We manufacture Bend Press Machine to bend sheet metal edges. Hydraulic Press Machines are used in metalworking industries
A bend press machine, also known as a press brake or bending press, is a powerful and versatile tool used for bending sheet metal and plate materials. It is commonly used in metal fabrication, manufacturing, and various industries that require precise and accurate bending operations. Here are some key features and information about bend press machines:
- Bending Capacity: Bend press machines come in various sizes and capacities, which determine the maximum thickness and length of the material that can be bent. The capacity can range from smaller machines designed for thin sheet metal to larger machines capable of bending thick plates.
- Hydraulic or Mechanical Operation: Bend press machines can be hydraulic or mechanical. Hydraulic press brakes use hydraulic cylinders to apply force, while mechanical press brakes use mechanical linkages and mechanisms. Hydraulic machines are generally more powerful and offer precise control over the bending process, while mechanical machines are often simpler and more suitable for lighter-duty applications.
- Bed and Ram: A bend press machine consists of a bed (also called a table) and a ram (also called a beam or slide). The material to be bent is placed on the bed, and the ram moves downward to apply force and bend the material. The ram can have various types of tooling, such as punches and dies, attached to perform specific bending operations.
- Bending Accuracy and Control: Bend press machines provide precise control over the bending process, allowing for accurate and repeatable bends. The operator can adjust parameters such as the bending angle, bend radius, and material positioning. Some machines are equipped with advanced CNC (Computer Numerical Control) systems that automate the bending process and offer high levels of precision and control.
- Tooling: Bend press machines use various types of tooling to achieve different bending configurations. The tooling consists of punches and dies that are selected based on the desired bending angle, material thickness, and other factors. The tooling can be changed and adjusted to accommodate different bending requirements.
- Safety Considerations: Operating a bend press machine requires adherence to strict safety guidelines. This includes proper training, wearing appropriate personal protective equipment (PPE), securing the material firmly, and avoiding hand or body contact with moving parts. Additionally, some machines are equipped with safety features such as guards and light curtains to ensure operator safety.
- Application Versatility: Bend press machines can be used for a wide range of bending applications, including forming bends, flanges, channels, boxes, and more. They are commonly used in industries such as automotive, aerospace, construction, metal fabrication, and HVAC (Heating, Ventilation, and Air Conditioning).
When using a bend press machine, it is essential to follow the manufacturer’s instructions and safety guidelines. Proper maintenance, including regular inspections and lubrication, is important to ensure the machine operates smoothly and accurately. Additionally, selecting the appropriate tooling and understanding the material properties will contribute to achieving high-quality bends.
It’s worth noting that larger and more advanced bend press machines may offer additional features and capabilities, such as multi-axis control, programmability, and automatic tool changing systems. These advanced machines are often utilized in high-production environments or for complex bending tasks.
Always refer to the machine’s documentation or consult the manufacturer for specific instructions, operating procedures, and safety guidelines for the particular bend press machine you are using.
Bend Press Machine
A bend press machine, also known as a press brake, is a powerful and versatile metalworking tool that utilizes hydraulic or mechanical force to bend, form, or straighten sheet metal into various shapes and components. It is widely used in various industries, including automotive, aerospace, construction, and manufacturing.
Key Components of a Bend Press Machine
A bend press machine consists of several crucial components that work together to achieve the desired bending or forming operation:
- Frame: The frame provides a sturdy and rigid structure to support the machine’s components and withstand the immense forces involved during operation. It typically consists of heavy-duty steel plates or beams.
- Hydraulic or Mechanical Drive System: The drive system is the heart of the press brake, generating the force required to bend the metal sheet. Hydraulic presses use hydraulic fluid to transmit pressure to the ram, while mechanical presses use a system of gears and levers.
- Ram: The ram is the movable part of the press brake that applies force directly to the workpiece. It is connected to the piston of the hydraulic cylinder or the drive system of a mechanical press.
- Tooling: Tooling, also known as dies and punches, is crucial in determining the specific shape or form of the workpiece. Dies provide the desired shape, while punches cut or pierce the material. Tooling can be customized to produce a wide range of shapes and sizes.
- Work Table: The work table provides a stable and adjustable surface for positioning and securing the workpiece during the bending operation. It can be adjusted to accommodate different workpiece sizes and heights.
- Control System: The control system manages the operation of the press brake, including ram movement, pressure control, and safety interlocks. It receives input from sensors, such as pressure transducers and position encoders, and controls the valves, actuators, and motor to regulate the machine’s behavior.
Working Principle of a Bend Press Machine
The working principle of a bend press machine can be summarized in the following steps:
- Workpiece Positioning: The workpiece is positioned and secured on the work table.
- Ram Movement: The ram, either driven by hydraulic pressure or mechanical force, moves towards the workpiece.
- Forming Operation: The ram applies force to the workpiece, causing it to bend or deform according to the shape of the tooling.
- Retraction: Once the desired shape is achieved, the ram retracts to its initial position.
- Unloading: The workpiece is removed from the work table.
Types of Bend Press Machines
Bend press machines can be categorized into two main types based on their drive system:
- Hydraulic Press Brakes: Hydraulic press brakes utilize hydraulic fluid to generate force, offering precise control over ram movement and pressure. They are commonly used for high-precision forming operations and applications requiring consistent results.
- Mechanical Press Brakes: Mechanical press brakes employ a mechanical drive system, typically using gears and levers to transfer force to the ram. They are known for their high production rates and ability to handle heavy-duty forming operations.
Applications of Bend Press Machines
Bend press machines are versatile tools used in various industries for a wide range of applications, including:
- Automotive Industry: Bending sheet metal components for vehicle bodies, frames, and structural parts
- Aerospace Industry: Forming and shaping aircraft parts, such as wings, fuselages, and control surfaces
- Construction Industry: Creating metal components for roofing, cladding, and structural elements
- Manufacturing Industry: Producing metal parts for appliances, electronics, machinery, and other products
- Appliance Industry: Shaping and forming sheet metal for various appliance components, such as cabinets, doors, and panels
- Electronics Industry: Bending and shaping metal parts for circuit boards, enclosures, and other electronic components
- Furniture Manufacturing: Creating metal frames, supports, and decorative elements for furniture
- HVAC Industry: Forming and shaping sheet metal components for air conditioning and ventilation systems
- Sign Manufacturing: Bending and cutting metal sheets for signage, lettering, and displays
- Metal Fabrication Industry: Producing a wide range of metal components for various applications, including construction, machinery, and consumer goods
History of Press Brake Machines
The origins of metal bending can be traced back to ancient civilizations, where blacksmiths used rudimentary tools to shape metal. As technology progressed, so did the methods of metal bending, leading to the development of more sophisticated machinery.
The first press brake machines emerged during the Industrial Revolution, driven by the need for more efficient and precise metalworking tools. Early press brake machines were manually operated, requiring significant physical effort and skill from the operator. Despite their limitations, these machines marked a significant advancement in the field of metal fabrication.
The 20th century witnessed substantial improvements in press brake technology. The introduction of hydraulic systems in the 1940s allowed for greater force and control, enabling the bending of thicker and tougher metals. This innovation revolutionized the industry, making hydraulic press brake machines the standard for many years.
In recent decades, the advent of computer numerical control (CNC) technology has transformed press brake machines once again. CNC press brake machines offer unparalleled precision and automation, allowing for complex bending operations to be performed with minimal human intervention. These machines are equipped with advanced software that can program and execute intricate bending sequences, ensuring consistency and accuracy.
Today, press brake machines continue to evolve, incorporating cutting-edge technologies such as robotics and artificial intelligence. These advancements are paving the way for even greater efficiency, flexibility, and precision in metal fabrication.
Types of Press Brake Machines
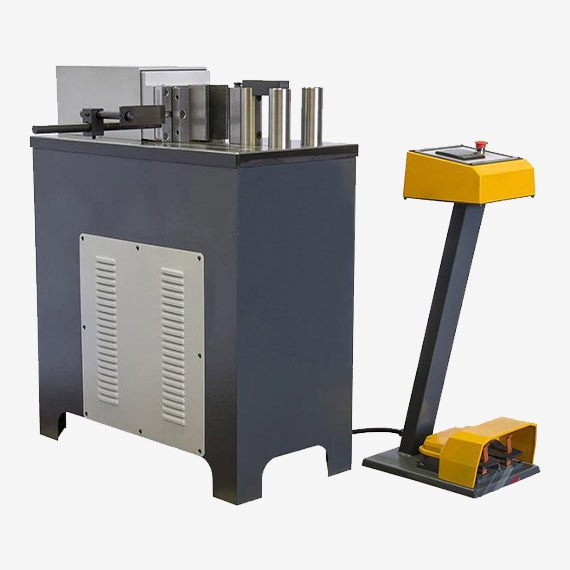
Press brake machines come in various types, each with its own features, advantages, and applications. Understanding the different types of press brake machines is essential for selecting the right equipment for specific metal bending tasks.
Manual Press Brake Machines
Features and Uses Manual press brake machines are the simplest type of press brakes, operated entirely by human effort. They are typically used for small-scale or low-volume production tasks, where high precision is not critical.
Advantages
- Cost-effective and affordable for small businesses
- Easy to operate and maintain
- Suitable for simple bending operations
Disadvantages
- Limited bending capacity and precision
- Labor-intensive and time-consuming
- Not suitable for high-volume production
Hydraulic Press Brake Machines
Features and Uses Hydraulic press brake machines use hydraulic fluid to generate the necessary force for bending metal sheets. They are widely used in various industries due to their versatility and reliability.
Advantages
- High bending capacity and precision
- Capable of handling thicker and tougher metals
- Smooth and consistent operation
Disadvantages
- Higher initial cost compared to manual machines
- Requires regular maintenance of hydraulic systems
- Potential for hydraulic fluid leaks
Electric Press Brake Machines
Features and Uses Electric press brake machines use electric motors to drive the bending process. They are known for their energy efficiency and precision.
Advantages
- Energy-efficient and environmentally friendly
- High precision and repeatability
- Lower operating costs compared to hydraulic machines
Disadvantages
- Limited force compared to hydraulic machines
- Higher initial cost than manual machines
- Requires skilled operators
CNC Press Brake Machines
Features and Uses CNC (Computer Numerical Control) press brake machines represent the pinnacle of press brake technology. They are equipped with advanced computer systems that control the bending process with exceptional precision.
Advantages
- Unmatched precision and accuracy
- Automated and programmable operations
- Suitable for complex and high-volume production
Disadvantages
- High initial cost and investment
- Requires skilled operators and programmers
- Complex maintenance and troubleshooting
Each type of press brake machine has its unique advantages and disadvantages, making it crucial to select the appropriate type based on specific production requirements and budget constraints.
Components of a Press Brake Machine
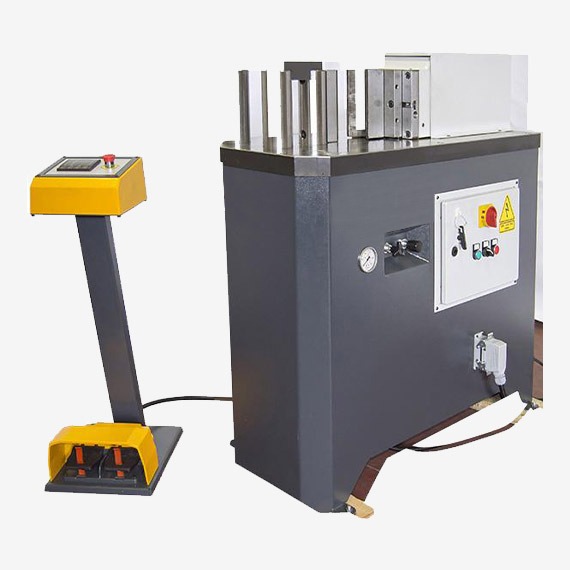
Press brake machines consist of several key components, each playing a vital role in the bending process. Understanding these components is essential for operating and maintaining the machine effectively.
Frame
The frame is the backbone of the press brake machine, providing structural support and stability. It is typically constructed from heavy-duty steel to withstand the forces exerted during the bending process.
Ram
The ram is a movable component that exerts force on the metal sheet, pressing it against the die to create the desired bend. The ram’s movement can be controlled manually, hydraulically, or electrically, depending on the type of press brake machine.
Die and Punch
The die and punch are the primary tools used in the bending process. The punch, attached to the ram, presses the metal sheet into the die, which is fixed to the machine’s bed. The shape and size of the die and punch determine the angle and radius of the bend.
Back Gauge
The back gauge is a positioning tool that helps in accurately aligning the metal sheet for bending. It ensures consistent bend angles and dimensions by providing a reference point for the sheet.
Control System
The control system manages the operation of the press brake machine. In manual machines, this may be a simple mechanical system, while hydraulic and electric machines use more advanced control systems. CNC press brake machines have sophisticated computer systems that program and control the entire bending process.
Safety Features
Press brake machines are equipped with various safety features to protect operators from accidents and injuries. These may include safety guards, emergency stop buttons, and light curtains that detect the presence of an operator’s hands near the bending area.
Working Principle
The basic working principle of a press brake machine involves applying a controlled force to bend metal sheets into specific shapes. Here are the key steps in the bending process:
- Sheet Positioning: The metal sheet is positioned on the machine’s bed, aligned against the back gauge to ensure precise placement.
- Tool Selection: The appropriate die and punch are selected based on the desired bend angle and radius. These tools are then installed on the machine.
- Bending Operation: The ram descends, pressing the punch into the metal sheet and forcing it into the die. This action creates the bend, with the angle and shape determined by the tools used and the force applied.
- Return Stroke: After the bend is completed, the ram ascends, releasing the pressure on the metal sheet. The sheet is then removed or repositioned for additional bends.
Precision and control are crucial in the bending process to ensure the accuracy and consistency of the bends. CNC press brake machines excel in this regard, as they use computer programming to control the ram’s movement and force, resulting in highly precise bends.
Applications of Press Brake Machines
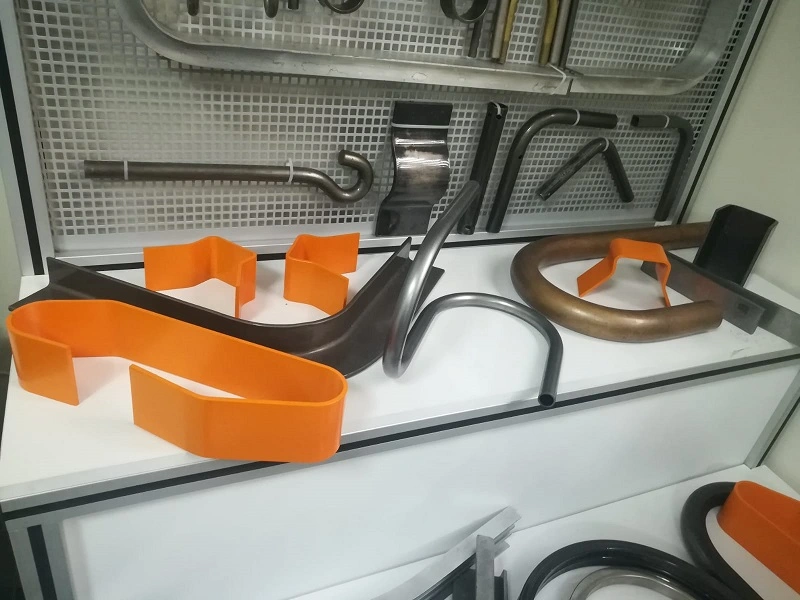
Press brake machines are used across various industries due to their versatility and precision. Here are some common applications:
- Automotive Industry: Manufacturing car body panels, chassis components, and brackets.
- Aerospace Industry: Producing aircraft parts, including wing components and fuselage sections.
- Construction Industry: Fabricating structural components, such as beams, columns, and brackets.
- Electronics Industry: Creating enclosures, chassis, and brackets for electronic devices.
- Furniture Industry: Making metal frames and components for furniture.
- HVAC Industry: Producing ductwork and ventilation components.
These machines are also used in creating custom metal parts and prototypes, showcasing their adaptability to various production needs.
Advantages of Using Press Brake Machines
Press brake machines offer several advantages that make them indispensable in metal fabrication:
- Precision and Accuracy: These machines can produce highly precise bends, ensuring that components meet exact specifications.
- Efficiency and Productivity: Press brake machines can perform complex bending operations quickly, increasing production efficiency.
- Versatility: They can handle a wide range of materials and thicknesses, making them suitable for various applications.
- Cost-effectiveness: By reducing material waste and increasing production speed, press brake machines can lower manufacturing costs.
Maintenance and Safety Tips
Proper maintenance and safety practices are essential for the efficient and safe operation of press brake machines. Here are some tips:
Routine Maintenance
- Regularly inspect the machine for wear and tear.
- Keep the machine clean and free from debris.
- Lubricate moving parts as recommended by the manufacturer.
- Check hydraulic fluid levels and replace as necessary.
Common Issues and Troubleshooting
- Misalignment of the die and punch: Adjust the alignment to ensure precise bends.
- Inconsistent bending angles: Check for wear on the tools and replace if needed.
- Hydraulic system leaks: Inspect seals and hoses, and replace any damaged components.
Safety Guidelines for Operators
- Always wear appropriate personal protective equipment (PPE).
- Ensure that safety guards and emergency stop buttons are in place and functional.
- Follow the manufacturer’s guidelines for safe operation.
- Undergo proper training before operating the machine.
Future Trends in Press Brake Technology
The future of press brake technology is shaped by advancements in automation, materials, and environmental considerations:
- Automation and Industry 4.0: The integration of robotics and IoT (Internet of Things) is enhancing the automation of press brake machines, leading to increased efficiency and reduced human intervention.
- Advanced Materials and Designs: The development of new materials and innovative designs is expanding the capabilities of press brake machines, allowing for more complex and precise bends.
- Environmental Considerations: Efforts to reduce energy consumption and minimize environmental impact are driving the adoption of electric press brake machines and other eco-friendly technologies.
Conclusion
Press brake machines are a cornerstone of modern metal fabrication, offering unmatched precision, efficiency, and versatility. From their historical evolution to the latest technological advancements, these machines continue to play a vital role in various industries.
Understanding the different types of press brake machines, their components, and working principles is essential for selecting the right equipment and maximizing its potential. By following proper maintenance and safety practices, operators can ensure the longevity and safe operation of these machines.
As we look to the future, advancements in automation, materials, and environmental sustainability will further enhance the capabilities of press brake machines, solidifying their place in the ever-evolving landscape of manufacturing.
Whether you are a seasoned professional or new to the field, this comprehensive guide provides valuable insights into the world of sheet metal bending press brake machines, highlighting their importance and potential in modern industry.
Components of a Press Brake Machine
Press brake machines consist of several key components, each playing a vital role in the bending process. Understanding these components is essential for operating and maintaining the machine effectively.
Frame
The frame is the backbone of the press brake machine, providing structural support and stability. Constructed from heavy-duty steel, the frame must be robust enough to withstand the significant forces exerted during the bending process. The frame’s design can vary depending on the machine type, but its primary function remains to ensure rigidity and durability.
Ram
The ram is a movable component that exerts force on the metal sheet, pressing it against the die to create the desired bend. The ram’s movement can be controlled manually, hydraulically, or electrically, depending on the type of press brake machine. In CNC press brakes, the ram’s motion is precisely controlled by computer programming, allowing for highly accurate and repeatable bends.
Die and Punch
The die and punch are the primary tools used in the bending process. The punch, attached to the ram, presses the metal sheet into the die, which is fixed to the machine’s bed. The shape and size of the die and punch determine the angle and radius of the bend. There are various types of dies and punches, each suited for different bending operations, such as V-dies, U-dies, and hemming dies.
Back Gauge
The back gauge is a positioning tool that helps in accurately aligning the metal sheet for bending. It ensures consistent bend angles and dimensions by providing a reference point for the sheet. Modern press brake machines often feature CNC-controlled back gauges, which can be programmed to automatically adjust positions for complex bending sequences, enhancing precision and efficiency.
Control System
The control system manages the operation of the press brake machine. In manual machines, this may be a simple mechanical system, while hydraulic and electric machines use more advanced control systems. CNC press brake machines have sophisticated computer systems that program and control the entire bending process. These systems can store multiple bending programs, allowing for quick setup and reduced downtime between jobs.
Safety Features
Press brake machines are equipped with various safety features to protect operators from accidents and injuries. These may include safety guards, emergency stop buttons, and light curtains that detect the presence of an operator’s hands near the bending area. Modern machines also incorporate safety sensors that halt the machine’s operation if a potential hazard is detected, ensuring a safer working environment.
Working Principle
https://www.youtube.com/embed/l8quDXXNNEg?feature=oembedWorking Principle
The basic working principle of a press brake machine involves applying a controlled force to bend metal sheets into specific shapes. Here are the key steps in the bending process:
- Sheet Positioning: The metal sheet is positioned on the machine’s bed, aligned against the back gauge to ensure precise placement. Proper alignment is crucial for achieving accurate and consistent bends.
- Tool Selection: The appropriate die and punch are selected based on the desired bend angle and radius. These tools are then installed on the machine. The selection of the correct tools is essential for achieving the desired bend geometry and avoiding damage to the metal sheet.
- Bending Operation: The ram descends, pressing the punch into the metal sheet and forcing it into the die. This action creates the bend, with the angle and shape determined by the tools used and the force applied. The bending process requires careful control of the ram’s speed and pressure to ensure precise and consistent results.
- Return Stroke: After the bend is completed, the ram ascends, releasing the pressure on the metal sheet. The sheet is then removed or repositioned for additional bends. In CNC press brakes, the return stroke and repositioning of the sheet can be automated, increasing efficiency and reducing operator fatigue.
Precision and control are crucial in the bending process to ensure the accuracy and consistency of the bends. CNC press brake machines excel in this regard, as they use computer programming to control the ram’s movement and force, resulting in highly precise bends. The ability to program complex bending sequences also allows for the efficient production of intricate parts with minimal manual intervention.
Applications of Press Brake Machines
https://www.youtube.com/embed/o1dG-pIFkTk?feature=oembedApplications of Press Brake Machines
Press brake machines are used across various industries due to their versatility and precision. Here are some common applications:
- Automotive Industry: Press brake machines are integral to manufacturing car body panels, chassis components, and brackets. These machines can produce complex shapes and bends required for modern vehicle designs, ensuring high precision and repeatability.
- Aerospace Industry: The aerospace industry demands high precision and stringent quality standards. Press brake machines are used to produce aircraft parts, including wing components and fuselage sections, where accuracy and consistency are paramount.
- Construction Industry: Press brake machines are utilized to fabricate structural components such as beams, columns, and brackets. These components must meet specific strength and dimensional requirements to ensure the safety and stability of buildings and other structures.
- Electronics Industry: In the electronics industry, press brake machines are used to create enclosures, chassis, and brackets for electronic devices. These components often require intricate bends and precise dimensions to accommodate various electronic components and assemblies.
- Furniture Industry: The furniture industry employs press brake machines to make metal frames and components for furniture. These machines enable the production of aesthetically pleasing and structurally sound furniture parts, such as legs, supports, and brackets.
- HVAC Industry: The HVAC industry uses press brake machines to produce ductwork and ventilation components. These machines can create complex bends and shapes needed for efficient air distribution and ventilation systems.
These machines are also used in creating custom metal parts and prototypes, showcasing their adaptability to various production needs. The ability to quickly and accurately produce custom components makes press brake machines valuable tools for manufacturers and fabricators across different industries.
Advantages of Using Press Brake Machines
Press brake machines offer several advantages that make them indispensable in metal fabrication:
- Precision and Accuracy: Press brake machines are designed to produce highly precise bends, ensuring that components meet exact specifications. CNC press brakes, in particular, offer unmatched precision and repeatability, allowing for the production of intricate and complex parts with tight tolerances.
- Efficiency and Productivity: These machines can perform complex bending operations quickly, increasing production efficiency. The automation capabilities of CNC press brakes reduce the need for manual intervention, leading to faster setup times and higher throughput.
- Versatility: Press brake machines can handle a wide range of materials and thicknesses, making them suitable for various applications. From thin aluminum sheets to thick steel plates, these machines can accommodate different bending requirements, providing flexibility in manufacturing processes.
- Cost-effectiveness: By reducing material waste and increasing production speed, press brake machines can lower manufacturing costs. The precision and efficiency of these machines minimize errors and rework, resulting in significant cost savings over time.
- Consistency: Press brake machines ensure consistent bend quality across multiple parts, which is essential for mass production. The ability to produce uniform parts enhances the overall quality and reliability of the final products.
- Customizability: Modern press brake machines, especially CNC models, offer high levels of customizability. Operators can program specific bending sequences and parameters, allowing for the production of custom parts tailored to unique design requirements.
- Reduced Labor Costs: Automation in CNC press brake machines reduces the need for skilled labor, lowering labor costs. These machines can operate with minimal supervision, enabling manufacturers to allocate human resources more efficiently.
- Enhanced Safety: Press brake machines are equipped with advanced safety features that protect operators from accidents and injuries. Safety guards, emergency stop buttons, and sensors contribute to a safer working environment, reducing the risk of workplace incidents.
These advantages highlight the critical role of press brake machines in modern metal fabrication, underscoring their value in achieving high-quality, efficient, and cost-effective manufacturing processes.
Maintenance and Safety Tips
Proper maintenance and safety practices are essential for the efficient and safe operation of press brake machines. Here are some tips:
Routine Maintenance
- Regular Inspection: Regularly inspect the machine for wear and tear. Check for any signs of damage or misalignment in the components, especially the die and punch.
- Cleaning: Keep the machine clean and free from debris. Accumulated dust and metal shavings can affect the machine’s performance and lead to premature wear.
- Lubrication: Lubricate moving parts as recommended by the manufacturer. Proper lubrication reduces friction and prevents wear, extending the machine’s lifespan.
- Hydraulic Fluid: Check hydraulic fluid levels and replace as necessary. Ensure that the hydraulic system is free from leaks and that the fluid is clean and at the proper level.
- Tool Maintenance: Inspect the die and punch for wear and replace them if needed. Sharp and well-maintained tools are crucial for achieving precise bends.
Common Issues and Troubleshooting
- Misalignment: Misalignment of the die and punch can result in inaccurate bends. Adjust the alignment to ensure precise bending operations.
- Inconsistent Bending Angles: Inconsistent bending angles may be due to worn tools or incorrect settings. Check the tools for wear and verify the machine’s settings.
- Hydraulic System Leaks: Hydraulic system leaks can affect the machine’s performance. Inspect seals and hoses regularly and replace any damaged components.
- Control System Errors: Errors in the control system, particularly in CNC machines, can disrupt operations. Ensure that the control system software is up-to-date and that any programming issues are addressed promptly.
Safety Guidelines for Operators
- Personal Protective Equipment (PPE): Always wear appropriate PPE, including safety glasses, gloves, and protective clothing, to prevent injuries.
- Safety Guards and Emergency Stops: Ensure that safety guards are in place and functional. Familiarize yourself with the location and operation of emergency stop buttons.
- Manufacturer Guidelines: Follow the manufacturer’s guidelines for safe operation. These guidelines provide crucial information on operating the machine safely and efficiently.
- Training: Undergo proper training before operating the machine. Training should cover machine operation, maintenance, and safety procedures.
- Awareness: Stay alert and aware of your surroundings while operating the machine. Avoid distractions and ensure that the work area is free from hazards.
By adhering to these maintenance and safety tips, operators can ensure the longevity, efficiency, and safe operation of press brake machines, minimizing downtime and reducing the risk of accidents.
Future Trends in Press Brake Technology
The future of press brake technology is shaped by advancements in automation, materials, and environmental considerations. Here are some key trends to watch:
Automation and Industry 4.0
The integration of robotics and the Internet of Things (IoT) is enhancing the automation of press brake machines. Industry 4.0 technologies enable machines to communicate and coordinate with each other, leading to increased efficiency and reduced human intervention. Automated press brake machines can perform complex bending operations with minimal oversight, improving productivity and precision.
Advanced Materials and Designs
The development of new materials and innovative designs is expanding the capabilities of press brake machines. Advanced materials, such as high-strength alloys and composites, require precise and powerful bending techniques. Modern press brake machines are being designed to handle these materials, enabling the production of more durable and lightweight components.
Environmental Considerations
Efforts to reduce energy consumption and minimize environmental impact are driving the adoption of electric press brake machines and other eco-friendly technologies. Electric press brakes are more energy-efficient than their hydraulic counterparts, producing less noise and requiring less maintenance. Additionally, manufacturers are exploring sustainable materials and processes to further reduce the environmental footprint of metal fabrication.
Smart Manufacturing
Smart manufacturing technologies, including artificial intelligence (AI) and machine learning, are being integrated into press brake machines. These technologies enable predictive maintenance, real-time monitoring, and adaptive control, enhancing machine performance and reducing downtime. AI-powered systems can optimize bending operations by analyzing data and making adjustments in real-time.
User-Friendly Interfaces
Future press brake machines are likely to feature more user-friendly interfaces, making them easier to operate and program. Touchscreen controls, intuitive software, and augmented reality (AR) training tools will simplify the operation of these machines, reducing the learning curve for operators.
These trends highlight the ongoing evolution of press brake technology, promising greater efficiency, precision, and sustainability in metal fabrication.
Conclusion
Press brake machines are a cornerstone of modern metal fabrication, offering unmatched precision, efficiency, and versatility. From their historical evolution to the latest technological advancements, these machines continue to play a vital role in various industries.
Understanding the different types of press brake machines, their components, and working principles is essential for selecting the right equipment and maximizing its potential. By following proper maintenance and safety practices, operators can ensure the longevity and safe operation of these machines.
As we look to the future, advancements in automation, materials, and environmental sustainability will further enhance the capabilities of press brake machines, solidifying their place in the ever-evolving landscape of manufacturing.
Whether you are a seasoned professional or new to the field, this comprehensive guide provides valuable insights into the world of sheet metal bending press brake machines, highlighting their importance and potential in modern industry.
Press brake machines will undoubtedly continue to evolve, driven by technological innovations and industry demands. Staying informed about these advancements and adopting best practices will enable manufacturers to leverage the full potential of press brake machines, ensuring continued success in their metal fabrication endeavors.
Overview of Bending and Press Machines in Industrial Applications
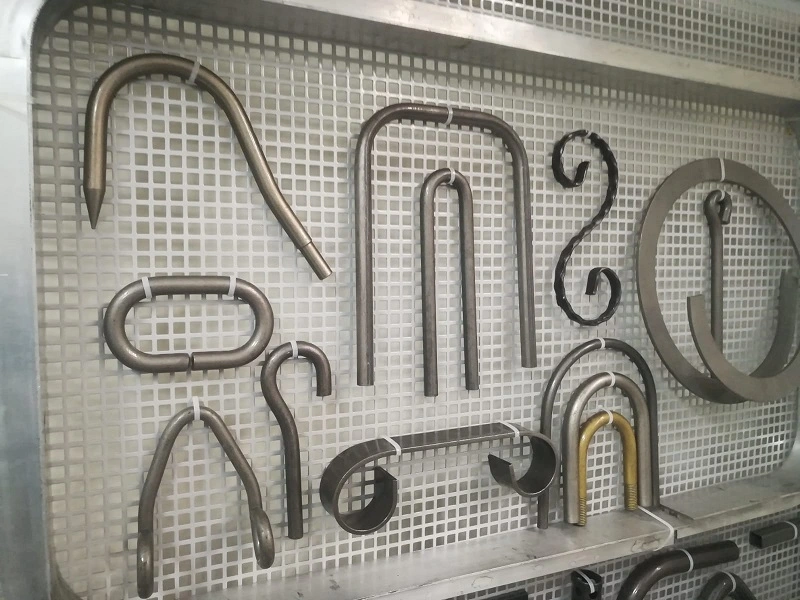
In the modern manufacturing and metalworking industries, bending and press machines are indispensable tools that shape, form, and modify metal and other materials with high precision. These machines are designed to handle various tasks, from simple bending operations to complex shaping processes, catering to a wide range of applications across multiple industries. The effectiveness and versatility of these machines make them critical in producing parts and components for automotive, aerospace, construction, and other heavy industries.
Bending and press machines are essential in transforming raw materials into finished products by applying force to alter the shape and properties of metals and other materials. The machines are designed to handle different materials, including steel, stainless steel (SS), aluminum, and more. These machines vary in size and capacity, from small, manual models used in workshops to large, automated systems in industrial manufacturing plants.
Types of Bending and Press Machines:
- Hydraulic Press Machines: Utilize hydraulic pressure to exert force, offering high precision and control in operations such as pressing, bending, and punching.
- Press Brake Machines: Specifically designed for bending sheet metal into various shapes by clamping the workpiece between a matching punch and die.
- Pipe Bending Machines: Used to bend pipes and tubes into desired angles and shapes, essential in plumbing, construction, and automotive industries.
- Sheet Metal Bending Machines: These machines focus on bending and shaping sheet metal, often used in fabrication shops and manufacturing lines.
Importance of Precision in Metalworking
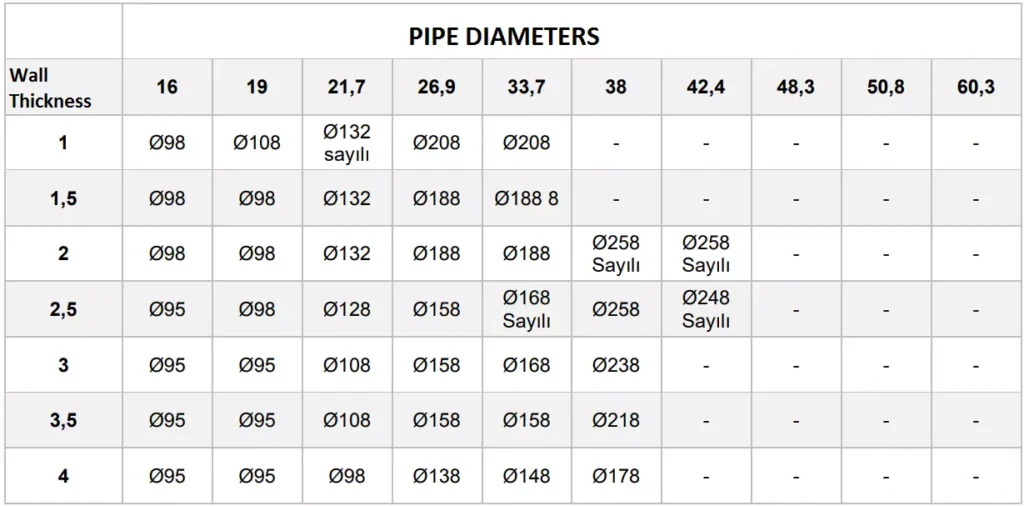
Precision is paramount in metalworking, as even minor deviations can lead to significant issues in the final product. Accurate bending and shaping are critical for ensuring that parts fit together correctly, maintain structural integrity, and meet the required specifications. The precision offered by modern bending and press machines allows manufacturers to produce complex components with tight tolerances, reducing the need for additional finishing processes and minimizing material waste.
Key Factors Influencing Precision:
- Machine Calibration: Proper calibration ensures the machine operates within the specified tolerances, providing consistent results.
- Tooling Quality: High-quality tools, such as dies and punches, are essential for achieving precise bends and shapes.
- Material Properties: Understanding the material’s properties, including its thickness, tensile strength, and ductility, is crucial for selecting the right machine settings.
- Operator Skill: Experienced operators can optimize machine settings and techniques to achieve the best results, even with challenging materials.
Overview of Bending and Press Machines
Bending and press machines are categorized based on their operating principles, applications, and the materials they handle. Below is a brief overview of some common types of bending and press machines:
1.3.1 Hydraulic Press Machines Hydraulic press machines operate by using a hydraulic cylinder to generate compressive force. They are highly versatile, allowing for various applications such as bending, forming, punching, and drawing. Hydraulic presses are known for their ability to exert high forces with great precision, making them ideal for heavy-duty applications. The introduction and working principles of hydraulic press machines will be discussed in more detail in the following sections.
1.3.2 Press Brake Machines Press brake machines are specialized machines used primarily for bending sheet metal. These machines utilize a combination of a punch and die to shape metal into specific angles and forms. Press brakes can be manual, hydraulic, or CNC-controlled, with each type offering different levels of automation and precision. The versatility of press brakes makes them a staple in metal fabrication shops.
