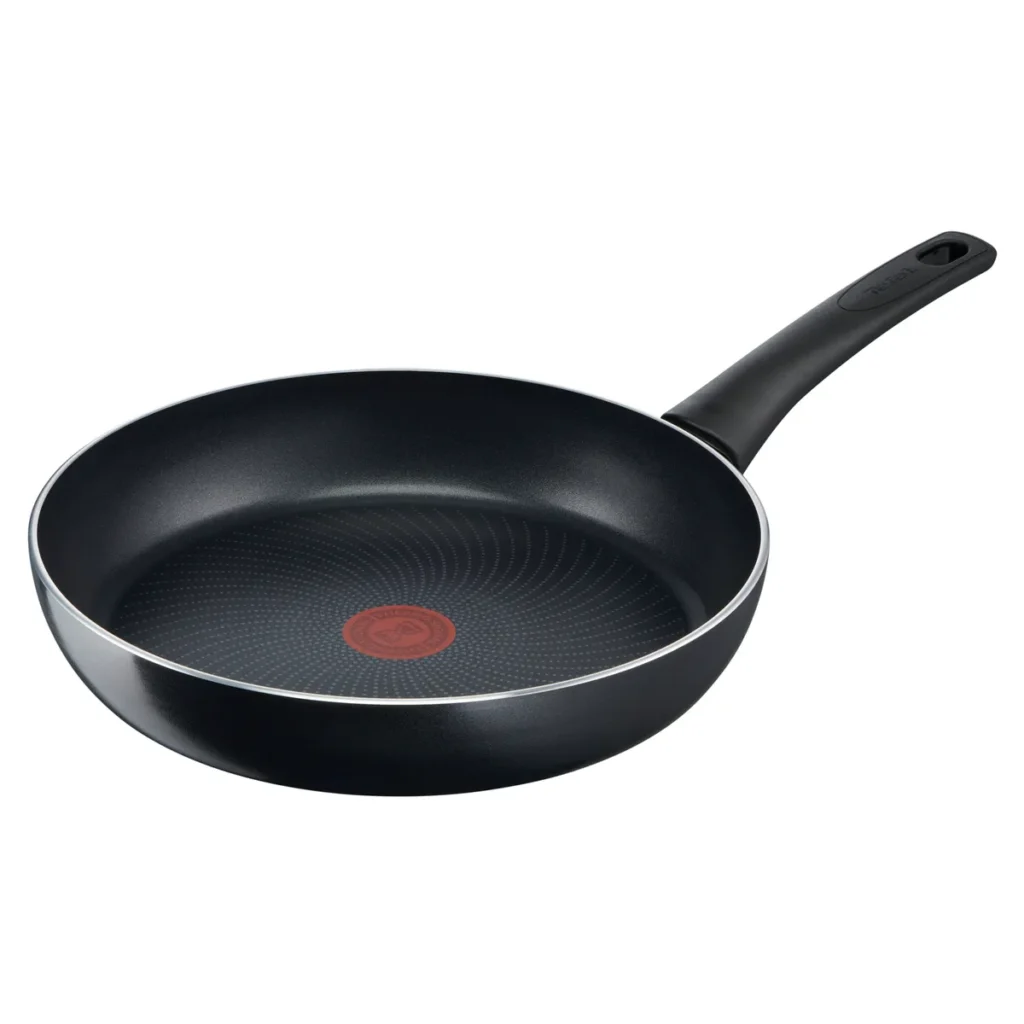
We explain How are Pans Made to bend sheet metal edges. Hydraulic Press Machines are used in metalworking industries
The manufacturing process for pans varies depending on the pan’s material, size, and desired features. However, there are some common steps involved in the production of most pans, including:
- Raw Material Preparation: The process begins with selecting the appropriate raw material, typically aluminum, stainless steel, cast iron, copper, or a combination of these materials. The material is inspected for defects and then cut into sheets or blanks of the desired size.
- Forming: The metal blanks are then heated to a specific temperature to make them malleable. Using various forming techniques, such as stamping, spinning, or forging, the blanks are shaped into the desired pan form. This involves creating the pan’s rounded base, side walls, handle attachment points, and any other unique features.
