The Aluminium Polishing Machine is a surface polishing buffing machine for aluminum parts. High quality & Low Price & Free Consultation from the manufacturer
Due to the different aluminum alloys, variations in the final surface finish may occur. Variations may also occur by the type of buffing equipment used, the type and size of the buff wheels, the peripheral speed of the buff, the type of abrasive composition used, and the operator’s technique. When using automatic equipment, the operator technique is replaced by a mechanical system controlling such variables as pressure, time cycle,
conveyor speed, and contact time against the buffing wheel, resulting in a more consistent finish.
Aluminum and its alloys are soft metals with a high frictional coefficient. As previously discussed, tripoli or silica is used for a cutdown or cut-and-shine operation on aluminum. Calcined alumina compounds are used for shine on the aluminum surface
Aluminium Polishing Machine
Aluminium polishing machines are essential tools for achieving a smooth, reflective finish on aluminum surfaces. They are widely used in various industries, including automotive, aerospace, electronics, and construction. These machines employ a combination of abrasive compounds and polishing wheels to remove imperfections, restore shine, and enhance the appearance of aluminum products.
Types of Aluminium Polishing Machines
- Bench Buffing Machines: These are compact machines designed for smaller workpieces or finishing tasks. They typically have a single spindle and are mounted on a benchtop.
- Floor Buffing Machines: These are larger machines used for polishing larger workpieces or continuous production lines. They may have multiple spindles and can be operated while the workpiece remains stationary.
- Automatic Buffing Machines: These machines are designed for high-volume production and offer automation for repetitive buffing tasks. They may employ robots or automated feeding systems to handle workpieces.
Components of Aluminium Polishing Machines
- Spindle: The spindle rotates the buffing wheel or mop, providing the driving force for polishing. It is typically connected to a motor that controls the rotational speed.
- Buffing Wheel or Mop: These are the abrasive components that come into contact with the aluminum workpiece. They are made of various materials, such as cotton, felt, or sisal, and are impregnated with polishing compounds.
- Polishing Compound: These compounds contain polishing agents, such as abrasives, lubricants, and extenders. They are applied to the buffing wheel or mop to achieve the desired polishing effect.
- Workpiece Holder or Fixture: These secure the workpiece in place while it is being buffed. They may be simple clamps or more complex fixtures designed for specific shapes or workpiece sizes.
- Dust Collection System: This system removes dust and debris generated during the buffing process. It typically consists of a hood, filter, and fan to collect and exhaust the airborne particles.
Applications of Aluminium Polishing Machines
- Automotive Industry: Aluminium polishing machines are used to polish car bodies, wheels, and trim, restoring their shine and removing scratches or imperfections.
- Aerospace Industry: These machines are used to polish aircraft components, such as wings, fuselages, and engine parts, to reduce drag and improve aerodynamic performance.
- Electronics Industry: Aluminium polishing machines are used to polish electronic components, such as housings, casings, and circuit boards, to achieve a clean, smooth finish and enhance their appearance.
- Construction Industry: Aluminium polishing machines are used to polish architectural components, such as railings, handrails, and door handles, to create a visually appealing and durable finish.
- Consumer Goods Industry: Aluminium polishing machines are used to polish appliances, cookware, and other consumer goods to enhance their appearance and extend their lifespan.
Benefits of Aluminium Polishing Machines
- Improved Appearance: Aluminium polishing machines restore the shine and luster of aluminum surfaces, enhancing the aesthetics of products and components.
- Enhanced Durability: Polishing removes imperfections and scratches, improving the surface quality of aluminum parts and extending their lifespan.
- Reduced Friction: Smoother aluminum surfaces reduce friction, improving the performance and efficiency of machinery and components.
- Corrosion Resistance: Polishing removes contaminants and polishes the surface, making it less susceptible to corrosion and oxidation.
- Ease of Cleaning: Smoother surfaces are easier to clean and maintain, reducing maintenance costs and downtime.
Conclusion
Aluminium polishing machines play a crucial role in various industries by restoring the shine, durability, and functionality of aluminum surfaces. By understanding the different types, components, and applications of aluminium polishing machines, manufacturers can effectively utilize these machines to enhance the quality and appearance of their aluminum products and components.
