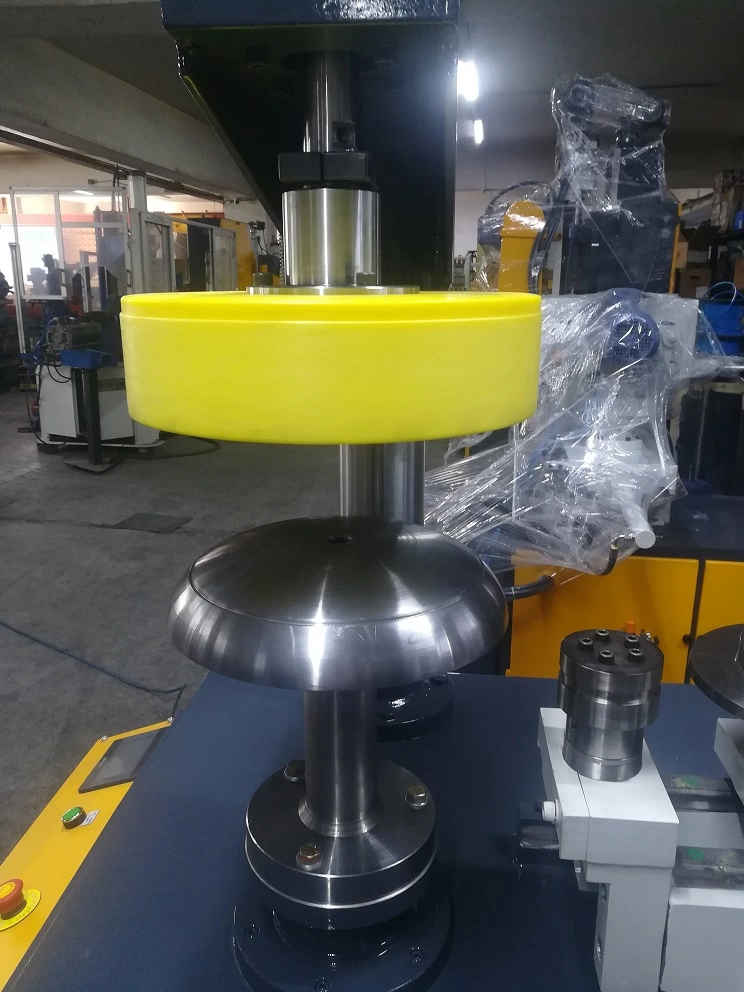
We manufacture a Sheet Metal Edge Rounding to round the sheet metal edges. These machines are used in metalworking industries
Sheet metal edge rounding is a process of removing sharp edges and creating rounded or chamfered edges on sheet metal components. This is done for various reasons, including safety, improved aesthetics, and enhanced functionality. Here are some common methods used for sheet metal edge rounding:
- Manual Deburring: Manual deburring involves using handheld tools such as deburring files, sandpaper, or abrasive pads to manually remove sharp edges and smooth the edges of the sheet metal. This method is suitable for small-scale or low-volume production and allows for precise control over the edge rounding process.
- Deburring Machines: Industrial deburring machines, such as vibratory or tumbling machines, can also be used for edge rounding of sheet metal. These machines utilize abrasive media or brushes to remove burrs and round the edges of the metal components. The sheet metal parts are placed in the machine, and the rotating or vibrating action of the machine results in controlled edge rounding.
- Edge Rounding Machines: Dedicated edge rounding machines are specifically designed for rounding the edges of sheet metal components. These machines employ various methods, such as abrasive belts, rotary tools, or brushes, to perform consistent and precise edge rounding. Edge rounding machines are available in different configurations, including standalone machines or attachments for other fabrication equipment.
- Laser Edge Rounding: Laser technology can be used to perform edge rounding on sheet metal. With laser edge rounding, a laser beam is precisely directed along the edges of the sheet metal component, melting and reshaping the edges to achieve the desired rounded profile. Laser edge rounding offers high precision and control, especially for complex shapes or intricate designs.
- CNC Machining: CNC machining processes, such as milling or routing, can also be utilized for sheet metal edge rounding. By using specially designed cutting tools or milling bits, the sharp edges of the sheet metal can be carefully removed, resulting in rounded edges. CNC machining offers flexibility and accuracy for edge rounding, particularly for larger or more intricate sheet metal parts.
When selecting a method for sheet metal edge rounding, consider factors such as the required level of precision, production volume, part complexity, and the desired final appearance. It is important to choose a method that matches the specific requirements of the application while ensuring efficient and consistent edge rounding results.
