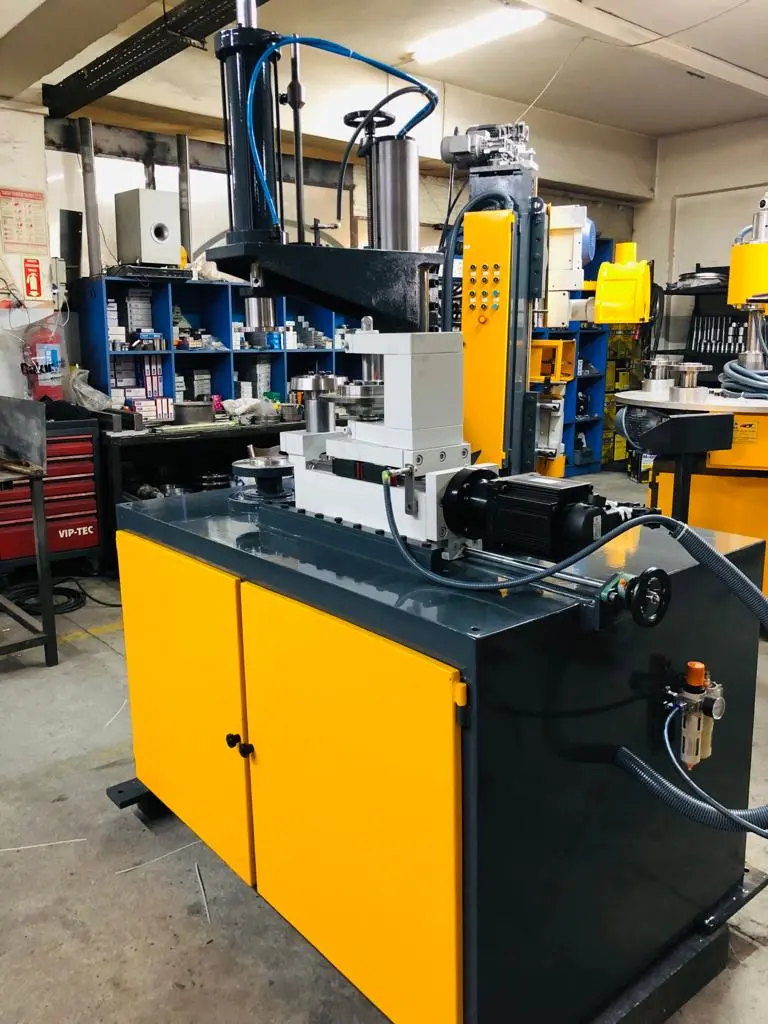
Edge cutting trimming machines play a crucial role in the production of hot water boiler production, ensuring precise dimensions and a smooth, consistent finish for various boiler components. These machines perform essential operations such as cutting, trimming, and beading to create the desired shape, profile, and strength for boiler components.
Types of Edge Cutting Trimming Machines for Hot Water Boiler Production
- Hydraulic Shearing Machines: Hydraulic shearing machines utilize a powerful hydraulic ram to force a sharp blade through the metal workpiece, producing a clean, straight edge. They are suitable for cutting various metal thicknesses and are commonly used for initial edge cutting of boiler components.
- Guillotine Shears: Guillotine shears employ a vertically mounted blade that descends onto the workpiece, cutting through it with a precise, downward motion. They offer high precision and are often used for trimming and sizing boiler components.
- Rotary Shearing Machines: Rotary shearing machines utilize a rotating blade that continuously cuts through the workpiece, producing a continuous edge. They are suitable for high-volume production and are often used for trimming and shaping boiler components.
Applications of Edge Cutting Trimming Machines in Hot Water Boiler Manufacturing
- Cutting Boiler Shell Plates: Edge cutting machines are used to precisely cut the edges of boiler shell plates, ensuring accurate dimensions for the boiler’s main body.
- Trimming Flanges and Openings: Trimming machines are used to refine the edges of flanges, openings, and other components, ensuring smooth, consistent finishes for proper sealing and connection.
- Beading Boiler Components: Beading machines are used to create raised ridges or lips along the edges of boiler components, providing reinforcement and strengthening the edges.
Benefits of Using Edge Cutting Trimming Machines for Hot Water Boiler Production
- Accuracy and Precision: These machines ensure precise cutting, trimming, and beading, producing components with accurate dimensions and consistent finishes.
- Efficiency and Speed: Automated machines significantly reduce production time and labor costs compared to manual methods. The high processing speed allows for rapid production of boiler components, meeting the demands of high-volume manufacturing.
- Consistency and Quality Control: Automated machines maintain consistent cutting, trimming, and beading operations, ensuring uniformity across all boiler components. This consistency contributes to high-quality products that meet industry standards.
- Versatility: These machines can handle various metal types and thicknesses, making them suitable for producing a wide range of boiler components. Their versatility allows for adapting to different boiler designs and specifications.
Safety Considerations for Operating Edge Cutting Trimming Machines
- Proper Training and Certification: Operators should receive proper training and certification in the operation of edge cutting trimming machines to ensure safe and efficient use.
- Personal Protective Equipment (PPE): Operators should wear appropriate PPE, including safety glasses, gloves, and hearing protection to minimize the risk of injuries from flying debris, sharp edges, or noise.
- Machine Guarding: Machinery should be equipped with proper guards to protect workers from moving parts and potential hazards.
- Emergency Stop Procedures: Train workers on emergency stop procedures and ensure they are readily accessible.
- Regular Maintenance: Maintain machinery in good working condition to prevent malfunctions and ensure safe operation.
Conclusion
Edge cutting trimming machines are essential equipment in the production of hot water boilers, contributing to the accuracy, efficiency, and quality of these critical components. By adhering to safety guidelines and utilizing these machines effectively, boiler manufacturers can ensure the production of high-quality boilers that meet industry standards and provide reliable hot water for various applications.
In hot water boiler production where blanks are deep-drawn by hydraulic presses, the cup-shaped parts are needed to edge cut and trimmed, and sometimes they need some special sheet forming operations such as bending, beading or curling.
Edge cutting of sheet metals is a one-way operation where the knife cuts the edges of the cylinder-shaped part
Edge trimming of sheet metals is a one-way but an action with duration, where the knife trims the burrs from the part. This operation can take a few seconds till the knife trims all the burrs from the edges of the part
Edge beading or bending of sheet metals is a one-way action, where the cutting mold bends the edges of the part into the inside. This is usually done for lids or parts that need to be welded later
Edge curling of sheet metals is a one way but an action with duration, where the curling molds curl the edges of the parts inside or outside
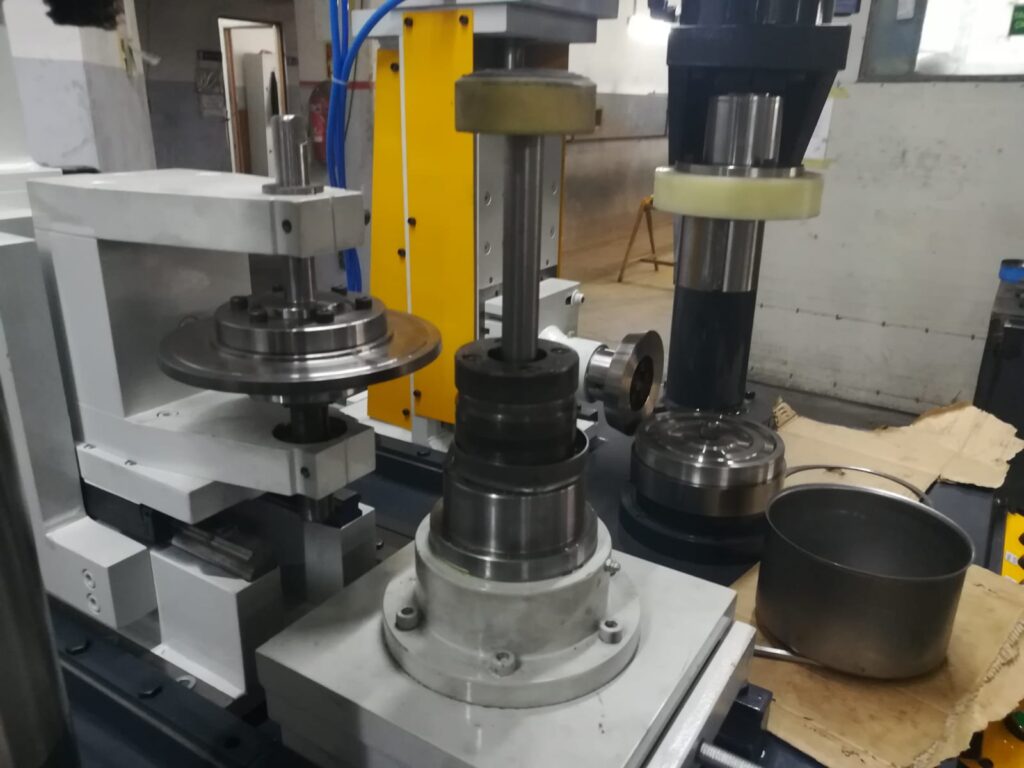
All the machines are tailor-made and designed with the technical drawings sent by the customer
An edge cutting and trimming machine for hot water boiler production is a specialized piece of equipment used in the manufacturing process of hot water boilers to trim and finish the edges of boiler components. This machine helps ensure that the boiler components have smooth, precise, and uniform edges, which are essential for the overall quality and safety of the hot water boilers. Here are some key features and functions of such a machine:
Key Features and Functions:
- Precision Trimming: The machine is equipped with cutting and trimming tools that are designed to precisely trim and finish the edges of various boiler components, such as boiler shells, tubes, and plates.
- Uniform Edge Profile: It ensures that the edges of the boiler components have a uniform profile, which is important for proper sealing and structural integrity.
- Smooth Edges: The machine is capable of creating smooth and burr-free edges, reducing the risk of leaks or weak points in the boiler’s structure.
- Automated Operation: Many edge cutting and trimming machines are automated or semi-automated, which improves efficiency and consistency in the production process.
- Customizable: The machine can be adjusted or customized to accommodate different boiler component sizes and shapes, allowing for versatility in production.
- Safety Features: Safety measures, such as guards and emergency stop mechanisms, are often incorporated to protect operators during the machine’s operation.
- Quality Control: The machine assists in maintaining consistent quality standards by ensuring that the edges meet specific requirements and tolerances.
- Efficiency: By automating the trimming process, these machines can significantly increase production efficiency, reduce labor costs, and improve overall manufacturing speed.
- Material Handling: Some machines may include material handling systems that feed the boiler components into the machine and remove them after trimming.
- Integration: The machine can be integrated into the production line for seamless and efficient manufacturing of hot water boilers.
Considerations for Selecting an Edge Cutting and Trimming Machine:
When selecting an edge cutting and trimming machine for hot water boiler production, consider the following factors:
- Boiler Component Variability: Ensure the machine can accommodate the range of boiler component sizes and shapes used in your production process.
- Production Volume: Choose a machine that can meet your production volume requirements, whether you have high or low production needs.
- Edge Quality: Assess the machine’s capability to deliver the required edge quality, including smoothness and uniformity.
- Automation Level: Determine the level of automation needed based on your production goals and available labor resources.
- Maintenance and Support: Consider the ease of maintenance and the availability of technical support for the machine.
- Cost: Evaluate the cost of the machine, including both the initial purchase price and ongoing operational costs.
- Safety Features: Ensure that the machine includes adequate safety features to protect operators.
- Compatibility: Verify that the machine is compatible with your existing production equipment and processes.
Edge cutting and trimming machines play a crucial role in ensuring the quality, safety, and efficiency of hot water boiler production. Choosing the right machine for your specific needs is essential to optimize your manufacturing process.
Hot Water Boiler Production with Edge Cutting Trimming
Hot water boilers play a crucial role in various applications, providing a source of hot water for heating, domestic use, and industrial processes. Their production involves a series of carefully controlled steps to ensure the safety, efficiency, and durability of these essential components. Here’s a detailed overview of the hot water boiler production process:
Raw Material Selection and Preparation:
- Material Selection: The choice of materials is critical for ensuring the strength, corrosion resistance, and heat transfer capabilities of hot water boilers. High-grade steel plates, stainless steel, or cast iron are commonly used, depending on the specific boiler design, operating pressure, and application requirements.
- Surface Preparation: The selected metal plates or castings undergo thorough surface preparation to remove any impurities, defects, or inconsistencies that could affect the welding process or the overall performance of the boiler. This may involve grinding, shot blasting, or chemical cleaning.
Cutting and Shaping:
- Edge Cutting Trimming: Edge cutting machines are used to precisely cut the edges of metal plates or castings to the desired dimensions for the boiler components. This ensures accurate sizing and prepares the pieces for further processing.
- Forming and Bending: Specialized forming and bending machines are used to shape the metal plates or castings into the required configurations. This may involve creating curved sections, forming flanges, or preparing openings for components such as tubes, valves, and fittings.
Welding and Fabrication:
- Welding: Professional welders utilize various welding techniques, such as arc welding, MIG welding, or TIG welding, to join the individual components of the boiler. The welds must meet stringent quality standards to ensure the integrity and pressure tightness of the boiler.
- Assembly: The various components of the boiler, including the shell, tubes, headers, and combustion chamber, are carefully assembled according to the boiler design and specifications. This involves aligning the components, securing them with welds or bolts, and ensuring proper alignment of tubes and openings.
Testing and Inspection:
- Non-Destructive Testing (NDT): Non-destructive testing methods, such as ultrasonic testing, radiographic testing, or dye penetrant testing, are employed to detect any defects or discontinuities in the welds and the overall structure of the boiler.
- Pressure Testing: The completed boiler is subjected to a rigorous pressure test to verify its ability to withstand the maximum operating pressure without leaks or structural failures.
- Hydraulic Testing: Hydraulic testing is performed to ensure the integrity of tubes, headers, and other water-carrying components by applying hydraulic pressure and checking for leaks.
Finishing and Packaging:
- Surface Finishing: The boiler’s exterior surfaces may undergo additional finishing treatments, such as painting or coating, to protect against corrosion and enhance the aesthetic appearance.
- Insulation: The boiler is insulated with fire-resistant materials to minimize heat loss and improve energy efficiency.
- Packaging and Shipping: The completed and tested boiler is carefully packaged and shipped to the intended destination, ensuring proper protection during transport and handling.
Quality Control and Safety:
Throughout the hot water boiler production process, strict quality control procedures are implemented to ensure that every boiler meets the highest standards of safety, performance, and reliability. This includes regular inspections, testing, and documentation to verify compliance with industry standards and regulatory requirements.
Additionally, safety remains paramount throughout the production process. Workers are provided with appropriate personal protective equipment (PPE) and training to minimize the risk of injuries from hazards such as hot surfaces, moving machinery, and welding fumes.
Precision Trimming
Precision trimming is a manufacturing process used to remove excess material or shape components with a high degree of accuracy and tight tolerances. This process is essential in various industries, including aerospace, automotive, electronics, medical devices, and more, where precise and consistent component dimensions are critical for product quality and performance. Precision trimming can involve cutting, machining, or finishing operations, and it aims to achieve the following objectives:
- Tight Tolerances: Precision trimming ensures that components meet very specific dimensional tolerances, often in the micron or sub-micron range. This level of precision is crucial for components that must fit together precisely or function within narrow specifications.
- Smooth and Burr-Free Edges: The process produces clean and smooth edges, free from burrs, rough surfaces, or defects. This is important for safety, as well as for components that require a high level of surface finish, such as optical or medical devices.
- Consistency: Precision trimming ensures that each component produced is nearly identical, reducing variability in the manufacturing process. Consistency is essential for maintaining product quality and performance.
- Complex Shapes: It enables the fabrication of complex and intricate shapes with tight dimensional control. This is particularly useful in industries like aerospace, where components often have complex geometries.
- Material Removal: Precision trimming can be used to remove excess material, reshape components, or achieve specific geometrical features, all while maintaining precise tolerances.
- Efficiency: The process is typically highly efficient, reducing material waste and minimizing the need for additional finishing or post-processing steps.
Methods and Techniques for Precision Trimming:
- CNC Machining: Computer Numerical Control (CNC) machining involves using computer-controlled machines, such as mills, lathes, or routers, to precisely cut, shape, and finish components. CNC machines offer high precision and repeatability.
- Wire EDM (Electrical Discharge Machining): Wire EDM uses a thin, electrically charged wire to cut through materials with high precision. It’s often used for intricate and complex shapes, especially in tool and die manufacturing.
- Laser Cutting and Laser Micromachining: Lasers are used to precisely cut, engrave, or ablate material. Laser cutting is commonly used for thin materials, while laser micromachining achieves very fine features on small components.
- Waterjet Cutting: Waterjet cutting uses a high-pressure stream of water mixed with abrasive particles to cut through various materials with precision. It’s especially suitable for materials that are sensitive to heat.
- Chemical Etching: Chemical etching involves selectively removing material from a component’s surface using chemical processes. It’s often used for fine and precise pattern or feature generation.
- Abrasive Jet Machining: Abrasive jet machining uses a high-velocity stream of abrasive particles to cut and shape materials. It’s used for precision machining of hard materials.
- Grinding and Polishing: Grinding and polishing operations are used to achieve high levels of precision and surface finish. They are often employed in the manufacturing of optical and medical components.
Precision trimming is a critical part of modern manufacturing, ensuring that components and products meet stringent quality and performance standards. It allows industries to produce highly accurate and consistent parts that are essential for various applications.
Industries working with our machinery
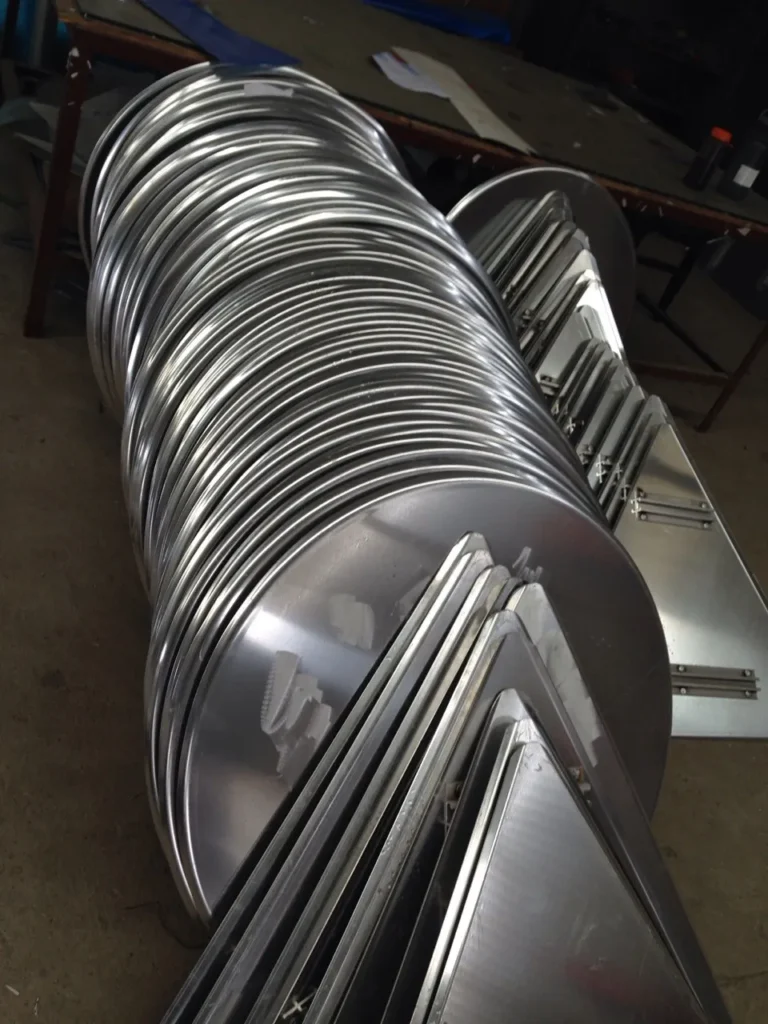
Trimming and beading machines are versatile tools that are used in a wide range of industries. Here are some of the most common industries that use trimming and beading machines:
Automotive Industry
The automotive industry is one of the largest users of trimming and beading machines. These machines are used to trim and bead car body panels, fenders, doors, and other sheet metal components. Trimming ensures precise dimensions and eliminates rough edges, while beading strengthens the sheet metal and provides reference points for alignment during assembly and welding.
Aerospace Industry
The aerospace industry also relies heavily on trimming and beading machines. These machines are used to fabricate lightweight and high-strength components for aircraft and spacecraft. The precise and consistent trimming and beading operations ensure the structural integrity of these critical components.
Appliance Manufacturing
Appliance manufacturing is another major user of trimming and beading machines. These machines are used to trim and bead the sheet metal components of refrigerators, washing machines, and other household appliances. Trimming and beading help to strengthen the appliances, improve their appearance, and facilitate assembly.
HVAC Industry
The HVAC industry uses trimming and beading machines to fabricate ductwork, fans, and other sheet metal components. Trimming ensures that the components fit together properly, while beading strengthens the components and provides rigidity.
Construction Industry
The construction industry uses trimming and beading machines to fabricate roofing panels, siding, and other sheet metal components for buildings. Trimming and beading help to ensure that the components are weatherproof and durable.
Metal Fabrication Industries
Trimming and beading machines are widely used in various metal fabrication industries, including electrical equipment manufacturing, medical device manufacturing, and industrial machinery manufacturing. These machines are used to trim and bead a wide range of sheet metal components for various applications.
In addition to these specific industries, trimming and beading machines are also used in a variety of other applications, including:
- Sign Manufacturing
- Furniture Manufacturing
- Toy Manufacturing
- Food and Beverage Processing Equipment Manufacturing
- Medical Device Manufacturing
The versatility and effectiveness of trimming and beading machines make them essential tools for a wide range of industries. These machines play a crucial role in producing high-quality, durable, and precisely dimensioned sheet metal components for a variety of applications.
- Cookware Kitchenware
- Defense
- Water Tank Manufacturing
- Solar Power Generator Manufacturing
- Electrical Motor Fan Cover Manufacturing
- Fire Extinguisher Manufacturing
- Exhaust Pipe Manufacturing
- LPG & LNG Tank Manufacturing
Trimming beading machines are specialized pieces of equipment used in various manufacturing industries to cut, shape, and form beads along the edges of metal sheets and other materials. These machines serve the critical function of enhancing the structural integrity and aesthetic appeal of products by creating precise and consistent beading.
Trimming beading machines are essential in processes where the appearance and durability of the edges are paramount. They are commonly employed in industries such as automotive, aerospace, HVAC, and consumer goods manufacturing, where precision and efficiency are crucial.
Importance in Industrial Applications
The primary importance of trimming beading machines lies in their ability to streamline manufacturing processes by automating edge-forming tasks that would otherwise be labor-intensive and prone to human error. By improving consistency and reducing waste, these machines contribute significantly to the overall productivity and cost-effectiveness of production lines.
Furthermore, trimming beading machines enhance the quality of finished products, ensuring they meet stringent industry standards and customer expectations. Their ability to produce uniform edges and beads also plays a vital role in the assembly and functionality of components, particularly in high-stakes industries like aerospace and automotive manufacturing.
Overview of the Content
This comprehensive guide aims to provide an in-depth exploration of trimming beading machines, covering their components, working principles, types, applications, technical specifications, maintenance, and emerging trends. By understanding these aspects, industry professionals can make informed decisions about implementing and optimizing trimming beading machines within their operations.
Components of Trimming Beading Machines
Base and Frame
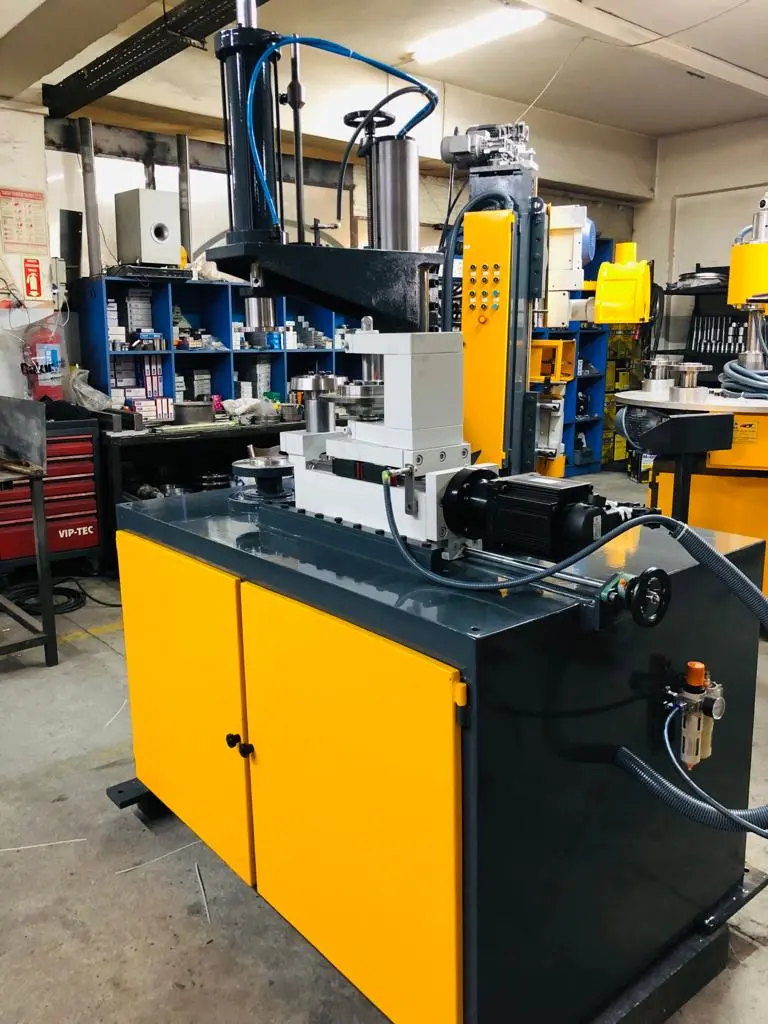
The base and frame of a trimming beading machine form its structural backbone, providing stability and support for all other components. Typically constructed from robust materials such as steel or cast iron, the frame ensures the machine can withstand the stresses of operation and maintain precision over time.
Materials Used
- Steel: Known for its durability and resistance to deformation, steel is commonly used in high-performance trimming beading machines. It offers excellent rigidity and longevity.
- Cast Iron: Preferred for its vibration-damping properties, cast iron frames help minimize noise and improve accuracy during operation.
Structural Design
- The structural design of trimming beading machines varies based on the specific model and intended application. Key considerations include the machine’s footprint, ease of access for maintenance, and adaptability to different manufacturing environments.
Cutting and Beading Tools
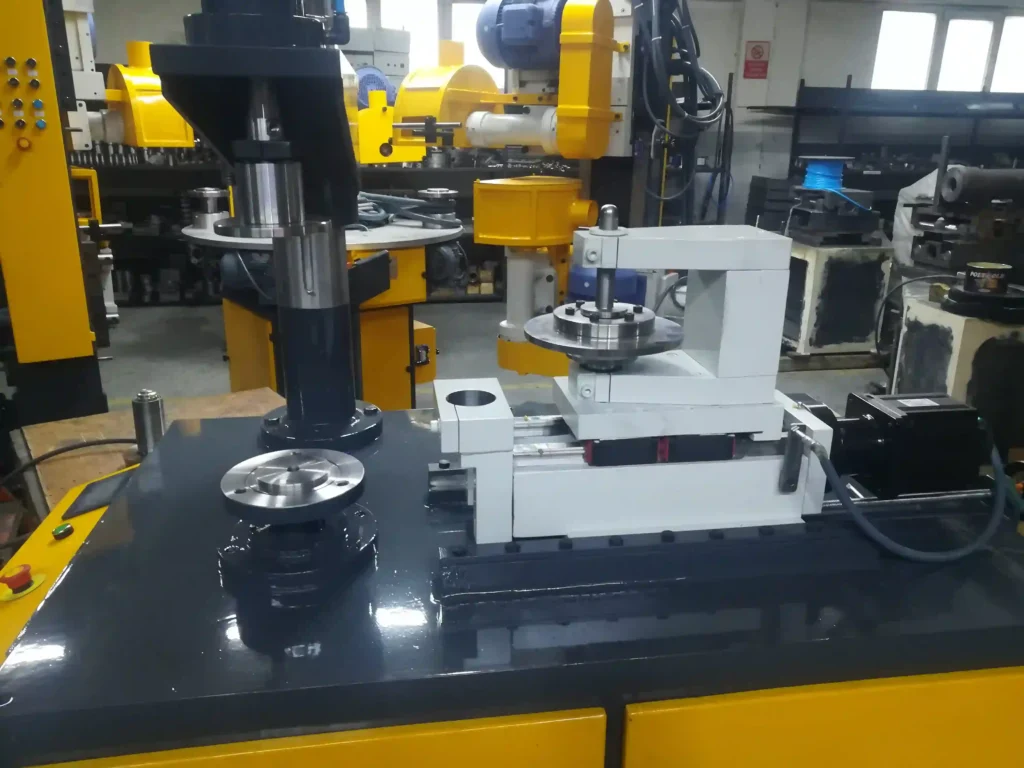
The cutting and beading tools are critical to the machine’s functionality, responsible for shaping and forming the edges of materials. These tools come in various shapes and sizes, tailored to the specific beading patterns and material thicknesses required.
