The buffing machine for metal is a surface polishing machine for metal parts such as cookware and kitchenware. Low prices & High Quality and Free Consultation
The main concern of most fabricators of stainless steel is to remove welds and machining marks and blend and simulate the final finish with the original mill finish or the sheet or coil stock. To refine the area of welds and machining marks, standard rough polishing procedures used are as those previously discussed.
Note that the final surface finish must closely approximate the original mill finish. There are eight basic stainless steel mill finishes used in the industry by product designers and architects. Mill finish Nos. 3, 4, 6, 7, and 8 are produced mechanically using some type of abrasive media and buffing wheels.
Finish Nos. 3 and 4 have proven to be the most popular among fabricators of dairy, kitchens, cafeterias, chemical equipment, and architectural and decorative structures. The simplest way to produce these blended finishes is with string wheels coated with greaseless abrasive compositions containing 80, 120, or 180 grit abrasive, operating at relatively low speeds
Narrow, flat, or curved areas can easily be blended with a portable power tool and a string wheel up to 8 inches in face width. Medium or very wide areas are finished with a string wheel log held with two hands or by two operators. Such a polishing log is made up of string wheel sections on a desired width shaft of a sufficiently powered portable tool.
The greaseless compound is applied to the rotating string wheel log and allowed to dry a few minutes. String wheel blending is then quickly accomplished in the direction of the lines of the original mill finish. Mill finishes Nos. 6, 7, and 8 are most generally used on consumer products,
although on some architectural sections, they are produced for contrasting patterns.
Buffing
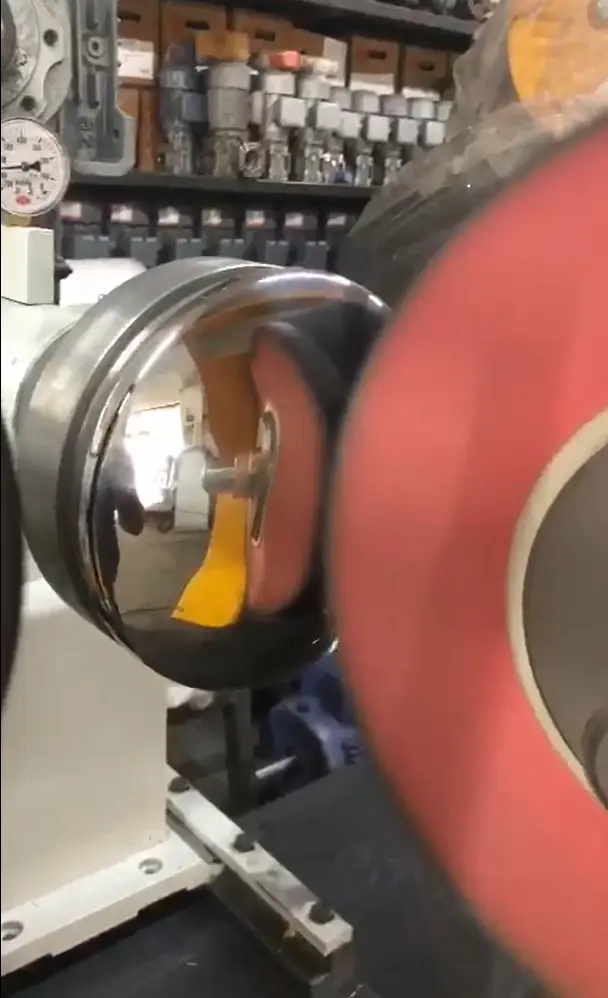
Buffing is a finishing process that utilizes an abrasive compound and a rotating wheel or mop to smooth and polish metal surfaces. It removes imperfections, scratches, and burrs, restoring the shine and luster of the metal. Buffing is widely used in various industries, including automotive, aerospace, jewelry, and metal fabrication, to enhance the appearance, durability, and performance of metal products and components.
Types of Buffing Processes
- Cut Buffing: Cut buffing employs coarse abrasives to remove heavy scratches, burrs, and imperfections from the metal surface. It is typically the first step in the buffing process.
- Color Buffing: Color buffing uses medium-grit abrasives to further smooth the surface and enhance the color of the metal. It follows cut buffing and precedes final polishing.
- Polishing: Polishing utilizes fine abrasives to achieve the desired level of smoothness and luster. It is the final step in the buffing process and produces a reflective, high-gloss finish.
Factors Affecting Buffing Results
- Abrasive Selection: The type and grit of the abrasive determine the aggressiveness of the buffing process. Coarse abrasives are used for initial cutting, while finer abrasives produce a smoother finish.
- Polishing Compound: The polishing compound contains abrasives, lubricants, and extenders that affect the polishing action. Different compounds are available for various metals and desired finishes.
- Buffing Wheel or Mop: The material and texture of the buffing wheel or mop influence the polishing effect. Cotton, felt, and sisal are common materials used for buffing wheels.
- Spindle Speed: The rotational speed of the spindle controls the intensity of the buffing process. Higher speeds produce a more aggressive polishing action, while slower speeds are better for fine polishing.
