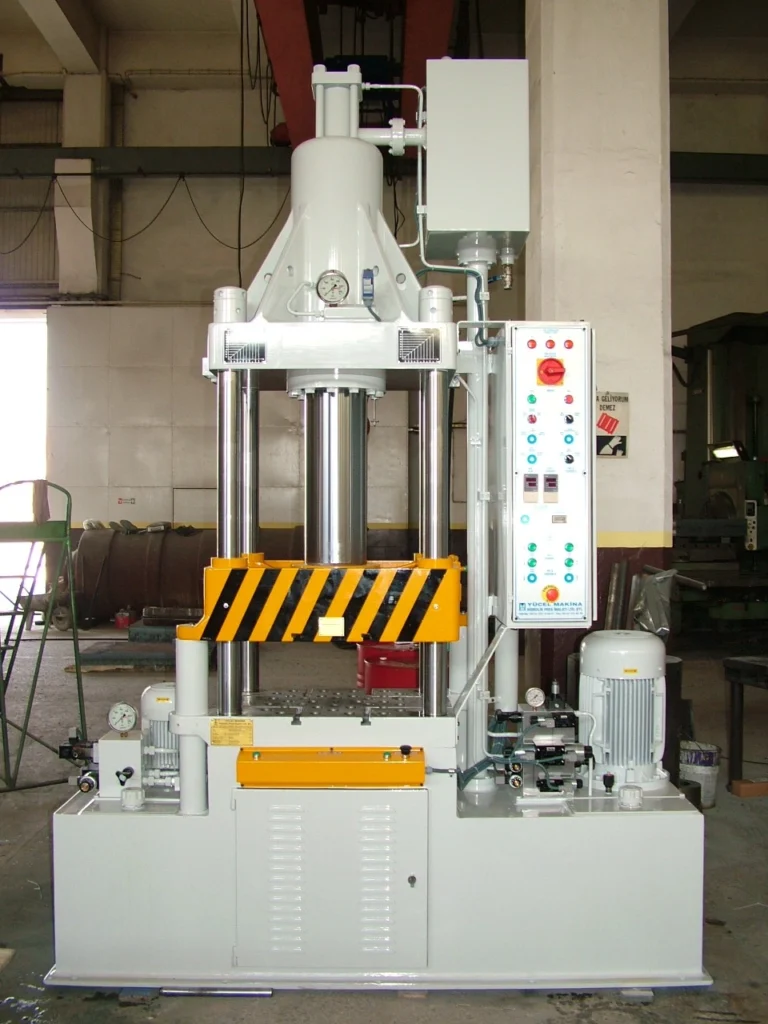
We manufacture a Bending Sheet Metal with Hydraulic Press to bend sheet metal edges. Bending Sheet Metal with Hydraulic Press is used in metalworking industries
Bending sheet metal using a hydraulic press is a common and efficient method in metal fabrication. Hydraulic presses provide the force necessary to bend the metal while maintaining control and precision. Here’s a general overview of the process:
- Material Preparation: Begin by selecting the appropriate sheet metal for the desired bend. Ensure that the metal is clean and free from any contaminants that could affect the bending process.
- Tooling Selection: Choose the appropriate tooling for the hydraulic press based on the desired bend angle and radius. The tooling typically consists of a punch (male die) and a die (female die) that work together to shape the metal. The dimensions of the tooling will depend on the specific bending requirements.
- Die Setup: Install the die on the hydraulic press, ensuring it is securely positioned and aligned with the punch. The die should match the desired bend angle and have the appropriate radius.
- Sheet Metal Placement: Position the sheet metal on the hydraulic press, aligning it with the die and punch. Ensure that the metal is flat and properly aligned to achieve an accurate and consistent bend.
- Pressure Adjustment: Adjust the pressure settings on the hydraulic press based on the thickness and properties of the sheet metal. The pressure should be sufficient to bend the metal without causing excessive deformation or damage.
- Bending Process: Activate the hydraulic press to apply force to the sheet metal. The press will exert pressure on the punch, which will push the metal into the die, creating the desired bend. The operator should carefully monitor the bending process to ensure it meets the desired specifications.
- Repeat if Needed: Depending on the complexity of the part and the number of bends required, the process may need to be repeated multiple times to achieve the desired shape. Each subsequent bend should be carefully aligned and executed to maintain accuracy.
It is important to note that the specific steps and parameters may vary depending on the size and capabilities of the hydraulic press, the thickness and type of sheet metal, and the desired bend specifications. Safety precautions, such as wearing appropriate personal protective equipment, should always be followed during the bending process.
It is recommended to consult the manufacturer’s guidelines and seek proper training before operating a hydraulic press for bending sheet metal.
Bending Sheet Metal with Hydraulic Press
Bending sheet metal with a hydraulic press is a common and effective method for shaping metal sheets into various forms. Hydraulic presses offer a controlled and precise way to apply force, ensuring consistent and accurate bends.
Preparing for Bending
- Material Selection: Choose the appropriate sheet metal material based on the desired properties, such as strength, corrosion resistance, and formability.
- Sheet Metal Preparation: Ensure the sheet metal is clean, free from debris, and flat. Mark the desired bend location clearly on the sheet metal.
- Tooling Selection: Select the appropriate bending tool, such as a V-die or a U-die, based on the desired bend angle and material thickness.
Bending Process
- Positioning the Sheet Metal: Place the sheet metal on the hydraulic press bed, aligning the bend line with the bending tool.
- Adjusting the Ram and Back Gauge: Adjust the ram height to ensure the correct amount of force is applied during bending. Position the back gauge to maintain the desired bend angle.
- Initiating the Bending Process: Activate the hydraulic press to apply force and bend the sheet metal. Move the ram slowly and evenly to ensure a smooth bend.
- Checking the Bend: Once the bending process is complete, inspect the bend for accuracy and consistency. Adjust the tooling or ram position if necessary.
Safety Precautions
- Wear Protective Gear: Always wear safety glasses, gloves, and appropriate clothing when operating a hydraulic press.
- Secure the Workpiece: Clamp the sheet metal securely to the press bed to prevent movement during bending.
- Avoid Distractions: Stay focused on the bending operation and avoid distractions.
- Maintain Proper Distance: Keep hands and body clear of moving parts of the press.
- Follow Manufacturer Instructions: Adhere to the specific instructions provided by the hydraulic press manufacturer.
Additional Tips
- Lubrication: Lubricate the bending tool and sheet metal to reduce friction and prevent damage.
- Gradual Bending: Apply force gradually to avoid overstressing the material.
- Multiple Bends: For complex shapes, perform multiple bends in stages to achieve the desired form.
- Experience: Practice bending techniques to develop the necessary skills and achieve consistent results.
Bending sheet metal with a hydraulic press requires a combination of proper technique, safety precautions, and appropriate tooling. By following these guidelines and practicing consistently, you can effectively shape sheet metal into various forms for your projects.
Material Preparation
Material preparation is an important step in the process of bending sheet metal using a hydraulic press. Proper material preparation ensures that the sheet metal is ready for bending and helps achieve accurate and consistent results. Here are some key aspects of material preparation:
- Material Selection: Choose the appropriate type and thickness of sheet metal for the desired application and bending requirements. Consider factors such as the material’s strength, flexibility, and suitability for the intended use. Common materials used for sheet metal bending include steel, aluminum, stainless steel, and copper.
- Material Thickness: Determine the thickness of the sheet metal, which will influence the bending parameters and the force required from the hydraulic press. Measure the thickness accurately using a caliper or other suitable measuring tool.
- Material Condition: Ensure that the sheet metal is clean and free from any dirt, oil, or other contaminants. Clean the surface of the sheet metal using solvents, degreasers, or other appropriate cleaning methods. This helps prevent any interference or defects during the bending process.
- Sheet Metal Layout: Plan the layout of the sheet metal to optimize material usage and minimize waste. Consider the dimensions and shape of the final part to determine the size and shape of the sheet metal required. Marking or layout tools can be used to indicate the bending lines or reference points on the sheet metal.
- Cutting and Shearing: If the sheet metal needs to be cut or sheared to the desired size or shape before bending, use appropriate cutting tools such as shears, nibblers, or laser cutting machines. Ensure clean and precise cuts to maintain accuracy during the bending process.
- Deburring: After cutting or shearing, deburr the edges of the sheet metal to remove any sharp or rough edges. This can be done using deburring tools, files, or sandpaper. Smooth edges minimize the risk of injury and ensure proper contact between the sheet metal and the bending tools.
- Material Protection: Consider applying protective coatings or films to the sheet metal surface, especially if the material is susceptible to scratching or damage during handling and bending. Protective coatings help maintain the surface finish and prevent any unwanted marks or blemishes.
Proper material preparation sets the foundation for successful sheet metal bending using a hydraulic press. It ensures that the sheet metal is clean, accurately sized, and free from contaminants or defects that could affect the bending process. By paying attention to material preparation, you can enhance the overall quality and efficiency of the bending operation.
Tooling Selection
Tooling selection is a crucial aspect of sheet metal bending with a hydraulic press. The choice of appropriate tooling determines the accuracy, quality, and efficiency of the bending process. Here are some key considerations for tooling selection:
- Bend Angle and Radius: Determine the required bend angle and radius for the sheet metal part. These specifications will guide the selection of the appropriate tooling. The tooling should match the desired bend angle and have the appropriate radius to achieve the desired shape.
- Tooling Types: There are various types of tooling available for sheet metal bending with a hydraulic press. The most common types include V-dies, U-dies, and custom dies. V-dies are typically used for straight bends, while U-dies are used for creating curved or U-shaped bends. Custom dies are designed for specific bending applications and can be fabricated to match unique part geometries.
- Die Width: The width of the die should be suitable for the width of the sheet metal being bent. It should provide sufficient support and contact area to ensure accurate and consistent bending. The die width should also take into account any additional material allowances required for springback, which is the tendency of the material to return to its original shape after bending.
- Die Opening Size: The die opening size, also known as the die gap or die clearance, is the space between the punch and die. It affects the bend radius and the overall bending result. The die opening size should be properly calculated based on the material thickness, bend angle, and other factors. It should allow for proper material flow during bending without causing excessive deformation or wrinkling.
- Tooling Materials: Consider the materials used for the tooling. Common materials for tooling include hardened steel, tool steel, and carbide. The choice of material depends on factors such as the material being bent, the required precision, and the expected tool life. Hardened and durable materials are preferred to withstand the forces and wear associated with sheet metal bending.
- Tooling Compatibility: Ensure that the selected tooling is compatible with the hydraulic press being used. Consider factors such as the tooling dimensions, mounting mechanisms, and the tonnage capacity of the press. The tooling should fit securely and accurately in the press, allowing for precise and repeatable bending operations.
- Supplier Support: Partner with reputable tooling suppliers who can provide guidance and support in selecting the appropriate tooling for your specific bending needs. They can offer expertise in tooling design, material selection, and troubleshooting to ensure successful bending operations.
Proper tooling selection is critical for achieving accurate and high-quality bends in sheet metal with a hydraulic press. It is recommended to consult with experienced tooling suppliers or manufacturers to ensure the right tooling is chosen for your specific bending requirements.
Die Setup
Die setup is an important step in the process of sheet metal bending with a hydraulic press. It involves properly positioning and aligning the die on the press to ensure accurate and consistent bends. Here are the key steps involved in die setup:
- Die Selection: Choose the appropriate die for the desired bend angle and radius. The die should match the specifications of the bend to be made. Consider factors such as the die width, opening size, and compatibility with the hydraulic press being used.
- Die Installation: Mount the die securely onto the press bed or the appropriate tooling attachment. Ensure that the die is aligned with the press and positioned accurately for the desired bending operation. The die should be securely fixed to prevent any movement or misalignment during the bending process.
- Die Alignment: Align the die with the punch (male die) to ensure proper contact and precise bending. The alignment should be perpendicular to the direction of the bend and parallel to the press bed. Use alignment tools, such as dial indicators or precision gauges, to verify and adjust the alignment as necessary.
- Die Positioning: Position the sheet metal properly in relation to the die and punch. Align the edge of the sheet metal with the desired bending line or reference point on the die. Ensure that the sheet metal is flat and properly supported to prevent any distortion or misalignment during bending.
- Die Clearance Adjustment: Adjust the die opening size or die clearance based on the thickness and properties of the sheet metal. The die clearance determines the bend radius and should be properly calculated or set according to the bending requirements. Consult the manufacturer’s guidelines or bending charts to determine the appropriate die clearance for the specific material and bend angle.
- Die Lubrication: Apply a suitable lubricant or release agent to the die surface to reduce friction and prevent the sheet metal from sticking to the die during bending. Lubrication helps in smooth material flow and minimizes the risk of scratching or damaging the sheet metal surface.
- Test Bend: Before proceeding with the actual production bending, perform a test bend to ensure that the die setup is properly adjusted and aligned. Make any necessary adjustments to the die position, alignment, or clearance to achieve the desired bend angle and quality.
Proper die setup is crucial for achieving accurate and repeatable bends in sheet metal. It ensures that the die is aligned, positioned, and adjusted correctly for the specific bending operation. Careful attention to die setup helps maintain consistency and quality throughout the bending process.
Sheet Metal Placement
Sheet metal placement is a crucial step in the process of bending sheet metal with a hydraulic press. Proper placement of the sheet metal ensures accurate and consistent bends. Here are some key considerations for sheet metal placement:
- Alignment with Die and Punch: Position the sheet metal on the hydraulic press bed, aligning it with the die and punch (male die). Ensure that the edge of the sheet metal aligns with the desired bending line or reference point on the die. This alignment ensures that the bend occurs precisely at the intended location.
- Proper Support: Provide proper support to the sheet metal to prevent excessive sagging or deformation during bending. Use suitable support tools, such as V-blocks or support fingers, to hold the sheet metal securely and distribute the bending forces evenly. The support should be placed close to the bend line to minimize any unsupported sections.
- Flatness: Ensure that the sheet metal is flat and free from any warping or buckling. If the sheet metal is not flat, flatten it before placing it on the press bed to ensure consistent and accurate bending. Use clamps or weights if necessary to hold the sheet metal flat during the bending process.
- Material Overhang: Determine the amount of material overhang required for the desired bend. The material overhang refers to the distance between the bend line and the edge of the sheet metal. It allows for material flow during bending and prevents incomplete or uneven bends. Consult bending charts or guidelines to determine the appropriate material overhang for the specific bend angle and material thickness.
- Sheet Metal Positioning: Position the sheet metal in a way that allows for easy access to the hydraulic press controls and operator’s line of sight. The operator should have a clear view of the bending operation to ensure proper control and safety.
- Sheet Metal Clamping: If necessary, use clamps or hold-down devices to secure the sheet metal in place during bending. This helps prevent any movement or shifting of the sheet metal during the bending process, ensuring accurate and consistent results.
- Safety Considerations: Prioritize safety when placing the sheet metal on the hydraulic press. Ensure that there are no obstructions or hazards in the surrounding area that could interfere with the bending operation. Always follow proper safety procedures, such as wearing personal protective equipment (PPE) and keeping hands clear of moving parts.
Proper placement of the sheet metal is essential for achieving accurate and high-quality bends with a hydraulic press. It ensures that the sheet metal is aligned, supported, and positioned correctly for the desired bending operation. Paying attention to sheet metal placement enhances the overall efficiency, precision, and safety of the bending process.
Pressure Adjustment
Pressure adjustment is a critical aspect of bending sheet metal with a hydraulic press. It involves setting the appropriate pressure to achieve the desired bend without damaging the material or the equipment. Here are the key steps for pressure adjustment:
- Understand the Material: Familiarize yourself with the material properties, including its thickness, tensile strength, and ductility. Different materials have different requirements in terms of bending pressure.
- Start with a Low Pressure: Begin by setting the hydraulic press to a relatively low pressure. This allows for a test bend to assess the material’s response and the accuracy of the bend.
- Perform Test Bends: Select a scrap piece of the same material and thickness as the sheet metal being bent. Place it in the desired position and perform a test bend. Observe the result and evaluate if the bend is accurate, without any cracking or excessive deformation. Adjust the pressure as needed.
- Consider Material Springback: Keep in mind that some materials exhibit springback, meaning they tend to return to their original shape after bending. Take springback into account when adjusting the pressure. A higher pressure might be required to compensate for the anticipated springback.
- Incremental Pressure Adjustments: Make incremental adjustments to the pressure. Increase or decrease the pressure gradually, testing the result after each adjustment. This allows for fine-tuning of the pressure to achieve the desired bend angle and quality.
- Observe Material Behavior: Pay attention to the behavior of the material during bending. Look for signs of excessive deformation, cracking, or wrinkling. These may indicate that the pressure is too high and should be reduced.
- Consult Bending Charts or Guidelines: Refer to bending charts or guidelines specific to the material being used. These resources provide recommended pressure ranges based on the material’s thickness and properties. They serve as a helpful reference for initial pressure adjustment.
- Operator Experience: Operator experience and skill play a crucial role in pressure adjustment. Experienced operators can often assess the material’s behavior and make appropriate adjustments based on their knowledge and expertise.
- Safety Considerations: While adjusting the pressure, always prioritize safety. Follow proper safety procedures, including wearing appropriate personal protective equipment (PPE) and keeping hands clear of moving parts.
- Document the Optimal Pressure: Once you have determined the optimal pressure for bending the specific material, document the pressure setting for future reference. This helps maintain consistency and efficiency in future bending operations.
Remember that pressure adjustment is an iterative process. It may require multiple test bends and adjustments to achieve the desired result. By paying attention to material behavior and making incremental pressure adjustments, you can ensure accurate and high-quality bends while preventing material damage or equipment failure.
Bending Process
The bending process is a common technique used to shape sheet metal into desired forms and angles. It involves the application of force to deform the material along a specific axis, resulting in a bent or formed shape. Here are the key steps involved in the bending process:
- Material Selection: Choose the appropriate type and thickness of sheet metal for the desired application. Consider factors such as material strength, ductility, and suitability for bending.
- Material Preparation: Ensure that the sheet metal is clean and free from any contaminants or debris that could affect the bending process. Remove any protective coatings or films, if necessary.
- Tooling Selection: Select the appropriate tooling for the bending operation. This includes the die (female die) and punch (male die), which form the desired bend shape. The tooling should match the specifications of the desired bend angle and radius.
- Die Setup: Set up the die and punch on the bending machine or hydraulic press. Align and secure the tooling properly to ensure accurate and consistent bends. Adjust the die clearance based on the material thickness and properties.
- Sheet Metal Placement: Position the sheet metal on the press bed, aligning it with the die and punch. Ensure proper support and alignment to prevent distortion or misalignment during bending.
- Pressure Adjustment: Set the appropriate bending pressure on the machine. This involves adjusting the hydraulic press or machine to apply the necessary force to deform the sheet metal. Refer to bending charts or guidelines for recommended pressure ranges based on material thickness and properties.
- Bending Operation: Activate the bending machine or hydraulic press to apply pressure to the sheet metal. The punch moves toward the die, deforming the material and creating the desired bend shape. The bending process may involve a single bend or multiple bends, depending on the desired form.
- Bend Angle Control: Monitor and control the bend angle during the process. This can be done visually or with the help of angle-measuring devices, such as protractors or digital angle finders. Make adjustments as needed to achieve the desired bend angle.
- Post-Bending Inspection: After the bending process, inspect the bent part for quality and accuracy. Check for any defects, such as cracks, wrinkles, or uneven bends. Use measuring tools, such as calipers or rulers, to verify dimensions and angles.
- Finishing Operations: Depending on the application, further finishing operations may be required, such as deburring, trimming, or surface treatment. These steps help remove sharp edges, improve aesthetics, and prepare the bent part for its intended use.
The bending process requires precision, proper tooling, and careful attention to detail to achieve accurate and high-quality results. By following the steps outlined above and adhering to best practices, you can successfully bend sheet metal to meet your specific design and fabrication requirements.
Hydraulic Cylinder:
A hydraulic cylinder is a mechanical actuator that converts hydraulic energy into linear mechanical force and motion. It is a key component in hydraulic systems, widely used in various industries for applications requiring precise and powerful movement, such as lifting, pushing, pulling, and positioning heavy loads or equipment.
Construction: A typical hydraulic cylinder consists of several main components:
- Cylinder Barrel: Also known as the cylinder tube, it serves as the main body of the cylinder, housing the other internal components.
- Piston: The piston is a cylindrical component that separates the fluid-filled areas of the cylinder into two chambers. When hydraulic pressure is applied to one side of the piston, it moves linearly, generating force and motion.
- Piston Rod: The piston rod is attached to the piston and extends through one end of the cylinder barrel. It transmits the force generated by the hydraulic pressure to the external load or mechanism.
- Seals: Seals, such as piston seals and rod seals, prevent hydraulic fluid from leaking past the piston and cylinder barrel, maintaining pressure within the cylinder and preventing contamination of the hydraulic system.
- End Caps: End caps, also known as cylinder heads or caps, seal the ends of the cylinder barrel and provide mounting points for the cylinder within the hydraulic system.
Operation: Hydraulic cylinders operate based on Pascal’s principle, which states that pressure exerted at any point in a confined fluid is transmitted equally in all directions throughout the fluid. When hydraulic fluid is pumped into one side of the cylinder, it applies pressure to the piston, causing it to move linearly and exert force on the piston rod. The piston rod then extends or retracts, depending on the direction of fluid flow and the desired motion of the cylinder.
Types: There are several types of hydraulic cylinders designed for different applications:
- Single-Acting Cylinder: Single-acting cylinders exert force in only one direction, typically extending the piston rod when hydraulic pressure is applied and using gravity, springs, or external forces to retract it.
- Double-Acting Cylinder: Double-acting cylinders exert force in both directions, extending and retracting the piston rod using hydraulic pressure applied alternately to each side of the piston.
- Telescopic Cylinder: Telescopic cylinders consist of nested stages or sleeves that extend and retract telescopically, providing a long stroke length with a compact retracted length, making them suitable for applications with limited space.
- Tie-Rod Cylinder: Tie-rod cylinders feature tie rods or bolts that connect the end caps to the cylinder barrel, providing structural support and stability under high loads or pressures.
- Welded Cylinder: Welded cylinders have a one-piece welded construction, with the end caps welded directly to the cylinder barrel, offering a compact and lightweight design suitable for space-constrained applications.
Applications: Hydraulic cylinders find applications in various industries, including:
- Construction: Hydraulic cylinders are used in construction equipment such as excavators, bulldozers, and cranes for lifting, digging, and pushing heavy loads.
- Manufacturing: Hydraulic cylinders are used in manufacturing machinery such as presses, injection molding machines, and metalworking equipment for shaping, forming, and assembling parts.
- Agriculture: Hydraulic cylinders are used in agricultural machinery such as tractors, harvesters, and irrigation systems for tasks such as plowing, seeding, and harvesting crops.
- Transportation: Hydraulic cylinders are used in transportation vehicles such as dump trucks, garbage trucks, and trailers for lifting, tipping, and dumping loads.
- Aerospace: Hydraulic cylinders are used in aircraft landing gear, cargo doors, and flight control systems for deploying, retracting, and controlling various components.
In conclusion, hydraulic cylinders are essential components in hydraulic systems, providing precise and powerful actuation for a wide range of industrial, mobile, and aerospace applications. Their robust construction, reliable operation, and versatility make them indispensable for tasks requiring linear force and motion in hydraulic machinery and equipment.
Actuator:
An actuator is a mechanical device used to convert energy into motion, force, or mechanical output. In the context of hydraulic systems, an actuator is specifically designed to generate linear or rotary motion using hydraulic fluid power. Actuators play a crucial role in various industrial, automotive, aerospace, and mobile applications, where precise and powerful movement is required to control valves, operate machinery, or perform mechanical tasks.
Construction and Components: While the specific construction of hydraulic actuators may vary depending on their application and design, they typically consist of the following main components:
- Cylinder: The cylinder serves as the primary housing for the actuator, containing the piston and hydraulic fluid. It is often made of high-strength materials such as steel or aluminum to withstand high pressures and loads.
- Piston: The piston is a cylindrical component that divides the cylinder into two chambers and transmits hydraulic pressure to generate linear motion. It is sealed against the cylinder walls using seals or rings to prevent fluid leakage.
- Piston Rod: The piston rod extends from the piston through one end of the cylinder and connects to the external load or mechanism. It transmits the force generated by the hydraulic pressure to produce linear motion or mechanical work.
- Seals: Seals, such as piston seals and rod seals, prevent hydraulic fluid from leaking past the piston and cylinder, maintaining pressure within the actuator and protecting against contamination.
- End Caps: End caps, also known as cylinder heads or caps, seal the ends of the cylinder and provide mounting points for the actuator within the hydraulic system.
Operation: Hydraulic actuators operate based on the principles of fluid power and Pascal’s law, which states that pressure exerted at any point in a confined fluid is transmitted equally in all directions. When hydraulic fluid is pumped into one side of the actuator cylinder, it applies pressure to the piston, causing it to move linearly. The piston rod attached to the piston then extends or retracts, depending on the direction of fluid flow and the desired motion of the actuator.
Types: There are several types of hydraulic actuators, each designed for specific applications and motion requirements:
- Linear Actuators: Linear actuators produce linear motion, extending or retracting a piston rod in a straight line.
- Rotary Actuators: Rotary actuators produce rotary motion, converting hydraulic pressure into rotational movement to turn a shaft or mechanism.
- Single-Acting Actuators: Single-acting actuators operate in one direction only, using hydraulic pressure to extend the piston rod and relying on external forces such as gravity or springs to retract it.
- Double-Acting Actuators: Double-acting actuators operate in both directions, using hydraulic pressure to extend and retract the piston rod alternately.
- Spring-Return Actuators: Spring-return actuators use hydraulic pressure to extend the piston rod, with a spring mechanism providing the force to retract it when hydraulic pressure is released.
Applications: Hydraulic actuators are used in a wide range of applications across various industries, including:
- Industrial Machinery: Hydraulic actuators are used in manufacturing machinery, robotics, material handling equipment, and assembly lines for tasks such as lifting, pushing, pulling, clamping, and positioning.
- Automotive: Hydraulic actuators are used in automotive applications such as brakes, steering systems, suspension systems, and convertible tops for controlling motion and providing mechanical assistance.
- Aerospace: Hydraulic actuators are used in aircraft flight control systems, landing gear, cargo doors, and thrust vectoring systems for precise control of aircraft movement and mechanical functions.
- Construction and Mining: Hydraulic actuators are used in construction equipment, mining machinery, and earthmoving vehicles for tasks such as excavating, lifting, loading, and dumping heavy materials.
- Marine: Hydraulic actuators are used in marine applications such as ship steering systems, winches, cranes, and hatch covers for controlling movement and performing mechanical tasks onboard ships and offshore platforms.
