The Automatic Buffing Machine is an inside polishing machine for metal surfaces. Low price & High quality & Free consultation. Buy anywhere.
Automatic buffing machines have revolutionized the metal polishing industry by providing a high degree of precision, efficiency, and consistency in buffing operations. These machines are designed to automate repetitive buffing tasks, significantly reducing labor costs and improving production output.
Components of Automatic Buffing Machines
- Workpiece Loading and Unloading System: This system automatically loads and unloads workpieces onto and from the buffing spindles, ensuring a continuous and uninterrupted buffing process.
- Buffing Spindles: The buffing spindles rotate the buffing wheels or mops, providing the driving force for polishing. They can be controlled individually or in groups to accommodate different buffing stages and workpiece geometries.
- Buffing Wheels or Mops: These are the abrasive components that come into contact with the workpiece. They are made of various materials, such as cotton, felt, or sisal, and are impregnated with polishing compounds.
- Polishing Compound Delivery System: This system automatically dispenses polishing compounds onto the buffing wheels or mops, ensuring a consistent supply of abrasives and lubricants throughout the buffing process.
- Workpiece Positioning and Orientation System: This system precisely positions and orients the workpiece relative to the buffing wheels or mops, ensuring uniform buffing and achieving the desired finish.
- Control System: The control system regulates the machine’s operation, including spindle speeds, buffing pressure, and compound delivery. It may incorporate programmable logic controllers (PLCs) to automate complex buffing sequences.
Benefits of Automatic Buffing Machines
- Increased Efficiency: Automatic buffing machines significantly reduce labor costs by eliminating the need for manual workpiece handling and buffing operations.
- Enhanced Consistency: These machines provide consistent buffing results, ensuring uniform finishes across all workpieces.
- Improved Quality: The precise control and automation of buffing parameters lead to higher quality finishes and fewer defects.
- Reduced Labor Costs: Automated buffing reduces labor dependency, lowering labor costs and improving overall production efficiency.
- Enhanced Safety: Automatic buffing machines minimize worker exposure to hazardous moving parts, abrasive dust, and metal particles.
Applications of Automatic Buffing Machines
- Automotive Industry: Automatic buffing machines are used to polish car bodies, wheels, and trim, restoring their shine and removing scratches or imperfections.
- Aerospace Industry: These machines are used to polish aircraft components, such as wings, fuselages, and engine parts, to reduce drag and improve aerodynamic performance.
- Jewelry Industry: Automatic buffing machines are used to polish jewelry pieces, such as rings, bracelets, and necklaces, to achieve a high-gloss finish and enhance their appearance.
- Metal Fabrication Industry: Automatic buffing machines are used to polish metal surfaces, such as tools, dies, and components, to remove burrs, scratches, and other imperfections, improving their appearance and functionality.
- Medical Device Industry: Automatic buffing machines are used to polish medical implants, surgical instruments, and other medical devices to achieve a smooth, clean finish that meets stringent hygiene standards.
Conclusion
Automatic buffing machines have become indispensable tools in various industries, providing a combination of efficiency, precision, and consistency in metal polishing operations. By automating repetitive tasks, reducing labor costs, and enhancing quality control, automatic buffing machines contribute to improved production processes, enhanced product quality, and reduced manufacturing costs.
