We manufacture What is CNC Bending Machine to bend sheet metal edges. Hydraulic Press Machines are used in metalworking industries
A CNC (Computer Numerical Control) bending machine is an advanced machine tool used for automated bending of sheet metal or other materials. It utilizes computer-controlled systems to precisely control the bending process, allowing for complex bending operations with high accuracy and repeatability. CNC bending machines offer several advantages over traditional manual bending methods, including increased productivity, flexibility, and efficiency.
Here are some key features and benefits of CNC bending machines:
- CNC Control System: CNC bending machines are equipped with sophisticated control systems that allow for precise programming and execution of bending operations. The operator can input bending parameters, such as bend angles, bend radius, and material thickness, into the CNC control interface.
- Automated Operation: Once the bending program is set, the CNC bending machine carries out the bending process automatically, without the need for manual intervention. This significantly reduces labor requirements and increases productivity.
- Precision and Repeatability: CNC bending machines offer high precision and repeatability in bending operations. The computer-controlled system ensures accurate positioning and control of the bending tool, resulting in consistent and precise bends, even for complex geometries.
- Versatility: CNC bending machines are versatile and can handle a wide range of materials, including various types of sheet metal, tubes, profiles, and more. They can accommodate different material thicknesses and lengths, making them suitable for diverse applications.
- Multi-Axis Bending: Advanced CNC bending machines often have multiple bending axes, allowing for the creation of complex and multi-dimensional bends. This capability enables the production of intricate and customized parts with high accuracy.
- Tooling Options: CNC bending machines support a variety of tooling options, including different types of bending punches, dies, and tool holders. This flexibility allows for the creation of different bending profiles and geometries to meet specific design requirements.
- Efficiency and Productivity: CNC bending machines offer increased efficiency and productivity compared to manual bending methods. They can execute multiple bends in a single setup, eliminating the need for manual repositioning and reducing production time.
- Operator-Friendly Interface: CNC bending machines typically have user-friendly interfaces, such as touchscreens or graphical interfaces, that simplify programming and operation. Operators can easily set up and adjust bending parameters, monitor the bending process, and make real-time adjustments if necessary.
- Safety Features: CNC bending machines incorporate various safety features to ensure operator safety during operation. These may include safety guards, emergency stop buttons, and light curtains to prevent accidents and injuries.
CNC bending machines are widely used in industries such as automotive, aerospace, electronics, and metal fabrication, where precise and efficient bending operations are required. They offer advanced capabilities, improved productivity, and consistent quality, making them a valuable asset in modern manufacturing processes.
What is CNC Bending Machine
A CNC bending machine, also known as a CNC press brake or CNC brake press, is a computer-numerically controlled (CNC) machine that utilizes a computer system to precisely bend sheet metal into various shapes and forms. It is widely used in various industries, including automotive, aerospace, construction, and manufacturing, due to its high precision, efficiency, and versatility.
Key Components of a CNC Bending Machine
A CNC bending machine consists of several crucial components that work together to achieve the desired bending operation:
- Frame: The frame provides a sturdy and rigid structure to support the machine’s components and withstand the forces involved during bending. It typically consists of heavy-duty steel plates or beams.
- Computer Control System: The computer control system is the heart of the machine, managing the bending process and ensuring precise control over ram movement, pressure application, and tool selection. It receives input from sensors, coordinates the actions of various actuators and motors, and executes the bending program.
- Hydraulic or Servo Drive System: The drive system provides the force required to bend the sheet metal. Hydraulic presses utilize hydraulic fluid to generate force, while servo presses employ electric motors and servomotors for precise control and high production rates.
- Ram and Die/Punch Assembly: The ram is the movable part of the machine that applies force directly to the workpiece. The die and punch, also known as tooling, determine the specific shape or form of the workpiece. The die provides the desired shape, while the punch cuts or pierces the material.
- Work Table and Backgauge: The work table provides a stable and adjustable surface for positioning and securing the workpiece. The backgauge ensures precise positioning of the workpiece relative to the die and punch.
- Safety Interlocks and Guards: Safety interlocks and guards protect the operator from potential hazards, such as accidental contact with the moving ram or tooling. They typically include sensors, switches, and physical barriers.
Working Principle of a CNC Bending Machine
The working principle of a CNC bending machine can be summarized in the following steps:
- Program Preparation: The desired bending program is created using CAD (Computer-Aided Design) software or specialized CNC programming software. The program specifies the bending angles, tooling selection, and bending sequence.
- Program Loading: The bending program is loaded into the machine’s computer control system.
- Workpiece Positioning and Clamping: The workpiece is accurately positioned on the work table and securely clamped to prevent movement during bending.
- Tool Selection: The appropriate die and punch are automatically selected based on the bending program and workpiece characteristics.
- Ram Movement: The ram, driven by the hydraulic or servo system, moves towards the workpiece according to the bending program’s instructions.
- Die and Punch Engagement: The die and punch engage with the workpiece, applying force to bend it according to the desired shape and angles specified in the program.
- Bending Operation: The workpiece is bent according to the programmed bending sequence and angles. Sensors monitor the bending process and provide feedback to the control system for precise control.
- Ram Retraction: Once the desired bend is achieved, the ram retracts to its initial position.
- Workpiece Unloading: The bent workpiece is removed from the work table.
Benefits of CNC Bending Machines
CNC bending machines offer several advantages over manual or semi-automatic bending methods:
- Precision: Computer-controlled systems ensure precise bending angles, consistent results, and minimal tolerances.
- High Production Rates: Automated machines can achieve high production rates, especially for repetitive bending tasks.
- Reduced Labor Costs: Automated machines reduce labor requirements and minimize the risk of human error, lowering labor costs.
- Flexibility: CNC machines can handle a wide range of sheet metal thicknesses, sizes, and shapes.
- Versatility: CNC machines can perform various bending operations, including simple bends, compound bends, and radius bends.
- Repeatability: CNC machines can consistently produce identical parts with minimal variation, ensuring quality control.
- Data Storage and Traceability: CNC machines can store bending programs and production data, facilitating traceability and process optimization.
Applications of CNC Bending Machines
CNC bending machines are widely used in various industries for a wide range of applications, including:
- Automotive Industry: Bending sheet metal components for vehicle bodies, frames, and structural parts
- Aerospace Industry: Forming and shaping aircraft parts, such as wings, fuselages, and control surfaces
- Construction Industry: Creating metal components for roofing, cladding, and structural elements
- Manufacturing Industry: Producing metal parts for appliances, electronics, machinery, and other products
- Appliance Industry: Shaping and forming sheet metal for various appliance components, such as cabinets, doors, and panels
CNC Control System
A CNC (Computer Numerical Control) control system is an integral part of CNC machines, including CNC bending machines. It is responsible for controlling the machine’s movements and operations based on the programmed instructions. The CNC control system consists of hardware and software components that work together to execute precise and automated machining processes. Here are the key elements of a CNC control system:
- CNC Controller: The CNC controller is the central unit that receives and interprets the program instructions. It manages the operation of the machine, coordinates the movement of axes, and controls auxiliary functions. The controller can be a standalone unit or integrated into the machine itself.
- Control Panel: The control panel provides the interface between the operator and the CNC controller. It typically consists of a display screen, keyboard, buttons, and other input devices. The operator uses the control panel to input and edit program instructions, monitor the machine’s status, and make adjustments as needed.
- Programming Software: CNC machines require programming to define the specific machining operations. Programming software, often referred to as CAM (Computer-Aided Manufacturing) software, is used to create the program instructions. The software allows the operator to define tool paths, specify machining parameters, and generate the program code.
- Program Storage: CNC control systems have memory storage where the program instructions are stored. This can include internal memory within the control unit or external storage devices such as USB drives or network connections. The program can be loaded into the CNC controller for execution when needed.
- Axes Control: CNC machines typically have multiple axes of motion, such as X, Y, and Z axes for 3-axis machines or additional axes for more complex machines. The CNC control system precisely controls the movement of each axis based on the programmed instructions. This allows for precise positioning and movement of the cutting or bending tools.
- Feedback Systems: CNC control systems incorporate feedback systems to monitor the machine’s position, speed, and other relevant parameters during operation. Encoders or sensors provide real-time feedback to the control system, allowing it to make adjustments and ensure accurate positioning and movement.
- Diagnostics and Monitoring: CNC control systems often include diagnostic features and monitoring capabilities to detect errors, tool wear, or any issues that may affect the machining process. This helps in troubleshooting and maintaining optimal performance.
- Connectivity and Networking: Advanced CNC control systems may have connectivity options to integrate with other manufacturing systems, such as network connections for data transfer, remote monitoring, or integration with computer networks.
The CNC control system is responsible for transforming the programmed instructions into precise machine movements, ensuring accuracy, repeatability, and automation in CNC machining processes. It plays a critical role in controlling the machine’s performance, productivity, and efficiency.
Automated Operation
Automated operation refers to the ability of a machine or system to perform tasks or processes without direct human intervention. In the context of CNC bending machines, automated operation means that the bending process is carried out automatically, guided by pre-programmed instructions and controlled by the CNC system. Here are some key aspects of automated operation in CNC bending machines:
- Programmed Instructions: The bending process starts with the creation of a bending program using CAM (Computer-Aided Manufacturing) software. The program contains specific instructions for the machine, including the bending angles, tooling requirements, material parameters, and any other relevant information.
- CNC Control System: The CNC control system interprets the programmed instructions and coordinates the movement of the machine’s axes and the operation of auxiliary functions. It controls the bending tool and the positioning of the sheet metal, ensuring precise and accurate bending.
- Material Handling: In an automated setup, material handling systems can be integrated with the CNC bending machine. These systems can automatically load and unload sheet metal, allowing for continuous and uninterrupted operation. This eliminates the need for manual handling of the material, increasing efficiency and reducing labor requirements.
- Tool Change and Setup: CNC bending machines can be equipped with tool changers that allow for automatic tool changes during the bending process. This enables the machine to switch between different bending tools or tooling setups without manual intervention. Tool changes can be programmed within the bending program, ensuring seamless transitions between different bending operations.
- Sensor Integration: Automated CNC bending machines may incorporate sensors and feedback systems to monitor the bending process in real-time. These sensors can detect deviations, such as material variations, tool wear, or alignment issues, and provide feedback to the CNC control system. The system can then make necessary adjustments to maintain precision and quality.
- Error Detection and Correction: The CNC control system continuously monitors the machine’s performance and can detect errors or abnormalities during the bending process. If an error is detected, such as incorrect tool positioning or excessive force, the system can automatically stop or adjust the operation to prevent further issues.
- Production Monitoring and Reporting: Automated CNC bending machines can generate reports and provide production data, including the number of bends completed, cycle times, and any error or downtime occurrences. This data can be used for quality control, process optimization, and production management.
Automated operation in CNC bending machines offers several advantages, including increased productivity, improved accuracy, reduced labor requirements, and consistent quality. It allows for efficient and uninterrupted bending processes, making it ideal for high-volume production and applications that require complex bending operations.
Programming Software
Programming software, also known as CAM (Computer-Aided Manufacturing) software, is used in CNC (Computer Numerical Control) machines, including CNC bending machines, to generate the instructions and code required to execute specific machining operations. The programming software plays a crucial role in translating design specifications into machine-readable instructions. Here are some key aspects of programming software for CNC bending machines:
- CAD Integration: Programming software often integrates with CAD (Computer-Aided Design) software to import and work with 2D or 3D models of the part or component to be bent. This allows the user to define the bending operations directly on the digital model, simplifying the programming process.
- Geometry Creation: Programming software provides tools to define the geometry of the part, including the shape, dimensions, and bending angles. Users can create or modify the part’s geometry using a variety of tools such as lines, arcs, curves, and splines. Some software may also offer automated features for generating complex geometries or working with standard shapes.
- Toolpath Generation: Once the part’s geometry is defined, the programming software generates the toolpath, which specifies the precise movements and positioning of the bending tool during the bending process. The software calculates the toolpath based on the desired bending angles, material properties, and tooling parameters. It ensures that the bending operations are carried out accurately and efficiently.
- Bending Parameters and Simulation: Programming software allows users to specify various bending parameters, such as bend radius, bend allowance, material thickness, and tooling dimensions. These parameters affect how the bending operation is performed. The software may also include simulation capabilities to visualize and verify the bending process before actual production, allowing users to detect and resolve any potential issues or collisions.
- Tooling Selection and Management: Programming software provides tools to select the appropriate bending tools or tooling setups for the desired bending operations. Users can choose from a library of standard tooling profiles or create custom tooling configurations. The software manages the tooling information and ensures that the generated toolpath is compatible with the selected tooling.
- Post-Processing: After the bending program is created, programming software performs post-processing to generate the machine-specific code that the CNC control system can understand. The software translates the toolpath and bending parameters into G-code or other machine-readable formats suitable for the CNC bending machine. The post-processed code can then be loaded into the CNC controller for execution.
- Optimization and Efficiency: Advanced programming software may include optimization features to improve the efficiency and accuracy of the bending process. This can include algorithms to minimize tool changes, optimize toolpath sequencing, optimize material usage, or reduce cycle times. These features help to maximize productivity and minimize material waste.
Programming software for CNC bending machines varies in terms of functionality, capabilities, and user interfaces. Different software options may be preferred depending on the complexity of the bending operations, the desired level of automation, and the specific needs of the manufacturing process.
Program Storage
Program storage in the context of CNC bending machines refers to the storage and management of bending programs or instructions that are used to control the machine’s operations. CNC bending machines rely on these programs to execute bending operations accurately and efficiently. Here are some common methods of program storage in CNC bending machines:
- Onboard Memory: Many CNC bending machines have onboard memory where bending programs can be stored directly within the machine. The programs are typically stored in the machine’s control unit or memory modules. This allows for quick and convenient access to the programs without the need for external storage devices.
- External Storage Devices: CNC bending machines may also support external storage devices such as USB drives, memory cards, or external hard drives. Bending programs can be saved and loaded from these devices as needed. This provides flexibility in program management, allowing for easy backup, transfer, and sharing of programs between different machines or systems.
- Network Storage: In networked manufacturing environments, CNC bending machines may be connected to a local area network (LAN) or an industrial network. In such cases, bending programs can be stored and managed on network servers or shared network drives. This enables centralized program storage, version control, and accessibility from multiple machines or workstations.
- Cloud Storage: Some modern CNC bending machines may offer cloud-based program storage and management. Bending programs are uploaded to a cloud server or platform, allowing for secure storage, remote access, and collaboration. This approach provides the advantage of centralized program management, real-time updates, and easy integration with other cloud-based manufacturing systems.
- Program Libraries: CNC bending machines often have the capability to create and organize program libraries. These libraries enable the categorization and storage of bending programs based on various criteria such as part types, customer orders, or specific production requirements. Program libraries make it easier to locate, retrieve, and reuse programs, saving time and effort in programming.
- Program Editing and Versioning: CNC bending machines typically provide built-in programming software or interfaces for editing and modifying bending programs directly on the machine. This allows operators or programmers to make adjustments to existing programs or create new programs on the fly. Some machines also offer version control features, allowing operators to save different versions of the same program for future reference or comparison.
Proper program storage is essential for maintaining a well-organized and efficient CNC bending process. It ensures that bending programs are easily accessible, protected from data loss, and can be retrieved whenever needed. The specific method of program storage depends on the capabilities of the CNC bending machine and the requirements of the manufacturing environment.
Toolpath Generation
Toolpath generation is a critical step in CNC (Computer Numerical Control) machining, including CNC bending machines. It involves the creation of a precise path that the machine’s cutting tool or bending tool will follow to shape the workpiece according to the desired design. Here’s an overview of the toolpath generation process for CNC bending machines:
- Input Geometry: The first step in toolpath generation is to input the geometry of the part or component that needs to be bent. This can be done by importing a 2D or 3D CAD (Computer-Aided Design) model of the part into the CNC bending machine’s software or programming system.
- Define Bending Parameters: Next, the operator or programmer specifies the bending parameters, which include parameters such as bend angle, bend radius, material thickness, and tooling information. These parameters are crucial for accurately generating the toolpath and ensuring the desired bending results.
- Toolpath Calculation: Based on the input geometry and bending parameters, the CNC bending machine’s software calculates the toolpath. The software takes into account factors such as tool dimensions, material properties, and machine constraints to determine the exact path that the bending tool will follow during the bending operation.
- Collision Detection and Avoidance: During toolpath generation, the software may include collision detection algorithms to ensure that the bending tool does not collide with the workpiece or any other obstructions. This helps prevent potential damage to the machine or the workpiece and ensures safe and accurate bending.
- Optimization: Depending on the software capabilities, toolpath optimization algorithms may be used to optimize the toolpath for factors such as minimizing material waste, reducing cycle time, or improving surface finish. These optimization techniques help maximize the efficiency and productivity of the CNC bending process.
- Simulation and Verification: Once the toolpath is generated, it can be simulated and verified using software-based simulation tools. This allows operators or programmers to visualize the bending process and check for any errors or issues before the actual bending operation takes place. Simulation helps identify and rectify any potential problems, ensuring that the bending process proceeds smoothly.
- Output Code Generation: After the toolpath is generated and verified, the CNC bending machine’s software generates the machine-specific code, typically G-code, that will be used to control the machine’s movements and operations. This code contains the precise instructions for the machine to execute the bending process based on the generated toolpath.
Toolpath generation is a crucial aspect of CNC bending as it directly influences the accuracy, quality, and efficiency of the bending process. Advanced software packages provide various features and capabilities for generating complex toolpaths, optimizing the bending process, and simulating the bending operation for improved productivity and precision.
Axes Control
In CNC bending machines, axes control refers to the management and coordination of the different axes or movements of the machine to accurately position and control the bending tool. CNC bending machines typically have multiple axes that control various aspects of the bending process. Here are the commonly used axes in CNC bending machines and their functions:
- X-Axis: The X-axis controls the horizontal movement of the bending tool. It determines the position of the tool along the length of the workpiece, allowing for accurate positioning of the bend.
- Y-Axis: The Y-axis controls the vertical movement of the bending tool. It determines the height or depth of the bending tool, ensuring the desired bending angle is achieved.
- Z-Axis: The Z-axis controls the movement of the bending tool in the depth direction. It adjusts the depth at which the tool penetrates into the workpiece during the bending process.
- R-Axis: The R-axis, also known as the rotation axis or back gauge axis, controls the rotation or movement of the back gauge. The back gauge provides support for the workpiece during bending and helps maintain consistent bend positions.
- C-Axis: The C-axis, or rotary axis, is used in machines with rotating tooling, such as rotary bending tools or rotary shear tools. It enables the rotation of the tool to achieve complex bending shapes or perform additional operations like cutting or notching.
- B-Axis: The B-axis, or bending axis, is specific to press brake machines and controls the movement of the bending beam or ram. It determines the bending angle and the force applied during the bending operation.
The axes control is achieved through the CNC control system, which receives commands from the program and translates them into precise movements of each axis. The control system sends signals to the machine’s servo motors or hydraulic systems, which drive the axes accordingly.
The CNC control system allows for precise positioning, speed control, and synchronization of the axes, ensuring accurate and repeatable bending operations. It enables complex bending sequences, multiple bends in different directions, and the ability to create intricate shapes.
Operators or programmers can input the desired coordinates and angles for each axis in the CNC program, and the control system will execute the movements accordingly. The control system also provides features such as backlash compensation, acceleration/deceleration control, and positioning feedback to further enhance the accuracy and control of the bending process.
Overall, the axes control in CNC bending machines is a fundamental aspect of achieving precise and consistent bending results while enabling the flexibility to produce a wide range of bending shapes and configurations.
CNC Tube Bending
CNC tube bending refers to the process of bending tubes or pipes using a computer numerical control (CNC) machine. This technology allows for precise, automated bending of tubes to achieve complex shapes and configurations. Here’s a detailed explanation:
CNC tube bending machines are equipped with computer-controlled axes that accurately manipulate the tube’s position and orientation during the bending process. These machines typically feature a bending head with various tooling, including mandrels, wiper dies, and pressure dies, to support and shape the tube as it is bent.
The CNC tube bending process begins with the design of the part using computer-aided design (CAD) software. The desired bend angles, radii, and dimensions are programmed into the CNC machine’s control system, specifying the bending parameters for each bend along the tube’s length.
Once the program is loaded into the CNC machine, the operator loads the tube or pipe into the bending machine’s clamp or collet. The machine automatically feeds the tube into the bending head, where it is clamped and positioned for bending.
During bending, the CNC machine precisely controls the movement of the tube and bending tools, following the programmed instructions to achieve the desired bend geometry. The machine may perform multiple bends in sequence, rotating the tube and adjusting its position as needed to create complex shapes and configurations.
CNC tube bending offers several advantages over traditional manual or semi-automatic bending methods. Firstly, it provides unmatched accuracy and repeatability, ensuring that each bent tube conforms precisely to the specified dimensions and tolerances. This level of precision is essential in industries such as aerospace, automotive, and medical, where tight tolerances are critical.
Additionally, CNC tube bending allows for increased efficiency and productivity. Once the bending program is set up, the machine can produce bent tubes rapidly and consistently, reducing lead times and increasing throughput compared to manual methods. This makes CNC tube bending ideal for high-volume production runs.
Furthermore, CNC tube bending offers greater flexibility and versatility in design. Complex bend geometries, including multiple radii, compound bends, and variable wall thicknesses, can be achieved with ease using CNC machines. This enables engineers and designers to create innovative and intricate tube assemblies for a wide range of applications.
In conclusion, CNC tube bending is a highly advanced and efficient method for producing precision bent tubes and pipes. By leveraging computer-controlled technology, CNC machines offer unmatched accuracy, repeatability, and versatility in tube bending operations, making them indispensable tools in modern manufacturing processes.
Automated Tube Bending:
Automated tube bending refers to the process of bending tubes or pipes using machinery and technology that minimizes manual intervention. This method streamlines production processes, enhances efficiency, and ensures precision in bending operations. Here’s a detailed explanation:
Automated tube bending involves the use of specialized machinery equipped with computerized controls and robotic capabilities to perform bending operations. These machines are designed to handle various tube sizes, materials, and bend configurations, making them versatile tools in manufacturing and fabrication industries.
The automated tube bending process begins with the preparation of bending programs using computer-aided design (CAD) or computer-aided manufacturing (CAM) software. Engineers and programmers define the desired bend angles, radii, and dimensions, along with any specific requirements for the part.
Once the bending program is created, it is loaded into the automated tube bending machine’s control system. The machine is then set up with the appropriate tooling, including mandrels, wiper dies, and pressure dies, to support and shape the tube during bending.
During operation, the automated tube bending machine feeds the tube into the bending head, where it is clamped and positioned for bending. The machine’s computerized controls precisely manipulate the tube and bending tools, following the programmed instructions to achieve the desired bend geometry.
Automated tube bending offers several key advantages over manual bending methods. Firstly, it reduces reliance on skilled labor, as the majority of bending operations are performed by the machine itself. This helps to minimize human error and ensures consistency in bend quality and accuracy.
Additionally, automated tube bending enhances productivity and throughput by streamlining production processes and reducing cycle times. With automated machines, multiple bends can be performed quickly and efficiently, allowing for high-volume production runs and shorter lead times.
Furthermore, automated tube bending enables greater flexibility and adaptability in manufacturing operations. Changes to bending programs can be made easily, allowing for rapid prototyping and design iteration. This flexibility is particularly valuable in industries with dynamic production requirements and evolving product designs.
In conclusion, automated tube bending is a highly efficient and versatile method for producing precision bent tubes and pipes. By leveraging advanced machinery and computerized controls, automated tube bending offers increased productivity, accuracy, and flexibility in manufacturing processes, making it an essential technology in modern fabrication operations.
Precision Tube Bending:
Precision tube bending is a specialized manufacturing process used to accurately bend tubes or pipes to precise specifications, tolerances, and geometries. This technique is essential in industries where accuracy and consistency are paramount, such as aerospace, automotive, and medical device manufacturing. Here’s an in-depth explanation:
Precision tube bending involves the manipulation of tubes or pipes to achieve specific bend radii, angles, and configurations with minimal distortion or variation. This process requires advanced machinery, precise tooling, and meticulous attention to detail to ensure that the final bent tubes meet stringent quality standards.
The precision tube bending process begins with careful planning and design. Engineers and designers use computer-aided design (CAD) software to create detailed drawings and models of the desired tube assemblies, specifying the bend locations, angles, radii, and tolerances.
Once the design is finalized, the bending program is developed using computer-aided manufacturing (CAM) software. This program contains instructions for the bending machine, detailing the sequence of bends, tooling requirements, and machine parameters needed to produce the desired tube geometry.
Next, the tube is loaded into the precision tube bending machine, which is equipped with specialized tooling and controls for accurate bending. Depending on the complexity of the bend, the machine may use mandrels, wiper dies, pressure dies, and other accessories to support and shape the tube during bending.
During the bending process, the machine precisely manipulates the tube, following the programmed instructions to achieve the specified bend angles and radii. Advanced sensors and feedback systems monitor the bending operation in real-time, ensuring that each bend meets the desired tolerances and dimensions.
Precision tube bending offers several key benefits over conventional bending methods. Firstly, it enables the production of complex tube geometries with unmatched accuracy and repeatability. This level of precision is essential in applications where tight tolerances are critical for proper fit, function, and performance.
Additionally, precision tube bending minimizes material waste and scrap by optimizing the use of raw materials. By achieving precise bend geometries with minimal distortion, manufacturers can maximize the yield from each tube length, reducing costs and enhancing efficiency.
Furthermore, precision tube bending ensures consistency and uniformity across production batches. With advanced CNC machinery and automated controls, manufacturers can replicate bending parameters precisely from one part to the next, eliminating variations and ensuring conformity to specifications.
In conclusion, precision tube bending is a sophisticated manufacturing process that enables the production of high-quality bent tubes and pipes with exceptional accuracy and consistency. By leveraging advanced machinery, precise tooling, and meticulous planning, precision tube bending offers numerous benefits for industries that demand the highest standards of quality and performance.
Computer-controlled Tube Bending:
Computer-controlled tube bending, also known as CNC tube bending, is a cutting-edge manufacturing process that utilizes computer numerical control (CNC) technology to bend tubes or pipes with precision and efficiency. This method offers numerous advantages over traditional manual bending techniques and is widely used in various industries for its accuracy, repeatability, and versatility. Here’s a comprehensive explanation:
Computer-controlled tube bending involves the use of CNC machines equipped with sophisticated software and automation capabilities to precisely control the bending operation. These machines are capable of bending tubes of various sizes, shapes, and materials to meet specific design requirements.
The process begins with the creation of a bending program using computer-aided design (CAD) or computer-aided manufacturing (CAM) software. Engineers or programmers input the desired bend angles, radii, and dimensions into the software, along with any additional parameters such as material type and thickness.
Once the bending program is created, it is transferred to the CNC tube bending machine’s control system. The machine is then set up with the appropriate tooling, which may include mandrels, wiper dies, pressure dies, and other accessories, depending on the requirements of the job.
The tube to be bent is loaded into the machine’s clamping mechanism, and the bending program is executed. The CNC machine precisely positions the tube and bending tools according to the programmed instructions, applying the necessary force and rotation to achieve the desired bend geometry.
During the bending process, sensors and feedback mechanisms monitor various parameters such as tube position, bend angle, and applied force, ensuring accuracy and consistency throughout the operation. Any deviations from the programmed parameters are immediately detected and corrected by the CNC system.
Computer-controlled tube bending offers several key benefits over manual bending methods. Firstly, it allows for the production of complex bend geometries with unparalleled precision and repeatability. This is particularly important in industries such as aerospace, automotive, and medical, where tight tolerances are critical for component performance and safety.
Additionally, CNC tube bending significantly reduces setup times and operator intervention compared to manual bending techniques. Once the bending program is created and loaded into the machine, the bending operation can be performed automatically, minimizing labor costs and maximizing efficiency.
Furthermore, computer-controlled tube bending enables rapid prototyping and design iteration, as changes to bending programs can be made quickly and easily using CAD/CAM software. This flexibility allows manufacturers to adapt to evolving design requirements and production demands with minimal downtime.
In conclusion, computer-controlled tube bending is a state-of-the-art manufacturing process that offers unparalleled precision, efficiency, and flexibility in bending tubes and pipes. By harnessing the power of CNC technology, manufacturers can achieve superior results in terms of accuracy, consistency, and productivity, making it an indispensable technique in modern fabrication operations.
CNC Mandrel Tube Bending:
CNC mandrel tube bending is an advanced manufacturing process that utilizes computer numerical control (CNC) technology and mandrels to bend tubes or pipes with precision and accuracy. This method is widely used in industries where tight tolerances and high-quality bends are required, such as aerospace, automotive, and medical device manufacturing. Let’s delve into the details of CNC mandrel tube bending:
- Mandrel Tube Bending Process:
- CNC mandrel tube bending begins with the preparation of a bending program using computer-aided design (CAD) or computer-aided manufacturing (CAM) software. This program defines the desired bend angles, radii, and dimensions for the tube.
- The bending program is then transferred to the CNC mandrel tube bending machine’s control system. The machine is set up with the appropriate mandrel and tooling, which supports the inner surface of the tube during bending to prevent collapse or deformation.
- The tube to be bent is loaded into the machine’s clamping mechanism, and the bending program is executed. The CNC machine precisely positions the tube and mandrel according to the programmed instructions, applying the necessary force and rotation to achieve the desired bend geometry.
- As the tube is bent, the mandrel supports the inner surface, ensuring uniform wall thickness and preventing wrinkling or distortion. The CNC machine monitors various parameters such as bend angle, mandrel position, and tube movement to ensure accuracy and consistency throughout the bending process.
- Advantages of CNC Mandrel Tube Bending:
- High Precision: CNC mandrel tube bending offers unmatched precision and repeatability, ensuring that each bend meets the specified tolerances and dimensions with minimal variation.
- Improved Surface Finish: By supporting the inner surface of the tube, mandrel tube bending produces smooth, wrinkle-free bends with superior surface finish, reducing the need for secondary finishing operations.
- Complex Geometries: CNC mandrel tube bending allows for the creation of complex bend geometries, including multiple radii, compound bends, and variable wall thicknesses, with ease and accuracy.
- Reduced Material Waste: The use of mandrels minimizes material waste by preventing collapse or distortion of the tube during bending, maximizing the yield from each tube length and reducing production costs.
- Applications of CNC Mandrel Tube Bending:
- CNC mandrel tube bending is used in various industries for the production of precision components and assemblies, including exhaust systems, roll cages, handrails, hydraulic tubing, and structural frames.
- It is particularly well-suited for applications where tight tolerances, smooth bends, and uniform wall thickness are critical for performance, reliability, and safety.
In conclusion, CNC mandrel tube bending is a highly advanced and efficient manufacturing process that offers unmatched precision, accuracy, and versatility in bending tubes and pipes. By leveraging CNC technology and mandrels, manufacturers can produce high-quality bent components with complex geometries, meeting the stringent requirements of diverse industries.
CNC Roll Tube Bending:
CNC roll tube bending is a sophisticated manufacturing process used to bend tubes or pipes using a set of rollers and computer numerical control (CNC) technology. This method offers precise control over the bending process, allowing for the creation of complex shapes and geometries with accuracy and repeatability. Here’s a detailed explanation of CNC roll tube bending:
- Roll Tube Bending Process:
- CNC roll tube bending begins with the preparation of a bending program using computer-aided design (CAD) or computer-aided manufacturing (CAM) software. This program defines the desired bend angles, radii, and dimensions for the tube.
- The bending program is then transferred to the CNC roll tube bending machine’s control system. The machine is equipped with a series of rollers arranged in a specific configuration to support and shape the tube during bending.
- The tube to be bent is loaded into the machine’s clamping mechanism, and the bending program is executed. The CNC machine precisely positions the tube and rollers according to the programmed instructions, applying the necessary force and rotation to achieve the desired bend geometry.
- As the tube is fed through the rollers, it is gradually bent to the specified shape. The CNC machine monitors various parameters such as bend angle, roller position, and tube movement to ensure accuracy and consistency throughout the bending process.
- Advantages of CNC Roll Tube Bending:
- Versatility: CNC roll tube bending machines can accommodate a wide range of tube sizes, shapes, and materials, making them suitable for diverse applications and industries.
- Complex Geometries: CNC roll tube bending allows for the creation of complex bend geometries, including large-radius bends, spiral bends, and elliptical bends, with precision and efficiency.
- High Productivity: CNC roll tube bending machines can bend tubes rapidly and continuously, resulting in high throughput and shorter lead times compared to manual bending methods.
- Minimal Distortion: The use of rollers distributes bending forces evenly along the length of the tube, minimizing distortion and maintaining consistent wall thickness throughout the bend.
- Applications of CNC Roll Tube Bending:
- CNC roll tube bending is used in various industries for the production of a wide range of components and assemblies, including handrails, exhaust systems, architectural structures, and industrial machinery.
- It is particularly well-suited for applications that require large-radius bends, smooth curves, and intricate shapes, such as decorative elements, structural frames, and artistic installations.
In conclusion, CNC roll tube bending is a highly versatile and efficient manufacturing process that offers precise control over tube bending operations. By leveraging CNC technology and rollers, manufacturers can produce high-quality bent components with complex geometries, meeting the requirements of diverse industries and applications.
