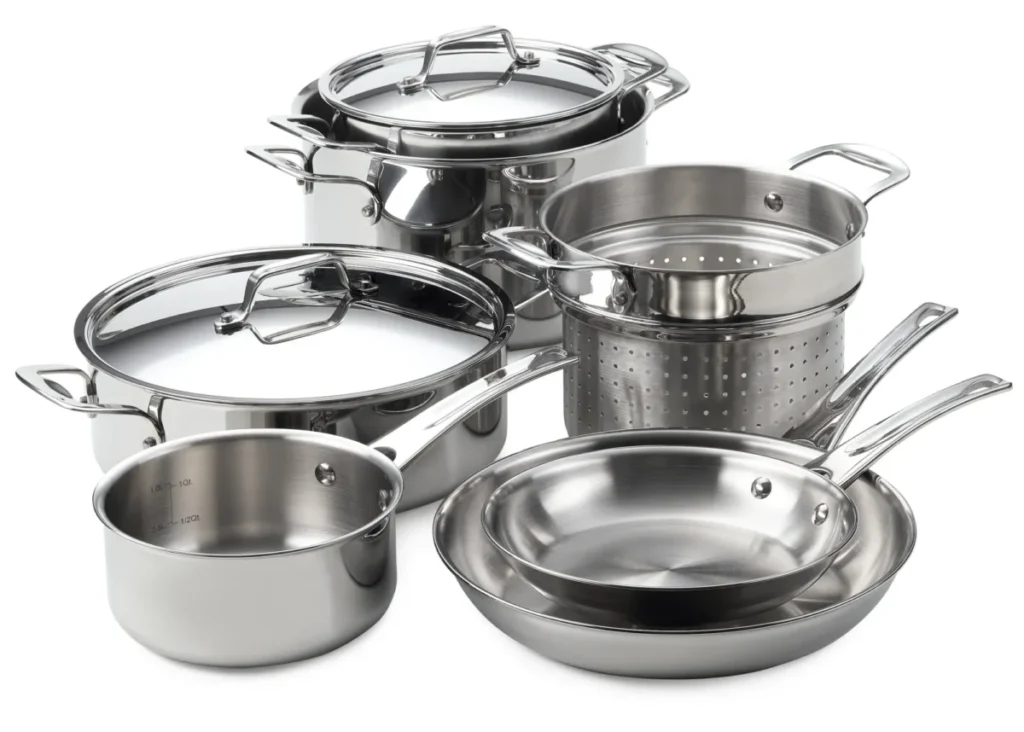
Sheet Metal Wok Manufacturing Machine: Sheet metal cookware manufacturing involves several processes that shape, form, and finish metal sheets into items like pots, pans, lids, and other utensils. Below is a breakdown of the main types of machinery used in a typical sheet metal cookware production line:
Sheet Metal Preparation Equipment
- Shearing Machine: Cuts large metal sheets into manageable sizes.
- Decoiling Machine: Unwinds coils of metal sheet (commonly stainless steel, aluminum, or copper).
- Leveling Machine: Flattens and removes coil set and crossbow from metal sheets.
Forming Machines
- Deep Drawing Press: The primary machine used to form cookware bodies from flat sheets by drawing the material into a die.
- Types: Hydraulic press, mechanical press, servo press.
- Trimming Press: Trims excess material from the edge of drawn cookware.
- Beading Machine: Rolls the rim to strengthen the edge and improve aesthetics.
Spinning and Rolling Machines
- Metal Spinning Lathe: Used especially for round cookware or complex shapes (like bowls or woks).
- Edge Rolling Machine: Forms curled or rolled edges on cookware.
Welding and Assembly
- Seam Welding Machine: Used to attach handles, spouts, or multi-part cookware pieces.
- Spot Welding Machine: For attaching small components like handle mounts.
Surface Finishing Equipment
- Polishing and Buffing Machines: Create smooth or mirror-like finishes.
- Sandblasting Machine: Provides matte or textured finishes.
- Anodizing/Coating Lines: For non-stick coatings, hard anodizing (aluminum), or enamel finishes (steel/cast iron).
Quality Control and Testing
- Leak Test Machine: Ensures welds and joints are airtight/watertight.
- Balancing Machine: For ensuring stability of round cookware on flat surfaces.
- Thickness Gauge: For checking wall thickness consistency.
Auxiliary Systems
- Tooling and Dies: Custom dies are needed for different shapes/sizes of cookware.
- Automation/Robotics: For handling, stacking, or moving parts between machines.
- CNC Press Brakes: For specific folding or edge work on certain cookware types.
In a typical sheet metal cookware manufacturing setup, the process starts with raw materials in the form of metal sheets or coils—usually stainless steel, aluminum, or copper. These sheets are first uncoiled using a decoiling machine, then leveled to remove any deformation. Next, a shearing machine cuts the sheet into blanks of appropriate size for forming. These blanks are then processed using a deep drawing press, which forms them into basic cookware shapes like pots or pans by pulling the sheet into a die under high pressure. Depending on the cookware design, this may involve multiple drawing steps with intermediate annealing.
After deep drawing, trimming presses remove excess material from the rim for a smooth and uniform edge. Edge finishing follows, often done by beading machines or edge rolling machines, which curl or roll the rim for strength and safety. For more complex shapes or round-bottom items like woks or bowls, metal spinning lathes come into play, shaping the cookware using rotational force and forming tools.
Welding equipment, such as spot or seam welders, is used for attaching handles, brackets, or other components. Handle bases may also be riveted depending on the design. Once the cookware is assembled, it moves to surface treatment and finishing. Polishing and buffing machines give the cookware a smooth or mirror finish, while sandblasting machines offer a matte or textured surface. For non-stick cookware or aluminum products, the parts go through a coating line where they’re treated with PTFE, ceramic coatings, or anodized for durability and aesthetics.
Each item is then subjected to quality control checks. Leak testers ensure that all joints are sealed, especially after welding. Thickness gauges check the consistency of the metal, while balancing machines ensure flatness and stability of round-bottomed items. Automation and robotic systems can be integrated at various points to improve productivity and consistency, especially in high-volume manufacturing. Tooling and custom dies are crucial throughout, as each cookware shape and size requires specific molds and forming tools. The entire setup can be scaled from semi-automatic to fully automated depending on production volume and investment level.
After quality control and inspection, the cookware typically proceeds to the final finishing and assembly stages. At this point, if the product requires further surface treatment—like applying decorative patterns, branding logos, or measurement markings—laser engraving or stamping machines are used. These add functional or branding elements without compromising material integrity.
Next comes handle installation. For cookware with plastic or bakelite handles, an additional step of screw fastening or overmolding is carried out. In some high-end setups, robotic arms perform automated handle assembly, ensuring precise alignment and torque control. If the cookware has glass lids, these are often produced in a parallel line and assembled later using similar riveting, crimping, or welding processes for handles and rims.
Packaging is the final step. Before packaging, items may pass through a cleaning station—typically an ultrasonic washer or high-pressure rinsing unit—to remove dust, oil, or fingerprints. Once clean, the cookware is dried using hot air tunnels and moved to a packaging station. This can involve automated wrapping machines that apply protective films, insert manuals, and box the products, or it can be done semi-manually depending on factory size and product variety.
Modern cookware factories often integrate enterprise resource planning (ERP) systems and machine monitoring software to track production efficiency, maintenance schedules, and inventory levels. Smart sensors on machines help detect wear or faults early, reducing downtime and ensuring consistent product quality.
In more advanced operations, energy efficiency and sustainability are factored into the design. For instance, recycling systems collect metal scrap from trimming and punching processes, which is then sent back for re-melting or reuse. Exhaust and fume extraction systems ensure a safe environment, especially in areas with coating or welding operations.
The entire cookware production line—from raw sheet handling to the final boxed product—can be modular, allowing manufacturers to customize their setup based on the type of cookware (e.g., pressure cookers, saucepans, fry pans, woks) and target market requirements.
Let me know if you’d like a complete list of machines with specifications or manufacturers, or a layout plan showing how a small-to-medium scale plant would be organized.
To further optimize production, many cookware manufacturers incorporate lean manufacturing principles and just-in-time (JIT) inventory systems. These methodologies minimize waste, reduce holding costs, and improve workflow efficiency. For instance, rather than producing large batches of the same product type, manufacturers can produce smaller, more flexible batches in line with customer demand, ensuring higher responsiveness to market needs.
In addition, modern machinery often integrates with Internet of Things (IoT) technology, allowing operators and supervisors to monitor machine performance in real-time. IoT sensors placed on machines can provide data on temperature, pressure, vibration, and other key operational metrics. This data can be analyzed for predictive maintenance, helping to avoid unexpected downtime by scheduling repairs or part replacements proactively.
Automated guided vehicles (AGVs) are increasingly used in larger factories to transport materials between machines and stations. This reduces manual labor and improves the consistency and speed of material handling. Additionally, AGVs can be integrated with warehouse management systems (WMS) to track raw material and finished product movements, ensuring that the right materials are at the right place at the right time.
In terms of sustainability, energy-efficient machines and practices have become a focal point for many manufacturers. The introduction of variable frequency drives (VFDs) and other energy-saving technologies ensures that machinery operates only at the necessary power levels, reducing electricity consumption. Additionally, the use of eco-friendly coatings and materials (such as water-based or low-VOC coatings) has gained traction as companies seek to reduce their environmental footprint.
In the context of high-volume production, automation plays a central role in maintaining consistent quality while reducing the reliance on human labor for repetitive tasks. Robots are often deployed for operations such as placing handles, attaching lids, or packing the finished products into cartons. In some cases, robotic arms can even perform intricate tasks like placing a protective film or wrapping the cookware with plastic for retail display.
To further enhance quality control, vision inspection systems are now being used for defect detection. These systems use cameras and artificial intelligence (AI) to detect any imperfections, such as surface scratches, deformations, or discoloration, ensuring that only flawless products move through to the next phase of packaging.
Once products are packaged, they are sent through an automated dispatch system. A warehouse management system (WMS) tracks and organizes these items, ensuring they are ready for shipment to retailers or directly to consumers. For large operations, cross-docking systems may be implemented to expedite the movement of goods from inbound trucks directly to outbound trucks, minimizing storage time and maximizing warehouse space efficiency.
In conclusion, a modern sheet metal cookware manufacturing process is highly automated, with advanced machinery handling everything from initial metal sheet preparation through to packaging. This results in greater efficiency, consistent product quality, and lower costs. Each stage of the process is interconnected, with real-time monitoring and data analysis improving overall operational performance.
Sheet Metal Broiling Pan Manufacturing Machine
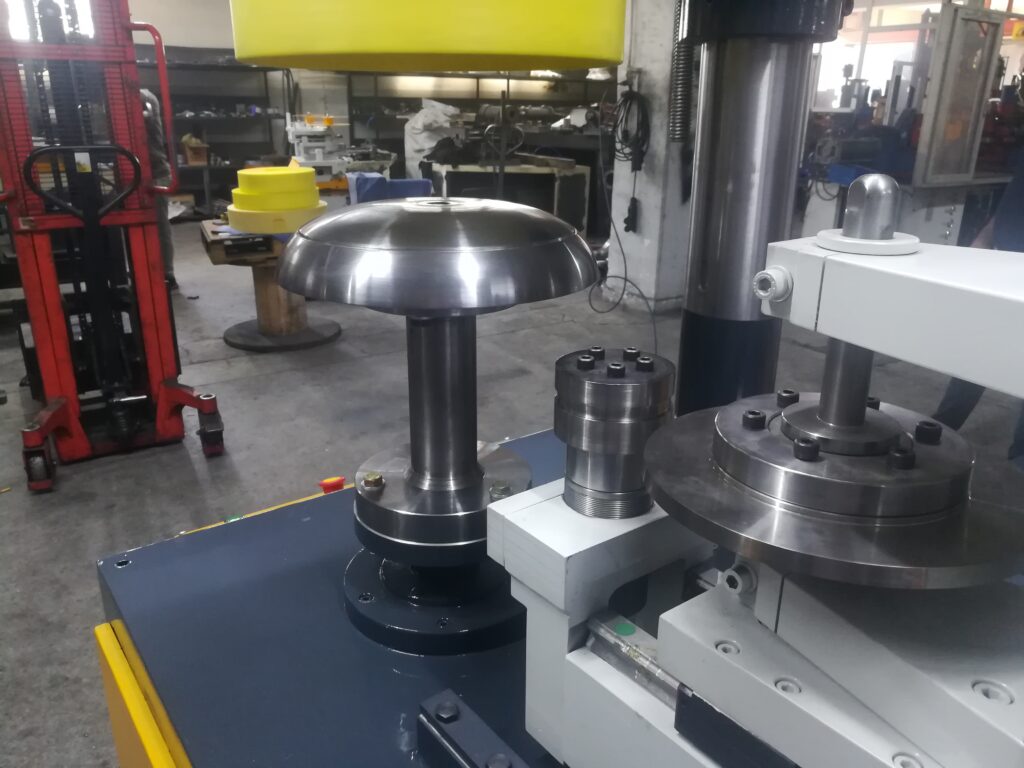
The manufacturing process for a sheet metal broiling pan involves several specialized machines designed to handle the material efficiently while forming, assembling, and finishing the pan to meet quality standards. Here’s a breakdown of the machinery and processes involved in the production of a broiling pan made from sheet metal:
1. Material Handling and Preparation
- Decoiling Machine: This is used for uncoiling the large metal sheets or coils, which could be made of stainless steel, aluminum, or other metals that are resistant to high temperatures and corrosion.
- Leveling Machine: After decoiling, the metal sheets are fed through a leveling machine that flattens them to remove any distortions or warps from the coil, ensuring uniformity before further processing.
- Shearing Machine: Once the metal is flattened, it is cut into the necessary sizes for the broiling pan using a shearing machine. The shears make precise cuts to form the pan’s base, edges, and any other parts.
2. Forming and Shaping the Pan
- Deep Drawing Press: This machine is used to form the base of the broiling pan by drawing the flat metal sheet into a mold. It creates a raised, shallow pan shape. For some broiling pans, additional deep drawing steps may be needed to form a deeper shape or specialized features like handles or edges.
- Stamping Press: If the pan design requires multiple individual parts (such as perforated surfaces or additional structural elements), a stamping press can be used to punch holes or create embossed patterns, typically to improve airflow or aesthetic appeal in broiling pans.
- Edge Beading/Rolling Machine: This machine is used to form a rolled edge or bead along the perimeter of the pan to strengthen the rim, create a smooth, safe finish, and allow for better handling, especially when the pan is hot.
3. Welding and Assembly
- Spot Welding Machine: In the case where the broiling pan consists of multiple parts (e.g., separate perforated inserts or handles), a spot welding machine is used to join these parts together. This machine creates precise welds that bond the metal securely.
- Seam Welding Machine: For continuous seams (such as around the edges of the pan), seam welding machines ensure a strong, even weld along the entire length of the edge, ensuring that the pan holds its shape and is structurally sound.
4. Handle and Component Attachment
- Riveting Machine: If the broiling pan uses rivets to attach handles, these are installed using a riveting machine, which secures the handles firmly in place.
- Injection Molding Machine (Optional): If the pan has plastic or Bakelite handles, they may be attached using an injection molding machine, which allows for the molding of non-metal parts to be affixed to the metal base of the pan.
- Welding or Screwing Machines: For more advanced broiling pans, robotic arms or automated machines may be used to attach parts such as silicone grips or lid handles, depending on the pan’s design.
5. Surface Treatment
- Polishing and Buffing Machines: These are used to give the broiling pan a smooth, shiny, or matte finish. Depending on the material (e.g., stainless steel), polishing can improve both the aesthetic and functionality of the pan.
- Sandblasting Machine: If a rougher, more textured finish is desired (for example, for aesthetic purposes or to reduce surface scratching), sandblasting is used to etch the surface with a fine texture.
- Coating Lines (Optional): Some broiling pans may undergo coating processes, such as anodizing (for aluminum) or PTFE (non-stick) coating. Coating lines may include spray systems, curing ovens, and electrostatic systems to apply coatings evenly and effectively.
6. Quality Control
- Leak Test Machine: This ensures that the broiling pan’s seams, especially around welded areas, do not leak or have weaknesses.
- Thickness Measurement Machine: A laser or ultrasonic thickness gauge checks that the sheet metal has been formed to the correct thickness throughout the pan.
- Visual Inspection: In some cases, a visual inspection station or automated vision system is used to look for any surface defects, alignment issues, or errors in manufacturing.
7. Packaging and Shipping
- Cleaning Stations: Once the pan is fully formed and finished, it often goes through a cleaning station to remove any residual oils, dust, or other contaminants.
- Automated Packaging System: After the broiling pans are cleaned and inspected, they are packaged using an automated packaging system. This system may wrap the pans in protective film or cardboard, and place them into boxes for shipment to retailers or end consumers.
- Heat Shrink Wrapping Machine: Some pans, especially those with non-stick coatings or delicate finishes, are heat-shrink wrapped for extra protection during transit.
The manufacturing process for a sheet metal broiling pan starts with preparing the raw material, typically stainless steel, aluminum, or another heat-resistant metal. First, the metal is uncoiled and flattened using a decoiling and leveling machine. Then, the material is cut into the desired shape with a shearing machine.
Next, deep drawing presses form the base of the pan, shaping it into a shallow dish. Depending on the design, stamping presses may add perforations or embossed patterns to improve heat distribution or for aesthetic purposes. The edges of the pan are reinforced using a beading or rolling machine, creating a smooth, safe rim.
For assembly, spot welding machines are used to attach various components, such as handles or reinforcement plates. If handles are made from materials like Bakelite or plastic, an injection molding machine may be used to form them and attach them to the pan.
Once the pan is assembled, surface treatments like polishing, sandblasting, or non-stick coatings are applied. These enhance both the functionality and appearance of the pan. Finally, the pan undergoes a thorough quality control process that checks for defects, ensures proper thickness, and tests for leaks before the product is cleaned, packaged, and prepared for shipment.
The process starts with raw metal coils, which are uncoiled, flattened, and cut to size. The metal is then formed into a pan shape using deep drawing presses, followed by edge beading or rolling for reinforcement. Spot welding or other assembly methods attach handles and components. After that, surface treatments like polishing or coating are applied for finish and durability. Finally, the product is inspected for quality, cleaned, and packaged for shipment.
The manufacturing of sheet metal broiling pans begins with the acquisition of raw material, typically stainless steel, aluminum, or other heat-resistant metals. The process starts by uncoiling the large rolls of metal sheets using a decoiling machine. These sheets are then passed through a leveling machine to flatten any coils that may have become deformed during transportation. Once the metal is flattened, it is ready to be cut into the required sizes for the broiling pans using a shearing machine. This ensures that the sheets are of the correct dimensions and ready for the next steps.
The next critical stage is shaping the metal. A deep drawing press is used to form the base of the broiling pan. In this process, a flat sheet of metal is drawn into a mold under high pressure, creating a shallow, curved shape. If the pan has any intricate features or additional parts (such as perforated inserts for better heat distribution), a stamping press may be used to punch holes or emboss patterns into the sheet.
Once the basic shape is formed, the edges of the pan are reinforced. This is often done using an edge beading machine or edge rolling machine, which rolls the rim of the pan to create a smooth, sturdy edge that is easier to handle and helps maintain the pan’s structural integrity. The reinforced edge also makes it safer to use by preventing sharp edges.
After the pan’s shape and edges are complete, it is time to assemble any additional components. If the broiling pan includes handles or lid attachments, a spot welding machine may be used to securely weld these parts onto the pan. In some cases, the handles may be molded separately from the metal body using injection molding machines to create handles from materials like Bakelite or plastic. These handles are then attached to the pan using screws or rivets.
Next comes the finishing process, where the broiling pan undergoes various treatments to improve its appearance and functionality. Polishing and buffing machines are used to give the metal a smooth, shiny, or matte finish, depending on the desired result. If a rougher texture or matte finish is needed, a sandblasting machine may be used to create a uniform surface texture across the pan. Additionally, some broiling pans, especially those made from aluminum, may undergo an anodizing process, which hardens the surface and adds a layer of corrosion resistance.
For non-stick broiling pans, a coating line applies a layer of PTFE (Teflon) or other non-stick coatings. These coatings are typically applied in a spray or dip method and then cured in a curing oven to ensure the coating adheres properly to the metal surface.
Once the pan is finished, it is inspected for quality assurance. This typically involves several checks: a visual inspection for any surface defects, a thickness gauge to ensure the correct material thickness is maintained, and a leak test machine to verify that there are no holes or weaknesses in the welds or seams. If any issues are found, the pan may be sent back for rework or scrapping, depending on the severity of the defect.
After passing inspection, the broiling pan is sent to a cleaning station, where any oils, dust, or residue from the manufacturing process are removed. This is usually done with high-pressure washing systems or ultrasonic cleaning, which ensures that the pan is spotless and safe for use.
Finally, the cleaned broiling pans are packaged for shipment. Automated packaging systems handle this step, wrapping the pans in protective film or cardboard and placing them into boxes for distribution. If necessary, heat-shrink wrapping is used to further protect the pans during shipping.
Throughout the manufacturing process, automation is often used to improve efficiency and consistency. Machines are frequently monitored with IoT (Internet of Things) sensors to track their performance, and predictive maintenance systems can alert operators when a machine requires servicing. This helps reduce downtime and ensures that the process runs smoothly, maintaining a high standard of product quality.
By integrating these machines and processes, manufacturers are able to produce high-quality broiling pans that are durable, efficient, and ready for use by consumers.
The production of sheet metal broiling pans starts with raw materials—metal coils like stainless steel or aluminum. These coils are first uncoiled using a decoiling machine, which flattens the metal to prepare it for the next steps. A shearing machine cuts the flattened metal sheets into the necessary sizes for the broiling pan.
Once the sheets are cut, they are formed into the pan’s shape using a deep drawing press. This press applies high pressure to form the metal into a shallow, curved pan shape. Additional features, like perforated sections for heat distribution, may be added using a stamping press. To reinforce the edges of the pan, an edge beading or rolling machine is used to create a smooth, durable rim.
Handles and other components are then added. Spot welding machines are used to attach metal handles, while non-metal handles, like plastic or Bakelite, are molded separately and then fastened to the pan. If the pan requires non-stick coating, it will go through a coating line where PTFE or other coatings are applied and cured in an oven.
Finally, the broiling pan undergoes quality control, where visual inspections, thickness measurements, and leak tests are performed to ensure there are no defects. After passing inspection, the pans are cleaned, typically using high-pressure washers, and packaged for shipment.
Automation and IoT technology are often incorporated throughout the process, improving efficiency, reducing downtime, and ensuring consistent product quality.
Sheet Metal Roasting Rack Manufacturing Machine
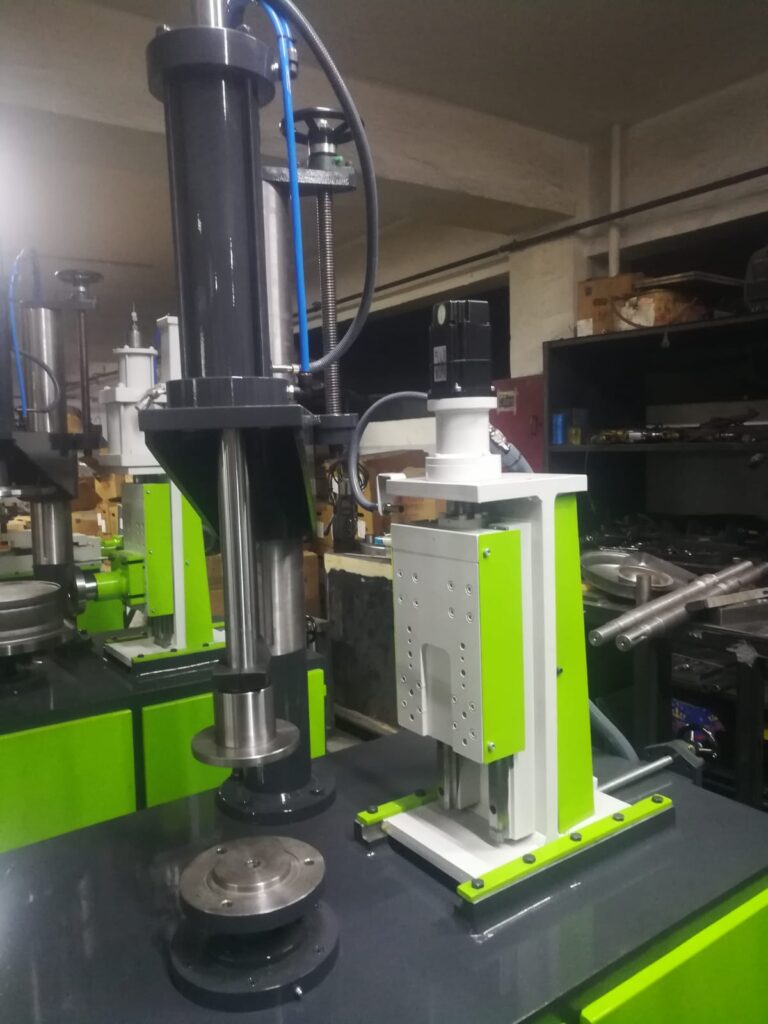
The manufacturing of a sheet metal roasting rack involves a series of specialized processes to transform raw metal sheets into a functional, durable rack designed for cooking. Below is an outline of the machinery and steps involved in the production of a typical sheet metal roasting rack:
1. Material Handling and Preparation
- Decoiling Machine: The process begins with uncoiling rolls of metal, typically stainless steel or other corrosion-resistant materials. The decoiling machine unrolls the metal sheets, which are then flattened for ease of further processing.
- Leveling Machine: After uncoiling, the metal is passed through a leveling machine that ensures it is flat and free from distortions or curls caused by the coil.
2. Cutting and Shaping the Metal
- Shearing Machine: The flattened sheets are then cut into manageable pieces of the appropriate size for the roasting rack using a shearing machine. This machine uses blades to make straight, precise cuts to form the base and side components of the rack.
- Notching or Punching Machine: For racks that require specific slots, holes, or features (such as air vents for heat circulation), a punching or notching machine is used. This process ensures that the sheet metal is appropriately perforated for both aesthetic and functional purposes.
3. Forming the Rack Structure
- Bending or Folding Machine: The individual parts of the roasting rack, like the edges or sides, are bent using a bending machine. This machine can create precise, sharp angles to form the side walls and support bars of the rack. For complex shapes, a CNC press brake might be used to achieve higher precision.
4. Welding and Assembly
- Spot Welding Machine: The frame and components of the roasting rack are then joined using a spot welding machine. Spot welding ensures that the different parts of the rack are securely attached at specific points without compromising the integrity of the metal.
- Seam Welding Machine: In some cases, continuous seams (such as for the edges of the rack or to attach mesh elements) may be welded using a seam welding machine. This ensures a strong bond and a smooth finish along the seams.
5. Adding Support Features
- Riveting Machine: If the roasting rack design requires riveted joints for extra strength (especially for attaching legs or side supports), a riveting machine is used to install the rivets at designated points.
- Handle Attachment (if applicable): If the roasting rack includes handles, they may be welded, riveted, or screwed into place, depending on the design. For non-metal handles, an injection molding machine may be used to create handles from heat-resistant plastics or Bakelite, which are then attached to the metal frame.
6. Surface Treatment and Coating
- Polishing and Buffing Machines: After the rack is assembled, the surface of the metal is polished and buffed to remove any rough edges and create a smooth, clean finish. This improves both the appearance and safety of the final product.
- Sandblasting Machine: For a more textured or matte finish, the roasting rack can undergo sandblasting. This process uses abrasive particles to roughen the surface, which can also help with improving the appearance and adhesion of any coatings.
- Coating Line (Optional): For additional protection, a non-stick coating such as PTFE (Teflon) may be applied to the roasting rack to make it easier to clean and enhance its non-stick properties. This coating process typically involves spraying the PTFE onto the surface and then curing it in an oven.
7. Quality Control
- Visual Inspection: The roasting rack undergoes a final inspection to check for any surface imperfections, alignment issues, or defects in the welds and joints.
- Strength Testing: Some manufacturers may perform load testing to ensure the rack can withstand the weight of roasting items, such as poultry or vegetables, without bending or breaking.
