We manufacture a Deburring Tool for Sheet Metal to round the sheet metal edges. These machines are used in metalworking industries
A deburring tool for sheet metal is a specialized tool used to remove burrs, sharp edges, and roughness from sheet metal after cutting, punching, or machining operations. Deburring is an important step in sheet metal fabrication to ensure smooth edges, improve safety, and enhance the overall appearance of the finished product. There are various types of deburring tools available, each designed for specific deburring applications. Here are a few common types:
- Handheld Deburring Tool: This is a manual tool typically consisting of a handle and a cutting blade. It is commonly used for deburring small areas or hard-to-reach places on sheet metal. The blade can be replaced or resharpened as needed.
- Deburring Files: Deburring files feature a series of teeth or ridges that effectively remove burrs from the edges of sheet metal. They are available in different shapes and sizes to suit various deburring requirements.
- Deburring Wheels: Deburring wheels are mounted on rotary tools such as bench grinders or handheld power tools. They consist of abrasive material (such as nylon, wire, or abrasive grains) embedded in a wheel or brush-like structure. When the wheel rotates against the sheet metal edge, it removes burrs and smoothes the surface.
- Countersink Tools: Countersink tools are used to create chamfered or countersunk holes in sheet metal. They can also be used for deburring by removing the sharp edges around the holes, leaving a smooth and tapered surface.
- Vibratory Deburring Machines: Vibratory deburring machines use vibratory motion and media (such as ceramic or plastic pellets) to remove burrs from sheet metal parts. The sheet metal parts are placed in the machine along with the media, and the vibrations cause the media to rub against the edges, effectively removing burrs.
- Tumbling Barrels: Tumbling barrels are cylindrical containers that rotate or tumble the sheet metal parts along with abrasive media. As the barrel rotates, the parts and media interact, resulting in deburring and edge-smoothing.
When selecting a deburring tool for sheet metal, consider factors such as the type and thickness of the metal, the size and complexity of the deburring task, and the desired level of precision. It’s also essential to follow safety guidelines and wear appropriate protective gear, such as gloves and safety glasses, when using deburring tools.
Deburring Tool for Sheet Metal
Deburring tools are specialized implements designed to effectively remove burrs, sharp edges, and imperfections from sheet metal components. These tools are crucial for maintaining the safety, functionality, and aesthetics of sheet metal products used in various industries.
Types of Deburring Tools for Sheet Metal:
- Hand-Held Deburring Tools:
These tools provide portability and convenient deburring for smaller sheet metal parts or in situations where access is limited. Common hand-held deburring tools include:
- Files: Files with varying coarseness levels are effective for removing burrs and smoothing out rough edges on sheet metal.
- Deburring Knives: Knives with rounded blades are specifically designed to trim and remove burrs from sheet metal edges.
- Deburring Wheels: Deburring wheels with abrasive grit are effective for deburring sheet metal edges.
- Power Deburring Tools:
These tools offer greater efficiency and power for deburring larger sheet metal components or in high-volume production. Examples include:
- Rotary Deburring Tools: Utilize rotating abrasive discs or belts to quickly remove burrs from sheet metal parts.
- Sanders: Sanders with appropriate abrasive belts can be used for deburring and surface finishing of sheet metal components.
- Stationary Deburring Machines:
For high-precision deburring or deburring complex shapes, specialized stationary machines offer consistent and precise results. These machines may utilize rotating cutters, abrasive belts, or a combination of both.
- Ultrasonic Deburring Systems:
For precision deburring of delicate sheet metal parts or complex geometries, ultrasonic deburring offers a gentle and effective method.
Choosing the Right Deburring Tool for Sheet Metal:
The choice of deburring tool for sheet metal depends on several factors, including:
- Size and shape of the sheet metal part: The tool should be able to accommodate the size and shape of the part comfortably.
- Material of the sheet metal part: The abrasive material used in the tool should be compatible with the material of the part.
- Desired level of precision: The tool should be able to achieve the desired level of precision for the application.
- Production volume: If high-volume production is required, a stationary machine may be more efficient.
- Safety features: The tool should incorporate adequate safety features to protect the operator from potential hazards.
Benefits of Using Deburring Tools for Sheet Metal:
- Improved safety: Deburring tools can reduce the risk of injuries to operators by removing sharp edges and burrs.
- Improved functionality: Rounded edges can prevent snagging and protect other components from damage.
- Enhanced aesthetics: A smooth, burr-free surface improves the overall appearance of sheet metal products.
- Increased efficiency: Power deburring tools and stationary machines can significantly reduce deburring time.
Applications of Deburring Tools for Sheet Metal:
- Automotive industry: Deburring car bodies, engine components, and other automotive parts.
- Aerospace manufacturing: Deburring precision sheet metal components for aircraft and spacecraft.
- Construction: Deburring sheet metal components for buildings, bridges, and other structures.
- Electronics manufacturing: Deburring sheet metal components for circuit boards, electronic devices, and other electronics.
- Consumer goods manufacturing: Deburring sheet metal components for appliances, furniture, and other consumer products.
