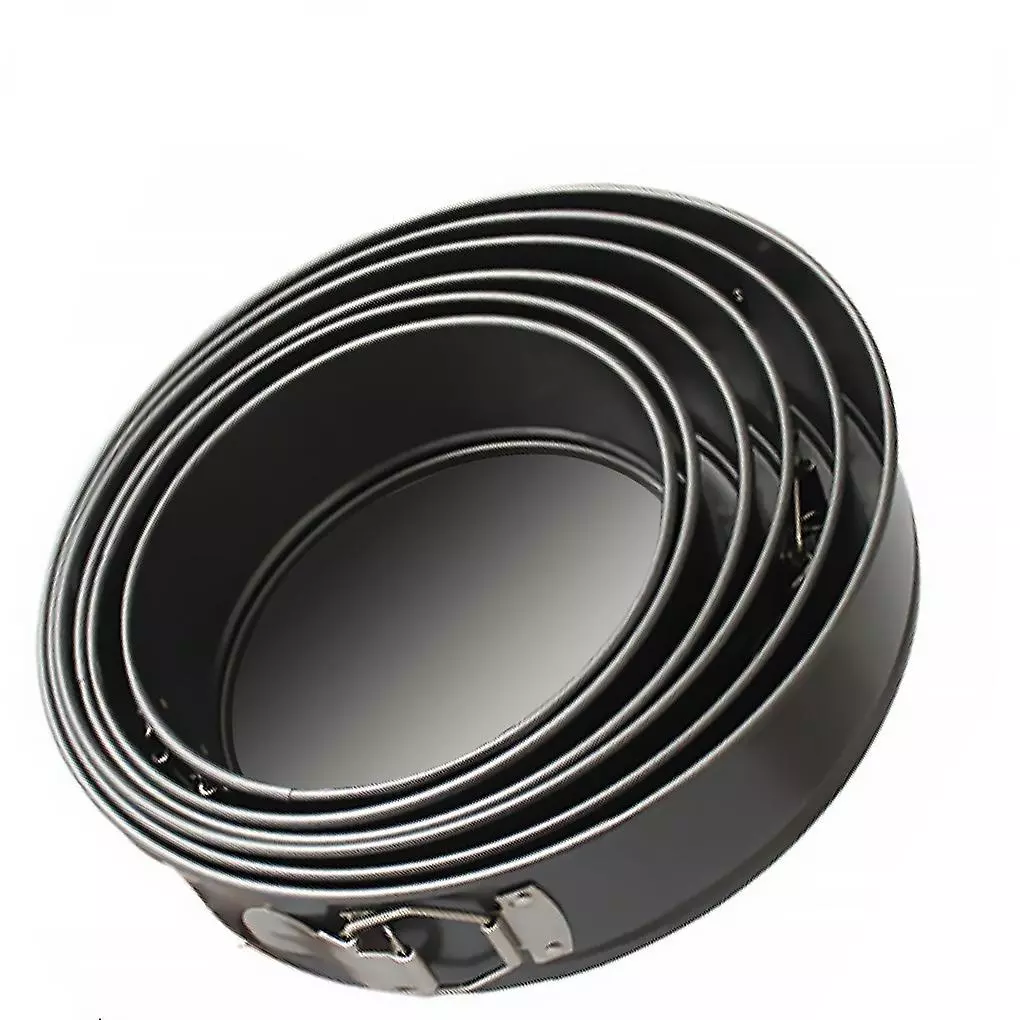
Baking molds manufacturing machines play a crucial role in the production of a wide variety of baked goods, from cakes and muffins to pastries and bread. These machines utilize various techniques to shape and form dough, batter, or other baking ingredients into the desired shapes and sizes, ensuring consistent results and high production efficiency.
Types of Baking Molds Manufacturing Machines
- Dough Sheeting Machines: These machines transform dough into uniform sheets of consistent thickness, preparing the material for subsequent shaping and forming operations. They typically employ rollers or belts to flatten and even out the dough.
- Depositing Machines: Depositing machines precisely deposit batter or dough into baking molds, ensuring consistent filling and accurate portion control. They can handle various consistencies, from pourable batters to thick doughs.