- Thickness Measurement: A thickness gauge is used to verify that the sheet metal used in the rack is consistent in thickness and meets manufacturing standards.
8. Cleaning and Packaging
- Cleaning Station: After all manufacturing processes are complete, the roasting rack is cleaned using a high-pressure washer or ultrasonic cleaning system to remove any oils, debris, or dust accumulated during production.
- Automated Packaging: Once cleaned and inspected, the roasting racks are packaged for shipment. Automated packaging systems may wrap the racks in protective plastic, box them, and label them for easy distribution.
Automation and Technology
Throughout the production of the sheet metal roasting rack, automation plays an important role. Machines are often equipped with IoT sensors to monitor performance in real-time. This data can be used for predictive maintenance to reduce downtime and ensure that the manufacturing process remains efficient. Additionally, robotic arms are sometimes used in assembly or packaging to improve the speed and consistency of production.
By using a combination of precise cutting, forming, welding, and surface treatment technologies, manufacturers can produce high-quality, durable roasting racks suitable for both home kitchens and commercial use.
The production of a sheet metal roasting rack begins with uncoiling and flattening metal sheets using a decoiling and leveling machine. The metal is then cut into the required size with a shearing machine. For racks that require perforations, a punching machine adds holes for ventilation.
Next, the rack’s frame is formed using a bending or folding machine to shape the edges and supports. These parts are then welded together using spot welding or seam welding machines to securely attach the components.
Handles are either welded or riveted into place, and non-metal handles may be molded separately using injection molding machines. The rack is then polished or sandblasted for a smooth finish.
For added protection, non-stick coatings may be applied, followed by a curing process. The rack undergoes visual inspection, strength testing, and thickness measurement to ensure quality.
The manufacturing process of a sheet metal roasting rack starts with the acquisition of raw materials, typically stainless steel, aluminum, or other heat-resistant metals. These materials are often supplied in the form of large coils of metal. The first step is decoiling, where the coil is unrolled, and then passed through a leveling machine to flatten it. This ensures that the metal is smooth and free from any distortions caused by the coil, ensuring that it’s ready for precision cutting and shaping.
Once the metal is flattened, it is then cut into the required dimensions for the roasting rack using a shearing machine. The shearing machine makes precise, straight cuts to form the main components of the roasting rack, including the base and side walls. If the rack requires any specific perforations for air circulation or additional features like drainage holes, a punching machine or notching machine is used to create these features at specific locations on the metal sheet. This step ensures that the roasting rack has the functional design needed for efficient heat distribution during roasting.
Next, the individual pieces of the roasting rack—such as the base, side walls, and any support beams—are formed into their final shapes. This is done using a bending or folding machine that applies pressure to the metal sheet to create sharp, accurate bends at the edges or where the side walls meet the base. In more complex designs, a CNC press brake may be used for high precision in creating these bends, allowing for tighter tolerances and better consistency across each piece of the batch.
Once the pieces are shaped, the next step is the assembly process. For many roasting racks, components such as legs, handles, or reinforcements need to be attached. This is done using spot welding machines, which are commonly employed to join the metal parts securely. Spot welding involves applying electrical current to the joint area, causing the metal to melt and fuse together at specific points. This ensures that each part of the roasting rack is firmly held in place without affecting the surrounding metal structure.
For racks that require additional structural integrity, such as the attachment of legs or crossbars, a riveting machine can be used to insert rivets and join parts together. This method provides a strong, durable connection, which is especially useful for maintaining the rack’s stability during use. If the design calls for non-metal handles made from heat-resistant materials like Bakelite or plastic, these parts are usually produced separately using an injection molding machine. Once molded, the handles are attached to the roasting rack either by welding, riveting, or mechanical fastening.
After the frame is fully assembled, the roasting rack moves on to the finishing process. This is where the aesthetic and functional qualities of the pan are enhanced. Polishing and buffing machines are employed to smooth and refine the surface, removing any rough spots or sharp edges. This ensures that the rack is not only visually appealing but also safe to handle. For a more textured or matte finish, a sandblasting machine can be used to create a uniform, non-glossy surface. This can also help improve the adhesion of any coatings that may be applied in the next steps.
One common finishing treatment for roasting racks, especially for those made from metals like aluminum or stainless steel, is the application of a non-stick coating. This is usually done using a coating line, where a layer of PTFE (Teflon) or other non-stick material is applied to the surface of the roasting rack. This coating is then cured in an oven, allowing it to adhere firmly to the metal. The non-stick surface helps prevent food from sticking to the rack and makes cleaning much easier.
After the rack has been finished, it undergoes a thorough quality control inspection. This may involve a visual inspection to check for any surface defects, scratches, or imperfections. Additionally, the roasting racks are often subjected to strength testing to ensure that they can support the weight of food during roasting without warping or bending. Thickness gauges may also be used to measure the consistency of the metal thickness to ensure that the material meets manufacturing standards.
Once the roasting racks pass quality control, they are cleaned to remove any oils, dust, or debris that accumulated during the manufacturing process. This cleaning is usually performed using high-pressure washers or an ultrasonic cleaning system to ensure that the racks are completely clean and safe for use.
The final step in the process is packaging. The roasted racks are typically handled by automated packaging systems that wrap each rack in protective film to prevent scratches or damage during shipping. They are then placed in boxes, labeled, and sealed for shipment to retailers or directly to consumers.
Throughout the entire manufacturing process, automation plays a key role in improving efficiency and consistency. Machines are often integrated with IoT sensors to monitor real-time data, such as temperature, pressure, and machine performance. This data can be analyzed to optimize production, predict when maintenance is needed, and improve the overall quality of the finished product.
By using a combination of cutting, forming, welding, coating, and inspection processes, manufacturers can produce high-quality sheet metal roasting racks that are durable, functional, and safe for consumer use.
The manufacturing of a sheet metal roasting rack starts with uncoiling and flattening raw metal sheets using decoiling and leveling machines. After this, the metal is cut to size using a shearing machine. Any required perforations, such as for ventilation, are made using a punching or notching machine.
The next step involves forming the rack’s components. This is done with a bending or folding machine, which shapes the metal into the sides, base, and other elements of the rack. These parts are then assembled together using spot welding or riveting, depending on the design. If the rack requires additional features like non-metal handles, they are made separately using injection molding machines and then attached to the metal frame.
Once the assembly is complete, the roasting rack undergoes finishing treatments. It may be polished or sandblasted for a smooth or textured surface, depending on the design. A non-stick coating like PTFE may be applied to improve the functionality and ease of cleaning. This coating is cured in an oven for durability.
After finishing, the roasting rack undergoes quality control, where it is visually inspected, strength-tested, and thickness-checked. It is then cleaned using high-pressure washing systems or ultrasonic cleaning.
Finally, the racks are packaged using automated systems that wrap and box them for shipment. Throughout the process, automation and IoT sensors are often employed to ensure efficiency and maintain high product quality.
The sheet metal roasting rack manufacturing process begins with the uncoiling of raw metal sheets, typically stainless steel or aluminum, using a decoiling machine. These sheets are then flattened and straightened by a leveling machine to ensure smoothness. Next, the metal is cut into precise sizes with a shearing machine, ready to be shaped into the rack.
The metal sheets are then formed into the desired structure using a bending or folding machine. This process creates the sides and base of the roasting rack. Any necessary holes or ventilation slots are punched using a punching machine. Once the components are shaped, they are assembled together using welding machines, such as spot welding, or riveted for added strength and stability.
After assembly, the rack undergoes surface treatment. It may be polished, buffed, or sandblasted to remove rough edges and enhance the appearance. For non-stick functionality, a coating like PTFE is applied and cured in an oven.
Quality control checks are conducted, including visual inspections for defects, strength testing to ensure durability, and thickness measurements to confirm material consistency. The racks are then cleaned using high-pressure washers or ultrasonic cleaning systems to remove any residues from manufacturing.
Finally, the roasting racks are packaged for shipping, often by automated systems, ensuring safe transport to customers. Throughout the process, automated machinery and IoT sensors help streamline production and maintain product quality.
Sheet Metal Casserole Dish Manufacturing Machine

The manufacturing process for a sheet metal casserole dish involves a series of precise steps using specialized machinery to transform raw metal sheets into functional and durable cooking dishes. Here’s a breakdown of the typical machinery and processes used in manufacturing a sheet metal casserole dish:
1. Material Preparation
- Decoiling Machine: The process begins with uncoiling large rolls of metal, typically stainless steel, aluminum, or other heat-resistant materials. The decoiling machine unwinds the coils of metal and straightens them, ensuring they are flat and ready for cutting.
- Leveling Machine: The metal sheet is passed through a leveling machine that ensures the metal is smooth, removing any distortions or warping from the coil. This ensures the metal is uniform for further processing.
2. Cutting the Metal
- Shearing Machine: Once the material is prepared, the metal is cut into the appropriate size for the casserole dish. A shearing machine uses blades to make straight, precise cuts to the metal sheet.
- Laser Cutting or Punching (Optional): In cases where more intricate shapes or designs are needed (such as for handles or vents), laser cutting machines or punching machines may be used. These machines can cut complex shapes or add specific features to the dish’s design.
3. Forming the Casserole Dish Shape
- Deep Drawing Press: The casserole dish shape is created by using a deep drawing press, which applies high pressure to the metal sheet, drawing it into a mold to create the shallow, rounded shape of the dish. The deep drawing press can also be used to create deeper or more intricate shapes, depending on the design.
- Embossing/Stamping Press (Optional): If the casserole dish design requires any embossed patterns for decoration or functionality, a stamping press is used. This can also be used to create additional textures on the surface of the dish for non-stick applications or aesthetic appeal.
4. Edge Forming and Reinforcement
- Beading or Edge Rolling Machine: After the dish shape is formed, the edges of the casserole dish are reinforced for both strength and safety. A beading or edge rolling machine is used to create a rolled edge that adds durability and provides a smooth finish.
- Flanging Machine: For casserole dishes that need a lip for attaching a lid or handles, a flanging machine is used to create a flange at the dish’s edge.
5. Assembly (Handles and Components)
- Spot Welding Machine: If the casserole dish design includes metal handles, spot welding machines are used to attach them securely to the dish. The welding process fuses the metal at specific points, ensuring that the handles are strong and durable.
- Riveting Machine: For some designs, rivets may be used instead of welding to attach handles or reinforcement components. A riveting machine installs these rivets to secure the handles or other parts of the dish.
6. Surface Treatment and Finishing
- Polishing and Buffing Machines: Once the casserole dish is assembled, it may undergo polishing and buffing to ensure a smooth, shiny finish or to create a more matte appearance, depending on the desired result.
- Sandblasting Machine: If a rougher or matte finish is required, a sandblasting machine may be used to create a consistent texture across the surface.
- Non-stick Coating (Optional): Many casserole dishes receive a non-stick coating like PTFE (Teflon). This is applied through a spraying or dipping process and then cured in an oven to form a durable, non-stick surface that makes the dish easier to clean and enhances its cooking performance.
7. Quality Control
- Visual Inspection: Each casserole dish undergoes a visual inspection to check for any surface defects, cracks, or imperfections. The appearance is checked to ensure the finish meets the required standards.
- Thickness Measurement: A thickness gauge is used to measure the metal thickness and ensure consistency across all dishes.
- Strength Testing: The casserole dish may undergo strength tests to verify that it can withstand high temperatures and the weight of food without deforming or breaking.
8. Cleaning and Packaging
- Cleaning Station: After manufacturing, the casserole dishes are cleaned to remove any oils, dust, or residues left from the production process. High-pressure washing or ultrasonic cleaning methods are often used.
- Automated Packaging: Once cleaned, the casserole dishes are packaged for shipment. Automated packaging systems handle the wrapping, boxing, and labeling of the products to prepare them for distribution.
Automation and Technology Integration
Throughout the manufacturing process, automation plays a key role in improving efficiency and precision. Machines are often equipped with IoT sensors that monitor performance and alert operators to any issues, reducing downtime and ensuring high-quality production. The entire process is designed to ensure consistency and minimize human error, from the initial decoiling to the final packaging.
This combination of cutting, forming, welding, coating, and finishing processes ensures that the sheet metal casserole dishes produced are durable, functional, and ready for use in the kitchen. Would you like more details on any specific part of the process or machinery used?
The manufacturing process for a sheet metal casserole dish starts with uncoiling large metal rolls using a decoiling machine, which flattens the metal. This is followed by cutting the metal into the required size with a shearing machine. If needed, laser cutting or punching machines are used for adding specific holes or shapes.
Next, a deep drawing press is used to form the dish’s shallow, rounded shape, while a stamping press can add any textures or designs. The edges of the dish are reinforced using an edge rolling machine or beading machine for durability and a smooth finish.
Handles are added through spot welding or riveting to ensure they are securely attached. After assembly, the casserole dish undergoes polishing and buffing for a smooth finish, and sometimes sandblasting for a textured look. A non-stick coating is applied if necessary, followed by curing in an oven.
Quality control checks are done to inspect for defects and measure thickness. The dishes are then cleaned using high-pressure washers or ultrasonic systems and finally packaged for shipment. Throughout the process, automation and IoT sensors ensure consistent quality and efficient production.
The manufacturing of a sheet metal casserole dish starts by uncoiling large rolls of metal using a decoiling machine, which flattens the material. The metal is then cut to size using a shearing machine. If the design requires specific shapes or holes, laser cutting or punching machines are used for precision.
The metal is then formed into the casserole dish shape using a deep drawing press, which creates the dish’s shallow form. Any decorative patterns or texturing are applied with a stamping press. The edges of the dish are reinforced and smoothed using an edge rolling or beading machine.
Handles are attached by spot welding or riveting. The dish is then polished, buffed, or sandblasted for the desired finish. A non-stick coating is applied if necessary, followed by a curing process in an oven.
The casserole dish undergoes quality control, including visual inspection and strength testing. Finally, the dish is cleaned and packaged for shipment. Automation and IoT sensors are used throughout the process to monitor and improve production efficiency.
The manufacturing process of a sheet metal casserole dish begins with the preparation of the raw material, typically stainless steel, aluminum, or another heat-resistant metal. Large rolls of metal, often referred to as coils, are uncoiled and prepared for further processing using a decoiling machine. This machine unrolls the metal and ensures that it is flat, removing any curvature or distortions that might have occurred during the coiling process. After this, the metal sheet is passed through a leveling machine to ensure that it is fully flat and free of any residual bends or imperfections.
Once the metal is prepared, it is cut to the required dimensions using a shearing machine. The shearing machine uses high-pressure blades to make clean, straight cuts along the edges of the metal, forming sheets of the correct size for the casserole dish. If the design requires intricate shapes, such as holes or slots, these are added at this stage using laser cutting or punching machines, which can precisely cut out complex patterns or features needed for handles, vents, or other elements of the dish.
The next step is the actual forming of the casserole dish shape. This is done using a deep drawing press. In this process, the flat metal sheet is placed into a mold, and a high-pressure punch is used to draw the metal downward into the mold, shaping it into the shallow, rounded form of the casserole dish. For more intricate or deeper shapes, multiple passes through the deep drawing press may be required to achieve the desired depth and form. In some cases, a stamping press is used to apply textures or patterns to the metal, which could be for decorative purposes or to create functional features like enhanced heat distribution or a non-stick surface.
Once the casserole dish shape is formed, the edges need to be reinforced for added strength and to eliminate sharp points that could cause safety concerns. This is done using an edge rolling machine or a beading machine, both of which bend or roll the edges of the dish to form a smooth, reinforced rim. This not only strengthens the dish but also gives it a finished look, ensuring that it is safe and aesthetically pleasing.
If the casserole dish requires handles, they are attached during the assembly phase. Spot welding is commonly used for metal handles, where heat is applied to the junction points to fuse the metal pieces together. Alternatively, riveting machines can be used to attach handles or other components, ensuring a secure, lasting bond. For casseroles with non-metal handles made from materials like plastic or Bakelite, the handles are often molded separately through injection molding and then attached to the metal parts.
After the assembly, the casserole dish undergoes a series of finishing processes. Polishing and buffing machines are employed to smooth the surface of the dish, removing any rough edges or imperfections that might remain from the manufacturing process. Depending on the desired final appearance, a sandblasting machine can also be used to create a matte or textured finish. This is sometimes done for aesthetic reasons or to improve the performance of coatings that may be applied later.
A key feature for many casserole dishes is a non-stick coating, which makes cooking and cleaning easier. This coating, usually made of PTFE (Teflon) or similar materials, is applied to the surface of the dish using a spraying or dipping method. After the coating is applied, the dish is placed in an oven for curing, which allows the non-stick layer to bond securely to the metal, forming a durable, easy-to-clean surface.
Once the casserole dish has been finished, it moves to the quality control stage. During this stage, each dish is carefully inspected for any surface defects, such as scratches, dents, or imperfections in the finish. The thickness of the metal is measured with a thickness gauge to ensure consistency across all units. In some cases, a strength test is performed to verify that the casserole dish can withstand high temperatures and the weight of food without warping or breaking.
The final step in the manufacturing process is cleaning and packaging. The casserole dishes are thoroughly cleaned to remove any oils, debris, or residues left from manufacturing. This cleaning is typically done using high-pressure washers or ultrasonic cleaning systems that ensure all traces of dirt or manufacturing residue are removed. Once cleaned, the casserole dishes are dried and prepared for shipment. Automated packaging systems are often used to wrap each dish in protective materials, box them, and label them for easy distribution.
Throughout the entire manufacturing process, automation and IoT sensors are integrated into the machinery to monitor the performance of each step. These sensors track factors such as temperature, pressure, and machine status, allowing for real-time adjustments and maintenance scheduling. This not only improves the efficiency of production but also ensures a high level of consistency and quality control across all units produced.
In summary, the process of making a sheet metal casserole dish involves a combination of cutting, forming, welding, coating, and finishing processes that transform raw metal sheets into a durable, functional, and aesthetically pleasing kitchen item. The integration of advanced machinery and automation helps to ensure that each casserole dish meets high standards for quality and performance, while also allowing for efficient production.
Sheet Metal Baking Pan Manufacturing Machine

The manufacturing of a sheet metal baking pan involves several specialized machines and processes to transform raw metal sheets into functional and durable pans. Below is a detailed breakdown of the typical steps and machinery used in the production of sheet metal baking pans:
1. Material Preparation
- Decoiling Machine: The manufacturing process begins with uncoiling large metal rolls, typically made from stainless steel, aluminum, or other suitable heat-resistant metals. The decoiling machine unrolls and flattens the metal, ensuring that it is smooth and uniform, removing any bends or distortions from the coiling process. Once the coil is flattened, the metal sheet is prepared for cutting.
- Leveling Machine: After decoiling, the metal is passed through a leveling machine to further flatten the material, ensuring it is even and free from any residual warping or imperfections. This ensures a smooth surface for accurate cutting and forming.
2. Cutting the Metal
- Shearing Machine: The next step involves cutting the metal into the required size and shape for the baking pan. A shearing machine uses high-pressure blades to make straight, precise cuts on the metal sheet. The machine can handle both simple cuts and more intricate shapes based on the pan design.
- Laser Cutting or Punching Machine (Optional): In some designs, where more complex shapes or perforations are required (such as for handles or drainage holes), laser cutting or punching machines may be used. These machines are capable of cutting out specific shapes with high precision, allowing for intricate designs to be added to the baking pan.
3. Forming the Baking Pan Shape
- Deep Drawing Press: Once the metal sheet is cut to size, the next step is forming the baking pan shape. This is typically done with a deep drawing press. In this process, the metal is placed into a mold, and a high-pressure punch is used to draw the sheet downward into the mold, shaping it into the shallow, rectangular, or square form of the baking pan. For pans with deeper sides, the process may be repeated, or multiple passes may be required to achieve the desired depth.
- Embossing or Stamping Press (Optional): If the design requires additional patterns, textures, or surface features—such as reinforcing ribs or decorative patterns—an embossing or stamping press is used. These machines can add texturing to the pan’s surface or reinforce certain parts of the pan to increase its strength and durability.
4. Edge Reinforcement
- Edge Rolling or Beading Machine: The edges of the baking pan are then reinforced to prevent sharp edges and improve durability. This is done using an edge rolling machine or beading machine, which rolls or bends the metal along the edge to create a smooth, reinforced lip. This lip not only adds strength but also ensures that the pan is safe to handle.
- Flanging Machine (Optional): For pans that require a lip or flange for attaching handles or lids, a flanging machine may be used. This machine creates a flat, outward-facing lip around the edges of the pan, which can be used to attach handles or other accessories.
5. Assembly (Handles and Components)
- Spot Welding Machine: If the baking pan design includes handles, these are typically added during the assembly stage. Spot welding machines are commonly used to attach metal handles to the sides of the pan. The process involves applying electrical current to the joints of the handle and pan, causing the metal to fuse together at the spot weld points.
- Riveting Machine: In some designs, instead of welding, riveting machines may be used to attach handles or reinforce parts of the pan. Riveting creates a permanent bond by inserting and securing a rivet through the metal.
6. Surface Treatment and Finishing
- Polishing and Buffing Machines: After the pan’s shape and components are assembled, the baking pan is polished and buffed to remove any rough edges or imperfections. Polishing machines create a smooth, shiny finish, while buffing machines add a lustrous sheen to the pan, ensuring it is aesthetically pleasing and safe to handle.
- Sandblasting Machine (Optional): For pans that require a matte or textured finish, a sandblasting machine can be used to add a uniform, non-reflective texture to the surface. This process is often used to prepare the pan for coating or to create a rustic look.
- Non-stick Coating Application: Many baking pans are coated with a non-stick surface to make cooking and cleaning easier. The most common material used for this is PTFE (Teflon), though other non-stick coatings are available. The pan is either dipped into the coating material or sprayed with the coating and then cured in an oven to create a durable, easy-to-clean surface.
7. Quality Control
- Visual Inspection: Every baking pan undergoes a visual inspection to check for defects, such as scratches, dents, or imperfections in the surface finish. The pan is also checked for uniformity in shape and size, ensuring it meets the required specifications.
- Thickness Measurement: A thickness gauge is used to measure the thickness of the metal at various points to ensure consistency and that the pan meets quality standards.
- Strength Testing: Some pans are subjected to strength tests to verify their durability. This might include tests to ensure that the pan can withstand high temperatures without warping or bending under the weight of food.
8. Cleaning and Packaging
- Cleaning System: After the manufacturing process is complete, the baking pans are thoroughly cleaned to remove any oils, dust, or residues left from the production process. This is typically done using high-pressure washers or ultrasonic cleaning systems to ensure that the pans are completely clean and free of any contaminants that could affect their performance.
- Automated Packaging System: Finally, the baking pans are packaged for shipment. Automated packaging systems wrap each pan in protective material to prevent scratches and damage during transport. The pans are then boxed, labeled, and prepared for shipment to retailers or consumers.
9. Automation and Technology Integration
Throughout the entire manufacturing process, automation plays a crucial role in ensuring efficiency and maintaining consistency. Many of the machines involved in the process are integrated with IoT sensors, allowing for real-time monitoring of production parameters like temperature, pressure, and machine performance. This data is used to optimize production, reduce downtime, and improve the quality of the final product.
Summary
The production of sheet metal baking pans involves a combination of cutting, forming, welding, coating, and finishing processes. Using specialized machinery such as shearing machines, deep drawing presses, and coating systems, manufacturers can produce high-quality, durable, and functional baking pans. Automation and quality control measures are integrated throughout the process to ensure consistent production and high product standards.
Sheet Metal Baking Pan Manufacturing Machine
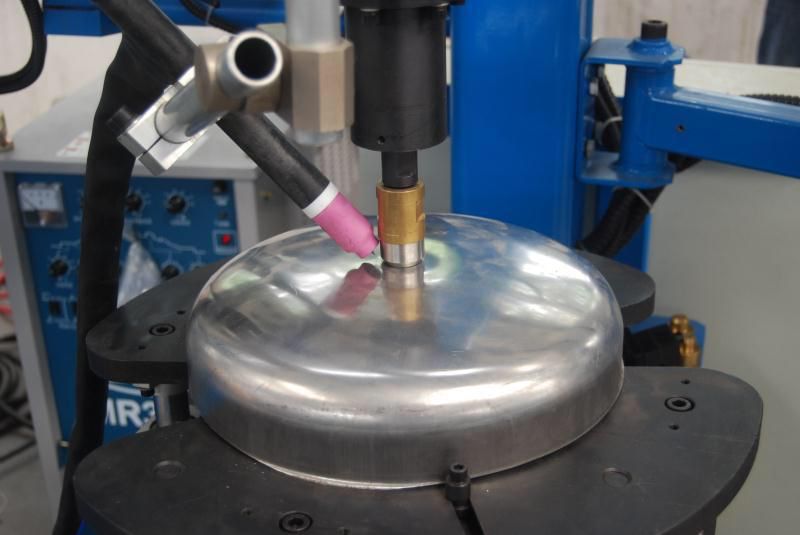
The manufacturing of sheet metal baking pans involves several specialized machines and processes to convert raw metal sheets into durable, functional pans suitable for baking. Here’s a breakdown of the typical machinery used in the production of these pans:
1. Material Preparation
- Decoiling Machine: The manufacturing process begins with decoiling, where large rolls of metal—usually stainless steel or aluminum—are unwound. The decoiling machine flattens the metal as it is unrolled, ensuring it is free from any curling or imperfections that might have developed during the coiling process.
- Leveling Machine: Once uncoiled, the metal sheet is passed through a leveling machine to smooth it out completely. This step ensures the metal is flat and straight, which is critical for accurate cutting and forming.
2. Cutting the Metal
- Shearing Machine: To obtain the correct dimensions for the baking pan, the metal sheet is cut to the required size using a shearing machine. This machine uses high-pressure blades to make straight, precise cuts on the metal. Depending on the design, the cut metal can be either rectangular, square, or shaped to the specific design of the pan.
- Laser Cutting or Punching (Optional): If the baking pan requires perforations or more complex shapes, such as ventilation holes or unique patterns, laser cutting or punching machines are used. These machines provide high precision for intricate shapes and are ideal for making features like handles, vents, or decorative cuts in the pan.
3. Forming the Baking Pan Shape
- Deep Drawing Press: To form the actual shape of the baking pan, a deep drawing press is used. This process involves placing the metal sheet into a mold, where a high-pressure punch draws the metal down into the mold, creating the pan’s shallow, rounded shape. The deep drawing press ensures the pan has smooth, uniform walls without any wrinkles or distortions.
- Embossing or Stamping Press (Optional): If the pan requires textured patterns or reinforcement along certain sections (for example, strengthening the bottom or creating ribs for added stability), an embossing or stamping press is used. These presses can imprint designs onto the surface of the metal, which not only improves the aesthetics of the pan but can also enhance its structural integrity.
4. Edge Reinforcement
- Edge Rolling or Beading Machine: After forming the pan shape, the edges are reinforced to improve strength and prevent sharp edges that could be hazardous. This is done using an edge rolling machine or beading machine, which rolls the edges of the pan into a smooth, reinforced lip. This step also contributes to the overall durability and safety of the pan.
- Flanging Machine (Optional): If the pan design requires a lip for attaching handles or lids, a flanging machine can be used to create a flat outward-facing lip around the edge of the pan. This feature is especially useful for pans with detachable handles or lids.
5. Assembly (Handles and Other Components)
- Spot Welding Machine: Many baking pans feature metal handles, which are typically attached using a spot welding machine. This process involves applying heat to specific points where the handle meets the pan, causing the metal to fuse together. Spot welding is fast and ensures a strong bond between the handle and the pan.
- Riveting Machine: For some designs, particularly those that require removable or more intricate handles, riveting machines may be used. Rivets are inserted through the metal and then expanded to create a secure, permanent bond.
6. Surface Treatment and Finishing
- Polishing and Buffing Machines: After assembly, the baking pan goes through a polishing and buffing process to ensure a smooth and shiny finish. Polishing removes any rough spots from the manufacturing process, while buffing adds a smooth, reflective surface.
- Sandblasting Machine (Optional): If a textured or matte finish is desired, the pan can be sandblasted. Sandblasting removes any roughness and gives the surface a uniform matte texture. This step is often used to improve the adhesion of coatings or to create a rustic or decorative finish.
