Metal spinning machines, also known as metal spinning lathes, are workhorses in sheet metal forming. These machines manipulate flat sheets of metal into precise, hollow, and rotationally symmetrical shapes. Their versatility allows them to produce a vast array of products, from simple cones used in kitchenware to complex rocket nose cones and decorative lampshades.
Metal spinning
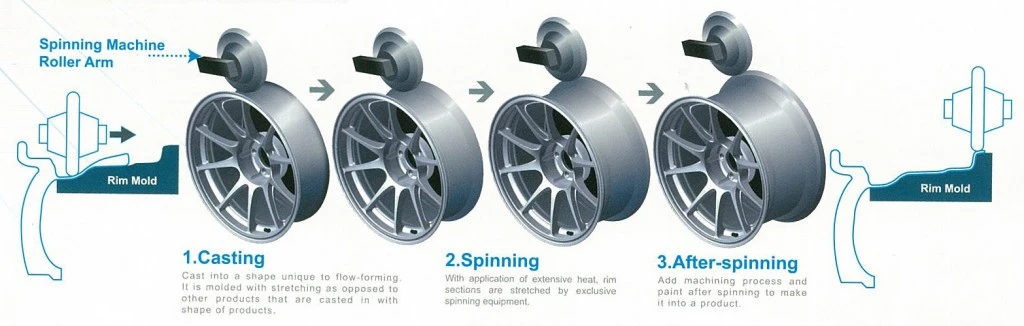
The core functionality of a metal spinning machine is fairly straightforward. A metal sheet is securely fastened to a rotating mandrel. This mandrel acts as a mold, pre-defining the final shape of the metal piece. A tool, typically a roller, is then pressed against the spinning sheet. As the lathe rotates the mandrel and sheet together, the roller tool is gradually guided along the length of the mandrel. This controlled pressure forces the sheet metal to conform to the contours of the mandrel, effectively shaping it into the desired form.
Metal spinning machines come in two primary configurations: manual and CNC (computer numerical control). Manual machines rely on the skill of a craftsperson who maneuvers a hand-held roller tool to shape the metal. CNC machines, on the other hand, are automated. They follow a pre-programmed digital blueprint to precisely control the movements of the roller tool, ensuring consistent and repeatable results.
The metal spinning process boasts several advantages. Firstly, it’s a relatively cost-effective way to manufacture high-quality parts. Secondly, it tackles intricate shapes with remarkable ease, something that can be challenging with other metal forming methods. Finally, metal spinning offers exceptional versatility. It can work with a broad spectrum of metals, including aluminum, steel, copper, and brass, making it a suitable choice for a wide range of applications.
Metal spinning, also known as spin forming or metal turning, is a metalworking process used to create axially symmetric parts. The metal spinning machine plays a critical role in this process, enabling the transformation of metal blanks into various shapes such as cones, cylinders, and hemispheres. This article explores the workings, components, advantages, and applications of metal spinning machines.
What is Metal Spinning?

Metal spinning is a manufacturing process in which a metal disc or tube is rotated at high speed and formed into a desired shape using localized pressure. This process is typically performed on a lathe, but specialized metal spinning machines are often used for industrial applications.
Components of a Metal Spinning Machine
- Lathe Bed: The base that supports the entire machine.
- Headstock: Houses the spindle and drive mechanism, which rotates the workpiece.
- Tailstock: Supports the other end of the workpiece and can be adjusted for length.
- Tool Post: Holds the forming tools that shape the metal.
- Forming Rollers: Tools that apply pressure to the spinning metal to shape it.
- Control System: Manages the speed, pressure, and movements of the machine.
How Metal Spinning Machines Work
- Setup: A metal blank is mounted onto the spindle and secured in place.
- Rotation: The spindle rotates the metal blank at high speed.
- Tool Application: Forming tools, typically rollers, are applied to the rotating metal blank, gradually shaping it against a pre-formed mold or mandrel.
- Shaping: The metal is stretched and compressed to conform to the shape of the mold.
- Finishing: The formed part is trimmed and finished as needed.
Advantages of Metal Spinning Machines
- Versatility: Capable of producing a wide range of shapes and sizes.
- Material Efficiency: Minimal waste compared to other metal forming processes.
- Cost-Effective: Lower tooling costs and shorter setup times.
- Strength and Quality: The process enhances the strength and grain structure of the metal.
- Customization: Easily adaptable for custom and short-run production.
Applications of Metal Spinning Machines
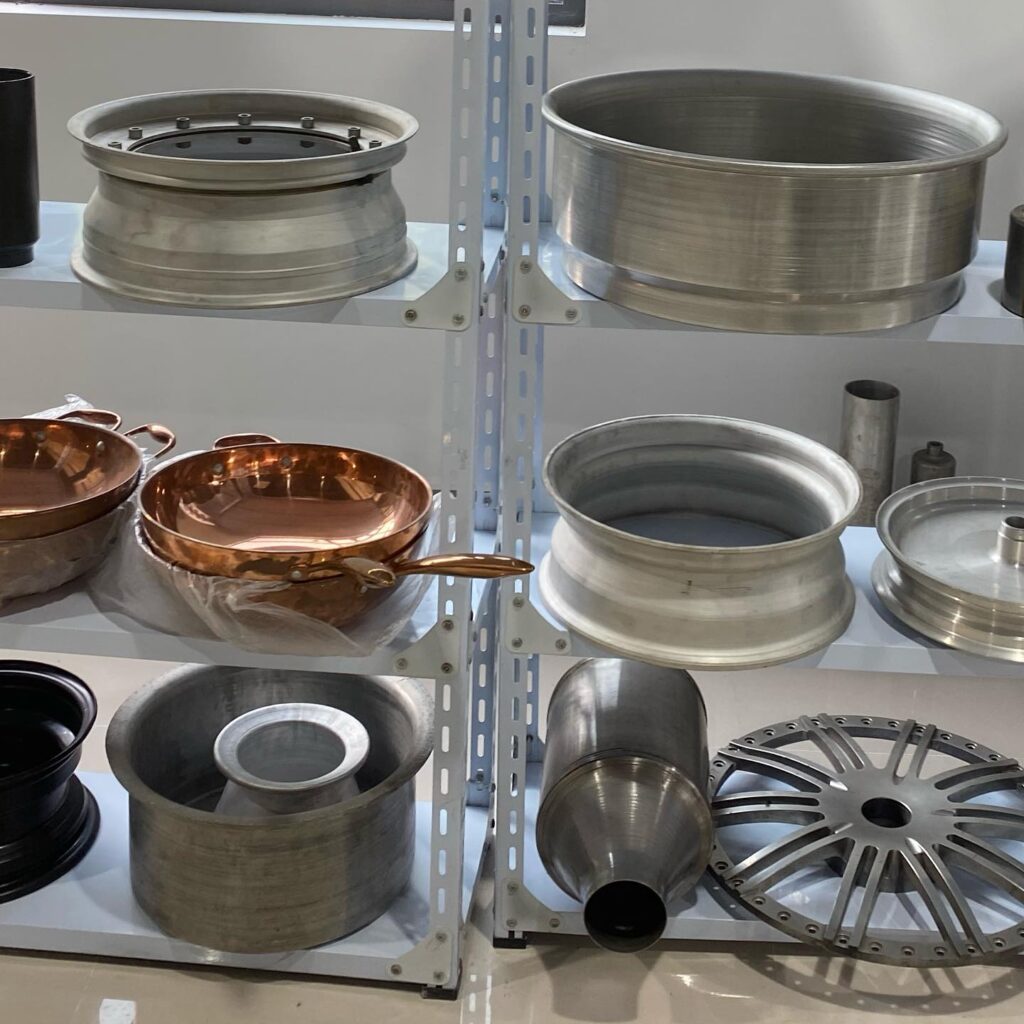
Metal spinning machines are used in various industries to produce parts such as:
- Automotive: Wheel rims, hubcaps, and exhaust components.
- Aerospace: Nose cones, engine components, and structural parts.
- Cookware: Pots, pans, and lids.
- Lighting: Reflectors and decorative fixtures.
- HVAC: Ductwork and ventilation components.
- Medical: Surgical instruments and components.
Safety Considerations
Operating metal spinning machines involves several safety risks. Adhering to safety protocols is crucial:
- Training: Operators must be adequately trained.
- Protective Equipment: Use of appropriate personal protective equipment (PPE).
- Regular Maintenance: Ensures the machinery operates safely.
- Emergency Procedures: Clear guidelines for handling emergencies.
Future Trends and Innovations
The future of metal spinning machines looks promising with ongoing technological advancements:
- Automation and CNC Technology: Integration of computerized controls for increased precision and efficiency.
- Eco-Friendly Processes: Development of more sustainable and energy-efficient methods.
- Advanced Materials: Exploration of new materials that can be spun, expanding the range of applications.
- Smart Manufacturing: Use of IoT and AI for real-time monitoring and optimization.
Conclusion
Metal spinning machines are vital tools in modern manufacturing, enabling the production of high-quality, axially symmetric parts with efficiency and precision. Their versatility, cost-effectiveness, and ability to enhance material properties make them indispensable in various industries. As technology continues to evolve, metal spinning machines will play an increasingly significant role in advancing manufacturing capabilities and meeting the demands of diverse applications.
Parts of a metal spinning machine
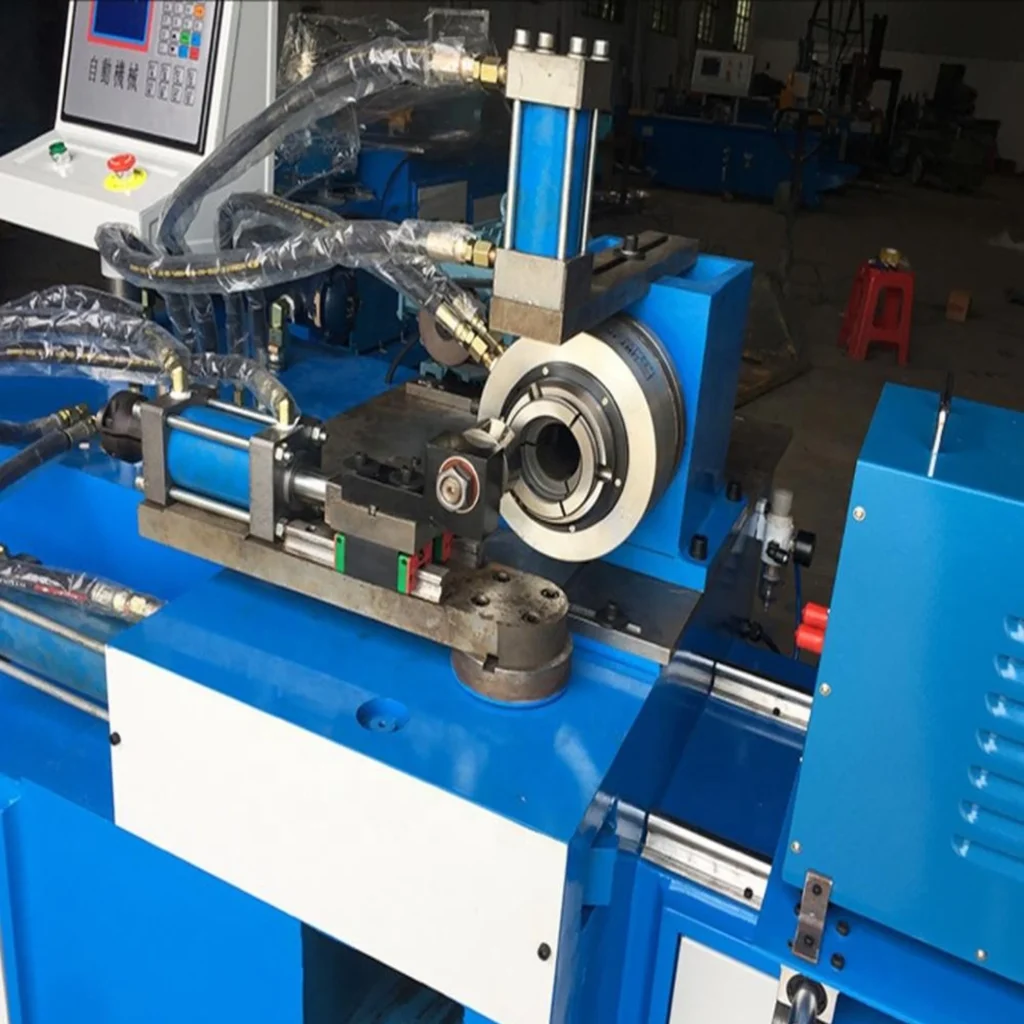
Metal spinning machines, also known as metal spinning lathes, are workhorses in sheet metal forming. These machines manipulate flat sheets of metal into precise, hollow, and rotationally symmetrical shapes. Their versatility allows them to produce a vast array of products, from simple cones used in kitchenware to complex rocket nose cones and decorative lampshades.
The core functionality of a metal spinning machine is fairly straightforward. A metal sheet is securely fastened to a rotating mandrel. This mandrel acts as a mold, pre-defining the final shape of the metal piece. A tool, typically a roller, is then pressed against the spinning sheet. As the lathe rotates the mandrel and sheet together, the roller tool is gradually guided along the length of the mandrel. This controlled pressure forces the sheet metal to conform to the contours of the mandrel, effectively shaping it into the desired form.
Metal spinning machines come in two primary configurations: manual and CNC (computer numerical control). Manual machines rely on the skill of a craftsperson who maneuvers a hand-held roller tool to shape the metal. CNC machines, on the other hand, are automated. They follow a pre-programmed digital blueprint to precisely control the movements of the roller tool, ensuring consistent and repeatable results.
