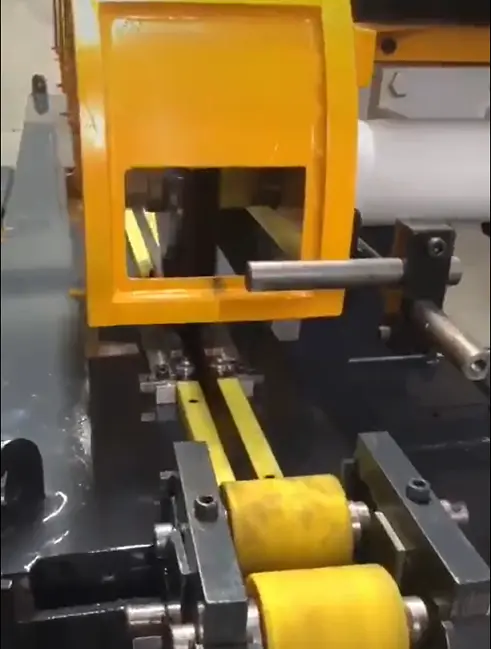
Flat surface polishing machine is mainly used for flat surface finishing applications, finishing and deburring of strips, satin and bright finishing of square tubes and pipes.
A flat surface polishing machine is a versatile tool used to achieve a smooth, polished finish on various flat surfaces, including sheet metal components, plastics, and even wood. It is widely used in various industries, including manufacturing, construction, and woodworking, to enhance the appearance, functionality, and durability of products.
Principle of Operation
Flat surface polishing machines typically operate on the principle of abrasive action. The machine utilizes abrasive belts, disks, or wheels coated with fine abrasive particles, such as aluminum oxide, silicon carbide, or diamond. These abrasives remove minute amounts of material from the surface, gradually leveling out imperfections and refining the finish.
Types of Flat Surface Polishing Machines
There are several types of flat surface polishing machines, each with its own characteristics and applications:
- Belt Polishers: Belt polishers utilize continuous abrasive belts that rotate over rollers. The workpiece is fed against the moving belt, creating a consistent and uniform polishing effect. Belt polishers are suitable for polishing large flat surfaces or for high-volume production.
- Disk Polishers: Disk polishers employ abrasive disks mounted on a rotating spindle. The workpiece is placed against the rotating disk, allowing for more precise polishing and control over the polishing action. Disk polishers are often used for polishing smaller surfaces or for delicate materials.
- Polishing Wheels: Polishing wheels, also known as buffing wheels, are made of various materials, such as cotton, felt, or sisal, and coated with abrasive compounds. The workpiece is pressed against the rotating wheel, achieving a high degree of polish and a refined finish. Polishing wheels are often used for final polishing stages or for polishing curved surfaces.
Applications of Flat Surface Polishing Machines
Flat surface polishing machines are used for a wide range of applications, including:
- Sheet Metal Polishing: Polishing sheet metal components enhances their appearance and removes imperfections, such as scratches, burrs, or welding marks. It also improves the surface smoothness, reducing friction and enhancing corrosion resistance.
- Plastic Polishing: Polishing plastic components removes mold lines, surface imperfections, and scratches, achieving a smooth, glossy finish. It also improves the clarity and transparency of plastics.
- Wood Polishing: Polishing wooden surfaces removes scratches, dents, and grain imperfections, resulting in a smooth, even finish. It also enhances the natural beauty of wood and protects it from moisture and wear.
- Stone Polishing: Polishing stones, such as granite or marble, removes surface imperfections and enhances their shine. It also improves the durability and stain resistance of stone surfaces.
- Metal Finishing: Flat surface polishing machines are used in various metal finishing processes, such as buffing, burnishing, and mirror polishing, to achieve high levels of surface refinement and reflectivity.
Factors Affecting Flat Surface Polishing
The effectiveness of flat surface polishing depends on several factors:
- Abrasive Material: The type and grit of the abrasive material determine the aggressiveness of the polishing action. Finer abrasives produce a smoother finish, while coarser abrasives remove more material and are used for initial polishing stages.