Deburring tools play an essential role in maintaining the quality and safety of sheet metal components across various industries. By effectively removing burrs and imperfections, deburring enhances the functionality, aesthetics, and overall value of sheet metal products.
Handheld Deburring Tool
A handheld deburring tool is a manual tool designed to remove burrs, sharp edges, and roughness from sheet metal surfaces. It is commonly used for smaller deburring tasks or in areas where access is limited. Here are some key features and considerations for a handheld deburring tool:
- Handle: The tool typically consists of a comfortable handle that provides a secure grip during operation. The handle may be made of plastic, rubber, or another non-slip material for enhanced control and safety.
- Blade or Cutter: The handheld deburring tool has a cutting element, such as a blade or cutter, that removes the burrs from the sheet metal. The blade can be made of high-speed steel (HSS), carbide, or another durable material to ensure efficient and long-lasting deburring performance.
- Adjustable or Replaceable Blade: Some handheld deburring tools have adjustable or replaceable blades, allowing you to customize the cutting depth or replace the blade when it becomes dull or worn out. This flexibility extends the tool’s lifespan and ensures consistent deburring results.
- Ergonomics: Look for a handheld deburring tool with an ergonomic design that reduces hand fatigue and improves comfort during prolonged use. Features like a cushioned grip and ergonomic shape can make a difference in user experience.
- Versatility: Consider the versatility of the deburring tool and its compatibility with various types and thicknesses of sheet metal. Some handheld deburring tools come with multiple blade options or adjustable settings, allowing you to adapt to different deburring requirements.
- Safety Features: Ensure that the handheld deburring tool has safety features to protect your hands during operation. This may include a blade guard or a retractable blade mechanism that covers the blade when not in use.
- Portability: As a handheld tool, portability is a key advantage. Consider the size, weight, and ease of carrying or storing the deburring tool, especially if you need to move around or work in different locations.
- Price and Brand: Compare different brands and models of handheld deburring tools to find the one that meets your requirements and budget. Consider factors such as durability, customer reviews, and warranty when making your selection.
Remember to follow proper safety guidelines when using any deburring tool, including wearing protective gloves and safety glasses. It’s also recommended to practice on scrap pieces of sheet metal before working on your actual project to become familiar with the tool and achieve desired deburring results.
Deburring Files
Deburring files are tools specifically designed for removing burrs, sharp edges, and roughness from sheet metal surfaces. They consist of a handle and a file portion with teeth or ridges that effectively shave away the burrs. Here are some key features and considerations for deburring files:
- File Type: Deburring files come in various types, including flat files, half-round files, triangular files, and needle files. Each file type has a specific shape and size that is suited for different deburring tasks. Consider the shape and size of the file based on the contours and dimensions of the sheet metal surface you need to deburr.
- File Teeth: The file portion of the deburring file contains teeth or ridges that remove the burrs from the metal surface. The teeth can be coarse or fine, depending on the level of aggressiveness required for the deburring task. Coarser teeth are more suitable for heavier burrs and rough edges, while finer teeth provide a smoother finish.
- File Material: Deburring files are typically made of hardened steel or carbide materials. Hardened steel files are more common and offer good durability and sharpness. Carbide files, on the other hand, are harder and can maintain their sharpness for longer, making them suitable for tougher metals or extended use.
- File Cut: Deburring files come in different cuts, denoting the coarseness of the teeth. The common cut types include bastard cut, second cut, and smooth cut. The choice of cut depends on the severity of the burrs and the desired finish. Bastard cut files have the coarsest teeth, second cut files have medium-coarse teeth, and smooth cut files have finer teeth for a smoother finish.
- Handle: The handle of a deburring file provides a comfortable grip and control during use. Look for handles with ergonomic designs and non-slip materials to ensure a secure grip and minimize hand fatigue during prolonged use.
- File Length: The length of the file determines the reach and accessibility to different areas of the sheet metal. Consider the size and shape of the sheet metal and select a deburring file length that allows you to effectively reach all the necessary areas.
- Maintenance and Cleaning: To maintain the effectiveness of the deburring file, it’s important to clean it regularly to remove metal shavings and debris. Use a file brush or a stiff wire brush to clean between the teeth and keep the file in good condition.
- Price and Brand: Compare different brands and models of deburring files based on their quality, durability, and price. Opt for reputable brands known for manufacturing high-quality tools.
When using deburring files, it’s important to apply consistent pressure and use smooth, controlled strokes along the burrs to avoid damaging the surrounding metal or creating new burrs. Work with caution and wear appropriate safety gear, such as gloves and safety glasses, to protect yourself from sharp edges and metal fragments.
Deburring Wheels
Deburring wheels are abrasive tools used for removing burrs, sharp edges, and surface imperfections from sheet metal and other materials. They are typically used with rotary tools such as bench grinders, die grinders, or handheld power tools. Deburring wheels consist of a wheel or brush-like structure embedded with abrasive material. Here are some key features and considerations for deburring wheels:
- Wheel Type: Deburring wheels come in different types, including abrasive nylon wheels, wire wheels, and abrasive composite wheels. Each type has its own characteristics and is suited for specific deburring applications. Consider the material and the severity of the burrs when choosing the appropriate deburring wheel type.
