We manufacture Cutter and Beading Machine, Trimming Flanging Machine, Trimming Beading Machine, Cutting and Beading Machine for sale.
A Cutter and Beading Machine is a metalforming machine used to simultaneously cut and bead a sheet metal strip, typically made of aluminum or steel. The machine is used to create a bead or edge on the sheet metal strip, which strengthens and stiffens the material while also adding a decorative element.
The machine consists of a feed roller, a cutting roller, and a beading roller. The sheet metal strip is fed into the machine through the feed roller, which moves the material forward at a controlled speed. The cutting roller then cuts the strip to the desired length while the beading roller creates a bead along the edge of the strip.
The machine can be adjusted to produce beads of different shapes and sizes, depending on the needs of the application. The finished product can be used for a variety of purposes, including as a trim or edge finish for metal panels or other structures.
Overall, the Cutter and Beading Machine is a versatile and efficient metalforming machine that can save time and labor in the fabrication process while also producing high-quality finished products.
Cutter and Beading Machine
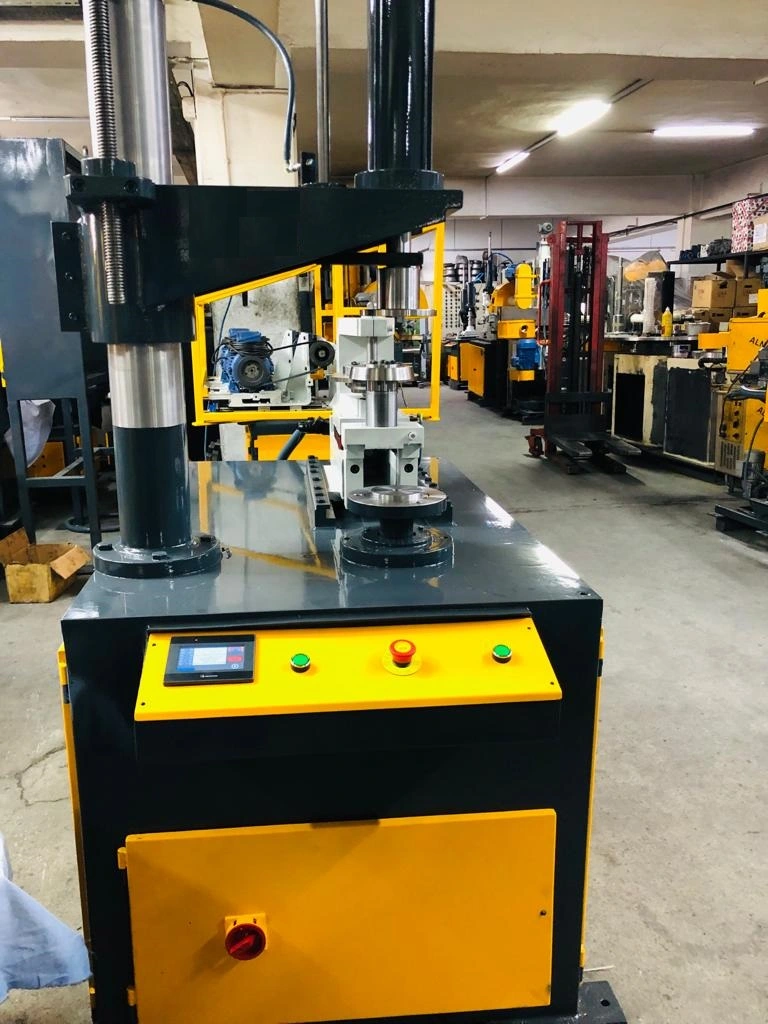
The Cutter and Beading Machine is a metalforming machinery used to cut and form sheet metal into different shapes and sizes. It is commonly used in the HVAC (Heating, Ventilation and Air Conditioning) industry to fabricate ductwork.
The machine typically consists of a set of rollers that feed the sheet metal through the machine. The first set of rollers cuts the sheet metal to the desired length, while the second set of rollers creates a bead or flange on the edge of the sheet. The beading process strengthens the edge of the sheet metal and makes it easier to join with other pieces of sheet metal.
Cutter and Beading Machines can vary in size and capacity depending on the needs of the user. They can be manual or fully automated and can be used for a wide range of applications including roofing, cladding, and ductwork fabrication.
Cutter and Beading Machine Parts
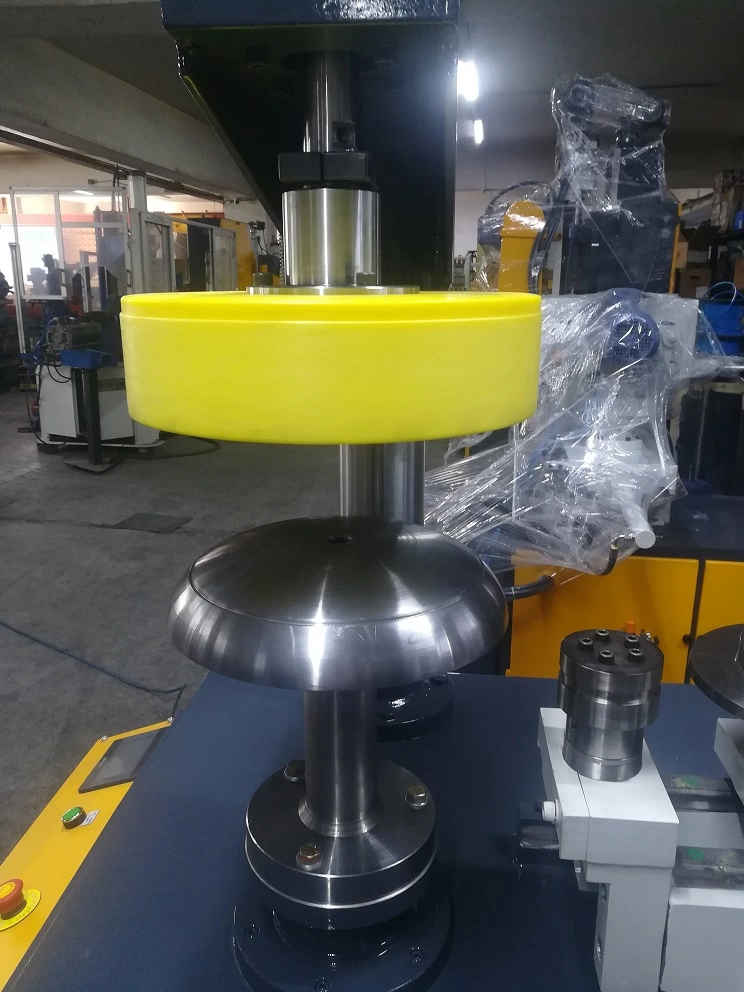
The main parts of a cutter and beading machine include:
- Base: The base provides the support and stability for the machine.
