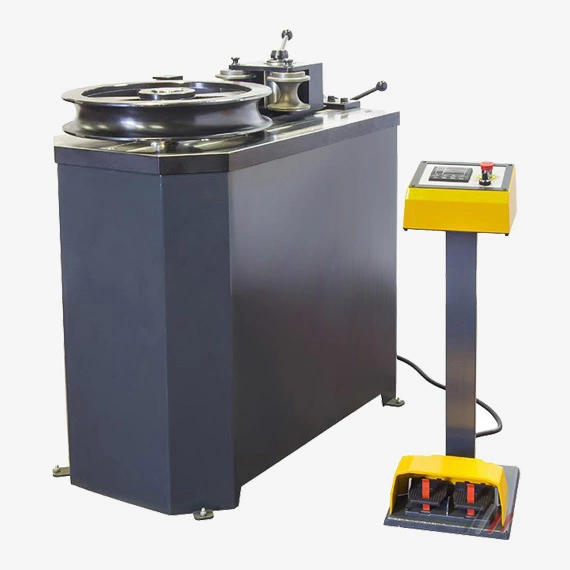
Tube Bending Machine Turkey. Tube Bending Machine Manufacturers. Tube Bending Machine Video. Tube Bending Machine Price and for Sale. Low Price & High Quality
Tube Bending Machine Turkey
A tube bending machine or a tube bender is a bending machine, designed to bend metal pipes in desired radius values. There are some different types of it, where according to the use of it, we offer:
- Automatic pipe bending machine
- Manual pipe bending machine
The automatic pipe bender operates in full automation and doesn’t need any intervention during the operation, where the manual one needs a constant attention.
According to the operating power, we offer
- Hydraulic pipe bending machine
- Mechanical pipe bending machine
After a desired power, we prefer to manufacture the tube benders with a hydraulic pump to support the necessary bending power
According to the control;
- CNC pipe bending machine
- NC pipe bending machine
A CNC pipe bending machine is operatoted by an industrial computer, where the NC pipe bending machine is operated by numeric values entered by the operator
Our pipe bending machine Turkey as a manufacturer
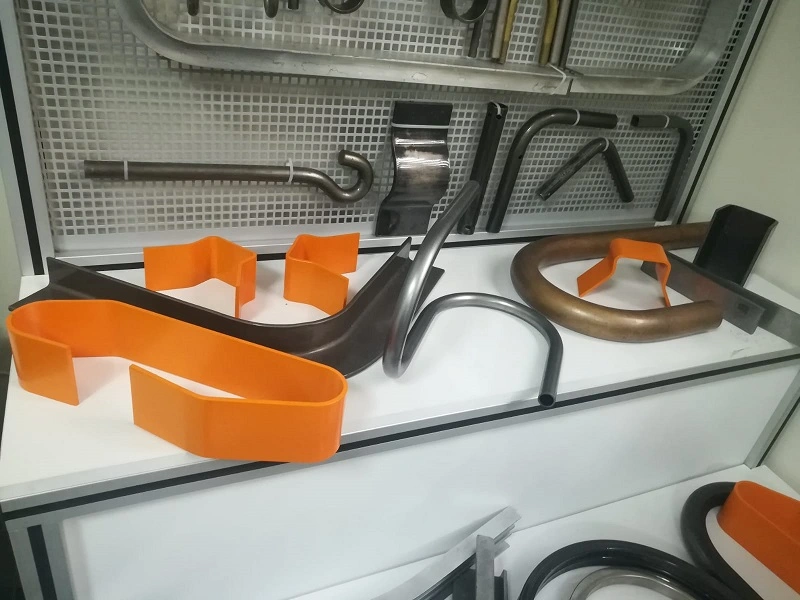
Below, you can check our main automatic hydraulic pipe bending machine range:
- EMS TB 42 Pipe bending machine
- EMS TB 60 Pipe bending machine
- EMS TB 76 Pipe bending machine
- EMS TB 100 Pipe bending machine
Above, each machine is named after the biggest diameter that can bent on the machine.
Application of Pipe Bending Machine Turkey
Main application areas of our automatic pipe bending machines are:
- Industrial – Industrial use means used in manufacturing, mining, or chemical process or in the operation of factories, processing plants, and similar sites.
- Automotive – Automotive engineers work as part of a team to design, develop, manufacture, and test vehicles.
- Agricultural – Agriculture is the art or science of cultivating soil, growing crops, and raising animals.
- Commercial Vehicles – Commercial vehicles are a type of motor vehicle used for loading goods
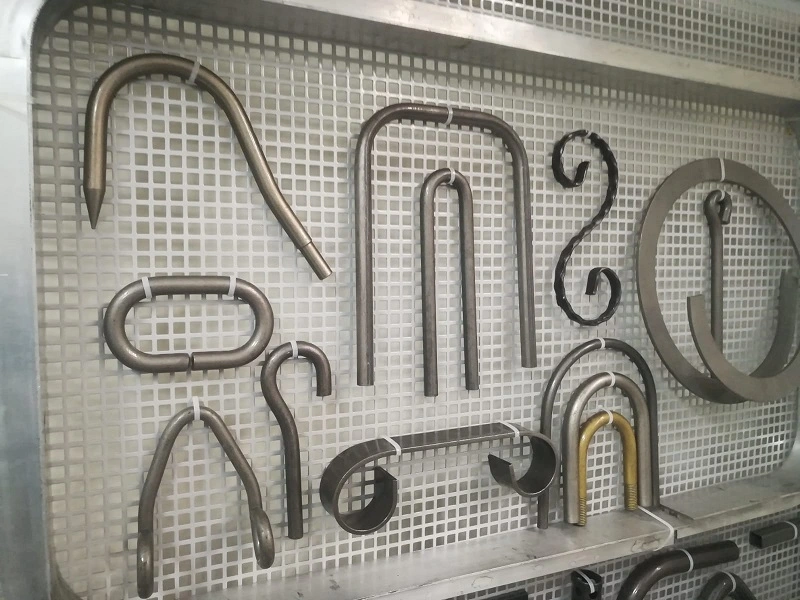
Parts of the Tube Bending Machine
Tube bending machines have various parts that work together to bend a tube accurately and consistently. Here are some of the key parts of a tube bending machine:
- Bend Die: The bend die is a critical component of a tube bending machine, as it determines the final shape of the bend. It is typically made of hardened steel and is available in various sizes and shapes to accommodate different tube sizes and bending angles.
- Clamp Die: The clamp die is used to hold the tube firmly in place during the bending process. It is designed to prevent the tube from slipping or twisting during the bend.
- Mandrel: The mandrel is an optional component that can be used to support the tube from the inside during the bend. It helps to prevent wrinkling and deformation of the tube, resulting in a smooth and consistent bend.
- Pressure Die: The pressure die is used to apply pressure to the outside of the tube during the bend, ensuring that it maintains its shape and does not collapse.
- Control System: The control system is the brain of the tube bending machine, and it manages the bending process. It typically includes a computer, software, and sensors that monitor the tube’s position, speed, and pressure during the bend.
- Drive System: The drive system provides the power to rotate the tube and move it through the bending process. It usually includes a motor, gearbox, and drive shafts.
- Bed: The bed is the main frame of the tube bending machine, providing a stable base for all the components. It is typically made of steel and is designed to withstand the forces generated during the bending process.
These are some of the critical parts of a tube bending machine, but there may be other components depending on the machine’s specific design and capabilities.
Turkey as a manufacturing hub
Turkey has become a significant manufacturing hub, especially in recent years, due to its strategic location, skilled workforce, and favorable economic policies. Turkey’s location at the crossroads of Europe, Asia, and the Middle East provides easy access to major markets and trade routes, making it an ideal location for manufacturers looking to expand their global reach.
The Turkish government has also implemented several policies aimed at promoting the country’s manufacturing industry, including tax incentives, investment subsidies, and export support programs. These policies have helped to attract both domestic and foreign companies to set up manufacturing operations in Turkey.
Turkey’s manufacturing industry is diverse and includes sectors such as automotive, electronics, textiles, food and beverages, and machinery. The country has a skilled and educated workforce, with a large pool of engineers and technicians, making it an attractive destination for manufacturers seeking to tap into the country’s technical expertise.
Additionally, Turkey’s manufacturing sector is known for its quality and competitiveness, with many Turkish companies producing high-quality products at competitive prices. This has helped to establish Turkey as a leading manufacturing hub in the region, and it continues to attract both domestic and foreign investment in various manufacturing sectors.
Overall, Turkey’s favorable location, skilled workforce, and supportive government policies have helped to establish it as a significant manufacturing hub, and it is likely to continue to attract investment in the years ahead.
Metal pipe bending machines are versatile tools used to shape and form various types of metal pipes into desired bends and curves. These machines are widely employed in a variety of industries, including plumbing, automotive, HVAC, and aerospace, to create precise bends that meet specific requirements.
Types of Metal Pipe Bending Machines
There are two primary types of metal pipe bending machines:
- Mandrel bending machines: These machines utilize an internal mandrel that supports the pipe during the bending process, ensuring consistent and precise bends without distortion or thinning of the material. Mandrel bending is particularly suitable for bending thin-walled or ductile metal pipes.
- Non-mandrel bending machines: These machines do not use an internal mandrel and instead rely on external pressure rollers to gradually deform the pipe or tube into the desired shape. Non-mandrel bending is well-suited for bending thicker-walled or harder metal pipes.
Key Features of Metal Pipe Bending Machines
- Bending capacity: This refers to the maximum pipe diameter and wall thickness that the machine can handle.
- Bending radius: This is the distance from the center of the pipe to the center of the bend. A larger bending radius creates a more gradual bend, reducing wrinkling and ovalization.
- Bending angle: This is the angle of the bend. Pipe bending machines can typically achieve bending angles of up to 180 degrees.
- Drive system: The drive system provides the power to bend the pipe. Pipe bending machines typically use hydraulic or electric drive systems.
- Control system: The control system regulates the bending process and ensures precise angle and radius control.
Applications of Metal Pipe Bending Machines
- Plumbing and piping: Pipe bending machines are used to create bends in pipes for water supply, drainage, and gas lines.
- Automotive industry: These machines are employed in the automotive industry to fabricate exhaust pipes, intake manifolds, and other tubular components with precise bends.
- HVAC systems: Pipe bending is used in HVAC systems to create bends for ductwork, refrigerant lines, and ventilation systems, ensuring smooth airflow and efficient operation.
- Furniture manufacturing: These machines are used in furniture manufacturing to produce curved metal frames for chairs, tables, and other furniture pieces, adding aesthetic appeal and functionality.
- Aerospace and defense: Pipe bending is crucial in the aerospace and defense industries for creating precise bends in aircraft components, hydraulic lines, and structural supports, ensuring the integrity and performance of critical components.
Benefits of Metal Pipe Bending Machines
- Precise bending: Pipe bending machines can achieve precise bending angles and radii, meeting stringent dimensional requirements for various applications.
- Reduced material waste: Optimized material usage minimizes waste and promotes cost-efficiency.
- Enhanced structural integrity: Precise bends maintain the structural integrity of the pipe, preventing premature failure or leaks.
- Improved flow characteristics: Preserving the pipe’s internal diameter ensures optimal flow capacity, reducing pressure drops and maintaining system efficiency.
- Increased versatility: Pipe bending machines can handle a wide range of pipe sizes, materials, and bending requirements, making them versatile tools for various industries.
Conclusion
The Pipe Bending Machine for Sale is our own production tube bending machine. Free consultation & Low Price & High Quality
Pipe bending machines are versatile tools used to shape and form various types of pipes and tubes. These machines utilize a mechanical bending mechanism to create precise bends and curves in the material. Pipe bending machines are widely used in a variety of industries, including plumbing, automotive, HVAC, and aerospace.
Types of Pipe Bending Machines
There are two main types of pipe bending machines:
- Mandrel bending machines use an internal mandrel to support the pipe during the bending process. This type of machine is typically used for bending thicker pipes and tubes.
- Non-mandrel bending machines do not use an internal mandrel. This type of machine is typically used for bending thinner pipes and tubes.
Key Features of Pipe Bending Machines
Pipe bending machines typically have the following key features:
- Bending radius: The bending radius is the distance from the center of the pipe to the center of the bend. A larger bending radius will create a more gradual bend, which can help to reduce wrinkling and ovalization.
- Bending angle: The bending angle is the angle of the bend. Pipe bending machines can typically achieve bending angles of up to 180 degrees.
- Drive system: The drive system provides the power to bend the pipe. Pipe bending machines typically use hydraulic or electric drive systems.
- Control system: The control system regulates the bending process and ensures precise angle and radius control.
Applications of Pipe Bending Machines
Pipe bending machines are used in a wide variety of applications, including:
- Plumbing: Pipe bending machines are used to create bends in pipes for water supply, drainage, and gas lines.
- Automotive: Pipe bending machines are used to create bends in exhaust pipes, intake manifolds, and other tubular components.
- HVAC: Pipe bending machines are used to create bends in ductwork, refrigerant lines, and ventilation systems.
- Furniture manufacturing: Pipe bending machines are used to create curved metal frames for chairs, tables, and other furniture pieces.
- Aerospace and defense: Pipe bending machines are used to create precise bends in aircraft components, hydraulic lines, and structural supports.
Safety Considerations for Pipe Bending Machine Operation
When operating a pipe bending machine, it is important to follow the manufacturer’s safety guidelines. Some of the key safety considerations include:
- Wear appropriate personal protective equipment (PPE): This includes safety glasses, gloves, and hearing protection.
- Secure the workpiece: The workpiece must be securely fastened to the machine’s worktable or clamping system to prevent it from moving or twisting during the bending process.
- Do not exceed the machine’s rated capacity: Overloading the machine can damage the machine and cause injury to the operator.
- Keep hands away from the bending area: The bending area can be dangerous, so it is important to keep hands away from the moving parts of the machine.
- Only operate the machine when authorized: Only authorized personnel should operate the machine.
- Read the operator’s manual: The operator’s manual contains important safety information and instructions for operating the machine.
Conclusion
Pipe bending machines are essential tools for a variety of industries. By following safety guidelines and using the machine correctly, pipe bending machines can be used to create precise bends in pipes and tubes for a variety of applications.
Tube Bender Manufacturer
Non-mandrel pipe bending machines are versatile tools used to shape and form various types of pipes and tubes without the need for a mandrel. These machines utilize a unique bending mechanism that gradually deforms the pipe or tube, creating precise bends and curves without internal support.
Advantages of Non-Mandrel Pipe Bending Machines
- Reduced Wrinkling and Ovalization: Unlike mandrel bending, non-mandrel bending minimizes wrinkling and ovalization of the pipe or tube, maintaining its structural integrity and preventing material thinning.
- Versatility: Non-mandrel machines can handle a wide range of pipe and tube sizes and materials, including steel, stainless steel, aluminum, and copper.
- Ease of Use: These machines are relatively easy to operate and require minimal setup, making them suitable for both skilled operators and beginners.
- Reduced Material Waste: Non-mandrel bending optimizes material usage, minimizing waste and promoting cost-efficiency.
- Precise Bending: Non-mandrel machines can achieve precise bending angles and radii, meeting stringent dimensional requirements.
Key Components of Non-Mandrel Pipe Bending Machines
- Frame: The frame provides the structural support for the machine and houses the bending mechanism.
- Bending Formers: These formers, also known as dies, shape the pipe or tube during the bending process.
- Pressure Roller System: The pressure rollers apply force to the pipe or tube, gradually deforming it into the desired shape.
- Drive System: The drive system powers the bending mechanism, providing the necessary torque to bend the pipe or tube.
- Control System: The control system regulates the bending process, ensuring precise angle and radius control.
Applications of Non-Mandrel Pipe Bending Machines
- Plumbing and Piping: Non-mandrel machines are widely used in plumbing and piping applications to create bends for water supply, drainage, and gas lines.
- Automotive Industry: These machines are employed in the automotive industry to fabricate exhaust pipes, intake manifolds, and other tubular components.
- HVAC Systems: Non-mandrel bending is used in HVAC systems to create bends for ductwork, refrigerant lines, and ventilation systems.
- Furniture Manufacturing: These machines are used in furniture manufacturing to produce curved metal frames for chairs, tables, and other furniture pieces.
- Aerospace and Defense: Non-mandrel bending is crucial in the aerospace and defense industries for creating precise bends in aircraft components, hydraulic lines, and structural supports.
Safety Considerations for Non-Mandrel Pipe Bending Machine Operation
- Wear Proper Personal Protective Equipment (PPE): Always wear appropriate PPE, including safety glasses, gloves, and hearing protection, when operating a non-mandrel pipe bending machine.
- Secure Workpiece Placement: Properly secure the pipe or tube to the machine’s worktable or clamping system to prevent it from moving or twisting during the bending process.
- Inspect the Bending Formers: Regularly inspect the bending formers for cracks, damage, or wear. Replace any damaged formers to ensure consistent and safe operation.
- Maintain Proper Clearance: Maintain adequate clearance between the operator and moving parts of the machine to prevent injuries.
- Follow Manufacturer Guidelines: Always follow the manufacturer’s operating instructions and safety guidelines for the specific non-mandrel pipe bending machine being used.
Conclusion
Non-mandrel pipe bending machines offer a versatile and efficient method for shaping and forming pipes and tubes without the need for a mandrel. Their ability to produce precise bends without material distortion makes them valuable tools in various industries, including plumbing, automotive, HVAC, furniture manufacturing, and aerospace. With proper safety precautions, training, and maintenance, non-mandrel pipe bending machines can contribute to efficient and safe manufacturing processes.
As a tube bender manufacturer; we design, manufacture and assembly our own hydraulic tube bender machines. In our tube bending machine range, we offer the following options:
- EMS TB 42 Pipe bending machine
- EMS TB 60 Pipe bending machine
- EMS TB 76 Pipe bending machine
- EMS TB 100 Pipe bending machine
All the machines above can be used as round tube benders and square tube bender machines.
The industry has two main categories for tube bending machines: Mandrel bender and Non-mandrel bender. All the pipe bending machines we manufacture are non-mandrel bender type.
Pipe Bending Machine for Sale
Metal pipe bending machines play a vital role in various industries, enabling the creation of precise and durable bends that meet specific functional and aesthetic requirements. Their versatility, efficiency, and ability to produce high-quality bends make them essential tools for manufacturing, construction, and other applications. With proper selection, operation, and maintenance, pipe bending machines can contribute to efficient, safe, and cost-effective production processes
Our pipe bending machines are copper tube bender, steel tube bender or aluminum tube bender. The machines are all manual tube bender machines except the operation is carried out by a foot pedal. The bending operation is automatic and the operator doesn’t have to do anything else than step on the pedal.
