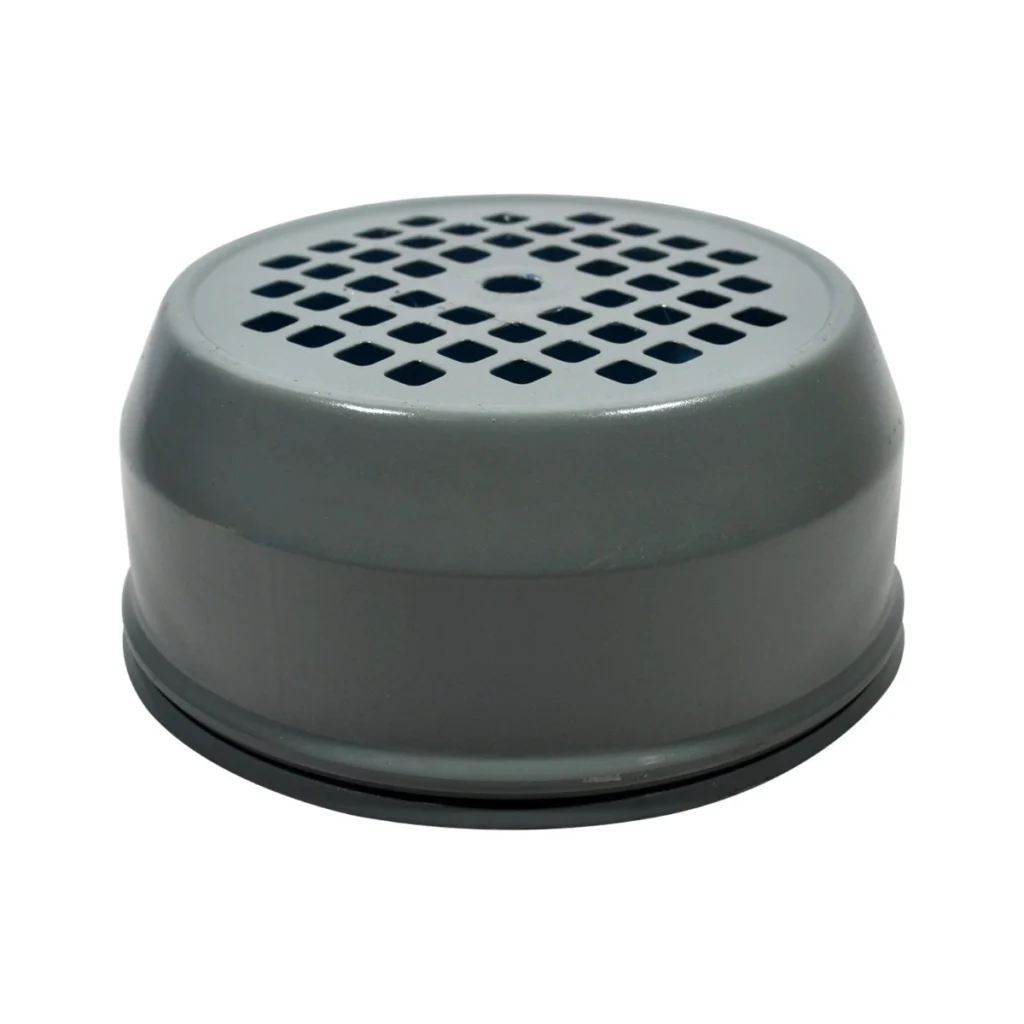
The water pump fan cover production machine is one of the machines that we manufacture for the water pump production companies.
A water pump fan is a crucial component in a water pump system, typically used in internal combustion engines to cool the engine by circulating coolant through the engine block and radiator. The fan assists in the cooling process by drawing air through the radiator, dissipating heat from the coolant, and preventing the engine from overheating. Here’s an overview of the water pump fan and its role in an engine cooling system:
Components and Functionality:
- Blades:
- The fan consists of blades attached to a hub. These blades are designed to move air efficiently.
- Hub:
- The hub is the central component to which the fan blades are attached. It connects to the water pump and is often driven by the engine’s crankshaft or through a belt drive system.
- Mounting Structure:
- The fan is mounted on the water pump or another location within the cooling system, ensuring proper alignment for effective air circulation.
- Drive Mechanism:
- The fan is typically driven by the engine, either directly or through a belt drive system. This ensures that the fan operates whenever the engine is running.
Operation:
- Coolant Circulation:
- As the water pump circulates coolant through the engine block and radiator, the coolant absorbs heat from the engine.
- Heat Dissipation:
- The hot coolant flows through the radiator, and the water pump fan draws air through the radiator fins. This process facilitates heat exchange, allowing the heat from the coolant to be transferred to the air.
- Airflow Control:
- The water pump fan controls the airflow through the radiator. When the engine temperature rises, the fan speed increases to enhance cooling. Some systems include a fan clutch that adjusts the fan’s engagement based on engine temperature.
- Thermal Regulation:
- The fan plays a crucial role in regulating the engine temperature, preventing it from reaching dangerous levels. Effective cooling ensures the engine operates within the optimal temperature range for performance and longevity.
- Auxiliary Fans (if applicable):
- Some vehicles have additional auxiliary fans that can be electrically controlled. These fans may operate independently of the engine speed and can be triggered by temperature sensors or air conditioning requirements.
Types of Fans:
- Mechanical Fans:
- Driven by the engine through a mechanical connection (e.g., fan belt).
- Electric Fans:
- Powered by an electric motor and controlled by a thermostat or other temperature-sensing mechanism.
The type of fan used depends on the specific design of the vehicle’s cooling system.
In summary, the water pump fan is a vital component in an engine’s cooling system, ensuring effective heat dissipation and preventing engine overheating. It plays a crucial role in maintaining the engine’s operational temperature within safe limits for optimal performance and longevity.
Water Pump Fan Cover Production Machine
The water pump fan cover production machine consists of the following machinery:
- Sheet Metal Decoiler
- Sheet Metal Press Feeding Line
- Eccentric Press for Circle Blanking
- Deep Drawing Press for the Drawing of the Water Pump Cover
- Edge Cutting and Trimming of the Water Pump Cover
- Edge Curling of the Water Pump Cover
The production of water pump fan covers involves several manufacturing processes, and various machines play a crucial role in shaping, forming, and assembling the components. Here’s a general overview of the types of machines and processes involved in the production of water pump fan covers:
- Sheet Metal Decoiler:
- Function: Uncoils the metal sheet from a coil, providing a continuous supply of material for the production line.
- Stamping or Cutting Machine:
- Function: Cuts the required shape from a metal sheet using processes such as stamping, laser cutting, or other cutting methods.
- Press Brake:
- Function: Bends the cut metal sheets into the desired form for the water pump fan cover.
- Roll Forming Machine:
- Function: Shapes the metal sheet into complex forms or adds specific features to the water pump fan cover.
- Welding Machine:
- Function: Joins together different components of the water pump fan cover securely. Welding is often used to assemble multiple parts.
- Powder Coating or Painting Machine:
- Function: Applies a protective coating to enhance the appearance and provide corrosion resistance to the water pump fan cover.
- Assembly Line:
- Function: Assembles various components of the water pump fan cover, including brackets or additional features.
- Edge Cutting and Trimming Machine:
- Function: Shapes and trims the edges of the water pump fan cover to ensure a clean and precise finish.
- Deep Drawing Press (if applicable):
- Function: Shapes metal sheets into complex and deep-drawn forms, especially useful for intricate designs or specific cover shapes.
- Quality Control Stations:
- Function: Inspects the water pump fan covers for dimensional accuracy, surface finish, and overall quality at different stages of production.
- CNC Machining (if applicable):
- Function: Utilized for precise machining operations, especially for features that require high precision.
- Packaging Machine:
- Function: Packs the finished water pump fan covers and prepares them for shipment.
The specific machines used can vary based on the design and material specifications of the water pump fan covers, as well as the production scale and efficiency requirements of the manufacturer. Additionally, quality control measures are integrated throughout the production process to ensure that the final products meet the required standards.
Sheet Metal Decoiler for the Water Pump Fan Cover Production Machine
Sheet metal decoiler is equipment that decoils the sheet metal from a coil. The decoiler moves in both directions in order to coil or decoil the sheet coil. A decoiler can be made as mechanical or hydraulic depending on the weight of the coil.
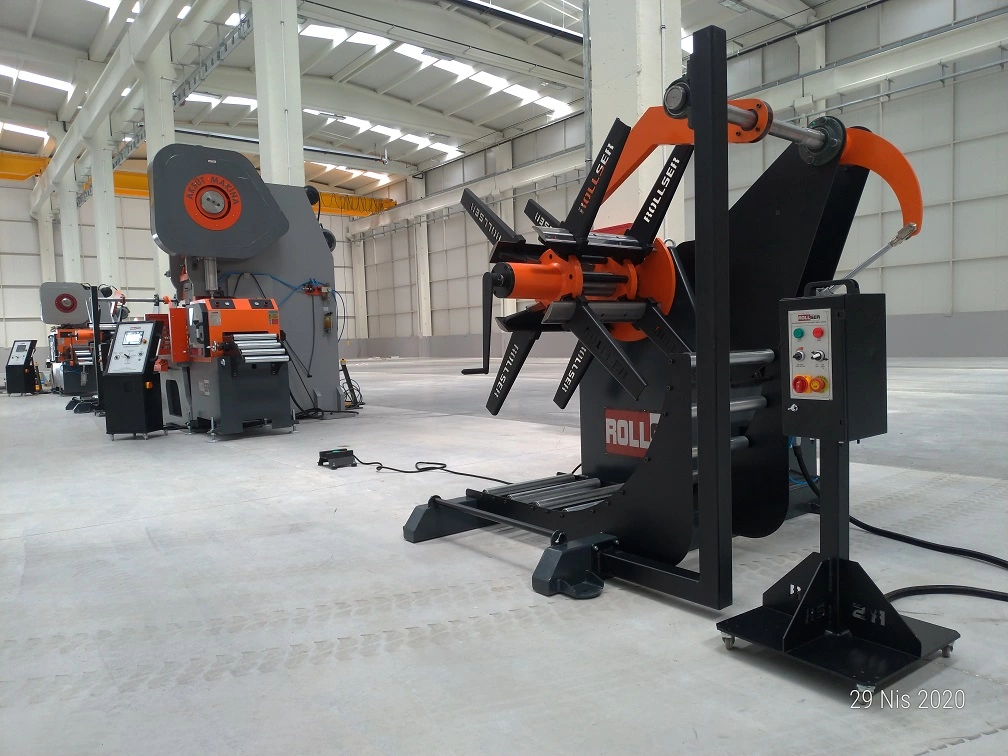
In the context of the water pump fan cover production machine, a sheet metal decoiler is an essential component that facilitates the continuous and automated feeding of metal sheets into the manufacturing process. The decoiler is responsible for unwinding and providing a steady supply of the metal sheet that will be shaped and formed to create the water pump fan covers. Here’s an overview of the sheet metal decoiler’s role in this production process:
- Material Handling:
- Material Type: The sheet metal decoiler is designed to handle metal coils, commonly made of materials such as aluminum or steel.
- Coil Size: It accommodates metal coils of the appropriate size for the water pump fan cover production.
- Loading the Coil:
- Loading Mechanism: The metal coil is loaded onto the decoiler. This can be done manually or, in more automated systems, with the assistance of lifting equipment.
- Decoiling:
- Uncoiling Mechanism: The sheet metal decoiler unwinds the metal strip from the coil, ensuring a continuous and controlled supply of material for the production line.
- Tension Control: Some decoilers have features for controlling the tension on the metal strip to prevent issues such as stretching or buckling.
- Straightening (Optional):
- Straightening Components: In some setups, the decoiler may be integrated with straightening components to ensure that the metal strip is flat and uniform before it enters the subsequent manufacturing processes.
- Material Quality: Straightening helps ensure that the material is in optimal condition for forming and shaping.
- Feeding into the Production Line:
- Integration with Machines: The decoiler is positioned in such a way that it feeds the uncoiled metal strip directly into the subsequent machines in the production line, such as stamping, cutting, or forming machines.
- Automation: In modern manufacturing setups, the decoiler is often integrated into an automated production line for seamless and efficient operation.
- Speed Control:
- Speed Adjustment: The speed at which the metal strip is fed into the production line can be controlled to match the processing speed of downstream machines. This synchronization is critical for a smooth and efficient manufacturing process.
- Safety Features:
- Safety Mechanisms: Decoilers may incorporate safety features such as emergency stop buttons, sensors, or guards to ensure the safety of operators and prevent accidents during the loading and decoiling process.
- Coil Changeover (Optional):
- Quick Changeover: In situations where different coil sizes or materials are used, some decoilers are designed for quick and efficient changeovers between coils to minimize downtime.
The sheet metal decoiler is an integral part of the overall water pump fan cover production machine. Its efficient operation ensures a continuous supply of material, contributing to the overall productivity and effectiveness of the manufacturing process.
After the decoiler, the sheet is transferred to the press by a press feeding line
Sheet Metal Press Feeding Line for Water Pump Fan Cover Production Machine
The sheet metal press feeding line is a complex piece of equipment, that consists of a servo driver and straightener. The Servo driver is an electromechanical device, used to drive the sheet into the molds of the press at a given distance. The distance here can be as small as 1/100 of an mm. This distance depends on the precision of the servo motor used in the driver. Before the servo driver, a straightener is also used to straighten the sheet after the decoiler.
