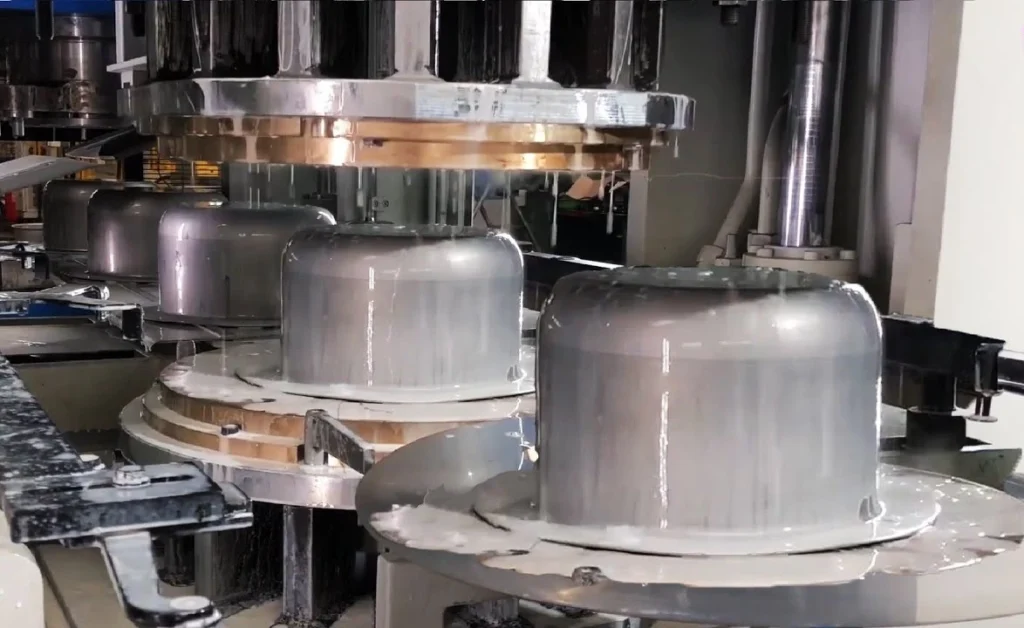
Fire Extinguisher Manufacturing Plant Cost and Machinery Prices from the Manufacturer. High quality & Low price & Free consultation
The cost of setting up a fire extinguisher manufacturing plant can vary depending on several factors, including the scale of the operation, production capacity, equipment selection, facility requirements, and location. Here are some key cost considerations when planning a fire extinguisher manufacturing plant:
- Facility Costs: This includes the purchase or lease of a suitable building or space for the manufacturing plant. The cost will depend on the location, size, condition, and amenities of the facility.
- Equipment Costs: Fire extinguisher manufacturing requires specialized equipment, such as cylinder manufacturing machinery, valve assembly machines, filling equipment, testing and quality control devices, powder coating or painting systems, labeling machines, and packaging equipment. The cost of these machines can vary based on their quality, capacity, and automation level.
- Raw Materials: The cost of raw materials, including steel or aluminum cylinders, extinguishing agents, valves, fittings, powder coatings, labels, and packaging materials, needs to be considered. The prices of these materials can fluctuate based on market conditions and suppliers.
- Utilities and Infrastructure: Costs related to utilities such as electricity, water, gas, and internet connection need to be factored in. Additionally, infrastructure requirements such as ventilation systems, compressed air supply, and fire safety systems will also contribute to the overall cost.
- Labor Costs: The cost of labor includes salaries or wages for production workers, technicians, engineers, quality control personnel, and administrative staff. Labor costs can vary depending on the skill level, local labor market, and any specific training requirements.
- Regulatory and Compliance Costs: Fire extinguisher manufacturing is subject to regulatory requirements and compliance standards. Costs associated with obtaining licenses, certifications, permits, and complying with safety regulations should be considered.
- Maintenance and Repair Costs: Machinery and equipment will require regular maintenance, servicing, and occasional repairs. These costs should be accounted for to ensure the smooth operation of the manufacturing plant.
