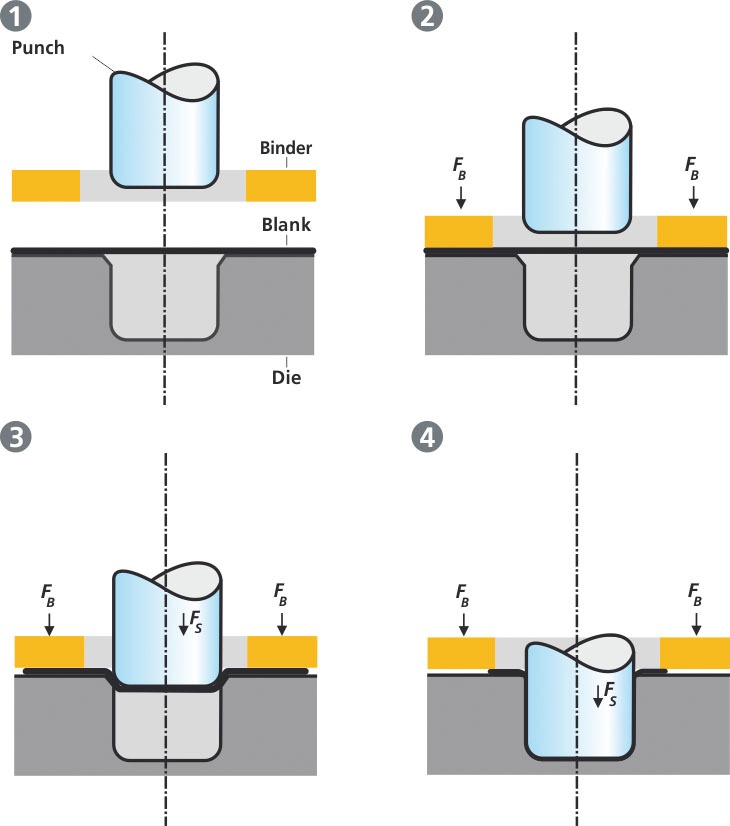
Deep Drawing Manufacturing: Hydraulic deep drawing presses are an essential piece of equipment in the manufacturing industry, utilized for forming sheet metal into desired shapes through a process called “deep drawing.” These presses use hydraulic fluid to exert force on a punch, which then presses a metal blank into a die, creating complex geometries with high precision.
The deep drawing process allows for the creation of cylindrical, box-shaped, and irregularly shaped components with a high degree of consistency. Hydraulic presses are favored for their ability to exert constant force over long distances, making them ideal for deep drawing processes that involve high-strength materials.
Historically, deep drawing presses were mechanical, relying on mechanical linkages to drive the punch. The evolution to hydraulic systems brought greater control over the force and speed of the press, leading to improvements in precision, safety, and operational efficiency. This shift has cemented hydraulic deep drawing presses as the technology of choice for industries requiring high-quality, complex metal forming.
Hydraulic deep drawing presses are widely used in automotive, aerospace, consumer electronics, medical devices, and more. Their ability to handle high-strength materials and produce intricate, precise shapes makes them invaluable in industries requiring both durability and complex designs.
Basic Principles of Deep Drawing Process
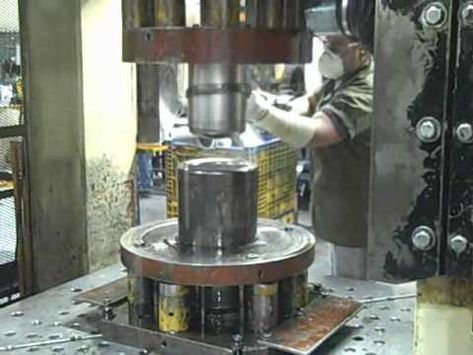
Deep drawing is a metal-forming process in which a flat sheet metal blank is radially drawn into a forming die by the mechanical action of a punch. The result is a part with a depth that exceeds its diameter, such as a cup or can.
The deep drawing process can be divided into several key stages:
- Blanking: The flat metal sheet is cut into a blank, typically a circular shape.
- Drawing: The blank is placed over a die cavity, and the punch pushes the blank into the die, forming the desired shape.
- Redrawing: If the depth of the part is greater than what can be achieved in a single stroke, the part may be redrawn through a series of dies to gradually achieve the final shape.
- Trimming and Finishing: After the deep drawing process, excess material is trimmed, and the part may undergo finishing processes to smooth out any rough edges.
The main characteristic of deep drawing is that the material undergoes plastic deformation, which is necessary for forming complex, deep geometries. The process requires careful control of various parameters, including the force applied, the speed of the punch, and the quality of the material to avoid common defects like tearing, wrinkling, or excessive thinning.
Hydraulic deep drawing presses play a critical role in this process. The hydraulic system provides consistent pressure, which is essential for achieving uniform part dimensions. Unlike mechanical presses, where the force can fluctuate, hydraulic presses offer precise control over the pressure applied during the drawing process, allowing for more accurate results. This is particularly important in high-volume production environments where consistency and quality are paramount.
Components of a Hydraulic Deep Drawing Press
The hydraulic deep drawing press is composed of several critical components, each playing a crucial role in the successful operation of the machine. Understanding these components is essential for optimizing the performance of the press and ensuring that the deep drawing process is both efficient and accurate.
- Hydraulic Cylinder: The hydraulic cylinder is the heart of the press, responsible for generating the force necessary for deep drawing. Hydraulic fluid is pumped into the cylinder, which moves the piston and creates the downward force needed to push the punch into the die.
- Punch and Die: The punch and die are the tools used to shape the metal blank. The punch is attached to the hydraulic cylinder and presses the blank into the die, which has the shape of the final part. The design and precision of the punch and die are critical for producing high-quality parts.
- Pressure System: The hydraulic pressure system controls the flow and pressure of the hydraulic fluid. It includes components such as pumps, valves, and reservoirs, which work together to ensure the correct amount of pressure is applied throughout the deep drawing process.
- Control System: Modern hydraulic deep drawing presses are equipped with computerized control systems that allow operators to precisely control the speed, force, and timing of the press. These systems also provide real-time feedback on press performance, allowing for adjustments to be made on the fly.
- Safety Mechanisms: Hydraulic presses are equipped with safety features to protect operators and equipment. These include emergency stop buttons, pressure relief valves, and guarding systems that prevent accidental contact with moving parts.
Each of these components plays a crucial role in ensuring that the hydraulic deep drawing press operates smoothly and efficiently. The integration of advanced control systems and safety mechanisms has made modern hydraulic presses more reliable and user-friendly than ever before.
Hydraulic System and Working Mechanism
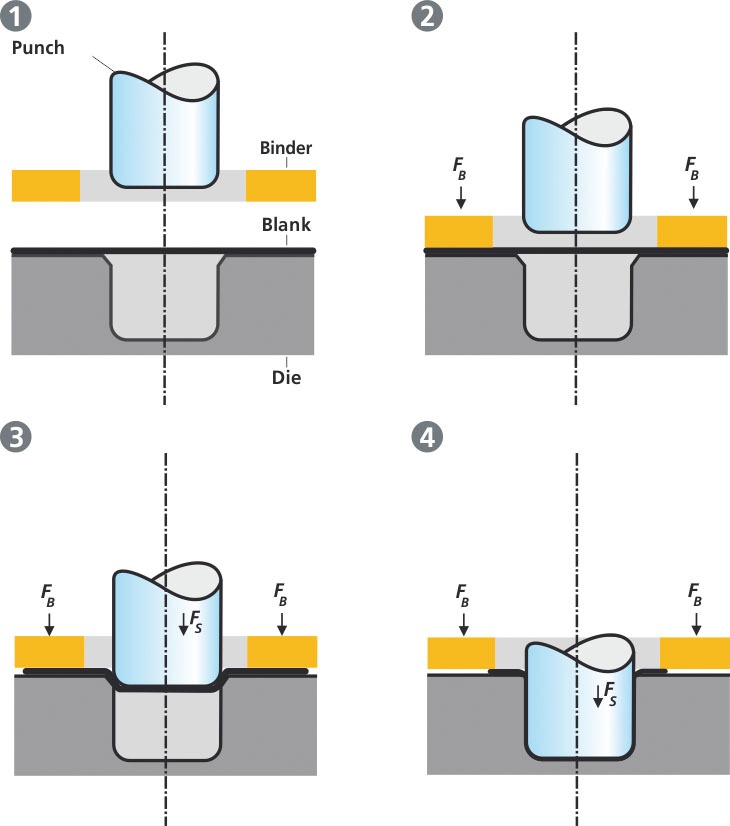
At the core of any hydraulic deep drawing press is the hydraulic system, which powers the press and controls the force applied during the deep drawing process. Understanding how this system works is essential for comprehending the advantages that hydraulic deep drawing presses offer in terms of precision, control, and adaptability.
How Hydraulic Systems Work
Hydraulic systems operate based on Pascal’s Law, which states that when a fluid is placed under pressure in a confined space, the pressure is transmitted equally in all directions. This principle allows hydraulic systems to generate large amounts of force with minimal input. In a hydraulic deep drawing press, a hydraulic pump is used to pressurize hydraulic fluid, which then moves through a series of valves and pipes to reach the hydraulic cylinder. The pressurized fluid exerts force on a piston within the cylinder, which in turn pushes the punch against the metal blank.
A key advantage of hydraulic systems is their ability to apply constant pressure over the full stroke of the piston. This ensures uniform force throughout the deep drawing process, allowing for more consistent and accurate parts compared to mechanical presses, where the force may vary at different points of the stroke.
Key Components of the Hydraulic System
The hydraulic system of a deep drawing press includes several important components that work together to ensure smooth and reliable operation:
- Hydraulic Fluid: The hydraulic fluid is the medium through which force is transmitted in the system. Typically, specialized hydraulic oils are used because they possess the right combination of viscosity, temperature stability, and lubricating properties. The quality and maintenance of hydraulic fluids are critical since contaminants or degraded fluids can lead to inefficiencies and even damage the system.
- Hydraulic Pump: The pump is responsible for generating pressure in the system by forcing the hydraulic fluid through the pipes and into the cylinder. There are different types of pumps used in hydraulic presses, including gear pumps, vane pumps, and piston pumps. The choice of pump depends on the specific requirements of the press, such as the pressure needed and the speed of operation.
- Valves and Regulators: Valves are used to control the flow of hydraulic fluid within the system, allowing the operator to precisely regulate the amount of pressure applied to the cylinder. Regulators are also used to ensure that the pressure does not exceed safe limits, preventing damage to the press and maintaining a safe working environment.
- Hydraulic Cylinder: The hydraulic cylinder is the component that converts the fluid pressure into mechanical force. The cylinder contains a piston that moves when the fluid is pressurized, creating the motion needed to drive the punch into the metal blank. Cylinders are typically made from high-strength materials to withstand the enormous forces generated during the deep drawing process.
- Pressure Accumulators: In some hydraulic systems, accumulators are used to store hydraulic fluid under pressure, which can then be released when needed. This allows for more efficient operation and provides a buffer to handle fluctuations in demand for pressure.
Working Mechanism of a Hydraulic Deep Drawing Press
The operation of a hydraulic deep drawing press can be broken down into several key stages:
- Initial Setup: Before the press is operated, the blank (a flat sheet of metal) is prepared and placed over the die. The die is mounted onto the lower bed of the press, while the punch is attached to the piston of the hydraulic cylinder.
- Pressure Build-up: Once the machine is set up, hydraulic fluid is pumped into the system, building pressure in the hydraulic cylinder. This pressure is carefully controlled to ensure that the correct amount of force is applied during the drawing process.
- Drawing Process: The press is activated, causing the hydraulic cylinder to drive the punch downward. As the punch moves into the die, it forces the blank into the desired shape. The constant pressure provided by the hydraulic system ensures that the blank deforms evenly, reducing the likelihood of defects such as wrinkling or tearing.
- Reversing the Cycle: After the drawing process is complete, the hydraulic system reverses the flow of fluid, retracting the piston and lifting the punch out of the die. The completed part is then removed, and the press is ready for the next cycle.
Advantages of Hydraulic Systems in Deep Drawing Presses
- Precise Control of Force: Hydraulic systems provide highly precise control over the force applied during the drawing process. Operators can adjust the pressure based on the specific requirements of each job, ensuring that the right amount of force is applied for different materials and part geometries.
- Constant Pressure Throughout Stroke: One of the key benefits of hydraulic presses is that they can maintain constant pressure throughout the entire stroke of the piston. This results in more uniform part quality and reduces the risk of defects compared to mechanical presses.
- Adaptability and Flexibility: Hydraulic presses are highly adaptable and can be adjusted to perform a wide range of tasks. For example, operators can modify the stroke length, pressure, and speed to accommodate different materials, part shapes, and production volumes.
- Reduced Wear and Tear: The smooth operation of hydraulic systems results in less wear and tear on the machine components compared to mechanical presses, where the high impact forces can cause damage over time. This reduces maintenance costs and extends the lifespan of the press.
Types of Hydraulic Deep Drawing Presses
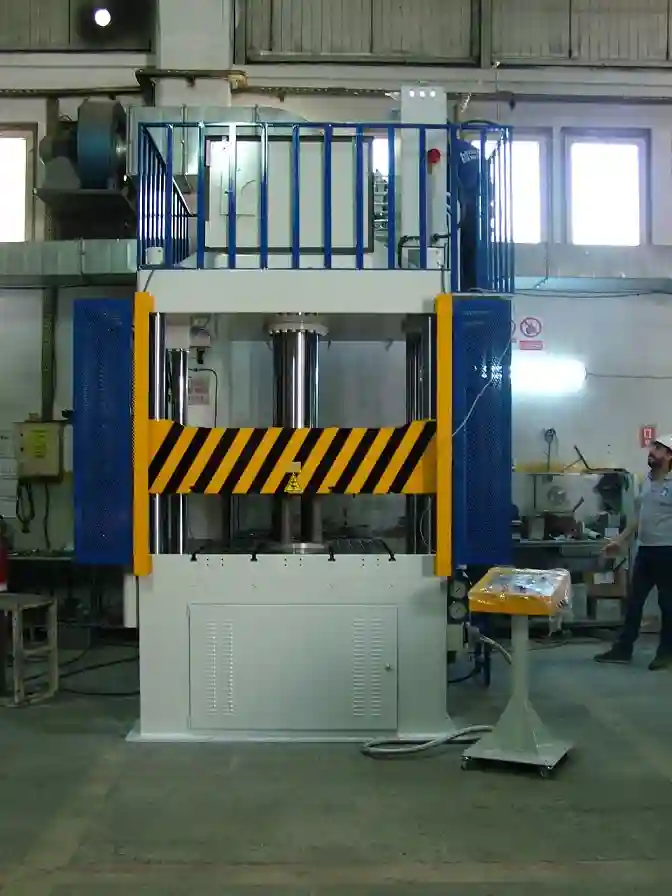
Hydraulic deep drawing presses come in various configurations, each designed to meet specific manufacturing requirements. The main types of hydraulic presses used in deep drawing applications include single-action, double-action, and triple-action presses. Understanding the differences between these types is crucial for selecting the right press for a particular application.
1. Single-Action Hydraulic Press
A single-action hydraulic press is the simplest type of press, using a single hydraulic cylinder to apply force. In this configuration, the blank is placed over the die, and the punch is driven into the die by the hydraulic cylinder. The force is applied in a single direction, hence the name “single-action.”
- Applications: Single-action presses are ideal for simpler deep drawing tasks, where the shape of the part is not too complex, and only moderate drawing depths are required. They are often used for producing parts such as cups, bowls, and shallow containers.
- Advantages: These presses are generally more affordable and easier to maintain compared to multi-action presses. They are also more compact, making them suitable for smaller manufacturing facilities.
- Limitations: Single-action presses are not as versatile as their double- and triple-action counterparts, as they lack the ability to handle more complex shapes or deeper draws.
2. Double-Action Hydraulic Press
Double-action hydraulic presses have two separate cylinders: one for the punch and another for the blank holder. This allows for more precise control over the drawing process, as the blank holder can be independently controlled to hold the metal blank in place while the punch draws it into the die.
- Applications: Double-action presses are commonly used for more complex parts that require greater precision and deeper draws. They are widely used in the automotive industry for forming large body panels, such as doors and hoods, where maintaining uniform material flow is critical.
- Advantages: The ability to control both the punch and the blank holder independently results in better control over the material flow, reducing the risk of defects like wrinkling or tearing. Double-action presses are also more versatile, as they can handle a wider range of part shapes and sizes.
- Limitations: These presses are more expensive and larger than single-action presses, making them more suitable for high-volume production environments.
3. Triple-Action Hydraulic Press
Triple-action hydraulic presses feature three separate cylinders: one for the punch, one for the blank holder, and a third for the ejector. The ejector is used to remove the finished part from the die after the drawing process is complete, allowing for continuous production with minimal downtime.
- Applications: Triple-action presses are used for highly complex deep drawing applications that require precise control over every aspect of the process. They are commonly used in industries such as aerospace, where parts often have intricate geometries and tight tolerances.
- Advantages: Triple-action presses offer the highest level of control and versatility, making them suitable for the most demanding deep drawing tasks. The use of an ejector system also improves production efficiency, as it reduces the time required to remove finished parts from the die.
- Limitations: These presses are the most expensive and require the largest amount of floor space. They also require more maintenance due to the increased complexity of the hydraulic system.
Key Considerations for Selecting a Hydraulic Deep Drawing Press
When selecting a hydraulic deep drawing press, several factors must be considered to ensure that the press meets the specific requirements of the production environment:
- Part Complexity: More complex parts with deeper draws and intricate geometries may require double- or triple-action presses for precise control.
- Production Volume: High-volume production environments may benefit from the continuous operation and efficiency offered by triple-action presses.
- Material Type: The type of material being formed will also influence the choice of press, as some materials require higher forces or more precise control over the drawing process.
Process Parameters Affecting Deep Drawing
The deep drawing process is highly sensitive to a range of parameters that can directly impact the quality, consistency, and overall success of the formed parts. Proper management of these parameters ensures defect-free production, reduces material waste, and improves production efficiency. The key parameters that influence deep drawing include blank holder force, drawing speed, lubrication, blank material properties, and the geometry of the die and punch.
1. Blank Holder Force
The blank holder force is the pressure applied to hold the metal blank in place during the drawing process. Its primary role is to control the material flow as the punch moves the blank into the die. If the blank holder force is too low, the material may wrinkle due to excessive material flow. On the other hand, if the force is too high, it can lead to tearing or cracking because the material cannot move freely enough into the die.
Achieving the correct balance in blank holder force is essential. Modern hydraulic deep drawing presses often feature adjustable blank holder systems, allowing operators to fine-tune the force to suit the specific material and part geometry. The use of dynamic control systems can further improve the process by automatically adjusting the force in real time as the press operates.
2. Drawing Speed
Drawing speed refers to the rate at which the punch moves into the die during the deep drawing process. It directly affects the material’s flow, the heat generated during forming, and the risk of defects like tearing or thinning. If the drawing speed is too fast, the material may not have enough time to flow into the die, leading to defects such as cracking or excessive thinning in certain areas.
Conversely, if the speed is too slow, production efficiency may suffer, and excessive friction between the blank and the die may result in surface defects or increased tool wear. Advanced hydraulic deep drawing presses often allow operators to control the drawing speed with great precision, enabling them to optimize the process for different materials and part geometries.
3. Lubrication Quality
Lubrication is a critical aspect of the deep drawing process, as it reduces friction between the blank and the die, minimizing wear on the tools and preventing surface defects on the finished part. The type and quality of lubrication used can significantly influence the success of the drawing operation.
- Metalworking Fluids (MWFs): Special lubricants known as MWFs are often used in deep drawing applications to ensure smooth material flow and reduce friction. These lubricants must be chosen based on factors such as material type, part geometry, and the drawing speed.
- Lubrication Techniques: Lubrication can be applied in different ways, including spraying, rolling, or coating the blank with a thin layer before the drawing process. Ensuring uniform lubrication is important to prevent localized friction, which can lead to defects like galling or surface scratches.
Improper or inadequate lubrication can result in an increase in tool wear, shortening the life of the die and punch, and may lead to inconsistent part quality.
4. Blank Material and Thickness
The material properties of the blank play a crucial role in the deep drawing process. Common materials used in deep drawing include aluminum, steel, brass, copper, and stainless steel, each with different formability characteristics. The choice of material is typically influenced by the requirements of the final part, such as strength, weight, corrosion resistance, and surface finish.
- Material Ductility: Ductile materials, which can undergo significant deformation without breaking, are ideal for deep drawing as they can be stretched into the desired shape without tearing. However, highly ductile materials also require precise control over process parameters to prevent wrinkling.
- Material Thickness: The thickness of the blank is another key factor. Thicker blanks require higher forces to be drawn into the die and may be prone to wrinkling if the blank holder force is not properly calibrated. Thinner blanks, while easier to form, are more susceptible to tearing or excessive thinning in high-stress areas.
Operators must take material properties into account when selecting press settings, including blank holder force, drawing speed, and lubrication requirements, to avoid defects and ensure optimal performance.
5. Die and Punch Geometry
The geometry of the die and punch determines the final shape of the part and plays a significant role in the material flow during the deep drawing process. Important aspects of die and punch design include:
- Corner Radius: The corner radius of the die and punch must be carefully designed to ensure smooth material flow and avoid excessive thinning or tearing. Sharp corners can cause the material to crack, while overly large radii may result in wrinkling.
- Die Clearance: The clearance between the punch and the die must be sufficient to allow for smooth material flow, but not so large that it causes wrinkling or uneven material distribution. The clearance is typically determined based on the thickness of the blank material.
- Draw Depth: The depth of the draw, or how far the punch pushes the blank into the die, is a critical parameter. Deeper draws require greater force and increase the risk of defects like tearing or thinning, especially in high-stress areas of the part. Proper control of the punch speed and blank holder force is essential to manage these risks.
6. Strategies to Avoid Defects
Several common defects can arise in the deep drawing process, including wrinkling, tearing, and thinning. By carefully controlling the key process parameters, operators can minimize the likelihood of these defects:
- Wrinkling: Wrinkling occurs when the material flows too freely into the die, often due to insufficient blank holder force. Adjusting the blank holder force and optimizing the lubrication can reduce wrinkling.
- Tearing: Tearing typically happens when the material is overstressed, either due to excessive drawing speed or insufficient lubrication. Reducing the punch speed and using high-quality lubricants can help prevent tearing.
- Thinning: Excessive thinning occurs when the material is stretched too much during the drawing process. Proper control of the punch speed and careful selection of the die and punch geometry are critical to minimizing thinning.
Advantages and Limitations of Hydraulic Deep Drawing Presses
Hydraulic deep drawing presses offer several advantages over traditional mechanical presses, particularly in terms of control, versatility, and performance. However, like any piece of industrial equipment, they also come with certain limitations that manufacturers must consider when choosing the right press for their operations.
Advantages and Limitations of Hydraulic Deep Drawing Presses
- Precise Control Over Force and Speed (continued)
Hydraulic presses allow for highly precise control over the force and speed applied during the deep drawing process. This precision is crucial for ensuring consistent part quality, especially for complex geometries and high-strength materials. The pressure can be adjusted throughout the stroke, which means that hydraulic presses are capable of maintaining a constant force over the entire cycle. This feature makes hydraulic presses ideal for deep drawing operations where material properties and thickness can vary significantly. - Versatility in Operation
Hydraulic deep drawing presses are extremely versatile and can be used for a wide variety of applications across different industries. Unlike mechanical presses, which are designed for specific tasks, hydraulic presses can be easily adjusted to accommodate different materials, part shapes, and production volumes. They can handle large, complex parts or multiple smaller parts simultaneously, making them well-suited for industries such as automotive, aerospace, and electronics manufacturing.Additionally, hydraulic presses are capable of multi-action operations, such as double- or triple-action presses, allowing them to perform different forming tasks in a single machine. This flexibility is a significant advantage in production environments that require a range of forming operations, reducing the need for multiple machines and minimizing setup times. - Handling of Complex Shapes and Deep Draws
Hydraulic deep drawing presses excel at handling parts with complex geometries and deep draws, which are often difficult or impossible to achieve with mechanical presses. The constant pressure and speed control provided by hydraulic systems make it easier to form intricate shapes without risking defects such as tearing, wrinkling, or excessive thinning. This capability is essential for industries like aerospace and automotive, where components often feature deep cavities and complex shapes that require precise forming. - Improved Safety and Operator Control
Modern hydraulic deep drawing presses are equipped with advanced safety features and control systems that protect both the operator and the equipment. These systems include emergency stop buttons, pressure relief valves, automatic overload protection, and guarding mechanisms that prevent accidental contact with moving parts. Additionally, the smooth and controlled motion of hydraulic systems reduces the risk of sudden mechanical failures or excessive forces that could cause injury or damage. - Energy Efficiency in High-Volume Production
Hydraulic presses have become more energy-efficient with the advent of modern control systems and the integration of servo-driven hydraulic systems. These innovations allow for better energy management by adjusting the power output based on the demand at each stage of the deep drawing process. As a result, hydraulic presses can be more energy-efficient in high-volume production compared to traditional mechanical presses, where energy consumption remains constant regardless of the workload. - Reduced Wear and Tear on Components
The smooth, controlled motion of hydraulic presses leads to reduced wear and tear on both the press components and the tooling used during the deep drawing process. Mechanical presses, by contrast, often experience higher levels of impact and stress, which can result in premature wear of critical components. This reduction in wear extends the lifespan of the machine and reduces the frequency and cost of maintenance.