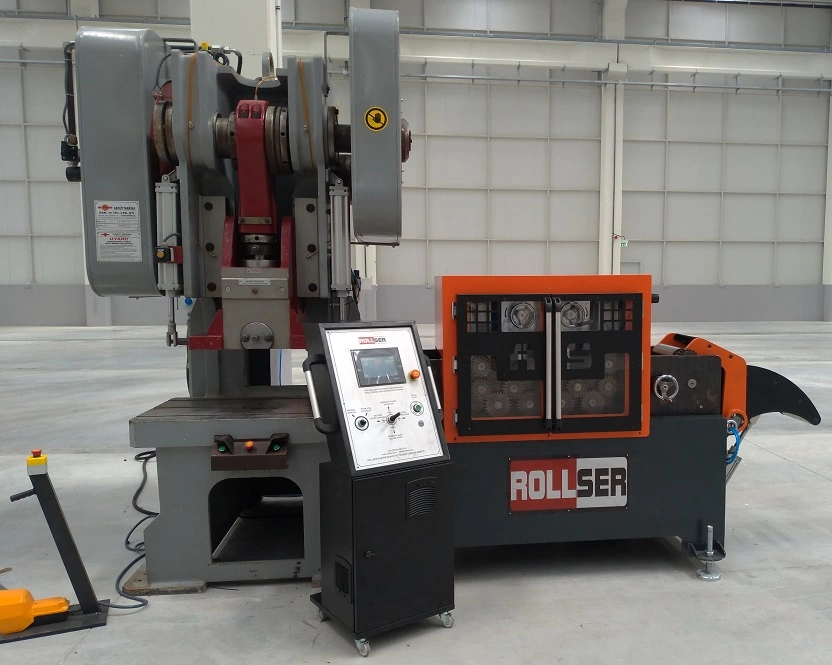
A sheet metal press feeding line is a key component in the production of water pump fan covers, especially when precision and efficiency are critical factors. This type of automated system is designed to feed and process metal sheets continuously, ensuring a smooth and efficient production line. Here’s an overview of how a sheet metal press feeding line functions in the context of water pump fan cover manufacturing:
1. Coil Unloading and Loading:
- Unloading: Metal coils (commonly aluminum or steel) are unloaded onto the press feeding line. This can be done manually or using automated equipment.
- Loading: The metal coils are loaded onto the decoiler, which is part of the press feeding line.
2. Decoiling and Straightening:
- Decoiling: The decoiler uncoils the metal strip from the coil, providing a continuous supply of material for the production line.
- Straightening: Some press feeding lines include straightening components to ensure that the metal strip is flat and even before it enters the press.
3. Feeding into the Press:
- Feeding Mechanism: The press feeding line is integrated with a press machine used for stamping or forming the metal into the shape of the water pump fan cover.
- Precision Feeding: The feeding mechanism ensures precise and consistent feeding of the metal strip into the press, allowing for accurate shaping and forming.
4. Die Changes and Quick Setup:
- Tooling Changes: Press feeding lines are designed to facilitate quick die changes and setup adjustments. This is important for manufacturers producing different designs or sizes of water pump fan covers.
- Tooling Automation: Some advanced systems may include automated tooling changes for increased efficiency.
5. Auto-Stacking or Collection:
- Stacking or Collection: Once the metal sheets are stamped or formed, the press feeding line may include mechanisms for auto-stacking or collecting the finished water pump fan covers.
- Conveyor Systems: Conveyor systems may be integrated to transport the finished products to the next stage in the production process.
6. Speed and Tension Control:
- Speed Adjustment: The speed of the press feeding line can be adjusted to match the production speed of downstream machines.
- Tension Control: Tension control features help maintain consistent tension on the metal strip, preventing issues such as wrinkling or buckling.
7. Quality Control:
- Inspection Points: Quality control measures may be integrated into the press feeding line to inspect the formed water pump fan covers for dimensional accuracy and surface quality during the manufacturing process.
8. Automation and Integration:
- PLC Controls: Programmable Logic Controller (PLC) systems are often used to control and coordinate the various components of the press feeding line.
- Integration with Other Machines: The press feeding line is integrated into the overall manufacturing process, working seamlessly with other machines and systems.
A well-designed sheet metal press feeding line enhances the efficiency, accuracy, and overall productivity of the water pump fan cover production process. It ensures a continuous and controlled flow of material into the press, resulting in high-quality and precisely formed products.
Eccentric Press for Circle Blanking for Water Pump Fan Cover Production Machine
The eccentric press is also another electromechanical equipment, that cuts out the circle blanks from the sheet metal rolls for further production. The eccentric press punches out the circle blanks by pressing the cutting mold into the sheet metal. This is a serial cutting operation for the circle cutting of sheet metals. After the circle cutting operation, we get the circle discs as below:

An eccentric press, also known as a mechanical press or crank press, is commonly used for metal forming operations, including circle blanking, in the production of components such as water pump fan covers. Circle blanking involves cutting circular shapes from sheet metal, which is a crucial step in manufacturing components like fan covers. Here’s how an eccentric press is typically used for circle blanking in the production of water pump fan covers:
- Material Preparation:
- Start with a flat sheet of metal, such as aluminum or steel, which is suitable for water pump fan cover production.
- Loading the Material:
- The metal sheet is loaded onto the bed or working area of the eccentric press. Fixturing or clamping mechanisms may be used to secure the sheet in place.
- Die Setup:
- The eccentric press is equipped with a circular-shaped die, which determines the size and shape of the blanked circle. The die is mounted on the press bed.
- Adjustments and Settings:
- Adjust the eccentric press settings, including the stroke length and speed, based on the desired dimensions of the circular blanks and the material being used.
- Circle Blanking Operation:
- As the press operates, the eccentric mechanism converts the rotary motion of the crankshaft into linear motion. The punch, attached to the eccentric portion of the crankshaft, descends and contacts the metal sheet through the circular die, cutting out the circular blank.
- Waste Removal:
- The cut circular blanks are separated from the remaining sheet material. The waste material may be expelled through openings in the die or collected for recycling.
- Quality Control:
- Inspect the cut circular blanks for dimensional accuracy and quality. Any defects or irregularities in the blanks are addressed.
- Tooling Maintenance:
- Regular maintenance of the circular cutting die is essential to ensure sharpness and precision in subsequent blanking operations.
- Automation (Optional):
- In some production setups, the eccentric press may be part of an automated system that includes material feeding, part ejection, and stacking of the cut blanks.
- Repeat Operation:
- The process is repeated for each cycle of the eccentric press, producing a continuous stream of circular blanks from the metal sheet.
The eccentric press is chosen for its simplicity, cost-effectiveness, and suitability for various metal forming operations. It’s particularly well-suited for applications like circle blanking, where the motion of the crankshaft can be translated into a controlled and repetitive punching action.
As with any industrial process, safety measures should be in place, and operators should be trained in the proper use of the eccentric press to ensure efficient and secure production.
Deep Drawing Press for the Drawing of the Water Pump Fan Cover Production Machine
A deep drawing press is a crucial machine in the manufacturing process of components like water pump fan covers, especially when the production involves shaping metal sheets into complex and deep-drawn forms. Deep drawing is a metal forming process where a flat sheet of metal is radially drawn into a forming die by the mechanical action of a punch. Here’s an overview of how a deep drawing press is utilized in the drawing of water pump fan covers:
- Material Preparation:
- Start with a flat sheet of metal, such as aluminum or steel, which is suitable for deep drawing in the production of water pump fan covers.
- Loading the Sheet:
- The metal sheet is loaded into the deep drawing press. This can be done manually or with the help of automated feeding systems.
- Die Setup:
- The deep drawing press is equipped with a die, which is a specialized tool that defines the shape of the final water pump fan cover. The die setup is crucial for achieving the desired form.
- The die may consist of multiple components, including the blank holder, die ring, and punch.
- Lubrication:
- To facilitate smooth material flow and reduce friction, lubrication is often applied to the metal sheet or the forming die.
- Blank Holder and Pressure Control:
- A blank holder or pressure pad may be used to hold the metal sheet in place during the drawing process, preventing wrinkles and ensuring even material flow.
- The pressure applied by the press is carefully controlled to avoid tearing or other defects in the drawn part.
- Deep Drawing Process:
- The press applies force through a punch, which moves into the die cavity, forcing the metal sheet to deform and take the shape of the die.
- Deep drawing is often a multi-stage process. The sheet may go through successive drawing operations to achieve the desired depth and form.
- Quality Control:
- After the deep drawing process, the formed parts are inspected for dimensional accuracy, surface finish, and any defects. Quality control measures may include visual inspection and measurements.
- Trimming and Finishing (if necessary):
- The formed water pump fan covers may undergo additional processes such as trimming, deburring, or finishing to achieve the final product specifications.
- Tool Maintenance:
- Regular maintenance of the forming dies is essential to ensure consistent quality and prolong the life of the tooling.
- Unloading the Formed Parts:
- Once the drawing process is complete, the formed water pump fan covers are ejected from the die. Automation, such as robotic systems, may be used for part handling and transfer.
The deep drawing press plays a central role in shaping metal sheets into the intricate and complex forms required for water pump fan covers, contributing to the efficiency and precision of the manufacturing process.
The water pump manufacturing factory companies or water pump manufacturer companies need to have these machines in comparison to water pump importer companies as the water pump importer companies usually by motors and pumps already in assembled form.
The other type of water pumps as die-casting motors and pumps
Edge Cutting and Trimming of the Water Pump Covers
The Edge cutting and trimming is the next step in a water pump production line. The water pump production line is a serial production line where each machine is the next step of the previous one.
The edge cutting and trimming process for water pump covers is crucial for refining the final appearance and ensuring the covers meet quality standards. This process involves shaping and refining the edges of the covers to achieve a clean and smooth finish. Here’s an overview of the edge cutting and trimming process for water pump covers:
- Material Inspection:
- Before the edge cutting and trimming process, the water pump covers undergo inspection for any imperfections or irregularities. This ensures that only high-quality covers move forward in the production process.
- Loading the Covers:
- The covers are loaded onto the work area or fixture of the edge cutting and trimming machine. Fixturing ensures stability during the cutting and trimming process.
- Edge Cutting:
- Cutting Tools: Various cutting tools can be used for edge cutting, including shearing machines, laser cutting machines, or water jet cutters.
- Precision Cutting: The cutting process is designed to remove excess material from the edges, creating a smooth and precise edge on the water pump covers.
- Trimming:
- Trimming Tools: Trimming is done to remove any unwanted protrusions or excess material that may be present on the surface of the water pump covers.
- Deburring: Trimming helps in deburring, which involves removing any sharp edges or burrs left from the cutting process.
- CNC Machining (Optional):
- In some cases, CNC (Computer Numerical Control) machining may be used for precise edge cutting and trimming. This is especially beneficial for complex shapes and intricate designs.
- Quality Control:
- Visual Inspection: After the edge cutting and trimming process, the covers undergo a visual inspection to ensure that the edges are smooth, and there are no defects.
- Dimensional Inspection: Measurements may be taken to verify that the covers meet the specified dimensions.
- Surface Finishing (Optional):
- Depending on the desired aesthetics and functional requirements, the covers may undergo additional surface finishing processes, such as polishing or coating.
- Packaging:
- Once the edge cutting and trimming, and any additional processes, are complete, the finished water pump covers are packaged and prepared for shipment.
The specific machinery used for edge cutting and trimming can vary based on the manufacturing facility and the characteristics of the water pump covers being produced. The goal is to achieve precise and uniform edges, ensuring the functionality and aesthetics of the final product. Additionally, these processes contribute to the overall quality and safety of the water pump covers.
The edge-cutting trimming and forming is a special metalworking process, designed to cut the rims of a pot or a pan after the deep-drawing operation. It is also called edge wrapping, edge beading, or edge crimping in some cases.
Edge Curling of the Water Pump Fan Cover Production Machine
The edge curling is a special metalworking operation that forms hollow curls on the edges of round sheet metal parts.
Edge curling in the context of water pump fan cover production involves shaping the edges of the metal sheet to create a curved or rolled profile. This process is typically performed to enhance the structural integrity of the fan cover, improve safety by eliminating sharp edges, and contribute to the overall aesthetics of the product. Here’s an overview of the edge curling process in the production of water pump fan covers:
- Material Preparation:
- Start with a flat metal sheet, commonly aluminum or steel, which has been cut to the desired size for the water pump fan cover.
- Loading the Metal Sheet:
- The metal sheet is loaded onto the edge curling machine, which is designed to shape the edges of the sheet.
- Edge Curling Machine:
- The edge curling machine is equipped with rollers or dies that apply pressure to the edges of the metal sheet.
- The rollers may have a specific profile or curvature to create the desired edge shape.
- Adjustments and Settings:
- The machine settings, including the pressure applied by the rollers and the positioning of the metal sheet, may be adjusted based on the design specifications of the water pump fan cover.
- Edge Curling Operation:
- The machine then performs the edge curling operation, gradually bending the edges of the metal sheet to create a curved or rolled profile.
- The speed and precision of the curling process are critical to achieving uniform and consistent results.
- Quality Control:
- After the edge curling operation, the formed edges are inspected for uniformity, smoothness, and adherence to design specifications.
- Any deviations or defects are addressed to ensure the quality of the final product.
- Further Processing:
- The water pump fan cover may undergo additional manufacturing processes, such as surface finishing, coating, or assembly, depending on the specific product requirements.
- Packaging:
- Once the edge curling and any additional processes are complete, the finished water pump fan covers are packaged and prepared for shipment.
Edge curling is an essential step in the production of water pump fan covers as it not only contributes to the product’s structural integrity but also enhances safety and aesthetics. The use of specialized machinery and precise control over the edge curling process ensures that the final product meets quality standards and design specifications.
Edge curling is a similar process to edge cutting or trimming by means of operation.