In conclusion, hydraulic actuators are essential components in hydraulic systems, providing precise and powerful motion control for a wide range of industrial, automotive, aerospace, and mobile applications. Their versatility, reliability, and efficiency make them indispensable for tasks requiring linear or rotary motion in hydraulic machinery and equipment, contributing to increased productivity, performance, and safety in various industries.
Piston:
The piston is a crucial component of hydraulic cylinders and actuators, serving as the primary mechanism for converting hydraulic energy into linear mechanical force and motion. It plays a fundamental role in the operation of hydraulic systems, facilitating the movement of fluid within the cylinder and generating the desired motion of the piston rod.
Construction and Design: Pistons are typically cylindrical in shape and are precision-machined to fit snugly within the cylinder bore. They are usually made from high-strength materials such as steel, aluminum, or composite alloys to withstand the pressures and loads encountered in hydraulic applications. The surface of the piston is often coated or treated to improve wear resistance and reduce friction against the cylinder walls.
Pistons may have various designs depending on the specific requirements of the hydraulic system:
- Single-Acting Pistons: Single-acting pistons have a smooth surface and are designed to transmit hydraulic pressure from one side of the piston to the other, generating linear motion in one direction.
- Double-Acting Pistons: Double-acting pistons feature seals or grooves on both sides of the piston, allowing hydraulic pressure to act on both sides alternately. This design enables bi-directional motion, with the piston extending and retracting based on the direction of fluid flow.
- Multiple Pistons: Some hydraulic cylinders may incorporate multiple pistons arranged in series or parallel configurations to increase force output or distribute load evenly across the cylinder bore. Multiple pistons may be connected by a common piston rod or operate independently, depending on the application requirements.
Function and Operation: The primary function of the piston in a hydraulic system is to transmit hydraulic pressure from the fluid to the piston rod, generating linear motion or force output. When hydraulic fluid is pumped into one side of the cylinder, it applies pressure to the piston, causing it to move in the direction of the applied force. The piston rod attached to the piston then extends or retracts, depending on the direction of fluid flow and the desired motion of the hydraulic cylinder or actuator.
The design and operation of the piston are critical factors in determining the performance and efficiency of hydraulic systems. Proper sealing and lubrication of the piston are essential to prevent fluid leakage, minimize friction, and ensure smooth and reliable operation. Additionally, the size, shape, and surface finish of the piston may be optimized to enhance fluid dynamics, reduce turbulence, and improve energy efficiency within the hydraulic cylinder.
Applications: Pistons are used in a wide range of hydraulic systems and applications across various industries, including:
- Construction Machinery: Hydraulic pistons are used in excavators, bulldozers, cranes, and other construction equipment for tasks such as lifting, pushing, digging, and material handling.
- Manufacturing Machinery: Hydraulic pistons are used in presses, injection molding machines, metalworking equipment, and assembly lines for shaping, forming, stamping, and assembling parts.
- Automotive Systems: Hydraulic pistons are used in automotive applications such as brakes, suspension systems, steering systems, and convertible tops for controlling motion and providing mechanical assistance.
- Aerospace Systems: Hydraulic pistons are used in aircraft flight control systems, landing gear, cargo doors, and thrust vectoring systems for precise control of aircraft movement and mechanical functions.
- Marine Systems: Hydraulic pistons are used in ship steering systems, winches, cranes, hatch covers, and propulsion systems for controlling movement and performing mechanical tasks onboard ships and offshore platforms.
In conclusion, pistons are essential components of hydraulic systems, providing the primary mechanism for converting hydraulic energy into linear mechanical motion. Their design, construction, and operation are critical factors in determining the performance, efficiency, and reliability of hydraulic cylinders and actuators across various industries and applications. Proper selection, maintenance, and optimization of pistons are essential to ensure smooth and reliable operation of hydraulic systems and equipment.
Cylinder Barrel:
The cylinder barrel is a fundamental component of hydraulic cylinders, providing the main housing for the piston, seals, and hydraulic fluid. It serves as the structural backbone of the cylinder, containing and guiding the movement of internal components to generate linear mechanical force and motion. The cylinder barrel is crucial for maintaining hydraulic pressure, preventing fluid leakage, and withstanding the loads and pressures encountered in hydraulic applications.
Construction and Materials: Cylinder barrels are typically cylindrical in shape, with precise dimensions and tolerances to ensure proper fit and function within the hydraulic system. They are often machined from high-strength materials such as steel, aluminum, or stainless steel, chosen for their durability, corrosion resistance, and compatibility with hydraulic fluids. The surface of the cylinder barrel may be honed or polished to reduce friction and wear and provide a smooth surface for the piston seals to glide against.
Function and Operation: The primary function of the cylinder barrel is to contain and guide the movement of the piston and piston rod within the hydraulic cylinder. When hydraulic pressure is applied to one side of the piston, it exerts force against the cylinder barrel, causing the piston to move linearly within the cylinder bore. The cylinder barrel provides a sealed chamber for the hydraulic fluid, ensuring that pressure is maintained and transmitted effectively to generate the desired motion of the piston rod.
The smoothness and roundness of the cylinder bore are critical factors in ensuring proper sealing and smooth operation of the hydraulic cylinder. Any imperfections or irregularities in the cylinder barrel surface can lead to leakage, increased friction, and reduced efficiency of the hydraulic system. Therefore, precision machining and quality control are essential in manufacturing cylinder barrels to meet the stringent requirements of hydraulic applications.
Applications: Cylinder barrels are used in a wide range of hydraulic systems and applications across various industries, including:
- Construction Machinery: Hydraulic cylinders with cylinder barrels are used in excavators, loaders, bulldozers, cranes, and other construction equipment for tasks such as lifting, pushing, digging, and material handling.
- Manufacturing Machinery: Hydraulic cylinders with cylinder barrels are used in presses, injection molding machines, metalworking equipment, and assembly lines for shaping, forming, stamping, and assembling parts.
- Automotive Systems: Hydraulic cylinders with cylinder barrels are used in automotive applications such as brakes, suspension systems, steering systems, and convertible tops for controlling motion and providing mechanical assistance.
- Aerospace Systems: Hydraulic cylinders with cylinder barrels are used in aircraft flight control systems, landing gear, cargo doors, and thrust vectoring systems for precise control of aircraft movement and mechanical functions.
- Marine Systems: Hydraulic cylinders with cylinder barrels are used in ship steering systems, winches, cranes, hatch covers, and propulsion systems for controlling movement and performing mechanical tasks onboard ships and offshore platforms.
In conclusion, the cylinder barrel is a critical component of hydraulic cylinders, providing the main housing for the piston and seals and guiding the movement of internal components to generate linear mechanical force and motion. Its construction, materials, and surface finish are essential factors in ensuring proper sealing, smooth operation, and reliable performance of hydraulic systems across various industries and applications. Proper selection, maintenance, and quality control of cylinder barrels are essential to ensure the longevity and efficiency of hydraulic cylinders in demanding operating conditions.
Piston Rod:
The piston rod is a vital component of hydraulic cylinders, serving as the primary linkage between the piston and the external load or mechanism. It transmits the force generated by hydraulic pressure to produce linear motion or mechanical work, allowing hydraulic cylinders to perform a wide range of tasks such as lifting, pushing, pulling, and positioning heavy loads or equipment.
Construction and Materials: Piston rods are typically cylindrical in shape and are precision-machined to fit securely within the piston and extend through one end of the cylinder barrel. They are often made from high-strength materials such as steel, chrome-plated steel, stainless steel, or alloy steel to withstand the high pressures, loads, and operating conditions encountered in hydraulic applications. The surface of the piston rod may be hardened, polished, or coated to improve wear resistance, corrosion resistance, and surface finish.
Function and Operation: The primary function of the piston rod is to transmit the force generated by hydraulic pressure from the piston to the external load or mechanism. When hydraulic fluid is pumped into one side of the cylinder, it applies pressure to the piston, causing it to move linearly within the cylinder bore. The piston rod attached to the piston then extends or retracts, depending on the direction of fluid flow and the desired motion of the hydraulic cylinder or actuator.
The design and construction of the piston rod are critical factors in determining the performance and reliability of hydraulic cylinders. Proper sizing, material selection, and surface treatment of the piston rod are essential to withstand the forces, pressures, and environmental conditions encountered in hydraulic applications. Additionally, the piston rod must be precisely aligned and supported to prevent bending, deflection, or misalignment during operation.
Sealing and Protection: Piston rods are often equipped with seals or gaskets to prevent hydraulic fluid from leaking past the piston and cylinder barrel. Common types of rod seals include O-rings, lip seals, wipers, and scraper rings, which provide a tight seal and protect the piston rod from contaminants such as dirt, moisture, and debris. In addition to seals, piston rods may be equipped with protective coatings or coverings to enhance corrosion resistance and extend service life.
Applications: Piston rods are used in a wide range of hydraulic systems and applications across various industries, including:
- Construction Machinery: Hydraulic cylinders with piston rods are used in excavators, loaders, bulldozers, cranes, and other construction equipment for tasks such as lifting, pushing, digging, and material handling.
- Manufacturing Machinery: Hydraulic cylinders with piston rods are used in presses, injection molding machines, metalworking equipment, and assembly lines for shaping, forming, stamping, and assembling parts.
- Automotive Systems: Hydraulic cylinders with piston rods are used in automotive applications such as brakes, suspension systems, steering systems, and convertible tops for controlling motion and providing mechanical assistance.
- Aerospace Systems: Hydraulic cylinders with piston rods are used in aircraft flight control systems, landing gear, cargo doors, and thrust vectoring systems for precise control of aircraft movement and mechanical functions.
- Marine Systems: Hydraulic cylinders with piston rods are used in ship steering systems, winches, cranes, hatch covers, and propulsion systems for controlling movement and performing mechanical tasks onboard ships and offshore platforms.
In conclusion, the piston rod is a critical component of hydraulic cylinders, serving as the primary linkage between the piston and the external load or mechanism. Its construction, materials, sealing, and protection are essential factors in ensuring proper transmission of force, reliable operation, and long-term performance of hydraulic systems across various industries and applications. Proper selection, maintenance, and installation of piston rods are essential to ensure the efficiency, safety, and reliability of hydraulic cylinders in demanding operating conditions.
Seals:
Seals are essential components of hydraulic systems, serving to prevent leakage of hydraulic fluid and to contain pressure within the system. They are critical for maintaining system integrity, preventing contamination, and ensuring optimal performance and reliability. Seals are used in various locations within hydraulic components such as cylinders, valves, pumps, and fittings, and they come in a variety of designs and materials to suit different operating conditions and requirements.
Types of Seals: There are several types of seals commonly used in hydraulic systems:
- O-Rings: O-rings are one of the most widely used types of seals in hydraulic systems. They are circular elastomeric seals with a cross-section resembling the letter “O” and are installed in grooves or glands to create a seal between mating surfaces. O-rings are simple, reliable, and cost-effective and can withstand a wide range of temperatures and pressures.
- Lip Seals: Lip seals, also known as shaft seals or oil seals, are used to seal rotary shafts in hydraulic pumps, motors, and actuators. They have a flexible lip that contacts the shaft surface to prevent leakage of hydraulic fluid. Lip seals may be single-lip or double-lip designs, depending on the application requirements.
- Wipers: Wipers, also known as scraper seals or dirt seals, are used to remove contaminants such as dirt, dust, and moisture from the surface of hydraulic cylinders or rods. They have a wiping edge that cleans the rod surface as it extends and retracts, preventing contaminants from entering the hydraulic system and damaging seals or components.
- Rod Seals: Rod seals are used to seal the piston rod of hydraulic cylinders and prevent leakage of hydraulic fluid from the cylinder bore. They are typically installed in the gland or housing at the end of the cylinder barrel and provide a dynamic sealing interface between the rod and cylinder bore.
- Piston Seals: Piston seals are used to seal the piston inside hydraulic cylinders and prevent leakage of hydraulic fluid from one side of the piston to the other. They are installed in grooves or glands on the piston and provide a static or dynamic sealing interface between the piston and cylinder barrel.
- Wear Rings: Wear rings are used to reduce friction and wear between moving components such as pistons and cylinders. They are typically installed between the piston and cylinder bore and provide a low-friction bearing surface that helps to maintain alignment and minimize clearance between mating parts.
Materials: Seals are made from a variety of materials to suit different operating conditions and requirements. Common materials used for hydraulic seals include:
- Nitrile Rubber (NBR): Nitrile rubber is a versatile elastomer with good resistance to oil, fuel, and hydraulic fluids. It is commonly used for O-rings, lip seals, and wipers in hydraulic systems.
- Polyurethane (PU): Polyurethane is a durable material with excellent wear resistance and mechanical properties. It is often used for rod seals, piston seals, and wear rings in high-pressure hydraulic applications.
- Fluorocarbon Rubber (FKM): Fluorocarbon rubber, also known as Viton®, is a high-performance elastomer with exceptional chemical resistance and temperature tolerance. It is commonly used for seals in hydraulic systems operating at high temperatures or with aggressive fluids.
- Polytetrafluoroethylene (PTFE): PTFE is a low-friction material with excellent chemical resistance and thermal stability. It is commonly used for lip seals, piston seals, and wear rings in hydraulic systems requiring low friction and high reliability.
Applications: Seals are used in a wide range of hydraulic systems and components across various industries, including:
- Hydraulic Cylinders: Seals are used to seal the piston and rod of hydraulic cylinders, preventing leakage and ensuring smooth operation.
- Hydraulic Pumps and Motors: Seals are used to seal the shafts and housings of hydraulic pumps and motors, preventing leakage and contamination of hydraulic fluid.
- Hydraulic Valves: Seals are used in hydraulic valves to control the flow of hydraulic fluid and prevent leakage between valve components.
- Hydraulic Fittings and Connectors: Seals are used in hydraulic fittings and connectors to create leak-tight connections between hydraulic components and piping or tubing.
In conclusion, seals are essential components of hydraulic systems, providing vital functions such as preventing leakage, containing pressure, and protecting components from contamination and wear. Proper selection, installation, and maintenance of seals are crucial to ensure the reliability, efficiency, and longevity of hydraulic systems across various industries and applications.
Rod Seal:
Rod seals are critical components of hydraulic cylinders, responsible for preventing leakage of hydraulic fluid from the cylinder bore and maintaining pressure within the system. They create a dynamic sealing interface between the piston rod and the cylinder bore, allowing the rod to move in and out of the cylinder while containing the hydraulic fluid and preventing contaminants from entering the system.
Construction and Design: Rod seals are typically made from elastomeric materials such as nitrile rubber (NBR), polyurethane (PU), fluorocarbon rubber (FKM), or polytetrafluoroethylene (PTFE). These materials offer excellent sealing properties, chemical resistance, and durability, making them suitable for use in hydraulic applications.
Rod seals may have various designs depending on the specific requirements of the hydraulic system:
- Single-Lip Seal: Single-lip rod seals have a single sealing lip that contacts the surface of the piston rod to create a seal. They are suitable for applications with moderate pressures and speeds and provide reliable sealing performance with low friction.
- Double-Lip Seal: Double-lip rod seals have two sealing lips that provide additional protection against leakage and contamination. They are ideal for applications with higher pressures, speeds, or demanding operating conditions, where enhanced sealing performance is required.
- Buffer Seal: Buffer seals, also known as secondary seals or backup rings, are often used in conjunction with rod seals to provide additional support and protection. They help to distribute pressure evenly across the sealing surface and prevent extrusion of the rod seal under high pressures.
Function and Operation: The primary function of the rod seal is to create a seal between the piston rod and the cylinder bore, preventing leakage of hydraulic fluid and maintaining pressure within the cylinder. When hydraulic pressure is applied to one side of the piston, it exerts force against the rod seal, causing it to compress against the rod surface and create a tight seal. As the piston rod moves in and out of the cylinder, the rod seal flexes and adapts to maintain a continuous seal, even under varying pressures and speeds.
Rod seals must provide effective sealing performance while allowing the piston rod to move smoothly and freely within the cylinder bore. They must withstand the forces, pressures, and temperatures encountered in hydraulic applications without deforming, extruding, or wearing prematurely. Proper sizing, installation, and maintenance of rod seals are essential to ensure reliable operation and long-term performance of hydraulic cylinders.
Applications: Rod seals are used in a wide range of hydraulic cylinders and applications across various industries, including:
- Construction Machinery: Hydraulic cylinders with rod seals are used in excavators, loaders, bulldozers, cranes, and other construction equipment for tasks such as lifting, pushing, digging, and material handling.
- Manufacturing Machinery: Hydraulic cylinders with rod seals are used in presses, injection molding machines, metalworking equipment, and assembly lines for shaping, forming, stamping, and assembling parts.
- Automotive Systems: Hydraulic cylinders with rod seals are used in automotive applications such as brakes, suspension systems, steering systems, and convertible tops for controlling motion and providing mechanical assistance.
- Aerospace Systems: Hydraulic cylinders with rod seals are used in aircraft flight control systems, landing gear, cargo doors, and thrust vectoring systems for precise control of aircraft movement and mechanical functions.
- Marine Systems: Hydraulic cylinders with rod seals are used in ship steering systems, winches, cranes, hatch covers, and propulsion systems for controlling movement and performing mechanical tasks onboard ships and offshore platforms.
In conclusion, rod seals are essential components of hydraulic cylinders, providing vital functions such as preventing leakage, maintaining pressure, and protecting components from contamination and wear. Proper selection, installation, and maintenance of rod seals are crucial to ensure the reliability, efficiency, and longevity of hydraulic systems across various industries and applications.
Piston Seal:
Piston seals are critical components of hydraulic cylinders, serving to seal the piston within the cylinder bore and prevent leakage of hydraulic fluid from one side of the piston to the other. They create a dynamic sealing interface between the piston and cylinder bore, allowing the piston to move smoothly and efficiently while containing the hydraulic pressure within the cylinder.
Construction and Design: Piston seals are typically made from elastomeric materials such as nitrile rubber (NBR), polyurethane (PU), fluorocarbon rubber (FKM), or polytetrafluoroethylene (PTFE). These materials offer excellent sealing properties, chemical resistance, and durability, making them suitable for use in hydraulic applications.
Piston seals may have various designs depending on the specific requirements of the hydraulic system:
- Single-Acting Seal: Single-acting piston seals are designed to seal hydraulic fluid on one side of the piston only. They are typically installed in grooves or glands on the piston and provide a dynamic sealing interface between the piston and cylinder bore.
- Double-Acting Seal: Double-acting piston seals are designed to seal hydraulic fluid on both sides of the piston. They are often used in applications where hydraulic pressure is applied alternately to both sides of the piston, allowing bi-directional movement of the piston within the cylinder bore.
- U-Cup Seal: U-cup piston seals, also known as lip seals or U-seals, have a U-shaped cross-section that provides excellent sealing performance and resistance to extrusion. They are suitable for high-pressure applications and can accommodate both single-acting and double-acting piston designs.
Function and Operation: The primary function of the piston seal is to create a seal between the piston and cylinder bore, preventing leakage of hydraulic fluid and maintaining pressure within the cylinder. When hydraulic pressure is applied to one side of the piston, it exerts force against the piston seal, causing it to compress against the cylinder bore and create a tight seal. As the piston moves within the cylinder bore, the piston seal flexes and adapts to maintain continuous contact with the cylinder wall, ensuring effective sealing performance throughout the piston stroke.
Piston seals must provide reliable sealing performance while allowing the piston to move smoothly and efficiently within the cylinder bore. They must withstand the forces, pressures, and temperatures encountered in hydraulic applications without deforming, extruding, or wearing prematurely. Proper sizing, installation, and maintenance of piston seals are essential to ensure reliable operation and long-term performance of hydraulic cylinders.
Applications: Piston seals are used in a wide range of hydraulic cylinders and applications across various industries, including:
- Construction Machinery: Hydraulic cylinders with piston seals are used in excavators, loaders, bulldozers, cranes, and other construction equipment for tasks such as lifting, pushing, digging, and material handling.
- Manufacturing Machinery: Hydraulic cylinders with piston seals are used in presses, injection molding machines, metalworking equipment, and assembly lines for shaping, forming, stamping, and assembling parts.
- Automotive Systems: Hydraulic cylinders with piston seals are used in automotive applications such as brakes, suspension systems, steering systems, and convertible tops for controlling motion and providing mechanical assistance.
- Aerospace Systems: Hydraulic cylinders with piston seals are used in aircraft flight control systems, landing gear, cargo doors, and thrust vectoring systems for precise control of aircraft movement and mechanical functions.
- Marine Systems: Hydraulic cylinders with piston seals are used in ship steering systems, winches, cranes, hatch covers, and propulsion systems for controlling movement and performing mechanical tasks onboard ships and offshore platforms.
In conclusion, piston seals are essential components of hydraulic cylinders, providing vital functions such as preventing leakage, maintaining pressure, and enabling smooth and efficient movement of the piston within the cylinder bore. Proper selection, installation, and maintenance of piston seals are crucial to ensure the reliability, efficiency, and longevity of hydraulic systems across various industries and applications.
Hydraulic Fluid:
Hydraulic fluid is a crucial element in hydraulic systems, serving as the medium for transmitting power and energy within the system. It is a specially formulated liquid or synthetic substance that is capable of transferring force from one component to another, enabling hydraulic machinery and equipment to perform a wide range of tasks with precision and efficiency.
Properties and Characteristics: Hydraulic fluids exhibit several key properties and characteristics that make them suitable for use in hydraulic systems:
- Viscosity: Hydraulic fluids have a specific viscosity that determines their flow characteristics and ability to transmit force within the system. Proper viscosity is essential for maintaining optimal performance and efficiency, as excessive viscosity can lead to sluggish operation, while insufficient viscosity can result in leakage and inadequate lubrication.
- Temperature Stability: Hydraulic fluids must maintain their viscosity and performance over a wide range of temperatures encountered in operating conditions. They should resist thinning at high temperatures and thickening at low temperatures to ensure consistent performance and protection of system components.
- Chemical Compatibility: Hydraulic fluids must be compatible with system materials such as seals, hoses, valves, and reservoirs to prevent degradation, corrosion, or swelling of components. They should also be resistant to oxidation, foaming, and contamination to maintain system cleanliness and reliability.
- Lubrication: Hydraulic fluids serve as lubricants for moving parts within hydraulic components, reducing friction, wear, and heat generation. Proper lubrication is essential for extending component life, minimizing downtime, and ensuring smooth and efficient operation of hydraulic systems.
- Sealing: Hydraulic fluids help to create a tight seal between moving components such as pistons, cylinders, and valves, preventing leakage and loss of hydraulic pressure. They also provide a barrier against contaminants such as dirt, moisture, and debris that can damage system components and degrade performance.
Types of Hydraulic Fluids: There are several types of hydraulic fluids available for use in hydraulic systems, each with its own advantages, limitations, and suitability for specific applications:
- Mineral Oil-Based Fluids: Mineral oil-based hydraulic fluids are the most common type and are derived from refined petroleum. They offer good lubrication, temperature stability, and cost-effectiveness and are suitable for general-purpose hydraulic applications.
- Synthetic Fluids: Synthetic hydraulic fluids are formulated from synthetic base stocks and offer superior performance characteristics compared to mineral oil-based fluids. They provide enhanced temperature stability, oxidation resistance, and wear protection and are often used in high-pressure, high-temperature, or environmentally sensitive applications.
- Biodegradable Fluids: Biodegradable hydraulic fluids are formulated from renewable sources such as vegetable oils or esters and are designed to minimize environmental impact in case of leakage or spillage. They offer biodegradability, low toxicity, and compatibility with environmentally sensitive areas but may have limited temperature and performance capabilities compared to mineral oil-based or synthetic fluids.
- Fire-Resistant Fluids: Fire-resistant hydraulic fluids are specially formulated to minimize the risk of fire or explosion in high-temperature or hazardous environments. They are available in various formulations such as water-based, phosphate ester-based, or synthetic fluids and offer enhanced safety and protection in applications where fire risk is a concern.
Applications: Hydraulic fluids are used in a wide range of hydraulic systems and applications across various industries, including:
- Construction Machinery: Hydraulic fluids are used in excavators, loaders, bulldozers, cranes, and other construction equipment for tasks such as lifting, pushing, digging, and material handling.
- Manufacturing Machinery: Hydraulic fluids are used in presses, injection molding machines, metalworking equipment, and assembly lines for shaping, forming, stamping, and assembling parts.
- Automotive Systems: Hydraulic fluids are used in automotive applications such as brakes, suspension systems, steering systems, and convertible tops for controlling motion and providing mechanical assistance.
- Aerospace Systems: Hydraulic fluids are used in aircraft flight control systems, landing gear, cargo doors, and thrust vectoring systems for precise control of aircraft movement and mechanical functions.
- Marine Systems: Hydraulic fluids are used in ship steering systems, winches, cranes, hatch covers, and propulsion systems for controlling movement and performing mechanical tasks onboard ships and offshore platforms.
In conclusion, hydraulic fluid is a vital component of hydraulic systems, serving as the medium for transmitting power, lubricating moving parts, creating seals, and maintaining system integrity and reliability. Proper selection, maintenance, and monitoring of hydraulic fluid are essential to ensure optimal performance, efficiency, and longevity of hydraulic systems across various industries and applications.
Hydraulic Pump:
A hydraulic pump is a mechanical device used to generate hydraulic pressure by converting mechanical energy into fluid energy. It plays a crucial role in hydraulic systems by supplying pressurized hydraulic fluid to power various hydraulic actuators, such as cylinders, motors, and valves, enabling them to perform work or control movement in a wide range of applications.
Types of Hydraulic Pumps:
- Gear Pumps: Gear pumps are among the most common types of hydraulic pumps and operate by meshing gears to pressurize hydraulic fluid. They are simple in design, cost-effective, and suitable for medium-pressure applications. However, they are not ideal for high-pressure or high-speed operations due to their limited efficiency and noise levels.
- Vane Pumps: Vane pumps utilize vanes mounted on a rotor to create chambers that trap and pressurize hydraulic fluid. They offer smooth and quiet operation, making them suitable for medium-pressure applications requiring precise control and low noise levels. Vane pumps are available in fixed and variable displacement configurations to accommodate different flow and pressure requirements.
- Piston Pumps: Piston pumps are capable of delivering high-pressure hydraulic fluid and are commonly used in heavy-duty applications requiring high power and efficiency. They operate by reciprocating pistons within cylinders to pressurize hydraulic fluid, offering superior performance and reliability compared to gear and vane pumps. Piston pumps are available in axial, radial, and bent-axis designs, each offering specific advantages in terms of efficiency, compactness, and versatility.
Function and Operation:
The primary function of a hydraulic pump is to generate hydraulic pressure by imparting mechanical energy to hydraulic fluid. When the pump is activated, it creates suction to draw hydraulic fluid from a reservoir or tank into its inlet port. The mechanical action of the pump then pressurizes the fluid and delivers it through its outlet port to the hydraulic system.
