We are one of the Deep Draw Press for Sale manufacturers. Deep drawing process & Deep drawing press & Double action deep drawing press & Triple action deep drawing press
Deep drawing is a manufacturing process of forming sheet metal stock, called blanks, into geometrical or irregular shapes that are more than half their diameters in depth. Deep drawing involves stretching the metal blank around a plug and then moving it into a moulding cutter called a die. Common shapes of deep drawn products including cylinders for Aluminium cans and cups for baking pans.
Deep Draw Press
A deep draw press is a type of metalworking press used to transform flat metal sheets into three-dimensional shapes. It is a versatile tool that can produce a wide range of products, including cooking pots, pans, automotive parts, and electrical enclosures.
How a Deep Draw Press Works:
- Blanking: A stamping press is used to cut out a flat blank from a sheet of metal. The blank size is slightly larger than the desired final shape to allow for metal flow during the drawing process.
- Heating: The blank may be heated to improve its formability and reduce the risk of cracking. Heating is particularly important for thicker materials or complex shapes.
- Loading: The blank is placed on the blank holder of the deep draw press. The blank holder firmly grips the blank around its edges, preventing it from wrinkling or buckling during the drawing process.
- Drawing: The punch, a tool with the desired shape of the final product, descends into the blank holder, forcing the blank into the desired shape. The blank flows over the punch, forming the desired three-dimensional shape.
- Trimming: Excess material around the edges of the drawn part is trimmed away using a trimming die. This ensures that the final part has a clean edge and meets the desired dimensions.
Types of Deep Draw Presses:
- Single-Action Deep Draw Presses: These presses use a single ram to perform both the drawing and trimming operations. They are relatively simple and inexpensive, but they are limited in the complexity of shapes they can produce.
- Double-Action Deep Draw Presses: These presses have two rams, one for drawing and one for trimming. This allows for more complex shapes to be produced, as the drawing ram can continue to draw the blank while the trimming ram trims the edges.
- Triple-Action Deep Draw Presses: These presses have three rams, one for drawing, one for trimming, and one for ejecting the finished part. They are used for producing the most complex shapes, such as those with undercut features or re-entrant angles.
Applications of Deep Draw Presses:
Deep draw presses are used in a wide variety of industries, including:
- Automotive Industry: Producing car body panels, fenders, hoods, and other automotive components.
- Appliance Industry: Manufacturing cooking pots, pans, sinks, and other appliance components.
- Aerospace Industry: Creating aircraft components, such as fuel tanks, fuselage sections, and engine housings.
- Electrical Industry: Producing electrical enclosures, housings, and components.
- Construction Industry: Manufacturing architectural panels, roofing components, and ventilation ducts.
Benefits of Using Deep Draw Presses:
Deep draw presses offer several advantages over other metalforming methods, such as stamping and casting:
- Versatility: Deep draw presses can produce a wide range of shapes, from simple cylinders to complex geometries.
- Accuracy: Deep draw presses can achieve high levels of accuracy and consistency in the dimensions of the finished parts.
- Efficiency: Deep draw presses can produce parts quickly and efficiently, making them a cost-effective manufacturing method.
- Material Savings: Deep draw presses can produce parts with minimal waste of material.
- Strength and Durability: Deep-drawn parts are generally stronger and more durable than those produced by other methods.
In conclusion, deep draw presses are versatile and powerful tools that play a crucial role in various industries. Their ability to produce complex shapes with high precision and efficiency makes them an essential part of modern manufacturing.
Irregular items, such as enclosure covers for truck oil filters and fire extinguishers, are also commonly manufactured by the deep drawing method. The drawing of sheet metal or commonly known as deep drawing is a process which a punch is used to force a sheet metal to flow between the surfaces of a punch a die. As a result, a cylindrical, conical or box-shaped part is formed in the die with minimal material scrap (Boljanovic, 2004). In this process, a flat sheet metal was kept under a blank holder force (BHF).
The blank holder should allow the material to slide into the die surface but at the same time, that force must be a great enough to prevent wrinkling of the sheet as it drawn as shown in Figure 2.1. The punch transferred the force through the punch and thus the punch transmits the force through the walls of the cup as it drawn into the die cavity (Singh, 2008). In deep drawing process, it can be divided into two types that is pure bending and ironing.