- Marketing and Sales Costs: Promoting and marketing the fire extinguishers, attending industry trade shows, advertising, and establishing distribution channels may require a budget allocation.
- Contingency and Miscellaneous Costs: It is advisable to allocate a portion of the budget for unforeseen expenses, contingencies, and miscellaneous costs that may arise during the setup and initial operation of the manufacturing plant.
It is challenging to provide an exact cost without specific details about the scale and scope of the manufacturing plant. The costs can range from hundreds of thousands to millions of dollars, depending on the factors mentioned above. Conducting a comprehensive feasibility study and working with industry experts can help in estimating the cost and developing a realistic budget for establishing a fire extinguisher manufacturing plant.
Fire Extinguisher Manufacturing Machine
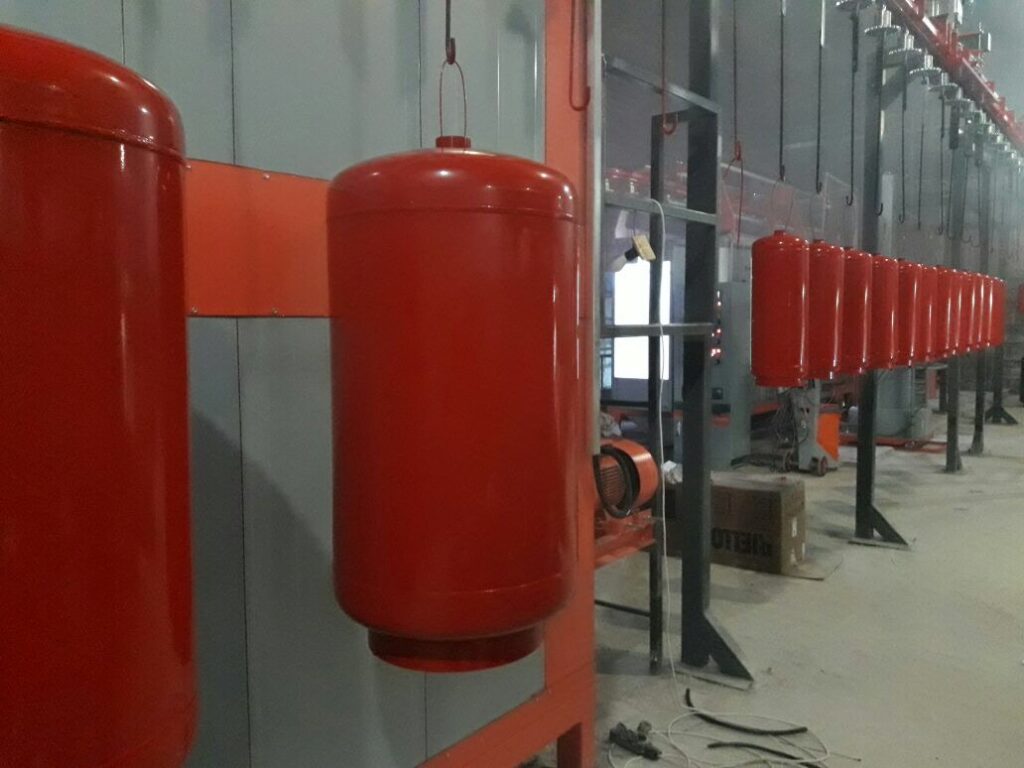
Fire extinguisher making machines are the latest technology in fire safety equipment. Fire extinguisher manufacturing machines are an essential part of the fire safety industry. The use of them is to create fire extinguishers. The aim of their design is to put out fires in a safe and effective manner. By using these machines, manufacturers can quickly and efficiently produce fire extinguishers that meet all safety requirements and standards. With the help of these machines, manufacturers can ensure that their products have those features: The first one is being up-to-date with the latest technology and regulations. The second one is providing customers with reliable fire protection solutions.
