We manufacture a Hydraulic Pipe Bending Machine Price to bend sheet metal edges. Hydraulic Press Machines are used in metalworking industries
A hydraulic pipe bending machine is a powerful tool that utilizes hydraulic pressure to bend metal pipes into various shapes and angles. It is commonly used in construction, plumbing, and industrial applications due to its ability to handle large-diameter pipes and achieve precise bending angles.
Key Components of a Hydraulic Pipe Bending Machine
A hydraulic pipe bending machine typically consists of the following components:
- Frame: The frame provides a sturdy base for the machine and supports the bending mechanism. It is typically made from heavy-duty steel or cast iron.
- Hydraulic Pump and Control System: The hydraulic pump and control system regulate the flow and pressure of hydraulic fluid, ensuring precise and controlled bending. It consists of a hydraulic pump, a control valve, and a pressure gauge.
- Hydraulic Cylinder: The hydraulic cylinder converts hydraulic fluid pressure into mechanical force to drive the bending mechanism. It consists of a piston, a rod, and a cylinder barrel.
- Bending Mechanism: The bending mechanism consists of a bending form, a pressure roller, and a mandrel. The bending form provides the desired shape, while the pressure roller applies force to bend the pipe, and the mandrel supports the pipe from the inside to prevent flattening.
- Work Table: The work table provides a stable surface for positioning and securing the pipe during bending. It may be adjustable to accommodate different pipe sizes and bending angles.
- Controls: The controls allow the user to operate the machine, including setting the bending angle, engaging the bending mechanism, and controlling the speed of the bending process.
Common Applications of Hydraulic Pipe Bending Machines
Hydraulic pipe bending machines are suitable for various applications, including:
- Bending large-diameter pipes (typically up to 2 inches or 50 mm)
- Forming piping systems for plumbing, heating, and ventilation
- Creating piping components for industrial applications, such as oil and gas pipelines
- Bending pipes for structural supports and frameworks
- Manufacturing pipes for railings, fences, and other decorative applications
Benefits of Hydraulic Pipe Bending Machines
Hydraulic pipe bending machines offer several advantages over manual and electric bending machines:
- High Bending Force: Hydraulic machines can generate immense force, allowing them to bend thick-walled and high-strength pipes.
- Precise Bending Control: Hydraulic systems offer precise control over bending angles, ensuring consistent and accurate results.
- Versatility: Hydraulic machines can handle a wide range of pipe sizes and materials, including steel, copper, and stainless steel.
- Efficient Operation: Hydraulic machines can bend pipes quickly and efficiently, reducing production time and cost.
Safety Precautions for Using Hydraulic Pipe Bending Machines
When using hydraulic pipe bending machines, it is crucial to follow strict safety protocols to prevent injuries and accidents:
- Thorough Training: Operators must receive comprehensive training on the operation, maintenance, and safety procedures of the hydraulic pipe bending machine.
- Personal Protective Equipment (PPE): Always wear appropriate PPE, including safety glasses, gloves, and hearing protection.
- Secure Pipe Placement: Properly secure the pipe in the machine’s bending form and pressure roller to prevent slippage and ensure accurate bending.
- Maintain Safe Distances: Maintain a safe distance from the bending mechanism and hydraulic components during operation.
- Regular Maintenance: Follow a strict maintenance schedule to ensure the machine is in optimal condition and free of potential hazards.
- Emergency Stop Procedures: Familiarize yourself with emergency stop procedures and be prepared to act quickly in case of an unexpected issue.
Hydraulic pipe bending machines are powerful and versatile tools that play a vital role in various industries. By adhering to strict safety protocols and operating the machine with proper training and technique, individuals can effectively bend pipes and create various piping systems and components.
Hydraulic Pipe Bending Machine
A hydraulic pipe bending machine utilizes hydraulic pressure to bend metal pipes into various shapes and angles. It is a powerful and versatile tool widely used in construction, plumbing, and industrial applications. The working principle of a hydraulic pipe bending machine involves the following steps:
- Pipe Preparation: The pipe is cut to the desired length and cleaned to remove any dirt, debris, or rust that could interfere with the bending process.
- Pipe Positioning: The pipe is placed on the worktable of the machine and secured in the bending form. The bending form provides the desired shape for the bend.
- Mandrel Insertion: A mandrel, typically made of steel or hardened plastic, is inserted into the pipe to provide internal support and prevent flattening during bending.
- Hydraulic Pressure Application: Hydraulic fluid is pumped into the hydraulic cylinder, generating immense force that pushes the pressure roller against the pipe.
- Bending Process: The pressure roller applies force to the pipe, causing it to bend around the bending form. The mandrel inside the pipe provides support and prevents flattening.
- Angle Control: The bending angle is precisely controlled by adjusting the amount of hydraulic pressure applied and the position of the pressure roller.
- Ram Retraction: Once the desired bending angle is achieved, the hydraulic pressure is released, and the ram retracts, releasing the pipe.
- Pipe Removal: The bent pipe is carefully removed from the machine.
- Inspection and Finishing: The bent pipe is inspected for any imperfections or cracks. If necessary, finishing touches may be applied, such as grinding or polishing.
Hydraulic pipe bending machines offer several advantages over manual and electric bending machines, including:
- High Bending Force: Hydraulic machines can generate immense force, allowing them to bend thick-walled and high-strength pipes.
- Precise Angle Control: Hydraulic systems offer precise control over bending angles, ensuring consistent and accurate results.
- Versatility: Hydraulic machines can handle a wide range of pipe sizes and materials, including steel, copper, and stainless steel.
- Efficient Operation: Hydraulic machines can bend pipes quickly and efficiently, reducing production time and cost.
Due to these advantages, hydraulic pipe bending machines are essential tools in various industries for creating piping systems, structural supports, and decorative components.
Hydraulic Cylinder:
A hydraulic cylinder is a fundamental component of hydraulic systems used in various industrial applications, including tube bending machines. This cylindrical mechanism converts hydraulic energy into linear mechanical force and motion. Here’s an in-depth look at the hydraulic cylinder:
The hydraulic cylinder comprises several key elements, including the cylinder barrel, piston, rod, seals, and hydraulic fluid. The cylinder barrel is a hollow cylindrical tube typically made of steel or aluminum, housing the piston and hydraulic fluid. The piston is a solid, cylindrical component that fits snugly inside the cylinder barrel and separates the internal space into two chambers: the rod side and the cap side.
The piston is connected to a piston rod, which extends through one end of the cylinder barrel and attaches to the load or machinery being actuated. When hydraulic pressure is applied to one side of the piston, it creates a force imbalance, causing the piston and piston rod to move in the desired direction. The hydraulic fluid is contained within the cylinder barrel and acts as the medium for transmitting force from one chamber to the other.
Seals are critical components of the hydraulic cylinder, ensuring that the hydraulic fluid remains contained within the cylinder and preventing leakage. Common types of seals used in hydraulic cylinders include piston seals, rod seals, wiper seals, and gland seals. These seals are typically made of rubber or polyurethane and are designed to withstand high pressures and temperatures.
Hydraulic cylinders come in various designs and configurations to suit different applications and operating conditions. Single-acting cylinders have one port for hydraulic fluid input, with the force exerted in one direction only. Double-acting cylinders have two ports, allowing hydraulic fluid to enter and exit the cylinder, enabling bidirectional movement of the piston.
In tube bending machines, hydraulic cylinders play a crucial role in applying bending force to the pipe or tube being bent. The hydraulic cylinder is actuated to push the bending die against the pipe, causing it to deform and take on the desired shape. Proper maintenance and inspection of hydraulic cylinders are essential to ensure reliable performance and prevent issues such as fluid leaks, seal failures, and piston damage.
In conclusion, the hydraulic cylinder is a vital component of hydraulic systems, providing linear mechanical force and motion in various industrial applications. Understanding its operation, design principles, and maintenance requirements is essential for ensuring the efficient and reliable performance of hydraulic equipment, including tube bending machines.
Ram:
The ram is a crucial component of a hydraulic pipe bending machine, serving as the moving part of the hydraulic cylinder responsible for applying force to the pipe during the bending process. Let’s delve into the intricacies of the ram:
The ram is typically a solid, cylindrical shaft that extends from the hydraulic cylinder and interfaces directly with the bending die or tooling. It is designed to withstand high levels of hydraulic pressure and transmit this force efficiently to the bending die to deform the pipe. The size and shape of the ram may vary depending on the specific application and requirements of the tube bending operation.
In hydraulic pipe bending machines, the ram is actuated by hydraulic pressure, which causes it to move linearly within the hydraulic cylinder. As the ram extends, it pushes against the bending die, exerting force on the pipe and causing it to bend to the desired angle and radius. The force applied by the ram must be carefully controlled and calibrated to ensure precise bending results and prevent damage to the pipe or tooling.
The ram is often equipped with seals and guide components to ensure smooth and controlled movement within the hydraulic cylinder. These seals help to maintain the integrity of the hydraulic system by preventing leakage of hydraulic fluid and contamination of the internal components. Guide components, such as bearings or bushings, help to stabilize the ram and prevent it from deflecting or binding during operation.
Proper maintenance of the ram is essential to ensure optimal performance and longevity of the hydraulic pipe bending machine. Regular inspection of the ram, seals, and guide components is necessary to detect any signs of wear, damage, or leakage. Any worn or damaged components should be promptly replaced to prevent issues such as fluid leaks, loss of bending accuracy, or system failure.
In conclusion, the ram plays a critical role in hydraulic pipe bending machines, serving as the primary mechanism for applying bending force to the pipe. Understanding its design, function, and maintenance requirements is essential for achieving accurate and reliable tube bending results while ensuring the safety and efficiency of the bending operation.
Piston:
The piston is a pivotal component within the hydraulic cylinder of a tube bending machine, responsible for converting hydraulic pressure into linear mechanical motion. Let’s delve deeper into the function and operation of the piston:
Functionally, the piston serves as a barrier within the hydraulic cylinder, dividing it into two distinct chambers: the cap end and the rod end. This division allows hydraulic pressure to act on one side of the piston, while the opposite side can simultaneously exhaust fluid or accommodate fluid displacement due to the piston’s movement.
Constructed typically from high-strength materials such as steel or aluminum, the piston is engineered to withstand significant hydraulic pressures without compromising its structural integrity. Its cylindrical shape ensures a snug fit within the cylinder barrel, minimizing fluid leakage and maximizing the efficiency of force transmission.
The piston’s movement within the cylinder is facilitated by the application of hydraulic pressure. When pressurized fluid enters the cap end of the cylinder, it exerts force on the piston, causing it to move linearly within the cylinder barrel. This movement, in turn, drives the piston rod connected to the load or machinery being actuated, thereby achieving the desired mechanical motion.
Seals play a critical role in maintaining the integrity of the piston within the hydraulic cylinder. Piston seals, typically made of high-performance elastomers or polymers, prevent hydraulic fluid from bypassing the piston and ensure efficient force transmission. These seals must exhibit excellent resilience, wear resistance, and compatibility with hydraulic fluids to ensure reliable performance over extended periods.
Proper maintenance of the piston and associated seals is essential to prevent hydraulic fluid leakage and maintain the efficiency of the hydraulic system. Regular inspection of the piston’s condition, seal integrity, and fluid levels helps identify potential issues early and address them promptly to avoid operational disruptions.
In conclusion, the piston serves as a vital component within the hydraulic cylinder of a tube bending machine, enabling the conversion of hydraulic pressure into linear mechanical motion. Its robust design, coupled with effective sealing mechanisms, ensures efficient force transmission and reliable operation of the hydraulic system, contributing to the overall performance and productivity of the tube bending process.
Cylinder Barrel:
The cylinder barrel is a foundational component of the hydraulic cylinder in tube bending machines, providing the housing for the piston and facilitating the conversion of hydraulic pressure into linear mechanical motion. Let’s explore the key aspects of the cylinder barrel:
Composition and Construction: The cylinder barrel is typically manufactured from high-strength materials such as steel, aluminum, or alloy steel, chosen for their durability, corrosion resistance, and ability to withstand high hydraulic pressures. The material selection ensures that the cylinder barrel can withstand the forces exerted during tube bending operations without deformation or failure.
The cylinder barrel is precision-machined to exacting tolerances to ensure a smooth and precise fit for the piston and associated seals. This precision machining is crucial for minimizing fluid leakage and maximizing the efficiency of force transmission within the hydraulic cylinder.
Chamber Division: One of the primary functions of the cylinder barrel is to divide the hydraulic cylinder into two distinct chambers: the cap end and the rod end. This division allows hydraulic pressure to act on one side of the piston while the opposite side accommodates fluid displacement or exhausts fluid during the piston’s movement.
Sealing Surfaces: The interior surface of the cylinder barrel, known as the bore, serves as the sealing surface for the piston seals. These seals prevent hydraulic fluid from bypassing the piston and ensure efficient force transmission. The bore must be meticulously machined to achieve the required surface finish and dimensional accuracy to maintain seal integrity and minimize fluid leakage.
Mounting and Integration: The cylinder barrel is typically mounted within the hydraulic system framework of the tube bending machine, either horizontally or vertically, depending on the specific machine design. It must be securely fastened to prevent movement or misalignment during operation, ensuring consistent and reliable performance.
Maintenance and Inspection: Regular maintenance and inspection of the cylinder barrel are essential to ensure optimal performance and longevity of the hydraulic cylinder. Periodic checks for signs of wear, damage, or corrosion are necessary to detect any issues early and address them promptly to prevent operational disruptions.
In conclusion, the cylinder barrel is a critical component of the hydraulic cylinder in tube bending machines, providing the housing for the piston and facilitating the conversion of hydraulic pressure into linear mechanical motion. Its robust construction, precise machining, and proper maintenance are essential for ensuring the efficiency, reliability, and longevity of the hydraulic system in tube bending operations.
Piston Rod:
The piston rod is a crucial component of the hydraulic cylinder in tube bending machines, serving as the link between the piston and the load or machinery being actuated. Here’s an in-depth look at the piston rod and its role in hydraulic systems:
- Functionality and Operation:
- The piston rod extends from the piston within the hydraulic cylinder and protrudes through one end of the cylinder barrel.
- As hydraulic pressure is applied to the piston, the piston rod transmits the resulting linear motion to the load or machinery connected to its free end.
- Material and Construction:
- Piston rods are typically made of high-strength materials such as chrome-plated steel or stainless steel to withstand the forces and stresses encountered during operation.
- These materials offer excellent durability, corrosion resistance, and fatigue strength, ensuring reliable performance over extended periods.
- Sealing and Protection:
- Piston rods are often equipped with seals, such as rod seals and wiper seals, to prevent contamination of the hydraulic fluid and protect the internal components of the hydraulic cylinder.
- Rod seals prevent hydraulic fluid from leaking past the piston rod, while wiper seals remove contaminants such as dirt, dust, and debris from the rod surface as it retracts into the cylinder.
- Mounting and Connection:
- The free end of the piston rod is typically attached to the load or machinery being actuated, either directly or through mechanical linkages.
- Mounting options include threaded connections, clevis mounts, eye mounts, or custom mounting configurations depending on the specific application requirements.
- Maintenance and Inspection:
- Regular inspection and maintenance of the piston rod are essential to ensure optimal performance and longevity of the hydraulic system.
- Inspections should include checks for signs of wear, corrosion, or damage to the rod surface, as well as the condition of the sealing elements.
- Safety Considerations:
- Proper maintenance of the piston rod and associated seals is crucial for preventing hydraulic fluid leaks and ensuring the safe operation of the hydraulic system.
- Any signs of wear, damage, or deterioration should be addressed promptly to prevent potential hazards and maintain operational safety.
In conclusion, the piston rod plays a critical role in hydraulic systems, transmitting linear motion from the piston to the load or machinery being actuated. Its robust construction, effective sealing, and proper maintenance are essential for ensuring reliable performance and operational safety in tube bending machines and other hydraulic applications.
Seals:
Seals are integral components within hydraulic pipe bending machines, ensuring the integrity of the hydraulic system by preventing leakage of hydraulic fluid and contamination from external elements. Let’s explore the various types and functions of seals in hydraulic systems:
- Piston Seals:
- Piston seals are located between the piston and the cylinder bore, sealing the dynamic interface and preventing hydraulic fluid from bypassing the piston.
- These seals are typically designed to withstand high pressures and provide reliable sealing performance under dynamic conditions.
- Rod Seals:
- Rod seals are installed on the piston rod and prevent leakage of hydraulic fluid from the rod side to the cap side of the cylinder.
- They also protect the hydraulic system from contamination by preventing external debris from entering the cylinder.
- Wiper Seals:
- Wiper seals, also known as scraper seals, are installed on the external surface of the piston rod and remove contaminants such as dirt, dust, and moisture as the rod retracts into the cylinder.
- By maintaining a clean rod surface, wiper seals help prevent damage to the rod seals and extend their service life.
- Gland Seals:
- Gland seals are located in the gland or housing at the end of the cylinder barrel and prevent leakage of hydraulic fluid from the cylinder.
- These seals provide static sealing between the piston rod and the cylinder bore and are typically designed to withstand both high pressures and low pressures.
- Static Seals:
- Static seals are used to seal non-moving connections and interfaces within the hydraulic system, such as flanges, fittings, and port connections.
- They prevent leakage of hydraulic fluid from static joints and maintain system integrity.
- O-Rings:
- O-rings are widely used in hydraulic systems as static and dynamic seals due to their simple design, versatility, and effectiveness.
- These elastomeric seals are installed in grooves or recesses and provide reliable sealing by deforming to conform to the mating surfaces.
- Backup Rings:
- Backup rings are often used in conjunction with O-rings and other seals to provide additional support and enhance sealing performance.
- They prevent extrusion of the elastomeric seal under high pressures and help maintain sealing integrity in demanding applications.
Proper selection, installation, and maintenance of seals are essential for ensuring the reliable performance and longevity of hydraulic pipe bending machines. Regular inspection of seals for wear, damage, or deterioration is necessary to detect potential issues early and prevent hydraulic fluid leaks or system failures. By understanding the functions and characteristics of different types of seals, operators can optimize the performance and efficiency of hydraulic systems in tube bending operations.
Hydraulic Pump:
The hydraulic pump is a critical component of hydraulic pipe bending machines, responsible for generating hydraulic pressure to power the hydraulic system. Let’s explore the function, operation, and types of hydraulic pumps used in tube bending machines:
- Functionality:
- The hydraulic pump converts mechanical energy, typically from an electric motor or engine, into hydraulic energy by pressurizing hydraulic fluid.
- This pressurized fluid is then transmitted through hydraulic hoses to actuate hydraulic cylinders, applying force to bend pipes during the bending process.
- Operation:
- Hydraulic pumps operate based on the principle of displacement, where mechanical energy is used to displace hydraulic fluid and create pressure.
- The pump draws hydraulic fluid from a reservoir or tank and delivers it to the hydraulic system at a higher pressure.
- As the pump operates, it generates flow, which is the volume of hydraulic fluid delivered per unit of time, and pressure, which is the force exerted by the fluid on the system components.
- Types of Hydraulic Pumps:
- Gear Pumps: These pumps are compact, simple in design, and suitable for low to medium pressure applications. They consist of two meshing gears that create a pumping action to displace hydraulic fluid.
- Vane Pumps: Vane pumps utilize rotating vanes mounted on a rotor to displace hydraulic fluid. They offer higher efficiency and quieter operation compared to gear pumps and are suitable for medium-pressure applications.
- Piston Pumps: Piston pumps are capable of delivering high-pressure hydraulic fluid and are commonly used in heavy-duty applications. They consist of pistons that reciprocate within cylinders to displace fluid.
- Axial Piston Pumps: Axial piston pumps feature pistons arranged parallel to the drive shaft and are capable of delivering high-pressure and high-flow rates. They are commonly used in demanding industrial applications.
- Maintenance and Inspection:
- Regular maintenance and inspection of the hydraulic pump are essential to ensure reliable performance and prevent system failures.
- Maintenance tasks may include checking fluid levels, inspecting pump components for wear or damage, and replacing worn seals or bearings.
- Monitoring pump performance parameters such as flow rate, pressure, and temperature can help detect potential issues early and prevent costly downtime.
- Safety Considerations:
- Operators should be trained in the safe operation and maintenance of hydraulic pumps to prevent accidents and injuries.
- Proper installation of the pump, including securing it to a stable base and ensuring adequate ventilation, is crucial for safe operation.
- Operators should be aware of potential hazards such as hydraulic fluid leaks, high-pressure fluid streams, and rotating components and take appropriate precautions to mitigate risks.
In conclusion, the hydraulic pump is a vital component of hydraulic pipe bending machines, providing the hydraulic pressure necessary to power the bending process. Understanding the operation, types, and maintenance requirements of hydraulic pumps is essential for ensuring the efficient and reliable performance of tube bending machines in industrial applications.
Hydraulic Reservoir:
The hydraulic reservoir, also known as the hydraulic tank or reservoir tank, is a crucial component of hydraulic pipe bending machines, serving as a storage vessel for hydraulic fluid. Let’s delve into the function, design, and importance of the hydraulic reservoir:
- Functionality:
- The primary function of the hydraulic reservoir is to store an adequate supply of hydraulic fluid for the hydraulic system.
- It acts as a reservoir for both the hydraulic fluid required for normal operation and a sump for collecting fluid returning from various hydraulic components.
- Hydraulic Fluid Storage:
- Hydraulic fluid is stored in the reservoir at atmospheric pressure, ready for use in the hydraulic system.
- The reservoir capacity is typically sized to accommodate the required volume of hydraulic fluid for the specific application and operating conditions.
- Fluid Cooling and Filtration:
- The reservoir provides a large surface area for dissipating heat generated during hydraulic system operation, helping to maintain optimal fluid temperature.
- It may include cooling fins or external heat exchangers to enhance heat dissipation and prevent overheating of the hydraulic fluid.
- Additionally, the reservoir often houses hydraulic fluid filters and strainers to remove contaminants and maintain fluid cleanliness.
- Fluid Level Monitoring:
- Many hydraulic reservoirs are equipped with sight gauges or level indicators to monitor the fluid level and ensure proper fluid replenishment as needed.
- Proper fluid level maintenance is essential for preventing cavitation, air ingestion, and system damage due to low fluid levels.
- Air Separation and Deaeration:
- Hydraulic reservoirs may incorporate baffles, weirs, or air separation devices to promote the separation of entrained air from the hydraulic fluid.
- Air removal is critical for maintaining hydraulic system efficiency and preventing cavitation and aeration issues that can lead to component damage.
- Material and Design:
- Hydraulic reservoirs are typically constructed from materials such as steel, aluminum, or plastic, chosen for their durability, corrosion resistance, and compatibility with hydraulic fluids.
- The design of the reservoir may vary depending on factors such as system size, operating environment, and space constraints.
- Maintenance and Inspection:
- Regular maintenance of the hydraulic reservoir is essential to ensure optimal hydraulic system performance and longevity.
- Maintenance tasks may include checking fluid levels, inspecting for leaks or damage, cleaning or replacing filters, and monitoring fluid condition.
- Proper fluid management practices, including periodic fluid analysis and replacement, help extend the life of hydraulic components and prevent system failures.
In conclusion, the hydraulic reservoir is a critical component of hydraulic pipe bending machines, providing storage, cooling, filtration, and air separation functions essential for the efficient and reliable operation of the hydraulic system. Understanding the function and importance of the hydraulic reservoir and implementing proper maintenance practices are essential for maximizing the performance and longevity of tube bending machines in industrial applications.
Hydraulic Hoses:
Hydraulic hoses play a vital role in hydraulic pipe bending machines, serving as the conduits for transmitting hydraulic fluid between various components of the hydraulic system. Let’s explore the functions, construction, and considerations related to hydraulic hoses:
- Functionality:
- Hydraulic hoses convey hydraulic fluid under pressure from the hydraulic pump to hydraulic cylinders, valves, actuators, and other hydraulic components within the tube bending machine.
- They provide a flexible and durable means of transmitting hydraulic power, allowing for movement and operation of machine components while withstanding high pressures and dynamic forces.
- Construction:
- Hydraulic hoses are typically constructed from layers of synthetic rubber or thermoplastic materials reinforced with high-tensile steel or textile braids or spirals.
- The inner tube, made of synthetic rubber or thermoplastic material, provides a barrier for hydraulic fluid and resists abrasion, corrosion, and chemical degradation.
- The reinforcement layer(s) enhance the hose’s strength and durability, providing resistance to high pressures, kinking, and external impacts.
- The outer cover, also made of synthetic rubber or thermoplastic material, protects the hose from environmental factors such as UV radiation, ozone, oil, and abrasion.
- Types of Hydraulic Hoses:
- Wire Braided Hoses: These hoses feature one or more layers of high-tensile steel wire braids for reinforcement and are suitable for medium to high-pressure applications.
- Wire Spiral Hoses: Wire spiral hoses utilize multiple layers of high-tensile steel wire spirals for reinforcement, providing increased strength and flexibility, making them ideal for high-pressure applications and demanding operating conditions.
- Thermoplastic Hoses: Thermoplastic hoses are lightweight, flexible, and resistant to abrasion and chemicals. They are often used in applications requiring flexibility and tight bend radii.
- Rubber Hoses: Rubber hoses are versatile and suitable for a wide range of hydraulic applications. They offer excellent flexibility, durability, and resistance to abrasion and environmental factors.
- Considerations:
- Proper hose selection is essential to ensure compatibility with the hydraulic fluid, operating pressure, temperature range, and application requirements.
- Hose length, diameter, and bend radius should be carefully chosen to accommodate system layout, movement, and operational needs without causing excessive strain or restriction.
- Regular inspection and maintenance of hydraulic hoses are necessary to detect signs of wear, damage, or deterioration, such as cracks, abrasions, bulges, or leaks.
- Hose assemblies should be installed and routed to minimize exposure to external hazards, such as sharp edges, hot surfaces, chemicals, and excessive bending or twisting, to prevent premature failure.
- Safety Considerations:
- Operators should be trained in proper hose handling, installation, routing, and maintenance procedures to prevent accidents, injuries, and hydraulic fluid leaks.
- Hose assemblies should be properly secured, supported, and protected to prevent chafing, kinking, or damage during operation.
- Hydraulic hoses should be inspected regularly for signs of damage or deterioration and replaced as needed to maintain system integrity and prevent hydraulic fluid leaks, which can pose safety hazards and cause environmental contamination.
In conclusion, hydraulic hoses are essential components of hydraulic pipe bending machines, facilitating the transmission of hydraulic power to various machine components. Understanding the functions, construction, types, considerations, and safety aspects of hydraulic hoses is crucial for ensuring the efficient, reliable, and safe operation of tube bending machines in industrial applications.
Control Valve:
The control valve is a critical component of hydraulic pipe bending machines, responsible for regulating the flow and direction of hydraulic fluid within the hydraulic system. Let’s delve into the functions, types, and importance of control valves in tube bending machines:
- Functionality:
- The control valve controls the flow rate, direction, and pressure of hydraulic fluid to actuate hydraulic cylinders, control the movement of machine components, and regulate the bending process.
- By adjusting the position of internal spools, ports, and orifices, the control valve directs hydraulic fluid to different parts of the hydraulic system, enabling precise control of machine movements and operations.
- Flow Control:
- Control valves regulate the flow of hydraulic fluid by adjusting the size of the flow passages or controlling the opening and closing of valve ports.
