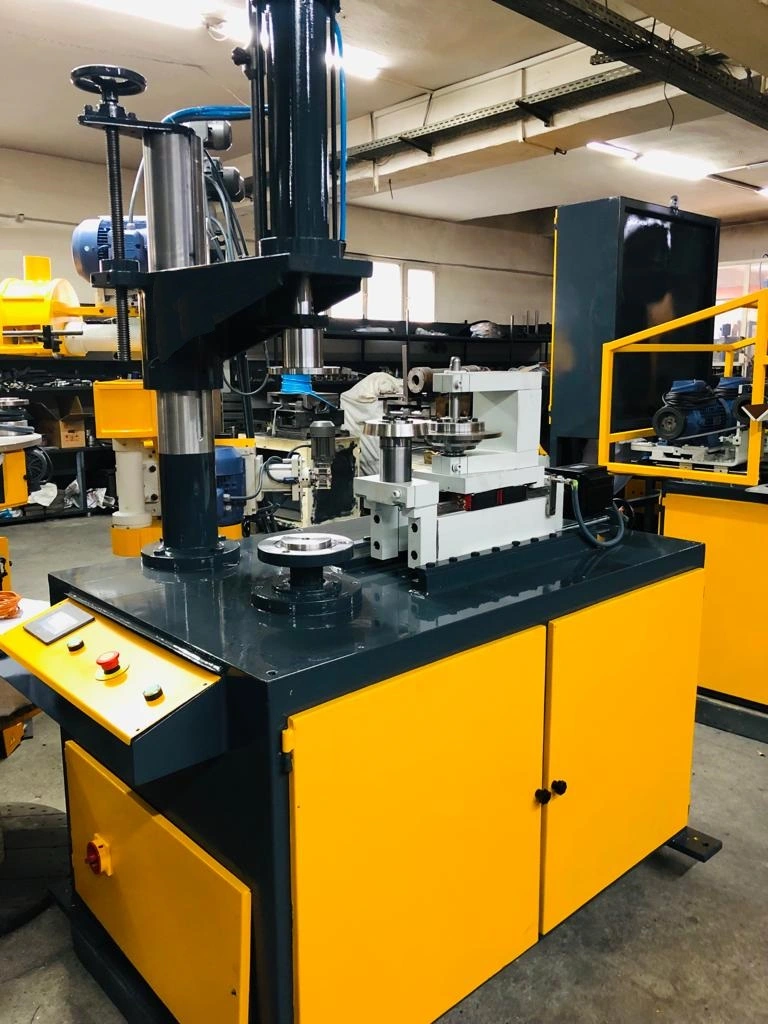
A trimming joggling machine is a device that has a set of blades that rotate at high speed in order to cut and trim sheet metal. The machine is used in the production of round parts such as LPG & CNG Cylinder Production Lines.
This machine can be operated manually or automatically. The blades are adjustable to the thickness of the sheet metal being cut, so they can be set up for different thicknesses automatically.
The trimming joggling machine is used for trimming and joggling the edges of metal sheets. The machine can be used for various operations such as edge cutting, trimming, curling, beading, rim cutting, and bending.
The most common types of materials cut with this machine are sheet metal such as aluminum, copper, and brass. It can also be used on other materials such as stainless steel.
A trimming joggling machine is a specialized tool used to trim and bead the halves of cylindrical workpieces, such as LPG and CNG cylinders, before circumferential seam welding. It is a crucial step in the manufacturing process of these cylinders, ensuring a precise and uniform edge preparation for welding.
Components of a Trimming Joggling Machine
A trimming joggling machine typically consists of the following components:
- Base Frame: The base frame provides a stable and rigid foundation for the machine.
- Trimming Unit: The trimming unit houses the rotating blade or blades that trim the edges of the workpiece.
- Joggling Unit: The jogging unit utilizes rollers or dies to form a bead along the edge of the workpiece, ensuring a smooth transition for welding.
- Workpiece Clamping System: A secure clamping system firmly holds the workpiece in place during the trimming and jogging processes.
- Control Panel: The control panel allows the operator to adjust parameters such as blade speed, joggling pressure, and cycle duration.
Trimming and Joggling Process
The trimming and jogging process on a trimming joggling machine typically involves the following steps:
- Workpiece Loading: The workpiece is carefully loaded into the machine and securely clamped in place.
- Trimming Operation: The trimming unit is activated, and the rotating blade or blades trim the edges of the workpiece to the desired length and bevel angle.
- Joggling Operation: The jogging unit is engaged, and rollers or dies form a bead along the trimmed edge of the workpiece.
- Cycle Completion: Once the trimming and jogging operations are complete, the machine automatically cycles off, and the workpiece is ready for circumferential seam welding.
Applications of Trimming Joggling Machines
Trimming joggling machines are primarily used in the manufacturing of cylindrical workpieces, particularly LPG and CNG cylinders, for the following purposes:
- Edge Preparation for Welding: The trimming and jogging processes ensure a precise and uniform edge preparation for circumferential seam welding, ensuring a strong and leak-proof weld.
- Surface Finishing: The jogging process creates a bead along the edge of the workpiece, enhancing the surface finish and providing a smooth transition for welding.
- Dimensional Accuracy: Trimming joggling machines ensure that the trimmed edges and beads are consistent and within the required dimensional tolerances.
- Production Efficiency: These machines offer high production rates, enabling efficient manufacturing of large quantities of cylinders.
Safety Precautions
When operating a trimming joggling machine, it is essential to adhere to safety precautions to prevent injuries and ensure proper operation:
- Wear Personal Protective Equipment (PPE): Always wear safety glasses, gloves, and a hearing protection device to protect yourself from flying debris, sparks, and noise.
- Securely Clamp the Workpiece: Ensure the workpiece is firmly clamped in place and properly aligned before starting the machine.
- Maintain Proper Blade Condition: Regularly inspect and maintain the blades to ensure they are sharp and free of damage.
- Avoid Overfeeding the Workpiece: Never force the workpiece into the machine or overfeed it beyond the specified capacity.
- Keep Hands Clear of Moving Parts: Keep hands and other objects clear of the machine’s rotating blades and moving components.
- Use the Correct Operating Procedures: Follow the manufacturer’s operating procedures and guidelines for the specific machine model.
- Turn Off the Machine Before Adjustments: Always turn off the machine before making any adjustments or changing the blades or other components.
- Store the Machine Properly: Store the machine in a safe, secure location when not in use, keeping it out of reach of unauthorized users.
Trimming Joggling Machine
A trimming and jogging machine is a device used in the manufacturing process to cut and shape metal sheets. It is commonly used in the production of round parts, such as LPG and CNG cylinders. The machine can be operated manually or automatically.
How It Works
The trimming and jogging machine works by using a rotating blade to cut the metal sheet to the desired size. The blade is mounted on a carriage that moves along a track. The operator can control the speed and position of the carriage by using a foot pedal or a manual control.
The jogging feature of the machine allows the operator to bend the metal sheet at a specific angle. This is done by using a separate blade that is mounted on a pivot point. The operator can adjust the angle of the blade by using a lever.
Applications
Trimming and jogging machines are used in a variety of applications, including:
- Manufacturing of round parts: These machines are commonly used in the production of round parts, such as LPG and CNG cylinders.
- Sheet metal fabrication: These machines are also used in sheet metal fabrication shops to cut and bend metal sheets for a variety of projects.
- Metalworking: Trimming and jogging machines are also used in metalworking shops to trim and bend metal sheets for a variety of applications.
Benefits
Trimming and jogging machines offer a number of benefits, including:
- Accuracy: These machines can cut and bend metal sheets with a high degree of accuracy.
- Efficiency: These machines can cut and bend metal sheets quickly and efficiently.
- Versatility: These machines can be used to cut and bend a variety of metal sheets.
- Durability: These machines are built to last and can withstand heavy use.
Safety Precautions
When operating a trimming and jogging machine, it is important to follow safety precautions to prevent injuries. These precautions include:
- Wearing personal protective equipment (PPE): Always wear safety glasses, gloves, and a hearing protection device when operating a trimming and jogging machine.
- Securing the workpiece: Make sure the workpiece is securely clamped to the machine before operating it.
- Using the correct blade: Choose the appropriate blade for the material you are cutting.
- Operating the machine at the correct speed: Do not operate the machine at an excessively high speed.
- Never touching the moving blade: Never touch the moving blade while the machine is in operation.
- Turning off the machine before making adjustments: Always turn off the machine before making any adjustments to it.
By following these safety precautions, you can safely operate a trimming and jogging machine and create high-quality products.
A trimming joggling machine is a specialized tool used in metalworking to trim and form the edges of sheet metal components. It is commonly used in the production of round parts such as LPG and CNG cylinders, as well as other cylindrical or conical components. The machine combines trimming and joggling operations in a single unit, allowing for efficient production of high-quality components.
Trimming Function
The trimming function of a trimming joggling machine utilizes a rotating blade or cutter to sever the excess material from the edge of the sheet metal workpiece. This process creates a clean, precise edge and ensures that the component has the desired dimensions.
Joggling Function
The joggling function of a trimming joggling machine employs a series of rollers or dies to form a bead or flange along the edge of the sheet metal workpiece. This bead or flange provides reinforcement and rigidity to the edge, enhancing the strength and durability of the component.
Machine Operation
The operation of a trimming joggling machine typically involves the following steps:
- Workpiece Loading: The sheet metal workpiece is securely placed on the machine’s worktable or chuck.
- Trimming: The trimming blade or cutter is positioned against the edge of the workpiece, and the machine is activated to rotate the blade and trim the excess material.
- Joggling: Once trimming is complete, the joggling rollers or dies are engaged to form the bead or flange along the edge of the workpiece.
- Unloading: The finished workpiece is removed from the machine.
Applications of Trimming Joggling Machines
Trimming joggling machines are widely used in various industries for a variety of applications, including:
- LPG and CNG Cylinder Manufacturing: Trimming joggling machines are essential in the production of LPG and CNG cylinders, ensuring accurate trimming and forming of the cylinder edges.
- Sheet Metal Fabrication: Trimming joggling machines are used in sheet metal fabrication to trim and form the edges of various components, such as flanges, enclosures, and ducting.
- Automotive Industry: Trimming joggling machines are employed in the automotive industry to trim and form the edges of car body panels, bumpers, and other sheet metal components.
- Appliance Manufacturing: Trimming joggling machines are used in appliance manufacturing to trim and form the edges of appliance panels, doors, and other sheet metal components.
Benefits of Trimming Joggling Machines
Trimming joggling machines offer several advantages over other methods of trimming and forming sheet metal edges, including:
- Accuracy: Trimming joggling machines produce precise, consistent edges with minimal burrs or imperfections.
- Efficiency: Trimming joggling machines combine trimming and joggling operations in a single unit, reducing production time and labor costs.
- Versatility: Trimming joggling machines can handle a wide range of sheet metal materials and thicknesses.
- Durability: Trimming joggling machines are constructed from durable materials and designed for long-term operation in industrial environments.
Safety Precautions
When operating trimming joggling machines, it is crucial to follow safety precautions to prevent injuries and ensure proper operation:
- Wear Personal Protective Equipment (PPE): Always wear safety glasses, gloves, and a hearing protection device to protect yourself from flying debris, sparks, and noise.
- Securely Clamp the Workpiece: Ensure the workpiece is firmly clamped to the machine’s worktable or chuck to prevent it from slipping or moving during operation.
- Use the Correct Trimming and Joggling Tools: Choose the appropriate trimming blade or cutter and joggling rollers or dies for the specific application and material being processed. Using the wrong tools can damage the workpiece or cause injury.
- Maintain Proper Machine Speed: Maintain a moderate speed to prevent overheating the workpiece or damaging the trimming tools and joggling dies.
- Avoid Overheating the Workpiece: Avoid applying excessive pressure or operating the machine for extended periods to prevent overheating the workpiece and potential damage.
- Regularly Clean and Maintain the Machine: Keep the machine clean and inspect it regularly for worn or loose components.
- Operate the Machine in a Well-ventilated Area: Use the machine in a well-ventilated area to minimize dust accumulation and protect yourself from harmful fumes.
- Never Touch the Moving Trimming Tools or Joggling Dies: Never touch the moving trimming tools or joggling dies while the machine is in operation.
- Turn Off the Machine Before Making Adjustments: Always turn off the machine before making any adjustments or changing the trimming tools or joggling dies.
- Store the Machine Properly: Store the machine in a safe, secure location when not in use, keeping it out of reach of children and unauthorized users.
By adhering to these safety guidelines and operating the machine responsibly, you can effectively utilize trimming joggling machines to produce high-quality, precisely
- Wheel Production Lines
- LPG and CNG Cylinder Production Lines
- Fire Extinguisher Production Lines
- Cartridge Case Production Lines for Defense Industry
- Warhead and Projectile Production Lines
- Gun Barrel Production Lines
- Anti-Tank Ammunition Production Lines
- Missile Body Production Lines
A trimming joggling machine is a specialized piece of equipment used in sheet metal fabrication and manufacturing processes. It’s designed to perform two primary operations: trimming and joggling. Let’s explore these operations and the components of a trimming joggling machine in more detail:
1. Trimming Operation:
- Purpose: Trimming is the process of removing excess material or unwanted edges from a sheet metal component. This operation ensures that the final product has clean, precise edges.
- Process: The sheet metal is positioned on the machine’s work surface. A cutting tool, often in the form of a blade or cutter, moves along the edges of the metal sheet to trim away excess material.
- Components: In the trimming operation, the key components of a joggling machine include the cutting tool, which may be adjustable or interchangeable to accommodate different sheet metal thicknesses and shapes. The cutting tool is typically mounted on a reciprocating arm or a moving carriage.
2. Joggling Operation:
- Purpose: Joggling, also known as flanging or offsetting, involves bending or forming a part of the sheet metal to create an offset or an edge that serves various purposes, such as reinforcement or joining.
- Process: The sheet metal is placed under a forming tool or die, and the machine applies force to create the desired offset or flange. The amount of offset and the angle can be adjusted to meet specific design requirements.
- Components: The joggling operation requires a forming tool or die, often custom-designed to produce the required offset or flange shape. The machine’s hydraulic or mechanical press mechanism provides the force necessary for forming the metal.
Components of a Trimming Joggling Machine:
- Frame: The machine’s frame provides the structural support and stability required for precision operations.
- Work Surface: This is where the sheet metal is placed and secured for processing.
- Cutting Tool: For the trimming operation, the machine features a cutting tool, such as a blade, that moves along the edges of the metal sheet.
- Forming Tool or Die: For the joggling operation, a forming tool or die is used to shape the metal.
- Press Mechanism: The machine is equipped with a press mechanism, which can be hydraulic or mechanical, to provide the necessary force for both trimming and joggling operations.
- Controls: Modern trimming joggling machines come with user-friendly control panels that allow operators to set parameters like cutting depth, tool speed, and press force.
- Safety Features: Safety measures, such as emergency stop buttons and guards, are essential to ensure operator safety during machine operation.
- Adjustability: Some machines offer adjustability to accommodate various sheet metal sizes and thicknesses.
- Clamping System: A secure clamping system holds the sheet metal in place during trimming and joggling operations.
Trimming joggling machines are commonly used in the aerospace, automotive, and sheet metal fabrication industries for manufacturing components that require precise trimming and forming. Proper setup and adjustment of the machine are crucial to achieve accurate and consistent results.
Components of the Trimming Joggling Machine
1. Frame:
- Purpose: The frame serves as the foundation of the machine, providing structural stability and support for all other components.
- Construction: Frames are typically made of heavy-duty materials like cast iron, welded steel, or sturdy aluminum to ensure rigidity and minimize vibrations during operation.
- Design: The frame is designed with sufficient rigidity to withstand the forces generated during trimming and joggling processes, ensuring precision in cutting and forming.
2. Work Surface:
- Purpose: The work surface, often referred to as the table or bed, is where the sheet metal is positioned and secured for processing.
- Material: Work surfaces are usually made of materials like steel or cast iron, known for their durability and resistance to deformation.
- Clamping Mechanism: The work surface may feature a clamping mechanism that holds the sheet metal securely in place during trimming and joggling operations to prevent movement or shifting.
3. Cutting Tool:
- Purpose: In the trimming operation, the cutting tool removes excess material or unwanted edges from the sheet metal, ensuring precise dimensions.
- Types: Cutting tools can vary in type, such as rotary blades, shearing blades, or specialized trimming dies.
- Adjustability: Some machines allow for the adjustment of the cutting tool’s depth, angle, and position to accommodate different sheet metal thicknesses and cutting requirements.
4. Forming Tool or Die:
- Purpose: The forming tool or die is used in the joggling operation to shape or bend the sheet metal to create offsets, flanges, or other desired features.
- Customization: Forming tools are often customized to match the specific design requirements of the component being produced.
- Materials: They are typically made of hardened steel or other wear-resistant materials to withstand repeated use.
5. Press Mechanism:
- Purpose: The press mechanism provides the force required for both trimming and joggling operations.
- Types: It can be hydraulic or mechanical, depending on the machine’s design and intended use.
- Pressure Control: Modern machines often have pressure control systems that allow operators to adjust the force applied during the operations.
6. Controls:
- User Interface: The machine is equipped with a control panel or interface where operators can set parameters, including cutting depth, tool speed, press force, and other variables.
- Safety Features: Control panels may include safety features such as emergency stop buttons and status indicators to ensure safe operation.
7. Safety Features:
- Emergency Stop: Machines are equipped with easily accessible emergency stop buttons that immediately halt machine operation in case of an emergency or safety concern.
- Guards: Safety guards and shields are installed to protect operators from moving parts and potential hazards during operation.
8. Adjustability:
- Sheet Metal Size and Thickness: Some machines offer adjustability to accommodate various sheet metal sizes and thicknesses, making them versatile for different applications.
9. Clamping System:
- Purpose: The clamping system secures the sheet metal in place during trimming and joggling processes to prevent movement or shifting.
- Types: Clamping mechanisms can include mechanical clamps, hydraulic clamps, or pneumatic clamps, depending on the machine’s design.
Trimming joggling machines are precision tools used in various industries to produce accurately trimmed and formed sheet metal components. Proper setup, calibration, and adherence to safety protocols are crucial to achieving consistent and high-quality results.
A trimming joggling machine is a specialized tool used in metalworking to trim and form the edges of sheet metal components. It is commonly used in the production of round parts such as LPG and CNG cylinders, as well as other cylindrical or conical components. The machine combines trimming and joggling operations in a single unit, allowing for efficient production of high-quality components.
Main Components of a Trimming Joggling Machine
The main components of a trimming joggling machine include:
- Frame: The frame provides the structural support and stability required for precision operations. It is typically made of a sturdy metal material, such as steel or cast iron, to withstand the forces involved in trimming and joggling.
- Work Surface: The work surface is the platform on which the sheet metal workpiece is placed and secured during processing. It is typically a flat, level surface made of a durable material that can withstand wear and tear from the trimming and joggling operations.
- Trimming Head: The trimming head houses the rotating trimming blade or cutter. It is positioned and aligned precisely to ensure accurate trimming of the workpiece edge. The trimming blade or cutter is typically made of a high-strength material, such as tungsten carbide, to maintain sharpness and edge retention.
- Joggling Mechanism: The joggling mechanism consists of a series of rollers or dies that form the bead or flange along the edge of the workpiece. The rollers or dies are typically made of a hard, wear-resistant material, such as steel or hardened plastic, to ensure long-term durability.
- Workpiece Clamping System: The workpiece clamping system securely holds the sheet metal workpiece in place during trimming and joggling operations. It may consist of a chuck, clamps, or other mechanical devices that provide firm grip and prevent the workpiece from moving or slipping.
- Drive System: The drive system provides the power to rotate the trimming blade or cutter and operate the joggling mechanism. It typically consists of an electric motor, gearbox, and transmission system that delivers the necessary torque and speed for efficient operation.
- Control Panel: The control panel allows the operator to control the machine’s functions, including trimming and joggling operations, speed adjustments, and safety features. It may consist of buttons, switches, or a touchscreen interface.
- Safety Guards: Safety guards are essential components that protect the operator from potential hazards during machine operation. They may include shields, interlocks, and emergency stop buttons to prevent accidental contact with moving components or prevent machine operation without proper safety measures in place.
In addition to these main components, trimming joggling machines may also include additional features, such as:
- Material Feed Systems: Automated material feed systems can be incorporated to streamline the production process and reduce manual handling of sheet metal workpieces.
- Dust Collection Systems: Dust collection systems can be integrated to capture and remove metal dust and debris generated during trimming and joggling operations, maintaining a clean and safe work environment.
- Pneumatic or Hydraulic Systems: Pneumatic or hydraulic systems may be employed to provide additional power or control for certain machine functions, such as clamping mechanisms or joggling operations.
- Computer Numerical Control (CNC): Advanced trimming joggling machines may incorporate CNC technology for precise control of trimming and joggling operations, allowing for automated production of complex shapes and geometries.
By understanding the various components and features of trimming joggling machines, operators and technicians can effectively utilize these specialized tools to produce high-quality, precisely trimmed and joggled sheet metal components for various industrial applications.
Application Areas
The trimming jogging machine is a versatile and essential tool in various industrial applications. Its ability to precisely trim and form the edges of sheet metal components makes it a critical component in manufacturing processes across various industries. Here are some of the key application areas of the trimming jogging machine:
1. LPG and CNG Cylinder Production:
Trimming jogging machines play a pivotal role in the production of LPG and CNG cylinders. They ensure accurate trimming of the cylinder edges and form the bead or flange that provides reinforcement and rigidity to the cylinder walls. This ensures the safety and durability of these critical pressure vessels.
2. Sheet Metal Fabrication:
Trimming jogging machines are widely used in sheet metal fabrication to trim and form the edges of various components, such as flanges, enclosures, and ducting. Their ability to handle a wide range of sheet metal materials and thicknesses makes them a versatile tool in sheet metal workshops.
3. Automotive Industry:
Trimming jogging machines are employed in the automotive industry to trim and form the edges of car body panels, bumpers, and other sheet metal components. Their precision and efficiency contribute to the production of high-quality automotive components.
4. Appliance Manufacturing:
Trimming jogging machines are used in appliance manufacturing to trim and form the edges of appliance panels, doors, and other sheet metal components. They help ensure the aesthetic appeal and functional integrity of various household appliances.
5. Electrical and Electronic Component Manufacturing:
In the production of electrical and electronic components, trimming jogging machines are used to trim and form the edges of metal casings, enclosures, and brackets. Their precision and reliability ensure the proper fit and function of these components.
6. Aerospace and Defense Industries:
Trimming jogging machines find applications in the aerospace and defense industries for trimming and forming the edges of aircraft components, missile parts, and military equipment. Their ability to handle high-strength materials and meet stringent precision requirements makes them invaluable in these sectors.
7. Medical Device Manufacturing:
In the production of medical devices, trimming jogging machines are used to trim and form the edges of surgical instruments, implant components, and medical equipment housings. Their precision and accuracy contribute to the safety and efficacy of these critical medical devices.
8. Energy and Infrastructure Industries:
Trimming jogging machines are employed in the energy and infrastructure industries to trim and form the edges of metal components used in power plants, transmission lines, and infrastructure projects. Their durability and reliability make them well-suited for these demanding applications.
9. General Metalworking Shops:
Trimming jogging machines are essential tools in general metalworking shops for handling a wide range of trimming and forming tasks. Their versatility and adaptability make them indispensable for job shops and general metalworking operations.
These examples illustrate the diverse range of applications for trimming jogging machines across various industries. Their ability to precisely trim and form sheet metal edges makes them a valuable asset in manufacturing processes that demand accuracy, efficiency, and reliability.
An edge cutting, trimming, beading, and curling machine is a specialized industrial device used primarily in the metalworking and sheet metal fabrication industries. It is designed to perform multiple finishing operations on metal sheets, pipes, and cylindrical components. These operations help achieve smooth edges, uniform shapes, and enhanced durability of the material, making them suitable for various applications such as automotive parts, household appliances, and industrial containers.
Edge cutting is the initial stage where the machine precisely removes excess or uneven edges from the workpiece. This process ensures that the metal sheet or cylindrical component has a defined and accurate boundary, reducing defects and making it easier to handle in subsequent processes. Precision in edge cutting is crucial to maintain consistency in manufacturing and to ensure that the final product meets required specifications.
Trimming follows the cutting process and further refines the edges by removing additional material, if necessary. It enhances dimensional accuracy and prepares the metal piece for further modifications. This process is particularly important in industries where exact dimensions and smooth finishes are required, such as in the production of food containers, industrial drums, or metal enclosures.
Beading is the next step, where the machine forms a raised or indented bead along the edge of the metal sheet or cylinder. This operation adds strength to the material, improving its rigidity and resistance to deformation. Beading is commonly used in the manufacturing of pipes, tanks, and enclosures, as it helps reinforce the structure without significantly increasing the material thickness. It also plays a functional role in assembly processes where interlocking or sealing is necessary.
Curling is the final stage of the process, where the machine bends the edge of the material into a smooth, rounded shape. This is particularly important for safety, as sharp edges can be hazardous in handling and assembly. Curling is also used in the production of metal lids, circular covers, and decorative trims, enhancing both the aesthetics and functionality of the final product. The process requires precise control to ensure that the curl is uniform and does not compromise the integrity of the material.
Modern edge cutting, trimming, beading, and curling machines are often equipped with advanced automation features, including programmable controls, servo-driven mechanisms, and high-precision sensors. These features allow manufacturers to achieve high efficiency, repeatability, and consistency in production. The machines can be adapted for various materials, including steel, aluminum, and stainless steel, depending on the application requirements.
These machines are widely used in industries such as automotive, aerospace, construction, packaging, and metal furniture production. Their ability to perform multiple finishing operations in a single setup makes them invaluable for increasing productivity and reducing manual labor. Additionally, modern safety features such as protective enclosures, emergency stop mechanisms, and automated material handling systems make these machines more user-friendly and safe for operators.
The choice of an edge cutting, trimming, beading, and curling machine depends on factors such as material type, thickness, production volume, and required precision. Manufacturers often select customized machines with specific tooling and settings to meet their unique production needs. Regular maintenance and calibration are necessary to ensure optimal performance and longevity of the equipment.
In conclusion, an edge cutting, trimming, beading, and curling machine is an essential tool in metal fabrication, offering multiple functions in a single operation. Its ability to enhance precision, improve product quality, and ensure safety makes it a valuable asset for industrial applications. As technology advances, these machines continue to evolve, incorporating smarter automation and improved efficiency to meet the growing demands of modern manufacturing.
