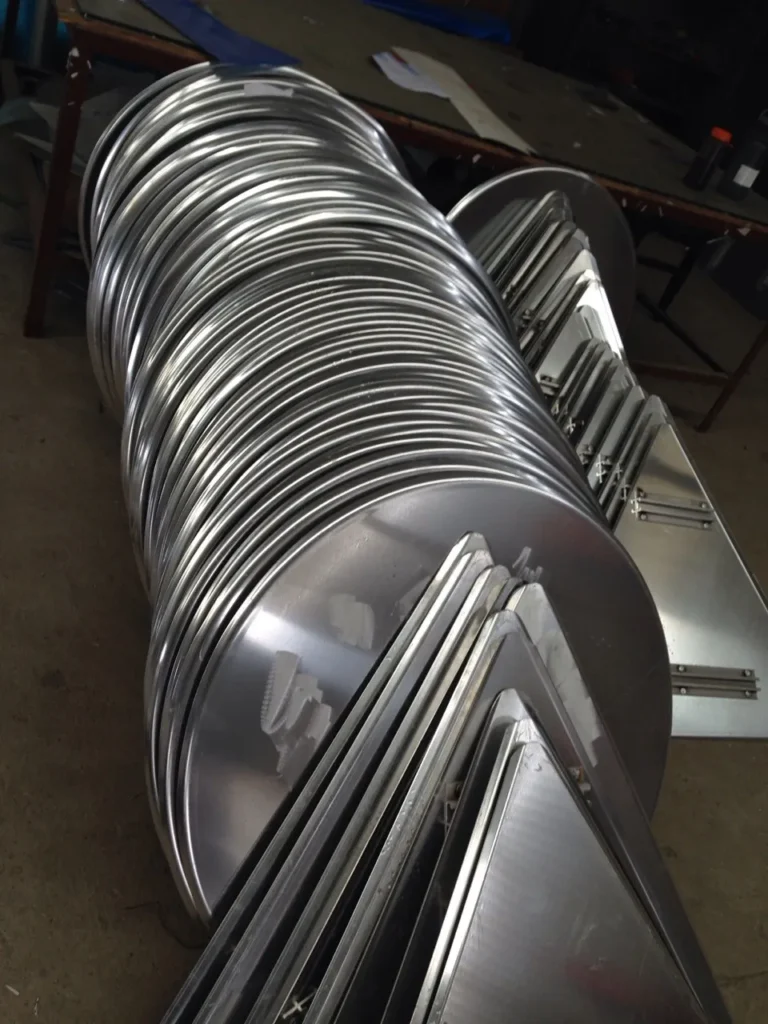
What is Sheet Metal and sheet metal forming with a hydraulic press? Sheet metal forming made with hydraulic presses are metalforming machines with high quality
Sheet Metal
When it comes to hydraulic presses and sheet metal applications, customization is often necessary to accommodate the specific requirements of sheet metal forming processes. Here are some key points regarding customization for sheet metal applications in hydraulic presses:
- Die Design: The design and customization of dies are crucial for shaping sheet metal in a hydraulic press. The dies can be customized to match the desired shape, size, and features of the sheet metal component being produced. Customized dies enable precise and repeatable forming of the sheet metal.
- Tooling Options: Hydraulic presses can be customized with various tooling options specifically designed for sheet metal applications. This may include tools such as blanking dies, bending tools, drawing dies, and deep-drawing dies. Each tooling option is customized to suit the specific forming operation required for the sheet metal.
- Pressure and Speed Control: Customization allows for precise control of the hydraulic pressure and speed during the forming process. This control is essential for achieving accurate and consistent results when working with different thicknesses and types of sheet metal. The customization of pressure and speed control ensures proper deformation without causing material damage.
- Safety Measures: Customization takes into account safety considerations for sheet metal applications. Safety features such as guards, sensors, and interlocks can be customized to protect operators and prevent accidents during the operation. Compliance with safety standards and regulations is a vital aspect of customization for sheet metal processes.
- Automation and Integration: Customized hydraulic presses can be equipped with automation and integration capabilities for sheet metal applications. This includes features such as robotic handling systems, automatic tool change systems, and integration with computer numerical control (CNC) systems. Automation and integration improve productivity, efficiency, and accuracy in sheet metal forming processes.
