Fire Extinguisher Manufacturing and Machinery needed for the Fire Extinguisher Production Line. High quality & Low price with Free consultation
Fire extinguisher manufacturing is a growing industry that has increased demand for its products in recent years. Fire extinguisher manufacturing requires specialized knowledge and expertise to ensure safety compliance.
Fire extinguisher manufacturing plays a vital role in safeguarding lives and properties. These devices are designed to suppress or extinguish fires in their early stages. They provide precious time for people to evacuate. And they reduce the risk of extensive damage. Fire extinguishers come in various types. They are water, foam, powder, and CO2, each suitable for specific types of fires. The manufacturing process involves intricate engineering, rigorous testing, and adherence. It is for stringent safety standards to guarantee their effectiveness. As a result, the product meets all safety standards and regulations.
Fire extinguishers are essential devices designed to control or extinguish small fires in emergency situations. They are critical components in the fire safety protocols of residential, commercial, and industrial settings. Fire extinguishers are often the first line of defense against fire hazards, providing a means to suppress flames before they escalate into more severe incidents. Their importance cannot be overstated, particularly in environments where the risk of fire is high due to the presence of flammable materials, electrical equipment, or industrial processes. This document aims to provide a comprehensive overview of fire extinguishers, covering their types, components, operational mechanisms, manufacturing processes, quality standards, challenges, and future trends in the industry.
Fire Extinguisher Manufacturing: Types of Fire Extinguishers
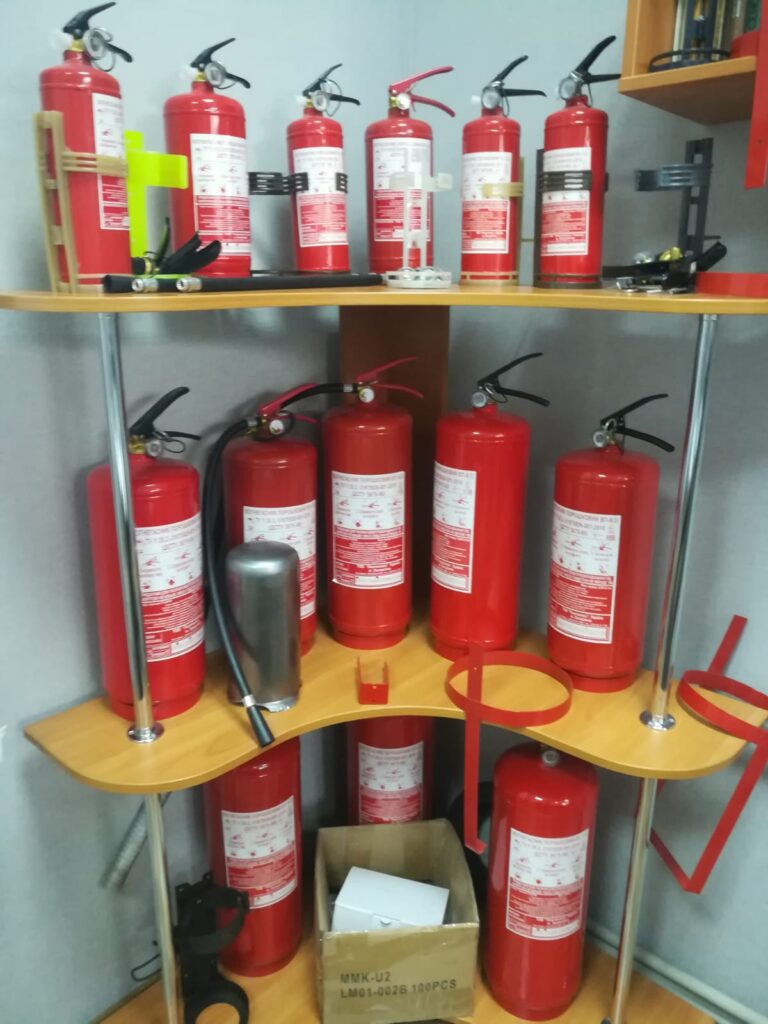
Fire extinguishers come in various types, each designed to tackle specific classes of fires. The primary types include water-based extinguishers, foam extinguishers, dry powder extinguishers, carbon dioxide extinguishers, and wet chemical extinguishers.