CNC Rotary Draw Tube Bending:
CNC rotary draw tube bending is a sophisticated manufacturing process used to bend tubes or pipes with precision and accuracy. This method relies on a rotary draw bending machine equipped with computer numerical control (CNC) technology to produce complex bends and shapes with consistency and repeatability. Let’s explore the details of CNC rotary draw tube bending:
- Rotary Draw Tube Bending Process:
- CNC rotary draw tube bending begins with the preparation of a bending program using computer-aided design (CAD) or computer-aided manufacturing (CAM) software. This program defines the desired bend angles, radii, and dimensions for the tube.
- The bending program is then transferred to the CNC rotary draw tube bending machine’s control system. The machine is equipped with a bending die, clamp, mandrel, and other tooling necessary for the bending operation.
- The tube to be bent is loaded into the machine’s clamp, and the mandrel is inserted into the tube to support the inner surface and prevent collapse during bending.
- As the bending program is executed, the CNC machine precisely positions the tube and bending die according to the programmed instructions. The tube is drawn around the bending die by the clamping mechanism, resulting in a smooth and accurate bend.
- Advanced sensors and feedback systems monitor various parameters such as bend angle, mandrel position, and tube movement to ensure accuracy and consistency throughout the bending process.
- Advantages of CNC Rotary Draw Tube Bending:
- High Precision: CNC rotary draw tube bending offers unmatched precision and repeatability, ensuring that each bend meets the specified tolerances and dimensions with minimal variation.
- Excellent Surface Finish: The use of mandrels and controlled bending forces results in smooth, wrinkle-free bends with superior surface finish, reducing the need for secondary finishing operations.
- Complex Geometries: CNC rotary draw tube bending allows for the creation of complex bend geometries, including multiple radii, compound bends, and tight-radius bends, with ease and accuracy.
- Minimal Distortion: The use of mandrels and controlled bending forces minimizes distortion and maintains consistent wall thickness throughout the bend, ensuring dimensional accuracy and structural integrity.
- Applications of CNC Rotary Draw Tube Bending:
- CNC rotary draw tube bending is used in various industries for the production of precision components and assemblies, including automotive exhaust systems, aerospace structures, hydraulic tubing, and medical devices.
- It is particularly well-suited for applications that require tight tolerances, smooth bends, and uniform wall thickness, such as fluid handling systems, instrumentation, and structural frameworks.
In conclusion, CNC rotary draw tube bending is a highly advanced and efficient manufacturing process that offers unparalleled precision, accuracy, and versatility in bending tubes and pipes. By leveraging CNC technology and mandrels, manufacturers can produce high-quality bent components with complex geometries, meeting the stringent requirements of diverse industries and applications.
CNC Compression Tube Bending:
CNC compression tube bending is a precision manufacturing process used to bend tubes or pipes using compression forces applied by a specialized bending machine controlled by computer numerical control (CNC) technology. This method offers high accuracy and repeatability, making it suitable for industries where precise bends are essential. Here’s a detailed explanation of CNC compression tube bending:
- Compression Tube Bending Process:
- CNC compression tube bending begins with the preparation of a bending program using computer-aided design (CAD) or computer-aided manufacturing (CAM) software. This program defines the desired bend angles, radii, and dimensions for the tube.
- The bending program is then transferred to the CNC compression tube bending machine’s control system. The machine is equipped with a bending die, clamp, and other tooling necessary for the bending operation.
- The tube to be bent is loaded into the machine’s clamp, and the bending die is positioned accordingly. The CNC machine applies compression forces to the tube at specific points along its length, causing it to deform and bend around the die.
- Advanced sensors and feedback systems monitor various parameters such as bend angle, clamp pressure, and tube movement to ensure accuracy and consistency throughout the bending process.
- Advantages of CNC Compression Tube Bending:
- High Precision: CNC compression tube bending offers precise control over bend angles and dimensions, ensuring that each bend meets the specified tolerances with minimal variation.
- Versatility: The compression bending process can accommodate a wide range of tube sizes, shapes, and materials, making it suitable for diverse applications and industries.
- Minimal Distortion: The controlled application of compression forces minimizes distortion and maintains consistent wall thickness throughout the bend, ensuring dimensional accuracy and structural integrity.
- Efficiency: CNC compression tube bending machines can bend tubes rapidly and continuously, resulting in high throughput and shorter lead times compared to manual bending methods.
- Applications of CNC Compression Tube Bending:
- CNC compression tube bending is used in various industries for the production of precision components and assemblies, including automotive exhaust systems, hydraulic tubing, HVAC systems, and furniture.
- It is particularly well-suited for applications that require tight tolerances, smooth bends, and uniform wall thickness, such as fluid conveyance systems, structural frameworks, and architectural elements.
In conclusion, CNC compression tube bending is a highly efficient and versatile manufacturing process that offers precise control over tube bending operations. By leveraging CNC technology and compression forces, manufacturers can produce high-quality bent components with accuracy and consistency, meeting the requirements of diverse industries and applications.
CNC Hydraulic Tube Bending:
CNC hydraulic tube bending is a precise manufacturing process used to bend tubes or pipes using hydraulic pressure controlled by computer numerical control (CNC) technology. This method offers high accuracy, repeatability, and versatility, making it suitable for a wide range of applications across various industries. Here’s a detailed explanation of CNC hydraulic tube bending:
- Hydraulic Tube Bending Process:
- CNC hydraulic tube bending begins with the preparation of a bending program using computer-aided design (CAD) or computer-aided manufacturing (CAM) software. This program specifies the desired bend angles, radii, and dimensions for the tube.
- The bending program is then transferred to the CNC hydraulic tube bending machine’s control system. The machine is equipped with hydraulic cylinders, mandrels, clamps, and other tooling necessary for the bending operation.
- The tube to be bent is loaded into the machine’s clamp, and the mandrel is inserted into the tube to support the inner surface and prevent collapse during bending.
- As the bending program is executed, the CNC machine controls the movement of hydraulic cylinders, applying pressure to specific points along the tube’s length to induce bending. The mandrel and clamps hold the tube in place to maintain dimensional accuracy and prevent distortion.
- Advanced sensors and feedback systems monitor various parameters such as bend angle, hydraulic pressure, and tube movement to ensure precision and consistency throughout the bending process.
- Advantages of CNC Hydraulic Tube Bending:
- High Precision: CNC hydraulic tube bending offers precise control over bend angles and dimensions, ensuring that each bend meets the specified tolerances with minimal variation.
- Versatility: Hydraulic tube bending machines can handle a wide range of tube sizes, shapes, and materials, making them suitable for diverse applications in industries such as automotive, aerospace, and construction.
- Efficiency: CNC hydraulic tube bending machines can bend tubes rapidly and continuously, resulting in high throughput and shorter lead times compared to manual bending methods.
- Minimal Distortion: The controlled application of hydraulic pressure minimizes distortion and maintains consistent wall thickness throughout the bend, ensuring dimensional accuracy and structural integrity.
- Applications of CNC Hydraulic Tube Bending:
- CNC hydraulic tube bending is used in various industries for the production of components and assemblies, including exhaust systems, roll cages, handrails, hydraulic tubing, and structural frames.
- It is particularly well-suited for applications that require precise bends, such as fluid conveyance systems, instrumentation, and architectural elements.
In conclusion, CNC hydraulic tube bending is a highly efficient and versatile manufacturing process that offers precise control over tube bending operations. By leveraging CNC technology and hydraulic pressure, manufacturers can produce high-quality bent components with accuracy and consistency, meeting the requirements of diverse industries and applications.
CNC Electric Tube Bending
CNC electric tube bending is an advanced manufacturing process used to bend tubes or pipes using electric servo motors controlled by computer numerical control (CNC) technology. This method offers high precision, flexibility, and efficiency, making it suitable for a wide range of applications across various industries. Let’s explore the details of CNC electric tube bending:
- Electric Tube Bending Process:
- CNC electric tube bending begins with the preparation of a bending program using computer-aided design (CAD) or computer-aided manufacturing (CAM) software. This program specifies the desired bend angles, radii, and dimensions for the tube.
- The bending program is then transferred to the CNC electric tube bending machine’s control system. The machine is equipped with electric servo motors, mandrels, clamps, and other tooling necessary for the bending operation.
- The tube to be bent is loaded into the machine’s clamp, and the mandrel is inserted into the tube to support the inner surface and prevent collapse during bending.
- As the bending program is executed, the CNC machine controls the movement of electric servo motors, which apply precise force and torque to specific points along the tube’s length to induce bending. The mandrel and clamps hold the tube in place to maintain dimensional accuracy and prevent distortion.
- Advanced sensors and feedback systems monitor various parameters such as bend angle, motor position, and tube movement to ensure precision and consistency throughout the bending process.
- Advantages of CNC Electric Tube Bending:
- High Precision: CNC electric tube bending offers precise control over bend angles and dimensions, ensuring that each bend meets the specified tolerances with minimal variation.
- Versatility: Electric tube bending machines can handle a wide range of tube sizes, shapes, and materials, making them suitable for diverse applications in industries such as automotive, aerospace, and furniture.
- Efficiency: CNC electric tube bending machines can bend tubes rapidly and continuously, resulting in high throughput and shorter lead times compared to manual bending methods.
- Energy Efficiency: Electric tube bending machines consume less energy compared to hydraulic systems, resulting in lower operating costs and reduced environmental impact.
- Applications of CNC Electric Tube Bending:
- CNC electric tube bending is used in various industries for the production of components and assemblies, including exhaust systems, roll cages, handrails, hydraulic tubing, and structural frames.
- It is particularly well-suited for applications that require precise bends and tight tolerances, such as automotive chassis components, medical devices, and aerospace structures.
In conclusion, CNC electric tube bending is a highly efficient and versatile manufacturing process that offers precise control over tube bending operations. By leveraging CNC technology and electric servo motors, manufacturers can produce high-quality bent components with accuracy and consistency, meeting the requirements of diverse industries and applications.
CNC Tube End Forming
CNC tube end forming is a specialized manufacturing process used to shape and modify the ends of tubes or pipes to meet specific requirements for assembly, connection, or functionality. This process involves the use of computer numerical control (CNC) technology to precisely control the shaping operations, ensuring accuracy, repeatability, and consistency. Here’s an in-depth explanation of CNC tube end forming:
- End Forming Operations:
- CNC tube end forming encompasses a variety of shaping operations performed on the ends of tubes or pipes. These operations may include flaring, flanging, expanding, reducing, swaging, beading, notching, threading, punching, and trimming, among others.
- Each end forming operation is designed to achieve a specific result, such as creating mating surfaces for welding or brazing, forming seals or connections, accommodating fittings or fasteners, enhancing structural integrity, or facilitating assembly with other components.
- CNC Technology:
- CNC tube end forming machines are equipped with computer-controlled axes, tooling, and programming capabilities to execute precise shaping operations according to predefined specifications.
- Engineers or programmers create end forming programs using computer-aided design (CAD) or computer-aided manufacturing (CAM) software, specifying the desired end shapes, dimensions, tolerances, and tooling paths.
- The CNC machine’s control system interprets the program and coordinates the movement of the machine’s components, including clamps, mandrels, dies, punches, and cutting tools, to perform the shaping operations with accuracy and repeatability.
- Advantages of CNC Tube End Forming:
- Precision and Accuracy: CNC tube end forming offers precise control over end dimensions, shapes, and tolerances, ensuring that each part meets the specified requirements with minimal variation.
- Consistency and Repeatability: CNC technology enables consistent and repeatable shaping operations, regardless of batch size or complexity, resulting in uniformity and reliability in the finished parts.
- Versatility: CNC tube end forming machines can accommodate a wide range of tube sizes, shapes, materials, and end forming operations, making them suitable for diverse applications and industries.
- Efficiency: CNC machines can perform end forming operations rapidly and automatically, reducing cycle times, labor costs, and material waste compared to manual or semi-automatic methods.
- Applications of CNC Tube End Forming:
- CNC tube end forming is used in various industries for the production of components and assemblies, including automotive exhaust systems, fluid handling systems, HVAC ductwork, furniture frames, and structural frameworks.
- It is particularly well-suited for applications that require precise end shapes, dimensions, and tolerances, such as tube fittings, connectors, adapters, couplings, flanges, and manifolds.
In conclusion, CNC tube end forming is a versatile and efficient manufacturing process that offers precise control over end shapes and dimensions, enabling the production of high-quality tube components with accuracy, repeatability, and consistency. By leveraging CNC technology, manufacturers can meet the diverse end forming requirements of different industries and applications effectively.
CNC Tube Cutting:
CNC tube cutting is a precision manufacturing process used to cut tubes or pipes to specific lengths with accuracy and repeatability. This process involves the use of computer numerical control (CNC) technology to control cutting operations, resulting in clean, precise cuts for various applications across different industries. Here’s a detailed explanation of CNC tube cutting:
- Cutting Methods:
- CNC tube cutting can be performed using various cutting methods, including sawing, milling, laser cutting, plasma cutting, and waterjet cutting.
- Each cutting method offers specific advantages in terms of cutting speed, accuracy, material compatibility, and cost-effectiveness, depending on the requirements of the application.
- CNC Technology:
- CNC tube cutting machines are equipped with computer-controlled axes, cutting tools, and programming capabilities to execute precise cutting operations according to predefined specifications.
- Engineers or programmers create cutting programs using computer-aided design (CAD) or computer-aided manufacturing (CAM) software, specifying the desired cut lengths, angles, dimensions, tolerances, and tooling paths.
- The CNC machine’s control system interprets the program and coordinates the movement of the machine’s components, including cutting heads, clamps, guides, and support structures, to perform the cutting operations with accuracy and repeatability.
- Advantages of CNC Tube Cutting:
- Precision and Accuracy: CNC tube cutting offers precise control over cut lengths, angles, and dimensions, ensuring that each part meets the specified requirements with minimal deviation.
- Speed and Efficiency: CNC machines can perform cutting operations rapidly and automatically, reducing cycle times and labor costs compared to manual cutting methods.
- Versatility: CNC tube cutting machines can accommodate a wide range of tube sizes, shapes, materials, and cutting methods, making them suitable for diverse applications and industries.
- Clean and Burr-Free Cuts: CNC cutting methods such as laser cutting and waterjet cutting produce clean, burr-free cuts with high precision, eliminating the need for secondary finishing operations.
- Applications of CNC Tube Cutting:
- CNC tube cutting is used in various industries for the production of components and assemblies, including automotive chassis, frame structures, roll cages, exhaust systems, furniture frames, and architectural elements.
- It is particularly well-suited for applications that require precise cut lengths, angles, and dimensions, such as tube fabrication, welding, assembly, and installation.
In conclusion, CNC tube cutting is a versatile and efficient manufacturing process that offers precise control over cutting operations, enabling the production of high-quality tube components with accuracy, repeatability, and consistency. By leveraging CNC technology and advanced cutting methods, manufacturers can meet the diverse cutting requirements of different industries and applications effectively.
Tube Flaring:
Tube flaring is a manufacturing process used to create a flared end on a tube or pipe for various applications, such as joining tubes together or forming connections with fittings. This process involves expanding the end of the tube outward in a conical shape to create a wider opening. Here’s a detailed explanation of tube flaring:
- Flaring Operations:
- Tube flaring can be performed using different methods, including manual flaring tools, hydraulic flaring machines, and CNC-controlled flaring equipment.
- The flaring process typically involves clamping the tube in a flaring die or fixture and applying force to expand the end of the tube gradually.
- Depending on the desired flare angle and shape, different flaring tools, such as mandrels, punches, and dies, may be used to achieve the desired result.
- Types of Flares:
- There are several types of flares commonly used in various industries, including:
- Single Flare: In a single flare, the tube end is flared outward at a single angle.
- Double Flare: In a double flare, the tube end is flared outward twice to create a more pronounced flare with a sealing surface.
- Triple Flare: In a triple flare, the tube end is flared outward three times to create a deep, tapered flare suitable for high-pressure applications.
- Inverted Flare: In an inverted flare, the tube end is flared inward to create a lip that provides a secure connection with a fitting or connector.
- There are several types of flares commonly used in various industries, including:
- Applications of Tube Flaring:
- Tube flaring is commonly used in industries such as automotive, aerospace, HVAC, plumbing, and hydraulic systems.
- It is often used to create connections between tubes and fittings, such as in brake lines, fuel lines, refrigeration systems, and hydraulic tubing.
- Flared tube ends provide a secure, leak-proof connection with fittings and improve the strength and integrity of the joint.
- Advantages of Tube Flaring:
- Secure Connections: Flared tube ends create a secure, leak-proof connection with fittings, ensuring reliable performance in demanding applications.
- Enhanced Strength: Flaring the tube end increases its strength and resistance to deformation, improving the overall integrity of the joint.
- Versatility: Tube flaring can be performed on various types of tubing materials, including copper, aluminum, steel, and stainless steel, making it suitable for a wide range of applications.
- Cost-Effectiveness: Tube flaring is a cost-effective method for creating connections between tubes and fittings, as it eliminates the need for additional components such as solder, adhesive, or compression fittings.
In conclusion, tube flaring is a versatile and widely used manufacturing process that provides secure, leak-proof connections between tubes and fittings in various industries. By employing the appropriate flaring method and equipment, manufacturers can produce high-quality flared tube ends that meet the specific requirements of their applications effectively.
Tube Swaging:
Tube swaging is a metal forming process used to reduce or increase the diameter of a tube or pipe by compressing or expanding its cross-section. This process involves applying radial force to the tube, causing it to conform to the shape of a die or mandrel. Here’s a detailed explanation of tube swaging:
- Swaging Operations:
- Tube swaging can be performed using various methods, including rotary swaging, axial swaging, and hydraulic swaging.
- The swaging process typically involves clamping the tube in a swaging machine and applying radial force to the tube using swaging dies, rollers, or mandrels.
- Depending on the desired outcome, swaging may be used to reduce the diameter of the tube (swage down) or increase it (swage up).
- Types of Swages:
- There are several types of swages commonly used in tube swaging operations, including:
- External Swage: In an external swage, the outside diameter of the tube is reduced by compressing it against a die or mandrel.
- Internal Swage: In an internal swage, the inside diameter of the tube is increased by expanding it using a mandrel or internal tooling.
- Tapered Swage: In a tapered swage, the diameter of the tube is gradually reduced or increased along its length to create a tapered shape.
- There are several types of swages commonly used in tube swaging operations, including:
- Applications of Tube Swaging:
- Tube swaging is used in various industries for a wide range of applications, including aerospace, automotive, HVAC, plumbing, and hydraulic systems.
- It is often used to create fittings, couplings, reducers, expanders, and other components that require precise changes in diameter.
- Swaged tubes provide a secure, leak-proof connection with fittings and improve the overall strength and integrity of the joint.
- Advantages of Tube Swaging:
- Precise Dimensional Control: Tube swaging allows for precise control over the diameter and wall thickness of the swaged portion, ensuring tight tolerances and dimensional accuracy.
- Improved Strength: Swaged tubes exhibit improved strength and resistance to deformation, making them suitable for high-pressure and high-stress applications.
- Versatility: Tube swaging can be performed on various types of tubing materials, including copper, aluminum, steel, and stainless steel, making it suitable for a wide range of applications.
- Cost-Effectiveness: Tube swaging is a cost-effective method for creating custom fittings and components, as it eliminates the need for welding, brazing, or machining operations.
In conclusion, tube swaging is a versatile and efficient metal forming process that allows for precise changes in the diameter of tubes or pipes. By employing the appropriate swaging method and equipment, manufacturers can produce high-quality swaged components that meet the specific requirements of their applications effectively.
Tube Notching:
Tube notching is a manufacturing process used to create precise cuts or grooves in the ends or along the length of tubes or pipes. This process is commonly used to prepare tubes for welding, assembly, or joining with other components. Here’s a detailed explanation of tube notching:
- Notching Operations:
- Tube notching can be performed using various methods, including manual notching tools, mechanical notchers, and CNC-controlled notching machines.
- The notching process typically involves clamping the tube in a notching fixture or machine and cutting or grinding away material to create the desired notch shape.
- Depending on the application and requirements, notches may be cut at different angles, depths, and locations on the tube.
- Types of Notches:
- There are several types of notches commonly used in tube notching operations, including:
- End Notch: An end notch is cut at the end of the tube to prepare it for welding or joining with another component.
- Offset Notch: An offset notch is cut along the length of the tube to create a step or groove for mating with another tube or component.
- V-Notch: A V-notch is cut at an angle to create a V-shaped groove for welding or assembly purposes.
- Saddle Notch: A saddle notch is cut to create a flat surface for joining tubes at an angle or intersection.
- There are several types of notches commonly used in tube notching operations, including:
- Applications of Tube Notching:
- Tube notching is used in various industries for a wide range of applications, including automotive, aerospace, fabrication, construction, and structural engineering.
- It is often used to prepare tubes for welding, assembly, or joining with other components in complex structures, frames, and assemblies.
- Notched tubes provide precise mating surfaces for welding, brazing, or mechanical connections, ensuring strong and reliable joints.
- Advantages of Tube Notching:
- Precise Fit: Tube notching allows for precise cuts and grooves to be made in tubes, ensuring tight tolerances and accurate fit-up with other components.
- Improved Strength: Notched tubes provide increased surface area for welding or mechanical connections, resulting in stronger and more durable joints.
- Versatility: Tube notching can be performed on various types of tubing materials, including steel, aluminum, stainless steel, and copper, making it suitable for a wide range of applications.
- Cost-Effectiveness: Tube notching is a cost-effective method for preparing tubes for welding or assembly, as it eliminates the need for complex machining or fabrication processes.
In conclusion, tube notching is a versatile and efficient manufacturing process that allows for precise cuts and grooves to be made in tubes or pipes. By employing the appropriate notching method and equipment, manufacturers can produce high-quality notched tubes that meet the specific requirements of their applications effectively.
Tube Piercing:
Tube piercing is a metalworking process used to create holes or perforations in tubes or pipes. This process involves forcing a pointed tool or punch through the wall of the tube to create a hole without removing any material. Here’s a detailed explanation of tube piercing:
- Piercing Operations:
- Tube piercing can be performed using various methods, including mechanical piercing presses, hydraulic piercing machines, and CNC-controlled piercing equipment.
- The piercing process typically involves clamping the tube in a piercing fixture or machine and aligning a piercing tool or punch with the desired location for the hole.
- The piercing tool is then forced through the wall of the tube using hydraulic pressure, mechanical force, or CNC-controlled movements, creating a hole of the specified size and shape.
- Depending on the application and requirements, multiple holes may be pierced in a single tube or pipe.
- Types of Piercings:
- There are several types of piercings commonly used in tube piercing operations, including:
- Round Piercing: Round holes are the most common type of piercing and are used for various applications, such as fluid flow, ventilation, or mounting hardware.
- Oval Piercing: Oval holes may be used for specific applications where space constraints or aesthetics are a consideration.
- Slot Piercing: Slots or elongated holes may be pierced in tubes for applications such as keyhole mounting or adjustable fastening.
- There are several types of piercings commonly used in tube piercing operations, including:
- Applications of Tube Piercing:
- Tube piercing is used in various industries for a wide range of applications, including automotive, aerospace, HVAC, plumbing, and fluid handling systems.
- It is often used to create holes for fluid flow, ventilation, drainage, mounting hardware, or fastening in tubes or pipes.
- Pierced tubes provide precise openings for the passage of fluids, gases, or mounting components, ensuring efficient operation and assembly.
- Advantages of Tube Piercing:
- Precision: Tube piercing allows for precise holes to be created in tubes or pipes with tight tolerances and accurate placement.
- Speed: Piercing operations can be performed rapidly and automatically using hydraulic or CNC-controlled equipment, resulting in high throughput and shorter lead times.
- Versatility: Tube piercing can be performed on various types of tubing materials, including steel, aluminum, stainless steel, and copper, making it suitable for a wide range of applications.
- Cost-Effectiveness: Tube piercing is a cost-effective method for creating holes in tubes or pipes, as it eliminates the need for drilling, punching, or machining operations.
In conclusion, tube piercing is a versatile and efficient manufacturing process that allows for precise holes to be created in tubes or pipes for various applications. By employing the appropriate piercing method and equipment, manufacturers can produce high-quality pierced tubes that meet the specific requirements of their applications effectively.
Tube Welding:
Tube welding is a manufacturing process used to join two or more tubes or pipes together permanently. This process involves the fusion of the mating surfaces of the tubes using heat and pressure, resulting in a strong and durable joint. Here’s a detailed explanation of tube welding:
- Welding Methods:
- Tube welding can be performed using various methods, including:
- Tungsten Inert Gas (TIG) Welding: TIG welding uses a non-consumable tungsten electrode to create an arc between the electrode and the workpiece, producing a weld pool that is shielded by an inert gas (such as argon). TIG welding is commonly used for welding thin-wall tubes and provides high-quality, precise welds.
- Metal Inert Gas (MIG) Welding: MIG welding uses a consumable wire electrode that is fed continuously into the weld pool, along with a shielding gas, to create a strong weld between the tubes. MIG welding is suitable for welding thicker-walled tubes and offers higher deposition rates compared to TIG welding.
- Flux-Cored Arc Welding (FCAW): FCAW welding uses a tubular wire electrode with flux inside, which provides a shielding gas and forms a slag to protect the weld pool. FCAW welding is often used for outdoor or high-wind welding applications and offers higher deposition rates than TIG welding.
- Submerged Arc Welding (SAW): SAW welding uses a granular flux that is fed continuously around the electrode, creating a submerged arc beneath the flux layer. SAW welding is commonly used for welding thick-walled tubes and offers high deposition rates and deep penetration.
- Tube welding can be performed using various methods, including:
- Welding Process:
- Tube welding begins with the preparation of the tubes, including cleaning the mating surfaces to remove contaminants and ensuring proper fit-up between the tubes.
- The welding process involves the application of heat to the mating surfaces of the tubes using a welding torch or electrode, along with the appropriate shielding gas or flux to protect the weld pool from atmospheric contamination.
- The welder manipulates the welding torch or electrode along the joint, ensuring proper penetration and fusion between the tubes.
- After welding, the weld bead may be cleaned, inspected, and finished as necessary to meet the requirements of the application.
- Advantages of Tube Welding:
- Strong and Durable Joints: Tube welding creates strong and durable joints that can withstand mechanical stresses, pressure, and temperature variations.
- Versatility: Tube welding can be used to join tubes or pipes made of various materials, including steel, stainless steel, aluminum, copper, and alloys.
- Cost-Effectiveness: Tube welding is a cost-effective method for joining tubes together permanently, as it eliminates the need for mechanical fasteners or adhesives and provides a reliable and long-lasting joint.
- High Production Rates: Welding processes such as MIG and FCAW offer high deposition rates, allowing for rapid welding of large quantities of tubes.
- Applications of Tube Welding:
- Tube welding is used in various industries for the fabrication of structural frameworks, piping systems, heat exchangers, pressure vessels, automotive components, and more.
- It is commonly used in applications where leak-proof and robust joints are required, such as fluid transport systems, gas pipelines, and structural assemblies.
In conclusion, tube welding is a versatile and widely used manufacturing process that provides strong and durable joints between tubes or pipes. By employing the appropriate welding method and equipment, manufacturers can produce high-quality welded tubes that meet the specific requirements of their applications effectively.
Tube Bending Dies:
Tube bending dies are essential components of tube bending machines used in the manufacturing process to shape tubes or pipes into desired configurations. These dies play a crucial role in determining the bend radius, angle, and overall quality of the bent tube. Here’s a detailed explanation of tube bending dies:
- Types of Tube Bending Dies:
- Mandrel Dies: Mandrel dies incorporate a mandrel, or internal support, that is inserted into the tube during bending to prevent collapsing or wrinkling of the inner wall. They are used for precision bending applications where tight tolerances and minimal distortion are required.
- Wiper Dies: Wiper dies feature a wiper or pressure pad that applies pressure to the outside of the tube to control wall thinning and improve bend quality. They are commonly used in rotary draw bending machines.
- Segmented Dies: Segmented dies consist of multiple individual segments that can be adjusted and repositioned to accommodate different tube diameters and bend radii. They offer flexibility and versatility in bending various tube sizes and shapes.
- Punch and Die Sets: Punch and die sets are used in rotary or press bending machines to deform the tube around a stationary or rotating die. They are suitable for high-volume production and can accommodate complex bend geometries.
- Compression Bending Dies: Compression bending dies compress the tube against a stationary or rotating form to induce bending. They are commonly used for large-radius bends and thick-walled tubes.
- Design Considerations:
- Material: Tube bending dies are typically made from hardened steel, carbide, or other durable materials to withstand the high pressures and stresses encountered during bending.
- Geometry: The geometry of the die, including the radius and profile, determines the shape of the bend and influences factors such as springback, wrinkling, and distortion.
- Surface Finish: The surface finish of the die affects the quality of the bend and the lifespan of the die. Smooth, polished surfaces reduce friction and wear, resulting in better bend quality and longer die life.
- Compatibility: Tube bending dies must be compatible with the specific tube bending machine and tooling system being used to ensure proper fit and performance.
- Applications of Tube Bending Dies:
- Tube bending dies are used in various industries for the production of bent tubes and pipes used in applications such as automotive exhaust systems, aerospace structures, HVAC ductwork, furniture frames, and architectural elements.
- They are essential for manufacturing components with precise bend angles, dimensions, and tolerances, meeting the requirements of diverse applications and industries.
- Maintenance and Care:
- Proper maintenance and care of tube bending dies are essential to ensure optimal performance and longevity. This includes regular inspection, cleaning, lubrication, and replacement of worn or damaged components.
- Die storage and handling practices should be followed to prevent damage and contamination, preserving the integrity and accuracy of the dies.
In conclusion, tube bending dies are critical components of tube bending machines that enable the precise shaping of tubes and pipes for various applications. By selecting the appropriate die design and maintaining proper care and maintenance practices, manufacturers can achieve high-quality bent components that meet the specific requirements of their applications effectively.
Tube Bending Machine Maintenance:
Tube bending machine maintenance is essential to ensure optimal performance, accuracy, and longevity of the equipment. Regular maintenance practices help prevent breakdowns, reduce downtime, and extend the lifespan of the machine. Here’s a detailed explanation of tube bending machine maintenance:
- Cleaning:
- Regular cleaning of the machine components, including the bending head, clamps, mandrels, dies, and guide rollers, is essential to remove dirt, debris, and metal shavings that can accumulate during operation.
- Use appropriate cleaning solvents and lubricants to keep the machine components free from rust and corrosion, especially in humid or corrosive environments.
- Lubrication:
- Lubricate moving parts, such as bearings, gears, slides, and hydraulic cylinders, according to the manufacturer’s recommendations to reduce friction, wear, and heat generation.
- Use high-quality lubricants suitable for the specific components and operating conditions of the machine to ensure smooth operation and prevent premature failure.
- Alignment:
- Regularly check and adjust the alignment of the machine components, including the bending head, mandrel, clamps, and guide rollers, to ensure accurate bending and prevent misalignment-related issues.
- Use precision measuring tools, such as dial indicators and laser alignment devices, to verify alignment and make necessary adjustments as needed.
- Inspecting Wear Parts:
- Periodically inspect wear parts, such as mandrels, dies, guide rollers, and tooling, for signs of wear, damage, or deformation.
- Replace worn or damaged parts promptly to maintain bending accuracy and prevent damage to the machine and workpieces.
- Hydraulic System Maintenance:
- Check hydraulic fluid levels, filters, hoses, and fittings regularly and replace or refill them as needed to ensure proper functioning of the hydraulic system.
- Inspect hydraulic cylinders, valves, pumps, and seals for leaks, damage, or malfunction and repair or replace them as necessary to prevent hydraulic system failures.
- Electrical System Maintenance:
- Inspect electrical components, such as switches, relays, motors, and control panels, for signs of wear, damage, or corrosion.
- Tighten loose connections, clean electrical contacts, and replace faulty components to ensure reliable operation of the electrical system.
- Safety Checks:
- Perform regular safety checks on the machine, including emergency stop buttons, safety guards, interlocks, and warning labels, to ensure compliance with safety regulations and protect operators from hazards.
- Train operators on safe operating procedures, including proper machine setup, tooling installation, material handling, and personal protective equipment (PPE) usage.
- Documentation and Records:
- Maintain detailed maintenance records, including inspection logs, service reports, repair records, and parts replacement history, to track the maintenance history of the machine and identify trends or recurring issues.
- Use maintenance management software or systems to schedule preventive maintenance tasks, track maintenance schedules, and generate maintenance reports for analysis and decision-making.
In conclusion, tube bending machine maintenance is crucial for ensuring the reliable performance, accuracy, and safety of the equipment. By following a comprehensive maintenance program that includes cleaning, lubrication, alignment, inspection, and safety checks, manufacturers can maximize the uptime and productivity of their tube bending machines while minimizing the risk of unplanned downtime and costly repairs.
Tube Bending Machine Safety:
Ensuring safety when operating tube bending machines is paramount to prevent accidents, injuries, and damage to equipment. Tube bending machines pose various hazards, including moving parts, high-pressure hydraulic systems, and sharp tooling, which require proper safety measures and precautions. Here’s a detailed explanation of tube bending machine safety:
- Operator Training:
- Provide comprehensive training to operators on the safe operation of tube bending machines, including machine setup, tooling installation, material handling, and emergency procedures.