Types and Materials
- High-Speed Steel (HSS): Known for its hardness and heat resistance, HSS is commonly used for cutting tools that need to maintain sharpness under demanding conditions.
- Carbide: Offering superior wear resistance and durability, carbide tools are ideal for high-volume production runs and materials that are difficult to machine.
Maintenance and Replacement
- Regular maintenance of cutting and beading tools is essential to ensure consistent performance. This includes sharpening or replacing worn tools and adjusting alignment to prevent defects in the finished products.
Drive Mechanism
The drive mechanism powers the machine’s operations, converting electrical energy into mechanical motion. It is a crucial component that directly influences the machine’s efficiency and performance.
Motor Types
- AC Motors: Widely used in trimming beading machines for their reliability and simplicity. AC motors offer consistent performance and are suitable for applications where speed control is not critical.
- Servo Motors: Preferred for applications requiring precise control and variable speeds. Servo motors enable dynamic adjustments to the machine’s operations, enhancing versatility and efficiency.
Energy Efficiency Considerations
- Modern trimming beading machines are designed with energy efficiency in mind, incorporating features like variable frequency drives (VFDs) to optimize power consumption and reduce operational costs.
Control Systems
Control systems govern the operation of trimming beading machines, allowing operators to configure settings, monitor performance, and ensure safety. These systems range from basic manual controls to sophisticated automated interfaces.
Manual vs. Automated Systems
- Manual Systems: Suitable for smaller operations or applications requiring frequent adjustments. Manual controls offer simplicity and direct operator oversight.
- Automated Systems: Essential for large-scale production environments, automated systems provide consistent performance, reduce human error, and enable integration with other machinery.
Integration with Industry 4.0 Technologies
- Trimming beading machines are increasingly adopting Industry 4.0 technologies, such as IoT sensors and data analytics, to enhance operational efficiency and enable predictive maintenance.
Working Principles
Detailed Description of the Trimming Process
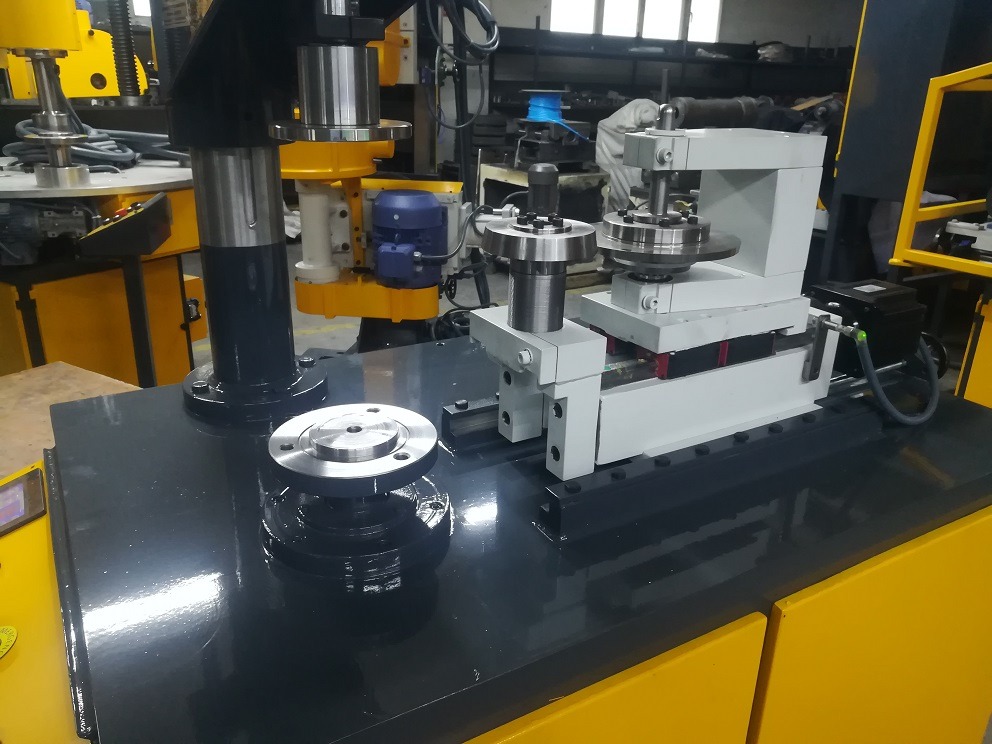
The trimming process involves cutting away excess material from the edges of a workpiece to achieve a desired shape or size. Trimming beading machines utilize specialized tools to perform this task with high precision and consistency.
- Material Feeding: The workpiece is fed into the machine, either manually or automatically, and positioned for trimming.
- Tool Engagement: Cutting tools engage the workpiece, removing excess material while following the predefined path and pattern.
- Material Removal: The machine’s cutting tools execute the trimming operation, guided by precise control systems to ensure uniformity.
- Quality Inspection: The trimmed edges are inspected for accuracy and quality, with adjustments made as necessary.
Beading Techniques and Variations
Beading is the process of forming beads along the edges of a workpiece, enhancing both its structural integrity and aesthetic appeal. Different techniques and variations are employed based on the material and intended application.
- Single Bead Formation: The simplest form of beading, involving a single continuous bead along the edge.
- Double Bead Formation: Utilized when additional strength or a decorative effect is desired, double beads consist of two parallel beads along the edge.
- Custom Bead Patterns: Some machines allow for custom bead patterns, tailored to specific design requirements or functional needs.
Workflow and Operational Steps
The workflow of a trimming beading machine is designed to maximize efficiency and ensure consistent output. Key operational steps include:
- Setup and Calibration: Operators configure the machine settings, such as tool alignment and material thickness, to match the requirements of the production run.
- Material Loading: Workpieces are loaded onto the machine, either manually or through automated systems, and positioned for processing.
- Trimming and Beading: The machine executes the trimming and beading operations, following the specified parameters and patterns.
- Quality Control: Finished pieces undergo quality control checks to verify dimensional accuracy and bead integrity.
- Adjustment and Maintenance: Regular adjustments and maintenance are performed to ensure optimal performance and address any issues that arise during operation.
Common Challenges and Solutions
Trimming beading machines can encounter various challenges during operation, which can impact performance and product quality. Common issues and their solutions include:
- Tool Wear and Dullness: Regular tool maintenance, including sharpening and replacement, is essential to maintain cutting precision and prevent defects.
- Material Deformation: Proper machine calibration and tool alignment help prevent material deformation during trimming and beading processes.
- Machine Downtime: Implementing predictive maintenance and monitoring systems can reduce downtime and improve overall equipment efficiency.
- Quality Variability: Consistent quality control checks and process adjustments help ensure uniformity and adherence to specifications.
Types of Trimming Beading Machines
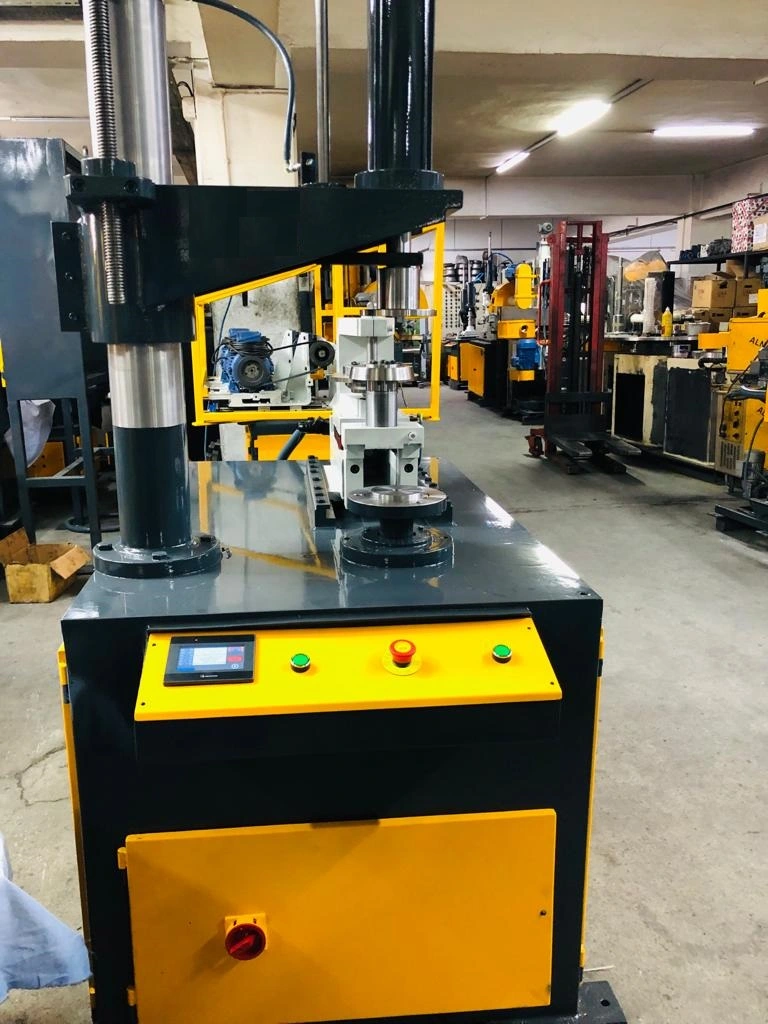
Trimming beading machines are available in various types, each suited to specific applications and production needs. Understanding the differences between these machines is crucial for selecting the right equipment for a given operation.
Manual Trimming Beading Machines
Features and Use Cases
- Manual trimming beading machines are operated entirely by human intervention, making them suitable for small-scale production or applications requiring frequent adjustments. These machines offer simplicity and ease of use, often utilized in workshops or small manufacturing facilities.
Advantages and Disadvantages
- Advantages:
- Cost-effective for low-volume production
- Flexibility to handle various materials and bead patterns
- Simple operation and maintenance
- Disadvantages:
- Limited throughput and productivity
- Higher labor costs due to manual operation
- Inconsistent quality due to human error
Semi-Automatic Trimming Beading Machines
Features and Use Cases
- Semi-automatic trimming beading machines combine manual input with automated processes, offering a balance between flexibility and efficiency. These machines are ideal for medium-scale production environments where speed and precision are important.
Advantages and Disadvantages
- Advantages:
- Improved productivity compared to manual machines
- Enhanced consistency and accuracy
- Reduced operator fatigue and error
- Disadvantages:
- Higher initial investment compared to manual machines
- Requires skilled operators for setup and adjustment
- Limited scalability for large-scale production
Fully Automatic Trimming Beading Machines
Features and Use Cases
- Fully automatic trimming beading machines offer the highest level of automation and efficiency, designed for large-scale production environments. These machines are equipped with advanced control systems and automation features, enabling continuous and consistent operation.
Advantages and Disadvantages
- Advantages:
- Maximum productivity and throughput
- Consistent quality and precision
- Integration with other automated systems and Industry 4.0 technologies
- Disadvantages:
- High initial cost and complexity
- Requires skilled technicians for maintenance and troubleshooting
- Limited flexibility for custom or small-batch production
Applications in Various Industries
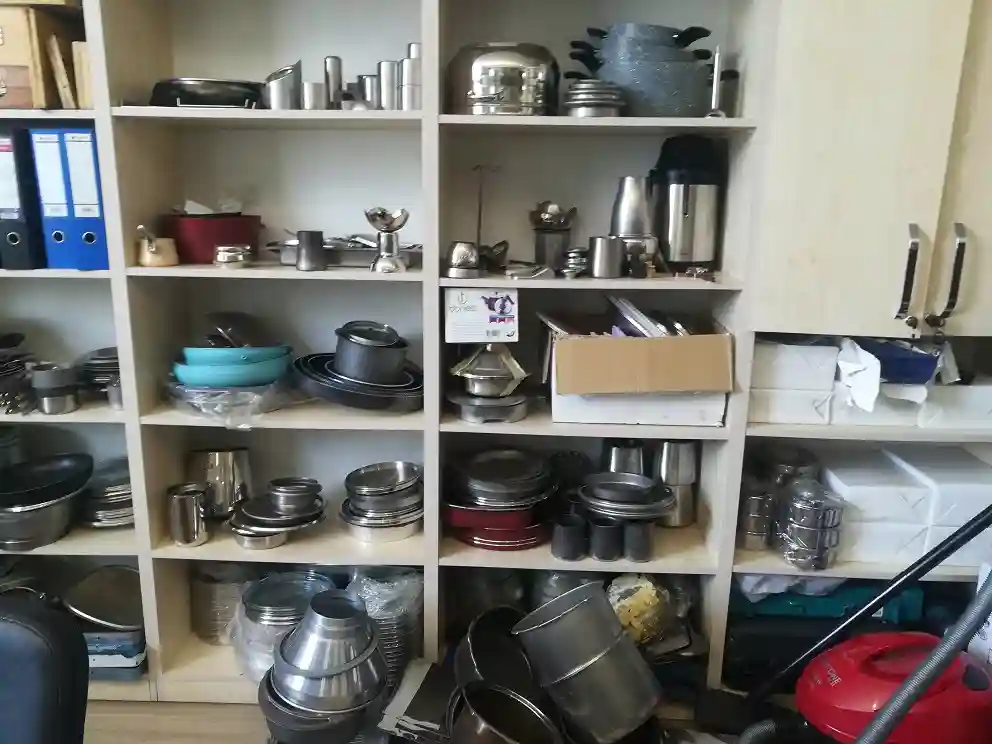
Trimming beading machines play a vital role in a wide range of industries, each benefiting from the precision and efficiency these machines offer. Here, we explore some of the key industries and their specific applications.
Automotive Industry
Specific Use Cases
- In the automotive industry, trimming beading machines are used for forming edges on components such as fenders, doors, hoods, and other body panels. These machines ensure that parts meet the strict dimensional tolerances required for assembly and safety.
Benefits in Automotive Manufacturing
- Improved part quality and consistency, reducing rework and waste
- Enhanced structural integrity of components, contributing to vehicle safety
- Increased production speed and efficiency, supporting high-volume manufacturing
Aerospace Industry
Specific Use Cases
- Aerospace manufacturing demands precision and reliability, making trimming beading machines essential for producing parts such as fuselage panels, wing components, and engine casings. These machines contribute to the stringent quality standards of the aerospace industry.
Benefits in Aerospace Manufacturing
- High precision and repeatability, ensuring compliance with aerospace standards
- Reduction in material waste and production costs
- Support for complex geometries and advanced materials
HVAC Industry
Specific Use Cases
- In the HVAC industry, trimming beading machines are used to form edges and beads on ductwork, vents, and other components. These machines help produce parts that are essential for efficient heating, ventilation, and air conditioning systems.
Benefits in HVAC Manufacturing
- Consistent part quality and fit, reducing installation time and costs
- Enhanced durability and performance of HVAC components
- Support for custom designs and specifications
Consumer Goods Industry
Specific Use Cases
- The consumer goods industry utilizes trimming beading machines for a variety of products, including appliances, electronics, and packaging. These machines help create aesthetically pleasing and functional components.
Benefits in Consumer Goods Manufacturing
- Improved product appearance and appeal
- Increased manufacturing efficiency and speed
- Support for diverse materials and product designs
Technical Specifications and Standards
Understanding the technical specifications and standards of trimming beading machines is crucial for selecting the right equipment and ensuring compliance with industry requirements.
International Standards and Compliance
Trimming beading machines must adhere to international standards to ensure safety, quality, and interoperability. Key standards include:
- ISO 9001: Quality management systems standard that ensures consistent product quality and customer satisfaction.
- ISO 12100: Safety of machinery – General principles for design, providing guidelines for reducing risks associated with machine operation.
- CE Marking: Conformity with European health, safety, and environmental protection standards.
Key Technical Specifications
Trimming beading machines have various technical specifications that influence their performance and suitability for specific applications. Key specifications include:
- Maximum Material Thickness: The thickest material the machine can handle, typically measured in millimeters or inches.
- Beading Speed: The rate at which the machine can form beads, often measured in meters per minute.
- Cutting Force: The amount of force exerted by the machine’s cutting tools, affecting its ability to handle different materials.
- Power Requirements: The electrical power needed for operation, influencing energy consumption and infrastructure needs.
Customization Options
Manufacturers often offer customization options to tailor trimming beading machines to specific requirements. Common customization options include:
- Tooling Variations: Custom tools and dies to accommodate unique bead patterns and material specifications.
- Automation Features: Integration of advanced control systems and automation technologies for enhanced performance.
- Material Handling Systems: Customized feeding and handling systems to improve workflow and reduce manual intervention.
Maintenance and Troubleshooting
Proper maintenance and troubleshooting are essential to ensuring the longevity and performance of trimming beading machines. Here, we outline key maintenance practices and common issues that operators may encounter.
Routine Maintenance Procedures
Regular maintenance helps prevent unexpected downtime and ensures consistent machine performance. Key maintenance procedures include:
- Tool Inspection and Replacement: Regularly inspect cutting and beading tools for wear and damage. Sharpen or replace tools as needed to maintain cutting precision.
- Lubrication: Ensure all moving parts are properly lubricated to reduce friction and wear.
- Alignment Checks: Verify tool alignment and calibration to prevent defects and ensure uniformity.
- Electrical System Inspection: Check electrical connections and components for signs of wear or damage, addressing issues promptly to prevent malfunctions.
Common Issues and Solutions
Trimming beading machines may encounter various issues during operation. Understanding these problems and their solutions is crucial for maintaining productivity and quality.
- Tool Wear and Dullness: Dull or worn tools can lead to poor cutting performance and defects. Regularly sharpen or replace tools to maintain quality.
- Material Jams: Misalignment or improper feeding can cause material jams, leading to downtime and damage. Ensure proper setup and alignment to prevent jams.
- Machine Vibration: Excessive vibration can impact precision and tool life. Check for loose components and ensure the machine is properly anchored to reduce vibration.
- Inconsistent Quality: Variability in bead quality and dimensions can arise from improper calibration or tool wear. Regularly inspect and adjust settings to maintain consistency.
Safety Considerations
Safety is paramount when operating trimming beading machines. Key safety considerations include:
- Personal Protective Equipment (PPE): Operators should wear appropriate PPE, such as gloves, safety glasses, and hearing protection, to minimize injury risk.
- Machine Guarding: Ensure all machine guards and safety features are in place and functional to prevent accidental contact with moving parts.
- Emergency Stops: Verify that emergency stop mechanisms are operational and accessible in case of emergencies.
- Training and Education: Provide thorough training to operators and maintenance personnel on safe machine operation and emergency procedures.
Latest Innovations and Trends
The field of trimming beading machines is continually evolving, with new technologies and trends shaping the future of manufacturing. Here, we explore some of the latest innovations and emerging trends in the industry.
Technological Advances
Advancements in technology are driving significant improvements in trimming beading machines, enhancing their capabilities and performance.
- Smart Sensors and IoT Integration: Trimming beading machines are increasingly incorporating smart sensors and IoT connectivity to monitor performance, predict maintenance needs, and optimize operations.
- Advanced Control Systems: New control systems offer greater precision and flexibility, enabling operators to achieve complex bead patterns and adapt to changing production requirements.
- Automation and Robotics: The integration of automation and robotics is transforming trimming beading machines, reducing manual labor, and increasing throughput.
Future Trends in Trimming Beading Machines
Several trends are shaping the future of trimming beading machines, influencing how they are designed and utilized.
- Sustainability and Energy Efficiency: Manufacturers are focusing on sustainability, developing machines with lower energy consumption and reduced environmental impact.
- Customization and Flexibility: As demand for custom products grows, trimming beading machines are becoming more adaptable, with features that support rapid reconfiguration and customization.
- Digitalization and Industry 4.0: The digital transformation of manufacturing is driving the adoption of Industry 4.0 technologies, enabling data-driven decision-making and enhanced machine performance.
Case Studies and Examples
Real-world examples and case studies demonstrate the impact of trimming beading machines in various industries, highlighting their benefits and applications.
- Automotive Manufacturing: A leading automotive manufacturer implemented advanced trimming beading machines to improve production efficiency and reduce defects, achieving significant cost savings and quality improvements.
- Aerospace Industry: An aerospace supplier adopted IoT-enabled trimming beading machines to enhance traceability and optimize maintenance, resulting in reduced downtime and improved compliance with industry standards.
- HVAC Production: A major HVAC manufacturer integrated automated trimming beading machines to increase production capacity and reduce manual labor, leading to faster lead times and higher product quality.
Choosing the Right Trimming Beading Machine
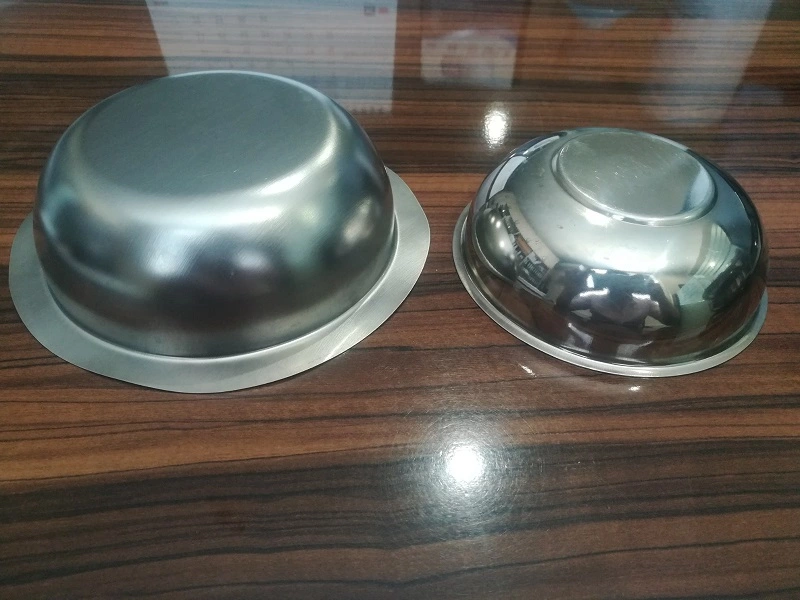
Selecting the right trimming beading machine is crucial for achieving optimal performance and meeting specific production needs. Here, we outline key factors to consider and offer guidance on the selection process.
Factors to Consider
When choosing a trimming beading machine, several factors should be considered to ensure the equipment meets operational requirements.
- Production Volume: Assess the production volume and throughput requirements to determine the appropriate machine type and capacity.
- Material Specifications: Consider the types of materials and thicknesses the machine will handle, ensuring compatibility with the equipment’s capabilities.
- Beading Patterns: Evaluate the complexity and variety of bead patterns needed, selecting machines that offer the necessary tooling and flexibility.
- Automation Needs: Determine the level of automation required, balancing productivity gains with cost considerations and operator expertise.
Cost vs. Benefit Analysis
Conducting a cost vs. benefit analysis helps evaluate the financial implications of investing in a trimming beading machine.
- Initial Investment: Assess the upfront cost of the machine, including installation and setup expenses.
- Operational Costs: Consider ongoing operational costs, such as energy consumption, maintenance, and labor.
- Return on Investment (ROI): Calculate the expected ROI by evaluating the machine’s impact on productivity, quality, and cost savings.
Vendor Selection and Partnerships
Choosing the right vendor and establishing strong partnerships are essential for acquiring quality equipment and support.
- Reputation and Experience: Evaluate potential vendors based on their reputation, experience, and track record in the industry.
- Technical Support and Service: Ensure the vendor offers comprehensive technical support, training, and maintenance services to maximize machine performance and uptime.
- Customization and Flexibility: Consider vendors that offer customization options and flexible solutions tailored to specific production needs.
Conclusion
Recap of Key Points
Trimming beading machines are essential tools in modern manufacturing, offering precision, efficiency, and versatility across a range of industries. Understanding their components, working principles, and applications is crucial for making informed decisions and optimizing production processes.
Final Thoughts on Trimming Beading Machines
As technology continues to advance, trimming beading machines are poised to play an increasingly important role in the manufacturing landscape. By embracing innovation and adopting best practices, manufacturers can leverage these machines to enhance quality, productivity, and competitiveness in their respective industries.
Components of Trimming Beading Machines
To provide a detailed exploration of the components of a trimming beading machine, we’ll delve deeper into each part, discussing their functions, materials, and importance. Here’s an expanded version of the Components of Trimming Beading Machines section:
Trimming beading machines consist of several integral components, each playing a crucial role in ensuring precise operation and high-quality output. Understanding these components can aid in the proper selection, operation, and maintenance of the machines.
Base and Frame
Functionality and Importance
The base and frame of a trimming beading machine serve as the foundation, providing structural support and stability. A well-designed frame is essential to withstand operational stresses and vibrations, ensuring accurate and consistent performance.
Materials Used
- Steel: Often used for its high tensile strength and durability. Steel frames provide rigidity, helping to maintain precision even under heavy loads.
- Cast Iron: Valued for its excellent vibration-damping properties. Cast iron is commonly used in applications where reducing machine noise and vibration is critical to maintaining accuracy.
- Aluminum Alloys: Used in some lightweight machines, aluminum alloys offer corrosion resistance and ease of handling, though they may lack the rigidity of steel or cast iron.
Structural Design
- Box-Type Frames: Provide superior rigidity and support. Box-type frames are designed to minimize deformation and ensure precise alignment of components.
- Open-Type Frames: Offer ease of access for maintenance and adjustments. Open frames are suitable for applications where quick changes and flexibility are required.
- Welded vs. Bolted Structures: Welded structures provide a solid and seamless frame, while bolted structures offer flexibility in assembly and disassembly for maintenance.
Cutting and Beading Tools
Role in Operation
Cutting and beading tools are at the heart of the trimming beading machine’s functionality. They are responsible for removing excess material and forming beads along the edges of workpieces.
Types of Tools
- Rotary Cutters: Used for continuous cutting operations, rotary cutters offer high speed and precision, ideal for long production runs.
- Punch and Die Sets: Employed for stamping and forming operations, punch and die sets provide versatility in creating complex bead patterns and shapes.
- Roller Dies: Utilized in forming continuous beads along the length of a workpiece. Roller dies offer consistent pressure and control, ensuring uniform bead formation.
Materials for Cutting Tools
- High-Speed Steel (HSS): Known for its hardness and ability to maintain a sharp edge at high temperatures. HSS is suitable for a wide range of cutting applications.
- Carbide: Offers superior wear resistance and durability, making it ideal for high-volume production and difficult-to-machine materials.
- Ceramic and Diamond Coatings: Used for specialized applications requiring extreme hardness and wear resistance. These coatings can extend the life of cutting tools and improve performance.
Maintenance and Replacement
Regular maintenance of cutting and beading tools is essential to ensure optimal performance. This includes:
- Tool Inspection: Conduct routine inspections to identify signs of wear or damage. Replace tools that have become dull or chipped.
- Sharpening: Maintain sharp edges on cutting tools to ensure precise cuts and prevent material deformation.
- Alignment and Calibration: Regularly check tool alignment and calibration to prevent defects and ensure uniformity in bead formation.
Drive Mechanism
Functionality and Importance
The drive mechanism powers the operation of trimming beading machines, converting electrical energy into mechanical motion. It directly influences the machine’s efficiency and performance.
Motor Types
- AC Motors: Commonly used for their reliability and low maintenance requirements. AC motors provide consistent performance and are suitable for applications where speed control is not critical.
- DC Motors: Offer precise speed control and are used in applications requiring variable speeds. DC motors can be paired with controllers to fine-tune performance.
- Servo Motors: Provide high precision and dynamic control, enabling rapid adjustments to speed and position. Servo motors are ideal for applications requiring complex bead patterns and high-speed operations.
