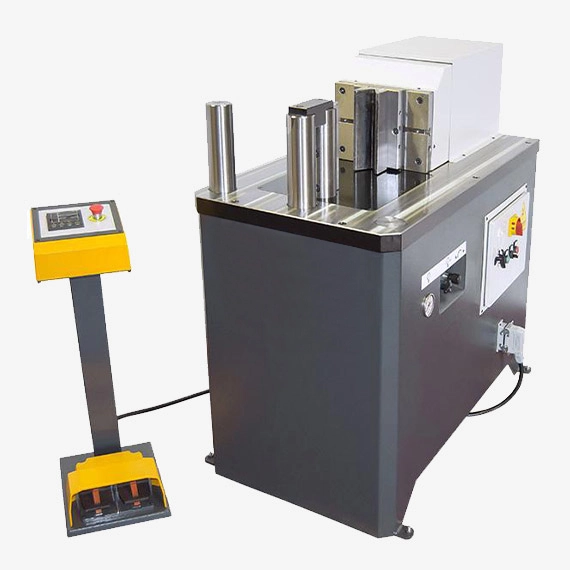
We manufacture Hydraulic Press Bending Attachments to bend sheet metal edges. Hydraulic Press Bending Attachments are used in metalworking industries
Hydraulic press bending attachments are specialized tools that can be used in conjunction with a hydraulic press to enhance the bending capabilities and efficiency. These attachments are designed to facilitate various bending operations and provide versatility in the types of bends that can be achieved. Here are some common hydraulic press bending attachments:
- V-Dies: V-dies are one of the most commonly used bending attachments for hydraulic presses. They consist of a pair of V-shaped grooves, one on the die (female die) and the other on the punch (male die). V-dies are versatile and can be used to create bends with different angles and radii by adjusting the position of the sheet metal within the V-grooves.
- U-Dies: U-dies feature a U-shaped groove on the die and a matching punch. They are typically used for creating U-shaped bends or channels in the sheet metal. U-dies are often used in applications such as forming flanges or creating curved profiles.
- Radius Dies: Radius dies are designed to create bends with a specific radius. They come in various sizes and shapes, allowing for precise bending of sheet metal to achieve consistent radii. Radius dies are commonly used in applications where precise curvature is required, such as in automotive or aerospace industries.
- Hemming Dies: Hemming dies are used to create hems or folded edges on sheet metal. They consist of a die and punch combination that allows the sheet metal to be bent over itself to form a closed hem. Hemming dies are commonly used in applications where a secure and neat edge finish is required, such as in the manufacturing of panels or enclosures.
- Box and Pan Brake Attachments: These attachments are used to convert a hydraulic press into a box and pan brake machine. They consist of segmented bending fingers that can be adjusted to create various box or pan shapes by bending the sheet metal along multiple points. Box and pan brake attachments are versatile and can handle complex bending operations, such as creating boxes, trays, or ductwork.
- Custom Bending Attachments: Depending on specific bending requirements, custom bending attachments can be designed and fabricated. These attachments are tailored to meet unique bending needs, such as forming intricate shapes, multiple bends, or specialty profiles. Custom bending attachments can enhance the versatility and productivity of a hydraulic press.
When selecting hydraulic press bending attachments, it’s important to consider factors such as the type and thickness of the sheet metal, the desired bend angles and radii, and the specific application requirements. Using the appropriate bending attachments ensures accurate and efficient bending operations while expanding the capabilities of the hydraulic press.
Hydraulic Press Bending Attachments
Hydraulic press bending attachments are accessories that extend the functionality of a hydraulic press, enabling it to perform various bending tasks on metal sheets or other materials. These attachments are designed to work seamlessly with hydraulic presses, providing precise and efficient bending operations.
Types of Hydraulic Press Bending Attachments
Hydraulic press bending attachments come in a variety of types, each catering to specific bending needs. Some common types include:
- V-die attachments: These attachments are used for creating precise and consistent bends in sheet metal. They feature a V-shaped groove that guides the material during bending, ensuring uniform angles and smooth transitions.
- U-die attachments: Similar to V-die attachments, U-die attachments are used for bending sheet metal, but they offer a wider opening compared to V-dies. This allows for bending wider materials or creating larger bends.
- Hemming attachments: Hemming attachments are specifically designed for creating hems, which are folded edges on sheet metal. They provide a clean and aesthetically pleasing finish to edges, preventing fraying and adding strength to the material.
- Beaded attachments: Beaded attachments are used for creating beads or raised ridges on sheet metal. These beads can serve various purposes, such as adding structural strength, improving rigidity, or enhancing aesthetics.
- Channel forming attachments: Channel forming attachments are designed to create channels or grooves in sheet metal. These channels can be used for various applications, such as wiring channels, ventilation ducts, or structural reinforcements.
Benefits of Using Hydraulic Press Bending Attachments
Hydraulic press bending attachments offer several advantages over manual bending methods or using specialized bending machines:
- Versatility: Hydraulic press bending attachments provide the flexibility to perform a wide range of bending operations, catering to various material types and shapes.
- Precision: These attachments ensure accurate and consistent bends, minimizing imperfections and maintaining dimensional integrity.
- Efficiency: Hydraulic presses provide rapid and powerful bending operations, significantly reducing production time compared to manual methods.
- Convenience: Hydraulic press bending attachments are easy to install and operate, making them suitable for both experienced and novice users.
- Cost-effectiveness: Hydraulic press bending attachments are relatively affordable, offering a cost-effective solution for enhancing the capabilities of a hydraulic press.
Applications of Hydraulic Press Bending Attachments
Hydraulic press bending attachments are widely used in various industries, including:
- Metal fabrication: Bending sheet metal for various components, such as enclosures, brackets, structural supports, and decorative elements.
- HVAC ductwork: Creating bends and shaping ductwork components for heating, ventilation, and air conditioning systems.