- Training should cover the identification of machine components, safety features, operating controls, and potential hazards associated with tube bending operations.
- Personal Protective Equipment (PPE):
- Require operators to wear appropriate PPE, including safety glasses, hearing protection, gloves, and protective clothing, to protect against flying debris, noise, burns, and cuts.
- Ensure that PPE is properly fitted, maintained, and used according to manufacturer recommendations and workplace safety regulations.
- Machine Guarding:
- Install and maintain machine guards, barriers, and safety interlocks to prevent access to hazardous areas, such as pinch points, rotating parts, and cutting zones, during machine operation.
- Guards should be designed to be secure, durable, and tamper-resistant, and they should not impede visibility or access to machine controls and tooling.
- Emergency Stop Controls:
- Install accessible emergency stop buttons or switches at multiple locations on the machine to allow operators to quickly stop machine operation in case of emergencies or hazardous situations.
- Test emergency stop controls regularly to ensure they function correctly and effectively interrupt machine operation when activated.
- Hydraulic System Safety:
- Implement lockout/tagout procedures to isolate and de-energize hydraulic systems before performing maintenance, service, or repair activities on tube bending machines.
- Inspect hydraulic hoses, fittings, and components regularly for leaks, damage, or deterioration and repair or replace them promptly to prevent hydraulic fluid spills or accidents.
- Tooling Safety:
- Handle and install tooling, such as mandrels, dies, and clamps, with caution to avoid pinch points, sharp edges, and crushing hazards.
- Ensure that tooling is properly secured, aligned, and inspected before each use to prevent tooling malfunctions, ejections, or accidents during bending operations.
- Material Handling:
- Establish safe material handling procedures, including the use of lifting equipment, fixtures, and supports, to safely position, load, and unload tubes or pipes onto the bending machine.
- Train operators on proper material handling techniques to prevent strains, sprains, and other musculoskeletal injuries associated with lifting and moving heavy or awkward objects.
- Safety Culture and Communication:
- Foster a safety-conscious work environment where employees feel empowered to report safety concerns, near misses, or incidents promptly.
- Encourage open communication, collaboration, and feedback among operators, supervisors, and safety personnel to identify hazards, implement corrective actions, and continuously improve safety practices.
In conclusion, tube bending machine safety is essential to protect operators, prevent accidents, and ensure the safe operation of equipment. By implementing comprehensive safety measures, providing adequate training and PPE, and fostering a safety-focused culture, manufacturers can create a safer work environment and reduce the risk of injuries and incidents associated with tube bending operations.
Tube Bending Machine Controls:
Tube bending machine controls are essential for operating, programming, and controlling the bending process accurately and efficiently. These controls enable operators to input bending parameters, monitor machine status, and adjust settings to achieve precise bends according to specifications. Here’s a detailed explanation of tube bending machine controls:
- Control Interface:
- Tube bending machines feature a control interface that allows operators to interact with the machine, input bending parameters, and monitor machine status.
- The control interface may consist of a touchscreen display, keypad, buttons, and knobs for navigating menus, entering data, and making adjustments.
- Programming Capabilities:
- Modern tube bending machines are equipped with programmable controls that allow operators to store and recall bending programs for different tube sizes, bend angles, and configurations.
- Programming capabilities may include the ability to input bend angles, bend radii, bend directions, and material properties, as well as sequence multiple bends in a single program.
- Axis Control:
- Tube bending machines typically have multiple axes of control, including the bending axis, mandrel axis (if applicable), clamp axis, and carriage axis.
- Operators can control each axis independently or in coordinated motion to execute precise bending sequences and achieve complex bend geometries.
- Motion Control:
- Motion control systems regulate the movement of the bending machine components, such as the bending head, mandrel, clamp, and carriage, during the bending process.
- Control parameters may include speed, acceleration, deceleration, positioning accuracy, and synchronization between multiple axes.
- Safety Features:
- Tube bending machine controls are equipped with safety features, such as emergency stop buttons, interlocks, and safety relays, to protect operators from hazards and prevent accidents during machine operation.
- Safety features may include collision detection, overload protection, and automatic shutdown in case of abnormal conditions or malfunctions.
- Diagnostic Tools:
- Some tube bending machine controls are equipped with diagnostic tools and monitoring functions that allow operators to troubleshoot machine issues, identify faults, and perform maintenance tasks.
- Diagnostic tools may include error code displays, alarm notifications, and built-in self-tests for verifying system integrity and functionality.
- Integration with CAD/CAM Systems:
- Advanced tube bending machine controls can be integrated with computer-aided design (CAD) and computer-aided manufacturing (CAM) systems to import bending data directly from CAD drawings and generate bending programs automatically.
- Integration with CAD/CAM systems streamlines the programming process, reduces manual data entry errors, and improves overall efficiency and accuracy.
- User Interface Customization:
- Tube bending machine controls may offer customization options for the user interface, allowing operators to personalize screen layouts, display preferences, and shortcut keys to suit their workflow and preferences.
In conclusion, tube bending machine controls play a critical role in the operation, programming, and control of bending processes. By providing intuitive interfaces, advanced programming capabilities, safety features, and integration with CAD/CAM systems, manufacturers can enhance productivity, accuracy, and efficiency in tube bending operations.
Tube Bending Machine Operation:
Operating a tube bending machine requires knowledge of machine setup, tooling installation, material handling, and bending techniques. Proper operation ensures accurate bends, optimal performance, and safe working conditions. Here’s a detailed explanation of tube bending machine operation:
- Machine Setup:
- Begin by ensuring that the tube bending machine is properly set up on a stable and level surface, with adequate space around it for material handling and access to controls.
- Check that all safety guards, barriers, and interlocks are in place and functioning correctly before operating the machine.
- Verify that the machine is properly aligned, calibrated, and configured for the desired bending application, including mandrel size, die selection, and tooling setup.
- Tooling Installation:
- Install the appropriate mandrel, dies, clamp blocks, and other tooling components onto the machine according to the bending requirements, tube size, and material properties.
- Ensure that the tooling components are securely fastened, aligned, and adjusted to prevent shifting or movement during bending operations.
- Follow manufacturer instructions and safety guidelines when installing and adjusting tooling to avoid accidents or damage to the machine.
- Material Handling:
- Prepare the tube or pipe material for bending by cutting it to the required length and deburring the ends to remove sharp edges or burrs that could interfere with bending.
- Position the tube or pipe material in the machine’s clamping mechanism, ensuring that it is securely held in place and aligned with the bending axis.
- Use proper lifting equipment, fixtures, and supports to handle heavy or long tubes safely and prevent strains or injuries to operators.
- Bending Process:
- Input bending parameters, such as bend angle, bend radius, and bend direction, into the machine’s control interface, either manually or by selecting a pre-programmed bending program.
- Activate the machine’s bending cycle, either manually or automatically, depending on the machine’s operating mode and control settings.
- Monitor the bending process closely, observing the tube’s movement, alignment, and interaction with the tooling to ensure proper bending and avoid errors or defects.
- Adjust machine settings, tooling positions, or material feed as needed to correct any deviations from the desired bend specifications during the bending process.
- Quality Control:
- Inspect the bent tube or pipe after each bending operation to verify that it meets the specified dimensions, tolerances, and quality standards.
- Measure key parameters, such as bend angle, bend radius, wall thickness, and straightness, using precision measuring tools, such as calipers, protractors, and CMMs.
- Reject any bent tubes or pipes that do not meet the required specifications and investigate the root causes of deviations to prevent recurrence in future bending operations.
- Safety Precautions:
- Follow all safety guidelines, procedures, and precautions provided by the machine manufacturer and workplace safety regulations when operating the tube bending machine.
- Wear appropriate personal protective equipment (PPE), including safety glasses, hearing protection, gloves, and protective clothing, to protect against hazards associated with bending operations.
- Never bypass or tamper with safety guards, interlocks, or emergency stop controls, and report any safety concerns or malfunctions to a supervisor or safety officer immediately.
In conclusion, proper operation of a tube bending machine requires attention to detail, adherence to safety protocols, and skill in machine setup, tooling installation, material handling, and bending techniques. By following best practices and safety guidelines, operators can achieve accurate bends, optimal performance, and safe working conditions in tube bending operations.
Tube Bending Machine Troubleshooting:
Tube bending machines, like any industrial equipment, may encounter issues during operation that can affect performance, accuracy, and efficiency. Troubleshooting these issues promptly and effectively is essential to minimize downtime and maintain productivity. Here’s a detailed explanation of tube bending machine troubleshooting:
- Identifying the Problem:
- Begin by identifying the specific symptoms or issues affecting the tube bending machine, such as inaccurate bends, material slipping, tooling damage, hydraulic leaks, or abnormal noises.
- Consult the machine operator, supervisor, or maintenance personnel to gather information about when the problem started, under what conditions it occurs, and any recent changes to machine settings or operations.
- Inspecting Machine Components:
- Conduct a visual inspection of the machine components, including tooling, clamps, mandrels, dies, guide rollers, and hydraulic systems, for signs of wear, damage, misalignment, or contamination.
- Look for loose bolts, broken parts, fluid leaks, worn bearings, misaligned components, or foreign objects that may be causing the problem.
- Checking Machine Settings:
- Review the machine settings, parameters, and program inputs to ensure that they are correct and consistent with the bending requirements, material specifications, and desired bend characteristics.
- Verify bend angle, bend radius, tooling positions, feed rates, and other parameters against the bending program or job setup sheet to identify any discrepancies.
- Performing Test Bends:
- Conduct test bends using scrap material or sample tubes to evaluate machine performance and diagnose bending issues.
- Monitor the bending process closely, observing tube movement, tooling interaction, and bend quality to identify any abnormalities or deviations from the expected results.
- Analyzing Bend Quality:
- Evaluate the quality of the bent tubes, including bend angle, bend radius, wall thickness, straightness, and surface finish, to determine if the machine is producing acceptable results.
- Use precision measuring tools, such as calipers, protractors, and CMMs, to quantify deviations from the specified dimensions and tolerances.
- Troubleshooting Specific Issues:
- Based on the symptoms and observations, troubleshoot specific issues by addressing potential causes systematically.
- Common issues and troubleshooting steps may include:
- Inaccurate bends: Check tooling alignment, mandrel position, and machine calibration.
- Material slipping: Inspect clamping mechanisms, adjust clamp pressure, or clean and lubricate clamps.
- Tooling damage: Replace worn or damaged tooling components, such as dies, mandrels, or guide rollers.
- Hydraulic leaks: Identify the source of the leak, repair or replace damaged hydraulic hoses, fittings, or seals, and replenish hydraulic fluid as needed.
- Abnormal noises: Inspect moving parts, bearings, gears, and drive mechanisms for wear, damage, or misalignment, and lubricate or repair as necessary.
- Documenting Findings and Solutions:
- Keep detailed records of troubleshooting activities, including observations, tests performed, findings, corrective actions taken, and outcomes.
- Use this information to develop preventive maintenance plans, update operating procedures, and train personnel to prevent recurrence of similar issues in the future.
- Seeking Expert Assistance:
- If troubleshooting efforts do not resolve the issue or if the problem persists, seek assistance from qualified technicians, engineers, or the machine manufacturer for further diagnosis and repair.
- Provide them with relevant information, such as machine model, serial number, error codes, and maintenance history, to facilitate the troubleshooting process.
In conclusion, effective troubleshooting of tube bending machines requires systematic investigation, analysis, and corrective action to address specific issues and maintain optimal machine performance. By following a structured approach and leveraging expertise, operators and maintenance personnel can diagnose problems accurately, implement timely solutions, and minimize downtime in tube bending operations.
Tube Bending Machine Maintenance Schedule:
Developing and adhering to a comprehensive maintenance schedule is crucial for ensuring the optimal performance, reliability, and longevity of tube bending machines. A well-planned maintenance program helps prevent breakdowns, minimize downtime, and extend the lifespan of the equipment. Here’s a detailed maintenance schedule for tube bending machines:
- Daily Maintenance:
- Clean machine components, including the bending head, clamps, mandrels, dies, and guide rollers, to remove dirt, debris, and metal shavings generated during operation.
- Inspect hydraulic hoses, fittings, and seals for leaks, damage, or deterioration, and repair or replace them as needed.
- Lubricate moving parts, such as bearings, gears, slides, and hydraulic cylinders, according to manufacturer recommendations to reduce friction and wear.
- Check safety features, such as emergency stop buttons, interlocks, and safety guards, to ensure they are functioning correctly.
- Weekly Maintenance:
- Inspect tooling components, including mandrels, dies, clamps, and guide rollers, for signs of wear, damage, or misalignment, and replace or adjust them as necessary.
- Verify machine alignment and calibration using precision measuring tools, such as dial indicators and laser alignment devices, and adjust as needed.
- Test emergency stop controls and safety features to ensure they respond appropriately in case of emergencies or hazardous situations.
- Clean and inspect electrical components, such as switches, relays, motors, and control panels, for signs of wear, damage, or corrosion, and perform maintenance as needed.
- Monthly Maintenance:
- Perform a thorough inspection of the machine structure, including frame, base, supports, and fasteners, for signs of wear, fatigue, or structural damage, and repair or reinforce as needed.
- Check hydraulic fluid levels, filters, and reservoirs, and replace or refill them as necessary to ensure proper functioning of the hydraulic system.
- Inspect pneumatic components, such as hoses, valves, and regulators, for leaks, damage, or malfunction, and repair or replace them as needed.
- Review maintenance logs, service reports, and operator feedback to identify any recurring issues or emerging maintenance needs and address them proactively.
- Quarterly Maintenance:
- Conduct a comprehensive inspection of all machine components, systems, and safety features, following manufacturer guidelines and maintenance procedures.
- Perform preventative maintenance tasks, such as lubrication, alignment checks, and calibration adjustments, to ensure the machine operates at peak performance.
- Test machine functionality and performance under load conditions to verify bending accuracy, repeatability, and consistency.
- Review and update maintenance procedures, checklists, and documentation based on lessons learned and feedback from operators and maintenance personnel.
- Annual Maintenance:
- Schedule professional inspection and servicing of critical machine components, such as hydraulic systems, electrical systems, and drive mechanisms, by qualified technicians.
- Conduct machine recalibration and alignment checks using advanced measurement tools and techniques to ensure accuracy and precision.
- Perform comprehensive cleaning, lubrication, and preventive maintenance tasks to prepare the machine for another year of reliable operation.
- Document and review the maintenance history, including service records, parts replacement, and performance improvements, to track the machine’s condition and identify areas for optimization.
In conclusion, a proactive maintenance schedule for tube bending machines is essential for maximizing uptime, productivity, and reliability while minimizing the risk of unplanned downtime and costly repairs. By following a structured maintenance program and adhering to scheduled maintenance tasks, manufacturers can ensure their tube bending machines remain in optimal condition and deliver consistent, high-quality results over their operational lifespan.
Tube Bending Machine Safety Precautions:
Safety is paramount when operating tube bending machines to prevent accidents, injuries, and damage to equipment. Implementing proper safety precautions and procedures ensures a safe working environment for operators and maintenance personnel. Here’s a detailed explanation of tube bending machine safety precautions:
- Operator Training:
- Provide comprehensive training to operators on the safe operation of tube bending machines, including machine setup, tooling installation, material handling, and emergency procedures.
- Ensure that operators are familiar with the machine controls, safety features, and potential hazards associated with tube bending operations.
- Offer refresher training sessions regularly to reinforce safety practices and update operators on new procedures or equipment.
- Personal Protective Equipment (PPE):
- Require operators to wear appropriate PPE, including safety glasses, hearing protection, gloves, and protective clothing, to protect against hazards such as flying debris, noise, burns, and cuts.
- Ensure that PPE is properly fitted, maintained, and used according to manufacturer recommendations and workplace safety regulations.
- Machine Guarding:
- Install and maintain machine guards, barriers, and safety interlocks to prevent access to hazardous areas, such as pinch points, rotating parts, and cutting zones, during machine operation.
- Ensure that guards are securely fastened, properly adjusted, and regularly inspected for damage or wear.
- Emergency Stop Controls:
- Install accessible emergency stop buttons or switches at multiple locations on the machine to allow operators to quickly stop machine operation in case of emergencies or hazardous situations.
- Test emergency stop controls regularly to ensure they function correctly and effectively interrupt machine operation when activated.
- Material Handling Safety:
- Establish safe material handling procedures, including the use of lifting equipment, fixtures, and supports, to safely position, load, and unload tubes or pipes onto the bending machine.
- Train operators on proper material handling techniques to prevent strains, sprains, and other musculoskeletal injuries associated with lifting and moving heavy or awkward objects.
- Tooling Safety:
- Handle and install tooling, such as mandrels, dies, and clamps, with caution to avoid pinch points, sharp edges, and crushing hazards.
- Ensure that tooling is properly secured, aligned, and inspected before each use to prevent tooling malfunctions, ejections, or accidents during bending operations.
- Hydraulic System Safety:
- Implement lockout/tagout procedures to isolate and de-energize hydraulic systems before performing maintenance, service, or repair activities on tube bending machines.
- Inspect hydraulic hoses, fittings, and components regularly for leaks, damage, or malfunction, and repair or replace them as necessary to prevent hydraulic fluid spills or accidents.
- Electrical Safety:
- Inspect electrical components, such as switches, relays, motors, and control panels, for signs of wear, damage, or corrosion.
- Ensure that electrical connections are tight, wires are properly insulated, and grounding is sufficient to prevent electrical hazards, such as shocks, short circuits, or fires.
- Safety Culture and Communication:
- Foster a safety-conscious work environment where employees feel empowered to report safety concerns, near misses, or incidents promptly.
- Encourage open communication, collaboration, and feedback among operators, supervisors, and safety personnel to identify hazards, implement corrective actions, and continuously improve safety practices.
In conclusion, implementing proper safety precautions and procedures is essential for preventing accidents and ensuring a safe working environment when operating tube bending machines. By prioritizing operator training, providing adequate PPE, implementing machine guarding, and promoting a safety-focused culture, manufacturers can minimize the risk of injuries and incidents associated with tube bending operations.
Tube Bending Machine: Material Considerations
Selecting the right material for tube bending is crucial to achieving precise bends, maintaining structural integrity, and meeting performance requirements. Various factors, such as material properties, formability, corrosion resistance, and cost, influence the choice of material for tube bending applications. Here’s a detailed explanation of material considerations for tube bending:
- Material Properties:
- Material properties, including yield strength, tensile strength, elongation, and hardness, determine how a material behaves during bending and its suitability for specific applications.
- Choose materials with sufficient ductility and elongation to withstand bending without cracking, wrinkling, or fracturing, while maintaining dimensional accuracy and surface finish.
- Material Formability:
- Consider the formability of the material, which refers to its ability to deform without fracture under applied stress, when selecting material for tube bending.
- Materials with high formability, such as aluminum, copper, and low-carbon steel, are easier to bend and require lower bending forces compared to materials with low formability, such as high-strength alloys and stainless steels.
- Wall Thickness:
- The wall thickness of the tube or pipe affects its bendability, springback behavior, and structural integrity during bending.
- Thinner-walled tubes are generally more flexible and easier to bend but may be prone to wrinkling or collapsing, while thicker-walled tubes require higher bending forces and may experience greater springback.
- Corrosion Resistance:
- Consider the environmental conditions, exposure to corrosive substances, and service requirements when selecting materials for tube bending applications.
- Choose materials with adequate corrosion resistance properties, such as stainless steel, corrosion-resistant alloys, or protective coatings, to ensure long-term durability and reliability in harsh environments.
- Surface Finish Requirements:
- Evaluate the surface finish requirements of the final product, including smoothness, cleanliness, and cosmetic appearance, when selecting materials for tube bending.
- Materials with good surface finish characteristics, such as stainless steel, brass, and polished aluminum, are suitable for applications where aesthetics and appearance are important.
- Cost Considerations:
- Factor in material costs, availability, and processing expenses when selecting materials for tube bending applications.
- Balance performance requirements with cost considerations to optimize material selection and achieve the desired balance of performance, quality, and affordability.
- Material Compatibility with Bending Processes:
- Consider the compatibility of the material with the bending process, including cold bending, hot bending, mandrel bending, rotary draw bending, or compression bending.
- Some materials may require specific bending techniques, tooling, or equipment to achieve desired bend characteristics and minimize defects or distortions.
- Post-Bending Treatments:
- Evaluate the effects of tube bending on material properties, such as work hardening, residual stresses, and dimensional changes, and consider post-bending treatments, such as stress relieving, annealing, or surface finishing, to mitigate potential issues.
In conclusion, selecting the right material for tube bending is a critical decision that impacts the performance, quality, and cost-effectiveness of the final product. By considering material properties, formability, corrosion resistance, surface finish requirements, cost considerations, and compatibility with bending processes, manufacturers can make informed decisions and achieve successful outcomes in tube bending applications.
Tube Bending Machine: Mandrel Considerations
The mandrel is a critical component in tube bending operations, providing internal support to prevent collapse or distortion of the tube during bending. Choosing the right mandrel and configuring it properly is essential for achieving accurate bends, maintaining tube integrity, and minimizing defects. Here’s a detailed explanation of mandrel considerations for tube bending:
- Mandrel Types:
- Fixed Mandrel: A fixed mandrel remains stationary inside the tube during bending, providing continuous internal support throughout the bending process.
- Floating Mandrel: A floating mandrel moves axially with the tube as it bends, allowing for greater flexibility and reduced friction between the mandrel and tube.
- Ball Mandrel: A ball mandrel consists of multiple spherical segments or bearings that conform to the inner diameter of the tube, providing uniform support and reducing the risk of surface marring or distortion.
- Plug Mandrel: A plug mandrel features a solid or hollow cylindrical body that fits snugly inside the tube and may include interchangeable tips or inserts to accommodate various tube diameters and bend radii.
- Mandrel Material:
- Choose mandrel materials that are durable, wear-resistant, and capable of withstanding high temperatures and pressures encountered during tube bending operations.
- Common mandrel materials include hardened steel, stainless steel, chrome-plated steel, and tungsten carbide, which offer high strength, hardness, and resistance to wear and deformation.
- Mandrel Coating or Surface Treatment:
- Consider applying coatings or surface treatments to mandrels to reduce friction, prevent galling, and improve lubrication between the mandrel and tube surfaces.
- Options may include PTFE (polytetrafluoroethylene) coatings, chrome plating, ceramic coatings, or diamond-like carbon (DLC) coatings, which provide low friction and high wear resistance.
- Mandrel Design and Configuration:
- Select mandrel designs and configurations based on tube diameter, wall thickness, bend radius, and material properties to ensure optimal support and minimal interference during bending.
- Choose mandrel lengths, diameters, and shapes that match the tube’s internal geometry and bending requirements, avoiding excessive protrusion or inadequate support.
- Mandrel Lubrication and Cooling:
- Apply lubricants or coolant to the mandrel surface to reduce friction, heat buildup, and material adhesion during bending.
- Use water-soluble lubricants, oils, or emulsions suitable for the tube material and bending process to improve surface finish, reduce tool wear, and extend mandrel life.
- Mandrel Retraction Mechanism:
- Incorporate a mandrel retraction mechanism into the bending machine to retract or remove the mandrel from the tube after bending, minimizing the risk of mandrel marks or indentations on the inner surface of the bend.
- Ensure that the mandrel retraction mechanism operates smoothly and reliably, with adjustable retraction speed and distance to accommodate different tube sizes and bend angles.
- Mandrel Maintenance and Inspection:
- Regularly inspect mandrels for signs of wear, damage, or deformation, such as scratches, dents, or surface irregularities, and replace or recondition them as needed.
- Clean and lubricate mandrels regularly to remove debris, prevent corrosion, and maintain smooth operation during bending operations.
In conclusion, selecting the right mandrel and configuring it properly is essential for achieving high-quality bends and maintaining tube integrity in tube bending operations. By considering mandrel types, materials, coatings, designs, lubrication, retraction mechanisms, and maintenance practices, manufacturers can optimize bending processes and achieve consistent, reliable results.
Tube Bending Machine: Die Considerations
Dies are essential components in tube bending machines, providing the external shape and support needed to form accurate bends in tubes and pipes. Choosing the right die and configuring it properly is crucial for achieving precise bends, minimizing wall thinning, and reducing defects. Here’s a detailed explanation of die considerations for tube bending:
- Die Types:
- Fixed Radius Die: A fixed radius die has a constant curvature along its entire length, allowing for consistent bends with a specified bend radius.
- Variable Radius Die: A variable radius die allows for the adjustment of the bend radius within a certain range, providing flexibility to accommodate different bending requirements.
- Wiper Die: A wiper die, also known as a pressure die or follower die, applies pressure to the outer surface of the tube to prevent wrinkling, ovality, or collapse during bending, especially in thin-walled or delicate materials.
- Die Material:
- Choose die materials that are durable, wear-resistant, and capable of withstanding high pressures and temperatures encountered during tube bending operations.
- Common die materials include tool steel, hardened steel, carbide inserts, and coated surfaces (e.g., chrome plating or DLC coating) to enhance wear resistance and prolong die life.
- Die Design and Geometry:
- Select die designs and geometries based on tube diameter, wall thickness, bend radius, and material properties to ensure proper support and deformation control during bending.
- Optimize die profiles, radii, angles, and surface finishes to minimize friction, reduce tool marks, and improve bend quality, especially in tight radius or complex bends.
- Die Configuration and Setup:
- Configure and install dies properly on the bending machine, ensuring alignment, clamping, and support to prevent movement or misalignment during bending.
- Use die inserts, shims, or spacers to accommodate different tube sizes, wall thicknesses, and bend radii, ensuring optimal contact and support along the entire length of the bend.
- Die Lubrication and Cooling:
- Apply lubricants or coolants to the die surfaces to reduce friction, heat buildup, and material adhesion during bending.
- Use water-soluble lubricants, oils, or emulsions suitable for the tube material and bending process to improve surface finish, reduce tool wear, and extend die life.
- Die Material Compatibility:
- Ensure that the die material is compatible with the tube material and bending process to avoid contamination, galling, or chemical reactions that could affect bend quality or die performance.
- Use die materials that are resistant to abrasion, adhesion, and chemical attack from the tube material and bending lubricants to maintain dimensional accuracy and surface finish.
- Die Maintenance and Inspection:
- Regularly inspect dies for signs of wear, damage, or deformation, such as chipping, cracking, or surface irregularities, and replace or recondition them as needed.
- Clean and lubricate dies regularly to remove debris, prevent corrosion, and maintain smooth operation during bending operations.
In conclusion, selecting the right die and configuring it properly is essential for achieving accurate and consistent bends in tube bending operations. By considering die types, materials, designs, lubrication, cooling, material compatibility, and maintenance practices, manufacturers can optimize bending processes and achieve high-quality results.
Tube Bending Machine: Bend Radius Considerations
The bend radius is a critical parameter in tube bending operations, influencing the overall shape, strength, and integrity of the bent tube or pipe. Selecting the appropriate bend radius and understanding its effects on material behavior and bend quality are essential for achieving desired results. Here’s a detailed explanation of bend radius considerations for tube bending:
- Definition of Bend Radius:
- The bend radius refers to the size of the arc formed during the bending process, measured from the centerline of the tube to the inner surface of the bend.
- It determines the curvature and tightness of the bend and is typically specified as a nominal value or a range of values depending on the bending application and material requirements.
- Minimum Bend Radius:
- The minimum bend radius is the smallest allowable bend radius for a given tube diameter and material, beyond which bending may cause defects such as wrinkling, flattening, or cracking.
- It is influenced by material properties, including yield strength, ductility, and elongation, as well as wall thickness, bend angle, and bending method.
- Factors Influencing Bend Radius:
- Material Properties: Different materials exhibit varying levels of bendability and elasticity, affecting their ability to withstand deformation without fracturing or wrinkling.
- Tube Diameter and Wall Thickness: Larger tube diameters and thinner wall thicknesses typically require larger bend radii to prevent distortion, flattening, or collapse during bending.
- Bend Angle: Tighter bend angles require smaller bend radii to achieve the desired curvature, while larger bend angles may allow for larger bend radii without compromising bend quality.
- Bending Method: Different bending methods, such as rotary draw bending, compression bending, or mandrel bending, may have specific requirements or limitations on bend radius based on machine capabilities and tooling design.
- Effects of Bend Radius on Material Behavior:
- Smaller Bend Radii: Tighter bend radii exert higher levels of stress and strain on the material, increasing the risk of material thinning, stretching, or fracturing, especially in high-strength or brittle materials.
- Larger Bend Radii: Larger bend radii distribute bending forces more evenly along the length of the tube, reducing the risk of material deformation and improving bend quality, but may require more space and longer tube lengths for bending.
- Bend Radius and Bend Quality:
- Selecting an appropriate bend radius is crucial for achieving high-quality bends with minimal defects, such as wrinkling, ovality, or surface irregularities.
- Optimal bend radii balance the requirements for bend tightness, material integrity, and bend quality to achieve the desired bend characteristics while avoiding excessive strain or deformation.
- Calculating Bend Radius:
- Bend radius calculations depend on various factors, including material properties, tube diameter, wall thickness, bend angle, and bending method.
- Manufacturers may use empirical formulas, bending charts, finite element analysis (FEA), or simulation software to determine suitable bend radii for specific bending applications.
In conclusion, understanding bend radius considerations is essential for achieving accurate and high-quality bends in tube bending operations. By considering material properties, tube diameter, wall thickness, bend angle, and bending method, manufacturers can select appropriate bend radii and optimize bending processes to meet performance requirements and quality standards.
Tube Bending Machine: Bend Angle Considerations
The bend angle is a crucial parameter in tube bending operations, determining the extent of the bend and influencing the overall shape, functionality, and structural integrity of the bent tube or pipe. Understanding the effects of bend angle and selecting the appropriate angle are essential for achieving desired results. Here’s a detailed explanation of bend angle considerations for tube bending:
- Definition of Bend Angle:
- The bend angle refers to the angular deviation from the straight axis of the tube or pipe caused by the bending process.
- It is typically measured in degrees and determines the extent of the bend, ranging from small angles (e.g., < 90 degrees) to large angles (e.g., > 90 degrees) depending on the application and design requirements.
- Effects of Bend Angle:
- Bend Tightness: Smaller bend angles result in tighter bends with sharper curvature, while larger bend angles produce more gradual bends with gentler curvature.
- Material Deformation: Higher bend angles exert greater levels of stress and strain on the material, increasing the risk of deformation, thinning, or wrinkling, especially in high-strength or brittle materials.
- Structural Integrity: Bend angle influences the structural integrity and load-bearing capacity of the bent tube, with larger bend angles potentially weakening the tube’s cross-section and reducing its strength or stiffness.
- Minimum Bend Angle:
- The minimum bend angle is the smallest allowable angle for a given tube diameter, wall thickness, and material, beyond which bending may cause defects such as kinking, buckling, or collapse.
- It is influenced by material properties, including yield strength, ductility, and elongation, as well as tube geometry, bend radius, and bending method.
- Maximum Bend Angle:
- The maximum bend angle is the largest allowable angle for a given tube diameter, wall thickness, and material, beyond which bending may become impractical or structurally unstable.
- It is influenced by material properties, bending machine capabilities, tooling design, and application requirements, with larger bend angles requiring specialized equipment or techniques.
- Bend Angle and Bend Quality:
- Selecting an appropriate bend angle is crucial for achieving high-quality bends with minimal defects, such as wrinkles, distortions, or surface irregularities.
- Optimal bend angles balance the requirements for bend tightness, material integrity, and bend quality to achieve the desired bend characteristics while maintaining dimensional accuracy and surface finish.
- Calculating Bend Angle:
- Bend angle calculations depend on various factors, including material properties, tube geometry, bend radius, and bending method.
- Manufacturers may use bending software, bending charts, or empirical formulas to determine suitable bend angles for specific bending applications, considering factors such as material elongation, springback, and tooling limitations.
In conclusion, understanding bend angle considerations is essential for achieving accurate and high-quality bends in tube bending operations. By considering material properties, tube geometry, bend radius, and application requirements, manufacturers can select appropriate bend angles and optimize bending processes to meet performance specifications and quality standards.
Tube Bending Machine: Springback Compensation Techniques
Springback is a common phenomenon in tube bending operations where the material tends to return partially to its original shape after being bent. Compensating for springback is essential for achieving accurate and repeatable bends, especially in applications requiring tight tolerances and precise geometries. Here are several techniques used to mitigate springback in tube bending:
- Overbending:
- Overbending involves bending the tube slightly beyond the desired angle to account for anticipated springback.
- By bending the tube past the target angle, the material will spring back to the desired angle, compensating for the springback effect.
- The amount of overbending depends on factors such as material properties, bend angle, bend radius, and tube diameter.
- Springback Analysis:
- Conducting springback analysis involves predicting the amount of springback based on material properties, tube geometry, bend radius, and bending method.
- Finite element analysis (FEA) and simulation software can simulate the bending process and predict the extent of springback, allowing for adjustments in bending parameters to compensate for the anticipated springback.
- Mandrel Design and Pressure Adjustment:
- Optimizing mandrel design and pressure adjustment can help reduce springback by providing internal support and controlling material deformation during bending.
- Using a mandrel with appropriate geometry, surface finish, and pressure settings helps maintain the desired bend shape and minimize springback effects.
- Die Design and Pressure Adjustment:
- Similar to mandrel design, optimizing die design and pressure adjustment can help reduce springback by controlling material deformation and ensuring proper support during bending.