- Non-stick Coating Application: Many baking pans are coated with a non-stick coating like PTFE (Teflon) to make them easier to clean. The coating is applied through spraying, dipping, or electrostatic processes and then baked or cured in an oven to ensure it adheres properly to the pan surface.
7. Quality Control
- Visual Inspection: Every pan undergoes a visual inspection to check for defects such as dents, scratches, or imperfections in the surface. Inspectors also ensure that the pan’s dimensions and shape are within tolerance.
- Thickness Measurement: A thickness gauge is used to ensure that the metal used for the baking pan is uniform in thickness. Consistent thickness ensures that the pan will heat evenly and perform well during use.
- Strength Testing: Some pans may undergo strength testing, where they are subjected to high temperatures or weight tests to confirm their durability and resistance to warping.
8. Cleaning and Packaging
- Cleaning System: After finishing and before packaging, the pans are cleaned to remove any oils, dust, or residues left over from manufacturing. This can be done using high-pressure washers or ultrasonic cleaning machines.
- Automated Packaging System: Finally, the cleaned pans are packaged for shipment. Automated packaging machines wrap the pans in protective materials to prevent scratches or damage during transport. The pans are then placed into boxes, labeled, and prepared for shipment.
9. Automation and IoT Integration
Throughout the manufacturing process, automation plays a key role in ensuring efficiency and maintaining consistent quality. Many machines are equipped with IoT sensors to monitor factors such as temperature, pressure, and machine performance. These sensors provide real-time data to operators, which allows for rapid adjustments to maintain high-quality production standards.
Summary
The production of sheet metal baking pans is a highly automated process that involves several key steps, including decoiling, cutting, forming, welding, coating, and finishing. Specialized machinery such as deep drawing presses, laser cutters, and non-stick coating systems ensure that the pans are durable, functional, and easy to clean. Quality control and automation ensure that each pan meets the required standards, making the entire manufacturing process efficient and reliable.
The production of a sheet metal baking pan begins with the preparation of the raw material. Typically made from stainless steel or aluminum, large coils of metal are unwound and flattened using a decoiling machine. This ensures the metal is smooth and free from distortions. Once uncoiled, a leveling machine is used to remove any remaining bends and ensure the sheet is perfectly flat for further processing.
Next, the metal sheet is cut into the required dimensions using a shearing machine, which makes precise, straight cuts. If intricate designs or features are needed, laser cutting or punching machines can be used to create specific shapes or perforations, such as holes for handles or decorative features.
The actual shape of the baking pan is then formed using a deep drawing press. This machine draws the metal sheet into a mold, creating the shallow, rounded form typical of baking pans. Additional textures or reinforcement patterns are applied using an embossing or stamping press, if required.
The edges of the pan are reinforced using an edge rolling machine or beading machine, creating smooth, durable edges. If handles are needed, they are attached via spot welding or riveting, depending on the design.
After the pan is assembled, the surface is treated for both appearance and functionality. Polishing and buffing machines are used to give the pan a smooth, shiny finish, and sandblasting can be employed to achieve a textured or matte surface. Many pans also receive a non-stick coating for easier cleaning, which is applied and then cured in an oven.
Finally, the pans undergo rigorous quality control checks to ensure they meet all specifications for strength, appearance, and performance. After cleaning and packaging, the pans are ready for distribution.
Throughout the process, automation and IoT sensors are integrated into the machinery to monitor production, optimize efficiency, and maintain quality standards.
The manufacturing of a sheet metal baking pan starts with uncoiling large rolls of metal, typically stainless steel or aluminum, using a decoiling machine. This machine flattens the metal to ensure it’s free from distortions. The metal is then passed through a leveling machine to remove any remaining bends.
The next step is cutting the metal into the appropriate dimensions using a shearing machine. If the design requires more complex shapes or features like handles or ventilation holes, laser cutting or punching machines are used for precise cuts.
To form the shape of the baking pan, a deep drawing press is used, where the metal sheet is drawn into a mold to create the pan’s shallow, rounded shape. Any additional textures or patterns are added using an embossing or stamping press.
The edges of the pan are reinforced with an edge rolling machine or beading machine to ensure smooth, durable edges. Handles are typically added through spot welding or riveting, depending on the design.
For the finishing touches, the pan is polished and buffed using polishing and buffing machines. Sandblasting can also be used for a matte or textured finish. Many pans receive a non-stick coating, which is applied and then cured in an oven.
The pans undergo quality control for defects and performance. Once cleaned and packaged, they are ready for distribution. Throughout the process, automation and IoT sensors are used to monitor and optimize production, ensuring high-quality output and efficient manufacturing.
After the manufacturing process of the sheet metal baking pan is completed, the pans undergo a detailed quality control phase. During this phase, each pan is thoroughly inspected for any defects, including dents, scratches, or any inconsistencies in shape or finish. Measurements are also taken to ensure that the pan meets the specified dimensions. Thickness gauges are used to measure the metal thickness at various points to ensure uniformity. If the pan has a non-stick coating, tests are done to confirm the integrity and consistency of the coating.
If any pans fail to meet the quality standards during inspection, they are either reworked or discarded. This step is crucial to maintaining the reliability of the product, as any minor defects could impact the pan’s performance, especially in terms of heat distribution and the ease of cleaning.
Cleaning and Packaging
Once the baking pans pass quality control, they are moved to the cleaning and packaging phase. This is where high-pressure washers or ultrasonic cleaning systems are used to remove any oils, dust, or residues from the manufacturing process. Cleaning ensures that the pans are ready for immediate use once they are purchased by consumers.
After cleaning, the pans are dried thoroughly and inspected once more for any remaining debris. Automated packaging systems then wrap the pans in protective materials such as bubble wrap or shrink wrap to prevent any damage during transport. Each pan is then boxed, labeled with the brand and product details, and prepared for shipment to distributors, retailers, or directly to consumers.
Automation and Technology
Throughout the manufacturing process, automation plays a key role in ensuring consistency and efficiency. Robotic arms are often used for tasks like handling and transporting pans between stages. Additionally, IoT (Internet of Things) sensors are integrated into the machinery to monitor production in real-time. These sensors collect data on factors such as temperature, pressure, and machine status, which are analyzed to optimize the production process. This allows for predictive maintenance and adjustments to the machinery, minimizing downtime and improving production rates.
Sustainability and Environmental Considerations
Modern sheet metal baking pan manufacturing also places a strong emphasis on sustainability. Manufacturers often recycle scrap metal generated during the cutting and forming stages. These scraps are melted down and reused in the production of new pans, which reduces waste and lowers the overall environmental impact of production. Additionally, energy-efficient machines and processes are utilized to minimize energy consumption throughout the manufacturing process.
Summary
In conclusion, the process of manufacturing a sheet metal baking pan involves several precise and automated steps, including decoiling, cutting, forming, reinforcing, assembling, finishing, and quality control. The use of advanced machinery ensures that each pan is durable, functional, and of high quality. Automation and technology not only streamline the production process but also contribute to maintaining high standards across all stages. Once completed, the pans are carefully cleaned, packaged, and prepared for distribution, ready for consumers to enjoy in their kitchens.
After quality control, the sheet metal baking pans undergo cleaning and packaging. High-pressure washers or ultrasonic cleaning systems remove any residual oils or manufacturing dust. Once cleaned, the pans are dried thoroughly and undergo another inspection to ensure they’re completely free of any contaminants.
Automated packaging systems then wrap the pans in protective materials like bubble wrap or shrink wrap to prevent damage during shipping. The pans are boxed, labeled with product details, and prepared for shipment to retailers or directly to consumers.
Throughout the entire manufacturing process, automation plays a key role in maintaining efficiency and consistency. Robotic arms are used for tasks like moving pans between stages, while IoT sensors monitor critical parameters like temperature and machine status to ensure optimal performance and predict any necessary maintenance.
Modern manufacturers are also focusing on sustainability by recycling scrap metal and using energy-efficient machines, reducing waste and environmental impact.
The result is a high-quality, durable baking pan that is ready for consumers, having gone through a streamlined, automated, and environmentally conscious production process.
After packaging, the sheet metal baking pans are ready to be distributed to the market. Depending on the manufacturer’s distribution model, these pans are either shipped to retailers, sold directly to consumers via online platforms, or sent to wholesalers. The packaging is designed to protect the pans during transportation and storage, ensuring that the products reach the customers in pristine condition.
Distribution and Retail
Once the pans reach the distribution points or retailers, they are stocked for sale. In retail environments, pans may be displayed with other cookware, and in some cases, manufacturers will provide promotional material or labels that highlight key features such as non-stick surfaces, durability, and heat resistance. These features are important selling points that help customers make informed purchasing decisions.
For online retailers, the pans are often cataloged with detailed descriptions, photos, and specifications. E-commerce platforms may offer customer reviews, which serve as valuable feedback for potential buyers.
Post-Sale Service and Customer Support
Some manufacturers also offer post-sale services to enhance customer satisfaction. This can include warranties or guarantees against defects in materials or workmanship. If customers experience issues such as warping, peeling of the non-stick coating, or other manufacturing defects, they may be eligible for a replacement or refund.
Manufacturers may also provide customer support for users who have questions about using or caring for their baking pans, including guidance on cleaning, storage, and proper usage. Offering comprehensive customer support helps to build brand loyalty and ensures customer satisfaction in the long term.
Market Trends and Innovation
The cookware industry, including sheet metal baking pans, is highly competitive, and manufacturers are always looking for ways to innovate. Some of the trends in baking pan manufacturing include:
- Advanced Coatings: Beyond traditional non-stick coatings, newer, more durable and safer coatings, like ceramic-based coatings, are gaining popularity.
- Improved Designs: Innovations in pan shapes, handles, and stacking abilities are being developed to meet the needs of more diverse consumer preferences.
- Sustainability: Many manufacturers are embracing environmentally friendly practices such as using recycled metals and eco-friendly coatings to meet the growing consumer demand for sustainable products.
Conclusion
In summary, the process of making sheet metal baking pans involves several critical steps, from material preparation and forming to cutting, finishing, and packaging. The use of advanced machines and automation ensures efficiency, consistency, and high-quality production. As the product moves from manufacturing to distribution, the focus on customer satisfaction, sustainability, and innovative designs ensures the pans remain competitive in the market.
Sheet Metal Griddle Pan Manufacturing Machine
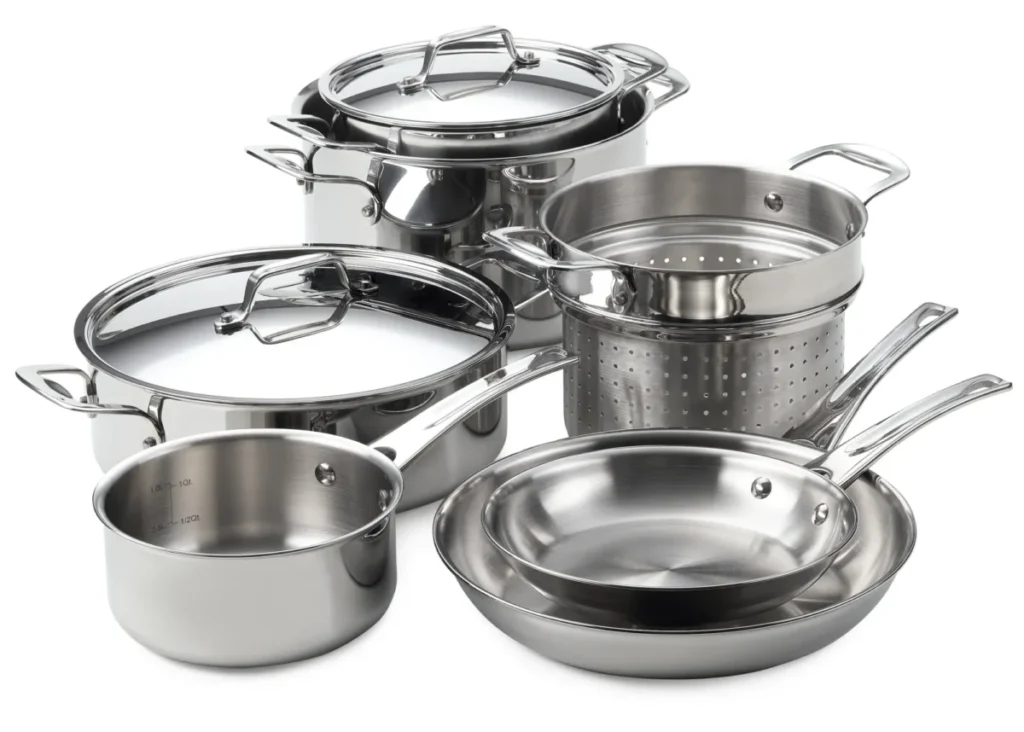
The manufacturing of sheet metal griddle pans involves several key processes, which require specialized machinery to transform raw metal sheets into durable, heat-efficient cooking tools. These griddles are typically made from aluminum or stainless steel, materials that offer excellent heat distribution and durability. Here’s an overview of the machinery and steps involved in producing sheet metal griddle pans:
1. Material Preparation
- Decoiling Machine: The production process begins with decoiling large rolls of metal, such as stainless steel or aluminum, which are unwound and flattened by a decoiling machine. This ensures that the metal is smooth and straight for further processing.
- Leveling Machine: The metal sheet is then passed through a leveling machine to eliminate any residual bends or warps, ensuring the sheet is perfectly flat and ready for cutting.
2. Cutting and Shaping
- Shearing Machine: The metal sheet is cut into the required dimensions using a shearing machine, which produces precise straight cuts. For griddle pans, this typically results in rectangular or square shapes.
- Laser Cutting or Punching Machine (Optional): For more complex features like ventilation holes or unique edge designs, laser cutting or punching machines are used. These machines are ideal for cutting intricate shapes, handle cutouts, or holes in the metal that improve both design and functionality.
3. Forming the Griddle Shape
- Deep Drawing Press: After cutting, the metal sheet is formed into the shallow, flat shape of a griddle pan using a deep drawing press. The metal sheet is placed into a mold, where a punch presses down on it to form the base and sides of the pan. This step requires precise control to ensure the griddle maintains a uniform thickness and shape.
- Embossing or Stamping Press (Optional): To add texture to the surface of the griddle (which can help with cooking performance or aesthetics), embossing or stamping presses are used. These can add patterns to the surface for better heat distribution, grip, or a decorative effect.
4. Reinforcing the Edges
- Edge Rolling or Beading Machine: The edges of the griddle pan are reinforced using an edge rolling machine or beading machine. These machines roll the edges of the pan to create a smooth, durable lip that is safe to handle and enhances the griddle’s structural strength.
- Flanging Machine (Optional): If the griddle pan design requires an outward-facing lip for attaching handles or additional reinforcement, a flanging machine can be used to create a sturdy flange around the edge of the pan.
5. Handle Attachment
- Spot Welding Machine: For griddles with metal handles, spot welding machines are typically used. The handles are positioned in place, and the spot welder applies heat to the contact points, fusing the handles securely to the pan.
- Riveting Machine (Optional): In some designs, handles may be attached using riveting. This is a common method for handles that require a detachable or more flexible connection to the pan.
6. Surface Treatment and Coating
- Polishing and Buffing Machines: Once the griddle pan is formed and assembled, it undergoes a polishing and buffing process. This ensures the surface is smooth, free from imperfections, and has an aesthetically pleasing finish.
- Sandblasting Machine: If a matte or textured finish is desired, the griddle pan may go through a sandblasting process. Sandblasting gives the metal a uniform, textured surface that can improve the griddle’s performance, such as better non-stick properties.
- Non-stick Coating Application: Many griddle pans are coated with a non-stick surface, typically PTFE (Teflon) or ceramic-based coatings. These coatings are applied using spraying, dipping, or electrostatic methods and then cured in an oven to ensure they adhere to the pan’s surface. Non-stick coatings are essential for ease of cleaning and preventing food from sticking during cooking.
7. Quality Control
- Visual and Dimensional Inspection: The griddle pans undergo rigorous visual inspections to check for defects such as dents, scratches, or incorrect shapes. Dimensional gauges are used to ensure that the pan’s size and thickness meet specifications.
- Strength Testing: The griddles are often subjected to strength testing to ensure they can withstand high cooking temperatures without warping or cracking. This may involve testing their resistance to thermal expansion or checking the bonding strength of welded handles.
8. Final Cleaning and Packaging
- Cleaning Systems: After the surface treatments and quality checks, the griddle pans are cleaned to remove any oils, dust, or residue from the manufacturing process. This is done using high-pressure washers or ultrasonic cleaning systems, ensuring that the pans are ready for use right out of the box.
- Packaging: The pans are then packed using automated packaging systems that wrap the griddles in protective materials like bubble wrap or shrink wrap. The packaging ensures that the pans are shielded from damage during shipping and storage. The griddles are then boxed, labeled, and ready for distribution.
9. Distribution
The completed and packaged griddle pans are then shipped to retailers, wholesalers, or directly to consumers. Retailers will display the griddles in stores, while online retailers will list the products with detailed descriptions and images. Some manufacturers may offer direct sales through their websites, providing a convenient shopping experience for customers.
Automation and Efficiency
Throughout the manufacturing process, automation plays a vital role in ensuring efficiency, consistency, and quality control. Machines are equipped with sensors and IoT (Internet of Things) technology that monitor various parameters, such as temperature and pressure. This data is used to optimize production, minimize downtime, and predict necessary maintenance, which contributes to higher throughput and reduced operational costs.
Sustainability Practices
Manufacturers increasingly focus on sustainability. Many companies recycle scrap metal, ensuring that the production process minimizes waste. Additionally, energy-efficient machines and environmentally friendly coatings help reduce the environmental footprint of the production process. As consumer demand for eco-friendly products grows, manufacturers are investing in sustainable practices to stay competitive and meet regulatory requirements.
Conclusion
The production of sheet metal griddle pans is a complex and highly automated process that involves several specialized machines for cutting, shaping, forming, reinforcing, and finishing the pans. With the help of advanced technology, these pans are produced with precision, ensuring they meet both functional and aesthetic standards. Non-stick coatings, handle attachment methods, and surface treatments enhance the usability and appearance of the pans, making them suitable for both home and commercial kitchens.
The process of manufacturing sheet metal griddle pans begins with the preparation of raw materials, typically stainless steel or aluminum, which are chosen for their excellent heat distribution properties. Large coils of metal are unwound using a decoiling machine, ensuring the material is flat and smooth for the next steps.
The metal sheet is then passed through a leveling machine, which removes any imperfections or bends from the material. Once leveled, the sheet is cut to the required size using a shearing machine. If more detailed shapes or designs are needed, laser cutting or punching machines are used for precision cuts.
To form the griddle pan’s shape, a deep drawing press molds the metal into the desired shallow, flat form. If textures or patterns are needed on the cooking surface for heat distribution or aesthetic purposes, an embossing or stamping press is used.
The edges of the griddle are reinforced using an edge rolling machine to ensure durability and smoothness. If handles are required, they are either welded in place using spot welding or attached via riveting.
Next, the griddle pan undergoes surface treatment, where it may be polished and buffed to give it a smooth finish. Some griddles are also sandblasted to create a matte surface or texture for better cooking performance. If a non-stick coating is desired, it is applied and cured in an oven.
Finally, the griddles are thoroughly inspected for quality, cleaned, and packaged. The packaging process includes wrapping the pans in protective materials to avoid damage during transport. Once packaged, the griddles are distributed to retailers or directly to consumers.
Throughout the process, automation and technology play an important role, ensuring that each pan is produced consistently and efficiently. Additionally, sustainability is increasingly prioritized, with manufacturers recycling metal scraps and using energy-efficient equipment.
Once the sheet metal griddle pans are packaged and prepared for shipment, the next phase involves logistics and distribution. Manufacturers typically work with a network of wholesalers, retailers, and e-commerce platforms to deliver products to both commercial and residential customers. During this phase, inventory tracking systems and automated warehouse management software are used to ensure accurate, timely deliveries and restocking.
At the retail level, the pans are marketed based on features like non-stick surfaces, compatibility with induction or gas cooktops, heat resistance, and ease of cleaning. Packaging often includes clear labeling of these features along with instructions for care and use. In the case of online sales, these details are translated into digital listings with photos, descriptions, and customer reviews that influence purchasing decisions.
In parallel, manufacturers engage in product development and innovation to stay competitive. Research and development teams might experiment with:
- New coating technologies for better non-stick performance and longer lifespan.
- Hybrid materials (e.g., aluminum cores with stainless steel exteriors) for superior heat distribution.
- Smart cooking features, such as embedded temperature sensors or detachable handles for compact storage.
- Ergonomic designs, including contoured grips or balanced weight for easier handling.
Additionally, customer feedback loops have become increasingly important. Feedback collected from online reviews, customer service inquiries, and product returns is analyzed to identify areas for improvement in design, durability, and usability. This feedback is integrated into the next generation of manufacturing specifications, ensuring continuous product enhancement.
Manufacturers also keep an eye on global regulations and standards, particularly those related to food safety, materials compliance (like FDA or EU standards), and environmental practices. Compliance is often verified through third-party testing and certification, which adds value and trustworthiness to the product.
As sustainability becomes a central concern, companies are adopting greener manufacturing practices. This includes:
- Using recyclable or biodegradable packaging.
- Implementing closed-loop water and cooling systems to reduce waste.
- Powering factories with renewable energy sources like solar or wind.
- Pursuing ISO 14001 certification for environmental management.
Ultimately, the life cycle of a sheet metal griddle pan—from raw material to a finished product in a customer’s kitchen—relies on a sophisticated interplay of engineering, automation, quality control, innovation, and environmental responsibility. Manufacturers who master this balance are best positioned to produce high-performance cookware that meets the evolving expectations of today’s home chefs and professional kitchens alike.
Sheet Metal Skillet Manufacturing Machine
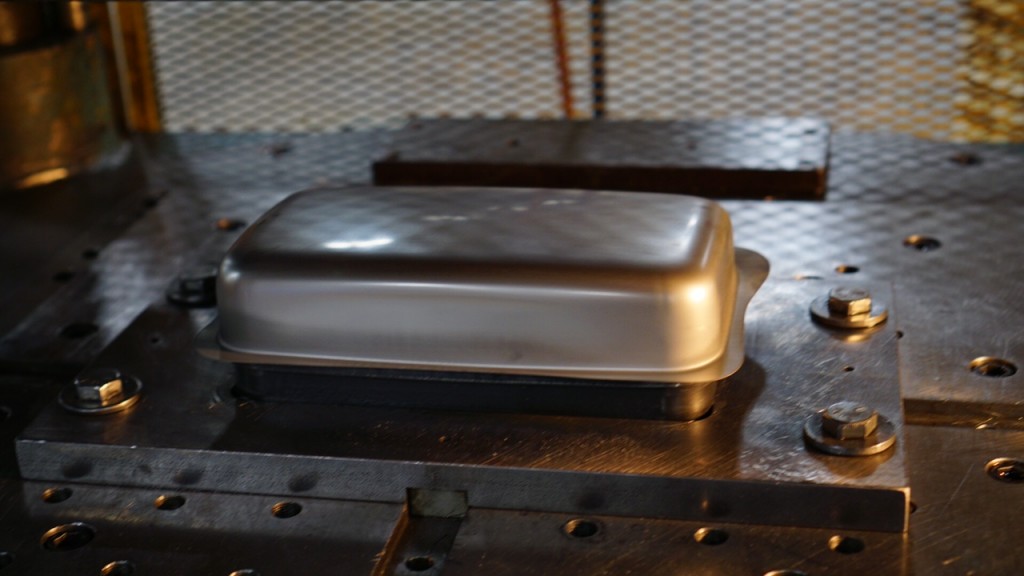
The sheet metal skillet manufacturing machine is part of a highly integrated and automated system designed to transform flat metal sheets—typically stainless steel, aluminum, or carbon steel—into finished skillets used in both domestic and commercial kitchens. Skillets, known for their slightly deeper sides and curved interior profiles compared to standard frying pans, require precision forming and robust construction to ensure long-lasting performance under high heat. Here’s a detailed walkthrough of how these machines function and how they fit into the larger manufacturing process.
The process begins with metal sheet preparation, where large coils of metal are fed into a decoiling and leveling unit. This machine unwinds the coil and flattens it to eliminate any curves or surface tension, preparing it for further processing. From there, a sheet feeding system guides the material into the hydraulic or servo-controlled blanking press, which cuts the metal into circular blanks, each corresponding to the size of the skillet to be produced.
These blanks are then transferred—either manually, robotically, or via conveyor belts—to the deep drawing press. This is one of the most critical machines in skillet manufacturing. It uses a matched set of dies to form the blank into the basic skillet shape, with raised sides and a flat bottom. Deep drawing must be precisely controlled to prevent wrinkling or tearing of the metal, and multiple draws (re-draws) are often needed to achieve the final depth and contour.
Once the skillet body is formed, it is passed to a trimming and flanging machine. This machine trims the upper edge of the pan for uniform height and then flanges the rim—either rolling it for strength or curling it over for a smooth edge. Some skillet models feature pouring spouts, which are pressed in at this stage using a hydraulic notching and forming press.
Next comes handle preparation and attachment. For metal handles, the process includes spot welding using a CNC-controlled welding machine, ensuring strong, consistent joints. If the skillet design requires riveted handles, a multi-station riveting machine performs the task with precision and speed. Plastic or bakelite handles are attached later during the finishing phase to avoid heat damage.
Surface finishing is carried out using buffing, grinding, and polishing machines. These machines smooth out the surface, remove tooling marks, and produce a satin or mirror finish, depending on the product design. Skillets requiring a non-stick surface move into a separate coating line. Here, a spray coating booth applies layers of PTFE (Teflon) or ceramic material, which is then cured in a high-temperature baking oven.
Each skillet goes through a rigorous quality control process. Laser scanners and vision systems check for deformities, dimensional accuracy, and coating uniformity. Hardness testers may be used on sample units to ensure that the drawing and annealing processes have maintained the desired material properties.
Before packaging, skillets are cleaned in a vibration-assisted ultrasonic bath to remove all residues, oils, and dust. They are then dried, often using air knives, and sent to an automated packaging line, where they are shrink-wrapped, labeled, and boxed for shipping.
Throughout the entire process, automation and real-time monitoring ensure consistency, high throughput, and minimal downtime. Machines are often equipped with PLC (Programmable Logic Controller) systems and HMI (Human-Machine Interface) panels that allow operators to adjust parameters, run diagnostics, and manage multiple production recipes with ease.
This sophisticated machinery setup not only supports mass production but also enables flexibility to produce different sizes and styles of skillets with minimal changeover time—essential for meeting the diverse demands of modern cookware markets.
Once the sheet metal skillet has passed through the final packaging stage, it enters the distribution pipeline, where logistics systems take over to ensure the product reaches its designated retailers, distributors, or direct consumers. Manufacturers rely on automated inventory systems to track production batches, manage storage in warehouses, and coordinate shipping schedules. These systems also help manage quality recalls or traceability issues if any arise later in the product’s lifecycle. In today’s global cookware market, skillets are often exported to multiple countries, so compliance with international standards such as FDA regulations in the United States, CE marking in Europe, or specific food-contact safety certifications in Asia is crucial. Labels, user manuals, and packaging materials are tailored accordingly during this phase, and the packaging line may apply region-specific information including languages, warranty details, and product registration codes.
Meanwhile, innovation continues in the background. Leading manufacturers are investing in smart manufacturing technologies, including machine learning algorithms to optimize press stroke parameters, predictive maintenance software for hydraulic systems, and robotic process automation for materials handling. These advances reduce downtime, improve energy efficiency, and increase overall yield. Research and development departments collaborate closely with materials scientists and surface engineers to create new skillet variants featuring improved non-stick coatings, reinforced layering techniques for better thermal diffusion, or multi-metal bonded bases to enhance compatibility with induction cooktops.
Customer feedback also feeds into this continuous improvement cycle. With the rise of e-commerce, online reviews and product ratings provide valuable insight into how well skillets perform in real-world kitchens. Issues like handle comfort, heat retention, coating longevity, and ease of cleaning are common themes that influence both marketing strategy and future design tweaks. Manufacturers use data analytics tools to sift through customer feedback, flagging patterns and correlating them with production batches or specific material suppliers to refine processes further.