- Pressure: The pressure applied to the workpiece during buffing affects the depth of cut and the overall polishing result. Excessive pressure can damage the workpiece, while too little pressure may not achieve the desired finish.
Safety Considerations for Buffing Operations
- Machine Guarding: Proper guards should be installed to prevent workers from accessing hazardous rotating parts, such as the buffing wheel or mop.
- Safety Interlocks: Safety interlocks prevent the buffing machine from operating if the guards are not in place or if the safety sensors detect an unsafe condition.
- Emergency Stop Buttons: Clearly marked emergency stop buttons should be readily accessible to enable workers to quickly halt the machine in case of an unsafe situation.
- Personal Protective Equipment (PPE): Workers should wear appropriate PPE, such as safety glasses, gloves, and respiratory protection, to minimize the risk of injuries from flying debris, abrasive dust, and metal particles.
Conclusion
Buffing plays a crucial role in various industries by restoring the shine, durability, and functionality of metal surfaces. By understanding the different types of buffing processes, factors affecting buffing results, and safety considerations, manufacturers can effectively utilize buffing machines to enhance the quality and appearance of their metal products and components.
Buffing machines
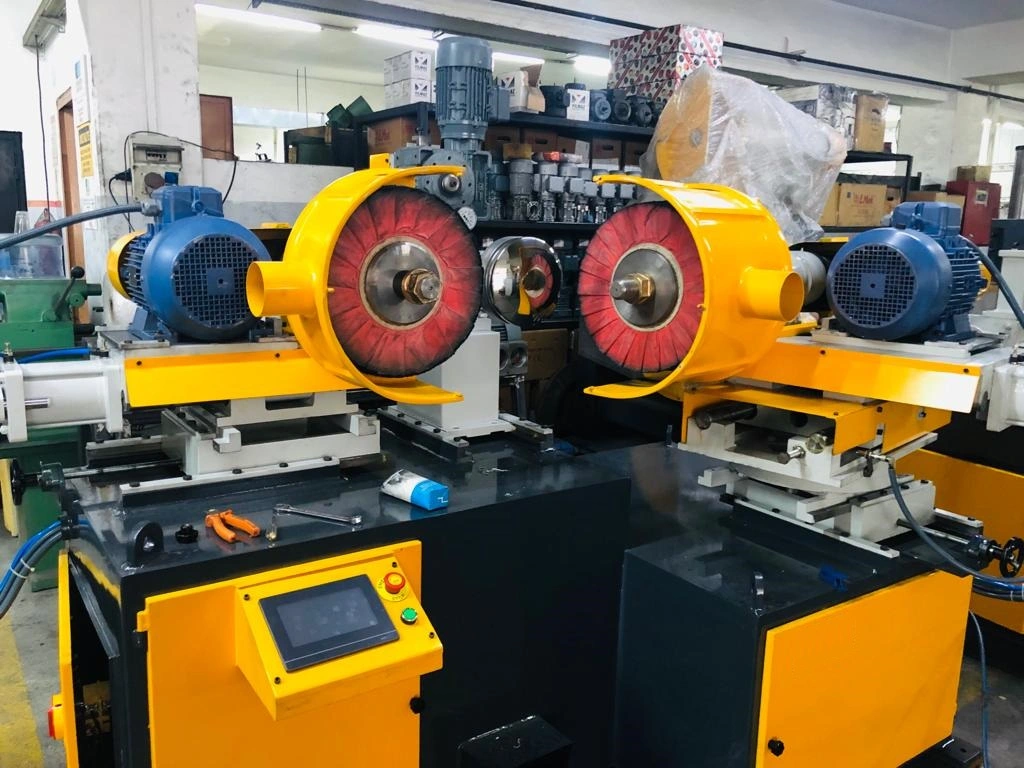
Buffing machines are essential tools for polishing and finishing metal surfaces, restoring their shine and removing imperfections. They employ various abrasives and polishing compounds to achieve the desired level of smoothness and luster. Buffing machines are used in a wide range of industries, including automotive, aerospace, jewelry, and metal fabrication.
Types of Buffing Machines
- Bench Buffing Machines: These are compact machines designed for smaller workpieces or finishing tasks. They typically have a single spindle and are mounted on a benchtop.
- Floor Buffing Machines: These are larger machines used for polishing larger workpieces or continuous production lines. They may have multiple spindles and can be operated while the workpiece remains stationary.
- Automatic Buffing Machines: These machines are designed for high-volume production and offer automation for repetitive buffing tasks. They may employ robots or automated feeding systems to handle workpieces.
Components of Buffing Machines
- Spindle: The spindle rotates the buffing wheel or mop, providing the driving force for polishing. It is typically connected to a motor that controls the rotational speed.
- Buffing Wheel or Mop: These are the abrasive components that come into contact with the workpiece. They are made of various materials, such as cotton, felt, or sisal, and are impregnated with polishing compounds.
- Polishing Compound: These compounds contain polishing agents, such as abrasives, lubricants, and extenders. They are applied to the buffing wheel or mop to achieve the desired polishing effect.
- Workpiece Holder or Fixture: These secure the workpiece in place while it is being buffed. They may be simple clamps or more complex fixtures designed for specific shapes or workpiece sizes.