- Abrasive Material: Deburring wheels are embedded with abrasive particles that perform the cutting and smoothing action. The abrasive material can vary, such as aluminum oxide, silicon carbide, or diamond particles. The choice of abrasive material depends on the hardness of the material being deburred and the desired finish.
- Wheel Density and Hardness: Deburring wheels can come in different densities and hardness levels. High-density wheels have more abrasive material packed together, providing a more aggressive cutting action. Lower-density wheels, on the other hand, are more flexible and suitable for contouring or fine deburring. Wheel hardness also affects the cutting action, with softer wheels conforming better to irregular surfaces.
- Wheel Grit: Deburring wheels are available in different grit sizes, which determine the coarseness of the abrasive particles. Coarser grits, such as 80 or 120, are more aggressive and suitable for heavy burr removal. Finer grits, such as 240 or 320, provide a smoother finish. Consider the level of burr removal required and the desired surface finish when selecting the appropriate grit size.
- Wheel Size: Deburring wheels come in various diameters and widths. The size of the wheel determines the coverage area and the contact surface with the material. Choose a wheel size that suits the size of the workpiece and allows for efficient deburring.
- Mounting Options: Deburring wheels can have different mounting options to be used with specific rotary tools. Common mounting options include arbor holes, threaded mounts, or quick-change systems. Ensure that the deburring wheel is compatible with the mounting mechanism of your chosen rotary tool.
- Speed and RPM: Deburring wheels have recommended operating speeds and RPM (revolutions per minute) limits. Consult the manufacturer’s recommendations for the maximum speed at which the wheel can be safely used to avoid damage or breakage.
- Safety Considerations: When using deburring wheels, always follow proper safety precautions. Wear protective goggles, gloves, and a face shield to protect yourself from flying debris. Ensure that the workpiece is securely held and use the appropriate guard or safety shield on the rotary tool.
- Replacement and Maintenance: Deburring wheels wear out over time and may require replacement. Regularly inspect the wheel for wear, damage, or clogging with debris. Clean the wheel periodically to remove accumulated metal shavings and abrasive particles.
Consider the specific deburring requirements, material type, and desired finish when selecting a deburring wheel. It’s advisable to experiment with different wheel types, grit sizes, and hardness levels on scrap pieces of sheet metal to determine the most suitable deburring wheel for your application.
Countersink Tools
Countersink tools are specialized cutting tools used to create chamfered or countersunk holes in sheet metal and other materials. These tools are designed to remove material around a hole, creating a conical or tapered shape that allows screws, bolts, or rivets to sit flush with the surface. Here are some key features and considerations for countersink tools:
- Countersink Angle: Countersink tools are available in various angles, typically ranging from 60 to 120 degrees. The angle determines the shape and depth of the countersunk hole. The most common countersink angles are 82 and 90 degrees. Consider the type of fasteners you will be using and the material thickness when selecting the appropriate countersink angle.
- Material and Coating: Countersink tools are made from high-speed steel (HSS), cobalt steel, or carbide. HSS countersinks are suitable for most general-purpose applications, while cobalt or carbide countersinks are more durable and can handle tougher materials like stainless steel. Some countersinks may also have coatings, such as titanium nitride (TiN), for increased wear resistance.
- Number of Flutes: Countersinks have flutes or cutting edges that remove material during the countersinking process. The number of flutes can vary, with three and four flutes being common. More flutes typically provide smoother and cleaner cuts, while fewer flutes may be more efficient for softer materials.
- Shank Size: Countersink tools come with different shank sizes to fit different types of drill chucks or power tools. Ensure that the countersink tool’s shank size matches the chuck or collet size of your drill or power tool.
- Adjustable or Non-adjustable: Some countersink tools have an adjustable depth stop or collar, allowing you to control the depth of the countersink hole. This feature is useful when you need consistent countersink depths across multiple workpieces. Non-adjustable countersinks have a fixed depth and are suitable for specific applications where a consistent depth is not critical.
- Single or Multi-step: Countersinks can be single-step or multi-step. Single-step countersinks have a single cutting edge and create a uniform chamfer or countersink angle in a single operation. Multi-step countersinks have multiple cutting edges of different sizes and angles, allowing you to create different chamfer sizes or countersink depths with one tool.
- Compatibility with Drill or Power Tools: Ensure that the countersink tool is compatible with the type of drill or power tool you will be using. Most countersinks have a hexagonal shank that can be inserted into a drill’s chuck, while others may require a specific type of chuck or adapter.
- Safety Considerations: When using countersink tools, always wear appropriate safety gear, including safety glasses and gloves, to protect yourself from flying debris. Secure the workpiece properly to prevent it from moving or spinning during the countersinking process.
Consider the material type, desired chamfer size and angle, and the specific application when selecting a countersink tool. It’s recommended to practice on scrap pieces of sheet metal or conduct tests on a small area before working on the actual project to ensure the desired countersink results.