1.3.3 Pipe Bending Machines Pipe bending machines are designed to bend pipes and tubes into various shapes and angles without compromising the material’s structural integrity. These machines are essential in industries such as plumbing, automotive, and construction, where precise pipe bends are required. Pipe bending machines can be hydraulic, pneumatic, mechanical, or electric, each offering different advantages depending on the application.
1.3.4 Sheet Metal Bending Machines Sheet metal bending machines focus on bending thin, flat sheets of metal into specific shapes. These machines are commonly used in the automotive and aerospace industries, where precision is critical. The machines can be manually operated, hydraulic, or CNC-controlled, offering various levels of control and automation.
Key Terminology and Concepts
Understanding the key terminology and concepts related to bending and press machines is essential for selecting the right equipment and optimizing its use. Below are some important terms that will be used throughout this document:
- Tonnage: The amount of force a machine can exert, usually measured in tons. For example, a 100-ton hydraulic press can exert 100 tons of force.
- Punch and Die: The tools used in press brake machines to shape metal. The punch presses into the die, which holds the workpiece.
- CNC (Computer Numerical Control): A method of automating machine tools using computers to control their movement and operation.
- Bend Radius: The radius of the inside curve of a bent section of metal. The bend radius is critical in determining the integrity and appearance of the bend.
- Ductility: The ability of a material to undergo deformation without breaking. Ductility is an important factor in bending operations.
Applications of Bending and Press Machines
Bending and press machines are used in a wide range of applications, from simple bending tasks to complex forming and shaping operations. Some common applications include:
- Automotive Industry: Producing car body parts, exhaust systems, and chassis components.
- Aerospace Industry: Manufacturing aircraft components, including fuselage panels and structural supports.
- Construction: Fabricating steel beams, columns, and other structural elements.
- Plumbing and HVAC: Bending pipes and tubes for plumbing, heating, and ventilation systems.
- Heavy Machinery: Forming and shaping parts for heavy equipment, such as cranes and bulldozers.
These applications highlight the versatility and importance of bending and press machines in modern manufacturing. The following sections will delve deeper into specific types of machines, their working principles, and the factors to consider when choosing the right equipment for your needs.
Hydraulic Press Machines: An Overview
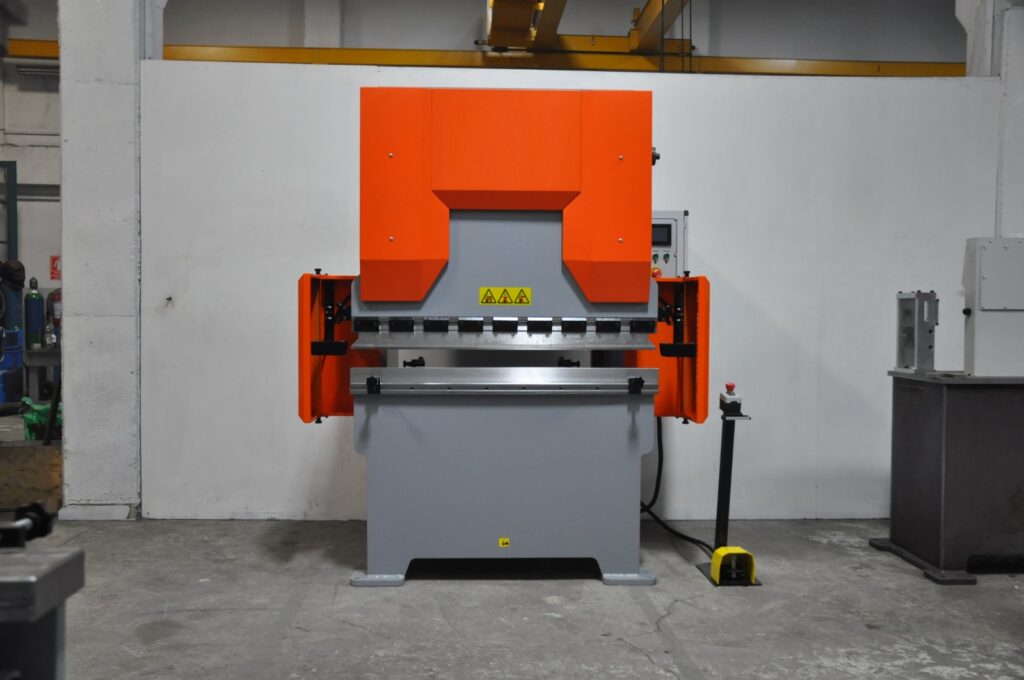
Hydraulic press machines are a cornerstone of modern manufacturing, offering unmatched power and precision in shaping, molding, and forming materials. These machines harness the power of hydraulics—a technology that uses fluid pressure to generate force—enabling them to perform tasks that require significant force with high accuracy. In this section, we will explore the fundamentals of hydraulic press machines, their working principles, various types, and key specifications that are critical for their selection and application in different industries.
2.1 Hydraulic Press Machine Introduction
Hydraulic press machines are used in a variety of industries for tasks that require compressive force. The concept behind hydraulic presses is based on Pascal’s law, which states that when pressure is applied to a confined fluid, the pressure is transmitted equally in all directions. This principle allows hydraulic presses to generate enormous amounts of force with relatively little input, making them highly efficient for industrial applications.
Key Characteristics:
- High Force Generation: Hydraulic presses can generate forces ranging from a few tons to several thousand tons, depending on the machine’s design and application.
- Versatility: These machines can perform a wide range of operations, including forging, stamping, bending, punching, and drawing.
- Precision: Hydraulic presses offer precise control over the applied force and movement, which is essential for tasks that require high accuracy.
- Customizability: Hydraulic presses can be customized with different types of tooling, making them adaptable to various tasks.
Hydraulic press machines are widely used in industries such as automotive manufacturing, aerospace, construction, and heavy machinery production. Their ability to handle large-scale operations with precision makes them a valuable asset in any industrial setting.
2.2 Hydraulic Press Machine Working Principles
The working of a hydraulic press machine is based on the simple but powerful principle of fluid mechanics. The machine typically consists of two cylinders: a smaller cylinder (called the slave cylinder) and a larger cylinder (called the master cylinder). These cylinders are connected by a pipe filled with hydraulic fluid, usually oil.
Working Process:
- Applying Force: When force is applied to the smaller cylinder (using a lever or a motor), it creates pressure in the hydraulic fluid.
- Pressure Transmission: According to Pascal’s law, the pressure in the fluid is transmitted equally throughout the system, causing the larger cylinder to move.
- Force Amplification: Because the larger cylinder has a greater surface area, the force exerted by it is much greater than the force applied to the smaller cylinder. This allows the machine to perform tasks that require significant force, such as pressing or bending metal.
Control Mechanisms:
- Pressure Control Valves: These valves regulate the amount of pressure applied to the hydraulic fluid, allowing the operator to control the force exerted by the machine.
- Flow Control Valves: These valves control the speed of the hydraulic fluid, which in turn controls the speed of the machine’s movement.
- Directional Control Valves: These valves direct the flow of hydraulic fluid to different parts of the system, enabling the machine to perform various operations.
Hydraulic press machines can be operated manually, semi-automatically, or fully automatically, depending on the level of control and automation required. Modern hydraulic presses often incorporate computerized control systems (CNC) for enhanced precision and efficiency.
2.3 Hydraulic Press Specifications
When selecting a hydraulic press machine, understanding its specifications is crucial to ensure that it meets the requirements of the intended application. Key specifications include:
2.3.1 Tonnage (Force Capacity)
- Definition: Tonnage refers to the maximum force that the hydraulic press can exert, usually measured in tons.
- Importance: The tonnage requirement depends on the material being processed and the operation being performed. For example, a higher tonnage is needed for tasks such as forging thick metal parts compared to bending thin sheets.
- Examples: A 100-ton hydraulic press is commonly used in medium-scale operations, while a 1000-ton hydraulic press is suitable for large-scale industrial applications.
2.3.2 Stroke Length
- Definition: Stroke length is the distance the press ram (the moving part of the machine that exerts force) can travel in one cycle.
- Importance: The stroke length determines the depth to which the material can be compressed or formed. It is particularly important in operations like deep drawing or molding.
- Adjustability: Many hydraulic presses allow the stroke length to be adjusted according to the specific requirements of the operation.
2.3.3 Bed Size
- Definition: The bed size is the working surface area of the press where the material is placed.
- Importance: The bed size must accommodate the dimensions of the workpiece being processed. A larger bed size is required for bigger workpieces.
- Customization: Some hydraulic presses offer interchangeable beds to handle different workpiece sizes.
2.3.4 Ram Speed
- Definition: Ram speed refers to the speed at which the press ram moves during operation.
- Importance: The speed of the ram can affect the quality of the operation. For example, slower speeds may be needed for precision tasks, while faster speeds are suitable for high-volume production.
- Control: Hydraulic presses often have adjustable ram speeds to suit different tasks.
2.3.5 Hydraulic System Pressure
- Definition: This is the pressure at which the hydraulic fluid operates within the system, usually measured in pounds per square inch (PSI) or bar.
- Importance: Higher system pressure allows for greater force generation but also requires more robust components to handle the increased stress.
- Safety: Hydraulic presses are equipped with safety mechanisms to prevent over-pressurization, which could lead to system failure.
2.4 100 Ton Hydraulic Press Specifications
A 100-ton hydraulic press is a versatile and commonly used machine in many industries, capable of handling a wide range of tasks from bending and forming to punching and drawing.
Key Specifications of a 100 Ton Hydraulic Press:
- Tonnage: 100 tons of maximum force, suitable for medium to large-scale operations.
- Stroke Length: Typically around 8 to 12 inches, with adjustability for different tasks.
- Bed Size: A standard bed size might be around 36 x 24 inches, but this can vary depending on the manufacturer.
- Ram Speed: Variable, often ranging from 10 to 30 mm/s, depending on the operation.
- System Pressure: Generally operates at around 3000 PSI, providing the necessary force without compromising safety.
Applications:
- Automotive Manufacturing: Used for pressing, forming, and shaping automotive parts.
- Metal Fabrication: Ideal for bending and shaping metal components in medium-scale production.
- Construction Equipment Manufacturing: Useful in the production of parts for heavy machinery and construction tools.
2.5 1000 Ton Hydraulic Press
The 1000-ton hydraulic press represents a significant leap in force capacity, making it suitable for the most demanding industrial applications. These machines are typically used in heavy industries where large-scale and high-force operations are required.
Key Specifications of a 1000 Ton Hydraulic Press:
- Tonnage: 1000 tons of maximum force, designed for heavy-duty tasks.
- Stroke Length: Can range from 12 to 24 inches, depending on the specific model and application.
- Bed Size: Large beds, often exceeding 72 x 48 inches, to accommodate massive workpieces.
- Ram Speed: Slower speeds, typically around 5 to 15 mm/s, due to the immense force being applied.
- System Pressure: Operates at high pressures, usually around 5000 PSI, to deliver the required force.
Applications:
- Shipbuilding: Used in the production of large metal components for ships and submarines.
- Aerospace: Essential for forming and shaping large aircraft components.
- Heavy Machinery Production: Involved in the manufacturing of parts for mining equipment, cranes, and other heavy-duty machinery.
2.6 Horizontal Hydraulic Press Machine
Horizontal hydraulic press machines differ from the more common vertical models in that the ram moves horizontally rather than vertically. This configuration is particularly useful for specific applications such as bending long pieces of metal or pressing components that are difficult to position vertically.
Advantages of Horizontal Hydraulic Press Machines:
- Versatility: Can handle a variety of tasks including bending, pressing, and straightening long workpieces.
- Ease of Operation: Easier to load and position large or awkwardly shaped workpieces.
- Space Efficiency: Horizontal presses can be more space-efficient in certain workshop layouts.
Applications:
- Railway Manufacturing: Used for bending and forming long steel rails.
- Pipeline Construction: Ideal for bending and forming large pipes used in oil, gas, and water pipelines.
- Structural Engineering: Employed in the production of long beams and structural components.
2.7 Small Horizontal Hydraulic Press
Small horizontal hydraulic presses are designed for applications that require less force and smaller workpieces. These machines are commonly used in workshops and smaller manufacturing facilities where space and budget constraints are factors.
Key Features:
- Compact Design: Takes up less space, making it ideal for small workshops.
- Lower Tonnage: Typically ranges from 10 to 50 tons, suitable for light to medium tasks.
- Ease of Use: Simple controls and operation, often with manual or semi-automatic settings.
Applications:
- Automotive Repair Shops: Used for pressing and straightening components like axles and shafts.
- Small Fabrication Shops: Ideal for bending and forming smaller metal parts.
- Maintenance Operations: Useful in on-site repairs and maintenance tasks where portability is required.
3. Press Brake Machines and Bending Applications
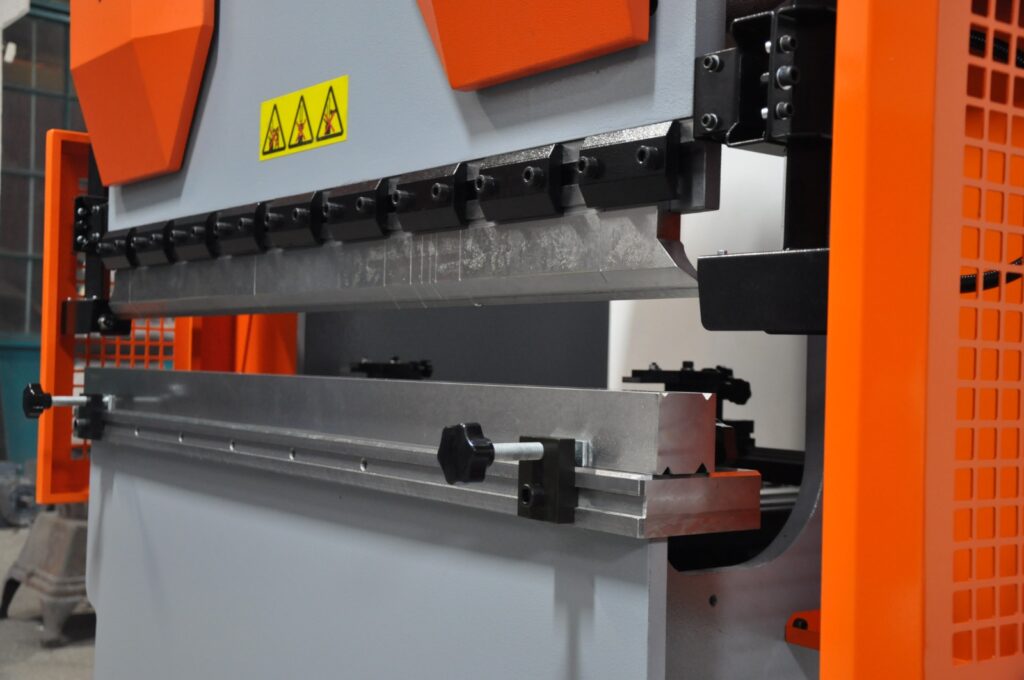
Press brake machines play a pivotal role in the metal fabrication industry, offering the precision and versatility required to transform flat metal sheets into complex shapes and structures. These machines are specifically designed for bending operations, making them indispensable in various manufacturing processes. This section delves into the functionality and applications of press brake machines, explores different bending techniques, and highlights the nuances of hydraulic press bending machines, including those tailored for sheet metal applications.
3.1 Press Brake Machine: Functionality and Applications
A press brake machine is a specialized tool used to bend and shape metal sheets and plates with high accuracy. Unlike general-purpose press machines, press brakes are specifically engineered to perform bending operations, making them essential in industries such as automotive, aerospace, construction, and manufacturing.
Key Functionalities:
- Bending: The primary function of a press brake is to bend metal sheets along a straight axis. This is achieved by clamping the metal between a punch and a die and applying force to create the desired angle.
- Forming: Beyond simple bends, press brakes can form complex shapes by combining multiple bending operations. This allows for the creation of intricate components required in various applications.
- Precision Cutting: Some advanced press brakes are equipped with features that allow for precise cutting or shearing of metal sheets during the bending process.
Applications:
- Automotive Industry: Manufacturing car body panels, chassis components, and exhaust systems.
- Aerospace Industry: Producing aircraft components, including fuselage sections and structural supports.
- Construction: Fabricating steel beams, columns, and other structural elements for buildings and infrastructure projects.
- Electronics: Creating enclosures and frames for electronic devices and appliances.
- Furniture Manufacturing: Designing and producing metal frames and supports for furniture pieces.
3.2 Press Brake Bending: Techniques and Precision
Bending is a fundamental operation in metalworking, and press brakes offer the precision and control necessary to achieve consistent and accurate results. Various bending techniques can be employed depending on the material, thickness, and desired outcome.
Bending Techniques:
- Air Bending: In this method, the punch presses the metal into the die without fully contacting it. This allows for greater flexibility in adjusting the bend angle and reduces stress on the material. Air bending is suitable for applications requiring variable angles and is widely used in sheet metal fabrication.Advantages:
- Versatility in bend angles.
- Reduced tooling wear.
- Lower force requirements compared to bottom bending.
- Bottom Bending (V-Die Bending): Here, the punch presses the metal all the way into the die, resulting in a more precise bend angle. This technique is ideal for applications where high accuracy and consistency are paramount.Advantages:
- Higher precision in bend angles.
- Better repeatability for mass production.
- Suitable for thicker materials.
- Coining: A specialized form of bottom bending where the metal is pressed into a highly precise shape within the die. Coining is used for intricate bends and is often employed in applications requiring fine details and superior surface finishes.
Precision Considerations:
- Tooling Quality: High-quality punches and dies are essential for achieving precise bends. The condition of the tooling directly impacts the accuracy and consistency of the bending process.
- Machine Calibration: Regular calibration ensures that the press brake operates within the specified tolerances, maintaining the precision of each bend.
- Material Properties: Understanding the ductility, tensile strength, and thickness of the material is crucial for selecting the appropriate bending parameters and avoiding defects such as cracking or warping.
- Operator Skill: Skilled operators can optimize machine settings and bending techniques to achieve the desired precision, especially when working with challenging materials or complex shapes.
3.3 Bend Press Machine: Overview
Bend press machines, often referred to interchangeably with press brake machines, are designed specifically for bending operations in metal fabrication. These machines vary in size, capacity, and control mechanisms, allowing them to cater to a wide range of applications from small workshops to large industrial facilities.
Types of Bend Press Machines:
- Manual Bend Press Machines: These are operated manually by the user, typically using a lever or hydraulic pump to apply force. They are suitable for small-scale operations and simple bending tasks.Advantages:
- Lower cost.
- Simplicity and ease of use.
- Ideal for light-duty applications.
- Hydraulic Bend Press Machines: Utilize hydraulic systems to apply force, offering greater control and higher tonnage capabilities compared to manual machines. They are widely used in medium to large-scale operations.Advantages:
- Higher force generation.
- Precise control over bending parameters.
- Suitable for a variety of materials and thicknesses.
- CNC Bend Press Machines: Equipped with computer numerical control (CNC) systems, these machines offer automated and programmable bending operations. They are ideal for high-precision and high-volume production environments.Advantages:
- Enhanced precision and repeatability.
- Ability to handle complex and intricate bends.
- Increased efficiency and reduced manual intervention.
Key Features:
- Adjustable Backgauges: Allow operators to set the precise location of the bend, ensuring consistency across multiple bends.
- Multiple Axes Control: Enables the machine to perform bends at various angles and positions without manual adjustments.
- Safety Features: Includes guards, emergency stop buttons, and sensors to ensure safe operation and protect operators from potential hazards.
3.4 Hydraulic Press Bending Machine
Hydraulic press bending machines combine the force-generating capabilities of hydraulic systems with the precision of press brakes to perform bending operations with high efficiency and accuracy. These machines are essential in applications where consistent and reliable bends are required, especially in medium to high-volume production settings.
Working Principles: Hydraulic press bending machines operate by using a hydraulic cylinder to exert force on the punch, which in turn bends the metal sheet against the die. The hydraulic system allows for smooth and controlled application of force, enabling precise bending angles and consistent results.
Advantages:
- High Force Capacity: Capable of handling thick and strong materials that require significant force to bend.
- Precision Control: Hydraulic systems offer fine control over the bending process, allowing for accurate and repeatable bends.
- Versatility: Suitable for a wide range of materials, including steel, aluminum, and stainless steel, making them adaptable to various industrial applications.
Applications:
- Automotive Manufacturing: Bending automotive body panels and structural components with high precision.
- Aerospace Industry: Forming aircraft parts that require exacting specifications and tight tolerances.
- Construction: Creating structural steel components for buildings and infrastructure projects.
- Heavy Machinery Production: Fabricating parts for construction equipment, mining machinery, and industrial tools.
3.5 Hydraulic Sheet Metal Bending Machine
Hydraulic sheet metal bending machines are specialized press brakes designed to handle the specific challenges associated with bending thin metal sheets. These machines leverage hydraulic systems to provide the necessary force and control for precise sheet metal fabrication.
Key Features:
- Enhanced Precision: Hydraulic systems ensure that each bend is executed with high accuracy, minimizing deviations and maintaining consistency.
- Adjustable Clamping Force: Allows for the secure holding of thin sheets without causing deformation or damage during the bending process.
- Integrated Control Systems: Modern hydraulic sheet metal bending machines often feature computerized controls for automated bending sequences, reducing manual intervention and increasing efficiency.
Benefits:
- Reduced Material Waste: Precise bending reduces the likelihood of errors and rework, leading to less material wastage and lower production costs.
- Increased Productivity: Automated and semi-automated systems enable faster production rates, meeting the demands of high-volume manufacturing.
- Versatility: Capable of handling a variety of sheet metal thicknesses and materials, making them suitable for diverse applications.
Applications:
- Appliance Manufacturing: Producing metal housings and components for household appliances such as refrigerators, washing machines, and ovens.
- Electronics Enclosures: Creating precise and compact metal enclosures for electronic devices and equipment.
- Furniture Manufacturing: Bending metal sheets for modern and ergonomic furniture designs.
- Signage and Displays: Forming metal panels used in signage, displays, and advertising materials.
3.6 Integration of CNC Technology in Press Brake Machines
The integration of Computer Numerical Control (CNC) technology into press brake machines has revolutionized the bending process, enhancing precision, efficiency, and flexibility. CNC press brakes are programmed with specific bending sequences, allowing for automated and repeatable operations that meet the stringent demands of modern manufacturing.
Advantages of CNC Press Brake Machines:
- Automation: Reduces the need for manual adjustments, minimizing human error and increasing production speed.
- Programmability: Allows for the storage and execution of complex bending programs, enabling the production of intricate shapes and multiple bends in a single setup.
- Consistency: Ensures that each bend is executed with the same precision, maintaining quality across large production runs.
- Ease of Use: User-friendly interfaces and software enable operators to input and modify bending programs with minimal training.
Applications:
- High-Precision Industries: Essential in industries such as aerospace and medical device manufacturing, where exacting standards must be met.
- Mass Production: Ideal for large-scale manufacturing where consistency and speed are critical.
- Customization: Facilitates the production of customized parts and components without significant downtime for setup changes.
3.7 Challenges and Considerations in Press Brake Bending
While press brake machines offer significant advantages in metal bending operations, several challenges and considerations must be addressed to ensure optimal performance and longevity of the equipment.
Common Challenges:
- Material Springback: After bending, materials tend to return partially to their original shape, known as springback. Proper compensation techniques and machine settings are required to achieve the desired final angle.
- Tooling Wear: Frequent bending operations can lead to wear and tear of punches and dies, affecting the quality of bends. Regular maintenance and timely replacement of tooling are essential.
- Setup Time: Adjusting machine settings and tooling for different bending tasks can be time-consuming, impacting overall productivity. CNC press brakes help mitigate this by enabling quick program changes.
- Operator Training: Skilled operators are necessary to manage machine settings, troubleshoot issues, and ensure consistent quality. Investing in training programs can enhance operational efficiency.
Key Considerations:
- Machine Selection: Choosing the right press brake machine involves assessing factors such as tonnage capacity, stroke length, bed size, and control systems based on the specific application requirements.
- Tooling Quality: High-quality punches and dies are crucial for achieving precise and consistent bends. Investing in durable tooling can reduce maintenance costs and improve overall performance.
- Maintenance Practices: Regular maintenance, including lubrication, inspection, and calibration, ensures that the press brake operates efficiently and extends its operational lifespan.
- Safety Measures: Implementing safety protocols, such as using protective guards and emergency stop mechanisms, protects operators and prevents accidents in the workplace.
3.8 Innovations in Press Brake Technology
Advancements in press brake technology continue to enhance the capabilities and efficiency of bending operations. Innovations such as servo-electric systems, advanced control software, and enhanced automation features are driving the evolution of press brake machines.
Servo-Electric Press Brakes: Servo-electric press brakes use electric motors to control the movement of the ram, offering precise positioning and energy-efficient operation. These machines provide faster cycle times and reduced maintenance compared to traditional hydraulic systems.
Advanced Control Software: Modern press brake machines are equipped with sophisticated software that enables real-time monitoring, automatic adjustments, and predictive maintenance. Features like automatic backgauges, bend allowance calculations, and integrated CAD/CAM systems streamline the bending process and improve accuracy.
Enhanced Automation: Automation features, including robotic loading and unloading, automated tool changes, and integrated quality control systems, increase productivity and reduce manual labor. These advancements are particularly beneficial in high-volume production environments where efficiency and consistency are paramount.
Sustainability Initiatives: Manufacturers are increasingly focusing on energy-efficient press brake machines that reduce power consumption and minimize environmental impact. Innovations such as regenerative braking systems and energy recovery mechanisms contribute to more sustainable manufacturing practices.
3.9 Case Studies: Press Brake Machines in Action
Automotive Manufacturing: In the automotive industry, press brake machines are used to fabricate various components such as door panels, chassis parts, and engine components. The precision offered by CNC press brakes ensures that each part meets the stringent quality standards required for vehicle assembly. For example, a major automotive manufacturer utilizes a fleet of 100-ton hydraulic press brakes to produce consistent and high-quality body panels, reducing production time and minimizing material waste.
Aerospace Industry: Aerospace manufacturers rely on hydraulic sheet metal bending machines to produce aircraft components with exacting specifications. The high precision and repeatability of CNC press brakes enable the production of complex parts such as fuselage sections and wing components. By integrating advanced control systems, aerospace companies can achieve the necessary tolerances and maintain the integrity of critical components.
Construction Sector: In the construction industry, press brake machines are used to fabricate structural steel elements like beams, columns, and trusses. Hydraulic press brakes with large bed sizes and high tonnage capacities are essential for handling the thick and heavy materials used in construction projects. For instance, a construction equipment manufacturer employs 1000-ton hydraulic press brakes to produce large steel beams, ensuring structural integrity and compliance with safety standards.
Electronics Manufacturing: Electronics manufacturers use small hydraulic sheet metal bending machines to create precise enclosures and frames for devices such as smartphones, laptops, and medical equipment. The ability to perform intricate bends with high accuracy ensures that the final products meet design specifications and fit seamlessly with other components.
3.10 Best Practices for Operating Press Brake Machines
To maximize the efficiency and lifespan of press brake machines, adhering to best practices is essential. These practices encompass proper machine setup, maintenance, and operational techniques that ensure consistent quality and safety.
Machine Setup:
- Accurate Alignment: Ensure that the punch and die are properly aligned to prevent uneven bends and reduce tooling wear.
- Proper Tooling Selection: Choose the appropriate punches and dies based on the material type, thickness, and desired bend angle.
- Parameter Optimization: Set the correct bending force, ram speed, and stroke length according to the material properties and bending requirements.
Maintenance:
- Regular Inspections: Conduct routine inspections of hydraulic systems, electrical components, and mechanical parts to identify and address potential issues early.
- Lubrication: Keep moving parts well-lubricated to reduce friction and prevent wear.
- Tooling Maintenance: Clean and maintain punches and dies to ensure optimal performance and extend their lifespan.
Operational Techniques:
- Consistent Feeding: Ensure that metal sheets are fed consistently into the press brake to maintain uniform bends.
- Monitoring and Adjustment: Continuously monitor the bending process and make necessary adjustments to maintain precision.
- Safety Protocols: Implement and enforce safety protocols, including the use of personal protective equipment (PPE) and adherence to operational guidelines.
Training and Education:
- Operator Training: Provide comprehensive training for operators to ensure they understand machine operation, safety procedures, and maintenance practices.
- Continuous Improvement: Encourage operators to stay updated with the latest techniques and technologies in press brake operations through ongoing education and training programs.
3.11 Conclusion
Press brake machines are integral to the metal fabrication industry, offering the precision and versatility required to produce a wide range of components and structures. Understanding the functionality, bending techniques, and specific applications of different press brake machines, including hydraulic and CNC models, is essential for optimizing their use in various industrial settings. By adhering to best practices and leveraging advancements in press brake technology, manufacturers can achieve high-quality results, enhance productivity, and maintain a competitive edge in the market.
In the following sections, we will explore other specialized bending machines, including pipe bending machines and sheet metal bending machines, to provide a comprehensive overview of the tools available for metal shaping and forming operations.
Pipe Bending Machines
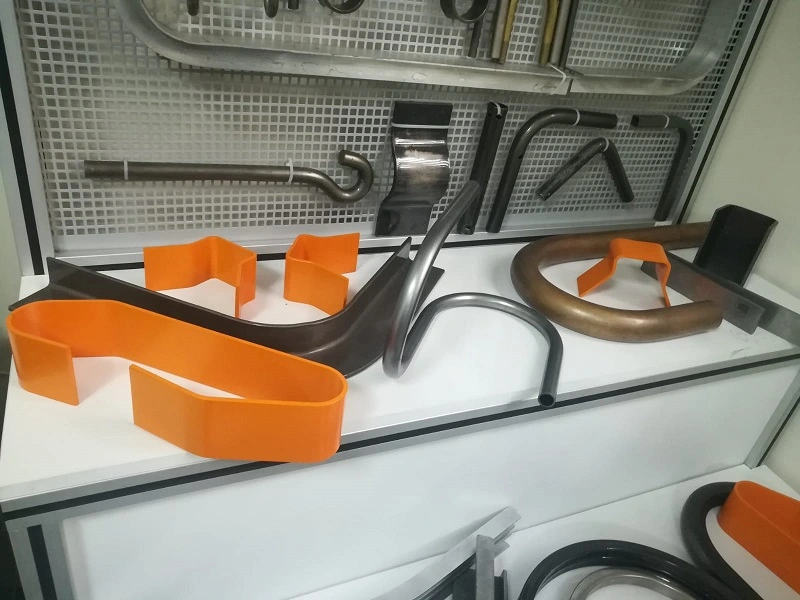
Pipe bending machines are essential tools in industries where precise and efficient bending of pipes and tubes is required. These machines are used to create complex pipe shapes that are crucial in various applications, from plumbing and construction to automotive and aerospace industries. In this section, we will explore the different types of pipe bending machines, including pneumatic, mechanical, hydraulic, and specialized machines for bending stainless steel (SS) and heavy pipes. We’ll also discuss the benefits and considerations for choosing the right pipe bending machine for specific applications.
4.1 Pneumatic Pipe Bending Machine
Pneumatic pipe bending machines utilize compressed air to generate the force needed to bend pipes. These machines are commonly used in applications that require moderate force and precision, making them suitable for a variety of industries, including automotive and HVAC (Heating, Ventilation, and Air Conditioning).
Working Principles:
- Air Compression: The machine operates by compressing air in a cylinder, which then forces a piston to move. This movement is transferred to the bending tool, which applies the necessary force to bend the pipe.
- Controlled Force: The force applied can be adjusted by regulating the air pressure, allowing for precise control over the bending process.
Advantages:
- Simplicity: Pneumatic systems are generally simpler and easier to maintain than hydraulic systems, with fewer components and less potential for leaks.
- Cost-Effectiveness: Pneumatic machines are often more affordable than their hydraulic counterparts, making them a good option for smaller operations.
- Safety: Pneumatic systems are inherently safer in environments where fire hazards are a concern, as they do not involve flammable fluids.
Applications:
- Automotive Industry: Bending exhaust pipes and other components where moderate force and precision are required.
- HVAC Systems: Shaping pipes and ducts for heating, ventilation, and air conditioning installations.
- General Fabrication: Suitable for bending tasks in small to medium-sized fabrication shops.
4.2 Mechanical Pipe Bending Machine
Mechanical pipe bending machines rely on mechanical force generated by gears, levers, and other mechanical components to bend pipes. These machines are known for their durability and reliability, making them suitable for high-volume production environments.
Working Principles:
- Mechanical Leverage: The machine uses mechanical leverage to amplify the force applied by the operator, allowing it to bend pipes with precision.
- Gear Systems: Gears and cams are often used to control the movement and force applied to the bending tool, ensuring consistent results.
Advantages:
- Durability: Mechanical pipe bending machines are built to last, with robust components that can withstand the rigors of high-volume production.
- Consistency: The use of gears and mechanical systems ensures consistent and repeatable bends, which is crucial in mass production.
- Ease of Use: These machines are typically straightforward to operate, with manual or semi-automatic controls that allow for precise adjustments.
Applications:
- Construction Industry: Bending steel pipes for structural applications, such as scaffolding and frameworks.
- Manufacturing: Producing bent pipes for various industrial products, including furniture, machinery, and equipment.
- Shipbuilding: Shaping pipes used in marine applications, where durability and precision are critical.
4.3 SS Pipe Bending Machine
Stainless steel (SS) pipes are widely used in industries that require corrosion-resistant and durable materials, such as food processing, pharmaceuticals, and chemical processing. Bending stainless steel pipes requires specialized machines that can handle the unique properties of this material without causing damage or deformation.
Key Features:
- Enhanced Tooling: SS pipe bending machines are equipped with hardened tooling that can withstand the high tensile strength of stainless steel, preventing tool wear and ensuring clean bends.
- Precision Control: These machines offer precise control over the bending process, allowing for tight bend radii and complex shapes without compromising the material’s integrity.
- Cooling Systems: Some SS pipe bending machines are equipped with cooling systems to prevent the material from overheating during the bending process, which could lead to discoloration or weakening of the stainless steel.
Advantages:
- Corrosion Resistance: SS pipe bending machines are designed to maintain the corrosion-resistant properties of stainless steel, making them ideal for applications in harsh environments.
- High Precision: The machines can produce precise bends with minimal springback, ensuring that the final product meets exact specifications.
- Versatility: Suitable for a wide range of applications, from sanitary piping in food processing to chemical transport lines in industrial settings.
Applications:
- Food and Beverage Industry: Bending pipes for sanitary processing lines, where cleanliness and corrosion resistance are paramount.
- Pharmaceutical Industry: Shaping pipes for sterile environments, including drug manufacturing and medical device production.
- Chemical Processing: Creating corrosion-resistant piping systems for transporting aggressive chemicals and other hazardous materials.
4.4 Steel Pipe Bending Machine
Steel pipe bending machines are designed to handle the rigors of bending steel pipes, which are commonly used in construction, infrastructure, and heavy industry. These machines are built to provide the necessary force and control to bend steel pipes without compromising their structural integrity.
Key Features:
- High Tonnage Capacity: Steel pipe bending machines are equipped with powerful hydraulic or mechanical systems capable of exerting the high forces required to bend steel.
- Robust Construction: The machines are built with heavy-duty frames and components to handle the stress of bending thick and strong steel pipes.
- Advanced Control Systems: Many steel pipe bending machines feature CNC controls, allowing for precise and automated bending processes.
Advantages:
- Strength and Durability: Steel pipe bending machines are capable of bending thick-walled and large-diameter steel pipes with high precision, ensuring that the final product meets structural requirements.
- Versatility: These machines can handle a wide range of steel pipe sizes and thicknesses, making them suitable for various applications in construction and heavy industry.
- Efficiency: The use of advanced control systems and automated features allows for efficient production, reducing labor costs and increasing throughput.
Applications:
- Construction: Bending steel pipes for structural applications, such as beams, columns, and supports in buildings and infrastructure projects.
- Oil and Gas Industry: Shaping steel pipes for pipelines, drilling rigs, and other critical infrastructure in the energy sector.
- Heavy Machinery Manufacturing: Producing bent steel components for construction equipment, mining machinery, and industrial tools.
4.5 Heavy Pipe Bending Machine
Heavy pipe bending machines are specialized for handling large-diameter and thick-walled pipes that require significant force to bend. These machines are used in industries where large-scale infrastructure projects and heavy-duty applications are common.
Key Features:
- High Force Capability: Heavy pipe bending machines are equipped with hydraulic systems capable of generating extremely high forces, often exceeding 1000 tons, to bend large and thick pipes.
