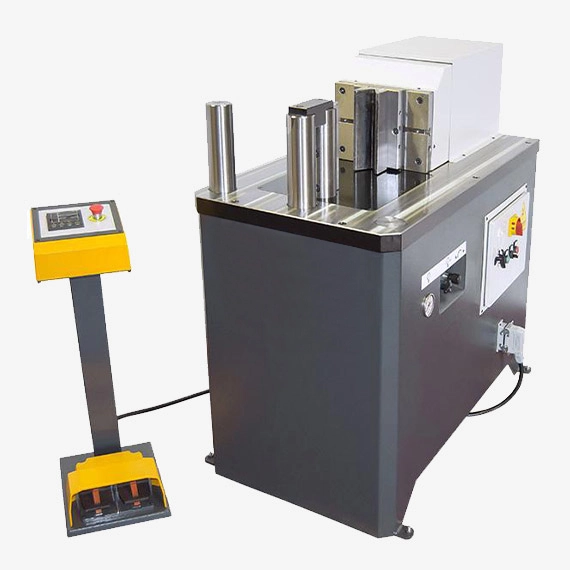
We manufacture Hydraulic Sheet Metal Bending Machine to bend sheet metal edges. Hydraulic Press Machines are used in metalworking industries
A hydraulic sheet metal bending machine, also known as a hydraulic press brake, is a specialized machine used for bending and shaping sheet metal with the application of hydraulic force. It is commonly used in various industries, including metal fabrication, manufacturing, automotive, and aerospace. Here are some key features and information about hydraulic sheet metal bending machines:
- Bending Capacity: Hydraulic sheet metal bending machines come in different sizes and capacities, which determine the maximum thickness and width of sheet metal they can handle. The capacity can range from smaller machines capable of bending thin gauge sheet metal to larger machines designed for thick and wide sheets.
- Hydraulic System: Hydraulic press brakes utilize hydraulic power to generate the necessary force for bending sheet metal. The hydraulic system consists of hydraulic cylinders, hydraulic pumps, valves, and a hydraulic fluid reservoir. The pressurized hydraulic fluid applies force to the machine’s ram, which in turn applies the bending force to the sheet metal.
- Bending Mechanism: Hydraulic sheet metal bending machines typically feature a mechanical or hydraulic bending mechanism. The mechanical mechanism involves the use of a mechanical linkage system and manually adjusted stops for precise bending angles. The hydraulic mechanism provides more precise control over the bending process and allows for automated or semi-automated bending with programmable controls.
- Control System: Hydraulic press brakes may have manual controls or advanced electronic control systems. Electronic control systems, such as a digital display or a programmable logic controller (PLC), offer precise control over bending angles, back gauge positioning, and other parameters. Some machines also feature pre-programmed bending sequences for increased efficiency.
- Back Gauge: Hydraulic press brakes often include a back gauge system. The back gauge is an adjustable stop that positions the sheet metal accurately for consistent bends. It can be manually adjusted or controlled electronically, allowing for precise positioning and repeatability.
- Safety Features: Hydraulic sheet metal bending machines are equipped with safety features to protect the operator during operation. These may include safety guards, emergency stop buttons, foot pedals for hands-free operation, and safety interlocks to prevent accidents.
- Tooling: Hydraulic press brakes use various types of tooling, such as upper and lower dies, to shape the sheet metal. The tooling selection depends on the specific bending requirements, including the desired bending angle, material thickness, and sheet metal type.
Hydraulic sheet metal bending machines offer precise and efficient bending capabilities, allowing for a wide range of complex shapes and angles in sheet metal fabrication. The specific features and capabilities of a hydraulic press brake can vary depending on the machine’s size, manufacturer, and model. It’s important to consult the machine’s documentation or the manufacturer for detailed information on the machine’s specifications, operating procedures, and safety guidelines.
Hydraulic Sheet Metal Bending Machine
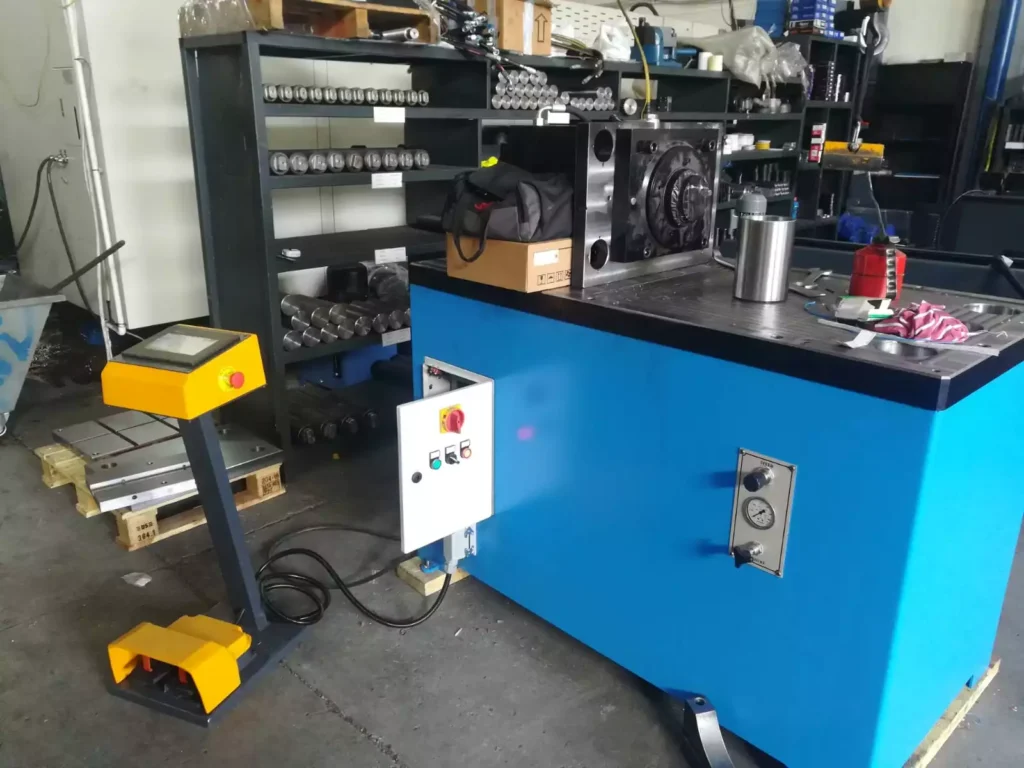
A hydraulic sheet metal bending machine is a specialized tool used to bend and shape sheet metal into various forms. It utilizes hydraulic pressure to generate the force required for bending, making it a powerful and versatile tool for metalworking applications.
