Friction screw press machines are versatile machines with a wide range of applications across various industries. These presses are known for their ability to generate high forging forces and precise control over the forging process. Here are some common application areas for friction screw presses:
Friction Screw Press for Sale
- Metal Forging:
- Hot Forging: Friction screw presses are widely used in hot forging processes to shape and deform metal components. They are used for producing automotive parts, aerospace components, industrial machinery, and more.
- Cold Forging: Some friction screw presses can be adapted for cold forging processes, which involve shaping metal at or near room temperature. This is common in the production of fasteners, bolts, and precision components.
- Die Forging:
- Friction screw presses are employed in die forging operations where metal blanks are pressed into dies to create intricate and precise shapes. This is common in the production of crankshafts, connecting rods, and other complex metal parts.
- Upsetting:
- Upsetting is a forging process in which the length of a metal workpiece is reduced while increasing its cross-sectional area. Friction screw presses are used for upsetting operations to create items like bolts, rivets, and axles.
- Coining:
- Coining is a precision forming process used in the minting industry to produce coins, tokens, and medals. Friction screw presses are employed to create precise and detailed impressions on metal blanks.
- Ballistics and Ammunition:
- In the defense industry, friction screw presses are used for manufacturing ammunition components, such as bullet casings and shells.
- Railway and Transportation:
- Friction screw presses play a role in manufacturing railway components, such as wheelsets, axles, and couplers, which require high strength and precision.
- Electrical and Electronics:
- They are used to produce various components for the electrical and electronics industry, including connectors, contacts, and terminal blocks.
- Aerospace:
- Aerospace applications include the production of critical components like landing gear parts, engine components, and structural elements that require high strength and precision.
- Automotive:
- In the automotive industry, friction screw presses are used to manufacture components such as crankshafts, gears, transmission parts, and suspension components.
- General Manufacturing:
- Friction screw presses find use in general manufacturing for various metalworking processes, including extrusion, drawing, and forming.
- Heavy Machinery:
- They are utilized in the production of heavy machinery and equipment components, including hydraulic cylinders, gears, and shafts.
- Tools and Hardware:
- Friction screw presses are employed to manufacture hand tools, hardware items, and other metal-based products that require precise shaping and durability.
- Shipbuilding:
- In shipbuilding, they are used for forging components like propeller shafts, anchor chains, and other critical parts of vessels.
- Energy Sector:
- Friction screw presses are used in the energy sector to produce components for power generation and distribution, including turbine shafts and generator parts.
These application areas demonstrate the versatility of friction screw presses in shaping and forming various metal components across a range of industries, where precision, strength, and consistency are critical requirements.
Hot forging is a crucial process in the manufacturing industry, used to form and shape metals under high temperatures. One of the key machines in this process is the friction screw press. This piece of equipment is valued for its ability to apply precise and controlled pressure, making it indispensable in producing high-quality forged components. This article will delve into the intricacies of friction screw press hot forging, exploring its components, working principles, advantages, and applications in various industries.
What is Hot Forging?
Hot forging involves shaping metals at high temperatures, typically above their recrystallization point. This process enhances the metal’s ductility, making it easier to form complex shapes without cracking. The benefits of hot forging include improved mechanical properties, refined grain structure, and the ability to produce large and intricate components.
Friction Screw Press: An Overview
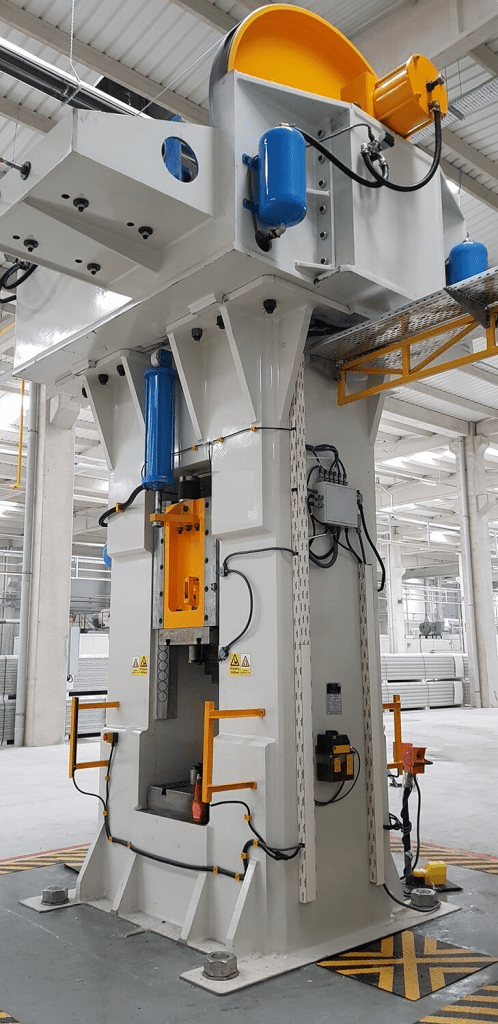
A friction screw press, also known as a screw press, is a type of machine used extensively in hot forging. Its operation relies on a screw mechanism driven by a flywheel and friction clutch. The design and technology of friction screw presses have evolved significantly over the years, incorporating advancements that enhance their efficiency and precision.
