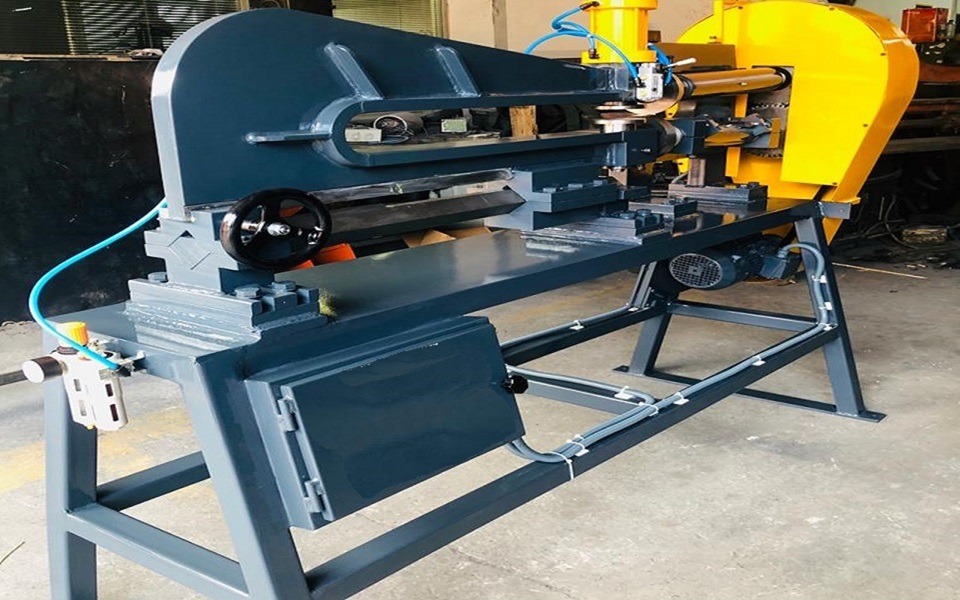
Cut Circle in Sheet Metal: Cutting a circle in sheet metal can be done using several methods depending on the size of the circle, the thickness of the metal, and the desired accuracy.
A circle cutting machine is a tool used to cut circular shapes out of various materials, such as metal, plastic, paper, or fabric. Here are some parts and features commonly found in circle-cutting machines:
- Cutting blade: The blade is the most important part of the circle cutting machine, and it can be made of different materials such as steel or tungsten carbide. The blade rotates as the machine is in use, cutting out the circular shape from the material.
- Cutting guide: The cutting guide holds the material in place and guides the blade along the cutting path. The guide is adjustable to accommodate different circle sizes.
- Cutting depth adjustment: The cutting depth adjustment allows the user to control the depth of the cut, which can be helpful when working with different materials.
- Base plate: The base plate is the surface on which the material is placed during cutting. It is typically made of a durable material like metal or plastic.
- Pivot arm: The pivot arm connects the cutting blade to the base plate and allows for precise control over the cutting angle and direction.
- Motor: The motor powers the blade and allows it to rotate quickly and efficiently.
- Safety features: Circle cutting machines may have safety features such as blade guards or automatic shut-off mechanisms to prevent injury or damage to the machine.
Circle cutting machines are used in a variety of industries, including metalworking, woodworking, and crafting. They are useful for creating circular shapes for products such as gears, wheels, and decorative items.
A circle cutting machine, also known as a circle cutter or disc cutter, is a specialized tool used to cut circular shapes from various materials, including paper, cardboard, plastic, fabric, and even thin metal sheets. These machines are commonly employed in industrial settings, craft workshops, and DIY projects.
Types of Circle Cutting Machines
Circle cutting machines come in various types, each with its own unique features and applications:
- Handheld Circle Cutters: These compact and portable machines are commonly used for cutting circles from paper, cardboard, and other lightweight materials. They typically feature a rotating blade or a punch-and-die mechanism to cut circles.
- Rotary Circle Cutters: These machines utilize a rotating blade mounted on a track or arm, allowing for precise cutting of circles in a variety of sizes. They are often used for cutting circles from fabric, leather, and other flexible materials.
- Hydraulic Circle Cutters: These powerful machines employ hydraulic pressure to cut circles from thicker materials, such as plastic sheets, thin metal sheets, and rubber. They offer high precision and cutting force for heavy-duty applications.
- CNC Circle Cutting Machines: These computer-numerically controlled (CNC) machines utilize computer programming to cut circles with exceptional precision and accuracy. They are commonly used in industrial settings for cutting circles from a wide range of materials.
Safety Precautions when using Circle Cutting Machines
When operating circle cutting machines, it is crucial to follow safety precautions to prevent injuries and ensure proper operation:
- Wear Personal Protective Equipment (PPE): Always wear safety glasses, gloves, and a cutting mat to protect yourself from sharp blades, flying debris, and potential cuts.
- Securely Clamp the Workpiece: Ensure the workpiece is firmly clamped to the machine’s work surface to prevent it from slipping or moving during cutting.
- Use the Correct Blade or Punch: Choose the appropriate blade or punch size and type for the material and desired circle size. Using the wrong blade or punch can damage the material or cause injury.
- Maintain Proper Blade or Punch Sharpness: Regularly sharpen or replace blades and punches to ensure they are sharp and maintain cutting efficiency. Dull blades can cause ragged edges and increase the risk of injury.
- Handle with Care: Always handle the machine with care, avoiding sudden movements or forceful actions that could lead to accidents.
- Never Touch the Moving Blade or Punch: Never touch the moving blade or punch while the machine is in operation.
- Turn Off the Machine Before Making Adjustments: Always turn off the machine before making any adjustments or changing the blade or punch.
- Store the Machine Properly: Store the machine in a safe, secure location when not in use, keeping it out of reach of children and unauthorized users.
By following these safety guidelines and operating the machine correctly, you can effectively utilize circle cutting machines to create precise circular shapes from various materials with minimal risk of injury.
Circle cutting machines are used in various industries, including:
- Metalworking: Circle cutting machines are commonly used in metalworking industries to cut circular shapes out of metals, such as steel, aluminum, and copper. They are used to make parts for machinery, automotive components, and other metal products.
- Woodworking: Circle cutting machines are also used in woodworking industries to cut circular shapes out of wood. They are used to make decorative wooden objects, such as clocks and signs, as well as to cut circular parts for furniture and other wooden products.
- Textile and apparel: Circle cutting machines are used in the textile and apparel industries to cut circular shapes out of fabric, leather, and other materials. They are used to make clothing, hats, bags, and other textile products.
- Craft and hobby: Circle cutting machines are popular among hobbyists and crafters, as they can be used to cut circular shapes out of a variety of materials. They are commonly used in scrapbooking, card making, and other paper crafts, as well as for creating decorative items like wreaths and ornaments.
- Manufacturing: Circle cutting machines are used in various manufacturing industries to cut circular shapes out of different materials. They are commonly used to make parts for machines and equipment, as well as for creating decorative and functional products.
In factories, where hydraulic presses manufacture deep drawn parts, as blank, sheet metal circles need to be prepared beforehand. These circles can either be manufactured by a mechanical press in serial production or needs to be cut as a square first, then the corners need to be trimmed by a machine to turn these square sheets into circles. This machine is called a circle cutting machine
A circle cutting machine is a machine that is used to cut a circle into a sheet of steel. Circle cutters are mainly used in metalworking to cut round steel sheets into circles. They come in two types: manual and automatic.
The first type of circle cutting machine is the manual type. This type of machine has large handles on both sides which are turned by hand to rotate the blade and produce the circular cut out from the metal sheet. The second type of circle cutting machine is automatic, which is much more efficient than its manual counterpart because it does not require any human input or labor to operate it.
For this purpose, we design and manufacture circle cutting machines, to cut the corners of sheet metals, which are later sent to hydraulic drawing presses for further operation
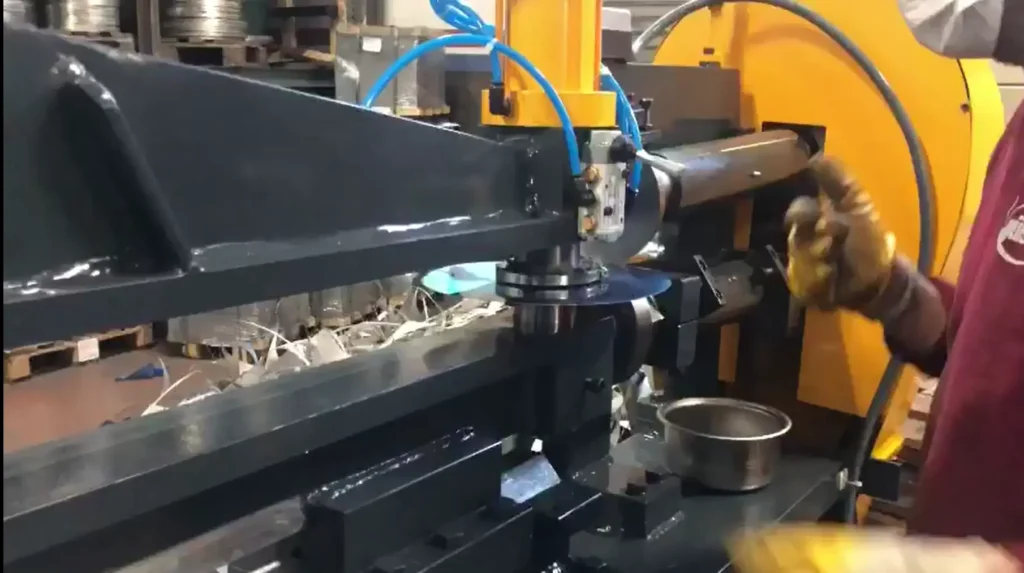
The capacity of our circle cutting machines is exceptionally high where an operator can get as high as 30 pcs per minute
The main body of the circle cutting machine is solid welded steel and knives to cut the sheet are made from high carbon high chromium steel
Circle cutting machine
A circle cutting machine for sheet metal is a specialized tool designed to cut precise circular shapes from metal sheets. These machines are widely used in industries such as metal fabrication, automotive manufacturing, HVAC, and construction. They enable workers to achieve accuracy, consistency, and efficiency in producing round components for various applications. The basic function of a circle cutting machine is to create circular cuts with a defined diameter in metal sheets of varying thicknesses. These machines come in different types, including manual, semi-automatic, and fully automated models, each suited for different levels of production and precision requirements.
Manual circle cutters require an operator to adjust the machine and guide the cutting process, while automated models use CNC technology to program precise cuts without continuous human intervention. The cutting process can be accomplished using different methods such as plasma cutting, laser cutting, oxy-fuel cutting, and mechanical shearing. Plasma cutting is preferred for its speed and ability to cut thick metal sheets with smooth edges. Laser cutting provides high precision and minimal material wastage, making it ideal for intricate designs.
Oxy-fuel cutting is commonly used for thick steel sheets due to its cost-effectiveness, while mechanical shearing relies on rotating blades or punches to create circular cuts. The choice of cutting method depends on factors such as material type, thickness, required precision, and production volume. Some circle cutting machines are portable, allowing workers to cut metal on-site, while others are stationary for industrial-scale operations. The machines typically consist of a base, a cutting head, and an adjustable arm or guide to ensure a consistent circular path. Many modern machines feature digital controls and automated settings to enhance precision and repeatability.
Safety features such as protective shields, emergency stop buttons, and fume extraction systems are integrated into advanced models to protect operators and maintain a clean work environment. Regular maintenance, including blade or nozzle replacement, lubrication of moving parts, and calibration of the cutting mechanism, is essential to ensure optimal performance and longevity of the machine. Choosing the right circle cutting machine involves considering factors such as sheet metal thickness, desired cut quality, production speed, and budget. Proper training for operators is also important to maximize efficiency and reduce errors. By investing in the right circle cutting machine, manufacturers and fabricators can improve productivity and achieve high-quality circular metal components with minimal waste.
Additional features of circle cutting machines can enhance their functionality and efficiency, making them more suitable for specific industrial needs. Some machines are equipped with motorized drive systems that automate the movement of the cutting head, reducing operator fatigue and improving accuracy. Advanced models may also include computer numerical control (CNC) technology, allowing for programmable cutting patterns, automatic diameter adjustments, and precise repeatability. These CNC machines are especially useful in industries requiring mass production of circular components with exact specifications.
The materials that can be processed by a circle cutting machine depend on the cutting method and the machine’s capabilities. Common metals include stainless steel, aluminum, copper, brass, and carbon steel. For high-strength alloys or specialized materials, advanced cutting techniques like fiber laser or waterjet cutting may be preferred to minimize heat-affected zones and material distortion. The ability to adjust cutting speed, pressure, and power settings enables operators to optimize the process for different materials and thicknesses.
In terms of design, some circle cutting machines feature interchangeable cutting heads, allowing users to switch between different cutting methods as needed. This flexibility is particularly beneficial for workshops handling diverse materials and project requirements. Additionally, machines with automated height control can maintain consistent cutting quality by adjusting for variations in sheet metal thickness or surface irregularities.
Efficiency and waste reduction are critical factors in modern manufacturing, and circle cutting machines contribute to these goals by ensuring precise cuts with minimal scrap. Some advanced systems incorporate nesting software, which optimizes the arrangement of circular cuts on a metal sheet to maximize material utilization. This feature is especially valuable in industries where raw material costs are high, such as aerospace and automotive manufacturing.
For heavy-duty applications, industrial-grade circle cutting machines are built with robust frames and high-power motors to handle large-diameter cuts in thick metal sheets. These machines are commonly used in shipbuilding, structural engineering, and heavy machinery production. Portable circle cutters, on the other hand, are designed for on-site applications such as pipeline fabrication, ventilation duct cutting, and maintenance work. Their lightweight and compact design make them easy to transport and operate in confined spaces.
Safety is a key consideration when using circle cutting machines, as high temperatures, sharp edges, and moving parts pose potential hazards. Operators should wear appropriate protective gear, including gloves, eye protection, and fire-resistant clothing, depending on the cutting method used. Machines equipped with fume extraction systems help to remove harmful gases and particulates generated during cutting, ensuring a safer work environment. Emergency stop functions, blade guards, and overload protection are also common safety features in modern machines.
Proper maintenance of a circle cutting machine is essential for ensuring long-term performance and reliability. Regular inspection of cutting components, lubrication of moving parts, and cleaning of dust or slag buildup can prevent downtime and extend the machine’s lifespan. Software updates and recalibration may be required for CNC models to maintain accuracy and efficiency. Operators should also follow manufacturer guidelines for replacing consumables, such as cutting nozzles, blades, or electrodes, based on usage and wear.
