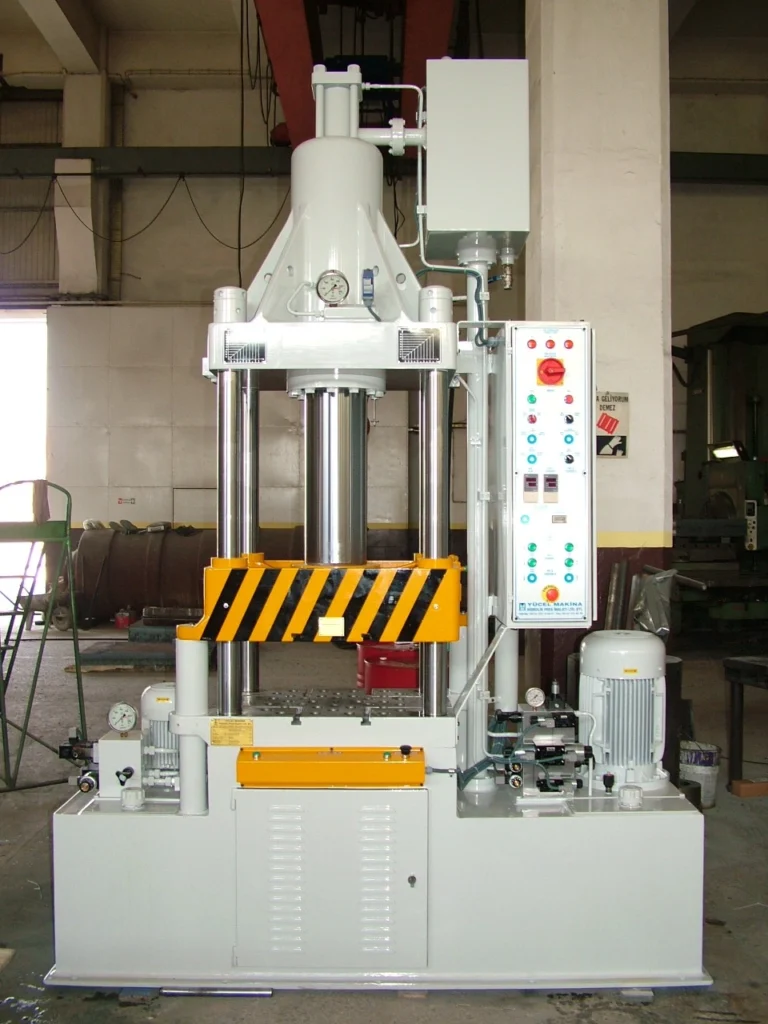
We manufacture the Fry Pan Making Machine to produce pans in different forms. These machines are used in metalworking industries for fry pan making operations
A fry pan making machine is a specialized piece of equipment designed to mass produce frying pans. These machines typically employ a combination of forming, shaping, and finishing processes to transform raw materials into finished frying pans.
Key Components of a Fry Pan Making Machine
- Feeding System: The feeding system supplies the raw material, typically aluminum or stainless steel, in the form of sheets or coils, to the machine.
- Forming Station: The forming station shapes the raw material into the desired frying pan shape. This may involve processes like stamping, spinning, or hydraulic forming.
- Trimming Unit: The trimming unit removes excess material from the edges of the formed frying pan, creating a clean and consistent shape.
- Handle Attachment Mechanism: The handle attachment mechanism secures the handle to the frying pan using techniques like riveting or welding.
- Coating System: The coating system applies a non-stick coating to the frying pan’s cooking surface, preventing food from sticking and ensuring easy cleaning.
- Quality Control System: The quality control system inspects the finished frying pans for defects, ensuring they meet the desired specifications for shape, size, and finish.
Operation of a Fry Pan Making Machine
- Material Feeding: The feeding system unwinds the raw material from a coil or feeds pre-cut sheets into the forming station.
- Forming Process: The forming station molds the raw material into the desired frying pan shape. The specific forming process depends on the type of machine and the desired pan design.
- Trimming and Finishing: The trimmed frying pan undergoes further processing to remove imperfections and create a smooth finish. This may involve sanding, buffing, or polishing.