Sheet Metal Edge Rounding
Sheet metal edge rounding is the process of removing the sharp edges of sheet metal parts and creating a smooth, rounded profile. This process is important for several reasons:
- Safety: Sharp edges on sheet metal can cause cuts, lacerations, and other injuries. Rounding off the edges makes them safer to handle and reduces the risk of injury.
- Aesthetics: Rounded edges make sheet metal parts look more finished and professional. This is especially important for parts that will be visible in the final product, such as appliance panels or car parts.
- Functionality: Rounded edges can prevent snagging, tearing, or abrasion of materials that come into contact with the sheet metal part. This is important for parts that need to move smoothly, such as conveyor belts or machinery components.
There are several different methods for rounding off sheet metal edges. The most common methods include:
- Deburring machines: These machines use abrasive belts or disks to grind down the sharp edges of the sheet metal. Deburring machines are a good choice for parts that have a lot of edges to be rounded.
- Milling machines: These machines use milling cutters to precisely round off edges. Milling machines are a good choice for parts that require a very high level of precision.
- Roll forming machines: These machines use a series of rollers to gradually bend and shape the edges of the sheet metal. Roll forming machines are a good choice for processing large, flat sheets of metal.
The specific method that is used to round off the edges of a sheet metal part will depend on the size, shape, and material of the part, as well as the desired level of precision.
Here are some additional benefits of sheet metal edge rounding:
- Reduced stress concentration: Rounded edges can help to reduce stress concentration in sheet metal parts, which can extend the life of the part.
- Improved paint adhesion: Rounded edges can improve the adhesion of paint and other coatings to sheet metal parts.
- Reduced noise: Rounded edges can help to reduce noise from vibrating sheet metal parts.
Overall, sheet metal edge rounding is an important process that can improve the safety, aesthetics, and functionality of sheet metal parts.
Manual Deburring
Manual deburring is a process of removing burrs, sharp edges, and imperfections from metal or other workpiece materials using handheld tools. This method allows for precise control and is commonly used for small-scale or low-volume deburring tasks. Here are some common tools and techniques used in manual deburring:
- Deburring Files: Deburring files have a flat or curved surface embedded with abrasive material. They are used to manually file away burrs and rough edges on metal surfaces. Deburring files come in various shapes and sizes to accommodate different types of deburring tasks.
- Handheld Deburring Tools: Handheld deburring tools are specifically designed for deburring applications. They often feature a comfortable handle and a replaceable or adjustable cutting blade. These tools can be used to remove burrs from edges, holes, and other hard-to-reach areas.
- Sandpaper or Emery Cloth: Sandpaper or emery cloth is a versatile abrasive material used in manual deburring. It can be wrapped around a block or held in hand to smooth out rough edges and remove burrs. Different grit sizes are available to achieve various levels of surface finish.
- Scraping Tools: Scraping tools, such as scrapers or scrapers with interchangeable blades, are used to scrape off burrs and rough edges. These tools work by applying pressure and scraping the surface of the workpiece to remove unwanted material.
- Brushes: Wire brushes or abrasive brushes can be used to manually deburr metal surfaces. They are effective for removing light burrs and surface imperfections. Wire brushes are available in various types, including steel, brass, or nylon bristles, depending on the material and the level of aggressiveness required.
- Handheld Rotary Tools: Handheld rotary tools, such as die grinders or Dremel tools, can be equipped with deburring attachments or abrasive bits to perform manual deburring. These tools offer high-speed rotation and precision control, making them suitable for intricate deburring tasks.
During manual deburring, it is important to wear appropriate personal protective equipment (PPE) such as safety goggles, gloves, and a dust mask to protect against flying debris and potential health hazards. Additionally, proper technique and attention to detail are essential to achieve consistent and high-quality deburring results.
Manual deburring is often preferred when dealing with small parts, complex geometries, or sensitive materials that require precise control and delicate handling. It allows for customization and adaptability, but it may not be as efficient for large-scale production compared to automated deburring methods.
Deburring Machines
Deburring machines are specialized equipment used for the removal of burrs, sharp edges, and other imperfections from workpiece surfaces. These machines are designed to streamline and automate the deburring process, improving efficiency and consistency. There are several types of deburring machines available, each suited for specific applications and workpiece materials. Here are some common types of deburring machines:
- Vibratory Deburring Machines: Vibratory deburring machines use vibratory motion to remove burrs and smooth workpiece surfaces. The workpieces, along with abrasive media and a deburring compound, are placed in a vibratory bowl or tub. The vibratory action causes the media to impact and abrade the workpiece surfaces, effectively removing burrs and achieving the desired finish.
- Tumbling Deburring Machines: Tumbling deburring machines work on a similar principle to vibratory machines but use a rotating drum or barrel. The workpieces, along with abrasive media and a deburring compound, are loaded into the drum, and the rotating action causes the media to interact with the workpieces, resulting in deburring and surface refinement.