- Large Bed Size: These machines feature expansive working areas to accommodate the size of the pipes being bent, allowing for precise positioning and control.
- Reinforced Components: The machines are built with reinforced frames, tooling, and hydraulic systems to handle the stress of bending heavy pipes without deformation.
Advantages:
- Capability: Heavy pipe bending machines can handle pipes with large diameters and thick walls, which are typically used in major infrastructure projects.
- Precision: Despite their size, these machines offer precise control over the bending process, ensuring that large pipes meet exacting specifications.
- Durability: Built to withstand the demands of heavy industry, these machines offer long service life and reliable performance in challenging environments.
Applications:
- Pipeline Construction: Bending large-diameter pipes for oil, gas, and water pipelines that span long distances and require precise engineering.
- Shipbuilding: Shaping heavy steel pipes for marine vessels, where durability and structural integrity are crucial.
- Power Generation: Producing bent pipes for power plants and energy infrastructure, including those used in nuclear and fossil fuel power generation.
4.6 Hydraulic Pipe Bending Machine
Hydraulic pipe bending machines are among the most versatile and powerful options for bending pipes in various industries. These machines utilize hydraulic pressure to apply force, offering precise control and the ability to handle a wide range of pipe sizes and materials.
Working Principles:
- Hydraulic Force: The machine uses a hydraulic cylinder to apply force to the bending tool, which then bends the pipe to the desired angle.
- Adjustable Pressure: Operators can adjust the hydraulic pressure to control the force applied, allowing for precise bends even in challenging materials.
Advantages:
- Versatility: Hydraulic pipe bending machines can handle a variety of materials, including steel, aluminum, and stainless steel, making them suitable for diverse applications.
- Precision: The hydraulic system offers fine control over the bending process, ensuring consistent results with minimal springback.
- Power: These machines are capable of generating significant force, allowing them to bend thick and strong pipes with ease.
Applications:
- Automotive Manufacturing: Bending exhaust pipes, roll cages, and other components where precision and strength are required.
- Aerospace Industry: Shaping pipes used in aircraft hydraulic systems, fuel lines, and other critical applications.
- Construction: Bending steel pipes for structural applications, such as beams, columns, and support structures.
4.7 Electric Pipe Bending Machine
Electric pipe bending machines offer an alternative to hydraulic and pneumatic systems, using electric motors to generate the force needed for bending operations. These machines are known for their energy efficiency, precision, and ease of use.
Key Features:
- Electric Motor Drive: The machine uses an electric motor to drive the bending tool, providing precise control over the bending process.
- Programmable Controls: Many electric pipe bending machines feature CNC or digital controls, allowing for automated and repeatable bending sequences.
- Quiet Operation: Electric machines tend to operate more quietly than hydraulic or pneumatic systems, making them suitable for environments where noise is a concern.
Advantages:
- Energy Efficiency: Electric pipe bending machines consume less energy compared to hydraulic systems, making them more cost-effective in the long run.
- Precision and Consistency: The use of electric motors and digital controls ensures precise and repeatable bends, which is critical in high-volume production.
- Ease of Maintenance: Electric machines have fewer moving parts compared to hydraulic systems, resulting in lower maintenance requirements and longer service life.
Applications:
- Furniture Manufacturing: Bending metal pipes for furniture frames, including chairs, tables, and shelving units.
- Medical Equipment: Shaping pipes used in medical devices and equipment, where precision and cleanliness are essential.
- Automotive Aftermarket: Producing custom exhaust systems, roll cages, and other automotive components.
4.8 Small Pipe Bending Machine
Small pipe bending machines are designed for applications that involve smaller-diameter pipes and require less force. These machines are commonly used in workshops, small-scale manufacturing, and maintenance operations.
Key Features:
- Compact Design: Small pipe bending machines are portable and space-efficient, making them ideal for use in confined spaces or on job sites.
- Manual or Semi-Automatic Operation: These machines are typically operated manually or with semi-automatic controls, offering a balance between control and ease of use.
- Versatility: Despite their small size, these machines can handle a variety of materials and bending angles, making them suitable for diverse applications.
Advantages:
- Portability: Small pipe bending machines are easy to transport and set up, making them ideal for on-site work and maintenance tasks.
- Cost-Effectiveness: These machines are typically more affordable than larger models, making them accessible to small businesses and workshops.
- Ease of Use: Simple controls and operation make these machines user-friendly, even for operators with limited experience.
Applications:
- Plumbing: Bending pipes for plumbing installations and repairs, including copper, PVC, and other materials.
- HVAC: Shaping small-diameter pipes for heating, ventilation, and air conditioning systems.
- DIY and Home Workshops: Suitable for hobbyists and small-scale fabricators working on custom projects.
4.9 Pipe Bending Machine Price Considerations
When selecting a pipe bending machine, understanding the factors that influence price is crucial to making an informed investment. The price of a pipe bending machine can vary significantly based on several key factors, including machine type, capacity, features, and brand.
Factors Influencing Price:
- Machine Type: Hydraulic and electric pipe bending machines are generally more expensive than pneumatic or mechanical models due to their advanced features and higher force capabilities.
- Capacity: Machines capable of bending larger-diameter or thicker-walled pipes typically cost more due to the increased force requirements and more robust construction.
- Control Systems: CNC-controlled machines with programmable features and automated bending sequences are priced higher than manual or semi-automatic models.
- Brand and Quality: Established brands with a reputation for quality and reliability often command higher prices, but they also offer better performance, durability, and support.
Cost vs. Functionality:
- Entry-Level Machines: Suitable for small-scale operations, workshops, and maintenance tasks, these machines offer basic functionality at a lower cost.
- Mid-Range Machines: Ideal for medium-sized businesses and manufacturers, offering a balance between price and advanced features.
- High-End Machines: Designed for large-scale production and heavy industry, these machines offer the highest levels of precision, automation, and durability but come at a premium price.
Making the Right Investment:
- Assessing Needs: Consider the specific requirements of your operation, including the types of materials, pipe sizes, and production volume, to choose a machine that meets your needs without overspending.
- Long-Term Value: While higher-end machines may have a higher initial cost, their durability, efficiency, and advanced features can lead to lower operational costs and better ROI over time.
- Supplier Support: Look for suppliers that offer good after-sales support, including training, maintenance, and parts availability, as this can significantly impact the total cost of ownership.
4.10 Conclusion
Pipe bending machines are crucial tools in various industries, offering the ability to shape and form pipes to precise specifications. Understanding the different types of pipe bending machines, including pneumatic, mechanical, hydraulic, and specialized machines for stainless steel and heavy pipes, is essential for selecting the right equipment for your needs. By considering factors such as machine capacity, control systems, and price, manufacturers and operators can make informed decisions that optimize productivity and ensure the quality of their products.
Sheet Metal Bending Machines
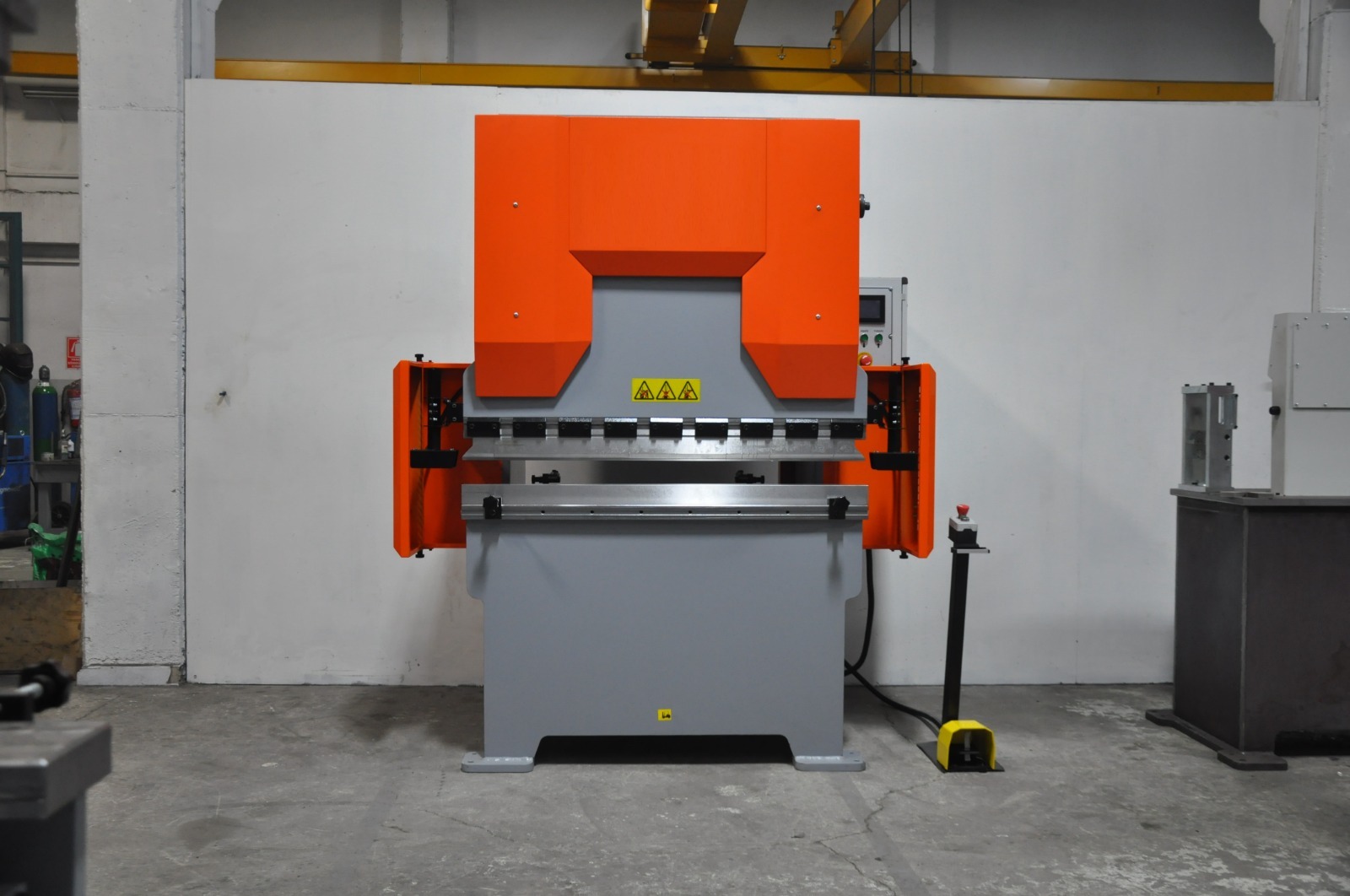
Sheet metal bending machines are essential in the fabrication of metal components, allowing manufacturers to create a wide range of shapes and structures from flat metal sheets. These machines are used across various industries, from automotive to aerospace, and play a critical role in producing everything from simple bends to complex geometries. In this section, we will explore the different types of sheet metal bending machines, including electric, hydraulic, automatic, and CNC-controlled machines. We will also discuss their applications, benefits, and factors to consider when selecting the right machine for specific tasks.
5.1 Electric Sheet Metal Bending Machine
Electric sheet metal bending machines use electric motors to generate the force needed to bend metal sheets. These machines are known for their energy efficiency, precision, and ease of use, making them a popular choice in many fabrication shops.
Key Features:
- Electric Motor Drive: These machines are driven by electric motors, which provide precise control over the bending process and allow for consistent and repeatable results.
- Programmable Controls: Many electric bending machines come with digital or CNC controls, enabling operators to program bending sequences and angles for automated operations.
- Quiet Operation: Electric machines tend to be quieter than hydraulic models, making them suitable for environments where noise reduction is important.
Advantages:
- Energy Efficiency: Electric machines are more energy-efficient than hydraulic machines, reducing operational costs over time.
- Precision: The electric motor provides consistent power, allowing for precise bends with minimal variability.
- Ease of Maintenance: With fewer moving parts and no hydraulic fluid, electric bending machines typically require less maintenance and have lower operating costs.
Applications:
- Light Fabrication: Suitable for bending thin sheets of metal, making them ideal for light fabrication tasks such as creating enclosures, brackets, and panels.
- Electronics Manufacturing: Used to bend metal components for electronic devices, where precision and consistency are critical.
- Custom Fabrication: Ideal for small workshops and custom fabrication businesses that require flexible and precise bending capabilities.
5.2 Small Sheet Bending Machine
Small sheet bending machines are designed for tasks that involve smaller pieces of sheet metal. These machines are typically more compact and easier to use, making them ideal for workshops and small-scale operations.
Key Features:
- Compact Design: Small sheet bending machines are designed to be portable and space-efficient, allowing them to be used in smaller workspaces.
- Manual or Semi-Automatic Operation: These machines often feature manual or semi-automatic controls, providing a balance between precision and ease of use.
- Versatile Tooling: Despite their size, small sheet bending machines can be equipped with a variety of tooling to handle different bending tasks.
Advantages:
- Portability: The compact size of these machines makes them easy to transport and set up, allowing for flexible use in different locations.
- Affordability: Small sheet bending machines are typically less expensive than larger models, making them accessible to small businesses and workshops.
- Ease of Use: Simple controls and operation make these machines user-friendly, even for operators with limited experience.
Applications:
- DIY and Custom Projects: Ideal for hobbyists and small-scale fabricators working on custom projects.
- Maintenance and Repair: Used in maintenance shops for bending small metal parts and components during repairs.
- Prototype Development: Suitable for creating prototypes and small production runs, where flexibility and quick setup are important.
5.3 Automatic Bending Machine
Automatic bending machines are designed to streamline the bending process by automating various aspects of the operation. These machines are equipped with advanced control systems that allow for precise and repeatable bending without the need for constant operator intervention.
Key Features:
- Automation: Automatic bending machines are capable of performing multiple bends in a single setup, reducing the need for manual adjustments and increasing productivity.
- CNC Controls: Many automatic bending machines are equipped with CNC (Computer Numerical Control) systems that allow for the programming of complex bending sequences.
- High Throughput: These machines are designed for high-volume production, making them ideal for industries that require large quantities of bent metal parts.
Advantages:
- Increased Efficiency: Automation reduces the time required for setup and bending, leading to higher production rates and lower labor costs.
- Consistency: Automatic machines ensure that each bend is executed with the same precision, reducing variability and improving product quality.
- Flexibility: The ability to program complex bending sequences allows for the production of intricate and custom shapes with minimal manual intervention.
Applications:
- Mass Production: Used in industries such as automotive and aerospace, where large quantities of parts with consistent quality are required.
- Complex Fabrication: Suitable for producing parts with multiple bends or intricate shapes that would be difficult to achieve manually.
- High-Precision Manufacturing: Ideal for applications where exacting tolerances and repeatability are essential, such as in the production of medical devices and electronics.
5.4 CNC Sheet Bending Machine
CNC sheet bending machines represent the pinnacle of precision and automation in sheet metal bending. These machines are controlled by computer numerical control (CNC) systems, which allow for highly accurate and repeatable bending operations.
Key Features:
- CNC Control: CNC sheet bending machines are equipped with computerized controls that allow operators to program and execute complex bending sequences with high precision.
- Automated Tooling: These machines often feature automated tooling systems that can change punches and dies as needed, further increasing efficiency and reducing setup time.
- Real-Time Monitoring: CNC systems provide real-time monitoring of the bending process, allowing operators to make adjustments on the fly and ensuring that each bend meets the required specifications.
Advantages:
- High Precision: CNC control ensures that each bend is performed with exacting accuracy, making these machines ideal for applications where precision is critical.
- Repeatability: The ability to store and recall bending programs allows for consistent results across multiple production runs, reducing variability and waste.
- Complexity: CNC sheet bending machines can perform intricate bends and form complex shapes that would be difficult or impossible to achieve with manual machines.
Applications:
- Aerospace Industry: Used to produce aircraft components with exacting tolerances and complex shapes.
- Automotive Manufacturing: Essential for the production of car body panels, chassis components, and other critical parts that require high precision.
- Electronics and Appliances: Ideal for creating metal enclosures, frames, and other components used in electronics and household appliances.
5.5 What is a CNC Bending Machine?
A CNC bending machine is a specialized type of bending machine that uses computer numerical control (CNC) to automate the bending process. CNC machines are programmed with specific instructions that control the movement of the machine’s bending tools, allowing for precise and repeatable operations.
How CNC Bending Machines Work:
- Programming: Operators program the CNC machine using specialized software, inputting parameters such as bend angles, material thickness, and sequence of operations.
- Tool Movement: The CNC system controls the movement of the bending tools, ensuring that each bend is executed according to the programmed instructions.
- Feedback Loops: CNC machines often include feedback systems that monitor the bending process in real-time, allowing for automatic adjustments to maintain precision.
Benefits of CNC Bending Machines:
- Precision: CNC bending machines offer unparalleled precision, with the ability to produce bends with tight tolerances and consistent quality.
- Efficiency: Automation reduces the time required for setup and bending, increasing throughput and reducing labor costs.
- Flexibility: The ability to program complex bending sequences allows for the production of custom and intricate shapes with minimal manual intervention.
Applications:
- Industrial Manufacturing: Used in high-volume production environments where consistency and precision are critical.
- Custom Fabrication: Ideal for producing custom parts and components, especially those with complex geometries.
- Prototyping: CNC bending machines are valuable in the development of prototypes, allowing for rapid iteration and precise adjustments.
5.6 Hydraulic Press Bending Machine
Hydraulic press bending machines combine the power of hydraulic systems with the precision of press brakes to perform bending operations with high efficiency and accuracy. These machines are widely used in industries that require consistent and reliable bends in a variety of materials, including steel, aluminum, and stainless steel.
Working Principles:
- Hydraulic Force: The machine uses a hydraulic cylinder to apply force to the bending tool, which then bends the metal sheet to the desired angle.
- Adjustable Pressure: Operators can adjust the hydraulic pressure to control the force applied, allowing for precise bends even in challenging materials.
Advantages:
- High Force Capacity: Hydraulic press bending machines are capable of exerting significant force, making them suitable for bending thick and strong materials.
- Precision: The hydraulic system provides fine control over the bending process, ensuring consistent results with minimal variability.
- Versatility: These machines can handle a wide range of materials and thicknesses, making them suitable for various industrial applications.
Applications:
- Automotive Manufacturing: Bending automotive body panels and structural components with high precision.
- Construction: Creating structural steel components for buildings and infrastructure projects.
- Heavy Machinery Production: Fabricating parts for construction equipment, mining machinery, and industrial tools.
5.7 Hydraulic Sheet Metal Bending Machine
Hydraulic sheet metal bending machines are specialized press brakes designed to handle the specific challenges associated with bending thin metal sheets. These machines leverage hydraulic systems to provide the necessary force and control for precise sheet metal fabrication.
Key Features:
- Enhanced Precision: Hydraulic systems ensure that each bend is executed with high accuracy, minimizing deviations and maintaining consistency.
- Adjustable Clamping Force: Allows for the secure holding of thin sheets without causing deformation or damage during the bending process.
- Integrated Control Systems: Modern hydraulic sheet metal bending machines often feature computerized controls for automated bending sequences, reducing manual intervention and increasing efficiency.
Benefits:
- Reduced Material Waste: Precise bending reduces the likelihood of errors and rework, leading to less material wastage and lower production costs.
- Increased Productivity: Automated and semi-automated systems enable faster production rates, meeting the demands of high-volume manufacturing.
- Versatility: Capable of handling a variety of sheet metal thicknesses and materials, making them suitable for diverse applications.
Applications:
- Appliance Manufacturing: Producing metal housings and components for household appliances such as refrigerators, washing machines, and ovens.
- Electronics Enclosures: Creating precise and compact metal enclosures for electronic devices and equipment.
- Furniture Manufacturing: Bending metal sheets for modern and ergonomic furniture designs.
5.8 Choosing the Right Sheet Metal Bending Machine
Selecting the right sheet metal bending machine involves considering several factors, including the material being bent, the required precision, production volume, and budget. Here are some key considerations to keep in mind:
Material Type and Thickness:
- Material: Different machines are better suited for specific materials. For example, hydraulic machines are ideal for thick steel sheets, while electric machines may be better for lighter materials.
- Thickness: The thickness of the material will determine the required force, with thicker materials needing more powerful machines.
Bending Precision:
- Tolerances: If your application requires tight tolerances, a CNC or hydraulic bending machine may be the best choice due to their precision and consistency.
- Complexity: For complex bending operations involving multiple bends or intricate shapes, a CNC machine will provide the necessary control and flexibility.
Production Volume:
- Low Volume: For small production runs or custom projects, a manual or small sheet bending machine may suffice.
- High Volume: For large-scale production, an automatic or CNC bending machine is more appropriate due to their higher efficiency and automation capabilities.
Budget Considerations:
- Initial Investment: CNC and hydraulic machines tend to have higher upfront costs but offer long-term benefits in precision, efficiency, and flexibility.
- Operating Costs: Consider the long-term costs of maintenance, energy consumption, and tooling when selecting a machine.
Supplier Support:
- After-Sales Service: Choose a supplier that offers good after-sales support, including maintenance, training, and access to spare parts.
- Warranty: Look for machines that come with a comprehensive warranty, which can protect your investment and reduce the risk of unexpected costs.
5.9 Future Trends in Sheet Metal Bending Machines
The field of sheet metal bending is constantly evolving, with new technologies and innovations improving the efficiency, precision, and versatility of bending machines. Here are some trends shaping the future of sheet metal bending:
Automation and Robotics:
- Increased Automation: Automation is becoming more prevalent in sheet metal bending, with robots and automated systems taking over tasks such as loading, unloading, and tool changes, leading to higher productivity and lower labor costs.
- Collaborative Robots: Also known as cobots, these robots work alongside human operators to assist with bending operations, enhancing efficiency while maintaining flexibility.
Advanced CNC Systems:
- Real-Time Monitoring: CNC systems are becoming more advanced, with features such as real-time monitoring, predictive maintenance, and automatic adjustments ensuring higher precision and reducing downtime.
- AI Integration: Artificial intelligence (AI) is being integrated into CNC systems to optimize bending processes, improve decision-making, and enhance overall efficiency.
Sustainability Initiatives:
- Energy Efficiency: Manufacturers are focusing on creating more energy-efficient bending machines that reduce power consumption without compromising performance.
- Material Waste Reduction: Innovations in tooling and process control are helping to reduce material waste, leading to more sustainable manufacturing practices.
Customization and Flexibility:
- Modular Machines: Modular designs allow for easy customization of bending machines, enabling manufacturers to adapt to different tasks and requirements without significant downtime.
- Flexible Tooling: Advances in tooling technology are allowing for more flexible and adaptable bending operations, making it easier to switch between different products and designs.
5.10 Conclusion
Sheet metal bending machines are vital tools in modern manufacturing, offering the precision, flexibility, and efficiency needed to produce high-quality metal components. Understanding the different types of machines—such as electric, hydraulic, automatic, and CNC models—and their specific applications is crucial for selecting the right equipment for your needs. By considering factors such as material type, bending precision, production volume, and budget, manufacturers can make informed decisions that enhance productivity and ensure the quality of their products.
Bending Press Machine Price Considerations
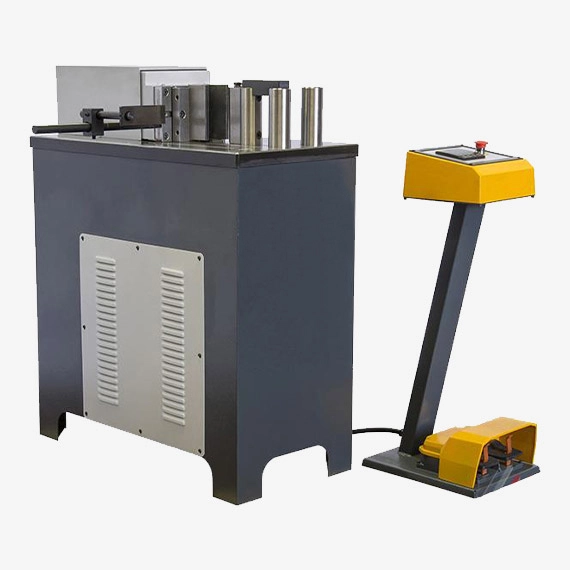
When investing in bending press machines, understanding the factors that influence pricing is essential for making an informed and cost-effective decision. Bending press machines come in various types and configurations, each with different features and capabilities that affect their overall cost. In this section, we will explore the key factors that determine the price of bending press machines, including specifications, features, brand reputation, and market demand. We will also discuss how to balance cost with functionality to ensure that you select the right machine for your specific needs.
6.1 Factors Affecting Bending Press Machine Price
The price of a bending press machine is influenced by several factors, including its type, specifications, features, brand, and market conditions. Understanding these factors can help you determine which machine offers the best value for your investment.
6.1.1 Machine Type
- Manual vs. Automated Machines: Manual bending press machines are generally less expensive than automated or CNC-controlled machines due to their simpler design and lower manufacturing costs. However, automated machines, while more expensive, offer greater efficiency, precision, and productivity, which can justify the higher initial investment.
- Hydraulic vs. Mechanical Presses: Hydraulic presses are typically more expensive than mechanical presses because of their complex hydraulic systems, which provide greater force and control. Mechanical presses, while less costly, may be more suitable for applications where speed is prioritized over precision.
6.1.2 Specifications and Capacity
- Tonnage: The tonnage, or force capacity, of a bending press machine is one of the primary factors influencing its price. Machines with higher tonnage are capable of bending thicker and stronger materials but come with a higher price tag due to the more robust construction and powerful hydraulic or mechanical systems required.
- Bed Size: The size of the machine’s bed, which determines the maximum size of the workpiece it can handle, also affects the price. Larger beds increase the machine’s versatility but require more material and engineering, leading to higher costs.
- Stroke Length: The stroke length, or the distance the press ram can travel, is another critical specification. Machines with longer stroke lengths can accommodate deeper bends, which adds to the complexity and cost of the machine.
6.1.3 Features and Technology
- CNC Controls: Bending press machines equipped with CNC (Computer Numerical Control) systems are significantly more expensive than those with manual or semi-automatic controls. CNC systems offer the ability to program and automate complex bending sequences, enhancing precision and productivity, which justifies their higher price.
- Automation and Robotics: Machines with advanced automation features, such as automatic tool changers, robotic loading and unloading, and real-time monitoring systems, command higher prices due to the added technology and the potential for increased production efficiency.
- Safety Features: Enhanced safety features, such as light curtains, safety guards, and emergency stop systems, can also contribute to the overall cost of the machine. These features are essential for protecting operators and ensuring compliance with safety regulations, particularly in high-volume production environments.
6.1.4 Brand and Quality
- Reputation: The reputation of the manufacturer or brand plays a significant role in the price of bending press machines. Established brands with a history of quality, reliability, and excellent after-sales support often charge a premium for their products. While these machines may be more expensive upfront, they often offer better performance, durability, and long-term value.
- Quality of Materials: The quality of the materials used in the construction of the machine, such as the steel for the frame and the components of the hydraulic system, affects both the machine’s durability and price. Higher-quality materials lead to longer-lasting machines but increase manufacturing costs.
6.1.5 Market Demand and Availability
- Supply and Demand: Market conditions, such as the balance between supply and demand, can also influence the price of bending press machines. During periods of high demand, prices may rise due to limited availability. Conversely, prices may decrease during periods of low demand or excess supply.
- Import and Export Costs: For machines that are imported, factors such as tariffs, shipping costs, and currency exchange rates can affect the final price. These costs can vary significantly depending on the country of origin and the location of the buyer.
6.2 Cost vs. Functionality: Making the Right Investment
When selecting a bending press machine, it is essential to balance cost with functionality to ensure that the machine meets your specific needs without exceeding your budget. Here are some strategies to help you make a cost-effective investment:
6.2.1 Assessing Your Needs
- Production Volume: Consider the volume of production when choosing a machine. If your operation involves high-volume production, investing in a more expensive, automated machine may be justified by the increased efficiency and reduced labor costs. For lower-volume operations, a less expensive manual or semi-automatic machine may be sufficient.
- Material Type and Thickness: The types of materials you work with, including their thickness and strength, will determine the necessary tonnage and capabilities of the machine. Ensure that the machine you choose can handle your specific material requirements without overpaying for unnecessary capacity.
- Complexity of Bends: If your applications involve complex bends or require high precision, investing in a CNC-controlled machine may be worth the higher cost. However, for simpler bends, a manual or mechanical machine may provide adequate functionality at a lower price.
6.2.2 Evaluating Long-Term Costs
- Operating Costs: Consider the long-term operating costs of the machine, including energy consumption, maintenance, and tooling. While a machine with advanced features may have a higher upfront cost, it could offer lower operating costs and higher efficiency, leading to savings over time.
- Durability and Reliability: Machines made with higher-quality materials and components tend to have longer service lives and require less maintenance. Investing in a durable, reliable machine can reduce downtime and maintenance costs, providing better long-term value.
- Resale Value: Some high-quality machines maintain their value well and can be resold at a good price if your needs change. This can offset some of the initial investment costs and provide flexibility in the future.
6.2.3 Exploring Financing and Leasing Options
- Financing: Many manufacturers and dealers offer financing options that allow you to spread the cost of the machine over time. This can make it easier to afford a higher-quality machine without straining your budget.
- Leasing: Leasing is another option that allows you to use a high-quality machine without the full upfront cost. Leasing can be particularly advantageous if you need the machine for a specific project or a limited time.
6.2.4 Considering Used or Refurbished Machines
- Used Machines: Purchasing a used bending press machine can be a cost-effective way to acquire high-quality equipment at a lower price. However, it is essential to thoroughly inspect the machine for wear and tear and ensure that it has been well-maintained.
- Refurbished Machines: Refurbished machines offer a middle ground between new and used equipment. These machines have been restored to good working condition and often come with warranties, providing reliability at a reduced cost.
6.2.5 Comparing Suppliers and Brands
- Supplier Reputation: Work with reputable suppliers who offer good after-sales support, including training, maintenance, and access to spare parts. A reliable supplier can significantly impact the total cost of ownership by helping you keep the machine in good working condition.
- Brand Comparison: Compare different brands and models to find the best balance between price and features. Look for reviews and case studies to understand how the machines perform in real-world applications and whether they meet industry standards.
6.3 Case Studies: Price Considerations in Real-World Scenarios
Case Study 1: Small Fabrication Shop A small metal fabrication shop required a bending press machine for custom projects involving light to medium-gauge steel. After evaluating their needs, they opted for a mid-range hydraulic press with manual controls. While they considered a CNC machine, the additional cost was not justified given their low production volume. The hydraulic press offered the necessary force and precision at a reasonable price, allowing the shop to handle a variety of projects without overextending their budget.
Case Study 2: High-Volume Automotive Manufacturer A large automotive manufacturer needed a new bending press machine to increase production efficiency for body panels. They chose a high-end CNC-controlled hydraulic press with automated tool changers and real-time monitoring. Although the machine was significantly more expensive than manual or semi-automatic models, the investment was justified by the increased throughput, reduced labor costs, and high precision required for automotive production. The machine’s advanced features also allowed for quicker setup times and reduced downtime, further enhancing productivity.
Case Study 3: Start-Up in the Aerospace Industry A start-up aerospace company needed a bending press machine capable of producing complex, high-precision components. Given their limited budget, they explored options for used and refurbished CNC machines. They found a reputable supplier offering a refurbished CNC press brake that met their specifications at a fraction of the cost of a new machine. The refurbished machine provided the precision and functionality needed for aerospace applications, allowing the start-up to meet industry standards without exceeding their budget.
6.4 Conclusion
When considering the purchase of a bending press machine, it is crucial to weigh the cost against the functionality and long-term value of the machine. Factors such as machine type, specifications, features, brand reputation, and market demand all play a significant role in determining the price. By carefully assessing your specific needs, evaluating long-term costs, exploring financing or leasing options, and comparing suppliers and brands, you can make a well-informed decision that balances cost with the required functionality. Whether you are a small shop or a large manufacturer, selecting the right bending press machine is an investment that can enhance productivity, improve product quality, and contribute to the overall success of your operation.
Introduction to Specialized Hydraulic Presses
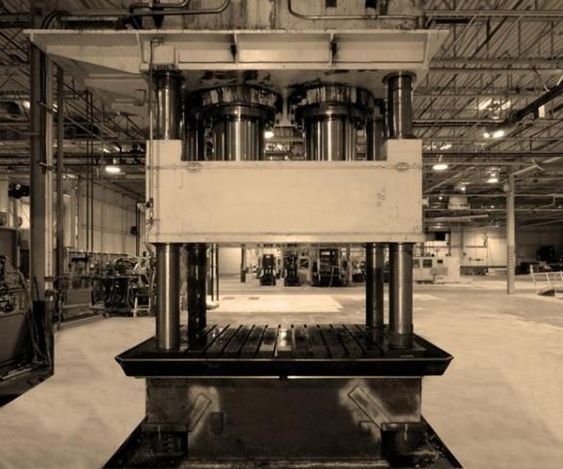
A hydraulic press is a mechanical device that uses a hydraulic cylinder to generate compressive force, transforming energy from hydraulic fluid into mechanical work. Hydraulic presses are an essential part of modern industrial manufacturing, offering precision and the capability to generate immense force. While general-purpose hydraulic presses are versatile and used in a wide range of industries, specialized hydraulic presses are designed for specific tasks, providing enhanced efficiency, precision, and performance for specialized applications.
1.1. What Makes a Hydraulic Press “Specialized”?
A hydraulic press becomes specialized when its design and functionality are tailored to a particular industrial task. These presses often feature unique configurations, custom components, or advanced control systems that allow them to perform specific tasks more effectively than standard presses. Specialized presses are used in industries such as automotive manufacturing, aerospace, medical device production, metalworking, and electronics, where the need for precision, speed, or high force is critical.
- Specialized tasks: While general-purpose presses can handle a variety of tasks, specialized presses are built to handle more complex operations such as deep drawing, isostatic pressing, metal forging, stamping, and transfer pressing. Each of these tasks requires specific pressure, stroke control, and precision that a standard press may not be able to deliver effectively.
- Customization: Specialized hydraulic presses often incorporate custom-built components such as specific dies, transfer mechanisms, or servo-controlled systems, making them suitable for precise manufacturing processes. These presses can also be designed with unique frame configurations, such as H-frame, C-frame, or four-column designs, each optimized for specific operational needs.
1.2. Importance of Specialized Hydraulic Presses in Industry
The increasing complexity of modern manufacturing processes, along with the demand for higher-quality products, has driven the need for specialized hydraulic presses. These machines not only improve the quality of finished products but also enhance productivity by reducing cycle times and increasing automation. Their ability to generate and control immense force with precision allows industries to achieve more complex and refined results than ever before.
- Automotive industry: Specialized hydraulic presses are critical in the automotive sector, where they are used to form body panels, chassis components, and internal engine parts. Presses such as deep drawing presses and forging presses enable the production of high-strength parts that meet safety and performance standards.
- Aerospace industry: In aerospace manufacturing, isostatic hydraulic presses are used to create high-strength, lightweight components like turbine blades and structural parts. These presses provide the precision needed to meet the stringent safety and durability requirements of the aerospace sector.
- Medical device manufacturing: The medical device industry relies on specialized presses to produce intricate components such as surgical instruments, implants, and diagnostic devices. The high precision and force control offered by these presses ensure that even the smallest tolerances are met.
1.3. How Specialized Presses Differ from Standard Hydraulic Presses
While both standard and specialized hydraulic presses operate on the same basic principle of using hydraulic pressure to generate force, the key difference lies in their design, control systems, and intended applications.
- Design differences: Specialized hydraulic presses often feature more robust or complex designs to handle specific tasks. For example, four-column hydraulic presses are designed to provide even pressure distribution for large or irregularly shaped workpieces, while C-frame presses are designed for easy access to the work area in small part production.
- Control systems: Specialized presses typically use advanced control systems, such as servo-hydraulic systems or CNC controls, to provide greater precision and automation. These control systems allow operators to adjust pressure, stroke length, and speed with high accuracy, which is essential in tasks that require exact force application.
- Application focus: While a general-purpose hydraulic press may be suitable for a wide variety of tasks, specialized presses are built to excel at specific operations. This specialization results in higher productivity, better quality, and lower error rates for those particular tasks.