- Molding Machines: Molding machines press dough or batter into molds, forming the desired shapes and contours of baked goods. They may employ stamping, compression, or injection molding techniques.
- Encrusting Machines: Encrusting machines encapsulate fillings within dough or batter, creating filled products like pies, pastries, and filled cookies. They precisely deposit and wrap the filling within the dough or batter.
- Cookie Wire Cutters: Cookie wire cutters utilize wire cutters to shape and cut dough into various cookie shapes. They offer precise and consistent cutting for a variety of cookie designs.
Key Components of Baking Molds Manufacturing Machines
- Frame: The sturdy frame provides the structural support for the entire machine, housing the various components and mechanisms.
- Feeding System: The feeding system supplies the dough, batter, or filling to the machine for processing and shaping. It may consist of hoppers, conveyors, or pumps.
- Shaping and Forming Mechanisms: These mechanisms manipulate the dough, batter, or filling to create the desired shapes and sizes. They may involve rollers, belts, stamps, pistons, or wire cutters.
- Control System: The control system regulates the machine’s operation, ensuring precise and consistent processing. It may include timers, sensors, and programmable logic controllers (PLCs).
- Molding Plates or Dies: Molding plates or dies provide the contours and shapes for the baked goods. They are typically made from durable materials like stainless steel or aluminum.
Applications of Baking Molds Manufacturing Machines
- Bread Production: These machines are used to shape dough into loaves, rolls, and other bread varieties.
- Cake and Muffin Production: They produce uniform batter for cakes, cupcakes, and muffins, ensuring consistent baking results.
- Pastry and Cookie Manufacturing: They form dough or batter into various pastry shapes, such as croissants, danishes, and cookies.
- Filled Product Manufacturing: They encapsulate fillings within dough or batter, creating filled pastries, pies, and filled cookies.
- Snack Food Production: They produce snack foods like crackers, pretzels, and tortilla chips.
Benefits of Baking Molds Manufacturing Machines
- Consistency: These machines ensure consistent product shapes, sizes, and filling distribution, enhancing product quality and brand reputation.
- Efficiency: They automate labor-intensive tasks, increasing production speed and reducing labor costs.
- Precision: They provide precise shaping and forming, minimizing waste and ensuring consistent product quality.
- Versatility: They can handle a wide range of doughs, batters, and fillings, catering to diverse product offerings.
- Scalability: They can be scaled up or down to meet fluctuating production demands.
Conclusion
Baking molds manufacturing machines are essential tools in the baking industry, enabling the production of a wide variety of baked goods with consistent quality, efficiency, and precision. By utilizing various techniques and incorporating advanced control systems, these machines play a vital role in meeting the demands of modern bakeries and food manufacturers.
As EMS Metalworking Machinery, one of the core machines we manufacture is the baking molds manufacturing machine. The baking molds are metal, coated round parts, with their edges curled with edge curling machines.
Punching presses manufacture the baking molds to cut out the sheet metal circles first. The coated cookware or bakeware products are top-rated beside the home cookware. The non-coated cookware is not very suitable for baking as the cakes can stick to non-coated surfaces. The non-stick coat (non-stick cookware is coated with polytetrafluoroethylene (PTFE) or as mostly known Teflon) is a special coating application applied to cookware or bakeware products that can be scratched.
