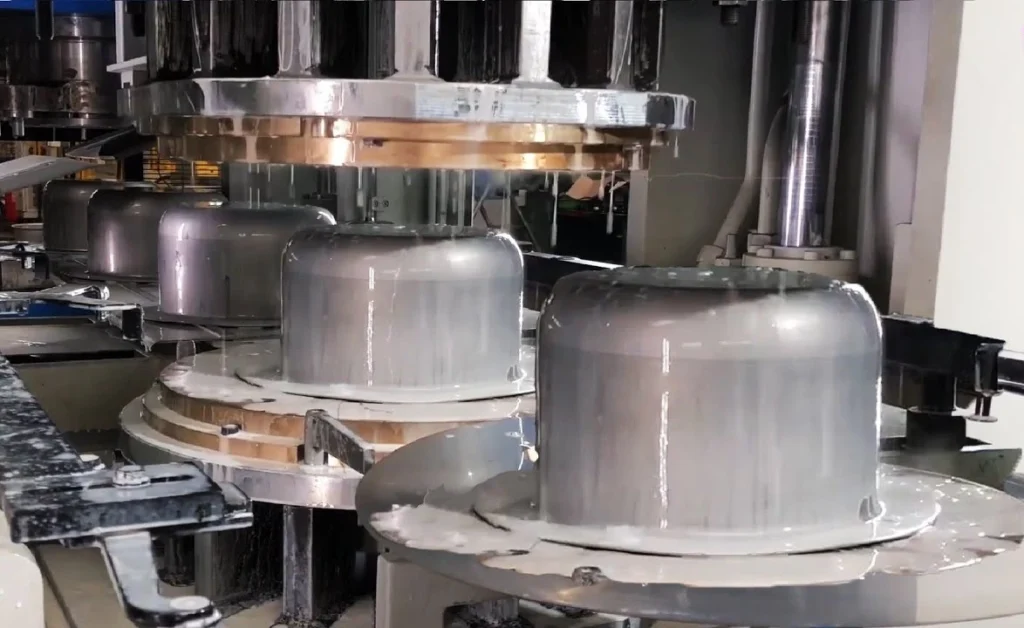
We manufacture the Hydraulic Press Machine to bend sheet metal edges. Hydraulic Press Machines are used in metalworking industries
A hydraulic press machine is a type of machinery that uses hydraulic pressure to generate force. It is commonly used in manufacturing processes to shape, mold, or deform materials such as metal, plastic, or rubber. Hydraulic press machines come in various sizes and capacities, ranging from small manual units to large industrial models that can exert thousands of tons of force.
The basic components of a hydraulic press machine include:
- Hydraulic pump: This component supplies the pressurized hydraulic fluid that powers the machine.
- Hydraulic cylinder: This component converts the hydraulic pressure into mechanical force, which is used to operate the machine. The hydraulic cylinder consists of a piston and cylinder, with the piston being pushed by the hydraulic fluid.
- Control system: This system controls the operation of the machine and includes components such as valves, switches, and sensors.
Some common applications of hydraulic press machines include:
- Metal forming: Hydraulic press machines are commonly used in the metalworking industry to bend, stamp, or shear metal sheets or plates.
- Plastic and rubber molding: Hydraulic press machines can also be used to mold plastic or rubber parts.
- Powder compaction: Powder compaction is a process in which powdered materials are compressed into solid shapes using a hydraulic press machine.
- Assembly: Hydraulic press machines can be used for assembly tasks such as pressing bearings or fitting parts together.
Overall, hydraulic press machines are versatile tools that are widely used in various industries for a range of applications. They offer high force, precision, and control, making them an essential tool for many manufacturing processes.
Hydraulic Press Machine
Hydraulic presses are versatile and powerful machines used in various industries. Their specifications vary depending on their intended application, workpiece size, and desired force output. Here’s a summary of key hydraulic press specifications:
- Capacity: The capacity of a hydraulic press refers to its maximum force output, typically measured in tons or kilonewtons (kN). This determines the type of workpieces and forming operations the press can handle.
- Stroke Length: The stroke length is the maximum distance the press ram can travel, determining the depth of forming operations and the range of workpiece sizes that can be accommodated.
- Work Table Size: The work table size determines the maximum size of the workpiece that can be placed on the press for operation.
- Ram Speed: The ram speed is the rate at which the ram moves during the pressing operation. This is important for controlling forming speed and ensuring proper material flow.
- Opening Height: The opening height is the distance between the work table and the ram when it is fully retracted. This determines the clearance needed for loading and unloading workpieces.
- Daylight: The daylight is the total vertical distance between the top of the work table and the bottom of the ram at its highest position. This determines the maximum thickness of the workpiece that can be accommodated.
- Pump Capacity: The pump capacity is the volume of hydraulic fluid the pump can deliver per unit time, measured in liters per minute (LPM) or gallons per minute (GPM). This determines the press’s ability to maintain pressure during operation.
- Motor Power: The motor power is the electrical power required to drive the hydraulic pump, typically measured in horsepower (HP) or kilowatts (kW). This determines the overall power consumption of the press.
- Control System: The control system determines the press’s operation modes, including manual, semi-automatic, and fully automatic control. It also manages ram movement, pressure control, and safety interlocks.
- Safety Features: Safety features are essential for preventing accidents and injuries during press operation. Common safety features include safety interlocks, light curtains, and emergency stop buttons.
