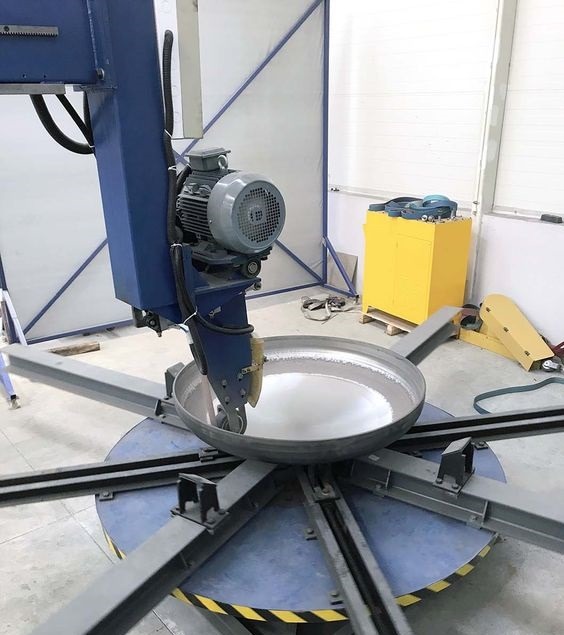
Tank Head Polishing Machine: The metal finishing and polishing machinery industry plays a critical role in the manufacturing sector, providing essential tools that enhance the quality, durability, and appearance of metal products. From aerospace to automotive, construction to consumer goods, the importance of precision metal finishing cannot be overstated. High-quality surface finishing not only improves the aesthetic appeal of metal products but also extends their lifespan, enhances resistance to corrosion, and ensures compliance with industry standards.
The demand for advanced metal finishing machines is driven by the need for efficiency, precision, and consistency in metalworking processes. As industries evolve, so too do the technologies behind these machines. Companies are increasingly seeking out machinery that offers a combination of high performance, ease of use, and adaptability to various types of metalworking tasks. This has led to the development and refinement of a wide range of specialized machines, each designed to meet specific needs within the metal fabrication process.
In this text, we will explore a variety of these machines, including the Tank Head Polishing Machine, Dry Metal Deburring Machine, Dry or Wet Metal Finishing Machine, Sheet Metal Leveling Machine, Sheet Metal Embossing Machine, Tube Polishing Machine, Pipe Profile Bending Machine, Sheet Metal Buffing Polishing Machine, Wheel Polishing Machine, Tank Dish End Polishing Machine, and Belt Grinder. Each section will provide an in-depth look at the functionality, applications, and benefits of these machines, helping you understand how they can enhance your manufacturing processes.
Tank Head Polishing Machine
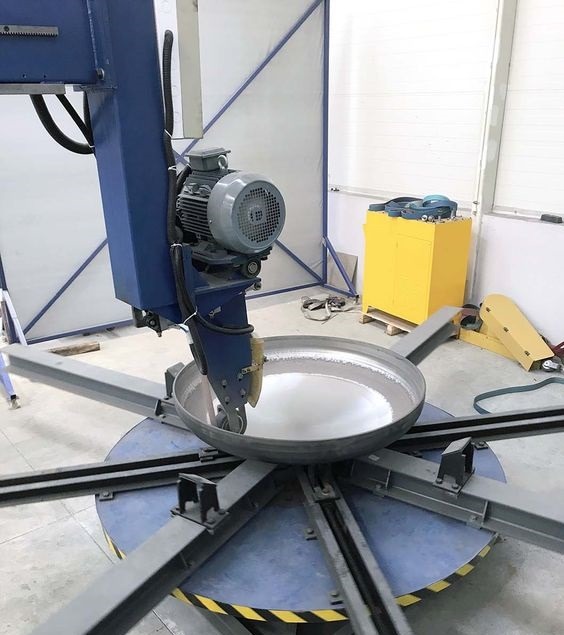
A Tank Head Polishing Machine is a specialized piece of equipment designed for polishing the heads of tanks, also known as dish ends. These machines are critical in industries where the aesthetic and structural quality of tank heads is paramount, such as in the production of pressure vessels, chemical tanks, and storage containers used in the food and beverage industry.
Functionality and Design
The Tank Head Polishing Machine is engineered to deliver a uniform and smooth finish across the curved surfaces of tank heads. It typically features a rotating table that holds the tank head in place, while a set of polishing tools or abrasive belts move systematically over the surface. The machine can handle different sizes and shapes of tank heads, offering flexibility for manufacturers that produce a variety of tank types.
These machines are equipped with advanced control systems that allow operators to adjust parameters such as polishing speed, pressure, and the type of abrasive material used. This ensures that the machine can achieve the desired finish, whether it’s a mirror-like shine or a matte surface, depending on the specific requirements of the application.
Industrial Applications
Tank Head Polishing Machines are widely used in industries where the internal and external surfaces of tanks need to be polished to high standards. These include:
- Food and Beverage Industry: Tanks used for storing and processing food products must have smooth, polished surfaces to prevent contamination and facilitate easy cleaning.
- Pharmaceutical Industry: Tanks in this industry require a high level of surface finish to maintain product purity and comply with strict hygiene standards.
- Chemical Industry: In chemical processing, polished tank heads help prevent corrosion and reduce the risk of contamination from chemical residues.
Advantages of Using a Tank Head Polishing Machine
Investing in a Tank Head Polishing Machine offers several advantages:
- Improved Quality: Achieves a consistent and high-quality finish that enhances the overall appearance and performance of the tank.
- Efficiency: Automates the polishing process, reducing the time and labor required compared to manual polishing methods.
- Versatility: Capable of handling a wide range of tank sizes and shapes, making it a versatile addition to any manufacturing operation.
- Cost Savings: By reducing the need for rework and minimizing material wastage, these machines can contribute to significant cost savings over time.
Dry Metal Deburring Machine

The Dry Metal Deburring Machine is a vital tool in metalworking, specifically designed to remove burrs—small, often sharp, imperfections left on metal surfaces after cutting, drilling, or milling operations. These burrs can affect the quality, safety, and functionality of metal components, making deburring an essential step in the manufacturing process.
Purpose and Key Features
A Dry Metal Deburring Machine is used to smooth out rough edges and remove excess material from metal parts without using any liquid or coolant. This dry process is particularly beneficial in environments where the use of water or other fluids is either undesirable or impractical. The machine employs abrasive belts, wheels, or brushes to methodically grind down the burrs, leaving the metal surface clean and smooth.
Key features of a Dry Metal Deburring Machine include:
- Abrasive Media Variety: Equipped to use different types of abrasive materials, including belts and brushes, depending on the specific requirements of the metal being processed.
- Adjustable Speed and Pressure: Operators can control the speed and pressure applied during deburring to suit the thickness, hardness, and type of metal, ensuring precision and preventing damage to delicate parts.
- Dust Collection Systems: Since the process is dry, effective dust collection systems are integrated into the machine to maintain a clean working environment and prevent airborne particles from affecting workers’ health or contaminating the workspace.
- Compact and Versatile Design: Many dry deburring machines are designed to be compact, making them suitable for use in a variety of manufacturing settings, from large-scale industrial plants to smaller workshops.
Applications in Manufacturing and Fabrication
Dry Metal Deburring Machines are used across a wide range of industries where metal parts need to be smooth, safe, and ready for assembly or further processing. Some of the key applications include:
- Automotive Industry: Deburring is crucial for the precision parts used in engines, transmissions, and other critical automotive components. Smooth edges help ensure proper fitting and function, reducing the risk of mechanical failure.