- Handle Attachment: The handle is attached to the frying pan using a secure and durable method, ensuring it can withstand regular use.
- Non-Stick Coating: The frying pan’s cooking surface is coated with a non-stick material, typically a polymer-based coating.
- Quality Control: Finished frying pans undergo quality control checks to ensure they meet the desired specifications and are free from defects.
Benefits of Using a Fry Pan Making Machine
- Increased Production Efficiency: Fry pan making machines can produce frying pans at a much faster rate than manual methods, significantly increasing production output.
- Improved Consistency and Quality: Machines ensure consistent shaping, trimming, and coating, resulting in frying pans with uniform dimensions, smooth finishes, and even non-stick coatings.
- Reduced Labor Costs: Automated machines eliminate the need for extensive manual labor, reducing labor costs and overall production expenses.
- Enhanced Safety: Machines minimize the risk of injuries associated with manual handling of hot materials and sharp tools.
- Versatility: Modern fry pan making machines can produce a wide range of frying pan sizes, shapes, and designs, catering to diverse market needs.
Fry Pan Making Machine
A fry pan making machine is a specialized piece of equipment designed to efficiently produce fry pans in a variety of sizes, shapes, and materials. These machines are typically found in large-scale manufacturing facilities that produce cookware on an industrial scale.
The basic operation of a fry pan making machine involves a series of automated steps that transform raw materials into finished fry pans. Here’s a simplified overview of the process:
- Material Preparation:a. Material Selection: The type of material used for the fry pan is determined based on the desired properties and characteristics, such as aluminum, stainless steel, or cast iron.b. Material Preparation: The raw material may undergo various preparation steps, such as cutting, cleaning, and shaping, to ensure it is ready for the forming process.
- Forming and Shaping:a. Pressing: The prepared material is fed into a stamping press, where it is pressed into the desired shape of the fry pan. This process involves applying high pressure to force the material into a die or mold.b. Spinning: For some fry pans with curved sides, spinning is used. A spinning chuck rotates a metal disc, and a roller is applied to gradually form the disc into the desired shape.
- Trimming and Finishing:a. Trimming: Excess material is trimmed from the edges of the fry pan to create a clean and consistent shape.b. Sanding: The fry pan may be sanded to remove any rough spots or imperfections and create a smooth surface.
- Handle Attachment:a. Drilling: Holes are drilled in the fry pan for handle attachment.b. Handle Riveting or Welding: Handles are attached to the fry pan using rivets or welding techniques, ensuring a secure and durable connection.
- Coating:a. Non-Stick Coating: For non-stick fry pans, a non-stick coating is applied to the cooking surface. This coating prevents food from sticking to the pan and ensures easy cleaning.b. Seasoning: For cast iron fry pans, seasoning is applied to create a non-stick surface. This involves heating the pan with oil or fat until a protective layer forms.
- Quality Control:a. Thorough Inspection: The fry pans undergo rigorous quality control checks to ensure they meet the desired specifications for shape, size, finish, and overall quality. This may involve visual inspection, dimensional checks, and material testing.
- Packaging and Shipping:a. Protective Packaging: The fry pans are carefully packaged using protective materials like cardboard boxes, bubble wrap, and foam padding to prevent damage during shipping.b. Shipping: The packaged fry pans are shipped to retailers or distributors for distribution and sale.
These represent the fundamental steps involved in the operation of a fry pan making machine. The specific details and technologies employed may vary depending on the manufacturer, the type of fry pan being produced, and the desired production volume. Fry pan making machines play a crucial role in the mass production of cookware, ensuring efficient and consistent production of high-quality fry pans for consumers worldwide.
Cookware manufacturing is a vital industry that plays a significant role in daily life. From professional chefs to home cooks, quality cookware is essential for preparing meals efficiently and safely. The manufacturing process involves a series of steps that transform raw materials into functional and aesthetically pleasing kitchen tools. This document explores the different types of cookware, the raw materials used, the detailed manufacturing processes, technological advancements, challenges, and future trends in the industry.