Investing in the right circle cutting machine can significantly enhance production efficiency, reduce material waste, and improve the overall quality of metal components. Whether for small-scale workshops or large industrial operations, selecting a machine with the appropriate cutting method, automation level, and material handling capabilities ensures optimal performance and return on investment.
Circle Cutting
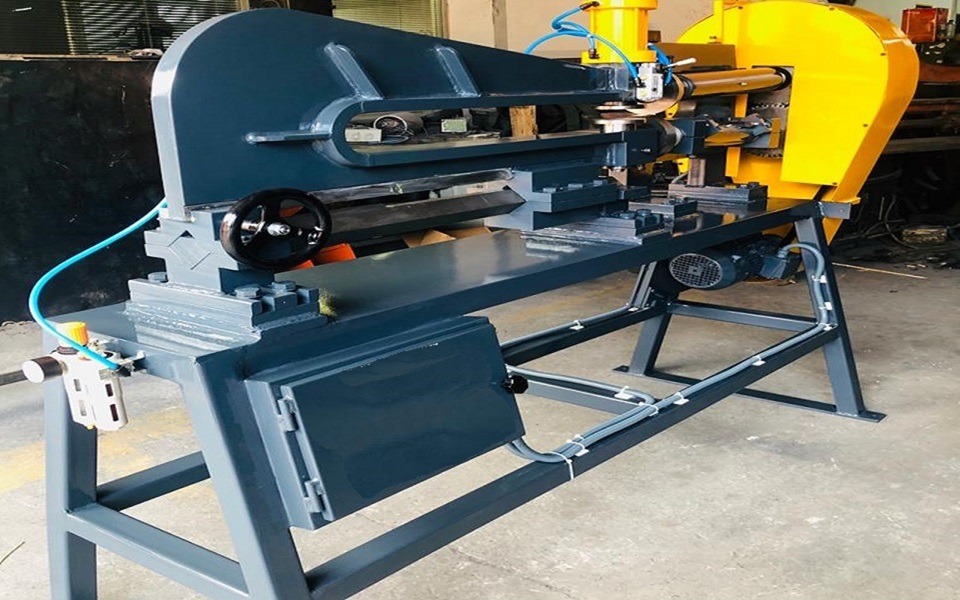
The versatility of circle cutting machines extends beyond standard metal fabrication, as they are used in specialized industries such as HVAC, aerospace, shipbuilding, and custom metalwork. In HVAC applications, for instance, precise circular cuts are necessary for manufacturing ductwork, ventilation openings, and flanges. The ability to quickly and accurately produce circular components ensures proper airflow and system efficiency. In aerospace and automotive industries, where precision is critical, high-tech circle cutting machines equipped with laser or waterjet technology are commonly used to create lightweight yet durable components. These advanced methods minimize heat distortion, preserving the mechanical properties of the materials.
In shipbuilding and heavy machinery manufacturing, thick steel plates often require large-diameter circular cuts for structural components, flanges, and reinforcements. Industrial-grade circle cutting machines with high-powered plasma or oxy-fuel cutting capabilities are typically employed for these tasks. The integration of CNC controls allows for precise customization of cut diameters, reducing manual adjustments and increasing efficiency. In the field of custom metalwork, artisans and fabricators use circle cutting machines to create intricate metal designs, sculptures, and decorative architectural elements. The precision of laser and plasma cutting machines makes them ideal for crafting detailed patterns in metal.
One of the key factors influencing the choice of a circle cutting machine is its power source and cutting capacity. Machines powered by electricity are the most common, offering stable and efficient operation for both manual and automated models. Pneumatic and hydraulic-powered machines provide additional force for cutting thick materials, making them suitable for heavy-duty industrial applications. The thickness and type of metal being processed determine the necessary cutting force, speed, and method. For example, thin aluminum sheets can be efficiently cut using a high-speed laser, while thick steel plates may require oxy-fuel cutting due to its deep penetration capability.
The integration of modern technologies in circle cutting machines has significantly improved accuracy, ease of use, and efficiency. Touchscreen interfaces, digital readouts, and automated positioning systems allow operators to input precise measurements and control the cutting process with minimal manual intervention. Some machines come with remote monitoring and diagnostic features, enabling technicians to track performance, identify issues, and perform maintenance remotely. Smart sensors in advanced models can detect variations in material thickness and adjust cutting parameters accordingly, reducing errors and ensuring uniform results.
Another aspect of circle cutting machines is their compatibility with additional accessories and attachments. For example, rotary indexing tables allow for automatic repositioning of the workpiece, enhancing production speed in mass manufacturing. Magnetic bases provide stability for portable cutting machines, ensuring precise operation even in challenging work environments. For applications requiring beveled edges, some machines include tilting heads or adjustable torch angles to create chamfered cuts, which are essential for weld preparation and assembly processes.
The environmental impact of cutting processes is also a consideration, especially in industries focused on sustainability. Waterjet cutting, for example, is an eco-friendly option that does not produce heat-affected zones or toxic fumes, making it ideal for industries with strict environmental regulations. Laser cutting, while highly precise, requires careful management of energy consumption and fume extraction to minimize environmental impact. Plasma and oxy-fuel cutting generate slag and gases that must be properly filtered and disposed of to comply with workplace safety and environmental standards.
Training and skill development are crucial for maximizing the efficiency of circle cutting machines. Operators must be familiar with machine controls, material properties, and safety procedures to achieve the best results. In industries where CNC cutting is prevalent, knowledge of CAD/CAM software is essential for designing and programming complex cutting patterns. Many manufacturers offer training programs and technical support to help users optimize machine performance and troubleshoot issues.
The future of circle cutting machines continues to evolve with advancements in automation, artificial intelligence, and smart manufacturing. Predictive maintenance using AI-driven analytics can anticipate component wear and suggest timely replacements, reducing unplanned downtime. Robotics integration allows for fully automated cutting cells, where machines can load, position, cut, and unload materials with minimal human intervention. As Industry 4.0 technologies advance, real-time data monitoring and cloud connectivity will enable greater efficiency, quality control, and production flexibility.
Ultimately, circle cutting machines play a vital role in modern metalworking industries by providing precision, efficiency, and versatility. Whether used in small workshops or large-scale manufacturing facilities, these machines enhance productivity and ensure high-quality results. The selection of the right machine depends on specific application requirements, material characteristics, and desired automation levels. With continuous technological improvements, these machines are becoming smarter, more energy-efficient, and more adaptable to the ever-evolving demands of industrial fabrication.
The integration of circle cutting machines into modern manufacturing processes has significantly streamlined production workflows, reducing manual labor while increasing output quality and consistency. These machines are now a fundamental part of industries that require precise circular cuts, from small fabrication shops to large-scale automated production facilities. The ability to automate cutting operations minimizes errors, reduces material waste, and enhances overall efficiency. With advancements in control systems and machine learning, newer models are capable of self-correcting cutting paths, adjusting speed and pressure based on real-time feedback from sensors that monitor material properties.
Customization and adaptability are key advantages of modern circle cutting machines. Many models now support multi-functional cutting heads that allow for different cutting techniques, such as switching between plasma and laser cutting within the same machine. This versatility ensures that manufacturers can handle a wide range of materials and cutting requirements without the need for multiple machines. Some machines are also equipped with interchangeable tooling systems, enabling them to perform additional operations like drilling, marking, or engraving, which can be particularly useful in industries requiring part traceability or branding.
One of the most significant improvements in circle cutting technology is the integration of software-driven precision. Many high-end machines now come equipped with CAD/CAM software that allows users to design cutting patterns digitally before execution. This not only improves accuracy but also reduces setup time and material waste. Operators can program the machine to cut multiple circles from a single sheet with minimal scrap, optimizing material usage. Some machines even feature AI-powered nesting algorithms that automatically arrange cutting patterns in the most efficient layout, further enhancing cost-effectiveness.
The impact of automation on circle cutting machines is particularly evident in large-scale manufacturing operations, where high production volumes require minimal downtime and consistent quality. Robotic arms are increasingly being integrated with CNC cutting systems to automate the loading, cutting, and unloading processes, eliminating manual handling and increasing efficiency. These robotic systems can operate around the clock, significantly boosting productivity while reducing human fatigue and the risk of errors. Additionally, automated material handling solutions, such as conveyor systems and stacking mechanisms, further streamline the workflow by ensuring continuous production without interruption.
For businesses operating in custom metal fabrication, the ability to quickly adjust cutting parameters and produce complex designs is crucial. Modern circle cutting machines offer intuitive user interfaces that allow operators to modify settings on the fly, making them ideal for prototyping and short-run production. The ability to cut intricate designs with minimal post-processing work is especially beneficial in industries such as signage, decorative metalwork, and artistic fabrication, where aesthetics and precision are equally important.
The durability and longevity of a circle cutting machine depend on proper maintenance and adherence to best practices in operation. Regular calibration, lubrication, and cleaning of cutting components are necessary to ensure smooth performance. Many machines now include predictive maintenance features that use sensors to monitor wear and tear, alerting operators when parts need replacement before they fail. This helps prevent unexpected breakdowns and reduces downtime. Additionally, manufacturers are increasingly using modular machine designs, allowing for easy upgrades and component replacements without the need for an entirely new machine.
Safety remains a primary concern in the operation of circle cutting machines, particularly those that use high-temperature cutting methods such as plasma and oxy-fuel. Proper ventilation and fume extraction systems are critical in preventing the accumulation of hazardous gases and particulates. Many machines are designed with automatic safety shutoffs, emergency stop buttons, and protective enclosures to minimize risks to operators. Adequate training is essential to ensure safe handling of both the machine and the materials being cut. In workplaces with high safety standards, compliance with industry regulations and certifications, such as OSHA or ISO safety guidelines, is mandatory for machine operation.
The global demand for more efficient and eco-friendly cutting solutions is driving research into new cutting technologies. Hybrid cutting machines that combine laser and waterjet technologies are being developed to achieve ultra-precise cuts with minimal environmental impact. Additionally, advancements in fiber laser cutting continue to improve energy efficiency and cutting speed while reducing operational costs. As sustainability becomes a growing priority in manufacturing, companies are looking for cutting solutions that minimize energy consumption and reduce waste.
Looking ahead, the evolution of circle cutting machines will likely be shaped by further developments in automation, artificial intelligence, and material science. Smart factories equipped with interconnected CNC cutting machines will be able to operate autonomously, with minimal human supervision, using real-time data analytics to optimize production. Augmented reality (AR) and virtual reality (VR) training modules may also become common, allowing operators to learn machine operation and troubleshooting in a simulated environment before handling the actual equipment.
The continued advancement of these machines ensures that they remain a vital part of modern industry, offering improved efficiency, precision, and versatility. Whether for mass production or custom fabrication, investing in the latest circle cutting technology provides businesses with a competitive edge in an increasingly demanding market.
A circle cutting machine for sheet metal typically consists of five main parts, each playing a crucial role in the cutting process.
- Cutting Head – This is the core component that performs the actual cutting. Depending on the cutting method, the head may contain a plasma torch, laser emitter, oxy-fuel nozzle, or mechanical blade. In advanced models, the cutting head is adjustable to accommodate different angles, depths, and speeds, ensuring precision and smooth edges.
- Base/Frame – The structural foundation of the machine provides stability and support during the cutting process. It ensures minimal vibrations, which is essential for maintaining cutting accuracy. The base may include mounting points, rails, or guides to assist in smooth movement and alignment of the cutting components.
- Rotary Arm/Guide Mechanism – This component controls the circular movement of the cutting tool, ensuring that the cutter follows a perfect circular path. Depending on the design, it may be manually adjustable or automatically controlled in CNC models. Some machines use a pivoting arm, while others rely on a track or programmed coordinates for precision.
- Control System – This includes the interface or software used to operate and program the machine. Manual machines have mechanical dials and levers, while CNC machines feature digital displays, touchscreens, and computer-based programming for precise and automated cutting. The control system adjusts speed, pressure, and cutting depth based on the material and project specifications.
- Power Source and Drive System – The power source varies depending on the machine type. Electric motors drive mechanical cutters, while plasma and laser cutters use high-energy power supplies. Hydraulic or pneumatic systems may also be used in heavy-duty machines to provide additional cutting force. The drive system moves the cutting head along its path, ensuring smooth and controlled operation.
Each of these components contributes to the efficiency, accuracy, and versatility of a circle cutting machine, making it an essential tool in metal fabrication and manufacturing.
Cutting Head
The cutting head is the most crucial component of a circle cutting machine for sheet metal, responsible for executing precise cuts based on the selected cutting method. It serves as the primary interface between the machine and the material, determining the accuracy, efficiency, and quality of the cutting process. Cutting heads can vary widely depending on the cutting technology used, including laser, plasma, oxy-fuel, waterjet, or mechanical blade cutting. The design and functionality of the cutting head must be optimized for the specific material, thickness, and required precision.
In modern machines, cutting heads are often equipped with advanced features such as height adjustment mechanisms, cooling systems, and automated focusing capabilities to enhance performance and durability. A key function of the cutting head is to direct the cutting energy precisely onto the workpiece, ensuring a clean and smooth cut. In laser cutting machines, the cutting head contains a focusing lens that concentrates the laser beam into an intense, fine point capable of melting, vaporizing, or burning through metal with minimal material distortion. The precision of laser cutting heads is enhanced through automated focal length adjustments, which compensate for variations in material thickness and maintain consistent cut quality. Plasma cutting heads, on the other hand, use a high-velocity jet of ionized gas to slice through metal by melting it with intense heat.
These cutting heads require proper gas flow regulation and nozzle maintenance to ensure stable and clean cuts. The nozzle design is critical in plasma cutting heads as it determines the shape and focus of the plasma arc, affecting cut precision and edge quality. In oxy-fuel cutting systems, the cutting head consists of a torch that mixes oxygen and a fuel gas such as acetylene or propane, creating a high-temperature flame that heats the metal to its ignition point before a stream of pure oxygen burns through the material. The cutting head in oxy-fuel machines typically has multiple nozzles to control the flame and oxygen flow, and it requires proper alignment to ensure efficient combustion and cutting performance. Waterjet cutting heads use a high-pressure stream of water, often mixed with an abrasive material, to erode the metal along a programmed cutting path.
These cutting heads require precision nozzles that can withstand extreme pressure levels while maintaining a steady, focused jet stream for accurate cuts. Mechanical cutting heads use rotating blades or punches to physically shear through metal, and they are commonly found in machines designed for thin sheets or softer metals. The durability of the cutting head is a key consideration, as continuous exposure to heat, pressure, and high-speed motion can cause wear over time. Many advanced cutting heads are designed with cooling systems, including air or water cooling, to prevent overheating and prolong their operational lifespan.