- Stepper Motors: Offer precise positioning and repeatability. Stepper motors are used in applications where incremental movements and accuracy are essential.
Energy Efficiency Considerations
- Variable Frequency Drives (VFDs): Used to optimize energy consumption by adjusting the motor’s speed and torque to match the operational needs. VFDs can significantly reduce energy costs and extend the life of the drive system.
- Regenerative Drives: Capture and reuse energy generated during deceleration, further improving energy efficiency and reducing operational costs.
Control Systems
Role in Operation
Control systems govern the operation of trimming beading machines, allowing operators to configure settings, monitor performance, and ensure safety. These systems range from basic manual controls to sophisticated automated interfaces.
Types of Control Systems
- Manual Controls: Suitable for smaller operations or applications requiring frequent adjustments. Manual controls offer simplicity and direct operator oversight.
- Programmable Logic Controllers (PLCs): Provide automation and flexibility, enabling operators to program complex operations and adjust settings on the fly. PLCs are widely used in industrial applications for their reliability and ease of use.
- Computer Numerical Control (CNC): Offers high precision and control, allowing for complex and repeatable operations. CNC systems are ideal for high-volume production and applications requiring intricate bead patterns.
- Human-Machine Interfaces (HMIs): Facilitate interaction between operators and machines, providing real-time data and control over machine settings. HMIs enhance usability and improve operational efficiency.
Integration with Industry 4.0 Technologies
Trimming beading machines are increasingly adopting Industry 4.0 technologies to enhance operational efficiency and enable predictive maintenance. Key advancements include:
- IoT Connectivity: Sensors and IoT devices provide real-time monitoring and data collection, enabling operators to track performance, detect anomalies, and predict maintenance needs.
- Data Analytics and Machine Learning: Advanced analytics and machine learning algorithms optimize machine performance by analyzing operational data and identifying trends or inefficiencies.
- Remote Monitoring and Control: Operators can access and control machines remotely, improving flexibility and enabling rapid response to issues.
Conclusion
The components of trimming beading machines play vital roles in ensuring precision, efficiency, and durability. By understanding these components, manufacturers can optimize their machines for specific applications, improve operational efficiency, and reduce downtime. Proper selection, maintenance, and integration of these components are essential for maximizing the performance and lifespan of trimming beading machines.
Tool Maintenance Tips for Trimming Beading Machines
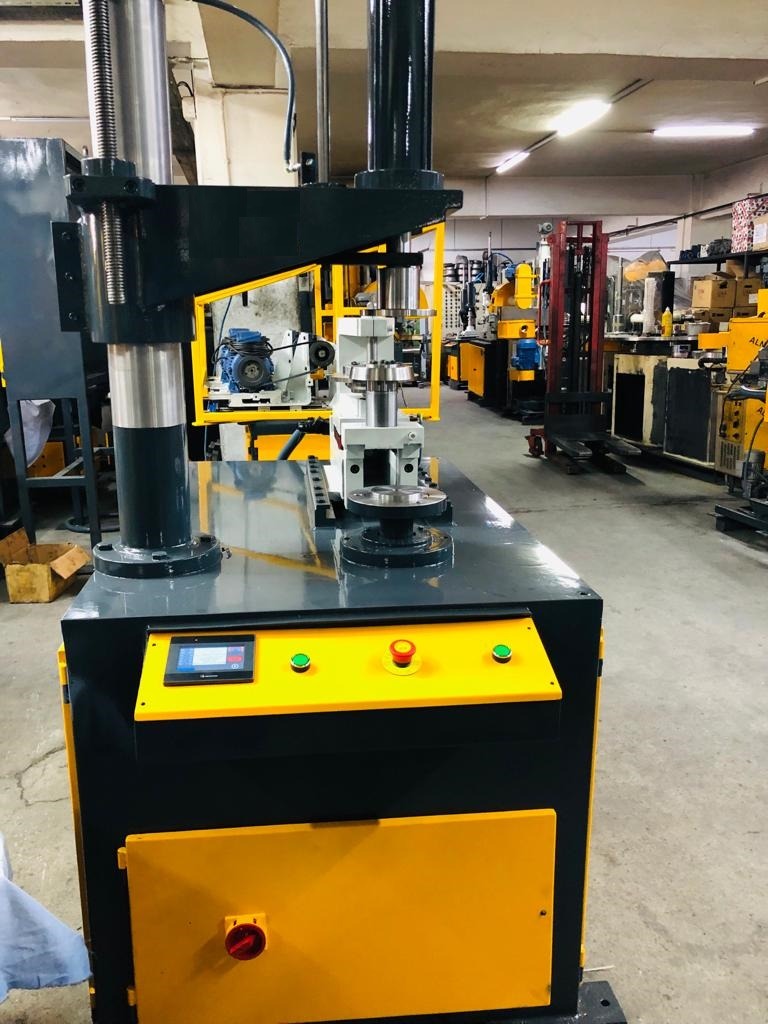
Maintaining the tools of a trimming beading machine is essential for ensuring long-term efficiency, precision, and reliability. Regular maintenance not only prolongs the lifespan of the tools but also ensures consistent quality of the finished products. Here are some detailed tool maintenance tips:
1. Regular Inspection and Assessment
Visual Inspection
- Daily Checks: Conduct visual inspections of cutting and beading tools at the start and end of each shift to identify any visible signs of wear, damage, or misalignment.
- Surface Examination: Look for chips, cracks, or signs of wear on the cutting edges and surfaces, as these can affect the tool’s performance and the quality of the beading.
Performance Monitoring
- Quality Checks: Routinely check the quality of the finished products for any signs of tool-related issues, such as burrs, uneven edges, or inconsistent beading.
- Operational Sounds: Listen for unusual noises during operation, which may indicate tool misalignment or wear.
2. Proper Cleaning and Lubrication
Cleaning Procedures
- Remove Debris: Regularly clean tools to remove metal shavings, dust, and other debris that can accumulate and affect performance.
- Use Appropriate Solvents: Employ non-corrosive cleaning solvents to remove stubborn residues without damaging the tool’s surface.
Lubrication
- Lubricant Selection: Use the correct type of lubricant for the specific tool material, such as oil-based lubricants for steel tools or dry lubricants for carbide tools.
- Regular Application: Apply lubricants at regular intervals to reduce friction, prevent overheating, and protect against corrosion.
3. Sharpening and Reconditioning
Sharpening Techniques
- Proper Tools: Use appropriate sharpening tools, such as diamond stones or grinding wheels, to maintain the cutting edge.
- Sharpening Angles: Follow the manufacturer’s recommendations for sharpening angles to ensure optimal cutting performance.
- Frequency: Establish a regular sharpening schedule based on tool usage and material hardness to maintain sharp edges.
Reconditioning Services
- Professional Reconditioning: Consider professional reconditioning services for heavily worn or damaged tools to restore them to their original specifications.
- Tool Replacement: Replace tools that have reached the end of their usable life to maintain performance and quality.
4. Alignment and Calibration
Tool Alignment
- Proper Setup: Ensure that tools are correctly aligned before each operation to prevent uneven wear and ensure accurate cuts and beads.
- Alignment Tools: Use precision alignment tools and gauges to verify proper tool positioning and alignment.
Calibration
- Regular Calibration: Regularly calibrate the machine and its components to ensure that tools operate within specified tolerances.
- Documentation: Keep detailed records of calibration activities and adjustments for quality control and maintenance purposes.
5. Storage and Handling
Tool Storage
- Protective Cases: Store tools in protective cases or racks to prevent damage when not in use.
- Controlled Environment: Maintain a clean, dry, and temperature-controlled environment to prevent corrosion and material degradation.
Handling Practices
- Proper Handling: Use appropriate handling techniques to prevent dropping or mishandling tools, which can lead to damage.
- Training: Train operators and maintenance personnel on proper handling and storage procedures to minimize accidental damage.
6. Documentation and Training
Maintenance Records
- Detailed Logs: Keep detailed records of all maintenance activities, including inspections, cleaning, sharpening, and replacements. This information can help track tool performance and identify patterns or issues.
- Tool Usage Records: Document tool usage, including hours of operation and materials processed, to anticipate maintenance needs and schedule downtime effectively.
Training and Education
- Operator Training: Provide comprehensive training for operators and maintenance personnel on proper tool care and maintenance procedures.
- Continuous Education: Stay updated on the latest tool maintenance techniques and technologies to improve maintenance practices and enhance tool longevity.
Conclusion
Effective tool maintenance is crucial for maximizing the performance and lifespan of trimming beading machines. By implementing these maintenance tips, manufacturers can ensure consistent product quality, reduce downtime, and extend the life of their tools. Regular inspections, proper cleaning and lubrication, alignment, and training are essential components of a comprehensive maintenance strategy.
Application Areas of Trimming Beading Machines
Trimming beading machines play a crucial role across various industries due to their ability to efficiently trim and bead the edges of metal and other materials. They are essential for achieving precision, consistency, and quality in manufacturing processes. Below, we delve into the primary application areas where these machines are indispensable:
1. Automotive Industry
Role and Importance
The automotive industry relies heavily on trimming beading machines to ensure the structural integrity and aesthetic quality of vehicle components. These machines are used to trim and form beads on various parts, contributing to the overall safety and appearance of vehicles.
Specific Applications
- Body Panels: Trimming beading machines are used to trim and bead the edges of doors, hoods, fenders, and trunk lids. This ensures a smooth fit and finish, reducing the risk of sharp edges and improving the vehicle’s aesthetic appeal.
- Exhaust Systems: Beading is essential for exhaust system components to ensure proper sealing and assembly. Trimming beading machines create precise beads that help maintain joint integrity under varying temperatures and pressures.
- Interior Components: These machines are used to create beaded edges on interior panels and trim pieces, enhancing the aesthetic quality and durability of the interior components.
Benefits
- Improved Safety: Proper beading enhances the strength and stability of components, contributing to vehicle safety.
- Aesthetic Appeal: Beading provides a polished and professional appearance, enhancing the overall look of the vehicle.
- Cost Efficiency: Automated trimming and beading reduce labor costs and increase production efficiency, enabling manufacturers to meet high-volume demands.
2. Aerospace Industry
Role and Importance
The aerospace industry demands the highest precision and quality standards, making trimming beading machines essential for manufacturing components that must withstand extreme conditions and stresses.
Specific Applications
- Fuselage Panels: Trimming beading machines are used to trim and bead the edges of fuselage panels, ensuring a precise fit and alignment during assembly. Beading enhances the panels’ structural integrity and resistance to aerodynamic forces.
- Wing Components: Beading is applied to wing components, such as flaps and ailerons, to improve their strength and performance. The precision of trimming beading machines ensures the components meet strict aerospace standards.
- Engine Components: In engine manufacturing, trimming beading machines are used to create precise beads on engine casings and ducts, improving thermal and mechanical performance.
Benefits
- Precision and Accuracy: Trimming beading machines provide the precision necessary to meet the stringent requirements of the aerospace industry.
- Enhanced Performance: Beaded components offer improved strength and aerodynamic performance, contributing to the overall efficiency of aircraft.
- Reliability: The consistent quality of beaded components ensures reliability and safety in critical aerospace applications.
3. HVAC Industry
Role and Importance
The HVAC (Heating, Ventilation, and Air Conditioning) industry utilizes trimming beading machines to manufacture components that require precise sealing and structural integrity.
Specific Applications
- Ductwork: Trimming beading machines are used to bead the edges of ductwork components, ensuring a tight seal and preventing air leaks. Proper beading also enhances the structural stability of ducts.
- Vents and Grilles: Beading is applied to vents and grilles to improve their strength and appearance. Trimming beading machines ensure a consistent fit and finish, contributing to the overall quality of HVAC systems.
- Heat Exchangers: In heat exchanger manufacturing, trimming beading machines create beads that enhance the thermal performance and durability of components.
Benefits
- Energy Efficiency: Beaded components improve sealing and reduce air leakage, enhancing the energy efficiency of HVAC systems.
- Durability: The structural integrity provided by beading ensures the long-term durability of HVAC components.
- Quality Assurance: Trimming beading machines deliver consistent quality, enabling manufacturers to meet industry standards and customer expectations.
4. Consumer Goods Industry
Role and Importance
In the consumer goods industry, trimming beading machines are employed to enhance the quality and appearance of a wide range of products, from household appliances to electronics.
Specific Applications
- Appliances: Trimming beading machines are used to create beaded edges on appliances such as refrigerators, ovens, and washing machines. This improves the aesthetic appeal and durability of the products.
- Electronics Enclosures: Beading is applied to electronic enclosures and casings to enhance their strength and provide a polished appearance. Trimming beading machines ensure a precise fit and finish, critical for protecting sensitive electronic components.
- Packaging: In packaging manufacturing, trimming beading machines create beads that improve the strength and sealing of containers, ensuring the protection and integrity of packaged goods.
Benefits
- Aesthetic Enhancement: Beading enhances the visual appeal of consumer products, contributing to customer satisfaction and brand image.
- Structural Integrity: Beaded edges provide added strength and resistance to wear and tear, extending the lifespan of consumer goods.
- Manufacturing Efficiency: Trimming beading machines increase production efficiency, allowing manufacturers to meet high demand while maintaining quality.
5. Metalworking Industry
Role and Importance
The metalworking industry utilizes trimming beading machines for a variety of applications where precision and consistency are paramount.
Specific Applications
- Sheet Metal Fabrication: Trimming beading machines are used to trim and bead sheet metal components for a range of applications, from construction to transportation.
- Custom Metal Components: Beading is applied to custom metal parts to enhance their strength and performance. Trimming beading machines enable the production of intricate and precise designs.
- Architectural Metalwork: In architectural metalwork, trimming beading machines create beaded edges on decorative elements, ensuring a high-quality finish.
Benefits
- Precision and Consistency: Trimming beading machines provide the accuracy required for complex metalworking applications.
- Versatility: These machines can handle a wide range of materials and thicknesses, accommodating diverse metalworking needs.
- Quality Assurance: The consistent quality of beaded metal components ensures they meet industry standards and project specifications.
6. Food and Beverage Industry
Role and Importance
In the food and beverage industry, trimming beading machines are used to manufacture components that require precise sealing and hygiene standards.
Specific Applications
- Food Containers: Trimming beading machines are used to create beaded edges on food containers, ensuring a tight seal and preventing contamination.
- Beverage Cans: Beading is applied to beverage cans to enhance their strength and resistance to pressure changes. Trimming beading machines ensure a uniform and reliable seal.
- Processing Equipment: In food processing equipment manufacturing, trimming beading machines create beads that improve the structural integrity and hygiene of components.
Benefits
- Food Safety: Beaded components provide secure sealing, preventing contamination and ensuring food safety.
- Durability: The added strength provided by beading ensures the longevity and reliability of food and beverage packaging.
- Efficiency: Trimming beading machines increase production efficiency, enabling manufacturers to meet high demand while maintaining quality and safety standards.
7. Medical Device Manufacturing
Role and Importance
The medical device manufacturing industry requires precision and reliability, making trimming beading machines essential for producing components that must meet strict standards.
Specific Applications
- Surgical Instruments: Trimming beading machines are used to create beaded edges on surgical instruments, enhancing their strength and safety.
- Medical Equipment Casings: Beading is applied to medical equipment casings to improve their structural integrity and provide a polished appearance.
- Implantable Devices: In the manufacturing of implantable devices, trimming beading machines create beads that ensure precision and compatibility with human tissue.
Benefits
- Precision and Accuracy: Trimming beading machines provide the precision necessary to meet the stringent requirements of medical device manufacturing.
- Reliability: Beaded components ensure reliability and safety in critical medical applications.
- Quality Assurance: The consistent quality of beaded medical components ensures they meet industry standards and regulatory requirements.
Conclusion
Trimming beading machines are versatile tools that play a vital role in various industries, from automotive to medical device manufacturing. Their ability to enhance the precision, consistency, and quality of components makes them indispensable for modern manufacturing processes. By understanding the specific applications and benefits of trimming beading machines, manufacturers can optimize their operations, improve product quality, and meet the demands of their respective industries.
Trimming Beading Tools
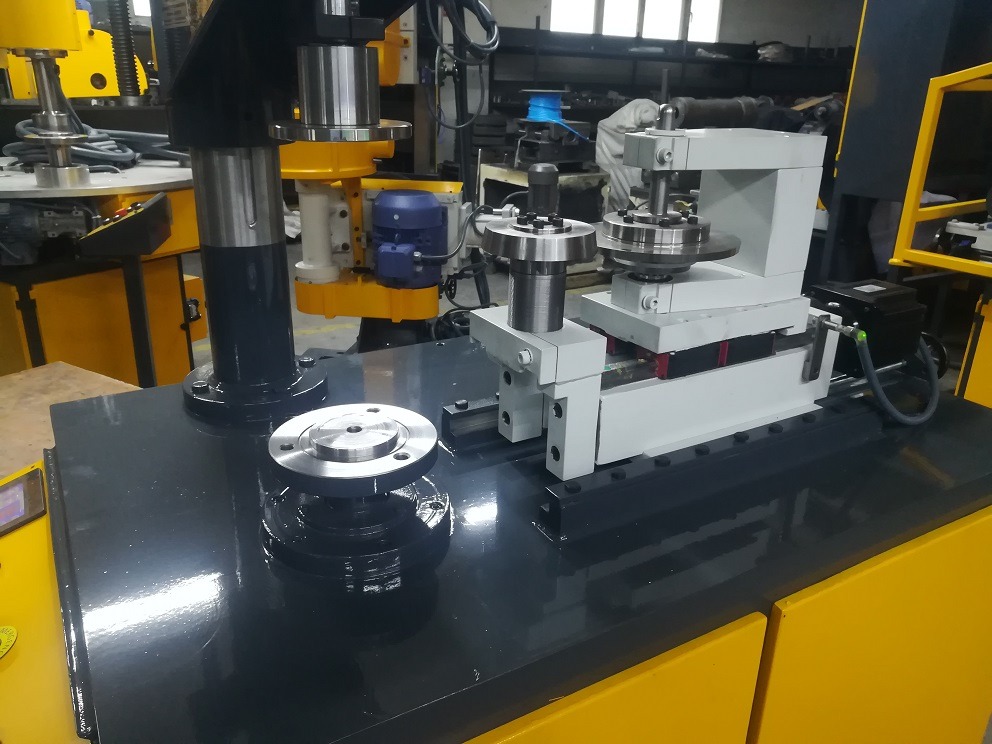
Trimming beading tools are critical components of trimming beading machines, directly responsible for cutting and forming beads on workpieces. Their design, material, and maintenance play a crucial role in determining the quality and efficiency of the trimming and beading process. Here’s an in-depth look at trimming beading tools, including their types, materials, maintenance, and considerations for selection:
Types of Trimming Beading Tools
Trimming beading tools come in various shapes and forms, each designed for specific tasks and applications. The choice of tools depends on the material being processed, the desired bead pattern, and the machine’s capabilities.
1. Rotary Cutters
Functionality
- Rotary cutters are used for continuous cutting operations and are ideal for long production runs.
- They provide high-speed cutting and precision, making them suitable for trimming operations that require clean and straight edges.
Applications
- Automotive body panels
- Sheet metal fabrication
- Packaging components
2. Punch and Die Sets
Functionality
- Punch and die sets are used for stamping and forming operations, allowing for the creation of complex bead patterns and shapes.
- They offer versatility and can be customized to meet specific design requirements.
Applications
- Complex bead patterns in aerospace components
- Decorative metalwork
- Custom metal parts
3. Roller Dies
Functionality
- Roller dies are utilized in forming continuous beads along the length of a workpiece.
- They apply consistent pressure and control, ensuring uniform bead formation.
Applications
- HVAC ductwork
- Metal enclosures
- Architectural metalwork
4. Serrated Cutters
Functionality
- Serrated cutters feature a toothed edge that is designed for gripping and cutting through tougher materials.
- They are often used in applications where a smooth finish is not critical but where material grip and precision are required.
Applications
- Heavy-duty metal cutting
- Thicker materials such as steel or titanium
5. Profile Tools
Functionality
- Profile tools are used to create specific bead profiles and shapes, including U-beads, V-beads, and more complex designs.
- These tools are customized to match the desired profile and are critical for applications requiring specific geometric shapes.
Applications
- Automotive trim components
- Custom metal profiles
- Precision sheet metal work
Materials for Trimming Beading Tools
The choice of material for trimming beading tools affects their performance, durability, and suitability for different applications. Key materials include:
1. High-Speed Steel (HSS)
Characteristics
- Known for its hardness and ability to maintain a sharp edge at high temperatures.
- Offers good wear resistance and is suitable for a wide range of cutting applications.
Advantages
- Cost-effective for general-purpose trimming and beading.
- Easy to sharpen and recondition.
Limitations
- May wear quickly in high-volume production or with abrasive materials.
2. Carbide
Characteristics
- Carbide tools offer superior wear resistance and durability, making them ideal for high-volume production and difficult-to-machine materials.
- Maintains sharpness and precision over extended periods.
Advantages
- Long tool life and reduced downtime for tool changes.
- Suitable for hard and abrasive materials.
Limitations
- Higher initial cost compared to HSS tools.
- More challenging to recondition and sharpen.
3. Ceramic and Diamond Coatings
Characteristics
- Ceramic and diamond coatings provide extreme hardness and wear resistance.
- Used for specialized applications requiring the highest levels of durability and precision.
Advantages
- Exceptional tool life and performance in demanding applications.
- Resistance to heat and wear, reducing tool degradation.
Limitations
- Very high cost, typically reserved for critical applications.
- Requires specialized equipment for sharpening and maintenance.
4. Tool Steel
Characteristics
- Tool steel is a versatile material that offers a good balance of strength, toughness, and wear resistance.
- Suitable for a variety of tool types and applications.
Advantages
- Cost-effective and easy to machine and customize.
- Provides a good balance between durability and flexibility.
Limitations
- May not perform as well as carbide or ceramic in highly abrasive conditions.
Maintenance of Trimming Beading Tools
Proper maintenance of trimming beading tools is essential for ensuring consistent performance and longevity. Here are some key maintenance practices:
1. Regular Inspection and Assessment
- Visual Inspections: Conduct regular visual inspections to identify signs of wear, damage, or misalignment.
- Performance Monitoring: Monitor tool performance by checking the quality of the finished products for any signs of tool-related issues, such as burrs or uneven edges.
2. Cleaning and Lubrication
- Cleaning Procedures: Regularly clean tools to remove metal shavings, dust, and debris that can accumulate and affect performance.
- Lubrication: Apply appropriate lubricants to reduce friction, prevent overheating, and protect against corrosion. Ensure that the correct type of lubricant is used for the specific tool material.
3. Sharpening and Reconditioning
- Sharpening Techniques: Use the appropriate sharpening tools, such as diamond stones or grinding wheels, to maintain the cutting edge. Follow manufacturer recommendations for sharpening angles.
- Reconditioning Services: Consider professional reconditioning services for heavily worn or damaged tools to restore them to their original specifications.
4. Alignment and Calibration
- Tool Alignment: Ensure that tools are correctly aligned before each operation to prevent uneven wear and ensure accurate cuts and beads.
- Calibration: Regularly calibrate the machine and its components to ensure that tools operate within specified tolerances.
5. Storage and Handling
- Proper Storage: Store tools in protective cases or racks to prevent damage when not in use. Maintain a clean, dry, and temperature-controlled environment.
- Handling Practices: Use appropriate handling techniques to prevent dropping or mishandling tools. Train operators on proper handling and storage procedures.
Considerations for Selecting Trimming Beading Tools
Selecting the right trimming beading tools requires careful consideration of several factors to ensure optimal performance and quality:
1. Material Compatibility
- Choose tools made from materials that are compatible with the workpiece material to ensure effective cutting and beading.
- Consider the hardness, abrasiveness, and thickness of the material when selecting tool materials and coatings.
2. Tool Geometry
- Select tools with the appropriate geometry for the desired bead profile and cutting requirements.
- Consider factors such as tool angle, shape, and size when choosing tools for specific applications.
3. Production Volume
- Consider the production volume and frequency of tool changes when selecting tools. High-volume production may require more durable materials such as carbide or ceramic.
4. Quality Requirements
- Evaluate the quality requirements of the finished product, including precision, surface finish, and consistency.
- Select tools that can meet the desired quality standards, taking into account the required tolerances and specifications.
5. Cost Considerations
- Balance the cost of tools with their expected performance and longevity. Consider the total cost of ownership, including maintenance and replacement costs.
6. Machine Compatibility
- Ensure that the selected tools are compatible with the specific trimming beading machine being used, including tool holders, spindles, and drive mechanisms.
Conclusion
Trimming beading tools are essential components of trimming beading machines, directly influencing the quality and efficiency of the manufacturing process. By understanding the different types of tools, their materials, and maintenance requirements, manufacturers can optimize their operations and ensure consistent, high-quality results. Proper tool selection, maintenance, and handling are key to maximizing performance and extending the lifespan of trimming beading tools.
Beading Machine Efficiency
Improving the efficiency of a beading machine is crucial for manufacturers seeking to enhance productivity, reduce costs, and maintain high-quality output. A beading machine’s efficiency is influenced by multiple factors, including machine design, tool selection, operational practices, and maintenance strategies. This guide will explore these factors in detail, providing insights into how efficiency can be optimized.
1. Machine Design and Configuration
The design and configuration of a beading machine have a significant impact on its efficiency. Considerations include the machine’s mechanical setup, automation capabilities, and adaptability to various production requirements.
Key Design Factors
- Automation Level: Automated beading machines can significantly improve efficiency by reducing manual intervention, minimizing errors, and increasing throughput. Machines with advanced control systems, such as CNC (Computer Numerical Control) or PLC (Programmable Logic Controllers), offer precise control over operations.
- Modular Design: Machines with modular components allow for quick changes and customization to accommodate different product specifications. This flexibility can lead to reduced downtime and faster setup times.
- Ergonomic Design: An ergonomic design reduces operator fatigue and error rates. Features such as user-friendly interfaces and adjustable components enhance operator comfort and efficiency.
Technological Integration
- Industry 4.0: Incorporating Industry 4.0 technologies, such as IoT (Internet of Things) sensors and data analytics, enables real-time monitoring of machine performance and predictive maintenance. This integration helps identify potential issues before they lead to downtime, ensuring continuous operation.
- Adaptive Controls: Machines equipped with adaptive control systems can automatically adjust settings based on real-time data, optimizing performance for varying materials and production requirements.
2. Tool Selection and Maintenance
The selection and maintenance of tools are critical to maximizing the efficiency of a beading machine. High-quality tools, combined with regular maintenance, ensure precision and longevity.
Tool Selection
- Material Compatibility: Choose tools that are compatible with the materials being processed. This minimizes wear and tear and ensures efficient operation. For example, carbide tools are ideal for high-volume production due to their durability and resistance to wear.
- Tool Geometry: Select tools with the appropriate geometry for the desired bead profile and cutting requirements. Proper tool geometry can reduce material waste and improve cycle times.
Tool Maintenance
- Routine Sharpening: Regularly sharpen tools to maintain their cutting efficiency. Dull tools increase cycle times and reduce product quality.
- Alignment and Calibration: Ensure tools are properly aligned and calibrated to prevent defects and ensure consistent bead formation.
- Inventory Management: Maintain an inventory of spare tools to prevent downtime in the event of tool failure or wear.
3. Operational Practices
Operational practices, including setup procedures, quality control, and process optimization, play a crucial role in enhancing beading machine efficiency.
Setup and Calibration
- Efficient Setup Procedures: Streamline setup procedures to reduce downtime between production runs. This includes using quick-change tooling systems and pre-configured settings.
- Calibration Checks: Regularly perform calibration checks to ensure the machine operates within specified tolerances. This prevents defects and reduces the need for rework.
Process Optimization
- Cycle Time Reduction: Analyze and optimize cycle times by identifying bottlenecks and implementing process improvements. This can include adjustments to machine speed, tool changes, and material handling.
- Lean Manufacturing Principles: Implement lean manufacturing principles to eliminate waste and improve process flow. Techniques such as 5S and value stream mapping can enhance efficiency.
- Continuous Improvement: Foster a culture of continuous improvement by encouraging operators and engineers to identify inefficiencies and propose solutions.
4. Quality Control and Inspection
Implementing robust quality control and inspection processes ensures that beading machines produce consistent and high-quality output, reducing waste and rework.