- Choosing the right die profile, surface finish, and pressure settings helps minimize friction, stress concentrations, and material rebound, improving bend accuracy and repeatability.
- Material Selection and Heat Treatment:
- Selecting materials with specific properties, such as high elongation or low springback, can help mitigate springback effects.
- Heat treatment processes, such as annealing or stress relieving, can help reduce residual stresses and improve material ductility, reducing the tendency for springback in certain materials.
- Incremental Bending:
- Incremental bending involves dividing the total bend angle into smaller increments and performing multiple bending steps to gradually achieve the desired angle.
- By incrementally bending the tube and allowing for relaxation between each bending step, springback effects can be minimized, and bend accuracy improved.
- Post-Bending Corrections:
- Post-bending correction techniques, such as cold setting or re-rolling, can be applied to adjust the final bend angle and compensate for springback deviations.
- These techniques involve applying controlled pressure or mechanical manipulation to the bent tube to achieve the desired geometry and tolerances.
In conclusion, mitigating springback in tube bending operations requires a combination of advanced techniques, including overbending, springback analysis, mandrel and die optimization, material selection, incremental bending, and post-bending corrections. By understanding the factors influencing springback and applying appropriate compensation techniques, manufacturers can achieve accurate and repeatable bends in tube bending applications.
Tube Bending Machine: Lubrication and Cooling Systems
Lubrication and cooling systems play crucial roles in tube bending operations, ensuring smooth operation, minimizing frictional forces, and extending tool life. Proper lubrication and cooling help reduce wear on bending tools, improve surface finish, and prevent material defects during bending. Here’s a detailed explanation of lubrication and cooling systems in tube bending machines:
- Lubrication Systems:
- Lubrication systems deliver lubricants to the contact points between the tube and bending tools, reducing friction, heat buildup, and wear during bending.
- Common lubricants used in tube bending include water-soluble oils, synthetic lubricants, emulsions, and solid lubricants (e.g., graphite or molybdenum disulfide).
- Lubrication systems may utilize spray nozzles, brushes, rollers, or immersion baths to apply lubricants to the tube surface, depending on the bending method and machine configuration.
- Proper lubrication helps improve bend quality, reduce tool wear, and minimize the risk of surface defects such as scoring, scratching, or galling.
- Cooling Systems:
- Cooling systems dissipate heat generated during bending and lubrication processes, maintaining tool and workpiece temperatures within safe operating limits.
- Water-based cooling systems, such as coolant sprays, misters, or flood cooling, are commonly used to remove heat from the bending zone and prevent thermal distortion or metallurgical changes in the material.
- Cooling systems may incorporate temperature sensors, flow meters, and control valves to regulate coolant flow rate, temperature, and distribution, ensuring consistent cooling across the bending zone.
- Effective cooling helps reduce tool wear, prevent material overheating, and improve dimensional accuracy and surface finish of the bent tube.
- Benefits of Lubrication and Cooling:
- Reduced Friction: Lubricants reduce friction between the tube and bending tools, allowing for smoother bending motion and reduced wear on tool surfaces.
- Heat Dissipation: Cooling systems remove heat generated during bending and lubrication processes, preventing overheating of the tube material and tooling and minimizing thermal distortion.
- Improved Surface Finish: Proper lubrication and cooling help achieve a smooth surface finish on the bent tube, minimizing scratches, scoring, or surface defects caused by friction or heat.
- Extended Tool Life: Lubrication and cooling systems help prolong the life of bending tools by reducing wear, thermal stress, and fatigue, resulting in lower maintenance costs and downtime.
- Maintenance and Monitoring:
- Regular maintenance and monitoring of lubrication and cooling systems are essential to ensure optimal performance and reliability.
- Operators should inspect lubrication nozzles, coolant lines, filters, and reservoirs regularly for leaks, blockages, or contamination and perform necessary cleaning, lubrication, or fluid replenishment as needed.
- Monitoring system parameters such as coolant flow rate, temperature, pressure, and fluid levels helps detect anomalies or malfunctions early and prevent potential issues during bending operations.
In conclusion, lubrication and cooling systems play critical roles in tube bending operations, providing essential lubrication and heat dissipation to ensure smooth and efficient bending processes. By implementing proper lubrication and cooling techniques and conducting regular maintenance and monitoring, manufacturers can achieve high-quality bends, prolong tool life, and minimize downtime in tube bending applications.
Tube Bending Machine: Mandrel Lubrication Techniques
Mandrel lubrication is essential in tube bending operations to reduce friction between the mandrel and the inner surface of the tube, preventing sticking, galling, and surface defects. Proper lubrication ensures smooth bending motion, improves bend quality, and prolongs mandrel life. Here’s an overview of mandrel lubrication techniques commonly used in tube bending machines:
- Spray Lubrication:
- Spray lubrication involves applying lubricant directly onto the mandrel surface or the inner surface of the tube using spray nozzles or misters.
- Lubricants are atomized into fine droplets and directed onto the contact points between the mandrel and the tube, forming a thin film that reduces friction and facilitates smooth bending motion.
- Spray lubrication systems may use water-soluble oils, synthetic lubricants, emulsions, or solid lubricants (e.g., graphite or molybdenum disulfide) depending on the bending application and material requirements.
- Drip Lubrication:
- Drip lubrication involves dripping lubricant onto the mandrel surface or into the tube through drip tubes or reservoirs located above the bending zone.
- Lubricants flow by gravity onto the mandrel or tube surface, providing continuous lubrication during bending operations and ensuring consistent lubricant coverage and distribution.
- Drip lubrication systems are suitable for long-duration bending operations or continuous production runs where regular lubricant replenishment is necessary.
- Roller Lubrication:
- Roller lubrication utilizes rotating rollers or pads impregnated with lubricant to transfer lubricant onto the mandrel surface as it rotates within the tube.
- Lubricant is evenly distributed across the mandrel surface by the rolling action of the lubricated rollers, ensuring uniform lubrication and minimizing excess lubricant buildup.
- Roller lubrication systems are commonly used in mandrel bending machines with continuous mandrel rotation, providing efficient and consistent lubrication without the need for external spray or drip systems.
- Immersion Lubrication:
- Immersion lubrication involves immersing the mandrel in a lubricant bath or reservoir before inserting it into the tube, ensuring complete coverage and saturation of the mandrel surface with lubricant.
- Lubricant is applied to the mandrel by submerging it in a tank or container filled with lubricant, allowing it to absorb lubricant and form a protective film before entering the bending zone.
- Immersion lubrication provides long-lasting lubrication and is suitable for high-speed bending operations or applications where frequent lubricant application is impractical.
- Brush Lubrication:
- Brush lubrication uses rotating or stationary brushes mounted on the mandrel or tube bending machine to apply lubricant to the mandrel surface.
- Brushes are impregnated with lubricant and make contact with the mandrel surface as it rotates or moves through the tube, transferring lubricant and ensuring uniform coverage along the entire length of the mandrel.
- Brush lubrication systems are effective in delivering controlled amounts of lubricant and are suitable for applications requiring precise lubricant application and minimal waste.
In conclusion, mandrel lubrication is essential for reducing friction, preventing sticking, and improving bend quality in tube bending operations. By selecting appropriate lubrication techniques, such as spray lubrication, drip lubrication, roller lubrication, immersion lubrication, or brush lubrication, manufacturers can achieve smooth and efficient bending processes while prolonging mandrel life and minimizing surface defects in bent tubes.
Tube Bending Machine: Die Lubrication Techniques
Die lubrication is crucial in tube bending operations to reduce friction between the die and the outer surface of the tube, preventing scratching, scoring, and material defects. Proper lubrication ensures smooth bending motion, improves bend quality, and extends die life. Here are several commonly used die lubrication techniques in tube bending machines:
- Spray Lubrication:
- Spray lubrication involves applying lubricant directly onto the die surface or the outer surface of the tube using spray nozzles or misters.
- Lubricants are atomized into fine droplets and directed onto the contact points between the die and the tube, forming a thin film that reduces friction and facilitates smooth bending motion.
- Spray lubrication systems may use water-soluble oils, synthetic lubricants, emulsions, or solid lubricants (e.g., graphite or molybdenum disulfide) depending on the bending application and material requirements.
- Roller Lubrication:
- Roller lubrication utilizes rotating rollers or pads impregnated with lubricant to transfer lubricant onto the die surface as the tube passes through the bending machine.
- Lubricant is evenly distributed across the die surface by the rolling action of the lubricated rollers, ensuring uniform lubrication and minimizing excess lubricant buildup.
- Roller lubrication systems are commonly used in tube bending machines with continuous tube feed, providing efficient and consistent lubrication without the need for external spray systems.
- Drip Lubrication:
- Drip lubrication involves dripping lubricant onto the die surface or onto the tube surface as it enters the bending zone through drip tubes or reservoirs located above the bending area.
- Lubricants flow by gravity onto the die or tube surface, providing continuous lubrication during bending operations and ensuring consistent lubricant coverage and distribution.
- Drip lubrication systems are suitable for long-duration bending operations or continuous production runs where regular lubricant replenishment is necessary.
- Brush Lubrication:
- Brush lubrication uses rotating or stationary brushes mounted on the die or tube bending machine to apply lubricant to the die surface.
- Brushes are impregnated with lubricant and make contact with the die surface as the tube passes through the bending machine, transferring lubricant and ensuring uniform coverage along the entire length of the die.
- Brush lubrication systems are effective in delivering controlled amounts of lubricant and are suitable for applications requiring precise lubricant application and minimal waste.
- Immersion Lubrication:
- Immersion lubrication involves immersing the die in a lubricant bath or reservoir before bending, ensuring complete coverage and saturation of the die surface with lubricant.
- Lubricant is applied to the die by submerging it in a tank or container filled with lubricant, allowing it to absorb lubricant and form a protective film before entering the bending zone.
- Immersion lubrication provides long-lasting lubrication and is suitable for high-speed bending operations or applications where frequent lubricant application is impractical.
In conclusion, die lubrication is essential for reducing friction, preventing scratching, and improving bend quality in tube bending operations. By selecting appropriate lubrication techniques, such as spray lubrication, roller lubrication, drip lubrication, brush lubrication, or immersion lubrication, manufacturers can achieve smooth and efficient bending processes while prolonging die life and minimizing surface defects in bent tubes.
Tube Bending Machine: Die Materials and Coatings
Die materials and coatings are critical components of tube bending machines, influencing the quality of bends, tool life, and overall efficiency of the bending process. Selecting the right die materials and coatings is essential for achieving precise bends, minimizing wear, and reducing maintenance costs. Here’s an overview of commonly used die materials and coatings in tube bending machines:
- Tool Steel:
- Tool steel, such as D2, H13, or A2, is a popular choice for die materials due to its high hardness, wear resistance, and toughness.
- Tool steel dies can withstand high pressures and temperatures encountered during bending operations, maintaining dimensional accuracy and surface finish over prolonged use.
- Tool steel dies are suitable for bending a wide range of materials, including mild steel, stainless steel, aluminum, and copper alloys.
- Carbide Inserts:
- Carbide inserts, such as tungsten carbide or carbide-tipped inserts, are used in die surfaces to enhance wear resistance and prolong die life.
- Carbide inserts are bonded or brazed onto the die surface, providing superior hardness, abrasion resistance, and thermal stability compared to conventional tool steel.
- Carbide inserts are particularly effective in bending abrasive or high-strength materials, such as titanium, inconel, or hardened steel, where tool wear is a concern.
- Hardened Steel:
- Hardened steel dies undergo heat treatment processes, such as quenching and tempering, to increase hardness, toughness, and wear resistance.
- Hardened steel dies offer improved durability and longevity compared to untreated tool steel, making them suitable for high-volume production and demanding bending applications.
- Hardened steel dies are commonly used in rotary draw bending, mandrel bending, and CNC bending machines for bending tubes with tight radii and complex geometries.
- Chrome Plating:
- Chrome plating is a surface treatment applied to die surfaces to improve hardness, corrosion resistance, and lubricity.
- Chrome-plated dies exhibit reduced friction, wear, and material adhesion during bending, resulting in smoother bend surfaces and improved dimensional accuracy.
- Chrome plating is suitable for bending applications where surface finish and precision are critical, such as automotive exhaust systems, furniture frames, and aerospace components.
- Diamond-Like Carbon (DLC) Coating:
- Diamond-like carbon (DLC) coating is a thin film coating applied to die surfaces to enhance hardness, lubricity, and wear resistance.
- DLC-coated dies offer superior performance in high-speed bending operations, reducing friction, heat buildup, and tool wear compared to conventional coatings.
- DLC coating is particularly effective in bending thin-walled tubes or delicate materials, where minimizing surface defects and maintaining bend quality are paramount.
- Ceramic Coatings:
- Ceramic coatings, such as titanium nitride (TiN) or aluminum oxide (Al2O3), are applied to die surfaces to improve hardness, abrasion resistance, and thermal stability.
- Ceramic-coated dies exhibit reduced wear, galling, and material pickup during bending, resulting in extended tool life and improved bend quality.
- Ceramic coatings are suitable for bending applications involving abrasive materials, high-temperature environments, or aggressive bending conditions.
In conclusion, selecting the right die materials and coatings is crucial for achieving high-quality bends, minimizing wear, and maximizing productivity in tube bending operations. By considering factors such as material properties, bending requirements, and application-specific challenges, manufacturers can choose the most suitable die materials and coatings to optimize bending processes and achieve consistent results.
Tube Bending Machine: Bend Quality Inspection Techniques
Bend quality inspection is essential in tube bending operations to ensure that bent tubes meet dimensional accuracy, surface finish requirements, and overall performance criteria. Implementing effective inspection techniques helps identify defects, deviations, and inconsistencies early in the production process, allowing for timely adjustments and improvements. Here are several commonly used bend quality inspection techniques in tube bending machines:
- Dimensional Measurement:
- Dimensional measurement involves using precision measuring tools, such as calipers, micrometers, or coordinate measuring machines (CMMs), to verify bend angles, radii, lengths, and other geometric parameters of the bent tube.
- Measurements are compared against engineering drawings, specifications, or quality standards to assess compliance and identify any deviations or out-of-tolerance conditions.
- Automated measurement systems with laser sensors or vision systems may be used for rapid and accurate inspection of multiple bends in high-volume production environments.
- Surface Inspection:
- Surface inspection techniques, such as visual inspection, profilometry, or surface roughness measurement, assess the surface finish and integrity of the bent tube.
- Operators visually inspect the tube surface for defects such as scratches, scoring, cracks, or surface irregularities that may affect functionality or aesthetics.
- Profilometers or surface roughness testers quantify surface roughness parameters, such as Ra (average roughness) or Rz (maximum roughness depth), to ensure that surface finish requirements are met.
- Wall Thickness Measurement:
- Wall thickness measurement techniques, such as ultrasonic testing (UT) or eddy current testing (ECT), assess the uniformity and integrity of the tube wall thickness along the length of the bend.
- Ultrasonic probes or eddy current sensors are used to detect variations or defects in wall thickness caused by material thinning, wrinkling, or stretching during bending.
- Wall thickness measurements are compared against specified tolerances to ensure that the bent tube meets strength, pressure, or weight requirements.
- Cross-Sectional Analysis:
- Cross-sectional analysis involves cutting and examining cross-sections of the bent tube to assess internal features, such as wall thickness variations, ovality, or distortion.
- Optical microscopy, scanning electron microscopy (SEM), or X-ray imaging techniques may be used to visualize internal defects, weld seams, or material microstructure changes induced by bending.
- Defect Detection Systems:
- Defect detection systems, such as non-destructive testing (NDT) methods like dye penetrant testing (DPT), magnetic particle testing (MPT), or visual inspection systems, identify surface or subsurface defects in the bent tube.
- These systems use dye penetrants, magnetic particles, or visual inspection algorithms to detect cracks, porosity, or discontinuities that may compromise the integrity or performance of the bent tube.
- Statistical Process Control (SPC):
- Statistical process control techniques monitor and analyze bend quality data in real-time to identify trends, variations, or abnormalities in the bending process.
- Control charts, histograms, or Pareto analysis are used to track key quality indicators, such as bend angle deviations, scrap rates, or rework levels, and implement corrective actions as needed to maintain process stability and product consistency.
In conclusion, bend quality inspection techniques are essential for ensuring the dimensional accuracy, surface finish, and structural integrity of bent tubes in tube bending operations. By implementing comprehensive inspection procedures and utilizing advanced measurement and analysis tools, manufacturers can identify and address quality issues early, optimize production processes, and deliver high-quality bent tubes that meet customer requirements and industry standards.
Tube Bending Machine: Bend Radius Selection
Selecting the appropriate bend radius is a critical aspect of tube bending operations, as it directly influences the quality, integrity, and functionality of the bent tube. Bend radius affects factors such as material deformation, tooling requirements, and bending forces, and must be carefully considered to achieve optimal results. Here’s a comprehensive explanation of bend radius selection in tube bending:
- Definition of Bend Radius:
- The bend radius refers to the curvature of the bent section of the tube, measured from the centerline of the bend to the inner surface of the tube.
- It determines the tightness of the bend and influences the degree of material deformation, springback, and stress distribution during bending.
- Minimum Bend Radius:
- The minimum bend radius is the smallest allowable radius for a given tube diameter, wall thickness, and material, beyond which bending may cause defects such as kinking, wrinkling, or collapse.
- It is determined by material properties, including yield strength, elongation, and ductility, as well as tube geometry and bending method.
- Bend Radius Guidelines:
- General guidelines and industry standards provide recommended minimum bend radii for different tube materials, diameters, and wall thicknesses based on empirical data and bending experience.
- These guidelines help ensure bend quality, minimize material thinning, and prevent excessive tool wear or damage during bending.
- Material Deformation:
- Smaller bend radii result in tighter bends with sharper curvature, causing greater levels of material deformation and strain on the inner and outer surfaces of the tube.
- Material deformation increases the risk of defects such as thinning, wrinkling, or cracking, especially in high-strength or brittle materials.
- Springback Considerations:
- Larger bend radii tend to exhibit reduced springback effects, as they impose lower levels of residual stress and strain on the material during bending.
- Springback refers to the tendency of the material to return partially to its original shape after bending and must be accounted for when selecting bend radii to achieve desired bend angles.
- Tooling Requirements:
- Smaller bend radii require tighter tooling, such as mandrels or dies, with corresponding profiles and dimensions to support the tube and maintain bend integrity.
- Larger bend radii may allow for simpler tooling configurations and reduced tool wear, as they impose lower bending forces and stress levels on the tooling components.
- Application Considerations:
- Bend radius selection depends on specific application requirements, including bend angle, bend direction, space constraints, and functional considerations such as flow characteristics or structural integrity.
- For example, tight bend radii may be preferred in compact or space-constrained applications, while larger bend radii may be necessary to minimize flow restrictions or stress concentrations in fluid-carrying tubes.
- Finite Element Analysis (FEA):
- Advanced simulation techniques, such as finite element analysis (FEA), can be used to predict and optimize bend radius selection by simulating bending processes and assessing material behavior, stress distribution, and springback effects.
- FEA allows for virtual experimentation with different bend radii, materials, and bending parameters to identify optimal bending configurations and mitigate potential issues before actual production.
In conclusion, selecting the appropriate bend radius is crucial for achieving accurate and high-quality bends in tube bending operations. By considering factors such as material properties, deformation characteristics, tooling requirements, and application considerations, manufacturers can choose suitable bend radii to optimize bend quality, minimize defects, and meet performance specifications in tube bending applications.
Tube Bending Machine: Mandrel Types and Applications
Mandrels are critical components in tube bending machines, providing internal support to prevent tube collapse, wrinkling, or deformation during bending. Different mandrel types are available to suit various bending applications, materials, and geometries. Understanding the characteristics and applications of different mandrel types is essential for achieving high-quality bends. Here’s an overview of common mandrel types and their applications:
- Ball Mandrels:
- Ball mandrels consist of a spherical or hemispherical tip mounted on a shaft, providing point contact with the inner surface of the tube during bending.
- Ball mandrels are suitable for bending applications requiring minimal tube distortion, such as thin-walled or delicate materials, where reducing mandrel-induced marks or scratches is crucial.
- They are commonly used in mandrel bending machines for producing tight-radius bends with excellent surface finish and dimensional accuracy.
- Plug Mandrels:
- Plug mandrels feature a cylindrical or tapered shape that closely matches the inner diameter of the tube, providing full-length support and uniform pressure distribution during bending.
- Plug mandrels are ideal for bending thick-walled or heavy-duty materials, where internal support is essential to prevent collapse or distortion.
- They are commonly used in rotary draw bending machines for bending structural components, exhaust systems, or hydraulic tubing requiring precise control over wall thinning and ovality.
- Ball Mandrel with Links:
- Ball mandrels with links consist of multiple ball segments interconnected by flexible links or springs, allowing for articulation and adjustment to accommodate varying tube geometries.
- Ball mandrels with links provide increased flexibility and adaptability compared to rigid mandrels, making them suitable for bending complex shapes, multiple bend radii, or asymmetrical profiles.
- They are commonly used in CNC bending machines for producing intricate bends in automotive frames, aerospace structures, or architectural components requiring precise control over bend angles and geometries.
- Pressure-Die Mandrels:
- Pressure-die mandrels combine internal mandrel support with external pressure application using hydraulic or mechanical dies, ensuring uniform deformation and dimensional accuracy during bending.
- Pressure-die mandrels are ideal for bending thick-walled or high-strength materials that require both internal and external support to maintain bend integrity and prevent distortion.
- They are commonly used in mandrel bending machines for producing heavy-duty components such as roll cages, chassis frames, or hydraulic cylinders requiring tight tolerances and consistent bend quality.
- Floating Mandrels:
- Floating mandrels feature a retractable design that allows them to move axially or rotate freely within the tube during bending, minimizing friction and material deformation.
- Floating mandrels are suitable for bending long or thin-walled tubes where mandrel-induced marks or wrinkles must be minimized, and internal support is required to prevent collapse or distortion.
- They are commonly used in CNC bending machines for producing long-length bends in automotive exhaust systems, conveyor systems, or heat exchanger tubing requiring smooth, wrinkle-free bends.
- Segmented Mandrels:
- Segmented mandrels consist of multiple interchangeable segments or inserts that can be adjusted or replaced to accommodate different tube diameters, wall thicknesses, or bend radii.
- Segmented mandrels offer versatility and cost-effectiveness by allowing for customization and reconfiguration to suit various bending requirements without the need for dedicated mandrels.
- They are commonly used in job shops, prototype development, or low-volume production environments where flexibility and adaptability are paramount.
In conclusion, selecting the appropriate mandrel type is crucial for achieving high-quality bends in tube bending operations. By understanding the characteristics and applications of different mandrel types, manufacturers can choose the most suitable mandrel for their specific bending requirements, materials, and geometries, ensuring consistent bend quality, dimensional accuracy, and production efficiency.
Tube Bending Machine: Bend Allowance Calculation
Bend allowance calculation is a fundamental aspect of tube bending operations, essential for determining the length of the straight tube required to achieve a desired bend angle and geometry accurately. Accurate bend allowance calculation ensures precise tube cutting, bending, and assembly, minimizing scrap and rework. Here’s a detailed explanation of bend allowance calculation in tube bending:
- Definition of Bend Allowance:
- Bend allowance refers to the additional length of material required to accommodate the deformation and elongation of the tube during bending, ensuring that the final bent shape matches the desired specifications.
- It compensates for the increase in material length along the neutral axis of the bend due to stretching and compression during bending.
- Factors Affecting Bend Allowance:
- Bend Radius: Smaller bend radii result in greater elongation and compression of the material along the neutral axis, requiring a larger bend allowance.
- Material Thickness: Thicker-walled tubes experience greater elongation and compression during bending, necessitating a larger bend allowance to compensate for material deformation.
- Material Type: Material properties such as yield strength, elongation, and ductility influence the amount of stretch and compression experienced during bending, affecting bend allowance calculations.
- Bend Angle: Greater bend angles result in increased material elongation and compression, requiring a larger bend allowance to achieve the desired bend geometry accurately.
- Bend Allowance Calculation Methods:
- There are several methods for calculating bend allowance, including empirical formulas, tables, software simulations, and CAD/CAM systems.
- The most common approach is the empirical method, which involves using mathematical formulas or tables based on material properties, bend radius, bend angle, and tube geometry to calculate bend allowance.
- Software simulations and CAD/CAM systems utilize finite element analysis (FEA) or numerical modeling techniques to predict material behavior, stress distribution, and bend deformation accurately, allowing for precise bend allowance calculation and optimization.
- Empirical Formulas:
- The most widely used empirical formula for calculating bend allowance is the K-factor method, which relates the bend allowance to the material thickness, bend radius, and bend angle.
- The K-factor represents the ratio of the neutral axis location to the material thickness and varies depending on the bending method, tooling configuration, and material properties.
- Other empirical formulas, such as the Bend Deduction (BD) or Bend Allowance (BA) formulas, may be used depending on specific bending requirements or industry standards.
- Bend Allowance Calculation Steps:
- Determine Material Properties: Identify the material type, thickness, yield strength, and elongation properties of the tube material.
- Select Bending Parameters: Determine the bend radius, bend angle, and bending method (e.g., rotary draw bending, mandrel bending, CNC bending).
- Calculate Bend Allowance: Use the selected bend allowance calculation method or formula to determine the required bend allowance for the given bending parameters.
- Apply Bend Allowance: Add the calculated bend allowance to the straight length of the tube to obtain the total length required for bending.
- Verify Accuracy: Validate the calculated bend allowance by performing test bends or simulations and adjusting as needed to achieve the desired bend geometry and dimensional accuracy.
- Importance of Accurate Bend Allowance:
- Accurate bend allowance calculation is crucial for achieving precise bend geometries, minimizing scrap and rework, and ensuring dimensional accuracy and fit-up in assembly.
- Incorrect bend allowance can result in deviations from design specifications, including overbending, underbending, or distortion of the bent tube, leading to quality issues and production delays.
In conclusion, bend allowance calculation is a critical step in tube bending operations, ensuring accurate and consistent bend geometries while minimizing material waste and production costs. By understanding the factors affecting bend allowance, selecting appropriate calculation methods, and verifying accuracy through testing or simulation, manufacturers can achieve optimal bend quality and efficiency in tube bending processes.
Tube Bending Machine: Springback Compensation Techniques
Springback is a common phenomenon in tube bending operations, where the material tends to return partially to its original shape after bending, leading to deviations from the desired bend angle and geometry. Springback compensation techniques are employed to mitigate the effects of springback, ensuring that the final bent tube conforms closely to design specifications. Here are several techniques used to compensate for springback in tube bending:
- Overbending:
- Overbending involves bending the tube slightly beyond the desired bend angle to account for the anticipated springback.
- By intentionally overbending the tube, the final springback-induced angle deviation brings the bent tube closer to the desired angle, compensating for the elastic recovery of the material.
- Overbending is typically applied empirically based on experience and trial-and-error adjustments, with the amount of overbend depending on material properties, bend radius, and bend angle.
- Springback Angle Adjustment:
- Springback angle adjustment techniques involve calculating and applying a corrective angle to the bending tooling or machine setup to counteract the anticipated springback.
- The corrective angle is determined based on empirical formulas, bend allowance calculations, or previous bend data, taking into account material properties, bend radius, and bend angle.
- Springback angle adjustments may be made manually by the operator or automatically using CNC programming or machine control systems to achieve the desired final bend geometry.
- Backward Angle Compensation:
- Backward angle compensation techniques involve bending the tube slightly in the opposite direction (backward) to the desired bend angle before performing the primary bend.
- The backward bend introduces additional residual stresses and strains into the material, counteracting the springback effect and resulting in a final bend angle closer to the target angle.
- Backward angle compensation is particularly effective for bending high-strength or springy materials where springback is more pronounced.
- Mandrel Design Optimization:
- Mandrel design optimization techniques focus on enhancing mandrel performance and effectiveness in supporting the inner surface of the tube during bending to minimize springback.
- Improvements in mandrel geometry, surface finish, material selection, and lubrication can reduce friction, improve material flow, and mitigate springback-induced defects such as wrinkling or collapse.
- Advanced mandrel designs, such as segmented or floating mandrels, allow for greater adaptability and control over bend geometry, enabling precise springback compensation in complex bending applications.
- Material Selection and Heat Treatment:
- Material selection and heat treatment processes can influence the magnitude of springback in tube bending by altering material properties such as yield strength, modulus of elasticity, and ductility.
- Selecting materials with lower yield strength or higher elongation properties can reduce springback tendencies, while heat treatment processes such as annealing or stress relieving can stabilize material microstructures and minimize residual stresses.
- Tailoring material properties through alloying, heat treatment, or cold working can optimize springback behavior and improve bend quality and consistency in tube bending applications.
- Finite Element Analysis (FEA):
- Finite element analysis (FEA) simulations allow for virtual modeling and prediction of springback behavior in tube bending processes, enabling optimization of bending parameters and tooling designs to minimize springback effects.
- FEA simulations consider material properties, geometric factors, boundary conditions, and loading conditions to accurately simulate the bending process and predict springback tendencies.
- By iteratively adjusting bending parameters and analyzing simulation results, manufacturers can optimize springback compensation strategies and achieve precise control over bend geometry and dimensional accuracy in tube bending operations.
In conclusion, springback compensation techniques are essential for achieving accurate and consistent bend geometries in tube bending operations. By employing methods such as overbending, angle adjustment, mandrel optimization, material selection, and FEA simulations, manufacturers can effectively mitigate the effects of springback, ensuring high-quality and dimensionally accurate bent tubes that meet design specifications and performance requirements.
Tube Bending Machine: Lubrication Systems and Importance
Lubrication systems play a crucial role in tube bending operations, facilitating smooth material flow, reducing friction, minimizing wear on tooling components, and improving bend quality and efficiency. Proper lubrication ensures that the bending process remains consistent, reliable, and free from defects. Here’s an in-depth look at lubrication systems used in tube bending machines and their importance:
- Types of Lubrication Systems:
- Flood Lubrication: Flood lubrication systems involve continuously applying a lubricant, such as oil or water-based coolant, directly onto the bending tooling and workpiece surface during the bending process. This ensures consistent lubrication and cooling, reducing friction and heat buildup.
- Mist Lubrication: Mist lubrication systems atomize lubricant into fine particles, creating a mist or spray that is directed onto the tooling and workpiece surfaces. Mist lubrication provides targeted lubrication and reduces waste compared to flood lubrication systems.
- Roller Lubrication: Roller lubrication systems apply lubricant to the bending mandrel or pressure rollers, ensuring smooth material flow and reducing friction between the mandrel and the inner surface of the tube.
- Importance of Lubrication in Tube Bending:
- Friction Reduction: Lubrication reduces friction between the tooling and the workpiece, allowing for smoother material flow and minimizing the risk of surface defects such as scratches, scoring, or galling.
- Heat Dissipation: Lubrication helps dissipate heat generated during the bending process, preventing overheating of the tooling and workpiece and reducing the risk of thermal distortion or metallurgical changes in the material.
- Tool Life Extension: Proper lubrication extends the life of bending tooling components, such as mandrels, dies, and pressure rollers, by reducing wear and abrasion, prolonging maintenance intervals, and minimizing downtime.
- Bend Quality Improvement: Lubrication ensures uniform material deformation and improves bend quality by reducing the risk of material thinning, wrinkling, or cracking, resulting in smoother bend surfaces and tighter dimensional tolerances.
- Chip Removal: Lubrication helps flush away chips, debris, and swarf generated during the bending process, preventing buildup and clogging of tooling components and ensuring continuous operation and reliability.
- Lubricant Selection Considerations:
- Compatibility: The lubricant should be compatible with the tube material, tooling materials, and machine components to avoid chemical reactions, corrosion, or damage.
- Lubricity: The lubricant should have high lubricity to reduce friction and improve material flow, ensuring smooth bending and minimizing surface defects.
- Cooling Properties: The lubricant should have effective cooling properties to dissipate heat generated during bending, preventing thermal distortion and maintaining material properties.
- Environmental Impact: Considerations such as biodegradability, toxicity, and environmental regulations should be taken into account when selecting lubricants to minimize environmental impact and ensure workplace safety.
- Maintenance and Monitoring:
- Regular maintenance and monitoring of lubrication systems are essential to ensure proper function and performance.
- Periodic inspection of lubricant levels, quality, and distribution ensures that the lubrication system operates effectively and prevents issues such as insufficient lubrication, contamination, or blockages.
- Lubrication system components, such as pumps, filters, hoses, and nozzles, should be inspected, cleaned, and replaced as needed to maintain optimal lubricant delivery and system integrity.
In conclusion, lubrication systems are critical components of tube bending machines, providing essential lubrication, cooling, and friction reduction during the bending process. By selecting the appropriate lubrication system and lubricants, implementing proper maintenance practices, and monitoring system performance, manufacturers can ensure smooth and efficient tube bending operations, minimize defects, and achieve high-quality bend results consistently.
Tube Bending Machine: Tooling Materials and Selection
Tooling materials play a crucial role in tube bending operations, influencing bend quality, tool life, and overall process efficiency. Selecting the appropriate tooling material is essential for achieving precise and consistent bends while minimizing wear, deformation, and defects. Here’s an in-depth exploration of common tooling materials used in tube bending machines and their selection criteria:
- Common Tooling Materials:
- Tool Steel (e.g., D2, A2, S7): Tool steel is a versatile and widely used material for tube bending tooling due to its excellent wear resistance, toughness, and machinability. It is suitable for a wide range of tube materials and bending applications.