Deep Drawing Presses
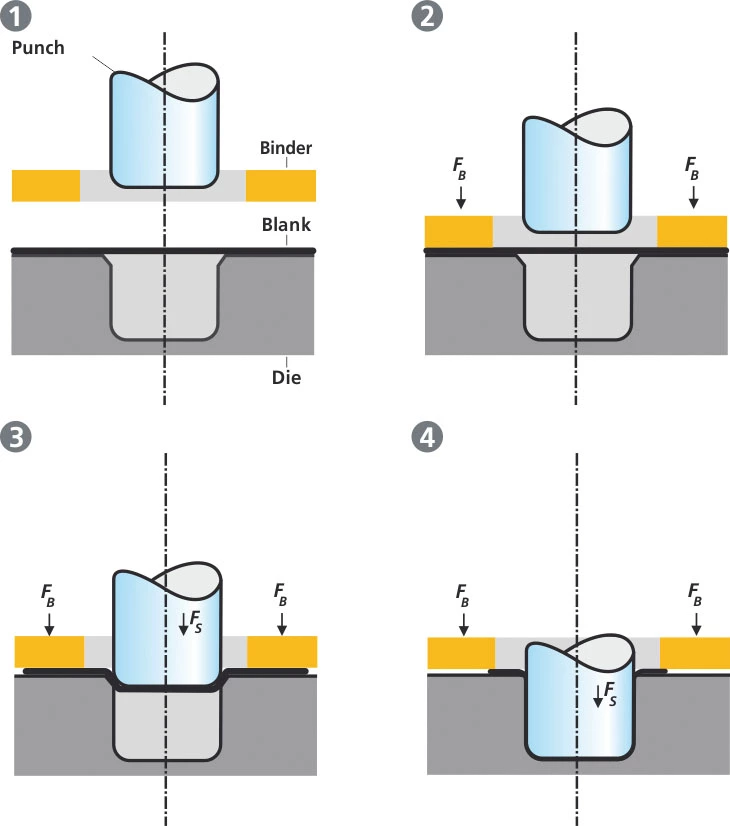
Deep drawing presses are a specialized type of hydraulic press used primarily for shaping metal sheets into deep, hollow shapes without compromising the integrity of the material. This process is commonly employed in the automotive, aerospace, packaging, and appliance industries to form components such as fuel tanks, kitchen sinks, and metal housings. The ability to create complex, seamless shapes from a single sheet of metal with minimal material wastage makes deep drawing presses essential for mass production applications.
2.1. Definition and Working Principle of Deep Drawing
Deep drawing is a metal forming process in which a flat sheet of metal (known as a blank) is gradually transformed into a deep, hollow shape through the application of pressure. During the deep drawing process, a punch pushes the metal sheet into a die cavity, stretching and compressing the material to form a desired shape. The term “deep” refers to the fact that the depth of the drawn part is greater than its diameter.
- Key components of a deep drawing press:
- Punch: The punch is the tool that applies pressure to the metal sheet and forces it into the die.
- Die: The die provides the cavity into which the metal is drawn to take the desired shape.
- Blank holder: This component holds the metal blank in place to prevent wrinkling and ensure uniform deformation.
- Hydraulic cylinder: The hydraulic system applies controlled force to the punch, enabling precise and consistent drawing.
The process begins with a metal blank being placed over the die. As the hydraulic press drives the punch downward, the metal sheet is forced into the die cavity, where it undergoes plastic deformation. The blank holder applies pressure to prevent the sheet from moving sideways or wrinkling as it is drawn into the die.
Stages of Deep Drawing
The deep drawing process can be broken down into several stages:
- Initial contact: The punch makes initial contact with the metal blank.
- Forming: The punch gradually pushes the blank into the die, causing the material to stretch and form around the punch.
- Final shaping: The material conforms to the shape of the die as the punch reaches the bottom of the stroke.
- Ejection: Once the desired shape is achieved, the punch is retracted, and the finished part is ejected from the die.
In more complex operations, multi-draw deep drawing presses may be used, which involve multiple stages of drawing to achieve deeper shapes or more intricate designs.
2.2. Design Characteristics of Deep Drawing Presses
Deep drawing presses are designed to handle the high forces and precise control needed for metal forming. Key design features include large hydraulic cylinders, robust frames, and advanced control systems to ensure accurate force application and material deformation.
- Frame design: Most deep drawing presses use an H-frame or four-column frame design to provide the structural support needed for high-force applications. These frames ensure that the force is evenly distributed across the die and blank, preventing misalignment or material deformation.
- Hydraulic system: Deep drawing presses use hydraulic cylinders to apply precise, consistent pressure during the drawing process. The hydraulic system allows operators to adjust the speed, force, and stroke length of the press, providing greater control over the depth and shape of the final product.
- Blank holders and force management: The blank holder plays a crucial role in maintaining the integrity of the material as it is drawn into the die. By applying controlled pressure to the blank, the holder prevents wrinkling or tearing, ensuring uniform deformation and a smooth final product.
Advanced deep drawing presses are often equipped with servo-hydraulic systems or CNC controls that provide automated control over the drawing process. These systems allow operators to program the press for specific tasks, adjust parameters such as pressure and stroke length, and monitor the process in real-time.
2.3. Applications of Deep Drawing Presses
Deep drawing presses are used in industries that require the production of deep, seamless, and hollow components from metal sheets. The process is widely employed in sectors such as automotive, aerospace, packaging, and appliances.
2.3.1. Automotive Industry
One of the largest users of deep drawing presses is the automotive industry, where they are employed to produce a variety of critical components. These include:
- Body panels: Car body panels such as doors, hoods, and fenders are often produced using deep drawing presses. The process ensures that these panels have smooth, uniform surfaces without joints or seams.
- Fuel tanks: Automotive fuel tanks are deep, hollow structures that are typically formed using deep drawing presses. The seamless nature of the deep drawing process helps prevent leaks and ensures the structural integrity of the tank.
- Chassis components: Various chassis components, including cross members and support structures, are manufactured using deep drawing presses for their strength and durability.
2.3.2. Aerospace Industry
In the aerospace sector, deep drawing presses are used to manufacture lightweight, high-strength components for aircraft and spacecraft. Some common applications include:
- Turbine engine components: Certain parts of turbine engines are made using deep drawing presses to create thin-walled, hollow structures that must withstand extreme temperatures and pressure.
- Structural components: Aircraft fuselages, frames, and bulkheads are formed using deep drawing processes to ensure they are lightweight and resistant to mechanical stress.
2.3.3. Packaging Industry
Deep drawing presses are commonly used in the packaging industry to manufacture metal cans, containers, and aluminum trays. This process allows for the mass production of seamless containers that are lightweight, durable, and cost-effective. Some common products include:
- Beverage cans: Aluminum cans for soda and beer are produced using deep drawing presses, ensuring a seamless design that holds pressure and maintains product integrity.
- Food containers: Metal food containers, such as those used for canned goods, are also made using deep drawing, allowing for rapid production of strong, lightweight containers.
2.3.4. Appliance Manufacturing
The appliance industry uses deep drawing presses to produce components such as:
- Sinks: Kitchen sinks, especially stainless steel varieties, are typically made using deep drawing presses. The process ensures that the sink has a smooth, seamless finish and is durable enough for everyday use.
- Cookware: Pots, pans, and other metal cookware are often produced using deep drawing processes, ensuring uniform shapes and smooth surfaces.
2.4. Advantages of Deep Drawing Presses
Deep drawing presses offer several key advantages over other metal forming processes, particularly in industries where high precision, large-scale production, and material efficiency are critical.
- High precision and repeatability: Deep drawing presses are capable of producing parts with high precision, ensuring that each component is consistent in terms of dimensions and quality. This is particularly important in industries such as automotive and aerospace, where tight tolerances are required.
- Minimal material waste: Deep drawing uses the initial metal blank efficiently, minimizing material wastage. This reduces production costs, especially when working with expensive metals like aluminum or stainless steel.
- Complex, seamless shapes: The ability to form deep, hollow, and complex shapes from a single metal sheet without the need for welding or additional assembly is one of the primary advantages of deep drawing presses. This results in stronger, more durable components.
- High-volume production: Deep drawing presses are ideal for high-volume production runs, offering faster cycle times and the ability to produce large quantities of parts in a short period.
2.5. Technological Advancements in Deep Drawing Presses
Over the years, significant advancements have been made in the technology used in deep drawing presses, improving their efficiency, precision, and ease of use. Some of the key innovations include:
- Servo-hydraulic systems: These systems combine hydraulic power with servo control, allowing for more precise force and speed control. This results in greater accuracy and reduced material waste.
- CNC controls: Computer Numerical Control (CNC) systems have been integrated into deep drawing presses, enabling fully automated operation. Operators can program the press for specific tasks, adjust parameters remotely, and monitor the entire process in real-time.
- Intelligent monitoring systems: Modern deep drawing presses often come equipped with sensors and real-time monitoring systems that track factors such as pressure, temperature, and material deformation. These systems allow operators to detect potential issues early and optimize the press for peak performance.
Isostatic Presses
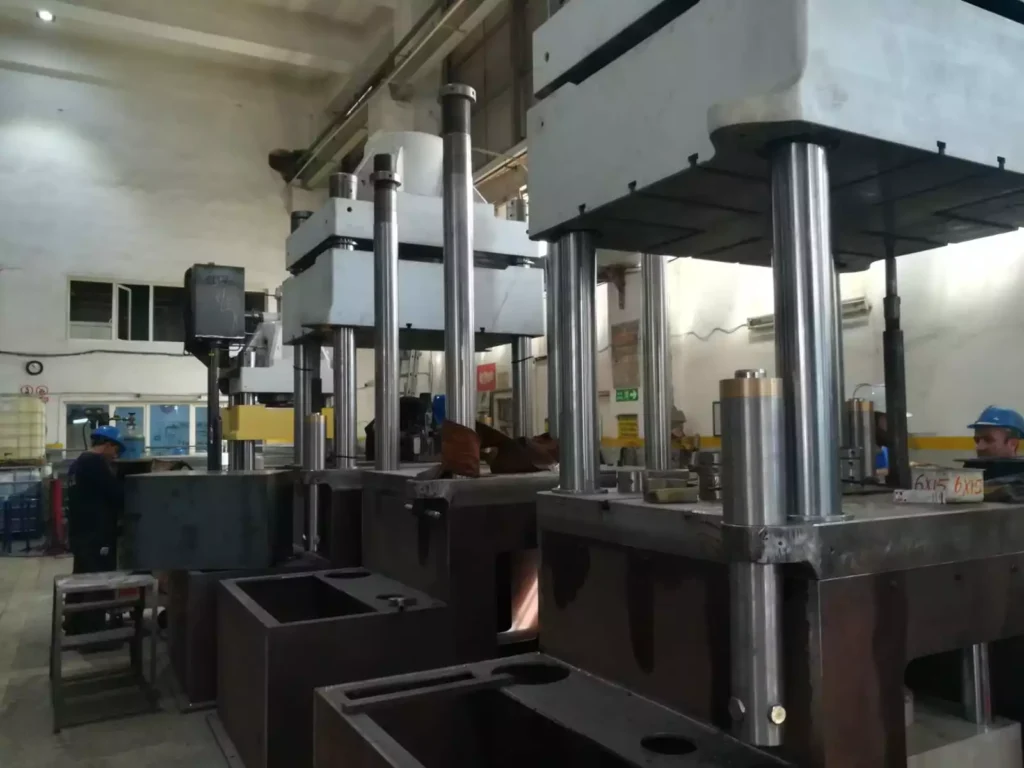
Isostatic presses are specialized hydraulic presses used to form materials under uniform pressure from all directions, ensuring that the material being pressed is evenly compressed. This technique is primarily employed in industries that require high-density, complex parts with excellent structural integrity, such as powder metallurgy, advanced ceramics, and the aerospace and medical device industries. Isostatic presses are particularly useful when working with materials that are difficult to shape through traditional pressing methods or that require precise control over porosity and density.
3.1. Working Principle of Isostatic Pressing
The key principle of isostatic pressing is the application of equal pressure from all directions on the material being formed. Unlike traditional hydraulic presses, which apply force from a single direction, isostatic presses use a fluid medium to transmit pressure uniformly across the material. This approach allows for consistent compression and ensures that the final product has uniform density and minimal internal stresses or defects.
The process can be categorized into two main types: Cold Isostatic Pressing (CIP) and Hot Isostatic Pressing (HIP). Both methods rely on similar principles but differ in terms of operating temperature and the type of material being processed.
3.1.1. Cold Isostatic Pressing (CIP)
In Cold Isostatic Pressing, the material being formed (typically a powdered metal or ceramic) is placed inside a flexible mold made of rubber or elastomer. This mold is then submerged in a pressure vessel filled with a liquid, such as water or oil. Hydraulic pumps are used to pressurize the fluid, which in turn applies uniform pressure to the mold, compressing the material from all sides.
- Working temperature: As the name suggests, cold isostatic pressing is carried out at room temperature. The primary purpose of CIP is to compact powders before sintering or further processing.
- Pressure range: The pressure applied in CIP typically ranges from 20,000 to 100,000 PSI (pounds per square inch), depending on the material and the desired density.
Once the material has been sufficiently compressed, it is removed from the mold and subjected to sintering (a heat treatment process) to solidify the material and achieve the final desired properties.
3.1.2. Hot Isostatic Pressing (HIP)
Hot Isostatic Pressing differs from CIP in that it combines the application of pressure with high temperatures. This method is used to both compact and sinter the material simultaneously, resulting in denser, more homogeneous parts with improved mechanical properties.
- Working temperature: In HIP, the material is placed inside a rigid mold or capsule, typically made of metal. The pressure vessel is filled with an inert gas, such as argon, which is then heated to temperatures ranging from 500°C to over 2000°C (930°F to 3600°F). The high temperature helps in sintering the material while the pressure consolidates it, eliminating porosity and improving density.
- Pressure range: HIP typically operates at pressures between 10,000 and 30,000 PSI, which is lower than CIP, but the combined effect of heat and pressure enables the material to achieve full densification.
HIP is commonly used to strengthen and densify metals, ceramics, and composites that require exceptional mechanical properties, such as those used in the aerospace and medical industries.
3.2. Key Components of Isostatic Presses
Isostatic presses have several essential components that enable them to apply uniform pressure to the material being formed. These components are critical for maintaining consistency and ensuring that the material is shaped and compressed evenly.
- Pressure vessel: The pressure vessel is the container in which the pressing takes place. It is designed to withstand extremely high pressures and, in the case of HIP, high temperatures as well. The vessel is filled with a fluid (in CIP) or gas (in HIP) that transmits the pressure uniformly.
- Mold or capsule: In CIP, the material is placed inside a flexible mold made of rubber or elastomer. In HIP, a rigid metal capsule is used to contain the material, which ensures that it holds its shape during the pressing and sintering process.
- Hydraulic system: The hydraulic system in an isostatic press is responsible for pressurizing the fluid or gas within the pressure vessel. In CIP, water or oil is used as the pressure-transmitting medium, while in HIP, an inert gas such as argon is used.
- Temperature control (for HIP): In hot isostatic presses, the pressure vessel is equipped with heating elements and temperature control systems to maintain the desired operating temperature during the pressing and sintering process.
3.3. Applications of Isostatic Presses
Isostatic presses are used in industries where material density and structural integrity are critical. The uniform pressure applied during isostatic pressing makes these machines ideal for applications that require the formation of complex shapes with minimal porosity.
3.3.1. Powder Metallurgy
One of the primary applications of isostatic presses is in powder metallurgy, where powdered metals are compressed into dense, high-strength parts. This process is used to produce components for various industries, including automotive, aerospace, and machinery manufacturing.
- High-performance parts: Parts produced using isostatic pressing often exhibit superior mechanical properties compared to those made with traditional pressing techniques. The uniform pressure ensures that the powder particles are densely packed, resulting in a stronger final product with fewer defects.
- Complex shapes: Isostatic presses allow manufacturers to create complex shapes that would be difficult or impossible to achieve with traditional forging or casting methods. This is particularly useful in producing components such as gears, bearings, and engine parts.
3.3.2. Advanced Ceramics
Advanced ceramics are used in industries ranging from electronics to aerospace, and isostatic pressing is an essential process for forming high-performance ceramic components.
- Electronics: Ceramic substrates used in electronic circuits must have excellent thermal and electrical properties, and isostatic pressing ensures that these components are produced with high density and uniformity.
- Aerospace and defense: In aerospace, isostatic presses are used to produce ceramic components that can withstand extreme temperatures and mechanical stress, such as heat shields and engine components.
3.3.3. Aerospace and Medical Applications
In the aerospace and medical industries, isostatic pressing is used to manufacture parts that require high strength, durability, and precision.
- Turbine blades: Hot isostatic pressing is used to densify turbine blades made from superalloys, ensuring they can withstand the extreme heat and pressure experienced in aircraft engines.
- Medical implants: The production of medical implants, such as hip and knee replacements, relies on isostatic pressing to form high-density metal parts that meet stringent biocompatibility and durability standards.
3.4. Advantages of Isostatic Presses
Isostatic presses offer several advantages over traditional pressing methods, particularly in industries that require precision and high material density.
- Uniform pressure distribution: The primary advantage of isostatic pressing is the uniform application of pressure from all directions. This ensures that the material is evenly compressed, resulting in higher density and fewer internal defects.
- Ability to form complex shapes: Isostatic presses are ideal for creating intricate, detailed parts that would be challenging to form using conventional methods. The flexible molds used in CIP allow for greater design flexibility, while HIP’s ability to combine heat and pressure enables the production of fully dense, sintered parts.
- Improved material properties: Parts produced using isostatic presses often exhibit superior mechanical properties, such as increased strength, hardness, and durability. This is particularly important in industries where parts are subjected to extreme conditions, such as aerospace and medical applications.
3.5. Industry Innovations in Isostatic Pressing
Recent advancements in isostatic pressing technology have further improved the efficiency and precision of these machines. Some of the most notable innovations include:
- 3D printed molds: Additive manufacturing technologies, such as 3D printing, are now being used to create molds for isostatic pressing. These custom molds allow manufacturers to produce complex, one-of-a-kind parts with greater accuracy and faster turnaround times.
- AI-driven process optimization: The integration of Artificial Intelligence (AI) and machine learning into isostatic pressing systems has enabled real-time monitoring and optimization of the pressing process. These technologies help identify potential defects early in the process and automatically adjust parameters to ensure consistent quality.
Transfer Hydraulic Presses
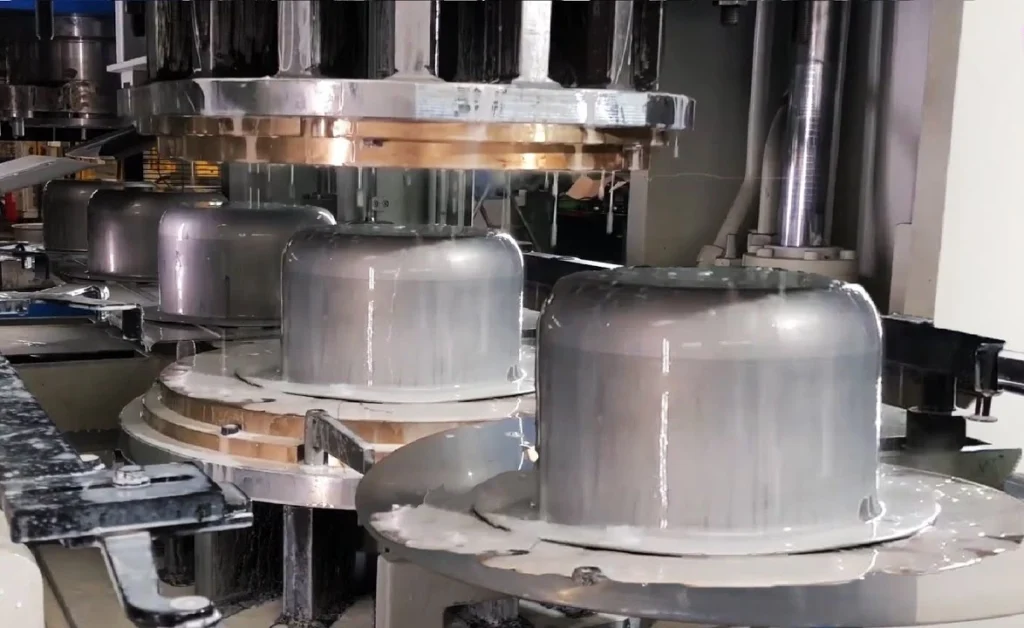
Transfer hydraulic presses are specialized machines designed for high-volume, multi-step production processes where multiple operations can be performed in sequence on a single part. These presses are commonly used in industries that require complex forming, stamping, or assembly tasks, particularly in large-scale manufacturing environments such as the automotive, appliance, and electrical component industries. The defining characteristic of a transfer hydraulic press is its ability to move parts from one station to the next automatically, reducing manual labor and increasing productivity.
4.1. Working Principle of Transfer Hydraulic Presses
The main advantage of a transfer hydraulic press is its ability to perform multiple operations in a single production cycle by moving the part between different workstations automatically. This functionality is achieved using an integrated transfer mechanism that picks up the part after each operation and moves it to the next station.
Stages of Operation in a Transfer Press
- Feeding and positioning: Raw material or partially formed parts are fed into the press, either manually or using automated feeders. The part is positioned at the first station, where the initial operation (such as cutting or forming) is performed.
- First operation: The press applies hydraulic pressure to the material, performing the first operation, such as stamping, drawing, or punching. Once this step is complete, the transfer mechanism takes over.
- Transfer to the next station: The part is picked up by a transfer arm or gripper and moved to the next station, where a secondary operation is performed. This could involve further shaping, bending, trimming, or assembly.
- Final operation and ejection: After all the required operations have been completed at the various stations, the finished part is ejected from the press. Depending on the complexity of the part, it may undergo several stages of transformation before reaching its final form.
The ability to carry out multiple operations without requiring the operator to intervene at each step significantly increases the efficiency and speed of the production process. The transfer system ensures that parts move seamlessly from one station to another, allowing for high-volume production with minimal downtime between operations.
4.2. Components of a Transfer Hydraulic Press
Transfer hydraulic presses are more complex than standard hydraulic presses, as they include additional mechanisms to facilitate the automatic movement of parts between workstations. The key components of a transfer hydraulic press include:
- Transfer mechanism: The transfer mechanism is a key feature that distinguishes transfer presses from other types of hydraulic presses. It is responsible for moving the part between stations during the production cycle. This mechanism can be a robotic arm, a gripper system, or a set of automated rails that lift and transfer the part without damaging it.
- Die sets and tooling: Transfer presses often use multiple die sets, each designed for a specific operation, such as cutting, bending, forming, or assembly. These die sets are positioned at different stations within the press, allowing for multiple processes to be carried out in sequence.
- Hydraulic system: As with all hydraulic presses, the hydraulic system provides the force needed to perform the various operations. In transfer presses, the hydraulic system must be precisely controlled to ensure that each operation is carried out with the correct amount of force and speed.
- Control systems: Transfer presses rely on advanced control systems, often equipped with Programmable Logic Controllers (PLCs) or Computer Numerical Control (CNC) systems. These systems coordinate the movements of the transfer mechanism, control the hydraulic pressure applied at each station, and monitor the overall operation of the press.
4.3. Applications of Transfer Hydraulic Presses
Transfer hydraulic presses are ideal for mass production environments where large quantities of parts need to be processed quickly and accurately. Some common applications of transfer presses include:
4.3.1. Automotive Manufacturing
The automotive industry is one of the largest users of transfer hydraulic presses. These presses are used to produce a wide range of components, from structural parts like chassis components and body panels to engine parts such as valve covers and housings.
- Stamping: Transfer presses are commonly used for stamping operations in automotive manufacturing, where large metal sheets are progressively shaped into car body panels or structural components. The ability to perform multiple stamping operations in sequence reduces production time and minimizes manual labor.
- Deep drawing and forming: Transfer presses are also used for deep drawing operations, where metal sheets are formed into deeper, more complex shapes such as fuel tanks, wheel rims, or exhaust components.
4.3.2. Appliance Manufacturing
In the appliance industry, transfer hydraulic presses are used to produce metal and plastic parts for household items such as washing machines, refrigerators, dishwashers, and stoves.
- Multi-stage forming: Many appliance components, such as metal brackets, frames, and enclosures, require multiple forming operations to achieve their final shape. Transfer presses streamline this process by allowing each step to be carried out in one machine, reducing the need for separate pressing operations.
- Assembly: Some transfer presses are equipped to perform simple assembly tasks, such as inserting fasteners or connecting parts, in addition to shaping and forming materials.
4.3.3. Electrical Component Production
The electronics industry uses transfer hydraulic presses for the production of metal housings, connectors, and casings for electronic devices. The high precision and automation capabilities of transfer presses make them ideal for producing the small, intricate parts required in modern electronics.
- High precision stamping: Transfer presses are used to stamp metal components for electrical connectors, terminals, and housings, ensuring that each part meets strict dimensional tolerances.
- Mass production of casings: In the production of electronics, the ability to quickly and accurately form metal casings and frames for devices like smartphones, laptops, and tablets is essential for meeting consumer demand.
4.4. Advantages of Transfer Hydraulic Presses
Transfer hydraulic presses offer several significant advantages over traditional hydraulic presses, particularly in large-scale production environments where multiple operations are needed to complete a part.
4.4.1. High Productivity
One of the primary advantages of transfer presses is their ability to increase productivity by performing multiple operations in a single cycle. Since the parts are automatically transferred from one station to the next, there is no need for manual intervention between steps, reducing cycle times and increasing output.
4.4.2. Automation and Labor Reduction
By automating the transfer process, transfer presses minimize the need for manual labor. This not only reduces labor costs but also improves consistency and accuracy, as human error is minimized during the production process. The use of robotic arms or automated transfer systems ensures that parts are moved precisely and consistently between stations.
4.4.3. Versatility
Transfer hydraulic presses are highly versatile machines capable of performing a wide range of operations, including cutting, stamping, forming, and even assembly. This versatility makes them ideal for industries that require complex, multi-step production processes.
4.4.4. Space Efficiency
By consolidating multiple operations into a single machine, transfer presses help save floor space in manufacturing facilities. Instead of requiring separate presses for each step of the process, a transfer press can perform all the necessary operations in one place, reducing the need for additional equipment and floor space.
4.5. Technological Advancements in Transfer Presses
As with other types of hydraulic presses, transfer hydraulic presses have benefited from technological advancements that improve efficiency, precision, and automation. Some key innovations in transfer press technology include:
- Integration with robotics: Many modern transfer hydraulic presses are equipped with robotic arms or gripper systems that handle the movement of parts between stations. These robots can be programmed to handle parts with extreme precision, ensuring that they are positioned correctly at each station and reducing the risk of damage or misalignment.
- CNC and PLC control systems: The integration of CNC and PLC control systems allows for greater automation and control over the press’s operation. Operators can program the press to perform specific tasks, adjust parameters like pressure and stroke length, and monitor the entire production process in real-time.
- IoT connectivity: Some transfer hydraulic presses are now equipped with Internet of Things (IoT) technology, allowing them to be connected to a larger network of machines and systems. This connectivity enables remote monitoring, predictive maintenance, and real-time data analysis, improving overall efficiency and reducing downtime.
Four-Column Hydraulic Presses
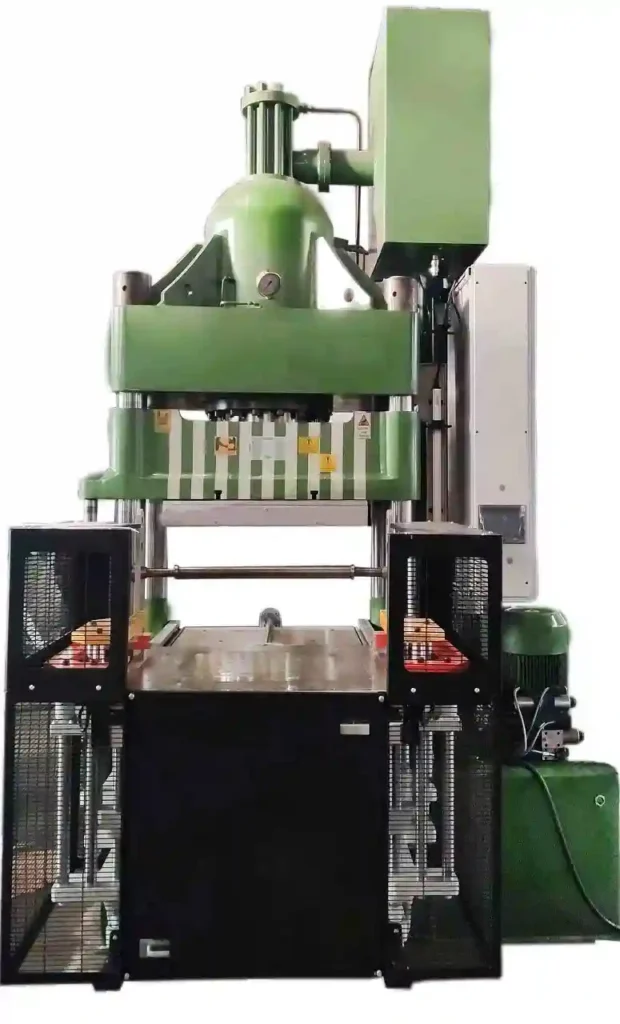
Four-column hydraulic presses, also known as four-post presses, are a type of hydraulic press characterized by their robust design, featuring four vertical columns that provide superior stability and even force distribution. These presses are widely used in industrial applications that require high precision, durability, and large force outputs. Their sturdy design makes them ideal for handling large workpieces and performing tasks such as deep drawing, die cutting, forging, and molding. Four-column presses are particularly favored in industries like aerospace, automotive, heavy machinery, and plastics.
5.1. Design and Structure of Four-Column Hydraulic Presses
The defining feature of four-column hydraulic presses is their frame design, which includes four vertical columns that support the upper and lower crossheads of the press. The columns are positioned at the corners of the press, allowing for the even distribution of force across the entire work area. This design provides exceptional rigidity and stability, making four-column presses ideal for high-force applications that require precise control over pressure and material deformation.
Key Components
- Four vertical columns: The four columns serve as the structural backbone of the press, ensuring stability and providing support to the upper and lower crossheads. These columns are typically made from high-strength steel to withstand the immense forces generated during operation.
- Upper and lower crossheads: The crossheads are the horizontal beams that connect the four columns. The upper crosshead supports the hydraulic cylinder, while the lower crosshead serves as the base of the press. These crossheads help distribute the load evenly, ensuring that the force applied by the hydraulic cylinder is spread across the entire surface of the workpiece.
- Hydraulic cylinder: The hydraulic cylinder is mounted on the upper crosshead and contains the piston that moves vertically to apply pressure to the material. The cylinder is driven by pressurized hydraulic fluid, which generates the force needed to deform or shape the material.
- Die sets: In applications such as metal forming or die cutting, four-column presses are equipped with die sets that shape the material as it is compressed between the punch and die.
Force Distribution and Stability
One of the primary advantages of the four-column design is its ability to evenly distribute force across the entire workpiece. In presses that do not have this type of frame, the force can be unevenly applied, leading to inconsistent results, material deformation, or damage. With four-column presses, the hydraulic cylinder applies pressure directly to the material, while the columns and crossheads ensure that this pressure is evenly distributed. This makes four-column presses particularly effective for forming large, complex parts or handling irregularly shaped workpieces.
5.2. Applications of Four-Column Hydraulic Presses
Four-column hydraulic presses are used in a wide variety of industrial applications, particularly in sectors where precision, force control, and large work areas are essential. Some common applications include:
5.2.1. Metal Forming and Deep Drawing
In the metalworking industry, four-column hydraulic presses are widely used for deep drawing, sheet metal forming, and stamping operations. These presses can handle large metal sheets and apply even pressure across the material, ensuring that the metal is formed uniformly without wrinkles or cracks.
- Automotive industry: Four-column presses are commonly used to form large automotive body panels, chassis components, and engine parts. Their ability to handle large workpieces and apply consistent pressure makes them ideal for producing high-strength, precision-engineered parts for vehicles.
- Appliance industry: These presses are also used in the production of metal components for household appliances, such as washing machine drums, refrigerator panels, and kitchen sink basins.
5.2.2. Die Cutting
Die cutting is another common application for four-column hydraulic presses, particularly in industries that require precision cutting of materials like plastic, rubber, leather, and metal. The stability and accuracy provided by the four-column design allow for precise control over the cutting process, ensuring that each part is cut to the correct dimensions.
- Plastics and rubber industry: In the production of plastic and rubber components, four-column presses are used to cut parts such as gaskets, seals, and packaging materials. The even force distribution ensures that each part is cut cleanly and consistently.
- Textiles and leather: In industries like textiles and leather manufacturing, four-column presses are used for die cutting fabric and leather materials into patterns for clothing, upholstery, and accessories.
5.2.3. Forging and Molding
In forging and molding applications, four-column hydraulic presses are used to apply large amounts of pressure to shape metal, plastic, or composite materials. These presses are often used in the production of high-strength parts that require uniform compression and precision.
- Aerospace industry: The aerospace sector relies on four-column hydraulic presses to forge critical components such as turbine blades, engine housings, and structural parts. The high precision and force capacity of these presses ensure that aerospace components meet strict safety and performance standards.
- Heavy machinery: In the production of heavy industrial equipment, four-column presses are used to forge large, high-strength parts like gears, shafts, and machine frames.
5.3. Advantages of Four-Column Hydraulic Presses
Four-column hydraulic presses offer several key advantages over other types of hydraulic presses, making them the preferred choice for many industrial applications.
5.3.1. Even Pressure Distribution
One of the most significant advantages of four-column presses is their ability to distribute pressure evenly across the workpiece. This is especially important in applications like deep drawing and die cutting, where uneven pressure can lead to defects or inconsistent results. The four-column design ensures that the hydraulic force is applied uniformly, improving product quality and reducing the likelihood of material failure.
5.3.2. Versatility in Handling Large Workpieces
Four-column presses are designed to accommodate large workpieces, making them ideal for industries that require the forming, cutting, or forging of large parts. The large work area provided by the press allows operators to handle complex or oversized materials that would be difficult to process using other types of presses.
5.3.3. High Force Capacity
Due to their robust design, four-column hydraulic presses can generate extremely high forces, often ranging from several tons to thousands of tons. This makes them well-suited for heavy-duty applications, such as metal forging or the production of large automotive components. The combination of high force capacity and even pressure distribution ensures that these presses can handle the most demanding tasks with precision and reliability.
5.3.4. Precision and Stability
The four-column design provides exceptional stability, reducing the risk of misalignment or deformation during the pressing process. This is particularly important in applications that require high precision, such as aerospace and automotive part production. The stability provided by the four-column frame ensures that the material is pressed evenly and accurately, resulting in high-quality parts with minimal defects.
5.4. Technological Advancements in Four-Column Presses
As with other hydraulic presses, four-column hydraulic presses have benefited from recent advancements in technology, particularly in areas such as automation, energy efficiency, and precision control. Some of the key innovations in four-column press technology include:
Servo-Hydraulic Systems
Many modern four-column hydraulic presses are equipped with servo-hydraulic systems, which provide more precise control over the press’s force, speed, and stroke length. Servo-hydraulic systems use servo motors to regulate the flow of hydraulic fluid, allowing operators to adjust the press’s parameters with a high degree of accuracy. This results in improved precision and energy efficiency, making four-column presses suitable for high-precision tasks that require tight tolerances.
CNC Integration
Computer Numerical Control (CNC) systems are increasingly being integrated into four-column hydraulic presses, allowing for fully automated operation. CNC-controlled presses can be programmed to perform specific tasks, such as deep drawing or die cutting, with minimal operator intervention. This increases productivity and reduces the risk of human error, while also allowing for greater flexibility in terms of press operation.
IoT and Smart Manufacturing
Some four-column hydraulic presses are now equipped with Internet of Things (IoT) connectivity, allowing them to be integrated into smart manufacturing environments. IoT-enabled presses can communicate with other machines and systems in the production line, providing real-time data on press performance, material usage, and maintenance needs. This connectivity allows for more efficient production management and predictive maintenance, reducing downtime and improving overall operational efficiency.
Forging Hydraulic Presses
Forging hydraulic presses are specialized machines designed to shape metal by applying high compressive forces. They are used in industries that require strong, high-quality metal parts with specific mechanical properties. Forging presses can process both hot and cold metals, making them suitable for a wide range of forging applications. These presses play a critical role in industries like automotive, aerospace, heavy machinery, and industrial equipment manufacturing, where parts need to withstand extreme stress and environmental conditions.