- Polishing Speed: The speed of the polishing machine affects the polishing rate and the level of finish. Higher speeds generally produce a faster polishing action, but excessive speed can damage the workpiece or cause overheating.
- Polishing Pressure: The pressure applied to the workpiece during polishing influences the polishing intensity and the depth of material removal. Excessive pressure can damage the workpiece, while insufficient pressure may result in an incomplete finish.
- Workpiece Material: The material of the workpiece affects the polishing process. Harder materials, such as metals or stones, require more aggressive polishing techniques, while softer materials, such as plastics or wood, require gentler polishing methods.
- Polishing Compound: Polishing compounds, often applied to abrasive belts or wheels, contain lubricants and polishing agents that enhance the polishing action and improve the final finish.
Conclusion
Flat surface polishing machines are essential tools for achieving smooth, polished surfaces on a wide range of materials. Their versatility, efficiency, and ability to produce high-quality finishes make them valuable assets in various industries. By understanding the principles of operation, types of machines, applications, and factors influencing the polishing process, users can effectively utilize flat surface polishing machines to enhance the appearance, functionality, and durability of their products.
The application is carried out by a continuous line with polishing stations on the moving conveyor. the flat surface part is fed manually or by a robot to the machine and the rolling polishing heads apply finishing to the part moving under
The machine is steel welded structure with an electrical control board, controlled by a PLC.
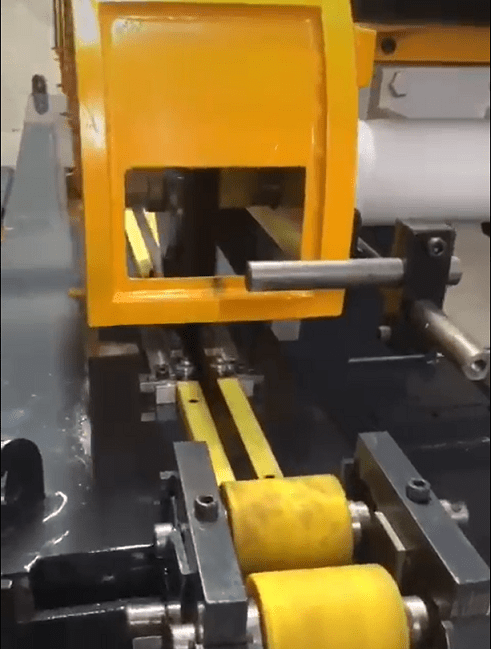
Belt Polishers as a Flat Surface Polishing Machine
Belt polishers are versatile and widely used machines for achieving a smooth, polished finish on various flat surfaces, including sheet metal components, plastics, and even wood. They are commonly employed in various industries, such as manufacturing, construction, and woodworking, to enhance the appearance, functionality, and durability of products.
Principle of Operation
Belt polishers utilize continuous abrasive belts that rotate over rollers. The workpiece is fed against the moving belt, creating a consistent and uniform polishing effect. The abrasive belt gradually removes minute amounts of material from the surface, leveling out imperfections and refining the finish.
Components of Belt Polishers
Belt polishers typically consist of the following components:
- Frame: The frame provides the structural support for the machine and houses the various components.
- Drive Motor: The drive motor powers the rotation of the abrasive belt. The motor’s speed can be adjusted to control the polishing intensity.
- Belt Tensioning System: The belt tensioning system maintains the proper tension on the abrasive belt, ensuring effective polishing action and preventing belt slippage.
- Contact Roller: The contact roller provides a flat surface against which the workpiece is pressed during polishing. The roller may be made of rubber, synthetic materials, or even metal, depending on the application.
- Abrasive Belt: The abrasive belt is the heart of the polishing process. It consists of a flexible backing material, such as cloth or paper, coated with fine abrasive particles, such as aluminum oxide, silicon carbide, or diamond. The grit and type of abrasive determine the aggressiveness of the polishing action.