Additionally, some cutting heads incorporate automatic height sensing and adjustment systems that detect variations in the workpiece surface and dynamically adjust the head position to maintain optimal cutting distance. This feature is especially important in plasma and laser cutting machines, where inconsistent height can lead to poor cut quality, excessive dross, or material warping. Regular maintenance of the cutting head is essential to ensure consistent performance. Operators must inspect and replace consumable parts such as nozzles, electrodes, lenses, and seals to prevent degradation of cut quality. Calibration of the cutting head is also necessary to maintain alignment with the programmed cutting path, especially in high-precision applications.
In CNC-controlled cutting machines, the cutting head is integrated with motion control systems that allow for intricate cutting patterns and automated adjustments based on programmed designs. Some advanced cutting heads feature multi-axis capabilities, enabling them to tilt or rotate for bevel cutting and more complex geometries. The evolution of cutting head technology continues to drive improvements in cutting speed, accuracy, and energy efficiency. With the integration of smart sensors, AI-driven process control, and adaptive cutting technologies, modern cutting heads are becoming more efficient and user-friendly, minimizing the need for manual adjustments and reducing material waste. As manufacturing demands grow and precision requirements become more stringent, cutting heads will remain a focal point of innovation in metal fabrication and industrial processing.
The efficiency and performance of a cutting head depend on multiple factors, including the quality of its components, the cutting technology used, and its ability to adapt to different materials and conditions. Modern cutting heads are designed to handle a variety of materials, such as stainless steel, aluminum, copper, and carbon steel, with varying thicknesses. The selection of the right cutting head configuration is critical for achieving the desired cut quality, efficiency, and cost-effectiveness. Different cutting methods require specific designs and operating conditions to function optimally. For instance, a laser cutting head requires a precise optical system to focus the laser beam to a fine point, while a plasma cutting head relies on controlled gas flow and electrode stability to maintain a steady arc.
One of the most important aspects of a cutting head is its ability to maintain a consistent distance from the workpiece. In advanced CNC cutting systems, height control mechanisms are integrated into the cutting head to compensate for material warping, uneven surfaces, or variations in sheet thickness. This is particularly essential in plasma and laser cutting processes, where an incorrect distance can result in poor edge quality, excessive slag, or even damage to the cutting head components. Some modern cutting heads utilize capacitive or optical sensors to measure the distance from the material and make real-time adjustments to keep the cut precise and uniform.
The durability of a cutting head also depends on the quality of its consumable components, such as nozzles, electrodes, lenses, and focusing elements. In plasma cutting systems, the electrode and nozzle work together to shape the arc and direct it toward the workpiece. These components experience wear over time due to the intense heat and electrical discharge, requiring periodic replacement to maintain cutting accuracy. In laser cutting heads, the lenses or fiber optics that focus the beam must remain clean and free from debris to prevent power loss and beam distortion. Advanced laser cutting heads may include automated lens cleaning systems to extend operational life and reduce maintenance frequency.
Another critical feature in modern cutting heads is cooling technology, which prevents overheating and extends the lifespan of the components. Plasma cutting heads typically use air or water cooling systems to dissipate heat from the electrode and nozzle, while laser cutting heads may incorporate active cooling with circulating coolant to maintain stable temperatures. Effective cooling not only enhances performance but also reduces the risk of thermal damage to the workpiece, ensuring cleaner cuts with minimal distortion.
Automation and integration with digital control systems have significantly improved the functionality of cutting heads in recent years. CNC-controlled cutting heads can execute complex cutting patterns with minimal manual intervention, allowing for greater precision and repeatability. Some cutting heads are equipped with motorized tilting mechanisms, enabling bevel cutting for weld preparation or specialized fabrication needs. Multi-axis cutting heads provide even greater flexibility, allowing for the creation of intricate three-dimensional cuts in a single operation. These advanced capabilities have become essential in industries such as aerospace, automotive manufacturing, and shipbuilding, where precision and efficiency are paramount.
In addition to functionality, safety features in cutting heads are increasingly being prioritized. High-energy cutting methods such as laser and plasma generate intense heat, sparks, and potentially harmful fumes, requiring protective measures to ensure operator safety. Some cutting heads are equipped with enclosed designs to contain sparks and reduce exposure to harmful emissions. In industrial environments, fume extraction systems are often integrated with the cutting head to remove smoke and particulates generated during cutting. In laser cutting systems, automatic beam shutoff mechanisms are implemented to prevent accidental exposure to high-intensity laser radiation.
As technology continues to advance, the future of cutting heads will see even more innovations focused on efficiency, automation, and precision. Developments in artificial intelligence and machine learning are paving the way for smart cutting heads that can analyze material properties in real-time and automatically adjust cutting parameters for optimal performance. Predictive maintenance systems using IoT technology can monitor the condition of cutting head components, alerting operators to potential issues before they lead to downtime. Additionally, advancements in energy-efficient cutting technologies will contribute to more sustainable manufacturing processes, reducing power consumption and material waste.
The role of the cutting head in a circle cutting machine cannot be overstated, as it directly impacts the quality, speed, and reliability of the cutting process. Whether using traditional oxy-fuel, plasma, laser, or waterjet technology, selecting the right cutting head and maintaining it properly ensures consistent results and long-term operational efficiency. With ongoing technological advancements, cutting heads are becoming more intelligent, adaptive, and capable of meeting the ever-evolving demands of modern metal fabrication and manufacturing industries.
The continuous advancement in cutting head technology has led to significant improvements in precision, efficiency, and adaptability across various metal fabrication industries. One of the most critical developments is the integration of adaptive control systems within cutting heads, allowing for real-time monitoring and adjustments during the cutting process. These systems utilize sensors and feedback mechanisms to measure factors such as material thickness, heat distribution, and cutting speed, ensuring optimal performance without manual intervention. This is particularly beneficial for high-precision applications where even minor variations in cutting parameters can impact the final product quality.
For instance, in plasma cutting, modern cutting heads incorporate arc voltage sensing technology to automatically adjust the torch height as the material surface changes. This eliminates inconsistencies caused by sheet metal warping or uneven surfaces, leading to cleaner cuts and reduced material waste. Similarly, laser cutting heads now feature auto-focus and beam diameter adjustment capabilities, enabling them to switch seamlessly between different materials and thicknesses without the need for manual recalibration. This level of automation not only enhances precision but also reduces setup time, making production processes more efficient.
Another major development in cutting head technology is the use of multi-functional heads that can perform additional operations beyond cutting. Some cutting heads are designed to integrate with marking, engraving, or drilling attachments, allowing for more complex manufacturing processes in a single operation. This is particularly useful in industries that require part identification, such as aerospace and automotive manufacturing, where serial numbers or logos must be etched onto components for traceability. Additionally, certain cutting heads are equipped with beveling features that allow them to cut at an angle, making them ideal for weld preparation and specialized fabrication tasks.
Durability and longevity remain critical factors in the design of cutting heads, especially in high-production environments where machines operate continuously. To extend the lifespan of cutting heads, manufacturers have developed advanced cooling techniques and wear-resistant materials for key components such as nozzles, lenses, and electrodes. In laser cutting, for example, cutting heads now include high-efficiency cooling systems that prevent thermal expansion of optical elements, maintaining beam integrity and reducing downtime due to overheating. Plasma cutting heads utilize reinforced electrodes and ceramic nozzle coatings to withstand the extreme temperatures and electrical stress associated with prolonged operation.
One of the most significant challenges in cutting head technology is maintaining consistent performance while minimizing consumable usage and energy consumption. To address this, engineers are developing intelligent power management systems that optimize cutting efficiency based on material properties and job specifications. These systems adjust power output, gas flow, and cutting speed dynamically, ensuring that the cutting head operates at peak efficiency while reducing overall energy costs. This not only makes the process more economical but also contributes to sustainable manufacturing practices by minimizing resource waste.
In addition to technological improvements, the design of cutting heads is evolving to accommodate new manufacturing trends, such as additive manufacturing and hybrid machining. Some modern cutting heads are now being integrated with robotic systems, allowing for more complex cutting geometries and enhanced automation. Robotic arms equipped with precision cutting heads can execute intricate cutting patterns with high repeatability, making them invaluable for industries that require detailed customization, such as medical device manufacturing and custom metal fabrication.
Safety remains a key focus in cutting head development, particularly in high-energy cutting processes like laser and plasma cutting. Advanced safety features are being incorporated into modern cutting heads to protect both operators and the equipment. For example, laser cutting heads now include real-time beam monitoring systems that detect irregularities in laser output and shut down the beam if an anomaly is detected. In plasma cutting, cutting heads are designed with automatic shielding gas control to prevent exposure to hazardous fumes and ensure a stable cutting environment. Many cutting heads also feature integrated collision detection systems that automatically retract the head in case of an unexpected obstruction, preventing damage to both the machine and the workpiece.
As industry demands continue to evolve, the role of cutting heads in precision manufacturing will only become more significant. Future advancements will likely focus on greater automation, enhanced material adaptability, and improved energy efficiency. Artificial intelligence is expected to play a major role in optimizing cutting head performance, with machine learning algorithms analyzing cutting data in real time to make automatic adjustments for optimal results. Additionally, developments in ultrafast laser technology and high-definition plasma cutting will further push the boundaries of what cutting heads can achieve in terms of speed, accuracy, and material versatility.
Ultimately, the cutting head is the heart of any circle cutting machine, and its continued evolution is shaping the future of metal fabrication. By incorporating advanced control systems, improved durability, and smarter automation features, modern cutting heads are becoming more efficient, reliable, and capable of handling increasingly complex manufacturing requirements. Whether used in small workshops or large-scale industrial facilities, the advancements in cutting head technology are revolutionizing the way sheet metal is processed, making production faster, more precise, and more cost-effective than ever before.
Base/Frame
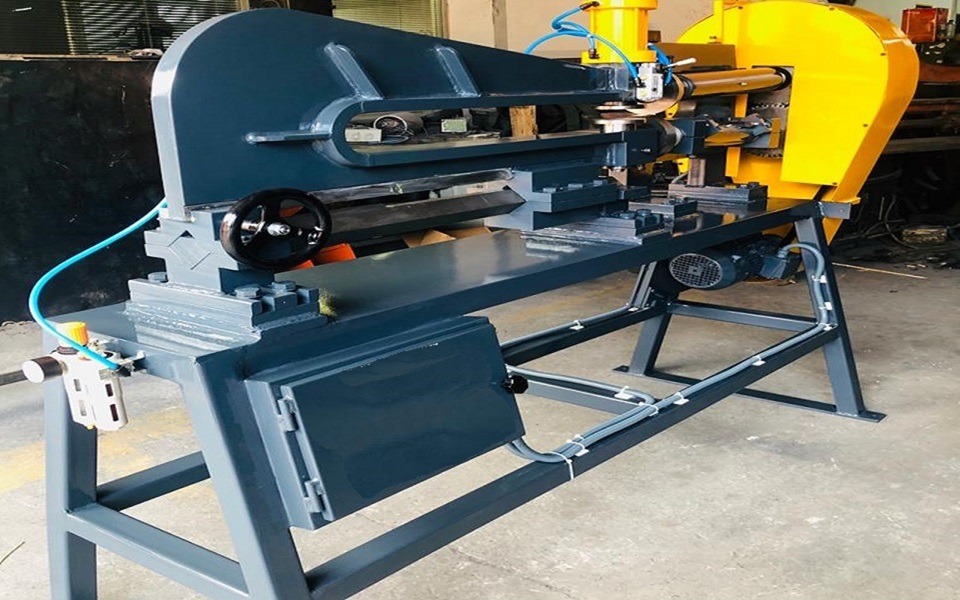
The base or frame of a circle cutting machine for sheet metal serves as the structural foundation, providing stability, support, and alignment for all other components. It plays a crucial role in ensuring precise and vibration-free operation, as any instability in the frame can lead to inaccuracies in cutting, excessive wear on mechanical parts, and reduced overall efficiency. The frame is typically constructed from heavy-duty materials such as steel or cast iron, designed to withstand the stress and forces generated during the cutting process. Its rigidity is essential for maintaining the accuracy of the cutting head’s movement, especially in high-precision applications such as CNC-controlled operations. A well-designed frame minimizes deflection and ensures that all moving parts function smoothly without unnecessary strain or misalignment.
The design of the base varies depending on the size and complexity of the machine. In small, manually operated machines, the base may be relatively simple, consisting of a sturdy metal plate with mounting brackets to hold the cutting head and guiding mechanisms. In contrast, large industrial machines often feature reinforced frames with integrated rails, ball screws, or linear guides that facilitate smooth and precise movement of the cutting components. Some high-end frames include damping systems that absorb vibrations caused by high-speed cutting, preventing distortions and improving the longevity of machine components. The weight and structural integrity of the base also impact the machine’s ability to handle different material thicknesses, as a robust frame can support heavier sheets without flexing or compromising accuracy.
Another key aspect of the base or frame is its role in material handling. Many modern circle cutting machines integrate worktables or slatted surfaces into the frame to support the sheet metal during cutting. These surfaces are often designed with replaceable slats that minimize heat buildup and prevent excessive warping of the material. In plasma and laser cutting machines, specialized bases with water tables or downdraft systems are incorporated to manage fumes, sparks, and slag produced during the cutting process. Water tables help dissipate heat and reduce airborne particulates, while downdraft systems use suction to remove smoke and debris, creating a safer and cleaner working environment.
The frame also provides the necessary support for additional automation features, such as motorized material feeding systems, rotary attachments for tube or pipe cutting, and robotic integration for fully automated production lines. In advanced CNC-controlled machines, the frame houses precision linear motion components that guide the cutting head with extreme accuracy. These motion systems may include servo motors, stepper motors, or rack-and-pinion drives, all of which require a stable and well-aligned base to function correctly. Misalignment or warping of the frame can lead to inconsistencies in cutting path execution, negatively affecting the final product quality.
Durability is a major consideration in frame design, as the machine must withstand years of continuous operation under demanding conditions. Many manufacturers employ stress-relief techniques such as annealing or vibration stress relief to ensure that the frame remains stable and does not deform over time. Protective coatings, such as powder coating or corrosion-resistant treatments, are applied to prevent rust and degradation, particularly in environments with high humidity or exposure to cutting fluids. Regular maintenance of the frame, including checking for loose bolts, structural integrity, and proper leveling, is essential to maintain the machine’s performance and prevent mechanical failures.
Portability and space efficiency are additional factors influencing base design, especially in smaller workshops where space is limited. Some compact circle cutting machines feature modular or foldable frames that allow for easier transport and storage. In contrast, large-scale industrial machines often require fixed, reinforced foundations to handle heavy loads and high-speed cutting forces. For mobile applications, such as on-site fabrication or construction work, lightweight yet sturdy frames are designed to balance portability with stability, ensuring that the machine can be transported and set up without compromising cutting accuracy.