Industries working with our machinery
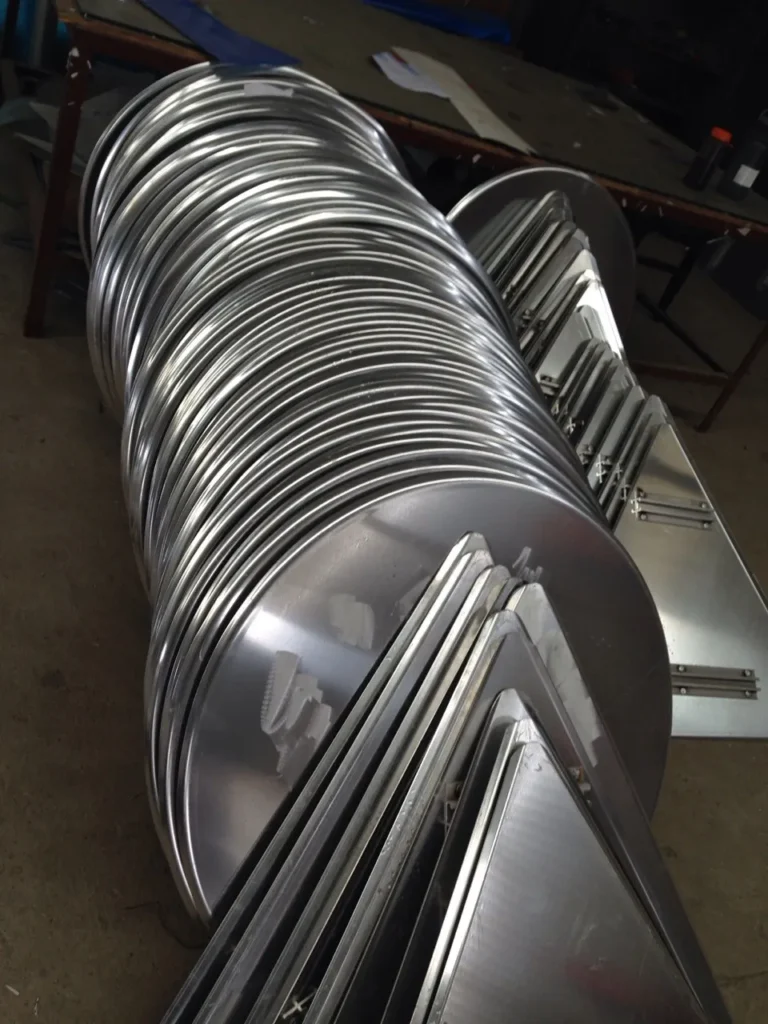
Trimming and beading machines are versatile tools that are used in a wide range of industries. Here are some of the most common industries that use trimming and beading machines:
Automotive Industry
The automotive industry is one of the largest users of trimming and beading machines. These machines are used to trim and bead car body panels, fenders, doors, and other sheet metal components. Trimming ensures precise dimensions and eliminates rough edges, while beading strengthens the sheet metal and provides reference points for alignment during assembly and welding.
Aerospace Industry
The aerospace industry also relies heavily on trimming and beading machines. These machines are used to fabricate lightweight and high-strength components for aircraft and spacecraft. The precise and consistent trimming and beading operations ensure the structural integrity of these critical components.
Appliance Manufacturing
Appliance manufacturing is another major user of trimming and beading machines. These machines are used to trim and bead the sheet metal components of refrigerators, washing machines, and other household appliances. Trimming and beading help to strengthen the appliances, improve their appearance, and facilitate assembly.
HVAC Industry
The HVAC industry uses trimming and beading machines to fabricate ductwork, fans, and other sheet metal components. Trimming ensures that the components fit together properly, while beading strengthens the components and provides rigidity.
Construction Industry
The construction industry uses trimming and beading machines to fabricate roofing panels, siding, and other sheet metal components for buildings. Trimming and beading help to ensure that the components are weatherproof and durable.
Metal Fabrication Industries
Trimming and beading machines are widely used in various metal fabrication industries, including electrical equipment manufacturing, medical device manufacturing, and industrial machinery manufacturing. These machines are used to trim and bead a wide range of sheet metal components for various applications.
In addition to these specific industries, trimming and beading machines are also used in a variety of other applications, including:
- Sign Manufacturing
- Furniture Manufacturing
- Toy Manufacturing
- Food and Beverage Processing Equipment Manufacturing
- Medical Device Manufacturing
The versatility and effectiveness of trimming and beading machines make them essential tools for a wide range of industries. These machines play a crucial role in producing high-quality, durable, and precisely dimensioned sheet metal components for a variety of applications.
- Cookware Kitchenware
- Defense
- Water Tank Manufacturing
- Solar Power Generator Manufacturing
- Electrical Motor Fan Cover Manufacturing
- Fire Extinguisher Manufacturing
- Exhaust Pipe Manufacturing
- LPG & LNG Tank Manufacturing
Trimming beading machines are specialized pieces of equipment used in various manufacturing industries to cut, shape, and form beads along the edges of metal sheets and other materials. These machines serve the critical function of enhancing the structural integrity and aesthetic appeal of products by creating precise and consistent beading.
Trimming beading machines are essential in processes where the appearance and durability of the edges are paramount. They are commonly employed in industries such as automotive, aerospace, HVAC, and consumer goods manufacturing, where precision and efficiency are crucial.
Importance in Industrial Applications
The primary importance of trimming beading machines lies in their ability to streamline manufacturing processes by automating edge-forming tasks that would otherwise be labor-intensive and prone to human error. By improving consistency and reducing waste, these machines contribute significantly to the overall productivity and cost-effectiveness of production lines.
Furthermore, trimming beading machines enhance the quality of finished products, ensuring they meet stringent industry standards and customer expectations. Their ability to produce uniform edges and beads also plays a vital role in the assembly and functionality of components, particularly in high-stakes industries like aerospace and automotive manufacturing.
Overview of the Content
This comprehensive guide aims to provide an in-depth exploration of trimming beading machines, covering their components, working principles, types, applications, technical specifications, maintenance, and emerging trends. By understanding these aspects, industry professionals can make informed decisions about implementing and optimizing trimming beading machines within their operations.
Components of Trimming Beading Machines
Base and Frame
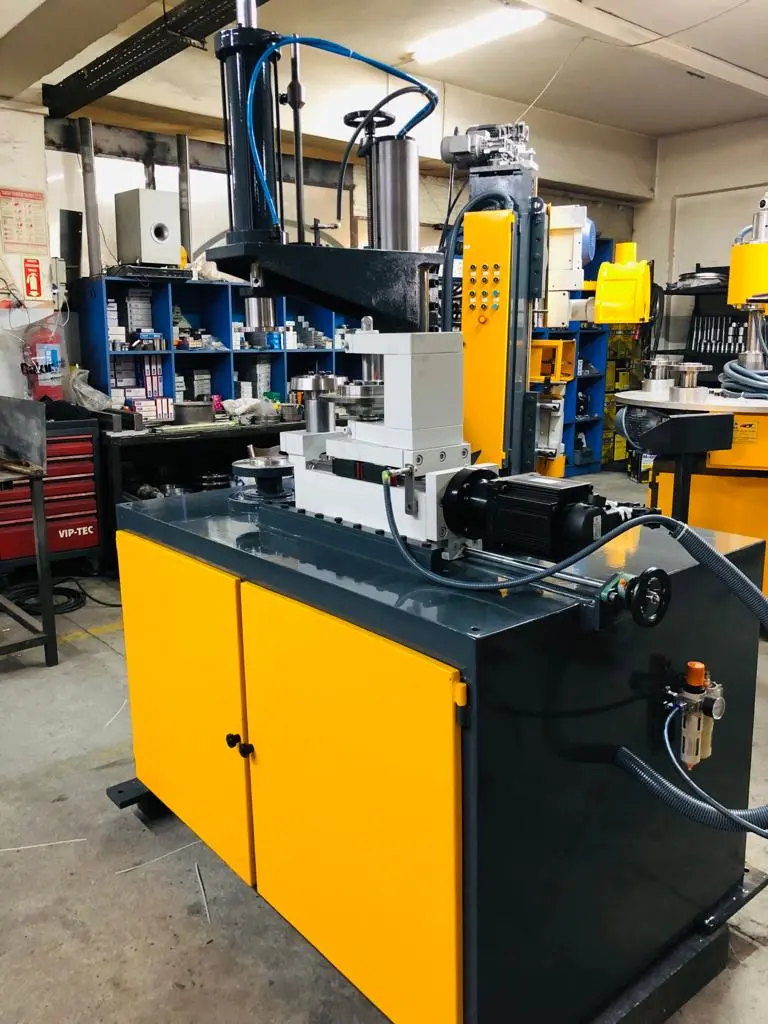
The base and frame of a trimming beading machine form its structural backbone, providing stability and support for all other components. Typically constructed from robust materials such as steel or cast iron, the frame ensures the machine can withstand the stresses of operation and maintain precision over time.
Materials Used
- Steel: Known for its durability and resistance to deformation, steel is commonly used in high-performance trimming beading machines. It offers excellent rigidity and longevity.
- Cast Iron: Preferred for its vibration-damping properties, cast iron frames help minimize noise and improve accuracy during operation.
Structural Design
- The structural design of trimming beading machines varies based on the specific model and intended application. Key considerations include the machine’s footprint, ease of access for maintenance, and adaptability to different manufacturing environments.
Cutting and Beading Tools
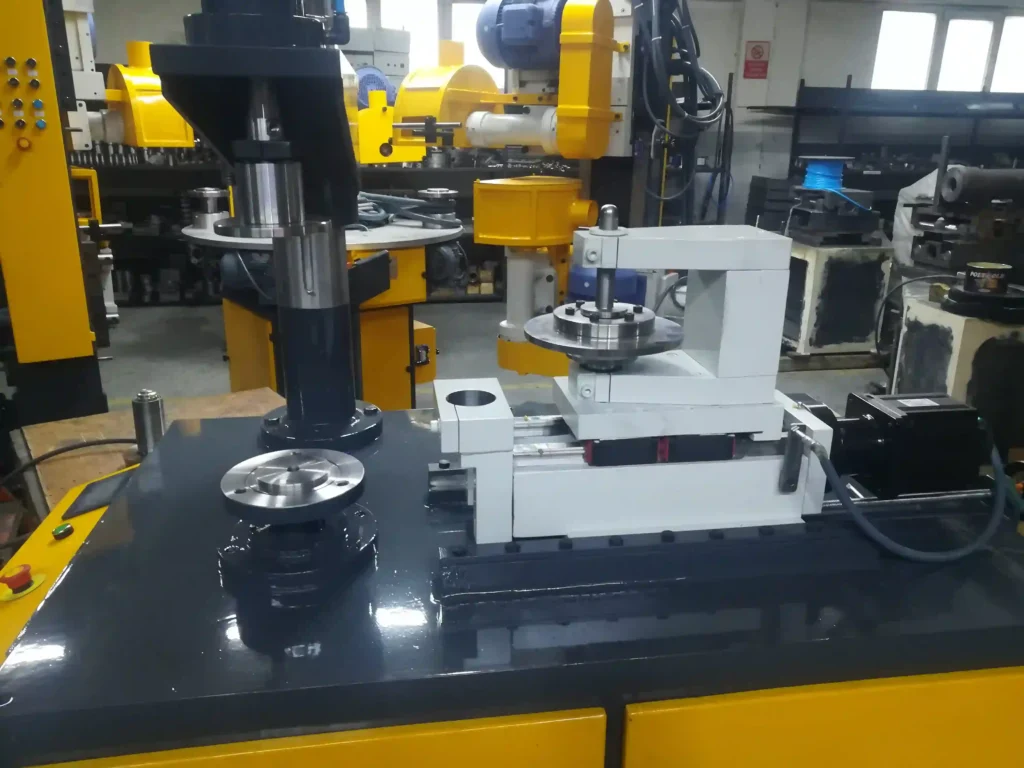
The cutting and beading tools are critical to the machine’s functionality, responsible for shaping and forming the edges of materials. These tools come in various shapes and sizes, tailored to the specific beading patterns and material thicknesses required.
Types and Materials
- High-Speed Steel (HSS): Known for its hardness and heat resistance, HSS is commonly used for cutting tools that need to maintain sharpness under demanding conditions.
- Carbide: Offering superior wear resistance and durability, carbide tools are ideal for high-volume production runs and materials that are difficult to machine.
Maintenance and Replacement
- Regular maintenance of cutting and beading tools is essential to ensure consistent performance. This includes sharpening or replacing worn tools and adjusting alignment to prevent defects in the finished products.
Drive Mechanism
The drive mechanism powers the machine’s operations, converting electrical energy into mechanical motion. It is a crucial component that directly influences the machine’s efficiency and performance.
Motor Types
- AC Motors: Widely used in trimming beading machines for their reliability and simplicity. AC motors offer consistent performance and are suitable for applications where speed control is not critical.
- Servo Motors: Preferred for applications requiring precise control and variable speeds. Servo motors enable dynamic adjustments to the machine’s operations, enhancing versatility and efficiency.
Energy Efficiency Considerations
- Modern trimming beading machines are designed with energy efficiency in mind, incorporating features like variable frequency drives (VFDs) to optimize power consumption and reduce operational costs.
Control Systems
Control systems govern the operation of trimming beading machines, allowing operators to configure settings, monitor performance, and ensure safety. These systems range from basic manual controls to sophisticated automated interfaces.
Manual vs. Automated Systems
- Manual Systems: Suitable for smaller operations or applications requiring frequent adjustments. Manual controls offer simplicity and direct operator oversight.