- Dust Collection System: A dust collection system is often incorporated to remove dust and debris generated during the polishing process, maintaining a clean and safe work environment.
Advantages of Belt Polishers
Belt polishers offer several advantages over other polishing methods:
- Efficiency: They provide a continuous polishing action, resulting in faster polishing times compared to hand polishing or other methods.
- Uniformity: The continuous belt motion ensures consistent polishing across the entire surface of the workpiece.
- Versatility: They can accommodate a wide range of workpiece sizes and materials, making them suitable for various applications.
- Cost-effectiveness: Abrasive belts are relatively inexpensive and can be easily replaced, making belt polishers a cost-effective solution for high-volume production.
Applications of Belt Polishers
Belt polishers are used for a wide range of applications, including:
- Sheet Metal Polishing: Polishing sheet metal components removes scratches, burrs, and imperfections, enhancing their appearance and reducing friction.
- Plastic Polishing: Polishing plastic components removes mold lines, surface imperfections, and scratches, achieving a smooth, glossy finish.
- Wood Polishing: Polishing wooden surfaces removes scratches, dents, and grain imperfections, resulting in a smooth, even finish.
- Stone Polishing: Polishing stones, such as granite or marble, removes surface imperfections and enhances their shine.
- Metal Finishing: Belt polishers are used in various metal finishing processes, such as buffing, burnishing, and mirror polishing, to achieve high levels of surface refinement and reflectivity.
Factors Affecting Belt Polishing
The effectiveness of belt polishing depends on several factors:
- Abrasive Belt Grit: The grit of the abrasive belt determines the level of material removal and the fineness of the polish. Finer grits produce a smoother finish, while coarser grits remove more material and are used for initial polishing stages.
- Belt Speed: The speed of the abrasive belt affects the polishing rate and the level of finish. Higher speeds generally produce a faster polishing action, but excessive speed can damage the workpiece or cause overheating.
- Belt Tension: The tension of the abrasive belt influences the polishing intensity and the ability to maintain contact with the workpiece. Excessive tension can damage the belt, while insufficient tension may result in an incomplete finish.
- Workpiece Material: The material of the workpiece affects the polishing process. Harder materials, such as metals or stones, require more aggressive polishing techniques, while softer materials, such as plastics or wood, require gentler polishing methods.
- Workpiece Preparation: The surface condition of the workpiece prior to polishing can affect the polishing outcome. Cleaning and removing any contaminants or debris from the workpiece surface is essential for achieving a consistent and high-quality finish.
Conclusion
Belt polishers are valuable tools for achieving smooth, polished surfaces on a wide range of materials. Their efficiency, versatility, and ability to produce high-quality finishes make them essential equipment in various industries. By understanding the principles of operation, components, advantages, applications, and factors influencing the polishing process, users can effectively utilize belt polishers to enhance the appearance, functionality, and durability of their products.
Disk Polishers as a Flat Surface Polishing Machine
Disk polishers, also known as buffing wheels or polishing wheels, are versatile tools used to achieve a smooth, polished finish on various flat and curved surfaces, including sheet metal components, plastics, and even wood. They are widely used in various industries, such as manufacturing, construction, and woodworking, to enhance the appearance, functionality, and durability of products.
Principle of Operation
Disk polishers employ abrasive disks mounted on a rotating spindle. The workpiece is placed against the rotating disk, allowing for more precise polishing and control over the polishing action compared to belt polishers. The abrasive disk gradually removes minute amounts of material from the surface, leveling out imperfections and refining the finish.
Types of Disk Polishers
There are several types of disk polishers, each with its own characteristics and applications:
- Single-Spindle Disk Polishers: Single-spindle disk polishers utilize a single abrasive disk mounted on a rotating spindle. They are suitable for polishing small to medium-sized workpieces and offer precise control over the polishing process.
