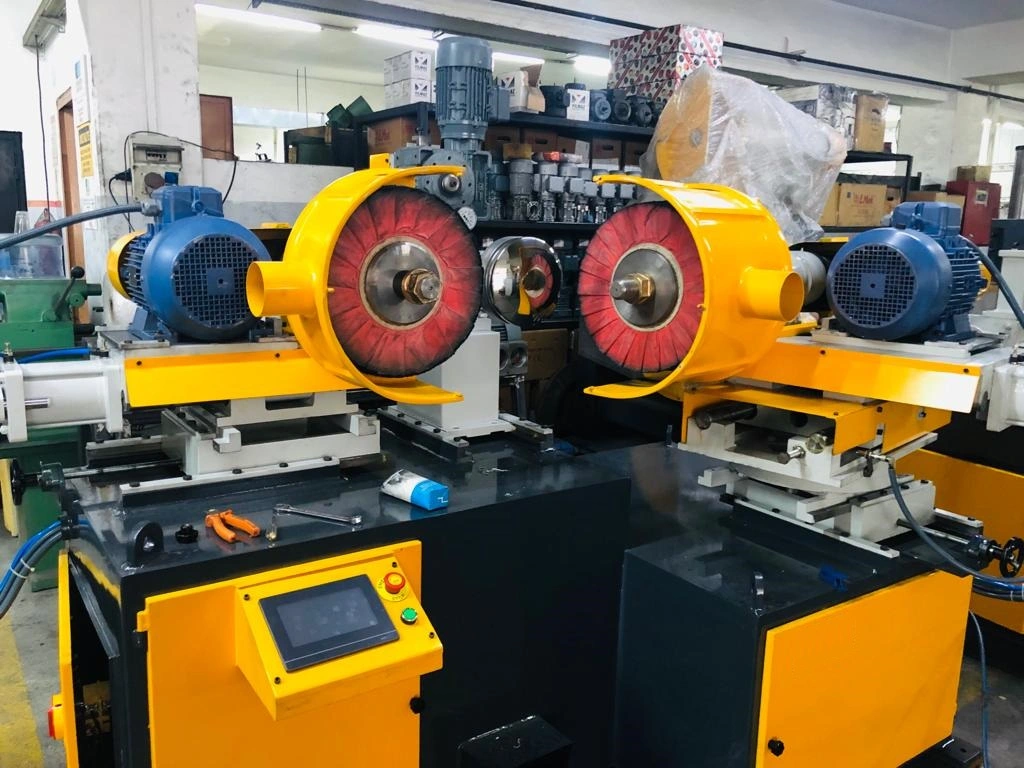
Polishing is the most important part of finishing in the cookware industry. For a shining surface, cookware kitchenware products need to be polished before packaging. Polishing is carried out by some different steps (For ex: Polishing Machine for Stainless Steel Cookware).
Polishing machines play a crucial role in the manufacturing of stainless steel cookware, imparting a gleaming finish that enhances both the aesthetic appeal and functionality of these culinary tools. These machines employ various polishing techniques to remove imperfections, smooth out surface irregularities, and achieve a desired level of reflectivity.
Types of Polishing Machines for Stainless Steel Cookware
- Belt Polishing Machines: Belt polishing machines utilize continuous abrasive belts that rotate over rollers. The stainless steel cookware piece is fed against the moving belt, creating a consistent and uniform polishing effect. This method is efficient and suitable for polishing large quantities of cookware.
- Disk Polishing Machines: Disk polishing machines employ abrasive disks mounted on a rotating spindle. The cookware piece is placed against the rotating disk, allowing for more precise polishing and control over the polishing action. This method is suitable for polishing smaller or intricate pieces of cookware.
- Buffing Machines: Buffing machines utilize soft abrasive wheels or compounds to achieve a high degree of polish. The cookware piece is placed against the rotating wheel, and the buffing compound is applied to further refine the surface finish. Buffing is often used as a final polishing step to achieve a mirror-like shine.