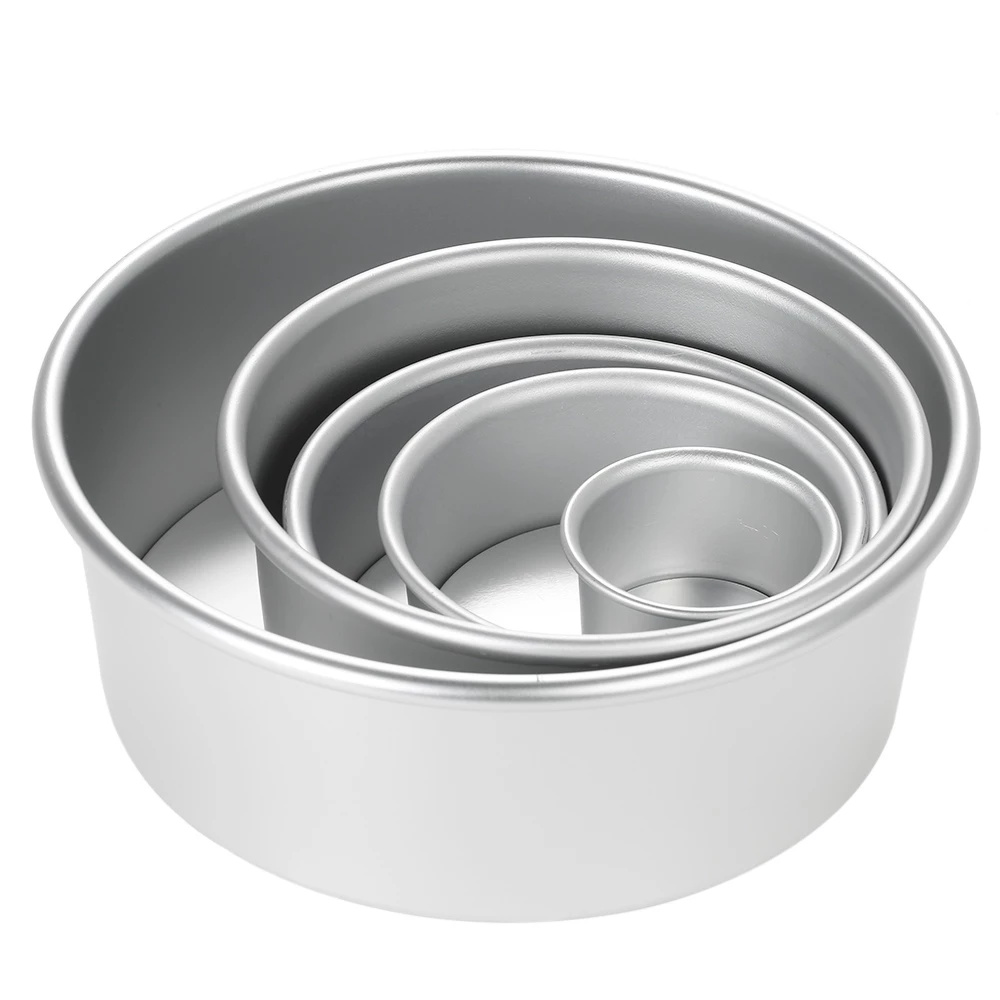
Baking Molds
Baking molds are indispensable tools in the baking industry, used to shape and form dough, batter, or other baking ingredients into the desired shapes and sizes. They come in a wide variety of materials, designs, and sizes, catering to the diverse needs of bakeries and food manufacturers.
Types of Baking Molds
- Round Baking Molds: These molds are typically used for cakes, cupcakes, and muffins. They come in various diameters and depths, accommodating different batter volumes and baking times.
- Rectangular Baking Molds: These molds are commonly used for bread, brownies, and lasagna. They offer a larger surface area for even baking and a rectangular shape that is versatile for various baked goods.
- Jelly Roll Pans: These molds have a shallow, rectangular shape with a raised lip, designed to prevent overflow during jelly roll baking. They are typically used for rolled cakes and desserts.
- Tartelet Pans: These molds have individual wells, typically circular or rectangular, for baking small pastries, such as tarts and tartlets. They come in various sizes and depths, accommodating different filling amounts.
- Cupcake Liners: These paper or silicone liners are placed in muffin tins to prevent sticking and enhance the appearance of cupcakes. They come in various colors and patterns.
Material Options for Baking Molds
- Stainless Steel: Stainless steel molds are durable, easy to clean, and resistant to corrosion, making them ideal for commercial baking applications.
- Aluminum: Aluminum molds are lightweight, heat conductive, and affordable, making them popular for home bakers.
- Non-Stick Silicone Molds: Silicone molds are flexible, non-stick, and easy to remove baked goods from. They are dishwasher-safe and can be used in both conventional and convection ovens.
- Porcelain or Glass Molds: Porcelain or glass molds can impart a unique look and feel to baked goods. They are often used for decorative cakes and desserts.
