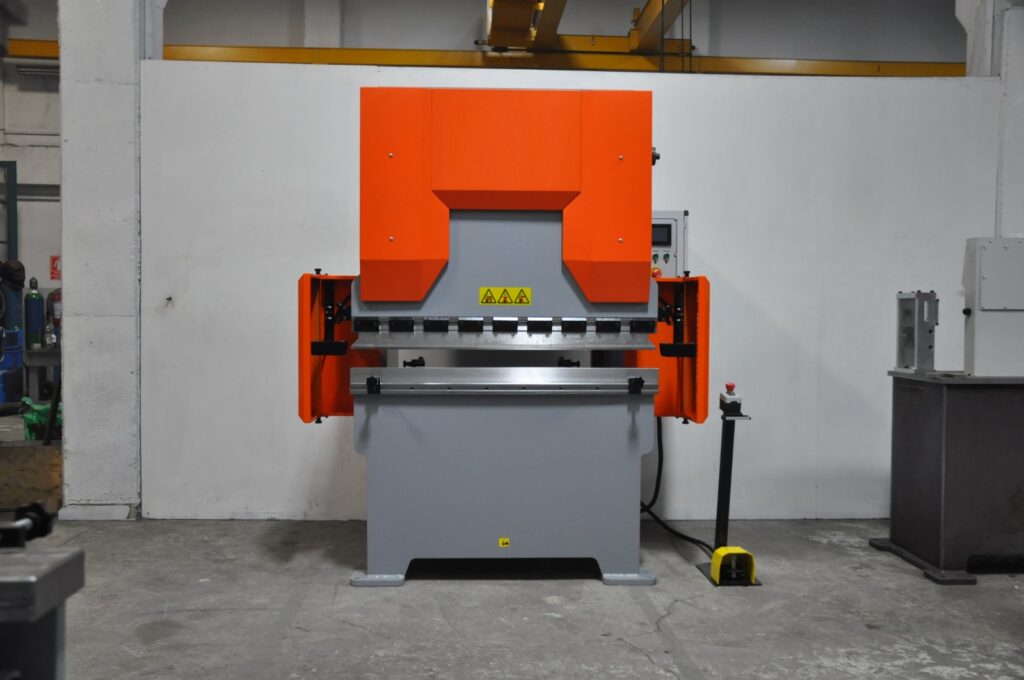
Steel Bending Machine Price: Steel bending machines are industrial tools used to shape steel into various forms and angles. These machines are essential in numerous industries, including construction, automotive, and manufacturing.
Types of Steel Bending Machines
The specific type of bending machine used depends on the desired shape, material thickness, and production volume. Here are some common types:
- Press Brakes
- Roll Bending Machines
- Tube Bending Machines
- Rebar Bending Machines
- Angle Bending Machines
Key Components of a Steel Bending Machine
- Frame
- Hydraulic or Mechanical System
- Bending Dies
- Clamping System
- Control System
Factors to Consider When Choosing a Steel Bending Machine
- Material thickness
- Bend angle and radius
- Production volume
- Automation level
- Budget
We manufacture a 20 ton Press Brake to bend sheet metal edges. 20 ton Press Brake is used in metalworking industries
A 20-ton press brake is a powerful and versatile machine used to bend sheet metal into various shapes and angles using hydraulic pressure. It is a common choice for small- to medium-sized metal fabrication shops due to its ability to handle a wide range of sheet metal thicknesses and produce precise bends.
Key Components of a 20-Ton Press Brake
- Frame: The frame provides a sturdy base for the machine and supports the bending mechanism. It is typically made from heavy-duty steel or cast iron to withstand the immense forces involved in bending sheet metal.
- Hydraulic System: The hydraulic system is the heart of the machine, generating and supplying pressurized hydraulic fluid to the bending mechanism. It consists of a hydraulic pump, hoses, valves, and a hydraulic cylinder. The hydraulic cylinder applies high-pressure hydraulic fluid to the ram, providing the force required to bend the sheet metal.
- Ram: The ram is a movable component that applies downward force onto the sheet metal. It is connected to the hydraulic cylinder and guided by rails to ensure precise movement and alignment during the bending process.
- Punch: The punch is a tooling component that forms the desired shape in the sheet metal. It is typically made from hardened steel or tool steel to withstand the abrasion and forces involved in bending. The punch’s profile corresponds to the desired bend shape.
- Die: The die is another tooling component that supports the sheet metal during bending. It is designed to match the shape of the punch to create the desired bend angle and prevent distortion. The die provides a stable surface against which the punch forces the sheet metal to bend.
- Work Table: The work table provides a stable and adjustable surface for positioning and securing the sheet metal during bending. It can be adjusted to accommodate different sheet metal sizes and bending angles, ensuring precise positioning.
- Back Gauge: The back gauge, also known as the depth stop, controls the distance between the rear edge of the sheet metal and the bending line. It ensures consistent bending positions and prevents the sheet metal from slipping during the bending process, maintaining accuracy and consistency.
- Controls: The control panel allows the operator to set and monitor the bending process. Modern press brakes often feature advanced computer controls for precise and automated operation. These controls enable operators to set bending angles, bending speeds, and other parameters, ensuring consistent and repeatable results.
Common Applications of 20-Ton Press Brakes
20-ton press brakes are widely used for a variety of applications in the metal fabrication industry:
- Bending sheet metal components for various products: These components include enclosures, brackets, ducts, structural components, and various other sheet metal parts.
- Manufacturing metal parts for appliances: 20-ton press brakes are used to create sheet metal components for appliances like refrigerators, washing machines, and dishwashers.
- Producing automotive components: These components include car body panels, brackets, frames, and other sheet metal parts used in automotive manufacturing.
- Creating custom-shaped sheet metal components: 20-ton press brakes can bend sheet metal into unique and custom shapes for specific applications.
- Prototyping sheet metal designs: These machines are used to create prototypes of sheet metal components to evaluate form, fit, and functionality before full-scale production.
- High-volume production of sheet metal components: 20-ton press brakes are designed for high-volume production, enabling efficient manufacturing of large quantities of sheet metal components for various industries.
Benefits of 20-Ton Press Brakes
20-ton press brakes offer several advantages over other bending methods, making them a popular choice in metal fabrication:
- High Bending Capacity: 20-ton press brakes can handle thicker sheet metal than manual or pneumatic bending machines, making them suitable for heavy-duty applications and bending thicker materials.
- Precision Bending: 20-ton press brakes provide precise control over the bending angle, ensuring consistent and accurate bends, even for complex shapes. The hydraulic system, punch, die, and back gauge contribute to precise bending results.
- High Production Rates: 20-ton press brakes are designed for high-volume production, enabling efficient manufacturing of large quantities of sheet metal components. Their automation capabilities further enhance production efficiency.
- Automation and Efficiency: Modern 20-ton press brakes can be automated, reducing labor costs and increasing production efficiency. Automated controls allow for repetitive and consistent bending operations, reducing human error and improving productivity.
- Durability and Reliability: 20-ton press brakes are built to withstand demanding industrial environments and provide reliable performance over extended periods. Their robust construction and components ensure long-lasting operation.
Safety Precautions for Operating 20-Ton Press Brakes
When operating 20-ton press brakes, it is crucial to adhere to strict safety
20 Ton Press Brake
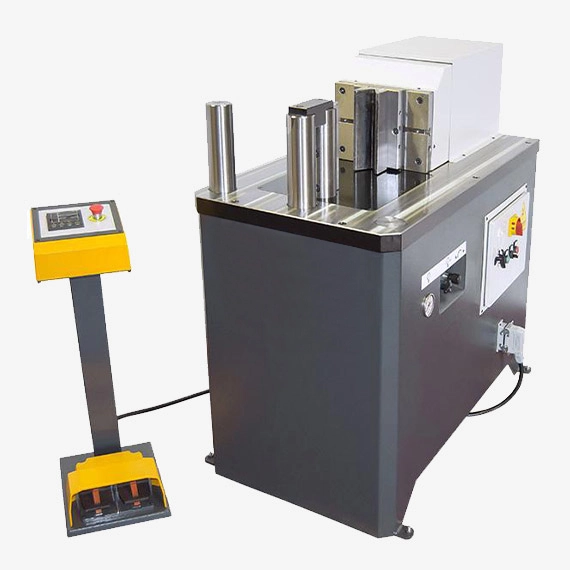
A 20-ton horizontal press machine is a versatile and powerful piece of equipment used for a wide range of metal fabrication tasks. It utilizes hydraulic pressure to apply force to a ram, which in turn forces a punch down onto sheet metal, bending it over a die to create the desired shape or angle. Horizontal press brakes are commonly used for bending sheet metal, forming extrusions, and stamping or punching out shapes.
Key Components of a 20-Ton Horizontal Press Machine
- Frame: The sturdy frame provides a solid base for the machine and supports the bending mechanism. It is typically constructed from heavy-duty steel or cast iron to withstand the immense forces involved in bending sheet metal.
- Hydraulic System: The heart of the machine, the hydraulic system generates and supplies pressurized hydraulic fluid to the bending mechanism. It consists of a hydraulic pump, hoses, valves, and a hydraulic cylinder. The hydraulic cylinder applies high-pressure hydraulic fluid to the ram, providing the force required to bend the sheet metal.
- Ram: The movable ram applies downward force onto the sheet metal. Connected to the hydraulic cylinder and guided by rails, it ensures precise movement and alignment during the bending process.
- Punch: The punch is a tooling component that forms the desired shape in the sheet metal. Typically made from hardened steel or tool steel to withstand abrasion and bending forces, its profile corresponds to the desired bend shape.
- Die: The die, another tooling component, supports the sheet metal during bending. Designed to match the punch’s shape, it creates the desired bend angle and prevents distortion. The die provides a stable surface against which the punch forces the sheet metal to bend.
- Work Table: The adjustable work table provides a stable surface for positioning and securing the sheet metal during bending. It accommodates different sheet metal sizes and bending angles, ensuring precise positioning.
