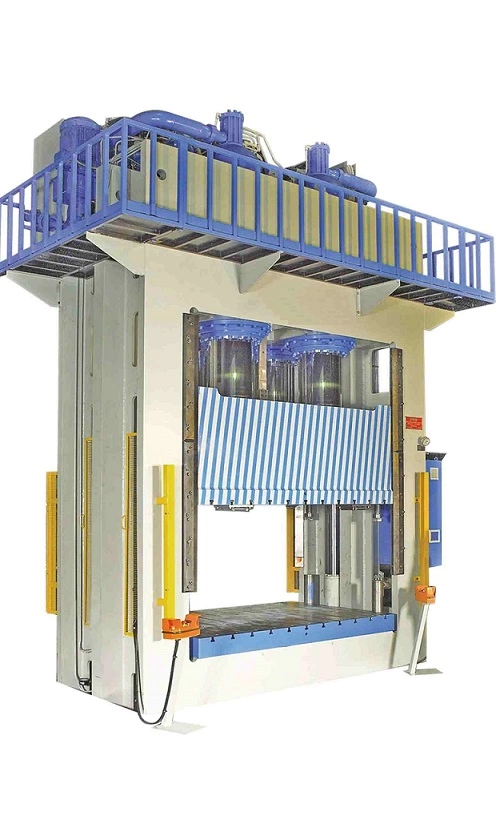
We manufacture Hydraulic Presses for the Automotive Industry. Hydraulic press lines for automotive OEMs and main parts. Free consultation with high quality.
Automotive Industry
Hydraulic presses play a vital role in the automotive industry, where they are used for a wide range of applications such as stamping, forming, punching, and assembling various parts and components. Here are some specific examples of how hydraulic presses are used in the automotive industry:
- Stamping and forming body panels: Hydraulic presses are commonly used to stamp and form sheet metal into body panels such as doors, hoods, fenders, and roofs. These presses can apply high forces and precise control to produce complex shapes and curves.
- Making engine and transmission parts: Hydraulic presses are used to make a wide range of engine and transmission components such as crankshafts, connecting rods, cylinder heads, and gears. These parts are typically made from high-strength metals and require precise control to ensure their accuracy and durability.
- Assembling automotive components: Hydraulic presses are also used for assembling various automotive components such as suspension systems, steering columns, and airbags. These presses can apply controlled force to join and fasten parts together, ensuring a strong and reliable connection.
- Testing automotive components: Hydraulic presses can be used to test the strength and durability of automotive components by subjecting them to various forces and conditions. This is important for ensuring that parts and components meet the required safety and performance standards.
Overall, hydraulic presses have become an essential tool in the automotive industry, enabling manufacturers to produce high-quality parts and components efficiently and effectively.
Stamping and Forming Body Panels
Stamping and forming body panels is one of the primary applications of hydraulic presses in the automotive industry. Body panels such as doors, hoods, fenders, and roofs are typically made from sheet metal and require precise stamping and forming operations to create the desired shape and curvature.
Hydraulic presses are well-suited for this application because they can apply high forces and precise control to the sheet metal during the stamping and forming process. The presses are typically equipped with specialized tooling such as dies, punches, and forming tools that are designed to create the specific shapes and contours required for each body panel.
The stamping and forming process typically involves feeding a flat sheet of metal into the press, which then applies pressure to the metal to create the desired shape. The press may use a single operation or a series of operations to create the final shape, depending on the complexity of the panel.
The finished body panels are then inspected for quality and accuracy before being sent on for further processing and assembly into the final vehicle. Overall, stamping and forming body panels is a critical application of hydraulic presses in the automotive industry, enabling manufacturers to produce high-quality, durable, and aesthetically pleasing body panels efficiently and effectively.
Making Engine and Transmission Parts
Hydraulic presses are also widely used in the automotive industry for making various engine and transmission parts. These parts include crankshafts, connecting rods, cylinder heads, and gears, among others. The parts are usually made from high-strength metals such as steel, aluminum, and titanium, which require precise control during the manufacturing process to ensure their accuracy and durability.