On the sustainability front, manufacturers are moving toward greener operations by installing solar panels on factory roofs, using water recycling systems for coolant management, and sourcing metal from mills that use recycled content. Even the coating materials are evolving—some brands have phased out PFAS-based coatings in favor of ceramic or plant-derived alternatives to appeal to environmentally conscious consumers. Furthermore, factories are minimizing packaging waste by switching to recyclable cartons, eliminating unnecessary plastic, and using QR codes instead of printed manuals.
Ultimately, the journey from raw sheet metal to a high-performance skillet is not just a mechanical transformation but a synthesis of engineering precision, environmental responsibility, market responsiveness, and digital intelligence. The machines used in this process are not static assets but dynamic hubs of productivity, constantly adapted and optimized to meet changing consumer demands, regulatory landscapes, and technological frontiers. The skillet that ends up on a stovetop represents not just functional cookware, but the culmination of an intricate, deeply integrated manufacturing ecosystem.
As the manufacturing ecosystem continues to evolve, the skillet production process is increasingly influenced by global trends in smart kitchens, consumer lifestyle shifts, and digital connectivity. Manufacturers are now exploring ways to integrate digital features into traditional cookware. For instance, some skillet designs are being prototyped with embedded temperature sensors that communicate with mobile apps via Bluetooth or Wi-Fi, allowing users to monitor cooking heat in real time. These additions require changes not only in product design but also in the manufacturing machinery, as new steps for embedding sensors, wiring, and protective coatings must be added to the production line without compromising efficiency or safety.
In tandem with these innovations, skillet manufacturers are partnering more frequently with culinary professionals and industrial designers to create products that align with modern cooking habits. From high-heat searing to oven-to-table versatility, today’s skillets are expected to meet both performance and aesthetic standards. This demand drives the customization of tooling dies and forming machines to accommodate new skillet shapes, tapered sides, or hybrid pan designs that combine attributes of a wok, frying pan, and sauté pan. With the help of CNC-based mold creation and rapid prototyping, new designs can be tested and implemented in production faster than ever before.
The globalization of the cookware industry has also made supply chain management a central concern. To maintain steady production, skillet manufacturing operations depend on timely deliveries of metal coils, handle materials, rivets, coatings, and packaging. Any disruption—whether from geopolitical shifts, environmental regulations, or raw material shortages—can slow down the entire process. In response, many manufacturers are adopting dual-sourcing strategies and investing in localizing supply chains to reduce dependence on distant vendors. Advanced ERP systems, integrated with real-time factory data, allow companies to respond dynamically to these challenges by adjusting production plans and material orders on the fly.
Another emerging focus area is worker safety and skill development. As machines become more sophisticated and automated, the role of factory personnel is shifting from manual labor to system supervision, diagnostics, and maintenance. Training programs now emphasize technical literacy, digital monitoring tools, and safety protocols associated with high-voltage machinery, robotic arms, and high-temperature curing ovens. Modern factories are designed not just for throughput, but for ergonomics and worker well-being, incorporating better lighting, noise-reduction systems, and ventilation controls to create healthier work environments.
As skillets reach end-users, the brand experience continues through customer support, warranty services, and increasingly, through digital ecosystems. Some companies provide mobile apps that offer cooking guides, maintenance tips, and even AI-generated recipes tailored to the specific skillet model purchased. This creates a long-term user engagement strategy that goes beyond a single transaction, turning a cookware product into a smart companion in the kitchen.
Looking ahead, the next generation of skillet manufacturing machines will likely incorporate even more AI-driven quality control, augmented reality-assisted maintenance, and blockchain-based material tracking for full transparency in sourcing and sustainability claims. In this trajectory, the humble skillet evolves into a sophisticated product of precision engineering, intelligent systems, and user-centered design—all made possible by the continuous advancement of specialized manufacturing machinery and production technologies.
As the skillet manufacturing process becomes even more advanced, there are several key areas in which emerging technologies are expected to make a significant impact. Artificial intelligence (AI) is already starting to play a critical role in predictive maintenance and quality control, and it is likely to become even more integral in future skillet production lines. AI algorithms can now predict when machines need servicing by analyzing patterns in performance and detecting anomalies that humans may miss. This reduces downtime, optimizes machine efficiency, and lowers maintenance costs by allowing for just-in-time repairs rather than waiting for something to break.
In terms of quality control, AI-driven vision systems are already being used to scan skillets for imperfections at various stages of production. These systems use high-resolution cameras and machine learning to identify even the most minute defects, such as surface scratches, uneven coating, or dimensional discrepancies. This process is far more accurate than traditional human inspections, ensuring that each skillet that leaves the production line is of the highest quality.
Additionally, augmented reality (AR) is poised to revolutionize the way factory workers interact with machinery and each other. For example, AR glasses could provide real-time, hands-free access to machine diagnostics, process data, and step-by-step troubleshooting guides, making it easier for workers to solve problems without needing to consult a manual. This can speed up response times to production issues and increase overall efficiency by reducing dependency on paper-based instructions or external expertise.
On the factory floor, robotic automation is becoming increasingly sophisticated, especially in processes that require precise, repetitive tasks. Robotic arms, equipped with advanced vision systems, are now capable of performing multi-stage operations, such as moving materials from one machine to another, welding handles, or applying coatings. These robots can work in collaboration with human operators to handle the more physically demanding or monotonous tasks, allowing workers to focus on areas that require more skill or oversight. This shift is expected to improve productivity and reduce the risk of human error.
Blockchain technology is also emerging as a tool for improving traceability and transparency in the skillet manufacturing process. By integrating blockchain into the supply chain, manufacturers can create a secure, transparent record of where materials come from and how they are processed at each step of the production journey. This level of transparency can be especially important when it comes to sustainability claims, such as whether materials are sourced ethically or whether the manufacturing process adheres to environmental standards. Blockchain could also be used to track the entire lifecycle of a skillet, offering consumers insight into its environmental impact and enabling brands to demonstrate their commitment to sustainability.
In terms of material innovation, manufacturers are exploring new, more sustainable materials that reduce environmental impact without sacrificing quality. For example, there is growing interest in using recycled metals for skillet production, reducing the need for mining new raw materials. Additionally, there are developments in creating eco-friendly coatings that maintain non-stick properties while avoiding harmful chemicals like PFAS, which are commonly used in traditional non-stick cookware. Companies are working with researchers to develop plant-based or ceramic alternatives that are safer for both the environment and consumers.
Sustainability in packaging is also becoming a priority for cookware manufacturers. With the rise of online shopping, packaging waste has become a significant environmental concern. Companies are moving toward using biodegradable, recyclable, or minimal packaging materials. Some manufacturers are even opting for zero-waste packaging solutions, which not only reduces waste but also strengthens their brand’s commitment to eco-consciousness.
As skillet manufacturing continues to adapt to these technological and environmental changes, the final product will likely be even more durable, efficient, and user-friendly. The combination of advanced machinery, AI, robotics, and sustainability efforts will likely result in a new era of high-performance cookware that is better suited to the needs of the modern consumer—one that balances functionality with environmental responsibility.
The future of skillet manufacturing, driven by these innovations, will be characterized by greater customization, enhanced performance, and increased responsibility to both consumers and the environment. As this industry evolves, manufacturers will need to stay agile, constantly adapting to new technologies and market demands, while ensuring that quality remains at the core of their production processes. The shift toward smart kitchens, sustainable practices, and technologically advanced cookware will undoubtedly shape the next generation of skillets, bringing new and exciting opportunities to both manufacturers and consumers.
Sheet Metal Ladle Manufacturing Machine
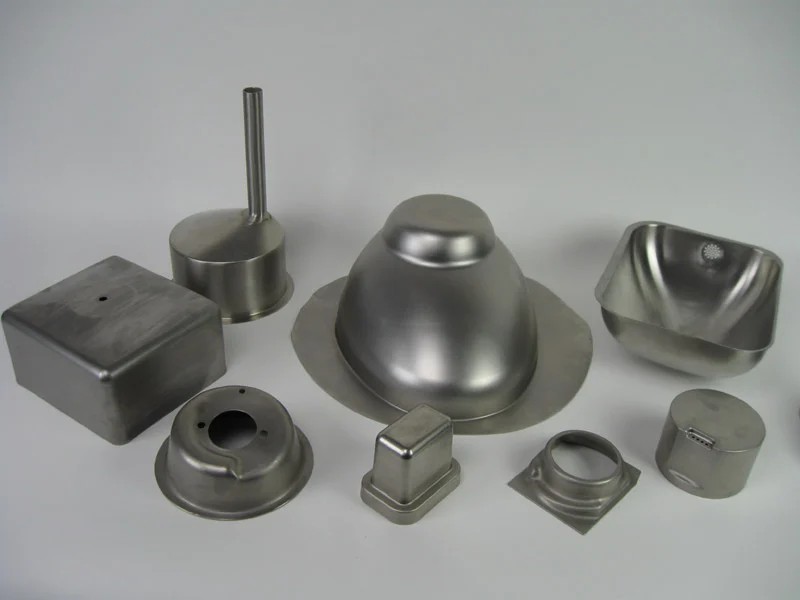
The sheet metal ladle manufacturing machine is designed to produce ladles, essential kitchen tools used for serving liquids like soup, sauces, or for deep frying. A ladle’s design, typically featuring a long handle and a deep bowl, is relatively simple but requires precision in both forming and finishing to ensure the final product performs well in high-heat environments while maintaining ergonomic usability.
The process of manufacturing sheet metal ladles starts with the preparation of the raw material, often stainless steel or aluminum due to their durability, heat resistance, and resistance to rust. The process begins with decoiling, where large coils of metal are unrolled using a decoiling machine to prepare the material for further processing. The metal sheets are then passed through a leveling machine to flatten them, ensuring they are free of imperfections and any initial curl or warping.
Once the sheet is leveled, it is cut into circular blanks that will form the base of the ladle. This is done using a blanking press, where the metal sheet is cut into a round shape. These blanks are then transferred to the next stage, the deep drawing press, where the round metal blank is drawn into the bowl-shaped form that gives the ladle its characteristic deep, curved shape. The deep drawing press uses a mold and a set of dies to stretch and form the metal into the desired depth, ensuring that the bowl is smooth and consistent.
After the bowl is formed, the next step is the creation of the handle. This is often a separate process and involves cutting and forming a long strip of metal into the handle shape using a cutting and bending machine. If the ladle design requires a curved handle, this is achieved using a curving press. The handle is then attached to the bowl of the ladle using a welding machine or riveting system, ensuring the joint is secure enough to handle the weight of liquids without failure. Some manufacturers may also employ laser welding or spot welding for a cleaner, stronger bond.
Once the ladle has been formed, it’s transferred to a trimming press where the edges are cleaned up and any excess material from the handle or bowl is removed. If the ladle design includes decorative or functional features like pouring spouts or texture on the handle, a stamping or embossing press is used. This allows the manufacturer to add unique design elements while maintaining the integrity of the ladle’s functionality.
After the basic shape and assembly are complete, the ladle undergoes surface finishing processes, which include polishing, buffing, and sometimes electropolishing to enhance the appearance and smoothness of the metal. The surface finish is critical, particularly for ladles, as it ensures easy cleaning and prevents food from sticking. Some ladles may also undergo coating applications if a non-stick or corrosion-resistant finish is desired. This could include PTFE coatings, anodizing for aluminum ladles, or other forms of protective treatment to ensure the ladle is both functional and aesthetically pleasing.
Finally, the ladle goes through a comprehensive quality control process, where each unit is inspected for any manufacturing defects such as cracks, scratches, or irregularities in the handle attachment. Advanced vision systems or manual inspections are performed to detect any flaws in the product. Ladles that meet the quality standards are then cleaned, dried, and packaged for shipment. Packaging materials are carefully selected to protect the ladles during transportation, ensuring they reach their destination free from damage.
Throughout the entire manufacturing process, automation plays a key role in enhancing efficiency, consistency, and production speed. From the cutting, forming, and welding stages to the finishing and packaging, advanced machinery ensures that each ladle is produced with high precision. Additionally, manufacturers are increasingly integrating sustainability practices into production by using recycled metals, reducing waste, and opting for eco-friendly packaging materials.
In addition to the traditional ladle designs, some manufacturers are exploring innovative designs with ergonomic handles, multi-purpose functionalities, or integration of smart technologies, such as temperature sensors to help cooks maintain ideal serving temperatures. These innovations are becoming increasingly popular in both the professional culinary world and the consumer market. As technology advances, ladle manufacturing is expected to continue evolving, offering better performance, durability, and user experience in the years to come.
As the manufacturing of sheet metal ladles continues to evolve, new technologies and advancements are pushing the boundaries of what is possible. Automation remains a cornerstone of the production process, enabling manufacturers to maintain high efficiency while minimizing human error. By integrating robotics into various stages of production, such as material handling, welding, and assembly, manufacturers are able to speed up the process, reduce labor costs, and achieve a higher degree of precision. Robotic arms equipped with specialized grippers are often used for tasks such as transferring ladle components between machines or performing delicate assembly tasks, allowing for greater flexibility and reducing the risk of defects during production.
In parallel with automation, the increasing use of data analytics and machine learning is helping manufacturers optimize their production lines. By analyzing data from sensors and machine performance, manufacturers can identify trends, detect inefficiencies, and predict potential failures before they occur. This predictive maintenance capability is not only cost-effective but also crucial in ensuring continuous production without unnecessary downtime, thus improving overall throughput.
Sustainability continues to be a major focus in ladle manufacturing. Companies are increasingly turning to green manufacturing practices, such as utilizing recycled metals in their production processes, which helps reduce the need for mining new materials and cuts down on the environmental impact of producing raw metal. Additionally, eco-friendly coatings and finishes are gaining traction, particularly for non-stick or corrosion-resistant ladles. These alternatives are not only safer for the environment but also meet the growing consumer demand for products that align with sustainable living principles.
Another key development is the move toward smart cookware. While ladles have traditionally been simple tools, there’s a growing trend of integrating technology into kitchen utensils, and ladles are no exception. Some companies are experimenting with temperature sensors embedded within the ladle’s handle, allowing users to monitor the temperature of the liquids they’re serving or cooking with. This is particularly useful in commercial kitchens where maintaining precise temperatures for sauces, soups, or stews is critical. Such features, along with the ability to sync with apps for tracking cooking progress, reflect the ongoing shift toward smart kitchen tools that offer both functionality and interactivity.
Innovation in design is another area of focus. Manufacturers are looking at ergonomics and how the shape, handle, and weight distribution of ladles can be optimized for comfort and ease of use. Whether it’s a more comfortable grip for extended use or a design that allows for better control while serving, these enhancements are driven by consumer feedback and an understanding of the evolving needs of kitchen users. Additionally, companies are exploring multi-functional ladles that can serve as both a cooking and serving tool, offering versatility for home cooks and professionals alike.
As these innovations take root, the market for ladles is expected to expand, not just in traditional markets but also in emerging regions where kitchenware demand is growing rapidly. To meet these needs, manufacturers will need to remain adaptable, incorporating new production methods and materials to stay competitive in a dynamic industry. The ladle of the future may be a far cry from the traditional version but will undoubtedly maintain its place as an essential, versatile kitchen tool that blends traditional design with modern technology.
As the demand for high-performance, multifunctional kitchen tools continues to grow, the evolution of ladle manufacturing will be shaped by several key trends. One major factor driving innovation is the increasing emphasis on customization. Consumers are seeking more personalized products, and cookware is no exception. The ability to create ladles with unique finishes, colors, or even customized handles allows manufacturers to cater to niche markets or offer a more tailored experience. Some manufacturers are already offering custom engraving or design options for handles, allowing consumers to personalize their kitchenware to suit their style or needs. This level of customization is made possible by advancements in laser engraving and 3D printing technologies, which are also being used for rapid prototyping of new ladle designs before they enter full-scale production.
Moreover, 3D printing is expected to play a more prominent role in ladle manufacturing as the technology matures. While 3D printing has traditionally been used for prototyping, it’s now entering the production phase for certain components. With 3D printing, manufacturers can create intricate ladle designs with less waste, faster turnaround times, and the ability to experiment with more complex shapes or features. For example, handles could be customized for specific ergonomic needs, or bowl shapes could be adjusted to suit different cooking styles or types of liquids. This approach offers endless possibilities in terms of both functionality and design, enabling manufacturers to meet the evolving tastes and demands of consumers.
As the market for premium cookware continues to expand, there’s also a growing interest in using luxury materials for ladle production. In addition to stainless steel and aluminum, manufacturers are experimenting with copper, titanium, or even carbon fiber to produce ladles that offer superior heat conductivity, lighter weight, or more durable finishes. These materials not only enhance the performance of the ladle but also appeal to consumers who are willing to invest in high-end, aesthetically pleasing kitchen tools. Some ladles, for example, may feature copper bowls for better heat retention or titanium handles for increased strength and resistance to corrosion. The use of such materials also offers an opportunity to create products that stand out in the competitive kitchenware market.
At the same time, the role of smart technology in cookware manufacturing is expected to increase. The integration of sensors, smart monitoring systems, and wireless communication could open new possibilities for ladles, such as smart ladles that automatically adjust temperature or volume settings based on the type of liquid being served or the user’s preferences. Imagine a ladle with built-in sensors that track the amount of liquid dispensed and send updates to a connected app, providing feedback on the cooking process. Such innovations would align with the broader trend toward connected kitchens, where kitchen devices work in tandem to enhance the cooking experience and improve efficiency.
In terms of sustainability, the future of ladle manufacturing is also looking toward closed-loop production systems. These systems focus on minimizing waste by reusing materials throughout the manufacturing process. For instance, metal scraps produced during the blanking and forming processes can be collected, melted down, and reused in the production of new ladles. This reduces the need for virgin materials, lowers the environmental footprint, and contributes to a circular economy. Additionally, advances in eco-friendly coatings and non-toxic finishes are reducing the reliance on harmful chemicals, making ladles safer for both the user and the environment. Manufacturers are also investing in energy-efficient production techniques, such as using solar power or improving the thermal efficiency of ovens used for heat treatments, which further supports their sustainability efforts.
The next frontier in ladle manufacturing will also see collaborations between different industries. For instance, partnerships between cookware manufacturers and food science experts could result in ladles that are specifically designed to handle particular types of cooking. Ladles intended for use in sous-vide cooking, for example, may have features that make them better suited for precise temperature control or ease of handling in water baths. Similarly, ladles designed for use in commercial kitchens might focus on durability and the ability to withstand long hours of high-temperature cooking.
As consumer preferences continue to evolve, the user experience will become an even more significant factor in ladle design. Beyond functionality, the look and feel of the ladle—how it fits in the hand, how well it performs in different cooking environments, and how easy it is to clean—will play an important role in driving purchasing decisions. Manufacturers are investing in ergonomics research to create handles that reduce strain during extended use, heat-resistant materials that make ladles comfortable to hold even when handling hot liquids, and dishwasher-safe designs that simplify the cleaning process.
The demand for ladles will likely keep increasing, especially as home cooking and culinary interest continues to rise globally. The ongoing innovation in materials, automation, and design, combined with sustainability efforts and the integration of smart technology, will shape the future of ladle manufacturing. As a result, the ladle will remain an essential kitchen tool, combining traditional craftsmanship with cutting-edge technology to meet the needs of modern consumers. Manufacturers will need to remain agile, continuously adapting to new trends, consumer desires, and technological advances to stay ahead of the competition and ensure that their ladles meet the highest standards of quality, performance, and sustainability.
As the ladle manufacturing industry evolves, a key factor will be the integration of advanced manufacturing techniques to address both production scalability and customization demands. One of the most promising advancements is additive manufacturing, commonly known as 3D metal printing. This process allows manufacturers to build ladles layer by layer using metal powders, enabling the production of highly complex and intricate designs that would be difficult or impossible to achieve with traditional methods. This could be particularly useful for creating specialized ladles, like those with intricate handle grips, non-standard bowl shapes, or built-in features such as integrated pour spouts or ergonomic reliefs for better user comfort. As additive manufacturing technologies become more affordable and efficient, we may see a shift toward more on-demand production, where customers can design their own ladles and have them printed and assembled for a bespoke kitchen experience.
Moreover, precision manufacturing is becoming increasingly crucial, especially with the rise of high-quality, luxury kitchenware. Companies are adopting laser cutting, precision stamping, and high-speed punching techniques to produce ladles with exceptional accuracy. These processes ensure that every ladle is produced with tight tolerances, resulting in consistency across large production runs and a product that performs reliably under demanding conditions. The rise of precision manufacturing is also encouraging ladle makers to experiment with new combinations of materials, such as stainless steel and carbon fiber or titanium and silicone, which offer unique attributes like lightweight durability or enhanced heat resistance.
At the same time, the global market for ladles and other cookware is undergoing significant shifts. In emerging economies, where growing middle-class populations are becoming increasingly interested in home cooking, there is rising demand for affordable yet durable kitchenware. As a result, manufacturers are focusing on developing cost-efficient production methods without compromising quality. Innovations in robotics and artificial intelligence (AI) are allowing factories to produce large quantities of ladles with high consistency while reducing labor costs and human error. Automated systems for inventory tracking, production planning, and material handling are also optimizing workflows, reducing downtime, and ensuring that factories can meet fluctuating demand with greater flexibility.
In established markets, particularly in North America and Europe, there is a shift toward premium, eco-conscious cookware. Consumers are increasingly seeking products that are not only functional but also align with their sustainability values. This demand is pushing ladle manufacturers to focus on eco-friendly production processes, from recycled metal sourcing to eco-conscious packaging. By reducing the environmental impact of the manufacturing process and offering products made from sustainable materials, ladle manufacturers can appeal to environmentally conscious consumers while also adhering to stricter regulations regarding resource usage and waste disposal.
Another significant trend influencing ladle manufacturing is the growing popularity of healthy cooking. As more consumers prioritize health-conscious cooking methods, such as low-oil frying and fat-free cooking, ladles are becoming more specialized. Ladles with non-stick coatings, for example, are increasingly in demand, as they allow users to cook and serve food with less fat while preventing foods from sticking to the surface. Additionally, there is an increasing demand for ladles that can withstand high-heat cooking without warping or degrading over time. Some ladles are now being designed with heat-resistant handles made from materials like silicone or bamboo, which provide a safer and more comfortable user experience during extended cooking sessions.
As the demand for specialty cookware rises, there is also an increasing trend toward multifunctional kitchen tools. Ladles, traditionally designed for serving liquids, are being reimagined for dual purposes. Some ladles now feature a built-in measuring scale on the handle, allowing cooks to measure out exact portions of liquids or sauces. Others are being designed with removable heads that can be swapped out to create different cooking effects, such as stirring or whisking, in addition to serving. These multi-functional ladles cater to busy consumers who prefer versatile tools that help streamline cooking tasks and save space in the kitchen.
Manufacturers are also turning to supply chain innovations to ensure a reliable flow of materials and finished products. For example, digital twins—virtual replicas of physical production systems—are being used to simulate manufacturing operations. By monitoring and optimizing production processes in real-time, digital twins enable ladle manufacturers to predict bottlenecks, optimize supply chains, and reduce waste. This kind of digital transformation allows for greater responsiveness to market demands and the efficient use of resources.
In the context of the globalized market, localization is becoming an increasingly important strategy. As manufacturers face the challenges of navigating tariffs, shipping costs, and regulatory constraints, many are moving toward regional manufacturing hubs to better serve local markets and mitigate supply chain risks. By establishing production facilities closer to key consumer bases, ladle manufacturers can reduce transportation costs, expedite shipping times, and take advantage of region-specific material sources or labor advantages. This trend is part of a broader shift toward localization of manufacturing driven by both economic and environmental factors.
As the next generation of ladle manufacturing machines is developed, the integration of artificial intelligence (AI) will likely play a bigger role in ensuring that each ladle is produced with the utmost precision. AI can help automate and optimize quality control checks, ensuring that each ladle meets the highest standards. For example, AI-powered vision systems can detect minute defects, such as cracks or inconsistencies in the finish, which might go unnoticed by human inspectors. AI can also help with predictive maintenance, forecasting potential breakdowns and allowing for preventative repairs to avoid costly downtimes.
Another significant trend will be the increasing demand for connected, “smart” ladles. As part of the larger trend of smart kitchens, ladles could soon come equipped with integrated sensors that connect to kitchen apps, allowing cooks to monitor things like temperature, volume, and the consistency of the liquid inside the ladle. This data could even be synced with smart stoves and ovens, creating a fully integrated cooking experience. For example, a smart ladle could alert the user when the soup inside is ready to serve or notify them if the temperature is too high, preventing burns or overcooking.
The continued evolution of ladle manufacturing reflects a broader trend within the cookware industry, which is constantly innovating to meet the changing needs of consumers. Whether it’s through advanced production technologies, sustainable practices, or the integration of smart capabilities, the ladle is transforming into a more sophisticated tool that blends traditional design with cutting-edge innovations. As these changes continue, ladle manufacturers will need to balance technological advancements with the timeless qualities that make a ladle an essential kitchen tool.
Sheet Metal Saucepan Manufacturing Machine
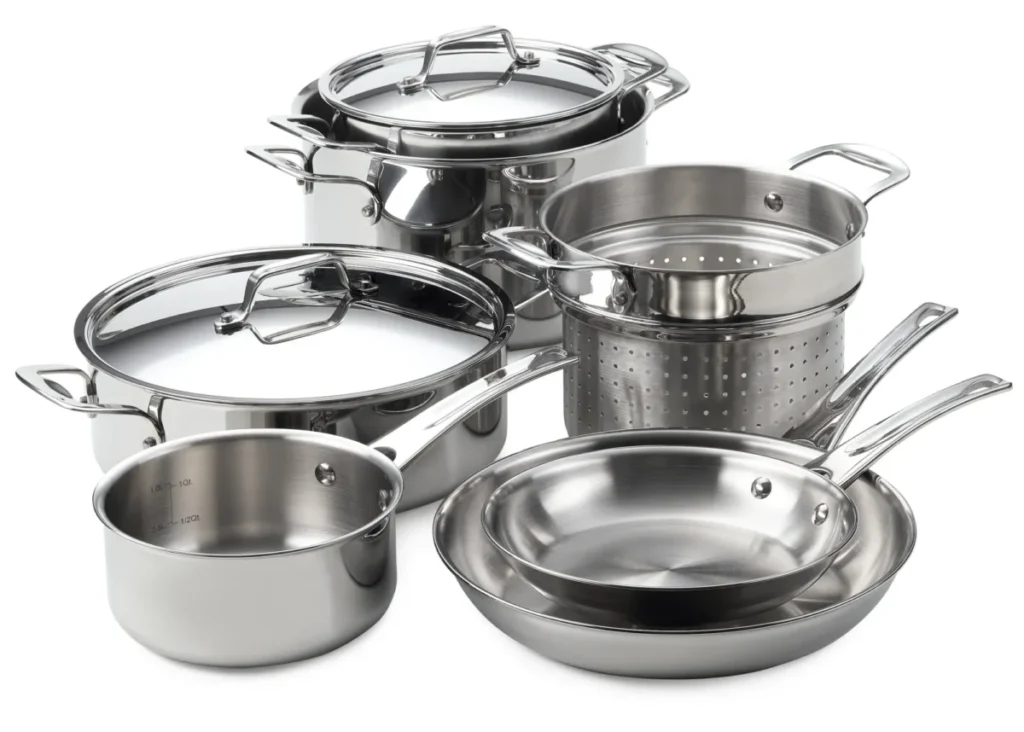
The sheet metal saucepan manufacturing machine is designed to produce high-quality saucepans typically used for cooking liquids such as sauces, soups, or stews. The manufacturing process of a saucepan involves a series of steps that transform raw sheet metal, often stainless steel or aluminum, into a functional and aesthetically pleasing cooking vessel.
The process begins with the acquisition of metal sheets that are generally rolled into large coils. These coils are then unrolled and fed into the production line using a decoiling machine. The raw metal sheet is typically stainless steel for durability and resistance to corrosion or aluminum for lighter weight and excellent heat conductivity. The material is then passed through a leveling machine, which flattens any imperfections and removes any curl or warping from the sheet, ensuring it is perfectly flat and ready for the next steps.