- Motor: The motor provides the power to run the machine and drive the cutting and beading tools.
- Cutting head: The cutting head is a rotating blade that is used to cut the metal sheet or plate.
- Beading head: The beading head is a pair of rollers that are used to form the edges of the metal sheet or plate.
- Feed rollers: The feed rollers are used to move the metal sheet or plate through the machine.
- Control panel: The control panel is used to control the machine’s functions, such as the speed of the cutting and beading heads and the feed rollers.
- Tooling: The tooling consists of various cutting and beading tools that can be changed out depending on the type of metal and the desired end result.
- Coolant system: The coolant system is used to lubricate and cool the cutting and beading heads during operation to prevent overheating and prolong the life of the machine.
- Chip tray: The chip tray collects the metal chips and debris that are produced during cutting and beading, making it easier to clean up and dispose of the waste material.
Beading Machine for Sheet Metal
Line 5 beading machine and line 7 beading machine are used to make sheet metal reinforced ribs during HVAC air duct processing. This machine can groove 5 or 7 reinforced ribs at the same time with stable working and high quality.
Our company can also customize multiple lines of grooving machines on the basis of customers’ demands. The metal sheet beading/grooving machine is a part of ventilation air duct manufacturing machines, it can be used with other rectangular HVAC tube forming machines together to finish a whole duct production, such as lock forming machine, pneumatic sheet metal folding machine, TDF flange forming machine, electric shearing machine, lock seam closing machine, clips cutting machine, etc.
Meanwhile, it will be very important to maintain the beading machine after you use it few months. The machine will be more smooth to use and use time will be longer if the operator adds lubrication oil to the parts before operating it. According to the different needs of every customer, EMS Metalworking Machinery can provide you with special cases of machines corresponding to customers’ requirements and actual use conditions.
As a professional manufacturer of ventilation air duct-making machines, the company can provide CNC HVAC whole duct-making machine lines and separate machines to meet different customers’ needs. Our address is Dongcheng Industrial Park, Bowang Town, Bowang District, Ma’anshan City, Anhui Province. Welcome people from all over the world to visit our factory and test machines.
What’s more, you can choose OEM service too. For after-sales service, we have skilled technicians who can teach you how to operate machines via video and we can also provide engineer overseas service or you can send the worker to our factory to learn the operation way.
Hydraulic presses are powerful machines used to apply a significant amount of force to an object through hydraulic fluid pressure. They are essential in various industrial applications, providing the necessary force for processes such as metal forming, stamping, bending, and molding. The versatility and efficiency of hydraulic presses make them indispensable tools in manufacturing and production lines. This document will explore the different types of hydraulic presses, their application areas, components, operational principles, manufacturing process, and the challenges and advancements in the industry.
Types of Hydraulic Presses
Hydraulic presses come in various designs, each suited to specific applications and requirements. The primary types of hydraulic presses include C-frame presses, H-frame presses, four-column presses, straightening presses, arbor presses, laminating presses, and transfer presses.
C-frame presses, also known as gap-frame presses, have a C-shaped frame that provides three-sided access to the work area. This design is ideal for applications requiring easy loading and unloading of materials.
H-frame presses, or two-post presses, have a robust H-shaped frame that offers excellent stability and strength. They are commonly used for heavy-duty tasks such as metal forming and straightening.
Four-column presses, or four-post presses, have four vertical columns that provide superior support and uniform force distribution. These presses are suitable for large-scale applications requiring high precision and repeatability.
Straightening presses are specialized hydraulic presses used to straighten bent or distorted metal components. They are widely used in the automotive and construction industries.
Arbor presses are smaller, manually operated hydraulic presses used for light-duty tasks such as assembly, riveting, and broaching. They are commonly found in workshops and small manufacturing facilities.
Laminating presses are used to bond multiple layers of material together under heat and pressure. These presses are essential in industries such as electronics, where laminated components are common.
Transfer presses are automated hydraulic presses that move the workpiece through multiple stations for different operations. They are highly efficient and used in high-volume production environments.
Application Areas
Hydraulic presses are employed in various industries, thanks to their ability to deliver consistent and precise force. Key application areas include:
Metal forming and forging: Hydraulic presses are crucial in shaping and forming metal parts through processes such as stamping, bending, and deep drawing. They are essential in the production of automotive parts, machinery components, and structural elements.
Automotive industry: In the automotive sector, hydraulic presses are used for manufacturing various parts, including body panels, chassis components, and engine parts. They play a critical role in ensuring the structural integrity and performance of vehicles.
Aerospace industry: The aerospace industry relies on hydraulic presses for forming and shaping high-strength materials used in aircraft components. Precision and reliability are paramount in this industry, making hydraulic presses indispensable.
Plastic and rubber molding: Hydraulic presses are used in the molding of plastic and rubber components, including automotive parts, household goods, and medical devices. They ensure consistent product quality and precision.
Electrical and electronics industry: In the electronics sector, hydraulic presses are used for laminating circuit boards, forming connectors, and assembling electronic components. They provide the necessary force and precision for delicate operations.
Medical device manufacturing: Hydraulic presses are used in the production of medical devices, including surgical instruments, implants, and diagnostic equipment. They ensure the high precision and quality required in the medical field.
Packaging industry: Hydraulic presses are employed in the packaging industry for forming and shaping packaging materials, such as cardboard, plastic, and metal. They help produce packaging solutions that are strong, durable, and aesthetically pleasing.