Polishing Techniques for Stainless Steel Cookware
- Initial Polishing: Initial polishing involves removing scratches, burrs, and imperfections from the stainless steel surface. This is typically done using coarser abrasive belts or disks to remove significant material and level out the surface.
- Intermediate Polishing: Intermediate polishing further refines the surface by removing finer imperfections and scratches. This stage utilizes medium-grit abrasives to create a smoother, more uniform finish.
- Final Polishing: Final polishing achieves the desired level of reflectivity. Finely grained abrasive belts, disks, or buffing compounds are used to eliminate even the smallest imperfections and create a mirror-like finish.
Safety Considerations for Polishing Stainless Steel Cookware
- Personal Protective Equipment (PPE): Workers should wear appropriate PPE, including gloves, safety glasses, and respiratory protection to prevent exposure to dust and debris generated during the polishing process.
- Machine Guarding: Machinery should be equipped with proper guards to protect workers from moving parts and potential hazards.
- Emergency Stop Procedures: Train workers on emergency stop procedures and ensure they are readily accessible.
- Regular Maintenance: Maintain machinery in good working condition to prevent malfunctions and ensure safe operation.
- Ventilation: Ensure adequate ventilation in the workspace to remove dust and debris generated during polishing.
By adhering to these safety guidelines, manufacturers can effectively utilize polishing machines to produce high-quality stainless steel cookware while maintaining a safe and healthy work environment.
For polishing of stainless steel, some of the main materials that are used, Canvas and leather are ideal for polishing wheels, although a wide variety of other materials, including cotton cloth, felt, leather, paper, plastic, sheepskin, rubber, and wool can also be used. Cotton or wool cloth are used for buffing wheels or mops. Polishing and buffing can also contribute to workplace safety. Buffing, for example, helps prevent corrosion in specialty plumbing. When applied to pipes found in dairy and pharmaceutical plants, it also destroys bacteria or mold and prevents corrosion, thus ensuring product safety.
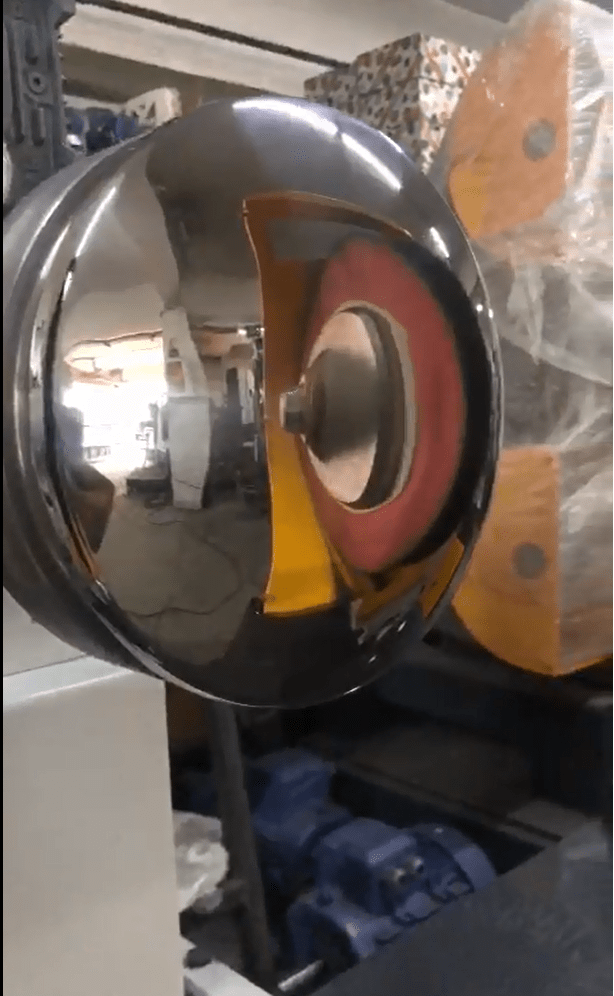
With our polishing machine, you can increase your capacity up to 300 parts/hour. All the polishing process is carried out automatically and programmed by a PLC.