Limitations of Hydraulic Deep Drawing Presses
- Higher Initial Cost
One of the primary limitations of hydraulic deep drawing presses is their higher initial cost compared to mechanical presses. The complexity of the hydraulic system, along with the need for specialized components such as pumps, valves, and hydraulic fluid reservoirs, contributes to a higher upfront investment. For manufacturers with limited budgets, this can be a significant barrier to adopting hydraulic technology. - Maintenance Complexity
While hydraulic presses tend to experience less wear and tear during operation, their maintenance requirements can be more complex than those of mechanical presses. Hydraulic systems rely on a variety of components, including pumps, valves, and fluid reservoirs, all of which must be regularly inspected and maintained to ensure optimal performance. Contaminants in the hydraulic fluid, such as dirt or metal particles, can cause system failures if not properly filtered out, adding to the maintenance burden.Furthermore, hydraulic fluid itself must be monitored and replaced periodically to prevent system inefficiencies or damage to the press. This ongoing need for fluid management adds to the operational costs and requires specialized knowledge. - Energy Consumption and Heat Generation
Although modern hydraulic presses are more energy-efficient than older models, they can still consume more energy than mechanical presses during certain operations. This is especially true in applications where high pressures or prolonged press cycles are required. Hydraulic systems can also generate a significant amount of heat during operation, particularly in high-volume production environments. Excessive heat can cause the hydraulic fluid to degrade over time, potentially leading to system inefficiencies or component failure.To mitigate these issues, manufacturers often invest in cooling systems or heat exchangers to manage the temperature of the hydraulic fluid, adding to the overall cost of the machine. - Larger Footprint and Space Requirements
Hydraulic presses typically require more floor space than mechanical presses due to the additional components involved, such as hydraulic fluid reservoirs, pumps, and control units. This larger footprint can be a disadvantage for manufacturers with limited space in their production facilities. Additionally, the installation process for a hydraulic press is more involved and may require specialized foundations or supports to accommodate the increased size and weight of the machine. - Slower Cycle Times for Certain Applications
Hydraulic presses generally operate more slowly than mechanical presses, particularly in applications that require fast cycle times. While the controlled, constant pressure of a hydraulic press is beneficial for complex deep drawing operations, it can result in slower production speeds compared to mechanical presses, which are capable of higher cycle rates. In high-volume, mass production environments where speed is critical, this slower cycle time may be a limitation.
Comparison with Mechanical Deep Drawing Presses
- Control and Precision: Hydraulic presses offer better control over the drawing process, particularly when handling complex parts or deep draws, whereas mechanical presses are typically faster but less precise.
- Cost: Mechanical presses are often less expensive and easier to maintain, but they may require more frequent repairs due to the higher impact forces involved.
- Efficiency: Hydraulic presses can be more energy-efficient in high-precision applications, while mechanical presses tend to be more efficient in high-speed, high-volume production environments.
Applications of Hydraulic Deep Drawing Presses in Different Industries
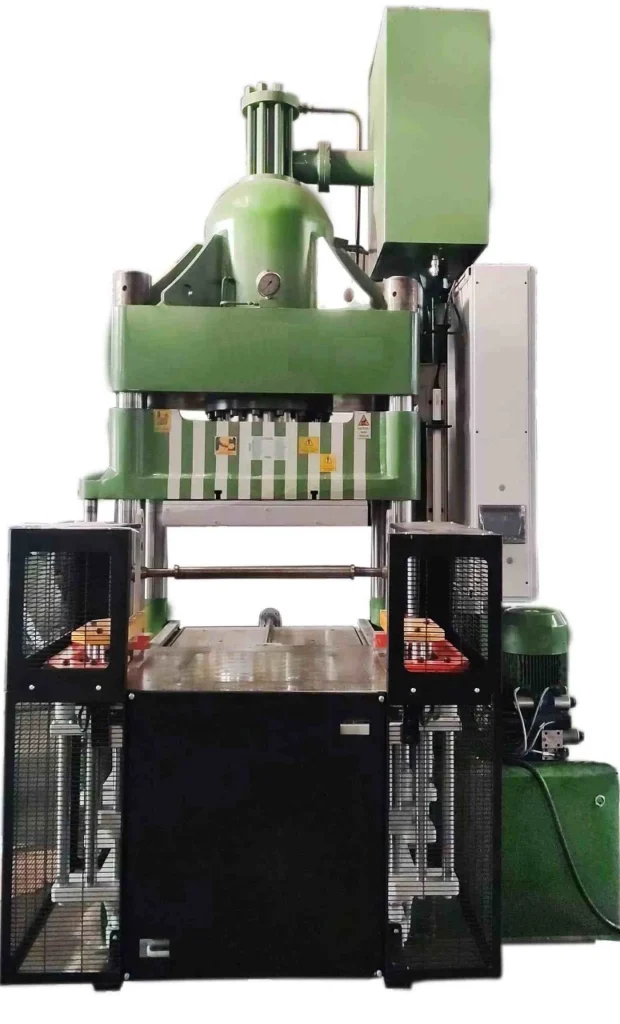
Hydraulic deep drawing presses play a vital role in numerous industries where precise metal forming is required. Their versatility, ability to handle complex shapes, and capacity for high-strength materials make them indispensable in fields ranging from automotive manufacturing to medical device production. Below are key industries where hydraulic deep drawing presses have a significant impact, along with specific applications.
1. Automotive Industry
The automotive industry is one of the largest consumers of hydraulic deep drawing presses. These presses are crucial for forming various metal components that require high precision and strength. The demand for lightweight, yet durable materials in vehicles has made deep drawing an essential process for car manufacturers.
- Car Body Panels: Hydraulic deep drawing presses are used to form large, complex panels such as doors, hoods, roof panels, and fenders. These parts must be manufactured with tight tolerances to ensure a proper fit and structural integrity.
- Fuel Tanks and Exhaust Components: Due to the need for high-strength materials in fuel tanks and exhaust systems, hydraulic deep drawing presses are widely used in the production of these components. The ability to maintain precise control over the drawing force and speed ensures the integrity of the material without compromising the structure.
- Chassis and Frame Components: Many chassis components, including cross members, brackets, and reinforcements, are deep drawn to ensure the highest levels of durability. The deep drawing process allows for the production of these parts with minimal material waste and consistent thickness, which is critical for safety.
2. Aerospace Industry
The aerospace industry requires components with extremely high precision, strength, and durability due to the harsh operational environments in which these parts must function. Hydraulic deep drawing presses are frequently used to manufacture complex, lightweight components that meet the rigorous standards of the industry.
- Aircraft Body Panels and Structural Components: Aerospace manufacturers use deep drawing presses to form structural components such as fuselage panels, wing components, and bulkheads. These parts must withstand high levels of stress and fatigue, making the deep drawing process ideal for ensuring uniform material distribution and strength.
- Engine Components: In jet engines and other aerospace propulsion systems, hydraulic presses are employed to form heat-resistant alloys and other high-strength materials into complex shapes. The precise control offered by hydraulic presses ensures that these critical components meet strict performance requirements.
- Landing Gear Components: Hydraulic deep drawing presses are also used to manufacture parts of landing gear systems, which need to be both lightweight and capable of withstanding extreme forces during takeoff and landing.
3. Consumer Electronics Industry
In the consumer electronics sector, hydraulic deep drawing presses are essential for producing thin, lightweight enclosures and components for devices like smartphones, laptops, and wearables. With the trend toward more compact and sleek designs, manufacturers rely on deep drawing technology to achieve high precision and finish quality.
- Device Enclosures and Casings: The metal enclosures for smartphones, tablets, and laptops are typically deep drawn to achieve seamless, lightweight structures that are both durable and aesthetically pleasing. The hydraulic press ensures that the material is evenly distributed and free from defects like thinning or tearing.
- Heat Sinks and Other Thermal Management Components: Many electronic devices rely on heat sinks and thermal management components made from metals such as aluminum or copper. Hydraulic deep drawing presses are used to form these components, ensuring they can effectively dissipate heat while maintaining a compact size.
4. Household Appliances
Hydraulic deep drawing presses are widely used in the production of household appliances such as washing machines, refrigerators, and microwave ovens. The need for large, robust metal components that are formed with precision makes deep drawing an ideal process for these products.
- Washer and Dryer Drums: The drums in washing machines and dryers are typically deep drawn from stainless steel to ensure durability and corrosion resistance. Hydraulic presses provide the necessary force to form these large, cylindrical parts without compromising their structural integrity.
- Refrigerator Liners and Panels: Hydraulic deep drawing presses are used to form the inner liners and panels of refrigerators. These components must be manufactured with tight tolerances to ensure proper insulation and assembly, while also being durable enough to withstand years of use.
5. Medical Devices and Equipment
The medical device industry requires high-precision, often small, components made from biocompatible materials such as stainless steel and titanium. Hydraulic deep drawing presses play a key role in manufacturing these critical parts, ensuring the highest levels of accuracy and consistency.
- Surgical Instruments and Implantable Devices: Many surgical instruments, such as forceps, scalpels, and clamps, are deep drawn from stainless steel or titanium. The hydraulic deep drawing process ensures these components are formed to precise specifications with smooth edges and surfaces, reducing the risk of contamination or material failure during use.
- Medical Implants: Complex medical implants, such as pacemaker enclosures and stents, require intricate forming processes that can only be achieved using hydraulic presses. The ability to control the force and speed of the drawing process ensures these delicate components are produced without defects, enhancing patient safety.
6. Packaging Industry
In the packaging industry, hydraulic deep drawing presses are used to manufacture various metal containers, including food and beverage cans, aerosol cans, and cosmetic containers. The deep drawing process is ideal for creating seamless, lightweight containers that are both functional and visually appealing.
- Metal Cans for Food and Beverages: Aluminum and steel cans for food and beverages are often deep drawn using hydraulic presses to ensure uniform thickness and high strength. The smooth surface finish and consistent dimensions of deep-drawn cans make them ideal for mass production and consumer use.
- Aerosol and Cosmetic Containers: Hydraulic deep drawing presses are also used to manufacture aerosol cans and cosmetic containers, which require precise forming to ensure proper functionality and aesthetic quality.
Future Trends in Industry Applications
As industries continue to push the boundaries of innovation, the demand for advanced deep drawing processes is expected to grow. Key trends influencing the future of hydraulic deep drawing presses include:
- Lightweight Materials: The use of lightweight materials such as aluminum and composites is becoming increasingly important, particularly in the automotive and aerospace industries. Hydraulic presses, with their precise control and versatility, are well-suited to forming these materials without compromising strength.
- Electrification and E-Mobility: The rise of electric vehicles (EVs) and other e-mobility solutions is driving demand for complex, high-strength components such as battery enclosures and electric motor housings. Hydraulic deep drawing presses are expected to play a crucial role in producing these parts efficiently.
- Sustainability: Manufacturers are increasingly focused on sustainability and reducing material waste. The deep drawing process, which can produce complex parts from a single piece of material, aligns with these goals by minimizing scrap and optimizing material use.
Recent Developments and Technological Advances
The technology behind hydraulic deep drawing presses has evolved significantly in recent years, driven by advancements in automation, digitalization, and material science. These developments have improved the performance, efficiency, and versatility of hydraulic presses, making them an essential part of modern manufacturing.
1. Digitalization and Automation
One of the most significant technological advances in hydraulic deep drawing presses is the integration of digital control systems and automation. These innovations have transformed the way hydraulic presses are operated, providing manufacturers with greater precision, flexibility, and productivity.
- CNC and PLC Systems: Modern hydraulic presses are often equipped with computer numerical control (CNC) or programmable logic controller (PLC) systems, which allow for automated control of the press parameters such as force, speed, and stroke length. These systems enable manufacturers to program complex forming sequences, reducing the need for manual adjustments and improving production consistency.
- Automated Tool Change Systems: In high-volume production environments, the ability to quickly change tools is critical for maintaining efficiency. Automated tool change systems have been developed to reduce downtime between production runs, allowing manufacturers to switch between different parts and materials with minimal disruption.
2. Integration with Industry 4.0 and Smart Manufacturing
The rise of Industry 4.0 has introduced new opportunities for hydraulic deep drawing presses to integrate with smart manufacturing systems. Through the use of sensors, data analytics, and machine learning, presses can now provide real-time feedback on performance and optimize production processes.
- Real-Time Monitoring: Sensors embedded in hydraulic presses can monitor key parameters such as pressure, temperature, and tool wear in real time. This data is transmitted to central control systems, allowing operators to make adjustments on the fly or trigger maintenance alerts before a failure occurs.
- Predictive Maintenance: Machine learning algorithms can analyze historical data from hydraulic presses to predict when maintenance is needed. This approach, known as predictive maintenance, reduces unplanned downtime by identifying potential issues before they lead to equipment failure.
Maintenance and Troubleshooting of Hydraulic Deep Drawing Presses
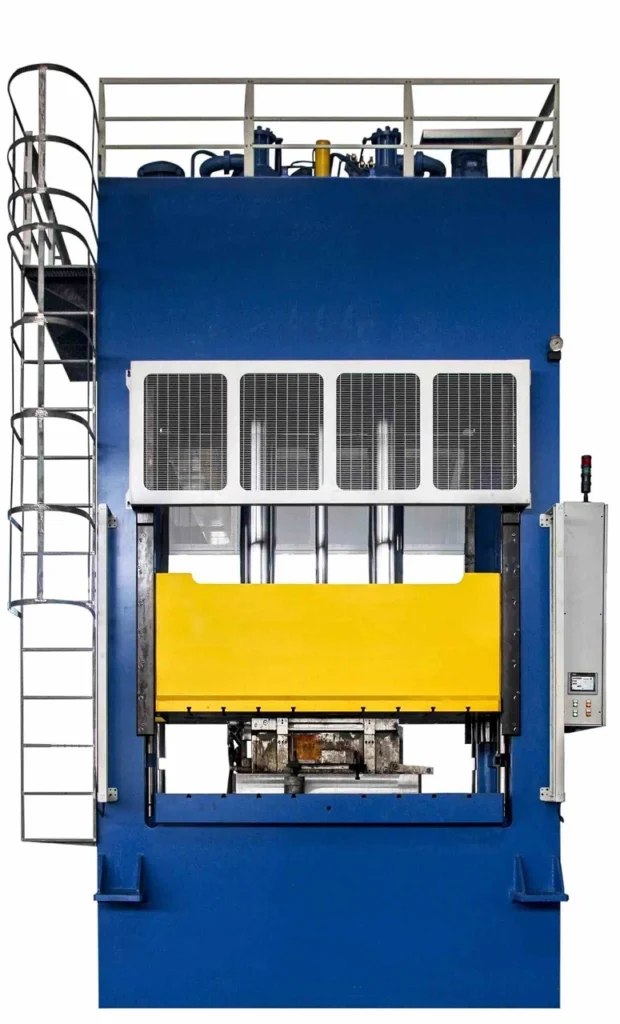
Maintenance is essential for ensuring the long-term performance, safety, and efficiency of hydraulic deep drawing presses. Given the complex nature of hydraulic systems, neglecting regular maintenance can lead to increased downtime, expensive repairs, and even equipment failure. To avoid these issues, manufacturers must implement a comprehensive maintenance program, which includes regular inspections, preventive maintenance, and troubleshooting.
1. Common Maintenance Practices
Routine maintenance practices for hydraulic deep drawing presses revolve around monitoring and maintaining the hydraulic system components, mechanical elements, and control systems. Some key maintenance tasks include:
- Hydraulic Fluid Monitoring: The hydraulic fluid is the lifeblood of the press. Over time, contaminants such as dirt, metal particles, and moisture can accumulate in the fluid, degrading its performance and causing damage to hydraulic components. Regularly checking the fluid for signs of contamination or degradation is crucial. In addition, hydraulic fluid levels should be monitored and maintained at the correct levels to avoid air entering the system, which can cause cavitation and system inefficiencies.
- Filter Replacement: Hydraulic systems include filters to remove contaminants from the fluid. Over time, these filters become clogged and must be replaced to maintain system performance. Clogged filters can cause reduced pressure, overheating, and wear on the hydraulic pump and valves.
- Seal Inspection and Replacement: The seals used in hydraulic cylinders and valves are prone to wear and tear over time. Leaking seals can lead to a loss of pressure and reduced performance. Regularly inspecting and replacing seals is an important preventive measure that ensures consistent press performance.
- Lubrication of Mechanical Components: While the hydraulic system provides the force required for deep drawing, mechanical components such as bearings, gears, and guideways still require proper lubrication to minimize friction and wear. Applying the appropriate lubricants at regular intervals is essential to prevent mechanical failures and extend the life of the press.
- System Calibration: Periodic calibration of the press’s control system ensures that the applied force, speed, and other critical parameters remain within acceptable tolerances. Calibration is particularly important in high-precision applications, where even small deviations can lead to defects in the finished parts.
2. Predictive Maintenance Techniques
Predictive maintenance has become an increasingly popular approach in modern manufacturing due to its ability to prevent costly breakdowns and extend the lifespan of hydraulic deep drawing presses. This approach leverages real-time data and advanced analytics to predict when maintenance is needed, rather than relying on fixed maintenance schedules.
- Condition Monitoring: Sensors are installed on key components such as hydraulic pumps, motors, and valves to monitor parameters like pressure, temperature, vibration, and oil quality. By continuously analyzing this data, manufacturers can detect early signs of wear or failure and schedule maintenance before a serious issue arises.
- Data Analytics and AI: Predictive maintenance systems often use machine learning algorithms to analyze historical data and identify patterns that indicate potential problems. This allows manufacturers to anticipate when components are likely to fail and perform maintenance only when necessary, reducing both downtime and maintenance costs.
3. Common Issues and Troubleshooting
Despite regular maintenance, hydraulic deep drawing presses can experience problems due to wear, environmental conditions, or unexpected failures. The most common issues include hydraulic system failures, mechanical malfunctions, and control system errors. Some common issues and their troubleshooting methods include:
- Hydraulic Fluid Leaks: Leaks can occur due to damaged seals, cracked hoses, or worn components. If a leak is detected, the source must be identified and repaired immediately to prevent a loss of pressure and damage to the system. Replacing worn seals, tightening fittings, or replacing damaged hoses can resolve the issue.
- Pressure Loss: If the press is unable to generate the required force, the cause is often a loss of hydraulic pressure. Possible causes include low hydraulic fluid levels, a clogged filter, or a malfunctioning pump. Checking fluid levels, replacing filters, and inspecting the pump can help restore pressure.
- Overheating: Hydraulic systems generate heat during operation, and if the system overheats, it can cause the hydraulic fluid to degrade and reduce system efficiency. Overheating may be caused by insufficient fluid levels, clogged filters, or excessive operating pressure. Addressing these issues by ensuring proper fluid levels and replacing filters can prevent overheating.
- Excessive Vibration or Noise: Excessive vibration or noise can be a sign of cavitation in the hydraulic system, which occurs when air enters the fluid. This can be caused by low fluid levels or a loose fitting. Ensuring the system is properly sealed and fluid levels are maintained can eliminate cavitation.
4. Ensuring Safety During Maintenance
Safety is paramount when performing maintenance on hydraulic deep drawing presses. The high pressures involved in the hydraulic system can pose serious hazards if not properly managed. Key safety measures include:
- Lockout/Tagout Procedures: Before performing any maintenance, the press should be de-energized, and lockout/tagout procedures should be followed to ensure the machine cannot be inadvertently started during maintenance.
- Pressure Release: Hydraulic systems should always be depressurized before any work is done on the system. This prevents accidental fluid release, which can cause injury or equipment damage.
- Personal Protective Equipment (PPE): Maintenance personnel should wear appropriate PPE, such as gloves, goggles, and protective clothing, to protect themselves from potential hazards.
Conclusion
Hydraulic deep drawing presses are an essential tool in modern manufacturing, offering unparalleled precision, control, and versatility for forming complex metal parts. Their ability to handle high-strength materials and produce parts with intricate geometries has made them indispensable in industries such as automotive, aerospace, consumer electronics, and medical devices.
The deep drawing process, powered by hydraulic systems, ensures uniform pressure throughout the entire stroke, resulting in consistent part quality and reduced risk of defects. With advancements in digital control systems, automation, and smart manufacturing technologies, hydraulic presses continue to evolve, offering greater efficiency, precision, and flexibility than ever before.
While hydraulic deep drawing presses have several advantages over traditional mechanical presses, including better control over pressure and the ability to handle more complex parts, they also come with challenges. These challenges include higher initial costs, more complex maintenance requirements, and larger space requirements. However, with proper maintenance and the use of predictive maintenance techniques, manufacturers can maximize the lifespan and efficiency of their hydraulic presses while minimizing downtime.
Looking to the future, hydraulic deep drawing presses will continue to play a crucial role in driving innovation across a range of industries, from the production of electric vehicle components to advanced medical devices. As manufacturing trends move toward increased automation, sustainability, and lightweight materials, hydraulic deep drawing presses will remain at the forefront of cutting-edge manufacturing technologies.
Deep drawing
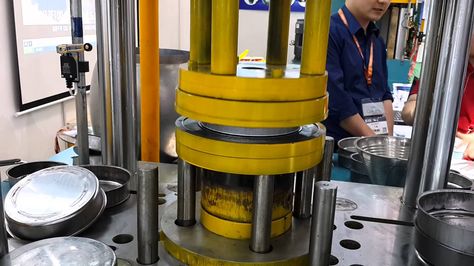
Deep drawing is a metal-forming process used to manufacture complex, hollow shapes from flat sheet metal. During the process, a metal blank is placed over a die cavity and pressed into the die by a punch, resulting in a part that has a depth greater than its diameter, such as a cup, cylinder, or box. This process is fundamental to manufacturing industries that require the creation of durable, precise, and lightweight components.
The deep drawing process is widely used in industries like automotive, aerospace, electronics, and packaging, where forming large volumes of metal parts with uniform thickness is critical. Products such as car body panels, fuel tanks, beverage cans, and kitchen sinks are typically produced through deep drawing.
This technique is favored due to its ability to create complex shapes with high structural integrity and minimal material waste. However, achieving high-quality parts through deep drawing requires a deep understanding of the mechanics behind the process, including the behavior of the material under stress, the forces applied by the punch, and the design of the die.
Deep drawing distinguishes itself from other metal-forming processes like stamping or bending due to the greater emphasis on stretching the metal without breaking it. To successfully complete a deep drawing process without defects, engineers must carefully control variables such as material properties, lubrication, punch speed, and blank holder force.
Fundamental Principles of Deep Drawing
The engineering behind deep drawing revolves around the mechanics of plastic deformation, the method by which the metal blank is stretched into a new shape without returning to its original form. Understanding the forces at play and how the metal reacts to these forces is key to successfully producing parts with uniform dimensions and minimal defects.
Plastic Deformation and Strain
During deep drawing, the metal blank is subjected to a combination of tensile and compressive stresses. As the punch presses the metal into the die, the material is forced to flow and stretch to conform to the shape of the die. This is referred to as plastic deformation, where the metal undergoes permanent deformation without cracking. The ability of a material to undergo plastic deformation without failure is a key characteristic in the deep drawing process.
Strain occurs as the metal is stretched by the punch, with different regions of the blank experiencing varying levels of strain. The outer edges of the blank experience tensile stress, while the material in contact with the punch and die is compressed. The strain distribution across the blank is a critical factor in determining the quality of the final part.
Key Components in Deep Drawing
- Punch: The punch is the tool that drives the metal blank into the die. The punch’s shape and speed play a crucial role in ensuring smooth material flow without introducing defects. The punch must be designed to apply sufficient force to stretch the material into the die without tearing it.
- Die: The die determines the final shape of the part. It needs to be precisely machined to match the part’s desired geometry. The clearance between the punch and the die is a critical factor in determining material flow and the part’s final thickness.
- Blank Holder: The blank holder, or hold-down ring, is used to control the material flow during the drawing process. Its primary function is to prevent the formation of wrinkles by applying uniform pressure around the blank’s edge. The correct amount of blank holder force ensures that the metal flows into the die smoothly, without stretching too much in one area.
Role of Friction and Lubrication
Friction plays a major role in the deep drawing process, especially at the interface between the blank, punch, and die. Too much friction can lead to tearing or thinning of the material, while too little friction may cause the blank to slip or wrinkle. The lubricant used in deep drawing serves to reduce friction, improve material flow, and prevent surface defects.
The selection of a lubricant depends on the material being drawn, the depth of the draw, and the speed of the process. Common lubricants include oils, greases, and specialized synthetic compounds that can withstand the high pressures and temperatures generated during the process.
Force Distribution in Deep Drawing
The force required for deep drawing depends on various factors, including material properties, sheet thickness, and the geometry of the die. As the punch pushes the blank into the die, the force needed increases due to the material’s resistance to deformation. This force is distributed unevenly across the blank, with the edges often experiencing higher forces than the center. Proper force distribution is essential for avoiding defects such as wrinkling, tearing, or excessive thinning.
Materials Used in Deep Drawing
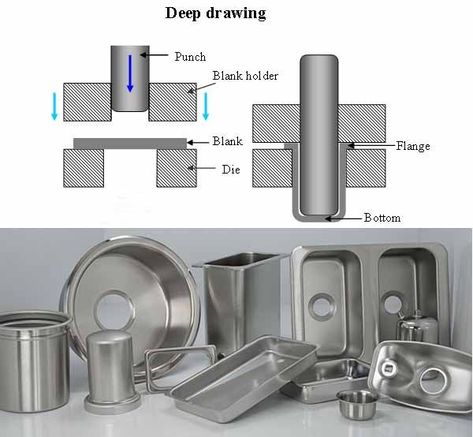
The success of the deep drawing process depends heavily on the material properties of the metal blank. Not all materials can be easily deep drawn; the material must have high ductility, allowing it to stretch without breaking. Additionally, formability, strength, and thickness play a crucial role in determining whether a material can be successfully drawn into complex shapes.
Common Materials in Deep Drawing
- Low-Carbon Steel:
- Low-carbon steel is one of the most common materials used in deep drawing due to its excellent formability and relatively low cost. Its ductility allows for significant deformation before failure, making it suitable for applications such as automotive panels and household appliances.
- Stainless Steel:
- Stainless steel is prized for its corrosion resistance and strength, but it is more difficult to deep draw than low-carbon steel. Special lubricants and precise control over process parameters are required to prevent defects when deep drawing stainless steel. It is commonly used for kitchen sinks, medical instruments, and aerospace components.
- Aluminum:
- Aluminum is a lightweight, ductile metal that is highly suitable for deep drawing applications where weight savings are essential. Automotive and aerospace industries often use deep-drawn aluminum parts for fuel tanks, body panels, and structural components. However, aluminum’s lower strength compared to steel requires adjustments to the punch speed and blank holder force.
- Copper and Brass:
- Copper and brass are often used in electrical applications, plumbing, and decorative products. Both materials offer good formability, though their higher cost makes them less common in large-scale deep drawing processes.
Material Properties Influencing Deep Drawing
- Ductility:
Ductility is the ability of a material to undergo significant plastic deformation before failure. The higher the ductility of the material, the easier it is to form deep-drawn parts without tearing or cracking. Materials like aluminum and low-carbon steel, which have high ductility, are ideal for deep drawing. - Yield Strength:
The yield strength of a material is the amount of stress it can withstand before it begins to deform plastically. Materials with lower yield strength are generally easier to draw, as they require less force to initiate deformation. However, if the material’s yield strength is too low, it may not be able to withstand the forces required for deep drawing without buckling or wrinkling. - Sheet Thickness:
Thicker sheets require more force to be drawn into the die but are less likely to tear compared to thinner sheets. However, they are more prone to wrinkling and require higher blank holder forces to ensure uniform material flow. Engineers must carefully balance sheet thickness with other process parameters to avoid defects. - Anisotropy:
The anisotropy of a material refers to its directional dependence on mechanical properties. In deep drawing, materials may behave differently based on the direction of the metal grains in the sheet. Materials with high anisotropy can result in uneven deformation, leading to defects such as earing (the formation of wavy edges).