Buffing
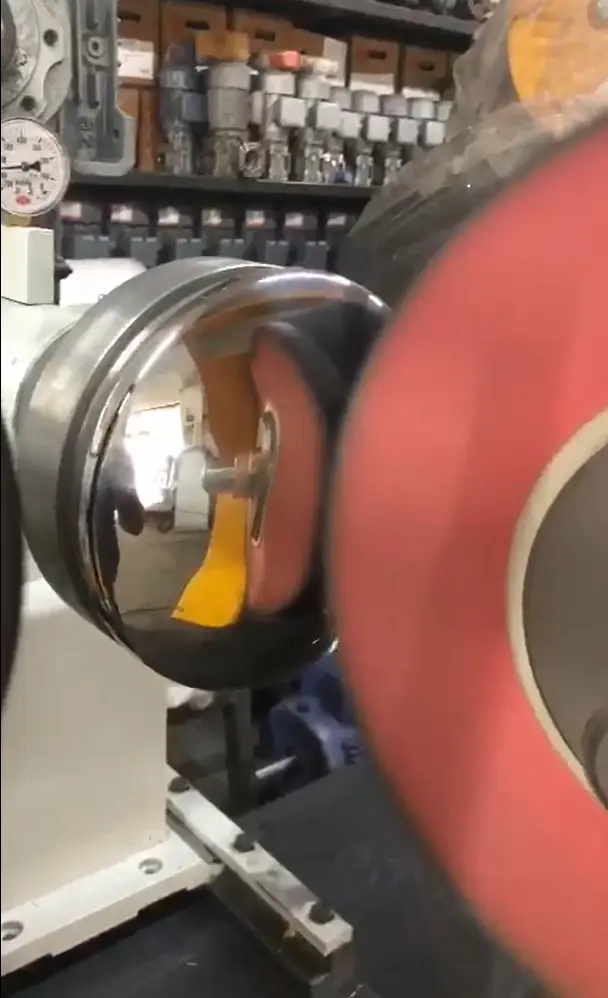
Buffing is a finishing process that utilizes an abrasive compound and a rotating wheel or mop to smooth and polish metal surfaces. It removes imperfections, scratches, and burrs, restoring the shine and luster of the metal. Buffing is widely used in various industries, including automotive, aerospace, jewelry, and metal fabrication, to enhance the appearance, durability, and performance of metal products and components.
Types of Buffing Processes
- Cut Buffing: Cut buffing employs coarse abrasives to remove heavy scratches, burrs, and imperfections from the metal surface. It is typically the first step in the buffing process.
- Color Buffing: Color buffing uses medium-grit abrasives to further smooth the surface and enhance the color of the metal. It follows cut buffing and precedes final polishing.
- Polishing: Polishing utilizes fine abrasives to achieve the desired level of smoothness and luster. It is the final step in the buffing process and produces a reflective, high-gloss finish.
Factors Affecting Buffing Results
- Abrasive Selection: The type and grit of the abrasive determine the aggressiveness of the buffing process. Coarse abrasives are used for initial cutting, while finer abrasives produce a smoother finish.
- Polishing Compound: The polishing compound contains abrasives, lubricants, and extenders that affect the polishing action. Different compounds are available for various metals and desired finishes.
- Buffing Wheel or Mop: The material and texture of the buffing wheel or mop influence the polishing effect. Cotton, felt, and sisal are common materials used for buffing wheels.
- Spindle Speed: The rotational speed of the spindle controls the intensity of the buffing process. Higher speeds produce a more aggressive polishing action, while slower speeds are better for fine polishing.
- Pressure: The pressure applied to the workpiece during buffing affects the depth of cut and the overall polishing result. Excessive pressure can damage the workpiece, while too little pressure may not achieve the desired finish.
Safety Considerations for Buffing Operations
- Machine Guarding: Proper guards should be installed to prevent workers from accessing hazardous rotating parts, such as the buffing wheel or mop.
- Safety Interlocks: Safety interlocks prevent the buffing machine from operating if the guards are not in place or if the safety sensors detect an unsafe condition.
- Emergency Stop Buttons: Clearly marked emergency stop buttons should be readily accessible to enable workers to quickly halt the machine in case of an unsafe situation.
- Personal Protective Equipment (PPE): Workers should wear appropriate PPE, such as safety glasses, gloves, and respiratory protection, to minimize the risk of injuries from flying debris, abrasive dust, and metal particles.
Conclusion
Buffing plays a crucial role in various industries by restoring the shine, durability, and functionality of metal surfaces. By understanding the different types of buffing processes, factors affecting buffing results, and safety considerations, manufacturers can effectively utilize buffing machines to enhance the quality and appearance of their metal products and components.
