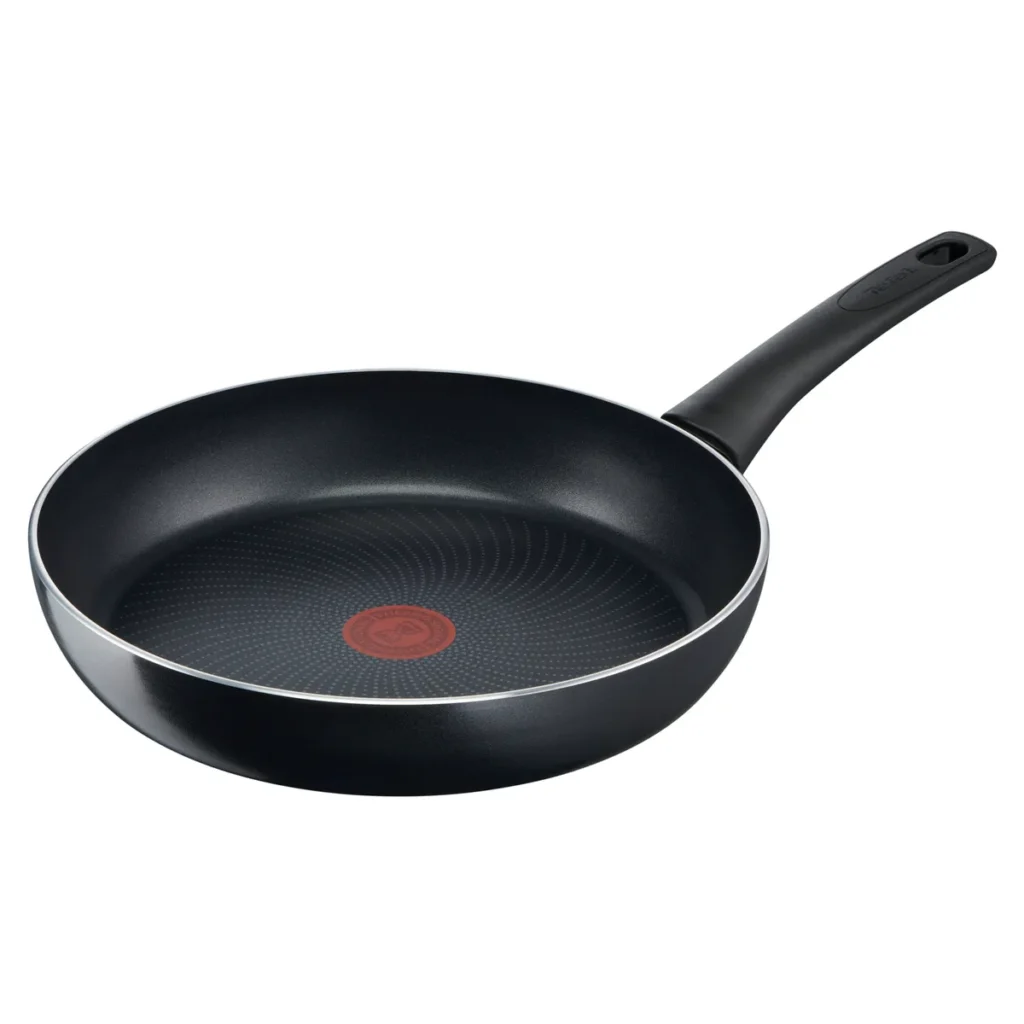
We manufacture a Frying Pan Manufacturing Process to bend sheet metal edges. Frying Pan Manufacturing Processes are used in metalworking industries
The manufacturing process of frying pans typically involves several steps, from material selection to final finishing. Here is a general overview of the frying pan manufacturing process:
- Material Selection: Choose a suitable material for the frying pan, such as stainless steel, cast iron, aluminum, or non-stick coated materials. Consider factors such as heat conductivity, durability, and non-stick properties based on the desired end product.
- Material Preparation: Prepare the selected material for the manufacturing process. This may involve cutting or shaping the material into the desired size and shape for the frying pan.