- Flow control valves can be configured as throttling valves, which restrict flow through an adjustable orifice, or as proportional valves, which vary flow in proportion to a control signal.
- Directional Control:
- Directional control valves determine the direction of hydraulic fluid flow within the hydraulic system, allowing for the activation and deactivation of hydraulic cylinders and actuators.
- These valves typically have multiple ports and spools that can be shifted to direct fluid flow to different hydraulic circuits, enabling forward, reverse, and neutral positions.
- Pressure Control:
- Pressure control valves maintain the desired pressure level within the hydraulic system by regulating the flow of hydraulic fluid or diverting excess fluid to a reservoir.
- Pressure relief valves protect hydraulic components from overpressurization by opening when system pressure exceeds a preset limit, allowing excess fluid to bypass the valve and return to the reservoir.
- Types of Control Valves:
- Directional Control Valves: Directional control valves include spool valves, poppet valves, and rotary valves, among others, and are used to control the direction of hydraulic fluid flow.
- Flow Control Valves: Flow control valves, such as needle valves, flow restrictors, and proportional valves, regulate the flow rate of hydraulic fluid to control the speed and motion of hydraulic cylinders and actuators.
- Pressure Control Valves: Pressure control valves include pressure relief valves, pressure reducing valves, and sequence valves, which maintain system pressure within safe operating limits and regulate pressure levels in specific hydraulic circuits.
- Importance:
- The control valve is crucial for achieving precise control and coordination of machine movements and operations during the tube bending process.
- Proper selection, installation, and adjustment of control valves are essential for optimizing machine performance, ensuring bending accuracy, and preventing damage to hydraulic components.
- Maintenance and Inspection:
- Regular maintenance and inspection of control valves are necessary to detect any signs of wear, damage, or malfunction and ensure proper functioning of the hydraulic system.
- Maintenance tasks may include cleaning, lubricating, adjusting, and replacing control valve components as needed to maintain optimal performance and reliability.
In conclusion, the control valve is a fundamental component of hydraulic pipe bending machines, providing control over the flow, direction, and pressure of hydraulic fluid to facilitate precise and efficient machine operations. Understanding the functions, types, importance, and maintenance requirements of control valves is essential for achieving accurate and reliable tube bending results in industrial applications.
Bending Die:
The bending die is a critical component of a hydraulic pipe bending machine, responsible for shaping the pipe or tube to the desired angle and radius during the bending process. Let’s explore the functions, types, and importance of bending dies in tube bending machines:
- Functionality:
- The bending die provides the form or shape around which the pipe or tube is bent, exerting pressure to deform the material and achieve the desired bend angle and radius.
- It supports and guides the pipe or tube during bending, ensuring proper alignment and preventing distortion or collapse of the material.
- Design and Construction:
- Bending dies are typically made from high-strength materials such as tool steel or alloy steel, chosen for their durability, wear resistance, and ability to withstand high bending forces.
- They are precision-machined to the desired bend angle and radius, with smooth and polished surfaces to minimize friction and prevent scratching or marring of the material being bent.
- Bending dies may be segmented or solid, depending on the complexity of the bend and the requirements of the application. Segmented dies allow for the bending of pipes with varying diameters and radii.
- Types of Bending Dies:
- Rotary Draw Dies: These dies are used in rotary draw bending machines, where the pipe or tube is clamped and drawn around the bending die by a rotating mandrel, creating precise bends with minimal distortion.
- Compression Bending Dies: Compression bending dies are used in compression bending machines, where the pipe or tube is bent by applying force directly to the material without the use of a mandrel. These dies typically have a rounded profile to support the outer surface of the material during bending.
- Roll Bending Dies: Roll bending dies are used in roll bending machines, where the pipe or tube is passed between three or four rollers to gradually bend it to the desired shape. These dies are typically adjustable to accommodate different pipe diameters and radii.
- Importance:
- The bending die plays a crucial role in determining the accuracy, quality, and repeatability of bends produced by the tube bending machine.
- Proper selection and setup of bending dies are essential for achieving precise bend angles and radii, minimizing distortion, and ensuring dimensional accuracy of bent components.
- Maintenance and Inspection:
- Regular maintenance and inspection of bending dies are necessary to ensure optimal performance and longevity.
- Maintenance tasks may include cleaning, lubricating, and inspecting the die surfaces for signs of wear, damage, or deformation. Worn or damaged dies should be repaired or replaced to maintain bending accuracy and quality.
In conclusion, the bending die is a critical component of hydraulic pipe bending machines, providing the form and support necessary to shape pipes and tubes accurately and efficiently. Understanding the functions, types, importance, and maintenance requirements of bending dies is essential for achieving high-quality and consistent tube bending results in industrial applications.
Mandrel:
The mandrel is a key component in tube bending machines, particularly in rotary draw bending systems, where it plays a crucial role in maintaining the integrity of the tube or pipe during the bending process. Let’s delve into the functions, types, and importance of mandrels in tube bending:
- Support and Control:
- The primary function of the mandrel is to support the inner surface of the tube or pipe during bending, preventing collapse or distortion, especially in thin-walled or delicate materials.
- By providing internal support, the mandrel helps maintain the roundness and dimensional accuracy of the bent tube or pipe, ensuring consistent bend quality.
- Types of Mandrels:
- Ball Mandrels: These mandrels feature a spherical ball or plug inserted into the tube or pipe, providing support while allowing for smooth rotation and movement during bending.
- Plug Mandrels: Plug mandrels consist of a solid cylindrical plug inserted into the tube or pipe, offering excellent support and control, particularly for tight-radius bends and thick-walled materials.
- Wiper/Drop-Down Mandrels: Wiper or drop-down mandrels are designed to retract or collapse during bending, allowing them to pass through tight bends without causing interference or distortion.
- Materials and Construction:
- Mandrels are typically made from materials such as steel, aluminum, or composite materials, chosen for their strength, durability, and resistance to wear and deformation.
- The surface of the mandrel may be coated or treated to reduce friction and minimize wear on the tube or pipe during bending.
- Adjustability and Customization:
- Many mandrels are adjustable or modular, allowing for easy customization to accommodate different tube diameters, wall thicknesses, and bend radii.
- Adjustable mandrels may feature interchangeable inserts or expandable segments that can be adjusted to match the specific requirements of each bending job.
- Importance:
- The mandrel is essential for achieving high-quality and accurate bends in tube bending operations, particularly for demanding applications requiring tight tolerances and minimal distortion.
- Proper selection and setup of the mandrel are crucial for preventing wrinkling, buckling, or collapsing of the tube or pipe during bending, ensuring the integrity and dimensional accuracy of the finished components.
- Maintenance and Inspection:
- Regular maintenance and inspection of mandrels are necessary to ensure optimal performance and longevity.
- Maintenance tasks may include cleaning, lubricating, and inspecting the mandrel surface for signs of wear, damage, or deformation. Worn or damaged mandrels should be repaired or replaced to maintain bending accuracy and quality.
In conclusion, the mandrel is a critical component in tube bending machines, providing internal support and control to ensure the integrity and dimensional accuracy of bent tubes and pipes. Understanding the functions, types, importance, and maintenance requirements of mandrels is essential for achieving high-quality and consistent tube bending results in industrial applications.
Pressure Die:
The pressure die, also known as the clamping die or pressure block, is an essential component of tube bending machines, particularly in rotary draw bending systems. It plays a crucial role in securely holding the tube or pipe in place during the bending process, ensuring accurate and repeatable bends. Let’s explore the functions, types, and importance of pressure dies in tube bending:
- Functionality:
- The primary function of the pressure die is to apply clamping force to the tube or pipe, holding it firmly against the bending die or mandrel during the bending process.
- By securely clamping the tube, the pressure die prevents slippage, buckling, or distortion, ensuring precise and consistent bends.
- Types of Pressure Dies:
- Fixed Pressure Dies: Fixed pressure dies are stationary components mounted on the machine frame, providing consistent clamping force throughout the bending process.
- Adjustable Pressure Dies: Adjustable pressure dies allow for fine-tuning of clamping force to accommodate different tube diameters, wall thicknesses, and bend radii. They may feature adjustable clamping arms, springs, or hydraulic actuators for precise control.
- Roller Pressure Dies: Roller pressure dies feature rollers or wheels that contact the outer surface of the tube, distributing clamping force evenly and minimizing surface marring or deformation.
- Materials and Construction:
- Pressure dies are typically made from hardened steel, aluminum, or other durable materials chosen for their strength, wear resistance, and ability to withstand high clamping forces.
- The surface of the pressure die may be coated or treated to reduce friction and minimize wear on the tube or pipe during clamping.
- Integration with Bending System:
- Pressure dies are integrated into the bending machine’s tooling setup, typically positioned opposite the bending die or mandrel to provide counter-pressure during bending.
- They may be mounted on adjustable arms, slides, or carriages to accommodate different tube sizes and bending configurations.
- Importance:
- The pressure die is critical for achieving accurate and repeatable bends in tube bending operations, particularly for tight-radius bends and thin-walled materials.
- Proper selection and setup of the pressure die are essential for preventing tube slippage, distortion, or wrinkling during bending, ensuring the integrity and dimensional accuracy of the finished components.
- Maintenance and Inspection:
- Regular maintenance and inspection of pressure dies are necessary to ensure optimal performance and longevity.
- Maintenance tasks may include cleaning, lubricating, and inspecting the pressure die surface for signs of wear, damage, or deformation. Worn or damaged pressure dies should be repaired or replaced to maintain bending accuracy and quality.
In conclusion, the pressure die is a critical component of tube bending machines, providing clamping force to securely hold the tube or pipe in place during bending. Understanding the functions, types, importance, and maintenance requirements of pressure dies is essential for achieving high-quality and consistent tube bending results in industrial applications.
Wiper Die:
In tube bending machines, the wiper die, also known as the wiper shoe or pressure die, serves a crucial role in maintaining the integrity and appearance of the tube or pipe during the bending process. Let’s delve into the functions, types, and importance of wiper dies in tube bending:
- Functionality:
- The primary function of the wiper die is to support the outer surface of the tube or pipe opposite the bend radius, providing counter-pressure to prevent wrinkles, distortions, or ovalization.
- By applying uniform pressure along the outer surface of the tube, the wiper die helps maintain the roundness and dimensional accuracy of the bend, ensuring high-quality results.
- Types of Wiper Dies:
- Fixed Wiper Dies: Fixed wiper dies are stationary components mounted on the machine frame, providing consistent counter-pressure throughout the bending process.
- Adjustable Wiper Dies: Adjustable wiper dies allow for fine-tuning of pressure to accommodate different tube diameters, wall thicknesses, and bend radii. They may feature adjustable shoes, springs, or hydraulic actuators for precise control.
- Materials and Construction:
- Wiper dies are typically made from hardened steel, aluminum, or other durable materials chosen for their strength, wear resistance, and ability to withstand high pressure.
- The surface of the wiper die may be coated or treated to reduce friction and minimize wear on the tube or pipe during bending.
- Integration with Bending System:
- Wiper dies are integrated into the bending machine’s tooling setup, positioned opposite the bending die or mandrel to provide counter-pressure during bending.
- They are often mounted on adjustable arms, slides, or carriages to accommodate different tube sizes and bending configurations.
- Importance:
- The wiper die is essential for achieving smooth, wrinkle-free bends in tube bending operations, particularly for thin-walled materials and tight-radius bends.
- Proper selection and setup of the wiper die are critical for preventing surface defects, such as wrinkles or indentations, and ensuring the integrity and appearance of the finished components.
- Maintenance and Inspection:
- Regular maintenance and inspection of wiper dies are necessary to ensure optimal performance and longevity.
- Maintenance tasks may include cleaning, lubricating, and inspecting the wiper die surface for signs of wear, damage, or deformation. Worn or damaged wiper dies should be repaired or replaced to maintain bending accuracy and quality.
In conclusion, the wiper die is a critical component of tube bending machines, providing counter-pressure to support the outer surface of the tube or pipe during bending. Understanding the functions, types, importance, and maintenance requirements of wiper dies is essential for achieving high-quality and consistent tube bending results in industrial applications.
Mandrel Lubrication System:
In tube bending machines, the mandrel lubrication system plays a crucial role in ensuring smooth and efficient bending operations while prolonging the life of the mandrel and reducing wear on the tube or pipe being bent. Let’s explore the functions, components, and importance of the mandrel lubrication system:
- Functionality:
- The mandrel lubrication system is designed to apply lubricant to the mandrel surface, reducing friction between the mandrel and the inner surface of the tube or pipe during bending.
- By minimizing friction, the lubrication system helps prevent galling, scoring, and scratching of the tube or pipe, ensuring smoother bends and preserving the integrity of the material.
- Components:
- Lubricant Reservoir: The lubricant reservoir stores the lubricant, such as oil or grease, used in the lubrication system. It may be integrated into the bending machine or mounted externally.
- Delivery System: The delivery system transports the lubricant from the reservoir to the mandrel surface. This may include hoses, tubes, or pipes connected to a pump or dispenser.
- Applicator: The applicator distributes the lubricant onto the mandrel surface during bending. This may be a spray nozzle, brush, roller, or pad, depending on the specific design of the lubrication system.
- Types of Lubricants:
- Oil-Based Lubricants: Oil-based lubricants, such as cutting oils or hydraulic oils, are commonly used in mandrel lubrication systems due to their lubricating properties and compatibility with metal surfaces.
- Grease: Grease lubricants are thicker and more viscous than oils, providing better adhesion to the mandrel surface and longer-lasting lubrication. They are often used in high-pressure bending applications or where continuous lubrication is required.
- Importance:
- The mandrel lubrication system is essential for ensuring smooth and efficient bending operations, reducing friction and wear on both the mandrel and the tube or pipe.
- Proper lubrication helps maintain bending accuracy, prevents surface defects such as scoring or scratching, and extends the life of bending tooling and equipment.
- Maintenance and Inspection:
- Regular maintenance and inspection of the mandrel lubrication system are necessary to ensure proper functioning and effectiveness.
- Maintenance tasks may include refilling the lubricant reservoir, checking for leaks or blockages in the delivery system, and cleaning or replacing applicator components as needed.
- Inspecting the mandrel surface for signs of wear, damage, or inadequate lubrication can help detect issues early and prevent costly repairs or downtime.
In conclusion, the mandrel lubrication system is a critical component of tube bending machines, ensuring smooth and efficient bending operations while prolonging the life of bending tooling and equipment. Understanding the functions, components, types of lubricants, and maintenance requirements of the mandrel lubrication system is essential for achieving high-quality and consistent tube bending results in industrial applications.
Pressure Die Lubrication System:
The pressure die lubrication system is a vital component of tube bending machines, particularly in rotary draw bending systems, where it plays a crucial role in reducing friction and wear between the pressure die and the outer surface of the tube or pipe being bent. Let’s explore the functions, components, and importance of the pressure die lubrication system:
- Functionality:
- The primary function of the pressure die lubrication system is to apply lubricant to the surface of the pressure die, reducing friction and minimizing wear during the bending process.
- By lubricating the contact surface between the pressure die and the tube or pipe, the lubrication system helps ensure smooth and consistent bending operations, preventing surface defects and prolonging the life of the bending tooling.
- Components:
- Lubricant Reservoir: The lubricant reservoir stores the lubricant used in the lubrication system, such as oil or grease. It may be integrated into the bending machine or mounted externally.
- Delivery System: The delivery system transports the lubricant from the reservoir to the pressure die surface. This may include hoses, tubes, or pipes connected to a pump or dispenser.
- Applicator: The applicator distributes the lubricant onto the surface of the pressure die during bending. This may be a spray nozzle, brush, roller, or pad, depending on the specific design of the lubrication system.
- Types of Lubricants:
- Oil-Based Lubricants: Oil-based lubricants, such as cutting oils or hydraulic oils, are commonly used in pressure die lubrication systems due to their lubricating properties and compatibility with metal surfaces.
- Grease: Grease lubricants are thicker and more viscous than oils, providing better adhesion to the pressure die surface and longer-lasting lubrication. They are often used in high-pressure bending applications or where continuous lubrication is required.
- Importance:
- The pressure die lubrication system is essential for reducing friction and wear between the pressure die and the tube or pipe, ensuring smooth and consistent bending operations.
- Proper lubrication helps maintain bending accuracy, prevents surface defects such as scoring or scratching, and extends the life of bending tooling and equipment.
- Maintenance and Inspection:
- Regular maintenance and inspection of the pressure die lubrication system are necessary to ensure proper functioning and effectiveness.
- Maintenance tasks may include refilling the lubricant reservoir, checking for leaks or blockages in the delivery system, and cleaning or replacing applicator components as needed.
- Inspecting the pressure die surface for signs of wear, damage, or inadequate lubrication can help detect issues early and prevent costly repairs or downtime.
In conclusion, the pressure die lubrication system is a critical component of tube bending machines, ensuring smooth and consistent bending operations while prolonging the life of bending tooling and equipment. Understanding the functions, components, types of lubricants, and maintenance requirements of the pressure die lubrication system is essential for achieving high-quality and consistent tube bending results in industrial applications.
Bend Angle Measurement System:
The bend angle measurement system is an essential feature of tube bending machines, providing accurate and reliable measurement of the bend angle to ensure precision and consistency in tube bending operations. Let’s explore the functions, types, and importance of bend angle measurement systems:
- Functionality:
- The primary function of the bend angle measurement system is to measure the angle of the tube or pipe as it is being bent, allowing operators to achieve the desired bend angle with high accuracy.
- By providing real-time feedback on the bend angle, the measurement system enables operators to make adjustments and corrections as needed to ensure the final product meets the required specifications.
- Types of Measurement Systems:
- Manual Protractors: Manual protractors are simple, handheld devices used to measure bend angles manually. They typically consist of a graduated scale and a rotating arm or pointer that is aligned with the bent tube to determine the angle.
- Digital Angle Gauges: Digital angle gauges utilize electronic sensors and display screens to provide accurate and precise measurements of bend angles. They may be mounted directly on the bending machine or used as handheld devices for convenience.
- Integrated Measurement Systems: Some tube bending machines feature integrated measurement systems that automatically measure the bend angle during the bending process. These systems may use sensors, encoders, or laser-based technologies to capture and display bend angle data in real time.
- Importance:
- The bend angle measurement system is critical for ensuring the accuracy and consistency of tube bending operations, particularly in applications where tight tolerances and precise angles are required.
- Accurate bend angle measurements help minimize scrap, rework, and material waste by ensuring that bent tubes meet the required specifications the first time.
- The measurement system also facilitates process control and quality assurance, allowing operators to monitor and adjust bending parameters as needed to achieve optimal results.
- Integration with Bending Process:
- Bend angle measurement systems are typically integrated into the tube bending machine’s control system, allowing for seamless operation and data feedback.
- Some advanced measurement systems may offer features such as automatic angle correction, tolerance monitoring, and data logging for process optimization and traceability.
- Maintenance and Calibration:
- Regular maintenance and calibration of the bend angle measurement system are essential to ensure accurate and reliable measurements.
- Maintenance tasks may include cleaning, inspection, and calibration of sensors, displays, and electronic components to maintain optimal performance and accuracy.
In conclusion, the bend angle measurement system is a critical component of tube bending machines, providing operators with accurate and reliable feedback on bend angles to ensure precision and consistency in tube bending operations. Understanding the functions, types, importance, and maintenance requirements of bend angle measurement systems is essential for achieving high-quality and consistent tube bending results in industrial applications.
Hydraulic Power Unit (HPU):
The hydraulic power unit (HPU) is a vital component of tube bending machines, providing the necessary hydraulic pressure and flow to operate various hydraulic components, including cylinders, valves, and actuators. Let’s explore the functions, components, and importance of hydraulic power units in tube bending machines:
- Functionality:
- The primary function of the hydraulic power unit is to generate hydraulic pressure and deliver hydraulic fluid to the hydraulic system of the tube bending machine.
- The hydraulic pressure generated by the HPU powers hydraulic cylinders, actuators, and other hydraulic components, enabling the bending, clamping, and movement of machine elements during the bending process.
- Components:
- Electric Motor: The HPU is typically powered by an electric motor, which drives the hydraulic pump to generate hydraulic pressure.
- Hydraulic Pump: The hydraulic pump is responsible for pressurizing hydraulic fluid and delivering it to the hydraulic system. Common types of hydraulic pumps include gear pumps, vane pumps, and piston pumps.
- Reservoir: The reservoir stores hydraulic fluid and helps dissipate heat generated during operation. It also provides a supply of fluid for the hydraulic system and allows for fluid level monitoring and maintenance.
- Filtration System: The filtration system removes contaminants and impurities from the hydraulic fluid, ensuring proper lubrication and preventing damage to hydraulic components.
- Control Valves: Control valves regulate the flow, direction, and pressure of hydraulic fluid within the hydraulic system, controlling the operation of hydraulic cylinders and actuators.
- Importance:
- The hydraulic power unit is essential for providing the hydraulic energy required to operate tube bending machines efficiently and accurately.
- Proper selection and sizing of the HPU are critical to ensure adequate hydraulic pressure and flow for the specific requirements of the bending application, such as material type, thickness, and bend radius.
- The HPU’s performance directly impacts the bending speed, accuracy, and repeatability of the tube bending machine, as well as the overall productivity and efficiency of the manufacturing process.
- Integration with Bending System:
- The hydraulic power unit is typically integrated into the tube bending machine’s control system, allowing for seamless operation and coordination of hydraulic components.
- The HPU may be equipped with sensors, gauges, and controls to monitor hydraulic pressure, temperature, and fluid level, as well as to adjust operating parameters as needed for optimal performance.
- Maintenance and Inspection:
- Regular maintenance and inspection of the hydraulic power unit are essential to ensure reliable operation and prevent downtime.
- Maintenance tasks may include checking fluid levels, inspecting hoses and fittings for leaks or damage, monitoring pump performance, and replacing filters as needed.
- Proper fluid management, including periodic fluid analysis and replacement, helps maintain hydraulic system cleanliness and performance over time.
In conclusion, the hydraulic power unit is a critical component of tube bending machines, providing the hydraulic energy necessary for bending operations. Understanding the functions, components, importance, and maintenance requirements of hydraulic power units is essential for achieving high-quality and efficient tube bending results in industrial applications.
Hydraulic Fluid:
Hydraulic fluid is a fundamental element in tube bending machines, serving as the medium for transmitting hydraulic power and enabling the movement of hydraulic components such as cylinders, valves, and actuators. Let’s explore the functions, types, properties, and importance of hydraulic fluid in tube bending machines:
- Functionality:
- The primary function of hydraulic fluid is to transfer hydraulic power from the hydraulic power unit to various hydraulic components within the tube bending machine.
- Hydraulic fluid transmits force from the hydraulic pump to hydraulic cylinders, actuators, and valves, facilitating the bending, clamping, and movement of machine elements during the bending process.
- Types of Hydraulic Fluid:
- Mineral Oil-Based Fluids: Mineral oil-based hydraulic fluids are the most commonly used type of hydraulic fluid, known for their compatibility with a wide range of hydraulic systems and components. They provide excellent lubrication and thermal stability.
- Synthetic Fluids: Synthetic hydraulic fluids, such as phosphate esters, polyalphaolefins (PAOs), and polyglycols, offer enhanced performance in extreme temperatures, high-pressure applications, and environments where fire resistance or biodegradability is required.
- Water-Based Fluids: Water-based hydraulic fluids are environmentally friendly alternatives to petroleum-based fluids, often used in applications where fire risk or environmental concerns are paramount. They provide good lubrication and cooling properties but may require additional corrosion protection.
- Biodegradable Fluids: Biodegradable hydraulic fluids are formulated to break down naturally in the environment, reducing environmental impact in case of leaks or spills. They are commonly used in environmentally sensitive areas or where regulatory compliance is required.
- Properties of Hydraulic Fluid:
- Viscosity: Viscosity refers to the resistance of a fluid to flow. Hydraulic fluids with appropriate viscosity ensure smooth and efficient operation of hydraulic components, preventing excessive wear and friction.
- Viscosity Index: The viscosity index (VI) indicates the change in viscosity of a fluid with temperature. Hydraulic fluids with a high VI maintain consistent performance over a wide temperature range, ensuring reliable operation in varying environmental conditions.
- Flash Point: The flash point is the temperature at which a fluid emits vapors that can ignite in the presence of an ignition source. Hydraulic fluids with high flash points reduce the risk of fire and ensure safety in hydraulic systems.
- Pour Point: The pour point is the temperature below which a fluid loses its flow characteristics and becomes too viscous to flow. Hydraulic fluids with low pour points remain fluid at low temperatures, ensuring operability in cold environments.
- Importance:
- Hydraulic fluid is essential for the proper functioning of tube bending machines, providing lubrication, cooling, and sealing properties to hydraulic components.
- Proper selection and maintenance of hydraulic fluid are crucial for ensuring the reliability, performance, and longevity of hydraulic systems, as well as the quality of tube bending operations.
- Hydraulic fluid also plays a role in system efficiency, energy consumption, and environmental impact, making it important to choose the right type of fluid for specific application requirements.
- Maintenance and Inspection:
- Regular maintenance and inspection of hydraulic fluid are necessary to ensure optimal performance and reliability of tube bending machines.
- Maintenance tasks may include monitoring fluid levels, checking for leaks or contamination, inspecting filters, and performing fluid analysis to assess fluid condition and identify any potential issues.
- Proper fluid management practices, such as filtration, contamination control, and periodic fluid replacement, help maintain hydraulic system cleanliness and performance over time.
In conclusion, hydraulic fluid is a critical component of tube bending machines, facilitating the transmission of hydraulic power and ensuring the proper operation of hydraulic systems. Understanding the functions, types, properties, importance, and maintenance requirements of hydraulic fluid is essential for achieving high-quality and efficient tube bending results in industrial applications.
Bending Machine Frame:
The bending machine frame is the structural backbone of the tube bending machine, providing support and rigidity to withstand bending forces and ensure accurate and consistent bending operations. Let’s explore the functions, construction, types, and importance of bending machine frames:
- Functionality:
- The primary function of the bending machine frame is to provide a stable and rigid platform for mounting and aligning the bending components, including the bending die, mandrel, pressure die, and hydraulic system.
- The frame absorbs bending forces and vibrations generated during the bending process, ensuring precision and repeatability in tube bending operations.
- Construction:
- Bending machine frames are typically constructed from high-strength materials such as steel or cast iron, chosen for their durability, stiffness, and resistance to deformation.
- The frame may be fabricated from welded steel plates or cast as a single-piece casting, depending on the size and configuration of the machine.
- Types of Frames:
- Open Frame: Open-frame bending machines feature a simple, open design with minimal enclosure around the bending components. They offer accessibility and ease of maintenance but may be less rigid than enclosed frame designs.
- Enclosed Frame: Enclosed-frame bending machines feature a fully enclosed structure surrounding the bending components, providing additional stiffness and protection against contamination and debris. They are commonly used in high-precision bending applications and environments with strict cleanliness requirements.
- Importance:
- The bending machine frame is critical for maintaining the accuracy and stability of tube bending operations, particularly in applications requiring tight tolerances and precise bends.
- A rigid and robust frame minimizes deflection and distortion during bending, ensuring that the bent tubes meet the required specifications and dimensional accuracy.
- Proper alignment and alignment of bending components within the frame are essential for achieving consistent and repeatable bending results, minimizing scrap and rework.
- Integration with Bending System:
- Bending machine frames are integrated with various components of the tube bending system, including the bending die, mandrel, pressure die, hydraulic system, and control interface.