The metal spinning process boasts several advantages. Firstly, it’s a relatively cost-effective way to manufacture high-quality parts. Secondly, it tackles intricate shapes with remarkable ease, something that can be challenging with other metal forming methods. Finally, metal spinning offers exceptional versatility. It can work with a broad spectrum of metals, including aluminum, steel, copper, and brass, making it a suitable choice for a wide range of applications.
Here are the key parts of a metal spinning machine:
- Headstock: This is the part of the machine that houses the electric motor and drive system. It is responsible for rotating the mandrel at high speeds.
- Tailstock: The tailstock is located at the opposite end of the lathe from the headstock. It provides support for the end of the mandrel and the metal blank.
- Mandrel: The mandrel is a precisely shaped form that replicates the desired final shape of the metal piece. The metal blank is clamped onto the mandrel.
- Drive Belt: The drive belt connects the motor in the headstock to the mandrel, transferring rotational power to spin the mandrel.
- Tailstock Die (follower rest or live center): The tailstock die applies pressure to the back of the metal blank to help it conform to the shape of the mandrel.
- Tool Rest: The tool rest provides support for the spinning tool (usually a roller) and allows the operator to control the pressure applied to the metal blank.
- Spinning Tool: The spinning tool, most commonly a roller with various profiles, is used to press against the metal blank and shape it over the mandrel. There are various types of spinning tools for different shaping applications.
- Foot Pedal (CNC machines only): A foot pedal allows the operator to control the start and stop functions of the CNC machine.
- CNC Control Unit (CNC machines only): This is the computer system that controls the automated movements of the machine based on a pre-programmed design.
Parts that can be manufactured by metal spinning
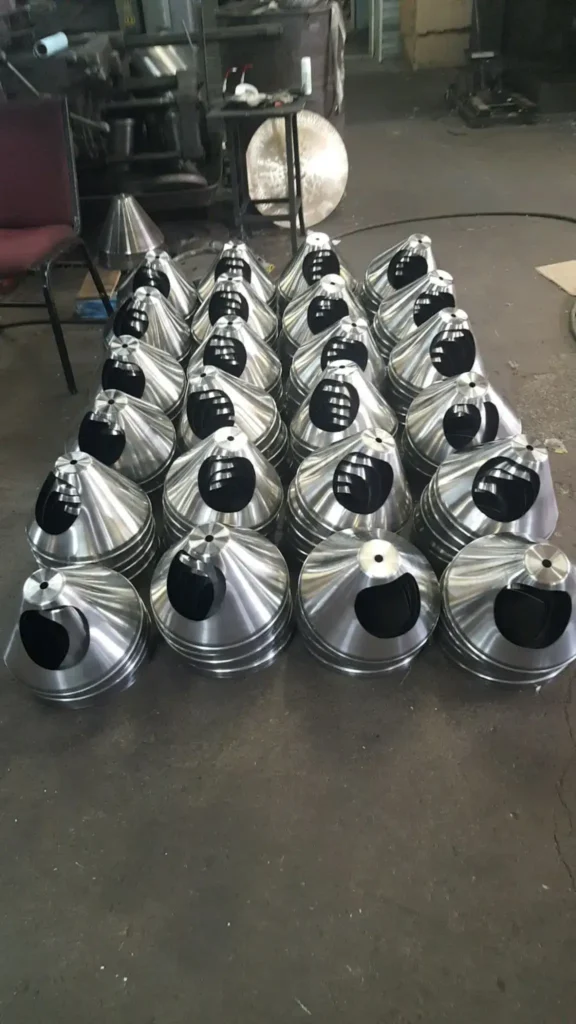
Metal spinning machines excel at producing a wide range of hollow, rotationally symmetrical parts. Here are some examples:
- Simple Shapes:
- Cones: Commonly used in kitchenware, lampshades, and funnels.
- Hemispheres: Found in applications like pressure vessel ends, light fixtures, and decorative spheres.
- Cylinders: Used for tubes, enclosures, and various machine components.
- Complex Shapes:
- Rocket nose cones: These require precise shaping for optimal aerodynamic performance.
- Radar dishes: The curved shape allows for efficient signal transmission and reception.
- Automotive parts: Wheel covers, air intake scoops, and some headlight housings can be spun.
- Lighting components: Reflectors and lamp shades with intricate curves are possible.
- Other Applications:
- Medical equipment: Cladding for medical instruments and certain sterile containers.
- Plumbing components: Decorative or custom-shaped pipe fittings.
- Telecommunication equipment: Parabolic dish antennas and waveguides.
Overall, metal spinning offers a versatile solution for creating a vast array of rotationally symmetrical parts, from everyday items to specialized components.
Mechanics of Sheet Metal Spinning
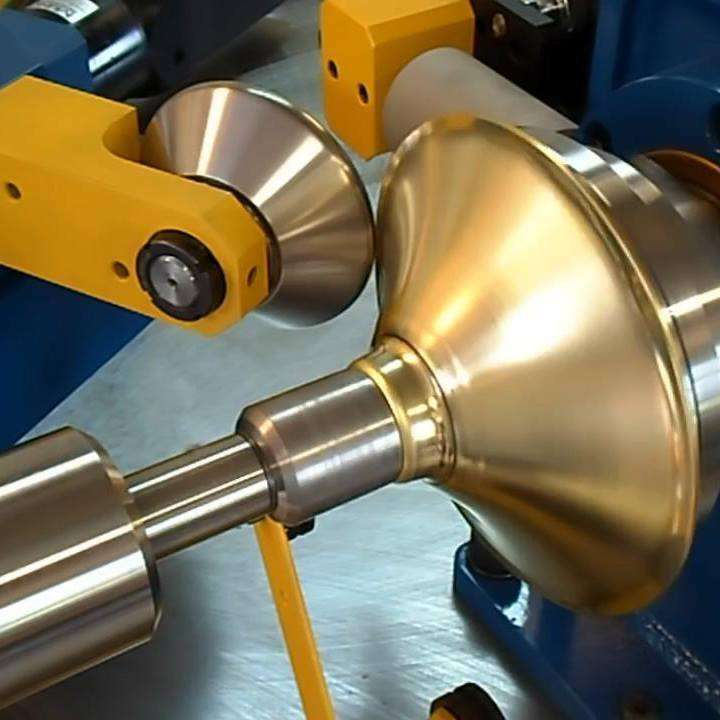
The mechanics of sheet metal spinning involve a combination of controlled force, material plasticity, and manipulation on a rotating form. Here’s a breakdown of the key aspects:
1. Material:
- Sheet metal is the starting point. The specific type chosen depends on the desired final product’s properties. Common options include aluminum, steel, copper, and brass. Each metal has its own work hardening characteristics, which influence how much shaping it can undergo without cracking.
2. Mandrel:
- The mandrel acts as a mold, replicating the final desired shape of the metal piece. It’s a precisely contoured form typically made of steel or wood. The metal sheet is clamped securely onto the mandrel.
3. Spinning Tool:
- The spinning tool, most commonly a roller with various profiles depending on the shaping needs, is used to press against the rotating metal sheet. As the lathe spins the mandrel and sheet together, the operator guides the roller along the mandrel’s length.
4. Deformation:
- The key to shaping the metal lies in applying controlled pressure with the spinning tool. This pressure causes plastic deformation in the metal sheet. Imagine stretching clay on a pottery wheel; metal spinning works similarly. The outer areas of the sheet experience stretching, while the material closer to the mandrel compresses slightly. This combined deformation allows the sheet to conform to the shape of the mandrel.
5. Work Hardening:
- As the metal sheet is deformed, it work hardens. This means the metal becomes stiffer and requires more force to shape further. Skilled metal spinners strategically apply pressure and use multiple passes with the spinning tool to achieve the desired shape without exceeding the metal’s capacity and causing cracks.
6. Thickness Variation:
- It’s important to note that the thickness of the metal sheet may not remain uniform throughout the spinning process. The areas experiencing stretching will become thinner, while compressed areas might see a slight thickening. Experienced operators consider this during material selection and factor in the final desired thickness.
7. Speed and Lubrication:
- The spinning process is typically performed at high speeds to minimize friction and heat generation. Lubrication is also crucial to reduce friction between the tool and the metal sheet, further aiding in shaping and extending tool life.
8. Manual vs. CNC Control:
- Metal spinning machines come in both manual and CNC varieties. Manual machines rely on the operator’s skill to manipulate the spinning tool and achieve the desired shape. CNC machines use a pre-programmed digital blueprint to control the tool’s movement precisely, ensuring consistent and repeatable results for complex shapes.
In essence, metal spinning utilizes controlled plastic deformation of sheet metal over a rotating form to create a desired shape. It’s a balance between applying enough force for shaping and managing the work hardening characteristics of the metal to achieve the final product without compromising its integrity.
Spinning Tool

In the world of metal spinning, the spinning tool is a crucial element responsible for shaping the sheet metal into the desired form. Here’s a closer look at these essential tools:
Types of Spinning Tools:
Spinning tools come in various shapes and profiles to accommodate different shaping requirements. Here are some common types:
- Roller: This is the most widely used spinning tool. It has a smooth, cylindrical profile and is ideal for creating basic shapes like cones, cylinders, and hemispheres. Variations of rollers exist with slightly curved profiles for achieving gentle bends.
- Forming Roller: This type of roller has a specific contour that matches a particular desired shape. It’s used for more complex shapes that require a precise profile.
- Planishing Roller: This roller has a broad, flat profile and is used for smoothing out the surface of the metal sheet after the initial shaping process is complete.
- Beading Roller: This tool features a grooved profile that creates decorative ridges or beads on the metal surface.
- Sipe Roller: This specialized roller has a sharp edge used for creating sharp corners and folds in the sheet metal.
Material:
Spinning tools are typically made from hardened steel to ensure they can withstand the pressure applied during the shaping process. Sometimes, other materials like nylon or wood might be used for specific applications where a softer touch is desired to avoid marking the metal surface.
Selection:
The selection of the appropriate spinning tool depends on several factors:
- Desired Shape: The profile of the tool needs to match the form you want to achieve in the metal sheet.
- Stage of Spinning: Different tools might be used for initial shaping, creating specific details, or smoothing the final product.
- Metal Type: The hardness and work hardening characteristics of the metal being spun can influence the tool selection. Softer metals might allow for the use of simpler rollers, while harder metals might require specialized tools.
Using the Spinning Tool:
The spinning tool is mounted on a tool rest on the metal spinning machine. The operator skillfully guides the tool along the length of the rotating mandrel, pressing it against the sheet metal to achieve the desired form. The pressure applied and the path of the tool are crucial for successful shaping.
In conclusion, the spinning tool acts as an extension of the metal spinner’s hand. With the right tool selection and skillful manipulation, these tools transform flat sheets of metal into a vast array of useful and beautiful shapes.
Article on Metal Spinning, Flow Forming, Shear Forming, and Wheel Forming Machines
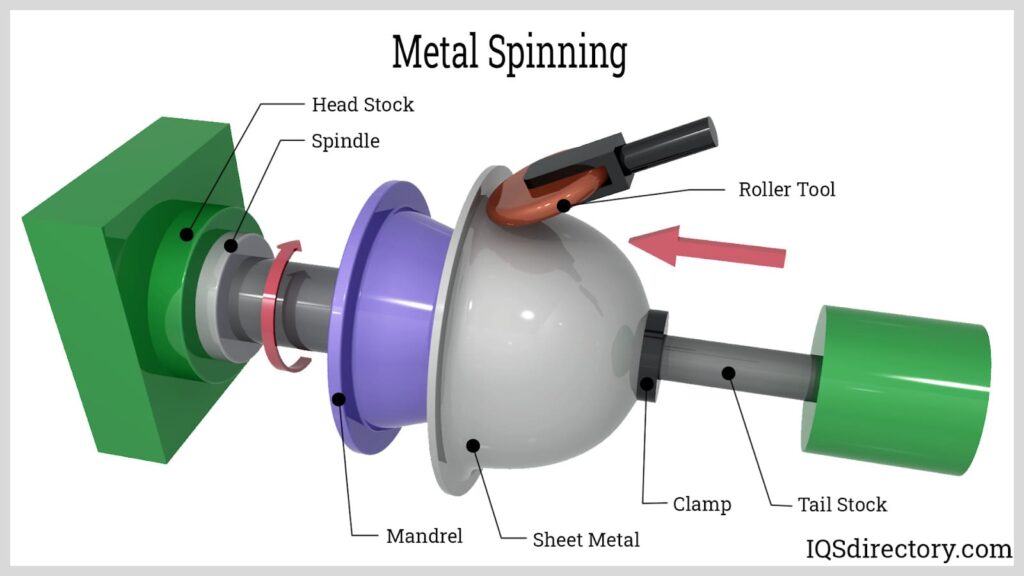
Metal forming processes are integral to modern manufacturing, enabling the production of complex and precise components across various industries. Among these processes, metal spinning, flow forming, shear forming, and wheel forming stand out due to their unique methodologies and wide-ranging applications. Each process offers distinct advantages, making them suitable for different industrial requirements.
The importance of these metal forming techniques cannot be overstated, as they play a crucial role in the automotive, aerospace, military, and industrial sectors. From producing lightweight components for aircraft to manufacturing robust parts for automobiles, these processes contribute significantly to technological advancement and economic growth.
In this article, we will delve into the intricacies of metal spinning, flow forming, shear forming, and wheel forming machines. We will explore their principles, processes, machines, applications, advantages, and challenges. By understanding these processes, manufacturers and engineers can make informed decisions about the best techniques to employ for specific projects.