Hydraulic pumps are typically driven by electric motors, internal combustion engines, or other power sources, depending on the application requirements. They may be operated manually, hydraulically, or electrically, with various control mechanisms such as manual valves, solenoids, or electronic controllers to regulate flow, pressure, and direction of hydraulic fluid.
Applications:
Hydraulic pumps are used in a wide range of hydraulic systems and applications across various industries, including:
- Construction Machinery: Hydraulic pumps are used in excavators, loaders, bulldozers, cranes, and other construction equipment for tasks such as lifting, pushing, digging, and material handling.
- Manufacturing Machinery: Hydraulic pumps are used in presses, injection molding machines, metalworking equipment, and assembly lines for shaping, forming, stamping, and assembling parts.
- Automotive Systems: Hydraulic pumps are used in automotive applications such as power steering systems, braking systems, suspension systems, and convertible tops for providing mechanical assistance and control.
- Aerospace Systems: Hydraulic pumps are used in aircraft flight control systems, landing gear, cargo doors, and thrust vectoring systems for precise control of aircraft movement and mechanical functions.
- Marine Systems: Hydraulic pumps are used in ship steering systems, winches, cranes, hatch covers, and propulsion systems for controlling movement and performing mechanical tasks onboard ships and offshore platforms.
In conclusion, hydraulic pumps are essential components of hydraulic systems, providing the mechanical energy necessary to pressurize hydraulic fluid and power various hydraulic actuators and mechanisms. Proper selection, installation, and maintenance of hydraulic pumps are crucial to ensure optimal performance, efficiency, and reliability of hydraulic systems across various industries and applications.
Hydraulic Valve:
A hydraulic valve is a mechanical device used to control the flow, direction, and pressure of hydraulic fluid within a hydraulic system. It plays a crucial role in regulating the operation of hydraulic actuators, such as cylinders and motors, by opening, closing, or diverting fluid flow in response to external signals or conditions.
Types of Hydraulic Valves:
- Directional Control Valves: Directional control valves regulate the direction of hydraulic fluid flow within a hydraulic system. They control the movement of hydraulic actuators by selectively directing fluid flow to either side of the actuator, causing it to extend, retract, or stop. Directional control valves may be manually operated, mechanically actuated, or solenoid-controlled and are available in various configurations such as spool, poppet, and rotary valves.
- Pressure Control Valves: Pressure control valves regulate the pressure of hydraulic fluid within a hydraulic system by adjusting the flow rate or diverting excess flow to a reservoir or another part of the system. They help to maintain a constant pressure level within the system, prevent overpressure conditions, and protect system components from damage. Pressure control valves include relief valves, pressure reducing valves, and sequence valves, each serving specific pressure regulation functions.
- Flow Control Valves: Flow control valves regulate the flow rate of hydraulic fluid within a hydraulic system by restricting or controlling the passage of fluid through a valve orifice. They allow precise control of actuator speed, acceleration, and deceleration, enabling smooth and efficient operation of hydraulic machinery and equipment. Flow control valves may be adjustable, non-adjustable, or proportional, depending on the desired flow control characteristics and requirements.
- Check Valves: Check valves, also known as one-way valves or non-return valves, allow fluid flow in one direction while preventing reverse flow in the opposite direction. They are commonly used to maintain system pressure, prevent backflow, and protect system components from damage caused by fluid surges or shock loads. Check valves may be spring-loaded, gravity-operated, or pilot-operated, depending on the application requirements.
Function and Operation:
The primary function of a hydraulic valve is to control the flow, direction, and pressure of hydraulic fluid within a hydraulic system. When the valve is actuated or manipulated, it opens, closes, or adjusts the flow passage to regulate the movement of hydraulic actuators, control system pressure, or divert fluid flow to different parts of the system.
Hydraulic valves may be operated manually, mechanically, hydraulically, or electrically, depending on the application requirements and control mechanisms used. They may incorporate various features such as spools, poppets, pistons, or balls to control fluid flow, and they may be designed for specific flow rates, pressure levels, and environmental conditions.
Applications:
Hydraulic valves are used in a wide range of hydraulic systems and applications across various industries, including:
- Construction Machinery: Hydraulic valves are used in excavators, loaders, bulldozers, cranes, and other construction equipment for controlling the movement of hydraulic cylinders, motors, and other actuators.
- Manufacturing Machinery: Hydraulic valves are used in presses, injection molding machines, metalworking equipment, and assembly lines for controlling the speed, force, and direction of hydraulic actuators.
- Automotive Systems: Hydraulic valves are used in automotive applications such as brakes, suspension systems, steering systems, and transmission systems for controlling fluid flow, pressure, and direction.
- Aerospace Systems: Hydraulic valves are used in aircraft flight control systems, landing gear, cargo doors, and thrust vectoring systems for precise control of hydraulic actuators and mechanisms.
- Marine Systems: Hydraulic valves are used in ship steering systems, winches, cranes, hatch covers, and propulsion systems for controlling fluid flow, pressure, and direction in marine environments.
In conclusion, hydraulic valves are essential components of hydraulic systems, providing control and regulation of fluid flow, direction, and pressure to enable the operation of hydraulic machinery and equipment. Proper selection, installation, and maintenance of hydraulic valves are crucial to ensure optimal performance, efficiency, and reliability of hydraulic systems across various industries and applications.
Hydraulic Actuator:
A hydraulic actuator is a mechanical device used to convert hydraulic pressure into mechanical motion or force. It plays a crucial role in hydraulic systems by transforming the energy stored in pressurized hydraulic fluid into linear or rotary motion, enabling the operation of various mechanical components and machinery.
Types of Hydraulic Actuators:
- Hydraulic Cylinder: A hydraulic cylinder is a linear actuator that consists of a cylindrical barrel, piston, and rod. When pressurized hydraulic fluid is introduced into one side of the cylinder, it exerts force on the piston, causing it to move linearly within the cylinder bore. The motion of the piston is transmitted through the rod, which can be connected to external components to perform mechanical work such as lifting, pushing, pulling, or bending.
- Hydraulic Motor: A hydraulic motor is a rotary actuator that converts hydraulic pressure into rotational motion. It typically consists of a housing, rotor, and output shaft. Pressurized hydraulic fluid is directed into the motor, where it interacts with internal components to create rotational force and drive the output shaft. Hydraulic motors are used in applications requiring continuous rotation, such as driving conveyor belts, winches, fans, and rotary actuators.
Function and Operation:
The primary function of a hydraulic actuator is to convert hydraulic energy into mechanical motion or force to perform work or control movement in hydraulic systems. When pressurized hydraulic fluid is introduced into the actuator, it applies force to internal components, causing them to move and generate motion or torque. The direction, speed, and force of the actuator’s movement are controlled by regulating the flow, pressure, and direction of hydraulic fluid within the system.
Hydraulic actuators may be operated manually, mechanically, hydraulically, or electrically, depending on the application requirements and control mechanisms used. They may incorporate various features such as pistons, cylinders, gears, or vanes to convert hydraulic energy into mechanical motion or force efficiently and reliably.
Applications:
Hydraulic actuators are used in a wide range of hydraulic systems and applications across various industries, including:
- Construction Machinery: Hydraulic cylinders and motors are used in excavators, loaders, bulldozers, cranes, and other construction equipment for tasks such as lifting, pushing, digging, and material handling.
- Manufacturing Machinery: Hydraulic actuators are used in presses, injection molding machines, metalworking equipment, and assembly lines for shaping, forming, stamping, and assembling parts.
- Automotive Systems: Hydraulic actuators are used in automotive applications such as brakes, suspension systems, steering systems, and convertible tops for controlling motion and providing mechanical assistance.
- Aerospace Systems: Hydraulic actuators are used in aircraft flight control systems, landing gear, cargo doors, and thrust vectoring systems for precise control of aircraft movement and mechanical functions.
- Marine Systems: Hydraulic actuators are used in ship steering systems, winches, cranes, hatch covers, and propulsion systems for controlling movement and performing mechanical tasks onboard ships and offshore platforms.
In conclusion, hydraulic actuators are essential components of hydraulic systems, providing the mechanical force or motion necessary to perform work or control movement in various mechanical components and machinery. Proper selection, installation, and maintenance of hydraulic actuators are crucial to ensure optimal performance, efficiency, and reliability of hydraulic systems across various industries and applications.
Hydraulic Reservoir:
A hydraulic reservoir, also known as a hydraulic tank or oil reservoir, is a storage container used to hold hydraulic fluid within a hydraulic system. It plays a crucial role in hydraulic systems by providing a reservoir for storing hydraulic fluid, dissipating heat generated during operation, and allowing air and contaminants to be removed from the system.
Function and Importance:
The primary function of a hydraulic reservoir is to store hydraulic fluid and provide a source of fluid for the hydraulic system. It serves several important purposes:
- Storage: The reservoir holds a supply of hydraulic fluid that can be used by the hydraulic system as needed. This ensures that there is an adequate supply of fluid available to maintain system pressure and lubricate moving parts.
- Heat Dissipation: During operation, hydraulic systems generate heat due to friction and energy transfer. The reservoir provides a large surface area for the hydraulic fluid to dissipate heat, helping to regulate the temperature of the fluid and prevent overheating of system components.
- Air Separation: Hydraulic fluid may contain air bubbles or entrained air that can degrade system performance and cause cavitation. The reservoir allows air to rise to the surface of the fluid, where it can be vented or released from the system through breather vents or air bleed valves.
- Contaminant Settlement: Contaminants such as dirt, debris, and moisture may accumulate in the hydraulic fluid over time, leading to increased wear and damage to system components. The reservoir allows these contaminants to settle at the bottom of the tank, where they can be periodically removed during maintenance.
- Fluid Level Monitoring: The reservoir typically includes a sight glass, dipstick, or level gauge to allow operators to monitor the fluid level and ensure that it remains within the recommended operating range. Maintaining proper fluid levels is essential for the reliable operation of the hydraulic system.
Design and Construction:
Hydraulic reservoirs come in various sizes, shapes, and configurations to suit different hydraulic system designs and requirements. They are typically constructed from steel, aluminum, or plastic materials and may be cylindrical, rectangular, or custom-shaped to fit within the available space in the equipment or machinery.
Hydraulic reservoirs may include additional features and components to enhance their functionality and performance:
- Fill Ports: Fill ports allow hydraulic fluid to be added to the reservoir easily. They may include filters or strainers to remove contaminants from incoming fluid.
- Breather Vents: Breather vents allow air to enter and exit the reservoir, preventing pressure buildup and vacuum formation during fluid displacement.
- Filters: Filters help to remove contaminants from the hydraulic fluid, ensuring that clean fluid is circulated throughout the system.
- Cooling Fins: Cooling fins or heat exchangers may be added to the reservoir to enhance heat dissipation and maintain optimal fluid temperature.
Applications:
Hydraulic reservoirs are used in a wide range of hydraulic systems and applications across various industries, including:
- Construction Machinery: Hydraulic reservoirs are used in excavators, loaders, bulldozers, cranes, and other construction equipment for storing hydraulic fluid and dissipating heat during operation.
- Manufacturing Machinery: Hydraulic reservoirs are used in presses, injection molding machines, metalworking equipment, and assembly lines for storing hydraulic fluid and maintaining system performance.
- Automotive Systems: Hydraulic reservoirs are used in automotive applications such as brakes, suspension systems, steering systems, and transmission systems for storing hydraulic fluid and ensuring reliable operation.
- Aerospace Systems: Hydraulic reservoirs are used in aircraft flight control systems, landing gear, cargo doors, and thrust vectoring systems for storing hydraulic fluid and regulating system temperature.
- Marine Systems: Hydraulic reservoirs are used in ship steering systems, winches, cranes, hatch covers, and propulsion systems for storing hydraulic fluid and maintaining system performance in marine environments.
In conclusion, hydraulic reservoirs are essential components of hydraulic systems, providing storage, heat dissipation, air separation, and contaminant settlement functions to ensure the reliable operation and longevity of hydraulic equipment and machinery across various industries and applications. Proper selection, installation, and maintenance of hydraulic reservoirs are crucial to optimize system performance, efficiency, and reliability.
Hydraulic Hose:
A hydraulic hose is a flexible conduit used to convey hydraulic fluid from one component to another within a hydraulic system. It plays a critical role in hydraulic systems by transmitting pressurized hydraulic fluid between hydraulic components, such as cylinders, motors, valves, and actuators, enabling the operation of machinery and equipment.
Construction and Materials:
Hydraulic hoses are typically constructed from multiple layers of synthetic rubber, thermoplastic, or Teflon materials, reinforced with braided or spiral-wound steel wire or textile fibers to withstand high pressures and provide flexibility. The inner layer, known as the tube, is designed to contain the hydraulic fluid and provide resistance to abrasion, chemicals, and heat. The reinforcement layer provides structural support and prevents the hose from expanding or bursting under pressure. The outer layer, known as the cover, protects the hose from environmental factors such as abrasion, weathering, and UV radiation.
Types of Hydraulic Hoses:
- Wire Braided Hoses: Wire braided hydraulic hoses consist of multiple layers of synthetic rubber or thermoplastic materials reinforced with one or more layers of braided steel wire. They offer high flexibility, durability, and resistance to abrasion and are suitable for medium to high-pressure hydraulic applications.
- Wire Spiral Hoses: Wire spiral hydraulic hoses feature a spiral-wound reinforcement layer, typically made of multiple layers of braided steel wire or high-tensile steel wire. They provide greater strength, resistance to pressure pulsation, and flexibility compared to wire braided hoses and are suitable for high-pressure hydraulic applications.
- Thermoplastic Hoses: Thermoplastic hydraulic hoses are constructed from synthetic thermoplastic materials such as nylon, polyurethane, or PVC, reinforced with braided or spiral-wound steel wire. They offer excellent flexibility, chemical resistance, and low weight, making them suitable for applications requiring tight bends, compact installations, or resistance to environmental factors.
- Teflon (PTFE) Hoses: Teflon hydraulic hoses are made from polytetrafluoroethylene (PTFE) material and feature a smooth bore for enhanced flow characteristics. They offer high temperature resistance, chemical compatibility, and low friction, making them suitable for applications requiring high temperature or corrosive fluid handling.
Function and Operation:
The primary function of a hydraulic hose is to transmit pressurized hydraulic fluid between hydraulic components within a hydraulic system. When pressurized hydraulic fluid is introduced into one end of the hose, it exerts force on the inner tube, causing it to expand and transmit hydraulic pressure to the opposite end of the hose. The reinforcement layer provides structural support and prevents the hose from expanding or bursting under pressure, while the outer cover protects the hose from external damage and environmental factors.
Hydraulic hoses may be connected to hydraulic components using various types of fittings, such as threaded, crimped, or quick-connect fittings, to create a secure and leak-free connection. Proper selection, installation, and maintenance of hydraulic hoses are essential to ensure reliable performance, prevent leakage, and extend the service life of hydraulic systems.
Applications:
Hydraulic hoses are used in a wide range of hydraulic systems and applications across various industries, including:
- Construction Machinery: Hydraulic hoses are used in excavators, loaders, bulldozers, cranes, and other construction equipment for transmitting hydraulic fluid to hydraulic cylinders, motors, and valves.
- Manufacturing Machinery: Hydraulic hoses are used in presses, injection molding machines, metalworking equipment, and assembly lines for conveying hydraulic fluid to hydraulic actuators and controls.
- Automotive Systems: Hydraulic hoses are used in automotive applications such as brakes, suspension systems, power steering systems, and hydraulic lifts for transmitting hydraulic pressure and controlling mechanical functions.
- Aerospace Systems: Hydraulic hoses are used in aircraft hydraulic systems, landing gear, flight control systems, and auxiliary power units for transmitting hydraulic fluid and controlling aircraft movement.
- Marine Systems: Hydraulic hoses are used in ship steering systems, winches, cranes, hatch covers, and propulsion systems for conveying hydraulic fluid and controlling mechanical functions onboard ships and offshore platforms.
In conclusion, hydraulic hoses are essential components of hydraulic systems, providing flexible and reliable transmission of pressurized hydraulic fluid between hydraulic components in various industries and applications. Proper selection, installation, and maintenance of hydraulic hoses are crucial to ensure optimal performance, efficiency, and reliability of hydraulic systems.
Hydraulic Filter:
A hydraulic filter is a component used to remove contaminants from hydraulic fluid within a hydraulic system. It plays a critical role in maintaining the cleanliness and reliability of hydraulic systems by removing particles, dirt, debris, and other contaminants that can cause wear, damage, and malfunction of system components.
Function and Importance:
The primary function of a hydraulic filter is to remove contaminants from hydraulic fluid to ensure that clean fluid is circulated throughout the hydraulic system. Contaminants such as dirt, debris, metal particles, rust, and varnish can enter the hydraulic system through various sources, including external contamination, component wear, and system maintenance activities. These contaminants can cause abrasion, erosion, corrosion, and blockage of system components, leading to decreased performance, increased downtime, and costly repairs.
Hydraulic filters help to protect hydraulic pumps, valves, cylinders, motors, and other components from damage caused by contaminants, ensuring the reliable operation and longevity of hydraulic systems. They help to maintain optimal fluid cleanliness levels, reduce system downtime, extend component life, and improve system efficiency and reliability.
Types of Hydraulic Filters:
- In-line Filters: In-line hydraulic filters are installed in the hydraulic fluid line between hydraulic components, such as pumps, valves, cylinders, and reservoirs. They typically consist of a filter housing and replaceable filter element, which captures and retains contaminants as hydraulic fluid flows through the filter.
- Suction Strainers: Suction strainers are installed at the inlet port of hydraulic pumps or reservoirs to prevent large particles and debris from entering the hydraulic system. They feature a mesh screen or perforated plate that traps contaminants while allowing hydraulic fluid to pass through.
- Return Line Filters: Return line filters are installed in the return line of hydraulic systems, between hydraulic components and the reservoir, to remove contaminants from hydraulic fluid before it returns to the reservoir. They help to maintain clean fluid in the reservoir and prevent contamination of hydraulic components.
- Pressure Filters: Pressure filters are installed in the pressure line of hydraulic systems, downstream of hydraulic pumps or valves, to remove contaminants from pressurized hydraulic fluid. They feature a filter element that captures contaminants as hydraulic fluid flows through the filter under pressure.
- Breather Filters: Breather filters are installed on hydraulic reservoirs or vent ports to prevent airborne contaminants, moisture, and particles from entering the hydraulic system. They help to maintain clean and dry hydraulic fluid within the reservoir and prevent contamination of the hydraulic system.
Selection and Maintenance:
Proper selection, installation, and maintenance of hydraulic filters are essential to ensure effective contaminant removal and optimal performance of hydraulic systems. When selecting hydraulic filters, factors such as flow rate, pressure rating, filtration efficiency, particle size rating, and compatibility with hydraulic fluid and system components should be considered.
Regular inspection, replacement, and maintenance of hydraulic filters are necessary to ensure that they continue to effectively remove contaminants from hydraulic fluid. Filters should be inspected periodically for signs of contamination, clogging, or damage, and replaced or cleaned as needed according to manufacturer recommendations and maintenance schedules.
Applications:
Hydraulic filters are used in a wide range of hydraulic systems and applications across various industries, including:
- Construction Machinery: Hydraulic filters are used in excavators, loaders, bulldozers, cranes, and other construction equipment for maintaining clean hydraulic fluid and protecting hydraulic components from contamination.
- Manufacturing Machinery: Hydraulic filters are used in presses, injection molding machines, metalworking equipment, and assembly lines for ensuring clean hydraulic fluid and preventing contamination-related issues.
- Automotive Systems: Hydraulic filters are used in automotive applications such as brakes, steering systems, suspension systems, and hydraulic lifts for maintaining clean hydraulic fluid and protecting system components from wear and damage.
- Aerospace Systems: Hydraulic filters are used in aircraft hydraulic systems, landing gear, flight control systems, and auxiliary power units for ensuring clean hydraulic fluid and preventing contamination-related failures.
- Marine Systems: Hydraulic filters are used in ship steering systems, winches, cranes, hatch covers, and propulsion systems for maintaining clean hydraulic fluid and protecting system components from corrosion and wear.
In conclusion, hydraulic filters are essential components of hydraulic systems, providing effective contaminant removal and protection of hydraulic components from wear, damage, and malfunction. Proper selection, installation, and maintenance of hydraulic filters are crucial to ensure optimal performance, efficiency, and reliability of hydraulic systems across various industries and applications.
Hydraulic Accumulator:
A hydraulic accumulator is a device used to store pressurized hydraulic fluid under high pressure. It plays a critical role in hydraulic systems by storing energy in the form of pressurized fluid and releasing it as needed to supplement pump flow, dampen pressure spikes, or provide emergency power in the event of pump failure.
Function and Importance:
The primary function of a hydraulic accumulator is to store hydraulic energy in the form of pressurized fluid and release it when required to perform work or control movement within a hydraulic system. It helps to maintain system pressure, reduce pump cycling, absorb shocks and vibrations, and provide backup power in case of pump failure or power loss.
Hydraulic accumulators are commonly used in hydraulic systems where rapid changes in flow or pressure occur, such as in mobile equipment, industrial machinery, and hydraulic presses. They help to improve system efficiency, performance, and reliability by providing supplemental energy and cushioning against pressure spikes and fluid surges.
Types of Hydraulic Accumulators:
- Piston Accumulators: Piston accumulators consist of a cylindrical housing, piston, and gas and fluid chambers. Pressurized hydraulic fluid is stored in the fluid chamber, while a compressible gas, such as nitrogen, is contained in the gas chamber. When hydraulic fluid is introduced into the accumulator, it compresses the gas, storing energy in the form of pressurized fluid. When fluid pressure drops, the compressed gas expands, forcing hydraulic fluid out of the accumulator to supplement system flow or pressure.
- Bladder Accumulators: Bladder accumulators consist of a pressure vessel, bladder, and gas and fluid chambers. The bladder, typically made of rubber or elastomeric material, separates the gas and fluid chambers. Pressurized hydraulic fluid is stored in the fluid chamber, while a compressible gas is contained in the gas chamber. When hydraulic fluid is introduced into the accumulator, it compresses the gas and expands the bladder, storing energy in the form of pressurized fluid. When fluid pressure drops, the compressed gas forces hydraulic fluid out of the accumulator to supplement system flow or pressure.
- Diaphragm Accumulators: Diaphragm accumulators are similar to bladder accumulators but use a flexible diaphragm instead of a bladder to separate the gas and fluid chambers. They operate on the same principle, with pressurized hydraulic fluid compressing the gas and expanding the diaphragm to store energy in the form of pressurized fluid.
Applications:
Hydraulic accumulators are used in a wide range of hydraulic systems and applications across various industries, including:
- Mobile Equipment: Hydraulic accumulators are used in construction machinery, agricultural equipment, material handling vehicles, and mining equipment for energy storage, shock absorption, and emergency power assistance.
- Industrial Machinery: Hydraulic accumulators are used in hydraulic presses, injection molding machines, metal forming equipment, and machine tools for energy storage, pressure control, and damping of pressure fluctuations.
- Aerospace Systems: Hydraulic accumulators are used in aircraft landing gear, flight control systems, and emergency power units for energy storage, backup power assistance, and shock absorption during landing and maneuvering.
- Marine Systems: Hydraulic accumulators are used in ship steering systems, winches, cranes, and propulsion systems for energy storage, pressure regulation, and emergency power assistance in marine environments.
- Energy Storage Systems: Hydraulic accumulators are used in hydraulic hybrid vehicles, regenerative braking systems, and renewable energy systems for storing energy and supplementing power during acceleration or peak demand periods.
In conclusion, hydraulic accumulators are essential components of hydraulic systems, providing energy storage, pressure control, and emergency power assistance in various industries and applications. Proper selection, installation, and maintenance of hydraulic accumulators are crucial to ensure optimal performance, efficiency, and reliability of hydraulic systems.
Hydraulic Pump:
A hydraulic pump is a mechanical device used to generate flow and create hydraulic pressure within a hydraulic system. It plays a fundamental role in hydraulic systems by converting mechanical energy into hydraulic energy, which is then used to power hydraulic actuators, such as cylinders and motors, and perform work in various applications across industries.
Function and Importance:
The primary function of a hydraulic pump is to generate flow and create hydraulic pressure by displacing hydraulic fluid from a reservoir and forcing it into the hydraulic system. This pressurized fluid is then transmitted to hydraulic actuators, where it exerts force or motion to perform work, such as lifting, pushing, pulling, or rotating.
Hydraulic pumps are essential components of hydraulic systems, providing the motive power required to operate hydraulic machinery and equipment efficiently. They help to transmit energy from power sources, such as electric motors, internal combustion engines, or hydraulic systems, to hydraulic actuators, enabling the controlled movement of mechanical components and the performance of various tasks.
Types of Hydraulic Pumps:
- Gear Pumps: Gear pumps consist of two or more meshing gears that rotate within a housing. As the gears rotate, they trap and displace hydraulic fluid from the inlet to the outlet of the pump, generating flow and creating pressure. Gear pumps are simple in design, cost-effective, and suitable for low to medium-pressure applications.
- Vane Pumps: Vane pumps consist of a rotor with sliding vanes that are forced against the pump housing by centrifugal force or springs. As the rotor rotates, the vanes trap and displace hydraulic fluid from the inlet to the outlet of the pump, generating flow and creating pressure. Vane pumps are compact, quiet, and suitable for medium-pressure applications.
- Piston Pumps: Piston pumps consist of one or more pistons that reciprocate within cylinders to trap and displace hydraulic fluid from the inlet to the outlet of the pump. Piston pumps may be axial piston, radial piston, or bent axis design, with varying configurations for high-pressure applications. They are efficient, durable, and suitable for a wide range of pressure and flow requirements.
Operation and Performance:
Hydraulic pumps operate based on the principle of fluid displacement, where mechanical energy is used to move hydraulic fluid from a low-pressure reservoir to a high-pressure system. The performance of a hydraulic pump is characterized by its flow rate, pressure rating, efficiency, and reliability, which depend on factors such as pump design, size, speed, and operating conditions.
Hydraulic pumps may be operated at fixed or variable speeds, depending on the application requirements and control mechanisms used. They may incorporate features such as pressure compensators, flow control valves, and load-sensing devices to regulate flow and pressure, optimize efficiency, and protect system components from overload or damage.
Applications:
Hydraulic pumps are used in a wide range of hydraulic systems and applications across various industries, including:
- Construction Machinery: Hydraulic pumps are used in excavators, loaders, bulldozers, cranes, and other construction equipment for powering hydraulic cylinders, motors, and controls.
- Manufacturing Machinery: Hydraulic pumps are used in presses, injection molding machines, metalworking equipment, and assembly lines for powering hydraulic actuators and controls.