- Aerospace Industry: In aerospace manufacturing, where safety and precision are paramount, deburring is an essential process for ensuring that metal parts meet strict specifications and do not pose any risk of injury or malfunction.
- Metal Fabrication: General metal fabrication, including the production of sheet metal parts, structural components, and machined pieces, relies on deburring machines to produce high-quality, defect-free surfaces.
Comparative Analysis: Dry vs. Wet Deburring Machines
When deciding between a Dry Metal Deburring Machine and a wet alternative, several factors come into play, each influencing the choice based on the specific needs of the manufacturing operation.
- Environmental Considerations: Dry deburring is more environmentally friendly as it eliminates the need for water or other coolants, reducing waste disposal concerns. It is ideal for facilities where water conservation is a priority or where liquid handling is challenging.
- Material Compatibility: Dry deburring is generally better suited for non-ferrous metals like aluminum, brass, and copper, which do not generate significant heat during processing. For harder metals like steel, wet deburring might be preferred to reduce heat build-up.
- Surface Finish Quality: Wet deburring can achieve finer finishes and is often used when a higher degree of surface smoothness is required. However, dry deburring is sufficient for most general-purpose applications and is often faster due to the absence of drying time.
- Cost Efficiency: Dry deburring machines tend to have lower operational costs since they do not require coolant systems or the maintenance associated with wet processing. They are also typically easier to clean and maintain.
In summary, Dry Metal Deburring Machines offer an efficient, cost-effective solution for removing burrs from metal parts, particularly in settings where water or other liquids are not viable. Their versatility and ease of use make them an indispensable tool in various metalworking industries.
Dry or Wet Metal Finishing Machine
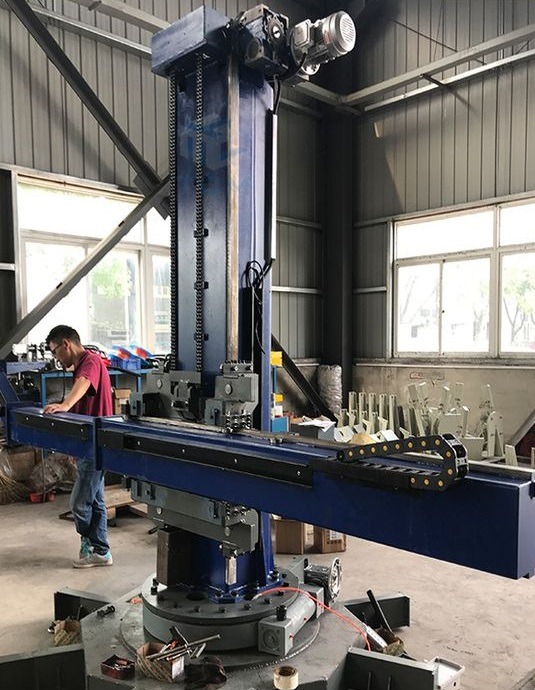
A Dry or Wet Metal Finishing Machine is a versatile tool designed to enhance the surface quality of metal products through various finishing processes. These machines are essential in industries where the final appearance, texture, and durability of metal components are critical. They can operate in either dry or wet modes, depending on the specific requirements of the task, offering flexibility to manufacturers across different sectors.
Understanding Metal Finishing Processes
Metal finishing is the process of altering the surface of a metal workpiece to achieve a desired texture, appearance, or performance characteristic. This can involve smoothing out rough edges, removing imperfections, or adding protective coatings. The type of finishing process used depends on the intended application of the metal part, ranging from aesthetic improvements to enhancing corrosion resistance.
A Dry or Wet Metal Finishing Machine can perform a variety of finishing tasks, including:
- Deburring: Removing sharp edges or burrs left after machining.
- Polishing: Creating a smooth, reflective surface that enhances the appearance of the metal.
- Grinding: Smoothing out rough surfaces to prepare the metal for further processing or final use.
- Sanding: Abrading the surface to remove old coatings, rust, or other contaminants.
Differences Between Dry and Wet Finishing Machines
While both dry and wet finishing machines are designed to improve the surface quality of metal products, they operate differently and are suited to distinct types of finishing tasks.
- Dry Metal Finishing Machines:
- No Liquid Required: These machines do not use any liquid during the finishing process, which makes them ideal for applications where water or coolant usage is not feasible.
- Faster Processing: The absence of liquid means there is no need for drying time, making the finishing process quicker.
- Dust Management: They are equipped with dust collection systems to handle the fine particles generated during the finishing process, maintaining a clean work environment.
- Lower Operating Costs: Since there’s no need for coolant systems, dry machines tend to be more economical in terms of both operation and maintenance.
- Wet Metal Finishing Machines:
- Cooling Effect: The use of water or coolant helps to reduce the heat generated during finishing, which is particularly useful when working with hard metals or when an exceptionally smooth finish is required.
- Enhanced Surface Finish: Wet finishing generally produces a finer surface finish, making it the preferred choice for applications where aesthetics are critical, such as in the production of high-end consumer goods or decorative metal parts.
- Cleaner Process: The liquid helps to wash away debris and dust, resulting in a cleaner finish and reducing the risk of airborne particles.
- Complex Maintenance: Wet machines require more maintenance due to the involvement of liquids, which can lead to issues such as rust or contamination if not properly managed.
Selecting the Right Machine for Your Needs
Choosing between a dry or wet metal finishing machine depends on several factors, including the type of metal being processed, the desired surface finish, and the specific requirements of the manufacturing process.
- Material Type: For softer metals or non-ferrous materials, a dry finishing machine may suffice, offering speed and cost efficiency. For harder metals, a wet machine may be necessary to manage the heat generated during the finishing process.
- Desired Finish: If a high-gloss or mirror-like finish is needed, a wet finishing machine is generally more effective. However, for general-purpose finishing where a smooth but not necessarily reflective surface is required, a dry machine is often adequate.
- Operational Environment: In facilities where water usage is restricted or where liquid waste management poses challenges, a dry machine is the better choice. Conversely, in environments where cleanliness and precision are paramount, wet finishing machines might be preferred.
- Budget Considerations: Dry machines tend to be more economical in terms of initial investment and ongoing maintenance. However, the choice should also consider the long-term quality of the finished product and the potential need for rework if the chosen machine does not meet the required standards.
In conclusion, Dry or Wet Metal Finishing Machines are crucial tools in the metalworking industry, offering flexibility and precision to meet a wide range of finishing needs. By understanding the differences between dry and wet processes, manufacturers can select the machine that best suits their production goals and operational constraints.
Sheet Metal Leveling Machine
The Sheet Metal Leveling Machine is a crucial piece of equipment in the metal fabrication industry, designed to correct distortions in sheet metal and ensure a flat, even surface. This process, known as leveling, is essential for preparing metal sheets for subsequent manufacturing processes, such as cutting, bending, or welding. By eliminating stresses and imperfections, the leveling machine enhances the quality and consistency of the final products.
Role in Metal Fabrication
In metal fabrication, precision is key. Even minor distortions in sheet metal can lead to significant issues during production, affecting the accuracy of cuts, bends, and welds. A Sheet Metal Leveling Machine addresses these challenges by applying a series of small, controlled bends to the metal sheet, effectively removing any internal stresses and flattening the material.
The leveling process is particularly important when working with thin metal sheets, which are more prone to warping and distortion. By passing the sheet through the leveling machine, manufacturers can achieve a uniform thickness and a perfectly flat surface, ensuring that the sheet metal meets the strict tolerances required in high-precision applications.