Our pipe bending machine for sale is also used as the exhaust tubing bender. Exhaust pipe manufacturing companies use our pipe bender to manufacture their exhaust pipes. Our tube benders are NC type. There is also a CNC tubing bender on the market for more complex tasks. These CNC tubing bender machines are almost always mandrel tube benders.
Regarding our tubing bender for sale types:
EMS TB42 can bend tubes or pipes up to 42 mm outer diameter
EMS TB60 can bend tubes or pipes up to 60 mm outer diameter
EMS TB76 can bend tubes or pipes up to 76 mm outer diameter
EMS TB100 can bend tubes or pipes up to 100 mm outer diameter
Furthermore, we manufacture pipe bender for sale for diameters less than 42 and more than 100mm for special cases.
Stainless Steel Tube Bender
For stainless steel pipes, we offer our stainless steel tube bender. This metal tube bender differs in its tube bender dies.
Hydraulic tube benders are versatile tools used to shape and form various types of tubes into desired bends and curves. These machines utilize hydraulic pressure to gradually deform the tube, creating precise bends without distortion or thinning of the material. Hydraulic tube benders are widely employed in various industries, including plumbing, automotive, aerospace, and furniture manufacturing.
Advantages of Hydraulic Tube Benders
- High Power and Precision: Hydraulic systems provide powerful and controlled bending force, enabling the production of precise bends with minimal material deformation.
- Versatility: Hydraulic tube benders can handle a wide range of tube sizes and materials, including steel, stainless steel, aluminum, and copper.
- Uniform Bends: The hydraulic system ensures consistent and repeatable bends, meeting stringent dimensional requirements for various applications.
- Reduced Material Waste: Precise bending minimizes material waste and promotes cost-effectiveness.
- Ease of Operation: Hydraulic tube benders are relatively easy to operate and require minimal setup, making them suitable for both skilled operators and beginners.
Key Components of Hydraulic Tube Benders
- Frame: The frame provides the structural support for the machine and houses the hydraulic system and bending mechanism.
- Hydraulic System: The hydraulic system generates and controls the pressure required to bend the tube.
- Bending Formers: These formers, also known as dies, shape the tube during the bending process based on the desired bend radius and angle.
- Pressure Roller System: The pressure rollers apply force to the tube, gradually deforming it into the desired shape.
- Control System: The control system regulates the bending process and ensures precise angle and radius control.
Applications of Hydraulic Tube Benders
- Plumbing and Piping: Hydraulic tube benders are used to create bends in pipes for water supply, drainage, and gas lines.
- Automotive Industry: These machines are employed in the automotive industry to fabricate exhaust pipes, intake manifolds, and other tubular components with precise bends.
- HVAC Systems: Hydraulic bending is used in HVAC systems to create bends for ductwork, refrigerant lines, and ventilation systems, ensuring smooth airflow and efficient operation.
- Furniture Manufacturing: These machines are used in furniture manufacturing to produce curved metal frames for chairs, tables, and other furniture pieces, adding aesthetic appeal and functionality.
- Aerospace and Defense: Hydraulic tube bending is crucial in the aerospace and defense industries for creating precise bends in aircraft components, hydraulic lines, and structural supports, ensuring the integrity and performance of critical components.
Safety Considerations for Hydraulic Tube Bender Operation
- Wear Proper Personal Protective Equipment (PPE): Always wear appropriate PPE, including safety glasses, gloves, and hearing protection, when operating a hydraulic tube bender.
- Secure Workpiece Placement: Properly secure the tube to the machine’s worktable or clamping system to prevent it from moving or twisting during the bending process.
- Inspect the Bending Formers: Regularly inspect the bending formers for cracks, damage, or wear. Replace any damaged formers to ensure consistent and safe operation.
- Maintain Proper Clearance: Maintain adequate clearance between the operator and moving parts of the machine to prevent injuries.
- Follow Manufacturer Guidelines: Always follow the manufacturer’s operating instructions and safety guidelines for the specific hydraulic tube bender being used.
Conclusion
Hydraulic tube benders offer a powerful and efficient method for shaping and forming tubes into precise bends. Their ability to handle a wide range of tube sizes and materials, coupled with their ease of operation and safety features, makes them valuable tools in various industries. With proper selection, operation, and maintenance, hydraulic tube benders can contribute to efficient, safe, and cost-effective manufacturing processes.
Tube Bending Equipment:
Tube bending equipment refers to machinery designed for the purpose of bending metal tubes or pipes to desired shapes and angles. These machines are commonly used in various industries such as automotive, aerospace, construction, and manufacturing. Tube bending equipment comes in various types and configurations to accommodate different tube materials, sizes, and bending requirements.
These machines typically consist of a bending die, clamp die, pressure die, mandrel (in some cases), and a bending arm or mechanism. Hydraulic or electric motors power the bending process, providing the force necessary to deform the tube to the desired shape. Some tube bending equipment utilizes CNC (Computer Numerical Control) technology for precise and automated bending operations, while others may rely on manual control.
Tube bending equipment can handle a wide range of tube materials including steel, stainless steel, aluminum, copper, and various alloys. The bending process can be categorized into several methods such as rotary draw bending, compression bending, and roll bending, each suitable for different tube materials and geometries.
These machines are crucial for fabricating components with complex shapes and tight tolerances. Applications of tube bending equipment include manufacturing exhaust systems, handrails, roll cages, hydraulic lines, and structural components.
Advanced features in modern tube bending equipment include automatic tool change systems, multi-stack bending capabilities, real-time monitoring and control systems, and safety features to prevent accidents during operation. Regular maintenance and calibration are essential to ensure the accuracy, reliability, and safety of tube bending equipment.
Tube Bender Machines:
Tube bender machines are sophisticated pieces of equipment designed for the precise and efficient bending of metal tubes. These machines are widely utilized across industries such as automotive, aerospace, HVAC (Heating, Ventilation, and Air Conditioning), and plumbing for manufacturing components with curved or angular geometries.
Tube bender machines come in various types and configurations, each tailored to specific bending requirements and tube materials. Hydraulic tube benders use hydraulic power to apply force and deform the tube, while electric tube benders utilize electric motors for the bending process. CNC (Computer Numerical Control) tube bender machines offer automated and programmable bending operations, allowing for high precision and repeatability.
The key components of a tube bender machine include the bending die, clamp die, mandrel (in some cases), pressure die, and bending arm or mechanism. These components work together to grip the tube securely, apply bending force, and control the bending process to achieve the desired bend radius and angle.
Tube bender machines can accommodate a wide range of tube sizes and materials, including steel, stainless steel, aluminum, copper, and various alloys. Depending on the application and material, different bending methods such as rotary draw bending, compression bending, or roll bending may be employed.
In addition to basic bending capabilities, modern tube bender machines often feature advanced functionalities such as multi-stack bending, automatic tool change systems, real-time monitoring and control, and safety mechanisms to prevent accidents during operation.
Efficient operation of tube bender machines requires proper setup, programming, and maintenance. Operators must ensure that the machine is calibrated correctly, tooling is in good condition, and safety protocols are followed to avoid damage to the machine or injury to personnel.
Overall, tube bender machines play a crucial role in the fabrication of various components with complex geometries, offering versatility, precision, and efficiency in tube bending applications.
Hydraulic Tube Bender:
A hydraulic tube bender is a specialized machine used for bending metal tubes or pipes using hydraulic force. These machines are widely employed in industries such as automotive, aerospace, construction, and manufacturing for fabricating components with curved or angled geometries.
At the heart of a hydraulic tube bender is a hydraulic system that generates the force necessary to deform the tube. This system typically comprises a hydraulic pump, hydraulic cylinders, valves, and hoses. The hydraulic pump pressurizes hydraulic fluid, which is then directed to the hydraulic cylinders to exert force on the tube, causing it to bend.
Hydraulic tube benders come in various configurations, including manual, semi-automatic, and fully automatic models. Manual hydraulic tube benders require the operator to manually control the bending process, while semi-automatic and fully automatic models offer greater levels of automation, allowing for programmable bending sequences and precise control over bend angles and radii.
Key components of a hydraulic tube bender include the bending die, clamp die, mandrel (if applicable), pressure die, and bending arm or mechanism. These components work together to secure the tube in place, apply bending force, and control the bending process to achieve the desired bend geometry.
Hydraulic tube benders can accommodate a wide range of tube sizes and materials, including steel, stainless steel, aluminum, copper, and various alloys. The bending process can be customized based on factors such as tube diameter, wall thickness, bend radius, and bend angle.
One of the advantages of hydraulic tube benders is their ability to exert high levels of force, making them suitable for bending thick-walled or high-strength materials. Additionally, hydraulic systems offer smooth and controlled bending motion, resulting in precise and repeatable bends.
Efficient operation of a hydraulic tube bender requires proper setup, calibration, and maintenance. Operators must ensure that the machine is equipped with the appropriate tooling, and safety protocols are followed to prevent accidents during operation.
Overall, hydraulic tube benders are indispensable tools for manufacturers seeking to produce complex tubular components with high precision and efficiency. Their versatility, reliability, and capability to handle a wide range of materials make them essential assets in modern fabrication facilities.
CNC Tube Bending:
CNC tube bending refers to the process of bending metal tubes or pipes using Computer Numerical Control (CNC) technology. This advanced manufacturing technique offers precise and automated control over the bending process, allowing for the fabrication of complex components with high accuracy and repeatability.
In CNC tube bending, the bending parameters such as bend angle, bend radius, and bend direction are programmed into a computer system, which controls the movement of the bending machine. CNC tube bending machines are equipped with servo motors, hydraulic actuators, or electric drives to apply force and deform the tube according to the programmed specifications.
The key advantage of CNC tube bending is its ability to produce intricate bends with tight tolerances, consistently and efficiently. This makes it ideal for applications requiring complex geometries, such as automotive exhaust systems, furniture frames, aerospace structures, and architectural elements.
CNC tube bending machines can handle a wide range of tube materials, including steel, stainless steel, aluminum, copper, and various alloys. They come in different configurations, including single-stack and multi-stack machines, allowing for multiple bends to be performed in a single setup.
The programming of CNC tube bending machines involves creating a bending sequence that specifies the order and parameters of each bend. This sequence can be generated using CAD/CAM (Computer-Aided Design/Computer-Aided Manufacturing) software, which allows for precise visualization and simulation of the bending process before actual fabrication.
One of the key benefits of CNC tube bending is its high productivity and efficiency. Once the bending program is set up, the machine can produce multiple identical components without the need for manual intervention, reducing labor costs and lead times.
However, CNC tube bending requires skilled operators and programmers to ensure optimal performance and quality. Proper tooling selection, machine calibration, and maintenance are also critical to achieving accurate and reliable results.
Overall, CNC tube bending offers manufacturers a versatile and cost-effective solution for producing complex tubular components with precision and efficiency, meeting the demands of modern industries for high-quality fabrication processes.
Mandrel Tube Bender:
A mandrel tube bender is a specialized machine used for bending metal tubes or pipes with the assistance of a mandrel. Mandrel bending is a technique used to maintain the shape and integrity of the tube during the bending process, particularly when tight radius bends or thin-walled tubing are involved.
The mandrel is a solid rod or flexible element inserted into the tube before bending. It supports the inner wall of the tube and prevents it from collapsing or deforming excessively during bending, ensuring consistent bend quality and minimizing wrinkling or distortion on the inside radius of the bend.
Mandrel tube benders are commonly used in industries such as automotive, aerospace, marine, and furniture manufacturing, where precise and smooth bends are required for applications such as exhaust systems, roll cages, handrails, and architectural elements.
The key components of a mandrel tube bender include the bending die, clamp die, mandrel assembly, pressure die, and bending arm or mechanism. The mandrel is typically mounted on a mandrel rod that moves axially through the tube during the bending process, supported by mandrel ball bearings to reduce friction and wear.
Mandrel tube bending can be performed using various types of bending machines, including hydraulic, electric, and CNC-controlled models. These machines apply bending force while simultaneously advancing the mandrel through the tube, ensuring uniform support and deformation throughout the bending cycle.
One of the advantages of mandrel tube bending is its ability to produce tight radius bends with minimal distortion, even in thin-walled tubing. This makes it suitable for applications requiring high-quality bends with smooth inner surfaces and precise dimensions.
However, mandrel tube bending requires careful setup and adjustment to ensure proper alignment and support of the mandrel within the tube. Additionally, the selection of mandrel materials and configurations must be tailored to the specific requirements of the bending application.
Overall, mandrel tube bending offers manufacturers a reliable and effective method for producing high-quality bent tubing components with tight tolerances and smooth internal surfaces, meeting the stringent requirements of diverse industrial applications.
Electric Tube Bending Machines:
Electric tube bending machines are advanced pieces of equipment used for bending metal tubes or pipes using electrically powered mechanisms. These machines offer precision, efficiency, and versatility in the fabrication of various tubular components across industries such as automotive, aerospace, furniture manufacturing, and HVAC (Heating, Ventilation, and Air Conditioning).
Unlike hydraulic tube benders that rely on hydraulic power, electric tube bending machines use electric motors to generate bending force and control the bending process. This allows for smoother and quieter operation compared to hydraulic systems, with precise control over bending parameters such as bend angle, radius, and speed.
Electric tube bending machines are available in different configurations, including manual, semi-automatic, and fully automatic models. Manual electric tube benders require the operator to control the bending process manually, while semi-automatic and fully automatic models offer programmable bending sequences and automated operation, reducing the need for manual intervention.
The key components of an electric tube bending machine include the bending die, clamp die, mandrel (if applicable), pressure die, and bending arm or mechanism. These components work together to secure the tube in place, apply bending force, and control the bending process to achieve the desired bend geometry.
Electric tube bending machines can handle a wide range of tube materials, including steel, stainless steel, aluminum, copper, and various alloys. They offer flexibility in bending operations, allowing for multiple bends, compound bends, and complex shapes to be achieved with high precision and repeatability.
One of the advantages of electric tube bending machines is their energy efficiency and environmental friendliness compared to hydraulic systems. Electric motors consume less energy and produce fewer emissions, making them a sustainable choice for manufacturers seeking to reduce their carbon footprint.
Efficient operation of electric tube bending machines requires proper setup, programming, and maintenance. Operators must ensure that the machine is calibrated correctly, tooling is in good condition, and safety protocols are followed to prevent accidents during operation.
Overall, electric tube bending machines provide manufacturers with a reliable and cost-effective solution for producing high-quality tubular components with precision and efficiency, meeting the demands of modern industries for advanced fabrication technologies.
Manual Pipe Bender:
A manual pipe bender is a simple yet effective tool used for bending metal pipes or tubes manually. It is commonly employed in workshops, garages, and small-scale manufacturing operations for bending pipes to desired angles and shapes. Manual pipe benders are versatile, portable, and easy to use, making them suitable for a wide range of applications in industries such as plumbing, automotive repair, and metal fabrication.
The design of a manual pipe bender typically consists of a sturdy frame, a bending lever or handle, and various dies or forms to accommodate different pipe sizes and bending radii. The pipe is clamped securely in place between the bending dies, and the operator applies force to the bending lever to deform the pipe to the desired angle.
Manual pipe benders come in different types, including lever-operated benders, rotary draw benders, and hinged benders, each offering unique advantages in terms of bending capabilities and ease of use. Lever-operated benders utilize a lever mechanism to apply bending force, while rotary draw benders use a rotating die to bend the pipe around a stationary mandrel. Hinged benders feature a hinged frame that allows for bending pipes in confined spaces or at awkward angles.
While manual pipe benders offer simplicity and affordability, they may have limitations in terms of bending capacity, precision, and repeatability compared to hydraulic or CNC-controlled benders. However, they are suitable for small-scale or occasional bending tasks where cost-effectiveness and ease of operation are priorities.
Manual pipe benders are commonly used for bending pipes in plumbing installations, vehicle exhaust systems, roll cages, handrails, and custom fabrication projects. They are particularly useful for onsite bending tasks where access to power sources or specialized equipment may be limited.
Efficient operation of a manual pipe bender requires proper technique, adequate support for the pipe during bending, and careful selection of bending dies to match the pipe diameter and material. Regular maintenance, such as lubrication of moving parts and inspection of wear components, is essential to ensure the longevity and performance of the bender.
Overall, manual pipe benders offer a practical and convenient solution for bending pipes in a variety of applications, providing flexibility and control over the bending process without the need for expensive machinery or complex setup procedures.
Automatic Pipe Bending:
Automatic pipe bending refers to the process of bending metal pipes or tubes using automated machinery equipped with advanced control systems. These machines offer high precision, efficiency, and repeatability in bending operations, making them ideal for high-volume production and complex bending geometries across various industries such as automotive, aerospace, HVAC, and furniture manufacturing.
In automatic pipe bending, the bending parameters such as bend angle, radius, and sequence are programmed into the machine’s control system, which then orchestrates the bending process without the need for manual intervention. Automatic pipe bending machines are typically equipped with hydraulic, electric, or servo-driven actuators to apply bending force and control the movement of the pipe during bending.
The key components of an automatic pipe bending machine include the bending die, clamp die, mandrel (if applicable), pressure die, and bending arm or mechanism. These components work together under the control of the machine’s software to secure the pipe, apply bending force, and achieve the desired bend geometry with high accuracy and consistency.
Automatic pipe bending machines come in various configurations, including CNC-controlled models, which offer advanced features such as multi-axis control, automatic tool change systems, and real-time monitoring of bending parameters. These machines can handle a wide range of pipe materials, including steel, stainless steel, aluminum, copper, and various alloys, and accommodate different pipe diameters and wall thicknesses.
One of the primary advantages of automatic pipe bending is its ability to achieve complex bending geometries with minimal setup time and material waste. The automated nature of the process allows for rapid production of components with consistent quality, reducing labor costs and increasing productivity.
Automatic pipe bending machines are commonly used for manufacturing components such as exhaust systems, roll cages, handrails, furniture frames, and structural elements. They offer versatility in bending operations, allowing for single bends, multiple bends, and compound bends to be performed in a single setup.
Efficient operation of automatic pipe bending machines requires skilled operators to program the bending sequences, set up the machine parameters, and ensure proper tooling selection. Regular maintenance and calibration are also essential to maintain the accuracy, reliability, and safety of the machine.
Overall, automatic pipe bending offers manufacturers a cost-effective and efficient solution for producing high-quality bent pipe components with precision and consistency, meeting the demands of modern manufacturing environments for advanced fabrication technologies.