Advancements in machine frame design continue to improve overall machine performance, with manufacturers focusing on enhanced rigidity, better vibration control, and more efficient material handling. The integration of smart sensors and real-time monitoring systems within the frame structure allows operators to detect misalignment, excessive vibration, or wear in critical areas before they lead to performance issues. Some high-end frames now include self-leveling technology, which automatically adjusts to uneven floors or surfaces to maintain perfect alignment for precision cutting.
The base or frame is not just a support structure but an integral component that directly impacts the efficiency, accuracy, and longevity of the entire circle cutting machine. Whether designed for small-scale manual operations or large industrial automation, a well-engineered frame provides the necessary foundation for achieving high-quality cuts with minimal errors. With continuous advancements in material science and machine design, the future of cutting machine frames will likely see further improvements in structural integrity, modularity, and intelligent monitoring capabilities, ensuring that these machines remain at the forefront of precision metal fabrication.
The evolution of base and frame design in circle cutting machines continues to focus on improving stability, precision, and adaptability to different industrial requirements. One of the key advancements in modern base construction is the use of hybrid materials, combining high-strength steel with vibration-dampening composites to enhance rigidity while reducing weight. These materials help minimize the effects of mechanical stress, preventing long-term deformation and ensuring that the machine retains its accuracy even after years of continuous operation. The inclusion of reinforced support structures within the frame, such as crossbeams and gussets, further enhances strength and prevents flexing, particularly in large-format machines designed for heavy-duty sheet metal cutting.
Another significant development in frame design is the integration of modular and customizable structures. Some manufacturers now offer frames that can be expanded or adjusted based on the size of the workpiece or the specific cutting requirements of different industries. Modular frames allow users to add extensions, additional support brackets, or specialized mounting points for attachments such as fume extraction systems, additional cutting heads, or robotic arms. This adaptability makes it easier for businesses to scale their operations without the need to invest in entirely new machines when production demands change.
In CNC-operated circle cutting machines, the accuracy of the frame alignment is crucial for ensuring smooth motion along the cutting path. Modern frames are designed with precision-ground linear rails, hardened guideways, and advanced motion control systems that reduce friction and enable high-speed operation without sacrificing accuracy. High-precision rack-and-pinion or ball screw drive systems are mounted directly onto the frame, ensuring consistent movement with minimal backlash. These systems require perfectly level and stable base structures, making the quality of the frame construction an essential factor in determining the overall performance of the machine.
For plasma and laser cutting machines, heat management is an important consideration in frame design. The intense heat generated during cutting can cause thermal expansion and distortion of the workpiece and even the machine itself. To counter this, manufacturers incorporate temperature-resistant materials and design frames with expansion joints or specialized cooling systems. Water tables, which are integrated into the base of some cutting machines, serve a dual purpose: they help dissipate heat from the cutting process while also reducing smoke, dust, and metal slag. Advanced downdraft tables, designed with powerful ventilation systems, actively extract fumes and airborne particles, maintaining a cleaner and safer working environment.
In the context of industrial automation, the base or frame also serves as a mounting point for auxiliary systems such as conveyor belts, robotic loading arms, and part-sorting mechanisms. Automated material handling solutions rely on a stable and well-aligned frame to ensure smooth transitions between different processing stages. In some high-end machines, the base structure includes embedded sensors that monitor vibrations, surface flatness, and machine alignment in real time. These smart monitoring systems alert operators to potential issues such as misalignment, excessive wear, or instability, allowing for preventive maintenance and reducing the risk of downtime.
Portability remains a key consideration for mobile or field-use cutting machines. Some portable circle cutting machines are designed with lightweight yet durable aluminum frames that allow for easy transport while still maintaining sufficient stability for precision cutting. Foldable legs, adjustable height settings, and compact footprints make these machines suitable for job site applications where space and mobility are critical. Despite their smaller size, these frames are engineered to provide sufficient rigidity to prevent wobbling and ensure consistent cutting performance.
As technology continues to advance, future developments in machine base and frame design are expected to focus on further improving durability, automation, and energy efficiency. The incorporation of smart materials with self-healing or adaptive properties could help enhance longevity by reducing wear and fatigue in high-stress areas. AI-driven frame monitoring systems, capable of predicting structural weaknesses before they lead to performance degradation, could become standard features in next-generation cutting machines. Additionally, advancements in 3D printing and composite manufacturing may enable the production of highly customized and lightweight frame structures that maintain exceptional strength while reducing material costs.
Ultimately, the base or frame of a circle cutting machine is far more than just a supporting structure; it is a fundamental component that affects every aspect of the machine’s performance, from precision and durability to automation and operator safety. Whether used in high-production manufacturing facilities or small workshops, the quality and design of the frame play a crucial role in determining the overall efficiency and reliability of the cutting process. As industries continue to demand higher precision, greater flexibility, and improved sustainability, innovations in frame construction will remain at the forefront of advancements in metal cutting technology.
The future of base and frame design in circle cutting machines is poised to incorporate even more advanced technologies, driven by the growing demands for precision, efficiency, and sustainability. One key trend that will influence frame design is the increased focus on reducing the environmental impact of manufacturing processes. Frames are likely to be designed with lighter, more eco-friendly materials that do not sacrifice strength or durability. For example, the use of recycled metals and sustainable composite materials could become more prevalent, contributing to a greener manufacturing footprint while still maintaining the performance standards required for cutting operations.
Moreover, energy-efficient base designs will become more common. As cutting machines continue to evolve toward greener operations, the base structure will play a significant role in reducing overall energy consumption. Machines may be equipped with integrated power management systems that optimize energy usage, ensuring that all components, including the base and frame, work in harmony to reduce waste. Some advanced frame systems could also include features like regenerative braking or energy recovery mechanisms, allowing excess energy generated during machine motion to be fed back into the system, contributing to overall energy savings.
A growing emphasis on automation and data-driven manufacturing will likely lead to more intelligent base structures. With the increasing integration of IoT (Internet of Things) and AI-powered sensors, the base or frame of a circle cutting machine could be equipped with smart monitoring systems capable of continuously analyzing machine health. These sensors will detect issues such as vibration levels, temperature changes, and wear patterns, providing real-time feedback that can be used to optimize machine performance and prevent breakdowns. These systems will also enable predictive maintenance, where the machine can notify operators of impending issues before they affect performance, thus reducing unplanned downtime. This will increase machine reliability, reduce maintenance costs, and enhance overall productivity.
The integration of autonomous systems into frame design is another area expected to advance. Automated alignment systems embedded into the base can adjust machine components to compensate for any misalignment, ensuring perfect cutting accuracy even under variable operating conditions. This level of automation could be beneficial in industries where cutting machines are used to process a variety of materials or complex geometries, as the system would be able to make real-time adjustments without operator input.
Another innovation on the horizon is the use of 3D printing or additive manufacturing to create custom frame components. As additive manufacturing technology continues to mature, it will allow for the production of complex, lightweight, and strong frame structures that traditional manufacturing methods cannot easily replicate. Custom-designed frames could be tailored to the specific needs of different cutting machines, further enhancing machine performance, reducing material waste, and accelerating production timelines. This process could also help reduce the time and costs associated with producing prototypes or designing bespoke frames for unique applications.
In terms of machine mobility, developments in robotics and advanced mobility systems will lead to more versatile and flexible base designs. For example, mobile circle cutting machines may incorporate robotic bases with autonomous movement capabilities, allowing them to move to different parts of a workshop or factory floor as needed. These autonomous systems could be programmed to transport the cutting machine to different workstations, enhancing workflow efficiency and reducing the need for manual handling of large and heavy equipment. In remote or difficult-to-access environments, such as offshore oil rigs or construction sites, robotic mobility could make it easier to deploy cutting machines where they are needed most.
Additionally, as industries move toward Industry 4.0 and greater connectivity, base structures will increasingly need to be compatible with other automated systems within the factory. This could include robotic arms, automated material handling systems, and centralized data management systems that track and analyze machine performance in real-time. A machine’s base would need to support these systems through integrated mounts, interfaces, and communication channels, allowing the cutting machine to seamlessly interact with other machines and systems in an interconnected production environment.
The importance of ergonomics in frame design will also increase, especially as machine operators’ comfort and safety become more closely tied to productivity and performance. Future base designs may feature adjustable elements, such as height-adjustable frames or tilting components, that can be customized for different operator needs. This adaptability would reduce operator fatigue, improve safety, and enhance overall machine usability, making it easier for workers to handle complex tasks with fewer physical demands.
In terms of structural enhancements, future frames may include integrated vibration-damping technologies that go beyond conventional materials. These damping systems could involve the use of piezoelectric materials or active vibration control systems, which can detect and counteract vibrations in real time, maintaining machine stability even in high-speed or high-torque cutting processes. Such innovations will be especially important in industries where ultra-precise cuts are required, such as in aerospace, automotive, or electronics manufacturing, where even the slightest vibration can lead to defects.
In conclusion, the ongoing development of circle cutting machine frames will continue to enhance the overall performance, flexibility, and sustainability of cutting operations. As industries demand faster, more precise, and environmentally friendly solutions, the base and frame of cutting machines will evolve to meet these needs. With smarter technologies, more sustainable materials, and greater integration with automation systems, the future of base design will ensure that cutting machines can keep pace with the ever-changing demands of modern manufacturing. Whether focusing on energy efficiency, automation, or mobility, these innovations will play a key role in improving the efficiency and precision of metal cutting while reducing costs and environmental impacts.
Rotary Arm/Guide Mechanism
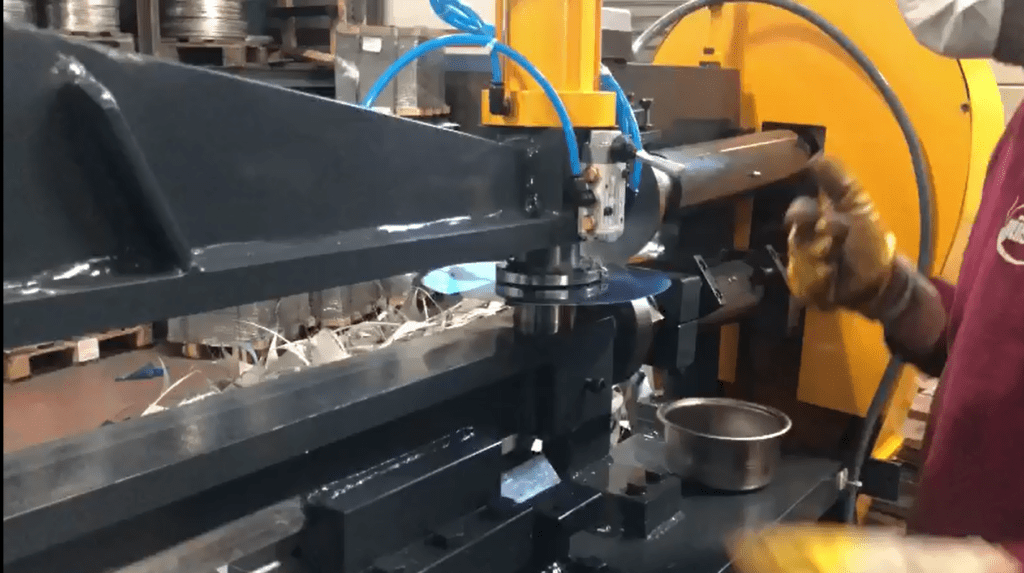
The rotary arm and guide mechanism in circle cutting machines play a crucial role in ensuring the accurate and precise movement of the cutting head. They are responsible for guiding the cutting tool in a circular motion, which is essential for producing consistent cuts on sheet metal. These mechanisms are designed to withstand the forces generated during the cutting process, ensuring that the cutting head remains stable and aligned throughout the operation. The rotary arm typically consists of a rotating shaft or arm attached to a motorized base, which can pivot or rotate around a fixed center point. The guide mechanism, often in the form of tracks, rails, or bearings, ensures smooth and controlled movement, enabling the cutting head to follow the desired path with high precision.
The guide mechanism is a key factor in determining the overall accuracy and quality of the cuts. It ensures that the cutting tool maintains a constant distance from the workpiece, preventing deviations that could result in uneven or imperfect cuts. In some advanced machines, the guide mechanism is integrated with CNC (computer numerical control) technology, allowing for highly precise adjustments based on programmed instructions. This integration enables the machine to automatically compensate for variations in material thickness, surface irregularities, or tool wear, ensuring consistent performance over time.
The materials used in the construction of the rotary arm and guide mechanism are critical to their durability and performance. High-strength alloys, such as steel or aluminum, are commonly used to ensure that these components can withstand the stresses of continuous operation without bending or wearing down. In high-speed machines, bearings and linear guides are often employed to reduce friction and ensure smooth motion. These elements are precision-engineered to minimize backlash and play, which could otherwise lead to inaccuracies in the cutting process.
Over time, advances in technology have led to the development of more efficient and reliable rotary arms and guide mechanisms. For example, the introduction of servo motors and stepper motors has improved the control and responsiveness of these systems, allowing for more precise and faster movements. These motors can be integrated with encoders and feedback systems, which provide real-time data to the machine’s control system. This enables the rotary arm to make minute adjustments during operation, improving cutting accuracy and minimizing the risk of errors.
Another important development in the rotary arm and guide mechanism is the implementation of automation. In modern machines, robotic arms are sometimes used to perform the rotary motion, especially in systems that require high levels of flexibility or complex movement patterns. These robotic arms are often equipped with advanced sensors and cameras, allowing them to detect the position of the cutting tool and automatically adjust the cutting path. This automation improves the overall efficiency of the system and reduces the need for manual intervention, making it possible to produce high-quality cuts with minimal downtime.
In some designs, the rotary arm is coupled with an adjustable counterweight system, which helps to balance the arm during its movement. This system is particularly useful in reducing the strain on the motor and bearings, which can extend the lifespan of these components and improve overall machine performance. Counterweights can be adjusted to accommodate different material sizes and weights, ensuring smooth operation even when cutting thicker or denser materials.
In certain cutting applications, the rotary arm and guide mechanism may also be equipped with a tilting feature. This allows the cutting head to adjust the angle at which it approaches the material, making it possible to cut at varying angles and create beveled edges. This added versatility is beneficial in industries such as automotive manufacturing, where parts often require angled cuts for welding or fitting purposes. The tilting mechanism is typically controlled by the CNC system, ensuring precise and repeatable adjustments.
As cutting technology continues to advance, new materials and coatings are being introduced to improve the performance of rotary arms and guide mechanisms. For instance, anti-wear coatings are applied to reduce friction and increase the lifespan of moving components. Additionally, newer bearing technologies, such as magnetic or air bearings, are being explored for their ability to provide smooth and frictionless motion, further enhancing the precision of the cutting process.
