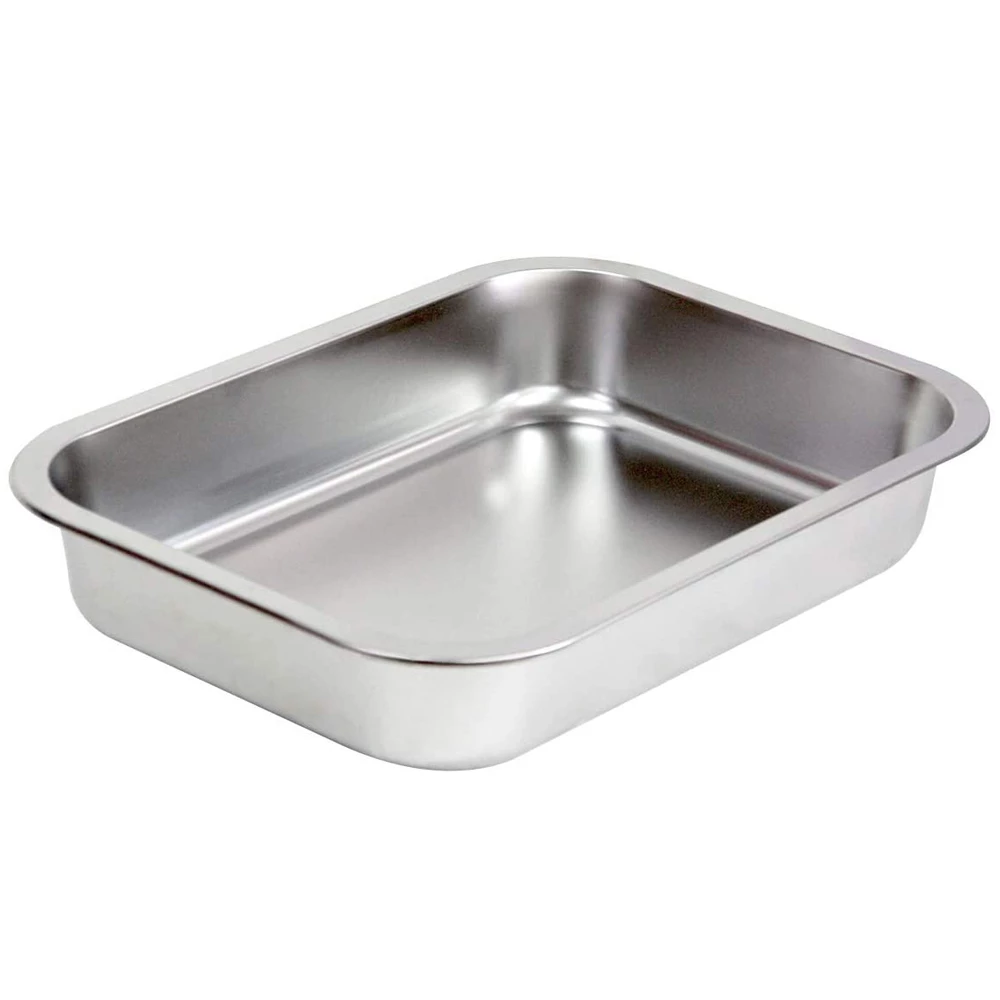
We explain below How to Smooth Sheet Metal Edges to round sheet metal edges. These machines are used in metalworking industries
Smoothing sheet metal edges is an essential process to eliminate sharp, jagged edges that can pose safety hazards and impair the functionality and aesthetics of metal parts. Several methods can be employed to effectively smooth sheet metal edges, each with its own suitability based on the material, size, shape, and desired finish of the component.
- Hand Files: Hand files offer a versatile and convenient option for smoothing small sheet metal edges or in situations where access is limited. A variety of file types with varying coarseness levels can be used to gradually remove burrs and imperfections, starting with coarse files for initial deburring and progressing to finer files for achieving a smooth finish.