Types of Cookware
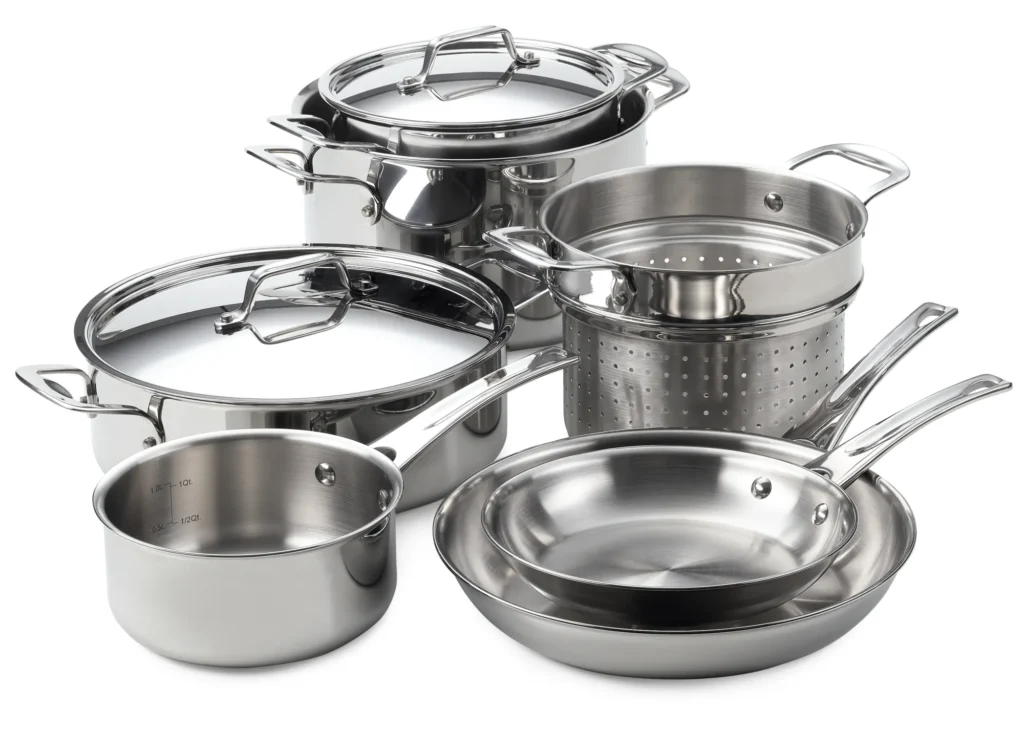
Cookware comes in various types, each with unique properties and manufacturing processes. The primary types include stainless steel, aluminum, cast iron, copper, non-stick, and ceramic cookware.
Stainless steel cookware is known for its durability, resistance to rust and corrosion, and non-reactive properties. It is often used in professional kitchens and for high-quality home cookware.
Aluminum cookware is lightweight, conducts heat well, and is typically more affordable than other types. It is often anodized or coated to prevent reaction with acidic foods.
Cast iron cookware is renowned for its excellent heat retention and even cooking. It is durable and can be used on various heat sources, including induction cooktops.
Copper cookware provides superior heat conductivity, allowing precise temperature control. It is often lined with stainless steel or tin to prevent reactions with food.
Non-stick cookware features a coating that prevents food from sticking, making it easy to clean. It is popular for low-fat cooking but requires careful handling to avoid damaging the coating.
Ceramic cookware is valued for its non-reactive surface and even heating. It is often used for baking and roasting due to its ability to withstand high temperatures.
Raw Materials and Sourcing
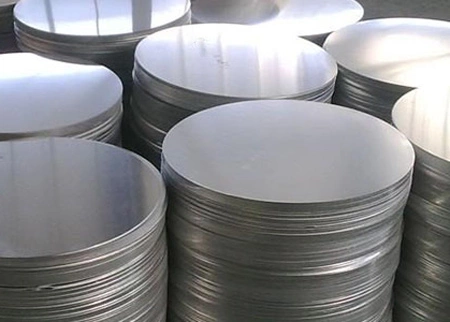
The selection and sourcing of raw materials are critical in cookware manufacturing. The quality of the final product depends heavily on the quality of the materials used.