Components of a Friction Screw Press
- Main Frame: The robust structure that supports all other components.
- Flywheel and Clutch: These control the rotational motion, converting it into linear force.
- Screw Mechanism: The core component that translates rotational energy into pressing force.
- Ram and Die Assembly: These parts directly interact with the workpiece to shape it.
- Control Systems: Modern presses include computerized controls for precision and safety.
How Friction Screw Press Works
The operation of a friction screw press can be broken down into several steps:
- Initial Setup: The workpiece is placed in the die.
- Engagement: The flywheel accelerates, and the clutch engages, transferring energy to the screw.
- Pressing: The screw drives the ram downward, applying force to shape the workpiece.
- Release: The clutch disengages, allowing the ram to return to its starting position.
- Final Product: The forged component is removed and inspected.
Advantages of Using Friction Screw Press for Hot Forging
- Precision and Control: The press provides accurate force application, essential for high-quality forging.
- Energy Efficiency: The design allows for efficient energy use, reducing operational costs.
- Versatility in Application: Suitable for a wide range of metals and component sizes.
- Durability and Maintenance: Built to withstand heavy-duty operations with minimal maintenance requirements.
Applications of Friction Screw Press Hot Forging
- Automotive Industry: Used in the production of engine components, gears, and axles.
- Aerospace Industry: Essential for creating high-strength, lightweight components.
- Construction and Heavy Machinery: Produces durable parts for heavy-duty applications.
- Other Industrial Applications: Applicable in the manufacturing of tools, agricultural equipment, and more.
Safety Considerations
Operating a friction screw press involves several safety risks. It’s crucial to adhere to strict safety protocols:
- Training: Operators must be adequately trained.
- Protective Equipment: Use of appropriate personal protective equipment (PPE).
- Regular Maintenance: Ensures the machinery operates safely.
- Emergency Procedures: Clear guidelines for handling emergencies.
Future Trends and Innovations
The future of friction screw press hot forging looks promising with ongoing technological advancements:
- Automation and AI: Integration of automated systems and artificial intelligence for enhanced precision.
- Eco-Friendly Technologies: Development of more energy-efficient and environmentally friendly processes.
- Material Innovations: Exploration of new materials that can be forged using friction screw presses.
Conclusion
Friction screw press hot forging is a pivotal process in modern manufacturing, offering numerous benefits in terms of precision, efficiency, and versatility. Its applications span various industries, contributing significantly to advancements in technology and industrial capabilities. As the industry continues to innovate, the role of friction screw presses in hot forging will remain vital, driving progress and setting new standards in manufacturing excellence.
Friction Press
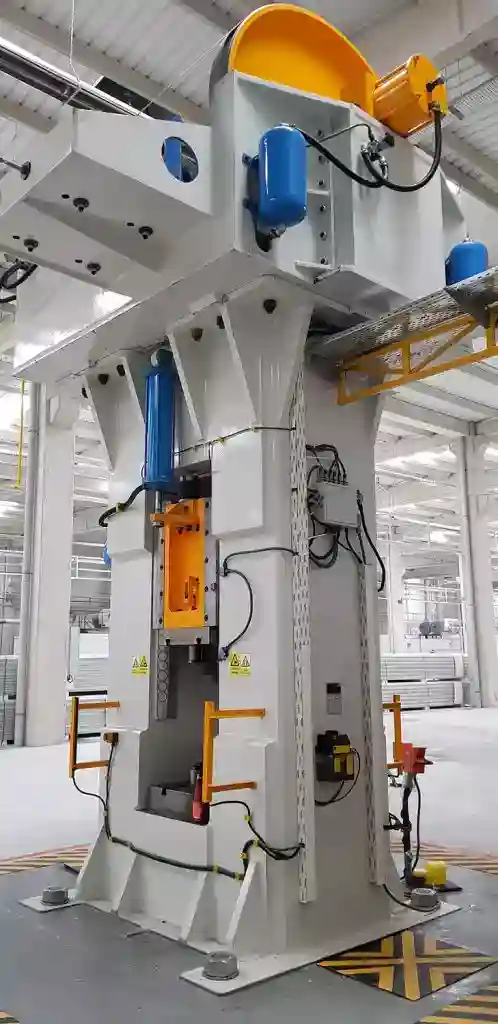
Friction presses play a crucial role in the manufacturing of various metal products, including pots and pans. These machines offer precision, efficiency, and control, making them ideal for producing high-quality cookware. This article explores the use of friction presses in the manufacturing process of pots and pans, detailing their operation, advantages, and impact on the industry.