The rotary arm and guide mechanism are not only important for the accuracy of the cuts but also for the overall speed and efficiency of the machine. By ensuring that the cutting tool moves smoothly and steadily, these components help to reduce the time required for each cutting operation. In high-volume manufacturing settings, this can significantly increase productivity and reduce operational costs. Furthermore, because the guide mechanism ensures consistent cutting paths, the need for rework or corrections is minimized, resulting in better material utilization and fewer waste products.
In addition to their mechanical function, the rotary arm and guide mechanism contribute to the overall safety of the machine. In many modern systems, these components are equipped with safety sensors that can detect obstructions or irregularities in the cutting path. If an issue is detected, the system can automatically stop the cutting operation to prevent damage to the workpiece or the machine itself. These safety features help protect both operators and equipment, ensuring a safer working environment.
The development of rotary arm and guide mechanisms will continue to evolve as industries demand even greater precision, speed, and automation. Future innovations may include fully integrated systems that can seamlessly communicate with other machines in a production line, allowing for synchronized operations and higher levels of automation. Additionally, as materials and cutting technologies improve, the rotary arm and guide mechanisms will be designed to handle increasingly diverse materials, thicknesses, and cutting methods, from traditional laser and plasma cutting to newer techniques such as water jet cutting or advanced hybrid systems.
Overall, the rotary arm and guide mechanism are vital components of circle cutting machines, ensuring that the cutting process is precise, efficient, and reliable. Their role in maintaining the alignment and movement of the cutting head directly affects the quality of the final product, making them essential for industries where accuracy and consistency are paramount. With continued advancements in technology, these mechanisms will only become more refined, offering enhanced performance and capabilities for an even broader range of cutting applications.
As industries continue to demand more advanced, precise, and efficient cutting solutions, the role of the rotary arm and guide mechanism in circle cutting machines will evolve to meet these needs. One key area of advancement is the incorporation of artificial intelligence (AI) and machine learning algorithms into the operation of the rotary arm and guide system. These technologies can be used to predict potential issues, optimize cutting paths, and adjust in real-time based on the feedback received from sensors and monitoring systems. For example, AI-driven systems can analyze cutting conditions and make real-time adjustments to optimize speed, accuracy, and efficiency, ensuring that the cutting head maintains its ideal position relative to the material. This level of intelligent control can drastically improve performance and reduce errors, especially in complex cutting operations.
In addition, the integration of advanced sensors and cameras into the rotary arm and guide mechanism will enable even finer levels of control. These sensors can monitor the position of the cutting head with incredible accuracy, providing instant feedback to the CNC system and allowing for rapid adjustments. This feedback loop helps maintain optimal cutting conditions, even when faced with variations in material characteristics or changes in the environment, such as temperature fluctuations that may affect the material or machine.
The continued miniaturization and refinement of components will also drive improvements in the design of the rotary arm and guide mechanism. Smaller, more efficient motors, coupled with advanced motion control technologies, will allow for smoother and faster movement without sacrificing precision. Additionally, the use of lightweight materials, such as carbon fiber or advanced composites, will reduce the overall weight of the rotary arm, making it easier to handle and reducing the strain on supporting structures. Lighter arms will also allow for more agile motion, which can be especially beneficial for machines that require rapid cutting speeds or need to perform intricate cuts with high precision.
Maintenance and durability will also see significant improvements in future rotary arm and guide mechanisms. As manufacturers seek to reduce downtime and increase operational efficiency, the development of self-lubricating components and longer-lasting bearings will be a focus. These innovations will not only reduce the frequency of required maintenance but also improve the overall lifespan of the machine. Additionally, predictive maintenance systems, which can alert operators to potential wear or mechanical failure before it occurs, will become more prevalent. This technology will allow for proactive repairs and adjustments, preventing costly breakdowns and keeping machines running at peak performance for longer periods.
Moreover, the integration of wireless communication systems and cloud computing will enhance the connectivity and data-sharing capabilities of the rotary arm and guide mechanism. Remote monitoring and control systems will allow operators and managers to track machine performance from any location, enabling faster decision-making and troubleshooting. Real-time data from the cutting process can be analyzed remotely, and any necessary adjustments can be made without the need for physical presence on-site, enhancing flexibility and responsiveness.
As circular cutting machines are used in an increasingly diverse range of industries—from aerospace and automotive to shipbuilding and metal fabrication—the versatility of the rotary arm and guide mechanism will become more critical. Machines will need to be adaptable to different materials, thicknesses, and cutting methods, and the rotary arm and guide system will be integral in achieving this flexibility. The future may see the development of multi-functional systems that can be easily reconfigured for different cutting processes, whether it’s traditional flame cutting, advanced laser cutting, or water jet cutting.
Additionally, safety features will continue to evolve to keep pace with technological advancements. The incorporation of automated safety systems into the rotary arm and guide mechanism will allow for real-time hazard detection, such as obstruction or malfunction of the cutting path. In such cases, the system can stop the cutting operation or trigger an emergency stop to prevent damage to the machine or injury to the operator. These safety features will be further enhanced by real-time data monitoring, ensuring that the machine operates within safe parameters at all times.
The development of hybrid systems, which combine multiple cutting technologies in a single machine, will place additional demands on the rotary arm and guide mechanism. These systems, for example, could use a combination of laser cutting for precision and plasma cutting for speed, requiring the rotary arm to seamlessly transition between different cutting tools. Such flexibility will be achieved through advanced control systems that can dynamically switch between cutting modes, ensuring that the cutting head remains stable and aligned in all settings.
The future of rotary arm and guide mechanisms in circle cutting machines will be marked by continuous innovation, with a focus on automation, precision, and durability. Whether through the adoption of AI, the use of advanced materials, or improvements in machine connectivity, these mechanisms will play a central role in shaping the next generation of cutting technologies. The drive for higher efficiency, greater versatility, and enhanced safety will ensure that these systems remain at the forefront of manufacturing, enabling industries to meet the demands of increasingly complex and diverse production processes.
The advancements in rotary arm and guide mechanisms will also bring about significant changes in machine adaptability and integration with other manufacturing systems. As industries increasingly embrace automation and smart manufacturing principles, the integration of these mechanisms with the broader ecosystem of factory machines will become essential. The rotary arm and guide systems will need to be compatible with automated material handling systems, such as robotic arms, conveyors, and automated inspection units. Seamless communication between these systems will enable more efficient workflows, reducing the need for human intervention and streamlining production lines.
The integration with automated material handling systems will allow the rotary arm to respond to real-time instructions from the factory’s central control system. This means that the machine could not only cut materials with greater precision but could also adapt to changes in the material flow, automatically adjusting its movements based on the arrival of new sheets or changes in the production schedule. For instance, the rotary arm could adjust its path or speed to accommodate different sheet sizes or thicknesses, improving efficiency and reducing the likelihood of errors. These capabilities would enhance production flexibility, especially in environments where quick setup changes and high-volume production are required.
Moreover, the future of rotary arm and guide mechanisms is expected to align with the principles of Industry 4.0, where real-time data exchange and machine-to-machine (M2M) communication are paramount. As more sensors and IoT devices are embedded into the rotary arm, the system will be able to gather and transmit performance data, such as cutting speed, power consumption, and vibration levels. This data can be analyzed by centralized software systems to optimize the cutting process, predict maintenance needs, and provide actionable insights that help operators make informed decisions. This data-driven approach will enhance not only performance but also predictive capabilities, allowing for preemptive actions that can prevent machine downtime and extend the lifespan of critical components.
The increasing sophistication of rotary arm and guide mechanisms will also lead to greater precision in cutting operations. For example, in industries where high-tolerance cuts are required—such as aerospace, medical device manufacturing, and electronics—enhanced rotary mechanisms will be designed to maintain alignment with incredible accuracy. This could involve the use of ultra-precise linear guides, air-bearing systems, or laser-guided alignment systems to ensure that the cutting head stays on track, even during high-speed operations. With these advancements, manufacturers will be able to produce parts with tighter tolerances and higher quality, which is crucial for industries where even small deviations can lead to significant defects.
Additionally, the development of hybrid and multi-tool cutting systems will place new demands on the rotary arm and guide mechanisms. These systems, which combine multiple cutting technologies such as plasma, laser, and oxy-fuel in one machine, will require advanced guidance systems capable of supporting the smooth switching between different cutting heads. The rotary arm and guide mechanism will need to be robust and versatile enough to handle the varying speeds, power levels, and motion requirements of each cutting tool. This adaptability will allow manufacturers to use the same machine for different applications, saving time and cost associated with changing machines or tools for each task.
An emerging trend that will influence rotary arm and guide mechanism design is the use of “smart” materials. These materials possess properties that allow them to respond to external stimuli, such as temperature or pressure changes. For instance, piezoelectric materials could be incorporated into the guide system to enhance precision by actively correcting misalignments in real-time. Smart coatings could also be applied to the rotary arm and guide rails to prevent wear and reduce friction, improving the overall performance and longevity of the system. These innovations would help to create even more reliable and efficient cutting machines capable of maintaining high performance for extended periods.
The influence of sustainability will also extend to the design of rotary arm and guide mechanisms. Manufacturers will increasingly focus on creating energy-efficient systems that not only reduce power consumption but also minimize material waste. By using advanced sensors to monitor the cutting process and adjust parameters in real time, the system can optimize cutting conditions to reduce scrap and maximize material utilization. This level of control, coupled with the ability to adjust speed and power based on the material type and thickness, will help achieve a more sustainable manufacturing process.
Moreover, in industries where cutting machines are used in harsh or remote environments, such as oil rigs or mining sites, the rotary arm and guide mechanism will need to be designed to withstand extreme conditions. This includes exposure to high temperatures, dust, moisture, and vibrations. Manufacturers will use corrosion-resistant materials, protective coatings, and advanced sealing techniques to ensure that the rotary arm and guide mechanism continue to function reliably even in these challenging environments. The addition of robust safety features, such as automatic shutoff systems in case of malfunction, will be critical for preventing accidents and ensuring safe operation in such high-risk settings.
The need for enhanced ergonomics and user-friendly operation will also shape the future of rotary arm and guide mechanisms. As operators play an increasingly important role in monitoring and adjusting machine performance, ease of use will be a key factor in the design of these systems. User interfaces that allow operators to easily adjust settings, monitor machine performance, and receive real-time feedback will be essential. This could include touch-screen controls, intuitive software, and augmented reality (AR) displays that provide a live visual representation of the cutting process. Such interfaces will make it easier for operators to interact with the machine, reduce errors, and improve overall operational efficiency.
Finally, as manufacturing processes become more global and interconnected, rotary arm and guide mechanisms will need to be designed with versatility in mind. Machines will be expected to work across a wide range of materials, cutting methods, and production scales. This means that the rotary arm and guide systems will need to be modular, easily adaptable to different types of materials and production processes. Manufacturers may offer customizable options, allowing operators to tailor the system to specific needs without requiring entirely new machinery for each different application.
In conclusion, the future of rotary arm and guide mechanisms in circle cutting machines is deeply connected to the trends of automation, smart manufacturing, precision cutting, and sustainability. As technology continues to advance, these mechanisms will become more intelligent, adaptable, and reliable, offering enhanced performance, efficiency, and flexibility. By integrating new technologies such as AI, advanced sensors, and smart materials, rotary arms and guide systems will play a pivotal role in transforming the cutting industry and meeting the ever-increasing demands for precision, versatility, and sustainability in manufacturing.
Control System
The control system in a circle cutting machine is the heart of its operation, serving as the brain that directs all of the machine’s movements, processes, and functions. It is responsible for interpreting input data, coordinating various components, and ensuring that the machine operates efficiently, accurately, and safely. Modern control systems in these machines are sophisticated and highly integrated, utilizing advanced technology to deliver precision cutting while enhancing productivity and reducing human error. These systems typically comprise a combination of hardware and software, with the software providing the intelligence and the hardware executing the commands.
At the core of the control system is the computer or programmable logic controller (PLC) that manages all operations, from controlling the motorized movement of the rotary arm and guide mechanism to adjusting the cutting speed and path. The PLC processes the inputs it receives from the operator and sensors, and based on pre-programmed instructions, it generates commands to control the movement of the machine components. The software integrated into the control system is typically customizable, allowing operators to input cutting specifications, adjust settings, and monitor performance in real-time. It also plays a crucial role in optimizing machine performance, reducing waste, and increasing the overall efficiency of the cutting process.
The control system’s interface is a key aspect of machine usability. In many modern systems, a user-friendly graphical interface allows operators to input commands, configure settings, and monitor the machine’s progress through touch-screen panels, buttons, or even voice commands. These interfaces have become more intuitive and feature-rich, enabling operators to easily adjust cutting parameters such as speed, pressure, and depth. In some cases, the system can also suggest optimal settings based on the material type, thickness, and desired cutting quality, streamlining the decision-making process and reducing setup time. This kind of intelligent system allows for greater flexibility and precision in the manufacturing process, accommodating a wide range of materials and cutting requirements.
One of the critical functions of the control system is to ensure the precise synchronization of all the moving parts within the cutting machine. This includes controlling the motors, actuators, and feedback loops to ensure smooth and accurate movement. For example, it must manage the speed and rotation of the rotary arm and guide mechanism, ensuring that the cutting head follows the exact circular path with minimal deviation. The control system also adjusts the pressure and feed rate to maintain consistent cutting performance, even when working with varying material thicknesses or densities. To achieve this, it relies on a network of sensors that constantly monitor the position, speed, and status of various components, feeding this information back into the system to make real-time adjustments.
In addition to basic motion control, the control system is also responsible for integrating with other systems, such as those used for material handling or quality inspection. For instance, the system might communicate with a conveyor belt or robotic arm to automatically feed materials into the machine. The control system can adjust the cutting process based on feedback from sensors that measure material properties or detect defects. If a material is deemed unsuitable for cutting, the system can stop the operation or prompt the operator to replace it. This level of integration helps reduce downtime, optimize workflow, and ensure that the cutting process is always operating under optimal conditions.
Another important function of the control system is safety. Cutting machines often operate under high-speed and high-temperature conditions, and a malfunction or failure could result in significant damage or safety hazards. The control system is designed to monitor critical machine parameters in real-time and to automatically shut down or trigger safety mechanisms when something goes wrong. For instance, if the machine detects an abnormal temperature rise in the cutting head or excessive vibration in the rotary arm, it can stop the process to prevent damage. These safety features are designed to protect both the machine and the operator, ensuring that the cutting process is both effective and safe.