- Machining: Once the pan’s basic shape is formed, it undergoes machining processes to remove excess material, smooth out rough edges, and achieve a uniform appearance. This may involve using cutting tools, grinding machines, and polishing tools.
- Heat Treatment: Depending on the material, the pan may undergo heat treatment to enhance its properties. For stainless steel pans, annealing can improve toughness and ductility. For cast iron pans, hardening and tempering can increase durability and hardness.
- Nonstick Coating Application (for nonstick pans): For nonstick pans, a nonstick coating is applied to the cooking surface. The type of coating used may vary depending on the desired properties, such as durability, heat resistance, and adherence to the pan’s material.
- Enamel coating: For enameled cast iron pans, a mixture of ceramic minerals, glass, and other additives is applied to the base and then fired in a high-temperature oven to cure and harden the coating.
- PTFE coating: For PTFE-coated pans, a thin layer of polytetrafluoroethylene (PTFE) is applied to the cooking surface. This coating is then cured using a variety of methods, such as baking or plasma spraying.
- Handle Assembly: The pan’s handle is attached securely using various methods, such as riveting, welding, or using heat-resistant adhesives. The handle should be ergonomically designed for comfort and heat resistance.
- Quality Control: Throughout the manufacturing process, rigorous quality control checks are performed to ensure that the pans meet the desired specifications. This includes inspecting the pan’s shape, dimensions, coating uniformity, handle attachment, and overall finish.
- Packaging and Shipping: Once the pans pass quality control checks, they are cleaned, packaged, and prepared for shipping. The packaging should protect the pans from damage during transportation and storage.
How are Pans Made
The manufacturing process for pans varies depending on the pan’s material, size, and desired features. However, the general process typically involves the following steps:
- Raw Material Preparation:
- The process begins with selecting the appropriate raw material, typically aluminum, stainless steel, cast iron, or copper. The material is inspected for defects and then cut into sheets or blanks of the desired size.
- Forming and Shaping:
- The metal blanks are then heated to a specific temperature to make them malleable. Using various forming techniques, such as stamping, spinning, forging, or extrusion, the blanks are shaped into the desired pan form. This involves creating the pan’s rounded base, side walls, and handle attachment points.
- Trimming and Finishing:
- Once the pan’s basic shape is formed, it undergoes trimming and finishing processes to remove excess material, smooth out rough edges, and achieve a uniform appearance. This may involve using cutting tools, sanding machines, and polishing tools.
- Nonstick Coating Application (for nonstick pans):
- For nonstick pans, a nonstick coating is applied to the pan’s cooking surface. The type of coating used may vary depending on the desired properties, such as durability, heat resistance, and adherence to the pan’s material.
- The coating application process typically involves several steps, such as degreasing the pan’s surface, applying a primer, spraying or dipping the pan in the nonstick coating material, and curing the coating in an oven to ensure proper adhesion.
- Handle Assembly:
- The pan’s handle is attached using various methods, such as riveting, welding, or using heat-resistant adhesives. The handle should be securely attached and designed to withstand frequent use and high temperatures.
- Quality Control:
- Throughout the manufacturing process, quality control checks are performed to ensure that the pans meet the desired specifications. This may involve inspecting the pan’s shape, dimensions, coating uniformity, handle attachment, and overall finish.
- Packaging and Shipping:
- Once the pans pass quality control checks, they are cleaned, packaged, and prepared for shipping. The packaging should protect the pans from damage during transportation and storage.
Additional Considerations:
- The specific manufacturing process may vary depending on the pan’s material, size, and desired features. For instance, some pans may undergo additional treatments, such as anodizing for aluminum pans or surface hardening for stainless steel pans.
- Environmental considerations are increasingly important in pan manufacturing. Manufacturers are adopting eco-friendly practices, such as using recycled materials, reducing energy consumption, and minimizing waste generation.
In addition to these general steps, here are some specific details about the manufacturing process for different types of pans:
- Cast Iron Pans: Cast iron pans are typically made by pouring molten iron into a sand mold, allowing it to cool and solidify into the desired shape. The pans are then finished by grinding and polishing to achieve a smooth surface.
- Stainless Steel Pans: Stainless steel pans are typically made by stamping or rolling stainless steel sheets into the desired shape. The pans may then be heat-treated to improve their strength and durability.