2. Metal Spinning
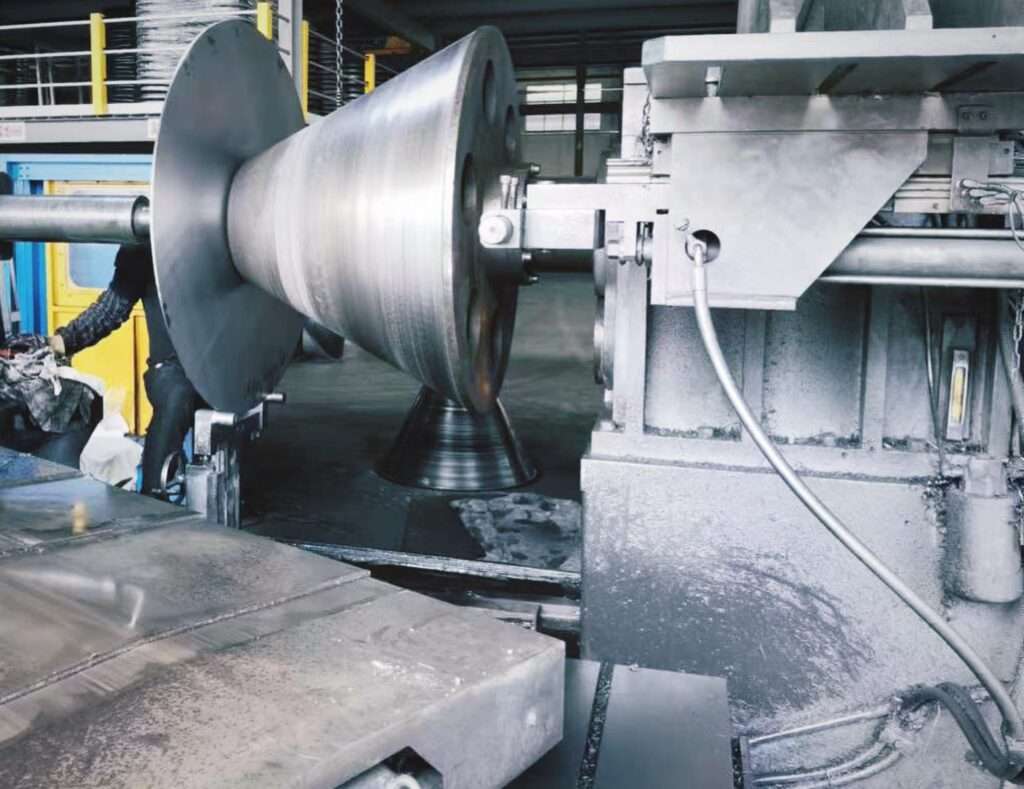
Principles and Process
Metal spinning, also known as spin forming or spinning, is a metalworking process that forms a sheet or tube of metal into an axially symmetric part. This process involves rotating a metal disc or tube at high speed while applying pressure with a tool to shape the metal around a mandrel. The metal is stretched and compressed, resulting in a seamless, symmetrical shape.
Historically, metal spinning dates back to ancient Egypt, where artisans used simple tools to spin and shape metals. Today, it has evolved into a sophisticated process that utilizes advanced machinery and technology. Metal spinning is versatile and can be performed manually or using Computer Numerical Control (CNC) machines.
There are several types of metal spinning, including:
- Conventional spinning: Involves manually manipulating the metal using a lathe.
- CNC spinning: Utilizes computerized machines to automate the spinning process, allowing for greater precision and repeatability.
- Shear spinning: Similar to conventional spinning but involves thinning the metal as it is spun.
The basic steps in the metal spinning process are as follows:
- Preparation: The metal blank is cut to the desired size and shape.
- Mounting: The blank is mounted onto a spinning lathe or CNC machine.
- Rotation: The blank is spun at high speed.
- Forming: A tool is applied to the spinning blank, shaping it around the mandrel.
- Finishing: The final product is trimmed and polished to achieve the desired finish.
Machines and Equipment
Metal spinning machines vary in complexity, from simple manual lathes to advanced CNC machines. These machines are designed to provide precise control over the spinning process, ensuring consistent and high-quality results.
Key components of metal spinning machines include:
- Spindle: Rotates the metal blank at high speed.
- Mandrel: Provides a form around which the metal is shaped.
- Tooling system: Includes various tools for applying pressure and shaping the metal.
- Control system: Manages the speed, pressure, and movement of the tools.
Recent advancements in metal spinning machinery have focused on improving efficiency, precision, and automation. CNC machines have revolutionized the metal spinning industry by allowing for complex shapes and designs that were previously impossible to achieve manually. These machines offer enhanced control over the spinning process, reducing material waste and increasing productivity.
Applications
Metal spinning is used across a wide range of industries due to its versatility and ability to produce high-quality, seamless components. Some common applications include:
- Aerospace: Manufacturing lightweight components such as cones, nozzles, and housings for aircraft engines.
- Automotive: Producing parts like wheel rims, exhaust components, and decorative trims.
- HVAC: Creating ductwork, vent hoods, and other components for heating, ventilation, and air conditioning systems.
- Lighting: Fabricating reflectors, lamp bases, and other lighting fixtures.
- Kitchenware: Producing pots, pans, and other cookware.
The ability to create complex shapes with minimal material waste makes metal spinning an attractive option for manufacturers seeking to optimize production and reduce costs.
Advantages and Challenges
Advantages of metal spinning include:
- Cost-efficiency: Metal spinning requires minimal tooling compared to other forming processes, reducing production costs.
- Flexibility: The process can be used with various materials, including aluminum, steel, and copper.
- Seamless components: Metal spinning produces parts without seams or joints, enhancing their structural integrity.
- Customization: The ability to create complex shapes and designs allows for greater customization and innovation.
Despite its advantages, metal spinning also presents certain challenges:
- Limited to symmetrical shapes: Metal spinning is best suited for axially symmetric components, limiting its application for non-symmetrical parts.
- Material limitations: Certain materials may be difficult to spin, requiring specialized equipment and expertise.
- Skill requirement: Manual metal spinning requires skilled operators, although CNC machines have mitigated this challenge.
3. Flow Forming
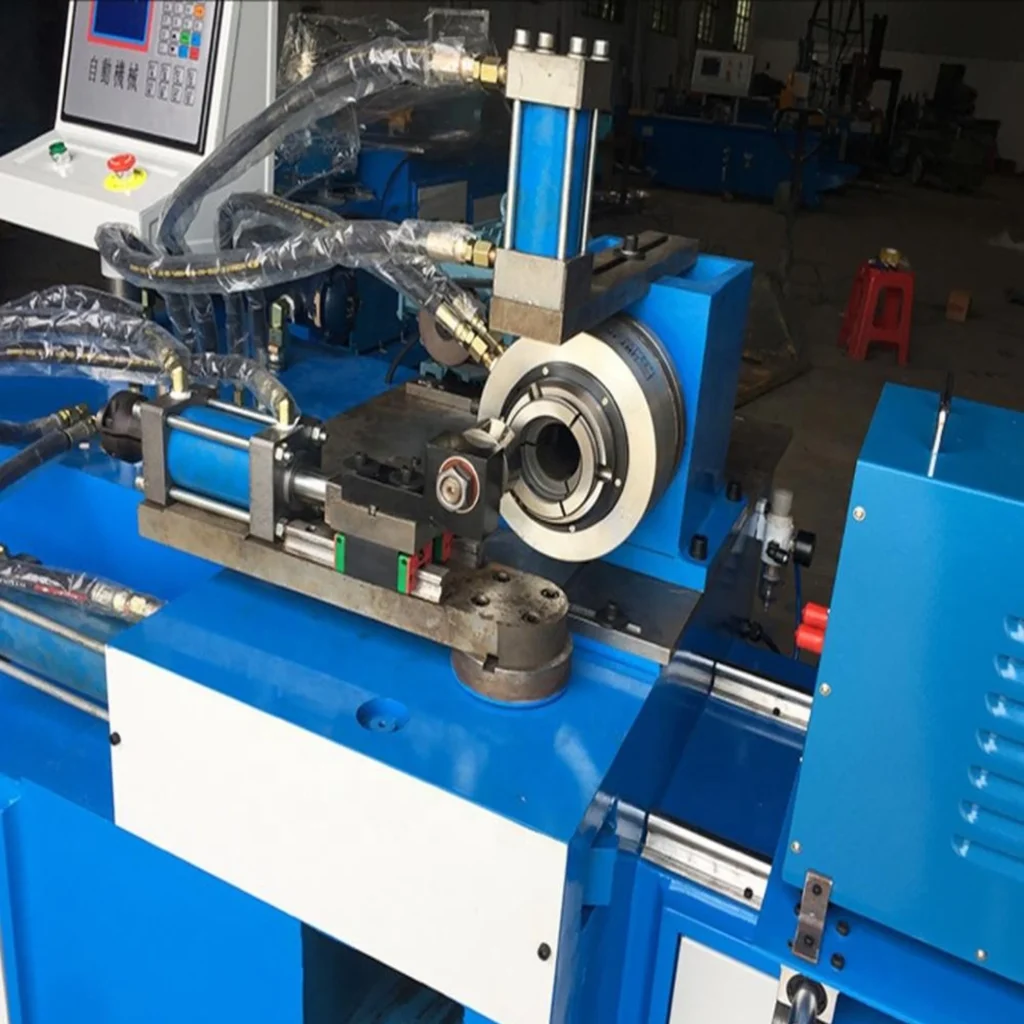
Flow forming, also known as rotary forming or flow turning, is an advanced metal forming process that transforms tubular blanks into precise, high-strength components. This process involves the controlled deformation of the metal blank, reducing its wall thickness and elongating its length.
Flow forming is distinct from other forming processes due to its ability to create thin-walled, seamless components with exceptional dimensional accuracy. The process is highly precise and allows for the creation of complex geometries and intricate designs.
The flow forming process consists of the following steps:
- Preparation: A tubular blank is cut to the desired length and pre-formed if necessary.
- Mounting: The blank is mounted onto a mandrel in a flow-forming machine.
- Rotation: The blank is rotated at high speed.
- Forming: Rollers apply pressure to the rotating blank, reducing its wall thickness and elongating its length.
- Finishing: The formed component is trimmed and finished to meet the desired specifications.
Flow forming can be performed using various methods, including:
- Forward flow forming: The rollers move in the same direction as the rotation of the blank, reducing the wall thickness and elongating the length.
- Reverse flow forming: The rollers move in the opposite direction of the blank’s rotation, allowing for greater control over the final shape.
- Tube spinning: Involves spinning the blank without altering its diameter, focusing on wall thickness reduction.
Machines and Equipment
Flow forming machines are highly specialized and designed to provide precise control over the forming process. These machines are equipped with advanced technology and automation capabilities to ensure consistent and high-quality results.
Key components of flow forming machines include:
- Spindle: Rotates the tubular blank at high speed.
- Mandrel: Provides support and shape for the forming process.
- Rollers: Apply controlled pressure to the blank, shaping it into the desired form.
- Control system: Manages the speed, pressure, and movement of the rollers, ensuring precision and accuracy.
Technological advancements in flow forming machinery have focused on improving automation, reducing material waste, and enhancing process control. Modern flow-forming machines utilize CNC technology to achieve precise and repeatable results, reducing the need for manual intervention and increasing productivity.
Applications
Flow forming is widely used in industries that require high-precision, thin-walled components. Some specific applications include:
- Aerospace: Manufacturing aircraft engine components, such as compressor cases and fan housings.
- Automotive: Producing lightweight, high-strength parts like drive shafts and wheel rims.
- Military: Creating artillery shells, missile casings, and other defense-related components.
- Industrial: Fabricating components for machinery and equipment, such as pump housings and pressure vessels.
The ability to produce components with tight tolerances and exceptional strength makes flow forming an ideal choice for industries that demand high-performance parts.
Advantages and Challenges
Advantages of flow forming include:
- Dimensional accuracy: Flow forming achieves tight tolerances and precise dimensions, ensuring high-quality components.
- Material efficiency: The process reduces material waste by minimizing the need for additional machining or finishing.
- Strength and durability: Flow-formed components exhibit enhanced mechanical properties, including increased strength and fatigue resistance.
- Design flexibility: The ability to create complex shapes and intricate designs allows for greater innovation and customization.
Despite its advantages, flow forming also presents certain challenges:
- Initial setup cost: Flow forming machines are specialized and can be expensive to purchase and maintain.
- Material limitations: Certain materials may be difficult to flow form, requiring specialized equipment and expertise.
- Process complexity: The process requires careful control and monitoring to achieve the desired results, necessitating skilled operators and advanced technology.
4. Shear Forming
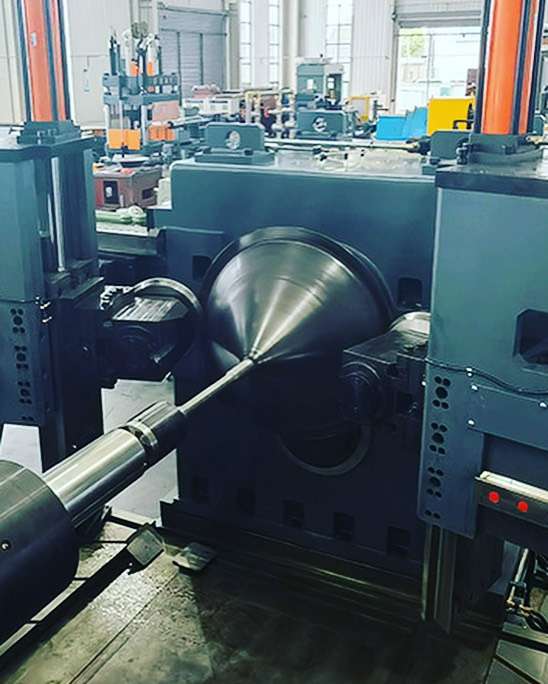
Shear forming, also known as shear spinning, is a metal forming process that produces axisymmetric components by reducing the wall thickness of a blank while maintaining its diameter. This process is similar to conventional spinning but involves a shearing action that allows for greater control over the final shape and thickness of the component.