In addition to these key specifications, hydraulic presses may also include additional features, such as adjustable work table height, tool change systems, and integrated data acquisition systems. The choice of specific features depends on the specific application and user requirements.
When selecting a hydraulic press, it’s crucial to consider the intended application, workpiece size, desired force output, and safety requirements. Consulting with press manufacturers or industry experts can help ensure the selection of the most suitable hydraulic press for the specific needs.
Industries
Hydraulic press machines are used in a wide range of industries, including:
- Automotive: Hydraulic press machines are used in the automotive industry to manufacture various parts such as body panels, engine components, and brake pads.
- Aerospace: Hydraulic press machines are used in the aerospace industry to produce components such as wings, fuselages, and landing gear.
- Construction: Hydraulic press machines are used in the construction industry to produce precast concrete parts such as pillars, beams, and slabs.
- Manufacturing: Hydraulic press machines are used in the manufacturing industry to produce a wide range of products such as consumer goods, electronics, and industrial equipment.
- Energy: Hydraulic press machines are used in the energy industry to produce components such as wind turbine blades, solar panels, and heat exchangers.
- Medical: Hydraulic press machines are used in the medical industry to manufacture parts such as surgical instruments, orthopedic implants, and dental products.
Overall, hydraulic press machines are versatile tools that find application in a wide range of industries for various purposes.
Operation
Hydraulic press machines work by using hydraulic pressure to generate force that is applied to a workpiece. The basic components of a hydraulic press machine include a hydraulic cylinder, a ram or piston, a hydraulic pump, and a control valve. Here’s how it works:
- Hydraulic fluid is pumped from a reservoir into the hydraulic cylinder through a high-pressure hose or pipe.
- The hydraulic cylinder contains a piston or ram that is driven by the hydraulic pressure. The piston moves towards the workpiece and applies a force to it.
- The control valve regulates the flow of hydraulic fluid to the cylinder, controlling the speed and force of the piston.
- The force applied to the workpiece can be increased or decreased by adjusting the hydraulic pressure, which is controlled by the hydraulic pump.
- Once the desired force is applied to the workpiece, the hydraulic pump stops and the pressure is maintained, allowing the workpiece to be held in place.
- The hydraulic press machine can be operated manually or with the help of a computerized control system, depending on the level of automation required.
Overall, hydraulic press machines are powerful and precise tools that are used to shape, form, and join a wide range of materials.
Hydraulic Press Machine Introduction
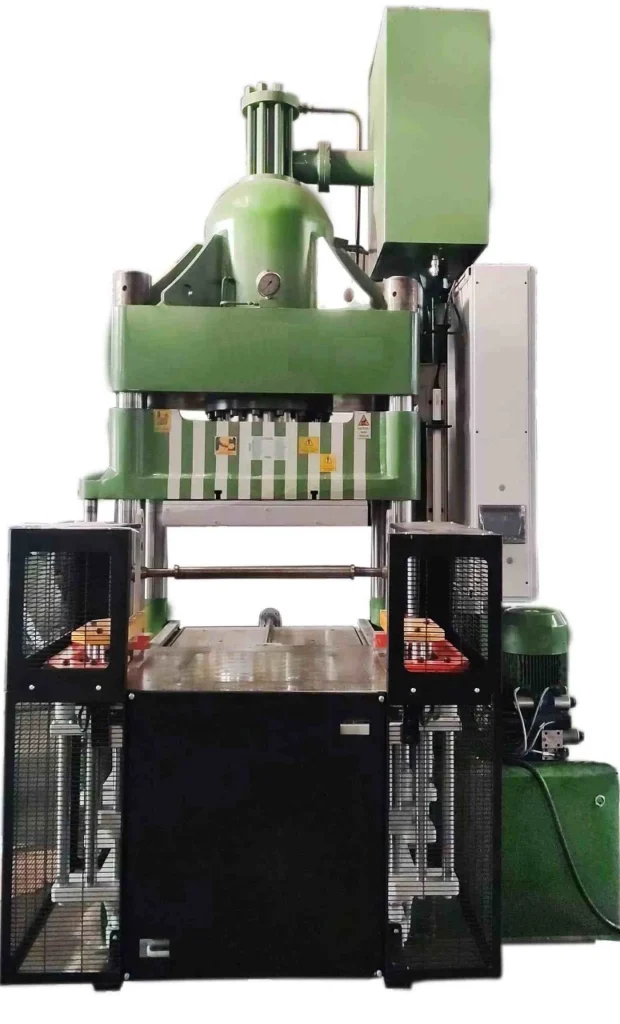
A hydraulic press machine is a powerful and versatile tool that utilizes hydraulic pressure to apply force to shape, form, or cut various materials, primarily metal workpieces. It operates based on Pascal’s law, which states that pressure applied to a confined fluid is transmitted equally in all directions throughout the fluid. This principle allows for the generation of immense force using a relatively small amount of applied pressure.
Key Components of a Hydraulic Press Machine
A hydraulic press machine consists of several key components that work together to achieve the desired forming or cutting operation:
- Hydraulic Cylinder: The hydraulic cylinder is the heart of the press, converting hydraulic pressure into mechanical force. It consists of a piston, cylinder barrel, and hydraulic seals. The size of the cylinder determines the maximum force the press can exert.