- The frame provides mounting points, guides, and supports for these components, ensuring proper alignment and coordination during bending operations.
- Maintenance and Inspection:
- Regular maintenance and inspection of the bending machine frame are necessary to ensure structural integrity and performance.
- Maintenance tasks may include checking for signs of wear, corrosion, or fatigue, inspecting welds and connections, and performing alignments and adjustments as needed to maintain machine accuracy and reliability.
In conclusion, the bending machine frame is a fundamental component of tube bending machines, providing the structural foundation and support necessary for accurate and consistent bending operations. Understanding the functions, construction, types, importance, and maintenance requirements of bending machine frames is essential for achieving high-quality and efficient tube bending results in industrial applications.
Bending Machine Controls:
Bending machine controls are the interface between operators and the bending machine, allowing for precise control and adjustment of bending parameters to achieve desired bending results. Let’s explore the functions, types, features, and importance of bending machine controls:
- Functionality:
- The primary function of bending machine controls is to enable operators to input bending parameters such as bend angle, bend radius, tube dimensions, and material properties.
- Controls allow operators to start, stop, and pause bending operations, as well as to adjust machine settings, speed, and tooling configurations.
- Types of Controls:
- Manual Controls: Manual controls consist of basic switches, knobs, and buttons that operators manipulate manually to control machine functions. They may include start/stop buttons, emergency stop switches, and manual override controls.
- Semi-Automatic Controls: Semi-automatic controls offer intermediate levels of automation, allowing operators to input bending parameters manually while the machine performs bending operations automatically. They may feature digital displays and input interfaces for parameter entry.
- Fully Automatic Controls: Fully automatic controls provide advanced levels of automation, with programmable features for setting up bending sequences, storing bending programs, and adjusting parameters automatically based on predefined criteria. They may include touch-screen interfaces, graphical user interfaces (GUIs), and integrated control systems for seamless operation.
- Features and Capabilities:
- Programmability: Bending machine controls allow operators to program and store bending sequences, reducing setup time and enabling consistent and repeatable bending results.
- Precision Control: Controls offer precise control over bending parameters such as bend angle, bend radius, and feed rate, ensuring accurate and consistent bending operations.
- Safety Features: Controls may include safety interlocks, sensors, and alarms to prevent accidents, detect malfunctions, and ensure operator safety during bending operations.
- Diagnostic Tools: Some controls feature built-in diagnostic tools and monitoring capabilities to detect and troubleshoot issues, optimize performance, and minimize downtime.
- Integration: Controls may integrate with other components of the bending system, such as hydraulic systems, measurement systems, and tooling, for seamless operation and data exchange.
- Importance:
- Bending machine controls are critical for achieving precise, efficient, and safe bending operations, regardless of the complexity of the bending process or the material being bent.
- Intuitive and user-friendly controls enhance operator productivity and confidence, allowing for faster setup, adjustment, and troubleshooting.
- Advanced control features enable automation, optimization, and customization of bending processes to meet specific application requirements and production goals.
- Maintenance and Upgrades:
- Regular maintenance and calibration of bending machine controls are necessary to ensure accurate and reliable operation.
- Upgrading controls with the latest software updates, firmware upgrades, or hardware improvements can enhance functionality, performance, and compatibility with evolving manufacturing needs and technologies.
In conclusion, bending machine controls are essential components that enable operators to program, control, and optimize bending operations for achieving desired bending results efficiently and accurately. Understanding the functions, types, features, importance, and maintenance requirements of bending machine controls is essential for maximizing productivity and quality in tube bending applications.
Safety Interlocks:
Safety interlocks are critical components of tube bending machines designed to protect operators, equipment, and materials from potential hazards during bending operations. Let’s explore the functions, types, features, and importance of safety interlocks in tube bending machines:
- Functionality:
- The primary function of safety interlocks is to prevent or mitigate accidents, injuries, and damage by ensuring that specific safety conditions are met before allowing the bending machine to operate.
- Safety interlocks may include physical barriers, sensors, switches, and software controls that detect unsafe conditions and interrupt machine operation to prevent hazards.
- Types of Safety Interlocks:
- Physical Barriers: Physical barriers, such as guards, shields, and enclosures, are installed around hazardous areas of the bending machine to prevent operator access during operation. Interlocks may be integrated into these barriers to disable machine functions when the barriers are opened or removed.
- Emergency Stop (E-stop) Systems: Emergency stop systems provide a quick and effective means of stopping machine operation in emergency situations. E-stop buttons or switches are located within easy reach of operators and instantly halt machine motion when activated.
- Safety Sensors: Safety sensors, such as light curtains, laser scanners, and pressure mats, detect the presence of operators or objects in hazardous areas and trigger machine shutdown if an intrusion is detected.
- Two-Hand Control Systems: Two-hand control systems require operators to use both hands simultaneously to activate machine functions, ensuring that operators maintain a safe distance from moving parts during operation.
- Features and Capabilities:
- Integration with Machine Controls: Safety interlocks integrate with the machine’s control system to monitor safety conditions and control machine operation. They may include programmable logic controllers (PLCs) or dedicated safety controllers for logic processing.
- Self-Checking and Monitoring: Some safety interlocks feature self-checking and diagnostic capabilities to verify proper operation and detect faults or malfunctions. They may include redundant sensors or feedback mechanisms to ensure reliability.
- Configurability: Safety interlocks may be configurable to adapt to different bending applications, safety standards, and operating environments. Operators may adjust sensitivity, response times, and other parameters to optimize safety performance.
- Importance:
- Safety interlocks are essential for protecting operators from injury and preventing damage to equipment and materials in tube bending operations.
- Compliance with safety regulations and standards, such as OSHA (Occupational Safety and Health Administration) regulations or ISO (International Organization for Standardization) safety standards, is facilitated by implementing effective safety interlock systems.
- By minimizing the risk of accidents and downtime, safety interlocks contribute to improved productivity, efficiency, and overall workplace safety culture.
- Maintenance and Testing:
- Regular maintenance, inspection, and testing of safety interlocks are necessary to ensure proper functioning and compliance with safety standards.
- Maintenance tasks may include cleaning, lubrication, adjustment, and replacement of components as needed to maintain reliability and performance.
- Periodic testing and validation of safety interlocks help identify potential issues and ensure that safety systems operate as intended in emergency situations.
In conclusion, safety interlocks are essential safety features of tube bending machines, providing protection against hazards and ensuring operator safety during bending operations. Understanding the functions, types, features, importance, and maintenance requirements of safety interlocks is crucial for creating a safe and productive working environment in tube bending applications.
Tube Measurement Systems:
Tube measurement systems are integral components of tube bending machines, enabling precise measurement of tube dimensions and alignment to ensure accurate and consistent bending results. Let’s delve into the functions, types, features, and importance of tube measurement systems:
- Functionality:
- Tube measurement systems are designed to accurately measure key parameters of the tube, including length, diameter, wall thickness, and straightness, before and after bending.
- These systems provide feedback to operators and machine controls, allowing for adjustments to bending parameters to compensate for variations in tube dimensions and ensure the desired bending outcome.
- Types of Tube Measurement Systems:
- Contact Measurement Systems: Contact measurement systems utilize physical probes, calipers, or micrometers to directly measure tube dimensions by making physical contact with the tube surface. They are precise but may require manual intervention and can potentially damage delicate surfaces.
- Non-Contact Measurement Systems: Non-contact measurement systems employ optical, laser, or vision-based technologies to measure tube dimensions without touching the surface. These systems offer high accuracy, fast measurement speeds, and non-destructive testing capabilities.
- Combination Systems: Some tube bending machines incorporate a combination of contact and non-contact measurement systems to leverage the advantages of both approaches. For example, a contact measurement system may be used for precise measurements of critical dimensions, while a non-contact system may be employed for rapid inspection of overall tube geometry.
- Features and Capabilities:
- Accuracy and Precision: Tube measurement systems offer high accuracy and precision, ensuring that bent tubes meet tight tolerances and dimensional specifications.
- Real-Time Feedback: Measurement systems provide real-time feedback to operators and machine controls, allowing for immediate adjustments to bending parameters to maintain dimensional accuracy and consistency.
- Automated Data Recording: Some measurement systems automatically record measurement data, providing documentation and traceability for quality assurance purposes and facilitating process optimization and analysis.
- Alignment Correction: Advanced measurement systems may include features for detecting and correcting tube misalignment or distortion before bending, reducing scrap and rework.
- Importance:
- Tube measurement systems are critical for achieving accurate and consistent bending results, particularly in applications where tight tolerances and precise dimensions are required.
- By providing real-time feedback and control, measurement systems help minimize scrap, rework, and material waste, improving productivity and reducing production costs.
- Measurement data captured by these systems can be used for quality control, process optimization, and compliance with regulatory requirements, enhancing overall manufacturing efficiency and competitiveness.
- Maintenance and Calibration:
- Regular maintenance and calibration of tube measurement systems are essential to ensure accurate and reliable performance.
- Maintenance tasks may include cleaning, calibration verification, sensor alignment, and software updates to maintain optimal functionality.
- Calibration should be performed at regular intervals according to manufacturer recommendations or industry standards to maintain traceability and compliance with quality requirements.
In conclusion, tube measurement systems are essential components of tube bending machines, providing accurate and reliable measurement of tube dimensions to ensure precise and consistent bending results. Understanding the functions, types, features, importance, and maintenance requirements of tube measurement systems is crucial for achieving high-quality and efficient tube bending in industrial applications.
Pressure Die:
The pressure die is a crucial component of tube bending machines, providing support and control to the outer surface of the tube or pipe during the bending process. Let’s explore the functions, types, features, and importance of the pressure die in tube bending:
- Functionality:
- The primary function of the pressure die is to exert controlled force against the outer surface of the tube or pipe being bent, preventing distortion, wrinkling, or collapse during the bending process.
- By supporting the tube or pipe against the bending radius, the pressure die helps maintain the desired cross-sectional shape and dimensional accuracy of the bent part.
- Types of Pressure Dies:
- Fixed Pressure Die: Fixed pressure dies are stationary components positioned at a predetermined distance from the bending die. They provide consistent support and pressure against the tube or pipe throughout the bending cycle.
- Spring-Loaded Pressure Die: Spring-loaded pressure dies feature a mechanism that allows them to retract or compress against the tube during bending, accommodating variations in tube diameter, wall thickness, and material properties. They provide flexibility and adaptability to different bending applications.
- Multi-Radius Pressure Die: Multi-radius pressure dies incorporate multiple radii or profiles to support complex bending geometries, such as compound bends or variable-radius bends. They offer versatility and precision for demanding bending requirements.
- Features and Capabilities:
- Material and Surface Finish: Pressure dies are typically made from hardened steel or other durable materials to withstand high bending forces and abrasion. They may have specialized surface coatings or treatments to reduce friction and wear.
- Adjustability: Some pressure dies feature adjustable or interchangeable components, such as inserts or pads, to accommodate different tube diameters, wall thicknesses, and bend radii.
- Cooling Systems: In high-speed or high-volume bending applications, pressure dies may incorporate cooling systems, such as water jackets or air channels, to dissipate heat generated by friction and maintain consistent bending performance.
- Sensing and Control: Advanced pressure dies may include sensors or load cells to monitor bending forces and provide feedback to machine controls for precise control and optimization of bending parameters.
- Importance:
- The pressure die plays a critical role in ensuring the dimensional accuracy, surface finish, and structural integrity of bent tubes or pipes.
- Proper selection and adjustment of the pressure die are essential for preventing defects such as wrinkling, collapsing, or ovality in the bent part and minimizing scrap and rework.
- By providing uniform support and pressure distribution, the pressure die helps achieve consistent and repeatable bending results, even in challenging bending applications or materials.
- Maintenance and Inspection:
- Regular maintenance and inspection of the pressure die are necessary to ensure proper functioning and performance.
- Maintenance tasks may include cleaning, lubrication, inspection for wear or damage, and adjustment of pressure and positioning mechanisms as needed.
- Inspecting bent parts for defects or inconsistencies can help identify issues with the pressure die and guide corrective actions to improve bending quality and productivity.
In conclusion, the pressure die is a critical component of tube bending machines, providing support and control to the outer surface of the tube or pipe during bending operations. Understanding the functions, types, features, importance, and maintenance requirements of pressure dies is essential for achieving high-quality and efficient tube bending results in industrial applications.
Bending Die:
The bending die is a fundamental component of tube bending machines, responsible for shaping the tube or pipe into the desired bend radius and angle. Let’s explore the functions, types, features, and importance of bending dies in tube bending:
- Functionality:
- The primary function of the bending die is to apply controlled force to the tube or pipe, inducing plastic deformation and forming it into the desired bend geometry.
- Bending dies come in various shapes and sizes to accommodate different bend radii, angles, and tube diameters, allowing for versatility in bending applications.
- Types of Bending Dies:
- Mandrel Dies: Mandrel dies incorporate a mandrel or internal support mechanism inside the tube or pipe to prevent collapse or wrinkling of the inner surface during bending. They are used in applications requiring tight bend radii or thin-walled tubes.
- Wiper Dies: Wiper dies feature a contoured surface that contacts the outer surface of the tube or pipe, providing support and guidance during bending. They are commonly used in rotary draw bending systems to ensure smooth and uniform bending.
- Radius Dies: Radius dies have a fixed radius profile that determines the bend radius of the tube or pipe. They are available in various radii sizes and configurations to accommodate different bending requirements.
- Variable Radius Dies: Variable radius dies allow for the adjustment of the bend radius during bending operations, providing flexibility to create complex bend geometries or gradual transitions between straight and curved sections.
- Features and Capabilities:
- Material and Coating: Bending dies are typically made from high-strength materials such as tool steel or carbide to withstand high bending forces and wear. They may have specialized coatings or surface treatments to reduce friction and extend tool life.
- Interchangeability: Some bending machines feature interchangeable bending die sets, allowing operators to quickly change dies to accommodate different tube sizes, bend radii, or bending configurations.
- Alignment and Guiding: Bending dies may incorporate features such as guides, rollers, or bearings to ensure proper alignment and smooth movement of the tube or pipe during bending, minimizing surface defects and distortion.
- Cooling Systems: In high-speed or high-volume bending applications, bending dies may incorporate cooling systems, such as water jackets or air channels, to dissipate heat generated by friction and maintain consistent bending performance.
- Importance:
- The bending die is critical for achieving the desired bend radius, angle, and dimensional accuracy of bent tubes or pipes.
- Proper selection and setup of the bending die are essential for minimizing defects such as wrinkling, ovality, or springback in the bent part and ensuring high-quality bending results.
- By providing controlled deformation and support, the bending die helps produce consistent and repeatable bends, even in challenging materials or geometries.
- Maintenance and Inspection:
- Regular maintenance and inspection of bending dies are necessary to ensure proper functioning and performance.
- Maintenance tasks may include cleaning, lubrication, inspection for wear or damage, and replacement of worn or damaged components.
- Inspecting bent parts for dimensional accuracy, surface finish, and defects can help identify issues with the bending die and guide corrective actions to improve bending quality and productivity.
In conclusion, the bending die is a critical component of tube bending machines, responsible for shaping tubes or pipes into the desired bend geometry. Understanding the functions, types, features, importance, and maintenance requirements of bending dies is essential for achieving high-quality and efficient tube bending results in industrial applications.
Mandrel:
The mandrel is a crucial component of tube bending machines, especially in applications involving tight bend radii or thin-walled tubing. It provides internal support to the tube during bending, preventing collapse and wrinkling of the inner surface. Let’s explore the functions, types, features, and importance of mandrels in tube bending:
- Functionality:
- The primary function of the mandrel is to support the inner surface of the tube or pipe during bending, preventing deformation, collapse, or wrinkling.
- By maintaining internal support, the mandrel ensures uniform wall thickness and dimensional accuracy of the bent part, particularly in applications with tight bend radii or thin-walled tubing.
- Types of Mandrels:
- Ball Mandrels: Ball mandrels feature a spherical or cylindrical shape with a smooth surface, allowing for easy insertion and movement inside the tube. They are commonly used in rotary draw bending systems for bending small-diameter tubes with tight radii.
- Plug Mandrels: Plug mandrels have a solid cylindrical shape with a tapered or profiled end that conforms to the desired bend geometry. They provide more extensive support along the length of the tube and are suitable for bending larger-diameter tubes or tubes with thicker walls.
- Ball and Link Mandrels: Ball and link mandrels combine the features of ball and plug mandrels, featuring a series of interconnected balls or links that provide flexible support and conformability to varying tube geometries.
- Features and Capabilities:
- Material and Coating: Mandrels are typically made from high-strength materials such as tool steel, stainless steel, or tungsten carbide to withstand bending forces and wear. They may have specialized coatings or surface treatments to reduce friction and improve lubricity.
- Adjustability: Some mandrels feature adjustable or interchangeable components, such as mandrel tips or inserts, to accommodate different tube diameters, wall thicknesses, and bend radii.
- Cooling Systems: In high-speed or high-volume bending applications, mandrels may incorporate cooling systems, such as water channels or air jets, to dissipate heat generated by friction and maintain consistent bending performance.
- Importance:
- Mandrels are essential for achieving high-quality bends, particularly in applications requiring tight tolerances, smooth surfaces, and uniform wall thickness.
- Proper selection and setup of the mandrel are critical for minimizing defects such as wrinkling, ovality, or springback in the bent part and ensuring dimensional accuracy and repeatability.
- By providing internal support and control, the mandrel helps produce consistent and repeatable bends, even in challenging materials or geometries.
- Maintenance and Inspection:
- Regular maintenance and inspection of mandrels are necessary to ensure proper functioning and performance.
- Maintenance tasks may include cleaning, lubrication, inspection for wear or damage, and replacement of worn or damaged components.
- Inspecting bent parts for dimensional accuracy, surface finish, and defects can help identify issues with the mandrel and guide corrective actions to improve bending quality and productivity.
In conclusion, the mandrel is a critical component of tube bending machines, providing internal support and control to prevent collapse and wrinkling of the inner surface during bending. Understanding the functions, types, features, importance, and maintenance requirements of mandrels is essential for achieving high-quality and efficient tube bending results in industrial applications.
Wiper Die:
The wiper die is an essential component in tube bending machines, particularly in rotary draw bending systems. It plays a crucial role in guiding and supporting the outer surface of the tube or pipe during bending, ensuring smooth and uniform deformation. Let’s explore the functions, types, features, and importance of wiper dies in tube bending:
- Functionality:
- The primary function of the wiper die is to provide support and guidance to the outer surface of the tube or pipe as it passes through the bending die during the bending process.
- By exerting controlled pressure against the tube, the wiper die helps prevent wrinkles, surface defects, and out-of-roundness, ensuring high-quality bends with uniform wall thickness.
- Types of Wiper Dies:
- Solid Wiper Dies: Solid wiper dies have a continuous, smooth surface that contacts the tube along its entire length, providing consistent support and guidance during bending. They are suitable for general-purpose bending applications with moderate bend radii and tube diameters.
- Segmented Wiper Dies: Segmented wiper dies feature multiple individual segments or fingers that can move independently to conform to the shape of the tube. They offer greater flexibility and adaptability to varying tube geometries, including complex or asymmetrical shapes.
- Roller Wiper Dies: Roller wiper dies incorporate rolling elements, such as bearings or rollers, that rotate or move along the tube surface during bending. They reduce friction and surface marring, particularly in applications with sensitive or polished tube materials.
- Features and Capabilities:
- Material and Coating: Wiper dies are typically made from hardened steel or other durable materials to withstand bending forces and wear. They may have specialized coatings or surface treatments to reduce friction and improve lubricity.
- Adjustability: Some wiper dies feature adjustable or interchangeable components, such as inserts or pads, to accommodate different tube diameters, wall thicknesses, and bend radii.
- Cooling Systems: In high-speed or high-volume bending applications, wiper dies may incorporate cooling systems, such as water channels or air jets, to dissipate heat generated by friction and maintain consistent bending performance.
- Importance:
- Wiper dies are essential for achieving high-quality bends with smooth surfaces, uniform wall thickness, and minimal distortion.
- Proper selection and setup of the wiper die are critical for minimizing defects such as wrinkles, surface imperfections, or out-of-roundness in the bent part and ensuring dimensional accuracy and repeatability.
- By providing external support and control, the wiper die helps produce consistent and repeatable bends, even in challenging materials or geometries.
- Maintenance and Inspection:
- Regular maintenance and inspection of wiper dies are necessary to ensure proper functioning and performance.
- Maintenance tasks may include cleaning, lubrication, inspection for wear or damage, and replacement of worn or damaged components.
- Inspecting bent parts for dimensional accuracy, surface finish, and defects can help identify issues with the wiper die and guide corrective actions to improve bending quality and productivity.
In conclusion, the wiper die is a critical component of tube bending machines, providing external support and guidance to ensure smooth and uniform deformation of tubes or pipes during bending. Understanding the functions, types, features, importance, and maintenance requirements of wiper dies is essential for achieving high-quality and efficient tube bending results in industrial applications.
Hydraulic System:
The hydraulic system is a fundamental component of tube bending machines, providing the power and control necessary to perform bending operations with precision and efficiency. Let’s explore the functions, types, features, and importance of hydraulic systems in tube bending:
- Functionality:
- The primary function of the hydraulic system is to generate and transmit hydraulic power to actuate the bending mechanisms, including the bending die, pressure die, mandrel (if applicable), and other components of the bending machine.
- Hydraulic systems use fluid pressure to apply force and control the movement of hydraulic cylinders, pistons, or actuators, allowing for precise and controlled bending operations.
- Types of Hydraulic Systems:
- Single-Acting Hydraulic Systems: Single-acting hydraulic systems use hydraulic pressure to actuate a single direction of movement, such as extending a hydraulic cylinder. They are simple, cost-effective, and suitable for basic bending applications with limited bending requirements.
- Double-Acting Hydraulic Systems: Double-acting hydraulic systems can apply hydraulic pressure to actuate both directions of movement, such as extending and retracting a hydraulic cylinder. They offer greater flexibility, control, and power for more complex bending operations and bending machine configurations.
- Hydraulic Power Units (HPUs): Hydraulic power units are standalone systems that include hydraulic pumps, reservoirs, valves, filters, and other components necessary for generating hydraulic power. They can be integrated with tube bending machines or used as standalone units for powering multiple hydraulic actuators or machines.
- Features and Capabilities:
- Pressure and Flow Control: Hydraulic systems feature pressure relief valves, flow control valves, and other components for regulating hydraulic pressure and flow rates, ensuring precise control and safety during bending operations.
- Variable Speed Control: Some hydraulic systems incorporate variable-speed pumps or hydraulic motors to adjust the speed and force of hydraulic actuators, allowing for precise control over bending speeds and forces.
- Integrated Controls: Hydraulic systems may include integrated control panels or interfaces for monitoring hydraulic parameters, adjusting settings, and coordinating bending operations with other machine functions.
- Energy Efficiency: Advanced hydraulic systems may feature energy-efficient components, such as variable-displacement pumps, regenerative circuits, or hydraulic accumulators, to minimize energy consumption and operating costs.
- Importance:
- The hydraulic system is essential for providing the power, control, and precision necessary to perform bending operations accurately and efficiently.
- Hydraulic systems enable tube bending machines to exert precise bending forces, control bending speeds, and maintain consistent bending parameters, resulting in high-quality bends with tight tolerances and minimal distortion.
- By automating bending operations and reducing manual effort, hydraulic systems improve productivity, throughput, and operator safety in tube bending applications.
- Maintenance and Inspection:
- Regular maintenance and inspection of hydraulic systems are essential to ensure proper functioning and performance.
- Maintenance tasks may include checking hydraulic fluid levels, inspecting hoses and fittings for leaks or damage, monitoring hydraulic pressure and temperature, and replacing filters or fluids as needed.
- Periodic testing and calibration of hydraulic components, such as pressure gauges and relief valves, help maintain optimal performance and safety.
In conclusion, the hydraulic system is a critical component of tube bending machines, providing the power, control, and precision necessary for accurate and efficient bending operations. Understanding the functions, types, features, importance, and maintenance requirements of hydraulic systems is essential for achieving high-quality and reliable tube bending results in industrial applications.
Servo Motor:
The servo motor is a key component in modern tube bending machines, offering precise control over bending operations and enhancing overall performance. Let’s explore the functions, features, types, and importance of servo motors in tube bending:
- Functionality:
- The primary function of the servo motor in tube bending machines is to provide controlled motion and positioning of bending components, such as the bending die, pressure die, and mandrel.
- Servo motors convert electrical signals from the machine’s control system into precise mechanical motion, allowing for accurate and repeatable positioning of bending tools and workpieces.
- Features and Capabilities:
- High Precision: Servo motors offer exceptional positional accuracy and repeatability, making them ideal for applications requiring tight tolerances and complex bend geometries.
- Variable Speed Control: Servo motors can operate at variable speeds, allowing for precise control over bending velocities and accelerations. This feature is particularly useful for achieving smooth transitions between bending operations and reducing cycle times.
- Instantaneous Response: Servo motors provide rapid response times to control signals, enabling real-time adjustments to bending parameters and ensuring precise synchronization between bending components.
- Programmability: Servo motors can be programmed to follow specific motion profiles, allowing for customizable bending sequences, multi-axis coordination, and complex motion trajectories.
- Feedback Systems: Many servo motors incorporate feedback devices, such as encoders or resolvers, to provide closed-loop control and feedback on position, velocity, and torque. This feedback ensures accurate motion control and helps compensate for errors or disturbances during bending operations.
- Types of Servo Motors:
- Brushed DC Servo Motors: Brushed DC servo motors are simple and cost-effective solutions for low-power applications requiring precise motion control. They are suitable for small to medium-sized tube bending machines.
- Brushless DC Servo Motors: Brushless DC servo motors offer higher power density, efficiency, and reliability compared to brushed DC motors. They are commonly used in medium to large-sized tube bending machines and offer excellent performance in demanding applications.
- AC Servo Motors: AC servo motors provide high torque and power output, making them suitable for heavy-duty bending applications and high-speed bending operations. They offer superior dynamic performance and energy efficiency.
- Linear Servo Motors: Linear servo motors provide linear motion directly without the need for rotary-to-linear conversion mechanisms. They are used in applications requiring precise linear positioning, such as CNC (Computer Numerical Control) tube bending machines.
- Importance:
- Servo motors play a crucial role in achieving precise, repeatable, and high-quality tube bending results, particularly in applications with stringent dimensional tolerances and complex bend geometries.
- By offering precise motion control and synchronization, servo motors help minimize scrap, rework, and material waste, improving overall production efficiency and cost-effectiveness.
- The versatility and programmability of servo motors enable tube bending machines to adapt to a wide range of bending requirements, from simple bends to complex multi-axis bends, while maintaining consistent quality and productivity.
In conclusion, servo motors are essential components in modern tube bending machines, providing precise motion control and positioning for achieving high-quality and efficient bending operations. Understanding the functions, features, types, and importance of servo motors is crucial for optimizing tube bending processes and achieving superior bending results in industrial applications.
Control System:
The control system in tube bending machines is the central nervous system that governs and coordinates all machine functions, ensuring precise and efficient bending operations. Let’s delve into the functions, features, types, and importance of control systems in tube bending:
- Functionality:
- The primary function of the control system is to interpret user inputs, process bending parameters, and command various machine components, such as servo motors, hydraulic actuators, and safety interlocks, to execute bending operations accurately.