- Material Handling: Customization may involve incorporating features for efficient material handling in sheet metal applications. This can include coil handling equipment, sheet feeding systems, and stacking mechanisms. Customized material handling solutions enhance productivity and streamline the overall production process.
Customization in hydraulic presses for sheet metal applications is essential to ensure precise forming, efficient production, and optimal results. Manufacturers and engineers work closely with clients to understand their specific requirements and develop customized solutions that meet their needs in terms of shape, size, material compatibility, safety, and productivity.
Die Design
Die design is a crucial aspect of customizing hydraulic presses for various sheet metal forming processes. The design of the die determines the final shape, size, and features of the formed sheet metal component. Here are some key considerations regarding die design in hydraulic press applications:
- Function and Purpose: The first step in die design is understanding the function and purpose of the formed sheet metal component. This includes determining the desired shape, dimensions, features, and tolerances. The die design should be tailored to achieve the desired outcome accurately.
- Material Compatibility: Die design takes into account the specific properties and characteristics of the sheet metal being formed. Different types of sheet metal, such as steel, aluminum, or stainless steel, may require different die designs due to variations in their elasticity, ductility, and other material properties. The die design should ensure proper deformation and minimize material damage or defects.
- Part Complexity: The complexity of the formed sheet metal part influences the die design. Simple parts may require a single-stage die, while more complex parts may necessitate multiple stages or progressive dies. The die design should consider the number of stages, the order of operations, and the required tooling for each stage.
- Die Material: The choice of die material is important for die design. The die material should have sufficient strength, wear resistance, and durability to withstand the forces and pressures exerted during the forming process. Common die materials include tool steel, carbide, and various hardened alloys.
- Die Geometry: The geometry of the die determines the final shape of the formed sheet metal. It includes features such as contours, radii, flanges, embossing, and cut-outs. The die geometry should be designed to ensure proper material flow, minimize stress concentrations, and achieve the desired dimensional accuracy.
- Clearance and Springback Compensation: Die design accounts for clearance, which is the space between the punch and the die. Adequate clearance is essential to allow for material flow and prevent excessive friction or binding. Additionally, springback, which is the elastic recovery of the sheet metal after forming, should be considered in the die design to achieve the desired final shape.
- Surface Finish and Tooling Maintenance: Die design considers the desired surface finish of the formed sheet metal component. Smooth surfaces, textured patterns, or specific finishes can be incorporated into the die design to achieve the desired appearance or functional requirements. The ease of tooling maintenance and replacement is also considered to ensure efficient and cost-effective operations.
Die design in hydraulic press applications involves a combination of engineering principles, experience, and iterative testing. The customization of die design ensures optimal performance, accuracy, and efficiency in sheet metal forming processes.
Tooling Options
Tooling options in hydraulic presses for sheet metal applications refer to the various tools and dies used to shape and form the sheet metal. Different tooling options are available depending on the specific sheet metal forming processes and desired outcomes. Here are some common tooling options used in hydraulic press applications:
- Blanking Dies: Blanking dies are used to cut out flat or complex-shaped sheet metal components from a larger sheet. They consist of a punch and a die with a sharp cutting edge. Blanking dies are commonly used in applications where precise and clean cutting is required.
- Bending Tools: Bending tools, also known as press brakes or bending dies, are used to bend sheet metal into desired angles or shapes. They typically consist of a punch and a matching die that provides the necessary contour to achieve the desired bend. Bending tools are essential for forming sheet metal components with straight edges or complex geometries.
- Drawing Dies: Drawing dies are used to shape sheet metal into deep-drawn components with concave or complex shapes. They involve the use of a punch and a die that gradually draw the sheet metal into the desired shape through a series of forming stages. Drawing dies are commonly used in the production of cups, cans, and other hollow parts.
- Progressive Dies: Progressive dies are used for high-volume production of complex sheet metal components. They consist of multiple stations, each performing a different forming operation in a sequential manner. Progressive dies allow for continuous feeding of the sheet metal strip, resulting in efficient and rapid forming of the desired part.