- Deburring Knives: Deburring knives feature sharp, rounded blades specifically designed to trim and remove burrs from metal edges. They provide precise control and are particularly effective for smoothing edges on thin or delicate sheet metal components.
- Deburring Wheels: Deburring wheels, also known as abrasive wheels, are mounted on power tools or specialized deburring machines. These wheels utilize abrasive grit to grind down edges and remove imperfections, offering a more efficient and powerful approach to smoothing sheet metal edges.
- Rotary Deburring Tools: Rotary deburring tools, such as Dremel or similar devices, are handheld power tools equipped with various attachments, including deburring discs and wheels. These tools offer versatility and portability for smoothing edges on a variety of shapes and sizes of sheet metal components.
- Sanding: Sanding can be used for both hand finishing and power sanding. Hand sanding involves using sandpaper of varying grit levels to manually smooth edges, while power sanding utilizes orbital sanders or belt sanders for a more efficient and consistent finish.
- Grinding: Grinding is a more aggressive method for smoothing sheet metal edges, typically used for heavy-duty applications or when removing significant imperfections. Grinding tools, such as angle grinders, utilize coarse abrasive wheels to grind down edges and remove burrs.
- Edge Rounding Machines: Edge rounding machines are specialized machines designed to create a smooth, rounded profile on the edges of sheet metal components. These machines offer precise control and consistency, particularly for large-scale production or when a specific edge radius is required.
- Ultrasonic Deburring: Ultrasonic deburring is a non-abrasive method that utilizes high-frequency vibrations to remove burrs and imperfections from delicate or precision sheet metal components. This method is particularly suitable for parts with intricate geometries or sensitive surfaces.
The choice of method for smoothing sheet metal edges depends on several factors, including:
- Material of the sheet metal: Different materials may require specific abrasive materials or deburring techniques.
- Size and shape of the sheet metal component: Smaller or irregularly shaped components may be better suited for hand tools, while larger or flat pieces may benefit from power tools or specialized machines.
- Desired level of precision: For high-precision applications, hand files or ultrasonic deburring may be preferred, while power tools or grinding may be suitable for less critical applications.
- Production volume: For high-volume production, power tools or specialized machines offer increased efficiency.
Regardless of the method chosen, smoothing sheet metal edges is essential for enhancing safety, improving functionality, and ensuring the aesthetic quality of metal components. By selecting the appropriate method based on the specific requirements of the application, manufacturers can achieve the desired finish and ensure the integrity of their metal parts.
How to Smooth Sheet Metal Edges
Deburring sheet metal edges is a crucial process in metalworking to remove burrs, sharp edges, and imperfections from the edges of sheet metal components. These imperfections can arise from various metalworking processes, such as cutting, stamping, or forming. Deburring is essential for several reasons:
- Safety: Sharp edges and burrs on sheet metal pose a significant safety hazard, increasing the risk of cuts, lacerations, and other injuries. Deburring removes these hazards, reducing the risk of accidents and enhancing worker safety.
- Aesthetics: Rounded edges and a smooth surface improve the overall appearance of sheet metal components, making them more visually appealing and aesthetically pleasing. This is particularly important for products that will be visible in the final product, such as appliance panels or architectural components.
- Functionality: Rounded edges can prevent snagging, tearing, or abrasion of materials that come into contact with the sheet metal component. This is important for parts that need to move smoothly, such as conveyor belts, machinery components, or packaging materials.
Methods for Deburring Sheet Metal Edges:
- Hand Deburring Tools:
For small sheet metal components or in situations where access is limited, hand-held tools offer a convenient option. Common hand-held deburring tools include:
- Files: Files with varying coarseness levels can be used to remove burrs and smooth out rough edges.
- Deburring Knives: Knives with rounded blades are specifically designed to trim and remove burrs from sheet metal edges.
- Deburring Wheels: Deburring wheels with abrasive grit are effective for deburring sheet metal edges.