- Forming the Pan Body: Use a forming process, such as deep drawing or metal spinning, to shape the material into the frying pan’s body. The material is pressed or spun to achieve the desired pan shape, including the bottom, sidewalls, and handle attachment points.
- Handle Attachment: Attach the handle to the pan body using welding, riveting, or screwing methods. The handle should be securely attached to ensure proper functionality and safety during use.
- Surface Treatment: Apply surface treatments to the frying pan, depending on the desired finish and functionality. This may include processes like polishing, grinding, or sandblasting to achieve a smooth surface. For non-stick pans, a non-stick coating may be applied following the manufacturer’s guidelines.
- Heat Treatment: Subject the frying pan to a heat treatment process to improve its strength, durability, and heat distribution properties. Heat treatment processes vary based on the material used and can include annealing, tempering, or hardening.
- Finishing and Polishing: Perform any necessary finishing and polishing processes to enhance the aesthetic appearance of the frying pan. This may involve buffing, polishing, or electroplating to achieve a desired surface finish.
- Quality Control: Implement quality control measures throughout the manufacturing process to ensure that the frying pans meet the required standards. Conduct inspections, dimensional checks, and functional tests to verify the quality, performance, and safety of the frying pans.
- Packaging: Package the finished frying pans in suitable packaging materials to protect them during storage and transportation. Label the packaging with relevant information, such as product details, safety instructions, and branding.
It’s important to note that the specific manufacturing process for frying pans can vary depending on factors such as the material used, manufacturing techniques, and desired end product. Manufacturers may have proprietary processes or variations to differentiate their products. The steps outlined above provide a general overview of the frying pan manufacturing process.
Frying Pan Manufacturing Process
The manufacturing process for frying pans involves several steps, from forming the pan’s shape to applying nonstick coatings and finishing touches. The specific details may vary depending on the pan’s material, size, and desired features, but the general process remains consistent.
1. Raw Material Preparation
- The process begins with selecting the appropriate raw material, typically aluminum or stainless steel. The material is inspected for defects and then cut into sheets or blanks of the desired size.
2. Forming and Shaping
- The metal blanks are then heated to a specific temperature to make them malleable. Using various forming techniques, such as stamping, spinning, or forging, the blanks are shaped into the desired frying pan form. This involves creating the pan’s rounded base, side walls, and handle attachment points.
3. Trimming and Finishing
- Once the pan’s basic shape is formed, it undergoes trimming and finishing processes to remove excess material, smooth out rough edges, and achieve a uniform appearance. This may involve using cutting tools, sanding machines, and polishing tools.
4. Nonstick Coating Application
- For nonstick pans, a nonstick coating is applied to the pan’s cooking surface. The type of coating used may vary depending on the desired properties, such as durability, heat resistance, and adherence to the pan’s material.
- The coating application process typically involves several steps, such as degreasing the pan’s surface, applying a primer, spraying or dipping the pan in the nonstick coating material, and curing the coating in an oven to ensure proper adhesion.
5. Handle Assembly
- The pan’s handle is attached using various methods, such as riveting, welding, or using heat-resistant adhesives. The handle should be securely attached and designed to withstand frequent use and high temperatures.
6. Quality Control
- Throughout the manufacturing process, quality control checks are performed to ensure that the pans meet the desired specifications. This may involve inspecting the pan’s shape, dimensions, coating uniformity, handle attachment, and overall finish.
7. Packaging and Shipping
- Once the pans pass quality control checks, they are cleaned, packaged, and prepared for shipping. The packaging should protect the pans from damage during transportation and storage.
Additional Considerations
- The specific manufacturing process may vary depending on the pan’s material, size, and desired features. For instance, some pans may undergo additional treatments, such as anodizing for aluminum pans or surface hardening for stainless steel pans.
- Environmental considerations are increasingly important in frying pan manufacturing. Manufacturers are adopting eco-friendly practices, such as using recycled materials, reducing energy consumption, and minimizing waste generation.
Material Selection
Material selection is a crucial aspect of manufacturing ceramic coated pans. The choice of materials impacts the performance, durability, and overall quality of the pans. Here are some key considerations in material selection for ceramic coated pans:
- Pan Base Material: The base material of the pan should possess good heat conductivity for efficient and even heat distribution during cooking. Common base materials used for ceramic coated pans include:
- Aluminum: Aluminum pans offer excellent heat conductivity, lightweight properties, and affordability. They heat up quickly and evenly, making them popular for ceramic coated pans.