Key Components of a Hydraulic Sheet Metal Bending Machine
A hydraulic sheet metal bending machine consists of several crucial components that work together to achieve the desired bending operation:
- Hydraulic Cylinder: The hydraulic cylinder is the heart of the machine, converting hydraulic fluid pressure into mechanical force. It consists of a piston and a cylinder barrel, and the fluid is pumped into the cylinder to push the piston, which applies force to the ram.
- Ram: The ram is the movable part of the machine that applies force directly to the workpiece. It is connected to the piston of the hydraulic cylinder.
- Tooling: Tooling, also known as dies and punches, is crucial in determining the specific shape or form of the workpiece. Dies provide the desired shape, while punches cut or pierce the material. Tooling can be customized to produce a wide range of shapes and sizes.
- Work Table: The work table provides a stable and adjustable surface for positioning and securing the workpiece during the bending operation. It can be adjusted to accommodate different workpiece sizes and heights.
- Control System: The control system manages the operation of the machine, including ram movement, pressure control, and safety interlocks. It receives input from sensors, such as pressure transducers and position encoders, and controls the valves, actuators, and motor to regulate the machine’s behavior.
Working Principle of a Hydraulic Sheet Metal Bending Machine
The working principle of a hydraulic sheet metal bending machine can be summarized in the following steps:
- Workpiece Positioning: The workpiece is positioned and secured on the work table.
- Ram Movement: The ram, driven by hydraulic pressure, moves towards the workpiece.
- Die and Punch Engagement: The ram applies force to the punch, pushing it against the die. The die and punch shape the workpiece according to the desired bend.
- Bending Operation: The workpiece is bent or deformed according to the shape of the tooling.
- Ram Retraction: Once the desired shape is achieved, the ram retracts to its initial position.
- Unloading: The workpiece is removed from the work table.
Benefits of Hydraulic Sheet Metal Bending Machines
Hydraulic sheet metal bending machines offer several advantages over other bending methods:
- Precision: Hydraulic presses provide precise control over ram movement and pressure, allowing for accurate and consistent bending.
- Versatility: Hydraulic presses can bend a wide range of sheet metal thicknesses and shapes, including simple bends, compound bends, and radius bends.
- High Production Rates: Hydraulic presses can achieve high production rates, especially when used in conjunction with automated systems.
- Ability to Handle Heavy Loads: Hydraulic presses can handle heavy loads, making them suitable for bending thick and large sheet metal components.
Applications of Hydraulic Sheet Metal Bending Machines
Hydraulic sheet metal bending machines are widely used in various industries for a wide range of applications:
- Automotive Industry: Bending sheet metal components for vehicle bodies, frames, and structural parts
- Aerospace Industry: Forming and shaping aircraft parts, such as wings, fuselages, and control surfaces
- Construction Industry: Creating metal components for roofing, cladding, and structural elements
- Manufacturing Industry: Producing metal parts for appliances, electronics, machinery, and other products
- Appliance Industry: Shaping and forming sheet metal for various appliance components, such as cabinets, doors, and panels
- Electronics Industry: Bending and shaping metal parts for circuit boards, enclosures, and other electronic components
- Furniture Manufacturing: Creating metal frames, supports, and decorative elements for furniture
- HVAC Industry: Forming and shaping sheet metal components for air conditioning and ventilation systems
- Sign Manufacturing: Bending and cutting metal sheets for signage, lettering, and displays
- Metal Fabrication Industry: Producing a wide range of metal components for various applications, including construction, machinery, and consumer goods
Horizontal Hydraulic Press Machine
A horizontal hydraulic press machine is a powerful and versatile tool that utilizes hydraulic pressure to apply force horizontally to a workpiece. It is commonly used in various industries, including metalworking, manufacturing, and construction, for a wide range of applications such as bending, straightening, pressing, and forming.
Key Components of a Horizontal Hydraulic Press Machine
- Frame: The frame provides the structural backbone for the press, ensuring stability and rigidity during operation. It is typically constructed from heavy-duty steel plates or castings and is designed to withstand the high forces generated during pressing operations.
- Hydraulic Cylinder: The hydraulic cylinder is the heart of the press, converting hydraulic pressure into mechanical force. It consists of a piston, cylinder barrel, and hydraulic seals. The size of the cylinder determines the maximum force the press can exert.
- Hydraulic Pump and Power Unit: The hydraulic pump and power unit supply hydraulic fluid to the cylinder, generating the required pressure for operation. The pump draws fluid from a reservoir and forces it through a series of valves and filters into the cylinder. The power unit regulates the pressure and flow of hydraulic fluid.