- Hydraulic Pump and Power Unit: The hydraulic pump and power unit supply hydraulic fluid to the cylinder, generating the required pressure for operation. The pump draws fluid from a reservoir and forces it through a series of valves and filters into the cylinder. The power unit regulates the pressure and flow of hydraulic fluid.
- Control System: The control system manages the operation of the press, including ram movement, pressure control, and safety interlocks. It receives input from sensors, such as pressure transducers and position encoders, and controls the valves and actuators to regulate the press’s behavior.
- Ram: The ram is the movable part of the press that applies force directly to the workpiece. It is connected to the piston of the hydraulic cylinder and slides along guides within the frame. The ram can be equipped with various tooling, such as dies, punches, or adapters, depending on the specific application.
- Work Table or Bed: The work table or bed provides a stable surface for positioning and securing the workpiece during the pressing operation. It is typically adjustable to accommodate different workpiece sizes and heights.
- Tooling: Tooling plays a crucial role in shaping or forming the workpiece. It consists of dies, punches, or adapters that are attached to the ram or work table. Dies provide the desired shape or form for the workpiece, while punches cut or pierce the material. Adapters allow for the connection of different tooling components.
Working Principle
The working principle of a hydraulic press machine can be summarized in the following steps:
- Hydraulic fluid is drawn from the reservoir into the hydraulic pump.
- The pump forces the hydraulic fluid through a series of valves and filters into the hydraulic cylinder.
- The hydraulic fluid pressure builds up in the cylinder, pushing against the piston.
- The force from the piston is transmitted to the ram, which applies force directly to the workpiece.
- The workpiece is compressed, shaped, or cut as a result of the applied force.
- Once the desired forming or cutting operation is complete, the pressure is released, and the ram retracts.
Advantages of Hydraulic Press Machines
Hydraulic press machines offer several advantages over other types of presses, such as mechanical presses:
- Precise control of force and speed: Hydraulic presses allow for precise control of the force applied to the workpiece and the speed at which the ram moves. This is essential for delicate forming operations and ensuring consistent product quality.
- Versatility: Hydraulic presses can be used for a wide range of forming and cutting operations, including bending, straightening, pressing, cutting, and coining. This makes them versatile tools for various applications.
- Overload protection: Hydraulic presses are equipped with overload protection mechanisms that prevent damage to the press or workpiece in case of excessive force.
- Smooth and quiet operation: Hydraulic presses operate smoothly and quietly compared to mechanical presses due to the use of hydraulic fluid.
- High power-to-size ratio: Hydraulic presses can generate a large amount of force compared to their size, making them compact and efficient machines.
Applications of Hydraulic Press Machines
Hydraulic press machines are widely used in various industries, including:
- Metalworking: Bending, forming, straightening, pressing, and cutting of metal components
- Manufacturing: Production of metal parts for automotive, aerospace, and other industries
- Construction: Forming and shaping of sheet metal components for roofing, cladding, and structural elements
- Recycling and scrap processing: Compacting of scrap metal for easier transportation and processing
- Composite materials: Forming and shaping of composite materials, such as carbon fiber or fiberglass
- Powder compaction: Compacting of metal powders into desired shapes for subsequent processing
- Pharmaceutical industry: Production of tablets and capsules
- Food processing: Pressing and forming of food items
- Electronics manufacturing: Assembly and riveting of electronic components
- Aerospace industry: Precision forming of aerospace components
Hydraulic Press Machine
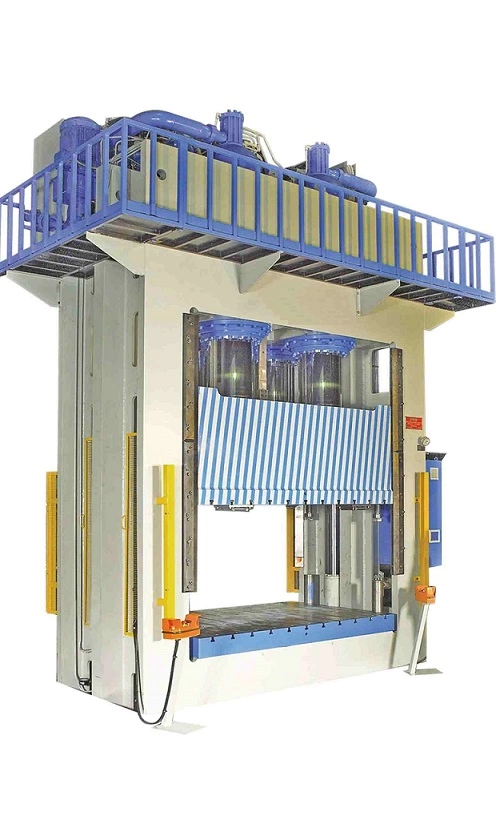
Hydraulic press machines are used in a wide range of industries for a variety of applications. Here are some examples:
- Automotive Industry: Hydraulic press machines are used in the production of automobile parts such as engine blocks, transmission components, and brake rotors.
- Aerospace Industry: The aerospace industry uses hydraulic press machines for forming aircraft components such as wings, fuselages, and landing gear.
- Manufacturing Industry: Hydraulic press machines are used in manufacturing for stamping, punching, and blanking operations.
- Construction Industry: Hydraulic press machines are used for bending and shaping steel for construction of buildings, bridges, and other structures.