Stages of the Deep Drawing Process
The deep drawing process consists of several stages, each playing a critical role in forming the final part with the desired dimensions and properties. Engineers must ensure that each stage is properly controlled to prevent defects and produce high-quality components.
1. Blanking
The first stage of the deep drawing process is blanking, where a flat sheet of metal is cut into a blank. The blank is typically circular and slightly larger than the final part to allow for material flow into the die. Blanking is performed using a punch and die set, with the punch cutting through the metal sheet to produce the desired blank size.
The quality of the blank is important because any imperfections, such as surface defects or rough edges, can propagate during the deep drawing process and lead to poor part quality. The blank must also be properly aligned with the die to ensure uniform material flow.
2. Drawing and Redrawing
The drawing stage is where the blank is pressed into the die by the punch. The punch moves downward, pushing the metal into the die cavity. As the punch descends, the material is forced to stretch and flow, taking the shape of the die. The success of this stage depends on maintaining the correct balance of blank holder force, punch speed, and lubrication.
If the depth of the part exceeds what can be achieved in a single stroke, the part may undergo redrawing. Redrawing involves repeating the drawing process in multiple stages, each time using a progressively smaller punch and die. This method allows for deeper parts to be formed without excessive thinning or tearing of the material.
3. Trimming and Finishing
After the part has been drawn to its final shape, excess material may need to be trimmed from the edges. This is particularly important in parts that require tight dimensional tolerances or smooth surfaces. Trimming is performed using specialized cutting tools, which remove any excess material and smooth out rough edges.
In some cases, parts may also undergo finishing processes, such as deburring, to remove any sharp edges or surface imperfections. Finishing is especially important in applications where surface quality is critical, such as in medical devices or consumer electronics.
4. Metal Flow During Drawing
The flow of metal during the drawing process is influenced by several factors, including the material’s ductility, the design of the die, and the force applied by the punch. During the initial stages of drawing, the material flows radially inward toward the center of the blank. As the punch moves deeper into the die, the material is stretched vertically, and its thickness decreases.
The flow stress of the material must be carefully controlled to prevent uneven deformation. If the material flows too quickly, it may cause wrinkling or tearing, while slow material flow can result in excessive thinning or uneven wall thickness.
5. Influence of Blank Holder Force and Punch Speed
The blank holder force is a critical parameter in deep drawing, as it controls the flow of material into the die. If the blank holder force is too low, the material may flow too freely, resulting in wrinkles. Conversely, if the force is too high, the material may not be able to flow into the die properly, leading to tearing or cracking.
The punch speed also plays a significant role in determining the quality of the final part. Higher punch speeds can increase productivity, but they also generate more heat and can lead to defects such as excessive thinning or surface defects. Lower punch speeds, on the other hand, provide more control over the material flow, but they slow down the production process.
Engineers must carefully balance the blank holder force and punch speed to achieve the best results in terms of part quality, material usage, and production efficiency.
Engineering Parameters Influencing Deep Drawing
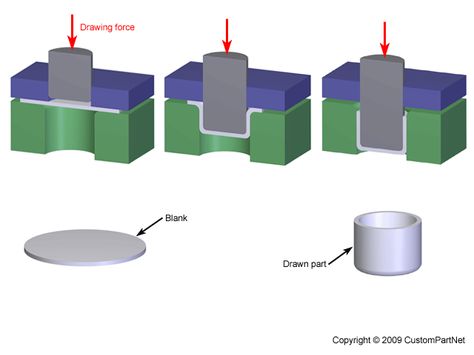
The quality and efficiency of the deep drawing process are highly dependent on various engineering parameters. By optimizing these parameters, engineers can achieve high-quality parts while minimizing defects and material waste.
1. Blank Holder Force
As discussed earlier, the blank holder force is essential for controlling the material flow during the deep drawing process. The force must be carefully adjusted based on the material being drawn, the part’s geometry, and the depth of the draw. Too much or too little force can result in defects such as wrinkling or tearing.
Dynamic blank holder systems have been developed to adjust the force in real-time during the drawing process. These systems use sensors and control algorithms to optimize the blank holder force throughout the drawing stroke, improving part quality and reducing the risk of defects.
2. Drawing Ratio and Limiting Drawing Ratio (LDR)
The drawing ratio is defined as the ratio of the blank diameter to the diameter of the drawn part. This ratio is an important measure of the severity of the drawing process. A higher drawing ratio indicates a more severe draw, which requires greater force and increases the likelihood of defects.
The limiting drawing ratio (LDR) is the maximum drawing ratio that can be achieved without causing failure (tearing or wrinkling) in the material. The LDR depends on factors such as material properties, punch and die design, and lubrication. Engineers must design the deep drawing process within the LDR to avoid defects.
3. Punch and Die Design
The design of the punch and die plays a crucial role in determining the success of the deep drawing process. Key design considerations include:
- Radius: The corner radius of the die and punch must be carefully designed to allow for smooth material flow. A small radius can cause the material to crack, while a large radius may lead to wrinkling or uneven material flow.
- Clearance: The clearance between the punch and the die is another critical factor. If the clearance is too small, the material may experience excessive thinning or tearing. Conversely, if the clearance is too large, the material may not deform properly, resulting in wrinkles.
- Shape: The shape of the punch and die determines the final geometry of the part. Complex shapes with deep cavities require precise punch and die design to ensure uniform material flow and avoid defects.
4. Drawing Speed and Pressure Control
The drawing speed affects the rate at which the material is deformed, while the pressure control ensures that the punch applies consistent force throughout the drawing process. Both parameters must be carefully controlled to prevent defects and ensure uniform part quality.
Modern hydraulic and servo-hydraulic presses allow for precise control over drawing speed and pressure. These presses can be programmed to adjust the speed and pressure based on the material’s behavior, ensuring optimal performance during the drawing process.
5. Effects of Lubrication and Friction
As mentioned earlier, lubrication is essential for reducing friction and ensuring smooth material flow. The choice of lubricant depends on factors such as the material being drawn, the depth of the draw, and the operating temperature. Dry film lubricants, synthetic oils, and water-based lubricants are commonly used in deep drawing applications.
Friction between the blank, punch, and die can lead to defects such as galling (material sticking to the punch or die) or surface scratches. Proper lubrication minimizes friction and helps prevent these defects, improving the overall quality of the part.
Common Defects in Deep Drawing
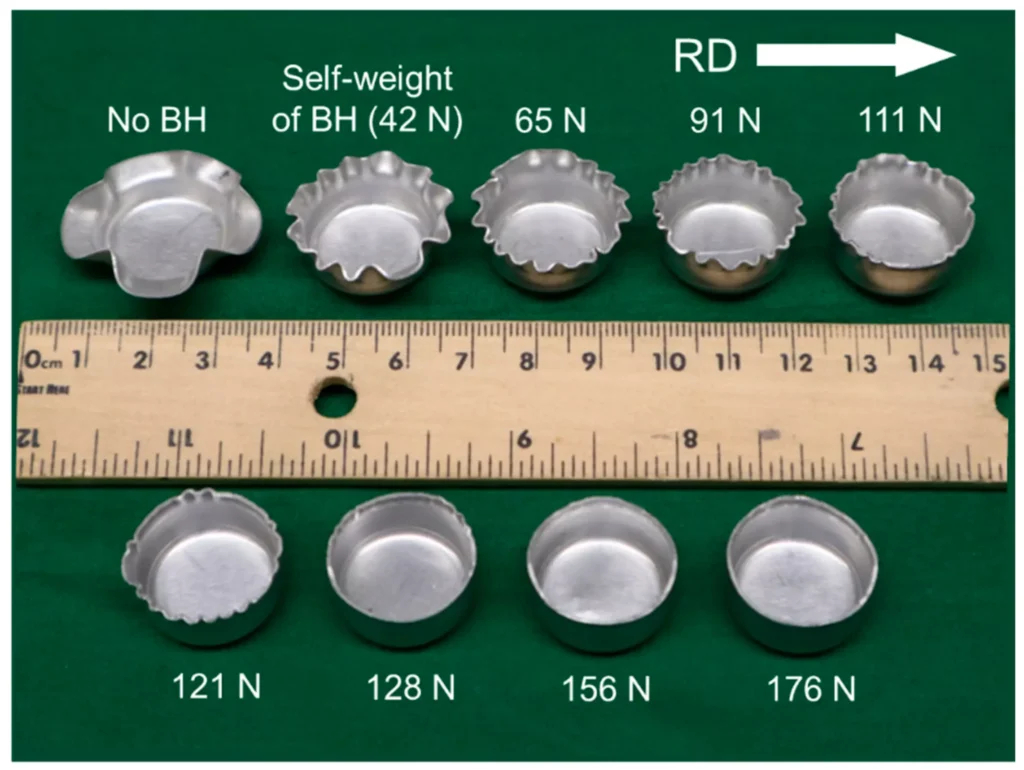
Despite careful planning and optimization, defects can still occur during the deep drawing process. These defects are often the result of improper control of process parameters, material properties, or tool design.
1. Wrinkling
Wrinkling occurs when the blank holder force is too low, allowing the material to flow too freely into the die. This results in excess material bunching up, forming wrinkles around the edges of the part. Wrinkling is more likely to occur in deeper draws or when drawing materials with low stiffness.
Solution:
Increasing the blank holder force or adjusting the lubrication can help prevent wrinkling. In some cases, redesigning the die to provide better material flow can also reduce the risk of wrinkling.
2. Tearing
Tearing is a catastrophic failure that occurs when the material is overstretched and can no longer withstand the applied forces. It often happens when the punch speed is too high, the material is too brittle, or the die design is not suitable for the material being drawn.
Solution:
Reducing the punch speed and ensuring that the material’s thickness and ductility are appropriate for the drawing process can help prevent tearing. Lubrication also plays a role in reducing the likelihood of tearing by minimizing friction.
3. Thinning and Earing
Thinning occurs when the material becomes too stretched in certain areas, resulting in a reduction in thickness. Thinning can weaken the part and increase the risk of failure during use. Earing, on the other hand, refers to the formation of wavy edges on the part due to anisotropy in the material’s grain structure.
Solution:
To avoid thinning, engineers must carefully control the punch speed, blank holder force, and lubrication. Earing can be minimized by selecting materials with lower anisotropy or adjusting the orientation of the blank relative to the material’s grain direction.
4. Galling and Surface Defects
Galling occurs when material from the blank adheres to the punch or die, causing scratches or rough surfaces on the part. Galling is more likely to occur when drawing hard materials or when lubrication is inadequate.
Solution:
Using proper lubrication and coating the punch and die with wear-resistant materials can reduce the risk of galling. Regular maintenance of the punch and die is also essential to prevent surface defects.
Technological Advances in Deep Drawing
The deep drawing process has evolved significantly with advancements in engineering, simulation, and automation technologies. These advances have improved the efficiency, precision, and quality of the process, enabling manufacturers to produce more complex parts with fewer defects.
1. Finite Element Analysis (FEA) and Simulation
Finite element analysis (FEA) is a computational technique used to simulate the behavior of materials under various conditions. In deep drawing, FEA allows engineers to predict how the material will deform during the drawing process, helping them optimize tool design, material selection, and process parameters.
Using FEA, engineers can simulate different scenarios, such as varying the blank holder force or changing the punch speed, to identify potential defects before they occur in production. This reduces the need for costly trial-and-error methods and shortens the time required to develop new products.
2. Automation and Control Systems
Automation has played a significant role in improving the productivity and precision of the deep drawing process. Modern hydraulic presses are equipped with CNC (Computer Numerical Control) systems that allow for precise control over process parameters such as punch speed, pressure, and blank holder force.
Automated tool change systems have also been developed to reduce downtime between production runs. These systems allow manufacturers to quickly switch between different punch and die sets, enabling greater flexibility in producing a variety of parts.
3. Advanced Materials and Coatings
New materials and surface coatings have been developed to improve the performance of punches and dies, reducing wear and increasing tool life. Hard coatings, such as titanium nitride (TiN) or diamond-like carbon (DLC), are applied to the surfaces of tools to reduce friction and prevent galling.
Additionally, advances in material science have led to the development of high-strength alloys that can be drawn into complex shapes without compromising part quality. These materials are particularly valuable in industries like aerospace and automotive, where lightweight, high-strength components are in high demand.
4. Industry 4.0 Integration
The integration of Industry 4.0 technologies, such as sensors, data analytics, and machine learning, has revolutionized the deep drawing process. Smart presses equipped with sensors can monitor key parameters, such as temperature, pressure, and tool wear, in real time. This data is transmitted to a central control system, allowing engineers to make adjustments on the fly or schedule maintenance before a failure occurs.
Predictive maintenance systems use machine learning algorithms to analyze historical data and predict when a press or tool will require maintenance. This reduces unplanned downtime and improves overall production efficiency.
Applications of Deep Drawing in Manufacturing
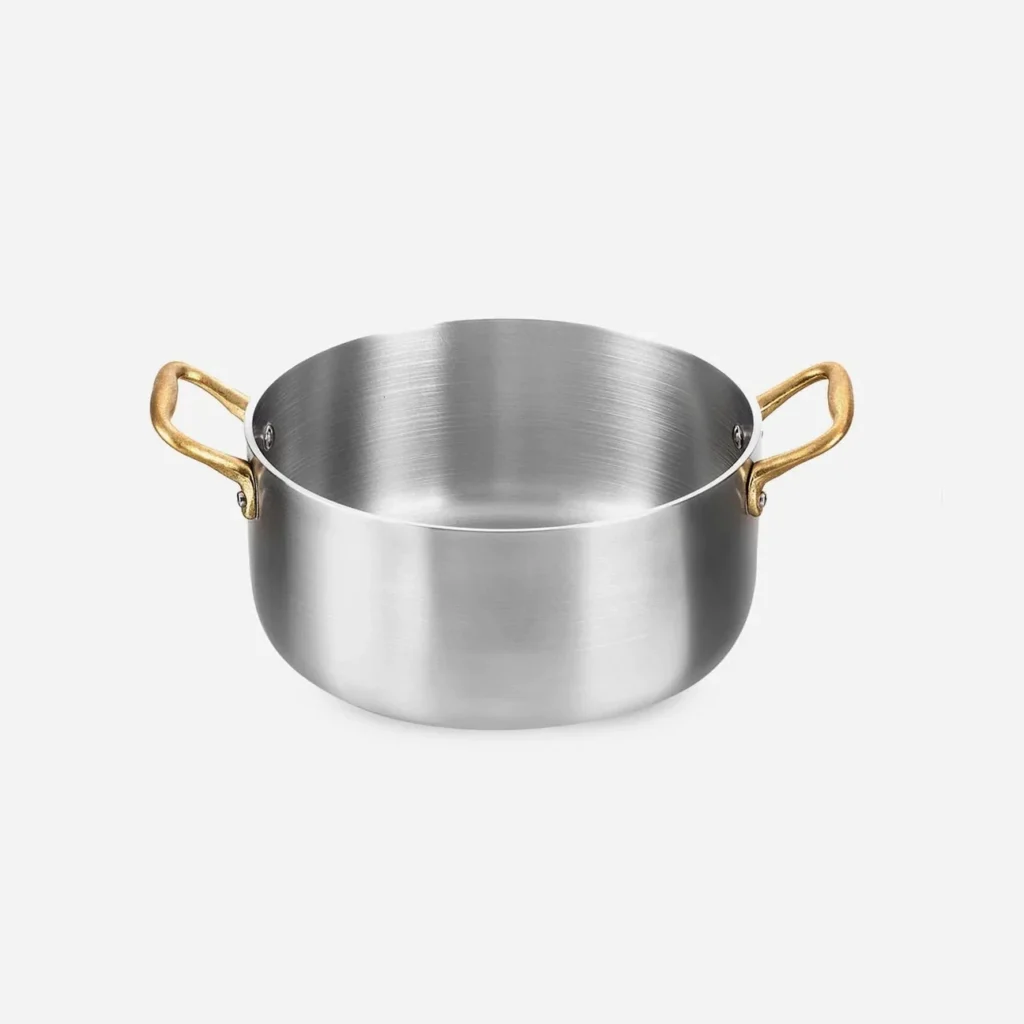
Deep drawing is a versatile process used in a wide range of industries to produce components with complex geometries and high precision. Below are some of the most common applications of deep drawing across different sectors.
1. Automotive Industry
In the automotive industry, deep drawing is used to manufacture parts such as car body panels, fuel tanks, and exhaust components. These parts require high strength and durability, making deep drawing an ideal process due to its ability to produce complex shapes with minimal material waste.
Lightweighting is a major trend in the automotive industry, and deep drawing is used to form lightweight materials like aluminum and high-strength steel into parts that meet stringent safety and performance requirements.
2. Aerospace Industry
The aerospace industry relies on deep drawing to produce components that are both lightweight and strong. Parts such as fuselage panels, engine components, and landing gear housings are often deep drawn from high-strength alloys. The precision and control offered by the deep drawing process make it ideal for producing parts with tight tolerances and complex geometries.
3. Electronics and Consumer Products
Deep drawing is widely used in the electronics and consumer goods industries to produce enclosures for devices like smartphones, laptops, and appliances. The ability to create thin, lightweight metal parts with a high-quality surface finish makes deep drawing suitable for these applications.
Heat sinks, battery enclosures, and connector components are also commonly produced using deep drawing, particularly when lightweight materials like aluminum are required.
4. Medical Devices and Packaging
In the medical industry, deep drawing is used to produce surgical instruments, implants, and medical device housings. The precision of the process is critical in ensuring that these components meet the stringent quality and safety standards required in the medical field.
In packaging, deep drawing is commonly used to produce metal cans, aerosol containers, and cosmetic containers, where lightweight, durable, and aesthetically pleasing packaging is important.
Conclusion
Deep drawing is a highly versatile and efficient metal-forming process that has become a cornerstone of modern manufacturing. Its ability to produce complex shapes with minimal material waste makes it invaluable in industries like automotive, aerospace, electronics, and medical devices. However, the success of the deep drawing process depends on a deep understanding of the engineering principles behind it, including material behavior, tool design, and process optimization.
As manufacturing continues to evolve, advances in technology are enhancing the deep drawing process. Finite element analysis (FEA), automation, and smart manufacturing systems are allowing engineers to achieve greater precision, reduce defects, and improve overall efficiency. Additionally, new materials and surface coatings are extending tool life and enabling the production of more complex, high-strength components.
Looking to the future, the integration of Industry 4.0 technologies and data analytics promises to further improve the deep drawing process, enabling manufacturers to predict failures, optimize production in real time, and reduce costs. As the demand for lightweight, high-strength components continues to grow, deep drawing will remain a critical process in the global manufacturing landscape.
To create a comprehensive 5,000-word technical text on Materials Used in Deep Drawing, we will cover various materials commonly used in the process, their specific properties, and how these properties affect deep drawing operations. The document will be structured to explore the fundamentals of deep drawing, material requirements, the behavior of various metals, and recent innovations in material science for deep drawing applications.
Introduction to Deep Drawing and Material Requirements
Deep drawing is a manufacturing process used to form sheet metal into three-dimensional shapes through the application of mechanical force. The process involves placing a flat metal blank over a die cavity and pushing it into the die using a punch, transforming the flat sheet into a hollow object, such as a cup, cylinder, or more complex geometries.
Material selection is one of the most critical factors influencing the success of deep drawing. The process subjects the material to significant stretching and compressive forces, requiring it to have sufficient ductility and strength to deform without tearing or wrinkling. The material must also have good formability characteristics to ensure smooth material flow during the process and maintain uniform thickness without defects.
Materials used in deep drawing must meet several criteria to avoid common issues like tearing, wrinkling, or excessive thinning. The key properties that influence a material’s suitability for deep drawing include ductility, yield strength, tensile strength, and formability. These properties vary across different metals and alloys, and the success of a deep drawing operation depends on the careful balance of these characteristics.
Common metals used in deep drawing include steel, aluminum, copper, brass, titanium, and nickel alloys, each offering distinct advantages and challenges. This document will explore these materials, focusing on how their unique properties make them suitable for deep drawing applications and their role in various industries.
Material Properties Critical to Deep Drawing
The ability of a material to undergo plastic deformation without failure is essential in the deep drawing process. Understanding key material properties helps engineers select the right metal for specific deep drawing applications.
1. Ductility and Plasticity
Ductility is the material’s ability to undergo significant plastic deformation before rupture. It is perhaps the most important property in deep drawing, as the process involves extensive stretching and bending of the material. Materials with high ductility, like low-carbon steel and aluminum, can be drawn into complex shapes without breaking.
Plasticity refers to the material’s ability to retain its deformed shape once the force is removed. In deep drawing, high plasticity ensures that the material can be stretched into the desired shape and maintain its new geometry without springing back or cracking.
2. Yield Strength and Tensile Strength
Yield strength is the amount of stress a material can withstand before it begins to deform plastically. Materials with lower yield strength are typically easier to draw because they deform under lower forces. However, they also tend to be more prone to wrinkling. Tensile strength refers to the maximum stress a material can endure before failure. In deep drawing, both yield and tensile strengths must be carefully considered to ensure that the material can withstand the applied forces without tearing or cracking.
3. Anisotropy and Its Effects
Anisotropy refers to the variation in material properties depending on the direction of the material grain. Many metals, especially those used in deep drawing, exhibit directional dependence due to the rolling process used to produce metal sheets. This directional behavior can cause issues like earing (formation of wavy edges) during deep drawing. Materials with high levels of anisotropy may experience uneven deformation, leading to defects in the final part.
4. Formability (n-value, r-value, and Elongation)
Formability is the material’s ability to undergo plastic deformation without failure. It is typically assessed using the n-value (strain hardening exponent), which indicates how much a material strengthens as it is stretched, and the r-value (plastic strain ratio), which measures the material’s resistance to thinning during drawing.
- n-value: Higher n-values indicate better resistance to necking, which allows for deeper draws without tearing.
- r-value: A high r-value suggests that the material will resist thinning, making it more suitable for deep drawing operations.
The elongation at break is another important measure of formability, indicating how much a material can be stretched before it fractures. Materials with high elongation, like aluminum and low-carbon steel, are ideal for deep drawing.
5. Work Hardening and Strain Hardening
Work hardening (or strain hardening) occurs when a material becomes stronger and less ductile as it is deformed. This property is critical in deep drawing, as it affects how the material behaves during multiple drawing stages. While work hardening improves the material’s resistance to failure, it also makes it more difficult to deform further, potentially leading to cracking or surface defects if not carefully managed.
Steel and Its Alloys in Deep Drawing
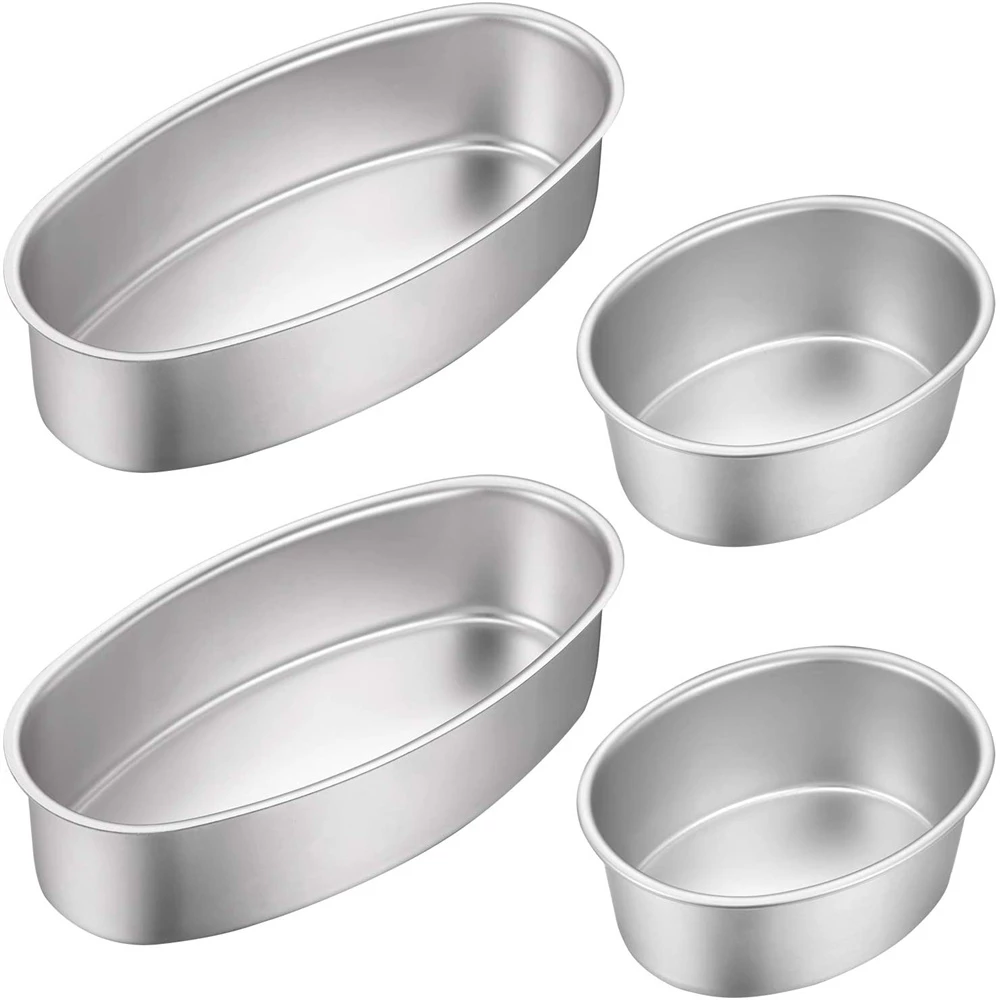
Steel is one of the most commonly used materials in deep drawing, thanks to its versatility, strength, and relatively low cost. Steel alloys come in a wide range of forms, each with distinct mechanical properties that make them suitable for different deep drawing applications.
1. Low-Carbon Steel: Properties and Applications
Low-carbon steel (also known as mild steel) is the most widely used material for deep drawing. It has a carbon content of less than 0.25%, which gives it excellent ductility and formability. Low-carbon steel can be drawn into deep, complex shapes without tearing or wrinkling, making it ideal for automotive body panels, household appliances, and various industrial components.