Technical Specifications and Performance
Sheet Metal Leveling Machines are designed to handle a wide range of materials and thicknesses, from thin aluminum sheets to thicker steel plates. Key technical features of these machines include:
- Adjustable Rollers: The machine uses multiple rollers, which can be adjusted to apply varying degrees of pressure to the sheet metal. This allows for precise control over the leveling process, ensuring that the metal is perfectly flat without causing damage or excessive thinning.
- Automatic Control Systems: Modern leveling machines are equipped with computerized control systems that automatically adjust the rollers based on the thickness and material of the sheet. This ensures consistent results and reduces the risk of operator error.
- High Throughput: These machines are capable of processing large volumes of sheet metal quickly and efficiently, making them ideal for use in high-production environments. Some models are designed to handle sheets at high speeds, ensuring that the leveling process does not become a bottleneck in the manufacturing workflow.
- Material Handling Options: Many leveling machines are integrated with material handling systems, such as coil feeders and stackers, which streamline the loading and unloading of sheet metal. This not only improves efficiency but also reduces the risk of damage during handling.
Key Industries Benefiting from Sheet Metal Leveling Machines
Sheet Metal Leveling Machines are used in a variety of industries where flat, stress-free metal sheets are essential for high-quality production. Some of the key industries include:
- Automotive Industry: In automotive manufacturing, sheet metal leveling is critical for ensuring that body panels and other components fit together perfectly. Any distortion in the metal can lead to gaps, misalignments, and other defects that compromise the quality and safety of the vehicle.
- Aerospace Industry: The aerospace sector demands the highest levels of precision in all components. Sheet metal leveling ensures that metal sheets used in aircraft structures are perfectly flat, reducing the risk of structural failures and improving overall safety.
- Construction Industry: In construction, leveled sheet metal is used for a variety of applications, including roofing, cladding, and structural components. Ensuring that the metal is flat and stress-free is essential for maintaining the integrity and durability of these structures.
- Consumer Electronics: The production of consumer electronics often involves the use of thin metal sheets for components such as casings and enclosures. Sheet metal leveling is essential for achieving the precise tolerances required in these applications, ensuring that components fit together seamlessly and function as intended.
Advantages of Using a Sheet Metal Leveling Machine
Investing in a Sheet Metal Leveling Machine offers several benefits:
- Enhanced Precision: The machine ensures that sheet metal is perfectly flat, which is essential for achieving the tight tolerances required in many industries.
- Improved Product Quality: By eliminating distortions and internal stresses, the leveling process enhances the overall quality and consistency of the final products.
- Increased Efficiency: Modern leveling machines are designed to process large volumes of sheet metal quickly, helping manufacturers meet production targets and reduce lead times.
- Versatility: These machines can handle a wide range of materials and thicknesses, making them suitable for use in various industries and applications.
In conclusion, the Sheet Metal Leveling Machine is an indispensable tool in the metal fabrication industry, ensuring that sheet metal is flat, stress-free, and ready for further processing. By investing in a high-quality leveling machine, manufacturers can improve the precision, quality, and efficiency of their production processes.
Sheet Metal Embossing Machine
A Sheet Metal Embossing Machine is a specialized piece of equipment used to create raised or recessed designs on sheet metal surfaces. This process, known as embossing, involves pressing a pattern or texture into the metal, adding both aesthetic and functional value to the material. Embossing is widely used in various industries for decorative purposes, as well as for practical applications like improving grip, adding structural rigidity, or increasing surface area for heat dissipation.
Overview of Embossing Processes
Embossing involves the use of matched male and female dies that are pressed into the sheet metal to create a three-dimensional pattern. The process can be performed on a variety of metals, including steel, aluminum, copper, and brass, and is commonly used to produce textures such as diamonds, squares, circles, and custom designs.
The Sheet Metal Embossing Machine is designed to handle this process efficiently, ensuring precise replication of the desired pattern across large batches of metal sheets. Depending on the application, the machine can be configured to emboss single sheets or continuous coils of metal, allowing for high-volume production.
How Sheet Metal Embossing Machines Work
The operation of a Sheet Metal Embossing Machine typically involves the following steps:
- Loading the Material: Sheet metal or metal coils are fed into the machine, where they are aligned and prepared for embossing.
- Die Pressing: The machine presses the male and female dies together with the sheet metal in between, imprinting the pattern onto the metal surface. The pressure applied during this process is carefully controlled to ensure uniform depth and detail in the embossed design.
- Material Handling: After embossing, the sheet metal is either stacked or rolled into coils for further processing or shipment. Advanced machines may include automated material handling systems to streamline this process.
- Quality Control: Modern embossing machines often incorporate inspection systems that check the quality and consistency of the embossed patterns, ensuring that each sheet meets the required specifications.
Industry Applications and Benefits
Sheet Metal Embossing Machines are used in a wide range of industries where both the decorative and functional aspects of embossed metal are valued. Key applications include:
- Architectural and Interior Design: Embossed metal sheets are used in building facades, interior wall panels, and ceiling tiles to add texture and visual interest. The embossed patterns can also help to diffuse light, create shadows, and add depth to surfaces.
- Automotive Industry: In automotive manufacturing, embossed sheet metal is used for interior components, such as dashboards and door panels, as well as exterior elements like running boards and foot pedals. The embossed textures can improve grip, enhance the appearance, and add structural strength to these components.
- HVAC Systems: Embossed metal is commonly used in heating, ventilation, and air conditioning systems to create surfaces with increased surface area for better heat exchange. The embossed patterns can also add rigidity to thin metal sheets, reducing the need for additional support structures.
- Packaging and Signage: The packaging industry uses embossed metal for creating attractive and durable containers, while the signage industry employs embossed metal sheets for producing high-visibility, weather-resistant signs.
Advantages of Using a Sheet Metal Embossing Machine
The use of a Sheet Metal Embossing Machine offers several key benefits, making it an invaluable tool in the production of high-quality metal products:
- Enhanced Aesthetics: Embossing adds visual appeal to metal surfaces, allowing manufacturers to create unique, eye-catching designs that stand out in the market.
- Increased Structural Integrity: The embossing process can strengthen sheet metal by adding rigidity and reducing flex, making it more durable and resistant to deformation.
- Improved Functionality: Embossed patterns can enhance the functionality of metal components by improving grip, increasing surface area for heat dissipation, and providing better fluid flow in certain applications.
- Customization: Modern embossing machines offer a high degree of customization, allowing manufacturers to create bespoke patterns that meet specific design requirements or brand standards.
- Cost-Effectiveness: Embossing is a relatively low-cost way to add value to sheet metal, especially in high-volume production runs where the cost per unit is minimized.
In conclusion, the Sheet Metal Embossing Machine is a versatile and powerful tool that adds both decorative and functional value to metal products. Its ability to create detailed, consistent patterns on sheet metal makes it essential for industries ranging from automotive to architecture. By investing in advanced embossing technology, manufacturers can enhance the appeal, strength, and performance of their metal products, giving them a competitive edge in the market.
Tube Polishing Machine
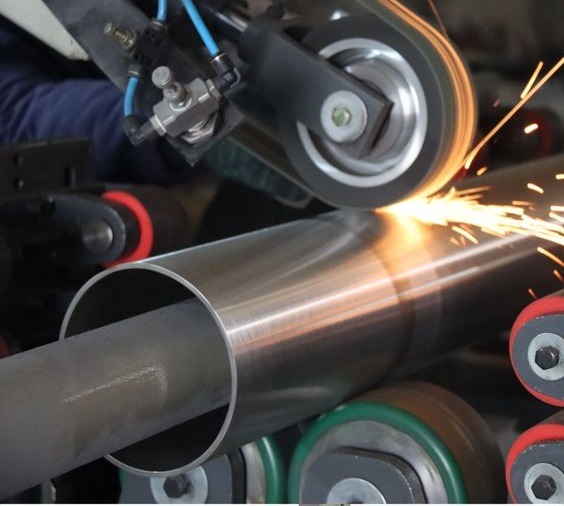
A Tube Polishing Machine is a specialized piece of equipment designed for the surface finishing of tubes and cylindrical parts. These machines are essential in industries where the surface quality of tubes is critical, such as in the automotive, aerospace, construction, and medical device sectors. The primary function of a tube polishing machine is to remove imperfections, enhance the surface finish, and prepare the tubes for further processing or final use.