Vibratory Deburring Machines
Vibratory deburring machines are equipment used for deburring, polishing, and finishing metal and other materials. These machines utilize vibratory motion combined with abrasive media to remove burrs, sharp edges, and surface imperfections from workpieces. Here are some key features and considerations for vibratory deburring machines:
- Vibratory Motion: Vibratory deburring machines utilize vibratory motion to agitate the workpieces and abrasive media. The motion can be circular or elliptical, and it helps to evenly distribute the abrasive media across the workpieces, ensuring consistent deburring and surface finishing.
- Bowl or Tub Design: Vibratory deburring machines typically have a bowl or tub-shaped container where the workpieces and abrasive media are placed. The shape and size of the container can vary depending on the capacity and type of workpieces being processed.
- Abrasive Media: These machines require abrasive media, such as ceramic or plastic pellets, to remove burrs and surface imperfections. The size, shape, and composition of the abrasive media can be chosen based on the specific deburring requirements and material being processed.
- Variable Speed and Amplitude: Vibratory deburring machines often feature adjustable speed and amplitude settings. This allows you to control the intensity of the vibration and tailor it to the specific needs of the workpieces and the desired deburring or surface finishing results.
- Water and Compound Flow: Some vibratory deburring machines have provisions for water and compound flow. Water helps to control the temperature and lubrication during the deburring process, while a compound can enhance the cleaning and deburring action. These features are particularly useful when processing materials prone to overheating or requiring additional cleaning.
- Separation and Media Discharge: Vibratory deburring machines may have built-in mechanisms for separating the workpieces from the abrasive media. This can include sieves or screens that allow the media to be discharged while retaining the workpieces, making it easier to handle and clean the finished parts.
- Safety Features: Ensure that the vibratory deburring machine has safety features in place, such as covers, interlocks, or emergency stop buttons, to protect operators and prevent accidents during operation.
- Size and Capacity: Consider the size and capacity of the vibratory deburring machine in relation to the size and quantity of the workpieces you intend to process. Choose a machine that can accommodate your workpiece size and production volume requirements.
- Maintenance and Cleaning: Vibratory deburring machines require regular maintenance to ensure optimal performance. This includes cleaning the machine, replacing worn-out parts, and monitoring the condition of the abrasive media. Follow the manufacturer’s recommendations for maintenance procedures and intervals.
- Price and Brand: Compare different brands and models of vibratory deburring machines based on their features, durability, and price. Opt for reputable brands known for manufacturing reliable and efficient equipment.
Vibratory deburring machines offer an efficient and effective way to deburr and finish workpieces in bulk. They are widely used in industries such as automotive, aerospace, metal fabrication, and more. However, it’s important to conduct trials and adjust the process parameters to achieve the desired deburring and finishing results for specific workpieces and materials.
Tumbling Barrels
Tumbling barrels, also known as rotary tumblers or barrel tumblers, are equipment used for various applications such as deburring, polishing, cleaning, and surface finishing of small parts and components. These machines consist of a rotating barrel or drum that holds the workpieces, along with abrasive media and sometimes a liquid compound. Here are some key features and considerations for tumbling barrels:
- Barrel Design: Tumbling barrels typically have a cylindrical or hexagonal shape and are made from durable materials such as steel or rubber. The barrel is designed to rotate and create a tumbling action that facilitates the deburring or finishing process.
- Capacity: Tumbling barrels come in different sizes and capacities to accommodate various workpiece quantities and sizes. Consider the volume and dimensions of the parts you need to process when selecting an appropriate barrel size.
- Rotation Speed: Tumbling barrels have adjustable rotation speeds to control the intensity and duration of the tumbling action. The speed can be adjusted to suit the specific requirements of the workpieces and the desired deburring or finishing results.
- Abrasive Media: Tumbling barrels require abrasive media to perform the deburring or finishing action. Common types of media include ceramic media, plastic media, or steel media. The choice of media depends on the material being processed, the desired finish, and the level of aggressiveness required.
- Liquid Compound: In some cases, a liquid compound may be added to the tumbling barrel to enhance the deburring or finishing process. The compound can improve the cutting action, provide lubrication, or aid in cleaning the workpieces.
- Separation and Media Discharge: Tumbling barrels may have built-in mechanisms for separating the workpieces from the abrasive media. This can include screens or mesh to retain the workpieces while allowing the media and debris to be discharged. Separation systems help streamline the process and make it easier to retrieve the finished parts.
- Safety Features: Ensure that the tumbling barrel is equipped with appropriate safety features, such as covers, interlocks, or emergency stop buttons, to protect operators and prevent accidents during operation.
- Maintenance and Cleaning: Tumbling barrels require regular maintenance to ensure optimal performance and longevity. This includes cleaning the barrel, replacing worn-out parts, and monitoring the condition of the media and compounds. Follow the manufacturer’s recommendations for maintenance procedures and intervals.
- Price and Brand: Compare different brands and models of tumbling barrels based on their features, durability, and price. Opt for reputable brands known for manufacturing reliable and efficient equipment.
Tumbling barrels are versatile machines used in various industries, including automotive, aerospace, jewelry, and metal fabrication. They offer an efficient and cost-effective way to process small parts in bulk, achieving consistent deburring, polishing, or surface finishing results. However, it’s important to select the appropriate media, compound, and process parameters based on the specific workpieces and desired outcomes. Conducting trials and adjusting the process variables will help optimize the performance of the tumbling barrel for your specific application.