- Food Processing Industry: Hydraulic press machines are used for juice extraction, oil extraction, and other food processing applications.
- Recycling Industry: Hydraulic press machines are used for baling and compacting recyclable materials such as paper, plastic, and metal.
- Medical Industry: Hydraulic press machines are used for manufacturing prosthetic limbs, surgical instruments, and other medical devices.
Overall, hydraulic press machines are versatile equipment that can be used in many industries where high force is required for shaping, forming, or compressing materials.
How does it work?
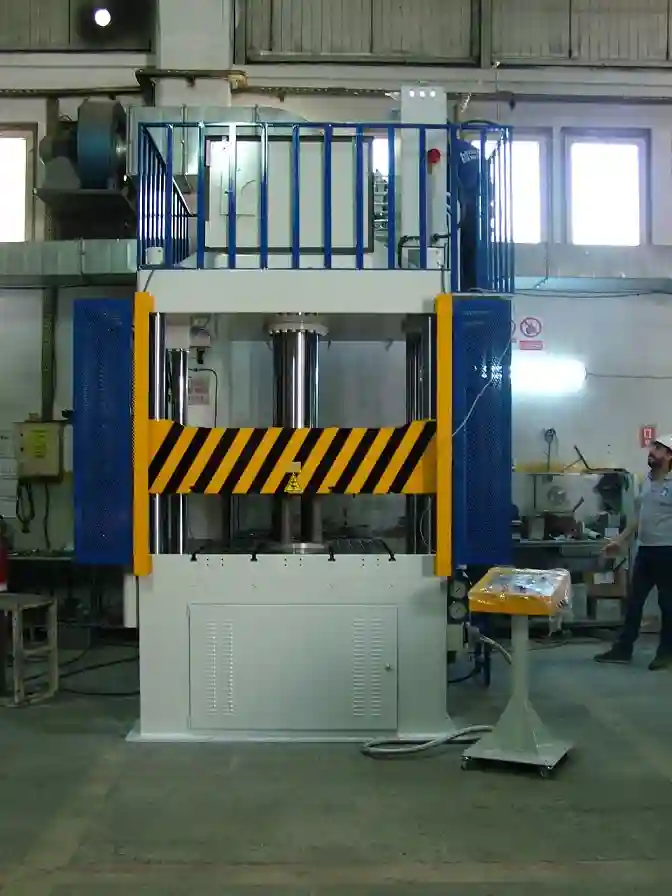
A hydraulic press machine works by using hydraulic pressure to exert force on a material or workpiece. The machine consists of a hydraulic system, a frame or housing, a press table or bed, and a tool or die.
Here’s how it works:
- Hydraulic System: The hydraulic system consists of a hydraulic pump, which converts mechanical energy into hydraulic pressure. The hydraulic fluid is then transmitted through hoses and pipes to the cylinder or cylinders, where it pushes a piston.
- Frame or Housing: The frame or housing supports the hydraulic system, press table or bed, and tool or die.
- Press Table or Bed: The press table or bed is where the material or workpiece is placed for shaping or compression. It is typically made of steel or other strong materials that can withstand the high pressures exerted by the hydraulic system.
- Tool or Die: The tool or die is the component that comes in contact with the workpiece and shapes it into the desired form.
When the machine is in operation, the hydraulic pump pressurizes the hydraulic fluid, which then flows through the hoses and pipes to the cylinder or cylinders. The piston in the cylinder is pushed out, exerting force on the material or workpiece placed on the press table or bed.
As the hydraulic fluid continues to flow, the piston continues to move, exerting more force on the workpiece. The amount of force exerted can be controlled by adjusting the pressure in the hydraulic system.
The tool or die is used to shape or compress the workpiece into the desired form. For example, a metal part can be bent, stamped, or cut into shape using a hydraulic press machine.
Overall, a hydraulic press machine works by using hydraulic pressure to exert force on a material or workpiece, allowing it to be shaped or compressed into the desired form.
A hydraulic press is a machine that uses a hydraulic cylinder to generate a compressive force. It is a fundamental tool in various industries, ranging from automotive to manufacturing, due to its ability to apply substantial force in a controlled manner. The history of hydraulic presses dates back to the 19th century, with significant advancements made by inventors like Joseph Bramah, who is often credited with creating the first hydraulic press in 1795. Bramah’s design utilized the principles of hydraulics, as outlined in Pascal’s Law, which states that pressure applied to a confined fluid is transmitted equally in all directions. This invention revolutionized many industrial processes by allowing for more efficient and powerful pressing operations.
In modern industry, hydraulic presses are indispensable due to their versatility and efficiency. They are used in forging, molding, metal forming, and even in the compaction of materials for recycling. Their ability to provide a consistent and controllable force makes them ideal for applications where precision and repeatability are crucial. As technology has progressed, so too has the design and functionality of hydraulic presses, incorporating advanced materials and computerized control systems to enhance performance and safety.
Hydraulic presses play a vital role in today’s industrial landscape, providing essential capabilities for manufacturing, construction, and beyond. Their development and refinement continue to drive innovation and efficiency in various fields, making them a cornerstone of modern engineering and production.