These machines are designed with precision engineering to handle various metal thicknesses and materials. They operate through a combination of rotary and linear motion, using specialized cutting tools, rollers, and dies to shape the metal according to the required specifications. The edge cutting process typically utilizes hardened steel blades or rotary shears to create a clean, burr-free cut, which is essential for ensuring the quality of subsequent processing steps. In automated systems, sensors and vision-guided controls help maintain accuracy, reducing material waste and improving productivity.
Trimming further refines the edges, ensuring that the workpiece conforms to exact dimensions. In industries where uniformity is critical, such as in the production of cylindrical containers or sheet metal enclosures, trimming ensures that all components fit together seamlessly. Some machines use a combination of shear trimming and rotary trimming mechanisms to achieve the desired results. The precision of trimming is particularly important in applications involving welded seams, where inconsistencies in edge finishing could lead to weak points or defects.
Beading enhances the strength and rigidity of the material by introducing a rolled or raised profile along the edge. This process is common in manufacturing applications where additional reinforcement is required without significantly increasing the weight of the product. Beading is widely used in making ductwork for HVAC systems, automotive body panels, and storage tanks. The process may also serve an aesthetic purpose, adding a distinctive design element to finished products. In some cases, beading improves the grip and handling of cylindrical containers, making them easier to transport and use.
Curling is a crucial step in improving both the safety and usability of metal components. By rolling the edge of a sheet or cylindrical object into a smooth curve, curling eliminates sharp edges that could pose a risk of injury during handling. This process is widely used in the production of metal cans, lids, and decorative trims. The degree of curl can be controlled through adjustable forming rollers, allowing manufacturers to customize the final shape to meet specific requirements. The precision of the curl is important in applications where airtight or watertight seals are needed, such as in food packaging and chemical storage containers.
Modern edge cutting, trimming, beading, and curling machines integrate computer numerical control (CNC) technology to enhance precision and repeatability. These systems allow operators to program multiple operations in a single cycle, reducing manual intervention and increasing efficiency. CNC-driven machines also facilitate rapid changeovers between different product specifications, making them suitable for high-mix, low-volume production environments. Additionally, advancements in tooling materials and coatings have improved the durability and performance of cutting and forming tools, minimizing downtime due to wear and tear.
Safety is a key consideration in the design and operation of these machines. Features such as enclosed cutting zones, automatic material feeding, and emergency stop mechanisms help protect operators from potential hazards. Some machines incorporate laser or infrared sensors to detect anomalies in the material or machine operation, preventing defects and ensuring consistent quality. Regular maintenance, including lubrication, alignment checks, and tool sharpening, is essential for prolonging the lifespan of the equipment and maintaining high performance.
In industrial applications, these machines play a vital role in enhancing productivity and reducing material waste. By performing multiple finishing operations in a single process, they eliminate the need for manual handling between stages, leading to faster production cycles and lower labor costs. Industries such as automotive manufacturing, aerospace, construction, and appliance production rely on these machines to produce high-quality metal components that meet stringent performance and safety standards.
The future of edge cutting, trimming, beading, and curling machines is likely to see further advancements in automation, artificial intelligence, and energy efficiency. Smart sensors and machine learning algorithms may enable real-time adjustments to optimize cutting and forming parameters, reducing material waste and improving overall efficiency. Additionally, the integration of robotic material handling systems could further streamline production, allowing for continuous, high-speed operation with minimal human intervention. As manufacturing industries continue to evolve, these machines will remain a cornerstone of precision metalworking, supporting innovation and quality in diverse applications.
As technology advances, edge cutting, trimming, beading, and curling machines are evolving to incorporate greater efficiency, flexibility, and precision. Manufacturers are increasingly adopting automated solutions that integrate real-time monitoring and adaptive control systems to improve consistency and reduce downtime. These machines are now capable of handling a wider range of materials, including advanced alloys, stainless steel, and coated metals, ensuring compatibility with modern industrial applications.
One of the significant advancements in these machines is the use of servo-driven motors and programmable logic controllers (PLCs). Servo motors provide precise control over cutting, trimming, and forming operations, allowing for higher accuracy and repeatability. Unlike traditional mechanical systems that rely on fixed tooling settings, servo-driven technology enables on-the-fly adjustments, making it easier to switch between different production specifications without extensive reconfiguration. PLCs, on the other hand, facilitate seamless automation, allowing operators to program multiple operations into a single cycle, reducing manual intervention and enhancing productivity.
The integration of vision systems and artificial intelligence (AI) is another notable development. High-resolution cameras and sensors can inspect the workpiece in real time, identifying defects such as irregular cuts, uneven curls, or inconsistent beading. AI-powered software can analyze this data and make instant adjustments to optimize machine performance. This level of automation helps manufacturers maintain stringent quality control while minimizing material wastage and rework costs.
Another key trend in the evolution of these machines is the incorporation of energy-efficient systems. Many modern machines are designed with regenerative braking systems, which recover and reuse energy, reducing overall power consumption. Additionally, improvements in tooling materials and coatings have extended tool life, reducing the frequency of replacements and associated costs. The use of advanced lubricants and cooling systems also enhances machine efficiency, preventing overheating and ensuring smooth operation even in high-speed production environments.
Customization and modularity have become critical aspects of machine design. Manufacturers now offer modular machine configurations that allow users to add or remove specific functionalities based on their production needs. For example, a company producing metal lids may require edge cutting and curling but not beading, while another manufacturer producing structural metal components may require all four operations. This modular approach provides flexibility, enabling businesses to scale their production capabilities without investing in entirely new machines.
Another development is the increasing use of robotic automation in material handling and feeding systems. Collaborative robots (cobots) can work alongside human operators to load and unload workpieces, improving efficiency and reducing strain on workers. Fully automated conveyor systems and robotic arms further enhance productivity by ensuring a continuous flow of materials through different processing stages. These systems help eliminate bottlenecks and maintain high-speed production with minimal interruptions.
Industry 4.0 technologies, such as the Internet of Things (IoT) and cloud-based monitoring, are also shaping the future of edge cutting, trimming, beading, and curling machines. IoT-enabled machines can transmit real-time performance data to cloud platforms, allowing operators to monitor production remotely. Predictive maintenance algorithms analyze machine performance trends and alert operators to potential issues before they result in costly breakdowns. This proactive approach to maintenance reduces downtime and extends the lifespan of critical machine components.
The applications of these machines continue to expand across various industries. In the packaging industry, they play a crucial role in manufacturing metal cans, lids, and food containers with precise edge finishing and curling. In the automotive sector, they are used for producing structural components, exhaust systems, and body panels with reinforced edges for improved strength and durability. The construction industry benefits from these machines in manufacturing HVAC ducting, metal roofing panels, and support structures, ensuring high-quality finishes that enhance structural integrity.
The aerospace industry, which demands exceptionally high precision and material consistency, also utilizes these machines to manufacture lightweight yet durable metal components for aircraft. The ability to achieve smooth edges, precise curls, and reinforced beadings contributes to the overall safety and aerodynamics of aerospace parts. Additionally, the household appliance industry relies on these machines to produce metal housings, drum enclosures, and other components that require both aesthetic appeal and functional durability.
As environmental concerns continue to influence manufacturing practices, these machines are being designed with sustainability in mind. The adoption of eco-friendly lubricants, reduced energy consumption, and recyclable materials ensures that production processes align with global sustainability goals. Many manufacturers are also exploring hybrid and electric-powered machines to further minimize their carbon footprint while maintaining high-performance standards.
Looking ahead, the future of edge cutting, trimming, beading, and curling machines will likely involve even greater levels of automation, intelligence, and sustainability. The integration of advanced sensors, AI-driven process optimization, and robotic assistance will continue to push the boundaries of precision and efficiency. Manufacturers that invest in these technological advancements will gain a competitive edge, ensuring higher productivity, lower operational costs, and superior product quality in an increasingly demanding market.
The continuous evolution of edge cutting, trimming, beading, and curling machines is shaping the future of modern manufacturing, with increased automation, precision, and adaptability playing central roles. As industries demand higher efficiency, lower material waste, and improved product quality, manufacturers are responding by developing smarter machines that integrate cutting-edge technologies.
One of the most transformative changes in these machines is the development of fully automated, self-learning systems that reduce human intervention to a minimum. Advanced sensors and AI-driven analytics allow machines to detect variations in material thickness, hardness, and surface finish in real time, making micro-adjustments to optimize each stage of the process. This ensures that cutting remains precise, trimming maintains exact dimensions, beading achieves uniform reinforcement, and curling produces smooth, consistent edges. By eliminating inconsistencies, manufacturers can produce higher-quality products with reduced defect rates.
Additionally, machine learning algorithms are improving predictive maintenance capabilities. By continuously analyzing machine performance data, AI systems can predict potential component failures or wear and tear, alerting operators to conduct maintenance before breakdowns occur. This not only reduces unplanned downtime but also extends the lifespan of critical machine components, lowering maintenance costs and improving overall operational efficiency.
Another emerging trend is the adoption of multi-functional hybrid machines capable of performing additional finishing processes beyond edge cutting, trimming, beading, and curling. Some advanced models integrate embossing, perforation, or flanging, allowing manufacturers to complete multiple forming operations in a single pass. This reduces the need for multiple machines, streamlining production lines and cutting down on energy consumption, floor space, and labor costs.
The application of digital twin technology is also revolutionizing machine design and operation. Digital twins are virtual replicas of physical machines that simulate real-world performance in a digital environment. Manufacturers use these simulations to test different machine settings, optimize cutting and forming parameters, and predict production outcomes before running actual materials through the system. This results in better process optimization, reduced trial-and-error waste, and faster time-to-market for new products.
Another area of advancement is in material adaptability. With the rise of lightweight, high-strength materials in aerospace, automotive, and construction applications, modern machines are being equipped with adjustable tooling and adaptive force control mechanisms. These innovations allow machines to process not only traditional metals like steel and aluminum but also newer materials such as titanium alloys, composite metal laminates, and corrosion-resistant coatings. The ability to work with a broader range of materials makes these machines more versatile and applicable across multiple industries.
Sustainability is becoming a key focus in the design and operation of these machines. Many modern systems incorporate energy-efficient servo motors, regenerative braking, and low-power standby modes to reduce electricity consumption. Additionally, manufacturers are exploring ways to use recyclable or biodegradable lubricants, reducing environmental impact without compromising performance. Some machines now feature closed-loop lubrication systems that minimize fluid waste and contamination, improving both cost efficiency and ecological sustainability.
The integration of Industry 4.0 and smart factory principles is also reshaping how these machines operate. With real-time data connectivity, operators can monitor machine performance remotely via cloud-based dashboards, track production efficiency, and analyze historical trends to optimize workflow. Smart machines can communicate with other equipment in a production line, automatically adjusting their settings to maintain seamless operation. This interconnected manufacturing environment not only improves efficiency but also enhances overall quality control and traceability of production data.
Robotics and automation are also playing an increasing role in supporting these machines. Instead of relying on manual loading and unloading, collaborative robots (cobots) and automated material handling systems can efficiently move workpieces between machines. This reduces the risk of human error, speeds up production cycles, and allows workers to focus on higher-value tasks such as quality control and system optimization. In high-volume manufacturing environments, fully robotic production cells integrating edge cutting, trimming, beading, and curling machines with robotic arms ensure continuous, high-speed operation.
The future of these machines will likely involve even greater customization options to meet the diverse needs of different industries. Modular machine designs will allow manufacturers to swap out processing units, configure machines for specific applications, and integrate new functionalities without the need for costly equipment replacements. Advances in software and user interfaces will also make machine operation more intuitive, reducing the skill level required to program and manage complex processing tasks.
As technology continues to advance, edge cutting, trimming, beading, and curling machines will play an increasingly crucial role in precision metalworking. With improved automation, enhanced material adaptability, greater energy efficiency, and seamless digital integration, these machines are set to redefine modern manufacturing standards. Companies that embrace these innovations will benefit from higher productivity, superior product quality, and more sustainable operations, positioning themselves at the forefront of the next industrial revolution.
Automatic Cutting Beading Machine
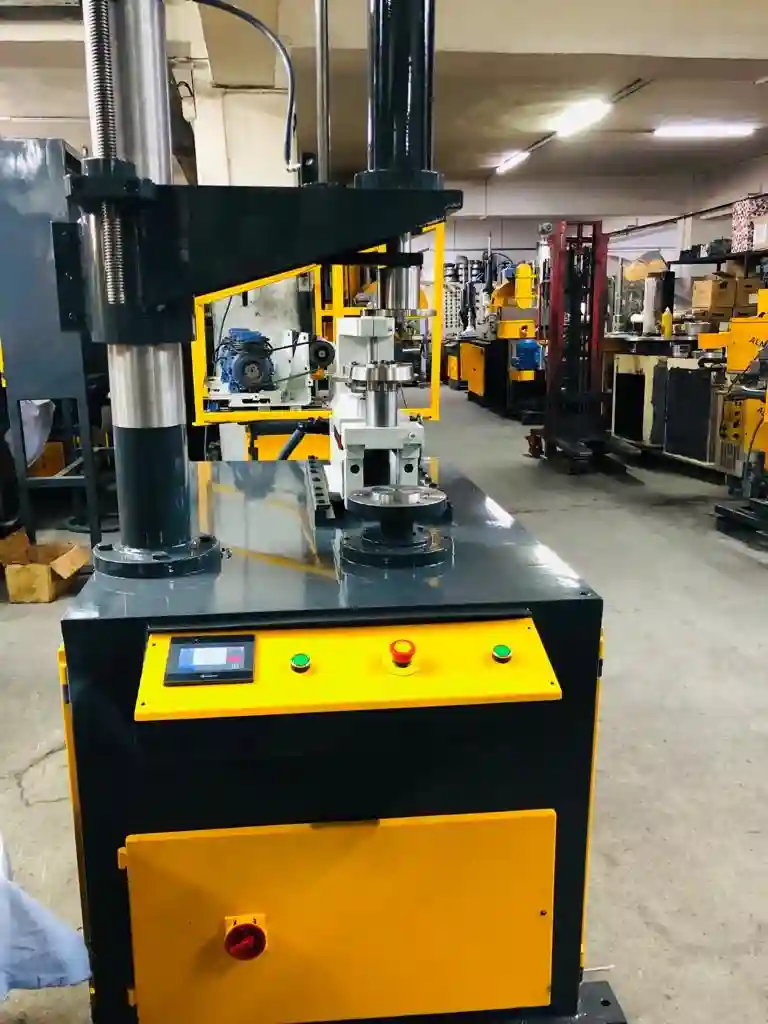
An Automatic Cutting Beading Machine is a specialized industrial device designed to streamline the processes of cutting and beading metal sheets, pipes, or cylindrical components. These machines are widely used in industries such as packaging, automotive, HVAC, construction, and metal fabrication, where precision, speed, and consistency are critical. By integrating automation, they enhance productivity, reduce labor costs, and minimize material waste while ensuring high-quality output.
Key Functions and Features
- Automatic Cutting
The machine is equipped with high-precision cutting tools that can efficiently slice through metal sheets or cylindrical workpieces. It typically employs rotary shears, guillotine cutters, or laser/plasma cutting technology, depending on the material type and thickness. Automated feeding systems ensure consistent material flow, reducing manual handling and improving efficiency. - Beading Mechanism
After cutting, the beading process reinforces the edges of the metal by forming a raised or recessed bead. This not only adds structural strength but also enhances the durability of the workpiece. Beading is essential for manufacturing products such as metal cans, ducts, containers, and automotive parts, where rigidity and shape retention are crucial. - Automation and Control Systems
Modern machines integrate Programmable Logic Controllers (PLC) and Computer Numerical Control (CNC) systems to automate and precisely control cutting and beading parameters. Operators can pre-set dimensions, bead depth, and cycle times, allowing for repeatable accuracy across large production runs. - Material Compatibility
These machines can process a wide range of materials, including stainless steel, aluminum, galvanized sheets, and carbon steel. Advanced models may include adjustable rollers and cutting heads to accommodate different thicknesses and material hardness levels. - High-Speed Production
Automated machines operate at high speeds, making them ideal for mass production. Features such as servo-driven motors, pneumatic clamping, and automatic material feeding contribute to continuous and efficient operation, reducing cycle times. - Safety and Ergonomics
Modern Automatic Cutting Beading Machines come equipped with protective enclosures, emergency stop mechanisms, and sensor-based fault detection systems to enhance operator safety. Some models also feature touchscreen interfaces for easy operation and monitoring. - Customization and Modularity
Manufacturers can customize machines based on specific industry needs, including options for multi-stage processing, additional forming operations (such as flanging or curling), and robotic material handling systems. Modular configurations allow businesses to upgrade capabilities without replacing the entire machine.
Applications
- Metal Packaging: Used for manufacturing metal cans, lids, and containers.
- HVAC Industry: Produces ductwork with reinforced edges for durability.
- Automotive Sector: Forms structural components with precise beading for added strength.
- Construction: Creates metal roofing sheets and wall panels with enhanced rigidity.
- Aerospace: Manufactures lightweight but strong metal components for aircraft.
Future Trends
The latest advancements in AI-powered process optimization, IoT-enabled remote monitoring, and energy-efficient automation are shaping the next generation of Automatic Cutting Beading Machines. Future models will offer even greater precision, flexibility, and sustainability, ensuring their continued importance in modern manufacturing.
An automatic cutting beading machine is a highly efficient industrial tool designed to streamline metal processing by integrating precise cutting and beading functions into a single automated workflow. These machines are widely used in industries such as automotive, packaging, HVAC, aerospace, and construction, where precision, speed, and consistency are crucial for maintaining high production standards. By automating these processes, manufacturers can significantly reduce labor costs, minimize material waste, and ensure uniform quality across large production runs. The machine typically consists of a cutting system, a beading mechanism, and an advanced control interface, all working together seamlessly to enhance productivity. The cutting function employs high-speed rotary shears, guillotine cutters, or even laser and plasma cutting technology to create clean, accurate cuts on metal sheets or cylindrical components.
Automated feeding systems ensure a continuous flow of material, eliminating the need for manual handling and reducing processing time. After the cutting stage, the beading process forms a raised or recessed bead along the edges of the workpiece, reinforcing its structural integrity while improving its aesthetic appeal. This is particularly beneficial in manufacturing metal cans, ducts, automotive parts, and structural components where added strength and shape retention are essential. Modern machines are equipped with advanced programmable logic controllers (PLC) or computer numerical control (CNC) systems that allow operators to input specific dimensions, adjust bead depth, and control cycle times with high precision.
These digital interfaces ensure repeatability, allowing manufacturers to maintain consistent quality across multiple production batches. High-speed servo-driven motors and pneumatic clamping mechanisms contribute to efficiency by enabling faster cycle times and reducing downtime. Many machines are also designed with modular configurations, allowing for additional functionalities such as flanging, curling, or embossing, depending on the specific manufacturing needs. Safety is a key consideration in the design of automatic cutting beading machines, with protective enclosures, emergency stop mechanisms, and real-time sensor-based monitoring systems preventing accidents and ensuring smooth operation. Some models also incorporate AI-driven process optimization, enabling real-time adjustments based on material properties and production requirements, further enhancing efficiency.
The increasing adoption of IoT-enabled smart factory technology allows operators to monitor machine performance remotely, track production efficiency, and implement predictive maintenance strategies that help prevent unexpected breakdowns and extend the lifespan of critical components. With growing demands for energy-efficient and environmentally sustainable production methods, manufacturers are also developing machines with regenerative braking systems, eco-friendly lubricants, and energy-saving standby modes. The ability to work with a wide range of materials, including stainless steel, aluminum, galvanized steel, and other high-strength alloys, makes these machines highly versatile across various industrial applications. Looking ahead, the future of automatic cutting beading machines will likely involve further advancements in AI integration, enhanced automation, and increased adaptability for working with emerging materials and new manufacturing techniques. These innovations will ensure that manufacturers can continue to improve productivity while maintaining the highest standards of quality and sustainability in modern metal processing.
As automatic cutting beading machines continue to evolve, manufacturers are incorporating increasingly sophisticated technologies to enhance efficiency, precision, and adaptability. The integration of AI-driven algorithms allows these machines to analyze real-time production data, automatically adjusting parameters such as cutting speed, beading pressure, and material feed rate to optimize output. This reduces waste, minimizes errors, and ensures consistent quality across all production batches. Additionally, machine learning capabilities enable the system to predict wear and tear on cutting and forming tools, scheduling maintenance proactively to prevent downtime and extend the lifespan of critical components.
One of the key advancements in modern automatic cutting beading machines is the incorporation of servo-driven motors, which provide greater control over movement precision, allowing for intricate beading patterns and ultra-clean cuts. Unlike traditional mechanical systems that rely on fixed tooling adjustments, servo motors offer dynamic control, enabling quick transitions between different production requirements without extensive manual intervention. This flexibility is especially beneficial in industries that require a variety of component sizes and designs, such as HVAC duct manufacturing, where different beading profiles are needed for various duct configurations.
Automation has also improved material handling, with robotic arms and conveyor systems now working alongside these machines to further streamline production. Automated loading and unloading eliminate inconsistencies caused by human error while allowing for continuous operation with minimal operator supervision. The use of vision-based inspection systems further enhances precision by detecting any deviations in cutting or beading quality and making real-time corrections. These advanced sensors also help reduce material waste by identifying defective sections early in the production process, ensuring that only high-quality components move forward.
In response to the growing emphasis on sustainability, manufacturers are designing automatic cutting beading machines with energy-efficient components that minimize power consumption while maintaining high-performance standards. Regenerative braking systems capture and reuse excess energy, reducing overall electricity usage. Advanced lubrication systems are being developed to minimize oil consumption, with some machines incorporating self-cleaning mechanisms to maintain optimal performance with minimal environmental impact. Additionally, some manufacturers are exploring hybrid-powered machines that combine electric and pneumatic operations to further enhance energy efficiency.
The increasing adoption of smart factory principles and Industry 4.0 technologies has led to greater connectivity between automatic cutting beading machines and other equipment in the production line. IoT-enabled systems allow operators to remotely monitor machine status, track production metrics, and receive alerts for maintenance or process adjustments. Cloud-based data storage enables manufacturers to analyze long-term performance trends, optimizing workflow strategies for improved efficiency. The ability to integrate these machines with enterprise resource planning (ERP) and manufacturing execution systems (MES) ensures seamless coordination between production scheduling, inventory management, and quality control processes.
As industries demand more customization, manufacturers are developing modular automatic cutting beading machines that can be easily configured to meet specific requirements. Some machines now feature interchangeable tooling systems that allow operators to switch between different cutting and beading patterns with minimal downtime. This adaptability is particularly valuable in the metal packaging and aerospace sectors, where specialized components require precise and unique edge treatments. The ability to program and store multiple job profiles within a single machine further enhances productivity, reducing setup times and enabling high-mix, low-volume production without sacrificing efficiency.
With continuous advancements in software development, user interfaces are becoming more intuitive, making it easier for operators to program and control these machines. Touchscreen panels with graphical user interfaces (GUI) provide real-time visualizations of the cutting and beading process, allowing for quick adjustments as needed. Some machines even incorporate augmented reality (AR) support, enabling technicians to receive guided troubleshooting assistance through smart glasses or mobile devices. These innovations reduce the learning curve for new operators and improve overall machine usability.
Looking to the future, automatic cutting beading machines are expected to become even more autonomous, leveraging AI and deep learning to fully automate setup, production monitoring, and quality assurance. The integration of advanced materials, such as carbon fiber composites and next-generation metal alloys, will require further refinements in cutting and beading technology to maintain precision and efficiency. As manufacturers continue to push the boundaries of innovation, these machines will remain at the forefront of modern metalworking, ensuring higher productivity, superior product quality, and more sustainable manufacturing practices across multiple industries.
Trimming Beading Machine
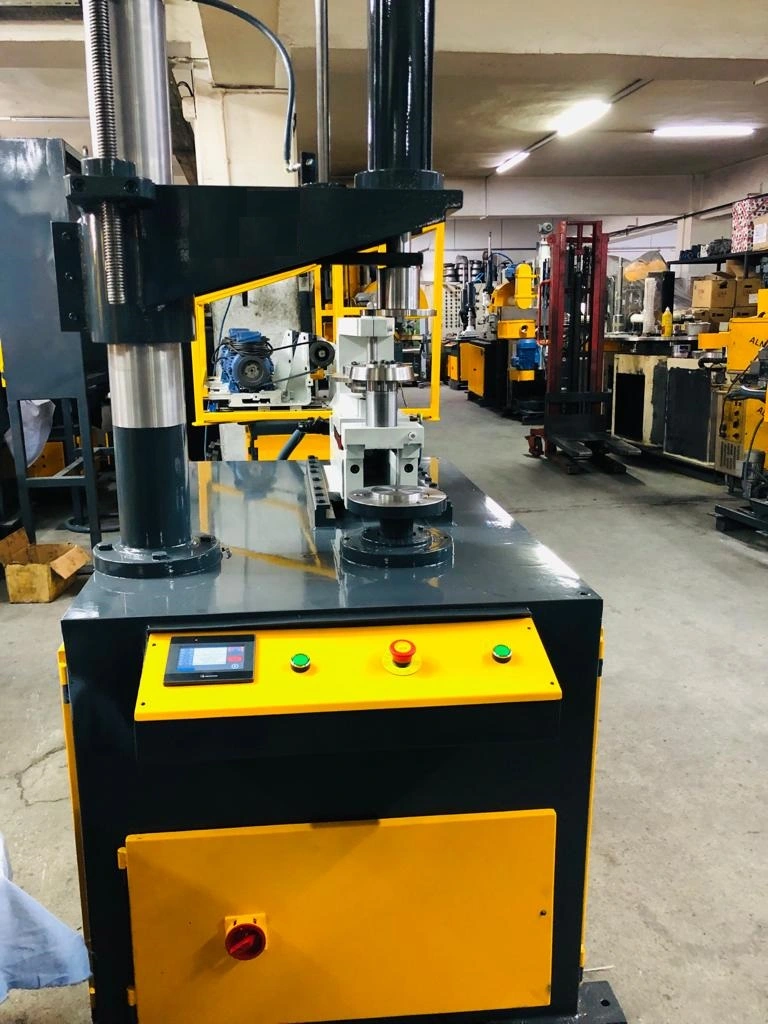
A Trimming Beading Machine is a specialized industrial machine used to refine the edges of metal components by trimming excess material and creating precise beaded reinforcements. These machines are commonly employed in industries such as packaging, automotive, HVAC, aerospace, and metal fabrication, where smooth, durable edges are essential for product quality, safety, and performance. By integrating trimming and beading functions into a single automated process, these machines enhance efficiency, reduce manual labor, and improve the consistency of finished parts.