Components of a Hydraulic Press
A hydraulic press comprises several key components that work together to generate and control the applied force. The main components include the frame, hydraulic cylinder, hydraulic pump, control valves, hydraulic fluid, pressure gauges and sensors, and die and tooling.
The frame is the main structure of the hydraulic press, providing stability and support for all other components. It is typically made of high-strength steel to withstand the significant forces generated during operation.
The hydraulic cylinder is the core component that generates the pressing force. It consists of a cylindrical chamber, a piston, and a piston rod. When hydraulic fluid is pumped into the cylinder, it moves the piston, which in turn applies force to the workpiece.
The hydraulic pump is responsible for generating the hydraulic fluid pressure needed to move the piston. It draws hydraulic fluid from a reservoir and delivers it to the cylinder under high pressure.
Control valves regulate the flow of hydraulic fluid to and from the cylinder, controlling the movement and force of the press. These valves can be manually operated or automated, depending on the press design.
Hydraulic fluid, typically oil, is the medium through which force is transmitted in the hydraulic system. It must have suitable properties, such as viscosity and lubricity, to ensure efficient operation and protect system components.
Pressure gauges and sensors monitor the hydraulic fluid pressure within the system. They provide real-time feedback to the operator or control system, ensuring safe and accurate press operation.
Die and tooling are the interchangeable components that come into direct contact with the workpiece. They are designed to shape, form, or cut the material as required by the specific application.
How Hydraulic Presses Work
Hydraulic presses operate based on Pascal’s principle, which states that pressure applied to a confined fluid is transmitted equally in all directions. This principle allows hydraulic presses to generate significant force with relatively small input pressure.
The operation of a hydraulic press begins with the hydraulic pump drawing fluid from the reservoir and delivering it to the cylinder. The control valves regulate the flow of fluid, directing it into the cylinder to move the piston. As the piston moves, it applies force to the workpiece placed between the die and tooling.
The hydraulic fluid plays a crucial role in this process, as it transmits the applied pressure and lubricates the system components. The pressure gauges and sensors continuously monitor the fluid pressure, providing feedback to ensure the press operates within safe limits.
The force generated by the hydraulic press can be precisely controlled by adjusting the hydraulic fluid pressure and the position of the control valves. This allows for accurate and repeatable operations, essential for high-quality manufacturing.
Manufacturing of Hydraulic Presses
The manufacturing of hydraulic presses involves several stages, from design and engineering to assembly and quality control. Each stage is critical to ensuring the press’s performance, reliability, and safety.
Design and engineering: The process begins with the design and engineering phase, where specifications for the press are developed based on the intended application. This includes selecting suitable materials, determining the required force and stroke, and designing the frame and hydraulic system.
Material selection: High-quality materials, such as high-strength steel for the frame and durable alloys for the hydraulic components, are selected to ensure the press’s longevity and performance.
Fabrication of components: The individual components of the hydraulic press, including the frame, cylinder, and pump, are fabricated using precision machining and manufacturing techniques. This ensures that each component meets the required tolerances and specifications.
Assembly process: The fabricated components are then assembled into the complete hydraulic press. This involves mounting the cylinder, pump, and control valves onto the frame, connecting the hydraulic lines, and installing the die and tooling.
Quality control and testing: Rigorous quality control measures are implemented throughout the manufacturing process to ensure the press meets all specifications and standards. This includes pressure testing the hydraulic system, verifying the accuracy of the control valves, and performing operational tests to ensure the press functions correctly.
Advancements and Innovations
The hydraulic press industry is continually evolving, driven by advancements in technology and increasing demands for efficiency and precision. Key innovations include automation and control systems, energy efficiency improvements, and smart hydraulic presses.
Automation and control systems: Modern hydraulic presses are often equipped with advanced control systems that automate the pressing process. This includes programmable logic controllers (PLCs), human-machine interfaces (HMIs), and sensors that monitor and adjust the press’s operation in real time. Automation improves efficiency, reduces the risk of human error, and enhances the consistency of the finished products.
Energy efficiency improvements: Manufacturers are focusing on developing hydraulic presses that consume less energy and have a smaller environmental footprint. This includes using variable displacement pumps, energy recovery systems, and optimizing the hydraulic system’s design to minimize energy losses.
Smart hydraulic presses: The integration of IoT (Internet of Things) technology into hydraulic presses has led to the development of smart presses. These presses can communicate with other machines and systems, providing real-time data on their status, performance, and maintenance needs. This connectivity allows for predictive maintenance, reducing downtime and extending the press’s lifespan.
Challenges in Hydraulic Press Manufacturing
The manufacturing of hydraulic presses presents several challenges, including precision and quality requirements, cost management, technological advancements, and environmental considerations.
Precision and quality requirements: Hydraulic presses must deliver consistent and precise force, which requires high levels of accuracy in the manufacturing process. Ensuring each component meets the required tolerances and specifications is critical to the press’s performance and reliability.
Cost management: The cost of materials, labor, and energy can significantly impact the overall cost of manufacturing hydraulic presses. Manufacturers must balance quality and cost to remain competitive in the market.
Technological advancements: Keeping up with technological advancements is essential for manufacturers to meet the evolving demands of the industry. This requires continuous investment in research and development to incorporate new technologies and improve existing designs.
Environmental considerations: Environmental regulations and sustainability concerns are increasingly important in hydraulic press manufacturing. Manufacturers must develop eco-friendly presses that consume less energy, use recyclable materials, and minimize their environmental impact.
A Cutter and Beading Machine is a type of sheet metal forming machine used primarily in HVAC ductwork fabrication, metal roofing, and other metalworking industries. It combines two essential operations:
🔧 1. Cutting Function:
- Purpose: To trim, cut, or notch sheet metal to desired sizes or shapes.
- Types of Cutting: Could include rotary shearing, slitting, or trimming.
- Blade Mechanism: Usually consists of rotary cutters or straight blades.
🔩 2. Beading Function:
- Purpose: To create beads (raised or indented ridges) on sheet metal.
- Why Beading?
- Increases rigidity and strength of the metal sheet.
- Prevents warping or oil-canning (distortion).
- Can be decorative in some applications.