- Power Deburring Tools:
For larger sheet metal components or high-volume production, power tools provide a more efficient and powerful solution. Examples include:
- Rotary Deburring Tools: These tools utilize rotating abrasive discs or belts to quickly remove burrs from sheet metal components.
- Sanders: Sanders with appropriate abrasive belts can be used for deburring and surface finishing of sheet metal components.
- Stationary Deburring Machines:
For high-precision deburring or deburring complex shapes, specialized stationary machines offer consistent and precise results. These machines may utilize rotating cutters, abrasive belts, or a combination of both.
- Ultrasonic Deburring Systems:
Ultrasonic deburring systems use high-frequency vibrations to remove burrs from delicate or precision sheet metal components. This method is gentle and non-abrasive, making it suitable for parts with intricate geometries or sensitive surfaces.
Factors to Consider When Choosing a Deburring Method:
- Sheet Size and Thickness: The size and thickness of the sheet metal component will determine the tool’s capacity and suitability.
- Desired Level of Precision: The required level of precision will dictate whether a hand-held tool, a power tool, or a specialized machine is more appropriate.
- Accessibility of Edges: The accessibility of the edges will influence whether a handheld or stationary tool is more suitable.
- Production Volume: For high-volume production, a power tool or a specialized machine may be necessary.
- Cost Considerations: The cost of different deburring methods and tools should be evaluated based on production volume and desired precision.
Conclusion:
Deburring sheet metal edges is an essential step in metalworking to ensure the safety, aesthetics, and functionality of sheet metal components. The choice of deburring method depends on factors such as sheet size, precision requirements, accessibility, production volume, and cost considerations. By effectively removing burrs and imperfections, deburring enhances the quality and safety of sheet metal products across various industries.
Deburring Tool for Metal
https://www.youtube.com/embed/mMRmnQuYgjE?feature=oembedDeburring Tool for Metal
Deburring tools are essential for removing burrs, sharp edges, and imperfections from metal components. These tools are crucial for maintaining the safety, functionality, and aesthetics of metal products across various industries.
Types of Deburring Tools for Metal:
- Hand-Held Deburring Tools: These tools provide portability and convenient deburring for smaller metal parts or in situations where access is limited. Common hand-held deburring tools include:
- Files: Files with varying coarseness levels are effective for removing burrs and smoothing out rough edges on metal.
- Deburring Knives: Knives with rounded blades are specifically designed to trim and remove burrs from metal edges.
- Deburring Wheels: Deburring wheels with abrasive grit are effective for deburring metal edges.
- Power Deburring Tools: These tools offer greater efficiency and power for deburring larger metal components or in high-volume production. Examples include:
- Rotary Deburring Tools: Utilize rotating abrasive discs or belts to quickly remove burrs from metal parts.
- Sanders: Sanders with appropriate abrasive belts can be used for deburring and surface finishing of metal components.
- Stationary Deburring Machines: For high-precision deburring or deburring complex shapes, specialized stationary machines offer consistent and precise results. These machines may utilize rotating cutters, abrasive belts, or a combination of both.
- Ultrasonic Deburring Systems: For precision deburring of delicate metal parts or complex geometries, ultrasonic deburring offers a gentle and effective method.