Water-based extinguishers are suitable for Class A fires, which involve ordinary combustibles such as wood, paper, and textiles. These extinguishers work by cooling the burning material below its ignition temperature.
Foam extinguishers are effective against both Class A and Class B fires. Class B fires involve flammable liquids like petrol, oil, and solvents. The foam forms a blanket over the burning liquid, cutting off the oxygen supply and preventing re-ignition.
Dry powder extinguishers are versatile and can be used on Class A, B, and C fires. Class C fires involve gases such as propane, butane, and methane. The powder works by interrupting the chemical reaction of the fire.
Carbon dioxide extinguishers are ideal for Class B and electrical fires. They work by displacing oxygen and reducing the heat with a cold discharge, effectively suffocating the fire.
Wet chemical extinguishers are specifically designed for Class F fires, which involve cooking oils and fats. The chemical forms a soap-like solution on the surface of the burning oil, creating a barrier that separates the fuel from oxygen and cools the flames.
There are also specialized extinguishers for metal fires, such as Class D extinguishers, which use agents like sodium chloride to smother the flames and absorb the heat.
Components of a Fire Extinguisher
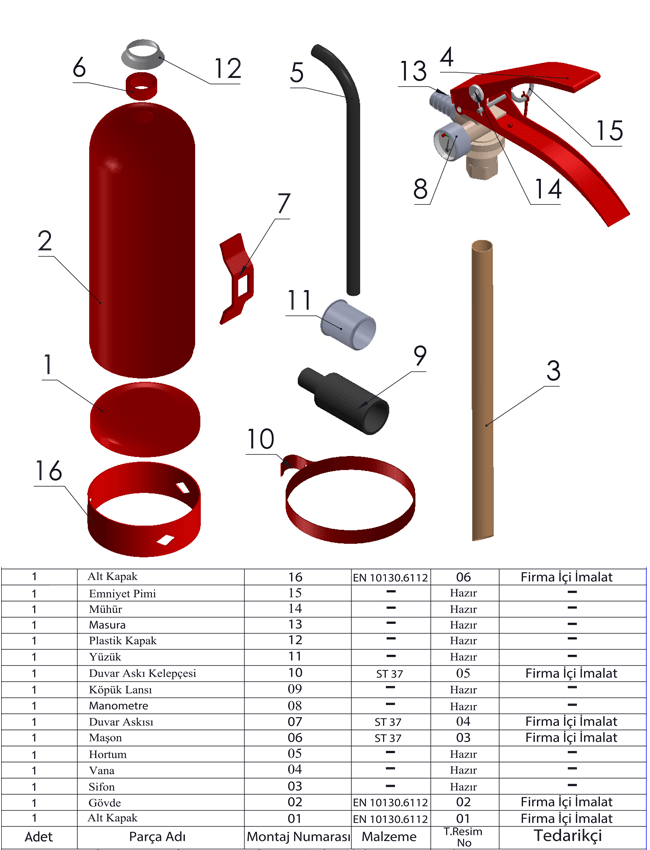
A fire extinguisher consists of several key components that work together to ensure effective operation. The main components include the cylinder, pressure gauge, discharge nozzle or hose, handle and trigger mechanism, and the extinguishing agent.
The cylinder is the main body of the extinguisher, typically made from steel or aluminum, designed to hold the extinguishing agent under pressure. The pressure gauge indicates the internal pressure of the extinguisher, ensuring it is within the operational range for effective use.