Hydraulic presses are well-suited for making engine and transmission parts because they can apply high forces and provide precise control over the shaping and forming of the metal. The presses are equipped with specialized tooling such as dies, punches, and forming tools that are designed to create the specific shapes and contours required for each part.
The manufacturing process typically begins with a raw material, such as a billet of metal, which is heated and then placed into the press. The press applies pressure to the metal, using the specialized tooling, to shape and form it into the desired part. Depending on the complexity of the part, multiple operations may be required to achieve the final shape and dimensions.
The finished parts are then subjected to various quality control measures to ensure that they meet the required specifications for strength, durability, and dimensional accuracy. These parts are then sent on for further processing and assembly into the final engine or transmission.
In summary, hydraulic presses play an essential role in the production of engine and transmission parts in the automotive industry, enabling manufacturers to produce high-quality, durable, and reliable parts efficiently and effectively.
Assembling Automotive Components
Hydraulic presses are also widely used in the automotive industry for assembling various components of a vehicle. These components include suspension systems, steering systems, brake systems, and other critical parts that require high precision and strength.
The hydraulic press can be used for a variety of assembly operations, including pressing bearings into housings, assembling shafts and gears, installing bushings, and pressing studs into hubs, among others. The press can also be used to assemble parts that have been fabricated using other manufacturing processes, such as stamping or forging.
The assembly process typically involves placing the parts to be assembled into the press and then applying pressure to them using specialized tooling, such as dies or punches, to ensure that they are aligned correctly and securely. The press may apply heat or use other techniques, such as vibration, to aid in the assembly process.
Once the parts are assembled, they are subjected to rigorous quality control measures to ensure that they meet the required specifications for strength, durability, and dimensional accuracy. These parts are then sent on for further processing and assembly into the final vehicle.
In summary, hydraulic presses are essential tools in the automotive industry for assembling various components of a vehicle. They enable manufacturers to produce high-quality, reliable parts that meet the required specifications efficiently and effectively.
Testing Automotive Components
Hydraulic presses are also commonly used in the automotive industry for testing and evaluating various components of a vehicle. Testing is an important part of the production process as it ensures that the components meet the required specifications and are safe for use in the final product.
One of the most common uses of hydraulic presses in testing automotive components is for performing compression and tension tests on materials. This involves subjecting the material to a controlled load or force, and measuring how it deforms or reacts under that load. This helps manufacturers to determine the material properties, such as strength, ductility, and elasticity, and to ensure that they meet the required specifications.
Hydraulic presses are also used for testing various components of a vehicle, such as suspension systems, steering systems, and brake systems. For example, hydraulic presses can be used to test the strength and durability of shock absorbers, by applying a controlled load or force and measuring how the shock absorber responds. This helps manufacturers to ensure that the components can withstand the loads and forces that they will encounter during normal use.
In addition, hydraulic presses can be used for testing the performance of various systems and components in the vehicle, such as airbags, seat belts, and other safety features. This helps to ensure that these systems are functioning correctly and meet the required safety standards.
Overall, hydraulic presses are essential tools in the automotive industry for testing and evaluating various components of a vehicle, helping manufacturers to ensure that they meet the required specifications and are safe for use in the final product.
Hydraulic presses are powerful machines used to apply a significant amount of force to an object through hydraulic fluid pressure. They are essential in various industrial applications, providing the necessary force for processes such as metal forming, stamping, bending, and molding. The versatility and efficiency of hydraulic presses make them indispensable tools in manufacturing and production lines. This document will explore the different types of hydraulic presses, their application areas, components, operational principles, manufacturing process, and the challenges and advancements in the industry.
Types of Hydraulic Presses
Hydraulic presses come in various designs, each suited to specific applications and requirements. The primary types of hydraulic presses include C-frame presses, H-frame presses, four-column presses, straightening presses, arbor presses, laminating presses, and transfer presses.
C-frame presses, also known as gap-frame presses, have a C-shaped frame that provides three-sided access to the work area. This design is ideal for applications requiring easy loading and unloading of materials.
H-frame presses, or two-post presses, have a robust H-shaped frame that offers excellent stability and strength. They are commonly used for heavy-duty tasks such as metal forming and straightening.