- Control System: The control system manages the operation of the press, including ram movement, pressure control, and safety interlocks. It receives input from sensors, such as pressure transducers and position encoders, and controls the valves and actuators to regulate the press’s behavior.
- Ram: The ram is the movable part of the press that applies force directly to the workpiece. It is connected to the piston of the hydraulic cylinder and slides along guides within the frame. The ram can be equipped with various tooling, such as dies, punches, or adapters, depending on the specific application.
- Work Table or Bed: The work table or bed provides a stable surface for positioning and securing the workpiece during the pressing operation. It is typically adjustable to accommodate different workpiece sizes and heights.
- Tooling: Tooling is a crucial component of horizontal hydraulic press machines, allowing the press to perform various forming operations. Common tooling options include dies, punches, adapters, and forming tools. Dies are used to shape the workpiece, while punches are used to cut or pierce material. Adapters are used to connect different tooling components, and forming tools are used for specific forming operations, such as bending or straightening.
- Safety Interlocks: Safety interlocks are essential components that prevent hazardous situations from occurring during press operation. They typically include sensors that detect the presence of an operator or workpiece, and they prevent the press from activating if safety conditions are not met.
- Gauges and Indicators: Gauges and indicators provide the operator with real-time information about the press’s operation, such as hydraulic pressure, ram position, and press force. This information is crucial for monitoring the press’s performance and ensuring safe operation.
- Electrical System: The electrical system powers the control system, hydraulic pump, and other electrical components of the press. It includes wiring, electrical panels, and various electrical components, such as motors, relays, and switches.
Types of Horizontal Hydraulic Press Machines
Horizontal hydraulic press machines come in various types, each with its specific characteristics and applications:
- Single-acting Presses: These presses have a single hydraulic cylinder that applies force in one direction. They are suitable for simple bending and straightening operations.
- Double-acting Presses: These presses have two hydraulic cylinders, allowing for force application in both directions. They are more versatile and can handle a wider range of pressing operations.
- Four-column Presses: These presses feature four columns that provide exceptional stability and rigidity, making them suitable for heavy-duty applications.
- C-frame Presses: These presses have a C-shaped frame, offering a more compact design and suitable for smaller workpieces.
Applications of Horizontal Hydraulic Press Machines
Horizontal hydraulic press machines are versatile tools used for a wide range of applications in various industries:
- Metalworking: Bending, straightening, forming, and coining of metal components for manufacturing.
- Construction: Pressing and forming of sheet metal components for construction applications, such as roofing, cladding, and structural elements.
- Automotive Industry: Forming of automotive components, such as body panels, brackets, and structural parts.
- Aerospace Industry: Precision forming of aerospace components, ensuring high strength, dimensional accuracy, and structural integrity.
- Industrial Applications: Pressing and forming of various components for industrial machinery, equipment, and tools.
Safety Considerations for Horizontal Hydraulic Press Machine Operation
Safety is paramount when operating horizontal hydraulic press machines. Operators must follow strict safety guidelines to prevent accidents and injuries. These guidelines include:
- Wearing appropriate personal protective equipment (PPE), including safety glasses, gloves, and hearing protection.
- Ensuring proper machine setup and maintenance, following the manufacturer’s instructions.
- Securing the workpiece firmly on the work table before operation.
What is a Horizontal Hydraulic Press?
A horizontal hydraulic press is a powerful machine that utilizes hydraulic pressure to apply force horizontally to a workpiece. It is commonly used in various industries, including metalworking, manufacturing, and construction, for a wide range of applications such as bending, straightening, pressing, and forming.
Key Components of a Horizontal Hydraulic Press
Horizontal hydraulic presses consist of several key components that work together to achieve the desired pressing operation. These components include:
- Frame: The frame provides the structural backbone for the press, ensuring stability and rigidity during operation. It is typically constructed from heavy-duty steel plates or castings and is designed to withstand the high forces generated during pressing operations.
- Hydraulic Cylinder: The hydraulic cylinder is the heart of the press, converting hydraulic pressure into mechanical force. It consists of a piston, cylinder barrel, and hydraulic seals. The size of the cylinder determines the maximum force the press can exert.
- Hydraulic Pump and Power Unit: The hydraulic pump and power unit supply hydraulic fluid to the cylinder, generating the required pressure for operation. The pump draws fluid from a reservoir and forces it through a series of valves and filters into the cylinder. The power unit regulates the pressure and flow of hydraulic fluid.
- Control System: The control system manages the operation of the press, including ram movement, pressure control, and safety interlocks. It receives input from sensors, such as pressure transducers and position encoders, and controls the valves and actuators to regulate the press’s behavior.
- Ram: The ram is the movable part of the press that applies force directly to the workpiece. It is connected to the piston of the hydraulic cylinder and slides along guides within the frame. The ram can be equipped with various tooling, such as dies, punches, or adapters, depending on the specific application.
- Work Table or Bed: The work table or bed provides a stable surface for positioning and securing the workpiece during the pressing operation. It is typically adjustable to accommodate different workpiece sizes and heights.
- Tooling: Tooling is a crucial component of horizontal hydraulic presses, allowing the press to perform various forming operations. Common tooling options include dies, punches, adapters, and forming tools. Dies are used to shape the workpiece, while punches are used to cut or pierce material. Adapters are used to connect different tooling components, and forming tools are used for specific forming operations, such as bending or straightening.
- Safety Interlocks: Safety interlocks are essential components that prevent hazardous situations from occurring during press operation. They typically include sensors that detect the presence of an operator or workpiece, and they prevent the press from activating if safety conditions are not met.