The mainframe of the polishing machine is welded construction, with a polishing station controlled by a lead screw to control the distance traveled by the polishing head into the pot
Metal Polishing Machine with Polishing Disc
Metal polishing is an important finishing process in the metalworking industry. The metal finishing machines can be classified as the following:
- Superfinishing Machines
- Microfinishing Machines
- Grinding Machines
- Deburring (Burr removing) Machines
- Centerless Grinding and Polishing Machines
- Flat Part & Surface Grinding Polishing Machine
Grinding metal can be carried out by abrasive discs, sanding material, leather, cotton, or cellulose-based components. The process has some levels depending on the surface hardness and abrasiveness of the grinding compound. The hardest is the sanding wheel and the softest is cotton-based micro-finishing applications
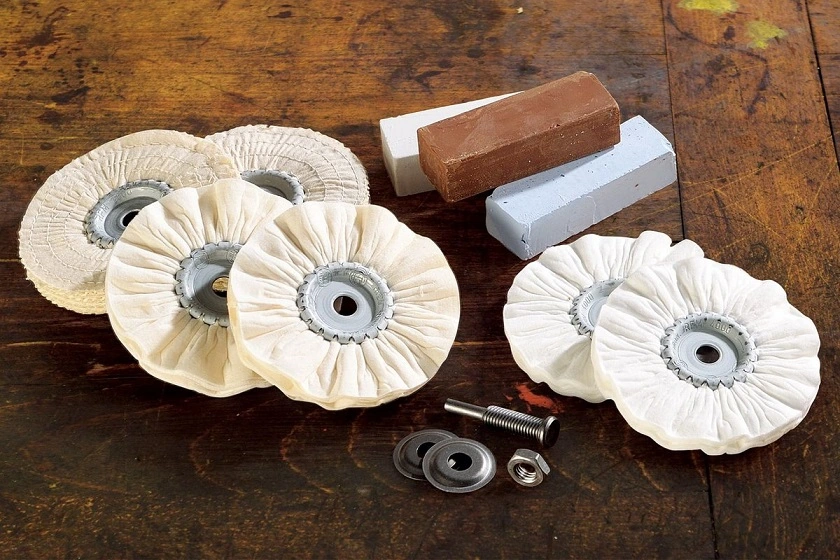
Polishing discs play a crucial role in metal polishing, offering a versatile and effective method for achieving a smooth, polished finish on various metal surfaces. These discs, also known as polishing wheels or buffing wheels, utilize abrasive compounds to gradually remove imperfections and refine the surface, resulting in a gleaming and aesthetically pleasing finish.
Types of Polishing Discs for Metal
- Sisal Discs: Sisal discs are made from natural sisal fibers, offering a relatively aggressive polishing action. They are often used for initial polishing stages to remove scratches, burrs, and imperfections from metal surfaces.
- Cotton Discs: Cotton discs are made from soft cotton fibers, providing a gentler polishing action. They are suitable for intermediate polishing stages to refine the surface and remove finer scratches.
- Felt Discs: Felt discs are made from compressed wool fibers, offering a versatile polishing action that can be tailored to various applications. They are often used for final polishing stages to achieve a high degree of polish and a mirror-like finish.
Abrasive Compounds for Metal Polishing
Abrasive compounds are essential components of metal polishing, containing a combination of abrasive particles, lubricating agents, and polishing agents. The type, grit, and concentration of abrasive particles determine the aggressiveness of the polishing action, while the lubricating agents and polishing agents enhance the finish and prevent overheating.
Metal Polishing Process with Polishing Disc
The metal polishing process with polishing discs typically involves several stages:
- Surface Preparation: The metal surface is thoroughly cleaned and degreased to remove any contaminants or debris that could affect the polishing process.
- Initial Polishing: Sisal discs with coarse abrasive compounds are used to remove scratches, burrs, and imperfections from the metal surface.
- Intermediate Polishing: Cotton discs with medium-grit abrasive compounds are used to refine the surface and remove finer scratches, creating a smoother finish.