- Brush Deburring Machines: Brush deburring machines employ rotating brushes with abrasive bristles to remove burrs and smooth workpiece surfaces. The workpieces are fed into the machine, and as they pass through, the rotating brushes come into contact with the workpiece surfaces, effectively removing burrs and providing a uniform finish.
- CNC Deburring Machines: CNC (Computer Numerical Control) deburring machines are automated systems that use precision cutting tools or brushes to perform deburring operations. These machines are programmed to follow specific tool paths and perform deburring on complex workpieces with high precision. CNC deburring machines are commonly used in industries that require intricate deburring tasks and high production volumes.
- Thermal Deburring Machines: Thermal deburring machines, also known as thermal energy method (TEM) machines or spark erosion machines, use a combination of heat and gas to remove burrs from workpiece surfaces. The workpieces are submerged in a chamber filled with a flammable gas, and an electric discharge is passed through the gas, causing a controlled explosion. The explosion removes the burrs from the workpiece surfaces. This method is especially suitable for complex and hard-to-reach areas.
- Laser Deburring Machines: Laser deburring machines utilize laser technology to remove burrs and sharp edges from workpieces. A focused laser beam is directed at the burrs, melting or vaporizing them away. Laser deburring offers high precision, minimal material removal, and can be used on a wide range of materials.
Deburring machines can vary in size, capacity, and level of automation. When choosing a deburring machine, consider factors such as the type and size of workpieces, the desired level of precision, production volume, and the specific deburring requirements of your application.
Edge Rounding Machines
Edge rounding machines are specialized equipment used to round the edges of workpieces, typically made of metal, to remove sharp edges, burrs, and improve the overall finish. These machines are designed to automate the edge rounding process, ensuring consistent and precise results. Here are some common types of edge rounding machines:
- Belt Edge Rounding Machines: Belt edge rounding machines utilize abrasive belts to round the edges of workpieces. The workpiece is fed through the machine, and the rotating abrasive belt makes contact with the edges, removing sharp corners and burrs while imparting a rounded profile. These machines often have adjustable belt tension and speed controls for precise edge rounding.
- Disc Edge Rounding Machines: Disc edge rounding machines use rotating abrasive discs to round the edges of workpieces. The workpiece is guided along the edge, and the rotating discs remove sharp edges and burrs, resulting in a rounded edge. These machines can have multiple discs with varying abrasive grits to achieve different levels of edge rounding.
- Brush Edge Rounding Machines: Brush edge rounding machines employ rotating abrasive brushes to round the edges of workpieces. The workpiece is passed through the machine, and the rotating brushes make contact with the edges, effectively removing sharp corners and burrs. These machines can use different types of brushes with various abrasive bristle materials to achieve the desired edge rounding effect.
- CNC Edge Rounding Machines: CNC (Computer Numerical Control) edge rounding machines are programmable machines that use precision cutting tools or brushes to perform automated edge rounding operations. These machines can follow specific tool paths and be programmed with various edge rounding profiles to accommodate different workpiece shapes and sizes. CNC edge rounding machines offer high precision and versatility for complex edge rounding requirements.
- Laser Edge Rounding Machines: Laser edge rounding machines utilize laser technology to selectively remove material from the edges of workpieces, creating rounded profiles. The laser beam is precisely directed at the edges, melting or vaporizing the material to achieve the desired rounding effect. Laser edge rounding machines offer high precision, minimal material removal, and are suitable for delicate or heat-sensitive materials.
Edge rounding machines can vary in size, configuration, and level of automation. When selecting an edge rounding machine, consider factors such as the type and size of workpieces, desired level of precision, production volume, and specific edge rounding requirements of your application.
Laser Edge Rounding
Laser edge rounding is a process that utilizes laser technology to round the edges of workpieces, such as metal or plastic components. It is a precise and controlled method for removing sharp edges, burrs, and creating rounded profiles. Here’s an overview of how laser edge rounding works:
- Laser Beam: A focused laser beam is generated using a laser source, such as a fiber laser or a CO2 laser. The laser beam is directed towards the edges of the workpiece.
- Heating and Melting: The laser beam is directed onto the edges of the workpiece, heating the material and causing it to melt. The heat is concentrated on the edges, allowing for controlled material removal.
- Material Removal: As the material melts, it is vaporized or blown away by assist gases, such as compressed air or nitrogen. The laser beam moves along the edges, gradually removing material and creating a rounded profile.
- Control and Precision: Laser edge rounding offers precise control over the process. The laser parameters, such as power, speed, and focus, can be adjusted to achieve the desired edge rounding effect. The process can be programmed and automated for consistent and repeatable results.