- Carbide (e.g., tungsten carbide): Carbide tooling offers superior hardness, abrasion resistance, and thermal stability compared to tool steel, making it ideal for high-volume production, abrasive materials, or demanding bending conditions.
- High-Speed Steel (HSS): HSS tooling combines high wear resistance with good toughness and heat resistance, making it suitable for general-purpose bending applications where a balance of performance and cost is desired.
- Chrome-Plated Steel: Chrome-plated tooling provides enhanced corrosion resistance and surface hardness, reducing friction and wear during bending operations. It is often used in applications requiring tight tolerances and smooth bend surfaces.
- Ceramics (e.g., alumina, silicon nitride): Ceramic tooling offers exceptional hardness, thermal stability, and chemical resistance, making it suitable for bending exotic or heat-sensitive materials and achieving ultra-precision bends.
- Selection Criteria:
- Material Compatibility: The tooling material should be compatible with the tube material to prevent material contamination, chemical reactions, or surface damage during bending. Considerations such as material hardness, ductility, and thermal conductivity should match the requirements of the tube material.
- Wear Resistance: Tooling materials should exhibit high wear resistance to withstand the abrasive effects of repeated bending cycles and maintain dimensional accuracy and surface finish over extended periods of use.
- Toughness and Impact Resistance: Tooling materials should possess adequate toughness and impact resistance to withstand bending forces, shock loading, and incidental impacts without fracturing or chipping.
- Heat Resistance: Tooling materials should maintain mechanical properties and dimensional stability at elevated temperatures encountered during bending, preventing softening, deformation, or thermal damage.
- Surface Finish: Tooling materials should have smooth and uniform surface finishes to minimize friction, reduce material adhesion, and prevent surface defects such as scoring, scratching, or galling on the bent tube.
- Cost Considerations: Tooling materials should offer a balance of performance and cost-effectiveness, taking into account factors such as tool life, maintenance requirements, and production volume.
- Tool Coatings and Treatments:
- Tool coatings, such as TiN (titanium nitride), TiCN (titanium carbonitride), or DLC (diamond-like carbon), can improve tooling performance by enhancing wear resistance, reducing friction, and preventing material buildup during bending.
- Surface treatments, such as heat treatment, nitriding, or cryogenic treatment, can modify tooling properties, such as hardness, toughness, and surface finish, to optimize performance and longevity in specific bending applications.
- Tooling Maintenance and Care:
- Regular inspection, cleaning, and maintenance of tooling components are essential to ensure optimal performance and longevity.
- Proper lubrication, coolant application, and chip removal help minimize friction, heat buildup, and wear on tooling surfaces during bending operations.
- Monitoring tool wear, dimensional accuracy, and surface finish of bent tubes allows for timely replacement or reconditioning of worn or damaged tooling components to maintain bend quality and consistency.
In conclusion, selecting the appropriate tooling material is critical for achieving high-quality and precise bends in tube bending operations. By considering factors such as material compatibility, wear resistance, toughness, heat resistance, and cost-effectiveness, manufacturers can choose the most suitable tooling material for their specific bending requirements, materials, and production conditions, ensuring optimal performance, efficiency, and bend quality in tube bending processes.
Tube Bending Machine: Tube End Forming
Tube end forming is a process that involves shaping, resizing, or adding features to the ends of tubes to meet specific functional or design requirements. It is commonly performed in conjunction with tube bending operations to produce finished components with precise dimensions, configurations, and end conditions. Here’s a detailed exploration of tube end forming processes, techniques, and applications:
- End Forming Processes:
- Expansion: Expansion involves enlarging the diameter of the tube end to achieve a snug fit with mating components or fittings. It is commonly used in applications such as tube-to-tube joints, connections to hoses or fittings, or sealing surfaces.
- Reduction: Reduction entails decreasing the diameter of the tube end to fit into a smaller opening or to create a stepped or tapered configuration. It is used in applications such as insertion into sockets, connectors, or mating components.
- Flaring: Flaring creates a flared or conical shape at the tube end, providing a smooth transition for mating with other components, enhancing structural integrity, or facilitating fluid flow. It is commonly used in applications such as brake lines, fuel lines, or fluid transfer systems.
- Swaging: Swaging involves compressing or reducing the diameter of the tube end to create a cylindrical or stepped shape, often used for joining tubes, forming lap joints, or creating mechanical connections.
- Beading: Beading adds a bead or raised feature to the tube end for reinforcement, sealing, or retention purposes. It is commonly used in applications such as fluid reservoirs, fuel tanks, or structural components requiring added strength or rigidity.
- Notching: Notching creates cutouts or grooves in the tube end to accommodate mating features, fasteners, or attachment points. It is used in applications such as frame construction, mounting brackets, or assembly fixtures.
- Chamfering: Chamfering involves beveling or cutting an angle on the edge of the tube end to facilitate insertion, alignment, or welding operations. It is commonly used in applications such as pipe fittings, structural joints, or weld preparations.
- End Forming Techniques:
- Cold Forming: Cold forming techniques involve deforming the tube end at ambient temperatures using specialized tooling, dies, or presses. Cold forming offers precise control over dimensional accuracy, surface finish, and material properties without requiring heating or annealing of the tube.
- Hot Forming: Hot forming techniques involve heating the tube end to elevated temperatures before shaping or resizing to improve ductility, reduce forming forces, or achieve complex geometries. Hot forming is commonly used for thick-walled or high-strength materials, intricate shapes, or large-scale production.
- Hydraulic Forming: Hydraulic forming utilizes hydraulic pressure to deform the tube end using a hydraulic press, ram, or bladder. Hydraulic forming offers high forming forces, uniform deformation, and flexibility in tooling configurations, making it suitable for a wide range of end forming applications.
- Applications of Tube End Forming:
- Tube end forming is widely used in various industries and applications, including automotive, aerospace, HVAC (heating, ventilation, and air conditioning), plumbing, furniture, and manufacturing.
- Common applications include tube-to-tube joints, tube-to-component connections, fluid transfer systems, structural frames, exhaust systems, hydraulic systems, and assembly fixtures.
- Tube end forming allows for the creation of complex geometries, tight tolerances, and tailored end conditions to meet specific performance, functional, and design requirements in diverse engineering applications.
In conclusion, tube end forming is a versatile and essential process in tube bending operations, enabling the production of finished components with precise dimensions, configurations, and end conditions. By utilizing various end forming processes, techniques, and applications, manufacturers can achieve optimal performance, functionality, and aesthetics in a wide range of engineering and manufacturing applications.
Tube Bending Machine: CNC Programming and Control
CNC (Computer Numerical Control) programming and control are integral to modern tube bending machines, enabling precise, automated, and repeatable bending operations. CNC technology allows manufacturers to produce complex bends with high accuracy and efficiency while minimizing setup time and material waste. Here’s an in-depth look at CNC programming and control in tube bending machines:
- CNC Programming Basics:
- CNC programming involves creating a set of instructions, known as G-code or M-code, that control the movements and operations of the tube bending machine.
- G-code commands specify the toolpath, feed rates, spindle speeds, tool changes, and other parameters required to perform the bending operation accurately.
- CNC programming can be performed manually using text-based programming languages such as G-code or through graphical user interfaces (GUIs) and software applications specifically designed for tube bending machines.
- Key Components of CNC Control:
- Control Unit: The control unit serves as the brain of the CNC system, interpreting the programmed instructions and translating them into precise movements and actions by the machine.
- Servo Motors: Servo motors drive the motion of the machine axes (e.g., X, Y, Z) based on the commands received from the control unit. They provide high-speed, high-precision positioning for accurate bending operations.
- Feedback Systems: Feedback systems, such as encoders or resolvers, provide real-time position feedback to the control unit, ensuring accurate positioning and compensation for any deviations or errors during bending.
- Human-Machine Interface (HMI): The HMI allows operators to interact with the CNC system, input programming parameters, monitor machine status, and diagnose issues through a user-friendly interface.
- Safety Systems: CNC control systems include safety features such as emergency stop buttons, interlocks, and safety sensors to protect operators and equipment from accidents or malfunctions.
- CNC Programming Steps:
- Part Design: The first step in CNC programming is to create a digital model or CAD (Computer-Aided Design) file of the desired part geometry, including bend angles, dimensions, and tolerances.
- Toolpath Generation: Next, the CNC programmer generates the toolpath or trajectory that the bending tool will follow to achieve the desired bend geometry. This may involve selecting bend sequences, calculating bend allowances, and optimizing tool movements for efficient bending.
- G-code Generation: Based on the toolpath and part geometry, the CNC programmer generates the G-code program that specifies the machine movements, tool actions, feed rates, and other parameters required to produce the part.
- Simulation and Verification: Before executing the program on the machine, the CNC programmer simulates the bending process using software or virtual machining environments to verify the correctness of the toolpath, detect collisions, and optimize cycle times.
- Machine Setup and Execution: Once the program is verified, the CNC operator loads the program into the machine control unit, sets up the workpiece and tooling, and executes the bending operation. The CNC control system precisely executes the programmed instructions to produce the finished part.
- Advantages of CNC Control in Tube Bending:
- Precision and Accuracy: CNC control enables precise control over bending parameters, resulting in accurate bend angles, dimensions, and tolerances, even for complex geometries.
- Repeatability: CNC programming allows for the replication of bending sequences and part geometries with high repeatability, ensuring consistent quality and performance across production batches.
- Efficiency: CNC automation reduces setup time, material waste, and manual intervention, leading to increased productivity, shorter lead times, and lower production costs.
- Flexibility: CNC programming offers flexibility to accommodate design changes, customization, or prototyping, allowing manufacturers to respond quickly to customer demands and market trends.
- Safety: CNC control systems incorporate safety features and interlocks to protect operators and equipment from accidents, ensuring a safe working environment.
In conclusion, CNC programming and control are essential capabilities of tube bending machines, enabling precise, automated, and efficient bending operations. By leveraging CNC technology, manufacturers can achieve superior part quality, consistency, and productivity while adapting to changing market demands and maintaining a competitive edge in the manufacturing industry.
Tube Bending Machine: Material Handling Systems
Material handling systems are essential components of tube bending machines, facilitating the efficient loading, positioning, and manipulation of workpieces during bending operations. These systems optimize workflow, minimize downtime, and ensure operator safety, contributing to overall productivity and efficiency. Here’s a comprehensive overview of material handling systems used in tube bending machines:
- Types of Material Handling Systems:
- Manual Loading: In manual loading systems, operators manually load and position workpieces onto the bending machine’s feeding mechanism, such as a conveyor belt, roller table, or loading arm. Manual loading systems are suitable for low-volume production or applications with varying part geometries and sizes.
- Automatic Loading: Automatic loading systems utilize robotic arms, gantry loaders, or pick-and-place mechanisms to automatically retrieve workpieces from storage racks, trays, or pallets and position them accurately onto the bending machine. Automatic loading systems are ideal for high-volume production, repetitive tasks, or applications requiring precise positioning and rapid cycle times.
- In-Line Feeding: In-line feeding systems transport workpieces continuously along a linear or rotary path, feeding them into the bending machine at predefined intervals or positions. In-line feeding systems are suitable for continuous production lines, integrated manufacturing cells, or applications with sequential bending operations.
- Offline Loading: Offline loading systems allow operators to load and prepare workpieces outside of the bending machine’s workspace, minimizing machine downtime and maximizing throughput. Offline loading systems may include material staging areas, part fixtures, or pre-loading stations for efficient workflow management.
- Key Features and Components:
- Feeding Mechanisms: Feeding mechanisms, such as conveyors, rollers, belts, or chains, transport workpieces from the loading area to the bending machine’s clamping and bending zones.
- Positioning Systems: Positioning systems, such as linear actuators, servo motors, or pneumatic cylinders, accurately position workpieces in the desired orientation and location for bending.
- Clamping Devices: Clamping devices, such as vise jaws, collets, or hydraulic clamps, securely hold the workpiece in place during bending to prevent movement or distortion.
- Gripping and Manipulation Tools: Gripping and manipulation tools, such as robotic end effectors, vacuum cups, or magnetic grippers, handle and manipulate workpieces with precision and reliability.
- Safety Features: Safety features, such as light curtains, interlocks, emergency stop buttons, and protective barriers, ensure operator safety and compliance with safety standards during material handling operations.
- Integration with Bending Process:
- Material handling systems are seamlessly integrated with the bending process to ensure smooth workflow and optimal machine utilization.
- Integration may involve synchronized movement between the material handling system and bending machine, real-time communication between control systems, and automated loading and unloading of workpieces.
- Advanced material handling systems may incorporate sensors, vision systems, or AI (Artificial Intelligence) algorithms to detect and correct errors, optimize cycle times, and adapt to variations in part geometry or material properties.
- Benefits of Material Handling Systems:
- Increased Productivity: Material handling systems streamline workflow, reduce setup time, and minimize manual intervention, leading to higher throughput and productivity.
- Improved Accuracy: Automated positioning and manipulation ensure consistent part positioning and alignment, resulting in accurate bend geometries and dimensional tolerances.
- Enhanced Safety: Material handling systems incorporate safety features to protect operators from hazards such as pinch points, entanglement, or falling objects, ensuring a safe working environment.
- Cost Savings: Efficient material handling reduces labor costs, material waste, and production downtime, maximizing the return on investment (ROI) of tube bending machines.
- Flexibility: Material handling systems support a wide range of workpiece sizes, shapes, and materials, enabling manufacturers to adapt to changing production requirements and customer demands.
In conclusion, material handling systems are integral components of tube bending machines, optimizing workflow, increasing productivity, and ensuring operator safety. By selecting the appropriate material handling system and integrating it seamlessly with the bending process, manufacturers can achieve efficient and reliable tube bending operations while maximizing operational efficiency and profitability.
Tube Bending Machine: Quality Control and Inspection
Quality control and inspection are essential aspects of tube bending operations to ensure that finished products meet specified requirements, adhere to quality standards, and satisfy customer expectations. Proper quality control measures help identify and rectify defects, minimize scrap, and maintain consistent product quality. Here’s an in-depth exploration of quality control and inspection techniques in tube bending:
- Key Quality Control Parameters:
- Bend Angle: The bend angle is a critical parameter that must conform to design specifications and tolerances. Variations in bend angle can affect the fit, form, and function of the finished part.
- Bend Radius: The bend radius determines the curvature of the bend and impacts factors such as material strength, fatigue life, and dimensional accuracy. Deviations from the specified bend radius can result in part rejection or performance issues.
- Bend Quality: Bend quality encompasses factors such as surface finish, dimensional accuracy, wall thinning, wrinkling, and ovality. High-quality bends exhibit smooth surfaces, uniform dimensions, and minimal defects.
- Dimensional Tolerances: Dimensional tolerances define acceptable variations in part dimensions and geometries. Tight tolerances ensure interchangeability, assembly compatibility, and functional performance.
- Material Integrity: Material integrity refers to the structural integrity, metallurgical properties, and material characteristics of the bent tube, including hardness, grain structure, and residual stresses. Material defects such as cracks, tears, or imperfections can compromise part performance and durability.
- Alignment and Straightness: Alignment and straightness ensure that the bent tube is free from twists, kinks, or distortions and maintains positional accuracy relative to mating components or assembly fixtures.
- Quality Control Techniques:
- In-Process Inspection: In-process inspection involves monitoring and verifying critical parameters during the bending process to detect deviations or defects in real-time. Techniques such as laser measurement, optical sensors, or vision systems provide immediate feedback and enable corrective actions to be taken promptly.
- Post-Process Inspection: Post-process inspection entails evaluating finished parts against quality criteria using measurement tools, gauges, fixtures, or coordinate measuring machines (CMMs). Inspections may include visual inspection, dimensional measurement, surface profilometry, hardness testing, or material analysis.
- Statistical Process Control (SPC): SPC techniques involve collecting and analyzing process data to monitor variations, trends, and anomalies in key quality parameters. Control charts, histograms, and statistical analyses help identify sources of variation, optimize process settings, and maintain process stability and capability.
- Non-Destructive Testing (NDT): NDT methods, such as ultrasonic testing, radiographic testing, eddy current testing, or dye penetrant testing, detect internal or surface defects in bent tubes without causing damage to the material. NDT techniques are used to verify material integrity, identify discontinuities, and ensure compliance with quality standards.
- First Article Inspection (FAI): FAI involves conducting comprehensive inspections and dimensional checks on the first few parts produced during a production run to validate manufacturing processes, tooling setups, and part conformance to design specifications. FAI ensures that subsequent parts meet quality requirements and customer expectations.
- Quality Assurance Practices:
- Standard Operating Procedures (SOPs): SOPs define standardized processes, procedures, and work instructions for tube bending operations, including setup, programming, machine operation, and inspection protocols. SOPs ensure consistency, repeatability, and adherence to quality standards.
- Training and Certification: Training programs provide operators, technicians, and quality personnel with the knowledge, skills, and competencies required to perform tube bending tasks effectively and safely. Certification programs validate proficiency and ensure compliance with industry standards and regulations.
- Calibration and Maintenance: Regular calibration and maintenance of equipment, measurement tools, and inspection instruments are essential to ensure accuracy, reliability, and traceability of measurement results. Calibration ensures that inspection equipment meets specified tolerances and remains in optimal working condition.
- Continuous Improvement: Continuous improvement initiatives, such as Lean manufacturing, Six Sigma, or Kaizen, focus on identifying and eliminating waste, optimizing processes, and enhancing product quality and customer satisfaction. Quality control data and feedback drive process improvements and corrective actions to prevent recurrence of defects and non-conformities.
In conclusion, quality control and inspection are critical aspects of tube bending operations to ensure that finished products meet quality standards, performance requirements, and customer expectations. By implementing robust quality control measures, utilizing advanced inspection techniques, and fostering a culture of quality assurance and continuous improvement, manufacturers can achieve consistent, reliable, and high-quality tube bending outcomes while minimizing defects, scrap, and rework.
Tube Bending Machine: Tool Wear and Maintenance
Tool wear and maintenance are crucial aspects of tube bending machine operation, as they directly impact bend quality, production efficiency, and tool longevity. Proper maintenance practices help minimize downtime, extend tool life, and ensure consistent performance of tube bending equipment. Here’s an in-depth exploration of tool wear mechanisms, maintenance techniques, and best practices:
- Tool Wear Mechanisms:
- Abrasive Wear: Abrasive wear occurs when hard particles or contaminants in the tube material or bending environment come into contact with the tool surface, gradually eroding the tool material. Factors such as material hardness, surface finish, lubrication, and cutting parameters influence abrasive wear.
- Adhesive Wear: Adhesive wear results from the transfer of material from the workpiece to the tool surface due to friction and contact pressure during bending. This leads to material buildup, galling, and surface scoring, affecting bend quality and tool performance.
- Fatigue Wear: Fatigue wear occurs as a result of repeated bending cycles, causing micro-cracks, deformation, and fracture of the tool material. High bending forces, cyclic loading, and stress concentrations in critical areas contribute to fatigue wear.
- Chemical Wear: Chemical wear involves the degradation or corrosion of tool surfaces due to exposure to aggressive chemicals, heat, moisture, or environmental factors. Chemical wear can lead to surface pitting, etching, or deterioration of tool properties.
- Tool Maintenance Techniques:
- Regular Inspection: Routine inspection of tooling components, such as mandrels, wiper dies, clamp dies, and pressure dies, helps identify signs of wear, damage, or deformation. Visual inspection, dimensional checks, and non-destructive testing methods assist in assessing tool condition and performance.
- Cleaning and Lubrication: Cleaning tool surfaces and applying lubricants or coatings reduce friction, prevent material adhesion, and extend tool life. Proper lubrication also helps dissipate heat, reduce wear, and improve bending performance.
- Sharpening and Reconditioning: Sharpening or regrinding worn tool surfaces restores cutting edges, geometries, and surface finishes, revitalizing tool performance and functionality. Precision grinding techniques ensure accurate dimensions and profiles while removing material defects and imperfections.
- Replacement and Replenishment: Periodic replacement or replenishment of consumable tooling components, such as inserts, bushings, guide rollers, or wear plates, maintains optimal bending performance and minimizes downtime due to tool failure or wear-related issues.
- Temperature Control: Maintaining consistent temperature conditions in the bending environment helps prevent thermal degradation, softening, or distortion of tool materials. Cooling systems, heat shields, or insulation measures mitigate heat-related wear and extend tool life.
- Best Practices for Tool Maintenance:
- Establish Preventive Maintenance Programs: Implementing scheduled maintenance routines, including cleaning, lubrication, inspection, and replacement intervals, ensures proactive management of tool wear and degradation.
- Document and Track Tool Performance: Keeping detailed records of tool usage, maintenance activities, wear patterns, and performance indicators helps identify trends, predict failure modes, and optimize maintenance schedules.
- Invest in High-Quality Tooling: Selecting premium-grade tooling materials, coatings, and treatments enhances wear resistance, durability, and performance, resulting in longer tool life and reduced maintenance costs over time.
- Train Operators and Maintenance Personnel: Providing comprehensive training programs for operators and maintenance personnel fosters awareness of tooling issues, proper handling techniques, and maintenance procedures, empowering them to troubleshoot problems and optimize tool performance.
- Monitor Process Parameters: Monitoring key process parameters, such as bending forces, temperatures, speeds, and material properties, allows for early detection of abnormal conditions, deviations, or trends that may indicate impending tool wear or failure.
In conclusion, effective tool wear management and maintenance practices are essential for maximizing the performance, reliability, and longevity of tube bending equipment. By understanding the mechanisms of tool wear, implementing proactive maintenance strategies, and adhering to best practices, manufacturers can minimize downtime, optimize production efficiency, and achieve consistent, high-quality tube bending outcomes.
Tube Bending Machine: Environmental Considerations
Environmental considerations in tube bending operations encompass various aspects related to energy consumption, waste generation, emissions, and sustainability practices. Implementing environmentally friendly practices not only reduces the environmental footprint of tube bending processes but also promotes resource efficiency, cost savings, and regulatory compliance. Here’s an overview of environmental considerations and best practices for tube bending operations:
- Energy Efficiency:
- Equipment Selection: Choosing energy-efficient tube bending machines with advanced features such as variable-speed drives, servo motors, and regenerative braking systems can significantly reduce energy consumption during operation.
- Process Optimization: Optimizing bending parameters, tooling configurations, and material handling techniques minimizes energy expenditure and maximizes process efficiency. Utilizing simulation software and predictive modeling tools helps identify energy-saving opportunities and optimize machine settings.
- Energy Recovery: Implementing energy recovery systems, such as heat exchangers or recuperators, captures and recycles waste heat generated during bending processes for heating, cooling, or other purposes, reducing overall energy demand.
- Waste Reduction and Recycling:
- Material Optimization: Minimizing material waste through efficient nesting, cutting, and bending strategies reduces raw material consumption and lowers production costs. Utilizing advanced CAD/CAM software and nesting algorithms optimizes material usage and maximizes material yield.
- Scrap Management: Segregating and recycling scrap materials, such as offcuts, trimmings, or scrap tubes, reduces landfill waste and conserves valuable resources. Establishing partnerships with recycling facilities or scrap metal vendors facilitates responsible disposal and recycling of waste materials.
- Lean Manufacturing Practices: Implementing lean manufacturing principles, such as just-in-time production, kanban systems, and inventory control, streamlines operations, reduces excess inventory, and minimizes waste generation throughout the production process.
- Emissions Control and Air Quality:
- Exhaust Ventilation: Installing efficient exhaust ventilation systems and dust collection equipment captures and removes airborne contaminants, particulates, and fumes generated during tube bending processes, improving indoor air quality and minimizing worker exposure to harmful emissions.
- Emission Reduction Technologies: Employing emission control technologies, such as catalytic converters, scrubbers, or filtration systems, reduces air pollutant emissions, including volatile organic compounds (VOCs), particulate matter, and hazardous gases, ensuring compliance with environmental regulations and standards.
- Sustainable Materials and Practices:
- Material Selection: Choosing sustainable materials, such as recycled metals, low-carbon alloys, or eco-friendly coatings, promotes environmental stewardship and reduces the ecological footprint of tube bending operations. Utilizing materials with eco-label certifications or compliance with environmental standards demonstrates a commitment to sustainability.
- Life Cycle Assessment (LCA): Conducting life cycle assessments evaluates the environmental impacts of tube bending processes from raw material extraction to end-of-life disposal. LCA helps identify opportunities for improvement, prioritize sustainable practices, and make informed decisions to minimize environmental impacts throughout the product life cycle.
- Regulatory Compliance and Certification:
- Environmental Regulations: Understanding and complying with applicable environmental regulations, permits, and standards ensures legal compliance and minimizes the risk of fines, penalties, or regulatory sanctions. Staying informed about evolving regulations and implementing proactive measures to address environmental concerns demonstrates corporate responsibility and fosters public trust.
- Environmental Management Systems (EMS): Implementing environmental management systems, such as ISO 14001 certification, establishes a framework for continuous improvement, risk mitigation, and environmental performance monitoring. EMS frameworks help organizations identify, assess, and manage environmental aspects and impacts associated with tube bending operations.
In conclusion, integrating environmental considerations into tube bending operations promotes sustainability, resource conservation, and responsible manufacturing practices. By adopting energy-efficient technologies, minimizing waste generation, controlling emissions, utilizing sustainable materials, and ensuring regulatory compliance, manufacturers can mitigate environmental impacts, reduce operational costs, and enhance their reputation as environmentally responsible organizations.
Tube Bending Machine: Safety Protocols and Risk Management
Safety protocols and risk management are paramount in tube bending operations to protect workers, prevent accidents, and ensure compliance with regulatory standards. Implementing comprehensive safety measures and fostering a culture of safety awareness contribute to a safe working environment and minimize the risk of injuries or incidents. Here’s an overview of safety protocols, risk assessment techniques, and best practices for tube bending machine operations:
- Machine Safety Features:
- Guarding and Enclosures: Installing machine guards, enclosures, and barriers around hazardous areas, such as bending zones, pinch points, and moving components, prevents accidental contact and reduces the risk of injuries.
- Emergency Stop Controls: Equipping tube bending machines with emergency stop buttons or switches enables operators to quickly halt machine operations in case of emergencies, entrapments, or unsafe conditions.
- Interlocks and Safety Sensors: Incorporating interlock systems, light curtains, safety mats, or presence sensors prevents machine activation when safety gates are open or when operators are in close proximity to hazardous areas, enhancing operator safety.
- Safe Start-up and Shutdown Procedures: Establishing standardized procedures for machine start-up, shutdown, and maintenance activities ensures that operators follow safe practices and adhere to safety protocols to minimize risks during machine operation.
- Operator Training and Certification:
- Safety Training Programs: Providing comprehensive safety training programs for operators, technicians, and maintenance personnel familiarizes them with machine operation procedures, hazard recognition, emergency response protocols, and personal protective equipment (PPE) requirements.
- Certification Requirements: Requiring operators to undergo certification or competency assessments verifies their proficiency in operating tube bending machines safely and ensures compliance with regulatory standards and industry best practices.
- Risk Assessment and Hazard Identification:
- Job Hazard Analysis (JHA): Conducting job hazard analyses evaluates potential hazards, risks, and exposure scenarios associated with specific tube bending tasks or work environments. JHA identifies preventive measures, controls, and safeguards to mitigate risks and prevent accidents.
- Safety Inspections: Regular inspections of tube bending machines, tooling, workstations, and workplace conditions identify safety deficiencies, equipment malfunctions, or ergonomic issues that may pose risks to operators. Prompt corrective actions address identified hazards and prevent accidents.
- Personal Protective Equipment (PPE):
- PPE Selection: Providing appropriate personal protective equipment, such as safety glasses, hearing protection, gloves, and protective clothing, protects operators from physical hazards, flying debris, noise, and chemical exposures encountered during tube bending operations.
- Fit and Comfort: Ensuring proper fit, comfort, and suitability of PPE encourages compliance and minimizes discomfort or distractions that may compromise operator safety and performance.
- Safety Culture and Continuous Improvement:
- Leadership Commitment: Demonstrating leadership commitment to safety, establishing clear safety policies, and fostering a culture of accountability and responsibility for safety at all levels of the organization promote employee engagement and ownership of safety initiatives.
- Employee Involvement: Involving employees in safety committees, hazard reporting systems, and safety improvement initiatives empowers them to contribute ideas, identify hazards, and participate in decision-making processes to enhance workplace safety.
- Incident Investigation and Analysis: Conducting thorough investigations of near misses, accidents, or incidents identifies root causes, systemic issues, and corrective actions to prevent recurrence and improve safety performance over time.
In conclusion, prioritizing safety protocols, risk management, and employee engagement in tube bending operations promotes a safe working environment, protects workers from hazards, and ensures compliance with regulatory requirements. By implementing comprehensive safety measures, providing adequate training and resources, and fostering a culture of continuous improvement, manufacturers can mitigate risks, prevent accidents, and safeguard the well-being of their workforce.
Tube Bending Machine: Hydraulic System Components
The hydraulic system is a critical component of tube bending machines, providing the power and control necessary for bending operations. Understanding the key components of the hydraulic system is essential for optimizing machine performance, ensuring reliability, and minimizing downtime. Here’s an overview of the main hydraulic system components in tube bending machines:
- Hydraulic Pump:
- The hydraulic pump is the heart of the hydraulic system, responsible for generating hydraulic pressure to power the bending process.
- Types of hydraulic pumps include gear pumps, vane pumps, and piston pumps, each offering different flow rates, pressure capabilities, and efficiency levels.
- The pump draws hydraulic fluid from the reservoir and delivers it to the hydraulic circuit at the required pressure to actuate the bending cylinder or hydraulic actuators.
- Hydraulic Reservoir:
- The hydraulic reservoir, also known as the hydraulic tank, stores hydraulic fluid and ensures proper fluid level and temperature control.
- The reservoir typically contains baffles, filters, and breathers to prevent fluid contamination, entrapped air, and overheating.
- Proper reservoir design and maintenance are essential to ensure adequate fluid supply, minimize foaming, and prevent cavitation in the hydraulic system.
- Hydraulic Cylinder:
- The hydraulic cylinder converts hydraulic pressure into linear motion to actuate the bending mechanism, clamp mechanism, or mandrel in tube bending machines.
- Cylinder types include single-acting cylinders, double-acting cylinders, telescopic cylinders, and special-purpose cylinders, depending on the application requirements and bending forces.
- Hydraulic cylinders feature piston rods, cylinder barrels, seals, and mounting arrangements designed to withstand high pressures and provide precise control over bending forces and movements.
- Control Valves:
- Control valves regulate the flow and direction of hydraulic fluid in the hydraulic system, enabling precise control over bending speed, force, and direction.
- Types of hydraulic control valves include directional control valves, pressure control valves, flow control valves, and proportional control valves, each serving specific functions in the hydraulic circuit.
- Valves may be manually operated, electrically actuated, or controlled by hydraulic pilot circuits, depending on the desired level of automation and control complexity.
- Hydraulic Hoses and Fittings:
- Hydraulic hoses and fittings convey hydraulic fluid between hydraulic components, such as the pump, cylinder, valves, and reservoir.
- Hoses are constructed from durable materials, such as rubber or thermoplastic, and reinforced with layers of wire or textile braids to withstand high pressures and dynamic loads.
- Proper hose routing, sizing, and installation practices ensure hydraulic system integrity, prevent leaks, and maintain hydraulic fluid cleanliness and contamination control.
- Hydraulic Fluid:
- Hydraulic fluid serves as the working medium in the hydraulic system, transmitting power, lubricating components, and dissipating heat generated during operation.
- Common hydraulic fluid types include mineral oil-based fluids, synthetic fluids, and water-glycol solutions, each offering specific performance characteristics, viscosity grades, and temperature ranges.
- Hydraulic fluid properties, such as viscosity, viscosity index, oxidation stability, and additive composition, are critical factors influencing hydraulic system performance, efficiency, and longevity.
- Hydraulic Filtration System:
- The hydraulic filtration system removes contaminants, particulates, and impurities from the hydraulic fluid to maintain system cleanliness, prevent component wear, and ensure hydraulic system reliability.
- Filtration components include hydraulic filters, strainers, breathers, and contamination indicators, strategically located throughout the hydraulic circuit to trap and remove debris, dirt, and water from the fluid.
- Proper filtration and maintenance practices, such as regular filter replacement, fluid analysis, and cleanliness standards, are essential to extend hydraulic component life and prevent system failures.
- Hydraulic Control System:
- The hydraulic control system comprises control panels, hydraulic actuators, sensors, and feedback mechanisms that regulate and monitor hydraulic system operation.
- Advanced control systems may incorporate programmable logic controllers (PLCs), human-machine interfaces (HMIs), and closed-loop feedback control algorithms to automate bending processes, optimize performance, and ensure precision and repeatability.
- Hydraulic control systems may also feature safety interlocks, alarms, and diagnostic functions to detect faults, protect equipment, and alert operators to abnormal operating conditions.
In conclusion, understanding the key hydraulic system components in tube bending machines is essential for optimizing machine performance, ensuring reliability, and minimizing downtime. By selecting high-quality components, maintaining proper fluid cleanliness, and implementing effective control and maintenance practices, manufacturers can maximize the efficiency, accuracy, and longevity of their tube bending equipment while ensuring safe and reliable operation.