- Final Polishing: Felt discs with fine-grit abrasive compounds or buffing compounds are used to achieve a high degree of polish and a mirror-like finish.
- Cleaning and Inspection: The polished metal surface is cleaned to remove any remaining polishing residue and inspected for any remaining imperfections or defects.
Factors Affecting Metal Polishing with Polishing Disc
- Disc Material: The material of the polishing disc, such as sisal, cotton, or felt, influences the aggressiveness of the polishing action.
- Abrasive Compound: The type, grit, and concentration of abrasive particles in the compound determine the aggressiveness of the polishing action and the level of finish.
- Polishing Speed: The speed of the polishing machine affects the polishing rate and the level of finish. Higher speeds generally produce a faster polishing action, but excessive speed can damage the workpiece or cause overheating.
- Polishing Pressure: The pressure applied to the workpiece during polishing influences the polishing intensity and the depth of material removal. Excessive pressure can damage the workpiece, while insufficient pressure may result in an incomplete finish.
- Workpiece Material: The material of the workpiece affects the polishing process. Harder materials, such as stainless steel or chrome, require more aggressive polishing techniques, while softer materials, such as aluminum or brass, require gentler polishing methods.
Conclusion
Polishing discs are essential tools for achieving a smooth, polished finish on various metal surfaces. Their versatility, effectiveness, and ability to produce high-quality finishes make them valuable equipment in diverse industries. By understanding the principles of metal polishing with polishing discs, selecting the appropriate disc and abrasive compound, and following a proper polishing process, users can effectively enhance the appearance and functionality of metal products.
Buffing Machines as a Polishing Machine
Buffing machines are versatile tools used to achieve a high degree of polish and a mirror-like finish on various surfaces, including metals, plastics, and even some types of wood. They are widely used in various industries, such as manufacturing, construction, and woodworking, to enhance the appearance, functionality, and durability of products.
Principle of Operation
Buffing machines utilize soft abrasive wheels or compounds to refine the surface of a workpiece. The workpiece is pressed against the rotating buffing wheel, and the abrasive compound removes minute amounts of material, leveling out imperfections and achieving a smooth, polished finish.
Types of Buffing Machines
- Single-Spindle Buffing Machines: Single-spindle buffing machines utilize a single buffing wheel mounted on a rotating spindle. They are suitable for polishing small to medium-sized workpieces and offer precise control over the polishing process.
- Multi-Spindle Buffing Machines: Multi-spindle buffing machines employ multiple buffing wheels mounted on a rotating spindle, allowing for simultaneous polishing of multiple workpieces or different areas of a single workpiece. They are suitable for high-volume production and offer increased efficiency.
- Automatic Buffing Machines: Automatic buffing machines utilize computer-controlled systems to automate the polishing process, ensuring consistency and reducing operator fatigue. They are suitable for high-precision applications and large-scale production.
Buffing Compounds
Buffing compounds are essential components of buffing machines, containing a combination of abrasive particles, lubricating agents, and polishing agents. The type and grit of the abrasive particles determine the aggressiveness of the polishing action, while the lubricating agents and polishing agents enhance the finish and prevent overheating.
Applications of Buffing Machines
Buffing machines are used for a wide range of applications, including:
- Metal Finishing: Buffing machines are used in various metal finishing processes, such as buffing, burnishing, and mirror polishing, to achieve high levels of surface refinement and reflectivity.
- Plastic Polishing: Buffing machines can be used to achieve a high gloss finish on plastic components, especially for optical components or decorative items.
- Wood Polishing: Buffing machines can be used to achieve a high gloss finish on certain types of wood, such as musical instruments or furniture.
- Jewelry Polishing: Buffing machines are commonly used in jewelry manufacturing to remove scratches, tarnish, and imperfections, achieving a gleaming finish.
Factors Affecting Buffing
The effectiveness of buffing depends on several factors:
- Buffing Wheel: The type, material, and hardness of the buffing wheel affect the polishing action. Softer wheels are used for delicate materials, while harder wheels are used for more aggressive polishing.