- Automotive industry: Forming and bending sheet metal parts for vehicles, such as body panels, structural components, and trim pieces.
- Appliance manufacturing: Bending sheet metal for appliances, such as refrigerators, ovens, washing machines, and dishwashers.
- Electronics industry: Creating bends and shaping metal enclosures for electronic devices, such as computers, telecommunications equipment, and consumer electronics.
Factors to Consider When Choosing Hydraulic Press Bending Attachments
When selecting hydraulic press bending attachments, several factors should be considered:
- Material type and thickness: Ensure the attachment is compatible with the material and thickness you intend to bend.
- Desired bend angle and shape: Choose the appropriate attachment based on the required bend angle and shape.
- Hydraulic press capacity: Verify that the attachment is suitable for the capacity of your hydraulic press.
- Attachment dimensions: Ensure the attachment’s dimensions are compatible with your hydraulic press and the workspace.
- Quality and reputation of the manufacturer: Opt for attachments from reputable manufacturers known for high-quality materials and construction.
Conclusion
Hydraulic press bending attachments are valuable additions to any workshop or manufacturing facility, expanding the capabilities of hydraulic presses and enabling precise, efficient bending operations. With a wide range of attachment types available, users can tailor their bending capabilities to meet specific material and application requirements.
V-Dies
V-dies are a commonly used bending attachment for hydraulic presses and are named after their distinctive V-shaped grooves. They consist of a pair of dies, one fixed (female die) and the other movable (male die or punch), with matching V-shaped grooves machined into them. V-dies are versatile tools that allow for the bending of sheet metal to create a variety of angles and radii.
Here are some key points about V-dies:
- Function: V-dies are primarily used for air bending, a common bending method where the sheet metal is bent by applying downward force with the punch onto the V-die. The angle of the bend is determined by the depth at which the sheet metal is placed in the V-groove.
- Adjustable Angle: V-dies offer adjustability in terms of bend angle. By changing the position of the sheet metal within the V-grooves, you can achieve different bend angles. This adjustability allows for flexibility in creating a range of bends without the need for changing tooling.
- Different V-Groove Sizes: V-dies come in various sizes to accommodate different sheet metal thicknesses and bending requirements. The size of the V-groove determines the radius of the bend that can be achieved. Smaller V-grooves produce tighter bends, while larger V-grooves result in larger bend radii.
- Multiple V-Die Sets: Hydraulic press machines often have multiple sets of V-dies available, each with different V-groove sizes. This allows for greater versatility in bending operations, enabling the operator to select the appropriate V-die set based on the desired bend radius and sheet metal thickness.
- Compatibility: V-dies can be used with various types of sheet metal, including steel, aluminum, stainless steel, and other metals that are suitable for bending. The choice of V-die depends on the specific material being used and its thickness.
- Support Accessories: Additional support accessories, such as backgauges and angle-measuring devices, can be used in conjunction with V-dies to assist with accurate positioning and angle control during the bending process. These accessories help ensure consistent and precise bends.
V-dies are widely used in industries such as metal fabrication, automotive, aerospace, and construction. They provide a versatile and efficient solution for bending sheet metal with a hydraulic press, offering flexibility in creating various bend angles and radii without the need for extensive tool changes.
U-Dies
U-dies are another type of bending attachment used in conjunction with hydraulic presses. They are named after their U-shaped grooves and are designed to create U-shaped bends or channels in sheet metal. U-dies consist of a fixed die (female die) and a movable punch (male die) with matching U-shaped grooves.
Here are some key points about U-dies:
- Function: U-dies are specifically designed for bending sheet metal to form U-shaped bends. The sheet metal is placed between the U-shaped grooves, and the downward force applied by the punch causes the material to deform and form the desired U-shape.
- U-Groove Size and Shape: U-dies are available in various sizes and shapes to accommodate different bending requirements. The size of the U-groove determines the depth and width of the U-shaped bend that can be achieved. Different U-die sizes allow for flexibility in creating U-shaped bends of varying dimensions.
- Material Compatibility: U-dies can be used with different types of sheet metal, such as steel, aluminum, stainless steel, and other metals suitable for bending. The choice of U-die depends on the specific material being used and its thickness.
- Bending Applications: U-dies are commonly used for applications that require U-shaped bends, such as forming flanges, channels, or curved profiles. They are widely used in industries like HVAC, automotive, and general metal fabrication.
- Support Accessories: Similar to V-dies, U-dies can be used in conjunction with support accessories like backgauges or angle-measuring devices to ensure accurate positioning and angle control during the bending process. These accessories assist in achieving consistent and precise U-shaped bends.
- Die Set Configurations: Hydraulic press machines often have multiple sets of U-dies available, each with different U-groove sizes. This allows for flexibility in creating U-shaped bends with varying dimensions and radii.
U-dies offer a practical solution for bending sheet metal into U-shaped forms. They provide versatility and efficiency in creating U-shaped bends with consistent dimensions. By selecting the appropriate U-die size and shape, operators can achieve accurate and repeatable U-shaped bends using hydraulic press machines.
Radius Dies
Radius dies are a type of bending attachment used in hydraulic presses to create bends with specific radii in sheet metal. They are designed to provide precise and consistent curvature to achieve rounded or curved bends. Radius dies consist of a fixed die (female die) and a movable punch (male die) with matching curved profiles.
Here are some key points about radius dies:
- Curvature and Radii: Radius dies are available in different profiles to create bends with specific radii. The radius of the die corresponds to the desired curvature of the bend. By selecting the appropriate radius die, operators can achieve consistent and accurate bends with a desired radius of curvature.
- Application Flexibility: Radius dies can be used for a variety of applications where precise curved bends are required. They are commonly used in industries such as automotive, aerospace, architectural, and manufacturing, where curved components or parts are needed.