- Multi-Spindle Disk Polishers: Multi-spindle disk polishers employ multiple abrasive disks mounted on a rotating spindle, allowing for simultaneous polishing of multiple workpieces or different areas of a single workpiece. They are suitable for high-volume production and offer increased efficiency.
- Flexible Disk Polishers: Flexible disk polishers utilize flexible abrasive disks that can adapt to curved surfaces and contoured shapes. They are suitable for polishing complex geometries and areas that are difficult to reach with traditional disk polishers.
Advantages of Disk Polishers
Disk polishers offer several advantages over other polishing methods:
- Precise Control: The direct contact between the workpiece and the abrasive disk allows for precise control over the polishing action and the level of material removal.
- Versatility: They can accommodate a wide range of workpiece sizes, shapes, and materials, making them suitable for various applications.
- Efficiency: They can achieve a high degree of polish in a relatively short time, making them efficient for production settings.
- Durability: Abrasive disks come in various grits and materials, allowing for tailoring the polishing process to specific requirements.
Applications of Disk Polishers
Disk polishers are used for a wide range of applications, including:
- Sheet Metal Polishing: Polishing sheet metal components removes scratches, burrs, and imperfections, enhancing their appearance and reducing friction.
- Plastic Polishing: Polishing plastic components removes mold lines, surface imperfections, and scratches, achieving a smooth, glossy finish.
- Wood Polishing: Polishing wooden surfaces removes scratches, dents, and grain imperfections, resulting in a smooth, even finish.
- Stone Polishing: Polishing stones, such as granite or marble, removes surface imperfections and enhances their shine.
- Metal Finishing: Disk polishers are used in various metal finishing processes, such as buffing, burnishing, and mirror polishing, to achieve high levels of surface refinement and reflectivity.
Factors Affecting Disk Polishing
The effectiveness of disk polishing depends on several factors:
- Abrasive Disk Grit: The grit of the abrasive disk determines the level of material removal and the fineness of the polish. Finer grits produce a smoother finish, while coarser grits remove more material and are used for initial polishing stages.
- Disk Rotation Speed: The rotation speed of the disk affects the polishing rate and the level of finish. Higher speeds generally produce a faster polishing action, but excessive speed can damage the workpiece or cause overheating.
- Disk Pressure: The pressure applied to the workpiece during polishing influences the polishing intensity and the depth of material removal. Excessive pressure can damage the workpiece, while insufficient pressure may result in an incomplete finish.
- Workpiece Material: The material of the workpiece affects the polishing process. Harder materials, such as metals or stones, require more aggressive polishing techniques, while softer materials, such as plastics or wood, require gentler polishing methods.
- Workpiece Preparation: The surface condition of the workpiece prior to polishing can affect the polishing outcome. Cleaning and removing any contaminants or debris from the workpiece surface is essential for achieving a consistent and high-quality finish.
Conclusion
Disk polishers are valuable tools for achieving smooth, polished finishes on a wide range of materials. Their versatility, controllability, and ability to produce high-quality finishes make them essential equipment in various industries. By understanding the principles of operation, types of disk polishers, advantages, applications, and factors influencing the polishing process, users can effectively utilize disk polishers to enhance the appearance, functionality, and durability of their products.
Polishing Wheels
Polishing wheels, also known as buffing wheels or buffing compounds, are essential tools used to achieve a smooth, polished finish on various surfaces, including sheet metal components, plastics, and even jewelry. They are commonly used in various industries, such as manufacturing, construction, and woodworking, to enhance the appearance, functionality, and durability of products.
Principle of Operation
Polishing wheels are typically mounted on a rotating spindle or shaft. The workpiece is pressed against the rotating wheel, allowing for the removal of minute amounts of material from the surface, leveling out imperfections and refining the finish. The abrasive particles in the polishing compound work in conjunction with the rotating wheel to achieve the desired polish.