In-Line Inspection
- Automated Inspection Systems: Use automated inspection systems to monitor product quality in real-time. This allows for immediate identification and correction of defects.
- Statistical Process Control (SPC): Implement SPC techniques to track and analyze production data. This helps identify trends and deviations, enabling proactive adjustments.
Feedback Loops
- Operator Feedback: Encourage operators to provide feedback on machine performance and quality issues. This insight can be invaluable for identifying areas for improvement.
- Customer Feedback: Collect and analyze customer feedback to identify quality issues and adjust processes accordingly.
5. Maintenance Strategies
A proactive maintenance strategy is essential for minimizing downtime and ensuring the long-term efficiency of beading machines.
Preventive Maintenance
- Scheduled Maintenance: Implement a regular maintenance schedule to address wear and tear before it leads to machine failure. This includes lubrication, alignment checks, and part replacements.
- Maintenance Logs: Maintain detailed logs of maintenance activities to track machine performance and identify recurring issues.
Predictive Maintenance
- Condition Monitoring: Use condition monitoring tools, such as vibration analysis and thermal imaging, to detect signs of impending failure.
- Data Analytics: Analyze maintenance and operational data to predict future maintenance needs, reducing unplanned downtime.
6. Training and Workforce Development
Investing in operator training and workforce development can enhance the efficiency of beading machines by ensuring proper machine operation and fostering a culture of continuous improvement.
Operator Training
- Skill Development: Provide comprehensive training on machine operation, maintenance procedures, and quality control. This ensures operators are equipped to maximize machine performance.
- Cross-Training: Implement cross-training programs to develop a versatile workforce capable of operating multiple machines and handling various tasks.
Continuous Learning
- Workshops and Seminars: Encourage participation in workshops and seminars to stay updated on the latest industry trends and technologies.
- Knowledge Sharing: Foster a culture of knowledge sharing among employees to disseminate best practices and innovations.
Conclusion
Enhancing the efficiency of a beading machine involves a multifaceted approach that encompasses machine design, tool selection, operational practices, quality control, maintenance strategies, and workforce development. By focusing on these areas, manufacturers can optimize machine performance, reduce costs, and maintain high-quality output. A commitment to continuous improvement and technological integration will ensure long-term efficiency and competitiveness in the industry.
Installation Requirements for Trimming Beading Machines
The installation of a trimming beading machine requires careful planning and consideration of various factors to ensure optimal performance and safety. Proper installation is crucial for maximizing efficiency, reducing downtime, and maintaining consistent product quality. Below, we explore the key installation requirements for trimming beading machines, covering site preparation, utility requirements, machine setup, safety considerations, and training.
1. Site Preparation
Preparing the installation site is a critical first step to ensure that the beading machine can be set up and operated efficiently. This involves selecting the appropriate location, ensuring structural support, and planning for space requirements.
Location Selection
- Proximity to Production Lines: The machine should be located near the relevant production lines to minimize material handling time and improve workflow efficiency.
- Access for Maintenance: Ensure that there is sufficient space around the machine for maintenance and repairs. Consider the accessibility of components that require frequent servicing.
Structural Support
- Floor Load Capacity: Verify that the floor can support the weight of the machine and any additional equipment. Reinforce the floor if necessary to prevent vibrations and ensure stability.
- Vibration Isolation: Implement vibration isolation measures, such as mounting the machine on anti-vibration pads, to reduce noise and prevent damage to nearby equipment.
Space Requirements
- Working Area: Allocate sufficient space for operators to work safely and efficiently, including room for tool changes, adjustments, and inspections.
- Material Handling: Plan for adequate space for the storage and handling of raw materials and finished products, including conveyors or material handling systems if necessary.
2. Utility Requirements
Ensuring that the necessary utilities are in place is essential for the proper operation of a trimming beading machine. This includes power supply, compressed air, and ventilation.
Power Supply
- Voltage and Amperage: Confirm that the power supply meets the machine’s voltage and amperage requirements. Most industrial beading machines require a three-phase power supply with specific voltage levels (e.g., 220V, 380V, or 440V).
- Electrical Connections: Ensure that electrical connections are made by a qualified electrician, adhering to local electrical codes and standards. Install circuit breakers and fuses as necessary to protect the machine and operators.
Compressed Air
- Air Supply: Some beading machines require compressed air for certain operations, such as clamping or pneumatic controls. Verify the machine’s air pressure and flow requirements and ensure a reliable supply.
- Air Quality: Install air filters and dryers to maintain air quality and prevent contaminants from affecting the machine’s performance.
Ventilation
- Dust and Fume Extraction: Provide adequate ventilation to remove dust, fumes, and other airborne contaminants generated during the beading process. Consider installing dust extraction systems or local exhaust ventilation to maintain air quality.
- Climate Control: Ensure that the installation area is climate-controlled to prevent temperature and humidity fluctuations that could affect machine performance and material quality.
3. Machine Setup and Alignment
Proper setup and alignment of the beading machine are critical to ensure precision and efficiency. This involves machine assembly, calibration, and testing.
Machine Assembly
- Component Installation: Assemble the machine according to the manufacturer’s instructions, ensuring that all components are correctly installed and secured.
- Tooling Installation: Install and configure the necessary cutting and beading tools, ensuring they are compatible with the materials and bead profiles required.
Alignment and Calibration
- Tool Alignment: Align tools with the workpiece to ensure accurate trimming and beading. Use precision alignment tools and gauges to verify correct positioning.
- Calibration: Calibrate the machine’s control systems to ensure that operations are performed within specified tolerances. This includes setting tool angles, cutting speeds, and beading pressures.
Testing and Verification
- Trial Runs: Conduct trial runs with sample materials to verify that the machine is operating correctly and producing the desired results. Adjust settings as needed to achieve optimal performance.
- Quality Inspection: Inspect finished samples for quality and consistency, checking for defects such as burrs, uneven edges, or incomplete beads.
4. Safety Considerations
Safety is a paramount concern during the installation and operation of a trimming beading machine. Implementing proper safety measures protects operators and equipment.
Machine Safety Features
- Emergency Stops: Ensure that emergency stop buttons are accessible and functioning correctly. Test the emergency stop system to verify its effectiveness.
- Safety Guards: Install safety guards and barriers to prevent accidental contact with moving parts. Ensure that guards are securely fastened and meet relevant safety standards.
Operator Safety
- Personal Protective Equipment (PPE): Provide operators with appropriate PPE, such as gloves, safety glasses, and hearing protection, to minimize injury risks.
- Safety Signage: Install safety signage to warn operators of potential hazards and remind them of safe operating procedures.
Compliance and Regulations
- Regulatory Compliance: Ensure that the installation complies with all relevant safety and environmental regulations. This may include OSHA standards in the United States or similar regulations in other countries.
- Risk Assessment: Conduct a risk assessment to identify potential hazards and implement mitigation measures.
5. Training and Workforce Development
Training operators and maintenance personnel is essential for ensuring safe and efficient machine operation.
Operator Training
- Machine Operation: Provide comprehensive training on machine operation, including setup, tool changes, and adjustments. Ensure that operators understand the machine’s control systems and safety features.
- Quality Control: Train operators on quality control procedures, including inspecting finished products for defects and making necessary adjustments.
Maintenance Training
- Routine Maintenance: Train maintenance personnel on routine maintenance tasks, such as lubrication, tool sharpening, and alignment checks.
- Troubleshooting: Provide training on troubleshooting common issues and performing repairs to minimize downtime.
Continuous Improvement
- Feedback Mechanisms: Encourage operators and maintenance personnel to provide feedback on machine performance and suggest improvements.
- Ongoing Training: Offer ongoing training opportunities to keep employees updated on the latest technologies and best practices.
Conclusion
Proper installation of a trimming beading machine involves careful consideration of site preparation, utility requirements, machine setup, safety considerations, and training. By addressing these factors, manufacturers can ensure that their machines operate efficiently, safely, and effectively, leading to improved productivity and product quality. A well-planned installation process lays the foundation for long-term success and competitiveness in the manufacturing industry.
Installation Time Estimate for a Trimming Beading Machine
Estimating the installation time for a trimming beading machine involves considering various factors, such as the complexity of the machine, site preparation, the availability of resources, and the experience of the installation team. While the specific time required can vary widely depending on these factors, I can provide a general breakdown of the installation steps and estimated time frames for each phase.
Here’s a detailed look at the various steps involved in the installation process and the estimated time required for each phase:
1. Pre-Installation Planning and Preparation
Estimated Time: 1-3 Days
- Site Inspection and Preparation: Conduct a thorough inspection of the installation site to ensure it meets the necessary requirements, such as floor strength, ventilation, and space availability. Prepare the site by clearing any obstructions and ensuring utilities are accessible.
- Utility Setup: Arrange for electrical connections, compressed air supply, and other necessary utilities. This might require coordination with electricians and other contractors to ensure compliance with safety standards.
- Logistics and Equipment Handling: Plan the delivery and handling of the machine and its components. This includes scheduling transportation and ensuring equipment like cranes or forklifts is available for moving heavy parts.
2. Machine Assembly
Estimated Time: 2-5 Days
- Unpacking and Inspection: Unpack the machine components and inspect them for any damage incurred during transportation. Verify that all components and accessories are present according to the packing list.
- Base and Frame Setup: Assemble the base and frame of the machine. This involves positioning and securing the machine to the floor, ensuring it is level and stable. Vibration pads or anchors may need to be installed, depending on the machine’s design and site requirements.
- Component Assembly: Assemble the various components of the machine, such as drive systems, control panels, cutting and beading tools, and other peripherals. This step can vary significantly depending on the complexity of the machine.
3. Electrical and Utility Connections
Estimated Time: 1-2 Days
- Electrical Wiring: Connect the machine to the power supply, ensuring that wiring is done by a certified electrician. Test the connections to verify proper voltage and amperage levels.
- Compressed Air and Pneumatics: Connect the compressed air supply if required by the machine. Verify that air pressure and flow meet the manufacturer’s specifications.
- Ventilation Systems: Install any necessary ventilation systems or dust extraction equipment to ensure a safe working environment.
4. Calibration and Testing
Estimated Time: 1-3 Days
- Tool Installation and Alignment: Install and align the cutting and beading tools. Use precision instruments to ensure correct alignment and positioning.
- System Calibration: Calibrate the machine’s control systems, including CNC or PLC settings, to ensure operations are within specified tolerances. This may involve setting up parameters for speed, pressure, and bead patterns.
- Trial Runs and Testing: Conduct trial runs using sample materials to verify machine operation. Inspect the finished products for quality and consistency, making necessary adjustments to settings.
5. Safety Checks and Final Adjustments
Estimated Time: 1 Day
- Safety Inspections: Conduct a thorough safety inspection to ensure all guards, emergency stops, and safety features are operational. Address any potential hazards identified during this inspection.
- Final Adjustments: Make final adjustments to optimize machine performance and address any remaining issues detected during testing.
6. Operator Training and Handover
Estimated Time: 1-3 Days
- Operator Training: Provide comprehensive training to operators and maintenance personnel on machine operation, maintenance procedures, and safety protocols.
- Handover: Conduct a formal handover process, providing documentation, manuals, and support contacts. Ensure that operators and technicians are comfortable with the machine’s operation and troubleshooting procedures.
Total Estimated Installation Time
Overall Time Estimate: 7-17 Days
This estimate assumes that all resources are available, and the installation team is experienced. The time required can vary based on the complexity of the machine, the readiness of the site, and the efficiency of the installation team.
Factors Influencing Installation Time
- Machine Complexity: More complex machines with advanced automation and control systems may require additional time for assembly, calibration, and testing.
- Site Readiness: Delays in site preparation, such as electrical work or structural modifications, can extend the installation timeline.
- Team Experience: Experienced installation teams can complete the process more quickly and efficiently, reducing potential delays.
- Logistical Challenges: Issues with transportation, equipment handling, or supply chain disruptions can affect the installation schedule.
- Customizations: Custom or modified machines may require additional time for assembly and configuration to meet specific requirements.
Conclusion
The installation of a trimming beading machine involves several phases, each with its own set of tasks and time requirements. By planning effectively, coordinating resources, and ensuring that the installation team is well-prepared, manufacturers can optimize the installation process, minimizing downtime and ensuring that the machine is up and running efficiently. Proper installation not only ensures immediate productivity but also lays the foundation for long-term machine performance and reliability.
An Edge Curling and Sheet Crimping Machine is a specialized piece of equipment used in metalworking and sheet fabrication industries. It is designed to modify the edges of sheet metal by curling or crimping them to achieve specific mechanical, aesthetic, or safety-related purposes. This type of machine plays a crucial role in various manufacturing processes, particularly in industries such as automotive, aerospace, HVAC, packaging, and metal container production.
Working Principle
The machine operates by feeding a sheet metal workpiece between rollers or dies that apply force to curl or crimp the edges. Depending on the configuration, the machine may employ different techniques such as:
- Edge Curling – This process involves rolling the sheet metal edge inward or outward to create a smooth, rounded finish. It is commonly used to eliminate sharp edges, enhance structural integrity, or facilitate assembly in joining operations.
- Sheet Crimping – This involves creating a series of corrugations or crimps along the edge or surface of the sheet metal to increase its strength and flexibility. This is often used in applications where sheets need to be joined or overlapped without additional welding or fasteners.
Types of Edge Curling and Crimping Machines
- Manual Machines – These are hand-operated or foot-pedal machines used for low-volume or custom fabrication. They offer high precision for small-scale operations.
- Semi-Automatic Machines – These machines use motorized rollers or hydraulic actuators to assist with the curling and crimping process, increasing efficiency while still allowing some manual control.
- Fully Automatic Machines – These are CNC-controlled or PLC-based systems that handle high-volume production with minimal human intervention. They ensure consistent quality and are widely used in industrial manufacturing.
Applications
- HVAC Ducting: Used to form and strengthen sheet metal ducts for air conditioning and ventilation systems.
- Metal Packaging: Used in tin can manufacturing to create curled edges for safety and sealing purposes.
- Automotive Industry: Employed in fender and body panel fabrication to enhance durability and aesthetics.
- Roofing and Cladding: Used in sheet metal roofing to provide weatherproofing and ease of installation.
- Aerospace and Defense: Utilized in aircraft component manufacturing where lightweight and strong metal parts are required.
Advantages of Using Edge Curling and Crimping Machines
- Improved Safety: Curled edges remove sharp points, reducing injury risks.
- Enhanced Strength: Crimped or curled edges provide additional stiffness to thin sheets.
- Better Aesthetic Appeal: Smooth, rounded edges create a more refined finish.
- Ease of Assembly: Crimped or curled edges allow for easier joining and welding of metal sheets.
- Cost Efficiency: Reduces material waste and improves production efficiency.
Factors to Consider When Choosing a Machine
- Material Compatibility: Ensure the machine can handle the required sheet metal type (e.g., aluminum, steel, stainless steel).
- Thickness Range: Machines vary in their ability to handle different sheet metal thicknesses.
- Production Volume: Choose between manual, semi-automatic, or automatic based on production needs.
- Customization Features: Some machines allow for interchangeable rollers or dies for different edge profiles.
- Power and Speed: Automated machines offer higher efficiency with adjustable speed settings.
Conclusion
Edge Curling and Sheet Crimping Machines are essential tools in metalworking and sheet fabrication industries. They provide a reliable method for enhancing the functionality, safety, and appearance of sheet metal components. With advancements in automation and control technology, modern machines offer increased efficiency, precision, and versatility, making them indispensable for industrial manufacturing applications.
Edge curling and sheet crimping machine
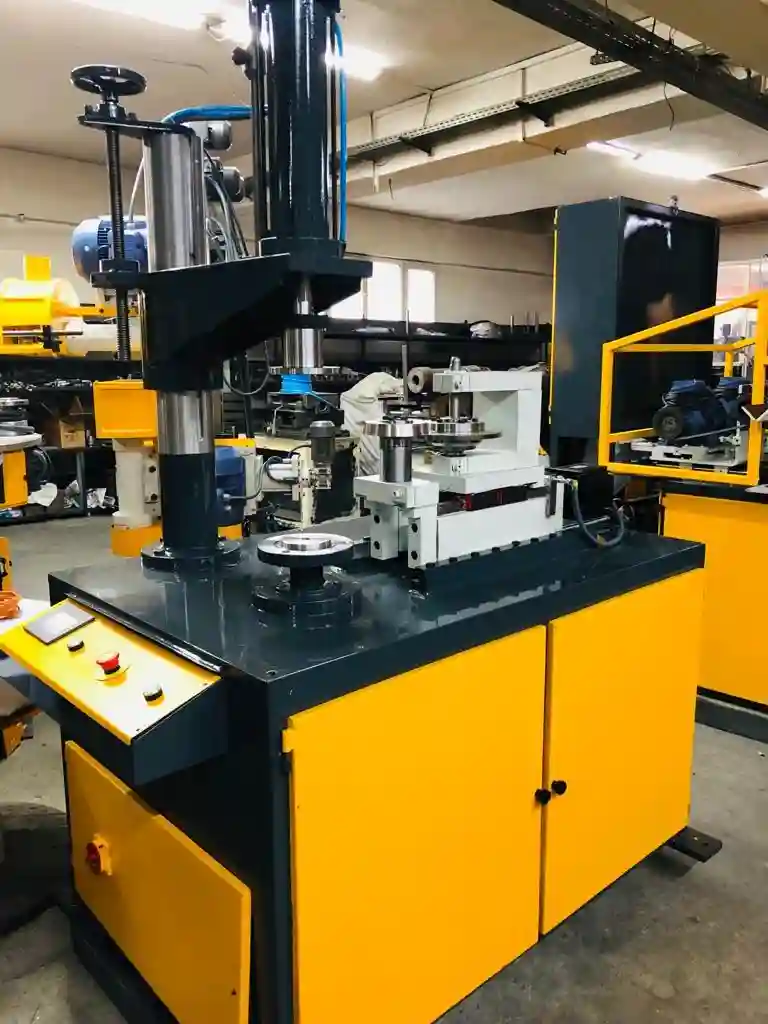
An edge curling and sheet crimping machine operates by applying mechanical force to the edges or surfaces of sheet metal to achieve a specific form or structural enhancement. The working principle involves feeding a sheet metal workpiece between rollers, dies, or forming tools that progressively shape the metal into the desired profile. The machine exerts controlled pressure and movement on the material, ensuring uniformity and consistency in the curling or crimping process. The process typically starts with the insertion of a flat sheet into the machine, where the edges come into contact with rotating rollers or forming dies. These rollers gradually bend or fold the edges inward or outward, depending on the intended final shape.
The curling operation rounds off the edges to create a smooth, tubular or semi-circular profile, which is commonly used to eliminate sharp edges, improve the structural rigidity of the component, and enhance its aesthetic appeal. Crimping, on the other hand, involves the formation of small corrugations or indentations along the edge or body of the sheet metal, increasing its mechanical strength and flexibility. The machine may use a series of passes, with each roller or die applying a progressive level of deformation until the final shape is achieved. In some automated systems, the process is controlled through a computer numerical control (CNC) system or programmable logic controllers (PLCs), which precisely regulate the pressure, speed, and feed rate to maintain consistency across multiple workpieces. The force applied by the rollers or forming tools is carefully calibrated to avoid excessive stress on the material, which could lead to cracks, warping, or material fatigue. Additionally, lubrication or specialized coatings may be used to reduce friction and ensure smooth operation. Depending on the complexity of the design, the machine may incorporate multiple sets of rollers or adjustable tooling to accommodate different edge profiles and metal thicknesses.
In high-speed industrial applications, automatic feeding systems and conveyor mechanisms are often integrated to enhance production efficiency. The process may also involve preheating or annealing in cases where the material requires additional ductility to prevent breakage during forming. The working principle remains consistent across various machine designs, with manual machines relying on operator control for material positioning and force application, while automated systems streamline the process with precision engineering and advanced control mechanisms. The outcome is a precisely curled or crimped edge that improves both the functionality and durability of the final product, making the machine an essential tool in industries such as automotive, aerospace, HVAC, roofing, and metal packaging.
The working principle of an edge curling and sheet crimping machine is based on controlled deformation of sheet metal using mechanical force, typically through rollers, dies, or specialized forming tools. The process begins with the insertion of a flat sheet into the machine, where guiding mechanisms align it properly for consistent shaping. Depending on whether the operation is curling or crimping, different sets of rollers or forming tools engage the material. In edge curling, the rollers gradually bend the sheet metal edges inward or outward in a progressive manner. This controlled bending ensures a smooth curvature without introducing cracks or stress concentrations.
The amount of curling depends on the specific roller geometry and the applied pressure. In contrast, crimping involves the creation of small, repetitive folds or indentations along the edge or surface of the sheet. These crimps add mechanical strength to the sheet without significantly increasing weight. The machine typically consists of a motorized drive mechanism that controls the movement of the rollers or dies. In manual or semi-automatic machines, operators may need to adjust pressure settings, feed rate, and roller positioning to achieve the desired shape. However, in automated systems, parameters such as roller pressure, speed, and depth of deformation are precisely controlled by computer numerical control (CNC) systems or programmable logic controllers (PLCs). These advanced controls ensure uniformity across multiple workpieces and minimize operator intervention.
The process may also involve the use of lubrication or specialized coatings on the rollers to reduce friction and prevent material damage. Some machines employ multi-stage forming, where the sheet undergoes multiple passes through different roller sets to gradually reach the final shape. This approach minimizes stress on the material and allows for more complex edge profiles. In high-production environments, additional automation features such as automatic feeding, conveyor integration, and real-time monitoring systems enhance efficiency and precision. The force applied by the rollers must be carefully calibrated based on the material properties, such as thickness, ductility, and tensile strength, to prevent defects like warping, tearing, or excessive thinning. Preheating or annealing may be incorporated in cases where the material requires increased malleability before forming. The final result is a sheet metal workpiece with curled or crimped edges that improve its structural integrity, ease of assembly, and overall aesthetic quality. These machines play a vital role in manufacturing processes across multiple industries, including automotive, aerospace, HVAC, metal roofing, and packaging, where precise edge forming is required to enhance durability and functionality.
The edge curling and sheet crimping machine operates with precision to ensure that each sheet metal workpiece undergoes consistent deformation without compromising material integrity. The rollers or forming tools exert a controlled force that gradually shapes the edges, allowing for a smooth transition from a flat sheet to a curled or crimped profile. In the case of edge curling, the process follows a carefully calculated progression where the metal is guided through a series of rollers that incrementally bend the edges. This progressive deformation ensures that stress is distributed evenly across the material, preventing fractures or unwanted thinning. Depending on the application, the curling may be partial, forming a semi-circular edge, or complete, creating a fully enclosed loop that can later be used for interlocking or joining with other components.
Crimping, on the other hand, involves the creation of ridges or folds along the sheet, achieved by pressing the material between specially designed dies. These crimps are strategically placed to enhance the sheet’s flexibility, allowing it to be bent or shaped further without losing strength. The depth and spacing of these crimps can be adjusted based on the roller or die settings, ensuring the final product meets the required specifications. Advanced machines allow for real-time adjustments, where operators or automated control systems modify pressure, feed rate, and roller positioning to accommodate different sheet metal types and thicknesses.
In high-precision applications, feedback sensors are integrated into the machine to monitor key parameters such as material tension, roller pressure, and deformation accuracy. These sensors provide real-time data to the control system, allowing for instant adjustments that optimize performance. Some machines also incorporate material tracking systems, where each sheet is scanned before processing to determine its exact dimensions and properties, ensuring consistent results across production batches. The use of servo motors in automated systems further enhances precision, allowing for smooth, controlled motion that minimizes mechanical stress and improves repeatability.
Lubrication is another critical aspect of the process, particularly in high-speed operations where friction can generate heat and wear down the rollers or dies. Specialized lubricants or coatings are applied to the metal surface, reducing resistance and ensuring a flawless finish. In certain cases, preheating is employed to soften the material, especially for metals that are prone to cracking when subjected to bending forces. This is particularly useful for materials like stainless steel or aluminum alloys, which may require additional treatment to achieve the desired form without compromising strength.
The effectiveness of the machine is also influenced by its structural design. Rigid, vibration-free frames ensure that all mechanical components maintain precise alignment during operation, preventing deviations that could lead to inconsistent curling or crimping. High-quality rollers, often made from hardened steel or coated with wear-resistant materials, ensure longevity and maintain accuracy over extended production cycles. The inclusion of quick-change tooling systems allows operators to switch between different edge profiles rapidly, increasing machine versatility and reducing downtime.
As production demands evolve, modern machines are designed to integrate with digital manufacturing environments. Smart automation systems allow machines to be linked with factory networks, enabling remote monitoring, data logging, and predictive maintenance. By analyzing performance trends, manufacturers can anticipate maintenance needs, reducing unexpected downtime and improving overall efficiency. This level of automation also facilitates mass customization, where machines automatically adjust settings based on specific design requirements, eliminating the need for manual recalibration.
Ultimately, the working principle of an edge curling and sheet crimping machine revolves around precision, controlled force application, and progressive shaping techniques. Whether for safety improvements, structural reinforcement, or aesthetic enhancements, these machines play a critical role in various industrial sectors. As technology continues to advance, their capabilities will only expand, incorporating smarter control systems, enhanced automation, and improved material adaptability to meet the evolving needs of modern manufacturing.
The working principle of an edge curling and sheet crimping machine is continuously refined through engineering advancements that enhance precision, efficiency, and versatility. As the sheet metal moves through the machine, the rollers, dies, or crimping mechanisms work in harmony to apply the necessary force in a controlled manner, gradually shaping the material to the desired form. This stepwise deformation is crucial in preventing excessive stress concentrations, which could otherwise lead to material failure such as cracking, wrinkling, or uneven thickness distribution.
In edge curling, the process is particularly sensitive to material properties such as ductility, thickness, and tensile strength. The metal is progressively curved along its edge by a sequence of forming rollers that each contribute incrementally to the final shape. If the force is applied too abruptly, the sheet may resist bending, resulting in irregular or incomplete curling. Therefore, the design of the roller profile and the spacing between each deformation stage are carefully calculated to ensure smooth transitions. The final curled edge not only improves safety by eliminating sharp metal edges but also adds rigidity and enhances the structural performance of the component.
In sheet crimping, the machine employs a set of dies or specially contoured rollers to create a series of ridges or corrugations along the surface or edges of the sheet. These crimps increase flexibility and provide additional strength without requiring extra material. The process is highly beneficial for applications where sheets need to be joined, as the crimping pattern allows for interlocking sections or facilitates welding and fastening. Crimping also helps in reducing metal fatigue, especially in applications where the sheet will be subjected to repeated bending or dynamic loading. The shape and depth of the crimps are determined by the die design and the pressure applied during the forming process.
The efficiency of the machine is largely dependent on the drive system, which controls the movement of the sheet and the rollers. High-precision servo motors or hydraulic actuators are commonly used in automated systems to ensure smooth operation and consistent shaping. These actuators allow for precise control over speed and force, reducing material waste and improving repeatability across large production runs. Some machines incorporate adaptive control algorithms that dynamically adjust processing parameters based on real-time feedback from sensors, ensuring optimal performance for different materials and thicknesses.
To further refine the process, advanced lubrication systems are employed to minimize friction and wear on the rollers and sheet surface. Lubricants help in preventing surface imperfections such as scratches, oxidation, or excessive heat buildup that can arise due to prolonged contact between the metal and forming tools. In some cases, cooling systems are integrated into the machine to dissipate heat, especially when working with high-strength materials that generate significant resistance during forming.
Another crucial aspect of the working principle is the integration of precision alignment and guiding mechanisms. The sheet must be fed into the machine in an exact position to prevent misalignment, which could result in inconsistent curling or crimping patterns. Automated systems often use optical or laser sensors to track the sheet’s position and make micro-adjustments in real-time. This ensures that each workpiece is processed accurately, regardless of minor variations in material dimensions or initial positioning.
For industrial-scale production, many edge curling and sheet crimping machines are designed with modular tooling systems that allow for quick adjustments or replacements of forming dies and rollers. This flexibility enables manufacturers to switch between different edge profiles or crimping patterns without requiring extensive reconfiguration. By reducing setup times, these modular systems improve production efficiency and adaptability to varying design requirements.
As manufacturing technology progresses, newer machine models are incorporating digital connectivity features that allow for real-time monitoring and remote operation. These smart systems enable operators to track machine performance, diagnose potential issues, and optimize workflow efficiency using centralized control platforms. Predictive maintenance technologies, powered by data analytics and artificial intelligence, are also being integrated to detect wear patterns and schedule maintenance before unexpected failures occur.