- Back Gauge: The back gauge, also known as the depth stop, controls the distance between the rear edge of the sheet metal and the bending line. It ensures consistent bending positions and prevents the sheet metal from slipping during the bending process, maintaining accuracy and consistency.
- Controls: The control panel allows the operator to set and monitor the bending process. Modern horizontal press brakes often feature advanced computer controls for precise and automated operation. These controls enable operators to set bending angles, bending speeds, and other parameters.
Common Applications of 20-Ton Horizontal Press Machines
20-ton horizontal press machines are widely used in various metal fabrication applications:
- Bending Sheet Metal Components: These machines are commonly used to bend sheet metal components for enclosures, brackets, ducts, structural components, and various other sheet metal parts.
- Forming Extrusions: Horizontal press brakes can form extrusions, which are shapes created by forcing metal through a die. This process is used to create various components, such as tubes, channels, and beams.
- Stamping and Punching: Horizontal press brakes can be used for stamping and punching operations, where a punch is used to cut or form shapes in sheet metal. This process is used to create components like washers, gaskets, and electrical connectors.
- Prototyping Sheet Metal Designs: These machines are employed to create prototypes of sheet metal components to evaluate form, fit, and functionality before full-scale production.
- High-Volume Production: 20-ton horizontal press brakes are designed for high-volume production, enabling efficient manufacturing of large quantities of sheet metal components.
Benefits of 20-Ton Horizontal Press Machines
20-ton horizontal press brakes offer several advantages for metal fabrication:
- Versatility: These machines can perform various operations, including bending, forming, stamping, and punching, making them versatile tools for metal fabrication.
- Precision Bending: Horizontal press brakes provide precise control over bending angles, ensuring consistent and accurate bends, even for complex shapes.
- High Production Rates: Designed for high-volume production, these machines enable efficient manufacturing of large quantities of sheet metal components.
- Automation and Efficiency: Modern horizontal press brakes can be automated, reducing labor costs and increasing production efficiency. Automated controls allow for repetitive and consistent operations.
- Durability and Reliability: Constructed to withstand demanding industrial environments, 20-ton horizontal press brakes offer reliable performance over extended periods.
Safety Precautions for Operating 20-Ton Horizontal Press Machines
When operating 20-ton horizontal press brakes, it is crucial to adhere to strict safety protocols:
- Thorough Training: Operators must receive comprehensive training on the specific machine model, its operation, and safety procedures.
- Personal Protective Equipment (PPE): Always wear appropriate PPE, including safety glasses, gloves, and hearing protection, to protect from flying debris, sharp edges, and noise.
Sheet metal bending is a fundamental process in manufacturing, playing a crucial role in the creation of various metal components and products. One of the most essential machines used in this process is the press brake machine. This powerful equipment is designed to bend and shape metal sheets with precision, efficiency, and consistency, making it indispensable in many industries, from automotive to aerospace.
The press brake machine’s ability to produce complex bends and shapes with high accuracy has revolutionized metal fabrication. By applying a controlled force through a punch and die, these machines can create intricate and precise metal parts that meet exact specifications. The evolution of press brake machines, from simple manual devices to sophisticated computer-controlled systems, reflects the technological advancements in the field of metalworking.
In this article, we will explore the history, types, components, working principles, and applications of press brake machines. We will also delve into the advantages of using these machines, maintenance and safety tips, and future trends in press brake technology. Whether you are an industry professional, a manufacturing enthusiast, or simply curious about this vital piece of machinery, this comprehensive guide will provide valuable insights into the world of sheet metal bending press brake machines.
History of Press Brake Machines
The origins of metal bending can be traced back to ancient civilizations, where blacksmiths used rudimentary tools to shape metal. As technology progressed, so did the methods of metal bending, leading to the development of more sophisticated machinery.
The first press brake machines emerged during the Industrial Revolution, driven by the need for more efficient and precise metalworking tools. Early press brake machines were manually operated, requiring significant physical effort and skill from the operator. Despite their limitations, these machines marked a significant advancement in the field of metal fabrication.
The 20th century witnessed substantial improvements in press brake technology. The introduction of hydraulic systems in the 1940s allowed for greater force and control, enabling the bending of thicker and tougher metals. This innovation revolutionized the industry, making hydraulic press brake machines the standard for many years.
In recent decades, the advent of computer numerical control (CNC) technology has transformed press brake machines once again. CNC press brake machines offer unparalleled precision and automation, allowing for complex bending operations to be performed with minimal human intervention. These machines are equipped with advanced software that can program and execute intricate bending sequences, ensuring consistency and accuracy.
Today, press brake machines continue to evolve, incorporating cutting-edge technologies such as robotics and artificial intelligence. These advancements are paving the way for even greater efficiency, flexibility, and precision in metal fabrication.
Types of Press Brake Machines
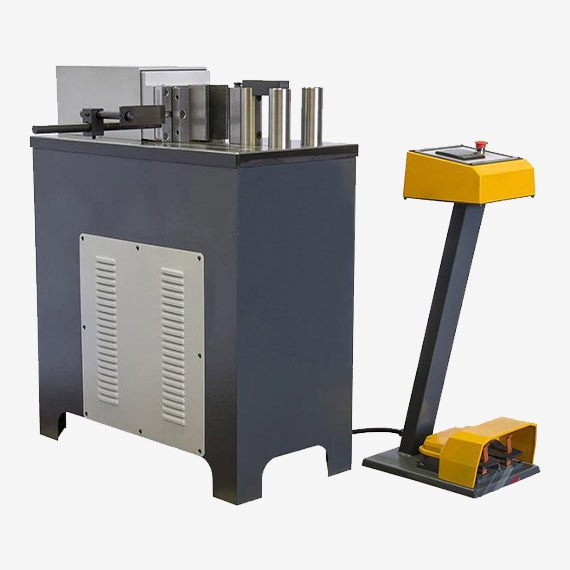
Press brake machines come in various types, each with its own features, advantages, and applications. Understanding the different types of press brake machines is essential for selecting the right equipment for specific metal bending tasks.
Manual Press Brake Machines
Features and Uses Manual press brake machines are the simplest type of press brakes, operated entirely by human effort. They are typically used for small-scale or low-volume production tasks, where high precision is not critical.
Advantages
- Cost-effective and affordable for small businesses
- Easy to operate and maintain
- Suitable for simple bending operations
Disadvantages
- Limited bending capacity and precision
- Labor-intensive and time-consuming
- Not suitable for high-volume production
Hydraulic Press Brake Machines
Features and Uses Hydraulic press brake machines use hydraulic fluid to generate the necessary force for bending metal sheets. They are widely used in various industries due to their versatility and reliability.
Advantages
- High bending capacity and precision
- Capable of handling thicker and tougher metals
- Smooth and consistent operation
Disadvantages
- Higher initial cost compared to manual machines
- Requires regular maintenance of hydraulic systems
- Potential for hydraulic fluid leaks
Electric Press Brake Machines
Features and Uses Electric press brake machines use electric motors to drive the bending process. They are known for their energy efficiency and precision.
Advantages
- Energy-efficient and environmentally friendly
- High precision and repeatability
- Lower operating costs compared to hydraulic machines
Disadvantages
- Limited force compared to hydraulic machines
- Higher initial cost than manual machines
- Requires skilled operators
CNC Press Brake Machines
Features and Uses CNC (Computer Numerical Control) press brake machines represent the pinnacle of press brake technology. They are equipped with advanced computer systems that control the bending process with exceptional precision.
Advantages
- Unmatched precision and accuracy
- Automated and programmable operations
- Suitable for complex and high-volume production
Disadvantages
- High initial cost and investment
- Requires skilled operators and programmers
- Complex maintenance and troubleshooting
Each type of press brake machine has its unique advantages and disadvantages, making it crucial to select the appropriate type based on specific production requirements and budget constraints.
Components of a Press Brake Machine
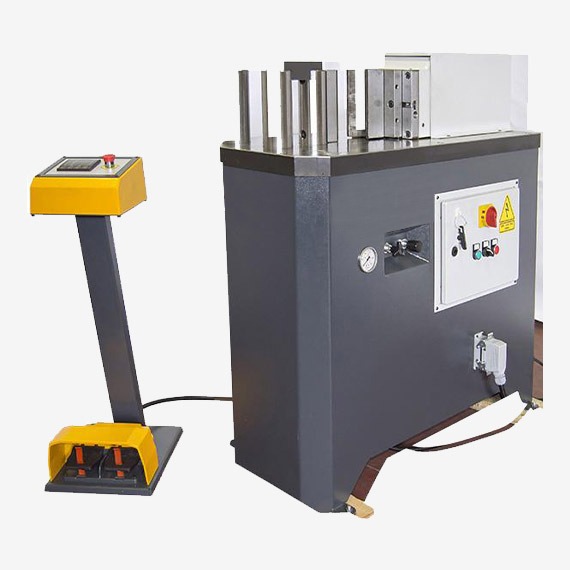
Press brake machines consist of several key components, each playing a vital role in the bending process. Understanding these components is essential for operating and maintaining the machine effectively.
Frame
The frame is the backbone of the press brake machine, providing structural support and stability. It is typically constructed from heavy-duty steel to withstand the forces exerted during the bending process.
Ram
The ram is a movable component that exerts force on the metal sheet, pressing it against the die to create the desired bend. The ram’s movement can be controlled manually, hydraulically, or electrically, depending on the type of press brake machine.
Die and Punch
The die and punch are the primary tools used in the bending process. The punch, attached to the ram, presses the metal sheet into the die, which is fixed to the machine’s bed. The shape and size of the die and punch determine the angle and radius of the bend.
Back Gauge
The back gauge is a positioning tool that helps in accurately aligning the metal sheet for bending. It ensures consistent bend angles and dimensions by providing a reference point for the sheet.
Control System
The control system manages the operation of the press brake machine. In manual machines, this may be a simple mechanical system, while hydraulic and electric machines use more advanced control systems. CNC press brake machines have sophisticated computer systems that program and control the entire bending process.
Safety Features
Press brake machines are equipped with various safety features to protect operators from accidents and injuries. These may include safety guards, emergency stop buttons, and light curtains that detect the presence of an operator’s hands near the bending area.