- Types of Beads: Straight beads, circular beads, or custom patterns depending on the rollers used.
⚙️ Key Components:
- Rollers: Interchangeable to accommodate different bead types or sizes.
- Crank or Motor: Manually operated or motorized depending on the machine size.
- Gauge Control: Adjusts for sheet thickness.
- Guide System: Keeps the sheet aligned during the operation.
🏭 Common Applications:
- HVAC duct fabrication
- Metal furniture
- Automotive panels
- Roofing and cladding
- Tank or drum fabrication
A cutter and beading machine is a multifunctional tool used in sheet metal fabrication, especially in industries like HVAC, roofing, and automotive. It performs two main tasks: cutting and beading sheet metal. The cutting function allows the operator to trim or slit metal sheets to precise dimensions, typically using rotary or straight blades. This ensures clean and accurate cuts for further forming or assembly.
The beading function adds strength to the sheet metal by forming raised or indented ridges called beads. These beads increase the rigidity of the sheet, helping prevent deformation, especially in large flat panels. Beading can also have aesthetic purposes or be used to create grooves for joining components.
The machine generally uses sets of rollers to perform the beading operation, and these rollers can be swapped out depending on the desired bead pattern. Some machines are manually operated using a hand crank, while larger or more industrial models are motorized for continuous operation. Adjustable gauges help handle different thicknesses of sheet metal, and guide rails keep the material aligned for accurate processing.
The cutter and beading machine is an essential tool in various industries where metal sheets need to be shaped, cut, and reinforced. The cutting function can be designed to handle different thicknesses of materials, from thin sheets of aluminum to thicker steel, allowing for a wide range of applications. It works by feeding the metal sheet into the machine, where rotating blades or shearing edges cut it into the specified lengths or shapes, often with minimal material waste.
The beading function, on the other hand, uses rollers to press a pattern into the metal sheet. The beads formed help to stiffen the metal, which is crucial for applications where strength is a concern, such as in the construction of ductwork or structural panels. The beads also help in the assembly of pieces by creating grooves or channels that can lock together. This is especially useful in the HVAC industry, where ducts need to maintain their shape and integrity over time, even when subjected to external pressure or forces.
While the two processes can sometimes be performed separately, combining them into one machine helps to streamline production, reduce equipment costs, and save on floor space in manufacturing environments. These machines can also come with additional features like adjustable bead sizes, different cutting mechanisms, or automated systems that increase efficiency and precision in high-volume production environments.
The versatility of cutter and beading machines makes them valuable not only in standard metalworking but also in creating custom-designed metal parts where both cutting and reinforcing are needed in a single operation. Depending on the machine’s sophistication, operators can adjust settings to accommodate different types of metal, bead profiles, and sheet sizes, making them adaptable to a variety of industrial tasks.
Road Sign Trimming Beading Machine
A Road Sign Trimming Beading Machine is a specialized tool used in the fabrication of road signs, particularly to trim, shape, and reinforce the metal sheets that are used to create traffic signs, highway markers, and other road signage. These machines combine both trimming and beading functionalities to produce signs that are both durable and highly visible.
The trimming function of the machine allows for precise cutting of the metal sheets, which are often aluminum or galvanized steel, into the required shape and size for road signs. The machine can handle different thicknesses of materials, allowing for cutting along straight edges or intricate contours to match the design specifications of the road signs. This ensures that the signs fit within the required dimensions and can be properly mounted or installed on posts.
The beading function is equally important. It adds raised ridges or grooves around the edges of the sign. These beads not only increase the mechanical strength of the sign but also improve its aesthetic appearance by giving the sign a more defined, professional finish. The beads also serve functional purposes, such as enhancing the rigidity of the material and helping to prevent warping or bending due to wind or other environmental factors.
Additionally, the beading around the edges can create a slightly reflective surface that increases the visibility of the road sign, especially at night when lights hit the sign at various angles. In some cases, the machine may also add additional features such as rounded edges or specific cutouts for mounting holes.
Road sign trimming beading machines are typically designed for high-speed, continuous operation, and they are commonly used in environments where large volumes of road signs need to be produced quickly and efficiently. These machines often come with adjustable settings to accommodate different sign shapes, sizes, and bead profiles, offering flexibility for custom road signage projects.
In summary, a road sign trimming beading machine combines the essential tasks of cutting and reinforcing road signs in one operation, providing both structural integrity and visual appeal to signs used in transportation and traffic management.
The road sign trimming beading machine plays a crucial role in ensuring the durability and longevity of traffic signs, which need to withstand harsh weather conditions, road vibrations, and constant exposure to sunlight. By integrating both trimming and beading functions, this machine enhances the production process, making it more efficient while ensuring consistency in the final product.
When producing road signs, the trimming function allows for precision cutting, ensuring that the metal sheets are cut to the exact size and shape needed for standard regulatory signs (such as speed limit signs, warning signs, or directional signs) or custom signage. This precise cutting is important for ensuring that the signs can fit within standardized frames, posts, or mounting fixtures used in road signage systems.
Beading the edges of the signs serves multiple purposes. The raised beads act as a reinforcement feature, preventing bending or warping of the thin metal sheets commonly used in sign production. This is particularly important for signs exposed to high winds, such as highway signs, which need to maintain their shape and visibility even in extreme weather. The beading also provides a finished, clean edge to the sign, which enhances its overall appearance and gives it a professional, polished look.
The machine’s ability to add reflective beads around the edges also contributes to increased safety. These beads can enhance the reflectivity of the sign’s border, making it more visible in low light or at night. In addition to this, the beads can help direct light more effectively, increasing the visibility of the sign from various angles. This added reflectivity is especially beneficial for road signs that need to be clearly visible to drivers, particularly in areas with poor lighting or during nighttime driving.
Road sign trimming beading machines are typically used in large-scale sign manufacturing plants, where speed, efficiency, and consistency are vital. Some advanced models are fully automated, capable of handling high volumes of signs with minimal operator intervention. These machines are equipped with programmable controls, which allow for quick adjustments to different sign sizes, bead shapes, and cutting patterns without the need for manual recalibration, thus improving production time and reducing the risk of errors.