Choosing the Right Deburring Tool for Metal
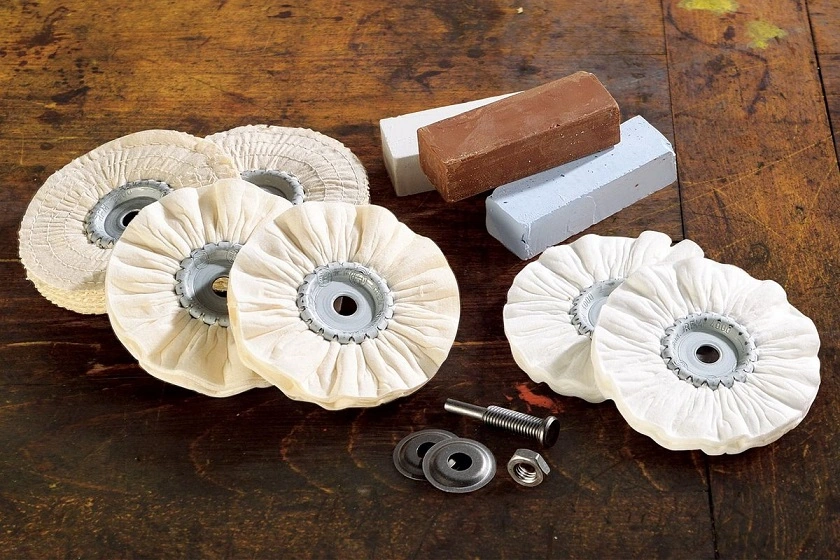
The choice of deburring tool for metal depends on several factors, including:
- Size and shape of the metal part: The tool should be able to accommodate the size and shape of the part comfortably.
- Material of the metal part: The abrasive material used in the tool should be compatible with the material of the part.
- Desired level of precision: The tool should be able to achieve the desired level of precision for the application.
- Production volume: If high-volume production is required, a stationary machine may be more efficient.
- Safety features: The tool should incorporate adequate safety features to protect the operator from potential hazards.
Benefits of Using Deburring Tools for Metal:
- Improved safety: Deburring tools can reduce the risk of injuries to operators by removing sharp edges and burrs.
- Improved functionality: Rounded edges can prevent snagging and protect other components from damage.
- Enhanced aesthetics: A smooth, burr-free surface improves the overall appearance of metal products.
- Increased efficiency: Power deburring tools and stationary machines can significantly reduce deburring time.
Applications of Deburring Tools for Metal:
- Automotive industry: Deburring car bodies, engine components, and other automotive parts.
- Aerospace manufacturing: Deburring precision metal components for aircraft and spacecraft.
- Construction: Deburring metal components for buildings, bridges, and other structures.
- Electronics manufacturing: Deburring metal components for circuit boards, electronic devices, and other electronics.
- Consumer goods manufacturing: Deburring metal components for appliances, furniture, and other consumer products.
Deburring tools play an essential role in maintaining the quality and safety of metal components across various industries. By effectively removing burrs and imperfections, deburring enhances the functionality, aesthetics, and overall value of metal products.
Metal deburring, grinding, and rounding are common applications in metalworking processes aimed at smoothing rough edges, removing burrs, and achieving a uniform finish on metal parts. Here’s a brief overview of each:
- Deburring: This process involves removing sharp edges or burrs left on metal parts after machining, cutting, or forming operations. It improves safety, functionality, and aesthetics of the parts.
- Grinding: Grinding is used to achieve precise dimensional control and surface finish. It involves using abrasive wheels or belts to remove material from a workpiece, often to prepare surfaces for further finishing or to achieve specific tolerances.
- Rounding: Rounding, also known as edge rounding, is done to soften sharp edges or corners on metal parts. It improves part handling, reduces the risk of injury, and can be aesthetically pleasing.
These processes are essential in various industries such as automotive, aerospace, manufacturing, and precision engineering, where metal parts must meet high standards of quality, safety, and performance.
- Deburring:
- Purpose: Deburring removes burrs, which are unwanted rough edges or protrusions on metal parts that result from machining, cutting, or forming processes.
- Methods: Deburring can be achieved through various methods such as manual deburring tools, abrasive stones, brushes, tumbling machines (vibratory or centrifugal), or chemical deburring solutions.
- Importance: Removing burrs improves the functional and aesthetic quality of metal parts. It also enhances safety by eliminating sharp edges that could cause injuries during handling or assembly.
- Grinding:
- Purpose: Grinding is used to achieve precise dimensional control, improve surface finish, and remove excess material from metal parts.
