We manufacture a Plate Bending Machine to bend sheet metal edges. Hydraulic Press Machines are used in metalworking industries
A plate bending machine, also known as a plate roll or plate rolling machine, is a type of equipment used to bend or roll metal plates into curved or cylindrical shapes. Plate bending machines are commonly used in metalworking industries for various applications such as manufacturing tanks, cylinders, pipes, and structural components. Here are some key aspects of a plate bending machine:
- Construction and Design: Plate bending machines are typically constructed with a sturdy frame or base that supports the bending components. The machine consists of three main components: the top roll (also known as the upper roll or bending roll), the bottom roll (also known as the lower roll or pinch roll), and the side roll(s). The rolls are usually powered by electric motors or hydraulic systems to apply force and control the bending process.
- Bending Capacity: The bending capacity of a plate bending machine refers to its ability to bend metal plates of different thicknesses and widths. The bending capacity is determined by factors such as the maximum plate thickness and width that the machine can handle. It’s important to choose a machine with the appropriate bending capacity to meet your specific bending requirements.
- Bending Techniques: Plate bending machines utilize different bending techniques to achieve various bending results. Common bending techniques include:
- Three-Roll Bending: This technique involves passing the metal plate between the top roll and the bottom roll while applying force to achieve the desired curvature. The side rolls are often used to assist in the bending process and maintain proper alignment of the plate.
- Four-Roll Bending: Four-roll bending machines have an additional side roll that provides better control and support during the bending process. This allows for more precise bending results and minimizes deformation of the plate.
- Control and Operation: Plate bending machines can be operated manually, semi-automatically, or with advanced computer numerical control (CNC) systems. Manual machines require the operator to adjust and control the bending process manually. Semi-automatic machines may have hydraulic or motorized adjustments for improved control. CNC plate bending machines offer the highest level of precision and automation, allowing for programmable bending sequences and precise control of bending parameters.
- Tooling and Dies: Plate bending machines use specialized tooling and dies to facilitate the bending process and achieve the desired curvature. These tooling components may include top rolls, bottom rolls, and side rolls with different profiles and sizes to accommodate various bending applications.
- Safety Features: Plate bending machines are equipped with safety features to protect operators and prevent accidents. These features may include emergency stop buttons, safety interlocks, and protective guarding to prevent access to hazardous areas during operation. Operators should be trained in safe machine operation and follow all safety guidelines to minimize risks.
- Maintenance and Support: Regular maintenance is crucial to ensure the proper functioning and longevity of a plate bending machine. This may involve lubrication, inspection of critical components, and periodic calibration. It’s important to have access to technical support and spare parts from the manufacturer or supplier to address any maintenance or repair needs.
When choosing a plate bending machine, consider your specific bending requirements, such as the thickness and width of the plates you’ll be working with, as well as the desired bending radius and curvature. Additionally, consider the reputation and reliability of the manufacturer or supplier to ensure you receive a high-quality machine that meets your needs.
Plate Bending Machine
A plate bending machine, also known as a plate rolling machine or simply a roll bending machine, is a specialized industrial equipment used to bend and shape metal plates and sheets into various forms, curves, and cylindrical shapes. These machines are commonly used in metal fabrication, manufacturing, and construction industries. Here are the key components and features of a plate bending machine:
- Rolls:
- The rolls are the central components of the plate bending machine. There are typically three rolls: two bottom rolls and one top roll.
- The rolls can be cylindrical or conical in shape, depending on the type of bending machine.
- The top roll is adjustable and exerts pressure on the metal plate to bend it as it passes through the rolls.
- Frame:
- The frame provides the structural support and stability for the machine.
- It is typically made of heavy-duty steel or cast iron to handle the high forces and stresses generated during the bending process.
- Hydraulic or Mechanical Drive:
- Plate bending machines can be powered by either hydraulic systems or mechanical means, such as gears and levers.
- Hydraulic systems offer precise control and are often preferred for heavy-duty applications.
- Control Panel:
- Modern plate bending machines are equipped with control panels that allow operators to adjust and control the bending process.
- Operators can set parameters such as the bending angle, curvature, and roll speeds.
- Support Rollers:
- Support rollers are often placed on both sides of the rolls to support and guide the metal plate as it passes through the machine.
- These rollers help ensure uniform bending and prevent material from skewing or twisting during the process.
- Tooling and Dies:
- Tooling and dies are used to create specific shapes and curves in the metal plate.
- Different tooling and dies can be installed based on the desired outcome, such as creating cylinders, cones, or various curved profiles.