Additionally, these machines may also be equipped with features like cutting tools for mounting holes or holes for bolts, enabling operators to prepare the signs for installation right after fabrication. This eliminates the need for additional steps or equipment, further streamlining the sign production process.
Overall, the road sign trimming beading machine is a vital piece of equipment in the modern road sign manufacturing industry, combining efficiency with functionality to create signs that are both structurally sound and highly visible, ensuring safety on the roads.
Continuing from where we left off, the road sign trimming beading machine also contributes significantly to improving the overall production workflow in sign manufacturing plants. The automation in these machines reduces the need for manual labor, which not only helps increase throughput but also minimizes the risk of human error, ensuring that the final product meets the required standards for quality and safety.
In some advanced versions, these machines incorporate CNC (Computer Numerical Control) systems, allowing for even greater precision and the ability to easily program complex designs. This is especially beneficial when producing customized signs with intricate shapes, symbols, or logos that require more detailed cutting and beading. CNC systems can handle different types of metals, adjusting the pressure and speed settings for various materials, thus improving the versatility of the machine and making it more adaptable to different projects.
Another advantage of using a road sign trimming beading machine is its ability to handle a wide range of materials. While aluminum is a common choice for road signs due to its light weight and resistance to rust, the machine can often be adjusted to handle other materials like galvanized steel, stainless steel, or even reflective films. This versatility allows manufacturers to produce a diverse range of signs suitable for various environments, whether they’re placed in urban areas or more rural, high-wind zones.
These machines are also designed to be user-friendly, with simple interfaces that allow operators to input measurements and select different cutting and beading options. Many models come with safety features like automatic shutdown if an issue is detected, as well as protective shields and sensors to prevent injury during operation.
For maintenance, road sign trimming beading machines are built with durability in mind, but regular upkeep is still essential to maintain optimal performance. This includes checking for any wear and tear on the cutting blades and rollers, lubricating moving parts, and ensuring the alignment of the rollers for consistent beading. Some machines even come with diagnostic systems that alert operators to potential maintenance issues before they result in operational downtime.
Moreover, the integration of these machines into a larger production line can allow manufacturers to speed up the entire process of sign creation. Once the sheets are cut and beaded, they may move on to the screen printing or vinyl application stages, where they are coated with the appropriate reflective materials or graphics. Some road sign trimming beading machines even have the capability to add the reflective coatings directly during the beading process, ensuring better integration between the structural and visual elements of the sign.
In environmentally conscious production settings, newer machines are being designed to be energy-efficient and reduce the amount of material waste. By optimizing cutting paths and minimizing scrap, manufacturers can make the most out of their raw materials, helping reduce costs and environmental impact. Some systems are also built with recycling features that allow for the reuse of scrap material, further enhancing sustainability.
In summary, the road sign trimming beading machine is more than just a tool for shaping metal. It’s a comprehensive solution that integrates cutting, beading, durability enhancement, and visibility improvement in one machine. As traffic safety becomes even more important globally, these machines are evolving to meet the needs of modern road sign manufacturing, offering faster production speeds, greater flexibility in materials, and enhanced precision—all while reducing costs and improving the final product’s performance.
Aluminium Tray Trimming Beading Machine
An Aluminum Tray Trimming Beading Machine is a specialized piece of equipment used in the production of aluminum trays, often utilized in industries like food service, packaging, and storage. This machine combines two critical operations: trimming and beading, to create trays with precise dimensions, reinforced edges, and a professional finish.
The trimming function is responsible for cutting aluminum sheets into specific sizes to form the trays. Aluminum trays come in various shapes, from rectangular to circular or custom designs, and the trimming machine ensures that the edges are cut cleanly and accurately. This trimming is essential for ensuring uniformity across large batches of trays, which is particularly important in mass production environments.
The beading function adds a raised ridge or groove along the edges of the tray. This bead enhances the structural integrity of the aluminum tray, preventing it from bending or warping under pressure or heat. The beading also adds to the tray’s aesthetic appeal, giving it a polished and professional finish. In practical terms, the beads serve multiple purposes: they make the tray more rigid, improve stacking capability, and help in aligning trays during transportation or storage. Additionally, the raised bead can make the tray easier to handle, especially when it’s being carried or moved in bulk.
These machines typically use rollers or dies to form the beading, and the width or depth of the bead can be adjusted based on the tray’s requirements. The rollers are designed to apply consistent pressure across the aluminum sheet, ensuring that the bead is uniform in shape and size. For large-scale operations, automated versions of these machines allow for high-speed production with minimal operator intervention.
One of the key advantages of an Aluminum Tray Trimming Beading Machine is its ability to handle different thicknesses of aluminum, which is crucial for producing trays with varying levels of strength or durability. Whether the trays are intended for light-duty use in food packaging or heavy-duty industrial applications, the machine can adjust its settings to accommodate different material gauges, ensuring the finished product meets the required standards.
These machines are generally designed for high-volume production, with features such as programmable controls that allow manufacturers to set different cutting and beading parameters for different tray sizes or designs. Some models can also integrate additional processes like hole punching for drainage or ventilation, corner rounding, or even surface treatment (like anodizing or coating) to further enhance the trays’ functionality and appearance.
For maintenance, it’s important to regularly check the rollers, blades, and die mechanisms to ensure they remain sharp and properly aligned. This helps to maintain the quality of both the trimming and beading processes. Machines with automatic lubrication systems or diagnostic tools can help reduce downtime by alerting operators to potential issues before they lead to production delays.
In conclusion, an Aluminum Tray Trimming Beading Machine is a versatile and highly efficient machine that significantly improves the production process for aluminum trays. By combining trimming and beading in a single machine, it reduces the need for multiple separate operations, speeds up production, and ensures the final product is durable, visually appealing, and consistent in quality. These machines are widely used in industries where aluminum trays are in high demand, ensuring that manufacturers can meet production needs while maintaining product standards.
An Aluminum Tray Trimming Beading Machine is a highly efficient tool used to streamline the process of producing aluminum trays, which are common in industries such as food packaging, storage, and even in medical or industrial applications. These machines combine the crucial operations of trimming and beading into one unit, which greatly speeds up production while ensuring the trays are both strong and visually appealing.