- Minimal Material Removal: Laser edge rounding is a non-contact process, meaning there is no physical contact between the laser and the workpiece. As a result, there is minimal material deformation or distortion, and only a small amount of material is removed during the rounding process.
- Versatility: Laser edge rounding can be applied to a wide range of materials, including metals like steel, stainless steel, aluminum, and various plastics. It is suitable for both thin and thick materials and can accommodate complex geometries and intricate part designs.
Benefits of laser edge rounding include precise control, minimal material removal, high-quality finishes, and the ability to work with various materials and part configurations. It is commonly used in industries such as automotive, aerospace, electronics, and medical devices where precise edge quality and safety are crucial.
It’s worth noting that laser edge rounding machines are specialized equipment designed for this specific process. These machines typically incorporate laser sources, motion control systems, and gas assist systems to ensure accurate and efficient edge rounding.
CNC Machining
CNC machining, which stands for Computer Numerical Control machining, is a manufacturing process that utilizes computer-controlled machines to create precise and complex parts from various materials. It involves the use of computerized instructions, known as G-code, to control the movement and operation of cutting tools and other machining processes. Here’s an overview of CNC machining:
- Design and Programming: The process starts with designing the part using computer-aided design (CAD) software. The CAD model is then translated into machine-readable instructions using computer-aided manufacturing (CAM) software. The CAM software generates the G-code, which contains the specific instructions for the CNC machine.
- Machine Setup: Once the G-code is generated, it is transferred to the CNC machine. The machine operator sets up the workpiece, fixturing, and cutting tools on the machine’s worktable or spindle. This involves securing the workpiece, installing the appropriate cutting tools, and setting the tool offsets and workpiece zero positions.
- Machining Operations: The CNC machine executes the programmed instructions to perform various machining operations. These operations can include milling, turning, drilling, boring, threading, and more. The cutting tools are precisely controlled and guided by the machine’s axes to remove material and shape the workpiece according to the programmed design.
- Automation and Control: CNC machines are highly automated and controlled by the CNC controller. The controller interprets the G-code instructions and coordinates the movements of the machine’s axes and spindle. It controls the tool feed rate, spindle speed, coolant flow, and other parameters to ensure accurate and efficient machining.
- Inspection and Quality Control: Throughout the machining process, quality control measures are implemented to ensure the accuracy and quality of the machined parts. This can include in-process inspections, dimensional measurements, and surface finish evaluations. CNC machines often have built-in probing systems that can measure and verify critical dimensions during the machining process.
- Finishing Operations: After the machining operations are complete, additional finishing operations may be performed to achieve the desired surface finish, such as deburring, polishing, or coating. These finishing operations can be done manually or using specialized equipment.
CNC machining offers several advantages, including high precision, repeatability, and the ability to create complex parts with tight tolerances. It is widely used in various industries, such as automotive, aerospace, electronics, medical devices, and more. CNC machines can work with a wide range of materials, including metals, plastics, wood, and composites.
It’s important to note that CNC machining requires skilled operators who are proficient in programming, setup, and operation of CNC machines. Additionally, the selection of appropriate cutting tools, toolpath optimization, and proper machine maintenance are critical for achieving optimal results in CNC machining.
Deburring Tool for Metal
https://www.youtube.com/embed/mMRmnQuYgjE?feature=oembedDeburring Tool for Metal
Deburring tools are essential for removing burrs, sharp edges, and imperfections from metal components. These tools are crucial for maintaining the safety, functionality, and aesthetics of metal products across various industries.
Types of Deburring Tools for Metal:
- Hand-Held Deburring Tools: These tools provide portability and convenient deburring for smaller metal parts or in situations where access is limited. Common hand-held deburring tools include:
- Files: Files with varying coarseness levels are effective for removing burrs and smoothing out rough edges on metal.
- Deburring Knives: Knives with rounded blades are specifically designed to trim and remove burrs from metal edges.
- Deburring Wheels: Deburring wheels with abrasive grit are effective for deburring metal edges.
- Power Deburring Tools: These tools offer greater efficiency and power for deburring larger metal components or in high-volume production. Examples include:
- Rotary Deburring Tools: Utilize rotating abrasive discs or belts to quickly remove burrs from metal parts.
- Sanders: Sanders with appropriate abrasive belts can be used for deburring and surface finishing of metal components.
- Stationary Deburring Machines: For high-precision deburring or deburring complex shapes, specialized stationary machines offer consistent and precise results. These machines may utilize rotating cutters, abrasive belts, or a combination of both.
- Ultrasonic Deburring Systems: For precision deburring of delicate metal parts or complex geometries, ultrasonic deburring offers a gentle and effective method.