- Gauges and Indicators: Gauges and indicators provide the operator with real-time information about the press’s operation, such as hydraulic pressure, ram position, and press force. This information is crucial for monitoring the press’s performance and ensuring safe operation.
- Electrical System: The electrical system powers the control system, hydraulic pump, and other electrical components of the press. It includes wiring, electrical panels, and various electrical components, such as motors, relays, and switches.
Applications of Horizontal Hydraulic Presses
Horizontal hydraulic presses are versatile machines used for a wide range of applications in various industries. Some common applications include:
- Metalworking: Bending, straightening, forming, and coining of metal components for manufacturing.
- Construction: Pressing and forming of sheet metal components for construction applications, such as roofing, cladding, and structural elements.
- Automotive Industry: Forming of automotive components, such as body panels, brackets, and structural parts.
- Aerospace Industry: Precision forming of aerospace components, ensuring high strength, dimensional accuracy, and structural integrity.
- Industrial Applications: Pressing and forming of various components for industrial machinery, equipment, and tools.
Safety Considerations for Horizontal Hydraulic Press Operation
Safety is paramount when operating horizontal hydraulic presses. Operators must follow strict safety guidelines to prevent accidents and injuries. These guidelines include:
- Wearing appropriate personal protective equipment (PPE), including safety glasses, gloves, and hearing protection.
- Ensuring proper machine setup and maintenance, following the manufacturer’s instructions.
- Securing the workpiece firmly on the work table before operation.
- Avoiding distractions while operating the press.
- Never operating the press with damaged components or under unsafe conditions.
- Receiving proper training and supervision before operating the press.
- Being aware of potential hazards, such as pinch points, moving parts, and high-pressure hydraulic fluid.
- Never operating the press under the influence of alcohol or drugs.
- Reporting any malfunctions or safety concerns to the appropriate personnel immediately.
Horizontal hydraulic presses play a vital role in various industries, enabling the production of high-quality components for a wide range of applications. By following safety guidelines and operating the press responsibly, operators can ensure safe and efficient
History of Press Brake Machines
The origins of metal bending can be traced back to ancient civilizations, where blacksmiths used rudimentary tools to shape metal. As technology progressed, so did the methods of metal bending, leading to the development of more sophisticated machinery.
The first press brake machines emerged during the Industrial Revolution, driven by the need for more efficient and precise metalworking tools. Early press brake machines were manually operated, requiring significant physical effort and skill from the operator. Despite their limitations, these machines marked a significant advancement in the field of metal fabrication.
The 20th century witnessed substantial improvements in press brake technology. The introduction of hydraulic systems in the 1940s allowed for greater force and control, enabling the bending of thicker and tougher metals. This innovation revolutionized the industry, making hydraulic press brake machines the standard for many years.
In recent decades, the advent of computer numerical control (CNC) technology has transformed press brake machines once again. CNC press brake machines offer unparalleled precision and automation, allowing for complex bending operations to be performed with minimal human intervention. These machines are equipped with advanced software that can program and execute intricate bending sequences, ensuring consistency and accuracy.
Today, press brake machines continue to evolve, incorporating cutting-edge technologies such as robotics and artificial intelligence. These advancements are paving the way for even greater efficiency, flexibility, and precision in metal fabrication.
Types of Press Brake Machines
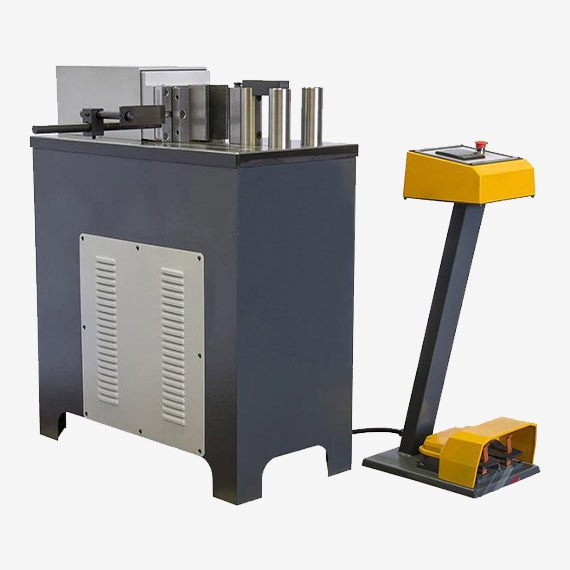
Press brake machines come in various types, each with its own features, advantages, and applications. Understanding the different types of press brake machines is essential for selecting the right equipment for specific metal bending tasks.
Manual Press Brake Machines
Features and Uses Manual press brake machines are the simplest type of press brakes, operated entirely by human effort. They are typically used for small-scale or low-volume production tasks, where high precision is not critical.
Advantages
- Cost-effective and affordable for small businesses
- Easy to operate and maintain
- Suitable for simple bending operations
Disadvantages
- Limited bending capacity and precision
- Labor-intensive and time-consuming
- Not suitable for high-volume production
Hydraulic Press Brake Machines
Features and Uses Hydraulic press brake machines use hydraulic fluid to generate the necessary force for bending metal sheets. They are widely used in various industries due to their versatility and reliability.
Advantages
- High bending capacity and precision
- Capable of handling thicker and tougher metals
- Smooth and consistent operation
Disadvantages
- Higher initial cost compared to manual machines
- Requires regular maintenance of hydraulic systems
- Potential for hydraulic fluid leaks
Electric Press Brake Machines
Features and Uses Electric press brake machines use electric motors to drive the bending process. They are known for their energy efficiency and precision.
