The CNC Buffing Machine is a polishing finishing machine for metal surfaces. Low Price & High Quality & Free consultation from the manufacturer
Buffing is the processing of a metal surface to give a desired finish. Depending on the desired finish, buffing has four basic categories: satin finishing, cutdown buffing, cut-and-color buffing, and luster buffing. Satin finishing produces a satin or directional lined finish; other types of satin finishing are brushed or Butler finishing.
Cutdown buffing produces an initial smoothness; cut-and-color buffing produces an intermediate luster; and luster buffing (color buffing) produces high reflectivity or mirror finish.
CNC Buffing Machine
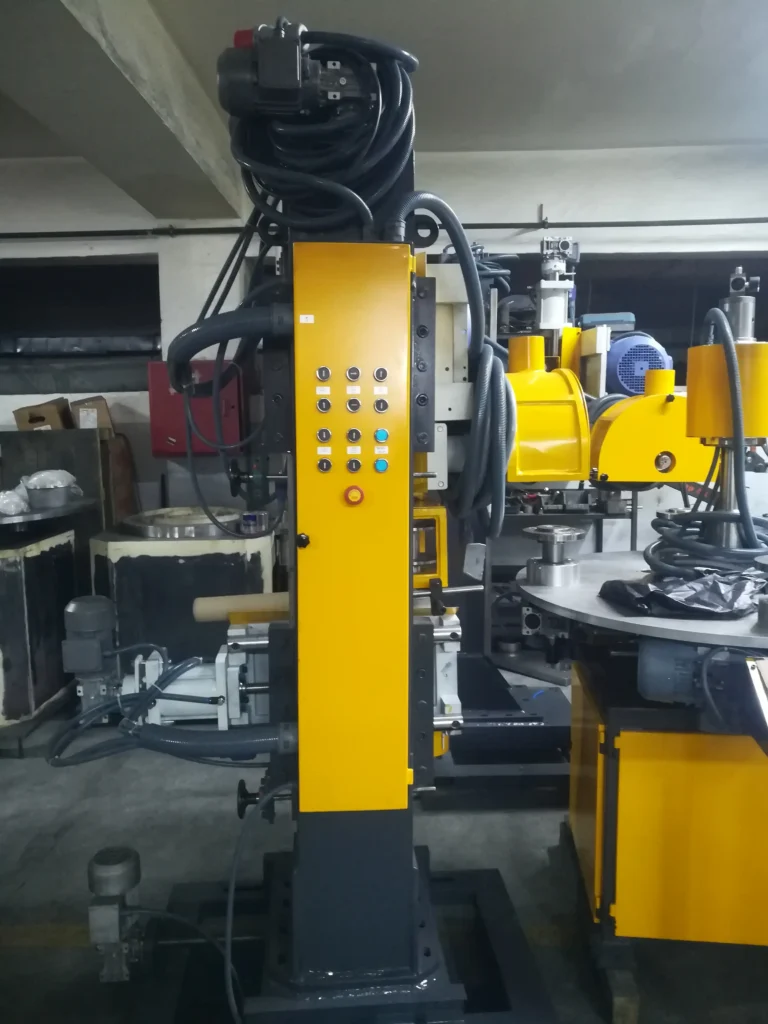
CNC buffing machines are advanced metal polishing machines that utilize computer numerical control (CNC) technology to automate and optimize the buffing process. They offer a combination of precision, efficiency, consistency, and flexibility, making them ideal for high-volume manufacturing operations and demanding applications.
Components of CNC Buffing Machines
- CNC Controller: The CNC controller is the heart of the machine, responsible for interpreting CNC code and controlling the machine’s movements. It utilizes software and algorithms to precisely guide the buffing tool along complex paths and maintain consistent polishing parameters.
- Robotic Arm: The robotic arm provides the dexterity and range of motion to manipulate the buffing tool and workpiece. It consists of multiple joints and actuators, controlled by the CNC controller, enabling precise positioning, orientation, and movement.
- Buffing Tool: The buffing tool is the interface between the robotic arm and the workpiece. It can be a buffing wheel, mop, or other abrasive component, depending on the specific application and desired finish. The robotic arm precisely controls the tool’s movement, pressure, and angle during polishing.