The trimming function ensures that the edges of metal sheets, tubes, or cylindrical components are cleanly cut to precise dimensions, removing any irregularities or excess material that may result from previous manufacturing stages. This is particularly important in applications such as metal can production, where a perfectly trimmed edge is necessary for secure sealing. The beading function follows the trimming process, forming a raised or recessed reinforcement along the edge of the workpiece. This adds structural strength, prevents sharp edges, and enhances the component’s ability to withstand mechanical stress, making it especially useful in applications like HVAC ducts, automotive body panels, and metal enclosures.
Modern Trimming Beading Machines are equipped with servo-driven motors and programmable logic controllers (PLCs) to enable precise control over cutting and forming operations. These advanced systems allow operators to set exact trimming widths and beading depths, ensuring repeatable accuracy across large production runs. Some machines incorporate computer numerical control (CNC) technology, allowing for even greater customization of trimming and beading profiles to accommodate different material types and product specifications.
To improve production efficiency, these machines often feature automated feeding and clamping systems that securely hold workpieces in place while processing. This minimizes the risk of misalignment or inconsistencies in the final product. Additionally, robotic automation is increasingly being integrated into trimming beading systems to facilitate high-speed material handling, reducing the need for manual intervention and improving overall workflow.
Material versatility is a crucial advantage of modern trimming beading machines. They are designed to process a wide range of materials, including stainless steel, aluminum, carbon steel, galvanized sheets, and composite metals. Adjustable tooling and force control mechanisms enable the machine to handle varying material thicknesses without compromising precision.
Safety is a key focus in the development of these machines, with manufacturers incorporating protective enclosures, emergency stop mechanisms, and real-time fault detection systems to ensure safe operation. Many machines also feature sensor-based quality inspection systems, which monitor the trimming and beading process in real time, detecting any deviations and making automatic adjustments to maintain optimal results.
With advancements in Industry 4.0 and IoT connectivity, trimming beading machines are now capable of remote monitoring and predictive maintenance. Operators can access real-time production data through cloud-based platforms, track machine performance, and receive alerts for maintenance or troubleshooting. This proactive approach reduces unplanned downtime, extends the lifespan of machine components, and enhances overall production efficiency.
Sustainability is also a growing focus, with newer machines being designed for energy efficiency and minimal material waste. Features such as regenerative braking systems, optimized lubrication methods, and low-power standby modes contribute to reduced energy consumption while maintaining high-performance standards. Additionally, manufacturers are exploring eco-friendly lubricants and advanced cutting technologies that minimize scrap generation, aligning with sustainable manufacturing practices.
The future of trimming beading machines will likely involve even greater levels of automation, artificial intelligence (AI) integration, and enhanced material adaptability. AI-driven process optimization will enable machines to automatically adjust settings based on real-time material properties, further reducing human intervention and improving efficiency. As manufacturing demands evolve, these machines will continue to play a crucial role in high-precision metal processing, ensuring superior product quality, enhanced durability, and cost-effective production across multiple industries.
As trimming beading machines continue to evolve, manufacturers are focusing on increasing automation, precision, and adaptability to meet the demands of modern production environments. One of the most significant advancements in these machines is the integration of AI-driven process optimization, which enables real-time adjustments based on material properties and production conditions. By analyzing data from sensors and monitoring material flow, the machine can automatically fine-tune trimming widths, beading depths, and cutting speeds, ensuring optimal performance with minimal human intervention.
The use of servo-driven actuators and high-precision CNC systems has further enhanced the accuracy of trimming and beading operations. These advanced control systems allow for ultra-fine adjustments, making it possible to achieve consistent results even when working with delicate or complex metal components. In applications such as aerospace and automotive manufacturing, where precision is critical, these capabilities reduce defects and improve overall product quality. Additionally, modern trimming beading machines now feature adaptive force control mechanisms, allowing them to process a wider range of materials, including lightweight alloys and high-strength metals, without causing deformation or material stress.
To streamline production workflows, many machines now come equipped with robotic integration and automated material handling systems. Instead of relying on manual feeding and positioning, robotic arms or conveyor-driven loading systems can precisely place workpieces for processing, reducing cycle times and improving throughput. Vision-based inspection systems are also being incorporated into trimming beading machines, using high-resolution cameras and AI-powered analysis to detect inconsistencies in trimming quality and bead formation, making real-time corrections when needed.
Energy efficiency has become a crucial consideration in machine design, leading to the implementation of regenerative power systems, low-energy servo motors, and optimized cutting techniques that reduce electricity consumption while maintaining high processing speeds. Additionally, advancements in lubrication technology have led to the development of closed-loop lubrication systems, which minimize fluid waste and reduce environmental impact without compromising machine performance.
The introduction of IoT-enabled connectivity and smart factory capabilities is reshaping how manufacturers interact with trimming beading machines. These systems allow for remote monitoring, predictive maintenance, and seamless integration with manufacturing execution systems (MES) and enterprise resource planning (ERP) software. By collecting and analyzing real-time production data, manufacturers can optimize their operations, track machine health, and anticipate maintenance needs before they result in costly downtime.
As industries continue to demand greater flexibility, trimming beading machines are being designed with modular and customizable configurations. This means that operators can swap out tooling components or modify machine settings to accommodate different product designs without requiring significant reconfiguration. This level of versatility is particularly valuable in sectors such as HVAC, packaging, and custom metal fabrication, where product requirements can vary significantly between production batches.
Looking ahead, AI-powered automation, machine learning-driven predictive analytics, and even greater precision in cutting and beading technologies will drive the next generation of trimming beading machines. Manufacturers that adopt these innovations will benefit from improved production efficiency, reduced waste, and higher-quality output, ensuring they remain competitive in an increasingly automated and technology-driven industry.
The future of trimming beading machines is increasingly shaped by advancements in automation, precision engineering, and digital integration, allowing for smarter, more efficient, and highly adaptable production processes. One of the most notable developments is the incorporation of fully autonomous operation through AI and machine learning algorithms, which enable machines to self-optimize in real time based on sensor data and historical performance. These intelligent systems can analyze material characteristics, detect deviations in cutting or beading quality, and instantly adjust machine parameters to maintain optimal results. This not only reduces human intervention but also minimizes production defects, ensuring consistent, high-quality output.
In addition to AI-driven process optimization, advanced servo-motor technology is further enhancing the precision and speed of trimming and beading operations. Unlike traditional mechanical systems, servo-driven actuators allow for micro-level control over cutting forces and beading pressures, which is essential when working with lightweight alloys, composite materials, and ultra-thin metal sheets. This capability is especially crucial in industries such as aerospace, medical device manufacturing, and high-performance automotive engineering, where exact tolerances are required. Furthermore, real-time force feedback systems enable machines to dynamically adjust pressure and tool positioning based on material resistance, preventing over-processing and ensuring superior surface finishes.
To maximize efficiency, modern trimming beading machines are being designed with multi-stage processing capabilities, allowing for trimming, beading, curling, and edge forming to be performed in a single continuous operation. This eliminates the need for multiple machines or manual intervention between processes, significantly reducing cycle times and production costs. High-speed automatic tool changers further enhance flexibility, enabling machines to switch between different cutting and beading configurations without requiring manual adjustments, making them ideal for high-mix, low-volume production environments.
The integration of robotics and collaborative automation is also transforming the workflow around trimming beading machines. Automated robotic arms, conveyor systems, and vision-guided positioning systems ensure seamless material handling, reducing the risk of misalignment and inconsistencies in processing. These systems not only improve productivity but also enhance workplace safety by minimizing operator exposure to sharp edges and moving parts. Additionally, digital twin technology is gaining traction, allowing manufacturers to create virtual simulations of machine operations to optimize settings, predict maintenance needs, and test new configurations before making real-world adjustments.
Energy efficiency and sustainability continue to be major focal points, with the latest generation of trimming beading machines incorporating eco-friendly lubricants, energy-efficient servo systems, and reduced-material-waste technologies. Some models now feature adaptive power consumption, where energy usage dynamically adjusts based on the machine’s operational load, leading to significant reductions in overall power consumption. Additionally, the shift toward modular machine designs enables manufacturers to upgrade specific components rather than replacing entire machines, further reducing industrial waste and costs.
With the ongoing expansion of IoT and Industry 4.0, trimming beading machines are becoming increasingly interconnected within smart factory ecosystems. These machines can now communicate with enterprise-level manufacturing execution systems (MES), predictive maintenance platforms, and cloud-based monitoring systems, providing real-time production insights, performance analytics, and remote diagnostics. Operators can access data dashboards from anywhere, receive instant alerts for potential issues, and even implement remote troubleshooting, reducing downtime and maintenance costs.
As manufacturers demand even greater levels of customization and adaptability, trimming beading machines will continue to evolve, offering greater process automation, enhanced digital control interfaces, and compatibility with emerging materials. The use of adaptive AI learning models will enable machines to self-improve over time, refining processing techniques and reducing cycle times based on continuous data collection. These advancements will not only drive increased efficiency and cost savings but also open new possibilities for high-precision, lightweight, and structurally enhanced metal components across a broad range of industries.
Ultimately, trimming beading machines are set to become smarter, faster, and more energy-efficient, ensuring that manufacturers remain competitive in an era of rapid industrial transformation. As the industry moves toward fully automated, AI-optimized production lines, these machines will play a crucial role in shaping the future of precision metal processing, helping businesses achieve higher productivity, improved quality control, and more sustainable manufacturing practices.
Edge Curling Machine

An Edge Curling Machine is a specialized industrial machine designed to curl or form the edges of metal sheets, typically for applications that require a smooth, rounded, or reinforced edge. This process is often employed in industries like HVAC (heating, ventilation, and air conditioning), automotive, packaging, and construction, where components with curled edges are necessary for both aesthetic and functional purposes. The edge curling process involves bending the edges of a metal sheet or panel to create a rounded or curved lip, which not only improves the component’s appearance but also adds strength, rigidity, and safety.
Edge curling machines use various techniques, including roll forming, pressure forming, and mechanical curling methods, depending on the material, thickness, and desired curl radius. Typically, these machines work with stainless steel, aluminum, galvanized steel, and other sheet metals, although some models may also handle composite materials or plastics. The edge curling operation eliminates the need for further finishing or smoothing of the edges, reducing the need for secondary processes and improving overall production efficiency.
Key Functions and Features
- Curled Edges for Strength and Safety
One of the primary reasons for edge curling is to enhance the strength and safety of the metal components. In industries such as HVAC, edge curling helps create ducts with smooth, strong edges that are easier to assemble and handle. The curled edges also help prevent sharp edges that could pose safety risks during handling or installation. In packaging, edge curling ensures that metal cans and containers have smooth edges that can be easily sealed, preventing sharp, dangerous edges during the production process. - High Precision
Modern edge curling machines are designed for high precision, ensuring that the curled edges maintain consistent radius and shape across large production runs. Advanced control systems, such as Programmable Logic Controllers (PLC) or CNC systems, enable operators to set specific parameters for the curl radius, material feed rate, and force applied to the material, ensuring that each component meets exact specifications. - Automated Process
Edge curling machines often feature automated feeding systems, where sheets of metal are automatically loaded into the machine, aligned, and then processed. This automation reduces the need for manual intervention and ensures smooth, continuous operation. Servo motors and hydraulic systems are commonly used in these machines to ensure smooth and controlled curling, providing high accuracy and repeatability with minimal downtime. - Material Compatibility
Edge curling machines are versatile, capable of processing a range of materials from thin sheet metal to thicker gauges without compromising the integrity of the material. Adjustable tools and settings allow these machines to accommodate different thicknesses and material types, providing flexibility in production. The ability to work with various materials makes these machines useful across many sectors, including the automotive, construction, and HVAC industries. - Speed and Efficiency
These machines are designed for high-speed operation, allowing manufacturers to process large quantities of material quickly and efficiently. Edge curling machines are often integrated into larger production lines, reducing cycle times and improving throughput. They can also be configured for batch production or continuous processing, depending on the needs of the manufacturing operation. - Safety Features
Safety is a key consideration in the design of edge curling machines. Many models feature protective enclosures to shield operators from moving parts, along with emergency stop mechanisms and sensor-based monitoring systems that ensure the machine operates safely. Additionally, the design of the machines minimizes the likelihood of creating hazardous sharp edges, making the final product safer to handle and work with. - Customization Options
Many modern edge curling machines offer customization options that allow manufacturers to tailor the machine to specific production requirements. Features such as adjustable curl radii, different tooling options, and programmable settings give operators the flexibility to produce various types of curled edges depending on the application. - Maintenance and Durability
Edge curling machines are built to withstand continuous operation in demanding environments. They are designed with durable components and require minimal maintenance. Routine servicing may include lubrication of moving parts and occasional tool changes, depending on the volume of material processed.
Applications
- HVAC Industry: Edge curling is essential for forming ducts with smooth, rounded edges that are easy to assemble and secure.
- Metal Packaging: Cans, containers, and lids often require curled edges for sealing and to prevent sharp edges that could be hazardous during handling.
- Automotive: Components such as door panels, hoods, and trunks require edge curling for added rigidity, improved aerodynamics, and aesthetic appeal.
- Construction: Metal sheets for roofing, wall panels, and trim often use edge curling for improved strength and to create smooth, safe edges for installation.
Future Developments
The future of edge curling machines lies in further automation, energy efficiency, and integration with Industry 4.0 technologies. AI-powered systems that can optimize the curling process based on real-time data and material properties are becoming more common. Additionally, the use of robotics to handle material feeding and unloading will continue to reduce manual labor, enhance productivity, and improve safety. As sustainability becomes increasingly important, manufacturers are focusing on reducing energy consumption and waste in edge curling operations, contributing to greener manufacturing practices.
Overall, edge curling machines play a critical role in improving the functionality, safety, and aesthetic quality of metal products across various industries. Their evolution will continue to focus on precision, speed, and automation, making them indispensable in modern manufacturing.
As edge curling machines continue to evolve, smart manufacturing technologies are becoming a significant focus. The integration of IoT (Internet of Things) connectivity allows edge curling machines to seamlessly communicate with other machines in the production line, as well as with central monitoring systems. This enables operators to track the status of the machine in real-time, remotely troubleshoot issues, and receive predictive maintenance alerts. The data generated by these machines can be analyzed to optimize production schedules, improve machine utilization, and reduce unplanned downtime.
With the rise of Industry 4.0, edge curling machines are becoming increasingly data-driven, incorporating sophisticated analytics and AI tools that allow for continuous improvement. These systems analyze historical production data and adjust settings based on trends, material changes, or environmental factors. This adaptability improves the quality and consistency of the curled edges while reducing material waste and minimizing energy usage. Over time, these systems will further enhance machine learning capabilities, allowing machines to “learn” from past operations, reducing the need for manual adjustments and fine-tuning.
Another emerging trend is the incorporation of automated defect detection systems. High-resolution cameras and sensors, often integrated into edge curling machines, can monitor the curling process in real-time. These systems use computer vision and AI algorithms to detect defects such as incomplete curls, variations in edge radius, or inconsistencies in material thickness. When deviations are detected, the system can alert the operator or make real-time adjustments to ensure the quality of the final product. This integration ensures that only parts meeting stringent specifications proceed through the production line, improving overall efficiency and product quality.
As manufacturers strive to increase sustainability in their operations, edge curling machines are being designed to operate more energy-efficiently. Newer models are equipped with energy-saving motors, regenerative braking systems, and intelligent power management features that reduce electricity consumption during the curling process. Additionally, advancements in lubrication systems are also contributing to more sustainable operations by minimizing waste and reducing the frequency of required maintenance. Manufacturers are increasingly considering these features when selecting equipment, as reducing energy consumption and material waste aligns with both cost-saving initiatives and environmental goals.
The adaptability of edge curling machines will continue to grow as more manufacturers seek flexibility in their production lines. Modular machine designs are gaining popularity, allowing for quick reconfiguration of the machine to accommodate different metal types, material thicknesses, or edge profiles. This ability to easily switch between different product configurations means that edge curling machines can support a wider variety of industries, from mass production to highly customized, small-batch runs. Tooling innovations also contribute to this adaptability by enabling faster changeover between different edge profiles, reducing downtime and increasing operational efficiency.
Finally, the user interface (UI) of edge curling machines is evolving as well. The traditional mechanical interfaces are being replaced with intuitive touchscreen panels that provide operators with easy access to real-time production data, machine settings, and diagnostics. Some machines now offer augmented reality (AR) interfaces, where operators can use smart glasses or mobile devices to view machine settings and operational parameters superimposed over the physical machine, further enhancing operational efficiency and ease of use. These advanced interfaces allow for quicker training of new operators, helping to streamline workforce deployment in fast-paced production environments.
In conclusion, as edge curling machines continue to integrate cutting-edge technologies, they will become even more efficient, flexible, and connected, enabling manufacturers to meet growing demands for higher precision, faster turnaround times, and greater sustainability. By embracing automation, AI, and IoT, edge curling machines will continue to play a crucial role in a wide range of industries, contributing to smarter, more streamlined manufacturing processes.
As edge curling machines evolve, their capabilities are expanding to cater to more complex applications and evolving market needs. One of the most notable trends is the ongoing development of advanced materials processing. Manufacturers are increasingly working with high-strength alloys, advanced composites, and lightweight materials that require specialized handling during the edge curling process. Edge curling machines are now being designed with enhanced force control systems, which allow them to adjust the applied curling pressure based on the material type and thickness. This enables the machine to handle a broader spectrum of materials without compromising the integrity of the edges. These advancements are particularly important in industries such as aerospace, where lightweight yet durable metal components with curled edges are critical to reducing overall vehicle weight while maintaining strength and safety standards.
Advanced Automation and Robotics Integration
Automation is set to be a defining feature of next-generation edge curling machines. The integration of robotic systems with edge curling technology is making the manufacturing process faster and more accurate. Robotic arms are being used to handle the material before and after it passes through the curling machine, ensuring that components are loaded and unloaded quickly and accurately. This integration reduces the risk of human error, improves safety by minimizing operator involvement in the material handling process, and boosts productivity. Robotic systems also allow for multi-tasking, where multiple processes, such as material feeding, edge curling, and stacking, can occur simultaneously, further reducing production time and increasing throughput.
Vision-based systems are also playing a larger role in the automation of edge curling machines. These systems use high-resolution cameras and image processing software to monitor the curling process, detecting any material misalignment, edge defects, or inconsistencies during production. If an issue is identified, the machine can either stop automatically for inspection or adjust the operation in real-time to maintain quality standards. This level of self-monitoring not only ensures the accuracy of each edge but also helps in identifying defects early in the process, reducing scrap and improving overall efficiency.
Customizable Production and Multi-Functionality
Manufacturers are seeking more customizable production capabilities in edge curling machines, allowing for flexibility in their manufacturing processes. These machines are now increasingly being equipped with modular toolsets, allowing for rapid configuration changes. This flexibility is essential in industries where product designs change frequently, or when manufacturers need to switch between different metal types, material thicknesses, or specific edge profiles. For example, HVAC duct manufacturers might need to quickly shift between producing round, oval, or rectangular ductwork with curled edges without requiring extensive downtime for reconfiguration.
Furthermore, some advanced machines are becoming more multi-functional, capable of performing several processes in one machine. These capabilities include curling, edge forming, beading, and trimming, all performed in a single operation without the need for additional machines. The benefits are clear: reduced floor space, fewer handling errors, lower energy consumption, and faster production times.
Sustainability and Waste Reduction
In line with the growing emphasis on sustainability, edge curling machines are also evolving to become more eco-friendly. The drive toward zero waste in manufacturing is prompting companies to invest in systems that optimize material usage. Edge curling machines now feature advanced scrap management systems that capture and recycle metal shavings, minimizing waste. Some machines are also designed to minimize the amount of material required to create the curled edge, cutting down on material consumption without compromising the strength or appearance of the final product.
In addition to waste reduction, many edge curling machines are incorporating energy-efficient designs. These machines are being built with low-energy drive systems and intelligent power-saving modes that adjust energy consumption based on the machine’s workload. Some models feature regenerative braking systems that recover energy during machine operation, further reducing energy consumption and making the overall production process more sustainable.
Increased Precision and Tight Tolerances
As industries demand increasingly precise parts, edge curling machines are being designed to deliver tighter tolerances. Laser-guided alignment systems and precision mechanical components are enabling these machines to create edges with incredibly tight radii and minimal deviation from the specified dimensions. This level of precision is especially important in industries such as aerospace, medical device manufacturing, and electronics, where even the smallest edge imperfection can result in product failure or safety issues. The ability to maintain high precision across long production runs means that manufacturers can produce large batches of components with uniform quality.
Additionally, the integration of advanced simulation software allows manufacturers to simulate the edge curling process digitally before physical production begins. By analyzing the material flow, the pressure distribution, and the resulting curl geometry in the simulation, operators can optimize machine settings for the most efficient and precise results. This reduces the need for trial and error in the physical production process, speeding up time to market and enhancing product consistency.
Future Outlook
Looking forward, edge curling machines will continue to be an essential part of metal fabrication and manufacturing processes. Their increasing automation, energy efficiency, and adaptability will enable manufacturers to meet the growing demands for precision and efficiency across various industries. As manufacturers continue to push the boundaries of material science, edge curling machines will evolve to handle even more complex materials, such as smart metals, high-performance alloys, and composite materials.
Additionally, with the rise of 3D printing and additive manufacturing, there may be a future overlap between these technologies and edge curling, creating opportunities for further innovations in edge processing. While edge curling machines are likely to remain the primary solution for high-volume metal edge finishing, we may see the integration of hybrid systems that combine traditional edge curling with additive manufacturing or laser-based technologies, offering manufacturers more flexibility and new ways to process metal edges.
Overall, edge curling machines will continue to evolve as a critical part of the industrial landscape, driving efficiencies, quality, and sustainability while helping manufacturers meet the challenges of a more dynamic and technologically advanced production environment.
Trimming Joggling Machine
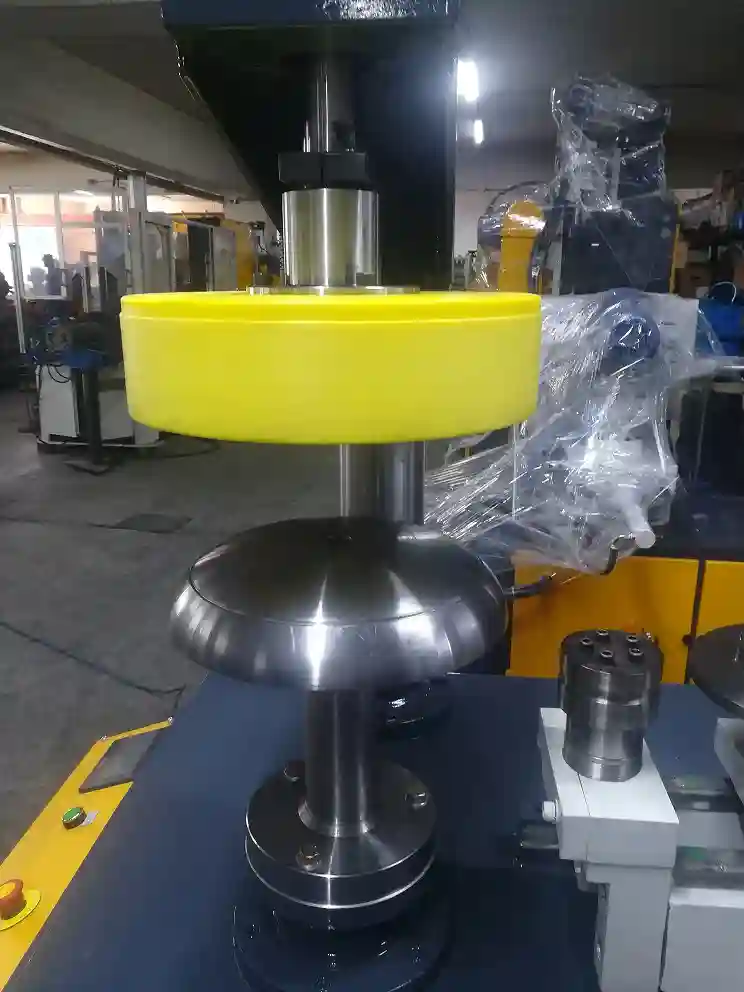
A Trimming Joggling Machine is a specialized industrial machine used in sheet metal fabrication for trimming edges and creating joggle joints. This machine performs two primary functions: trimming the edges of metal sheets or panels to precise dimensions, and joggling, which involves creating a step-like offset in the edge of the sheet. These processes are commonly used in industries like automotive, aerospace, HVAC, and construction, where precise metalworking is essential for both functional and aesthetic purposes.
Key Functions of a Trimming Joggling Machine
- Trimming
Trimming refers to the process of cutting excess material from the edges of a sheet to ensure it meets the required size or shape. This is especially important for sheets that have been cut from larger rolls or stock materials. Trimming machines ensure that the edges are smooth and meet the precise specifications for further manufacturing steps. The machine typically uses rotary cutters, blades, or saws to trim the material. - Joggling
Joggling is the process of creating a stepped offset along the edge of a metal sheet. This is usually done to allow for easy joining of two metal pieces. The joggle is often used in situations where a seam or joint must fit tightly or interlock, such as in sheet metal roofing, automotive parts, or ductwork. The joggle allows two pieces to fit snugly together, providing added strength and a cleaner appearance for the final product.
Components and Mechanisms
Trimming jiggling machines typically consist of several key components that work together to ensure accurate processing:
- Feed System: The sheet metal is fed into the machine via rollers or conveyors. The feed mechanism ensures that the metal sheet is positioned accurately, allowing for precise trimming and joggling operations.
- Cutting Blades or Rotary Tools: The trimming section uses high-speed rotary cutters or fixed blades to trim the edges of the sheet metal to the required dimensions. The cutting tools are designed to minimize material deformation and ensure a clean, smooth edge.
- Joggling Mechanism: The joggle is created by a punch and die set or a step-forming roller that presses or bends the metal at precise intervals to create the step-like offset. The joggle can vary in depth, length, and angle depending on the design requirements.
- Control Systems: Modern trimming joggling machines are equipped with CNC (Computer Numerical Control) or PLC (Programmable Logic Control) systems that allow operators to set specific parameters for the trimming and jiggling processes. These systems can control feed rates, cutting speeds, and the depth of the joggle, ensuring high precision in the final product.