Key properties of low-carbon steel include:
- High ductility: Allows for deep drawing without failure.
- Good weldability: Makes it easy to join parts after forming.
- Cost-effectiveness: Low-carbon steel is relatively inexpensive compared to other metals used in deep drawing.
Low-carbon steel is often used in automotive applications, such as the production of car body panels, doors, hoods, and fenders, where large, lightweight, and structurally sound parts are required. The material’s formability ensures that manufacturers can produce large volumes of parts with uniform quality.
2. High-Strength Low-Alloy (HSLA) Steel: Advantages and Challenges
High-strength low-alloy (HSLA) steels contain small amounts of alloying elements like chromium, vanadium, and manganese, which increase their strength without significantly reducing ductility. HSLA steels offer a higher strength-to-weight ratio than low-carbon steels, making them ideal for applications where both strength and weight reduction are critical, such as in automotive and structural components.
Advantages of HSLA steel in deep drawing include:
- Higher strength: Allows for thinner, lighter parts without sacrificing structural integrity.
- Improved wear resistance: HSLA steel is more resistant to wear, reducing tool wear during deep drawing.
Challenges with HSLA steels include:
- Lower ductility: While HSLA steels have improved strength, their lower ductility compared to low-carbon steel makes them more prone to tearing and cracking during deep drawing.
- Higher drawing forces required: HSLA steels require more force to be drawn into complex shapes, which can lead to increased tool wear and energy consumption.
3. Stainless Steel: Formability, Limitations, and Uses
Stainless steel is known for its corrosion resistance, strength, and ability to withstand high temperatures, making it ideal for applications in harsh environments. It is used in a variety of industries, including food processing, medical devices, and aerospace, where durability and hygiene are important.
The most common grades of stainless steel used in deep drawing are 304 and 316, which offer a balance between formability and strength. However, stainless steel is more difficult to draw than low-carbon steel due to its higher yield strength and tendency to work harden.
Key challenges with stainless steel in deep drawing include:
- Increased tool wear: Stainless steel’s hardness can lead to higher tool wear, requiring more frequent maintenance of punches and dies.
- Springback: Stainless steel has a tendency to spring back after deformation, making it harder to achieve tight dimensional tolerances.
4. Advanced High-Strength Steels (AHSS)
Advanced high-strength steels (AHSS), such as dual-phase (DP) steel and transformation-induced plasticity (TRIP) steel, have been developed to meet the demands of modern automotive manufacturing, where weight reduction and crash performance are critical.
- Dual-phase steel (DP): Combines a soft ferritic phase with a hard martensitic phase, offering excellent strength and ductility. It is commonly used in automotive safety components like B-pillars and structural reinforcements.
- TRIP steel: Utilizes the transformation of retained austenite into martensite during deformation, providing a high strength-to-weight ratio and excellent energy absorption in crash scenarios.
While AHSS offers excellent mechanical properties for deep drawing, it is more difficult to form due to its higher strength and reduced ductility compared to traditional steels. This increases the risk of tearing and requires more precise control over process parameters.
5. Innovations in Steel for Deep Drawing
Recent advancements in steel metallurgy have focused on improving the formability of high-strength steels for deep drawing applications. Some of these innovations include:
- Third-generation AHSS: These steels combine the high strength of AHSS with improved ductility, allowing for better formability in deep drawing processes.
- Press-hardened steel (PHS): PHS is used to form ultra-high-strength components through a process known as hot forming. This involves heating the steel before drawing it into shape, which reduces the risk of cracking and allows for complex geometries to be formed.
Aluminum and Its Alloys
Aluminum is favored in deep drawing applications that require lightweight, corrosion-resistant parts. It is commonly used in industries such as automotive, aerospace, and electronics, where weight reduction is a key priority.
1. Why Aluminum is Favored in Lightweight Applications
Aluminum is significantly lighter than steel, with a density approximately one-third that of steel. This makes it ideal for applications where weight reduction is critical, such as in transportation (to improve fuel efficiency) and consumer electronics (to create lightweight, portable devices).
Key advantages of aluminum in deep drawing include:
- High ductility: Aluminum can be stretched into complex shapes without cracking.
- Corrosion resistance: Aluminum naturally forms a protective oxide layer, making it resistant to corrosion in most environments.
- Recyclability: Aluminum can be easily recycled without losing its properties, making it a sustainable choice for manufacturers.
2. 1000-Series (Pure Aluminum): Formability and Applications
The 1000-series of aluminum alloys consists of commercially pure aluminum, which offers excellent formability due to its high ductility and low yield strength. However, its relatively low strength limits its use to applications where mechanical strength is not the primary requirement.
Applications of 1000-series aluminum in deep drawing include:
- Food packaging: Aluminum cans and containers are often made from 1000-series alloys due to their formability and corrosion resistance.
- Consumer goods: Lightweight aluminum components for household appliances and electronic devices are often deep drawn from pure aluminum.
3. 5000-Series Aluminum Alloys: Marine, Automotive, and Aerospace Applications
The 5000-series aluminum alloys contain magnesium as the primary alloying element, which improves the material’s strength without significantly reducing ductility. These alloys are used in applications where a balance of strength and formability is required.
Applications of 5000-series aluminum in deep drawing include:
- Marine industry: Aluminum components for boats and ships are often drawn from 5000-series alloys due to their corrosion resistance in saltwater environments.
- Automotive industry: Lightweight components, such as body panels and structural reinforcements, are often made from 5000-series alloys to reduce vehicle weight and improve fuel efficiency.
- Aerospace industry: Aircraft structural components are often drawn from high-strength aluminum alloys in the 5000 and 6000 series.
4. Challenges of Aluminum in Deep Drawing
Despite its many advantages, aluminum presents several challenges in the deep drawing process, including:
- Cracking: Aluminum has a lower elongation at break compared to steel, making it more prone to cracking during deep drawing, especially in high-strength alloys.
- Springback: Like stainless steel, aluminum tends to spring back after being deformed, making it difficult to achieve tight tolerances.
- Lubrication requirements: Aluminum requires specialized lubricants to reduce friction during deep drawing. Without proper lubrication, aluminum can stick to the punch and die, causing defects like galling.
5. Recent Developments in Aluminum Alloys for Deep Drawing
Researchers have developed new aluminum alloys with improved formability for deep drawing applications. These innovations include:
- Aluminum-lithium alloys: These alloys offer a higher strength-to-weight ratio than traditional aluminum alloys, making them ideal for aerospace applications.
- Heat-treatable alloys: Advances in heat treatment processes have improved the formability of aluminum alloys, allowing for deeper draws without cracking or tearing.
Copper and Brass in Deep Drawing
Copper and brass are frequently used in deep drawing for applications that require high thermal or electrical conductivity, corrosion resistance, or aesthetic appeal.
1. Copper: Ductility, Thermal Conductivity, and Electrical Applications
Copper is highly ductile and exhibits excellent formability, making it suitable for deep drawing applications where complex shapes are required. Its high thermal and electrical conductivity make it the material of choice for components such as:
- Electrical connectors
- Heat exchangers
- Plumbing fittings
Due to its softness, copper can be drawn into deep, intricate shapes without excessive force. However, copper’s tendency to work harden during deformation can complicate the deep drawing process, requiring careful control over drawing speed and lubrication.
2. Brass Alloys: Formability and Uses in Plumbing, Electrical, and Decorative Products
Brass, an alloy of copper and zinc, offers good formability and is often used in decorative applications as well as functional components like:
- Plumbing fixtures
- Electrical contacts
- Musical instruments
The zinc content in brass improves its strength and corrosion resistance while maintaining sufficient ductility for deep drawing. Cartridge brass (70% copper, 30% zinc) is commonly used in deep drawing for applications like bullet casings and architectural components due to its excellent balance of strength and formability.
3. Challenges with Copper and Brass in Deep Drawing
Copper and brass present several challenges during the deep drawing process, including:
- Work hardening: Copper and brass work harden quickly during deformation, which can lead to cracking if the material becomes too brittle. To avoid this, manufacturers may use intermediate annealing processes to restore the material’s ductility between drawing stages.
- Friction and galling: Both copper and brass can stick to the punch and die during drawing, leading to surface defects. Specialized lubricants, such as graphite-based lubricants, are often required to reduce friction and prevent galling.
4. Lubrication Requirements and Solutions for Copper and Brass
Lubrication is critical in deep drawing copper and brass, as their soft, ductile nature makes them prone to sticking and galling. Water-based lubricants, oil-based lubricants, and dry film coatings are commonly used to improve material flow and protect the surface of the workpiece.
Titanium and Its Alloys
Titanium is known for its exceptional strength-to-weight ratio, corrosion resistance, and biocompatibility, making it an ideal material for industries such as aerospace, medical devices, and automotive.
1. Unique Properties of Titanium: Strength-to-Weight Ratio, Corrosion Resistance
Titanium’s high strength-to-weight ratio allows for the production of lightweight, durable components that can withstand extreme conditions. Its natural corrosion resistance also makes it suitable for applications in chemical processing, marine environments, and biomedical implants.
2. Medical and Aerospace Applications
Titanium’s biocompatibility and resistance to corrosion make it the material of choice for medical implants such as hip and knee replacements. In the aerospace industry, titanium alloys are used to manufacture components such as turbine blades, aircraft frames, and fasteners due to their ability to withstand high temperatures and harsh environments.
3. Difficulties in Forming Titanium: High Springback, Galling
Despite its advantages, titanium is challenging to form through deep drawing due to its high strength and springback effect. Springback occurs when the material tries to return to its original shape after being deformed, making it difficult to achieve precise tolerances.
Additionally, titanium has a tendency to gall, meaning that material from the blank can adhere to the punch or die during drawing. This can lead to surface defects and increased tool wear.
4. Innovations in Tooling and Lubrication for Drawing Titanium
To address these challenges, manufacturers have developed specialized tooling materials and lubricants to improve the deep drawing of titanium. These include:
- Coated punches and dies: Titanium nitride (TiN) and diamond-like carbon (DLC) coatings are applied to reduce galling and extend tool life.
- High-performance lubricants: Synthetic lubricants and solid film coatings are used to reduce friction and improve material flow during the deep drawing process.
Nickel Alloys in Deep Drawing
Nickel-based alloys are known for their high strength, corrosion resistance, and ability to withstand extreme temperatures, making them essential in industries like aerospace, chemical processing, and power generation.
1. Properties of Nickel-Based Alloys: Heat and Corrosion Resistance
Nickel alloys are often used in environments where extreme heat and corrosive chemicals are present. For example, Inconel and Hastelloy are two common nickel-based alloys used in deep drawing due to their resistance to oxidation and corrosion at high temperatures.
2. Applications in Extreme Environments: Aerospace, Chemical Processing
In the aerospace industry, nickel alloys are used for components such as turbine blades, exhaust systems, and heat exchangers, where the material must maintain its strength and resist oxidation at high temperatures. In the chemical processing industry, nickel alloys are used in reactors, pipes, and valves that handle corrosive fluids and gases.
3. Challenges in Deep Drawing Nickel Alloys: Hardening, Tool Wear
Nickel alloys tend to work harden rapidly during deformation, which increases the risk of cracking and tool wear during deep drawing. The high strength of nickel alloys also requires higher drawing forces, which can lead to increased tool wear and material galling.
4. Techniques to Improve Formability
To improve the formability of nickel alloys in deep drawing, several techniques are employed, including:
- Heat treatments: Annealing the material between drawing stages helps to reduce work hardening and restore ductility.
- Tool coatings: Applying hard coatings such as TiN or ceramic coatings to punches and dies reduces tool wear and galling, extending tool life and improving the quality of the finished part.
Magnesium Alloys in Deep Drawing
Magnesium alloys are gaining popularity in industries like automotive and aerospace due to their extremely lightweight properties. However, their use in deep drawing is still limited due to the challenges associated with forming magnesium.
1. Lightweighting Advantages of Magnesium Alloys
Magnesium is one of the lightest structural metals available, making it ideal for applications where weight reduction is critical. In the automotive industry, magnesium is used to reduce the overall weight of vehicles, leading to improved fuel efficiency and reduced emissions.
2. Applications in Automotive and Aerospace Industries
In the automotive industry, magnesium alloys are used to produce components such as gearboxes, steering wheels, and dashboard frames. In the aerospace industry, magnesium is used in aircraft seats, bracketry, and engine components to reduce weight while maintaining strength.
3. Challenges: Brittleness, Forming Temperatures, and Lubrication
Magnesium alloys are more brittle than aluminum and steel, making them more prone to cracking during deep drawing. Additionally, magnesium has a narrow range of forming temperatures, meaning that it must be heated to a specific temperature range to avoid cracking.
Magnesium also requires specialized lubricants during deep drawing to reduce friction and prevent galling. Without proper lubrication, magnesium alloys can stick to the punch and die, leading to surface defects.
4. Recent Research in Forming Magnesium for Deep Drawing
Researchers are exploring new methods to improve the deep drawing of magnesium alloys, including:
- Hot forming: Heating the magnesium to its optimal forming temperature improves ductility and reduces the risk of cracking.
- Alloy development: New magnesium alloys with improved ductility are being developed to overcome the brittleness of traditional magnesium alloys.
Recent Developments in Material Science for Deep Drawing
Advances in material science and technology have significantly improved the deep drawing process, enabling manufacturers to produce more complex and high-strength components.
1. Development of Ultra-Lightweight Materials
Researchers are continually developing new ultra-lightweight materials that offer high strength and formability, making them ideal for deep drawing applications. These materials are critical in industries like automotive and aerospace, where reducing weight without sacrificing strength is a top priority.
2. Advances in Coatings for Reducing Friction
To improve material flow and reduce tool wear, advanced coatings are being applied to punches and dies in deep drawing operations. Diamond-like carbon (DLC) coatings and ceramic coatings are among the most commonly used, offering excellent wear resistance and reducing the risk of galling.
3. Simulation Tools for Predicting Material Behavior in Deep Drawing
The use of finite element analysis (FEA) and other simulation tools allows engineers to predict how materials will behave during the deep drawing process. These tools help optimize tool design, material selection, and process parameters, reducing the need for costly trial-and-error methods.
4. Smart Materials and Adaptive Forming Technologies
Smart materials that can change their properties in response to external stimuli, such as temperature or pressure, are being explored for use in deep drawing. These materials could enable more efficient and precise forming processes by adapting to the forces applied during deep drawing.
Conclusion
Material selection is one of the most critical factors in the success of the deep drawing process. The materials used must have the right combination of ductility, strength, and formability to withstand the stresses and strains of deep drawing without failing. Different metals, such as steel, aluminum, copper, brass, titanium, and nickel alloys, each offer unique properties that make them suitable for different deep drawing applications.
Recent advancements in material science, such as the development of ultra-lightweight alloys and advanced coatings, have improved the performance of materials used in deep drawing. Additionally, the use of simulation tools and smart materials has enabled more precise control over the deep drawing process, reducing defects and improving efficiency.
As industries continue to demand lightweight, high-strength components, the development of new materials and technologies for deep drawing will play a crucial role in advancing manufacturing capabilities.
The Fundamental Principles of Deep Drawing: A Comprehensive Exploration
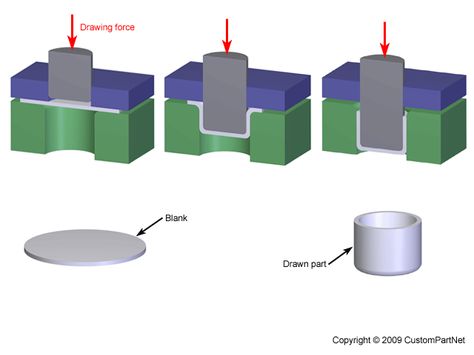
Deep drawing is a widely used manufacturing process that involves transforming flat sheet metal into complex three-dimensional shapes by applying mechanical force. It is a critical technique in industries such as automotive, aerospace, electronics, and packaging, where high precision, repeatability, and strength are essential. The success of the deep drawing process hinges on understanding the underlying mechanical and material principles involved. This text will delve into these fundamental principles, covering the mechanics of deep drawing, material properties, stress-strain behavior, tool design, process parameters, and common issues and solutions.
Introduction to Deep Drawing
Deep drawing is a sheet metal forming process in which a flat metal blank is radially drawn into a forming die by the mechanical action of a punch. The process can produce parts with a depth greater than their diameter, making it distinct from other metal forming techniques such as stamping or bending. Deep drawing is commonly used to manufacture cylindrical, box-shaped, and complex hollow parts, such as beverage cans, automotive body panels, kitchen sinks, and fuel tanks.
The deep drawing process is highly versatile, capable of producing components with intricate geometries and tight tolerances. It also ensures uniform material thickness and high structural integrity, making it ideal for industries requiring both aesthetic quality and durability. However, achieving defect-free deep drawing requires a thorough understanding of the fundamental principles governing material behavior, tool design, and process control.
The key factors influencing the deep drawing process include material properties, the interaction between the punch and die, friction, blank holder force, and lubrication. These factors determine the success of the process and the quality of the final part. By exploring the mechanical principles and parameters that control deep drawing, we can optimize the process to minimize defects such as wrinkling, tearing, and thinning, while maximizing efficiency and product quality.
Mechanics of Deep Drawing
The deep drawing process is governed by the principles of plastic deformation, which refers to the permanent change in the shape of a material when subjected to external forces. Understanding the mechanics of plastic deformation is critical for controlling how the sheet metal flows into the die and forms the desired shape.
2.1. Plastic Deformation and Stress-Strain Relationship
The deep drawing process involves the application of mechanical force to a metal blank, causing it to stretch and flow into a die cavity. This deformation occurs in the plastic region of the material’s stress-strain curve, meaning that the material is permanently deformed and does not return to its original shape once the force is removed.
The stress-strain relationship is a fundamental concept in understanding how materials behave under load. It describes how a material deforms (strain) in response to an applied stress. The elastic region of the curve represents the reversible deformation, while the plastic region represents permanent deformation. In deep drawing, the material must be deformed plastically to achieve the desired shape without cracking.
The amount of deformation a material can undergo before failure is determined by its ductility, which is a key material property in deep drawing. Ductile materials, such as low-carbon steel and aluminum, can withstand significant plastic deformation before rupturing, making them suitable for deep drawing applications.
2.2. Forces in Deep Drawing
The primary forces in deep drawing include the punch force, blank holder force, and frictional forces. These forces interact to control the flow of the material and determine the final shape and quality of the drawn part.
- Punch Force: The punch force is the force applied by the punch to drive the blank into the die. It must be high enough to overcome the material’s resistance to deformation, but not so high that it causes the material to tear. The punch force increases as the depth of the draw increases, and its magnitude depends on factors such as material properties, sheet thickness, and die geometry.
- Blank Holder Force: The blank holder force is applied by a blank holder or hold-down ring to prevent the edges of the blank from wrinkling as it is drawn into the die. Insufficient blank holder force can lead to wrinkling, while excessive force can restrict material flow and cause tearing. Achieving the correct blank holder force is essential for maintaining material flow and preventing defects.
- Frictional Forces: Friction plays a critical role in the deep drawing process, particularly at the interfaces between the blank, punch, and die. Friction opposes material flow, increasing the required punch force and influencing the distribution of stresses in the blank. While some friction is necessary to control material flow, excessive friction can lead to thinning, tearing, and tool wear. Proper lubrication is essential to minimize friction and ensure smooth material flow.
2.3. Flow of Material
Material flow during deep drawing is a complex interaction of tensile, compressive, and shear stresses. As the punch moves downward, it stretches the material radially inward toward the die cavity. The blank undergoes tensile stress at the outer edges, while the material near the punch is subjected to compressive stress as it is forced into the die.
Material flow is influenced by factors such as the material’s ductility, the shape and geometry of the die, and the blank holder force. Flow stress, which is the stress required to continue deforming the material, must be carefully controlled to avoid defects. If the material flows too quickly, it can result in wrinkling, while slow material flow can lead to excessive thinning or tearing.
Material Properties in Deep Drawing
Material selection is one of the most important aspects of the deep drawing process. Different materials behave differently under stress, and their properties directly influence how they respond to the forces applied during deep drawing. The key material properties that determine a material’s suitability for deep drawing include ductility, yield strength, tensile strength, anisotropy, and work hardening. Understanding these properties helps engineers optimize the process and select the best material for a given application.
3.1. Ductility
Ductility refers to a material’s ability to undergo significant plastic deformation before rupturing. Materials with high ductility, such as low-carbon steel and aluminum, are preferred for deep drawing because they can be stretched and formed into complex shapes without cracking. The greater the material’s ductility, the deeper the part can be drawn without failure. Ductility is especially important in deep drawing because the material undergoes large deformations, particularly in the flange area where tensile stress is concentrated.
Elongation at break, which measures the strain a material can withstand before fracturing, is commonly used as an indicator of ductility. Materials with high elongation values are more capable of undergoing the large strains associated with deep drawing, while materials with low elongation are more prone to tearing.
3.2. Yield Strength and Tensile Strength
Yield strength is the stress at which a material begins to deform plastically. In deep drawing, materials with lower yield strength are generally preferred because they require less force to deform. A lower yield strength allows the material to flow more easily into the die cavity without tearing or wrinkling. However, materials with excessively low yield strength may be prone to wrinkling or excessive thinning due to their inability to resist compressive forces.
Tensile strength, on the other hand, is the maximum stress a material can withstand before it fractures. While tensile strength is important for ensuring that the material does not rupture during drawing, it is not as critical as yield strength in most deep drawing applications. The material is typically stressed beyond its yield point but below its tensile strength.
Balancing yield strength and tensile strength is essential in deep drawing. The material should be soft enough to be drawn easily, but strong enough to resist tearing during the drawing process.
3.3. Anisotropy
Anisotropy refers to the directional dependence of a material’s mechanical properties. In deep drawing, anisotropy can significantly influence how the material deforms during the process. Most sheet metals exhibit some degree of planar anisotropy, which arises from the rolling process used to manufacture the sheets. This anisotropy can cause non-uniform deformation, leading to defects such as earing, which refers to the formation of wavy edges around the drawn part.
The degree of anisotropy in a material is characterized by the r-value (plastic strain ratio), which measures the material’s resistance to thinning during deformation. A higher r-value indicates that the material is less likely to thin out, making it more suitable for deep drawing. Materials with low anisotropy are preferred for deep drawing because they deform more uniformly and are less prone to defects.
3.4. Work Hardening and Strain Hardening
Work hardening (also known as strain hardening) occurs when a material becomes stronger and more resistant to deformation as it is plastically deformed. While work hardening improves the material’s resistance to tearing, it also makes it more difficult to deform further, which can complicate the deep drawing process.
Strain hardening is described by the n-value (strain hardening exponent), which measures how much a material strengthens as it is deformed. A higher n-value indicates better resistance to localized necking, which is critical for deep drawing, especially for deeper or more complex parts. However, excessive work hardening can lead to problems like tearing, surface defects, and increased tool wear.
In deep drawing, materials must balance ductility and work hardening. While some level of work hardening is desirable for strength and durability, excessive work hardening can make the material too brittle to be drawn into deep or complex shapes without failure.
Tooling in Deep Drawing
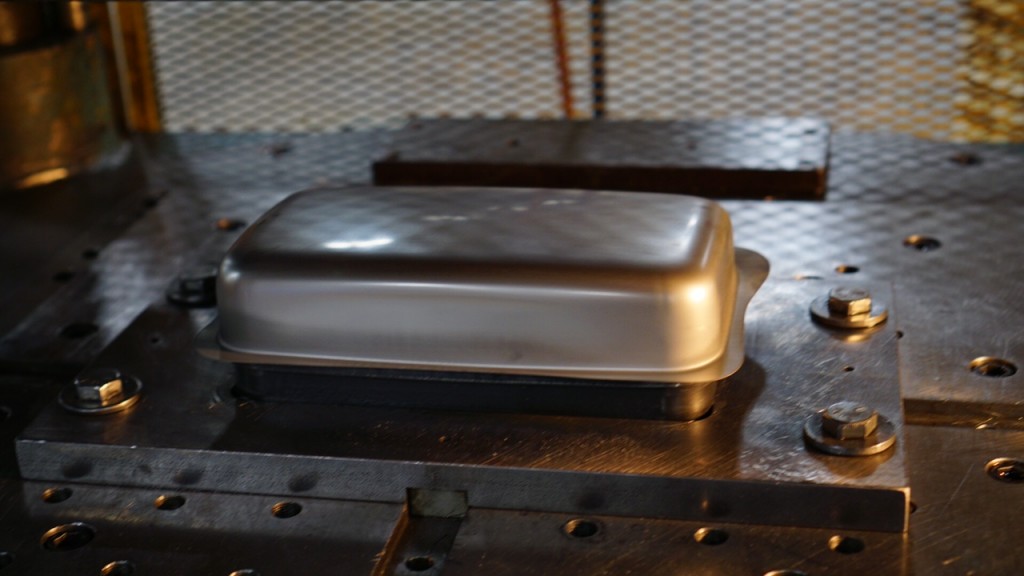
Tool design is critical to the success of the deep drawing process. The key components of the tooling system include the punch, die, and blank holder. Each tool must be precisely designed and manufactured to ensure smooth material flow, prevent defects, and produce parts with the desired geometry and dimensions. The design of these tools directly affects the forces acting on the material and determines how the material deforms during drawing.
4.1. Punch Design
The punch is responsible for pushing the blank into the die and forming the part. Its design, including its shape, size, and surface finish, is crucial to controlling material flow and minimizing defects such as tearing or thinning. Punches can have a variety of shapes depending on the desired part geometry, including cylindrical, conical, or box-shaped profiles.
Key considerations for punch design include:
- Shape and Geometry: The punch must match the desired shape of the final part. Complex geometries, such as those with deep cavities or intricate details, require carefully designed punches to control material flow and prevent localized thinning.
- Radius: The corner radius of the punch plays a critical role in the drawing process. A small radius can lead to high localized stresses, which increases the risk of tearing or cracking. Conversely, a large radius may result in wrinkling or uneven material flow. The punch radius should be optimized to ensure smooth deformation and uniform material distribution.
- Surface Finish: The punch’s surface finish affects friction between the punch and the blank. A smooth surface reduces friction, allowing for better material flow, while a rough surface may increase friction and cause defects such as galling or scratching.
4.2. Die Design
The die is the tool into which the metal blank is drawn to form the desired shape. The design of the die, including its geometry, clearance, and surface finish, is crucial for controlling material flow, minimizing friction, and ensuring consistent part dimensions.