- Automotive Systems: Hydraulic pumps are used in automotive applications such as power steering systems, braking systems, suspension systems, and convertible tops for providing hydraulic assistance and control.
- Aerospace Systems: Hydraulic pumps are used in aircraft flight control systems, landing gear, cargo doors, and auxiliary power units for providing hydraulic power and control.
- Marine Systems: Hydraulic pumps are used in ship steering systems, winches, cranes, hatch covers, and propulsion systems for providing hydraulic power and control in marine environments.
In conclusion, hydraulic pumps are essential components of hydraulic systems, providing the motive power required to operate hydraulic machinery and equipment efficiently. Proper selection, installation, and maintenance of hydraulic pumps are crucial to ensure optimal performance, efficiency, and reliability of hydraulic systems across various industries and applications.
Hydraulic Valve:
A hydraulic valve is a mechanical device used to control the flow, direction, and pressure of hydraulic fluid within a hydraulic system. It plays a crucial role in regulating the operation of hydraulic machinery and equipment by directing fluid flow to hydraulic actuators, such as cylinders and motors, and controlling their movement and function.
Function and Importance:
The primary function of a hydraulic valve is to regulate the flow, direction, and pressure of hydraulic fluid within a hydraulic system to perform specific tasks and control the movement of mechanical components. Hydraulic valves help to start, stop, and modulate fluid flow, change the direction of fluid flow, and regulate fluid pressure to achieve desired system performance and operation.
Hydraulic valves are essential components of hydraulic systems, providing precise and reliable control over hydraulic fluid flow and pressure to ensure the efficient and safe operation of machinery and equipment. They help to optimize system performance, energy efficiency, and productivity while protecting system components from overload, damage, and malfunction.
Types of Hydraulic Valves:
- Directional Control Valves: Directional control valves regulate the direction of hydraulic fluid flow within a hydraulic system. They control the movement of hydraulic actuators, such as cylinders and motors, by directing fluid flow to different ports or circuits to achieve desired motion, such as extending, retracting, stopping, or reversing.
- Pressure Control Valves: Pressure control valves regulate the pressure of hydraulic fluid within a hydraulic system by controlling the flow of fluid to maintain desired pressure levels. They help to prevent overpressure conditions, regulate system pressure, and protect system components from damage caused by excessive pressure.
- Flow Control Valves: Flow control valves regulate the flow rate of hydraulic fluid within a hydraulic system by controlling the rate of fluid flow through a valve orifice or passage. They help to control the speed of hydraulic actuators, adjust the flow distribution in hydraulic circuits, and optimize system performance and efficiency.
- Proportional Valves: Proportional valves provide continuous and precise control over the flow, direction, and pressure of hydraulic fluid within a hydraulic system. They use electronic or hydraulic control signals to modulate valve operation and achieve precise control over system parameters, such as flow rate, pressure, and direction.
- Check Valves: Check valves allow hydraulic fluid to flow in one direction while preventing reverse flow or backflow in the opposite direction. They help to maintain system integrity, prevent fluid leakage, and protect system components from damage caused by reverse flow or pressure surges.
Operation and Performance:
Hydraulic valves operate based on various principles, such as spool displacement, poppet action, or pilot control, depending on the valve type and design. They may be operated manually, mechanically, hydraulically, or electrically, depending on the application requirements and control mechanisms used.
The performance of a hydraulic valve is characterized by its flow capacity, pressure rating, response time, leakage rate, and reliability, which depend on factors such as valve design, size, materials, and operating conditions. Proper selection, installation, and maintenance of hydraulic valves are crucial to ensure optimal performance, efficiency, and reliability of hydraulic systems.
Applications:
Hydraulic valves are used in a wide range of hydraulic systems and applications across various industries, including:
- Construction Machinery: Hydraulic valves are used in excavators, loaders, bulldozers, cranes, and other construction equipment for controlling the movement of hydraulic cylinders, motors, and controls.
- Manufacturing Machinery: Hydraulic valves are used in presses, injection molding machines, metalworking equipment, and assembly lines for controlling the operation of hydraulic actuators and controls.
- Automotive Systems: Hydraulic valves are used in automotive applications such as brakes, steering systems, suspension systems, and transmission systems for controlling fluid flow, direction, and pressure.
- Aerospace Systems: Hydraulic valves are used in aircraft flight control systems, landing gear, cargo doors, and thrust vectoring systems for precise control of hydraulic fluid flow and pressure.
- Marine Systems: Hydraulic valves are used in ship steering systems, winches, cranes, hatch covers, and propulsion systems for controlling fluid flow, direction, and pressure in marine environments.
In conclusion, hydraulic valves are essential components of hydraulic systems, providing precise and reliable control over fluid flow, direction, and pressure to achieve desired system performance and operation. Proper selection, installation, and maintenance of hydraulic valves are crucial to ensure optimal performance, efficiency, and reliability of hydraulic systems across various industries and applications.
Hydraulic Actuator:
A hydraulic actuator is a mechanical device used to convert hydraulic energy into mechanical motion or force. It plays a vital role in hydraulic systems by transforming the pressure and flow of hydraulic fluid into linear or rotary motion to perform work in various applications across industries.
Function and Importance:
The primary function of a hydraulic actuator is to translate the energy stored in pressurized hydraulic fluid into mechanical motion or force to perform specific tasks or control the movement of mechanical components within a hydraulic system. Hydraulic actuators help to convert hydraulic energy into useful work, such as lifting, pushing, pulling, rotating, or controlling the position of loads or equipment.
Hydraulic actuators are essential components of hydraulic systems, providing precise and reliable control over mechanical motion and force to operate machinery and equipment efficiently. They offer advantages such as high force-to-weight ratio, smooth and precise operation, variable speed and force control, and suitability for a wide range of applications and operating conditions.
Types of Hydraulic Actuators:
- Hydraulic Cylinders: Hydraulic cylinders are linear actuators that convert hydraulic energy into linear motion. They consist of a cylindrical housing, piston, and rod assembly, with hydraulic fluid acting on one side of the piston to extend or retract the rod. Hydraulic cylinders are used in various applications, such as lifting, pressing, clamping, tilting, and positioning.
- Hydraulic Motors: Hydraulic motors are rotary actuators that convert hydraulic energy into rotary motion. They consist of a rotor, shaft, and housing assembly, with hydraulic fluid driving the rotor to rotate the shaft. Hydraulic motors are used in applications such as driving machinery, rotating equipment, powering conveyors, and driving vehicle wheels.
- Hydraulic Rotary Actuators: Hydraulic rotary actuators are rotary actuators that convert hydraulic energy into rotary motion. They consist of a piston or vane mechanism housed within a cylindrical housing, with hydraulic fluid acting on the mechanism to produce rotary motion. Hydraulic rotary actuators are used in applications such as valve actuation, robotic manipulators, material handling, and positioning systems.
- Hydraulic Linear Actuators: Hydraulic linear actuators are specialized linear actuators designed for specific applications or requirements. They may include features such as built-in hydraulic cylinders, hydraulic motors, or customized designs to meet specific performance, size, or mounting requirements.
Operation and Performance:
Hydraulic actuators operate based on the principle of fluid power, where pressurized hydraulic fluid is used to exert force or motion on mechanical components. The performance of a hydraulic actuator is characterized by factors such as force, speed, stroke length, efficiency, accuracy, and reliability, which depend on factors such as actuator type, size, design, and operating conditions.
Hydraulic actuators may be operated manually, mechanically, hydraulically, or electrically, depending on the application requirements and control mechanisms used. They may incorporate features such as position feedback, speed control, force limiting, and overload protection to enhance performance, safety, and reliability.
Applications:
Hydraulic actuators are used in a wide range of hydraulic systems and applications across various industries, including:
- Construction Machinery: Hydraulic actuators are used in excavators, loaders, bulldozers, cranes, and other construction equipment for lifting, pushing, pulling, and positioning heavy loads and materials.
- Manufacturing Machinery: Hydraulic actuators are used in presses, injection molding machines, metalworking equipment, and assembly lines for pressing, clamping, bending, cutting, and positioning operations.
- Automotive Systems: Hydraulic actuators are used in automotive applications such as brakes, steering systems, suspension systems, and convertible tops for controlling vehicle motion, stability, and comfort.
- Aerospace Systems: Hydraulic actuators are used in aircraft flight control systems, landing gear, cargo doors, and thrust vectoring systems for controlling aircraft movement, landing, and cargo handling.
- Marine Systems: Hydraulic actuators are used in ship steering systems, winches, cranes, hatch covers, and propulsion systems for controlling vessel movement, cargo handling, and propulsion.
In conclusion, hydraulic actuators are essential components of hydraulic systems, providing precise and reliable control over mechanical motion and force to perform work in various applications across industries. Proper selection, installation, and maintenance of hydraulic actuators are crucial to ensure optimal performance, efficiency, and reliability of hydraulic systems.
Hydraulic Reservoir:
A hydraulic reservoir, also known as a hydraulic tank or hydraulic sump, is a container used to store hydraulic fluid within a hydraulic system. It plays a crucial role in hydraulic systems by providing a reservoir for storing hydraulic fluid, dissipating heat, releasing entrained air, and allowing for fluid expansion and contraction.
Function and Importance:
The primary function of a hydraulic reservoir is to store hydraulic fluid and provide a stable supply of fluid to the hydraulic system as needed. Hydraulic reservoirs help to ensure proper fluid levels, prevent air entrapment, remove contaminants, and dissipate heat generated during system operation. They also allow for the expansion and contraction of hydraulic fluid due to temperature changes and system dynamics.
Hydraulic reservoirs are essential components of hydraulic systems, providing a centralized location for storing and managing hydraulic fluid while maintaining system integrity, performance, and reliability. They help to extend the service life of hydraulic components, reduce maintenance requirements, and optimize system efficiency and operation.
Design and Construction:
Hydraulic reservoirs are typically constructed from materials such as steel, aluminum, or plastic and may be integrated into other hydraulic system components, such as hydraulic pumps, valves, or actuators, or mounted externally as standalone units. They may feature various design elements, such as baffles, partitions, sight glasses, filters, breathers, and access ports, to facilitate fluid management, air release, filtration, and inspection.
Hydraulic reservoirs may be designed with features such as volume markings, drain plugs, level indicators, temperature gauges, and fluid level sensors to monitor fluid levels, temperature, and condition and facilitate maintenance and troubleshooting.
Operation and Maintenance:
The operation and maintenance of hydraulic reservoirs involve monitoring fluid levels, temperature, and condition, checking for leaks, replenishing fluid as needed, and periodically inspecting and cleaning the reservoir and associated components. Proper maintenance of hydraulic reservoirs helps to ensure optimal fluid quality, system performance, and reliability.
Applications:
Hydraulic reservoirs are used in a wide range of hydraulic systems and applications across various industries, including:
- Construction Machinery: Hydraulic reservoirs are used in excavators, loaders, bulldozers, cranes, and other construction equipment for storing hydraulic fluid and providing a stable supply of fluid to hydraulic components.
- Manufacturing Machinery: Hydraulic reservoirs are used in presses, injection molding machines, metalworking equipment, and assembly lines for storing hydraulic fluid and dissipating heat generated during system operation.
- Automotive Systems: Hydraulic reservoirs are used in automotive applications such as brakes, steering systems, suspension systems, and convertible tops for storing hydraulic fluid and maintaining system performance and reliability.
- Aerospace Systems: Hydraulic reservoirs are used in aircraft landing gear, flight control systems, and auxiliary power units for storing hydraulic fluid and providing a stable supply of fluid to hydraulic components during flight and ground operations.
- Marine Systems: Hydraulic reservoirs are used in ship steering systems, winches, cranes, hatch covers, and propulsion systems for storing hydraulic fluid and maintaining system performance and reliability in marine environments.
In conclusion, hydraulic reservoirs are essential components of hydraulic systems, providing a centralized location for storing and managing hydraulic fluid while maintaining system integrity, performance, and reliability. Proper selection, installation, and maintenance of hydraulic reservoirs are crucial to ensure optimal fluid management and system operation across various industries and applications.
Hydraulic Hose:
A hydraulic hose is a flexible conduit used to transmit hydraulic fluid between hydraulic components within a hydraulic system. It plays a crucial role in hydraulic systems by providing a pathway for the flow of pressurized hydraulic fluid to power hydraulic actuators, such as cylinders and motors, and perform work in various applications across industries.
Function and Importance:
The primary function of a hydraulic hose is to convey pressurized hydraulic fluid from one hydraulic component to another within a hydraulic system. Hydraulic hoses help to transmit energy from hydraulic pumps or power sources to hydraulic actuators, allowing for controlled movement and operation of machinery and equipment.
Hydraulic hoses are essential components of hydraulic systems, providing a flexible and durable connection between hydraulic components while accommodating movement, vibration, and temperature fluctuations. They help to optimize system performance, reliability, and safety by ensuring efficient fluid transmission and minimizing leakage, downtime, and maintenance requirements.
Construction and Materials:
Hydraulic hoses are typically constructed from layers of synthetic rubber, thermoplastic, or synthetic textile fibers reinforced with high-strength steel or synthetic wire braids or spirals. The construction and materials of hydraulic hoses are selected based on factors such as operating pressure, temperature, fluid compatibility, abrasion resistance, flexibility, and environmental conditions.
Hydraulic hoses may feature various layers, such as inner tubes, reinforcement layers, and outer covers, designed to withstand the operating conditions and performance requirements of hydraulic systems. They may also incorporate features such as abrasion-resistant covers, flame-resistant covers, and conductive layers for specific applications or regulatory requirements.
Types of Hydraulic Hoses:
- Wire-Braided Hydraulic Hoses: Wire-braided hydraulic hoses consist of a synthetic rubber inner tube reinforced with one or more layers of high-tensile steel wire braids. They are suitable for medium to high-pressure hydraulic applications and offer flexibility, durability, and resistance to abrasion.
- Wire-Spiral Hydraulic Hoses: Wire-spiral hydraulic hoses consist of a synthetic rubber inner tube reinforced with multiple layers of high-tensile steel wire spirals. They are suitable for high-pressure hydraulic applications and provide enhanced strength, flexibility, and resistance to abrasion and pressure surges.
- Thermoplastic Hydraulic Hoses: Thermoplastic hydraulic hoses consist of a thermoplastic inner tube reinforced with one or more layers of synthetic textile or wire braids. They are suitable for medium to high-pressure hydraulic applications and offer flexibility, lightweight, and resistance to abrasion, chemicals, and UV exposure.
- Hybrid Hydraulic Hoses: Hybrid hydraulic hoses combine features of wire-braided and thermoplastic hoses to provide a balance of flexibility, strength, and performance. They may feature a synthetic rubber or thermoplastic inner tube reinforced with wire braids or spirals for use in various hydraulic applications.
Operation and Maintenance:
The operation and maintenance of hydraulic hoses involve proper selection, installation, inspection, and replacement to ensure optimal performance, reliability, and safety. Hydraulic hoses should be selected based on the specific requirements of the hydraulic system, including operating pressure, temperature, fluid compatibility, and environmental conditions.
Regular inspection of hydraulic hoses for signs of wear, damage, leaks, or degradation is essential to identify potential issues and prevent hydraulic system failures. Hoses should be replaced or repaired as needed according to manufacturer recommendations, maintenance schedules, and regulatory requirements to ensure safe and reliable operation of hydraulic systems.
Applications:
Hydraulic hoses are used in a wide range of hydraulic systems and applications across various industries, including:
- Construction Machinery: Hydraulic hoses are used in excavators, loaders, bulldozers, cranes, and other construction equipment for transmitting hydraulic fluid to hydraulic cylinders, motors, and controls.
- Manufacturing Machinery: Hydraulic hoses are used in presses, injection molding machines, metalworking equipment, and assembly lines for powering hydraulic actuators and controls.
- Automotive Systems: Hydraulic hoses are used in automotive applications such as brakes, steering systems, suspension systems, and hydraulic lifts for transmitting hydraulic fluid and controlling vehicle motion.
- Aerospace Systems: Hydraulic hoses are used in aircraft landing gear, flight control systems, and auxiliary power units for transmitting hydraulic fluid and controlling aircraft movement and operation.
- Marine Systems: Hydraulic hoses are used in ship steering systems, winches, cranes, hatch covers, and propulsion systems for transmitting hydraulic fluid and controlling vessel movement and operation.
In conclusion, hydraulic hoses are essential components of hydraulic systems, providing a flexible and durable connection between hydraulic components while accommodating movement, vibration, and temperature fluctuations. Proper selection, installation, and maintenance of hydraulic hoses are crucial to ensure optimal performance, reliability, and safety of hydraulic systems across various industries and applications.
Hydraulic Filtration:
Hydraulic filtration is the process of removing contaminants, such as dirt, debris, and particles, from hydraulic fluid within a hydraulic system. It plays a critical role in maintaining the cleanliness and integrity of hydraulic fluid, preventing damage to hydraulic components, and ensuring the efficient and reliable operation of hydraulic systems.
Function and Importance:
The primary function of hydraulic filtration is to remove contaminants from hydraulic fluid to maintain fluid cleanliness and protect hydraulic components from wear, damage, and malfunction. Hydraulic filters help to trap and retain particles, debris, water, and other contaminants that can degrade fluid quality, reduce system efficiency, and cause premature component failure.
Hydraulic filtration is essential for maintaining the performance, reliability, and longevity of hydraulic systems, as contaminated fluid can lead to increased friction, corrosion, cavitation, and fluid breakdown, resulting in reduced system efficiency and increased maintenance costs.
Types of Hydraulic Filters:
- In-Line Filters: In-line filters are installed directly in the hydraulic fluid circuit and remove contaminants as fluid flows through them. They may be mounted in-line with hydraulic hoses, pipes, or reservoirs and come in various configurations, such as cartridge filters, spin-on filters, and suction strainers.
- Return Line Filters: Return line filters are installed in the return line of hydraulic systems and remove contaminants from hydraulic fluid as it returns to the reservoir. They help to ensure that only clean fluid is reintroduced into the system, preventing contamination of hydraulic components.
- Pressure Line Filters: Pressure line filters are installed in the pressure line of hydraulic systems and remove contaminants from hydraulic fluid before it reaches hydraulic actuators or controls. They help to protect sensitive components from damage caused by contamination and ensure proper system operation.
- Offline Filtration Systems: Offline filtration systems are standalone units that continuously filter hydraulic fluid outside the main hydraulic system. They may include features such as high-efficiency filtration media, multiple stages of filtration, and fluid monitoring and conditioning capabilities to provide comprehensive contamination control.
Filtration Media and Efficiency:
Hydraulic filters use various types of filtration media, such as cellulose, synthetic fibers, metal mesh, and microglass, to trap and retain contaminants of different sizes and shapes. The efficiency of a hydraulic filter depends on factors such as the filtration media, pore size, surface area, and design, which determine its ability to capture and retain contaminants at specified micron levels.
Hydraulic filters are rated based on their particle removal efficiency, expressed as a percentage of particles captured at a specific micron size. Common filtration ratings include nominal filtration, absolute filtration, and beta ratio, which provide information about the filter’s ability to remove contaminants of various sizes and concentrations.
Operation and Maintenance:
The operation and maintenance of hydraulic filtration systems involve regular inspection, replacement, and monitoring of hydraulic filters to ensure optimal performance and reliability. Hydraulic filters should be inspected periodically for signs of clogging, damage, or degradation and replaced or cleaned according to manufacturer recommendations and maintenance schedules.
Proper maintenance of hydraulic filters helps to ensure effective contamination control, minimize fluid degradation, and extend the service life of hydraulic components. In addition to filter maintenance, other best practices for hydraulic filtration include proper fluid handling, storage, and sampling to prevent contamination and maintain fluid cleanliness.
Applications:
Hydraulic filtration is used in a wide range of hydraulic systems and applications across various industries, including:
- Construction Machinery: Hydraulic filtration is used in excavators, loaders, bulldozers, cranes, and other construction equipment for maintaining hydraulic fluid cleanliness and protecting hydraulic components from wear and damage.
- Manufacturing Machinery: Hydraulic filtration is used in presses, injection molding machines, metalworking equipment, and assembly lines for ensuring clean hydraulic fluid and reliable operation of hydraulic systems.
- Automotive Systems: Hydraulic filtration is used in automotive applications such as brakes, steering systems, suspension systems, and hydraulic lifts for maintaining fluid cleanliness and prolonging the service life of hydraulic components.
- Aerospace Systems: Hydraulic filtration is used in aircraft landing gear, flight control systems, and auxiliary power units for ensuring clean hydraulic fluid and safe and reliable aircraft operation.
- Marine Systems: Hydraulic filtration is used in ship steering systems, winches, cranes, hatch covers, and propulsion systems for maintaining fluid cleanliness and protecting hydraulic components from wear and damage in marine environments.
In conclusion, hydraulic filtration is essential for maintaining the cleanliness and integrity of hydraulic fluid, preventing damage to hydraulic components, and ensuring the efficient and reliable operation of hydraulic systems across various industries and applications. Proper selection, installation, and maintenance of hydraulic filters are crucial to ensure optimal filtration performance and system reliability.
Hydraulic Fluid:
Hydraulic fluid is a specially formulated liquid used to transmit power within hydraulic systems. It plays a crucial role in hydraulic systems by providing a medium for transmitting energy from hydraulic pumps to hydraulic actuators, lubricating moving parts, sealing hydraulic components, dissipating heat, and protecting system components from wear, corrosion, and contamination.
Function and Importance:
The primary function of hydraulic fluid is to transmit power within hydraulic systems by converting mechanical energy into hydraulic energy and vice versa. Hydraulic fluid transfers force from hydraulic pumps to hydraulic actuators, such as cylinders and motors, to perform work, such as lifting, pushing, pulling, or rotating, in various applications across industries.
Hydraulic fluid also serves other important functions in hydraulic systems, including lubricating moving parts to reduce friction and wear, sealing hydraulic components to prevent leakage and maintain system integrity, dissipating heat generated during system operation, and protecting system components from corrosion, oxidation, and contamination.
Properties of Hydraulic Fluid:
Hydraulic fluids have specific properties that make them suitable for use in hydraulic systems. These properties include:
- Viscosity: The viscosity of hydraulic fluid determines its resistance to flow and influences its ability to lubricate moving parts and transmit power within hydraulic systems. Hydraulic fluids with higher viscosity provide better lubrication and sealing but may require higher pump pressures to overcome friction.
- Flash Point and Fire Resistance: The flash point of hydraulic fluid indicates its susceptibility to ignition and combustion. Hydraulic fluids with higher flash points are less likely to ignite and burn in the presence of high temperatures or sparks, making them suitable for use in high-temperature or hazardous environments.
- Pour Point and Cold Weather Performance: The pour point of hydraulic fluid indicates its ability to flow at low temperatures without solidifying or becoming viscous. Hydraulic fluids with lower pour points have better cold weather performance and can flow more easily in sub-zero temperatures, ensuring reliable operation of hydraulic systems in cold climates.
- Anti-Wear and Extreme Pressure Properties: Hydraulic fluids contain additives such as anti-wear agents and extreme pressure additives to protect system components from wear and damage under high-pressure and high-load conditions. These additives form a protective film on metal surfaces, reducing friction and preventing metal-to-metal contact.
- Oxidation and Corrosion Resistance: Hydraulic fluids are formulated to resist oxidation and corrosion to maintain their chemical stability and performance over time. Oxidation inhibitors and corrosion inhibitors are added to hydraulic fluids to prevent the degradation of fluid properties and the formation of sludge, varnish, or acid buildup.
Types of Hydraulic Fluids:
- Mineral Oil-Based Hydraulic Fluids: Mineral oil-based hydraulic fluids are the most commonly used type of hydraulic fluid and are derived from refined petroleum crude oil. They offer good lubrication, cooling, and sealing properties and are suitable for a wide range of hydraulic applications.
- Synthetic Hydraulic Fluids: Synthetic hydraulic fluids are formulated from synthetic base oils and additives to provide enhanced performance and properties compared to mineral oil-based fluids. They offer improved viscosity-temperature characteristics, oxidation resistance, and fire resistance and are suitable for demanding hydraulic applications.
- Biodegradable Hydraulic Fluids: Biodegradable hydraulic fluids are formulated from renewable or biodegradable base oils and additives to minimize environmental impact and ecological harm in case of spills or leaks. They offer comparable performance to mineral oil-based fluids and are used in environmentally sensitive areas or applications.
- Water-Based Hydraulic Fluids: Water-based hydraulic fluids are formulated from water and additives such as glycols, polymers, or surfactants to provide hydraulic energy transmission and lubrication. They offer advantages such as fire resistance, biodegradability, and environmental friendliness but may require additional corrosion protection and maintenance.
Operation and Maintenance:
The operation and maintenance of hydraulic fluid involve proper selection, monitoring, and maintenance to ensure optimal performance, reliability, and longevity of hydraulic systems. Hydraulic fluid should be selected based on factors such as operating temperature, pressure, compatibility with system materials, and environmental considerations.
Regular monitoring of hydraulic fluid condition, including viscosity, cleanliness, contamination levels, and chemical properties, is essential to detect and prevent issues such as fluid degradation, contamination, or fluid loss. Hydraulic fluid should be replaced or replenished according to manufacturer recommendations, maintenance schedules, and regulatory requirements to maintain system performance and reliability.
Proper maintenance of hydraulic fluid also involves proper storage, handling, and disposal to prevent contamination, degradation, or environmental harm. Hydraulic fluid should be stored in clean, sealed containers, handled with care to avoid contamination, and disposed of according to local regulations and environmental guidelines.
Applications:
Hydraulic fluid is used in a wide range of hydraulic systems and applications across various industries, including:
- Construction Machinery: Hydraulic fluid is used in excavators, loaders, bulldozers, cranes, and other construction equipment for powering hydraulic cylinders, motors, and controls.
- Manufacturing Machinery: Hydraulic fluid is used in presses, injection molding machines, metalworking equipment, and assembly lines for transmitting hydraulic power and performing various manufacturing operations.
- Automotive Systems: Hydraulic fluid is used in automotive applications such as brakes, steering systems, suspension systems, and transmissions for transmitting hydraulic power and controlling vehicle motion and operation.
- Aerospace Systems: Hydraulic fluid is used in aircraft landing gear, flight control systems, and auxiliary power units for transmitting hydraulic power and controlling aircraft movement and operation.
- Marine Systems: Hydraulic fluid is used in ship steering systems, winches, cranes, hatch covers, and propulsion systems for transmitting hydraulic power and controlling vessel movement and operation.
In conclusion, hydraulic fluid is a vital component of hydraulic systems, providing a medium for transmitting power, lubricating moving parts, sealing hydraulic components, dissipating heat, and protecting system components. Proper selection, monitoring, and maintenance of hydraulic fluid are essential to ensure optimal performance, reliability, and longevity of hydraulic systems across various industries and applications.