The discharge nozzle or hose directs the extinguishing agent towards the fire. Depending on the type of extinguisher, the nozzle design may vary to optimize the delivery of the agent. The handle and trigger mechanism allow the user to control the discharge of the extinguishing agent. When the handle is squeezed, the trigger mechanism opens a valve, releasing the agent.
The extinguishing agent itself varies depending on the type of fire extinguisher. It can be water, foam, dry powder, carbon dioxide, or a wet chemical solution, each formulated to combat specific fire classes effectively.
How Fire Extinguishers Work
The operational mechanism of fire extinguishers varies according to the type of extinguisher. Understanding how each type works is crucial for effective fire suppression.
Water-based extinguishers work by cooling the burning material. When the extinguisher is activated, water is expelled under pressure, soaking the combustibles and lowering their temperature below the ignition point.
Foam extinguishers create a thick foam that blankets the burning liquid, cutting off the oxygen supply and preventing the vapor from reaching the flames. This dual action of smothering and cooling makes foam extinguishers effective for both Class A and B fires.
Dry powder extinguishers interrupt the chemical reaction of the fire. The powder forms a barrier between the fuel and the oxygen, effectively smothering the flames and stopping the fire from spreading.
Carbon dioxide extinguishers work by displacing oxygen around the fire and releasing a cold discharge that cools the fuel. This makes them suitable for Class B and electrical fires, where using water-based extinguishers would be hazardous.
Wet chemical extinguishers contain a special solution that reacts with cooking oils and fats to form a soapy layer on the surface, cutting off the oxygen supply and cooling the flames. This reaction is particularly effective in commercial kitchens where Class F fires are common.
Manufacturing of Fire Extinguishers
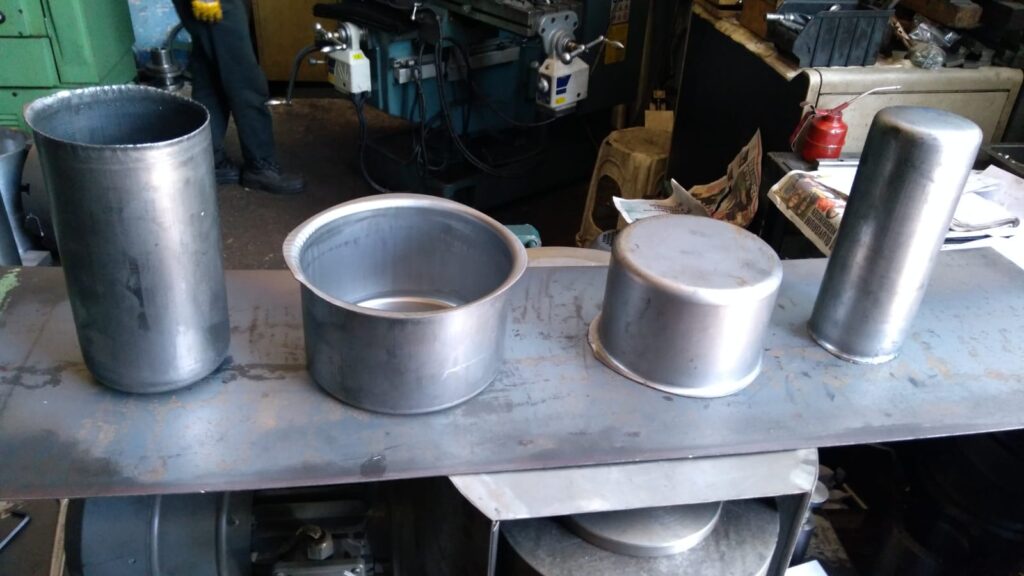
The manufacturing process of fire extinguishers involves several stages, from raw material sourcing to final assembly and quality control.
Raw materials such as steel or aluminum are sourced for cylinder production. These materials must meet stringent quality standards to ensure the durability and safety of the extinguisher. The design and engineering phase involves creating specifications for each component, ensuring they meet the required performance criteria.