Deburring Tool for Metal
https://www.youtube.com/embed/mMRmnQuYgjE?feature=oembedDeburring Tool for Metal
Deburring tools are essential for removing burrs, sharp edges, and imperfections from metal components. These tools are crucial for maintaining the safety, functionality, and aesthetics of metal products across various industries.
Types of Deburring Tools for Metal:
- Hand-Held Deburring Tools: These tools provide portability and convenient deburring for smaller metal parts or in situations where access is limited. Common hand-held deburring tools include:
- Files: Files with varying coarseness levels are effective for removing burrs and smoothing out rough edges on metal.
- Deburring Knives: Knives with rounded blades are specifically designed to trim and remove burrs from metal edges.
- Deburring Wheels: Deburring wheels with abrasive grit are effective for deburring metal edges.
- Power Deburring Tools: These tools offer greater efficiency and power for deburring larger metal components or in high-volume production. Examples include:
- Rotary Deburring Tools: Utilize rotating abrasive discs or belts to quickly remove burrs from metal parts.
- Sanders: Sanders with appropriate abrasive belts can be used for deburring and surface finishing of metal components.
- Stationary Deburring Machines: For high-precision deburring or deburring complex shapes, specialized stationary machines offer consistent and precise results. These machines may utilize rotating cutters, abrasive belts, or a combination of both.
- Ultrasonic Deburring Systems: For precision deburring of delicate metal parts or complex geometries, ultrasonic deburring offers a gentle and effective method.
Choosing the Right Deburring Tool for Metal
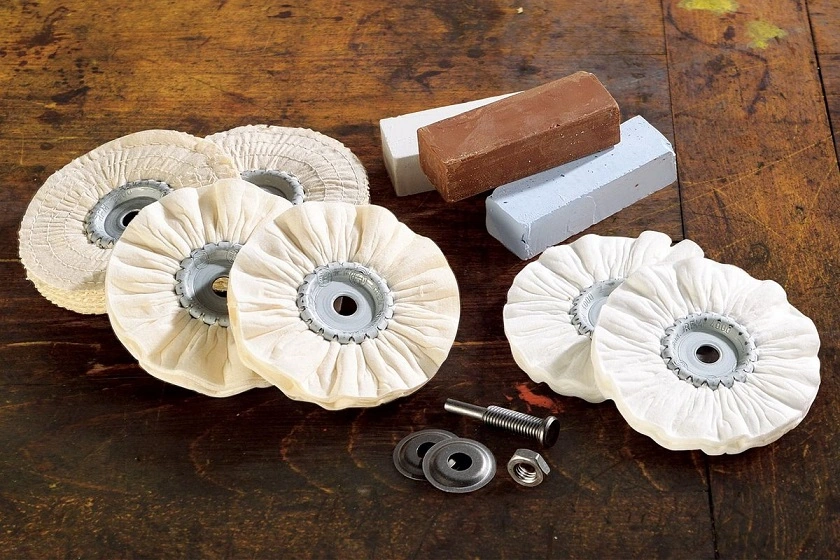
The choice of deburring tool for metal depends on several factors, including:
- Size and shape of the metal part: The tool should be able to accommodate the size and shape of the part comfortably.
- Material of the metal part: The abrasive material used in the tool should be compatible with the material of the part.
- Desired level of precision: The tool should be able to achieve the desired level of precision for the application.
- Production volume: If high-volume production is required, a stationary machine may be more efficient.
- Safety features: The tool should incorporate adequate safety features to protect the operator from potential hazards.
Benefits of Using Deburring Tools for Metal:
- Improved safety: Deburring tools can reduce the risk of injuries to operators by removing sharp edges and burrs.
- Improved functionality: Rounded edges can prevent snagging and protect other components from damage.
- Enhanced aesthetics: A smooth, burr-free surface improves the overall appearance of metal products.
- Increased efficiency: Power deburring tools and stationary machines can significantly reduce deburring time.
Applications of Deburring Tools for Metal:
- Automotive industry: Deburring car bodies, engine components, and other automotive parts.
- Aerospace manufacturing: Deburring precision metal components for aircraft and spacecraft.
- Construction: Deburring metal components for buildings, bridges, and other structures.
- Electronics manufacturing: Deburring metal components for circuit boards, electronic devices, and other electronics.
- Consumer goods manufacturing: Deburring metal components for appliances, furniture, and other consumer products.
Deburring tools play an essential role in maintaining the quality and safety of metal components across various industries. By effectively removing burrs and imperfections, deburring enhances the functionality, aesthetics, and overall value of metal products.
Metal deburring, grinding, and rounding are common applications in metalworking processes aimed at smoothing rough edges, removing burrs, and achieving a uniform finish on metal parts. Here’s a brief overview of each:
- Deburring: This process involves removing sharp edges or burrs left on metal parts after machining, cutting, or forming operations. It improves safety, functionality, and aesthetics of the parts.
- Grinding: Grinding is used to achieve precise dimensional control and surface finish. It involves using abrasive wheels or belts to remove material from a workpiece, often to prepare surfaces for further finishing or to achieve specific tolerances.