- Automated Systems: Essential for large-scale production environments, automated systems provide consistent performance, reduce human error, and enable integration with other machinery.
Integration with Industry 4.0 Technologies
- Trimming beading machines are increasingly adopting Industry 4.0 technologies, such as IoT sensors and data analytics, to enhance operational efficiency and enable predictive maintenance.
Working Principles
Detailed Description of the Trimming Process
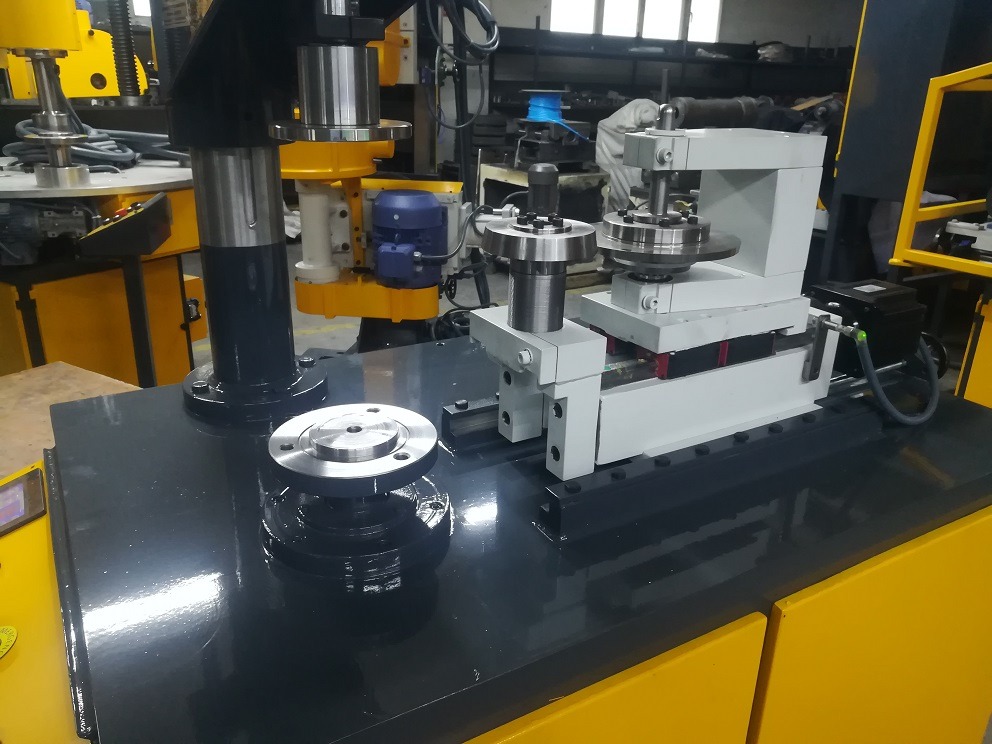
The trimming process involves cutting away excess material from the edges of a workpiece to achieve a desired shape or size. Trimming beading machines utilize specialized tools to perform this task with high precision and consistency.
- Material Feeding: The workpiece is fed into the machine, either manually or automatically, and positioned for trimming.
- Tool Engagement: Cutting tools engage the workpiece, removing excess material while following the predefined path and pattern.
- Material Removal: The machine’s cutting tools execute the trimming operation, guided by precise control systems to ensure uniformity.
- Quality Inspection: The trimmed edges are inspected for accuracy and quality, with adjustments made as necessary.
Beading Techniques and Variations
Beading is the process of forming beads along the edges of a workpiece, enhancing both its structural integrity and aesthetic appeal. Different techniques and variations are employed based on the material and intended application.
- Single Bead Formation: The simplest form of beading, involving a single continuous bead along the edge.
- Double Bead Formation: Utilized when additional strength or a decorative effect is desired, double beads consist of two parallel beads along the edge.
- Custom Bead Patterns: Some machines allow for custom bead patterns, tailored to specific design requirements or functional needs.
Workflow and Operational Steps
The workflow of a trimming beading machine is designed to maximize efficiency and ensure consistent output. Key operational steps include:
- Setup and Calibration: Operators configure the machine settings, such as tool alignment and material thickness, to match the requirements of the production run.
- Material Loading: Workpieces are loaded onto the machine, either manually or through automated systems, and positioned for processing.
- Trimming and Beading: The machine executes the trimming and beading operations, following the specified parameters and patterns.
- Quality Control: Finished pieces undergo quality control checks to verify dimensional accuracy and bead integrity.
- Adjustment and Maintenance: Regular adjustments and maintenance are performed to ensure optimal performance and address any issues that arise during operation.
Common Challenges and Solutions
Trimming beading machines can encounter various challenges during operation, which can impact performance and product quality. Common issues and their solutions include:
- Tool Wear and Dullness: Regular tool maintenance, including sharpening and replacement, is essential to maintain cutting precision and prevent defects.
- Material Deformation: Proper machine calibration and tool alignment help prevent material deformation during trimming and beading processes.
- Machine Downtime: Implementing predictive maintenance and monitoring systems can reduce downtime and improve overall equipment efficiency.
- Quality Variability: Consistent quality control checks and process adjustments help ensure uniformity and adherence to specifications.
Types of Trimming Beading Machines
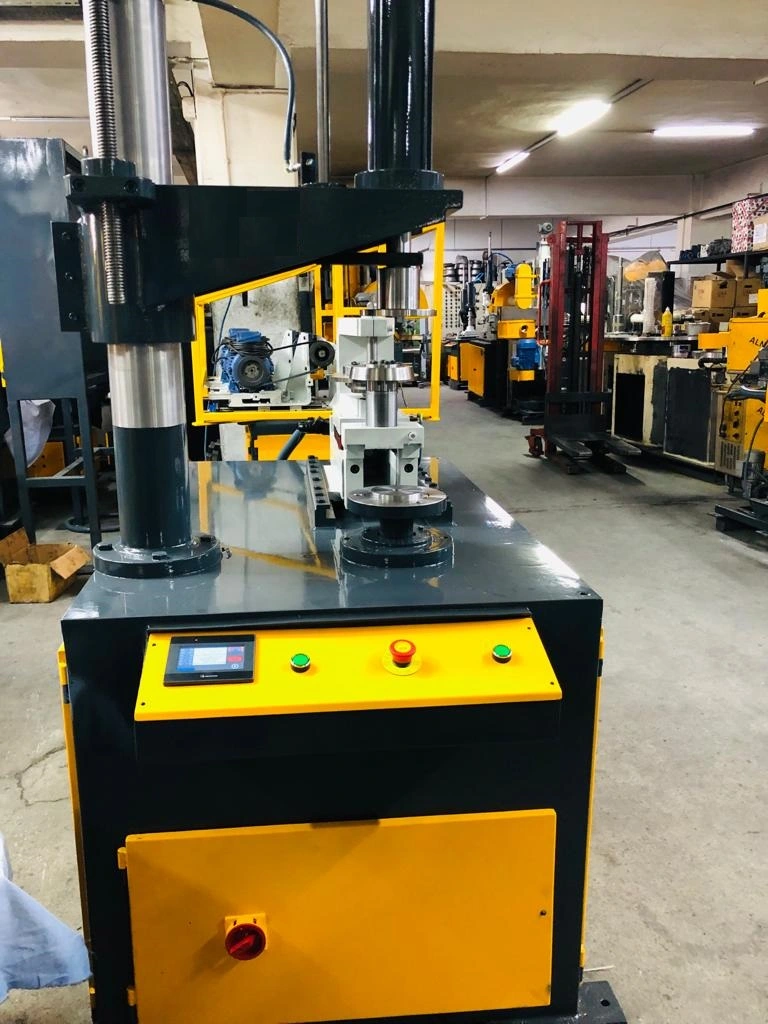
Trimming beading machines are available in various types, each suited to specific applications and production needs. Understanding the differences between these machines is crucial for selecting the right equipment for a given operation.
Manual Trimming Beading Machines
Features and Use Cases
- Manual trimming beading machines are operated entirely by human intervention, making them suitable for small-scale production or applications requiring frequent adjustments. These machines offer simplicity and ease of use, often utilized in workshops or small manufacturing facilities.
Advantages and Disadvantages
- Advantages:
- Cost-effective for low-volume production
- Flexibility to handle various materials and bead patterns
- Simple operation and maintenance
- Disadvantages:
- Limited throughput and productivity
- Higher labor costs due to manual operation
- Inconsistent quality due to human error
Semi-Automatic Trimming Beading Machines
Features and Use Cases
- Semi-automatic trimming beading machines combine manual input with automated processes, offering a balance between flexibility and efficiency. These machines are ideal for medium-scale production environments where speed and precision are important.
Advantages and Disadvantages
- Advantages:
- Improved productivity compared to manual machines
- Enhanced consistency and accuracy
- Reduced operator fatigue and error
- Disadvantages:
- Higher initial investment compared to manual machines
- Requires skilled operators for setup and adjustment
- Limited scalability for large-scale production
Fully Automatic Trimming Beading Machines
Features and Use Cases
- Fully automatic trimming beading machines offer the highest level of automation and efficiency, designed for large-scale production environments. These machines are equipped with advanced control systems and automation features, enabling continuous and consistent operation.
Advantages and Disadvantages
- Advantages:
- Maximum productivity and throughput
- Consistent quality and precision
- Integration with other automated systems and Industry 4.0 technologies
- Disadvantages:
- High initial cost and complexity
- Requires skilled technicians for maintenance and troubleshooting
- Limited flexibility for custom or small-batch production
Applications in Various Industries
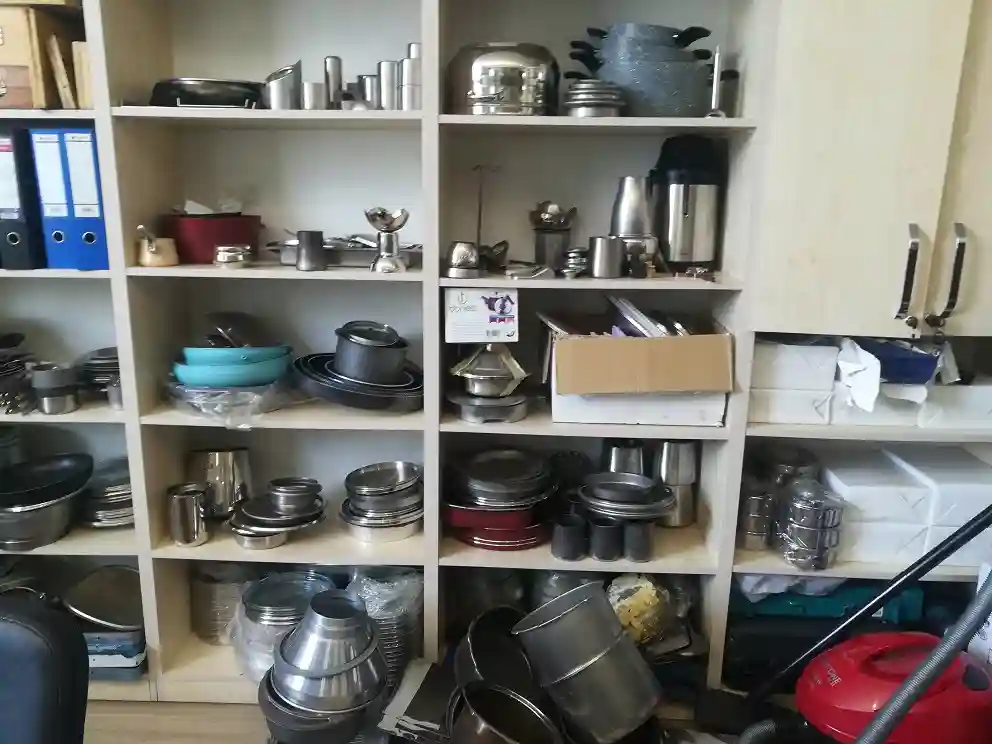
Trimming beading machines play a vital role in a wide range of industries, each benefiting from the precision and efficiency these machines offer. Here, we explore some of the key industries and their specific applications.
Automotive Industry
Specific Use Cases
- In the automotive industry, trimming beading machines are used for forming edges on components such as fenders, doors, hoods, and other body panels. These machines ensure that parts meet the strict dimensional tolerances required for assembly and safety.
Benefits in Automotive Manufacturing
- Improved part quality and consistency, reducing rework and waste
- Enhanced structural integrity of components, contributing to vehicle safety
- Increased production speed and efficiency, supporting high-volume manufacturing
Aerospace Industry
Specific Use Cases
- Aerospace manufacturing demands precision and reliability, making trimming beading machines essential for producing parts such as fuselage panels, wing components, and engine casings. These machines contribute to the stringent quality standards of the aerospace industry.
Benefits in Aerospace Manufacturing
- High precision and repeatability, ensuring compliance with aerospace standards
- Reduction in material waste and production costs
- Support for complex geometries and advanced materials
HVAC Industry
Specific Use Cases
- In the HVAC industry, trimming beading machines are used to form edges and beads on ductwork, vents, and other components. These machines help produce parts that are essential for efficient heating, ventilation, and air conditioning systems.
Benefits in HVAC Manufacturing
- Consistent part quality and fit, reducing installation time and costs
- Enhanced durability and performance of HVAC components
- Support for custom designs and specifications
Consumer Goods Industry
Specific Use Cases
- The consumer goods industry utilizes trimming beading machines for a variety of products, including appliances, electronics, and packaging. These machines help create aesthetically pleasing and functional components.
Benefits in Consumer Goods Manufacturing
- Improved product appearance and appeal
- Increased manufacturing efficiency and speed
- Support for diverse materials and product designs
Technical Specifications and Standards
Understanding the technical specifications and standards of trimming beading machines is crucial for selecting the right equipment and ensuring compliance with industry requirements.