The production process begins with cylinder manufacturing, where sheets of metal are cut, formed, and welded into the cylindrical shape. The cylinders are then treated to prevent corrosion and tested for pressure resistance. Once the cylinders pass these tests, they move on to the assembly line.
During assembly, various components such as the pressure gauge, handle, trigger mechanism, and discharge nozzle are fitted to the cylinder. The extinguisher is then filled with the appropriate extinguishing agent under controlled conditions to ensure accurate filling and prevent contamination.
Quality control is a critical aspect of the manufacturing process. Each extinguisher undergoes rigorous testing to verify its functionality, pressure stability, and discharge performance. Testing includes checking for leaks, ensuring the correct pressure, and validating the effectiveness of the extinguishing agent.
Quality Standards and Certifications
Fire extinguishers must comply with various international and local quality standards and certifications to ensure their reliability and safety. Standards such as those set by the National Fire Protection Association (NFPA), Underwriters Laboratories (UL), and the International Organization for Standardization (ISO) specify the requirements for design, performance, and testing of fire extinguishers.
The certification process involves third-party testing to verify that the extinguishers meet these standards. Manufacturers must provide documentation and samples for evaluation, and only those extinguishers that pass the stringent tests receive certification.
Compliance with these standards is crucial for manufacturers, as it not only ensures the safety and effectiveness of their products but also enhances their credibility in the market.
Challenges in Fire Extinguisher Manufacturing
The manufacturing of fire extinguishers presents several challenges, including material sourcing, technological advancements, regulatory compliance, and environmental concerns.
Material sourcing and cost management are critical challenges, as manufacturers need to obtain high-quality materials at competitive prices. Fluctuations in material costs can impact production expenses and pricing strategies.
Technological advancements also pose challenges, as manufacturers must continuously innovate to keep up with new developments in fire suppression technology. This requires significant investment in research and development to create more effective and user-friendly extinguishers.
Regulatory compliance is another major challenge, as manufacturers must adhere to stringent standards and regulations. Keeping up with changing regulations and ensuring compliance can be resource-intensive.
Environmental concerns and sustainability are increasingly important in fire extinguisher manufacturing. Manufacturers are under pressure to develop eco-friendly extinguishing agents and recyclable materials to minimize their environmental impact.
Future Trends in Fire Extinguisher Manufacturing
The future of fire extinguisher manufacturing is likely to be shaped by innovations in technology, eco-friendly materials, and smart systems.
Innovations in extinguisher technology are expected to focus on improving the efficiency and effectiveness of fire suppression. This includes developing new extinguishing agents that can tackle a wider range of fire classes and enhance user safety.
Smart extinguishers equipped with sensors and connectivity features are also on the horizon. These extinguishers can provide real-time data on their status, alert users to maintenance needs, and even integrate with building management systems for automated fire response.
Eco-friendly materials and agents are becoming a priority as manufacturers strive to reduce their environmental footprint. Research into biodegradable agents and recyclable components is expected to lead to greener fire extinguishers.
Conclusion
Fire extinguishers play a critical role in fire safety, providing an essential means of suppressing fires in their early stages. Understanding the different types of extinguishers, their components, and how they work is crucial for effective fire response. The manufacturing process of fire extinguishers involves careful sourcing of materials, precise engineering, and rigorous quality control to ensure their reliability and safety.
Challenges in the industry include material sourcing, technological advancements, regulatory compliance, and environmental concerns. However, future trends such as smart extinguishers and eco-friendly materials promise to drive innovation and sustainability in the industry.
As fire risks continue to evolve, the fire extinguisher manufacturing industry must adapt and innovate to meet the demands of safety and environmental responsibility. Through continued research and development, manufacturers can enhance the effectiveness and sustainability of fire extinguishers, contributing to a safer world.