- Stainless Steel: Stainless steel pans provide durability, resistance to corrosion, and a polished appearance. However, stainless steel has lower heat conductivity compared to aluminum, so it is often used as a base material in combination with an aluminum or copper core for improved heat distribution.
- Ceramic Coating Material: The ceramic coating material is a critical component of ceramic coated pans. It should offer excellent nonstick properties, durability, and heat resistance. The specific composition of the ceramic coating material varies among manufacturers and can include ceramic particles, binders, and additives. The coating material should be chosen to provide optimal nonstick performance while ensuring safety and compliance with applicable regulations.
- Surface Preparation Material: The material used for surface preparation before the application of the ceramic coating can affect the bonding and adhesion of the coating. Common surface preparation methods include sanding, polishing, or chemical etching. The material used for these processes should be compatible with the base material and promote good adhesion of the ceramic coating.
- Handle Material: The handle of the pan should be made from a material that provides heat resistance, comfortable grip, and durability. Common handle materials include heat-resistant plastics, silicone, or stainless steel.
- Overall Construction: In addition to the specific materials used, the overall construction of the pan should be considered. Factors such as the thickness and quality of the base material, the bonding methods used, and the presence of reinforcing layers (e.g., multiple layers of aluminum or stainless steel) can contribute to the overall strength, durability, and performance of the ceramic coated pan.
Manufacturers carefully select materials based on factors such as cost, performance, availability, and customer preferences. Material selection is a balancing act to ensure that the chosen materials offer the desired functionality, quality, and value for the ceramic coated pans.
Material Preparation
Material preparation is an important step in the manufacturing process of ceramic coated pans. It involves various procedures to ensure that the base material and the ceramic coating material are properly prepared before application. Here are some common aspects of material preparation:
- Base Material Cleaning: The base material, such as aluminum or stainless steel, needs to be thoroughly cleaned to remove any contaminants, dirt, or oils that could interfere with the bonding of the ceramic coating. Cleaning methods can include degreasing, washing, or using solvents to ensure a clean surface.
- Surface Conditioning: Depending on the base material, surface conditioning techniques may be employed to enhance the adhesion of the ceramic coating. For example, abrasive methods like sanding or shot blasting can be used to roughen the surface slightly, creating microscopic grooves that allow for better coating adhesion.
- Surface Treatment: In some cases, a surface treatment process is employed to improve the bonding properties between the base material and the ceramic coating. Surface treatments may include processes like chemical etching or applying a primer or bonding agent that enhances adhesion.
- Ceramic Coating Preparation: The ceramic coating material is typically prepared by mixing ceramic particles, binders, and additives. The composition and formulation can vary depending on the desired properties of the coating, such as nonstick performance, durability, and heat resistance. The materials are mixed and processed to achieve a uniform and well-dispersed coating material.
- Coating Material Filtering: To remove any impurities or particles that may affect the quality of the coating, the ceramic coating material is often passed through filters. This step ensures a clean and consistent coating material before application.
- Coating Material Mixing: Proper mixing of the ceramic coating material is important to ensure uniform distribution of the ceramic particles, binders, and additives. Mixing techniques can include mechanical mixing, stirring, or using specialized mixing equipment to achieve a homogeneous mixture.
By properly preparing the base material and the ceramic coating material, manufacturers can enhance the adhesion, durability, and overall quality of the ceramic coated pans. Material preparation is a critical step to ensure that the subsequent coating application and curing processes result in a high-quality and reliable product.
Forming the Pan Body
Forming the pan body is a key step in the manufacturing process of ceramic coated pans. The pan body refers to the overall shape and structure of the pan, including the cooking surface, sides, and bottom. Here’s an overview of the process of forming the pan body:
- Sheet Metal Selection: The base material for the pan body is typically a sheet metal, such as aluminum or stainless steel. The sheet metal is selected based on the desired properties of the pan, including heat conductivity, durability, and weight.