Choosing the Right Deburring Tool for Metal
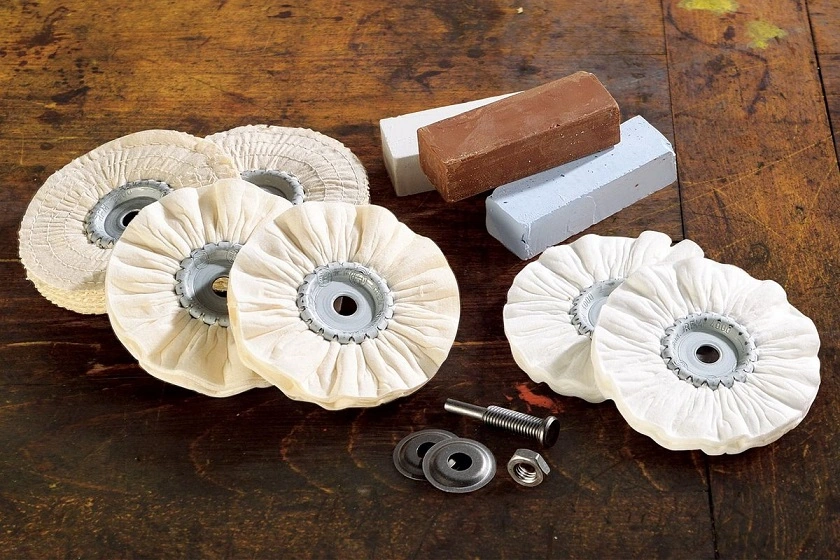
The choice of deburring tool for metal depends on several factors, including:
- Size and shape of the metal part: The tool should be able to accommodate the size and shape of the part comfortably.
- Material of the metal part: The abrasive material used in the tool should be compatible with the material of the part.
- Desired level of precision: The tool should be able to achieve the desired level of precision for the application.
- Production volume: If high-volume production is required, a stationary machine may be more efficient.
- Safety features: The tool should incorporate adequate safety features to protect the operator from potential hazards.
Benefits of Using Deburring Tools for Metal:
- Improved safety: Deburring tools can reduce the risk of injuries to operators by removing sharp edges and burrs.
- Improved functionality: Rounded edges can prevent snagging and protect other components from damage.
- Enhanced aesthetics: A smooth, burr-free surface improves the overall appearance of metal products.
- Increased efficiency: Power deburring tools and stationary machines can significantly reduce deburring time.
Applications of Deburring Tools for Metal:
- Automotive industry: Deburring car bodies, engine components, and other automotive parts.
- Aerospace manufacturing: Deburring precision metal components for aircraft and spacecraft.
- Construction: Deburring metal components for buildings, bridges, and other structures.
- Electronics manufacturing: Deburring metal components for circuit boards, electronic devices, and other electronics.
- Consumer goods manufacturing: Deburring metal components for appliances, furniture, and other consumer products.
Deburring tools play an essential role in maintaining the quality and safety of metal components across various industries. By effectively removing burrs and imperfections, deburring enhances the functionality, aesthetics, and overall value of metal products.
Metal deburring, grinding, and rounding are common applications in metalworking processes aimed at smoothing rough edges, removing burrs, and achieving a uniform finish on metal parts. Here’s a brief overview of each:
- Deburring: This process involves removing sharp edges or burrs left on metal parts after machining, cutting, or forming operations. It improves safety, functionality, and aesthetics of the parts.
- Grinding: Grinding is used to achieve precise dimensional control and surface finish. It involves using abrasive wheels or belts to remove material from a workpiece, often to prepare surfaces for further finishing or to achieve specific tolerances.
- Rounding: Rounding, also known as edge rounding, is done to soften sharp edges or corners on metal parts. It improves part handling, reduces the risk of injury, and can be aesthetically pleasing.
These processes are essential in various industries such as automotive, aerospace, manufacturing, and precision engineering, where metal parts must meet high standards of quality, safety, and performance.
- Deburring:
- Purpose: Deburring removes burrs, which are unwanted rough edges or protrusions on metal parts that result from machining, cutting, or forming processes.
- Methods: Deburring can be achieved through various methods such as manual deburring tools, abrasive stones, brushes, tumbling machines (vibratory or centrifugal), or chemical deburring solutions.
- Importance: Removing burrs improves the functional and aesthetic quality of metal parts. It also enhances safety by eliminating sharp edges that could cause injuries during handling or assembly.
- Grinding:
- Purpose: Grinding is used to achieve precise dimensional control, improve surface finish, and remove excess material from metal parts.
- Types: There are several types of grinding processes, including surface grinding, cylindrical grinding, centerless grinding, and internal grinding, each suited for specific part geometries and surface requirements.
- Equipment: Grinding machines use abrasive wheels (grinding wheels or belts) that rotate at high speeds to grind away material from the workpiece.