- Nonstick Pans: Nonstick pans are typically coated with a ceramic or enamel coating. This coating is applied to the pan’s surface using various methods, such as dipping, spraying, or firing. The coating is then cured in a high-temperature oven to ensure proper adhesion and hardening.
- Copper Pans: Copper pans are typically made by hammering or rolling copper sheets into the desired shape. The pans are then polished to a high shine.
The manufacturing process for pans is a complex and sophisticated operation that involves a variety of techniques and materials. By understanding the different steps involved, you can appreciate the craftsmanship and engineering that goes into creating the pans that we use in our kitchens every day.
Types of Cookware
Cookware comes in various types, each with unique properties and manufacturing processes. The primary types include stainless steel, aluminum, cast iron, copper, non-stick, and ceramic cookware.
Stainless steel cookware is known for its durability, resistance to rust and corrosion, and non-reactive properties. It is often used in professional kitchens and for high-quality home cookware.
Aluminum cookware is lightweight, conducts heat well, and is typically more affordable than other types. It is often anodized or coated to prevent reaction with acidic foods.
Cast iron cookware is renowned for its excellent heat retention and even cooking. It is durable and can be used on various heat sources, including induction cooktops.
Copper cookware provides superior heat conductivity, allowing precise temperature control. It is often lined with stainless steel or tin to prevent reactions with food.
Non-stick cookware features a coating that prevents food from sticking, making it easy to clean. It is popular for low-fat cooking but requires careful handling to avoid damaging the coating.
Ceramic cookware is valued for its non-reactive surface and even heating. It is often used for baking and roasting due to its ability to withstand high temperatures.
Raw Materials and Sourcing
The selection and sourcing of raw materials are critical in cookware manufacturing. The quality of the final product depends heavily on the quality of the materials used.
For stainless steel cookware, high-grade stainless steel alloys such as 18/10 (18% chromium, 10% nickel) are commonly used. These alloys offer excellent durability and resistance to corrosion.
Aluminum cookware typically uses pure aluminum or aluminum alloys. Pure aluminum is soft and lightweight, while alloys provide added strength and durability.
Cast iron cookware is made from iron alloys with a high carbon content. The iron is melted and poured into molds to create the desired shapes.
Copper cookware uses high-purity copper, often with a lining of stainless steel or tin to prevent reactions with food.
Non-stick cookware starts with a base of aluminum or stainless steel, to which a non-stick coating such as PTFE (polytetrafluoroethylene) is applied.
Ceramic cookware is made from natural clay, which is shaped and fired at high temperatures to create a hard, non-porous surface.
Quality control of raw materials involves rigorous testing and inspection to ensure they meet industry standards. Environmental considerations also play a role in material selection, with manufacturers increasingly opting for sustainable and eco-friendly options.
Manufacturing Process
The manufacturing process of cookware involves several stages, each crucial for producing high-quality products.
Forming
Forming is the initial stage where the raw materials are shaped into cookware.
Casting: Involves pouring molten metal into molds to create the desired shape. This method is commonly used for cast iron and some types of aluminum cookware.
Stamping: Uses heavy machinery to stamp out shapes from sheets of metal. This process is often used for stainless steel and aluminum cookware.
Spinning: Involves rotating a metal disc and shaping it over a form using a lathe. This method is used for making items like pots and pans from stainless steel and aluminum.
Surface Preparation
Surface preparation ensures the cookware’s surface is smooth and ready for coating or finishing.
Grinding: Removes any rough edges and surface imperfections using abrasive wheels.
Polishing: Uses finer abrasives to create a smooth, shiny surface on the cookware.
Sandblasting: Blasts the surface with fine particles to clean and texture it, preparing it for further finishing.
Coating and Finishing
Coating and finishing enhance the cookware’s performance and appearance.
Non-stick Coating Application: Involves applying a non-stick layer, usually PTFE, to the cookware surface. The coating is then baked to cure it.
Enameling: Applies a glass-like coating to metal cookware, providing a durable, non-reactive surface. This process is commonly used for cast iron and steel cookware.
Anodizing: Involves electrochemically treating aluminum to create a hard, non-reactive surface. Anodized aluminum cookware is known for its durability and resistance to corrosion.
Assembly and Attachment
Handles and knobs are attached to the cookware, ensuring they are secure and ergonomic.