As circle cutting machines evolve, so too does the sophistication of their control systems. The trend toward automation and smarter manufacturing processes has led to the development of control systems that incorporate advanced algorithms and machine learning techniques. These systems can predict and respond to potential issues before they occur, making adjustments to the cutting parameters or machine movements without requiring operator intervention. For example, the system might detect patterns in the way materials are fed into the machine and adjust the cutting speed or pressure accordingly, compensating for slight variations in material properties or environmental conditions. This predictive capability helps ensure that the cutting process remains consistent and high-quality, even as operating conditions change.
Moreover, the integration of Internet of Things (IoT) technology into the control system allows for remote monitoring and control of the cutting machine. Through a network of sensors and cloud-based platforms, operators and maintenance teams can access real-time data about the machine’s performance from anywhere in the world. This remote capability enhances the ability to troubleshoot issues, track machine health, and optimize performance, even if the machine is located in a different facility or on a remote job site. It also facilitates predictive maintenance, as the system can analyze performance data over time and identify trends that suggest potential failure points. By identifying and addressing issues before they cause a breakdown, this capability can significantly reduce downtime and extend the lifespan of the machine.
The increasing complexity and capabilities of control systems also mean that more advanced training and expertise are required to operate and maintain these machines. While earlier systems were often controlled by simple switches or manual settings, modern systems require skilled operators who are familiar with both the machine’s software and hardware. Many cutting machines now feature advanced diagnostic and troubleshooting tools that guide operators through the process of identifying and fixing issues. In addition, operators may need to understand how to interpret the data generated by the system, such as performance metrics, error codes, and sensor outputs, to make informed decisions about machine adjustments.
In the future, control systems will continue to evolve as part of the broader trend toward smart factories and Industry 4.0. The development of artificial intelligence, machine learning, and deep learning technologies will enable control systems to become even more autonomous, making more complex decisions on their own based on real-time data and historical performance data. These systems may even be able to collaborate with other machines in the factory, sharing data and optimizing production processes in real-time to maximize efficiency and minimize waste.
The control system’s role in sustainability will also grow in importance. By optimizing the cutting process, control systems can help minimize energy consumption and reduce material waste. For example, they can adjust the cutting speed and path to reduce the amount of scrap material generated during the process. Additionally, through data analysis and feedback from sensors, the system can detect inefficiencies or suboptimal conditions, enabling operators to make adjustments that reduce the environmental impact of the manufacturing process.
In conclusion, the control system in a circle cutting machine is a vital component that directly influences the machine’s performance, safety, and efficiency. As cutting technology advances, the sophistication of control systems will continue to increase, with a focus on automation, real-time data processing, predictive maintenance, and enhanced safety features. By integrating advanced technologies such as AI, IoT, and machine learning, control systems will be able to handle more complex tasks, make smarter decisions, and optimize machine performance, enabling manufacturers to meet the demands of modern production environments while ensuring sustainability and reducing costs.
As the control system continues to evolve, its role will expand to encompass more sophisticated functions that enhance overall manufacturing processes. One of the key developments will be in the integration of augmented reality (AR) and virtual reality (VR) interfaces. By combining the power of AR/VR with the control system, operators will be able to visualize the cutting process in real-time, as well as simulate various cutting scenarios before the actual operation begins. This would allow them to foresee potential issues, adjust settings, and make more informed decisions, all without physically interacting with the machine.
The integration of these technologies could also make operator training more effective. Instead of relying solely on traditional hands-on training, operators could use VR simulations to familiarize themselves with the system’s operations and troubleshooting methods. They would be able to practice handling emergencies, adjusting parameters, or even maintaining the machine in a safe and controlled environment, minimizing risk and improving skill development. This could be especially beneficial in environments where the machines are complex, and quick, accurate decision-making is crucial.
In addition to AR and VR, the role of big data and analytics in the control system will also continue to grow. As manufacturing becomes increasingly data-driven, the control system will be able to collect vast amounts of data from sensors, production logs, and machine usage patterns. By analyzing this data, manufacturers will gain insights into the overall efficiency of their machines, detecting areas for improvement and further optimization. For example, the system could track the frequency of specific adjustments, performance trends, or even operator behavior. This information could help identify best practices or predict when parts might need replacement, further extending the life of the machinery.
Advanced analytics could also help in achieving greater customization of the cutting process. By tracking the specific requirements of different projects, such as material types, sheet sizes, and cutting complexities, the control system can recommend or automatically apply the optimal settings for each new job. Over time, as the system learns from past performance, it can suggest improvements to cutting strategies, helping manufacturers achieve higher levels of precision while reducing operational costs.
Another area where control systems are likely to advance is in energy management. In industrial settings, energy consumption is a significant cost, and many manufacturers are looking for ways to reduce their energy footprint. The control system can play a crucial role in this effort by optimizing the energy usage of various machine components. By continuously monitoring power consumption, the system can identify patterns that indicate energy waste or inefficiencies and adjust parameters to minimize energy usage without sacrificing performance. For example, the system could lower motor speeds during idle periods, adjust the cooling system to operate only when necessary, or switch off non-critical components during low-demand operations.
The integration of renewable energy sources into the manufacturing process is another possibility. The control system could be designed to prioritize the use of on-site solar or wind power when available, helping companies reduce their reliance on grid energy and lower their environmental impact. Additionally, the system could integrate energy storage solutions, such as batteries, to store excess energy generated during off-peak hours for use during peak demand times, further reducing costs and enhancing sustainability.
Security will continue to be a critical aspect of the control system. As machines become more connected to networks and the Internet of Things (IoT), the risk of cyber-attacks grows. Hackers could potentially gain control of the cutting machine, disrupt production, or cause physical damage. To combat these threats, the control system will need to integrate advanced cybersecurity measures. These could include encrypted communication protocols, multi-factor authentication for remote access, and real-time monitoring of network activity to detect unusual behavior. Additionally, automated backup systems could be implemented to restore machine settings in case of a cyber-attack or system failure.
As the industry continues to adopt artificial intelligence (AI) and machine learning, the control system will increasingly leverage these technologies for decision-making. The ability of AI to analyze large datasets and make decisions in real time will allow the system to make optimizations on the fly, adjusting parameters for maximum efficiency and output. The system could also use machine learning algorithms to continuously improve its performance. By analyzing historical data on cutting jobs, materials, and machine behavior, the system could learn patterns that lead to the best outcomes, and it could apply this knowledge to future jobs, continuously refining its cutting strategy.
For instance, if a certain material consistently produces higher-quality cuts when processed at a slower speed, the AI-powered control system will recognize this trend and recommend—or even automatically implement—slower speeds for similar materials in the future. This level of adaptability ensures that the machine continues to perform at its best, even as variables such as material types, thickness, and external conditions change over time.
In the long term, the control system could even integrate with larger enterprise resource planning (ERP) systems, further enhancing coordination between the cutting machine and other manufacturing processes. By sharing data between departments, such as inventory management, order scheduling, and maintenance, the control system can ensure that the machine operates as part of a larger, more synchronized production workflow. For example, if the system detects a delay in material delivery or a potential scheduling conflict, it could automatically adjust the cutting timeline or pause the operation until the material is ready, optimizing production without human intervention.
The development of more advanced, adaptive, and intelligent control systems will not only improve the performance of circle cutting machines but also redefine how manufacturers approach production. Through automation, real-time data analysis, and increased integration with other systems, these machines will become more flexible, efficient, and capable of handling complex tasks with minimal oversight. As the control systems evolve to support the next generation of manufacturing, they will help companies improve operational efficiency, reduce costs, enhance precision, and contribute to the ongoing trend of smarter, more sustainable production processes.
Looking ahead, the role of control systems in circle cutting machines will continue to expand as new technologies and manufacturing philosophies emerge. One significant advancement on the horizon is the increased use of digital twins. A digital twin is a virtual replica of a physical system, in this case, the cutting machine, which can simulate its behavior and performance in real-time. By integrating a digital twin into the control system, manufacturers will be able to monitor the machine’s performance in a virtual environment, making adjustments and predicting outcomes before implementing changes on the actual machine. This approach not only improves predictive maintenance and troubleshooting but also allows for virtual testing of new cutting strategies or machine configurations, enabling faster innovation cycles and reducing the risks associated with physical changes.
Moreover, digital twins can provide a detailed, real-time view of the entire production process. By linking the virtual model of the cutting machine to the broader factory environment, the control system can synchronize with other machines, sensors, and production lines. This holistic view will allow for real-time optimization across multiple systems, reducing inefficiencies, eliminating bottlenecks, and enhancing throughput. For instance, if the control system detects that a machine downstream of the cutting station is experiencing delays, it could automatically adjust the cutting schedule to minimize idle time and keep the entire production line running smoothly.
In parallel with digital twins, advancements in 5G technology will further transform how control systems operate. The high-speed, low-latency capabilities of 5G will allow machines to communicate with each other and the broader factory network more effectively, enabling even faster data exchanges between systems. This will be particularly beneficial in real-time decision-making, where milliseconds matter. Control systems will be able to send and receive data from sensors, robots, and other machines instantly, allowing for immediate adjustments to the cutting process. This increased connectivity will also facilitate the adoption of cloud-based platforms, where data can be processed, analyzed, and shared across multiple locations. Manufacturers could remotely monitor and control their cutting machines from anywhere, allowing for centralized management of operations, more responsive customer support, and streamlined maintenance processes.
The potential for control systems to integrate with artificial intelligence (AI) and advanced data analytics will also enable more advanced, autonomous decision-making capabilities. AI-powered systems can analyze vast amounts of production data, learning from each cut and optimizing parameters for each new job. For instance, the system could not only adjust for material variations but also adapt cutting strategies based on operator feedback and performance data over time. By continuously refining its approach, the system will be able to reduce cutting time, minimize waste, and ensure the highest quality cuts for every sheet of material.
AI will also support the development of autonomous inspection systems, which can identify defects or quality issues in real-time. These inspection systems can be integrated directly into the control system, allowing the machine to immediately adjust its cutting process in response to detected imperfections. For example, if a defect is identified in the material, the machine could adjust its cutting parameters to ensure that only the usable portion of the material is processed, reducing scrap and improving yield. In more advanced scenarios, AI could predict potential defects in materials even before they are introduced into the cutting machine, allowing for better sorting and preparation of materials ahead of time.
The growing focus on sustainability will drive the development of more energy-efficient control systems. As energy costs continue to rise and environmental regulations become stricter, manufacturers will be under increasing pressure to reduce their energy consumption and minimize their environmental impact. Control systems will play a critical role in this effort by continuously optimizing power usage. For example, advanced algorithms could enable the system to automatically adjust the cutting speed and power consumption based on material properties, thickness, and cutting requirements. This optimization will help minimize energy usage during each phase of the cutting process, while still maintaining the required precision and quality.
Another important area for development is the integration of circular economy principles into the control system’s operation. A circular economy emphasizes the reuse, recycling, and repurposing of materials, which has significant implications for cutting processes. The control system could be designed to track material usage and waste more effectively, allowing manufacturers to identify opportunities to recycle or repurpose scrap materials. For example, the system could automatically sort and process offcuts or remnants, transforming them into usable products for other applications. This not only reduces waste but also contributes to a more sustainable manufacturing process.
As we move toward fully autonomous factories, control systems will need to support increased collaboration between machines. In a smart factory, machines will be interconnected through a centralized digital ecosystem that allows them to work together seamlessly. Control systems will play a key role in coordinating these interactions, ensuring that machines are operating at peak efficiency while sharing information in real time. This interconnectedness will allow for continuous optimization, with each machine adjusting its operations based on data from others, creating a dynamic, self-optimizing production environment.
In such an environment, predictive maintenance will be a key feature of the control system. By continuously collecting data from sensors embedded in the machine, the control system will be able to detect signs of wear and tear, such as excessive vibration or temperature changes. This data will be analyzed in real-time to predict when components are likely to fail, allowing for maintenance to be scheduled before a failure occurs. By preventing unplanned downtime, predictive maintenance will reduce maintenance costs, increase machine availability, and extend the overall lifespan of the equipment.
The ultimate goal for control systems in circle cutting machines is to achieve a high level of automation, precision, and adaptability while also enhancing overall manufacturing efficiency. These systems will not only be able to optimize the cutting process itself but also coordinate seamlessly with other machines, sensors, and enterprise systems to drive continuous improvements across the entire production process. With AI, IoT, and other advanced technologies working in concert, control systems will be able to make smarter, more autonomous decisions, improve machine performance, and contribute to more sustainable and cost-effective manufacturing operations.
As these systems evolve, the role of the operator will change as well. Rather than focusing on day-to-day adjustments and troubleshooting, operators will shift toward overseeing the broader system, making strategic decisions, and ensuring that all components are functioning together smoothly. This shift will require a new set of skills and expertise, as operators will need to understand both the technology behind the control systems and the broader context in which they operate. Training and education will be critical to ensuring that the workforce is prepared for these new roles and can maximize the benefits of increasingly intelligent and interconnected control systems.
In conclusion, the future of control systems in circle cutting machines is closely tied to advancements in automation, AI, machine learning, and digitalization. These systems will become more intelligent, autonomous, and interconnected, offering manufacturers enhanced efficiency, precision, and sustainability. As the technology continues to evolve, control systems will be at the forefront of transforming the cutting industry, enabling manufacturers to meet the demands of a rapidly changing production environment while improving operational performance and reducing environmental impact.
Cutting Blades
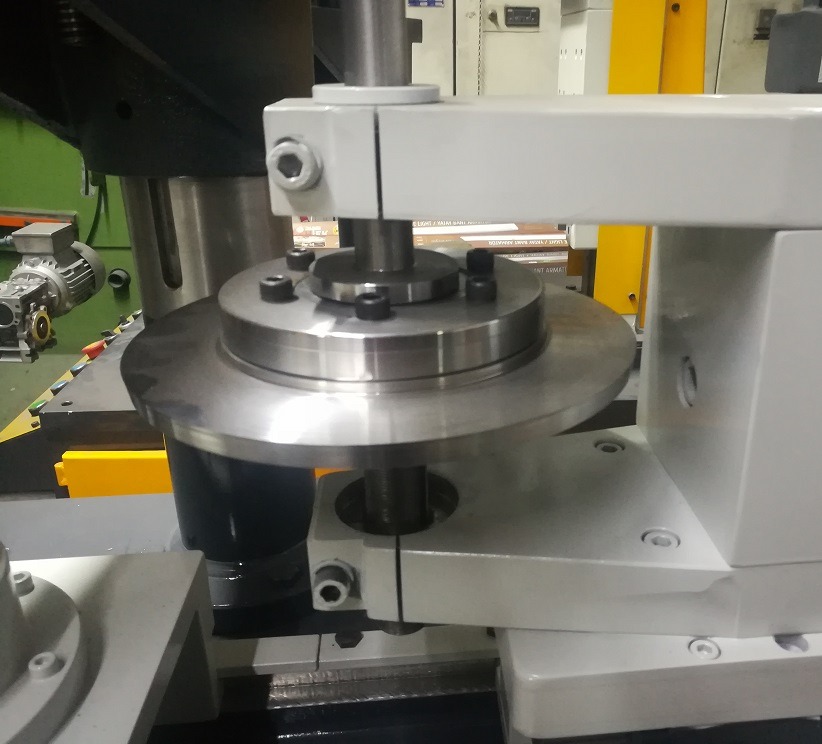
Cutting blades are essential components of any circle cutting machine, serving as the primary tool for achieving the precision cuts that these machines are designed for. They are tasked with cutting through various materials, including metals, plastics, and composites, depending on the specific requirements of the application. The design, material, and sharpness of cutting blades play a crucial role in determining the efficiency, accuracy, and quality of the cutting process. These blades are often subjected to high levels of stress, heat, and wear, making the selection of the right type of blade and proper maintenance essential to achieving optimal cutting performance.