Industrial Tube Bending Equipment:
Industrial tube bending equipment encompasses a range of machinery designed for bending metal tubes or pipes in industrial settings. These machines are crucial for various manufacturing processes across industries such as automotive, aerospace, construction, and infrastructure development.
Industrial tube bending equipment is available in different types and configurations to accommodate diverse bending requirements and production volumes. Hydraulic tube benders utilize hydraulic power to apply force and deform the tube, while electric tube benders use electric motors for bending operations. CNC (Computer Numerical Control) tube bending machines offer automated and programmable bending sequences, allowing for high precision and repeatability in bending operations.
The key components of industrial tube bending equipment include the bending die, clamp die, mandrel (if applicable), pressure die, and bending arm or mechanism. These components work together to grip the tube securely, apply bending force, and control the bending process to achieve the desired bend geometry.
Industrial tube bending equipment can handle a wide range of tube materials, including steel, stainless steel, aluminum, copper, and various alloys. The bending process can be customized based on factors such as tube diameter, wall thickness, bend radius, and bend angle to meet specific application requirements.
One of the primary advantages of industrial tube bending equipment is its ability to produce complex bends with high precision and efficiency. These machines offer versatility in bending operations, allowing for single bends, multiple bends, and compound bends to be performed in a single setup.
Industrial tube bending equipment is commonly used for manufacturing components such as exhaust systems, roll cages, handrails, hydraulic lines, structural elements, and various other tubular components used in industrial machinery and equipment.
Efficient operation of industrial tube bending equipment requires skilled operators to set up the machines, select appropriate tooling, and program bending sequences. Regular maintenance and calibration are also essential to ensure the accuracy, reliability, and safety of the equipment.
Overall, industrial tube bending equipment plays a vital role in modern manufacturing processes, offering manufacturers a cost-effective and efficient solution for producing high-quality tubular components with precision and consistency.
Metal Pipe Bending:
Metal pipe bending is the process of deforming metal pipes to achieve specific angles, curves, or shapes. It is a crucial fabrication technique employed across various industries, including construction, plumbing, automotive, aerospace, and manufacturing, to produce components with custom geometries and functionalities.
The metal pipe bending process can be carried out using different methods and equipment, depending on factors such as the material, pipe diameter, wall thickness, bend radius, and required precision. Common methods of metal pipe bending include:
- Manual Bending: Manual bending involves using handheld tools such as pipe benders or tube benders to bend pipes manually. This method is suitable for small-scale or onsite bending tasks where flexibility and portability are required.
- Hydraulic Bending: Hydraulic pipe bending utilizes hydraulic force to deform metal pipes. Hydraulic pipe bending machines offer precise control over bending parameters and are suitable for bending thick-walled or high-strength materials.
- CNC Bending: CNC (Computer Numerical Control) pipe bending involves automated bending processes controlled by computer programs. CNC pipe bending machines offer high precision, repeatability, and efficiency, making them ideal for high-volume production and complex bending geometries.
- Roll Bending: Roll bending is a method of bending pipes using rollers to gradually deform the pipe along its length. This method is commonly used for bending large-diameter pipes or achieving long-radius bends.
Metal pipe bending can be performed on various types of metal pipes, including steel, stainless steel, aluminum, copper, brass, and alloys. The choice of material depends on factors such as strength requirements, corrosion resistance, and cost considerations.
Applications of metal pipe bending are diverse and include manufacturing components such as pipelines, exhaust systems, handrails, frames, chassis, roll cages, and structural elements. Metal pipe bending is essential for creating custom solutions tailored to specific project requirements in industries ranging from infrastructure and construction to automotive and aerospace.
Efficient operation of metal pipe bending processes requires proper tooling selection, machine setup, and skilled operators to ensure accurate and consistent results. Regular maintenance and calibration of bending equipment are also essential to uphold quality standards and productivity.
Overall, metal pipe bending is a fundamental fabrication technique that enables the production of complex and customized components essential for various industrial applications, contributing to innovation and advancement across diverse sectors.
Steel Tube Bending:
Steel tube bending is a manufacturing process that involves the deformation of steel tubes to create specific shapes, angles, or curves. It is widely used across industries such as automotive, construction, aerospace, and furniture manufacturing for fabricating components with custom geometries and structural integrity.
The steel tube bending process can be achieved using various methods and equipment, depending on factors such as the diameter, wall thickness, bend radius, and required precision. Common methods of steel tube bending include:
- Hydraulic Bending: Hydraulic tube bending machines use hydraulic force to deform steel tubes. These machines offer precise control over bending parameters and are suitable for bending thick-walled or high-strength steel tubes.
- CNC Bending: CNC (Computer Numerical Control) tube bending involves automated bending processes controlled by computer programs. CNC tube bending machines offer high precision, repeatability, and efficiency, making them ideal for high-volume production and complex bending geometries.
- Roll Bending: Roll bending is a method of bending steel tubes using rollers to gradually deform the tube along its length. This method is commonly used for bending large-diameter steel tubes or achieving long-radius bends.
Steel tube bending can be performed on various grades of steel, including carbon steel, stainless steel, alloy steel, and tool steel. The choice of steel grade depends on factors such as strength requirements, corrosion resistance, and environmental conditions.
Applications of steel tube bending are diverse and include manufacturing components such as exhaust systems, roll cages, handrails, frames, chassis, structural elements, and furniture frames. Steel tube bending is essential for creating custom solutions tailored to specific project requirements in industries ranging from infrastructure and construction to automotive and aerospace.
Efficient operation of steel tube bending processes requires proper tooling selection, machine setup, and skilled operators to ensure accurate and consistent results. Regular maintenance and calibration of bending equipment are also essential to uphold quality standards and productivity.
Overall, steel tube bending is a versatile fabrication technique that enables the production of complex and customized components essential for various industrial applications, contributing to innovation and advancement across diverse sectors.
Aluminum Pipe Bender:
An aluminum pipe bender is a specialized tool or machine used for bending aluminum pipes to achieve specific angles, curves, or shapes. These bending machines are essential in various industries, including automotive, aerospace, construction, and manufacturing, where aluminum pipes are commonly used due to their lightweight, corrosion resistance, and high strength-to-weight ratio.
Aluminum pipe bending can be performed using different methods and equipment, depending on factors such as the pipe diameter, wall thickness, bend radius, and required precision. Common methods of aluminum pipe bending include:
- Manual Bending: Manual bending involves using handheld tools such as pipe benders or tube benders to bend aluminum pipes manually. This method is suitable for small-scale or onsite bending tasks where flexibility and portability are required.
- Hydraulic Bending: Hydraulic pipe bending utilizes hydraulic force to deform aluminum pipes. Hydraulic pipe bending machines offer precise control over bending parameters and are suitable for bending thick-walled or high-strength aluminum pipes.
- CNC Bending: CNC (Computer Numerical Control) pipe bending involves automated bending processes controlled by computer programs. CNC pipe bending machines offer high precision, repeatability, and efficiency, making them ideal for high-volume production and complex bending geometries.
- Roll Bending: Roll bending is a method of bending aluminum pipes using rollers to gradually deform the pipe along its length. This method is commonly used for bending large-diameter aluminum pipes or achieving long-radius bends.
Aluminum pipe bending can be performed on various grades and alloys of aluminum, including 6061-T6, 6063-T6, and 5052-H32. The choice of aluminum alloy depends on factors such as strength requirements, corrosion resistance, and specific application needs.
Applications of aluminum pipe bending are diverse and include manufacturing components such as automotive exhaust systems, aircraft frames, HVAC (Heating, Ventilation, and Air Conditioning) ducts, handrails, and structural elements. Aluminum pipe bending is essential for creating custom solutions tailored to specific project requirements in industries ranging from transportation and aerospace to construction and architecture.
Efficient operation of aluminum pipe bending processes requires proper tooling selection, machine setup, and skilled operators to ensure accurate and consistent results. Regular maintenance and calibration of bending equipment are also essential to uphold quality standards and productivity.
Overall, aluminum pipe bending is a versatile fabrication technique that enables the production of lightweight, durable, and corrosion-resistant components essential for various industrial applications, contributing to innovation and advancement across diverse sectors.
Exhaust Pipe Bender:
An exhaust pipe bender is a specialized machine used for bending metal pipes or tubes to fabricate exhaust systems for vehicles, machinery, or industrial equipment. These machines are essential in automotive repair shops, custom car fabrication shops, and manufacturing facilities where custom exhaust systems are designed and fabricated.
Exhaust pipe benders are designed specifically to handle the unique requirements of bending exhaust pipes, which often have tight bends, complex shapes, and varying diameters to fit specific vehicle models or performance needs. These machines come in various types and configurations, including manual, hydraulic, electric, and CNC-controlled models, each offering different levels of precision, automation, and flexibility.
The key components of an exhaust pipe bender include the bending die, clamp die, mandrel (if applicable), pressure die, and bending arm or mechanism. These components work together to grip the exhaust pipe securely, apply bending force, and control the bending process to achieve the desired bend geometry while maintaining the structural integrity of the pipe.
Exhaust pipe benders can handle a wide range of pipe materials, including stainless steel, aluminized steel, mild steel, and titanium, commonly used in exhaust system fabrication. They offer flexibility in bending operations, allowing for single bends, multiple bends, and compound bends to be performed in a single setup to create intricate exhaust system designs.
One of the primary advantages of exhaust pipe benders is their ability to produce custom exhaust systems tailored to specific vehicle models or performance requirements. Whether it’s a performance-oriented header system for a sports car or a durable exhaust system for a heavy-duty truck, exhaust pipe benders enable fabricators to meet the diverse needs of their customers.
Efficient operation of exhaust pipe benders requires proper tooling selection, machine setup, and skilled operators to ensure accurate and consistent results. Regular maintenance and calibration of bending equipment are also essential to uphold quality standards and productivity in exhaust system fabrication.
Overall, exhaust pipe benders play a crucial role in the automotive industry and aftermarket, enabling the fabrication of high-quality, custom exhaust systems that enhance vehicle performance, sound, and aesthetics, while meeting regulatory standards for emissions and noise levels.
Bender Dies:
Bender dies are essential components used in tube bending machines to shape and deform metal tubes or pipes into desired configurations. These dies come in various shapes and sizes to accommodate different tube diameters, wall thicknesses, bend radii, and bending methods, allowing for versatility and precision in the bending process.
The primary function of bender dies is to support and guide the tube during bending, ensuring that the bending forces are applied evenly and consistently across the tube’s cross-section. Bender dies are typically made from hardened steel or other durable materials to withstand the high pressures and stresses involved in the bending process.
There are several types of bender dies commonly used in tube bending machines, including:
- Bending Die: The bending die is the primary die used to deform the tube and create the desired bend geometry. It is shaped to match the desired bend radius and angle and is mounted on the bending arm or mechanism of the tube bending machine.
- Clamp Die: The clamp die holds the tube securely in place during the bending process, preventing it from slipping or rotating. It is typically mounted opposite the bending die and applies pressure to grip the tube firmly against the bending die.
- Mandrel Die: In mandrel bending, a mandrel die is used to support the inner wall of the tube and prevent it from collapsing or deforming excessively during bending. Mandrel dies come in various designs, including ball mandrels, plug mandrels, and wiper mandrels, depending on the specific bending requirements.
- Pressure Die: The pressure die assists in controlling the deformation of the tube and maintaining its shape during bending. It applies additional pressure to the outside of the tube, helping to prevent wrinkling or distortion on the inside radius of the bend.
Bender dies are critical components in tube bending operations, as they directly influence the quality, accuracy, and consistency of the bent tubes. Proper selection and setup of bender dies are essential to ensure that the bending process produces precise and repeatable results, meeting the specifications and requirements of the intended application.
Regular maintenance and inspection of bender dies are also necessary to identify any signs of wear or damage and prevent issues such as uneven bending, material wrinkling, or tube ovality. By ensuring the proper functioning of bender dies, manufacturers can achieve high-quality bent tubes with tight tolerances and smooth surfaces, meeting the demands of diverse industrial applications.
Tube Bending Tools:
Tube bending tools encompass a range of equipment and accessories used in the process of bending metal tubes or pipes to achieve specific shapes, angles, or configurations. These tools are essential in various industries such as automotive, aerospace, HVAC (Heating, Ventilation, and Air Conditioning), plumbing, and manufacturing, where custom tube bending is required for component fabrication.
The key tube bending tools include:
- Pipe Benders: Pipe benders are handheld or machine-mounted tools used to deform metal tubes or pipes manually or automatically. They apply bending force to the tube to create bends of various angles and radii.
- Tube Benders: Similar to pipe benders, tube benders are specifically designed for bending tubes and are available in manual, hydraulic, electric, and CNC-controlled models for different bending applications and requirements.
- Bender Dies: Bender dies are components used in tube bending machines to support and guide the tube during bending. They come in various shapes and sizes to accommodate different tube diameters, bend radii, and bending methods.
- Mandrels: Mandrels are used in mandrel bending to support the inner wall of the tube and prevent it from collapsing or deforming excessively during bending. They come in various designs, including ball mandrels, plug mandrels, and wiper mandrels, depending on the specific bending requirements.
- Clamps: Clamps are used to hold the tube securely in place during the bending process, preventing it from slipping or rotating. They apply pressure to grip the tube firmly against the bending die or mandrel.
- Pressure Dies: Pressure dies assist in controlling the deformation of the tube and maintaining its shape during bending. They apply additional pressure to the outside of the tube, helping to prevent wrinkling or distortion on the inside radius of the bend.
- Cutting Tools: Cutting tools such as tube cutters, saws, or shears are used to cut tubes to the required length before bending or to trim excess material after bending.
- Measuring and Marking Tools: Measuring tools such as rulers, calipers, and protractors are used to measure tube dimensions and angles accurately. Marking tools such as markers, scribes, or chalk are used to mark the tube surface for bending or cutting.
Efficient operation of tube bending processes requires proper selection, setup, and maintenance of tube bending tools. Operators must ensure that the tools are compatible with the tube material, size, and bending requirements to achieve accurate and consistent bending results.
Overall, tube bending tools play a crucial role in the fabrication of custom tubular components, offering manufacturers the flexibility, precision, and versatility required to meet the demands of diverse industrial applications.
Tube Bending Process:
The tube bending process involves deforming metal tubes or pipes to create specific shapes, angles, or configurations for various industrial applications. It is a critical fabrication technique used in industries such as automotive, aerospace, HVAC (Heating, Ventilation, and Air Conditioning), construction, and manufacturing, where custom tubular components are required for product assembly.
The tube bending process can be divided into several key steps:
- Tube Selection: The process begins with selecting the appropriate tube material, diameter, wall thickness, and length based on the requirements of the intended application. Factors such as material properties, corrosion resistance, and mechanical strength are considered during tube selection.
- Tube Preparation: Before bending, the tube may need to be cut to the required length using cutting tools such as tube cutters, saws, or shears. Any burrs or sharp edges resulting from cutting are removed to ensure smooth bending without damage to the tube surface.
- Tooling Setup: The next step involves setting up the tube bending machine with the necessary tooling, including bending dies, mandrels (if applicable), clamps, pressure dies, and other accessories. The tooling setup is adjusted to accommodate the tube diameter, bend radius, bend angle, and other bending parameters.
- Clamping: The tube is securely clamped in place between the bending dies to prevent movement or slippage during the bending process. Clamping pressure is applied evenly to grip the tube firmly without causing deformation or distortion.
- Bending: Once the tube is properly clamped, the bending process begins. Depending on the type of tube bending machine used (e.g., manual, hydraulic, electric, CNC-controlled), bending force is applied to deform the tube gradually to the desired angle or shape. The bending die and mandrel (if used) guide the tube’s deformation, ensuring smooth and uniform bending without wrinkling or distortion.
- Mandrel Removal (if applicable): In mandrel bending, the mandrel is gradually withdrawn from the tube as the bending process progresses to prevent interference and ensure proper tube support. The mandrel removal may be automated or manual, depending on the machine configuration.
- Inspection: After bending, the bent tube is inspected visually and dimensionally to ensure that it meets the specified tolerances and quality standards. Any defects or deviations from the desired geometry are identified and addressed as necessary.
- Finishing: Depending on the application requirements, the bent tube may undergo additional finishing operations such as deburring, cleaning, coating, or surface treatment to enhance its appearance, durability, and functionality.
Efficient operation of the tube bending process requires skilled operators, proper tooling selection, machine setup, and adherence to safety protocols. Regular maintenance and calibration of bending equipment are also essential to ensure consistent and accurate bending results.
Overall, the tube bending process is a versatile fabrication technique that enables the production of custom tubular components with precision and efficiency, meeting the diverse needs of modern industries for complex and innovative product designs.
Tube Bending Techniques:
Tube bending techniques encompass a variety of methods used to deform metal tubes or pipes to achieve specific shapes, angles, or configurations. These techniques are essential in industries such as automotive, aerospace, HVAC (Heating, Ventilation, and Air Conditioning), construction, and manufacturing, where custom tubular components are required for product assembly.
The choice of tube bending technique depends on factors such as the tube material, diameter, wall thickness, bend radius, bend angle, and required precision. Common tube bending techniques include:
- Manual Bending: Manual bending involves using handheld tools such as pipe benders or tube benders to deform tubes or pipes manually. This technique is suitable for small-scale or onsite bending tasks where flexibility and portability are required.
- Hydraulic Bending: Hydraulic tube bending utilizes hydraulic force to deform metal tubes or pipes. Hydraulic tube bending machines offer precise control over bending parameters and are suitable for bending thick-walled or high-strength materials.
- Electric Bending: Electric tube bending machines use electric motors to generate bending force and control the bending process. These machines offer smooth and controlled bending motion, making them suitable for applications requiring high precision and repeatability.
- CNC Bending: CNC (Computer Numerical Control) tube bending involves automated bending processes controlled by computer programs. CNC tube bending machines offer high precision, repeatability, and efficiency, making them ideal for high-volume production and complex bending geometries.
- Roll Bending: Roll bending is a method of bending tubes using rollers to gradually deform the tube along its length. This technique is commonly used for bending large-diameter tubes or achieving long-radius bends.
- Mandrel Bending: Mandrel bending utilizes a mandrel (a solid rod or flexible element) inserted into the tube to support the inner wall and prevent collapse or deformation during bending. This technique is used to achieve tight radius bends or maintain the tube’s shape and integrity.
- Compression Bending: Compression bending involves deforming the tube against a fixed form or die to achieve the desired bend geometry. This technique is suitable for bending thin-walled tubes or achieving precise bend angles.