- Workpiece Holding Fixture: The workpiece holding fixture securely positions the workpiece during the buffing process. It can be a simple clamp or a more complex fixture designed for specific workpiece shapes or sizes.
- Polishing Compound Delivery System: This system automatically dispenses polishing compounds onto the buffing tool, ensuring a consistent supply of abrasives and lubricants throughout the polishing process. It may utilize pumps, valves, and sensors to control the compound flow precisely.
- Dust Collection System: Removes airborne dust and debris generated during polishing to prevent respiratory hazards and maintain a clean work environment.
Applications of CNC Buffing Machines
CNC buffing machines are primarily used in large-scale manufacturing operations where high volume, precision, consistency, and flexibility are critical. They are particularly well-suited for applications such as:
- Automotive Industry: Polishing car bodies, wheels, and trim to achieve a uniform, high-quality finish across a wide range of models and variants.
- Aerospace Industry: Polishing aircraft components, such as wings, fuselages, and engine parts, to reduce drag, improve aerodynamic performance, and meet stringent quality standards for critical components.
- Electronics Industry: Polishing electronic components, such as housings, casings, and circuit boards, to achieve a clean, smooth finish, enhance aesthetics, and protect against corrosion, especially for high-end devices.
- Construction Industry: Polishing architectural components, such as railings, handrails, and door handles, to create a visually appealing and durable finish, especially for large-scale construction projects or high-end architectural elements.
- Consumer Goods Industry: Polishing appliances, cookware, and other consumer goods to enhance their appearance, extend their lifespan, and maintain consistent quality across large production runs, especially for premium products or luxury brands.
Benefits of CNC Buffing Machines
CNC buffing machines offer several advantages over traditional manual or semi-automated buffing methods:
- Precision: CNC technology ensures precise and consistent polishing, eliminating human error and achieving a uniform finish across all workpieces.
- Efficiency: CNC machines can operate continuously with minimal breaks, significantly increasing production output and reducing labor costs.
- Consistency: CNC machines maintain consistent polishing parameters, ensuring consistent results across all workpieces, even for complex shapes or intricate details.
- Flexibility: CNC machines can be programmed for a wide range of polishing tasks, accommodating different workpiece shapes, sizes, and desired finishes.
- Reduced Labor Costs: Automation eliminates the need for manual labor, reducing labor costs and improving overall production efficiency.
- Safety: CNC machines minimize worker exposure to hazardous moving parts, abrasive dust, and metal particles, promoting a safer work environment.
Conclusion
CNC buffing machines represent a significant advancement in metal finishing technology, offering a combination of precision, efficiency, consistency, and flexibility. Their ability to automate complex buffing tasks, maintain consistent quality standards, and adapt to diverse workpiece requirements makes them indispensable tools in large-scale manufacturing operations and demanding applications. As technology continues to evolve, CNC buffing machines are expected to play an increasingly crucial role in various industries, contributing to improved product quality, reduced manufacturing costs, enhanced worker safety, and increased production flexibility.
Types of Buffing Compounds Compositions
The greaseless compound is used to produce a satin finish or a directional lined finish. The greaseless compound contains water, glue, and abrasive. As its name implies, it retains the abrasive on the buffing wheel in a grease-free environment, leaving the surface of the finished part clean and free of greasy residue.
The principal uses of the greaseless compounds are for satin finishing or flexible deburring. Generally, the abrasive contained in such compounds is silicon carbide or fused aluminum oxide. Grades are available in abrasive sizing from 80 grit to finer depending on the degree of dullness required on a particular base metal. Silicon carbide abrasives are used for the finishing of stainless steel and aluminum.
Aluminum oxide grades are used for brass and other nonferrous metals, as well as for carbon steel prior to plating. To produce a finer satin finish on nonferrous materials, fine emery and hard silica are used. For Butler finishes on silver plate and sterling, fine buffing powders of unfused aluminum oxide and soft silica are used. Greaseless compounds are applied to a revolving buff by frictional transfer.
The buff speed is 4,000 to 6,000 surface feet per minute (SFM). The material then melts on the cotton buff, adheres to the peripheral surface, and dries in a short period of time. This produces a dry, abrasive-coated wheel with a flexible surface. The buffing wheels on which greaseless compounds can be applied are sewn muslin buffs, pocketed buffs, full disk loose buffs, and strong wheels. The coarser the abrasive particle, the duller the satin finish; the finer the abrasive particle, the brighter will be the satin finish.