- Dust Collection System: This system removes dust and debris generated during the buffing process. It typically consists of a hood, filter, and fan to collect and exhaust the airborne particles.
Applications of Buffing Machines
- Automotive Industry: Buffing machines are used to polish car bodies, wheels, and trim, restoring their shine and removing scratches or imperfections.
- Aerospace Industry: Buffing machines are used to polish aircraft components, such as wings, fuselages, and engine parts, to reduce drag and improve aerodynamic performance.
- Jewelry Industry: Buffing machines are used to polish jewelry pieces, such as rings, bracelets, and necklaces, to achieve a high-gloss finish and enhance their appearance.
- Metal Fabrication Industry: Buffing machines are used to polish metal surfaces, such as tools, dies, and components, to remove burrs, scratches, and other imperfections, improving their appearance and functionality.
Benefits of Buffing Machines
- Improved Appearance: Buffing machines restore the shine and luster of metal surfaces, enhancing the aesthetics of products and components.
- Enhanced Durability: Buffing removes imperfections and scratches, improving the surface quality of metal parts and extending their lifespan.
- Reduced Friction: Smoother metal surfaces reduce friction, improving the performance and efficiency of machinery and components.
- Corrosion Resistance: Buffing removes contaminants and polishes the surface, making it less susceptible to corrosion and oxidation.
- Ease of Cleaning: Smoother surfaces are easier to clean and maintain, reducing maintenance costs and downtime.
Basic Stainless Steel Sheet Finish Designation
The following list of stainless steel sheet finish designations includes a brief description of how each finish is obtained.
Unpolished Finish No. 1: A dull finish produced by hot rolling to specified
thickness, followed by annealing and descaling.
Unpolished Finish No. 2D: A dull finish produced by cold rolling to a specified thickness, followed by annealing and descaling. May also be accomplished by a final, light roll pass on dull rolls.
Unpolished Finish No. 2B: A bright finish commonly produced in the same way as No. 2D, except that the annealed and descaled sheet receives a final, light cold-roll pass on polished rolls. This is a general-purpose, cold-rolled finish, and is more readily polished than the No. 1 or No. 2D finishes.
Polished Finish No. 3: An intermediate polished finish generally used where a semi-polished surface is required for subsequent finishing operations following fabrication, or as a final finish with a 50- or 80-grit abrasive compound.
Polished Finish No. 4: A general-purpose bright polished finish obtained with a 100 to 180 mesh abrasive, following initial grinding with coarser abrasives.
Buffed Finish No. 6: A soft satin finish having lower reflectivity than a No. 4 finish. It is produced with a greaseless compound, #200 grit, top dressed with white rouge or chromium green rouge.
Buffed Finish No. 7: A highly reflective finish produced by buffing a surface that has first been refined to approximate a No. 6 finish, then buffed lightly with a white rouge without removing satin finish lines.
Buffed Finish No. 8: The most reflective finish commonly produced. It is
obtained by flexible polishing with successively finer abrasive compounds, then buffing extensively with a very fine chromium green rouge bar compound.
Cut Buffing
Cut buffing is an essential step in the metal polishing process, responsible for removing heavy scratches, burrs, and imperfections from the metal surface. It utilizes coarse abrasives to achieve a consistent and smooth base for subsequent polishing stages.
Purpose of Cut Buffing
The primary purpose of cut buffing is to prepare the metal surface for further polishing steps. By removing deep scratches, burrs, and imperfections, cut buffing creates a uniform and smooth base that allows for finer abrasives to achieve a high-gloss finish.
Process of Cut Buffing
Cut buffing typically involves the following steps:
- Selection of Abrasives: Coarse abrasives, such as aluminum oxide or silicon carbide, are chosen to provide the aggressive cutting action required for initial buffing.
- Preparation of Polishing Compound: A cut buffing compound, containing coarse abrasives, lubricants, and extenders, is applied to the buffing wheel or mop.
- Buffing Technique: The workpiece is held firmly against the rotating buffing wheel or mop, applying consistent pressure to achieve uniform buffing.
- Monitoring Progress: The buffing process is monitored to ensure that deep scratches and imperfections are removed without damaging the underlying metal surface.
Safety Considerations for Cut Buffing
- Machine Guarding: Proper guards should be installed to prevent workers from accessing hazardous rotating parts, such as the buffing wheel or mop.
- Safety Interlocks: Safety interlocks prevent the cut buffing machine from operating if the guards are not in place or if the safety sensors detect an unsafe condition.
- Emergency Stop Buttons: Clearly marked emergency stop buttons should be readily accessible to enable workers to quickly halt the machine in case of an unsafe situation.
- Personal Protective Equipment (PPE): Workers should wear appropriate PPE, such as safety glasses, gloves, and respiratory protection, to minimize the risk of injuries from flying debris, abrasive dust, and metal particles.
Benefits of Cut Buffing
- Scratch Removal: Cut buffing effectively removes deep scratches and imperfections, restoring a smooth and consistent surface to the metal.
- Burr Removal: It eliminates burrs and rough edges, improving the overall appearance and quality of the metal workpiece.