Fire extinguisher equipment is an essential safety tool for controlling fires in various settings, including machine shops, offices, homes, and public spaces. The use of a fire extinguisher for a machine shop is very critical. The risk of fires must be high due to the presence of flammable materials, equipment, and machinery. Due to that, a fire extinguisher manufacturing machine can produce reliable and efficient fire extinguishers. As a result, they can help control fires in a machine shop and prevent significant damage to property and loss of life.
The mission of fire extinguisher manufacturing machines is to produce fire extinguishers efficiently and to the highest quality standards. These machines have equipment with various components that work together to produce high-quality extinguishers efficiently. One of the key components is the cylinder forming machine. This machine shapes the metal sheets into cylindrical shapes that form the body of the extinguisher. The cylinder forming machine has equipment with rollers that bend the metal sheets to the required diameter and length. And following that, a welding system seals the seam to create a seamless cylinder.
Fire extinguisher making machines are the latest technology in fire safety equipment. Fire extinguisher manufacturing machines are an essential part of the fire safety industry. The use of them is to create fire extinguishers. The aim of their design is to put out fires in a safe and effective manner. By using these machines, manufacturers can quickly and efficiently produce fire extinguishers that meet all safety requirements and standards. With the help of these machines, manufacturers can ensure that their products have those features: The first one is being up-to-date with the latest technology and regulations. The second one is providing customers with reliable fire protection solutions.
The Process of Fire Extinguisher Manufacturing Machine
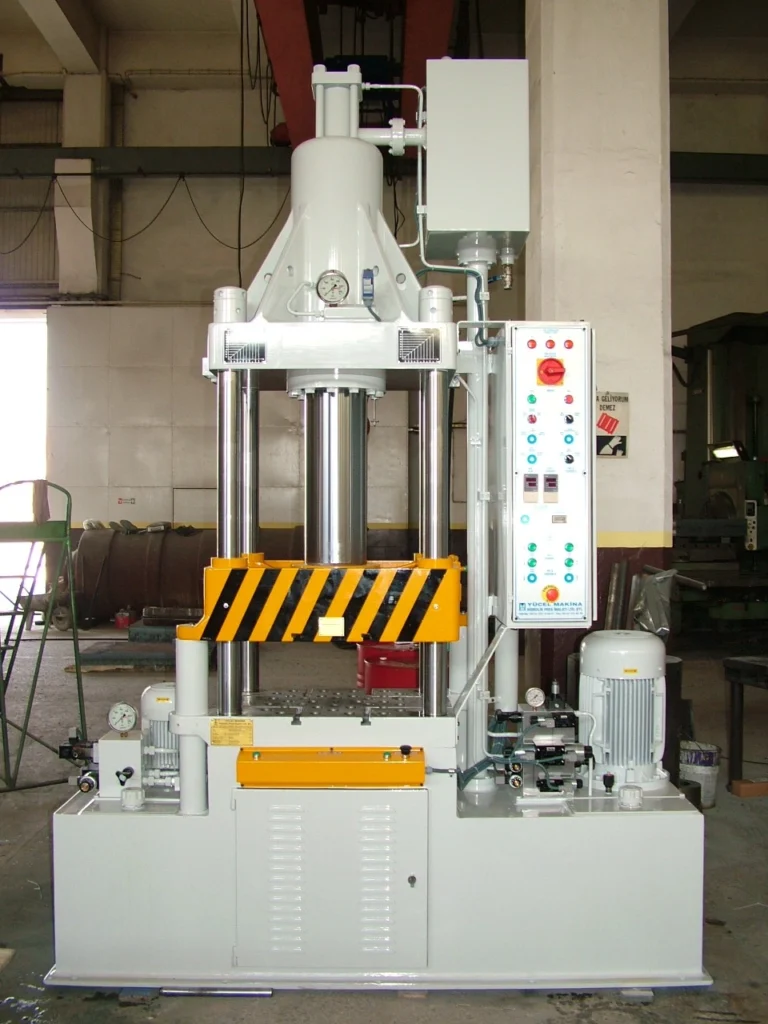
The fire extinguisher manufacturing process involves several critical steps, from cylinder forming to filling and testing. Whole the process requires precision and expertise to ensure that the final product is safe and effective. Once the cylinder is formed, it is moved to the next station, where the valve and handle are attached. The valve is the heart of the extinguisher. As it regulates the flow of the extinguishing agent. Additionally, it allows the user to control the discharge. The purpose of attaching the handle is to the valve to provide a grip for the user to hold the extinguisher.