- Material Compatibility: Radius dies can be used with various types of sheet metal, including steel, aluminum, stainless steel, and other metals suitable for bending. The choice of radius die depends on the specific material being used and its thickness.
- Die Configuration: Radius dies are typically available as a set consisting of multiple dies with different radii. This allows operators to choose the appropriate die for the desired bend radius. The die set may include different radii to accommodate a range of bending requirements.
- Precision and Consistency: Radius dies provide precise and consistent curvature to the sheet metal during the bending process. This ensures that the resulting bends have a uniform radius and meet the desired specifications.
- Support Accessories: To achieve accurate and repeatable bends using radius dies, operators can use support accessories such as backgauges or angle-measuring devices. These accessories assist in positioning the sheet metal and controlling the bend angle, resulting in consistent and precise curved bends.
Radius dies offer a specialized solution for creating bends with specific radii in sheet metal. They provide the ability to achieve smooth and precise curved bends, allowing for the production of components with consistent shapes and dimensions. By selecting the appropriate radius die and utilizing proper techniques, operators can achieve high-quality curved bends using hydraulic press machines.
Hemming Dies
Hemming dies are specialized bending attachments used in hydraulic presses to create folded edges or hems on sheet metal. They are designed to fold the edge of the sheet metal over itself, resulting in a secure and neat finished edge. Hemming dies consist of a fixed die (female die) and a movable punch (male die) with matching profiles that enable the folding action.
Here are some key points about hemming dies:
- Folding Mechanism: Hemming dies use a folding mechanism to bend the edge of the sheet metal over itself. The punch presses down on the edge of the sheet metal, while the die supports and guides the material to facilitate the folding process.
- Folded Edge Formation: The hemming process involves folding the edge of the sheet metal back onto itself, creating a double-layered fold. This provides enhanced strength, stability, and a clean finished appearance to the edge.
- Hemming Types: Hemming dies can facilitate different types of hems, such as a single hem or a double hem. A single hem involves folding the edge of the sheet metal once, while a double hem involves folding the edge twice, resulting in a more secure and reinforced edge.
- Material Compatibility: Hemming dies can be used with various types of sheet metal, including steel, aluminum, stainless steel, and other metals suitable for bending. The choice of hemming die depends on the specific material being used and its thickness.
- Applications: Hemming dies are commonly used in industries such as automotive, aerospace, appliance manufacturing, and general sheet metal fabrication. They are often employed in applications where a finished, folded edge is required, such as in the production of panels, enclosures, or structural components.
- Support Accessories: To ensure accurate and repeatable hemming operations, support accessories like backgauges or angle-measuring devices can be used. These accessories assist in positioning the sheet metal and controlling the folding angle, resulting in consistent and precise hemmed edges.
Hemming dies provide a reliable and efficient solution for creating folded edges or hems on sheet metal. They offer enhanced edge strength and a professional finish to the sheet metal components. By utilizing proper hemming techniques and selecting the appropriate hemming die, operators can achieve consistent and high-quality hemmed edges using hydraulic press machines.
Box and Pan Brake Attachments
Box and pan brake attachments are accessories used with hydraulic presses or other bending machines to perform box and pan bending operations. These attachments allow for the bending of sheet metal to create boxes, pans, trays, and other similar structures with multiple sides and complex shapes. They consist of segmented fingers or clamping bars that can be adjusted to accommodate various box and pan configurations.
Here are some key points about box and pan brake attachments:
- Adjustable Fingers or Clamping Bars: The box and pan brake attachments feature segmented fingers or clamping bars that can be individually adjusted. These segments can be moved closer or farther apart to create the desired width and depth for bending the sheet metal.
- Multiple Bending Options: Box and pan brake attachments provide versatility in bending operations. They can be used to create different angles and radii in the sheet metal, allowing for the formation of various box and pan shapes.
- Support for Complex Shapes: The adjustable fingers or clamping bars can be positioned to accommodate complex shapes, such as boxes with uneven sides, flanges, or angled bends. This versatility allows for the creation of customized structures based on specific design requirements.
- Material Compatibility: Box and pan brake attachments can be used with different types of sheet metal, including steel, aluminum, stainless steel, and other metals suitable for bending. The choice of attachment depends on the specific material being used and its thickness.
- Accuracy and Precision: The segmented fingers or clamping bars provide precise bending control, ensuring accurate and repeatable results. This allows for consistent dimensions and angles in the formed box and pan structures.
- Time and Labor Saving: Box and pan brake attachments streamline the process of creating boxes and pans, reducing the need for manual forming or additional tooling. They help save time and labor by simplifying complex bending operations.
Box and pan brake attachments are commonly used in industries such as metal fabrication, HVAC, electrical enclosures, and general manufacturing. They offer a practical solution for bending sheet metal into boxes, pans, and similar structures with multiple sides and varying dimensions. By adjusting the fingers or clamping bars, operators can achieve precise and customized bending results using hydraulic press machines or other compatible bending equipment.
Custom Bending Attachments
Custom bending attachments refer to specialized tools or accessories that are specifically designed and manufactured for unique or specific bending applications. These attachments are tailored to meet specific requirements, such as bending complex shapes, forming intricate patterns, or achieving precise dimensions that may not be possible with standard bending tools.
Here are some key points about custom bending attachments:
- Tailored Design: Custom bending attachments are designed to fit the specific needs of the application. They are often developed based on detailed specifications or drawings provided by the customer. The design takes into consideration factors such as the desired bending angles, radii, dimensions, and material characteristics.
- Specialized Functionality: Custom bending attachments can be engineered to perform specialized bending operations that are not achievable with standard tools. This may include bending materials with unique properties, forming intricate patterns, creating complex geometries, or achieving specific tolerances.
- Enhanced Versatility: Custom bending attachments offer increased versatility and flexibility compared to standard tools. They can be designed to accommodate different types of materials, thicknesses, and shapes, allowing for a wider range of bending applications.