Fire extinguishers are an essential safety component in any home or business. As such, the demand for fire extinguisher manufacturing plants is on the rise. Fire extinguisher manufacturing plants are responsible for producing fire extinguishers that meet rigorous safety standards and provide effective protection against fires.
It is important to ensure that fire extinguisher manufacturing dates are up-to-date. So that use of them can be effective in the event of a fire. Manufacturers carefully determine the fire extinguisher manufacturing date. They adhere to industry standards and regulations to ensure their reliability and efficacy. In this essay, we will discuss the importance of checking the fire extinguisher manufacturing date, as well as provide tips on how to do it correctly. Additionally, it will cover some common use cases for fire extinguishers. And lastly, it explains why the manufacturing of them is regular.
Fire extinguisher manufacturing involves the production of devices designed to suppress or extinguish small fires. It is a process that requires careful attention to detail, adherence to safety standards, and compliance with applicable regulations. Here is an overview of the fire extinguisher manufacturing process:
- Design and Planning: The first step in fire extinguisher manufacturing is the design and planning phase. This involves determining the types of fire extinguishers to be produced, selecting appropriate materials, and developing specifications and drawings.
- Raw Material Procurement: The next step is procuring the necessary raw materials for manufacturing. Common materials include cylinders (usually made of steel or aluminum), valves, handles, pressure gauges, extinguishing agents (such as water, foam, or dry chemical powders), and various accessories.
- Cylinder Preparation: The cylinders are prepared for assembly by cleaning and inspecting them for any defects or imperfections. The cylinders may also undergo surface treatment processes, such as sandblasting or coating, to enhance their durability and corrosion resistance.
- Component Manufacturing: The manufacturing of various components, such as valves, handles, pressure gauges, and accessories, takes place concurrently. These components are typically manufactured using specialized machinery or processes specific to each component type.
- Assembly: Once the components are ready, the fire extinguishers are assembled. This involves fitting the valves, handles, pressure gauges, and other accessories onto the cylinders according to the specific design and specifications. The assembly process requires precise alignment, proper sealing, and secure fastening of the components.
- Extinguishing Agent Filling: The extinguishing agent, which can vary depending on the type of fire extinguisher, is filled into the assembled cylinders. The filling process must be carefully controlled to ensure the correct amount of agent is added and that there are no leaks or contamination.
- Pressure Testing: The filled fire extinguishers undergo pressure testing to verify their structural integrity and pressure containment capability. This involves subjecting the extinguishers to hydraulic or pneumatic pressure to ensure they can withstand the internal pressure generated during operation.
- Finishing and Inspection: After pressure testing, the fire extinguishers undergo final finishing processes, such as painting or labeling, to enhance their appearance and provide important information to users. A thorough inspection is conducted to check for any manufacturing defects, ensure proper assembly, and verify compliance with quality standards.
- Packaging and Distribution: The fire extinguishers are packaged appropriately to protect them during transportation and storage. Packaging materials should provide adequate cushioning and secure containment. The extinguishers are then ready for distribution to customers or retail outlets.
- Quality Control and Certification: Throughout the manufacturing process, quality control measures are implemented to ensure the fire extinguishers meet the required quality standards and regulatory compliance. Certification by recognized certification bodies may be obtained to validate the extinguishers’ compliance with relevant standards and regulations.
Fire extinguisher manufacturing requires strict adherence to safety protocols, quality control measures, and compliance with regulations to ensure the production of reliable and effective devices. Manufacturers should closely follow industry standards and best practices to ensure the manufacturing process produces high-quality fire extinguishers that can effectively suppress fires and safeguard lives and property.