Hydraulic Pump:
A hydraulic pump is a mechanical device used to generate flow and pressure of hydraulic fluid within a hydraulic system. It plays a crucial role in hydraulic systems by converting mechanical energy into hydraulic energy to power hydraulic actuators, such as cylinders and motors, and perform work in various applications across industries.
Function and Importance:
The primary function of a hydraulic pump is to convert mechanical energy, typically provided by an electric motor, internal combustion engine, or other power source, into hydraulic energy by pressurizing hydraulic fluid. Hydraulic pumps generate flow and pressure of hydraulic fluid to transmit power from the pump to hydraulic actuators, allowing for controlled movement and operation of machinery and equipment.
Hydraulic pumps are essential components of hydraulic systems, providing the necessary flow and pressure of hydraulic fluid to drive hydraulic actuators and perform work in various applications. They help to optimize system performance, efficiency, and reliability by ensuring adequate fluid supply, pressure regulation, and control over hydraulic components.
Types of Hydraulic Pumps:
- Gear Pumps: Gear pumps are the simplest type of hydraulic pump and consist of two meshing gears that rotate in opposite directions within a housing. As the gears rotate, they trap and pressurize hydraulic fluid, forcing it out of the pump’s discharge port. Gear pumps are compact, efficient, and cost-effective but may produce pulsating flow and noise.
- Vane Pumps: Vane pumps consist of a rotor with vanes that slide in and out of slots within a circular housing. As the rotor rotates, centrifugal force pushes the vanes outward, trapping and pressurizing hydraulic fluid between the vanes and the housing. Vane pumps offer smooth and quiet operation, moderate efficiency, and resistance to contamination.
- Piston Pumps: Piston pumps use reciprocating pistons to pressurize hydraulic fluid within a cylinder block or housing. As the pistons move back and forth, they draw in and expel hydraulic fluid through inlet and outlet ports. Piston pumps are highly efficient, capable of high pressures and flows, and available in various configurations, such as axial piston, radial piston, and bent-axis piston pumps.
Operation and Performance:
Hydraulic pumps operate based on the principle of positive displacement, where a fixed volume of hydraulic fluid is trapped and pressurized within the pump’s chambers and expelled through outlet ports. The performance of a hydraulic pump is characterized by factors such as flow rate, pressure rating, efficiency, speed, and reliability, which depend on factors such as pump type, size, design, and operating conditions.
Hydraulic pumps may be operated manually, mechanically, hydraulically, or electrically, depending on the application requirements and control mechanisms used. They may incorporate features such as variable displacement, pressure compensation, load sensing, and hydraulic control valves to optimize performance, efficiency, and control over hydraulic systems.
Applications:
Hydraulic pumps are used in a wide range of hydraulic systems and applications across various industries, including:
- Construction Machinery: Hydraulic pumps are used in excavators, loaders, bulldozers, cranes, and other construction equipment for powering hydraulic cylinders, motors, and controls.
- Manufacturing Machinery: Hydraulic pumps are used in presses, injection molding machines, metalworking equipment, and assembly lines for providing hydraulic power and controlling various manufacturing operations.
- Automotive Systems: Hydraulic pumps are used in automotive applications such as power steering systems, braking systems, suspension systems, and convertible tops for providing hydraulic power and controlling vehicle motion and operation.
- Aerospace Systems: Hydraulic pumps are used in aircraft landing gear, flight control systems, and auxiliary power units for providing hydraulic power and controlling aircraft movement and operation.
- Marine Systems: Hydraulic pumps are used in ship steering systems, winches, cranes, hatch covers, and propulsion systems for providing hydraulic power and controlling vessel movement and operation.
In conclusion, hydraulic pumps are essential components of hydraulic systems, providing the necessary flow and pressure of hydraulic fluid to drive hydraulic actuators and perform work in various applications across industries. Proper selection, installation, and maintenance of hydraulic pumps are crucial to ensure optimal performance, efficiency, and reliability of hydraulic systems.
Hydraulic Motor:
A hydraulic motor is a mechanical device used to convert hydraulic energy into mechanical energy in hydraulic systems. It plays a crucial role in hydraulic systems by receiving pressurized hydraulic fluid from a hydraulic pump and converting it into rotary or linear motion to drive machinery and equipment in various applications across industries.
Function and Importance:
The primary function of a hydraulic motor is to convert the pressure and flow of hydraulic fluid into mechanical torque and rotational or linear motion to drive hydraulic actuators, such as shafts, gears, wheels, or cylinders, and perform work in hydraulic systems. Hydraulic motors receive pressurized hydraulic fluid from a hydraulic pump and convert it into mechanical power to drive machinery and equipment.
Hydraulic motors are essential components of hydraulic systems, providing the necessary power and motion to drive hydraulic actuators and perform work in various applications. They help to optimize system performance, efficiency, and reliability by converting hydraulic energy into mechanical energy with high efficiency and control over speed, torque, and direction of motion.
Types of Hydraulic Motors:
- Gear Motors: Gear motors consist of meshing gears that rotate within a housing and convert hydraulic pressure into rotary motion. As hydraulic fluid enters the motor, it applies force to the gears, causing them to rotate and drive an output shaft. Gear motors are compact, simple, and cost-effective but may produce pulsating output and require external bearings for support.
- Vane Motors: Vane motors consist of a rotor with vanes that slide in and out of slots within a circular housing and convert hydraulic pressure into rotary motion. As hydraulic fluid enters the motor, it pushes the vanes outward, causing the rotor to rotate and drive an output shaft. Vane motors offer smooth operation, high starting torque, and good efficiency but may be sensitive to contamination.
- Piston Motors: Piston motors use reciprocating pistons to convert hydraulic pressure into rotary or linear motion. As hydraulic fluid enters the motor, it applies force to pistons within cylinders, causing them to reciprocate and drive an output shaft or piston rod. Piston motors are highly efficient, capable of high speeds and torques, and available in various configurations, such as axial piston, radial piston, and bent-axis piston motors.
Operation and Performance:
Hydraulic motors operate based on the principle of positive displacement, where pressurized hydraulic fluid enters the motor and applies force to internal components, causing them to move and generate mechanical motion. The performance of a hydraulic motor is characterized by factors such as speed, torque, efficiency, displacement, and control, which depend on factors such as motor type, size, design, and operating conditions.
Hydraulic motors may be operated at fixed or variable speeds and torques, depending on the application requirements and control mechanisms used. They may incorporate features such as variable displacement, pressure compensation, load sensing, and hydraulic control valves to optimize performance, efficiency, and control over hydraulic systems.
Applications:
Hydraulic motors are used in a wide range of hydraulic systems and applications across various industries, including:
- Construction Machinery: Hydraulic motors are used in excavators, loaders, bulldozers, cranes, and other construction equipment for driving hydraulic pumps, winches, conveyors, and other machinery and equipment.
- Manufacturing Machinery: Hydraulic motors are used in presses, injection molding machines, metalworking equipment, and assembly lines for driving conveyors, agitators, pumps, and other machinery and equipment.
- Automotive Systems: Hydraulic motors are used in automotive applications such as power windows, convertible tops, seat adjustments, and windshield wipers for driving mechanisms and systems.
- Aerospace Systems: Hydraulic motors are used in aircraft landing gear, flight control systems, and auxiliary power units for driving actuators, pumps, and other systems.
- Marine Systems: Hydraulic motors are used in ship steering systems, winches, cranes, hatch covers, and propulsion systems for driving pumps, actuators, and other systems.
In conclusion, hydraulic motors are essential components of hydraulic systems, providing the necessary power and motion to drive machinery and equipment in various applications across industries. Proper selection, installation, and maintenance of hydraulic motors are crucial to ensure optimal performance, efficiency, and reliability of hydraulic systems.
Hydraulic Valve:
A hydraulic valve is a mechanical device used to control the flow, pressure, and direction of hydraulic fluid within a hydraulic system. It plays a crucial role in regulating the operation of hydraulic components, such as cylinders, motors, and actuators, and controlling the flow of hydraulic fluid to perform work in various applications across industries.
Function and Importance:
The primary function of a hydraulic valve is to regulate the flow, pressure, and direction of hydraulic fluid within a hydraulic system to control the operation of hydraulic components and machinery. Hydraulic valves receive signals from manual controls, electrical solenoids, or other devices and adjust their internal mechanisms to open, close, or modulate the flow of hydraulic fluid according to system requirements.
Hydraulic valves are essential components of hydraulic systems, providing precise control over fluid flow, pressure, and direction to optimize system performance, efficiency, and reliability. They help to regulate the speed, force, and direction of hydraulic actuators and perform work in various applications, including lifting, lowering, pushing, pulling, and rotating.
Types of Hydraulic Valves:
- Directional Control Valves: Directional control valves regulate the flow of hydraulic fluid to control the direction of movement of hydraulic actuators. They include various types such as spool valves, poppet valves, and rotary valves, and are used to control single or multiple actuators and perform functions such as forward, reverse, stop, and hold.
- Pressure Control Valves: Pressure control valves regulate the pressure of hydraulic fluid within a hydraulic system to maintain system pressure within desired limits. They include relief valves, pressure reducing valves, and sequence valves, and are used to protect hydraulic components from overpressure, control system pressure, and prioritize fluid flow to different circuits.
- Flow Control Valves: Flow control valves regulate the flow rate of hydraulic fluid within a hydraulic system to control the speed of hydraulic actuators. They include throttling valves, check valves, and flow divider/combiner valves, and are used to adjust fluid flow to actuators, control cylinder speed, and synchronize multiple actuators.
- Proportional Valves: Proportional valves regulate the flow, pressure, or direction of hydraulic fluid proportionally to a control signal, allowing for precise control over hydraulic system parameters. They include proportional directional control valves, proportional pressure control valves, and proportional flow control valves and are used in applications requiring accurate and responsive control.
Operation and Performance:
Hydraulic valves operate based on various principles, including spool displacement, poppet action, rotary motion, and proportional control, depending on the type and design of the valve. The performance of a hydraulic valve is characterized by factors such as flow capacity, pressure rating, response time, leakage rate, and reliability, which depend on factors such as valve type, size, design, and operating conditions.
Hydraulic valves may be operated manually, mechanically, hydraulically, pneumatically, or electrically, depending on the application requirements and control mechanisms used. They may incorporate features such as pilot-operated, servo-operated, or remote-controlled operation to optimize performance, efficiency, and control over hydraulic systems.
Applications:
Hydraulic valves are used in a wide range of hydraulic systems and applications across various industries, including:
- Construction Machinery: Hydraulic valves are used in excavators, loaders, bulldozers, cranes, and other construction equipment for controlling hydraulic cylinders, motors, and controls.
- Manufacturing Machinery: Hydraulic valves are used in presses, injection molding machines, metalworking equipment, and assembly lines for controlling hydraulic actuators and performing various manufacturing operations.
- Automotive Systems: Hydraulic valves are used in automotive applications such as brakes, steering systems, suspension systems, and transmissions for controlling hydraulic pressure, flow, and direction.
- Aerospace Systems: Hydraulic valves are used in aircraft landing gear, flight control systems, and auxiliary power units for controlling hydraulic actuators, pumps, and other systems.
- Marine Systems: Hydraulic valves are used in ship steering systems, winches, cranes, hatch covers, and propulsion systems for controlling hydraulic power, flow, and direction.
In conclusion, hydraulic valves are essential components of hydraulic systems, providing precise control over fluid flow, pressure, and direction to regulate the operation of hydraulic components and machinery in various applications across industries. Proper selection, installation, and maintenance of hydraulic valves are crucial to ensure optimal performance, efficiency, and reliability of hydraulic systems.
Hydraulic Cylinder:
A hydraulic cylinder is a mechanical device used to convert hydraulic energy into linear motion or force in hydraulic systems. It plays a crucial role in various applications across industries by providing controlled movement or force to perform work such as lifting, pushing, pulling, or bending.
Function and Importance:
The primary function of a hydraulic cylinder is to convert the pressure and flow of hydraulic fluid into linear motion or force to drive mechanical loads or perform work in hydraulic systems. Hydraulic cylinders consist of a cylindrical barrel, piston, rod, seals, and ports for hydraulic fluid inlet and outlet. When pressurized hydraulic fluid enters the cylinder, it applies force to the piston, causing it to move linearly and exert force on the connected load or machinery.
Hydraulic cylinders are essential components of hydraulic systems, providing precise control over movement and force to perform various tasks in applications such as construction, manufacturing, automotive, aerospace, and marine industries. They offer advantages such as high force output, smooth and precise motion control, compact design, and reliability.
Types of Hydraulic Cylinders:
- Single-Acting Cylinders: Single-acting cylinders have a single hydraulic port for fluid inlet and rely on an external force, such as a spring or gravity, to return the piston to its initial position once hydraulic pressure is released. They are used in applications where force is required in one direction only, such as lifting or pressing.
- Double-Acting Cylinders: Double-acting cylinders have two hydraulic ports for fluid inlet and outlet, allowing hydraulic fluid to act on both sides of the piston for bidirectional movement. They are used in applications where force is required in both directions, such as pushing and pulling.
- Telescopic Cylinders: Telescopic cylinders consist of nested cylinders or stages that extend and retract telescopically to provide longer stroke lengths while maintaining a compact design. They are used in applications where space is limited or long stroke lengths are required, such as dump trucks, cranes, and agricultural equipment.
- Rotary Cylinders: Rotary cylinders convert hydraulic energy into rotary motion instead of linear motion, allowing for rotational movement of connected loads or machinery. They are used in applications such as rotary indexing tables, rotary actuators, and rotating fixtures.
Operation and Performance:
Hydraulic cylinders operate based on the principle of Pascal’s law, where pressure applied to hydraulic fluid in a confined space is transmitted equally in all directions, resulting in linear movement of the piston. The performance of a hydraulic cylinder is characterized by factors such as stroke length, bore size, rod diameter, force output, speed, accuracy, and reliability, which depend on factors such as cylinder type, size, design, and operating conditions.
Hydraulic cylinders may be operated manually, mechanically, hydraulically, or electrically, depending on the application requirements and control mechanisms used. They may incorporate features such as cushioning, position sensing, load sensing, and feedback control to optimize performance, efficiency, and safety.
Applications:
Hydraulic cylinders are used in a wide range of applications across various industries, including:
- Construction Machinery: Hydraulic cylinders are used in excavators, loaders, bulldozers, cranes, and other construction equipment for lifting, pushing, digging, and moving heavy loads and materials.
- Manufacturing Machinery: Hydraulic cylinders are used in presses, injection molding machines, metalworking equipment, and assembly lines for clamping, punching, bending, and pressing operations.
- Automotive Systems: Hydraulic cylinders are used in automotive applications such as brakes, steering systems, suspension systems, and convertible tops for actuating mechanisms and systems.
- Aerospace Systems: Hydraulic cylinders are used in aircraft landing gear, flight control systems, cargo doors, and auxiliary power units for actuating mechanisms and systems.
- Marine Systems: Hydraulic cylinders are used in ship steering systems, winches, cranes, hatch covers, and propulsion systems for actuating mechanisms and systems.
In conclusion, hydraulic cylinders are essential components of hydraulic systems, providing controlled linear motion or force to perform work in various applications across industries. Proper selection, installation, and maintenance of hydraulic cylinders are crucial to ensure optimal performance, efficiency, and reliability of hydraulic systems.
Hydraulic Accumulator:
A hydraulic accumulator is a mechanical device used to store hydraulic energy in the form of pressurized hydraulic fluid. It plays a crucial role in hydraulic systems by providing auxiliary power, energy storage, pressure regulation, and shock absorption to improve system performance, efficiency, and safety in various applications across industries.
Function and Importance:
The primary function of a hydraulic accumulator is to store pressurized hydraulic fluid under high pressure and release it when needed to supplement or augment the flow and pressure of hydraulic systems. Hydraulic accumulators consist of a pressure vessel, bladder, piston, or diaphragm, and are charged with hydraulic fluid to store potential energy in the form of compressed gas or spring force.
Hydraulic accumulators are essential components of hydraulic systems, providing various functions such as energy storage, pressure regulation, shock absorption, emergency power, and leakage compensation. They help to optimize system performance, efficiency, and reliability by storing excess energy during low demand periods and releasing it during high demand periods, reducing peak power requirements and improving system response and stability.
Types of Hydraulic Accumulators:
- Bladder Accumulators: Bladder accumulators consist of a pressure vessel divided into two chambers by a flexible bladder or diaphragm. One chamber contains hydraulic fluid, while the other contains compressed gas, typically nitrogen. When hydraulic fluid enters the accumulator, it compresses the gas, storing potential energy. When hydraulic pressure drops, the compressed gas expands, forcing hydraulic fluid out of the accumulator.
- Piston Accumulators: Piston accumulators consist of a pressure vessel with a movable piston separating hydraulic fluid from compressed gas or spring force. When hydraulic fluid enters the accumulator, it compresses the gas or spring, storing potential energy. When hydraulic pressure drops, the compressed gas expands, pushing the piston and forcing hydraulic fluid out of the accumulator.
- Diaphragm Accumulators: Diaphragm accumulators consist of a pressure vessel divided into two chambers by a flexible diaphragm. One chamber contains hydraulic fluid, while the other contains compressed gas or spring force. When hydraulic fluid enters the accumulator, it compresses the gas or spring, storing potential energy. When hydraulic pressure drops, the compressed gas expands, deflecting the diaphragm and forcing hydraulic fluid out of the accumulator.
Operation and Performance:
Hydraulic accumulators operate based on the principle of storing potential energy in the form of compressed gas or spring force and releasing it as kinetic energy to supplement or augment hydraulic systems. The performance of a hydraulic accumulator is characterized by factors such as capacity, pressure rating, response time, leakage rate, and reliability, which depend on factors such as accumulator type, size, design, and operating conditions.
Hydraulic accumulators may be charged manually, mechanically, or hydraulically, depending on the application requirements and control mechanisms used. They may incorporate features such as gas pre-charge, volume compensation, and bladder monitoring to optimize performance, efficiency, and safety.
Applications:
Hydraulic accumulators are used in a wide range of applications across various industries, including:
- Industrial Machinery: Hydraulic accumulators are used in presses, injection molding machines, metalworking equipment, and assembly lines for energy storage, pressure regulation, and shock absorption.
- Mobile Equipment: Hydraulic accumulators are used in excavators, loaders, bulldozers, cranes, and other mobile equipment for energy storage, emergency power, and auxiliary functions.
- Automotive Systems: Hydraulic accumulators are used in automotive applications such as brakes, suspension systems, and hydraulic hybrid vehicles for energy recovery, pressure regulation, and shock absorption.
- Aerospace Systems: Hydraulic accumulators are used in aircraft landing gear, flight control systems, and emergency power units for energy storage, pressure regulation, and emergency operations.
- Marine Systems: Hydraulic accumulators are used in ship steering systems, winches, cranes, hatch covers, and propulsion systems for energy storage, pressure regulation, and shock absorption.
In conclusion, hydraulic accumulators are essential components of hydraulic systems, providing energy storage, pressure regulation, and shock absorption to improve system performance, efficiency, and safety in various applications across industries. Proper selection, installation, and maintenance of hydraulic accumulators are crucial to ensure optimal performance, efficiency, and reliability of hydraulic systems.
Hydraulic Filter:
A hydraulic filter is a mechanical device used to remove contaminants from hydraulic fluid in hydraulic systems. It plays a crucial role in maintaining the cleanliness and integrity of hydraulic fluid to ensure optimal performance, efficiency, and reliability of hydraulic components and machinery in various applications across industries.
Function and Importance:
The primary function of a hydraulic filter is to remove solid particles, water, air, and other contaminants from hydraulic fluid to prevent damage to hydraulic components, reduce wear and tear, and extend the service life of hydraulic systems. Hydraulic filters consist of a filter element, housing, and fittings, and are installed in hydraulic systems to trap and retain contaminants while allowing clean hydraulic fluid to pass through.
Hydraulic filters are essential components of hydraulic systems, providing critical protection against contamination-induced failures, system downtime, and maintenance costs. They help to optimize system performance, efficiency, and reliability by maintaining the cleanliness and integrity of hydraulic fluid, reducing component wear and tear, and minimizing the risk of system failure and downtime.
Types of Hydraulic Filters:
- Suction Filters: Suction filters are installed on the inlet side of hydraulic pumps to remove contaminants from incoming hydraulic fluid before it enters the hydraulic system. They typically consist of a mesh screen or perforated metal element to trap large particles and debris.
- Return Filters: Return filters are installed on the return line of hydraulic systems to remove contaminants from hydraulic fluid returning to the reservoir. They typically consist of a filter element with a high dirt-holding capacity to capture contaminants suspended in hydraulic fluid.
- Pressure Filters: Pressure filters are installed on the pressure line of hydraulic systems to remove contaminants from pressurized hydraulic fluid before it reaches hydraulic components. They typically consist of a filter element with a high filtration efficiency to trap contaminants under high pressure.
- Offline Filters: Offline filters are portable or stationary filtration units installed outside the main hydraulic system to continuously or periodically filter hydraulic fluid and maintain cleanliness levels. They typically consist of a filter element, pump, motor, and reservoir for hydraulic fluid.
Operation and Performance:
Hydraulic filters operate by trapping contaminants within the filter element while allowing clean hydraulic fluid to pass through and return to the hydraulic system. The performance of a hydraulic filter is characterized by factors such as filtration efficiency, dirt-holding capacity, pressure drop, flow rate, and service life, which depend on factors such as filter type, size, media, design, and operating conditions.
Hydraulic filters may incorporate features such as bypass valves, indicator gauges, and differential pressure indicators to optimize performance, efficiency, and reliability. Bypass valves allow hydraulic fluid to bypass the filter element if it becomes clogged, preventing pressure spikes and ensuring continuous operation. Indicator gauges and differential pressure indicators provide visual or electronic signals of filter clogging and the need for maintenance.
Applications:
Hydraulic filters are used in a wide range of hydraulic systems and applications across various industries, including:
- Industrial Machinery: Hydraulic filters are used in presses, injection molding machines, metalworking equipment, and assembly lines for maintaining cleanliness and integrity of hydraulic fluid.
- Mobile Equipment: Hydraulic filters are used in excavators, loaders, bulldozers, cranes, and other mobile equipment for protecting hydraulic components and systems from contamination.
- Automotive Systems: Hydraulic filters are used in automotive applications such as power steering systems, braking systems, and transmission systems for maintaining cleanliness and integrity of hydraulic fluid.
- Aerospace Systems: Hydraulic filters are used in aircraft landing gear, flight control systems, and auxiliary power units for protecting hydraulic components and systems from contamination.
- Marine Systems: Hydraulic filters are used in ship steering systems, winches, cranes, hatch covers, and propulsion systems for maintaining cleanliness and integrity of hydraulic fluid.
In conclusion, hydraulic filters are essential components of hydraulic systems, providing critical protection against contamination-induced failures, system downtime, and maintenance costs. Proper selection, installation, and maintenance of hydraulic filters are crucial to ensure optimal performance, efficiency, and reliability of hydraulic systems.
Hydraulic Hose:
A hydraulic hose is a flexible, reinforced tube used to transmit hydraulic fluid between hydraulic components in hydraulic systems. It plays a crucial role in conveying pressurized hydraulic fluid to power hydraulic actuators and machinery in various applications across industries.
Function and Importance:
The primary function of a hydraulic hose is to transmit pressurized hydraulic fluid between hydraulic components, such as pumps, valves, cylinders, and motors, in hydraulic systems. Hydraulic hoses provide a flexible and reliable means of conveying hydraulic fluid under high pressure and varying operating conditions while accommodating movement, vibration, and temperature fluctuations.
Hydraulic hoses are essential components of hydraulic systems, providing critical connections between hydraulic components and allowing for controlled movement and operation of machinery and equipment. They help to optimize system performance, efficiency, and reliability by transmitting hydraulic energy with minimal pressure drop, fluid leakage, and downtime.
Types of Hydraulic Hoses:
- Rubber Hydraulic Hoses: Rubber hydraulic hoses are the most common type of hydraulic hose and are made from synthetic rubber compounds reinforced with braided or spiral layers of high-tensile steel wire or synthetic fibers. They offer flexibility, durability, and resistance to abrasion, oil, weather, and temperature extremes.
- Thermoplastic Hydraulic Hoses: Thermoplastic hydraulic hoses are made from thermoplastic materials such as nylon, polyurethane, or polyester reinforced with braided or spiral layers of high-tensile synthetic fibers. They offer lightweight, flexibility, and resistance to abrasion, oil, chemicals, and ultraviolet (UV) radiation.
- Metal Hydraulic Hoses: Metal hydraulic hoses are made from stainless steel or other metal alloys and consist of corrugated metal tubes with welded or swaged end fittings. They offer high pressure capability, resistance to corrosion, and durability in harsh environments but may be less flexible than rubber or thermoplastic hoses.
- Composite Hydraulic Hoses: Composite hydraulic hoses combine the properties of rubber, thermoplastic, and metal materials to provide specific performance characteristics such as flexibility, pressure rating, chemical resistance, and temperature range. They are used in specialized applications where standard hoses may not meet requirements.
Operation and Performance:
Hydraulic hoses operate by transmitting pressurized hydraulic fluid between hydraulic components while accommodating movement, vibration, and temperature fluctuations. The performance of a hydraulic hose is characterized by factors such as pressure rating, temperature range, flexibility, abrasion resistance, oil resistance, and service life, which depend on factors such as hose type, size, reinforcement, design, and operating conditions.
Hydraulic hoses may be selected based on parameters such as maximum working pressure, burst pressure, minimum bend radius, temperature rating, and compatibility with hydraulic fluids and environmental conditions. They may incorporate features such as wire or textile reinforcement, abrasion-resistant covers, and crimped or threaded end fittings to optimize performance, durability, and reliability.
Applications:
Hydraulic hoses are used in a wide range of hydraulic systems and applications across various industries, including:
- Construction Machinery: Hydraulic hoses are used in excavators, loaders, bulldozers, cranes, and other construction equipment for transmitting hydraulic fluid to power hydraulic cylinders, motors, and controls.
- Manufacturing Machinery: Hydraulic hoses are used in presses, injection molding machines, metalworking equipment, and assembly lines for transmitting hydraulic fluid to operate hydraulic actuators and controls.
- Automotive Systems: Hydraulic hoses are used in automotive applications such as brakes, steering systems, suspension systems, and transmissions for transmitting hydraulic fluid to actuate mechanisms and systems.
- Aerospace Systems: Hydraulic hoses are used in aircraft landing gear, flight control systems, cargo doors, and auxiliary power units for transmitting hydraulic fluid to operate mechanisms and systems.
- Marine Systems: Hydraulic hoses are used in ship steering systems, winches, cranes, hatch covers, and propulsion systems for transmitting hydraulic fluid to operate mechanisms and systems.