- Precision and Accuracy: Custom attachments are engineered with precision to ensure accurate and repeatable bending results. They can incorporate features such as adjustable components, precise measurement systems, or specialized control mechanisms to achieve the desired bending specifications.
- Material Compatibility: Custom bending attachments can be designed for use with various types of materials, including metals, plastics, composites, or other specialized materials. The selection of materials for the attachment depends on factors such as the material being bent, its thickness, and the specific application requirements.
- Application-Specific Considerations: Custom bending attachments take into account specific application considerations, such as production volume, workflow efficiency, operator ergonomics, and safety requirements. The attachment can be designed to integrate seamlessly into the existing bending equipment or production line.
Custom bending attachments are typically developed through collaboration between the manufacturer or designer and the customer. The design process involves understanding the specific bending needs, conducting feasibility studies, creating prototypes, and performing testing to ensure the attachment meets the desired specifications.
By utilizing custom bending attachments, manufacturers can enhance their capabilities, increase productivity, and achieve precise and customized bending results. These attachments enable the bending of challenging or unique shapes, contributing to the production of specialized components or products.
Hydraulic Metal Press
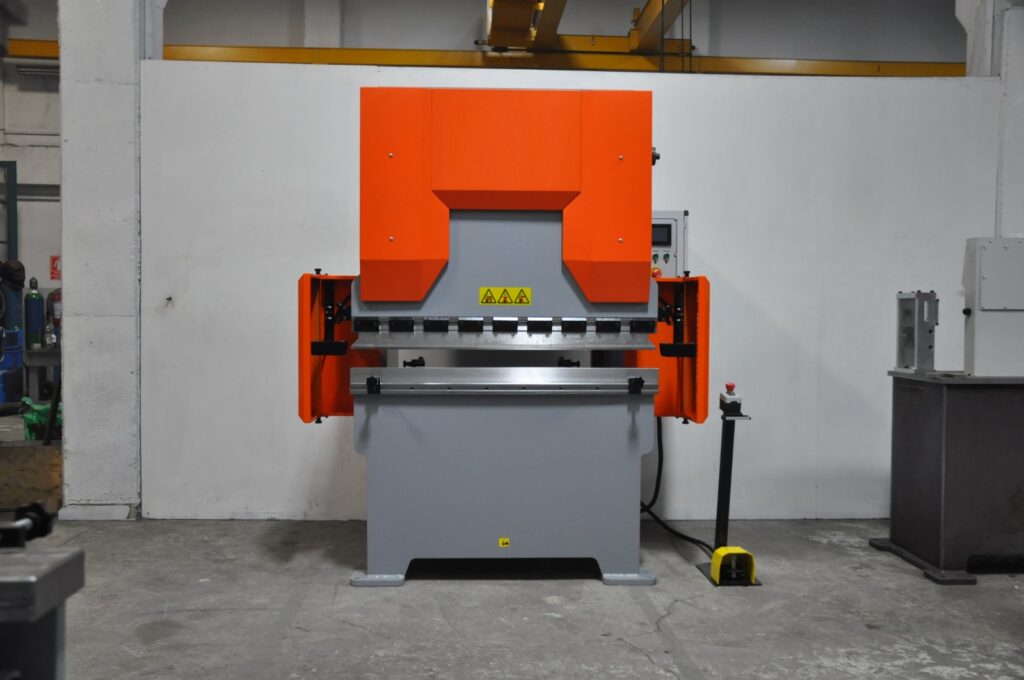
A hydraulic metal press is a powerful industrial tool used to shape and form metal sheets into various components. It utilizes hydraulic pressure to apply a controlled force, enabling precise and efficient bending, forming, and stamping operations. Hydraulic metal presses are widely used in various industries, including metal fabrication, automotive manufacturing, appliance production, and electronics assembly.
Components of a Hydraulic Metal Press
A hydraulic metal press typically consists of the following components:
- Frame: The frame provides the rigid support for the press’s components. It typically consists of a heavy-duty steel structure.
- Hydraulic Ram: The hydraulic ram is the main component that applies force to the metal sheet. It is powered by hydraulic fluid, which is pressurized by a hydraulic pump.
- Hydraulic Pump: The hydraulic pump is responsible for generating the pressurized fluid that powers the hydraulic ram. It can be electric or hydraulically driven.
- Hydraulic Reservoir: The hydraulic reservoir stores the hydraulic fluid that is circulated within the system. It also helps regulate the temperature and pressure of the fluid.
- Control Panel: The control panel allows the operator to control the press’s functions, such as ram speed, force, and stroke length.
- Tooling: Tooling includes dies, punches, and other attachments that are used to shape the metal sheet into the desired form. Tooling is interchangeable, allowing the press to perform various operations.
Types of Hydraulic Metal Presses
There are several types of hydraulic metal presses, each designed for specific applications:
- C-Frame Presses: C-frame presses are the most common type of hydraulic metal press. They offer a simple and versatile design, suitable for a wide range of bending and forming operations.
- H-Frame Presses: H-frame presses are designed for heavy-duty applications, where high tonnage and precise bending are required. They feature a more robust frame and can handle thicker metal sheets.
4-Column Presses:** 4-column presses provide exceptional stability and precision, making them ideal for high-precision forming and stamping operations. They feature four vertical columns that support the frame and ensure uniform force distribution.
Applications of Hydraulic Metal Presses
Hydraulic metal presses are used in a wide range of applications, including:
- Bending: Hydraulic presses are commonly used to bend sheet metal into various shapes, such as boxes, enclosures, brackets, and channels.
- Forming: Hydraulic presses can form complex shapes in sheet metal, such as curves, domes, and flanges.
- Stamping: Hydraulic presses are used to stamp out metal parts from sheet metal blanks. Stamping is used to create components with intricate details and precise dimensions.