Fire Extinguisher Manufacturing Plant Cost
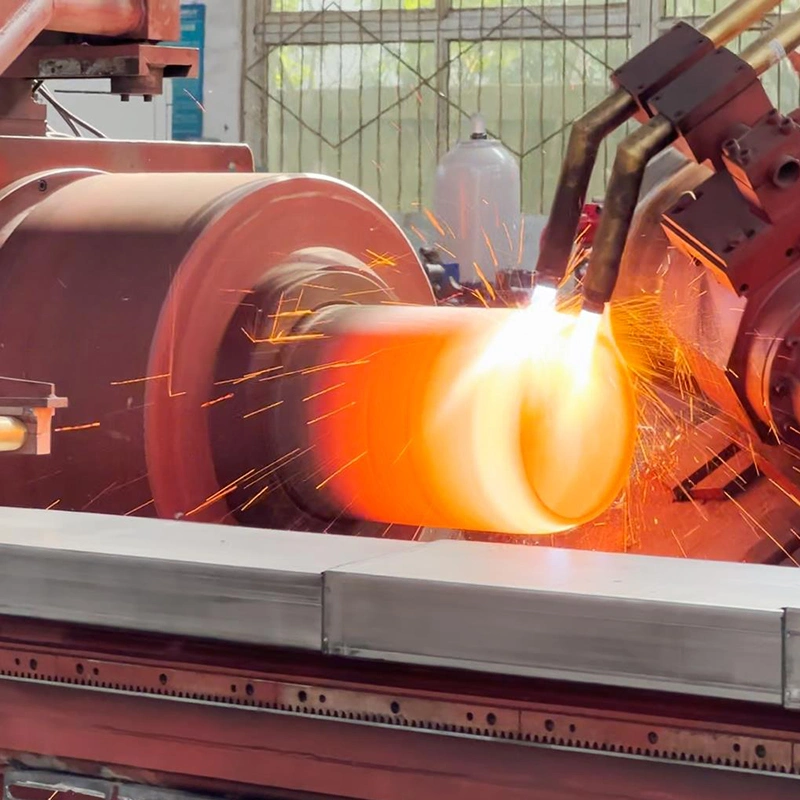
The establishment of a fire extinguisher manufacturing plant involves careful planning and considerable investment. From choosing an appropriate location to acquiring machinery and raw materials, every step demands attention. The aim is to detail and comply with safety regulations. Furthermore, the costs associated with setup, raw materials, labor, and compliance add to the financial considerations. By understanding the intricacies of the manufacturing process and estimating costs accurately, entrepreneurs can embark on this essential venture. They can contribute to fire safety and protection in various settings.
The cost of setting up a fire extinguisher manufacturing plant depends on the size, location, and type of equipment required. An experienced team of engineers and technicians is necessary to build a successful fire extinguisher manufacturing plant. The cost of the equipment for this type of manufacturing can vary with the type and quality of materials used. Additionally, adhering to safety regulations is important. To ensure that all products meet industry standards. With proper planning and implementation, fire extinguisher manufacturers can create a safe workplace environment. While providing quality products at competitive prices.
The cost of establishing a fire extinguisher manufacturing plant can vary. Significantly those factors are such as size, location, and technology used. The cost of setting up a plant includes purchasing the necessary equipment. Also, it includes training staff and obtaining certifications from relevant authorities. Additionally, it is important to consider the ongoing costs relevant to running a plant such as maintenance and repairs. With the right infrastructure in place, fire extinguisher manufacturers can ensure that their products are safe and reliable. While also keeping their production costs low.
Fire extinguisher manufacturing is an important industry that provides vital safety equipment to individuals and businesses around the world. It requires a significant investment. In terms of capital, materials, and labor to build and operate a fire extinguisher manufacturing plant. The cost of setting up a fire extinguisher manufacturing plant can vary greatly depending on the size of the facility, the type of machinery used, and other factors.