Next, the flat metal sheet is cut into round blanks using a blanking press. These blanks are the base shape of the saucepan. The round metal pieces are then moved to a deep drawing press where they are transformed into a cylindrical shape. The deep drawing press uses a set of dies to press the blank metal sheet into a mold, forming the base and sides of the saucepan. This process requires precise control to ensure that the walls are uniform in thickness and that the base of the saucepan is deep enough to allow for efficient cooking.
Once the saucepan shape has been formed, it is often necessary to perform trimming to clean up the edges. A trimming press is used to remove any excess material around the lip of the saucepan, creating a smooth and uniform edge. The next step involves the creation of the handle. The handle of the saucepan is typically made of a heat-resistant material such as stainless steel, aluminum, or bakelite, though silicone-coated handles are also becoming increasingly popular due to their heat resistance and ergonomic design. These handles are typically created by either casting, forging, or stamping, depending on the material being used.
The handle is then attached to the body of the saucepan using a welding machine, riveting system, or screws, depending on the design and desired strength of the connection. If welding is used, it is often done with laser welding or spot welding for a cleaner, more efficient bond, which reduces the potential for defects and provides a smooth finish. In high-end saucepans, cast handles are often used for added durability and aesthetics.
After the body and handle are assembled, the saucepan undergoes a variety of finishing processes. This may include polishing, buffing, and sometimes electropolishing to give the saucepan a smooth and shiny finish, which enhances its appearance and makes it easier to clean. Surface coatings such as non-stick finishes or anodizing (for aluminum saucepans) may also be applied at this stage to enhance the saucepan’s functionality. These coatings make the saucepan easier to clean and provide better heat distribution while cooking.
For non-stick pans, a coating process involving PTFE (Polytetrafluoroethylene) or ceramic coatings is applied to the interior surface of the saucepan. These coatings create a smooth, non-porous surface that reduces the need for oils or fats in cooking and prevents food from sticking. These coatings are applied using a spraying system or dipping system, followed by curing in an oven to ensure that the coating bonds effectively to the metal surface.
Once the saucepan has been fully assembled and finished, it undergoes a comprehensive quality control process. This includes visual inspection to check for defects such as scratches, cracks, or uneven surfaces, as well as functional tests such as checking the handle strength or testing the non-stick coating for consistency and durability. Automated vision systems or manual inspections are used to detect these defects, ensuring that only high-quality saucepans make it to the market.
Finally, after passing inspection, the saucepans are thoroughly cleaned, dried, and packaged. Packaging is designed to protect the product during transport while also showcasing the saucepan’s features. Eco-friendly packaging is becoming increasingly popular in response to growing consumer demand for sustainable products, with manufacturers opting for recycled cardboard or biodegradable materials for packaging.
Automation plays a major role in the manufacturing of sheet metal saucepans. From blanking presses to robotic welding and automated polishing stations, machines and robotics increase production efficiency while maintaining consistent quality. Advanced data analytics and machine learning are also being incorporated into production lines to monitor machine performance and predict maintenance needs, which reduces downtime and improves overall efficiency.
The use of sustainable manufacturing practices is increasingly important in the saucepan industry. Many manufacturers are focusing on reducing material waste by using recycled metals, especially stainless steel, in their production processes. Additionally, the use of energy-efficient production equipment and eco-friendly coatings ensures that saucepans are produced with minimal environmental impact.
As technology continues to advance, we can expect further innovations in saucepan design and manufacturing. The integration of smart technology into cookware is one example, with manufacturers exploring ways to incorporate temperature sensors or smart handles that alert users when the cooking temperature has been reached. These innovations would cater to the growing trend of connected kitchens, where various kitchen tools communicate with each other to improve cooking efficiency and experience.
Overall, the sheet metal saucepan manufacturing process is a complex combination of material preparation, precise shaping, assembly, and finishing techniques. Automation and innovative technologies continue to improve efficiency and quality, allowing manufacturers to meet the growing demand for high-quality, durable, and functional cookware. As sustainability and consumer preferences for smart kitchen tools evolve, we can expect the saucepan manufacturing process to continue adapting to meet these new challenges.
The sheet metal saucepan manufacturing process begins with the selection of high-quality raw materials, typically stainless steel or aluminum, which are carefully chosen for their durability, heat conductivity, and corrosion resistance. These metals are typically delivered in large coils, which are then fed into specialized decoiling machines to unroll and flatten the material, removing any imperfections or curl. Once the metal is prepared, it is cut into round blanks using a blanking press. These blanks serve as the base of the saucepan, and they are carefully measured to ensure that the final product will have the correct proportions.
The next phase involves deep drawing, where the blanks are shaped into a cylindrical form using a deep drawing press. This process is crucial as it creates the body of the saucepan, forming the base and the sides into a smooth, uniform shape. After the drawing, any excess material around the lip is trimmed to create a clean, smooth edge. The next step focuses on creating the handle of the saucepan, which is typically made from a material like stainless steel, aluminum, or Bakelite. These handles are often forged or cast to ensure strength and durability. Once the handle is formed, it is welded or riveted to the body of the saucepan. In many cases, laser welding or spot welding is used to create a strong and seamless bond between the handle and the pan.
Once the saucepan body and handle are securely attached, the saucepan is subjected to various finishing processes. These processes may include polishing, buffing, or electropolishing to create a shiny, smooth finish. Non-stick coatings are applied to the interior surfaces of the saucepan to improve cooking performance and make cleaning easier. The most common non-stick coatings used are PTFE (Teflon) and ceramic coatings, which are applied using spray or dip systems before being cured in an oven to ensure the coating bonds effectively. In addition to non-stick surfaces, some saucepans may undergo anodizing, particularly if they are made of aluminum, to create a durable, corrosion-resistant surface that also enhances heat conductivity.
After finishing, each saucepan undergoes strict quality control checks. These inspections include visual checks for defects such as scratches, dents, or inconsistencies, as well as functional testing to ensure that handles are securely attached and that the non-stick coating performs as expected. Automated vision systems or manual inspection processes are used to detect any flaws in the product before it moves to the next stage. If the saucepan passes all tests, it is thoroughly cleaned and dried to remove any remaining oils or residues before being packaged. Packaging is designed to protect the product during shipping while also providing an opportunity to display the saucepan’s features and quality. Manufacturers are increasingly opting for eco-friendly packaging, using materials like recycled cardboard or biodegradable options in response to consumer demand for sustainable products.
Automation plays an integral role in the saucepan manufacturing process, as robotic systems and automated machinery ensure precise production and greater efficiency. From blanking presses and deep drawing machines to robotic welding arms, technology minimizes human error, improves consistency, and speeds up the production process. Advanced machine learning and data analytics are also being integrated into production lines to optimize workflows, predict maintenance needs, and monitor quality control, further enhancing the efficiency of the manufacturing process.
Sustainability is a growing focus in cookware production, and many manufacturers are adopting green manufacturing practices. Recycled metals, particularly stainless steel, are increasingly being used in saucepan production, reducing the need for mining new materials and lowering the environmental impact of manufacturing. Additionally, energy-efficient production methods, such as using solar power or optimizing factory heating systems, help reduce the carbon footprint of the manufacturing process. The use of eco-friendly coatings and finishes, such as those that are free from toxic chemicals, is also gaining popularity as part of the effort to minimize the environmental impact of cookware.
As the cookware industry continues to innovate, the trend toward smart kitchen tools is influencing saucepan design. The integration of sensors and smart technology into cookware is becoming more common. For example, temperature sensors may be embedded into the saucepan to allow users to monitor the cooking temperature in real-time, or smart handles could alert the user when the pan has reached a specific heat threshold. These innovations are part of the larger movement toward connected kitchens, where kitchen appliances and tools communicate with each other to improve cooking efficiency.
Overall, the process of manufacturing sheet metal saucepans involves a combination of traditional techniques, such as stamping and welding, alongside advanced automation and innovative technologies. As consumer demand for high-quality, durable, and eco-friendly cookware grows, manufacturers are continually refining their production methods, integrating new materials and designs, and adopting sustainable practices to remain competitive in the global market.
As manufacturers continue to refine their methods for producing sheet metal saucepans, a focus on consumer needs is leading to further customization options. The market now demands more than just functional cookware — there is also an emphasis on aesthetic appeal and personalization. As such, manufacturers are experimenting with a variety of finishes and designs, offering consumers more choices in terms of color, texture, and style. For instance, some manufacturers are offering saucepans with matte finishes or colored coatings that provide both visual appeal and added durability. Others are looking into engraving techniques, allowing for custom designs or logos to be added to the cookware, appealing to those looking for personalized or premium kitchen items.
In addition to customization, the trend toward multi-functional cookware is becoming more pronounced. Consumers are increasingly looking for products that can serve more than one purpose. For example, a saucepan with a detachable handle could be used as both a stovetop cooking tool and an oven-safe dish. Similarly, stackable saucepans or nesting designs are becoming more popular in response to limited kitchen storage space. These innovations are pushing manufacturers to adapt their designs to meet the evolving needs of modern consumers.
Another trend driving changes in saucepan manufacturing is the rise of health-conscious cooking. With more people focusing on preparing healthier meals at home, there is growing demand for cookware that supports low-fat, low-oil cooking methods. Non-stick coatings are now designed to be more durable, enabling users to cook without relying on excessive oils, fats, or butter. Additionally, there is an increasing focus on the use of non-toxic materials in cookware production. Brands are responding by offering PFOA-free and PTFE-free options, using safer materials that provide peace of mind to consumers who are concerned about chemicals leaching into their food.
The shift toward smart cooking technology is also influencing saucepan manufacturing. The integration of sensors or smart technology into cookware is an area of growing interest. For example, some manufacturers are exploring temperature-sensing technologies that would allow a saucepan to communicate with other smart kitchen devices, ensuring precise temperature control. This could help prevent overheating or burning, which is a common challenge when cooking delicate dishes. Smart saucepans might even alert users when it’s time to stir, or when the food has reached the desired temperature, improving overall cooking precision.
Additionally, advanced materials are being incorporated into the saucepan manufacturing process. Beyond traditional metals like stainless steel and aluminum, there are experiments with composite materials that combine metals with ceramics or other compounds to enhance heat distribution and retention. These materials can also reduce the overall weight of the saucepan, which appeals to consumers looking for cookware that is both durable and lightweight. The use of induction-compatible materials is another trend, as more homes switch to induction cooktops, which require cookware with specific magnetic properties. Manufacturers are now ensuring that their saucepans are suitable for induction cooking, providing versatility for consumers who may switch between different types of stoves.
Looking toward the future, robotics and artificial intelligence (AI) are likely to play an even bigger role in saucepan manufacturing. From robotic arms that assemble the components to AI systems that monitor production quality in real time, the use of smart technology in factories will help ensure that saucepans are made to the highest standards while reducing human error and improving efficiency. AI could also help optimize the supply chain, predicting demand patterns and ensuring that materials are sourced in a timely manner to avoid shortages or delays in production.
In conclusion, the sheet metal saucepan manufacturing process is evolving rapidly, influenced by consumer demands for higher quality, sustainability, and innovative features. Manufacturers are adopting advanced technologies and materials, embracing automation, and focusing on consumer-centric designs to create cookware that not only meets functional needs but also appeals to modern lifestyle choices. Whether through eco-friendly practices, customizable options, or smart features, the saucepan of the future will continue to push the boundaries of design and manufacturing technology.
Sheet Metal Steamer Basket Manufacturing Machine
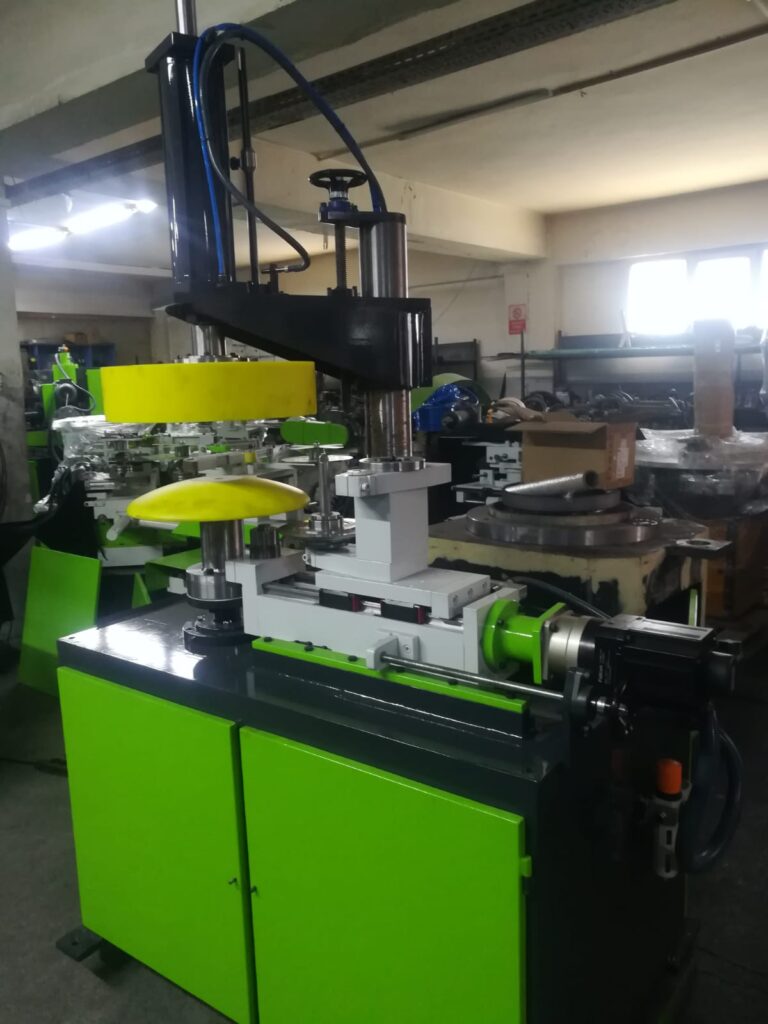
The sheet metal steamer basket manufacturing machine is designed to produce steamer baskets, which are essential kitchen tools used to cook food using steam. These baskets are typically made of stainless steel or aluminum for their strength, corrosion resistance, and ability to withstand high temperatures. The process of manufacturing a steamer basket from sheet metal involves several key stages, each requiring specialized equipment to ensure precision and quality.
The process begins with raw sheet metal, typically purchased in rolls of stainless steel or aluminum. These metal sheets are unrolled and flattened using a decoiling machine. The metal is then cut into the required shape using a blanking press or laser cutter, depending on the complexity of the design. In some cases, laser cutting is preferred for more intricate patterns, especially those found in the perforated body of the steamer basket.
Next, the flat metal sheets are shaped into the circular form of the basket. This step is typically performed using a deep drawing press. The process involves pressing the flat metal sheet into a mold to form the side walls and bottom of the steamer basket. The result is a cylindrical shape that provides the necessary surface area for steam to pass through while holding the food inside. The deep drawing press also ensures that the metal is evenly distributed and that the steamer basket walls are uniform in thickness.
Once the shape is formed, the next stage involves perforating the steamer basket. This is done using punching or stamping machines, which create the small holes or slits in the metal that allow steam to pass through. The perforations need to be evenly spaced and of a size that ensures the steamer basket is efficient at transferring steam while also holding the food securely. Depending on the design, the perforations can be made in a variety of patterns, including round, oval, or diamond-shaped holes.
After perforating, the steamer basket undergoes trimming to ensure that the edges are smooth and free from any sharp or uneven areas. A trimming press or laser cutting machine is used to clean up the edges of the steamer basket, ensuring that the final product is safe to handle. The edges are usually bent over slightly to create a smooth, rounded finish, preventing injury or discomfort for users when handling the basket.
The next step is the attachment of the handles. Steamer baskets typically feature handles on either side for easy lifting and maneuvering. These handles are usually made of stainless steel or other heat-resistant materials, and they are either welded or riveted onto the sides of the basket. In some cases, the handles are formed through casting or stamping, while welding is the most common method of attachment due to its durability and strength. The handles are designed to be ergonomic and heat-resistant to ensure safety during use.
Once the basket and handles are fully assembled, the steamer basket undergoes a series of finishing processes. These processes include polishing and buffing to ensure the steamer basket has a smooth, shiny finish. Electropolishing is sometimes used, especially for high-end models, to improve the surface finish and corrosion resistance. Additionally, some steamer baskets are treated with a protective coating or are subjected to anodizing (in the case of aluminum), which enhances durability and resistance to wear and tear.
To ensure that the steamer baskets are of high quality and free from defects, quality control inspections are performed at various stages of the manufacturing process. These inspections include checks for perforation accuracy, handle attachment strength, edge smoothness, and overall appearance. Automated vision systems are increasingly being used for these inspections, as they can quickly detect defects such as uneven perforations or poorly welded handles.
Once the steamer baskets pass quality control, they are thoroughly cleaned to remove any dust, oils, or residues from the manufacturing process. After cleaning, the baskets are packaged for shipment. The packaging is designed to protect the steamer baskets during transit and to provide an appealing presentation for consumers. Many manufacturers are now opting for eco-friendly packaging, using recycled materials to meet growing consumer demand for sustainability.
The automation of the manufacturing process plays a crucial role in increasing the efficiency and consistency of steamer basket production. From automated punching and perforating systems to robotic arms that handle the welding of handles, automation reduces labor costs, increases production speeds, and ensures that each steamer basket meets the highest quality standards.
Additionally, advancements in material science are playing an increasingly important role in the development of steamer baskets. For example, the use of composite materials in steamer basket manufacturing is on the rise. These materials combine metals with ceramics or other compounds to enhance heat distribution, reduce weight, and improve durability. The integration of induction-compatible materials is also becoming more common, as many modern kitchens use induction cooktops that require specific cookware properties for optimal performance.
As steamer baskets are used for cooking food by steaming, which is often seen as a healthier cooking method, the focus on safe materials and eco-friendly production practices is particularly strong. Manufacturers are increasingly emphasizing the use of non-toxic coatings and ensuring that their products do not contain harmful chemicals, such as PFOA or PFAS. This is especially important as consumers become more health-conscious and seek cookware that aligns with their wellness and environmental values.
Finally, the continued advancement of smart kitchen technology may also influence the design of steamer baskets in the future. With the growing trend of smart kitchens, there could be opportunities to integrate sensors into steamer baskets that could communicate with other kitchen appliances. For instance, a smart steamer basket might alert users when the water level is low, or it could sync with a smart oven or stove to optimize cooking time and temperature.
In summary, the manufacturing of sheet metal steamer baskets involves a complex series of steps, from cutting and shaping the metal to attaching handles, perforating the basket, and applying finishing touches. Advanced technologies like automation, precision cutting, and smart technology integration are making the process more efficient and allowing for higher-quality, more innovative products. As the demand for health-conscious cooking continues to rise, steamer baskets are likely to see further advancements in design, materials, and functionality, making them an even more essential tool in the modern kitchen.
The continued evolution of sheet metal steamer basket manufacturing is shaped by both technological advancements and changing consumer preferences. As sustainability and eco-consciousness continue to gain importance in the marketplace, manufacturers are focusing on reducing their environmental footprint throughout the production process. One of the most significant areas of focus is the sourcing and use of recycled materials. Many steamer baskets are now being made from recycled stainless steel or aluminum, which not only reduces the demand for raw materials but also lowers the overall energy consumption involved in manufacturing. This trend aligns with the broader shift in the cookware industry towards more sustainable practices, responding to consumer demands for products that are both durable and environmentally responsible.
In addition to using recycled materials, energy-efficient production techniques are also being prioritized. Manufacturers are investing in more energy-efficient furnaces, presses, and machinery, which can significantly lower energy consumption during the shaping, cutting, and finishing processes. The use of solar energy in factories and the adoption of green building technologies are part of a larger trend toward making cookware manufacturing more eco-friendly. These measures not only benefit the environment but also reduce operational costs in the long run, making the manufacturing process more cost-effective.
Another trend in steamer basket manufacturing is the growing interest in multifunctional cookware. Consumers are looking for kitchen tools that serve more than one purpose. In this context, steamer baskets are being redesigned to work in conjunction with other cooking devices, such as pressure cookers, slow cookers, or even microwave ovens. Some steamer baskets now feature adjustable or removable tiers, allowing them to accommodate different food items in one go, making them more versatile. This adaptability appeals to busy consumers who appreciate cookware that saves time and space, particularly in smaller kitchens.
Manufacturers are also integrating modular designs into steamer baskets. These baskets can be customized by adding or removing components, such as extra steamer tiers or trays that allow users to steam multiple types of food at once. These designs not only increase the functionality of the product but also cater to the growing trend of personalized or customizable kitchenware, which allows consumers to tailor their cookware to their unique needs.
As consumer demand for health-conscious cooking tools rises, steamer baskets made from non-toxic materials continue to be in high demand. As mentioned earlier, the focus is on ensuring that the materials used in manufacturing steamer baskets are free from harmful chemicals such as PFOA, PFAS, or lead. There is also an increasing demand for natural materials, such as bamboo or ceramic-coated steel, which offer an alternative to traditional metals. These materials are often marketed as being more natural, safer, and free from synthetic coatings, giving health-conscious consumers peace of mind when using their cookware.
Manufacturers are also exploring innovative surface coatings that are both functional and aesthetic. Ceramic coatings have become a popular choice due to their ability to provide a non-stick surface without the use of chemicals like PTFE. These coatings offer the benefits of easy cleaning, a natural cooking surface, and a reduced risk of harmful chemicals leaching into food. Hard anodized aluminum is another material growing in popularity due to its durability, heat distribution properties, and resistance to corrosion. These coatings and materials ensure that steamer baskets are not only effective but also safe and long-lasting.
Technological innovations in smart kitchen appliances are also influencing steamer basket design. Some manufacturers are exploring ways to incorporate sensors into steamer baskets to make cooking even more efficient. For example, temperature or moisture sensors could be embedded into the basket to ensure that the correct cooking conditions are maintained throughout the steaming process. These smart features could communicate with other kitchen appliances, like a smart stove, oven, or multifunctional pressure cooker, to optimize cooking times and temperatures based on real-time data. Additionally, mobile apps may soon be able to sync with cookware to give users real-time feedback on their cooking, creating a more connected and interactive kitchen experience.
The integration of robotics into steamer basket manufacturing is also transforming the industry. Robots equipped with vision systems can now assist in the inspection and packaging process, improving product quality and consistency. These robots can quickly identify defects in the perforations, edges, or handles, ensuring that only perfectly manufactured baskets move forward in the production process. Automated assembly lines that handle repetitive tasks such as handle attachment, perforation, and polishing have significantly increased the speed and efficiency of manufacturing, making it possible to meet the growing demand for high-quality steamer baskets.
In terms of consumer education, brands are increasingly focusing on demonstrating the health benefits of steaming food. Manufacturers are using social media, influencers, and online content to educate customers about the benefits of using a steamer basket for cooking, such as retaining more nutrients, reducing the need for added fats, and creating healthier meals overall. This marketing approach, combined with a growing interest in plant-based diets and clean eating, is boosting the popularity of steamer baskets, which are often associated with health-conscious cooking.
With the increasing competition in the global cookware market, manufacturers are also exploring ways to differentiate their products. Some companies are introducing premium models that feature innovative designs or exclusive materials, such as copper-steel hybrids or handcrafted steel baskets. These premium offerings are typically marketed toward high-end consumers who are looking for unique and long-lasting cookware, often coupled with lifetime warranties or specialized care instructions to ensure product longevity.
In summary, the manufacturing process for sheet metal steamer baskets continues to evolve as technology, sustainability, and consumer demand shape the cookware industry. From recycled materials and energy-efficient production techniques to multifunctional designs and smart technology integration, the future of steamer basket manufacturing looks poised for even more innovation. As manufacturers continue to respond to the needs of health-conscious and eco-aware consumers, we can expect the steamer basket to become an increasingly essential tool in the modern kitchen, offering a blend of functionality, design, and sustainability that meets the demands of today’s consumer.
As the manufacturing of sheet metal steamer baskets continues to evolve, there are several emerging trends and innovations that promise to shape the future of cookware production. These trends are driven by advancements in materials science, consumer preferences, and the broader movement toward sustainability in the kitchenware industry. Let’s explore these factors further:
Advanced Materials and Composites
The development of new materials is one of the most exciting aspects of steamer basket manufacturing. While stainless steel and aluminum remain the dominant materials used, manufacturers are increasingly experimenting with composite materials that combine the best properties of different materials to create products that are not only more durable but also lighter and more heat-efficient.
For instance, titanium-coated stainless steel is gaining popularity due to its lightweight yet strong nature, as well as its resistance to corrosion. These materials are becoming more common in premium products, as consumers seek cookware that can withstand years of use while maintaining an attractive appearance. Additionally, ceramic-infused metals or nano-coatings are being explored to offer a non-stick surface without relying on synthetic chemicals.
Copper-core steamer baskets are another example of material innovation. Copper is known for its excellent heat conductivity, and combining it with stainless steel creates a highly efficient cooking vessel that heats up quickly and evenly. These premium steamer baskets are typically more expensive, but they appeal to discerning chefs and home cooks who value top-tier performance.
Health-Conscious Features
As more consumers adopt healthier lifestyles, the demand for cookware that supports these habits continues to grow. Steamer baskets, being central to the steaming process—which is known for preserving nutrients better than other cooking methods—are in high demand. Manufacturers are responding by focusing on non-toxic materials and natural finishes that meet strict health and safety standards.
In response to this trend, there’s been a push for steamer baskets to be free from potentially harmful chemicals like PFOA, PFAS, and other substances that are commonly found in traditional non-stick coatings. Instead, companies are turning to ceramic coatings that are completely free of these chemicals, offering a non-toxic, safe cooking surface.
Bamboo-steamer baskets, though not metal, are an increasingly popular choice due to their natural properties and the perception of being a healthier alternative to synthetic materials. Though less durable than metal baskets, they are valued for their eco-friendly appeal and their ability to steam food effectively. Some manufacturers are even combining metal and bamboo to create hybrid products that combine the benefits of both materials, creating a steamer basket that is both natural and durable.
Smart Cookware Integration
The growing trend of smart kitchens is beginning to make its way into cookware, and steamer baskets are no exception. As home kitchens become more connected, cookware with built-in sensor technology is becoming increasingly common. For example, manufacturers are exploring ways to embed temperature sensors or moisture sensors within steamer baskets, providing real-time feedback to users through a smartphone app or directly to the kitchen’s smart appliances.
These smart features could help users achieve more consistent steaming results by automatically adjusting cooking times, temperatures, or even moisture levels based on the food being cooked. For instance, a smart steamer basket could work in conjunction with an app to alert the cook when food is perfectly steamed, or adjust the cooking parameters if the food is not steaming evenly.
In addition to improving cooking precision, the integration of sensors could also offer safety features. A sensor could alert the user if the water level in the steamer has dropped too low, preventing the steamer basket from burning or overheating. Such features could make the steaming process more foolproof, especially for novice cooks.
Customization and Personalization
Consumers are increasingly interested in customization and personalization in their cookware. In the case of steamer baskets, manufacturers are exploring ways to offer more options for personalization. This might include the ability to choose from a variety of handle designs, colors, or even decorative elements like embossed patterns or monogramming.
For example, some high-end cookware brands now offer bespoke or limited-edition steamer baskets, where customers can select materials, finishes, and even add personalized engravings. This trend aligns with a broader shift toward personalized kitchenware that allows consumers to express their style while also investing in high-quality, functional products.
Modular designs are also gaining popularity, allowing customers to create a customized steamer basket system. Some steamer baskets are now designed with stackable tiers or removable components, allowing users to add or remove layers depending on the food they are preparing. These modular baskets can be easily adapted for different cooking tasks, offering maximum versatility in the kitchen.
Eco-Friendly Manufacturing Practices
Sustainability has become a key concern for both consumers and manufacturers alike, with the cookware industry striving to reduce its environmental impact. As a result, manufacturers of steamer baskets are focusing on reducing waste and adopting eco-friendly production processes.
One key area of improvement is in packaging. Many companies are transitioning to using recycled materials for packaging or opting for minimalistic packaging that reduces waste. For example, some brands have eliminated plastic packaging altogether, instead using biodegradable or recycled cardboard to package their steamer baskets. Others are offering bulk packaging for customers who wish to purchase multiple baskets, further reducing packaging waste.