- Rounding: Rounding, also known as edge rounding, is done to soften sharp edges or corners on metal parts. It improves part handling, reduces the risk of injury, and can be aesthetically pleasing.
These processes are essential in various industries such as automotive, aerospace, manufacturing, and precision engineering, where metal parts must meet high standards of quality, safety, and performance.
- Deburring:
- Purpose: Deburring removes burrs, which are unwanted rough edges or protrusions on metal parts that result from machining, cutting, or forming processes.
- Methods: Deburring can be achieved through various methods such as manual deburring tools, abrasive stones, brushes, tumbling machines (vibratory or centrifugal), or chemical deburring solutions.
- Importance: Removing burrs improves the functional and aesthetic quality of metal parts. It also enhances safety by eliminating sharp edges that could cause injuries during handling or assembly.
- Grinding:
- Purpose: Grinding is used to achieve precise dimensional control, improve surface finish, and remove excess material from metal parts.
- Types: There are several types of grinding processes, including surface grinding, cylindrical grinding, centerless grinding, and internal grinding, each suited for specific part geometries and surface requirements.
- Equipment: Grinding machines use abrasive wheels (grinding wheels or belts) that rotate at high speeds to grind away material from the workpiece.
- Applications: Grinding is crucial for preparing surfaces for further finishing operations (such as polishing or plating), achieving tight tolerances, or removing defects like surface imperfections or weld seams.
- Rounding (Edge Rounding):
- Purpose: Rounding, or edge rounding, involves smoothing sharp edges or corners on metal parts.
- Methods: This can be done through mechanical methods like deburring tools with radius edges, vibratory or centrifugal tumbling processes with rounded media, or automated edge rounding machines.
- Benefits: Rounding improves part handling safety by reducing the risk of cuts or scratches. It also enhances the part’s appearance and can be critical for components that interact with other parts or personnel during assembly or use.
These processes are fundamental in metalworking industries where precision, quality, and safety are paramount. They ensure that metal parts meet exacting standards for functionality, durability, and aesthetics demanded by various applications, from automotive and aerospace to electronics and consumer goods manufacturing.
Deburring
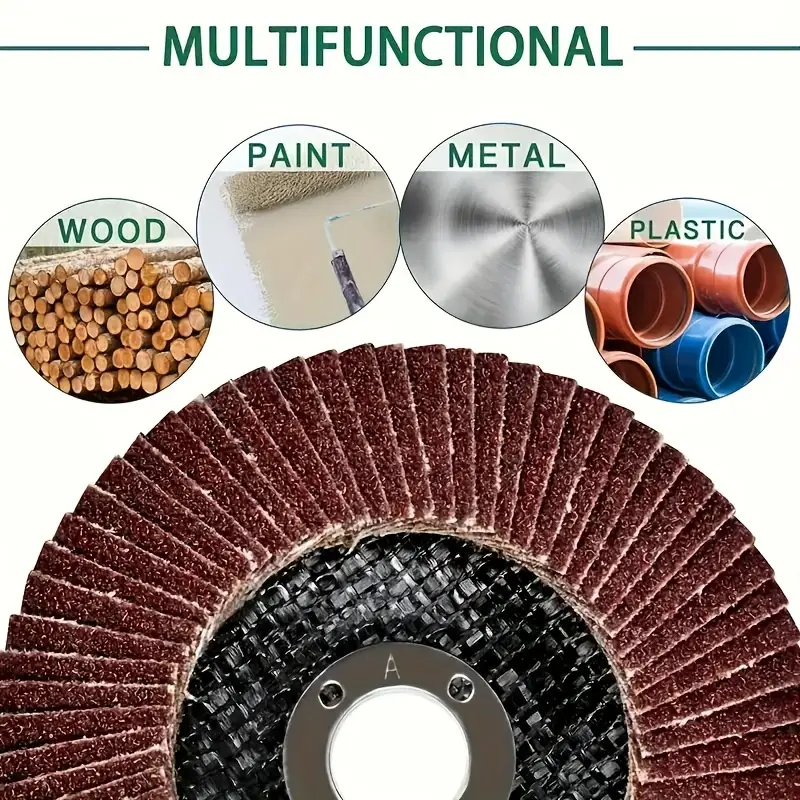
Deburring is a critical process in metalworking that involves the removal of burrs, which are unwanted rough edges or protrusions on metal parts. These burrs typically occur as a result of machining, cutting, or forming operations such as drilling, milling, stamping, or punching.
Importance of Deburring:
- Safety: Removing burrs eliminates sharp edges that can cause injuries during handling or assembly of parts.
- Functionality: Deburring ensures that parts fit together properly without interference from protrusions or rough edges.
- Aesthetics: Smooth edges improve the appearance of parts and enhance overall product quality.
- Performance: Burrs can affect the performance of moving parts or components that require precise tolerances.
Methods of Deburring:
- Manual Deburring Tools: Hand tools such as files, deburring knives, scrapers, or abrasive pads are used to manually remove burrs from small or intricate parts.