Working Principle
The basic working principle of a press brake machine involves applying a controlled force to bend metal sheets into specific shapes. Here are the key steps in the bending process:
- Sheet Positioning: The metal sheet is positioned on the machine’s bed, aligned against the back gauge to ensure precise placement.
- Tool Selection: The appropriate die and punch are selected based on the desired bend angle and radius. These tools are then installed on the machine.
- Bending Operation: The ram descends, pressing the punch into the metal sheet and forcing it into the die. This action creates the bend, with the angle and shape determined by the tools used and the force applied.
- Return Stroke: After the bend is completed, the ram ascends, releasing the pressure on the metal sheet. The sheet is then removed or repositioned for additional bends.
Precision and control are crucial in the bending process to ensure the accuracy and consistency of the bends. CNC press brake machines excel in this regard, as they use computer programming to control the ram’s movement and force, resulting in highly precise bends.
Applications of Press Brake Machines
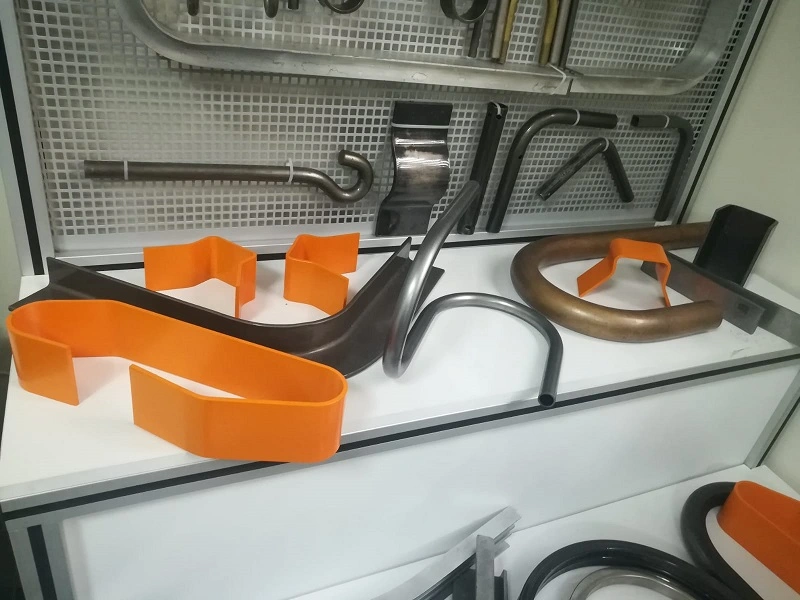
Press brake machines are used across various industries due to their versatility and precision. Here are some common applications:
- Automotive Industry: Manufacturing car body panels, chassis components, and brackets.
- Aerospace Industry: Producing aircraft parts, including wing components and fuselage sections.
- Construction Industry: Fabricating structural components, such as beams, columns, and brackets.
- Electronics Industry: Creating enclosures, chassis, and brackets for electronic devices.
- Furniture Industry: Making metal frames and components for furniture.
- HVAC Industry: Producing ductwork and ventilation components.
These machines are also used in creating custom metal parts and prototypes, showcasing their adaptability to various production needs.
Advantages of Using Press Brake Machines
Press brake machines offer several advantages that make them indispensable in metal fabrication:
- Precision and Accuracy: These machines can produce highly precise bends, ensuring that components meet exact specifications.
- Efficiency and Productivity: Press brake machines can perform complex bending operations quickly, increasing production efficiency.
- Versatility: They can handle a wide range of materials and thicknesses, making them suitable for various applications.
- Cost-effectiveness: By reducing material waste and increasing production speed, press brake machines can lower manufacturing costs.
Maintenance and Safety Tips
Proper maintenance and safety practices are essential for the efficient and safe operation of press brake machines. Here are some tips:
Routine Maintenance
- Regularly inspect the machine for wear and tear.
- Keep the machine clean and free from debris.
- Lubricate moving parts as recommended by the manufacturer.
- Check hydraulic fluid levels and replace as necessary.
Common Issues and Troubleshooting
- Misalignment of the die and punch: Adjust the alignment to ensure precise bends.
- Inconsistent bending angles: Check for wear on the tools and replace if needed.
- Hydraulic system leaks: Inspect seals and hoses, and replace any damaged components.
Safety Guidelines for Operators
- Always wear appropriate personal protective equipment (PPE).
- Ensure that safety guards and emergency stop buttons are in place and functional.
- Follow the manufacturer’s guidelines for safe operation.
- Undergo proper training before operating the machine.
Future Trends in Press Brake Technology
The future of press brake technology is shaped by advancements in automation, materials, and environmental considerations:
- Automation and Industry 4.0: The integration of robotics and IoT (Internet of Things) is enhancing the automation of press brake machines, leading to increased efficiency and reduced human intervention.
- Advanced Materials and Designs: The development of new materials and innovative designs is expanding the capabilities of press brake machines, allowing for more complex and precise bends.
- Environmental Considerations: Efforts to reduce energy consumption and minimize environmental impact are driving the adoption of electric press brake machines and other eco-friendly technologies.
Conclusion
Press brake machines are a cornerstone of modern metal fabrication, offering unmatched precision, efficiency, and versatility. From their historical evolution to the latest technological advancements, these machines continue to play a vital role in various industries.
Understanding the different types of press brake machines, their components, and working principles is essential for selecting the right equipment and maximizing its potential. By following proper maintenance and safety practices, operators can ensure the longevity and safe operation of these machines.
As we look to the future, advancements in automation, materials, and environmental sustainability will further enhance the capabilities of press brake machines, solidifying their place in the ever-evolving landscape of manufacturing.
Whether you are a seasoned professional or new to the field, this comprehensive guide provides valuable insights into the world of sheet metal bending press brake machines, highlighting their importance and potential in modern industry.
Components of a Press Brake Machine
Press brake machines consist of several key components, each playing a vital role in the bending process. Understanding these components is essential for operating and maintaining the machine effectively.
Frame
The frame is the backbone of the press brake machine, providing structural support and stability. Constructed from heavy-duty steel, the frame must be robust enough to withstand the significant forces exerted during the bending process. The frame’s design can vary depending on the machine type, but its primary function remains to ensure rigidity and durability.
Ram
The ram is a movable component that exerts force on the metal sheet, pressing it against the die to create the desired bend. The ram’s movement can be controlled manually, hydraulically, or electrically, depending on the type of press brake machine. In CNC press brakes, the ram’s motion is precisely controlled by computer programming, allowing for highly accurate and repeatable bends.
Die and Punch
The die and punch are the primary tools used in the bending process. The punch, attached to the ram, presses the metal sheet into the die, which is fixed to the machine’s bed. The shape and size of the die and punch determine the angle and radius of the bend. There are various types of dies and punches, each suited for different bending operations, such as V-dies, U-dies, and hemming dies.
Back Gauge
The back gauge is a positioning tool that helps in accurately aligning the metal sheet for bending. It ensures consistent bend angles and dimensions by providing a reference point for the sheet. Modern press brake machines often feature CNC-controlled back gauges, which can be programmed to automatically adjust positions for complex bending sequences, enhancing precision and efficiency.
Control System
The control system manages the operation of the press brake machine. In manual machines, this may be a simple mechanical system, while hydraulic and electric machines use more advanced control systems. CNC press brake machines have sophisticated computer systems that program and control the entire bending process. These systems can store multiple bending programs, allowing for quick setup and reduced downtime between jobs.
Safety Features
Press brake machines are equipped with various safety features to protect operators from accidents and injuries. These may include safety guards, emergency stop buttons, and light curtains that detect the presence of an operator’s hands near the bending area. Modern machines also incorporate safety sensors that halt the machine’s operation if a potential hazard is detected, ensuring a safer working environment.
Working Principle
https://www.youtube.com/embed/l8quDXXNNEg?feature=oembedWorking Principle
The basic working principle of a press brake machine involves applying a controlled force to bend metal sheets into specific shapes. Here are the key steps in the bending process:
- Sheet Positioning: The metal sheet is positioned on the machine’s bed, aligned against the back gauge to ensure precise placement. Proper alignment is crucial for achieving accurate and consistent bends.
- Tool Selection: The appropriate die and punch are selected based on the desired bend angle and radius. These tools are then installed on the machine. The selection of the correct tools is essential for achieving the desired bend geometry and avoiding damage to the metal sheet.
- Bending Operation: The ram descends, pressing the punch into the metal sheet and forcing it into the die. This action creates the bend, with the angle and shape determined by the tools used and the force applied. The bending process requires careful control of the ram’s speed and pressure to ensure precise and consistent results.
- Return Stroke: After the bend is completed, the ram ascends, releasing the pressure on the metal sheet. The sheet is then removed or repositioned for additional bends. In CNC press brakes, the return stroke and repositioning of the sheet can be automated, increasing efficiency and reducing operator fatigue.
Precision and control are crucial in the bending process to ensure the accuracy and consistency of the bends. CNC press brake machines excel in this regard, as they use computer programming to control the ram’s movement and force, resulting in highly precise bends. The ability to program complex bending sequences also allows for the efficient production of intricate parts with minimal manual intervention.
Applications of Press Brake Machines
https://www.youtube.com/embed/o1dG-pIFkTk?feature=oembedApplications of Press Brake Machines
Press brake machines are used across various industries due to their versatility and precision. Here are some common applications:
- Automotive Industry: Press brake machines are integral to manufacturing car body panels, chassis components, and brackets. These machines can produce complex shapes and bends required for modern vehicle designs, ensuring high precision and repeatability.
- Aerospace Industry: The aerospace industry demands high precision and stringent quality standards. Press brake machines are used to produce aircraft parts, including wing components and fuselage sections, where accuracy and consistency are paramount.
- Construction Industry: Press brake machines are utilized to fabricate structural components such as beams, columns, and brackets. These components must meet specific strength and dimensional requirements to ensure the safety and stability of buildings and other structures.