Bench Buffing Machines
Bench buffing machines are compact and versatile polishing tools designed for smaller workpieces or finishing tasks. They are typically mounted on a benchtop and offer a single spindle for rotating buffing wheels or mops. These machines are commonly used in various industries, including automotive, jewelry, metal fabrication, and woodworking.
Components of Bench Buffing Machines
- Spindle: The spindle is the central rotating shaft that drives the buffing wheel or mop. It is connected to a motor that controls the rotational speed, allowing for adjustments based on the desired polishing effect.
- Buffing Wheel or Mop: These are the abrasive components that directly contact the workpiece. They are made from various materials, such as cotton, felt, or sisal, and are impregnated with polishing compounds to achieve the desired finish.
- Polishing Compound: Polishing compounds contain abrasives, lubricants, and extenders that determine the aggressiveness of the polishing action. Different compounds are available for various metals, desired finishes, and workpiece sizes.
- Workpiece Holder or Fixture: This component securely holds the workpiece in place while it is being buffed. It can be a simple clamp or a more complex fixture designed for specific workpiece shapes or sizes.
- Dust Collection System: To prevent the spread of airborne dust and debris generated during the buffing process, bench buffing machines often have a dust collection system. This typically consists of a hood, filter, and fan to capture and exhaust the particles.
- Foot Pedal or Switch: Bench buffing machines are typically controlled using a foot pedal or switch that activates the spindle and polishing wheel. This allows the operator to maintain control while keeping both hands on the workpiece.
Applications of Bench Buffing Machines
Bench buffing machines are versatile tools used for a wide range of polishing applications, including:
- Automotive Industry: Polishing car bodies, wheels, and trim to restore shine and remove scratches.
- Jewelry Industry: Polishing jewelry pieces, such as rings, bracelets, and necklaces, to achieve a high-gloss finish.
- Metal Fabrication Industry: Polishing metal components, such as tools, dies, and hardware, to remove burrs, imperfections, and improve surface quality.
- Woodworking Industry: Polishing wooden surfaces, such as furniture, musical instruments, and decorative items, to enhance their appearance and protect against wear.
- Hobby and DIY Projects: Polishing various materials, including metals, plastics, and gemstones, for hobbyists and DIY enthusiasts.
Benefits of Bench Buffing Machines
- Compact and Portable: Their small size and lightweight construction make them easy to transport and use in various workspaces.
- Easy to Operate: The simple design and intuitive controls make them user-friendly, even for those with limited experience in buffing.
- Versatility: They can accommodate a variety of workpiece sizes and shapes, making them suitable for a wide range of applications.
- Cost-Effective: They are generally more affordable than larger buffing machines, making them a cost-effective option for small-scale operations.
- Suitable for Finishing Tasks: They are particularly well-suited for final polishing stages and finishing touches on smaller workpieces.
Safety Considerations for Bench Buffing Machines
- Personal Protective Equipment (PPE): Wear appropriate PPE, including safety glasses, gloves, and respiratory protection, to minimize the risk of injuries from flying debris, abrasive dust, and metal particles.
- Machine Guarding: Ensure proper guards are installed around the rotating buffing wheel or mop to prevent worker contact with hazardous moving parts.
- Safe Work Practices: Follow safe work practices, such as maintaining a firm grip on the workpiece and avoiding loose clothing or jewelry that could become entangled in the machine.
- Emergency Stop Button: Clearly marked emergency stop buttons should be readily accessible to enable workers to halt the machine quickly in case of an unsafe situation.
Conclusion
Bench buffing machines provide an efficient and versatile solution for polishing smaller workpieces or performing finishing tasks. Their compact size, ease of operation, and affordability make them a valuable tool for various industries and hobbyists. By adhering to safety guidelines and using appropriate techniques, bench buffing machines can effectively enhance the appearance, durability, and functionality of various materials.