International Standards and Compliance
Trimming beading machines must adhere to international standards to ensure safety, quality, and interoperability. Key standards include:
- ISO 9001: Quality management systems standard that ensures consistent product quality and customer satisfaction.
- ISO 12100: Safety of machinery – General principles for design, providing guidelines for reducing risks associated with machine operation.
- CE Marking: Conformity with European health, safety, and environmental protection standards.
Key Technical Specifications
Trimming beading machines have various technical specifications that influence their performance and suitability for specific applications. Key specifications include:
- Maximum Material Thickness: The thickest material the machine can handle, typically measured in millimeters or inches.
- Beading Speed: The rate at which the machine can form beads, often measured in meters per minute.
- Cutting Force: The amount of force exerted by the machine’s cutting tools, affecting its ability to handle different materials.
- Power Requirements: The electrical power needed for operation, influencing energy consumption and infrastructure needs.
Customization Options
Manufacturers often offer customization options to tailor trimming beading machines to specific requirements. Common customization options include:
- Tooling Variations: Custom tools and dies to accommodate unique bead patterns and material specifications.
- Automation Features: Integration of advanced control systems and automation technologies for enhanced performance.
- Material Handling Systems: Customized feeding and handling systems to improve workflow and reduce manual intervention.
Maintenance and Troubleshooting
Proper maintenance and troubleshooting are essential to ensuring the longevity and performance of trimming beading machines. Here, we outline key maintenance practices and common issues that operators may encounter.
Routine Maintenance Procedures
Regular maintenance helps prevent unexpected downtime and ensures consistent machine performance. Key maintenance procedures include:
- Tool Inspection and Replacement: Regularly inspect cutting and beading tools for wear and damage. Sharpen or replace tools as needed to maintain cutting precision.
- Lubrication: Ensure all moving parts are properly lubricated to reduce friction and wear.
- Alignment Checks: Verify tool alignment and calibration to prevent defects and ensure uniformity.
- Electrical System Inspection: Check electrical connections and components for signs of wear or damage, addressing issues promptly to prevent malfunctions.
Common Issues and Solutions
Trimming beading machines may encounter various issues during operation. Understanding these problems and their solutions is crucial for maintaining productivity and quality.
- Tool Wear and Dullness: Dull or worn tools can lead to poor cutting performance and defects. Regularly sharpen or replace tools to maintain quality.
- Material Jams: Misalignment or improper feeding can cause material jams, leading to downtime and damage. Ensure proper setup and alignment to prevent jams.
- Machine Vibration: Excessive vibration can impact precision and tool life. Check for loose components and ensure the machine is properly anchored to reduce vibration.
- Inconsistent Quality: Variability in bead quality and dimensions can arise from improper calibration or tool wear. Regularly inspect and adjust settings to maintain consistency.
Safety Considerations
Safety is paramount when operating trimming beading machines. Key safety considerations include:
- Personal Protective Equipment (PPE): Operators should wear appropriate PPE, such as gloves, safety glasses, and hearing protection, to minimize injury risk.
- Machine Guarding: Ensure all machine guards and safety features are in place and functional to prevent accidental contact with moving parts.
- Emergency Stops: Verify that emergency stop mechanisms are operational and accessible in case of emergencies.
- Training and Education: Provide thorough training to operators and maintenance personnel on safe machine operation and emergency procedures.
Latest Innovations and Trends
The field of trimming beading machines is continually evolving, with new technologies and trends shaping the future of manufacturing. Here, we explore some of the latest innovations and emerging trends in the industry.
Technological Advances
Advancements in technology are driving significant improvements in trimming beading machines, enhancing their capabilities and performance.
- Smart Sensors and IoT Integration: Trimming beading machines are increasingly incorporating smart sensors and IoT connectivity to monitor performance, predict maintenance needs, and optimize operations.
- Advanced Control Systems: New control systems offer greater precision and flexibility, enabling operators to achieve complex bead patterns and adapt to changing production requirements.
- Automation and Robotics: The integration of automation and robotics is transforming trimming beading machines, reducing manual labor, and increasing throughput.
Future Trends in Trimming Beading Machines
Several trends are shaping the future of trimming beading machines, influencing how they are designed and utilized.
- Sustainability and Energy Efficiency: Manufacturers are focusing on sustainability, developing machines with lower energy consumption and reduced environmental impact.
- Customization and Flexibility: As demand for custom products grows, trimming beading machines are becoming more adaptable, with features that support rapid reconfiguration and customization.
- Digitalization and Industry 4.0: The digital transformation of manufacturing is driving the adoption of Industry 4.0 technologies, enabling data-driven decision-making and enhanced machine performance.
Case Studies and Examples
Real-world examples and case studies demonstrate the impact of trimming beading machines in various industries, highlighting their benefits and applications.
- Automotive Manufacturing: A leading automotive manufacturer implemented advanced trimming beading machines to improve production efficiency and reduce defects, achieving significant cost savings and quality improvements.
- Aerospace Industry: An aerospace supplier adopted IoT-enabled trimming beading machines to enhance traceability and optimize maintenance, resulting in reduced downtime and improved compliance with industry standards.
- HVAC Production: A major HVAC manufacturer integrated automated trimming beading machines to increase production capacity and reduce manual labor, leading to faster lead times and higher product quality.
Choosing the Right Trimming Beading Machine
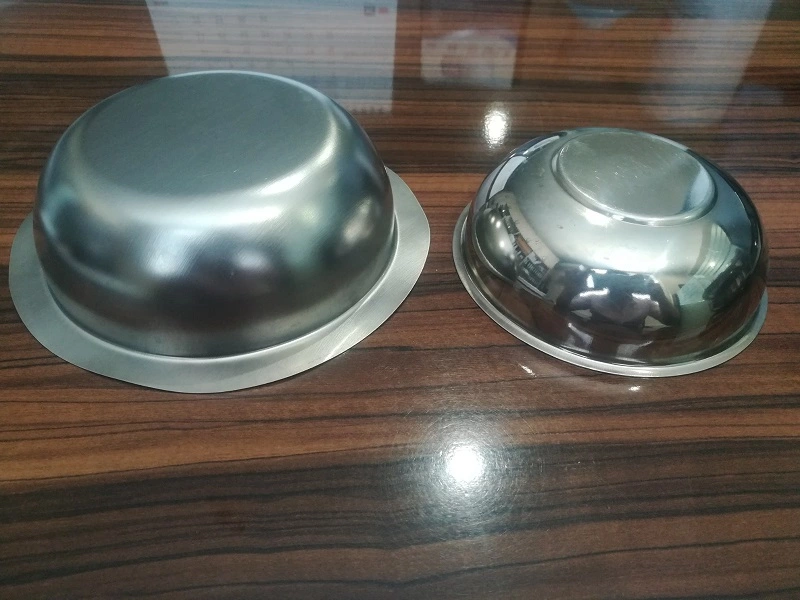
Selecting the right trimming beading machine is crucial for achieving optimal performance and meeting specific production needs. Here, we outline key factors to consider and offer guidance on the selection process.
Factors to Consider
When choosing a trimming beading machine, several factors should be considered to ensure the equipment meets operational requirements.
- Production Volume: Assess the production volume and throughput requirements to determine the appropriate machine type and capacity.
- Material Specifications: Consider the types of materials and thicknesses the machine will handle, ensuring compatibility with the equipment’s capabilities.
- Beading Patterns: Evaluate the complexity and variety of bead patterns needed, selecting machines that offer the necessary tooling and flexibility.
- Automation Needs: Determine the level of automation required, balancing productivity gains with cost considerations and operator expertise.
Cost vs. Benefit Analysis
Conducting a cost vs. benefit analysis helps evaluate the financial implications of investing in a trimming beading machine.
- Initial Investment: Assess the upfront cost of the machine, including installation and setup expenses.
- Operational Costs: Consider ongoing operational costs, such as energy consumption, maintenance, and labor.
- Return on Investment (ROI): Calculate the expected ROI by evaluating the machine’s impact on productivity, quality, and cost savings.
Vendor Selection and Partnerships
Choosing the right vendor and establishing strong partnerships are essential for acquiring quality equipment and support.
- Reputation and Experience: Evaluate potential vendors based on their reputation, experience, and track record in the industry.
- Technical Support and Service: Ensure the vendor offers comprehensive technical support, training, and maintenance services to maximize machine performance and uptime.
- Customization and Flexibility: Consider vendors that offer customization options and flexible solutions tailored to specific production needs.
Conclusion
Recap of Key Points
Trimming beading machines are essential tools in modern manufacturing, offering precision, efficiency, and versatility across a range of industries. Understanding their components, working principles, and applications is crucial for making informed decisions and optimizing production processes.
Final Thoughts on Trimming Beading Machines
As technology continues to advance, trimming beading machines are poised to play an increasingly important role in the manufacturing landscape. By embracing innovation and adopting best practices, manufacturers can leverage these machines to enhance quality, productivity, and competitiveness in their respective industries.
Components of Trimming Beading Machines
To provide a detailed exploration of the components of a trimming beading machine, we’ll delve deeper into each part, discussing their functions, materials, and importance. Here’s an expanded version of the Components of Trimming Beading Machines section:
Trimming beading machines consist of several integral components, each playing a crucial role in ensuring precise operation and high-quality output. Understanding these components can aid in the proper selection, operation, and maintenance of the machines.
Base and Frame
Functionality and Importance
The base and frame of a trimming beading machine serve as the foundation, providing structural support and stability. A well-designed frame is essential to withstand operational stresses and vibrations, ensuring accurate and consistent performance.
Materials Used
- Steel: Often used for its high tensile strength and durability. Steel frames provide rigidity, helping to maintain precision even under heavy loads.
- Cast Iron: Valued for its excellent vibration-damping properties. Cast iron is commonly used in applications where reducing machine noise and vibration is critical to maintaining accuracy.
- Aluminum Alloys: Used in some lightweight machines, aluminum alloys offer corrosion resistance and ease of handling, though they may lack the rigidity of steel or cast iron.
Structural Design
- Box-Type Frames: Provide superior rigidity and support. Box-type frames are designed to minimize deformation and ensure precise alignment of components.
- Open-Type Frames: Offer ease of access for maintenance and adjustments. Open frames are suitable for applications where quick changes and flexibility are required.
- Welded vs. Bolted Structures: Welded structures provide a solid and seamless frame, while bolted structures offer flexibility in assembly and disassembly for maintenance.
Cutting and Beading Tools
Role in Operation
Cutting and beading tools are at the heart of the trimming beading machine’s functionality. They are responsible for removing excess material and forming beads along the edges of workpieces.
Types of Tools
- Rotary Cutters: Used for continuous cutting operations, rotary cutters offer high speed and precision, ideal for long production runs.
- Punch and Die Sets: Employed for stamping and forming operations, punch and die sets provide versatility in creating complex bead patterns and shapes.
- Roller Dies: Utilized in forming continuous beads along the length of a workpiece. Roller dies offer consistent pressure and control, ensuring uniform bead formation.
Materials for Cutting Tools
- High-Speed Steel (HSS): Known for its hardness and ability to maintain a sharp edge at high temperatures. HSS is suitable for a wide range of cutting applications.
- Carbide: Offers superior wear resistance and durability, making it ideal for high-volume production and difficult-to-machine materials.
- Ceramic and Diamond Coatings: Used for specialized applications requiring extreme hardness and wear resistance. These coatings can extend the life of cutting tools and improve performance.
Maintenance and Replacement
Regular maintenance of cutting and beading tools is essential to ensure optimal performance. This includes:
- Tool Inspection: Conduct routine inspections to identify signs of wear or damage. Replace tools that have become dull or chipped.
- Sharpening: Maintain sharp edges on cutting tools to ensure precise cuts and prevent material deformation.
- Alignment and Calibration: Regularly check tool alignment and calibration to prevent defects and ensure uniformity in bead formation.
Drive Mechanism
Functionality and Importance
The drive mechanism powers the operation of trimming beading machines, converting electrical energy into mechanical motion. It directly influences the machine’s efficiency and performance.
Motor Types
- AC Motors: Commonly used for their reliability and low maintenance requirements. AC motors provide consistent performance and are suitable for applications where speed control is not critical.
- DC Motors: Offer precise speed control and are used in applications requiring variable speeds. DC motors can be paired with controllers to fine-tune performance.
- Servo Motors: Provide high precision and dynamic control, enabling rapid adjustments to speed and position. Servo motors are ideal for applications requiring complex bead patterns and high-speed operations.
- Stepper Motors: Offer precise positioning and repeatability. Stepper motors are used in applications where incremental movements and accuracy are essential.
Energy Efficiency Considerations
- Variable Frequency Drives (VFDs): Used to optimize energy consumption by adjusting the motor’s speed and torque to match the operational needs. VFDs can significantly reduce energy costs and extend the life of the drive system.
- Regenerative Drives: Capture and reuse energy generated during deceleration, further improving energy efficiency and reducing operational costs.
Control Systems
Role in Operation
Control systems govern the operation of trimming beading machines, allowing operators to configure settings, monitor performance, and ensure safety. These systems range from basic manual controls to sophisticated automated interfaces.
Types of Control Systems
- Manual Controls: Suitable for smaller operations or applications requiring frequent adjustments. Manual controls offer simplicity and direct operator oversight.
- Programmable Logic Controllers (PLCs): Provide automation and flexibility, enabling operators to program complex operations and adjust settings on the fly. PLCs are widely used in industrial applications for their reliability and ease of use.
- Computer Numerical Control (CNC): Offers high precision and control, allowing for complex and repeatable operations. CNC systems are ideal for high-volume production and applications requiring intricate bead patterns.