- Safety Features:
- Plate bending machines are equipped with safety features such as emergency stop buttons, guards, and interlocks to protect operators from accidents.
- Pre-Bending Capability:
- Many plate bending machines have the capability to perform pre-bending, which involves bending the leading and trailing edges of the plate before the main bending operation.
- Pre-bending ensures a more precise and uniform curvature along the entire length of the plate.
- Material Handling:
- Some plate bending machines are equipped with material handling systems, such as conveyors or infeed/outfeed tables, to assist in loading and unloading large and heavy plates.
- CNC Control:
- Advanced plate bending machines may feature CNC (Computer Numerical Control) systems for automated and precise bending.
- CNC control allows for the creation of complex shapes and the storage of bending programs for different jobs.
Plate bending machines are used in a wide range of applications, including the production of cylindrical tanks, pipes, pressure vessels, and various curved components used in industries such as shipbuilding, construction, and metalworking. The choice of a plate bending machine depends on the thickness and type of material to be bent, as well as the specific bending requirements of the project.
A plate bending machine is a specialized tool used to shape metal plates into various angles and forms. It is a versatile machine that can be used for a variety of applications, including manufacturing, construction, and repair work.
Types of Plate Bending Machines
There are three main types of plate bending machines:
- Mechanical plate bending machines: These machines use a mechanical drive to bend the plate. They are the most basic type of plate bending machine and are typically used for bending small- to medium-sized plates.
- Hydraulic plate bending machines: These machines use hydraulic pressure to bend the plate. They are more powerful than mechanical plate bending machines and can bend larger plates.
- CNC plate bending machines: These machines are computer-controlled and can bend plates with very precise accuracy. They are typically used for high-volume production or for bending complex shapes.
Common Applications of Plate Bending Machines
Plate bending machines are used for a variety of applications, including:
- Manufacturing: Plate bending machines are used to manufacture a wide variety of metal products, such as brackets, cabinets, and railings.
- Construction: Plate bending machines are used to construct metal structures, such as buildings, bridges, and fences.
- Repair work: Plate bending machines are used to repair damaged metal objects, such as cars, appliances, and machinery.
Benefits of Plate Bending Machines
Plate bending machines offer several benefits, including:
- Precision: Plate bending machines can produce very precise bends, which is important for many applications.
- Versatility: Plate bending machines can be used to bend a wide variety of shapes and sizes of plates.
- Efficiency: Plate bending machines can be used to bend plates quickly and efficiently, which can save time and money.
Safety Precautions for Plate Bending Machines
When using plate bending machines, it is important to follow safety precautions to prevent injuries. Some of the most important safety precautions include:
- Wear personal protective equipment (PPE) such as safety glasses, gloves, and hearing protection.
- Secure the plate to the machine before bending.
- Do not overload the machine.
- Keep your hands away from the bending jaws and rollers.
- Be aware of the machine’s power source.
- Stop the machine before making any adjustments.
By following these safety precautions, you can help to prevent injuries and ensure the safe operation of plate bending machines.
Application Areas
Plate bending machines find applications in various industries and are essential tools for shaping and bending metal plates and sheets. Here are some of the primary application areas where plate bending machines are used:
- Metal Fabrication:
- Plate bending machines are extensively used in metal fabrication shops for bending and forming metal sheets and plates into a wide range of shapes and profiles.
- They are used to create curved and contoured parts, such as cylinders, cones, and arcs, which are used in the manufacture of various products.
- Shipbuilding:
- Shipyards utilize plate bending machines to bend and shape metal plates to form the hulls and other structural components of ships and boats.
- These machines are crucial for achieving the curved and contoured shapes needed in ship construction.
- Aerospace Industry:
- In the aerospace industry, plate bending machines are used to fabricate curved and aerodynamic components for aircraft and spacecraft.
- They play a vital role in producing wing sections, fuselage parts, and engine components.
- Oil and Gas Industry:
- Plate bending machines are employed to manufacture components for the oil and gas industry, including pipes, tanks, pressure vessels, and pipeline segments.
- These machines help create cylindrical and conical shapes required for storage and transport of liquids and gases.
- Construction:
- In construction, plate bending machines are used to produce curved and rolled sections of metal for architectural elements, such as curved facades, canopies, and roof structures.
- They are also used for bending metal plates and beams for structural purposes.
- Automotive Industry:
- Automotive manufacturers utilize plate bending machines for shaping and forming various metal components, including exhaust pipes, chassis parts, and body panels.