Shear forming is distinct from flow forming in that it focuses on altering the thickness of the blank while maintaining its diameter. This process is highly versatile and can be used to create a wide range of components with varying shapes and sizes.
The shear forming process consists of the following steps:
- Preparation: A blank is cut to the desired size and shape.
- Mounting: The blank is mounted onto a mandrel in a shear-forming machine.
- Rotation: The blank is rotated at high speed.
- Forming: A tool applies pressure to the rotating blank, reducing its wall thickness and shaping it into the desired form.
- Finishing: The formed component is trimmed and finished to meet the desired specifications.
Machines and Equipment
Shear forming machines are designed to provide precise control over the forming process, ensuring consistent and high-quality results. These machines are equipped with advanced technology and automation capabilities to optimize the shear-forming process.
Key components of shear forming machines include:
- Spindle: Rotates the blank at high speed.
- Mandrel: Provides support and shape for the forming process.
- Tooling system: Includes various tools for applying pressure and shaping the metal.
- Control system: Manages the speed, pressure, and movement of the tools, ensuring precision and accuracy.
Innovations in shear-forming technology have focused on improving process control, reducing material waste, and enhancing automation. Modern shear-forming machines utilize CNC technology to achieve precise and repeatable results, reducing the need for manual intervention and increasing productivity.
Applications
Shear forming is used in a wide range of industries due to its versatility and ability to produce high-quality, axisymmetric components. Some specific applications include:
- Aerospace: Manufacturing components such as turbine disks, flanges, and structural parts.
- Automotive: Producing parts like pulleys, hubs, and other rotational components.
- Industrial: Fabricating components for machinery and equipment, such as pump housings and pressure vessels.
- Medical: Creating components for medical devices and equipment, such as surgical instruments and implants.
The ability to create components with varying thicknesses and complex shapes makes shear forming an attractive option for manufacturers seeking to optimize production and reduce costs.
Advantages and Challenges
Advantages of shear forming include:
- Material efficiency: The process reduces material waste by minimizing the need for additional machining or finishing.
- Design flexibility: The ability to create complex shapes and varying thicknesses allows for greater innovation and customization.
- Strength and durability: Shear-formed components exhibit enhanced mechanical properties, including increased strength and fatigue resistance.
- Cost-effectiveness: Shear forming requires minimal tooling compared to other forming processes, reducing production costs.
Despite its advantages, shear forming also presents certain challenges:
- Limited to axisymmetric shapes: Shear forming is best suited for components with rotational symmetry, limiting its application for non-symmetrical parts.
- Material limitations: Certain materials may be difficult to shear form, requiring specialized equipment and expertise.
- Process complexity: The process requires careful control and monitoring to achieve the desired results, necessitating skilled operators and advanced technology.
5. Wheel Forming
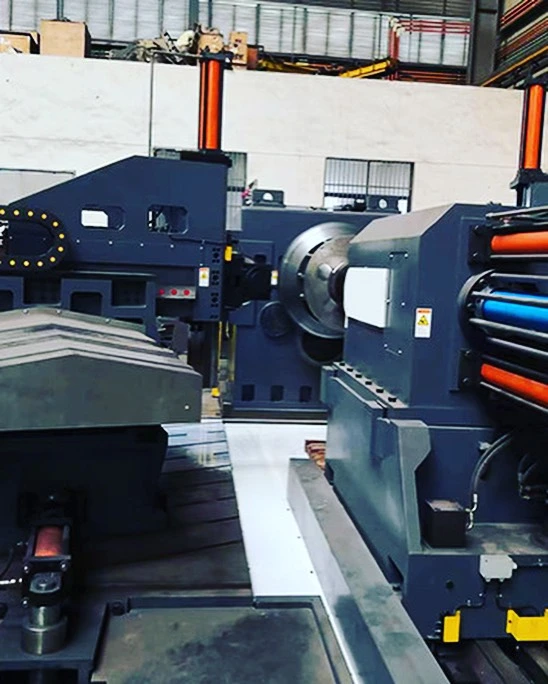
Wheel forming is a specialized metal forming process used to produce wheels for various applications, particularly in the automotive and aerospace industries. This process involves shaping a metal blank into a wheel by applying pressure and force through a series of rollers or dies.
Wheel forming is distinct from other metal forming processes due to its focus on creating wheels and other rotational components. The process is highly efficient and allows for the production of lightweight, high-strength wheels with complex geometries.
The wheel-forming process consists of the following steps:
- Preparation: A metal blank is cut to the desired size and shape.
- Mounting: The blank is mounted onto a wheel-forming machine.
- Rotation: The blank is rotated at high speed.
- Forming: Rollers or dies apply pressure to the rotating blank, shaping it into the desired wheel form.
- Finishing: The formed wheel is trimmed and finished to meet the desired specifications.
Machines and Equipment
Wheel forming machines are highly specialized and designed to provide precise control over the forming process. These machines are equipped with advanced technology and automation capabilities to ensure consistent and high-quality results.
Key components of wheel forming machines include:
- Spindle: Rotates the blank at high speed.
- Mandrel: Provides support and shape for the forming process.
- Rollers or dies: Apply controlled pressure to the blank, shaping it into the desired wheel form.
- Control system: Manages the speed, pressure, and movement of the rollers or dies, ensuring precision and accuracy.
Recent advancements in wheel-forming technology have focused on improving automation, reducing material waste, and enhancing process control. Modern wheel-forming machines utilize CNC technology to achieve precise and repeatable results, reducing the need for manual intervention and increasing productivity.
Applications
Wheel forming is widely used in industries that require high-quality, lightweight wheels and rotational components. Some specific applications include:
- Automotive: Manufacturing wheels for cars, trucks, and motorcycles.
- Aerospace: Producing wheels for aircraft landing gear and other rotational components.
- Industrial: Fabricating wheels for machinery and equipment, such as conveyor systems and transport vehicles.
- Consumer goods: Creating wheels for bicycles, skateboards, and other consumer products.
The ability to produce wheels with tight tolerances and exceptional strength makes wheel forming an ideal choice for industries that demand high-performance rotational components.
Advantages and Challenges
Advantages of wheel forming include:
- Lightweight and high strength: Wheel-forming produces lightweight wheels with exceptional strength and durability.
- Dimensional accuracy: The process achieves tight tolerances and precise dimensions, ensuring high-quality wheels.
- Material efficiency: Wheel forming reduces material waste by minimizing the need for additional machining or finishing.
- Design flexibility: The ability to create complex geometries and intricate designs allows for greater innovation and customization.
Despite its advantages, wheel forming also presents certain challenges:
- Initial setup cost: Wheel forming machines are specialized and can be expensive to purchase and maintain.
- Material limitations: Certain materials may be difficult to wheel form, requiring specialized equipment and expertise.
- Process complexity: The process requires careful control and monitoring to achieve the desired results, necessitating skilled operators and advanced technology.
6. Comparative Analysis
In this section, we will compare metal spinning, flow forming, shear forming, and wheel forming processes to understand their differences, advantages, and suitability for various applications.
Comparison of Processes:
- Metal Spinning vs. Flow Forming: Metal spinning focuses on forming axially symmetric parts by rotating a blank around a mandrel, while flow forming involves reducing the wall thickness of a tubular blank through controlled deformation. Flow forming is more suitable for thin-walled, high-precision components, while metal spinning is ideal for larger, symmetrical parts.
- Shear Forming vs. Flow Forming: Shear forming and flow forming both involve reducing the wall thickness of a blank, but shear forming maintains the blank’s diameter, whereas flow forming can elongate the blank. Shear forming is preferred for components with varying thicknesses, while flow forming is used for high-precision, thin-walled parts.
- Wheel Forming vs. Other Processes: Wheel forming is specifically designed for creating wheels and rotational components, making it unique among the other processes. It offers advantages in producing lightweight, high-strength wheels with complex geometries, but is limited to wheel and rotational component applications.
Suitability for Different Applications:
- Aerospace: Flow forming and shear forming are highly suitable for aerospace applications due to their ability to produce high-precision, lightweight components with enhanced mechanical properties.
- Automotive: Metal spinning and wheel forming are commonly used in the automotive industry for manufacturing wheels, exhaust components, and decorative trims.
- Industrial: All four processes are utilized in various industrial applications, depending on the specific requirements of the components being produced.
- Consumer Goods: Metal spinning and wheel forming are popular choices for producing consumer goods, such as cookware, lighting fixtures, and wheels for bicycles and skateboards.
Technical and Economic Considerations:
- Material Costs: Metal spinning and shear forming require minimal tooling and have lower material costs, making them cost-effective options for certain applications.
- Process Complexity: Flow forming and wheel forming involve more complex processes and require advanced technology, resulting in higher initial setup costs but offering greater precision and quality.
- Production Volume: Metal spinning and wheel forming are suitable for both low and high-volume production, while flow forming and shear forming are more efficient for high-volume production due to their precision and automation capabilities.
7. Future Trends and Developments
The metal forming industry is constantly evolving, with new technologies and innovations shaping the future of metal spinning, flow forming, shear forming, and wheel forming processes. Some emerging trends and developments include:
- Additive Manufacturing Integration: Combining traditional metal forming processes with additive manufacturing techniques to create complex components with enhanced properties and reduced material waste.
- Automation and Industry 4.0: Increasing automation and the adoption of Industry 4.0 technologies, such as IoT and AI, to improve process control, efficiency, and productivity in metal forming operations.
- Advanced Materials: The development of new materials and alloys that are more suitable for metal forming processes, allowing for greater innovation and customization.
- Sustainability and Environmental Impact: Focus on reducing the environmental impact of metal forming processes through energy-efficient machinery and sustainable material sourcing.
As these trends continue to evolve, metal spinning, flow forming, shear forming, and wheel forming processes will play an increasingly important role in manufacturing, driving innovation and efficiency across various industries.
8. Conclusion
Metal spinning, flow forming, shear forming, and wheel forming are essential metal forming processes that offer unique advantages and capabilities for producing high-quality, precise components across various industries. Each process has its strengths and challenges, making them suitable for different applications and requirements.
By understanding the principles, machines, applications, and advantages of these processes, manufacturers and engineers can make informed decisions about the best techniques to employ for specific projects. As the metal forming industry continues to evolve, these processes will play a crucial role in driving innovation, efficiency, and sustainability in manufacturing.
Choosing the right materials for metal forming processes such as metal spinning, flow forming, shear forming, and wheel forming is crucial for achieving desired product characteristics, performance, and quality. Each process has specific material requirements based on the mechanical properties, formability, and intended application. Here’s an overview of recommended materials for each process:
Metal Spinning
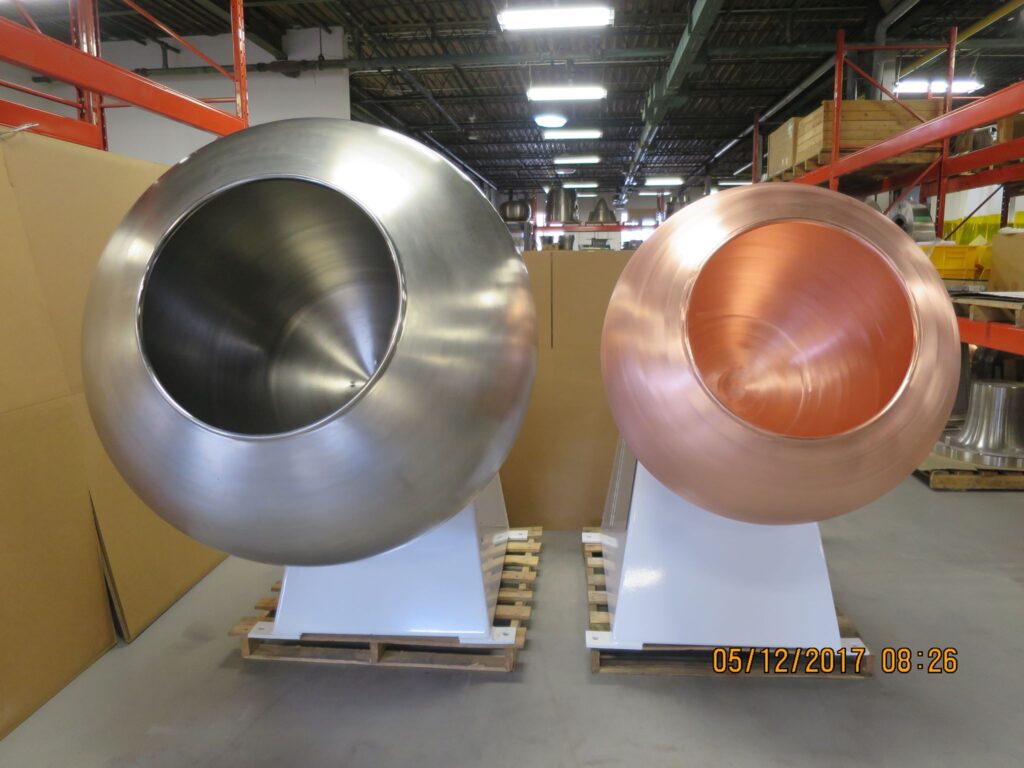
Metal spinning is a versatile process that can work with a variety of metals. Key material properties to consider include ductility, malleability, and tensile strength. Here are some commonly used materials in metal spinning:
- Aluminum and Aluminum Alloys
- Properties: Lightweight, corrosion-resistant, good thermal and electrical conductivity.
- Applications: Aerospace components, automotive parts, cookware, and decorative items.
- Stainless Steel
- Properties: High corrosion resistance, strength, and durability.
- Applications: Food processing equipment, medical devices, and architectural components.
- Copper and Copper Alloys
- Properties: Excellent thermal and electrical conductivity, corrosion resistance, and antimicrobial properties.
- Applications: Lighting fixtures, electrical components, and decorative items.