Advantages
- Energy-efficient and environmentally friendly
- High precision and repeatability
- Lower operating costs compared to hydraulic machines
Disadvantages
- Limited force compared to hydraulic machines
- Higher initial cost than manual machines
- Requires skilled operators
CNC Press Brake Machines
Features and Uses CNC (Computer Numerical Control) press brake machines represent the pinnacle of press brake technology. They are equipped with advanced computer systems that control the bending process with exceptional precision.
Advantages
- Unmatched precision and accuracy
- Automated and programmable operations
- Suitable for complex and high-volume production
Disadvantages
- High initial cost and investment
- Requires skilled operators and programmers
- Complex maintenance and troubleshooting
Each type of press brake machine has its unique advantages and disadvantages, making it crucial to select the appropriate type based on specific production requirements and budget constraints.
Components of a Press Brake Machine
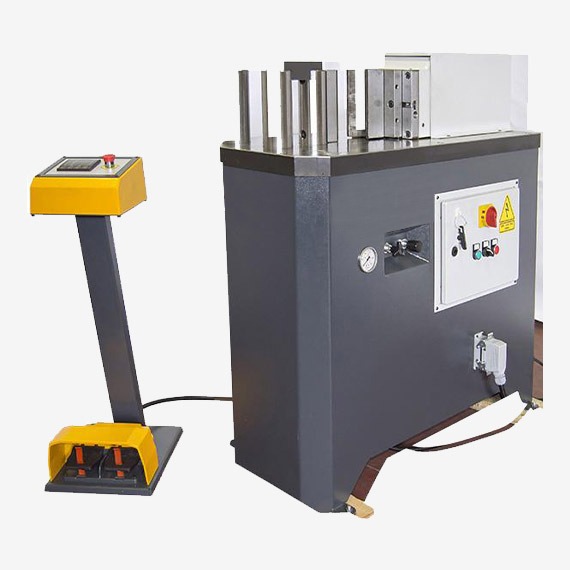
Press brake machines consist of several key components, each playing a vital role in the bending process. Understanding these components is essential for operating and maintaining the machine effectively.
Frame
The frame is the backbone of the press brake machine, providing structural support and stability. It is typically constructed from heavy-duty steel to withstand the forces exerted during the bending process.
Ram
The ram is a movable component that exerts force on the metal sheet, pressing it against the die to create the desired bend. The ram’s movement can be controlled manually, hydraulically, or electrically, depending on the type of press brake machine.
Die and Punch
The die and punch are the primary tools used in the bending process. The punch, attached to the ram, presses the metal sheet into the die, which is fixed to the machine’s bed. The shape and size of the die and punch determine the angle and radius of the bend.
Back Gauge
The back gauge is a positioning tool that helps in accurately aligning the metal sheet for bending. It ensures consistent bend angles and dimensions by providing a reference point for the sheet.
Control System
The control system manages the operation of the press brake machine. In manual machines, this may be a simple mechanical system, while hydraulic and electric machines use more advanced control systems. CNC press brake machines have sophisticated computer systems that program and control the entire bending process.
Safety Features
Press brake machines are equipped with various safety features to protect operators from accidents and injuries. These may include safety guards, emergency stop buttons, and light curtains that detect the presence of an operator’s hands near the bending area.
Working Principle
The basic working principle of a press brake machine involves applying a controlled force to bend metal sheets into specific shapes. Here are the key steps in the bending process:
- Sheet Positioning: The metal sheet is positioned on the machine’s bed, aligned against the back gauge to ensure precise placement.
- Tool Selection: The appropriate die and punch are selected based on the desired bend angle and radius. These tools are then installed on the machine.
- Bending Operation: The ram descends, pressing the punch into the metal sheet and forcing it into the die. This action creates the bend, with the angle and shape determined by the tools used and the force applied.
- Return Stroke: After the bend is completed, the ram ascends, releasing the pressure on the metal sheet. The sheet is then removed or repositioned for additional bends.
Precision and control are crucial in the bending process to ensure the accuracy and consistency of the bends. CNC press brake machines excel in this regard, as they use computer programming to control the ram’s movement and force, resulting in highly precise bends.
Applications of Press Brake Machines
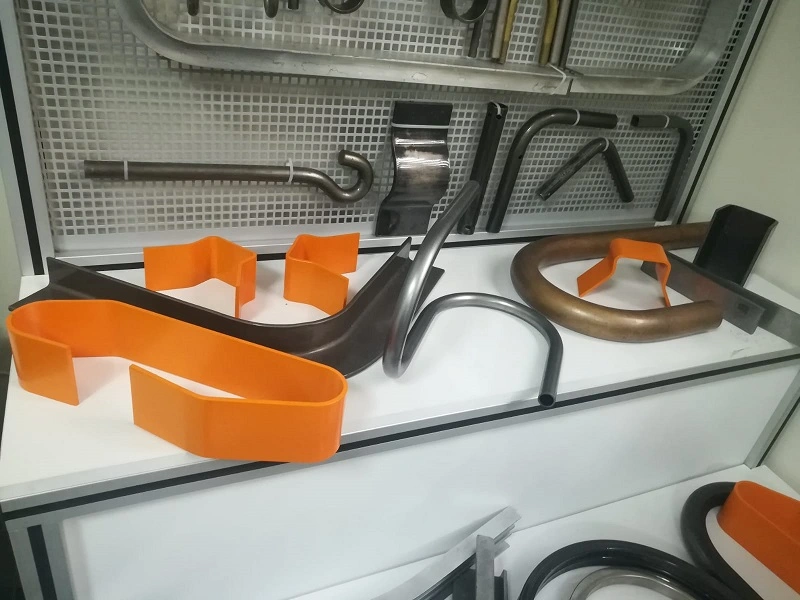
Press brake machines are used across various industries due to their versatility and precision. Here are some common applications:
- Automotive Industry: Manufacturing car body panels, chassis components, and brackets.