- These machines aid in achieving the desired contours and shapes for vehicle parts.
- Railroad and Transportation:
- Plate bending machines are involved in producing curved and rolled sections for railroad tracks, tram rails, and the construction of transportation infrastructure.
- They help create smooth curves and bends in rail components.
- Energy Sector:
- In the energy sector, plate bending machines are used to fabricate components for power plants, including pressure vessels, heat exchangers, and boilers.
- They enable the production of specialized components that can withstand high temperatures and pressures.
- Manufacturing of Tanks and Silos:
- Plate bending machines are essential for manufacturing storage tanks, silos, and containers used in various industries, including agriculture, food processing, and chemicals.
- These machines ensure the structural integrity of storage vessels.
- Artistic and Architectural Metalwork:
- Plate bending machines are employed in artistic and architectural metalwork to create custom and ornamental metal elements, such as decorative railings, sculptures, and artwork.
- They enable artists and craftsmen to achieve complex and artistic metal forms.
Plate bending machines come in various sizes and configurations to accommodate different plate thicknesses and bending requirements. The versatility and precision of these machines make them indispensable tools in a wide range of industrial and manufacturing processes.
History of Press Brake Machines
The origins of metal bending can be traced back to ancient civilizations, where blacksmiths used rudimentary tools to shape metal. As technology progressed, so did the methods of metal bending, leading to the development of more sophisticated machinery.
The first press brake machines emerged during the Industrial Revolution, driven by the need for more efficient and precise metalworking tools. Early press brake machines were manually operated, requiring significant physical effort and skill from the operator. Despite their limitations, these machines marked a significant advancement in the field of metal fabrication.
The 20th century witnessed substantial improvements in press brake technology. The introduction of hydraulic systems in the 1940s allowed for greater force and control, enabling the bending of thicker and tougher metals. This innovation revolutionized the industry, making hydraulic press brake machines the standard for many years.
In recent decades, the advent of computer numerical control (CNC) technology has transformed press brake machines once again. CNC press brake machines offer unparalleled precision and automation, allowing for complex bending operations to be performed with minimal human intervention. These machines are equipped with advanced software that can program and execute intricate bending sequences, ensuring consistency and accuracy.
Today, press brake machines continue to evolve, incorporating cutting-edge technologies such as robotics and artificial intelligence. These advancements are paving the way for even greater efficiency, flexibility, and precision in metal fabrication.
Types of Press Brake Machines
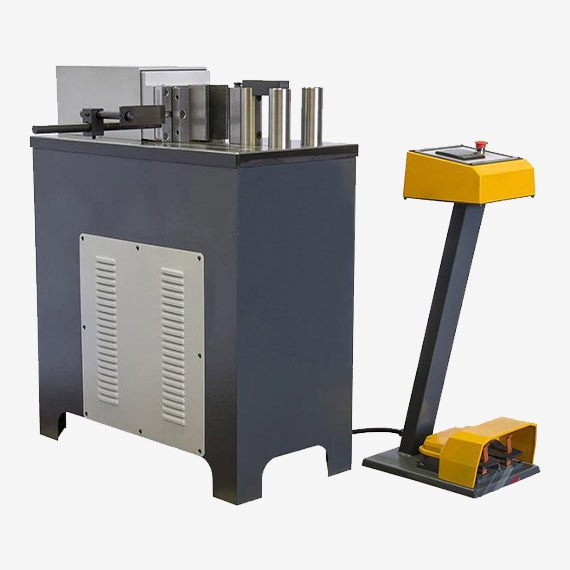
Press brake machines come in various types, each with its own features, advantages, and applications. Understanding the different types of press brake machines is essential for selecting the right equipment for specific metal bending tasks.
Manual Press Brake Machines
Features and Uses Manual press brake machines are the simplest type of press brakes, operated entirely by human effort. They are typically used for small-scale or low-volume production tasks, where high precision is not critical.
Advantages
- Cost-effective and affordable for small businesses
- Easy to operate and maintain
- Suitable for simple bending operations
Disadvantages
- Limited bending capacity and precision
- Labor-intensive and time-consuming
- Not suitable for high-volume production
Hydraulic Press Brake Machines
Features and Uses Hydraulic press brake machines use hydraulic fluid to generate the necessary force for bending metal sheets. They are widely used in various industries due to their versatility and reliability.