Key factors in die design include:
- Die Shape and Geometry: The die must be designed to match the desired shape of the part. The geometry of the die cavity determines how the material will flow during the drawing process. Complex part geometries, such as those with multiple features or deep cavities, require precise die design to prevent defects such as wrinkling, tearing, or uneven wall thickness.
- Die Radius: The die entry radius is one of the most important aspects of die design. A small die radius can lead to excessive thinning or tearing of the material, while a large die radius may cause wrinkling or excessive stretching. The die radius must be carefully selected based on the material properties and the desired depth of the draw.
- Clearance Between Punch and Die: The clearance between the punch and the die is the gap through which the material flows as it is drawn into the die cavity. The clearance is typically slightly larger than the thickness of the blank to allow for material flow without excessive thinning or tearing. Incorrect clearance can result in defects such as wrinkles, tears, or uneven thickness distribution.
4.3. Blank Holder Design
The blank holder (also known as a hold-down ring) plays a critical role in controlling the flow of material into the die during the drawing process. The blank holder applies pressure to the edges of the blank, preventing it from wrinkling or folding as it is drawn into the die. However, the blank holder force must be carefully controlled to avoid defects.
Key considerations for blank holder design include:
- Force Distribution: The blank holder must apply uniform pressure around the circumference of the blank to ensure even material flow. Uneven pressure can lead to wrinkling or tearing at the edges of the part. In some cases, adjustable blank holders or segmented blank holders are used to apply variable pressure based on the material’s behavior during drawing.
- Blank Holder Force: The force applied by the blank holder is critical to preventing defects. Too little force can result in wrinkling, while too much force can restrict material flow and cause tearing. The optimal blank holder force depends on the material properties, part geometry, and depth of the draw.
- Lubrication and Friction: The blank holder’s interaction with the blank can generate friction, which affects material flow. Proper lubrication is essential to reduce friction and ensure smooth material movement. Lubricants must be carefully selected based on the material being drawn and the surface finish of the blank holder.
Process Parameters in Deep Drawing
Controlling the process parameters in deep drawing is essential for producing high-quality parts and minimizing defects. These parameters include blank holder force, drawing speed, drawing ratio, and lubrication. By optimizing these parameters, engineers can ensure smooth material flow, uniform thickness distribution, and consistent part geometry.
5.1. Blank Holder Force
The blank holder force is one of the most critical parameters in the deep drawing process. It controls the material flow into the die and prevents the blank from wrinkling or folding as it is drawn. The correct blank holder force depends on the material properties, the part geometry, and the depth of the draw.
Optimizing blank holder force:
- Too little force: If the blank holder force is too low, the material will flow too freely into the die, resulting in wrinkling or folding at the edges of the part.
- Too much force: If the blank holder force is too high, the material may not flow into the die properly, leading to tearing or cracking. Excessive blank holder force can also cause excessive thinning or uneven wall thickness in the part.
To optimize blank holder force, engineers often use dynamic blank holder systems that adjust the force in real time during the drawing process. These systems use sensors and control algorithms to monitor material flow and adjust the force based on the material’s behavior.
5.2. Drawing Ratio and Limiting Drawing Ratio (LDR)
The drawing ratio is the ratio of the blank diameter to the diameter of the drawn part. It is a measure of the severity of the drawing process. A higher drawing ratio indicates a more severe draw, requiring greater force and increasing the likelihood of defects such as wrinkling or tearing.
The limiting drawing ratio (LDR) is the maximum drawing ratio that can be achieved without causing failure in the material. The LDR depends on the material properties, such as ductility and formability, as well as the design of the punch, die, and blank holder. To achieve a successful deep draw, engineers must design the process to stay within the material’s LDR.
Maximizing drawing ratio:
- Material selection: Materials with high ductility and formability, such as low-carbon steel and aluminum, can achieve higher drawing ratios without failure. Engineers must select materials that can withstand the strains imposed by deep drawing without tearing or wrinkling.
- Process optimization: By optimizing parameters such as blank holder force, punch speed, and lubrication, engineers can increase the drawing ratio while minimizing the risk of defects.
5.3. Drawing Speed
The drawing speed affects the rate at which the material is deformed and drawn into the die. Drawing speed influences the material’s behavior, the heat generated during the process, and the risk of defects such as tearing or surface defects.
Optimizing drawing speed:
- High drawing speed: While high drawing speeds can increase productivity, they can also generate more heat due to friction, leading to defects such as excessive thinning or surface cracking. High speeds can also increase the risk of tearing, especially in brittle materials.
- Low drawing speed: Lower drawing speeds provide more control over material flow, reducing the risk of defects. However, slow drawing speeds reduce productivity and can increase the overall cycle time for each part.
Hydraulic deep drawing presses allow for precise control over drawing speed, enabling engineers to optimize the process based on the material properties and part geometry. In some cases, variable-speed systems are used to adjust the speed throughout the drawing process, providing faster speeds during initial stages and slower speeds as the part is drawn deeper into the die.
5.4. Lubrication
Lubrication plays a critical role in reducing friction between the blank, punch, and die during deep drawing. Proper lubrication ensures smooth material flow, minimizes tool wear, and reduces the risk of defects such as galling, surface scratches, or thinning.
Selecting the right lubricant:
- Material-specific lubricants: Different materials require different types of lubricants. For example, aluminum requires high-viscosity lubricants to prevent galling, while steel may benefit from oil-based or synthetic lubricants to reduce friction and heat generation.
- Lubricant application: Lubricants can be applied in various ways, including spraying, rolling, or coating the blank. Uniform application is essential to prevent localized friction, which can lead to surface defects or uneven material flow.
Deep Drawing Process
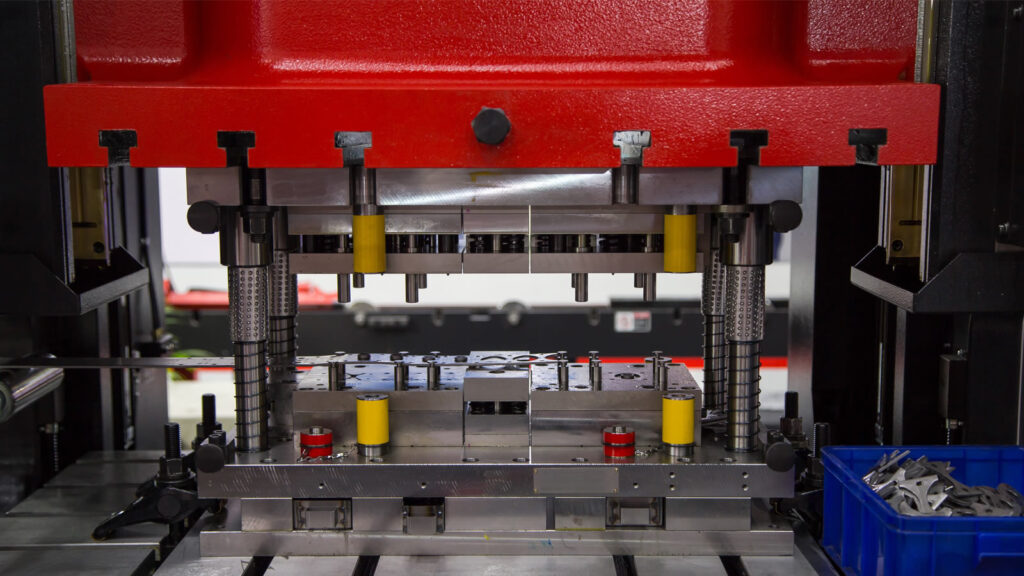
The deep drawing process is one of the most widely used metal forming techniques in modern manufacturing. From producing everyday household items like sinks and cooking pots to manufacturing critical components in the automotive, aerospace, and electronics industries, deep drawing plays a vital role in shaping sheet metal into three-dimensional products with a high degree of precision and efficiency.
This 10,000-word document will provide a thorough exploration of the deep drawing process, covering its fundamental principles, technical aspects, key variables, equipment, material selection, challenges, defect prevention, and recent advancements. The explanation will also include real-world applications and best practices for optimizing the deep drawing process.
Introduction to Deep Drawing
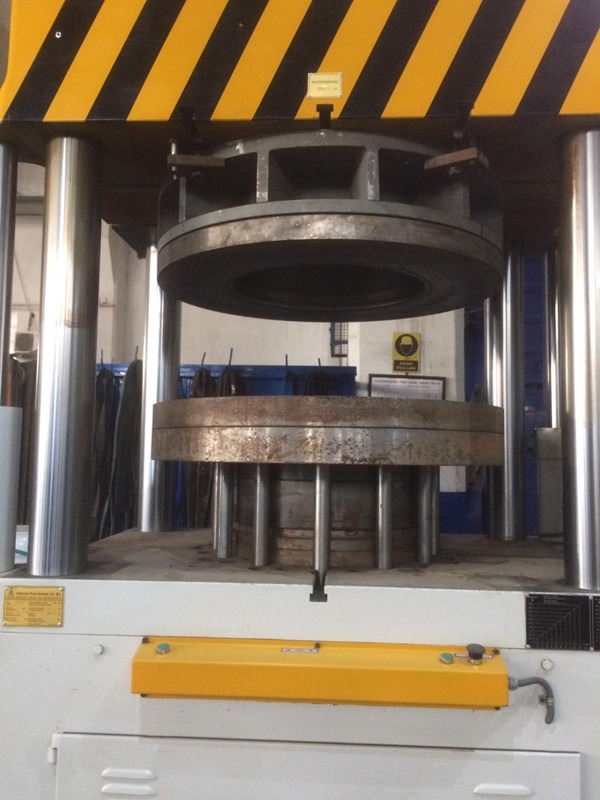
Deep drawing is a metal forming process in which a flat sheet of metal, referred to as a blank, is radially drawn into a forming die by the mechanical action of a punch. The process transforms the flat sheet into a hollow, cylindrical, or box-shaped part, where the depth of the drawn part is often greater than its diameter. This method distinguishes deep drawing from other forming techniques like stamping or bending, where the depth of the formed part is relatively shallow.
The process involves subjecting the metal blank to significant tensile and compressive forces that cause the material to deform plastically and take the shape of the die cavity. The result is a component with uniform thickness, smooth surfaces, and precise dimensions.
The deep drawing process is commonly used for producing components such as:
- Cylindrical parts: beverage cans, cups, and pots
- Box-shaped parts: battery enclosures, automotive fuel tanks
- Complex geometries: automotive body panels, aerospace components
1.2 Historical Background
The deep drawing process can trace its roots to ancient metalworking practices, but it wasn’t until the 19th century that deep drawing became a common industrial practice. Early methods of metal forming were largely manual and relied on hammers and rudimentary dies to shape metal. However, the invention of the hydraulic press in the late 1800s revolutionized the deep drawing process, allowing for more precise control over pressure and speed, and enabling the mass production of deep-drawn parts.
The development of more advanced materials, tooling, and lubrication technologies during the 20th century further enhanced the deep drawing process. Today, with the advent of computer-controlled hydraulic presses, servo-driven systems, and finite element analysis (FEA) simulations, deep drawing has evolved into a highly sophisticated and efficient manufacturing technique.
1.3 Importance in Manufacturing Industries
Deep drawing is integral to many manufacturing industries due to its ability to produce high-quality, durable components with complex geometries in large volumes. Some of the key industries that rely on deep drawing include:
- Automotive Industry: Deep drawing is used to manufacture critical automotive components such as body panels, fuel tanks, and transmission housings. These parts need to be strong, lightweight, and produced in high volumes with consistent quality.
- Aerospace Industry: The aerospace sector relies on deep drawing for components like fuselage panels, landing gear components, and engine housings, where precision, strength, and weight savings are paramount.
- Consumer Goods and Electronics: The production of household items such as cookware, kitchen sinks, and electronic device enclosures often involves deep drawing to create seamless, aesthetically pleasing, and structurally sound products.
- Packaging Industry: Beverage cans, food containers, and cosmetic packaging are frequently deep drawn from materials like aluminum and tin, where uniformity, surface finish, and material efficiency are essential.
The versatility of deep drawing, coupled with advances in automation and material science, makes it a preferred process for a wide range of industries, particularly when manufacturing parts that require high precision, repeatability, and strength.
Fundamental Principles of Deep Drawing
To fully understand the deep drawing process, it’s important to explore the fundamental principles that govern material behavior, force distribution, and the interaction between tooling and the blank. These principles are rooted in the mechanics of plastic deformation and the stress-strain relationship of the material.
2.1 Plastic Deformation and Material Flow
Deep drawing relies on the plastic deformation of the material, which refers to its ability to undergo permanent change in shape when subjected to a force beyond its elastic limit. When a blank is placed on a die and subjected to force from a punch, the material in the blank flows radially toward the die cavity. During this process, the material must undergo significant tensile and compressive stresses to conform to the die’s shape.
Plastic deformation occurs in two main regions:
- Tensile deformation: This takes place in the flange area of the blank, where the material is stretched and pulled into the die.
- Compressive deformation: In areas closer to the punch and die interface, the material is compressed as it flows into the die, conforming to the shape of the punch and die cavity.
The material must have enough ductility (the ability to undergo significant plastic deformation before failure) to withstand these stresses without tearing or cracking. As the material is drawn, it becomes thinner in certain regions, especially near the corners and edges of the part, where the greatest amount of stretching occurs.
2.2 Stress-Strain Behavior in Deep Drawing
The stress-strain relationship is critical in understanding how a material behaves during deep drawing. This relationship is typically depicted in a stress-strain curve, which shows how a material responds to an applied load.
- Elastic region: At the initial stages of loading, the material deforms elastically, meaning that it will return to its original shape if the load is removed. In deep drawing, however, the material is intentionally deformed beyond this point to achieve permanent shape changes.
- Plastic region: Beyond the elastic limit, the material enters the plastic region, where it deforms permanently. The stress required to continue deforming the material is known as flow stress. Flow stress increases as the material is drawn deeper into the die, particularly in areas where the material is stretched the most.
- Necking and failure: If the material is stretched too far, it can undergo necking, a localized reduction in cross-sectional area that precedes tearing or cracking. Preventing necking and controlling strain distribution is a key challenge in deep drawing.
Materials with high tensile strength and ductility, such as low-carbon steel and aluminum, are better suited for deep drawing because they can withstand higher levels of strain without failure. The ability to distribute strain uniformly throughout the blank is crucial for avoiding defects like tearing or wrinkling.
2.3 Key Forces in Deep Drawing
Several forces are involved in the deep drawing process, each of which must be carefully controlled to ensure successful material flow and avoid defects.
- Punch Force: The punch applies force to the blank, driving it into the die cavity. The magnitude of the punch force depends on factors such as material thickness, material properties, the depth of the draw, and friction at the punch-blank interface. The punch force must be sufficient to overcome the material’s resistance to deformation but not so high that it causes tearing or excessive thinning.
- Blank Holder Force: The blank holder applies pressure around the edges of the blank to prevent it from wrinkling as it is drawn into the die. The blank holder force must be optimized; too little force allows the material to wrinkle, while too much force restricts material flow, increasing the risk of tearing. The blank holder force is usually applied by hydraulic or mechanical systems, and modern presses may feature adjustable or dynamic blank holders that allow for real-time adjustments.
- Frictional Forces: Friction plays a significant role in deep drawing, particularly at the interfaces between the punch, die, and blank. While friction helps control material flow, excessive friction increases the punch force and can lead to defects like galling (where material adheres to the die) or thinning. Proper lubrication is essential to reduce friction and ensure smooth material movement.
2.4 Material Flow in Deep Drawing
Material flow during deep drawing is a complex interaction of tensile, compressive, and shear stresses. As the punch moves downward and draws the blank into the die, the material undergoes various deformations, including stretching, bending, and compressing. These deformations must be managed carefully to achieve the desired part shape without defects.
Flow behavior in deep drawing can be summarized as follows:
- Radial flow: The material flows radially inward toward the punch as the blank is drawn into the die. This flow creates tensile stresses in the flange, which can lead to thinning if the material is not properly supported by the blank holder.
- Compressive stresses: In the areas of the blank that contact the die, the material undergoes compressive stresses as it is pushed into the die cavity. This helps form the shape of the part but must be balanced with the tensile stresses to avoid wrinkling or tearing.
- Thinning: The material tends to thin out at the areas experiencing the greatest tensile stress, particularly near the punch corners. Proper control of punch speed, blank holder force, and lubrication helps to distribute the thinning evenly and minimize the risk of failure.
Equipment and Tooling in Deep Drawing
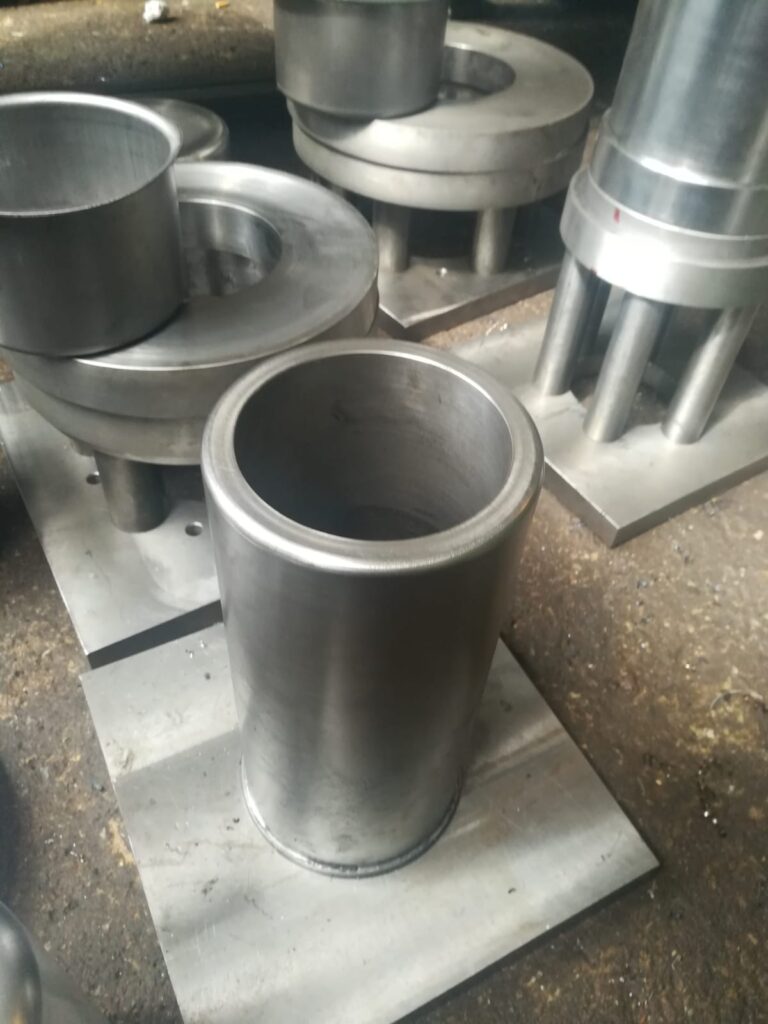
The success of the deep drawing process heavily depends on the design and precision of the equipment and tooling used. Tooling refers to the components that interact with the material during the drawing process, including the punch, die, and blank holder. Each of these tools plays a specific role in shaping the material and must be designed to accommodate the material properties, part geometry, and process parameters.
3.1 Components of a Deep Drawing Press
The primary machine used in deep drawing is the deep drawing press, which can be mechanical, hydraulic, or servo-driven. Each type of press has specific advantages and is chosen based on the material being drawn, the complexity of the part, and production requirements.
- Mechanical Presses: Mechanical presses operate using a flywheel and crankshaft mechanism that converts rotational motion into linear motion. These presses are known for their high speed and precision, making them ideal for high-volume production of shallow-drawn parts. However, they lack the flexibility to control force and speed throughout the stroke, which can limit their use in complex or deep draws.
- Hydraulic Presses: Hydraulic presses use a hydraulic system to apply force, offering more precise control over force, speed, and stroke length. These presses are capable of generating high forces and are preferred for deep draws, as they can maintain consistent force throughout the stroke. The flexibility of hydraulic presses makes them suitable for a wide range of materials and part geometries.
- Servo-Driven Presses: Servo-driven presses use electric motors to control the movement of the ram, allowing for precise control over speed and force. These presses offer the highest level of flexibility, enabling dynamic adjustments during the drawing process. Servo-driven presses are often used in advanced manufacturing applications that require high precision and real-time control over process parameters.
3.2 Punch Design in Deep Drawing
The punch is a critical component that drives the blank into the die to form the desired part shape. The punch is responsible for applying the necessary force to deform the material, and its design directly influences the success of the deep drawing process.
Key considerations for punch design include:
- Shape and Geometry: The shape of the punch must match the desired shape of the final part. Punches can have cylindrical, conical, or box-like geometries depending on the complexity of the part being formed. Complex shapes, such as those with deep cavities or intricate details, require precise punch design to control material flow and prevent defects like tearing or thinning.
- Punch Radius: The punch corner radius is a crucial design parameter. A sharp punch radius can result in high localized stresses, increasing the likelihood of tearing or cracking at the corners of the drawn part. Conversely, a larger punch radius helps distribute stress more evenly, reducing the risk of defects but may lead to wrinkling if not properly controlled. Optimizing the punch radius based on the material properties and part geometry is essential to ensure smooth material flow and uniform thickness distribution.
- Surface Finish and Coatings: The surface finish of the punch affects friction at the punch-blank interface, which in turn influences material flow. A smooth surface finish reduces friction, allowing the material to flow more easily, while a rough surface can increase friction and lead to defects like galling (adhesion of material to the punch). To reduce wear and improve the longevity of the tooling, punches may be coated with materials such as titanium nitride (TiN) or diamond-like carbon (DLC) coatings, which provide excellent wear resistance and reduce friction.
3.3 Die Design in Deep Drawing
The die is the component into which the metal blank is drawn by the punch, shaping the blank into the desired form. The design of the die plays a critical role in controlling material flow, minimizing friction, and ensuring the final part meets dimensional specifications.
Key aspects of die design include:
- Die Cavity Shape: The geometry of the die cavity determines the shape of the final part. Complex part geometries, such as those with sharp corners or deep cavities, require precise die design to control material flow and avoid defects such as wrinkling, tearing, or uneven wall thickness.
- Die Radius: The die entry radius (the radius at the top edge of the die where the blank first enters the die cavity) is one of the most critical aspects of die design. A small die radius can result in high localized stress, leading to tearing or excessive thinning of the material. Conversely, a large die radius may reduce stress concentrations but can lead to wrinkling or material folding. The die radius must be optimized based on the material properties and the depth of the draw.
- Clearance Between Punch and Die: The clearance between the punch and die is the gap through which the material flows as it is drawn into the die cavity. The clearance is typically slightly larger than the thickness of the blank to allow for material flow without excessive thinning or tearing. Incorrect clearance can result in defects such as wrinkles, tears, or uneven thickness distribution. The clearance must be carefully calculated based on the material properties and part dimensions.
3.4 Blank Holder Design
The blank holder (also known as a hold-down ring) is used to apply pressure to the edges of the blank during the drawing process, preventing it from wrinkling or folding as it is drawn into the die. The design of the blank holder and the force it applies are critical to ensuring smooth material flow and preventing defects.
Key considerations for blank holder design include:
- Force Distribution: The blank holder must apply uniform pressure around the circumference of the blank to ensure even material flow. Uneven pressure can lead to wrinkling or tearing at the edges of the part. In some cases, adjustable blank holders or segmented blank holders are used to apply variable pressure based on the material’s behavior during drawing.
- Blank Holder Force: The force applied by the blank holder must be carefully controlled to avoid defects. Too little force allows the material to wrinkle, while too much force restricts material flow, leading to tearing. The optimal blank holder force depends on factors such as material thickness, part geometry, and the depth of the draw. In modern deep drawing presses, dynamic blank holder systems can adjust the force in real time to optimize material flow and prevent defects.
- Lubrication and Friction Management: The interaction between the blank holder and the blank generates friction, which affects material flow. Proper lubrication is essential to reduce friction and ensure smooth material movement. Lubricants must be carefully selected based on the material being drawn and the surface finish of the blank holder. In advanced deep drawing operations, dry film lubricants or coated tooling may be used to reduce friction and improve process efficiency.
3.5 Tool Coatings and Wear Prevention
The wear and tear on tooling during deep drawing can significantly affect the quality of the final parts and the overall efficiency of the process. Tooling must withstand high stresses, friction, and contact with abrasive materials, which can lead to premature wear if not properly addressed.
Common tool coatings for deep drawing include:
- Titanium Nitride (TiN): TiN is a popular coating material for punches and dies due to its hardness, wear resistance, and low friction properties. It helps reduce tool wear and improves the longevity of the tooling, especially when working with hard or abrasive materials like stainless steel.
- Diamond-Like Carbon (DLC): DLC coatings provide excellent hardness, wear resistance, and low friction, making them ideal for deep drawing applications involving hard-to-form materials like titanium or nickel-based alloys. DLC coatings can significantly reduce the risk of galling and improve tool life.
- Ceramic Coatings: Ceramic coatings offer high-temperature resistance, wear resistance, and low friction, making them suitable for deep drawing applications where the tooling is subjected to extreme heat and pressure.
By applying these coatings to the punch and die, manufacturers can reduce friction, minimize tool wear, and improve the overall efficiency and longevity of the deep drawing process.
Stages of the Deep Drawing Process
The deep drawing process is a multi-stage operation that transforms a flat metal blank into a three-dimensional part through a series of forming steps. Each stage of the process plays a critical role in shaping the material, controlling material flow, and achieving the desired part geometry. The primary stages of the deep drawing process include blanking, drawing, redrawing, and trimming.
4.1 Blanking
The first stage of the deep drawing process is blanking, where a flat sheet of metal is cut into a circular or rectangular shape known as a blank. The blank is typically cut from a larger sheet using a punch and die set. Blanking is a critical step because any imperfections in the blank, such as rough edges or surface defects, can lead to defects during the subsequent drawing stages.
Key considerations for blanking include:
- Material Selection: The material used for the blank must have sufficient ductility to undergo the large deformations associated with deep drawing. Common materials include low-carbon steel, aluminum, stainless steel, and copper. The material’s thickness, yield strength, and formability must be carefully considered to ensure successful drawing.
- Blank Size and Shape: The size and shape of the blank are determined by the dimensions of the final part. The blank must be slightly larger than the part to allow for material flow during drawing. In some cases, the blank may have a circular shape for cylindrical parts or a rectangular shape for box-like parts. Proper blank alignment with the punch and die is essential to avoid defects.
- Surface Finish and Edge Quality: The surface finish of the blank and the quality of the edges are critical to ensuring smooth material flow during drawing. Rough or uneven edges can cause tearing or wrinkling during the drawing process. The edges of the blank must be clean and free from burrs or sharp corners that could interfere with material flow.