In conclusion, hydraulic hoses are essential components of hydraulic systems, providing flexible and reliable connections between hydraulic components to transmit pressurized hydraulic fluid and power machinery and equipment in various applications across industries. Proper selection, installation, and maintenance of hydraulic hoses are crucial to ensure optimal performance, efficiency, and reliability of hydraulic systems.
Hydraulic Pump:
A hydraulic pump is a mechanical device used to generate flow and create hydraulic pressure in hydraulic systems. It plays a crucial role in providing the primary power source to drive hydraulic actuators, motors, and machinery in various applications across industries.
Function and Importance:
The primary function of a hydraulic pump is to convert mechanical energy into hydraulic energy by generating flow and creating pressure in hydraulic fluid. Hydraulic pumps receive mechanical input, such as rotation or reciprocation, and use it to pressurize hydraulic fluid, which is then transmitted to hydraulic components to perform work.
Hydraulic pumps are essential components of hydraulic systems, providing the primary power source to drive hydraulic actuators, motors, and machinery. They help to optimize system performance, efficiency, and reliability by generating the necessary flow and pressure of hydraulic fluid to meet application requirements and control system operation.
Types of Hydraulic Pumps:
- Gear Pumps: Gear pumps consist of meshing gears that rotate within a housing to generate flow and create pressure in hydraulic fluid. They are simple, cost-effective, and suitable for low to medium pressure applications but may produce pulsating flow and require close tolerances for efficient operation.
- Vane Pumps: Vane pumps consist of vanes that slide in and out of slots within a circular housing to generate flow and create pressure in hydraulic fluid. They offer smooth and quiet operation, good efficiency, and self-priming capability but may be sensitive to contamination and require periodic maintenance.
- Piston Pumps: Piston pumps use reciprocating pistons to generate flow and create pressure in hydraulic fluid. They offer high efficiency, high pressure capability, and variable displacement control but may be more complex, expensive, and sensitive to system conditions than gear or vane pumps.
- Axial Piston Pumps: Axial piston pumps consist of pistons arranged in a circular array around a central shaft to generate flow and create pressure in hydraulic fluid. They offer high efficiency, high pressure capability, and variable displacement control and are commonly used in high-performance hydraulic systems.
Operation and Performance:
Hydraulic pumps operate based on the principle of positive displacement, where fixed or variable volumes of hydraulic fluid are moved and pressurized to generate flow and create pressure. The performance of a hydraulic pump is characterized by factors such as flow rate, pressure rating, efficiency, displacement, speed, and control, which depend on factors such as pump type, size, design, and operating conditions.
Hydraulic pumps may be operated at fixed or variable speeds and displacements, depending on the application requirements and control mechanisms used. They may incorporate features such as pressure compensation, load sensing, and hydraulic control valves to optimize performance, efficiency, and control over hydraulic systems.
Applications:
Hydraulic pumps are used in a wide range of hydraulic systems and applications across various industries, including:
- Construction Machinery: Hydraulic pumps are used in excavators, loaders, bulldozers, cranes, and other construction equipment for powering hydraulic cylinders, motors, and controls.
- Manufacturing Machinery: Hydraulic pumps are used in presses, injection molding machines, metalworking equipment, and assembly lines for powering hydraulic actuators and controls.
- Automotive Systems: Hydraulic pumps are used in automotive applications such as power steering systems, braking systems, and suspension systems for powering mechanisms and systems.
- Aerospace Systems: Hydraulic pumps are used in aircraft landing gear, flight control systems, cargo doors, and auxiliary power units for powering mechanisms and systems.
- Marine Systems: Hydraulic pumps are used in ship steering systems, winches, cranes, hatch covers, and propulsion systems for powering mechanisms and systems.
In conclusion, hydraulic pumps are essential components of hydraulic systems, providing the primary power source to drive hydraulic actuators, motors, and machinery in various applications across industries. Proper selection, installation, and maintenance of hydraulic pumps are crucial to ensure optimal performance, efficiency, and reliability of hydraulic systems.
Hydraulic Motor:
A hydraulic motor is a mechanical device used to convert hydraulic energy into rotary motion in hydraulic systems. It plays a crucial role in powering rotating machinery, equipment, and systems in various applications across industries.
Function and Importance:
The primary function of a hydraulic motor is to convert the pressure and flow of hydraulic fluid into rotary motion to drive rotating machinery, equipment, and systems. Hydraulic motors receive pressurized hydraulic fluid from a hydraulic pump and use it to generate rotational torque, which is then transmitted to drive shafts, gears, or other mechanical components.
Hydraulic motors are essential components of hydraulic systems, providing the primary power source to drive rotary actuators, pumps, fans, conveyors, winches, and other rotating machinery. They help to optimize system performance, efficiency, and reliability by converting hydraulic energy into mechanical work with high torque, speed, and precision.
Types of Hydraulic Motors:
- Gear Motors: Gear motors consist of intermeshing gears that rotate within a housing to generate rotary motion in hydraulic fluid. They offer simple construction, low cost, and high torque at low speeds but may produce pulsating output and require close tolerances for efficient operation.
- Vane Motors: Vane motors consist of vanes that slide in and out of slots within a circular housing to generate rotary motion in hydraulic fluid. They offer smooth operation, good efficiency, and high torque at low speeds but may be sensitive to contamination and require periodic maintenance.
- Piston Motors: Piston motors use reciprocating pistons to generate rotary motion in hydraulic fluid. They offer high efficiency, high torque at high speeds, and variable displacement control but may be more complex, expensive, and sensitive to system conditions than gear or vane motors.
- Radial Piston Motors: Radial piston motors consist of pistons arranged radially around a central shaft to generate rotary motion in hydraulic fluid. They offer high torque, high efficiency, and variable displacement control and are commonly used in high-performance hydraulic systems.
Operation and Performance:
Hydraulic motors operate based on the principle of positive displacement, where pressurized hydraulic fluid is used to drive rotating components, such as gears, vanes, or pistons. The performance of a hydraulic motor is characterized by factors such as torque, speed, efficiency, displacement, control, and reliability, which depend on factors such as motor type, size, design, and operating conditions.
Hydraulic motors may be operated at fixed or variable speeds and displacements, depending on the application requirements and control mechanisms used. They may incorporate features such as pressure compensation, load sensing, and hydraulic control valves to optimize performance, efficiency, and control over hydraulic systems.
Applications:
Hydraulic motors are used in a wide range of hydraulic systems and applications across various industries, including:
- Construction Machinery: Hydraulic motors are used in excavators, loaders, bulldozers, cranes, and other construction equipment for powering rotating machinery, such as excavator arms, buckets, and winches.
- Manufacturing Machinery: Hydraulic motors are used in conveyors, mixers, crushers, and other manufacturing equipment for powering rotating machinery and systems.
- Automotive Systems: Hydraulic motors are used in automotive applications such as power windows, power seats, windshield wipers, and convertible tops for powering mechanisms and systems.
- Aerospace Systems: Hydraulic motors are used in aircraft auxiliary power units, landing gear, cargo doors, and engine actuators for powering mechanisms and systems.
- Marine Systems: Hydraulic motors are used in ship steering systems, winches, cranes, hatch covers, and propulsion systems for powering mechanisms and systems.
In conclusion, hydraulic motors are essential components of hydraulic systems, providing the primary power source to drive rotating machinery, equipment, and systems in various applications across industries. Proper selection, installation, and maintenance of hydraulic motors are crucial to ensure optimal performance, efficiency, and reliability of hydraulic systems.
Hydraulic Valve:
A hydraulic valve is a mechanical device used to control the flow, direction, and pressure of hydraulic fluid in hydraulic systems. It plays a crucial role in regulating the operation of hydraulic components, machinery, and equipment in various applications across industries.
Function and Importance:
The primary function of a hydraulic valve is to control the flow, direction, and pressure of hydraulic fluid to regulate the operation of hydraulic systems. Hydraulic valves receive signals from control devices, such as levers, switches, or solenoids, and use them to open, close, or modulate the flow of hydraulic fluid to actuate hydraulic cylinders, motors, and other components.
Hydraulic valves are essential components of hydraulic systems, providing precise control over the movement, speed, force, and direction of hydraulic actuators and machinery. They help to optimize system performance, efficiency, and safety by controlling the flow of hydraulic fluid to meet application requirements and operational conditions.
Types of Hydraulic Valves:
- Directional Control Valves: Directional control valves control the flow of hydraulic fluid to actuate hydraulic actuators, such as cylinders and motors, in specific directions. They include valves such as spool valves, poppet valves, and rotary valves, and may be manually operated, mechanically actuated, or electrically controlled.
- Pressure Control Valves: Pressure control valves control the pressure of hydraulic fluid within hydraulic systems to prevent overloading, overspeeding, or damage to hydraulic components. They include valves such as relief valves, pressure reducing valves, and sequence valves, and may be set to open or close at predetermined pressure levels.
- Flow Control Valves: Flow control valves control the rate of flow of hydraulic fluid within hydraulic systems to regulate the speed, direction, or force of hydraulic actuators and machinery. They include valves such as throttle valves, check valves, and flow dividers, and may be adjustable or non-adjustable.
- Proportional Valves: Proportional valves control the flow, direction, and pressure of hydraulic fluid in proportion to input signals from control devices, such as voltage or current. They offer precise and variable control over hydraulic systems and are used in applications requiring fine-tuning of hydraulic parameters.
Operation and Performance:
Hydraulic valves operate based on the principles of fluid dynamics and control theory, where hydraulic fluid is directed, regulated, or modulated to achieve desired flow, direction, and pressure within hydraulic systems. The performance of a hydraulic valve is characterized by factors such as flow rate, pressure drop, response time, leakage rate, and reliability, which depend on factors such as valve type, size, design, and operating conditions.
Hydraulic valves may be operated manually, mechanically, hydraulically, or electrically, depending on the application requirements and control mechanisms used. They may incorporate features such as pilot operation, proportional control, position feedback, and load sensing to optimize performance, efficiency, and safety.
Applications:
Hydraulic valves are used in a wide range of hydraulic systems and applications across various industries, including:
- Construction Machinery: Hydraulic valves are used in excavators, loaders, bulldozers, cranes, and other construction equipment for controlling the movement, speed, and force of hydraulic cylinders and motors.
- Manufacturing Machinery: Hydraulic valves are used in presses, injection molding machines, metalworking equipment, and assembly lines for controlling the operation of hydraulic actuators and controls.
- Automotive Systems: Hydraulic valves are used in automotive applications such as brakes, steering systems, suspension systems, and transmissions for controlling the flow, direction, and pressure of hydraulic fluid.
- Aerospace Systems: Hydraulic valves are used in aircraft landing gear, flight control systems, cargo doors, and auxiliary power units for controlling the movement, speed, and force of hydraulic actuators and systems.
- Marine Systems: Hydraulic valves are used in ship steering systems, winches, cranes, hatch covers, and propulsion systems for controlling the operation of hydraulic actuators and systems.
In conclusion, hydraulic valves are essential components of hydraulic systems, providing precise control over the flow, direction, and pressure of hydraulic fluid to regulate the operation of hydraulic components, machinery, and equipment in various applications across industries. Proper selection, installation, and maintenance of hydraulic valves are crucial to ensure optimal performance, efficiency, and reliability of hydraulic systems.
Hydraulic Cylinder:
A hydraulic cylinder is a mechanical device used to convert hydraulic energy into linear motion in hydraulic systems. It plays a crucial role in powering machinery, equipment, and systems that require linear force or motion in various applications across industries.
Function and Importance:
The primary function of a hydraulic cylinder is to convert the pressure and flow of hydraulic fluid into linear motion to actuate mechanical components, such as pistons, arms, or platforms. Hydraulic cylinders consist of a cylindrical barrel, piston, rod, and seals, and are installed in hydraulic systems to generate pushing or pulling forces in a straight line.
Hydraulic cylinders are essential components of hydraulic systems, providing the primary power source to drive mechanical motion, such as lifting, pushing, pulling, bending, or pressing. They help to optimize system performance, efficiency, and reliability by converting hydraulic energy into mechanical work with high force, precision, and control.
Types of Hydraulic Cylinders:
- Single-Acting Cylinders: Single-acting cylinders have one port for hydraulic fluid to enter and act on one side of the piston, while the other side is vented to the atmosphere or equipped with a spring to return the piston. They provide force in one direction only and are typically used in applications where gravity or external forces assist in retracting the piston.
- Double-Acting Cylinders: Double-acting cylinders have two ports for hydraulic fluid to enter and act on both sides of the piston, allowing for force generation in both directions of travel. They are commonly used in applications where precise control over extension and retraction forces is required.
- Telescopic Cylinders: Telescopic cylinders consist of multiple nested stages that extend and retract in a telescoping fashion to provide extended stroke lengths within a compact envelope. They are commonly used in applications with limited space or height restrictions, such as dump trucks, cranes, and aerial lifts.
- Rotary Cylinders: Rotary cylinders convert hydraulic energy into rotary motion instead of linear motion and are used to actuate rotary mechanisms, such as shafts, gears, or levers. They are commonly used in applications such as indexing tables, rotary actuators, and machine tools.
Operation and Performance:
Hydraulic cylinders operate based on the principle of Pascal’s Law, where pressure exerted on hydraulic fluid is transmitted equally in all directions to generate force and motion. The performance of a hydraulic cylinder is characterized by factors such as bore diameter, rod diameter, stroke length, speed, force, precision, and reliability, which depend on factors such as cylinder type, size, design, and operating conditions.
Hydraulic cylinders may be operated at fixed or variable speeds and forces, depending on the application requirements and control mechanisms used. They may incorporate features such as cushioning, position sensing, and load holding to optimize performance, efficiency, and safety.
Applications:
Hydraulic cylinders are used in a wide range of hydraulic systems and applications across various industries, including:
- Construction Machinery: Hydraulic cylinders are used in excavators, loaders, bulldozers, cranes, and other construction equipment for lifting, pushing, pulling, and bending operations.
- Manufacturing Machinery: Hydraulic cylinders are used in presses, injection molding machines, metalworking equipment, and assembly lines for clamping, stamping, bending, and pressing operations.
- Automotive Systems: Hydraulic cylinders are used in automotive applications such as lifts, hoists, jacks, and tailgates for lifting, lowering, and tilting operations.
- Aerospace Systems: Hydraulic cylinders are used in aircraft landing gear, flight control systems, cargo doors, and auxiliary power units for actuating mechanisms and systems.
- Marine Systems: Hydraulic cylinders are used in ship steering systems, winches, cranes, hatch covers, and propulsion systems for actuating mechanisms and systems.
In conclusion, hydraulic cylinders are essential components of hydraulic systems, providing linear force and motion to power machinery, equipment, and systems in various applications across industries. Proper selection, installation, and maintenance of hydraulic cylinders are crucial to ensure optimal performance, efficiency, and reliability of hydraulic systems.
Hydraulic Accumulator:
A hydraulic accumulator is a mechanical device used to store hydraulic energy in the form of pressurized fluid in hydraulic systems. It plays a crucial role in providing supplemental power, damping pressure fluctuations, and absorbing shocks in various applications across industries.
Function and Importance:
The primary function of a hydraulic accumulator is to store pressurized hydraulic fluid under low or high pressure and release it as needed to supplement the output of hydraulic pumps, actuators, or systems. Hydraulic accumulators consist of a pressure vessel, hydraulic fluid, gas or spring, and seals, and are installed in hydraulic systems to provide energy storage, shock absorption, and pressure regulation.
Hydraulic accumulators are essential components of hydraulic systems, providing supplemental power, energy efficiency, and safety by storing excess energy during low demand periods and releasing it during peak demand or emergencies. They help to optimize system performance, efficiency, and reliability by reducing pressure fluctuations, minimizing pump load variations, and protecting hydraulic components from damage.
Types of Hydraulic Accumulators:
- Hydro-pneumatic Accumulators: Hydro-pneumatic accumulators consist of a pressure vessel divided into two chambers by a flexible diaphragm or piston. One chamber contains hydraulic fluid, while the other chamber contains compressed gas, typically nitrogen. They store energy in the form of compressed gas and hydraulic fluid and are commonly used in applications requiring high energy density, such as hydraulic presses, cranes, and elevators.
- Bladder Accumulators: Bladder accumulators consist of a pressure vessel divided into two chambers by a flexible bladder. One chamber contains hydraulic fluid, while the other chamber contains compressed gas, typically nitrogen. They store energy in the form of compressed gas and hydraulic fluid and are commonly used in applications requiring high energy density, such as hydraulic presses, cranes, and elevators.
- Piston Accumulators: Piston accumulators consist of a pressure vessel with a piston separating hydraulic fluid from compressed gas. They store energy in the form of compressed gas and are commonly used in applications requiring high pressure and flow rates, such as hydraulic systems in heavy machinery, offshore platforms, and power plants.
Operation and Performance:
Hydraulic accumulators operate based on the principles of gas compression and hydraulic fluid displacement, where hydraulic fluid is pressurized by compressed gas or spring force to store energy. The performance of a hydraulic accumulator is characterized by factors such as pressure rating, volume capacity, gas precharge, response time, and reliability, which depend on factors such as accumulator type, size, design, and operating conditions.
Hydraulic accumulators may be configured to provide different functions, such as energy storage, shock absorption, pressure regulation, or emergency power, depending on the application requirements and control mechanisms used. They may incorporate features such as safety valves, rupture discs, and pressure gauges to optimize performance, efficiency, and safety.
Applications:
Hydraulic accumulators are used in a wide range of hydraulic systems and applications across various industries, including:
- Construction Machinery: Hydraulic accumulators are used in excavators, loaders, bulldozers, cranes, and other construction equipment for energy storage, shock absorption, and emergency power.
- Manufacturing Machinery: Hydraulic accumulators are used in presses, injection molding machines, metalworking equipment, and assembly lines for energy storage, pressure regulation, and emergency power.
- Automotive Systems: Hydraulic accumulators are used in automotive applications such as suspension systems, braking systems, and transmission systems for energy storage, damping pressure fluctuations, and emergency power.
- Aerospace Systems: Hydraulic accumulators are used in aircraft landing gear, flight control systems, cargo doors, and auxiliary power units for energy storage, shock absorption, and emergency power.
- Marine Systems: Hydraulic accumulators are used in ship steering systems, winches, cranes, hatch covers, and propulsion systems for energy storage, pressure regulation, and emergency power.
In conclusion, hydraulic accumulators are essential components of hydraulic systems, providing supplemental power, energy storage, shock absorption, and pressure regulation in various applications across industries. Proper selection, installation, and maintenance of hydraulic accumulators are crucial to ensure optimal performance, efficiency, and reliability of hydraulic systems.
Hydraulic Filter:
A hydraulic filter is a mechanical device used to remove contaminants from hydraulic fluid in hydraulic systems. It plays a crucial role in maintaining the cleanliness, performance, and reliability of hydraulic components, machinery, and equipment in various applications across industries.
Function and Importance:
The primary function of a hydraulic filter is to remove solid particles, water, air, and other contaminants from hydraulic fluid to prevent damage, wear, and malfunction of hydraulic components. Hydraulic filters consist of a filter element, housing, seals, and fittings, and are installed in hydraulic systems to trap and retain contaminants while allowing clean hydraulic fluid to flow through.
Hydraulic filters are essential components of hydraulic systems, providing critical protection against contamination-induced failures, downtime, and maintenance costs. They help to optimize system performance, efficiency, and reliability by maintaining the cleanliness of hydraulic fluid within specified cleanliness levels and prolonging the service life of hydraulic components and equipment.
Types of Hydraulic Filters:
- Suction Filters: Suction filters are installed on the inlet side of hydraulic pumps to remove contaminants from incoming hydraulic fluid before it enters the pump. They typically consist of a mesh screen or perforated metal element to trap large particles and debris.
- Pressure Filters: Pressure filters are installed downstream of hydraulic pumps or within hydraulic circuits to remove contaminants from pressurized hydraulic fluid. They typically consist of a filter element, housing, and bypass valve and may use pleated paper, wire mesh, or synthetic media to trap particles.
- Return Filters: Return filters are installed on the return line of hydraulic systems to remove contaminants from hydraulic fluid returning to the reservoir. They typically consist of a filter element, housing, and bypass valve and may use cellulose, fiberglass, or synthetic media to capture contaminants.
- Bypass Filters: Bypass filters are installed in parallel with main hydraulic filters to provide additional filtration of hydraulic fluid. They typically consist of a fine mesh or depth media element to remove smaller particles and may be used in high-contamination environments or critical systems.
Operation and Performance:
Hydraulic filters operate based on the principles of filtration, where contaminants are trapped and retained within the filter media while clean hydraulic fluid passes through. The performance of a hydraulic filter is characterized by factors such as filtration efficiency, pressure drop, dirt-holding capacity, flow rate, and service life, which depend on factors such as filter type, size, media, design, and operating conditions.
Hydraulic filters may be selected based on parameters such as micron rating, beta ratio, ISO cleanliness code, flow rate, pressure rating, temperature range, and compatibility with hydraulic fluids and environmental conditions. They may incorporate features such as bypass valves, differential pressure indicators, and integral magnets to optimize performance, efficiency, and reliability.
Applications:
Hydraulic filters are used in a wide range of hydraulic systems and applications across various industries, including:
- Construction Machinery: Hydraulic filters are used in excavators, loaders, bulldozers, cranes, and other construction equipment for protecting hydraulic pumps, valves, cylinders, and motors from contamination.
- Manufacturing Machinery: Hydraulic filters are used in presses, injection molding machines, metalworking equipment, and assembly lines for maintaining the cleanliness of hydraulic fluid and prolonging the service life of hydraulic components.
- Automotive Systems: Hydraulic filters are used in automotive applications such as power steering systems, braking systems, and transmission systems for filtering hydraulic fluid and preventing contamination-induced failures.
- Aerospace Systems: Hydraulic filters are used in aircraft landing gear, flight control systems, cargo doors, and auxiliary power units for ensuring the cleanliness and reliability of hydraulic systems in critical aerospace applications.
- Marine Systems: Hydraulic filters are used in ship steering systems, winches, cranes, hatch covers, and propulsion systems for protecting hydraulic components from contamination and maintaining system performance and reliability.
In conclusion, hydraulic filters are essential components of hydraulic systems, providing critical protection against contamination-induced failures, downtime, and maintenance costs. Proper selection, installation, and maintenance of hydraulic filters are crucial to ensure optimal performance, efficiency, and reliability of hydraulic systems.
Hydraulic Hose:
A hydraulic hose is a flexible, reinforced conduit used to transmit hydraulic fluid between hydraulic components, machinery, and systems in hydraulic systems. It plays a crucial role in conveying pressurized hydraulic fluid while accommodating movement, vibration, and temperature fluctuations in various applications across industries.
Function and Importance:
The primary function of a hydraulic hose is to transmit pressurized hydraulic fluid between hydraulic components, such as pumps, valves, cylinders, and motors, while accommodating movement, vibration, and temperature fluctuations. Hydraulic hoses consist of an inner tube, reinforcement layer(s), cover, and fittings, and are installed in hydraulic systems to convey hydraulic fluid under high pressure, flow, and temperature conditions.
Hydraulic hoses are essential components of hydraulic systems, providing critical connectivity, flexibility, and durability to ensure the safe and efficient operation of hydraulic machinery, equipment, and systems. They help to optimize system performance, efficiency, and reliability by transmitting hydraulic power while withstanding mechanical stresses, environmental exposure, and chemical degradation.
Types of Hydraulic Hoses:
- Rubber Hoses: Rubber hydraulic hoses are commonly used in hydraulic systems due to their flexibility, durability, and resistance to abrasion, ozone, and weathering. They are typically constructed with a synthetic rubber inner tube, reinforcement layers of high-tensile steel wire or textile braids, and a synthetic rubber cover.
- Thermoplastic Hoses: Thermoplastic hydraulic hoses are lightweight, flexible, and resistant to abrasion, chemicals, and UV radiation. They are typically constructed with a thermoplastic inner tube, reinforcement layers of high-tensile synthetic fibers, and a thermoplastic or polyurethane cover.
- Metal Hoses: Metal hydraulic hoses, also known as stainless steel hoses, are used in applications requiring high pressure, temperature, or corrosive resistance. They are typically constructed with a metal inner tube, reinforcement layers of stainless steel wire braids, and a metal or synthetic cover.
- Composite Hoses: Composite hydraulic hoses combine the advantages of rubber, thermoplastic, and metal hoses to provide flexibility, durability, and resistance to abrasion, chemicals, and temperature extremes. They are typically constructed with multiple layers of different materials, such as rubber, thermoplastic, and metal, to meet specific application requirements.
Operation and Performance:
Hydraulic hoses operate based on the principles of fluid dynamics and material science, where pressurized hydraulic fluid is transmitted through a conduit while accommodating movement, vibration, and temperature fluctuations. The performance of a hydraulic hose is characterized by factors such as pressure rating, temperature range, flexibility, abrasion resistance, chemical compatibility, and service life, which depend on factors such as hose type, size, construction, and operating conditions.
Hydraulic hoses may be selected based on parameters such as hose diameter, length, bend radius, working pressure, burst pressure, temperature rating, and compatibility with hydraulic fluids and environmental conditions. They may incorporate features such as wire reinforcement, textile braiding, spiral wrapping, and protective covers to optimize performance, flexibility, and durability.
Applications:
Hydraulic hoses are used in a wide range of hydraulic systems and applications across various industries, including:
- Construction Machinery: Hydraulic hoses are used in excavators, loaders, bulldozers, cranes, and other construction equipment for transmitting hydraulic fluid to actuate hydraulic cylinders, motors, and controls.
- Manufacturing Machinery: Hydraulic hoses are used in presses, injection molding machines, metalworking equipment, and assembly lines for transmitting hydraulic fluid to power hydraulic actuators, valves, and controls.
- Automotive Systems: Hydraulic hoses are used in automotive applications such as power steering systems, braking systems, suspension systems, and transmission systems for transmitting hydraulic fluid to actuate mechanisms and controls.
- Aerospace Systems: Hydraulic hoses are used in aircraft landing gear, flight control systems, cargo doors, and auxiliary power units for transmitting hydraulic fluid to actuate mechanisms and controls in critical aerospace applications.
- Marine Systems: Hydraulic hoses are used in ship steering systems, winches, cranes, hatch covers, and propulsion systems for transmitting hydraulic fluid to actuate mechanisms and controls in harsh marine environments.
In conclusion, hydraulic hoses are essential components of hydraulic systems, providing critical connectivity, flexibility, and durability to ensure the safe and efficient operation of hydraulic machinery, equipment, and systems. Proper selection, installation, and maintenance of hydraulic hoses are crucial to ensure optimal performance, efficiency, and reliability of hydraulic systems.