- Control systems monitor and regulate bending parameters such as bend angle, bend radius, bend speed, and material feed rate, ensuring adherence to design specifications and quality standards.
- Advanced control systems may incorporate feedback mechanisms, predictive algorithms, and adaptive controls to optimize bending performance, minimize cycle times, and adapt to changing process conditions in real-time.
- Features and Capabilities:
- User Interface: Control systems feature intuitive user interfaces, such as touchscreen displays or graphical interfaces, for inputting bending parameters, selecting bending programs, and monitoring machine status.
- Programmability: Control systems allow users to create, store, and recall bending programs or recipes for different tube sizes, bend configurations, and material types. This feature facilitates rapid setup and changeover between production runs.
- Diagnostic Tools: Control systems provide diagnostic tools and error reporting capabilities to identify and troubleshoot issues quickly, minimizing downtime and maximizing machine uptime.
- Integration: Control systems may integrate with other manufacturing systems, such as CAD/CAM (Computer-Aided Design/Computer-Aided Manufacturing) software, ERP (Enterprise Resource Planning) systems, or factory automation networks, to streamline production workflows and data exchange.
- Remote Monitoring and Control: Some control systems offer remote monitoring and control capabilities, allowing operators to monitor machine performance, adjust parameters, and troubleshoot issues from remote locations, enhancing flexibility and responsiveness in production environments.
- Types of Control Systems:
- CNC (Computer Numerical Control) Systems: CNC control systems use computerized algorithms and numerical commands to control machine axes and execute bending operations with precision. They are highly versatile and adaptable to a wide range of bending applications, from simple to complex geometries.
- PLC (Programmable Logic Controller) Systems: PLC control systems are commonly used in tube bending machines for basic control functions, such as sequencing machine operations, monitoring inputs and outputs, and implementing safety interlocks.
- Hydraulic Control Systems: Hydraulic control systems manage hydraulic actuators, valves, and pumps to regulate hydraulic pressure, flow rates, and direction of motion during bending operations. They are essential for precise and reliable control of hydraulic components in the bending machine.
- Importance:
- The control system is critical for achieving accurate, repeatable, and high-quality tube bending results while maximizing productivity and efficiency.
- By providing precise control over bending parameters and machine components, control systems help minimize scrap, rework, and material waste, optimizing resource utilization and reducing production costs.
- Advanced control features and capabilities enable tube bending machines to adapt to changing production requirements, accommodate diverse bending applications, and maintain competitiveness in dynamic manufacturing environments.
In conclusion, the control system is the backbone of tube bending machines, orchestrating and optimizing bending operations to achieve precise and efficient results. Understanding the functions, features, types, and importance of control systems is essential for maximizing the performance and capabilities of tube bending machines in industrial applications.
Material Feed System:
The material feed system in tube bending machines is responsible for accurately positioning and feeding the tube or pipe through the bending machine, ensuring precise bending operations. Let’s explore the functions, features, types, and importance of material feed systems in tube bending:
- Functionality:
- The primary function of the material feed system is to position the tube or pipe accurately in relation to the bending die, pressure die, and mandrel (if applicable) to ensure proper bending geometry and dimensional accuracy.
- Material feed systems control the speed, direction, and positioning of the tube or pipe as it enters the bending machine, allowing for precise alignment and synchronization with bending operations.
- Advanced material feed systems may incorporate sensors, actuators, and feedback mechanisms to detect and correct deviations in tube position or alignment during feeding, minimizing errors and optimizing bending quality.
- Features and Capabilities:
- Variable Speed Control: Material feed systems offer variable speed control to adjust the rate of tube feeding according to bending requirements, material properties, and machine capabilities. This feature enables precise control over bending speeds and accelerations, minimizing distortion and optimizing cycle times.
- Automatic Centering: Some material feed systems feature automatic centering mechanisms that align the tube or pipe with the bending die and other bending components, ensuring symmetrical bending and minimizing off-center errors.
- Material Handling: Material feed systems may include additional features for handling and manipulating tubes or pipes before and after bending, such as loading and unloading mechanisms, rotary tables, or conveyor systems.
- Safety Interlocks: Material feed systems incorporate safety interlocks and guarding to prevent accidents and ensure operator safety during tube feeding and bending operations. Safety features may include presence sensors, emergency stop buttons, and protective enclosures.
- Types of Material Feed Systems:
- Push Feed Systems: Push feed systems use mechanical or pneumatic actuators to push the tube or pipe through the bending machine. They are simple, cost-effective solutions suitable for low to medium-speed bending applications.
- Pull Feed Systems: Pull feed systems use gripper jaws, clamps, or rollers to pull the tube or pipe through the bending machine. They offer greater control and stability, particularly for high-speed bending operations and long tube lengths.
- Hydraulic Feed Systems: Hydraulic feed systems use hydraulic actuators to control the movement and positioning of the tube or pipe during feeding. They offer precise control over feeding forces and velocities, making them suitable for demanding bending applications with tight tolerances.
- Importance:
- The material feed system is critical for achieving accurate and repeatable tube bending results by ensuring proper positioning and alignment of the tube or pipe with bending components.
- Precise control over material feeding speeds, positions, and alignments helps minimize errors, scrap, and rework, improving bending quality and productivity.
- Advanced material feed features and capabilities enable tube bending machines to handle a wide range of tube sizes, materials, and bending geometries, enhancing versatility and adaptability in manufacturing environments.
In conclusion, the material feed system is a vital component of tube bending machines, providing precise control over tube positioning and feeding to achieve accurate and efficient bending operations. Understanding the functions, features, types, and importance of material feed systems is essential for optimizing tube bending processes and achieving high-quality bending results in industrial applications.
Bend Angle Measurement System:
The bend angle measurement system in tube bending machines is crucial for ensuring the accuracy and consistency of bent parts by precisely measuring the angle of each bend. Let’s explore the functions, features, types, and importance of bend angle measurement systems in tube bending:
- Functionality:
- The primary function of the bend angle measurement system is to accurately measure the angle of each bend formed in the tube or pipe during the bending process.
- Bend angle measurement systems typically use sensors, encoders, or optical devices to detect the angular position of the tube or bending components relative to a reference point.
- The measured bend angles are compared against target values specified in bending programs or production requirements to verify bending accuracy and ensure dimensional conformity of bent parts.
- Features and Capabilities:
- High Accuracy: Bend angle measurement systems offer high accuracy and resolution, enabling precise measurement of bend angles with tight tolerances.
- Real-Time Feedback: Some bend angle measurement systems provide real-time feedback to the machine control system, allowing for immediate adjustments to bending parameters to correct deviations from target bend angles.
- Multiple Measurement Points: Advanced bend angle measurement systems may include multiple measurement points along the length of the tube or pipe to capture bend angles at different locations, ensuring uniformity and consistency of bending across the entire workpiece.
- Non-Contact Measurement: Non-contact measurement techniques, such as laser sensors or vision systems, eliminate the need for physical contact with the tube or pipe, reducing the risk of damage or contamination to the workpiece.
- Types of Bend Angle Measurement Systems:
- Rotary Encoders: Rotary encoders are commonly used to measure the rotational position of bending components, such as the bending die or mandrel, relative to a reference point. They provide high-resolution angle measurement and are suitable for applications requiring precise control over bend angles.
- Inclinometers: Inclinometers, or tilt sensors, measure the inclination or tilt angle of the tube or bending components relative to the horizontal or vertical axis. They are compact, cost-effective solutions for measuring bend angles and are often integrated directly into bending machine tooling.
- Laser Measurement Systems: Laser measurement systems use laser sensors or scanners to measure the deflection of a laser beam as it interacts with the bent tube or pipe. They offer non-contact measurement, high accuracy, and versatility for measuring bend angles in various tube geometries and materials.
- Importance:
- The bend angle measurement system is critical for verifying bending accuracy, ensuring dimensional conformity, and meeting quality standards for bent parts.
- Accurate bend angle measurement helps minimize scrap, rework, and material waste by identifying deviations from target bend angles and enabling timely adjustments to bending parameters.
- Reliable bend angle measurement ensures consistency and repeatability of bending results, reducing variability in finished parts and enhancing overall product quality and reliability.
In conclusion, the bend angle measurement system is an essential component of tube bending machines, providing accurate and reliable measurement of bend angles to ensure the quality and dimensional accuracy of bent parts. Understanding the functions, features, types, and importance of bend angle measurement systems is crucial for optimizing tube bending processes and achieving high-quality bending results in industrial applications.
Pressure Die:
The pressure die is a critical component of tube bending machines, providing essential support and control during the bending process to ensure accurate and high-quality bends. Let’s explore the functions, features, types, and importance of pressure dies in tube bending:
- Functionality:
- The primary function of the pressure die is to exert controlled pressure against the outer surface of the tube or pipe during bending, preventing flattening, wrinkling, or distortion of the material.
- By providing support and confinement to the outer diameter of the tube, the pressure die helps maintain the roundness and dimensional accuracy of the bent part, particularly in applications with thin-walled tubing or tight bend radii.
- Features and Capabilities:
- Profiled Surface: Pressure dies feature a contoured or profiled surface that matches the curvature of the bending die, ensuring uniform contact and distribution of pressure along the length of the tube during bending.
- Adjustability: Some pressure dies are adjustable or interchangeable to accommodate different tube diameters, wall thicknesses, and bend radii. This feature allows for versatility in bending applications and facilitates quick setup and changeover between production runs.
- Material and Coating: Pressure dies are typically made from hardened steel, carbide, or other wear-resistant materials to withstand bending forces and minimize wear. They may have specialized coatings or surface treatments to reduce friction and improve durability.
- Cooling Systems: In high-speed or high-volume bending applications, pressure dies may incorporate cooling systems, such as water jackets or air channels, to dissipate heat generated by friction and maintain consistent bending performance.
- Types of Pressure Dies:
- Fixed Pressure Dies: Fixed pressure dies have a stationary design and apply constant pressure against the tube throughout the bending process. They are suitable for straightforward bending applications with consistent tube properties and bend requirements.
- Spring-Loaded Pressure Dies: Spring-loaded pressure dies use springs or pneumatic actuators to apply variable pressure against the tube, allowing for compensation of variations in tube diameter, ovality, or material properties. They provide flexibility and adaptability to changing bending conditions.
- Hydraulic Pressure Dies: Hydraulic pressure dies use hydraulic actuators to control the application of pressure against the tube, offering precise control over pressure levels and distribution. They are suitable for demanding bending applications requiring high force and accuracy.
- Importance:
- The pressure die is essential for achieving accurate and high-quality bends by providing support and control to the outer surface of the tube during bending.
- Proper selection and setup of the pressure die are critical for minimizing defects such as flattening, wrinkling, or ovality in the bent part and ensuring dimensional accuracy and repeatability.
- By exerting controlled pressure and confinement, the pressure die helps produce consistent and repeatable bends, even in challenging materials or geometries.
In conclusion, the pressure die is a crucial component of tube bending machines, providing essential support and control to ensure accurate and high-quality bends. Understanding the functions, features, types, and importance of pressure dies is essential for achieving optimal tube bending results in industrial applications.
Bending Die:
The bending die is a core component of tube bending machines, responsible for imparting the desired bend geometry to the tube or pipe. Let’s explore the functions, features, types, and importance of bending dies in tube bending:
- Functionality:
- The primary function of the bending die is to shape the tube or pipe into the desired bend radius and angle during the bending process.
- Bending dies come in various profiles and sizes to accommodate different bend radii, bend angles, and tube diameters, allowing for flexibility in bending applications.
- By providing the bending form, the bending die determines the final shape and dimensional accuracy of the bent part.
- Features and Capabilities:
- Profiled Surface: Bending dies feature a contoured or profiled surface that matches the desired bend geometry, ensuring uniform deformation and consistent bend quality.
- Material and Coating: Bending dies are typically made from hardened steel, tool steel, or carbide to withstand bending forces and minimize wear. They may have specialized coatings or surface treatments, such as chrome plating or nitriding, to improve durability and reduce friction.
- Adjustability: Some bending dies are adjustable or interchangeable to accommodate different bend radii, angles, and tube sizes. This feature allows for versatility in bending applications and facilitates quick setup and changeover between production runs.
- Multi-Stack Capability: Advanced bending dies may incorporate multiple stackable segments or inserts, allowing for the creation of complex bend profiles and multi-radius bends in a single operation.
- Types of Bending Dies:
- Rotary Draw Dies: Rotary draw bending dies are commonly used in rotary draw tube bending machines. They feature a fixed or rotating profiled surface against which the tube is bent using a bending arm or mandrel. Rotary draw dies offer precise control over bend radii and angles and are suitable for tight-radius bends and complex geometries.
- Wiper Dies: Wiper dies provide support and guidance to the outer surface of the tube during bending, ensuring smooth deformation and minimizing surface imperfections. They are often used in conjunction with rotary draw dies to improve bend quality and consistency.
- Compression Bending Dies: Compression bending dies compress the tube along its inside radius while bending, allowing for tighter bend radii and reducing wrinkling or distortion of the outer surface. They are commonly used in CNC (Computer Numerical Control) tube bending machines for producing tight-radius bends in thin-walled tubing.
- Importance:
- The bending die is crucial for achieving accurate and repeatable bends in tube or pipe, determining the final shape and dimensional accuracy of the bent part.
- Proper selection and setup of the bending die are essential for minimizing defects such as ovality, wrinkling, or springback in the bent part and ensuring dimensional consistency and repeatability.
- By providing the bending form, the bending die enables tube bending machines to produce a wide range of bend profiles and geometries to meet diverse application requirements.
In conclusion, the bending die is a fundamental component of tube bending machines, shaping the tube or pipe into the desired bend geometry with precision and accuracy. Understanding the functions, features, types, and importance of bending dies is essential for achieving optimal tube bending results in industrial applications.
Mandrel:
The mandrel is a crucial component in tube bending machines, especially for bending applications requiring tight radii, preventing tube deformation, and maintaining bend quality. Let’s delve into the functions, features, types, and importance of mandrels in tube bending:
- Functionality:
- The primary function of the mandrel is to support the inner radius of the tube during bending, preventing collapse, wrinkling, or ovality and maintaining the roundness and dimensional accuracy of the bent part.
- Mandrels exert inward pressure against the inner surface of the tube or pipe, counteracting the compressive forces generated during bending and ensuring uniform deformation and bend quality.
- By providing internal support, the mandrel allows for tighter bend radii, reduced wall thinning, and improved surface finish in bent parts, particularly in thin-walled or delicate materials.
- Features and Capabilities:
- Profiled Design: Mandrels feature a contoured or profiled surface that matches the desired bend geometry, ensuring uniform support and contact along the inner radius of the tube.
- Material and Coating: Mandrels are typically made from hardened steel, tool steel, or other wear-resistant materials to withstand bending forces and minimize wear. They may have specialized coatings or surface treatments, such as chrome plating or Teflon coating, to reduce friction and prevent material adhesion.
- Adjustability: Some mandrels are adjustable or interchangeable to accommodate different tube diameters, wall thicknesses, and bend radii. This feature allows for versatility in bending applications and facilitates quick setup and changeover between production runs.
- Support Structures: Mandrels may incorporate support structures, such as ball bearings, rollers, or sliding sleeves, to reduce friction, enhance stability, and facilitate smooth movement within the tube during bending.
- Types of Mandrels:
- Ball Mandrels: Ball mandrels consist of a spherical or cylindrical ball mounted on a shaft or spindle. They provide point contact with the inner surface of the tube and are suitable for applications requiring tight bend radii and minimal wall thinning.
- Plug Mandrels: Plug mandrels feature a solid or hollow cylindrical design that inserts into the tube or pipe during bending. They offer uniform support along the entire length of the bend and are suitable for applications with longer bending lengths or heavier wall thicknesses.
- Floating Mandrels: Floating mandrels incorporate a flexible or articulated design that allows for radial movement or deflection within the tube during bending. They are useful for bending applications with complex geometries or variable wall thicknesses, minimizing mandrel interference and improving bend quality.
- Importance:
- The mandrel is essential for achieving accurate and high-quality bends by providing internal support and preventing deformation of the tube or pipe during bending.
- Proper selection and setup of the mandrel are critical for minimizing defects such as collapse, wrinkling, or ovality in the bent part and ensuring dimensional accuracy and repeatability.
- By supporting the inner radius, the mandrel enables tube bending machines to produce tight-radius bends, thin-walled tubing, and complex geometries with consistent quality and reliability.
In conclusion, the mandrel is a vital component of tube bending machines, providing essential support and control to ensure accurate and high-quality bends in tube or pipe. Understanding the functions, features, types, and importance of mandrels is essential for achieving optimal tube bending results in industrial applications.
Wiper Die:
The wiper die is a critical component in tube bending machines, working in conjunction with the bending die to improve bend quality and reduce surface imperfections. Let’s explore the functions, features, types, and importance of wiper dies in tube bending:
- Functionality:
- The primary function of the wiper die is to support and guide the outer surface of the tube or pipe during bending, ensuring smooth deformation and minimizing surface imperfections such as wrinkles, scratches, or gouges.
- Wiper dies apply pressure against the outer surface of the tube, smoothing out irregularities and providing additional support to prevent distortion or ovality during bending.
- By working in tandem with the bending die, the wiper die helps produce uniform and consistent bends with improved surface finish and dimensional accuracy.
- Features and Capabilities:
- Profiled Surface: Wiper dies feature a contoured or profiled surface that matches the curvature of the bending die, ensuring uniform contact and distribution of pressure along the length of the tube during bending.
- Material and Coating: Wiper dies are typically made from hardened steel, tool steel, or carbide to withstand bending forces and minimize wear. They may have specialized coatings or surface treatments, such as chrome plating or nitriding, to improve durability and reduce friction.
- Adjustability: Some wiper dies are adjustable or interchangeable to accommodate different bend radii, angles, and tube sizes. This feature allows for versatility in bending applications and facilitates quick setup and changeover between production runs.
- Cooling Systems: In high-speed or high-volume bending applications, wiper dies may incorporate cooling systems, such as water jackets or air channels, to dissipate heat generated by friction and maintain consistent bending performance.
- Types of Wiper Dies:
- Roller Wiper Dies: Roller wiper dies feature one or more rollers that apply pressure against the outer surface of the tube or pipe, smoothing out wrinkles and irregularities during bending. They offer uniform support and are suitable for a wide range of tube sizes and materials.
- Shoe Wiper Dies: Shoe wiper dies consist of a contoured shoe or pad that presses against the outer surface of the tube, providing broad contact and support during bending. They are often used in conjunction with roller wiper dies to improve surface finish and reduce friction.
- Floating Wiper Dies: Floating wiper dies incorporate a flexible or articulated design that allows for radial movement or deflection during bending. They minimize marking or marring of the tube surface and are suitable for delicate or polished materials requiring gentle handling.
- Importance:
- The wiper die is essential for improving bend quality, reducing surface imperfections, and enhancing the appearance and performance of bent parts.
- Proper selection and setup of the wiper die are critical for minimizing defects such as scratches, gouges, or wrinkles in the bent part and ensuring dimensional accuracy and repeatability.
- By providing additional support and smoothing out irregularities, the wiper die helps produce consistent and repeatable bends with improved surface finish and aesthetic appeal.
In conclusion, the wiper die is a fundamental component of tube bending machines, working in tandem with the bending die to improve bend quality and reduce surface imperfections. Understanding the functions, features, types, and importance of wiper dies is essential for achieving optimal tube bending results in industrial applications.
Clamp Die:
The clamp die is a critical component in tube bending machines, responsible for securely holding the tube or pipe in place during the bending process. Let’s explore the functions, features, types, and importance of clamp dies in tube bending:
- Functionality:
- The primary function of the clamp die is to provide a secure grip on the tube or pipe to prevent movement or slippage during bending.
- Clamp dies hold the tube firmly in position relative to the bending die, pressure die, and mandrel (if applicable), ensuring accurate alignment and consistent bend geometry.
- By maintaining proper clamping force and alignment, the clamp die helps produce uniform and repeatable bends with minimal distortion or deviation from desired specifications.
- Features and Capabilities:
- Jaw Design: Clamp dies feature jaws or clamping surfaces that engage with the outer surface of the tube or pipe, applying sufficient pressure to hold it securely in place without causing damage.
- Adjustability: Some clamp dies are adjustable or interchangeable to accommodate different tube diameters, wall thicknesses, and bend radii. This feature allows for versatility in bending applications and facilitates quick setup and changeover between production runs.
- Material and Coating: Clamp dies are typically made from hardened steel, tool steel, or carbide to withstand clamping forces and minimize wear. They may have specialized coatings or surface treatments, such as chrome plating or nitriding, to improve durability and reduce friction.
- Actuation Mechanisms: Clamp dies may incorporate manual, pneumatic, hydraulic, or electric actuation mechanisms to apply clamping force quickly and consistently. Some systems may include sensors or feedback devices to monitor clamping pressure and ensure proper engagement.
- Types of Clamp Dies:
- Vise-Style Clamp Dies: Vise-style clamp dies feature two opposing jaws that close together to grip the tube or pipe securely. They offer strong and reliable clamping force and are suitable for a wide range of tube sizes and materials.
- Collet-Style Clamp Dies: Collet-style clamp dies use a set of nested or expanding collets to grip the tube from the inside, providing uniform clamping pressure along the entire circumference. They are particularly useful for thin-walled tubing or delicate materials requiring gentle handling.
- Hydraulic Clamp Dies: Hydraulic clamp dies use hydraulic actuators to apply precise and adjustable clamping force to the tube. They offer high clamping force and control and are suitable for heavy-duty bending applications or high-speed production environments.
- Importance:
- The clamp die is essential for maintaining tube stability and alignment during bending, ensuring accurate and repeatable bend geometry.
- Proper selection and setup of the clamp die are critical for minimizing defects such as slippage, misalignment, or distortion in the bent part and ensuring dimensional accuracy and repeatability.
- By providing secure clamping, the clamp die helps produce consistent and high-quality bends, reducing scrap, rework, and production costs.
In conclusion, the clamp die is a vital component of tube bending machines, providing essential clamping force and stability to ensure accurate and repeatable bends. Understanding the functions, features, types, and importance of clamp dies is essential for achieving optimal tube bending results in industrial applications.
Mandrel Lubrication System:
The mandrel lubrication system is a critical component of tube bending machines, responsible for ensuring smooth operation of the mandrel and minimizing friction between the mandrel and the inner surface of the tube during bending. Let’s explore the functions, features, types, and importance of mandrel lubrication systems in tube bending:
- Functionality:
- The primary function of the mandrel lubrication system is to apply a lubricant to the mandrel surface, reducing friction and preventing galling or scoring of the tube’s inner surface during bending.
- By reducing friction, the lubrication system helps prolong the life of the mandrel, minimize wear on bending tooling, and improve bend quality by preventing surface defects such as scratches or gouges.
- Proper lubrication also enhances bending efficiency, reduces energy consumption, and ensures consistent performance of the tube bending machine.
- Features and Capabilities:
- Lubricant Delivery: Mandrel lubrication systems may utilize various methods for delivering lubricant to the mandrel surface, including spray nozzles, drip feeders, or brush applicators. The lubricant is typically applied directly to the mandrel just before it enters the tube.
- Lubricant Type: The lubricant used in mandrel lubrication systems can vary depending on the application requirements and material compatibility. Common lubricants include oil-based lubricants, water-soluble lubricants, and dry lubricants such as graphite or molybdenum disulfide.
- Adjustability: Some mandrel lubrication systems allow for adjustable flow rates, spray patterns, or lubricant types to accommodate different tube materials, wall thicknesses, and bending conditions.
- Monitoring and Control: Advanced mandrel lubrication systems may incorporate monitoring and control features to ensure proper lubricant application and prevent over-lubrication or under-lubrication. This can include sensors, flow meters, or automated control systems.
- Types of Mandrel Lubrication Systems:
- Manual Lubrication Systems: Manual mandrel lubrication systems require operators to apply lubricant to the mandrel surface manually, either using a spray bottle, brush, or applicator. While simple and inexpensive, manual systems may be prone to inconsistency and require frequent monitoring and adjustment.
- Automatic Lubrication Systems: Automatic mandrel lubrication systems are integrated into the tube bending machine and operate automatically during bending cycles. They provide consistent and precise lubricant application, reducing operator intervention and ensuring uniform lubrication across all bending operations.
- Centralized Lubrication Systems: Centralized lubrication systems supply lubricant to multiple components of the tube bending machine, including the mandrel, bending dies, and clamp dies, from a centralized reservoir or distribution system. They offer efficiency, convenience, and centralized control over lubrication processes.
- Importance:
- The mandrel lubrication system is essential for minimizing friction and wear on the mandrel and tube during bending, ensuring smooth operation and high-quality bends.
- Proper lubrication helps prevent surface defects such as scratches, scoring, or galling on the inner surface of the tube, improving bend quality and appearance.
- By reducing friction, the mandrel lubrication system enhances bending efficiency, prolongs tooling life, and minimizes energy consumption, leading to cost savings and increased productivity.
In conclusion, the mandrel lubrication system plays a critical role in tube bending machines, ensuring smooth operation, minimizing friction, and improving bend quality. Understanding the functions, features, types, and importance of mandrel lubrication systems is essential for optimizing tube bending processes and achieving high-quality bends in industrial applications.
Bend Radius Compensation System:
The bend radius compensation system is a crucial feature in tube bending machines, designed to ensure accurate bending results by compensating for material springback and achieving the desired final bend radius. Let’s delve into the functions, features, types, and importance of bend radius compensation systems in tube bending:
- Functionality:
- The primary function of the bend radius compensation system is to adjust the bending process to compensate for material springback, which occurs when the tube or pipe attempts to return to its original shape after bending.
- By applying additional bending force or extending the bending cycle, the compensation system counteracts material springback, allowing the bent part to achieve the desired final bend radius accurately.
- Bend radius compensation systems help ensure dimensional accuracy, consistency, and repeatability of bent parts, particularly in applications with tight tolerances or critical bend requirements.
- Features and Capabilities:
- Springback Prediction: Advanced bend radius compensation systems may incorporate algorithms or models to predict the amount of material springback based on factors such as material properties, tube geometry, and bending parameters.
- Adjustable Parameters: Bend radius compensation systems allow operators to adjust various parameters, such as bending force, mandrel position, or bend angle, to fine-tune the bending process and achieve the desired final bend radius.
- Real-Time Feedback: Some compensation systems provide real-time feedback during the bending process, monitoring key variables such as mandrel pressure, tube position, and bend angle, and making automatic adjustments to ensure accurate compensation for springback.
- Multi-Step Bending: In complex bending applications, bend radius compensation systems may coordinate multi-step bending sequences, including pre-bending, over-bending, or springback correction, to achieve precise final bend geometries.
- Types of Bend Radius Compensation Systems:
- Manual Compensation: Manual bend radius compensation systems require operators to adjust bending parameters based on their experience or empirical data to compensate for material springback. While simple and cost-effective, manual systems may be prone to inconsistency and require skilled operators.
- Programmable Compensation: Programmable bend radius compensation systems use predefined bending programs or algorithms to automatically adjust bending parameters based on input parameters such as material type, tube size, bend radius, and bend angle. They offer accuracy, repeatability, and ease of use.
- Closed-Loop Compensation: Closed-loop bend radius compensation systems incorporate sensors, actuators, and feedback mechanisms to continuously monitor bending parameters and dynamically adjust the bending process in real-time to compensate for material springback. They offer the highest level of accuracy and control, particularly in demanding or high-speed bending applications.