History of Press Brake Machines
The origins of metal bending can be traced back to ancient civilizations, where blacksmiths used rudimentary tools to shape metal. As technology progressed, so did the methods of metal bending, leading to the development of more sophisticated machinery.
The first press brake machines emerged during the Industrial Revolution, driven by the need for more efficient and precise metalworking tools. Early press brake machines were manually operated, requiring significant physical effort and skill from the operator. Despite their limitations, these machines marked a significant advancement in the field of metal fabrication.
The 20th century witnessed substantial improvements in press brake technology. The introduction of hydraulic systems in the 1940s allowed for greater force and control, enabling the bending of thicker and tougher metals. This innovation revolutionized the industry, making hydraulic press brake machines the standard for many years.
In recent decades, the advent of computer numerical control (CNC) technology has transformed press brake machines once again. CNC press brake machines offer unparalleled precision and automation, allowing for complex bending operations to be performed with minimal human intervention. These machines are equipped with advanced software that can program and execute intricate bending sequences, ensuring consistency and accuracy.
Today, press brake machines continue to evolve, incorporating cutting-edge technologies such as robotics and artificial intelligence. These advancements are paving the way for even greater efficiency, flexibility, and precision in metal fabrication.
Types of Press Brake Machines
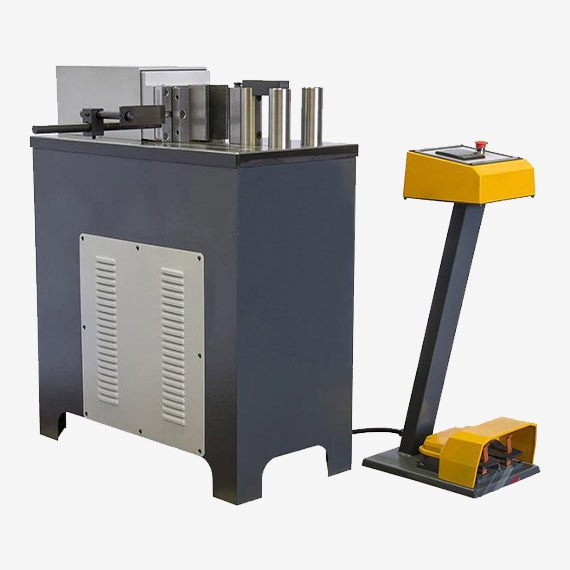
Press brake machines come in various types, each with its own features, advantages, and applications. Understanding the different types of press brake machines is essential for selecting the right equipment for specific metal bending tasks.
Manual Press Brake Machines
Features and Uses Manual press brake machines are the simplest type of press brakes, operated entirely by human effort. They are typically used for small-scale or low-volume production tasks, where high precision is not critical.
Advantages
- Cost-effective and affordable for small businesses
- Easy to operate and maintain
- Suitable for simple bending operations
Disadvantages
- Limited bending capacity and precision
- Labor-intensive and time-consuming
- Not suitable for high-volume production
Hydraulic Press Brake Machines
Features and Uses Hydraulic press brake machines use hydraulic fluid to generate the necessary force for bending metal sheets. They are widely used in various industries due to their versatility and reliability.
Advantages
- High bending capacity and precision
- Capable of handling thicker and tougher metals
- Smooth and consistent operation
Disadvantages
- Higher initial cost compared to manual machines
- Requires regular maintenance of hydraulic systems
- Potential for hydraulic fluid leaks
Electric Press Brake Machines
Features and Uses Electric press brake machines use electric motors to drive the bending process. They are known for their energy efficiency and precision.
Advantages
- Energy-efficient and environmentally friendly
- High precision and repeatability
- Lower operating costs compared to hydraulic machines
Disadvantages
- Limited force compared to hydraulic machines
- Higher initial cost than manual machines
- Requires skilled operators
CNC Press Brake Machines
Features and Uses CNC (Computer Numerical Control) press brake machines represent the pinnacle of press brake technology. They are equipped with advanced computer systems that control the bending process with exceptional precision.
Advantages
- Unmatched precision and accuracy
- Automated and programmable operations
- Suitable for complex and high-volume production
Disadvantages
- High initial cost and investment
- Requires skilled operators and programmers
- Complex maintenance and troubleshooting
Each type of press brake machine has its unique advantages and disadvantages, making it crucial to select the appropriate type based on specific production requirements and budget constraints.
Components of a Press Brake Machine
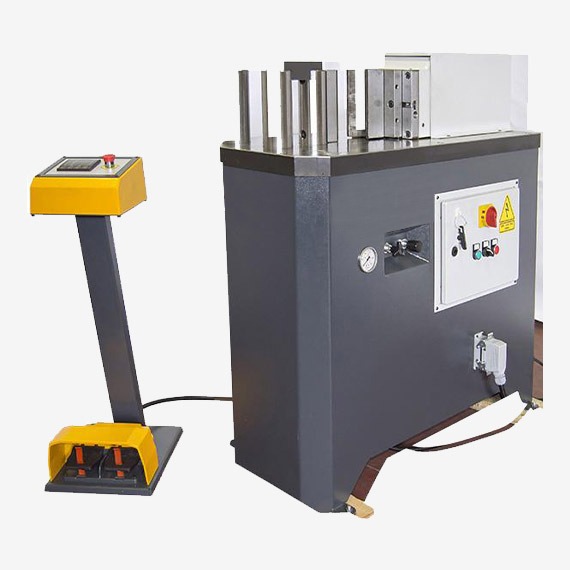
Press brake machines consist of several key components, each playing a vital role in the bending process. Understanding these components is essential for operating and maintaining the machine effectively.
Frame
The frame is the backbone of the press brake machine, providing structural support and stability. It is typically constructed from heavy-duty steel to withstand the forces exerted during the bending process.
Ram
The ram is a movable component that exerts force on the metal sheet, pressing it against the die to create the desired bend. The ram’s movement can be controlled manually, hydraulically, or electrically, depending on the type of press brake machine.
Die and Punch
The die and punch are the primary tools used in the bending process. The punch, attached to the ram, presses the metal sheet into the die, which is fixed to the machine’s bed. The shape and size of the die and punch determine the angle and radius of the bend.
Back Gauge
The back gauge is a positioning tool that helps in accurately aligning the metal sheet for bending. It ensures consistent bend angles and dimensions by providing a reference point for the sheet.
Control System
The control system manages the operation of the press brake machine. In manual machines, this may be a simple mechanical system, while hydraulic and electric machines use more advanced control systems. CNC press brake machines have sophisticated computer systems that program and control the entire bending process.
Safety Features
Press brake machines are equipped with various safety features to protect operators from accidents and injuries. These may include safety guards, emergency stop buttons, and light curtains that detect the presence of an operator’s hands near the bending area.
Working Principle
The basic working principle of a press brake machine involves applying a controlled force to bend metal sheets into specific shapes. Here are the key steps in the bending process:
- Sheet Positioning: The metal sheet is positioned on the machine’s bed, aligned against the back gauge to ensure precise placement.
- Tool Selection: The appropriate die and punch are selected based on the desired bend angle and radius. These tools are then installed on the machine.
- Bending Operation: The ram descends, pressing the punch into the metal sheet and forcing it into the die. This action creates the bend, with the angle and shape determined by the tools used and the force applied.
- Return Stroke: After the bend is completed, the ram ascends, releasing the pressure on the metal sheet. The sheet is then removed or repositioned for additional bends.
Precision and control are crucial in the bending process to ensure the accuracy and consistency of the bends. CNC press brake machines excel in this regard, as they use computer programming to control the ram’s movement and force, resulting in highly precise bends.
Applications of Press Brake Machines
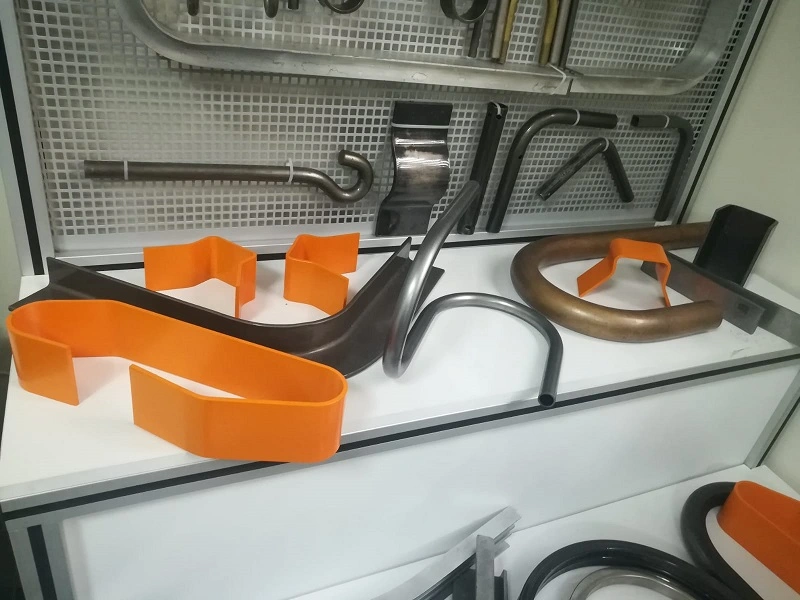
Press brake machines are used across various industries due to their versatility and precision. Here are some common applications:
- Automotive Industry: Manufacturing car body panels, chassis components, and brackets.
- Aerospace Industry: Producing aircraft parts, including wing components and fuselage sections.
- Construction Industry: Fabricating structural components, such as beams, columns, and brackets.
- Electronics Industry: Creating enclosures, chassis, and brackets for electronic devices.
- Furniture Industry: Making metal frames and components for furniture.
- HVAC Industry: Producing ductwork and ventilation components.
These machines are also used in creating custom metal parts and prototypes, showcasing their adaptability to various production needs.
Advantages of Using Press Brake Machines
Press brake machines offer several advantages that make them indispensable in metal fabrication:
- Precision and Accuracy: These machines can produce highly precise bends, ensuring that components meet exact specifications.
- Efficiency and Productivity: Press brake machines can perform complex bending operations quickly, increasing production efficiency.
- Versatility: They can handle a wide range of materials and thicknesses, making them suitable for various applications.
- Cost-effectiveness: By reducing material waste and increasing production speed, press brake machines can lower manufacturing costs.
Maintenance and Safety Tips
Proper maintenance and safety practices are essential for the efficient and safe operation of press brake machines. Here are some tips:
Routine Maintenance
- Regularly inspect the machine for wear and tear.
- Keep the machine clean and free from debris.
- Lubricate moving parts as recommended by the manufacturer.
- Check hydraulic fluid levels and replace as necessary.
Common Issues and Troubleshooting
- Misalignment of the die and punch: Adjust the alignment to ensure precise bends.
- Inconsistent bending angles: Check for wear on the tools and replace if needed.
- Hydraulic system leaks: Inspect seals and hoses, and replace any damaged components.
Safety Guidelines for Operators
- Always wear appropriate personal protective equipment (PPE).
- Ensure that safety guards and emergency stop buttons are in place and functional.
- Follow the manufacturer’s guidelines for safe operation.
- Undergo proper training before operating the machine.
Future Trends in Press Brake Technology
The future of press brake technology is shaped by advancements in automation, materials, and environmental considerations:
- Automation and Industry 4.0: The integration of robotics and IoT (Internet of Things) is enhancing the automation of press brake machines, leading to increased efficiency and reduced human intervention.
- Advanced Materials and Designs: The development of new materials and innovative designs is expanding the capabilities of press brake machines, allowing for more complex and precise bends.
- Environmental Considerations: Efforts to reduce energy consumption and minimize environmental impact are driving the adoption of electric press brake machines and other eco-friendly technologies.
Conclusion
Press brake machines are a cornerstone of modern metal fabrication, offering unmatched precision, efficiency, and versatility. From their historical evolution to the latest technological advancements, these machines continue to play a vital role in various industries.
Understanding the different types of press brake machines, their components, and working principles is essential for selecting the right equipment and maximizing its potential. By following proper maintenance and safety practices, operators can ensure the longevity and safe operation of these machines.
As we look to the future, advancements in automation, materials, and environmental sustainability will further enhance the capabilities of press brake machines, solidifying their place in the ever-evolving landscape of manufacturing.
Whether you are a seasoned professional or new to the field, this comprehensive guide provides valuable insights into the world of sheet metal bending press brake machines, highlighting their importance and potential in modern industry.
Components of a Press Brake Machine
Press brake machines consist of several key components, each playing a vital role in the bending process. Understanding these components is essential for operating and maintaining the machine effectively.
Frame
The frame is the backbone of the press brake machine, providing structural support and stability. Constructed from heavy-duty steel, the frame must be robust enough to withstand the significant forces exerted during the bending process. The frame’s design can vary depending on the machine type, but its primary function remains to ensure rigidity and durability.
Ram
The ram is a movable component that exerts force on the metal sheet, pressing it against the die to create the desired bend. The ram’s movement can be controlled manually, hydraulically, or electrically, depending on the type of press brake machine. In CNC press brakes, the ram’s motion is precisely controlled by computer programming, allowing for highly accurate and repeatable bends.
Die and Punch
The die and punch are the primary tools used in the bending process. The punch, attached to the ram, presses the metal sheet into the die, which is fixed to the machine’s bed. The shape and size of the die and punch determine the angle and radius of the bend. There are various types of dies and punches, each suited for different bending operations, such as V-dies, U-dies, and hemming dies.
Back Gauge
The back gauge is a positioning tool that helps in accurately aligning the metal sheet for bending. It ensures consistent bend angles and dimensions by providing a reference point for the sheet. Modern press brake machines often feature CNC-controlled back gauges, which can be programmed to automatically adjust positions for complex bending sequences, enhancing precision and efficiency.
Control System
The control system manages the operation of the press brake machine. In manual machines, this may be a simple mechanical system, while hydraulic and electric machines use more advanced control systems. CNC press brake machines have sophisticated computer systems that program and control the entire bending process. These systems can store multiple bending programs, allowing for quick setup and reduced downtime between jobs.
Safety Features
Press brake machines are equipped with various safety features to protect operators from accidents and injuries. These may include safety guards, emergency stop buttons, and light curtains that detect the presence of an operator’s hands near the bending area. Modern machines also incorporate safety sensors that halt the machine’s operation if a potential hazard is detected, ensuring a safer working environment.
Working Principle
https://www.youtube.com/embed/l8quDXXNNEg?feature=oembedWorking Principle
The basic working principle of a press brake machine involves applying a controlled force to bend metal sheets into specific shapes. Here are the key steps in the bending process:
- Sheet Positioning: The metal sheet is positioned on the machine’s bed, aligned against the back gauge to ensure precise placement. Proper alignment is crucial for achieving accurate and consistent bends.
- Tool Selection: The appropriate die and punch are selected based on the desired bend angle and radius. These tools are then installed on the machine. The selection of the correct tools is essential for achieving the desired bend geometry and avoiding damage to the metal sheet.
- Bending Operation: The ram descends, pressing the punch into the metal sheet and forcing it into the die. This action creates the bend, with the angle and shape determined by the tools used and the force applied. The bending process requires careful control of the ram’s speed and pressure to ensure precise and consistent results.
- Return Stroke: After the bend is completed, the ram ascends, releasing the pressure on the metal sheet. The sheet is then removed or repositioned for additional bends. In CNC press brakes, the return stroke and repositioning of the sheet can be automated, increasing efficiency and reducing operator fatigue.
Precision and control are crucial in the bending process to ensure the accuracy and consistency of the bends. CNC press brake machines excel in this regard, as they use computer programming to control the ram’s movement and force, resulting in highly precise bends. The ability to program complex bending sequences also allows for the efficient production of intricate parts with minimal manual intervention.
Applications of Press Brake Machines
https://www.youtube.com/embed/o1dG-pIFkTk?feature=oembedApplications of Press Brake Machines
Press brake machines are used across various industries due to their versatility and precision. Here are some common applications:
- Automotive Industry: Press brake machines are integral to manufacturing car body panels, chassis components, and brackets. These machines can produce complex shapes and bends required for modern vehicle designs, ensuring high precision and repeatability.
- Aerospace Industry: The aerospace industry demands high precision and stringent quality standards. Press brake machines are used to produce aircraft parts, including wing components and fuselage sections, where accuracy and consistency are paramount.
- Construction Industry: Press brake machines are utilized to fabricate structural components such as beams, columns, and brackets. These components must meet specific strength and dimensional requirements to ensure the safety and stability of buildings and other structures.
- Electronics Industry: In the electronics industry, press brake machines are used to create enclosures, chassis, and brackets for electronic devices. These components often require intricate bends and precise dimensions to accommodate various electronic components and assemblies.
- Furniture Industry: The furniture industry employs press brake machines to make metal frames and components for furniture. These machines enable the production of aesthetically pleasing and structurally sound furniture parts, such as legs, supports, and brackets.
- HVAC Industry: The HVAC industry uses press brake machines to produce ductwork and ventilation components. These machines can create complex bends and shapes needed for efficient air distribution and ventilation systems.
These machines are also used in creating custom metal parts and prototypes, showcasing their adaptability to various production needs. The ability to quickly and accurately produce custom components makes press brake machines valuable tools for manufacturers and fabricators across different industries.
Advantages of Using Press Brake Machines
Press brake machines offer several advantages that make them indispensable in metal fabrication:
- Precision and Accuracy: Press brake machines are designed to produce highly precise bends, ensuring that components meet exact specifications. CNC press brakes, in particular, offer unmatched precision and repeatability, allowing for the production of intricate and complex parts with tight tolerances.
- Efficiency and Productivity: These machines can perform complex bending operations quickly, increasing production efficiency. The automation capabilities of CNC press brakes reduce the need for manual intervention, leading to faster setup times and higher throughput.
- Versatility: Press brake machines can handle a wide range of materials and thicknesses, making them suitable for various applications. From thin aluminum sheets to thick steel plates, these machines can accommodate different bending requirements, providing flexibility in manufacturing processes.
- Cost-effectiveness: By reducing material waste and increasing production speed, press brake machines can lower manufacturing costs. The precision and efficiency of these machines minimize errors and rework, resulting in significant cost savings over time.
- Consistency: Press brake machines ensure consistent bend quality across multiple parts, which is essential for mass production. The ability to produce uniform parts enhances the overall quality and reliability of the final products.
- Customizability: Modern press brake machines, especially CNC models, offer high levels of customizability. Operators can program specific bending sequences and parameters, allowing for the production of custom parts tailored to unique design requirements.
- Reduced Labor Costs: Automation in CNC press brake machines reduces the need for skilled labor, lowering labor costs. These machines can operate with minimal supervision, enabling manufacturers to allocate human resources more efficiently.
- Enhanced Safety: Press brake machines are equipped with advanced safety features that protect operators from accidents and injuries. Safety guards, emergency stop buttons, and sensors contribute to a safer working environment, reducing the risk of workplace incidents.
These advantages highlight the critical role of press brake machines in modern metal fabrication, underscoring their value in achieving high-quality, efficient, and cost-effective manufacturing processes.
Maintenance and Safety Tips
Proper maintenance and safety practices are essential for the efficient and safe operation of press brake machines. Here are some tips:
Routine Maintenance
- Regular Inspection: Regularly inspect the machine for wear and tear. Check for any signs of damage or misalignment in the components, especially the die and punch.
- Cleaning: Keep the machine clean and free from debris. Accumulated dust and metal shavings can affect the machine’s performance and lead to premature wear.
- Lubrication: Lubricate moving parts as recommended by the manufacturer. Proper lubrication reduces friction and prevents wear, extending the machine’s lifespan.
- Hydraulic Fluid: Check hydraulic fluid levels and replace as necessary. Ensure that the hydraulic system is free from leaks and that the fluid is clean and at the proper level.
- Tool Maintenance: Inspect the die and punch for wear and replace them if needed. Sharp and well-maintained tools are crucial for achieving precise bends.
Common Issues and Troubleshooting
- Misalignment: Misalignment of the die and punch can result in inaccurate bends. Adjust the alignment to ensure precise bending operations.
- Inconsistent Bending Angles: Inconsistent bending angles may be due to worn tools or incorrect settings. Check the tools for wear and verify the machine’s settings.
- Hydraulic System Leaks: Hydraulic system leaks can affect the machine’s performance. Inspect seals and hoses regularly and replace any damaged components.
- Control System Errors: Errors in the control system, particularly in CNC machines, can disrupt operations. Ensure that the control system software is up-to-date and that any programming issues are addressed promptly.
Safety Guidelines for Operators
- Personal Protective Equipment (PPE): Always wear appropriate PPE, including safety glasses, gloves, and protective clothing, to prevent injuries.
- Safety Guards and Emergency Stops: Ensure that safety guards are in place and functional. Familiarize yourself with the location and operation of emergency stop buttons.
- Manufacturer Guidelines: Follow the manufacturer’s guidelines for safe operation. These guidelines provide crucial information on operating the machine safely and efficiently.
- Training: Undergo proper training before operating the machine. Training should cover machine operation, maintenance, and safety procedures.
- Awareness: Stay alert and aware of your surroundings while operating the machine. Avoid distractions and ensure that the work area is free from hazards.
By adhering to these maintenance and safety tips, operators can ensure the longevity, efficiency, and safe operation of press brake machines, minimizing downtime and reducing the risk of accidents.
Future Trends in Press Brake Technology
The future of press brake technology is shaped by advancements in automation, materials, and environmental considerations. Here are some key trends to watch:
Automation and Industry 4.0
The integration of robotics and the Internet of Things (IoT) is enhancing the automation of press brake machines. Industry 4.0 technologies enable machines to communicate and coordinate with each other, leading to increased efficiency and reduced human intervention. Automated press brake machines can perform complex bending operations with minimal oversight, improving productivity and precision.
Advanced Materials and Designs
The development of new materials and innovative designs is expanding the capabilities of press brake machines. Advanced materials, such as high-strength alloys and composites, require precise and powerful bending techniques. Modern press brake machines are being designed to handle these materials, enabling the production of more durable and lightweight components.
Environmental Considerations
Efforts to reduce energy consumption and minimize environmental impact are driving the adoption of electric press brake machines and other eco-friendly technologies. Electric press brakes are more energy-efficient than their hydraulic counterparts, producing less noise and requiring less maintenance. Additionally, manufacturers are exploring sustainable materials and processes to further reduce the environmental footprint of metal fabrication.
Smart Manufacturing
Smart manufacturing technologies, including artificial intelligence (AI) and machine learning, are being integrated into press brake machines. These technologies enable predictive maintenance, real-time monitoring, and adaptive control, enhancing machine performance and reducing downtime. AI-powered systems can optimize bending operations by analyzing data and making adjustments in real-time.
User-Friendly Interfaces
Future press brake machines are likely to feature more user-friendly interfaces, making them easier to operate and program. Touchscreen controls, intuitive software, and augmented reality (AR) training tools will simplify the operation of these machines, reducing the learning curve for operators.
These trends highlight the ongoing evolution of press brake technology, promising greater efficiency, precision, and sustainability in metal fabrication.
Conclusion
Press brake machines are a cornerstone of modern metal fabrication, offering unmatched precision, efficiency, and versatility. From their historical evolution to the latest technological advancements, these machines continue to play a vital role in various industries.
Understanding the different types of press brake machines, their components, and working principles is essential for selecting the right equipment and maximizing its potential. By following proper maintenance and safety practices, operators can ensure the longevity and safe operation of these machines.
As we look to the future, advancements in automation, materials, and environmental sustainability will further enhance the capabilities of press brake machines, solidifying their place in the ever-evolving landscape of manufacturing.
Whether you are a seasoned professional or new to the field, this comprehensive guide provides valuable insights into the world of sheet metal bending press brake machines, highlighting their importance and potential in modern industry.
Press brake machines will undoubtedly continue to evolve, driven by technological innovations and industry demands. Staying informed about these advancements and adopting best practices will enable manufacturers to leverage the full potential of press brake machines, ensuring continued success in their metal fabrication endeavors.
Overview of Bending and Press Machines in Industrial Applications
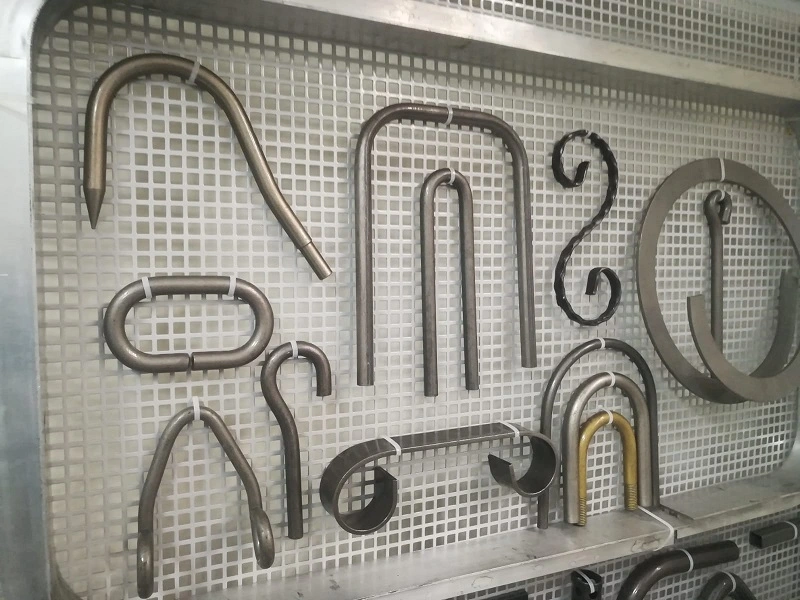
In the modern manufacturing and metalworking industries, bending and press machines are indispensable tools that shape, form, and modify metal and other materials with high precision. These machines are designed to handle various tasks, from simple bending operations to complex shaping processes, catering to a wide range of applications across multiple industries. The effectiveness and versatility of these machines make them critical in producing parts and components for automotive, aerospace, construction, and other heavy industries.
Bending and press machines are essential in transforming raw materials into finished products by applying force to alter the shape and properties of metals and other materials. The machines are designed to handle different materials, including steel, stainless steel (SS), aluminum, and more. These machines vary in size and capacity, from small, manual models used in workshops to large, automated systems in industrial manufacturing plants.
Types of Bending and Press Machines:
- Hydraulic Press Machines: Utilize hydraulic pressure to exert force, offering high precision and control in operations such as pressing, bending, and punching.
- Press Brake Machines: Specifically designed for bending sheet metal into various shapes by clamping the workpiece between a matching punch and die.
- Pipe Bending Machines: Used to bend pipes and tubes into desired angles and shapes, essential in plumbing, construction, and automotive industries.
- Sheet Metal Bending Machines: These machines focus on bending and shaping sheet metal, often used in fabrication shops and manufacturing lines.
Importance of Precision in Metalworking
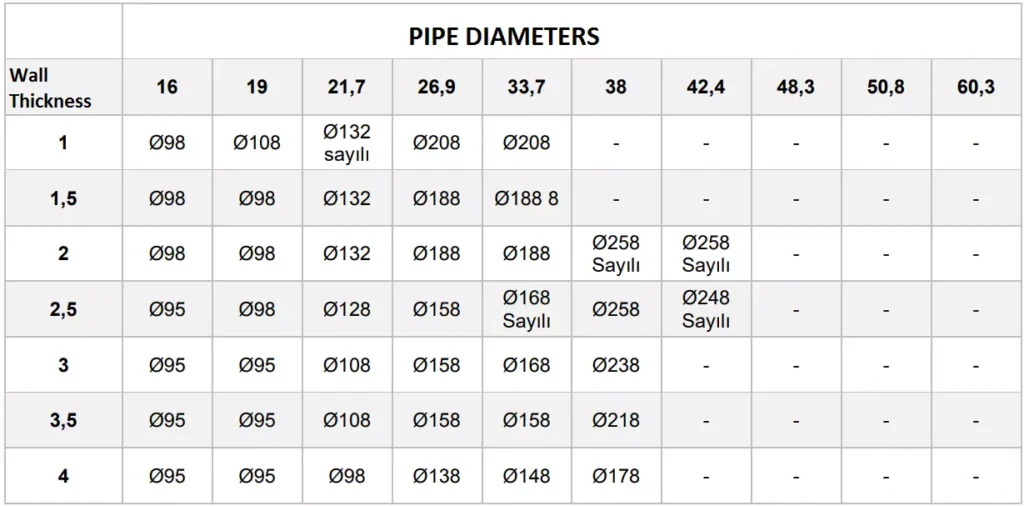
Precision is paramount in metalworking, as even minor deviations can lead to significant issues in the final product. Accurate bending and shaping are critical for ensuring that parts fit together correctly, maintain structural integrity, and meet the required specifications. The precision offered by modern bending and press machines allows manufacturers to produce complex components with tight tolerances, reducing the need for additional finishing processes and minimizing material waste.
Key Factors Influencing Precision:
- Machine Calibration: Proper calibration ensures the machine operates within the specified tolerances, providing consistent results.
- Tooling Quality: High-quality tools, such as dies and punches, are essential for achieving precise bends and shapes.
- Material Properties: Understanding the material’s properties, including its thickness, tensile strength, and ductility, is crucial for selecting the right machine settings.
- Operator Skill: Experienced operators can optimize machine settings and techniques to achieve the best results, even with challenging materials.
Overview of Bending and Press Machines
Bending and press machines are categorized based on their operating principles, applications, and the materials they handle. Below is a brief overview of some common types of bending and press machines:
1.3.1 Hydraulic Press Machines Hydraulic press machines operate by using a hydraulic cylinder to generate compressive force. They are highly versatile, allowing for various applications such as bending, forming, punching, and drawing. Hydraulic presses are known for their ability to exert high forces with great precision, making them ideal for heavy-duty applications. The introduction and working principles of hydraulic press machines will be discussed in more detail in the following sections.
1.3.2 Press Brake Machines Press brake machines are specialized machines used primarily for bending sheet metal. These machines utilize a combination of a punch and die to shape metal into specific angles and forms. Press brakes can be manual, hydraulic, or CNC-controlled, with each type offering different levels of automation and precision. The versatility of press brakes makes them a staple in metal fabrication shops.
1.3.3 Pipe Bending Machines Pipe bending machines are designed to bend pipes and tubes into various shapes and angles without compromising the material’s structural integrity. These machines are essential in industries such as plumbing, automotive, and construction, where precise pipe bends are required. Pipe bending machines can be hydraulic, pneumatic, mechanical, or electric, each offering different advantages depending on the application.
1.3.4 Sheet Metal Bending Machines Sheet metal bending machines focus on bending thin, flat sheets of metal into specific shapes. These machines are commonly used in the automotive and aerospace industries, where precision is critical. The machines can be manually operated, hydraulic, or CNC-controlled, offering various levels of control and automation.
Key Terminology and Concepts
Understanding the key terminology and concepts related to bending and press machines is essential for selecting the right equipment and optimizing its use. Below are some important terms that will be used throughout this document:
- Tonnage: The amount of force a machine can exert, usually measured in tons. For example, a 100-ton hydraulic press can exert 100 tons of force.
- Punch and Die: The tools used in press brake machines to shape metal. The punch presses into the die, which holds the workpiece.
- CNC (Computer Numerical Control): A method of automating machine tools using computers to control their movement and operation.
- Bend Radius: The radius of the inside curve of a bent section of metal. The bend radius is critical in determining the integrity and appearance of the bend.
- Ductility: The ability of a material to undergo deformation without breaking. Ductility is an important factor in bending operations.
Applications of Bending and Press Machines
Bending and press machines are used in a wide range of applications, from simple bending tasks to complex forming and shaping operations. Some common applications include:
- Automotive Industry: Producing car body parts, exhaust systems, and chassis components.
- Aerospace Industry: Manufacturing aircraft components, including fuselage panels and structural supports.
- Construction: Fabricating steel beams, columns, and other structural elements.
- Plumbing and HVAC: Bending pipes and tubes for plumbing, heating, and ventilation systems.
- Heavy Machinery: Forming and shaping parts for heavy equipment, such as cranes and bulldozers.
These applications highlight the versatility and importance of bending and press machines in modern manufacturing. The following sections will delve deeper into specific types of machines, their working principles, and the factors to consider when choosing the right equipment for your needs.