- Human-Machine Interfaces (HMIs): Facilitate interaction between operators and machines, providing real-time data and control over machine settings. HMIs enhance usability and improve operational efficiency.
Integration with Industry 4.0 Technologies
Trimming beading machines are increasingly adopting Industry 4.0 technologies to enhance operational efficiency and enable predictive maintenance. Key advancements include:
- IoT Connectivity: Sensors and IoT devices provide real-time monitoring and data collection, enabling operators to track performance, detect anomalies, and predict maintenance needs.
- Data Analytics and Machine Learning: Advanced analytics and machine learning algorithms optimize machine performance by analyzing operational data and identifying trends or inefficiencies.
- Remote Monitoring and Control: Operators can access and control machines remotely, improving flexibility and enabling rapid response to issues.
Conclusion
The components of trimming beading machines play vital roles in ensuring precision, efficiency, and durability. By understanding these components, manufacturers can optimize their machines for specific applications, improve operational efficiency, and reduce downtime. Proper selection, maintenance, and integration of these components are essential for maximizing the performance and lifespan of trimming beading machines.
Tool Maintenance Tips for Trimming Beading Machines
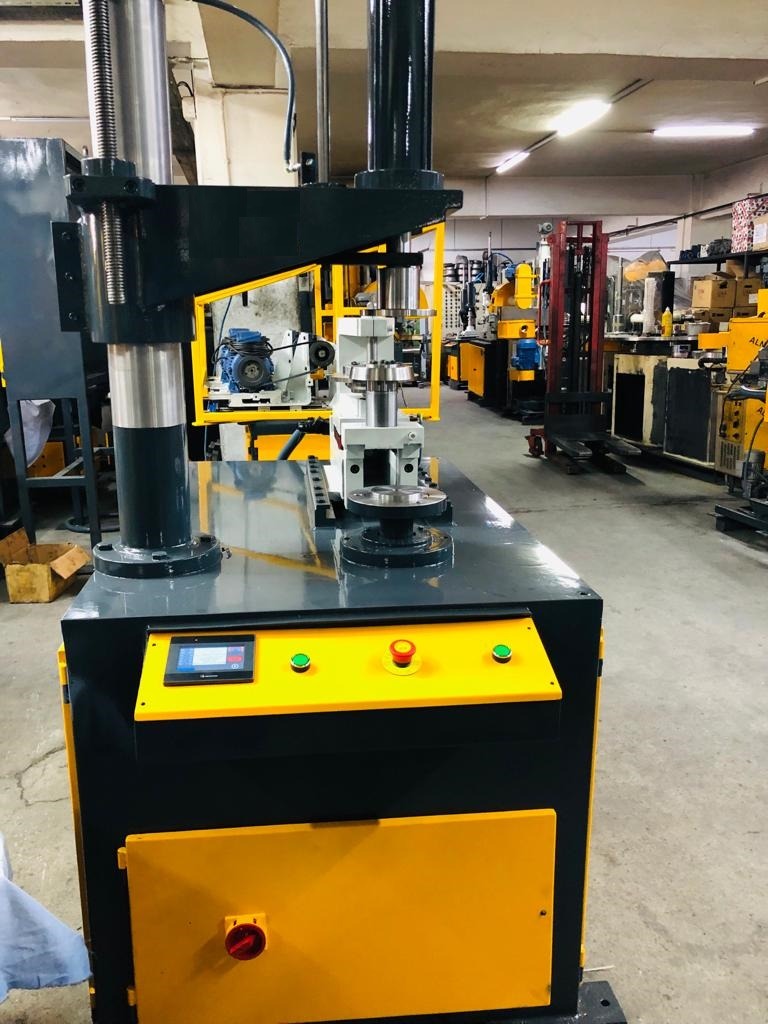
Maintaining the tools of a trimming beading machine is essential for ensuring long-term efficiency, precision, and reliability. Regular maintenance not only prolongs the lifespan of the tools but also ensures consistent quality of the finished products. Here are some detailed tool maintenance tips:
1. Regular Inspection and Assessment
Visual Inspection
- Daily Checks: Conduct visual inspections of cutting and beading tools at the start and end of each shift to identify any visible signs of wear, damage, or misalignment.
- Surface Examination: Look for chips, cracks, or signs of wear on the cutting edges and surfaces, as these can affect the tool’s performance and the quality of the beading.
Performance Monitoring
- Quality Checks: Routinely check the quality of the finished products for any signs of tool-related issues, such as burrs, uneven edges, or inconsistent beading.
- Operational Sounds: Listen for unusual noises during operation, which may indicate tool misalignment or wear.
2. Proper Cleaning and Lubrication
Cleaning Procedures
- Remove Debris: Regularly clean tools to remove metal shavings, dust, and other debris that can accumulate and affect performance.
- Use Appropriate Solvents: Employ non-corrosive cleaning solvents to remove stubborn residues without damaging the tool’s surface.
Lubrication
- Lubricant Selection: Use the correct type of lubricant for the specific tool material, such as oil-based lubricants for steel tools or dry lubricants for carbide tools.
- Regular Application: Apply lubricants at regular intervals to reduce friction, prevent overheating, and protect against corrosion.
3. Sharpening and Reconditioning
Sharpening Techniques
- Proper Tools: Use appropriate sharpening tools, such as diamond stones or grinding wheels, to maintain the cutting edge.
- Sharpening Angles: Follow the manufacturer’s recommendations for sharpening angles to ensure optimal cutting performance.
- Frequency: Establish a regular sharpening schedule based on tool usage and material hardness to maintain sharp edges.
Reconditioning Services
- Professional Reconditioning: Consider professional reconditioning services for heavily worn or damaged tools to restore them to their original specifications.
- Tool Replacement: Replace tools that have reached the end of their usable life to maintain performance and quality.
4. Alignment and Calibration
Tool Alignment
- Proper Setup: Ensure that tools are correctly aligned before each operation to prevent uneven wear and ensure accurate cuts and beads.
- Alignment Tools: Use precision alignment tools and gauges to verify proper tool positioning and alignment.
Calibration
- Regular Calibration: Regularly calibrate the machine and its components to ensure that tools operate within specified tolerances.
- Documentation: Keep detailed records of calibration activities and adjustments for quality control and maintenance purposes.
5. Storage and Handling
Tool Storage
- Protective Cases: Store tools in protective cases or racks to prevent damage when not in use.
- Controlled Environment: Maintain a clean, dry, and temperature-controlled environment to prevent corrosion and material degradation.
Handling Practices
- Proper Handling: Use appropriate handling techniques to prevent dropping or mishandling tools, which can lead to damage.
- Training: Train operators and maintenance personnel on proper handling and storage procedures to minimize accidental damage.
6. Documentation and Training
Maintenance Records
- Detailed Logs: Keep detailed records of all maintenance activities, including inspections, cleaning, sharpening, and replacements. This information can help track tool performance and identify patterns or issues.
- Tool Usage Records: Document tool usage, including hours of operation and materials processed, to anticipate maintenance needs and schedule downtime effectively.
Training and Education
- Operator Training: Provide comprehensive training for operators and maintenance personnel on proper tool care and maintenance procedures.
- Continuous Education: Stay updated on the latest tool maintenance techniques and technologies to improve maintenance practices and enhance tool longevity.
Conclusion
Effective tool maintenance is crucial for maximizing the performance and lifespan of trimming beading machines. By implementing these maintenance tips, manufacturers can ensure consistent product quality, reduce downtime, and extend the life of their tools. Regular inspections, proper cleaning and lubrication, alignment, and training are essential components of a comprehensive maintenance strategy.
Application Areas of Trimming Beading Machines
Trimming beading machines play a crucial role across various industries due to their ability to efficiently trim and bead the edges of metal and other materials. They are essential for achieving precision, consistency, and quality in manufacturing processes. Below, we delve into the primary application areas where these machines are indispensable:
1. Automotive Industry
Role and Importance
The automotive industry relies heavily on trimming beading machines to ensure the structural integrity and aesthetic quality of vehicle components. These machines are used to trim and form beads on various parts, contributing to the overall safety and appearance of vehicles.
Specific Applications
- Body Panels: Trimming beading machines are used to trim and bead the edges of doors, hoods, fenders, and trunk lids. This ensures a smooth fit and finish, reducing the risk of sharp edges and improving the vehicle’s aesthetic appeal.
- Exhaust Systems: Beading is essential for exhaust system components to ensure proper sealing and assembly. Trimming beading machines create precise beads that help maintain joint integrity under varying temperatures and pressures.
- Interior Components: These machines are used to create beaded edges on interior panels and trim pieces, enhancing the aesthetic quality and durability of the interior components.
Benefits
- Improved Safety: Proper beading enhances the strength and stability of components, contributing to vehicle safety.
- Aesthetic Appeal: Beading provides a polished and professional appearance, enhancing the overall look of the vehicle.
- Cost Efficiency: Automated trimming and beading reduce labor costs and increase production efficiency, enabling manufacturers to meet high-volume demands.
2. Aerospace Industry
Role and Importance
The aerospace industry demands the highest precision and quality standards, making trimming beading machines essential for manufacturing components that must withstand extreme conditions and stresses.
Specific Applications
- Fuselage Panels: Trimming beading machines are used to trim and bead the edges of fuselage panels, ensuring a precise fit and alignment during assembly. Beading enhances the panels’ structural integrity and resistance to aerodynamic forces.
- Wing Components: Beading is applied to wing components, such as flaps and ailerons, to improve their strength and performance. The precision of trimming beading machines ensures the components meet strict aerospace standards.
- Engine Components: In engine manufacturing, trimming beading machines are used to create precise beads on engine casings and ducts, improving thermal and mechanical performance.
Benefits
- Precision and Accuracy: Trimming beading machines provide the precision necessary to meet the stringent requirements of the aerospace industry.
- Enhanced Performance: Beaded components offer improved strength and aerodynamic performance, contributing to the overall efficiency of aircraft.
- Reliability: The consistent quality of beaded components ensures reliability and safety in critical aerospace applications.
3. HVAC Industry
Role and Importance
The HVAC (Heating, Ventilation, and Air Conditioning) industry utilizes trimming beading machines to manufacture components that require precise sealing and structural integrity.
Specific Applications
- Ductwork: Trimming beading machines are used to bead the edges of ductwork components, ensuring a tight seal and preventing air leaks. Proper beading also enhances the structural stability of ducts.
- Vents and Grilles: Beading is applied to vents and grilles to improve their strength and appearance. Trimming beading machines ensure a consistent fit and finish, contributing to the overall quality of HVAC systems.
- Heat Exchangers: In heat exchanger manufacturing, trimming beading machines create beads that enhance the thermal performance and durability of components.
Benefits
- Energy Efficiency: Beaded components improve sealing and reduce air leakage, enhancing the energy efficiency of HVAC systems.
- Durability: The structural integrity provided by beading ensures the long-term durability of HVAC components.
- Quality Assurance: Trimming beading machines deliver consistent quality, enabling manufacturers to meet industry standards and customer expectations.
4. Consumer Goods Industry
Role and Importance
In the consumer goods industry, trimming beading machines are employed to enhance the quality and appearance of a wide range of products, from household appliances to electronics.
Specific Applications
- Appliances: Trimming beading machines are used to create beaded edges on appliances such as refrigerators, ovens, and washing machines. This improves the aesthetic appeal and durability of the products.
- Electronics Enclosures: Beading is applied to electronic enclosures and casings to enhance their strength and provide a polished appearance. Trimming beading machines ensure a precise fit and finish, critical for protecting sensitive electronic components.
- Packaging: In packaging manufacturing, trimming beading machines create beads that improve the strength and sealing of containers, ensuring the protection and integrity of packaged goods.
Benefits
- Aesthetic Enhancement: Beading enhances the visual appeal of consumer products, contributing to customer satisfaction and brand image.
- Structural Integrity: Beaded edges provide added strength and resistance to wear and tear, extending the lifespan of consumer goods.
- Manufacturing Efficiency: Trimming beading machines increase production efficiency, allowing manufacturers to meet high demand while maintaining quality.
5. Metalworking Industry
Role and Importance
The metalworking industry utilizes trimming beading machines for a variety of applications where precision and consistency are paramount.
Specific Applications
- Sheet Metal Fabrication: Trimming beading machines are used to trim and bead sheet metal components for a range of applications, from construction to transportation.
- Custom Metal Components: Beading is applied to custom metal parts to enhance their strength and performance. Trimming beading machines enable the production of intricate and precise designs.
- Architectural Metalwork: In architectural metalwork, trimming beading machines create beaded edges on decorative elements, ensuring a high-quality finish.
Benefits
- Precision and Consistency: Trimming beading machines provide the accuracy required for complex metalworking applications.
- Versatility: These machines can handle a wide range of materials and thicknesses, accommodating diverse metalworking needs.
- Quality Assurance: The consistent quality of beaded metal components ensures they meet industry standards and project specifications.
6. Food and Beverage Industry
Role and Importance
In the food and beverage industry, trimming beading machines are used to manufacture components that require precise sealing and hygiene standards.
Specific Applications
- Food Containers: Trimming beading machines are used to create beaded edges on food containers, ensuring a tight seal and preventing contamination.
- Beverage Cans: Beading is applied to beverage cans to enhance their strength and resistance to pressure changes. Trimming beading machines ensure a uniform and reliable seal.
- Processing Equipment: In food processing equipment manufacturing, trimming beading machines create beads that improve the structural integrity and hygiene of components.
Benefits
- Food Safety: Beaded components provide secure sealing, preventing contamination and ensuring food safety.
- Durability: The added strength provided by beading ensures the longevity and reliability of food and beverage packaging.