Buffing Wheel or Mop
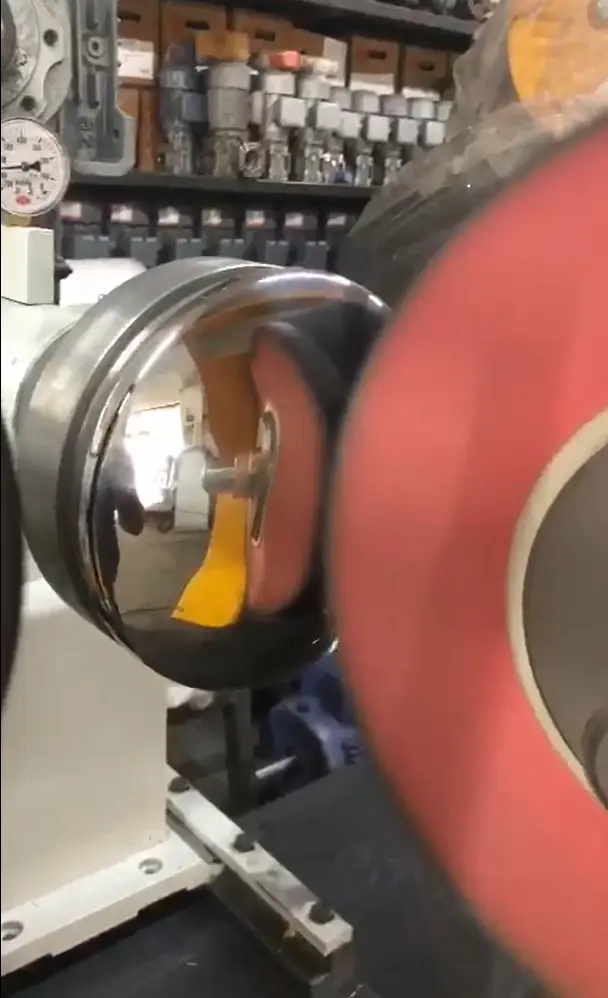
Buffing wheels and mops are essential components of buffing machines, providing the abrasive interface that polishes and refines metal surfaces. They are made from various materials, each with unique properties that influence their polishing action and suitability for different applications.
Types of Buffing Wheels and Mops
- Cotton Buffing Wheels: These are the most common type of buffing wheel, offering a balance of cutting action and finishing ability. They are suitable for a wide range of metals and polishing stages, from cut buffing to final polishing.
- Felt Buffing Wheels: Felt buffing wheels are softer and more flexible than cotton wheels, making them ideal for final polishing stages and achieving a high-gloss finish. They can also be used for polishing delicate surfaces or intricate shapes.
- Sisal Buffing Wheels: Sisal buffing wheels are made from a natural fiber that provides a more aggressive cutting action compared to cotton or felt wheels. They are primarily used for initial cut buffing stages to remove deep scratches, burrs, and imperfections.
- Buffing Mops: Buffing mops are similar to buffing wheels but typically have a more open structure, allowing for better ventilation and heat dissipation. They are often used for buffing large, flat surfaces or applying polishing compounds.
Selection of Buffing Wheels and Mops
The choice of buffing wheel or mop depends on several factors, including:
- Polishing Stage: The stage of the buffing process dictates the type of abrasive action required. Cut buffing requires a more aggressive wheel like sisal, while final polishing requires a softer wheel like felt or cotton.
- Metal Type: Different metals have varying hardness and reactivity to abrasives. For harder metals, a denser wheel like sisal may be needed, while softer metals may require a softer wheel like cotton or felt.
- Workpiece Shape and Size: The shape and size of the workpiece influence the choice of wheel or mop. For intricate shapes, a flexible felt mop may be suitable, while larger, flat surfaces may require a buffing wheel.
- Desired Finish: The desired level of polish dictates the fineness of the abrasives impregnated in the wheel or mop. For a high-gloss finish, finer abrasives are used, while a matte finish may require coarser abrasives.
Care and Maintenance of Buffing Wheels and Mops
Proper care and maintenance of buffing wheels and mops extend their lifespan and ensure consistent polishing performance:
- Cleaning: Regularly clean the wheel or mop to remove accumulated debris and polishing compounds. Use appropriate solvents or cleaning agents recommended by the manufacturer.
- Dressing: Dressing involves truing the wheel or mop to maintain its shape and balance. Use a dressing tool or a diamond-impregnated dressing stick to remove uneven wear and restore a consistent surface.