- Electronics Industry: In the electronics industry, press brake machines are used to create enclosures, chassis, and brackets for electronic devices. These components often require intricate bends and precise dimensions to accommodate various electronic components and assemblies.
- Furniture Industry: The furniture industry employs press brake machines to make metal frames and components for furniture. These machines enable the production of aesthetically pleasing and structurally sound furniture parts, such as legs, supports, and brackets.
- HVAC Industry: The HVAC industry uses press brake machines to produce ductwork and ventilation components. These machines can create complex bends and shapes needed for efficient air distribution and ventilation systems.
These machines are also used in creating custom metal parts and prototypes, showcasing their adaptability to various production needs. The ability to quickly and accurately produce custom components makes press brake machines valuable tools for manufacturers and fabricators across different industries.
Advantages of Using Press Brake Machines
Press brake machines offer several advantages that make them indispensable in metal fabrication:
- Precision and Accuracy: Press brake machines are designed to produce highly precise bends, ensuring that components meet exact specifications. CNC press brakes, in particular, offer unmatched precision and repeatability, allowing for the production of intricate and complex parts with tight tolerances.
- Efficiency and Productivity: These machines can perform complex bending operations quickly, increasing production efficiency. The automation capabilities of CNC press brakes reduce the need for manual intervention, leading to faster setup times and higher throughput.
- Versatility: Press brake machines can handle a wide range of materials and thicknesses, making them suitable for various applications. From thin aluminum sheets to thick steel plates, these machines can accommodate different bending requirements, providing flexibility in manufacturing processes.
- Cost-effectiveness: By reducing material waste and increasing production speed, press brake machines can lower manufacturing costs. The precision and efficiency of these machines minimize errors and rework, resulting in significant cost savings over time.
- Consistency: Press brake machines ensure consistent bend quality across multiple parts, which is essential for mass production. The ability to produce uniform parts enhances the overall quality and reliability of the final products.
- Customizability: Modern press brake machines, especially CNC models, offer high levels of customizability. Operators can program specific bending sequences and parameters, allowing for the production of custom parts tailored to unique design requirements.
- Reduced Labor Costs: Automation in CNC press brake machines reduces the need for skilled labor, lowering labor costs. These machines can operate with minimal supervision, enabling manufacturers to allocate human resources more efficiently.
- Enhanced Safety: Press brake machines are equipped with advanced safety features that protect operators from accidents and injuries. Safety guards, emergency stop buttons, and sensors contribute to a safer working environment, reducing the risk of workplace incidents.
These advantages highlight the critical role of press brake machines in modern metal fabrication, underscoring their value in achieving high-quality, efficient, and cost-effective manufacturing processes.
Maintenance and Safety Tips
Proper maintenance and safety practices are essential for the efficient and safe operation of press brake machines. Here are some tips:
Routine Maintenance
- Regular Inspection: Regularly inspect the machine for wear and tear. Check for any signs of damage or misalignment in the components, especially the die and punch.
- Cleaning: Keep the machine clean and free from debris. Accumulated dust and metal shavings can affect the machine’s performance and lead to premature wear.
- Lubrication: Lubricate moving parts as recommended by the manufacturer. Proper lubrication reduces friction and prevents wear, extending the machine’s lifespan.
- Hydraulic Fluid: Check hydraulic fluid levels and replace as necessary. Ensure that the hydraulic system is free from leaks and that the fluid is clean and at the proper level.
- Tool Maintenance: Inspect the die and punch for wear and replace them if needed. Sharp and well-maintained tools are crucial for achieving precise bends.
Common Issues and Troubleshooting
- Misalignment: Misalignment of the die and punch can result in inaccurate bends. Adjust the alignment to ensure precise bending operations.
- Inconsistent Bending Angles: Inconsistent bending angles may be due to worn tools or incorrect settings. Check the tools for wear and verify the machine’s settings.
- Hydraulic System Leaks: Hydraulic system leaks can affect the machine’s performance. Inspect seals and hoses regularly and replace any damaged components.
- Control System Errors: Errors in the control system, particularly in CNC machines, can disrupt operations. Ensure that the control system software is up-to-date and that any programming issues are addressed promptly.
Safety Guidelines for Operators
- Personal Protective Equipment (PPE): Always wear appropriate PPE, including safety glasses, gloves, and protective clothing, to prevent injuries.
- Safety Guards and Emergency Stops: Ensure that safety guards are in place and functional. Familiarize yourself with the location and operation of emergency stop buttons.
- Manufacturer Guidelines: Follow the manufacturer’s guidelines for safe operation. These guidelines provide crucial information on operating the machine safely and efficiently.
- Training: Undergo proper training before operating the machine. Training should cover machine operation, maintenance, and safety procedures.
- Awareness: Stay alert and aware of your surroundings while operating the machine. Avoid distractions and ensure that the work area is free from hazards.
By adhering to these maintenance and safety tips, operators can ensure the longevity, efficiency, and safe operation of press brake machines, minimizing downtime and reducing the risk of accidents.
Future Trends in Press Brake Technology
The future of press brake technology is shaped by advancements in automation, materials, and environmental considerations. Here are some key trends to watch:
Automation and Industry 4.0
The integration of robotics and the Internet of Things (IoT) is enhancing the automation of press brake machines. Industry 4.0 technologies enable machines to communicate and coordinate with each other, leading to increased efficiency and reduced human intervention. Automated press brake machines can perform complex bending operations with minimal oversight, improving productivity and precision.
Advanced Materials and Designs
The development of new materials and innovative designs is expanding the capabilities of press brake machines. Advanced materials, such as high-strength alloys and composites, require precise and powerful bending techniques. Modern press brake machines are being designed to handle these materials, enabling the production of more durable and lightweight components.
Environmental Considerations
Efforts to reduce energy consumption and minimize environmental impact are driving the adoption of electric press brake machines and other eco-friendly technologies. Electric press brakes are more energy-efficient than their hydraulic counterparts, producing less noise and requiring less maintenance. Additionally, manufacturers are exploring sustainable materials and processes to further reduce the environmental footprint of metal fabrication.
Smart Manufacturing
Smart manufacturing technologies, including artificial intelligence (AI) and machine learning, are being integrated into press brake machines. These technologies enable predictive maintenance, real-time monitoring, and adaptive control, enhancing machine performance and reducing downtime. AI-powered systems can optimize bending operations by analyzing data and making adjustments in real-time.
User-Friendly Interfaces
Future press brake machines are likely to feature more user-friendly interfaces, making them easier to operate and program. Touchscreen controls, intuitive software, and augmented reality (AR) training tools will simplify the operation of these machines, reducing the learning curve for operators.
These trends highlight the ongoing evolution of press brake technology, promising greater efficiency, precision, and sustainability in metal fabrication.
Conclusion
Press brake machines are a cornerstone of modern metal fabrication, offering unmatched precision, efficiency, and versatility. From their historical evolution to the latest technological advancements, these machines continue to play a vital role in various industries.
Understanding the different types of press brake machines, their components, and working principles is essential for selecting the right equipment and maximizing its potential. By following proper maintenance and safety practices, operators can ensure the longevity and safe operation of these machines.
As we look to the future, advancements in automation, materials, and environmental sustainability will further enhance the capabilities of press brake machines, solidifying their place in the ever-evolving landscape of manufacturing.
Whether you are a seasoned professional or new to the field, this comprehensive guide provides valuable insights into the world of sheet metal bending press brake machines, highlighting their importance and potential in modern industry.
Press brake machines will undoubtedly continue to evolve, driven by technological innovations and industry demands. Staying informed about these advancements and adopting best practices will enable manufacturers to leverage the full potential of press brake machines, ensuring continued success in their metal fabrication endeavors.
Cold forming machines are industrial machines used to shape and form metal materials at room temperature, without the application of heat. This process is typically used to produce parts with high precision and mechanical properties, including strength, hardness, and dimensional accuracy.
Here’s an overview of the key elements of cold forming machines:
Types of Cold Forming Processes:
- Stamping: The material is placed between dies and pressed into shape using a press machine. This is commonly used for producing flat parts.
- Roll Forming: The material is passed through a series of rollers to gradually form it into a desired shape. This is ideal for producing long lengths of materials, such as channels or profiles.
- Cold Heading: This is typically used to form fasteners such as bolts and screws. The process involves the deformation of the metal into a specific shape by compressing it in a die.
- Bending: Involves bending the metal to a required angle without heating it.
- Extrusion: In cold extrusion, the material is forced through a die to create long parts with consistent cross-sections.
Advantages of Cold Forming:
- Improved Material Properties: Cold forming increases the strength and hardness of the material due to work hardening.
- High Precision: The process can create parts with tight tolerances and fine detail.
- Cost Efficiency: It is often more cost-effective than hot forming because it eliminates the need for heating and the associated energy costs.
- Minimal Waste: Cold forming typically results in very little waste material, making it more efficient in terms of material usage.
Applications:
Cold forming is used in a wide range of industries, including automotive, aerospace, electronics, construction, and general manufacturing, to create components like gears, shafts, brackets, fasteners, and electrical connectors.
Cold forming machines are designed to shape metal materials at room temperature, utilizing pressure to mold or bend them into specific shapes. Unlike hot forming processes that require heating the material to high temperatures, cold forming relies on the metal’s ductility at ambient temperatures, which is particularly advantageous for maintaining material integrity and achieving high precision in the final products. This process is commonly used in industries where parts need to be made with high strength and durability, such as automotive, aerospace, and electronics.
In cold forming, the material is typically fed into a machine, where it undergoes various stages of deformation, such as stamping, rolling, heading, or bending. The shaping process is carried out through mechanical presses or rollers, which apply controlled force to the metal. One of the key benefits of cold forming is that it enhances the material’s mechanical properties. For example, the metal’s strength is often increased due to the work hardening that occurs during the process. Cold forming can also produce very precise and complex shapes, which is crucial for applications requiring tight tolerances or intricate details.
Additionally, cold forming can reduce material waste because it generally involves processes like stamping or extrusion, where the metal is used efficiently and little scrap is generated. It’s also a cost-effective method compared to other forming processes, as there’s no need for heating, which saves on energy and time. The resulting products tend to be highly durable, with improved surface finishes, and can be used for parts like gears, fasteners, and structural components.