The evolution of edge curling and sheet crimping machines is driven by the need for greater precision, faster production speeds, and enhanced material handling capabilities. Whether used for forming sheet metal in automotive, aerospace, construction, or packaging industries, these machines remain an essential part of modern fabrication processes. With continued advancements in automation, material science, and digital integration, the working principle behind these machines will continue to evolve, pushing the boundaries of efficiency and manufacturing excellence.
Types of Edge Curling and Crimping Machines
Edge curling and sheet crimping machines come in various types, each designed to suit different production requirements, material specifications, and automation levels. These machines can be classified based on their operation mode, level of automation, and specific application. Below are the primary types of edge curling and crimping machines used in the metal fabrication industry:
1. Manual Edge Curling and Crimping Machines
Manual machines are the simplest type, typically operated by hand or with foot pedals. They are designed for low-volume production, prototyping, or custom fabrication where precision is required but automation is not necessary. These machines feature manually adjustable rollers or dies that shape the metal as it is fed through. Operators control the pressure, feed rate, and alignment to ensure consistent results. Manual machines are often used in small workshops, sheet metal repair shops, and craft industries where customization is a priority.
2. Semi-Automatic Edge Curling and Crimping Machines
Semi-automatic machines use a combination of manual feeding and motorized rollers to improve efficiency while still allowing operator control over the process. These machines typically feature powered rollers that apply consistent force to the sheet metal, reducing the physical effort required by the operator. Adjustable settings allow for variations in edge curling radius and crimping depth. Semi-automatic machines are ideal for medium-scale production environments where precision and repeatability are needed without full automation. They are commonly used in HVAC ductwork, roofing sheet production, and small-scale metal packaging manufacturing.
3. Fully Automatic Edge Curling and Crimping Machines
Fully automatic machines are equipped with motorized feeding systems, computer-controlled rollers, and programmable settings that allow for high-speed production with minimal human intervention. These machines use servo motors or hydraulic actuators to precisely control the pressure, speed, and roller positioning. Advanced models may also include CNC (Computer Numerical Control) or PLC (Programmable Logic Controller) systems for precise automation. Fully automatic machines are used in high-volume manufacturing industries, such as automotive, aerospace, and metal can production, where efficiency, speed, and consistency are critical.
4. Roll Forming-Based Curling and Crimping Machines
Some machines integrate edge curling and crimping into a continuous roll forming process. Roll forming machines feature multiple sets of rollers that progressively shape the metal as it moves through the system. This method is highly efficient for producing long, uniform sheet metal components with curled or crimped edges. These machines are commonly used in large-scale roofing, cladding, and structural sheet metal production. They are particularly effective for processing thin-gauge metals in continuous coils rather than discrete sheet pieces.
5. Hydraulic Edge Curling and Crimping Machines
Hydraulic-powered machines use hydraulic cylinders to apply pressure to the sheet metal, offering higher force and precision compared to mechanical systems. These machines are well-suited for working with thicker and harder metals, such as stainless steel or heavy-gauge aluminum. The hydraulic mechanism ensures smooth operation and can handle complex edge curling and crimping designs. They are commonly used in industrial applications where high-strength materials are processed, such as heavy-duty ductwork, structural components, and high-strength containers.
6. Pneumatic Edge Curling and Crimping Machines
Pneumatic machines use compressed air to drive the forming rollers or dies. These machines are typically used for lightweight sheet metals and applications requiring rapid cycle times. They are preferred in industries where speed and automation are essential but where hydraulic systems would be excessive. Pneumatic systems provide precise force control and can be easily integrated into automated production lines for high-speed processing. They are commonly used in tin can manufacturing, food packaging, and lightweight metal component production.
7. CNC Edge Curling and Crimping Machines
CNC (Computer Numerical Control) edge curling and crimping machines are the most advanced type, offering fully programmable control over the entire forming process. These machines use servo-driven rollers and advanced software to precisely shape the edges of sheet metal according to predefined specifications. CNC machines allow for complex edge profiles, multi-stage curling, and variable crimping patterns. They are widely used in precision industries such as aerospace, medical equipment, and high-end architectural metalwork.
8. Portable Edge Curling and Crimping Machines
Portable or handheld edge curling and crimping machines are designed for on-site applications, allowing operators to form sheet metal edges without requiring a large, stationary machine. These machines are typically powered by electric or pneumatic motors and are used in applications such as HVAC duct installation, roofing sheet adjustments, and metal repair work. Portable machines are convenient for contractors, repair technicians, and fieldwork operations where mobility is necessary.
9. Special-Purpose Edge Curling and Crimping Machines
Some machines are custom-designed for specific applications, such as producing curled edges for metal packaging, creating interlocking seams for ductwork, or forming decorative edge details in architectural metal panels. These machines may incorporate additional features such as embossing, beading, or edge sealing to meet specialized industry needs. Manufacturers often develop these machines based on unique customer requirements for industries like metal furniture, appliance manufacturing, or artistic metal fabrication.
Conclusion
The choice of an edge curling and sheet crimping machine depends on factors such as production volume, material type, required precision, and level of automation. Manual and semi-automatic machines are suitable for small to medium-scale operations, while fully automatic and CNC-controlled machines are essential for high-volume industrial production. Hydraulic and pneumatic systems offer additional power and efficiency, making them ideal for heavy-duty applications. As manufacturing technology continues to evolve, edge curling and crimping machines are becoming more advanced, incorporating digital controls, automation, and material adaptability to meet the growing demands of modern metal fabrication industries.
Edge curling and sheet crimping machines come in various types, each designed to meet specific production requirements, levels of automation, and material handling capabilities. Manual machines are the simplest form, operated by hand or foot pedal, making them suitable for small-scale production, repair work, and custom fabrications where precision is needed without automation. Semi-automatic machines improve efficiency by integrating powered rollers while still requiring operator input for feeding and adjustments, making them ideal for medium-volume manufacturing processes such as HVAC ductwork, roofing sheets, and lightweight structural components. Fully automatic machines eliminate the need for manual control by incorporating motorized feeding systems, servo-driven rollers, and computer-controlled settings, allowing for high-speed production with consistent quality. These are widely used in industries requiring mass production, such as automotive, aerospace, and metal packaging.
Roll forming-based machines integrate curling and crimping as part of a continuous metal forming process, using multiple sets of rollers that gradually shape the metal sheet as it moves through. This method is highly efficient for processing long sheets or coils, commonly found in roofing, cladding, and structural applications. Hydraulic edge curling and crimping machines rely on hydraulic pressure to apply force, making them well-suited for heavy-duty applications and working with thick or high-strength metals like stainless steel and aluminum. These machines provide smooth operation and are used in industries requiring structural rigidity, such as industrial containers, reinforced ducts, and load-bearing sheet components. Pneumatic machines, on the other hand, use compressed air to drive the rollers or dies, making them a suitable choice for lightweight sheet metals and applications where high-speed processing is essential, such as tin can manufacturing and food packaging.
CNC-controlled machines represent the most advanced type, utilizing computer programming to precisely control roller movement, pressure, and feed rate. These machines allow for complex edge profiles, variable crimping patterns, and multi-stage forming with high precision, making them indispensable in aerospace, high-end architectural metalwork, and specialized industrial applications. Portable edge curling and crimping machines are designed for on-site applications, allowing operators to modify sheet metal edges without requiring a fixed machine setup. These are commonly used in HVAC duct installation, metal roofing adjustments, and field repair work. Special-purpose machines are custom-designed for unique applications, such as creating interlocking seams for ducts, adding decorative edges to architectural panels, or forming specialized packaging components. These machines often incorporate additional features like embossing, beading, or edge sealing to enhance the final product’s functionality and aesthetic appeal.
As manufacturing technology evolves, modern edge curling and crimping machines increasingly integrate digital automation, sensor feedback, and predictive maintenance features, ensuring greater efficiency, precision, and adaptability. The choice of a machine depends on factors such as production scale, material properties, required speed, and industry-specific demands. Manual and semi-automatic machines cater to small to mid-scale operations, while fully automatic, hydraulic, and CNC systems serve high-volume industries where precision and consistency are paramount. The continuous advancement of these machines enables manufacturers to optimize metal forming processes, reduce production time, and improve product quality, solidifying their role as essential tools in modern metalworking and fabrication industries.
The evolution of edge curling and sheet crimping machines has led to increasingly sophisticated systems that optimize efficiency, precision, and adaptability across various industries. As demand for higher production speeds and tighter tolerances grows, manufacturers continuously refine these machines by integrating advanced control systems, high-performance materials, and automation technologies. In fully automated and CNC-controlled machines, servo motors and hydraulic actuators precisely regulate roller movement, pressure application, and material feed rates, ensuring uniform results with minimal operator intervention. These intelligent systems incorporate feedback sensors that monitor real-time processing conditions, adjusting parameters dynamically to compensate for material variations and maintain consistent edge curling or crimping profiles.
Modern machines are also designed for greater versatility, allowing manufacturers to switch between different edge profiles and crimping patterns without requiring extensive reconfiguration. Quick-change tooling systems enable rapid adjustments, reducing downtime and increasing overall productivity. In high-volume production environments, these machines integrate seamlessly with digital manufacturing ecosystems, utilizing programmable logic controllers (PLCs) and networked automation to synchronize operations with upstream and downstream processes. Predictive maintenance capabilities further enhance reliability by analyzing performance data to anticipate potential component wear, allowing for timely servicing that prevents unexpected breakdowns and production delays.
Material science advancements have also played a crucial role in improving the efficiency of edge curling and crimping machines. High-strength alloys, specialized coatings, and wear-resistant roller materials extend machine lifespan while maintaining consistent forming quality. Lubrication and cooling systems help mitigate friction and heat buildup, reducing tool wear and preserving surface integrity, especially when working with high-strength metals or complex profiles. In some applications, preheating or controlled annealing is used to improve material ductility, preventing cracks or distortions during the forming process.
With the ongoing push for sustainable manufacturing, modern edge curling and crimping machines incorporate energy-efficient motors, optimized power consumption, and material waste reduction strategies. Advanced simulation and modeling tools allow manufacturers to optimize machine settings before production, reducing trial-and-error adjustments and minimizing scrap. Additionally, digital twin technology enables real-time monitoring and remote diagnostics, allowing operators to fine-tune machine performance from a centralized interface.
As industries such as automotive, aerospace, construction, and packaging demand higher quality and efficiency, edge curling and crimping machines continue to evolve, offering greater precision, automation, and adaptability. The ability to handle diverse materials, support complex design requirements, and integrate with smart manufacturing systems ensures that these machines remain indispensable in modern production environments. The future of edge forming technology will likely see further advancements in AI-driven process optimization, enhanced material adaptability, and fully autonomous operation, reinforcing their critical role in industrial metalworking and fabrication.
The continued advancement of edge curling and sheet crimping machines is shaping the future of metal fabrication by pushing the boundaries of precision, automation, and efficiency. As manufacturing industries demand tighter tolerances and higher production speeds, machine designs are incorporating even more intelligent control systems. AI-driven automation is becoming a key feature, where machine learning algorithms analyze production data to optimize parameters such as roller pressure, feed speed, and material handling in real time. This ensures not only higher consistency in edge formation but also reduces errors, material waste, and rework.
The integration of robotics into edge curling and crimping machines is another major development, particularly in fully automated production lines where robotic arms feed sheets into the machines, adjust positioning, and transfer formed parts to the next stage in the manufacturing process. This eliminates the need for manual handling, enhancing both productivity and workplace safety. The use of cobots (collaborative robots) is also on the rise, enabling human operators to work alongside machines without the risk of injury. These cobots assist in setting up tooling, monitoring production, and performing quality control checks to ensure each sheet meets the required specifications.
Another key area of innovation lies in material adaptability. Traditionally, edge curling and crimping machines have been optimized for standard sheet metals such as mild steel, aluminum, and stainless steel. However, with the increasing use of advanced materials like high-strength alloys, composite sheets, and hybrid metal-plastic laminates, machines are evolving to handle a wider range of substrates. This includes the development of adaptive forming technologies that adjust roller pressure and forming speeds based on real-time feedback from material sensors. Such advancements allow manufacturers to work with lightweight, high-performance materials while maintaining structural integrity and aesthetic quality.
The emergence of digital twin technology is also transforming how these machines are operated and maintained. Digital twins create virtual models of physical machines, allowing engineers to simulate different edge curling and crimping processes before running actual production. This predictive modeling helps optimize settings, troubleshoot potential issues, and refine machine performance without wasting materials. Additionally, remote monitoring systems enable real-time diagnostics and maintenance scheduling, reducing unexpected downtime and improving overall equipment efficiency.
Sustainability is becoming a growing concern in the manufacturing industry, and edge curling and crimping machines are adapting to meet environmental goals. Energy-efficient motors, regenerative braking systems, and smart power management are being integrated to reduce electricity consumption. Additionally, manufacturers are developing eco-friendly lubrication and coating solutions that minimize harmful emissions while still ensuring smooth metal forming. Waste reduction is also a priority, with machines now capable of optimizing sheet usage to minimize scrap, as well as integrating with recycling systems to reclaim excess material for reuse.
Looking ahead, the future of edge curling and crimping machines will be driven by further advancements in AI, automation, and digital connectivity. Self-learning machines that automatically adapt to new materials and designs, predictive maintenance systems that eliminate unexpected failures, and fully interconnected smart factories where machines communicate seamlessly are all on the horizon. These developments will not only enhance production efficiency but also open new possibilities for complex metal forming applications in aerospace, automotive, construction, and emerging industries such as renewable energy and electric vehicle manufacturing. The role of edge curling and crimping machines in modern metalworking is set to expand, cementing their place as a vital component in high-precision manufacturing.
Edge curling and sheet crimping machines play a crucial role in a wide range of industries by providing solutions for shaping and joining sheet metal. Their applications extend across many sectors where metal forming is essential for both functional and aesthetic purposes. These machines are utilized in the following key industries and applications:
1. Automotive Industry
In the automotive sector, edge curling and crimping machines are used to form metal edges for various components, such as body panels, trim parts, and structural elements. Curling is often used for creating smooth, rounded edges on metal sheets to ensure safety by eliminating sharp edges. Crimping is used in the production of parts like heat exchangers, radiators, and gaskets, providing a secure, interlocking design that enhances durability and performance. These machines are also used to create corrugated metal sheets for structural reinforcement in vehicles, including car bodies and chassis.
2. Aerospace Industry
The aerospace industry relies on edge curling and crimping machines to produce lightweight, high-strength components for aircraft, spacecraft, and other aviation applications. Edge curling is often applied to components such as wing panels, fuselage sections, and tail assemblies to create smooth edges that prevent sharp corners, improve aerodynamics, and reduce the risk of damage. Crimping is used in fuel tanks, air ducts, and other pressure-sensitive components where a secure, leak-proof seal is necessary. The precision and consistency of these machines are critical for meeting the stringent quality and safety standards required in aerospace manufacturing.
3. HVAC (Heating, Ventilation, and Air Conditioning)
In the HVAC industry, edge curling and crimping machines are widely used to form metal sheets that are used in ducts, vents, and other HVAC components. Edge curling is particularly important for creating safe, smooth edges in air ducts, which are essential for easy handling, transportation, and assembly. Crimping is commonly used to create interlocking seams that securely join sheet metal pieces together, reducing the need for additional fasteners or welding. These machines help increase production speed and improve the overall quality of HVAC systems, ensuring better performance and longevity.
4. Roofing and Cladding
Edge curling and crimping machines are essential for the production of roofing panels and cladding systems. These machines are used to create the distinctive curled edges on roofing sheets, which helps prevent water leakage and enhances the panel’s structural integrity. Crimping is used to form interlocking profiles that allow for easier installation of roofing materials, providing a secure, weather-resistant seal. In the cladding industry, these machines are used to create corrugated metal sheets, providing both strength and aesthetic appeal to building facades.
5. Metal Packaging
In the metal packaging industry, edge curling and crimping machines are vital for producing items such as cans, bottles, and metal containers. Edge curling is used to create smooth, sealed edges on cans and lids, preventing sharp edges and ensuring a secure, tight fit. Crimping plays a key role in the manufacturing of beverage cans and food containers, where it helps form a secure closure that maintains product integrity and prevents contamination. These machines enable high-speed production with precise control over material handling, essential for the mass production of packaging items.
6. Electrical and Electronics Industry
Edge curling and crimping machines are used to form metal enclosures, connectors, and terminals in the electrical and electronics industry. Crimping, in particular, is widely used to attach connectors to wires, ensuring a reliable electrical connection that can withstand high currents without failure. Edge curling is used in the production of electrical cabinets and housings, where smooth, rounded edges are required for both safety and aesthetic purposes. These machines are also used to create cable shields and protective enclosures for sensitive electronics, ensuring that components are securely housed and insulated.
7. Metal Furniture and Appliances
Edge curling and crimping machines are used to fabricate metal parts for furniture and household appliances. For instance, these machines are employed to form the edges of metal furniture components, such as tables, chairs, and shelving units, to ensure that they are safe to handle. Crimping is often used in appliance manufacturing to form durable, secure seams in parts like washing machine bodies, refrigerators, and stoves. The precision provided by these machines is crucial for maintaining the structural integrity and visual appeal of the finished products.
8. Construction and Structural Metalwork
In construction, edge curling and crimping machines are used to produce metal profiles and components for building frameworks, reinforced structures, and decorative elements. Crimped edges are used in steel beams, columns, and plates to improve the material’s flexibility and strength. Edge curling helps create smooth, safe edges on sheet metal used in facade cladding, curtain walls, and other architectural elements. These machines enable the fabrication of complex designs and large-scale metal components needed for modern construction projects, including commercial and residential buildings.
9. Medical Equipment and Devices
The medical industry also benefits from edge curling and crimping machines, particularly in the production of components for medical devices and equipment. These machines are used to form parts such as metal casings for medical instruments, pressure vessels, and equipment housings. Crimping ensures that metal components are securely fastened, providing leak-proof seals and ensuring the structural integrity of devices. Edge curling is often applied to smooth the edges of surgical instruments and equipment, reducing the risk of injury and improving safety.
10. Renewable Energy
In the renewable energy sector, edge curling and crimping machines are employed in the production of components for wind turbines, solar panels, and other energy-generation systems. Crimping is used to create secure, interlocking connections for electrical systems in solar panels and wind turbine components. Edge curling is essential in creating smooth edges on large metal sheets used in wind turbine blades, providing the necessary aerodynamics and reducing the risk of material fatigue over time. These machines help ensure that the parts used in renewable energy systems are both durable and efficient.
Conclusion
Edge curling and sheet crimping machines have applications across a broad range of industries that require precise metal forming for safety, durability, and efficiency. From the automotive and aerospace sectors to HVAC, packaging, construction, and medical device manufacturing, these machines play an essential role in shaping metal sheets and components to meet the stringent requirements of modern industries. Their ability to create secure, smooth edges and interlocking seams ensures structural integrity, reduces manufacturing costs, and enhances the performance of the final product. With continued advancements in automation and material adaptability, the applications of edge curling and crimping machines are likely to expand further, supporting innovation across many industries.
Edge curling and sheet crimping machines are crucial across a wide variety of industries where metal forming is necessary for both functional and aesthetic purposes. In the automotive industry, these machines are widely used to form edges on body panels, structural parts, and components such as heat exchangers and radiators. Curling helps to eliminate sharp edges, improving safety and handling, while crimping ensures secure connections and interlocking parts for enhanced durability. In aerospace, the need for high precision is critical, and these machines are used to shape metal components for aircraft, spacecraft, and aviation parts. Curling creates smooth edges to reduce the risk of damage and improve aerodynamics, while crimping ensures leak-proof seals for fuel tanks and other pressurized components.
The HVAC industry uses these machines for producing ducts and air handling components, where edge curling ensures smooth, safe edges and crimping forms strong, secure joints that reduce the need for additional fasteners or welding. In roofing and cladding, edge curling machines form rounded edges to prevent water leakage and enhance the strength of roofing panels, while crimping ensures secure interlocking seams for easy installation and weather resistance. For the metal packaging sector, these machines are essential for manufacturing cans, bottles, and other containers, where curling forms smooth, sealed edges and crimping creates tight closures that maintain the integrity of the packaging.
In the electrical and electronics industry, edge curling and crimping machines are used to form enclosures, connectors, and terminals. Crimping is particularly important for attaching connectors to wires, ensuring reliable electrical connections. Curling is applied to smooth and round edges on enclosures and housings, providing safety and aesthetic appeal. The metal furniture and appliances sectors also rely on these machines for creating metal components for furniture, household appliances, and equipment. Curling is used to ensure safe, rounded edges, while crimping forms secure, durable seams.
In the construction and structural metalwork industries, these machines are used for fabricating metal profiles for building frameworks, decorative elements, and structural components. Crimping is often used in steel beams, columns, and plates to enhance strength and flexibility, while curling creates smooth edges for metal sheets used in facades and architectural features. In the medical equipment industry, edge curling and crimping are applied to form durable, safe, and functional components for medical devices, instrument housings, and pressure vessels.
In the renewable energy sector, these machines are employed in the manufacturing of components for wind turbines, solar panels, and other energy systems. Crimping ensures secure electrical connections in solar panels and wind turbine components, while edge curling is used to shape turbine blades and other large metal parts, enhancing their aerodynamics and durability. As industries evolve and demand more precision and efficiency in their manufacturing processes, edge curling and crimping machines will continue to play a vital role in ensuring that metal parts and components meet the highest standards of quality, safety, and performance. The ongoing advancements in automation and material adaptability will further expand the scope of these machines across various industries, making them an essential tool in modern manufacturing.
Advantages of Using Edge Curling and Crimping Machines
Using edge curling and crimping machines offers several advantages across various industries, especially in metal forming applications where precision, safety, and efficiency are critical. These advantages are vital for ensuring high-quality outputs while optimizing production processes. Some of the key benefits include:
- Improved Safety: One of the primary benefits of edge curling is the removal of sharp edges from metal sheets, which significantly reduces the risk of injury to operators during handling, assembly, and installation. This safety feature is essential in industries such as automotive, HVAC, and metal packaging, where workers are regularly in contact with metal parts.
- Enhanced Structural Integrity: Edge curling and crimping contribute to the overall strength and durability of metal components. By creating smooth, rounded edges and secure crimped seams, these machines help reinforce the material’s structural integrity, making components more resilient to mechanical stress, fatigue, and external forces. This is particularly important in sectors like aerospace, automotive, and construction, where safety and performance are critical.
- Increased Production Efficiency: Automated and semi-automatic edge curling and crimping machines speed up the metal forming process by reducing the need for manual labor, minimizing errors, and ensuring consistent results. This leads to higher throughput and improved manufacturing efficiency, making it possible to meet high production demands while maintaining quality standards. The ability to form and shape large volumes of metal quickly without compromising precision is an essential factor in industries such as metal packaging and HVAC.
- Cost-Effectiveness: By reducing the need for additional manual labor and minimizing scrap material through optimized forming processes, edge curling and crimping machines help reduce operational costs. The precision of these machines ensures minimal waste and maximum material utilization, which can lead to significant cost savings in material consumption, especially when working with expensive metals.
- Better Joint Quality: Crimping creates strong, interlocking seams that provide secure connections between metal parts. This is particularly beneficial in applications where the integrity of joints is essential, such as in fuel tanks, automotive parts, HVAC ducts, and metal packaging. The resulting crimped joints are more durable and less prone to leakage or failure compared to other methods, such as welding or riveting.
- Versatility and Flexibility: Modern edge curling and crimping machines are highly versatile, capable of handling a wide range of materials, thicknesses, and designs. This allows manufacturers to produce custom metal components with different edge profiles, crimping patterns, and forming characteristics based on specific requirements. The machines can be easily adjusted to accommodate various applications in industries such as aerospace, construction, and medical devices.
- Aesthetic Appeal: Curling and crimping contribute to the aesthetic quality of metal products by providing a smooth, polished finish. For instance, edge curling eliminates rough edges, giving metal panels and parts a clean, finished appearance. In architectural applications, this is particularly important for maintaining the visual appeal of metal facades and roofing systems. Crimping, especially when used in decorative metalwork, also contributes to the overall design by creating uniform, neat seams.
- Reduced Manual Labor: By automating the edge curling and crimping processes, these machines reduce the amount of manual labor required, allowing operators to focus on other important tasks in the production process. This also reduces the physical strain on workers, improving overall ergonomics in the workplace. In high-volume manufacturing settings, automation leads to more streamlined operations and reduces the risk of human error.
- Higher Precision and Consistency: Edge curling and crimping machines are designed to provide consistent results with high precision. This consistency is vital for ensuring that components meet strict quality control standards. In industries like aerospace, automotive, and electronics, where even the slightest variation in dimensions can affect performance, the precision offered by these machines is indispensable.
- Ease of Integration into Automated Production Lines: Many modern edge curling and crimping machines can be integrated into fully automated production lines, allowing for seamless coordination with other manufacturing processes. This integration leads to more efficient workflow management, reduces production bottlenecks, and enhances overall system performance. Automated systems also offer the ability to monitor production in real time, making it easier to identify and address issues quickly.
- Minimized Environmental Impact: With the ability to optimize material use and reduce waste, these machines contribute to more sustainable manufacturing practices. Additionally, the use of energy-efficient motors, reduced energy consumption, and recyclable metal materials help manufacturers minimize their environmental footprint. Sustainable practices such as these are increasingly becoming a priority in industries focused on reducing their ecological impact.
- Customization Capabilities: Many edge curling and crimping machines are customizable to meet specific manufacturing needs. Operators can adjust settings such as the roller pressure, feed rate, and material tension, which allows them to create unique edge profiles and crimping designs that suit specialized applications. This flexibility is particularly useful in industries like custom metal furniture or unique architectural features.
Overall, edge curling and crimping machines offer a combination of safety, precision, efficiency, and cost-effectiveness that makes them indispensable in metalworking industries. Their ability to automate and optimize metal forming processes results in higher-quality products, reduced waste, and increased profitability for manufacturers, while also contributing to enhanced safety and sustainability in the production environment.
When selecting an edge curling and crimping machine, several factors need to be considered to ensure the right fit for the specific needs of the production process. These factors will influence the machine’s performance, efficiency, and the quality of the final product. Here are some of the key considerations:
- Material Type and Thickness: Different machines are designed to handle various types of materials, including aluminum, steel, stainless steel, and other metals. The thickness of the material is also a crucial factor; some machines are better suited for thinner materials, while others are designed for heavier, thicker sheets. It’s important to choose a machine that can accommodate the specific material type and thickness required for the production process.
- Production Volume: The scale of production plays a significant role in determining the appropriate machine. For high-volume production, fully automated machines with high throughput are essential to meet demand efficiently. These machines typically offer faster processing speeds, higher precision, and less manual intervention. In contrast, for lower-volume or custom fabrication work, manual or semi-automatic machines may be more suitable due to their lower cost and ability to handle smaller batches or specific customizations.
- Edge Profile Requirements: The type of edge profile needed for the final product is a major consideration. Some machines are designed to form specific edge shapes, such as round or smooth curls, while others can create more complex profiles. Ensure the machine can accommodate the desired edge shape, whether it’s a simple curled edge, a flanged edge, or a more intricate crimped or folded design.
- Crimping and Curling Features: Some machines specialize in curling, while others are better suited for crimping. Depending on the application, it may be necessary to have a machine that can perform both operations effectively. Machines with adjustable settings for curling pressure, crimping depth, and other parameters allow for greater flexibility in creating various forms and profiles, which is especially important in industries like HVAC, automotive, and packaging.
- Automation and Control: The level of automation and control offered by the machine will impact both production efficiency and ease of use. Fully automated machines reduce the need for operator intervention, increase production speed, and ensure consistent quality. However, they typically come at a higher cost. Semi-automatic machines may offer a balance between cost and efficiency, while manual machines are often more affordable but require more direct operator involvement.
- Precision and Accuracy: The quality of the edge curling and crimping process relies heavily on the machine’s precision and accuracy. If your product requires tight tolerances and high-quality finishes, investing in a machine with advanced control systems, such as CNC (Computer Numerical Control), may be necessary. These machines can precisely control roller movements, pressure, and feed rates, ensuring high levels of accuracy and repeatability.