- Surface Preparation: Cut buffing creates a uniform base for subsequent polishing stages, ensuring a high-quality finish.
- Durability Enhancement: By removing surface imperfections, cut buffing contributes to the durability and longevity of the metal product.
- Appearance Improvement: It restores the shine and luster of the metal, enhancing its aesthetic appeal.
Conclusion
Cut buffing plays a critical role in the metal polishing process, providing the foundation for achieving a high-quality finish. By carefully selecting abrasives, applying appropriate buffing techniques, and adhering to safety guidelines, cut buffing effectively removes deep scratches, burrs, and imperfections, preparing the metal surface for further polishing and enhancing the overall appearance, durability, and functionality of metal products and components.
Color Buffing
Color buffing, also known as intermediate buffing, is a crucial step in the metal polishing process, bridging the gap between cut buffing and final polishing. It utilizes medium-grit abrasives to further refine the surface, eliminate residual scratches, and enhance the color of the metal.
Purpose of Color Buffing
Color buffing serves several important purposes in the metal polishing process:
- Scratch Removal: It removes finer scratches left behind by cut buffing, achieving a smoother and more refined surface.
- Surface Refinement: Color buffing further refines the metal surface, preparing it for the final polishing stage.
- Color Enhancement: It brings out the natural color of the metal, intensifying its luster and enhancing its visual appeal.
Process of Color Buffing
Color buffing typically involves the following steps:
- Selection of Abrasives: Medium-grit abrasives, such as silicon carbide or emery, are chosen to provide a balance between cutting action and surface refinement.
- Preparation of Polishing Compound: A color buffing compound, containing medium-grit abrasives, lubricants, and extenders, is applied to the buffing wheel or mop.
- Buffing Technique: The workpiece is held firmly against the rotating buffing wheel or mop, applying consistent pressure to achieve uniform buffing.
- Monitoring Progress: The color buffing process is monitored to ensure that finer scratches are removed and the desired color is achieved without over-polishing and reducing the surface texture.
Safety Considerations for Color Buffing
- Machine Guarding: Proper guards should be installed to prevent workers from accessing hazardous rotating parts, such as the buffing wheel or mop.
- Safety Interlocks: Safety interlocks prevent the color buffing machine from operating if the guards are not in place or if the safety sensors detect an unsafe condition.
- Emergency Stop Buttons: Clearly marked emergency stop buttons should be readily accessible to enable workers to quickly halt the machine in case of an unsafe situation.
- Personal Protective Equipment (PPE): Workers should wear appropriate PPE, such as safety glasses, gloves, and respiratory protection, to minimize the risk of injuries from flying debris, abrasive dust, and metal particles.
Benefits of Color Buffing
- Finer Scratch Removal: Color buffing effectively removes finer scratches left behind by cut buffing, achieving a smoother and more polished surface.
- Enhanced Color: It intensifies the natural color of the metal, enhancing its aesthetic appeal and highlighting its unique characteristics.
- Preparation for Final Polishing: Color buffing creates a refined surface that is ready for the final polishing stage, ensuring a high-quality finish.
- Durability Enhancement: By removing finer scratches and imperfections, color buffing contributes to the overall durability of the metal product.
- Appearance Improvement: It enhances the overall appearance of the metal, restoring its shine and luster.
Conclusion
Color buffing plays a vital role in the metal polishing process, refining the surface and enhancing the color of the metal. By carefully selecting abrasives, applying appropriate buffing techniques, and adhering to safety guidelines, color buffing effectively prepares the metal for the final polishing stage and contributes to achieving a high-quality, visually appealing, and durable finished product.
Polishing
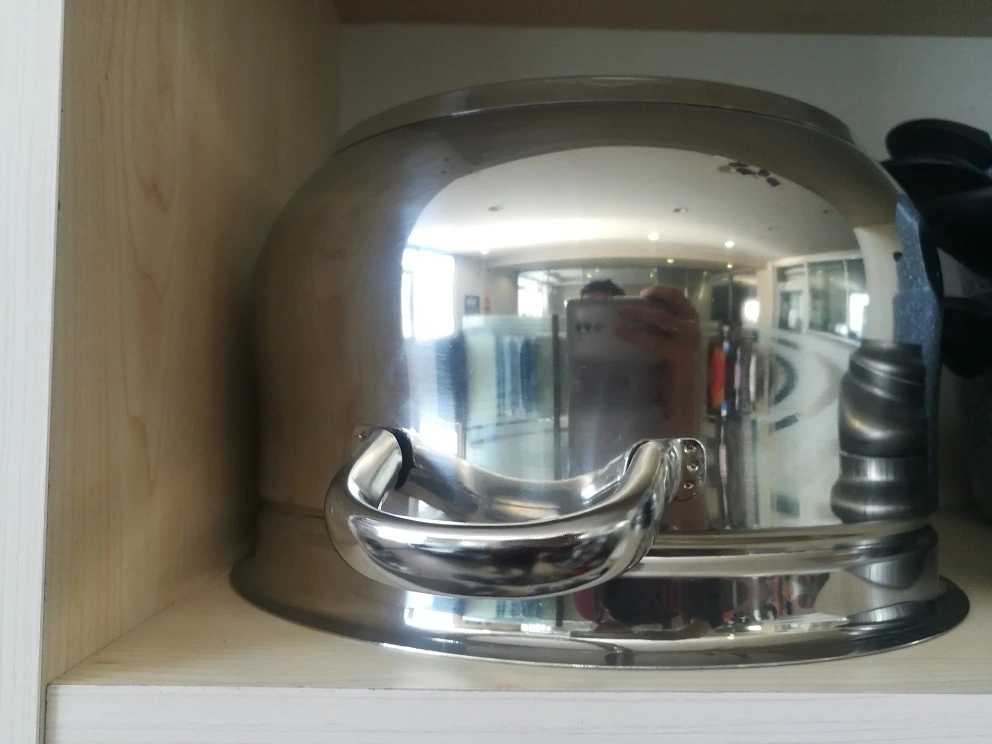
Polishing is the final step in the metal polishing process, responsible for achieving a high-gloss, mirror-like finish on the metal surface. It utilizes fine abrasives and polishing compounds to remove residual scratches and imperfections, creating a smooth, reflective surface.