Manufacturers are also investing in sustainable materials that minimize the environmental impact of their products. For instance, instead of using new metals, some companies are utilizing recycled stainless steel or aluminum in their production process. This reduces the need for mining raw materials, conserves energy, and helps reduce overall emissions.
Global Trends and Expanding Markets
As demand for high-quality, sustainable cookware increases worldwide, manufacturers are increasingly looking to global markets. Asian markets, particularly in countries like China, Japan, and India, present significant opportunities for the growth of steamer basket sales, as steaming is a traditional cooking method in these regions. Additionally, the growing interest in plant-based diets and clean eating in Western markets is contributing to the popularity of steamer baskets in countries like the United States and Europe.
To cater to these global markets, manufacturers are adjusting their products to meet local needs. For example, steamer baskets made from bamboo or wicker may be more popular in Asian markets, while stainless steel or ceramic-coated baskets are gaining traction in Europe and North America due to their durability and modern aesthetics. Additionally, manufacturers may also adapt the size, shape, or capacity of the baskets to align with local cooking practices.
Looking to the Future: 3D Printing and Automation
As automation and additive manufacturing (3D printing) technologies advance, steamer basket production may see revolutionary changes. The use of 3D printing to produce complex, customized designs could allow for the creation of steamer baskets with more intricate perforation patterns or unique shapes that would be difficult to achieve with traditional manufacturing methods. This could open up new possibilities for both functional and decorative designs, allowing consumers to personalize their cookware even further.
Automation in factories will also continue to increase, allowing manufacturers to produce large volumes of steamer baskets at a lower cost while maintaining high levels of precision. The combination of robotics, AI-driven quality control, and automated assembly lines will lead to faster production speeds and reduced labor costs, further enhancing the competitiveness of steamer basket manufacturers in the global market.
In conclusion, the future of sheet metal steamer basket manufacturing looks bright, with a growing focus on sustainability, health-conscious features, and smart technology. As the cookware industry adapts to consumer preferences and advances in manufacturing technologies, steamer baskets will continue to evolve, offering more customization options, improved functionality, and environmentally friendly solutions. Whether through the use of innovative materials, integration with smart kitchen devices, or the adoption of green production practices, the future of steamer baskets will undoubtedly provide a mix of tradition, innovation, and personalization for both home cooks and professional chefs alike.
Sheet Metal Baking Pan Manufacturing Machine
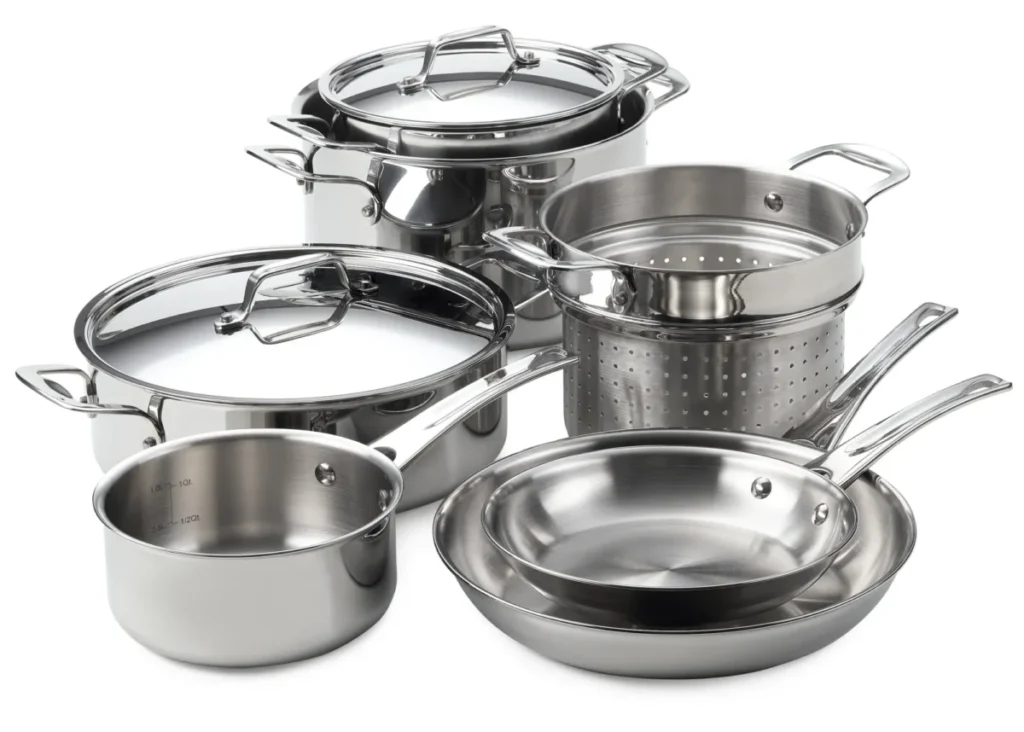
The sheet metal baking pan manufacturing machine is used to produce baking pans that are commonly made of materials such as stainless steel, aluminum, or other metals. These baking pans are essential kitchen tools used for baking cakes, breads, cookies, and other baked goods. The manufacturing process involves several key stages, each requiring specialized equipment to ensure precision, durability, and high-quality finished products.
1. Raw Material Preparation
The manufacturing process begins with raw sheet metal typically purchased in rolls or sheets. The most common materials used for baking pans are stainless steel, aluminum, and sometimes carbon steel due to their durability, heat conductivity, and non-reactivity with food. The raw material is unrolled, flattened, and prepared for further processing using decoiling machines or shearing machines. These machines cut the metal sheets into the required dimensions, based on the size and shape of the baking pan to be produced.
2. Cutting and Shaping
Once the metal sheets are cut to size, the next step is shaping the pan’s walls. This is typically done through die cutting or laser cutting, depending on the complexity of the design. The process usually involves the use of press brakes, punching machines, or laser cutters that cut and shape the metal to form the sides, base, and rims of the pan.
For pans with specific shapes or designs (such as rectangular, square, round, or more intricate patterns), dies are created to shape the metal precisely. In some cases, custom molds are used, especially for specialized designs such as cupcake pans or muffin tins.
3. Deep Drawing
In the case of some baking pans, the metal is subjected to a process called deep drawing. This process involves using a press to press the metal sheet into a mold to form a container-like shape, such as a cake pan or loaf pan. The deep drawing press applies pressure to the metal, stretching it into the desired shape. This ensures uniform thickness throughout the pan and prevents any weak spots in the walls or base.
Deep drawing is particularly useful for creating pans with deep sides, such as for baking bread or cakes. It also helps in maintaining consistent dimensions across large production runs, ensuring that all the pans are uniform in size and shape.
4. Edge Forming and Trimming
After the basic shape is formed, the edges of the baking pan are typically trimmed to remove any excess metal, which can be sharp or irregular. The trimming process uses a trimming press or laser cutter to clean up the edges. This is a critical step in the production process, as it ensures that the pans have smooth, safe edges for handling.
In addition to trimming, the edges of the baking pan are often folded or bent slightly to create a more durable and smoother finish. The folding process involves using machines that press and shape the metal to form a rounded or flat lip around the edge, which can improve the pan’s strength and make it easier to handle without damaging the contents.
5. Perforating (if applicable)
Certain types of baking pans, such as cookie sheets or baking trays, may require perforations to allow air circulation during the baking process. These perforations are usually made by punching machines that create a pattern of small holes throughout the base of the pan. The purpose of perforations is to enhance heat distribution and allow for more even cooking by facilitating better airflow.
The perforating process also helps reduce the weight of the pan, making it easier to handle while still maintaining the necessary strength for baking.
6. Handle and Special Features
For certain baking pans, such as lasagna pans, roasting pans, or braising pans, handles may need to be added. These handles are typically made from stainless steel or aluminum and can be attached using welding, riveting, or screws, depending on the design and the manufacturer’s preference.
Handles need to be securely attached to the pan to ensure that they can withstand the weight of the pan when filled with hot food. Ergonomic handles are also a common feature, especially for larger or heavier pans, to make lifting and moving the pan easier and safer.
Some advanced models of baking pans may also feature non-stick coatings, which can be applied during this stage or in later stages of production. PTFE (polytetrafluoroethylene) or ceramic coatings are typically used to provide a non-stick surface, making it easier to remove baked goods from the pan and clean the pan after use.
7. Surface Finishing
Once the pan has been shaped, trimmed, and perforated, it goes through a series of finishing processes to improve its appearance and performance. The surface of the pan is often polished using abrasive wheels or brushes to remove any burrs or rough areas from the surface. This also enhances the visual appeal of the baking pan by providing a shiny, smooth finish.
In some cases, electropolishing is used, especially for stainless steel pans, to achieve an even smoother surface. This process removes microscopic imperfections and improves the overall corrosion resistance of the metal. Electropolishing also provides a sleek and shiny finish that is highly resistant to staining or tarnishing, ensuring that the baking pan maintains its attractive appearance over time.
If the baking pan has a non-stick coating, this is typically applied after the surface has been polished and cleaned. The coating process can vary depending on the material, but it usually involves dipping the pan into a non-stick solution or applying a powder coating, which is then cured in an oven.
8. Quality Control and Inspection
Throughout the manufacturing process, quality control inspections are performed at various stages. This ensures that the pans meet the required dimensions, strength, and performance standards. Key aspects of inspection include checking for uniformity in size and shape, confirming that the edges are smooth and safe, testing the durability of the non-stick coating, and ensuring that perforations (if applicable) are properly placed and sized.
Automated vision systems or manual inspection are commonly used for this purpose. Any pans that do not meet the necessary standards are removed from the production line for rework or disposal. This step ensures that only high-quality baking pans reach the market.
9. Packaging and Shipping
Once the baking pans have passed quality control, they are thoroughly cleaned to remove any dust, oil, or residue from the manufacturing process. After cleaning, the pans are carefully packaged for shipment. The packaging is designed to protect the pans from damage during transit, often using corrugated cardboard, foam inserts, or bubble wrap.
For retail sales, the packaging may also include branding, care instructions, or product specifications to help consumers understand how to use and maintain the pans. Many manufacturers also use eco-friendly packaging made from recycled materials in response to growing consumer demand for sustainable products.
10. Automation in Baking Pan Manufacturing
The baking pan manufacturing process is increasingly automated to improve efficiency and reduce production costs. Robotic arms and automated guided vehicles (AGVs) are used to move materials and finished products throughout the factory. In addition, computer-controlled machines that handle cutting, trimming, shaping, and coating can operate with high precision and at faster speeds than traditional methods.
Automated systems can also help to improve consistency in the final products, ensuring that each baking pan is made to the same specifications and quality standards. Additionally, automation allows manufacturers to scale up production to meet growing demand while maintaining a high level of quality control.
Conclusion
The manufacturing of sheet metal baking pans is a highly technical process that involves cutting, shaping, and finishing metal sheets into functional and durable kitchen products. The steps include raw material preparation, deep drawing, edge forming, perforating (if applicable), surface finishing, and packaging. Automation, smart technology, and sustainability are also transforming the industry, leading to faster production, improved quality, and more eco-friendly manufacturing practices. As consumer preferences continue to evolve, baking pan manufacturers will continue to innovate with materials, designs, and coatings to meet the needs of modern home bakers and professional chefs alike.
The sheet metal baking pan manufacturing process involves a series of steps designed to transform raw metal into high-quality, durable pans suitable for baking. It starts with raw sheet metal, typically stainless steel or aluminum, which is unrolled and cut into the desired size using decoiling and shearing machines. These sheets are then shaped using methods like die cutting or laser cutting, depending on the complexity of the design. For certain types of pans, such as cake or loaf pans, deep drawing is used to press the metal into molds, ensuring that the sides are even and the thickness is consistent. After shaping, the edges are trimmed and folded to create smooth, durable edges that are safe for handling. In some cases, perforations are made in the pan to allow for better airflow, especially in baking trays or cookie sheets.
Handles are sometimes added to the pans, either through welding or riveting, providing easier handling, particularly for larger pans. Non-stick coatings may be applied at this stage to improve the usability of the pans and make cleaning easier, with materials like PTFE or ceramic coatings being commonly used. Once the pans are fully shaped, coated, and finished, they undergo a rigorous quality control process. This ensures that each pan meets the required standards for size, durability, and performance. Inspections look for any imperfections, from uneven edges to coating flaws, to ensure only high-quality products are sent to market.
After passing inspection, the pans are cleaned thoroughly and then packaged for shipment. Packaging is designed to protect the pans during transit and is often done using eco-friendly materials to align with sustainability efforts. In modern manufacturing, automation plays a significant role in increasing efficiency. Robotics and automated systems handle everything from moving materials to performing quality control checks, allowing for faster production with consistent results. As demand for high-quality and sustainable products grows, baking pan manufacturers continue to innovate with new materials, designs, and coatings, all while adhering to eco-friendly practices to reduce their environmental impact. This ensures that the pans not only meet the needs of modern bakers but also support a more sustainable future in cookware manufacturing.
As the baking pan manufacturing industry continues to evolve, several trends are emerging that are shaping the way these products are designed and produced. One significant trend is the increasing demand for sustainable materials. Consumers are becoming more conscious of the environmental impact of their purchases, and cookware manufacturers are responding by incorporating recycled metals and using more eco-friendly coatings. For example, many manufacturers are transitioning to recycled stainless steel or aluminum, reducing the need for virgin materials and lowering the carbon footprint associated with production. Additionally, the use of eco-friendly packaging materials, such as biodegradable or recyclable cardboard, is gaining traction to minimize waste and improve sustainability.
Another trend in the baking pan manufacturing process is the incorporation of non-toxic, non-stick coatings that are safer for both health and the environment. Traditional non-stick coatings often contain harmful chemicals like PFOA or PTFE, but consumers are increasingly seeking alternatives made from natural materials such as ceramic coatings or silicone that do not release toxic fumes or chemicals during cooking. These alternatives are gaining popularity, especially in premium products, as they provide a healthier option without compromising the convenience and performance of non-stick surfaces.
Manufacturers are also exploring smart cookware options, integrating technology into baking pans to enhance user experience. Smart baking pans could feature built-in sensors that communicate with a smartphone or kitchen appliance, providing real-time feedback on the pan’s temperature, the doneness of baked goods, or even alerting the user when baking is complete. These innovations help take the guesswork out of baking, ensuring that results are consistent every time. This trend towards connected cookware is becoming a part of the larger movement toward smart kitchens, where appliances and tools work together seamlessly to improve cooking efficiency and accuracy.
Customization is another growing trend in the baking pan industry. As consumers seek products that reflect their personal tastes, manufacturers are offering more options for customized designs. Consumers can choose from various shapes, sizes, colors, and even personalized engravings, turning baking pans into unique items that can complement their kitchen décor or make thoughtful gifts. Modular designs are also becoming more popular, where baking pans are designed to be stackable or adjustable, allowing users to adapt their pans to different cooking needs. These modular pans often feature removable inserts or interchangeable parts, making them versatile and easy to store.
Additionally, the demand for more durable, long-lasting products continues to grow. Many modern consumers are looking for high-quality cookware that can withstand frequent use and last for many years. Manufacturers are addressing this demand by improving the strength and resilience of baking pans. For example, hard-anodized aluminum or cast iron is being used for certain high-performance pans because of their superior heat conductivity and long-term durability. Similarly, the use of reinforced coatings or thicker metal gauges helps to prevent warping or bending, ensuring that the pans maintain their shape even under high temperatures.
The baking pan market is also influenced by the globalization of culinary trends. With baking becoming more popular across various cultures and regions, manufacturers are adapting their products to meet the needs of diverse markets. For example, in Asia, where steam cooking is popular, steamer trays and bamboo-lined pans are becoming more common, while in Europe and North America, multi-functional pans that can be used for baking, roasting, and even grilling are gaining popularity. This globalization has led to the development of pan designs that cater to different cooking techniques, allowing manufacturers to offer a broader range of products for international markets.
In conclusion, the sheet metal baking pan manufacturing industry is undergoing significant transformations driven by consumer demand for sustainability, health-conscious features, smart technology, and customization. As manufacturers continue to innovate, they are exploring new materials, coatings, and production methods to meet these changing demands. Whether through the use of advanced non-stick coatings, eco-friendly packaging, or integrating smart technology, the baking pan industry is evolving to create products that are not only more functional and versatile but also more aligned with the values of modern consumers. As these trends continue to shape the market, baking pan manufacturers will find new ways to improve performance, meet consumer preferences, and stay competitive in an increasingly dynamic marketplace.
Sheet Metal Pizza Pan Manufacturing Machine
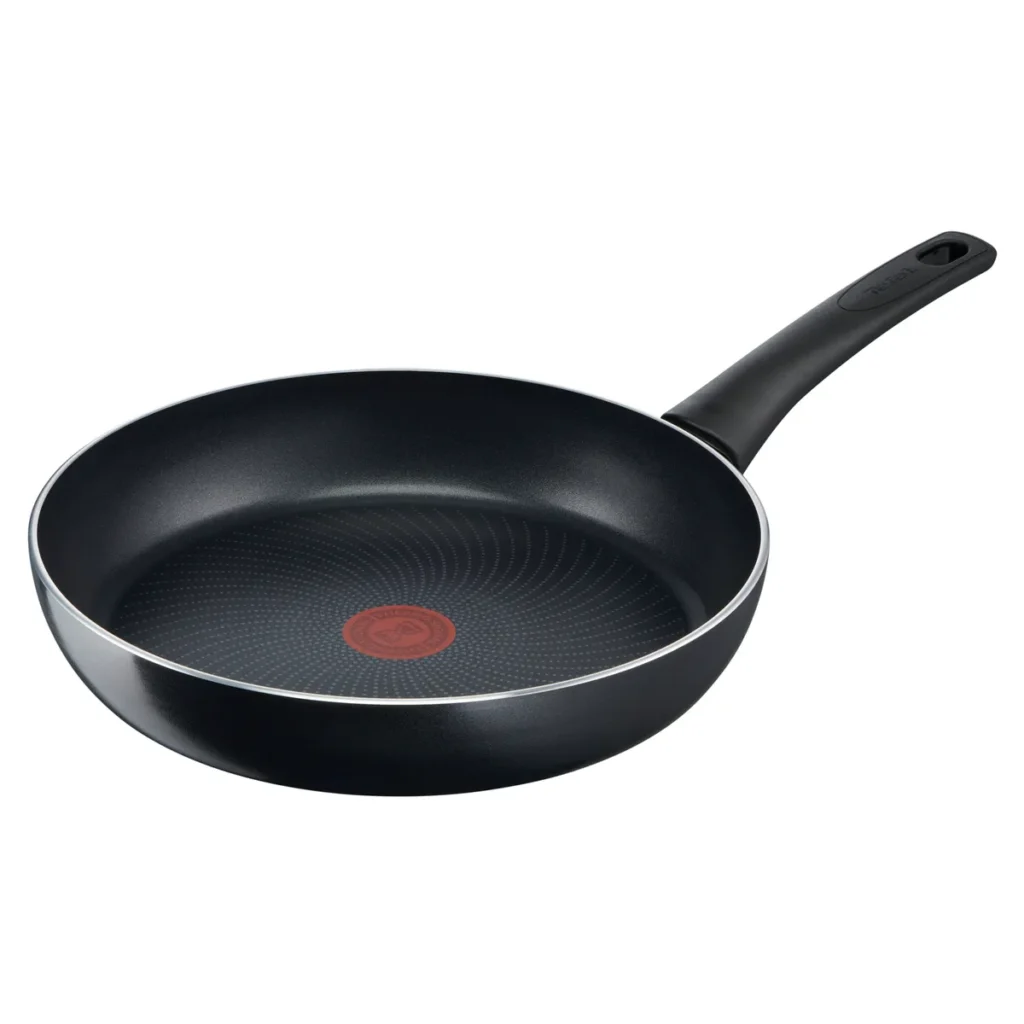
The sheet metal pizza pan manufacturing machine is designed to produce high-quality pizza pans from sheet metal, typically aluminum or stainless steel. These pans are essential for baking pizzas in both home kitchens and commercial settings, where durability and heat conductivity are important. The manufacturing process involves several steps that include shaping, trimming, coating, and finishing to ensure that the final product meets industry standards for performance and safety. Here’s an overview of the process:
1. Material Selection and Preparation
The manufacturing process begins with the selection of high-quality sheet metal, often in the form of large rolls or sheets. The most commonly used materials for pizza pans are aluminum due to its excellent heat conductivity and stainless steel for its durability and corrosion resistance. The sheets are inspected for quality and prepared for further processing by uncoiling, straightening, and cutting them to the required dimensions. Machines like decoilers, shearing machines, or slitting machines are typically used for this step.
2. Cutting and Shaping
Once the metal sheets are prepared, they are cut into round shapes to form the base of the pizza pan. The cutting process typically involves punching or laser cutting using specialized dies and machines. Die-cutting presses are often employed to create a round blank, with the size of the blank determining the size of the pizza pan. For standard pizza pans, the diameter can range from small personal pans to large commercial sizes.
In some cases, water jet cutting or laser cutting may be used for more intricate designs, particularly for pans that have specific edge profiles or perforations for improved airflow. The cutting process ensures that the metal sheets are accurately shaped before moving on to the next stages.
3. Edge Forming and Trimming
After the base of the pizza pan is cut, the edges are then formed and trimmed to create a smooth, consistent finish. Edge forming typically involves folding or beading the edges of the pan to create a sturdy, non-sharp lip that is easy to handle. This can be done using a rolling machine or press brake that bends the edge of the metal sheet around a mold or die. In some cases, the edges may also be reinforced to enhance the pan’s durability and prevent any warping during the baking process.
The trimming process involves removing excess material from around the edges to ensure a clean, precise final shape. This is typically done with a trimming press or laser cutting, ensuring that the pan’s dimensions are correct and the edges are smooth.
4. Perforation (Optional)
Some pizza pans feature perforations (small holes punched in the base) to allow better air circulation during the baking process. These perforations ensure that the heat is evenly distributed throughout the pizza, resulting in a crispier crust. Perforating machines are used to create a pattern of holes in the base of the pizza pan. This step is optional and is generally used for thin crust pizzas or commercial-grade pans.
The perforation process ensures that the air can flow evenly under the pizza, which prevents moisture buildup and helps the crust cook evenly. The size and pattern of the perforations depend on the type of pizza the pan is designed for.
5. Surface Coating
To improve the non-stick properties of the pizza pan and make it easier to clean, non-stick coatings are often applied to the surface of the pan. This can be done using PTFE (Teflon) coatings or ceramic coatings, both of which provide a smooth, non-reactive surface. Non-stick coatings prevent dough from sticking to the pan and allow for easier removal of the pizza once it is baked.
For commercial-grade pizza pans, the coating may be applied using spraying systems or dipping processes. The pans are then subjected to baking or curing in high-temperature ovens to set the coating and ensure it adheres properly. In some cases, anodizing (for aluminum pans) is used to increase the surface hardness and resistance to corrosion, creating a more durable and long-lasting product.
6. Heat Treatment (for Stainless Steel)
If the pizza pan is made from stainless steel, it may go through a heat treatment process to improve its strength and durability. Heat treatment involves heating the stainless steel to a specific temperature and then cooling it rapidly, a process known as quenching, which strengthens the metal. This step ensures that the pan maintains its shape and structural integrity during high-heat baking.
For aluminum pans, heat treatment is not always necessary, as aluminum naturally has good thermal conductivity and resistance to warping. However, some manufacturers may choose to hard anodize aluminum for additional durability.
7. Quality Control and Inspection
After the pans are formed, coated, and treated, they undergo a thorough quality control inspection. This inspection ensures that the pizza pans meet the required standards for size, shape, and functionality. Key factors checked during quality control include edge smoothness, non-stick coating uniformity, dimensions, strength (to ensure the pans do not warp or bend), and overall surface quality.
Some manufacturers use vision systems to automate inspection, while others rely on manual inspection by quality control specialists. Any pans that do not meet the required standards are removed from the production line and either reworked or discarded.
8. Packaging and Shipping
Once the pizza pans have passed inspection, they are carefully packaged for shipment. Packaging typically involves placing the pans in protective boxes or blister packs to prevent damage during transit. For retail sale, packaging may also include branding or care instructions to ensure consumers know how to use and maintain their pizza pans.
For bulk shipping to commercial kitchens or restaurants, pizza pans are typically stacked in boxes or pallets, often with protective inserts to avoid scratches or damage. Eco-friendly packaging is also increasingly being used, aligning with consumer demand for sustainable products.
9. Automation in Production
Modern pizza pan manufacturing is highly automated, with robotic arms and automated guided vehicles (AGVs) handling tasks such as transporting raw materials, moving finished products, and packing. Automated systems help increase production speed and accuracy while maintaining consistency in quality. These systems also reduce labor costs and improve efficiency in high-volume production settings.
The incorporation of computer numerical control (CNC) machines has also allowed for more precise cutting, shaping, and coating application. These automated systems work with high precision, ensuring that each pizza pan is uniform in size and shape, which is critical in the competitive foodservice market.
Conclusion
The sheet metal pizza pan manufacturing machine plays a crucial role in producing high-quality pans that are both durable and functional. Through a combination of cutting, shaping, coating, and finishing processes, manufacturers create pizza pans that ensure even cooking, easy cleaning, and long-lasting performance. With advancements in automation, material innovation, and sustainability, the pizza pan manufacturing process continues to evolve, offering consumers and foodservice professionals reliable, high-performance products. Whether for home use or commercial kitchens, the high-quality manufacturing of pizza pans ensures that they can withstand the rigors of baking and provide excellent results every time.
The sheet metal pizza pan manufacturing machine is designed to produce high-quality pizza pans from sheet metal, typically aluminum or stainless steel. These pans are essential for baking pizzas in both home kitchens and commercial settings, where durability and heat conductivity are important. The manufacturing process begins with selecting high-quality sheet metal, which is uncoiled and straightened. Then, the metal sheets are cut into the desired round shapes using punching, die-cutting, or laser-cutting methods, ensuring that the pans meet the required size specifications. Once the base of the pan is formed, the edges are rolled or folded to create smooth, durable rims that are easy to handle and prevent sharp edges.
Some pizza pans feature perforations to enhance airflow during baking, which helps achieve a crispy crust. This process involves punching small holes into the pan, ensuring uniform heat distribution for an even cook. Depending on the type of pizza pan, additional features like reinforced edges or non-stick coatings are added at this stage. Non-stick coatings are commonly applied to prevent dough from sticking to the pan and to make cleaning easier. These coatings can be made from materials like PTFE or ceramic, and they are baked into the pans to ensure durability. For stainless steel pans, heat treatments are often performed to enhance the strength of the material, ensuring that the pan can withstand high temperatures without warping.
Once the pans are shaped, coated, and heat-treated, they undergo quality control inspections to ensure they meet specific standards for durability, heat conductivity, and appearance. This process checks for defects such as uneven coatings, warping, or incorrect dimensions. The pans that pass inspection are then cleaned and packaged for shipment. Packaging ensures that the pans remain protected during transportation, and eco-friendly materials are often used to align with sustainability efforts. In commercial settings, the pans are typically shipped in bulk, while retail products may be individually boxed with branding or care instructions.
Automation plays a significant role in modern pizza pan manufacturing. Robotic systems handle various tasks, such as moving materials, cutting metal, applying coatings, and packing the pans, improving both speed and consistency in production. These systems not only increase efficiency but also help maintain product quality across large volumes. The integration of computer numerical control (CNC) machines has made it possible to achieve high levels of precision in cutting, shaping, and finishing the pans. With advances in technology and a growing focus on sustainability, manufacturers are developing more durable and eco-friendly pizza pans that meet both consumer demands and industry standards. As the market for high-quality cookware continues to grow, innovations in material selection, design, and production processes will keep the pizza pan manufacturing process evolving to deliver better performance, longer-lasting products, and a more environmentally conscious approach to production.
As the pizza pan manufacturing process evolves, several innovations are shaping the future of production, particularly focusing on sustainability, efficiency, and product performance. One notable trend is the increasing demand for eco-friendly materials. Manufacturers are moving away from traditional materials that are difficult to recycle and turning toward more sustainable alternatives. For example, using recycled aluminum for pizza pans reduces the environmental impact by minimizing the need for virgin materials, while also reducing energy consumption during production. Recycled metals can offer the same durability and performance as non-recycled materials, making them a viable and environmentally conscious option for cookware manufacturing.