- Applications: Grinding is crucial for preparing surfaces for further finishing operations (such as polishing or plating), achieving tight tolerances, or removing defects like surface imperfections or weld seams.
- Rounding (Edge Rounding):
- Purpose: Rounding, or edge rounding, involves smoothing sharp edges or corners on metal parts.
- Methods: This can be done through mechanical methods like deburring tools with radius edges, vibratory or centrifugal tumbling processes with rounded media, or automated edge rounding machines.
- Benefits: Rounding improves part handling safety by reducing the risk of cuts or scratches. It also enhances the part’s appearance and can be critical for components that interact with other parts or personnel during assembly or use.
These processes are fundamental in metalworking industries where precision, quality, and safety are paramount. They ensure that metal parts meet exacting standards for functionality, durability, and aesthetics demanded by various applications, from automotive and aerospace to electronics and consumer goods manufacturing.
Deburring
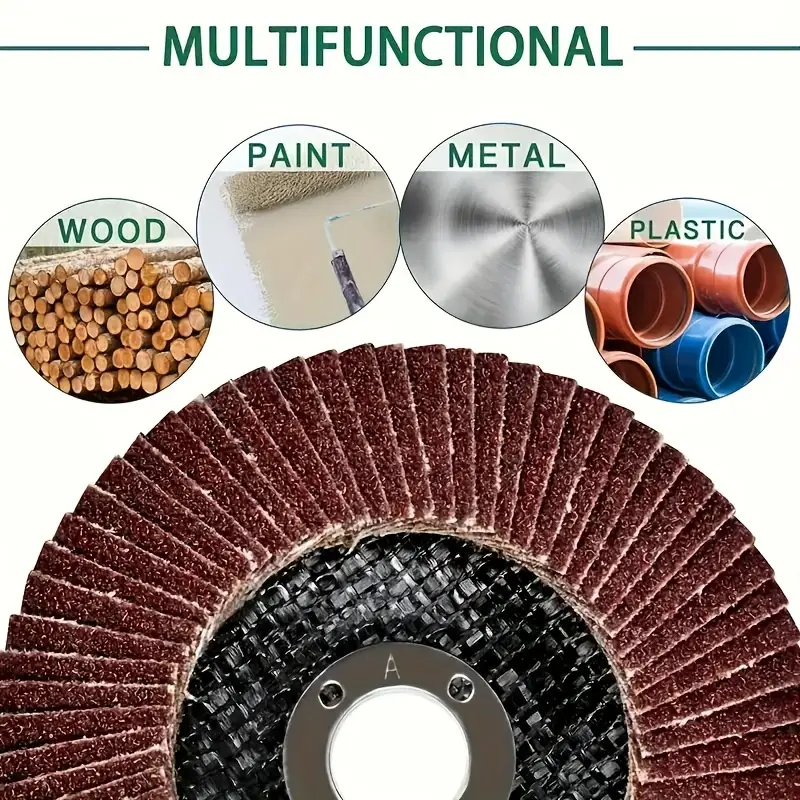
Deburring is a critical process in metalworking that involves the removal of burrs, which are unwanted rough edges or protrusions on metal parts. These burrs typically occur as a result of machining, cutting, or forming operations such as drilling, milling, stamping, or punching.
Importance of Deburring:
- Safety: Removing burrs eliminates sharp edges that can cause injuries during handling or assembly of parts.
- Functionality: Deburring ensures that parts fit together properly without interference from protrusions or rough edges.
- Aesthetics: Smooth edges improve the appearance of parts and enhance overall product quality.
- Performance: Burrs can affect the performance of moving parts or components that require precise tolerances.
Methods of Deburring:
- Manual Deburring Tools: Hand tools such as files, deburring knives, scrapers, or abrasive pads are used to manually remove burrs from small or intricate parts.
- Abrasive Stones and Brushes: Rotary tools equipped with abrasive stones or brushes can be used to remove burrs from larger or more accessible surfaces.
- Tumbling Machines: Vibratory or centrifugal tumbling machines use abrasive media (such as ceramic or plastic pellets) to deburr multiple parts simultaneously. This method is effective for small to medium-sized parts with complex geometries.
- Chemical Deburring: Chemical solutions or processes can be employed to selectively dissolve burrs, particularly in internal passages or complex shapes where mechanical methods may be challenging.
Deburring Considerations:
- Material Type: Different metals (e.g., aluminum, steel, titanium) require specific deburring techniques due to variations in hardness and machinability.
- Part Geometry: Deburring methods are chosen based on the size, shape, and accessibility of the burrs and the part itself.
- Quality Control: Inspecting parts after deburring ensures that all burrs are removed and that the part meets required specifications.
