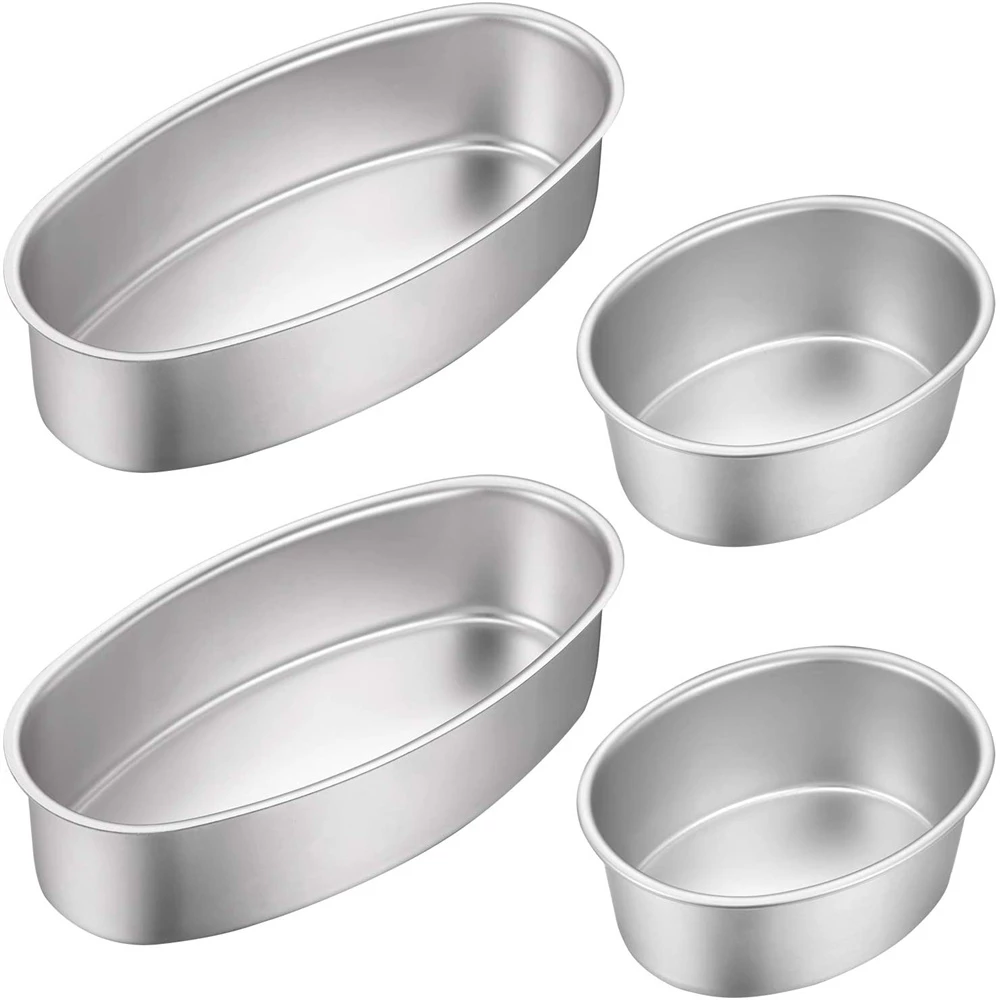
We manufacture Aluminium Cookware Manufacturing processes to cut metal in different forms. These machines are used in metalworking industries for cutting operations
The manufacturing process for aluminum cookware typically involves several steps:
- Material preparation: The raw material, which is usually aluminum sheets or discs, is prepared by cutting it into the appropriate size and shape for the cookware being produced.
- Forming: The prepared material is then formed into the shape of the cookware through a process called deep drawing. This involves placing the material into a die, which is a specialized tool that shapes the material through a series of presses and punches.
- Trimming and Finishing: After the cookware has been formed, it is trimmed to remove any excess material and smooth out any rough edges. Depending on the desired finish, the surface may also be polished or textured.
- Heat treatment: The cookware is then heat-treated to improve its strength and durability. This involves heating the cookware to a high temperature and then cooling it rapidly to create a specific crystalline structure.
- Coating: Some aluminum cookware may also be coated with a non-stick material or another protective coating to prevent food from sticking and to enhance durability.