- Types: There are several types of grinding processes, including surface grinding, cylindrical grinding, centerless grinding, and internal grinding, each suited for specific part geometries and surface requirements.
- Equipment: Grinding machines use abrasive wheels (grinding wheels or belts) that rotate at high speeds to grind away material from the workpiece.
- Applications: Grinding is crucial for preparing surfaces for further finishing operations (such as polishing or plating), achieving tight tolerances, or removing defects like surface imperfections or weld seams.
- Rounding (Edge Rounding):
- Purpose: Rounding, or edge rounding, involves smoothing sharp edges or corners on metal parts.
- Methods: This can be done through mechanical methods like deburring tools with radius edges, vibratory or centrifugal tumbling processes with rounded media, or automated edge rounding machines.
- Benefits: Rounding improves part handling safety by reducing the risk of cuts or scratches. It also enhances the part’s appearance and can be critical for components that interact with other parts or personnel during assembly or use.
These processes are fundamental in metalworking industries where precision, quality, and safety are paramount. They ensure that metal parts meet exacting standards for functionality, durability, and aesthetics demanded by various applications, from automotive and aerospace to electronics and consumer goods manufacturing.
Deburring
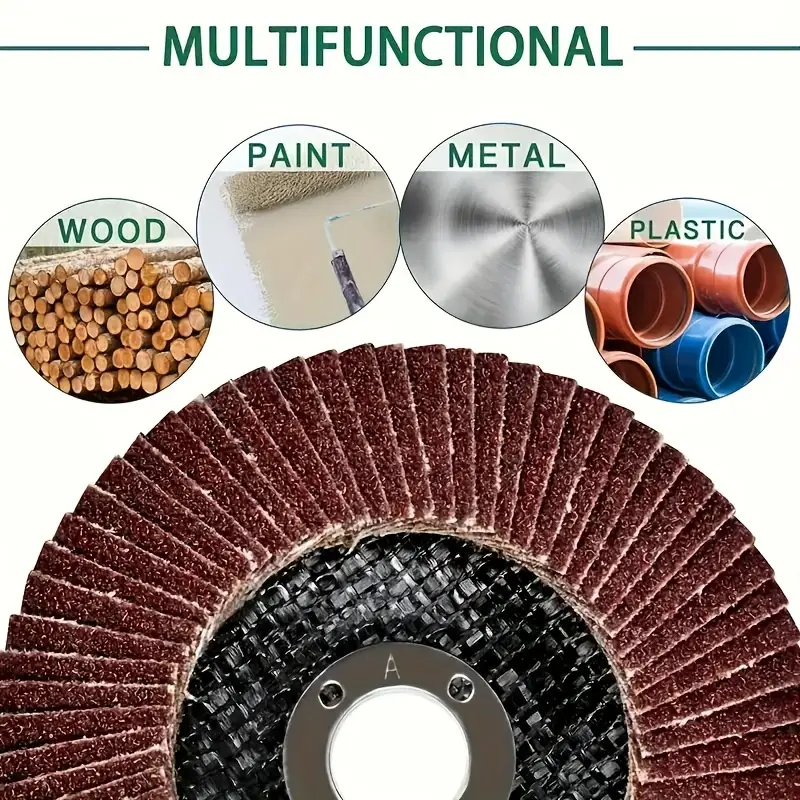
Deburring is a critical process in metalworking that involves the removal of burrs, which are unwanted rough edges or protrusions on metal parts. These burrs typically occur as a result of machining, cutting, or forming operations such as drilling, milling, stamping, or punching.
Importance of Deburring:
- Safety: Removing burrs eliminates sharp edges that can cause injuries during handling or assembly of parts.
- Functionality: Deburring ensures that parts fit together properly without interference from protrusions or rough edges.
- Aesthetics: Smooth edges improve the appearance of parts and enhance overall product quality.
- Performance: Burrs can affect the performance of moving parts or components that require precise tolerances.