6.1. Working Principle of Forging Hydraulic Presses
The forging process involves deforming a metal workpiece by applying pressure to force it into a desired shape. Forging hydraulic presses are equipped with a hydraulic system that generates the immense pressure required to deform metal, typically using a punch and die set to compress the metal into a specific shape. The key advantage of hydraulic presses in forging is their ability to apply consistent and controllable pressure over a long stroke length, which ensures precision and uniformity in the final product.
Types of Forging Processes
There are two main types of forging processes that can be performed using hydraulic presses: hot forging and cold forging.
- Hot forging: In this process, the metal workpiece is heated to a temperature where it becomes malleable and easier to shape. Hot forging is typically used for metals like steel, aluminum, and titanium, which require high temperatures to achieve the desired level of deformation. Hydraulic presses apply pressure to the heated metal, compressing it into the die cavity to form the desired shape. The high temperature allows the metal to flow more easily, reducing the force required for shaping.
- Cold forging: In cold forging, the metal is shaped at or near room temperature. Cold forging is generally used for softer metals or applications where a high degree of dimensional accuracy and surface finish is required. Since cold forging does not involve heating, the metal undergoes work hardening, which increases its strength. However, cold forging requires higher forces than hot forging because the metal is less malleable at lower temperatures.
Forging Press Components
Forging hydraulic presses share many components with other types of hydraulic presses, but they are specifically designed to handle the immense pressures and extreme conditions required for forging. Some of the key components of a forging hydraulic press include:
- Hydraulic cylinder: The hydraulic cylinder is responsible for generating the force that drives the piston downward, applying pressure to the metal workpiece. Forging presses use large hydraulic cylinders capable of producing thousands of tons of force.
- Piston and ram: The piston, housed within the hydraulic cylinder, moves up and down to apply pressure. The ram is the component that physically contacts the metal workpiece, pressing it into the die to form the desired shape.
- Die set: The die set consists of two parts: the upper die (attached to the ram) and the lower die (mounted on the press bed). The shape of the dies determines the final shape of the forged part. Hydraulic presses use interchangeable dies to create a wide variety of parts, from simple geometries to complex shapes.
- Cooling system: Since hot forging involves working with high temperatures, forging hydraulic presses are typically equipped with cooling systems to dissipate heat and maintain the proper operating temperature. The cooling system helps prevent overheating, which could damage the hydraulic components or affect press performance.
6.2. Hot vs. Cold Forging in Hydraulic Presses
Both hot forging and cold forging have their advantages, and the choice between the two depends on the type of metal being forged and the desired properties of the final part.
Hot Forging
- Process: In hot forging, the metal is heated to temperatures ranging from 700°C to 1250°C (1300°F to 2300°F), depending on the material. At these high temperatures, the metal becomes more ductile and easier to shape. The hydraulic press then applies pressure to deform the heated metal, forcing it into the shape of the die.
- Advantages:
- Easier material flow: The high temperature makes the metal more malleable, allowing it to flow easily into complex shapes with less force.
- Reduction in material defects: Hot forging reduces the likelihood of defects such as porosity or cracking, as the metal’s internal structure is more uniform at high temperatures.
- Improved mechanical properties: The heat treatment that occurs during hot forging improves the toughness, ductility, and fatigue resistance of the forged part.
- Disadvantages:
- Energy consumption: Hot forging requires a significant amount of energy to heat the metal, making it less energy-efficient than cold forging.
- Potential for scale formation: When metals are heated, they can form an oxide layer on their surface, known as scale, which must be removed in post-forging processes like cleaning or machining.
Cold Forging
- Process: Cold forging is performed at room temperature or near-room temperature. It is typically used for softer metals, such as aluminum or copper, or when high precision and excellent surface finish are required.
- Advantages:
- Increased strength through work hardening: Since the metal is not heated during cold forging, the material undergoes work hardening, which increases its strength and durability.
- High precision and surface finish: Cold forging allows for tighter dimensional tolerances and better surface finish, reducing the need for secondary machining processes.
- Energy efficiency: Cold forging does not require heating the metal, resulting in lower energy consumption and cost savings compared to hot forging.
- Disadvantages:
- Higher force required: Since the metal is less malleable at room temperature, cold forging requires higher forces to shape the material. Hydraulic presses used for cold forging must be capable of generating extremely high pressures.
- Limited to softer metals or small parts: Cold forging is best suited for softer metals or smaller parts. Attempting to cold forge large, high-strength metals like steel can result in cracking or other defects.
6.3. Applications of Forging Hydraulic Presses
Forging hydraulic presses are used in industries that require high-strength, high-performance parts. The forging process produces components that are stronger and more durable than parts made using other metal forming methods, making hydraulic forging presses indispensable in industries such as automotive, aerospace, and heavy machinery manufacturing.
6.3.1. Automotive Industry
The automotive industry is one of the largest users of forging hydraulic presses, particularly for the production of engine and drivetrain components. Forging provides the strength and durability needed for parts that must withstand high stress, such as:
- Crankshafts: Crankshafts, which convert linear motion into rotational motion in an engine, are forged using hydraulic presses to ensure they can endure high loads and torque. Forging also improves the grain structure of the metal, enhancing its fatigue resistance.
- Connecting rods: Forged connecting rods are used to link the piston to the crankshaft in an engine. These components are subjected to extreme forces, and forging ensures they have the necessary strength to operate reliably.
- Gears and axles: Forged gears and axles are used in transmissions and drivetrains, where high strength and precision are essential for smooth operation and long service life.
6.3.2. Aerospace Industry
In the aerospace industry, forged components are used in critical applications where strength, lightweight, and reliability are paramount. Aerospace parts are often made from high-performance alloys, such as titanium and nickel-based superalloys, which are well-suited for forging. Some common aerospace applications include:
- Turbine blades: Hydraulic forging presses are used to shape turbine blades for jet engines. These blades must withstand extreme temperatures and high mechanical stress, making forging the ideal manufacturing method to ensure their durability and performance.
- Landing gear components: Forged components in landing gear systems must be able to absorb impact and resist wear, making them ideal candidates for the forging process. Hydraulic presses can produce landing gear components with superior strength and toughness.
- Structural parts: Hydraulic presses are used to forge structural components for aircraft frames, ensuring they are lightweight yet strong enough to endure the stresses of flight.
6.3.3. Heavy Machinery and Industrial Equipment
Forging hydraulic presses are essential in the production of heavy machinery and industrial equipment that require high-strength, wear-resistant parts. Examples of applications in this industry include:
- Forged gears and shafts: In heavy equipment such as excavators, bulldozers, and mining machinery, forged gears and shafts provide the strength and durability needed to operate in harsh environments and under heavy loads.
- Hydraulic cylinders: Hydraulic presses are used to forge high-strength cylinders and pistons used in the hydraulic systems of heavy machinery. These components must withstand high pressure and wear over extended periods.
- Tools and dies: The tooling industry relies on forging presses to produce dies, molds, and tools used in metal forming, stamping, and cutting operations. Forging ensures that these tools have the hardness and wear resistance required for demanding applications.
6.4. Advantages of Forging Hydraulic Presses
Forging hydraulic presses offer several advantages over other metal forming methods, particularly when it comes to producing high-strength, precision components.
6.4.1. Superior Mechanical Properties
The forging process results in parts with superior mechanical properties compared to casting or machining. Forged parts have a more refined grain structure, which improves their strength, toughness, and fatigue resistance. This makes forging the ideal choice for components that will be subjected to high stress or extreme conditions.
6.4.2. Precision and Repeatability
Hydraulic forging presses provide precise control over the pressure, speed, and stroke length of the press, ensuring consistent results and high repeatability. This precision is critical in industries like aerospace and automotive, where parts must meet tight tolerances and high-quality standards.
6.4.3. Versatility
Forging hydraulic presses are versatile machines capable of handling a wide range of metals and producing a variety of shapes and sizes. Whether forging small, intricate parts or large, heavy-duty components, hydraulic presses can be adapted to meet the specific needs of the application.
6.4.4. Improved Surface Finish
Forging results in parts with a smooth surface finish and uniform dimensions, reducing the need for post-processing such as machining or grinding. This not only saves time but also reduces material waste and costs.
6.5. Technological Advancements in Forging Hydraulic Presses
Recent innovations in forging hydraulic press technology have further improved the efficiency, precision, and energy efficiency of these machines.
Servo-Hydraulic Systems
Many modern forging presses are equipped with servo-hydraulic systems that provide more precise control over the press’s force, speed, and stroke length. These systems use servo motors to regulate the flow of hydraulic fluid, allowing for greater accuracy and energy savings. Servo-hydraulic systems also enable faster cycle times, increasing productivity.
Automation and Robotics
Automation is playing an increasingly important role in forging operations. Robotic arms and automated part handling systems are being integrated into forging presses to load and unload parts, reducing the need for manual labor and improving consistency. Automated systems can also monitor the forging process in real-time, detecting and correcting any deviations to ensure high-quality parts.
Smart Forging Systems
With the advent of Industry 4.0 technologies, smart forging systems are becoming more common. These systems use sensors, IoT connectivity, and machine learning algorithms to optimize the forging process in real-time. Smart forging presses can adjust parameters such as pressure and stroke length based on real-time data, improving product quality and reducing downtime.
C-Frame Hydraulic Presses
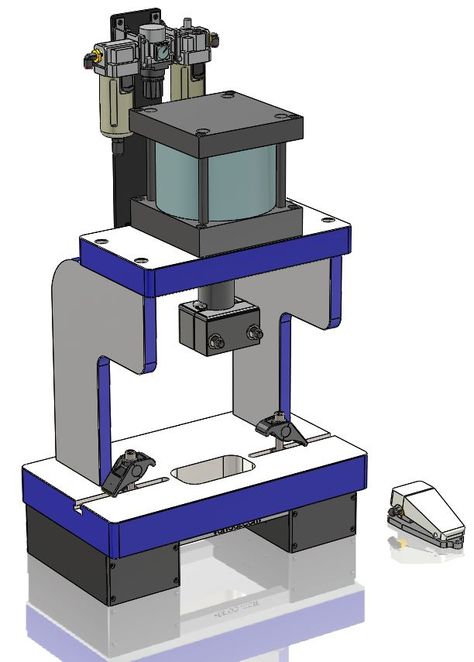
C-frame hydraulic presses are a popular type of hydraulic press characterized by their open-front design, which resembles the shape of the letter “C.” This design allows easy access to the working area from three sides, making C-frame presses ideal for applications that require frequent loading and unloading of materials. These presses are commonly used in precision metalworking, assembly line tasks, and light manufacturing applications where space efficiency, versatility, and accessibility are essential.
C-frame presses are often favored for tasks like punching, bending, stamping, and assembly, especially when dealing with smaller workpieces or components. Their compact design makes them suitable for small workshops and production lines, as they require less floor space than larger, multi-column presses.
7.1. Design and Structure of C-Frame Hydraulic Presses
The defining feature of a C-frame hydraulic press is its open-front design, which offers operators easy access to the press’s working area. The frame is shaped like the letter “C,” with the hydraulic cylinder and ram mounted at the top and the working table or bed at the bottom. This open design allows for unrestricted access to the workpiece, simplifying material handling, part loading, and unloading.
Key Components of a C-Frame Hydraulic Press
- C-shaped frame: The frame is the structural element of the press, providing support and housing the hydraulic system. It is typically made from high-strength steel to withstand the forces generated during pressing operations.
- Hydraulic cylinder: The hydraulic cylinder is mounted at the top of the press, containing a piston that moves the ram vertically. The cylinder generates the force needed to press, punch, or bend the material.
- Ram and punch: The ram is the moving component of the press that applies force to the workpiece. It is connected to the piston inside the hydraulic cylinder. A punch or other tooling is often attached to the ram to perform specific operations, such as cutting or forming.
- Work table or bed: The work table or bed is the surface where the material or part is placed during the pressing operation. This surface may have slots or holes for mounting dies or other tools used in metal forming, stamping, or bending processes.
- Controls: C-frame presses are often equipped with manual or automated controls to regulate pressure, stroke length, and speed. More advanced models may feature programmable logic controllers (PLCs) or computer numerical control (CNC) systems for precision control.
7.2. Applications of C-Frame Hydraulic Presses
C-frame hydraulic presses are versatile machines suitable for a variety of applications across multiple industries. Their open-front design and ease of access make them particularly useful for tasks that require frequent handling of parts or small components. Some of the most common applications include:
7.2.1. Precision Metal Forming
In precision metalworking, C-frame hydraulic presses are often used for punching, stamping, and bending small metal components. These presses offer the precision and control necessary for high-quality metal forming, ensuring that each part is shaped accurately and consistently.
- Electronics industry: In the electronics sector, C-frame presses are used to punch and form metal housings and components for devices like smartphones, tablets, and computers. The precision offered by these presses ensures that each part meets strict tolerances and quality standards.
- Automotive industry: C-frame presses are used to produce small metal parts for vehicles, such as brackets, clips, and connectors. Their compact design and precision make them ideal for producing components that require tight tolerances and consistent quality.
7.2.2. Assembly Line Tasks
C-frame presses are commonly used in assembly lines for tasks like inserting bearings, fasteners, or rivets into larger components. The open-front design allows operators to quickly load and unload parts, increasing the efficiency of the assembly process.
- Automotive assembly: C-frame presses are used in automotive assembly lines to insert bearings, bushings, and other small components into larger assemblies such as engine blocks, transmission housings, or suspension components.
- Electronics assembly: In the electronics industry, C-frame presses are used to assemble small components like connectors, terminals, or circuit boards. The compact design and precision control allow for efficient handling of delicate electronic parts.
7.2.3. Light Manufacturing
C-frame presses are ideal for light manufacturing applications, where small parts need to be formed, stamped, or assembled. Their compact size and versatility make them suitable for workshops, laboratories, and smaller production facilities.
- Jewelry making: In the jewelry industry, C-frame presses are used for precision metal forming tasks, such as stamping intricate designs onto metal surfaces or forming small components for rings, bracelets, and necklaces.
- Prototype development: In research and development labs, C-frame presses are often used to produce prototypes of new products. Their precision and flexibility make them suitable for small production runs and experimental projects.
7.3. Advantages of C-Frame Hydraulic Presses
C-frame hydraulic presses offer several advantages that make them an attractive choice for many industries and applications.
7.3.1. Compact and Space-Efficient Design
One of the most significant advantages of C-frame presses is their compact size. These presses are designed to fit in smaller workspaces, making them ideal for workshops, assembly lines, and facilities with limited floor space. Despite their small footprint, C-frame presses can generate significant force, making them capable of handling a wide range of tasks.
7.3.2. Easy Access to the Work Area
The open-front design of a C-frame press provides easy access to the working area, allowing operators to quickly load and unload materials. This design is especially beneficial for applications that require frequent handling of parts, such as assembly line tasks or small-batch production. The open design also makes it easier to position materials accurately within the press, reducing setup time and improving overall efficiency.
7.3.3. High Precision and Control
C-frame hydraulic presses offer precise control over force, stroke length, and speed, making them ideal for applications that require high precision. Many C-frame presses are equipped with advanced control systems, such as servo-hydraulic or CNC controls, which allow operators to program specific parameters for each task. This level of control ensures consistent, high-quality results, even in applications that require tight tolerances.
7.3.4. Versatility
C-frame presses are highly versatile machines that can be used for a wide range of tasks, from metal forming and stamping to assembly and punching. Their compact size and flexibility make them suitable for both small-batch production and high-volume manufacturing environments. Additionally, C-frame presses can be easily customized with different tooling and accessories to meet the specific needs of each application.
7.4. Limitations of C-Frame Hydraulic Presses
While C-frame hydraulic presses offer many advantages, they also have some limitations that may make them less suitable for certain applications.
7.4.1. Lower Force Capacity
C-frame presses typically generate lower force than larger hydraulic presses, such as H-frame or four-column presses. As a result, they may not be suitable for heavy-duty applications that require extremely high pressures or large workpieces. C-frame presses are best suited for light to medium-duty tasks, such as small part production or assembly work.
7.4.2. Risk of Frame Deformation
Because of their open-front design, C-frame presses can be prone to frame deformation under high loads. The lack of structural support on one side of the frame means that the press may flex or bend if subjected to excessive force, potentially affecting the accuracy and quality of the work. This limitation makes C-frame presses less suitable for applications that require very high pressures or heavy materials.
7.4.3. Limited Work Area
While the open-front design of C-frame presses provides easy access to the work area, it also limits the size of the workpiece that can be processed. Larger workpieces may not fit within the compact frame of a C-frame press, making it less suitable for large-scale manufacturing or heavy-duty metal forming.
7.5. Technological Advancements in C-Frame Presses
Recent technological advancements have enhanced the performance and functionality of C-frame hydraulic presses, making them even more versatile and efficient.
Servo-Hydraulic Systems
Many modern C-frame presses are equipped with servo-hydraulic systems, which offer more precise control over the force, speed, and stroke length of the press. Servo-hydraulic systems use servo motors to regulate the flow of hydraulic fluid, allowing operators to make fine adjustments to the press’s operation. This level of control improves accuracy, reduces material waste, and increases energy efficiency.
CNC Controls
CNC-controlled C-frame presses are becoming more common in industries that require high precision and automation. CNC systems allow operators to program the press for specific tasks, such as punching or forming, and automate the entire process. This reduces the need for manual intervention, improves consistency, and increases production speed.
Smart Press Technology
Some C-frame hydraulic presses are now equipped with smart technology, such as sensors and IoT connectivity, which allow for real-time monitoring of press performance. Smart presses can track factors such as pressure, stroke length, and material deformation, providing valuable data for optimizing the pressing process and ensuring consistent product quality.
H-Frame Hydraulic Presses
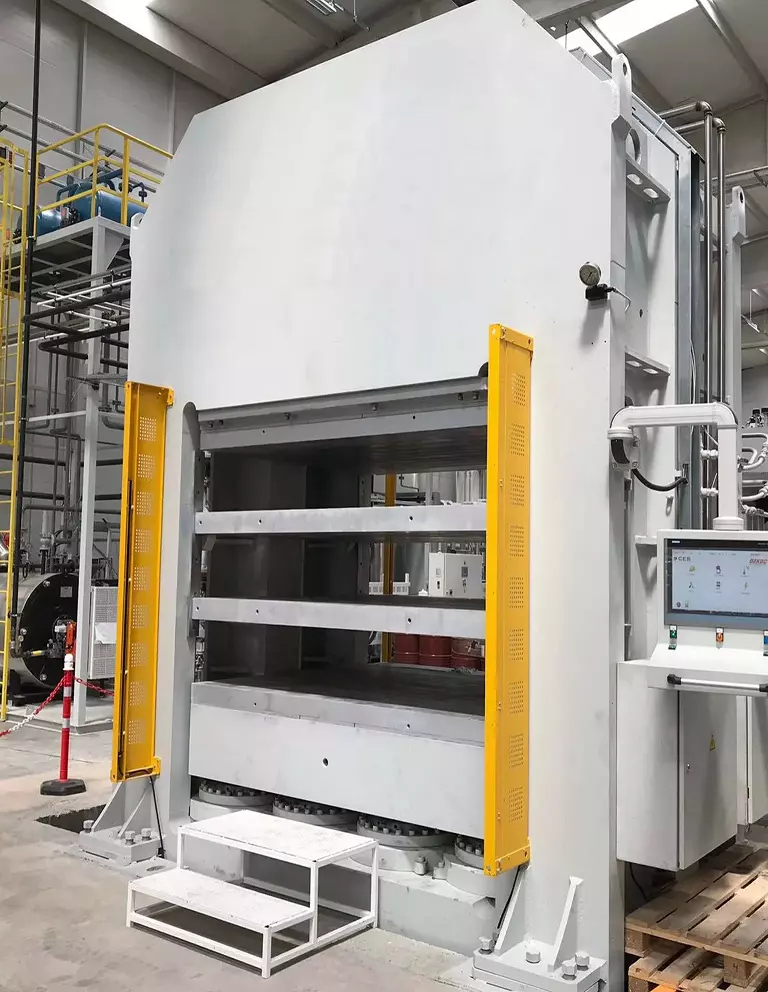
H-frame hydraulic presses, named for their distinct H-shaped frame, are among the most versatile and widely used hydraulic presses in industrial settings. This type of press features a frame with two vertical columns connected by horizontal crossbars, forming an “H” structure that provides exceptional stability and support during pressing operations. H-frame presses are known for their robust design, high force capacity, and versatility, making them ideal for tasks such as metal forming, bending, straightening, punching, and stamping. They are commonly used in industries such as automotive, metalworking, aerospace, manufacturing, and repair shops.
8.1. Design and Structure of H-Frame Hydraulic Presses
The key feature of an H-frame hydraulic press is its rigid frame design, which provides the necessary support to handle high-force applications. The frame consists of two vertical columns and two horizontal crossbars, creating a sturdy structure that can withstand immense pressure without flexing or deforming. The large, open space between the columns allows for easy access to the work area and accommodates various workpiece sizes.
Key Components
- Vertical columns: The two vertical columns provide the structural support for the press. They are typically made from high-strength steel to ensure they can handle the heavy loads generated during pressing operations.
- Horizontal crossbars: The upper and lower crossbars connect the vertical columns and provide stability to the frame. The upper crossbar supports the hydraulic cylinder and ram, while the lower crossbar serves as the bed where the workpiece is placed.
- Hydraulic cylinder and ram: The hydraulic cylinder is mounted on the upper crossbar and houses the piston that drives the ram downward to apply pressure to the workpiece. The ram moves vertically, pressing the material against the die or tool located on the bed.
- Work table or bed: The bed is where the workpiece is placed during the pressing operation. It may include slots or holes for mounting tooling, dies, or jigs. The open design of the H-frame allows for larger workpieces to be processed compared to other press types like C-frame presses.
- Control systems: H-frame presses are equipped with manual or automated controls that regulate the press’s force, stroke length, and speed. More advanced models may include CNC controls or programmable logic controllers (PLCs) for automated operation and precise control over the pressing process.
8.2. Applications of H-Frame Hydraulic Presses
H-frame hydraulic presses are used in a wide range of industrial applications, particularly those that require high force and precise control. Their versatility and strength make them suitable for both heavy-duty and light-duty tasks, from metalworking to assembly work.
8.2.1. Metalworking and Fabrication
H-frame presses are commonly used in metalworking for tasks such as bending, forming, straightening, and punching metal parts. Their ability to generate significant force, combined with the large work area, allows operators to process various sizes and shapes of metal sheets, plates, and components.
- Bending and forming: H-frame presses are used to bend metal sheets and plates into specific shapes. By applying controlled force, the press can form complex bends and curves without damaging the material.
- Straightening: In metal fabrication, H-frame presses are often used to straighten bent or deformed metal parts. By applying pressure in the opposite direction of the bend, the press can restore the part to its original shape.
- Punching and cutting: H-frame presses can also be used for punching holes or cutting shapes into metal sheets. The high force capacity of the press ensures clean, precise cuts, even in thicker materials.
8.2.2. Automotive Repair and Manufacturing
In the automotive industry, H-frame presses are used for both repair work and manufacturing of vehicle components. The ability to generate consistent force and handle large workpieces makes H-frame presses ideal for tasks such as pressing bearings, straightening chassis components, and assembling automotive parts.
- Bearing installation: H-frame presses are frequently used in automotive repair shops to press bearings into place in engine blocks, transmissions, and wheel hubs. The precise control over pressure ensures that bearings are installed correctly without damaging the surrounding components.
- Chassis straightening: In automotive repair, H-frame presses are used to straighten bent or damaged chassis components. By applying controlled pressure, the press can restore the structural integrity of the vehicle’s frame.
- Component manufacturing: H-frame presses are used in automotive manufacturing to form, stamp, and assemble various parts, such as suspension components, engine mounts, and body panels. The press’s large work area and high force capacity allow for efficient processing of automotive parts.
8.2.3. Aerospace Industry
In the aerospace industry, H-frame hydraulic presses are used for the precision forming of high-strength components, such as structural parts, engine housings, and turbine blades. The high-pressure capabilities of H-frame presses ensure that aerospace components meet the stringent quality and safety standards required for aviation.
- Forming complex shapes: H-frame presses are used to form complex, high-strength parts from metals like aluminum, titanium, and composites. These parts are essential for aircraft structures, where strength and weight are critical factors.
- Stamping and punching: H-frame presses are also used for stamping and punching operations, where precise holes or cutouts are needed in metal sheets or plates used in aircraft construction.
8.2.4. Plastic and Rubber Molding
H-frame presses are used in the plastic and rubber molding industries to compress materials into molds, creating finished products with precise shapes and dimensions. These presses apply consistent force, ensuring that the molded parts are uniform and free of defects.
- Compression molding: In compression molding, plastic or rubber material is placed in a mold, and the H-frame press applies pressure to form the material into the desired shape. This process is commonly used to manufacture components like seals, gaskets, and housings.
- Die cutting: H-frame presses are also used for die-cutting operations in the plastics and rubber industries, where sheets of material are cut into specific shapes for products such as packaging, gaskets, or seals.
8.3. Advantages of H-Frame Hydraulic Presses
H-frame hydraulic presses offer several advantages over other types of hydraulic presses, making them the preferred choice for many industrial applications.
8.3.1. High Force Capacity
H-frame presses are designed to handle high-force applications, often generating forces ranging from a few tons to thousands of tons. This makes them ideal for tasks like metal forming, punching, and stamping, where large amounts of pressure are needed to shape or cut materials. The robust construction of the H-frame ensures that the press can handle heavy loads without flexing or deforming.
8.3.2. Versatility
One of the key advantages of H-frame presses is their versatility. These presses can be used for a wide range of tasks, from light-duty assembly work to heavy-duty metal forming and fabrication. The open design of the H-frame allows operators to work with large workpieces, making the press suitable for industries that require the processing of oversized parts or materials.
8.3.3. Precision and Control
H-frame hydraulic presses offer precise control over pressure, stroke length, and speed, making them suitable for applications that require high precision. Many H-frame presses are equipped with servo-hydraulic or CNC control systems, which allow operators to program specific parameters for each task. This level of control ensures consistent, high-quality results, even in applications that require tight tolerances.
8.3.4. Durability and Stability
The rigid frame design of H-frame presses provides excellent stability and durability, making them capable of withstanding the stresses of heavy-duty industrial applications. The frame’s ability to distribute force evenly across the workpiece ensures that the material is pressed accurately, reducing the risk of misalignment or material deformation.
8.4. Technological Advancements in H-Frame Hydraulic Presses
Recent advancements in H-frame hydraulic press technology have improved the efficiency, precision, and versatility of these machines, making them even more valuable in modern manufacturing environments.
Servo-Hydraulic Systems
Many modern H-frame presses are equipped with servo-hydraulic systems, which provide greater control over the press’s force, speed, and stroke length. Servo-hydraulic systems use servo motors to regulate the flow of hydraulic fluid, allowing operators to make fine adjustments to the press’s operation. This results in improved accuracy, faster cycle times, and increased energy efficiency.
CNC and PLC Controls
H-frame hydraulic presses are increasingly being equipped with CNC and PLC control systems that allow for fully automated operation. CNC-controlled presses can be programmed to perform specific tasks, such as bending, stamping, or forming, with minimal operator intervention. This automation increases productivity, reduces the risk of human error, and allows for greater flexibility in terms of press operation.
Smart Manufacturing and IoT Integration
As part of the Industry 4.0 movement, H-frame presses are now being integrated into smart manufacturing environments using IoT (Internet of Things) connectivity. IoT-enabled presses can communicate with other machines in the production line, providing real-time data on press performance, material usage, and maintenance needs. This connectivity enables more efficient production management and predictive maintenance, reducing downtime and improving overall operational efficiency.
Stamping Hydraulic Presses
Stamping hydraulic presses are specialized machines designed for high-speed metal stamping operations, which involve cutting, shaping, and forming sheet metal using dies. These presses apply a large force over a short period, making them suitable for mass production in industries like automotive, electronics, appliances, and aerospace. Stamping hydraulic presses are highly efficient and capable of producing large quantities of precision parts with minimal material waste, making them an essential tool in modern manufacturing.
9.1. Working Principle of Stamping Hydraulic Presses
The stamping process involves placing a sheet of metal, known as a blank, into the press where a punch and die are used to shape or cut the material. The hydraulic press applies force to the punch, which drives the blank into the die, forming the desired shape. Stamping presses are capable of performing a variety of tasks, including blanking, piercing, bending, embossing, and coining, all of which are critical for producing metal components with precise dimensions and surface finishes.
Key Stamping Operations
- Blanking: This operation involves cutting a flat piece of metal from a larger sheet. The blank serves as the starting material for further operations or as the final product.
- Piercing: Piercing is the process of punching holes or shapes into the metal sheet, which is commonly used to create holes for fasteners or electrical components.
- Bending: In bending operations, the metal sheet is deformed into a specific angle or shape without cutting it. This is used to form parts like brackets, panels, and frames.
- Embossing: Embossing involves creating raised or recessed designs on the surface of the metal. This operation is often used for decorative purposes or to add rigidity to the part.
- Coining: Coining is a precision stamping operation where the material is compressed between the punch and die to create fine details, such as logos or serial numbers, with a high degree of accuracy.
The force generated by the hydraulic system is transferred through the ram to the punch, which compresses the material against the die. Hydraulic presses are known for their smooth and controlled force application, allowing for high-precision operations, even in high-speed production environments. The force can be adjusted based on the material and thickness of the blank, ensuring that each part is stamped accurately and consistently.
9.2. Components of Stamping Hydraulic Presses
Stamping hydraulic presses consist of several key components that work together to perform high-speed metal stamping operations. Each component plays a critical role in ensuring the efficiency and precision of the stamping process.
Key Components
- Frame: The frame is the structural foundation of the press and provides the support needed to handle the large forces generated during stamping. Stamping hydraulic presses typically use an H-frame or C-frame design, depending on the size of the press and the type of operation. H-frame presses are more common for large-scale, high-force operations, while C-frame presses are used for smaller, lighter tasks.
- Hydraulic system: The hydraulic system provides the force required to perform the stamping operation. It consists of a hydraulic pump, cylinders, and fluid reservoirs that work together to pressurize the hydraulic fluid and move the ram.
- Ram: The ram is the moving part of the press that transfers the hydraulic force to the punch. It moves vertically, pressing the punch against the material to perform the stamping operation.
- Die and punch: The die and punch are the tools used to shape the material. The punch applies pressure to the blank, forcing it into the die cavity, where it is cut or shaped into the desired form. Dies are typically custom-made for specific parts, ensuring that each stamped piece meets precise dimensional requirements.
- Control system: Stamping hydraulic presses are equipped with control systems that allow operators to regulate the force, speed, and stroke length of the press. Advanced presses often feature CNC controls or programmable logic controllers (PLCs) for automated operation and precise control over the stamping process.
9.3. Applications of Stamping Hydraulic Presses
Stamping hydraulic presses are used in a variety of industries to produce metal parts that require high precision, fast production speeds, and complex shapes. Some of the most common applications include:
9.3.1. Automotive Industry
In the automotive industry, stamping hydraulic presses are essential for producing large quantities of body panels, chassis components, and engine parts. The speed and precision of stamping presses make them ideal for mass production, where consistent quality and tight tolerances are critical.
- Body panels: Automotive body panels, such as doors, hoods, fenders, and roofs, are typically produced using stamping hydraulic presses. These panels must be shaped accurately to fit together seamlessly, and stamping presses ensure that each panel is produced to exact specifications.
- Chassis components: Stamping presses are used to form various chassis components, including cross members, support beams, and suspension brackets. The ability to stamp complex shapes quickly and consistently makes these presses indispensable for automotive manufacturing.
- Engine parts: Stamping hydraulic presses are also used to produce small engine components, such as valve covers, brackets, and housings. These parts must meet strict dimensional tolerances to ensure proper engine performance.
9.3.2. Electronics and Appliances
In the electronics and appliance industries, stamping presses are used to produce small metal parts, such as housings, connectors, and frames. The precision and speed of stamping hydraulic presses make them ideal for producing large quantities of parts used in consumer electronics, household appliances, and industrial equipment.
- Metal housings: Stamping hydraulic presses are used to form metal housings for electronic devices, such as smartphones, laptops, and tablets. These housings must be lightweight, durable, and precisely shaped to fit internal components.
- Connectors: Electrical connectors and terminals are often produced using stamping presses, where small metal parts are stamped and shaped into connectors that ensure reliable electrical connections in devices.
- Appliance components: Stamping presses are used to produce metal components for household appliances, such as washing machines, refrigerators, and dishwashers. These components include brackets, enclosures, and panels, all of which require precision and durability.
9.3.3. Aerospace Industry
In the aerospace industry, stamping hydraulic presses are used to produce lightweight, high-strength components for aircraft and spacecraft. The ability to produce precision parts with minimal material waste is critical in aerospace manufacturing, where weight reduction and structural integrity are essential.
- Aircraft panels: Stamping presses are used to form thin, lightweight panels for aircraft fuselages, wings, and control surfaces. These parts must be shaped with extreme precision to ensure aerodynamic performance and structural strength.
- Turbine components: Stamping hydraulic presses are also used to produce small components for aircraft engines, such as turbine blades and housings. These parts must withstand high temperatures and mechanical stress, making precision stamping a crucial part of the manufacturing process.
9.3.4. Industrial and Consumer Goods
Stamping hydraulic presses are widely used in the production of industrial and consumer goods, where they are used to manufacture metal parts for products like tools, packaging, and hardware.
- Packaging: Stamping presses are used to produce metal cans, containers, and lids for the food and beverage industry. The ability to quickly stamp large quantities of metal packaging ensures a consistent supply of lightweight, durable containers.
- Tools and hardware: Stamping presses are used to form metal parts for hand tools, fasteners, and hardware. The precision and strength of these presses ensure that each part is produced to the exact specifications required for reliable performance.
9.4. Advantages of Stamping Hydraulic Presses
Stamping hydraulic presses offer several advantages over other types of metal forming equipment, making them the preferred choice for high-speed, high-precision manufacturing.
9.4.1. High Speed and Efficiency
Stamping hydraulic presses are capable of high-speed operation, allowing manufacturers to produce large quantities of parts in a short amount of time. This is especially important in industries like automotive and electronics, where production volumes are high, and cycle times must be minimized. The rapid cycling of the press, combined with its ability to handle continuous feeds of material, makes it an efficient solution for mass production.
9.4.2. Precision and Consistency
Hydraulic presses provide consistent and precise force throughout the entire stroke, ensuring that each part is stamped with the same level of accuracy. This is critical in industries where even minor deviations can result in parts that do not fit or function properly. Stamping presses can be equipped with advanced control systems, such as servo-hydraulic or CNC controls, which allow operators to adjust the force, speed, and stroke length with high precision.
9.4.3. Versatility in Part Design
Stamping presses are capable of producing a wide range of shapes, sizes, and designs, making them highly versatile. The use of interchangeable dies allows manufacturers to switch between different part designs quickly, enabling flexible production lines that can adapt to changing product requirements. This versatility is particularly valuable in industries like automotive and electronics, where product designs evolve rapidly.
9.4.4. Minimal Material Waste
The stamping process is designed to maximize material efficiency, with minimal waste generated during production. Stamping presses can be used to nest parts within the metal sheet, ensuring that as much material as possible is utilized. This reduces material costs and minimizes the environmental impact of the manufacturing process.
9.5. Technological Advancements in Stamping Hydraulic Presses
Advances in stamping press technology have improved the efficiency, precision, and automation of these machines, making them even more valuable in modern manufacturing environments.
Servo-Hydraulic Systems
Many modern stamping hydraulic presses are equipped with servo-hydraulic systems, which combine the power of hydraulics with the precision control of servo motors. Servo-hydraulic presses offer improved accuracy, faster cycle times, and greater energy efficiency compared to traditional hydraulic presses. The ability to precisely control the force and speed of the press allows for better material handling and reduces the risk of defects.
CNC Controls
CNC-controlled stamping presses are increasingly common in industries that require high precision and automation. CNC systems allow operators to program specific parameters for each part, such as stroke length, force, and feed rate. This level of automation improves consistency, reduces setup time, and increases production speed. CNC systems also enable quick die changes, allowing manufacturers to switch between different part designs with minimal downtime.
IoT and Smart Manufacturing
As part of the Industry 4.0 revolution, stamping hydraulic presses are being integrated into smart manufacturing systems that use IoT connectivity and real-time data monitoring. IoT-enabled presses can communicate with other machines in the production line, providing real-time data on press performance, material usage, and maintenance needs. This connectivity allows manufacturers to optimize production schedules, reduce downtime, and improve overall efficiency.