- Rotary Draw Bending: Rotary draw bending utilizes a rotating die to bend the tube around a stationary mandrel. This technique offers precise control over bend angles and radii, making it suitable for high-precision bending applications.
Efficient operation of tube bending techniques requires proper tooling selection, machine setup, and skilled operators to ensure accurate and consistent results. Regular maintenance and calibration of bending equipment are also essential to uphold quality standards and productivity in tube bending operations.
Overall, tube bending techniques offer manufacturers a versatile and cost-effective solution for producing custom tubular components with precision and efficiency, meeting the demands of diverse industrial applications.
Tube Bending Machine Manufacturers:
Tube bending machine manufacturers design, produce, and distribute a wide range of machinery and equipment used in the fabrication of metal tubes or pipes. These manufacturers play a crucial role in supplying the industry with innovative and reliable solutions for bending tubes to meet the diverse needs of various applications across industries such as automotive, aerospace, construction, and manufacturing. Here are some prominent tube bending machine manufacturers:
- AMOB: AMOB is a global manufacturer of tube bending machines based in Portugal. They offer a comprehensive range of hydraulic, electric, and hybrid tube bending machines, as well as CNC-controlled models for high-precision bending applications.
- Bend-Tech: Bend-Tech is a leading manufacturer of tube and pipe bending software and equipment based in the United States. They specialize in CNC tube bending machines, roll benders, and software solutions for tube fabrication and design.
- BLM Group: BLM Group is an international manufacturer of tube and pipe processing equipment headquartered in Italy. They offer a wide range of tube bending machines, laser tube cutting systems, end-forming machines, and automation solutions for tube processing.
- Ercolina: Ercolina, part of the CML Group, is a manufacturer of tube and pipe bending machines based in the United States. They specialize in compact and portable tube benders, as well as CNC-controlled mandrel bending machines for a variety of bending applications.
- Horn Machine Tools: Horn Machine Tools is a manufacturer of tube bending machines based in the United States. They offer a range of hydraulic and CNC tube benders, as well as end-forming machines and custom solutions for tube fabrication.
- Langbow: Langbow is a manufacturer of tube bending machines based in the United Kingdom. They specialize in CNC tube bending machines, roll benders, and ancillary equipment for tube fabrication and bending applications.
- Schwarze-Robitec: Schwarze-Robitec, part of the InnoLas Solutions group, is a manufacturer of tube and pipe bending machines based in Germany. They offer a wide range of CNC-controlled tube bending machines, mandrel benders, and automation solutions for tube processing.
- Transfluid: Transfluid is a global manufacturer of tube bending and forming machines based in Germany. They specialize in CNC tube bending machines, end-forming machines, and tube processing systems for automotive, aerospace, and other industries.
These manufacturers supply a diverse range of tube bending machines tailored to specific bending requirements, production volumes, and budget considerations. They often provide comprehensive support services, including installation, training, maintenance, and technical assistance, to ensure optimal performance and customer satisfaction.
Tube Bending Machine Types:
Tube bending machines come in various types and configurations, each suited to different bending requirements, production volumes, and precision levels. Understanding the different types of tube bending machines is crucial for selecting the most suitable equipment for specific applications. Here are some common types of tube bending machines:
- Manual Tube Benders:
- Manual tube benders are operated by hand and are suitable for low-volume bending tasks or onsite fabrication where portability is essential. They are simple to use and cost-effective but require physical effort and skill to achieve accurate bends.
- Hydraulic Tube Benders:
- Hydraulic tube benders use hydraulic power to apply bending force to the tube. They offer precise control over bending parameters such as angle and radius and are suitable for bending thick-walled or high-strength tubes. Hydraulic tube benders are available in manual, semi-automatic, and fully automatic configurations.
- Electric Tube Benders:
- Electric tube benders utilize electric motors to generate bending force and control the bending process. They offer smooth and quiet operation with precise control over bending parameters. Electric tube benders are suitable for a wide range of tube materials and can be programmed for automated bending sequences.
- CNC Tube Benders:
- CNC (Computer Numerical Control) tube benders are automated machines controlled by computer programs. They offer high precision, repeatability, and efficiency in bending operations, making them ideal for high-volume production and complex bending geometries. CNC tube benders can perform multiple bends, compound bends, and variable radius bends with minimal setup time.
- Mandrel Tube Benders:
- Mandrel tube benders use a mandrel (a solid rod or flexible element) inserted into the tube to support the inner wall and prevent collapse or deformation during bending. They are suitable for achieving tight radius bends or maintaining the tube’s shape and integrity, particularly for thin-walled or high-precision bending applications.
- Roll Benders:
- Roll benders deform tubes using rollers to gradually bend the tube along its length. They are commonly used for bending large-diameter tubes or achieving long-radius bends. Roll benders offer versatility in bending operations and can produce symmetrical and asymmetrical bends with minimal distortion.
- Rotary Draw Benders:
- Rotary draw benders use a rotating die to bend the tube around a stationary mandrel. They offer precise control over bend angles and radii and are suitable for high-precision bending applications. Rotary draw benders can achieve tight radius bends and complex bend geometries with minimal material distortion.
By understanding the capabilities and limitations of each type of tube bending machine, manufacturers can select the most suitable equipment for their specific bending requirements, ensuring optimal performance, efficiency, and quality in tube fabrication processes.
Tube Bending Machine Operation:
Operating a tube bending machine requires a combination of technical knowledge, skill, and attention to detail to achieve accurate and consistent bending results. Whether using a manual, hydraulic, electric, CNC, or other type of tube bending machine, the following steps outline the basic operation process:
- Machine Setup:
- Begin by setting up the tube bending machine according to the specifications of the bending job. This includes installing the appropriate bending dies, mandrels (if applicable), clamps, and other tooling required for the specific tube diameter, wall thickness, bend radius, and bend angle.
- Tube Preparation:
- Prepare the tube for bending by cutting it to the required length using cutting tools such as tube cutters, saws, or shears. Ensure that the tube ends are square and free of burrs or sharp edges that could affect the bending process.
- Clamping:
- Clamp the tube securely in place between the bending dies to prevent movement or slippage during bending. Apply clamping pressure evenly to grip the tube firmly without causing deformation or distortion.
- Bending Sequence:
- Determine the bending sequence based on the desired bend geometry and the capabilities of the tube bending machine. Consider factors such as the number of bends, bend angles, and bend radii to optimize the bending process for efficiency and accuracy.
- Bending Process:
- Initiate the bending process according to the machine’s operating instructions. Apply bending force gradually and consistently to deform the tube to the desired angle or shape. Monitor the bending operation closely to ensure that the tube remains aligned and does not experience excessive stress or deformation.
- Mandrel Control (if applicable):
- If using mandrel bending, control the position and movement of the mandrel to support the inner wall of the tube and prevent collapse or deformation. Adjust the mandrel pressure and withdrawal speed as needed to achieve optimal bending results.
- Inspection:
- After bending, inspect the bent tube visually and dimensionally to ensure that it meets the specified tolerances and quality standards. Check for any defects, wrinkles, or distortions that may require corrective action.
- Finishing:
- Depending on the application requirements, the bent tube may undergo additional finishing operations such as deburring, cleaning, coating, or surface treatment to enhance its appearance, durability, and functionality.
- Machine Maintenance:
- After completing the bending job, perform routine maintenance tasks on the tube bending machine to ensure its optimal performance and longevity. This may include lubricating moving parts, inspecting wear components, and calibrating machine settings.
By following these steps and adhering to best practices for tube bending machine operation, operators can achieve accurate, repeatable, and high-quality bending results, meeting the requirements of diverse industrial applications. Regular training, practice, and experience are essential for mastering the art of tube bending machine operation.
Tube Bending Machine Safety:
Operating a tube bending machine involves inherent risks, including potential hazards such as crushing, entanglement, and exposure to sharp edges or high-pressure hydraulics. To ensure the safety of operators and bystanders, it’s essential to adhere to strict safety protocols and guidelines. Here are key safety measures to consider when working with tube bending machines:
- Training and Certification:
- Ensure that operators receive comprehensive training on the safe operation of tube bending machines before using them. Training should cover machine setup, tooling installation, bending procedures, emergency procedures, and hazard awareness. Operators should also be certified to operate the specific type of machine they will be using.
- Machine Inspection:
- Conduct pre-operation inspections of the tube bending machine to check for any signs of damage, wear, or malfunction. Inspect components such as hydraulic systems, clamps, bending dies, mandrels, and safety guards to ensure they are in good working condition.
- Personal Protective Equipment (PPE):
- Require operators to wear appropriate personal protective equipment (PPE) when operating tube bending machines. This may include safety glasses, ear protection, gloves, and steel-toed shoes to protect against potential hazards such as flying debris, noise, and crush injuries.
- Machine Guarding:
- Install machine guards and safety interlocks to prevent access to moving parts and hazardous areas during machine operation. Guarding should be designed to prevent accidental contact with pinch points, rotating components, and hydraulic systems.
- Emergency Stop Controls:
- Ensure that tube bending machines are equipped with easily accessible emergency stop controls that allow operators to quickly stop machine operation in case of an emergency or hazardous situation. Test emergency stop functionality regularly to verify proper operation.
- Safe Work Practices:
- Establish and enforce safe work practices for operating tube bending machines, including proper lifting techniques, material handling procedures, and machine setup procedures. Encourage operators to work methodically and attentively to minimize the risk of accidents or injuries.
- Material Handling:
- Use proper lifting equipment, such as cranes or hoists, to handle heavy tubes or materials safely. Ensure that tubes are properly supported and secured during loading, unloading, and bending to prevent accidents caused by falling or shifting materials.
- Hydraulic System Safety:
- Exercise caution when working with hydraulic systems to avoid hydraulic fluid leaks, bursts, or pressure spikes. Follow manufacturer recommendations for hydraulic system maintenance, inspection, and troubleshooting to prevent accidents or equipment damage.
- Emergency Response Procedures:
- Establish clear emergency response procedures for handling accidents, injuries, or machine malfunctions. Provide training to operators on how to respond to emergencies effectively, including first aid procedures, evacuation routes, and communication protocols.
- Regular Maintenance:
- Implement a regular maintenance schedule for tube bending machines to ensure their safe and reliable operation. This includes routine inspections, lubrication, calibration, and repair of worn or damaged components.
By prioritizing safety and implementing these measures, operators can minimize the risk of accidents and injuries associated with tube bending machine operation, creating a safer working environment for everyone involved. Additionally, fostering a culture of safety awareness and accountability among operators and supervisors is essential for maintaining a safe workplace.
Tube Bending Machine Maintenance:
Proper maintenance of tube bending machines is essential to ensure optimal performance, reliability, and longevity. Regular maintenance helps prevent unexpected breakdowns, reduces downtime, and extends the lifespan of the equipment. Here are key maintenance tasks to perform on tube bending machines:
- Scheduled Inspections:
- Conduct regular inspections of the tube bending machine to check for signs of wear, damage, or misalignment. Inspect components such as hydraulic systems, electrical wiring, clamps, bending dies, mandrels, and safety guards. Look for leaks, loose bolts, worn bearings, and other issues that may affect machine operation.
- Lubrication:
- Lubricate moving parts, bearings, and guide rails according to the manufacturer’s recommendations. Use the appropriate lubricants and grease types for each component to ensure smooth operation and prevent premature wear.
- Cleaning:
- Keep the machine clean and free of debris, dust, and metal shavings that can accumulate over time. Use compressed air, brushes, and cleaning solvents to remove dirt and debris from moving parts, electrical components, and hydraulic systems.
- Tooling Maintenance:
- Inspect bending dies, mandrels, clamps, and other tooling regularly for signs of wear, damage, or deformation. Replace worn or damaged tooling to ensure accurate and consistent bending results. Store tooling properly when not in use to prevent damage or corrosion.
- Hydraulic System Maintenance:
- Check hydraulic fluid levels regularly and top up or replace fluid as needed. Inspect hydraulic hoses, fittings, and seals for signs of leaks, cracks, or deterioration. Clean or replace hydraulic filters to ensure proper fluid filtration and system performance.
- Electrical System Maintenance:
- Inspect electrical wiring, connectors, switches, and controls for signs of wear, damage, or corrosion. Tighten loose connections and replace worn or damaged components as necessary. Test safety features such as emergency stop controls and interlocks to verify proper operation.
- Alignment and Calibration:
- Check the alignment of bending dies, mandrels, and guide rails to ensure they are properly aligned and parallel. Use precision measuring tools such as dial indicators or laser alignment devices to verify alignment and make adjustments as needed. Calibrate machine settings such as bend angles and bend radii to ensure accurate bending results.
- Operator Training:
- Provide ongoing training to machine operators on proper machine maintenance procedures, including daily inspections, lubrication schedules, and troubleshooting techniques. Encourage operators to report any abnormalities or issues with the machine promptly.
- Manufacturer Recommendations:
- Follow the manufacturer’s recommendations and guidelines for machine maintenance, including recommended service intervals, lubricants, spare parts, and troubleshooting procedures. Refer to the machine’s operation manual or contact the manufacturer for specific maintenance instructions.
- Record Keeping:
- Keep detailed records of maintenance activities, including inspection reports, lubrication schedules, repairs, and spare parts inventory. Document any maintenance issues or abnormalities observed during inspections and track their resolution over time.
By implementing a proactive maintenance program and adhering to these guidelines, manufacturers can ensure the optimal performance, reliability, and safety of their tube bending machines, ultimately maximizing productivity and minimizing downtime in tube fabrication operations.
Tube Bending Machine Troubleshooting:
Despite regular maintenance, tube bending machines may encounter issues that affect their performance and efficiency. Troubleshooting these issues promptly is essential to minimize downtime and maintain production schedules. Here are common problems encountered with tube bending machines and steps to troubleshoot them:
- Uneven Bends:
- Issue: The tube bends are not uniform or consistent, resulting in uneven angles or radii.
- Troubleshooting:
- Check the alignment of bending dies, mandrels, and guide rails to ensure they are properly aligned and parallel.
- Verify that the clamping pressure is applied evenly across the tube to prevent slippage or distortion during bending.
- Inspect the tooling for signs of wear or damage and replace worn components as needed.
- Adjust machine settings such as bend speed, pressure, and feed rate to optimize bending performance.
- Wrinkling or Cracking:
- Issue: The tube surface exhibits wrinkles, cracks, or deformations, particularly on the inner radius of the bend.
- Troubleshooting:
- Increase mandrel pressure or use a different mandrel type to support the inner wall of the tube and prevent collapse or deformation.
- Reduce the bend radius or increase the bend angle to minimize stress concentrations and prevent material failure.
- Check the tube material and wall thickness to ensure it is suitable for the bending process and application requirements.
- Inspect the tooling for sharp edges or defects that may cause scratching or gouging on the tube surface.
- Hydraulic System Issues:
- Issue: The hydraulic system experiences leaks, pressure fluctuations, or slow response times.
- Troubleshooting:
- Check hydraulic fluid levels and top up or replace fluid as needed. Inspect hydraulic hoses, fittings, and seals for signs of leaks or damage.
- Clean or replace hydraulic filters to ensure proper fluid filtration and system performance.
- Inspect hydraulic pump, valves, and cylinders for signs of wear, damage, or malfunction. Tighten loose connections and replace worn components as needed.
- Verify that the hydraulic system is properly pressurized and calibrated according to manufacturer specifications.
- Electrical System Malfunctions:
- Issue: The electrical system experiences issues such as power loss, faulty controls, or erratic behavior.
- Troubleshooting:
- Check electrical connections, switches, and controls for signs of damage, corrosion, or loose connections. Tighten loose connections and replace damaged components as needed.
- Test electrical circuits and components using a multimeter or other diagnostic tools to identify faulty or malfunctioning parts.
- Verify that emergency stop controls and safety interlocks are functioning properly and are not engaged inadvertently.
- Consult the machine’s operation manual or contact the manufacturer for specific troubleshooting procedures and recommendations.
- Material Jams or Blockages:
- Issue: The tube bending machine experiences material jams or blockages, preventing the bending process from completing.
- Troubleshooting:
- Clear any debris, metal shavings, or obstructions from the bending dies, clamps, and mandrels.
- Verify that the tube is properly aligned and seated in the bending machine to prevent binding or interference during bending.
- Check for worn or damaged tooling that may be causing material jams or blockages. Replace worn components as needed.
- Adjust machine settings such as feed rate, pressure, or speed to optimize material flow and prevent jams during bending.
- Abnormal Noise or Vibration:
- Issue: The tube bending machine produces abnormal noise, vibration, or resonance during operation.
- Troubleshooting:
- Inspect the machine’s mechanical components, including bearings, gears, and drive mechanisms, for signs of wear or damage. Replace worn or damaged parts as needed.
- Check for loose or misaligned components that may be causing noise or vibration. Tighten bolts and fasteners and realign components as needed.
- Lubricate moving parts and bearings according to the manufacturer’s recommendations to reduce friction and noise.
- Test the machine under different operating conditions to identify the source of the noise or vibration and take corrective action accordingly.
- Programming or Control Issues (for CNC Machines):
- Issue: The CNC tube bending machine experiences programming errors, control system malfunctions, or erratic behavior.
- Troubleshooting:
- Review the bending program and verify that it is correctly configured with the desired bend parameters, tooling specifications, and material properties.
- Check for software updates or patches that may address known bugs or compatibility issues with the control system.
- Reset the control system to factory settings and reprogram the machine if necessary. Ensure that all parameters and settings are entered accurately and consistently.
- Consult the machine’s operation manual or contact the manufacturer’s technical support team for assistance with troubleshooting and resolving programming or control issues.
By systematically troubleshooting and addressing these common problems, operators can maintain the performance and reliability of tube bending machines, minimizing downtime and ensuring consistent quality in tube fabrication operations. Regular monitoring, preventive maintenance, and operator training are essential for identifying and resolving issues promptly to keep production running smoothly.
Tube Bending Machine Calibration:
Calibrating a tube bending machine is essential to ensure accurate and repeatable bending results, especially in CNC-controlled machines where precise control over bending parameters is critical. Calibration involves verifying and adjusting various machine settings, tooling configurations, and control parameters to match the desired bending specifications. Here are the key steps involved in calibrating a tube bending machine:
- Tooling Inspection:
- Begin by inspecting the bending dies, mandrels (if applicable), clamps, and other tooling components for signs of wear, damage, or misalignment. Ensure that the tooling is clean, properly installed, and in good working condition.
- Tooling Setup:
- Set up the bending machine with the appropriate tooling, including bending dies, mandrels, and clamps, to match the dimensions and specifications of the tubes to be bent. Verify that the tooling is aligned and secured according to the manufacturer’s recommendations.