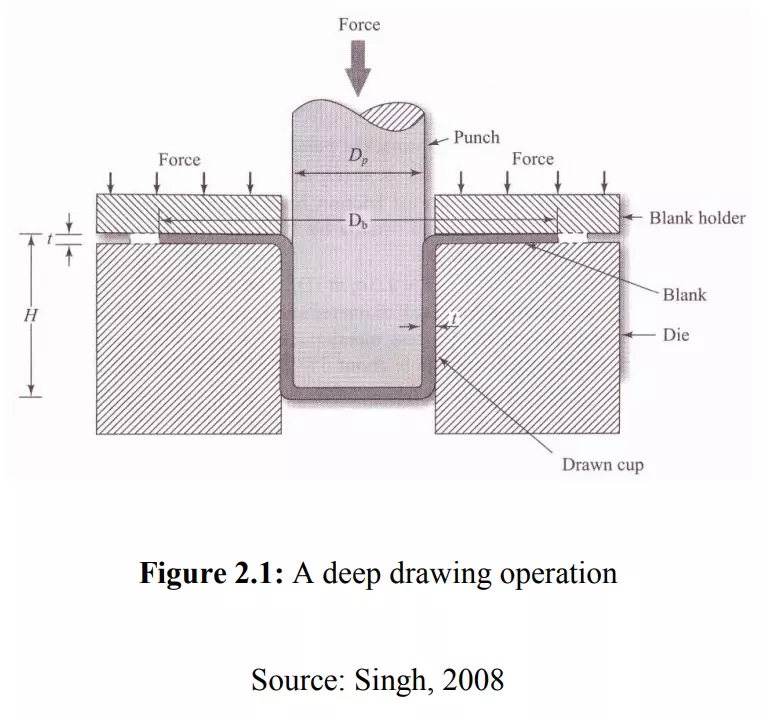
Pure Bending in Deep Draw Press
Pure bending is type of deep drawing without a reduction in the thickness of the workpiece material while in ironing, it a deep drawing with a reduction in the thickness of the workpiece material (Boljanovic, 2004). A schematic illustration of these two types of deep drawing is shown in Figure 2.2. From the Figure 2.1, it is clear that the basic tools for deep drawing are the punch, the drawing die ring, and the blank holder. However, some products cannot be drawn in a single draw and requires secondary drawing that is redrawing process. As a result, the design of the die will be more complicated as a progressive die is normally required to allow multiple drawing operations under one production line.
A percentage reduction of 48% is considered excellent on the first draw. Succeeding draws are smaller. There should be no appreciable change in the thickness of the material between the blank and the finished part.
Results of deep drawing are mostly empirical in nature and research has been done only limited almost exclusively to the drawing of cylindrical cup. For other shapes theoretical analysis is too much complicated and has no practical significance (Singh, 2008). In deep drawing process, there are several factors that can be affected the process which are categorized into two groups:
Materials for Deep Draw Press
Material and friction factors, and tool and equipment factors. Thus it is important before running the deep drawing process, these factors was considered well to prevent an undesirable result like earing, fracturing, and wrinkling. In Figure 2.3, it shows clearly these two factors (material and friction, tool and equipment) that need to consider in deep drawing process. Recently more studies have been develop by refer to these factors in order make an improvement while running deep drawing process.
Formability Test
Sheet metal formability is undergoing a transition from art to science.
Formability within each forming mode can be related to specific metal formability parameters. The successful sheet metal forming process which is can be converts initially from flat to desired shape. There are many major failures that always happened such as splitting, wrinkling or shape distortion.
The formability test is use to access of sheet to be deformed into useful part. The testing can be divided into two types: Intrinsic and simulative. The intrinsic tests measure the basic material properties under certain stress strain states, for example the uniaxial tensile test and the plane strain tensile test. Traditional evaluation of formability is based on both intrinsic tests and simulative tests.
The intrinsic tests measure the basic characteristic properties of materials that can be related to their formability. These tests provide comprehensive information that is insensitive to the thickness and surface condition of the material. Examples of intrinsic tests are Hydraulic Bulge test, Marciniak In-Plane Sheet torsion test, and Miyauchi shear test.
The simulative test can provide limited specific information that may be sensitive to factors other than material properties like the thickness, surface condition, surface lubrication and etc. Subject the material to deformation that closely resembles the deformation that occurs in a particular forming operation.
Hydraulic presses are powerful machines used to apply a significant amount of force to an object through hydraulic fluid pressure. They are essential in various industrial applications, providing the necessary force for processes such as metal forming, stamping, bending, and molding. The versatility and efficiency of hydraulic presses make them indispensable tools in manufacturing and production lines. This document will explore the different types of hydraulic presses, their application areas, components, operational principles, manufacturing process, and the challenges and advancements in the industry.