The use of non-toxic, environmentally friendly coatings is another growing trend in the pizza pan manufacturing industry. Traditional non-stick coatings may contain harmful chemicals like PFOA or PTFE, which can release toxic fumes when overheated. As consumer awareness about health and safety increases, manufacturers are opting for ceramic coatings or silicone-based non-stick surfaces that are free from harmful chemicals. These alternative coatings are not only safer but also offer enhanced cooking performance, ensuring that food doesn’t stick to the pan, while being easy to clean.
Additionally, there is a growing focus on smart cookware technologies. The rise of the smart kitchen means that more and more cooking appliances and tools are being designed with connectivity in mind. For pizza pans, this could include integrating temperature sensors that sync with smartphone apps or kitchen appliances. Such innovations would allow users to monitor and adjust the cooking temperature of the pizza pan in real time, ensuring consistent results every time. These smart features can provide greater precision in cooking, as well as better control over the quality of baked products.
In terms of design, manufacturers are also offering more customization options for consumers. As people become more interested in personalized and unique kitchen tools, manufacturers are providing ways to create bespoke pizza pans that reflect individual preferences. Customers can choose from various sizes, shapes, and even add engravings or custom designs to their pizza pans. This trend toward personalization is gaining traction as consumers seek products that align with their individual tastes and needs.
Moreover, advanced manufacturing technologies like 3D printing are beginning to influence the pizza pan production process. Though still in its early stages for cookware, 3D printing allows for the creation of highly customizable, intricate pan designs that were previously difficult or impossible to achieve with traditional manufacturing methods. These technologies allow manufacturers to experiment with new shapes, textures, and features that can enhance the performance of pizza pans, providing more options for consumers.
The industry is also responding to the globalization of food trends. As pizza culture spreads worldwide, there is increasing demand for specialized pizza pans designed for different types of pizzas, such as Neapolitan-style, deep-dish, or thin-crust pizzas. Manufacturers are creating pizza pans with specific characteristics tailored to these regional styles, such as pans with varying depths or coatings that optimize heat distribution for certain baking methods.
In addition to focusing on performance and innovation, durability remains a key factor in pizza pan design. With consumers seeking products that will last for years, manufacturers are investing in high-quality materials that can withstand frequent use in both home and commercial kitchens. For example, hard-anodized aluminum or cast iron pizza pans offer superior heat retention and longevity compared to standard aluminum pans, making them highly desirable for serious home bakers and restaurant professionals alike. These pans are less likely to warp, corrode, or lose their non-stick properties over time, ensuring a longer lifespan.
Another important consideration is the rise of multifunctional cookware. In response to the growing popularity of multi-use kitchen tools, pizza pans are being designed with added versatility. Some pizza pans can now double as baking trays or serving platters, reducing the need for multiple items in the kitchen and offering greater convenience for users. These pans may come with features like removable handles or stackable designs for easier storage, while still maintaining their effectiveness for cooking pizza.
Finally, the manufacturing of pizza pans is seeing an emphasis on quality control and precision. With increasing consumer demand for high-performance products, manufacturers are investing in automated quality control systems that use sensors and imaging technology to detect even the smallest defects in the production line. This ensures that each pizza pan meets the highest standards before it reaches the consumer, guaranteeing consistency in both function and aesthetics.
In conclusion, the pizza pan manufacturing process is becoming more sophisticated as manufacturers incorporate sustainable practices, advanced technologies, and consumer-driven innovations into their products. From the use of eco-friendly materials and non-toxic coatings to the integration of smart features and customization options, the industry is adapting to meet the needs of modern consumers. As demand for high-quality, versatile, and sustainable cookware continues to rise, pizza pan manufacturers will continue to innovate, offering products that not only enhance the cooking experience but also align with the values of health-conscious, environmentally aware consumers. With advancements in material science, manufacturing techniques, and product design, the future of pizza pan production looks promising, ensuring that pizza lovers can continue to enjoy perfectly baked pies for years to come.
Sheet Metal Wok Manufacturing Machine
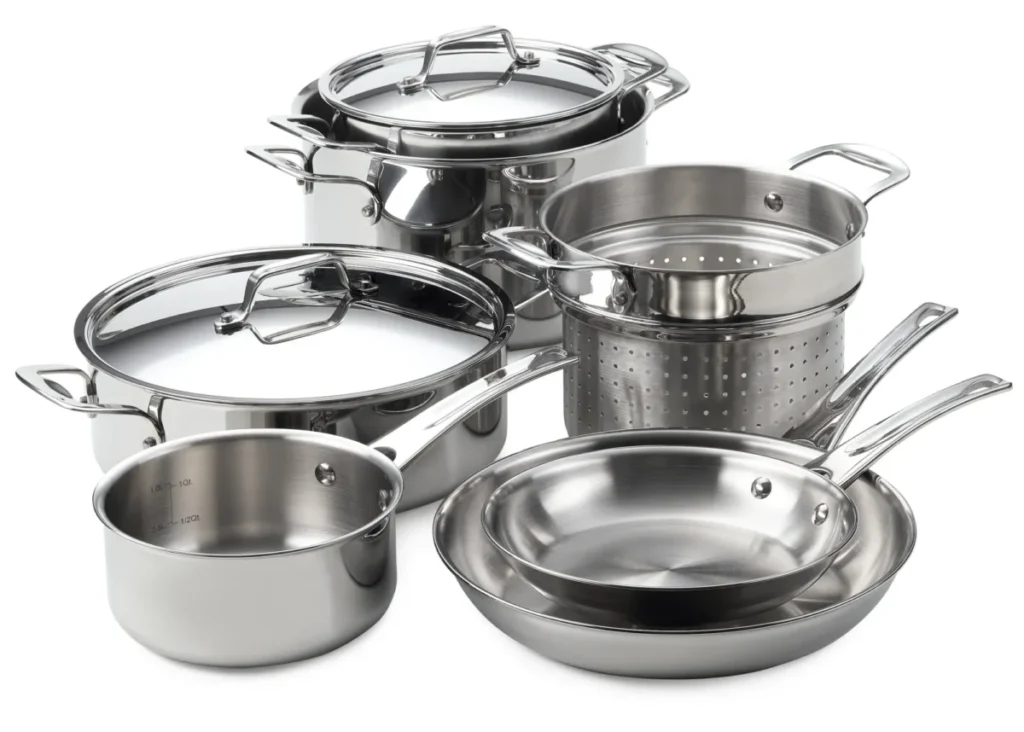
The sheet metal wok manufacturing machine is designed to produce high-quality woks, which are essential cookware in Asian cuisine, known for their unique round-bottom design that allows for efficient cooking at high temperatures. The manufacturing process for creating sheet metal woks involves various stages of shaping, forming, coating, and finishing to ensure they perform well on stovetops and last over time. Here’s an outline of the key steps in the production process of a sheet metal wok:
The first stage of wok production begins with material selection. Woks are typically made from metals like carbon steel, stainless steel, or aluminum, depending on the desired qualities of the finished product. Carbon steel is particularly favored for its excellent heat conductivity and ability to develop a natural non-stick surface after seasoning. Stainless steel woks are chosen for their durability and resistance to corrosion, while aluminum woks are lightweight and conduct heat efficiently but are less common for professional use. The raw material typically comes in the form of large sheets or coils, which are carefully inspected for quality and prepared for further processing.
Once the material is ready, the sheet metal is cut to size. The material is fed into a shearing machine or laser cutting machine to cut the sheet into the desired dimensions for the wok. In some cases, punching machines may also be used to create circular blanks, which are later shaped into the final wok form. The diameter of the wok will vary depending on the intended use, with small woks for home kitchens and larger versions for commercial use.
After the sheet metal is cut into blanks, the next step is forming the wok’s shape. This step is essential for creating the wok’s iconic round-bottomed structure. The wok blanks are placed in a press-forming machine or hydraulic press, where they are shaped using a combination of pressure and heat. The metal is formed into a shallow bowl shape that gradually tapers toward the bottom. The process typically involves a deep-drawing press to ensure that the wok has the characteristic curve that allows for even heat distribution during cooking.
Once the wok is shaped, the edges are often trimmed and smoothed to ensure that they are free from sharp edges. Edge forming machines or manual trimming processes are employed to create a smooth, even lip that is both aesthetically pleasing and safe to handle. This step may also involve beading or folding the edge to reinforce the wok, making it more resistant to warping during high-heat cooking.
The next step in wok manufacturing is handle attachment. Many woks have wooden or metal handles that are affixed to the body of the wok. For metal handles, welding or riveting is typically used to secure them in place. Wooden handles, commonly found on traditional woks, are attached using a brazing or riveting process. Wooden handles are often shaped to provide a comfortable grip and may be treated with a heat-resistant finish to prevent damage from prolonged exposure to high heat.
In some cases, woks undergo a seasoning process, especially for carbon steel woks, which require an initial layer of oil to create a non-stick coating. The wok is heated to a high temperature, and a thin layer of oil is applied to the surface, which then carbonizes to form a protective layer. This seasoning improves the wok’s non-stick properties and enhances its cooking performance. Stainless steel woks, on the other hand, do not require seasoning, but may receive a protective coating to prevent oxidation and improve longevity.
For added non-stick properties, especially for aluminum or stainless steel woks, some manufacturers apply a non-stick coating during the manufacturing process. This can be done using spray or dip coating methods, followed by a curing process in a high-temperature oven. Non-stick coatings like PTFE or ceramic-based coatings are often used to prevent food from sticking and to make cleaning easier.
Once the wok has been formed, handled, and coated, it undergoes a quality control inspection. The wok is checked for defects in the material, shape, handle attachment, and coating. The wok is also tested for its heat resistance and overall durability, ensuring it can withstand high cooking temperatures without warping or degrading. Additionally, the non-stick coating is checked for uniformity and effectiveness.
Finally, the woks are packaged and prepared for shipment. Depending on the market, woks may be packaged individually or in bulk for commercial sales. Retail packaging may include information about the material, care instructions, and branding, while woks for industrial kitchens may be bulk-packed for easy distribution. Protective packaging is used to prevent damage during transit, ensuring that each wok arrives at its destination in excellent condition.
Modern manufacturing processes for woks often involve automation, particularly for repetitive tasks like cutting, forming, and handling. Robotic arms and automated guided vehicles (AGVs) are used to transport materials and finished products, reducing labor costs and increasing production efficiency. Automation ensures that woks are produced quickly, accurately, and consistently, with minimal human intervention. Some manufacturers also employ computer numerical control (CNC) machines for precise shaping and coating, further enhancing the quality of the final product.
As consumer preferences shift toward sustainability and health-conscious cooking, wok manufacturers are increasingly focusing on the use of eco-friendly materials and coatings. For instance, recycled metals and biodegradable packaging are becoming more common in wok production. Furthermore, as the popularity of wok-based cooking continues to spread, manufacturers are innovating with new features like ergonomic handles, multi-functional designs, and induction compatibility for electric stovetops.
The global demand for woks has also led to innovations in design customization. Consumers now have the option to choose from various sizes, materials, and handle types, and some manufacturers even offer personalized engraving for a unique touch. With the rise of the home-cooking and Asian cuisine trend, demand for high-quality woks continues to grow, leading to greater diversity in product offerings.
In conclusion, the sheet metal wok manufacturing process combines various techniques such as cutting, forming, welding, and coating to produce durable, high-performance cooking tools. The industry is evolving with a focus on sustainability, efficiency, and innovative designs, as manufacturers seek to meet the demands of a growing global market. With advancements in materials, automation, and custom features, the future of wok manufacturing looks promising, ensuring that both home cooks and professional chefs can enjoy reliable, long-lasting cooking tools that enhance their culinary experiences.
The sheet metal wok manufacturing process continues to evolve as advancements in material science, automation, and consumer preferences shape the industry. As consumer awareness about environmental sustainability grows, manufacturers are placing increased importance on eco-friendly production methods. The shift toward using recycled metals in the creation of woks is becoming more prevalent, reducing the need for virgin materials and lowering the carbon footprint of the manufacturing process. Recycled aluminum and carbon steel are often sourced from post-consumer products and industrial scraps, providing a more sustainable alternative without compromising the quality or performance of the cookware.
At the same time, the manufacturing process benefits from innovative coatings designed to improve the performance and longevity of woks. While traditional woks are prized for their ability to develop a natural non-stick surface with use, modern coatings like ceramic non-stick or PTFE-free solutions are becoming increasingly popular. These coatings are applied in a manner that ensures a smooth, easy-to-clean surface without compromising the wok’s heat conductivity. Manufacturers are also working to improve the heat retention properties of woks, especially for those designed for induction cooking, a growing trend among home cooks and professional chefs alike. Induction-compatible woks have special bases made from materials that enable them to heat evenly when used on induction stoves, contributing to more efficient cooking.
In terms of design and usability, the demand for ergonomic handles and lightweight materials has been steadily increasing. Consumers are looking for woks that are comfortable to handle, even during high-temperature cooking. Wooden handles, traditionally used for their ability to stay cool while cooking, are now often paired with metal bodies, and innovations like soft-touch handles are gaining popularity for providing a secure grip during stir-frying and tossing ingredients. Some woks even feature detachable handles or collapsible designs, aimed at improving storage options for consumers with limited kitchen space.
Furthermore, manufacturers are paying more attention to multi-functional cookware that can serve a variety of purposes. Modern woks are designed not only for stir-frying but also for steaming, braising, deep-frying, and even smoking. These versatile designs are appealing to consumers who prefer kitchen tools that can serve multiple functions, saving space and enhancing convenience. This multi-use approach is especially important in the context of small kitchen appliances and space-saving cookware trends, which are gaining momentum due to the growing popularity of apartment living and minimalist home design.
Automation plays a critical role in the manufacturing process of sheet metal woks, as robots and automated machines improve both efficiency and precision. Automated systems are used throughout the production line for tasks such as cutting, forming, welding, and coating. Robotic arms handle the loading and unloading of materials, while automated guided vehicles (AGVs) transport finished products to packaging or storage areas. The automation of these processes allows for high-volume production, faster turnaround times, and a reduction in human error, ensuring that every wok is consistent in quality and free of defects. Moreover, the use of computer numerical control (CNC) machines allows manufacturers to achieve greater precision in shaping the wok, ensuring it has a consistent form that meets design specifications.
The role of quality control remains paramount in the wok manufacturing process, as woks must meet stringent standards for performance, durability, and safety. The woks are carefully inspected at various stages of production to check for defects such as warping, cracking, or improper coating application. Additionally, the handles are tested for secure attachment, and the overall heat distribution of the wok is assessed to ensure it will perform well during cooking. Woks are also checked for compliance with international safety standards to ensure they are free from harmful chemicals like PFOA and lead, especially in non-stick varieties.
As the global demand for woks increases, manufacturers are expanding their product offerings to cater to diverse markets. Wok sizes range from small, personal-use woks to large commercial-sized models that can cook large quantities of food for restaurants or catering businesses. The materials used in manufacturing woks also vary based on regional preferences. For example, in markets where traditional carbon steel woks are favored, the production process emphasizes the creation of woks that can develop a seasoned patina over time. On the other hand, in regions where stainless steel or non-stick materials are more popular, the focus is on producing durable, low-maintenance woks that require minimal seasoning or coating upkeep.
Packaging has also seen innovations aimed at both protecting the product during transit and appealing to environmentally conscious consumers. Instead of using plastic packaging, manufacturers are opting for biodegradable or recyclable materials such as cardboard and paper to package their woks. Packaging designs often highlight the wok’s key features, such as its heat retention capabilities, non-stick surface, and handle design, while providing instructions on proper care and seasoning (for carbon steel woks). The packaging also often includes information about the environmental impact of the materials used, reinforcing the manufacturer’s commitment to sustainability.
In addition to the increased focus on sustainability, the manufacturing of sheet metal woks is influenced by rising consumer interest in healthier cooking options. Since woks are used for stir-frying, which typically requires little oil and cooks food quickly at high temperatures, they are often seen as a healthier alternative to other cooking methods. To appeal to this trend, manufacturers are incorporating non-toxic coatings that do not release harmful chemicals when heated, allowing consumers to enjoy the benefits of wok cooking without worrying about the potential health risks associated with low-quality non-stick pans.
The growing trend of home cooking and global cuisine is also contributing to the demand for high-quality woks. As people explore new cuisines, particularly Asian cooking, the wok has gained popularity due to its versatility and effectiveness in preparing stir-fries, noodles, curries, and other traditional dishes. As a result, manufacturers are focusing on creating woks that can handle a wide range of cooking techniques, making them suitable for both professional chefs and amateur cooks alike.
In conclusion, the sheet metal wok manufacturing process is continually evolving in response to shifting consumer preferences and technological advancements. With a focus on sustainability, innovation, and efficiency, manufacturers are producing woks that meet the demands of modern kitchens, combining durability, versatility, and ease of use in one essential piece of cookware. As the market for high-quality woks continues to grow, so too will the production techniques, ensuring that woks remain an indispensable tool for cooking enthusiasts and professionals around the world.
As the demand for high-quality woks continues to rise, manufacturers are expanding their focus not just on the functional aspects of wok production, but also on consumer experience and global market trends. One of the primary areas of innovation is the integration of smart technology into cookware. Though still relatively new, smart woks with embedded temperature sensors or Bluetooth connectivity are starting to emerge in the market. These woks can connect to smartphones or smart kitchen appliances, providing real-time temperature monitoring and alerts for optimal cooking performance. Such smart features allow users to fine-tune their cooking process, resulting in more precise control over the heat and cooking time, ensuring better cooking outcomes. This is particularly beneficial for users who want consistent results for different types of dishes, especially delicate stir-fries or dishes requiring precise heat control.
The increasing popularity of multicultural cooking has also led manufacturers to develop specialized woks suited for different cooking styles. For example, in some regions, woks with flat bottoms are preferred, as they are more suitable for modern stoves, including electric and induction cooktops. On the other hand, traditional round-bottom woks remain popular in places where gas stoves with high heat outputs are more common. To cater to both needs, manufacturers are creating hybrid models that feature slightly rounded bottoms, optimized for both gas and induction cooking, offering greater versatility for consumers. These changes in design ensure that consumers across various regions can enjoy the benefits of wok cooking regardless of their kitchen setup.
Another factor that is influencing wok manufacturing is the growing interest in multifunctional cookware. As consumers seek to simplify their kitchens and reduce the number of items they need, wok manufacturers are adapting by designing woks that can serve multiple purposes. Some woks now come with features that allow them to be used as steaming baskets or even sauté pans. These multipurpose woks come with removable steamer inserts or lids that provide added functionality, allowing consumers to steam vegetables, fish, or dumplings in the same vessel they use for stir-frying. This increased flexibility is a key selling point for those with limited kitchen space or those who value versatility in their cooking tools.
Customization options are also becoming more popular, as consumers look for personalized kitchen products. Manufacturers now offer woks in various sizes, designs, and materials, and some even allow for engraving or personalized branding. Whether it’s a custom handle design, a unique finish, or a special engraving to commemorate a particular occasion, these personalized options are appealing to a growing number of consumers who want their cookware to reflect their individual style.
The design and ergonomics of wok handles have also been a point of significant innovation. While traditional woks often feature long, wooden handles for ease of handling and heat resistance, newer models are incorporating handles that provide greater comfort and control during cooking. Many modern woks feature soft-grip silicone handles, or handles that are ergonomically designed for better weight distribution, making them easier to maneuver during high-heat cooking or when tossing ingredients. Some manufacturers are even introducing foldable handles, which allow for easier storage, especially in smaller kitchens where space is limited. For large, commercial-grade woks, the handles are often reinforced for added strength and durability, able to withstand heavy use in a professional setting.
On the sustainability front, the push for more eco-conscious practices is evident throughout the wok manufacturing process. Manufacturers are turning to biodegradable and recyclable packaging materials as a way to reduce their environmental impact. Wok production facilities are also focusing on energy efficiency, reducing waste, and utilizing renewable energy sources where possible. In terms of the woks themselves, there is an increasing demand for naturally sourced, non-toxic materials. For example, cast iron woks are seeing a resurgence due to their durability, ability to retain heat, and the fact that they require no coatings that could potentially leach chemicals. This trend reflects a broader consumer preference for more natural, chemical-free cookware options.
The growth of online shopping and direct-to-consumer sales has also had a significant impact on wok manufacturing and marketing. With many consumers now purchasing cookware online, manufacturers are placing greater emphasis on branding, packaging, and digital marketing. Detailed product descriptions, care instructions, and instructional videos have become more commonplace, helping consumers understand how to get the best results from their woks. Manufacturers are also offering wok care kits that include oils, cleaning tools, and seasoning instructions for carbon steel woks, providing a more complete customer experience.
As the market for woks becomes increasingly competitive, manufacturers are also differentiating themselves by offering specialized chef-oriented woks designed for professional kitchens. These woks are typically made from high-grade materials, such as carbon steel or stainless steel, and are designed for heavy-duty use. Features like thicker gauge metals for improved heat distribution, reinforced edges, and removable handles are common in these models. Such professional-grade woks cater to high-volume kitchens, ensuring that they can withstand the demands of a commercial environment while maintaining optimal performance over time.
Furthermore, the rise of health-conscious cooking has impacted wok designs. The traditional wok, which often requires little or no oil for stir-frying, aligns perfectly with modern trends of cooking with minimal fats. The versatility of the wok for quick cooking at high temperatures preserves nutrients in vegetables and proteins, making it an attractive option for those following low-fat or plant-based diets. This shift toward healthier cooking methods has led to the development of woks that cater specifically to these dietary preferences, with non-stick and eco-friendly coatings that make cooking and cleaning easier without compromising on performance.
In conclusion, the future of sheet metal wok manufacturing looks set to continue evolving with an emphasis on innovation, sustainability, technology integration, and consumer customization. From incorporating smart features and multifunctional capabilities to focusing on ergonomic designs and environmentally friendly materials, wok manufacturers are working to meet the needs of modern cooks around the world. With a blend of traditional craftsmanship and cutting-edge technology, the wok remains a timeless and essential piece of cookware, and its production is increasingly aligned with both performance and sustainability goals.
As wok manufacturers continue to innovate and adapt to changing consumer preferences, the future of sheet metal wok production holds exciting possibilities. The growing demand for global cuisine and the continued popularity of Asian cooking techniques ensure that the wok will remain a staple in kitchens around the world. With advancements in materials, production processes, and consumer trends, the wok is evolving to meet the needs of modern cooks while maintaining its traditional characteristics that make it such a versatile and beloved cooking tool.
One significant area of growth in wok production is the integration of smart cooking technology into cookware. As more kitchens become equipped with smart appliances and internet-connected devices, there is increasing interest in woks that can offer a more high-tech cooking experience. For instance, woks with built-in sensors that track temperature fluctuations, cooking progress, and even offer recipes or cooking tips via smartphone apps are gaining traction. These woks could also send alerts when the heat is too high or when the food is cooked to perfection, ensuring better results for even the most novice cooks. The ability to sync with other smart kitchen appliances, such as induction cooktops or smart stoves, would allow for seamless integration into a connected kitchen ecosystem, making wok cooking more efficient and intuitive.
Alongside smart technology, there is a growing trend toward multi-functional cookware. Manufacturers are designing woks that can easily transition from one cooking method to another, allowing for a more diverse range of meals to be prepared with a single piece of cookware. Some woks now come with detachable grills, steamer trays, or lids that allow them to function as multi-tier steamers, deep fryers, or even braisers. This flexibility caters to home cooks who want to maximize their kitchen tools, offering versatility and convenience while minimizing the number of pots and pans needed in the kitchen.
As concerns over environmental impact grow, sustainable practices in wok manufacturing are becoming even more critical. In addition to using recycled metals, many manufacturers are turning to eco-friendly coatings that are free from harmful chemicals such as PFOA, PFOS, and other substances often found in conventional non-stick coatings. Manufacturers are also opting for natural, non-toxic finishes such as ceramic-based or cast-iron-based coatings, which are not only safer for the environment but also safer for consumers’ health. This trend reflects the increasing demand for green products in the cookware industry, as consumers become more conscientious about the materials and chemicals used in the products they purchase.
The increasing focus on ergonomics in cookware design also plays a significant role in wok production. As home cooking becomes a more widespread hobby and professional chefs continue to rely on woks in high-heat environments, comfort and control are paramount. Wok handles, traditionally made of wood, are now being redesigned to include heat-resistant silicone or soft-touch plastic, ensuring that cooks can handle the wok comfortably, even during long cooking sessions. Additionally, longer handles or helper handles are being integrated into wok designs, making it easier to stir-fry or toss ingredients without worrying about the wok slipping or becoming difficult to maneuver. These ergonomic improvements are particularly important for users who may have mobility or strength concerns, ensuring that the wok remains a user-friendly and safe kitchen tool.
Another emerging trend in wok production is the rise of induction-compatible woks, which have become more popular due to the increasing use of induction cooktops in modern kitchens. These cooktops require cookware with a magnetic base, which means traditional woks with thin or non-ferrous bottoms need to be specially adapted for induction cooking. To meet this demand, wok manufacturers are introducing woks with ferrous bases that are specifically designed to be compatible with induction cooktops. This innovation allows users to enjoy the benefits of wok cooking on induction stoves, providing a convenient and energy-efficient cooking method without sacrificing the wok’s signature performance.
In parallel with the push for induction compatibility, there is an increasing focus on creating multi-layered woks that offer better heat retention and distribution. Clad woks, which feature layers of different metals like aluminum and stainless steel, are designed to offer superior heat conductivity while ensuring durability and longevity. These woks are particularly beneficial for people who want to use their woks on a variety of stovetops, including induction, gas, or electric, as the multiple layers provide uniform heat distribution that helps prevent food from burning or cooking unevenly.
Additionally, the trend toward customization in cookware extends to woks. Some manufacturers offer personalized options where consumers can choose specific sizes, materials, finishes, and even handle designs. Personalized engraving is also becoming a popular feature, allowing consumers to add a unique touch to their woks. This trend not only appeals to individual tastes but also caters to the growing demand for giftable cookware, as woks with custom engravings or special designs make thoughtful presents for cooking enthusiasts or newlyweds.
The rise of the home-cooking revolution also plays a significant role in driving wok production. As more people embrace cooking at home, often exploring cuisines from different cultures, woks are becoming an essential kitchen tool for a variety of cooking styles. Stir-frying, steaming, braising, and deep-frying are just a few of the techniques that woks excel at, making them an indispensable tool for anyone looking to experiment with diverse recipes. The versatility of the wok in handling high-heat cooking and multiple ingredients, all while retaining flavor and nutrients, makes it especially popular for healthy, fast cooking. As people become more health-conscious and seek efficient cooking methods that preserve the nutritional value of ingredients, woks are perfectly positioned to meet these needs.
The global market for woks continues to expand as the cookware reaches new audiences. In regions where wok cooking was traditionally less popular, manufacturers are seeing increased interest in Asian-inspired cooking tools. This has led to the expansion of wok production to accommodate various culinary preferences, including woks designed for specific types of cooking or specialized diets, such as vegan, gluten-free, or low-fat cooking. As woks are introduced into new markets, manufacturers are also tailoring their marketing strategies to educate consumers on the benefits and techniques of wok cooking, helping to grow the market even further.
In conclusion, the future of sheet metal wok manufacturing is driven by technological innovation, sustainability, consumer customization, and the growing popularity of global cuisines. With advancements in materials, smart technology, and design, woks are becoming more versatile, user-friendly, and environmentally conscious than ever before. Manufacturers are not only focused on creating cookware that delivers exceptional cooking performance but also on meeting the diverse needs of today’s consumers, who demand products that are efficient, sustainable, and adaptable to a variety of cooking styles and dietary preferences. The continued evolution of wok production promises a future where this iconic cooking tool remains an essential part of kitchens worldwide, enhancing the culinary experience for home cooks and professionals alike.