- Material Selection:
- Select the appropriate tube material, diameter, wall thickness, and length for calibration. Use test tubes or scrap material with known properties to simulate actual bending conditions and verify the machine’s performance.
- Program Verification (for CNC Machines):
- If using a CNC tube bending machine, verify that the bending program is correctly configured with the desired bend parameters, including bend angles, radii, feed rates, and tooling selections. Review the program code to ensure accuracy and consistency.
- Test Bends:
- Perform test bends on the calibration material using the selected tooling and bending parameters. Measure the resulting bend angles, radii, and dimensions using precision measuring tools such as protractors, calipers, or coordinate measuring machines (CMM).
- Adjustment and Fine-Tuning:
- Compare the measured bend angles and dimensions with the desired specifications and adjust the machine settings accordingly. This may involve fine-tuning parameters such as bend speed, pressure, mandrel position, and clamp pressure to achieve the desired bending results.
- Repeat Testing:
- Repeat the test bending process multiple times, making incremental adjustments as needed, until the measured bend angles and dimensions consistently match the desired specifications within acceptable tolerances.
- Documentation and Record-Keeping:
- Document the calibration process, including the machine settings, tooling configurations, test results, and any adjustments made during calibration. Maintain detailed records of calibration activities for future reference and quality assurance purposes.
- Verification and Validation:
- Once calibration is complete, verify the accuracy and repeatability of the machine’s bending performance by performing additional test bends on different materials and tube profiles. Validate the machine’s capability to produce accurate and consistent bends across a range of bending parameters.
- Periodic Recalibration:
- Schedule periodic recalibration of the tube bending machine to ensure that it maintains its accuracy and performance over time. Regular calibration intervals may vary depending on factors such as machine usage, environmental conditions, and quality control requirements.
By following these steps and maintaining a systematic approach to calibration, operators can ensure that tube bending machines produce accurate, repeatable, and high-quality bends that meet the specifications and requirements of diverse industrial applications. Calibration is essential for achieving consistent results and maintaining the integrity of tube fabrication processes.
Tube Bending Machine Software:
Tube bending machine software plays a crucial role in modern tube fabrication processes, particularly in CNC-controlled machines, by providing advanced programming capabilities, simulation tools, and automation features. Here’s an overview of the key aspects and functionalities of tube bending machine software:
- CAD/CAM Integration:
- Many tube bending machine software packages offer integration with computer-aided design (CAD) and computer-aided manufacturing (CAM) software. This allows users to import 3D models of tube assemblies or components directly into the bending software for programming and simulation.
- Bend Simulation:
- Bend simulation features enable users to visualize and analyze the bending process before actual production begins. Users can simulate the bending of tube geometries, verify bend angles, radii, and clearances, and detect potential collisions or interference issues.
- Programming Interface:
- Tube bending machine software provides an intuitive programming interface for defining bending sequences, parameters, and tooling configurations. Users can input bend angles, bend radii, tube lengths, and other specifications directly into the software to generate bending programs.
- Automatic Collision Detection:
- Advanced software packages include automatic collision detection algorithms that identify potential collisions between the tube, tooling, and machine components during the bending process. This helps prevent machine damage and ensures safe and efficient operation.
- Optimization Algorithms:
- Optimization algorithms optimize the bending sequence and tooling setup to minimize material waste, reduce setup time, and improve production efficiency. These algorithms analyze the geometry of the tube assembly and recommend the most efficient bending strategy.
- Offline Programming:
- Offline programming capabilities allow users to program and simulate bending operations offline, away from the production floor. This enables operators to optimize bending programs, test different bending strategies, and troubleshoot potential issues without disrupting production.
- Material Database:
- Tube bending machine software often includes a material database with predefined material properties such as elasticity, yield strength, and elongation. Users can select the appropriate material from the database, and the software automatically adjusts bending parameters accordingly.
- Post-Processing:
- After programming the bending sequence, users can generate machine-specific code (such as G-code for CNC machines) for execution on the tube bending machine. Post-processing features ensure compatibility with different machine controllers and optimize code for efficient machine operation.
- Data Analysis and Reporting:
- Some software packages offer data analysis and reporting tools that provide insights into bending performance, productivity, and quality metrics. Users can track bending cycle times, material utilization, error rates, and other key performance indicators for process optimization.
- Integration with Machine Controls:
- Tube bending machine software integrates seamlessly with the machine’s control system, enabling real-time communication and data exchange between the software and the machine. This allows operators to monitor and control bending operations directly from the software interface.
Overall, tube bending machine software enhances productivity, accuracy, and flexibility in tube fabrication processes by providing powerful programming, simulation, and optimization tools. By leveraging advanced software capabilities, manufacturers can streamline production workflows, reduce setup time, and improve overall process efficiency.
Tube Bending Machine Safety Features:
Tube bending machines are equipped with various safety features to protect operators, bystanders, and the equipment itself from potential hazards and accidents. These safety features are designed to mitigate risks associated with machine operation and ensure compliance with safety regulations and standards. Here are some common safety features found in tube bending machines:
- Emergency Stop (E-stop) Button:
- An emergency stop button allows operators to quickly stop machine operation in case of an emergency or hazardous situation. Activating the E-stop immediately halts all machine functions, including hydraulic movement, motorized components, and bending operations.
- Safety Interlocks:
- Safety interlocks prevent machine operation when certain conditions are not met or when safety guards are open or removed. For example, interlocks may prevent bending operations if the safety enclosure door is open or if the clamping mechanism is not engaged.
- Light Curtains or Area Sensors:
- Light curtains or area sensors create a detection zone around the machine to detect the presence of operators or objects within the machine’s operating area. If an obstruction is detected, the machine automatically stops or enters a safe mode to prevent collisions or accidents.
- Two-Hand Control:
- Two-hand control systems require operators to use both hands to initiate machine operation, reducing the risk of accidental activation. This feature ensures that operators maintain a safe distance from moving components during machine setup and operation.
- Guarding and Enclosures:
- Protective guards and enclosures shield operators from moving parts, pinch points, and rotating components during machine operation. Guards are designed to prevent access to hazardous areas and minimize the risk of contact with machine components.
- Hydraulic Overload Protection:
- Hydraulic overload protection mechanisms safeguard against excessive hydraulic pressure or force during bending operations. If the pressure exceeds predetermined limits, the system automatically releases pressure or stops the bending process to prevent damage to the machine or tooling.
- Automatic Tooling Locking:
- Automatic tooling locking mechanisms secure bending dies, mandrels, and other tooling in place during machine operation to prevent accidental dislodgement or movement. This feature ensures stability and consistency in bending operations.
- Warning Alarms and Indicators:
- Warning alarms and indicators alert operators to potential safety hazards, malfunctions, or abnormal conditions during machine operation. Audible alarms, visual indicators, or on-screen messages prompt operators to take corrective action or stop the machine if necessary.
- Operator Training and Safety Procedures:
- Comprehensive operator training programs and safety procedures educate operators on safe machine operation, hazard awareness, emergency response protocols, and proper use of personal protective equipment (PPE). Training empowers operators to identify and mitigate risks effectively.
- Compliance with Safety Standards:
- Tube bending machines are designed and manufactured in compliance with international safety standards and regulations, such as ISO 13857, ANSI B11.1, and OSHA requirements. Compliance ensures that machines meet stringent safety criteria and undergo rigorous testing and certification processes.
By incorporating these safety features into tube bending machines and promoting a culture of safety awareness among operators and maintenance personnel, manufacturers can minimize the risk of accidents, injuries, and equipment damage in tube fabrication operations. Safety should always be a top priority in the design, operation, and maintenance of tube bending machines to ensure a safe and productive working environment.
Tube Bending Machine Applications:
Tube bending machines play a vital role in various industries where the fabrication of curved or shaped tubes is required. These versatile machines offer precise control over bending parameters, allowing manufacturers to produce complex tube geometries for a wide range of applications. Here are some common industries and applications where tube bending machines are used:
- Automotive Industry:
- Tube bending machines are extensively used in the automotive industry for fabricating exhaust systems, roll cages, chassis components, and fluid transfer systems. Bends with tight radii and complex geometries are often required to fit within limited space constraints in vehicle assemblies.
- Aerospace Industry:
- In the aerospace industry, tube bending machines are used to manufacture structural components, hydraulic lines, fuel systems, and ducting for aircraft and spacecraft. High-precision bending is essential to meet strict performance, weight, and safety requirements in aerospace applications.
- Construction and Architecture:
- Tube bending machines are employed in the construction and architecture sectors to fabricate curved or ornamental metal components for building structures, staircases, handrails, and decorative elements. Bends with aesthetically pleasing profiles and consistent dimensions enhance the visual appeal of architectural designs.
- Furniture and Interior Design:
- In furniture manufacturing and interior design, tube bending machines are used to create curved metal frames, supports, and accents for chairs, tables, lighting fixtures, and other furnishings. Curved metal elements add visual interest and functionality to furniture designs.
- Medical Equipment:
- Tube bending machines play a crucial role in the production of medical equipment and devices such as hospital beds, patient lifts, IV stands, and diagnostic equipment. Bends with precise angles and radii are required to ensure ergonomic design and functionality in medical applications.
- Oil and Gas Industry:
- The oil and gas industry utilizes tube bending machines to fabricate pipelines, tubing, and structural components for offshore platforms, refineries, and petrochemical facilities. Bends with high-pressure ratings and corrosion resistance are essential for transporting fluids and gases safely and efficiently.
- Industrial Machinery:
- Tube bending machines are integrated into various types of industrial machinery and equipment, including conveyor systems, material handling equipment, hydraulic presses, and packaging machinery. Curved tubes and pipes are used for conveying materials, transferring fluids, and actuating mechanical components.
- Renewable Energy:
- In the renewable energy sector, tube bending machines are used to fabricate components for solar panel mounting systems, wind turbine towers, and geothermal heat exchangers. Curved metal structures support renewable energy infrastructure and optimize energy capture and distribution.
- Marine and Shipbuilding:
- Tube bending machines are employed in the marine and shipbuilding industry to manufacture piping systems, railing, and structural components for ships, boats, and offshore platforms. Bends with precise dimensions and corrosion-resistant coatings withstand harsh marine environments.
- Recreational Vehicles and Sports Equipment:
- Tube bending machines are used in the production of recreational vehicles (RVs), bicycles, motorcycles, and sports equipment such as ski poles, handlebars, and roll cages. Curved metal components provide strength, durability, and functionality in recreational and athletic applications.
By serving diverse industries and applications, tube bending machines contribute to the fabrication of a wide range of products and structures that enhance our daily lives, from transportation vehicles to architectural landmarks to medical devices. The versatility and precision of tube bending technology continue to drive innovation and creativity across industries, shaping the world around us.
Tube Bending Machine Automation:
Automation in tube bending machines has revolutionized the manufacturing industry by improving efficiency, precision, and productivity in tube fabrication processes. Automated tube bending systems leverage advanced technologies such as robotics, computer numerical control (CNC), and artificial intelligence (AI) to streamline production workflows and minimize manual intervention. Here are key aspects of tube bending machine automation:
- CNC Control:
- Computer numerical control (CNC) technology is at the heart of automated tube bending machines. CNC systems use pre-programmed instructions to control machine movements, including bending angles, feed rates, and tooling changes, with high precision and repeatability.
- Programmable Bending Sequences:
- Automated tube bending machines allow users to program complex bending sequences and geometries using intuitive software interfaces. Operators can define bend angles, radii, lengths, and tooling configurations for multiple bends in a single setup, minimizing manual adjustments and setup time.
- Batch and Job Management:
- Automation software enables batch processing and job management capabilities, allowing operators to queue multiple bending jobs and optimize production schedules. The software automatically selects and executes the appropriate bending programs based on job priorities and machine availability.
- Material Handling Systems:
- Automated tube bending systems may incorporate material handling equipment such as robotic arms, conveyors, and loaders/unloaders to streamline the loading and unloading of tubes. Robotic arms can pick, position, and feed tubes to the bending machine, increasing throughput and reducing manual labor.
- In-Process Measurement and Monitoring:
- Automated tube bending machines may feature in-process measurement and monitoring systems to verify bend angles, dimensions, and tolerances during production. Sensors, cameras, or laser scanners inspect the bent tubes in real-time, allowing for immediate adjustments or corrections as needed.
- Tooling Changeover Automation:
- Tooling changeover automation mechanisms enable quick and seamless interchangeability of bending dies, mandrels, and other tooling components. Automated tool changers minimize downtime between production runs and reduce the need for manual intervention by operators.
- Error Detection and Correction:
- Automated tube bending systems incorporate error detection algorithms and feedback mechanisms to identify deviations from programmed parameters or quality standards. The system can automatically pause, adjust, or scrap out-of-specification parts to maintain product quality and consistency.
- Remote Monitoring and Control:
- Some automated tube bending machines offer remote monitoring and control capabilities, allowing operators to oversee production activities, access machine status reports, and troubleshoot issues remotely via computer or mobile device. Remote access improves flexibility and responsiveness in production management.
- Predictive Maintenance:
- Automation software may include predictive maintenance features that monitor machine health, analyze performance data, and anticipate potential maintenance needs or failures. By proactively addressing maintenance issues, predictive maintenance reduces unplanned downtime and extends equipment lifespan.
- Integration with Manufacturing Systems:
- Automated tube bending machines can integrate seamlessly with enterprise resource planning (ERP) systems, manufacturing execution systems (MES), and other production management software. Data exchange between systems enables real-time monitoring, data analytics, and performance optimization across the manufacturing workflow.
By embracing automation technologies in tube bending processes, manufacturers can achieve higher throughput, lower production costs, and improved quality control, positioning themselves for success in today’s competitive manufacturing landscape. Automation enables manufacturers to meet evolving customer demands for faster turnaround times, customization options, and consistent product quality while maximizing operational efficiency and profitability.
Tube Bending Machine Innovations:
Innovations in tube bending machine technology continue to drive advancements in manufacturing processes, enabling greater precision, efficiency, and versatility in tube fabrication. From software enhancements to hardware improvements, these innovations push the boundaries of what is possible in tube bending. Here are some recent innovations in tube bending machine technology:
- AI-Driven Automation:
- Integration of artificial intelligence (AI) algorithms into tube bending machine software enables predictive maintenance, process optimization, and error detection. AI-driven automation enhances productivity and reliability while reducing downtime and material waste.
- Augmented Reality (AR) Assistance:
- AR-assisted tube bending systems overlay digital information onto the physical workspace, providing operators with real-time guidance, instructions, and visualizations during setup and operation. AR technology improves accuracy and efficiency while reducing training time for operators.
- Digital Twin Simulation:
- Digital twin simulation software creates virtual replicas of tube bending machines, allowing operators to simulate and optimize bending processes before physical production begins. Digital twin technology minimizes setup time, material waste, and trial-and-error iterations.
- Hybrid Bending Technologies:
- Hybrid tube bending machines combine different bending technologies, such as rotary draw bending, roll bending, and compression bending, into a single platform. Hybrid bending systems offer flexibility to handle diverse tube geometries and materials while achieving complex bend profiles.
- Adaptive Tooling Systems:
- Adaptive tooling systems feature self-adjusting or flexible tooling components that automatically adapt to variations in tube dimensions, wall thicknesses, and materials. Adaptive tooling improves setup flexibility and reduces the need for manual adjustments between production runs.
- Additive Manufacturing Integration:
- Integration of additive manufacturing (3D printing) technologies into tube bending processes enables the fabrication of custom tooling, fixtures, and support structures with intricate geometries. Additive manufacturing enhances design freedom and reduces lead times for tooling production.
- Smart Sensors and IoT Connectivity:
- Smart sensors embedded in tube bending machines collect real-time data on machine performance, process parameters, and environmental conditions. IoT connectivity enables remote monitoring, predictive maintenance, and data-driven decision-making for optimized production.
- Material Formability Analysis:
- Advanced material formability analysis software predicts and optimizes tube bending processes based on material properties, such as elasticity, yield strength, and strain hardening behavior. Material formability analysis ensures consistent bend quality and reduces the risk of defects or failures.
- Green Manufacturing Solutions:
- Green manufacturing initiatives focus on sustainability and environmental responsibility in tube bending processes. Innovations such as energy-efficient hydraulic systems, eco-friendly lubricants, and recyclable materials promote resource conservation and reduce carbon footprint.
- Collaborative Robotics (Cobots):
- Collaborative robots (cobots) work alongside human operators to perform repetitive or physically demanding tasks in tube bending operations. Cobots enhance productivity, safety, and ergonomics by automating routine tasks and allowing operators to focus on higher-value activities.
These innovations in tube bending machine technology drive continuous improvement and innovation in manufacturing, paving the way for enhanced productivity, quality, and competitiveness in diverse industries. By embracing cutting-edge technologies and solutions, manufacturers can stay ahead of the curve and meet the evolving demands of the global marketplace.
Tube Bending Machine Maintenance Checklist:
Regular maintenance is crucial for ensuring the optimal performance, reliability, and longevity of tube bending machines. By following a comprehensive maintenance checklist, operators can identify and address potential issues proactively, minimizing downtime and maximizing productivity. Here’s a detailed maintenance checklist for tube bending machines:
- Daily Inspection:
- Check for any signs of damage, wear, or abnormalities on the machine’s components, including hydraulic systems, electrical wiring, tooling, clamps, and safety guards.
- Inspect the machine for loose bolts, fasteners, or connections that may need tightening.
- Verify that emergency stop controls, safety interlocks, and warning indicators are functioning properly.
- Lubrication:
- Lubricate moving parts, bearings, and guide rails according to the manufacturer’s recommendations and maintenance schedule.
- Use the appropriate lubricants and grease types for each component to ensure smooth operation and prevent premature wear.
- Cleaning:
- Keep the machine clean and free of debris, dust, and metal shavings that can accumulate during operation.
- Use compressed air, brushes, and cleaning solvents to remove dirt and debris from moving parts, electrical components, and hydraulic systems.
- Tooling Inspection:
- Inspect bending dies, mandrels, clamps, and other tooling components for signs of wear, damage, or deformation.
- Replace worn or damaged tooling to ensure accurate and consistent bending results.
- Store tooling properly when not in use to prevent damage or corrosion.
- Hydraulic System Maintenance:
- Check hydraulic fluid levels and top up or replace fluid as needed.
- Inspect hydraulic hoses, fittings, and seals for signs of leaks, cracks, or deterioration.
- Clean or replace hydraulic filters to ensure proper fluid filtration and system performance.