- Assembling: Hydraulic presses can be used to assemble metal components by pressing them together or inserting fasteners.
- Coining: Hydraulic presses can be used for coining operations, where metal is compressed into a die to create detailed designs or patterns.
Benefits of Using Hydraulic Metal Presses
Hydraulic metal presses offer several advantages over other metal forming methods:
- Precision: Hydraulic presses provide precise and consistent bending and forming operations.
- Force Control: Hydraulic presses allow for controlled application of force, ensuring uniform shaping and minimizing material damage.
- Versatility: Hydraulic presses can be used for a wide range of operations, from simple bending to complex forming and stamping.
- Efficiency: Hydraulic presses offer rapid cycle times, making them efficient for production environments.
- Safety: Hydraulic presses are designed with safety features to protect operators from hazards.
Safety Precautions for Hydraulic Metal Presses
When operating a hydraulic metal press, it is crucial to follow safety precautions to prevent injuries:
- Proper Training: Operators should receive proper training on the operation and safety procedures of the hydraulic press.
- Protective Gear: Wear safety glasses, gloves, and appropriate clothing to protect against flying debris and potential hazards.
- Secure Workpiece: Secure the workpiece firmly to the press bed to prevent movement during operation.
- Maintain Clearance: Keep hands and body clear of moving parts of the press.
- Emergency Stop: Be familiar with the location and operation of the emergency stop button.
- Regular Maintenance: Conduct regular maintenance and inspections to ensure the press is in proper working condition.
Conclusion
Hydraulic metal presses are powerful and versatile tools that play a vital role in various industries. Their ability to apply precise and controlled force makes them ideal for shaping and forming metal sheets into various components. By following proper safety precautions and operating techniques, hydraulic metal presses can be used safely and efficiently to produce high-quality metal parts.
Application Areas
Hydraulic metal presses are used in a wide range of applications, including:
Metal fabrication: Hydraulic presses are commonly used to bend, form, and stamp sheet metal into various components for metal fabrication projects. They are used to create parts for various industries, such as automotive, construction, aerospace, and appliance manufacturing.
Automotive industry: Hydraulic presses are essential tools in the automotive industry, used to produce various components such as body panels, structural supports, and trim pieces. They are also used for stamping out parts such as brackets, hinges, and fasteners.
Construction industry: Hydraulic presses are used in the construction industry to form and shape metal components for structures, such as beams, columns, and roof trusses. They are also used to manufacture components for construction equipment, such as cranes, bulldozers, and excavators.
Aerospace industry: Hydraulic presses play a crucial role in the aerospace industry, used to produce high-precision components for aircraft and spacecraft. They are used for forming and shaping complex shapes in lightweight materials such as aluminum, titanium, and composites.
Appliance manufacturing: Hydraulic presses are widely used in appliance manufacturing to produce components for various appliances, such as refrigerators, ovens, washing machines, and dishwashers. They are used for bending, forming, and stamping sheet metal components.
Electronics industry: Hydraulic presses are used in the electronics industry to create enclosures for electronic devices, such as computers, telecommunications equipment, and consumer electronics. They are also used to form and shape metal components within electronic devices.
Powder metallurgy: Hydraulic presses are used in powder metallurgy to compact and form metal powders into various shapes. This process is used to produce components with high density, precise dimensions, and complex geometries.
Recycling and scrap metal processing: Hydraulic presses are used in recycling and scrap metal processing to compact and compress scrap metal for easier transportation and processing. They are also used to separate different types of scrap metal based on their properties.
These are just a few examples of the many application areas of hydraulic metal presses. Their versatility and ability to apply precise force make them valuable tools in a wide range of industries.
A small press brake machine is a compact tool used for bending sheet metal into various shapes. It’s ideal for small-scale operations or workshops with limited space. Here’s a basic rundown of what to look for and expect:
Key Features:
- Capacity: Check the maximum bending length and thickness it can handle. Small machines are often used for lighter and thinner materials.
- Controls: Modern machines may have manual, hydraulic, or even CNC controls for precision.
- Tooling: Look at the types of dies and punches included or available, as these determine the range of shapes and angles you can create.
- Frame and Build: Ensure it’s robust enough for your needs while still being compact.
- Safety Features: Safety guards and emergency stops are crucial for safe operation.
Applications:
- Prototype Development: Useful for making small runs or prototypes with custom bends.
- Small Batch Production: Ideal for low-volume production runs.
- DIY Projects: Great for hobbyists or small business owners.
Do you need specific recommendations or have any particular requirements for your projects?
A small press brake machine for sheet metal bending consists of several key components that work together to achieve precise bends. Here’s an overview of the main components:
1. Frame
- Description: The frame is the backbone of the press brake, providing structural support and stability. It is typically made of heavy-duty steel to withstand the forces involved in bending.
- Importance: A sturdy frame ensures accuracy and prevents deformation during operation.
2. Ram (or Slide)
- Description: The ram is the moving part of the press brake that holds the upper die and moves vertically to apply force to the sheet metal.
- Types: Can be powered by manual, hydraulic, mechanical, or electric systems, depending on the type of press brake.
- Importance: The ram’s movement and force application are crucial for precise bending.
3. Bed
- Description: The bed is the fixed part of the press brake that holds the lower die. It provides a stable surface against which the sheet metal is bent.
- Importance: The bed must be level and sturdy to ensure accurate bends.
4. Punch and Die
- Punch: The tool attached to the ram that presses the sheet metal into the die.
- Die: The tool attached to the bed that shapes the metal as the punch presses into it.
- Types: Different shapes and sizes for various bending operations (e.g., V-dies, U-dies, offset dies).
- Importance: The choice of punch and die determines the bend shape and angle.
5. Back Gauge
- Description: A mechanical or computerized device that positions the sheet metal accurately for bending.
- Function: Allows for precise placement and repeatability in bends.
- Importance: Ensures consistency in multi-bend operations.