Servo-Hydraulic Presses
Servo-hydraulic presses are advanced hydraulic presses that combine the power and reliability of traditional hydraulic systems with the precision and efficiency of servo motors. These presses provide improved control over force, speed, and positioning, making them ideal for applications that require high accuracy and repeatability. Servo-hydraulic presses are used in industries such as automotive, aerospace, electronics, and medical device manufacturing, where precision and energy efficiency are critical.
The key advantage of servo-hydraulic presses lies in their ability to adjust parameters dynamically during operation, allowing for more precise control over the pressing process. This flexibility, combined with the energy efficiency offered by servo motors, has made servo-hydraulic presses a popular choice in industries where both performance and sustainability are priorities.
10.1. Working Principle of Servo-Hydraulic Presses
A servo-hydraulic press functions similarly to a traditional hydraulic press, with one key difference: the hydraulic system is controlled by servo motors instead of a constant-speed electric motor. Servo motors provide precise control over the movement of the hydraulic fluid, allowing operators to adjust the speed, pressure, and position of the ram with a high degree of accuracy.
Key Components
- Servo motor: The servo motor is responsible for controlling the hydraulic pump, which in turn pressurizes the hydraulic fluid. Unlike traditional hydraulic presses, where the pump runs at a constant speed, the servo motor can vary the speed and pressure of the pump based on the specific requirements of the task.
- Hydraulic system: The hydraulic system, which consists of a pump, reservoir, and hydraulic fluid, generates the force needed to move the ram and perform the pressing operation. In a servo-hydraulic press, the hydraulic system is controlled by the servo motor, which allows for precise adjustments in real-time.
- Ram: The ram is the component that moves up and down to apply force to the workpiece. The position and speed of the ram can be controlled with extreme precision in a servo-hydraulic press, allowing for more accurate pressing operations.
- Control system: Servo-hydraulic presses are equipped with advanced control systems, often featuring CNC or PLC controls, which allow operators to program specific parameters for each operation. These control systems enable automated operation, real-time monitoring, and adjustments to force, speed, and stroke length.
10.2. Applications of Servo-Hydraulic Presses
Servo-hydraulic presses are used in industries that require precise control over the pressing process, particularly for tasks that involve complex part shapes, tight tolerances, or energy efficiency requirements. Some of the most common applications include:
10.2.1. Automotive Industry
In the automotive industry, servo-hydraulic presses are used to manufacture components such as body panels, chassis parts, and engine components. The ability to adjust pressing parameters dynamically ensures that each part is formed with precision, reducing defects and ensuring that the parts meet strict safety and performance standards.
- Precision stamping: Servo-hydraulic presses are used for precision stamping of automotive body panels, where exact dimensional accuracy is critical. The ability to control the press’s force and speed ensures that each panel is formed without defects like wrinkling or tearing.
- Chassis and suspension components: In the production of chassis and suspension components, servo-hydraulic presses offer the precision needed to form parts that must withstand high stress and mechanical loads. The ability to control the pressing process ensures that the parts meet stringent safety requirements.
10.2.2. Aerospace Industry
The aerospace industry relies on servo-hydraulic presses to produce lightweight, high-strength components that must meet exacting quality standards. Servo-hydraulic presses are used to form parts such as turbine blades, engine housings, and structural components for aircraft.
- Turbine blade production: Servo-hydraulic presses are used to forge turbine blades for jet engines. These blades must be formed with extreme precision to ensure they can withstand high temperatures and mechanical stress.
- Aircraft panels and structural parts: The ability to control the force and speed of the press allows manufacturers to produce aircraft panels and structural parts with minimal material waste, ensuring that each part is lightweight and strong.
10.2.3. Electronics Industry
In the electronics industry, servo-hydraulic presses are used to produce small, intricate components such as metal housings, connectors, and terminals. The precision offered by these presses ensures that each part is produced to exact specifications, which is critical in the production of electronic devices.
- Metal stamping: Servo-hydraulic presses are used for metal stamping of electronic components, where tight tolerances and high precision are essential. The ability to control the press’s movement ensures that each component is formed with the required accuracy.
- Connector and terminal production: The electronics industry relies on servo-hydraulic presses to produce small connectors and terminals that must meet exact dimensional tolerances. The precise control offered by these presses ensures that each part is manufactured with consistency and quality.
10.2.4. Medical Device Manufacturing
The medical device industry requires precision and repeatability in the production of components such as surgical instruments, implants, and diagnostic equipment. Servo-hydraulic presses are used to manufacture these components with the accuracy needed to meet stringent regulatory standards.
- Implant production: Servo-hydraulic presses are used to produce medical implants, such as hip and knee replacements. These parts must be formed with precision to ensure they fit properly and function reliably.
- Surgical instruments: In the production of surgical instruments, the ability to control the pressing process ensures that each instrument is formed to the exact specifications required for medical procedures.
10.3. Advantages of Servo-Hydraulic Presses
Servo-hydraulic presses offer several advantages over traditional hydraulic presses, making them the preferred choice for industries that require precision, energy efficiency, and flexibility.
10.3.1. Precise Control
One of the main advantages of servo-hydraulic presses is the precise control they offer over force, speed, and position. The servo motor allows operators to adjust the pressing parameters dynamically, ensuring that each part is formed with the required accuracy. This level of control is especially important in industries like aerospace and medical device manufacturing, where even minor deviations can result in parts that do not meet quality standards.
10.3.2. Energy Efficiency
Servo-hydraulic presses are more energy-efficient than traditional hydraulic presses, as the servo motor only uses energy when the press is in motion. In contrast, traditional hydraulic presses run continuously, even when no pressing operation is taking place, which results in wasted energy. The ability to control the motor’s speed and power consumption allows servo-hydraulic presses to operate more efficiently, reducing energy costs and the press’s overall environmental impact.
10.3.3. Flexibility
Servo-hydraulic presses offer greater flexibility compared to traditional hydraulic presses. The ability to adjust parameters such as force, speed, and stroke length allows manufacturers to use the same press for multiple tasks, reducing the need for additional equipment. This flexibility is especially valuable in industries like automotive and electronics, where product designs and requirements can change frequently.
10.3.4. Faster Cycle Times
Servo-hydraulic presses can achieve faster cycle times than traditional hydraulic presses due to their ability to accelerate and decelerate quickly. The precise control over the press’s movement allows for shorter press cycles, increasing productivity and reducing downtime.
10.3.5. Reduced Maintenance
Servo-hydraulic presses typically require less maintenance than traditional hydraulic presses. The use of servo motors eliminates the need for constant-speed electric motors, which reduces wear and tear on the hydraulic system. Additionally, the ability to monitor the press’s performance in real-time using IoT sensors and smart technology allows operators to detect potential issues before they result in costly downtime.
10.4. Technological Advancements in Servo-Hydraulic Presses
Recent advancements in servo-hydraulic press technology have further improved their performance, precision, and efficiency, making them even more valuable in modern manufacturing environments.
Smart Press Technology
Servo-hydraulic presses are increasingly being equipped with smart technology, such as IoT connectivity and real-time data monitoring. Smart presses can collect data on pressing force, stroke length, and material deformation, allowing manufacturers to optimize the pressing process and ensure consistent product quality. This data can also be used for predictive maintenance, reducing downtime and improving overall efficiency.
AI and Machine Learning
Artificial intelligence (AI) and machine learning algorithms are being integrated into servo-hydraulic presses to optimize pressing parameters in real-time. These systems can analyze data from previous operations and adjust the press’s settings to improve performance, reduce material waste, and increase efficiency.
Energy Recovery Systems
Some servo-hydraulic presses are now equipped with energy recovery systems, which capture the energy generated during the pressing process and reuse it for future operations. This technology reduces the overall energy consumption of the press, making it more sustainable and cost-effective.
Introduction to H-Frame Hydraulic Presses
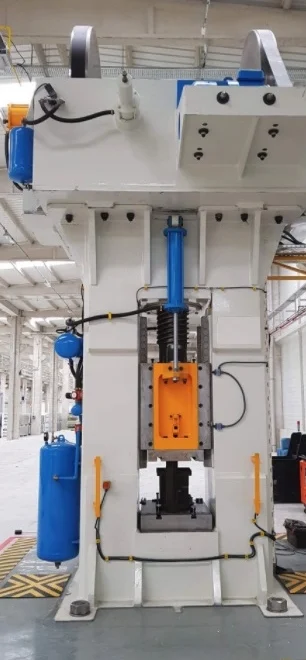
Hydraulic presses are essential tools in modern manufacturing, offering immense power and precision for a wide range of metal forming, molding, and assembly operations. Among the various types of hydraulic presses available today, the H-frame hydraulic press stands out as one of the most versatile and widely used designs. Named for its distinctive H-shaped frame, this press configuration offers exceptional stability and force distribution, making it ideal for high-force applications that require precision and reliability.
The H-frame design consists of two vertical columns and two horizontal crossbars that provide support for the hydraulic cylinder and the press bed. This rigid frame structure ensures that the press can handle the high forces required for tasks such as bending, straightening, forming, punching, and stamping large workpieces. The open space between the columns allows for easy access to the work area, enabling operators to process larger components than what might be possible with other types of presses, such as C-frame presses.
One of the key advantages of H-frame hydraulic presses is their ability to generate evenly distributed force across the workpiece, reducing the risk of deformation or misalignment. This makes them particularly valuable in industries that require high levels of precision, such as the automotive, aerospace, and metalworking industries. H-frame presses are also commonly used in maintenance and repair operations, where their ability to apply consistent pressure is essential for tasks like pressing bearings into place or straightening bent metal parts.
H-frame hydraulic presses come in a variety of sizes and configurations, ranging from small, manual presses used in workshops to large, automated systems capable of producing thousands of tons of force. Modern H-frame presses are equipped with advanced control systems that allow for precise adjustments to pressure, speed, and stroke length, making them suitable for both heavy-duty industrial applications and precision manufacturing tasks.
In addition to their versatility, H-frame hydraulic presses are known for their durability and reliability. The robust construction of the frame ensures that the press can withstand the high stresses of continuous operation, while the hydraulic system provides consistent force throughout the press cycle. With proper maintenance, H-frame presses can operate for many years, making them a cost-effective solution for manufacturers who require a reliable, high-performance press.
The enduring popularity of H-frame hydraulic presses can be attributed to their flexibility, power, and precision. Whether used for metal forming, molding, or assembly, these presses play a critical role in modern manufacturing, providing the strength and control needed to produce high-quality parts and components.
Historical Evolution of H-Frame Hydraulic Presses
The development of H-frame hydraulic presses is closely linked to the broader history of hydraulic press technology and its evolution over the centuries. Understanding how H-frame presses emerged as a standard in the manufacturing industry requires an exploration of early hydraulic press innovations, the impact of industrialization, and advancements in hydraulic system design.
2.1. Early Development of Hydraulic Presses
The principles of hydraulics have been understood for centuries, with the invention of the hydraulic press commonly attributed to Joseph Bramah, an English engineer who patented the first practical hydraulic press in 1795. Bramah’s design utilized Pascal’s Law, which states that when pressure is applied to a confined fluid, it is transmitted equally in all directions. This discovery enabled the development of a machine capable of generating significant force using a relatively small amount of pressure, laying the groundwork for modern hydraulic press technology.
The original hydraulic press designed by Bramah was used primarily for packing and compressing materials, such as cotton and paper. While these early presses were relatively simple, the concept of using hydraulics to amplify force revolutionized various industries, leading to the gradual improvement and diversification of hydraulic press designs.
2.2. Evolution of the H-Frame Design
The H-frame hydraulic press emerged as a result of the need for greater stability and force distribution during pressing operations. As hydraulic press applications expanded, there was a demand for more robust structures that could handle larger forces without flexing or deforming. The H-frame design, with its vertical columns and horizontal crossbars, provided a solution by creating a rigid, stable frame that could support high loads.
This configuration allowed for even distribution of force across the workpiece, reducing the risk of material deformation and ensuring consistent quality. The open space between the columns also provided easier access to the work area, enabling operators to process larger components and allowing for more versatility in industrial applications.
2.3. Influence of Industrialization on Hydraulic Press Technology
The Industrial Revolution, which began in the late 18th century, had a profound impact on the development and use of hydraulic presses, including the H-frame design. The mass production of goods, driven by advancements in machinery and manufacturing processes, led to an increased demand for powerful and reliable press equipment. Hydraulic presses were employed in various industries, such as metalworking, automotive, and construction, for tasks like metal forming, stamping, and bending.
During the 19th and early 20th centuries, significant advancements were made in hydraulic systems, including improvements in hydraulic pumps, cylinders, and fluid control mechanisms. These innovations allowed for the development of more powerful and efficient H-frame hydraulic presses, which became widely adopted in manufacturing and heavy industry.
2.4. The Shift from Mechanical to Hydraulic Systems
Before the widespread adoption of hydraulic presses, mechanical presses were the dominant technology used for metal forming and related applications. Mechanical presses operated using a flywheel, gears, and crank mechanisms to generate force. While they were effective for certain tasks, mechanical presses had limitations in terms of controlling force and adjusting stroke length.
The transition to hydraulic systems offered several advantages over mechanical presses, including:
- Variable force control: Hydraulic presses could apply a consistent force throughout the entire stroke, unlike mechanical presses where the force varied depending on the position of the crank.
- Adjustable stroke length: Hydraulic systems allowed operators to control the stroke length more precisely, making them suitable for a wider range of applications.
- Greater flexibility: Hydraulic presses could easily accommodate different tooling and dies, enabling rapid changes between tasks.
As these benefits became more evident, the H-frame hydraulic press gained popularity as a versatile and powerful solution for manufacturing operations. Its ability to generate significant force while providing precise control over the pressing process made it suitable for tasks that required high accuracy, such as automotive manufacturing, aerospace production, and metal fabrication.
2.5. Key Milestones in the Development of H-Frame Hydraulic Presses
Over the decades, several key milestones have marked the evolution of H-frame hydraulic presses, including:
- Introduction of high-pressure hydraulic systems: In the mid-20th century, advancements in hydraulic technology led to the development of high-pressure systems capable of generating thousands of tons of force. This increased the capabilities of H-frame presses, making them suitable for heavy-duty applications like forging and metal forming.
- Adoption of servo-hydraulic systems: The integration of servo-hydraulic technology allowed for more precise control of pressure, speed, and stroke length in H-frame presses. This innovation improved the accuracy and efficiency of pressing operations, enabling manufacturers to produce high-quality components with tight tolerances.
- Integration with computer numerical control (CNC): The adoption of CNC control systems revolutionized the operation of H-frame hydraulic presses, allowing for automated and programmable control over the pressing process. CNC integration enabled more complex operations, such as multi-stage forming, automated assembly, and precision stamping.
- Development of smart manufacturing systems: With the advent of Industry 4.0, H-frame hydraulic presses have been integrated into smart manufacturing environments that use IoT connectivity and real-time data monitoring. These systems enable predictive maintenance, performance optimization, and seamless integration with other manufacturing equipment.
Today, H-frame hydraulic presses are recognized as a cornerstone of modern manufacturing, providing the strength, versatility, and precision required for a wide range of industrial applications. Their continued development and integration with advanced technologies ensure that they remain relevant in an ever-evolving industrial landscape.
Design and Construction of H-Frame Hydraulic Presses
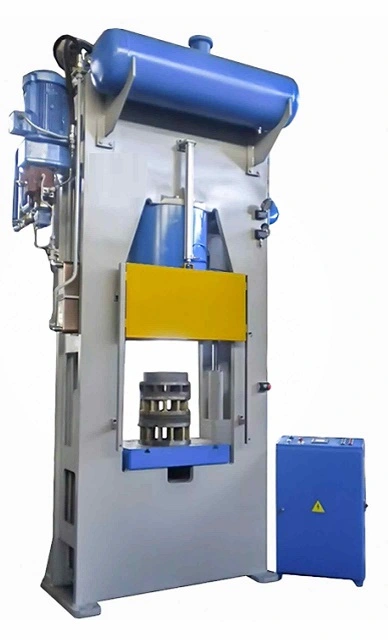
The H-frame hydraulic press is known for its robust construction, stability, and versatility. Its design consists of a simple yet effective configuration that includes two vertical columns and two horizontal crossbars forming an “H” shape, hence the name. This structural design allows the press to distribute force evenly, maintain rigidity under high loads, and accommodate various industrial applications.
3.1. Structural Overview: The H-Frame Design
The H-frame design is characterized by a symmetrical structure, which provides excellent support and stability. The two vertical columns serve as the primary supports, while the two horizontal crossbars connect these columns and house key components like the hydraulic cylinder, ram, and bed. This design ensures that the press can withstand the forces generated during pressing operations without flexing or deforming.
Key Characteristics of the H-Frame Design
- Symmetry: The symmetrical arrangement of the vertical columns and horizontal crossbars helps to balance the distribution of force across the entire structure.
- Open Work Area: The open space between the columns allows for easy access to the workpiece and enables the press to handle larger components compared to other press types like C-frame presses.
- Modular Design Options: The H-frame configuration can be easily customized with different accessories, die sets, and control systems to suit specific industrial requirements.
3.2. Key Components of H-Frame Hydraulic Presses
H-frame hydraulic presses consist of several key components that work together to perform pressing operations with precision and consistency.
3.2.1. Vertical Columns
The vertical columns are the backbone of the H-frame press. They provide the structural support needed to handle the immense forces generated during pressing. The columns are typically made of high-strength steel to ensure they can withstand heavy loads without buckling or bending.
- Reinforcement and thickness: The columns are designed with sufficient thickness and reinforcement to prevent deformation during high-pressure operations.
- Guide rails: Some H-frame presses feature guide rails mounted on the columns to ensure the ram moves vertically without tilting or misalignment.
3.2.2. Horizontal Crossbars
The upper and lower crossbars connect the vertical columns, providing structural stability and support for the hydraulic components.
- Upper crossbar: The upper crossbar supports the hydraulic cylinder and ram, allowing them to apply pressure to the workpiece.
- Lower crossbar (bed): The lower crossbar, also known as the bed, serves as the base where the workpiece is placed during pressing operations. It may include slots or holes for mounting dies, tooling, or fixtures.
3.2.3. Hydraulic Cylinder
The hydraulic cylinder is a critical component that generates the force needed to perform pressing operations. It consists of a piston, ram, and cylinder housing, which work together to convert hydraulic fluid pressure into mechanical force.
- Single-acting vs. double-acting cylinders: H-frame presses can use either single-acting cylinders, where hydraulic fluid only acts on one side of the piston, or double-acting cylinders, which allow fluid to act on both sides for greater control over the ram’s movement.
- Cylinder bore size and stroke length: The size of the cylinder bore and stroke length determine the press’s force capacity and the range of motion for the ram.
3.2.4. Ram and Punch
The ram is the moving component that transmits the force from the hydraulic cylinder to the workpiece. It is typically connected to a punch or other tooling used to shape, cut, or press the material.
- Ram guides: To ensure the ram moves vertically without deviation, guide rails or bushings may be installed to reduce lateral movement and improve precision.
- Punches and tooling: The ram can be fitted with various tooling, such as punches, dies, or forming tools, depending on the specific operation.
3.2.5. Work Table or Bed
The work table or bed is the surface where the workpiece is placed during pressing operations. It is usually made from hardened steel to withstand the impact and pressure of repeated pressing. The bed may also include:
- T-slots or mounting holes for securing dies, tooling, or fixtures.
- Adjustable positioning to accommodate different workpiece sizes and shapes.
3.2.6. Control Systems
Modern H-frame hydraulic presses are equipped with various control systems to regulate pressure, speed, and stroke length.
- Manual controls: Some basic H-frame presses use manual controls, such as hand-operated levers or foot pedals, to operate the press.
- Automated controls: Advanced presses are equipped with programmable logic controllers (PLCs) or computer numerical control (CNC) systems that allow for automated operation and precise adjustments.
- Servo-hydraulic systems: These systems use servo motors to control the hydraulic pump, enabling greater precision in pressure and speed adjustments.
3.3. Importance of Stability and Force Distribution in H-Frame Presses
The design of H-frame hydraulic presses ensures that the forces generated during pressing operations are evenly distributed across the structure. This stability is crucial for maintaining the accuracy and quality of the pressed components.
- Reduced risk of deformation: The rigid frame design minimizes flexing or bending, which could otherwise lead to inconsistencies in the workpiece.
- Consistent force application: The even distribution of force across the press bed ensures that the entire surface of the workpiece is subjected to uniform pressure, improving the overall quality of the formed or shaped part.
- Improved precision: The combination of stability and precise control systems in H-frame presses allows for high levels of accuracy, even when pressing large or complex workpieces.
3.4. Customization Options in H-Frame Hydraulic Presses
H-frame hydraulic presses can be customized to meet the specific needs of various industries and applications. Some common customization options include:
- Different tonnage capacities: H-frame presses are available in a range of force capacities, from small manual presses producing a few tons of force to large industrial presses capable of thousands of tons.
- Specialized tooling and accessories: Custom tooling, such as embossing dies, forming tools, and punches, can be fitted to the press for specific applications.
- Multi-station setups: Some H-frame presses can be configured with multiple stations to perform sequential operations, such as stamping, forming, and assembly.
- Hydraulic system configurations: The hydraulic system can be tailored with different pump types, cylinder arrangements, and fluid reservoirs to achieve the desired force and speed.
3.5. Material Choices and Durability of H-Frame Structures
The durability and longevity of an H-frame hydraulic press depend on the materials used in its construction.
- High-strength steel: Most H-frame presses are made from high-strength steel that can endure the stress of heavy-duty operations. This ensures the press maintains its structural integrity over time.
- Surface treatments: Surface treatments, such as chrome plating or heat treatment, may be applied to certain components, like the ram or work bed, to enhance durability and reduce wear.
Working Principle of H-Frame Hydraulic Presses
The H-frame hydraulic press operates based on the principles of hydraulic pressure and force amplification. It uses a hydraulic system to generate force, which is then applied to a workpiece to perform various tasks such as bending, forming, stamping, punching, or compression molding. The fundamental working principle is governed by Pascal’s Law, which states that pressure applied to a confined fluid is transmitted equally in all directions.
4.1. Basic Hydraulic Press Operation
The basic operation of an H-frame hydraulic press involves the following steps:
- Generating Hydraulic Pressure: The press’s hydraulic system consists of a hydraulic pump, fluid reservoir, and hydraulic cylinders. The pump pressurizes the hydraulic fluid (usually oil), which is stored in a reservoir and then sent through a system of valves and hoses to the hydraulic cylinder.
- Actuating the Hydraulic Cylinder: The pressurized hydraulic fluid enters the cylinder chamber, where it acts on the piston inside the hydraulic cylinder. The fluid pressure creates a mechanical force that pushes the piston and the attached ram downward to apply force on the workpiece.
- Applying Force to the Workpiece: The ram moves vertically, pressing against the workpiece placed on the bed. Depending on the application, the ram may be fitted with various tools, such as dies, punches, or forming attachments, to shape, cut, or compress the material.
- Returning the Ram to its Initial Position: Once the pressing operation is complete, the hydraulic pressure is released, and the ram is returned to its initial position, ready for the next operation. In double-acting hydraulic cylinders, pressurized fluid can be used on both sides of the piston to control the movement in both directions.
4.2. Force Transmission and Movement in H-Frame Designs
The structure of the H-frame hydraulic press ensures that the force is transmitted uniformly across the workpiece. The H-shaped frame supports the hydraulic cylinder and ram, providing a stable base for force application. The vertical columns and horizontal crossbars help maintain rigidity and distribute the force evenly, which is crucial for achieving consistent results.
Key Elements in Force Transmission
- Hydraulic cylinder: The hydraulic cylinder converts fluid pressure into mechanical force. The piston inside the cylinder moves vertically, driving the ram to apply pressure to the workpiece.
- Ram guides: Ram guides or bushings ensure that the ram moves straight and does not tilt or shift laterally. This alignment is essential for maintaining the precision and quality of the pressing operation.
- Bed support: The work bed serves as the base where the material is placed, and its robust construction ensures that it can handle the high forces without deforming.
4.3. Hydraulic Cylinder and Pump Mechanics
The hydraulic cylinder and pump work together to generate the force needed for pressing operations. Understanding the mechanics of these components is crucial for optimizing the performance of an H-frame hydraulic press.
4.3.1. Hydraulic Pump Operation
The hydraulic pump draws fluid from the reservoir and pressurizes it, sending it into the hydraulic system. The type of pump used can vary depending on the force requirements of the press:
- Gear pumps: Known for their simplicity and reliability, gear pumps are commonly used in basic hydraulic systems.
- Vane pumps: Vane pumps offer a good balance between pressure and flow rate, making them suitable for presses that need moderate control.
- Piston pumps: These pumps provide high-pressure capabilities and are often used in heavy-duty presses that generate thousands of tons of force.
4.3.2. Cylinder Mechanics
The cylinder bore size, stroke length, and piston diameter all play a role in determining the force output and range of motion. Larger bore sizes and pistons can generate higher forces, while longer stroke lengths provide more flexibility in pressing different workpiece sizes.
4.4. Application of Force to Workpieces
The ability of an H-frame hydraulic press to apply force uniformly makes it suitable for a variety of industrial applications. The way the press applies force to a workpiece can be customized to achieve different outcomes.
4.4.1. Metal Forming
In metal forming, the ram and die are used to shape the metal workpiece into the desired form. The press applies steady, controlled pressure to bend or stretch the metal without causing cracks or deformities. Common metal forming tasks include:
- Bending: Creating angles and curves in metal sheets.
- Stamping: Forming metal shapes or embossing designs onto sheets.
- Punching: Cutting holes or shapes in metal sheets.
4.4.2. Compression Molding
In compression molding, the press is used to shape materials like plastics, rubber, or composites by compressing them into a mold. The H-frame hydraulic press ensures consistent pressure throughout the molding process, resulting in uniform parts with minimal defects.
4.4.3. Assembly Operations
For assembly tasks, H-frame presses are used to press bearings, bushings, or other components into place. The press applies precise pressure to ensure the components fit snugly and securely, reducing the risk of damage.
4.5. Importance of Pressure Control and Force Distribution
The control of hydraulic pressure and force distribution is crucial for achieving high-quality pressing results. Advanced control systems in modern H-frame hydraulic presses allow operators to fine-tune the pressure, speed, and stroke length, enabling greater precision in various applications.
4.5.1. Pressure Regulation
Pressure regulation ensures that the hydraulic system maintains a consistent force during the press cycle. Relief valves, pressure regulators, and flow controls are used to monitor and adjust the pressure to prevent overloading or underperformance.
4.5.2. Force Distribution
The even distribution of force across the press bed ensures that the entire workpiece is subjected to uniform pressure. This is essential for applications like sheet metal forming or compression molding, where uneven pressure can lead to warping or defects.
4.6. Control Systems and Automation in Modern H-Frame Presses
Modern H-frame hydraulic presses are equipped with automated control systems, such as CNC, PLC, or servo-hydraulic systems, that enhance the precision and efficiency of pressing operations.
4.6.1. Programmable Logic Controllers (PLCs)
PLCs allow operators to program specific parameters for each pressing task, such as force levels, stroke lengths, and cycle speeds. This automation reduces the need for manual adjustments and improves productivity.
4.6.2. Servo-Hydraulic Control
Servo-hydraulic systems use servo motors to control the hydraulic pump, providing real-time adjustments to the press’s force and speed. This capability allows for dynamic pressure control, which is beneficial in tasks requiring high precision.
4.6.3. IoT Integration and Smart Presses
With the integration of IoT connectivity, H-frame hydraulic presses can be connected to smart manufacturing networks. These smart presses provide real-time data on performance metrics, predictive maintenance alerts, and process optimization insights.
Key Applications of H-Frame Hydraulic Presses
H-frame hydraulic presses are versatile machines used across numerous industries due to their ability to generate significant force while maintaining precision and stability. Their robust design, open work area, and customizable configurations make them suitable for a wide range of applications. Below are some of the most common uses of H-frame hydraulic presses in various industries.
5.1. Metal Forming and Fabrication
One of the primary applications of H-frame hydraulic presses is in metal forming and fabrication. The press is used to manipulate metal sheets, plates, and other materials into various shapes and sizes. Key metal forming tasks performed using H-frame presses include bending, straightening, forming, stamping, and punching.
- Bending: H-frame hydraulic presses are used to create precise bends and curves in metal sheets. By applying controlled pressure, the press can shape the metal without causing cracks or material fatigue, making it suitable for producing brackets, frames, panels, and angles.
- Straightening: When metal parts become bent or warped during manufacturing, H-frame presses can be used to straighten them. This is common in industries like metalworking and construction, where steel beams, bars, or rods need to be restored to their original shape.
- Forming complex shapes: The press can also be used to form intricate shapes or components by using specialized dies. This capability is valuable in automotive and aerospace applications, where parts need to meet strict design specifications.
5.2. Automotive Manufacturing
The automotive industry is a major user of H-frame hydraulic presses. These machines are essential for producing various car components and parts that require high precision, durability, and strength. Common applications in the automotive industry include pressing bearings, forming chassis components, and punching engine parts.
- Pressing bearings: H-frame presses are widely used in automotive repair and assembly lines to press bearings into place in engine blocks, wheel hubs, and transmissions. The ability to apply precise pressure ensures that the bearings are installed correctly without causing damage to surrounding components.
- Chassis components: In manufacturing chassis components like cross members, support beams, and suspension parts, H-frame presses are used to form or shape metal parts with consistent quality. The press’s ability to handle large workpieces makes it ideal for producing these structural components.
- Punching and stamping engine parts: H-frame presses can perform high-precision punching and stamping operations to produce small engine components, such as valve covers, brackets, and housings. The press ensures each part is formed accurately, meeting the required tolerances for reliable engine performance.
5.3. Aerospace Industry
In the aerospace industry, H-frame hydraulic presses are used to produce lightweight, high-strength components that must meet exacting quality standards. Aerospace manufacturing often involves forming, punching, or stamping materials like aluminum, titanium, and composites.
- Forming lightweight structural components: H-frame presses are used to shape aircraft panels, fuselages, and wing structures, where the material must be lightweight yet strong. The precision and even force distribution provided by the H-frame design ensure that these components meet stringent aerodynamic and structural requirements.
- Turbine blades and high-strength parts: Hydraulic presses are used to form parts for jet engines, such as turbine blades and engine housings, where materials need to be shaped to withstand high temperatures and mechanical stress.
5.4. Heavy Machinery and Industrial Equipment
The heavy machinery and industrial equipment industries rely on H-frame hydraulic presses for producing large, high-strength components used in construction, mining, and agricultural equipment. Common applications include forging, stamping, and shaping parts such as gears, shafts, bearings, and machine components.
- Forging and stamping gears and shafts: H-frame hydraulic presses are used to forge metal into shapes like gears and shafts, which are crucial components in heavy machinery. The press applies consistent pressure to ensure that each part is formed to the exact specifications required for high performance.
- Compression molding in rubber and plastics: In the production of rubber seals, plastic housings, and gaskets, H-frame presses are used for compression molding, where the material is shaped and hardened under high pressure and heat.
5.5. General Maintenance and Repair
H-frame hydraulic presses are not only used in manufacturing but also play a crucial role in maintenance and repair work. Their ability to generate high force with precision makes them ideal for tasks such as straightening bent parts and pressing bearings.
- Straightening bent parts: In repair shops, H-frame presses are commonly used to restore bent metal parts, such as axles, rods, and framework, to their original shape. By applying controlled pressure in the opposite direction of the bend, the press can gradually straighten the part without causing further damage.
- Pressing bearings into place: H-frame presses are used to install bearings into various mechanical systems, including engines, gearboxes, and machinery. The press ensures that the bearings are seated securely, improving the reliability and longevity of the equipment.
5.6. Assembly and Production Lines
H-frame hydraulic presses are frequently integrated into assembly lines and production facilities, where they are used to perform sequential operations on a workpiece. These presses can be customized to handle different tasks, such as multi-stage manufacturing and assembly operations.
- Multi-stage manufacturing: H-frame presses can be configured with multiple stations to carry out sequential operations, such as forming, cutting, punching, and bending. This setup increases productivity by reducing the need to transfer parts between different machines.
- Assembly operations in automated settings: H-frame presses are used in automated production lines to perform tasks such as riveting, joining, and inserting components. The ability to automate these processes ensures consistency, speed, and reduced labor costs.
5.7. Specialized Applications
In addition to the common uses mentioned above, H-frame hydraulic presses are employed in various specialized applications, where their precision, force capacity, and customization options make them suitable for unique industrial tasks.
- Medical device manufacturing: In the production of medical devices and surgical tools, H-frame presses are used to shape and form metal components with tight tolerances, ensuring that each part meets stringent healthcare standards.
- Art and sculpture: Artists and sculptors use H-frame hydraulic presses to shape metal, plastics, and other materials into creative designs. The press’s ability to apply controlled pressure enables the creation of intricate shapes and patterns.
- Prototype development: In research and development labs, H-frame presses are used to create prototypes and test samples. Their flexibility and precision make them ideal for small-batch production runs, where new materials or designs are being evaluated.
Advantages of H-Frame Hydraulic Presses
H-frame hydraulic presses offer several advantages that make them the preferred choice for a wide range of industrial applications. These presses are recognized for their versatility, high force capacity, precision, and stability, making them suitable for tasks ranging from metal forming to assembly operations. Below are some of the key benefits that set H-frame hydraulic presses apart from other types of presses.
6.1. High Force Capacity and Structural Integrity
One of the primary advantages of H-frame hydraulic presses is their ability to generate high force, which makes them suitable for heavy-duty applications. The robust H-frame design ensures that the press can handle significant loads without compromising structural integrity.
- Handling High-Pressure Tasks: The H-frame press can produce forces ranging from a few tons to several thousand tons, allowing it to perform high-pressure tasks such as metal forging, stamping, and bending. The ability to generate consistent force throughout the stroke length ensures that even thick or tough materials can be shaped or compressed effectively.
- Structural Integrity for Heavy-Duty Applications: The H-shaped frame, with its vertical columns and horizontal crossbars, provides excellent stability, which prevents the press from flexing or deforming under high loads. This structural integrity is essential for applications that require consistent pressure, such as precision stamping and compression molding.
6.2. Versatility Across a Wide Range of Applications
H-frame hydraulic presses are incredibly versatile, capable of performing multiple tasks with different materials. This adaptability makes them suitable for a wide range of industries, including automotive, aerospace, metalworking, plastic molding, and maintenance.
- Metal Forming and Fabrication: The press is commonly used for tasks such as bending, straightening, stamping, punching, and forming metal components. The ability to adjust force, speed, and stroke length allows operators to customize the press for specific metalworking tasks.
- Compression Molding: H-frame presses can be used to mold rubber, plastics, and composites by applying uniform pressure to a mold, ensuring the material takes on the desired shape. This process is often used in the production of gaskets, seals, and plastic housings.
- Assembly and Maintenance: The precision and control offered by H-frame presses make them ideal for assembly tasks, such as pressing bearings into place or installing bushings. They are also used in repair shops to straighten bent parts or press components back into shape.
6.3. Precision and Control: Why H-Frames are Ideal for High-Accuracy Work
Precision is a key requirement in many manufacturing processes, and H-frame hydraulic presses provide the control and accuracy needed for high-quality results.
- Adjustable Pressure and Stroke Control: Modern H-frame presses come equipped with advanced control systems that allow operators to fine-tune the pressure, speed, and stroke length. This level of control ensures that the press can produce consistent results, even when working with materials that require tight tolerances.
- Dynamic Force Application: The press can apply force dynamically, meaning that the pressure can be adjusted in real-time based on the requirements of the task. This capability is particularly valuable in applications like metal forming, where different stages of the process may require varying levels of force.
- Automation and Precision Control Systems: Many H-frame hydraulic presses are integrated with computer numerical control (CNC) or programmable logic controllers (PLCs) that allow for automated operation and greater accuracy in complex tasks. Servo-hydraulic systems also provide real-time adjustments to force and speed, enhancing the precision of the press.
6.4. Stability and Even Force Distribution: Ensuring Quality Results
The H-frame design offers exceptional stability and ensures that the force applied to the workpiece is distributed evenly. This characteristic is crucial for maintaining the quality of the finished product and preventing defects.
- Minimizing Deformation and Warping: The even distribution of force across the press bed helps reduce the risk of deformation or warping, especially in materials like sheet metal or plastics. The rigid frame design prevents the press from bending under load, ensuring consistent force application.