Components of a Hydraulic Press
Hydraulic presses are complex machines composed of several essential components that work together to generate and apply force. Each component plays a crucial role in the operation and efficiency of the press. Below are the primary components of a hydraulic press:
1. Frame
The frame of a hydraulic press is the structural backbone that supports the entire machine. It must be robust and capable of withstanding the high forces generated during operation. Frames are typically made of heavy-duty steel or cast iron to ensure durability and stability. The design of the frame can vary, with common configurations including C-frame, H-frame, and four-post designs, each suited to different applications and space constraints.
2. Hydraulic Cylinder
The hydraulic cylinder is the component responsible for generating the pressing force. It consists of a cylindrical barrel, a piston, and a piston rod. Hydraulic fluid is pumped into the cylinder, pushing the piston and rod to create a compressive force. The cylinder’s size and capacity determine the amount of force the press can exert, with larger cylinders providing greater force. Hydraulic cylinders are often constructed from high-strength steel to withstand high pressures and ensure longevity.
3. Hydraulic Pump
The hydraulic pump is the heart of the hydraulic system, supplying the press with the necessary hydraulic fluid under pressure. It converts mechanical energy into hydraulic energy by drawing fluid from the reservoir and pumping it into the hydraulic cylinder. There are various types of hydraulic pumps, including gear pumps, vane pumps, and piston pumps, each offering different levels of efficiency and performance. The selection of the pump depends on the specific requirements of the press, such as flow rate and pressure capacity.
4. Control Valves
Control valves are essential for regulating the flow and pressure of the hydraulic fluid within the system. They allow the operator to control the movement and force of the hydraulic cylinder, enabling precise adjustments during operation. Common types of control valves include directional control valves, pressure relief valves, and flow control valves. These valves ensure the hydraulic system operates safely and efficiently by preventing overpressure and ensuring the correct fluid flow.
5. Reservoir
The reservoir, also known as the hydraulic tank, stores the hydraulic fluid used by the press. It is designed to hold a sufficient volume of fluid to keep the system operating smoothly. The reservoir also helps dissipate heat generated during operation, preventing the hydraulic fluid from overheating. It typically includes filters to remove contaminants from the fluid, maintaining the cleanliness and efficiency of the hydraulic system.
6. Pressure Gauges
Pressure gauges are used to monitor the hydraulic system’s pressure levels, ensuring they remain within safe operating limits. Accurate pressure readings are crucial for maintaining the press’s performance and preventing damage to the components. These gauges are usually installed at various points in the hydraulic circuit, such as near the pump and the cylinder, providing real-time feedback to the operator.
Each component of a hydraulic press must be carefully designed and maintained to ensure optimal performance and longevity. The interplay of these components allows hydraulic presses to deliver the powerful, precise force needed for a wide range of industrial applications.
Working Principle of Hydraulic Presses
Hydraulic presses operate based on the principles of fluid mechanics, specifically Pascal’s Law, which states that when a pressure is applied to a confined fluid, the pressure change occurs throughout the entire fluid. This fundamental principle allows hydraulic presses to generate substantial force with minimal input. Understanding the working principle involves examining the role of each component in the system and how they interact to create the pressing force.
Pascal’s Law
Pascal’s Law is the cornerstone of hydraulic press operation. It states that pressure applied to a confined fluid is transmitted equally in all directions. In practical terms, this means that when hydraulic fluid is pumped into a cylinder, the pressure exerted on the fluid is distributed uniformly throughout the cylinder, generating a force on the piston. This force is then transmitted through the piston rod to the object being pressed.
Force and Pressure Transmission
In a hydraulic press, the force generated depends on the pressure of the hydraulic fluid and the surface area of the piston. The formula used to calculate this force is:
Force=Pressure×Area\text{Force} = \text{Pressure} \times \text{Area}Force=Pressure×Area
Where:
- Force is the output force exerted by the press.
- Pressure is the hydraulic fluid pressure.
- Area is the surface area of the piston.
By increasing the pressure or the surface area of the piston, the force generated by the press can be significantly amplified. This capability allows hydraulic presses to handle tasks that require high force, such as metal forming and forging.
Operation Process
The operation of a hydraulic press involves several key steps:
- Hydraulic Fluid Supply: The hydraulic pump draws hydraulic fluid from the reservoir and pressurizes it, directing it into the hydraulic cylinder.
- Piston Movement: As the pressurized fluid enters the cylinder, it pushes against the piston, causing it to move. The piston rod, attached to the piston, extends outward, transmitting the force to the press’s working surface.
- Pressing Action: The object to be pressed is placed on the press’s working surface. As the piston rod extends, it applies a compressive force to the object. The magnitude of this force can be precisely controlled by adjusting the hydraulic fluid pressure and flow.
- Return Stroke: Once the pressing operation is complete, the control valves redirect the hydraulic fluid, allowing the piston to retract. This return stroke is typically aided by a return spring or by reversing the fluid flow using the hydraulic pump.
- Cycle Repeat: The press is now ready for the next cycle. The operator can adjust the parameters as needed for different operations, such as changing the force, speed, or stroke length.
Advantages of Hydraulic Presses
- Precision Control: Hydraulic presses offer precise control over the force and speed of the pressing operation, allowing for accurate and repeatable results.
- High Force Generation: Hydraulic systems can generate substantial force with relatively small input, making them ideal for heavy-duty applications.
- Versatility: Hydraulic presses can be used for a wide range of applications, from metal forming and stamping to plastic molding and compacting materials.
- Safety: Modern hydraulic presses are equipped with safety features such as pressure relief valves and emergency stop buttons, ensuring safe operation.