Fire Extinguisher Manufacturing Process
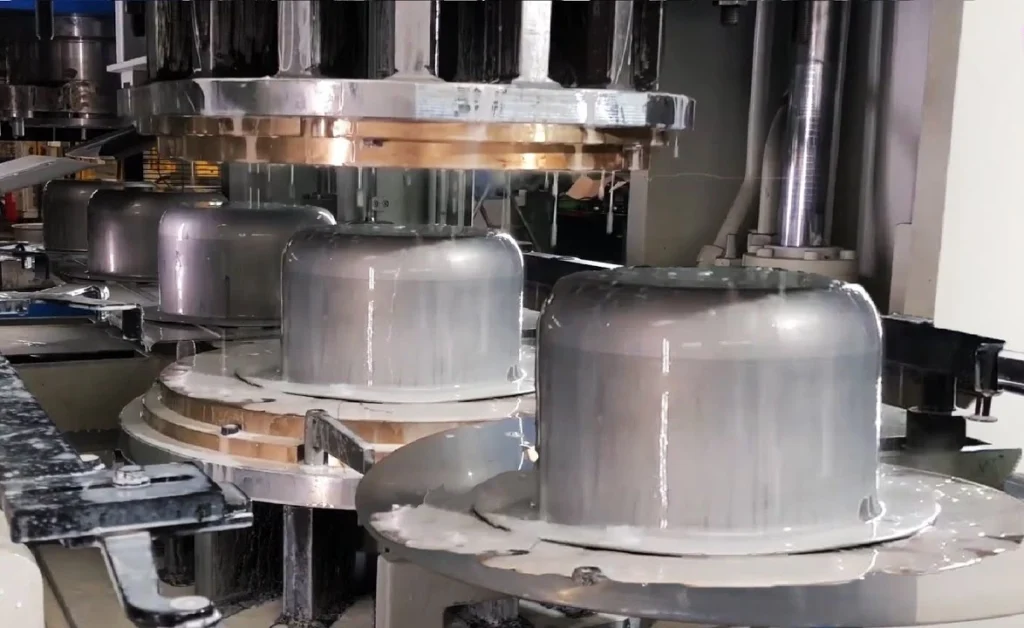
The fire extinguisher manufacturing process encompasses several stages. It begins with the design and selection of materials. And it concludes with rigorous testing and quality control measures. While specific methodologies may vary among manufacturers, we will discuss the fundamental steps.
The first step is design and planning. The design stage involves engineering and designing a fire extinguisher that meets the necessary safety standards. This includes determining the type, size, and capacity of the extinguisher. As well as selecting appropriate materials. The next step is material selection. Fire extinguishers are typically composed of a metal cylinder, a pressure vessel, an extinguishing agent, and various mechanical components. Choosing these materials carefully provides ensuring durability, resistance to corrosion, and compatibility with the extinguishing agent.
The manufacturing process continues with the fabrication of the metal cylinder. Steel or aluminum is commonly used for its strength and resistance to high pressures. Shaping, welding, and testing the metal is to ensure its integrity and ability to contain the extinguishing agent. The following step is assembly and filling. During the assembly stage, the process is fitting the cylinder with essential components such as valves, pressure gauges, handles, and discharge nozzles. The extinguishing agent, specific to the extinguisher type (e.g., water, foam, dry chemical), is then filled under controlled conditions. The reason is to achieve the required pressure and volume.
The last step is testing and quality control. Quality control plays a crucial role in fire extinguisher manufacturing. Each extinguisher must undergo rigorous testing to ensure it meets safety standards and functional requirements. Pressure tests, leakage checks, and discharge tests are conducted to validate the extinguisher’s performance and reliability.
Fire Extinguisher Manufacturing Companies
Fire extinguishers are a critical component of safety and security in many industries. Manufacturing fire extinguishers require specialized knowledge and expertise. The reason is to ensure that the product meets all safety standards and regulations. As a fire extinguisher supplier, it is important to have access to reliable manufacturers. They can provide quality products at competitive prices.