Functionality and Design
The Tube Polishing Machine is engineered to polish tubes of various diameters and lengths, achieving a smooth and uniform surface. These machines typically consist of several key components:
- Polishing Heads: The machine is equipped with multiple polishing heads or abrasive belts that rotate around the tube as it is fed through the machine. These heads can be adjusted to apply different levels of pressure and use various abrasive materials to achieve the desired finish.
- Variable Speed Control: Operators can adjust the speed of the polishing heads and the feed rate of the tube, allowing for precise control over the polishing process. This ensures that the machine can handle a range of materials, from soft metals like aluminum to harder materials like stainless steel.
- Support Rollers: The tube is supported by rollers that guide it through the polishing heads, ensuring consistent contact with the abrasive surfaces and preventing any deformation during the process.
- Dust Collection System: Polishing generates dust and debris, so these machines are often equipped with integrated dust collection systems that keep the workspace clean and safe.
Versatile Applications Across Industries
Tube Polishing Machines are used in various industries where high-quality, polished tubes are required. Some of the key applications include:
- Automotive Industry: Polished tubes are used in exhaust systems, hydraulic lines, and other automotive components where smooth surfaces are essential for performance and durability. Tube polishing ensures that these components meet strict quality standards and have an attractive, defect-free finish.
- Aerospace Industry: In aerospace manufacturing, the surface finish of tubes is critical for both aesthetic and functional reasons. Polished tubes are often used in structural components, fuel lines, and other parts where precision and corrosion resistance are paramount.
- Construction and Architecture: Polished metal tubes are commonly used in architectural designs, such as railings, support structures, and decorative elements. The tube polishing process enhances the appearance of these components, ensuring they meet the aesthetic standards of modern architecture.
- Medical Device Manufacturing: In the medical field, polished tubes are used in the production of surgical instruments, implants, and medical equipment. The smooth, polished surface of these tubes is essential for ensuring cleanliness, reducing friction, and meeting stringent hygiene standards.
How Tube Polishing Machines Improve Surface Quality
The polishing process significantly improves the surface quality of tubes, making them suitable for high-precision applications. The benefits of using a Tube Polishing Machine include:
- Surface Smoothness: Polishing removes surface irregularities, scratches, and burrs, resulting in a smooth, uniform finish that is both visually appealing and functionally superior.
- Corrosion Resistance: By polishing the surface, the machine reduces the risk of corrosion, which is particularly important in industries where tubes are exposed to harsh environments or corrosive substances.
- Improved Aesthetics: A polished tube has a high-quality finish that enhances the overall appearance of the product, making it suitable for visible applications in consumer products and architectural designs.
- Enhanced Mechanical Properties: Polishing can improve the mechanical properties of the tube, such as fatigue strength and wear resistance, by eliminating surface defects that could lead to failure under stress.
Advantages of Using a Tube Polishing Machine
Investing in a Tube Polishing Machine offers several significant advantages for manufacturers:
- Increased Productivity: These machines are designed for high-throughput production, allowing manufacturers to polish large volumes of tubes quickly and efficiently.
- Consistency and Precision: Automated tube polishing ensures that each tube is polished to the same standard, eliminating variability and ensuring consistent quality across production runs.
- Cost Efficiency: By reducing the need for manual polishing and minimizing material waste, tube polishing machines can lower production costs and increase profitability.
- Flexibility: These machines can be adjusted to polish tubes of different sizes and materials, making them a versatile addition to any manufacturing operation.
In conclusion, the Tube Polishing Machine is a vital tool for achieving high-quality surface finishes on tubes used in a wide range of industries. Its ability to deliver consistent, precise polishing makes it indispensable for manufacturers who require superior surface quality and durability in their products. By investing in advanced tube polishing technology, companies can enhance the performance, appearance, and longevity of their metal tubes, ensuring they meet the demanding standards of their industries.
Pipe Profile Bending Machine
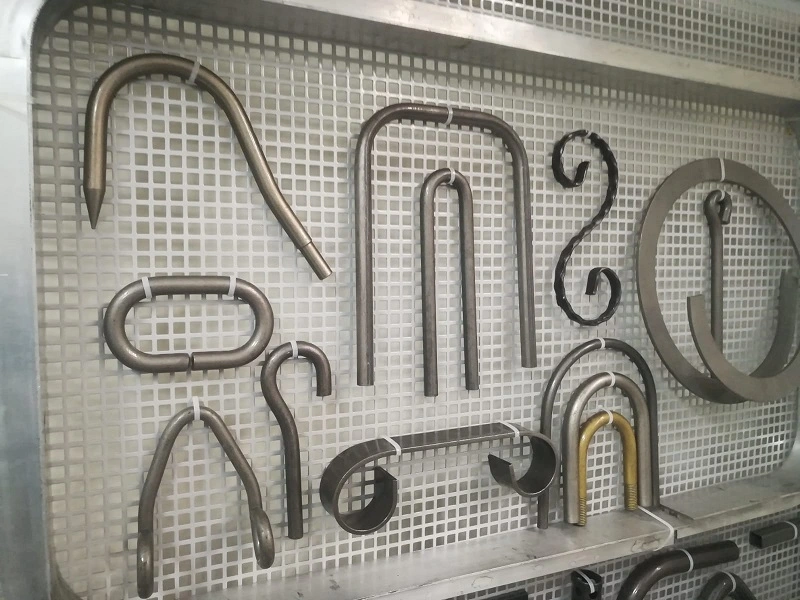
A Pipe Profile Bending Machine is a specialized piece of equipment designed to bend pipes and profiles into specific shapes and angles without compromising the integrity of the material. These machines are essential in industries where precision bending of pipes and profiles is required, such as in construction, automotive, aerospace, and shipbuilding. The ability to accurately bend pipes and profiles ensures that they meet the precise specifications needed for complex installations and assemblies.
Understanding Pipe Bending Techniques
Pipe bending is a process used to permanently deform pipes and tubes into a desired angle or curvature. There are several techniques used in pipe bending, each with its advantages depending on the material, diameter, and thickness of the pipe, as well as the required bend radius.
- Mandrel Bending: In this technique, a mandrel is inserted into the pipe to provide internal support during bending. This prevents the pipe from collapsing or wrinkling, making it ideal for tight radius bends on thin-walled pipes.
- Rotary Draw Bending: This method uses a set of dies to bend the pipe by rotating it around a fixed radius. Rotary draw bending is highly accurate and is often used in applications where consistent, precise bends are required.
- Roll Bending: In roll bending, the pipe is passed through a series of rollers that gradually shape it into the desired curve. This method is suitable for creating large-radius bends and is commonly used for bending profiles and structural components.
- Compression Bending: This technique involves pushing the pipe into a stationary die to achieve the bend. It is a cost-effective method for simple bends but is less precise than other techniques.