- Efficiency: Trimming beading machines increase production efficiency, enabling manufacturers to meet high demand while maintaining quality and safety standards.
7. Medical Device Manufacturing
Role and Importance
The medical device manufacturing industry requires precision and reliability, making trimming beading machines essential for producing components that must meet strict standards.
Specific Applications
- Surgical Instruments: Trimming beading machines are used to create beaded edges on surgical instruments, enhancing their strength and safety.
- Medical Equipment Casings: Beading is applied to medical equipment casings to improve their structural integrity and provide a polished appearance.
- Implantable Devices: In the manufacturing of implantable devices, trimming beading machines create beads that ensure precision and compatibility with human tissue.
Benefits
- Precision and Accuracy: Trimming beading machines provide the precision necessary to meet the stringent requirements of medical device manufacturing.
- Reliability: Beaded components ensure reliability and safety in critical medical applications.
- Quality Assurance: The consistent quality of beaded medical components ensures they meet industry standards and regulatory requirements.
Conclusion
Trimming beading machines are versatile tools that play a vital role in various industries, from automotive to medical device manufacturing. Their ability to enhance the precision, consistency, and quality of components makes them indispensable for modern manufacturing processes. By understanding the specific applications and benefits of trimming beading machines, manufacturers can optimize their operations, improve product quality, and meet the demands of their respective industries.
Trimming Beading Tools
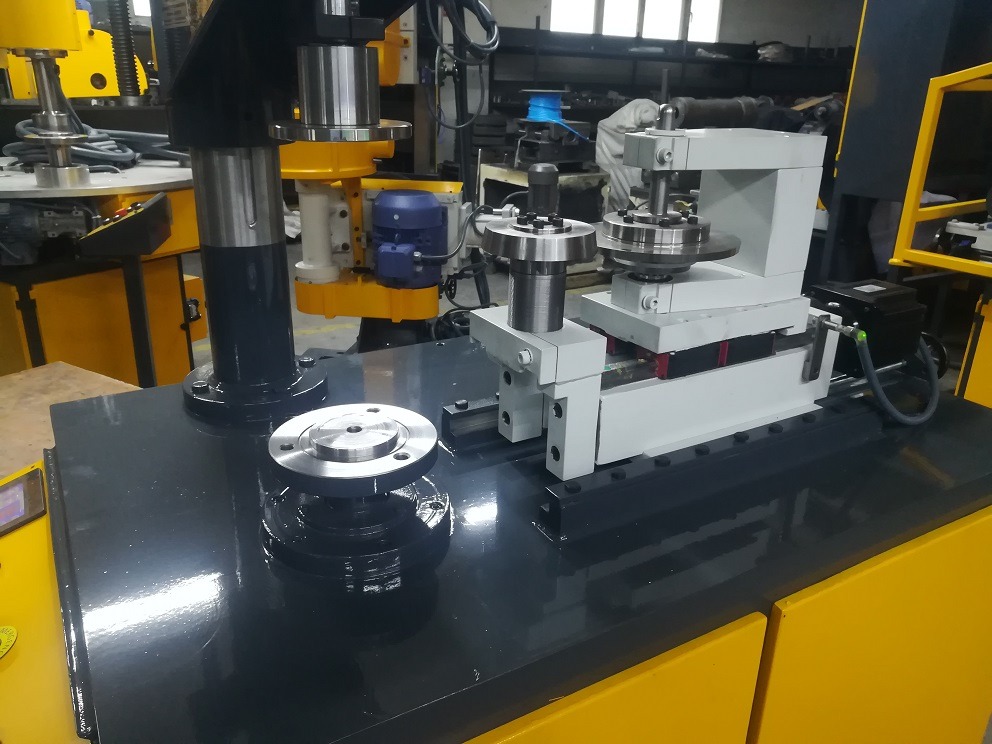
Trimming beading tools are critical components of trimming beading machines, directly responsible for cutting and forming beads on workpieces. Their design, material, and maintenance play a crucial role in determining the quality and efficiency of the trimming and beading process. Here’s an in-depth look at trimming beading tools, including their types, materials, maintenance, and considerations for selection:
Types of Trimming Beading Tools
Trimming beading tools come in various shapes and forms, each designed for specific tasks and applications. The choice of tools depends on the material being processed, the desired bead pattern, and the machine’s capabilities.
1. Rotary Cutters
Functionality
- Rotary cutters are used for continuous cutting operations and are ideal for long production runs.
- They provide high-speed cutting and precision, making them suitable for trimming operations that require clean and straight edges.
Applications
- Automotive body panels
- Sheet metal fabrication
- Packaging components
2. Punch and Die Sets
Functionality
- Punch and die sets are used for stamping and forming operations, allowing for the creation of complex bead patterns and shapes.
- They offer versatility and can be customized to meet specific design requirements.
Applications
- Complex bead patterns in aerospace components
- Decorative metalwork
- Custom metal parts
3. Roller Dies
Functionality
- Roller dies are utilized in forming continuous beads along the length of a workpiece.
- They apply consistent pressure and control, ensuring uniform bead formation.
Applications
- HVAC ductwork
- Metal enclosures
- Architectural metalwork
4. Serrated Cutters
Functionality
- Serrated cutters feature a toothed edge that is designed for gripping and cutting through tougher materials.
- They are often used in applications where a smooth finish is not critical but where material grip and precision are required.
Applications
- Heavy-duty metal cutting
- Thicker materials such as steel or titanium
5. Profile Tools
Functionality
- Profile tools are used to create specific bead profiles and shapes, including U-beads, V-beads, and more complex designs.
- These tools are customized to match the desired profile and are critical for applications requiring specific geometric shapes.
Applications
- Automotive trim components
- Custom metal profiles
- Precision sheet metal work
Materials for Trimming Beading Tools
The choice of material for trimming beading tools affects their performance, durability, and suitability for different applications. Key materials include:
1. High-Speed Steel (HSS)
Characteristics
- Known for its hardness and ability to maintain a sharp edge at high temperatures.
- Offers good wear resistance and is suitable for a wide range of cutting applications.
Advantages
- Cost-effective for general-purpose trimming and beading.
- Easy to sharpen and recondition.
Limitations
- May wear quickly in high-volume production or with abrasive materials.
2. Carbide
Characteristics
- Carbide tools offer superior wear resistance and durability, making them ideal for high-volume production and difficult-to-machine materials.
- Maintains sharpness and precision over extended periods.
Advantages
- Long tool life and reduced downtime for tool changes.
- Suitable for hard and abrasive materials.
Limitations
- Higher initial cost compared to HSS tools.
- More challenging to recondition and sharpen.
3. Ceramic and Diamond Coatings
Characteristics
- Ceramic and diamond coatings provide extreme hardness and wear resistance.
- Used for specialized applications requiring the highest levels of durability and precision.
Advantages
- Exceptional tool life and performance in demanding applications.
- Resistance to heat and wear, reducing tool degradation.
Limitations
- Very high cost, typically reserved for critical applications.
- Requires specialized equipment for sharpening and maintenance.
4. Tool Steel
Characteristics
- Tool steel is a versatile material that offers a good balance of strength, toughness, and wear resistance.
- Suitable for a variety of tool types and applications.
Advantages
- Cost-effective and easy to machine and customize.
- Provides a good balance between durability and flexibility.
Limitations
- May not perform as well as carbide or ceramic in highly abrasive conditions.
Maintenance of Trimming Beading Tools
Proper maintenance of trimming beading tools is essential for ensuring consistent performance and longevity. Here are some key maintenance practices:
1. Regular Inspection and Assessment
- Visual Inspections: Conduct regular visual inspections to identify signs of wear, damage, or misalignment.
- Performance Monitoring: Monitor tool performance by checking the quality of the finished products for any signs of tool-related issues, such as burrs or uneven edges.
2. Cleaning and Lubrication
- Cleaning Procedures: Regularly clean tools to remove metal shavings, dust, and debris that can accumulate and affect performance.
- Lubrication: Apply appropriate lubricants to reduce friction, prevent overheating, and protect against corrosion. Ensure that the correct type of lubricant is used for the specific tool material.
3. Sharpening and Reconditioning
- Sharpening Techniques: Use the appropriate sharpening tools, such as diamond stones or grinding wheels, to maintain the cutting edge. Follow manufacturer recommendations for sharpening angles.
- Reconditioning Services: Consider professional reconditioning services for heavily worn or damaged tools to restore them to their original specifications.
4. Alignment and Calibration
- Tool Alignment: Ensure that tools are correctly aligned before each operation to prevent uneven wear and ensure accurate cuts and beads.
- Calibration: Regularly calibrate the machine and its components to ensure that tools operate within specified tolerances.
5. Storage and Handling
- Proper Storage: Store tools in protective cases or racks to prevent damage when not in use. Maintain a clean, dry, and temperature-controlled environment.
- Handling Practices: Use appropriate handling techniques to prevent dropping or mishandling tools. Train operators on proper handling and storage procedures.
Considerations for Selecting Trimming Beading Tools
Selecting the right trimming beading tools requires careful consideration of several factors to ensure optimal performance and quality:
1. Material Compatibility
- Choose tools made from materials that are compatible with the workpiece material to ensure effective cutting and beading.
- Consider the hardness, abrasiveness, and thickness of the material when selecting tool materials and coatings.
2. Tool Geometry
- Select tools with the appropriate geometry for the desired bead profile and cutting requirements.
- Consider factors such as tool angle, shape, and size when choosing tools for specific applications.
3. Production Volume
- Consider the production volume and frequency of tool changes when selecting tools. High-volume production may require more durable materials such as carbide or ceramic.
4. Quality Requirements
- Evaluate the quality requirements of the finished product, including precision, surface finish, and consistency.
- Select tools that can meet the desired quality standards, taking into account the required tolerances and specifications.
5. Cost Considerations
- Balance the cost of tools with their expected performance and longevity. Consider the total cost of ownership, including maintenance and replacement costs.
6. Machine Compatibility
- Ensure that the selected tools are compatible with the specific trimming beading machine being used, including tool holders, spindles, and drive mechanisms.
Conclusion
Trimming beading tools are essential components of trimming beading machines, directly influencing the quality and efficiency of the manufacturing process. By understanding the different types of tools, their materials, and maintenance requirements, manufacturers can optimize their operations and ensure consistent, high-quality results. Proper tool selection, maintenance, and handling are key to maximizing performance and extending the lifespan of trimming beading tools.
Beading Machine Efficiency
Improving the efficiency of a beading machine is crucial for manufacturers seeking to enhance productivity, reduce costs, and maintain high-quality output. A beading machine’s efficiency is influenced by multiple factors, including machine design, tool selection, operational practices, and maintenance strategies. This guide will explore these factors in detail, providing insights into how efficiency can be optimized.
1. Machine Design and Configuration
The design and configuration of a beading machine have a significant impact on its efficiency. Considerations include the machine’s mechanical setup, automation capabilities, and adaptability to various production requirements.
Key Design Factors
- Automation Level: Automated beading machines can significantly improve efficiency by reducing manual intervention, minimizing errors, and increasing throughput. Machines with advanced control systems, such as CNC (Computer Numerical Control) or PLC (Programmable Logic Controllers), offer precise control over operations.
- Modular Design: Machines with modular components allow for quick changes and customization to accommodate different product specifications. This flexibility can lead to reduced downtime and faster setup times.
- Ergonomic Design: An ergonomic design reduces operator fatigue and error rates. Features such as user-friendly interfaces and adjustable components enhance operator comfort and efficiency.
Technological Integration
- Industry 4.0: Incorporating Industry 4.0 technologies, such as IoT (Internet of Things) sensors and data analytics, enables real-time monitoring of machine performance and predictive maintenance. This integration helps identify potential issues before they lead to downtime, ensuring continuous operation.
- Adaptive Controls: Machines equipped with adaptive control systems can automatically adjust settings based on real-time data, optimizing performance for varying materials and production requirements.
2. Tool Selection and Maintenance
The selection and maintenance of tools are critical to maximizing the efficiency of a beading machine. High-quality tools, combined with regular maintenance, ensure precision and longevity.
Tool Selection
- Material Compatibility: Choose tools that are compatible with the materials being processed. This minimizes wear and tear and ensures efficient operation. For example, carbide tools are ideal for high-volume production due to their durability and resistance to wear.
- Tool Geometry: Select tools with the appropriate geometry for the desired bead profile and cutting requirements. Proper tool geometry can reduce material waste and improve cycle times.
Tool Maintenance
- Routine Sharpening: Regularly sharpen tools to maintain their cutting efficiency. Dull tools increase cycle times and reduce product quality.
- Alignment and Calibration: Ensure tools are properly aligned and calibrated to prevent defects and ensure consistent bead formation.
- Inventory Management: Maintain an inventory of spare tools to prevent downtime in the event of tool failure or wear.
3. Operational Practices
Operational practices, including setup procedures, quality control, and process optimization, play a crucial role in enhancing beading machine efficiency.
Setup and Calibration
- Efficient Setup Procedures: Streamline setup procedures to reduce downtime between production runs. This includes using quick-change tooling systems and pre-configured settings.
- Calibration Checks: Regularly perform calibration checks to ensure the machine operates within specified tolerances. This prevents defects and reduces the need for rework.
Process Optimization
- Cycle Time Reduction: Analyze and optimize cycle times by identifying bottlenecks and implementing process improvements. This can include adjustments to machine speed, tool changes, and material handling.
- Lean Manufacturing Principles: Implement lean manufacturing principles to eliminate waste and improve process flow. Techniques such as 5S and value stream mapping can enhance efficiency.
- Continuous Improvement: Foster a culture of continuous improvement by encouraging operators and engineers to identify inefficiencies and propose solutions.