Buffing Abrasives for the Automatic Buffing Machine
Buffing abrasives are essential components of automatic buffing machines, playing a crucial role in achieving the desired surface finish on metal workpieces. The type and grit of abrasives used depend on the specific buffing stage and the desired finish.
Types of Buffing Abrasives
- Aluminum Oxide: Aluminum oxide is a versatile abrasive commonly used in cut buffing and color buffing stages. It is known for its aggressive cutting action and ability to remove deep scratches and imperfections.
- Silicon Carbide: Silicon carbide is another widely used abrasive, particularly in color buffing and final polishing stages. It offers a balance of cutting action and surface refinement, effectively removing finer scratches and enhancing the color of the metal.
- Emery: Emery is a natural abrasive composed of corundum and magnetite. It is primarily used in cut buffing and color buffing stages, providing a medium-aggressive cutting action to remove scratches and imperfections.
- Tripoli: Tripoli is a natural abrasive composed of silica and clay. It is commonly used in final polishing stages due to its fine grit and gentle polishing action. It effectively removes minute scratches and produces a high-gloss finish.
- Rouge: Rouge is a natural abrasive composed of iron oxide. It is primarily used in final polishing stages, providing a very fine polishing action to achieve a mirror-like finish.
Selection of Buffing Abrasives
The selection of buffing abrasives depends on the specific buffing stage and the desired finish.
- Cut Buffing: Coarse abrasives, such as aluminum oxide or silicon carbide, are used to remove deep scratches, burrs, and imperfections.
- Color Buffing: Medium-grit abrasives, such as silicon carbide or emery, are used to refine the surface, eliminate finer scratches, and enhance the color of the metal.
- Final Polishing: Fine abrasives, such as tripoli or rouge, are used to achieve a high-gloss, mirror-like finish on the stainless steel surface.
Grit Size of Buffing Abrasives
The grit size of buffing abrasives determines the aggressiveness of the cutting action.
- Coarse Grit: Coarse-grit abrasives are used for initial buffing stages to remove deep scratches and imperfections.
- Medium Grit: Medium-grit abrasives are used for intermediate buffing stages to refine the surface and remove finer scratches.
- Fine Grit: Fine-grit abrasives are used for final polishing stages to achieve a high-gloss finish.
Compatibility with Automatic Buffing Machines
Buffing abrasives should be compatible with the automatic buffing machine’s specifications and the type of polishing compound being used. Proper compatibility ensures optimal performance and prevents damage to the machine or the workpiece.
Conclusion
Buffing abrasives play a critical role in achieving the desired surface finish on metal workpieces processed by automatic buffing machines. By carefully selecting the appropriate type and grit of abrasives based on the specific buffing stage and desired finish, manufacturers can ensure consistent, high-quality results and extend the lifespan of their automatic buffing machines.
Aluminum Oxide and Other Powders
Aluminum oxide powders, fused and unfused, are the abrasives most commonly used in the buffing of hard metals. Chromium oxide is used to achieve the highest reflectivity (color) on stainless steel, chromium, and nickel plate. To achieve a high reflectivity (color) on brass, gold, copper, and silver, iron oxide is generally used. Aluminum oxide is chemically represented as Al2O3.
The unfused aluminum oxide is white in color. This is manufactured from
bauxite or hydrated aluminum oxide by heating it at elevated temperatures. This heating process, called calcination, gives the abrasive the common name calcinated alumina. The higher the calcination temperature, the more water of hydration is driven off and the harder the crystalline material becomes.
When the calcinated temperature is about 950oC, the product produced is a soft alumina having a porous structure. This type of abrasive is used for luster or color buffing. When the calcined temperature is about 1,250oC, a harder alumina is produced. This type of abrasive is used for cutting. Soft aluminas are used to produce luster or a higher reflectivity on all metals, both ferrous and nonferrous. The harder aluminas will cut and remove more metal from the surface of castings or extrusions of aluminum, brass, and other metals.