- Abrasive Stones and Brushes: Rotary tools equipped with abrasive stones or brushes can be used to remove burrs from larger or more accessible surfaces.
- Tumbling Machines: Vibratory or centrifugal tumbling machines use abrasive media (such as ceramic or plastic pellets) to deburr multiple parts simultaneously. This method is effective for small to medium-sized parts with complex geometries.
- Chemical Deburring: Chemical solutions or processes can be employed to selectively dissolve burrs, particularly in internal passages or complex shapes where mechanical methods may be challenging.
Deburring Considerations:
- Material Type: Different metals (e.g., aluminum, steel, titanium) require specific deburring techniques due to variations in hardness and machinability.
- Part Geometry: Deburring methods are chosen based on the size, shape, and accessibility of the burrs and the part itself.
- Quality Control: Inspecting parts after deburring ensures that all burrs are removed and that the part meets required specifications.
Deburring is essential in industries such as aerospace, automotive, electronics, and precision engineering, where high-quality, safe, and functional metal components are crucial.
Grinding
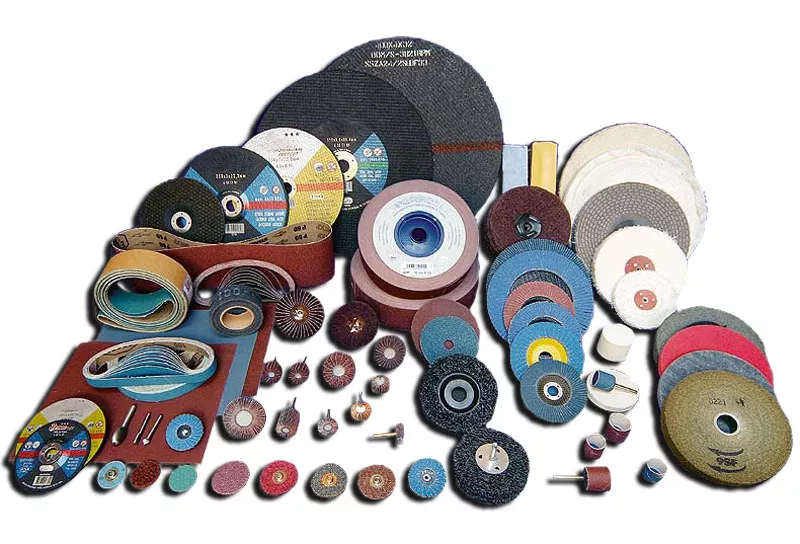
Grinding is a machining process used to remove material from a workpiece to achieve desired dimensions and surface finish. It is a versatile process widely used in various industries for both roughing and finishing operations on metal and other materials.
Purpose of Grinding
- Dimensional Control: Grinding allows for precise control over the dimensions of a workpiece, achieving tight tolerances that are difficult to achieve through other machining processes.
- Surface Finish: By using abrasive grains bonded into wheels or belts, grinding can produce smooth surfaces with low roughness values, enhancing the appearance and functionality of the parts.
- Material Removal: Grinding efficiently removes excess material, such as weld beads, casting flash, or stock material from forgings or billets, preparing the workpiece for subsequent operations.
Types of Grinding Processes:
- Surface Grinding: Involves grinding flat surfaces to achieve a smooth finish. It is commonly used for finishing hardened steel, cast iron, and similar materials.
- Cylindrical Grinding: Used to grind the outside diameter of cylindrical workpieces. It is ideal for creating precise roundness and surface finishes on shafts, rods, and other cylindrical components.
- Centerless Grinding: A type of cylindrical grinding where the workpiece is supported between two wheels: the grinding wheel and a regulating wheel. It is used for high-volume production of cylindrical parts with consistent dimensional accuracy.
- Internal Grinding: Grinding the inside diameter of a workpiece. It is used to create precise bores or holes with a smooth surface finish.
Equipment and Tools:
- Grinding Machines: Include surface grinders, cylindrical grinders, centerless grinders, and internal grinders, each designed for specific grinding applications.
- Grinding Wheels: Made from abrasive grains bonded together in various shapes and sizes. Types include aluminum oxide, silicon carbide, and diamond, each suited to different materials and applications.
Applications of Grinding:
- Manufacturing: Grinding is essential in the production of precision components for automotive, aerospace, medical devices, and consumer electronics.
- Tool and Die Making: Used for sharpening cutting tools and dies to maintain sharp edges and precise dimensions.
- Repair and Maintenance: Grinding is also employed for repairing worn or damaged parts by restoring their original dimensions and surface finish.
Grinding is a fundamental machining process that plays a crucial role in achieving the required dimensional accuracy, surface quality, and overall performance of metal parts in modern manufacturing.