- Storage: Store buffing wheels and mops properly to prevent damage and maintain their shape. Hang them on dedicated hooks or store them in a protective container.
- Inspection: Regularly inspect buffing wheels and mops for signs of wear, damage, or contamination. Replace or repair damaged wheels or mops to ensure safety and performance.
Conclusion
Buffing wheels and mops play a crucial role in achieving the desired finish on metal surfaces. By understanding the different types, selection criteria, and maintenance practices, manufacturers and hobbyists can effectively utilize buffing wheels and mops to enhance the appearance, durability, and functionality of their metal products and projects.
Designations of Finishing grades done by an Aluminium Polishing Machine
- Series (a) As fabricated. No buffing or polishing is required.
- Series (b) Medium bright soft textured satin finish.
- Series (c) Bright buffed finish over soft texture satin.
- Series (d) Bright buffed finish on the original surface.
- Series (e) Coarse directional satin finish.
- Series (f) Medium directional satin finish.
- Series (g) Fine directional satin finish.
- Series (h) Hand-rubbed satin-type finish (small areas only).
- Series (i) Brushed finish.
- Series (j) Nondirectional satin finish.
The following recommendations are step-by-step instructions for obtaining the designated architectural finishes.
Aluminium Polishing Machine Grades
- Series (b) Finishes Polish with a wheel coated with an abrasive and cement paste with 80 to 150 grit on sewn or ventilated buffs, lightly lubricated with a special bar or liquid lubricants. Buff speed 6,000 sfm. Final polish with a wheel coated with an abrasive and cement paste with 320 grit using the same buff and the same speed.
- Series (c) Finishes Polish with an abrasive and cement paste-coated wheel, 320 grit on sewn or ventilated buff. Light lubrication with a special bar or liquid lubricant. Bright buff with clean working tripoli bar compound or liquid tripoli buffing compound on ventilated, sewn, or loose buff. Buff speed 7,000 sfm.
- Series (d) Finishes Bright buff only over the original surface as for series (c) finishes. No prior polishing is required.
- Series (e) Finishes Coarse satin finish with a greaseless compound of 80 grit over glue base buff sizing on a ventilated or sewn buff, or with liquid abrasive 80 grit on the same type buff. Lubricate the dried compound head with a special bar or liquid lubricant. Buff speed 6,000 sfm.
- Series (f) Finishes Medium satin finish with greaseless compound, 120 grit, over a blue base buff sizing on ventilated or sewn buffs, or with liquid abrasive 120 grit on the same type buff. Lubricate the dried compound head with a special bar or liquid lubricant.
- Series (g) Finishes Fine satin finish with greaseless compound, 150 grit, on a ventilated, sewn, or loose buff, or with liquid abrasive 150 grit on the same type of buff. Lubricate the dried compound head with a special bar or liquid lubricant. Buff speed 6,000 sfm.
- Series (h) Finishes Hand-rubbed finish, using coarse steel wool lubricated with a special liquid lubricant. Final rubbing with No. 0 steel wool.
- Series (i) Finishes Brush-type finish produced with string wheels coated with greaseless compound, 80 grit. String wheel speed 6,000 sfm. The buff head may require some light lubrication with a special bar lubricant, depending on the alloy of aluminum. Nylon-impregnated wheels are also used for this finish.
- Series (j) Finishes: Brush-type finish produced with a string wheel coated with greaseless compound, 80 grit, but operated at a slow speed of 2,000 to 3,000 sfm.
May also require some light lubrication with a special bar lubricant. Again, nylon-impregnated wheels may also be used. When high-production satin finishing is required for series (e), (f), (g), and (i), use a liquid greaseless abrasive. Such compositions may be applied automatically with properly designed spray equipment. Light lubrication of the satin-finished head, when required, is done with non misting, low-atomizing spray equipment.