- Aerospace Industry: Producing aircraft parts, including wing components and fuselage sections.
- Construction Industry: Fabricating structural components, such as beams, columns, and brackets.
- Electronics Industry: Creating enclosures, chassis, and brackets for electronic devices.
- Furniture Industry: Making metal frames and components for furniture.
- HVAC Industry: Producing ductwork and ventilation components.
These machines are also used in creating custom metal parts and prototypes, showcasing their adaptability to various production needs.
Advantages of Using Press Brake Machines
Press brake machines offer several advantages that make them indispensable in metal fabrication:
- Precision and Accuracy: These machines can produce highly precise bends, ensuring that components meet exact specifications.
- Efficiency and Productivity: Press brake machines can perform complex bending operations quickly, increasing production efficiency.
- Versatility: They can handle a wide range of materials and thicknesses, making them suitable for various applications.
- Cost-effectiveness: By reducing material waste and increasing production speed, press brake machines can lower manufacturing costs.
Maintenance and Safety Tips
Proper maintenance and safety practices are essential for the efficient and safe operation of press brake machines. Here are some tips:
Routine Maintenance
- Regularly inspect the machine for wear and tear.
- Keep the machine clean and free from debris.
- Lubricate moving parts as recommended by the manufacturer.
- Check hydraulic fluid levels and replace as necessary.
Common Issues and Troubleshooting
- Misalignment of the die and punch: Adjust the alignment to ensure precise bends.
- Inconsistent bending angles: Check for wear on the tools and replace if needed.
- Hydraulic system leaks: Inspect seals and hoses, and replace any damaged components.
Safety Guidelines for Operators
- Always wear appropriate personal protective equipment (PPE).
- Ensure that safety guards and emergency stop buttons are in place and functional.
- Follow the manufacturer’s guidelines for safe operation.
- Undergo proper training before operating the machine.
Future Trends in Press Brake Technology
The future of press brake technology is shaped by advancements in automation, materials, and environmental considerations:
- Automation and Industry 4.0: The integration of robotics and IoT (Internet of Things) is enhancing the automation of press brake machines, leading to increased efficiency and reduced human intervention.
- Advanced Materials and Designs: The development of new materials and innovative designs is expanding the capabilities of press brake machines, allowing for more complex and precise bends.
- Environmental Considerations: Efforts to reduce energy consumption and minimize environmental impact are driving the adoption of electric press brake machines and other eco-friendly technologies.
Conclusion
Press brake machines are a cornerstone of modern metal fabrication, offering unmatched precision, efficiency, and versatility. From their historical evolution to the latest technological advancements, these machines continue to play a vital role in various industries.
Understanding the different types of press brake machines, their components, and working principles is essential for selecting the right equipment and maximizing its potential. By following proper maintenance and safety practices, operators can ensure the longevity and safe operation of these machines.
As we look to the future, advancements in automation, materials, and environmental sustainability will further enhance the capabilities of press brake machines, solidifying their place in the ever-evolving landscape of manufacturing.
Whether you are a seasoned professional or new to the field, this comprehensive guide provides valuable insights into the world of sheet metal bending press brake machines, highlighting their importance and potential in modern industry.
Components of a Press Brake Machine
Press brake machines consist of several key components, each playing a vital role in the bending process. Understanding these components is essential for operating and maintaining the machine effectively.
Frame
The frame is the backbone of the press brake machine, providing structural support and stability. Constructed from heavy-duty steel, the frame must be robust enough to withstand the significant forces exerted during the bending process. The frame’s design can vary depending on the machine type, but its primary function remains to ensure rigidity and durability.
Ram
The ram is a movable component that exerts force on the metal sheet, pressing it against the die to create the desired bend. The ram’s movement can be controlled manually, hydraulically, or electrically, depending on the type of press brake machine. In CNC press brakes, the ram’s motion is precisely controlled by computer programming, allowing for highly accurate and repeatable bends.
Die and Punch
The die and punch are the primary tools used in the bending process. The punch, attached to the ram, presses the metal sheet into the die, which is fixed to the machine’s bed. The shape and size of the die and punch determine the angle and radius of the bend. There are various types of dies and punches, each suited for different bending operations, such as V-dies, U-dies, and hemming dies.
Back Gauge
The back gauge is a positioning tool that helps in accurately aligning the metal sheet for bending. It ensures consistent bend angles and dimensions by providing a reference point for the sheet. Modern press brake machines often feature CNC-controlled back gauges, which can be programmed to automatically adjust positions for complex bending sequences, enhancing precision and efficiency.
Control System
The control system manages the operation of the press brake machine. In manual machines, this may be a simple mechanical system, while hydraulic and electric machines use more advanced control systems. CNC press brake machines have sophisticated computer systems that program and control the entire bending process. These systems can store multiple bending programs, allowing for quick setup and reduced downtime between jobs.
Safety Features
Press brake machines are equipped with various safety features to protect operators from accidents and injuries. These may include safety guards, emergency stop buttons, and light curtains that detect the presence of an operator’s hands near the bending area. Modern machines also incorporate safety sensors that halt the machine’s operation if a potential hazard is detected, ensuring a safer working environment.