- Importance:
- The bend radius compensation system is essential for achieving accurate and repeatable bend geometries by compensating for material springback and ensuring dimensional conformity of bent parts.
- Proper compensation for springback helps minimize errors, scrap, and rework in tube bending operations, improving productivity, efficiency, and overall product quality.
- Bend radius compensation systems enable tube bending machines to handle a wide range of materials, geometries, and bend requirements with precision and reliability, enhancing versatility and adaptability in manufacturing environments.
In conclusion, the bend radius compensation system is a critical feature in tube bending machines, ensuring accurate and consistent bend geometries by compensating for material springback. Understanding the functions, features, types, and importance of bend radius compensation systems is essential for optimizing tube bending processes and achieving high-quality bends in industrial applications.
Electro-Hydraulic System:
The electro-hydraulic system is a key component in modern tube bending machines, providing precise control over hydraulic actuators and other hydraulic functions through electrical signals. Let’s explore the functions, features, types, and importance of electro-hydraulic systems in tube bending:
- Functionality:
- The primary function of the electro-hydraulic system is to convert electrical signals into hydraulic power, controlling various hydraulic components such as cylinders, valves, pumps, and motors in the tube bending machine.
- By combining the advantages of hydraulic power with electronic control, the electro-hydraulic system offers precise and responsive operation, allowing for accurate positioning, speed control, force regulation, and synchronization of bending operations.
- Electro-hydraulic systems enable advanced automation, integration with CNC (Computer Numerical Control) systems, and programmable control of bending parameters, enhancing productivity, flexibility, and quality in tube bending applications.
- Features and Capabilities:
- Proportional Control: Electro-hydraulic systems utilize proportional valves or servo valves to regulate hydraulic flow and pressure precisely, providing smooth and accurate control over bending forces, speeds, and positions.
- Closed-Loop Feedback: Some electro-hydraulic systems incorporate sensors, encoders, or load cells to provide closed-loop feedback on bending parameters, allowing for real-time monitoring, adjustment, and compensation to maintain desired performance and accuracy.
- Programmable Logic: Electro-hydraulic systems may include programmable logic controllers (PLCs) or microprocessor-based control units to execute predefined bending programs, sequences, or algorithms, enabling automated operation and adaptability to varying production requirements.
- Integration with CNC Systems: Electro-hydraulic systems can interface with CNC systems or other control devices to synchronize bending operations with part programs, CAD/CAM software, or production databases, facilitating seamless integration into manufacturing workflows.
- Types of Electro-Hydraulic Systems:
- Open-loop Systems: Open-loop electro-hydraulic systems operate without feedback control, relying on predefined input signals or commands to regulate hydraulic functions. They are simple, cost-effective solutions suitable for basic bending applications with less stringent accuracy requirements.
- Closed-loop Systems: Closed-loop electro-hydraulic systems incorporate feedback sensors or devices to monitor hydraulic performance and adjust control parameters in real-time, ensuring precise and consistent bending results. They offer higher accuracy, repeatability, and versatility for demanding bending applications.
- Proportional Hydraulic Systems: Proportional electro-hydraulic systems utilize proportional valves or servo valves to modulate hydraulic flow and pressure in proportion to electrical input signals, providing smooth, responsive, and accurate control over bending forces and movements.
- Importance:
- The electro-hydraulic system plays a crucial role in tube bending machines, providing precise and responsive control over hydraulic functions to achieve accurate and repeatable bending results.
- By combining hydraulic power with electronic control, electro-hydraulic systems offer versatility, flexibility, and adaptability to varying bending requirements, materials, and geometries.
- Electro-hydraulic systems enable advanced automation, integration with CNC systems, and programmable control of bending parameters, enhancing productivity, efficiency, and quality in tube bending operations.
In conclusion, the electro-hydraulic system is a vital component of modern tube bending machines, providing precise control over hydraulic functions and enabling advanced automation and integration capabilities. Understanding the functions, features, types, and importance of electro-hydraulic systems is essential for optimizing tube bending processes and achieving high-quality bends in industrial applications.
Safety Interlock System:
The safety interlock system is a critical feature in tube bending machines, designed to enhance operator safety and prevent accidents during machine operation. Let’s explore the functions, features, types, and importance of safety interlock systems in tube bending:
- Functionality:
- The primary function of the safety interlock system is to prevent unauthorized access to hazardous areas of the tube bending machine and to ensure that operators follow proper safety procedures during machine setup, operation, and maintenance.
- Safety interlock systems use sensors, switches, or other devices to detect the presence or position of operators, machine components, or workpieces, and to control access to machine functions accordingly.
- By enforcing safety protocols and interlocking critical machine functions, the safety interlock system helps reduce the risk of accidents, injuries, and damage to equipment or property.
- Features and Capabilities:
- Access Control: Safety interlock systems restrict access to machine controls, tooling, and moving parts, preventing operators from entering hazardous areas or performing unsafe actions while the machine is in operation.
- Emergency Stop: Safety interlock systems include emergency stop buttons or switches that immediately halt machine operation in case of an emergency, allowing operators to quickly stop the machine and prevent accidents or injuries.
- Door Interlocks: Some safety interlock systems incorporate door interlocks or safety gates that prevent machine operation when access doors or panels are open, ensuring that operators cannot reach into the machine’s working area while it is running.
- Position Monitoring: Safety interlock systems may monitor the position or movement of machine components, such as the bending arm, clamp dies, or mandrel, to ensure that they are in a safe position before allowing machine operation to proceed.
- Types of Safety Interlock Systems:
- Mechanical Interlocks: Mechanical safety interlock systems use physical barriers, such as guards, covers, or safety fences, to prevent access to hazardous areas and to ensure that machine components are properly positioned before operation.
- Electrical Interlocks: Electrical safety interlock systems use electrical signals or switches to control machine functions and to detect the presence or position of operators, workpieces, or machine components. They may include sensors, limit switches, or proximity switches to monitor machine status and enforce safety protocols.
- Programmable Interlocks: Programmable safety interlock systems utilize programmable logic controllers (PLCs) or microprocessor-based control units to implement complex safety protocols, logic, and interlocking sequences. They offer flexibility, adaptability, and customization options to suit specific safety requirements and application scenarios.
- Importance:
- The safety interlock system is essential for protecting operators, preventing accidents, and ensuring compliance with safety regulations and standards in tube bending operations.
- Proper implementation of safety interlock systems helps reduce the risk of injuries, damage to equipment, and production downtime due to accidents or incidents in industrial environments.
- Safety interlock systems promote a safe working environment, instill confidence in operators, and contribute to overall productivity, efficiency, and morale in manufacturing facilities.
In conclusion, the safety interlock system is a fundamental feature of tube bending machines, providing critical safety functions to protect operators, prevent accidents, and ensure compliance with safety regulations. Understanding the functions, features, types, and importance of safety interlock systems is essential for maintaining a safe and productive working environment in tube bending operations.
Bend Angle Measurement System:
The bend angle measurement system is a key component in tube bending machines, providing accurate measurement and control of bend angles to ensure precise bending results. Let’s explore the functions, features, types, and importance of bend angle measurement systems in tube bending:
- Functionality:
- The primary function of the bend angle measurement system is to measure the angle of the bent tube or pipe accurately during the bending process.
- Bend angle measurement systems use sensors, encoders, or other devices to detect the position or movement of the bending arm, mandrel, or tube, and to calculate the bend angle based on the change in position or displacement.
- By providing real-time feedback on bend angles, the measurement system allows operators to monitor and adjust bending parameters to achieve the desired bend geometry and dimensional accuracy.
- Features and Capabilities:
- Accuracy: Bend angle measurement systems offer high accuracy and repeatability, ensuring precise measurement of bend angles within tight tolerances.
- Real-Time Monitoring: Measurement systems provide real-time monitoring of bend angles during the bending process, allowing operators to detect deviations from target angles and make immediate adjustments to maintain quality and consistency.
- Data Logging: Some measurement systems include data logging capabilities to record bend angle measurements, process parameters, and production data for quality control, analysis, and documentation purposes.
- Integration with Control Systems: Measurement systems can interface with CNC (Computer Numerical Control) systems or other control devices to synchronize bend angle measurement with bending operations, enabling automated control and optimization of bending processes.
- Types of Bend Angle Measurement Systems:
- Encoder-Based Systems: Encoder-based measurement systems use rotary encoders or linear encoders to track the movement of machine components such as the bending arm or mandrel and to calculate bend angles based on angular or linear displacement.
- Inclinometer Systems: Inclinometer-based measurement systems use inclinometers or tilt sensors to measure the inclination or tilt of the bent tube or pipe relative to a reference plane, providing accurate bend angle measurements without direct contact with the tube.
- Laser Measurement Systems: Laser-based measurement systems project a laser beam onto the surface of the bent tube or pipe and measure the reflected beam to determine the bend angle. They offer non-contact measurement and high accuracy, especially for complex geometries or reflective materials.
- Importance:
- The bend angle measurement system is essential for ensuring dimensional accuracy, consistency, and quality in tube bending operations.
- Accurate measurement of bend angles allows operators to verify bend geometry, detect deviations from specifications, and make necessary adjustments to achieve desired results.
- Measurement systems enable process optimization, quality control, and documentation of bending parameters, contributing to overall productivity, efficiency, and customer satisfaction.
In conclusion, the bend angle measurement system is a critical component of tube bending machines, providing accurate measurement and control of bend angles to ensure precise bending results. Understanding the functions, features, types, and importance of bend angle measurement systems is essential for optimizing tube bending processes and achieving high-quality bends in industrial applications.
Tube Feeding System:
The tube feeding system is an integral part of tube bending machines, responsible for accurately positioning and feeding the tube or pipe into the bending area for processing. Let’s delve into the functions, features, types, and importance of tube feeding systems in tube bending:
- Functionality:
- The primary function of the tube feeding system is to advance the tube or pipe into the bending area with precision and consistency, ensuring proper alignment and engagement with bending dies and tooling.
- Tube feeding systems control the movement of the tube along its longitudinal axis, facilitating accurate positioning for bending operations and minimizing material waste or errors due to misalignment or improper feeding.
- By providing controlled and uniform feeding of the tube, the feeding system enables efficient bending cycles, reduces setup time, and enhances productivity in tube bending processes.
- Features and Capabilities:
- Material Handling: Tube feeding systems are capable of handling various types of tubing materials, including stainless steel, aluminum, copper, and titanium, with different diameters, wall thicknesses, and surface finishes.
- Feeding Mechanisms: Feeding systems may utilize different mechanisms for advancing the tube, such as grippers, rollers, belts, or chain conveyors, depending on the material properties, bend requirements, and production environment.
- Adjustability: Some feeding systems offer adjustable feed rates, stroke lengths, and positioning accuracy to accommodate different tube sizes, bend radii, and bending sequences. This feature allows for versatility and flexibility in bending operations.
- Integration with Control Systems: Feeding systems can interface with CNC (Computer Numerical Control) systems or other control devices to synchronize tube feeding with bending operations, enabling automated setup, operation, and optimization of bending processes.
- Types of Tube Feeding Systems:
- Roller Feed Systems: Roller feed systems use sets of powered or gravity-fed rollers to grip and advance the tube along its length, providing smooth and continuous feeding with minimal friction or distortion. They are suitable for handling long lengths of tubing and materials with smooth surfaces.
- Gripper Feed Systems: Gripper feed systems utilize pneumatic, hydraulic, or mechanical grippers to clamp onto the tube and move it incrementally into the bending area. They offer precise positioning and control, making them ideal for applications requiring high accuracy and repeatability.
- Belt Conveyor Systems: Belt conveyor systems use flexible belts or bands to convey the tube along a predefined path, allowing for gentle handling and support during feeding. They are suitable for transporting tubes with irregular shapes, fragile surfaces, or complex geometries.
- Chain Conveyor Systems: Chain conveyor systems utilize chains or slats to move the tube along a guided track, providing robust and reliable feeding for heavy-duty applications or harsh operating environments.
- Importance:
- The tube feeding system is crucial for ensuring proper alignment, positioning, and engagement of the tube during bending operations, leading to accurate and consistent bend geometries.
- Accurate tube feeding reduces setup time, minimizes material waste, and enhances productivity in tube bending processes, resulting in cost savings and improved efficiency.
- Feeding systems enable automation, integration with control systems, and optimization of bending parameters, contributing to overall quality, repeatability, and competitiveness in manufacturing operations.
In conclusion, the tube feeding system is a critical component of tube bending machines, providing controlled and precise feeding of the tube for bending operations. Understanding the functions, features, types, and importance of tube feeding systems is essential for optimizing tube bending processes and achieving high-quality bends in industrial applications.
Mandrel Extraction System:
The mandrel extraction system is an essential component in tube bending machines, designed to remove the mandrel from the bent tube or pipe after the bending process is completed. Let’s explore the functions, features, types, and importance of mandrel extraction systems in tube bending:
- Functionality:
- The primary function of the mandrel extraction system is to safely and efficiently remove the mandrel from the inside of the bent tube without causing damage to the tube or mandrel.
- After the bending process, the mandrel extraction system engages with the mandrel, releases it from the tube, and withdraws it from the bent section, leaving the finished part with the desired bend geometry.
- Mandrel extraction systems ensure smooth and uninterrupted production by facilitating the rapid removal and reinsertion of mandrels between bending cycles.
- Features and Capabilities:
- Gripper Mechanism: Mandrel extraction systems typically employ gripper mechanisms, collets, or expanding fingers to securely grip the mandrel and facilitate its removal from the tube.
- Adjustability: Some mandrel extraction systems offer adjustable settings for grip pressure, mandrel extraction speed, and mandrel release timing, allowing for customization to accommodate different tube materials, sizes, and bending configurations.
- Automation: Advanced mandrel extraction systems may incorporate automation features such as pneumatic or hydraulic actuators, sensors, and programmable control logic to automate the mandrel extraction process, reducing operator intervention and cycle times.
- Safety Features: Mandrel extraction systems include safety interlocks, guards, or sensors to prevent accidental engagement or entrapment of operators’ hands or tools during mandrel removal operations, ensuring a safe working environment.
- Types of Mandrel Extraction Systems:
- Manual Extraction Systems: Manual mandrel extraction systems require operators to manually engage with the mandrel, release it from the tube, and withdraw it from the bending area using hand tools or levers. While simple and cost-effective, manual systems may be slower and require more operator intervention.
- Semi-Automated Extraction Systems: Semi-automated mandrel extraction systems utilize pneumatic or hydraulic actuators to assist operators in gripping and extracting the mandrel from the tube. Operators still oversee the process but benefit from reduced physical effort and increased efficiency compared to manual systems.
- Fully Automated Extraction Systems: Fully automated mandrel extraction systems integrate with the tube bending machine’s control system to automatically engage, release, and extract the mandrel from the bent tube without operator intervention. They offer the highest level of efficiency, consistency, and productivity for high-volume production environments.
- Importance:
- The mandrel extraction system is critical for completing the tube bending process and producing finished parts with the desired bend geometry.
- Efficient mandrel extraction reduces cycle times, increases throughput, and improves overall productivity in tube bending operations.
- Proper mandrel extraction ensures the integrity of bent parts by minimizing the risk of tube distortion, scratching, or damage during mandrel removal.
In conclusion, the mandrel extraction system is a vital component of tube bending machines, enabling the safe and efficient removal of mandrels from bent tubes. Understanding the functions, features, types, and importance of mandrel extraction systems is essential for optimizing tube bending processes and achieving high-quality bends in industrial applications.
Mandrel Lubrication System:
The mandrel lubrication system is a crucial component of tube bending machines, ensuring smooth operation of the mandrel and minimizing friction between the mandrel and the inner surface of the tube during bending. Let’s delve into the functions, features, types, and importance of mandrel lubrication systems in tube bending:
- Functionality:
- The primary function of the mandrel lubrication system is to apply a lubricant to the surface of the mandrel before it enters the tube or pipe to be bent.
- By reducing friction between the mandrel and the inner surface of the tube, the lubrication system helps prevent galling, scratching, or scoring of the tube, resulting in smoother bends and improved surface finish.
- Mandrel lubrication systems ensure the longevity of the mandrel by minimizing wear and extending its operational lifespan.
- Features and Capabilities:
- Lubricant Delivery: Mandrel lubrication systems may utilize various methods for delivering lubricant to the mandrel surface, including spray nozzles, drip feeders, or brush applicators. The lubricant is typically applied directly to the mandrel just before it enters the tube.
- Lubricant Type: The lubricant used in mandrel lubrication systems can vary depending on the application requirements and material compatibility. Common lubricants include oil-based lubricants, water-soluble lubricants, and dry lubricants such as graphite or molybdenum disulfide.
- Adjustability: Some mandrel lubrication systems allow for adjustable flow rates, spray patterns, or lubricant types to accommodate different tube materials, wall thicknesses, and bending conditions.
- Monitoring and Control: Advanced mandrel lubrication systems may incorporate monitoring and control features to ensure proper lubricant application and prevent over-lubrication or under-lubrication. This can include sensors, flow meters, or automated control systems.
- Types of Mandrel Lubrication Systems:
- Manual Lubrication Systems: Manual mandrel lubrication systems require operators to apply lubricant to the mandrel surface manually, either using a spray bottle, brush, or applicator. While simple and inexpensive, manual systems may be prone to inconsistency and require frequent monitoring and adjustment.
- Automatic Lubrication Systems: Automatic mandrel lubrication systems are integrated into the tube bending machine and operate automatically during bending cycles. They provide consistent and precise lubricant application, reducing operator intervention and ensuring uniform lubrication across all bending operations.
- Centralized Lubrication Systems: Centralized lubrication systems supply lubricant to multiple components of the tube bending machine, including the mandrel, bending dies, and clamp dies, from a centralized reservoir or distribution system. They offer efficiency, convenience, and centralized control over lubrication processes.
- Importance:
- The mandrel lubrication system is essential for minimizing friction and wear on the mandrel and tube during bending, ensuring smooth operation and high-quality bends.
- Proper lubrication helps prevent surface defects such as scratches, scoring, or galling on the inner surface of the tube, improving bend quality and appearance.
- By reducing friction, the mandrel lubrication system enhances bending efficiency, prolongs tooling life, and minimizes energy consumption, leading to cost savings and increased productivity.
In conclusion, the mandrel lubrication system plays a critical role in tube bending machines, providing essential lubrication to minimize friction and ensure smooth bending operations. Understanding the functions, features, types, and importance of mandrel lubrication systems is essential for achieving high-quality bends and maximizing the performance of tube bending processes in industrial applications.
Pressure Die System:
The pressure die system is a fundamental component of tube bending machines, essential for achieving accurate and consistent bends by providing support and control over the outside diameter of the tube during the bending process. Let’s explore the functions, features, types, and importance of pressure die systems in tube bending:
- Functionality:
- The primary function of the pressure die system is to maintain contact with the outer surface of the tube or pipe throughout the bending process, preventing distortion, ovality, or wrinkling of the tube and ensuring uniform bending.
- Pressure die systems exert force against the tube as it is being bent, providing support and stability to counteract the internal forces generated during bending, particularly in cases of thin-walled or lightweight tubing.
- By controlling the tube’s cross-sectional shape and preventing collapse or deformation, the pressure die system helps achieve precise bend geometries, tight radii, and high-quality finishes in bent parts.
- Features and Capabilities:
- Die Configuration: Pressure die systems may consist of multiple dies arranged in various configurations, including V-shaped, roller, or ball dies, to accommodate different tube geometries, materials, and bending requirements.
- Material and Coatings: Pressure dies are typically made from hardened steel or carbide materials to withstand high contact pressures and resist wear from repeated bending cycles. Some dies may also feature coatings or surface treatments to reduce friction and improve longevity.
- Adjustability: Some pressure die systems offer adjustable settings for die position, pressure, or contact force, allowing operators to optimize bending parameters and adapt to various tube sizes, wall thicknesses, and bend radii.
- Cooling and Lubrication: Advanced pressure die systems may incorporate cooling or lubrication mechanisms to dissipate heat generated during bending and minimize friction between the die and the tube, improving bend quality and tooling lifespan.
- Types of Pressure Die Systems:
- Fixed Pressure Die Systems: Fixed pressure die systems maintain a constant pressure or contact force against the tube throughout the bending process. They are simple, reliable, and suitable for standard bending applications with consistent tube properties.
- Spring-Loaded Pressure Die Systems: Spring-loaded pressure die systems use springs or pneumatic actuators to apply variable pressure against the tube, adjusting automatically to accommodate variations in tube diameter, wall thickness, or material properties.
- Hydraulic Pressure Die Systems: Hydraulic pressure die systems utilize hydraulic cylinders or actuators to apply controlled pressure against the tube, offering precise force regulation and dynamic adjustment capabilities for complex bending operations.
- Importance:
- The pressure die system is critical for maintaining dimensional accuracy, surface finish, and structural integrity in bent parts by providing support and control over the tube’s outer surface during bending.
- Properly designed and adjusted pressure die systems help minimize defects such as wrinkles, ovality, or distortion in bent tubes, ensuring high-quality bends and reducing scrap rates in production.
- Pressure die systems contribute to overall productivity, efficiency, and profitability in tube bending operations by enabling faster setup, more consistent results, and extended tooling life.
In conclusion, the pressure die system is a fundamental element of tube bending machines, essential for achieving accurate, high-quality bends in tubes and pipes. Understanding the functions, features, types, and importance of pressure die systems is crucial for optimizing tube bending processes and ensuring reliable performance in industrial applications.
Wiper Die System:
The wiper die system is a critical component in tube bending machines, designed to prevent wrinkling, flattening, or distortion of the inner radius of the tube during the bending process. Let’s explore the functions, features, types, and importance of wiper die systems in tube bending:
- Functionality:
- The primary function of the wiper die system is to support and guide the inner wall of the tube or pipe as it bends around the bend die, ensuring uniform contact and preventing deformation or imperfections on the inner radius of the bend.
- Wiper dies exert pressure against the inner surface of the tube, smoothing out wrinkles, wrinkles, or irregularities that may occur during bending, particularly in cases of tight radii or thin-walled tubing.
- By maintaining consistent wall thickness and curvature along the inner radius of the bend, the wiper die system helps achieve precise bend geometries, smooth contours, and high-quality finishes in bent parts.
- Features and Capabilities:
- Die Configuration: Wiper die systems typically consist of multiple segments or inserts arranged in a circular or semi-circular configuration, matching the inner radius of the bend. They may feature different profiles or contours to accommodate various tube sizes, wall thicknesses, and bend radii.
- Material and Coatings: Wiper dies are often made from hardened steel, carbide, or other wear-resistant materials to withstand high contact pressures and resist wear from repeated bending cycles. Some dies may also feature coatings or surface treatments to reduce friction and improve lubricity.
- Adjustability: Some wiper die systems offer adjustable settings for die position, pressure, or clearance, allowing operators to optimize bending parameters and adapt to different tube materials, wall thicknesses, and bend configurations.
- Cooling and Lubrication: Advanced wiper die systems may incorporate cooling or lubrication mechanisms to dissipate heat generated during bending and minimize friction between the die and the tube, improving bend quality and tooling lifespan.
- Types of Wiper Die Systems:
- Fixed Wiper Die Systems: Fixed wiper die systems maintain a constant position and pressure against the inner surface of the tube throughout the bending process. They are simple, reliable, and suitable for standard bending applications with consistent tube properties.
- Spring-Loaded Wiper Die Systems: Spring-loaded wiper die systems use springs or pneumatic actuators to apply variable pressure against the inner surface of the tube, adjusting automatically to accommodate variations in tube diameter, wall thickness, or material properties.
- Hydraulic Wiper Die Systems: Hydraulic wiper die systems utilize hydraulic cylinders or actuators to apply controlled pressure against the inner surface of the tube, offering precise force regulation and dynamic adjustment capabilities for complex bending operations.
- Importance:
- The wiper die system is essential for achieving uniform wall thickness, smooth contours, and high-quality finishes in bent tubes by preventing wrinkling, flattening, or distortion of the inner radius.
- Properly designed and adjusted wiper die systems help minimize defects and imperfections in bent tubes, ensuring dimensional accuracy, surface finish, and structural integrity in finished parts.
- Wiper die systems contribute to overall productivity, efficiency, and profitability in tube bending operations by reducing scrap rates, minimizing rework, and extending tooling life.
In conclusion, the wiper die system is a critical element of tube bending machines, essential for achieving accurate, high-quality bends in tubes and pipes. Understanding the functions, features, types, and importance of wiper die systems is crucial for optimizing tube bending processes and ensuring reliable performance in industrial applications.
Mandrel Lubrication System:
The mandrel lubrication system is a critical component of tube bending machines, ensuring smooth operation of the mandrel and minimizing friction between the mandrel and the inner surface of the tube during bending. Let’s delve into the functions, features, types, and importance of mandrel lubrication systems in tube bending:
- Functionality:
- The primary function of the mandrel lubrication system is to apply a lubricant to the surface of the mandrel before it enters the tube or pipe to be bent.
- By reducing friction between the mandrel and the inner surface of the tube, the lubrication system helps prevent galling, scratching, or scoring of the tube, resulting in smoother bends and improved surface finish.
- Mandrel lubrication systems ensure the longevity of the mandrel by minimizing wear and extending its operational lifespan.
- Features and Capabilities:
- Lubricant Delivery: Mandrel lubrication systems may utilize various methods for delivering lubricant to the mandrel surface, including spray nozzles, drip feeders, or brush applicators. The lubricant is typically applied directly to the mandrel just before it enters the tube.
- Lubricant Type: The lubricant used in mandrel lubrication systems can vary depending on the application requirements and material compatibility. Common lubricants include oil-based lubricants, water-soluble lubricants, and dry lubricants such as graphite or molybdenum disulfide.
- Adjustability: Some mandrel lubrication systems allow for adjustable flow rates, spray patterns, or lubricant types to accommodate different tube materials, wall thicknesses, and bending conditions.
- Monitoring and Control: Advanced mandrel lubrication systems may incorporate monitoring and control features to ensure proper lubricant application and prevent over-lubrication or under-lubrication. This can include sensors, flow meters, or automated control systems.
- Types of Mandrel Lubrication Systems:
- Manual Lubrication Systems: Manual mandrel lubrication systems require operators to apply lubricant to the mandrel surface manually, either using a spray bottle, brush, or applicator. While simple and inexpensive, manual systems may be prone to inconsistency and require frequent monitoring and adjustment.
- Automatic Lubrication Systems: Automatic mandrel lubrication systems are integrated into the tube bending machine and operate automatically during bending cycles. They provide consistent and precise lubricant application, reducing operator intervention and ensuring uniform lubrication across all bending operations.
- Centralized Lubrication Systems: Centralized lubrication systems supply lubricant to multiple components of the tube bending machine, including the mandrel, bending dies, and clamp dies, from a centralized reservoir or distribution system. They offer efficiency, convenience, and centralized control over lubrication processes.
- Importance:
- The mandrel lubrication system is essential for minimizing friction and wear on the mandrel and tube during bending, ensuring smooth operation and high-quality bends.
- Proper lubrication helps prevent surface defects such as scratches, scoring, or galling on the inner surface of the tube, improving bend quality and appearance.
- By reducing friction, the mandrel lubrication system enhances bending efficiency, prolongs tooling life, and minimizes energy consumption, leading to cost savings and increased productivity.