Types of Polishing and Buffing Machines
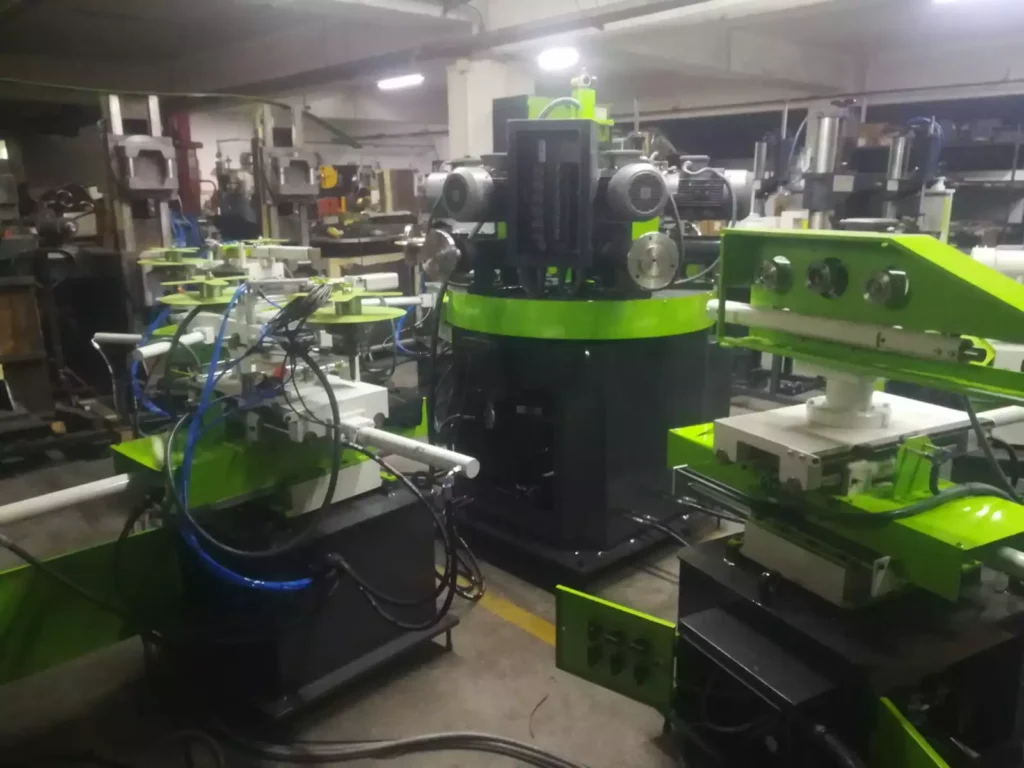
Manual Machines
Manual polishing and buffing machines are the most basic type, requiring direct human operation. These machines are suitable for small-scale operations and tasks that need a hands-on approach. They are typically used for intricate work where precision and control are paramount.
Key Features:
- Simple design and operation.
- Cost-effective for small jobs.
- Ideal for detailed and delicate work.
Applications:
- Jewelry and watchmaking.
- Small metal parts in the automotive and aerospace industries.
Semi-Automatic Machines
Semi-automatic polishing and buffing machines combine manual and automated features. They allow for greater control over the process while improving efficiency compared to fully manual machines. Operators can set parameters and oversee the operation, making adjustments as necessary.
Key Features:
- Enhanced control with automated functions.
- Increased efficiency and throughput.
- Suitable for medium-scale operations.
Applications:
- Mid-sized manufacturing units.
- Complex parts requiring a balance of manual oversight and automation.
CNC (Computer Numerical Control) Machines
CNC polishing and buffing machines represent the pinnacle of automation and precision in surface finishing. These machines use computer-controlled systems to manage the movement and operation of polishing tools with high accuracy. CNC machines are highly programmable, allowing for the automation of complex and repetitive tasks.
Key Features:
- High precision and repeatability.
- Ability to handle complex shapes and surfaces.
- Programmable for different tasks and materials.
Benefits:
- Consistent and high-quality finishes.
- Reduced labor costs and increased productivity.
- Flexibility in manufacturing processes.
Applications:
- Aerospace components.
- High-end automotive parts.
- Medical devices and implants.
NC (Numerical Control) Machines
NC machines, while similar to CNC machines, are generally less sophisticated and do not offer the same level of flexibility and automation. They are controlled by pre-set instructions but lack the advanced programmability of CNC systems.
Key Features:
- Automated control with limited programmability.