- Silicone-Coated Baking Pans: These pans provide the non-stick properties of silicone without the flexibility, making them suitable for heavy-duty baking tasks.
Choosing Baking Molds
The type of baking mold chosen depends on the specific baked good being prepared. For instance, round molds are ideal for cakes, rectangular molds for bread, and tartlet pans for tarts and tartlets.
Material selection is also crucial. Stainless steel is best for professional baking due to its durability and resistance to corrosion. Aluminum is a good choice for home bakers seeking affordability and lightweight molds. Non-stick silicone molds are convenient for easy removal of baked goods. Porcelain or glass molds provide a decorative touch for special occasions. Silicone-coated baking pans offer a balance of non-stick properties and durability.
Care and Maintenance of Baking Molds
- Hand Washing: Hand-washing is recommended for most baking molds to prevent damage from harsh detergents or dishwasher cycles.
- Scouring: Use a soft sponge and mild dish soap to gently clean the molds. Avoid abrasive cleaners that could scratch or damage the material.
- Air Drying: Allow the molds to air dry completely before storing them. This prevents moisture buildup and the potential for mold or mildew growth.
- Lubrication (Optional): For silicone molds, apply a thin layer of non-stick cooking spray or vegetable oil after washing and drying. This helps prevent sticking and extends the mold’s lifespan.
- Storage: Store baking molds in a clean, dry, and well-ventilated area. Avoid stacking heavy items on top of the molds, as this could deform or damage them.
By understanding the different types, materials, and care requirements of baking molds, bakers and food manufacturers can make informed decisions to achieve consistent, high-quality results.
Non-stick Coating for Stainless Steel Baking Molds Manufacturing Machine
The non-stick coating for stainless steel baking molds manufacturing machine is as first the punching press to cut the sheet circles out. These punching machines can cut stainless steel sheets as well as many other materials.
The circle sheets are pressed into baking mold bottom layers. We will also need another machine to produce the peripheral sheets of the baking molds.
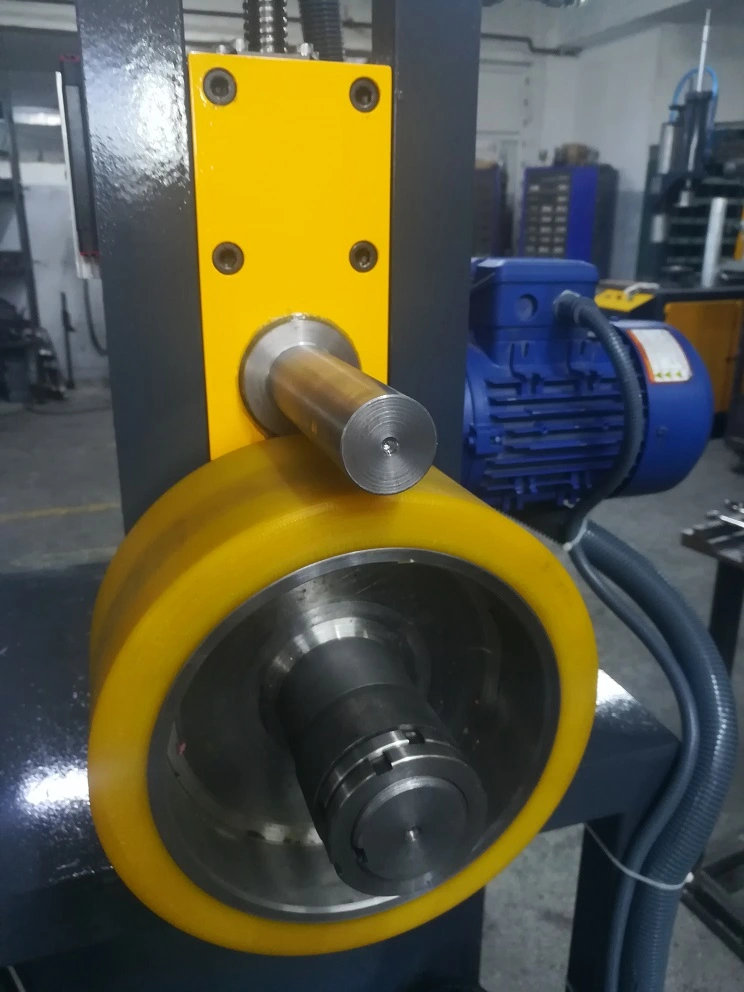
Applying a non-stick coating to stainless steel baking molds is a common practice in the manufacturing process to prevent food from sticking and make the molds easier to clean. The non-stick coating creates a smooth surface that reduces the likelihood of baked goods adhering to the mold. Here’s a general overview of the process for applying a non-stick coating to stainless steel baking molds:
- Cleaning and Preparation: Before applying the non-stick coating, the stainless steel molds need to be thoroughly cleaned to remove any contaminants or residues. The surface should be smooth and free from any imperfections that could affect the adhesion of the coating.