- Packaging: The finished cookware is then packaged for shipping to retail stores or distributors.
Overall, the manufacturing process for aluminum cookware involves several steps that require specialized equipment and skilled labor. The end result is a durable, versatile product that is widely used in kitchens around the world.
Aluminium Cookware Manufacturing Process
The manufacturing process of aluminum cookware involves several steps to transform raw aluminum into high-quality cooking vessels. Here’s a comprehensive overview of the key phases involved:
- Raw Material Preparation:
- Alumina Smelting: Pure aluminum is extracted from bauxite ore through a multi-step process involving crushing, digesting, and refining to produce alumina, a high-purity crystalline form of aluminum oxide.
- Electrolysis: Alumina is further refined through electrolysis, a process that separates aluminum from its oxygen atoms. The alumina is dissolved in a molten salt bath, and an electric current is passed through the solution, causing the aluminum ions to migrate to the cathode, where they are collected and form pure aluminum ingots.
- Rolling and Extrusion:
- The aluminum ingots are heated to a molten state and then cast into slabs or billets. These slabs are then passed through a series of rollers to reduce their thickness and achieve the desired gauge (thickness) for the cookware material.
- For complex shapes, the aluminum is subjected to extrusion, a process where the molten metal is forced through a shaped die, creating long, continuous extruded tubes or sheets.
- Blanking and Deep Drawing:
- The extruded aluminum sheets or tubes are cut into individual blanks using a stamping press or laser cutting machine. These blanks are then subjected to deep drawing, a process that utilizes a punch and die to deform the metal into the desired pot shape, ensuring consistent wall thickness and smooth contours.
- Forming and Welding:
- The deep-drawn pot blanks undergo further forming processes, such as spinning and flanging, to create specific features like handles, lids, and spouts. These components are then welded onto the pot body using either MIG (metal inert gas) welding or TIG (tungsten inert gas) welding, ensuring strong and durable joints.
- Heat Treatment and Annealing:
- To improve the mechanical properties and reduce the internal stresses of the aluminum cookware, the pots are subjected to heat treatment processes. This involves heating the pots to a specific temperature range and then cooling them slowly to achieve the desired hardness, ductility, and strength.
- Polishing and Finishing:
- The cookware undergoes a series of polishing and finishing steps to remove any surface imperfections and achieve a smooth, non-stick surface. This typically involves grinding, buffing, and anodizing, which creates a thin, oxide layer that enhances corrosion resistance and provides a durable non-stick coating.
- Quality Control and Inspection:
- Each piece of cookware undergoes rigorous quality control inspections to ensure that it meets the specified standards for dimensions, surface finish, and overall quality. Inspectors check for any defects, blemishes, or irregularities, and any non-conforming items are either reworked or scrapped.
- Packaging and Distribution:
- The finished aluminum cookware is carefully packaged to protect it from damage during transportation and storage. The packaging typically consists of protective foam inserts, cardboard boxes, and labels that identify the product and its specifications.
- Compliance and Certification:
- The manufacturers of aluminum cookware adhere to strict safety standards and regulations to ensure that their products are safe for consumers. This includes testing for lead and other harmful substances and obtaining certifications from relevant safety agencies.
Steps of the Aluminium Cookware Manufacturing Process
- Material selection: The type and quality of aluminum used in the cookware is an important consideration. High-quality aluminum sheets or discs with a consistent thickness and purity are typically used to ensure the best results in terms of durability, heat distribution, and cooking performance.
- Lubrication: During the deep drawing process, lubrication reduces friction between the material and the die and prevents tearing or cracking. Different types of lubricants, such as oil or wax, may be used depending on the type of aluminum and the specific manufacturing process.
- Testing and inspection: Throughout the manufacturing process, the cookware may be tested and inspected to ensure that it meets the desired quality and performance standards. This may involve visual inspection, measurement, and testing for strength, durability, and heat distribution.
- Recycling: Aluminum is a highly recyclable material, and many manufacturers incorporate recycling into their production processes. Scrap aluminum from the manufacturing process can be collected and recycled, reducing waste and minimizing the environmental impact of the production process.
Overall, the manufacturing process for aluminum cookware involves a range of specialized equipment and skilled labor, and requires attention to detail at each step to ensure that the end product meets the desired quality and performance standards.