Hydraulic presses are essential tools in many industrial processes due to their ability to apply controlled, high-force pressure. Their operation relies on the fundamental principles of hydraulics, enabling them to perform a variety of tasks with precision and efficiency.
Materials Used in Manufacturing Hydraulic Presses
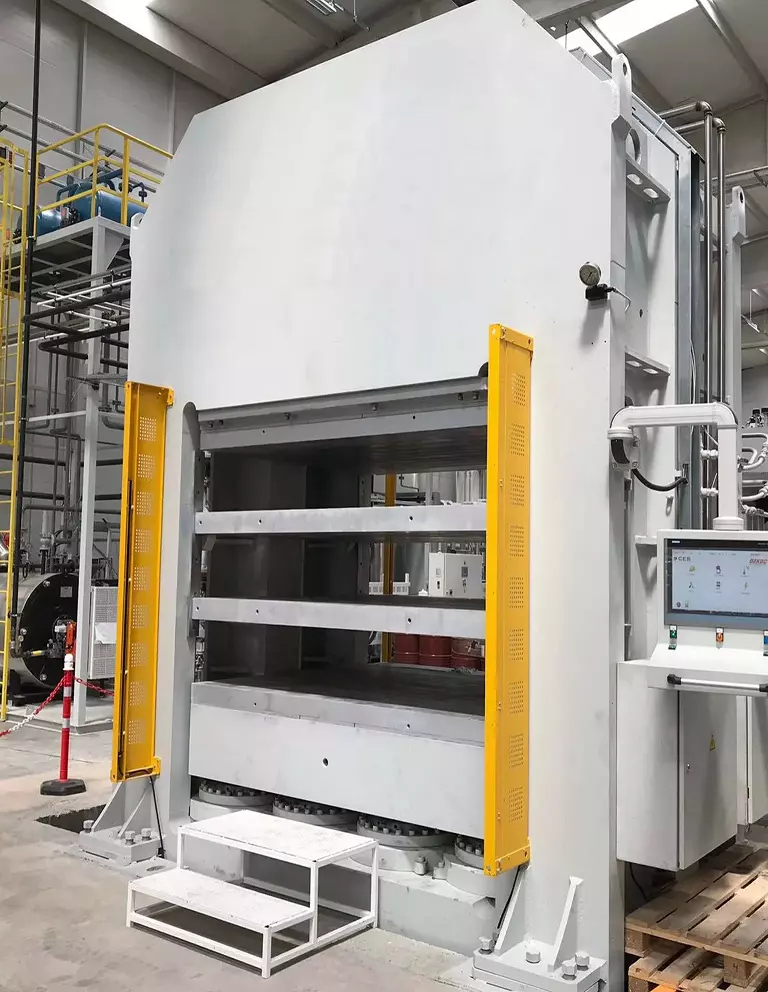
The manufacturing of hydraulic presses requires the use of high-quality materials to ensure durability, reliability, and performance under high pressure. Different components of a hydraulic press are made from specific materials suited to their functions. Here are the primary materials used in the construction of hydraulic presses:
Metals
- Steel
- Frame and Structure: The frame and structural components of hydraulic presses are typically made from high-strength steel. This material provides the necessary rigidity and strength to withstand the substantial forces generated during operation. Steel is also used for the press’s bed, columns, and other load-bearing elements due to its excellent mechanical properties and durability.
- Cylinders and Pistons: Hydraulic cylinders and pistons are often made from hardened steel or alloy steel. These materials can endure high pressures and resist wear and deformation over time. The surfaces of the pistons and cylinder bores are usually precision-machined and treated to minimize friction and enhance longevity.
- Cast Iron
- Base and Frame Components: Cast iron is sometimes used for the base and certain frame components of hydraulic presses. It is chosen for its excellent compressive strength and vibration-damping properties, which help in maintaining stability during operation.
- Aluminum
- Lightweight Components: Aluminum is used in the construction of certain lightweight components, such as control panels, covers, and non-load-bearing parts. Its lower density compared to steel makes it ideal for reducing the overall weight of the press without compromising strength.
Seals and Gaskets
- Rubber
- Seals: Rubber seals are essential for preventing hydraulic fluid leaks in the hydraulic system. They are used in the hydraulic cylinders, pumps, and control valves. Rubber’s elasticity and resilience make it ideal for creating tight seals that can withstand the pressures within the system.
- Polyurethane
- Gaskets and Seals: Polyurethane is used for gaskets and seals due to its excellent resistance to wear, chemicals, and high pressures. It provides a durable sealing solution that maintains its integrity over a wide range of operating conditions.
Lubricants
- Hydraulic Fluids
- Lubrication and Power Transmission: Hydraulic fluids, also known as hydraulic oils, are critical for the operation of hydraulic presses. These fluids transmit power, lubricate moving parts, and act as a coolant. High-quality hydraulic fluids are formulated to provide optimal viscosity, thermal stability, and anti-wear properties. Common types include mineral-based oils, synthetic fluids, and biodegradable options for environmentally sensitive applications.
Other Materials
- High-Strength Alloys
- Specialized Components: Certain components of hydraulic presses, such as high-pressure fittings and fasteners, are made from high-strength alloys. These materials offer superior mechanical properties and corrosion resistance, ensuring reliable performance in demanding environments.