Alumina
When alumina is heated to 1,850oC, fused aluminum oxide (Al2O3 ) is produced. This material is made in an electric furnace at approximately 2,000oC. Bauxite, when mixed with alumina and other oxide materials, produces a specific crystalline structure whose hardness can be varied to meet specified physical properties. This fused mass is then cooled and crushed.
In the crushing process, the material is ground, screened to the appropriate size, treated magnetically, and acid washed. It is then rescreened to its final classification (grit sizing). The difference between fused aluminum oxide and calcined alumina is that the fused oxide is of a crystalline structure that is much harder than the calcined alumina. Fused aluminum oxide is used mainly on abrasive belts or setup wheels for polishing. As for buffing, fused aluminum oxide is used for cutting down ferrous metals. The abrasive sizing is generally from 60 grit to -325 grit for buffing compounds.
rescreened to its final classification (grit sizing). The difference between fused aluminum oxide and calcined alumina is that the fused oxide is of a crystalline structure that is much harder than the calcined alumina. Fused aluminum oxide is used mainly on abrasive belts or setup wheels for polishing. As for buffing, fused aluminum oxide is used for cutting down
ferrous metals. The abrasive sizing is generally from 60 grit to -325 grit for buffing compounds.
Tripoli
Tripoli is considered to be microcrystalline silica, which is made naturally. It is highly suitable for buffing aluminum, brass, copper, and zinc die cast or other white metals. Tripoli and silica can be used as a cutting abrasive or a so-called cut-and-color abrasive for nonferrous metals.
Tripoli should not be classified as an amorphous silica, but it is microcrystalline in nature. Crystalline silica may cause delayed lung injury for people when exposed to it over a long period. Users of products containing these abrasives should be aware of this possibility and should wear a mask and work in a ventilated area.
Silicon Carbide
Silicon carbide (SiC) is of a crystalline structure that is harder than fused aluminum oxide. It is formed by mixing coke and silica in an electric furnace at approximately 1,900 to 2,400oC. The material is cooled, ground, and sifted to the required grit size similar to the processing of fused aluminum oxide. The crystalline structure of SiC is hexagonal.
Red Rouge
The chemical formula for rouge is Fe2O3; it is also called the jeweler’s rouge. Its purity is 99% ferric oxide. The crystalline structure of ferric oxide is spherical. Rouge is used mainly on precious metals to give an exceptionally high luster
Green Rouge
The chemical formula for chromium green oxide is Cr2O3. The hardness of chromium oxide is 9 Mohs as opposed to iron oxide, which is 6 Mohs and is used to produce an exceptional luster or color on ferrous as well as nonferrous metals. These abrasives mentioned represent a small percentage of material available to give a specific finish required on a particular substrate.
See Table I for typical hardness values. Although the wheel speeds for buffing with grease bars will vary greatly from job to job and operator to operator, the figures in surface feet per minute given in Tables II and III will serve as a guide for hand buffing operations.
Buffing wheel speeds for automatic operation may vary with the design of the machine and the contact of the work to the wheel. It can, therefore, be more definitely fixed without depending on the physical ability of the hand buffer to maintain the correct position and pressure against the wheel.