- Speed and Throughput: Depending on the production requirements, the speed and throughput of the machine may be a critical factor. High-speed machines are essential for industries that require mass production, such as packaging, automotive, or construction. Machines with adjustable speeds or variable cycle times allow manufacturers to tailor production rates to match specific needs.
- Flexibility and Customization: Some machines offer customization options to suit different types of products or materials. For instance, adjustable roller setups, modular tooling, and variable feed mechanisms allow the machine to be adapted for a range of tasks. If your production involves diverse products or custom metal parts, a flexible machine capable of being reconfigured for different processes is essential.
- Maintenance and Durability: A machine’s longevity and ease of maintenance are vital factors to consider. Look for machines that are built with durable, high-quality materials and that have readily available spare parts. Additionally, consider the machine’s maintenance requirements, such as lubrication, tool replacement, and cleaning. Machines with predictive maintenance features that alert operators to potential issues before they result in downtime can be especially valuable in high-volume environments.
- Energy Efficiency: In today’s manufacturing landscape, energy efficiency is becoming an increasingly important consideration. Machines that consume less power, incorporate energy-saving motors, and have optimized power management systems contribute to reducing operational costs over time. Energy-efficient machines are particularly valuable in industries with high production volumes, as they help minimize the overall environmental impact and reduce electricity bills.
- Operator Training and Ease of Use: Machines with user-friendly interfaces and clear operating instructions can reduce the learning curve for operators, ensuring smoother and more efficient production. If the machine requires specialized knowledge to operate or maintain, it’s important to factor in the cost and time for training. Some machines come with advanced features like touchscreens, programmable settings, and remote control options that simplify the setup and monitoring processes.
- Cost and Budget: The upfront cost of the machine, along with its long-term operating and maintenance costs, should be carefully evaluated. While high-end, fully automated machines may offer advanced features and efficiency, they also come with a higher initial investment. On the other hand, manual or semi-automatic machines are more affordable but may require more labor and time to achieve the same output. Balancing the machine’s capabilities with the budget available is essential to achieving a cost-effective solution.
- After-Sales Support and Service: Reliable after-sales support, including installation, maintenance, and troubleshooting, is an important factor in selecting a machine. A strong support network can minimize downtime and ensure that the machine operates optimally throughout its lifecycle. Look for manufacturers that offer comprehensive warranty packages, technical support, and maintenance services to help address potential issues quickly.
- Space and Layout Considerations: The physical size and layout of the machine should be compatible with the available space in the production facility. For example, fully automated machines often require more space due to their complex setups and associated components. Ensure the machine can fit comfortably into your facility without obstructing other processes or workflow, and that it is easily accessible for maintenance and operation.
- Compliance with Industry Standards: Depending on the industry, the machine may need to meet specific regulatory standards related to safety, emissions, or product quality. Ensure that the chosen machine complies with relevant industry regulations and certifications to avoid any legal or operational issues.
By considering these factors, manufacturers can select an edge curling and crimping machine that best fits their specific needs, ensuring a productive and efficient metal forming process that meets both operational and product quality requirements.
When selecting an edge curling and crimping machine, it’s important to consider several factors that can significantly impact production efficiency and product quality. One of the first considerations is the material type and thickness. Different machines are designed to handle specific materials such as steel, aluminum, or stainless steel, and varying material thicknesses. It’s important to choose a machine that accommodates the specific material type and thickness for the intended application. The production volume also plays a major role; high-volume operations generally require fully automated machines that can process large quantities quickly and consistently. For smaller batches or custom work, semi-automatic or manual machines may be more cost-effective and flexible.
The desired edge profile is another critical factor. Machines are often tailored to produce specific edge profiles, so it’s essential to ensure the machine can form the desired edge type, whether it’s a rounded curl or a more complex crimped design. Additionally, the specific curling and crimping features needed will determine the best machine to use. Some machines specialize in one function or the other, while others can handle both processes. Machines with adjustable settings provide greater flexibility in achieving various shapes and forms, which can be especially valuable in industries like automotive or HVAC.
The level of automation and control also affects production efficiency. Automated machines reduce the need for manual labor, streamline production, and maintain consistency, but they typically come at a higher initial cost. Semi-automatic or manual machines may be more affordable but require more operator involvement. Precision is also a key factor; machines that offer high accuracy and tight tolerances are critical for industries like aerospace, medical, and electronics, where even slight variations can lead to performance issues or safety concerns.
Speed and throughput are essential considerations, especially in high-demand industries. Machines with faster processing speeds and higher throughput capabilities can help meet tight production deadlines, whereas slower machines might be more suitable for niche or low-volume work. Flexibility and customization options are another key factor, especially when dealing with a variety of materials or custom designs. Machines that allow for adjustments to accommodate different product types and material characteristics can reduce the need for purchasing multiple machines and improve overall production efficiency.
Maintenance and durability are also important to ensure long-term performance. Machines that require minimal maintenance and are built with high-quality, durable components will offer better longevity and reduce downtime. Machines with easily accessible parts and comprehensive service options are preferable to reduce the impact of any needed repairs or maintenance. Energy efficiency has become increasingly important as manufacturers look to reduce operational costs and their environmental impact. Machines with lower energy consumption can help to keep costs down, especially in high-production environments.
The ease of use and operator training requirements should also be factored in. Machines that are easy to operate, with clear interfaces and minimal complexity, will reduce training time and improve overall efficiency. Additionally, strong after-sales support is essential. A manufacturer that offers installation, technical support, and ongoing maintenance services will ensure the machine runs smoothly and any issues are addressed promptly, preventing costly downtimes.
Lastly, it’s important to evaluate the cost and budget. While more advanced, automated machines might offer significant productivity gains, they come with a higher upfront cost. On the other hand, manual or semi-automatic machines, although less expensive, may require more labor or take longer to produce the same amount of output. Ensuring that the machine fits within the budget while still meeting production requirements is essential for making a cost-effective decision.
By considering all these factors, manufacturers can choose the most suitable edge curling and crimping machine for their specific needs, ensuring an efficient, cost-effective, and high-quality production process.
When choosing an edge curling and crimping machine, several important factors must be considered to ensure the machine meets specific production requirements and operational needs. These factors help to optimize the machine’s performance, ensure efficiency, and improve the quality of the final product.
One of the primary considerations is the material type and thickness. Different machines are designed to process specific materials, such as aluminum, steel, or stainless steel, and various thicknesses. It’s essential to select a machine that can handle the material you plan to work with, ensuring optimal performance and preventing material damage. The production volume also plays a crucial role. High-volume operations require machines with high throughput and automation capabilities to meet production deadlines and ensure consistent quality. Conversely, low-volume or custom jobs might benefit from semi-automatic or manual machines, which offer more flexibility but may not be as fast.
The edge profile required for the final product is another key factor. Different machines can produce various edge shapes, such as rounded, smooth, or crimped edges. Choosing a machine that can create the specific edge profile required for your application is crucial, whether for aesthetic purposes or functional requirements. Crimping and curling features are also important; some machines are designed for one function, while others offer both. Machines with adjustable settings for curling pressure and crimping depth allow for customization based on specific needs, which is particularly valuable in industries with varying product designs.
The level of automation and control is also an important consideration. Fully automated machines typically offer higher production speeds, consistency, and minimal operator involvement, but they often come at a higher initial cost. Semi-automatic machines provide a balance between automation and operator control, making them a good option for companies looking to reduce labor costs while maintaining some level of manual intervention. Precision and accuracy are critical in industries where tight tolerances are required, such as aerospace or medical device manufacturing. Machines that offer precise control over the curling and crimping processes are essential for ensuring high-quality results.
The speed and throughput capabilities of the machine are essential for ensuring the machine can handle the production demands. Faster machines with higher throughput are necessary for industries like packaging or automotive manufacturing, where large quantities of parts need to be processed quickly. However, for smaller-scale production or custom jobs, machines with adjustable speeds or slower cycle times may be more appropriate.
Flexibility and customization options are also worth considering, especially if the machine needs to accommodate a range of materials, product sizes, or edge profiles. Machines that offer adjustable rollers, changeable tooling, or programmable settings allow manufacturers to handle a wide variety of tasks without investing in multiple machines.
The maintenance and durability of the machine are critical to long-term performance. Machines that are built to last and require minimal maintenance help reduce downtime and operational costs over time. Machines with durable components and readily available replacement parts ensure that the machine remains operational for many years.
Energy efficiency is becoming increasingly important, particularly in large-scale production environments. Machines that consume less power contribute to reducing overall energy costs and help to lower the environmental footprint of the production process.
Operator ease of use is another factor to consider, as machines with intuitive interfaces and user-friendly controls reduce the need for extensive training. This can increase productivity and reduce the risk of operational errors. Additionally, after-sales support is an important factor when choosing a machine. Having access to reliable technical support, spare parts, and maintenance services ensures that any issues are resolved quickly and efficiently, minimizing downtime.
Finally, the cost of the machine should be evaluated, including both the initial investment and ongoing operational costs. High-end automated machines may have significant upfront costs but can offer higher production rates and lower labor costs in the long term. Alternatively, manual or semi-automatic machines can be more affordable upfront but may incur higher labor and maintenance costs over time.
By carefully considering these factors, manufacturers can select the most suitable edge curling and crimping machine for their specific needs, ensuring efficiency, quality, and cost-effectiveness in their production processes.
How Do You Manufacture Cookware?

Manufacturing cookware involves several steps, from material selection to finishing and quality control. The process can vary depending on the type of cookware being produced, such as pots, pans, and bakeware, and the material used, such as stainless steel, aluminum, cast iron, or nonstick-coated cookware. Below is an overview of the general process of manufacturing cookware:
1. Material Selection
The first step in cookware manufacturing is choosing the right material. Common materials include:
- Stainless steel: Known for its durability, rust resistance, and high heat resistance. It is commonly used in high-quality cookware.
- Aluminum: Lightweight and an excellent heat conductor, often used for frying pans and sauté pans. Sometimes, it’s anodized for additional durability and nonstick properties.
- Cast iron: Known for its heat retention and durability, used in skillets, Dutch ovens, and other heavy-duty cookware.
- Copper: Used for its superior heat conductivity but requires a lining, such as stainless steel, due to its reactivity with food.
- Nonstick coating: Materials like Teflon or ceramic are often applied to cookware to make them easier to clean and to prevent food from sticking.
The selection of material depends on the desired characteristics of the cookware, such as heat distribution, durability, and ease of cleaning.
2. Metal Forming
Once the material is selected, the cookware components are shaped through various metal forming processes:
- Stamping or Pressing: Metal sheets are fed into a machine where they are pressed or stamped into the shape of the cookware (such as a pan, lid, or pot). The sheet metal is typically cut into the desired size and then pressed into a mold to create the base shape.
- Casting: For materials like cast iron or some aluminum cookware, molten metal is poured into a mold and allowed to cool, solidifying into the desired shape. This process is ideal for heavy-duty cookware.
- Rolling: Metal sheets may be rolled to a thinner form, particularly for aluminum cookware, which is then shaped into pans or pots.
In some cases, cookware is made by spinning, where a circular disc of metal is spun at high speeds on a lathe, forming it into a bowl or pan shape.
3. Assembly
After the individual pieces of cookware are formed, they are assembled. This step involves attaching components such as handles, lids, and any additional features (e.g., pouring spouts or helper handles).
- Handle Attachment: Handles are usually made from materials like metal, plastic, or heat-resistant silicone. They are attached to the cookware via screws, rivets, or welding, depending on the design.
- Lid Assembly: For cookware with lids, handles are typically attached to the lids via similar methods, ensuring the lid fits securely onto the pot or pan.
4. Surface Treatment
Cookware often undergoes surface treatments to enhance performance, appearance, and safety:
- Nonstick Coating: For cookware like frying pans, a nonstick coating is applied to make cooking and cleaning easier. This coating can be sprayed or baked onto the cookware’s surface. Nonstick coatings are made from materials like PTFE (Teflon) or ceramic-based solutions.
- Anodizing (for aluminum): Aluminum cookware can be anodized to create a hard, corrosion-resistant surface. Anodizing involves an electrochemical process that thickens the metal’s oxide layer, which improves durability and enhances its nonstick properties.
- Polishing and Buffing: Stainless steel and other metals are often polished to create a shiny, smooth surface. This also helps to improve the cookware’s aesthetic appeal.
5. Heat Treatment
Some cookware, especially cast iron or certain stainless steel pieces, undergoes heat treatment to strengthen the metal and improve its performance. Cast iron cookware is often seasoned after casting to create a natural nonstick surface. For other metals, heat treatment can also help to improve their hardness and resistance to wear and corrosion.
6. Quality Control
Once the cookware has been assembled, surface-treated, and heat-treated, it undergoes a series of quality control checks to ensure that it meets industry standards for safety, durability, and performance. This includes:
- Inspection for defects: Any defects such as cracks, warping, or imperfections in the finish are checked and corrected.
- Testing for heat conductivity: The cookware’s ability to heat evenly is tested to ensure that it meets the expected performance standards.
- Safety tests: For nonstick cookware, tests are performed to ensure that the coating is free from harmful chemicals and adheres properly to the surface.
7. Packaging and Distribution
Once the cookware passes quality control, it is cleaned, packed, and prepared for shipment. Packaging includes protective materials to prevent scratches or damage during transport, and labeling with brand, safety instructions, and usage guidelines.
8. Additional Considerations
- Environmental Considerations: In today’s manufacturing environment, there’s a growing emphasis on sustainable practices. Many manufacturers focus on using recycled materials for cookware, as well as reducing energy consumption during production.
- Innovation: Newer cookware designs often incorporate advanced technologies, such as improved nonstick coatings, hybrid materials (such as copper and stainless steel), or induction-compatible bases for efficient cooking on induction cooktops.
By following these manufacturing steps, cookware is produced to meet the needs of the consumer, providing durable, functional, and safe cooking tools that can withstand high temperatures and frequent use in the kitchen.
Material selection is a critical aspect of cookware manufacturing as it directly affects the performance, durability, safety, and overall quality of the finished product. The choice of material influences the cookware’s ability to conduct and retain heat, its resistance to corrosion, its weight, and its ease of cleaning. Different materials offer various benefits and drawbacks, so selecting the right material requires careful consideration of the intended use, cooking methods, and desired characteristics of the cookware.
One of the most commonly used materials is stainless steel, known for its resistance to rust, staining, and corrosion. It is durable and often used in high-end cookware for its ability to withstand high temperatures without warping. Stainless steel also provides an attractive, shiny finish, but it is a poor conductor of heat on its own, which is why many high-quality stainless steel pans include a layer of aluminum or copper at the base to improve heat distribution. Aluminum, on the other hand, is prized for its excellent heat conductivity. It heats up quickly and distributes heat evenly, making it ideal for frying pans and sauté pans.
However, raw aluminum can be prone to scratching, denting, and reacting with acidic foods. To address these issues, aluminum cookware is often anodized, a process that creates a hard, non-reactive surface that is both scratch-resistant and corrosion-resistant. For cookware requiring even better heat retention, cast iron is an excellent choice. Cast iron pots and pans are known for their ability to retain and evenly distribute heat, making them ideal for slow-cooking, frying, and baking. Cast iron cookware is durable and can last for generations if properly cared for. However, it is heavy and prone to rust if not properly seasoned or maintained. Many cast iron pans are now coated with enamel, which helps to prevent rust and makes cleaning easier while still maintaining the heat-retention benefits. Copper, known for its superior heat conductivity, is often used in premium cookware for its ability to quickly adjust to temperature changes.
Copper cookware allows for precise temperature control and is often used by professional chefs. However, copper is reactive with certain foods, which is why it is often lined with stainless steel. While copper provides excellent performance, it requires regular polishing to maintain its appearance and is generally more expensive than other materials. Nonstick coatings are commonly applied to cookware to reduce the need for oil or butter and make cooking and cleaning easier. These coatings, typically made of PTFE (polytetrafluoroethylene) or ceramic-based compounds, prevent food from sticking to the surface and help in creating healthier meals with less fat. Nonstick cookware is lightweight, easy to clean, and offers good cooking performance, but the coatings can wear out over time, especially with the use of metal utensils or excessive heat. There are also concerns about the safety of nonstick coatings, particularly older ones that may contain PFOA (perfluorooctanoic acid), which has been linked to health risks. As a result, newer nonstick cookware is often marketed as PFOA-free. Another material often used for specialized cookware is carbon steel. Similar to cast iron, carbon steel has excellent heat retention properties and is favored by professional chefs for its ability to achieve a perfect sear on meats.
Carbon steel cookware is lighter than cast iron but requires seasoning and maintenance to develop a nonstick patina and prevent rusting. As with cast iron, it can be reactive with acidic foods, but it is beloved in the culinary world for its versatility and heat responsiveness. The choice of material also depends on the type of cooking being done. For example, induction-compatible cookware must have a magnetic base, which is why materials like stainless steel with an iron base or cast iron are often used. On the other hand, non-induction cookware can be made from a wider range of materials, including aluminum or copper. The material also impacts the cookware’s weight, with cast iron being heavy but excellent for slow-cooking, while aluminum is lightweight and easier to handle for everyday tasks. Ultimately, material selection is a balancing act between durability, functionality, cost, and the specific cooking needs of the consumer. Understanding the properties of each material, such as heat conductivity, weight, ease of cleaning, and maintenance, allows manufacturers to produce cookware that meets both functional and aesthetic requirements, delivering a product that performs well over time and enhances the cooking experience.
Metal Forming
Metal forming is a crucial process in the manufacture of cookware, as it shapes and molds the raw metal materials into the desired cookware components, such as pots, pans, and lids. The metal forming process can vary depending on the material being used and the complexity of the cookware design. Generally, the first step in metal forming begins with the preparation of the metal sheets or blanks, which are often purchased in rolls or sheets. These metal sheets are typically cut to size based on the specifications of the cookware design. For cookware made of aluminum, stainless steel, or copper, the metal sheets are the starting point, and the shaping process will determine the final form of the piece.
The first technique used in metal forming is stamping or pressing, where metal sheets are placed in a die, and a press is used to force the metal into the shape of the cookware. This process is commonly used for items like frying pans or saucepans, where the base of the pan is formed from a single sheet of metal. The metal is pressed into a mold that shapes it into the bowl-like form of the cookware, and the edges are either curled or flattened to form the pan’s rim. Stamping allows for high production rates, making it ideal for cookware manufacturing on a large scale. Another method of metal forming is spinning, used mainly for aluminum cookware and some other metals.
In this process, a flat metal disc is placed onto a rotating spindle, and a tool is applied to the surface to shape the disc into a cylindrical form. The spinning process is ideal for creating uniform, lightweight cookware pieces, such as pie pans, bowls, or some types of sauté pans. This method also offers flexibility in design and can be used to create cookware with a wide range of shapes and sizes. Another common metal forming technique is casting, which is typically used for cookware made of cast iron or sometimes aluminum. In this process, the metal is melted and poured into a mold that holds the desired shape. The metal is allowed to cool and solidify in the mold, taking on the shape of the cookware component. Cast iron cookware, for example, is created using this method to form heavy-duty pieces such as Dutch ovens, skillets, and griddles.
The casting process is ideal for creating durable and heat-retentive cookware, but it tends to result in a heavier product, making it less ideal for those who prefer lightweight cookware. Some cookware also undergoes forging, a process in which a metal billet is heated and then hammered into shape using a die. Forging is less common in cookware manufacturing but is used for making high-quality, heavy-duty items like certain knives or specialized kitchen tools. This method can produce cookware with excellent durability and strength but is more time-consuming and expensive than other metal-forming techniques. For certain types of cookware, such as pots and pans with multi-layered bases, rolling is used. In this process, metal sheets or strips are passed through rollers to reduce their thickness and increase their length. This is commonly used for creating the multi-ply cookware, where several layers of metal are fused together to create a durable, heat-conductive base. For example, a stainless steel pot may have a core of aluminum to improve heat distribution, with stainless steel on the outside for durability and appearance.
The rolling process ensures that the metal is evenly distributed, resulting in uniform thickness and consistent quality. Lastly, for cookware with specific features like handles, spouts, or rims, welding, riveting, or fastening may be used. Handles are often welded or riveted onto the body of the cookware, ensuring that they are securely attached and capable of withstanding high temperatures and the rigors of daily cooking. Similarly, the edges of cookware pieces may be rolled or crimped to ensure a secure and finished look, while adding strength to the piece. Each of these metal-forming techniques plays an important role in creating cookware that is both functional and aesthetically pleasing. The specific methods chosen will depend on factors like the type of material, the design of the cookware, and the intended purpose.
For example, cookware meant for high-heat cooking, such as cast iron or certain aluminum pans, may require more robust forming processes like casting or forging to create a durable, heat-retentive product. Meanwhile, cookware intended for more delicate tasks, such as saucepans or nonstick frypans, may be formed using stamping or spinning to create a lighter, more evenly heated piece. The quality of the metal-forming process directly impacts the final product’s performance, durability, and overall aesthetic, and it is a fundamental part of ensuring the cookware meets the necessary standards for safety and functionality.
Assembly is a key step in the cookware manufacturing process where all the individual components are brought together to create the final product. Once the various parts of the cookware, such as the body, handles, lids, and base, are fabricated, they are assembled into a fully functional and durable piece. The first stage of the assembly process typically involves attaching the handles to the cookware body. Handles are often made from materials like stainless steel, plastic, or heat-resistant silicone, depending on the design and intended use of the cookware. The handles are either welded, riveted, or screwed onto the cookware body, ensuring they are securely attached and can withstand the high temperatures and frequent handling associated with cooking.
For some cookware, handles may be designed to be detachable for easier storage, while for others, permanent attachment is preferred to ensure durability and safety. Once the handles are securely fixed in place, the next step in the assembly process often involves attaching lids. Lids are typically made of materials similar to the cookware body, such as stainless steel or tempered glass. The lids are designed to fit tightly onto the cookware to retain heat and moisture during cooking. In some cases, the lid may feature a small vent to allow steam to escape, preventing excessive pressure buildup. For safety and convenience, the lid handle is often made of heat-resistant material, and it is carefully attached to the lid, ensuring a comfortable grip. Another aspect of assembly is the attachment of any additional features or components that the cookware might require. For example, some cookware, such as frying pans, may include pouring spouts to make it easier to pour liquids without spills.
These spouts are carefully integrated into the cookware body and are welded or fastened to ensure they remain firmly in place during use. Similarly, cookware designed with special features, like nonstick coatings or induction compatibility, may require additional steps in assembly to incorporate these elements effectively. The nonstick coating, for instance, may be applied in a separate step, after the cookware body is formed, while induction-compatible cookware may include a layer of magnetic material added to the base. Once all the components have been properly attached, the cookware undergoes additional checks for quality control. This includes testing the strength and security of the handles and lid, ensuring that all parts fit together correctly, and verifying that the cookware meets safety standards. For example, if the cookware has a nonstick surface, the coating’s adherence and uniformity are tested to ensure it will last through regular use and cleaning. Additionally, any seams or joints from the assembly process are inspected to ensure there are no weaknesses or leaks, especially in cookware items like pressure cookers or stews that require a tight seal.
During assembly, some cookware pieces may also receive additional finishing touches, such as polishing or buffing. This is common for stainless steel cookware, which may be polished to achieve a smooth, shiny finish that is both aesthetically pleasing and easy to clean. The buffing process ensures that there are no sharp edges or rough spots that could affect the performance or safety of the cookware. After assembly and finishing, the cookware typically undergoes a final inspection and testing phase. This ensures that all the pieces meet the manufacturer’s standards for quality, durability, and functionality. The cookware is checked for consistency in shape, size, and finish, and any cosmetic defects are corrected.
The assembled cookware is then cleaned and prepared for packaging, ensuring that it is free from any oils, dust, or residues that may have accumulated during the manufacturing process. The assembly stage plays a significant role in determining the overall quality and durability of the cookware. Ensuring that the handles are securely attached, the lids fit properly, and all additional features are incorporated correctly is essential for producing high-performance cookware. A well-assembled piece will not only function effectively but also be safe, durable, and easy to use. The attention to detail in this stage is critical to ensuring that the final product meets both the manufacturer’s and the consumer’s expectations, providing a cookware item that performs consistently and lasts over time.
Surface treatment is an essential part of cookware manufacturing, as it enhances the performance, durability, and aesthetic appeal of the finished product. It involves a series of processes designed to improve the surface characteristics of the cookware, such as heat resistance, corrosion resistance, nonstick properties, and appearance. The specific surface treatment applied depends on the material of the cookware and the desired qualities of the final product. For many cookware items, particularly those made of stainless steel or aluminum, polishing and buffing are common surface treatments used to achieve a smooth, shiny finish. Polishing helps to remove any surface imperfections or scratches left from the forming and manufacturing processes, ensuring that the cookware looks attractive and is easy to clean.
This treatment is particularly important for cookware that is intended for high-end kitchens, where appearance plays a key role in product appeal. In addition to improving aesthetics, polishing stainless steel cookware also helps to make it more resistant to food particles sticking to the surface, making cleaning easier. Another vital surface treatment is the application of nonstick coatings, which are especially common in frying pans, skillets, and other cookware intended for low-fat cooking. Nonstick coatings, such as PTFE (polytetrafluoroethylene, commonly known as Teflon) or ceramic-based coatings, are applied to the cookware to create a smooth, slick surface that prevents food from sticking during cooking. This surface treatment reduces the need for oils and fats, promoting healthier cooking while making the cookware easier to clean. Nonstick coatings are applied by spraying or dipping the cookware in the coating material, which is then cured by baking it in an oven to form a durable, even layer.
While nonstick coatings improve performance, they can wear down over time, especially with excessive heat or the use of metal utensils, so it’s crucial to follow proper care instructions. For cookware made from aluminum or other metals, anodizing is another important surface treatment used to enhance durability and resistance to corrosion. Anodizing involves an electrochemical process that thickens the metal’s natural oxide layer, creating a harder, more durable surface. This treatment makes aluminum cookware more resistant to scratches, dents, and discoloration, while also improving its resistance to rust and corrosion. Anodized aluminum cookware is also less likely to react with acidic foods, which can cause discoloration or affect the flavor of the food being cooked. Anodizing also allows for the creation of colored cookware, as the process can incorporate dyes into the oxide layer, giving the cookware a range of attractive colors.
For cast iron cookware, seasoning is a critical surface treatment that not only prevents rust but also creates a natural nonstick surface. Seasoning involves coating the cookware with a thin layer of oil and then heating it to a high temperature, which causes the oil to polymerize and form a hard, nonstick coating on the surface of the cast iron. This process helps to prevent the cookware from rusting while improving its cooking performance by allowing for better heat retention and distribution. Over time, cast iron cookware develops a more seasoned surface with regular use, enhancing its nonstick qualities. Additionally, some cast iron cookware may be enameled, with a layer of vitreous enamel applied to the surface. This enamel coating prevents rust and provides a smooth, easy-to-clean surface, while also offering improved heat retention. Enamel-coated cast iron cookware combines the best of both worlds—durability and heat retention from cast iron, and the easy maintenance and protection of enamel.
For cookware that is exposed to high levels of heat and wear, such as cookware used on induction stoves or for heavy-duty cooking, heat treatment is often applied to further improve durability and performance. Heat treatment, which includes processes like tempering and hardening, strengthens the cookware, making it more resistant to damage from high temperatures or impacts. In some cases, cookware may also undergo additional surface treatments to improve its resistance to stains, discoloration, or abrasion. This is especially important for cookware used in commercial kitchens, where the demand for long-lasting, high-performance tools is critical. In addition to functional surface treatments, many cookware items undergo decorative or branding treatments, such as laser etching or screen printing. These treatments are used to add logos, markings, or other decorative elements to the surface of the cookware, enhancing its branding and appeal to consumers. Surface treatments can also play a role in enhancing the cookware’s ability to interact with specific cooking surfaces.
For example, cookware intended for use on induction stoves requires a ferrous material in the base to allow for magnetic interaction with the induction burner. In such cases, the base of the cookware may be treated with a special process to ensure the proper magnetic properties. Overall, surface treatment is a crucial aspect of cookware production that directly impacts the cookware’s performance, longevity, and ease of use. The right surface treatment not only makes the cookware more durable and effective at heat conduction but also improves its safety, ease of cleaning, and visual appeal. The application of nonstick coatings, anodizing, polishing, and seasoning, among other treatments, ensures that the cookware can withstand the rigors of daily cooking while providing a superior cooking experience.