Advantages
- High bending capacity and precision
- Capable of handling thicker and tougher metals
- Smooth and consistent operation
Disadvantages
- Higher initial cost compared to manual machines
- Requires regular maintenance of hydraulic systems
- Potential for hydraulic fluid leaks
Electric Press Brake Machines
Features and Uses Electric press brake machines use electric motors to drive the bending process. They are known for their energy efficiency and precision.
Advantages
- Energy-efficient and environmentally friendly
- High precision and repeatability
- Lower operating costs compared to hydraulic machines
Disadvantages
- Limited force compared to hydraulic machines
- Higher initial cost than manual machines
- Requires skilled operators
CNC Press Brake Machines
Features and Uses CNC (Computer Numerical Control) press brake machines represent the pinnacle of press brake technology. They are equipped with advanced computer systems that control the bending process with exceptional precision.
Advantages
- Unmatched precision and accuracy
- Automated and programmable operations
- Suitable for complex and high-volume production
Disadvantages
- High initial cost and investment
- Requires skilled operators and programmers
- Complex maintenance and troubleshooting
Each type of press brake machine has its unique advantages and disadvantages, making it crucial to select the appropriate type based on specific production requirements and budget constraints.
Components of a Press Brake Machine
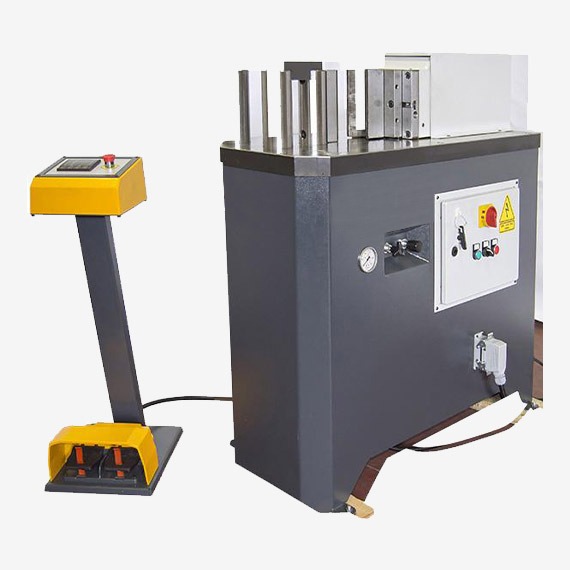
Press brake machines consist of several key components, each playing a vital role in the bending process. Understanding these components is essential for operating and maintaining the machine effectively.
Frame
The frame is the backbone of the press brake machine, providing structural support and stability. It is typically constructed from heavy-duty steel to withstand the forces exerted during the bending process.
Ram
The ram is a movable component that exerts force on the metal sheet, pressing it against the die to create the desired bend. The ram’s movement can be controlled manually, hydraulically, or electrically, depending on the type of press brake machine.
Die and Punch
The die and punch are the primary tools used in the bending process. The punch, attached to the ram, presses the metal sheet into the die, which is fixed to the machine’s bed. The shape and size of the die and punch determine the angle and radius of the bend.
Back Gauge
The back gauge is a positioning tool that helps in accurately aligning the metal sheet for bending. It ensures consistent bend angles and dimensions by providing a reference point for the sheet.
Control System
The control system manages the operation of the press brake machine. In manual machines, this may be a simple mechanical system, while hydraulic and electric machines use more advanced control systems. CNC press brake machines have sophisticated computer systems that program and control the entire bending process.
Safety Features
Press brake machines are equipped with various safety features to protect operators from accidents and injuries. These may include safety guards, emergency stop buttons, and light curtains that detect the presence of an operator’s hands near the bending area.
Working Principle
The basic working principle of a press brake machine involves applying a controlled force to bend metal sheets into specific shapes. Here are the key steps in the bending process:
- Sheet Positioning: The metal sheet is positioned on the machine’s bed, aligned against the back gauge to ensure precise placement.
- Tool Selection: The appropriate die and punch are selected based on the desired bend angle and radius. These tools are then installed on the machine.
- Bending Operation: The ram descends, pressing the punch into the metal sheet and forcing it into the die. This action creates the bend, with the angle and shape determined by the tools used and the force applied.
- Return Stroke: After the bend is completed, the ram ascends, releasing the pressure on the metal sheet. The sheet is then removed or repositioned for additional bends.
Precision and control are crucial in the bending process to ensure the accuracy and consistency of the bends. CNC press brake machines excel in this regard, as they use computer programming to control the ram’s movement and force, resulting in highly precise bends.