Four-column presses, or four-post presses, have four vertical columns that provide superior support and uniform force distribution. These presses are suitable for large-scale applications requiring high precision and repeatability.
Straightening presses are specialized hydraulic presses used to straighten bent or distorted metal components. They are widely used in the automotive and construction industries.
Arbor presses are smaller, manually operated hydraulic presses used for light-duty tasks such as assembly, riveting, and broaching. They are commonly found in workshops and small manufacturing facilities.
Laminating presses are used to bond multiple layers of material together under heat and pressure. These presses are essential in industries such as electronics, where laminated components are common.
Transfer presses are automated hydraulic presses that move the workpiece through multiple stations for different operations. They are highly efficient and used in high-volume production environments.
Application Areas
Hydraulic presses are employed in various industries, thanks to their ability to deliver consistent and precise force. Key application areas include:
Metal forming and forging: Hydraulic presses are crucial in shaping and forming metal parts through processes such as stamping, bending, and deep drawing. They are essential in the production of automotive parts, machinery components, and structural elements.
Automotive industry: In the automotive sector, hydraulic presses are used for manufacturing various parts, including body panels, chassis components, and engine parts. They play a critical role in ensuring the structural integrity and performance of vehicles.
Aerospace industry: The aerospace industry relies on hydraulic presses for forming and shaping high-strength materials used in aircraft components. Precision and reliability are paramount in this industry, making hydraulic presses indispensable.
Plastic and rubber molding: Hydraulic presses are used in the molding of plastic and rubber components, including automotive parts, household goods, and medical devices. They ensure consistent product quality and precision.
Electrical and electronics industry: In the electronics sector, hydraulic presses are used for laminating circuit boards, forming connectors, and assembling electronic components. They provide the necessary force and precision for delicate operations.
Medical device manufacturing: Hydraulic presses are used in the production of medical devices, including surgical instruments, implants, and diagnostic equipment. They ensure the high precision and quality required in the medical field.
Packaging industry: Hydraulic presses are employed in the packaging industry for forming and shaping packaging materials, such as cardboard, plastic, and metal. They help produce packaging solutions that are strong, durable, and aesthetically pleasing.
Components of a Hydraulic Press
A hydraulic press comprises several key components that work together to generate and control the applied force. The main components include the frame, hydraulic cylinder, hydraulic pump, control valves, hydraulic fluid, pressure gauges and sensors, and die and tooling.
The frame is the main structure of the hydraulic press, providing stability and support for all other components. It is typically made of high-strength steel to withstand the significant forces generated during operation.
The hydraulic cylinder is the core component that generates the pressing force. It consists of a cylindrical chamber, a piston, and a piston rod. When hydraulic fluid is pumped into the cylinder, it moves the piston, which in turn applies force to the workpiece.
The hydraulic pump is responsible for generating the hydraulic fluid pressure needed to move the piston. It draws hydraulic fluid from a reservoir and delivers it to the cylinder under high pressure.
Control valves regulate the flow of hydraulic fluid to and from the cylinder, controlling the movement and force of the press. These valves can be manually operated or automated, depending on the press design.
Hydraulic fluid, typically oil, is the medium through which force is transmitted in the hydraulic system. It must have suitable properties, such as viscosity and lubricity, to ensure efficient operation and protect system components.
Pressure gauges and sensors monitor the hydraulic fluid pressure within the system. They provide real-time feedback to the operator or control system, ensuring safe and accurate press operation.
Die and tooling are the interchangeable components that come into direct contact with the workpiece. They are designed to shape, form, or cut the material as required by the specific application.
How Hydraulic Presses Work
Hydraulic presses operate based on Pascal’s principle, which states that pressure applied to a confined fluid is transmitted equally in all directions. This principle allows hydraulic presses to generate significant force with relatively small input pressure.
The operation of a hydraulic press begins with the hydraulic pump drawing fluid from the reservoir and delivering it to the cylinder. The control valves regulate the flow of fluid, directing it into the cylinder to move the piston. As the piston moves, it applies force to the workpiece placed between the die and tooling.
The hydraulic fluid plays a crucial role in this process, as it transmits the applied pressure and lubricates the system components. The pressure gauges and sensors continuously monitor the fluid pressure, providing feedback to ensure the press operates within safe limits.