Hydraulic Press Machines: An Overview
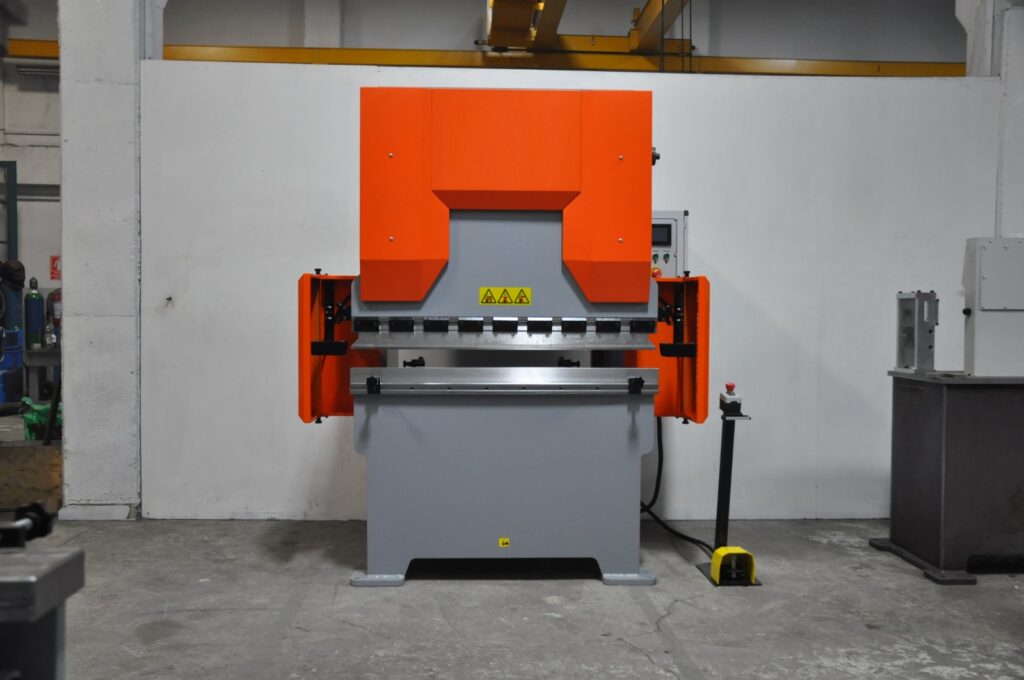
Hydraulic press machines are a cornerstone of modern manufacturing, offering unmatched power and precision in shaping, molding, and forming materials. These machines harness the power of hydraulics—a technology that uses fluid pressure to generate force—enabling them to perform tasks that require significant force with high accuracy. In this section, we will explore the fundamentals of hydraulic press machines, their working principles, various types, and key specifications that are critical for their selection and application in different industries.
2.1 Hydraulic Press Machine Introduction
Hydraulic press machines are used in a variety of industries for tasks that require compressive force. The concept behind hydraulic presses is based on Pascal’s law, which states that when pressure is applied to a confined fluid, the pressure is transmitted equally in all directions. This principle allows hydraulic presses to generate enormous amounts of force with relatively little input, making them highly efficient for industrial applications.
Key Characteristics:
- High Force Generation: Hydraulic presses can generate forces ranging from a few tons to several thousand tons, depending on the machine’s design and application.
- Versatility: These machines can perform a wide range of operations, including forging, stamping, bending, punching, and drawing.
- Precision: Hydraulic presses offer precise control over the applied force and movement, which is essential for tasks that require high accuracy.
- Customizability: Hydraulic presses can be customized with different types of tooling, making them adaptable to various tasks.
Hydraulic press machines are widely used in industries such as automotive manufacturing, aerospace, construction, and heavy machinery production. Their ability to handle large-scale operations with precision makes them a valuable asset in any industrial setting.
2.2 Hydraulic Press Machine Working Principles
The working of a hydraulic press machine is based on the simple but powerful principle of fluid mechanics. The machine typically consists of two cylinders: a smaller cylinder (called the slave cylinder) and a larger cylinder (called the master cylinder). These cylinders are connected by a pipe filled with hydraulic fluid, usually oil.
Working Process:
- Applying Force: When force is applied to the smaller cylinder (using a lever or a motor), it creates pressure in the hydraulic fluid.
- Pressure Transmission: According to Pascal’s law, the pressure in the fluid is transmitted equally throughout the system, causing the larger cylinder to move.
- Force Amplification: Because the larger cylinder has a greater surface area, the force exerted by it is much greater than the force applied to the smaller cylinder. This allows the machine to perform tasks that require significant force, such as pressing or bending metal.
Control Mechanisms:
- Pressure Control Valves: These valves regulate the amount of pressure applied to the hydraulic fluid, allowing the operator to control the force exerted by the machine.
- Flow Control Valves: These valves control the speed of the hydraulic fluid, which in turn controls the speed of the machine’s movement.
- Directional Control Valves: These valves direct the flow of hydraulic fluid to different parts of the system, enabling the machine to perform various operations.
Hydraulic press machines can be operated manually, semi-automatically, or fully automatically, depending on the level of control and automation required. Modern hydraulic presses often incorporate computerized control systems (CNC) for enhanced precision and efficiency.
2.3 Hydraulic Press Specifications
When selecting a hydraulic press machine, understanding its specifications is crucial to ensure that it meets the requirements of the intended application. Key specifications include:
2.3.1 Tonnage (Force Capacity)
- Definition: Tonnage refers to the maximum force that the hydraulic press can exert, usually measured in tons.
- Importance: The tonnage requirement depends on the material being processed and the operation being performed. For example, a higher tonnage is needed for tasks such as forging thick metal parts compared to bending thin sheets.
- Examples: A 100-ton hydraulic press is commonly used in medium-scale operations, while a 1000-ton hydraulic press is suitable for large-scale industrial applications.
2.3.2 Stroke Length
- Definition: Stroke length is the distance the press ram (the moving part of the machine that exerts force) can travel in one cycle.
- Importance: The stroke length determines the depth to which the material can be compressed or formed. It is particularly important in operations like deep drawing or molding.
- Adjustability: Many hydraulic presses allow the stroke length to be adjusted according to the specific requirements of the operation.
2.3.3 Bed Size
- Definition: The bed size is the working surface area of the press where the material is placed.
- Importance: The bed size must accommodate the dimensions of the workpiece being processed. A larger bed size is required for bigger workpieces.
- Customization: Some hydraulic presses offer interchangeable beds to handle different workpiece sizes.
2.3.4 Ram Speed
- Definition: Ram speed refers to the speed at which the press ram moves during operation.
- Importance: The speed of the ram can affect the quality of the operation. For example, slower speeds may be needed for precision tasks, while faster speeds are suitable for high-volume production.
- Control: Hydraulic presses often have adjustable ram speeds to suit different tasks.
2.3.5 Hydraulic System Pressure
- Definition: This is the pressure at which the hydraulic fluid operates within the system, usually measured in pounds per square inch (PSI) or bar.
- Importance: Higher system pressure allows for greater force generation but also requires more robust components to handle the increased stress.
- Safety: Hydraulic presses are equipped with safety mechanisms to prevent over-pressurization, which could lead to system failure.
2.4 100 Ton Hydraulic Press Specifications
A 100-ton hydraulic press is a versatile and commonly used machine in many industries, capable of handling a wide range of tasks from bending and forming to punching and drawing.
Key Specifications of a 100 Ton Hydraulic Press:
- Tonnage: 100 tons of maximum force, suitable for medium to large-scale operations.
- Stroke Length: Typically around 8 to 12 inches, with adjustability for different tasks.
- Bed Size: A standard bed size might be around 36 x 24 inches, but this can vary depending on the manufacturer.
- Ram Speed: Variable, often ranging from 10 to 30 mm/s, depending on the operation.
- System Pressure: Generally operates at around 3000 PSI, providing the necessary force without compromising safety.
Applications:
- Automotive Manufacturing: Used for pressing, forming, and shaping automotive parts.
- Metal Fabrication: Ideal for bending and shaping metal components in medium-scale production.
- Construction Equipment Manufacturing: Useful in the production of parts for heavy machinery and construction tools.
2.5 1000 Ton Hydraulic Press
The 1000-ton hydraulic press represents a significant leap in force capacity, making it suitable for the most demanding industrial applications. These machines are typically used in heavy industries where large-scale and high-force operations are required.
Key Specifications of a 1000 Ton Hydraulic Press:
- Tonnage: 1000 tons of maximum force, designed for heavy-duty tasks.
- Stroke Length: Can range from 12 to 24 inches, depending on the specific model and application.
- Bed Size: Large beds, often exceeding 72 x 48 inches, to accommodate massive workpieces.
- Ram Speed: Slower speeds, typically around 5 to 15 mm/s, due to the immense force being applied.
- System Pressure: Operates at high pressures, usually around 5000 PSI, to deliver the required force.
Applications:
- Shipbuilding: Used in the production of large metal components for ships and submarines.
- Aerospace: Essential for forming and shaping large aircraft components.
- Heavy Machinery Production: Involved in the manufacturing of parts for mining equipment, cranes, and other heavy-duty machinery.
2.6 Horizontal Hydraulic Press Machine
Horizontal hydraulic press machines differ from the more common vertical models in that the ram moves horizontally rather than vertically. This configuration is particularly useful for specific applications such as bending long pieces of metal or pressing components that are difficult to position vertically.
Advantages of Horizontal Hydraulic Press Machines:
- Versatility: Can handle a variety of tasks including bending, pressing, and straightening long workpieces.
- Ease of Operation: Easier to load and position large or awkwardly shaped workpieces.
- Space Efficiency: Horizontal presses can be more space-efficient in certain workshop layouts.
Applications:
- Railway Manufacturing: Used for bending and forming long steel rails.
- Pipeline Construction: Ideal for bending and forming large pipes used in oil, gas, and water pipelines.
- Structural Engineering: Employed in the production of long beams and structural components.
2.7 Small Horizontal Hydraulic Press
Small horizontal hydraulic presses are designed for applications that require less force and smaller workpieces. These machines are commonly used in workshops and smaller manufacturing facilities where space and budget constraints are factors.
Key Features:
- Compact Design: Takes up less space, making it ideal for small workshops.
- Lower Tonnage: Typically ranges from 10 to 50 tons, suitable for light to medium tasks.
- Ease of Use: Simple controls and operation, often with manual or semi-automatic settings.
Applications:
- Automotive Repair Shops: Used for pressing and straightening components like axles and shafts.
- Small Fabrication Shops: Ideal for bending and forming smaller metal parts.
- Maintenance Operations: Useful in on-site repairs and maintenance tasks where portability is required.
3. Press Brake Machines and Bending Applications
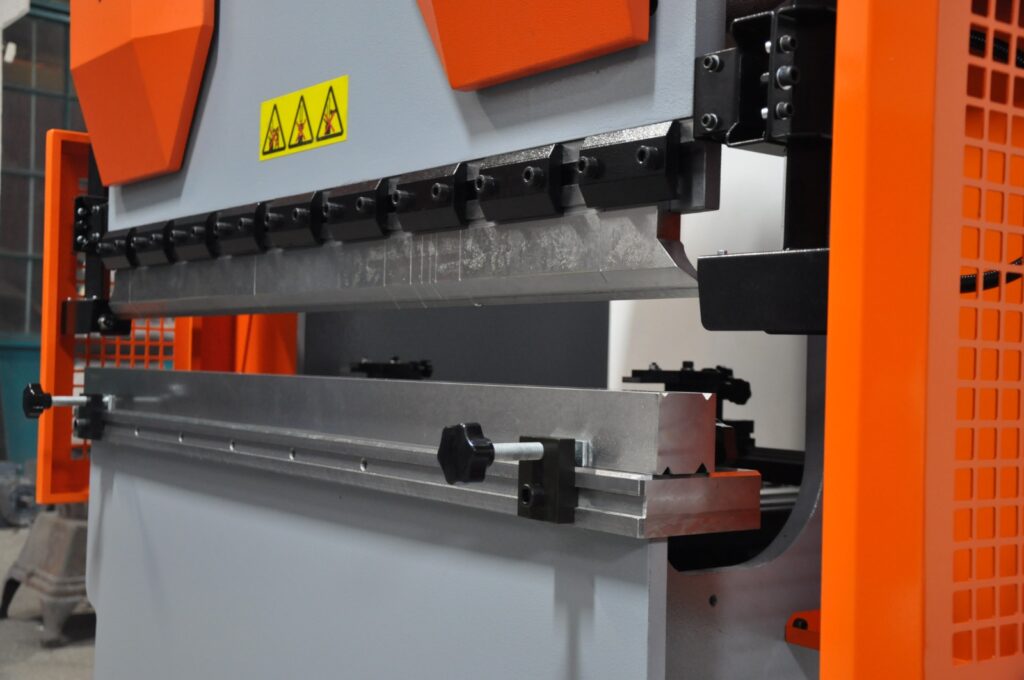
Press brake machines play a pivotal role in the metal fabrication industry, offering the precision and versatility required to transform flat metal sheets into complex shapes and structures. These machines are specifically designed for bending operations, making them indispensable in various manufacturing processes. This section delves into the functionality and applications of press brake machines, explores different bending techniques, and highlights the nuances of hydraulic press bending machines, including those tailored for sheet metal applications.
3.1 Press Brake Machine: Functionality and Applications
A press brake machine is a specialized tool used to bend and shape metal sheets and plates with high accuracy. Unlike general-purpose press machines, press brakes are specifically engineered to perform bending operations, making them essential in industries such as automotive, aerospace, construction, and manufacturing.
Key Functionalities:
- Bending: The primary function of a press brake is to bend metal sheets along a straight axis. This is achieved by clamping the metal between a punch and a die and applying force to create the desired angle.
- Forming: Beyond simple bends, press brakes can form complex shapes by combining multiple bending operations. This allows for the creation of intricate components required in various applications.
- Precision Cutting: Some advanced press brakes are equipped with features that allow for precise cutting or shearing of metal sheets during the bending process.
Applications:
- Automotive Industry: Manufacturing car body panels, chassis components, and exhaust systems.
- Aerospace Industry: Producing aircraft components, including fuselage sections and structural supports.
- Construction: Fabricating steel beams, columns, and other structural elements for buildings and infrastructure projects.
- Electronics: Creating enclosures and frames for electronic devices and appliances.
- Furniture Manufacturing: Designing and producing metal frames and supports for furniture pieces.
3.2 Press Brake Bending: Techniques and Precision
Bending is a fundamental operation in metalworking, and press brakes offer the precision and control necessary to achieve consistent and accurate results. Various bending techniques can be employed depending on the material, thickness, and desired outcome.
Bending Techniques:
- Air Bending: In this method, the punch presses the metal into the die without fully contacting it. This allows for greater flexibility in adjusting the bend angle and reduces stress on the material. Air bending is suitable for applications requiring variable angles and is widely used in sheet metal fabrication.Advantages:
- Versatility in bend angles.
- Reduced tooling wear.
- Lower force requirements compared to bottom bending.
- Bottom Bending (V-Die Bending): Here, the punch presses the metal all the way into the die, resulting in a more precise bend angle. This technique is ideal for applications where high accuracy and consistency are paramount.Advantages:
- Higher precision in bend angles.
- Better repeatability for mass production.
- Suitable for thicker materials.
- Coining: A specialized form of bottom bending where the metal is pressed into a highly precise shape within the die. Coining is used for intricate bends and is often employed in applications requiring fine details and superior surface finishes.
Precision Considerations:
- Tooling Quality: High-quality punches and dies are essential for achieving precise bends. The condition of the tooling directly impacts the accuracy and consistency of the bending process.
- Machine Calibration: Regular calibration ensures that the press brake operates within the specified tolerances, maintaining the precision of each bend.
- Material Properties: Understanding the ductility, tensile strength, and thickness of the material is crucial for selecting the appropriate bending parameters and avoiding defects such as cracking or warping.
- Operator Skill: Skilled operators can optimize machine settings and bending techniques to achieve the desired precision, especially when working with challenging materials or complex shapes.
3.3 Bend Press Machine: Overview
Bend press machines, often referred to interchangeably with press brake machines, are designed specifically for bending operations in metal fabrication. These machines vary in size, capacity, and control mechanisms, allowing them to cater to a wide range of applications from small workshops to large industrial facilities.
Types of Bend Press Machines:
- Manual Bend Press Machines: These are operated manually by the user, typically using a lever or hydraulic pump to apply force. They are suitable for small-scale operations and simple bending tasks.Advantages:
- Lower cost.
- Simplicity and ease of use.
- Ideal for light-duty applications.
- Hydraulic Bend Press Machines: Utilize hydraulic systems to apply force, offering greater control and higher tonnage capabilities compared to manual machines. They are widely used in medium to large-scale operations.Advantages:
- Higher force generation.
- Precise control over bending parameters.
- Suitable for a variety of materials and thicknesses.
- CNC Bend Press Machines: Equipped with computer numerical control (CNC) systems, these machines offer automated and programmable bending operations. They are ideal for high-precision and high-volume production environments.Advantages:
- Enhanced precision and repeatability.
- Ability to handle complex and intricate bends.
- Increased efficiency and reduced manual intervention.
Key Features:
- Adjustable Backgauges: Allow operators to set the precise location of the bend, ensuring consistency across multiple bends.
- Multiple Axes Control: Enables the machine to perform bends at various angles and positions without manual adjustments.
- Safety Features: Includes guards, emergency stop buttons, and sensors to ensure safe operation and protect operators from potential hazards.
3.4 Hydraulic Press Bending Machine
Hydraulic press bending machines combine the force-generating capabilities of hydraulic systems with the precision of press brakes to perform bending operations with high efficiency and accuracy. These machines are essential in applications where consistent and reliable bends are required, especially in medium to high-volume production settings.
Working Principles: Hydraulic press bending machines operate by using a hydraulic cylinder to exert force on the punch, which in turn bends the metal sheet against the die. The hydraulic system allows for smooth and controlled application of force, enabling precise bending angles and consistent results.
Advantages:
- High Force Capacity: Capable of handling thick and strong materials that require significant force to bend.
- Precision Control: Hydraulic systems offer fine control over the bending process, allowing for accurate and repeatable bends.
- Versatility: Suitable for a wide range of materials, including steel, aluminum, and stainless steel, making them adaptable to various industrial applications.
Applications:
- Automotive Manufacturing: Bending automotive body panels and structural components with high precision.
- Aerospace Industry: Forming aircraft parts that require exacting specifications and tight tolerances.
- Construction: Creating structural steel components for buildings and infrastructure projects.
- Heavy Machinery Production: Fabricating parts for construction equipment, mining machinery, and industrial tools.
3.5 Hydraulic Sheet Metal Bending Machine
Hydraulic sheet metal bending machines are specialized press brakes designed to handle the specific challenges associated with bending thin metal sheets. These machines leverage hydraulic systems to provide the necessary force and control for precise sheet metal fabrication.
Key Features:
- Enhanced Precision: Hydraulic systems ensure that each bend is executed with high accuracy, minimizing deviations and maintaining consistency.
- Adjustable Clamping Force: Allows for the secure holding of thin sheets without causing deformation or damage during the bending process.
- Integrated Control Systems: Modern hydraulic sheet metal bending machines often feature computerized controls for automated bending sequences, reducing manual intervention and increasing efficiency.
Benefits:
- Reduced Material Waste: Precise bending reduces the likelihood of errors and rework, leading to less material wastage and lower production costs.
- Increased Productivity: Automated and semi-automated systems enable faster production rates, meeting the demands of high-volume manufacturing.
- Versatility: Capable of handling a variety of sheet metal thicknesses and materials, making them suitable for diverse applications.
Applications:
- Appliance Manufacturing: Producing metal housings and components for household appliances such as refrigerators, washing machines, and ovens.
- Electronics Enclosures: Creating precise and compact metal enclosures for electronic devices and equipment.
- Furniture Manufacturing: Bending metal sheets for modern and ergonomic furniture designs.
- Signage and Displays: Forming metal panels used in signage, displays, and advertising materials.
3.6 Integration of CNC Technology in Press Brake Machines
The integration of Computer Numerical Control (CNC) technology into press brake machines has revolutionized the bending process, enhancing precision, efficiency, and flexibility. CNC press brakes are programmed with specific bending sequences, allowing for automated and repeatable operations that meet the stringent demands of modern manufacturing.
Advantages of CNC Press Brake Machines:
- Automation: Reduces the need for manual adjustments, minimizing human error and increasing production speed.
- Programmability: Allows for the storage and execution of complex bending programs, enabling the production of intricate shapes and multiple bends in a single setup.
- Consistency: Ensures that each bend is executed with the same precision, maintaining quality across large production runs.
- Ease of Use: User-friendly interfaces and software enable operators to input and modify bending programs with minimal training.
Applications:
- High-Precision Industries: Essential in industries such as aerospace and medical device manufacturing, where exacting standards must be met.
- Mass Production: Ideal for large-scale manufacturing where consistency and speed are critical.
- Customization: Facilitates the production of customized parts and components without significant downtime for setup changes.
3.7 Challenges and Considerations in Press Brake Bending
While press brake machines offer significant advantages in metal bending operations, several challenges and considerations must be addressed to ensure optimal performance and longevity of the equipment.
Common Challenges:
- Material Springback: After bending, materials tend to return partially to their original shape, known as springback. Proper compensation techniques and machine settings are required to achieve the desired final angle.
- Tooling Wear: Frequent bending operations can lead to wear and tear of punches and dies, affecting the quality of bends. Regular maintenance and timely replacement of tooling are essential.
- Setup Time: Adjusting machine settings and tooling for different bending tasks can be time-consuming, impacting overall productivity. CNC press brakes help mitigate this by enabling quick program changes.
- Operator Training: Skilled operators are necessary to manage machine settings, troubleshoot issues, and ensure consistent quality. Investing in training programs can enhance operational efficiency.
Key Considerations:
- Machine Selection: Choosing the right press brake machine involves assessing factors such as tonnage capacity, stroke length, bed size, and control systems based on the specific application requirements.
- Tooling Quality: High-quality punches and dies are crucial for achieving precise and consistent bends. Investing in durable tooling can reduce maintenance costs and improve overall performance.
- Maintenance Practices: Regular maintenance, including lubrication, inspection, and calibration, ensures that the press brake operates efficiently and extends its operational lifespan.
- Safety Measures: Implementing safety protocols, such as using protective guards and emergency stop mechanisms, protects operators and prevents accidents in the workplace.
3.8 Innovations in Press Brake Technology
Advancements in press brake technology continue to enhance the capabilities and efficiency of bending operations. Innovations such as servo-electric systems, advanced control software, and enhanced automation features are driving the evolution of press brake machines.
Servo-Electric Press Brakes: Servo-electric press brakes use electric motors to control the movement of the ram, offering precise positioning and energy-efficient operation. These machines provide faster cycle times and reduced maintenance compared to traditional hydraulic systems.
Advanced Control Software: Modern press brake machines are equipped with sophisticated software that enables real-time monitoring, automatic adjustments, and predictive maintenance. Features like automatic backgauges, bend allowance calculations, and integrated CAD/CAM systems streamline the bending process and improve accuracy.
Enhanced Automation: Automation features, including robotic loading and unloading, automated tool changes, and integrated quality control systems, increase productivity and reduce manual labor. These advancements are particularly beneficial in high-volume production environments where efficiency and consistency are paramount.
Sustainability Initiatives: Manufacturers are increasingly focusing on energy-efficient press brake machines that reduce power consumption and minimize environmental impact. Innovations such as regenerative braking systems and energy recovery mechanisms contribute to more sustainable manufacturing practices.
3.9 Case Studies: Press Brake Machines in Action
Automotive Manufacturing: In the automotive industry, press brake machines are used to fabricate various components such as door panels, chassis parts, and engine components. The precision offered by CNC press brakes ensures that each part meets the stringent quality standards required for vehicle assembly. For example, a major automotive manufacturer utilizes a fleet of 100-ton hydraulic press brakes to produce consistent and high-quality body panels, reducing production time and minimizing material waste.
Aerospace Industry: Aerospace manufacturers rely on hydraulic sheet metal bending machines to produce aircraft components with exacting specifications. The high precision and repeatability of CNC press brakes enable the production of complex parts such as fuselage sections and wing components. By integrating advanced control systems, aerospace companies can achieve the necessary tolerances and maintain the integrity of critical components.
Construction Sector: In the construction industry, press brake machines are used to fabricate structural steel elements like beams, columns, and trusses. Hydraulic press brakes with large bed sizes and high tonnage capacities are essential for handling the thick and heavy materials used in construction projects. For instance, a construction equipment manufacturer employs 1000-ton hydraulic press brakes to produce large steel beams, ensuring structural integrity and compliance with safety standards.
Electronics Manufacturing: Electronics manufacturers use small hydraulic sheet metal bending machines to create precise enclosures and frames for devices such as smartphones, laptops, and medical equipment. The ability to perform intricate bends with high accuracy ensures that the final products meet design specifications and fit seamlessly with other components.
3.10 Best Practices for Operating Press Brake Machines
To maximize the efficiency and lifespan of press brake machines, adhering to best practices is essential. These practices encompass proper machine setup, maintenance, and operational techniques that ensure consistent quality and safety.
Machine Setup:
- Accurate Alignment: Ensure that the punch and die are properly aligned to prevent uneven bends and reduce tooling wear.
- Proper Tooling Selection: Choose the appropriate punches and dies based on the material type, thickness, and desired bend angle.
- Parameter Optimization: Set the correct bending force, ram speed, and stroke length according to the material properties and bending requirements.
Maintenance:
- Regular Inspections: Conduct routine inspections of hydraulic systems, electrical components, and mechanical parts to identify and address potential issues early.
- Lubrication: Keep moving parts well-lubricated to reduce friction and prevent wear.
- Tooling Maintenance: Clean and maintain punches and dies to ensure optimal performance and extend their lifespan.
Operational Techniques:
- Consistent Feeding: Ensure that metal sheets are fed consistently into the press brake to maintain uniform bends.
- Monitoring and Adjustment: Continuously monitor the bending process and make necessary adjustments to maintain precision.
- Safety Protocols: Implement and enforce safety protocols, including the use of personal protective equipment (PPE) and adherence to operational guidelines.
Training and Education:
- Operator Training: Provide comprehensive training for operators to ensure they understand machine operation, safety procedures, and maintenance practices.
- Continuous Improvement: Encourage operators to stay updated with the latest techniques and technologies in press brake operations through ongoing education and training programs.
3.11 Conclusion
Press brake machines are integral to the metal fabrication industry, offering the precision and versatility required to produce a wide range of components and structures. Understanding the functionality, bending techniques, and specific applications of different press brake machines, including hydraulic and CNC models, is essential for optimizing their use in various industrial settings. By adhering to best practices and leveraging advancements in press brake technology, manufacturers can achieve high-quality results, enhance productivity, and maintain a competitive edge in the market.
In the following sections, we will explore other specialized bending machines, including pipe bending machines and sheet metal bending machines, to provide a comprehensive overview of the tools available for metal shaping and forming operations.
Pipe Bending Machines
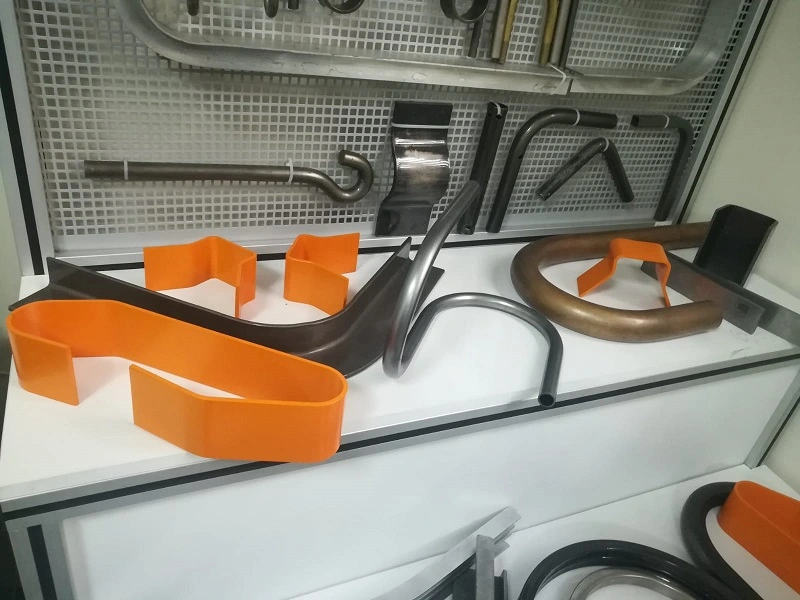
Pipe bending machines are essential tools in industries where precise and efficient bending of pipes and tubes is required. These machines are used to create complex pipe shapes that are crucial in various applications, from plumbing and construction to automotive and aerospace industries. In this section, we will explore the different types of pipe bending machines, including pneumatic, mechanical, hydraulic, and specialized machines for bending stainless steel (SS) and heavy pipes. We’ll also discuss the benefits and considerations for choosing the right pipe bending machine for specific applications.
4.1 Pneumatic Pipe Bending Machine
Pneumatic pipe bending machines utilize compressed air to generate the force needed to bend pipes. These machines are commonly used in applications that require moderate force and precision, making them suitable for a variety of industries, including automotive and HVAC (Heating, Ventilation, and Air Conditioning).
Working Principles:
- Air Compression: The machine operates by compressing air in a cylinder, which then forces a piston to move. This movement is transferred to the bending tool, which applies the necessary force to bend the pipe.
- Controlled Force: The force applied can be adjusted by regulating the air pressure, allowing for precise control over the bending process.
Advantages:
- Simplicity: Pneumatic systems are generally simpler and easier to maintain than hydraulic systems, with fewer components and less potential for leaks.
- Cost-Effectiveness: Pneumatic machines are often more affordable than their hydraulic counterparts, making them a good option for smaller operations.
- Safety: Pneumatic systems are inherently safer in environments where fire hazards are a concern, as they do not involve flammable fluids.
Applications:
- Automotive Industry: Bending exhaust pipes and other components where moderate force and precision are required.
- HVAC Systems: Shaping pipes and ducts for heating, ventilation, and air conditioning installations.
- General Fabrication: Suitable for bending tasks in small to medium-sized fabrication shops.
4.2 Mechanical Pipe Bending Machine
Mechanical pipe bending machines rely on mechanical force generated by gears, levers, and other mechanical components to bend pipes. These machines are known for their durability and reliability, making them suitable for high-volume production environments.
Working Principles:
- Mechanical Leverage: The machine uses mechanical leverage to amplify the force applied by the operator, allowing it to bend pipes with precision.
- Gear Systems: Gears and cams are often used to control the movement and force applied to the bending tool, ensuring consistent results.
Advantages:
- Durability: Mechanical pipe bending machines are built to last, with robust components that can withstand the rigors of high-volume production.
- Consistency: The use of gears and mechanical systems ensures consistent and repeatable bends, which is crucial in mass production.
- Ease of Use: These machines are typically straightforward to operate, with manual or semi-automatic controls that allow for precise adjustments.
Applications:
- Construction Industry: Bending steel pipes for structural applications, such as scaffolding and frameworks.
- Manufacturing: Producing bent pipes for various industrial products, including furniture, machinery, and equipment.
- Shipbuilding: Shaping pipes used in marine applications, where durability and precision are critical.
4.3 SS Pipe Bending Machine
Stainless steel (SS) pipes are widely used in industries that require corrosion-resistant and durable materials, such as food processing, pharmaceuticals, and chemical processing. Bending stainless steel pipes requires specialized machines that can handle the unique properties of this material without causing damage or deformation.
Key Features:
- Enhanced Tooling: SS pipe bending machines are equipped with hardened tooling that can withstand the high tensile strength of stainless steel, preventing tool wear and ensuring clean bends.
- Precision Control: These machines offer precise control over the bending process, allowing for tight bend radii and complex shapes without compromising the material’s integrity.
- Cooling Systems: Some SS pipe bending machines are equipped with cooling systems to prevent the material from overheating during the bending process, which could lead to discoloration or weakening of the stainless steel.
Advantages:
- Corrosion Resistance: SS pipe bending machines are designed to maintain the corrosion-resistant properties of stainless steel, making them ideal for applications in harsh environments.
- High Precision: The machines can produce precise bends with minimal springback, ensuring that the final product meets exact specifications.
- Versatility: Suitable for a wide range of applications, from sanitary piping in food processing to chemical transport lines in industrial settings.
Applications:
- Food and Beverage Industry: Bending pipes for sanitary processing lines, where cleanliness and corrosion resistance are paramount.
- Pharmaceutical Industry: Shaping pipes for sterile environments, including drug manufacturing and medical device production.
- Chemical Processing: Creating corrosion-resistant piping systems for transporting aggressive chemicals and other hazardous materials.
4.4 Steel Pipe Bending Machine
Steel pipe bending machines are designed to handle the rigors of bending steel pipes, which are commonly used in construction, infrastructure, and heavy industry. These machines are built to provide the necessary force and control to bend steel pipes without compromising their structural integrity.
Key Features:
- High Tonnage Capacity: Steel pipe bending machines are equipped with powerful hydraulic or mechanical systems capable of exerting the high forces required to bend steel.
- Robust Construction: The machines are built with heavy-duty frames and components to handle the stress of bending thick and strong steel pipes.
- Advanced Control Systems: Many steel pipe bending machines feature CNC controls, allowing for precise and automated bending processes.
Advantages:
- Strength and Durability: Steel pipe bending machines are capable of bending thick-walled and large-diameter steel pipes with high precision, ensuring that the final product meets structural requirements.
- Versatility: These machines can handle a wide range of steel pipe sizes and thicknesses, making them suitable for various applications in construction and heavy industry.
- Efficiency: The use of advanced control systems and automated features allows for efficient production, reducing labor costs and increasing throughput.
Applications:
- Construction: Bending steel pipes for structural applications, such as beams, columns, and supports in buildings and infrastructure projects.
- Oil and Gas Industry: Shaping steel pipes for pipelines, drilling rigs, and other critical infrastructure in the energy sector.
- Heavy Machinery Manufacturing: Producing bent steel components for construction equipment, mining machinery, and industrial tools.
4.5 Heavy Pipe Bending Machine
Heavy pipe bending machines are specialized for handling large-diameter and thick-walled pipes that require significant force to bend. These machines are used in industries where large-scale infrastructure projects and heavy-duty applications are common.