Cookware manufacturing is a vital industry that plays a significant role in daily life. From professional chefs to home cooks, quality cookware is essential for preparing meals efficiently and safely. The manufacturing process involves a series of steps that transform raw materials into functional and aesthetically pleasing kitchen tools. This document explores the different types of cookware, the raw materials used, the detailed manufacturing processes, technological advancements, challenges, and future trends in the industry.
Types of Cookware
Cookware comes in various types, each with unique properties and manufacturing processes. The primary types include stainless steel, aluminum, cast iron, copper, non-stick, and ceramic cookware.
Stainless steel cookware is known for its durability, resistance to rust and corrosion, and non-reactive properties. It is often used in professional kitchens and for high-quality home cookware.
Aluminum cookware is lightweight, conducts heat well, and is typically more affordable than other types. It is often anodized or coated to prevent reaction with acidic foods.
Cast iron cookware is renowned for its excellent heat retention and even cooking. It is durable and can be used on various heat sources, including induction cooktops.
Copper cookware provides superior heat conductivity, allowing precise temperature control. It is often lined with stainless steel or tin to prevent reactions with food.
Non-stick cookware features a coating that prevents food from sticking, making it easy to clean. It is popular for low-fat cooking but requires careful handling to avoid damaging the coating.
Ceramic cookware is valued for its non-reactive surface and even heating. It is often used for baking and roasting due to its ability to withstand high temperatures.
Raw Materials and Sourcing
The selection and sourcing of raw materials are critical in cookware manufacturing. The quality of the final product depends heavily on the quality of the materials used.
For stainless steel cookware, high-grade stainless steel alloys such as 18/10 (18% chromium, 10% nickel) are commonly used. These alloys offer excellent durability and resistance to corrosion.
Aluminum cookware typically uses pure aluminum or aluminum alloys. Pure aluminum is soft and lightweight, while alloys provide added strength and durability.
Cast iron cookware is made from iron alloys with a high carbon content. The iron is melted and poured into molds to create the desired shapes.
Copper cookware uses high-purity copper, often with a lining of stainless steel or tin to prevent reactions with food.
Non-stick cookware starts with a base of aluminum or stainless steel, to which a non-stick coating such as PTFE (polytetrafluoroethylene) is applied.
Ceramic cookware is made from natural clay, which is shaped and fired at high temperatures to create a hard, non-porous surface.
Quality control of raw materials involves rigorous testing and inspection to ensure they meet industry standards. Environmental considerations also play a role in material selection, with manufacturers increasingly opting for sustainable and eco-friendly options.
Manufacturing Process
The manufacturing process of cookware involves several stages, each crucial for producing high-quality products.
Forming
Forming is the initial stage where the raw materials are shaped into cookware.
Casting: Involves pouring molten metal into molds to create the desired shape. This method is commonly used for cast iron and some types of aluminum cookware.
Stamping: Uses heavy machinery to stamp out shapes from sheets of metal. This process is often used for stainless steel and aluminum cookware.
Spinning: Involves rotating a metal disc and shaping it over a form using a lathe. This method is used for making items like pots and pans from stainless steel and aluminum.
Surface Preparation
Surface preparation ensures the cookware’s surface is smooth and ready for coating or finishing.
Grinding: Removes any rough edges and surface imperfections using abrasive wheels.
Polishing: Uses finer abrasives to create a smooth, shiny surface on the cookware.
Sandblasting: Blasts the surface with fine particles to clean and texture it, preparing it for further finishing.
Coating and Finishing
Coating and finishing enhance the cookware’s performance and appearance.
Non-stick Coating Application: Involves applying a non-stick layer, usually PTFE, to the cookware surface. The coating is then baked to cure it.
Enameling: Applies a glass-like coating to metal cookware, providing a durable, non-reactive surface. This process is commonly used for cast iron and steel cookware.
Anodizing: Involves electrochemically treating aluminum to create a hard, non-reactive surface. Anodized aluminum cookware is known for its durability and resistance to corrosion.
Assembly and Attachment
Handles and knobs are attached to the cookware, ensuring they are secure and ergonomic.