Methods of Deburring:
- Manual Deburring Tools: Hand tools such as files, deburring knives, scrapers, or abrasive pads are used to manually remove burrs from small or intricate parts.
- Abrasive Stones and Brushes: Rotary tools equipped with abrasive stones or brushes can be used to remove burrs from larger or more accessible surfaces.
- Tumbling Machines: Vibratory or centrifugal tumbling machines use abrasive media (such as ceramic or plastic pellets) to deburr multiple parts simultaneously. This method is effective for small to medium-sized parts with complex geometries.
- Chemical Deburring: Chemical solutions or processes can be employed to selectively dissolve burrs, particularly in internal passages or complex shapes where mechanical methods may be challenging.
Deburring Considerations:
- Material Type: Different metals (e.g., aluminum, steel, titanium) require specific deburring techniques due to variations in hardness and machinability.
- Part Geometry: Deburring methods are chosen based on the size, shape, and accessibility of the burrs and the part itself.
- Quality Control: Inspecting parts after deburring ensures that all burrs are removed and that the part meets required specifications.
Deburring is essential in industries such as aerospace, automotive, electronics, and precision engineering, where high-quality, safe, and functional metal components are crucial.
Grinding
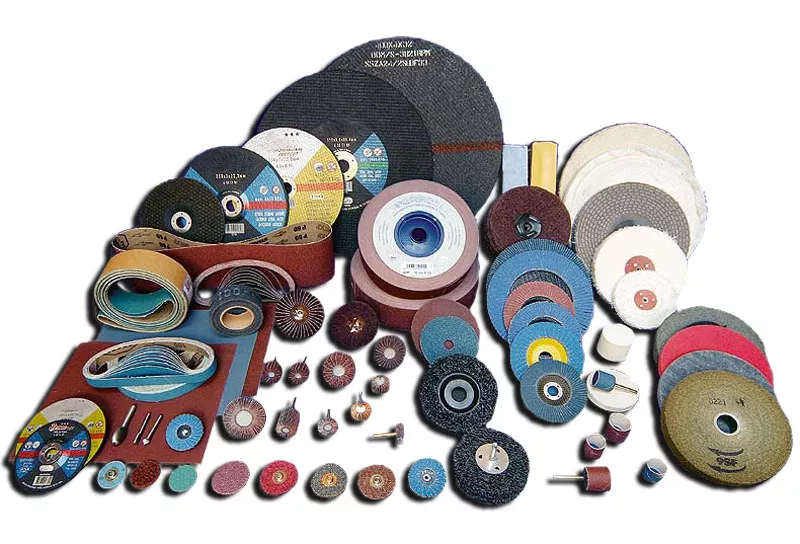
Grinding is a machining process used to remove material from a workpiece to achieve desired dimensions and surface finish. It is a versatile process widely used in various industries for both roughing and finishing operations on metal and other materials.
Purpose of Grinding
- Dimensional Control: Grinding allows for precise control over the dimensions of a workpiece, achieving tight tolerances that are difficult to achieve through other machining processes.
- Surface Finish: By using abrasive grains bonded into wheels or belts, grinding can produce smooth surfaces with low roughness values, enhancing the appearance and functionality of the parts.
- Material Removal: Grinding efficiently removes excess material, such as weld beads, casting flash, or stock material from forgings or billets, preparing the workpiece for subsequent operations.
Types of Grinding Processes:
- Surface Grinding: Involves grinding flat surfaces to achieve a smooth finish. It is commonly used for finishing hardened steel, cast iron, and similar materials.
- Cylindrical Grinding: Used to grind the outside diameter of cylindrical workpieces. It is ideal for creating precise roundness and surface finishes on shafts, rods, and other cylindrical components.
- Centerless Grinding: A type of cylindrical grinding where the workpiece is supported between two wheels: the grinding wheel and a regulating wheel. It is used for high-volume production of cylindrical parts with consistent dimensional accuracy.