The versatility of cold forming machines makes them suitable for a wide range of materials, including steel, aluminum, and other metals. Their applications are diverse, extending across different sectors, such as manufacturing parts for the automotive industry, aerospace components, electrical connectors, and hardware. The process continues to be a preferred choice for producing high-quality, high-strength metal parts in a highly efficient manner.
Cold forming machines are versatile and highly efficient, particularly in industries requiring high-volume production of complex metal parts. The machines typically use specialized dies and tooling to apply compressive force on the material, shaping it without the need for heat. This not only conserves energy but also helps maintain the metal’s original properties, such as hardness and tensile strength. For example, during cold heading, the metal is deformed in a series of dies to create components like bolts, nuts, and rivets, often with minimal waste.
One of the standout features of cold forming is its ability to produce parts with enhanced mechanical properties, particularly in terms of strength and hardness. This is because the process induces a phenomenon known as “work hardening,” where the metal becomes stronger as it is deformed, which can be beneficial for applications that require durable, high-performance components. This is especially true in industries like aerospace and automotive manufacturing, where parts must withstand high levels of stress and pressure.
The precision that cold forming offers is another key advantage. With the use of high-precision tools and equipment, cold forming can produce parts that meet tight tolerances and have intricate geometries. This is critical for applications such as electronics, where small, detailed components are often required, or for making complex fasteners used in automotive assemblies. The machines are capable of delivering consistent results over large production runs, which is essential for mass manufacturing operations.
Cold forming machines can handle a wide range of materials, from mild steel to high-strength alloys, and can be tailored to suit specific production needs. Whether using a mechanical press, a hydraulic press, or a rolling mill, manufacturers can select the type of cold forming machine that best fits the material and complexity of the part being produced. The process also allows for different variations of forming techniques, such as impact or shear forces, to achieve the desired shape and properties.
Overall, the appeal of cold forming machines lies in their ability to produce parts with high precision, enhanced material properties, and minimal waste, all while being energy efficient and cost-effective. Whether for mass production or custom parts, cold forming continues to be a fundamental process in modern manufacturing, enabling the creation of high-quality metal components used across a broad spectrum of industries.
Steel Bending Machine
A steel bending machine is a type of industrial equipment used to bend steel and other metal materials into various shapes and angles. The process is commonly employed in construction, manufacturing, and fabrication industries to create steel components that need to be formed into specific configurations, such as angles, curves, or circular shapes. Steel bending machines are designed to handle different grades and thicknesses of steel, ensuring high precision and repeatability for mass production or custom fabrication needs.
These machines typically use mechanical or hydraulic systems to apply controlled force to the steel, bending it around a die or mandrel. Depending on the design of the machine and the complexity of the bending operation, the process can either involve a single-axis bend (such as in pipe bending) or multi-axis bends for more complex shapes (as in structural beams or metal frames). Steel bending machines can also be used to create bends at precise angles, allowing for a high level of control over the final product.
One of the key features of steel bending machines is their ability to produce clean, accurate bends without causing excessive deformation or material stress. This is crucial in maintaining the structural integrity and appearance of the bent steel, particularly for applications where the steel will bear loads or be visible in the finished product. For example, in the construction of metal frames for buildings or bridges, precise bending is essential for ensuring the stability and strength of the structure.
Steel bending machines come in several different types, each suited for specific bending needs:
- Press Brake: One of the most common types, press brakes use a punch and die to apply force to the steel sheet, bending it into the desired shape. These machines are typically used for sheet metal bending and can accommodate various thicknesses and lengths of material.
- Roll Bending Machine: Used for bending metal plates or bars into curves, these machines have rollers that gradually shape the steel by passing it through the machine. Roll bending is commonly used for producing cylindrical shapes or large-radius bends.
- Pipe Bender: These machines are specialized for bending pipes and tubes, making them ideal for applications like plumbing, HVAC systems, and automotive exhaust systems. They use either rotary or rotary draw bending methods to shape the pipe into the required angles without kinking.
- Section Bender: Section benders are designed for bending structural steel sections, such as I-beams, H-beams, and channels. They are commonly used in the fabrication of frames and other structural components.
In addition to their versatility, steel bending machines are designed to be efficient, reducing the amount of time required for each bend and minimizing waste. Automation features in some advanced models also enable faster setups, higher production rates, and improved accuracy.
Overall, steel bending machines are crucial for the production of metal components that require precise, consistent bends. They are widely used in industries ranging from construction and infrastructure to automotive and aerospace, where structural integrity and precision are key.
Steel bending machines are essential tools in various industries that require the bending of steel and other metal materials into specific shapes and angles. These machines are designed to provide precise control over the bending process, ensuring that steel components maintain their structural integrity and meet required specifications. The bending process typically involves applying force to the material using either mechanical or hydraulic systems, allowing the metal to be shaped around a die or mandrel. This technique is widely used in construction, manufacturing, and fabrication, where steel needs to be bent for structural components, pipes, frames, and other applications.
These machines are capable of handling a range of steel types and thicknesses, allowing for versatility in the types of products they can produce. The ability to produce accurate bends without causing deformation is a key feature of steel bending machines. This ensures that the steel retains its strength and appearance after the bending process. Whether creating steel frames for buildings, bending pipes for plumbing, or forming metal components for machinery, the precision provided by these machines is crucial for the quality and safety of the final product.
Steel bending machines can perform various bending operations, depending on the type of machine and the complexity of the task. Some machines use press brakes to apply force to steel sheets, shaping them into the desired angle or form. Others, such as roll bending machines, can gradually bend metal plates or bars into curves or circular shapes. For specialized bending of pipes and tubes, pipe benders are used to create smooth, consistent bends without compromising the integrity of the material. In addition, section benders are designed to bend larger structural steel components, such as beams and channels, which are often needed for larger-scale construction projects.
The versatility of steel bending machines is enhanced by the range of automation features available on modern models. Automated controls allow for faster setups and higher production rates, making them ideal for high-volume production or complex, custom fabrication tasks. With the ability to bend a variety of materials and achieve precise results, these machines reduce waste and improve efficiency, ensuring that the steel is used effectively.
In industries like automotive, construction, and aerospace, where strength, durability, and accuracy are essential, steel bending machines play a vital role in the production of metal components. They are fundamental tools in ensuring that steel parts meet exacting standards while maintaining cost efficiency and reducing production time.
Cutting Machine for Sheet Metal
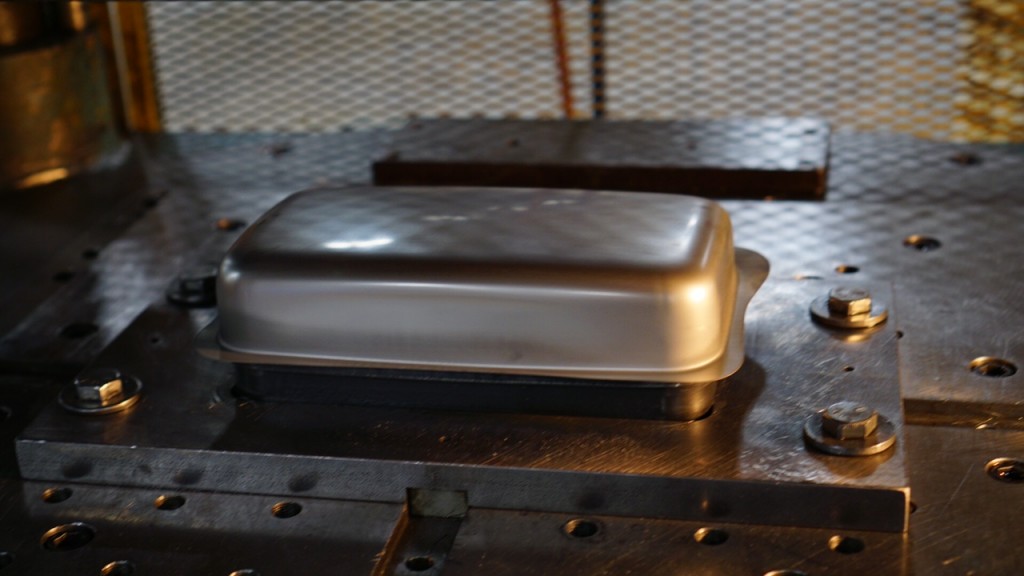
A cutting machine for sheet metal is a vital tool in industries where metal sheets need to be cut into specific shapes and sizes for various applications. These machines are designed to efficiently and accurately cut through different types of metal sheets, including steel, aluminum, and other alloys, with minimal waste and high precision. The process involves applying mechanical force, heat, or a combination of both to separate or shape the metal sheets according to the desired specifications.
Cutting machines for sheet metal can come in various types, each suited for different cutting needs and materials. Some of the most common types of cutting machines include shears, laser cutters, plasma cutters, and water jet cutters. Shearing machines, for example, are widely used for straight-line cutting of thin metal sheets, while more advanced technologies like laser cutting offer the ability to create intricate designs with high precision, especially for thinner materials. Plasma cutting, on the other hand, is often used for thicker materials, offering high-speed cuts with a high degree of accuracy.
These machines offer significant advantages, such as high cutting speed, minimal distortion of the material, and the ability to handle complex geometries. For example, laser cutting machines use a high-powered laser to focus energy onto the metal, vaporizing it along the cutting path. Plasma cutters utilize a high-temperature plasma stream to melt and blow away the metal, while water jet cutters use a high-pressure stream of water mixed with abrasives to cut through the material without generating heat, which helps to maintain the material’s integrity.
The choice of cutting machine depends on several factors, including the type of metal, thickness, complexity of the cut, and production volume. For large production runs, automated cutting machines may be employed to increase efficiency and reduce labor costs, while custom or small-batch production may rely on more manual or semi-automated machines for greater flexibility.
In industries like automotive, construction, aerospace, and metal fabrication, sheet metal cutting machines are essential for creating a wide range of components such as car panels, structural beams, ducts, and enclosures. Their ability to deliver precise cuts quickly and consistently makes them indispensable tools in modern manufacturing.