In conclusion, the mandrel lubrication system plays a critical role in tube bending machines, providing essential lubrication to minimize friction and ensure smooth bending operations. Understanding the functions, features, types, and importance of mandrel lubrication systems is crucial for achieving high-quality bends and maximizing the performance of tube bending processes in industrial applications.
Wiper Die System:
The wiper die system is a critical component in tube bending machines, designed to prevent wrinkling, flattening, or distortion of the inner radius of the tube during the bending process. Let’s explore the functions, features, types, and importance of wiper die systems in tube bending:
- Functionality:
- The primary function of the wiper die system is to support and guide the inner wall of the tube or pipe as it bends around the bend die, ensuring uniform contact and preventing deformation or imperfections on the inner radius of the bend.
- Wiper dies exert pressure against the inner surface of the tube, smoothing out wrinkles, wrinkles, or irregularities that may occur during bending, particularly in cases of tight radii or thin-walled tubing.
- By maintaining consistent wall thickness and curvature along the inner radius of the bend, the wiper die system helps achieve precise bend geometries, smooth contours, and high-quality finishes in bent parts.
- Features and Capabilities:
- Die Configuration: Wiper die systems typically consist of multiple segments or inserts arranged in a circular or semi-circular configuration, matching the inner radius of the bend. They may feature different profiles or contours to accommodate various tube sizes, wall thicknesses, and bend radii.
- Material and Coatings: Wiper dies are often made from hardened steel, carbide, or other wear-resistant materials to withstand high contact pressures and resist wear from repeated bending cycles. Some dies may also feature coatings or surface treatments to reduce friction and improve lubricity.
- Adjustability: Some wiper die systems offer adjustable settings for die position, pressure, or clearance, allowing operators to optimize bending parameters and adapt to different tube materials, wall thicknesses, and bend configurations.
- Cooling and Lubrication: Advanced wiper die systems may incorporate cooling or lubrication mechanisms to dissipate heat generated during bending and minimize friction between the die and the tube, improving bend quality and tooling lifespan.
- Types of Wiper Die Systems:
- Fixed Wiper Die Systems: Fixed wiper die systems maintain a constant position and pressure against the inner surface of the tube throughout the bending process. They are simple, reliable, and suitable for standard bending applications with consistent tube properties.
- Spring-Loaded Wiper Die Systems: Spring-loaded wiper die systems use springs or pneumatic actuators to apply variable pressure against the inner surface of the tube, adjusting automatically to accommodate variations in tube diameter, wall thickness, or material properties.
- Hydraulic Wiper Die Systems: Hydraulic wiper die systems utilize hydraulic cylinders or actuators to apply controlled pressure against the inner surface of the tube, offering precise force regulation and dynamic adjustment capabilities for complex bending operations.
- Importance:
- The wiper die system is essential for achieving uniform wall thickness, smooth contours, and high-quality finishes in bent tubes by preventing wrinkling, flattening, or distortion of the inner radius.
- Properly designed and adjusted wiper die systems help minimize defects and imperfections in bent tubes, ensuring dimensional accuracy, surface finish, and structural integrity in finished parts.
- Wiper die systems contribute to overall productivity, efficiency, and profitability in tube bending operations by reducing scrap rates, minimizing rework, and extending tooling life.
In conclusion, the wiper die system is a critical element of tube bending machines, essential for achieving accurate, high-quality bends in tubes and pipes. Understanding the functions, features, types, and importance of wiper die systems is crucial for optimizing tube bending processes and ensuring reliable performance in industrial applications.
Parts of Hydraulic Pipe Bender:
The hydraulic pipe bender is a versatile tool used in various industries for bending pipes and tubes with precision and efficiency. Understanding its components is essential for proper operation and maintenance. Let’s explore the key parts of a hydraulic pipe bender:
- Hydraulic Cylinder:
- The hydraulic cylinder is the primary power source of the bender, responsible for generating the force needed to bend the pipe.
- It consists of a cylindrical barrel containing a piston that moves linearly when hydraulic fluid is pressurized, exerting force on the pipe through a bending die.
- Bending Die:
- The bending die is a specialized tool that shapes the pipe or tube into the desired bend radius and angle.
- It typically consists of a stationary die and a moving die, which come together to deform the pipe when pressure is applied by the hydraulic cylinder.
- Clamping System:
- The clamping system holds the pipe securely in place during the bending process to prevent slipping or movement.
- It may include clamping jaws, vise-like mechanisms, or hydraulic clamps that grip the pipe firmly to the bending die assembly.
- Mandrel:
- In some hydraulic pipe benders, a mandrel is used to support the inner wall of the pipe during bending, preventing collapse or distortion.
- The mandrel is inserted into the pipe before bending and is typically withdrawn afterward using a mandrel extraction system.
- Pressure Die:
- The pressure die provides additional support to the outer wall of the pipe, ensuring uniform bending and preventing deformation.
- It applies pressure against the pipe surface opposite the bending die, helping to maintain the pipe’s shape and integrity during bending.
- Control Panel:
- The control panel houses the controls and interface for operating the hydraulic pipe bender.
- It may include buttons, switches, and digital displays for adjusting bending parameters such as angle, radius, and speed.
- Hydraulic Power Unit:
- The hydraulic power unit supplies pressurized hydraulic fluid to the hydraulic cylinder, enabling it to generate bending force.
- It typically includes a reservoir, pump, motor, valves, and hoses for hydraulic fluid distribution.
- Frame and Base:
- The frame and base provide structural support and stability to the hydraulic pipe bender.
- They are often made of heavy-duty materials such as steel or cast iron to withstand the bending forces and vibrations generated during operation.
- Foot Pedal or Remote Control:
- Some hydraulic pipe benders are equipped with a foot pedal or remote control device for hands-free operation.
- These controls allow the operator to activate the bending process while maintaining a safe distance from the machine.
- Safety Features:
- Various safety features may be incorporated into hydraulic pipe benders to protect operators and prevent accidents.
- These may include emergency stop buttons, safety interlocks, protective guards, and warning lights.
Understanding the function and role of each part of the hydraulic pipe bender is essential for safe and efficient operation, as well as for troubleshooting and maintenance tasks. Regular inspection and maintenance of these components ensure the longevity and reliability of the bender for years of productive use.
Overview of Bending and Press Machines in Industrial Applications
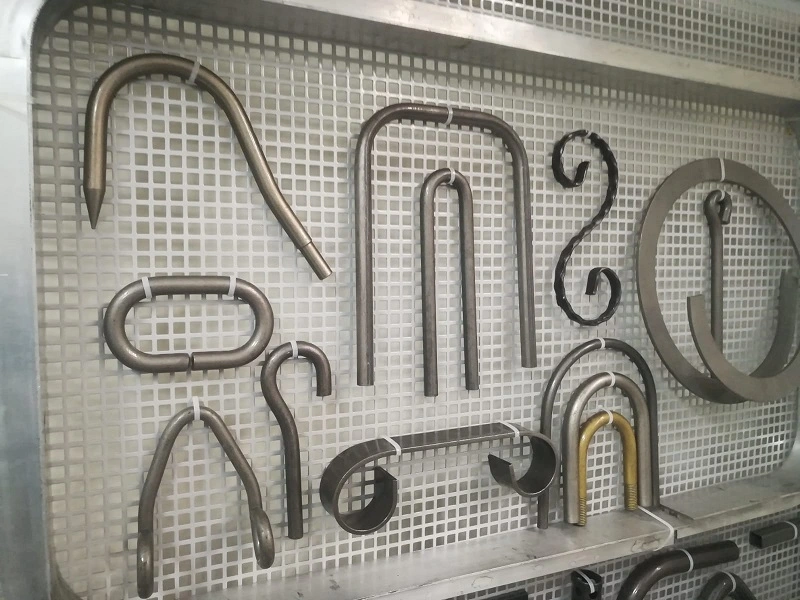
In the modern manufacturing and metalworking industries, bending and press machines are indispensable tools that shape, form, and modify metal and other materials with high precision. These machines are designed to handle various tasks, from simple bending operations to complex shaping processes, catering to a wide range of applications across multiple industries. The effectiveness and versatility of these machines make them critical in producing parts and components for automotive, aerospace, construction, and other heavy industries.
Bending and press machines are essential in transforming raw materials into finished products by applying force to alter the shape and properties of metals and other materials. The machines are designed to handle different materials, including steel, stainless steel (SS), aluminum, and more. These machines vary in size and capacity, from small, manual models used in workshops to large, automated systems in industrial manufacturing plants.
Types of Bending and Press Machines:
- Hydraulic Press Machines: Utilize hydraulic pressure to exert force, offering high precision and control in operations such as pressing, bending, and punching.
- Press Brake Machines: Specifically designed for bending sheet metal into various shapes by clamping the workpiece between a matching punch and die.
- Pipe Bending Machines: Used to bend pipes and tubes into desired angles and shapes, essential in plumbing, construction, and automotive industries.
- Sheet Metal Bending Machines: These machines focus on bending and shaping sheet metal, often used in fabrication shops and manufacturing lines.
Importance of Precision in Metalworking
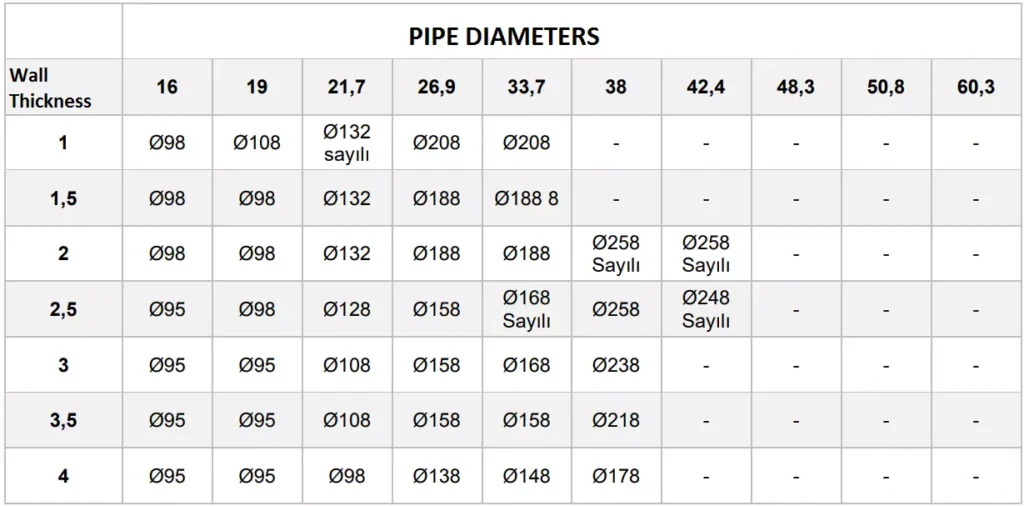
Precision is paramount in metalworking, as even minor deviations can lead to significant issues in the final product. Accurate bending and shaping are critical for ensuring that parts fit together correctly, maintain structural integrity, and meet the required specifications. The precision offered by modern bending and press machines allows manufacturers to produce complex components with tight tolerances, reducing the need for additional finishing processes and minimizing material waste.
Key Factors Influencing Precision:
- Machine Calibration: Proper calibration ensures the machine operates within the specified tolerances, providing consistent results.
- Tooling Quality: High-quality tools, such as dies and punches, are essential for achieving precise bends and shapes.
- Material Properties: Understanding the material’s properties, including its thickness, tensile strength, and ductility, is crucial for selecting the right machine settings.
- Operator Skill: Experienced operators can optimize machine settings and techniques to achieve the best results, even with challenging materials.
Overview of Bending and Press Machines
Bending and press machines are categorized based on their operating principles, applications, and the materials they handle. Below is a brief overview of some common types of bending and press machines:
1.3.1 Hydraulic Press Machines Hydraulic press machines operate by using a hydraulic cylinder to generate compressive force. They are highly versatile, allowing for various applications such as bending, forming, punching, and drawing. Hydraulic presses are known for their ability to exert high forces with great precision, making them ideal for heavy-duty applications. The introduction and working principles of hydraulic press machines will be discussed in more detail in the following sections.
1.3.2 Press Brake Machines Press brake machines are specialized machines used primarily for bending sheet metal. These machines utilize a combination of a punch and die to shape metal into specific angles and forms. Press brakes can be manual, hydraulic, or CNC-controlled, with each type offering different levels of automation and precision. The versatility of press brakes makes them a staple in metal fabrication shops.
1.3.3 Pipe Bending Machines Pipe bending machines are designed to bend pipes and tubes into various shapes and angles without compromising the material’s structural integrity. These machines are essential in industries such as plumbing, automotive, and construction, where precise pipe bends are required. Pipe bending machines can be hydraulic, pneumatic, mechanical, or electric, each offering different advantages depending on the application.
1.3.4 Sheet Metal Bending Machines Sheet metal bending machines focus on bending thin, flat sheets of metal into specific shapes. These machines are commonly used in the automotive and aerospace industries, where precision is critical. The machines can be manually operated, hydraulic, or CNC-controlled, offering various levels of control and automation.
Key Terminology and Concepts
Understanding the key terminology and concepts related to bending and press machines is essential for selecting the right equipment and optimizing its use. Below are some important terms that will be used throughout this document:
- Tonnage: The amount of force a machine can exert, usually measured in tons. For example, a 100-ton hydraulic press can exert 100 tons of force.
- Punch and Die: The tools used in press brake machines to shape metal. The punch presses into the die, which holds the workpiece.
- CNC (Computer Numerical Control): A method of automating machine tools using computers to control their movement and operation.
- Bend Radius: The radius of the inside curve of a bent section of metal. The bend radius is critical in determining the integrity and appearance of the bend.
- Ductility: The ability of a material to undergo deformation without breaking. Ductility is an important factor in bending operations.
Applications of Bending and Press Machines
Bending and press machines are used in a wide range of applications, from simple bending tasks to complex forming and shaping operations. Some common applications include:
- Automotive Industry: Producing car body parts, exhaust systems, and chassis components.
- Aerospace Industry: Manufacturing aircraft components, including fuselage panels and structural supports.
- Construction: Fabricating steel beams, columns, and other structural elements.
- Plumbing and HVAC: Bending pipes and tubes for plumbing, heating, and ventilation systems.
- Heavy Machinery: Forming and shaping parts for heavy equipment, such as cranes and bulldozers.
These applications highlight the versatility and importance of bending and press machines in modern manufacturing. The following sections will delve deeper into specific types of machines, their working principles, and the factors to consider when choosing the right equipment for your needs.
Hydraulic Press Machines: An Overview
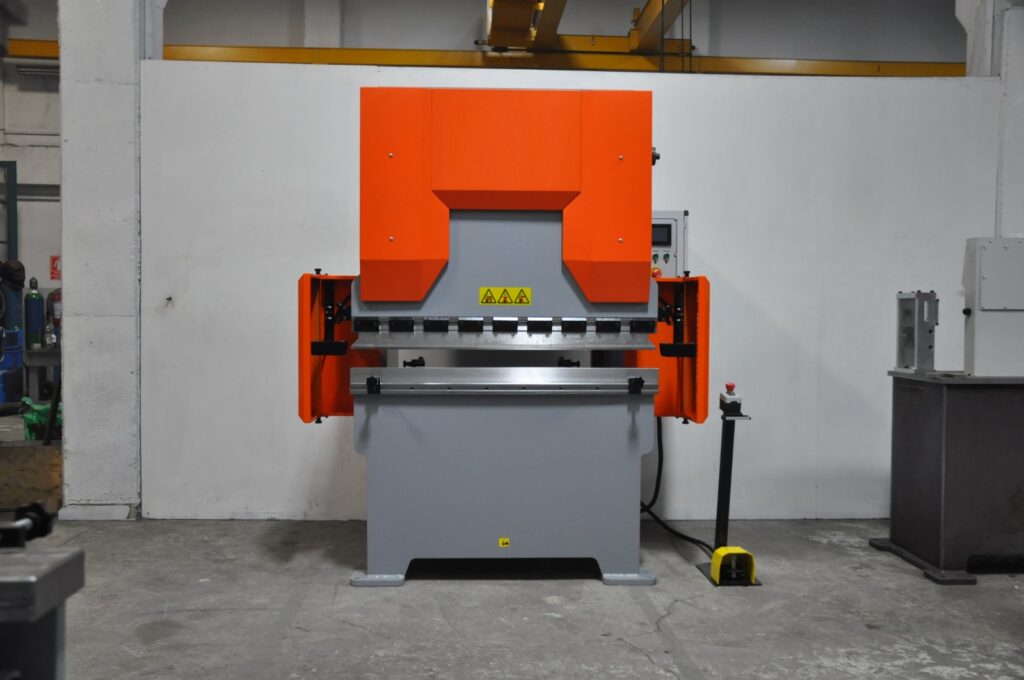
Hydraulic press machines are a cornerstone of modern manufacturing, offering unmatched power and precision in shaping, molding, and forming materials. These machines harness the power of hydraulics—a technology that uses fluid pressure to generate force—enabling them to perform tasks that require significant force with high accuracy. In this section, we will explore the fundamentals of hydraulic press machines, their working principles, various types, and key specifications that are critical for their selection and application in different industries.
2.1 Hydraulic Press Machine Introduction
Hydraulic press machines are used in a variety of industries for tasks that require compressive force. The concept behind hydraulic presses is based on Pascal’s law, which states that when pressure is applied to a confined fluid, the pressure is transmitted equally in all directions. This principle allows hydraulic presses to generate enormous amounts of force with relatively little input, making them highly efficient for industrial applications.
Key Characteristics:
- High Force Generation: Hydraulic presses can generate forces ranging from a few tons to several thousand tons, depending on the machine’s design and application.
- Versatility: These machines can perform a wide range of operations, including forging, stamping, bending, punching, and drawing.
- Precision: Hydraulic presses offer precise control over the applied force and movement, which is essential for tasks that require high accuracy.
- Customizability: Hydraulic presses can be customized with different types of tooling, making them adaptable to various tasks.
Hydraulic press machines are widely used in industries such as automotive manufacturing, aerospace, construction, and heavy machinery production. Their ability to handle large-scale operations with precision makes them a valuable asset in any industrial setting.
2.2 Hydraulic Press Machine Working Principles
The working of a hydraulic press machine is based on the simple but powerful principle of fluid mechanics. The machine typically consists of two cylinders: a smaller cylinder (called the slave cylinder) and a larger cylinder (called the master cylinder). These cylinders are connected by a pipe filled with hydraulic fluid, usually oil.
Working Process:
- Applying Force: When force is applied to the smaller cylinder (using a lever or a motor), it creates pressure in the hydraulic fluid.
- Pressure Transmission: According to Pascal’s law, the pressure in the fluid is transmitted equally throughout the system, causing the larger cylinder to move.
- Force Amplification: Because the larger cylinder has a greater surface area, the force exerted by it is much greater than the force applied to the smaller cylinder. This allows the machine to perform tasks that require significant force, such as pressing or bending metal.
Control Mechanisms:
- Pressure Control Valves: These valves regulate the amount of pressure applied to the hydraulic fluid, allowing the operator to control the force exerted by the machine.
- Flow Control Valves: These valves control the speed of the hydraulic fluid, which in turn controls the speed of the machine’s movement.
- Directional Control Valves: These valves direct the flow of hydraulic fluid to different parts of the system, enabling the machine to perform various operations.
Hydraulic press machines can be operated manually, semi-automatically, or fully automatically, depending on the level of control and automation required. Modern hydraulic presses often incorporate computerized control systems (CNC) for enhanced precision and efficiency.
2.3 Hydraulic Press Specifications
When selecting a hydraulic press machine, understanding its specifications is crucial to ensure that it meets the requirements of the intended application. Key specifications include:
2.3.1 Tonnage (Force Capacity)
- Definition: Tonnage refers to the maximum force that the hydraulic press can exert, usually measured in tons.
- Importance: The tonnage requirement depends on the material being processed and the operation being performed. For example, a higher tonnage is needed for tasks such as forging thick metal parts compared to bending thin sheets.
- Examples: A 100-ton hydraulic press is commonly used in medium-scale operations, while a 1000-ton hydraulic press is suitable for large-scale industrial applications.
2.3.2 Stroke Length
- Definition: Stroke length is the distance the press ram (the moving part of the machine that exerts force) can travel in one cycle.
- Importance: The stroke length determines the depth to which the material can be compressed or formed. It is particularly important in operations like deep drawing or molding.
- Adjustability: Many hydraulic presses allow the stroke length to be adjusted according to the specific requirements of the operation.
2.3.3 Bed Size
- Definition: The bed size is the working surface area of the press where the material is placed.
- Importance: The bed size must accommodate the dimensions of the workpiece being processed. A larger bed size is required for bigger workpieces.
- Customization: Some hydraulic presses offer interchangeable beds to handle different workpiece sizes.
2.3.4 Ram Speed
- Definition: Ram speed refers to the speed at which the press ram moves during operation.
- Importance: The speed of the ram can affect the quality of the operation. For example, slower speeds may be needed for precision tasks, while faster speeds are suitable for high-volume production.
- Control: Hydraulic presses often have adjustable ram speeds to suit different tasks.
2.3.5 Hydraulic System Pressure
- Definition: This is the pressure at which the hydraulic fluid operates within the system, usually measured in pounds per square inch (PSI) or bar.
- Importance: Higher system pressure allows for greater force generation but also requires more robust components to handle the increased stress.
- Safety: Hydraulic presses are equipped with safety mechanisms to prevent over-pressurization, which could lead to system failure.
2.4 100 Ton Hydraulic Press Specifications
A 100-ton hydraulic press is a versatile and commonly used machine in many industries, capable of handling a wide range of tasks from bending and forming to punching and drawing.
Key Specifications of a 100 Ton Hydraulic Press:
- Tonnage: 100 tons of maximum force, suitable for medium to large-scale operations.
- Stroke Length: Typically around 8 to 12 inches, with adjustability for different tasks.
- Bed Size: A standard bed size might be around 36 x 24 inches, but this can vary depending on the manufacturer.
- Ram Speed: Variable, often ranging from 10 to 30 mm/s, depending on the operation.
- System Pressure: Generally operates at around 3000 PSI, providing the necessary force without compromising safety.
Applications:
- Automotive Manufacturing: Used for pressing, forming, and shaping automotive parts.
- Metal Fabrication: Ideal for bending and shaping metal components in medium-scale production.
- Construction Equipment Manufacturing: Useful in the production of parts for heavy machinery and construction tools.
2.5 1000 Ton Hydraulic Press
The 1000-ton hydraulic press represents a significant leap in force capacity, making it suitable for the most demanding industrial applications. These machines are typically used in heavy industries where large-scale and high-force operations are required.
Key Specifications of a 1000 Ton Hydraulic Press:
- Tonnage: 1000 tons of maximum force, designed for heavy-duty tasks.
- Stroke Length: Can range from 12 to 24 inches, depending on the specific model and application.
- Bed Size: Large beds, often exceeding 72 x 48 inches, to accommodate massive workpieces.
- Ram Speed: Slower speeds, typically around 5 to 15 mm/s, due to the immense force being applied.
- System Pressure: Operates at high pressures, usually around 5000 PSI, to deliver the required force.
Applications:
- Shipbuilding: Used in the production of large metal components for ships and submarines.
- Aerospace: Essential for forming and shaping large aircraft components.
- Heavy Machinery Production: Involved in the manufacturing of parts for mining equipment, cranes, and other heavy-duty machinery.
2.6 Horizontal Hydraulic Press Machine
Horizontal hydraulic press machines differ from the more common vertical models in that the ram moves horizontally rather than vertically. This configuration is particularly useful for specific applications such as bending long pieces of metal or pressing components that are difficult to position vertically.
Advantages of Horizontal Hydraulic Press Machines:
- Versatility: Can handle a variety of tasks including bending, pressing, and straightening long workpieces.
- Ease of Operation: Easier to load and position large or awkwardly shaped workpieces.
- Space Efficiency: Horizontal presses can be more space-efficient in certain workshop layouts.
Applications:
- Railway Manufacturing: Used for bending and forming long steel rails.
- Pipeline Construction: Ideal for bending and forming large pipes used in oil, gas, and water pipelines.
- Structural Engineering: Employed in the production of long beams and structural components.
2.7 Small Horizontal Hydraulic Press
Small horizontal hydraulic presses are designed for applications that require less force and smaller workpieces. These machines are commonly used in workshops and smaller manufacturing facilities where space and budget constraints are factors.
Key Features:
- Compact Design: Takes up less space, making it ideal for small workshops.
- Lower Tonnage: Typically ranges from 10 to 50 tons, suitable for light to medium tasks.
- Ease of Use: Simple controls and operation, often with manual or semi-automatic settings.
Applications:
- Automotive Repair Shops: Used for pressing and straightening components like axles and shafts.
- Small Fabrication Shops: Ideal for bending and forming smaller metal parts.
- Maintenance Operations: Useful in on-site repairs and maintenance tasks where portability is required.
3. Press Brake Machines and Bending Applications
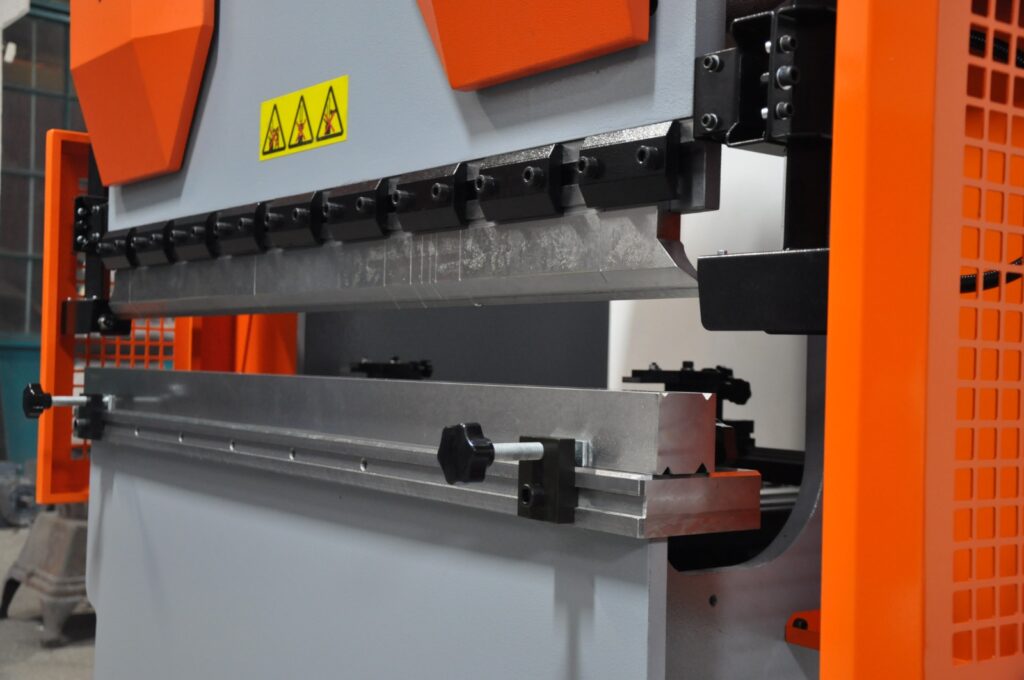
Press brake machines play a pivotal role in the metal fabrication industry, offering the precision and versatility required to transform flat metal sheets into complex shapes and structures. These machines are specifically designed for bending operations, making them indispensable in various manufacturing processes. This section delves into the functionality and applications of press brake machines, explores different bending techniques, and highlights the nuances of hydraulic press bending machines, including those tailored for sheet metal applications.