Deburring is essential in industries such as aerospace, automotive, electronics, and precision engineering, where high-quality, safe, and functional metal components are crucial.
Grinding
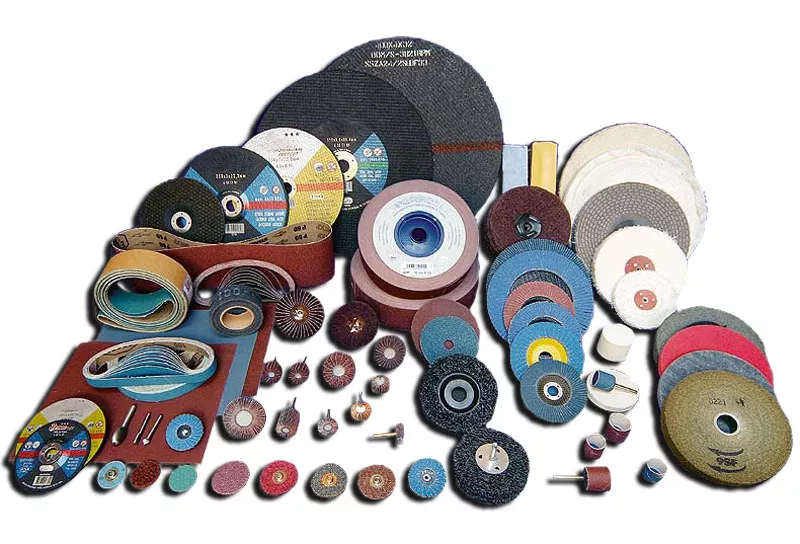
Grinding is a machining process used to remove material from a workpiece to achieve desired dimensions and surface finish. It is a versatile process widely used in various industries for both roughing and finishing operations on metal and other materials.
Purpose of Grinding
- Dimensional Control: Grinding allows for precise control over the dimensions of a workpiece, achieving tight tolerances that are difficult to achieve through other machining processes.
- Surface Finish: By using abrasive grains bonded into wheels or belts, grinding can produce smooth surfaces with low roughness values, enhancing the appearance and functionality of the parts.
- Material Removal: Grinding efficiently removes excess material, such as weld beads, casting flash, or stock material from forgings or billets, preparing the workpiece for subsequent operations.
Types of Grinding Processes:
- Surface Grinding: Involves grinding flat surfaces to achieve a smooth finish. It is commonly used for finishing hardened steel, cast iron, and similar materials.
- Cylindrical Grinding: Used to grind the outside diameter of cylindrical workpieces. It is ideal for creating precise roundness and surface finishes on shafts, rods, and other cylindrical components.
- Centerless Grinding: A type of cylindrical grinding where the workpiece is supported between two wheels: the grinding wheel and a regulating wheel. It is used for high-volume production of cylindrical parts with consistent dimensional accuracy.
- Internal Grinding: Grinding the inside diameter of a workpiece. It is used to create precise bores or holes with a smooth surface finish.
Equipment and Tools:
- Grinding Machines: Include surface grinders, cylindrical grinders, centerless grinders, and internal grinders, each designed for specific grinding applications.
- Grinding Wheels: Made from abrasive grains bonded together in various shapes and sizes. Types include aluminum oxide, silicon carbide, and diamond, each suited to different materials and applications.
Applications of Grinding:
- Manufacturing: Grinding is essential in the production of precision components for automotive, aerospace, medical devices, and consumer electronics.
- Tool and Die Making: Used for sharpening cutting tools and dies to maintain sharp edges and precise dimensions.
- Repair and Maintenance: Grinding is also employed for repairing worn or damaged parts by restoring their original dimensions and surface finish.
Grinding is a fundamental machining process that plays a crucial role in achieving the required dimensional accuracy, surface quality, and overall performance of metal parts in modern manufacturing.