Bar Compounds
Bar compounds contain two types of ingredients; binder and abrasive. The
binder can consist of one or more materials taken from animal or vegetable fats as well as petroleum and similarly derived products. Animal fats are such materials as fatty acids, tallows, and glycerides.
Waxes can be from vegetable, insect, or petroleum-based products. Petroleum-based or vegetable-based oils also may be used. The animal and vegetable materials are more saponifiable and will produce a water-soluble soap when combined with an alkali.
Petroleum, mineral oils, and waxes are unsaponifiable and, therefore, might create subsequent cleaning problems. Each ingredient is added to the binder to transmit a specific effect to the bar compound such as lubricity, degree of hardness, or improved adherence to a buffing wheel. A binder also controls the amount of frictional heat that can be developed on a surface. This is called a slip. There is a wide range of abrasives used in buffing compounds, a few of which will be described.
Buffing Abrasives for the CNC Buffing Machine
Aluminum oxide powders, fused and unfused, are the abrasives most commonly used in the buffing of hard metals. Chromium oxide is used to achieve the highest reflectivity (color) on stainless steel, chromium, and nickel plate. To achieve a high reflectivity (color) on brass, gold, copper, and silver, iron oxide is generally used. Aluminum oxide is chemically represented as Al2O3.
The unfused aluminum oxide is white in color. This is manufactured from
bauxite or hydrated aluminum oxide by heating it at elevated temperatures. This heating process, called calcination, gives the abrasive the common name calcinated alumina. The higher the calcination temperature, the more water of hydration is driven off and the harder the crystalline material becomes.
When the calcinated temperature is about 950oC, the product produced is a soft alumina having a porous structure. This type of abrasive is used for luster or color buffing. When the calcined temperature is about 1,250oC, a harder alumina is produced. This type of abrasive is used for cutting. Soft aluminas are used to produce luster or a higher reflectivity on all metals, both ferrous and nonferrous. The harder aluminas will cut and remove more metal from the surface of castings or extrusions of aluminum, brass, and other metals.
Abrasive wheels for the CNC Buffing Machine
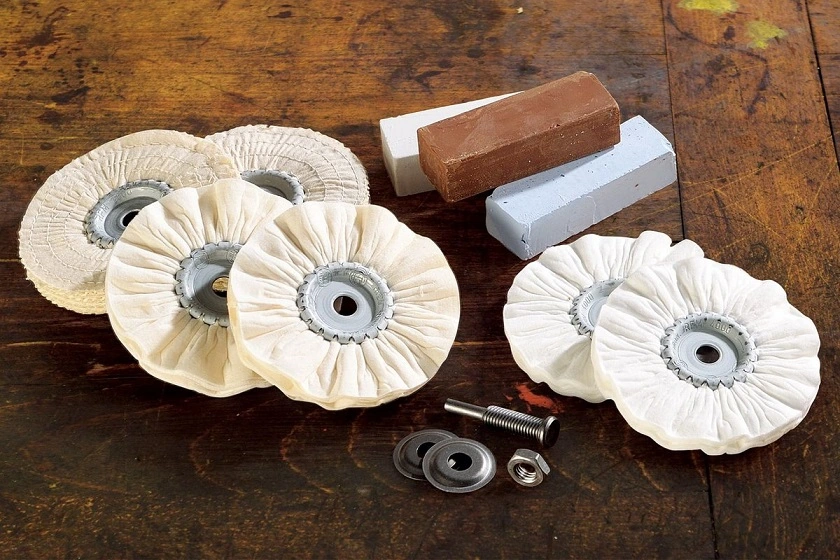
When alumina is heated to 1,850oC, fused aluminum oxide (Al2O3 ) is produced. This material is made in an electric furnace at approximately 2,000oC. Bauxite, when mixed with alumina and other oxide materials, produces a specific crystalline structure whose hardness can be varied to meet specified physical properties. This fused mass is then cooled and crushed.
In the crushing process, the material is ground, screened to the appropriate size, treated magnetically, and acid washed. It is then rescreened to its final classification (grit sizing). The difference between fused aluminum oxide and calcined alumina is that the fused oxide is of a crystalline structure that is much harder than the calcined alumina. Fused aluminum oxide is used mainly on abrasive belts or setup wheels for polishing. As for buffing, fused aluminum oxide is used for cutting down ferrous metals. The abrasive sizing is generally from 60 grit to -325 grit for buffing compounds.