Handles and Knobs: Made from materials such as stainless steel, plastic, or silicone, are attached using riveting, welding, or screwing.
Riveting and Welding: Securely attach handles and other components to the cookware, ensuring they can withstand regular use.
Quality Control and Testing
Quality control is critical in cookware manufacturing to ensure the final products meet safety and performance standards.
Inspection Procedures: Involve visual and mechanical inspection of cookware to detect any defects or irregularities.
Performance Testing: Includes tests for heat distribution, durability, and resistance to scratching and corrosion.
Safety Standards Compliance: Ensures that the cookware meets all relevant safety standards and regulations, such as those set by the FDA or other regulatory bodies.
Technological Advancements in Cookware Manufacturing
Technological advancements are continually improving the efficiency, quality, and sustainability of cookware manufacturing.
Automation and Robotics: Modern manufacturing facilities often use automated systems and robotics to handle repetitive tasks, improving consistency and reducing labor costs.
Advanced Materials: Research into new materials and coatings has led to the development of cookware with improved performance, such as better non-stick properties and enhanced durability.
Sustainable Manufacturing Practices: Manufacturers are increasingly adopting eco-friendly practices, such as using recycled materials, reducing energy consumption, and minimizing waste.
Smart Cookware: The integration of smart technology into cookware, such as temperature sensors and connectivity features, is a growing trend, providing users with more control and information during cooking.
Challenges in Cookware Manufacturing
Cookware manufacturing faces several challenges, including maintaining quality and consistency, cost management, technological advancements, and environmental regulations.
Maintaining Quality and Consistency: Ensuring that every piece of cookware meets high standards of quality and performance is challenging, particularly in high-volume production.
Cost Management: Balancing the costs of materials, labor, and production while remaining competitive in the market requires careful planning and efficiency.
Technological Advancements: Keeping up with rapid technological changes and integrating new technologies into existing manufacturing processes can be demanding.
Environmental Regulations: Compliance with environmental regulations requires manufacturers to adopt sustainable practices and invest in eco-friendly technologies, which can be costly and complex.
Future Trends in Cookware Manufacturing
The future of cookware manufacturing is likely to be shaped by innovations in materials, enhanced functionality, and sustainability.
Innovations in Materials: Continued research into new materials and coatings will likely result in cookware with superior performance, such as improved heat distribution and non-stick properties.
Enhanced Functionality and Features: Cookware with added features, such as smart technology, will provide users with more control and convenience during cooking.
Eco-friendly and Sustainable Products: As consumers become more environmentally conscious, demand for eco-friendly cookware made from sustainable materials and produced using green manufacturing practices will likely increase.
Conclusion
Cookware manufacturing is a complex and multifaceted industry that produces essential tools for cooking. Understanding the various types of cookware, raw materials, manufacturing processes, and technological advancements is crucial for producing high-quality products. Despite challenges such as maintaining quality, managing costs, and complying with environmental regulations, the industry continues to evolve and innovate. Future trends in materials, functionality, and sustainability promise to drive the industry forward, ensuring that cookware remains a vital part of daily life and culinary excellence.
EMS Metalworking Machinery
We design, manufacture and assembly metalworking machinery such as:
- Hydraulic transfer press
- Glass mosaic press
- Hydraulic deep drawing press
- Casting press
- Hydraulic cold forming press
- Hydroforming press
- Composite press
- Silicone rubber moulding press
- Brake pad press
- Melamine press
- SMC & BMC Press
- Labrotaroy press
- Edge cutting trimming machine
- Edge curling machine
- Trimming beading machine
- Trimming joggling machine
- Cookware production line
- Pipe bending machine
- Profile bending machine
- Bandsaw for metal
- Cylindrical welding machine
- Horizontal pres and cookware
- Kitchenware, hotelware
- Bakeware and cuttlery production machinery
as a complete line as well as an individual machine such as:
- Edge cutting trimming beading machines
- Polishing and grinding machines for pot and pans
- Hydraulic drawing presses
- Circle blanking machines
- Riveting machine
- Hole punching machines
- Press feeding machine
You can check our machinery at work at: EMS Metalworking Machinery – YouTube
Applications:
- Beading and ribbing
- Flanging
- Trimming
- Curling
- Lock-seaming
- Ribbing
- Flange-punching