- Electrical System Inspection:
- Inspect electrical wiring, connectors, switches, and controls for signs of wear, damage, or corrosion.
- Tighten loose connections and replace worn or damaged components as needed.
- Test emergency stop controls, safety interlocks, and machine controls to verify proper operation.
- Alignment and Calibration:
- Check the alignment of bending dies, mandrels, and guide rails to ensure they are properly aligned and parallel.
- Use precision measuring tools such as dial indicators or laser alignment devices to verify alignment and make adjustments as needed.
- Calibrate machine settings such as bend angles and bend radii to ensure accurate bending results.
- Operator Training and Safety Procedures:
- Provide ongoing training to machine operators on proper maintenance procedures, including daily inspections, lubrication schedules, and troubleshooting techniques.
- Emphasize the importance of safety protocols, hazard awareness, and proper use of personal protective equipment (PPE) during machine operation.
- Documentation and Record-Keeping:
- Maintain detailed records of maintenance activities, including inspection reports, lubrication schedules, repairs, and spare parts inventory.
- Document any maintenance issues or abnormalities observed during inspections and track their resolution over time.
- Manufacturer Recommendations:
- Follow the manufacturer’s recommendations and guidelines for machine maintenance, including recommended service intervals, lubricants, spare parts, and troubleshooting procedures.
- Refer to the machine’s operation manual or contact the manufacturer for specific maintenance instructions and technical support.
By adhering to this maintenance checklist and conducting regular inspections and servicing, operators can ensure the safe and reliable operation of tube bending machines, minimize the risk of breakdowns or accidents, and prolong the lifespan of the equipment. Preventive maintenance is key to maintaining peak performance and maximizing productivity in tube fabrication operations.
Tube Bending Machine Safety Guidelines:
Safety is paramount when operating tube bending machines to prevent accidents, injuries, and damage to equipment. Following comprehensive safety guidelines ensures a safe working environment for operators and other personnel involved in tube bending operations. Here are essential safety guidelines for tube bending machine operation:
- Operator Training:
- All operators should receive thorough training on the safe operation of tube bending machines before using the equipment. Training should cover machine controls, emergency procedures, hazard awareness, and proper use of personal protective equipment (PPE).
- Read and Understand Manuals:
- Operators should read and understand the machine’s operation manual, safety instructions, and warning labels before operating the equipment. Familiarity with the machine’s controls, features, and safety mechanisms is essential for safe operation.
- Wear Personal Protective Equipment (PPE):
- Operators must wear appropriate PPE, including safety glasses, hearing protection, gloves, and steel-toed boots, to protect against potential hazards such as flying debris, noise, and impact injuries.
- Inspect the Machine:
- Conduct a pre-operation inspection of the tube bending machine to check for any signs of damage, wear, or malfunction. Ensure that all safety guards, interlocks, and emergency stop controls are in place and functioning properly.
- Secure Workpiece:
- Secure the workpiece firmly in place using clamps or fixtures before starting the bending process. Proper workpiece fixation prevents movement or slippage during bending, reducing the risk of accidents.
- Use Correct Tooling:
- Use the correct bending dies, mandrels, and tooling specified for the tube material, size, and bending requirements. Ensure that tooling is installed and aligned properly to prevent binding, deflection, or tool breakage during bending.
- Avoid Hand Contact:
- Keep hands and fingers away from moving parts, pinch points, and rotating components during machine operation. Do not attempt to reach into the bending area while the machine is running.
- Monitor Machine Operation:
- Maintain constant vigilance over the tube bending machine while it is in operation. Watch for any abnormal sounds, vibrations, or movements that may indicate a problem with the machine or tooling.
- Emergency Stop:
- Familiarize yourself with the location and operation of the emergency stop (E-stop) button on the machine. In case of an emergency or hazardous situation, press the E-stop button to immediately halt machine operation.
- Proper Handling of Materials:
- Handle tubes and materials with care to avoid injuries and accidents. Lift and carry materials using proper lifting techniques and equipment, and be mindful of sharp edges and heavy loads.
- Clear Work Area:
- Keep the work area clean and free of clutter, tools, and debris that could pose a tripping or slipping hazard. Maintain clear pathways and emergency exits for quick evacuation if needed.
- Report Hazards and Incidents:
- Report any safety hazards, near misses, or incidents to a supervisor or safety officer immediately. Addressing safety concerns promptly helps prevent accidents and improves overall workplace safety.
By adhering to these safety guidelines and practicing good safety habits, operators can minimize the risk of accidents and ensure a safe working environment when operating tube bending machines. Safety awareness, proper training, and adherence to safety protocols are essential for protecting personnel and equipment in tube fabrication operations.
Tube Bending Machine: Preventive Maintenance Guide
Preventive maintenance is essential for keeping tube bending machines in optimal working condition, reducing downtime, and extending their lifespan. A proactive approach to maintenance helps identify potential issues before they escalate into costly problems. Here’s a preventive maintenance guide for tube bending machines:
- Daily Maintenance:
- Clean the machine thoroughly, removing any debris, dust, or metal shavings from the working area, tooling, and components.
- Check for leaks, loose bolts, or abnormal sounds during operation. Address any issues promptly.
- Weekly Maintenance:
- Inspect hydraulic hoses, fittings, and seals for signs of wear or damage. Replace any worn or damaged components.
- Lubricate moving parts, bearings, and guide rails according to the manufacturer’s recommendations.
- Monthly Maintenance:
- Perform a comprehensive inspection of all machine components, including electrical wiring, switches, and controls.
- Verify the alignment of bending dies, mandrels, and tooling. Make adjustments if necessary.
- Quarterly Maintenance:
- Check the condition of hydraulic fluid and filters. Replace the hydraulic fluid and filters if they are contaminated or degraded.
- Conduct a test bend using scrap material to verify the accuracy and consistency of bending results.
- Bi-annual Maintenance:
- Inspect the electrical system, including wiring, connectors, and relays, for signs of wear or corrosion. Clean or replace any damaged components.
- Verify the calibration of machine settings such as bend angles and radii. Recalibrate if necessary.
- Annual Maintenance:
- Disassemble and inspect critical components such as the bending head, clamping mechanism, and pressure dies for wear, damage, or fatigue.
- Replace worn or damaged components and perform any necessary repairs or adjustments.
- Spare Parts Inventory:
- Maintain an inventory of commonly used spare parts, including seals, bearings, hydraulic fittings, and electrical components.
- Replace spare parts as needed during routine maintenance to minimize downtime.
- Software Updates:
- Keep the machine’s software and firmware up to date with the latest updates and patches provided by the manufacturer.
- Ensure compatibility with new features and improvements to optimize machine performance.
- Documentation and Record-Keeping:
- Keep detailed records of all maintenance activities, including inspection reports, repairs, parts replacements, and calibration data.
- Use a maintenance log or software system to track maintenance schedules and upcoming tasks.
- Operator Training:
- Provide ongoing training for machine operators on preventive maintenance procedures, including daily inspections, lubrication schedules, and troubleshooting techniques.
- Empower operators to identify and report potential maintenance issues early to prevent downtime and maintain productivity.
By following this preventive maintenance guide and adhering to a regular maintenance schedule, operators can ensure the reliable performance of tube bending machines and minimize the risk of unexpected breakdowns or malfunctions. Preventive maintenance is a proactive strategy for optimizing machine uptime, reducing maintenance costs, and maximizing the return on investment in tube bending equipment.
Tube Bending Machine: Troubleshooting Guide
Troubleshooting is essential for identifying and resolving issues that may arise during tube bending machine operation. By systematically diagnosing and addressing problems, operators can minimize downtime and maintain productivity. Here’s a troubleshooting guide for common issues encountered with tube bending machines:
- Machine Does Not Power On:
- Check the power source to ensure the machine is receiving electricity.
- Verify that the power cord is securely connected and not damaged.
- Inspect the circuit breaker or fuse box for tripped breakers or blown fuses.
- Hydraulic System Not Functioning:
- Check hydraulic fluid levels and top up if necessary.
- Inspect hydraulic hoses, fittings, and seals for leaks or damage. Replace as needed.
- Ensure that the hydraulic pump is running and generating sufficient pressure.
- Electrical Issues:
- Verify that all electrical connections are secure and properly connected.
- Check for loose wires, damaged connectors, or corroded terminals.
- Test electrical components such as switches, relays, and sensors for functionality.
- Tooling Problems:
- Inspect bending dies, mandrels, and tooling components for wear, damage, or misalignment.
- Verify that the tooling is installed correctly and securely fastened.
- Replace worn or damaged tooling as needed to ensure accurate bending results.
- Bending Inaccuracies:
- Check the calibration of machine settings such as bend angles, radii, and feed rates.
- Verify the alignment of bending dies, mandrels, and guide rails. Adjust if necessary.
- Ensure that material feed and clamping mechanisms are operating smoothly.
- Machine Vibration or Noise:
- Inspect the machine for loose bolts, fasteners, or components that may be causing vibration.
- Check for worn or damaged bearings, bushings, or drive belts.
- Lubricate moving parts and bearings to reduce friction and noise.
- Safety System Malfunctions:
- Test emergency stop controls, safety interlocks, and light curtains for proper operation.
- Check for obstructions or debris that may be interfering with safety sensors.
- Verify that safety guards and enclosures are in place and functioning correctly.
- Material Feeding Issues:
- Ensure that the material feed mechanism is aligned properly and free from obstructions.
- Check for burrs, debris, or irregularities on the material that may impede feeding.
- Adjust feed rollers or guides as needed to facilitate smooth material feeding.
- Program Errors or Malfunctions:
- Review the bending program for errors or inconsistencies in bend angles, lengths, or tooling selections.
- Verify that the correct program is loaded and selected for the desired bending operation.
- Check for software updates or patches that may address program bugs or glitches.
- Consult Manufacturer Documentation:
- If troubleshooting steps do not resolve the issue, refer to the machine’s operation manual or contact the manufacturer for technical support.
- Provide detailed information about the problem encountered, including any error codes or symptoms observed, to facilitate troubleshooting and resolution.
By following this troubleshooting guide and systematically addressing issues as they arise, operators can maintain the reliable performance of tube bending machines and minimize downtime in tube fabrication operations. Regular maintenance, operator training, and prompt resolution of problems are key to ensuring optimal productivity and efficiency in tube bending processes.
Tube Bending Machine: Safety Procedures
Operating tube bending machines requires strict adherence to safety procedures to prevent accidents, injuries, and damage to equipment. Here’s a comprehensive guide to safety procedures for tube bending machine operation:
- Operator Training:
- All operators must undergo comprehensive training on the safe operation of tube bending machines.
- Training should cover machine controls, emergency procedures, hazard awareness, and proper use of personal protective equipment (PPE).
- Read and Understand Manuals:
- Operators should read and understand the machine’s operation manual, safety instructions, and warning labels before operating the equipment.
- Familiarity with the machine’s controls, features, and safety mechanisms is essential for safe operation.
- Wear Personal Protective Equipment (PPE):
- Operators must wear appropriate PPE, including safety glasses, hearing protection, gloves, and steel-toed boots, to protect against potential hazards such as flying debris, noise, and impact injuries.
- Machine Inspection:
- Conduct a pre-operation inspection of the tube bending machine to check for any signs of damage, wear, or malfunction.
- Ensure that all safety guards, interlocks, and emergency stop controls are in place and functioning properly.
- Secure Workpiece:
- Secure the workpiece firmly in place using clamps or fixtures before starting the bending process.
- Proper workpiece fixation prevents movement or slippage during bending, reducing the risk of accidents.
- Tooling Inspection:
- Inspect bending dies, mandrels, clamps, and other tooling components for signs of wear, damage, or deformation.
- Replace worn or damaged tooling to ensure accurate and consistent bending results.
- Avoid Hand Contact:
- Keep hands and fingers away from moving parts, pinch points, and rotating components during machine operation.
- Do not attempt to reach into the bending area while the machine is running.
- Monitor Machine Operation:
- Maintain constant vigilance over the tube bending machine while it is in operation.
- Watch for any abnormal sounds, vibrations, or movements that may indicate a problem with the machine or tooling.
- Emergency Stop:
- Familiarize yourself with the location and operation of the emergency stop (E-stop) button on the machine.
- In case of an emergency or hazardous situation, press the E-stop button to immediately halt machine operation.
- Proper Handling of Materials:
- Handle tubes and materials with care to avoid injuries and accidents.
- Lift and carry materials using proper lifting techniques and equipment, and be mindful of sharp edges and heavy loads.
- Clear Work Area:
- Keep the work area clean and free of clutter, tools, and debris that could pose a tripping or slipping hazard.
- Maintain clear pathways and emergency exits for quick evacuation if needed.
- Report Hazards and Incidents:
- Report any safety hazards, near misses, or incidents to a supervisor or safety officer immediately.
- Addressing safety concerns promptly helps prevent accidents and improves overall workplace safety.
By following these safety procedures and practices, operators can minimize the risk of accidents and ensure a safe working environment when operating tube bending machines. Safety awareness, proper training, and adherence to safety protocols are essential for protecting personnel and equipment in tube fabrication operations.
Tube Bending Machine: Quality Control Measures
Ensuring quality control is crucial in tube bending operations to produce accurate, consistent, and defect-free parts. Implementing effective quality control measures helps maintain product integrity, meet customer specifications, and minimize waste. Here are essential quality control measures for tube bending machine operations:
- Material Inspection:
- Conduct thorough inspections of raw materials, including tubes and pipes, to ensure they meet specified dimensions, tolerances, and material properties.
- Verify material composition, wall thickness, and surface finish to prevent defects and ensure proper bendability.
- Tooling Verification:
- Inspect bending dies, mandrels, clamps, and other tooling components to ensure they are in good condition and free from damage or wear.
- Verify that tooling dimensions and profiles match the desired bend specifications and material requirements.
- Setup Verification:
- Verify machine setup parameters, including bend angles, radii, lengths, and feed rates, before initiating production runs.
- Use precision measuring tools such as calipers, micrometers, and protractors to confirm setup accuracy and consistency.
- First Article Inspection (FAI):
- Perform a first article inspection on the initial parts produced in a production run to verify conformance to customer specifications and quality standards.
- Compare measured dimensions and bend angles against engineering drawings or CAD models to identify any deviations or discrepancies.
- In-Process Inspection:
- Implement in-process inspection checkpoints at key stages of the bending process to monitor part quality and detect defects or variations early.
- Use visual inspection, measurement tools, and non-destructive testing methods to assess bend accuracy, surface finish, and dimensional integrity.
- Bend Angle Measurement:
- Use precision angle measurement tools such as angle gauges, digital protractors, or optical comparators to verify bend angles and ensure compliance with specified tolerances.
- Calibrate measurement equipment regularly to maintain accuracy and reliability.
- Dimensional Control:
- Measure critical dimensions such as bend radius, wall thickness, and centerline radius to verify part conformance and dimensional accuracy.
- Document measurement data and compare results against established quality criteria to identify trends or deviations.
- Surface Inspection:
- Inspect bent tubes for surface defects, such as scratches, dents, wrinkles, or surface irregularities, that may affect part integrity or functionality.
- Use visual inspection or surface profiling techniques to assess surface quality and identify imperfections.
- Final Inspection:
- Conduct a final inspection of finished parts to ensure they meet all specified requirements and quality standards before releasing them for assembly or shipment.
- Document inspection results and generate inspection reports for traceability and quality assurance purposes.
- Continuous Improvement:
- Implement feedback mechanisms to capture insights from quality control processes and identify opportunities for process improvement or corrective actions.
- Foster a culture of continuous improvement and quality excellence to drive ongoing enhancements in product quality, efficiency, and customer satisfaction.
By implementing robust quality control measures throughout the tube bending process, manufacturers can maintain high product quality standards, meet customer expectations, and enhance their competitive edge in the marketplace. Quality control is integral to achieving operational excellence and delivering value to customers in tube fabrication operations.
Tube Bending Machine: Environmental Considerations
While operating tube bending machines, it’s essential to consider environmental factors to minimize the impact on the surroundings and promote sustainable manufacturing practices. Here are key environmental considerations for tube bending machine operations:
- Energy Efficiency:
- Optimize machine settings and operating parameters to minimize energy consumption during tube bending operations.
- Use energy-efficient hydraulic systems, motors, and controls to reduce power consumption and environmental impact.
- Waste Reduction:
- Implement waste reduction strategies to minimize material waste generated during tube bending processes.
- Optimize nesting layouts and material utilization to maximize the yield from raw materials and reduce scrap generation.
- Recycling and Reuse:
- Establish recycling programs to collect and recycle scrap metal, chips, and other waste generated during tube bending operations.
- Explore opportunities to reuse or repurpose scrap materials within the manufacturing process or supply chain.
- Emissions Control:
- Install and maintain emissions control devices such as dust collectors, fume extractors, and air filtration systems to capture airborne pollutants generated during tube bending operations.
- Use low-emission lubricants and cutting fluids to minimize air pollution and environmental impact.
- Hazardous Materials Management:
- Properly manage and dispose of hazardous materials such as hydraulic fluids, lubricants, and coolant fluids used in tube bending processes.
- Follow regulatory guidelines and best practices for handling, storage, and disposal of hazardous substances to prevent environmental contamination.
- Water Conservation:
- Implement water conservation measures to minimize water usage in cooling and lubrication systems associated with tube bending machines.
- Recycle or reuse water where feasible, and invest in water-efficient equipment and technologies to reduce overall water consumption.
- Noise Reduction:
- Implement noise control measures such as soundproofing enclosures, barriers, and damping materials to minimize noise pollution from tube bending operations.
- Conduct regular noise assessments and provide hearing protection for workers exposed to high noise levels.
- Green Supply Chain Practices:
- Collaborate with suppliers to source materials and components from environmentally responsible sources with minimal environmental impact.
- Evaluate suppliers based on their commitment to sustainability, environmental management practices, and adherence to green certifications or standards.
- Environmental Compliance:
- Ensure compliance with local, regional, and national environmental regulations governing air quality, water quality, waste management, and hazardous materials handling.
- Monitor changes in environmental regulations and proactively adapt processes and practices to meet evolving compliance requirements.
- Environmental Awareness and Education:
- Foster environmental awareness and education among employees, suppliers, and stakeholders to promote a culture of environmental responsibility and sustainability.
- Provide training on environmental best practices, pollution prevention techniques, and the importance of minimizing environmental impact in tube bending operations.
By incorporating these environmental considerations into tube bending machine operations, manufacturers can minimize their environmental footprint, mitigate risks to the environment and public health, and contribute to a more sustainable future for the manufacturing industry. Environmental stewardship and sustainability are integral to responsible business practices and long-term success in today’s global marketplace.