After the valve and handle are attached, the extinguishing agent is filled into the cylinder. Depending on the type of extinguisher being manufactured, the filling process may involve adding dry powder, foam, carbon dioxide, or water-based agents. The filling process must be precise to ensure that the extinguisher contains the correct amount of the extinguishing agent. Once filling the cylinder, the final step is to test the extinguisher to ensure it meets safety standards. The testing process involves checking the pressure of the extinguisher and the performance of the valve and nozzle. Performing a leak test is also necessary to ensure that the cylinder is airtight and can maintain pressure over time.
Fire extinguishers come in different sizes and types, including dry powder, foam, carbon dioxide, and water-based extinguishers. The fire extinguisher manufacturing process involves assembling the various components of the extinguisher. These are such as the cylinder, valve, handle, and extinguishing agent. And the last one is testing the final product to ensure it meets safety standards.
Being A Fire Extinguisher Manufacturing Machine Manufacturer
Fire extinguisher making machines are used by fire fighting equipment manufacturers worldwide, including in Turkey. Firefighting equipment manufacturers worldwide, including those in Turkey, rely on these machines to produce reliable and efficient extinguishers. Turkey is among the leading producers of fire extinguisher production machines globally. As one of the firefighting equipment manufacturers in Turkey, EMS Metalworking Machinery produces superior fire extinguisher making machines. Our mission is to make you able to produce a range of qualified extinguishers suitable for different types of fires.
Since our establishment, EMS Metalworking Machinery has been an advanced leader in the development and manufacture of reliable fire extinguisher manufacturing machines. We offer a complete line of fire extinguishers for machine shops to manufacture fire fighting equipment. Our mission is to provide a customized fire extinguisher making machines product range that meets our customer’s needs. Because, we manufacture reliable, low maintenance, and cost-effective fire extinguisher making machines that can seamlessly provide you to do fire fighting equipment manufacturing.
In conclusion, the fire extinguisher making machine is an essential tool for producing high-quality fire extinguishers that can save lives and protect property in case of a fire. Our product group of fire extinguisher manufacturing machines can meet the highest safety standards in a machine shop. For those interested in learning more about the fire extinguisher manufacturing process, our company has many resources available. We can provide the fire extinguisher manufacturing process pdf documents and industry associations that provide guidance and support to manufacturers.
Fire extinguishers are essential devices designed to control or extinguish small fires in emergency situations. They are critical components in the fire safety protocols of residential, commercial, and industrial settings. Fire extinguishers are often the first line of defense against fire hazards, providing a means to suppress flames before they escalate into more severe incidents. Their importance cannot be overstated, particularly in environments where the risk of fire is high due to the presence of flammable materials, electrical equipment, or industrial processes. This document aims to provide a comprehensive overview of fire extinguishers, covering their types, components, operational mechanisms, manufacturing processes, quality standards, challenges, and future trends in the industry.