Hydraulic Pump:
A hydraulic pump is a mechanical device used to generate flow and pressure of hydraulic fluid in hydraulic systems. It plays a crucial role in providing the primary power source to drive hydraulic machinery, equipment, and systems in various applications across industries.
Function and Importance:
The primary function of a hydraulic pump is to convert mechanical energy, typically from an electric motor, engine, or other power source, into hydraulic energy by pressurizing hydraulic fluid. Hydraulic pumps create flow and pressure of hydraulic fluid to actuate hydraulic cylinders, motors, valves, and controls, enabling the operation of hydraulic machinery and equipment.
Hydraulic pumps are essential components of hydraulic systems, providing the primary power source to drive hydraulic actuators, controls, and systems. They help to optimize system performance, efficiency, and reliability by delivering precise flow and pressure of hydraulic fluid to meet application requirements and operational conditions.
Types of Hydraulic Pumps:
- Gear Pumps: Gear pumps consist of intermeshing gears that rotate within a housing to generate flow and pressure of hydraulic fluid. They offer simple construction, low cost, and smooth operation but may produce pulsating flow and require close tolerances for efficient operation.
- Vane Pumps: Vane pumps consist of vanes that slide in and out of slots within a circular housing to generate flow and pressure of hydraulic fluid. They offer smooth operation, low noise, and good efficiency but may be sensitive to contamination and require periodic maintenance.
- Piston Pumps: Piston pumps use reciprocating pistons to generate flow and pressure of hydraulic fluid. They offer high efficiency, high pressure capability, and variable displacement control but may be more complex, expensive, and sensitive to system conditions than gear or vane pumps.
- Axial Piston Pumps: Axial piston pumps consist of pistons arranged axially around a central shaft to generate flow and pressure of hydraulic fluid. They offer high efficiency, high pressure capability, and variable displacement control and are commonly used in high-performance hydraulic systems.
Operation and Performance:
Hydraulic pumps operate based on the principles of fluid dynamics and mechanical engineering, where mechanical energy is converted into hydraulic energy by displacing hydraulic fluid. The performance of a hydraulic pump is characterized by factors such as flow rate, pressure rating, efficiency, displacement, control, and reliability, which depend on factors such as pump type, size, design, and operating conditions.
Hydraulic pumps may be operated at fixed or variable speeds and displacements, depending on the application requirements and control mechanisms used. They may incorporate features such as pressure compensation, load sensing, and hydraulic control valves to optimize performance, efficiency, and control over hydraulic systems.
Applications:
Hydraulic pumps are used in a wide range of hydraulic systems and applications across various industries, including:
- Construction Machinery: Hydraulic pumps are used in excavators, loaders, bulldozers, cranes, and other construction equipment for powering hydraulic cylinders, motors, valves, and controls.
- Manufacturing Machinery: Hydraulic pumps are used in presses, injection molding machines, metalworking equipment, and assembly lines for powering hydraulic actuators, valves, and controls.
- Automotive Systems: Hydraulic pumps are used in automotive applications such as power steering systems, braking systems, suspension systems, and transmission systems for powering hydraulic actuators and controls.
- Aerospace Systems: Hydraulic pumps are used in aircraft landing gear, flight control systems, cargo doors, and auxiliary power units for powering hydraulic actuators and controls in critical aerospace applications.
- Marine Systems: Hydraulic pumps are used in ship steering systems, winches, cranes, hatch covers, and propulsion systems for powering hydraulic actuators and controls in harsh marine environments.
In conclusion, hydraulic pumps are essential components of hydraulic systems, providing the primary power source to drive hydraulic machinery, equipment, and systems in various applications across industries. Proper selection, installation, and maintenance of hydraulic pumps are crucial to ensure optimal performance, efficiency, and reliability of hydraulic systems.
Hydraulic Motor:
A hydraulic motor is a mechanical device used to convert hydraulic energy into rotational motion in hydraulic systems. It plays a crucial role in powering machinery, equipment, and systems that require rotary motion in various applications across industries.
Function and Importance:
The primary function of a hydraulic motor is to convert the pressure and flow of hydraulic fluid into rotational motion to drive mechanical components, such as shafts, gears, or wheels. Hydraulic motors consist of a rotor, cylinder block, pistons, and seals, and are installed in hydraulic systems to provide rotary power output while accommodating variable speed and torque requirements.
Hydraulic motors are essential components of hydraulic systems, providing the primary power source to drive rotary machinery, equipment, and systems. They help to optimize system performance, efficiency, and reliability by converting hydraulic energy into mechanical work with high torque, precision, and control.
Types of Hydraulic Motors:
- Gear Motors: Gear motors use intermeshing gears to convert hydraulic energy into rotational motion. They offer simple construction, low cost, and smooth operation but may produce pulsating torque and require close tolerances for efficient operation.
- Vane Motors: Vane motors use sliding vanes to convert hydraulic energy into rotational motion. They offer smooth operation, low noise, and good efficiency but may be sensitive to contamination and require periodic maintenance.
- Piston Motors: Piston motors use reciprocating pistons to convert hydraulic energy into rotational motion. They offer high efficiency, high torque capability, and variable displacement control but may be more complex, expensive, and sensitive to system conditions than gear or vane motors.
- Axial Piston Motors: Axial piston motors use axial pistons arranged around a central shaft to convert hydraulic energy into rotational motion. They offer high efficiency, high torque capability, and variable displacement control and are commonly used in high-performance hydraulic systems.
Operation and Performance:
Hydraulic motors operate based on the principles of fluid dynamics and mechanical engineering, where hydraulic energy is converted into rotational motion by pushing or pulling on mechanical components. The performance of a hydraulic motor is characterized by factors such as torque, speed, efficiency, displacement, control, and reliability, which depend on factors such as motor type, size, design, and operating conditions.
Hydraulic motors may be operated at fixed or variable speeds and displacements, depending on the application requirements and control mechanisms used. They may incorporate features such as pressure compensation, load sensing, and hydraulic control valves to optimize performance, efficiency, and control over hydraulic systems.
Applications:
Hydraulic motors are used in a wide range of hydraulic systems and applications across various industries, including:
- Construction Machinery: Hydraulic motors are used in excavators, loaders, bulldozers, cranes, and other construction equipment for powering hydraulic winches, drives, and attachments.
- Manufacturing Machinery: Hydraulic motors are used in machine tools, conveyors, lifts, and robots for powering rotary actuators, drives, and mechanisms.
- Automotive Systems: Hydraulic motors are used in automotive applications such as fan drives, seat adjusters, convertible tops, and power windows for powering rotary mechanisms and systems.
- Aerospace Systems: Hydraulic motors are used in aircraft landing gear, flight control systems, cargo doors, and auxiliary power units for powering rotary mechanisms and systems in critical aerospace applications.
- Marine Systems: Hydraulic motors are used in ship propulsion systems, steering systems, winches, and thrusters for powering rotary mechanisms and systems in harsh marine environments.
In conclusion, hydraulic motors are essential components of hydraulic systems, providing the primary power source to drive rotary machinery, equipment, and systems in various applications across industries. Proper selection, installation, and maintenance of hydraulic motors are crucial to ensure optimal performance, efficiency, and reliability of hydraulic systems.
Hydraulic Valve:
A hydraulic valve is a mechanical device used to control the flow, direction, and pressure of hydraulic fluid in hydraulic systems. It plays a crucial role in regulating the operation of hydraulic machinery, equipment, and systems in various applications across industries.
Function and Importance:
The primary function of a hydraulic valve is to regulate the flow, direction, and pressure of hydraulic fluid to control the movement and operation of hydraulic actuators, motors, and systems. Hydraulic valves consist of a valve body, spool, poppet, or other control elements, and are installed in hydraulic systems to provide precise control over hydraulic fluid flow, direction, and pressure.
Hydraulic valves are essential components of hydraulic systems, providing critical control and regulation of hydraulic fluid to ensure the safe, efficient, and reliable operation of hydraulic machinery and equipment. They help to optimize system performance, efficiency, and reliability by enabling precise control over hydraulic actuation, motion, and force.
Types of Hydraulic Valves:
- Directional Control Valves: Directional control valves control the direction of hydraulic fluid flow between different ports in hydraulic systems. They include various types such as spool valves, poppet valves, rotary valves, and cartridge valves, and are used to control the movement of hydraulic actuators, motors, and systems.
- Pressure Control Valves: Pressure control valves regulate the pressure of hydraulic fluid within hydraulic systems. They include various types such as relief valves, pressure-reducing valves, sequence valves, and counterbalance valves, and are used to protect hydraulic components from overpressure, control system pressure, and maintain system stability.
- Flow Control Valves: Flow control valves regulate the flow rate of hydraulic fluid within hydraulic systems. They include various types such as throttle valves, check valves, flow dividers, and flow regulators, and are used to control the speed, direction, and synchronization of hydraulic actuators, motors, and systems.
- Proportional Valves: Proportional valves provide proportional control over the flow, direction, and pressure of hydraulic fluid within hydraulic systems. They include various types such as proportional directional valves, proportional pressure valves, and proportional flow control valves, and are used to provide precise and variable control over hydraulic actuation, motion, and force.
Operation and Performance:
Hydraulic valves operate based on the principles of fluid dynamics and mechanical engineering, where hydraulic fluid flow is controlled by manipulating valve elements such as spools, poppets, or pistons. The performance of a hydraulic valve is characterized by factors such as flow capacity, pressure rating, response time, accuracy, repeatability, and reliability, which depend on factors such as valve type, size, design, and operating conditions.
Hydraulic valves may be operated manually, mechanically, electrically, pneumatically, or hydraulically, depending on the application requirements and control mechanisms used. They may incorporate features such as position feedback, pilot control, and proportional control to optimize performance, efficiency, and control over hydraulic systems.
Applications:
Hydraulic valves are used in a wide range of hydraulic systems and applications across various industries, including:
- Construction Machinery: Hydraulic valves are used in excavators, loaders, bulldozers, cranes, and other construction equipment for controlling hydraulic cylinders, motors, and systems.
- Manufacturing Machinery: Hydraulic valves are used in presses, injection molding machines, metalworking equipment, and assembly lines for controlling hydraulic actuators, valves, and controls.
- Automotive Systems: Hydraulic valves are used in automotive applications such as power steering systems, braking systems, suspension systems, and transmission systems for controlling hydraulic actuators and controls.
- Aerospace Systems: Hydraulic valves are used in aircraft landing gear, flight control systems, cargo doors, and auxiliary power units for controlling hydraulic actuators and controls in critical aerospace applications.
- Marine Systems: Hydraulic valves are used in ship steering systems, winches, cranes, hatch covers, and propulsion systems for controlling hydraulic actuators and controls in harsh marine environments.
In conclusion, hydraulic valves are essential components of hydraulic systems, providing critical control and regulation of hydraulic fluid to ensure the safe, efficient, and reliable operation of hydraulic machinery, equipment, and systems. Proper selection, installation, and maintenance of hydraulic valves are crucial to ensure optimal performance, efficiency, and reliability of hydraulic systems.
Hydraulic Cylinder:
A hydraulic cylinder is a mechanical actuator used to convert hydraulic energy into linear motion in hydraulic systems. It plays a crucial role in powering machinery, equipment, and systems that require straight-line force and motion in various applications across industries.
Function and Importance:
The primary function of a hydraulic cylinder is to convert the pressure and flow of hydraulic fluid into linear motion to move mechanical components, such as pistons, rods, or platforms. Hydraulic cylinders consist of a cylindrical barrel, piston, rod, seals, and ports, and are installed in hydraulic systems to provide straight-line force and motion for actuating mechanisms, controls, and systems.
Hydraulic cylinders are essential components of hydraulic systems, providing precise control and regulation of linear motion to ensure the safe, efficient, and reliable operation of hydraulic machinery and equipment. They help to optimize system performance, efficiency, and reliability by providing high force output, precise positioning, and smooth operation.
Types of Hydraulic Cylinders:
- Single-Acting Cylinders: Single-acting cylinders use hydraulic pressure to extend the piston rod in one direction, while a spring, gravity, or external force returns the piston rod to its original position. They are typically used in applications requiring unidirectional force and motion, such as lifting, pressing, or clamping.
- Double-Acting Cylinders: Double-acting cylinders use hydraulic pressure to extend and retract the piston rod in both directions. They are typically used in applications requiring bidirectional force and motion, such as pushing, pulling, or lifting with controlled speed and force.
- Telescopic Cylinders: Telescopic cylinders consist of nested cylindrical sections that extend and retract to provide multiple stages of linear motion within a compact space. They are typically used in applications requiring long stroke lengths or limited installation space, such as dump trucks, cranes, or agricultural equipment.
- Rotary Cylinders: Rotary cylinders convert hydraulic energy into rotary motion to provide angular movement or torque. They are typically used in applications requiring rotary actuation, such as indexing, clamping, or positioning.
Operation and Performance:
Hydraulic cylinders operate based on the principles of fluid dynamics and mechanical engineering, where hydraulic pressure is applied to one side of the piston to generate linear motion of the piston rod. The performance of a hydraulic cylinder is characterized by factors such as stroke length, bore size, rod diameter, force output, speed, accuracy, and reliability, which depend on factors such as cylinder type, size, design, and operating conditions.
Hydraulic cylinders may be operated manually, mechanically, electrically, or hydraulically, depending on the application requirements and control mechanisms used. They may incorporate features such as cushioning, position feedback, and force measurement to optimize performance, efficiency, and control over hydraulic systems.
Applications:
Hydraulic cylinders are used in a wide range of hydraulic systems and applications across various industries, including:
- Construction Machinery: Hydraulic cylinders are used in excavators, loaders, bulldozers, cranes, and other construction equipment for lifting, pushing, pulling, and positioning heavy loads and materials.
- Manufacturing Machinery: Hydraulic cylinders are used in presses, injection molding machines, metalworking equipment, and assembly lines for clamping, forming, bending, and stamping operations.
- Automotive Systems: Hydraulic cylinders are used in automotive applications such as lifting, lowering, tilting, and positioning vehicle components and assemblies during assembly, testing, and maintenance.
- Aerospace Systems: Hydraulic cylinders are used in aircraft landing gear, flight control systems, cargo doors, and auxiliary power units for actuating mechanisms and controls in critical aerospace applications.
- Marine Systems: Hydraulic cylinders are used in ship steering systems, winches, cranes, hatch covers, and propulsion systems for actuating mechanisms and controls in harsh marine environments.
In conclusion, hydraulic cylinders are essential components of hydraulic systems, providing precise control and regulation of linear motion to ensure the safe, efficient, and reliable operation of hydraulic machinery, equipment, and systems. Proper selection, installation, and maintenance of hydraulic cylinders are crucial to ensure optimal performance, efficiency, and reliability of hydraulic systems.
Hydraulic Reservoir:
A hydraulic reservoir, also known as a hydraulic tank or hydraulic oil reservoir, is a storage container used to hold hydraulic fluid in hydraulic systems. It plays a crucial role in providing a stable supply of hydraulic fluid, dissipating heat, and removing contaminants to maintain the performance and reliability of hydraulic systems.
Function and Importance:
The primary function of a hydraulic reservoir is to store hydraulic fluid and provide a stable supply to hydraulic pumps, motors, valves, cylinders, and other components within a hydraulic system. Hydraulic reservoirs also serve several important secondary functions, including:
- Heat Dissipation: Hydraulic reservoirs act as heat exchangers, dissipating heat generated by hydraulic components and system operation. This helps to prevent overheating of hydraulic fluid and components, which can lead to reduced performance, accelerated wear, and system failures.
- Air Separation: Hydraulic reservoirs allow entrained air and gases to separate from hydraulic fluid, preventing air bubbles and cavitation within the system. This helps to maintain hydraulic system efficiency, responsiveness, and stability by minimizing air-induced problems such as sponginess, noise, and reduced performance.
- Contaminant Settlement: Hydraulic reservoirs allow contaminants such as dirt, debris, and water to settle out of hydraulic fluid, preventing them from circulating through the system and causing damage to hydraulic components. This helps to maintain hydraulic fluid cleanliness and prolong the service life of system components.
- Fluid Level Monitoring: Hydraulic reservoirs typically include sight gauges, level indicators, or electronic sensors to monitor the level and condition of hydraulic fluid. This allows operators to visually inspect fluid levels, detect leaks, and perform maintenance tasks such as fluid replenishment, filtration, and contamination control.
Types of Hydraulic Reservoirs:
- Open Reservoirs: Open reservoirs are simple, unpressurized containers that allow hydraulic fluid to be exposed to the atmosphere. They are typically used in low-pressure, low-contamination environments and may require additional filtration and maintenance to ensure hydraulic fluid cleanliness.
- Closed Reservoirs: Closed reservoirs are sealed containers that prevent hydraulic fluid from being exposed to the atmosphere. They are typically pressurized to maintain system cleanliness and stability, and may include features such as breathers, filters, and baffles to control contamination, foaming, and fluid movement.
- Pressurized Reservoirs: Pressurized reservoirs are sealed containers that are pressurized to maintain hydraulic fluid cleanliness and stability. They are typically used in high-pressure, high-contamination environments and may include features such as bladder accumulators, diaphragm accumulators, or piston accumulators to maintain pressure and absorb fluid shocks.
- Integrated Reservoirs: Integrated reservoirs are hydraulic components that combine the functions of a reservoir, filter, cooler, and other accessories into a single unit. They are typically compact, space-saving designs that provide efficient and reliable hydraulic fluid storage, conditioning, and distribution in a single package.
Operation and Performance:
Hydraulic reservoirs operate based on the principles of fluid dynamics and thermodynamics, where hydraulic fluid is stored, circulated, and conditioned to maintain system performance and reliability. The performance of a hydraulic reservoir is characterized by factors such as capacity, shape, construction, material, filtration, cooling, and pressurization, which depend on factors such as reservoir type, size, design, and operating conditions.
Hydraulic reservoirs may be designed with features such as baffles, partitions, screens, magnets, breathers, filters, coolers, heaters, and level sensors to optimize performance, efficiency, and reliability. Proper selection, installation, and maintenance of hydraulic reservoirs are crucial to ensure optimal hydraulic system operation and longevity.
Applications:
Hydraulic reservoirs are used in a wide range of hydraulic systems and applications across various industries, including:
- Construction Machinery: Hydraulic reservoirs are used in excavators, loaders, bulldozers, cranes, and other construction equipment for storing hydraulic fluid and maintaining system performance and reliability.
- Manufacturing Machinery: Hydraulic reservoirs are used in presses, injection molding machines, metalworking equipment, and assembly lines for storing hydraulic fluid and providing a stable supply to hydraulic components and systems.
- Automotive Systems: Hydraulic reservoirs are used in automotive applications such as power steering systems, braking systems, suspension systems, and transmission systems for storing hydraulic fluid and maintaining system performance and reliability.
- Aerospace Systems: Hydraulic reservoirs are used in aircraft landing gear, flight control systems, cargo doors, and auxiliary power units for storing hydraulic fluid and providing a stable supply to critical hydraulic components and systems.
- Marine Systems: Hydraulic reservoirs are used in ship steering systems, winches, cranes, hatch covers, and propulsion systems for storing hydraulic fluid and maintaining system performance and reliability in harsh marine environments.
In conclusion, hydraulic reservoirs are essential components of hydraulic systems, providing a stable supply of hydraulic fluid, dissipating heat, and removing contaminants to maintain the performance and reliability of hydraulic machinery, equipment, and systems. Proper selection, installation, and maintenance of hydraulic reservoirs are crucial to ensure optimal hydraulic system operation and longevity.
Hydraulic Filter:
A hydraulic filter is a mechanical device used to remove contaminants from hydraulic fluid in hydraulic systems. It plays a crucial role in maintaining the cleanliness and integrity of hydraulic fluid, protecting hydraulic components from damage, and ensuring the reliable operation of hydraulic machinery and equipment.
Function and Importance:
The primary function of a hydraulic filter is to remove solid particles, debris, water, and other contaminants from hydraulic fluid to prevent them from circulating through the hydraulic system and causing damage to hydraulic components. Hydraulic filters consist of a filter medium, housing, end caps, seals, and ports, and are installed in hydraulic systems to provide effective filtration of hydraulic fluid.
Hydraulic filters are essential components of hydraulic systems, providing critical protection and contamination control to ensure the safe, efficient, and reliable operation of hydraulic machinery and equipment. They help to optimize system performance, efficiency, and longevity by maintaining hydraulic fluid cleanliness within specified ISO cleanliness levels.
Types of Hydraulic Filters:
- Depth Filters: Depth filters use a porous filter medium, such as cellulose, paper, or fiberglass, to trap contaminants throughout the thickness of the filter element. They offer high dirt-holding capacity and are effective at capturing solid particles and debris but may have higher pressure drops and require periodic replacement.
- Surface Filters: Surface filters use a pleated or woven filter medium, such as polyester, nylon, or metal mesh, to capture contaminants on the surface of the filter element. They offer lower pressure drops and longer service life but may have lower dirt-holding capacity and require regular cleaning or backwashing.
- Micron Filters: Micron filters use a defined pore size, such as 5 microns, 10 microns, or 25 microns, to capture contaminants of specific sizes from hydraulic fluid. They offer precise filtration and are effective at removing fine particles and contaminants but may have higher pressure drops and require frequent maintenance.
- Bypass Filters: Bypass filters divert a portion of hydraulic fluid flow through a secondary filter circuit, allowing for continuous filtration of hydraulic fluid while minimizing pressure drops and flow restrictions. They offer extended filtration capacity and can remove contaminants down to submicron levels but may require additional plumbing and maintenance.
Operation and Performance:
Hydraulic filters operate based on the principles of fluid dynamics and filtration, where hydraulic fluid is passed through the filter medium, and contaminants are captured and retained while clean fluid flows through. The performance of a hydraulic filter is characterized by factors such as filtration efficiency, dirt-holding capacity, pressure drop, flow rate, and service life, which depend on factors such as filter type, size, media, design, and operating conditions.
Hydraulic filters may be installed in various locations within hydraulic systems, including in-line, off-line, suction, return, and pressure locations, depending on the application requirements and contamination control strategy used. They may incorporate features such as bypass valves, indicators, gauges, and heaters to optimize performance, efficiency, and reliability.
Applications:
Hydraulic filters are used in a wide range of hydraulic systems and applications across various industries, including:
- Construction Machinery: Hydraulic filters are used in excavators, loaders, bulldozers, cranes, and other construction equipment for removing contaminants from hydraulic fluid and protecting hydraulic components from damage.
- Manufacturing Machinery: Hydraulic filters are used in presses, injection molding machines, metalworking equipment, and assembly lines for maintaining hydraulic fluid cleanliness and ensuring the reliable operation of hydraulic systems.
- Automotive Systems: Hydraulic filters are used in automotive applications such as power steering systems, braking systems, suspension systems, and transmission systems for removing contaminants from hydraulic fluid and protecting hydraulic components from wear and tear.
- Aerospace Systems: Hydraulic filters are used in aircraft landing gear, flight control systems, cargo doors, and auxiliary power units for maintaining hydraulic fluid cleanliness and ensuring the reliable operation of critical hydraulic components and systems.
- Marine Systems: Hydraulic filters are used in ship steering systems, winches, cranes, hatch covers, and propulsion systems for removing contaminants from hydraulic fluid and protecting hydraulic components from corrosion and damage in harsh marine environments.
In conclusion, hydraulic filters are essential components of hydraulic systems, providing critical protection and contamination control to ensure the safe, efficient, and reliable operation of hydraulic machinery, equipment, and systems. Proper selection, installation, and maintenance of hydraulic filters are crucial to ensure optimal hydraulic system performance, efficiency, and longevity.
Hydraulic Pump:
A hydraulic pump is a mechanical device used to generate flow and provide pressure to hydraulic fluid in hydraulic systems. It plays a crucial role in powering machinery, equipment, and systems that require hydraulic force and motion in various applications across industries.
Function and Importance:
The primary function of a hydraulic pump is to convert mechanical energy into hydraulic energy by pressurizing and circulating hydraulic fluid within a hydraulic system. Hydraulic pumps consist of a housing, inlet port, outlet port, drive shaft, pistons, gears, or vanes, and are installed in hydraulic systems to provide the primary power source for hydraulic machinery, equipment, and systems.
Hydraulic pumps are essential components of hydraulic systems, providing the force and pressure necessary to actuate hydraulic cylinders, motors, valves, and actuators. They help to optimize system performance, efficiency, and reliability by providing precise control over hydraulic fluid flow, pressure, and power output.
Types of Hydraulic Pumps:
- Gear Pumps: Gear pumps use intermeshing gears to pressurize and circulate hydraulic fluid within a hydraulic system. They offer simple construction, low cost, and smooth operation but may have lower efficiency and limited pressure and flow capabilities compared to other pump types.
- Vane Pumps: Vane pumps use sliding vanes to pressurize and circulate hydraulic fluid within a hydraulic system. They offer smooth operation, low noise, and moderate efficiency but may be sensitive to contamination and require periodic maintenance.
- Piston Pumps: Piston pumps use reciprocating pistons to pressurize and circulate hydraulic fluid within a hydraulic system. They offer high efficiency, high pressure, and variable displacement control but may be more complex, expensive, and sensitive to system conditions than gear or vane pumps.
- Axial Piston Pumps: Axial piston pumps use axial pistons arranged around a central shaft to pressurize and circulate hydraulic fluid within a hydraulic system. They offer high efficiency, high pressure, and variable displacement control and are commonly used in high-performance hydraulic systems.
Operation and Performance:
Hydraulic pumps operate based on the principles of fluid dynamics and mechanical engineering, where mechanical energy is converted into hydraulic energy by displacing hydraulic fluid and creating pressure within the system. The performance of a hydraulic pump is characterized by factors such as flow rate, pressure rating, efficiency, displacement, control, and reliability, which depend on factors such as pump type, size, design, and operating conditions.
Hydraulic pumps may be operated at fixed or variable speeds and displacements, depending on the application requirements and control mechanisms used. They may incorporate features such as pressure compensation, load sensing, and hydraulic control valves to optimize performance, efficiency, and control over hydraulic systems.
Applications:
Hydraulic pumps are used in a wide range of hydraulic systems and applications across various industries, including:
- Construction Machinery: Hydraulic pumps are used in excavators, loaders, bulldozers, cranes, and other construction equipment for powering hydraulic cylinders, motors, valves, and controls.
- Manufacturing Machinery: Hydraulic pumps are used in presses, injection molding machines, metalworking equipment, and assembly lines for powering hydraulic actuators, tools, and controls.
- Automotive Systems: Hydraulic pumps are used in automotive applications such as power steering systems, braking systems, suspension systems, and convertible tops for powering hydraulic actuators and controls.
- Aerospace Systems: Hydraulic pumps are used in aircraft landing gear, flight control systems, cargo doors, and auxiliary power units for powering hydraulic actuators and controls in critical aerospace applications.