Types of Hydraulic Presses
Hydraulic presses come in various designs, each suited to specific applications and requirements. The primary types of hydraulic presses include C-frame presses, H-frame presses, four-column presses, straightening presses, arbor presses, laminating presses, and transfer presses.
C-frame presses, also known as gap-frame presses, have a C-shaped frame that provides three-sided access to the work area. This design is ideal for applications requiring easy loading and unloading of materials.
H-frame presses, or two-post presses, have a robust H-shaped frame that offers excellent stability and strength. They are commonly used for heavy-duty tasks such as metal forming and straightening.
Four-column presses, or four-post presses, have four vertical columns that provide superior support and uniform force distribution. These presses are suitable for large-scale applications requiring high precision and repeatability.
Straightening presses are specialized hydraulic presses used to straighten bent or distorted metal components. They are widely used in the automotive and construction industries.
Arbor presses are smaller, manually operated hydraulic presses used for light-duty tasks such as assembly, riveting, and broaching. They are commonly found in workshops and small manufacturing facilities.
Laminating presses are used to bond multiple layers of material together under heat and pressure. These presses are essential in industries such as electronics, where laminated components are common.
Transfer presses are automated hydraulic presses that move the workpiece through multiple stations for different operations. They are highly efficient and used in high-volume production environments.
Application Areas
Hydraulic presses are employed in various industries, thanks to their ability to deliver consistent and precise force. Key application areas include:
Metal forming and forging: Hydraulic presses are crucial in shaping and forming metal parts through processes such as stamping, bending, and deep drawing. They are essential in the production of automotive parts, machinery components, and structural elements.
Automotive industry: In the automotive sector, hydraulic presses are used for manufacturing various parts, including body panels, chassis components, and engine parts. They play a critical role in ensuring the structural integrity and performance of vehicles.
Aerospace industry: The aerospace industry relies on hydraulic presses for forming and shaping high-strength materials used in aircraft components. Precision and reliability are paramount in this industry, making hydraulic presses indispensable.
Plastic and rubber molding: Hydraulic presses are used in the molding of plastic and rubber components, including automotive parts, household goods, and medical devices. They ensure consistent product quality and precision.
Electrical and electronics industry: In the electronics sector, hydraulic presses are used for laminating circuit boards, forming connectors, and assembling electronic components. They provide the necessary force and precision for delicate operations.
Medical device manufacturing: Hydraulic presses are used in the production of medical devices, including surgical instruments, implants, and diagnostic equipment. They ensure the high precision and quality required in the medical field.
Packaging industry: Hydraulic presses are employed in the packaging industry for forming and shaping packaging materials, such as cardboard, plastic, and metal. They help produce packaging solutions that are strong, durable, and aesthetically pleasing.
Components of a Hydraulic Press
A hydraulic press comprises several key components that work together to generate and control the applied force. The main components include the frame, hydraulic cylinder, hydraulic pump, control valves, hydraulic fluid, pressure gauges and sensors, and die and tooling.
The frame is the main structure of the hydraulic press, providing stability and support for all other components. It is typically made of high-strength steel to withstand the significant forces generated during operation.
The hydraulic cylinder is the core component that generates the pressing force. It consists of a cylindrical chamber, a piston, and a piston rod. When hydraulic fluid is pumped into the cylinder, it moves the piston, which in turn applies force to the workpiece.
The hydraulic pump is responsible for generating the hydraulic fluid pressure needed to move the piston. It draws hydraulic fluid from a reservoir and delivers it to the cylinder under high pressure.
Control valves regulate the flow of hydraulic fluid to and from the cylinder, controlling the movement and force of the press. These valves can be manually operated or automated, depending on the press design.
Hydraulic fluid, typically oil, is the medium through which force is transmitted in the hydraulic system. It must have suitable properties, such as viscosity and lubricity, to ensure efficient operation and protect system components.
Pressure gauges and sensors monitor the hydraulic fluid pressure within the system. They provide real-time feedback to the operator or control system, ensuring safe and accurate press operation.
Die and tooling are the interchangeable components that come into direct contact with the workpiece. They are designed to shape, form, or cut the material as required by the specific application.
How Hydraulic Presses Work
Hydraulic presses operate based on Pascal’s principle, which states that pressure applied to a confined fluid is transmitted equally in all directions. This principle allows hydraulic presses to generate significant force with relatively small input pressure.