Applications of Press Brake Machines
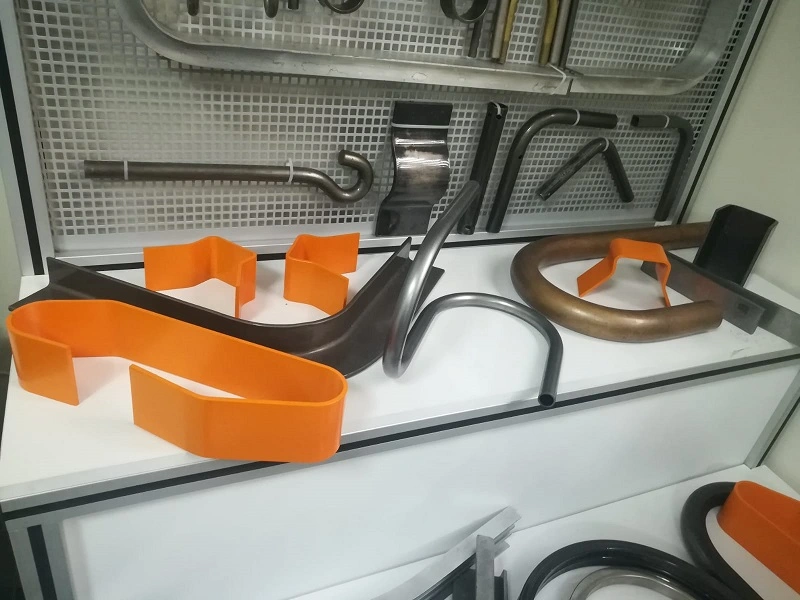
Press brake machines are used across various industries due to their versatility and precision. Here are some common applications:
- Automotive Industry: Manufacturing car body panels, chassis components, and brackets.
- Aerospace Industry: Producing aircraft parts, including wing components and fuselage sections.
- Construction Industry: Fabricating structural components, such as beams, columns, and brackets.
- Electronics Industry: Creating enclosures, chassis, and brackets for electronic devices.
- Furniture Industry: Making metal frames and components for furniture.
- HVAC Industry: Producing ductwork and ventilation components.
These machines are also used in creating custom metal parts and prototypes, showcasing their adaptability to various production needs.
Advantages of Using Press Brake Machines
Press brake machines offer several advantages that make them indispensable in metal fabrication:
- Precision and Accuracy: These machines can produce highly precise bends, ensuring that components meet exact specifications.
- Efficiency and Productivity: Press brake machines can perform complex bending operations quickly, increasing production efficiency.
- Versatility: They can handle a wide range of materials and thicknesses, making them suitable for various applications.
- Cost-effectiveness: By reducing material waste and increasing production speed, press brake machines can lower manufacturing costs.
Maintenance and Safety Tips
Proper maintenance and safety practices are essential for the efficient and safe operation of press brake machines. Here are some tips:
Routine Maintenance
- Regularly inspect the machine for wear and tear.
- Keep the machine clean and free from debris.
- Lubricate moving parts as recommended by the manufacturer.
- Check hydraulic fluid levels and replace as necessary.
Common Issues and Troubleshooting
- Misalignment of the die and punch: Adjust the alignment to ensure precise bends.
- Inconsistent bending angles: Check for wear on the tools and replace if needed.
- Hydraulic system leaks: Inspect seals and hoses, and replace any damaged components.
Safety Guidelines for Operators
- Always wear appropriate personal protective equipment (PPE).
- Ensure that safety guards and emergency stop buttons are in place and functional.
- Follow the manufacturer’s guidelines for safe operation.
- Undergo proper training before operating the machine.
Future Trends in Press Brake Technology
The future of press brake technology is shaped by advancements in automation, materials, and environmental considerations:
- Automation and Industry 4.0: The integration of robotics and IoT (Internet of Things) is enhancing the automation of press brake machines, leading to increased efficiency and reduced human intervention.
- Advanced Materials and Designs: The development of new materials and innovative designs is expanding the capabilities of press brake machines, allowing for more complex and precise bends.
- Environmental Considerations: Efforts to reduce energy consumption and minimize environmental impact are driving the adoption of electric press brake machines and other eco-friendly technologies.
Conclusion
Press brake machines are a cornerstone of modern metal fabrication, offering unmatched precision, efficiency, and versatility. From their historical evolution to the latest technological advancements, these machines continue to play a vital role in various industries.
Understanding the different types of press brake machines, their components, and working principles is essential for selecting the right equipment and maximizing its potential. By following proper maintenance and safety practices, operators can ensure the longevity and safe operation of these machines.