- Composites and Plastics
- Non-Structural Parts: Composites and high-performance plastics are used for non-structural parts such as protective covers, handles, and control knobs. These materials are lightweight, durable, and resistant to corrosion, making them suitable for various auxiliary components.
Manufacturing Process of Hydraulic Presses
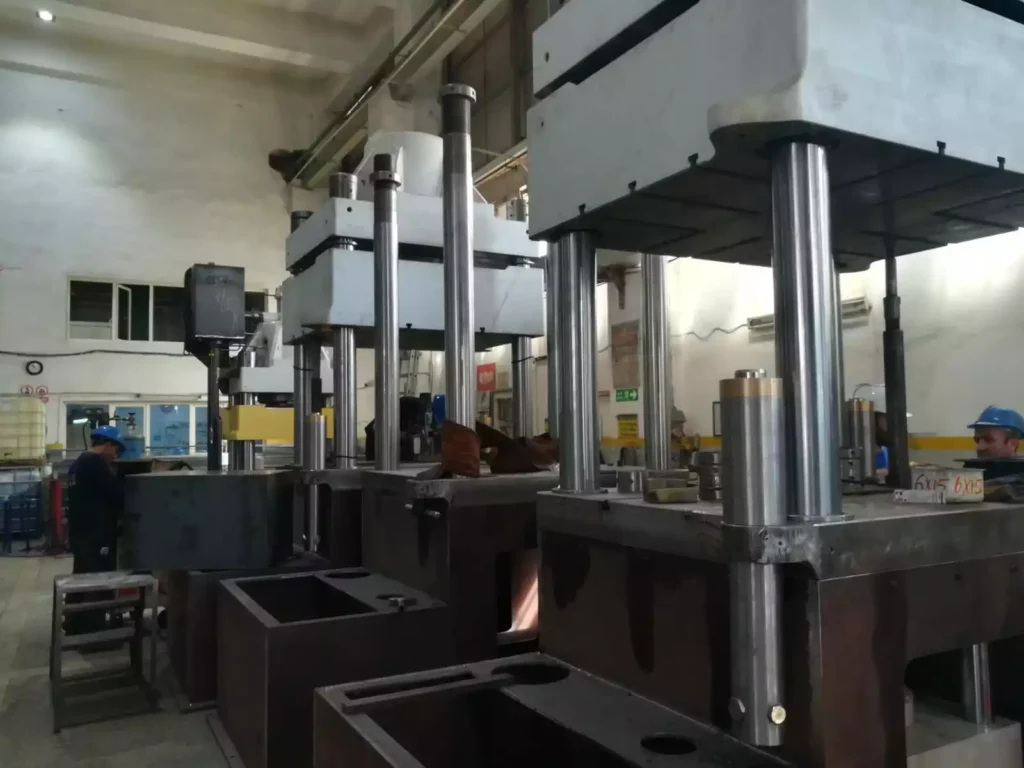
The manufacturing of hydraulic presses involves several key stages, each requiring precision engineering and attention to detail. Here’s an overview of the typical manufacturing process:
1. Design and Engineering
- Conceptual Design: The process begins with the conceptual design, where engineers determine the specifications and requirements for the hydraulic press. This includes defining the force capacity, stroke length, and application-specific features.
- CAD Modeling: Detailed computer-aided design (CAD) models are created, allowing for precise planning of the press’s components and overall structure. These models help in visualizing the final product and making necessary adjustments before production.
2. Material Selection and Procurement
- Choosing Materials: Based on the design specifications, appropriate materials are selected for each component. Engineers consider factors such as strength, durability, and cost when choosing materials.
- Sourcing Materials: High-quality raw materials are sourced from reputable suppliers. This ensures that the components meet the required standards for performance and reliability.
3. Machining and Assembly
- Component Fabrication: Individual components are manufactured using various machining processes, such as cutting, milling, drilling, and welding. Precision machining is crucial to ensure that each part fits together perfectly and operates smoothly.
- Assembly: The fabricated components are assembled into the final hydraulic press. This involves installing the hydraulic cylinder, pump, control valves, and other components into the frame. Careful alignment and calibration are necessary to ensure optimal performance.
4. Quality Control and Testing
- Inspection: Each component undergoes rigorous inspection to verify its dimensions, material properties, and overall quality. Non-destructive testing methods, such as ultrasonic or magnetic particle testing, may be used to detect any internal defects.
- Performance Testing: The assembled hydraulic press is subjected to performance testing to ensure it meets the specified force and pressure requirements. This includes testing the hydraulic system for leaks, verifying the control system’s functionality, and conducting load tests.
- Final Adjustments: Based on the test results, final adjustments are made to the press to optimize its performance. This may involve recalibrating the hydraulic system, fine-tuning the control valves, or reinforcing certain components.
5. Finishing and Delivery
- Surface Treatment: The hydraulic press components undergo surface treatments, such as painting or coating, to protect against corrosion and enhance their appearance.
- Packaging and Shipping: Once the press is fully assembled and tested, it is carefully packaged to prevent damage during transportation. It is then shipped to the customer or end-user, ready for installation and operation.
The manufacturing of hydraulic presses requires a combination of skilled engineering, precise machining, and thorough quality control to produce a reliable and efficient machine. Each step in the process is critical to ensuring that the final product meets the high standards required for industrial applications.