- Cutting and Blanking: The selected sheet metal is cut into specific sizes and shapes according to the design and dimensions of the pan. This can be done using various cutting techniques, such as shearing or laser cutting. Blanking involves removing excess material to obtain the desired blank shape.
- Forming: The blanked sheet metal is then formed into the desired shape of the pan body. Forming can be accomplished through various processes, including:
- Deep Drawing: In deep drawing, a blank is placed over a die and then forced into the die cavity using a punch. The sheet metal is stretched and shaped to create the pan body, including the depth and curvature of the cooking surface.
- Stamping or Pressing: Stamping or pressing processes may be used to shape the sides or create specific features of the pan, such as handles or ridges. This involves using a die and a press to deform the sheet metal into the desired shape.
- Bending and Flanging: Bending operations are performed to shape the edges and rims of the pan. This can involve using bending machines or presses to create the desired flanges or lip around the perimeter of the pan.
- Trimming and Finishing: After forming, the edges of the pan body may be trimmed to remove excess material and achieve a clean, uniform shape. The pan body may also undergo additional finishing processes, such as sanding or polishing, to smooth out any rough edges or surface imperfections.
Forming the pan body requires precision and expertise to ensure that the desired shape, dimensions, and structural integrity of the pan are achieved. Manufacturers use specialized machinery, such as hydraulic presses, stamping equipment, or deep drawing machines, to carry out the forming operations accurately and efficiently. The formed pan bodies are then ready for subsequent processes, such as surface preparation and ceramic coating application, to complete the manufacturing of ceramic coated pans.
Handle Attachment
Handle attachment is an important step in the manufacturing process of ceramic coated pans. The handle provides a means for users to safely and conveniently hold and manipulate the pan during cooking. Here’s an overview of the process of handle attachment:
- Handle Selection: The handle for the ceramic coated pan is typically made from heat-resistant materials such as plastic, silicone, or stainless steel. The selection of the handle material depends on factors such as heat resistance, durability, comfort, and design aesthetics.
- Handle Design: The handle is designed to fit the specific shape and size of the pan. It may feature ergonomic contours, grips, or other design elements to ensure a comfortable and secure grip for the user.
- Handle Preparation: Before attaching the handle to the pan, the handle may undergo surface preparation processes. This can include cleaning, sanding, or other treatments to ensure proper adhesion between the handle and the pan body.
- Attachment Method: There are several methods used for attaching handles to ceramic coated pans. Common methods include:
- Riveting: Rivets are commonly used to attach handles to pans. Holes are drilled in the pan body and handle, and rivets are inserted through the holes and secured to hold the handle in place.
- Welding: In some cases, handles are welded directly to the pan body. This involves heating the handle and pan body at specific points of attachment and fusing them together through welding processes.
- Screw Fastening: Screws or bolts can be used to attach handles to the pan body. Holes are drilled in the pan body and handle, and screws are inserted and tightened to secure the handle in place.
- Testing and Quality Control: After handle attachment, the pan undergoes testing and quality control measures to ensure proper attachment and stability. This may include checking the tightness of fasteners, verifying the handle’s stability, and evaluating overall functionality.
Proper handle attachment is crucial for the safety and usability of the ceramic coated pan. Manufacturers follow specific procedures and quality control measures to ensure that handles are securely and reliably attached to the pan bodies. This ensures that users can confidently handle and manipulate the pan during cooking without concerns of the handle detaching or compromising the overall integrity of the pan.
Surface Treatment
Surface treatment is an essential step in the manufacturing process of ceramic coated pans. It involves various processes and techniques to prepare the surface of the pan for the application of the ceramic coating. The surface treatment ensures proper adhesion of the coating, enhances durability, and contributes to the overall quality of the finished product. Here are some common surface treatment methods:
- Cleaning: The surface of the pan is thoroughly cleaned to remove any dirt, oil, grease, or contaminants that may hinder the adhesion of the ceramic coating. Cleaning methods may include using solvents, degreasers, or specialized cleaning agents to ensure a clean surface.
- Sanding or Abrasive Blasting: Depending on the base material and the desired finish, the surface of the pan may undergo sanding or abrasive blasting. These processes remove surface imperfections, smooth out rough areas, and create a textured surface that promotes better adhesion of the ceramic coating.