Types of Polishing Wheels
There are several types of polishing wheels, each with its own characteristics and applications:
- Wheel Material: Polishing wheels are made from various materials, including cotton, felt, or sisal. The material of the wheel affects the polishing action and the type of material it can be used on. For example, cotton wheels are gentler and are well-suited for polishing softer materials like plastics or wood, while felt wheels are more aggressive and can be used for polishing metals or other hard materials.
- Backing Material: Backing materials are the rigid structures that support the abrasive compound in the polishing wheel. They are typically made from materials like wood, metal, or plastic. The backing material provides stability and support during the polishing process.
- Abrasive Compound: Abrasive compounds are the key ingredients in polishing wheels that remove material from the workpiece surface. They are made up of finely ground particles of abrasive materials, such as aluminum oxide, silicon carbide, or diamond. The grit of the abrasive determines the level of material removal and the fineness of the polish. Coarser grits remove more material and are used for initial polishing stages, while finer grits produce a smoother finish.
- Compound Application: Polishing compounds can be applied to the polishing wheel in several ways. They can be pre-applied to the wheel during manufacturing, or they can be applied manually during the polishing process using a compound applicator.
- Shape and Sizing: Polishing wheels come in various shapes and sizes to accommodate different workpiece sizes and shapes. From small, flat wheels for polishing intricate details to large, contoured wheels for polishing large surfaces, there is a polishing wheel that can be adapted to the specific polishing application.
Applications of Polishing Wheels
Polishing wheels are used for a wide range of applications, including:
- Metal Polishing: Polishing wheels are used to remove scratches, burrs, and imperfections from metal surfaces, enhancing their appearance and reducing friction.
- Plastic Polishing: Polishing wheels are used to remove mold lines, surface imperfections, and scratches from plastic components, achieving a smooth, glossy finish.
- Wood Polishing: Polishing wheels are used to remove scratches, dents, and grain imperfections from wooden surfaces, resulting in a smooth, even finish.
- Jewelry Polishing: Polishing wheels are used to remove tarnish and scratches from jewelry, restoring their shine and luster.
- Other Applications: Polishing wheels are also used in polishing other materials, such as glass, stone, and even some types of fabric.
Factors Affecting Polishing with Wheels
The effectiveness of polishing with wheels depends on several factors:
- Wheel Speed: The speed of the rotating polishing wheel affects the polishing rate and the level of finish. Higher speeds generally produce a faster polishing action, but excessive speed can damage the workpiece or cause overheating.
- Workpiece Material: The material of the workpiece affects the polishing process. Harder materials, such as metals or stones, require more aggressive polishing techniques, while softer materials, such as plastics or wood, require gentler polishing methods.
- Polishing Compound: The type of polishing compound used depends on the material being polished and the desired level of finish. Coarser compounds are used for initial polishing stages, while finer compounds are used for final polishing.
- Polishing Pressure: The pressure applied to the workpiece during polishing influences the polishing intensity and the depth of material removal. Excessive pressure can damage the workpiece, while insufficient pressure may result in an incomplete finish.
- Water or Lubricant: In some polishing applications, water or a lubricant is used to cool the workpiece and the polishing wheel, prevent overheating, and enhance the polishing action.
Conclusion
Polishing wheels are versatile tools that can be used to achieve a variety of polishing effects on various materials. By understanding the principles of operation, types of polishing wheels, applications, and factors affecting polishing with wheels, users can effectively utilize polishing wheels to enhance
Flat Surface Polishing
Flat surface polishing is a crucial process in various industries, including manufacturing, construction, and woodworking, to achieve a smooth, polished finish on various flat surfaces. This process enhances the appearance, functionality, and durability of products and materials.
Common Methods for Flat Surface Polishing
- Belt Polishing: Belt polishers utilize continuous abrasive belts that rotate over rollers. The workpiece is fed against the moving belt, creating a consistent and uniform polishing effect. This method is suitable for polishing large flat surfaces or for high-volume production.