Types of Fire Extinguishers
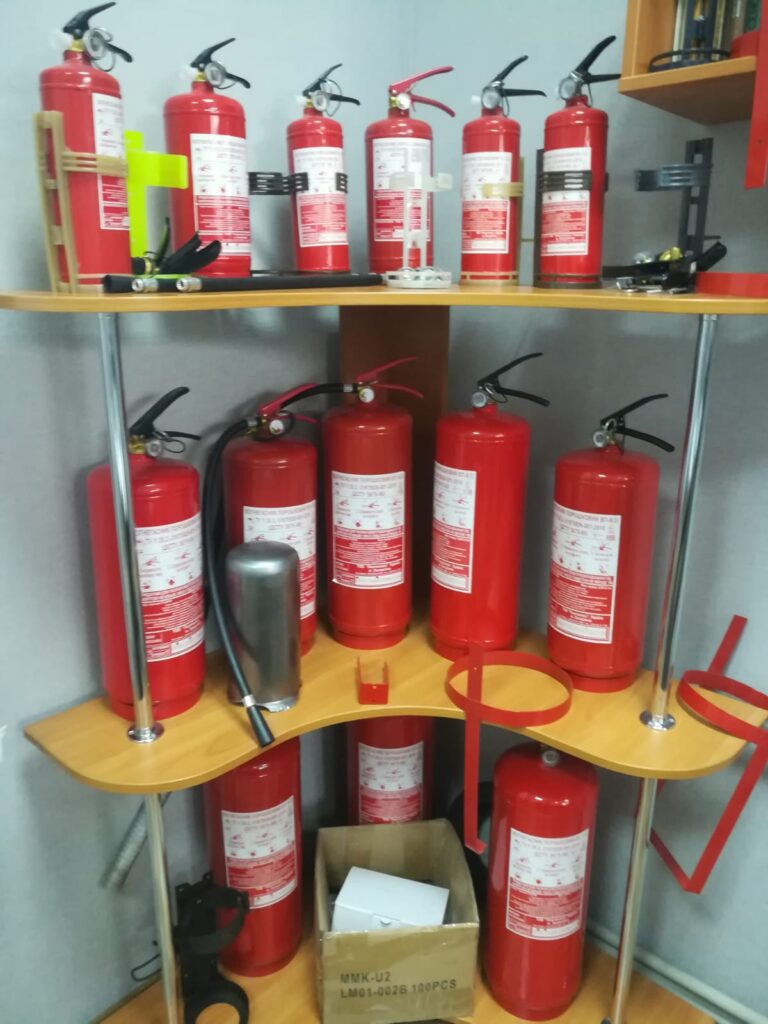
Fire extinguishers come in various types, each designed to tackle specific classes of fires. The primary types include water-based extinguishers, foam extinguishers, dry powder extinguishers, carbon dioxide extinguishers, and wet chemical extinguishers.
Water-based extinguishers are suitable for Class A fires, which involve ordinary combustibles such as wood, paper, and textiles. These extinguishers work by cooling the burning material below its ignition temperature.
Foam extinguishers are effective against both Class A and Class B fires. Class B fires involve flammable liquids like petrol, oil, and solvents. The foam forms a blanket over the burning liquid, cutting off the oxygen supply and preventing re-ignition.
Dry powder extinguishers are versatile and can be used on Class A, B, and C fires. Class C fires involve gases such as propane, butane, and methane. The powder works by interrupting the chemical reaction of the fire.
Carbon dioxide extinguishers are ideal for Class B and electrical fires. They work by displacing oxygen and reducing the heat with a cold discharge, effectively suffocating the fire.
Wet chemical extinguishers are specifically designed for Class F fires, which involve cooking oils and fats. The chemical forms a soap-like solution on the surface of the burning oil, creating a barrier that separates the fuel from oxygen and cools the flames.
There are also specialized extinguishers for metal fires, such as Class D extinguishers, which use agents like sodium chloride to smother the flames and absorb the heat.