- Chemical Etching: Chemical etching involves applying chemical solutions to the surface of the pan to create micro-roughness or increase surface energy. This process enhances the bonding properties between the base material and the ceramic coating, promoting better adhesion and durability.
- Surface Conditioning: Surface conditioning techniques may be employed to prepare the surface for coating application. This can include methods such as mechanical abrasion, brushing, or polishing to ensure a smooth, even surface and promote good coating adhesion.
- Pre-Treatment Coatings: In some cases, a pre-treatment coating or primer is applied to the surface of the pan. This coating acts as a bonding agent, enhancing the adhesion of the subsequent ceramic coating. Pre-treatment coatings may contain adhesion promoters or specific chemical compounds to facilitate the bonding process.
- Surface Activation: Surface activation methods, such as plasma treatment or corona treatment, may be utilized to increase the surface energy of the pan. This improves the wettability and adhesion of the ceramic coating, leading to better coating coverage and durability.
The specific surface treatment method used depends on factors such as the base material, the type of ceramic coating, and the desired finish of the pan. Manufacturers carefully select and optimize the surface treatment process to ensure optimal adhesion, durability, and overall quality of the ceramic coated pans.
Heat Treatment
Heat treatment is a critical step in the manufacturing process of ceramic coated pans. It involves subjecting the pans to controlled heating and cooling processes to enhance the properties of both the base material and the ceramic coating. Heat treatment can improve the hardness, durability, and overall performance of the pans. Here are some common heat treatment techniques used:
- Pre-Heating: Before applying the ceramic coating, the pans may undergo a pre-heating process. This involves heating the pan body to a specific temperature to remove any residual moisture, oils, or contaminants and prepare the surface for coating application. Pre-heating also helps to prevent thermal shock when the ceramic coating is applied.
- Ceramic Coating Curing: After the ceramic coating is applied to the pans, they are typically subjected to a curing process. This involves heating the pans to a specific temperature and holding them at that temperature for a specified period. The curing process allows the ceramic coating to chemically bond and form a durable, heat-resistant surface.
- Annealing: Annealing is a heat treatment process that involves heating the pans to a specific temperature and then gradually cooling them. This process relieves internal stresses, improves the ductility, and enhances the overall mechanical properties of the base material. Annealing can help reduce the risk of warping or distortion during the manufacturing process.
- Tempering: Tempering is a heat treatment technique that follows the hardening process. After the pans are heated to a high temperature and rapidly cooled (quenched) to increase their hardness, they are then tempered by reheating them to a lower temperature. Tempering improves the toughness and reduces the brittleness of the pans, making them less prone to cracking or breaking.
- Stress Relieving: Stress relieving is a heat treatment process used to minimize residual stresses that may have developed during the manufacturing process. The pans are heated to a specific temperature and held for a sufficient period to allow internal stresses to redistribute and relax. Stress relieving helps to improve the stability and dimensional integrity of the pans.
The specific heat treatment parameters, including temperature, duration, and cooling rate, depend on the base material, the desired properties of the pans, and the type of ceramic coating used. Manufacturers carefully control these parameters to ensure consistent and optimal heat treatment results. Proper heat treatment plays a crucial role in enhancing the performance, durability, and overall quality of ceramic coated pans.
Finishing and Polishing
Finishing and polishing are important steps in the manufacturing process of ceramic coated pans. These processes are carried out after the ceramic coating has been applied and heat-treated. Finishing and polishing aim to enhance the appearance, smoothness, and overall quality of the pans. Here’s an overview of the finishing and polishing steps:
- Surface Inspection: Before starting the finishing and polishing process, the pans undergo a thorough inspection to identify any surface defects or imperfections. This may include checking for uneven coating thickness, rough areas, or visual defects that need to be addressed.
- Grinding and Sanding: In some cases, rough areas or imperfections on the surface of the pans may be ground or sanded to create a smooth and even surface. This is done using specialized grinding or sanding equipment and abrasives of varying grit sizes. The goal is to remove any unevenness and create a uniform surface finish.