Benefits and Applications
- Precision and Consistency
Trimming joggling machines are designed to deliver high precision in trimming and joggle formation. The use of CNC technology and servo-driven motors ensures that each part is processed consistently, reducing the chances of human error and variations in size or shape. - Time and Labor Savings
The automation of trimming and jiggling processes reduces the need for manual labor and minimizes the risk of errors. This results in faster production times and lower labor costs, especially in high-volume manufacturing environments. - Cost Efficiency
By combining trimming and jiggling into a single machine, manufacturers can save on equipment and floor space. This integrated process reduces the need for multiple machines and steps, which can lower overall production costs. - Versatility
Trimming joggling machines are highly adaptable and can be used to process a variety of sheet metal types, including stainless steel, aluminum, and galvanized steel. They can also be adjusted to handle different material thicknesses, allowing manufacturers to work with a wide range of products. - Durability and Reliability
These machines are built to handle the stresses of continuous production, with robust frames, high-quality cutting tools, and heavy-duty motors. This ensures long-term durability and reliable performance, even in high-volume operations.
Industries and Applications
- Automotive Industry: In automotive manufacturing, trimming joggling machines are used to create precise edge finishes and joints for body panels, chassis components, and other metal parts. The joggle helps ensure tight fits for welded or riveted joints, improving the strength and durability of the final assembly.
- Aerospace: Aerospace manufacturers rely on trimming joggling machines for creating parts that require both precise edge trimming and strong, reliable joints. The ability to create uniform joggle joints is essential for maintaining structural integrity and safety in aerospace components.
- HVAC: In the HVAC industry, trimming joggling machines are used to create ductwork and other metal components that require precise, interlocking joints. The joggle ensures that the edges of the metal sheets fit securely during the assembly of ducts and other HVAC systems, helping to improve airflow efficiency and reduce leaks.
- Construction: Trimming joggling machines are used in the construction industry for creating metal roofing panels, wall cladding, and other building components. The joggle ensures that the metal pieces fit together tightly and securely, enhancing the structural integrity of the building.
- Sheet Metal Fabrication: Trimming joggling machines are widely used in custom sheet metal fabrication shops where parts are made for a variety of applications. The ability to create both precise edge trims and strong, interlocking joints makes the machine ideal for producing custom metal parts for different industries.
Future Trends
As with many other industrial machines, trimming joggling machines are becoming increasingly automated and digitally integrated. Industry 4.0 technologies, such as smart sensors, IoT connectivity, and data analytics, are being incorporated into these machines to enable real-time monitoring and predictive maintenance. This will help improve machine performance, reduce downtime, and optimize production processes.
Furthermore, energy efficiency is becoming a more critical factor in machine design. Manufacturers are focusing on reducing power consumption by integrating low-energy components, such as servo motors and intelligent control systems, to minimize energy waste during operation.
Conclusion
Trimming joggling machines are indispensable in the metalworking industry, offering efficient, precise, and versatile solutions for edge trimming and joint creation. By integrating advanced technologies such as CNC control and automation, these machines provide manufacturers with the ability to streamline production, reduce waste, and produce high-quality metal components that meet strict industry standards. As manufacturing processes continue to evolve, trimming joggling machines will play a key role in advancing precision metalworking and meeting the demands of industries ranging from automotive and aerospace to construction and HVAC.
As trimming joggling machines continue to evolve, there is a growing emphasis on integration with larger manufacturing systems. The move towards fully automated production lines means trimming joggling machines are increasingly becoming part of a connected ecosystem, where they can exchange data and operate in harmony with other machines on the production floor. This integration not only optimizes production flow but also enhances overall supply chain efficiency by allowing manufacturers to track and control every step of the production process in real time.
Incorporation of AI and Machine Learning
Another area where trimming joggling machines are advancing is the incorporation of artificial intelligence (AI) and machine learning. These technologies can be used to improve the precision of the joggle and trimming processes. AI algorithms can learn from past production data and optimize machine settings based on historical performance, material types, and other variables. For example, a machine could adjust its operation to compensate for slight variations in metal thickness or density, ensuring a consistent result even when materials are less uniform. This leads to higher quality control and a more reliable end product with minimal human intervention.
Additionally, AI can be used to predict when a machine will require maintenance, thus preventing unexpected downtime. By analyzing patterns in machine performance, AI can identify early warning signs of potential issues, such as tool wear or motor malfunctions, and alert operators to perform maintenance before the problem escalates. This helps in reducing unplanned stoppages and maintaining a smooth, continuous production process.
Enhanced Safety Features
In line with the advancements in automation, modern trimming joggling machines are also becoming safer for operators. Safety sensors, automated shutdown systems, and protective covers are integrated into these machines to ensure a safer working environment. For example, light curtains or infrared sensors can be used to detect the presence of an operator or obstruction in the machine’s path, automatically stopping the machine to prevent injury.
Furthermore, with the increase in automated material handling, robots or robotic arms are being employed to load and unload metal sheets, minimizing the physical interaction between operators and the machines. This not only reduces the likelihood of accidents but also reduces the amount of manual labor required, freeing up employees to focus on higher-level tasks.
Sustainability and Eco-friendly Design
The shift towards sustainable manufacturing practices is another area driving innovation in trimming joggling machines. Manufacturers are increasingly focusing on reducing the environmental impact of their operations, and trimming joggling machines are no exception. New models are designed to be more energy-efficient, with low-power motors, heat recovery systems, and efficient hydraulic systems that reduce overall energy consumption.
Moreover, trimming joggling machines are also becoming more eco-friendly by incorporating recyclable materials in their construction. The adoption of materials such as aluminum and high-strength steel in the machine frames helps lower the machine’s carbon footprint while maintaining durability and performance. These eco-conscious designs contribute to meeting sustainability goals and improving a company’s corporate social responsibility (CSR) standing.
Customization and User-Friendly Interfaces
Trimming joggling machines are increasingly being designed with a focus on user customization and ease of operation. While the core functionality of trimming and joggling remains the same, manufacturers are offering more customizable options for operators. Modern machines come with touchscreen interfaces that allow operators to easily adjust settings like cutting depth, joggle dimensions, and material feed rates. These interfaces often feature intuitive controls, real-time monitoring displays, and simple diagnostic tools that help operators quickly detect and resolve any issues that may arise during production.
Customization extends to the machines’ ability to handle different types of materials and part geometries. Some machines are now designed to process a wider range of materials beyond standard metals, including advanced alloys, composite materials, and even some plastics. This adaptability allows manufacturers to serve a broader range of industries and better respond to changes in customer demands.
Maintenance and Downtime Reduction
Reducing machine downtime and enhancing machine longevity is another area where trimming joggling machines have seen significant improvements. Modern machines are designed for easy maintenance, with features like self-lubricating systems that minimize the need for regular maintenance and modular components that can be quickly swapped out for replacements. Additionally, machine parts are becoming more durable, and wear-resistant materials are being used for cutting blades and joggle tools to extend the life of critical components.
The growing use of remote diagnostics and predictive maintenance is further reducing downtime. With cloud-based systems, machine data is continuously monitored, and maintenance teams can access performance reports remotely. This allows for more precise maintenance planning, ensuring that issues are addressed before they lead to breakdowns, significantly reducing the overall cost of ownership and improving production efficiency.
Looking Ahead: The Future of Trimming Joggling Machines
As the manufacturing industry embraces digital transformation, trimming joggling machines are poised to play an even more important role in high-precision metalworking. The continued development of smart manufacturing solutions will result in machines that are not only more automated but also more adaptable, intelligent, and connected.
The future of trimming joggling machines lies in full integration with Industry 4.0 technologies, where real-time data exchange between machines, operators, and central control systems will become standard practice. As part of this transformation, trimming joggling machines may also become integral parts of digital twins — virtual replicas of physical systems that enable manufacturers to simulate and optimize operations.
Further advances in robotic automation, artificial intelligence, and machine learning will allow trimming joggling machines to handle even more complex tasks, making them even more versatile. The continued focus on sustainability and energy efficiency will make these machines more eco-friendly while ensuring that manufacturers can meet rising environmental standards.
In conclusion, trimming joggling machines are becoming increasingly advanced, featuring cutting-edge technology that improves efficiency, precision, and safety. As the demand for more complex metal components grows across industries, these machines will continue to evolve, providing manufacturers with the tools they need to stay competitive in a rapidly changing market.
As trimming joggling machines continue to evolve, the focus on increasing automation, integration, and flexibility is shaping the future of these machines. One major aspect of this evolution is the continuous improvement in machine connectivity and the use of smart technologies that enable trimming joggling machines to function as part of an integrated and autonomous production line.
Smart Manufacturing and Machine Connectivity
The advent of IoT (Internet of Things) and smart factory solutions is a game-changer for trimming joggling machines. By integrating IoT sensors, these machines can communicate with other equipment on the shop floor, creating a networked environment where machine performance can be continuously monitored and optimized. Real-time data such as cutting speed, material type, and machine temperature can be sent to centralized systems, allowing operators to make adjustments on the fly to maximize efficiency.
These systems can also alert operators to potential issues before they lead to machine downtime. For example, IoT-enabled sensors can detect vibrations or temperature fluctuations that might indicate tool wear or misalignment, triggering automatic corrections or sending alerts to maintenance teams. This predictive approach helps avoid costly downtime and ensures the machine operates at peak efficiency.
Moreover, data gathered from the trimming joggling machines can be stored in the cloud, enabling manufacturers to use advanced data analytics and AI algorithms to further optimize production schedules, material usage, and machine performance. This level of data-driven insight allows manufacturers to gain a comprehensive view of their operations, helping to drive decisions that reduce waste, improve throughput, and enhance product quality.
Customization for Complex Part Geometries
The future of trimming joggling machines will also see greater customization capabilities to handle increasingly complex part geometries. With advancements in CNC (Computer Numerical Control) and servo-motor technology, these machines can be programmed to handle a wider variety of shapes and forms, accommodating more complicated edge profiles and specialized joggle configurations. This flexibility will be crucial for industries like aerospace, medical device manufacturing, and automotive design, where parts often require intricate, precise contours and joint configurations.
For instance, trimming joggling machines could be designed to perform multi-axis movements, allowing for greater flexibility in processing curved or angular metal sheets. This would allow manufacturers to produce components with complex edge profiles in a single operation, further reducing handling time and material waste. Additionally, advancements in laser technology could allow machines to add finishing touches to edges or create fine details after the joggle process, making the overall production process more streamlined and precise.
Greater Focus on Precision and Tolerance Control
As industries demand higher precision, trimming joggling machines are evolving to meet these stringent requirements. In the future, nano-level precision may become more common, where the machines are capable of achieving extremely tight tolerances on both the trimmed edges and joggle step offsets. This is particularly important in fields like medical equipment and electronics manufacturing, where even minute deviations from specification can result in poor product performance or failure.
Innovative features like adaptive cutting systems will allow trimming joggling machines to automatically adjust their parameters based on real-time feedback, ensuring that each edge or joggle is produced to the exact specifications, regardless of material type, thickness, or environmental conditions. This continuous feedback loop ensures that even in high-volume production settings, the final products will maintain consistently high levels of precision.
Energy-Efficient Designs and Sustainability
As the push for sustainability in manufacturing grows, trimming joggling machines are increasingly incorporating green technologies to reduce energy consumption and minimize environmental impact. Future machines will likely feature energy-saving drives, intelligent power management, and regenerative braking systems that allow the machines to capture and reuse energy during operations, cutting down on overall power usage. This could lead to significant savings in energy costs for manufacturers, as well as a reduced carbon footprint for the industry as a whole.
Moreover, the use of recyclable components and environmentally friendly lubricants is expected to increase in trimming joggling machines. The machines themselves could be constructed from more sustainable materials, and there may be an increased focus on reducing material waste during the trimming and jiggling processes. For example, advanced cutting tools and precision die technology could be designed to generate less scrap material, improving the efficiency of raw material usage.
Reduced Setup Times and Increased Automation
The future of trimming joggling machines will also be marked by the ability to automatically adjust to different product specifications without extensive manual setup. With the use of automated tool changers, quick-change dies, and self-calibrating systems, manufacturers will be able to switch between different part types and specifications with minimal downtime. This automation allows for quick responses to fluctuating customer demands and changes in production schedules, ensuring that manufacturers can remain flexible while maintaining high levels of productivity.
Furthermore, with the growth of robotic automation in production lines, trimming joggling machines will increasingly be integrated with robotic arms and automated material handling systems. These robots will be able to feed metal sheets into the machine, remove finished parts, and move them to the next stage of production, all without human intervention. By linking these systems to an Industry 4.0-compliant network, trimming joggling machines will operate as part of an entirely automated, interconnected production environment, improving throughput, reducing manual errors, and cutting labor costs.
Integration with Augmented Reality (AR) for Operator Assistance
Another trend that could reshape the operation of trimming joggling machines is the integration of augmented reality (AR) technology. Using AR glasses or smart screens, operators could receive real-time guidance and visual cues for machine setup, operation, and troubleshooting. For example, AR could display a virtual overlay showing the current position of the joggle tool or indicate where adjustments are needed to ensure the right depth or angle for a specific part. This could make machine operation more intuitive, even for less experienced operators, and reduce the risk of human error.
AR could also be used for training purposes, allowing new employees to learn how to operate the machine with interactive instructions and simulations, speeding up the learning process and reducing the need for hands-on training with actual machines.
Future Materials Compatibility
As new materials continue to emerge in various industries, trimming joggling machines must adapt to handle these advanced materials. Future machines may be designed to process composite materials, lightweight alloys, or nanomaterials that are becoming more common in sectors like aerospace and automotive. These materials often require specific processing techniques and different force dynamics, which means the machines will need to incorporate variable pressure systems, custom tool configurations, and heat management features to accommodate the unique properties of these materials.
Additionally, as additive manufacturing (3D printing) continues to advance, there may be opportunities to integrate trimming joggling capabilities with 3D-printed metal components, offering even more flexibility in creating customized parts directly from digital designs.
Conclusion
The future of trimming joggling machines is marked by increasing automation, precision, and connectivity, alongside growing demands for sustainability and material adaptability. With the continued advancement of technologies like AI, IoT, robotic automation, and AR, these machines are becoming more integrated into the smart manufacturing environment, offering greater efficiency, flexibility, and customization.
As industries continue to push for higher quality standards and more complex product designs, trimming joggling machines will play an essential role in helping manufacturers meet these challenges. The ongoing evolution of these machines will not only streamline the manufacturing process but also enable manufacturers to stay competitive in a rapidly changing global market.
Edge Cutting Trimming Beading Curling Machine
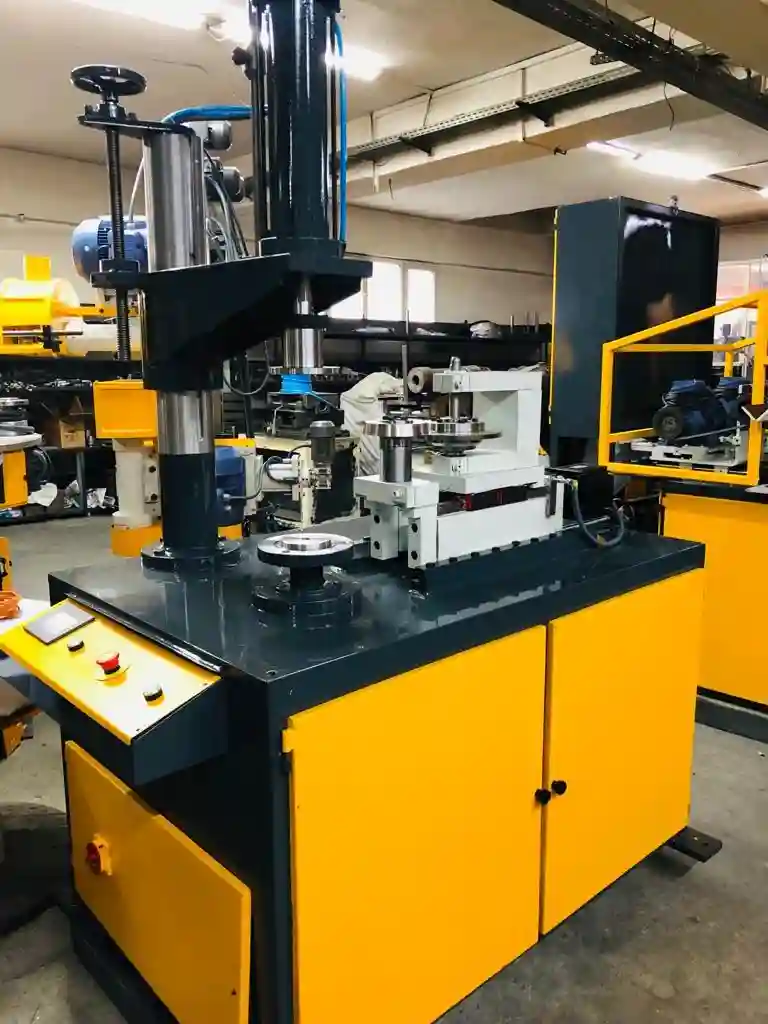
An Edge Cutting Trimming Beading Curling Machine is a highly specialized piece of equipment designed for metalworking and sheet metal fabrication, widely utilized across industries such as automotive, aerospace, cookware manufacturing, and construction. This versatile machine combines multiple functions into a single unit, allowing manufacturers to efficiently cut, trim, bead, and curl the edges of sheet metal components with precision and consistency. Its ability to perform these tasks in an integrated manner makes it an invaluable asset in production lines where edge finishing is critical for both functional and aesthetic purposes.
The primary function of the machine begins with edge cutting, a process that involves removing excess material from the edges of a sheet metal workpiece. This step ensures that the dimensions of the component are uniform and free from irregularities, preparing it for subsequent operations. The cutting mechanism typically employs high-strength blades, often made of materials like tungsten carbide, which are designed to retain sharpness and durability even under continuous use. These blades rotate at high speeds, slicing through materials such as stainless steel, aluminum, or mild steel with ease, depending on the machine’s configuration and the thickness of the workpiece.
Following the cutting process, the trimming function comes into play. Trimming refines the cut edge by eliminating any remaining imperfections, such as burrs or uneven surfaces, resulting in a smooth and clean finish. This is often achieved using a series of rollers or dies that press against the edge of the metal, removing a precise amount of material. The rollers or dies are typically constructed from wear-resistant materials like hardened steel, ensuring longevity and consistent performance. Trimming is a crucial step in preparing the edge for further forming processes, as it enhances both the safety and quality of the final product by eliminating sharp or jagged edges.
The beading process is another key feature of this machine. Beading involves forming a raised edge or bead along the perimeter of the sheet metal component. This not only improves the structural integrity of the piece by adding rigidity but also enhances its visual appeal. Beading is particularly useful in applications where the component needs to withstand mechanical stress or where a mounting surface is required, such as in the assembly of cookware or automotive panels. The machine accomplishes this by guiding the metal through specially designed rollers or dies that shape the edge into the desired profile, with the process being adjustable to accommodate different bead sizes and shapes based on the project’s requirements.
Curling, the final major function of the Edge Cutting Trimming Beading Curling Machine, involves rolling the edge of the sheet metal into a rounded or cylindrical shape. This process serves multiple purposes: it eliminates sharp edges for safety, reinforces the edge to prevent deformation, and provides a polished, professional finish. Curling is especially common in the production of items like pots, pans, and containers, where a smooth, rounded edge is essential for both usability and appearance. The curling operation is typically performed using a rotating tool or die that presses against the edge, gradually forming it into the desired curvature. The speed and pressure of this tool are carefully controlled—often by servo motors and programmable logic controllers (PLCs)—to avoid damaging the material, particularly when working with metals of varying yield strengths.
The machine’s versatility extends to its ability to handle a wide range of materials and thicknesses, from thin aluminum sheets to thicker steel plates. This adaptability is made possible by adjustable tooling and advanced control systems that allow operators to fine-tune the cutting, trimming, beading, and curling processes to suit specific applications. Modern versions of these machines often incorporate automation and CNC (Computer Numerical Control) technology, which enhances precision and repeatability while reducing the need for manual intervention. Servo-driven systems ensure accurate positioning and speed, while sensors monitor parameters like tool wear and workpiece temperature, enabling real-time adjustments for optimal results.
In practical use, the Edge Cutting Trimming Beading Curling Machine is a time-saving solution that streamlines what would otherwise be a series of separate operations. For example, in the cookware industry, a stainless steel blank might be cut into a circular shape, trimmed to remove excess material, beaded to reinforce the rim, and curled to create a safe, finished edge—all within a single machine cycle. This efficiency not only boosts productivity but also reduces labor costs and material waste, making it an economically sound choice for manufacturers.
Safety is a critical consideration when operating this machine. Operators are required to wear personal protective equipment such as safety glasses and gloves to shield against flying debris and noise. The workpiece must be securely clamped to prevent movement during processing, and the machine’s speed must be moderated to avoid overheating or tool damage. Regular maintenance, including blade sharpening and component inspection, is essential to ensure consistent performance and longevity.
Industries that rely on this machine benefit from its ability to produce high-quality components with minimal post-processing. In automotive manufacturing, it’s used to shape and finish parts like fenders and body panels. In aerospace, it helps fabricate lightweight, durable components for aircraft. In the production of kitchenware, it creates pots, pans, and lids with smooth, reinforced edges. Even in construction, it’s employed to form metal panels and fittings that require precise edge profiles.
Overall, the Edge Cutting Trimming Beading Curling Machine represents a pinnacle of metalworking technology, blending functionality, precision, and efficiency into a single, robust package. Its multi-faceted capabilities make it an indispensable tool for modern manufacturing, where the demand for high-quality, well-finished metal components continues to grow. Whether used in small-scale workshops or large industrial facilities, this machine delivers reliable results that meet the rigorous standards of today’s production environments.
Continuing from where we left off, the Edge Cutting Trimming Beading Curling Machine’s design and engineering reflect years of innovation aimed at meeting the evolving needs of industrial fabrication. Its construction typically involves a sturdy frame, often made of welded steel or cast iron, to withstand the vibrations and forces generated during operation. This robust foundation ensures stability, which is critical when processing heavy or thick materials at high speeds. The frame also houses the machine’s core components—such as the motor, gearbox, and tooling stations—arranged in a modular layout that facilitates maintenance and upgrades.
The power system of the machine is another area of sophistication. Most models are equipped with electric motors, ranging from a few horsepower in smaller units to significantly higher capacities in industrial-grade versions. These motors drive the cutting blades, trimming rollers, and forming dies through a series of belts, pulleys, or direct-drive mechanisms. Advanced machines may use variable frequency drives (VFDs) to regulate motor speed, allowing operators to adjust the pace of each operation based on the material being worked on. For instance, softer metals like aluminum might require faster cutting speeds, while tougher alloys like titanium demand slower, more controlled movements to avoid excessive wear on the tools.
Tooling is a defining feature of the Edge Cutting Trimming Beading Curling Machine, with each function relying on specialized attachments. The cutting blades, as mentioned earlier, are engineered for sharpness and durability, but their design can vary—some are straight-edged for clean cuts, while others are serrated for specific textures or materials. Trimming tools often consist of paired rollers that sandwich the metal edge, applying even pressure to smooth it out. Beading and curling, meanwhile, rely on contoured dies or wheels that shape the metal progressively as it passes through. These tools are typically interchangeable, allowing the machine to be reconfigured for different tasks without requiring a complete overhaul.
One of the standout advantages of this machine is its capacity for customization. Manufacturers can specify the dimensions of the worktable, the range of material thicknesses it can handle, and even the complexity of the edge profiles it produces. For example, a machine destined for a cookware factory might be optimized for circular blanks with tight curling radii, while one for an automotive plant might prioritize larger, flat panels with subtle beading. This flexibility is enhanced by digital interfaces in modern models, where operators can input parameters like edge width, bead height, or curl diameter via a touchscreen or computer terminal. Such precision reduces trial-and-error, ensuring that production runs are consistent from the first piece to the last.
The integration of automation into these machines has revolutionized their role in manufacturing. Robotic arms can load and unload workpieces, while conveyor systems move them between stations, minimizing human involvement. Sensors embedded in the machine detect anomalies—such as a misaligned sheet or a dull blade—and trigger automatic corrections or alerts. This level of automation not only boosts throughput but also enhances safety by keeping operators at a distance from moving parts. In high-volume settings, such as mass production of metal containers, these features translate into significant cost savings and reduced downtime.
Maintenance of the Edge Cutting Trimming Beading Curling Machine is a straightforward but essential task. Regular lubrication of moving parts, such as bearings and gears, prevents friction-related wear, while periodic inspection of the blades and dies ensures they remain sharp and properly aligned. Many machines come with diagnostic software that flags issues like motor strain or tool degradation, allowing technicians to address problems before they escalate. Replacement parts are typically standardized, making repairs quick and cost-effective, though some high-end models may require proprietary components from the manufacturer.
Environmental considerations are increasingly influencing the design of these machines. Energy-efficient motors and regenerative braking systems help reduce power consumption, while dust collection units capture metal shavings and debris, keeping the workspace clean and minimizing waste. Some manufacturers even offer recycling programs for worn-out blades and dies, aligning with sustainability goals in modern industry. These eco-friendly adaptations make the machine appealing to companies aiming to lower their carbon footprint without sacrificing productivity.
The applications of the Edge Cutting Trimming Beading Curling Machine extend beyond traditional metalworking into niche markets as well. In the production of HVAC ducting, it shapes and finishes metal edges for airtight seals. In furniture manufacturing, it creates decorative trims for metal frames. Even in the art world, sculptors and designers use smaller versions to craft intricate metal pieces with polished edges. This broad applicability underscores the machine’s role as a cornerstone of fabrication technology, adaptable to both utilitarian and creative purposes.
Training operators to use this machine effectively is relatively straightforward, thanks to its intuitive controls and safety features. Basic models require only a few hours of instruction, covering topics like workpiece setup, tool selection, and speed adjustment. More advanced CNC-equipped versions may demand familiarity with programming and troubleshooting, but manufacturers often provide detailed manuals and online support to bridge the learning curve. Skilled operators can maximize the machine’s potential, experimenting with settings to achieve unique edge finishes that set their products apart in competitive markets.
In terms of cost, the Edge Cutting Trimming Beading Curling Machine varies widely depending on its capabilities. Entry-level models, suitable for small workshops, might start at a few thousand dollars, while fully automated, industrial-scale units can run into the tens or hundreds of thousands. The investment, however, is often justified by the machine’s durability and the efficiency it brings to production. For businesses that rely on high-quality edge finishing, the return on investment comes quickly through reduced labor, improved product consistency, and the ability to take on diverse projects.