Working Principle
https://www.youtube.com/embed/l8quDXXNNEg?feature=oembedWorking Principle
The basic working principle of a press brake machine involves applying a controlled force to bend metal sheets into specific shapes. Here are the key steps in the bending process:
- Sheet Positioning: The metal sheet is positioned on the machine’s bed, aligned against the back gauge to ensure precise placement. Proper alignment is crucial for achieving accurate and consistent bends.
- Tool Selection: The appropriate die and punch are selected based on the desired bend angle and radius. These tools are then installed on the machine. The selection of the correct tools is essential for achieving the desired bend geometry and avoiding damage to the metal sheet.
- Bending Operation: The ram descends, pressing the punch into the metal sheet and forcing it into the die. This action creates the bend, with the angle and shape determined by the tools used and the force applied. The bending process requires careful control of the ram’s speed and pressure to ensure precise and consistent results.
- Return Stroke: After the bend is completed, the ram ascends, releasing the pressure on the metal sheet. The sheet is then removed or repositioned for additional bends. In CNC press brakes, the return stroke and repositioning of the sheet can be automated, increasing efficiency and reducing operator fatigue.
Precision and control are crucial in the bending process to ensure the accuracy and consistency of the bends. CNC press brake machines excel in this regard, as they use computer programming to control the ram’s movement and force, resulting in highly precise bends. The ability to program complex bending sequences also allows for the efficient production of intricate parts with minimal manual intervention.
Applications of Press Brake Machines
https://www.youtube.com/embed/o1dG-pIFkTk?feature=oembedApplications of Press Brake Machines
Press brake machines are used across various industries due to their versatility and precision. Here are some common applications:
- Automotive Industry: Press brake machines are integral to manufacturing car body panels, chassis components, and brackets. These machines can produce complex shapes and bends required for modern vehicle designs, ensuring high precision and repeatability.
- Aerospace Industry: The aerospace industry demands high precision and stringent quality standards. Press brake machines are used to produce aircraft parts, including wing components and fuselage sections, where accuracy and consistency are paramount.
- Construction Industry: Press brake machines are utilized to fabricate structural components such as beams, columns, and brackets. These components must meet specific strength and dimensional requirements to ensure the safety and stability of buildings and other structures.
- Electronics Industry: In the electronics industry, press brake machines are used to create enclosures, chassis, and brackets for electronic devices. These components often require intricate bends and precise dimensions to accommodate various electronic components and assemblies.
- Furniture Industry: The furniture industry employs press brake machines to make metal frames and components for furniture. These machines enable the production of aesthetically pleasing and structurally sound furniture parts, such as legs, supports, and brackets.
- HVAC Industry: The HVAC industry uses press brake machines to produce ductwork and ventilation components. These machines can create complex bends and shapes needed for efficient air distribution and ventilation systems.
These machines are also used in creating custom metal parts and prototypes, showcasing their adaptability to various production needs. The ability to quickly and accurately produce custom components makes press brake machines valuable tools for manufacturers and fabricators across different industries.
Advantages of Using Press Brake Machines
Press brake machines offer several advantages that make them indispensable in metal fabrication:
- Precision and Accuracy: Press brake machines are designed to produce highly precise bends, ensuring that components meet exact specifications. CNC press brakes, in particular, offer unmatched precision and repeatability, allowing for the production of intricate and complex parts with tight tolerances.
- Efficiency and Productivity: These machines can perform complex bending operations quickly, increasing production efficiency. The automation capabilities of CNC press brakes reduce the need for manual intervention, leading to faster setup times and higher throughput.
- Versatility: Press brake machines can handle a wide range of materials and thicknesses, making them suitable for various applications. From thin aluminum sheets to thick steel plates, these machines can accommodate different bending requirements, providing flexibility in manufacturing processes.
- Cost-effectiveness: By reducing material waste and increasing production speed, press brake machines can lower manufacturing costs. The precision and efficiency of these machines minimize errors and rework, resulting in significant cost savings over time.
- Consistency: Press brake machines ensure consistent bend quality across multiple parts, which is essential for mass production. The ability to produce uniform parts enhances the overall quality and reliability of the final products.
- Customizability: Modern press brake machines, especially CNC models, offer high levels of customizability. Operators can program specific bending sequences and parameters, allowing for the production of custom parts tailored to unique design requirements.
- Reduced Labor Costs: Automation in CNC press brake machines reduces the need for skilled labor, lowering labor costs. These machines can operate with minimal supervision, enabling manufacturers to allocate human resources more efficiently.
- Enhanced Safety: Press brake machines are equipped with advanced safety features that protect operators from accidents and injuries. Safety guards, emergency stop buttons, and sensors contribute to a safer working environment, reducing the risk of workplace incidents.
These advantages highlight the critical role of press brake machines in modern metal fabrication, underscoring their value in achieving high-quality, efficient, and cost-effective manufacturing processes.
Maintenance and Safety Tips
Proper maintenance and safety practices are essential for the efficient and safe operation of press brake machines. Here are some tips:
Routine Maintenance
- Regular Inspection: Regularly inspect the machine for wear and tear. Check for any signs of damage or misalignment in the components, especially the die and punch.
- Cleaning: Keep the machine clean and free from debris. Accumulated dust and metal shavings can affect the machine’s performance and lead to premature wear.
- Lubrication: Lubricate moving parts as recommended by the manufacturer. Proper lubrication reduces friction and prevents wear, extending the machine’s lifespan.
- Hydraulic Fluid: Check hydraulic fluid levels and replace as necessary. Ensure that the hydraulic system is free from leaks and that the fluid is clean and at the proper level.