Purpose of Polishing
The primary purpose of polishing is to enhance the appearance and aesthetic appeal of the metal workpiece. By removing minute scratches and imperfections, polishing produces a reflective surface that reflects light and enhances the visual impact of the metal.
Process of Polishing
Polishing typically involves the following steps:
- Selection of Abrasives: Fine abrasives, such as tripoli or rouge, are chosen to provide a gentle polishing action without removing the surface texture.
- Preparation of Polishing Compound: A polishing compound, containing fine abrasives, lubricants, and extenders, is applied to the buffing wheel or mop.
- Buffing Technique: The workpiece is held firmly against the rotating buffing wheel or mop, applying light pressure to achieve a consistent and controlled polishing action.
- Monitoring Progress: The polishing process is monitored to ensure that a high-gloss finish is achieved without over-polishing and removing the desired surface texture.
Safety Considerations for Polishing
- Machine Guarding: Proper guards should be installed to prevent workers from accessing hazardous rotating parts, such as the buffing wheel or mop.
- Safety Interlocks: Safety interlocks prevent the polishing machine from operating if the guards are not in place or if the safety sensors detect an unsafe condition.
- Emergency Stop Buttons: Clearly marked emergency stop buttons should be readily accessible to enable workers to quickly halt the machine in case of an unsafe situation.
- Personal Protective Equipment (PPE): Workers should wear appropriate PPE, such as safety glasses, gloves, and respiratory protection, to minimize the risk of injuries from flying debris, abrasive dust, and metal particles.
Benefits of Polishing
- High-Gloss Finish: Polishing produces a mirror-like finish that enhances the visual appeal of the metal workpiece.
- Improved Light Reflection: The reflective surface enhances the aesthetic appeal and highlights the unique characteristics of the metal.
- Surface Smoothing: Polishing removes minute scratches and imperfections, creating a smooth and even surface.
- Protection from Corrosion: A polished surface is less susceptible to corrosion and oxidation, extending the lifespan of the metal product.
- Enhanced Cleanability: A smooth, polished surface is easier to clean and maintain, reducing maintenance costs and downtime.
Conclusion
Polishing is the culmination of the metal polishing process, transforming the metal surface into a reflective and visually appealing masterpiece. By carefully selecting abrasives, employing appropriate buffing techniques, and adhering to safety guidelines, polishing effectively achieves a high-gloss finish, enhancing the aesthetic appeal, durability, and functionality of metal products and components.
Types of Polishing and Buffing Machines
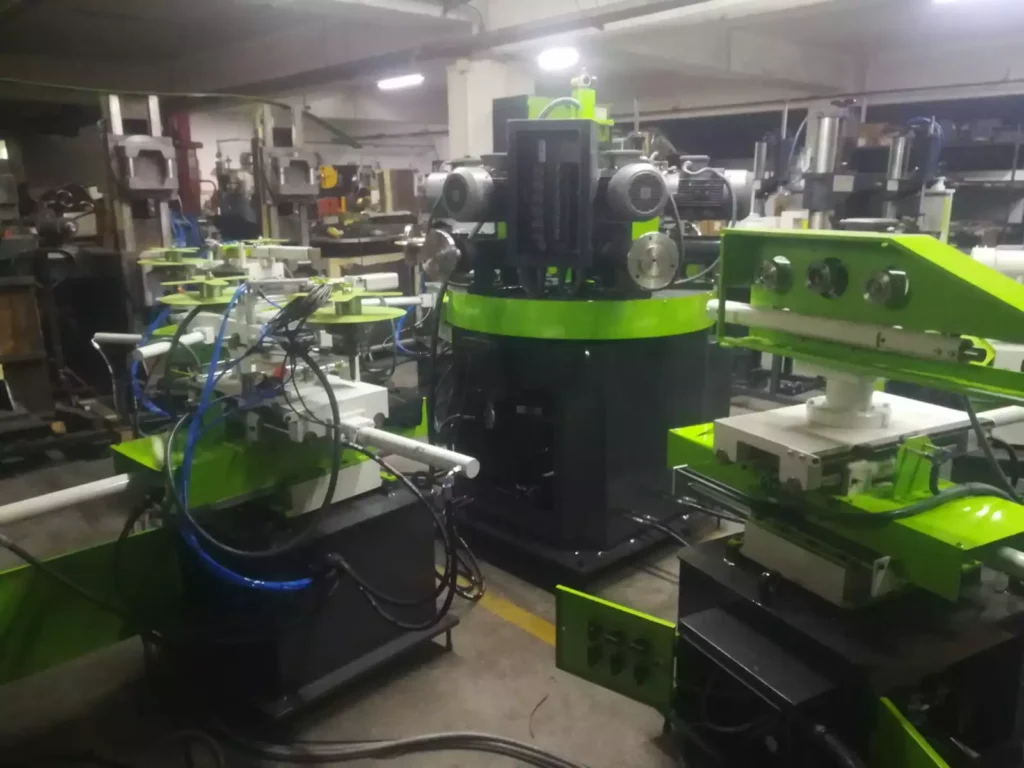
Manual Machines
Manual polishing and buffing machines are the most basic type, requiring direct human operation. These machines are suitable for small-scale operations and tasks that need a hands-on approach. They are typically used for intricate work where precision and control are paramount.