Application Areas of Hydraulic Presses
Hydraulic presses are versatile machines used across various industries due to their ability to apply substantial force with precision and control. Their applications span a wide range of fields, each leveraging the unique capabilities of hydraulic presses to enhance productivity and achieve specific manufacturing goals. Below are some of the key application areas of hydraulic presses:
1. Automotive Industry
- Metal Forming and Stamping
- Hydraulic presses are extensively used in the automotive industry for forming and stamping metal parts. These processes involve shaping metal sheets into components such as car body panels, chassis parts, and structural elements. The precision and high force of hydraulic presses ensure that the formed parts meet stringent quality standards.
- Assembly and Disassembly
- Hydraulic presses assist in the assembly and disassembly of various automotive components. They are used to press-fit bearings, bushings, and other components into their respective housings. The controlled force application prevents damage and ensures proper fitment.
- Powder Metallurgy
- In the production of automotive parts through powder metallurgy, hydraulic presses compact metal powders into solid forms. This method is used to manufacture gears, pistons, and other complex parts with high strength and precision.
2. Aerospace Industry
- Component Manufacturing
- The aerospace industry relies on hydraulic presses for manufacturing critical components such as aircraft wings, fuselage panels, and engine parts. The ability to apply uniform force ensures the structural integrity and precision of these components.
- Composite Materials
- Hydraulic presses are used in the production of composite materials, which are essential for lightweight and high-strength aerospace components. They help in molding and curing composite materials, ensuring consistent quality and performance.
- Maintenance and Repair
- During maintenance and repair operations, hydraulic presses are used to disassemble and reassemble parts, such as landing gear components and turbine blades. Their precise control prevents damage to sensitive components during these operations.
3. Manufacturing and Metal Forming
- Sheet Metal Fabrication
- In general manufacturing, hydraulic presses are used for fabricating sheet metal parts. They perform tasks such as bending, punching, and cutting with high precision, making them ideal for producing custom metal parts and prototypes.
- Forging and Extrusion
- Hydraulic presses are employed in forging and extrusion processes to shape metal billets into desired forms. These processes are crucial for producing parts with superior mechanical properties, such as crankshafts, connecting rods, and valve bodies.
- Plastic and Rubber Molding
- Beyond metalworking, hydraulic presses are also used for molding plastic and rubber parts. They apply consistent pressure and heat to mold materials into complex shapes, used in products ranging from automotive parts to consumer goods.
4. Construction Industry
- Concrete and Brick Making
- Hydraulic presses are used in the construction industry for making concrete blocks, bricks, and pavers. They apply pressure to molds filled with concrete or clay, compacting the material and forming strong, uniform building components.
- Pre-stressed Concrete Components
- In the production of pre-stressed concrete elements, hydraulic presses apply force to tension steel cables within concrete beams or slabs. This process enhances the strength and load-bearing capacity of the components, making them suitable for bridges, buildings, and other structures.
- Material Handling and Processing
- Hydraulic presses are used for material handling tasks such as compacting waste materials, crushing rocks, and processing construction debris. Their ability to apply high force makes them ideal for these demanding applications.
5. Recycling and Waste Management
- Metal Recycling
- In recycling facilities, hydraulic presses are used to compact scrap metal into bales for easier handling and transportation. They also assist in shearing and cutting metal into smaller pieces for further processing and melting.
- Plastic and Paper Recycling
- Hydraulic presses compact plastic and paper waste into dense bales, reducing the volume and facilitating efficient recycling. The consistent pressure application ensures that the bales are tightly packed and stable.
- E-Waste Processing
- For the recycling of electronic waste, hydraulic presses are used to crush and separate components such as circuit boards, cables, and casings. This process aids in the recovery of valuable materials and the safe disposal of hazardous components.
Conclusion
Hydraulic presses are indispensable tools in many industries due to their ability to apply controlled, high-force pressure in a precise manner. From automotive and aerospace manufacturing to construction and recycling, their versatility and efficiency make them a cornerstone of modern industrial processes.
The continuous development and refinement of hydraulic press technology will likely lead to even broader applications and improved performance in the future. Their critical role in manufacturing and other sectors underscores the importance of understanding their components, working principles, and the materials used in their construction.
EMS Metalworking Machinery
We design, manufacture and assembly metalworking machinery such as:
- Hydraulic transfer press
- Glass mosaic press
- Hydraulic deep drawing press
- Casting press
- Hydraulic cold forming press
- Hydroforming press
- Composite press
- Silicone rubber moulding press
- Brake pad press
- Melamine press
- SMC & BMC Press
- Labrotaroy press
- Edge cutting trimming machine
- Edge curling machine
- Trimming beading machine
- Trimming joggling machine
- Cookware production line
- Pipe bending machine
- Profile bending machine
- Bandsaw for metal
- Cylindrical welding machine
- Horizontal pres and cookware
- Kitchenware, hotelware
- Bakeware and cuttlery production machinery
as a complete line as well as an individual machine such as:
- Edge cutting trimming beading machines
- Polishing and grinding machines for pot and pans
- Hydraulic drawing presses
- Circle blanking machines
- Riveting machine
- Hole punching machines
- Press feeding machine
You can check our machinery at work at: EMS Metalworking Machinery – YouTube
Applications:
- Beading and ribbing
- Flanging
- Trimming
- Curling
- Lock-seaming
- Ribbing
- Flange-punching