- Tool Maintenance: Inspect the die and punch for wear and replace them if needed. Sharp and well-maintained tools are crucial for achieving precise bends.
Common Issues and Troubleshooting
- Misalignment: Misalignment of the die and punch can result in inaccurate bends. Adjust the alignment to ensure precise bending operations.
- Inconsistent Bending Angles: Inconsistent bending angles may be due to worn tools or incorrect settings. Check the tools for wear and verify the machine’s settings.
- Hydraulic System Leaks: Hydraulic system leaks can affect the machine’s performance. Inspect seals and hoses regularly and replace any damaged components.
- Control System Errors: Errors in the control system, particularly in CNC machines, can disrupt operations. Ensure that the control system software is up-to-date and that any programming issues are addressed promptly.
Safety Guidelines for Operators
- Personal Protective Equipment (PPE): Always wear appropriate PPE, including safety glasses, gloves, and protective clothing, to prevent injuries.
- Safety Guards and Emergency Stops: Ensure that safety guards are in place and functional. Familiarize yourself with the location and operation of emergency stop buttons.
- Manufacturer Guidelines: Follow the manufacturer’s guidelines for safe operation. These guidelines provide crucial information on operating the machine safely and efficiently.
- Training: Undergo proper training before operating the machine. Training should cover machine operation, maintenance, and safety procedures.
- Awareness: Stay alert and aware of your surroundings while operating the machine. Avoid distractions and ensure that the work area is free from hazards.
By adhering to these maintenance and safety tips, operators can ensure the longevity, efficiency, and safe operation of press brake machines, minimizing downtime and reducing the risk of accidents.
Future Trends in Press Brake Technology
The future of press brake technology is shaped by advancements in automation, materials, and environmental considerations. Here are some key trends to watch:
Automation and Industry 4.0
The integration of robotics and the Internet of Things (IoT) is enhancing the automation of press brake machines. Industry 4.0 technologies enable machines to communicate and coordinate with each other, leading to increased efficiency and reduced human intervention. Automated press brake machines can perform complex bending operations with minimal oversight, improving productivity and precision.
Advanced Materials and Designs
The development of new materials and innovative designs is expanding the capabilities of press brake machines. Advanced materials, such as high-strength alloys and composites, require precise and powerful bending techniques. Modern press brake machines are being designed to handle these materials, enabling the production of more durable and lightweight components.
Environmental Considerations
Efforts to reduce energy consumption and minimize environmental impact are driving the adoption of electric press brake machines and other eco-friendly technologies. Electric press brakes are more energy-efficient than their hydraulic counterparts, producing less noise and requiring less maintenance. Additionally, manufacturers are exploring sustainable materials and processes to further reduce the environmental footprint of metal fabrication.
Smart Manufacturing
Smart manufacturing technologies, including artificial intelligence (AI) and machine learning, are being integrated into press brake machines. These technologies enable predictive maintenance, real-time monitoring, and adaptive control, enhancing machine performance and reducing downtime. AI-powered systems can optimize bending operations by analyzing data and making adjustments in real-time.
User-Friendly Interfaces
Future press brake machines are likely to feature more user-friendly interfaces, making them easier to operate and program. Touchscreen controls, intuitive software, and augmented reality (AR) training tools will simplify the operation of these machines, reducing the learning curve for operators.
These trends highlight the ongoing evolution of press brake technology, promising greater efficiency, precision, and sustainability in metal fabrication.
Conclusion
Press brake machines are a cornerstone of modern metal fabrication, offering unmatched precision, efficiency, and versatility. From their historical evolution to the latest technological advancements, these machines continue to play a vital role in various industries.
Understanding the different types of press brake machines, their components, and working principles is essential for selecting the right equipment and maximizing its potential. By following proper maintenance and safety practices, operators can ensure the longevity and safe operation of these machines.
As we look to the future, advancements in automation, materials, and environmental sustainability will further enhance the capabilities of press brake machines, solidifying their place in the ever-evolving landscape of manufacturing.
Whether you are a seasoned professional or new to the field, this comprehensive guide provides valuable insights into the world of sheet metal bending press brake machines, highlighting their importance and potential in modern industry.
Press brake machines will undoubtedly continue to evolve, driven by technological innovations and industry demands. Staying informed about these advancements and adopting best practices will enable manufacturers to leverage the full potential of press brake machines, ensuring continued success in their metal fabrication endeavors.
EMS Metalworking Machinery
We design, manufacture and assembly metalworking machinery such as:
- Hydraulic transfer press
- Glass mosaic press
- Hydraulic deep drawing press
- Casting press
- Hydraulic cold forming press
- Hydroforming press
- Composite press
- Silicone rubber moulding press
- Brake pad press
- Melamine press
- SMC & BMC Press
- Labrotaroy press
- Edge cutting trimming machine
- Edge curling machine
- Trimming beading machine
- Trimming joggling machine
- Cookware production line
- Pipe bending machine
- Profile bending machine
- Bandsaw for metal
- Cylindrical welding machine
- Horizontal pres and cookware
- Kitchenware, hotelware
- Bakeware and cuttlery production machinery
as a complete line as well as an individual machine such as:
- Edge cutting trimming beading machines
- Polishing and grinding machines for pot and pans
- Hydraulic drawing presses
- Circle blanking machines
- Riveting machine
- Hole punching machines
- Press feeding machine
You can check our machinery at work at: EMS Metalworking Machinery – YouTube
Applications:
- Beading and ribbing
- Flanging
- Trimming
- Curling
- Lock-seaming
- Ribbing
- Flange-punching