- Suitable for less complex tasks.
- Cost-effective compared to CNC machines.
Applications:
- Standardized parts in automotive and metalworking industries.
- Tasks that do not require frequent changes in setup.
Applications of Polishing and Buffing Machines
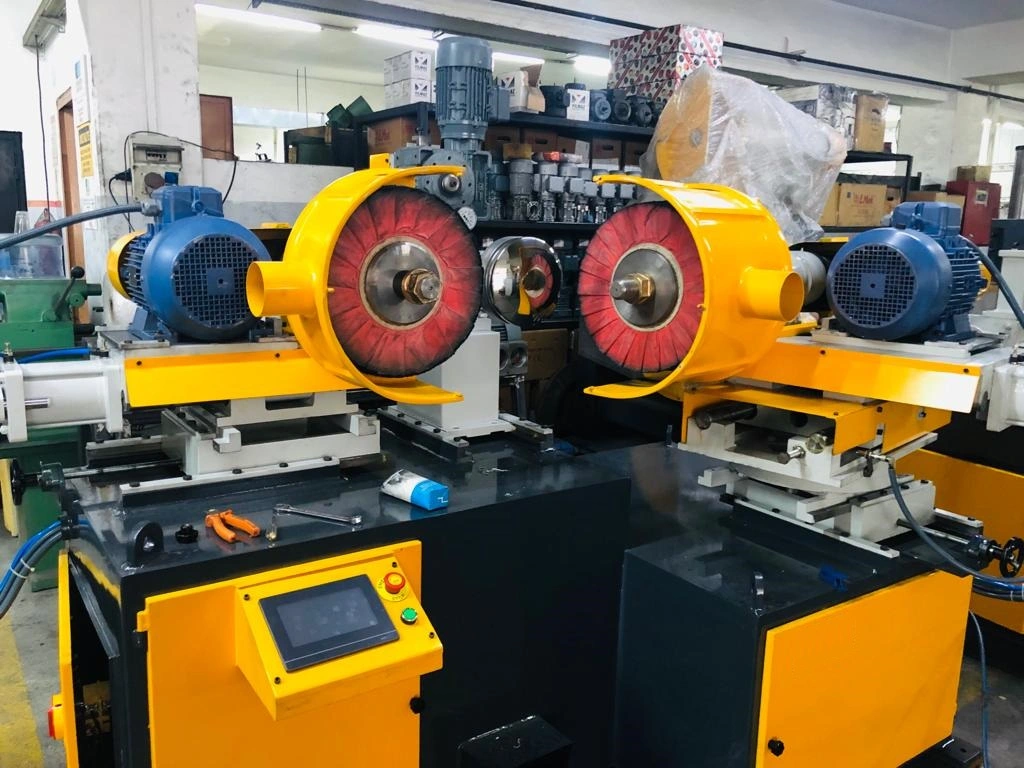
Automotive Industry
In the automotive industry, polishing and buffing are essential for achieving high-quality finishes on car parts. This includes the polishing of body panels, trim pieces, and engine components to enhance both aesthetics and performance.
Key Uses:
- Surface finishing of body panels.
- Polishing of chrome and aluminum trim.
- Buffing of engine and transmission parts.
Aerospace Industry
The aerospace industry demands the highest standards of precision and quality. Polishing and buffing are critical for ensuring the smooth surfaces necessary for aerodynamics and the performance of critical components.
Key Uses:
- Polishing turbine blades and engine parts.
- Finishing structural components for reduced drag.
- Ensuring the integrity of critical safety parts.
Metalworking Industry
In metalworking, polishing and buffing machines are used to finish metal parts, improving their appearance, resistance to corrosion, and overall quality.
Key Uses:
- Buffing of steel and aluminum parts.
- Finishing of tools and machinery components.
- Surface preparation for coating and painting.
Jewelry and Watchmaking
Precision and aesthetic appeal are paramount in jewelry and watchmaking. Polishing and buffing machines ensure that each piece has a flawless finish.
Key Uses:
- Polishing of precious metals and gemstones.
- Buffing intricate watch parts.
- Achieving high-shine finishes on jewelry.