- Disk Polishing: Disk polishers employ abrasive disks mounted on a rotating spindle. The workpiece is placed against the rotating disk, allowing for more precise polishing and control over the polishing action compared to belt polishers. This method is suitable for polishing smaller surfaces or for delicate materials.
- Hand Polishing: Hand polishing, while less efficient than machine-based methods, offers greater control and can be used on delicate or irregular surfaces. It involves using hand-held polishing tools, such as abrasive pads or buffing wheels, to achieve the desired finish.
Factors Affecting Flat Surface Polishing
- Abrasive Material: The type and grit of the abrasive material determine the aggressiveness of the polishing action. Finer abrasives produce a smoother finish, while coarser abrasives remove more material and are used for initial polishing stages.
- Polishing Speed: The speed of the polishing machine or the movement of the hand-held tool affects the polishing rate and the level of finish. Higher speeds generally produce a faster polishing action, but excessive speed can damage the workpiece or cause overheating.
- Polishing Pressure: The pressure applied to the workpiece during polishing influences the polishing intensity and the depth of material removal. Excessive pressure can damage the workpiece, while insufficient pressure may result in an incomplete finish.
- Workpiece Material: The material of the workpiece affects the polishing process. Harder materials, such as metals or stones, require more aggressive polishing techniques, while softer materials, such as plastics or wood, require gentler polishing methods.
- Polishing Compound: Polishing compounds, often applied to abrasive belts or disks, contain lubricants and polishing agents that enhance the polishing action and improve the final finish.
Applications of Flat Surface Polishing
- Sheet Metal Polishing: Polishing sheet metal components removes scratches, burrs, and imperfections, enhancing their appearance and reducing friction. It also improves the surface smoothness, reducing friction and enhancing corrosion resistance.
- Plastic Polishing: Polishing plastic components removes mold lines, surface imperfections, and scratches, achieving a smooth, glossy finish. It also improves the clarity and transparency of plastics.
- Wood Polishing: Polishing wooden surfaces removes scratches, dents, and grain imperfections, resulting in a smooth, even finish. It also enhances the natural beauty of wood and protects it from moisture and wear.
- Stone Polishing: Polishing stones, such as granite or marble, removes surface imperfections and enhances their shine. It also improves the durability and stain resistance of stone surfaces.
- Metal Finishing: Flat surface polishing machines are used in various metal finishing processes, such as buffing, burnishing, and mirror polishing, to achieve high levels of surface refinement and reflectivity.
Conclusion
Flat surface polishing is an essential process for achieving smooth, polished finishes on a wide range of materials. By understanding the principles of operation, methods, factors affecting the polishing process, and various applications, users can effectively utilize flat surface polishing techniques to enhance the appearance, functionality, and durability of products and materials.
EMS Metalworking Machinery
We design, manufacture and assembly metalworking machinery such as:
- Hydraulic transfer press
- Glass mosaic press
- Hydraulic deep drawing press
- Casting press
- Hydraulic cold forming press
- Hydroforming press
- Composite press
- Silicone rubber moulding press
- Brake pad press
- Melamine press
- SMC & BMC Press
- Labrotaroy press
- Edge cutting trimming machine
- Edge curling machine
- Trimming beading machine
- Trimming joggling machine
- Cookware production line
- Pipe bending machine
- Profile bending machine
- Bandsaw for metal
- Cylindrical welding machine
- Horizontal pres and cookware
- Kitchenware, hotelware
- Bakeware and cuttlery production machinery
as a complete line as well as an individual machine such as:
- Edge cutting trimming beading machines
- Polishing and grinding machines for pot and pans
- Hydraulic drawing presses
- Circle blanking machines
- Riveting machine
- Hole punching machines
- Press feeding machine
You can check our machinery at work at: EMS Metalworking Machinery – YouTube
Applications:
- Beading and ribbing
- Flanging
- Trimming
- Curling
- Lock-seaming
- Ribbing
- Flange-punching