- Buffing Compound: The type and grit of the buffing compound determine the aggressiveness of the polishing action and the level of finish. Coarser compounds are used for initial polishing stages, while finer compounds are used for final polishing.
- Workpiece Material: The material of the workpiece affects the polishing process. Harder materials, such as metals or stones, require more aggressive polishing techniques, while softer materials, such as plastics or wood, require gentler polishing methods.
- Polishing Pressure: The pressure applied to the workpiece during buffing influences the polishing intensity and the depth of material removal. Excessive pressure can damage the workpiece, while insufficient pressure may result in an incomplete finish.
- Workpiece Preparation: The surface condition of the workpiece prior to buffing can affect the polishing outcome. Cleaning and removing any contaminants or debris from the workpiece surface is essential for achieving a consistent and high-quality finish.
Conclusion
Buffing machines are valuable tools for achieving a high degree of polish and a mirror-like finish on various materials. Their versatility, controllability, and ability to produce high-quality finishes make them essential equipment in various industries. By understanding the principles of operation, types of buffing machines, buffing compounds, applications, and factors influencing the buffing process, users can effectively utilize buffing machines to enhance the appearance, functionality, and durability of their products.
The Grinding Automation for Cookware Kitchenware Products such as Pots and Pans
Grinding automation plays a crucial role in the manufacturing of cookware and kitchenware products, particularly in the production of pots and pans. Automated grinding systems provide several advantages over traditional manual grinding methods, including increased efficiency, consistency, and precision.
Benefits of Grinding Automation for Cookware
- Increased Efficiency: Automated grinding systems can operate continuously and consistently, significantly reducing production time and labor costs compared to manual grinding.
- Enhanced Consistency: Automated systems maintain consistent pressure, speed, and grinding patterns, ensuring uniformity across all cookware pieces. This consistency is essential for achieving a uniform finish and maintaining product quality.
- Improved Precision: Automated grinding systems can precisely control the removal of material, ensuring consistent wall thickness and surface smoothness. This precision is critical for producing high-quality cookware that meets performance and durability standards.
- Reduced Human Error: Automated systems eliminate the risk of human error, such as inconsistent grinding pressure or uneven grinding patterns, which can lead to defects and variations in product quality.
- Improved Working Conditions: Automated grinding systems reduce the physical strain and repetitive motions associated with manual grinding, improving worker safety and reducing the risk of musculoskeletal disorders.
Types of Grinding Automation for Cookware
- CNC Grinding Machines: CNC (Computer Numerical Control) grinding machines utilize computer-controlled programming to precisely guide the grinding process. These machines offer high precision and flexibility, allowing for complex grinding patterns and customized cookware designs.
- Robotic Grinding Systems: Robotic grinding systems employ robotic arms equipped with grinding tools to automate the grinding process. These systems provide even greater flexibility and can be integrated into automated production lines for continuous grinding.
- Automated Grinding Lines: Automated grinding lines incorporate multiple grinding stations, each equipped with CNC grinding machines or robotic grinding systems. These lines enable high-volume production and maintain consistent grinding quality throughout the manufacturing process.
Applications of Grinding Automation in Cookware Manufacturing
Grinding automation is widely used in various stages of cookware manufacturing, including:
- Edge Grinding: Automated grinding systems can precisely bevel and smooth the edges of pots and pans, enhancing their appearance and safety.
- Surface Grinding: Automated systems can grind the entire surface of cookware to achieve a uniform finish and remove imperfections.
- Interior Grinding: Automated grinding can precisely shape the interior of pots and pans, ensuring consistent cooking performance and reducing food sticking.
- Handle Grinding: Automated grinding can shape and smooth the handles of cookware, improving ergonomics and aesthetics.
- Lid Grinding: Automated grinding can precisely bevel and finish the lids of pots and pans, ensuring a proper fit and seal.
Conclusion
Grinding automation has revolutionized the manufacturing of cookware and kitchenware products, providing significant benefits in terms of efficiency, consistency, precision, and reduced human error. As cookware designs become more complex and demand for high-quality products increases, automated grinding systems will continue to play an essential role in the cookware industry.