Electronics Industry
In the electronics industry, surface preparation is crucial for the functionality and longevity of components. Polishing and buffing machines are used to prepare surfaces for assembly and coating.
Key Uses:
- Polishing of semiconductor wafers.
- Buffing of electronic enclosures and cases.
- Surface preparation for circuit boards.
Medical Device Manufacturing
The medical industry relies on highly polished surfaces for both functionality and hygiene. Polishing and buffing machines ensure that surgical instruments and implants meet stringent standards.
Key Uses:
- Polishing surgical instruments.
- Finishing orthopedic implants.
- Ensuring biocompatibility of medical devices.
Consumer Goods
Polishing and buffing are also used in the production of consumer goods, enhancing the aesthetic appeal and durability of everyday items.
Key Uses:
- Finishing of household appliances.
- Polishing of kitchen utensils and cutlery.
- Buffing of decorative items and hardware.
Production Process of Polishing and Buffing Machines
Design and Engineering
The production of polishing and buffing machines begins with design and engineering. This involves conceptualizing the machine, creating detailed CAD models, and planning the manufacturing process.
Steps:
- Conceptual design and feasibility studies.
- Detailed engineering using CAD software.
- Prototype development and testing.
Material Selection
Selecting the right materials is crucial for the durability and performance of polishing and buffing machines. Common materials include high-grade steels, aluminum alloys, and composite materials for specific parts.
Considerations:
- Durability and wear resistance.
- Weight and strength.
- Compatibility with various polishing materials.
Manufacturing Techniques
Manufacturing polishing and buffing machines involves several techniques, including machining, welding, assembly, and quality control. Each step is critical to ensuring the final product meets industry standards.
Techniques:
- CNC machining of components.
- Welding and fabrication of the machine frame.
- Assembly of mechanical and electronic parts.
- Rigorous testing and quality assurance.
Quality Control
Quality control is an integral part of the production process, ensuring that each machine meets the required specifications and performs reliably.
Methods:
- In-process inspections.
- Final testing of performance and safety.
- Certification to industry standards.
Materials Polished with Industrial Machines

Metals
Metals are the most common materials polished with industrial machines. This includes a wide range of metals used in various industries.
Examples:
- Stainless steel.
- Aluminum.
- Brass.
- Titanium.
Plastics
Certain types of plastics can also be polished to achieve a smooth and glossy finish, particularly in the electronics and consumer goods industries.
Examples:
- Acrylics.
- Polycarbonates.
- PVC.
Wood
Polishing wood can enhance its natural beauty and protect it from damage. This is commonly done in furniture making and decorative items.
Examples:
- Hardwood (oak, mahogany).
- Softwood (pine, cedar).
- Engineered wood (plywood, MDF).
Ceramics and Glass
Polishing ceramics and glass is delicate work that requires specialized techniques to avoid cracking and chipping.
Examples:
- Fine china.
- Glassware.
- Porcelain tiles.
Composites
Composites are used in advanced industries such as aerospace and automotive. Polishing these materials requires specialized equipment to handle their unique properties.
Examples:
- Carbon fiber.
- Fiberglass.
- Kevlar.
Advantages of Using CNC and NC Machines
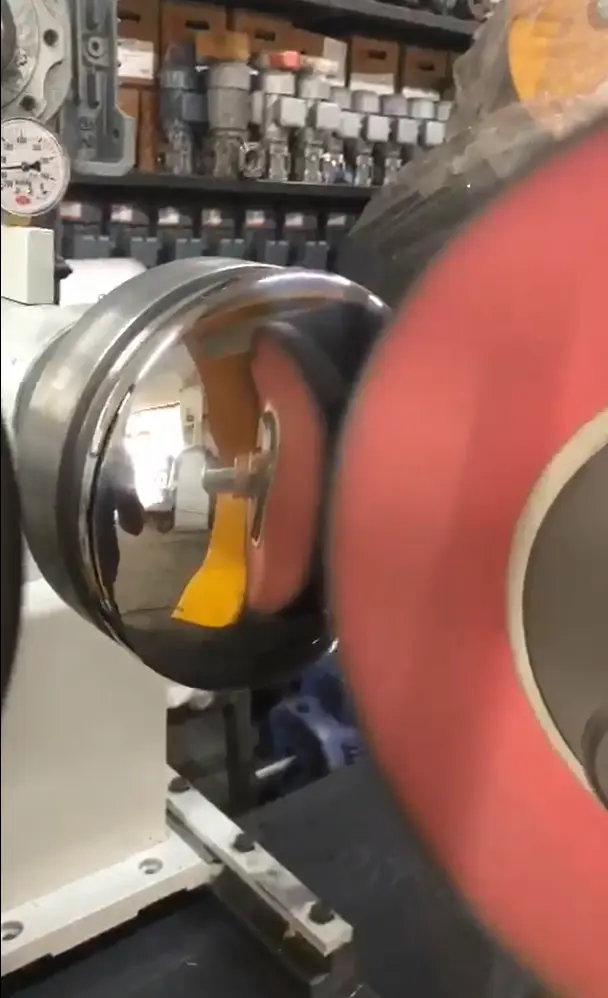
Precision and Consistency
CNC and NC machines offer unmatched precision and consistency, ensuring that each part meets exact specifications.