The trimming function of the machine is designed to cut aluminum sheets into precise shapes and sizes, turning large, raw metal into trays ready for further processing. This cutting is vital for maintaining consistency in the tray dimensions, ensuring they fit perfectly in stackable designs, packaging systems, or any other intended use. The machine is capable of handling different thicknesses of aluminum, allowing for the creation of trays that meet various durability requirements, from lightweight trays to more robust ones used in industrial environments.
Beading is the second function, which involves forming a raised edge around the perimeter of the tray. This bead serves to reinforce the tray, making it more rigid and less likely to bend or deform under pressure. It also improves the tray’s overall strength, which is especially important for trays that will be stacked or loaded with goods. Additionally, the beading adds a professional finish to the tray, giving it clean, uniform edges that are aesthetically pleasing. The beads can also help the trays align better during transportation and storage, as they make it easier to stack them securely.
The beading process typically uses rollers or dies, which apply pressure to the aluminum sheet to create consistent ridges along the edges. The size and depth of the beads can be adjusted depending on the tray’s design or the specific strength requirements. Advanced models of these machines may offer programmable settings, allowing operators to easily switch between different tray sizes and bead patterns without requiring major adjustments, making the production process even more efficient.
For industries that require large volumes of trays, these machines can run at high speeds, ensuring quick turnaround times. Automation in these machines means less manual labor is needed, which reduces human error and increases consistency across production runs. This is particularly important when producing trays for commercial or industrial purposes, where reliability and uniformity are key. Some machines may also include features like hole-punching for drainage or ventilation, corner rounding for a smoother finish, or even additional surface treatments to improve the appearance or performance of the tray, such as anodizing or coating.
Maintenance of these machines typically involves keeping the rollers, blades, and dies in good condition to ensure precise trimming and beading. Regular checks and lubrication can help prevent downtime, while more advanced models may have self-diagnosing features that alert operators to potential issues before they affect production. This minimizes disruptions and ensures the machine continues to perform at its best.
Overall, the Aluminum Tray Trimming Beading Machine is an essential piece of equipment for manufacturers looking to produce high-quality aluminum trays in a streamlined, efficient manner. By combining trimming and beading into one process, it reduces production time, cuts down on the need for multiple machines, and ensures that each tray produced is both strong and aesthetically pleasing, meeting the requirements of various industries.
In addition to the speed and efficiency improvements, the Aluminum Tray Trimming Beading Machine offers significant cost savings for manufacturers. By integrating both trimming and beading into a single process, the machine eliminates the need for separate equipment for each operation, which reduces overhead costs and saves on floor space. The ability to produce high volumes of aluminum trays with minimal manual intervention further helps lower labor costs and increases overall productivity.
These machines are also highly versatile, capable of producing a wide range of tray sizes and designs. Depending on the machine’s features, it can handle different aluminum alloys and thicknesses, allowing manufacturers to produce trays with varying strength characteristics. For instance, trays used in food packaging may require a lighter, more flexible aluminum, while trays used for industrial purposes may need thicker, more durable aluminum to withstand heavier loads.
The flexibility of the machine also extends to the types of beads it can create. Beads can be adjusted for different depths and profiles, depending on the specific application. For example, a deeper bead might be necessary for a tray intended to carry heavier items, while a shallow bead might be sufficient for a lighter-duty tray. This level of customization ensures that manufacturers can meet the precise specifications required by their customers, whether for standard, mass-produced trays or more customized, niche products.
In terms of product quality, the consistent beading and clean trimming ensure that every tray produced meets the required standards for both appearance and functionality. The smooth edges provided by the beading reduce the risk of cuts or injuries when handling the trays, which is particularly important in industries like foodservice or healthcare. Additionally, the increased rigidity from the beading helps prevent deformation during use or transport, ensuring that the trays maintain their shape and integrity even under stress.
Another key benefit is the environmental impact. As sustainability becomes increasingly important across industries, the Aluminum Tray Trimming Beading Machine can help reduce material waste. The ability to cut aluminum sheets precisely reduces scrap material, and in many cases, scrap aluminum can be recycled or repurposed. The machine’s efficiency also ensures that production runs are optimized, reducing energy consumption and making the process more environmentally friendly.
For businesses focusing on high-volume production, these machines are especially valuable due to their automated capabilities. With automated systems in place, operators can focus on monitoring the machine’s performance rather than making manual adjustments, which further increases the speed and consistency of production. Many modern machines are equipped with advanced control systems, which can store different program settings for a variety of tray designs, making it easy to switch between production runs without a significant setup time.
The ergonomic design of these machines also plays a role in improving the overall production process. Many machines are designed to be user-friendly, with intuitive interfaces that allow operators to input parameters such as tray size, bead depth, and cutting patterns with ease. This user-friendliness, coupled with automated functions, reduces the learning curve for new operators and helps maintain consistent output quality.
Overall, the Aluminum Tray Trimming Beading Machine is a powerful tool that enhances the efficiency, versatility, and quality of aluminum tray production. With its ability to trim and bead in one operation, this machine helps manufacturers meet high demands for consistent, durable, and visually appealing trays. It is an indispensable piece of equipment for industries that rely on aluminum trays, ensuring that production processes are streamlined, costs are reduced, and final products meet both functional and aesthetic requirements.
As the demand for aluminum trays continues to grow across various industries, the Aluminum Tray Trimming Beading Machine’s capabilities are becoming even more integral to meeting production needs efficiently. Its role in the automated production process ensures manufacturers can scale operations quickly while maintaining high standards of quality control. The ability to operate at high speeds with minimal human intervention reduces the risk of production delays and ensures that manufacturers can meet deadlines, whether for a large order of foodservice trays or for a more specialized run of industrial-grade trays.
With advancements in machine technology, some modern aluminum tray trimming beading machines are equipped with smart features. These can include real-time monitoring systems, where sensors and software continuously check the quality of the tray’s dimensions, bead consistency, and trim precision. This ensures that trays meet the exact specifications every time, and any discrepancies can be immediately corrected without halting the entire production line. These smart features reduce waste, improve uptime, and optimize machine performance, providing a high degree of reliability even in long shifts or high-production environments.