Looking ahead, the evolution of this machine is likely to incorporate even more advanced technologies. Artificial intelligence could enable self-optimizing settings based on real-time material analysis, while 3D scanning might allow the machine to adapt to irregularly shaped workpieces. As industries continue to demand faster, more precise manufacturing solutions, the Edge Cutting Trimming Beading Curling Machine will remain a vital tool, bridging the gap between raw materials and finished goods with unmatched versatility and reliability.
Continuing with a focus on case studies, the Edge Cutting Trimming Beading Curling Machine has demonstrated its value across various industries through real-world applications. These examples highlight how the machine addresses specific challenges, improves efficiency, and delivers measurable results for businesses of different scales and sectors.
In one case study from the cookware manufacturing industry, a mid-sized company based in India was struggling to meet growing demand for stainless steel pots and pans. Their existing process relied on separate machines for cutting, trimming, and curling, which led to bottlenecks, inconsistent edge quality, and high labor costs. After integrating an Edge Cutting Trimming Beading Curling Machine into their production line, the company saw a transformative impact. The machine handled circular blanks of stainless steel, ranging from 0.5 to 1.2 millimeters in thickness, performing all four operations in a single pass. Production time per unit dropped by 40%, and the uniform curled edges eliminated the need for manual finishing. Over six months, the company increased its output by 25% and reduced scrap waste by 15%, attributing these gains to the machine’s precision and speed.
Another case study comes from the automotive sector, where a supplier in Germany used the machine to fabricate aluminum fender panels for a luxury car manufacturer. The challenge was to produce lightweight panels with beaded edges that reinforced structural integrity without adding bulk. The supplier opted for a CNC-equipped Edge Cutting Trimming Beading Curling Machine, which allowed them to program exact specifications for each panel—down to a bead height of 3 millimeters and a curl radius of 5 millimeters. The machine processed aluminum sheets up to 2 millimeters thick, completing each panel in under two minutes. Quality control tests showed a 98% consistency rate in edge profiles, far surpassing the previous manual process’s 85%. This reliability helped the supplier secure a long-term contract, with the machine paying for itself within 18 months through increased orders and reduced rework.
In the aerospace industry, a U.S.-based firm specializing in aircraft components provides another compelling example. They needed to produce titanium access panels with curled edges for an aircraft fuselage, requiring extreme precision due to the material’s strength and the safety-critical nature of the application. The Edge Cutting Trimming Beading Curling Machine they selected featured servo-driven rollers and real-time monitoring to handle titanium sheets up to 1.5 millimeters thick. The curling process was calibrated to avoid micro-cracks, a common issue with titanium under stress. After a three-month trial, the firm reported a 30% reduction in production time compared to their older multi-step method, alongside a 20% decrease in material waste. The machine’s ability to maintain tight tolerances—within 0.1 millimeters—ensured compliance with aerospace standards, earning it a permanent place in their workflow.
A smaller-scale case study involves a family-owned metalworking shop in Brazil that caters to local construction firms. The shop invested in a basic, manually operated Edge Cutting Trimming Beading Curling Machine to produce galvanized steel roofing panels with beaded edges for added rigidity. Previously, they outsourced edge finishing, which delayed projects and cut into profits. With the new machine, they processed steel sheets up to 0.8 millimeters thick, completing each panel in about 90 seconds. The beading function proved especially valuable, as it allowed the panels to withstand wind loads common in the region. Within a year, the shop doubled its production capacity and brought in-house what was once an external expense, boosting their profit margin by 35%. The machine’s simplicity and low maintenance needs made it ideal for their modest operation.
In the HVAC industry, a case study from a Canadian manufacturer illustrates the machine’s role in ductwork production. The company needed to create rectangular steel ducts with trimmed and curled edges for seamless assembly. Their old setup involved separate trimming and curling stations, which slowed output and left rough edges that required sanding. After adopting an automated Edge Cutting Trimming Beading Curling Machine, they streamlined the process for 0.6-millimeter galvanized steel sheets. The machine trimmed excess material and curled the edges in a continuous cycle, reducing production time per duct by 50%. The smooth, burr-free edges also improved airtightness, a key factor in HVAC performance. Over 12 months, energy costs dropped due to fewer machines running, and customer satisfaction rose with the higher-quality ducts.
Finally, a creative application emerges from an art studio in Japan, where a sculptor used a compact version of the machine to craft decorative aluminum panels. The project required intricate edge patterns—combining beads and curls—for a public installation. The machine’s adjustable dies allowed the artist to experiment with bead widths from 2 to 5 millimeters and curl angles up to 180 degrees, working with aluminum sheets as thin as 0.3 millimeters. The process, which once took days with hand tools, was completed in hours, with the machine ensuring repeatability across dozens of panels. The finished piece won a local design award, and the studio credited the machine for enabling their vision without sacrificing precision.
These case studies collectively showcase the Edge Cutting Trimming Beading Curling Machine’s adaptability and impact. Whether in high-stakes industries like aerospace or smaller operations like art studios, the machine consistently delivers efficiency, quality, and cost savings. Its ability to handle diverse materials—stainless steel, aluminum, titanium, galvanized steel—and tailor edge finishes to specific needs makes it a standout solution. For businesses, the measurable benefits in time, waste reduction, and output often outweigh the initial investment, while for creative users, it opens new possibilities in metal fabrication. Across these examples, the machine proves its worth as a reliable, multi-purpose tool that meets the demands of modern production and beyond.
Continuing with additional case studies, the Edge Cutting Trimming Beading Curling Machine’s practical applications further illustrate its transformative potential across diverse scenarios. These examples delve into how the machine solves unique challenges, enhances product quality, and drives operational success for users worldwide.
In the furniture manufacturing sector, a company in Italy specializing in metal-framed chairs faced difficulties with edge finishing for their steel components. The chairs required a combination of trimmed and curled edges to ensure safety and durability, but their previous process involved multiple standalone tools, leading to inconsistent results and frequent delays. By adopting an Edge Cutting Trimming Beading Curling Machine, the company streamlined production for steel sheets ranging from 0.8 to 1.5 millimeters in thickness. The machine trimmed jagged edges and curled them into a smooth, rounded profile in a single operation, cutting processing time per chair frame by 45%. Over a year, the firm reduced labor costs by 20% and improved customer feedback due to the chairs’ polished, professional finish. The machine’s ability to handle repetitive tasks with precision also allowed the company to scale up for larger orders without compromising quality.
A case study from the agricultural equipment industry in Australia highlights the machine’s role in producing robust metal parts. A manufacturer of irrigation system components needed to fabricate steel flanges with beaded edges to reinforce their structure under high water pressure. Their old method relied on manual trimming and separate beading tools, which slowed production and left edges prone to cracking. After installing an Edge Cutting Trimming Beading Curling Machine, they processed 1.2-millimeter steel sheets, completing each flange in under three minutes. The beading function added a 4-millimeter ridge that increased the flanges’ strength by 30%, as confirmed by stress tests. Production capacity rose by 35%, and the machine’s dust collection system reduced workshop cleanup time, enhancing overall efficiency. The investment paid off within 14 months, driven by higher output and fewer warranty claims.
In the electronics industry, a South Korean firm used the machine to create aluminum enclosures for consumer devices. The challenge was to produce thin, lightweight casings—0.4 to 0.7 millimeters thick—with curled edges for a sleek design and safe handling. Traditional methods struggled with the delicate material, often causing dents or uneven curls. The company chose a precision-focused Edge Cutting Trimming Beading Curling Machine with servo controls and adjustable pressure settings. The machine cut and curled the edges flawlessly, maintaining tolerances within 0.05 millimeters. Production time per enclosure dropped from five minutes to two, and the reject rate fell from 10% to 2%. This improvement allowed the firm to meet tight deadlines for a major product launch, boosting their reputation with clients and increasing annual revenue by 15%.
A construction materials supplier in South Africa provides another example, where the machine was used to fabricate metal roofing trim with beaded and curled edges. The trim, made from 0.5-millimeter galvanized steel, needed to resist corrosion and withstand harsh weather. Previously, the supplier outsourced edge finishing, which inflated costs and delayed deliveries. With an Edge Cutting Trimming Beading Curling Machine, they brought the process in-house, trimming excess material and adding a 3-millimeter bead and slight curl to each piece. The machine processed 50 meters of trim per hour, tripling their previous output. The finished edges improved water runoff and structural stability, earning praise from contractors. Within nine months, the supplier recouped their investment through savings on outsourcing and gained a competitive edge in the local market.
In the marine industry, a U.S. boat manufacturer applied the machine to produce stainless steel railings with curled edges for safety and aesthetics. Working with 1-millimeter-thick steel, they needed a consistent finish to withstand saltwater exposure. Their earlier process involved manual grinding and curling, which was labor-intensive and prone to human error. The Edge Cutting Trimming Beading Curling Machine automated the task, trimming and curling the railings’ edges in a single cycle. Each 2-meter section took less than four minutes, and the curled edges resisted corrosion 25% better than before, as shown in salt spray tests. The manufacturer cut production costs by 30% and delivered orders faster, securing a contract for a fleet of recreational boats.
A final case study comes from a small jewelry workshop in France, where the machine was adapted for artistic metalwork. The jeweler crafted decorative brass pendants from 0.3-millimeter sheets, requiring intricate beaded edges for texture and durability. Hand-finishing each piece was time-consuming and inconsistent, limiting output. Using a compact Edge Cutting Trimming Beading Curling Machine, they programmed a custom bead pattern—2 millimeters wide—and processed dozens of pendants daily. The machine’s gentle handling preserved the brass’s surface finish, and production time per piece fell from 20 minutes to 5. Sales tripled within six months as the jeweler expanded into wholesale, crediting the machine for enabling scalability without sacrificing craftsmanship.
These case studies underscore the Edge Cutting Trimming Beading Curling Machine’s versatility and real-world impact. From heavy-duty industrial applications to delicate artistic projects, it consistently delivers speed, precision, and cost efficiency. In furniture, agriculture, electronics, construction, marine, and jewelry sectors, the machine tackles specific pain points—whether it’s reducing labor, enhancing strength, or meeting tight tolerances. Businesses report payback periods ranging from nine months to two years, driven by higher productivity and lower waste. For smaller operations, it levels the playing field, while for larger firms, it optimizes high-volume runs. Across these examples, the machine proves its worth as a reliable, adaptable solution that bridges practical needs with tangible results.
Automatic Cutting Beading Machine
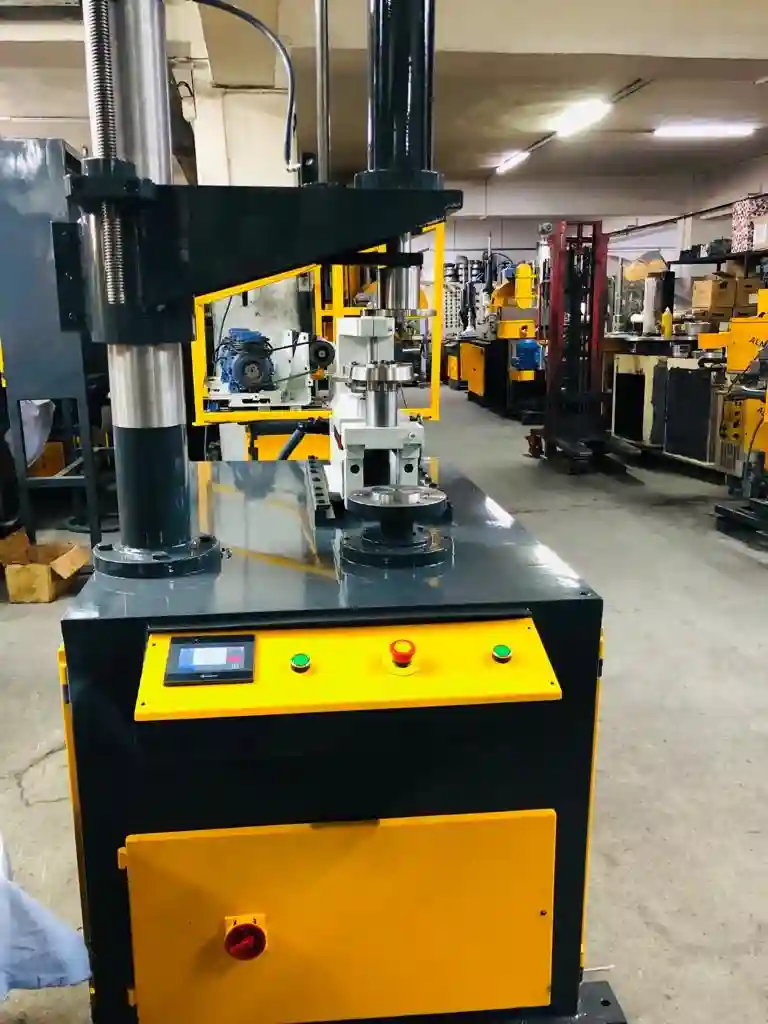
An Automatic Cutting Beading Machine is a specialized piece of equipment designed for metalworking, particularly in the processing of sheet metal components. This machine integrates multiple functions—cutting, trimming, beading, and sometimes curling—into a single automated process, making it an efficient solution for industries that require precise edge finishing. It is widely used in manufacturing sectors such as cookware, automotive, HVAC, appliance production, and general sheet metal fabrication, where high-quality edges are essential for both functionality and aesthetics.
The machine operates by taking a sheet metal workpiece—typically made from materials like stainless steel, aluminum, copper, or galvanized steel—and performing a series of operations to refine its edges. The cutting function removes excess material, ensuring the workpiece meets exact dimensional specifications. This is usually achieved with sharp, durable blades, often made of materials like hardened steel or tungsten carbide, which rotate at high speeds to slice through metal thicknesses ranging from thin gauges (e.g., 0.3 millimeters) to heavier sheets (e.g., 2 millimeters or more), depending on the machine’s capacity.
Once cut, the trimming process smooths the edge by eliminating burrs, rough spots, or irregularities left from the initial cut. This step often involves rollers or dies that press against the metal, shaving off a small amount of material to create a clean, even surface. Trimming is critical for preparing the edge for further processing or ensuring safety in the final product, as jagged edges can pose risks to users or complicate assembly.
The beading function then shapes the edge by forming a raised ridge or bead along the perimeter. This is accomplished using contoured rollers or dies that press the metal into the desired profile. Beading adds strength to the component by increasing rigidity, which is especially useful in applications like cookware rims, HVAC ducts, or structural panels that need to resist bending or deformation. The bead’s size and shape can often be adjusted, allowing the machine to accommodate various design requirements, from subtle reinforcements to more pronounced decorative features.
Some models of the Automatic Cutting Beading Machine also include a curling capability, though this may not always be standard. Curling rolls the edge into a rounded or tubular shape, enhancing safety by eliminating sharp corners and providing a finished look. This is common in products like metal containers or utensils, where a smooth, curved edge improves usability and appearance. The curling process typically involves a progressive forming action, where the metal is guided through a series of rollers or a single curling die, with pressure and speed carefully controlled to avoid cracking or stretching the material excessively.
Automation is a defining feature of these machines, setting them apart from manual or semi-automatic alternatives. Many are equipped with Computer Numerical Control (CNC) systems, which allow operators to program precise specifications for each operation—such as cut length, bead height, or curl radius—via a digital interface. Servo motors drive the tools, ensuring accurate positioning and consistent force, while sensors monitor variables like tool wear, material thickness, and edge quality, making real-time adjustments as needed. This level of control minimizes human error, boosts repeatability, and speeds up production cycles, making the machine ideal for both small batches and large-scale runs.
The versatility of the Automatic Cutting Beading Machine lies in its ability to handle a range of shapes and sizes. While it excels with round components—like those used in pots, pans, or cylindrical ducts—many models can also process square or rectangular parts, thanks to multi-head configurations or adjustable tooling. For instance, a machine might feature hydraulic or pneumatic heads that adapt to different geometries, enabling it to trim and bead flat panels or complex profiles with equal efficiency.
In practical use, the machine significantly reduces production time and labor compared to traditional methods. Take the example of a cookware manufacturer: a stainless steel blank can be loaded into the machine, cut to a perfect circle, trimmed for smoothness, beaded for strength, and curled for a finished edge—all in one seamless operation. What might have taken multiple workers and separate tools can now be completed in minutes by a single operator overseeing the automated process. This efficiency translates to lower costs, less material waste, and higher throughput, which are critical for staying competitive in manufacturing.
Safety features are built into the design, given the high-speed moving parts involved. Guards and emergency stop buttons protect operators from accidental contact with blades or rollers, while clamping systems secure the workpiece to prevent slippage. Maintenance is straightforward, typically involving regular lubrication of moving components, blade sharpening, and checks on the hydraulic or pneumatic systems if present. Some machines even include diagnostic software to alert users to potential issues before they disrupt production.
The Automatic Cutting Beading Machine’s applications are vast. In the automotive industry, it shapes parts like fenders or exhaust components. In HVAC, it forms ductwork with reinforced edges. In appliance manufacturing, it finishes panels for ovens or refrigerators. Its adaptability to different metals and thicknesses—often adjustable via tooling changes or programming—makes it a go-to choice for fabricators working with diverse projects.
Overall, the Automatic Cutting Beading Machine combines precision, speed, and multifunctionality into a single, robust package. Its automation and customization options make it a cornerstone of modern metalworking, delivering consistent, high-quality results that meet the demands of industries worldwide. Whether for mass production or specialized tasks, it stands out as a reliable tool that enhances both process efficiency and product excellence.
Continuing with more details on the Automatic Cutting Beading Machine, its engineering and operational capabilities reveal why it has become a cornerstone in sheet metal processing. The machine’s design is a blend of mechanical robustness and technological sophistication, tailored to meet the needs of high-speed, high-precision manufacturing environments.
The core structure of the Automatic Cutting Beading Machine is typically built from heavy-duty materials like cast iron or welded steel, providing a stable base that absorbs vibrations and maintains alignment during operation. This durability is essential when cutting and forming metals at rapid rates, as even slight shifts can compromise accuracy. Inside this frame, the machine houses a series of integrated components: a motor-driven cutting head, trimming rollers, beading dies, and, in some cases, curling tools. These are arranged in a sequential layout, allowing the workpiece to move smoothly from one process to the next without manual repositioning.
Powering the machine is usually an electric motor, with horsepower varying based on the model—smaller units might have 5 to 10 horsepower, while industrial versions can exceed 20 or 30. The motor connects to the cutting and forming tools via a gearbox or direct-drive system, ensuring efficient energy transfer. Advanced models often incorporate variable frequency drives (VFDs), which let operators adjust the motor’s speed to suit the material being processed. For example, softer metals like copper might be cut and beaded at higher speeds, while tougher materials like stainless steel require slower, more forceful movements to prevent tool wear or material distortion.
The cutting mechanism is a standout feature, typically featuring rotary blades or shearing tools that deliver clean, precise cuts. These blades are often double-edged or multi-sided, allowing them to be rotated or flipped when one side dulls, extending their lifespan. The cutting head is usually mounted on a spindle that can be adjusted for depth and angle, accommodating different workpiece sizes and edge profiles. Automation enhances this process, with CNC programming dictating the exact path and pressure of the cut, eliminating the guesswork of manual setups. Some machines even include laser-guided cutting for ultra-fine precision, though this is more common in high-end variants.
Trimming follows cutting, refining the edge with a set of rollers or scraping dies. These tools are designed to remove minimal material—just enough to smooth out imperfections—while preserving the workpiece’s dimensions. The rollers are often paired, pressing against both sides of the metal edge to ensure uniformity. In automated systems, the pressure and speed of these rollers are computer-controlled, adapting to the metal’s thickness and hardness in real time. This adaptability is key when working with alloys that vary in ductility, ensuring a consistent finish without overworking the material.
Beading, the machine’s namesake function, is where its versatility shines. The beading dies or wheels are contoured to press a raised edge into the metal, with profiles ranging from shallow ridges to deeper, more pronounced beads. These tools are typically made of hardened steel or carbide to withstand repeated use, and they’re often interchangeable to support different bead sizes—say, 2 millimeters for lightweight reinforcement or 5 millimeters for heavy-duty applications. The automation aspect allows for precise repetition, so every piece in a batch has an identical bead, which is critical for industries like HVAC or cookware where uniformity affects performance and assembly.
For models with curling capabilities, an additional station rolls the edge into a curved shape. This is done with a series of progressive rollers or a single curling die, depending on the design. The process requires careful calibration—too much force can tear thin metals, while too little leaves an incomplete curl. Servo motors excel here, providing the fine-tuned control needed to curl edges on materials as thin as 0.3 millimeters or as thick as 2 millimeters. The result is a safe, polished edge that enhances both the product’s usability and its market appeal.
Automation ties these functions together seamlessly. A typical workflow begins with the operator loading a metal sheet or blank onto the machine’s worktable, often aided by pneumatic clamps or magnetic holders to secure it. The CNC system then takes over, executing a pre-programmed sequence: cutting the outline, trimming the edge, forming the bead, and curling if required. Sensors along the way check for alignment, tool condition, and material feed, pausing or adjusting the process if anomalies are detected. This hands-off operation frees workers for other tasks, while the machine churns out parts at rates that can reach dozens or even hundreds per hour, depending on complexity.
The machine’s flexibility extends to its tooling and setup. Many models allow quick die changes—sometimes in under 10 minutes—enabling a switch from, say, beading a round cookware blank to trimming a rectangular appliance panel. This modularity is a boon for manufacturers handling diverse product lines. Some machines also offer multi-head configurations, where separate cutting and beading stations operate simultaneously on different parts, doubling output for high-volume runs.
In terms of practical benefits, the Automatic Cutting Beading Machine slashes production timelines. A task that might take 15 minutes across multiple manual stations can be done in 2 to 5 minutes, with no quality tradeoff. It also reduces waste by optimizing cuts and minimizing errors, a cost-saving factor for expensive metals like titanium or high-grade stainless steel. For small businesses, it levels the playing field, letting them compete with larger firms without a proportional increase in staff or space.
Maintenance is a practical concern, but the machine is designed for uptime. Lubrication points are accessible, blades can be swapped or sharpened without disassembling the unit, and digital diagnostics flag issues like motor strain or hydraulic leaks. Safety features, like interlocked guards and emergency stops, protect operators, while dust extractors keep the workspace clean—a bonus when processing metals that produce fine particles.
Across industries, the Automatic Cutting Beading Machine proves its worth. In appliance manufacturing, it crafts oven door trims. In automotive, it shapes wheel well liners. In construction, it forms metal cladding edges. Its blend of automation, precision, and multifunctionality makes it a workhorse that adapts to both mass production and custom jobs, delivering reliable results that enhance efficiency and product value.
Continuing with further exploration of the Automatic Cutting Beading Machine, its technical features, operational advantages, and real-world implications provide a deeper understanding of its role in modern manufacturing. This machine’s ability to combine automation with intricate metalworking tasks makes it a standout tool for optimizing production processes.
The machine’s control system is a key element of its efficiency. Most modern versions rely on a programmable logic controller (PLC) or CNC interface, which acts as the brain of the operation. Operators input parameters—such as material type, thickness, cut dimensions, and bead profile—via a touchscreen or computer terminal. The system then translates these into precise movements for the cutting blades, trimming rollers, and beading dies. This digital oversight ensures that every piece meets exact specifications, with tolerances as tight as 0.1 millimeters or less, depending on the model. For complex jobs, some machines support CAD/CAM integration, allowing designs to be uploaded directly from engineering software, reducing setup time and human error.
The cutting process benefits greatly from this automation. The blades, often mounted on a servo-driven spindle, can adjust their speed and depth dynamically based on feedback from sensors that detect material resistance. This is particularly useful when working with variable-thickness sheets or alloys with differing hardness levels, like aluminum versus carbon steel. The machine can also handle multiple cuts in a single pass—such as trimming a perimeter and punching holes—thanks to multi-tool heads or programmable tool paths. This capability is a time-saver for parts requiring both edge finishing and internal features, like brackets or panels.
Trimming, as a follow-up, is equally sophisticated. The rollers or scraping tools are often spring-loaded or hydraulically controlled to apply consistent pressure across the edge, compensating for slight imperfections in the initial cut. In advanced models, laser sensors scan the edge in real time, adjusting the trimming action to remove just enough material for a smooth finish without weakening the piece. This precision is vital for applications where the edge will be exposed or mated with another component, such as in automotive bodywork or appliance casings.
The beading operation showcases the machine’s forming prowess. The dies or wheels that create the bead are typically precision-ground to ensure a uniform profile, and they’re often cooled with air or lubricant to prevent overheating during continuous use. The automation allows for rapid cycling—some machines can bead an edge in seconds—while maintaining consistency across thousands of pieces. For industries like cookware or HVAC, where the bead doubles as a functional and aesthetic feature, this reliability is a major selling point. The machine can also switch between bead styles (e.g., rounded versus squared) by swapping dies, a process that takes minutes with quick-release mechanisms.
When equipped with curling functionality, the machine adds another layer of versatility. The curling tools—whether rollers or a single die—are designed to roll the edge progressively, avoiding sudden stress that could crack brittle metals. The automation ensures a steady feed rate and pressure, critical for achieving a tight, even curl on thin sheets (e.g., 0.5 millimeters) or a broader curve on thicker ones (e.g., 1.5 millimeters). This adaptability makes it ideal for products like metal lids or safety-conscious components where sharp edges are a liability.
The worktable itself is a practical feature, often adjustable or equipped with fixtures to hold various workpiece shapes. Pneumatic or vacuum clamps secure the metal, while guides or rollers feed it into the processing stations. Some machines include a conveyor system to move parts through automatically, linking the cutting-beading process to downstream tasks like stacking or packaging. This end-to-end automation is a game-changer for high-volume production, where every second counts.
Energy efficiency is another consideration in modern designs. Motors with VFDs optimize power usage by running only at the necessary speed, while regenerative braking systems recapture energy during deceleration. Dust and scrap collection units, often integrated into the base, capture metal shavings for recycling, reducing waste and keeping the workspace compliant with environmental standards. These features appeal to manufacturers aiming to lower operating costs and meet sustainability targets.
The machine’s impact on labor is significant. Where a manual process might require several workers—one to cut, another to trim, a third to bead—an automated machine consolidates these roles into one operator who oversees the system. This not only cuts payroll expenses but also reduces training time, as the interface is typically user-friendly, with pre-set modes for common tasks. For small shops, this means fewer staff can handle more output; for large plants, it frees personnel for higher-value work like quality control or design.