4.2 Drawing
The drawing stage is the core of the deep drawing process, where the blank is transformed into a three-dimensional shape by being drawn into a die cavity using a punch. During this stage, the blank undergoes significant tensile and compressive stresses as it flows into the die and takes on the desired shape.
Key steps in the drawing process include:
- Punch Movement: The punch moves downward, pressing the blank into the die cavity. As the blank is drawn into the die, it is stretched and compressed to conform to the shape of the die. The punch must apply sufficient force to overcome the material’s resistance to deformation without causing tearing or excessive thinning.
- Material Flow: As the blank is drawn into the die, the material flows radially inward toward the punch. The outer edges of the blank are subjected to tensile stresses, while the material near the punch and die interface is compressed. Proper control of material flow is essential to prevent defects such as wrinkling, tearing, or uneven wall thickness.
- Blank Holder Pressure: The blank holder applies pressure to the edges of the blank to prevent wrinkling. The blank holder force must be carefully controlled to allow the material to flow into the die without restriction. Too much blank holder pressure can cause the material to tear, while too little pressure can result in wrinkling.
4.3 Redrawing
In cases where the depth of the part exceeds the material’s ability to be drawn in a single pass, a secondary operation known as redrawing is performed. Redrawing involves repeating the drawing process in multiple stages, with each stage using a progressively smaller punch and die to achieve the desired depth.
Key considerations for redrawing include:
- Redrawing Ratio: The redrawing ratio is the ratio of the diameter of the blank after the first drawing stage to the diameter of the blank after the redrawing stage. The redrawing ratio determines the severity of the redrawing process and the amount of material that must be stretched to achieve the desired depth. If the redrawing ratio is too high, the material may tear or become excessively thinned.
- Intermediate Annealing: In some cases, the material may undergo work hardening during the initial drawing stage, making it more difficult to deform further. To restore the material’s ductility, an intermediate annealing process may be performed between drawing stages. Annealing involves heating the material to a specific temperature to relieve internal stresses and restore its ability to undergo plastic deformation.
4.4 Trimming and Finishing
After the part has been drawn to its final shape, excess material may need to be removed from the edges. This is done through a process called trimming, where specialized cutting tools are used to remove any excess material and smooth out the edges of the part. Trimming is especially important in applications where dimensional accuracy and surface quality are critical.
Finishing processes may also be required to achieve the desired surface quality or dimensional accuracy. Common finishing processes include deburring, polishing, and surface treatments such as anodizing or plating. These processes help to remove sharp edges, improve surface finish, and enhance the part’s corrosion resistance or aesthetic appeal.
Materials Used in Deep Drawing
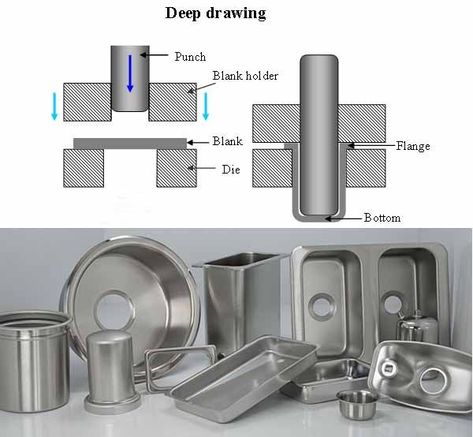
Material selection is a critical aspect of the deep drawing process. The material must have the right combination of ductility, formability, strength, and thickness to withstand the stresses imposed during drawing without failing. Different metals exhibit different behaviors during deep drawing, and each has specific advantages and limitations depending on the application.
5.1 Low-Carbon Steel
Low-carbon steel, also known as mild steel, is one of the most commonly used materials in deep drawing due to its excellent formability and cost-effectiveness. Low-carbon steel has a relatively low yield strength and high ductility, allowing it to be drawn into deep and complex shapes without tearing or cracking.
- Advantages: Low-carbon steel is easy to form, weld, and machine. It offers good strength and durability, making it suitable for applications in the automotive and construction industries. Parts such as automotive body panels, fuel tanks, and structural components are often made from low-carbon steel.
- Limitations: Low-carbon steel is susceptible to corrosion, so it may require surface treatments such as galvanizing or painting to improve its corrosion resistance.
5.2 Aluminum
Aluminum is widely used in deep drawing for applications that require lightweight, corrosion-resistant parts. It is commonly used in industries such as automotive, aerospace, and packaging, where weight reduction is a key priority.
- Advantages: Aluminum is lightweight, highly ductile, and has excellent corrosion resistance. It is ideal for applications where weight savings are critical, such as in the production of automotive body panels, aircraft components, and beverage cans. Aluminum is also highly recyclable, making it a sustainable choice for many manufacturers.
- Limitations: Aluminum is more prone to springback than other metals, meaning it tends to return to its original shape after being deformed. This can make it challenging to achieve tight dimensional tolerances. Additionally, aluminum requires specialized lubricants to reduce friction during the drawing process.
5.3 Stainless Steel
Stainless steel is known for its high strength, excellent corrosion resistance, and ability to withstand high temperatures. It is commonly used in industries such as food processing, medical devices, and aerospace, where durability and hygiene are important.
- Advantages: Stainless steel offers excellent mechanical properties and corrosion resistance, making it ideal for applications where the part will be exposed to harsh environments or high temperatures. Stainless steel is commonly used to manufacture kitchen sinks, medical instruments, and aircraft components.
- Limitations: Stainless steel is more difficult to draw than low-carbon steel or aluminum due to its higher yield strength and tendency to work harden. It requires higher drawing forces and specialized tooling to prevent tearing or cracking.
5.4 Copper and Brass
Copper and brass are frequently used in deep drawing for applications that require high thermal or electrical conductivity, corrosion resistance, or aesthetic appeal.
- Advantages: Copper is highly ductile and exhibits excellent formability, making it suitable for deep drawing applications where complex shapes are required. Its high thermal and electrical conductivity make it the material of choice for components such as electrical connectors, heat exchangers, and plumbing fittings.
- Limitations: Copper and brass tend to work harden quickly during deformation, which can complicate the deep drawing process. Intermediate annealing may be required to restore ductility between drawing stages.
5.5 Titanium
Titanium is known for its exceptional strength-to-weight ratio, corrosion resistance, and biocompatibility, making it an ideal material for industries such as aerospace, medical devices, and automotive.
- Advantages: Titanium’s high strength-to-weight ratio allows for the production of lightweight, durable components that can withstand extreme conditions. Its natural corrosion resistance also makes it suitable for applications in chemical processing, marine environments, and biomedical implants.
- Limitations: Titanium is challenging to form through deep drawing due to its high strength and springback effect. Springback occurs when the material tries to return to its original shape after being deformed, making it difficult to achieve precise tolerances. Titanium also has a tendency to gall, meaning that material from the blank can adhere to the punch or die during drawing.
5.6 Magnesium Alloys
Magnesium alloys are gaining popularity in industries like automotive and aerospace due to their extremely lightweight properties. However, their use in deep drawing is still limited due to the challenges associated with forming magnesium.
- Advantages: Magnesium is one of the lightest structural metals available, making it ideal for applications where weight reduction is critical. In the automotive industry, magnesium is used to reduce the overall weight of vehicles, leading to improved fuel efficiency and reduced emissions.
- Limitations: Magnesium alloys are more brittle than aluminum and steel, making them more prone to cracking during deep drawing. Additionally, magnesium has a narrow range of forming temperatures, meaning that it must be heated to a specific temperature range to avoid cracking.
Process Variables and Parameters in Deep Drawing
The quality and efficiency of the deep drawing process are highly dependent on several process variables and parameters, including blank holder force, punch speed, drawing ratio, and lubrication. By optimizing these parameters, engineers can produce high-quality parts while minimizing defects such as wrinkling, tearing, or thinning.
6.1 Blank Holder Force
The blank holder force is one of the most critical parameters in deep drawing. It controls the material flow into the die and prevents the blank from wrinkling or folding as it is drawn. The correct blank holder force depends on the material properties, the part geometry, and the depth of the draw.
Optimizing blank holder force:
- Too little force: If the blank holder force is too low, the material will flow too freely into the die, resulting in wrinkling or folding at the edges of the part.
- Too much force: If the blank holder force is too high, the material may not flow into the die properly, leading to tearing or cracking. Excessive blank holder force can also cause excessive thinning or uneven wall thickness in the part.
To optimize blank holder force, engineers often use dynamic blank holder systems that adjust the force in real time during the drawing process. These systems use sensors and control algorithms to monitor material flow and adjust the force based on the material’s behavior.
6.2 Punch Speed and Pressure
The punch speed affects the rate at which the material is deformed and drawn into the die. Punch speed influences the material’s behavior, the heat generated during the process, and the risk of defects such as tearing or surface defects.
Optimizing punch speed:
- High punch speed: While high punch speeds can increase productivity, they can also generate more heat due to friction, leading to defects such as excessive thinning or surface cracking. High speeds can also increase the risk of tearing, especially in brittle materials.
- Low punch speed: Lower punch speeds provide more control over material flow, reducing the risk of defects. However, slow punch speeds reduce productivity and can increase the overall cycle time for each part.
Hydraulic and servo-driven deep drawing presses allow for precise control over punch speed and pressure, enabling engineers to optimize the process based on the material properties and part geometry.
6.3 Drawing Ratio and Limiting Drawing Ratio (LDR)
The drawing ratio is the ratio of the blank diameter to the diameter of the drawn part. It is a measure of the severity of the drawing process. A higher drawing ratio indicates a more severe draw, requiring greater force and increasing the likelihood of defects such as wrinkling or tearing.
The limiting drawing ratio (LDR) is the maximum drawing ratio that can be achieved without causing failure in the material. The LDR depends on the material properties, such as ductility and formability, as well as the design of the punch, die, and blank holder. To achieve a successful deep draw, engineers must design the process to stay within the material’s LDR.
Maximizing drawing ratio:
- Material selection: Materials with high ductility and formability, such as low-carbon steel and aluminum, can achieve higher drawing ratios without failure. Engineers must select materials that can withstand the strains imposed by deep drawing without tearing or wrinkling.
- Process optimization: By optimizing parameters such as blank holder force, punch speed, and lubrication, engineers can increase the drawing ratio while minimizing the risk of defects.
6.4 Lubrication and Friction Management
Lubrication plays a critical role in reducing friction between the blank, punch, and die during deep drawing. Proper lubrication ensures smooth material flow, minimizes tool wear, and reduces the risk of defects such as galling, surface scratches, or thinning.
Selecting the right lubricant:
- Material-specific lubricants: Different materials require different types of lubricants. For example, aluminum requires high-viscosity lubricants to prevent galling, while steel may benefit from oil-based or synthetic lubricants to reduce friction and heat generation.
- Lubricant application: Lubricants can be applied in various ways, including spraying, rolling, or coating the blank. Uniform application is essential to prevent localized friction, which can lead to surface defects or uneven material flow.
In advanced deep drawing operations, dry film lubricants or coated tooling may be used to improve process efficiency and reduce friction. These specialized lubricants and coatings help ensure consistent material flow and prevent defects.
Defects in Deep Drawing and Their Solutions
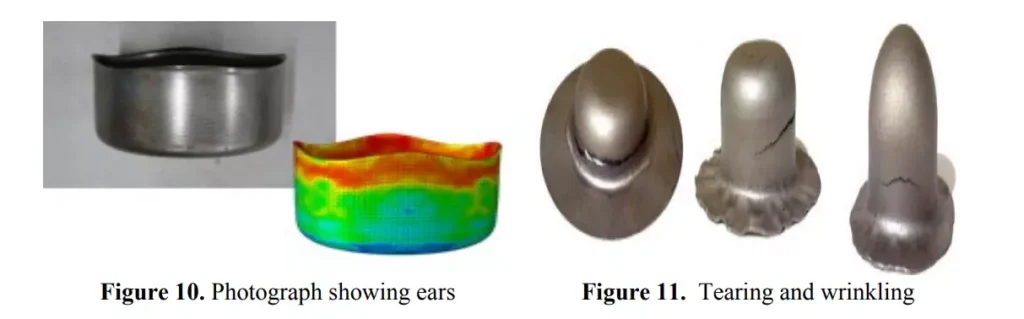
Despite careful planning and optimization, defects can occur during the deep drawing process. These defects are often the result of improper control of process parameters, material properties, or tool design. Some common defects in deep drawing include wrinkling, tearing, thinning, and earing.
7.1 Wrinkling
Wrinkling occurs when the blank holder force is too low, allowing the material to flow too freely into the die. This results in excess material bunching up, forming wrinkles around the edges of the part. Wrinkling is more likely to occur in deeper draws or when drawing materials with low stiffness.
Solution: Increasing the blank holder force or adjusting the lubrication can help prevent wrinkling. In some cases, redesigning the die to provide better material flow can also reduce the risk of wrinkling.
7.2 Tearing
Tearing is a catastrophic failure that occurs when the material is overstretched and can no longer withstand the applied forces. It often happens when the punch speed is too high, the material is too brittle, or the die design is not suitable for the material being drawn.
Solution: Reducing the punch speed and ensuring that the material’s thickness and ductility are appropriate for the drawing process can help prevent tearing. Lubrication also plays a role in reducing the likelihood of tearing by minimizing friction.
7.3 Thinning
Thinning occurs when the material becomes too stretched in certain areas, resulting in a reduction in thickness. Thinning can weaken the part and increase the risk of failure during use. Proper control of punch speed, blank holder force, and lubrication can help to distribute the thinning evenly and minimize the risk of failure.
7.4 Earing
Earing refers to the formation of wavy edges on the part due to anisotropy in the material’s grain structure. Materials with high levels of anisotropy may deform unevenly, resulting in ears or flanges around the edges of the part.
Solution: To avoid earing, engineers can select materials with lower anisotropy or adjust the orientation of the blank relative to the material’s grain direction.
Finite Element Analysis (FEA) and Simulation in Deep Drawing
Finite Element Analysis (FEA) is a computational technique used to simulate the behavior of materials during the deep drawing process. FEA allows engineers to predict how the material will deform under various conditions and optimize the design of the punch, die, and process parameters.
8.1 Role of FEA in Process Optimization
FEA is widely used in the deep drawing process to analyze material flow, stress distribution, and potential defects. By simulating the deep drawing process in a virtual environment, engineers can identify potential problems before they occur in production, reducing the need for costly trial-and-error methods.
8.2 Simulation Tools for Predicting Material Behavior
Simulation tools such as ABAQUS, ANSYS, and LS-DYNA are commonly used to model the deep drawing process. These tools can simulate the interaction between the punch, die, and blank, as well as the material’s response to different process parameters.
FEA simulations provide valuable insights into:
- Stress and strain distribution: FEA can predict how the material will deform under various loads, allowing engineers to optimize the punch and die design to reduce the risk of tearing or wrinkling.
- Material flow: Simulation tools can model how the material flows into the die cavity, helping engineers optimize blank holder force and lubrication to ensure smooth material movement.
- Defect prediction: By simulating the deep drawing process, engineers can identify potential defects such as thinning, wrinkling, or earing and adjust the process parameters to prevent them.
8.3 Case Studies on FEA in Deep Drawing
Several case studies have demonstrated the effectiveness of FEA in optimizing the deep drawing process. For example, in the automotive industry, FEA simulations have been used to design lightweight body panels with improved crash performance while minimizing material waste. In the aerospace industry, FEA has been used to optimize the deep drawing of complex components with tight tolerances, reducing the risk of defects and improving production efficiency.
Recent Advancements in Deep Drawing Technology
The deep drawing process has evolved significantly with advancements in technology, particularly in areas such as automation, smart manufacturing, servo-controlled presses, and advanced coatings and lubricants.
9.1 Automation and Smart Manufacturing
Automation has played a significant role in improving the productivity and precision of the deep drawing process. Modern hydraulic and servo-driven presses are equipped with CNC (Computer Numerical Control) systems that allow for precise control over process parameters such as punch speed, pressure, and blank holder force.
Smart manufacturing systems enable real-time monitoring and adjustment of process variables, improving part quality and reducing the risk of defects. Predictive maintenance systems use sensors and data analytics to monitor the condition of the tooling and equipment, allowing manufacturers to schedule maintenance before a failure occurs.
9.2 Servo-Controlled Presses and Real-Time Monitoring
Servo-controlled presses offer dynamic control over the punch speed and force, allowing for real-time adjustments during the drawing process. These presses are ideal for applications that require complex part geometries or tight tolerances, as they can adapt to changes in material behavior and process conditions.
Real-time monitoring systems use sensors to track key process variables such as temperature, pressure, and tool wear. By analyzing this data, engineers can make adjustments on the fly to optimize the process and prevent defects.
9.3 Advanced Coatings and Lubricants
Recent advancements in coating and lubrication technology have improved the performance of deep drawing tools. Diamond-Like Carbon (DLC) coatings and ceramic coatings offer excellent wear resistance and low friction, reducing tool wear and improving the quality of the finished parts.
In addition, new synthetic lubricants and dry film coatings have been developed to improve material flow, reduce friction, and prevent galling. These advanced lubricants are especially useful in applications involving hard-to-form materials such as titanium or nickel-based alloys.
9.4 Multi-Stage Deep Drawing for Complex Geometries
For parts with deep cavities or intricate details, a single drawing stage may not be sufficient to achieve the desired shape. Multi-stage deep drawing involves using multiple drawing stages, with each stage gradually forming the part into its final shape. This approach allows for the production of complex geometries while minimizing the risk of defects such as tearing or excessive thinning.
Applications of Deep Drawing in Various Industries
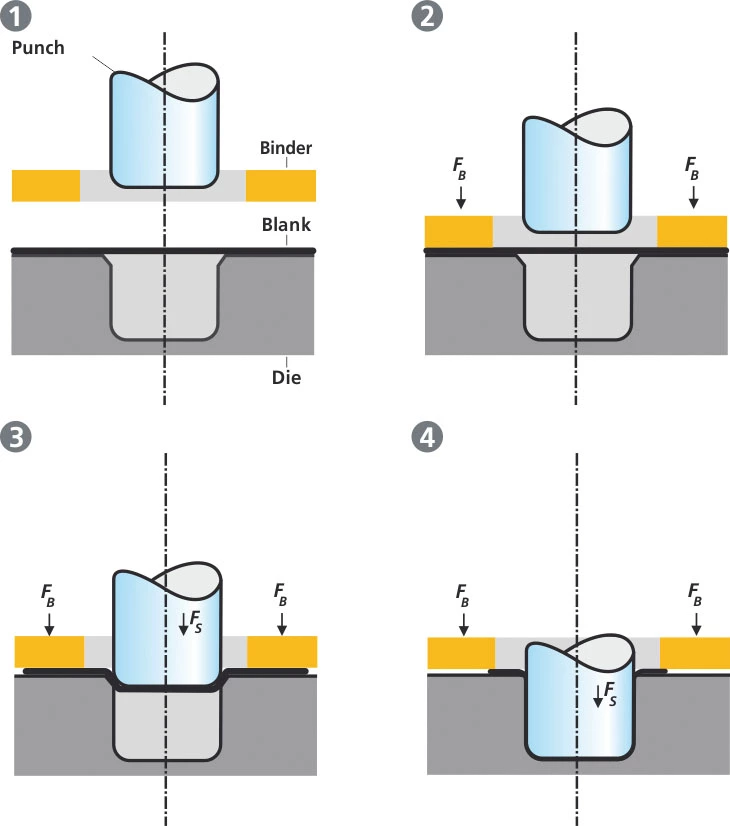
The versatility of the deep drawing process makes it suitable for a wide range of industries, including automotive, aerospace, electronics, medical devices, and packaging.
10.1 Automotive Industry
In the automotive industry, deep drawing is used to manufacture components such as body panels, fuel tanks, and transmission housings. These parts need to be strong, lightweight, and produced in high volumes with consistent quality.
Automotive manufacturers rely on deep drawing to produce parts with complex shapes and tight tolerances. The process is particularly useful for producing large parts with smooth surfaces and uniform thickness, such as door panels, hoods, and fenders.
10.2 Aerospace Industry
The aerospace industry requires components that are both lightweight and strong, making deep drawing an ideal process for manufacturing parts such as fuselage panels, engine components, and landing gear housings. These parts must withstand extreme conditions, including high temperatures and pressures, while maintaining their structural integrity.
Deep drawing allows aerospace manufacturers to produce components with high precision and repeatability, ensuring that parts meet the stringent quality and safety standards required in the industry.
10.3 Electronics and Consumer Goods
In the electronics and consumer goods industries, deep drawing is used to produce device enclosures, heat sinks, battery housings, and connector components. These parts require high dimensional accuracy and a smooth surface finish, making deep drawing an ideal process for their production.
The ability to create thin, lightweight metal parts with high structural integrity makes deep drawing a preferred method for manufacturing enclosures for smartphones, laptops, and household appliances.
10.4 Medical Devices and Packaging
In the medical field, deep drawing is used to produce components such as surgical instruments, implants, and medical device enclosures. The process allows for the production of parts with tight tolerances and high surface quality, which are critical in ensuring the safety and efficacy of medical devices.
Deep drawing is also widely used in the packaging industry to manufacture metal cans, aerosol containers, and food packaging. These products require high material efficiency and uniformity, making deep drawing an ideal process for their production.
Best Practices for Optimizing the Deep Drawing Process
To achieve the best results in deep drawing, manufacturers must implement best practices in tooling design, process optimization, and material selection.
11.1 Tooling Maintenance and Care
Proper maintenance of the tooling is essential for ensuring consistent part quality and extending tool life. Regular inspection and maintenance of punches, dies, and blank holders can prevent defects caused by tool wear or misalignment.
11.2 Process Optimization Techniques
By optimizing process parameters such as blank holder force, punch speed, and lubrication, manufacturers can improve material flow, reduce the risk of defects, and increase production efficiency.
11.3 Reducing Material Waste and Improving Efficiency
To reduce material waste, manufacturers can use simulation tools such as FEA to optimize blank size and shape. In addition, multi-stage deep drawing can be used to minimize material thinning and prevent tearing, resulting in higher material efficiency.
Sustainability in Deep Drawing
As sustainability becomes increasingly important in manufacturing, deep drawing offers several advantages in terms of energy efficiency, material recyclability, and waste reduction.
12.1 Energy Efficiency in Presses
Modern hydraulic and servo-driven presses are designed to be energy-efficient, reducing the overall energy consumption of the deep drawing process. By optimizing process parameters and using automation, manufacturers can further reduce their energy footprint.
12.2 Recyclability of Materials
Most of the materials used in deep drawing, such as steel, aluminum, and copper, are highly recyclable. This allows manufacturers to reduce waste and contribute to a circular economy by recycling scrap material generated during the drawing process.
12.3 Reducing Environmental Impact in Metal Forming
By reducing material waste, improving energy efficiency, and using environmentally friendly lubricants, manufacturers can minimize the environmental impact of the deep drawing process. Implementing sustainable practices in deep drawing not only benefits the environment but also helps reduce operational costs.
Conclusion
The deep drawing process is a versatile and efficient method for producing high-quality metal parts with complex geometries and tight tolerances. From automotive body panels to medical devices, deep drawing plays a crucial role in a wide range of industries.
By understanding the fundamental principles of deep drawing, optimizing process parameters, and selecting the right materials, manufacturers can achieve high-quality parts with minimal defects. Recent advancements in technology, such as automation, smart manufacturing, and simulation tools, have further enhanced the deep drawing process, enabling manufacturers to produce more complex parts with greater efficiency.
As industries continue to demand lightweight, durable, and high-precision components, the deep drawing process will remain a vital part of modern manufacturing. The future of deep drawing lies in the integration of sustainable practices, advanced materials, and innovative technologies, which will help manufacturers meet the evolving needs of the market.
Distinguishing Between Deep Drawing and Other Metal Forming Techniques
Metal forming is a broad field in manufacturing that includes numerous techniques to shape metal into desired forms. Among these, deep drawing is a highly specialized process used to produce hollow shapes from flat metal blanks. However, there are many other metal forming techniques, each with its own set of characteristics, applications, advantages, and limitations.
This 10,000-word exploration aims to distinguish between deep drawing and other major metal forming techniques, such as stamping, forging, bending, rolling, extrusion, hydroforming, and spinning. By understanding the key principles, processes, applications, and technical differences, we can better appreciate how deep drawing fits within the broader landscape of metal forming technologies.
Introduction to Metal Forming Processes
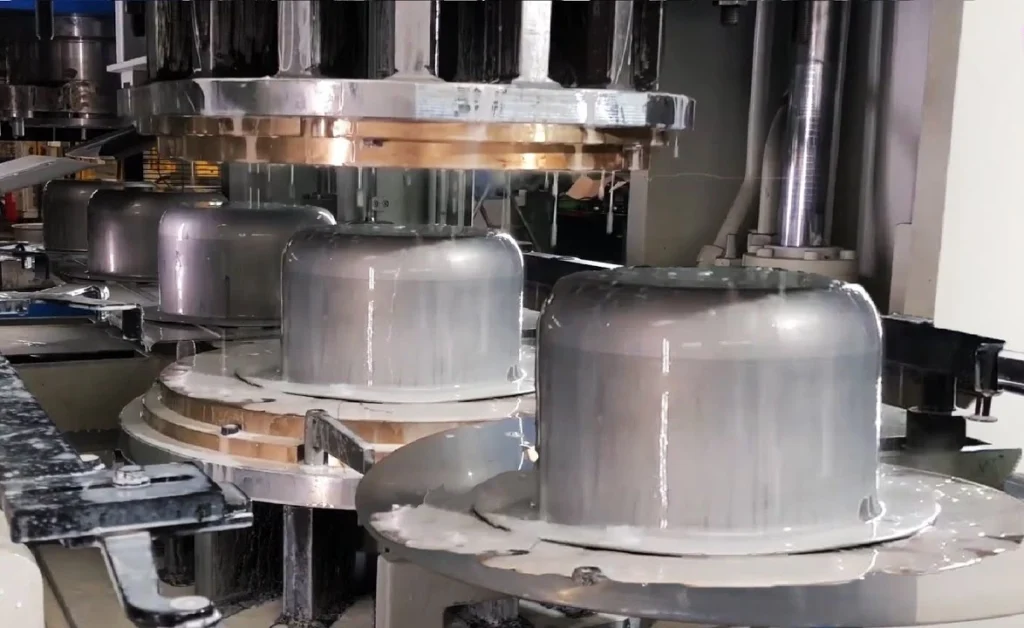
Metal forming is a group of manufacturing processes in which plastic deformation is used to change the shape of metal workpieces into desired forms. These processes rely on the material’s ability to undergo plastic deformation without breaking. Metal forming plays a crucial role in various industries, from automotive to aerospace, as it enables the creation of complex shapes with high strength and minimal material waste.