Key Features:
- Simple design and operation.
- Cost-effective for small jobs.
- Ideal for detailed and delicate work.
Applications:
- Jewelry and watchmaking.
- Small metal parts in the automotive and aerospace industries.
Semi-Automatic Machines
Semi-automatic polishing and buffing machines combine manual and automated features. They allow for greater control over the process while improving efficiency compared to fully manual machines. Operators can set parameters and oversee the operation, making adjustments as necessary.
Key Features:
- Enhanced control with automated functions.
- Increased efficiency and throughput.
- Suitable for medium-scale operations.
Applications:
- Mid-sized manufacturing units.
- Complex parts requiring a balance of manual oversight and automation.
CNC (Computer Numerical Control) Machines
CNC polishing and buffing machines represent the pinnacle of automation and precision in surface finishing. These machines use computer-controlled systems to manage the movement and operation of polishing tools with high accuracy. CNC machines are highly programmable, allowing for the automation of complex and repetitive tasks.
Key Features:
- High precision and repeatability.
- Ability to handle complex shapes and surfaces.
- Programmable for different tasks and materials.
Benefits:
- Consistent and high-quality finishes.
- Reduced labor costs and increased productivity.
- Flexibility in manufacturing processes.
Applications:
- Aerospace components.
- High-end automotive parts.
- Medical devices and implants.
NC (Numerical Control) Machines
NC machines, while similar to CNC machines, are generally less sophisticated and do not offer the same level of flexibility and automation. They are controlled by pre-set instructions but lack the advanced programmability of CNC systems.
Key Features:
- Automated control with limited programmability.
- Suitable for less complex tasks.
- Cost-effective compared to CNC machines.
Applications:
- Standardized parts in automotive and metalworking industries.
- Tasks that do not require frequent changes in setup.
Applications of Polishing and Buffing Machines
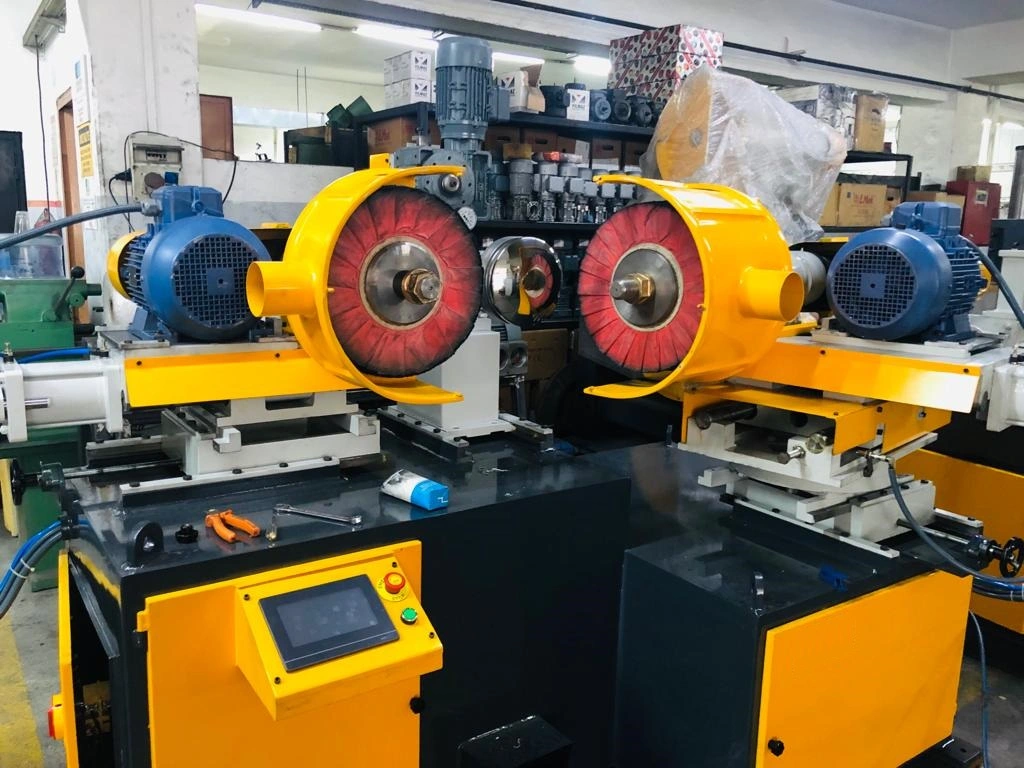
Automotive Industry
In the automotive industry, polishing and buffing are essential for achieving high-quality finishes on car parts. This includes the polishing of body panels, trim pieces, and engine components to enhance both aesthetics and performance.