Types of Polishing and Buffing Machines
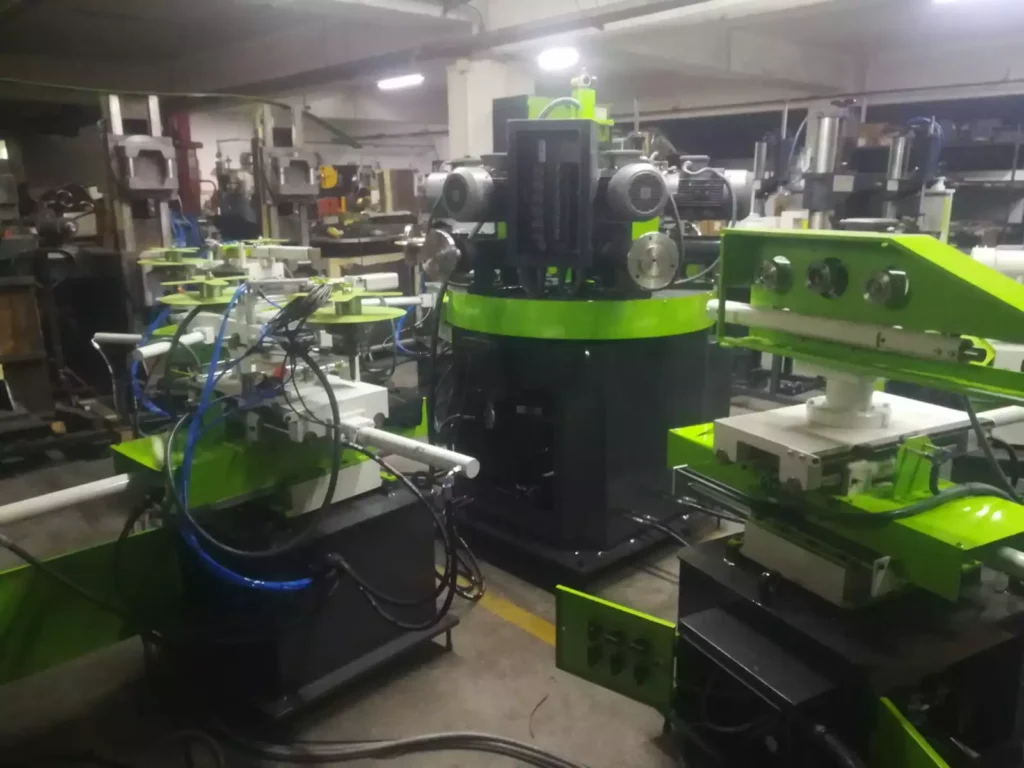
Manual Machines
Manual polishing and buffing machines are the most basic type, requiring direct human operation. These machines are suitable for small-scale operations and tasks that need a hands-on approach. They are typically used for intricate work where precision and control are paramount.
Key Features:
- Simple design and operation.
- Cost-effective for small jobs.
- Ideal for detailed and delicate work.
Applications:
- Jewelry and watchmaking.
- Small metal parts in the automotive and aerospace industries.
Semi-Automatic Machines
Semi-automatic polishing and buffing machines combine manual and automated features. They allow for greater control over the process while improving efficiency compared to fully manual machines. Operators can set parameters and oversee the operation, making adjustments as necessary.
Key Features:
- Enhanced control with automated functions.
- Increased efficiency and throughput.
- Suitable for medium-scale operations.
Applications:
- Mid-sized manufacturing units.
- Complex parts requiring a balance of manual oversight and automation.
CNC (Computer Numerical Control) Machines
CNC polishing and buffing machines represent the pinnacle of automation and precision in surface finishing. These machines use computer-controlled systems to manage the movement and operation of polishing tools with high accuracy. CNC machines are highly programmable, allowing for the automation of complex and repetitive tasks.
Key Features:
- High precision and repeatability.
- Ability to handle complex shapes and surfaces.
- Programmable for different tasks and materials.
Benefits:
- Consistent and high-quality finishes.
- Reduced labor costs and increased productivity.
- Flexibility in manufacturing processes.