For stainless steel cookware, high-grade stainless steel alloys such as 18/10 (18% chromium, 10% nickel) are commonly used. These alloys offer excellent durability and resistance to corrosion.
Aluminum cookware typically uses pure aluminum or aluminum alloys. Pure aluminum is soft and lightweight, while alloys provide added strength and durability.
Cast iron cookware is made from iron alloys with a high carbon content. The iron is melted and poured into molds to create the desired shapes.
Copper cookware uses high-purity copper, often with a lining of stainless steel or tin to prevent reactions with food.
Non-stick cookware starts with a base of aluminum or stainless steel, to which a non-stick coating such as PTFE (polytetrafluoroethylene) is applied.
Ceramic cookware is made from natural clay, which is shaped and fired at high temperatures to create a hard, non-porous surface.
Quality control of raw materials involves rigorous testing and inspection to ensure they meet industry standards. Environmental considerations also play a role in material selection, with manufacturers increasingly opting for sustainable and eco-friendly options.
Manufacturing Process
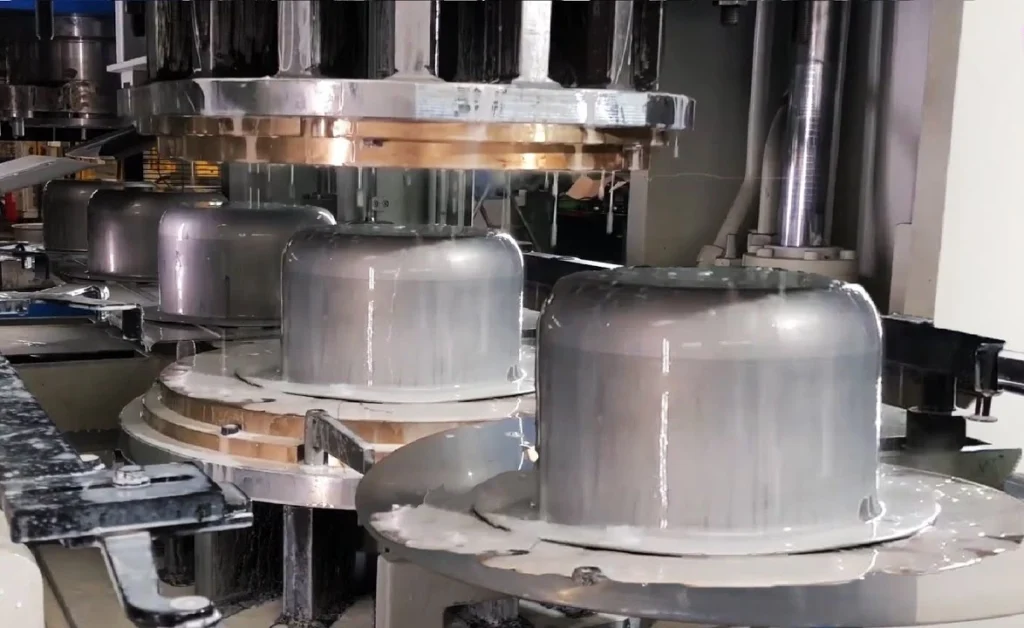
The manufacturing process of cookware involves several stages, each crucial for producing high-quality products.
Forming
Forming is the initial stage where the raw materials are shaped into cookware.
Casting: Involves pouring molten metal into molds to create the desired shape. This method is commonly used for cast iron and some types of aluminum cookware.
Stamping: Uses heavy machinery to stamp out shapes from sheets of metal. This process is often used for stainless steel and aluminum cookware.
Spinning: Involves rotating a metal disc and shaping it over a form using a lathe. This method is used for making items like pots and pans from stainless steel and aluminum.
Surface Preparation
Surface preparation ensures the cookware’s surface is smooth and ready for coating or finishing.
Grinding: Removes any rough edges and surface imperfections using abrasive wheels.
Polishing: Uses finer abrasives to create a smooth, shiny surface on the cookware.
Sandblasting: Blasts the surface with fine particles to clean and texture it, preparing it for further finishing.
Coating and Finishing
Coating and finishing enhance the cookware’s performance and appearance.