As we look to the future, advancements in automation, materials, and environmental sustainability will further enhance the capabilities of press brake machines, solidifying their place in the ever-evolving landscape of manufacturing.
Whether you are a seasoned professional or new to the field, this comprehensive guide provides valuable insights into the world of sheet metal bending press brake machines, highlighting their importance and potential in modern industry.
Components of a Press Brake Machine
Press brake machines consist of several key components, each playing a vital role in the bending process. Understanding these components is essential for operating and maintaining the machine effectively.
Frame
The frame is the backbone of the press brake machine, providing structural support and stability. Constructed from heavy-duty steel, the frame must be robust enough to withstand the significant forces exerted during the bending process. The frame’s design can vary depending on the machine type, but its primary function remains to ensure rigidity and durability.
Ram
The ram is a movable component that exerts force on the metal sheet, pressing it against the die to create the desired bend. The ram’s movement can be controlled manually, hydraulically, or electrically, depending on the type of press brake machine. In CNC press brakes, the ram’s motion is precisely controlled by computer programming, allowing for highly accurate and repeatable bends.
Die and Punch
The die and punch are the primary tools used in the bending process. The punch, attached to the ram, presses the metal sheet into the die, which is fixed to the machine’s bed. The shape and size of the die and punch determine the angle and radius of the bend. There are various types of dies and punches, each suited for different bending operations, such as V-dies, U-dies, and hemming dies.
Back Gauge
The back gauge is a positioning tool that helps in accurately aligning the metal sheet for bending. It ensures consistent bend angles and dimensions by providing a reference point for the sheet. Modern press brake machines often feature CNC-controlled back gauges, which can be programmed to automatically adjust positions for complex bending sequences, enhancing precision and efficiency.
Control System
The control system manages the operation of the press brake machine. In manual machines, this may be a simple mechanical system, while hydraulic and electric machines use more advanced control systems. CNC press brake machines have sophisticated computer systems that program and control the entire bending process. These systems can store multiple bending programs, allowing for quick setup and reduced downtime between jobs.
Safety Features
Press brake machines are equipped with various safety features to protect operators from accidents and injuries. These may include safety guards, emergency stop buttons, and light curtains that detect the presence of an operator’s hands near the bending area. Modern machines also incorporate safety sensors that halt the machine’s operation if a potential hazard is detected, ensuring a safer working environment.
Working Principle
https://www.youtube.com/embed/l8quDXXNNEg?feature=oembedWorking Principle
The basic working principle of a press brake machine involves applying a controlled force to bend metal sheets into specific shapes. Here are the key steps in the bending process:
- Sheet Positioning: The metal sheet is positioned on the machine’s bed, aligned against the back gauge to ensure precise placement. Proper alignment is crucial for achieving accurate and consistent bends.
- Tool Selection: The appropriate die and punch are selected based on the desired bend angle and radius. These tools are then installed on the machine. The selection of the correct tools is essential for achieving the desired bend geometry and avoiding damage to the metal sheet.
- Bending Operation: The ram descends, pressing the punch into the metal sheet and forcing it into the die. This action creates the bend, with the angle and shape determined by the tools used and the force applied. The bending process requires careful control of the ram’s speed and pressure to ensure precise and consistent results.
- Return Stroke: After the bend is completed, the ram ascends, releasing the pressure on the metal sheet. The sheet is then removed or repositioned for additional bends. In CNC press brakes, the return stroke and repositioning of the sheet can be automated, increasing efficiency and reducing operator fatigue.
Precision and control are crucial in the bending process to ensure the accuracy and consistency of the bends. CNC press brake machines excel in this regard, as they use computer programming to control the ram’s movement and force, resulting in highly precise bends. The ability to program complex bending sequences also allows for the efficient production of intricate parts with minimal manual intervention.
Applications of Press Brake Machines
https://www.youtube.com/embed/o1dG-pIFkTk?feature=oembedApplications of Press Brake Machines
Press brake machines are used across various industries due to their versatility and precision. Here are some common applications:
- Automotive Industry: Press brake machines are integral to manufacturing car body panels, chassis components, and brackets. These machines can produce complex shapes and bends required for modern vehicle designs, ensuring high precision and repeatability.
- Aerospace Industry: The aerospace industry demands high precision and stringent quality standards. Press brake machines are used to produce aircraft parts, including wing components and fuselage sections, where accuracy and consistency are paramount.
- Construction Industry: Press brake machines are utilized to fabricate structural components such as beams, columns, and brackets. These components must meet specific strength and dimensional requirements to ensure the safety and stability of buildings and other structures.