- Surface Treatment: The stainless steel surface may undergo a treatment to enhance adhesion. This could involve processes such as sandblasting or chemical etching to create a slightly roughened surface that improves the bond between the metal and the non-stick coating.
- Primer Application: A primer or bonding agent is applied to the prepared surface. The primer helps the non-stick coating adhere better to the stainless steel substrate.
- Non-Stick Coating Application: There are various types of non-stick coatings available, and the choice depends on factors such as the intended use of the baking molds and the desired properties of the coating. Common non-stick coatings include polytetrafluoroethylene (PTFE), often known by the brand name Teflon, and ceramic-based coatings.
- PTFE Coating: This is a fluoropolymer coating that provides excellent non-stick properties. It is resistant to high temperatures and is commonly used for bakeware.
- Ceramic Coating: Ceramic coatings are known for their durability and resistance to scratching. They can provide a smooth, non-stick surface.
- Curing or Baking: After the non-stick coating is applied, the baking molds typically go through a curing or baking process. This involves heating the molds to a specific temperature for a certain duration. Curing helps the coating bond to the surface and ensures that it forms a durable and effective non-stick layer.
- Quality Control: The coated baking molds undergo quality control checks to ensure that the non-stick coating is uniform, adheres properly, and meets the desired standards.
It’s important for manufacturers to follow industry regulations and standards when applying non-stick coatings to ensure the safety and quality of the final product.
These baking mold manufacturing machines can produce round sheet metals for the peripheral surrounding of the bakeware. The sheet metal strip is placed between the idle shaft and the rotating roller. When the electric motor rotates the rotating roller, the straight sheet metal strip turns into a round baking mold as below:
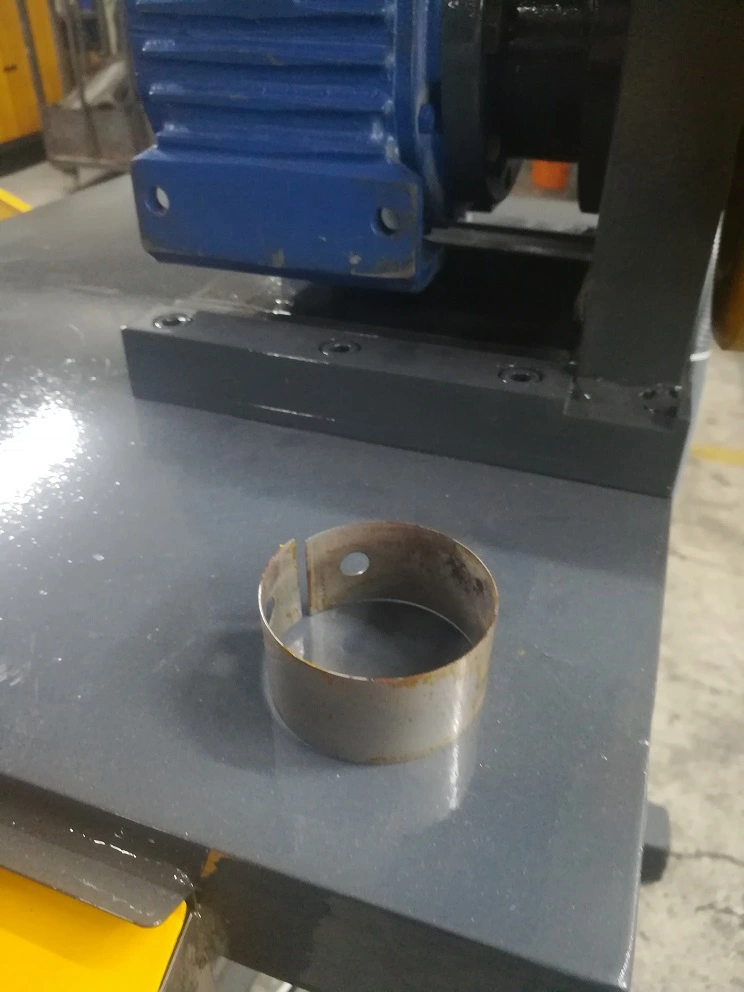
Then the edges of the baking molds are processed by the edge curling machine. The edge curling machine can curl the edges of the
- Baking molds
- Removable Bottom Non-Stick Metal Bake Mould Square Cake Pan Bakeware Carbon Steel Cakes Molds cake baking pans baking trays
- Factory wholesale stainless steel round adjustable cake mousse ring 6 to 12-inch cake baking molds