Rounding
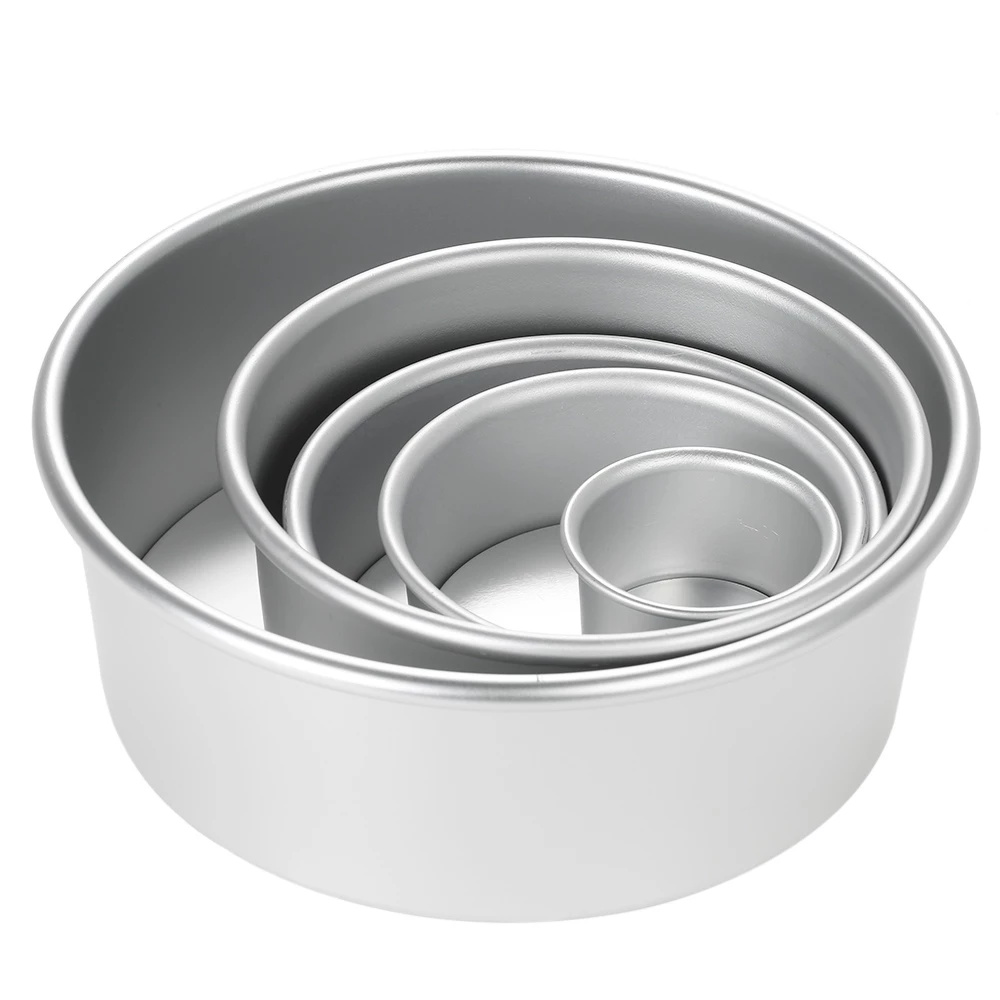
Rounding, also known as edge rounding or radiusing, is a finishing process used to smooth sharp edges and corners on metal parts. This process is essential for improving safety, enhancing aesthetics, and ensuring proper functionality of the parts, especially in applications where handling and contact with personnel or other components are involved.
Purpose and Benefits of Rounding:
- Safety: Rounded edges reduce the risk of injuries during handling, assembly, or use by eliminating sharp points or edges that could cause cuts or abrasions.
- Aesthetics: Smooth, rounded edges enhance the appearance of metal parts, making them more visually appealing and professional in finished products.
- Functionality: Rounding can improve the performance of parts by reducing stress concentrations at corners, which can extend the service life of components subjected to cyclic loading or wear.
Methods of Rounding:
- Manual Methods: Hand tools such as files, deburring tools with radiused edges, or abrasive pads can be used for small-scale rounding operations on accessible edges and corners.
- Machine Rounding: Automated edge rounding machines or dedicated deburring machines equipped with specialized tools can efficiently round edges and corners of larger or complex-shaped parts.
- Tumbling Processes: Vibratory or centrifugal tumbling machines using abrasive media (e.g., ceramic or plastic pellets) can uniformly round edges of multiple parts simultaneously. This method is effective for small to medium-sized parts with consistent edge profiles.
Considerations for Rounding:
- Part Geometry: The shape and size of the part influence the choice of rounding method. Complex geometries may require specialized equipment or multiple processes to achieve uniform rounding.
- Material Compatibility: Different metals (e.g., aluminum, stainless steel, titanium) and alloys have varying hardness and machinability characteristics, which may affect the choice of rounding tools and methods.
- Surface Finish Requirements: Rounding should maintain or improve the overall surface finish of the part, ensuring it meets functional and aesthetic specifications.
Applications of Rounding:
- Consumer Products: Rounding is crucial in industries such as furniture manufacturing, where rounded edges on metal components improve safety and user comfort.
- Automotive and Aerospace: Parts like brackets, panels, and housings benefit from rounded edges to prevent injuries during assembly and maintenance operations.
- Medical Devices: Ensuring smooth, rounded edges on surgical instruments and equipment enhances patient safety and ease of handling.
Rounding plays a vital role in enhancing the usability, safety, and appearance of metal parts across various industries, contributing to overall product quality and customer satisfaction.