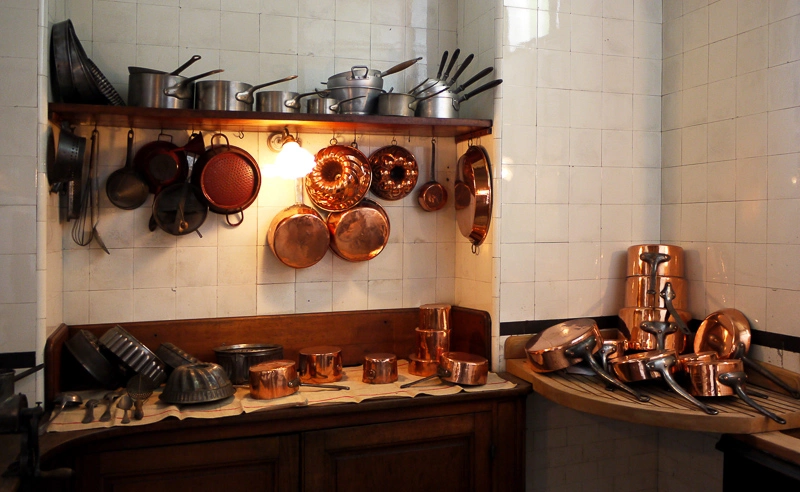
We manufacture the machinery for How Copper Pots are Made in different forms. These machines are used in metalworking industries for production.
We manufacture the machines for making copper pots in different forms. Our experience with how copper pots are made has advanced significantly in recent years.
People use coppers for centuries in the manufacturing of kitchenware and cooking utensils. And copper pots are no exception. Professional chefs and home cooks alike value copper pots highly due to copper pots are good for cooking and worth money. However, copper pot cooking safety is an important consideration for anyone who uses copper pots in their cooking. Copper is a reactive metal. That means it can react with certain foods and liquids and create harmful compounds. To minimize the risk of this happening, you should use copper pots that are lined with another metal during manufacturing time. This will prevent the copper from coming into direct contact with the food.
Meanwhile, copper pot making machinery is becoming increasingly popular as a way to make high-quality copper pans. This type of machinery allows for faster and more efficient production of copper pans. This can happen with the benefit of being able to customize the shape and size of each pan. The machinery also helps to reduce waste. It is capable of recycling scrap copper into usable raw materials. With this type of machinery, manufacturers can create beautiful and unique copper pans that are both durable and cost-effective.
Copper pot making machines are revolutionizing the way of making copper pans are made. By automating the process of copper pan production, these machines can produce high-quality pans. These pans have greater speed and precision than ever before. In this essay, we will explore the process of copper pot making ( how copper pots are made/ how copper pans are made) and the machinery used for it.
How Copper Pots are Made
The manufacturing process for copper pots involves several steps, including:
- Material Preparation:
- Copper sheets or coils are received at the manufacturing facility.
- The sheets or coils are inspected for defects and imperfections.
- If necessary, the sheets are cut into smaller pieces to match the desired pot sizes.
- Blanking and Pressing:
- A stamping press is used to cut out circular blanks from the prepared copper sheets.
- The blanks are then placed in a hydraulic press, which shapes them into the desired pot form.
- The first pressing creates a shallow pot shape, while subsequent pressings gradually deepen the pot and form its walls.
- Annealing:
- Copper is a soft metal that can become work-hardened during the pressing process.
- To restore the copper’s ductility and prevent cracking, the pot blanks are subjected to annealing.
- Annealing involves heating the copper to a specific temperature and then cooling it slowly, allowing the metal to relax and regain its malleability.
- Spinning and Forming:
- The annealed pot blanks are placed on a spinning lathe, which rotates the blank while a shaping tool is pressed against it.
- The spinning process further forms the pot’s walls and bottom, ensuring a smooth and consistent surface.
- Additional forming processes, such as flanging and beading, may be applied to create specific features like handles, rims, and spouts.
- Tinning or Nickel Lining:
- Copper is a reactive metal that can react with acidic foods, causing discoloration and metallic taste.
- To prevent this, the interior of the pot is typically lined with a non-reactive metal, such as tin or nickel.
- Tinning involves dipping the pot in molten tin, while nickel lining is applied using an electroplating process.
- Polishing and Finishing:
- The exterior of the copper pot is polished to achieve a desired finish, which may range from a bright, reflective shine to a more antiqued or rustic look.
- Polishing involves using progressively finer abrasives to remove surface imperfections and create a smooth, aesthetically pleasing surface.