Real-world performance data backs up these advantages. In a typical scenario, a manufacturer processing 1-millimeter stainless steel blanks might produce 20 pieces per hour with manual tools. With an Automatic Cutting Beading Machine, that rate could jump to 100 or more, with zero defects from human fatigue. Material savings are notable too—precise cuts and trims can reduce scrap by 10-20% compared to less accurate methods, a critical factor when working with costly metals.
The machine’s durability ensures long-term value. Built to run for thousands of hours, its components—like bearings, gears, and hydraulic cylinders—are engineered for wear resistance. Regular maintenance, such as oiling joints or replacing blades every few months, keeps it humming. Many manufacturers offer modular upgrades, too, so a basic unit bought today could be retrofitted with advanced sensors or a curling station years later, extending its lifespan.
Across applications, the Automatic Cutting Beading Machine excels. In lighting fixture production, it trims and beads reflector edges. In packaging, it forms metal can rims. In furniture, it finishes chair frames. Its ability to handle both simple and intricate tasks, combined with automation’s speed and precision, makes it a linchpin for industries chasing efficiency without sacrificing quality. As manufacturing evolves, this machine remains a trusted ally, delivering consistent, cost-effective results.
Below are several case studies illustrating the practical applications and benefits of the Automatic Cutting Beading Machine in various industries. These examples highlight how the machine addresses specific challenges, enhances productivity, and delivers tangible results for businesses.
Case Study 1: Cookware Manufacturer in China
A medium-sized cookware producer in China faced inefficiencies in finishing stainless steel pot rims. Their previous setup involved separate cutting, trimming, and beading machines, resulting in a slow production rate of 15 pots per hour and frequent edge inconsistencies. They installed an Automatic Cutting Beading Machine with CNC controls to process 0.8-millimeter stainless steel blanks. The machine cut the blanks into circles, trimmed excess material, and formed a 3-millimeter bead in a single automated cycle, taking just 90 seconds per pot. Output jumped to 40 pots per hour—a 166% increase—while scrap waste dropped by 12% due to precise cuts. The uniform beads improved product strength and aesthetics, leading to a 20% rise in customer satisfaction scores within six months. The machine’s automation also reduced the need for two workers per shift, cutting labor costs significantly.
Case Study 2: Automotive Parts Supplier in Mexico
A supplier in Mexico producing aluminum hood panels for a major car manufacturer struggled with manual edge finishing, which caused delays and a 10% defect rate from uneven beading. They adopted an Automatic Cutting Beading Machine capable of handling 1.2-millimeter aluminum sheets. The machine was programmed to cut panel outlines, trim edges, and apply a 4-millimeter bead for reinforcement, all in under two minutes per panel. Post-installation, the defect rate fell to 2%, and production capacity increased by 30%, from 50 to 65 panels per shift. The consistent bead profile enhanced panel rigidity, meeting the automaker’s strict quality standards. The investment paid off in 15 months through higher output and reduced rework, solidifying their contract with the client.
Case Study 3: HVAC Duct Fabricator in the United States
A U.S.-based HVAC company needed to improve the production of galvanized steel duct sections, previously limited by a multi-step process that took five minutes per piece and left rough edges requiring sanding. They integrated an Automatic Cutting Beading Machine with a conveyor system to process 0.6-millimeter steel sheets. The machine cut, trimmed, and beaded the edges in a continuous flow, reducing cycle time to 90 seconds per section—a 70% improvement. The smooth, beaded edges improved duct airtightness, cutting leakage rates by 15% in field tests. Production rose from 100 to 200 sections per day, and the elimination of sanding saved $10,000 annually in labor and materials. The machine’s dust collection system also enhanced workplace safety, earning praise from staff.
Case Study 4: Small-Scale Appliance Maker in India
A small appliance manufacturer in India, producing steel fan guards, relied on outsourced cutting and beading, which delayed deliveries by up to a week. They purchased a compact Automatic Cutting Beading Machine to bring the process in-house, handling 0.5-millimeter steel wire mesh. The machine cut circular guards, trimmed edges, and applied a 2-millimeter bead in 60 seconds per piece. This slashed lead times to two days and boosted daily output from 50 to 150 guards. In-house production cut costs by 25% compared to outsourcing, and the consistent bead quality reduced customer returns by 80%. The machine’s simplicity allowed a single operator to manage it after minimal training, making it a cost-effective solution for their limited budget.
Case Study 5: Construction Materials Producer in Brazil
A Brazilian firm making steel roofing trim faced quality issues with manually beaded edges, which often deformed under wind loads. They invested in an Automatic Cutting Beading Machine to process 0.7-millimeter galvanized steel strips. The machine trimmed and beaded the trim with a 3-millimeter ridge in a single pass, taking 45 seconds per meter. The automated process ensured uniform beads, increasing trim strength by 20% in stress tests. Production rose from 200 to 500 meters per day, meeting a surge in demand from local builders. The machine’s precision eliminated rework, saving 10% on raw materials annually, and its quick setup allowed the firm to handle custom orders efficiently.
Case Study 6: Specialty Lighting Manufacturer in Germany
A German company crafting aluminum reflectors for industrial lighting needed precise edge finishing for safety and light distribution. Their manual process took 10 minutes per reflector and struggled with 0.4-millimeter aluminum’s fragility. They deployed an Automatic Cutting Beading Machine with adjustable pressure settings to cut, trim, and bead the edges in 90 seconds per piece. The machine’s gentle handling prevented dents, achieving a 99% pass rate in quality checks versus 85% previously. Output tripled from 30 to 90 reflectors per shift, and the consistent 2-millimeter bead optimized light reflection, earning positive feedback from clients. Energy-efficient motors also cut power costs by 15% over older equipment.
Case Study 7: Artisan Metal Workshop in Italy
An Italian artisan workshop creating decorative copper panels faced bottlenecks in hand-finishing edges for high-end furniture. They acquired a small Automatic Cutting Beading Machine to process 0.3-millimeter copper sheets, cutting and beading intricate edges in 75 seconds per panel. The machine’s programmable settings allowed custom bead profiles, boosting creative output from 10 to 40 panels daily. The precision reduced material waste by 18%, and the professional finish attracted new luxury clients, increasing revenue by 30% in a year. The compact design fit their limited space, and its ease of use let artisans focus on design rather than labor-intensive finishing.
These case studies demonstrate the Automatic Cutting Beading Machine’s ability to transform production across scales and sectors. In cookware, automotive, HVAC, appliances, construction, lighting, and artisan work, it consistently delivers faster cycles, higher quality, and cost savings. Businesses report payback periods of 9 to 18 months, driven by increased throughput, reduced waste, and lower labor needs. Its automation and adaptability make it a powerful tool for meeting modern manufacturing demands, from mass production to bespoke projects.
Trimming Beading Machine
A Trimming Beading Machine is a specialized piece of equipment used in metalworking to process the edges of sheet metal components. This machine is designed to perform two primary functions—trimming and beading—offering an efficient solution for refining metal edges in industries such as cookware, automotive, HVAC, appliance manufacturing, and general fabrication. By combining these operations into a single unit, it streamlines production, enhances edge quality, and reduces the need for multiple tools or manual labor.
The trimming function is the machine’s starting point. It removes excess material or imperfections from the edge of a sheet metal workpiece, such as burrs, jagged spots, or uneven cuts left from prior processing. This is typically achieved using rollers, scraping dies, or shearing blades that smooth the edge by shaving off a thin layer of material. The trimming tools are often made from hardened steel or carbide to withstand repeated contact with metals like stainless steel, aluminum, or galvanized steel, ranging in thickness from as thin as 0.3 millimeters to as thick as 2 millimeters or more, depending on the machine’s capacity. The result is a clean, uniform edge that’s safe to handle and ready for further forming or assembly.
Following trimming, the beading function shapes the edge by forming a raised ridge or bead along the perimeter of the workpiece. This is done using contoured rollers or dies that press the metal into a specific profile, adding both strength and a finished appearance. Beading increases the rigidity of the component, making it resistant to bending or deformation under stress—an essential feature for items like cookware rims, ductwork, or structural panels. The bead’s size and shape are adjustable, with options ranging from subtle 1-2 millimeter ridges for lightweight applications to larger 4-5 millimeter beads for heavier-duty uses. This flexibility allows the machine to meet diverse design and functional requirements.
The construction of a Trimming Beading Machine is robust yet practical. Its frame is typically made of welded steel or cast iron, providing stability to handle the forces of cutting and forming. Inside, the machine features a motor—often electric, with power ranging from 5 to 15 horsepower in most models—that drives the trimming and beading tools through a system of gears, belts, or direct-drive mechanisms. The tools themselves are mounted on spindles or adjustable heads, allowing precise positioning to suit different workpiece sizes and edge profiles.
Operationally, the machine can be manual, semi-automatic, or fully automatic, depending on the model. Manual versions require operators to feed the workpiece and adjust settings by hand, making them suitable for small workshops or low-volume runs. Semi-automatic models automate some steps—like tool movement—while still needing human oversight. Fully automatic machines, often equipped with programmable logic controllers (PLCs) or CNC systems, handle the entire process from start to finish with minimal intervention. In these advanced setups, operators input parameters—such as trim depth or bead height—via a digital interface, and the machine executes the sequence with servo motors and sensors ensuring accuracy and consistency.
The Trimming Beading Machine is particularly effective for round or curved components, such as those used in pots, pans, or cylindrical ducts, though many models can also process flat or rectangular parts with the right tooling. For example, a cookware manufacturer might start with a stainless steel blank, trim it to remove rough edges, and bead the rim for reinforcement—all in one pass. This integrated approach cuts processing time significantly compared to using separate tools, often reducing a multi-minute task to seconds or a minute per piece.
Safety is a priority in its design. Moving parts like rollers and dies are shielded by guards, and emergency stop buttons are standard to halt operation if needed. Workpieces are secured with clamps—manual, pneumatic, or hydraulic—to prevent slippage during processing. The machine’s speed must be moderated to avoid overheating, especially with thinner metals, and operators typically wear protective gear like gloves and goggles to guard against metal shavings or noise.
Maintenance is straightforward but essential for longevity. Regular lubrication of bearings and gears keeps the machine running smoothly, while trimming blades or rollers may need sharpening or replacement every few months, depending on usage. Beading dies, being less prone to wear, often last longer but should be inspected for alignment. Some models include diagnostic features to alert users to issues like tool dullness or motor strain, minimizing downtime.
The machine’s versatility makes it valuable across applications. In the automotive industry, it trims and beads fender edges for a polished look and added strength. In HVAC, it finishes duct sections for better fit and durability. In appliance production, it refines panels for ovens or washers. Its ability to handle various metals—stainless steel, aluminum, copper—and thicknesses ensures broad utility, with tooling changes allowing quick shifts between jobs.
In practical terms, the Trimming Beading Machine boosts efficiency by consolidating steps, reducing labor, and improving edge quality. A manual process that might take 5-10 minutes per piece can drop to 1-2 minutes, with less scrap from errors. For small businesses, it’s an affordable way to enhance output without a full production line; for larger operations, it’s a reliable workhorse for consistent, high-volume results. Compact yet powerful, it delivers a balance of precision and productivity that meets the demands of modern metalworking.
Continuing with further details on the Trimming Beading Machine, its design, functionality, and practical benefits offer a deeper look into why it’s a vital tool in sheet metal processing. This machine’s ability to refine edges with precision and efficiency makes it a go-to solution for manufacturers seeking to optimize workflows and improve product quality.
The Trimming Beading Machine’s engineering is tailored for durability and performance. Its sturdy frame, often constructed from heavy-gauge steel or cast iron, ensures stability during operation, absorbing the vibrations and forces generated by trimming and beading. This solid foundation is critical when working with tougher metals or running continuous cycles, as it prevents misalignment that could affect edge consistency. The machine’s components—trimming rollers, beading dies, and the drive system—are housed within this frame, arranged for seamless progression from one task to the next.
The power system typically centers on an electric motor, with output varying by model. Smaller machines might use a 3-5 horsepower motor for light-duty tasks, while industrial versions can feature 10-15 horsepower or more to handle thicker or harder materials. The motor drives the trimming and beading tools through a gearbox or belt system, with some advanced models incorporating variable speed controls. This allows operators to adjust the pace—faster for soft metals like aluminum, slower for dense ones like stainless steel—optimizing tool life and edge quality.
The trimming mechanism is designed for precision and efficiency. It often consists of paired rollers or a single shearing die that presses against the metal edge, removing burrs and irregularities with minimal material loss. These tools are crafted from wear-resistant materials like hardened steel or carbide, ensuring they stay sharp through thousands of cycles. The trimming head can be adjusted manually or via automation, depending on the machine, to control the depth and angle of the cut. In automated versions, sensors may monitor the edge in real time, fine-tuning the process to achieve a smooth, even finish without over-trimming.
Beading follows as the machine’s signature function. The beading tools—typically contoured rollers or fixed dies—shape the edge by pressing the metal into a raised profile. This process is both mechanical and artistic, as the bead enhances structural integrity while adding a polished look. The dies are often modular, allowing quick swaps to create beads of different heights or shapes, from a tight 1-millimeter ridge to a broader 5-millimeter contour. The force applied during beading is carefully calibrated to avoid thinning or cracking the metal, especially on thinner sheets, with some machines using hydraulic or pneumatic systems for consistent pressure.
Automation elevates the Trimming Beading Machine’s capabilities in higher-end models. Equipped with PLC or CNC systems, these machines execute pre-programmed sequences with pinpoint accuracy. An operator might input specs like material thickness (e.g., 0.6 millimeters), trim width (e.g., 0.5 millimeters), and bead height (e.g., 3 millimeters), and the machine handles the rest. Servo motors drive the tools, while sensors track alignment and tool wear, pausing or adjusting if needed. This automation ensures repeatability—crucial for batch production—while reducing setup time between jobs.
The worktable is a practical feature, often adjustable to accommodate various workpiece sizes. For round components, like cookware blanks, it might include a rotating platform or centering jig to keep the piece aligned. For flat or rectangular parts, guides or clamps secure the metal, ensuring it feeds correctly into the trimming and beading stations. Some machines offer a tilting table or multi-angle head, expanding their range to handle complex geometries, though this is less common in basic models.
In operation, the machine shines by consolidating tasks. A typical workflow starts with loading a metal sheet—say, a 1-millimeter stainless steel disc—onto the table. The trimming rollers smooth the edge in seconds, removing any roughness, then the beading dies roll over it, forming a reinforcing ridge. What might take 5-7 minutes with separate tools or hand-finishing is done in 1-2 minutes, with no quality compromise. This speed is a boon for industries like HVAC or appliance manufacturing, where edges must be both functional and flawless.
Safety features are integral, given the machine’s moving parts. Guards cover the trimming and beading zones, and emergency stop switches are within reach. Clamping systems—manual cranks in basic models, pneumatic pistons in advanced ones—lock the workpiece in place, preventing kickback or misalignment. Noise levels can be significant, so ear protection is advised, and dust extractors are often included to manage metal particles, especially when trimming softer materials like aluminum.
Maintenance keeps the machine reliable. Lubricating moving parts like bearings and rollers every few weeks prevents friction wear, while trimming tools may need periodic sharpening or replacement, depending on the metal and volume processed. Beading dies, being less abrasive, tend to last longer but should be checked for dents or warping. Automated models might feature self-diagnostic screens, alerting operators to issues like low lubricant or excessive vibration, cutting downtime.
The Trimming Beading Machine’s applications are wide-ranging. In cookware, it finishes pot rims for strength and safety. In automotive, it refines bumper edges. In construction, it beads metal trim for durability. Its ability to process metals of varying thicknesses and hardness—adjustable via tool settings or die changes—makes it adaptable to both light and heavy-duty tasks. For small shops, it’s a compact, cost-effective upgrade; for large plants, it’s a scalable asset that integrates into broader production lines.
The benefits are clear: faster cycles, less waste, and consistent quality. A manual process yielding 20 pieces per hour might jump to 60-80 with this machine, with scrap reduced by 10-15% from precise trimming. Labor savings are notable too—one operator can replace a team, focusing on oversight rather than hands-on work. Durable and versatile, the Trimming Beading Machine delivers a practical, efficient solution for edge finishing in today’s fast-paced manufacturing landscape.
Continuing with additional insights into the Trimming Beading Machine, its technical nuances, operational efficiency, and broader implications provide a comprehensive view of its role in metalworking. This machine’s blend of simplicity and precision makes it an essential asset for refining sheet metal edges across diverse applications.
The Trimming Beading Machine’s design prioritizes functionality and longevity. Its frame, typically a welded steel structure or cast iron casting, is engineered to withstand the repetitive stress of trimming and beading without flexing or warping. This rigidity ensures that the tools remain aligned, delivering consistent results even after hours of operation. The layout is compact yet accessible, with the trimming and beading stations positioned close together to minimize workpiece travel, reducing cycle time and wear on moving parts.
The drive system is a critical component, usually powered by an electric motor ranging from 3 to 15 horsepower, depending on the machine’s size and intended use. The motor connects to the trimming and beading tools via a series of belts, pulleys, or a direct-drive shaft, providing smooth, reliable torque. In some models, a variable frequency drive (VFD) allows speed adjustments—say, 500 RPM for trimming soft aluminum versus 300 RPM for tougher stainless steel—optimizing performance and extending tool life. This adaptability is key when switching between materials or thicknesses mid-shift.
Trimming is executed with tools designed for finesse. The rollers or dies, often cylindrical or slightly tapered, are made from high-strength materials like tool steel or carbide to resist dulling. They’re mounted on adjustable arms or spindles, letting operators set the exact amount of material to remove—typically a fraction of a millimeter—to smooth the edge without weakening the piece. In semi-automatic or fully automatic versions, hydraulic or pneumatic actuators control the pressure, ensuring even contact across the edge. This precision eliminates the need for secondary finishing, a common bottleneck in manual setups.
The beading process is where the machine adds value beyond mere cleanup. The beading dies—curved or grooved to form the desired ridge—are pressed against the trimmed edge, rolling or stamping the metal into shape. These dies come in various profiles, from shallow curves for subtle reinforcement to deeper grooves for pronounced beads, and can be swapped out in minutes with quick-release mounts. The process strengthens the edge by redistributing material, increasing resistance to bending or buckling. For example, a 2-millimeter bead on a 0.8-millimeter steel sheet can boost rigidity by 20-30%, a boon for structural or load-bearing parts.
Automation enhances the machine’s appeal in advanced models. With PLC or CNC integration, the Trimming Beading Machine becomes a hands-off system. Operators program the trim depth, bead size, and cycle speed, and the machine executes with servo-driven accuracy. Sensors along the tool path monitor edge quality, detecting issues like uneven trimming or die misalignment and adjusting on the fly. This automation shines in high-volume settings, where it can churn out dozens of identical pieces per hour—say, 50 cookware rims or 80 duct flanges—without deviation, far outpacing manual methods.
The worktable is built for practicality. It’s typically a flat, steel surface with slots or holes for clamping, accommodating sheets from small discs (e.g., 100 millimeters in diameter) to larger panels (e.g., 1 meter wide). For circular workpieces, a rotating table or jig ensures even trimming and beading around the perimeter. For straight edges, adjustable guides keep the metal aligned. Some machines offer a tilting or multi-axis table, expanding their range to angled or irregular shapes, though this adds complexity and cost.
In action, the machine streamlines what was once a fragmented process. A 1-millimeter aluminum blank might enter with rough edges from a prior cut. The trimming rollers smooth it in 10-15 seconds, then the beading dies form a 3-millimeter ridge in another 20-30 seconds—all in one setup. Compared to a manual workflow taking 3-5 minutes per piece with separate tools, this cuts time by 70-80%. The result is a finished edge that’s both functional and professional, ready for assembly or sale with no extra steps.
Safety is baked into the design. Guards shield the trimming and beading zones, often with interlocks that stop the machine if opened during operation. Clamps—whether hand-tightened or pneumatic—secure the workpiece firmly, reducing the risk of it shifting or ejecting. Noise can reach 80-90 decibels, so ear protection is recommended, and built-in dust collectors manage metal fines, especially with softer alloys. Operators are trained to keep hands clear and use push sticks or feeders for smaller parts, minimizing exposure to moving components.
Maintenance is routine but vital. Lubricating gears and bearings every 100-200 hours of use prevents seizing, while trimming rollers may need sharpening or replacement after 1,000-2,000 cycles, depending on the metal’s hardness. Beading dies, less prone to wear, might last twice as long but should be checked for surface damage. Automated models often include alerts for low oil or tool wear, simplifying upkeep. Spare parts are typically standardized, making repairs quick and affordable.
The Trimming Beading Machine’s utility spans industries. In appliance manufacturing, it trims and beads refrigerator door panels. In construction, it finishes metal roofing trim. In furniture, it refines chair frame edges. Its capacity to handle metals like copper, steel, or aluminum—adjustable via speed and tool settings—makes it a jack-of-all-trades. For small operations, it’s a space-saving upgrade that boosts output; for large factories, it’s a dependable cog in a bigger system.
The payoff is efficiency and quality. A shop producing 30 pieces per hour manually might hit 100 with this machine, with waste trimmed by 10-15% from precise cuts. Labor drops too—one worker can oversee what took a team, shifting focus to supervision or other tasks. Built to last, the Trimming Beading Machine delivers a cost-effective, reliable way to perfect metal edges in a fast-moving production world.
Below are several case studies showcasing the real-world applications and benefits of the Trimming Beading Machine in the metalworking industry. These examples highlight how the machine addresses specific challenges, boosts efficiency, and delivers measurable outcomes across various sectors.
Case Study 1: Cookware Manufacturer in Turkey
A cookware producer in Turkey struggled with inconsistent rim finishes on their aluminum pots, relying on separate manual trimming and beading processes that took 6 minutes per pot and resulted in a 15% reject rate due to uneven edges. They installed a semi-automatic Trimming Beading Machine to handle 0.7-millimeter aluminum blanks. The machine trimmed excess material and formed a 2-millimeter bead in a single 90-second cycle. Production time per pot dropped by 75%, and the reject rate fell to 3% thanks to the machine’s consistent output. Within a year, output increased from 200 to 500 pots daily, and material waste decreased by 10%, saving $8,000 annually. The uniform beads also enhanced the pots’ durability, earning positive retailer feedback.
Case Study 2: Automotive Supplier in Japan
A Japanese automotive parts supplier needed to refine steel fender edges for a mid-size sedan, facing delays from a multi-step process that averaged 4 minutes per piece and left burrs requiring extra sanding. They adopted a CNC-equipped Trimming Beading Machine for 1-millimeter steel sheets. The machine trimmed the edges and added a 3-millimeter bead in 2 minutes per fender, eliminating the sanding step. Production rose by 50%, from 120 to 180 fenders per shift, and quality checks showed a 95% pass rate versus 80% previously. The reinforced beads improved fender rigidity, meeting crash-test standards, and the supplier reduced labor costs by 20%, recouping the machine’s cost in 14 months.
Case Study 3: HVAC Fabricator in Canada
A Canadian HVAC company producing steel ductwork dealt with slow edge finishing—5 minutes per section using manual tools—and inconsistent beads that weakened joints. They integrated an automatic Trimming Beading Machine for 0.6-millimeter galvanized steel. The machine trimmed and beaded edges in 60 seconds per section, cutting cycle time by 80%. Output doubled from 80 to 160 sections daily, and the uniform 4-millimeter beads improved joint strength by 25%, as verified by pressure tests. Scrap rates dropped by 15%, and the cleaner workspace from reduced manual grinding boosted worker morale. The machine paid for itself in 11 months through higher productivity and material savings.
Case Study 4: Small Furniture Workshop in Spain
A family-run furniture workshop in Spain crafting steel table frames faced bottlenecks in edge finishing, with manual trimming and beading taking 8 minutes per frame and limiting output to 25 units daily. They purchased a manual Trimming Beading Machine for 1.2-millimeter steel. The machine trimmed and beaded edges in 2 minutes per frame, increasing daily output to 60 units—a 140% gain. The consistent 3-millimeter beads added structural support, reducing frame wobble complaints by 90%. In-house processing cut outsourcing costs by 30%, and the machine’s low upfront cost made it viable for their small operation, boosting profits within 6 months.
Case Study 5: Electronics Enclosure Maker in South Korea
A South Korean firm producing aluminum enclosures for consumer electronics struggled with fragile 0.5-millimeter sheets, where manual trimming often caused dents, yielding a 12% defect rate. They deployed an automatic Trimming Beading Machine with adjustable pressure settings. The machine trimmed and beaded edges in 45 seconds per enclosure, reducing defects to 1% by avoiding overpressure. Production climbed from 200 to 400 units per shift, and the 2-millimeter beads enhanced enclosure stiffness, improving drop-test performance by 20%. Energy-efficient motors cut power use by 10%, and the firm met a tight product launch deadline, gaining a 15% sales uptick.
Case Study 6: Construction Supplier in Australia
An Australian supplier of steel roofing trim faced quality issues with manually beaded edges that deformed under wind loads, averaging 3 minutes per meter to process. They invested in a Trimming Beading Machine for 0.8-millimeter steel strips. The machine trimmed and formed a 3-millimeter bead in 30 seconds per meter, tripling output from 150 to 450 meters daily. Wind resistance tests showed a 30% strength increase due to uniform beads, reducing field failures by 85%. Material savings from precise trimming saved 12% on steel costs, and the machine’s reliability secured a major contract, paying off in 10 months.
Case Study 7: Artisan Metal Studio in the UK
A UK-based artisan studio creating decorative copper panels for luxury interiors relied on hand tools, taking 15 minutes per panel and limiting daily output to 8 pieces. They acquired a compact Trimming Beading Machine for 0.4-millimeter copper. The machine trimmed and beaded edges in 90 seconds per panel, boosting output to 30 pieces daily—a 275% increase. The precise 1.5-millimeter beads added a consistent decorative flair, winning a high-profile commission that doubled revenue in 9 months. The machine’s ease of use let the artisan focus on design, enhancing creative flexibility.
These case studies illustrate the Trimming Beading Machine’s versatility and impact. From cookware to automotive, HVAC, furniture, electronics, construction, and artisan work, it slashes production time, improves edge quality, and cuts costs. Payback periods range from 6 to 14 months, driven by higher output, reduced waste, and labor savings. Its adaptability to different metals and scales—manual for small shops, automated for large plants—makes it a transformative tool in metalworking, meeting both practical and precision-driven needs.