6. Control System
- Manual Controls: Levers and dials used for simple operations.
- CNC Controls: Computerized systems that allow for complex programming and automation of bends.
- Importance: The control system impacts ease of use, precision, and efficiency.
7. Foot Pedal or Control Panel
- Description: A user interface for operating the press brake, typically used to control the movement of the ram.
- Function: Allows the operator to start and stop the bending process safely.
- Importance: Ensures safety and precision in operation.
8. Safety Features
- Safety Guards: Protective barriers to prevent accidental contact with moving parts.
- Emergency Stop Button: Allows for immediate cessation of machine operation in case of emergency.
- Light Curtains or Laser Guards: Sensors that stop the machine if they detect an obstruction in the bending area.
- Importance: Safety features are crucial to protect operators from injury.
9. Hydraulic System (if applicable)
- Description: In hydraulic press brakes, this system uses fluid pressure to move the ram.
- Components: Includes hydraulic pumps, valves, and cylinders.
- Importance: Provides smooth and adjustable force for precise bending.
10. Motor and Drive System
- Description: Powers the movement of the ram and other mechanical components.
- Types: Can be electric or hydraulic, depending on the machine type.
- Importance: Ensures efficient and consistent machine operation.
Conclusion
Understanding these components will help you select the right press brake for your specific needs and ensure proper operation and maintenance. If you have further questions about any of these components or need advice on a specific model, feel free to ask!
Press brakes are machines used to bend and shape sheet metal, and they come in various types to suit different applications and requirements. Each type of press brake has unique characteristics and advantages. Here’s a detailed overview of the main types of press brakes:
1. Mechanical Press Brakes
Description
- Mechanical press brakes use a flywheel powered by an electric motor. The energy stored in the flywheel is transferred to the ram through a clutch and crank mechanism, providing precise and consistent force.
Advantages
- Speed: They are generally faster than hydraulic press brakes, making them suitable for high-production environments.
- Precision: Offers precise control over the bending process, ensuring consistent results.
- Cost-Effective: Often more affordable than other types, both in terms of purchase price and maintenance.
Disadvantages
- Limited Flexibility: Not as versatile as hydraulic models, especially for complex bends.
- Maintenance: Requires regular maintenance of mechanical components like the clutch and crank.
Applications
- Ideal for repetitive tasks and high-volume production of simpler bends.
2. Hydraulic Press Brakes
Description
- Hydraulic press brakes use hydraulic cylinders to move the ram. The hydraulic fluid is pumped into the cylinders, creating pressure that moves the ram downwards for bending.
Advantages
- Versatility: Can handle a wide range of materials and bend angles, including complex and acute bends.
- Adjustable Force: Allows for precise control over the bending force, making it suitable for various materials and thicknesses.
- Safety: Often equipped with advanced safety features and overload protection.
Disadvantages
- Speed: Generally slower than mechanical press brakes.
- Cost: Higher initial cost and maintenance expenses due to hydraulic components.
Applications
- Suitable for a variety of bending tasks, from simple to complex, and used in industries requiring versatility and precision.
3. Pneumatic Press Brakes
Description
- Pneumatic press brakes use compressed air to move the ram. They are generally used for lighter and less demanding applications.
Advantages
- Simplicity: Easier to operate and maintain than hydraulic and mechanical press brakes.
- Cost-Effective: Lower initial and operational costs.
- Environmentally Friendly: Uses air, which is more eco-friendly than hydraulic fluid.
Disadvantages
- Limited Force: Not suitable for heavy-duty applications or thick materials.
- Precision: Less precise compared to hydraulic or mechanical press brakes.
Applications
- Best for light-duty applications and smaller workshops that work with thinner materials.
4. Electric Press Brakes
Description
- Electric press brakes, also known as servo-electric press brakes, use electric motors and ball screws to move the ram.
Advantages
- Efficiency: Highly energy-efficient, consuming power only during operation.
- Precision: Offers excellent accuracy and repeatability in bends.
- Environmentally Friendly: Does not require hydraulic fluid, reducing environmental impact.
Disadvantages
- Cost: Typically more expensive than mechanical or hydraulic models.
- Limited Force: May not be suitable for very heavy-duty applications compared to hydraulic models.
Applications
- Ideal for precision work in industries like electronics, aerospace, and automotive, where accuracy is crucial.
5. CNC Press Brakes
Description
- CNC (Computer Numerical Control) press brakes use computerized controls to automate the bending process. They can be either hydraulic, mechanical, or electric.
Advantages
- Automation: Allows for automated and highly precise bending, reducing manual intervention.
- Versatility: Can handle complex bending tasks with ease, including multi-axis operations.
- Efficiency: Reduces setup time and increases production speed and consistency.
Disadvantages
- Cost: Higher initial investment and maintenance costs due to advanced technology.
- Complexity: Requires skilled operators to program and manage the CNC system.
Applications
- Used in high-precision industries for complex and varied bending tasks, including aerospace, automotive, and manufacturing.
6. Hydro-Mechanical Press Brakes
Description
- Hydro-mechanical press brakes combine hydraulic and mechanical systems. They use a hydraulic system to drive a mechanical linkage, providing the force for bending.
Advantages
- Power: Provides high bending force, suitable for heavy-duty applications.
- Control: Offers precise control over bending operations, similar to hydraulic press brakes.
Disadvantages
- Complexity: More complex than purely mechanical or hydraulic systems, requiring skilled maintenance.
- Cost: Typically more expensive due to the combined system.
Applications
- Suitable for heavy-duty applications requiring both power and precision.