A cutting machine for sheet metal is an essential piece of equipment used in various industries to precisely cut metal sheets into specific shapes and sizes. These machines are designed to handle a wide range of materials like steel, aluminum, and other metals, making them versatile tools in metalworking and manufacturing processes. The cutting process can be accomplished through different methods, each suited to different types of metal, thicknesses, and desired results.
Machines like shears are commonly used for straight-line cutting of thinner sheets, providing quick and clean cuts. These machines apply a mechanical force to the metal, making them ideal for mass production of simple, straight cuts. For more intricate or detailed designs, technologies like laser cutting are often used. Laser cutters employ a focused laser beam to melt or vaporize the metal along the cutting path, offering extremely high precision. This method is particularly useful for thin materials or parts that require intricate patterns and detailed shapes.
Plasma cutting is another popular technique, particularly when dealing with thicker materials. Plasma cutters use an ionized gas stream, which reaches temperatures high enough to melt the metal, allowing it to be blown away along the cutting path. This method is known for its speed and ability to cut through metals with varying thicknesses, but it may generate more heat, which can sometimes affect the surrounding material.
Water jet cutting is a process that uses a high-pressure stream of water, often mixed with abrasives, to cut through metal sheets. This method has the advantage of not generating heat, which can prevent the material from warping or losing its mechanical properties. Water jet cutting is especially effective for materials that are sensitive to heat, like aluminum and copper.
The choice of cutting machine depends on several factors such as the material to be cut, the thickness of the metal, the complexity of the cuts required, and the scale of production. Some machines are designed for high-volume, automated cutting, while others are more suitable for custom or smaller production runs, offering flexibility and adaptability for different jobs.
Cutting machines for sheet metal are crucial in industries like automotive, aerospace, construction, and general metal fabrication. They are used to create components ranging from car body panels to structural supports and ducts. The ability of these machines to produce precise, consistent cuts quickly is key to ensuring the quality and efficiency of the manufacturing process. These machines also help to reduce material waste and labor costs, making them valuable tools for improving productivity in metalworking operations.
The continued development and refinement of cutting machines for sheet metal have further enhanced their capabilities, making them more efficient, accurate, and cost-effective. With advancements in automation, modern cutting machines can integrate with computer numerical control (CNC) systems, allowing for precise control over the cutting process and reducing the need for manual intervention. CNC machines are particularly beneficial for applications that require repeated, high-precision cuts, ensuring that every part produced meets the same exacting standards.
Automation has also increased the speed of cutting operations, significantly reducing production time. This is particularly valuable in industries where time is critical, such as automotive manufacturing, where large quantities of parts must be produced quickly and with high consistency. Automated material handling systems can further optimize the process by automatically loading and unloading materials, improving throughput, and minimizing the risk of human error.
Another major advantage of modern cutting machines is their ability to minimize material waste. Laser cutting, for example, is known for its efficiency in material usage, as the narrow width of the laser beam allows for cuts that are almost as narrow as the material thickness, reducing scrap. Additionally, advanced software used in these machines can optimize the layout of the cuts to make the most of the available sheet material, further minimizing waste and maximizing material yield.
Maintenance and operational costs have also improved with newer models, thanks to advances in machine design, durability, and automation. Many cutting machines now include monitoring systems that track performance and alert operators to any issues before they lead to downtime. These systems help ensure that machines operate at peak efficiency, reducing unexpected repairs and maintenance costs.
The versatility of sheet metal cutting machines also allows them to be used in a wide range of industries beyond automotive and aerospace. For instance, in architecture and construction, they are used to cut metal panels for building facades, roofing systems, and structural reinforcements. In electronics, cutting machines help produce components like enclosures, connectors, and heat sinks, where precision is critical to the function of the final product. Even in the energy sector, these machines play a role in manufacturing components for wind turbines, solar panels, and oil rigs.
With their ability to adapt to different materials, thicknesses, and cut complexities, sheet metal cutting machines remain indispensable in modern manufacturing. As technology continues to evolve, the machines will likely become even more precise, faster, and more energy-efficient, making them even more essential to industries that rely on the creation of high-quality metal components.
Joggle Machine
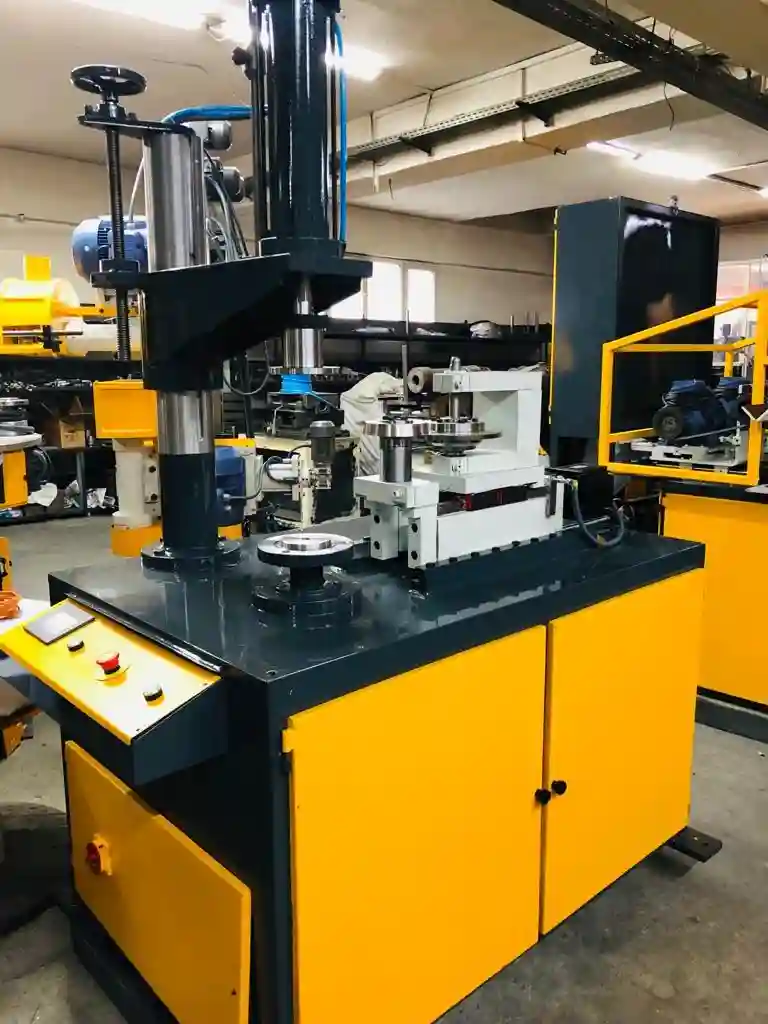
A joggle machine is a specialized piece of equipment used in metalworking to create a joggle, which is a small, controlled offset or step in a metal sheet or part. This offset is typically used to align parts, create a more secure fit between metal pieces, or prepare components for welding. The joggle process is especially important in industries like aerospace, automotive, and construction, where precise alignment and the ability to fit components together smoothly are crucial.
The joggle machine works by applying force to a metal sheet or part, bending it in a specific way to create the desired offset or step. The process can be used to form joggles in various materials, including aluminum, steel, and other alloys, with different thicknesses. These machines are designed to provide accurate and consistent results, ensuring that the joggle is uniform and fits perfectly with the corresponding part.
In applications like sheet metal fabrication, the joggle is often used to create flanges or joining points where two metal parts need to be connected. By adding a small offset, a joggle ensures that the parts align correctly and create a tight, secure fit for welding, bolting, or riveting. This can improve the strength and stability of the joint and can also help with the assembly process, reducing the potential for misalignment or gaps.
Joggle machines are typically equipped with adjustable dies or tools that allow the operator to control the size and angle of the joggle, depending on the specific requirements of the part. These machines are often integrated into automated production lines to facilitate the mass production of metal components with joggles. In some cases, CNC-controlled joggle machines offer high precision and repeatability, ensuring that each part is consistently formed to the required specifications.
The ability to create precise joggles using a joggle machine is essential for industries that require high-quality, durable metal parts. Whether for aerospace applications, where the integrity of joints is critical, or for automotive and construction projects, the joggle machine plays a vital role in ensuring the successful assembly of metal components.
A joggle machine is an essential tool in metalworking used to create a joggle, which is a controlled offset or step in metal sheets or parts. The joggle process helps ensure precise alignment between metal components, especially in applications that require tight fits for welding, bolting, or riveting. The offset created by the joggle machine allows for smoother assembly and a more secure connection between parts, which is critical in industries such as aerospace, automotive, and construction.
These machines work by applying force to a metal piece to form a specific offset at a precise angle or distance. The result is an evenly shaped step or bend in the metal, which helps components fit together with minimal gaps or misalignment. This can be particularly important in industries where components need to fit together perfectly to maintain strength and structural integrity, such as in aircraft fuselages, automotive frames, or building structural supports.
Joggle machines are designed for accuracy and repeatability, ensuring that every joggle is made to the exact specifications required for a particular application. The process allows manufacturers to produce parts that can be easily joined together, providing both mechanical stability and ease of assembly. The machine typically uses adjustable dies or tooling to control the size and shape of the joggle, allowing operators to tailor the process to different materials, thicknesses, and part configurations.
In modern manufacturing, many joggle machines are automated or CNC-controlled, which adds a level of precision and efficiency. Automation makes it easier to produce large batches of components with consistent results, reducing the chance of errors and ensuring that each part is identical. This is particularly useful in mass production settings where high precision and high throughput are crucial.
Joggle machines are crucial in industries where parts must meet strict tolerances and fit together perfectly, whether for structural strength, ease of assembly, or both. The machine’s ability to create precise joggles ensures that components will align correctly during the assembly process, reducing the risk of defects and improving overall product quality. As technology evolves, the joggle machine continues to be an important part of the manufacturing process, especially in industries that require durable, high-quality metal parts.