Non-stick Coating Application: Involves applying a non-stick layer, usually PTFE, to the cookware surface. The coating is then baked to cure it.
Enameling: Applies a glass-like coating to metal cookware, providing a durable, non-reactive surface. This process is commonly used for cast iron and steel cookware.
Anodizing: Involves electrochemically treating aluminum to create a hard, non-reactive surface. Anodized aluminum cookware is known for its durability and resistance to corrosion.
Assembly and Attachment
Handles and knobs are attached to the cookware, ensuring they are secure and ergonomic.
Handles and Knobs: Made from materials such as stainless steel, plastic, or silicone, are attached using riveting, welding, or screwing.
Riveting and Welding: Securely attach handles and other components to the cookware, ensuring they can withstand regular use.
Quality Control and Testing
Quality control is critical in cookware manufacturing to ensure the final products meet safety and performance standards.
Inspection Procedures: Involve visual and mechanical inspection of cookware to detect any defects or irregularities.
Performance Testing: Includes tests for heat distribution, durability, and resistance to scratching and corrosion.
Safety Standards Compliance: Ensures that the cookware meets all relevant safety standards and regulations, such as those set by the FDA or other regulatory bodies.
Technological Advancements in Cookware Manufacturing
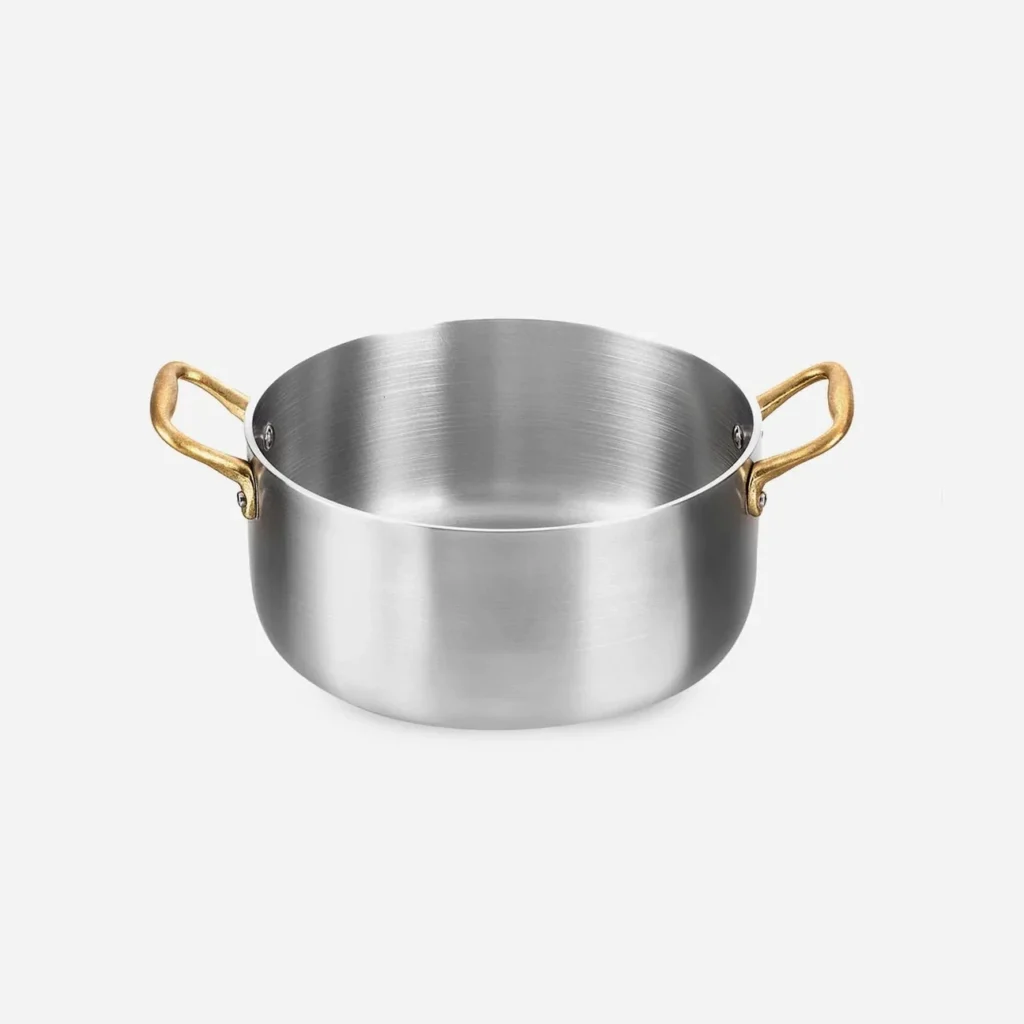
Technological advancements are continually improving the efficiency, quality, and sustainability of cookware manufacturing.