The design of cutting blades varies depending on the specific type of cutting machine and the material being processed. In circle cutting machines, the blades are typically round and feature a sharp edge that can smoothly rotate along a circular path to make precise cuts. They are mounted on a rotating shaft or motorized system that allows them to move around the material, cutting in a smooth, continuous motion. The round shape of the blades makes them ideal for cutting circular shapes, and their sharpness ensures that the material is cut cleanly without excessive burrs or deformation.
The material composition of cutting blades is one of the most important factors influencing their performance and longevity. The blades are often made from high-speed steel (HSS), carbide, or coated with materials like titanium nitride to increase hardness, wear resistance, and cutting performance. High-speed steel blades are commonly used for cutting softer materials such as mild steel, aluminum, or plastic. They offer a good balance of hardness and toughness but are more prone to wear over time, especially when cutting tougher materials. Carbide blades, on the other hand, are used for harder materials like stainless steel, titanium, or high-strength alloys. Carbide is a much harder material, allowing the blades to maintain their sharpness longer and withstand higher cutting temperatures, making them ideal for heavy-duty applications.
The sharpness of the cutting blade is another critical factor that determines its effectiveness. A sharp blade requires less force to make cuts, which reduces the stress on the machine and minimizes the risk of material deformation. It also ensures that the cut is clean and smooth, with fewer imperfections or rough edges. Over time, however, blades will naturally lose their sharpness due to wear and exposure to the cutting material. Dull blades can cause the machine to work harder, leading to increased energy consumption and longer cutting times. They can also result in poor-quality cuts, which may require additional finishing or rework.
To maintain cutting performance, blades must be regularly sharpened or replaced. Some cutting blades are designed with a replaceable tip or edge, allowing for easier maintenance without the need to replace the entire blade. In other cases, the blade may need to be ground or honed to restore its sharpness. Some machines even feature built-in blade sharpening systems, where the blade can be sharpened in place, reducing downtime and improving overall efficiency. Blade sharpening, however, requires precision and care, as improper sharpening techniques can damage the blade, leading to reduced cutting performance or failure.
In addition to the material and sharpness, the blade’s geometry also plays an important role in its cutting efficiency. Blades can have different tooth shapes, angles, and profiles, depending on the cutting requirements. For example, some blades may have a tooth geometry designed for cutting through thicker materials or reducing vibration, while others may be optimized for high-speed cutting or minimizing heat generation. The right blade geometry helps to ensure that the machine operates smoothly and that the material is cut with minimal resistance, reducing the chances of tool breakage or excessive wear.
The coating of cutting blades is another important factor that can significantly impact their performance and durability. Many cutting blades are coated with materials such as titanium nitride (TiN), which provides a hard, wear-resistant layer on the surface of the blade. These coatings increase the blade’s resistance to heat and corrosion, allowing it to last longer and perform better under high-stress conditions. Coatings can also help reduce friction during the cutting process, resulting in less heat buildup and smoother cuts. While coatings can significantly enhance blade performance, they can also add to the cost of the blades, so manufacturers must balance the benefits of coatings with their budgetary considerations.
The cooling of the cutting process is also important for maintaining blade performance and preventing damage. When blades cut through materials, especially metals, they generate a significant amount of heat due to the friction between the blade and the material. Excessive heat can cause the blade to lose its sharpness more quickly, warp, or even crack. To prevent overheating, many cutting systems are equipped with cooling systems that use water, oil, or air to cool the cutting area and reduce the temperature of the blade. Proper cooling not only prolongs the life of the blade but also ensures better cutting performance and quality.
Additionally, the type of material being cut plays a significant role in determining the type of blade needed. For example, when cutting thin sheet metal, a high-speed steel blade may be sufficient to handle the load, but cutting thicker or tougher materials like stainless steel or high-strength alloys may require carbide-tipped or coated blades. The cutting blade must be matched to the material’s hardness, thickness, and density to ensure efficient cutting. Using the wrong type of blade can lead to poor-quality cuts, premature blade wear, or even failure, resulting in downtime and increased operational costs.
One of the emerging trends in the cutting blade industry is the development of more specialized and custom-made blades designed for specific applications. As industries become more diverse and manufacturing requirements grow more complex, the demand for cutting blades that are optimized for specific materials or cutting tasks has increased. Custom-designed blades can incorporate unique features, such as specialized coatings, specific geometries, or materials that are tailored to meet the exact demands of the job. This can result in higher cutting efficiency, longer blade life, and better overall performance.
In industries where high-precision cutting is critical, such as aerospace, automotive, or electronics manufacturing, cutting blades need to meet stringent tolerances and specifications. In these applications, the blades must not only be sharp and durable but also consistently produce high-quality cuts with minimal deviation. These blades are often subjected to rigorous testing to ensure that they can withstand the demands of precision cutting without failure. Specialized blades for these industries may also feature advanced coatings to resist heat, corrosion, and wear, ensuring that they maintain their performance over extended periods of use.
The future of cutting blades in circle cutting machines will likely involve even more advancements in materials science, coatings, and blade geometry. As cutting technologies continue to evolve, the demand for cutting blades that can perform under increasingly challenging conditions will drive innovation in blade design. New materials such as superhard composites, ceramics, and advanced alloys may become more commonly used in blade construction, providing enhanced durability and cutting performance. Additionally, advancements in machine learning and predictive analytics could allow cutting machines to adjust their operations based on the condition of the cutting blade, optimizing performance and minimizing the need for manual intervention.
In conclusion, cutting blades are a fundamental component of circle cutting machines, and their design, material composition, sharpness, and maintenance directly impact the performance and quality of the cutting process. Selecting the appropriate blade for a given application is crucial for achieving efficient and precise cuts while minimizing wear and prolonging the life of the blade. With ongoing advancements in materials, coatings, and blade geometry, the future of cutting blades in circle cutting machines will likely see continued improvements in efficiency, durability, and performance, ultimately contributing to higher-quality manufacturing and reduced operational costs.
As cutting blade technology continues to evolve, there is also an increased focus on sustainability within the industry. One aspect of this is the development of more eco-friendly materials for blades and coatings. Traditional cutting blades often rely on metals and coatings that, while effective, may not be the most sustainable options in the long term. Manufacturers are exploring alternative materials that offer comparable durability and performance but have a lower environmental impact. For example, there is growing interest in the use of recycled metals and composites in blade construction, which can help reduce the demand for new raw materials and lower the overall environmental footprint of the manufacturing process.
In addition to the materials used in the blades themselves, sustainable cutting practices are also becoming more important. As industries seek to reduce waste and improve resource efficiency, manufacturers are looking for ways to optimize the cutting process to minimize scrap and improve material utilization. Cutting blades with higher precision, for example, can help reduce the amount of waste material generated during the cutting process. By achieving cleaner cuts with less burr, deformation, or waste, these blades can contribute to more sustainable production practices.
Another emerging trend is the adoption of digital technologies that can further optimize the cutting process and the performance of cutting blades. Through the use of sensors, data analytics, and machine learning, manufacturers can monitor the condition of cutting blades in real-time and adjust the cutting parameters to extend the life of the blade. These technologies can detect early signs of wear, misalignment, or damage, allowing for proactive maintenance and reducing the need for frequent blade replacements. By keeping blades in optimal condition for longer periods, manufacturers can reduce waste, lower costs, and improve the sustainability of their operations.
Furthermore, advancements in coating technologies may also contribute to more sustainable cutting practices. Coatings like titanium nitride (TiN) or diamond-like carbon (DLC) have been shown to extend the life of cutting blades significantly, reducing the frequency of blade replacements. These coatings help prevent wear, corrosion, and heat buildup, improving both performance and longevity. As coating technologies improve, they may become more cost-effective and environmentally friendly, providing manufacturers with longer-lasting, high-performance cutting blades that reduce waste and lower environmental impact.
The role of automation and robotics in the cutting process also holds potential for further improving the efficiency and sustainability of cutting operations. Automated systems can help optimize the cutting process, reducing waste by ensuring that the material is used as efficiently as possible. Robots can be programmed to adjust cutting parameters based on real-time data, optimizing the angle, speed, and force applied to the cutting blade. These systems can also minimize the risk of human error, which can lead to inefficient cutting practices, increased waste, or damaged blades.
In addition, as manufacturers continue to adopt Industry 4.0 principles and integrate cutting machines into smarter, more connected systems, the entire lifecycle of the cutting blades can be monitored and optimized. Data from multiple sources, such as sensors embedded in the cutting machine, operator input, and material specifications, can be integrated to create a comprehensive view of blade performance. This data-driven approach allows manufacturers to better understand the wear patterns of blades, optimize the timing of maintenance, and forecast when blades are likely to need replacement.
With the increasing push for sustainability, the development of cutting blades will likely focus on both performance and environmental impact. As technologies advance, manufacturers will be able to produce cutting blades that are not only more efficient, durable, and precise but also contribute to a more sustainable, circular economy. This evolution in blade technology will be essential in meeting the growing demands of industries that prioritize environmental responsibility, while still ensuring the highest levels of productivity and quality.
As cutting blades become more specialized and tailored to specific applications, there will also be an emphasis on designing blades that can handle a wider variety of materials and cutting tasks. Advances in blade coatings, materials science, and geometry will enable the production of multi-purpose blades capable of cutting through a range of materials without sacrificing performance or longevity. These all-purpose blades will be increasingly popular in industries where versatility is key, such as the automotive or aerospace sectors, where manufacturers often need to cut a range of materials with varying properties and thicknesses.
The cutting blade market is also likely to see innovations in blade recycling programs. As manufacturers become more environmentally conscious, there is potential for the development of closed-loop systems where used blades can be returned, reprocessed, and reused. By incorporating blade recycling into their operational practices, companies can help reduce the demand for new raw materials and ensure that used blades are disposed of in a sustainable manner. This could also lead to the development of specialized programs where blades are refurbished or reconditioned before being put back into use, extending their life cycle and reducing overall costs.
The demand for longer-lasting and more efficient cutting blades is expected to increase as industries continue to push for higher productivity and better quality. As competition intensifies, manufacturers will focus on maximizing the performance of their cutting machines by investing in cutting-edge blade technology. This will likely involve further research into new materials and advanced coating technologies that enhance the blades’ ability to withstand wear, heat, and corrosion, all while maintaining high cutting precision.
In conclusion, cutting blades will continue to play a central role in the performance of circle cutting machines, and ongoing advancements in materials, coatings, and design will further enhance their effectiveness and longevity. As manufacturers seek to optimize their operations, reduce waste, and improve sustainability, the cutting blade industry will evolve to meet these demands. Through technological innovation and a greater focus on environmental responsibility, cutting blades will not only deliver high-quality performance but also contribute to the broader goals of efficiency and sustainability in modern manufacturing.
Circle cutting machines can easily be used with stainless steel, aluminum, copper, and tin sheets for various industrial applications. The steel circles later are used to deep draw parts with a hydraulic press. For long-duration high-quality parts you can contact us as your supplier from our main page
For a better analysis of our circle blank cutting machine, you can check our video below
Our circle cutting machines are hand-operated. Hand-operated operations are safer as the operator needs to control the machine with his hands and he will need to keep his hands on the control board to operate the machine. Circle cutter machines are essential in production facilities where there is a deep drawing press. Deep drawing presses use round sheets to form vase forms by deep drawings.
With our round corner cutting machines or sheet metal circle cutting machines you can have a capacity as high as 1 piece in 4 seconds. With this capacity, you can feed 2 hydraulic presses with one 1 circle cutting machine easily
Circle cutting machines are versatile tools used in various industries and applications for precisely cutting circular shapes from a wide range of materials. They are commonly employed in industrial settings, craft workshops, and DIY projects.
Industrial Applications
- Manufacturing: Circle cutting machines are used in various manufacturing processes, such as cutting circular gaskets, seals, and components from rubber, plastic, and thin metal sheets. They are also used to cut circular patterns in fabrics and textiles for clothing and industrial applications.
- Packaging: Circle cutting machines are essential in the packaging industry for cutting circular packaging materials, such as cardboard discs, labels, and packaging inserts. They ensure precise dimensions and consistent quality for product packaging.
- Graphic Design and Printing: Circle cutting machines are used in graphic design and printing studios to cut circular shapes from paper, cardboard, and other materials for creating promotional materials, signage, and decorative elements.
Craft and DIY Applications
- Scrapbooking and Paper Crafts: Circle cutting machines are popular among scrapbookers and paper crafters for cutting circular embellishments, decorative shapes, and photo mats. They provide a precise and efficient way to create custom elements for scrapbooking projects.
- Jewelry Making: Circle cutting machines are used in jewelry making to cut circular shapes from leather, felt, and other materials for creating jewelry components, such as pendants, earrings, and bracelets. They ensure consistent shapes and sizes for jewelry designs.
- Home Décor and DIY Projects: Circle cutting machines are versatile tools for DIY projects, such as cutting circular patterns from fabrics for quilting, sewing, and home décor accents. They can also be used to cut circular shapes from materials like felt, foam, and cork for crafting projects.
- Model Making and Architectural Design: Circle cutting machines are used in model making and architectural design to cut circular shapes from various materials, such as cardboard, balsa wood, and foam, for creating models and prototypes. They provide precision and accuracy for detailed work.
General Safety Guidelines
When operating circle cutting machines, safety is paramount. Always follow these general guidelines:
- Wear Personal Protective Equipment (PPE): Always wear safety glasses, gloves, and a cutting mat to protect yourself from sharp blades, flying debris, and potential cuts.
- Securely Clamp the Workpiece: Ensure the workpiece is firmly clamped to the machine’s work surface to prevent it from slipping or moving during cutting.