- Marine Systems: Hydraulic pumps are used in ship steering systems, winches, cranes, hatch covers, and propulsion systems for powering hydraulic actuators and controls in harsh marine environments.
In conclusion, hydraulic pumps are essential components of hydraulic systems, providing the primary power source for hydraulic machinery, equipment, and systems in various applications across industries. Proper selection, installation, and maintenance of hydraulic pumps are crucial to ensure optimal performance, efficiency, and reliability of hydraulic systems.
Hydraulic Motor:
A hydraulic motor is a mechanical device used to convert hydraulic energy into rotary motion in hydraulic systems. It plays a crucial role in powering machinery, equipment, and systems that require rotational force and motion in various applications across industries.
Function and Importance:
The primary function of a hydraulic motor is to convert the pressure and flow of hydraulic fluid into rotational motion to drive mechanical components, such as shafts, gears, or wheels. Hydraulic motors consist of a housing, inlet port, outlet port, drive shaft, pistons, gears, or vanes, and are installed in hydraulic systems to provide rotary power for hydraulic machinery, equipment, and systems.
Hydraulic motors are essential components of hydraulic systems, providing the rotary power necessary to drive hydraulic pumps, fans, conveyors, winches, and other rotating equipment. They help to optimize system performance, efficiency, and reliability by providing precise control over rotational speed, torque, and power output.
Types of Hydraulic Motors:
- Gear Motors: Gear motors use intermeshing gears to convert hydraulic energy into rotary motion. They offer simple construction, low cost, and moderate efficiency but may have limited speed and torque capabilities compared to other motor types.
- Vane Motors: Vane motors use sliding vanes to convert hydraulic energy into rotary motion. They offer smooth operation, low noise, and moderate efficiency but may be sensitive to contamination and require periodic maintenance.
- Piston Motors: Piston motors use reciprocating pistons to convert hydraulic energy into rotary motion. They offer high efficiency, high torque, and variable displacement control but may be more complex, expensive, and sensitive to system conditions than gear or vane motors.
- Radial Piston Motors: Radial piston motors use radial pistons arranged around a central shaft to convert hydraulic energy into rotary motion. They offer high efficiency, high torque, and variable displacement control and are commonly used in high-performance hydraulic systems.
Operation and Performance:
Hydraulic motors operate based on the principles of fluid dynamics and mechanical engineering, where hydraulic energy is converted into rotary motion by displacing hydraulic fluid and creating torque within the motor. The performance of a hydraulic motor is characterized by factors such as speed, torque, efficiency, displacement, control, and reliability, which depend on factors such as motor type, size, design, and operating conditions.
Hydraulic motors may be operated at fixed or variable speeds and displacements, depending on the application requirements and control mechanisms used. They may incorporate features such as pressure compensation, speed regulation, and directional control to optimize performance, efficiency, and control over hydraulic systems.
Applications:
Hydraulic motors are used in a wide range of hydraulic systems and applications across various industries, including:
- Construction Machinery: Hydraulic motors are used in excavators, loaders, bulldozers, cranes, and other construction equipment for driving hydraulic pumps, fans, conveyors, winches, and other rotating equipment.
- Manufacturing Machinery: Hydraulic motors are used in presses, injection molding machines, metalworking equipment, and assembly lines for driving hydraulic pumps, fans, conveyors, and other rotating equipment.
- Automotive Systems: Hydraulic motors are used in automotive applications such as power steering systems, braking systems, convertible tops, and windshield wipers for driving hydraulic pumps, fans, and other rotating equipment.
- Aerospace Systems: Hydraulic motors are used in aircraft landing gear, flight control systems, cargo doors, and auxiliary power units for driving hydraulic pumps, fans, and other rotating equipment in critical aerospace applications.
- Marine Systems: Hydraulic motors are used in ship steering systems, winches, cranes, propulsion systems, and auxiliary power units for driving hydraulic pumps, fans, and other rotating equipment in harsh marine environments.
In conclusion, hydraulic motors are essential components of hydraulic systems, providing the rotary power necessary to drive hydraulic machinery, equipment, and systems in various applications across industries. Proper selection, installation, and maintenance of hydraulic motors are crucial to ensure optimal performance, efficiency, and reliability of hydraulic systems.
Hydraulic Valve:
A hydraulic valve is a mechanical device used to control the flow, direction, and pressure of hydraulic fluid in hydraulic systems. It plays a crucial role in regulating the operation of hydraulic machinery, equipment, and systems by directing the flow of hydraulic fluid to actuate hydraulic actuators, cylinders, motors, and other components.
Function and Importance:
The primary function of a hydraulic valve is to control the flow, direction, and pressure of hydraulic fluid within a hydraulic system to achieve desired motion, force, and performance. Hydraulic valves consist of a valve body, spool, poppet, or ball, and are installed in hydraulic systems to provide precise control over hydraulic fluid flow, direction, and pressure.
Hydraulic valves are essential components of hydraulic systems, providing critical control and regulation of hydraulic fluid to ensure the safe, efficient, and reliable operation of hydraulic machinery, equipment, and systems. They help to optimize system performance, efficiency, and reliability by providing precise control over motion, force, and speed.
Types of Hydraulic Valves:
- Directional Control Valves: Directional control valves control the direction of hydraulic fluid flow within a hydraulic system to actuate hydraulic actuators, cylinders, motors, and other components. They include various types such as spool valves, poppet valves, and ball valves, and may be manually operated, mechanically operated, electrically operated, or hydraulically operated.
- Pressure Control Valves: Pressure control valves control the pressure of hydraulic fluid within a hydraulic system to regulate system pressure, prevent overpressure conditions, and protect hydraulic components from damage. They include various types such as relief valves, pressure-reducing valves, sequence valves, and counterbalance valves, and may be set to open or close at specific pressure thresholds.
- Flow Control Valves: Flow control valves control the flow rate of hydraulic fluid within a hydraulic system to regulate system flow, adjust actuator speed, and optimize system performance. They include various types such as throttle valves, check valves, and flow control valves, and may be adjustable or fixed in flow rate.
- Proportional Control Valves: Proportional control valves control the flow, direction, and pressure of hydraulic fluid within a hydraulic system proportionally to an input signal, such as voltage or current. They offer precise control over hydraulic system operation, allowing for variable flow, speed, and force control in real-time.
Operation and Performance:
Hydraulic valves operate based on the principles of fluid dynamics and mechanical engineering, where hydraulic fluid flow is regulated by the position, configuration, and operation of valve components such as spools, poppets, or balls. The performance of a hydraulic valve is characterized by factors such as flow rate, pressure rating, response time, accuracy, repeatability, and reliability, which depend on factors such as valve type, size, design, and operating conditions.
Hydraulic valves may be operated manually, mechanically, electrically, or hydraulically, depending on the application requirements and control mechanisms used. They may incorporate features such as pressure compensation, flow regulation, position feedback, and fail-safe mechanisms to optimize performance, efficiency, and reliability.
Applications:
Hydraulic valves are used in a wide range of hydraulic systems and applications across various industries, including:
- Construction Machinery: Hydraulic valves are used in excavators, loaders, bulldozers, cranes, and other construction equipment for controlling the operation of hydraulic actuators, cylinders, motors, and other components.
- Manufacturing Machinery: Hydraulic valves are used in presses, injection molding machines, metalworking equipment, and assembly lines for controlling the operation of hydraulic actuators, cylinders, motors, and other components.
- Automotive Systems: Hydraulic valves are used in automotive applications such as power steering systems, braking systems, suspension systems, and transmission systems for controlling the operation of hydraulic actuators, cylinders, motors, and other components.
- Aerospace Systems: Hydraulic valves are used in aircraft landing gear, flight control systems, cargo doors, and auxiliary power units for controlling the operation of hydraulic actuators, cylinders, motors, and other components in critical aerospace applications.
- Marine Systems: Hydraulic valves are used in ship steering systems, winches, cranes, propulsion systems, and auxiliary power units for controlling the operation of hydraulic actuators, cylinders, motors, and other components in harsh marine environments.
In conclusion, hydraulic valves are essential components of hydraulic systems, providing critical control and regulation of hydraulic fluid to ensure the safe, efficient, and reliable operation of hydraulic machinery, equipment, and systems. Proper selection, installation, and maintenance of hydraulic valves are crucial to ensure optimal performance, efficiency, and reliability of hydraulic systems.
Hydraulic Hose:
A hydraulic hose is a flexible, reinforced tube used to convey hydraulic fluid under high pressure in hydraulic systems. It plays a crucial role in transmitting hydraulic power between hydraulic components, allowing for the operation of hydraulic machinery, equipment, and systems across various industries.
Function and Importance:
The primary function of a hydraulic hose is to transmit hydraulic fluid under high pressure between hydraulic components such as pumps, valves, cylinders, motors, and actuators within a hydraulic system. Hydraulic hoses consist of an inner tube, reinforcement layer(s), and outer cover, and are designed to withstand high pressure, temperature, and environmental conditions encountered in hydraulic applications.
Hydraulic hoses are essential components of hydraulic systems, providing critical fluid transmission and power transfer capabilities to ensure the safe, efficient, and reliable operation of hydraulic machinery, equipment, and systems. They help to optimize system performance, flexibility, and longevity by providing a durable and reliable connection between hydraulic components.
Types of Hydraulic Hoses:
- Rubber Hydraulic Hoses: Rubber hydraulic hoses are the most common type of hydraulic hoses and are suitable for a wide range of hydraulic applications. They are made of synthetic rubber materials such as NBR, EPDM, or SBR and are reinforced with high-tensile steel wire or textile braids to withstand high pressure and provide flexibility.
- Thermoplastic Hydraulic Hoses: Thermoplastic hydraulic hoses are lightweight and flexible hoses made of thermoplastic materials such as nylon, polyurethane, or PVC. They are reinforced with synthetic fibers or aramid yarns to provide high pressure capability and resistance to abrasion, chemicals, and UV radiation.
- Metal Hydraulic Hoses: Metal hydraulic hoses, also known as metal hoses or flexible metal hoses, are constructed of stainless steel or other metal alloys and are used in high-temperature, high-pressure, or corrosive hydraulic applications. They provide excellent resistance to heat, chemicals, and mechanical abuse but may be less flexible than rubber or thermoplastic hoses.
- Composite Hydraulic Hoses: Composite hydraulic hoses are hybrid hoses made of a combination of materials such as rubber, thermoplastic, and metal layers. They offer a balance of flexibility, durability, and performance characteristics and are suitable for specialized hydraulic applications requiring specific properties.
Operation and Performance:
Hydraulic hoses operate based on the principles of fluid dynamics and material science, where hydraulic fluid is transmitted under pressure through the hose assembly to actuate hydraulic components within a hydraulic system. The performance of a hydraulic hose is characterized by factors such as pressure rating, temperature rating, flexibility, abrasion resistance, chemical compatibility, and service life, which depend on factors such as hose type, size, construction, and operating conditions.
Hydraulic hoses may be designed with various reinforcement layers, such as braids, spirals, or helices, to provide strength, flexibility, and resistance to pressure, temperature, and environmental conditions. They may incorporate features such as smooth inner surfaces, anti-static properties, and flame-resistant covers to optimize performance, safety, and reliability in specific hydraulic applications.
Applications:
Hydraulic hoses are used in a wide range of hydraulic systems and applications across various industries, including:
- Construction Machinery: Hydraulic hoses are used in excavators, loaders, bulldozers, cranes, and other construction equipment for transmitting hydraulic power between hydraulic components such as pumps, valves, cylinders, motors, and actuators.
- Manufacturing Machinery: Hydraulic hoses are used in presses, injection molding machines, metalworking equipment, and assembly lines for transmitting hydraulic power between hydraulic components such as pumps, valves, cylinders, motors, and actuators.
- Automotive Systems: Hydraulic hoses are used in automotive applications such as power steering systems, braking systems, suspension systems, and transmission systems for transmitting hydraulic power between hydraulic components such as pumps, valves, cylinders, motors, and actuators.
- Aerospace Systems: Hydraulic hoses are used in aircraft landing gear, flight control systems, cargo doors, and auxiliary power units for transmitting hydraulic power between hydraulic components such as pumps, valves, cylinders, motors, and actuators in critical aerospace applications.
- Marine Systems: Hydraulic hoses are used in ship steering systems, winches, cranes, propulsion systems, and auxiliary power units for transmitting hydraulic power between hydraulic components such as pumps, valves, cylinders, motors, and actuators in harsh marine environments.
In conclusion, hydraulic hoses are essential components of hydraulic systems, providing critical fluid transmission and power transfer capabilities to ensure the safe, efficient, and reliable operation of hydraulic machinery, equipment, and systems. Proper selection, installation, and maintenance of hydraulic hoses are crucial to ensure optimal performance, flexibility, and longevity of hydraulic systems.
Hydraulic Fitting:
A hydraulic fitting is a mechanical device used to connect, terminate, or adapt hydraulic hoses, tubes, or components within a hydraulic system. It plays a crucial role in establishing leak-tight connections, routing hydraulic fluid, and facilitating the assembly and maintenance of hydraulic systems across various industries.
Function and Importance:
The primary function of a hydraulic fitting is to provide a secure and reliable connection between hydraulic components such as hoses, tubes, pipes, valves, cylinders, motors, and actuators within a hydraulic system. Hydraulic fittings consist of a body, threads, seals, and other features, and are designed to withstand high pressure, temperature, and environmental conditions encountered in hydraulic applications.
Hydraulic fittings are essential components of hydraulic systems, providing critical fluid transfer and containment capabilities to ensure the safe, efficient, and reliable operation of hydraulic machinery, equipment, and systems. They help to optimize system performance, integrity, and longevity by providing a durable and leak-free connection between hydraulic components.
Types of Hydraulic Fittings:
- Threaded Fittings: Threaded fittings use threads to connect hydraulic components such as hoses, tubes, pipes, valves, and adapters. They include various types such as NPT (National Pipe Thread), BSP (British Standard Pipe), JIC (Joint Industry Council), SAE (Society of Automotive Engineers), and metric threads, and may be straight, elbow, tee, or cross configurations.
- Flared Fittings: Flared fittings use flared ends to connect hydraulic components such as tubes, pipes, hoses, and adapters. They include various types such as SAE flared fittings, DIN (Deutsches Institut für Normung) flared fittings, and JIC flared fittings, and require a precise flaring process to ensure a leak-tight connection.
- Compression Fittings: Compression fittings use compression rings or ferrules to connect hydraulic components such as tubes, pipes, hoses, and adapters. They include various types such as single ferrule fittings, double ferrule fittings, and bite-type fittings, and require proper assembly to ensure a secure and leak-free connection.
- Quick Disconnect Fittings: Quick disconnect fittings use push-to-connect or pull-to-connect mechanisms to quickly and easily connect or disconnect hydraulic components such as hoses, tubes, valves, and cylinders. They include various types such as flat-face couplings, poppet-style couplings, and screw-to-connect couplings, and are commonly used in applications requiring frequent assembly and disassembly.
Operation and Performance:
Hydraulic fittings operate based on the principles of mechanical engineering and fluid dynamics, where hydraulic components are connected and sealed to prevent leaks and maintain hydraulic system integrity. The performance of a hydraulic fitting is characterized by factors such as pressure rating, temperature rating, thread type, connection type, material compatibility, and corrosion resistance, which depend on factors such as fitting type, size, design, and operating conditions.
Hydraulic fittings may be made of various materials such as steel, stainless steel, brass, aluminum, or plastic, depending on the application requirements and environmental conditions. They may incorporate features such as O-rings, seals, swivels, or locknuts to optimize performance, reliability, and ease of installation.
Applications:
Hydraulic fittings are used in a wide range of hydraulic systems and applications across various industries, including:
- Construction Machinery: Hydraulic fittings are used in excavators, loaders, bulldozers, cranes, and other construction equipment for connecting hydraulic hoses, tubes, pipes, valves, cylinders, and motors.
- Manufacturing Machinery: Hydraulic fittings are used in presses, injection molding machines, metalworking equipment, and assembly lines for connecting hydraulic hoses, tubes, pipes, valves, cylinders, and motors.
- Automotive Systems: Hydraulic fittings are used in automotive applications such as power steering systems, braking systems, suspension systems, and transmission systems for connecting hydraulic hoses, tubes, pipes, valves, cylinders, and motors.
- Aerospace Systems: Hydraulic fittings are used in aircraft landing gear, flight control systems, cargo doors, and auxiliary power units for connecting hydraulic hoses, tubes, pipes, valves, cylinders, and motors in critical aerospace applications.
- Marine Systems: Hydraulic fittings are used in ship steering systems, winches, cranes, propulsion systems, and auxiliary power units for connecting hydraulic hoses, tubes, pipes, valves, cylinders, and motors in harsh marine environments.
In conclusion, hydraulic fittings are essential components of hydraulic systems, providing critical fluid transfer and containment capabilities to ensure the safe, efficient, and reliable operation of hydraulic machinery, equipment, and systems. Proper selection, installation, and maintenance of hydraulic fittings are crucial to ensure optimal performance, integrity, and longevity of hydraulic systems.
Hydraulic Reservoir:
A hydraulic reservoir, also known as a hydraulic tank or hydraulic reservoir tank, is a container used to store hydraulic fluid in a hydraulic system. It plays a crucial role in maintaining hydraulic fluid levels, temperature, and cleanliness to ensure the proper operation and performance of hydraulic machinery, equipment, and systems across various industries.
Function and Importance:
The primary function of a hydraulic reservoir is to store hydraulic fluid to provide a ready supply for hydraulic system operation. Hydraulic reservoirs serve several important purposes in hydraulic systems:
- Fluid Storage: Hydraulic reservoirs store hydraulic fluid to ensure an adequate supply for hydraulic system operation. They help to maintain consistent fluid levels and pressure within the system, preventing cavitation, aeration, and performance issues.
- Temperature Regulation: Hydraulic reservoirs help to regulate hydraulic fluid temperature by dissipating heat generated during system operation. They may incorporate features such as cooling fins, heat exchangers, or circulation systems to dissipate heat and maintain optimal fluid temperature.
- Air Separation: Hydraulic reservoirs help to separate air or gas bubbles from hydraulic fluid, allowing them to rise to the surface and escape from the system. This prevents air entrainment, foaming, and performance degradation in hydraulic systems.
- Contaminant Filtration: Hydraulic reservoirs may incorporate filtration systems, such as breather filters, strainers, or magnetic filters, to remove contaminants such as dirt, debris, and particles from hydraulic fluid. This helps to maintain fluid cleanliness and prevent damage to hydraulic components.
- Fluid Level Monitoring: Hydraulic reservoirs may be equipped with fluid level indicators, sight glasses, or sensors to monitor hydraulic fluid levels and ensure proper maintenance and replenishment of fluid as needed.
Types of Hydraulic Reservoirs:
- Open Reservoirs: Open reservoirs are simple containers open to the atmosphere and are commonly used in low-pressure hydraulic systems. They may be cylindrical, rectangular, or custom-shaped and are often mounted above or adjacent to hydraulic equipment for gravity-fed fluid delivery.
- Closed Reservoirs: Closed reservoirs are sealed containers pressurized with a bladder, diaphragm, or gas cushion and are commonly used in high-pressure hydraulic systems. They help to maintain consistent fluid pressure and prevent contamination or fluid loss due to external factors.
- Steel Reservoirs: Steel reservoirs are durable and corrosion-resistant and are commonly used in heavy-duty industrial applications. They may be welded or bolted construction and may incorporate features such as baffles, partitions, or compartments for fluid management.
- Aluminum Reservoirs: Aluminum reservoirs are lightweight and cost-effective and are commonly used in mobile equipment and vehicles. They offer good thermal conductivity and may be extruded, cast, or fabricated construction.
- Plastic Reservoirs: Plastic reservoirs are lightweight, corrosion-resistant, and cost-effective and are commonly used in small hydraulic systems or applications requiring portability. They may be molded or fabricated construction and are available in various materials such as polyethylene, polypropylene, or PVC.
Operation and Maintenance:
Hydraulic reservoirs operate passively, relying on gravity, pressure differentials, and fluid dynamics to store, regulate, and circulate hydraulic fluid within the system. Proper operation and maintenance of hydraulic reservoirs are crucial to ensure optimal performance, cleanliness, and reliability of hydraulic systems.
Maintenance tasks for hydraulic reservoirs may include:
- Regular inspection of fluid levels, temperature, and cleanliness.
- Periodic fluid sampling and analysis to monitor fluid condition and contamination levels.
- Replacement or replenishment of hydraulic fluid as needed.
- Cleaning or replacement of filtration elements, breathers, and other components.
- Inspection and repair of reservoir seals, gaskets, and fittings to prevent leaks or contamination ingress.
- Inspection of mounting brackets, supports, and accessories for proper installation and alignment.
Applications:
Hydraulic reservoirs are used in a wide range of hydraulic systems and applications across various industries, including:
- Construction Machinery: Hydraulic reservoirs are used in excavators, loaders, bulldozers, cranes, and other construction equipment for storing hydraulic fluid and regulating fluid temperature and cleanliness.
- Manufacturing Machinery: Hydraulic reservoirs are used in presses, injection molding machines, metalworking equipment, and assembly lines for storing hydraulic fluid and ensuring proper fluid levels and cleanliness.
- Automotive Systems: Hydraulic reservoirs are used in automotive applications such as power steering systems, braking systems, suspension systems, and transmission systems for storing hydraulic fluid and regulating fluid temperature and cleanliness.
- Aerospace Systems: Hydraulic reservoirs are used in aircraft landing gear, flight control systems, cargo doors, and auxiliary power units for storing hydraulic fluid and ensuring proper fluid levels and cleanliness in critical aerospace applications.
- Marine Systems: Hydraulic reservoirs are used in ship steering systems, winches, cranes, propulsion systems, and auxiliary power units for storing hydraulic fluid and regulating fluid temperature and cleanliness in harsh marine environments.
In conclusion, hydraulic reservoirs are essential components of hydraulic systems, providing critical fluid storage, temperature regulation, and contamination control capabilities to ensure the safe, efficient, and reliable operation of hydraulic machinery, equipment, and systems. Proper selection, installation, and maintenance of hydraulic reservoirs are crucial to ensure optimal performance, cleanliness, and longevity of hydraulic systems.
Hydraulic Accumulator:
A hydraulic accumulator is a mechanical device used to store hydraulic energy in the form of pressurized fluid. It plays a crucial role in maintaining hydraulic system pressure, absorbing shocks, smoothing pressure pulsations, and providing emergency power in hydraulic systems across various industries.
Function and Importance:
The primary function of a hydraulic accumulator is to store hydraulic energy by compressing hydraulic fluid under pressure, which can be released on demand to supplement pump flow, absorb shocks, or maintain system pressure during power loss. Hydraulic accumulators consist of a pressure vessel, gas chamber, fluid port, gas port, and other components, and are installed in hydraulic systems to provide auxiliary hydraulic energy storage and control.
Hydraulic accumulators are essential components of hydraulic systems, providing critical energy storage and control capabilities to ensure the safe, efficient, and reliable operation of hydraulic machinery, equipment, and systems. They help to optimize system performance, efficiency, and reliability by providing a source of stored energy for various hydraulic functions.
Types of Hydraulic Accumulators:
- Bladder Accumulators: Bladder accumulators use a flexible elastomeric bladder to separate hydraulic fluid from a compressible gas charge, such as nitrogen. They offer high energy storage capacity, fast response times, and consistent pressure control but may be sensitive to fluid contamination and require periodic maintenance.
- Piston Accumulators: Piston accumulators use a movable piston to separate hydraulic fluid from a compressible gas charge within a cylindrical chamber. They offer high pressure ratings, precise pressure control, and durability but may have limited energy storage capacity and slower response times compared to bladder accumulators.
- Diaphragm Accumulators: Diaphragm accumulators use a flexible diaphragm to separate hydraulic fluid from a compressible gas charge within a cylindrical chamber. They offer moderate energy storage capacity, fast response times, and resistance to fluid contamination but may have limited pressure ratings compared to bladder or piston accumulators.
- Spring-loaded Accumulators: Spring-loaded accumulators use a coiled spring to store energy mechanically and are typically used in low-pressure or low-flow hydraulic systems. They offer simple construction, low cost, and compact size but may have limited energy storage capacity and pressure ratings compared to gas-charged accumulators.
Operation and Performance:
Hydraulic accumulators operate based on the principles of fluid dynamics, gas compression, and mechanical engineering, where hydraulic fluid is pressurized by compressing a gas charge within a sealed chamber. The performance of a hydraulic accumulator is characterized by factors such as energy storage capacity, pressure rating, response time, efficiency, and reliability, which depend on factors such as accumulator type, size, design, and operating conditions.
Hydraulic accumulators may be used for various functions in hydraulic systems, including:
- Energy Storage: Hydraulic accumulators store hydraulic energy when hydraulic system pressure exceeds a set level, which can be released on demand to supplement pump flow, absorb shocks, or maintain system pressure during power loss.
- Shock Absorption: Hydraulic accumulators absorb hydraulic shocks and pressure pulsations generated by rapid changes in flow or direction within hydraulic systems, protecting components from damage and reducing noise and vibration.
- Emergency Power: Hydraulic accumulators provide emergency hydraulic power for critical system functions such as emergency braking, steering, or actuation in the event of pump failure or power loss.
- Peak Demand Smoothing: Hydraulic accumulators smooth out peak demand periods in hydraulic systems by supplementing pump flow during high-demand periods and reducing pressure fluctuations, improving system efficiency and performance.
Applications:
Hydraulic accumulators are used in a wide range of hydraulic systems and applications across various industries, including:
- Construction Machinery: Hydraulic accumulators are used in excavators, loaders, bulldozers, cranes, and other construction equipment for energy storage, shock absorption, and emergency power in hydraulic systems.
- Manufacturing Machinery: Hydraulic accumulators are used in presses, injection molding machines, metalworking equipment, and assembly lines for energy storage, shock absorption, and peak demand smoothing in hydraulic systems.
- Automotive Systems: Hydraulic accumulators are used in automotive applications such as power steering systems, braking systems, suspension systems, and transmission systems for energy storage, shock absorption, and emergency power in hydraulic systems.
- Aerospace Systems: Hydraulic accumulators are used in aircraft landing gear, flight control systems, cargo doors, and auxiliary power units for energy storage, shock absorption, and emergency power in critical aerospace applications.
- Marine Systems: Hydraulic accumulators are used in ship steering systems, winches, cranes, propulsion systems, and auxiliary power units for energy storage, shock absorption, and emergency power in harsh marine environments.
In conclusion, hydraulic accumulators are essential components of hydraulic systems, providing critical energy storage and control capabilities to ensure the safe, efficient, and reliable operation of hydraulic machinery, equipment, and systems. Proper selection, installation, and maintenance of hydraulic accumulators are crucial to ensure optimal performance, efficiency, and reliability of hydraulic systems.