Advantages of Using Profile Bending Machines
Pipe Profile Bending Machines offer several advantages that make them indispensable in various industries:
- Precision Bending: These machines are designed to achieve high levels of precision, ensuring that each bend meets the exact specifications required for the application. This is particularly important in industries where even slight deviations can lead to significant issues in assembly or performance.
- Versatility: Profile bending machines can handle a wide range of materials, including steel, aluminum, copper, and stainless steel. They can also accommodate different pipe diameters and thicknesses, making them suitable for a variety of bending tasks.
- Efficiency: These machines are capable of bending pipes and profiles quickly and efficiently, reducing production time and increasing throughput. This is particularly beneficial in high-volume manufacturing environments.
- Reduced Material Waste: By providing consistent, accurate bends, profile bending machines minimize material waste, which can result in cost savings for manufacturers.
- Customization: Advanced machines allow for customization of the bending process, enabling manufacturers to produce complex shapes and profiles that would be difficult or impossible to achieve with manual bending techniques.
Industries That Rely on Pipe Profile Bending Machines

Several industries rely on Pipe Profile Bending Machines for their precision and versatility:
- Construction Industry: In construction, bent pipes and profiles are used in structural frameworks, railings, and piping systems. Profile bending machines ensure that these components are shaped accurately to fit the specific requirements of each project.
- Automotive Industry: The automotive sector uses bent pipes in exhaust systems, chassis components, and roll cages. Precision bending is essential to ensure that these parts fit correctly and function as intended.
- Aerospace Industry: In aerospace manufacturing, bent profiles and pipes are used in aircraft structures, hydraulic systems, and fuel lines. The high level of precision provided by profile bending machines is critical for ensuring the safety and performance of these components.
- Shipbuilding: In shipbuilding, large pipes and profiles are bent to create structural components and piping systems that must withstand the harsh conditions at sea. Profile bending machines provide the accuracy and strength needed for these demanding applications.
- Energy Sector: The energy sector, including oil and gas, relies on bent pipes for pipelines, rigs, and refineries. Profile bending machines help create the complex pipe systems required for efficient energy production and distribution.
How Profile Bending Machines Enhance Production
Profile bending machines significantly enhance the production process by providing manufacturers with the tools they need to create precise, consistent bends in pipes and profiles. The key benefits of using these machines in production include:
- Increased Accuracy: Automated bending machines reduce the likelihood of errors, ensuring that each bend is performed according to exact specifications. This is especially important in industries where precision is critical.
- Time Savings: These machines are designed to perform bends quickly, allowing for faster production cycles. This helps manufacturers meet tight deadlines and increase overall productivity.
- Reduced Labor Costs: By automating the bending process, these machines reduce the need for manual labor, lowering production costs and reducing the risk of injury to workers.
- Flexibility in Design: With the ability to produce a wide range of bend angles and profiles, these machines offer manufacturers greater flexibility in design, enabling them to meet the unique needs of their customers.
In conclusion, Pipe Profile Bending Machines are essential tools for industries that require precise, efficient bending of pipes and profiles. Their ability to handle a variety of materials and shapes makes them indispensable for manufacturing components that meet strict specifications and quality standards. By investing in these machines, manufacturers can improve their production processes, reduce costs, and ensure the highest levels of accuracy and consistency in their products.
Sheet Metal Buffing Polishing Machine
The Sheet Metal Buffing Polishing Machine is a crucial tool in the metal finishing industry, designed to enhance the surface quality of sheet metal through buffing and polishing processes. These machines are used to achieve a smooth, reflective, and aesthetically pleasing finish on metal surfaces, making them indispensable in industries where appearance and surface integrity are paramount.
The Importance of Buffing in Metal Finishing
Buffing is a finishing process that involves smoothing the surface of metal to remove imperfections and create a high-gloss finish. This process is typically performed after initial grinding or sanding stages and is essential for achieving the desired surface quality in various applications. Polishing, which is often used interchangeably with buffing, involves further refining the surface to increase its reflectivity and smoothness.
A Sheet Metal Buffing Polishing Machine uses specialized buffing wheels or abrasive belts to perform this process, ensuring that the metal sheet has a uniform and flawless finish. This machine is especially important in industries where the visual appeal of metal products is a key selling point.
Features of Sheet Metal Buffing Polishing Machines
These machines are designed to handle large, flat sheets of metal, providing a consistent and high-quality finish across the entire surface. Key features of a Sheet Metal Buffing Polishing Machine include:
- Adjustable Buffing Speed: The speed of the buffing wheels or belts can be adjusted to suit the material and the desired finish. Slower speeds are often used for delicate materials or finer finishes, while higher speeds are suitable for more aggressive buffing.
- Multiple Buffing Stations: Advanced machines may feature multiple buffing stations, allowing for different stages of buffing and polishing to be completed in one pass. This improves efficiency and ensures a consistent finish.
- Automatic Feed System: These machines are equipped with an automatic feed system that moves the sheet metal through the buffing process at a controlled rate, ensuring even coverage and reducing the likelihood of operator error.
- Dust and Debris Collection: Buffing generates fine dust and debris, so these machines are often equipped with integrated dust collection systems to maintain a clean work environment and protect workers’ health.
- Material Compatibility: Designed to work with a variety of metals, including aluminum, stainless steel, and copper, these machines offer flexibility in handling different types of sheet metal.
How to Choose the Right Machine for Your Operation
Selecting the right Sheet Metal Buffing Polishing Machine involves considering several factors based on the specific needs of your operation:
- Material Type: Different metals require different buffing techniques. For example, stainless steel may need a more robust machine with higher power, while softer metals like aluminum require a gentler touch to avoid damage.
- Desired Finish: The level of finish you need—whether it’s a simple smooth surface or a high-gloss mirror finish—will determine the type of machine and buffing compounds you should use. Machines with multiple buffing stations may be necessary for achieving more complex finishes.
- Production Volume: For high-volume operations, a machine with a high throughput rate and multiple buffing stations will be essential to keep up with production demands. Conversely, smaller operations might prioritize versatility and ease of use over speed.
- Automation and Control: Depending on the complexity of your operations, you may require a machine with advanced automation features, such as programmable settings and automatic material feeding. This can reduce the need for manual intervention and improve consistency.
- Maintenance and Durability: Investing in a robust machine that is easy to maintain will save time and reduce downtime in the long run. Look for machines made from durable materials with accessible components for regular maintenance.
Applications Across Industries
Sheet Metal Buffing Polishing Machines are used in a variety of industries where the surface quality of metal sheets is critical:
- Automotive Industry: Polished sheet metal is used in exterior body panels, trim components, and interior details. A high-quality finish enhances the visual appeal of the vehicle and helps protect against corrosion.
- Aerospace Industry: In aerospace, polished sheet metal is used for both functional and aesthetic purposes, including aircraft skins, interior panels, and structural components. A smooth, polished surface reduces drag and improves fuel efficiency.
- Consumer Goods: Many consumer products, such as appliances, electronics, and furniture, feature polished metal surfaces that contribute to their overall appearance and durability. Buffing and polishing ensure that these products meet high aesthetic standards.
- Architectural and Decorative Applications: Polished metal sheets are commonly used in architectural elements, including facades, interior walls, and decorative panels. The high-gloss finish adds a modern, sophisticated look to buildings and interiors.
Advantages of Using a Sheet Metal Buffing Polishing Machine
Investing in a Sheet Metal Buffing Polishing Machine provides several significant benefits for manufacturers:
- Improved Aesthetics: A polished finish enhances the appearance of metal products, making them more attractive to customers and increasing their market value.
- Increased Durability: Buffing and polishing remove surface imperfections that could lead to corrosion or wear, improving the longevity of metal products.