Types of Polishing and Buffing Machines
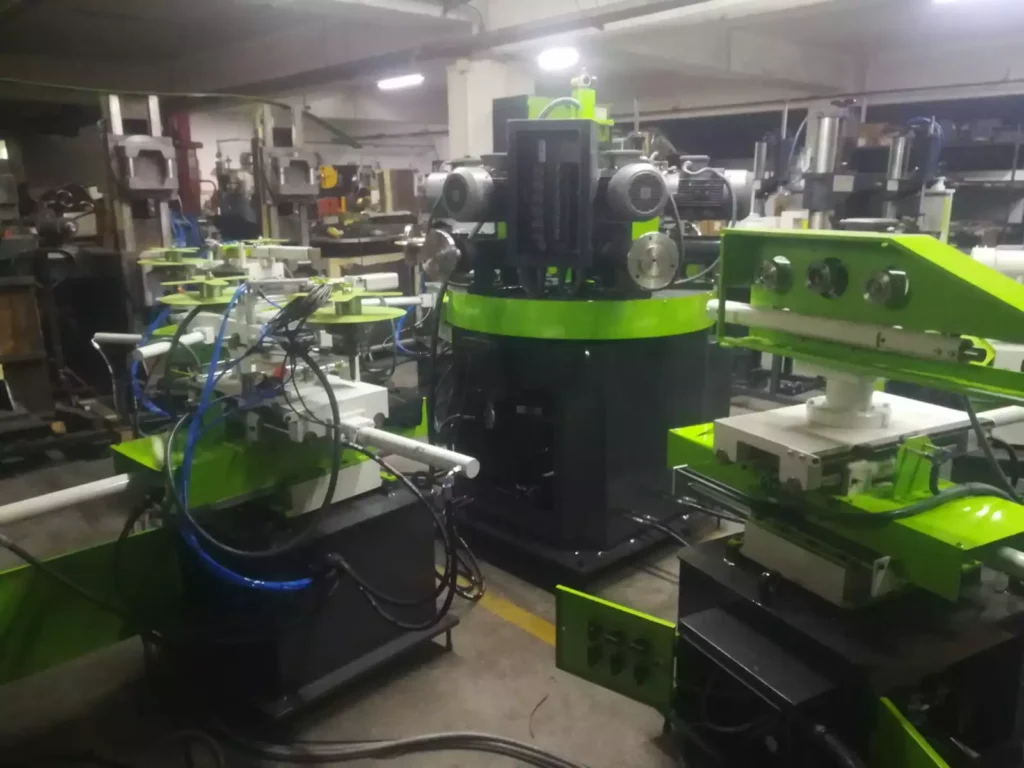
Manual Machines
Manual polishing and buffing machines are the most basic type, requiring direct human operation. These machines are suitable for small-scale operations and tasks that need a hands-on approach. They are typically used for intricate work where precision and control are paramount.
Key Features:
- Simple design and operation.
- Cost-effective for small jobs.
- Ideal for detailed and delicate work.
Applications:
- Jewelry and watchmaking.
- Small metal parts in the automotive and aerospace industries.
Semi-Automatic Machines
Semi-automatic polishing and buffing machines combine manual and automated features. They allow for greater control over the process while improving efficiency compared to fully manual machines. Operators can set parameters and oversee the operation, making adjustments as necessary.
Key Features:
- Enhanced control with automated functions.
- Increased efficiency and throughput.
- Suitable for medium-scale operations.
Applications:
- Mid-sized manufacturing units.
- Complex parts requiring a balance of manual oversight and automation.
CNC (Computer Numerical Control) Machines
CNC polishing and buffing machines represent the pinnacle of automation and precision in surface finishing. These machines use computer-controlled systems to manage the movement and operation of polishing tools with high accuracy. CNC machines are highly programmable, allowing for the automation of complex and repetitive tasks.
Key Features:
- High precision and repeatability.
- Ability to handle complex shapes and surfaces.
- Programmable for different tasks and materials.
Benefits:
- Consistent and high-quality finishes.
- Reduced labor costs and increased productivity.
- Flexibility in manufacturing processes.
Applications:
- Aerospace components.
- High-end automotive parts.
- Medical devices and implants.
NC (Numerical Control) Machines
NC machines, while similar to CNC machines, are generally less sophisticated and do not offer the same level of flexibility and automation. They are controlled by pre-set instructions but lack the advanced programmability of CNC systems.
Key Features:
- Automated control with limited programmability.
- Suitable for less complex tasks.
- Cost-effective compared to CNC machines.
Applications:
- Standardized parts in automotive and metalworking industries.
- Tasks that do not require frequent changes in setup.