- Buffing and Polishing: After the initial grinding and sanding, the pans are subjected to buffing and polishing processes to achieve a desired level of smoothness and shine. This involves using polishing compounds, pads, or wheels with varying levels of abrasiveness. The pans are carefully buffed and polished to remove fine scratches, refine the surface, and create a lustrous finish.
- Cleaning and Washing: Once the finishing and polishing process is complete, the pans undergo thorough cleaning and washing to remove any residual polishing compounds, debris, or contaminants. This ensures that the pans are clean and ready for packaging and distribution.
- Final Inspection: After finishing and polishing, the pans undergo a final inspection to ensure that the desired surface finish has been achieved and that there are no visible defects or blemishes. This includes checking for uniformity, smoothness, and overall aesthetic appeal.
Finishing and polishing are crucial for creating ceramic coated pans that not only perform well but also have an attractive appearance. These processes require skilled operators and the use of specialized equipment and materials. By carefully carrying out finishing and polishing, manufacturers can produce high-quality pans that meet the desired standards of performance, aesthetics, and customer satisfaction.
Quality Control
Quality control is a crucial aspect of the manufacturing process for ceramic coated pans. It ensures that the pans meet the required standards of quality, performance, and durability. Quality control involves a series of inspections, tests, and measures to identify and address any potential defects or issues. Here are some key aspects of quality control in the manufacturing of ceramic coated pans:
- Incoming Material Inspection: The quality control process starts with the inspection of incoming raw materials. This includes verifying the quality and specifications of the base materials, ceramic coatings, and any other components used in the pan production. Material samples may be tested to ensure they meet the desired standards.
- In-Process Inspection: Throughout the manufacturing process, inspections are carried out at various stages to monitor the quality and integrity of the pans. This can include checks for proper surface preparation, ceramic coating application, curing, heat treatment, and other critical steps. Inspections may be visual, dimensional, or involve specialized testing equipment.
- Coating Thickness Measurement: Ceramic coated pans require a specific thickness of the ceramic coating for optimal performance. Quality control measures include checking the thickness of the coating using specialized instruments such as coating thickness gauges. This ensures that the coating meets the required specifications.
- Adhesion Testing: Adhesion between the ceramic coating and the pan’s surface is crucial for durability. Quality control involves conducting adhesion tests to assess the bond strength of the coating. This can include methods such as cross-cut adhesion testing or tape adhesion testing to ensure that the coating adheres properly to the pan.
- Functional Performance Testing: Quality control may involve functional performance testing to ensure that the pans perform as intended. This can include tests for heat distribution, non-stick properties, scratch resistance, durability, and other performance parameters. These tests are conducted to ensure that the pans meet the desired standards of performance and functionality.
- Final Inspection: Before the pans are packaged and shipped, a final inspection is conducted to ensure that they meet all quality criteria. This includes checks for overall appearance, finish, cleanliness, proper handle attachment, and any other specific requirements. Random sampling or 100% inspection may be carried out to ensure consistency and adherence to quality standards.
- Documentation and Record-Keeping: Quality control processes include the documentation and record-keeping of inspection results, test data, and any non-conformities found. This documentation serves as a reference for traceability, troubleshooting, and continuous improvement of the manufacturing process.
By implementing robust quality control measures, manufacturers can ensure that ceramic coated pans meet the desired standards of quality, performance, and customer satisfaction. Quality control helps identify and rectify any issues early in the production process, resulting in consistent and reliable products for consumers.
Packaging
Packaging plays a crucial role in the manufacturing and distribution of ceramic coated pans. It not only protects the pans during transportation and storage but also presents an opportunity to enhance the brand image and provide a positive customer experience. Here are some key aspects of packaging for ceramic coated pans:
- Packaging Design: The packaging design should be visually appealing, informative, and aligned with the brand identity. It may include the brand logo, product images, features, and other relevant information. The design should attract attention on store shelves and effectively communicate the value of the product.
- Protective Packaging Materials: To ensure the pans are well-protected during transit, appropriate packaging materials should be used. This may include cardboard boxes, foam inserts, or other cushioning materials to prevent damage from impacts or rough handling. The packaging materials should be sturdy and durable to withstand the rigors of transportation.