- Consistent Quality: These machines ensure a uniform finish across all sheet metal products, reducing variability and ensuring that every piece meets the same high standards.
- Time and Cost Efficiency: Automated buffing and polishing processes save time and reduce labor costs compared to manual finishing methods. They also minimize material waste by ensuring that the polishing is done correctly the first time.
In conclusion, the Sheet Metal Buffing Polishing Machine is an essential tool for achieving high-quality, aesthetically pleasing finishes on sheet metal products. By investing in the right machine, manufacturers can improve the appearance, durability, and overall quality of their metal products, giving them a competitive edge in their respective markets.
Wheel Polishing Machine
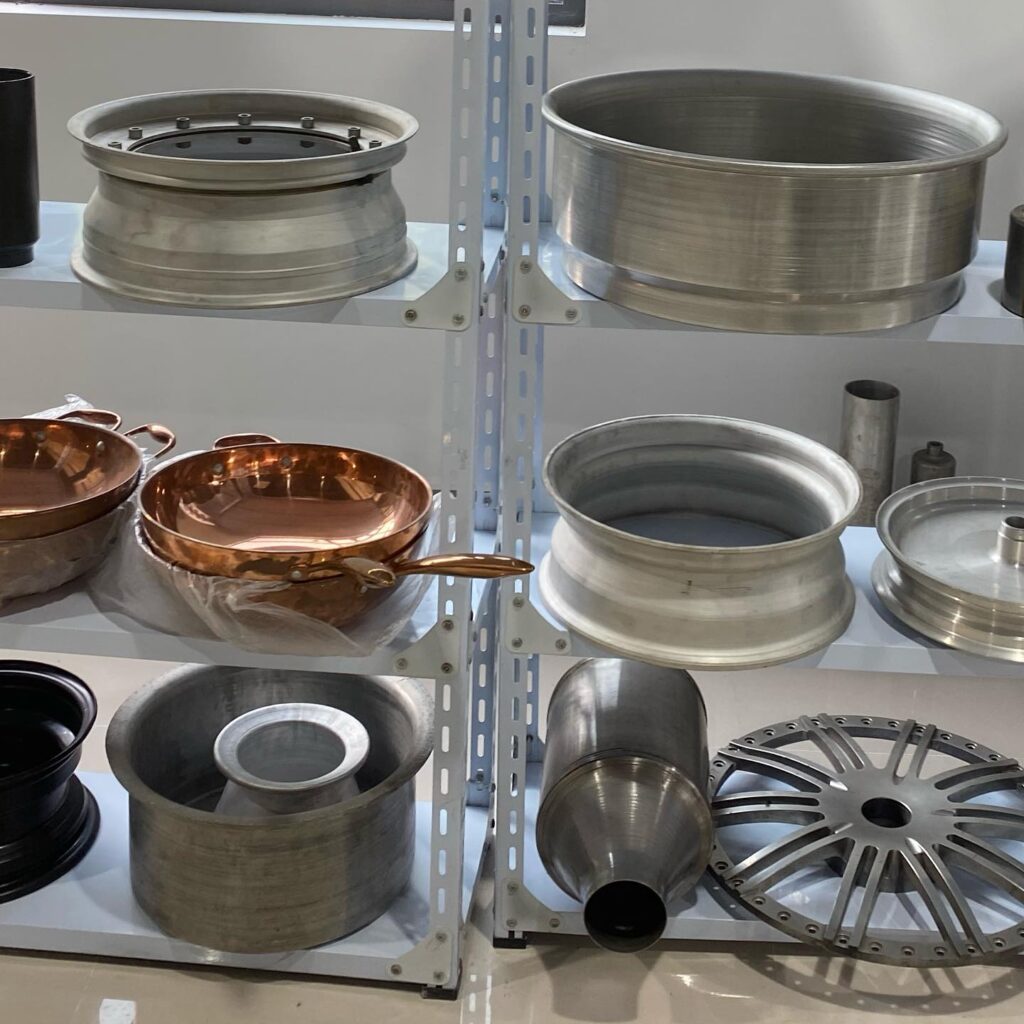
A Wheel Polishing Machine is a specialized piece of equipment designed to restore and enhance the surface finish of wheels, primarily in the automotive and aerospace industries. These machines are used to polish the surfaces of wheels, ensuring a smooth, reflective, and aesthetically pleasing finish. The process of wheel polishing not only improves the appearance of the wheels but also contributes to their longevity by removing imperfections that could lead to corrosion or wear over time.
What is a Wheel Polishing Machine?
A Wheel Polishing Machine is engineered to polish the entire surface of a wheel, including the face, spokes, and inner barrel. These machines typically use a combination of rotating abrasive wheels, buffing pads, and polishing compounds to achieve a mirror-like finish on the wheel’s surface. They are capable of handling wheels made from various materials, including aluminum, steel, and alloy, and are designed to accommodate different wheel sizes and designs.
Key features of a Wheel Polishing Machine include:
- Rotating Polishing Heads: The machine uses rotating polishing heads equipped with abrasive materials to smooth out the wheel’s surface. These heads can be adjusted to reach different parts of the wheel, ensuring a consistent finish across all areas.
- Variable Speed Control: The speed of the polishing heads can be adjusted to match the material and condition of the wheel, providing flexibility in the polishing process.
- Automation and Precision: Many wheel polishing machines are automated, allowing for precise control over the polishing process. This ensures that each wheel is polished to the same high standard, reducing the likelihood of errors or inconsistencies.
- Dust Collection Systems: Polishing wheels generates dust and debris, so these machines often include integrated dust collection systems to keep the workspace clean and safe.
Applications in Automotive and Manufacturing
Wheel Polishing Machines are used extensively in the automotive industry, where the appearance and condition of wheels are critical factors for both aesthetic and functional reasons. However, their applications extend beyond automotive manufacturing into other sectors as well:
- Automotive Industry: Polished wheels are a key component of vehicle aesthetics, particularly in high-end and custom cars. Wheel polishing machines are used to achieve the desired finish on factory wheels, aftermarket wheels, and wheels being restored or refurbished.
- Aerospace Industry: In aerospace, polished wheels are used on landing gear and other components where surface smoothness and corrosion resistance are critical. The high-quality finish provided by wheel polishing machines helps ensure that these parts meet stringent safety and performance standards.
- Custom and Aftermarket Wheels: The custom wheel market often demands highly polished, mirror-like finishes that can only be achieved through professional polishing. Wheel polishing machines are essential for producing these high-end finishes consistently.
- Manufacturing and Repair Shops: Manufacturing facilities and repair shops use these machines to maintain and restore the appearance of wheels. This is especially important for maintaining the value of vehicles and machinery, where wheel condition can impact both aesthetics and performance.
Enhancing Productivity with Advanced Wheel Polishing Machines
Investing in advanced Wheel Polishing Machines can significantly enhance productivity and improve the quality of the finished product. The key benefits of using these machines include:
- Consistency and Quality: Automated wheel polishing machines provide consistent, repeatable results, ensuring that every wheel is polished to the same high standard. This reduces the need for rework and increases customer satisfaction.
- Time Efficiency: These machines can polish wheels much faster than manual methods, allowing manufacturers and repair shops to increase throughput and meet tight deadlines.
- Cost Savings: By reducing the time and labor required to polish wheels, these machines help lower operational costs. They also minimize material waste by ensuring that the polishing process is done correctly the first time.
- Versatility: Wheel polishing machines are designed to handle a wide range of wheel sizes, designs, and materials, making them suitable for various applications across different industries.