The force generated by the hydraulic press can be precisely controlled by adjusting the hydraulic fluid pressure and the position of the control valves. This allows for accurate and repeatable operations, essential for high-quality manufacturing.
Manufacturing of Hydraulic Presses
The manufacturing of hydraulic presses involves several stages, from design and engineering to assembly and quality control. Each stage is critical to ensuring the press’s performance, reliability, and safety.
Design and engineering: The process begins with the design and engineering phase, where specifications for the press are developed based on the intended application. This includes selecting suitable materials, determining the required force and stroke, and designing the frame and hydraulic system.
Material selection: High-quality materials, such as high-strength steel for the frame and durable alloys for the hydraulic components, are selected to ensure the press’s longevity and performance.
Fabrication of components: The individual components of the hydraulic press, including the frame, cylinder, and pump, are fabricated using precision machining and manufacturing techniques. This ensures that each component meets the required tolerances and specifications.
Assembly process: The fabricated components are then assembled into the complete hydraulic press. This involves mounting the cylinder, pump, and control valves onto the frame, connecting the hydraulic lines, and installing the die and tooling.
Quality control and testing: Rigorous quality control measures are implemented throughout the manufacturing process to ensure the press meets all specifications and standards. This includes pressure testing the hydraulic system, verifying the accuracy of the control valves, and performing operational tests to ensure the press functions correctly.
Advancements and Innovations
The hydraulic press industry is continually evolving, driven by advancements in technology and increasing demands for efficiency and precision. Key innovations include automation and control systems, energy efficiency improvements, and smart hydraulic presses.
Automation and control systems: Modern hydraulic presses are often equipped with advanced control systems that automate the pressing process. This includes programmable logic controllers (PLCs), human-machine interfaces (HMIs), and sensors that monitor and adjust the press’s operation in real time. Automation improves efficiency, reduces the risk of human error, and enhances the consistency of the finished products.
Energy efficiency improvements: Manufacturers are focusing on developing hydraulic presses that consume less energy and have a smaller environmental footprint. This includes using variable displacement pumps, energy recovery systems, and optimizing the hydraulic system’s design to minimize energy losses.
Smart hydraulic presses: The integration of IoT (Internet of Things) technology into hydraulic presses has led to the development of smart presses. These presses can communicate with other machines and systems, providing real-time data on their status, performance, and maintenance needs. This connectivity allows for predictive maintenance, reducing downtime and extending the press’s lifespan.
Challenges in Hydraulic Press Manufacturing
The manufacturing of hydraulic presses presents several challenges, including precision and quality requirements, cost management, technological advancements, and environmental considerations.
Precision and quality requirements: Hydraulic presses must deliver consistent and precise force, which requires high levels of accuracy in the manufacturing process. Ensuring each component meets the required tolerances and specifications is critical to the press’s performance and reliability.
Cost management: The cost of materials, labor, and energy can significantly impact the overall cost of manufacturing hydraulic presses. Manufacturers must balance quality and cost to remain competitive in the market.
Technological advancements: Keeping up with technological advancements is essential for manufacturers to meet the evolving demands of the industry. This requires continuous investment in research and development to incorporate new technologies and improve existing designs.
Environmental considerations: Environmental regulations and sustainability concerns are increasingly important in hydraulic press manufacturing. Manufacturers must develop eco-friendly presses that consume less energy, use recyclable materials, and minimize their environmental impact.
Conclusion
Hydraulic presses are essential machines in various industries, providing the necessary force for processes such as metal forming, stamping, and molding. Understanding the different types of hydraulic presses, their components, and how they work is crucial for effective application and operation.
The manufacturing process of hydraulic presses involves careful design and engineering, material selection, precision fabrication, and rigorous quality control. Despite the challenges, advancements in technology and innovations are driving the industry forward, leading to more efficient, precise, and environmentally friendly hydraulic presses.
As industries continue to evolve, the hydraulic press industry must adapt and innovate to meet the demands of efficiency, precision, and sustainability. Through continuous research and development, manufacturers can enhance the performance and reliability of hydraulic presses, contributing to the success of various industrial applications.