- Product Labelling: Each package should include clear and accurate labelling that provides essential information about the product. This may include the product name, size, material composition, care instructions, and any relevant certifications or compliance labels. The labelling should comply with legal requirements and industry standards.
- User Manuals and Instruction Guides: If applicable, user manuals or instruction guides should be included in the packaging. These documents provide information on the proper use, care, and maintenance of the ceramic coated pans. Clear and concise instructions can help customers make the most of their purchase and ensure the longevity of the pans.
- Branding and Marketing Materials: Packaging provides an opportunity for branding and marketing. Including promotional materials such as coupons, warranty information, or product catalogs can encourage customer loyalty and future purchases. Branded packaging elements, such as stickers or tags, can reinforce brand recognition and create a positive brand experience.
- Sustainability Considerations: As sustainability becomes increasingly important, manufacturers may opt for eco-friendly packaging options. This can include using recyclable materials, minimizing packaging waste, or utilizing packaging materials with reduced environmental impact. Sustainable packaging choices can resonate with environmentally conscious consumers and align with corporate social responsibility goals.
- Compliance and Safety: Packaging should comply with relevant regulations and safety standards. This includes considerations such as proper labeling of hazardous materials, compliance with weight restrictions for shipping, and adherence to any specific packaging requirements of different regions or markets.
Proper packaging ensures that ceramic coated pans reach customers in good condition, with all necessary information and a positive brand experience. Manufacturers should carefully consider packaging design, materials, labeling, and sustainability to create packaging that is functional, visually appealing, and aligned with their brand values.
Types of Cookware
Cookware comes in various types, each with unique properties and manufacturing processes. The primary types include stainless steel, aluminum, cast iron, copper, non-stick, and ceramic cookware.
Stainless steel cookware is known for its durability, resistance to rust and corrosion, and non-reactive properties. It is often used in professional kitchens and for high-quality home cookware.
Aluminum cookware is lightweight, conducts heat well, and is typically more affordable than other types. It is often anodized or coated to prevent reaction with acidic foods.
Cast iron cookware is renowned for its excellent heat retention and even cooking. It is durable and can be used on various heat sources, including induction cooktops.
Copper cookware provides superior heat conductivity, allowing precise temperature control. It is often lined with stainless steel or tin to prevent reactions with food.
Non-stick cookware features a coating that prevents food from sticking, making it easy to clean. It is popular for low-fat cooking but requires careful handling to avoid damaging the coating.
Ceramic cookware is valued for its non-reactive surface and even heating. It is often used for baking and roasting due to its ability to withstand high temperatures.
Raw Materials and Sourcing
The selection and sourcing of raw materials are critical in cookware manufacturing. The quality of the final product depends heavily on the quality of the materials used.
For stainless steel cookware, high-grade stainless steel alloys such as 18/10 (18% chromium, 10% nickel) are commonly used. These alloys offer excellent durability and resistance to corrosion.
Aluminum cookware typically uses pure aluminum or aluminum alloys. Pure aluminum is soft and lightweight, while alloys provide added strength and durability.
Cast iron cookware is made from iron alloys with a high carbon content. The iron is melted and poured into molds to create the desired shapes.
Copper cookware uses high-purity copper, often with a lining of stainless steel or tin to prevent reactions with food.
Non-stick cookware starts with a base of aluminum or stainless steel, to which a non-stick coating such as PTFE (polytetrafluoroethylene) is applied.
Ceramic cookware is made from natural clay, which is shaped and fired at high temperatures to create a hard, non-porous surface.
Quality control of raw materials involves rigorous testing and inspection to ensure they meet industry standards. Environmental considerations also play a role in material selection, with manufacturers increasingly opting for sustainable and eco-friendly options.
Manufacturing Process
The manufacturing process of cookware involves several stages, each crucial for producing high-quality products.
Forming
Forming is the initial stage where the raw materials are shaped into cookware.
Casting: Involves pouring molten metal into molds to create the desired shape. This method is commonly used for cast iron and some types of aluminum cookware.
Stamping: Uses heavy machinery to stamp out shapes from sheets of metal. This process is often used for stainless steel and aluminum cookware.