Key Features:
- High Force Capability: Heavy pipe bending machines are equipped with hydraulic systems capable of generating extremely high forces, often exceeding 1000 tons, to bend large and thick pipes.
- Large Bed Size: These machines feature expansive working areas to accommodate the size of the pipes being bent, allowing for precise positioning and control.
- Reinforced Components: The machines are built with reinforced frames, tooling, and hydraulic systems to handle the stress of bending heavy pipes without deformation.
Advantages:
- Capability: Heavy pipe bending machines can handle pipes with large diameters and thick walls, which are typically used in major infrastructure projects.
- Precision: Despite their size, these machines offer precise control over the bending process, ensuring that large pipes meet exacting specifications.
- Durability: Built to withstand the demands of heavy industry, these machines offer long service life and reliable performance in challenging environments.
Applications:
- Pipeline Construction: Bending large-diameter pipes for oil, gas, and water pipelines that span long distances and require precise engineering.
- Shipbuilding: Shaping heavy steel pipes for marine vessels, where durability and structural integrity are crucial.
- Power Generation: Producing bent pipes for power plants and energy infrastructure, including those used in nuclear and fossil fuel power generation.
4.6 Hydraulic Pipe Bending Machine
Hydraulic pipe bending machines are among the most versatile and powerful options for bending pipes in various industries. These machines utilize hydraulic pressure to apply force, offering precise control and the ability to handle a wide range of pipe sizes and materials.
Working Principles:
- Hydraulic Force: The machine uses a hydraulic cylinder to apply force to the bending tool, which then bends the pipe to the desired angle.
- Adjustable Pressure: Operators can adjust the hydraulic pressure to control the force applied, allowing for precise bends even in challenging materials.
Advantages:
- Versatility: Hydraulic pipe bending machines can handle a variety of materials, including steel, aluminum, and stainless steel, making them suitable for diverse applications.
- Precision: The hydraulic system offers fine control over the bending process, ensuring consistent results with minimal springback.
- Power: These machines are capable of generating significant force, allowing them to bend thick and strong pipes with ease.
Applications:
- Automotive Manufacturing: Bending exhaust pipes, roll cages, and other components where precision and strength are required.
- Aerospace Industry: Shaping pipes used in aircraft hydraulic systems, fuel lines, and other critical applications.
- Construction: Bending steel pipes for structural applications, such as beams, columns, and support structures.
4.7 Electric Pipe Bending Machine
Electric pipe bending machines offer an alternative to hydraulic and pneumatic systems, using electric motors to generate the force needed for bending operations. These machines are known for their energy efficiency, precision, and ease of use.
Key Features:
- Electric Motor Drive: The machine uses an electric motor to drive the bending tool, providing precise control over the bending process.
- Programmable Controls: Many electric pipe bending machines feature CNC or digital controls, allowing for automated and repeatable bending sequences.
- Quiet Operation: Electric machines tend to operate more quietly than hydraulic or pneumatic systems, making them suitable for environments where noise is a concern.
Advantages:
- Energy Efficiency: Electric pipe bending machines consume less energy compared to hydraulic systems, making them more cost-effective in the long run.
- Precision and Consistency: The use of electric motors and digital controls ensures precise and repeatable bends, which is critical in high-volume production.
- Ease of Maintenance: Electric machines have fewer moving parts compared to hydraulic systems, resulting in lower maintenance requirements and longer service life.
Applications:
- Furniture Manufacturing: Bending metal pipes for furniture frames, including chairs, tables, and shelving units.
- Medical Equipment: Shaping pipes used in medical devices and equipment, where precision and cleanliness are essential.
- Automotive Aftermarket: Producing custom exhaust systems, roll cages, and other automotive components.
4.8 Small Pipe Bending Machine
Small pipe bending machines are designed for applications that involve smaller-diameter pipes and require less force. These machines are commonly used in workshops, small-scale manufacturing, and maintenance operations.
Key Features:
- Compact Design: Small pipe bending machines are portable and space-efficient, making them ideal for use in confined spaces or on job sites.
- Manual or Semi-Automatic Operation: These machines are typically operated manually or with semi-automatic controls, offering a balance between control and ease of use.
- Versatility: Despite their small size, these machines can handle a variety of materials and bending angles, making them suitable for diverse applications.
Advantages:
- Portability: Small pipe bending machines are easy to transport and set up, making them ideal for on-site work and maintenance tasks.
- Cost-Effectiveness: These machines are typically more affordable than larger models, making them accessible to small businesses and workshops.
- Ease of Use: Simple controls and operation make these machines user-friendly, even for operators with limited experience.
Applications:
- Plumbing: Bending pipes for plumbing installations and repairs, including copper, PVC, and other materials.
- HVAC: Shaping small-diameter pipes for heating, ventilation, and air conditioning systems.
- DIY and Home Workshops: Suitable for hobbyists and small-scale fabricators working on custom projects.
4.9 Pipe Bending Machine Price Considerations
When selecting a pipe bending machine, understanding the factors that influence price is crucial to making an informed investment. The price of a pipe bending machine can vary significantly based on several key factors, including machine type, capacity, features, and brand.
Factors Influencing Price:
- Machine Type: Hydraulic and electric pipe bending machines are generally more expensive than pneumatic or mechanical models due to their advanced features and higher force capabilities.
- Capacity: Machines capable of bending larger-diameter or thicker-walled pipes typically cost more due to the increased force requirements and more robust construction.
- Control Systems: CNC-controlled machines with programmable features and automated bending sequences are priced higher than manual or semi-automatic models.
- Brand and Quality: Established brands with a reputation for quality and reliability often command higher prices, but they also offer better performance, durability, and support.
Cost vs. Functionality:
- Entry-Level Machines: Suitable for small-scale operations, workshops, and maintenance tasks, these machines offer basic functionality at a lower cost.
- Mid-Range Machines: Ideal for medium-sized businesses and manufacturers, offering a balance between price and advanced features.
- High-End Machines: Designed for large-scale production and heavy industry, these machines offer the highest levels of precision, automation, and durability but come at a premium price.
Making the Right Investment:
- Assessing Needs: Consider the specific requirements of your operation, including the types of materials, pipe sizes, and production volume, to choose a machine that meets your needs without overspending.
- Long-Term Value: While higher-end machines may have a higher initial cost, their durability, efficiency, and advanced features can lead to lower operational costs and better ROI over time.
- Supplier Support: Look for suppliers that offer good after-sales support, including training, maintenance, and parts availability, as this can significantly impact the total cost of ownership.
4.10 Conclusion
Pipe bending machines are crucial tools in various industries, offering the ability to shape and form pipes to precise specifications. Understanding the different types of pipe bending machines, including pneumatic, mechanical, hydraulic, and specialized machines for stainless steel and heavy pipes, is essential for selecting the right equipment for your needs. By considering factors such as machine capacity, control systems, and price, manufacturers and operators can make informed decisions that optimize productivity and ensure the quality of their products.
Sheet Metal Bending Machines
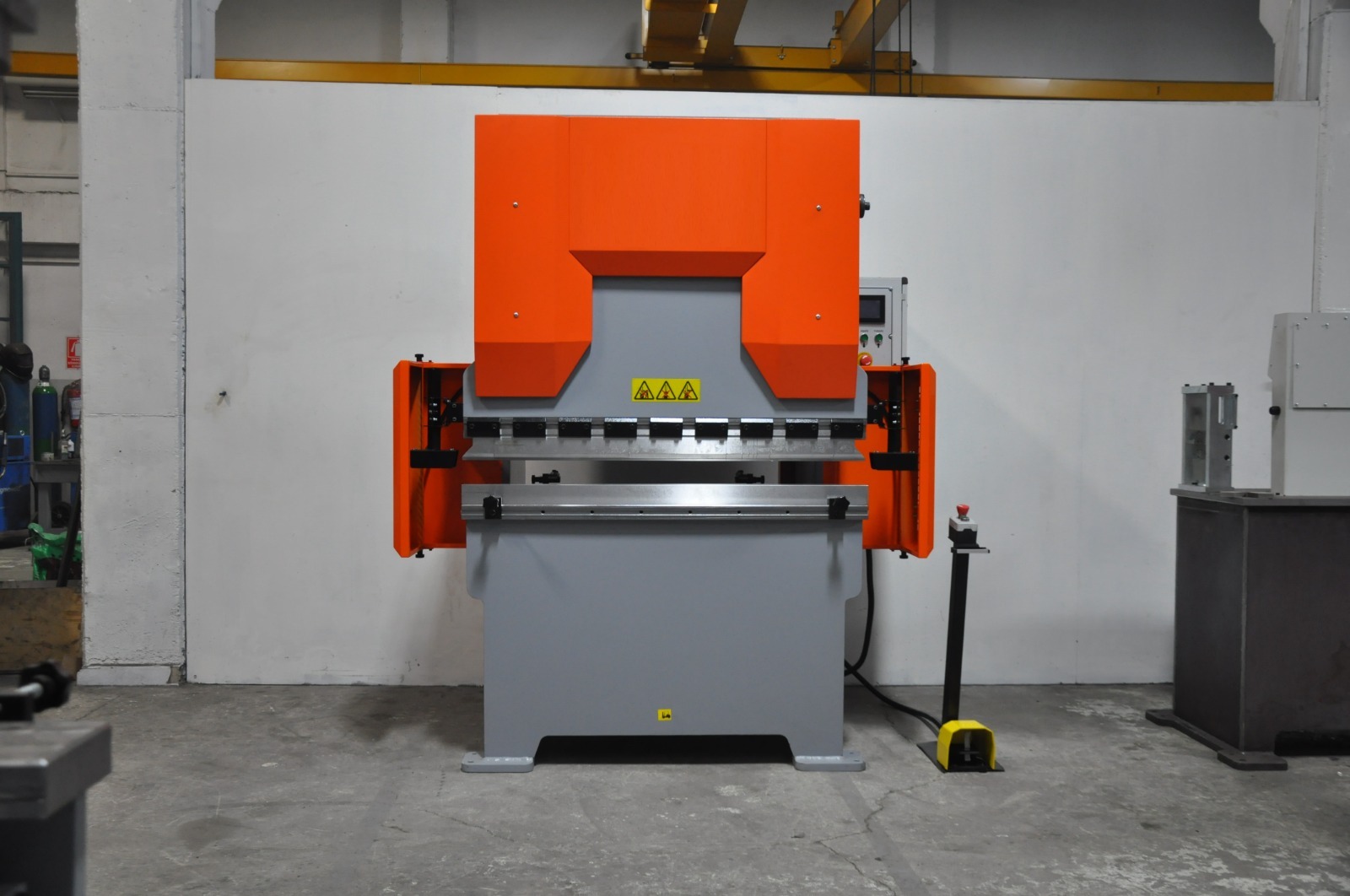
Sheet metal bending machines are essential in the fabrication of metal components, allowing manufacturers to create a wide range of shapes and structures from flat metal sheets. These machines are used across various industries, from automotive to aerospace, and play a critical role in producing everything from simple bends to complex geometries. In this section, we will explore the different types of sheet metal bending machines, including electric, hydraulic, automatic, and CNC-controlled machines. We will also discuss their applications, benefits, and factors to consider when selecting the right machine for specific tasks.
5.1 Electric Sheet Metal Bending Machine
Electric sheet metal bending machines use electric motors to generate the force needed to bend metal sheets. These machines are known for their energy efficiency, precision, and ease of use, making them a popular choice in many fabrication shops.
Key Features:
- Electric Motor Drive: These machines are driven by electric motors, which provide precise control over the bending process and allow for consistent and repeatable results.
- Programmable Controls: Many electric bending machines come with digital or CNC controls, enabling operators to program bending sequences and angles for automated operations.
- Quiet Operation: Electric machines tend to be quieter than hydraulic models, making them suitable for environments where noise reduction is important.
Advantages:
- Energy Efficiency: Electric machines are more energy-efficient than hydraulic machines, reducing operational costs over time.
- Precision: The electric motor provides consistent power, allowing for precise bends with minimal variability.
- Ease of Maintenance: With fewer moving parts and no hydraulic fluid, electric bending machines typically require less maintenance and have lower operating costs.
Applications:
- Light Fabrication: Suitable for bending thin sheets of metal, making them ideal for light fabrication tasks such as creating enclosures, brackets, and panels.
- Electronics Manufacturing: Used to bend metal components for electronic devices, where precision and consistency are critical.
- Custom Fabrication: Ideal for small workshops and custom fabrication businesses that require flexible and precise bending capabilities.
5.2 Small Sheet Bending Machine
Small sheet bending machines are designed for tasks that involve smaller pieces of sheet metal. These machines are typically more compact and easier to use, making them ideal for workshops and small-scale operations.
Key Features:
- Compact Design: Small sheet bending machines are designed to be portable and space-efficient, allowing them to be used in smaller workspaces.
- Manual or Semi-Automatic Operation: These machines often feature manual or semi-automatic controls, providing a balance between precision and ease of use.
- Versatile Tooling: Despite their size, small sheet bending machines can be equipped with a variety of tooling to handle different bending tasks.
Advantages:
- Portability: The compact size of these machines makes them easy to transport and set up, allowing for flexible use in different locations.
- Affordability: Small sheet bending machines are typically less expensive than larger models, making them accessible to small businesses and workshops.
- Ease of Use: Simple controls and operation make these machines user-friendly, even for operators with limited experience.
Applications:
- DIY and Custom Projects: Ideal for hobbyists and small-scale fabricators working on custom projects.
- Maintenance and Repair: Used in maintenance shops for bending small metal parts and components during repairs.
- Prototype Development: Suitable for creating prototypes and small production runs, where flexibility and quick setup are important.
5.3 Automatic Bending Machine
Automatic bending machines are designed to streamline the bending process by automating various aspects of the operation. These machines are equipped with advanced control systems that allow for precise and repeatable bending without the need for constant operator intervention.
Key Features:
- Automation: Automatic bending machines are capable of performing multiple bends in a single setup, reducing the need for manual adjustments and increasing productivity.
- CNC Controls: Many automatic bending machines are equipped with CNC (Computer Numerical Control) systems that allow for the programming of complex bending sequences.
- High Throughput: These machines are designed for high-volume production, making them ideal for industries that require large quantities of bent metal parts.
Advantages:
- Increased Efficiency: Automation reduces the time required for setup and bending, leading to higher production rates and lower labor costs.
- Consistency: Automatic machines ensure that each bend is executed with the same precision, reducing variability and improving product quality.
- Flexibility: The ability to program complex bending sequences allows for the production of intricate and custom shapes with minimal manual intervention.
Applications:
- Mass Production: Used in industries such as automotive and aerospace, where large quantities of parts with consistent quality are required.
- Complex Fabrication: Suitable for producing parts with multiple bends or intricate shapes that would be difficult to achieve manually.
- High-Precision Manufacturing: Ideal for applications where exacting tolerances and repeatability are essential, such as in the production of medical devices and electronics.
5.4 CNC Sheet Bending Machine
CNC sheet bending machines represent the pinnacle of precision and automation in sheet metal bending. These machines are controlled by computer numerical control (CNC) systems, which allow for highly accurate and repeatable bending operations.
Key Features:
- CNC Control: CNC sheet bending machines are equipped with computerized controls that allow operators to program and execute complex bending sequences with high precision.
- Automated Tooling: These machines often feature automated tooling systems that can change punches and dies as needed, further increasing efficiency and reducing setup time.
- Real-Time Monitoring: CNC systems provide real-time monitoring of the bending process, allowing operators to make adjustments on the fly and ensuring that each bend meets the required specifications.
Advantages:
- High Precision: CNC control ensures that each bend is performed with exacting accuracy, making these machines ideal for applications where precision is critical.
- Repeatability: The ability to store and recall bending programs allows for consistent results across multiple production runs, reducing variability and waste.
- Complexity: CNC sheet bending machines can perform intricate bends and form complex shapes that would be difficult or impossible to achieve with manual machines.
Applications:
- Aerospace Industry: Used to produce aircraft components with exacting tolerances and complex shapes.
- Automotive Manufacturing: Essential for the production of car body panels, chassis components, and other critical parts that require high precision.
- Electronics and Appliances: Ideal for creating metal enclosures, frames, and other components used in electronics and household appliances.
5.5 What is a CNC Bending Machine?
A CNC bending machine is a specialized type of bending machine that uses computer numerical control (CNC) to automate the bending process. CNC machines are programmed with specific instructions that control the movement of the machine’s bending tools, allowing for precise and repeatable operations.
How CNC Bending Machines Work:
- Programming: Operators program the CNC machine using specialized software, inputting parameters such as bend angles, material thickness, and sequence of operations.
- Tool Movement: The CNC system controls the movement of the bending tools, ensuring that each bend is executed according to the programmed instructions.
- Feedback Loops: CNC machines often include feedback systems that monitor the bending process in real-time, allowing for automatic adjustments to maintain precision.
Benefits of CNC Bending Machines:
- Precision: CNC bending machines offer unparalleled precision, with the ability to produce bends with tight tolerances and consistent quality.
- Efficiency: Automation reduces the time required for setup and bending, increasing throughput and reducing labor costs.
- Flexibility: The ability to program complex bending sequences allows for the production of custom and intricate shapes with minimal manual intervention.
Applications:
- Industrial Manufacturing: Used in high-volume production environments where consistency and precision are critical.
- Custom Fabrication: Ideal for producing custom parts and components, especially those with complex geometries.
- Prototyping: CNC bending machines are valuable in the development of prototypes, allowing for rapid iteration and precise adjustments.
5.6 Hydraulic Press Bending Machine
Hydraulic press bending machines combine the power of hydraulic systems with the precision of press brakes to perform bending operations with high efficiency and accuracy. These machines are widely used in industries that require consistent and reliable bends in a variety of materials, including steel, aluminum, and stainless steel.
Working Principles:
- Hydraulic Force: The machine uses a hydraulic cylinder to apply force to the bending tool, which then bends the metal sheet to the desired angle.
- Adjustable Pressure: Operators can adjust the hydraulic pressure to control the force applied, allowing for precise bends even in challenging materials.
Advantages:
- High Force Capacity: Hydraulic press bending machines are capable of exerting significant force, making them suitable for bending thick and strong materials.
- Precision: The hydraulic system provides fine control over the bending process, ensuring consistent results with minimal variability.
- Versatility: These machines can handle a wide range of materials and thicknesses, making them suitable for various industrial applications.
Applications:
- Automotive Manufacturing: Bending automotive body panels and structural components with high precision.
- Construction: Creating structural steel components for buildings and infrastructure projects.
- Heavy Machinery Production: Fabricating parts for construction equipment, mining machinery, and industrial tools.
5.7 Hydraulic Sheet Metal Bending Machine
Hydraulic sheet metal bending machines are specialized press brakes designed to handle the specific challenges associated with bending thin metal sheets. These machines leverage hydraulic systems to provide the necessary force and control for precise sheet metal fabrication.
Key Features:
- Enhanced Precision: Hydraulic systems ensure that each bend is executed with high accuracy, minimizing deviations and maintaining consistency.
- Adjustable Clamping Force: Allows for the secure holding of thin sheets without causing deformation or damage during the bending process.
- Integrated Control Systems: Modern hydraulic sheet metal bending machines often feature computerized controls for automated bending sequences, reducing manual intervention and increasing efficiency.
Benefits:
- Reduced Material Waste: Precise bending reduces the likelihood of errors and rework, leading to less material wastage and lower production costs.
- Increased Productivity: Automated and semi-automated systems enable faster production rates, meeting the demands of high-volume manufacturing.
- Versatility: Capable of handling a variety of sheet metal thicknesses and materials, making them suitable for diverse applications.
Applications:
- Appliance Manufacturing: Producing metal housings and components for household appliances such as refrigerators, washing machines, and ovens.
- Electronics Enclosures: Creating precise and compact metal enclosures for electronic devices and equipment.
- Furniture Manufacturing: Bending metal sheets for modern and ergonomic furniture designs.
5.8 Choosing the Right Sheet Metal Bending Machine
Selecting the right sheet metal bending machine involves considering several factors, including the material being bent, the required precision, production volume, and budget. Here are some key considerations to keep in mind:
Material Type and Thickness:
- Material: Different machines are better suited for specific materials. For example, hydraulic machines are ideal for thick steel sheets, while electric machines may be better for lighter materials.
- Thickness: The thickness of the material will determine the required force, with thicker materials needing more powerful machines.
Bending Precision:
- Tolerances: If your application requires tight tolerances, a CNC or hydraulic bending machine may be the best choice due to their precision and consistency.
- Complexity: For complex bending operations involving multiple bends or intricate shapes, a CNC machine will provide the necessary control and flexibility.
Production Volume:
- Low Volume: For small production runs or custom projects, a manual or small sheet bending machine may suffice.
- High Volume: For large-scale production, an automatic or CNC bending machine is more appropriate due to their higher efficiency and automation capabilities.
Budget Considerations:
- Initial Investment: CNC and hydraulic machines tend to have higher upfront costs but offer long-term benefits in precision, efficiency, and flexibility.
- Operating Costs: Consider the long-term costs of maintenance, energy consumption, and tooling when selecting a machine.
Supplier Support:
- After-Sales Service: Choose a supplier that offers good after-sales support, including maintenance, training, and access to spare parts.
- Warranty: Look for machines that come with a comprehensive warranty, which can protect your investment and reduce the risk of unexpected costs.
5.9 Future Trends in Sheet Metal Bending Machines
The field of sheet metal bending is constantly evolving, with new technologies and innovations improving the efficiency, precision, and versatility of bending machines. Here are some trends shaping the future of sheet metal bending:
Automation and Robotics:
- Increased Automation: Automation is becoming more prevalent in sheet metal bending, with robots and automated systems taking over tasks such as loading, unloading, and tool changes, leading to higher productivity and lower labor costs.
- Collaborative Robots: Also known as cobots, these robots work alongside human operators to assist with bending operations, enhancing efficiency while maintaining flexibility.
Advanced CNC Systems:
- Real-Time Monitoring: CNC systems are becoming more advanced, with features such as real-time monitoring, predictive maintenance, and automatic adjustments ensuring higher precision and reducing downtime.
- AI Integration: Artificial intelligence (AI) is being integrated into CNC systems to optimize bending processes, improve decision-making, and enhance overall efficiency.
Sustainability Initiatives:
- Energy Efficiency: Manufacturers are focusing on creating more energy-efficient bending machines that reduce power consumption without compromising performance.
- Material Waste Reduction: Innovations in tooling and process control are helping to reduce material waste, leading to more sustainable manufacturing practices.
Customization and Flexibility:
- Modular Machines: Modular designs allow for easy customization of bending machines, enabling manufacturers to adapt to different tasks and requirements without significant downtime.
- Flexible Tooling: Advances in tooling technology are allowing for more flexible and adaptable bending operations, making it easier to switch between different products and designs.
5.10 Conclusion
Sheet metal bending machines are vital tools in modern manufacturing, offering the precision, flexibility, and efficiency needed to produce high-quality metal components. Understanding the different types of machines—such as electric, hydraulic, automatic, and CNC models—and their specific applications is crucial for selecting the right equipment for your needs. By considering factors such as material type, bending precision, production volume, and budget, manufacturers can make informed decisions that enhance productivity and ensure the quality of their products.
Bending Press Machine Price Considerations
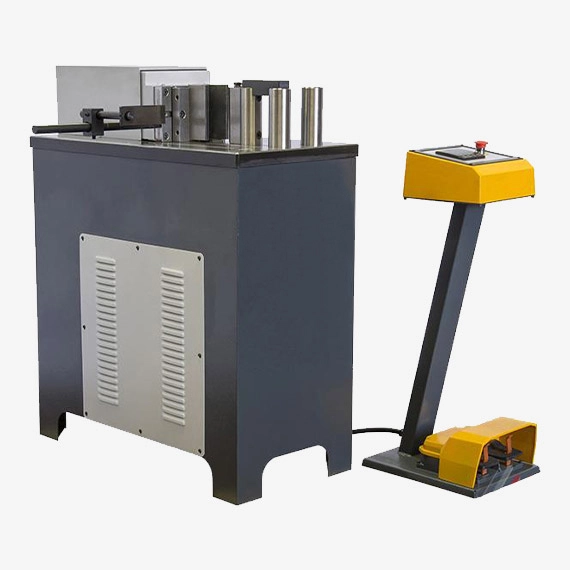
When investing in bending press machines, understanding the factors that influence pricing is essential for making an informed and cost-effective decision. Bending press machines come in various types and configurations, each with different features and capabilities that affect their overall cost. In this section, we will explore the key factors that determine the price of bending press machines, including specifications, features, brand reputation, and market demand. We will also discuss how to balance cost with functionality to ensure that you select the right machine for your specific needs.
6.1 Factors Affecting Bending Press Machine Price
The price of a bending press machine is influenced by several factors, including its type, specifications, features, brand, and market conditions. Understanding these factors can help you determine which machine offers the best value for your investment.
6.1.1 Machine Type
- Manual vs. Automated Machines: Manual bending press machines are generally less expensive than automated or CNC-controlled machines due to their simpler design and lower manufacturing costs. However, automated machines, while more expensive, offer greater efficiency, precision, and productivity, which can justify the higher initial investment.
- Hydraulic vs. Mechanical Presses: Hydraulic presses are typically more expensive than mechanical presses because of their complex hydraulic systems, which provide greater force and control. Mechanical presses, while less costly, may be more suitable for applications where speed is prioritized over precision.
6.1.2 Specifications and Capacity
- Tonnage: The tonnage, or force capacity, of a bending press machine is one of the primary factors influencing its price. Machines with higher tonnage are capable of bending thicker and stronger materials but come with a higher price tag due to the more robust construction and powerful hydraulic or mechanical systems required.
- Bed Size: The size of the machine’s bed, which determines the maximum size of the workpiece it can handle, also affects the price. Larger beds increase the machine’s versatility but require more material and engineering, leading to higher costs.
- Stroke Length: The stroke length, or the distance the press ram can travel, is another critical specification. Machines with longer stroke lengths can accommodate deeper bends, which adds to the complexity and cost of the machine.
6.1.3 Features and Technology
- CNC Controls: Bending press machines equipped with CNC (Computer Numerical Control) systems are significantly more expensive than those with manual or semi-automatic controls. CNC systems offer the ability to program and automate complex bending sequences, enhancing precision and productivity, which justifies their higher price.
- Automation and Robotics: Machines with advanced automation features, such as automatic tool changers, robotic loading and unloading, and real-time monitoring systems, command higher prices due to the added technology and the potential for increased production efficiency.
- Safety Features: Enhanced safety features, such as light curtains, safety guards, and emergency stop systems, can also contribute to the overall cost of the machine. These features are essential for protecting operators and ensuring compliance with safety regulations, particularly in high-volume production environments.
6.1.4 Brand and Quality
- Reputation: The reputation of the manufacturer or brand plays a significant role in the price of bending press machines. Established brands with a history of quality, reliability, and excellent after-sales support often charge a premium for their products. While these machines may be more expensive upfront, they often offer better performance, durability, and long-term value.
- Quality of Materials: The quality of the materials used in the construction of the machine, such as the steel for the frame and the components of the hydraulic system, affects both the machine’s durability and price. Higher-quality materials lead to longer-lasting machines but increase manufacturing costs.
6.1.5 Market Demand and Availability
- Supply and Demand: Market conditions, such as the balance between supply and demand, can also influence the price of bending press machines. During periods of high demand, prices may rise due to limited availability. Conversely, prices may decrease during periods of low demand or excess supply.
- Import and Export Costs: For machines that are imported, factors such as tariffs, shipping costs, and currency exchange rates can affect the final price. These costs can vary significantly depending on the country of origin and the location of the buyer.
6.2 Cost vs. Functionality: Making the Right Investment
When selecting a bending press machine, it is essential to balance cost with functionality to ensure that the machine meets your specific needs without exceeding your budget. Here are some strategies to help you make a cost-effective investment:
6.2.1 Assessing Your Needs
- Production Volume: Consider the volume of production when choosing a machine. If your operation involves high-volume production, investing in a more expensive, automated machine may be justified by the increased efficiency and reduced labor costs. For lower-volume operations, a less expensive manual or semi-automatic machine may be sufficient.
- Material Type and Thickness: The types of materials you work with, including their thickness and strength, will determine the necessary tonnage and capabilities of the machine. Ensure that the machine you choose can handle your specific material requirements without overpaying for unnecessary capacity.
- Complexity of Bends: If your applications involve complex bends or require high precision, investing in a CNC-controlled machine may be worth the higher cost. However, for simpler bends, a manual or mechanical machine may provide adequate functionality at a lower price.
6.2.2 Evaluating Long-Term Costs
- Operating Costs: Consider the long-term operating costs of the machine, including energy consumption, maintenance, and tooling. While a machine with advanced features may have a higher upfront cost, it could offer lower operating costs and higher efficiency, leading to savings over time.
- Durability and Reliability: Machines made with higher-quality materials and components tend to have longer service lives and require less maintenance. Investing in a durable, reliable machine can reduce downtime and maintenance costs, providing better long-term value.
- Resale Value: Some high-quality machines maintain their value well and can be resold at a good price if your needs change. This can offset some of the initial investment costs and provide flexibility in the future.
6.2.3 Exploring Financing and Leasing Options
- Financing: Many manufacturers and dealers offer financing options that allow you to spread the cost of the machine over time. This can make it easier to afford a higher-quality machine without straining your budget.
- Leasing: Leasing is another option that allows you to use a high-quality machine without the full upfront cost. Leasing can be particularly advantageous if you need the machine for a specific project or a limited time.
6.2.4 Considering Used or Refurbished Machines
- Used Machines: Purchasing a used bending press machine can be a cost-effective way to acquire high-quality equipment at a lower price. However, it is essential to thoroughly inspect the machine for wear and tear and ensure that it has been well-maintained.
- Refurbished Machines: Refurbished machines offer a middle ground between new and used equipment. These machines have been restored to good working condition and often come with warranties, providing reliability at a reduced cost.
6.2.5 Comparing Suppliers and Brands
- Supplier Reputation: Work with reputable suppliers who offer good after-sales support, including training, maintenance, and access to spare parts. A reliable supplier can significantly impact the total cost of ownership by helping you keep the machine in good working condition.
- Brand Comparison: Compare different brands and models to find the best balance between price and features. Look for reviews and case studies to understand how the machines perform in real-world applications and whether they meet industry standards.
6.3 Case Studies: Price Considerations in Real-World Scenarios
Case Study 1: Small Fabrication Shop A small metal fabrication shop required a bending press machine for custom projects involving light to medium-gauge steel. After evaluating their needs, they opted for a mid-range hydraulic press with manual controls. While they considered a CNC machine, the additional cost was not justified given their low production volume. The hydraulic press offered the necessary force and precision at a reasonable price, allowing the shop to handle a variety of projects without overextending their budget.
Case Study 2: High-Volume Automotive Manufacturer A large automotive manufacturer needed a new bending press machine to increase production efficiency for body panels. They chose a high-end CNC-controlled hydraulic press with automated tool changers and real-time monitoring. Although the machine was significantly more expensive than manual or semi-automatic models, the investment was justified by the increased throughput, reduced labor costs, and high precision required for automotive production. The machine’s advanced features also allowed for quicker setup times and reduced downtime, further enhancing productivity.
Case Study 3: Start-Up in the Aerospace Industry A start-up aerospace company needed a bending press machine capable of producing complex, high-precision components. Given their limited budget, they explored options for used and refurbished CNC machines. They found a reputable supplier offering a refurbished CNC press brake that met their specifications at a fraction of the cost of a new machine. The refurbished machine provided the precision and functionality needed for aerospace applications, allowing the start-up to meet industry standards without exceeding their budget.
6.4 Conclusion
When considering the purchase of a bending press machine, it is crucial to weigh the cost against the functionality and long-term value of the machine. Factors such as machine type, specifications, features, brand reputation, and market demand all play a significant role in determining the price. By carefully assessing your specific needs, evaluating long-term costs, exploring financing or leasing options, and comparing suppliers and brands, you can make a well-informed decision that balances cost with the required functionality. Whether you are a small shop or a large manufacturer, selecting the right bending press machine is an investment that can enhance productivity, improve product quality, and contribute to the overall success of your operation.
EMS Metalworking Machinery
We design, manufacture and assembly metalworking machinery such as:
- Hydraulic transfer press
- Glass mosaic press
- Hydraulic deep drawing press
- Casting press
- Hydraulic cold forming press
- Hydroforming press
- Composite press
- Silicone rubber moulding press
- Brake pad press
- Melamine press
- SMC & BMC Press
- Labrotaroy press
- Edge cutting trimming machine
- Edge curling machine
- Trimming beading machine
- Trimming joggling machine
- Cookware production line
- Pipe bending machine
- Profile bending machine
- Bandsaw for metal
- Cylindrical welding machine
- Horizontal pres and cookware
- Kitchenware, hotelware
- Bakeware and cuttlery production machinery
as a complete line as well as an individual machine such as:
- Edge cutting trimming beading machines
- Polishing and grinding machines for pot and pans
- Hydraulic drawing presses
- Circle blanking machines
- Riveting machine
- Hole punching machines
- Press feeding machine
You can check our machinery at work at: EMS Metalworking Machinery – YouTube
Applications:
- Beading and ribbing
- Flanging
- Trimming
- Curling
- Lock-seaming
- Ribbing
- Flange-punching