Applications:
- Aerospace components.
- High-end automotive parts.
- Medical devices and implants.
NC (Numerical Control) Machines
NC machines, while similar to CNC machines, are generally less sophisticated and do not offer the same level of flexibility and automation. They are controlled by pre-set instructions but lack the advanced programmability of CNC systems.
Key Features:
- Automated control with limited programmability.
- Suitable for less complex tasks.
- Cost-effective compared to CNC machines.
Applications:
- Standardized parts in automotive and metalworking industries.
- Tasks that do not require frequent changes in setup.
Applications of Polishing and Buffing Machines
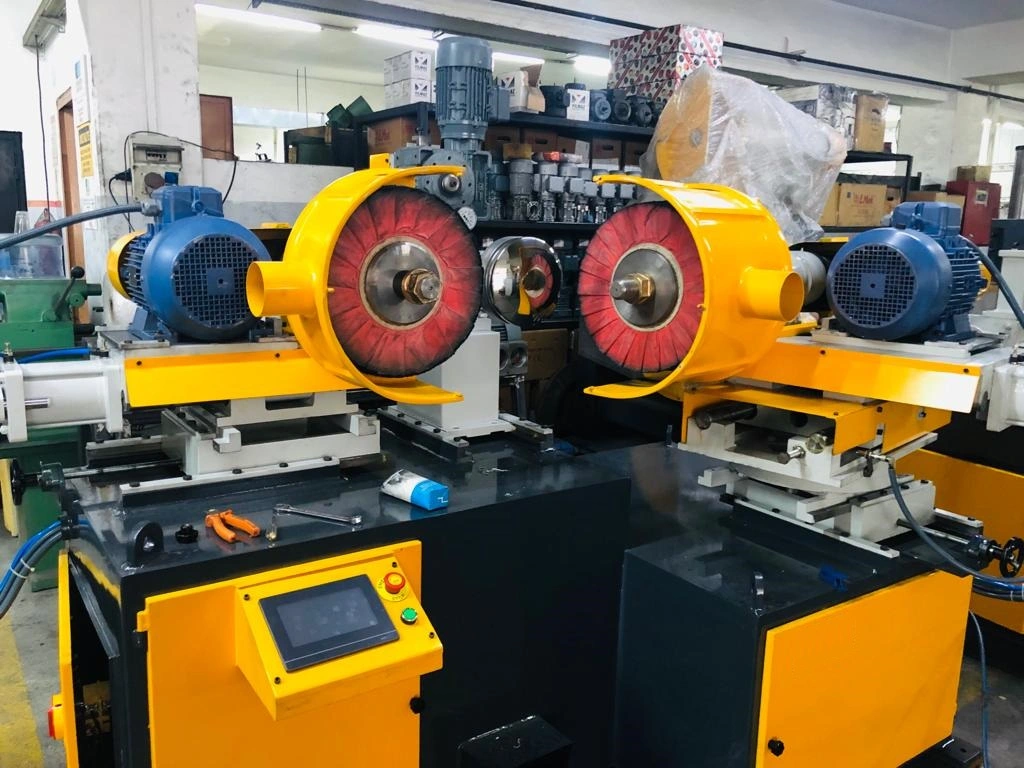
Automotive Industry
In the automotive industry, polishing and buffing are essential for achieving high-quality finishes on car parts. This includes the polishing of body panels, trim pieces, and engine components to enhance both aesthetics and performance.
Key Uses:
- Surface finishing of body panels.
- Polishing of chrome and aluminum trim.
- Buffing of engine and transmission parts.
Aerospace Industry
The aerospace industry demands the highest standards of precision and quality. Polishing and buffing are critical for ensuring the smooth surfaces necessary for aerodynamics and the performance of critical components.
Key Uses:
- Polishing turbine blades and engine parts.
- Finishing structural components for reduced drag.
- Ensuring the integrity of critical safety parts.
Metalworking Industry
In metalworking, polishing and buffing machines are used to finish metal parts, improving their appearance, resistance to corrosion, and overall quality.
Key Uses:
- Buffing of steel and aluminum parts.
- Finishing of tools and machinery components.
- Surface preparation for coating and painting.
Jewelry and Watchmaking
Precision and aesthetic appeal are paramount in jewelry and watchmaking. Polishing and buffing machines ensure that each piece has a flawless finish.