- High Stability for Large Workpieces: H-frame presses are well-suited for handling large workpieces that may be difficult to process using other types of presses, such as C-frame presses. The open work area allows for greater flexibility in positioning the material, while the frame’s stability ensures that the press can handle the high forces required for large parts.
- Precision Alignment: The vertical columns and ram guides ensure that the ram moves smoothly and remains aligned throughout the pressing operation, reducing the risk of misalignment or lateral movement that could compromise the quality of the workpiece.
6.5. Ability to Handle Large Workpieces and Complex Shapes
H-frame hydraulic presses are ideal for tasks involving large or irregularly shaped workpieces. Their open-front design allows operators to position materials easily and handle parts that may not fit within other press configurations.
- Accommodating Different Sizes and Shapes: The open design of the H-frame press enables operators to work with large sheets, panels, bars, and other sizable materials. The press can also be fitted with specialized tooling to accommodate complex shapes or multi-stage operations, such as forming, trimming, and piercing.
- Flexibility in Tooling and Setup: The H-frame configuration allows for the use of interchangeable tooling, such as different dies, punches, or forming attachments, making it easy to adapt the press for various applications. This flexibility is beneficial in industries where product designs or manufacturing requirements change frequently.
6.6. Customization Potential for Specific Industry Needs
H-frame hydraulic presses can be customized to meet the specific requirements of different industries. Manufacturers can choose from various options for tonnage capacity, stroke length, bed size, and control systems to create a press that is optimized for their application.
- Wide Range of Tonnage Capacities: H-frame presses are available in different force capacities, from a few tons to thousands of tons, making it possible to find the right press for tasks ranging from light assembly work to heavy metal forming.
- Modular Design Options: Some H-frame presses feature modular components, such as interchangeable rams, beds, or hydraulic systems, allowing users to reconfigure the press for different tasks. This modularity increases the versatility of the press and extends its service life.
- Industry-Specific Customizations: Customizations can include servo-hydraulic systems for real-time force adjustments, CNC controls for automated operation, and IoT connectivity for integration with smart manufacturing systems. These enhancements improve the press’s performance in applications like precision metalworking, automotive assembly, and aerospace manufacturing.
6.7. Cost-Effectiveness for Heavy-Duty Manufacturing
H-frame hydraulic presses are a cost-effective solution for industries that require reliable, high-performance pressing equipment. Their durability, versatility, and ease of maintenance contribute to long-term savings and operational efficiency.
- Long Service Life: The robust construction of the H-frame press ensures that it can withstand continuous use in demanding environments. With proper maintenance, an H-frame press can last for many years, making it a wise investment for manufacturers.
- Lower Maintenance Costs: Compared to more complex machinery, H-frame hydraulic presses have fewer moving parts, which reduces the likelihood of breakdowns and lowers maintenance costs. Routine maintenance, such as inspecting hydraulic fluid levels, cleaning filters, and checking for leaks, is usually sufficient to keep the press in good working condition.
- Reduced Material Waste: The precision and control offered by H-frame presses help reduce material waste during pressing operations. By ensuring that each part is formed accurately, the press minimizes the need for secondary processing or rework, saving time and material costs.
6.8. Safety Features and Operator Protection
Modern H-frame hydraulic presses are equipped with various safety features designed to protect operators and prevent accidents.
- Emergency Stop Mechanisms: Emergency stop buttons allow operators to halt the press immediately if a problem is detected. This feature is essential for preventing accidents during high-pressure operations.
- Guarding and Light Curtains: Many H-frame presses are equipped with safety guards or light curtains that detect the presence of hands or objects in the work area. These systems automatically stop the press if a safety breach is detected, reducing the risk of injury.
- Pressure Relief Valves: Pressure relief valves prevent overloading by releasing excess hydraulic pressure, ensuring that the press operates within safe limits.
6.9. Sustainability and Energy Efficiency
The integration of advanced control systems and energy-efficient components has made modern H-frame hydraulic presses more sustainable.
- Energy-Efficient Hydraulic Systems: Newer models of H-frame presses feature energy-saving hydraulic pumps that operate only when the press is in use. This reduces energy consumption and lowers operational costs.
- Use of Eco-Friendly Hydraulic Fluids: Some presses are compatible with biodegradable hydraulic fluids, which minimize environmental impact in case of a leak or spill.
- Energy Recovery Systems: In some servo-hydraulic presses, energy recovery systems are used to capture and reuse the energy generated during the press cycle, further improving energy efficiency.
Comparison to Other Types of Hydraulic Presses
H-frame hydraulic presses are one of several types of hydraulic presses used in industrial applications. Each type of press has its own advantages and limitations, making certain designs more suitable for specific tasks. This section compares H-frame hydraulic presses with other common types, such as C-frame presses, four-column presses, and servo-hydraulic presses, to highlight their unique characteristics and appropriate use cases.
7.1. H-Frame vs. C-Frame Hydraulic Presses
C-frame hydraulic presses, also known as gap-frame presses, feature an open-front design that resembles the shape of the letter “C.” This design provides easy access to the work area from three sides, making it ideal for tasks that require frequent loading and unloading of small workpieces.
Advantages of H-Frame Presses Over C-Frame Presses
- Higher Stability and Force Distribution: The H-frame design provides better stability and even force distribution compared to C-frame presses. This is particularly important for high-pressure tasks and large workpieces, where stability is essential to prevent frame deformation and ensure consistent results.
- Higher Force Capacity: H-frame presses generally have higher force capacities than C-frame presses, making them suitable for heavy-duty applications, such as forging, deep drawing, and metal forming.
Advantages of C-Frame Presses Over H-Frame Presses
- Compact Size and Space Efficiency: C-frame presses have a smaller footprint and are more space-efficient, making them ideal for workshops or production lines with limited space.
- Ease of Access: The open-front design allows operators to load and unload materials quickly, making C-frame presses better suited for tasks like assembly, small part production, and repetitive stamping operations.
7.2. H-Frame vs. Four-Column Hydraulic Presses
Four-column hydraulic presses, also known as four-post presses, have four vertical columns that support the upper and lower crossheads, providing a large, open work area. This design is known for its ability to evenly distribute force across the entire workpiece.
Advantages of H-Frame Presses Over Four-Column Presses
- Flexibility in Customization: H-frame presses are often more easily customizable than four-column presses. The frame design allows for modifications to accommodate different tooling, stroke lengths, and bed sizes, making them suitable for a wider range of applications.
- Cost-Effectiveness: H-frame presses tend to be more affordable than four-column presses with similar force capacities. This makes them a cost-effective choice for industries that require high-performance pressing equipment without the need for a large open work area.
Advantages of Four-Column Presses Over H-Frame Presses
- Larger Work Area: Four-column presses offer a larger, open work area, which is advantageous for handling large or irregularly shaped workpieces. This design is particularly useful in applications like deep drawing and large sheet metal forming, where space is needed for material movement.
- Greater Stability for Large Workpieces: The four-column structure provides enhanced stability when handling heavy or oversized materials, ensuring consistent pressure across the entire surface of the workpiece.
7.3. H-Frame vs. Servo-Hydraulic Presses
Servo-hydraulic presses integrate servo motor technology into the hydraulic system, allowing for precise control over force, speed, and position. These presses are often used in applications that require high precision and variable pressure settings.
Advantages of H-Frame Presses Over Servo-Hydraulic Presses
- Lower Initial Cost: H-frame hydraulic presses are generally less expensive than servo-hydraulic presses, making them more accessible for businesses with budget constraints.
- Simplicity in Operation: H-frame presses have a more straightforward hydraulic system, which makes them easier to maintain and operate compared to the complex servo-hydraulic systems. This simplicity can be beneficial in environments where operator training is limited.
Advantages of Servo-Hydraulic Presses Over H-Frame Presses
- Precision Control and Automation: Servo-hydraulic presses offer real-time adjustments to force, speed, and stroke length, allowing for greater accuracy in complex pressing tasks. The ability to fine-tune parameters makes servo-hydraulic presses suitable for industries like electronics, medical device manufacturing, and aerospace.
- Energy Efficiency: The integration of servo motors allows for better energy management, as the motor only consumes energy when needed. This makes servo-hydraulic presses more energy-efficient than traditional hydraulic presses, reducing operational costs.
7.4. When to Choose H-Frame Presses Over Other Types
H-frame hydraulic presses are the ideal choice for tasks that require high force capacity, stability, and versatility. The decision to use an H-frame press over other types depends on the specific requirements of the application.
H-Frame Presses Are Ideal For:
- Heavy-Duty Applications: Tasks such as metal forging, stamping, deep drawing, and compression molding require presses that can generate significant force and maintain structural integrity under high loads.
- Large Workpieces: When handling large sheets, panels, or irregularly shaped components, the H-frame’s stability and ability to accommodate different tooling make it a suitable choice.
- Customizable Setups: Industries that require customizable setups with interchangeable tooling, modular components, or multiple workstations can benefit from the flexibility of the H-frame design.
Other Press Types Are Better Suited For:
- High-Precision, Low-Tonnage Tasks: For tasks that demand high precision but do not require significant force, such as electronics manufacturing or fine metalwork, servo-hydraulic or C-frame presses may be more appropriate.
- Compact Workspaces: C-frame presses are ideal for workshops or production lines where space is limited, as their open-front design facilitates quick material handling and operator access.
- Large-Scale Metal Forming: For tasks that require a large open work area and consistent pressure distribution over extensive surfaces, such as large sheet metal forming or deep drawing, four-column presses may be the better option.
Technological Advancements in H-Frame Hydraulic Presses
Recent technological advancements have significantly improved the performance, efficiency, and precision of H-frame hydraulic presses, making them more versatile and suitable for modern industrial applications. These innovations include the integration of servo-hydraulic systems, automated control, IoT connectivity, and energy-efficient components, which collectively enhance the functionality of H-frame presses and expand their range of applications.
8.1. Integration of Servo-Hydraulic Systems for Precision Control
Servo-hydraulic systems have brought significant advancements to H-frame hydraulic presses by combining the power of hydraulics with the precision of servo motor technology. In servo-hydraulic presses, a servo motor is used to control the hydraulic pump, allowing for real-time adjustments to pressure, speed, and stroke length.
Key Benefits of Servo-Hydraulic Systems
- Enhanced Precision and Accuracy: Servo-hydraulic technology enables precise control over the force and movement of the ram, making it suitable for high-precision applications such as metal forming, stamping, and assembly tasks that require tight tolerances.
- Variable Pressure Settings: Unlike traditional hydraulic systems, where pressure is fixed, servo-hydraulic presses allow operators to adjust pressure dynamically based on the requirements of the specific task. This capability helps prevent material damage and defects during pressing operations.
- Energy Efficiency: The use of servo motors allows the press to consume energy only when needed, reducing overall energy consumption and operational costs. This makes servo-hydraulic presses more sustainable and eco-friendly.
8.2. Adoption of CNC and PLC Controls for Automation
The integration of Computer Numerical Control (CNC) and Programmable Logic Controllers (PLCs) has revolutionized the operation of H-frame hydraulic presses by enabling automated control and programming of complex tasks.
Advantages of CNC and PLC Integration
- Automated Operation: CNC and PLC systems allow operators to program specific parameters for each pressing task, including force levels, stroke length, ram speed, and dwell time. This automation increases productivity by reducing the need for manual adjustments.
- Consistency and Repeatability: By using automated control systems, H-frame presses can produce consistent results with high repeatability, ensuring that each part meets the required specifications. This is especially beneficial in industries such as automotive and aerospace, where product quality is critical.
- Multi-Stage Operations: CNC and PLC controls make it possible to perform multi-stage operations, such as forming, trimming, and punching, in a single setup. This capability streamlines the production process and reduces the time needed to switch between tasks.
8.3. IoT and Smart Manufacturing Integration
The adoption of Industry 4.0 technologies has brought IoT connectivity and smart manufacturing capabilities to H-frame hydraulic presses. These advancements enable real-time monitoring, predictive maintenance, and process optimization.
Benefits of IoT-Enabled H-Frame Presses
- Real-Time Data Monitoring: IoT-enabled presses can collect real-time data on parameters such as pressure, stroke length, cycle time, and hydraulic fluid temperature. This data can be analyzed to optimize the pressing process, identify areas for improvement, and ensure consistent product quality.
- Predictive Maintenance: By monitoring the condition of the press and its components, IoT systems can detect signs of wear and tear or potential issues before they result in machine failure. This predictive maintenance approach helps reduce downtime and extend the service life of the press.
- Remote Control and Diagnostics: IoT connectivity allows operators and technicians to remotely monitor the press’s performance and diagnose problems. This capability is especially useful for multi-site manufacturing operations, where presses in different locations can be managed from a central control hub.
8.4. Energy Efficiency Innovations in Modern H-Frame Presses
As energy efficiency becomes a greater priority in manufacturing, new technologies have been developed to reduce the energy consumption of H-frame hydraulic presses. These innovations not only help companies lower their operational costs but also support sustainability initiatives.
Energy-Saving Hydraulic Pumps
- Variable Displacement Pumps: Modern H-frame presses are often equipped with variable displacement pumps, which adjust the amount of hydraulic fluid being pumped based on the press’s requirements. This reduces energy waste by supplying only the necessary amount of fluid.
- Servo-Driven Pumps: Servo-driven pumps use servo motors to control the flow of hydraulic fluid. They are more efficient than traditional pumps because they can modulate speed and pressure according to the task, leading to lower energy consumption.
Energy Recovery Systems
- Regenerative Circuits: Some H-frame presses are equipped with regenerative hydraulic circuits that capture and reuse energy generated during the press cycle. This technology helps reduce energy consumption by recycling the energy used in the pressing operation.
- Energy Storage Systems: Hydraulic accumulators can be used to store excess energy generated during the press cycle. This stored energy can then be released to assist with subsequent press operations, reducing the demand on the hydraulic pump.
8.5. Advances in Safety Features for Operator Protection
Safety is a top priority in industrial environments, and H-frame hydraulic presses have benefited from advancements in safety features that protect operators from accidents.
Light Curtains and Guarding Systems
- Light Curtains: Light curtains create an invisible barrier around the work area. If the barrier is broken, the press will automatically stop to prevent injury. This feature is widely used in automated production lines to enhance operator safety.
- Safety Guarding: H-frame presses can be equipped with physical guards that prevent hands or tools from entering dangerous areas. These guards are designed to ensure that the operator remains at a safe distance from the moving parts of the press.
Emergency Stop Mechanisms
- Multiple Emergency Stop Buttons: Modern H-frame presses feature emergency stop buttons that are placed in strategic locations to allow operators to quickly halt the press in case of an emergency. Some models even have foot-operated safety pedals.
- Automatic Pressure Relief Systems: Pressure relief valves and safety interlocks ensure that the press does not exceed its maximum pressure limit, preventing equipment damage and operator injury.
8.6. Customizable Tooling and Modular Design Advancements
The ability to customize tooling and use a modular design enhances the flexibility and adaptability of H-frame hydraulic presses. This allows manufacturers to quickly adapt the press for different tasks.
Quick-Change Tooling
- Interchangeable Tool Sets: H-frame presses can be equipped with interchangeable tool sets that allow operators to switch between different tools, such as dies, punches, and forming attachments, with minimal downtime.
- Automated Tool Change Systems: Automated tool changers enable the press to switch between tools without manual intervention, reducing setup time and increasing productivity.
Modular Frames for Easy Upgrades
- Modular Frame Components: Some H-frame presses feature modular frames that can be easily upgraded or reconfigured to meet changing production requirements. For example, the press bed, ram, or hydraulic system can be modified to accommodate different materials or processes.
- Scalable Tonnage Capacities: Modular designs also allow for scalable tonnage capacities, enabling manufacturers to upgrade the press to a higher force capacity without replacing the entire machine.
8.7. Smart Technology Integration for Process Optimization
The integration of smart technology, including machine learning and artificial intelligence (AI), is transforming the capabilities of H-frame hydraulic presses. These technologies enable presses to self-optimize and improve process efficiency.
AI-Driven Process Optimization
- Adaptive Control Systems: AI-driven control systems can adjust pressing parameters in real time based on feedback from sensors, ensuring optimal performance for each task. This capability reduces material waste and improves cycle times.
- Machine Learning for Predictive Maintenance: By analyzing data collected from previous operations, machine learning algorithms can predict when maintenance will be needed, allowing for proactive repairs that reduce the risk of unexpected downtime.
Cloud-Based Data Analysis
- Cloud Connectivity: Some smart H-frame presses are connected to cloud-based platforms that store and analyze data on press performance. This data can be accessed remotely, allowing manufacturers to make data-driven decisions and continuously optimize production processes.
- Big Data for Quality Control: Using big data analytics, manufacturers can detect patterns in the pressing process that may indicate quality issues, allowing for timely adjustments to maintain high product standards.
Safety Considerations for Operating H-Frame Hydraulic Presses
H-frame hydraulic presses are powerful machines that can pose risks to operators if not used safely. Ensuring operator safety requires understanding the potential hazards associated with hydraulic presses, following safety standards, using protective features, and practicing proper maintenance and training. This section covers key safety considerations and best practices for the safe operation of H-frame hydraulic presses.
9.1. Overview of Hydraulic Press Safety Standards
Various organizations set safety standards for hydraulic press operation, which are designed to protect workers and reduce the risk of accidents. Key safety standards include:
- Occupational Safety and Health Administration (OSHA): OSHA provides guidelines on safe press operation, including requirements for guarding, emergency stop mechanisms, and training for operators.
- American National Standards Institute (ANSI): The ANSI B11.2 standard outlines the safety requirements for hydraulic and pneumatic presses, including guidelines for mechanical guards, control systems, and safety interlocks.
- European Machinery Directive (CE Marking): In Europe, hydraulic presses must meet the CE marking requirements to ensure they comply with European safety standards.
Compliance with these standards helps to minimize risks and ensure a safe working environment.
9.2. Common Hazards Associated with Hydraulic Press Operation
Operating an H-frame hydraulic press involves certain risks that must be managed to prevent accidents. Some common hazards include:
- Crushing Injuries: The most significant risk is the potential for crushing injuries if an operator’s hand or body part is caught between the ram and the bed. The immense force generated by the press can cause severe injury or death.
- High-Pressure Fluid Leaks: Hydraulic fluid leaks under high pressure can be dangerous, as they can cause injection injuries if the fluid penetrates the skin. Additionally, leaks can lead to slips and falls if the fluid spills on the floor.
- Ejection of Parts or Material: If a workpiece is not securely clamped or the press is overloaded, there is a risk that parts or materials could be ejected from the press at high speed, potentially injuring nearby workers.
- Mechanical Failures: Failures in components such as cylinders, valves, or hydraulic lines can lead to unexpected press movements or loss of pressure, creating hazardous conditions.
9.3. Key Safety Features in H-Frame Hydraulic Presses
Modern H-frame hydraulic presses come equipped with various safety features that help protect operators from accidents and injuries.
9.3.1. Guarding and Light Curtains
- Guarding: Physical guards are used to prevent operators from reaching into the danger zone during press operation. These guards may be made of metal, plastic, or transparent materials to provide visibility while maintaining protection.
- Light Curtains: Light curtains create a virtual barrier around the work area. If an operator’s hand or body part crosses the light beam while the press is in motion, the machine automatically stops to prevent injury.
9.3.2. Emergency Stop Buttons
- Multiple Emergency Stop Buttons: Emergency stop buttons are typically placed in accessible locations around the press, allowing operators to quickly halt the press if a hazardous situation arises. Some presses also have foot-operated emergency stops for added convenience.
- Redundant Safety Systems: In some presses, redundant safety systems are used to ensure that the press stops immediately if the emergency stop is activated, even if there is a failure in one part of the control system.
9.3.3. Pressure Relief Valves and Interlocks
- Pressure Relief Valves: These valves help prevent over-pressurization of the hydraulic system by releasing excess pressure, thereby protecting the press and operators from damage.
- Safety Interlocks: Interlock systems prevent the press from operating if the guards or doors are not in place. This ensures that operators cannot accidentally start the press when it is in an unsafe condition.
9.4. Importance of Regular Maintenance and Inspection
Regular maintenance and inspection are crucial for ensuring that an H-frame hydraulic press remains in safe operating condition. A preventive maintenance program helps identify potential issues before they result in machine failure or accidents.
9.4.1. Hydraulic System Maintenance
- Checking Hydraulic Fluid Levels: Hydraulic fluid should be kept at the recommended level and replaced regularly to ensure proper operation. Contaminated or low fluid levels can affect the press’s performance and increase the risk of failure.
- Inspecting Hoses and Seals for Leaks: Regular inspection of hoses, seals, and cylinders can help identify leaks early, preventing accidents related to high-pressure fluid ejection.
9.4.2. Mechanical Component Inspection
- Checking for Wear and Tear: The frame, ram guides, tooling, and bolts should be inspected for signs of wear or damage. Replacing worn components helps maintain the integrity of the press and reduces the risk of mechanical failure.
- Ram Alignment: Ensuring the ram is properly aligned reduces the likelihood of misaligned pressing, which can cause defects in the workpiece and pose safety risks.
9.5. Training and Certification for Operators
Operators of H-frame hydraulic presses must be properly trained to understand the safe operation procedures and potential hazards associated with these machines.
9.5.1. Safety Training Programs
- Hands-On Training: New operators should undergo hands-on training with experienced personnel to learn how to operate the press safely. This training should cover basic operations, emergency procedures, and safety features.
- Refresher Courses: Periodic safety training and refresher courses help keep operators up to date on new safety practices, regulations, and machine upgrades.
9.5.2. Operator Certification
- Certification Programs: In some industries, operators must obtain certification to work with hydraulic presses. Certification programs ensure that workers have the necessary skills and knowledge to operate the press safely.
- Compliance with Safety Regulations: Certified operators are better equipped to comply with safety regulations and standards set by organizations like OSHA, ANSI, or CE, reducing the risk of workplace accidents.
9.6. Best Practices for Safe Operation in Industrial Settings
Adhering to best practices for safe operation helps minimize risks when using H-frame hydraulic presses.
9.6.1. Using Proper Personal Protective Equipment (PPE)
- Gloves, Goggles, and Hearing Protection: Operators should wear appropriate PPE, such as gloves, safety goggles, and hearing protection, to protect against potential injuries from flying debris, loud noises, or sharp edges.
- Fire-Resistant Clothing: When working with hot materials or combustible fluids, fire-resistant clothing can reduce the risk of burns or fire-related injuries.
9.6.2. Implementing Lockout/Tagout Procedures
- Lockout/Tagout (LOTO): LOTO procedures ensure that the press is fully de-energized and locked out before maintenance or repair work is performed. This prevents accidental activation and protects workers during servicing.
9.6.3. Ensuring the Workpiece is Securely Clamped
- Proper Clamping and Positioning: Before operating the press, the workpiece should be securely clamped and properly positioned to prevent it from shifting or being ejected during the pressing operation.
Introduction to Four-Column Hydraulic Presses
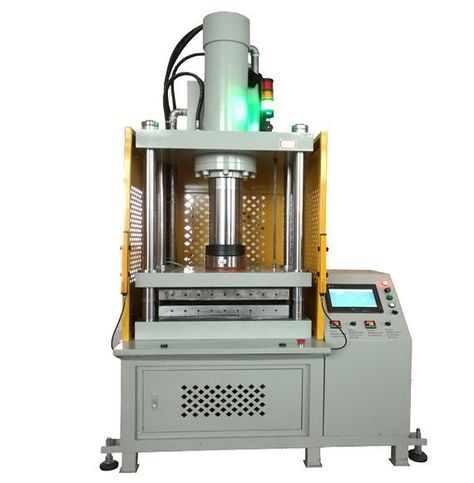
Four-column hydraulic presses are powerful and versatile machines that utilize hydraulic pressure to perform a variety of metal forming, molding, and assembly operations. The name “four-column” comes from the press’s structural design, which includes four vertical columns that provide support for the upper and lower crossheads, creating a large, open work area. This design allows for the even distribution of force across the entire workpiece, making four-column presses ideal for tasks that require high precision and consistency.
Four-column hydraulic presses are used in various industries, including automotive, aerospace, electronics, appliance manufacturing, and plastics and rubber molding. Their ability to generate significant force while maintaining precise control over pressure and movement makes them suitable for tasks such as deep drawing, stamping, embossing, and compression molding.
The unique design of four-column hydraulic presses offers several advantages over other press types, such as H-frame or C-frame presses. The four-column structure provides greater stability and accessibility, allowing operators to work with large or irregularly shaped workpieces. Additionally, the open work area makes it easier to handle complex tooling and multi-stage operations.
Modern four-column presses are equipped with advanced control systems, such as servo-hydraulic, CNC, or PLC automation, which allow for precise adjustments to force, speed, and stroke length. These features enable manufacturers to achieve high-quality results while maximizing productivity and minimizing material waste. Furthermore, recent technological advancements, including IoT connectivity and energy-efficient hydraulic systems, have improved the efficiency and safety of four-column hydraulic presses.
As the demand for high-quality, precision-manufactured parts continues to grow, the role of four-column hydraulic presses in modern manufacturing remains crucial. Their versatility, durability, and ability to handle heavy-duty operations make them an indispensable tool in industries where performance and reliability are paramount.
Historical Evolution of Four-Column Hydraulic Presses
The development of four-column hydraulic presses is part of the broader history of hydraulic press technology, which dates back centuries. Understanding the evolution of these presses involves examining early innovations in hydraulic systems, the emergence of the four-column design, and the impact of industrialization on hydraulic press adoption.
2.1. Early Development of Hydraulic Presses
The concept of using hydraulic pressure to generate force dates back to ancient times, but the first practical application of hydraulic principles for pressing tasks came with the invention of the hydraulic press by Joseph Bramah in 1795. Bramah’s design utilized Pascal’s Law, which states that pressure applied to a confined fluid is transmitted equally in all directions, allowing a relatively small input force to be amplified to generate significant pressing power.
Bramah’s early hydraulic presses were used for tasks like packing and material compression, but they laid the foundation for the development of more advanced hydraulic systems that would emerge in the coming centuries.
2.2. Emergence of the Four-Column Design
The four-column hydraulic press design was developed in response to the need for greater stability, even force distribution, and a larger open work area. The introduction of four vertical columns provided structural support for the upper and lower crossheads, ensuring that the press could handle high loads without flexing or bending. This design improvement allowed for the even distribution of force across the entire workpiece, making it ideal for tasks such as deep drawing, embossing, and large metal forming.
The four-column structure also created a large, open work area, which allowed operators to access the workpiece from all sides. This accessibility made it easier to handle large or irregularly shaped materials, as well as complex multi-stage operations that required different tools or dies.
2.3. Influence of Industrialization on Hydraulic Press Adoption
The Industrial Revolution, which began in the late 18th century, significantly accelerated the development and adoption of hydraulic presses, including the four-column design. The rapid growth of manufacturing and industrial production created a demand for powerful and reliable press equipment that could be used for mass production. Hydraulic presses were well-suited for a wide range of tasks, such as metal forming, stamping, forging, and molding.
The versatility and force capacity of four-column hydraulic presses made them a valuable tool in industries like automotive, aerospace, metalworking, and plastics manufacturing. As industrial processes became more complex, the need for high-precision, heavy-duty press equipment grew, leading to further innovations in hydraulic press technology.
2.4. Evolution of Hydraulic Systems and Technology
Throughout the 19th and 20th centuries, significant advancements were made in hydraulic systems, leading to the development of more efficient and powerful four-column presses. Some of the key innovations that contributed to the evolution of four-column hydraulic presses include:
- Improved Hydraulic Pumps: Early hydraulic pumps were relatively simple, but advancements in pump design, such as the introduction of gear pumps, vane pumps, and piston pumps, allowed for higher pressures and more consistent force application. These improvements made hydraulic presses more efficient and reliable.
- Development of Double-Acting Cylinders: The introduction of double-acting hydraulic cylinders allowed for precise control over the movement of the ram, enabling better control of the pressing process. This innovation was particularly important for applications that required variable stroke lengths or multi-stage operations.
- Adoption of Servo-Hydraulic Technology: The integration of servo-hydraulic systems in the late 20th century enabled greater precision in controlling force, speed, and position. Servo-hydraulic technology allowed operators to adjust pressing parameters dynamically, making four-column presses suitable for tasks that required high accuracy and repeatability.
2.5. Key Milestones in Four-Column Hydraulic Press Development
Several key milestones have marked the evolution of four-column hydraulic presses, helping to shape their modern capabilities:
- Introduction of High-Pressure Hydraulic Systems: The development of high-pressure hydraulic systems in the mid-20th century allowed four-column presses to generate forces of thousands of tons, making them suitable for heavy-duty applications like metal forging, deep drawing, and compression molding.
- Incorporation of Computer Numerical Control (CNC): The integration of CNC control systems in four-column presses enabled automated and programmable control over pressing operations. This development improved the precision, consistency, and productivity of the pressing process.
- Advances in Safety Features: Modern four-column hydraulic presses are equipped with advanced safety features, such as light curtains, emergency stop mechanisms, and pressure relief valves, to protect operators and prevent accidents.
- Integration with Industry 4.0 Technologies: In recent years, four-column presses have been integrated into smart manufacturing environments using IoT connectivity, real-time data monitoring, and predictive maintenance. These technologies help optimize press performance, improve energy efficiency, and reduce downtime.
Today, four-column hydraulic presses are recognized for their versatility, precision, and ability to handle heavy-duty operations, making them a cornerstone of modern manufacturing across a wide range of industries.
Design and Structure of Four-Column Hydraulic Presses
Four-column hydraulic presses are known for their robust design, which provides stability and flexibility for a wide range of applications. The design features four vertical columns that support the upper and lower crossheads, creating an open work area that allows for even force distribution across the workpiece. This section delves into the structural components, customization options, and material choices used in four-column hydraulic presses.
3.1. Structural Overview: The Four-Column Design
The four-column design is characterized by its symmetrical structure, which includes four vertical columns arranged around the press bed. This configuration provides excellent support for the upper crosshead, where the hydraulic cylinder and ram are mounted, and the lower crosshead, which serves as the base for the work table.
Key Characteristics of the Four-Column Design
- Symmetry and Stability: The symmetrical arrangement of the columns ensures balanced force distribution, which minimizes the risk of deformation or misalignment during pressing operations. This stability is particularly important for applications requiring high precision, such as metal forming and compression molding.
- Open Work Area: The open space created by the four-column structure provides easy access to the workpiece from multiple sides, making it suitable for handling large or irregularly shaped materials and for multi-stage operations that involve different tools or dies.
- Modular Configurations: The four-column design allows for various customization options, such as interchangeable rams, hydraulic systems, and tooling. This modularity makes the press adaptable to different industrial requirements.
3.2. Key Components of Four-Column Hydraulic Presses
The key components of a four-column hydraulic press work together to provide the force, precision, and control necessary for a variety of tasks. These components include the vertical columns, upper and lower crossheads, hydraulic cylinder, ram and punch, work table, and control systems.
3.2.1. Vertical Columns
The vertical columns are the main structural elements of the press. They provide support for the upper and lower crossheads, ensuring that the frame remains stable during high-force operations.
- Material Strength and Durability: The columns are typically made from high-strength steel or other durable materials to withstand heavy loads. They may also feature surface treatments, such as chrome plating or heat treatment, to enhance wear resistance.
- Guide Bushings and Sleeves: To ensure smooth movement of the ram, guide bushings or sleeves are installed along the columns. These components help maintain alignment, preventing the ram from tilting or shifting laterally.
3.2.2. Upper and Lower Crossheads
The upper and lower crossheads connect the vertical columns and serve as key support structures for the press.
- Upper Crosshead: The upper crosshead houses the hydraulic cylinder and provides support for the ram. It is designed to handle the forces generated during pressing without deforming.
- Lower Crosshead: The lower crosshead, also known as the base or bed, provides a stable platform for the work table. It may include T-slots or mounting holes for securing tooling, dies, or fixtures.
3.2.3. Hydraulic Cylinder
The hydraulic cylinder is responsible for generating the force needed to perform pressing operations. It consists of a piston, cylinder housing, and ram.
- Single-Acting vs. Double-Acting Cylinders: Single-acting cylinders use hydraulic fluid to move the ram in one direction, while double-acting cylinders allow for controlled movement in both directions, offering greater flexibility.
- Cylinder Bore Size and Stroke Length: The size of the cylinder bore and stroke length determine the press’s force capacity and range of motion. Larger bores and longer strokes are used for heavy-duty applications.
3.2.4. Ram and Punch
The ram is the moving component that transmits force from the hydraulic cylinder to the workpiece. It can be fitted with different punches, forming tools, or dies depending on the specific operation.
- Precision Alignment: To ensure that the ram remains aligned during pressing, it is guided along the columns using bushings or linear guides. This precision helps maintain the quality of the workpiece.
- Customizable Tooling: The ram can be fitted with a variety of tooling options, allowing the press to perform tasks such as punching, stamping, forming, or embossing.
3.2.5. Work Table or Bed
The work table, located on the lower crosshead, is where the workpiece is placed during pressing. It is usually made from hardened steel to withstand the impact and pressure generated by the press.
- T-Slots and Mounting Holes: The work table may feature T-slots or mounting holes for securing tooling, jigs, or fixtures, ensuring that the workpiece remains stable during the pressing operation.
- Adjustable Positioning: Some four-column presses have adjustable work tables that can be moved vertically to accommodate different workpiece sizes.
3.2.6. Control Systems
Modern four-column hydraulic presses are equipped with various control systems to regulate force, speed, stroke length, and automation levels.
- Manual Controls: Basic models may use manual levers or foot pedals to operate the press, providing simple control over pressing operations.
- Automated Controls: Advanced presses are equipped with Programmable Logic Controllers (PLCs) or Computer Numerical Control (CNC) systems for automated operation. These systems allow for precise adjustments and programmable press cycles.
- Servo-Hydraulic Systems: Servo-hydraulic technology enables real-time adjustments to pressure and speed, enhancing the press’s precision and efficiency.
3.3. Importance of Stability and Force Distribution
The four-column design ensures even force distribution across the entire workpiece, which is crucial for maintaining high-quality results and preventing material defects.
- Minimizing Deformation and Warping: The balanced force distribution reduces the risk of deforming the workpiece, especially during tasks like deep drawing or compression molding, where uniform pressure is essential.
- Stability for Large Workpieces: The four-column structure provides stability when handling large or irregularly shaped materials, ensuring that the press remains steady under heavy loads.
- Alignment Accuracy: The vertical columns and ram guides ensure that the ram moves in a straight line, maintaining alignment and preventing lateral movement during pressing.
3.4. Customization Options in Four-Column Hydraulic Presses
Four-column hydraulic presses can be customized to meet the specific requirements of different applications. Some common customization options include:
- Variable Tonnage Capacities: Presses are available in a range of force capacities, from a few tons to thousands of tons, making them suitable for both light-duty and heavy-duty tasks.
- Modular Components: The press’s components, such as the ram, work table, or hydraulic system, can be modified to accommodate different tasks.
- Advanced Control Systems: Customizations may include servo-hydraulic controls, CNC automation, or IoT connectivity for integration with smart manufacturing environments.
3.5. Material Choices and Durability
The durability and longevity of a four-column hydraulic press are influenced by the materials used in its construction.
- High-Strength Steel: The columns, crossheads, and work table are typically made from high-strength steel to withstand the forces generated during pressing.
- Surface Treatments: Components may receive chrome plating, heat treatment, or other surface treatments to improve wear resistance and extend the service life of the press.
Working Principle of Four-Column Hydraulic Presses
The working principle of a four-column hydraulic press is based on hydraulic pressure and force transmission through a system of fluid mechanics, enabling the machine to perform tasks like stamping, molding, forming, and compression. The hydraulic system converts fluid pressure into mechanical force, which is applied to a workpiece via the press’s ram. The process relies on Pascal’s Law, which states that pressure applied to a confined fluid is transmitted equally in all directions.
4.1. Basic Hydraulic Press Operation
A four-column hydraulic press operates by generating hydraulic pressure that moves the ram, allowing it to apply force to the workpiece placed on the work table. The basic operation involves several key steps:
- Generating Hydraulic Pressure: The press uses a hydraulic pump to pressurize the hydraulic fluid (usually oil), which is stored in a reservoir. The pump pushes the fluid into the hydraulic cylinder, where it generates force on the piston.
- Moving the Ram: The pressurized fluid enters the hydraulic cylinder and acts on the piston, which drives the ram downward. This movement allows the press to apply force to the workpiece on the bed, performing tasks such as forming, stamping, or compressing.