Steps in the Wheel Polishing Process
The process of polishing a wheel using a Wheel Polishing Machine typically involves several steps:
- Preparation: The wheel is cleaned and inspected for any damage or imperfections. If necessary, repairs or sanding are done to remove deep scratches or curb damage before polishing begins.
- Initial Polishing: The wheel is mounted onto the machine, and the initial polishing stage begins using coarse abrasive materials to remove surface imperfections and smooth the wheel’s surface.
- Fine Polishing: The wheel undergoes a series of polishing stages, each using progressively finer abrasives to refine the surface and achieve a smoother finish.
- Buffing: In the final stage, the wheel is buffed using soft polishing pads and compounds to bring out a high-gloss, mirror-like finish.
- Inspection and Finishing: After polishing, the wheel is inspected to ensure it meets quality standards. Any final touches are made, and the wheel is cleaned and prepared for reinstallation or shipment.
Advantages of Using a Wheel Polishing Machine
The use of a Wheel Polishing Machine offers several key advantages for businesses in the automotive, aerospace, and manufacturing sectors:
- Enhanced Appearance: A polished wheel significantly enhances the overall appearance of a vehicle or aircraft, contributing to its aesthetic appeal and market value.
- Improved Durability: Polishing removes surface imperfections that can lead to corrosion, extending the lifespan of the wheel and maintaining its structural integrity.
- Customer Satisfaction: High-quality polished wheels are highly desirable in both the consumer and commercial markets. Providing a flawless finish can lead to increased customer satisfaction and repeat business.
- Competitive Edge: By offering superior polishing services, businesses can differentiate themselves from competitors and attract more clients who value quality and attention to detail.
In conclusion, the Wheel Polishing Machine is a vital tool for achieving the high-quality, reflective finishes that are essential in the automotive and aerospace industries. Its ability to deliver consistent, professional results makes it an indispensable part of any operation that values the appearance and performance of wheels. By investing in advanced wheel polishing technology, businesses can enhance their productivity, reduce costs, and ensure that their products meet the highest standards of quality and aesthetics.
Tank Dish End Polishing Machine
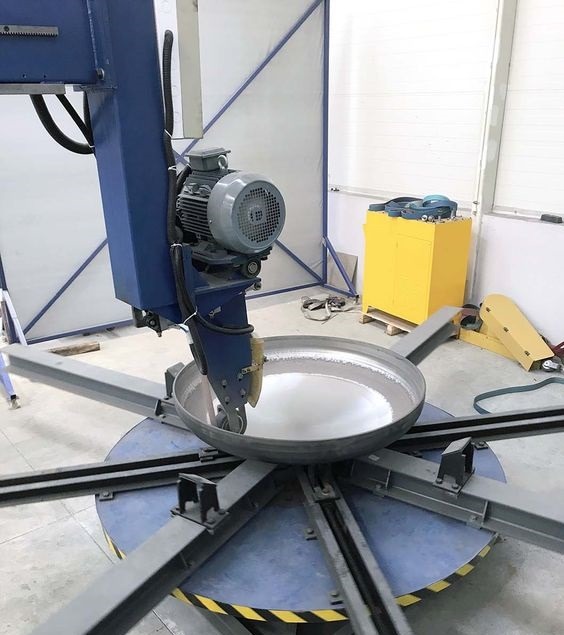
A Tank Dish End Polishing Machine is a specialized piece of equipment designed to polish the concave or convex ends of tanks, commonly referred to as dish ends. These machines are essential in industries where the quality, appearance, and surface finish of tank ends are critical, such as in the production of pressure vessels, storage tanks, and industrial containers used in sectors like food and beverage, pharmaceuticals, chemicals, and energy.
Significance of Tank Dish End Polishing in Industry
The dish ends of tanks play a crucial role in maintaining the structural integrity and functionality of the tank. They are typically made from metals like stainless steel, carbon steel, or aluminum, which require a high-quality finish to meet industry standards. The polishing process not only enhances the aesthetic appeal of the dish ends but also improves their performance by reducing the risk of corrosion, facilitating easier cleaning, and ensuring compliance with hygiene and safety regulations.
A Tank Dish End Polishing Machine is specifically engineered to handle the unique challenges associated with polishing these curved surfaces, delivering a consistent and smooth finish across the entire dish end.
Technical Aspects of Tank Dish End Polishing Machines
Tank Dish End Polishing Machines are designed to accommodate the complex geometry of dish ends, ensuring that every part of the surface is uniformly polished. Key technical features of these machines include:
- Rotating Worktable: The dish end is typically mounted on a rotating worktable that allows it to be polished evenly. The rotation ensures that the polishing tools cover the entire surface, including hard-to-reach areas.
- Articulated Polishing Arms: These machines are equipped with articulated polishing arms that can move in multiple directions to follow the contours of the dish end. This ensures consistent pressure and coverage, even on the most curved surfaces.
- Variable Speed Control: The polishing speed can be adjusted depending on the material and the desired finish. This flexibility allows for precise control over the polishing process, ensuring that the final product meets specific quality requirements.
- Abrasive Tools: The machine uses a variety of abrasive tools, such as polishing pads, belts, or wheels, which can be selected based on the material of the dish end and the required finish. These tools are designed to remove surface imperfections and create a smooth, reflective finish.
- Dust and Debris Management: Polishing generates dust and debris, particularly when working with metal. These machines are equipped with dust collection systems to keep the workspace clean and safe, as well as to prevent contamination of the polished surface.
Application Areas and Benefits
Tank Dish End Polishing Machines are used in various industries where the quality and cleanliness of tank surfaces are critical:
- Food and Beverage Industry: In this sector, tanks are used for processing and storing food products, beverages, and dairy. The dish ends of these tanks must be polished to a high standard to prevent contamination, facilitate cleaning, and ensure compliance with food safety regulations.
- Pharmaceutical Industry: Tanks used in the pharmaceutical industry require a polished finish to maintain product purity and prevent the buildup of residues that could affect the quality of the pharmaceuticals. Polished surfaces also make it easier to clean and sterilize the tanks, which is essential for maintaining hygiene standards.
- Chemical Industry: In chemical processing, polished dish ends help to prevent corrosion and contamination, ensuring the safe storage and handling of chemicals. The smooth surface finish also reduces the risk of chemical reactions that could be triggered by surface imperfections.
- Energy Sector: Tanks used in the energy sector, particularly in oil and gas, require a polished finish to withstand harsh environmental conditions and to ensure the structural integrity of the tanks over time.
Advantages of Using a Tank Dish End Polishing Machine
Investing in a Tank Dish End Polishing Machine offers several significant advantages for manufacturers:
- Improved Surface Quality: These machines are designed to achieve a high-quality finish on the dish ends of tanks, which enhances both the appearance and performance of the tanks. A smooth, polished surface reduces the risk of corrosion and contamination, and facilitates easier cleaning.
- Consistency and Precision: Automated polishing ensures that each dish end is polished to the same high standard, reducing variability and ensuring consistent quality across production batches.
- Increased Productivity: These machines are capable of handling large dish ends and processing them quickly, which helps manufacturers meet production targets and reduce lead times.
- Cost Efficiency: By automating the polishing process, manufacturers can reduce labor costs and minimize material waste. The precise control offered by these machines also reduces the need for rework, further enhancing cost efficiency.
- Compliance with Industry Standards: Polished dish ends are often required to meet specific industry standards, particularly in regulated sectors like food, pharmaceuticals, and chemicals. Investing in a high-quality polishing machine helps ensure that your products comply with these standards, reducing the risk of non-compliance penalties.