A polishing machine for stainless steel cookware is a specialized piece of equipment used in the manufacturing or finishing processes of stainless steel pots, pans, and other cookware. Its primary purpose is to achieve a polished, smooth, and aesthetically pleasing surface on stainless steel cookware products. Here are the key components and features of a polishing machine designed for this purpose:
Components:
- Polishing Wheels or Buffing Wheels:
- The heart of the polishing machine is the polishing or buffing wheels. These wheels are made of various materials, such as cotton, sisal, or felt, and are coated with polishing compounds.
- Different wheels and compounds are used for various stages of the polishing process, starting with coarse abrasives and progressing to finer ones for achieving a mirror-like finish.
- Drive System:
- The polishing wheels are driven by an electric motor or another power source. The motor provides the necessary rotational force to turn the wheels at the required speed.
- Control Panel:
- Modern polishing machines come with a control panel that allows operators to adjust the machine’s settings, including the rotation speed of the polishing wheels.
- Some machines may have digital controls for precise adjustment.
- Supporting Structure:
- The machine typically has a sturdy frame or supporting structure that holds the polishing wheels and supports the cookware during the polishing process.
- Workpiece Holders:
- Cookware items, such as pots and pans, need to be securely held in place while being polished. Specialized holders or fixtures are often included to accommodate various cookware shapes and sizes.
Features:
- Material Compatibility:
- Polishing machines for stainless steel cookware are designed to work specifically with stainless steel, ensuring that the material’s unique properties are properly addressed during polishing.
- Polishing Compounds:
- These machines often include a system for applying polishing compounds to the rotating wheels. These compounds aid in removing imperfections and creating a high-gloss finish.
- Adjustable Speed:
- The rotation speed of the polishing wheels is adjustable to accommodate different types of cookware and the desired finish quality.
- Safety Features:
- Safety is a priority in the operation of these machines. They may include safety guards and emergency stop features to protect operators from accidents.
- Dust Collection:
- Polishing stainless steel can generate dust and debris. Some machines have built-in dust collection systems to keep the workspace clean and reduce operator exposure to airborne particles.
- Quality Control:
- To ensure consistent quality, some machines may feature sensors or measurement systems to monitor the quality of the polished surface and make real-time adjustments if necessary.
- Automation:
- In larger-scale manufacturing operations, automated polishing machines may be used to streamline the process and maintain uniform quality across a high volume of cookware products.
Polishing machines for stainless steel cookware are commonly used in cookware manufacturing plants and metalworking workshops. They play a crucial role in enhancing the visual appeal of stainless steel cookware products, making them more attractive to consumers. The quality and consistency of the polishing process are essential to achieving a glossy and mirror-like finish, which is a hallmark of premium stainless steel cookware.
EMS Metalworking Machinery
We design, manufacture and assembly metalworking machinery such as:
- Hydraulic transfer press
- Glass mosaic press
- Hydraulic deep drawing press
- Casting press
- Hydraulic cold forming press
- Hydroforming press
- Composite press
- Silicone rubber moulding press
- Brake pad press
- Melamine press
- SMC & BMC Press
- Labrotaroy press
- Edge cutting trimming machine
- Edge curling machine
- Trimming beading machine
- Trimming joggling machine
- Cookware production line
- Pipe bending machine
- Profile bending machine
- Bandsaw for metal
- Cylindrical welding machine
- Horizontal pres and cookware
- Kitchenware, hotelware
- Bakeware and cuttlery production machinery
as a complete line as well as an individual machine such as:
- Edge cutting trimming beading machines
- Polishing and grinding machines for pot and pans
- Hydraulic drawing presses
- Circle blanking machines
- Riveting machine
- Hole punching machines
- Press feeding machine
You can check our machinery at work at: EMS Metalworking Machinery – YouTube
Applications:
- Beading and ribbing
- Flanging
- Trimming
- Curling
- Lock-seaming
- Ribbing
- Flange-punching