As joggle machines evolve, advancements in technology have led to more sophisticated models capable of handling a wider range of materials and offering greater flexibility in production. Modern joggle machines, especially those with CNC (Computer Numerical Control) capabilities, can be programmed to perform complex joggle patterns with high precision, enabling manufacturers to meet increasingly stringent design specifications. This automation has significantly reduced the amount of manual labor required, improving both the efficiency and consistency of the production process.
The ability to create multiple joggles on a single part is another feature that modern machines offer, making them even more versatile. This capability allows for the creation of intricate, multi-step designs that would have been difficult or time-consuming to produce manually. The machines can handle various types of metal, including aluminum, steel, stainless steel, and other alloys, and are capable of producing joggles on metal sheets of different thicknesses. This broad capability makes them useful in a variety of applications, from complex aerospace parts to more routine automotive and construction components.
Furthermore, joggle machines are often integrated with other machines in a fully automated production line, which can significantly speed up the entire fabrication process. By linking the joggle machine with cutting, bending, and welding systems, manufacturers can streamline the creation of parts, reducing handling times and improving the overall flow of production. This integration helps reduce costs, minimize errors, and shorten lead times, allowing businesses to meet demand more effectively.
In industries where quality control is critical, the precision offered by modern joggle machines is invaluable. Automated systems often come with built-in inspection capabilities, ensuring that each part meets required specifications before it moves to the next stage of production. This ensures that defective or misaligned components are caught early, preventing costly mistakes further down the production line.
Joggle machines also contribute to sustainability efforts in manufacturing by minimizing material waste. The precise nature of the joggle, along with automated layout optimization, allows manufacturers to make the best use of available material, reducing scrap and enhancing overall material efficiency. This is particularly important in industries where high-cost materials like titanium or high-strength alloys are used, making the efficient use of resources a priority.
As manufacturing processes continue to advance, joggle machines will likely become even more automated, precise, and versatile, ensuring their place as essential tools for producing high-quality, reliable components in a wide range of industries. Their role in creating secure, well-aligned joints between metal parts will remain crucial for building products that meet the exacting standards of sectors like aerospace, automotive, and construction, where safety and performance are of the utmost importance.
Sheet Metal Machinery
Sheet metal machinery encompasses a range of equipment used to shape, cut, form, and finish metal sheets into specific shapes or components. These machines are crucial in industries such as automotive, aerospace, construction, and general manufacturing, where precision and efficiency are essential for producing metal parts and assemblies.
One of the most common machines in sheet metal fabrication is the shearing machine, used to cut metal sheets into straight lines. Shears can handle different materials and thicknesses, providing clean and precise cuts. Laser cutting machines are another widely used tool, which utilize a high-powered laser to cut through sheet metal with exceptional precision. Laser cutters are particularly beneficial for intricate patterns and fine details, making them suitable for applications that require detailed work.
Press brakes are used to bend sheet metal into various angles and shapes. They work by applying force through a punch and die mechanism, allowing manufacturers to create parts like metal brackets, frames, and enclosures. These machines can handle both simple and complex bends, and more advanced models use CNC controls to ensure high precision and repeatability in production.
Roll forming machines are used for producing continuous profiles from metal sheets. By passing the metal through a series of rollers, roll forming machines gradually shape the metal into specific profiles, such as channels, beams, and roofing panels. This process is often used for high-volume production of long, uniform shapes.
Punch presses are used to create holes, slots, or other forms in metal sheets by using a punch and die system. These machines can be automated to perform multiple operations in one cycle, making them ideal for mass production of components like electrical panels, ventilation ducts, and other sheet metal products that require holes or complex shapes.
CNC machines, like CNC punching machines or CNC laser cutters, offer advanced automation and control, allowing for highly precise and efficient production of complex sheet metal parts. These machines are typically controlled by computer programs, which makes them ideal for mass production or jobs requiring consistent quality across large volumes.
Flanging machines and joggle machines are also used in sheet metal fabrication. A flanging machine is designed to create a flange or lip on the edge of a sheet metal piece, which can then be used for joining or securing other parts. Joggle machines, as previously mentioned, are used to create controlled offsets or steps in the metal, ensuring perfect alignment for welding or other assembly processes.
Finally, welding machines, such as spot welders and TIG/MIG welders, play a critical role in sheet metal fabrication, allowing metal sheets to be permanently joined together. These machines are crucial for the final assembly of metal parts and ensure that components remain securely fastened, providing the necessary strength and durability.
Overall, sheet metal machinery is a diverse and essential aspect of modern manufacturing, enabling the efficient production of high-quality metal components used in a wide range of industries. Whether cutting, bending, forming, or joining, these machines offer the precision, speed, and reliability required for producing durable and accurate metal parts.
Sheet metal machinery is a vital part of modern manufacturing, enabling the production of a wide variety of metal components used in different industries. These machines handle different processes such as cutting, bending, forming, punching, and welding, allowing manufacturers to produce precise and durable parts that meet specific design requirements. The versatility of sheet metal machinery is evident in the different types of machines available, each designed for specific tasks but often capable of performing a variety of operations depending on the setup and tooling used.
Machines like shearing machines are fundamental for cutting sheet metal into manageable sizes. They provide straight cuts with high precision, ensuring that the material is ready for further processing. Laser cutting machines, on the other hand, offer higher precision and can handle intricate designs, allowing manufacturers to create complex patterns and shapes in thin to medium-thickness metals. Their ability to focus a laser beam on a precise area makes them perfect for tasks requiring fine details and clean cuts, reducing the need for post-processing.
Press brakes are integral for bending sheet metal into the desired angles or shapes. The press brake’s ability to apply force through a punch and die mechanism makes it possible to create everything from simple bends to more complex geometries, all with high repeatability. Modern press brakes, especially those with CNC controls, provide manufacturers with more flexibility and accuracy, ensuring parts are consistently bent to exact specifications across large production runs.
Roll forming machines are essential for continuous production of profiles from metal sheets. This process is especially useful for high-volume manufacturing, such as in the production of roofing materials or metal channels used in construction. The process involves passing metal through a series of rollers to shape it into the desired profile, ensuring that the final product is uniform and consistent.
Punch presses are another critical piece of sheet metal machinery. These machines create holes, slots, or other complex shapes in sheet metal by applying a punching force. With the ability to carry out multiple operations within a single cycle, punch presses are ideal for high-speed production of parts like electrical enclosures, ventilation ducts, or automotive components. The automation available in modern punch presses allows for faster production times and ensures precision even in high-volume runs.
CNC sheet metal machinery, such as CNC laser cutters or CNC punching machines, brings advanced automation and control to the process. These machines are controlled by computer programs, which means parts can be produced with a high level of accuracy and consistency. The ability to input detailed designs and quickly make adjustments via software gives manufacturers the flexibility to adapt to different orders, ensuring that even complex parts are produced efficiently.
Welding machines also play a crucial role in sheet metal fabrication, providing the means to join parts together securely. Spot welders, MIG (Metal Inert Gas) welders, and TIG (Tungsten Inert Gas) welders are commonly used for joining sheet metal parts, with each method offering specific advantages depending on the materials and joint requirements. These machines ensure that the final assembled parts are durable and capable of withstanding the forces and conditions they will face in their respective applications.
In the production of sheet metal parts, other specialized machines, such as flanging machines, which create flanges or lips for joining metal pieces, and joggle machines, which create precise offsets in metal sheets, are also essential. These machines ensure that metal components can be joined seamlessly during assembly, whether for structural applications, electrical enclosures, or automotive parts.
The development of automated and CNC-controlled sheet metal machinery has revolutionized the manufacturing process, reducing human error, increasing speed, and improving precision. This has allowed for faster turnaround times, reduced material waste, and higher-quality products. As industries demand higher levels of customization and faster production times, sheet metal machinery continues to evolve, offering greater capabilities and versatility to meet the needs of modern manufacturing.
As the demand for faster, more accurate, and cost-effective production continues to grow, sheet metal machinery is becoming more advanced and automated. Technological innovations are enhancing the performance of these machines, making them more efficient, versatile, and capable of producing increasingly complex parts with minimal waste. The integration of robotics and artificial intelligence (AI) in sheet metal fabrication is one example of how automation is transforming the industry. Automated systems can now handle material handling, loading, and unloading tasks, reducing labor costs and improving overall efficiency in production lines.
For instance, automated material handling systems are often integrated with CNC punch presses, laser cutting machines, and press brakes, allowing for seamless operation without manual intervention. These systems can automatically load metal sheets onto the machine, manage inventory, and remove finished parts from the production line. The automation of these processes ensures a continuous workflow, reducing downtime between operations and improving throughput, which is especially beneficial in high-volume production environments.
Moreover, the software used in modern sheet metal machinery has advanced significantly. CAD (Computer-Aided Design) and CAM (Computer-Aided Manufacturing) software are now commonly used to design parts and generate machine instructions. These software systems help optimize the cutting and bending process, reducing material waste and ensuring that parts are made with minimal scrap. Software also allows manufacturers to easily make changes to designs and adapt to new production requirements, providing greater flexibility and efficiency in production schedules.
In addition to enhancing production efficiency, the evolution of sheet metal machinery has also focused on improving sustainability. As manufacturers seek to reduce their environmental impact, newer machines are being designed to use less energy and generate less waste. Laser cutting machines, for example, are highly efficient in terms of material usage, producing precise cuts that minimize waste. Similarly, advancements in press brake technology have resulted in machines that can work with thinner materials, reducing energy consumption and waste generated during bending.
The flexibility of modern sheet metal machinery also allows manufacturers to produce parts with more complex geometries, enabling the creation of custom metal components for industries like aerospace, automotive, and medical device manufacturing. In aerospace, for example, sheet metal machinery is used to create lightweight and durable parts for aircraft structures, while in automotive manufacturing, it is used for precision parts like body panels and frames. The ability to produce parts with intricate designs and exact specifications is key to meeting the stringent requirements of these industries.
Maintenance and support for sheet metal machinery have also improved, with remote monitoring and diagnostic tools being increasingly integrated into machines. These tools allow manufacturers to monitor the performance of their equipment in real-time, identifying potential issues before they result in costly downtime. Predictive maintenance technology can analyze machine data and provide alerts for scheduled maintenance, helping to extend the life of the machinery and reduce the likelihood of unexpected failures.