Applications of Polishing and Buffing Machines
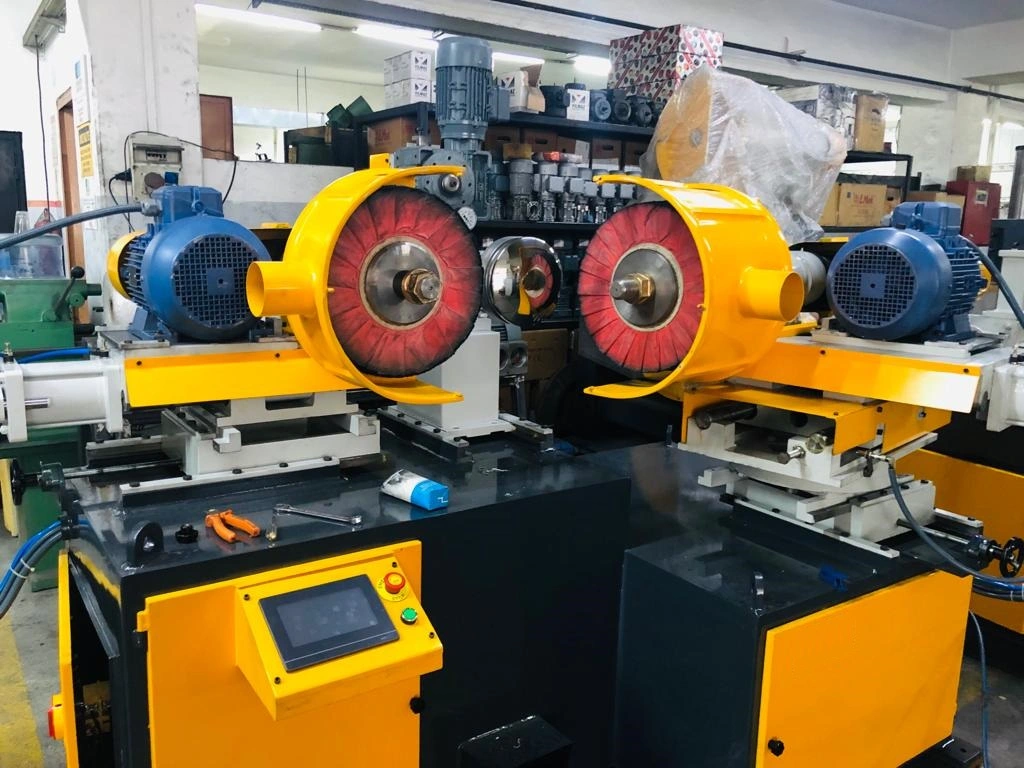
Automotive Industry
In the automotive industry, polishing and buffing are essential for achieving high-quality finishes on car parts. This includes the polishing of body panels, trim pieces, and engine components to enhance both aesthetics and performance.
Key Uses:
- Surface finishing of body panels.
- Polishing of chrome and aluminum trim.
- Buffing of engine and transmission parts.
Aerospace Industry
The aerospace industry demands the highest standards of precision and quality. Polishing and buffing are critical for ensuring the smooth surfaces necessary for aerodynamics and the performance of critical components.
Key Uses:
- Polishing turbine blades and engine parts.
- Finishing structural components for reduced drag.
- Ensuring the integrity of critical safety parts.
Metalworking Industry
In metalworking, polishing and buffing machines are used to finish metal parts, improving their appearance, resistance to corrosion, and overall quality.
Key Uses:
- Buffing of steel and aluminum parts.
- Finishing of tools and machinery components.
- Surface preparation for coating and painting.
Jewelry and Watchmaking
Precision and aesthetic appeal are paramount in jewelry and watchmaking. Polishing and buffing machines ensure that each piece has a flawless finish.
Key Uses:
- Polishing of precious metals and gemstones.
- Buffing intricate watch parts.
- Achieving high-shine finishes on jewelry.
Electronics Industry
In the electronics industry, surface preparation is crucial for the functionality and longevity of components. Polishing and buffing machines are used to prepare surfaces for assembly and coating.
Key Uses:
- Polishing of semiconductor wafers.
- Buffing of electronic enclosures and cases.
- Surface preparation for circuit boards.