3.1 Press Brake Machine: Functionality and Applications
A press brake machine is a specialized tool used to bend and shape metal sheets and plates with high accuracy. Unlike general-purpose press machines, press brakes are specifically engineered to perform bending operations, making them essential in industries such as automotive, aerospace, construction, and manufacturing.
Key Functionalities:
- Bending: The primary function of a press brake is to bend metal sheets along a straight axis. This is achieved by clamping the metal between a punch and a die and applying force to create the desired angle.
- Forming: Beyond simple bends, press brakes can form complex shapes by combining multiple bending operations. This allows for the creation of intricate components required in various applications.
- Precision Cutting: Some advanced press brakes are equipped with features that allow for precise cutting or shearing of metal sheets during the bending process.
Applications:
- Automotive Industry: Manufacturing car body panels, chassis components, and exhaust systems.
- Aerospace Industry: Producing aircraft components, including fuselage sections and structural supports.
- Construction: Fabricating steel beams, columns, and other structural elements for buildings and infrastructure projects.
- Electronics: Creating enclosures and frames for electronic devices and appliances.
- Furniture Manufacturing: Designing and producing metal frames and supports for furniture pieces.
3.2 Press Brake Bending: Techniques and Precision
Bending is a fundamental operation in metalworking, and press brakes offer the precision and control necessary to achieve consistent and accurate results. Various bending techniques can be employed depending on the material, thickness, and desired outcome.
Bending Techniques:
- Air Bending: In this method, the punch presses the metal into the die without fully contacting it. This allows for greater flexibility in adjusting the bend angle and reduces stress on the material. Air bending is suitable for applications requiring variable angles and is widely used in sheet metal fabrication.Advantages:
- Versatility in bend angles.
- Reduced tooling wear.
- Lower force requirements compared to bottom bending.
- Bottom Bending (V-Die Bending): Here, the punch presses the metal all the way into the die, resulting in a more precise bend angle. This technique is ideal for applications where high accuracy and consistency are paramount.Advantages:
- Higher precision in bend angles.
- Better repeatability for mass production.
- Suitable for thicker materials.
- Coining: A specialized form of bottom bending where the metal is pressed into a highly precise shape within the die. Coining is used for intricate bends and is often employed in applications requiring fine details and superior surface finishes.
Precision Considerations:
- Tooling Quality: High-quality punches and dies are essential for achieving precise bends. The condition of the tooling directly impacts the accuracy and consistency of the bending process.
- Machine Calibration: Regular calibration ensures that the press brake operates within the specified tolerances, maintaining the precision of each bend.
- Material Properties: Understanding the ductility, tensile strength, and thickness of the material is crucial for selecting the appropriate bending parameters and avoiding defects such as cracking or warping.
- Operator Skill: Skilled operators can optimize machine settings and bending techniques to achieve the desired precision, especially when working with challenging materials or complex shapes.
3.3 Bend Press Machine: Overview
Bend press machines, often referred to interchangeably with press brake machines, are designed specifically for bending operations in metal fabrication. These machines vary in size, capacity, and control mechanisms, allowing them to cater to a wide range of applications from small workshops to large industrial facilities.
Types of Bend Press Machines:
- Manual Bend Press Machines: These are operated manually by the user, typically using a lever or hydraulic pump to apply force. They are suitable for small-scale operations and simple bending tasks.Advantages:
- Lower cost.
- Simplicity and ease of use.
- Ideal for light-duty applications.
- Hydraulic Bend Press Machines: Utilize hydraulic systems to apply force, offering greater control and higher tonnage capabilities compared to manual machines. They are widely used in medium to large-scale operations.Advantages:
- Higher force generation.
- Precise control over bending parameters.
- Suitable for a variety of materials and thicknesses.
- CNC Bend Press Machines: Equipped with computer numerical control (CNC) systems, these machines offer automated and programmable bending operations. They are ideal for high-precision and high-volume production environments.Advantages:
- Enhanced precision and repeatability.
- Ability to handle complex and intricate bends.
- Increased efficiency and reduced manual intervention.
Key Features:
- Adjustable Backgauges: Allow operators to set the precise location of the bend, ensuring consistency across multiple bends.
- Multiple Axes Control: Enables the machine to perform bends at various angles and positions without manual adjustments.
- Safety Features: Includes guards, emergency stop buttons, and sensors to ensure safe operation and protect operators from potential hazards.
3.4 Hydraulic Press Bending Machine
Hydraulic press bending machines combine the force-generating capabilities of hydraulic systems with the precision of press brakes to perform bending operations with high efficiency and accuracy. These machines are essential in applications where consistent and reliable bends are required, especially in medium to high-volume production settings.
Working Principles: Hydraulic press bending machines operate by using a hydraulic cylinder to exert force on the punch, which in turn bends the metal sheet against the die. The hydraulic system allows for smooth and controlled application of force, enabling precise bending angles and consistent results.
Advantages:
- High Force Capacity: Capable of handling thick and strong materials that require significant force to bend.
- Precision Control: Hydraulic systems offer fine control over the bending process, allowing for accurate and repeatable bends.
- Versatility: Suitable for a wide range of materials, including steel, aluminum, and stainless steel, making them adaptable to various industrial applications.
Applications:
- Automotive Manufacturing: Bending automotive body panels and structural components with high precision.
- Aerospace Industry: Forming aircraft parts that require exacting specifications and tight tolerances.
- Construction: Creating structural steel components for buildings and infrastructure projects.
- Heavy Machinery Production: Fabricating parts for construction equipment, mining machinery, and industrial tools.
3.5 Hydraulic Sheet Metal Bending Machine
Hydraulic sheet metal bending machines are specialized press brakes designed to handle the specific challenges associated with bending thin metal sheets. These machines leverage hydraulic systems to provide the necessary force and control for precise sheet metal fabrication.
Key Features:
- Enhanced Precision: Hydraulic systems ensure that each bend is executed with high accuracy, minimizing deviations and maintaining consistency.
- Adjustable Clamping Force: Allows for the secure holding of thin sheets without causing deformation or damage during the bending process.
- Integrated Control Systems: Modern hydraulic sheet metal bending machines often feature computerized controls for automated bending sequences, reducing manual intervention and increasing efficiency.
Benefits:
- Reduced Material Waste: Precise bending reduces the likelihood of errors and rework, leading to less material wastage and lower production costs.
- Increased Productivity: Automated and semi-automated systems enable faster production rates, meeting the demands of high-volume manufacturing.
- Versatility: Capable of handling a variety of sheet metal thicknesses and materials, making them suitable for diverse applications.
Applications:
- Appliance Manufacturing: Producing metal housings and components for household appliances such as refrigerators, washing machines, and ovens.
- Electronics Enclosures: Creating precise and compact metal enclosures for electronic devices and equipment.
- Furniture Manufacturing: Bending metal sheets for modern and ergonomic furniture designs.
- Signage and Displays: Forming metal panels used in signage, displays, and advertising materials.
3.6 Integration of CNC Technology in Press Brake Machines
The integration of Computer Numerical Control (CNC) technology into press brake machines has revolutionized the bending process, enhancing precision, efficiency, and flexibility. CNC press brakes are programmed with specific bending sequences, allowing for automated and repeatable operations that meet the stringent demands of modern manufacturing.
Advantages of CNC Press Brake Machines:
- Automation: Reduces the need for manual adjustments, minimizing human error and increasing production speed.
- Programmability: Allows for the storage and execution of complex bending programs, enabling the production of intricate shapes and multiple bends in a single setup.
- Consistency: Ensures that each bend is executed with the same precision, maintaining quality across large production runs.
- Ease of Use: User-friendly interfaces and software enable operators to input and modify bending programs with minimal training.
Applications:
- High-Precision Industries: Essential in industries such as aerospace and medical device manufacturing, where exacting standards must be met.
- Mass Production: Ideal for large-scale manufacturing where consistency and speed are critical.
- Customization: Facilitates the production of customized parts and components without significant downtime for setup changes.
3.7 Challenges and Considerations in Press Brake Bending
While press brake machines offer significant advantages in metal bending operations, several challenges and considerations must be addressed to ensure optimal performance and longevity of the equipment.
Common Challenges:
- Material Springback: After bending, materials tend to return partially to their original shape, known as springback. Proper compensation techniques and machine settings are required to achieve the desired final angle.
- Tooling Wear: Frequent bending operations can lead to wear and tear of punches and dies, affecting the quality of bends. Regular maintenance and timely replacement of tooling are essential.
- Setup Time: Adjusting machine settings and tooling for different bending tasks can be time-consuming, impacting overall productivity. CNC press brakes help mitigate this by enabling quick program changes.
- Operator Training: Skilled operators are necessary to manage machine settings, troubleshoot issues, and ensure consistent quality. Investing in training programs can enhance operational efficiency.
Key Considerations:
- Machine Selection: Choosing the right press brake machine involves assessing factors such as tonnage capacity, stroke length, bed size, and control systems based on the specific application requirements.
- Tooling Quality: High-quality punches and dies are crucial for achieving precise and consistent bends. Investing in durable tooling can reduce maintenance costs and improve overall performance.
- Maintenance Practices: Regular maintenance, including lubrication, inspection, and calibration, ensures that the press brake operates efficiently and extends its operational lifespan.
- Safety Measures: Implementing safety protocols, such as using protective guards and emergency stop mechanisms, protects operators and prevents accidents in the workplace.
3.8 Innovations in Press Brake Technology
Advancements in press brake technology continue to enhance the capabilities and efficiency of bending operations. Innovations such as servo-electric systems, advanced control software, and enhanced automation features are driving the evolution of press brake machines.
Servo-Electric Press Brakes: Servo-electric press brakes use electric motors to control the movement of the ram, offering precise positioning and energy-efficient operation. These machines provide faster cycle times and reduced maintenance compared to traditional hydraulic systems.
Advanced Control Software: Modern press brake machines are equipped with sophisticated software that enables real-time monitoring, automatic adjustments, and predictive maintenance. Features like automatic backgauges, bend allowance calculations, and integrated CAD/CAM systems streamline the bending process and improve accuracy.
Enhanced Automation: Automation features, including robotic loading and unloading, automated tool changes, and integrated quality control systems, increase productivity and reduce manual labor. These advancements are particularly beneficial in high-volume production environments where efficiency and consistency are paramount.
Sustainability Initiatives: Manufacturers are increasingly focusing on energy-efficient press brake machines that reduce power consumption and minimize environmental impact. Innovations such as regenerative braking systems and energy recovery mechanisms contribute to more sustainable manufacturing practices.
3.9 Case Studies: Press Brake Machines in Action
Automotive Manufacturing: In the automotive industry, press brake machines are used to fabricate various components such as door panels, chassis parts, and engine components. The precision offered by CNC press brakes ensures that each part meets the stringent quality standards required for vehicle assembly. For example, a major automotive manufacturer utilizes a fleet of 100-ton hydraulic press brakes to produce consistent and high-quality body panels, reducing production time and minimizing material waste.
Aerospace Industry: Aerospace manufacturers rely on hydraulic sheet metal bending machines to produce aircraft components with exacting specifications. The high precision and repeatability of CNC press brakes enable the production of complex parts such as fuselage sections and wing components. By integrating advanced control systems, aerospace companies can achieve the necessary tolerances and maintain the integrity of critical components.
Construction Sector: In the construction industry, press brake machines are used to fabricate structural steel elements like beams, columns, and trusses. Hydraulic press brakes with large bed sizes and high tonnage capacities are essential for handling the thick and heavy materials used in construction projects. For instance, a construction equipment manufacturer employs 1000-ton hydraulic press brakes to produce large steel beams, ensuring structural integrity and compliance with safety standards.
Electronics Manufacturing: Electronics manufacturers use small hydraulic sheet metal bending machines to create precise enclosures and frames for devices such as smartphones, laptops, and medical equipment. The ability to perform intricate bends with high accuracy ensures that the final products meet design specifications and fit seamlessly with other components.
3.10 Best Practices for Operating Press Brake Machines
To maximize the efficiency and lifespan of press brake machines, adhering to best practices is essential. These practices encompass proper machine setup, maintenance, and operational techniques that ensure consistent quality and safety.
Machine Setup:
- Accurate Alignment: Ensure that the punch and die are properly aligned to prevent uneven bends and reduce tooling wear.
- Proper Tooling Selection: Choose the appropriate punches and dies based on the material type, thickness, and desired bend angle.
- Parameter Optimization: Set the correct bending force, ram speed, and stroke length according to the material properties and bending requirements.
Maintenance:
- Regular Inspections: Conduct routine inspections of hydraulic systems, electrical components, and mechanical parts to identify and address potential issues early.
- Lubrication: Keep moving parts well-lubricated to reduce friction and prevent wear.
- Tooling Maintenance: Clean and maintain punches and dies to ensure optimal performance and extend their lifespan.
Operational Techniques:
- Consistent Feeding: Ensure that metal sheets are fed consistently into the press brake to maintain uniform bends.
- Monitoring and Adjustment: Continuously monitor the bending process and make necessary adjustments to maintain precision.
- Safety Protocols: Implement and enforce safety protocols, including the use of personal protective equipment (PPE) and adherence to operational guidelines.
Training and Education:
- Operator Training: Provide comprehensive training for operators to ensure they understand machine operation, safety procedures, and maintenance practices.
- Continuous Improvement: Encourage operators to stay updated with the latest techniques and technologies in press brake operations through ongoing education and training programs.
3.11 Conclusion
Press brake machines are integral to the metal fabrication industry, offering the precision and versatility required to produce a wide range of components and structures. Understanding the functionality, bending techniques, and specific applications of different press brake machines, including hydraulic and CNC models, is essential for optimizing their use in various industrial settings. By adhering to best practices and leveraging advancements in press brake technology, manufacturers can achieve high-quality results, enhance productivity, and maintain a competitive edge in the market.
In the following sections, we will explore other specialized bending machines, including pipe bending machines and sheet metal bending machines, to provide a comprehensive overview of the tools available for metal shaping and forming operations.
Pipe Bending Machines
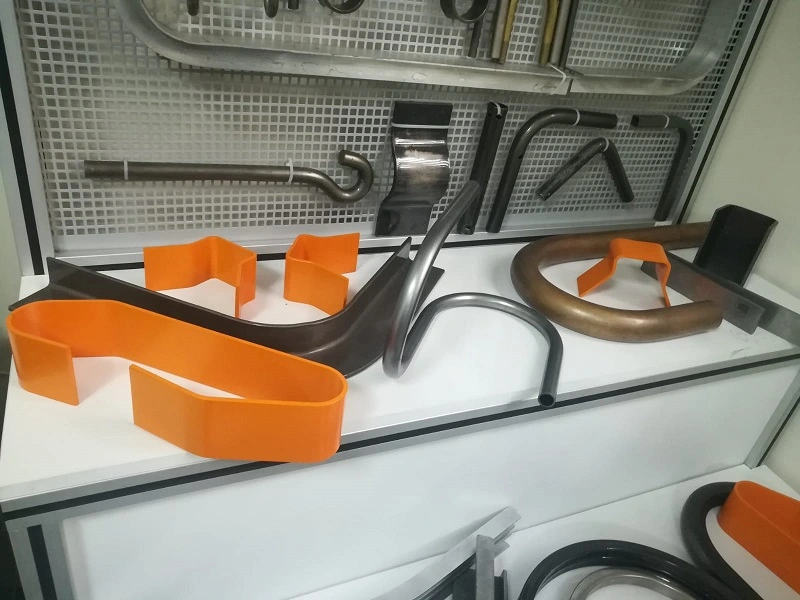
Pipe bending machines are essential tools in industries where precise and efficient bending of pipes and tubes is required. These machines are used to create complex pipe shapes that are crucial in various applications, from plumbing and construction to automotive and aerospace industries. In this section, we will explore the different types of pipe bending machines, including pneumatic, mechanical, hydraulic, and specialized machines for bending stainless steel (SS) and heavy pipes. We’ll also discuss the benefits and considerations for choosing the right pipe bending machine for specific applications.
4.1 Pneumatic Pipe Bending Machine
Pneumatic pipe bending machines utilize compressed air to generate the force needed to bend pipes. These machines are commonly used in applications that require moderate force and precision, making them suitable for a variety of industries, including automotive and HVAC (Heating, Ventilation, and Air Conditioning).
Working Principles:
- Air Compression: The machine operates by compressing air in a cylinder, which then forces a piston to move. This movement is transferred to the bending tool, which applies the necessary force to bend the pipe.
- Controlled Force: The force applied can be adjusted by regulating the air pressure, allowing for precise control over the bending process.
Advantages:
- Simplicity: Pneumatic systems are generally simpler and easier to maintain than hydraulic systems, with fewer components and less potential for leaks.
- Cost-Effectiveness: Pneumatic machines are often more affordable than their hydraulic counterparts, making them a good option for smaller operations.
- Safety: Pneumatic systems are inherently safer in environments where fire hazards are a concern, as they do not involve flammable fluids.
Applications:
- Automotive Industry: Bending exhaust pipes and other components where moderate force and precision are required.
- HVAC Systems: Shaping pipes and ducts for heating, ventilation, and air conditioning installations.
- General Fabrication: Suitable for bending tasks in small to medium-sized fabrication shops.
4.2 Mechanical Pipe Bending Machine
Mechanical pipe bending machines rely on mechanical force generated by gears, levers, and other mechanical components to bend pipes. These machines are known for their durability and reliability, making them suitable for high-volume production environments.
Working Principles:
- Mechanical Leverage: The machine uses mechanical leverage to amplify the force applied by the operator, allowing it to bend pipes with precision.
- Gear Systems: Gears and cams are often used to control the movement and force applied to the bending tool, ensuring consistent results.
Advantages:
- Durability: Mechanical pipe bending machines are built to last, with robust components that can withstand the rigors of high-volume production.
- Consistency: The use of gears and mechanical systems ensures consistent and repeatable bends, which is crucial in mass production.
- Ease of Use: These machines are typically straightforward to operate, with manual or semi-automatic controls that allow for precise adjustments.
Applications:
- Construction Industry: Bending steel pipes for structural applications, such as scaffolding and frameworks.
- Manufacturing: Producing bent pipes for various industrial products, including furniture, machinery, and equipment.
- Shipbuilding: Shaping pipes used in marine applications, where durability and precision are critical.
4.3 SS Pipe Bending Machine
Stainless steel (SS) pipes are widely used in industries that require corrosion-resistant and durable materials, such as food processing, pharmaceuticals, and chemical processing. Bending stainless steel pipes requires specialized machines that can handle the unique properties of this material without causing damage or deformation.
Key Features:
- Enhanced Tooling: SS pipe bending machines are equipped with hardened tooling that can withstand the high tensile strength of stainless steel, preventing tool wear and ensuring clean bends.
- Precision Control: These machines offer precise control over the bending process, allowing for tight bend radii and complex shapes without compromising the material’s integrity.
- Cooling Systems: Some SS pipe bending machines are equipped with cooling systems to prevent the material from overheating during the bending process, which could lead to discoloration or weakening of the stainless steel.
Advantages:
- Corrosion Resistance: SS pipe bending machines are designed to maintain the corrosion-resistant properties of stainless steel, making them ideal for applications in harsh environments.
- High Precision: The machines can produce precise bends with minimal springback, ensuring that the final product meets exact specifications.
- Versatility: Suitable for a wide range of applications, from sanitary piping in food processing to chemical transport lines in industrial settings.
Applications:
- Food and Beverage Industry: Bending pipes for sanitary processing lines, where cleanliness and corrosion resistance are paramount.
- Pharmaceutical Industry: Shaping pipes for sterile environments, including drug manufacturing and medical device production.
- Chemical Processing: Creating corrosion-resistant piping systems for transporting aggressive chemicals and other hazardous materials.
4.4 Steel Pipe Bending Machine
Steel pipe bending machines are designed to handle the rigors of bending steel pipes, which are commonly used in construction, infrastructure, and heavy industry. These machines are built to provide the necessary force and control to bend steel pipes without compromising their structural integrity.
Key Features:
- High Tonnage Capacity: Steel pipe bending machines are equipped with powerful hydraulic or mechanical systems capable of exerting the high forces required to bend steel.
- Robust Construction: The machines are built with heavy-duty frames and components to handle the stress of bending thick and strong steel pipes.
- Advanced Control Systems: Many steel pipe bending machines feature CNC controls, allowing for precise and automated bending processes.
Advantages:
- Strength and Durability: Steel pipe bending machines are capable of bending thick-walled and large-diameter steel pipes with high precision, ensuring that the final product meets structural requirements.
- Versatility: These machines can handle a wide range of steel pipe sizes and thicknesses, making them suitable for various applications in construction and heavy industry.
- Efficiency: The use of advanced control systems and automated features allows for efficient production, reducing labor costs and increasing throughput.
Applications:
- Construction: Bending steel pipes for structural applications, such as beams, columns, and supports in buildings and infrastructure projects.
- Oil and Gas Industry: Shaping steel pipes for pipelines, drilling rigs, and other critical infrastructure in the energy sector.
- Heavy Machinery Manufacturing: Producing bent steel components for construction equipment, mining machinery, and industrial tools.
4.5 Heavy Pipe Bending Machine
Heavy pipe bending machines are specialized for handling large-diameter and thick-walled pipes that require significant force to bend. These machines are used in industries where large-scale infrastructure projects and heavy-duty applications are common.
Key Features:
- High Force Capability: Heavy pipe bending machines are equipped with hydraulic systems capable of generating extremely high forces, often exceeding 1000 tons, to bend large and thick pipes.
- Large Bed Size: These machines feature expansive working areas to accommodate the size of the pipes being bent, allowing for precise positioning and control.
- Reinforced Components: The machines are built with reinforced frames, tooling, and hydraulic systems to handle the stress of bending heavy pipes without deformation.
Advantages:
- Capability: Heavy pipe bending machines can handle pipes with large diameters and thick walls, which are typically used in major infrastructure projects.
- Precision: Despite their size, these machines offer precise control over the bending process, ensuring that large pipes meet exacting specifications.
- Durability: Built to withstand the demands of heavy industry, these machines offer long service life and reliable performance in challenging environments.
Applications:
- Pipeline Construction: Bending large-diameter pipes for oil, gas, and water pipelines that span long distances and require precise engineering.
- Shipbuilding: Shaping heavy steel pipes for marine vessels, where durability and structural integrity are crucial.
- Power Generation: Producing bent pipes for power plants and energy infrastructure, including those used in nuclear and fossil fuel power generation.
4.6 Hydraulic Pipe Bending Machine
Hydraulic pipe bending machines are among the most versatile and powerful options for bending pipes in various industries. These machines utilize hydraulic pressure to apply force, offering precise control and the ability to handle a wide range of pipe sizes and materials.
Working Principles:
- Hydraulic Force: The machine uses a hydraulic cylinder to apply force to the bending tool, which then bends the pipe to the desired angle.
- Adjustable Pressure: Operators can adjust the hydraulic pressure to control the force applied, allowing for precise bends even in challenging materials.
Advantages:
- Versatility: Hydraulic pipe bending machines can handle a variety of materials, including steel, aluminum, and stainless steel, making them suitable for diverse applications.
- Precision: The hydraulic system offers fine control over the bending process, ensuring consistent results with minimal springback.
- Power: These machines are capable of generating significant force, allowing them to bend thick and strong pipes with ease.
Applications:
- Automotive Manufacturing: Bending exhaust pipes, roll cages, and other components where precision and strength are required.
- Aerospace Industry: Shaping pipes used in aircraft hydraulic systems, fuel lines, and other critical applications.
- Construction: Bending steel pipes for structural applications, such as beams, columns, and support structures.
4.7 Electric Pipe Bending Machine
Electric pipe bending machines offer an alternative to hydraulic and pneumatic systems, using electric motors to generate the force needed for bending operations. These machines are known for their energy efficiency, precision, and ease of use.
Key Features:
- Electric Motor Drive: The machine uses an electric motor to drive the bending tool, providing precise control over the bending process.
- Programmable Controls: Many electric pipe bending machines feature CNC or digital controls, allowing for automated and repeatable bending sequences.
- Quiet Operation: Electric machines tend to operate more quietly than hydraulic or pneumatic systems, making them suitable for environments where noise is a concern.
Advantages:
- Energy Efficiency: Electric pipe bending machines consume less energy compared to hydraulic systems, making them more cost-effective in the long run.
- Precision and Consistency: The use of electric motors and digital controls ensures precise and repeatable bends, which is critical in high-volume production.
- Ease of Maintenance: Electric machines have fewer moving parts compared to hydraulic systems, resulting in lower maintenance requirements and longer service life.
Applications:
- Furniture Manufacturing: Bending metal pipes for furniture frames, including chairs, tables, and shelving units.
- Medical Equipment: Shaping pipes used in medical devices and equipment, where precision and cleanliness are essential.
- Automotive Aftermarket: Producing custom exhaust systems, roll cages, and other automotive components.
4.8 Small Pipe Bending Machine
Small pipe bending machines are designed for applications that involve smaller-diameter pipes and require less force. These machines are commonly used in workshops, small-scale manufacturing, and maintenance operations.
Key Features:
- Compact Design: Small pipe bending machines are portable and space-efficient, making them ideal for use in confined spaces or on job sites.
- Manual or Semi-Automatic Operation: These machines are typically operated manually or with semi-automatic controls, offering a balance between control and ease of use.
- Versatility: Despite their small size, these machines can handle a variety of materials and bending angles, making them suitable for diverse applications.
Advantages:
- Portability: Small pipe bending machines are easy to transport and set up, making them ideal for on-site work and maintenance tasks.
- Cost-Effectiveness: These machines are typically more affordable than larger models, making them accessible to small businesses and workshops.
- Ease of Use: Simple controls and operation make these machines user-friendly, even for operators with limited experience.
Applications:
- Plumbing: Bending pipes for plumbing installations and repairs, including copper, PVC, and other materials.
- HVAC: Shaping small-diameter pipes for heating, ventilation, and air conditioning systems.
- DIY and Home Workshops: Suitable for hobbyists and small-scale fabricators working on custom projects.
4.9 Pipe Bending Machine Price Considerations
When selecting a pipe bending machine, understanding the factors that influence price is crucial to making an informed investment. The price of a pipe bending machine can vary significantly based on several key factors, including machine type, capacity, features, and brand.
Factors Influencing Price:
- Machine Type: Hydraulic and electric pipe bending machines are generally more expensive than pneumatic or mechanical models due to their advanced features and higher force capabilities.
- Capacity: Machines capable of bending larger-diameter or thicker-walled pipes typically cost more due to the increased force requirements and more robust construction.
- Control Systems: CNC-controlled machines with programmable features and automated bending sequences are priced higher than manual or semi-automatic models.
- Brand and Quality: Established brands with a reputation for quality and reliability often command higher prices, but they also offer better performance, durability, and support.
Cost vs. Functionality:
- Entry-Level Machines: Suitable for small-scale operations, workshops, and maintenance tasks, these machines offer basic functionality at a lower cost.
- Mid-Range Machines: Ideal for medium-sized businesses and manufacturers, offering a balance between price and advanced features.
- High-End Machines: Designed for large-scale production and heavy industry, these machines offer the highest levels of precision, automation, and durability but come at a premium price.