- Coining Dies: Coining dies are used to create highly accurate and precise features, such as embossing, debossing, or lettering, on sheet metal components. The punch and die in a coining die set exert significant pressure on the sheet metal to achieve the desired impression or texture.
- Hemming Tools: Hemming tools are used to create folded or rolled edges on sheet metal components. They involve a combination of bending and overlapping operations to secure the edges of the sheet metal. Hemming tools are commonly used in the automotive industry for joining body panels.
- Forming Tools: Forming tools are customized dies used to shape sheet metal into specific contours or complex geometries. They can include features such as flanges, ribs, embossing, or cut-outs. Forming tools are designed to achieve precise dimensional accuracy and desired surface finishes.
- Piercing and Punching Tools: Piercing and punching tools are used to create holes, slots, or other cut-outs in sheet metal components. They involve the use of a punch and a matching die to remove the material and create the desired opening.
The selection of tooling options depends on factors such as the desired shape, size, complexity of the sheet metal component, and the specific forming operation required. Customization of tooling options ensures the optimal performance and accuracy in shaping and forming sheet metal using hydraulic presses.
Pressure and Speed Control
Pressure and speed control are critical aspects of hydraulic press operations, as they allow for precise and controlled forming of sheet metal. Here’s an overview of pressure and speed control in hydraulic presses:
Pressure Control:
- Hydraulic System: Hydraulic presses use a hydraulic system consisting of a hydraulic pump, cylinders, valves, and control mechanisms to generate and regulate hydraulic pressure. The hydraulic pump supplies pressurized hydraulic fluid to the cylinders.
- Pressure Regulation: Hydraulic valves, such as pressure relief valves and pressure control valves, are employed to regulate the hydraulic pressure. These valves control the flow of hydraulic fluid and adjust the pressure level to achieve the desired force on the sheet metal. Pressure sensors are often used to provide feedback on the actual pressure being applied.
- Pressure Adjustment: The pressure in the hydraulic system can be adjusted to accommodate different sheet metal materials, thicknesses, and forming operations. The operator or control system can set the desired pressure level based on the specific requirements of the forming process.
- Pressure Holding: Once the desired pressure is reached, the hydraulic system maintains the pressure throughout the forming operation. This ensures consistent force application and accurate shaping of the sheet metal.
Speed Control:
- Speed Regulation: Hydraulic presses offer control over the speed of the ram or punch movement during the forming process. This control is achieved through the adjustment of flow control valves or proportional valves in the hydraulic system.
- Speed Adjustment: The operator or control system can adjust the speed of the ram or punch based on the specific requirements of the forming operation. Slower speeds may be used for more intricate or delicate forming processes, while faster speeds may be suitable for larger-scale production.
- Speed Profiles: Hydraulic presses can be programmed to follow specific speed profiles, such as ramp-up, dwell, and ramp-down phases. This allows for precise control of the speed throughout the forming process, accommodating different stages of the operation.
- Safety Considerations: Speed control in hydraulic presses often incorporates safety features, such as adjustable speed limits, emergency stop functions, or safety interlocks. These features ensure safe operation and prevent accidents or damage during the forming process.
The ability to control pressure and speed in hydraulic presses provides flexibility, accuracy, and repeatability in sheet metal forming operations. Operators and control systems can tailor these parameters to the specific material, part geometry, and desired outcome, resulting in precise and efficient sheet metal forming.
Safety Measures
Safety measures are of paramount importance in hydraulic press operations to ensure the well-being of operators and prevent accidents. Here are some key safety measures commonly implemented in hydraulic press systems:
- Machine Guarding: Hydraulic presses should be equipped with appropriate machine guarding to prevent access to hazardous areas during operation. This includes physical barriers, safety enclosures, interlocks, and presence-sensing devices to detect operator presence and interrupt machine operation when necessary.
- Emergency Stop (E-Stop): An easily accessible emergency stop button or control is essential in case of any unexpected hazard or emergency. Activating the emergency stop should immediately halt all machine functions, bringing the hydraulic press to a safe and controlled stop.