Handles and Knobs: Made from materials such as stainless steel, plastic, or silicone, are attached using riveting, welding, or screwing.
Riveting and Welding: Securely attach handles and other components to the cookware, ensuring they can withstand regular use.
Quality Control and Testing
Quality control is critical in cookware manufacturing to ensure the final products meet safety and performance standards.
Inspection Procedures: Involve visual and mechanical inspection of cookware to detect any defects or irregularities.
Performance Testing: Includes tests for heat distribution, durability, and resistance to scratching and corrosion.
Safety Standards Compliance: Ensures that the cookware meets all relevant safety standards and regulations, such as those set by the FDA or other regulatory bodies.
Technological Advancements in Cookware Manufacturing
Technological advancements are continually improving the efficiency, quality, and sustainability of cookware manufacturing.
Automation and Robotics: Modern manufacturing facilities often use automated systems and robotics to handle repetitive tasks, improving consistency and reducing labor costs.
Advanced Materials: Research into new materials and coatings has led to the development of cookware with improved performance, such as better non-stick properties and enhanced durability.
Sustainable Manufacturing Practices: Manufacturers are increasingly adopting eco-friendly practices, such as using recycled materials, reducing energy consumption, and minimizing waste.
Smart Cookware: The integration of smart technology into cookware, such as temperature sensors and connectivity features, is a growing trend, providing users with more control and information during cooking.
Challenges in Cookware Manufacturing
Cookware manufacturing faces several challenges, including maintaining quality and consistency, cost management, technological advancements, and environmental regulations.
Maintaining Quality and Consistency: Ensuring that every piece of cookware meets high standards of quality and performance is challenging, particularly in high-volume production.
Cost Management: Balancing the costs of materials, labor, and production while remaining competitive in the market requires careful planning and efficiency.
Technological Advancements: Keeping up with rapid technological changes and integrating new technologies into existing manufacturing processes can be demanding.
Environmental Regulations: Compliance with environmental regulations requires manufacturers to adopt sustainable practices and invest in eco-friendly technologies, which can be costly and complex.
Future Trends in Cookware Manufacturing
The future of cookware manufacturing is likely to be shaped by innovations in materials, enhanced functionality, and sustainability.
Innovations in Materials: Continued research into new materials and coatings will likely result in cookware with superior performance, such as improved heat distribution and non-stick properties.
Enhanced Functionality and Features: Cookware with added features, such as smart technology, will provide users with more control and convenience during cooking.
Eco-friendly and Sustainable Products: As consumers become more environmentally conscious, demand for eco-friendly cookware made from sustainable materials and produced using green manufacturing practices will likely increase.
Conclusion
Cookware manufacturing is a complex and multifaceted industry that produces essential tools for cooking. Understanding the various types of cookware, raw materials, manufacturing processes, and technological advancements is crucial for producing high-quality products. Despite challenges such as maintaining quality, managing costs, and complying with environmental regulations, the industry continues to evolve and innovate. Future trends in materials, functionality, and sustainability promise to drive the industry forward, ensuring that cookware remains a vital part of daily life and culinary excellence.
EMS Metalworking Machinery
We design, manufacture and assembly metalworking machinery such as:
- Hydraulic transfer press
- Glass mosaic press
- Hydraulic deep drawing press
- Casting press
- Hydraulic cold forming press
- Hydroforming press
- Composite press
- Silicone rubber moulding press
- Brake pad press
- Melamine press
- SMC & BMC Press
- Labrotaroy press
- Edge cutting trimming machine
- Edge curling machine
- Trimming beading machine
- Trimming joggling machine
- Cookware production line
- Pipe bending machine
- Profile bending machine
- Bandsaw for metal
- Cylindrical welding machine
- Horizontal pres and cookware
- Kitchenware, hotelware
- Bakeware and cuttlery production machinery
as a complete line as well as an individual machine such as:
- Edge cutting trimming beading machines
- Polishing and grinding machines for pot and pans
- Hydraulic drawing presses
- Circle blanking machines
- Riveting machine
- Hole punching machines
- Press feeding machine
You can check our machinery at work at: EMS Metalworking Machinery – YouTube
Applications:
- Beading and ribbing
- Flanging
- Trimming
- Curling
- Lock-seaming
- Ribbing
- Flange-punching