Moreover, the data tracking and reporting capabilities of these machines allow manufacturers to analyze production trends and identify areas for improvement. Data on machine efficiency, scrap material, production rates, and maintenance schedules can be gathered and used to make informed decisions about future production runs. By leveraging this data, manufacturers can further streamline their processes and increase the return on investment in the machine.
In terms of adaptability, the aluminum tray trimming beading machine can be customized for specific needs. For example, manufacturers may want to produce trays with particular edge finishes, deeper beads for added strength, or custom shapes to meet customer requirements. Machines can be equipped with a variety of interchangeable rollers, dies, or cutting tools to accommodate these needs. The flexibility in design options allows for quick adjustments, meaning that manufacturers can produce a wide range of aluminum tray types without needing a new machine for each design. This versatility also supports the production of small-batch, custom orders, providing manufacturers with the ability to cater to specialized markets or niche products.
For industries where hygiene and safety are paramount, like the food service sector, these machines offer another advantage by producing trays with smooth, safe edges. The beading process helps to ensure that trays are easy to handle, reducing the risk of cuts or injuries. The smooth, rounded edges are also more easily cleaned, making the trays ideal for environments where sanitation is a priority.
The ability to produce trays that are both lightweight and durable is another significant benefit. Aluminum trays are favored for being strong yet light enough for handling, storage, and transport. The beading process increases the strength-to-weight ratio of the trays, giving them additional durability without adding unnecessary weight. This is particularly important in industries like food packaging, where weight plays a key role in logistics, and in industrial settings where heavy-duty trays are needed but must remain manageable.
Looking ahead, the future of aluminum tray production is likely to involve more integration with Industry 4.0 technologies, including IoT (Internet of Things) connectivity. Machines could become even more interconnected, allowing for remote monitoring, predictive maintenance, and even automated reordering of raw materials based on production needs. This level of integration will help ensure that production processes remain efficient, cost-effective, and capable of meeting ever-increasing demand.
Ultimately, the Aluminum Tray Trimming Beading Machine represents a combination of efficiency, quality, and versatility in the manufacturing process. It enables producers to meet the diverse needs of their customers while maintaining high standards of performance. Whether producing large quantities of disposable foodservice trays or specialized industrial trays, the machine’s combination of trimming, beading, and customizability ensures that manufacturers can handle a wide variety of production requirements, enhancing their ability to stay competitive in the marketplace.
Square and Rectangular Tray Trimming Beading Machine
A Square and Rectangular Tray Trimming Beading Machine is a specialized machine designed to streamline the production of square and rectangular trays, which are commonly used in industries like food packaging, storage, and medical applications. This machine performs two essential functions: trimming and beading. The combination of these two operations allows manufacturers to produce high-quality, precise trays that are both durable and visually appealing, with the added benefit of a faster, more efficient production process.
The trimming function of the machine is responsible for cutting raw metal sheets (usually aluminum or stainless steel) into the precise square or rectangular dimensions needed for the trays. The machine ensures clean, straight cuts, allowing manufacturers to produce trays that fit exact specifications for use in various applications. Whether it’s a standard size for foodservice use or a custom size for a specialized product, the trimming function ensures consistency across all trays produced. These precise cuts are essential for making sure that the trays fit properly in stacks or align well during transport and storage.
The beading function adds a raised ridge along the edges of the tray. This bead serves multiple purposes: it strengthens the tray by increasing rigidity, making it less likely to bend or warp under pressure, and it also gives the tray a clean, professional finish. The beaded edge not only enhances the tray’s strength but also makes it easier to handle, as the raised edges improve grip. In addition, the beads can make the tray more resistant to deformation, which is especially important for trays that will carry heavy or hot items.
These machines are often equipped with adjustable rollers or dies that can be customized to create different bead profiles or depths, depending on the tray’s requirements. This flexibility allows manufacturers to produce trays with varying levels of strength or different edge designs. The bead can be shallow or deep, depending on the strength required, and the machine can be adjusted to create different sizes and shapes of beads for different tray designs.
The square and rectangular tray trimming beading machine is typically designed for high-volume production, making it a key tool for manufacturers who need to produce large batches of trays quickly. Automated controls often allow for easy programming of different tray sizes, bead shapes, and trimming dimensions, reducing setup time and increasing production efficiency. The machine can run continuously with minimal operator intervention, and modern models may come with CNC (Computer Numerical Control) systems, which ensure even greater precision and consistency.
For maintenance, it’s important to regularly check the trimming blades, rollers, and dies to ensure they are sharp, aligned, and in good working condition. This helps to prevent issues like uneven cuts or inconsistent beads, which could affect the quality of the trays. Many advanced machines feature diagnostic systems that alert operators when maintenance is needed, helping to avoid downtime and keep production running smoothly.
In industries like foodservice or pharmaceuticals, where trays must meet certain hygiene standards, the beading process also ensures smooth, rounded edges that are easier to clean and less likely to cause injury during handling. The trays are generally lighter due to the material used, but the beading process adds strength without increasing the weight significantly.
Overall, a Square and Rectangular Tray Trimming Beading Machine is an indispensable piece of equipment in modern manufacturing settings, where efficiency, precision, and quality are key. By combining trimming and beading into a single process, it significantly reduces production time, improves the durability of the trays, and ensures consistency across large batches. Whether for food packaging, medical trays, or industrial applications, this machine helps manufacturers meet a variety of market demands while maintaining high standards for strength, design, and performance.
The Square and Rectangular Tray Trimming Beading Machine is an essential tool for manufacturers seeking to produce precise and durable trays in high volumes. Its dual functionality of trimming and beading allows for the efficient production of trays that are both structurally sound and visually appealing. The trimming operation ensures that raw materials, usually metal sheets like aluminum, are cut accurately into the desired square or rectangular shapes. This is crucial for ensuring that the trays fit into standardized storage, stacking, or transport systems, maintaining uniformity across the entire batch.
The beading feature adds raised edges around the perimeter of the tray. These beads reinforce the tray’s structure, increasing its resistance to bending, warping, or deformation under weight or external stress. The beads not only enhance the tray’s strength but also improve its appearance by giving it a finished, professional look. The smooth, rounded edges resulting from the beading process also make the tray safer to handle, reducing the risk of injury from sharp edges and making it easier to clean, which is especially important in industries where hygiene is critical.