- Electronics Industry: In the electronics industry, press brake machines are used to create enclosures, chassis, and brackets for electronic devices. These components often require intricate bends and precise dimensions to accommodate various electronic components and assemblies.
- Furniture Industry: The furniture industry employs press brake machines to make metal frames and components for furniture. These machines enable the production of aesthetically pleasing and structurally sound furniture parts, such as legs, supports, and brackets.
- HVAC Industry: The HVAC industry uses press brake machines to produce ductwork and ventilation components. These machines can create complex bends and shapes needed for efficient air distribution and ventilation systems.
These machines are also used in creating custom metal parts and prototypes, showcasing their adaptability to various production needs. The ability to quickly and accurately produce custom components makes press brake machines valuable tools for manufacturers and fabricators across different industries.
Advantages of Using Press Brake Machines
Press brake machines offer several advantages that make them indispensable in metal fabrication:
- Precision and Accuracy: Press brake machines are designed to produce highly precise bends, ensuring that components meet exact specifications. CNC press brakes, in particular, offer unmatched precision and repeatability, allowing for the production of intricate and complex parts with tight tolerances.
- Efficiency and Productivity: These machines can perform complex bending operations quickly, increasing production efficiency. The automation capabilities of CNC press brakes reduce the need for manual intervention, leading to faster setup times and higher throughput.
- Versatility: Press brake machines can handle a wide range of materials and thicknesses, making them suitable for various applications. From thin aluminum sheets to thick steel plates, these machines can accommodate different bending requirements, providing flexibility in manufacturing processes.
- Cost-effectiveness: By reducing material waste and increasing production speed, press brake machines can lower manufacturing costs. The precision and efficiency of these machines minimize errors and rework, resulting in significant cost savings over time.
- Consistency: Press brake machines ensure consistent bend quality across multiple parts, which is essential for mass production. The ability to produce uniform parts enhances the overall quality and reliability of the final products.
- Customizability: Modern press brake machines, especially CNC models, offer high levels of customizability. Operators can program specific bending sequences and parameters, allowing for the production of custom parts tailored to unique design requirements.
- Reduced Labor Costs: Automation in CNC press brake machines reduces the need for skilled labor, lowering labor costs. These machines can operate with minimal supervision, enabling manufacturers to allocate human resources more efficiently.
- Enhanced Safety: Press brake machines are equipped with advanced safety features that protect operators from accidents and injuries. Safety guards, emergency stop buttons, and sensors contribute to a safer working environment, reducing the risk of workplace incidents.
These advantages highlight the critical role of press brake machines in modern metal fabrication, underscoring their value in achieving high-quality, efficient, and cost-effective manufacturing processes.
Maintenance and Safety Tips
Proper maintenance and safety practices are essential for the efficient and safe operation of press brake machines. Here are some tips:
Routine Maintenance
- Regular Inspection: Regularly inspect the machine for wear and tear. Check for any signs of damage or misalignment in the components, especially the die and punch.
- Cleaning: Keep the machine clean and free from debris. Accumulated dust and metal shavings can affect the machine’s performance and lead to premature wear.
- Lubrication: Lubricate moving parts as recommended by the manufacturer. Proper lubrication reduces friction and prevents wear, extending the machine’s lifespan.
- Hydraulic Fluid: Check hydraulic fluid levels and replace as necessary. Ensure that the hydraulic system is free from leaks and that the fluid is clean and at the proper level.
- Tool Maintenance: Inspect the die and punch for wear and replace them if needed. Sharp and well-maintained tools are crucial for achieving precise bends.
Common Issues and Troubleshooting
- Misalignment: Misalignment of the die and punch can result in inaccurate bends. Adjust the alignment to ensure precise bending operations.
- Inconsistent Bending Angles: Inconsistent bending angles may be due to worn tools or incorrect settings. Check the tools for wear and verify the machine’s settings.
- Hydraulic System Leaks: Hydraulic system leaks can affect the machine’s performance. Inspect seals and hoses regularly and replace any damaged components.
- Control System Errors: Errors in the control system, particularly in CNC machines, can disrupt operations. Ensure that the control system software is up-to-date and that any programming issues are addressed promptly.
Safety Guidelines for Operators
- Personal Protective Equipment (PPE): Always wear appropriate PPE, including safety glasses, gloves, and protective clothing, to prevent injuries.
- Safety Guards and Emergency Stops: Ensure that safety guards are in place and functional. Familiarize yourself with the location and operation of emergency stop buttons.