4. Quality Control and Inspection
Implementing robust quality control and inspection processes ensures that beading machines produce consistent and high-quality output, reducing waste and rework.
In-Line Inspection
- Automated Inspection Systems: Use automated inspection systems to monitor product quality in real-time. This allows for immediate identification and correction of defects.
- Statistical Process Control (SPC): Implement SPC techniques to track and analyze production data. This helps identify trends and deviations, enabling proactive adjustments.
Feedback Loops
- Operator Feedback: Encourage operators to provide feedback on machine performance and quality issues. This insight can be invaluable for identifying areas for improvement.
- Customer Feedback: Collect and analyze customer feedback to identify quality issues and adjust processes accordingly.
5. Maintenance Strategies
A proactive maintenance strategy is essential for minimizing downtime and ensuring the long-term efficiency of beading machines.
Preventive Maintenance
- Scheduled Maintenance: Implement a regular maintenance schedule to address wear and tear before it leads to machine failure. This includes lubrication, alignment checks, and part replacements.
- Maintenance Logs: Maintain detailed logs of maintenance activities to track machine performance and identify recurring issues.
Predictive Maintenance
- Condition Monitoring: Use condition monitoring tools, such as vibration analysis and thermal imaging, to detect signs of impending failure.
- Data Analytics: Analyze maintenance and operational data to predict future maintenance needs, reducing unplanned downtime.
6. Training and Workforce Development
Investing in operator training and workforce development can enhance the efficiency of beading machines by ensuring proper machine operation and fostering a culture of continuous improvement.
Operator Training
- Skill Development: Provide comprehensive training on machine operation, maintenance procedures, and quality control. This ensures operators are equipped to maximize machine performance.
- Cross-Training: Implement cross-training programs to develop a versatile workforce capable of operating multiple machines and handling various tasks.
Continuous Learning
- Workshops and Seminars: Encourage participation in workshops and seminars to stay updated on the latest industry trends and technologies.
- Knowledge Sharing: Foster a culture of knowledge sharing among employees to disseminate best practices and innovations.
Conclusion
Enhancing the efficiency of a beading machine involves a multifaceted approach that encompasses machine design, tool selection, operational practices, quality control, maintenance strategies, and workforce development. By focusing on these areas, manufacturers can optimize machine performance, reduce costs, and maintain high-quality output. A commitment to continuous improvement and technological integration will ensure long-term efficiency and competitiveness in the industry.
Installation Requirements for Trimming Beading Machines
The installation of a trimming beading machine requires careful planning and consideration of various factors to ensure optimal performance and safety. Proper installation is crucial for maximizing efficiency, reducing downtime, and maintaining consistent product quality. Below, we explore the key installation requirements for trimming beading machines, covering site preparation, utility requirements, machine setup, safety considerations, and training.
1. Site Preparation
Preparing the installation site is a critical first step to ensure that the beading machine can be set up and operated efficiently. This involves selecting the appropriate location, ensuring structural support, and planning for space requirements.
Location Selection
- Proximity to Production Lines: The machine should be located near the relevant production lines to minimize material handling time and improve workflow efficiency.
- Access for Maintenance: Ensure that there is sufficient space around the machine for maintenance and repairs. Consider the accessibility of components that require frequent servicing.
Structural Support
- Floor Load Capacity: Verify that the floor can support the weight of the machine and any additional equipment. Reinforce the floor if necessary to prevent vibrations and ensure stability.
- Vibration Isolation: Implement vibration isolation measures, such as mounting the machine on anti-vibration pads, to reduce noise and prevent damage to nearby equipment.
Space Requirements
- Working Area: Allocate sufficient space for operators to work safely and efficiently, including room for tool changes, adjustments, and inspections.
- Material Handling: Plan for adequate space for the storage and handling of raw materials and finished products, including conveyors or material handling systems if necessary.
2. Utility Requirements
Ensuring that the necessary utilities are in place is essential for the proper operation of a trimming beading machine. This includes power supply, compressed air, and ventilation.
Power Supply
- Voltage and Amperage: Confirm that the power supply meets the machine’s voltage and amperage requirements. Most industrial beading machines require a three-phase power supply with specific voltage levels (e.g., 220V, 380V, or 440V).
- Electrical Connections: Ensure that electrical connections are made by a qualified electrician, adhering to local electrical codes and standards. Install circuit breakers and fuses as necessary to protect the machine and operators.
Compressed Air
- Air Supply: Some beading machines require compressed air for certain operations, such as clamping or pneumatic controls. Verify the machine’s air pressure and flow requirements and ensure a reliable supply.
- Air Quality: Install air filters and dryers to maintain air quality and prevent contaminants from affecting the machine’s performance.
Ventilation
- Dust and Fume Extraction: Provide adequate ventilation to remove dust, fumes, and other airborne contaminants generated during the beading process. Consider installing dust extraction systems or local exhaust ventilation to maintain air quality.
- Climate Control: Ensure that the installation area is climate-controlled to prevent temperature and humidity fluctuations that could affect machine performance and material quality.
3. Machine Setup and Alignment
Proper setup and alignment of the beading machine are critical to ensure precision and efficiency. This involves machine assembly, calibration, and testing.
Machine Assembly
- Component Installation: Assemble the machine according to the manufacturer’s instructions, ensuring that all components are correctly installed and secured.
- Tooling Installation: Install and configure the necessary cutting and beading tools, ensuring they are compatible with the materials and bead profiles required.
Alignment and Calibration
- Tool Alignment: Align tools with the workpiece to ensure accurate trimming and beading. Use precision alignment tools and gauges to verify correct positioning.
- Calibration: Calibrate the machine’s control systems to ensure that operations are performed within specified tolerances. This includes setting tool angles, cutting speeds, and beading pressures.
Testing and Verification
- Trial Runs: Conduct trial runs with sample materials to verify that the machine is operating correctly and producing the desired results. Adjust settings as needed to achieve optimal performance.
- Quality Inspection: Inspect finished samples for quality and consistency, checking for defects such as burrs, uneven edges, or incomplete beads.
4. Safety Considerations
Safety is a paramount concern during the installation and operation of a trimming beading machine. Implementing proper safety measures protects operators and equipment.
Machine Safety Features
- Emergency Stops: Ensure that emergency stop buttons are accessible and functioning correctly. Test the emergency stop system to verify its effectiveness.
- Safety Guards: Install safety guards and barriers to prevent accidental contact with moving parts. Ensure that guards are securely fastened and meet relevant safety standards.
Operator Safety
- Personal Protective Equipment (PPE): Provide operators with appropriate PPE, such as gloves, safety glasses, and hearing protection, to minimize injury risks.
- Safety Signage: Install safety signage to warn operators of potential hazards and remind them of safe operating procedures.
Compliance and Regulations
- Regulatory Compliance: Ensure that the installation complies with all relevant safety and environmental regulations. This may include OSHA standards in the United States or similar regulations in other countries.
- Risk Assessment: Conduct a risk assessment to identify potential hazards and implement mitigation measures.
5. Training and Workforce Development
Training operators and maintenance personnel is essential for ensuring safe and efficient machine operation.
Operator Training
- Machine Operation: Provide comprehensive training on machine operation, including setup, tool changes, and adjustments. Ensure that operators understand the machine’s control systems and safety features.
- Quality Control: Train operators on quality control procedures, including inspecting finished products for defects and making necessary adjustments.
Maintenance Training
- Routine Maintenance: Train maintenance personnel on routine maintenance tasks, such as lubrication, tool sharpening, and alignment checks.
- Troubleshooting: Provide training on troubleshooting common issues and performing repairs to minimize downtime.
Continuous Improvement
- Feedback Mechanisms: Encourage operators and maintenance personnel to provide feedback on machine performance and suggest improvements.
- Ongoing Training: Offer ongoing training opportunities to keep employees updated on the latest technologies and best practices.
Conclusion
Proper installation of a trimming beading machine involves careful consideration of site preparation, utility requirements, machine setup, safety considerations, and training. By addressing these factors, manufacturers can ensure that their machines operate efficiently, safely, and effectively, leading to improved productivity and product quality. A well-planned installation process lays the foundation for long-term success and competitiveness in the manufacturing industry.
Installation Time Estimate for a Trimming Beading Machine
Estimating the installation time for a trimming beading machine involves considering various factors, such as the complexity of the machine, site preparation, the availability of resources, and the experience of the installation team. While the specific time required can vary widely depending on these factors, I can provide a general breakdown of the installation steps and estimated time frames for each phase.
Here’s a detailed look at the various steps involved in the installation process and the estimated time required for each phase:
1. Pre-Installation Planning and Preparation
Estimated Time: 1-3 Days
- Site Inspection and Preparation: Conduct a thorough inspection of the installation site to ensure it meets the necessary requirements, such as floor strength, ventilation, and space availability. Prepare the site by clearing any obstructions and ensuring utilities are accessible.
- Utility Setup: Arrange for electrical connections, compressed air supply, and other necessary utilities. This might require coordination with electricians and other contractors to ensure compliance with safety standards.
- Logistics and Equipment Handling: Plan the delivery and handling of the machine and its components. This includes scheduling transportation and ensuring equipment like cranes or forklifts is available for moving heavy parts.
2. Machine Assembly
Estimated Time: 2-5 Days
- Unpacking and Inspection: Unpack the machine components and inspect them for any damage incurred during transportation. Verify that all components and accessories are present according to the packing list.
- Base and Frame Setup: Assemble the base and frame of the machine. This involves positioning and securing the machine to the floor, ensuring it is level and stable. Vibration pads or anchors may need to be installed, depending on the machine’s design and site requirements.
- Component Assembly: Assemble the various components of the machine, such as drive systems, control panels, cutting and beading tools, and other peripherals. This step can vary significantly depending on the complexity of the machine.
3. Electrical and Utility Connections
Estimated Time: 1-2 Days
- Electrical Wiring: Connect the machine to the power supply, ensuring that wiring is done by a certified electrician. Test the connections to verify proper voltage and amperage levels.
- Compressed Air and Pneumatics: Connect the compressed air supply if required by the machine. Verify that air pressure and flow meet the manufacturer’s specifications.
- Ventilation Systems: Install any necessary ventilation systems or dust extraction equipment to ensure a safe working environment.
4. Calibration and Testing
Estimated Time: 1-3 Days
- Tool Installation and Alignment: Install and align the cutting and beading tools. Use precision instruments to ensure correct alignment and positioning.
- System Calibration: Calibrate the machine’s control systems, including CNC or PLC settings, to ensure operations are within specified tolerances. This may involve setting up parameters for speed, pressure, and bead patterns.
- Trial Runs and Testing: Conduct trial runs using sample materials to verify machine operation. Inspect the finished products for quality and consistency, making necessary adjustments to settings.
5. Safety Checks and Final Adjustments
Estimated Time: 1 Day
- Safety Inspections: Conduct a thorough safety inspection to ensure all guards, emergency stops, and safety features are operational. Address any potential hazards identified during this inspection.
- Final Adjustments: Make final adjustments to optimize machine performance and address any remaining issues detected during testing.
6. Operator Training and Handover
Estimated Time: 1-3 Days
- Operator Training: Provide comprehensive training to operators and maintenance personnel on machine operation, maintenance procedures, and safety protocols.
- Handover: Conduct a formal handover process, providing documentation, manuals, and support contacts. Ensure that operators and technicians are comfortable with the machine’s operation and troubleshooting procedures.
Total Estimated Installation Time
Overall Time Estimate: 7-17 Days
This estimate assumes that all resources are available, and the installation team is experienced. The time required can vary based on the complexity of the machine, the readiness of the site, and the efficiency of the installation team.
Factors Influencing Installation Time
- Machine Complexity: More complex machines with advanced automation and control systems may require additional time for assembly, calibration, and testing.
- Site Readiness: Delays in site preparation, such as electrical work or structural modifications, can extend the installation timeline.
- Team Experience: Experienced installation teams can complete the process more quickly and efficiently, reducing potential delays.
- Logistical Challenges: Issues with transportation, equipment handling, or supply chain disruptions can affect the installation schedule.
- Customizations: Custom or modified machines may require additional time for assembly and configuration to meet specific requirements.
Conclusion
The installation of a trimming beading machine involves several phases, each with its own set of tasks and time requirements. By planning effectively, coordinating resources, and ensuring that the installation team is well-prepared, manufacturers can optimize the installation process, minimizing downtime and ensuring that the machine is up and running efficiently. Proper installation not only ensures immediate productivity but also lays the foundation for long-term machine performance and reliability.
EMS Metalworking Machinery
We design, manufacture and assembly metalworking machinery such as:
- Hydraulic transfer press
- Glass mosaic press
- Hydraulic deep drawing press
- Casting press
- Hydraulic cold forming press
- Hydroforming press
- Composite press
- Silicone rubber moulding press
- Brake pad press
- Melamine press
- SMC & BMC Press
- Labrotaroy press
- Edge cutting trimming machine
- Edge curling machine
- Trimming beading machine
- Trimming joggling machine
- Cookware production line
- Pipe bending machine
- Profile bending machine
- Bandsaw for metal
- Cylindrical welding machine
- Horizontal pres and cookware
- Kitchenware, hotelware
- Bakeware and cuttlery production machinery
as a complete line as well as an individual machine such as:
- Edge cutting trimming beading machines
- Polishing and grinding machines for pot and pans
- Hydraulic drawing presses
- Circle blanking machines
- Riveting machine
- Hole punching machines
- Press feeding machine
You can check our machinery at work at: EMS Metalworking Machinery – YouTube
Applications:
- Beading and ribbing
- Flanging
- Trimming
- Curling
- Lock-seaming
- Ribbing
- Flange-punching