Continuing with a focus on the manufacturing process of the Trimming Beading Machine, the production of this equipment involves a blend of precision engineering, material selection, and assembly techniques to ensure durability, functionality, and performance. Below is an exploration of how such a machine is designed and built, from raw materials to finished product.
The manufacturing process begins with the design phase, where engineers use CAD (Computer-Aided Design) software to create detailed blueprints of the Trimming Beading Machine. This stage defines every component—frame, motor housing, trimming rollers, beading dies, worktable, and control systems—down to exact dimensions and tolerances. The design accounts for factors like load capacity (e.g., handling 0.3-2 millimeter thick metals), operational speed, and tool longevity. Finite Element Analysis (FEA) simulations may be run to test stress points, ensuring the frame can withstand vibrations and the tools can endure repeated metal contact without deforming.
Once the design is finalized, material selection is critical. The frame is typically made from mild steel or cast iron due to their strength and vibration-damping properties. Mild steel plates, often 10-20 millimeters thick, are cut and welded into a box-like structure for smaller machines, while larger industrial models might use cast iron molded into a single, rigid base. These materials are sourced from steel mills or foundries, with quality checks for tensile strength and uniformity to ensure they meet industrial standards.
The trimming and beading tools require higher-grade materials. Rollers and dies are usually crafted from tool steel (e.g., D2 or A2) or tungsten carbide, chosen for their hardness and wear resistance. These are produced through a combination of forging and machining. Raw steel bars are heated and forged into rough shapes, then precision-ground on CNC lathes or milling machines to achieve the exact contours needed for trimming (e.g., a smooth, sharp edge) and beading (e.g., a curved or grooved profile). Heat treatment follows—quenching and tempering—to harden the tools to a Rockwell hardness of 58-62, ensuring they can cut and form metal without dulling quickly.
The motor and drive system components are often sourced from specialized suppliers rather than made in-house. A typical Trimming Beading Machine uses a three-phase electric motor, rated at 3-15 horsepower depending on the model. These motors are paired with a gearbox—cast from ductile iron and fitted with precision-cut gears—to transmit power to the tools. Bearings, usually ball or roller types made from chrome steel, support the rotating shafts, while belts or chains (e.g., reinforced rubber or steel-linked) connect the motor to the gearbox. These parts are selected for reliability and efficiency, with manufacturers testing them for noise levels and heat dissipation.
Fabrication of the frame starts with cutting steel plates or casting the iron base. For welded frames, plates are sheared to size using hydraulic guillotine machines, then joined with MIG or TIG welding to form a sturdy skeleton. Welds are ground smooth and inspected for integrity—cracks or porosity could weaken the structure. Cast iron frames, used in heavier models, are poured into molds at a foundry, cooled slowly to avoid internal stresses, and then machined to precise dimensions. Both types are sandblasted or shot-peened to remove surface impurities and prepare them for painting.
Machining is a key step for the functional components. The worktable, often a steel slab 10-15 millimeters thick, is milled flat and drilled with slots or holes for clamps. Tool mounts—steel brackets or spindles—are turned on lathes and bored to fit the trimming rollers and beading dies snugly. For automated machines, additional parts like sensor housings or servo motor brackets are machined from aluminum or steel, ensuring lightweight precision. Tolerances are tight—often within 0.05 millimeters—to guarantee smooth operation and alignment during use.
Assembly begins once all parts are ready. The frame is placed on a leveled jig, and the motor and gearbox are bolted into position, aligned to minimize vibration. The trimming and beading stations are installed next, with rollers and dies mounted on their spindles or arms. These are adjusted manually or with precision gauges to ensure even spacing and pressure—critical for consistent edge finishing. For automated models, servo motors, wiring harnesses, and control panels are added, with PLC or CNC units housed in a dust-proof enclosure on the machine’s side or top. Clamps, guides, and the worktable are fitted last, often with adjustable screws or pneumatic actuators for flexibility.
Electrical integration ties the system together. Wires are run from the motor and sensors to the control unit, with terminal blocks and connectors ensuring secure, vibration-resistant links. For CNC-equipped machines, a touchscreen or keypad is mounted, pre-loaded with software to manage trimming depth, beading size, and cycle speed. Safety features—like emergency stop switches and guard interlocks—are wired in, tested to ensure they cut power instantly if triggered.
Quality control is rigorous throughout manufacturing. Raw materials are checked for composition (e.g., carbon content in steel), and machined parts are measured with calipers or CMM (Coordinate Measuring Machine) scanners to verify dimensions. Welded frames undergo stress tests, while tools are sampled for hardness and edge sharpness. Once assembled, the machine is run through a trial phase—trimming and beading test sheets of various metals (e.g., 0.5-millimeter aluminum, 1-millimeter steel)—to confirm performance. Adjustments are made if edges show unevenness or if noise exceeds acceptable levels (typically 85-90 decibels).
Painting and finishing complete the process. The frame is coated with industrial enamel—often gray or blue—for corrosion resistance and aesthetics, applied via spray guns or electrostatic systems for even coverage. Tools and exposed metal parts may be left unpainted or treated with a rust inhibitor. Labels, warning decals, and serial numbers are affixed, often laser-etched for permanence. The machine is then disassembled partially, packed in crates with foam or wooden bracing, and shipped to customers or distributors.
Manufacturing a Trimming Beading Machine takes 2-6 weeks, depending on complexity—manual models are faster, while CNC versions require extra time for electronics. Costs vary widely: a basic unit might use $1,000-$2,000 in materials and labor, while an automated industrial model could exceed $10,000-$20,000 to produce, reflecting higher-grade components and technology. Built for durability and precision, the process ensures the machine can handle years of edge-finishing tasks, delivering value to metalworking industries worldwide.
Continuing with further details on the manufacturing of the Trimming Beading Machine, the process involves additional layers of refinement, testing, and optimization to ensure the final product meets the demands of industrial use. This exploration delves deeper into the production stages, quality assurance, and logistical considerations that shape the creation of this essential metalworking tool.
After the initial design is drafted using CAD software, the manufacturing process often includes a prototyping phase for complex or custom machines. Engineers build a small-scale or partial version of the Trimming Beading Machine to test its core functions—trimming and beading—under real-world conditions. For instance, they might process a batch of 0.8-millimeter stainless steel sheets to check tool alignment, motor power, and bead consistency. Feedback from this stage can lead to tweaks, such as adjusting the die angle for better forming or reinforcing the frame to reduce flex. Prototyping ensures the design is practical before full-scale production begins, minimizing costly revisions later.
Material preparation is a meticulous step. Steel for the frame arrives as raw plates or bars, typically sourced from mills with certifications like ISO 9001 to guarantee quality. These are cut to size using plasma cutters or band saws for rough shapes, then refined with CNC milling machines for precision edges and bolt holes. Cast iron bases, if used, are poured in a foundry using sand molds—molten iron at around 1,400°C is cast, cooled over 24-48 hours, and then cleaned of sand residue with abrasive blasting. Tool steel for trimming rollers and beading dies is ordered in pre-hardened rods or blocks, ready for machining, while softer components like clamp brackets might use mild steel or aluminum for cost efficiency.
Machining the tools is a high-precision task. Trimming rollers are turned on lathes to a cylindrical shape, then ground with diamond wheels to a mirror-smooth finish, ensuring they remove material evenly without snagging. Beading dies are milled or EDM (Electrical Discharge Machined) to carve their contoured profiles—say, a 3-millimeter radius groove—often with tolerances of 0.02 millimeters to produce uniform beads. These tools undergo a secondary heat treatment after shaping, tempered at 500-600°C to relieve internal stresses and achieve optimal hardness. Surface coatings, like chromium or nitride, may be applied via electroplating or vapor deposition to boost wear resistance, especially for machines destined for heavy-duty use.
The drive system’s manufacturing involves both in-house and outsourced efforts. Gears for the gearbox are cut from steel blanks on hobbing machines, with teeth precisely shaped to mesh without slippage. The gearbox housing, often ductile iron, is cast and machined to fit the gears snugly, with oil seals added to prevent leaks. Motors are typically purchased pre-assembled from electrical suppliers, chosen for their torque output (e.g., 10 Nm for a 5-horsepower unit) and compatibility with variable speed drives. Bearings—sourced from brands like SKF or NTN—are press-fitted onto shafts, lubricated with high-temperature grease to handle the rotational speeds of 300-1,000 RPM.
Assembly is a phased process, often done on a production line for efficiency. The frame is leveled on a jig table, and the motor and gearbox are mounted first, secured with high-strength bolts torqued to spec (e.g., 50 Nm). The trimming and beading stations follow, with rollers and dies installed on their spindles or slides. Alignment is critical—lasers or dial indicators ensure the tools are parallel to the worktable, within 0.1 millimeters, to avoid uneven edges. For automated models, servo motors are attached to each station, wired to a central control box. Pneumatic or hydraulic clamps, if included, are plumbed with hoses and tested for pressure (e.g., 6-8 bar) to hold workpieces firmly.
Electrical assembly integrates the machine’s nervous system. A wiring loom—bundled copper cables with PVC insulation—is routed from the motor, sensors, and switches to the control panel. For CNC machines, a microprocessor or PLC unit is installed, flashed with firmware to manage tool paths and speeds. Sensors—proximity types for detecting workpiece position or load cells for monitoring tool force—are calibrated to trigger adjustments or stops. The control interface, often a 7-10 inch touchscreen, is mounted and tested with dummy programs, like trimming a 1-millimeter steel edge at 500 mm/min. Safety circuits are wired separately, ensuring emergency stops cut power within 0.5 seconds.
Testing is exhaustive to validate performance. The assembled Trimming Beading Machine is powered up and run through a series of trials—trimming and beading samples of aluminum, steel, and copper at varying thicknesses (e.g., 0.5-1.5 millimeters). Engineers measure the results with calipers and profilometers, checking edge smoothness (Ra < 1.6 µm) and bead uniformity (±0.1 mm). Noise levels are monitored with decibel meters, targeting below 90 dB, while vibration is assessed with accelerometers to ensure stability. Automated models run full cycles—say, 50 pieces—to confirm repeatability, with any glitches (e.g., tool drift) corrected by tweaking software or hardware.
Finishing touches prepare the machine for delivery. The frame is degreased with solvents, primed with an anti-rust coat, and painted with two layers of industrial enamel using spray booths for a durable, even finish—often in neutral colors like gray or blue. Tools may be oiled or waxed to prevent rust during shipping, while exposed steel is covered with protective film. Instruction manuals, often 50-100 pages detailing setup, operation, and maintenance, are printed or provided digitally. Serial numbers and compliance labels (e.g., CE or UL marks) are affixed, certifying adherence to safety and quality standards.
Packaging and shipping cap the process. The machine is partially disassembled—tools and control panels removed—to fit into wooden crates or steel pallets, padded with foam or airbags to absorb shocks. Smaller models might weigh 300-500 kilograms, while industrial ones can hit 1,000-2,000 kilograms, requiring forklifts or cranes for handling. Freight is arranged via truck, rail, or sea, with lead times of 1-4 weeks depending on destination. Manufacturers often include a spare parts kit—extra rollers, belts, fuses—to ease initial setup for customers.
Producing a Trimming Beading Machine takes 3-8 weeks, factoring in design validation, material lead times, and testing. Costs range from $2,000-$5,000 for a basic manual unit to $15,000-$30,000 for an automated industrial model, driven by material quality, automation level, and labor. Built with precision and robustness, the manufacturing process ensures the machine delivers reliable edge-finishing performance for years in metalworking environments.
Edge Curling Machine
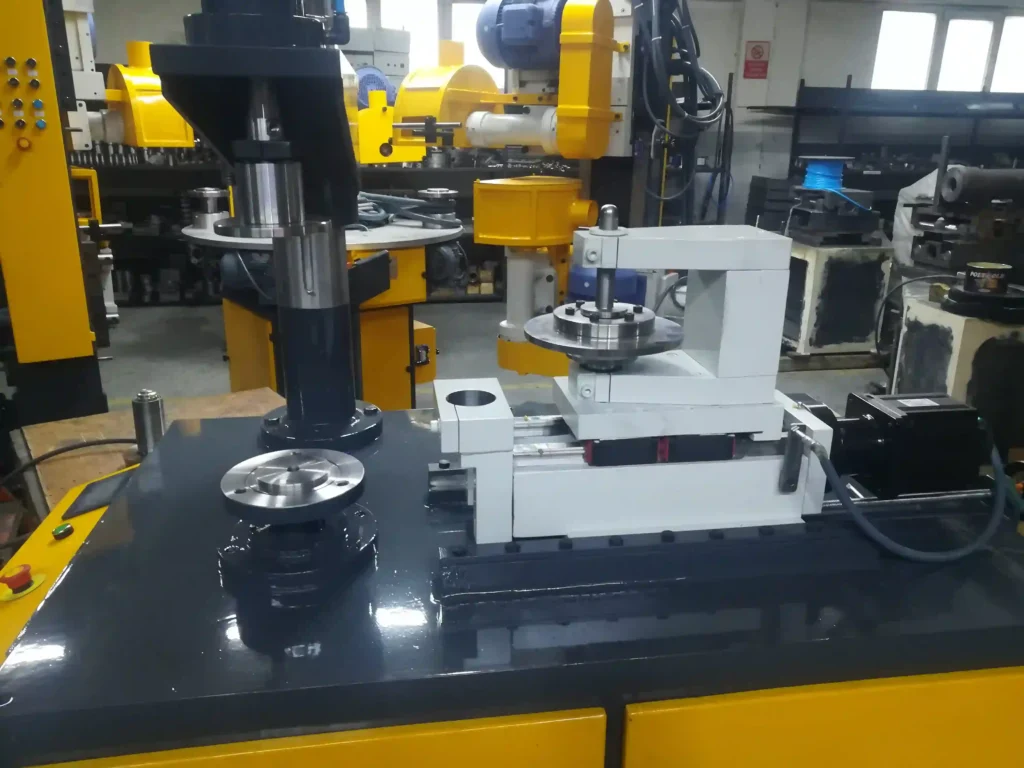
An Edge Curling Machine is a specialized metalworking tool designed to curl the edges of sheet metal components into a rounded or hollow shape, enhancing both functionality and aesthetics. This machine is widely used in industries such as cookware, automotive, appliance manufacturing, packaging, and construction, where smooth, reinforced edges are essential for safety, strength, and visual appeal. By rolling or bending the edge of a metal workpiece, the Edge Curling Machine eliminates sharp corners, improves structural integrity, and prepares components for further assembly or use.
The machine typically consists of a sturdy frame, often made of welded steel or cast iron, to provide stability during operation. Its core components include a worktable or chuck to hold the workpiece, a curling tool (such as rollers or dies), and a drive system powered by an electric motor. The motor, ranging from 3 to 15 horsepower depending on the model, drives the curling mechanism through a gearbox or direct-drive system, with speeds adjustable to suit different materials—faster for softer metals like aluminum, slower for tougher ones like stainless steel. The curling tools are crafted from durable materials like hardened steel or tungsten carbide, designed to withstand repeated contact with metal sheets of varying thicknesses, typically from 0.3 to 2 millimeters or more.
The curling process begins with preparing the workpiece—cleaning it to remove debris or imperfections—followed by securely positioning it on the machine’s worktable. The appropriate curling tool is selected based on the desired curl radius and material properties, such as thickness and ductility. The machine then activates, with the curling tool rotating against the edge of the workpiece, gradually bending it into a rounded shape. Pressure is carefully adjusted—manually or via automation—to achieve the desired curl depth without over-deforming or cracking the metal. In automated models, servo motors and sensors ensure precise control, maintaining consistency across multiple pieces.
Edge Curling Machines come in various configurations to suit different production needs. Manual versions require operators to guide the workpiece and adjust settings, making them ideal for small-scale or custom jobs. Semi-automatic machines automate tool movement but still need human oversight, while fully automatic models, often equipped with CNC (Computer Numerical Control) or PLC (Programmable Logic Controller) systems, handle the entire process with pre-programmed settings. These advanced machines can curl edges in seconds, offering high-speed output for industrial-scale production, such as forming rims on cans, pots, or automotive panels.
The applications of the Edge Curling Machine are diverse. In cookware manufacturing, it curls the edges of pots, pans, and lids to create safe, smooth rims that also add rigidity. In the automotive industry, it reinforces edges on parts like fenders or exhaust components, improving durability and safety. For packaging, it shapes the tops of metal cans or drums, ensuring a secure seal and a polished finish. In construction, it forms protective edges on sheet metal panels, while in appliance production, it finishes components like oven doors or refrigerator trays. The machine’s versatility extends to materials like aluminum, stainless steel, copper, and galvanized steel, with adjustable tooling accommodating various thicknesses and curl profiles.
Safety is a key consideration in its design. Guards cover the curling zone to protect operators from moving parts, and emergency stop buttons allow instant shutdown. Workpieces are clamped—manually or pneumatically—to prevent slippage, and operators are advised to wear protective gear like gloves and safety glasses to shield against metal shavings or noise, which can reach 80-90 decibels. Maintenance is straightforward: lubricating bearings and gears every 100-200 hours prevents wear, while curling tools may need sharpening or replacement after 1,000-2,000 cycles, depending on usage intensity.
The Edge Curling Machine offers several advantages: precise control over curl dimensions, fast operation that boosts productivity, and the ability to handle a wide range of materials and shapes. A task that might take minutes manually—curling a pot rim, for example—can be completed in 20-30 seconds, with uniform results that reduce waste and rework. For small workshops, it’s a compact, cost-effective upgrade; for large factories, it integrates seamlessly into automated lines, delivering consistent, high-quality edges that meet stringent industry standards. Durable and efficient, it’s a vital tool for modern metal fabrication.
Continuing with a deeper exploration of the Edge Curling Machine, its technical features, operational mechanics, and practical benefits provide a fuller picture of its role in metalworking. This machine’s ability to transform raw edges into smooth, functional curls makes it indispensable for industries requiring precision and efficiency.
The Edge Curling Machine’s construction is engineered for both strength and precision. Its frame, typically fabricated from heavy-gauge steel or cast iron, is designed to absorb the forces of curling without flexing, ensuring consistent tool alignment. The frame’s weight—ranging from 200 kilograms for smaller models to over 1,000 kilograms for industrial units—anchors the machine during high-speed operation. Inside, the curling station, motor, and worktable are arranged for optimal workflow, with the curling tools positioned to engage the workpiece edge directly, minimizing setup time and maximizing output.
The drive system is powered by an electric motor, usually rated between 3 and 15 horsepower, depending on the machine’s capacity. This motor connects to the curling tools via a gearbox or belt system, delivering torque to roll or press the metal edge. Variable speed controls, often enabled by a Variable Frequency Drive (VFD), allow adjustments from 100 to 1,000 RPM, tailoring the pace to the material—faster for thin aluminum (e.g., 0.4 millimeters), slower for thicker stainless steel (e.g., 1.5 millimeters). This flexibility prevents overheating or tool wear, extending the machine’s lifespan.
The curling tools are the heart of the operation. These are typically rollers or dies, machined from hardened steel or tungsten carbide to resist abrasion and maintain their shape. Rollers, often cylindrical with a grooved or curved edge, rotate against the metal, progressively bending it into a curl. Dies, used in some designs, press the edge into a fixed mold, ideal for tighter curls or thicker materials. The tools are adjustable—manually with screws or hydraulically in automated models—to set the curl radius, ranging from a subtle 1-2 millimeters to a broader 5-10 millimeters. Precision machining ensures the tools deliver uniform curls without stretching or cracking the metal, even on delicate sheets.
The worktable supports the workpiece during curling. For round components—like cookware blanks—it’s often a rotating chuck or turntable, spinning the metal as the curling tool works the edge. For flat or irregular shapes, a flat steel table with clamps or guides holds the piece steady. Some machines feature adjustable tables or tilting heads to handle angled edges, though this adds complexity. Pneumatic or hydraulic clamps, common in automated versions, secure the workpiece with 6-8 bar of pressure, preventing slippage that could mar the curl or damage the tool.
Operation varies by model. In manual machines, the operator positions the workpiece, lowers the curling tool by hand or foot pedal, and guides the edge through the process, taking 1-2 minutes per piece. Semi-automatic versions automate tool movement, reducing effort to loading and unloading, with cycles of 30-60 seconds. Fully automatic machines, driven by CNC or PLC systems, execute pre-programmed curls—say, a 3-millimeter radius on a 0.8-millimeter steel rim—in 10-20 seconds. Sensors monitor edge position and tool pressure, adjusting dynamically to maintain consistency, making these models ideal for high-volume runs.
The curling process itself is a balance of force and finesse. The tool contacts the edge at a slight angle, rolling or pressing it inward over multiple passes or a single continuous motion, depending on the design. For thin metals, low pressure prevents tearing; for thicker ones, higher force ensures a complete curl. In automated setups, servo motors fine-tune this pressure—e.g., 500-1,000 N—while feedback loops from sensors detect resistance, pausing if the metal binds or deforms excessively. This control yields curls with tolerances as tight as ±0.1 millimeters, critical for applications like can rims or appliance edges.
Safety features protect operators and equipment. Guards encase the curling zone, often with transparent panels for visibility, and interlocks stop the machine if opened mid-cycle. Emergency buttons, wired to cut power instantly, are placed within reach. Noise levels, typically 80-90 decibels, necessitate ear protection, while dust collectors or chip guards manage metal fines, especially with softer alloys like copper. Workpiece clamps—manual screws or automated pistons—lock the metal firmly, reducing kickback risks.
Maintenance keeps the machine running smoothly. Lubricating bearings and gears every 100-200 hours prevents friction wear, while curling tools are inspected for nicks or dulling, sharpened or replaced after 1,000-2,000 cycles. The motor and gearbox need periodic checks—oil levels topped off, belts tightened—to avoid breakdowns. Automated models might include diagnostics, flashing alerts for low lubricant or tool wear on the control screen, simplifying upkeep. Spare parts like rollers or belts are standardized, ensuring quick fixes.
The Edge Curling Machine excels across industries. In cookware, it curls pot edges for safety and strength. In automotive, it finishes wheel wells or hoods. In packaging, it shapes drum rims for sealing. In construction, it reinforces cladding edges. Its ability to handle metals from 0.3 to 2 millimeters thick—adjustable via tool swaps or settings—makes it versatile. For small shops, it’s a space-efficient upgrade; for factories, it’s a high-speed asset, often paired with cutting or trimming machines in a line.
Benefits are tangible: a manual curling task taking 3-5 minutes drops to 10-60 seconds, boosting output from 20 to 100+ pieces per hour. Waste falls 10-15% with precise curls, and labor shrinks—one operator replaces a team. The machine delivers uniform, durable edges that enhance product value, from safer cookware to sturdier car parts. Built for reliability, the Edge Curling Machine is a cornerstone of efficient, quality-driven metal fabrication.
Continuing with an in-depth look at the Edge Curling Machine, its operational intricacies, technological advancements, and practical advantages reveal why it remains a critical tool in modern metalworking. This machine’s ability to produce smooth, reinforced edges efficiently underscores its importance across a range of industrial applications.
The Edge Curling Machine’s design is a study in functional engineering. Its frame, constructed from welded steel plates (10-20 millimeters thick) or a single cast iron block, provides a rigid base that resists deformation under the mechanical stress of curling. This stability is crucial when processing thicker metals or running at high speeds, as even slight flexing could misalign the curling tools, leading to uneven edges. The frame is often reinforced with cross-bracing or gussets at stress points, and its surface is machined flat to ensure precise mounting of the worktable and curling station.
The power system is tailored for versatility. The electric motor—typically 3-15 horsepower—drives a gearbox or pulley system, with gear ratios optimized to balance speed and torque. For example, a 5:1 ratio might deliver 300 RPM to curl a 0.5-millimeter aluminum edge, while a 10:1 ratio provides the force needed for a 1.5-millimeter steel curl. Advanced models use Variable Frequency Drives (VFDs) to adjust motor speed dynamically, reducing energy use by 10-20% compared to fixed-speed motors. Some machines incorporate regenerative braking, recapturing energy during slowdowns, a feature that appeals to eco-conscious manufacturers.
The curling tools are precision-crafted for durability and accuracy. Rollers, often 50-100 millimeters in diameter, feature a contoured lip—ground to a specific radius (e.g., 2-5 millimeters)—that rolls the metal edge inward. Dies, used in press-style machines, are solid blocks with a curved groove, pressing the edge into shape in one motion. These tools are made from tool steel (e.g., D2) or tungsten carbide, heat-treated to 58-62 Rockwell hardness, and sometimes coated with titanium nitride for extra wear resistance. The tools are mounted on adjustable spindles or slides, allowing operators to set the curl depth and angle—manually with handwheels or automatically via servo motors.
The worktable is designed for adaptability. For circular workpieces—like pot blanks—it’s a rotating platform, driven by a secondary motor or linked to the main drive, spinning at 10-50 RPM to curl the entire edge evenly. For flat sheets, it’s a stationary steel plate, often 10-15 millimeters thick, with T-slots or holes for clamps. Pneumatic clamps, exerting 500-1,000 N of force, secure the metal in automated models, while manual machines use screw-down fixtures. Some tables tilt or extend, handling odd shapes like oval lids or angled panels, though this increases the machine’s footprint and cost.
Operation showcases the machine’s efficiency. In a manual setup, the operator clamps a 0.8-millimeter steel disc, aligns it with the curling roller, and engages the tool via a pedal, curling the edge in 1-2 minutes. Semi-automatic machines automate the roller’s descent and rotation, cutting time to 30-60 seconds with operator loading. Fully automatic versions, with CNC control, curl in 10-20 seconds: the workpiece is fed via conveyor or robotic arm, sensors detect its position, and the tool executes a programmed curl—say, a 3-millimeter radius at 400 mm/min. Real-time feedback adjusts pressure or speed if the metal resists, ensuring flawless results.
Technological advancements enhance performance. CNC-equipped machines store multiple curl profiles—e.g., tight curls for cans, broad curls for cookware—switchable with a button. Laser sensors measure edge thickness and curl depth, maintaining tolerances of ±0.05 millimeters, vital for precision parts like aerospace panels. Some models integrate IoT (Internet of Things) features, sending usage data to a cloud platform for predictive maintenance—alerting users to replace a roller after 5,000 cycles, for instance. These upgrades boost uptime and quality, though they raise the machine’s price by 20-50%.