- Brass and Bronze
- Properties: Corrosion resistance, electrical conductivity, and aesthetic appeal.
- Applications: Musical instruments, plumbing components, and decorative items.
- Carbon and Low-Alloy Steels
- Properties: High strength and durability.
- Applications: Automotive components, industrial machinery, and construction parts.
- Titanium and Titanium Alloys
- Properties: High strength-to-weight ratio, corrosion resistance, and biocompatibility.
- Applications: Aerospace components, medical implants, and sports equipment.
Flow Forming
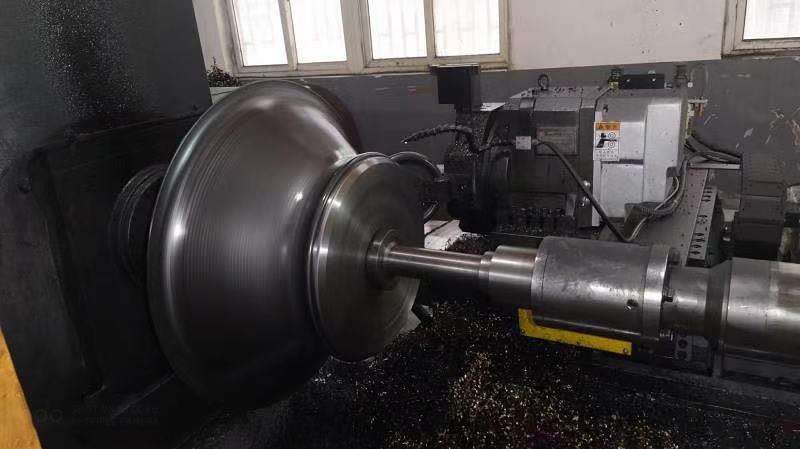
Flow forming is ideal for materials that require high strength, precision, and reduced weight. Materials should exhibit good ductility and work hardening properties. Recommended materials for flow forming include:
- Aluminum Alloys
- Properties: Lightweight, corrosion-resistant, and high formability.
- Applications: Aerospace components, automotive parts, and military applications.
- High-Strength Low-Alloy (HSLA) Steels
- Properties: Enhanced mechanical properties and good formability.
- Applications: Automotive components, structural parts, and pressure vessels.
- Stainless Steel
- Properties: Corrosion resistance, strength, and durability.
- Applications: Aerospace and defense components, medical devices, and industrial equipment.
- Nickel and Nickel Alloys
- Properties: High-temperature resistance, corrosion resistance, and strength.
- Applications: Aerospace components, gas turbine engines, and chemical processing equipment.
- Titanium Alloys
- Properties: High strength-to-weight ratio, corrosion resistance, and biocompatibility.
- Applications: Aerospace components, medical implants, and military applications.
Shear Forming
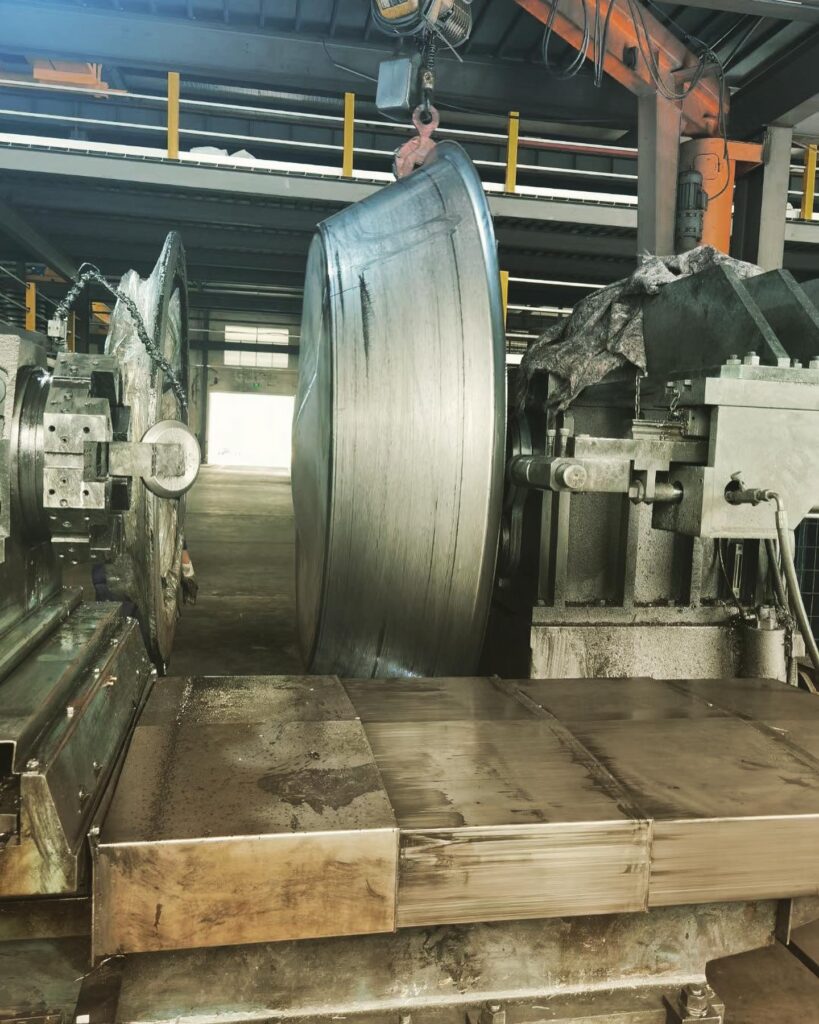
Shear forming is suitable for materials with good ductility and shear formability. This process is often used for producing components with varying thicknesses. Recommended materials include:
- Aluminum and Aluminum Alloys
- Properties: Lightweight, corrosion-resistant, and good formability.
- Applications: Aerospace components, automotive parts, and consumer goods.
- Stainless Steel
- Properties: Corrosion resistance, strength, and durability.
- Applications: Industrial equipment, medical devices, and structural components.
- Carbon and Low-Alloy Steels
- Properties: High strength and wear resistance.
- Applications: Automotive components, machinery parts, and construction materials.
- Copper and Copper Alloys
- Properties: Good thermal and electrical conductivity, corrosion resistance.
- Applications: Electrical components, plumbing fixtures, and decorative items.
- Titanium and Titanium Alloys
- Properties: High strength-to-weight ratio and corrosion resistance.
- Applications: Aerospace components, medical devices, and sports equipment.
Wheel Forming
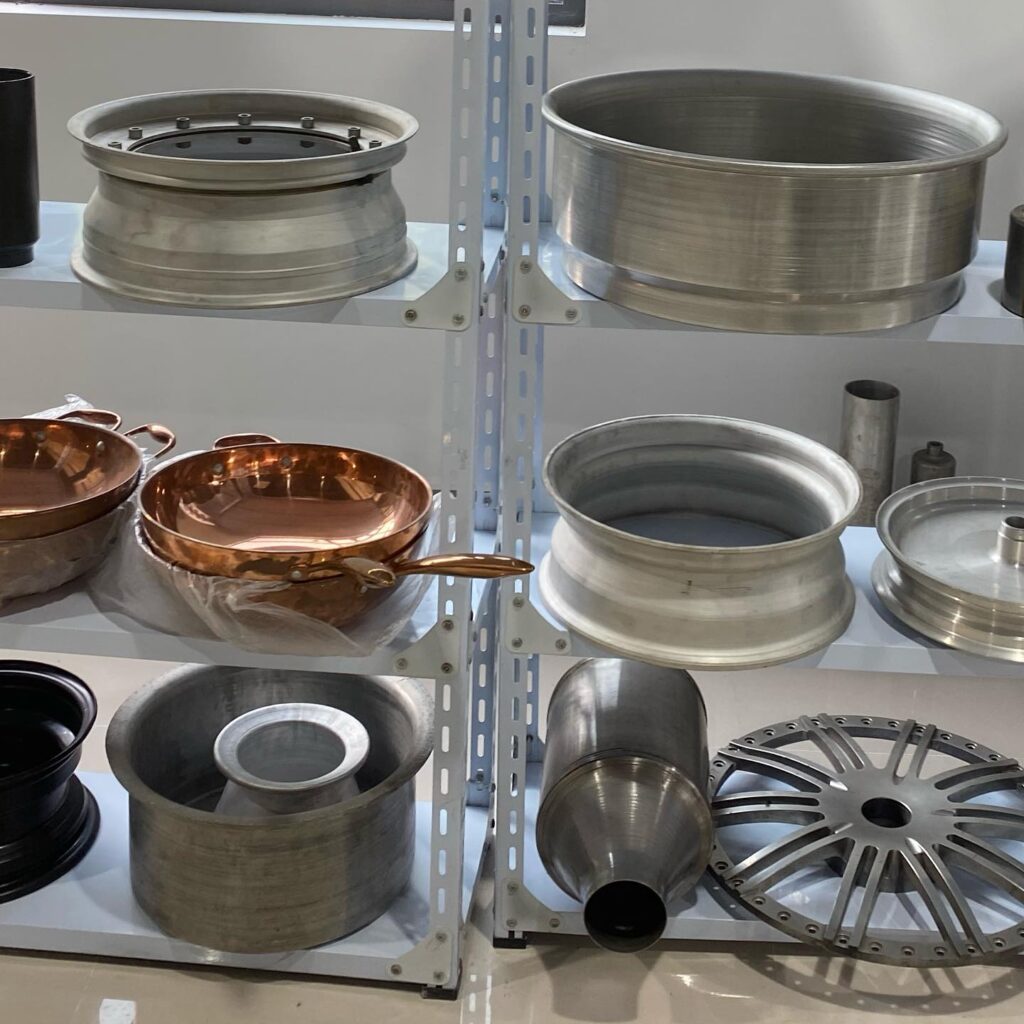
Wheel forming is used to create wheels and other rotational components, requiring materials with high strength and fatigue resistance. Recommended materials for wheel forming include:
- Aluminum Alloys
- Properties: Lightweight, corrosion-resistant, and high strength.
- Applications: Automotive wheels, aerospace components, and bicycle wheels.
- Magnesium Alloys
- Properties: Lightweight, good damping properties, and machinability.
- Applications: Automotive wheels, aerospace components, and electronics casings.
- Stainless Steel
- Properties: Corrosion resistance, strength, and durability.
- Applications: Heavy-duty industrial wheels, transportation equipment, and marine applications.
- Carbon and Low-Alloy Steels
- Properties: High strength, wear resistance, and durability.
- Applications: Heavy-duty automotive wheels, industrial machinery, and construction equipment.
- Titanium Alloys
- Properties: High strength-to-weight ratio, corrosion resistance, and fatigue resistance.
- Applications: Aerospace wheels, high-performance automotive wheels, and sports equipment.
Factors to Consider When Selecting Materials
When choosing materials for metal forming processes, several factors should be considered:
- Mechanical Properties: Ensure the material has the required strength, ductility, and toughness for the specific application.
- Formability: Consider the material’s ability to be formed without cracking or defects, as well as its work hardening characteristics.
- Corrosion Resistance: Select materials that can withstand the operating environment, especially for applications exposed to harsh conditions.
- Cost and Availability: Evaluate the cost-effectiveness and availability of the material, considering both short-term and long-term production needs.
- Application Requirements: Consider the specific requirements of the application, such as weight, thermal conductivity, electrical conductivity, and aesthetic appeal.
- Sustainability: Evaluate the environmental impact of the material and consider options that align with sustainability goals.
By carefully selecting the appropriate materials, manufacturers can optimize the metal forming process, reduce costs, and ensure high-quality, reliable components. If you need more detailed information or have specific applications in mind, feel free to ask!
Metal Spinning Machine Components

The components of machines used in metal forming processes such as metal spinning, flow forming, shear forming, and wheel forming are designed to deliver precise control and high-quality production. Each machine type is equipped with specialized parts that cater to the unique demands of the specific forming process. Below is an overview of the key components for each machine type, explaining their functions and significance.
Metal spinning machines range from manual lathes to advanced CNC-controlled systems. The fundamental components of a metal spinning machine include:
- Spindle:
- Function: The spindle is the rotating axis of the machine that holds and spins the metal blank at high speeds. It is crucial for maintaining balance and precision during the spinning process.
- Significance: Ensures consistent rotation speed and stability, allowing for uniform metal forming.
- Chuck or Mandrel:
- Function: Holds the metal blank in place and serves as the shaping mold for the final product. The mandrel determines the shape of the spun piece.
- Significance: Provides support and defines the final geometry of the component.
- Tailstock:
- Function: Supports the other end of the workpiece opposite the spindle, preventing wobble and maintaining alignment during spinning.
- Significance: Ensures stability and precision by supporting the blank throughout the process.
- Tool Rest and Tools:
- Function: The tool rest supports various forming tools, which are used to apply pressure and shape the metal as it spins.
- Types of Tools: Rollers, spoons, and other custom tools can be used depending on the desired shape and complexity of the component.
- Significance: Allows the operator or CNC program to apply pressure precisely and control the forming process.
- Bed:
- Function: The foundation that supports the entire machine structure, providing a stable platform for all operations.
- Significance: Ensures the rigidity and stability necessary for high-precision metal spinning.
- Control System:
- Function: Manages machine operations, including spindle speed, tool position, and pressure. In CNC machines, this includes programming capabilities for automated and complex spinning tasks.
- Significance: Provides precise control over the spinning process, enabling complex shapes and repeatable operations.
- Drive System:
- Function: Powers the spindle and other moving parts of the machine. This can include motors, belts, and gears.
- Significance: Ensures consistent power delivery and control over the machine’s movements.
Flow Forming Machine Components
Flow forming machines are highly specialized and designed to produce thin-walled components with precision. Key components include:
- Spindle and Chuck:
- Function: Similar to metal spinning, the spindle rotates the blank at high speed while the chuck securely holds it in place.