Tube Bending Machine: Cost Reduction Strategies
Reducing costs in tube bending operations is essential for improving profitability and maintaining competitiveness in the manufacturing industry. Here are key strategies to minimize costs associated with tube bending machines:
- Optimized Material Utilization:
- Implement nesting software to optimize material usage and minimize scrap during tube cutting and bending processes.
- Design parts and assemblies with optimized geometries to reduce material waste and maximize material yield.
- Lean Manufacturing Practices:
- Implement lean manufacturing principles such as 5S, value stream mapping, and kaizen to identify and eliminate waste in tube bending operations.
- Streamline production workflows, reduce setup times, and improve overall efficiency to lower production costs.
- Inventory Management:
- Implement just-in-time (JIT) inventory practices to minimize inventory holding costs and reduce excess material storage.
- Utilize inventory management software to track material usage, monitor stock levels, and optimize replenishment schedules.
- Equipment Maintenance:
- Implement a proactive maintenance program to minimize unplanned downtime and reduce repair costs associated with tube bending machines.
- Conduct regular inspections, lubrication, and preventive maintenance to prolong equipment lifespan and optimize performance.
- Energy Efficiency:
- Upgrade to energy-efficient tube bending machines and auxiliary equipment to reduce energy consumption and lower utility costs.
- Implement energy management strategies such as lighting retrofits, equipment scheduling, and energy monitoring to identify and reduce energy waste.
- Tooling Optimization:
- Invest in high-quality tooling and dies that offer longer tool life and better performance, reducing tooling replacement costs and downtime.
- Implement tool management systems to track tool usage, monitor wear, and schedule maintenance or replacement as needed.
- Labor Efficiency:
- Cross-train employees to perform multiple tasks and roles within tube bending operations, maximizing workforce flexibility and productivity.
- Implement performance incentives, training programs, and workflow optimizations to improve labor efficiency and reduce labor costs.
- Process Automation:
- Invest in automation technologies such as robotic loading and unloading systems, CNC controls, and robotic welding to increase production throughput and reduce labor costs.
- Automate repetitive tasks and manual processes to minimize human error, improve consistency, and free up labor for higher-value activities.
- Supplier Negotiation:
- Negotiate favorable terms and pricing with suppliers for raw materials, tooling, and consumables used in tube bending operations.
- Explore alternative suppliers, sourcing options, and bulk purchasing strategies to reduce material costs and improve supply chain efficiency.
- Continuous Improvement:
- Foster a culture of continuous improvement and innovation to identify and implement cost-saving opportunities throughout tube bending operations.
- Encourage employee involvement, idea generation, and process optimization initiatives to drive sustainable cost reductions and operational efficiencies.
By implementing these cost reduction strategies and continuously optimizing processes, manufacturers can improve profitability, enhance competitiveness, and achieve long-term success in tube bending operations. Cost reduction efforts should be aligned with overall business goals and objectives, focusing on maximizing value and efficiency across the entire manufacturing value chain.
Tube Bending Machine: Workflow Optimization
Optimizing the workflow in tube bending operations is crucial for maximizing efficiency, reducing lead times, and improving overall productivity. Here are key strategies to streamline the workflow and enhance performance in tube bending machine operations:
- Process Mapping:
- Map out the entire tube bending process from raw material procurement to finished product delivery.
- Identify each step in the process, including material handling, cutting, bending, inspection, and packaging.
- Value Stream Analysis:
- Conduct a value stream analysis to identify value-added and non-value-added activities in the tube bending process.
- Eliminate waste and inefficiencies by optimizing process flow and reorganizing workstations for smoother operations.
- Batching and Sequencing:
- Group similar parts or orders together to minimize setup times and maximize production efficiency.
- Sequence production runs to minimize changeovers and optimize machine utilization.
- Standardized Work Instructions:
- Develop standardized work instructions for tube bending machine setup, operation, and maintenance.
- Ensure consistency and repeatability by providing clear guidelines and procedures for operators to follow.
- Cross-Training:
- Cross-train operators to perform multiple tasks within tube bending operations, including machine setup, programming, and quality inspection.
- Increase workforce flexibility and agility to adapt to changing production demands and minimize bottlenecks.
- Equipment Layout and Ergonomics:
- Optimize the layout of equipment, workstations, and material flow to minimize unnecessary movement and improve efficiency.
- Ensure that workstations are ergonomically designed to reduce operator fatigue and enhance productivity.
- Automation and Robotics:
- Invest in automation technologies such as robotic loading and unloading systems, CNC controls, and automated tool changers to increase throughput and reduce manual labor.
- Automate repetitive tasks and material handling processes to free up operators for higher-value activities.
- Real-Time Monitoring and Control:
- Implement real-time monitoring systems to track machine performance, production metrics, and quality indicators.
- Use data analytics and visualization tools to identify trends, detect anomalies, and make data-driven decisions for process optimization.
- Continuous Improvement Culture:
- Foster a culture of continuous improvement and innovation among employees, encouraging them to identify and implement process enhancements.
- Conduct regular kaizen events, problem-solving workshops, and improvement projects to address inefficiencies and drive performance improvements.
- Supplier Collaboration:
- Collaborate closely with suppliers to optimize supply chain logistics, lead times, and inventory management.
- Develop strategic partnerships with suppliers to ensure timely delivery of raw materials and components to support production schedules.
By implementing these workflow optimization strategies, manufacturers can streamline tube bending operations, reduce cycle times, and increase overall efficiency. Continuous improvement efforts should focus on eliminating waste, increasing flexibility, and enhancing value-added activities throughout the production process.
Tube Bending Machine: Industry Trends
Staying abreast of industry trends is crucial for manufacturers involved in tube bending operations to remain competitive and capitalize on emerging opportunities. Here are some notable trends shaping the tube bending machine industry:
- Advanced Automation:
- Increasing adoption of automation technologies such as robotic bending cells, CNC controls, and integrated production systems to enhance productivity, precision, and flexibility in tube bending operations.
- Industry 4.0 Integration:
- Integration of Industry 4.0 principles and technologies, including IoT (Internet of Things), data analytics, and digital connectivity, to enable real-time monitoring, predictive maintenance, and remote diagnostics for tube bending machines.
- Additive Manufacturing (AM):
- Exploration of additive manufacturing techniques, such as 3D printing and metal deposition, for producing customized tooling, fixtures, and components used in tube bending processes, offering design flexibility and shorter lead times.
- Digital Twin Technology:
- Adoption of digital twin technology to create virtual replicas of tube bending machines, enabling simulation, optimization, and predictive modeling of machine performance and process parameters for improved efficiency and reliability.
- Energy Efficiency and Sustainability:
- Emphasis on energy-efficient machine designs, eco-friendly materials, and sustainable manufacturing practices to minimize environmental impact and meet regulatory requirements while reducing operating costs.
- Hybrid Manufacturing Solutions:
- Integration of additive manufacturing with traditional subtractive processes, such as tube bending and machining, to create hybrid manufacturing solutions that combine the strengths of both technologies for enhanced part quality and complexity.
- Customization and Personalization:
- Growing demand for customized and personalized products in various industries, driving the need for flexible tube bending solutions capable of producing small batch sizes, complex geometries, and unique designs efficiently.
- Smart Factory Concepts:
- Implementation of smart factory concepts and digital manufacturing platforms to optimize production workflows, streamline supply chain management, and enable agile, demand-driven manufacturing in tube bending operations.
- Materials Innovation:
- Exploration of advanced materials, including high-strength alloys, composite materials, and lightweight structures, for applications requiring superior performance, durability, and weight reduction in tube bending applications.
- Augmented Reality (AR) and Virtual Reality (VR):
- Adoption of AR and VR technologies for training, maintenance, and troubleshooting purposes, enabling operators to visualize complex processes, interact with digital models, and perform tasks more efficiently in tube bending operations.
By staying informed about these industry trends and embracing innovation, manufacturers can position themselves for success in the evolving landscape of tube bending machine technology and meet the evolving needs of their customers. Adaptation to these trends can lead to improved efficiency, enhanced product quality, and greater competitiveness in the market.
Tube Bending Machine: Maintenance Procedures
Regular maintenance is essential for ensuring the optimal performance, reliability, and longevity of tube bending machines. Here’s a comprehensive guide to maintenance procedures for tube bending machines:
- Daily Maintenance:
- Clean the machine thoroughly, removing any debris, chips, or coolant from the work area, tooling, and components.
- Check hydraulic fluid levels and top up if necessary. Inspect hoses, fittings, and seals for leaks or damage.
- Lubricate moving parts, bearings, and guide rails according to the manufacturer’s recommendations.
- Weekly Maintenance:
- Inspect electrical components, including wiring, connectors, and switches, for signs of wear, damage, or corrosion.
- Check pneumatic components, such as valves, cylinders, and hoses, for leaks or air pressure loss. Replace worn or damaged parts as needed.
- Verify the alignment of bending dies, mandrels, and tooling. Adjust if necessary to ensure accurate bending results.
- Monthly Maintenance:
- Conduct a comprehensive inspection of all machine components, including frame, drive system, and control panel.
- Check for signs of wear, fatigue, or misalignment in critical components. Replace worn or damaged parts and perform any necessary repairs.
- Clean and inspect the hydraulic system, including filters, reservoir, and pump. Replace hydraulic fluid and filters if contaminated or degraded.
- Quarterly Maintenance:
- Perform a test bend using scrap material to verify the accuracy and consistency of bending results. Adjust machine settings as needed.
- Inspect safety features, including emergency stop controls, safety interlocks, and light curtains, for proper operation. Test functionality and address any issues promptly.
- Semi-annual Maintenance:
- Disassemble and inspect critical components such as the bending head, clamping mechanism, and pressure dies for wear, damage, or fatigue.
- Verify the calibration of machine settings such as bend angles and radii. Recalibrate if necessary to maintain accuracy and repeatability.
- Annual Maintenance:
- Perform a thorough inspection of the electrical system, including wiring, relays, and control panels. Clean and tighten connections as needed.
- Check for software updates or firmware upgrades provided by the manufacturer. Install updates to ensure compatibility and performance optimization.
- Spare Parts Inventory:
- Maintain an inventory of commonly used spare parts, including seals, bearings, hydraulic fittings, and electrical components.
- Replace spare parts as needed during routine maintenance to minimize downtime and ensure uninterrupted operation.
- Documentation and Record-Keeping:
- Keep detailed records of all maintenance activities, including inspection reports, repairs, parts replacements, and calibration data.
- Use a maintenance log or software system to track maintenance schedules, upcoming tasks, and equipment history for reference.
By following these maintenance procedures and adhering to a regular maintenance schedule, operators can ensure the reliable performance of tube bending machines and minimize the risk of unexpected breakdowns or malfunctions. Preventive maintenance is key to maximizing equipment uptime, optimizing productivity, and prolonging the lifespan of tube bending machines.
Tube Bending Machine: Troubleshooting Guide
Troubleshooting is an essential skill for operators to quickly identify and resolve issues with tube bending machines. Here’s a troubleshooting guide to help diagnose and address common problems:
- Machine Does Not Power On:
- Check the power source to ensure it’s connected and operational.
- Inspect the power cord for damage or loose connections.
- Verify that the circuit breaker or fuse hasn’t tripped or blown.
- Hydraulic System Malfunction:
- Check hydraulic fluid levels and top up if low.
- Inspect hydraulic hoses and fittings for leaks or damage.
- Verify that the hydraulic pump is functioning correctly.
- Electrical Issues:
- Inspect electrical connections for loose wires or damaged components.
- Check for blown fuses or tripped circuit breakers.
- Test electrical components such as switches and relays for functionality.
- Tooling Problems:
- Inspect bending dies, mandrels, and tooling for damage or wear.
- Verify that tooling is installed correctly and securely fastened.
- Replace worn or damaged tooling as needed.
- Bending Inaccuracies:
- Check the calibration of machine settings such as bend angles and radii.
- Verify the alignment of bending dies and mandrels.
- Ensure proper material clamping and feeding.
- Machine Vibration or Noise:
- Inspect the machine for loose bolts or fasteners.
- Check for worn or damaged bearings or drive components.
- Lubricate moving parts and bearings as needed.
- Safety System Malfunctions:
- Test emergency stop controls and safety interlocks.
- Inspect safety guards and sensors for proper operation.
- Clear any obstructions from safety devices.
- Material Feeding Issues:
- Ensure that the material feed mechanism is aligned and functioning properly.
- Check for obstructions or debris in the feeding system.
- Adjust feed rollers or guides as needed.
- Program Errors:
- Review the bending program for errors or inconsistencies.
- Verify that the correct program is loaded and selected.
- Check for software updates or patches.
- Consult Manufacturer Documentation:
- If troubleshooting steps do not resolve the issue, refer to the machine’s operation manual or contact the manufacturer for technical support.
- Provide detailed information about the problem encountered for effective troubleshooting.
By systematically diagnosing and addressing issues using this troubleshooting guide, operators can minimize downtime and maintain the efficient operation of tube bending machines. Regular maintenance and proper operation are essential for preventing problems and ensuring long-term reliability.
Tube Bending Machine: Safety Procedures
Safety is paramount in tube bending machine operations to prevent accidents, injuries, and damage to equipment. Here’s a comprehensive guide to safety procedures for tube bending machine operation:
- Operator Training:
- Provide comprehensive training to operators on the safe operation of tube bending machines.
- Training should cover machine controls, emergency procedures, hazard recognition, and proper use of personal protective equipment (PPE).
- Read and Understand Manuals:
- Ensure operators read and understand the machine’s operation manual, safety instructions, and warning labels before operation.
- Familiarity with the machine’s features, controls, and safety mechanisms is essential for safe operation.
- Personal Protective Equipment (PPE):
- Require operators to wear appropriate PPE, including safety glasses, hearing protection, gloves, and steel-toed boots.
- PPE helps protect against potential hazards such as flying debris, noise, and impact injuries.
- Machine Inspection:
- Conduct pre-operation inspections of the tube bending machine to check for any signs of damage, wear, or malfunction.
- Ensure all safety guards, interlocks, and emergency stop controls are in place and functioning correctly.
- Secure Workpiece:
- Secure the workpiece firmly using clamps or fixtures before initiating the bending process.
- Proper workpiece fixation prevents movement or slippage during bending, reducing the risk of accidents.
- Tooling Inspection:
- Inspect bending dies, mandrels, and other tooling components for wear, damage, or misalignment.
- Ensure tooling is installed correctly and securely fastened to prevent accidents during operation.
- Avoid Hand Contact:
- Keep hands and fingers away from moving parts, pinch points, and rotating components during machine operation.
- Never attempt to reach into the bending area while the machine is running.
- Monitor Machine Operation:
- Maintain constant vigilance over the tube bending machine while it’s in operation.
- Watch for any abnormal sounds, vibrations, or movements that may indicate a problem with the machine or tooling.
- Emergency Stop:
- Familiarize operators with the location and operation of the emergency stop (E-stop) button on the machine.
- In case of an emergency or hazardous situation, instruct operators to press the E-stop button to immediately halt machine operation.
- Proper Handling of Materials:
- Handle tubes and materials with care to avoid injuries and accidents.
- Use proper lifting techniques and equipment, and be mindful of sharp edges and heavy loads to prevent accidents.
- Report Hazards and Incidents:
- Encourage operators to report any safety hazards, near misses, or incidents to a supervisor or safety officer immediately.
- Prompt reporting helps identify potential risks and prevent accidents from recurring.
By adhering to these safety procedures, operators can minimize the risk of accidents and create a safe working environment in tube bending operations. Regular safety training, equipment inspections, and hazard awareness are essential for protecting personnel and maintaining a culture of safety in the workplace.
Tube Bending Machine: Quality Control Measures
Quality control is crucial in tube bending operations to ensure that products meet specifications and standards consistently. Here are key quality control measures for tube bending machine operations:
- Material Inspection:
- Thoroughly inspect raw materials such as tubes and pipes for dimensional accuracy, surface defects, and material composition before bending.
- Verify material certifications and test reports to ensure compliance with specifications.
- Tooling Verification:
- Inspect bending dies, mandrels, and other tooling components for wear, damage, or misalignment.
- Verify that tooling dimensions and profiles match the desired bend specifications and material requirements.
- Setup Verification:
- Verify machine setup parameters, including bend angles, radii, and lengths, before initiating production runs.
- Use precision measuring tools to confirm setup accuracy and consistency.
- First Article Inspection (FAI):
- Perform a first article inspection on the initial parts produced in a production run to verify conformance to customer specifications and quality standards.
- Compare measured dimensions and bend angles against engineering drawings or CAD models.
- In-Process Inspection:
- Implement in-process inspection checkpoints at key stages of the bending process to monitor part quality and detect defects or variations early.
- Use visual inspection, measurement tools, and non-destructive testing methods as appropriate.
- Bend Angle Measurement:
- Use precision angle measurement tools such as angle gauges or optical comparators to verify bend angles and ensure compliance with specified tolerances.
- Calibrate measurement equipment regularly to maintain accuracy.
- Dimensional Control:
- Measure critical dimensions such as bend radius, wall thickness, and centerline radius to verify part conformance and dimensional accuracy.
- Document measurement data and compare results against established quality criteria.
- Surface Inspection:
- Inspect bent tubes for surface defects such as scratches, dents, or wrinkles that may affect part integrity or appearance.
- Use visual inspection or surface profiling techniques to assess surface quality and identify imperfections.
- Final Inspection:
- Conduct a final inspection of finished parts to ensure they meet all specified requirements and quality standards before release for assembly or shipment.
- Document inspection results and generate inspection reports for traceability and quality assurance purposes.
- Continuous Improvement:
- Implement feedback mechanisms to capture insights from quality control processes and identify opportunities for process improvement or corrective actions.
- Foster a culture of continuous improvement and quality excellence to drive ongoing enhancements in product quality, efficiency, and customer satisfaction.
By implementing these quality control measures, manufacturers can ensure that tube bending operations consistently produce high-quality parts that meet customer requirements and specifications. Quality control is integral to achieving customer satisfaction, maintaining competitive advantage, and sustaining business success in the long term.
Tube Bending Machine: Environmental Considerations
In the context of tube bending machine operations, it’s essential to consider environmental factors and adopt practices that minimize the ecological footprint of manufacturing processes. Here are key environmental considerations:
- Energy Efficiency:
- Utilize energy-efficient tube bending machines equipped with modern motors, drives, and controls to minimize energy consumption during operation.