- Use the Correct Blade or Punch: Choose the appropriate blade or punch size and type for the material and desired circle size. Using the wrong blade or punch can damage the material or cause injury.
- Maintain Proper Blade or Punch Sharpness: Regularly sharpen or replace blades and punches to ensure they are sharp and maintain cutting efficiency. Dull blades can cause ragged edges and increase the risk of injury.
- Handle with Care: Always handle the machine with care, avoiding sudden movements or forceful actions that could lead to accidents.
- Never Touch the Moving Blade or Punch: Never touch the moving blade or punch while the machine is in operation.
- Turn Off the Machine Before Making Adjustments: Always turn off the machine before making any adjustments or changing the blade or punch.
- Store the Machine Properly: Store the machine in a safe, secure location when not in use, keeping it out of reach of children and unauthorized users.
By adhering to these safety guidelines and operating the machine responsibly, you can effectively utilize circle cutting machines for various applications while minimizing the risk of injury.
Sheet Metal Circle Cutter Machine
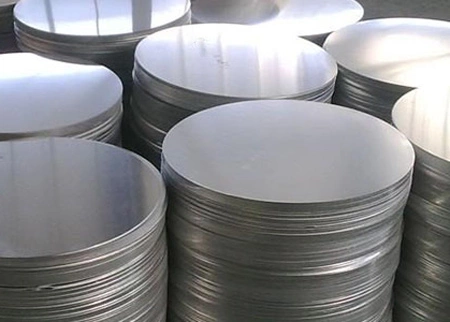
How do you cut a circle in sheet metal?
Our sheet metal circle cutter machine can cut from as small as 2″ of circle blanks on sheet metal surfaces up to 12″ in diameter. The circle diameter to be cut can be arranged on the machine. The cutting tool is made from high-carbon cutting steel specially produced for metal cutting operations. The frame of the machine is complete welded steel and all the machinery goes through stress-relieving after the manufacturing is finished. Circle cutting machines are widely used in the cookware industry.
How do you cut big circles in metal?
with our sheet metal circle cutting machine, you can cut circle blanks from square metal sheets with sheet thickness starting from 0.1 mm up to 5 mm. The diameter also can be arranged from 5 cm up to 30 cm.
The circle cutting machine is a type of machine that can cut circles out of metal sheets. It is also called an automatic circle cutter or a steel circle cutter.
It is used to cut circles out of metal sheets. The machine has a circular blade that rotates around the circumference of the sheet. The operator sets the size and radius of the desired hole and then presses start to begin cutting.
The circle cutting machine is an automatic machine that cuts circles from flat steel sheets.
The circle cutting machine is a type of metalworking equipment that is used to cut circles in sheet metal. This equipment can be used for a variety of purposes, including manufacturing and construction. The round steel sheet, which is the most common material used in the process, can be cut into circles using this machine.
Methods for Cutting Circles in Sheet Metal
- Hole Saw: For smaller circles, a hole saw can be used. It’s a cylindrical tool with teeth around the edge.
- Plasma Cutter: For larger circles or thicker metal, a plasma cutter offers precise cutting.
- Laser Cutter: Provides the highest accuracy and speed for cutting circles, especially in complex shapes.
- Water Jet Cutting: Similar to laser cutting, but uses a high-pressure water jet with abrasive particles.
- Manual Cutting: For smaller, less precise circles, a metal cutting saw or even a grinder can be used, but this method is time-consuming and requires skill.
- Circle Cutter: A specialized tool for cutting circles, available in manual and electric versions.
Factors to Consider
- Metal Thickness: Thicker metal requires more powerful cutting tools.
- Circle Diameter: Larger circles may require different cutting methods.
- Desired Accuracy: For precise circles, laser or water jet cutting is ideal.
- Material Type: Some metals might require specific cutting techniques.
Safety Precautions
- Always wear appropriate safety gear, including eye protection, gloves, and hearing protection.
- Ensure the workpiece is securely clamped to prevent movement.
- Follow the manufacturer’s instructions for the cutting tool you are using.
Adjustable Circle Cutter for Metal
An adjustable circle cutter typically consists of a central body that houses a pilot drill bit and an adjustable cutting blade.expand_more The pilot drill bit, usually made of high-speed steel (HSS) for durability, ensures the cutter stays centered while drilling into the metal. The cutting blade, also crafted from HSS for its ability to handle tough materials, is the workhorse of the tool.exclamation It can be adjusted outwards or inwards using a screw mechanism, allowing you to set the desired cutting diameter. Some models come with replaceable blades for extended use.
Operational Advantages
- Versatility: The key benefit of an adjustable circle cutter is its ability to cut various hole sizes within its range. This eliminates the need to purchase and carry multiple hole saws for different sized holes.
- Precision: When used correctly, adjustable circle cutters can produce clean, burr-free holes with minimal material distortion. The pilot drill bit helps maintain accuracy throughout the cutting process.
- Cost-Effective: Compared to buying multiple hole saws, an adjustable circle cutter offers a more economical solution for creating holes in various sizes.
- Drill Press Compatibility: Most adjustable circle cutters are designed for use with a drill press.expand_more The secure mounting of the drill press ensures stability and control while cutting, leading to cleaner cuts.exclamation
Factors to Consider When Choosing an Adjustable Circle Cutter
- Cutting Capacity: Adjustable circle cutters come with different maximum cutting diameters. Choose one that accommodates your typical hole size requirements. Common ranges include 1 inch to 6 inches, 2 inches to 12 inches, and even larger options for heavy-duty applications.
- Material Compatibility: While most adjustable circle cutters can handle sheet metal, brass, aluminum, and soft steel, some may not be suitable for very hard metals. Ensure the cutter you choose is rated for the type of metal you plan to work with.exclamation
- Shank Size: The shank is the part of the cutter that fits into the drill press chuck. Make sure the shank size of the cutter matches the chuck capacity of your drill press. Common shank sizes include 3/8 inch and 1/2 inch.
- Pilot Drill Bit Size: The pilot drill bit size should complement the cutting blade size.exclamation It ensures the cutter remains centered and prevents the metal from binding during the cutting process. Some adjustable circle cutters come with replaceable pilot drill bits.expand_more
Using an Adjustable Circle Cutter Safely and Effectively
- Clamp Your Workpiece Securely: Always ensure your metal sheet is firmly clamped to a stable work surface to prevent movement during cutting.expand_more
- Lubricate the Cutter: Use a cutting lubricant to reduce friction and extend the life of the blade.
- Start with a Pilot Hole (Optional): For thicker metals, drilling a pilot hole slightly smaller than the desired cut diameter can help center the adjustable circle cutter and make the cutting process smoother.
- Apply Moderate Pressure: Let the cutter do the work. Don’t force it through the metal, as this can cause the blade to bind or break.
- Maintain a Steady Speed: Use a moderate and consistent drill press speed for optimal cutting performance. Refer to the manufacturer’s instructions for recommended speeds based on the material and hole diameter.
With proper selection, use, and care, an adjustable circle cutter can become a valuable tool in your metalworking arsenal, saving you time, money, and effort while delivering clean and precise holes in your projects.
Which machine is used to cut rings or circular sheet metal?
There are two main machines used for cutting rings or circular sheet metal, each with its own advantages:
- Circular Shears: These machines are specifically designed for cutting out rings and discs from sheet metal. They typically have a stationary lower blade and a rotating upper blade that travels along a circular track. The metal sheet is fed between the blades, resulting in a clean, continuous cut. Circular shears can handle a wider range of metal thicknesses compared to some adjustable circle cutters.
- Adjustable Circle Cutters: As discussed previously, these versatile tools can be used to create circular holes in sheet metal. However, with some adjustments, they can also be used to cut out rings. This method involves making two cuts with the adjustable circle cutter: one for the inner diameter of the ring and another for the outer diameter. While less specialized than circular shears, adjustable circle cutters offer more flexibility in terms of creating holes of various sizes within their range.
Circular Shears
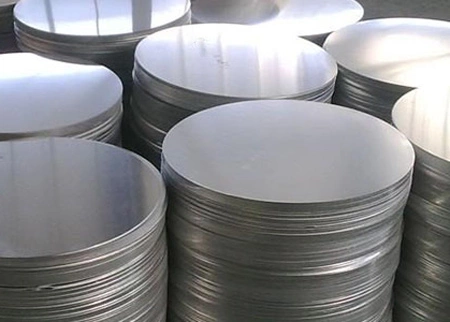
Circular shears, also known as rotary shears or ring shears, are specialized machines designed for efficiently and precisely cutting out rings and discs from sheet metal. They are ideal for high-volume production environments or applications requiring consistent, clean cuts in various ring sizes.
How They Work:
A circular shear typically has a sturdy base that houses the cutting mechanism. This mechanism consists of two key components:
- Lower Blade: This is a stationary, sharp blade secured to the base of the machine. It’s usually made from high-quality tool steel for durability.
- Upper Blade: This is a rotating blade mounted on an arm that travels along a circular track. The arm can be adjusted to set the desired cutting diameter for the ring. The upper blade is also crafted from tool steel for clean and efficient cutting.
Operation and Advantages:
- Simple Operation: Circular shears are relatively straightforward to operate. Once the sheet metal is positioned and the desired cutting diameter is set, the operator engages the machine. The upper blade rotates and presses against the sheet metal, shearing it cleanly along the pre-determined circular path.
- High Production Rate: Circular shears excel in production environments where repetitive cutting of rings is needed. They can handle a wider range of metal thicknesses compared to some adjustable circle cutters, making them suitable for heavier-duty applications.
- Clean and Accurate Cuts: The shearing action produces clean, burr-free edges on the cut rings. Additionally, the precise adjustment mechanism ensures consistent ring diameters throughout the cutting process.
- Versatility: While primarily used for rings, some circular shears offer the ability to make straight cuts as well. This adds to their overall functionality.
Choosing the Right Circular Shear:
When selecting a circular shear, consider the following factors:
- Cutting Capacity: Circular shears come with different maximum cutting diameters and throat depths (the maximum width of sheet metal they can handle). Choose one that accommodates your typical ring size and sheet metal thickness requirements.
- Material Compatibility: Ensure the shear is rated for the type of metal you plan to cut. Some models may be suitable for tougher materials like stainless steel.
- Power Source: Circular shears can be manually operated, powered by electric motors, or hydraulically driven. Electric and hydraulic models offer greater cutting force and efficiency for thicker metals.
- Additional Features: Some circular shears come with features like adjustable cutting speeds, digital displays for precise diameter settings, and foot pedals for hands-free operation.
Safety Considerations:
Always follow safety precautions when operating a circular shear, including wearing safety glasses, gloves, and proper clothing. Ensure the machine is properly secured and the sheet metal is firmly clamped in place before starting the cut.
In conclusion, circular shears are a powerful and efficient solution for cutting rings and discs from sheet metal. Their ability to handle high volumes, produce clean cuts, and accommodate various ring sizes makes them a valuable asset for metalworking professionals.
Adjustable Circle Cutter
Adjustable circle cutters, while not as specialized as circular shears, offer a versatile and cost-effective solution for creating holes in sheet metal. They can also be used, with a bit more work, to cut out rings.
How They Work:
An adjustable circle cutter is a more compact tool compared to a circular shear. It typically consists of:
- Central Body: This houses the mechanism for adjusting the cutting diameter.
- Pilot Drill Bit: Made from high-speed steel (HSS) for strength, it drills a pilot hole to center the cutter and prevent wandering.
- Adjustable Cutting Blade: Also crafted from HSS, this blade can be moved inwards or outwards using a screw mechanism to set the desired cutting diameter.
- Shank: This fits into the chuck of a drill press, providing stability and power for cutting.
Advantages:
- Versatility: The key benefit is the ability to cut various hole sizes within its range, eliminating the need for multiple hole saws.
- Cost-Effective: Compared to buying numerous hole saws, an adjustable circle cutter offers a more economical solution.
- Drill Press Compatibility: Most models are designed for use with a drill press, which provides stability and control for cleaner cuts.
- Can Cut Rings (with some effort): By making two cuts with the adjustable circle cutter (one for the inner and outer diameter), you can create rings from sheet metal.
Things to Consider When Choosing an Adjustable Circle Cutter:
- Cutting Capacity: Choose a cutter that accommodates your typical hole size requirements. Common ranges include 1 inch to 6 inches, 2 inches to 12 inches, and even larger options.
- Material Compatibility: Ensure the cutter is rated for the type of metal you plan to work with, such as sheet metal, brass, aluminum, or soft steel.
- Shank Size: Match the shank size of the cutter to the chuck capacity of your drill press (common sizes are 3/8 inch and 1/2 inch).
- Pilot Drill Bit Size: This should complement the cutting blade size for optimal centering and cutting performance. Some models come with replaceable pilot drill bits.
Using an Adjustable Circle Cutter Effectively:
- Clamp Your Workpiece Securely: Ensure the metal sheet is firmly clamped to prevent movement during cutting.
- Lubricate the Cutter: Use a cutting lubricant to reduce friction and extend blade life.
- Pilot Hole (Optional): For thicker metals, consider drilling a pilot hole slightly smaller than the desired cut for better centering and smoother cutting.
- Moderate Pressure: Let the cutter do the work. Don’t force it, as this can damage the blade.
- Maintain a Steady Speed: Use a moderate and consistent drill press speed for optimal results. Refer to the manufacturer’s instructions for recommended speeds based on material and hole diameter.
While not a replacement for a dedicated circular shear for high-volume ring cutting, adjustable circle cutters offer a practical and adaptable solution for various hole-making needs in sheet metal, with the added bonus of creating rings when required.
EMS Metalworking Machines
We design, manufacture and assembly metalworking machinery such as:
- Hydraulic transfer press
- Glass mosaic press
- Hydraulic deep drawing press
- Casting press
- Hydraulic cold forming press
- Hydroforming press
- Composite press
- Silicone rubber moulding press
- Brake pad press
- Melamine press
- SMC & BMC Press
- Labrotaroy press
- Edge cutting trimming machine
- Edge curling machine
- Trimming beading machine
- Trimming joggling machine
- Cookware production line
- Pipe bending machine
- Profile bending machine
- Bandsaw for metal
- Cylindrical welding machine
- Horizontal pres and cookware
- Kitchenware, hotelware
- Bakeware and cuttlery production machinery
as a complete line as well as an individual machine such as:
- Edge cutting trimming beading machines
- Polishing and grinding machines for pot and pans
- Hydraulic drawing presses
- Circle blanking machines
- Riveting machine
- Hole punching machines
- Press feeding machine
You can check our machinery at work at: EMS Metalworking Machinery – YouTube
Applications:
- Beading and ribbing
- Flanging
- Trimming
- Curling
- Lock-seaming
- Ribbing
- Flange-punching