- Significance: Provides stability and precision necessary for reducing wall thickness accurately.
- Mandrel:
- Function: Serves as the internal form around which the blank is shaped. It supports the workpiece during the forming process.
- Significance: Defines the internal dimensions and helps achieve the desired wall thickness.
- Rollers:
- Function: The primary forming tools that apply pressure to the rotating blank, reducing its wall thickness and elongating it.
- Types of Rollers: Can be single or multiple rollers depending on the process and desired outcomes.
- Significance: Enables controlled deformation of the material, achieving precise dimensions and properties.
- Tool Post:
- Function: Holds the rollers and positions them for precise contact with the workpiece. Can adjust roller position and pressure.
- Significance: Allows fine control of the forming process, ensuring consistency and accuracy.
- Tailstock:
- Function: Supports the opposite end of the workpiece, ensuring it remains aligned and stable during forming.
- Significance: Provides additional support, especially for longer components.
- Control System:
- Function: Oversees the machine’s operations, controlling spindle speed, roller position, and pressure. In CNC machines, it handles complex forming paths and sequences.
- Significance: Provides automation and precision control, essential for high-quality production.
- Drive System:
- Function: Powers the spindle and rollers, using motors and gearing systems to deliver the necessary force and speed.
- Significance: Ensures consistent operation and control over the forming process.
- Cooling System:
- Function: Manages heat generated during the forming process, often using cooling fluids to prevent overheating.
- Significance: Maintains material properties and prevents machine wear by dissipating heat.
Shear Forming Machine Components
Shear forming machines share similarities with both metal spinning and flow forming machines but have specific components tailored to the shearing action:
- Spindle:
- Function: Rotates the blank at high speed, providing the necessary force for shearing.
- Significance: Ensures consistent rotation for uniform wall thickness reduction.
- Mandrel:
- Function: Supports the workpiece and defines its internal shape. It may also help control wall thickness.
- Significance: Critical for achieving the desired internal dimensions and structural integrity.
- Shear Tools:
- Function: Specialized tools that apply localized pressure, shearing the metal and reducing wall thickness while maintaining diameter.
- Significance: Enables the unique thinning characteristic of shear forming, allowing for complex component profiles.
- Tool Post:
- Function: Positions and supports shear tools, allowing precise adjustments for pressure and angle.
- Significance: Provides control over the shearing process, enabling accurate and consistent results.
- Tailstock:
- Function: Provides support for the workpiece opposite the spindle, ensuring stability and alignment.
- Significance: Ensures component stability and precision throughout the forming process.
- Control System:
- Function: Manages machine operations, controlling tool position, spindle speed, and shearing pressure. CNC systems allow for complex and automated operations.
- Significance: Enables precision and repeatability, crucial for producing high-quality components.
- Drive System:
- Function: Powers the spindle and shear tools, using motors, belts, and gears to control speed and force.
- Significance: Delivers consistent power for effective shearing and forming.
- Cooling and Lubrication System:
- Function: Manages heat and friction during forming, using fluids to cool and lubricate the workpiece and tools.
- Significance: Reduces wear, maintains material properties, and improves tool life.
Wheel Forming Machine Components
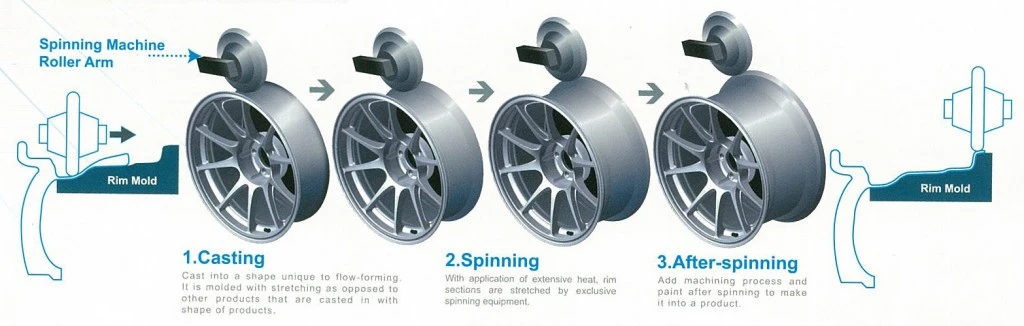
Wheel forming machines are specifically designed to produce wheels and other rotational components. Key components include:
- Spindle and Chuck:
- Function: Rotates the wheel blank at high speed, securing it in place for forming.
- Significance: Provides stability and precision, ensuring uniform wheel formation.
- Rollers or Dies:
- Function: Form the wheel by applying pressure to the rotating blank, shaping it into the desired wheel profile.
- Types of Dies: May include pre-forming and finishing dies for different stages of the process.
- Significance: Enables precise shaping of the wheel, achieving complex geometries and high strength.
- Mandrel:
- Function: Supports the blank and defines the internal geometry of the wheel.
- Significance: Ensures accurate internal dimensions and structural integrity.
- Tool Post:
- Function: Holds and positions rollers or dies, allowing for precise adjustments during the forming process.
- Significance: Provides control over the forming process, ensuring consistency and accuracy.
- Control System:
- Function: Manages machine operations, controlling spindle speed, die position, and pressure. CNC systems provide automation and precision.
- Significance: Ensures high-quality production with repeatable results.
- Drive System:
- Function: Powers the spindle and rollers/dies, delivering the necessary force and speed for forming.
- Significance: Ensures consistent operation and control over the forming process.
- Cooling and Lubrication System:
- Function: Manages heat and friction during forming, using fluids to cool and lubricate the workpiece and tools.
- Significance: Prevents overheating, reduces wear, and maintains material properties.
- Support Frames and Guides:
- Function: Provide structural support and guide the blank through the forming process, ensuring alignment and stability.
- Significance: Enhances machine stability and ensures accurate and consistent wheel formation.
Conclusion
The machines used in metal spinning, flow forming, shear forming, and wheel forming processes are complex systems equipped with specialized components designed to meet the unique demands of each process. By understanding these components and their functions, manufacturers can optimize the forming process, improve product quality, and achieve precise, high-performance components.
Metal Spinning Application Areas
The metal forming processes of metal spinning, flow forming, shear forming, and wheel forming are integral to a wide range of industries, each offering unique capabilities and advantages. Here’s an overview of the application areas for these processes, highlighting how they are utilized to create specific products and components across various sectors:
Metal spinning is a versatile process capable of producing axially symmetric components with seamless construction. Its applications span several industries due to its ability to efficiently produce complex shapes with high structural integrity.
Aerospace
- Components:
- Nose cones
- Rocket casings
- Jet engine parts
- Advantages:
- Metal spinning is ideal for aerospace applications where lightweight and high-strength components are critical. The process allows for the creation of complex shapes with excellent surface finishes and minimal material waste.
Automotive
- Components:
- Wheel rims
- Exhaust system parts
- Airbag components
- Advantages:
- In the automotive industry, metal spinning is used to produce lightweight and durable components. The process’s flexibility allows for the creation of custom parts with intricate designs, contributing to vehicle performance and aesthetics.
HVAC (Heating, Ventilation, and Air Conditioning)
- Components:
- Ductwork
- Ventilation hoods
- Fan housings
- Advantages:
- Metal spinning produces seamless components that ensure efficient airflow and minimal leakage. The process can handle various materials, making it suitable for applications requiring corrosion resistance and thermal stability.
Lighting
- Components:
- Reflectors
- Lampshades
- Fixture bases
- Advantages:
- In lighting applications, metal spinning is used to create aesthetically pleasing and functional components. The process can produce complex shapes with smooth finishes, enhancing both the performance and appearance of lighting products.
Consumer Products
- Components:
- Cookware (pots, pans, bowls)
- Musical instruments (cymbals, drums)
- Decorative items
- Advantages:
- The versatility of metal spinning allows for the production of consumer goods with intricate designs and high-quality finishes. The process is cost-effective, especially for small to medium production runs.
Flow Forming Application Areas
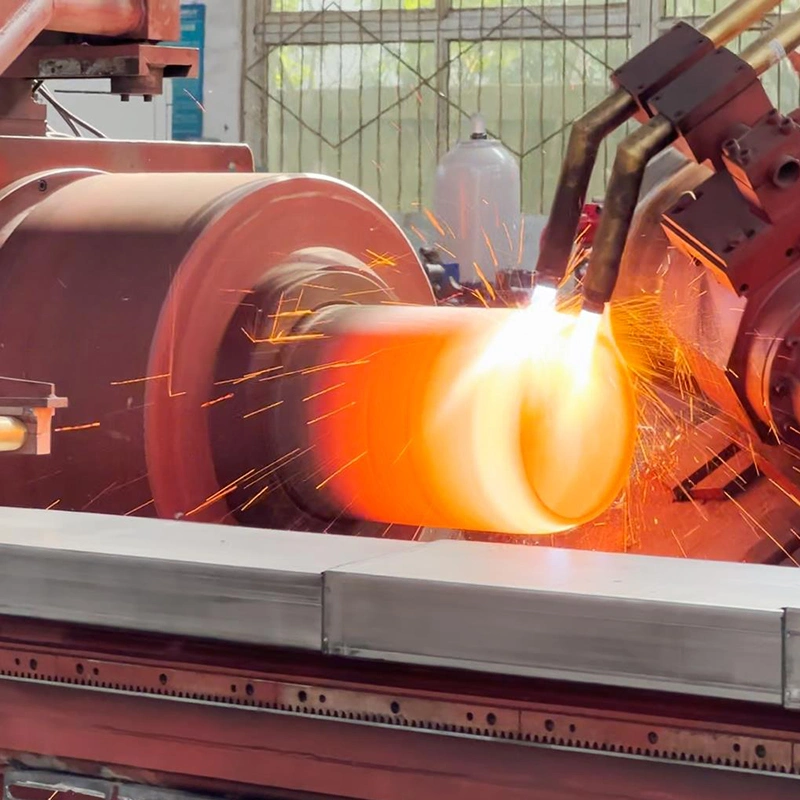
Flow forming is a precision metal forming process that excels in producing thin-walled, high-strength components. It is favored in industries that require parts with tight tolerances and enhanced mechanical properties.
Aerospace
- Components:
- Jet engine casings
- Missile casings
- Fuel tanks
- Advantages:
- Flow forming is used to produce high-performance aerospace components with superior strength-to-weight ratios. The process allows for the creation of complex geometries with exceptional precision, meeting the stringent requirements of the aerospace industry.
Automotive
- Components:
- Drive shafts
- Transmission parts
- Wheel rims
- Advantages:
- In the automotive industry, flow forming is used to manufacture lightweight, high-strength components that improve vehicle efficiency and performance. The process reduces material waste and allows for the production of parts with precise dimensions and surface finishes.
Military and Defense
- Components:
- Artillery shells
- Missile bodies
- Armored vehicle parts
- Advantages:
- Flow forming is ideal for producing defense components that require high strength, durability, and precision. The process can handle various materials, including high-strength alloys, making it suitable for demanding military applications.
Industrial
- Components:
- Pressure vessels
- Pump housings
- Cylindrical tanks
- Advantages:
- Flow forming is used to create industrial components that require high structural integrity and dimensional accuracy. The process allows for the efficient production of thin-walled parts with uniform thickness, reducing material usage and production costs.
Shear Forming Application Areas
Shear forming is a metal forming process that excels in producing axisymmetric components with varying thicknesses. It is suitable for applications that require precise control over wall thickness and complex profiles.
Aerospace
- Components:
- Turbine disks
- Engine flanges
- Structural components
- Advantages:
- Shear forming is used in aerospace applications to produce components with enhanced mechanical properties and precise dimensions. The process’s ability to control wall thickness is critical for optimizing weight and performance.
Automotive
- Components:
- Pulleys
- Hubs
- Rotational components
- Advantages:
- In the automotive industry, shear forming is used to manufacture lightweight and durable components. The process’s precision and flexibility allow for the creation of custom parts with complex shapes and varying thicknesses.
Medical
- Components:
- Surgical instruments
- Implants
- Medical device components
- Advantages:
- Shear forming is suitable for producing medical components that require high precision and biocompatibility. The process can handle various materials, including stainless steel and titanium, making it ideal for medical applications.
Industrial
- Components:
- Pump housings
- Pressure vessel components
- Machinery parts
- Advantages:
- Shear forming is used in industrial applications to produce high-quality components with precise dimensions and uniform wall thickness. The process’s ability to create complex profiles makes it suitable for a wide range of industrial products.
Wheel Forming Application Areas
Wheel forming is a specialized process used to produce wheels and other rotational components. It is widely used in industries that require high-performance wheels with complex geometries and enhanced mechanical properties.
Automotive
- Components:
- Car wheels
- Motorcycle wheels
- Racing wheels
- Advantages:
- Wheel forming is used to produce automotive wheels with superior strength, durability, and lightweight characteristics. The process allows for the creation of wheels with intricate designs and tight tolerances, enhancing vehicle performance and aesthetics.
Aerospace
- Components:
- Aircraft landing gear wheels
- Helicopter rotor hubs
- Turbine wheels
- Advantages:
- In the aerospace industry, wheel forming is used to manufacture high-performance wheels and rotational components. The process’s precision and material efficiency are critical for meeting the stringent requirements of aerospace applications.
Industrial
- Components:
- Conveyor wheels
- Heavy machinery wheels
- Transport vehicle wheels
- Advantages:
- Wheel forming is used to produce industrial wheels with exceptional strength and durability. The process’s ability to create complex geometries and uniform dimensions makes it suitable for demanding industrial applications.
Consumer Goods
- Components:
- Bicycle wheels
- Skateboard wheels
- Rollerblade wheels
- Advantages:
- In the consumer goods sector, wheel forming is used to produce wheels with high performance and aesthetic appeal. The process allows for the efficient production of wheels with consistent quality and design.