What is a Friction Press?
A friction press, also known as a screw press, is a type of mechanical press that utilizes a flywheel and a screw mechanism to apply pressure. This design allows for precise control over the force and speed of the pressing process, making it suitable for a wide range of forging applications, including the production of cookware.
Components of a Friction Press
- Main Frame: Provides structural support and stability.
- Flywheel and Clutch: Control the rotational motion and convert it into linear force.
- Screw Mechanism: Translates rotational energy into pressing force.
- Ram and Die Assembly: Interact with the workpiece to shape it.
- Control Systems: Ensure precision and safety during operation.
How Friction Presses are Used in Cookware Manufacturing
- Material Preparation: The raw material, usually a metal sheet, is cut to size.
- Heating: The metal sheet is heated to the appropriate forging temperature.
- Positioning: The heated metal sheet is placed in the die of the friction press.
- Pressing: The press applies force to shape the metal into the desired form of a pot or pan.
- Cooling and Finishing: The shaped cookware is cooled and undergoes finishing processes such as trimming and polishing.
Advantages of Using Friction Presses for Pots and Pans
- Precision and Control: Enables the production of high-quality cookware with consistent thickness and shape.
- Efficiency: The process is fast and can be automated, reducing production time.
- Versatility: Suitable for different types of metals and a variety of cookware designs.
- Durability: Friction presses are robust and can handle heavy-duty operations with minimal maintenance.
Applications in the Cookware Industry
Friction presses are used to manufacture various types of cookware, including:
- Pots: Different sizes and shapes for cooking.
- Pans: Frying pans, sauté pans, and more.
- Lids: Precisely fitting lids for pots and pans.
Safety Considerations
Operating friction presses involves several safety risks. It is crucial to adhere to strict safety protocols, including:
- Training: Operators must be adequately trained.
- Protective Equipment: Use of appropriate personal protective equipment (PPE).
- Regular Maintenance: Ensures the machinery operates safely.
- Emergency Procedures: Clear guidelines for handling emergencies.
Future Trends and Innovations
The future of friction presses in cookware manufacturing looks promising with ongoing technological advancements:
- Automation and AI: Integration of automated systems and artificial intelligence for enhanced precision.
- Eco-Friendly Technologies: Development of more energy-efficient and environmentally friendly processes.
- Material Innovations: Exploration of new materials that can be forged using friction presses.
Conclusion
Friction presses are essential in the manufacturing of high-quality cookware. Their precision, efficiency, and versatility make them ideal for producing pots, pans, and other kitchen essentials. As technology continues to advance, the role of friction presses in cookware manufacturing will remain vital, driving innovation and setting new standards in the industry.
EMS Metalworking Machinery
We design, manufacture and assembly metalworking machinery such as:
- Hydraulic transfer press
- Glass mosaic press
- Hydraulic deep drawing press
- Casting press
- Hydraulic cold forming press
- Hydroforming press
- Composite press
- Silicone rubber moulding press
- Brake pad press
- Melamine press
- SMC & BMC Press
- Labrotaroy press
- Edge cutting trimming machine
- Edge curling machine
- Trimming beading machine
- Trimming joggling machine
- Cookware production line
- Pipe bending machine
- Profile bending machine
- Bandsaw for metal
- Cylindrical welding machine
- Horizontal pres and cookware
- Kitchenware, hotelware
- Bakeware and cuttlery production machinery
as a complete line as well as an individual machine such as:
- Edge cutting trimming beading machines
- Polishing and grinding machines for pot and pans
- Hydraulic drawing presses
- Circle blanking machines
- Riveting machine
- Hole punching machines
- Press feeding machine
You can check our machinery at work at: EMS Metalworking Machinery – YouTube
Applications:
- Beading and ribbing
- Flanging
- Trimming
- Curling
- Lock-seaming
- Ribbing
- Flange-punching