- Returning the Ram: Once the pressing operation is complete, the pressure is released, and the ram is returned to its original position. In double-acting cylinders, the hydraulic fluid can be used on both sides of the piston to control the ram’s upward and downward movement.
4.2. Hydraulic Cylinder and Pump Mechanics
The hydraulic cylinder and pump play crucial roles in the functioning of a four-column hydraulic press, determining the amount of force generated and the efficiency of the pressing process.
4.2.1. Hydraulic Pumps
- Gear Pumps: These pumps are simple and reliable, providing a steady flow of hydraulic fluid at low to moderate pressure. They are suitable for basic press applications.
- Vane Pumps: Vane pumps are efficient and provide a balance between flow rate and pressure, making them suitable for applications that require moderate control.
- Piston Pumps: Piston pumps offer high-pressure capabilities and are commonly used in heavy-duty four-column hydraulic presses that need to generate significant force for tasks like metal forging or compression molding.
4.2.2. Hydraulic Cylinders
- Single-Acting Cylinders: In single-acting cylinders, the hydraulic fluid acts on one side of the piston to move the ram downward. The return motion relies on gravity or spring force.
- Double-Acting Cylinders: Double-acting cylinders use hydraulic fluid on both sides of the piston, allowing for controlled movement in both directions. This is beneficial for applications requiring precise ram positioning.
4.3. Force Transmission and Movement in Four-Column Presses
The design of the four-column hydraulic press ensures that force is transmitted evenly across the workpiece, providing consistent pressure and high-quality results. The force generated by the hydraulic cylinder is transmitted through the ram, which moves vertically to press against the workpiece.
Key Elements in Force Transmission
- Even Force Distribution: The four-column structure helps distribute force evenly across the ram and workpiece, reducing the risk of material deformation or warping.
- Ram Guides and Bushings: Guides and bushings along the vertical columns help maintain the ram’s alignment, ensuring smooth movement and preventing lateral shifts.
4.4. Application of Force to Workpieces
The force applied by a four-column hydraulic press can be used for a variety of tasks, including forming, compression, molding, and cutting. The versatility of the press makes it suitable for different materials, such as metal, plastic, rubber, and composites.
4.4.1. Metal Forming
In metal forming operations, the press can be used to shape metal sheets, plates, and components. Processes such as deep drawing, stamping, and embossing require consistent force application, which is achievable with a four-column press.
4.4.2. Compression Molding
For compression molding, the press is used to shape materials like plastics, rubber, or composites by applying force to a mold. This process ensures the material fills the mold cavity, taking on the desired shape.
4.4.3. Stamping and Punching
In stamping and punching applications, the press can cut or shape metal sheets using dies. The four-column design ensures even pressure distribution, allowing for clean cuts and precise shapes.
4.5. Importance of Pressure Control and Even Force Distribution
Accurate control of hydraulic pressure and even force distribution is essential for achieving high-quality results in pressing operations. Advanced control systems in modern four-column hydraulic presses allow for precise adjustments to pressure, speed, and stroke length.
4.5.1. Pressure Regulation
- Relief Valves and Regulators: Pressure relief valves and regulators are used to maintain consistent hydraulic pressure during pressing, preventing overloading or underperformance.
- Flow Control Valves: Flow control valves adjust the speed at which hydraulic fluid moves through the system, allowing for fine-tuning of ram movement.
4.5.2. Force Distribution
The even distribution of force across the press bed ensures that the entire workpiece experiences uniform pressure. This is crucial for applications like deep drawing, where inconsistent force can lead to defects.
4.6. Advanced Control Systems in Modern Four-Column Presses
Modern four-column hydraulic presses are equipped with automated control systems, such as CNC, PLC, or servo-hydraulic systems, to improve the precision and efficiency of pressing operations.
4.6.1. Programmable Logic Controllers (PLCs)
PLCs allow operators to program specific parameters, such as force levels, stroke length, and ram speed, for each task. This automation enhances consistency and productivity.
4.6.2. Servo-Hydraulic Control
Servo-hydraulic systems use servo motors to control the hydraulic pump, providing real-time adjustments to the press’s operation. This technology is especially useful for applications requiring high precision.
4.6.3. IoT and Smart Press Integration
With the integration of IoT connectivity, four-column hydraulic presses can be connected to smart manufacturing systems, enabling real-time data monitoring, predictive maintenance, and process optimization.
Key Applications of Four-Column Hydraulic Presses
Four-column hydraulic presses are versatile machines used across a wide range of industries due to their ability to deliver high force, precision, and consistent pressure. Their robust design, large work area, and ability to handle diverse materials make them suitable for various industrial applications. This section explores the key applications of four-column hydraulic presses in different industries.
5.1. Metal Forming and Fabrication
Metal forming is one of the primary applications for four-column hydraulic presses, which can be used to shape metal sheets, plates, and components into different forms. The press’s ability to distribute force evenly and handle large workpieces makes it ideal for several metal forming tasks.
- Deep Drawing: In deep drawing, a metal sheet is shaped into a hollow object by being forced into a die cavity. The four-column design allows for even force distribution across the sheet, ensuring that the material is stretched uniformly without tearing or wrinkling. This process is used to produce items such as cans, tanks, and automotive body panels.
- Stamping: Metal stamping involves cutting or forming metal sheets using dies and punches. Four-column hydraulic presses are used for high-precision stamping operations, where the even force distribution ensures clean cuts and precise shapes. This is especially important in industries such as automotive and electronics, where parts must meet strict tolerances.
- Embossing: Embossing is the process of creating raised or recessed designs on metal surfaces. Four-column presses can be used to apply the necessary pressure to emboss patterns, logos, or text onto metal parts. The open work area allows for easy handling of large metal sheets during embossing.
5.2. Automotive Manufacturing
The automotive industry relies heavily on four-column hydraulic presses for the production of various components. The ability of these presses to handle large forces and ensure precision makes them suitable for critical automotive manufacturing tasks.
- Forming Body Panels: In the production of automotive body panels, such as doors, hoods, fenders, and roof panels, four-column hydraulic presses are used to shape metal sheets into the desired contours. The press’s stability and ability to generate consistent pressure help prevent defects in the panels, ensuring that they fit together seamlessly during assembly.
- Stamping Chassis Components: Chassis components, such as cross members, suspension parts, and structural reinforcements, are often stamped using four-column presses. The press’s force capacity allows for the forming of high-strength materials that are required for the structural integrity of the vehicle.
- Pressing Engine and Transmission Components: Four-column hydraulic presses are used to form or stamp engine parts, gear housings, and transmission components. The press ensures that these parts meet the tight tolerances needed for proper engine performance.
5.3. Aerospace Industry
In the aerospace industry, where precision, strength, and lightweight components are critical, four-column hydraulic presses play a crucial role in forming various materials used in aircraft and spacecraft.
- Forming Lightweight Structural Components: Four-column presses are used to form aircraft panels, wing sections, and fuselage parts made from aluminum, titanium, and composite materials. The ability to apply consistent pressure across large workpieces ensures that these components meet strict aerodynamic and structural requirements.
- Pressing High-Strength Alloys: In aerospace manufacturing, high-strength alloys are often used to produce parts that need to withstand extreme conditions, such as jet engine components and landing gear structures. Four-column hydraulic presses are used to form these materials into the required shapes while maintaining the integrity of the alloy.
- Precision Forming for Satellite Components: For satellite manufacturing, four-column presses are used to shape delicate components that require precise tolerances. The press’s ability to apply controlled force helps ensure the integrity and functionality of these specialized parts.
5.4. Plastic and Rubber Molding
The plastic and rubber industries use four-column hydraulic presses for compression molding, where the material is shaped under high pressure to create durable, complex parts.
- Compression Molding for Plastic Parts: In compression molding, plastic materials are placed in a mold cavity and subjected to high pressure from the press. This process is used to manufacture items like automotive components, appliance parts, and electrical housings. The large work area of the four-column press allows for the production of parts with varying sizes and shapes.
- Forming Rubber Seals and Gaskets: Four-column hydraulic presses are also used for molding rubber products, such as seals, gaskets, and bushings. The consistent pressure ensures uniform material flow into the mold, resulting in high-quality finished products.
- Thermoset and Thermoplastic Molding: The press can handle both thermoset and thermoplastic materials, making it versatile for producing parts that require different curing processes.
5.5. Electronics and Appliance Manufacturing
The electronics and appliance industries often require precision stamping and forming of small metal and plastic components. Four-column hydraulic presses provide the necessary force and control to manufacture these parts with high accuracy.
- Stamping Metal Housings: Four-column hydraulic presses are used to stamp metal housings for electronic devices, such as smartphones, laptops, and tablets. The press ensures that each housing is formed with the exact dimensions needed to fit internal components securely.
- Forming Electrical Connectors: The press is also used to shape and stamp electrical connectors, terminals, and contacts. The precision offered by four-column presses ensures that these small components meet the dimensional tolerances required for reliable electrical connections.
- Molding Appliance Components: In the appliance industry, four-column presses are used to mold parts such as control panels, handles, and trim pieces. The press can be customized with specific tooling to accommodate different molding requirements.
5.6. Specialty Manufacturing and Custom Applications
Four-column hydraulic presses are used in specialized manufacturing for unique or custom applications where precision, customization, and versatility are crucial.
- Medical Device Manufacturing: The medical industry uses four-column presses to form surgical tools, implants, and diagnostic equipment. The press’s ability to achieve tight tolerances is essential for producing high-quality medical components.
- Art and Sculpture: Artists and sculptors use four-column hydraulic presses to shape materials such as metal, plastic, or clay for sculptures, art pieces, and decorative items. The open work area of the press allows for creative freedom when working with large or irregularly shaped materials.
- Prototyping and Small Batch Production: In research and development, four-column presses are used to create prototypes and test samples. Their versatility makes them suitable for small-batch production runs, where manufacturers need to evaluate new materials, designs, or processes.
5.7. Woodworking and Composite Materials
Four-column hydraulic presses are also used in woodworking and composite manufacturing for tasks such as laminating, pressing plywood, and forming fiber-reinforced plastics.
- Laminating Wood Panels: In woodworking, four-column presses are used to laminate wood panels, plywood, or veneers. The press applies consistent pressure across the entire surface, ensuring that the adhesive bonds evenly and the layers are securely pressed together.
- Forming Composite Parts: For composite materials, such as carbon fiber or glass fiber-reinforced plastics, four-column presses can be used to shape components used in automotive, aerospace, and sports equipment manufacturing. The press ensures that the composite material is fully consolidated, resulting in strong, lightweight parts.
Advantages of Four-Column Hydraulic Presses
Four-column hydraulic presses are favored in numerous industries due to their unique advantages, which include high force capacity, precision, versatility, and a large, open work area. These benefits make them suitable for a wide range of applications, from heavy-duty metal forming to precision molding. Below are the key advantages of four-column hydraulic presses and how they contribute to improved manufacturing processes.
6.1. High Force Capacity and Even Force Distribution
One of the primary advantages of four-column hydraulic presses is their ability to generate high force levels, making them suitable for heavy-duty applications. The robust design ensures that the press can handle substantial loads without compromising structural integrity.
- Handling Heavy-Duty Tasks: Four-column presses can produce forces ranging from a few tons to thousands of tons, allowing them to perform high-pressure tasks such as metal forging, deep drawing, compression molding, and stamping.
- Even Force Distribution Across the Work Area: The symmetrical four-column structure ensures that the force is evenly distributed across the entire surface of the workpiece. This balanced force application is essential for tasks that require uniform pressure, such as compression molding, deep drawing, and embossing, as it reduces the risk of material deformation.
6.2. Large Work Area and Accessibility
The open design of four-column hydraulic presses provides a large work area, allowing operators to handle large workpieces or irregularly shaped materials with ease.
- Accommodating Large Components: The open space between the columns enables operators to work with large sheets, panels, or long workpieces that would be difficult to process using other press types, such as C-frame or H-frame presses.
- Ease of Multi-Stage Operations: The open design allows for multi-stage operations, where multiple tools or dies can be used sequentially in the same press setup. This flexibility is particularly valuable in applications such as progressive stamping or forming complex shapes.
6.3. Versatility for a Wide Range of Applications
Four-column hydraulic presses are highly versatile, capable of performing a variety of tasks across different industries. This adaptability makes them suitable for industries ranging from automotive to plastics and rubber molding.
- Metal Forming and Fabrication: Four-column presses can be used for deep drawing, stamping, bending, forging, and other metal forming tasks, making them indispensable in industries such as automotive, aerospace, and metalworking.
- Compression Molding for Plastics and Rubber: The press can mold plastic and rubber parts by applying uniform pressure, ensuring that the material flows into the mold cavity completely. This process is used to manufacture items like seals, gaskets, appliance components, and automotive parts.
- Assembly and Custom Operations: Four-column presses are often used for assembly tasks, such as pressing bearings into place or joining components. Their versatility also allows for custom applications in niche industries, such as medical device manufacturing and artistic metalworking.
6.4. Precision and Control: Ideal for High-Accuracy Work
Precision is a critical requirement in many manufacturing processes, and four-column hydraulic presses provide the control and accuracy needed for high-quality results.
- Advanced Control Systems for Precision: Modern four-column presses come equipped with servo-hydraulic systems, CNC, or PLC controls, allowing operators to fine-tune parameters such as force, stroke length, ram speed, and dwell time. This level of control ensures consistent results, even in tasks that require tight tolerances.
- Real-Time Adjustments: The press can make real-time adjustments to the applied force, speed, and stroke length during pressing operations, enhancing the precision of the press. This capability is particularly valuable in applications like metal forming and compression molding, where different stages of the process may require varying levels of force.
- Eliminating Material Defects: The press’s ability to distribute force evenly and control pressure accurately reduces the risk of defects, such as warping, cracking, or improper material flow, ensuring that each part meets the required specifications.
6.5. Durability and Stability in Heavy-Duty Operations
The robust construction of four-column hydraulic presses ensures their durability and stability, even in demanding industrial environments. This durability makes them suitable for continuous use in applications that involve high pressures, heavy loads, and large workpieces.
- Long Service Life: Four-column presses are built from high-strength materials, such as hardened steel, that can withstand the stress of heavy-duty operations. With proper maintenance, these presses can operate for many years, providing a long-term solution for manufacturers.
- Resisting Deformation: The stable design of the four-column structure ensures that the press frame does not deform or bend under high loads, maintaining the accuracy and quality of pressing operations.
- Stable Performance for Large Workpieces: When working with large or heavy materials, the press’s stability ensures that the ram movement remains smooth and precise, which is crucial for tasks such as forming structural components or compression molding.
6.6. Customization Potential for Industry-Specific Needs
Four-column hydraulic presses can be customized to meet the specific requirements of different industries, enhancing their suitability for various applications.
- Variable Tonnage Capacities and Stroke Lengths: Manufacturers can choose from presses with different force capacities and stroke lengths, depending on the tasks they need to perform. This flexibility allows for customization to meet industry-specific requirements.
- Modular Frame Components: Some four-column presses feature modular frames that can be easily upgraded or reconfigured to accommodate changes in production needs. For example, the ram, work table, or hydraulic system can be modified for different materials or processes.
- Integration with Advanced Technology: Customization options may include servo-hydraulic controls, CNC systems, or IoT connectivity for smart manufacturing. These enhancements improve the press’s capabilities in applications such as precision metalworking, automated production lines, and smart factories.
6.7. Cost-Effectiveness for Mass Production
Four-column hydraulic presses provide a cost-effective solution for industries that require high-performance pressing equipment. Their efficiency, versatility, and ease of maintenance contribute to long-term cost savings.
- High Production Efficiency: The ability to perform multi-stage operations, coupled with automated control systems, increases production efficiency. The press can produce large quantities of parts with consistent quality, making it suitable for mass production in industries like automotive and electronics.
- Low Maintenance Requirements: The simplicity of the hydraulic system and the durability of the press’s components result in low maintenance costs. Routine maintenance, such as checking hydraulic fluid levels, inspecting hoses, and cleaning filters, is typically sufficient to keep the press in good working condition.
- Reduced Material Waste: The precision and control offered by four-column presses help minimize material waste during pressing operations. By ensuring that each part is formed accurately, the press reduces the need for rework or secondary processing, saving time and resources.
6.8. Safety Features for Operator Protection
Modern four-column hydraulic presses are equipped with various safety features that help protect operators and prevent accidents.
- Light Curtains and Guarding Systems: Light curtains create a virtual safety barrier around the press’s work area. If the light beam is interrupted, the press will stop immediately to protect the operator. Physical guarding systems can also be installed to prevent access to dangerous areas.
- Emergency Stop Buttons and Redundant Safety Systems: Emergency stop mechanisms are located at various points around the press, allowing operators to halt the machine instantly if necessary. Some presses also feature redundant safety systems to ensure that the press stops even if one component fails.
- Pressure Relief and Overload Protection: Pressure relief valves and overload protection systems prevent the press from exceeding its maximum pressure capacity, safeguarding both the machine and the operator from potential hazards.
6.9. Environmental Sustainability and Energy Efficiency
The integration of advanced technology and energy-efficient components has made modern four-column hydraulic presses more environmentally sustainable.
- Energy-Efficient Hydraulic Pumps: Modern presses use variable displacement pumps that adjust the amount of hydraulic fluid delivered based on the press’s requirements. This reduces energy consumption and minimizes hydraulic fluid waste.
- Energy Recovery Systems: Some four-column presses feature energy recovery systems that capture and reuse energy generated during the press cycle, further improving efficiency.
- Use of Eco-Friendly Hydraulic Fluids: Hydraulic systems can use biodegradable fluids that are less harmful to the environment in case of a leak, supporting sustainability efforts.
Technological Advancements in Four-Column Hydraulic Presses
Recent technological advancements have significantly enhanced the performance, efficiency, and safety of four-column hydraulic presses, making them more versatile and capable of meeting the demands of modern manufacturing. These innovations include the integration of servo-hydraulic systems, automated control, IoT connectivity, and energy-efficient components, which collectively expand the range of applications for four-column presses.
7.1. Servo-Hydraulic Systems for Precision Control
Servo-hydraulic systems combine the benefits of hydraulic power with the precision control of servo motors, resulting in improved accuracy and energy efficiency. This technology has become increasingly popular in four-column hydraulic presses, particularly in applications that require high precision and variable pressure settings.
Key Benefits of Servo-Hydraulic Systems
- Enhanced Precision and Accuracy: Servo-hydraulic technology allows for precise control over the force, speed, and position of the ram, making it suitable for tasks such as metal forming, stamping, and compression molding. The ability to make real-time adjustments ensures that pressing parameters are optimized for each operation.
- Variable Pressure Settings: Unlike traditional hydraulic systems, which maintain a constant pressure, servo-hydraulic systems enable operators to adjust pressure dynamically during the pressing process. This capability helps prevent material defects and damage, especially in processes that involve complex shapes or fragile materials.
- Energy Efficiency: By using servo motors to control the hydraulic pump, the system can reduce energy consumption by only using power when needed. This makes servo-hydraulic presses more sustainable and cost-effective in terms of energy use.
7.2. CNC and PLC Automation
The integration of Computer Numerical Control (CNC) and Programmable Logic Controllers (PLCs) in four-column hydraulic presses has revolutionized the way these machines are operated, allowing for automated control, programmable settings, and precision adjustments.
Advantages of CNC and PLC Integration
- Automated Operation: CNC and PLC systems enable operators to program specific parameters for each task, such as force levels, stroke length, and dwell time. This automation enhances productivity by minimizing manual intervention and reducing setup time.
- Consistency and Repeatability: Automated control ensures that each pressing operation is performed with consistent accuracy, which is crucial for applications that require tight tolerances or high repeatability, such as automotive manufacturing and electronics production.
- Multi-Stage Operations and Complex Forming Tasks: CNC systems make it possible to perform multi-stage operations, such as progressive stamping or deep drawing, in a single setup. This capability improves efficiency and reduces the time required for tool changes.
7.3. IoT and Smart Manufacturing Integration
As part of the Industry 4.0 revolution, IoT connectivity and smart manufacturing capabilities have been incorporated into four-column hydraulic presses. These technologies enable real-time monitoring, predictive maintenance, and process optimization, helping manufacturers achieve higher productivity and operational efficiency.
Benefits of IoT-Enabled Four-Column Presses
- Real-Time Data Monitoring: IoT-enabled presses collect real-time data on parameters such as pressure, stroke length, cycle time, and hydraulic fluid temperature. This data can be used to optimize the pressing process, ensuring consistent quality and identifying areas for improvement.
- Predictive Maintenance and Reduced Downtime: By monitoring the condition of critical components, IoT systems can detect signs of wear or potential issues before they lead to machine failure. This predictive maintenance approach helps prevent unexpected downtime and extends the lifespan of the press.
- Remote Control and Diagnostics: IoT connectivity allows operators and maintenance teams to remotely monitor the press’s performance and diagnose problems. This feature is particularly useful in multi-site manufacturing operations, where presses in different locations can be managed from a central control hub.
7.4. Energy Efficiency Innovations
Reducing energy consumption is a priority in modern manufacturing, and new technologies have made four-column hydraulic presses more energy-efficient and eco-friendly.
Energy-Saving Hydraulic Pumps
- Variable Displacement Pumps: Variable displacement pumps adjust the flow of hydraulic fluid according to the press’s requirements, reducing energy waste by supplying only the necessary amount of fluid. This technology helps lower operational costs and supports sustainability initiatives.
- Servo-Driven Pumps: Servo-driven pumps are controlled by servo motors, which modulate speed and pressure to match the pressing operation’s demands. This capability results in higher energy efficiency compared to traditional pumps.
Energy Recovery Systems
- Regenerative Circuits: Some four-column presses are equipped with regenerative hydraulic circuits that capture and reuse energy generated during the pressing process. This energy recovery technology reduces the overall energy consumption of the press, making it more sustainable.
- Energy Storage with Hydraulic Accumulators: Hydraulic accumulators can store excess energy generated during the press cycle and release it to assist with future press operations, further reducing the demand on the hydraulic pump.
7.5. Safety Enhancements for Operator Protection
Modern four-column hydraulic presses are equipped with advanced safety features designed to protect operators and minimize the risk of accidents.
Light Curtains, Safety Guards, and Emergency Stops
- Light Curtains: Light curtains create an invisible safety barrier around the press’s work area. If the barrier is breached, the press automatically stops, preventing potential injuries.
- Safety Guards: Physical guards help prevent operators from accessing dangerous areas during press operation. These guards are designed to ensure that workers remain at a safe distance from the moving parts of the press.
- Emergency Stop Mechanisms: Emergency stop buttons are strategically placed around the press, allowing operators to quickly halt the press in case of an emergency. Some presses also feature foot-operated emergency stops for added convenience.
Pressure Relief Valves and Redundant Safety Systems
- Pressure Relief Valves: These valves protect the hydraulic system from over-pressurization by releasing excess pressure, safeguarding both the press and the operator.
- Redundant Safety Systems: To ensure maximum safety, some presses incorporate redundant systems that provide backup protection in case one safety feature fails. This includes dual-circuit safety controls and fail-safe mechanisms.
7.6. Customizable Tooling and Modular Design Innovations
The ability to customize tooling and use modular designs enhances the flexibility of four-column hydraulic presses, making them suitable for a variety of applications.
Quick-Change Tooling
- Interchangeable Tool Sets: Four-column presses can be equipped with interchangeable tooling, such as different dies, forming tools, and punches, allowing operators to quickly switch between tasks without significant downtime.
- Automated Tool Change Systems: Automated tool changers further reduce downtime by enabling the press to switch tools without manual intervention. This is particularly beneficial in automated production lines where speed and efficiency are critical.
Modular Frame Components
- Scalable Tonnage Capacities: Modular designs allow for scalable tonnage capacities, enabling manufacturers to increase the press’s force capacity without having to replace the entire machine.
- Upgradable Hydraulic and Control Systems: The modularity of some four-column presses allows for easy upgrades to hydraulic components, control systems, or servo-hydraulic technology, ensuring that the press remains up-to-date with evolving manufacturing needs.
7.7. Smart Technology Integration for Process Optimization
The integration of smart technology, such as machine learning and artificial intelligence (AI), is transforming four-column hydraulic presses into self-optimizing machines capable of improving efficiency and product quality.
AI-Driven Process Optimization
- Adaptive Control Systems: AI-driven control systems can adjust pressing parameters in real-time based on feedback from sensors, optimizing performance for each task. This reduces material waste and shortens cycle times.
- Predictive Analytics for Maintenance: By analyzing historical data, machine learning algorithms can predict when maintenance is needed, allowing for proactive servicing that minimizes downtime.
Cloud Connectivity and Data Analysis
- Cloud-Based Monitoring: Smart presses connected to the cloud can store and analyze data on press performance, providing insights for continuous improvement and quality control.
- Big Data for Quality Assurance: Using big data analytics, manufacturers can identify patterns in the pressing process that may indicate quality issues, allowing for timely adjustments to maintain high product standards.
Introduction to Hydraulic Press Applications
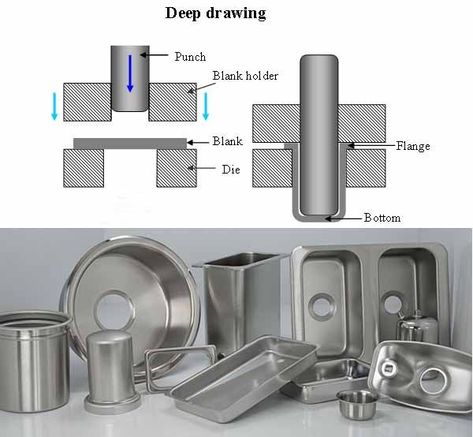
Hydraulic presses are versatile machines used to perform a variety of operations, including forming, stamping, forging, molding, bonding, and pressing. They work by applying hydraulic pressure to generate the force needed for these tasks. The hydraulic system uses pressurized fluid to create a controlled and consistent force, allowing the press to handle a wide range of materials and applications with precision and reliability.
The flexibility of hydraulic press technology has made it a cornerstone of modern manufacturing across multiple industries. From the automotive and aerospace sectors to plastics, electronics, and consumer products, hydraulic presses are used to produce components and products that are essential to everyday life. The different types of hydraulic presses, such as four-column, H-frame, C-frame, and servo-hydraulic presses, provide options to suit specific manufacturing needs.
The ability of hydraulic presses to generate significant force while maintaining control over the pressing parameters makes them suitable for tasks requiring high precision and repeatability. Whether it’s shaping metal sheets for automotive body panels, molding plastic housings for electronic devices, or forging heavy-duty components for construction equipment, hydraulic presses play a crucial role in ensuring the quality and performance of the finished products.
With advancements in press technology, including automation, servo control, and IoT integration, the applications of hydraulic presses continue to expand, offering new opportunities for efficient and sustainable manufacturing. This text will explore a wide range of products that are produced using hydraulic presses, highlighting the importance of this technology in various industries.
Metal Forming and Fabrication Products
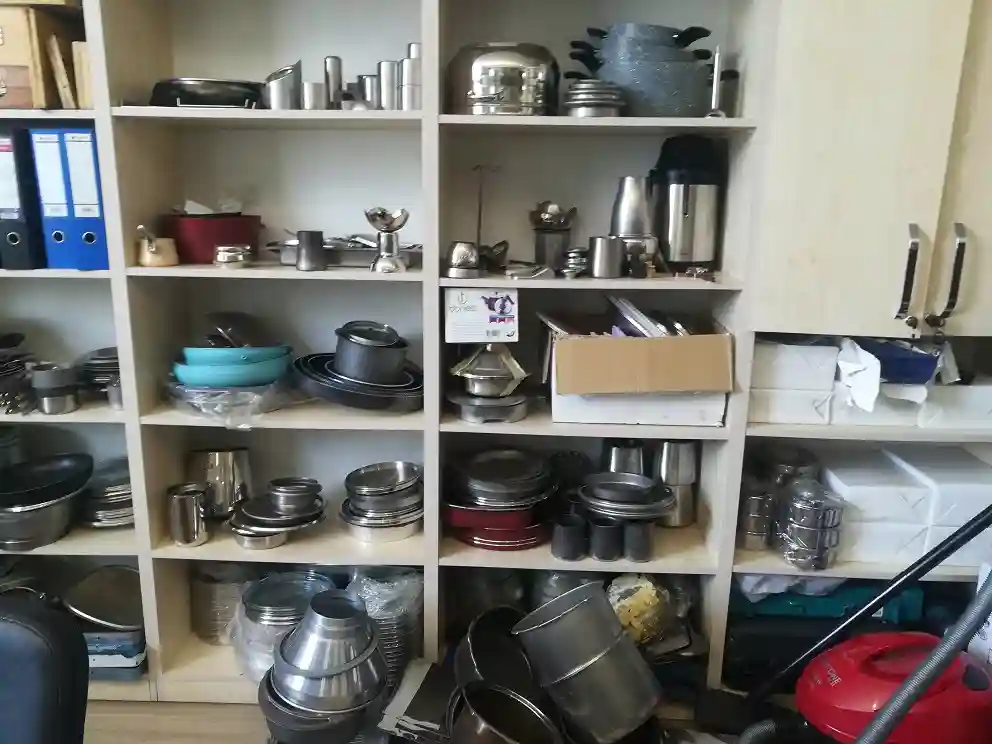
Hydraulic presses are widely used in metal forming and fabrication due to their ability to generate high force and apply it with precision. The even distribution of force across the workpiece makes them ideal for shaping metal sheets, plates, and components. This section explores various products produced through metal forming using hydraulic presses, including automotive parts, aerospace components, construction materials, and industrial tools.
2.1. Automotive Parts
The automotive industry relies heavily on hydraulic presses for manufacturing various metal parts, ensuring the components meet strict safety and performance standards. Common products include:
- Body Panels: Hydraulic presses are used to shape metal sheets into car body panels, such as doors, hoods, trunks, and fenders. The pressing operation ensures the panels are formed with the precise contours needed for aerodynamics, aesthetics, and structural integrity.
- Chassis Components: The chassis of a vehicle is made up of several parts, such as cross members, frames, and suspension components, that require metal forming. Hydraulic presses can shape high-strength steel or aluminum alloys used in these components to provide durability and crash resistance.
- Engine and Transmission Parts: Hydraulic presses are also used in the production of engine components, gear housings, and transmission parts. These metal parts need to meet strict tolerances to ensure efficient performance, and the precision offered by hydraulic presses helps achieve this.
2.2. Aerospace Components
In the aerospace industry, components need to be lightweight yet strong enough to withstand extreme conditions. Hydraulic presses are used to shape various materials, including aluminum, titanium, and composite alloys.
- Aircraft Panels: The body of an aircraft consists of wing panels, fuselage sections, and control surfaces, which are formed from lightweight materials. Hydraulic presses ensure that these components meet the strict dimensional tolerances required for aerodynamic performance.
- Structural Components: Hydraulic presses are used to manufacture high-strength structural components for aircraft, such as bulkheads, ribs, and frames, which help distribute stress across the aircraft’s structure.
- High-Strength Alloys: Aerospace components often involve forming high-strength alloys for parts like landing gear assemblies, turbine blades, and engine housings. The presses ensure that these materials are shaped without compromising their mechanical properties.
2.3. Construction and Heavy Machinery
Construction materials and heavy machinery parts require durability to withstand harsh environments and heavy loads. Hydraulic presses produce various metal components used in construction and industrial applications.
- Gears and Shafts: Hydraulic presses are used to forge gears and shafts used in construction equipment, industrial machinery, and agricultural vehicles. The pressing process ensures the components have the strength and precision required for heavy-duty use.
- Structural Beams: Hydraulic presses are employed in shaping steel beams and metal girders for construction projects, such as bridges, buildings, and industrial facilities. The even force distribution ensures uniformity and reduces the risk of structural failures.
- Fasteners and Connectors: Presses are used to manufacture various metal fasteners, such as bolts, nuts, and connectors, which are essential for assembling machinery and constructing buildings.
2.4. Household and Industrial Tools
Hydraulic presses are also used in the production of various household and industrial tools, where metal forming is essential for creating parts that meet specific functional requirements.
- Wrenches and Pliers: Hand tools like wrenches, pliers, and screwdrivers are made from forged metal, using hydraulic presses to shape and harden the components. The precision forming process ensures the tools have the proper dimensions and strength for repeated use.
- Blades and Cutting Tools: Blades, such as saw blades, scissors, and knives, are produced using hydraulic presses to shape and sharpen the metal. This ensures the cutting edge has the desired profile and hardness for effective performance.
Compression Molding Products
Compression molding is a manufacturing process used to shape thermosetting plastics, rubber, and composite materials by applying heat and pressure in a mold cavity. Hydraulic presses play a crucial role in this process, as they can generate the necessary force to ensure that the material fills the mold completely, creating durable, high-quality parts. Below are some of the key products produced through compression molding using hydraulic presses, including plastic components, rubber products, and composite materials.
3.1. Plastic Components
Compression molding is widely used to produce various plastic parts for different industries, where hydraulic presses ensure that the material flows evenly into the mold, producing parts with consistent quality and minimal defects.
- Automotive Interior Parts: Many interior components in vehicles, such as dashboard panels, door trims, and center consoles, are produced using compression molding. Hydraulic presses apply pressure and heat to form durable plastic parts that fit precisely within the vehicle’s interior.
- Electrical Housings: Electrical products, such as switches, circuit breaker casings, and junction boxes, often have molded plastic housings that provide insulation and protection for internal components. Hydraulic presses are used to form these housings to meet safety and dimensional standards.
- Appliance Components: Household appliances, such as microwaves, refrigerators, and washing machines, use plastic parts that are formed through compression molding. Hydraulic presses shape components like control panels, handles, and internal brackets, ensuring durability and heat resistance.
3.2. Rubber Products
Rubber molding is another key application of hydraulic presses, especially for products that require elasticity, durability, and the ability to withstand extreme temperatures.
- Seals and Gaskets: Hydraulic presses are used to produce various rubber seals, gaskets, and O-rings, which are essential for sealing applications in automotive, industrial, and plumbing systems. The consistent pressure applied during molding ensures that the seals maintain their shape and elasticity for reliable performance.
- Rubber Bushings and Mounts: Automotive suspension components, such as bushings and engine mounts, are made from molded rubber to absorb vibration and reduce noise. Hydraulic presses help mold these parts with precise dimensions and material properties to ensure optimal functionality.
- Tires and Belts: Some tire components and rubber belts used in machinery are also produced using compression molding. The press ensures uniform material distribution within the mold, leading to products that meet strict performance requirements.
3.3. Composite Materials
Composite materials, such as fiber-reinforced plastics and carbon fiber composites, are used in industries requiring strong, lightweight components. Hydraulic presses enable the molding of these materials into complex shapes.
- Fiber-Reinforced Plastics: Fiber-reinforced plastic components, used in automotive, marine, and construction applications, are made through compression molding. Hydraulic presses ensure that the fibers are properly aligned within the plastic matrix, providing maximum strength and durability.
- Carbon Fiber Parts: Carbon fiber-reinforced materials are commonly used in high-performance applications, such as aerospace components, sports equipment, and luxury car parts. Hydraulic presses mold these components to exact specifications, ensuring that they are lightweight while offering excellent strength.
- Sports Equipment (e.g., Bicycles, Helmets): Compression molding is also used to manufacture sports equipment, including bicycle frames, helmets, and protective gear. Hydraulic presses help form these items from composite materials, ensuring they meet safety standards and performance requirements.
EMS Metalworking Machinery
We design, manufacture and assembly metalworking machinery such as:
- Hydraulic transfer press
- Glass mosaic press
- Hydraulic deep drawing press
- Casting press
- Hydraulic cold forming press
- Hydroforming press
- Composite press
- Silicone rubber moulding press
- Brake pad press
- Melamine press
- SMC & BMC Press
- Labrotaroy press
- Edge cutting trimming machine
- Edge curling machine
- Trimming beading machine
- Trimming joggling machine
- Cookware production line
- Pipe bending machine
- Profile bending machine
- Bandsaw for metal
- Cylindrical welding machine
- Horizontal pres and cookware
- Kitchenware, hotelware
- Bakeware and cuttlery production machinery
as a complete line as well as an individual machine such as:
- Edge cutting trimming beading machines
- Polishing and grinding machines for pot and pans
- Hydraulic drawing presses
- Circle blanking machines
- Riveting machine
- Hole punching machines
- Press feeding machine
You can check our machinery at work at: EMS Metalworking Machinery – YouTube
Applications:
- Beading and ribbing
- Flanging
- Trimming
- Curling
- Lock-seaming
- Ribbing
- Flange-punching