Components of a Fire Extinguisher
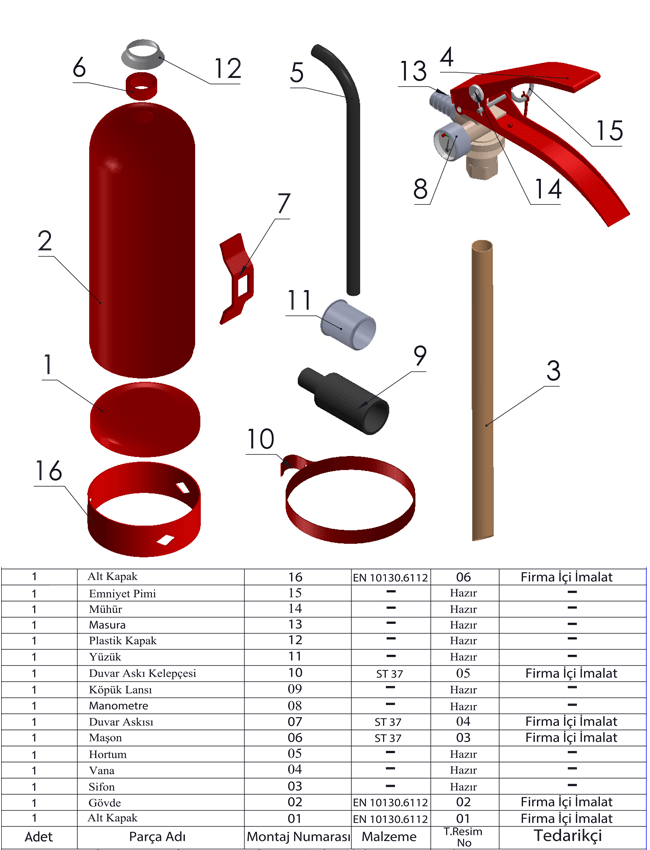
A fire extinguisher consists of several key components that work together to ensure effective operation. The main components include the cylinder, pressure gauge, discharge nozzle or hose, handle and trigger mechanism, and the extinguishing agent.
The cylinder is the main body of the extinguisher, typically made from steel or aluminum, designed to hold the extinguishing agent under pressure. The pressure gauge indicates the internal pressure of the extinguisher, ensuring it is within the operational range for effective use.
The discharge nozzle or hose directs the extinguishing agent towards the fire. Depending on the type of extinguisher, the nozzle design may vary to optimize the delivery of the agent. The handle and trigger mechanism allow the user to control the discharge of the extinguishing agent. When the handle is squeezed, the trigger mechanism opens a valve, releasing the agent.
The extinguishing agent itself varies depending on the type of fire extinguisher. It can be water, foam, dry powder, carbon dioxide, or a wet chemical solution, each formulated to combat specific fire classes effectively.
How Fire Extinguishers Work
The operational mechanism of fire extinguishers varies according to the type of extinguisher. Understanding how each type works is crucial for effective fire suppression.
Water-based extinguishers work by cooling the burning material. When the extinguisher is activated, water is expelled under pressure, soaking the combustibles and lowering their temperature below the ignition point.
Foam extinguishers create a thick foam that blankets the burning liquid, cutting off the oxygen supply and preventing the vapor from reaching the flames. This dual action of smothering and cooling makes foam extinguishers effective for both Class A and B fires.
Dry powder extinguishers interrupt the chemical reaction of the fire. The powder forms a barrier between the fuel and the oxygen, effectively smothering the flames and stopping the fire from spreading.
Carbon dioxide extinguishers work by displacing oxygen around the fire and releasing a cold discharge that cools the fuel. This makes them suitable for Class B and electrical fires, where using water-based extinguishers would be hazardous.
Wet chemical extinguishers contain a special solution that reacts with cooking oils and fats to form a soapy layer on the surface, cutting off the oxygen supply and cooling the flames. This reaction is particularly effective in commercial kitchens where Class F fires are common.