Making the Right Investment:
- Assessing Needs: Consider the specific requirements of your operation, including the types of materials, pipe sizes, and production volume, to choose a machine that meets your needs without overspending.
- Long-Term Value: While higher-end machines may have a higher initial cost, their durability, efficiency, and advanced features can lead to lower operational costs and better ROI over time.
- Supplier Support: Look for suppliers that offer good after-sales support, including training, maintenance, and parts availability, as this can significantly impact the total cost of ownership.
4.10 Conclusion
Pipe bending machines are crucial tools in various industries, offering the ability to shape and form pipes to precise specifications. Understanding the different types of pipe bending machines, including pneumatic, mechanical, hydraulic, and specialized machines for stainless steel and heavy pipes, is essential for selecting the right equipment for your needs. By considering factors such as machine capacity, control systems, and price, manufacturers and operators can make informed decisions that optimize productivity and ensure the quality of their products.
Sheet Metal Bending Machines
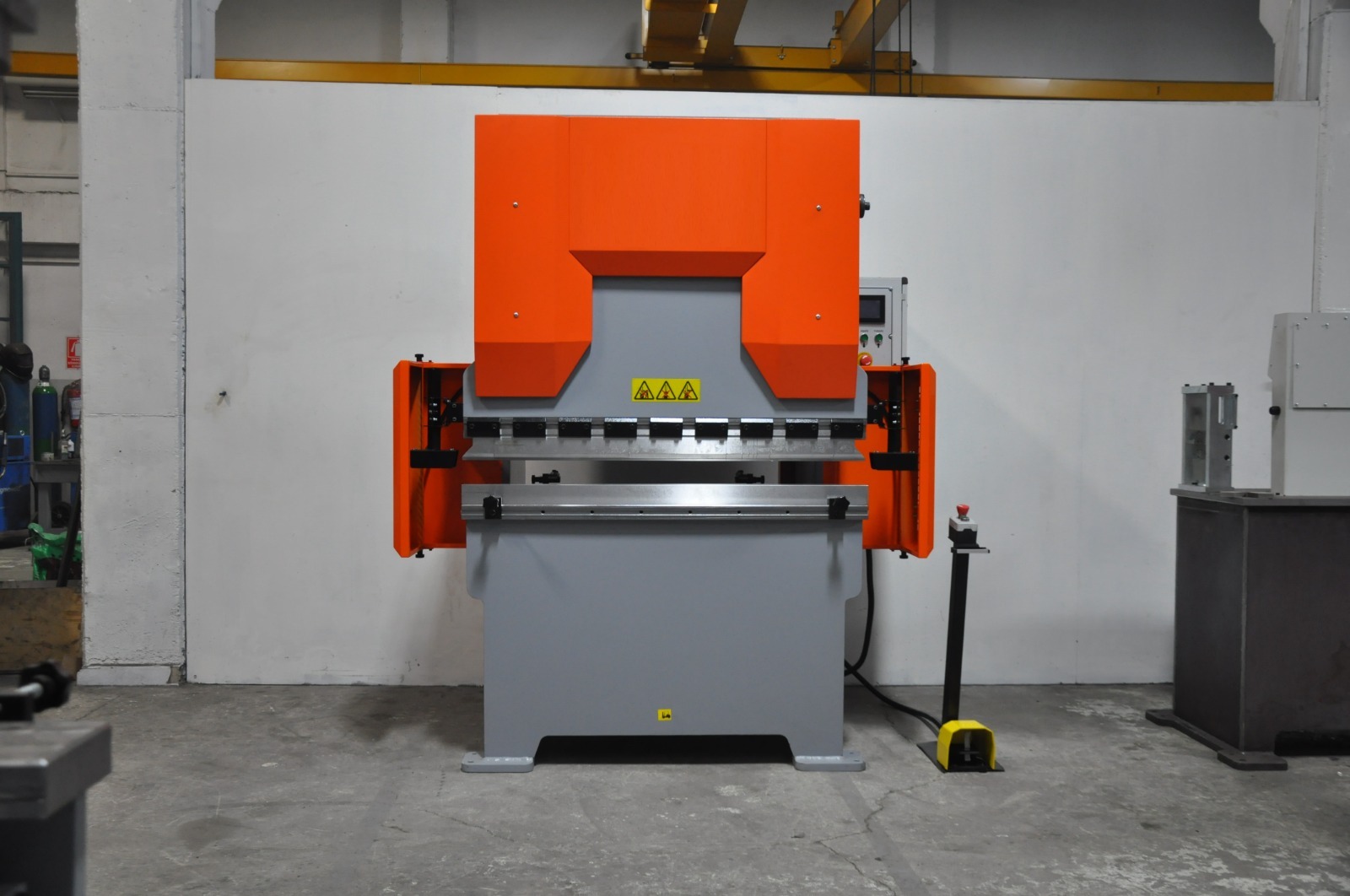
Sheet metal bending machines are essential in the fabrication of metal components, allowing manufacturers to create a wide range of shapes and structures from flat metal sheets. These machines are used across various industries, from automotive to aerospace, and play a critical role in producing everything from simple bends to complex geometries. In this section, we will explore the different types of sheet metal bending machines, including electric, hydraulic, automatic, and CNC-controlled machines. We will also discuss their applications, benefits, and factors to consider when selecting the right machine for specific tasks.
5.1 Electric Sheet Metal Bending Machine
Electric sheet metal bending machines use electric motors to generate the force needed to bend metal sheets. These machines are known for their energy efficiency, precision, and ease of use, making them a popular choice in many fabrication shops.
Key Features:
- Electric Motor Drive: These machines are driven by electric motors, which provide precise control over the bending process and allow for consistent and repeatable results.
- Programmable Controls: Many electric bending machines come with digital or CNC controls, enabling operators to program bending sequences and angles for automated operations.
- Quiet Operation: Electric machines tend to be quieter than hydraulic models, making them suitable for environments where noise reduction is important.
Advantages:
- Energy Efficiency: Electric machines are more energy-efficient than hydraulic machines, reducing operational costs over time.
- Precision: The electric motor provides consistent power, allowing for precise bends with minimal variability.
- Ease of Maintenance: With fewer moving parts and no hydraulic fluid, electric bending machines typically require less maintenance and have lower operating costs.
Applications:
- Light Fabrication: Suitable for bending thin sheets of metal, making them ideal for light fabrication tasks such as creating enclosures, brackets, and panels.
- Electronics Manufacturing: Used to bend metal components for electronic devices, where precision and consistency are critical.
- Custom Fabrication: Ideal for small workshops and custom fabrication businesses that require flexible and precise bending capabilities.
5.2 Small Sheet Bending Machine
Small sheet bending machines are designed for tasks that involve smaller pieces of sheet metal. These machines are typically more compact and easier to use, making them ideal for workshops and small-scale operations.
Key Features:
- Compact Design: Small sheet bending machines are designed to be portable and space-efficient, allowing them to be used in smaller workspaces.
- Manual or Semi-Automatic Operation: These machines often feature manual or semi-automatic controls, providing a balance between precision and ease of use.
- Versatile Tooling: Despite their size, small sheet bending machines can be equipped with a variety of tooling to handle different bending tasks.
Advantages:
- Portability: The compact size of these machines makes them easy to transport and set up, allowing for flexible use in different locations.
- Affordability: Small sheet bending machines are typically less expensive than larger models, making them accessible to small businesses and workshops.
- Ease of Use: Simple controls and operation make these machines user-friendly, even for operators with limited experience.
Applications:
- DIY and Custom Projects: Ideal for hobbyists and small-scale fabricators working on custom projects.
- Maintenance and Repair: Used in maintenance shops for bending small metal parts and components during repairs.
- Prototype Development: Suitable for creating prototypes and small production runs, where flexibility and quick setup are important.
5.3 Automatic Bending Machine
Automatic bending machines are designed to streamline the bending process by automating various aspects of the operation. These machines are equipped with advanced control systems that allow for precise and repeatable bending without the need for constant operator intervention.
Key Features:
- Automation: Automatic bending machines are capable of performing multiple bends in a single setup, reducing the need for manual adjustments and increasing productivity.
- CNC Controls: Many automatic bending machines are equipped with CNC (Computer Numerical Control) systems that allow for the programming of complex bending sequences.
- High Throughput: These machines are designed for high-volume production, making them ideal for industries that require large quantities of bent metal parts.
Advantages:
- Increased Efficiency: Automation reduces the time required for setup and bending, leading to higher production rates and lower labor costs.
- Consistency: Automatic machines ensure that each bend is executed with the same precision, reducing variability and improving product quality.
- Flexibility: The ability to program complex bending sequences allows for the production of intricate and custom shapes with minimal manual intervention.
Applications:
- Mass Production: Used in industries such as automotive and aerospace, where large quantities of parts with consistent quality are required.
- Complex Fabrication: Suitable for producing parts with multiple bends or intricate shapes that would be difficult to achieve manually.
- High-Precision Manufacturing: Ideal for applications where exacting tolerances and repeatability are essential, such as in the production of medical devices and electronics.
5.4 CNC Sheet Bending Machine
CNC sheet bending machines represent the pinnacle of precision and automation in sheet metal bending. These machines are controlled by computer numerical control (CNC) systems, which allow for highly accurate and repeatable bending operations.
Key Features:
- CNC Control: CNC sheet bending machines are equipped with computerized controls that allow operators to program and execute complex bending sequences with high precision.
- Automated Tooling: These machines often feature automated tooling systems that can change punches and dies as needed, further increasing efficiency and reducing setup time.
- Real-Time Monitoring: CNC systems provide real-time monitoring of the bending process, allowing operators to make adjustments on the fly and ensuring that each bend meets the required specifications.
Advantages:
- High Precision: CNC control ensures that each bend is performed with exacting accuracy, making these machines ideal for applications where precision is critical.
- Repeatability: The ability to store and recall bending programs allows for consistent results across multiple production runs, reducing variability and waste.
- Complexity: CNC sheet bending machines can perform intricate bends and form complex shapes that would be difficult or impossible to achieve with manual machines.
Applications:
- Aerospace Industry: Used to produce aircraft components with exacting tolerances and complex shapes.
- Automotive Manufacturing: Essential for the production of car body panels, chassis components, and other critical parts that require high precision.
- Electronics and Appliances: Ideal for creating metal enclosures, frames, and other components used in electronics and household appliances.
5.5 What is a CNC Bending Machine?
A CNC bending machine is a specialized type of bending machine that uses computer numerical control (CNC) to automate the bending process. CNC machines are programmed with specific instructions that control the movement of the machine’s bending tools, allowing for precise and repeatable operations.
How CNC Bending Machines Work:
- Programming: Operators program the CNC machine using specialized software, inputting parameters such as bend angles, material thickness, and sequence of operations.
- Tool Movement: The CNC system controls the movement of the bending tools, ensuring that each bend is executed according to the programmed instructions.
- Feedback Loops: CNC machines often include feedback systems that monitor the bending process in real-time, allowing for automatic adjustments to maintain precision.
Benefits of CNC Bending Machines:
- Precision: CNC bending machines offer unparalleled precision, with the ability to produce bends with tight tolerances and consistent quality.
- Efficiency: Automation reduces the time required for setup and bending, increasing throughput and reducing labor costs.
- Flexibility: The ability to program complex bending sequences allows for the production of custom and intricate shapes with minimal manual intervention.
Applications:
- Industrial Manufacturing: Used in high-volume production environments where consistency and precision are critical.
- Custom Fabrication: Ideal for producing custom parts and components, especially those with complex geometries.
- Prototyping: CNC bending machines are valuable in the development of prototypes, allowing for rapid iteration and precise adjustments.
5.6 Hydraulic Press Bending Machine
Hydraulic press bending machines combine the power of hydraulic systems with the precision of press brakes to perform bending operations with high efficiency and accuracy. These machines are widely used in industries that require consistent and reliable bends in a variety of materials, including steel, aluminum, and stainless steel.
Working Principles:
- Hydraulic Force: The machine uses a hydraulic cylinder to apply force to the bending tool, which then bends the metal sheet to the desired angle.
- Adjustable Pressure: Operators can adjust the hydraulic pressure to control the force applied, allowing for precise bends even in challenging materials.
Advantages:
- High Force Capacity: Hydraulic press bending machines are capable of exerting significant force, making them suitable for bending thick and strong materials.
- Precision: The hydraulic system provides fine control over the bending process, ensuring consistent results with minimal variability.
- Versatility: These machines can handle a wide range of materials and thicknesses, making them suitable for various industrial applications.
Applications:
- Automotive Manufacturing: Bending automotive body panels and structural components with high precision.
- Construction: Creating structural steel components for buildings and infrastructure projects.
- Heavy Machinery Production: Fabricating parts for construction equipment, mining machinery, and industrial tools.
5.7 Hydraulic Sheet Metal Bending Machine
Hydraulic sheet metal bending machines are specialized press brakes designed to handle the specific challenges associated with bending thin metal sheets. These machines leverage hydraulic systems to provide the necessary force and control for precise sheet metal fabrication.
Key Features:
- Enhanced Precision: Hydraulic systems ensure that each bend is executed with high accuracy, minimizing deviations and maintaining consistency.
- Adjustable Clamping Force: Allows for the secure holding of thin sheets without causing deformation or damage during the bending process.
- Integrated Control Systems: Modern hydraulic sheet metal bending machines often feature computerized controls for automated bending sequences, reducing manual intervention and increasing efficiency.
Benefits:
- Reduced Material Waste: Precise bending reduces the likelihood of errors and rework, leading to less material wastage and lower production costs.
- Increased Productivity: Automated and semi-automated systems enable faster production rates, meeting the demands of high-volume manufacturing.
- Versatility: Capable of handling a variety of sheet metal thicknesses and materials, making them suitable for diverse applications.
Applications:
- Appliance Manufacturing: Producing metal housings and components for household appliances such as refrigerators, washing machines, and ovens.
- Electronics Enclosures: Creating precise and compact metal enclosures for electronic devices and equipment.
- Furniture Manufacturing: Bending metal sheets for modern and ergonomic furniture designs.
5.8 Choosing the Right Sheet Metal Bending Machine
Selecting the right sheet metal bending machine involves considering several factors, including the material being bent, the required precision, production volume, and budget. Here are some key considerations to keep in mind:
Material Type and Thickness:
- Material: Different machines are better suited for specific materials. For example, hydraulic machines are ideal for thick steel sheets, while electric machines may be better for lighter materials.
- Thickness: The thickness of the material will determine the required force, with thicker materials needing more powerful machines.
Bending Precision:
- Tolerances: If your application requires tight tolerances, a CNC or hydraulic bending machine may be the best choice due to their precision and consistency.
- Complexity: For complex bending operations involving multiple bends or intricate shapes, a CNC machine will provide the necessary control and flexibility.
Production Volume:
- Low Volume: For small production runs or custom projects, a manual or small sheet bending machine may suffice.
- High Volume: For large-scale production, an automatic or CNC bending machine is more appropriate due to their higher efficiency and automation capabilities.
Budget Considerations:
- Initial Investment: CNC and hydraulic machines tend to have higher upfront costs but offer long-term benefits in precision, efficiency, and flexibility.
- Operating Costs: Consider the long-term costs of maintenance, energy consumption, and tooling when selecting a machine.
Supplier Support:
- After-Sales Service: Choose a supplier that offers good after-sales support, including maintenance, training, and access to spare parts.
- Warranty: Look for machines that come with a comprehensive warranty, which can protect your investment and reduce the risk of unexpected costs.
5.9 Future Trends in Sheet Metal Bending Machines
The field of sheet metal bending is constantly evolving, with new technologies and innovations improving the efficiency, precision, and versatility of bending machines. Here are some trends shaping the future of sheet metal bending:
Automation and Robotics:
- Increased Automation: Automation is becoming more prevalent in sheet metal bending, with robots and automated systems taking over tasks such as loading, unloading, and tool changes, leading to higher productivity and lower labor costs.
- Collaborative Robots: Also known as cobots, these robots work alongside human operators to assist with bending operations, enhancing efficiency while maintaining flexibility.
Advanced CNC Systems:
- Real-Time Monitoring: CNC systems are becoming more advanced, with features such as real-time monitoring, predictive maintenance, and automatic adjustments ensuring higher precision and reducing downtime.
- AI Integration: Artificial intelligence (AI) is being integrated into CNC systems to optimize bending processes, improve decision-making, and enhance overall efficiency.
Sustainability Initiatives:
- Energy Efficiency: Manufacturers are focusing on creating more energy-efficient bending machines that reduce power consumption without compromising performance.
- Material Waste Reduction: Innovations in tooling and process control are helping to reduce material waste, leading to more sustainable manufacturing practices.
Customization and Flexibility:
- Modular Machines: Modular designs allow for easy customization of bending machines, enabling manufacturers to adapt to different tasks and requirements without significant downtime.
- Flexible Tooling: Advances in tooling technology are allowing for more flexible and adaptable bending operations, making it easier to switch between different products and designs.
5.10 Conclusion
Sheet metal bending machines are vital tools in modern manufacturing, offering the precision, flexibility, and efficiency needed to produce high-quality metal components. Understanding the different types of machines—such as electric, hydraulic, automatic, and CNC models—and their specific applications is crucial for selecting the right equipment for your needs. By considering factors such as material type, bending precision, production volume, and budget, manufacturers can make informed decisions that enhance productivity and ensure the quality of their products.
Bending Press Machine Price Considerations
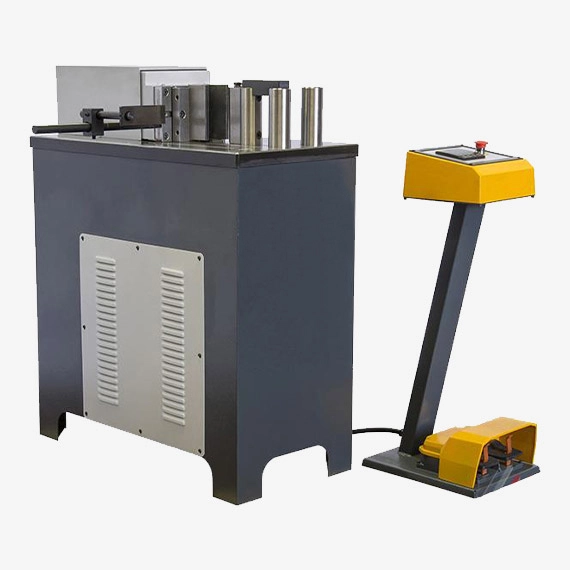
When investing in bending press machines, understanding the factors that influence pricing is essential for making an informed and cost-effective decision. Bending press machines come in various types and configurations, each with different features and capabilities that affect their overall cost. In this section, we will explore the key factors that determine the price of bending press machines, including specifications, features, brand reputation, and market demand. We will also discuss how to balance cost with functionality to ensure that you select the right machine for your specific needs.
6.1 Factors Affecting Bending Press Machine Price
The price of a bending press machine is influenced by several factors, including its type, specifications, features, brand, and market conditions. Understanding these factors can help you determine which machine offers the best value for your investment.
6.1.1 Machine Type
- Manual vs. Automated Machines: Manual bending press machines are generally less expensive than automated or CNC-controlled machines due to their simpler design and lower manufacturing costs. However, automated machines, while more expensive, offer greater efficiency, precision, and productivity, which can justify the higher initial investment.
- Hydraulic vs. Mechanical Presses: Hydraulic presses are typically more expensive than mechanical presses because of their complex hydraulic systems, which provide greater force and control. Mechanical presses, while less costly, may be more suitable for applications where speed is prioritized over precision.
6.1.2 Specifications and Capacity
- Tonnage: The tonnage, or force capacity, of a bending press machine is one of the primary factors influencing its price. Machines with higher tonnage are capable of bending thicker and stronger materials but come with a higher price tag due to the more robust construction and powerful hydraulic or mechanical systems required.
- Bed Size: The size of the machine’s bed, which determines the maximum size of the workpiece it can handle, also affects the price. Larger beds increase the machine’s versatility but require more material and engineering, leading to higher costs.
- Stroke Length: The stroke length, or the distance the press ram can travel, is another critical specification. Machines with longer stroke lengths can accommodate deeper bends, which adds to the complexity and cost of the machine.
6.1.3 Features and Technology
- CNC Controls: Bending press machines equipped with CNC (Computer Numerical Control) systems are significantly more expensive than those with manual or semi-automatic controls. CNC systems offer the ability to program and automate complex bending sequences, enhancing precision and productivity, which justifies their higher price.
- Automation and Robotics: Machines with advanced automation features, such as automatic tool changers, robotic loading and unloading, and real-time monitoring systems, command higher prices due to the added technology and the potential for increased production efficiency.
- Safety Features: Enhanced safety features, such as light curtains, safety guards, and emergency stop systems, can also contribute to the overall cost of the machine. These features are essential for protecting operators and ensuring compliance with safety regulations, particularly in high-volume production environments.
6.1.4 Brand and Quality
- Reputation: The reputation of the manufacturer or brand plays a significant role in the price of bending press machines. Established brands with a history of quality, reliability, and excellent after-sales support often charge a premium for their products. While these machines may be more expensive upfront, they often offer better performance, durability, and long-term value.
- Quality of Materials: The quality of the materials used in the construction of the machine, such as the steel for the frame and the components of the hydraulic system, affects both the machine’s durability and price. Higher-quality materials lead to longer-lasting machines but increase manufacturing costs.
6.1.5 Market Demand and Availability
- Supply and Demand: Market conditions, such as the balance between supply and demand, can also influence the price of bending press machines. During periods of high demand, prices may rise due to limited availability. Conversely, prices may decrease during periods of low demand or excess supply.
- Import and Export Costs: For machines that are imported, factors such as tariffs, shipping costs, and currency exchange rates can affect the final price. These costs can vary significantly depending on the country of origin and the location of the buyer.
6.2 Cost vs. Functionality: Making the Right Investment
When selecting a bending press machine, it is essential to balance cost with functionality to ensure that the machine meets your specific needs without exceeding your budget. Here are some strategies to help you make a cost-effective investment:
6.2.1 Assessing Your Needs
- Production Volume: Consider the volume of production when choosing a machine. If your operation involves high-volume production, investing in a more expensive, automated machine may be justified by the increased efficiency and reduced labor costs. For lower-volume operations, a less expensive manual or semi-automatic machine may be sufficient.
- Material Type and Thickness: The types of materials you work with, including their thickness and strength, will determine the necessary tonnage and capabilities of the machine. Ensure that the machine you choose can handle your specific material requirements without overpaying for unnecessary capacity.
- Complexity of Bends: If your applications involve complex bends or require high precision, investing in a CNC-controlled machine may be worth the higher cost. However, for simpler bends, a manual or mechanical machine may provide adequate functionality at a lower price.
6.2.2 Evaluating Long-Term Costs
- Operating Costs: Consider the long-term operating costs of the machine, including energy consumption, maintenance, and tooling. While a machine with advanced features may have a higher upfront cost, it could offer lower operating costs and higher efficiency, leading to savings over time.
- Durability and Reliability: Machines made with higher-quality materials and components tend to have longer service lives and require less maintenance. Investing in a durable, reliable machine can reduce downtime and maintenance costs, providing better long-term value.
- Resale Value: Some high-quality machines maintain their value well and can be resold at a good price if your needs change. This can offset some of the initial investment costs and provide flexibility in the future.
6.2.3 Exploring Financing and Leasing Options
- Financing: Many manufacturers and dealers offer financing options that allow you to spread the cost of the machine over time. This can make it easier to afford a higher-quality machine without straining your budget.
- Leasing: Leasing is another option that allows you to use a high-quality machine without the full upfront cost. Leasing can be particularly advantageous if you need the machine for a specific project or a limited time.
6.2.4 Considering Used or Refurbished Machines
- Used Machines: Purchasing a used bending press machine can be a cost-effective way to acquire high-quality equipment at a lower price. However, it is essential to thoroughly inspect the machine for wear and tear and ensure that it has been well-maintained.
- Refurbished Machines: Refurbished machines offer a middle ground between new and used equipment. These machines have been restored to good working condition and often come with warranties, providing reliability at a reduced cost.
6.2.5 Comparing Suppliers and Brands
- Supplier Reputation: Work with reputable suppliers who offer good after-sales support, including training, maintenance, and access to spare parts. A reliable supplier can significantly impact the total cost of ownership by helping you keep the machine in good working condition.
- Brand Comparison: Compare different brands and models to find the best balance between price and features. Look for reviews and case studies to understand how the machines perform in real-world applications and whether they meet industry standards.
6.3 Case Studies: Price Considerations in Real-World Scenarios
Case Study 1: Small Fabrication Shop A small metal fabrication shop required a bending press machine for custom projects involving light to medium-gauge steel. After evaluating their needs, they opted for a mid-range hydraulic press with manual controls. While they considered a CNC machine, the additional cost was not justified given their low production volume. The hydraulic press offered the necessary force and precision at a reasonable price, allowing the shop to handle a variety of projects without overextending their budget.
Case Study 2: High-Volume Automotive Manufacturer A large automotive manufacturer needed a new bending press machine to increase production efficiency for body panels. They chose a high-end CNC-controlled hydraulic press with automated tool changers and real-time monitoring. Although the machine was significantly more expensive than manual or semi-automatic models, the investment was justified by the increased throughput, reduced labor costs, and high precision required for automotive production. The machine’s advanced features also allowed for quicker setup times and reduced downtime, further enhancing productivity.
Case Study 3: Start-Up in the Aerospace Industry A start-up aerospace company needed a bending press machine capable of producing complex, high-precision components. Given their limited budget, they explored options for used and refurbished CNC machines. They found a reputable supplier offering a refurbished CNC press brake that met their specifications at a fraction of the cost of a new machine. The refurbished machine provided the precision and functionality needed for aerospace applications, allowing the start-up to meet industry standards without exceeding their budget.
6.4 Conclusion
When considering the purchase of a bending press machine, it is crucial to weigh the cost against the functionality and long-term value of the machine. Factors such as machine type, specifications, features, brand reputation, and market demand all play a significant role in determining the price. By carefully assessing your specific needs, evaluating long-term costs, exploring financing or leasing options, and comparing suppliers and brands, you can make a well-informed decision that balances cost with the required functionality. Whether you are a small shop or a large manufacturer, selecting the right bending press machine is an investment that can enhance productivity, improve product quality, and contribute to the overall success of your operation.
EMS Metalworking Machinery
We design, manufacture and assembly metalworking machinery such as:
- Hydraulic transfer press
- Glass mosaic press
- Hydraulic deep drawing press
- Casting press
- Hydraulic cold forming press
- Hydroforming press
- Composite press
- Silicone rubber moulding press
- Brake pad press
- Melamine press
- SMC & BMC Press
- Labrotaroy press
- Edge cutting trimming machine
- Edge curling machine
- Trimming beading machine
- Trimming joggling machine
- Cookware production line
- Pipe bending machine
- Profile bending machine
- Bandsaw for metal
- Cylindrical welding machine
- Horizontal pres and cookware
- Kitchenware, hotelware
- Bakeware and cuttlery production machinery
as a complete line as well as an individual machine such as:
- Edge cutting trimming beading machines
- Polishing and grinding machines for pot and pans
- Hydraulic drawing presses
- Circle blanking machines
- Riveting machine
- Hole punching machines
- Press feeding machine
You can check our machinery at work at: EMS Metalworking Machinery – YouTube
Applications:
- Beading and ribbing
- Flanging
- Trimming
- Curling
- Lock-seaming
- Ribbing
- Flange-punching