Benefits:
- Uniform finishes across large batches.
- High accuracy in complex geometries.
- Reduced human error.
Efficiency and Speed
These machines significantly reduce processing times, increasing overall productivity and allowing for faster turnaround times.
Benefits:
- Rapid processing of parts.
- Increased throughput.
- Shorter lead times.
Automation and Flexibility
Automation allows for continuous operation and the ability to handle multiple tasks without manual intervention.
Benefits:
- Customizable for various tasks.
- Minimal supervision required.
- Adaptable to different materials and shapes.
Cost-effectiveness
While the initial investment in CNC and NC machines can be high, the long-term savings in labor and increased efficiency make them cost-effective.
Benefits:
- Lower labor costs.
- High return on investment.
- Reduced material waste.
Challenges and Considerations
Initial Investment Costs
The cost of purchasing and installing CNC and NC machines can be significant, making it a major consideration for businesses.
Factors:
- Budgeting for high-quality machinery.
- Evaluating long-term benefits versus initial costs.
Maintenance and Upkeep
Regular maintenance is essential to ensure the longevity and performance of these machines.
Considerations:
- Scheduled maintenance and repairs.
- Availability of spare parts.
- Training for maintenance personnel.
Training and Skilled Labor
Operating CNC and NC machines requires skilled operators who understand the intricacies of programming and machine control.
Considerations:
- Investing in operator training.
- Ensuring continuous education on new technologies.
- Retaining skilled labor.
Technological Advancements
Keeping up with the latest advancements in technology is crucial for maintaining a competitive edge.
Considerations:
- Upgrading machinery and software.
- Staying informed about industry trends.
- Investing in research and development.
Future Trends in Polishing and Buffing Technology
Advancements in Automation and AI
The integration of artificial intelligence in polishing and buffing machines is set to revolutionize the industry by enhancing precision and efficiency.
Trends:
- AI-driven process optimization.
- Predictive maintenance using machine learning.
- Autonomous operation and monitoring.
Sustainable Practices
Sustainability is becoming increasingly important in manufacturing, with a focus on eco-friendly materials and processes.
Trends:
- Use of recyclable materials.
- Energy-efficient machinery.
- Reduction of waste and emissions.
Integration with Industry 4.0
Industry 4.0 involves the integration of smart technologies and IoT in manufacturing processes, providing real-time data and improving overall efficiency.
Trends:
- Smart manufacturing systems.
- Real-time monitoring and analytics.
- Enhanced connectivity and automation.
Conclusion
Industrial polishing and buffing machines play a vital role in various industries, ensuring that products meet the highest standards of quality and performance. From manual to advanced CNC and NC machines, each type offers unique benefits and is suited to different applications. Understanding the production processes, materials, and advantages of these machines is essential for businesses looking to improve their manufacturing capabilities. As technology continues to evolve, the future of polishing and buffing machines looks promising, with advancements in automation, sustainability, and smart manufacturing paving the way for more efficient and effective production methods.
By investing in the right equipment and staying informed about industry trends, manufacturers can achieve superior finishes, reduce costs, and maintain a competitive edge in their respective markets.