Spinning: Involves rotating a metal disc and shaping it over a form using a lathe. This method is used for making items like pots and pans from stainless steel and aluminum.
Surface Preparation
Surface preparation ensures the cookware’s surface is smooth and ready for coating or finishing.
Grinding: Removes any rough edges and surface imperfections using abrasive wheels.
Polishing: Uses finer abrasives to create a smooth, shiny surface on the cookware.
Sandblasting: Blasts the surface with fine particles to clean and texture it, preparing it for further finishing.
Coating and Finishing
Coating and finishing enhance the cookware’s performance and appearance.
Non-stick Coating Application: Involves applying a non-stick layer, usually PTFE, to the cookware surface. The coating is then baked to cure it.
Enameling: Applies a glass-like coating to metal cookware, providing a durable, non-reactive surface. This process is commonly used for cast iron and steel cookware.
Anodizing: Involves electrochemically treating aluminum to create a hard, non-reactive surface. Anodized aluminum cookware is known for its durability and resistance to corrosion.
Assembly and Attachment
Handles and knobs are attached to the cookware, ensuring they are secure and ergonomic.
Handles and Knobs: Made from materials such as stainless steel, plastic, or silicone, are attached using riveting, welding, or screwing.
Riveting and Welding: Securely attach handles and other components to the cookware, ensuring they can withstand regular use.
Quality Control and Testing
Quality control is critical in cookware manufacturing to ensure the final products meet safety and performance standards.
Inspection Procedures: Involve visual and mechanical inspection of cookware to detect any defects or irregularities.
Performance Testing: Includes tests for heat distribution, durability, and resistance to scratching and corrosion.
Safety Standards Compliance: Ensures that the cookware meets all relevant safety standards and regulations, such as those set by the FDA or other regulatory bodies.
Technological Advancements in Cookware Manufacturing
Technological advancements are continually improving the efficiency, quality, and sustainability of cookware manufacturing.
Automation and Robotics: Modern manufacturing facilities often use automated systems and robotics to handle repetitive tasks, improving consistency and reducing labor costs.
Advanced Materials: Research into new materials and coatings has led to the development of cookware with improved performance, such as better non-stick properties and enhanced durability.
Sustainable Manufacturing Practices: Manufacturers are increasingly adopting eco-friendly practices, such as using recycled materials, reducing energy consumption, and minimizing waste.
Smart Cookware: The integration of smart technology into cookware, such as temperature sensors and connectivity features, is a growing trend, providing users with more control and information during cooking.
Challenges in Cookware Manufacturing
Cookware manufacturing faces several challenges, including maintaining quality and consistency, cost management, technological advancements, and environmental regulations.
Maintaining Quality and Consistency: Ensuring that every piece of cookware meets high standards of quality and performance is challenging, particularly in high-volume production.
Cost Management: Balancing the costs of materials, labor, and production while remaining competitive in the market requires careful planning and efficiency.
Technological Advancements: Keeping up with rapid technological changes and integrating new technologies into existing manufacturing processes can be demanding.
Environmental Regulations: Compliance with environmental regulations requires manufacturers to adopt sustainable practices and invest in eco-friendly technologies, which can be costly and complex.
Future Trends in Cookware Manufacturing
The future of cookware manufacturing is likely to be shaped by innovations in materials, enhanced functionality, and sustainability.
Innovations in Materials: Continued research into new materials and coatings will likely result in cookware with superior performance, such as improved heat distribution and non-stick properties.
Enhanced Functionality and Features: Cookware with added features, such as smart technology, will provide users with more control and convenience during cooking.
Eco-friendly and Sustainable Products: As consumers become more environmentally conscious, demand for eco-friendly cookware made from sustainable materials and produced using green manufacturing practices will likely increase.
Conclusion
Cookware manufacturing is a complex and multifaceted industry that produces essential tools for cooking. Understanding the various types of cookware, raw materials, manufacturing processes, and technological advancements is crucial for producing high-quality products. Despite challenges such as maintaining quality, managing costs, and complying with environmental regulations, the industry continues to evolve and innovate. Future trends in materials, functionality, and sustainability promise to drive the industry forward, ensuring that cookware remains a vital part of daily life and culinary excellence.