Metal forming can be broadly classified into two categories:
- Bulk forming, where the entire volume of the material is deformed (e.g., forging, extrusion, and rolling).
- Sheet forming, where only the surface area is deformed (e.g., stamping, deep drawing, and bending).
Metal forming techniques are typically categorized by the amount of force applied, the temperature of the process (hot or cold forming), and the tools or dies used.
1.2 Classification of Metal Forming Techniques
The main types of metal forming techniques include:
- Deep Drawing: A sheet metal process where a blank is radially drawn into a forming die by the action of a punch, producing parts with depths greater than their diameters.
- Stamping: A process that shapes metal by applying high force to a blank, often through cutting, bending, or embossing actions, to produce flat parts with intricate details.
- Forging: Involves shaping metal using localized compressive forces, often at high temperatures, to create parts with excellent mechanical properties.
- Bending: A process where metal is plastically deformed to achieve an angular shape, often used to create simple, linear components.
- Rolling: Involves passing metal through rollers to reduce its thickness or change its cross-section.
- Extrusion: Forces metal through a die to create parts with a constant cross-sectional profile.
- Hydroforming: A process where high-pressure fluid is used to shape metal, often for lightweight components.
- Spinning: Involves rotating a metal disc and pressing it against a mold to create axially symmetric parts.
1.3 The Role of Deep Drawing in Modern Manufacturing
Among these processes, deep drawing holds a unique place in manufacturing due to its ability to produce parts with significant depth, structural integrity, and minimal material waste. The process is especially suited for making hollow parts, such as fuel tanks, automotive body panels, and beverage cans. Deep drawing offers advantages like high volume production, tight tolerances, and uniform material thickness.
However, deep drawing has its own limitations and is not always the best choice for all metal forming applications. Other metal forming techniques, like stamping or forging, are often better suited for different geometries, material thicknesses, and production requirements. Understanding the distinctions between deep drawing and these other techniques is essential for choosing the right manufacturing process.
Deep Drawing Process: Definition, Principles, and Applications
2.1 What is Deep Drawing?
Deep drawing is a metal forming process in which a flat sheet metal blank is placed over a die cavity and pushed into the die by a punch. The punch forces the metal to stretch and conform to the shape of the die, resulting in a hollow part that can have a depth greater than its diameter. The blank material undergoes both tensile and compressive stresses as it flows into the die.
In deep drawing, the blank is clamped between a blank holder and a die, while the punch descends and pushes the blank into the die cavity. The punch and die are typically made from hardened steel or other high-strength materials to withstand the high forces required for deformation.
Deep drawing can be performed at room temperature (cold forming) or at elevated temperatures (hot forming), depending on the material being used and the depth of the draw.
2.2 Key Components: Punch, Die, and Blank Holder
The three main components of the deep drawing process are the punch, die, and blank holder:
- Punch: The punch is the tool that drives the blank into the die cavity. Its geometry defines the internal shape of the part being drawn.
- Die: The die is the tool that shapes the external surface of the part. The blank flows into the die cavity, forming the desired shape.
- Blank Holder: The blank holder prevents the blank from wrinkling as it is drawn into the die. It applies pressure to the edges of the blank, controlling material flow and ensuring smooth deformation.
2.3 Material Flow and Deformation in Deep Drawing
The deep drawing process involves significant plastic deformation of the metal blank. The material experiences a combination of tensile and compressive forces as it is stretched and drawn into the die.
- Tensile Stress: The edges of the blank, particularly in the flange region, are subjected to tensile stresses as the material is pulled inward by the punch.
- Compressive Stress: The material inside the die, near the punch, experiences compressive stresses as it is forced to conform to the shape of the die.
The material must have sufficient ductility to undergo the necessary deformation without tearing or cracking. The drawing ratio, defined as the ratio of the blank diameter to the punch diameter, is an important factor in determining the severity of the deformation. High drawing ratios can increase the risk of defects such as wrinkling, thinning, or tearing.
2.4 Applications of Deep Drawing in Industry
Deep drawing is used to produce a wide range of parts across various industries. Its ability to create complex geometries with uniform wall thickness and high structural integrity makes it a popular choice for components that require durability and precision.
Key applications of deep drawing include:
- Automotive industry: Deep drawing is used to manufacture body panels, fuel tanks, and exhaust components. These parts must be lightweight yet strong to improve vehicle performance and safety.
- Aerospace industry: In aerospace, deep drawing is used to produce fuselage sections, engine housings, and structural components that need to withstand extreme conditions while remaining lightweight.
- Packaging industry: Beverage cans, food containers, and cosmetic packaging are often deep drawn from materials like aluminum or steel to create durable, uniform containers.
- Medical devices: Surgical instruments, implants, and medical device housings are often deep drawn from stainless steel or titanium for their corrosion resistance and biocompatibility.
While deep drawing is highly effective for certain applications, it is not suitable for all metal forming needs. Other metal forming techniques, such as stamping, forging, and hydroforming, may offer better solutions for specific geometries, material types, or production requirements.
Stamping vs. Deep Drawing
3.1 Definition and Principles of Stamping
Stamping is a metal forming process in which flat sheet metal is placed into a stamping press and shaped by applying high force with a punch and die. Stamping is a broad category that includes various operations such as blanking, punching, bending, embossing, and coining. It is primarily used to produce flat or shallow parts with intricate details, and it can be performed at high speeds for mass production.
The stamping process involves using a die set that contains a male and female die. As the punch presses the sheet metal into the die, the material is deformed to take the shape of the die cavity. Stamping is a high-speed process, often performed in progressive stamping presses, which can perform multiple operations in a single stroke.
3.2 Key Differences Between Stamping and Deep Drawing
While both stamping and deep drawing use a punch and die to shape metal, there are several key differences between the two processes:
- Forming Depth: In stamping, the depth of the part is generally shallow, and the process is primarily used to create flat or slightly contoured shapes. In contrast, deep drawing is specifically designed to produce parts with significant depth, often with a depth greater than the diameter of the blank.
- Material Deformation: Stamping typically involves cutting, bending, or embossing the metal, but the material does not undergo the same level of stretching and plastic deformation as in deep drawing. Deep drawing requires the material to flow into the die cavity, undergoing significant tensile and compressive stresses.
- Speed and Productivity: Stamping is much faster than deep drawing and is often used for high-volume production of smaller, simpler parts. Stamping presses can cycle at very high speeds, making them ideal for producing parts like brackets, clips, and fasteners. Deep drawing, on the other hand, is slower due to the need for precise control over material flow and deformation.
- Tooling: Stamping typically requires progressive dies that perform multiple operations (e.g., cutting, bending, punching) in a single stroke. Deep drawing requires specialized tooling, including blank holders and punches designed to manage the complex material flow and deformation involved in producing deep parts.
3.3 Material Deformation and Forming Depth
The amount of material deformation and forming depth are key differentiators between stamping and deep drawing.
- Stamping: The material deformation in stamping is relatively minor compared to deep drawing. The sheet metal is typically cut, bent, or formed into shallow features. Parts produced by stamping rarely have significant depth, and the material does not undergo the large-scale stretching seen in deep drawing.
- Deep Drawing: Deep drawing requires significant plastic deformation as the blank is stretched and drawn into the die. The forming depth in deep drawing can be substantial, often resulting in parts that are much deeper than those produced by stamping. The process must carefully manage the tensile and compressive stresses to avoid defects such as wrinkling, tearing, or thinning.
3.4 Applications of Stamping in Industry
Stamping is widely used in industries that require the mass production of small, shallow, or flat metal parts. Common applications include:
- Automotive: Stamping is used to produce small components like brackets, clips, and connectors, as well as larger flat parts like body panels. Stamping’s speed and efficiency make it ideal for high-volume production.
- Electronics: Stamping is often used to produce small, precise parts for electronic devices, including connectors, terminals, and circuit board components.
- Household Appliances: Stamped metal parts are found in many household appliances, from washing machines to refrigerators. These parts are often flat or slightly contoured and require minimal forming depth.
- Aerospace: Stamping is used to produce fasteners, brackets, and shields for aerospace applications. These parts need to be lightweight, durable, and produced to tight tolerances.
While stamping is highly efficient for producing flat or shallow parts in large quantities, it is not suitable for parts with significant depth or complex geometries. For those types of parts, deep drawing or other metal forming techniques are more appropriate.
Forging vs. Deep Drawing
4.1 Definition and Principles of Forging
Forging is a metal forming process that involves shaping metal by applying compressive forces, usually using a hammer or press. Forging can be performed at high temperatures (hot forging) or at room temperature (cold forging), depending on the material and the part’s requirements. The process is used to create parts with excellent mechanical properties, such as high strength, toughness, and fatigue resistance.
In forging, the material is typically heated to make it more malleable and is then deformed by a die or hammer. Forging can be classified into several types:
- Open-die forging: The metal is compressed between flat or simple-shaped dies, allowing it to flow freely in multiple directions.
- Closed-die forging: The metal is compressed in a die that contains the shape of the final part, resulting in more precise and complex geometries.
- Cold forging: The metal is formed at room temperature, often resulting in better surface finish and tighter tolerances but requiring higher forces.
4.2 Key Differences Between Forging and Deep Drawing
Forging and deep drawing differ in several important ways:
- Forming Forces: Forging relies on compressive forces to shape metal, while deep drawing uses a combination of tensile and compressive forces to deform a sheet into a hollow shape. Forging typically involves much higher forces than deep drawing, particularly in the case of hot forging.
- Material Deformation: In forging, the material is compressed to shape it, often involving significant changes in cross-sectional area. In deep drawing, the material is stretched and drawn into the die, maintaining much of its original thickness, especially in the flange area.
- Part Geometry: Forging is used to produce parts with solid cross-sections, such as gears, crankshafts, and tools, whereas deep drawing is used to produce hollow parts like cups, tanks, and enclosures.
- Temperature: Forging often involves heating the material to make it more malleable, especially in hot forging. Deep drawing, in contrast, is typically a cold forming process, though it can be performed at elevated temperatures for certain materials.
4.3 Hot Forging and Cold Forging: How They Compare to Deep Drawing
- Hot Forging: In hot forging, the material is heated above its recrystallization temperature, which reduces its strength and increases its ductility. This allows the material to be deformed more easily, resulting in complex shapes with minimal internal stresses. Hot forging is used to create parts with excellent mechanical properties but requires careful control of temperature and cooling rates.
- Cold Forging: Cold forging is performed at or near room temperature, resulting in parts with a better surface finish and tighter dimensional tolerances than hot forging. However, cold forging requires much higher forces, and the material is more prone to work hardening. Cold forging is typically used for smaller parts, such as fasteners or fittings.
Deep Drawing: Unlike forging, deep drawing is almost always a cold forming process. The material is deformed at room temperature, allowing for high precision and smooth surface finishes. Deep drawing is well-suited for producing large, hollow parts, while cold forging is better for smaller, solid parts.
4.4 Applications of Forging in Industry
Forging is commonly used in industries that require high-strength components capable of withstanding heavy loads and stress. Applications include:
- Automotive: Forged components like crankshafts, connecting rods, and gears are essential for the high-strength requirements of internal combustion engines and transmission systems.
- Aerospace: Forged parts are used in critical aerospace applications, such as landing gear, turbine blades, and structural components, where material strength and reliability are paramount.
- Tools and Hardware: Forged tools, such as wrenches, hammers, and pliers, benefit from the high toughness and durability that forging provides.
- Oil and Gas: Forged components like valves, flanges, and drill heads are widely used in the oil and gas industry, where they are exposed to high pressures and harsh conditions.
Bending vs. Deep Drawing
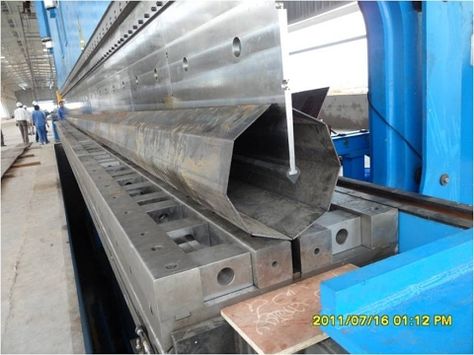
5.1 Definition and Principles of Bending
Bending is a metal forming process in which a sheet metal workpiece is plastically deformed to achieve a specific angular or curved shape. Bending is typically performed using press brakes or other specialized equipment, and it is one of the most common processes used in sheet metal fabrication.
Bending involves clamping the workpiece on a die and applying force to the blank using a punch. The material is deformed by bending around a specific axis, creating an angle or curve without changing the material’s thickness significantly. Bending can be used to produce a wide variety of shapes, such as L-bends, U-bends, or more complex profiles.
There are several types of bending operations:
- Air Bending: The punch presses the material into the die, but the material does not fully conform to the die shape, resulting in a springback effect.
- Bottoming: The material is pressed into the die cavity until it fully conforms to the shape of the die, providing more precise angles and dimensions.
- Coining: Coining is a high-pressure bending process in which the material is plastically deformed into the shape of the die, creating very tight tolerances and sharp angles.
5.2 Key Differences Between Bending and Deep Drawing
Bending and deep drawing differ significantly in their objectives, methods, and applications:
- Deformation: In bending, the material is plastically deformed along a single axis, typically forming an angular or curved shape. The material is not stretched or drawn into a deep cavity, as it is in deep drawing. Bending is a simpler process, with minimal material stretching and no changes in thickness.
- Geometry: Bending is used to create angular or curved shapes, such as brackets, frames, or channels. Deep drawing, on the other hand, produces hollow shapes, such as cups, boxes, or tanks, with depths that are often greater than their width.
- Tooling: Bending requires relatively simple tools, typically a punch and die, to form the desired angle or curve. In deep drawing, the tooling is more complex, involving a punch, die, and blank holder to control the material flow into the die.
- Forming Depth: The depth of deformation in bending is generally shallow, and the material does not undergo significant stretching. In contrast, deep drawing involves significant depth and material flow, with more complex stress and strain distributions.
5.3 Types of Bending: Air Bending, Bottoming, and Coining
- Air Bending: In air bending, the material is not pressed all the way into the die cavity. Instead, the punch applies pressure to bend the material, and the angle is determined by the depth of the punch stroke. Air bending allows for flexibility in the bending angle but results in less precise tolerances due to springback.
- Bottoming: Bottoming is a more precise bending process in which the material is pressed fully into the die, conforming to the die’s shape. This process provides better accuracy and control over the final angle, with less springback than air bending.
- Coining: Coining is a high-force bending process in which the material is squeezed between the punch and die to create very tight tolerances and sharp angles. Coining is typically used for small, high-precision parts where exact dimensions are required.
5.4 Applications of Bending in Industry
Bending is widely used in industries that require angular or curved metal parts. Applications include:
- Automotive: Bending is used to create components such as brackets, frames, and reinforcements in automotive manufacturing.
- Construction: Metal frames, supports, and structural components for buildings are often produced through bending processes.
- Furniture: Metal furniture components, such as chair frames or table legs, are often bent into shape using press brakes or other bending equipment.
- Consumer Goods: Bending is commonly used in the production of consumer products such as appliance housings, shelving, and brackets.
While bending is ideal for creating simple angular or curved shapes, it cannot produce the deep, hollow parts that deep drawing excels at. For parts requiring significant depth or more complex geometries, deep drawing is the preferred process.
Rolling vs. Deep Drawing
6.1 Definition and Principles of Rolling
Rolling is a metal forming process in which metal stock is passed between two or more rotating rolls to reduce its thickness or change its cross-sectional shape. Rolling is one of the most common and essential processes in metalworking, as it allows for the mass production of flat sheet metal, plates, bars, and strips.
Rolling is typically divided into two main types:
- Hot Rolling: In hot rolling, the metal is heated above its recrystallization temperature before being passed through the rolls. This reduces the material’s strength and allows for easier deformation, making it suitable for large reductions in thickness.
- Cold Rolling: Cold rolling is performed at room temperature, resulting in better surface finish, tighter tolerances, and increased material strength due to work hardening.
6.2 Key Differences Between Rolling and Deep Drawing
Rolling and deep drawing differ in their objectives, the nature of the deformation, and the final part geometries:
- Deformation Process: In rolling, the metal is compressed and elongated as it passes between the rotating rolls. This process reduces the thickness of the material and changes its cross-sectional shape. Deep drawing, in contrast, involves stretching the material into a hollow shape, with significant depth relative to its width.
- Product Geometry: Rolling is used to produce long, flat products like sheets, plates, and bars, as well as profiles with constant cross-sectional shapes like I-beams or rails. Deep drawing is used to produce hollow, three-dimensional parts with varying cross-sections and significant depth.
- Material Flow: In rolling, the material flows parallel to the rolls, and the thickness is reduced uniformly across the width of the workpiece. In deep drawing, the material flows radially inward as it is drawn into the die cavity, with localized thinning in areas of high tensile stress.
6.3 Hot Rolling and Cold Rolling: Comparison with Deep Drawing
- Hot Rolling: Hot rolling is used to produce large quantities of sheet metal, plates, and bars with significant reductions in thickness. Hot-rolled products typically have a rougher surface finish and looser tolerances compared to cold-rolled products. The material is less prone to cracking during hot rolling due to its lower strength at elevated temperatures.
- Cold Rolling: Cold rolling is performed after hot rolling to improve the surface finish, increase material strength through work hardening, and achieve tighter dimensional tolerances. Cold-rolled products are commonly used in applications requiring precise thickness and surface quality, such as automotive panels or appliance housings.
Deep Drawing: Unlike rolling, which is primarily focused on reducing thickness and shaping long products, deep drawing is concerned with creating hollow, three-dimensional parts with significant depth. The process involves more complex material flow and deformation, as the blank is stretched into the die cavity.
6.4 Applications of Rolling in Industry
Rolling is one of the most fundamental processes in metalworking, with applications in various industries:
- Construction: Rolled steel beams, plates, and sheets are used extensively in construction projects, from skyscrapers to bridges.
- Automotive: Cold-rolled steel sheets are used to manufacture automotive body panels, frames, and structural components.
- Aerospace: Rolled aluminum and titanium sheets are used in aircraft manufacturing for components such as fuselage panels, wing skins, and internal structures.
- Manufacturing: Rolled steel and aluminum sheets are used in the production of consumer goods, appliances, and machinery.
While rolling is ideal for producing long, flat products or profiles, it is not suitable for producing hollow, deep-drawn parts. Deep drawing is the preferred process for applications that require complex geometries and significant forming depth.
Extrusion vs. Deep Drawing
7.1 Definition and Principles of Extrusion
Extrusion is a metal forming process in which a billet of metal is forced through a die to create a long part with a constant cross-sectional profile. The material is pushed or pulled through the die by applying a compressive force, resulting in a continuous product with a uniform shape along its length.
There are two main types of extrusion:
- Direct Extrusion: In direct extrusion, the material is pushed through the die in the same direction as the applied force.
- Indirect Extrusion: In indirect extrusion, the die moves toward the billet while the billet remains stationary. This reduces friction between the material and the die, resulting in lower required force.
Extrusion can be performed at high temperatures (hot extrusion) or at room temperature (cold extrusion), depending on the material and the part requirements.
7.2 Key Differences Between Extrusion and Deep Drawing
Extrusion and deep drawing differ significantly in their deformation methods and the types of parts they produce:
- Deformation Process: In extrusion, the material is forced through a die to create a long part with a constant cross-sectional profile. The material flows in one direction, and the entire length of the product has the same shape. In deep drawing, the material is stretched and drawn into a die cavity, creating a hollow part with a variable cross-section.
- Part Geometry: Extrusion produces long, continuous parts like tubes, rods, and channels, which have the same cross-sectional shape throughout their length. Deep drawing, on the other hand, produces three-dimensional, hollow parts with complex geometries, such as cups, tanks, and enclosures.
- Tooling: Extrusion requires a die with a fixed cross-sectional profile, which defines the shape of the extruded product. Deep drawing requires more complex tooling, including a punch, die, and blank holder, to control the material flow and deformation during the process.
7.3 Types of Extrusion: Direct and Indirect
- Direct Extrusion: In direct extrusion, the billet is placed in a container and pushed through the die using a ram. This is the most common form of extrusion and is used to produce parts like tubing, bars, and profiles.
- Indirect Extrusion: In indirect extrusion, the die moves toward the stationary billet, reducing friction and requiring less force than direct extrusion. This method is often used for softer materials, such as aluminum and magnesium, to produce long, uniform profiles.
7.4 Applications of Extrusion in Industry
Extrusion is used to produce a wide range of products with constant cross-sectional profiles. Applications include:
- Automotive: Extruded aluminum profiles are used to create structural components, frames, and crash management systems in automotive manufacturing.
- Construction: Extruded steel and aluminum products, such as window frames, door frames, and roofing profiles, are widely used in the construction industry.
- Aerospace: Extruded titanium and aluminum components are used in aircraft structures, where lightweight, high-strength parts are essential.
- Manufacturing: Extrusion is used to produce a variety of consumer goods, from appliance components to sports equipment.
Extrusion is ideal for creating long, continuous parts with uniform cross-sections, but it is not suitable for producing hollow parts with varying depths or complex geometries. Deep drawing is the preferred process for parts that require significant depth and intricate shapes.
Hydroforming vs. Deep Drawing
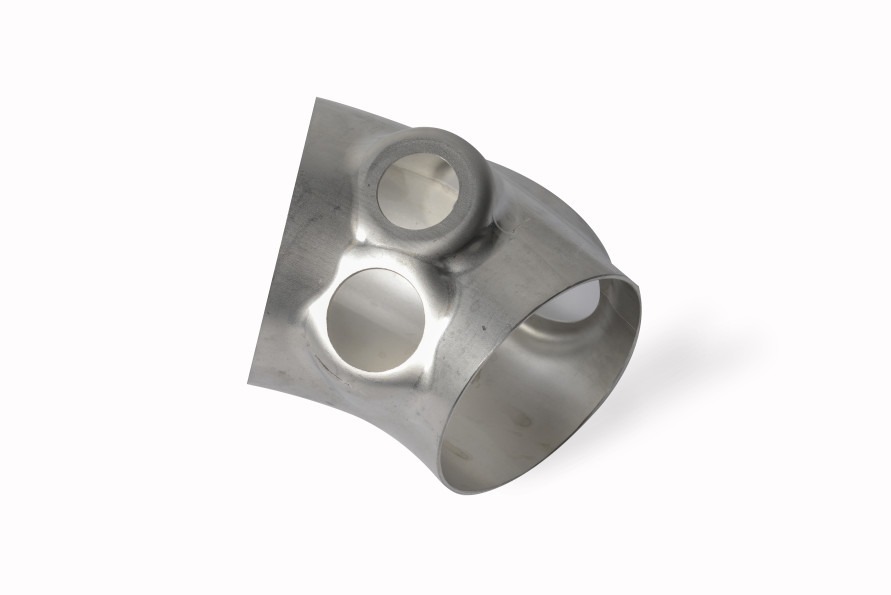
8.1 Definition and Principles of Hydroforming
Hydroforming is a metal forming process that uses high-pressure fluid to shape a metal blank or tube into a desired form. Unlike deep drawing, which relies on mechanical force from a punch, hydroforming uses fluid pressure to press the metal into a die, allowing for more uniform deformation and the creation of complex, lightweight parts.
There are two main types of hydroforming:
- Sheet Hydroforming: In sheet hydroforming, a flat sheet metal blank is placed over a die, and high-pressure fluid is used to push the blank into the die cavity, forming the desired shape.
- Tube Hydroforming: In tube hydroforming, a hollow tube is placed inside a die, and high-pressure fluid is injected into the tube, causing it to expand and conform to the shape of the die.
8.2 Key Differences Between Hydroforming and Deep Drawing
Hydroforming and deep drawing differ in the way force is applied to the material and the types of parts they produce:
- Force Application: In hydroforming, the material is shaped by the application of high-pressure fluid, which presses the material against the die. In deep drawing, the material is deformed by mechanical force applied by a punch. The use of fluid pressure in hydroforming results in more uniform material flow and less risk of wrinkling or tearing.
- Part Complexity: Hydroforming is capable of producing parts with more complex geometries than deep drawing, including asymmetric shapes, sharp corners, and variable wall thicknesses. Deep drawing is more suited for symmetrical, hollow parts like cylinders and boxes.
- Forming Depth: Hydroforming can achieve greater forming depth than deep drawing without causing defects like tearing or thinning. The fluid pressure in hydroforming distributes the forces more evenly, allowing for deeper, more intricate shapes to be formed.
8.3 Pressure-Controlled vs. Force-Controlled Processes
The key distinction between hydroforming and deep drawing lies in the way the material is deformed:
- Pressure-Controlled (Hydroforming): In hydroforming, the material is deformed by applying high-pressure fluid, which presses the blank or tube into the die. The fluid pressure can be precisely controlled, allowing for more uniform material deformation and reduced risk of defects like wrinkling or tearing.
- Force-Controlled (Deep Drawing): In deep drawing, the material is deformed by mechanical force from a punch. The force must be carefully controlled to avoid overstressing the material, which can lead to defects such as tearing, thinning, or wrinkling.
8.4 Applications of Hydroforming in Industry
Hydroforming is widely used in industries that require lightweight, complex, and high-strength components. Applications include:
- Automotive: Hydroforming is used to produce structural components like engine cradles, frame rails, and suspension parts. The process allows for the creation of lightweight, strong parts with complex geometries that would be difficult to achieve with traditional forming methods.
- Aerospace: In aerospace, hydroforming is used to create aircraft fuselage sections, engine components, and structural parts that require high strength and precision.
- Bicycle Manufacturing: Hydroforming is used to create lightweight, high-strength bicycle frames with complex shapes and varying tube diameters.
- Appliance Manufacturing: Hydroformed components are used in household appliances such as refrigerators, ovens, and washing machines, where complex shapes and high structural integrity are required.
While hydroforming is ideal for producing complex, lightweight parts, it is more expensive and slower than deep drawing due to the specialized equipment and high-pressure systems required. For simpler, symmetrical parts, deep drawing remains a more cost-effective solution.
Spinning vs. Deep Drawing
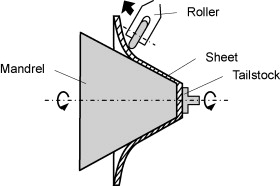
9.1 Definition and Principles of Metal Spinning
Metal spinning, also known as spin forming or spinning, is a metal forming process in which a metal disc or tube is rotated at high speed and pressed against a forming tool to create a cylindrical or conical shape. The process is typically performed on a lathe, where the workpiece is clamped in a chuck and spun at high speeds while a forming tool gradually presses the material against a mandrel or mold.