Rounding
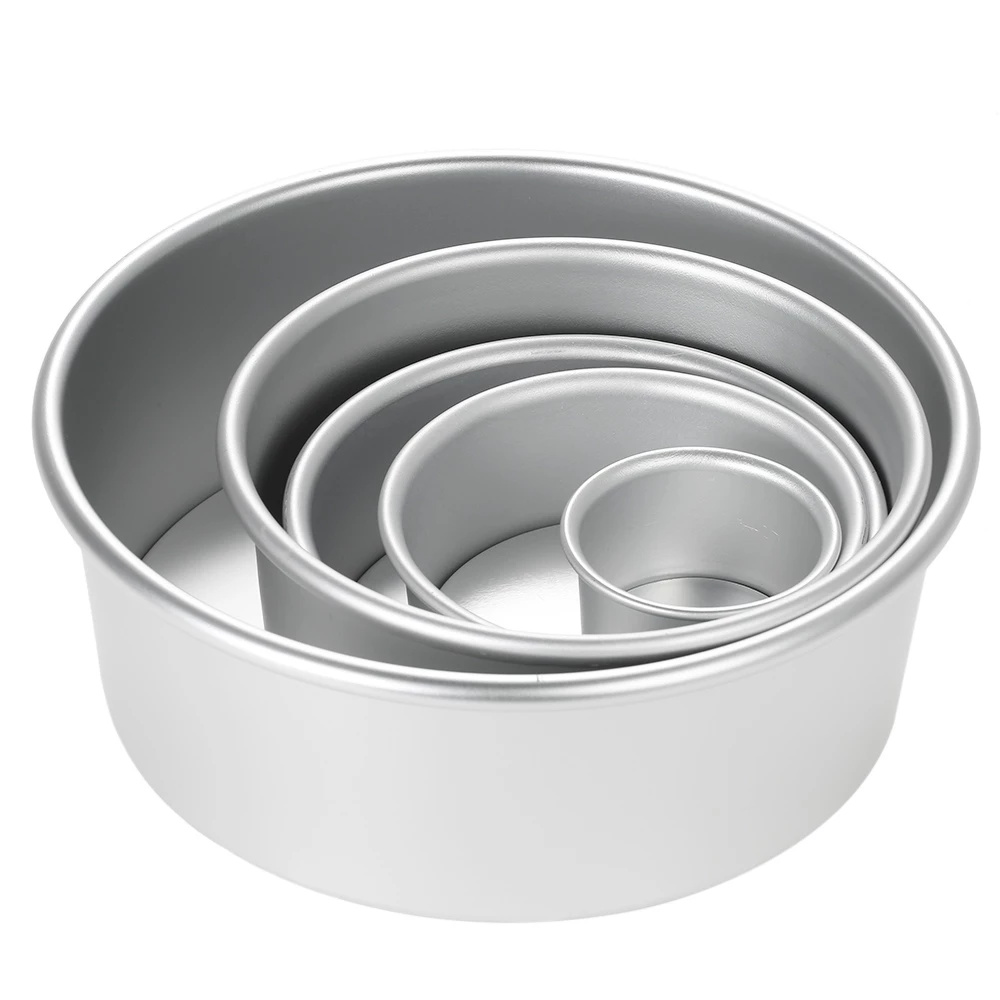
Rounding, also known as edge rounding or radiusing, is a finishing process used to smooth sharp edges and corners on metal parts. This process is essential for improving safety, enhancing aesthetics, and ensuring proper functionality of the parts, especially in applications where handling and contact with personnel or other components are involved.
Purpose and Benefits of Rounding:
- Safety: Rounded edges reduce the risk of injuries during handling, assembly, or use by eliminating sharp points or edges that could cause cuts or abrasions.
- Aesthetics: Smooth, rounded edges enhance the appearance of metal parts, making them more visually appealing and professional in finished products.
- Functionality: Rounding can improve the performance of parts by reducing stress concentrations at corners, which can extend the service life of components subjected to cyclic loading or wear.
Methods of Rounding:
- Manual Methods: Hand tools such as files, deburring tools with radiused edges, or abrasive pads can be used for small-scale rounding operations on accessible edges and corners.
- Machine Rounding: Automated edge rounding machines or dedicated deburring machines equipped with specialized tools can efficiently round edges and corners of larger or complex-shaped parts.
- Tumbling Processes: Vibratory or centrifugal tumbling machines using abrasive media (e.g., ceramic or plastic pellets) can uniformly round edges of multiple parts simultaneously. This method is effective for small to medium-sized parts with consistent edge profiles.
Considerations for Rounding:
- Part Geometry: The shape and size of the part influence the choice of rounding method. Complex geometries may require specialized equipment or multiple processes to achieve uniform rounding.
- Material Compatibility: Different metals (e.g., aluminum, stainless steel, titanium) and alloys have varying hardness and machinability characteristics, which may affect the choice of rounding tools and methods.
- Surface Finish Requirements: Rounding should maintain or improve the overall surface finish of the part, ensuring it meets functional and aesthetic specifications.
Applications of Rounding:
- Consumer Products: Rounding is crucial in industries such as furniture manufacturing, where rounded edges on metal components improve safety and user comfort.
- Automotive and Aerospace: Parts like brackets, panels, and housings benefit from rounded edges to prevent injuries during assembly and maintenance operations.
- Medical Devices: Ensuring smooth, rounded edges on surgical instruments and equipment enhances patient safety and ease of handling.
Rounding plays a vital role in enhancing the usability, safety, and appearance of metal parts across various industries, contributing to overall product quality and customer satisfaction.