Automation and Robotics: Modern manufacturing facilities often use automated systems and robotics to handle repetitive tasks, improving consistency and reducing labor costs.
Advanced Materials: Research into new materials and coatings has led to the development of cookware with improved performance, such as better non-stick properties and enhanced durability.
Sustainable Manufacturing Practices: Manufacturers are increasingly adopting eco-friendly practices, such as using recycled materials, reducing energy consumption, and minimizing waste.
Smart Cookware: The integration of smart technology into cookware, such as temperature sensors and connectivity features, is a growing trend, providing users with more control and information during cooking.
Challenges in Cookware Manufacturing
Cookware manufacturing faces several challenges, including maintaining quality and consistency, cost management, technological advancements, and environmental regulations.
Maintaining Quality and Consistency: Ensuring that every piece of cookware meets high standards of quality and performance is challenging, particularly in high-volume production.
Cost Management: Balancing the costs of materials, labor, and production while remaining competitive in the market requires careful planning and efficiency.
Technological Advancements: Keeping up with rapid technological changes and integrating new technologies into existing manufacturing processes can be demanding.
Environmental Regulations: Compliance with environmental regulations requires manufacturers to adopt sustainable practices and invest in eco-friendly technologies, which can be costly and complex.
Future Trends in Cookware Manufacturing
The future of cookware manufacturing is likely to be shaped by innovations in materials, enhanced functionality, and sustainability.
Innovations in Materials: Continued research into new materials and coatings will likely result in cookware with superior performance, such as improved heat distribution and non-stick properties.
Enhanced Functionality and Features: Cookware with added features, such as smart technology, will provide users with more control and convenience during cooking.
Eco-friendly and Sustainable Products: As consumers become more environmentally conscious, demand for eco-friendly cookware made from sustainable materials and produced using green manufacturing practices will likely increase.
Conclusion
Cookware manufacturing is a complex and multifaceted industry that produces essential tools for cooking. Understanding the various types of cookware, raw materials, manufacturing processes, and technological advancements is crucial for producing high-quality products. Despite challenges such as maintaining quality, managing costs, and complying with environmental regulations, the industry continues to evolve and innovate. Future trends in materials, functionality, and sustainability promise to drive the industry forward, ensuring that cookware remains a vital part of daily life and culinary excellence.
EMS Metalworking Machinery
We design, manufacture and assembly metalworking machinery such as:
- Hydraulic transfer press
- Glass mosaic press
- Hydraulic deep drawing press
- Casting press
- Hydraulic cold forming press
- Hydroforming press
- Composite press
- Silicone rubber moulding press
- Brake pad press
- Melamine press
- SMC & BMC Press
- Labrotaroy press
- Edge cutting trimming machine
- Edge curling machine
- Trimming beading machine
- Trimming joggling machine
- Cookware production line
- Pipe bending machine
- Profile bending machine
- Bandsaw for metal
- Cylindrical welding machine
- Horizontal pres and cookware
- Kitchenware, hotelware
- Bakeware and cuttlery production machinery
as a complete line as well as an individual machine such as:
- Edge cutting trimming beading machines
- Polishing and grinding machines for pot and pans
- Hydraulic drawing presses
- Circle blanking machines
- Riveting machine
- Hole punching machines
- Press feeding machine
You can check our machinery at work at: EMS Metalworking Machinery – YouTube
Applications:
- Beading and ribbing
- Flanging
- Trimming
- Curling
- Lock-seaming
- Ribbing
- Flange-punching