Key Uses:
- Polishing of precious metals and gemstones.
- Buffing intricate watch parts.
- Achieving high-shine finishes on jewelry.
Electronics Industry
In the electronics industry, surface preparation is crucial for the functionality and longevity of components. Polishing and buffing machines are used to prepare surfaces for assembly and coating.
Key Uses:
- Polishing of semiconductor wafers.
- Buffing of electronic enclosures and cases.
- Surface preparation for circuit boards.
Medical Device Manufacturing
The medical industry relies on highly polished surfaces for both functionality and hygiene. Polishing and buffing machines ensure that surgical instruments and implants meet stringent standards.
Key Uses:
- Polishing surgical instruments.
- Finishing orthopedic implants.
- Ensuring biocompatibility of medical devices.
Consumer Goods
Polishing and buffing are also used in the production of consumer goods, enhancing the aesthetic appeal and durability of everyday items.
Key Uses:
- Finishing of household appliances.
- Polishing of kitchen utensils and cutlery.
- Buffing of decorative items and hardware.
Production Process of Polishing and Buffing Machines
Design and Engineering
The production of polishing and buffing machines begins with design and engineering. This involves conceptualizing the machine, creating detailed CAD models, and planning the manufacturing process.
Steps:
- Conceptual design and feasibility studies.
- Detailed engineering using CAD software.
- Prototype development and testing.
Material Selection
Selecting the right materials is crucial for the durability and performance of polishing and buffing machines. Common materials include high-grade steels, aluminum alloys, and composite materials for specific parts.
Considerations:
- Durability and wear resistance.
- Weight and strength.
- Compatibility with various polishing materials.
Manufacturing Techniques
Manufacturing polishing and buffing machines involves several techniques, including machining, welding, assembly, and quality control. Each step is critical to ensuring the final product meets industry standards.
Techniques:
- CNC machining of components.
- Welding and fabrication of the machine frame.
- Assembly of mechanical and electronic parts.
- Rigorous testing and quality assurance.
Quality Control
Quality control is an integral part of the production process, ensuring that each machine meets the required specifications and performs reliably.
Methods:
- In-process inspections.
- Final testing of performance and safety.
- Certification to industry standards.
Materials Polished with Industrial Machines

Metals
Metals are the most common materials polished with industrial machines. This includes a wide range of metals used in various industries.
Examples:
- Stainless steel.
- Aluminum.
- Brass.
- Titanium.
Plastics
Certain types of plastics can also be polished to achieve a smooth and glossy finish, particularly in the electronics and consumer goods industries.
Examples:
- Acrylics.
- Polycarbonates.
- PVC.
Wood
Polishing wood can enhance its natural beauty and protect it from damage. This is commonly done in furniture making and decorative items.
Examples:
- Hardwood (oak, mahogany).
- Softwood (pine, cedar).
- Engineered wood (plywood, MDF).
Ceramics and Glass
Polishing ceramics and glass is delicate work that requires specialized techniques to avoid cracking and chipping.
Examples:
- Fine china.
- Glassware.
- Porcelain tiles.
Composites
Composites are used in advanced industries such as aerospace and automotive. Polishing these materials requires specialized equipment to handle their unique properties.
Examples:
- Carbon fiber.
- Fiberglass.
- Kevlar.