Manufacturing of Fire Extinguishers
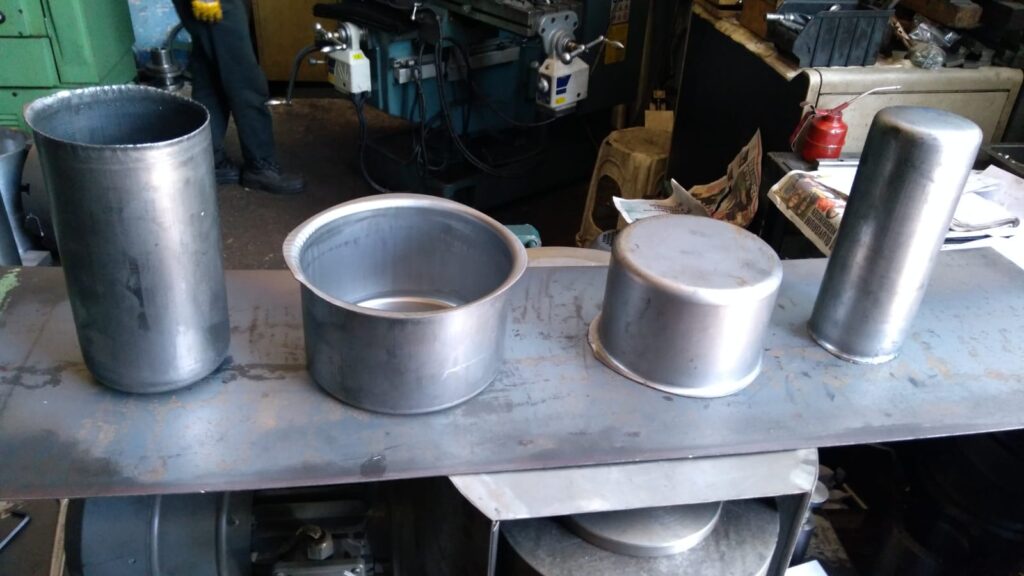
The manufacturing process of fire extinguishers involves several stages, from raw material sourcing to final assembly and quality control.
Raw materials such as steel or aluminum are sourced for cylinder production. These materials must meet stringent quality standards to ensure the durability and safety of the extinguisher. The design and engineering phase involves creating specifications for each component, ensuring they meet the required performance criteria.
The production process begins with cylinder manufacturing, where sheets of metal are cut, formed, and welded into the cylindrical shape. The cylinders are then treated to prevent corrosion and tested for pressure resistance. Once the cylinders pass these tests, they move on to the assembly line.
During assembly, various components such as the pressure gauge, handle, trigger mechanism, and discharge nozzle are fitted to the cylinder. The extinguisher is then filled with the appropriate extinguishing agent under controlled conditions to ensure accurate filling and prevent contamination.
Quality control is a critical aspect of the manufacturing process. Each extinguisher undergoes rigorous testing to verify its functionality, pressure stability, and discharge performance. Testing includes checking for leaks, ensuring the correct pressure, and validating the effectiveness of the extinguishing agent.
Quality Standards and Certifications
Fire extinguishers must comply with various international and local quality standards and certifications to ensure their reliability and safety. Standards such as those set by the National Fire Protection Association (NFPA), Underwriters Laboratories (UL), and the International Organization for Standardization (ISO) specify the requirements for design, performance, and testing of fire extinguishers.
The certification process involves third-party testing to verify that the extinguishers meet these standards. Manufacturers must provide documentation and samples for evaluation, and only those extinguishers that pass the stringent tests receive certification.
Compliance with these standards is crucial for manufacturers, as it not only ensures the safety and effectiveness of their products but also enhances their credibility in the market.
Challenges in Fire Extinguisher Manufacturing
The manufacturing of fire extinguishers presents several challenges, including material sourcing, technological advancements, regulatory compliance, and environmental concerns.
Material sourcing and cost management are critical challenges, as manufacturers need to obtain high-quality materials at competitive prices. Fluctuations in material costs can impact production expenses and pricing strategies.
Technological advancements also pose challenges, as manufacturers must continuously innovate to keep up with new developments in fire suppression technology. This requires significant investment in research and development to create more effective and user-friendly extinguishers.
Regulatory compliance is another major challenge, as manufacturers must adhere to stringent standards and regulations. Keeping up with changing regulations and ensuring compliance can be resource-intensive.
Environmental concerns and sustainability are increasingly important in fire extinguisher manufacturing. Manufacturers are under pressure to develop eco-friendly extinguishing agents and recyclable materials to minimize their environmental impact.
Future Trends in Fire Extinguisher Manufacturing
The future of fire extinguisher manufacturing is likely to be shaped by innovations in technology, eco-friendly materials, and smart systems.
Innovations in extinguisher technology are expected to focus on improving the efficiency and effectiveness of fire suppression. This includes developing new extinguishing agents that can tackle a wider range of fire classes and enhance user safety.