- Two-Hand Controls: Two-hand controls require the simultaneous use of both hands to initiate the machine’s operation. This ensures that operators keep their hands clear of the hazardous areas during the press cycle and helps prevent accidental activation of the machine.
- Safety Interlocks: Safety interlocks are devices or systems that ensure certain conditions are met before the machine can operate. For example, the press may only activate when the safety guard is closed and secured. Interlocks help prevent the machine from operating when safety measures are compromised.
- Training and Education: Operators should receive comprehensive training on the safe operation of hydraulic presses. They should be familiar with the machine’s controls, safety features, emergency procedures, and safe work practices. Ongoing training and education should be provided to keep operators updated with best practices and safety guidelines.
- Risk Assessments: Regular risk assessments should be conducted to identify and mitigate potential hazards associated with hydraulic press operations. This involves evaluating the machine, work environment, and tasks performed to identify potential risks and implement appropriate control measures.
- Personal Protective Equipment (PPE): Operators should wear appropriate personal protective equipment, such as safety glasses, gloves, hearing protection, and safety footwear, to protect themselves from potential hazards, including flying debris, noise, and crushing risks.
- Maintenance and Inspection: Regular maintenance and inspection of the hydraulic press are essential to ensure its safe and efficient operation. This includes inspecting hydraulic components, checking for leaks, verifying the integrity of safety devices, and promptly addressing any maintenance or repair needs.
- Lockout/Tagout (LOTO): LOTO procedures should be implemented to control hazardous energy sources during maintenance or servicing activities. This involves isolating and locking out energy sources to prevent accidental energization of the machine during maintenance or repair work.
- Compliance with Standards: Hydraulic presses should be designed, manufactured, and operated in compliance with relevant safety standards and regulations, such as those provided by organizations like OSHA (Occupational Safety and Health Administration) or ISO (International Organization for Standardization).
Implementing these safety measures helps mitigate risks and create a safe working environment when operating hydraulic presses. It is essential to prioritize safety at all times and ensure that operators are trained, aware, and actively engaged in following safe work practices.
Automation and Integration
Automation and integration play a significant role in enhancing the efficiency, productivity, and accuracy of hydraulic press operations. Here are some key aspects of automation and integration in hydraulic press systems:
- Robotic Handling Systems: Automation can be achieved by integrating robotic handling systems with hydraulic presses. Robots can be programmed to handle the loading and unloading of sheet metal components, tooling changeovers, and other material handling tasks. This reduces the need for manual intervention and improves overall process efficiency.
- Automatic Tool Change Systems: Hydraulic presses can be equipped with automatic tool change systems that allow for quick and seamless tooling changeovers. This eliminates the need for manual adjustments and reduces downtime between different forming operations. Automatic tool change systems enable efficient production and flexibility in sheet metal applications.
- Computer Numerical Control (CNC) Integration: CNC integration involves connecting the hydraulic press with a computer numerical control system. This allows for precise control and programming of press operations, including the movement of the ram, pressure, speed, and other parameters. CNC integration ensures repeatability, accuracy, and ease of process control.
- Data Acquisition and Monitoring: Automation and integration enable the collection of data during hydraulic press operations. Sensors and monitoring systems can capture data on parameters such as pressure, force, temperature, and cycle times. This data can be utilized for process optimization, quality control, and predictive maintenance.
- Process Control and Sequencing: Automation allows for the implementation of complex process control and sequencing in hydraulic press operations. The control system can be programmed to follow specific sequences, adjust parameters based on real-time feedback, and ensure consistent and precise forming of sheet metal components.
- Integration with Manufacturing Execution Systems (MES): Hydraulic presses can be integrated with MES, which is a software system that manages and controls the entire manufacturing process. Integration with MES enables real-time production monitoring, scheduling, inventory management, and data analysis for improved overall production efficiency.
- Human-Machine Interface (HMI): Automation and integration often involve the use of user-friendly HMI systems. These interfaces allow operators to interact with the hydraulic press, monitor process parameters, set operating parameters, and receive alerts or notifications. Intuitive HMIs facilitate easy operation and monitoring of the automated processes.