- Implement energy-saving measures such as optimizing machine settings, scheduling production runs during off-peak hours, and investing in energy-efficient lighting and HVAC systems.
- Waste Reduction and Recycling:
- Implement waste reduction strategies to minimize scrap generation during tube bending operations.
- Encourage recycling of metal scrap, chips, and other waste materials generated during the manufacturing process.
- Partner with recycling facilities to ensure proper disposal and recycling of waste materials in an environmentally responsible manner.
- Emissions Control:
- Install and maintain emissions control equipment such as dust collectors, fume extractors, and air filtration systems to minimize air pollution from tube bending operations.
- Use low-emission lubricants, coolants, and cutting fluids to reduce the release of volatile organic compounds (VOCs) and harmful airborne contaminants.
- Hazardous Materials Management:
- Properly manage and dispose of hazardous materials such as hydraulic fluids, lubricants, and chemical cleaners used in tube bending processes.
- Implement spill prevention measures and containment systems to minimize the risk of environmental contamination from hazardous materials.
- Water Conservation:
- Implement water conservation practices to minimize water usage in cooling and lubrication systems associated with tube bending machines.
- Recycle or reuse water where feasible, and invest in water-efficient equipment and technologies to reduce overall water consumption.
- Noise Reduction:
- Implement noise control measures such as soundproofing enclosures, barriers, and damping materials to minimize noise pollution from tube bending operations.
- Conduct regular noise assessments and provide hearing protection for workers exposed to high noise levels.
- Sustainable Materials Selection:
- Consider using sustainable materials such as recycled metals or environmentally friendly alloys in tube bending applications where feasible.
- Evaluate the environmental impact of materials throughout their lifecycle, from extraction and processing to disposal, and choose materials with lower environmental footprints.
- Environmental Compliance:
- Ensure compliance with local, regional, and national environmental regulations governing air quality, water quality, waste management, and hazardous materials handling.
- Stay informed about changes in environmental regulations and proactively adapt processes and practices to meet evolving compliance requirements.
By integrating these environmental considerations into tube bending machine operations, manufacturers can minimize their environmental impact, reduce resource consumption, and contribute to a more sustainable manufacturing industry. Environmental stewardship is essential for mitigating environmental risks and ensuring the long-term viability of manufacturing processes in a rapidly changing world.
Tube Bending Machine: Industry Trends
Understanding industry trends is crucial for manufacturers to stay competitive and adapt to changing market demands in tube bending machine operations. Here are some prominent trends shaping the industry:
- Advanced Automation:
- Increasing adoption of automation technologies such as robotic bending cells, CNC controls, and integrated production systems to enhance productivity, precision, and flexibility in tube bending operations.
- Industry 4.0 Integration:
- Integration of Industry 4.0 principles and technologies, including IoT (Internet of Things), data analytics, and digital connectivity, to enable real-time monitoring, predictive maintenance, and remote diagnostics for tube bending machines.
- Additive Manufacturing (AM):
- Exploration of additive manufacturing techniques, such as 3D printing and metal deposition, for producing customized tooling, fixtures, and components used in tube bending processes, offering design flexibility and shorter lead times.
- Digital Twin Technology:
- Adoption of digital twin technology to create virtual replicas of tube bending machines, enabling simulation, optimization, and predictive modeling of machine performance and process parameters for improved efficiency and reliability.
- Energy Efficiency and Sustainability:
- Emphasis on energy-efficient machine designs, eco-friendly materials, and sustainable manufacturing practices to minimize environmental impact and meet regulatory requirements while reducing operating costs.
- Hybrid Manufacturing Solutions:
- Integration of additive manufacturing with traditional subtractive processes, such as tube bending and machining, to create hybrid manufacturing solutions that combine the strengths of both technologies for enhanced part quality and complexity.
- Customization and Personalization:
- Growing demand for customized and personalized products in various industries, driving the need for flexible tube bending solutions capable of producing small batch sizes, complex geometries, and unique designs efficiently.
- Smart Factory Concepts:
- Implementation of smart factory concepts and digital manufacturing platforms to optimize production workflows, streamline supply chain management, and enable agile, demand-driven manufacturing in tube bending operations.
- Materials Innovation:
- Exploration of advanced materials, including high-strength alloys, composite materials, and lightweight structures, for applications requiring superior performance, durability, and weight reduction in tube bending applications.
- Augmented Reality (AR) and Virtual Reality (VR):
- Adoption of AR and VR technologies for training, maintenance, and troubleshooting purposes, enabling operators to visualize complex processes, interact with digital models, and perform tasks more efficiently in tube bending operations.
By staying informed about these industry trends and embracing innovation, manufacturers can position themselves for success in the evolving landscape of tube bending machine technology and meet the evolving needs of their customers. Adaptation to these trends can lead to improved efficiency, enhanced product quality, and greater competitiveness in the market.
Tube Bending Machine: Maintenance Procedures
Regular maintenance is essential for ensuring the optimal performance, reliability, and longevity of tube bending machines. Here’s a comprehensive guide to maintenance procedures for tube bending machines:
- Daily Maintenance:
- Clean the machine thoroughly, removing any debris, chips, or coolant from the work area, tooling, and components.
- Check hydraulic fluid levels and top up if necessary. Inspect hoses, fittings, and seals for leaks or damage.
- Lubricate moving parts, bearings, and guide rails according to the manufacturer’s recommendations.
- Weekly Maintenance:
- Inspect electrical components, including wiring, connectors, and switches, for signs of wear, damage, or corrosion.
- Check pneumatic components, such as valves, cylinders, and hoses, for leaks or air pressure loss. Replace worn or damaged parts as needed.
- Verify the alignment of bending dies, mandrels, and tooling. Adjust if necessary to ensure accurate bending results.
- Monthly Maintenance:
- Conduct a comprehensive inspection of all machine components, including frame, drive system, and control panel.
- Check for signs of wear, fatigue, or misalignment in critical components. Replace worn or damaged parts and perform any necessary repairs.
- Clean and inspect the hydraulic system, including filters, reservoir, and pump. Replace hydraulic fluid and filters if contaminated or degraded.
- Quarterly Maintenance:
- Perform a test bend using scrap material to verify the accuracy and consistency of bending results. Adjust machine settings as needed.
- Inspect safety features, including emergency stop controls, safety interlocks, and light curtains, for proper operation. Test functionality and address any issues promptly.
- Semi-annual Maintenance:
- Disassemble and inspect critical components such as the bending head, clamping mechanism, and pressure dies for wear, damage, or fatigue.
- Verify the calibration of machine settings such as bend angles and radii. Recalibrate if necessary to maintain accuracy and repeatability.
- Annual Maintenance:
- Perform a thorough inspection of the electrical system, including wiring, relays, and control panels. Clean and tighten connections as needed.
- Check for software updates or firmware upgrades provided by the manufacturer. Install updates to ensure compatibility and performance optimization.
- Spare Parts Inventory:
- Maintain an inventory of commonly used spare parts, including seals, bearings, hydraulic fittings, and electrical components.
- Replace spare parts as needed during routine maintenance to minimize downtime and ensure uninterrupted operation.
- Documentation and Record-Keeping:
- Keep detailed records of all maintenance activities, including inspection reports, repairs, parts replacements, and calibration data.
- Use a maintenance log or software system to track maintenance schedules, upcoming tasks, and equipment history for reference.
By following these maintenance procedures and adhering to a regular maintenance schedule, operators can ensure the reliable performance of tube bending machines and minimize the risk of unexpected breakdowns or malfunctions. Preventive maintenance is key to maximizing equipment uptime, optimizing productivity, and prolonging the lifespan of tube bending machines.
Tube Bending Machine: Troubleshooting Guide
Troubleshooting is an essential skill for operators to quickly identify and resolve issues with tube bending machines. Here’s a troubleshooting guide to help diagnose and address common problems:
- Machine Does Not Power On:
- Check the power source to ensure it’s connected and operational.
- Inspect the power cord for damage or loose connections.
- Verify that the circuit breaker or fuse hasn’t tripped or blown.
- Hydraulic System Malfunction:
- Check hydraulic fluid levels and top up if low.
- Inspect hydraulic hoses and fittings for leaks or damage.
- Verify that the hydraulic pump is functioning correctly.
- Electrical Issues:
- Inspect electrical connections for loose wires or damaged components.
- Check for blown fuses or tripped circuit breakers.
- Test electrical components such as switches and relays for functionality.
- Tooling Problems:
- Inspect bending dies, mandrels, and tooling for damage or wear.
- Verify that tooling is installed correctly and securely fastened.
- Replace worn or damaged tooling as needed.
- Bending Inaccuracies:
- Check the calibration of machine settings such as bend angles and radii.
- Verify the alignment of bending dies and mandrels.
- Ensure proper material clamping and feeding.
- Machine Vibration or Noise:
- Inspect the machine for loose bolts or fasteners.
- Check for worn or damaged bearings or drive components.
- Lubricate moving parts and bearings as needed.
- Safety System Malfunctions:
- Test emergency stop controls and safety interlocks.
- Inspect safety guards and sensors for proper operation.
- Clear any obstructions from safety devices.
- Material Feeding Issues:
- Ensure that the material feed mechanism is aligned and functioning properly.
- Check for obstructions or debris in the feeding system.
- Adjust feed rollers or guides as needed.
- Program Errors:
- Review the bending program for errors or inconsistencies.
- Verify that the correct program is loaded and selected.
- Check for software updates or firmware upgrades.
- Consult Manufacturer Documentation:
- If troubleshooting steps do not resolve the issue, refer to the machine’s operation manual or contact the manufacturer for technical support.
- Provide detailed information about the problem encountered for effective troubleshooting.
By systematically diagnosing and addressing issues using this troubleshooting guide, operators can minimize downtime and maintain the efficient operation of tube bending machines. Regular maintenance and proper operation are essential for preventing problems and ensuring long-term reliability.
Tube Bending Machine: Safety Procedures
Safety is paramount in tube bending machine operations to prevent accidents, injuries, and damage to equipment. Here’s a comprehensive guide to safety procedures for tube bending machine operation:
- Operator Training:
- Provide comprehensive training to operators on the safe operation of tube bending machines.
- Training should cover machine controls, emergency procedures, hazard recognition, and proper use of personal protective equipment (PPE).
- Read and Understand Manuals:
- Ensure operators read and understand the machine’s operation manual, safety instructions, and warning labels before operation.
- Familiarity with the machine’s features, controls, and safety mechanisms is essential for safe operation.
- Personal Protective Equipment (PPE):
- Require operators to wear appropriate PPE, including safety glasses, hearing protection, gloves, and steel-toed boots.
- PPE helps protect against potential hazards such as flying debris, noise, and impact injuries.
- Machine Inspection:
- Conduct pre-operation inspections of the tube bending machine to check for any signs of damage, wear, or malfunction.
- Ensure all safety guards, interlocks, and emergency stop controls are in place and functioning correctly.
- Secure Workpiece:
- Secure the workpiece firmly using clamps or fixtures before initiating the bending process.
- Proper workpiece fixation prevents movement or slippage during bending, reducing the risk of accidents.
- Tooling Inspection:
- Inspect bending dies, mandrels, and other tooling components for wear, damage, or misalignment.
- Verify that tooling is installed correctly and securely fastened to prevent accidents during operation.
- Avoid Hand Contact:
- Keep hands and fingers away from moving parts, pinch points, and rotating components during machine operation.
- Never attempt to reach into the bending area while the machine is running.
- Monitor Machine Operation:
- Maintain constant vigilance over the tube bending machine while it’s in operation.
- Watch for any abnormal sounds, vibrations, or movements that may indicate a problem with the machine or tooling.
- Emergency Stop:
- Familiarize operators with the location and operation of the emergency stop (E-stop) button on the machine.
- In case of an emergency or hazardous situation, instruct operators to press the E-stop button to immediately halt machine operation.
- Proper Handling of Materials:
- Handle tubes and materials with care to avoid injuries and accidents.
- Use proper lifting techniques and equipment, and be mindful of sharp edges and heavy loads to prevent accidents.
- Report Hazards and Incidents:
- Encourage operators to report any safety hazards, near misses, or incidents to a supervisor or safety officer immediately.
- Prompt reporting helps identify potential risks and prevent accidents from recurring.
By adhering to these safety procedures, operators can minimize the risk of accidents and create a safe working environment in tube bending operations. Regular safety training, equipment inspections, and hazard awareness are essential for protecting personnel and maintaining a culture of safety in the workplace.
Tube Bending Machine: Quality Control Measures
Quality control is crucial in tube bending operations to ensure that products meet specifications and standards consistently. Here are key quality control measures for tube bending machine operations:
- Material Inspection:
- Thoroughly inspect raw materials such as tubes and pipes for dimensional accuracy, surface defects, and material composition before bending.
- Verify material certifications and test reports to ensure compliance with specifications.
- Tooling Verification:
- Inspect bending dies, mandrels, and other tooling components for wear, damage, or misalignment.
- Verify that tooling dimensions and profiles match the desired bend specifications and material requirements.
- Setup Verification:
- Verify machine setup parameters, including bend angles, radii, and lengths, before initiating production runs.
- Use precision measuring tools to confirm setup accuracy and consistency.
- First Article Inspection (FAI):
- Perform a first article inspection on the initial parts produced in a production run to verify conformance to customer specifications and quality standards.
- Compare measured dimensions and bend angles against engineering drawings or CAD models.
- In-Process Inspection:
- Implement in-process inspection checkpoints at key stages of the bending process to monitor part quality and detect defects or variations early.
- Use visual inspection, measurement tools, and non-destructive testing methods as appropriate.
- Bend Angle Measurement:
- Use precision angle measurement tools such as angle gauges or optical comparators to verify bend angles and ensure compliance with specified tolerances.
- Calibrate measurement equipment regularly to maintain accuracy.
- Dimensional Control:
- Measure critical dimensions such as bend radius, wall thickness, and centerline radius to verify part conformance and dimensional accuracy.
- Document measurement data and compare results against established quality criteria.
- Surface Inspection:
- Inspect bent tubes for surface defects such as scratches, dents, or wrinkles that may affect part integrity or appearance.
- Use visual inspection or surface profiling techniques to assess surface quality and identify imperfections.
- Final Inspection:
- Conduct a final inspection of finished parts to ensure they meet all specified requirements and quality standards before release for assembly or shipment.
- Document inspection results and generate inspection reports for traceability and quality assurance purposes.
- Continuous Improvement:
- Implement feedback mechanisms to capture insights from quality control processes and identify opportunities for process improvement or corrective actions.
- Foster a culture of continuous improvement and quality excellence to drive ongoing enhancements in product quality, efficiency, and customer satisfaction.
By implementing these quality control measures, manufacturers can ensure that tube bending operations consistently produce high-quality parts that meet customer requirements and specifications. Quality control is integral to achieving customer satisfaction, maintaining competitive advantage, and sustaining business success in the long term.
Tube Bending Machine: Environmental Considerations
In the context of tube bending machine operations, it’s essential to consider environmental factors and adopt practices that minimize the ecological footprint of manufacturing processes. Here are key environmental considerations:
- Energy Efficiency:
- Utilize energy-efficient tube bending machines equipped with modern motors, drives, and controls to minimize energy consumption during operation.
- Implement energy-saving measures such as optimizing machine settings, scheduling production runs during off-peak hours, and investing in energy-efficient lighting and HVAC systems.
- Waste Reduction and Recycling:
- Implement waste reduction strategies to minimize scrap generation during tube bending operations.
- Encourage recycling of metal scrap, chips, and other waste materials generated during the manufacturing process.
- Partner with recycling facilities to ensure proper disposal and recycling of waste materials in an environmentally responsible manner.
- Emissions Control:
- Install and maintain emissions control equipment such as dust collectors, fume extractors, and air filtration systems to minimize air pollution from tube bending operations.
- Use low-emission lubricants, coolants, and cutting fluids to reduce the release of volatile organic compounds (VOCs) and harmful airborne contaminants.
- Hazardous Materials Management:
- Properly manage and dispose of hazardous materials such as hydraulic fluids, lubricants, and chemical cleaners used in tube bending processes.
- Implement spill prevention measures and containment systems to minimize the risk of environmental contamination from hazardous materials.
- Water Conservation:
- Implement water conservation practices to minimize water usage in cooling and lubrication systems associated with tube bending machines.
- Recycle or reuse water where feasible, and invest in water-efficient equipment and technologies to reduce overall water consumption.
- Noise Reduction:
- Implement noise control measures such as soundproofing enclosures, barriers, and damping materials to minimize noise pollution from tube bending operations.
- Conduct regular noise assessments and provide hearing protection for workers exposed to high noise levels.
- Sustainable Materials Selection:
- Consider using sustainable materials such as recycled metals or environmentally friendly alloys in tube bending applications where feasible.
- Evaluate the environmental impact of materials throughout their lifecycle, from extraction and processing to disposal, and choose materials with lower environmental footprints.
- Environmental Compliance:
- Ensure compliance with local, regional, and national environmental regulations governing air quality, water quality, waste management, and hazardous materials handling.
- Stay informed about changes in environmental regulations and proactively adapt processes and practices to meet evolving compliance requirements.
By integrating these environmental considerations into tube bending machine operations, manufacturers can minimize their environmental impact, reduce resource consumption, and contribute to a more sustainable manufacturing industry. Environmental stewardship is essential for mitigating environmental risks and ensuring the long-term viability of manufacturing processes in a rapidly changing world.
EMS Metalworking Machinery
We design, manufacture and assembly metalworking machinery such as:
- Hydraulic transfer press
- Glass mosaic press
- Hydraulic deep drawing press
- Casting press
- Hydraulic cold forming press
- Hydroforming press
- Composite press
- Silicone rubber moulding press
- Brake pad press
- Melamine press
- SMC & BMC Press
- Labrotaroy press
- Edge cutting trimming machine
- Edge curling machine
- Trimming beading machine
- Trimming joggling machine
- Cookware production line
- Pipe bending machine
- Profile bending machine
- Bandsaw for metal
- Cylindrical welding machine
- Horizontal pres and cookware
- Kitchenware, hotelware
- Bakeware and cuttlery production machinery
as a complete line as well as an individual machine such as:
- Edge cutting trimming beading machines
- Polishing and grinding machines for pot and pans
- Hydraulic drawing presses
- Circle blanking machines
- Riveting machine
- Hole punching machines
- Press feeding machine
You can check our machinery at work at: EMS Metalworking Machinery – YouTube
Applications:
- Beading and ribbing
- Flanging
- Trimming
- Curling
- Lock-seaming
- Ribbing
- Flange-punching