Key Uses:
- Surface finishing of body panels.
- Polishing of chrome and aluminum trim.
- Buffing of engine and transmission parts.
Aerospace Industry
The aerospace industry demands the highest standards of precision and quality. Polishing and buffing are critical for ensuring the smooth surfaces necessary for aerodynamics and the performance of critical components.
Key Uses:
- Polishing turbine blades and engine parts.
- Finishing structural components for reduced drag.
- Ensuring the integrity of critical safety parts.
Metalworking Industry
In metalworking, polishing and buffing machines are used to finish metal parts, improving their appearance, resistance to corrosion, and overall quality.
Key Uses:
- Buffing of steel and aluminum parts.
- Finishing of tools and machinery components.
- Surface preparation for coating and painting.
Jewelry and Watchmaking
Precision and aesthetic appeal are paramount in jewelry and watchmaking. Polishing and buffing machines ensure that each piece has a flawless finish.
Key Uses:
- Polishing of precious metals and gemstones.
- Buffing intricate watch parts.
- Achieving high-shine finishes on jewelry.
Electronics Industry
In the electronics industry, surface preparation is crucial for the functionality and longevity of components. Polishing and buffing machines are used to prepare surfaces for assembly and coating.
Key Uses:
- Polishing of semiconductor wafers.
- Buffing of electronic enclosures and cases.
- Surface preparation for circuit boards.
Medical Device Manufacturing
The medical industry relies on highly polished surfaces for both functionality and hygiene. Polishing and buffing machines ensure that surgical instruments and implants meet stringent standards.
Key Uses:
- Polishing surgical instruments.
- Finishing orthopedic implants.
- Ensuring biocompatibility of medical devices.
Consumer Goods
Polishing and buffing are also used in the production of consumer goods, enhancing the aesthetic appeal and durability of everyday items.
Key Uses:
- Finishing of household appliances.
- Polishing of kitchen utensils and cutlery.
- Buffing of decorative items and hardware.
Production Process of Polishing and Buffing Machines
Design and Engineering
The production of polishing and buffing machines begins with design and engineering. This involves conceptualizing the machine, creating detailed CAD models, and planning the manufacturing process.
Steps:
- Conceptual design and feasibility studies.
- Detailed engineering using CAD software.
- Prototype development and testing.
Material Selection
Selecting the right materials is crucial for the durability and performance of polishing and buffing machines. Common materials include high-grade steels, aluminum alloys, and composite materials for specific parts.
Considerations:
- Durability and wear resistance.
- Weight and strength.
- Compatibility with various polishing materials.
Manufacturing Techniques
Manufacturing polishing and buffing machines involves several techniques, including machining, welding, assembly, and quality control. Each step is critical to ensuring the final product meets industry standards.
Techniques:
- CNC machining of components.
- Welding and fabrication of the machine frame.
- Assembly of mechanical and electronic parts.
- Rigorous testing and quality assurance.
Quality Control
Quality control is an integral part of the production process, ensuring that each machine meets the required specifications and performs reliably.
Methods:
- In-process inspections.
- Final testing of performance and safety.
- Certification to industry standards.
Materials Polished with Industrial Machines

Metals
Metals are the most common materials polished with industrial machines. This includes a wide range of metals used in various industries.
Examples:
- Stainless steel.
- Aluminum.
- Brass.
- Titanium.
Plastics
Certain types of plastics can also be polished to achieve a smooth and glossy finish, particularly in the electronics and consumer goods industries.
Examples:
- Acrylics.
- Polycarbonates.
- PVC.
Wood
Polishing wood can enhance its natural beauty and protect it from damage. This is commonly done in furniture making and decorative items.
Examples:
- Hardwood (oak, mahogany).
- Softwood (pine, cedar).
- Engineered wood (plywood, MDF).
Ceramics and Glass
Polishing ceramics and glass is delicate work that requires specialized techniques to avoid cracking and chipping.
Examples:
- Fine china.
- Glassware.
- Porcelain tiles.
Composites
Composites are used in advanced industries such as aerospace and automotive. Polishing these materials requires specialized equipment to handle their unique properties.
Examples:
- Carbon fiber.
- Fiberglass.
- Kevlar.