- Remote Monitoring and Control: Automation and integration enable remote monitoring and control of hydraulic press operations. Through network connectivity, operators can access and monitor the press performance, diagnose issues, and even control the system remotely. This facilitates remote troubleshooting, maintenance, and support.
Automation and integration in hydraulic press systems improve productivity, reduce manual labor, enhance process control, and enable better data-driven decision-making. These advancements in technology contribute to increased efficiency, accuracy, and overall competitiveness in sheet metal manufacturing processes.
Material Handling
Material handling in the context of hydraulic press operations refers to the movement, positioning, and manipulation of sheet metal or other workpieces within the press system. Efficient material handling is crucial to ensure smooth and productive workflow. Here are some aspects of material handling in hydraulic press applications:
- Loading and Unloading: Material handling involves the loading of sheet metal or workpieces onto the press bed and the subsequent unloading of formed components. This can be done manually by operators or automated using robotic handling systems. Proper lifting and positioning techniques should be followed to ensure operator safety and prevent damage to the workpieces.
- Feeding Systems: In high-volume production, automated feeding systems can be integrated with hydraulic presses to facilitate continuous material feeding. These systems can include roll feeders, coil handling equipment, or vibratory feeders to deliver sheet metal to the press. The feeding systems ensure a steady supply of material, reducing downtime and improving overall productivity.
- Tooling Changeover: Material handling also encompasses the handling of tooling during changeover between different forming operations. Hydraulic presses may be equipped with automatic tool change systems, which facilitate quick and efficient tooling swaps. Material handling considerations during tool changeover include safe removal and storage of tooling and proper alignment of new tooling.
- Workpiece Positioning: Material handling includes the precise positioning of the workpiece within the press for accurate forming. This can be achieved through the use of positioning pins, fixtures, or guides. Proper alignment and secure clamping of the workpiece ensure consistent and reliable forming results.
- Part Ejection: After the forming operation, material handling involves the ejection of formed components from the press. This can be done manually or automated using pneumatic or robotic systems. Ejection mechanisms should be designed to safely and efficiently remove the formed parts without causing damage or injury.
- Material Storage and Retrieval: Material handling also includes the storage and retrieval of sheet metal or workpieces before and after press operations. Proper storage systems, such as racks or pallets, should be implemented to organize and protect the materials. Retrieval processes should be designed for easy access and efficient workflow.
- Material Inspection and Sorting: Material handling may involve inspecting and sorting formed components based on quality criteria. This can include visual inspection, dimensional measurement, or automated inspection systems. Sorting mechanisms, such as conveyors or bins, are used to separate parts based on their quality or specific characteristics.
- Material Waste Management: Effective material handling encompasses the proper management of waste material generated during hydraulic press operations. This includes collecting and disposing of scrap or excess material in a safe and organized manner. Recycling or reusing waste material whenever possible contributes to sustainability and cost-effectiveness.
Efficient material handling in hydraulic press operations minimizes downtime, maximizes productivity, ensures operator safety, and promotes overall process efficiency. It involves a combination of manual and automated techniques tailored to the specific requirements of the sheet metal forming process
Hydraulic presses are powerful machines used to apply a significant amount of force to an object through hydraulic fluid pressure. They are essential in various industrial applications, providing the necessary force for processes such as metal forming, stamping, bending, and molding. The versatility and efficiency of hydraulic presses make them indispensable tools in manufacturing and production lines. This document will explore the different types of hydraulic presses, their application areas, components, operational principles, manufacturing process, and the challenges and advancements in the industry.
Types of Hydraulic Presses
Hydraulic presses come in various designs, each suited to specific applications and requirements. The primary types of hydraulic presses include C-frame presses, H-frame presses, four-column presses, straightening presses, arbor presses, laminating presses, and transfer presses.
C-frame presses, also known as gap-frame presses, have a C-shaped frame that provides three-sided access to the work area. This design is ideal for applications requiring easy loading and unloading of materials.
H-frame presses, or two-post presses, have a robust H-shaped frame that offers excellent stability and strength. They are commonly used for heavy-duty tasks such as metal forming and straightening.
Four-column presses, or four-post presses, have four vertical columns that provide superior support and uniform force distribution. These presses are suitable for large-scale applications requiring high precision and repeatability.