- Handle Attachment:
- The pot handle, typically made from stainless steel or brass, is securely attached to the pot body using rivets, welds, or brazing.
- The handle is designed for comfort and grip, and it should be strong enough to withstand the weight of the pot and its contents.
- Quality Control:
- Each pot is inspected for defects, surface finish, and overall quality.
- Inspectors check for any imperfections in the copper, the lining, and the handle attachment.
- Pots that do not meet the quality standards are either reworked or rejected.
- Packaging and Shipping:
- The finished copper pots are cleaned and packaged for shipment.
- The packaging protects the pots from scratches and damage during transportation.
The manufacturing process for copper pots is designed to produce durable, high-quality cookware that combines traditional craftsmanship with modern techniques. Copper pots are valued for their exceptional heat conductivity, which allows for even cooking and precise temperature control.
The Process of Copper Pot Making
The cookware manufacturing process, such as copper pot making is a time-honored craft that requires skill and patience. The process begins with sheets of copper by cutting into desired shapes and sizes. Then, forming these sheets into the shape of a pot, pan, or bowl using a spinning technique is the second step. Spinning involves placing the copper sheet on a spinning lathe and using specialized tools to shape it into the desired form. The spinning process requires precision and expertise to ensure that the final product is symmetrical and uniform in thickness.
The process of making copper pots involves several steps, including shaping, joining, and finishing. The first step is to select the copper sheet. It is typically between 1.5 and 2.5 mm thick, depending on the size of the pot. The operator cuts the sheet into the appropriate size and shape using a cutting machine. Then, the next step is heating the sheet to make it malleable and easier to shape.
The shaping of the copper sheet requires using a hammer and a mold. The mold is necessary to shape the copper sheet into the desired form, while the hammer is necessary to carefully beat the copper into shape. This process is repeated until the copper sheet is formed into a pot or pan.
The next step is to join the copper pieces together using solder. After melting the solder and applying it to the joint between two pieces of copper, you have a strong and durable bond. By removing the excess solder, the operator can give it a smooth and shiny finish by cleaning and polishing the pot.
Copper Uttensils with the Similar Processes to Cooper Pots Manufacturing
Copper utensils are copper pans, bowls, stills, etc. Copper pan making and copper bowl making follow a similar process to copper pot making. The only difference is the shape and size of the end product. However, the quality of the craftsmanship remains the same. And each piece is made with the same care and attention to detail.
Making a copper pot still is a process that is used to make distilled spirits, such as whiskey and vodka. The process involves heating a mixture of fermented grains or fruits and capturing the steam that is released. The steam then condenses back into a liquid, resulting in a highly concentrated alcohol. In this case, copper is necessary to use in the construction of the still. Because it helps to remove unwanted flavors and impurities from the final product, resulting in a cleaner, smoother taste.
The Machinery Used For Copper Pot Making
The machinery used for copper pot making has advanced significantly in recent years. The usage rate of modern copper utensils making machines is increasing to shape and cut copper sheets. These machines have reduced the time and labor required for the process. These machines use hydraulic pressure to shape the copper sheet. This allows for greater precision and consistency in the final product.
Modern copper utensils making machines use computer-controlled spinning lathes to ensure that each pot, pan, still, or bowl has a perfect shape and is uniform in thickness. These machines also can create intricate designs and patterns on the surface of the copper. They can add an aesthetic appeal to the final product.
Also, making a copper pot still is another popular application for copper in the kitchen. The usage area of a copper pot still is to distill alcohol and other liquids. And it is an essential tool for anyone interested in home brewing or distilling. The process of making a copper pot still is similar to that of making a copper pot. The additional step is creating a distillation column to separate the alcohol from the liquid.
The use of these machines has allowed for more intricate designs to be created with far less effort than traditional methods. The use of copper pot making machinery has drastically reduced costs. Also, it has improved production times, allowing for more creative designs and faster delivery times to customers.
Manufacturing of Copper Pots Making
Copper pot making machines have revolutionized the way copper pans are made. These machines can quickly and accurately form pans from sheets of copper. As a result, this saves time and money in the production process. With the advent of modern copper utensils making machines, the process has become faster and more efficient. Besides, still maintains the high-quality craftsmanship that is synonymous with copper pots.
In conclusion, copper pot making is a skilled craft that requires precision and expertise. Therefore, we can guarantee that our customers will receive consistent, reliable performance from our company’s products. With our copper pot machines and the experience we have gained in this field, we can meet all needs and provide variable solutions for an invaluable tool for any workshop or production line.