- Manufacturer Guidelines: Follow the manufacturer’s guidelines for safe operation. These guidelines provide crucial information on operating the machine safely and efficiently.
- Training: Undergo proper training before operating the machine. Training should cover machine operation, maintenance, and safety procedures.
- Awareness: Stay alert and aware of your surroundings while operating the machine. Avoid distractions and ensure that the work area is free from hazards.
By adhering to these maintenance and safety tips, operators can ensure the longevity, efficiency, and safe operation of press brake machines, minimizing downtime and reducing the risk of accidents.
Future Trends in Press Brake Technology
The future of press brake technology is shaped by advancements in automation, materials, and environmental considerations. Here are some key trends to watch:
Automation and Industry 4.0
The integration of robotics and the Internet of Things (IoT) is enhancing the automation of press brake machines. Industry 4.0 technologies enable machines to communicate and coordinate with each other, leading to increased efficiency and reduced human intervention. Automated press brake machines can perform complex bending operations with minimal oversight, improving productivity and precision.
Advanced Materials and Designs
The development of new materials and innovative designs is expanding the capabilities of press brake machines. Advanced materials, such as high-strength alloys and composites, require precise and powerful bending techniques. Modern press brake machines are being designed to handle these materials, enabling the production of more durable and lightweight components.
Environmental Considerations
Efforts to reduce energy consumption and minimize environmental impact are driving the adoption of electric press brake machines and other eco-friendly technologies. Electric press brakes are more energy-efficient than their hydraulic counterparts, producing less noise and requiring less maintenance. Additionally, manufacturers are exploring sustainable materials and processes to further reduce the environmental footprint of metal fabrication.
Smart Manufacturing
Smart manufacturing technologies, including artificial intelligence (AI) and machine learning, are being integrated into press brake machines. These technologies enable predictive maintenance, real-time monitoring, and adaptive control, enhancing machine performance and reducing downtime. AI-powered systems can optimize bending operations by analyzing data and making adjustments in real-time.
User-Friendly Interfaces
Future press brake machines are likely to feature more user-friendly interfaces, making them easier to operate and program. Touchscreen controls, intuitive software, and augmented reality (AR) training tools will simplify the operation of these machines, reducing the learning curve for operators.
These trends highlight the ongoing evolution of press brake technology, promising greater efficiency, precision, and sustainability in metal fabrication.
Conclusion
Press brake machines are a cornerstone of modern metal fabrication, offering unmatched precision, efficiency, and versatility. From their historical evolution to the latest technological advancements, these machines continue to play a vital role in various industries.
Understanding the different types of press brake machines, their components, and working principles is essential for selecting the right equipment and maximizing its potential. By following proper maintenance and safety practices, operators can ensure the longevity and safe operation of these machines.
As we look to the future, advancements in automation, materials, and environmental sustainability will further enhance the capabilities of press brake machines, solidifying their place in the ever-evolving landscape of manufacturing.
Whether you are a seasoned professional or new to the field, this comprehensive guide provides valuable insights into the world of sheet metal bending press brake machines, highlighting their importance and potential in modern industry.
Press brake machines will undoubtedly continue to evolve, driven by technological innovations and industry demands. Staying informed about these advancements and adopting best practices will enable manufacturers to leverage the full potential of press brake machines, ensuring continued success in their metal fabrication endeavors.
EMS Metalworking Machinery
We design, manufacture and assembly metalworking machinery such as:
- Hydraulic transfer press
- Glass mosaic press
- Hydraulic deep drawing press
- Casting press
- Hydraulic cold forming press
- Hydroforming press
- Composite press
- Silicone rubber moulding press
- Brake pad press
- Melamine press
- SMC & BMC Press
- Labrotaroy press
- Edge cutting trimming machine
- Edge curling machine
- Trimming beading machine
- Trimming joggling machine
- Cookware production line
- Pipe bending machine
- Profile bending machine
- Bandsaw for metal
- Cylindrical welding machine
- Horizontal pres and cookware
- Kitchenware, hotelware
- Bakeware and cuttlery production machinery
as a complete line as well as an individual machine such as:
- Edge cutting trimming beading machines
- Polishing and grinding machines for pot and pans
- Hydraulic drawing presses
- Circle blanking machines
- Riveting machine
- Hole punching machines
- Press feeding machine
You can check our machinery at work at: EMS Metalworking Machinery – YouTube
Applications:
- Beading and ribbing
- Flanging
- Trimming
- Curling
- Lock-seaming
- Ribbing
- Flange-punching