Advantages of Using CNC and NC Machines
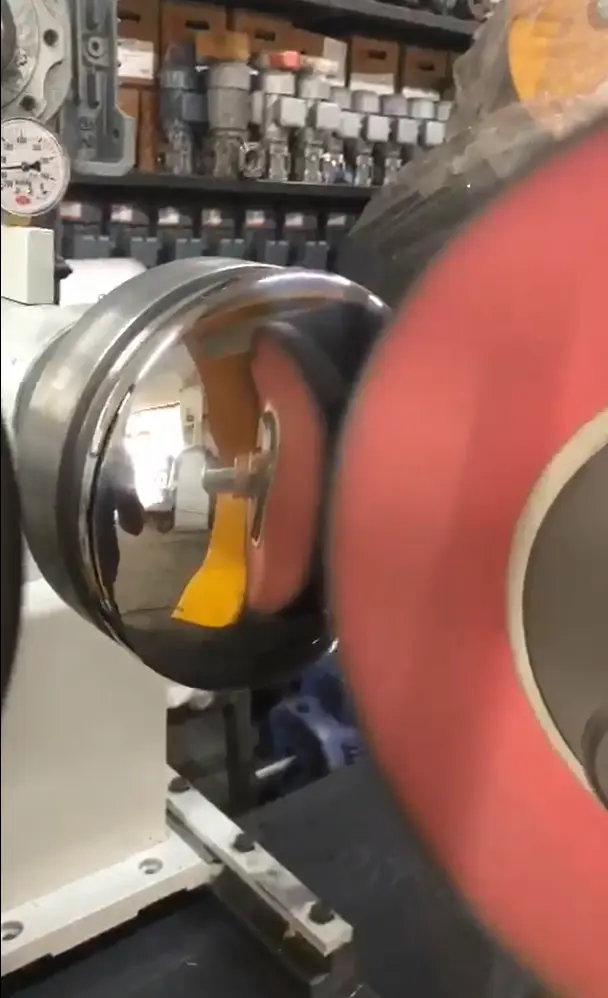
Precision and Consistency
CNC and NC machines offer unmatched precision and consistency, ensuring that each part meets exact specifications.
Benefits:
- Uniform finishes across large batches.
- High accuracy in complex geometries.
- Reduced human error.
Efficiency and Speed
These machines significantly reduce processing times, increasing overall productivity and allowing for faster turnaround times.
Benefits:
- Rapid processing of parts.
- Increased throughput.
- Shorter lead times.
Automation and Flexibility
Automation allows for continuous operation and the ability to handle multiple tasks without manual intervention.
Benefits:
- Customizable for various tasks.
- Minimal supervision required.
- Adaptable to different materials and shapes.
Cost-effectiveness
While the initial investment in CNC and NC machines can be high, the long-term savings in labor and increased efficiency make them cost-effective.
Benefits:
- Lower labor costs.
- High return on investment.
- Reduced material waste.
Challenges and Considerations
Initial Investment Costs
The cost of purchasing and installing CNC and NC machines can be significant, making it a major consideration for businesses.
Factors:
- Budgeting for high-quality machinery.
- Evaluating long-term benefits versus initial costs.
Maintenance and Upkeep
Regular maintenance is essential to ensure the longevity and performance of these machines.
Considerations:
- Scheduled maintenance and repairs.
- Availability of spare parts.
- Training for maintenance personnel.
Training and Skilled Labor
Operating CNC and NC machines requires skilled operators who understand the intricacies of programming and machine control.
Considerations:
- Investing in operator training.
- Ensuring continuous education on new technologies.
- Retaining skilled labor.
Technological Advancements
Keeping up with the latest advancements in technology is crucial for maintaining a competitive edge.
Considerations:
- Upgrading machinery and software.
- Staying informed about industry trends.
- Investing in research and development.
Future Trends in Polishing and Buffing Technology
Advancements in Automation and AI
The integration of artificial intelligence in polishing and buffing machines is set to revolutionize the industry by enhancing precision and efficiency.
Trends:
- AI-driven process optimization.
- Predictive maintenance using machine learning.
- Autonomous operation and monitoring.
Sustainable Practices
Sustainability is becoming increasingly important in manufacturing, with a focus on eco-friendly materials and processes.
Trends:
- Use of recyclable materials.
- Energy-efficient machinery.
- Reduction of waste and emissions.
Integration with Industry 4.0
Industry 4.0 involves the integration of smart technologies and IoT in manufacturing processes, providing real-time data and improving overall efficiency.
Trends:
- Smart manufacturing systems.
- Real-time monitoring and analytics.
- Enhanced connectivity and automation.
Conclusion
Industrial polishing and buffing machines play a vital role in various industries, ensuring that products meet the highest standards of quality and performance. From manual to advanced CNC and NC machines, each type offers unique benefits and is suited to different applications. Understanding the production processes, materials, and advantages of these machines is essential for businesses looking to improve their manufacturing capabilities. As technology continues to evolve, the future of polishing and buffing machines looks promising, with advancements in automation, sustainability, and smart manufacturing paving the way for more efficient and effective production methods.
By investing in the right equipment and staying informed about industry trends, manufacturers can achieve superior finishes, reduce costs, and maintain a competitive edge in their respective markets.