Heat treatment is a critical process in cookware manufacturing, as it plays a vital role in enhancing the strength, durability, and performance of various cookware materials. This process involves controlled heating and cooling of the metal to alter its physical properties, making the cookware more resistant to wear, deformation, and thermal damage. Different types of cookware materials, such as cast iron, stainless steel, aluminum, and carbon steel, benefit from specific heat treatment techniques designed to optimize their characteristics for cooking. In the case of cast iron cookware, heat treatment begins with the casting process, where molten iron is poured into molds and allowed to solidify.
However, even after casting, the cookware often undergoes additional heat treatment to further improve its properties. One of the most common techniques is seasoning, which involves coating the cookware with a thin layer of oil or fat and then heating it to a high temperature. This causes the oil to polymerize, forming a durable, nonstick surface that also protects the cookware from rust. Seasoning enhances the cookware’s heat retention and distribution capabilities, making it ideal for slow-cooking and frying. For raw cast iron, heat treatment strengthens the metal, allowing it to withstand the rigors of high-heat cooking. Another type of heat treatment applied to cast iron is tempering, which involves reheating the cast iron to a lower temperature to relieve internal stresses and reduce brittleness. This process increases the toughness and resilience of the cookware, helping to prevent cracking or breaking under extreme conditions. Aluminum cookware, particularly when anodized, also benefits from heat treatment. Anodizing involves an electrochemical process where aluminum is submerged in an electrolyte solution and subjected to an electric current. This process thickens the natural oxide layer on the surface of the aluminum, creating a harder, more durable surface that is resistant to scratches, corrosion, and staining.
The aluminum is then heat-treated to further enhance its strength and to ensure that the anodized surface is firmly bonded to the metal. Heat treatment of anodized aluminum cookware also improves its resistance to warping, allowing it to maintain its shape and cooking performance over time. Stainless steel cookware, which is widely used for its durability and resistance to corrosion, can also benefit from heat treatment to improve its mechanical properties. In many cases, stainless steel cookware is subjected to a process called hardening, which involves heating the steel to a high temperature and then rapidly cooling it, typically by quenching it in water or oil. This process increases the hardness of the steel, making it more resistant to scratching and wear.
Additionally, stainless steel may be annealed, which involves heating the steel to a specific temperature and allowing it to cool slowly. Annealing relieves internal stresses in the metal, making it less prone to cracking or warping under heat. For cookware materials such as carbon steel, heat treatment is essential for developing the right balance between hardness and flexibility. Carbon steel cookware is often heat-treated through a process of hardening and tempering. Hardening involves heating the carbon steel to a high temperature and then rapidly cooling it, which increases its hardness. Tempering follows, where the steel is reheated to a lower temperature and cooled slowly to reduce brittleness and improve toughness. This combination of hardening and tempering gives carbon steel cookware its unique properties, such as excellent heat retention and a naturally nonstick surface that improves with use. Carbon steel cookware, like cast iron, requires seasoning to develop a protective, nonstick coating that enhances its cooking performance. Heat treatment is also used in the production of cookware designed for induction cooking.
Cookware that is compatible with induction cooktops must have a ferrous base to interact with the magnetic field created by the induction stove. To achieve this, certain cookware pieces may undergo a heat treatment process to ensure that the base is magnetically responsive. In some cases, a layer of magnetic steel is bonded to the base of the cookware, and heat treatment ensures the proper properties for effective induction cooking. The heat treatment process not only enhances the performance of cookware materials but also improves their longevity. By controlling the temperature and cooling rates during heat treatment, manufacturers can create cookware that is resistant to warping, cracking, and corrosion. This is especially important for high-performance cookware that must withstand frequent use, high heat, and the stresses of cooking.
Overall, heat treatment is an essential process in cookware manufacturing, enabling manufacturers to fine-tune the properties of the materials used and produce cookware that delivers superior cooking performance and longevity. Whether it’s through hardening, tempering, seasoning, or anodizing, heat treatment ensures that cookware is strong, durable, and capable of withstanding the demands of everyday cooking. The process not only improves the physical properties of the cookware but also contributes to its ease of use, safety, and long-term reliability.
Quality control is an essential aspect of cookware manufacturing, ensuring that each product meets the required standards for performance, safety, and durability. The goal of quality control is to maintain consistency and reliability across all units, so that consumers can trust the cookware to perform effectively and last over time. From the initial stages of production to the final inspection, quality control involves rigorous testing, inspection, and monitoring to identify and address any potential defects or inconsistencies in the cookware.
One of the first steps in quality control occurs during the selection of raw materials. Manufacturers carefully choose the metals, coatings, and other materials used to produce cookware, ensuring that they meet specific standards for strength, heat conductivity, and safety. For example, stainless steel must be of a certain grade to resist rust and corrosion, while aluminum must meet specific requirements for thickness and durability. Quality control in this stage often involves testing materials for their chemical composition and physical properties, such as tensile strength and resistance to high temperatures. Once the raw materials are chosen, the manufacturing process begins, and quality control is implemented throughout each phase of production.
During the forming and shaping stages, the cookware is carefully monitored to ensure that it is accurately molded, pressed, or spun into the desired shape. At this point, quality control checks are done to verify the dimensions of the cookware, ensuring that each piece meets the specifications and tolerances set for the design. Any deviations in shape or size are corrected before moving on to the next stage, as even small discrepancies can affect the functionality and aesthetics of the cookware. After the cookware has been formed, it often undergoes additional surface treatments such as polishing, anodizing, or applying nonstick coatings. Quality control at this stage involves inspecting the finish of the cookware, ensuring that it is smooth, uniform, and free from defects. For cookware with nonstick coatings, special attention is given to the adhesion of the coating to the surface, as an improperly applied coating can result in peeling, scratching, or reduced performance over time. In addition to visual inspection, the nonstick coating may also undergo tests for durability, such as abrasion resistance tests, to ensure that it will maintain its properties through regular use.
Another critical stage for quality control is during the assembly process. Handles, lids, and other components must be securely attached to the cookware body. During this stage, quality control checks ensure that the handles are properly welded, riveted, or screwed into place, with no loose or improperly fastened parts. The lids must fit securely, and any features such as pouring spouts or vents must function correctly. The cookware is tested for ease of use, safety, and comfort, ensuring that the handles do not overheat during cooking and are ergonomic for handling. After assembly, the cookware is subject to rigorous functional testing. This may include heat resistance tests to ensure that the cookware can withstand high temperatures without warping or deteriorating. For nonstick cookware, performance tests are conducted to verify that the coating provides the expected level of nonstick properties, allowing food to be easily removed and making the cookware easy to clean. Additionally, cookware is often subjected to stress tests, such as drop tests, to simulate the stresses it may endure in everyday use, ensuring that it can handle impacts without breaking or losing its integrity.
Quality control also involves monitoring for safety compliance. This includes ensuring that the cookware is free from harmful chemicals or materials, especially with regard to nonstick coatings, which may contain substances like PFOA in older formulations. Modern nonstick cookware is often tested for PFOA-free certifications to meet health and safety regulations. Similarly, cookware that is intended for induction cooking must be tested to ensure that it has the necessary magnetic properties to function properly with induction stoves. Additionally, cookware must be tested for proper heat distribution to ensure even cooking, preventing issues such as hot spots or uneven heating that could affect food preparation. Once the cookware passes all functional and safety tests, it undergoes final inspections before being packaged. This final inspection includes checking the overall appearance of the cookware for any cosmetic defects, such as scratches, dents, or discoloration. The cookware is also checked for consistency in weight and size to ensure that each unit matches the specifications.
Any defects identified at this stage result in the cookware being rejected or sent back for rework. If the cookware passes the final inspection, it is cleaned and prepared for packaging. Quality control at this stage ensures that the cookware is free from any residue or contaminants that may have accumulated during manufacturing, and it is packaged in a way that protects it from damage during shipping and handling. Throughout the entire cookware production process, quality control is crucial for maintaining high standards and ensuring that each unit performs well, is safe to use, and meets the expectations of the consumer. By implementing rigorous testing and inspection at every step of the manufacturing process, manufacturers can detect and address issues before the cookware reaches the market. Ultimately, quality control helps to maintain the brand’s reputation, reduce customer complaints, and ensure that the cookware will provide a satisfactory cooking experience for its users.
Edge Cutting Machine for Sheet Metal Pots
An edge cutting machine for sheet metal pots is a specialized piece of equipment used in the cookware manufacturing industry to cut and shape the edges of metal sheets, specifically designed for the production of pots and similar cookware items. These machines are crucial in ensuring the precise and clean cutting of metal sheets, which will later be formed into pot bodies. The edge cutting process ensures that the metal sheets are trimmed to the correct dimensions, while the edges are shaped for further processing, such as curling, crimping, or welding. The machine is designed to handle a variety of metal materials, including aluminum, stainless steel, and carbon steel, which are commonly used in cookware manufacturing.
The operation of an edge cutting machine involves the use of sharp, durable blades or shearing tools that are powered by hydraulic, mechanical, or pneumatic systems. These machines are capable of cutting through metal sheets of varying thickness and can perform multiple cuts in a single operation, ensuring that the edges are clean, smooth, and consistent across all units. The cutting process can be done in different styles depending on the final design of the cookware, such as straight cuts, curved cuts, or more intricate shapes required for specific designs.
Once the metal sheets are cut, the edges are often prepared for the next stage in the production process. For pots, this often involves curling or crimping the edges to create a smooth, rounded rim that enhances both the safety and aesthetic appeal of the finished product. This process not only prepares the sheets for further shaping but also strengthens the structure of the cookware, allowing for better handling during cooking and reducing the likelihood of sharp edges that could be dangerous.
In addition to ensuring precise cuts, modern edge cutting machines often include features like automated measurements, sensors for detecting sheet alignment, and adjustable cutting speed to optimize productivity and precision. Automation in edge cutting machines allows for high-speed, high-volume production, making them ideal for large-scale cookware manufacturing operations. It also minimizes human error, improves consistency in the final product, and ensures that the cookware meets quality standards before moving to the next stages of production.
In some cases, the edge cutting machine may also be integrated into a larger manufacturing system, which includes additional machines for forming, shaping, and assembling the cookware. This integration streamlines the production process, allowing for continuous, efficient production lines with minimal downtime. The overall goal is to ensure that every pot produced has uniform, high-quality edges, which contributes to the overall quality, functionality, and durability of the final product.
Overall, the edge cutting machine plays a crucial role in the cookware manufacturing process, as it ensures that the metal sheets are prepared with precision for further forming and finishing steps. This enhances the overall efficiency of the manufacturing process and results in cookware that is functional, safe, and aesthetically appealing.
After the edge cutting process, the sheet metal undergoes additional steps to ensure the final product meets the necessary specifications for both performance and appearance. These steps typically involve further shaping, joining, and finishing processes, where the edge cutting machine plays a pivotal role in preparing the raw material for subsequent stages.
One of the next key stages after edge cutting is the shaping process, where the cut metal sheets are formed into the shape of a pot. This could include spinning, stamping, or deep drawing, depending on the design of the cookware. The edge of the metal sheet that has been cut will often be further manipulated by machines that roll, curl, or crimp the edges to provide a smooth, rounded rim. This is important not only for aesthetic purposes but also to prevent the possibility of sharp edges that could pose a risk to the end-user. In some cases, the edges may also be reinforced for additional strength or to allow for the attachment of handles and lids in later stages.
The next process typically involves welding or joining various parts of the cookware. For example, if the pot is designed with a separate base and body, the edge of the cut sheet metal will be welded or soldered to form the base of the pot. Additionally, in cases where the cookware features handles, the edges of the body may need to be specially prepped for handle attachment, often requiring smooth, consistent edges for a secure fit.
The surface treatment process, which can include polishing, anodizing, or applying nonstick coatings, may also involve specific preparation of the edges. Properly cut and shaped edges ensure that surface treatments are evenly applied and that any coatings or finishes adhere correctly. For example, a well-cut edge allows for more even distribution of nonstick coatings, which is especially important for performance cookware like frying pans and pots. If the edges are not smooth or properly prepared, it may result in uneven application, reducing the cookware’s effectiveness and longevity.
Additionally, quality control procedures remain crucial after edge cutting to ensure that the edges meet specific standards. The machine may be calibrated and adjusted to handle variations in metal thickness or ensure consistency in the cut dimensions, so each unit conforms to the same specifications. After cutting, the metal edges are inspected to ensure there are no burrs, jagged sections, or other imperfections. Often, deburring or edge finishing is performed using a grinding or brushing process to ensure smooth, safe edges.
As with many manufacturing processes, automation and advanced technologies have improved the efficiency and precision of edge cutting machines. Modern machines can incorporate features like automatic feeding systems, which allow for continuous production without the need for manual intervention. Additionally, with the inclusion of sensors, edge cutting machines can detect irregularities in the material, such as warping or misalignment, ensuring that only high-quality pieces proceed to the next stage of production. This reduces waste and minimizes the likelihood of defects in the final cookware product.
Another significant benefit of edge cutting machines is their ability to handle various sheet metal materials that are commonly used in cookware production. Different metals, such as stainless steel, aluminum, and copper, each have unique properties, and the cutting machine needs to be versatile enough to accommodate these variations. The machine’s cutting tools must be durable enough to handle the hardness and thickness of different metals, and adjustments may be required depending on the material to ensure clean, precise cuts.
In larger manufacturing operations, edge cutting machines are typically integrated into automated production lines, allowing for high-speed and large-volume production with minimal human oversight. This not only improves productivity but also helps reduce manufacturing costs by optimizing time and material use. Automated systems can monitor production rates, track material usage, and adjust settings in real-time to maximize efficiency and quality.
Ultimately, the edge cutting machine serves as the foundational equipment in the cookware manufacturing process, preparing the sheet metal for the complex steps that follow. Whether the cookware is made from stainless steel, aluminum, or other materials, the precision provided by the edge cutting machine ensures that the final product meets the required specifications for strength, safety, and appearance. Through advanced technology, improved automation, and precise controls, these machines help ensure that the cookware production process is both efficient and effective, resulting in high-quality pots and pans ready for consumer use.
Milk Can Manufacturing Line
A milk can manufacturing line is a production system designed to efficiently produce metal milk cans used for storing and transporting milk in both commercial and industrial settings. The line consists of a series of interconnected machines and processes that take raw materials, such as stainless steel or aluminum sheets, and convert them into finished milk cans. These cans are then used primarily in dairy farms, food processing plants, and dairy product storage facilities. The design and operation of a milk can manufacturing line focus on high precision, durability, and hygiene, as milk cans need to withstand harsh conditions and be easy to clean to prevent contamination.
The manufacturing process typically involves several stages, each with specific equipment dedicated to one or more tasks. Below is an outline of the key stages involved in a milk can manufacturing line:
1. Material Preparation: The process begins with the procurement of raw materials, typically stainless steel sheets or aluminum, which are chosen for their resistance to corrosion, ease of cleaning, and ability to withstand the rigors of milk storage. The material is typically in the form of coils or sheets, which are unrolled and fed into the production line. At this stage, the material may be cut to specific sizes or shapes as required for the next steps.
2. Shaping and Forming: The next step in the process involves shaping the material into the desired form of the milk can. A series of machines, such as press machines, hydraulic presses, and rolling machines, are used to form the body of the milk can. The first step is typically to cut the material into a blank (a flat, circular piece of metal) and then use a deep-drawing process or stamping process to form the cylindrical shape of the can. This stage ensures that the metal is uniformly shaped, and any imperfections or wrinkles are removed.
3. Bottom and Top Formation: Once the cylindrical body is formed, the next step is to attach the bottom and top lids of the milk can. For the bottom, a separate circular metal sheet is often used, which is either welded or rolled onto the cylindrical body. In some cases, the bottom may be pre-formed with a concave shape to allow for easier stacking or better durability when the can is in use. Similarly, the top part of the can may include an opening or nozzle for pouring milk, which is formed through stamping or cutting.
4. Welding and Joining: In many cases, the edges of the cylindrical body and the bottom and top parts are welded together using automated welding machines. This ensures a strong and secure connection, providing the necessary sealing properties for the can. The welding process is often done using techniques like TIG (Tungsten Inert Gas) welding, which is ideal for materials like stainless steel or aluminum. After welding, any excess material or seams are ground or polished to create a smooth surface.
5. Handle Attachment: Milk cans are typically designed with sturdy handles for easy transportation. These handles are attached to the body of the can using rivets or welding. In the case of large cans, additional reinforcement may be added to ensure that the handles can support the weight of the filled can. This process requires precision to ensure that the handles are securely fastened and evenly aligned on both sides of the can.
6. Surface Treatment and Cleaning: To ensure hygiene and extend the lifespan of the milk can, surface treatment is an essential step in the manufacturing process. The cans are typically cleaned and degreased to remove any oil, dirt, or contaminants that may have been introduced during the manufacturing process. Surface treatments such as passivation or coating are applied to improve corrosion resistance and make the cans easier to clean. In some cases, food-grade coatings or linings are applied to the interior of the cans to protect the milk from interacting with the metal, which could lead to contamination or degradation of the milk’s quality.
7. Inspection and Testing: Once the cans have been formed, welded, and treated, they undergo a series of quality control inspections to ensure they meet the required standards. This may include dimensional checks to verify that the cans are the correct size and shape, as well as testing for structural integrity to ensure that the welding and handle attachments are secure. Pressure tests may also be conducted to ensure that the cans do not leak when filled with milk.
8. Printing and Branding: In many cases, milk cans are branded with the company’s logo, product details, or other markings for identification purposes. This is often done using automated printing or labeling machines. Depending on the design, the cans may be decorated with a screen printing or laser marking process to apply logos or batch information.
9. Packaging: After inspection and branding, the finished milk cans are carefully packaged and prepared for shipment. The cans may be grouped into bundles, stacked, and placed into cartons or pallets for easier transportation and storage. Packaging also ensures that the cans are protected from potential damage during transit.
10. Final Quality Control: Before the cans leave the manufacturing facility, a final quality control check is conducted. This includes checking the packaging, ensuring that the cans are free from defects, and verifying that they meet the specific requirements for use in food-grade applications. Some manufacturers also conduct random spot checks on the cans for performance, such as conducting leak tests and checking the durability of handles and lids.
Automation and Efficiency: Modern milk can manufacturing lines are highly automated, with robots and automated conveyors used throughout the production process to reduce manual labor, increase precision, and improve efficiency. Automation allows for higher production rates while minimizing the risk of human error, ensuring that each can meets the necessary safety and quality standards. Automated systems also allow for continuous monitoring of the production process, enabling real-time adjustments to optimize performance and reduce waste.
Conclusion: The milk can manufacturing line is a complex and highly efficient system that converts raw metal materials into durable, high-quality milk cans. Each stage of the process, from material preparation and forming to surface treatment, welding, and final inspection, ensures that the finished product meets the necessary safety, hygiene, and functional standards. Advances in automation, precision machining, and quality control have significantly improved the speed, efficiency, and reliability of milk can production, allowing manufacturers to meet the demands of the dairy industry and ensure that milk is stored and transported safely.
The milk can manufacturing process continues with high emphasis on automation, precision, and safety. As the production line progresses, the cans are subjected to various checks and tests to ensure they meet the highest standards of quality. After the welding and handle attachment stages, the cans undergo detailed cleaning processes. Cleaning is essential to remove any residual oils, lubricants, or dust that may have accumulated during the manufacturing process. This is typically achieved using automated washing systems that subject the cans to high-pressure water and cleaning agents, followed by drying to ensure they are free from any moisture that could affect the final product.
Once cleaned, the cans are typically subjected to surface treatment processes that enhance their corrosion resistance, durability, and ease of cleaning. Stainless steel and aluminum milk cans are often passivated, a process that treats the metal to enhance its resistance to rust and oxidation. In some cases, food-safe coatings or linings are applied to the interior of the cans to prevent the metal from reacting with the milk, thereby maintaining its taste and quality. This also ensures that the milk remains fresh during storage and transportation. These coatings are designed to be non-toxic, non-reactive, and easy to clean, which is essential in maintaining hygienic standards.
Quality control remains a critical part of the process, ensuring that each milk can meets rigorous standards. The cans undergo dimensional inspections, which verify that the cans are within the specified size and shape parameters. Structural integrity is also tested to ensure that the welding and seam areas are secure and there are no weak points that could result in leaks or failure during use. This may involve pressure testing, where the cans are filled with air or water and sealed to check for leaks. For the handle attachments, additional checks are performed to verify that they are secure, well-placed, and capable of withstanding the weight and pressure that the filled can will exert.
Following the inspection, many milk cans are branded, often through an automated printing or labeling system. This stage allows the manufacturer to apply logos, batch numbers, or product information to the surface of the cans, which is essential for traceability and marketing purposes. The printing process is highly accurate, ensuring that the logos and text are clear, sharp, and properly aligned. Laser etching can also be used for more permanent branding.
Once the cans pass the quality inspection and branding stages, they are carefully packaged. The packaging is designed to protect the cans during transportation and handling, ensuring they arrive at their destination in pristine condition. The cans are typically stacked in bundles and placed in protective cartons or on pallets, ready for shipping. Packaging also makes handling more efficient, allowing for easier movement of the cans through logistics channels.
Before the cans are shipped, a final quality control check is done to ensure the entire production lot meets the necessary safety, quality, and hygiene standards. This is especially important in food-grade production, where even minor imperfections could affect the safety of the product. A combination of visual inspection and physical testing ensures that every can is ready for use in the dairy industry.
Throughout the entire manufacturing process, automation plays a significant role in improving speed, reducing human error, and ensuring consistency. Automated systems monitor production parameters, track material usage, and even adjust production speeds based on real-time data, maximizing efficiency. Robots and automated conveyors transport the cans from one stage of production to another, allowing for continuous operation and minimal downtime. The use of advanced robotics and machine learning systems in quality control further enhances the accuracy of inspections, reducing defects and improving overall production quality.
Overall, the milk can manufacturing line combines advanced machinery, automated systems, and stringent quality control procedures to produce reliable, high-quality milk cans that meet the specific needs of the dairy industry. From material preparation to the final packaging, each step in the production line ensures that the milk cans are durable, hygienic, and capable of storing milk safely and efficiently for transportation and distribution. With continual advancements in technology, milk can manufacturing is becoming more efficient, environmentally friendly, and responsive to the evolving demands of the food industry.
Edge Cutting Trimming and Forming Machine
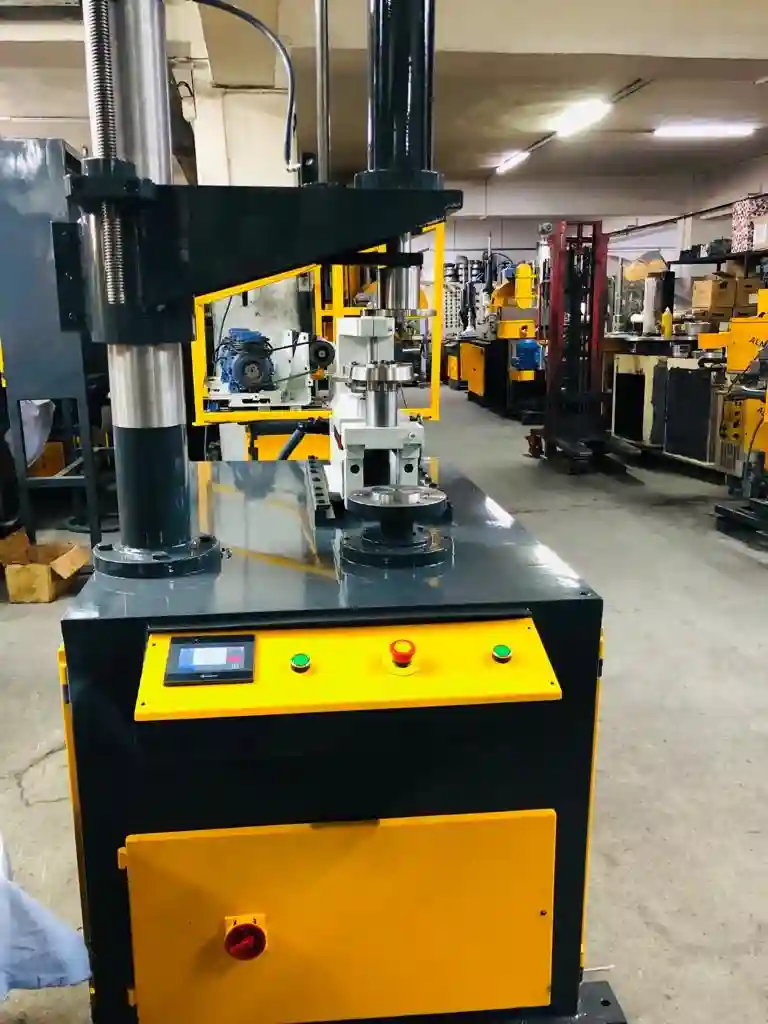
An edge cutting, trimming, and forming machine is a specialized piece of equipment used in various industries, particularly in the production of cookware, metal containers, and other metal-based products, to ensure that the edges of metal sheets or components are cut, trimmed, and formed with precision. These machines are essential for shaping and finishing the edges of sheet metal, removing excess material, and preparing the metal for further processing, such as welding, coating, or assembly. They are designed to enhance productivity, reduce manual labor, and ensure the final product meets high-quality standards for both appearance and functionality.
The operation of an edge cutting, trimming, and forming machine typically involves several interconnected processes:
Edge Cutting: The first function of the machine is to cut the metal sheets to the required size. This process involves cutting the edges of the sheets or removing excess material from the edges. The machine uses high-precision cutting tools, such as rotary blades, shearing blades, or lasers, to ensure that the edges are clean and even. This step is crucial because it ensures that the metal pieces are uniform in size and shape, allowing for further operations like forming or welding to proceed smoothly.
Trimming: After the metal sheets are cut, the trimming process is used to remove any small, unwanted portions from the edges. Trimming helps remove burrs, rough edges, or other imperfections that can occur during the cutting process. This is particularly important when manufacturing products like cookware, where sharp or uneven edges can compromise both the aesthetics and safety of the product. Trimming is usually done using rotary or oscillating blades that gently remove excess material while keeping the overall size and shape intact.
Forming: After cutting and trimming, the metal edges need to be shaped or formed into a desired profile or contour. The forming process is used to bend, curl, or press the edges into specific shapes needed for the product. For example, in cookware production, the edges of metal sheets are often curled or crimped to create smooth rims, preventing sharp edges that could harm users. Forming machines may use hydraulic presses, rollers, or pneumatic tools to apply controlled pressure and bend the metal into the desired shape.
The edge cutting, trimming, and forming machine can operate with different configurations depending on the specific needs of the production process. It may be part of an integrated production line that handles multiple stages of metal processing or may be a standalone piece of equipment. Modern machines typically feature automated systems that control cutting speeds, blade positioning, and forming pressure, ensuring precise and consistent results across high volumes of production.
The machines are typically equipped with adjustable settings, allowing operators to modify the cutting, trimming, and forming processes to accommodate different material types, thicknesses, and product sizes. The ability to fine-tune settings ensures that the machine can handle a wide range of tasks and adapt to various manufacturing requirements. Some machines may even incorporate sensors or cameras to detect material alignment, ensuring that cuts and trims are made at the correct locations and that the metal sheets are correctly positioned for forming.
Edge cutting, trimming, and forming machines are particularly important for industries that require high levels of precision and consistency. In cookware production, for instance, the machine ensures that the edges of metal pots, pans, or lids are uniformly shaped, with smooth and rounded edges that enhance both the safety and aesthetic appeal of the products. Similarly, in the automotive, aerospace, and packaging industries, the precision offered by these machines allows manufacturers to create components that fit together seamlessly, ensuring the integrity and functionality of the final products.
In addition to improving production speed and efficiency, these machines also contribute to overall safety. By automating the cutting and trimming processes, the risk of manual errors and injury is minimized, as operators are less likely to come into direct contact with sharp edges or rotating blades. Moreover, the precise forming of metal edges ensures that products are free from sharp, dangerous areas that could pose a risk during handling or use.
Overall, the edge cutting, trimming, and forming machine is a crucial tool in modern manufacturing, offering significant improvements in precision, safety, and efficiency. Whether used in cookware production, metal fabrication, or other industries, these machines ensure that metal components are cut, trimmed, and formed with the highest standards of quality, ready for further processing or final assembly.