Comparison Summary
Type | Advantages | Disadvantages | Applications |
---|---|---|---|
Mechanical | Fast, precise, cost-effective | Limited flexibility, requires maintenance | High-volume, repetitive tasks |
Hydraulic | Versatile, adjustable force, safe | Slower, higher cost | Complex bending tasks in various industries |
Pneumatic | Simple, cost-effective, eco-friendly | Limited force, less precise | Light-duty applications with thin materials |
Electric | Efficient, precise, eco-friendly | Expensive, limited force | Precision work in electronics, aerospace, etc. |
CNC | Automated, versatile, efficient | Expensive, complex | High-precision tasks in aerospace, automotive |
Hydro-Mechanical | Powerful, controlled bending | Complex, expensive | Heavy-duty applications requiring precision |
Conclusion
Choosing the right type of press brake depends on your specific needs, including the type of materials, the complexity of the bends, production volume, and budget constraints. If you need further assistance in selecting a press brake for your specific application, feel free to ask!
General Maintenance Tips
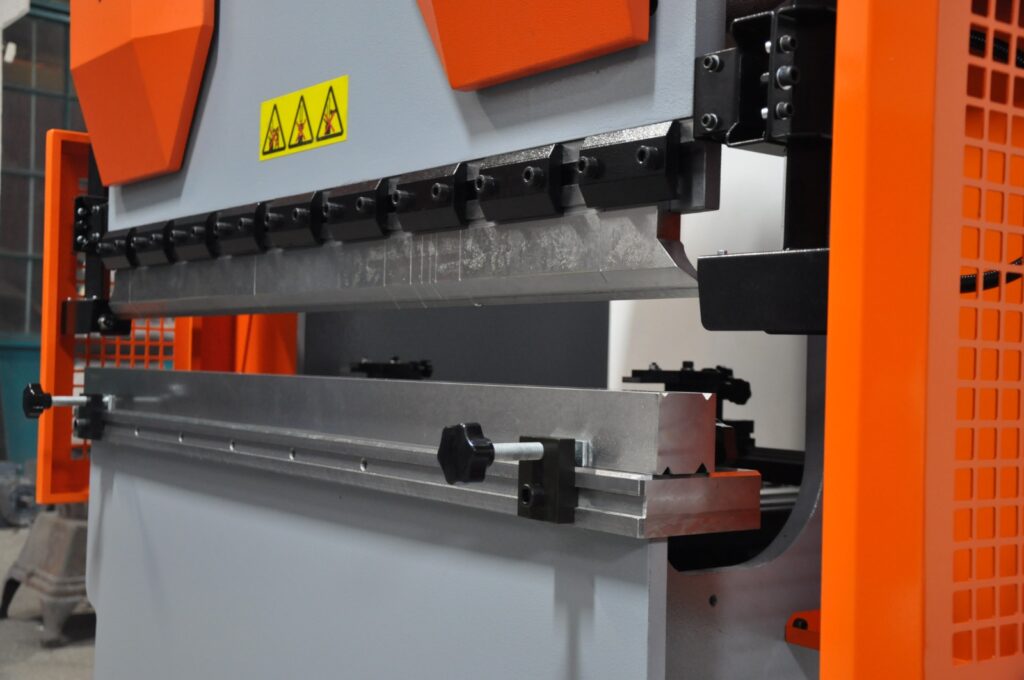
1. Regular Cleaning
- Daily Cleaning: Clean the machine surfaces and components daily to remove dust, metal shavings, and debris. Use a soft brush or cloth to clean sensitive areas.
- Lubrication: Lubricate all moving parts regularly according to the manufacturer’s specifications. This includes the ram, guide rails, and back gauge.
- Hydraulic System: Check for hydraulic fluid leaks and ensure that the hydraulic oil is clean and at the correct level.
2. Inspection and Monitoring
- Visual Inspection: Conduct a visual inspection of the machine before and after each use. Look for signs of wear, damage, or misalignment.
- Check Bolts and Fasteners: Ensure that all bolts, nuts, and fasteners are tight and secure. Loose components can lead to misalignment and damage.
- Monitor Performance: Pay attention to any unusual noises or changes in machine performance, which may indicate potential issues.
3. Electrical System Checks
- Wiring Inspection: Regularly inspect the wiring and electrical connections for signs of wear or damage. Replace any damaged wires immediately.
- Control Panel: Ensure that the control panel and buttons are functioning correctly. Test all safety switches and emergency stop buttons to verify they work properly.
4. Hydraulic System Maintenance
- Oil Quality and Level: Check the hydraulic oil regularly for contamination or degradation. Replace the oil according to the manufacturer’s recommendations.
- Hydraulic Filters: Inspect and replace hydraulic filters as needed to prevent contamination and ensure optimal system performance.
- Check for Leaks: Inspect hoses, seals, and connections for leaks. Repair or replace any faulty components immediately.
5. Tooling Maintenance
- Die and Punch Inspection: Inspect the dies and punches for wear or damage. Ensure they are properly aligned and seated in the machine.
- Tooling Alignment: Regularly check the alignment of the tooling to prevent uneven wear and ensure accurate bends.
- Storage: Store dies and punches in a clean, dry environment to prevent rust and damage.
6. Calibration and Adjustment
- Back Gauge Calibration: Regularly calibrate the back gauge to ensure precise positioning and accurate bends.
- Ram Alignment: Check and adjust the ram alignment periodically to maintain consistent bending accuracy.
- CNC System Calibration: If using a CNC press brake, regularly update and calibrate the CNC system to ensure accurate programming and operation.
Specific Maintenance Tips for Different Types of Press Brakes
Mechanical Press Brakes
- Clutch and Brake Maintenance: Regularly inspect and adjust the clutch and brake mechanisms for wear. Replace any worn components as needed.
- Flywheel Inspection: Check the flywheel for cracks or damage and ensure it spins smoothly without wobbling.
Hydraulic Press Brakes
- Hydraulic Cylinder Inspection: Regularly check the hydraulic cylinders for leaks or damage and ensure they operate smoothly.
- Pressure Settings: Verify that the hydraulic pressure settings are within the manufacturer’s specifications.