Straightening presses are specialized hydraulic presses used to straighten bent or distorted metal components. They are widely used in the automotive and construction industries.
Arbor presses are smaller, manually operated hydraulic presses used for light-duty tasks such as assembly, riveting, and broaching. They are commonly found in workshops and small manufacturing facilities.
Laminating presses are used to bond multiple layers of material together under heat and pressure. These presses are essential in industries such as electronics, where laminated components are common.
Transfer presses are automated hydraulic presses that move the workpiece through multiple stations for different operations. They are highly efficient and used in high-volume production environments.
Application Areas
Hydraulic presses are employed in various industries, thanks to their ability to deliver consistent and precise force. Key application areas include:
Metal forming and forging: Hydraulic presses are crucial in shaping and forming metal parts through processes such as stamping, bending, and deep drawing. They are essential in the production of automotive parts, machinery components, and structural elements.
Automotive industry: In the automotive sector, hydraulic presses are used for manufacturing various parts, including body panels, chassis components, and engine parts. They play a critical role in ensuring the structural integrity and performance of vehicles.
Aerospace industry: The aerospace industry relies on hydraulic presses for forming and shaping high-strength materials used in aircraft components. Precision and reliability are paramount in this industry, making hydraulic presses indispensable.
Plastic and rubber molding: Hydraulic presses are used in the molding of plastic and rubber components, including automotive parts, household goods, and medical devices. They ensure consistent product quality and precision.
Electrical and electronics industry: In the electronics sector, hydraulic presses are used for laminating circuit boards, forming connectors, and assembling electronic components. They provide the necessary force and precision for delicate operations.
Medical device manufacturing: Hydraulic presses are used in the production of medical devices, including surgical instruments, implants, and diagnostic equipment. They ensure the high precision and quality required in the medical field.
Packaging industry: Hydraulic presses are employed in the packaging industry for forming and shaping packaging materials, such as cardboard, plastic, and metal. They help produce packaging solutions that are strong, durable, and aesthetically pleasing.
Components of a Hydraulic Press
A hydraulic press comprises several key components that work together to generate and control the applied force. The main components include the frame, hydraulic cylinder, hydraulic pump, control valves, hydraulic fluid, pressure gauges and sensors, and die and tooling.
The frame is the main structure of the hydraulic press, providing stability and support for all other components. It is typically made of high-strength steel to withstand the significant forces generated during operation.
The hydraulic cylinder is the core component that generates the pressing force. It consists of a cylindrical chamber, a piston, and a piston rod. When hydraulic fluid is pumped into the cylinder, it moves the piston, which in turn applies force to the workpiece.
The hydraulic pump is responsible for generating the hydraulic fluid pressure needed to move the piston. It draws hydraulic fluid from a reservoir and delivers it to the cylinder under high pressure.
Control valves regulate the flow of hydraulic fluid to and from the cylinder, controlling the movement and force of the press. These valves can be manually operated or automated, depending on the press design.
Hydraulic fluid, typically oil, is the medium through which force is transmitted in the hydraulic system. It must have suitable properties, such as viscosity and lubricity, to ensure efficient operation and protect system components.
Pressure gauges and sensors monitor the hydraulic fluid pressure within the system. They provide real-time feedback to the operator or control system, ensuring safe and accurate press operation.
Die and tooling are the interchangeable components that come into direct contact with the workpiece. They are designed to shape, form, or cut the material as required by the specific application.
How Hydraulic Presses Work
Hydraulic presses operate based on Pascal’s principle, which states that pressure applied to a confined fluid is transmitted equally in all directions. This principle allows hydraulic presses to generate significant force with relatively small input pressure.
The operation of a hydraulic press begins with the hydraulic pump drawing fluid from the reservoir and delivering it to the cylinder. The control valves regulate the flow of fluid, directing it into the cylinder to move the piston. As the piston moves, it applies force to the workpiece placed between the die and tooling.
The hydraulic fluid plays a crucial role in this process, as it transmits the applied pressure and lubricates the system components. The pressure gauges and sensors continuously monitor the fluid pressure, providing feedback to ensure the press operates within safe limits.