The edge cutting, trimming, and forming machine plays a vital role in enhancing the overall efficiency and quality of metalworking processes. By automating the edge processing tasks, it minimizes human error and ensures uniformity across large volumes of production. The ability to adjust the machine’s settings allows manufacturers to work with various materials, including stainless steel, aluminum, copper, and others, accommodating different thicknesses and properties for diverse applications. The precision provided by these machines not only improves the quality of the edges but also optimizes the overall functionality of the final product.
The cutting and trimming processes performed by these machines are essential for preparing metal sheets for further operations, such as welding, assembling, or finishing. After trimming the rough edges and removing burrs or sharp parts, the metal becomes much easier to handle and work with in subsequent stages. In the case of cookware manufacturing, for instance, the smooth and well-defined edges created by these machines not only improve the product’s appearance but also contribute to the safety of the user. Similarly, in other industries, the proper shaping of edges ensures that components fit together properly during assembly and that any final products meet the required tolerances.
With the integration of advanced technologies such as CNC (computer numerical control) programming, these machines are able to perform complex edge shaping and trimming tasks with a high degree of accuracy and repeatability. This is particularly beneficial in high-volume manufacturing environments, where consistent results are crucial to maintaining product standards and meeting production quotas. Additionally, the automation reduces the need for manual labor and cuts down on the time spent on each piece, leading to faster turnaround times and reduced production costs.
Edge cutting, trimming, and forming machines are also adaptable to various end products. Whether it is cookware, automotive components, or packaging materials, the machine can be reconfigured to handle the specific requirements of each product, ensuring that the metal sheets are processed according to the correct dimensions and specifications. As industries evolve and demand increases for higher-quality, more precisely crafted products, these machines have become indispensable in meeting these needs while maintaining cost-effectiveness.
In addition to their precision and versatility, these machines are often designed with user-friendly interfaces, allowing operators to control and monitor the process with ease. The automation not only improves operational efficiency but also reduces human intervention, allowing workers to focus on overseeing the process rather than handling manual tasks. With advanced monitoring systems, operators can quickly identify and address any issues that may arise during production, further improving the reliability and continuity of the manufacturing line.
Moreover, as sustainability becomes increasingly important, these machines also contribute to minimizing material waste. By making precise cuts and trims, they ensure that the maximum usable material is extracted from the initial sheets, reducing excess scrap material. Additionally, these machines are designed to work efficiently, consuming minimal energy while delivering high productivity. In industries where environmental concerns are paramount, these benefits are crucial for meeting both operational and sustainability goals.
In summary, edge cutting, trimming, and forming machines are critical components in modern manufacturing, providing a level of precision, consistency, and efficiency that traditional manual methods cannot match. By improving the quality of metal components and reducing production costs, these machines play an essential role in producing high-quality products across a wide range of industries. As technological advancements continue to enhance their capabilities, these machines will remain indispensable for manufacturers seeking to stay competitive and meet the evolving demands of the market.
Edge cutting trimming and beading machine for fire extinguisher production
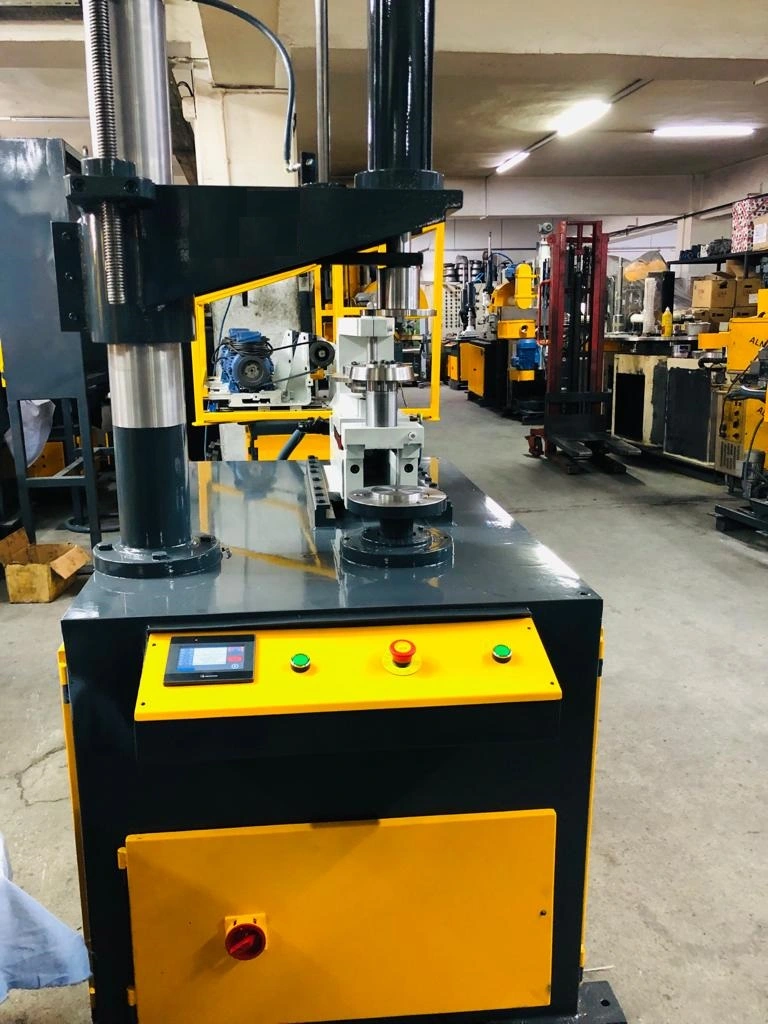
An edge cutting, trimming, and beading machine for fire extinguisher production is a specialized piece of equipment used in the manufacturing of metal fire extinguishers, particularly the cylindrical bodies that house the extinguishing agent. These machines are critical in shaping and preparing the metal parts, ensuring precision, safety, and structural integrity of the final product. Fire extinguishers must meet stringent safety standards, and the components must be perfectly fabricated to withstand high-pressure conditions, mechanical stress, and harsh environments.
The edge cutting, trimming, and beading machine is designed to perform several functions that are integral to the production process of fire extinguisher bodies. First, the metal sheets, usually made of steel or aluminum, are fed into the machine. The machine cuts the edges of the sheets to the precise dimensions required, ensuring that the material is the right size for forming the cylindrical body. The cutting process also eliminates any rough or uneven edges from the material, which could interfere with subsequent steps or compromise the product’s structural integrity.
Once the metal sheets are cut to the correct size, the machine moves on to the trimming process. During this stage, any excess material, such as burrs or irregularities around the edges, is removed. Trimming ensures that the edges are smooth and free from any imperfections that could cause issues during the forming or welding stages. This step is crucial to the overall quality of the fire extinguisher body, as any sharp or uneven edges could lead to defects in the finished product, affecting both its appearance and strength.
The beading process follows trimming and involves the creation of a raised bead or lip along the edges of the sheet metal. Beading is particularly important in fire extinguisher production because it strengthens the cylindrical body and improves its ability to withstand internal pressure. The beaded edge also makes it easier to weld the body, providing a strong, consistent seal. Beading is typically done using rollers or dies that press the edges of the metal into a raised pattern, forming a smooth, continuous bead around the circumference of the sheet.
After the beading process, the edges of the metal are typically prepared for welding, which is the next step in the production process. The beaded edges provide additional strength and are essential for ensuring that the two halves of the cylindrical body are securely welded together, preventing any leaks or structural weaknesses in the finished fire extinguisher.
In the case of fire extinguisher production, these machines are designed with high precision to ensure that the cuts, trims, and beads are uniform across all units. Precision is critical because fire extinguishers must meet strict industry standards for performance, reliability, and safety. Any deviation from the required measurements or imperfections in the metal can lead to product failure, which is especially dangerous given the role fire extinguishers play in emergency situations.
Modern edge cutting, trimming, and beading machines for fire extinguisher production are often automated, allowing for continuous, high-speed production. These machines are equipped with computer numerical control (CNC) systems that control the cutting, trimming, and beading processes with a high degree of accuracy. The automation not only improves the speed of production but also reduces the risk of human error and ensures that each fire extinguisher body is fabricated to the exact specifications needed.
Another important feature of these machines is their ability to handle a variety of materials and thicknesses. Fire extinguisher bodies are typically made from steel or aluminum, and these machines are designed to handle different metals with ease. The ability to adjust machine settings for different material types and thicknesses ensures that the final product maintains the strength and durability required to safely contain pressurized contents.
In addition to increasing production efficiency, these machines also contribute to safety and quality control in the fire extinguisher manufacturing process. Since fire extinguishers must be capable of withstanding high pressure without failing, the precise shaping and strengthening of the metal during the edge cutting, trimming, and beading stages ensures that the final product is safe for use. Any inconsistencies in these stages could lead to weak points in the body, compromising the safety of the fire extinguisher.
Overall, an edge cutting, trimming, and beading machine for fire extinguisher production plays a crucial role in ensuring that the metal parts of the extinguisher are accurately shaped, trimmed, and reinforced for strength. By automating these processes, manufacturers can produce fire extinguishers at a faster rate while maintaining consistent quality. This machine helps improve the efficiency of the manufacturing line, ensures safety standards are met, and ultimately contributes to the reliability and effectiveness of fire extinguishers in emergency situations.
The edge cutting, trimming, and beading machine for fire extinguisher production is crucial in ensuring the metal components are accurately shaped, precisely trimmed, and reinforced for strength and durability. These machines improve the efficiency and consistency of manufacturing while minimizing human error, contributing significantly to the safety and functionality of the final product. The cutting and trimming processes ensure that the raw metal sheets, which are typically steel or aluminum, are properly sized and free from any imperfections or irregularities that could affect later processes or the structural integrity of the fire extinguisher body.
The beading process adds an important structural element, strengthening the edges of the metal body, which is vital for ensuring the fire extinguisher can withstand high internal pressure. This added strength is particularly important for preventing leaks or deformations when the fire extinguisher is subjected to the pressure of the pressurized extinguishing agent inside. Beading also facilitates the welding process, as the raised edges help create a more secure bond when the body of the fire extinguisher is welded together. This step is especially crucial for the fire extinguisher to maintain its pressure-resistance and ensure its long-term reliability.
The automation of these processes is another key advantage, as it allows for high-speed production without sacrificing precision. Modern machines use CNC (Computer Numerical Control) systems to guide the cutting, trimming, and beading processes. This level of automation ensures that every fire extinguisher body is produced to the same exacting standards, with minimal variations. This uniformity is critical for safety, as even minor discrepancies in the metal’s dimensions or strength could compromise the performance of the fire extinguisher.
By using a combination of advanced machinery, automated processes, and precise control systems, fire extinguisher manufacturers can meet the strict regulatory standards required for such safety-critical products. The edge cutting, trimming, and beading machine helps manufacturers reduce costs by improving productivity and eliminating the need for manual labor, while also ensuring that the final product meets the high standards expected of fire safety equipment.
The ability to work with a range of materials and metal thicknesses ensures that the machine is versatile enough to handle the diverse requirements of fire extinguisher production. Adjusting settings on the machine allows for fine-tuning of the cutting and beading processes depending on the specific material being used. This flexibility is essential in producing fire extinguishers of varying sizes and designs, which may be used for different applications, from small portable extinguishers to large industrial units.
In terms of safety, the machine contributes to ensuring the fire extinguisher’s structural integrity by reducing the potential for defects. A properly beaded edge strengthens the body, while a smooth, clean trim eliminates any possibility of sharp, irregular edges that could cause issues during handling or when assembling other components, such as valves or handles. The result is a fire extinguisher that is both reliable and safe to use, capable of performing optimally when it is needed most.
Overall, an edge cutting, trimming, and beading machine is an integral part of the fire extinguisher manufacturing process. Its automation, precision, and ability to handle various materials and thicknesses make it an essential tool for modern manufacturers. The machine helps improve production efficiency, ensures safety, and maintains high-quality standards in the final product, ensuring that fire extinguishers are made to withstand the rigorous demands of emergency situations and provide effective fire suppression.
Edge Cutting Trimming Machine for Hot Water Boiler Production
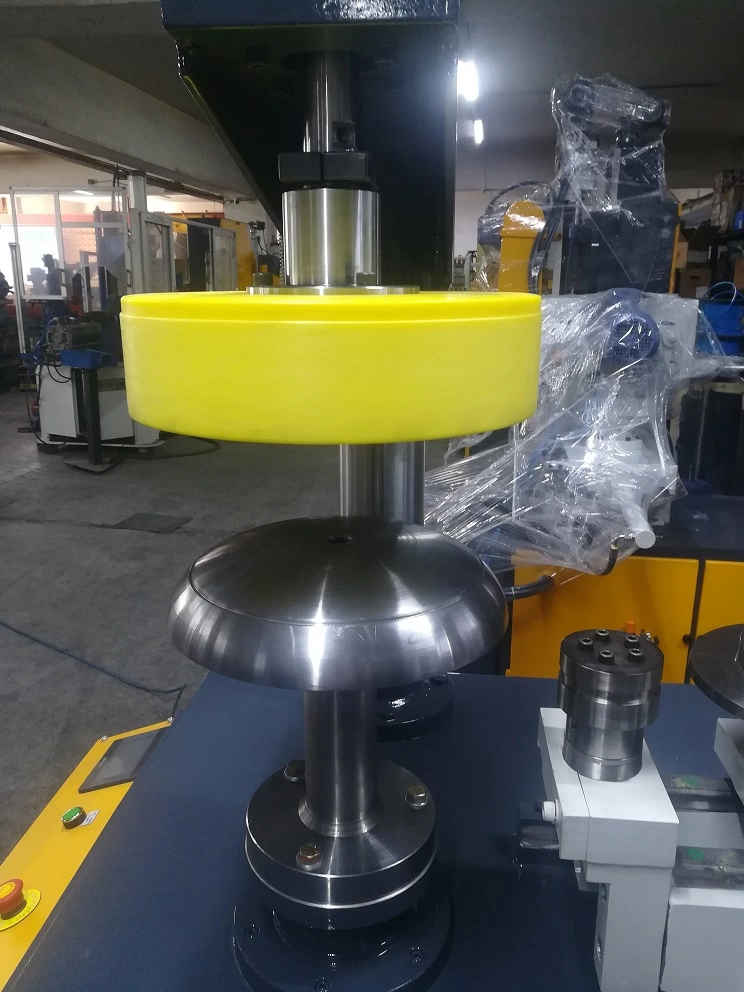
An edge cutting and trimming machine for hot water boiler production is a crucial piece of equipment used in the manufacturing process of hot water boilers, specifically for cutting and trimming the edges of the metal sheets that form the outer casing or other components of the boiler. These machines play an essential role in ensuring that the metal components are precisely cut and free from sharp or rough edges, which are necessary for the safety, durability, and overall performance of the final product. Boilers are subject to high pressures and temperatures, so every component, including the casing, pipes, and seams, must be fabricated with the utmost precision.
The edge cutting and trimming process begins with feeding large metal sheets, often made of steel or stainless steel, into the machine. These sheets typically have rough, uneven, or burr-ridden edges that need to be precisely cut or trimmed to meet the required dimensions for further processing. The machine’s cutting tools, which can include rotary blades, shearing tools, or lasers, are used to slice through the metal, ensuring that the material is the correct size for shaping and assembly. The edge cutting process must be done with great care to avoid any deformation or loss of material that could affect the boiler’s final fit and function.
Following the edge cutting, the trimming process begins. Trimming is necessary to remove any excess material, such as burrs, sharp edges, or irregularities left behind from the cutting process. These rough edges can cause issues later on in the assembly process, where they may interfere with welding or other joining techniques. By trimming the edges, the machine ensures that the metal sheets are clean and smooth, making them easier to handle and further process. In hot water boiler production, this step is critical, as sharp or uneven edges could pose safety risks during manufacturing or in the use of the final product.
These machines typically feature adjustable settings, allowing the operator to modify cutting speeds and trimming parameters to suit different materials or thicknesses. This flexibility is especially important in boiler production, as various types of metal may be used, such as carbon steel, stainless steel, or alloys, each with unique properties. The ability to adjust the machine’s settings ensures that all components of the boiler are cut and trimmed to precise specifications, regardless of the material used.
One of the key advantages of an edge cutting and trimming machine is its ability to automate these tasks. This reduces the need for manual labor, speeds up production, and minimizes human error. Automation ensures that the cuts are consistently precise, which is critical in boiler production, where even slight discrepancies can affect the efficiency and safety of the system. The machine’s automation capabilities also help improve production speed, reducing the time required to manufacture each component and increasing overall output.
Another important feature of these machines is their ability to work with high-pressure materials. Hot water boilers are subjected to high temperatures and pressure, so the materials used in their construction must be free from any defects or weaknesses that could compromise their integrity. The edge cutting and trimming machine ensures that the metal sheets are prepared for further forming and welding, providing clean, smooth edges that facilitate the next steps in the production process. The precise cutting and trimming contribute to the structural integrity of the boiler, reducing the likelihood of leaks, cracks, or failures in the final product.
In the hot water boiler manufacturing process, after edge cutting and trimming, the metal sheets are often subjected to further processing, such as forming, welding, or heat treatment. The precision provided by the edge cutting and trimming machine ensures that the components fit together perfectly, making the assembly process much easier and more efficient. For example, when the sheets are welded to form the boiler casing or other parts, the smooth edges created by the cutting and trimming machine help ensure that the welds are strong and secure, contributing to the overall durability and performance of the boiler.
Furthermore, these machines contribute to the safety of the production process. By eliminating sharp edges and reducing the need for manual intervention, operators are less likely to come into contact with dangerous, jagged metal. This improves workplace safety and helps maintain a smooth, efficient manufacturing environment.
Overall, an edge cutting and trimming machine for hot water boiler production plays a vital role in ensuring that the metal components are fabricated with high precision, safety, and efficiency. The machine’s ability to cut and trim metal sheets to exact specifications is essential for creating the various parts of the boiler, from the outer casing to the internal components. The automation and precision of these machines enhance the overall quality of the final product, ensuring that the hot water boiler performs reliably under high pressure and temperature conditions, and meets all safety standards for use in homes, businesses, and industrial settings.
The edge cutting and trimming machine for hot water boiler production is integral to achieving the precise fabrication of metal components that make up the boiler system. As these systems are designed to operate under high pressure and temperature, the components must be crafted with utmost precision to ensure they function safely and efficiently over time. The machine plays a crucial role in preparing the metal sheets, typically made from durable materials like carbon steel or stainless steel, by trimming and cutting them to the required dimensions and removing any burrs or sharp edges. This ensures that the material is smooth, uniform, and ready for further processing such as forming or welding.
The ability to fine-tune cutting speeds, trimming pressures, and other parameters allows the machine to handle different metal thicknesses and types, which is important because hot water boilers are often constructed using materials that need to withstand high internal pressure and thermal stresses. By adjusting these settings, manufacturers can ensure that each metal part, whether it’s a casing, valve, or piping component, is precisely prepared to fit together during assembly.
This process not only prepares the material for further forming but also eliminates potential problems that could arise later in the production line. For instance, rough or uneven edges could lead to poor welds, weak joints, or leaks, which would compromise the integrity of the boiler. By ensuring smooth and consistent edges, the edge cutting and trimming machine directly contributes to the overall reliability of the finished product.
Automation in these machines is key to their effectiveness. By automating the edge cutting and trimming processes, manufacturers can significantly increase production speed while reducing the likelihood of human error. Automation ensures that every cut is precise and consistent across all parts, making it easier to meet stringent quality control standards and reducing the likelihood of defects that could lead to costly repairs or product failures. The precision achieved also helps streamline subsequent steps in the production process, such as welding and heat treatment, by ensuring the parts are correctly aligned and ready for those operations.
Moreover, the edge cutting and trimming machine enhances safety in the production environment. By removing sharp edges and minimizing the need for manual handling, the machine reduces the risks posed by sharp metal and minimizes operator exposure to hazards. This not only protects workers but also helps maintain a more efficient and uninterrupted production process, as safety concerns are addressed proactively.
As hot water boilers are designed for long-term use under rigorous conditions, the precision achieved in the edge cutting and trimming process is vital for ensuring that each component performs as expected throughout the lifespan of the product. The machine ensures that metal sheets are properly prepared for further steps, which is essential for the high-quality welding, forming, and assembly processes that follow. The result is a well-made, durable, and reliable boiler that performs efficiently and safely, meeting the highest industry standards.
Edge Cutting Trimming Machine for the Cookware Industry
An edge cutting and trimming machine for the cookware industry is an essential piece of equipment used in the production of various cookware items, such as pots, pans, lids, and other metal-based kitchen products. The machine is specifically designed to cut, trim, and prepare the edges of metal sheets that are used in manufacturing cookware components. These machines are crucial for ensuring that the final cookware products have smooth, precise edges, free from burrs or sharp points, which is essential for both safety and aesthetics.
In cookware production, the metal sheets, typically made from stainless steel, aluminum, or other heat-resistant alloys, are often pre-cut to size but need further processing to refine their edges. The edge cutting function of the machine ensures that the metal sheets are cut to the precise dimensions required for the specific cookware item. This is important for creating uniform shapes and ensuring that the parts fit together correctly during the assembly process. Any discrepancies in the size of the metal sheets can result in difficulties during forming or welding and can negatively affect the final product’s functionality.
After the initial cut, the trimming process is performed to remove any excess material or imperfections that remain along the edges of the sheets. This could include removing rough edges, burrs, or any irregularities that might have resulted from the cutting process. Trimming is crucial in cookware manufacturing because sharp, uneven edges can pose safety hazards to the user and can also hinder further processing, such as welding or coating. The trimming machine ensures that the edges of the cookware parts are smooth and free from dangerous burrs, making them easier and safer to handle during assembly and use.
In addition to cutting and trimming, the machine may also be equipped to perform other tasks, such as rounding or curling the edges of the cookware. In many cases, cookware items such as pots and pans require a rounded or curled edge to prevent sharp corners and to facilitate easier handling by users. The curling or beading of edges also adds structural strength to the cookware, making it more durable and capable of withstanding repeated use in cooking environments. This process is often accomplished through specialized rollers or dies, which mold the metal into a smooth, curved shape.
Automation in edge cutting and trimming machines for the cookware industry allows for faster production speeds and higher consistency. Modern machines are typically controlled through computer numerical control (CNC) systems, which allow for precise adjustments in cutting speeds, trimming pressures, and edge formations. This level of automation reduces the risk of human error and ensures that every piece of cookware is made to the exact specifications required for quality and safety. The machine’s ability to adjust to different materials and thicknesses also makes it versatile and able to handle a range of cookware products.
These machines are designed to increase production efficiency while maintaining high safety standards. With automated trimming and cutting, manufacturers can produce large quantities of cookware with uniform edges that meet strict industry standards. The consistency of the edges is critical for both the appearance and functionality of the cookware. Smooth, well-defined edges not only improve the aesthetic appeal of the product but also ensure that the cookware is comfortable to handle and free from any sharp or jagged areas that could cause injury.
By streamlining the production process, edge cutting and trimming machines also contribute to cost reduction. Automation reduces labor costs, speeds up production, and minimizes material waste, ensuring that every piece of metal is used efficiently. These machines are also built for durability and reliability, capable of operating for long hours in high-volume manufacturing environments. Their efficiency in cutting, trimming, and shaping the metal ensures that the cookware is ready for subsequent processes such as welding, coating, or further finishing, ensuring the final product meets the high standards required for commercial and consumer use.
In summary, an edge cutting and trimming machine for the cookware industry plays a vital role in ensuring that metal cookware parts are accurately cut, trimmed, and shaped to the highest standards. The machine enhances safety, improves production efficiency, and ensures that the final products are of superior quality, both in terms of function and appearance. With the ability to handle different materials, thicknesses, and design requirements, these machines are indispensable for manufacturers who produce cookware that is both safe and durable.
An edge cutting and trimming machine for the cookware industry is integral to the production of high-quality kitchen items. The metal sheets, typically made from materials like stainless steel, aluminum, or other durable alloys, undergo precision cutting and trimming to ensure they meet the required specifications for further processing. The cutting function of the machine ensures that the metal sheets are sized correctly, which is essential for the consistent production of various cookware items such as pots, pans, and lids. Accurate sizing ensures that components fit together seamlessly during subsequent assembly stages, helping to reduce defects and maintain uniformity across the production line.
After the initial cut, the trimming process removes any imperfections left behind, such as rough edges or burrs, that could pose safety risks or hinder further operations like welding or coating. In cookware manufacturing, these sharp or uneven edges could be a potential source of injury for consumers, so trimming is essential to ensure that the final products are safe to use. The smooth edges also make the products more aesthetically pleasing, which is important for consumer appeal, especially in the competitive cookware market. Furthermore, well-trimmed edges help streamline other manufacturing processes, such as joining or welding, ensuring that components fit properly and that welds are strong and consistent.
In some cases, the machine may also be designed to curl or round the edges of the cookware parts. This additional process is often necessary for ensuring that the cookware has rounded edges, which not only improves its handling but also reinforces its structural integrity. Rounded or curled edges provide added strength, preventing the metal from becoming weak or prone to damage over time. Additionally, this feature contributes to the overall user experience, as it makes cookware easier to handle and reduces the risk of injury from sharp corners. The ability to adjust the machine for different edge shapes and profiles enhances its versatility, allowing manufacturers to produce a wide variety of cookware items with varying edge requirements.
Automated systems, particularly those controlled by CNC (computer numerical control), allow for precise and repeatable cuts and trims, ensuring consistency across large production runs. These automated machines can handle complex tasks with high speed, making them essential for maintaining a steady, efficient production line. The precision provided by CNC-controlled edge cutting and trimming machines helps manufacturers meet tight quality control standards, reducing the likelihood of errors or defects in the finished product. As cookware is often subjected to heat and pressure, such precision is crucial for ensuring the product’s longevity and performance. Consistently smooth and accurately shaped edges improve the cookware’s safety, function, and durability.
The edge cutting and trimming machine is adaptable, allowing for various material types and thicknesses to be processed. This flexibility is particularly important for the cookware industry, as different products require different material specifications, depending on their design, usage, and performance requirements. Whether working with thin-gauge aluminum for lightweight frying pans or thicker stainless steel for heavy-duty pots, the machine can be adjusted to accommodate different metals and thicknesses, ensuring that the final product meets the specific needs of the cookware.
Additionally, the efficiency of edge cutting and trimming machines helps reduce material waste. By ensuring that only the necessary amount of material is used for each product, the machines contribute to more sustainable manufacturing practices. The ability to maximize material utilization reduces costs and helps manufacturers meet environmental goals by minimizing waste and energy consumption. The automation of these machines further reduces labor costs and speeds up production times, helping manufacturers meet market demand more effectively while keeping operational costs low.
These machines are built to handle high volumes of production, ensuring that they can operate continuously in demanding manufacturing environments. Their reliability is essential for maintaining smooth production workflows and meeting deadlines for both small and large production runs. In high-volume production, the precision and speed of edge cutting and trimming machines allow manufacturers to increase output while maintaining consistent quality, ultimately helping them meet consumer expectations and industry standards.
In conclusion, edge cutting and trimming machines are indispensable for the cookware industry, as they ensure that the metal components used in cookware are precisely cut, smooth, and ready for further processing. These machines help improve safety, enhance product quality, and streamline the production process, all while maintaining high efficiency and reducing waste. By using automated systems to control cutting, trimming, and edge shaping, manufacturers can produce cookware that is durable, functional, and safe, meeting both consumer demand and industry standards.
EMS Metalworking Machinery
We design, manufacture and assembly metalworking machinery such as:
- Hydraulic transfer press
- Glass mosaic press
- Hydraulic deep drawing press
- Casting press
- Hydraulic cold forming press
- Hydroforming press
- Composite press
- Silicone rubber moulding press
- Brake pad press
- Melamine press
- SMC & BMC Press
- Labrotaroy press
- Edge cutting trimming machine
- Edge curling machine
- Trimming beading machine
- Trimming joggling machine
- Cookware production line
- Pipe bending machine
- Profile bending machine
- Bandsaw for metal
- Cylindrical welding machine
- Horizontal pres and cookware
- Kitchenware, hotelware
- Bakeware and cuttlery production machinery
as a complete line as well as an individual machine such as:
- Edge cutting trimming beading machines
- Polishing and grinding machines for pot and pans
- Hydraulic drawing presses
- Circle blanking machines
- Riveting machine
- Hole punching machines
- Press feeding machine
You can check our machinery at work at: EMS Metalworking Machinery – YouTube
Applications:
- Beading and ribbing
- Flanging
- Trimming
- Curling
- Lock-seaming
- Ribbing
- Flange-punching