Medical Device Manufacturing
The medical industry relies on highly polished surfaces for both functionality and hygiene. Polishing and buffing machines ensure that surgical instruments and implants meet stringent standards.
Key Uses:
- Polishing surgical instruments.
- Finishing orthopedic implants.
- Ensuring biocompatibility of medical devices.
Consumer Goods
Polishing and buffing are also used in the production of consumer goods, enhancing the aesthetic appeal and durability of everyday items.
Key Uses:
- Finishing of household appliances.
- Polishing of kitchen utensils and cutlery.
- Buffing of decorative items and hardware.
Production Process of Polishing and Buffing Machines
Design and Engineering
The production of polishing and buffing machines begins with design and engineering. This involves conceptualizing the machine, creating detailed CAD models, and planning the manufacturing process.
Steps:
- Conceptual design and feasibility studies.
- Detailed engineering using CAD software.
- Prototype development and testing.
Material Selection
Selecting the right materials is crucial for the durability and performance of polishing and buffing machines. Common materials include high-grade steels, aluminum alloys, and composite materials for specific parts.
Considerations:
- Durability and wear resistance.
- Weight and strength.
- Compatibility with various polishing materials.
Manufacturing Techniques
Manufacturing polishing and buffing machines involves several techniques, including machining, welding, assembly, and quality control. Each step is critical to ensuring the final product meets industry standards.
Techniques:
- CNC machining of components.
- Welding and fabrication of the machine frame.
- Assembly of mechanical and electronic parts.
- Rigorous testing and quality assurance.
Quality Control
Quality control is an integral part of the production process, ensuring that each machine meets the required specifications and performs reliably.
Methods:
- In-process inspections.
- Final testing of performance and safety.
- Certification to industry standards.
Materials Polished with Industrial Machines

Metals
Metals are the most common materials polished with industrial machines. This includes a wide range of metals used in various industries.
Examples:
- Stainless steel.
- Aluminum.
- Brass.
- Titanium.
Plastics
Certain types of plastics can also be polished to achieve a smooth and glossy finish, particularly in the electronics and consumer goods industries.
Examples:
- Acrylics.
- Polycarbonates.
- PVC.
Wood
Polishing wood can enhance its natural beauty and protect it from damage. This is commonly done in furniture making and decorative items.
Examples:
- Hardwood (oak, mahogany).
- Softwood (pine, cedar).
- Engineered wood (plywood, MDF).
Ceramics and Glass
Polishing ceramics and glass is delicate work that requires specialized techniques to avoid cracking and chipping.
Examples:
- Fine china.
- Glassware.
- Porcelain tiles.
Composites
Composites are used in advanced industries such as aerospace and automotive. Polishing these materials requires specialized equipment to handle their unique properties.
Examples:
- Carbon fiber.
- Fiberglass.
- Kevlar.
Advantages of Using CNC and NC Machines
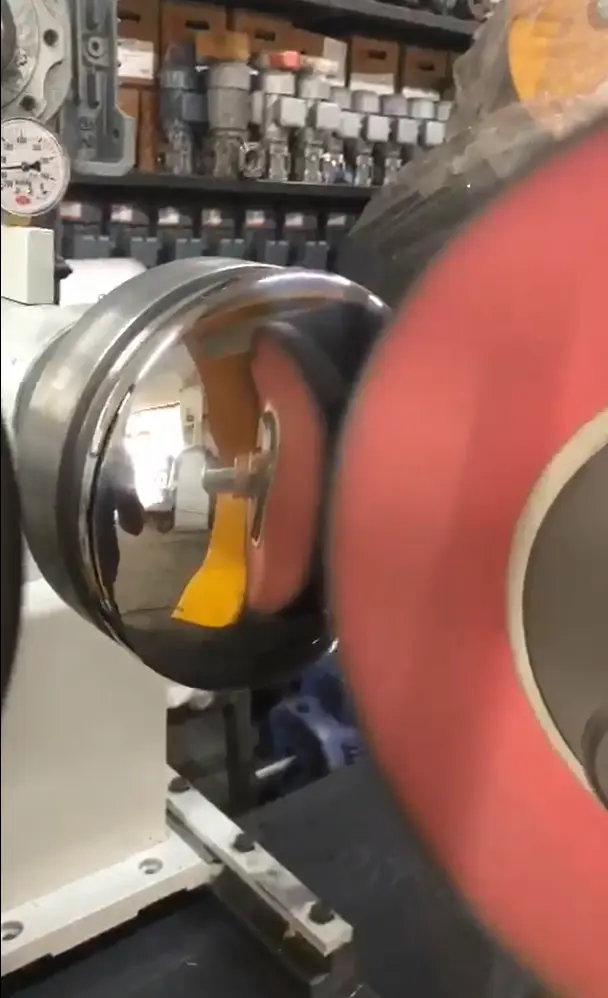
Precision and Consistency
CNC and NC machines offer unmatched precision and consistency, ensuring that each part meets exact specifications.