These fire extinguisher manufacturing companies have a wide range of products to offer. Ranging from basic handheld units to complex automatic systems. Usage of all of them can be in commercial buildings and other public areas. The quality of these products is also top-notch. It ensures they meet all safety standards and regulations set by the government. With their help, as a customer, we can all feel safer knowing. As a result, we have access to reliable firefighting equipment when we need it most.
Fire extinguishers are an essential safety device for any home or business. Fire extinguisher manufacturing companies are responsible for producing a wide range of fire extinguishers. These companies use advanced technology and reliable materials to create products. They meet global safety and performance standards. They also employ stringent quality control measures to ensure that their products are reliable and effective in emergencies. Also, they are tailored to meet diverse fire risks and environments. These companies typically employ experts in fire safety engineering. Furthermore, the materials science, and product design to develop effective and reliable fire extinguishers. They follow stringent quality control measures to adhere to industry standards and regulations. Additionally, they ensure that the final products are safe and efficient.
As such, the demand for fire extinguisher manufacturing companies in developing countries is on the rise. India is one of the leaders in this industry, with many fire extinguisher manufacturing companies operating in the country. With the increasing demand for fire extinguishers, these companies have become an integral part of India’s economy.
At EMS Metalworking Machinery, we strive to provide our customers with the best possible products for their fire protection needs. We partner with experienced manufacturers. Those use cutting-edge technology and materials to create fire extinguishers of the highest quality. Our team has the experienced know-how to provide our customers with the best service possible. For example, we provide from helping them find the right product for their needs, by providing reliable delivery times and after-sales service. We use advanced technologies and processes to ensure that our products are reliable and effective. Furthermore, we also provide training services to help customers understand how to use their fire extinguishers correctly. With the help of these companies, our customers can be sure that their premises are adequately protected from any potential fires.
Being a Fire Extinguisher Supplier
Whether you need a fire extinguisher supplier near you or an online provider, there are plenty of options available to meet your needs. From traditional brick-and-mortar stores to online suppliers, it is important to find a reliable source for your fire protection needs. With careful research and consideration, you can find a trustworthy fire extinguisher manufacturer who can provide quality products at competitive prices.
As a fire extinguisher supplier, our company specializes in the manufacturing, distribution, and maintenance of fire extinguishers. They are responsible for producing these essential safety devices that can save lives and property in the event of a fire emergency. Their role extends beyond the manufacturing process as they often offer additional services. Those are such as installation, training, and regular maintenance to ensure the optimal performance of the extinguishers.
Fire extinguisher suppliers provide the materials needed to manufacture fire extinguishers, including tanks, valves, nozzles, and hoses. They also offer technical support and advice on how to properly install and maintain fire extinguishers. With more businesses looking for reliable fire extinguisher suppliers near them, it is important to understand the process of manufacturing these life-saving devices.
EMS Metalworking Machinery
We design, manufacture and assembly metalworking machinery such as:
- Hydraulic transfer press
- Glass mosaic press
- Hydraulic deep drawing press
- Casting press
- Hydraulic cold forming press
- Hydroforming press
- Composite press
- Silicone rubber moulding press
- Brake pad press
- Melamine press
- SMC & BMC Press
- Labrotaroy press
- Edge cutting trimming machine
- Edge curling machine
- Trimming beading machine
- Trimming joggling machine
- Cookware production line
- Pipe bending machine
- Profile bending machine
- Bandsaw for metal
- Cylindrical welding machine
- Horizontal pres and cookware
- Kitchenware, hotelware
- Bakeware and cuttlery production machinery
as a complete line as well as an individual machine such as:
- Edge cutting trimming beading machines
- Polishing and grinding machines for pot and pans
- Hydraulic drawing presses
- Circle blanking machines
- Riveting machine
- Hole punching machines
- Press feeding machine
You can check our machinery at work at: EMS Metalworking Machinery – YouTube
Applications:
- Beading and ribbing
- Flanging
- Trimming
- Curling
- Lock-seaming
- Ribbing
- Flange-punching