- Internal Grinding: Grinding the inside diameter of a workpiece. It is used to create precise bores or holes with a smooth surface finish.
Equipment and Tools:
- Grinding Machines: Include surface grinders, cylindrical grinders, centerless grinders, and internal grinders, each designed for specific grinding applications.
- Grinding Wheels: Made from abrasive grains bonded together in various shapes and sizes. Types include aluminum oxide, silicon carbide, and diamond, each suited to different materials and applications.
Applications of Grinding:
- Manufacturing: Grinding is essential in the production of precision components for automotive, aerospace, medical devices, and consumer electronics.
- Tool and Die Making: Used for sharpening cutting tools and dies to maintain sharp edges and precise dimensions.
- Repair and Maintenance: Grinding is also employed for repairing worn or damaged parts by restoring their original dimensions and surface finish.
Grinding is a fundamental machining process that plays a crucial role in achieving the required dimensional accuracy, surface quality, and overall performance of metal parts in modern manufacturing.
Rounding
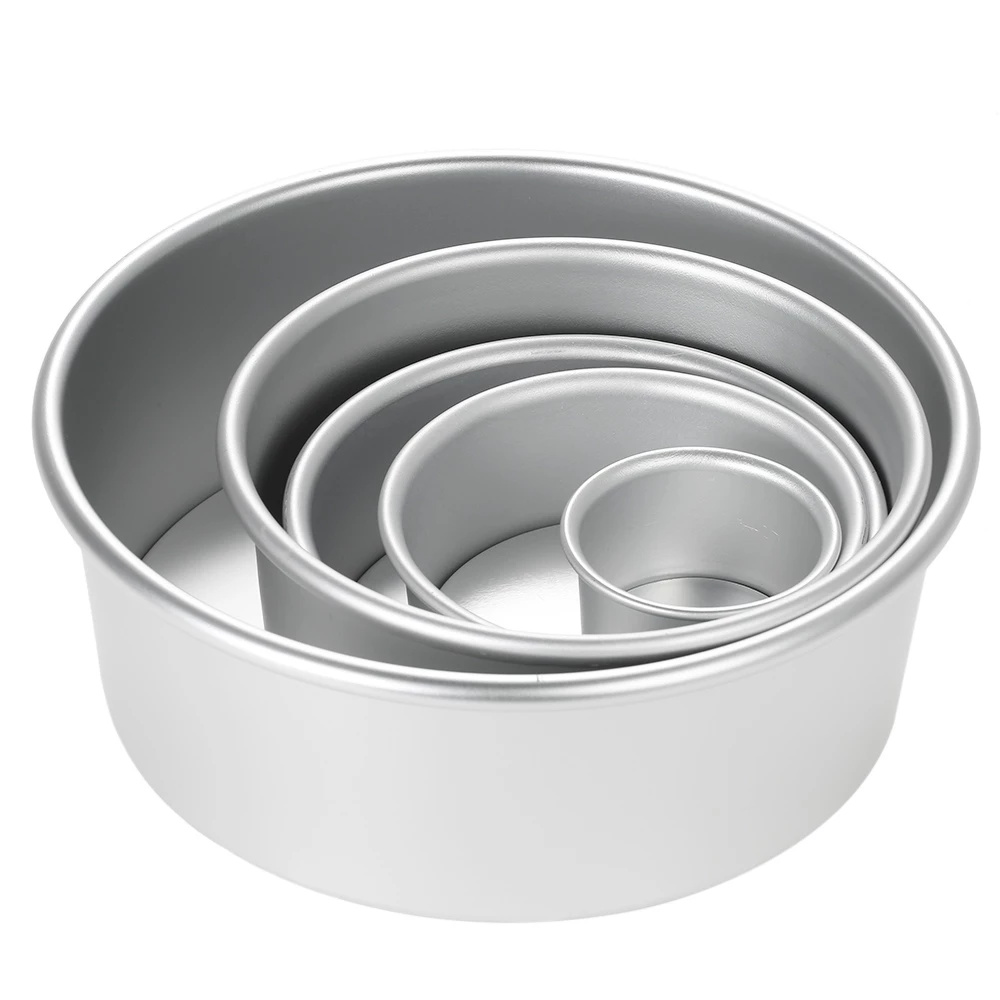
Rounding, also known as edge rounding or radiusing, is a finishing process used to smooth sharp edges and corners on metal parts. This process is essential for improving safety, enhancing aesthetics, and ensuring proper functionality of the parts, especially in applications where handling and contact with personnel or other components are involved.