Benefits:
- Uniform finishes across large batches.
- High accuracy in complex geometries.
- Reduced human error.
Efficiency and Speed
These machines significantly reduce processing times, increasing overall productivity and allowing for faster turnaround times.
Benefits:
- Rapid processing of parts.
- Increased throughput.
- Shorter lead times.
Automation and Flexibility
Automation allows for continuous operation and the ability to handle multiple tasks without manual intervention.
Benefits:
- Customizable for various tasks.
- Minimal supervision required.
- Adaptable to different materials and shapes.
Cost-effectiveness
While the initial investment in CNC and NC machines can be high, the long-term savings in labor and increased efficiency make them cost-effective.
Benefits:
- Lower labor costs.
- High return on investment.
- Reduced material waste.
Challenges and Considerations
Initial Investment Costs
The cost of purchasing and installing CNC and NC machines can be significant, making it a major consideration for businesses.
Factors:
- Budgeting for high-quality machinery.
- Evaluating long-term benefits versus initial costs.
Maintenance and Upkeep
Regular maintenance is essential to ensure the longevity and performance of these machines.
Considerations:
- Scheduled maintenance and repairs.
- Availability of spare parts.
- Training for maintenance personnel.
Training and Skilled Labor
Operating CNC and NC machines requires skilled operators who understand the intricacies of programming and machine control.
Considerations:
- Investing in operator training.
- Ensuring continuous education on new technologies.
- Retaining skilled labor.
Technological Advancements
Keeping up with the latest advancements in technology is crucial for maintaining a competitive edge.
Considerations:
- Upgrading machinery and software.
- Staying informed about industry trends.
- Investing in research and development.
Future Trends in Polishing and Buffing Technology
Advancements in Automation and AI
The integration of artificial intelligence in polishing and buffing machines is set to revolutionize the industry by enhancing precision and efficiency.
Trends:
- AI-driven process optimization.
- Predictive maintenance using machine learning.
- Autonomous operation and monitoring.
Sustainable Practices
Sustainability is becoming increasingly important in manufacturing, with a focus on eco-friendly materials and processes.
Trends:
- Use of recyclable materials.
- Energy-efficient machinery.
- Reduction of waste and emissions.
Integration with Industry 4.0
Industry 4.0 involves the integration of smart technologies and IoT in manufacturing processes, providing real-time data and improving overall efficiency.
Trends:
- Smart manufacturing systems.
- Real-time monitoring and analytics.
- Enhanced connectivity and automation.
Conclusion
Industrial polishing and buffing machines play a vital role in various industries, ensuring that products meet the highest standards of quality and performance. From manual to advanced CNC and NC machines, each type offers unique benefits and is suited to different applications. Understanding the production processes, materials, and advantages of these machines is essential for businesses looking to improve their manufacturing capabilities. As technology continues to evolve, the future of polishing and buffing machines looks promising, with advancements in automation, sustainability, and smart manufacturing paving the way for more efficient and effective production methods.
By investing in the right equipment and staying informed about industry trends, manufacturers can achieve superior finishes, reduce costs, and maintain a competitive edge in their respective markets.