Advantages of Using CNC and NC Machines
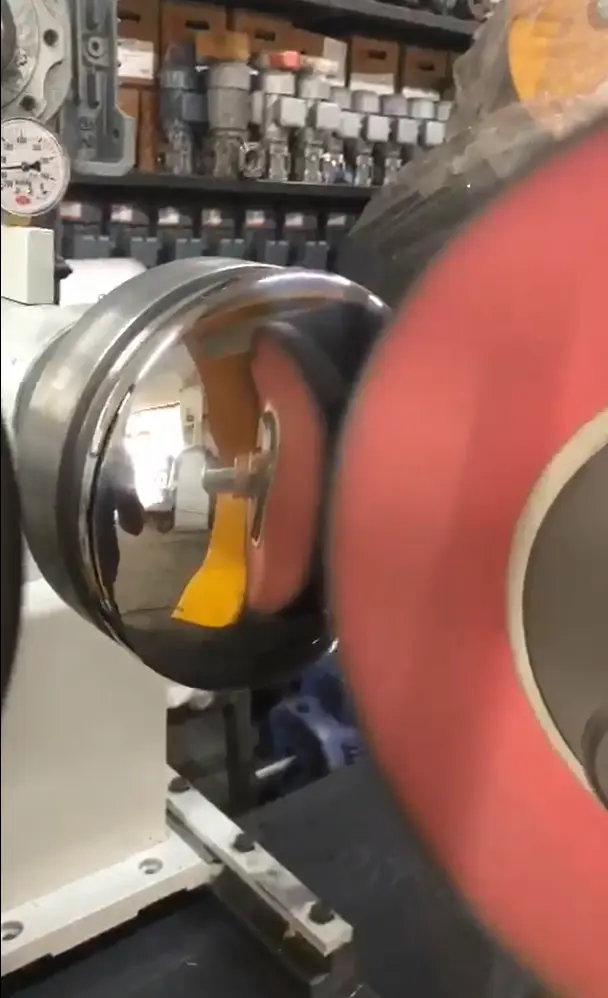
Precision and Consistency
CNC and NC machines offer unmatched precision and consistency, ensuring that each part meets exact specifications.
Benefits:
- Uniform finishes across large batches.
- High accuracy in complex geometries.
- Reduced human error.
Efficiency and Speed
These machines significantly reduce processing times, increasing overall productivity and allowing for faster turnaround times.
Benefits:
- Rapid processing of parts.
- Increased throughput.
- Shorter lead times.
Automation and Flexibility
Automation allows for continuous operation and the ability to handle multiple tasks without manual intervention.
Benefits:
- Customizable for various tasks.
- Minimal supervision required.
- Adaptable to different materials and shapes.
Cost-effectiveness
While the initial investment in CNC and NC machines can be high, the long-term savings in labor and increased efficiency make them cost-effective.
Benefits:
- Lower labor costs.
- High return on investment.
- Reduced material waste.
Challenges and Considerations
Initial Investment Costs
The cost of purchasing and installing CNC and NC machines can be significant, making it a major consideration for businesses.
Factors:
- Budgeting for high-quality machinery.
- Evaluating long-term benefits versus initial costs.
Maintenance and Upkeep
Regular maintenance is essential to ensure the longevity and performance of these machines.
Considerations:
- Scheduled maintenance and repairs.
- Availability of spare parts.
- Training for maintenance personnel.
Training and Skilled Labor
Operating CNC and NC machines requires skilled operators who understand the intricacies of programming and machine control.
Considerations:
- Investing in operator training.
- Ensuring continuous education on new technologies.
- Retaining skilled labor.
Technological Advancements
Keeping up with the latest advancements in technology is crucial for maintaining a competitive edge.
Considerations:
- Upgrading machinery and software.
- Staying informed about industry trends.
- Investing in research and development.
Future Trends in Polishing and Buffing Technology
Advancements in Automation and AI
The integration of artificial intelligence in polishing and buffing machines is set to revolutionize the industry by enhancing precision and efficiency.
Trends:
- AI-driven process optimization.
- Predictive maintenance using machine learning.
- Autonomous operation and monitoring.
Sustainable Practices
Sustainability is becoming increasingly important in manufacturing, with a focus on eco-friendly materials and processes.
Trends:
- Use of recyclable materials.
- Energy-efficient machinery.
- Reduction of waste and emissions.
Integration with Industry 4.0
Industry 4.0 involves the integration of smart technologies and IoT in manufacturing processes, providing real-time data and improving overall efficiency.
Trends:
- Smart manufacturing systems.
- Real-time monitoring and analytics.
- Enhanced connectivity and automation.
Conclusion
Industrial polishing and buffing machines play a vital role in various industries, ensuring that products meet the highest standards of quality and performance. From manual to advanced CNC and NC machines, each type offers unique benefits and is suited to different applications. Understanding the production processes, materials, and advantages of these machines is essential for businesses looking to improve their manufacturing capabilities. As technology continues to evolve, the future of polishing and buffing machines looks promising, with advancements in automation, sustainability, and smart manufacturing paving the way for more efficient and effective production methods.
By investing in the right equipment and staying informed about industry trends, manufacturers can achieve superior finishes, reduce costs, and maintain a competitive edge in their respective markets.