Spinning is used to create axially symmetric parts, such as bowls, cones, and domes. The process can be performed manually or using CNC (computer numerical control) lathes for higher precision and repeatability.
9.2 Key Differences Between Spinning and Deep Drawing
Spinning and deep drawing are both used to create hollow, symmetrical parts, but they differ in several key aspects:
- Deformation Process: In spinning, the material is deformed by applying pressure while the workpiece rotates, gradually shaping it into the desired form. The deformation is progressive, with the material being pressed against the mandrel over multiple passes. In deep drawing, the material is deformed in a single stroke as the punch forces the blank into the die cavity.
- Part Complexity: Spinning is ideal for creating axially symmetric parts with smooth, gradual curves, such as cones, domes, and cylinders. Deep drawing is better suited for creating parts with more complex geometries, including deep cavities, sharp corners, and varying cross-sections.
- Tooling: Spinning requires relatively simple tooling, typically consisting of a mandrel and forming tool. In deep drawing, the tooling is more complex, involving a punch, die, and blank holder to control material flow and deformation.
9.3 Manual vs. CNC Spinning: How It Compares to Deep Drawing
- Manual Spinning: In manual spinning, the operator uses hand tools to press the material against the mandrel while the workpiece rotates. Manual spinning is ideal for low-volume production and custom parts, but it requires a high level of skill and is slower than CNC spinning or deep drawing.
- CNC Spinning: CNC spinning uses computer-controlled lathes to automate the spinning process, allowing for higher precision, repeatability, and speed. CNC spinning can produce parts with tighter tolerances and more complex geometries than manual spinning.
Compared to deep drawing, CNC spinning offers greater flexibility in terms of part design and can produce parts with more complex curves and varying wall thicknesses. However, deep drawing is more efficient for high-volume production of symmetrical parts with consistent depth and geometry.
9.4 Applications of Spinning in Industry
Metal spinning is used in a variety of industries to produce hollow, axially symmetric parts. Applications include:
- Aerospace: Spinning is used to produce components such as nose cones, engine cowlings, and reflectors for aircraft and spacecraft.
- Lighting and Reflectors: Spinning is commonly used to create light reflectors, lamp housings, and domes for lighting applications.
- Household Goods: Spinning is used to produce household items such as pots, pans, bowls, and vases.
- Automotive: Spinning is used to create wheel rims, hubcaps, and other cylindrical automotive components.
While spinning is ideal for producing cylindrical or conical parts with smooth, curved surfaces, it is not as well-suited for parts with complex geometries, sharp corners, or deep cavities. For those types of parts, deep drawing is the preferred process.
Comparison of Material Selection in Deep Drawing and Other Metal Forming Techniques
Material selection plays a critical role in determining the success of any metal forming process, including deep drawing, stamping, forging, bending, rolling, extrusion, hydroforming, and spinning. Each process requires specific material properties to ensure the material can withstand the stresses and deformations without failing.
10.1 Deep Drawing: Suitable Materials and Properties
In deep drawing, the material must have sufficient ductility to undergo significant plastic deformation without cracking or tearing. Materials commonly used in deep drawing include:
- Low-Carbon Steel: Low-carbon steel offers excellent formability, making it suitable for deep drawing applications such as automotive body panels, fuel tanks, and appliance housings.
- Aluminum: Aluminum is lightweight and has good ductility, making it ideal for deep-drawn parts in the automotive, aerospace, and packaging industries. However, aluminum requires specialized lubricants to prevent galling during the drawing process.
- Stainless Steel: Stainless steel is used in deep drawing applications that require high corrosion resistance and strength, such as medical devices, kitchen sinks, and exhaust components.
- Copper and Brass: Copper and brass are used in deep drawing applications where electrical conductivity, thermal conductivity, and aesthetic appeal are important, such as in the production of electrical connectors and decorative items.
The key material properties that affect deep drawing include:
- Ductility: The ability of the material to undergo plastic deformation without cracking.
- Yield Strength: Lower yield strength is preferred for deep drawing, as it allows the material to flow more easily into the die cavity.
- Formability: Materials with good formability can be drawn into complex shapes without tearing or wrinkling.
- Anisotropy: Materials with low anisotropy deform more uniformly during deep drawing, reducing the risk of defects such as earing or uneven thickness distribution.
10.2 Material Selection in Stamping, Forging, Bending, Rolling, Extrusion, Hydroforming, and Spinning
Stamping: Materials used in stamping must have good formability, but the process does not require the same level of ductility as deep drawing. Common materials include:
- Steel: Low-carbon steel and high-strength steel are commonly used in stamping for automotive parts, appliances, and consumer goods.
- Aluminum: Aluminum is used in stamping applications that require lightweight parts, such as automotive body panels and electronic enclosures.
Forging: Materials used in forging must have high strength, toughness, and resistance to fatigue. Common materials include:
- Carbon Steel: Widely used in forging for components like gears, shafts, and connecting rods.
- Alloy Steel: Used in applications that require higher strength and toughness than carbon steel.
- Aluminum: Used in applications where lightweight and corrosion resistance are critical, such as in the aerospace and automotive industries.
Bending: Materials used in bending must have good ductility and resistance to cracking. Common materials include:
- Steel: Low-carbon steel is widely used for bending applications in construction, automotive, and manufacturing.
- Aluminum: Aluminum is used in bending for lightweight structures, frames, and enclosures.
Rolling: Materials used in rolling must have good malleability and the ability to withstand compressive forces. Common materials include:
- Steel: Steel is the most common material for rolling, used to produce sheets, plates, bars, and structural profiles.
- Aluminum: Aluminum is used in rolling to create lightweight sheets and plates for the aerospace, automotive, and construction industries.
Extrusion: Materials used in extrusion must have good flow properties and resistance to cracking. Common materials include:
- Aluminum: Aluminum is the most commonly extruded material, used for structural components, tubes, and profiles in the automotive and construction industries.
- Magnesium: Magnesium is used in extrusion for lightweight parts in the automotive and electronics industries.
Hydroforming: Materials used in hydroforming must have good ductility and the ability to withstand high-pressure fluid without cracking. Common materials include:
- Aluminum: Aluminum is widely used in hydroforming for lightweight automotive and aerospace components.
- Stainless Steel: Stainless steel is used in hydroforming for high-strength, corrosion-resistant parts such as exhaust systems and structural components.
Spinning: Materials used in spinning must have good ductility and the ability to withstand repeated deformation without cracking. Common materials include:
- Aluminum: Aluminum is commonly used in spinning for the production of cookware, lighting reflectors, and automotive components.
- Copper and Brass: Copper and brass are used in spinning for decorative items, electrical components, and plumbing fittings.
10.3 How Material Behavior Influences the Choice of Forming Process
The choice of material and forming process is influenced by several factors, including the material’s mechanical properties, formability, and the desired part geometry. Key considerations include:
- Ductility: Materials with high ductility, such as aluminum and low-carbon steel, are well-suited for deep drawing, hydroforming, and spinning. Materials with lower ductility, such as high-strength steel or titanium, may be more suitable for stamping or forging.
- Yield Strength: Lower yield strength materials are preferred for processes that involve significant plastic deformation, such as deep drawing and hydroforming. Higher yield strength materials are used in processes like forging and stamping, where compressive forces are dominant.
- Forming Depth: Deep drawing, hydroforming, and spinning are better suited for producing parts with significant forming depth, while stamping, bending, and rolling are better suited for shallow or flat parts.
Tooling and Equipment Comparison in Deep Drawing and Other Metal Forming Techniques
Tooling and equipment are critical components of any metal forming process. The design of the tooling and the choice of equipment can significantly impact the quality, speed, and cost of production.
11.1 Tooling Design in Deep Drawing vs. Stamping, Forging, and Bending
Deep Drawing: The tooling in deep drawing consists of a punch, die, and blank holder. The punch pushes the blank into the die cavity, while the blank holder prevents the material from wrinkling as it is drawn into the die. The tooling must be designed to control material flow and deformation, ensuring that the part is drawn without tearing or excessive thinning.
Stamping: Stamping requires progressive dies that perform multiple operations (e.g., cutting, bending, punching) in a single stroke. The dies must be carefully designed to achieve precise cuts and bends while minimizing material waste and defects.
Forging: Forging requires heavy-duty dies that can withstand the high compressive forces involved in shaping metal. The dies must be designed to create the desired part geometry while allowing for material flow and flash formation.
Bending: Bending requires relatively simple tooling, typically consisting of a punch and die. The tooling must be designed to achieve the desired bending angle while preventing cracking or excessive thinning at the bend radius.
11.2 Equipment Types: Mechanical, Hydraulic, and Servo-Driven Presses
Deep Drawing: Deep drawing is typically performed on hydraulic presses, which provide precise control over force and speed. Servo-driven presses are also used for deep drawing, allowing for real-time adjustments to process parameters such as punch speed and blank holder force.
Stamping: Stamping is commonly performed on mechanical presses, which operate at high speeds and are well-suited for high-volume production of small, shallow parts. Hydraulic presses are used for more complex stamping operations that require precise control over force and speed.
Forging: Forging requires mechanical or hydraulic presses that can apply high compressive forces to shape the metal. Hot forging is typically performed on hydraulic presses, while cold forging is performed on mechanical presses.
Bending: Bending is performed on press brakes or other specialized bending machines. These machines can be mechanical, hydraulic, or servo-driven, depending on the required precision and production volume.
11.3 Tool Wear and Maintenance in Deep Drawing Compared to Other Processes
Deep Drawing: Tool wear in deep drawing is influenced by factors such as material hardness, lubrication, and punch speed. The punch, die, and blank holder must be regularly inspected and maintained to prevent defects such as surface scratches, thinning, or tearing. Coatings such as titanium nitride (TiN) or diamond-like carbon (DLC) are commonly applied to tooling to reduce wear and extend tool life.
Stamping: Stamping dies experience wear due to the high-speed nature of the process and the repetitive cutting, punching, and bending operations. Regular maintenance and sharpening of the dies are required to maintain part quality and extend tool life.
Forging: Forging dies are subjected to extreme forces and temperatures, leading to significant tool wear. Heat-resistant coatings and lubricants are used to reduce wear and extend tool life. Regular maintenance is critical to prevent defects such as die cracking or surface defects in the forged parts.
Bending: Tool wear in bending is less severe than in processes like deep drawing or forging. However, the punch and die must be regularly inspected for wear to prevent cracking or thinning at the bend radius. Lubrication is often used to reduce friction and wear during the bending process.
Defects in Deep Drawing vs. Other Metal Forming Techniques
Each metal forming technique is prone to specific defects that can compromise the quality of the final part. Understanding the common defects in each process and how to prevent them is essential for achieving high-quality, defect-free parts.
12.1 Common Defects in Deep Drawing
Wrinkling: Wrinkling occurs when the blank holder force is too low, allowing the material to flow too freely into the die. Wrinkles form around the edges of the part, compromising its surface quality and structural integrity.
Tearing: Tearing occurs when the material is overstretched and can no longer withstand the tensile stresses. This is often caused by excessive punch speed or insufficient ductility in the material.
Thinning: Thinning occurs when the material is stretched too much in certain areas, leading to a reduction in thickness. This weakens the part and increases the risk of failure during use.
Earing: Earing is caused by anisotropy in the material’s grain structure, resulting in uneven deformation during deep drawing. This leads to the formation of ears or flanges around the edges of the part.
12.2 Defects in Stamping, Forging, and Bending
Stamping Defects:
- Burrs: Sharp edges or material protrusions left on the part after cutting or punching.
- Cracking: Occurs when the material is overstressed during bending or punching operations.
- Dimensional Variations: Caused by improper alignment of the dies or variations in material thickness.
Forging Defects:
- Flash: Excess material that is squeezed out of the die cavity during forging, which must be trimmed off in a secondary operation.
- Die Cracking: Caused by excessive stress or improper die maintenance.
- Surface Defects: Caused by improper die lubrication or tool wear.
Bending Defects:
- Cracking: Occurs when the material is bent beyond its ductility limits, leading to cracks along the bend radius.
- Springback: The tendency of the material to return to its original shape after bending, resulting in incorrect angles.
- Wrinkling: Caused by insufficient support or improper tooling during the bending process.
12.3 Defect Prevention Strategies in Different Metal Forming Processes
Deep Drawing:
- Increase the blank holder force to prevent wrinkling.
- Use lubrication to reduce friction and improve material flow.
- Select materials with high ductility to reduce the risk of tearing.
- Optimize punch speed to prevent overstretching and thinning.
Stamping:
- Maintain and sharpen dies regularly to reduce burr formation and improve dimensional accuracy.
- Use progressive dies to perform multiple operations in a single stroke, reducing the risk of misalignment.
- Optimize material thickness and die clearance to prevent cracking and dimensional variations.
Forging:
- Use preheating to reduce material strength and improve formability in hot forging operations.
- Apply heat-resistant coatings to dies to reduce wear and improve surface quality.
- Regularly inspect and maintain forging dies to prevent cracking and surface defects.
Bending:
- Select materials with high ductility to reduce the risk of cracking during bending.
- Use springback compensation techniques to achieve accurate bend angles.
- Ensure proper tool alignment and support to prevent wrinkling and surface defects.
Automation and Technological Advancements in Deep Drawing and Other Metal Forming Techniques
Technological advancements in automation, computer-aided design (CAD), and finite element analysis (FEA) have significantly improved the efficiency, precision, and flexibility of metal forming processes, including deep drawing, stamping, forging, and bending.
13.1 Automation in Deep Drawing: Servo-Driven Presses and CNC Control
Automation has revolutionized the deep drawing process by improving precision, repeatability, and production speed. Servo-driven presses and CNC (computer numerical control) systems allow for real-time adjustments to process parameters such as punch speed, blank holder force, and lubrication, enabling manufacturers to optimize the process for different materials and part geometries.
Benefits of automation in deep drawing include:
- Improved Precision: Servo-driven presses provide precise control over punch speed and force, resulting in tighter tolerances and higher part quality.
- Real-Time Monitoring: CNC systems allow for real-time monitoring of key process variables, such as temperature, pressure, and tool wear, enabling manufacturers to make adjustments on the fly and prevent defects.
- Increased Productivity: Automation reduces cycle times and increases production efficiency, making it possible to produce high-quality parts in large volumes.
13.2 Automation in Stamping, Forging, Bending, and Hydroforming
Stamping: Stamping has long been an automated process, with progressive stamping presses capable of performing multiple operations in a single stroke. Automation has improved the speed and precision of stamping, enabling manufacturers to produce small, intricate parts in high volumes with minimal manual intervention.
Forging: Automation in forging has improved the precision and repeatability of the process. Robotic automation is often used to handle heavy workpieces and position them in the forging dies, reducing the risk of injury to operators and improving production speed.
Bending: Automation in bending is achieved through the use of CNC press brakes, which allow for precise control over bend angles, force, and speed. CNC press brakes can be programmed to perform complex bending sequences with high accuracy and repeatability.
Hydroforming: Hydroforming has benefited from advancements in CNC control and servo-driven presses, which allow for precise control over fluid pressure and part geometry. Automation has made it possible to produce complex, lightweight parts with greater consistency and accuracy.
13.3 Finite Element Analysis (FEA) in Deep Drawing vs. Other Forming Techniques
Finite Element Analysis (FEA) is a powerful computational tool used to simulate the behavior of materials during metal forming processes. FEA allows engineers to predict how a material will deform under various conditions and optimize the design of tooling and process parameters to prevent defects.
In deep drawing, FEA is used to:
- Predict Material Flow: FEA simulations can model the flow of material into the die cavity, helping engineers optimize punch speed, blank holder force, and lubrication to ensure smooth material movement.
- Analyze Stress and Strain: FEA allows engineers to predict areas of high stress or strain in the material, enabling them to make adjustments to the tooling or process parameters to prevent defects such as tearing, wrinkling, or thinning.
- Optimize Tool Design: FEA simulations can be used to optimize the design of the punch, die, and blank holder to ensure that the material is deformed evenly and that the final part meets dimensional specifications.
In other metal forming processes, FEA is used for similar purposes:
- Stamping: FEA is used to simulate cutting, bending, and punching operations, allowing engineers to optimize die clearance, punch speed, and material thickness to prevent defects such as cracking, burrs, or dimensional variations.
- Forging: FEA is used to predict material flow and stress distribution during forging, enabling engineers to optimize die design, preheating temperature, and material flow to reduce defects and improve part quality.
- Bending: FEA is used to simulate the bending process and predict springback, allowing engineers to optimize tooling design and process parameters to achieve accurate bend angles.
13.4 Industry 4.0 Integration in Metal Forming Processes
Industry 4.0 refers to the integration of digital technologies, automation, and data analytics into manufacturing processes. In metal forming, Industry 4.0 technologies such as smart sensors, real-time data monitoring, and predictive maintenance are transforming the way parts are produced.
Key Industry 4.0 technologies in metal forming include:
- Smart Sensors: Smart sensors are used to monitor key process variables such as temperature, pressure, and tool wear in real time. This data can be analyzed to make real-time adjustments to process parameters, improving part quality and reducing downtime.
- Predictive Maintenance: Predictive maintenance systems use data analytics to monitor the condition of tooling and equipment, allowing manufacturers to schedule maintenance before a failure occurs. This reduces downtime and extends the life of the tooling and equipment.
- Digital Twins: Digital twins are virtual models of physical processes that can be used to simulate and optimize metal forming operations. By creating a digital twin of a deep drawing or stamping process, engineers can test different tooling designs and process parameters before implementing them in production.
Applications Across Industries: Deep Drawing vs. Other Metal Forming Techniques
Different industries rely on a variety of metal forming processes to produce parts with specific properties, shapes, and performance characteristics. The choice of process depends on factors such as part geometry, material requirements, production volume, and cost.
14.1 Automotive Industry: Deep Drawing vs. Stamping and Forging
Deep Drawing in Automotive: Deep drawing is widely used in the automotive industry to produce large, lightweight parts such as body panels, fuel tanks, and exhaust components. The process allows for the creation of parts with complex geometries and uniform wall thickness, making it ideal for structural components that require strength and durability.
Stamping in Automotive: Stamping is used to produce smaller, shallow parts such as brackets, clips, and fasteners. Stamping is a high-speed process that allows for the mass production of small parts with intricate details, making it ideal for high-volume automotive manufacturing.
Forging in Automotive: Forging is used to produce high-strength components such as crankshafts, connecting rods, and gears. These parts must withstand high loads and stresses, making forging the preferred process for critical drivetrain components.
14.2 Aerospace Industry: Hydroforming and Spinning vs. Deep Drawing
Deep Drawing in Aerospace: Deep drawing is used to produce components such as fuselage sections, engine housings, and structural parts. These parts require high strength, low weight, and tight tolerances, making deep drawing a suitable process for aerospace applications.
Hydroforming in Aerospace: Hydroforming is used to produce complex, lightweight components such as wing ribs, engine mounts, and exhaust systems. The process allows for the creation of parts with more complex geometries and deeper forming depths than deep drawing, making it ideal for certain aerospace applications.
Spinning in Aerospace: Spinning is used to produce axially symmetric parts such as nose cones, engine cowlings, and reflectors. The process allows for the creation of large, smooth, curved surfaces, making it suitable for parts that require aerodynamic efficiency.
14.3 Electronics and Consumer Goods: Bending, Stamping, and Deep Drawing
Deep Drawing in Electronics: Deep drawing is used to produce enclosures for electronic devices, such as smartphone housings, battery enclosures, and connector components. The process allows for the creation of thin, lightweight parts with high structural integrity and precise dimensions.
Stamping in Electronics: Stamping is used to produce small, precise parts for electronic devices, including connectors, terminals, and circuit board components. The high-speed nature of stamping makes it ideal for mass-producing small, intricate parts.
Bending in Consumer Goods: Bending is commonly used in the production of consumer products such as appliance housings, furniture frames, and brackets. Bending allows for the creation of simple, angular shapes with high precision and repeatability.
14.4 Medical Devices: Deep Drawing vs. Hydroforming and Spinning
Deep Drawing in Medical Devices: Deep drawing is used to produce medical device components such as surgical instruments, implants, and device enclosures. The process allows for the creation of parts with tight tolerances, smooth surfaces, and high corrosion resistance, making it ideal for medical applications.
Hydroforming in Medical Devices: Hydroforming is used to produce complex, lightweight components such as prosthetics, implants, and surgical instruments. The process allows for the creation of parts with more intricate geometries and deeper forming depths than deep drawing, making it suitable for certain medical applications.
Spinning in Medical Devices: Spinning is used to produce axially symmetric components such as implants, surgical tools, and device housings. The process allows for the creation of smooth, curved surfaces with high precision, making it ideal for parts that require biocompatibility and corrosion resistance.
Conclusion: Choosing Between Deep Drawing and Other Metal Forming Techniques
Metal forming processes, such as deep drawing, stamping, forging, bending, rolling, extrusion, hydroforming, and spinning, each offer unique advantages and limitations depending on the application. The choice of metal forming technique depends on factors such as part geometry, material requirements, production volume, and cost.
Deep drawing is ideal for producing hollow, three-dimensional parts with complex geometries, high strength, and uniform wall thickness. It is widely used in industries such as automotive, aerospace, packaging, and medical devices. However, deep drawing may not be the best choice for parts that require minimal forming depth, intricate details, or long, continuous profiles.
Stamping is a high-speed process that is best suited for producing flat or shallow parts with intricate details in large quantities. Forging is ideal for producing high-strength components that must withstand heavy loads and stress, while bending is used to create simple angular or curved shapes.
Rolling and extrusion are used to produce long, continuous parts with uniform cross-sectional profiles, while hydroforming and spinning are ideal for producing complex, lightweight parts with deep forming depths and smooth, curved surfaces.
Ultimately, the choice between deep drawing and other metal forming techniques depends on the specific requirements of the part, including its shape, material properties, and performance criteria. By carefully evaluating these factors, manufacturers can select the most appropriate metal forming process to meet their production goals and ensure high-quality, defect-free parts.
EMS Metalworking Machinery: Your Trusted Partner in Precision Metalworking
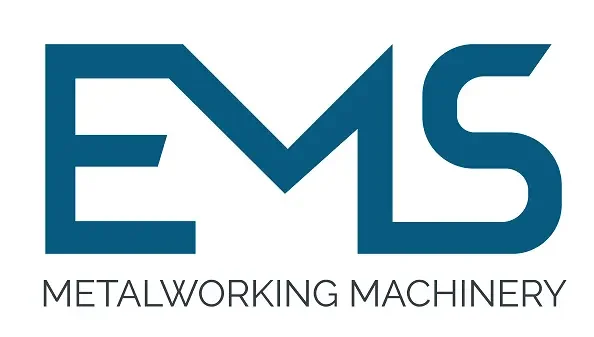
EMS Metalworking Machinery is a leading manufacturer of high-quality metalworking equipment, dedicated to providing innovative solutions that meet the evolving needs of industries worldwide. With a rich history of excellence and a commitment to technological advancement, we have earned a reputation for delivering cutting-edge machinery that ensures precision, efficiency, and durability.
Our Product Range:
- CNC Spinning Lathes: From precision bench lathes to heavy-duty industrial models, our lathes offer unmatched accuracy and performance for a wide range of applications, including machining shafts, gears, and other cylindrical components.
- Milling Machines: Our milling machines are designed to provide exceptional cutting capabilities and versatility, enabling you to create complex shapes and intricate details with ease. Whether you need a horizontal or vertical milling machine, we have the perfect solution for your needs.
- Drilling Machines: Our drilling machines are built to deliver precise and powerful drilling operations, ensuring clean holes and exceptional surface finishes. From sensitive bench drills to heavy-duty radial drills, we offer a comprehensive range to suit various applications.
- Grinding Machines: Our grinding machines are engineered for precision and efficiency, allowing you to achieve the highest levels of surface finish and dimensional accuracy. Whether you need a surface grinder, cylindrical grinder, or tool grinder, we have the equipment to meet your specific requirements.
- Sawing Machines: Our sawing machines are designed for fast and accurate cutting of metals, providing clean cuts and minimal burrs. From band saws to circular saws, we offer a variety of options to suit different materials and cutting needs.
- Custom Machinery: In addition to our standard product line, we also specialize in custom machinery fabrication. Our experienced engineers can work with you to design and build tailored solutions that meet your unique requirements and optimize your production processes.
Why Choose EMS Metalworking Machinery:
- Quality: Our machines are crafted with the highest quality materials and components, ensuring long-lasting performance and reliability.
- Precision: We are committed to delivering machinery that meets the most stringent tolerances and standards, ensuring exceptional accuracy in your metalworking operations.
- Innovation: We continuously invest in research and development to stay at the forefront of technological advancements, offering innovative solutions that enhance your productivity and efficiency.
- Customer Support: Our dedicated team of experts is always available to provide comprehensive support, from machine selection and installation to maintenance and troubleshooting.
- Customization: We understand that every business has unique needs, and we offer flexible customization options to tailor our machines to your specific requirements.
At EMS Metalworking Machinery, we are more than just a supplier of equipment; we are your trusted partner in metalworking success. By choosing EMS, you can be confident in the quality, reliability, and performance of your machinery, enabling you to achieve your business goals and stay ahead of the competition.
EMS Metalworking Machinery
We design, manufacture and assembly metalworking machinery such as:
- Hydraulic transfer press
- Glass mosaic press
- Hydraulic deep drawing press
- Casting press
- Hydraulic cold forming press
- Hydroforming press
- Composite press
- Silicone rubber moulding press
- Brake pad press
- Melamine press
- SMC & BMC Press
- Labrotaroy press
- Edge cutting trimming machine
- Edge curling machine
- Trimming beading machine
- Trimming joggling machine
- Cookware production line
- Pipe bending machine
- Profile bending machine
- Bandsaw for metal
- Cylindrical welding machine
- Horizontal pres and cookware
- Kitchenware, hotelware
- Bakeware and cuttlery production machinery
as a complete line as well as an individual machine such as:
- Edge cutting trimming beading machines
- Polishing and grinding machines for pot and pans
- Hydraulic drawing presses
- Circle blanking machines
- Riveting machine
- Hole punching machines
- Press feeding machine
You can check our machinery at work at: EMS Metalworking Machinery – YouTube
Applications:
Flange-punching
Beading and ribbing
Flanging
Trimming
Curling
Lock-seaming
Ribbing