The force generated by the hydraulic press can be precisely controlled by adjusting the hydraulic fluid pressure and the position of the control valves. This allows for accurate and repeatable operations, essential for high-quality manufacturing.
Manufacturing of Hydraulic Presses
The manufacturing of hydraulic presses involves several stages, from design and engineering to assembly and quality control. Each stage is critical to ensuring the press’s performance, reliability, and safety.
Design and engineering: The process begins with the design and engineering phase, where specifications for the press are developed based on the intended application. This includes selecting suitable materials, determining the required force and stroke, and designing the frame and hydraulic system.
Material selection: High-quality materials, such as high-strength steel for the frame and durable alloys for the hydraulic components, are selected to ensure the press’s longevity and performance.
Fabrication of components: The individual components of the hydraulic press, including the frame, cylinder, and pump, are fabricated using precision machining and manufacturing techniques. This ensures that each component meets the required tolerances and specifications.
Assembly process: The fabricated components are then assembled into the complete hydraulic press. This involves mounting the cylinder, pump, and control valves onto the frame, connecting the hydraulic lines, and installing the die and tooling.
Quality control and testing: Rigorous quality control measures are implemented throughout the manufacturing process to ensure the press meets all specifications and standards. This includes pressure testing the hydraulic system, verifying the accuracy of the control valves, and performing operational tests to ensure the press functions correctly.
Advancements and Innovations
The hydraulic press industry is continually evolving, driven by advancements in technology and increasing demands for efficiency and precision. Key innovations include automation and control systems, energy efficiency improvements, and smart hydraulic presses.
Automation and control systems: Modern hydraulic presses are often equipped with advanced control systems that automate the pressing process. This includes programmable logic controllers (PLCs), human-machine interfaces (HMIs), and sensors that monitor and adjust the press’s operation in real time. Automation improves efficiency, reduces the risk of human error, and enhances the consistency of the finished products.
Energy efficiency improvements: Manufacturers are focusing on developing hydraulic presses that consume less energy and have a smaller environmental footprint. This includes using variable displacement pumps, energy recovery systems, and optimizing the hydraulic system’s design to minimize energy losses.
Smart hydraulic presses: The integration of IoT (Internet of Things) technology into hydraulic presses has led to the development of smart presses. These presses can communicate with other machines and systems, providing real-time data on their status, performance, and maintenance needs. This connectivity allows for predictive maintenance, reducing downtime and extending the press’s lifespan.
Challenges in Hydraulic Press Manufacturing
The manufacturing of hydraulic presses presents several challenges, including precision and quality requirements, cost management, technological advancements, and environmental considerations.
Precision and quality requirements: Hydraulic presses must deliver consistent and precise force, which requires high levels of accuracy in the manufacturing process. Ensuring each component meets the required tolerances and specifications is critical to the press’s performance and reliability.
Cost management: The cost of materials, labor, and energy can significantly impact the overall cost of manufacturing hydraulic presses. Manufacturers must balance quality and cost to remain competitive in the market.
Technological advancements: Keeping up with technological advancements is essential for manufacturers to meet the evolving demands of the industry. This requires continuous investment in research and development to incorporate new technologies and improve existing designs.
Environmental considerations: Environmental regulations and sustainability concerns are increasingly important in hydraulic press manufacturing. Manufacturers must develop eco-friendly presses that consume less energy, use recyclable materials, and minimize their environmental impact.
Conclusion
Hydraulic presses are essential machines in various industries, providing the necessary force for processes such as metal forming, stamping, and molding. Understanding the different types of hydraulic presses, their components, and how they work is crucial for effective application and operation.
The manufacturing process of hydraulic presses involves careful design and engineering, material selection, precision fabrication, and rigorous quality control. Despite the challenges, advancements in technology and innovations are driving the industry forward, leading to more efficient, precise, and environmentally friendly hydraulic presses.
As industries continue to evolve, the hydraulic press industry must adapt and innovate to meet the demands of efficiency, precision, and sustainability. Through continuous research and development, manufacturers can enhance the performance and reliability of hydraulic presses, contributing to the success of various industrial applications.