- Carbon Steel Cakes Molds Non-Stick Metal Bake Mould Round Cake Baking Pan Removable Bottom Bakeware Cake Supplies
- Individual Molds Egg Tart Molds Pudding Molds Cups Mini Chocolate Molten Pans Carbon Steel Cupcake Cake Cookie Pudding Mold Round Nonstick Popover Bakeware Tumblers (2.6 x 2 x 1.3 Inch)
- Mini Tube Pan Set, 4-Inch 4Pcs Non-Stick Kugelhopf Mold for Oven and Instant Pot Baking
- Round Cookie Cutters Set 12 Pieces Biscuit Cookie Cutters Circle Pastry Cutters Round Donut Ring Molds for Baking for Pastries Doughs Doughnuts
- Egg Tart Molds, Mini Tart Pans, Muffin Cake Mold, Steel Mini Pie Pans Muffin Baking Cups Cupcake Cake Cookie Lined Mold Tin Baking Tool (2.5 inches)
- Pack Egg Tart Molds Tiny Pie Tartlets Dessert Mold Pans Tin Puto Cup Bakeware Muffin Cupcake Cake Cookie Mold Baking Tool, Round Reusable Nonstick (25)
- Mini Geometric Shaped Cookie Biscuit Cutter Set 24 Rectangle Square Heart Triangle Round Tiny Circle Baking Stainless Steel Metal Molds
- Cake Ring Molds Stainless Steel Ring Molds for Cooking Pastry Rings Cake Mousse Mold with Pusher,3.15in Diameter, Set of 6
- Plating/forming Stainless Steel Ring Mold Sets (4 rings)
- Round Cake Ring Mold, Stainless Steel 3-inch Dessert Mousse Molds with Pusher & Lifter Cooking Rings, Tuna Tartare Mold (Include 4 Rings and 1 Pusher)
EMS Metalworking Machinery
We design, manufacture and assembly metalworking machinery such as:
- Hydraulic transfer press
- Glass mosaic press
- Hydraulic deep drawing press
- Casting press
- Hydraulic cold forming press
- Hydroforming press
- Composite press
- Silicone rubber moulding press
- Brake pad press
- Melamine press
- SMC & BMC Press
- Labrotaroy press
- Edge cutting trimming machine
- Edge curling machine
- Trimming beading machine
- Trimming joggling machine
- Cookware production line
- Pipe bending machine
- Profile bending machine
- Bandsaw for metal
- Cylindrical welding machine
- Horizontal pres and cookware
- Kitchenware, hotelware
- Bakeware and cuttlery production machinery
as a complete line as well as an individual machine such as:
- Edge cutting trimming beading machines
- Polishing and grinding machines for pot and pans
- Hydraulic drawing presses
- Circle blanking machines
- Riveting machine
- Hole punching machines
- Press feeding machine
You can check our machinery at work at: EMS Metalworking Machinery – YouTube
Applications:
- Beading and ribbing
- Flanging
- Trimming
- Curling
- Lock-seaming
- Ribbing
- Flange-punching