Conclusion
The metal forming processes of metal spinning, flow forming, shear forming, and wheel forming offer unique capabilities and advantages, making them suitable for a wide range of applications across various industries. By understanding the strengths and limitations of each process, manufacturers can select the most appropriate technique for their specific needs, optimizing production efficiency and product quality.
Metal spinning is a manufacturing process used to shape a sheet metal into a hollow, symmetrical part. It’s often referred to as “spin forming” and is typically performed on a lathe machine. The process involves the following steps:
- Setup: A flat metal disc or blank is placed on a spinning lathe, which is usually made from aluminum, copper, steel, or other metals. The blank is clamped onto the lathe’s chuck.
- Spinning: The lathe spins the metal blank at high speed, while a tool (usually a roller or a mandrel) is applied against the surface of the spinning blank. The tool forces the metal to conform to the desired shape.
- Forming: As the metal is spun, the tool gradually moves along the blank, shaping it into the desired form. The metal stretches under pressure to achieve the required geometry, such as cones, cylinders, hemispheres, or other intricate shapes.
- Finishing: After the desired shape is achieved, the piece is removed from the lathe. It may undergo additional processes, such as trimming, sanding, polishing, or welding to achieve the final design.
Advantages of Metal Spinning:
- It is a cost-effective method for producing low to medium volume parts.
- The process can be used for both simple and complex geometries.
- High precision and smooth surfaces are often achieved, reducing the need for secondary finishing processes.
- Less material waste compared to other metal shaping methods like casting.
Applications: Metal spinning is commonly used in industries such as aerospace, automotive, medical devices, and home appliances. It’s particularly useful for creating parts like exhaust cones, decorative bowls, lamp shades, and turbine components.
Metal spinning is a versatile manufacturing process used to shape sheet metal into hollow, symmetrical parts by spinning it at high speeds. It involves placing a flat metal disc or blank on a lathe and applying pressure with a tool that gradually forces the metal into the desired shape. The process begins with the blank being secured in a chuck and the lathe spinning it at high speeds. As the metal is spun, the shaping tool, usually a roller or mandrel, is applied to the surface, pushing the metal outward to conform to a specific design. The spinning action causes the metal to stretch, forming intricate shapes like cones, cylinders, and hemispheres. Once the desired shape is achieved, the piece is removed from the lathe and may undergo further processes, such as trimming or polishing.
The process is highly efficient, producing parts with precise dimensions and smooth surfaces, often reducing the need for secondary finishing. Metal spinning is particularly advantageous when producing low to medium-volume parts since it uses less material and produces fewer defects than other methods like casting. It finds applications in a wide range of industries, including aerospace, automotive, medical devices, and home appliances, where components like exhaust cones, decorative items, and turbine parts are common.
Metal spinning can also be a highly flexible process in terms of the types of materials that can be used. Common metals like aluminum, brass, copper, stainless steel, and titanium are frequently spun due to their malleability when heated and their ability to form clean, smooth surfaces. The thickness of the sheet metal can vary, and metal spinning is capable of handling both thin and thick gauge materials, depending on the complexity and size of the part being produced.
One of the key benefits of metal spinning is its ability to create complex, high-strength parts without the need for expensive molds or dies, which are typically required for casting or forging. This makes it particularly valuable for producing prototype components or small production runs, where the cost of tooling can be prohibitive. Additionally, the process is more energy-efficient than other metal forming techniques because it doesn’t require heating the material to high temperatures—spinning is typically done at room temperature or with only minor heat applied.
Another advantage of metal spinning is its capacity for producing parts with minimal material waste. Since the process involves forming the metal into the desired shape rather than cutting away excess material, the resulting parts are typically more material-efficient. This reduces both waste and cost, making it an environmentally friendly option for certain types of production.
However, there are limitations. Metal spinning is most effective when producing symmetrical shapes with simple geometries. While it can be used for more complex designs, the process is generally limited to parts with gradual curves. Sharp corners or deep recesses can be challenging to achieve, and the process may not be suitable for extremely intricate or tight tolerances without additional post-processing. Additionally, the size of the part is constrained by the capabilities of the spinning lathe, meaning that extremely large or small parts may require different techniques.
In terms of quality, the process produces parts with high precision and surface finish, often eliminating the need for additional finishing or machining. However, there may be some surface blemishes or variations depending on the material used and the precision of the spinning tool. These can often be removed or smoothed out in post-processing.
Overall, metal spinning remains a valuable technique in various industries, particularly for producing medium-to-low volume runs of high-quality, lightweight parts. Its versatility, material efficiency, and cost-effectiveness make it a compelling choice for certain manufacturing applications, especially when precision and material conservation are important.
Metal Spinning Tools
In metal spinning, the tools used play a crucial role in shaping the metal into the desired form. The main tools involved are designed to control the movement of the material, ensure precision, and achieve the right surface finish. These tools typically include:
- Spinning Lathe: The central piece of equipment used for metal spinning. It’s a specialized lathe designed to rotate the metal blank at high speeds. The spinning lathe holds the blank in place while various other tools are used to form the material. There are manual, semi-automatic, and fully automatic lathes depending on the complexity of the job.
- Mandrel: A mandrel is a tool that acts as a form or core around which the metal is spun. It is especially useful when producing parts with deep or hollow shapes. The metal is stretched over the mandrel, which provides the internal shape of the part, ensuring uniformity. Mandrels can be made from a variety of materials, including steel or aluminum, and are often used in conjunction with a spinning tool to maintain the desired curvature.
- Spinning Rollers: These are the primary tools used to shape the metal as it spins on the lathe. A spinning roller applies pressure against the rotating blank, forcing it to stretch and conform to the mandrel or the tool’s shape. The roller is typically mounted on a tool holder that can be moved along the surface of the blank as it spins. These rollers come in various sizes, shapes, and materials depending on the metal being spun and the desired finish.
- Tool Holder: A tool holder is used to hold the spinning rollers and other tools in place during the metal spinning process. It can be adjusted to apply different amounts of pressure and control the movement of the roller. The tool holder is often designed to be precisely adjustable, ensuring the desired shaping of the metal as it spins.
- Backing Plate: A backing plate is often used in conjunction with the mandrel to support the material during the spinning process. It helps keep the metal in place, especially when dealing with larger or heavier blanks. It also provides additional support and stability to prevent the material from warping during shaping.
- Cutting Tools: After the spinning process, the workpiece often needs trimming or refining. Cutting tools such as shears or rotary cutters are used to trim excess material, creating a smooth edge or final shape. These tools can also be used for deburring and finishing processes to ensure the part meets the required specifications.
- Burnishing Tool: A burnishing tool is used to smooth and polish the surface of the spun part. It helps improve the surface finish and can be used to remove any marks or imperfections left by the spinning process. This tool is especially useful when a high-quality surface finish is required.
- Tailstock: A tailstock is used to support the free end of the rotating workpiece, particularly when producing long parts. It ensures that the part remains stable during the spinning process, preventing it from wobbling or shifting out of alignment. The tailstock can be adjusted to accommodate different sizes and shapes of parts.
Each of these tools plays a specific role in the metal spinning process, from initial shaping to final finishing, ensuring that the resulting components meet the desired specifications in terms of both shape and surface quality. The selection and proper use of these tools are crucial for achieving optimal results in metal spinning, whether it’s for high-volume production or custom, one-off parts.
In metal spinning, the tools involved are designed to control and shape the metal with high precision. The spinning lathe is the core piece of equipment, rotating the metal blank at high speeds to allow it to be formed. The blank is held in place while other tools apply pressure or force to stretch and mold the material into the desired shape. A mandrel is often used in the process, acting as a form around which the metal is spun. It provides the internal structure of the part, ensuring it takes on the proper dimensions, especially for deep or hollow parts. Mandrels are typically made from materials like steel or aluminum, and they help maintain the uniformity of the shape as the metal is worked.
Spinning rollers are the primary tools used to push and form the metal as it spins on the lathe. These rollers are positioned against the rotating blank, and their pressure causes the metal to stretch over the mandrel or shape it as desired. The rollers are mounted on a tool holder that can be moved along the surface, allowing for controlled shaping. The amount of pressure applied by the rollers can be adjusted to influence the final result. A backing plate is also used in some cases to support the metal as it spins, ensuring stability and helping prevent warping during the shaping process.
Once the shape is formed, cutting tools such as shears or rotary cutters are used to trim the excess material, creating smooth edges or refining the final shape. These tools can also be used for deburring, ensuring that the part is free from sharp edges or imperfections. A burnishing tool might be used at the end of the process to smooth and polish the surface, removing any marks left from the spinning or cutting. The burnishing tool helps achieve a high-quality surface finish, which is often essential, particularly in applications where aesthetics or tight tolerances are important.
A tailstock is often used to support the free end of the rotating workpiece, especially when working with longer or larger parts. It prevents any wobbling or misalignment during the spinning process, ensuring stability throughout the operation. The tailstock can be adjusted for different sizes or shapes of parts to provide the necessary support. Each of these tools plays a specific role in achieving the precise shape, surface finish, and structural integrity required in the final spun part. Their effective use ensures high-quality results, whether for small custom runs or more extensive production.
The versatility of metal spinning tools extends to the adaptability of the equipment for different types of materials and designs. For example, the spinning lathe can be adjusted to work with various types of metals, from soft materials like aluminum to harder ones such as stainless steel or titanium. The choice of tooling and settings depends on the specific material being spun, as harder metals may require more pressure or special types of rollers to prevent damage or excessive wear. The tool holders and rollers can also be customized to match the geometry of the parts being produced, allowing for fine-tuned control over the shaping process.
In more advanced setups, computer numerical control (CNC) machines may be used to automate and refine the process, allowing for higher precision and more complex geometries. CNC-controlled spinning lathes can program tool movements and adjust settings in real time, improving consistency and reducing human error, particularly for intricate or detailed parts. These machines are also capable of handling multi-step processes, where multiple tools are used sequentially to achieve the final shape, all while maintaining tight tolerances.
Another consideration in metal spinning is the use of lubrication or cooling agents during the process. The high pressures applied by the rollers can generate significant heat, especially with harder metals, which could cause the material to deform or wear the tools more quickly. Lubricants help reduce friction, allowing the tools to move smoothly over the metal’s surface and also help keep the workpiece cool, preventing overheating and material degradation. This is especially important when spinning metals with low thermal conductivity or when dealing with very thin blanks that may heat up quickly.
The quality of the finished part also depends on the proper maintenance of these tools. Regular inspections and replacement of worn-out components, such as rollers and mandrels, are essential to ensure the process remains consistent. Over time, the tools will naturally wear due to the constant pressure and friction involved in the spinning process, so keeping them in top condition is key to producing high-quality parts. Furthermore, the precision of the tool holder adjustments, the alignment of the lathe, and the calibration of CNC systems can all influence the overall accuracy of the parts being spun.
Metal spinning is also particularly useful for applications requiring high-strength components with lightweight properties, such as in aerospace or automotive industries. The process is capable of producing strong, durable parts without the need for welding or other joining techniques, making it ideal for creating seamless, one-piece parts. In addition, because spinning works by stretching the material rather than cutting it, the grain structure of the metal is preserved, which can enhance the strength and integrity of the final product.
Overall, metal spinning tools, when properly selected and maintained, play a critical role in achieving precision, efficiency, and high-quality finishes in a wide range of applications, from simple to complex geometries, and from low to high-volume production.
What is Metal Spinning Process Step by Step
The metal spinning process involves several key steps that work together to shape a sheet metal blank into a desired form. Here’s a step-by-step breakdown of the metal spinning process:
- Preparation of the Metal Blank: The process starts by selecting and preparing a flat metal sheet or disc, also known as a blank. This blank is typically made from materials such as aluminum, brass, copper, steel, or other metals. The blank is usually cut to a specific size based on the dimensions of the finished part.
- Securing the Blank on the Spinning Lathe: The metal blank is mounted onto a spinning lathe. The lathe spins the blank at high speeds. The blank is clamped onto the lathe’s chuck (the part of the lathe that holds the workpiece in place), ensuring it remains stable and secure during the spinning process.
- Using a Mandrel (if applicable): A mandrel may be used during the process, particularly when working with deep or hollow shapes. The mandrel acts as a form around which the metal is spun, providing internal support to the workpiece. It ensures that the final part has the desired shape, such as a cone or a cylindrical form.
- Forming the Metal: The primary forming action begins when a spinning roller or forming tool applies pressure to the surface of the rotating blank. The spinning lathe rotates the blank at high speed while the roller moves along the surface. This action forces the metal to stretch and conform to the desired shape. The roller moves along the radius of the blank, gradually shaping it into the final geometry, such as cones, cylinders, or hemispherical shapes.
- Shaping the Metal with Precision: The tool holder, which holds the spinning roller, is adjusted as needed to apply the correct amount of pressure to the metal. The tool follows a predetermined path, ensuring the material is formed uniformly. Depending on the complexity of the part, the process may involve multiple stages of tooling, where different rollers or tools are used to progressively refine the shape.
- Trimming Excess Material: After the desired shape is formed, excess material or any irregularities on the edge of the part are trimmed off. This can be done with cutting tools like shears or rotary cutters. The trimming process ensures that the part has smooth, clean edges and is closer to its final dimensions.
- Polishing and Finishing: Once the shape is complete and excess material has been removed, the part often requires surface finishing. This can include processes like burnishing, sanding, or polishing. A burnishing tool is commonly used to smooth and enhance the surface quality, ensuring the part is free from any tool marks or imperfections. This is particularly important when a smooth, aesthetically pleasing surface is required.
- Inspection and Quality Control: After the part is fully formed, it undergoes inspection to check for any defects, such as warping, dimensional errors, or surface imperfections. The finished part is measured against the design specifications to ensure it meets the required tolerances. If necessary, additional adjustments can be made during the inspection process.