Purpose and Benefits of Rounding:
- Safety: Rounded edges reduce the risk of injuries during handling, assembly, or use by eliminating sharp points or edges that could cause cuts or abrasions.
- Aesthetics: Smooth, rounded edges enhance the appearance of metal parts, making them more visually appealing and professional in finished products.
- Functionality: Rounding can improve the performance of parts by reducing stress concentrations at corners, which can extend the service life of components subjected to cyclic loading or wear.
Methods of Rounding:
- Manual Methods: Hand tools such as files, deburring tools with radiused edges, or abrasive pads can be used for small-scale rounding operations on accessible edges and corners.
- Machine Rounding: Automated edge rounding machines or dedicated deburring machines equipped with specialized tools can efficiently round edges and corners of larger or complex-shaped parts.
- Tumbling Processes: Vibratory or centrifugal tumbling machines using abrasive media (e.g., ceramic or plastic pellets) can uniformly round edges of multiple parts simultaneously. This method is effective for small to medium-sized parts with consistent edge profiles.
Considerations for Rounding:
- Part Geometry: The shape and size of the part influence the choice of rounding method. Complex geometries may require specialized equipment or multiple processes to achieve uniform rounding.
- Material Compatibility: Different metals (e.g., aluminum, stainless steel, titanium) and alloys have varying hardness and machinability characteristics, which may affect the choice of rounding tools and methods.
- Surface Finish Requirements: Rounding should maintain or improve the overall surface finish of the part, ensuring it meets functional and aesthetic specifications.
Applications of Rounding:
- Consumer Products: Rounding is crucial in industries such as furniture manufacturing, where rounded edges on metal components improve safety and user comfort.
- Automotive and Aerospace: Parts like brackets, panels, and housings benefit from rounded edges to prevent injuries during assembly and maintenance operations.
- Medical Devices: Ensuring smooth, rounded edges on surgical instruments and equipment enhances patient safety and ease of handling.
Rounding plays a vital role in enhancing the usability, safety, and appearance of metal parts across various industries, contributing to overall product quality and customer satisfaction.
EMS Metalworking Machinery
We design, manufacture and assembly metalworking machinery such as:
- Hydraulic transfer press
- Glass mosaic press
- Hydraulic deep drawing press
- Casting press
- Hydraulic cold forming press
- Hydroforming press
- Composite press
- Silicone rubber moulding press
- Brake pad press
- Melamine press
- SMC & BMC Press
- Labrotaroy press
- Edge cutting trimming machine
- Edge curling machine
- Trimming beading machine
- Trimming joggling machine
- Cookware production line
- Pipe bending machine
- Profile bending machine
- Bandsaw for metal
- Cylindrical welding machine
- Horizontal pres and cookware
- Kitchenware, hotelware
- Bakeware and cuttlery production machinery
as a complete line as well as an individual machine such as:
- Edge cutting trimming beading machines
- Polishing and grinding machines for pot and pans
- Hydraulic drawing presses
- Circle blanking machines
- Riveting machine
- Hole punching machines
- Press feeding machine
You can check our machinery at work at: EMS Metalworking Machinery – YouTube
Applications:
- Beading and ribbing
- Flanging
- Trimming
- Curling
- Lock-seaming
- Ribbing
- Flange-punching