Overall, the future of sheet metal machinery is moving toward even greater automation, precision, and sustainability. With the continuous improvement of technology, manufacturers are better equipped to meet the growing demand for high-quality, cost-effective, and customized metal parts across various industries. The integration of advanced software, automation, and energy-efficient technologies is setting the stage for a new era of sheet metal fabrication that will help drive innovation and productivity in manufacturing.
Steel Bending Machine
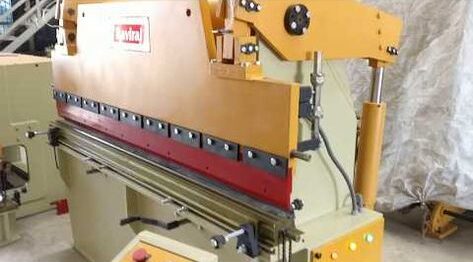
A steel bending machine is a type of industrial equipment used to bend steel and other metals into various shapes and angles. These machines are essential in industries like construction, automotive, aerospace, and metal fabrication, where precise bending of steel is required to create parts such as beams, brackets, frames, and other structural components. Steel bending machines apply force to metal to deform it, creating a bend at a desired angle or radius, which is critical in producing parts that fit specific design requirements.
There are different types of steel bending machines, each suited for specific tasks and types of bending. Press brakes are the most commonly used steel bending machines in industrial settings. They work by using a punch and die system to bend steel sheets or plates. The machine applies controlled force to the metal, bending it at a specific angle. Press brakes can handle a range of steel thicknesses, and modern versions are often CNC (Computer Numerical Control) machines, which allows for highly accurate and repeatable bends.
Angle bending machines are another type of machine used specifically for bending angle steel or structural steel sections. These machines are designed to handle the bending of angles, flats, and square bars into specific shapes or curves. They are widely used in the production of metal frames, columns, and other structural components that require precise bends in specific directions.
Roll bending machines are used to create curves or arcs in steel plates or sheets. These machines feature a set of rollers that gradually bend the metal as it passes through them. Roll bending is often used to create cylindrical shapes or large, curved structures, such as pipes or tanks. The machine applies pressure evenly across the steel sheet to form the desired curve, making it an ideal choice for creating round shapes or large-radius bends.
For more complex and precise bending tasks, CNC bending machines are increasingly common in steel bending operations. These machines offer advanced control, allowing for multiple bends to be performed in a single cycle. With CNC technology, operators can input specific parameters and designs, and the machine will automatically adjust to produce parts with high precision. CNC bending machines also improve efficiency by reducing human error and speeding up production times, making them ideal for high-volume manufacturing.
The process of bending steel is highly dependent on the type of steel being used, as different grades and thicknesses of steel may require varying amounts of force or different bending techniques. Some steel bending machines are equipped with adjustable settings to accommodate these variables, allowing for more flexibility in production.
Steel bending machines are crucial for the construction of metal frames, vehicle parts, industrial machinery, and structural supports. They help manufacturers create high-quality, durable metal parts with the exact specifications needed for assembly. Modern machines are designed for high efficiency, precision, and ease of use, making them essential tools in industries where metalworking is a key component of production. Additionally, the integration of advanced technologies such as automation and CNC systems has made steel bending machines faster, more accurate, and more cost-effective, improving overall productivity in metal fabrication.
Steel bending machines play a pivotal role in the metalworking industry by ensuring the precise bending of steel into various shapes and forms. These machines are designed to work with different grades and thicknesses of steel, making them highly versatile and essential for producing a wide range of parts and components. Whether it’s bending metal sheets, creating curved shapes, or forming angles and structural elements, steel bending machines provide the accuracy and control needed for these tasks.
In addition to press brakes and angle bending machines, there are hydraulic steel bending machines, which offer greater control over the bending process. Hydraulic systems use fluid pressure to apply force, providing smooth and precise bends. These machines are especially useful for handling large or heavy materials, as the hydraulic system can generate significant bending force with minimal physical effort. They are commonly used in construction and heavy industries where large steel components need to be bent to precise specifications.
The mandrel bending machine is another type of steel bending equipment, which is used for creating tight-radius bends without compromising the integrity of the material. Mandrel bending prevents the steel from collapsing or wrinkling during the bend, making it ideal for applications that require a smooth, consistent bend without any deformation. This method is particularly useful in industries like aerospace and automotive, where the aesthetic and structural quality of the bends is critical.
Automation and digital control technologies have significantly enhanced the capabilities of steel bending machines. With CNC systems, operators can input specific bending parameters, and the machine will automatically adjust to meet the required specifications. This has not only improved the accuracy of bends but also reduced human error and increased the speed of production. CNC bending machines also allow for complex, multi-bend components to be produced in a single cycle, improving efficiency and consistency in the manufacturing process.
Steel bending machines are also designed to be highly adaptable, allowing for adjustments in parameters such as bending radius, angle, and force to suit different types of steel and desired outcomes. With the ability to bend steel at a range of angles or to create specific curves and profiles, these machines are widely used in industries where custom metal parts are required. For example, in the automotive industry, steel bending machines are used to create frames, chassis, and other structural components that must meet precise tolerances. Similarly, in construction, these machines are used to bend steel rods and bars for reinforcing concrete structures.
The ability to work with different shapes, sizes, and types of steel is what makes steel bending machines such versatile tools. Whether it’s bending flat steel sheets, hollow sections, round bars, or square bars, these machines provide manufacturers with the tools to create high-quality metal parts that are durable, functional, and fit within the required design parameters. Moreover, the machines’ ability to integrate with other equipment in automated production lines ensures that the bending process is just one part of a seamless and efficient manufacturing workflow.
As technological advancements continue, steel bending machines are becoming faster, more efficient, and more accurate. The integration of AI, machine learning, and predictive maintenance technologies ensures that the machines run at optimal performance levels, minimizing downtime and improving the overall productivity of manufacturing operations. As the demand for customized and high-quality steel components continues to grow across various industries, steel bending machines will remain an integral part of the metal fabrication process.
The continued evolution of steel bending machines is pushing the boundaries of efficiency and precision in metal fabrication. With the integration of advanced technologies such as robotics and IoT (Internet of Things), these machines are becoming more autonomous and intelligent. Robotic arms, for example, are being used to automate the loading, unloading, and handling of steel pieces, reducing labor costs and enhancing production speed. This automation allows for 24/7 operation without the need for constant manual oversight, leading to significant increases in throughput and efficiency.
IoT-enabled steel bending machines can now collect real-time data from the manufacturing process, such as the machine’s operational status, performance metrics, and maintenance needs. This data can be analyzed to optimize the bending process, detect issues early, and predict when maintenance is needed. Predictive maintenance is a particularly important development, as it helps reduce unplanned downtime and extends the lifespan of the machines. By addressing potential issues before they result in breakdowns, manufacturers can avoid costly interruptions and maintain continuous production.
Furthermore, energy efficiency is becoming an increasingly important consideration in the design of steel bending machines. Manufacturers are focusing on creating machines that consume less energy while still providing the high levels of performance required in industrial settings. Energy-efficient designs help companies reduce operating costs and meet environmental sustainability goals. For example, hydraulic systems in steel bending machines are being optimized to use less power while maintaining their bending capabilities. This is particularly important in large-scale operations, where energy consumption can significantly impact overall costs.
Another key trend is the development of flexible bending solutions that can accommodate a broader range of materials, including not just steel but also aluminum, copper, and other metals. As industries increasingly require multi-material solutions, bending machines are being designed to handle a wider variety of materials with different properties and thicknesses. This capability allows manufacturers to produce parts that meet a diverse set of specifications without needing to invest in multiple machines for each material.
In addition, advancements in software are making it easier for operators to design, program, and manage the bending process. Software solutions are becoming more intuitive, with user-friendly interfaces that allow operators to input bending specifications, simulate the bending process, and optimize machine settings for maximum efficiency and minimal waste. These software tools can also integrate with other aspects of the production line, such as cutting and welding machines, providing a seamless workflow and improving overall production planning.
One of the most significant impacts of these advancements is in customization. Steel bending machines are becoming more capable of producing complex, one-off designs with the same efficiency as large-volume production. This opens up new possibilities for industries like architecture, where bespoke, intricately bent steel components are often needed for unique designs. The ability to quickly adapt to custom designs while maintaining precision and consistency is a game-changer for industries that rely on specialized steel components.
As the manufacturing landscape continues to evolve, the role of steel bending machines will remain critical in shaping the future of metalworking. Their ability to produce high-quality, precisely bent steel parts efficiently and at scale ensures their continued importance in industries that rely on metal components. With ongoing advancements in automation, energy efficiency, and software integration, steel bending machines will continue to provide manufacturers with the tools needed to meet the growing demands for precision, customization, and sustainability in modern production processes.
EMS Metalworking Machines
We design, manufacture and assembly metalworking machinery such as:
- Hydraulic transfer press
- Glass mosaic press
- Hydraulic deep drawing press
- Casting press
- Hydraulic cold forming press
- Hydroforming press
- Composite press
- Silicone rubber moulding press
- Brake pad press
- Melamine press
- SMC & BMC Press
- Labrotaroy press
- Edge cutting trimming machine
- Edge curling machine
- Trimming beading machine
- Trimming joggling machine
- Cookware production line
- Pipe bending machine
- Profile bending machine
- Bandsaw for metal
- Cylindrical welding machine
- Horizontal pres and cookware
- Kitchenware, hotelware
- Bakeware and cuttlery production machinery
as a complete line as well as an individual machine such as:
- Edge cutting trimming beading machines
- Polishing and grinding machines for pot and pans
- Hydraulic drawing presses
- Circle blanking machines
- Riveting machine
- Hole punching machines
- Press feeding machine
You can check our machinery at work at: EMS Metalworking Machinery – YouTube
Applications:
- Beading and ribbing
- Flanging
- Trimming
- Curling
- Lock-seaming
- Ribbing
- Flange-punching