In conclusion, the Tank Dish End Polishing Machine is an essential tool for manufacturers who need to achieve high-quality finishes on the dish ends of tanks. Its ability to deliver consistent, precise, and smooth polishing makes it invaluable in industries where the surface quality of tanks is critical. By investing in this technology, manufacturers can improve the appearance, durability, and performance of their tanks, ensuring that they meet the stringent requirements of their respective industries.
Belt Grinder
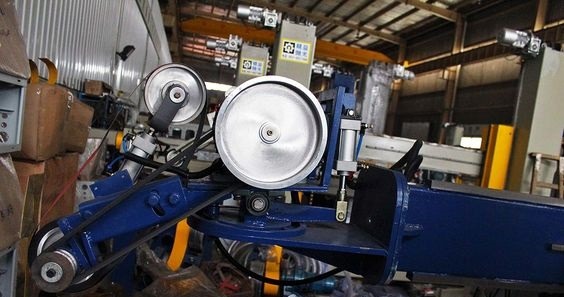
A Belt Grinder is a versatile and powerful tool used in metalworking to shape, smooth, and finish metal surfaces. This machine employs a continuous abrasive belt to grind, sand, or polish metal workpieces, making it an essential piece of equipment in fabrication shops, machine shops, and manufacturing facilities. The Belt Grinder is widely used in various industries for tasks ranging from heavy stock removal to fine finishing, offering a combination of speed, efficiency, and precision.
Versatility and Use Cases in Metalworking
The Belt Grinder is renowned for its versatility, making it suitable for a wide range of metalworking applications. Depending on the type of abrasive belt used and the machine’s configuration, it can be employed for different tasks:
- Stock Removal: The Belt Grinder excels in removing large amounts of material quickly. It is commonly used to grind down welds, remove burrs, or shape metal parts. The coarse abrasive belts are ideal for heavy-duty grinding operations, allowing operators to efficiently reduce the thickness or change the profile of a metal workpiece.
- Surface Preparation: Before metal parts can be painted, coated, or welded, they often need to be cleaned and prepared. A Belt Grinder can be used to remove rust, scale, or old coatings from metal surfaces, creating a clean and smooth surface ready for further processing.
- Deburring: After cutting, drilling, or machining, metal parts often have sharp edges or burrs that need to be removed. The Belt Grinder is effective at deburring these parts, leaving smooth edges that are safe to handle and ready for assembly.
- Finishing and Polishing: By using finer abrasive belts, the Belt Grinder can produce a polished finish on metal surfaces. This is particularly important in applications where the appearance of the final product is crucial, such as in architectural metalwork, automotive parts, or consumer goods.
Key Features of a High-Performance Belt Grinder
Belt Grinders are designed to provide a combination of power, speed, and control, enabling operators to achieve precise results in a variety of metalworking tasks. Some of the key features of a high-performance Belt Grinder include:
- Adjustable Belt Speed: The speed of the abrasive belt can be adjusted to match the specific requirements of the task at hand. Lower speeds are ideal for delicate finishing work, while higher speeds are used for aggressive grinding and material removal.
- Tilt and Swivel Functions: Many Belt Grinders allow the work table or the belt arm to tilt or swivel, providing greater flexibility in positioning the workpiece and the belt. This feature is particularly useful for grinding angles, curves, or complex shapes.
- Interchangeable Belts: The ability to quickly change belts is a critical feature, allowing operators to switch between different grit sizes or types of abrasives depending on the task. This versatility enhances the machine’s utility across various applications.
- Robust Construction: A well-built Belt Grinder is constructed from durable materials, ensuring stability and reducing vibrations during operation. This leads to more precise grinding and extends the machine’s lifespan.
- Dust Collection System: Grinding metal generates a significant amount of dust and debris. Many Belt Grinders are equipped with dust collection systems to maintain a clean work environment and protect the health of operators.
Industry Adoption and Best Practices
The Belt Grinder is widely adopted across various industries due to its versatility and effectiveness. Some of the key industries and applications include:
- Metal Fabrication: In metal fabrication shops, the Belt Grinder is used for shaping, deburring, and finishing metal parts, making it an indispensable tool in the production process. Fabricators rely on the grinder’s ability to quickly prepare metal surfaces for welding, coating, or assembly.
- Automotive Industry: In the automotive sector, Belt Grinders are used to prepare metal parts for assembly, smooth out welds, and create polished finishes on components like exhaust systems, body panels, and trim pieces.
- Aerospace Industry: Precision is critical in aerospace manufacturing, and Belt Grinders are used to achieve the exacting tolerances required for aircraft components. They are also employed to deburr and finish parts to ensure they meet stringent safety and performance standards.
- Tool and Die Making: Belt Grinders play a crucial role in tool and die making, where they are used to grind, shape, and finish precision tools and molds. The grinder’s ability to handle different materials and produce fine finishes is essential in this industry.
- Artisanal Metalwork: Artists and craftsmen in the metalworking field use Belt Grinders to create custom pieces, from jewelry to sculptures. The machine’s versatility allows them to shape, grind, and polish metal to achieve their desired artistic effects.
Best Practices for Using a Belt Grinder
To get the most out of a Belt Grinder and ensure safe operation, it is important to follow best practices:
- Choose the Right Belt: Selecting the appropriate abrasive belt for the material and task is crucial. Coarse belts are suitable for rapid material removal, while finer belts are better for finishing.
- Maintain Proper Belt Tension: Ensuring that the belt is properly tensioned will prevent slippage and ensure consistent grinding results. Regularly check and adjust the tension as needed.
- Wear Protective Gear: Grinding generates sparks, debris, and noise. Always wear appropriate personal protective equipment (PPE), including safety glasses, gloves, hearing protection, and a dust mask.
- Keep the Work Area Clean: Regularly clean the work area and the machine to prevent the buildup of dust and debris, which can affect the performance of the grinder and pose safety hazards.
- Inspect the Machine Regularly: Perform routine maintenance checks on the Belt Grinder to ensure it is in good working condition. This includes inspecting belts for wear, checking the alignment of components, and ensuring the dust collection system is functioning properly.
In conclusion, the Belt Grinder is an essential tool in metalworking, offering unmatched versatility and performance in shaping, smoothing, and finishing metal surfaces. Whether used for heavy-duty grinding or fine polishing, this machine is indispensable across a wide range of industries, from automotive to aerospace. By following best practices and investing in a high-quality Belt Grinder, manufacturers can achieve precise, efficient, and high-quality results in their metalworking operations.
EMS Metalworking Machines
We design, manufacture and assembly metalworking machinery such as:
- Hydraulic transfer press
- Glass mosaic press
- Hydraulic deep drawing press
- Casting press
- Hydraulic cold forming press
- Hydroforming press
- Composite press
- Silicone rubber moulding press
- Brake pad press
- Melamine press
- SMC & BMC Press
- Labrotaroy press
- Edge cutting trimming machine
- Edge curling machine
- Trimming beading machine
- Trimming joggling machine
- Cookware production line
- Pipe bending machine
- Profile bending machine
- Bandsaw for metal
- Cylindrical welding machine
- Horizontal pres and cookware
- Kitchenware, hotelware
- Bakeware and cuttlery production machinery
as a complete line as well as an individual machine such as:
- Edge cutting trimming beading machines
- Polishing and grinding machines for pot and pans
- Hydraulic drawing presses
- Circle blanking machines
- Riveting machine
- Hole punching machines
- Press feeding machine
You can check our machinery at work at: EMS Metalworking Machinery – YouTube
Applications:
Flange-punching
Beading and ribbing
Flanging
Trimming
Curling
Lock-seaming
Ribbing