The operation of a hydraulic press begins with the hydraulic pump drawing fluid from the reservoir and delivering it to the cylinder. The control valves regulate the flow of fluid, directing it into the cylinder to move the piston. As the piston moves, it applies force to the workpiece placed between the die and tooling.
The hydraulic fluid plays a crucial role in this process, as it transmits the applied pressure and lubricates the system components. The pressure gauges and sensors continuously monitor the fluid pressure, providing feedback to ensure the press operates within safe limits.
The force generated by the hydraulic press can be precisely controlled by adjusting the hydraulic fluid pressure and the position of the control valves. This allows for accurate and repeatable operations, essential for high-quality manufacturing.
Manufacturing of Hydraulic Presses
The manufacturing of hydraulic presses involves several stages, from design and engineering to assembly and quality control. Each stage is critical to ensuring the press’s performance, reliability, and safety.
Design and engineering: The process begins with the design and engineering phase, where specifications for the press are developed based on the intended application. This includes selecting suitable materials, determining the required force and stroke, and designing the frame and hydraulic system.
Material selection: High-quality materials, such as high-strength steel for the frame and durable alloys for the hydraulic components, are selected to ensure the press’s longevity and performance.
Fabrication of components: The individual components of the hydraulic press, including the frame, cylinder, and pump, are fabricated using precision machining and manufacturing techniques. This ensures that each component meets the required tolerances and specifications.
Assembly process: The fabricated components are then assembled into the complete hydraulic press. This involves mounting the cylinder, pump, and control valves onto the frame, connecting the hydraulic lines, and installing the die and tooling.
Quality control and testing: Rigorous quality control measures are implemented throughout the manufacturing process to ensure the press meets all specifications and standards. This includes pressure testing the hydraulic system, verifying the accuracy of the control valves, and performing operational tests to ensure the press functions correctly.
Advancements and Innovations
The hydraulic press industry is continually evolving, driven by advancements in technology and increasing demands for efficiency and precision. Key innovations include automation and control systems, energy efficiency improvements, and smart hydraulic presses.
Automation and control systems: Modern hydraulic presses are often equipped with advanced control systems that automate the pressing process. This includes programmable logic controllers (PLCs), human-machine interfaces (HMIs), and sensors that monitor and adjust the press’s operation in real time. Automation improves efficiency, reduces the risk of human error, and enhances the consistency of the finished products.
Energy efficiency improvements: Manufacturers are focusing on developing hydraulic presses that consume less energy and have a smaller environmental footprint. This includes using variable displacement pumps, energy recovery systems, and optimizing the hydraulic system’s design to minimize energy losses.
Smart hydraulic presses: The integration of IoT (Internet of Things) technology into hydraulic presses has led to the development of smart presses. These presses can communicate with other machines and systems, providing real-time data on their status, performance, and maintenance needs. This connectivity allows for predictive maintenance, reducing downtime and extending the press’s lifespan.
Challenges in Hydraulic Press Manufacturing
The manufacturing of hydraulic presses presents several challenges, including precision and quality requirements, cost management, technological advancements, and environmental considerations.
Precision and quality requirements: Hydraulic presses must deliver consistent and precise force, which requires high levels of accuracy in the manufacturing process. Ensuring each component meets the required tolerances and specifications is critical to the press’s performance and reliability.
Cost management: The cost of materials, labor, and energy can significantly impact the overall cost of manufacturing hydraulic presses. Manufacturers must balance quality and cost to remain competitive in the market.
Technological advancements: Keeping up with technological advancements is essential for manufacturers to meet the evolving demands of the industry. This requires continuous investment in research and development to incorporate new technologies and improve existing designs.
Environmental considerations: Environmental regulations and sustainability concerns are increasingly important in hydraulic press manufacturing. Manufacturers must develop eco-friendly presses that consume less energy, use recyclable materials, and minimize their environmental impact.
Conclusion
Hydraulic presses are essential machines in various industries, providing the necessary force for processes such as metal forming, stamping, and molding. Understanding the different types of hydraulic presses, their components, and how they work is crucial for effective application and operation.
The manufacturing process of hydraulic presses involves careful design and engineering, material selection, precision fabrication, and rigorous quality control. Despite the challenges, advancements in technology and innovations are driving the industry forward, leading to more efficient, precise, and environmentally friendly hydraulic presses.
As industries continue to evolve, the hydraulic press industry must adapt and innovate to meet the demands of efficiency, precision, and sustainability. Through continuous research and development, manufacturers can enhance the performance and reliability of hydraulic presses, contributing to the success of various industrial applications.