- Final Removal and Clean-Up: After inspection, the part is removed from the lathe and undergoes final cleaning to remove any oils, lubricants, or debris from the surface. This ensures that the part is ready for its intended use or for any additional processes, such as coating or assembly.
Throughout the metal spinning process, precise control is essential to ensure that the desired shape and surface finish are achieved. The key steps—blank preparation, forming, trimming, finishing, and inspection—work together to produce high-quality, accurate parts with minimal material waste. The flexibility of metal spinning makes it suitable for producing a wide range of geometries, from simple to complex shapes, and is often used in industries like aerospace, automotive, and medical devices.
The metal spinning process begins with preparing the metal blank, which is typically a flat sheet or disc of metal that will be shaped into the final part. This blank is selected based on the material type and thickness required for the final part. Once the blank is ready, it is mounted securely onto a spinning lathe, where it will be rotated at high speeds. The blank is clamped onto the lathe’s chuck to hold it firmly in place as it spins.
For parts that require internal support or deeper shapes, a mandrel is often used. This tool is placed inside the metal blank, acting as a form around which the metal will be spun. The mandrel ensures that the inside of the final part retains the desired shape, such as a cylindrical or conical form. The metal blank begins to stretch and conform to the mandrel as pressure is applied.
The next stage involves using a spinning roller or forming tool, which is moved along the surface of the rotating blank. This roller presses against the metal, forcing it to stretch and take on the shape of the tool or mandrel. As the tool moves along the blank, the metal is gradually formed into the desired geometry. The pressure applied by the roller is carefully controlled to avoid over-stretching or damaging the material, ensuring uniform thickness and smooth curves.
Once the basic shape is achieved, excess material around the edges of the part is trimmed using cutting tools like shears or rotary cutters. This step ensures that the final part has clean, smooth edges and is closer to the desired size. In some cases, if the part requires a higher quality surface, additional polishing or burnishing may be necessary. This process smooths the surface, removing any imperfections left from the forming process and enhancing the part’s finish.
After the forming and finishing stages, the part is inspected to ensure that it meets the design specifications. The dimensions and surface finish are checked to confirm that the part is free of defects such as warping or misalignment. If necessary, further adjustments can be made to refine the part. Once the inspection is complete, the part is cleaned to remove any oils, lubricants, or debris used during the process, ensuring the part is ready for its intended use or additional treatments like coating or assembly.
The metal spinning process combines precision, control, and the ability to produce complex shapes with minimal material waste, making it a valuable technique in industries where high-quality, lightweight parts are required.
As the metal spinning process continues, its versatility and efficiency become apparent in the range of shapes and sizes it can produce. For example, the spinning process can create not only simple geometric shapes like cones and cylinders, but also more complex parts with intricate curvatures. The ability to handle both thick and thin materials allows metal spinning to be used for a wide variety of applications, from lightweight components for aerospace to robust parts for automotive or industrial machinery.
One of the notable advantages of metal spinning is its ability to preserve the grain structure of the material, which enhances the strength and durability of the finished part. This is because the process stretches and forms the metal without cutting or shearing it. As a result, parts made through metal spinning tend to exhibit high resistance to stress and wear, which is crucial in industries where performance under pressure or extreme conditions is required.
Another aspect of the process is its cost-effectiveness, especially when it comes to low to medium production volumes. Unlike casting or forging, metal spinning does not require expensive molds or dies. The process is highly adaptable, and changes to the design or specifications can often be made quickly without the need for retooling, making it ideal for prototyping or small-batch production. Additionally, the metal spinning process generates minimal material waste, as the material is formed into shape rather than being cut away, further reducing costs and increasing efficiency.
However, metal spinning is not without limitations. While it excels in forming symmetrical shapes, it is not suitable for producing highly complex or irregular geometries, such as those with sharp angles or intricate internal features. This can be overcome to some extent with additional machining or secondary processes, but it does mean that metal spinning is best suited for parts with relatively simple or gradual curves. The size of the part is also constrained by the size of the spinning lathe, so very large components may require other methods like forging or casting.
Additionally, the process is highly dependent on the skill and experience of the operator. Proper adjustment of the tool pressure, lathe speed, and roller position is crucial for achieving the desired result. In more advanced applications, automated or CNC-controlled spinning lathes can help ensure consistency and precision, but for more traditional setups, an experienced operator is key to managing the nuances of the process effectively.
In conclusion, metal spinning is a highly effective, adaptable, and efficient manufacturing process that allows for the creation of strong, durable, and precise parts with minimal waste. Its flexibility in terms of material choice, geometry, and production volume makes it an ideal choice for industries requiring high-quality, lightweight components, while its cost-effectiveness and ability to preserve the material’s grain structure make it an attractive option for both large and small-scale manufacturing needs.
What is Metal Spinning Process
The metal spinning process, also known as spin forming, is a manufacturing technique used to shape a sheet of metal into a hollow, symmetrical part. This process involves rotating a flat metal blank at high speeds while a tool (usually a roller) is applied to the material, shaping it as it spins. The process allows for the creation of complex, high-precision parts, typically used in industries like aerospace, automotive, and manufacturing. The key aspects of the metal spinning process include the use of a lathe to spin the metal blank, a mandrel to support the material (if needed), and forming tools to stretch and shape the metal into the desired geometry.
The process begins by securing a metal blank, typically a circular piece of sheet metal, onto a spinning lathe. The lathe rotates the blank at high speeds. A forming tool, often a spinning roller, is then applied against the surface of the rotating blank. The tool pushes the metal over a mandrel or the shape of the tool itself, gradually stretching the material to conform to the desired shape. The pressure applied by the tool causes the metal to stretch and take on the form of the mandrel, which might be a cylindrical or conical shape, depending on the design.
The metal is worked in a controlled manner, allowing it to retain its grain structure, which often results in parts with good strength and durability. Once the desired shape is achieved, excess material around the edges is trimmed, and any imperfections can be smoothed out using burnishing or polishing tools. The part is then inspected to ensure it meets the required specifications, and any necessary finishing steps are carried out.
Metal spinning is widely used to create seamless, high-strength components with minimal material waste, offering a cost-effective solution for producing both simple and complex shapes, especially when only moderate production volumes are required.
The metal spinning process allows for the creation of seamless, lightweight, and durable parts by stretching a sheet metal blank over a rotating tool. As the blank spins, the material is progressively formed by the pressure applied from a roller or other forming tool, causing the metal to conform to the shape of a mandrel or the tool itself. The high-speed rotation of the blank combined with the applied pressure helps the metal maintain a uniform thickness and shape as it stretches, which is essential for creating symmetrical parts.
Once the metal is formed into the desired shape, any excess material or rough edges are trimmed using cutting tools such as shears or rotary cutters. This trimming step refines the part, ensuring it matches the exact specifications. Depending on the part’s final requirements, additional finishing processes like polishing or burnishing may be applied to achieve a smooth surface. This helps to remove tool marks or imperfections that could remain from the spinning process, especially in cases where a high-quality surface finish is needed.
The process is highly adaptable, allowing for the production of a wide range of geometries, from simple cylindrical shapes to more complex forms like cones, hemispheres, or custom designs. However, metal spinning is best suited for symmetrical shapes and may be limited when trying to form parts with intricate internal features or sharp angles.
One of the main benefits of metal spinning is its cost-effectiveness, especially for small to medium production runs. The process doesn’t require the use of expensive molds or dies, making it an ideal option for prototyping or when flexibility is needed in design. Additionally, metal spinning generates minimal waste compared to other techniques like casting, as the material is stretched and not cut away. The material’s grain structure is also preserved during the process, which often results in parts that have enhanced strength and durability, making metal spinning particularly valuable in applications where structural integrity is critical.
Ultimately, metal spinning is a versatile and efficient manufacturing process that produces high-quality, strong, and lightweight parts with relatively low material waste. Its precision and ability to work with a variety of metals make it a preferred choice for many industries that require custom, durable components.
Metal Spinning Machine
A metal spinning machine is a specialized piece of equipment used in the metal spinning process to shape sheet metal into hollow, symmetrical parts. These machines are designed to rotate the metal blank at high speeds, while applying pressure through various tools to form the metal into a specific shape. Metal spinning machines come in different types, depending on the complexity of the part being produced and the level of automation required.
The core components of a metal spinning machine include the following:
- Spinning Lathe: The spinning lathe is the heart of the machine, responsible for rotating the metal blank at high speeds. The lathe holds the metal blank in place, allowing it to spin while a tool is applied to the surface. The lathe may be manual, semi-automatic, or fully automated, with higher-end models offering precise control over speed and tool movement for complex shapes.
- Mandrel (optional): A mandrel is a supporting tool placed inside the metal blank, especially when forming deep or hollow shapes. The mandrel serves as a form around which the metal is stretched, ensuring that the internal shape of the part remains consistent. The use of a mandrel is common in the production of parts with more intricate geometries.
- Tool Holder and Forming Tools: The tool holder supports the spinning roller or other forming tools that apply pressure to the rotating metal blank. These tools stretch the metal over the mandrel or along the machine’s form, gradually shaping the material. In some machines, the tool holder is adjustable to allow for different shaping operations and to apply the right amount of pressure during the forming process.
- Rollers: The primary forming tool in a metal spinning machine is a spinning roller. The roller is moved across the rotating metal blank to shape the material. The pressure applied by the roller causes the metal to conform to the desired shape. The roller’s movement, as well as its pressure, can be adjusted to achieve the correct curvature or geometry of the part.
- Tailstock: A tailstock is a support that stabilizes the free end of the workpiece during the spinning process. It prevents the metal part from wobbling or misaligning while it is being shaped. This is particularly important when spinning larger or longer parts, ensuring that the part remains stable and the shaping process remains accurate.
- Control System: Modern metal spinning machines may feature computerized controls (CNC), which allow for highly precise movements and automated adjustments. CNC systems can adjust the rotation speed, tool position, and pressure in real time, allowing for greater consistency and the ability to produce complex shapes with minimal human intervention.
- Cutting and Finishing Tools: After the spinning operation, metal spinning machines often include tools for trimming excess material and refining the shape. This can involve rotary cutters, shears, or other finishing tools that remove any unwanted material or sharp edges from the part. Some machines may also have burnishing or polishing tools that improve the surface finish of the final product.
Overall, a metal spinning machine allows for the efficient production of high-precision parts with minimal material waste. The machine is adaptable to various materials, part sizes, and designs, making it a versatile tool in industries such as aerospace, automotive, medical device manufacturing, and more. The combination of precise control over the forming process and the ability to work with a variety of metals makes metal spinning machines invaluable for creating high-strength, lightweight components.
A metal spinning machine is designed to provide high precision and versatility when shaping sheet metal into hollow, symmetrical parts. The machine’s key function is to rotate the metal blank at high speeds while applying pressure through forming tools, gradually shaping the metal into the desired form. This is achieved through a spinning lathe that holds the metal blank firmly in place and spins it while tools such as rollers are applied to shape the material. The use of a mandrel, when necessary, ensures that the internal shape of the part remains intact and consistent, especially for parts that require deeper or more intricate forms.
The spinning lathe at the heart of the machine can vary in terms of automation. Basic models are manually operated, while more advanced machines may feature CNC (computer numerical control) for precise adjustments to speed, pressure, and tool movement. This enables the machine to produce complex shapes with high consistency and minimal manual intervention. The machine also includes a tool holder that holds the spinning rollers or other forming tools, which apply the necessary pressure to stretch and shape the metal. The rollers are adjusted for movement, pressure, and contact with the blank to ensure that the material takes on the correct geometry.
For larger or longer parts, a tailstock is used to stabilize the free end of the workpiece, ensuring the part remains aligned and preventing it from wobbling as it is formed. The tailstock can be moved to accommodate different sizes of parts. Once the shaping is complete, excess material or rough edges are trimmed off using rotary cutters or shears. These tools ensure that the part has smooth, clean edges, meeting the required specifications.
In more advanced metal spinning machines, automated cutting and finishing tools may be included to further refine the part’s shape and surface. These machines can incorporate burnishing tools to smooth the surface and improve the finish, removing any tool marks or imperfections that might have resulted from the spinning process. Modern systems allow operators to make quick changes and adjustments to the machine, ensuring a high level of flexibility and reducing downtime when switching between different production runs or part designs.
Overall, metal spinning machines are highly adaptable and efficient, allowing for the production of high-quality, durable parts with minimal material waste. They are particularly useful for creating lightweight yet strong components in industries such as aerospace, automotive, and manufacturing, where precision and strength are paramount. The machine’s flexibility in terms of design and material compatibility makes it a valuable tool for producing a wide range of parts, from simple to complex shapes, with exceptional accuracy.
EMS Metalworking Machines
We design, manufacture and assembly metalworking machinery such as:
- Hydraulic transfer press
- Glass mosaic press
- Hydraulic deep drawing press
- Casting press
- Hydraulic cold forming press
- Hydroforming press
- Composite press
- Silicone rubber moulding press
- Brake pad press
- Melamine press
- SMC & BMC Press
- Labrotaroy press
- Edge cutting trimming machine
- Edge curling machine
- Trimming beading machine
- Trimming joggling machine
- Cookware production line
- Pipe bending machine
- Profile bending machine
- Bandsaw for metal
- Cylindrical welding machine
- Horizontal pres and cookware
- Kitchenware, hotelware
- Bakeware and cuttlery production machinery
as a complete line as well as an individual machine such as:
- Edge cutting trimming beading machines
- Polishing and grinding machines for pot and pans
- Hydraulic drawing presses
- Circle blanking machines
- Riveting machine
- Hole punching machines
- Press feeding machine
You can check our machinery at work at: EMS Metalworking Machinery – YouTube
Applications:
- Beading and ribbing
- Flanging
- Trimming
- Curling
- Lock-seaming
- Ribbing
- Flange-punching