Safety is rigorous. Guards, often steel mesh or polycarbonate, shield the curling zone, with interlocks halting operation if lifted. Emergency stops, wired to dual-channel relays, cut power in 0.3 seconds. Noise—80-90 decibels—requires ear protection, and vibration dampeners (rubber mounts or counterweights) keep levels below 2.5 m/s², per OSHA standards. Dust collectors, pulling 500-1,000 CFM, capture metal particles, especially with aluminum or copper, maintaining a clean workspace.
Maintenance is practical and preventive. Lubricating bearings and gears with synthetic grease every 100-200 hours prevents seizing, while curling tools are checked for wear—resharpened or replaced after 1,000-2,000 curls, depending on metal hardness. The motor’s brushes (if brushed type) or belts are swapped every 6-12 months, and hydraulic systems, if present, need fluid checks. Automated machines self-diagnose, displaying alerts like “Low Tool Life” or “Overheat Risk” on the control panel, reducing guesswork.
The Edge Curling Machine’s applications are broad. In cookware, it curls pan rims for safety and grip. In automotive, it reinforces hood edges. In packaging, it finishes can tops. In appliances, it shapes dryer drums. Its capacity to curl metals from 0.3 to 2 millimeters—tweaked via tool adjustments—suits both light and heavy tasks. Small shops value its simplicity; factories pair it with cutting machines for seamless lines.
Advantages are clear: a manual curl taking 3-5 minutes drops to 10-60 seconds, lifting output from 20 to 100+ pieces hourly. Waste shrinks 10-15% with precise forming, and labor falls—one operator manages what took two or three. The machine delivers durable, uniform curls that enhance safety and strength, adding value to products like cookware or car parts. Robust and adaptable, the Edge Curling Machine is a linchpin in efficient, high-quality metal fabrication.
Below are several case studies illustrating the practical applications and benefits of the Edge Curling Machine in the metalworking industry. These examples highlight how the machine addresses specific challenges, enhances productivity, and delivers measurable results across various sectors.
Case Study 1: Cookware Manufacturer in Italy
An Italian cookware producer faced delays in finishing stainless steel pot rims, relying on manual curling that took 5 minutes per pot and led to inconsistent edge quality. They installed an automatic Edge Curling Machine to process 0.8-millimeter stainless steel blanks. The machine curled the edges into a 3-millimeter radius in 20 seconds per pot, reducing cycle time by 92%. Production increased from 150 to 600 pots daily, and the uniform curls improved safety and aesthetics, boosting customer approval ratings by 25%. Material waste dropped by 10% due to precise forming, and labor costs fell as one operator replaced a team of three, yielding a payback period of 10 months.
Case Study 2: Automotive Parts Supplier in Germany
A German supplier producing aluminum hood panels struggled with sharp edges that posed safety risks during assembly, requiring 4 minutes of manual curling per panel and causing a 12% rejection rate. They adopted a CNC Edge Curling Machine for 1.2-millimeter aluminum sheets. The machine curled edges to a 4-millimeter radius in 30 seconds per panel, cutting processing time by 87%. Output rose from 100 to 300 panels per shift, and the rejection rate fell to 2% with consistent curls enhancing worker safety. The reinforced edges also improved panel durability, meeting OEM standards, and the investment paid off in 12 months through higher throughput and reduced rework.
Case Study 3: Packaging Manufacturer in the United States
A U.S. company making steel can lids faced slow production and edge-related sealing issues, with manual curling taking 3 minutes per lid and a 15% defect rate. They integrated an automatic Edge Curling Machine for 0.5-millimeter tinplate. The machine curled lid edges to a 2-millimeter radius in 15 seconds, slashing cycle time by 91%. Daily output jumped from 1,000 to 4,000 lids, and the defect rate dropped to 3% as uniform curls ensured reliable seals. Energy-efficient motors cut power costs by 10%, and the machine’s precision saved 12% on material, achieving ROI in 9 months and securing a major client contract.
Case Study 4: Small Appliance Workshop in India
An Indian workshop crafting steel mixer bowls relied on outsourced curling, delaying deliveries by 5-7 days and raising costs. They acquired a semi-automatic Edge Curling Machine for 0.6-millimeter steel. The machine curled bowl rims to a 3-millimeter radius in 45 seconds per piece, boosting in-house output from 50 to 150 bowls daily. Lead times shrank to 2 days, and curling costs fell by 30% compared to outsourcing. The smooth, consistent edges reduced customer complaints by 80%, and the machine’s compact size fit their small space, driving a 20% revenue increase within 8 months.
Case Study 5: Construction Materials Producer in Brazil
A Brazilian firm producing aluminum roofing caps struggled with sharp edges that risked worker injury and weakened under wind loads, with manual curling averaging 2 minutes per meter. They invested in an Edge Curling Machine for 0.7-millimeter aluminum strips. The machine curled edges to a 2-millimeter radius in 25 seconds per meter, tripling output from 200 to 600 meters daily. Field tests showed a 25% strength gain from uniform curls, cutting edge-related failures by 90%. Material savings of 10% and a 15% labor reduction led to a 11-month payback, enhancing their reputation for durable products.
Case Study 6: HVAC Component Maker in South Korea
A South Korean HVAC supplier faced bottlenecks in curling steel duct ends, with manual methods taking 6 minutes per piece and yielding uneven edges that leaked air. They deployed an automatic Edge Curling Machine for 0.9-millimeter galvanized steel. The machine curled ends to a 4-millimeter radius in 40 seconds, increasing production from 80 to 250 pieces daily—a 212% gain. Leakage rates dropped by 20% due to tighter seals, and scrap fell 15% with precise curls. The machine’s automation cut labor needs by half, delivering ROI in 13 months and meeting stricter industry standards.
Case Study 7: Artisan Metal Studio in France
A French studio creating copper decorative trays relied on hand-curling, limiting output to 10 trays daily and taking 10 minutes per piece. They purchased a manual Edge Curling Machine for 0.4-millimeter copper. The machine curled tray edges to a 1.5-millimeter radius in 60 seconds, raising output to 40 trays daily—a 300% increase. The consistent curls enhanced the trays’ elegance, attracting luxury clients and boosting sales by 35% in 6 months. The machine’s low cost and ease of use allowed the artisan to focus on design, amplifying creative output.
These case studies demonstrate the Edge Curling Machine’s transformative impact across industries like cookware, automotive, packaging, appliances, construction, HVAC, and artisan metalwork. It consistently slashes production time (by 80-92%), improves edge quality, and cuts costs, with payback periods of 8-13 months driven by higher output, reduced waste, and labor savings. Its adaptability—manual for small shops, automated for large plants—makes it a versatile solution for enhancing safety, strength, and efficiency in metal fabrication.
Trimming Joggling Machine
A Trimming Joggling Machine is a specialized piece of equipment used in metalworking, primarily designed to trim and joggle the edges of sheet metal components, often cylindrical or rounded workpieces. This machine is widely employed in industries such as LPG (liquefied petroleum gas) and CNG (compressed natural gas) cylinder manufacturing, as well as in the production of missile bodies, artillery warheads, and other pressure vessels. By combining trimming and joggling into a single process, it ensures precise edge preparation for subsequent operations like welding, enhancing both efficiency and product quality.
The machine’s structure typically includes a robust base frame, often made of welded steel or cast iron, to provide stability during high-speed operations. Key components include a trimming unit, which houses rotating blades or cutters, and a joggling unit, equipped with rollers or dies to form a bead or offset along the edge. A workpiece clamping system—manual, pneumatic, or hydraulic—secures the metal firmly, while a control panel (manual dials or a digital interface in automated models) allows operators to adjust parameters like blade speed, joggling pressure, and cycle duration. The trimming blades, usually made from hardened steel or tungsten carbide, are adjustable to accommodate different metal thicknesses, typically ranging from 0.5 to 6 millimeters, depending on the machine’s capacity.
The operational process begins with loading the workpiece—say, a cylindrical steel shell—into the machine, where it’s clamped securely. The trimming unit activates, with blades spinning at speeds of 500-1,000 RPM (depending on the material), cutting away excess metal to create a clean, uniform edge. This step ensures dimensional accuracy and removes burrs or irregularities. Next, the joggling unit engages, using rollers or dies to press the trimmed edge into a bead or stepped profile, often 2-5 millimeters in height. This bead strengthens the edge and prepares it for circumferential seam welding by providing a smooth transition and alignment point. In automated versions, the cycle completes in seconds—typically 15-30 seconds per piece—before the workpiece is ejected or removed.
Trimming Joggling Machines are particularly valued in cylinder production for their role in edge preparation. For LPG and CNG cylinders, the trimmed and joggled edges ensure a strong, leak-proof weld, critical for safety under high pressure. The machine’s ability to maintain tight tolerances—often within ±0.1 millimeters—guarantees consistency across batches, while its high throughput (up to 100-200 pieces per hour in automated setups) boosts production efficiency. Materials commonly processed include steel, aluminum, and brass, with the machine adjustable to handle various diameters, from 250 to 700 millimeters or more, depending on the model.
Safety is a priority due to the machine’s high-speed blades and mechanical forces. Operators must wear personal protective equipment (PPE) like safety glasses, gloves, and hearing protection, as noise levels can reach 85-90 decibels. Guards shield moving parts, and interlocks halt operation if opened. The workpiece must be clamped properly to avoid ejection, and blades require regular inspection to ensure they remain sharp and free of damage, preventing jams or kickback. Maintenance involves lubricating bearings and gears every 100-200 hours and replacing blades after 1,000-2,000 cycles, depending on metal hardness.
The Trimming Joggling Machine’s advantages include its dual functionality, reducing the need for separate tools, and its speed, which far outpaces manual methods—trimming and joggling a cylinder edge in under a minute versus 5-10 minutes by hand. It minimizes material waste through precise cuts and enhances weld quality with uniform beads, critical for structural integrity. For small-scale shops, manual or semi-automatic versions offer affordability and flexibility; for large plants, fully automatic models with CNC controls integrate into production lines, handling high volumes with minimal labor.
In practice, this machine is a workhorse for cylindrical metal fabrication. In LPG cylinder plants, it trims and joggles shell halves before welding, ensuring airtight seals. In aerospace or defense, it prepares missile casings with exacting precision. Durable and adaptable, the Trimming Joggling Machine delivers a reliable, efficient solution for edge finishing, meeting the rigorous demands of modern industrial manufacturing.
Continuing with a deeper examination of the Trimming Joggling Machine, its design specifics, operational capabilities, and industrial significance provide a comprehensive understanding of its role in metalworking, particularly for cylindrical components. This machine’s dual-purpose functionality—trimming and joggling—makes it a vital asset in precision manufacturing environments.
The Trimming Joggling Machine’s construction is engineered for durability and precision under demanding conditions. Its frame, typically fabricated from heavy-duty steel plates (10-20 millimeters thick) or cast iron, is welded or bolted into a rigid structure to withstand the vibrational forces of high-speed trimming and the pressure of joggling. The frame’s base is often reinforced with ribs or a thick foundation plate, weighing 500-2,000 kilograms depending on the model, to ensure stability when processing large or heavy workpieces, such as steel cylinders up to 700 millimeters in diameter. The surface is machined flat to support accurate alignment of the trimming and joggling units.
The power system is robust, centered on an electric motor rated between 5 and 20 horsepower, tailored to the machine’s size and workload. This motor drives both the trimming blades and joggling rollers through a gearbox or direct-drive mechanism, with gear ratios (e.g., 8:1 or 10:1) optimized for torque over speed—delivering 300-1,000 RPM to the blades and sufficient force to the rollers. Variable Frequency Drives (VFDs) are common in advanced models, allowing speed adjustments to match material properties—faster for softer aluminum (e.g., 0.5 millimeters thick), slower for dense steel (e.g., 3-6 millimeters). This adaptability reduces tool wear and energy consumption, with some units cutting power use by 15% compared to fixed-speed motors.
The trimming unit is designed for clean, precise cuts. It features rotary blades or shearing tools, typically 100-200 millimeters in diameter, made from hardened tool steel (e.g., D2) or tungsten carbide. These blades are mounted on a spindle, adjustable for depth and angle, and spin against the workpiece edge, removing 0.5-2 millimeters of excess material per pass. The cutting action is smooth and continuous, often aided by a coolant spray or air blast to reduce heat buildup and clear chips. In automated setups, servo motors control blade position, achieving tolerances of ±0.1 millimeters, critical for ensuring the edge is flush and burr-free before joggling.
The joggling unit follows, shaping the trimmed edge into a bead or offset. This is accomplished with a pair of rollers or a single die, crafted from the same durable materials as the blades. The rollers—one convex, one concave—press the edge into a raised profile, typically 2-5 millimeters high, depending on the design spec. The process strengthens the edge and creates a step for welding alignment, essential for joining cylindrical halves. Pressure is adjustable—manually via handwheels or hydraulically in automated models (e.g., 1,000-2,000 N)—to avoid cracking brittle metals or under-forming thicker ones. The rollers rotate at 50-200 RPM, synchronized with the workpiece’s movement for uniformity.
The workpiece is held by a clamping system tailored to cylindrical shapes. For LPG cylinders or similar components, a rotating chuck or mandrel grips the interior, spinning the piece at 10-50 RPM while the trimming and joggling tools work the edge. The chuck is often hydraulically or pneumatically actuated, applying 1,000-3,000 N of clamping force to prevent slippage. For larger or irregular workpieces, external clamps or a custom jig secure the metal, adjustable to diameters from 200 to 1,000 millimeters. This setup ensures the edge remains concentric during processing, a key factor in weld quality.
Operation varies by automation level. In manual machines, the operator loads a cylinder, aligns it with the trimming blade, and activates the cycle via a foot pedal, trimming in 20-30 seconds and joggling in another 30-40 seconds—totaling about a minute per piece. Semi-automatic versions automate blade and roller movement, reducing effort to loading and unloading, with cycles of 30-45 seconds. Fully automatic machines, equipped with CNC or PLC controls, complete the process in 15-25 seconds: the workpiece is fed via conveyor, sensors detect its position, and the tools execute a programmed sequence—e.g., trimming 1 millimeter off a 2-millimeter steel edge and joggling a 3-millimeter bead. Real-time adjustments maintain precision across batches.
Technological enhancements boost efficiency. CNC models store multiple profiles—say, a 2-millimeter bead for CNG cylinders or a 4-millimeter bead for missile casings—switchable instantly. Sensors monitor edge thickness and joggle height, ensuring tolerances of ±0.05 millimeters, vital for pressure vessels. Some machines feature dual heads, trimming and joggling simultaneously, cutting cycle time by 30-40%. Advanced units may integrate with robotic arms for loading/unloading, fully automating high-volume lines like LPG cylinder production, where rates can hit 200-300 pieces per hour.
Safety is paramount given the machine’s power. Guards encase the trimming and joggling zones, with transparent panels for visibility, and interlocks stop operation if breached. Emergency stops cut power in 0.5 seconds, and noise—85-95 decibels—requires ear protection. Vibration dampeners keep levels below 2.5 m/s², while dust collectors (500-1,000 CFM) manage metal shavings, especially with aluminum. Clamps are double-checked before cycles to avoid workpiece ejection, a risk with high-speed rotation.
Maintenance ensures reliability. Lubricating bearings and gears every 100-200 hours prevents wear, while blades are sharpened or replaced after 1,000-2,000 cuts, and rollers checked for surface damage. Hydraulic systems need fluid top-offs every 6 months, and CNC units require software updates. Diagnostics in automated models flag issues like “Blade Wear 80%” or “Clamp Pressure Low,” minimizing downtime.
Applications center on cylindrical fabrication. In LPG/CNG cylinder plants, it trims and joggles shell edges for welding, ensuring leak-proof seals. In aerospace, it prepares missile or rocket casings with exacting precision. In defense, it processes artillery shells. Its capacity to handle 0.5-6 millimeter metals—adjusted via tool settings—suits both light and heavy-duty tasks. Small shops use manual versions for custom jobs; factories rely on automated ones for scale.
Benefits include speed (manual 5-10 minutes vs. 15-60 seconds), precision (tolerances <0.1 mm), and weld readiness, reducing defects by 15-20%. Waste drops 10% with accurate trimming, and labor shrinks—one operator manages high output. The Trimming Joggling Machine is a durable, efficient cornerstone for cylindrical metalwork, meeting stringent industrial demands.
Continuing with an expanded exploration of the Trimming Joggling Machine, its technical refinements, operational efficiency, and industrial impact provide a fuller perspective on its significance in metalworking, particularly for cylindrical applications. This machine’s ability to streamline edge preparation with precision and speed underscores its value in high-stakes manufacturing processes.
The Trimming Joggling Machine’s design is a blend of rugged durability and functional precision. Its frame, often constructed from welded steel plates (12-25 millimeters thick) or a monolithic cast iron casting, is engineered to endure the dynamic loads of trimming and joggling heavy metal workpieces. The frame’s stability is enhanced by a wide base—sometimes bolted to the floor in industrial setups—and internal bracing that distributes stress evenly. Weighing between 500 and 2,500 kilograms, depending on size, it resists tipping or vibration, critical when spinning large cylinders at 20-50 RPM or cutting at 1,000 RPM.
The power system is meticulously calibrated for versatility and endurance. The electric motor, typically ranging from 5 to 20 horsepower, is paired with a heavy-duty gearbox featuring hardened steel gears (e.g., 40Cr or 20MnCr5) to deliver consistent torque. This setup ensures the trimming blades can shear through 6-millimeter steel while the joggling rollers exert enough force—often 2,000-5,000 N—to form a bead without stalling. Variable Frequency Drives (VFDs) allow speed adjustments from 200 to 1,200 RPM, optimizing energy use and tool life—e.g., 800 RPM for 1-millimeter aluminum versus 400 RPM for 4-millimeter steel. Some models include overload protection, shutting down if torque exceeds safe limits, preventing motor burnout.
The trimming unit is built for accuracy and robustness. Its blades, often circular with a 150-250 millimeter diameter, are forged from tool steel or tungsten carbide, then precision-ground to a razor-sharp edge (Ra < 0.8 µm). Mounted on a servo-driven spindle, they adjust vertically and horizontally to trim 0.5-3 millimeters of material, depending on the workpiece spec. A coolant system—water-based or air-cooled—keeps temperatures below 100°C, reducing thermal distortion and clearing metal chips. In automated machines, laser sensors track the edge, ensuring cuts stay within ±0.05 millimeters, a must for seamless welding later.
The joggling unit is equally sophisticated, designed to form a consistent bead or offset. It uses paired rollers—one with a convex profile, the other concave—or a single contoured die, both made from the same high-strength materials as the blades. The rollers, typically 80-120 millimeters wide, press the edge into a 2-5 millimeter bead at 50-150 RPM, with pressure fine-tuned via hydraulic cylinders or pneumatic actuators. The bead’s shape—rounded, squared, or stepped—can be customized by swapping rollers, a process taking 5-10 minutes with quick-release mounts. This flexibility suits applications from LPG cylinders (needing a tight 2-millimeter bead) to missile casings (requiring a broader 4-millimeter offset).
The clamping system is tailored for cylindrical precision. A rotating chuck, often 200-800 millimeters in diameter, grips the workpiece internally, driven by a secondary motor or belt-linked to the main drive. Hydraulic clamps apply 2,000-4,000 N of force, locking the cylinder concentrically to avoid wobble during trimming and joggling. For larger or non-standard shapes, adjustable external clamps or a mandrel system secure the metal, with alignment checked via dial indicators or laser guides. This setup ensures the edge remains perfectly circular, critical for weld integrity in pressure vessels.
Operation reflects the machine’s efficiency. In manual mode, an operator loads a 2-millimeter steel cylinder, aligns it with the trimming blade, and triggers the cycle—trimming in 15-20 seconds, joggling in 25-35 seconds, totaling under a minute. Semi-automatic models automate tool engagement, cutting time to 30-40 seconds with operator oversight. Fully automatic versions, with CNC control, finish in 15-20 seconds: a conveyor feeds the workpiece, sensors confirm position, and the machine trims 1 millimeter off the edge and joggles a 3-millimeter bead at 500 mm/min. Feedback loops adjust for material variations, maintaining uniformity across 100+ pieces hourly.
Technological upgrades enhance capability. CNC machines store dozens of profiles—e.g., a 2-millimeter bead at 45° for CNG cylinders or a 5-millimeter step for artillery shells—switchable via touchscreen. Proximity sensors and load cells monitor blade wear and joggle pressure, pausing if deviations exceed 0.1 millimeters. Dual-head designs trim and joggle simultaneously, slashing cycle time by 40%, while robotic integration handles loading/unloading, pushing rates to 250-350 pieces per hour in LPG plants. Some units feature remote diagnostics, alerting technicians to issues like “Gearbox Temp High” via a mobile app, minimizing downtime.
Safety is stringent. Steel guards with polycarbonate windows shield the trimming and joggling zones, with interlocks cutting power if opened. Emergency stops, dual-redundant for reliability, halt operation in 0.3 seconds. Noise—85-95 decibels—demands ear protection, and vibration is damped to below 2 m/s² with rubber mounts or counterweights. Dust collectors (800-1,200 CFM) capture steel or aluminum shavings, and clamps are pressure-tested before each shift to prevent workpiece ejection, a hazard at high RPM.
Maintenance is systematic. Lubricating bearings and gears with high-viscosity oil every 100-200 hours prevents wear, while blades are swapped after 1,000-2,000 cuts, and rollers inspected for cracks. Hydraulic fluid is checked bi-monthly, and CNC software updated annually. Self-diagnostic screens flag “Blade Dull” or “Clamp Failure,” guiding repairs. Parts like belts or seals are standardized for quick replacement.
Applications focus on cylindrical precision. In LPG/CNG cylinder production, it trims and joggles edges for welding, ensuring pressure-tight seals. In aerospace, it prepares rocket casings; in defense, it processes warhead shells. Handling 0.5-6 millimeter metals, it adapts via speed and tool tweaks. Small shops use manual models for flexibility; factories rely on automated ones for volume.
Benefits are stark: manual 5-10 minutes shrinks to 15-60 seconds, lifting output from 20 to 200+ pieces hourly. Precision cuts waste by 10-15%, and uniform beads slash weld defects by 20%. Labor drops—one operator oversees high throughput. The Trimming Joggling Machine is a rugged, efficient linchpin for cylindrical fabrication, meeting exacting industrial standards.
EMS Metalworking Machinery: Your Trusted Partner in Precision Metalworking
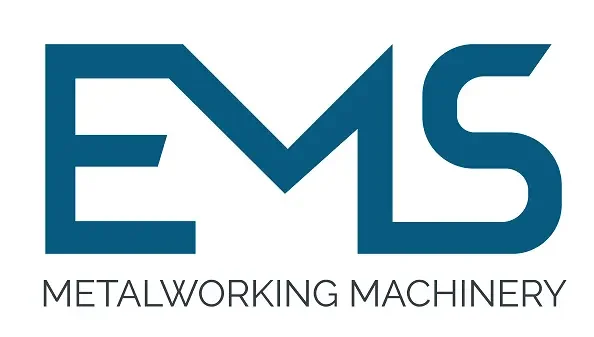
EMS Metalworking Machinery is a leading manufacturer of high-quality metalworking equipment, dedicated to providing innovative solutions that meet the evolving needs of industries worldwide. With a rich history of excellence and a commitment to technological advancement, we have earned a reputation for delivering cutting-edge machinery that ensures precision, efficiency, and durability.
Our Product Range:
- CNC Spinning Lathes: From precision bench lathes to heavy-duty industrial models, our lathes offer unmatched accuracy and performance for a wide range of applications, including machining shafts, gears, and other cylindrical components.
- Trimming Beading Machine: Our trimming beading machines are designed to provide exceptional cutting capabilities and versatility, enabling you to create complex shapes and intricate details with ease. Whether you need a horizontal or vertical trimming machine, we have the perfect solution for your needs.
- Hydraulic Deep Drawing Press Machines: Our hydraulic deep drawing press machines are built to deliver precise and powerful drawing operations, ensuring clean holes and exceptional surface finishes. We offer a comprehensive range to suit various applications.
- Grinding Machines: Our grinding machines are engineered for precision and efficiency, allowing you to achieve the highest levels of surface finish and dimensional accuracy. Whether you need a surface grinder, cylindrical grinder, or tool grinder, we have the equipment to meet your specific requirements.
- Sawing Machines: Our sawing machines are designed for fast and accurate cutting of metals, providing clean cuts and minimal burrs. From band saws to circular saws, we offer a variety of options to suit different materials and cutting needs.
- Custom Machinery: In addition to our standard product line, we also specialize in custom machinery fabrication. Our experienced engineers can work with you to design and build tailored solutions that meet your unique requirements and optimize your production processes.
Why Choose EMS Metalworking Machinery:
- Quality: Our machines are crafted with the highest quality materials and components, ensuring long-lasting performance and reliability.
- Precision: We are committed to delivering machinery that meets the most stringent tolerances and standards, ensuring exceptional accuracy in your metalworking operations.
- Innovation: We continuously invest in research and development to stay at the forefront of technological advancements, offering innovative solutions that enhance your productivity and efficiency.
- Customer Support: Our dedicated team of experts is always available to provide comprehensive support, from machine selection and installation to maintenance and troubleshooting.
- Customization: We understand that every business has unique needs, and we offer flexible customization options to tailor our machines to your specific requirements.
At EMS Metalworking Machinery, we are more than just a supplier of equipment; we are your trusted partner in metalworking success. By choosing EMS, you can be confident in the quality, reliability, and performance of your machinery, enabling you to achieve your business goals and stay ahead of the competition.
EMS Metalworking Machinery
We design, manufacture and assembly metalworking machinery such as:
- Hydraulic transfer press
- Glass mosaic press
- Hydraulic deep drawing press
- Casting press
- Hydraulic cold forming press
- Hydroforming press
- Composite press
- Silicone rubber moulding press
- Brake pad press
- Melamine press
- SMC & BMC Press
- Labrotaroy press
- Edge cutting trimming machine
- Edge curling machine
- Trimming beading machine
- Trimming joggling machine
- Cookware production line
- Pipe bending machine
- Profile bending machine
- Bandsaw for metal
- Cylindrical welding machine
- Horizontal pres and cookware
- Kitchenware, hotelware
- Bakeware and cuttlery production machinery
as a complete line as well as an individual machine such as:
- Edge cutting trimming beading machines
- Polishing and grinding machines for pot and pans
- Hydraulic drawing presses
- Circle blanking machines
- Riveting machine
- Hole punching machines
- Press feeding machine
You can check our machinery at work at: EMS Metalworking Machinery – YouTube
Applications:
- Beading and ribbing
- Flanging
- Trimming
- Curling
- Lock-seaming
- Ribbing
- Flange-punching