One of the standout features of the Square and Rectangular Tray Trimming Beading Machine is its ability to work with a variety of material thicknesses. Manufacturers can use it to produce trays that range from lightweight options used in food packaging to heavy-duty trays designed for industrial applications. This flexibility is possible due to adjustable rollers or dies, which allow for customization of the bead’s depth and width, and the trimming settings to suit different tray requirements.
These machines are designed for high-speed, automated production, which is crucial in industries that require large volumes of trays. With automated controls and programmable settings, manufacturers can quickly switch between different tray sizes, bead profiles, and trim patterns, making the machine versatile enough to handle a range of production needs. The automation reduces manual labor and increases production efficiency, ensuring a faster turnaround time on orders while maintaining high-quality output.
Moreover, modern Square and Rectangular Tray Trimming Beading Machines are often equipped with features like CNC control systems for precise and repeatable operations, which are critical when producing large quantities of trays with consistent quality. The ability to control settings electronically makes it easier to achieve precise cuts and uniform beads across multiple runs, reducing the chances of variation between trays.
Maintenance for these machines is generally straightforward, though it does require regular checks to ensure that the trimming blades, rollers, and beading dies are sharp, aligned, and functioning correctly. With proper upkeep, these machines can operate continuously for long hours without significant downtime. Some models are equipped with diagnostic tools that help operators identify potential issues before they affect production, helping to minimize the risk of equipment failure and keep the manufacturing process smooth.
In industries like foodservice, pharmaceuticals, or even electronics packaging, the trays produced by these machines must meet specific standards for safety, hygiene, and durability. The beading process helps ensure that the trays are safe to handle and easy to clean, while the trimming ensures that each tray fits within industry guidelines for size and shape. In the foodservice industry, for example, aluminum trays need to be lightweight for easy handling but strong enough to hold hot foods or liquids without warping. The square and rectangular designs produced by the machine are ideal for standardized uses, where the dimensions of the trays need to meet specific operational needs, such as fitting inside ovens, display cabinets, or food transport containers.
The Square and Rectangular Tray Trimming Beading Machine plays a key role in the automation of tray production, making it easier to meet high-demand, high-quality manufacturing standards. Whether it’s for disposable food trays, durable industrial trays, or custom packaging solutions, this machine ensures that trays are both practical and aesthetically pleasing. Its combination of trimming and beading, along with its flexibility in adjusting for different material thicknesses, makes it an indispensable piece of equipment for manufacturers aiming to keep pace with growing production demands while maintaining product quality and consistency.
The Square and Rectangular Tray Trimming Beading Machine also plays an important role in the sustainability efforts of manufacturers. With efficient use of raw materials and the ability to optimize cutting patterns, this machine helps minimize scrap and waste, which is especially important in industries looking to reduce their environmental footprint. In addition, many machines are designed to use recyclable materials like aluminum, which can be reused for future production runs, ensuring that manufacturers can both save on costs and contribute to a more sustainable production process.
Another significant advantage of the machine is its ability to integrate seamlessly into automated production lines, enhancing overall workflow. For manufacturers who produce trays alongside other packaging materials, the machine can easily be incorporated into a larger system where trays are produced, packed, and prepared for shipment with minimal manual handling. This integration allows for smoother transitions between different stages of production, further enhancing operational efficiency.
The machine’s versatility also supports the production of customized trays for various industries. Whether it’s a unique size or a tray with special beading patterns or features like holes for drainage, the Square and Rectangular Tray Trimming Beading Machine can handle specialized requests without the need for entirely new equipment or setups. This is especially beneficial in industries that require bespoke packaging or trays for specific products, such as high-end food packaging, medical trays, or trays for electronic components.
Manufacturers can also take advantage of the cost-saving benefits offered by these machines. By automating the trimming and beading processes, they eliminate the need for manual labor, reducing labor costs and freeing up employees for more complex tasks. Furthermore, automated trimming and beading ensure that each tray is produced to the exact same specifications, maintaining high quality and reducing the chances of errors or defective trays that would need to be discarded or reworked.
The safety features of modern machines are also worth noting. The beading process often involves high-pressure rollers and sharp trimming blades, so it’s crucial that the machine is designed with proper safeguards. Many machines come equipped with safety barriers, emergency shutoff switches, and sensors that can detect any malfunctions or irregularities in operation. These features help protect operators from accidents and ensure the machine runs smoothly.
As businesses expand and demand for square and rectangular trays increases, the Square and Rectangular Tray Trimming Beading Machine’s role becomes even more critical. Its high output capacity and quick changeover capabilities make it ideal for manufacturers looking to meet both large-scale production needs and custom orders efficiently. In industries where time-sensitive production and delivery are essential, this machine allows manufacturers to maintain tight schedules while producing trays that are high in quality and suitable for a wide range of applications.
In conclusion, the Square and Rectangular Tray Trimming Beading Machine is a pivotal piece of machinery for companies looking to optimize their production processes and meet the needs of a diverse and demanding market. With its combination of cutting-edge technology, customization options, and efficiency benefits, this machine is an indispensable tool for the modern manufacturing environment. Its ability to handle high-volume production, while also offering flexibility for custom designs and materials, ensures that it remains a go-to solution for companies in a variety of industries, from foodservice to industrial packaging.
Conclusion
Hydraulic presses are essential machines in various industries, providing the necessary force for processes such as metal forming, stamping, and molding. Understanding the different types of hydraulic presses, their components, and how they work is crucial for effective application and operation.
The manufacturing process of hydraulic presses involves careful design and engineering, material selection, precision fabrication, and rigorous quality control. Despite the challenges, advancements in technology and innovations are driving the industry forward, leading to more efficient, precise, and environmentally friendly hydraulic presses.
As industries continue to evolve, the hydraulic press industry must adapt and innovate to meet the demands of efficiency, precision, and sustainability. Through continuous research and development, manufacturers can enhance the performance and reliability of hydraulic presses, contributing to the success of various industrial applications.