Pneumatic Press Brakes
- Air Compressor Maintenance: Regularly inspect and maintain the air compressor, checking for leaks or damage.
- Air Filter Replacement: Replace air filters as needed to ensure clean and efficient air supply.
Electric Press Brakes
- Servo Motor Maintenance: Inspect and maintain servo motors, ensuring they are clean and operating efficiently.
- Ball Screw Inspection: Regularly check ball screws for wear and ensure proper lubrication.
Safety Considerations
- Training: Ensure that all operators are adequately trained in the safe operation and maintenance of the press brake.
- Safety Devices: Regularly test safety devices, such as light curtains, laser guards, and emergency stop buttons, to ensure they function correctly.
- Personal Protective Equipment (PPE): Require operators to wear appropriate PPE, such as gloves, safety glasses, and steel-toed boots.
Scheduled Maintenance
- Daily Maintenance: Perform basic cleaning, inspection, and lubrication tasks daily.
- Weekly Maintenance: Conduct more thorough inspections, including checking hydraulic oil levels and electrical connections.
- Monthly Maintenance: Perform comprehensive inspections, including calibration and alignment checks.
- Annual Maintenance: Schedule a professional service technician to conduct a detailed inspection and maintenance of the machine.
Conclusion
Regular maintenance of press brakes is essential to ensure safe and efficient operation. By following these tips and adhering to the manufacturer’s maintenance schedule, you can extend the life of your press brake and reduce the risk of unexpected breakdowns. If you have any specific maintenance questions or need further assistance, feel free to ask!
Installation Tips for Press Brake Machines

1. Site Preparation
Space Requirements
- Measure the Area: Ensure that the installation area is large enough to accommodate the press brake, including space for operators and maintenance access. Consider the dimensions of the machine and the bending material.
- Ceiling Height: Verify that the ceiling height is sufficient to allow for the full range of motion of the press brake’s ram and any required overhead clearances.
Floor Requirements
- Level Surface: The floor should be level and able to support the weight of the press brake and any associated loads. Use a level to check the surface.
- Foundation: For larger machines, consider a reinforced concrete foundation to prevent vibrations and ensure stability. Follow the manufacturer’s specifications for foundation thickness and reinforcement.
Environmental Conditions
- Temperature and Humidity: The installation area should have a controlled environment to prevent rust and corrosion. Extreme temperatures or humidity levels can affect machine performance.
- Ventilation: Ensure adequate ventilation to remove heat generated by the machine and prevent overheating.
2. Electrical and Power Requirements
Electrical Supply
- Voltage and Amperage: Check the machine’s electrical specifications for required voltage, amperage, and phase. Ensure that the power supply matches these requirements.
- Wiring and Circuit Breakers: Install appropriate wiring and circuit breakers to handle the machine’s electrical load. Use a licensed electrician to ensure compliance with local codes and standards.
Grounding
- Proper Grounding: Ensure the machine is properly grounded to prevent electrical shocks and equipment damage. Use appropriate grounding rods and wires.
3. Hydraulic and Pneumatic Systems
Hydraulic System
- Hydraulic Fluid: Fill the hydraulic system with the recommended hydraulic fluid. Check for leaks and ensure that all hoses and fittings are secure.
- Pressure Settings: Set the hydraulic pressure according to the manufacturer’s specifications. Adjust pressure relief valves as needed.
Pneumatic System (if applicable)
- Air Supply: Ensure a clean, dry air supply for pneumatic systems. Install air filters and dryers to remove moisture and contaminants.
4. Machine Setup and Alignment
Positioning
- Alignment: Use a precision level and alignment tools to ensure the press brake is properly aligned. Check that the ram and bed are parallel and that the back gauge is aligned correctly.
- Anchor the Machine: Secure the press brake to the foundation or floor using anchor bolts, following the manufacturer’s guidelines.
Tooling Installation
- Die and Punch Installation: Carefully install the dies and punches, ensuring they are correctly seated and aligned. Use the correct tools and follow the manufacturer’s instructions for safe installation.
5. Control System Setup
CNC System Initialization (if applicable)
- Software Installation: Install any required software and updates for CNC systems. Ensure compatibility with the control unit.
- Calibration: Calibrate the CNC system, including the back gauge and ram, to ensure accurate operation.
Manual Control Setup
- Control Panel Inspection: Verify that all buttons, switches, and indicators are functioning correctly. Check for any loose connections.
6. Safety Features and Devices
Safety Guards
- Install Guards: Install any provided safety guards, barriers, and light curtains to protect operators from moving parts and pinch points.
- Test Safety Devices: Test all safety devices, such as emergency stop buttons and interlocks, to ensure they function correctly.
Operator Safety Training
- Training Programs: Provide comprehensive training for operators, covering machine operation, safety procedures, and emergency response.
7. Testing and Calibration
Initial Testing
- Test Runs: Conduct initial test runs using scrap material to verify machine performance and accuracy. Check for alignment issues or mechanical problems.
- Adjustments: Make any necessary adjustments to the ram, back gauge, and tooling alignment to ensure accurate bending.
Calibration Checks
- Precision Calibration: Use precision measuring tools to check the accuracy of bends. Adjust settings as needed to achieve desired results.
8. Documentation and Compliance
Manufacturer’s Manual
- Review Documentation: Thoroughly review the manufacturer’s manual and installation guidelines to ensure compliance with all requirements.
- Warranty Registration: Register the machine’s warranty with the manufacturer and keep records of installation and maintenance activities.
Regulatory Compliance
- Local Codes and Standards: Ensure that the installation complies with local building codes, electrical standards, and safety regulations.
Conclusion
Proper installation of a press brake machine is essential for safe and efficient operation. By following these detailed installation tips and adhering to the manufacturer’s instructions, you can ensure a successful setup and minimize the risk of issues during operation. If you have any specific questions or need further assistance, feel free to ask!