Smart extinguishers equipped with sensors and connectivity features are also on the horizon. These extinguishers can provide real-time data on their status, alert users to maintenance needs, and even integrate with building management systems for automated fire response.
Eco-friendly materials and agents are becoming a priority as manufacturers strive to reduce their environmental footprint. Research into biodegradable agents and recyclable components is expected to lead to greener fire extinguishers.
Conclusion
Fire extinguishers play a critical role in fire safety, providing an essential means of suppressing fires in their early stages. Understanding the different types of extinguishers, their components, and how they work is crucial for effective fire response. The manufacturing process of fire extinguishers involves careful sourcing of materials, precise engineering, and rigorous quality control to ensure their reliability and safety.
Challenges in the industry include material sourcing, technological advancements, regulatory compliance, and environmental concerns. However, future trends such as smart extinguishers and eco-friendly materials promise to drive innovation and sustainability in the industry.
As fire risks continue to evolve, the fire extinguisher manufacturing industry must adapt and innovate to meet the demands of safety and environmental responsibility. Through continued research and development, manufacturers can enhance the effectiveness and sustainability of fire extinguishers, contributing to a safer world.
Fire Extinguisher Manufacturing Plant
A fire extinguisher manufacturing plant is a facility that produces fire extinguishers for commercial and industrial use. The plant typically has a number of different departments, including:
- Metalworking: This department is responsible for the production of the metal components of the fire extinguisher, such as the canister, valve, and hose. This may involve stamping, welding, and machining.
- Powder Filling: This department is responsible for filling the fire extinguisher with the extinguishing agent, which is typically a dry powder or water-based solution. The powder is stored in silos and is transported to the filling machines using pneumatic or hydraulic systems.
- Gas Filling: This department is responsible for filling the fire extinguisher with the pressurized gas that propels the extinguishing agent. The gas is typically compressed air or nitrogen. The gas is stored in cylinders and is transported to the filling machines using pneumatic or hydraulic systems.
- Testing and Inspection: This department is responsible for testing the fire extinguishers to ensure that they meet all safety standards. This may involve pressure testing, flow testing, and leak testing.
- Packaging: This department is responsible for packaging the fire extinguishers for shipment. This may involve shrink-wrapping, labeling, and palletizing.
The plant will also have a number of other departments, such as quality control, maintenance, and administration.
Fire extinguisher manufacturing plants must comply with a number of safety regulations, including:
- OSHA (Occupational Safety and Health Administration) regulations
- NFPA (National Fire Protection Association) standards
The plant must also have a number of safety procedures in place, such as:
- Lockout/Tagout procedures
- Hazard Communication (HazCom) program
- Emergency response plan
Fire extinguisher manufacturing is a critical industry that plays a vital role in protecting people and property from fire. The plants must operate safely and efficiently to ensure that they can produce high-quality fire extinguishers that meet all safety standards.
EMS Metalworking Machinery
We design, manufacture and assembly metalworking machinery such as:
- Hydraulic transfer press
- Glass mosaic press
- Hydraulic deep drawing press
- Casting press
- Hydraulic cold forming press
- Hydroforming press
- Composite press
- Silicone rubber moulding press
- Brake pad press
- Melamine press
- SMC & BMC Press
- Labrotaroy press
- Edge cutting trimming machine
- Edge curling machine
- Trimming beading machine
- Trimming joggling machine
- Cookware production line
- Pipe bending machine
- Profile bending machine
- Bandsaw for metal
- Cylindrical welding machine
- Horizontal pres and cookware
- Kitchenware, hotelware
- Bakeware and cuttlery production machinery
as a complete line as well as an individual machine such as:
- Edge cutting trimming beading machines
- Polishing and grinding machines for pot and pans
- Hydraulic drawing presses
- Circle blanking machines
- Riveting machine
- Hole punching machines
- Press feeding machine
You can check our machinery at work at: EMS Metalworking Machinery – YouTube
Applications:
- Beading and ribbing
- Flanging
- Trimming
- Curling
- Lock-seaming
- Ribbing
- Flange-punching