Sheet Metal Griddle Manufacturing Machine
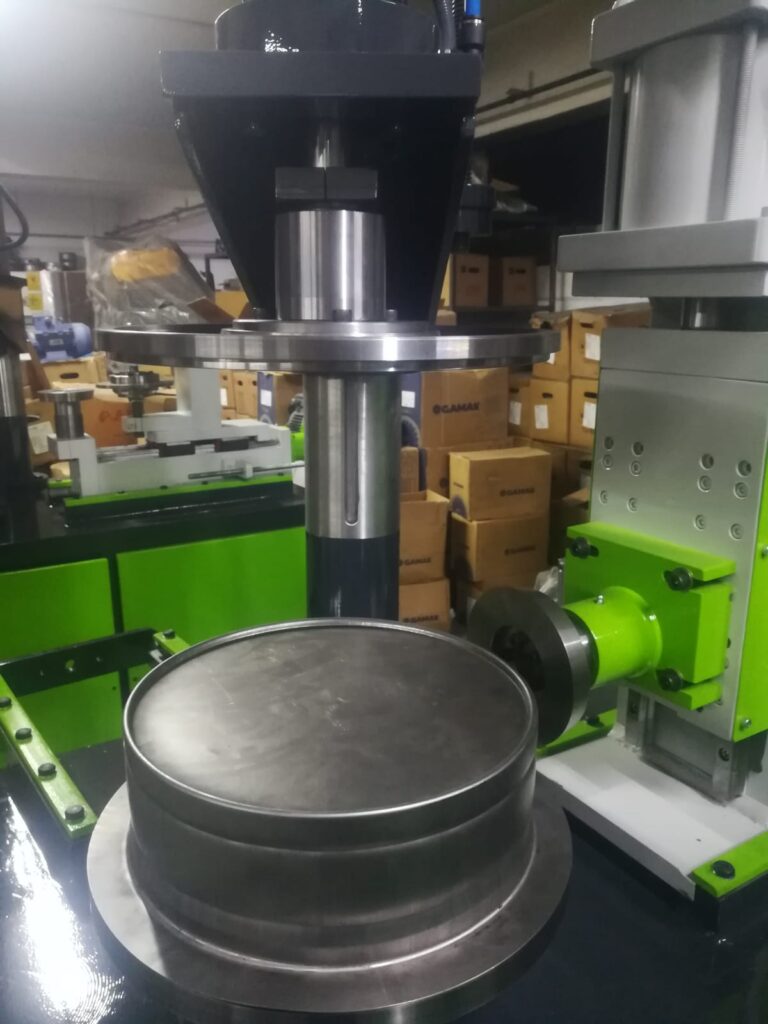
The manufacturing of sheet metal griddles involves a series of specialized processes to create durable, heat-conductive, and ergonomic griddles suitable for both home and commercial kitchens. A griddle is typically a flat cooking surface used for preparing a variety of foods such as pancakes, eggs, bacon, and burgers. The manufacturing process of sheet metal griddles must ensure high heat retention, even distribution, and resilience under continuous use. Here’s a breakdown of the main components of the sheet metal griddle manufacturing machine:
1. Material Selection and Preparation
The process begins with the selection of metal sheets, which are usually made from carbon steel, stainless steel, or aluminum, depending on the desired properties of the griddle. Stainless steel is often chosen for its resistance to corrosion and ease of cleaning, while carbon steel is valued for its heat retention properties, which make it ideal for griddles used in high-heat cooking. Aluminum is lightweight and offers good heat conductivity but is less durable than steel options.
Once the material is selected, it is cut to size using laser cutting machines or shearing tools. This step ensures that the sheet metal pieces are ready for the shaping and forming processes that will follow. The metal sheets must be flattened and checked for any defects before moving on to the next step.
2. Forming and Shaping
Once the metal sheets are prepared, the next step is forming. The sheets are fed into press machines or roll forming machines where they are shaped into the griddle’s characteristic flat or slightly concave form. If the griddle is designed for induction cooking, a special magnetic base may be added during this process to ensure compatibility with induction cooktops.
For commercial griddles, which often require larger dimensions, hydraulic presses may be used to handle the heavier gauge metal. Deep drawing is also utilized for producing deeper, more complex shapes if needed. The forming machines ensure that the metal takes the desired shape without warping or distorting, which could affect heat distribution and cooking performance.
3. Surface Treatment
After the griddle shape is formed, the metal surface undergoes a treatment to enhance both its aesthetic appearance and functional qualities. The surface treatment includes processes like polishing or brushing to give the griddle a smooth and uniform finish.
For non-stick griddles, an application of a ceramic or PTFE coating may be performed to ensure the surface is easy to clean and reduces the amount of oil or fat needed for cooking. The coating process requires precise temperature control to ensure the coating adheres well without compromising the griddle’s heat conductivity. Alternatively, some commercial griddles may have a seasoned cast-iron surface that develops a natural non-stick patina with use.
4. Edge Beading and Reinforcement
The edges of the griddle are often beaded or reinforced to provide extra strength and a clean finish. Edge beading machines roll the edges to a specific radius or profile, creating a strong, smooth edge that can resist wear and tear during cooking and cleaning. This step also helps prevent the griddle from warping at the edges, which could lead to heat distribution problems.
In some models, the griddle may feature reinforced edges or a lip around the perimeter to keep grease or liquids from spilling over. For commercial griddles, additional reinforcements may be added to handle heavy-duty use and to prevent the warping that can occur with prolonged exposure to high heat.
5. Handle and Support Attachment
Once the main body of the griddle is formed, the next step is to attach handles or support legs, depending on the design. Handle attachment can involve welding or using rivets to securely fix heat-resistant handles made from materials such as wood, stainless steel, or silicone to the griddle. Handles must be carefully positioned to provide a secure and ergonomic grip for users, particularly when lifting or moving a hot griddle.
For commercial models, which are usually larger and require sturdier support, legs or a mounting system are added. These can be made from stainless steel or cast iron and are designed to withstand heavy use while ensuring the griddle remains stable during cooking. Commercial griddles may also include wheeled bases for easy mobility in professional kitchens.
6. Welding and Assembly
For models that require more complex construction, components like handles, supports, or additional reinforcement elements are welded together. This ensures that all parts of the griddle are securely joined. For larger commercial griddles, spot welding or TIG welding (Tungsten Inert Gas welding) may be used for creating a high-quality and durable joint.
The assembly process may also involve attaching thermostatic controls or griddle plate inserts (if applicable). For electrical griddles, this step includes wiring the heating elements to the base plate, ensuring that the electrical connections are properly insulated and sealed to avoid any safety hazards.
7. Quality Control and Testing
Once the griddles are fully assembled, they undergo rigorous quality control and testing procedures. The griddles are checked for defects such as cracks, warped edges, or improper coating application. For non-stick griddles, manufacturers test the effectiveness of the non-stick coating and ensure it adheres well to the metal.
Testing also includes ensuring that the griddle heats evenly and efficiently. For electric griddles, electrical safety tests are conducted, including checks for proper insulation and secure connections. For gas griddles, manufacturers test for gas leaks and flame regulation.
Some manufacturers may also conduct drop tests or stress tests to ensure the griddle can withstand the stresses of daily cooking in both home and commercial settings.
8. Packaging and Shipping
After passing all quality tests, the griddles are cleaned, polished, and prepared for packaging. The packaging is designed to protect the griddles during transit and handling. Many manufacturers use eco-friendly packaging materials such as recyclable cardboard and biodegradable packing peanuts to meet sustainability standards and consumer preferences.
Instruction manuals for care, cleaning, and operation are included with each griddle, providing useful information for the consumer. The griddles are then sent to distribution centers, retailers, or directly to consumers, depending on the sales model.
Key Considerations for Griddle Manufacturing
- Heat Retention and Distribution: One of the most crucial factors in manufacturing sheet metal griddles is ensuring they can retain and evenly distribute heat. Proper material choice and surface treatment are essential for achieving optimal cooking performance.
- Durability: Griddles need to withstand prolonged exposure to high heat without warping, discoloration, or deterioration. Quality control ensures that all griddles meet stringent durability standards.
- User Safety and Ergonomics: Designing griddles with safe, heat-resistant handles and stable bases is essential for preventing accidents and ensuring user comfort during cooking.
- Sustainability: As eco-consciousness grows among consumers, the use of recycled materials and sustainable production methods is becoming increasingly important.
Conclusion
The manufacturing process of sheet metal griddles is highly specialized, involving a combination of precision machining, material science, surface treatments, and rigorous testing. The goal is to produce a high-quality, durable, and functional cooking tool that provides users with the best possible cooking experience, whether in a home kitchen or a commercial setting. Manufacturers are continually innovating to meet the evolving demands for versatile and sustainable cookware, ensuring that sheet metal griddles remain an essential part of kitchens around the world.
The sheet metal griddle manufacturing machine involves a systematic approach to create griddles that are durable, efficient, and suitable for various cooking environments. The following key steps in the manufacturing process highlight the transformation of raw material into a high-quality griddle:
1. Material Sourcing
The process starts with the selection of appropriate metals. Common materials for griddles include stainless steel, carbon steel, and aluminum, each chosen for their specific heat conduction properties, corrosion resistance, and strength. Stainless steel is preferred for its resistance to rust, while carbon steel provides excellent heat retention.
2. Cutting the Metal
The chosen sheet metal is cut into precise dimensions using laser cutting, plasma cutting, or shearing techniques. These methods ensure the metal sheets are accurately sized for the griddle design, which could range from smaller home-use models to larger, commercial-scale units. For more complex shapes, water jet cutting may also be used to handle intricate designs.
3. Forming and Shaping
Once the metal sheets are cut, they undergo press forming to create the flat or slightly concave cooking surface of the griddle. This process is performed with hydraulic presses or roll forming machines, which carefully mold the sheet metal into the required shape. For griddles with deeper designs or unique contours, additional shaping processes such as deep drawing might be used to create more complex forms.
4. Edge Treatment
The edges of the griddle are treated to avoid sharp, unfinished edges that could be a safety hazard or create weak points in the design. This is done by beading, which rolls the edges to create a smooth, rounded finish, or by adding additional reinforcements for increased durability. For models with raised edges, this helps in containing grease or cooking liquids.
5. Surface Treatment
To improve the griddle’s performance and ease of cleaning, the surface undergoes treatments like polishing, brushing, or coating. Non-stick coatings, like Teflon or ceramic-based finishes, may be applied to prevent food from sticking, making cleanup easier. Anodizing or electropolishing processes can also enhance the metal’s resistance to corrosion, particularly in commercial models used in high-humidity environments.
6. Handle and Support Attachment
The next step involves attaching handles or legs to the griddle. Handles may be made from heat-resistant plastic, wood, or metal and are securely fixed using rivets or welding. For commercial-grade griddles, stainless steel supports or reinforced legs are often added to ensure stability and ease of use.
7. Welding and Assembly
For more intricate designs, various parts of the griddle may be welded together. This includes welding sidewalls, legs, or any other structural components. For electrical or gas-powered griddles, welding and assembly also involve ensuring that heating elements, gas connections, and electrical wiring are securely integrated into the griddle design.
8. Quality Control and Testing
Before the griddles are ready for shipment, they undergo a thorough quality control process. This ensures that each griddle meets strict standards for heat distribution, durability, and safety. Testing includes checks for even heating, non-stick coating quality, and resilience under high heat. For electric griddles, electrical safety tests are performed, and for gas griddles, checks for leaks and proper flame control are crucial.
9. Packaging and Distribution
After passing inspection, the griddles are cleaned and carefully packaged to avoid damage during shipping. Packaging is designed to be both protective and eco-friendly, using recyclable materials. Griddles are then distributed to retailers or directly to consumers, often with an instruction manual outlining care, cleaning, and operational guidelines.
10. Customization and Special Features
Some manufacturers offer customizable features, such as personalized handles or size variations, catering to consumer preferences or special needs. Commercial griddles may have additional features like adjustable heat controls, grease traps, or multiple cooking zones to enhance functionality and versatility.
The entire process emphasizes precision, safety, and quality to produce a griddle that provides consistent cooking results, long-lasting performance, and ease of maintenance. The Sheet Metal Griddle Manufacturing Machine plays a crucial role in automating these steps, ensuring efficiency, and allowing for large-scale production while maintaining product consistency.
In addition to the key manufacturing processes outlined, the Sheet Metal Griddle Manufacturing Machine continues to evolve to incorporate technological advancements and respond to consumer demands. Below are additional considerations and innovations that enhance the production and functionality of sheet metal griddles:
11. Advancements in Material Technology
With ongoing developments in material science, manufacturers are increasingly exploring advanced alloys and composite materials to improve the griddle’s performance. Newer materials, such as hybrid metals combining stainless steel with other elements, may offer enhanced heat retention, thermal stability, and lightweight properties without sacrificing durability. The integration of materials with thermal-responsive qualities helps in creating griddles that heat up faster, retain heat more effectively, and cool down at a more consistent rate, improving overall cooking efficiency.
12. Smart Griddle Technology
As kitchen appliances become smarter, the demand for smart griddles has emerged. Manufacturers are incorporating Wi-Fi or Bluetooth capabilities into their griddle designs. These innovations allow users to control cooking temperature, time, and even receive alerts directly on their smartphones or other connected devices. Some griddles can now be programmed with preset cooking modes for specific foods, enabling consistent results with minimal effort. Integrated sensors can monitor the cooking surface’s temperature, adjusting heat settings automatically to ensure optimal cooking conditions. This feature adds convenience for both professional chefs and home cooks who prefer a more hands-off approach to cooking.
13. Energy Efficiency and Environmental Impact
As sustainability becomes a primary concern for both manufacturers and consumers, energy-efficient griddles are gaining popularity. For electric griddles, new energy-saving technologies are being integrated to ensure that heat is distributed effectively, reducing energy consumption without compromising performance. Manufacturers are also adopting solar-powered griddles for certain outdoor models, especially those designed for camping or eco-conscious customers. Furthermore, the production of griddles is increasingly utilizing recycled metals and other sustainable materials to minimize environmental impact.
14. Customization for Specialized Cooking Styles
Consumer preferences for specific cooking styles have led to a rise in specialized griddle designs. Some griddles are tailored for specific diets or cooking techniques, such as griddles designed for low-fat cooking, gluten-free grilling, or vegan-friendly cooking. Others are designed to accommodate specific cuisines like American-style griddles for pancakes or Asian-style griddles for stir-frying. Customization also extends to surface texture, where griddles can be created with varying degrees of roughness or smoothness to suit particular cooking needs, such as creating crispier crusts or achieving a tender finish.
15. Integration with Commercial Kitchens
For large-scale production, particularly in commercial kitchens, manufacturers are offering modular griddle systems that can be customized based on the kitchen’s specific requirements. These systems allow for multiple griddles to be linked together, enabling shared heating elements or variable temperature zones that can accommodate different cooking techniques at the same time. Commercial griddles also come with enhanced grease management systems, quick-release mechanisms for easy cleaning, and more robust support structures to withstand frequent use and heavy-duty cooking.
16. Precision in Temperature Control
Modern griddles are becoming more adept at precise temperature control, thanks to the integration of thermostatic controls and digital readouts. High-end electric and commercial griddles now feature advanced digital thermostats that provide exact temperature settings, ensuring perfect cooking every time. This precision is essential in professional kitchens, where the consistency of dishes like pancakes, burgers, and eggs relies heavily on consistent surface temperature. The ability to maintain a specific temperature helps reduce cooking time and ensures food is cooked evenly.
17. Maintenance and Longevity
Manufacturers are also focusing on the longevity of their griddles. Anti-corrosion coatings and tougher metal finishes are applied to extend the lifespan of griddles, especially in environments where they are subjected to high heat, oils, and acidic food residues. Additionally, modular components that are easy to replace (e.g., heating elements, grease trays) allow for easy repairs, which can extend the griddle’s usable life and provide more value to the consumer.
18. Consumer Education
As part of the griddle manufacturing process, many companies are focusing on educating consumers about the importance of proper care and maintenance. This includes providing guides on how to season and care for different types of griddles, particularly cast iron or carbon steel griddles, which require periodic seasoning to maintain their non-stick properties. Educational materials also include tips for cleaning, storing, and repairing the griddles to help consumers get the most out of their cookware investment.
19. Expansion into New Markets
While griddles have traditionally been associated with American breakfast foods and outdoor cooking, manufacturers are seeing an increase in demand for internationally inspired griddles. For example, teppanyaki-style griddles are gaining popularity for home use, offering a fun and interactive cooking experience for families. Similarly, flat-top griddles used in Latin American cooking, such as for arepas or tacos, are being adapted for domestic kitchens. Manufacturers are responding to these trends by designing griddles that accommodate different fuel sources (electric, gas, induction) and multi-zone cooking, allowing consumers to experiment with new cooking techniques.
20. Health-Conscious Cooking
The rise in health-conscious eating has led to the production of health-focused griddles designed to reduce fat content in cooked foods. Some griddles are equipped with built-in grease drainage systems that allow excess fats and oils to flow away from the cooking surface, reducing the fat content of the food being prepared. This feature, combined with non-stick surfaces and eco-friendly coatings, helps ensure that griddles are not only functional but also meet the needs of health-conscious consumers.
Conclusion
The evolution of sheet metal griddle manufacturing machines reflects broader trends in both consumer demand and manufacturing technology. Innovations in material science, energy efficiency, smart technology, and sustainability are driving the production of more versatile, user-friendly, and environmentally responsible griddles. From home kitchens to large-scale commercial operations, the need for durable, precise, and multifunctional cooking tools continues to shape the future of griddle manufacturing. As consumer preferences shift toward more personalized, health-conscious, and technology-driven solutions, manufacturers are adapting to create the next generation of griddles that meet the diverse needs of modern cooks.
Sheet Metal Roasting Pan Manufacturing Machine
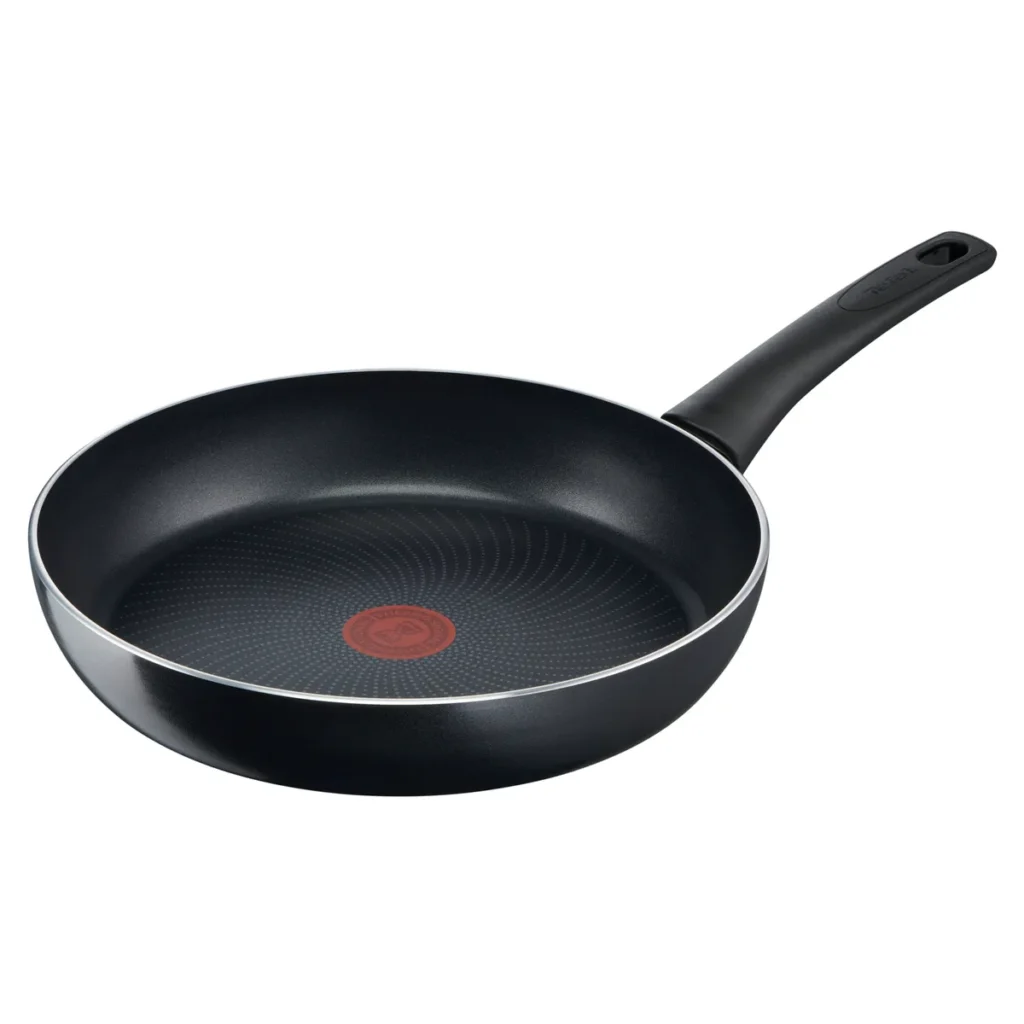
The Sheet Metal Roasting Pan Manufacturing Machine is a sophisticated industrial system designed to produce high-quality roasting pans used in domestic and commercial kitchens. These pans are essential for cooking meats, vegetables, and casseroles at high temperatures, and their design requires careful attention to heat distribution, structural integrity, and ergonomic handling. The machine facilitates the efficient, precise, and scalable production of roasting pans by automating a range of processes from raw material handling to final shaping and finishing.
The process begins with raw sheet metal, typically stainless steel, carbon steel, or aluminum, being fed into the machine. Stainless steel is often chosen for its rust resistance and durability, while aluminum is favored for its lightweight nature and excellent heat conductivity. The metal sheets are unrolled and cut into blanks using high-precision shearing or CNC-controlled laser cutters. This ensures uniformity and minimizes waste.
Next, the blanks are sent through a deep drawing or stamping station, where hydraulic or mechanical presses shape them into the initial pan form. This involves stretching the metal into a mold to create the pan’s base and walls in a single, seamless process, which enhances the structural strength and prevents leaks. The machines may include multi-die tooling to accommodate different pan sizes and shapes, from shallow trays to deeper roasters with ribbed or grooved bottoms for improved air circulation during cooking.
Once the basic form is established, the pans undergo edge trimming and flanging, where excess material is removed and the edges are curled or rolled to create smooth, safe rims that improve user safety and pan durability. In some cases, a reinforcing bead is added around the top edge to prevent warping during high-temperature cooking.
For roasting pans that require handles, the machine incorporates a robotic welding or riveting system. Handles may be stamped from the same metal or made from heat-resistant plastics or composite materials, then attached securely. The machine ensures that handle attachment points are uniform and robust, using sensors and torque feedback mechanisms for quality assurance.
The pans then move through surface treatment stations, which may include polishing, brushing, or electrochemical passivation to enhance corrosion resistance. Some pans receive non-stick coatings or are anodized to improve cooking performance and simplify cleaning. This coating process is carefully controlled by the machine to ensure even application and adherence, followed by curing ovens that harden the coating at controlled temperatures.
Following surface finishing, the roasting pans go through quality control checkpoints. Automated inspection systems with high-resolution cameras check for surface defects, dimensional accuracy, and handle alignment. Any deviation triggers a reject mechanism or flags the item for rework.
Finally, the finished roasting pans are automatically labeled, packaged, and prepared for distribution. Packaging may include cardboard inserts and plastic film to protect the pans during transit. The entire system is designed for high throughput, energy efficiency, and low manual intervention, making it suitable for modern cookware production lines that demand both speed and precision.
This comprehensive machinery setup ensures that every roasting pan produced meets strict standards of quality, functionality, and aesthetics. Manufacturers benefit from reduced labor costs, faster production cycles, and the ability to adapt quickly to new pan designs or market trends, thanks to the machine’s modular and programmable features.
The sheet metal roasting pan manufacturing machine continues to play a central role in streamlining cookware production by integrating automation, precision engineering, and adaptability into a single cohesive system. After the roasting pans are formed, edge-finished, and coated, additional value-added features may be incorporated depending on product specifications or customer demand. For example, embossed branding or decorative patterns can be added to the base or sidewalls using metal embossing rollers or stamping units. This not only reinforces brand identity but can also improve structural rigidity. Some designs include venting holes, ridges, or raised surfaces on the pan interior to elevate food slightly and promote more even air circulation during roasting—features that require precision machining and customized tooling.
To further enhance the functionality of the roasting pans, many machines are equipped with stations for attaching removable or foldable racks that nest within the pan body. These racks are typically made of stainless steel wire and are formed on dedicated wire-bending lines, then assembled in-line with the pan body using robotic arms. The machine must be finely tuned to align and insert these racks without damaging the coated or polished surfaces of the pans. For premium models, integrated lid manufacturing systems may also be synchronized with the pan line, ensuring a complete product with tight dimensional tolerances. These lids are usually stamped, pressed, and shaped with a separate set of dies, often fitted with a knob or handle in a similar fashion to the pan itself.
Post-assembly, the machine guides the finished product through a final cleaning stage where residual oils, dust, and metal particles from machining are removed using ultrasonic cleaners or high-pressure air and water jets. This step is crucial to meet food safety regulations and prepare the pans for immediate consumer use. Drying chambers and air knives are used to ensure all moisture is removed to prevent oxidation, especially before packaging. At this stage, serialization and batch tracking barcodes or QR codes may be laser-engraved or labeled onto the pan for inventory management and traceability, especially for commercial kitchen-grade products.
The automation doesn’t end with production—integrated packaging systems handle sorting, nesting of pans, and automatic boxing. These systems are designed to reduce human handling and increase speed. Pans may be shrink-wrapped individually or packed in sets, with custom inserts for accessories. Robotic palletizers then load the boxes onto pallets ready for warehousing or direct shipment. With demand fluctuating based on seasonal buying trends or promotional campaigns, many modern sheet metal roasting pan manufacturing machines include smart production management software that allows operators to quickly adjust production volume, size runs, or switch between pan models with minimal downtime through intuitive touch-screen interfaces and programmable logic controllers.
Modern versions of these machines are also built with a strong focus on sustainability. Systems for recycling excess metal trim and offcuts are fully integrated, feeding scrap directly back into melting or reprocessing units. Additionally, many factories now incorporate real-time energy monitoring tools and environmentally optimized exhaust and ventilation systems to reduce the carbon footprint of the entire production line. This is especially important for facilities that seek ISO 14001 environmental certification or aim to comply with regional and international standards for green manufacturing.
As culinary preferences shift and new cooking technologies emerge, roasting pans must adapt in both form and function. This demand pushes machine developers to continually refine die designs, press tolerances, coating formulations, and attachment mechanisms. The flexibility built into these manufacturing systems ensures that cookware producers can swiftly introduce innovations like dual-purpose pans, stackable sets, or induction-ready bases. As a result, the sheet metal roasting pan manufacturing machine represents not only an engineering achievement but also a dynamic platform for culinary innovation, capable of supporting the evolving demands of global food culture and modern kitchens.
With the continual push for innovation and efficiency, the sheet metal roasting pan manufacturing machine has evolved into a digitally integrated system where data-driven insights guide much of the operational workflow. Embedded sensors and machine learning algorithms now play a critical role in predictive maintenance and real-time quality assurance. These systems monitor parameters like press force, material stress, and alignment tolerances, flagging anomalies before they affect product quality. This proactive approach minimizes downtime, reduces material waste, and helps maintain a consistent standard across thousands of units per production cycle.
Another area of advancement is robotic handling and part orientation, where collaborative robots—or cobots—assist human operators in repositioning parts or loading blanks into the press systems. These cobots are equipped with vision systems and adaptive grippers, enabling them to handle multiple pan sizes and orientations without the need for retooling. Their flexibility significantly boosts throughput while preserving worker safety by reducing manual lifting and handling of heavy or hot materials.
Adaptive tooling is also gaining popularity. These are intelligent die systems that adjust their behavior based on the material properties of each batch of metal. For instance, minor variations in sheet thickness or hardness can affect how the metal forms under pressure. Using real-time feedback, the machine dynamically compensates for these differences, ensuring consistent product dimensions and structural strength across varied input materials. This is especially useful when working with recycled or mixed-alloy metal stocks.
Looking ahead, integration with digital twins—virtual replicas of the manufacturing line—enables simulation of new pan designs or process changes before physical adjustments are made. Engineers can test everything from metal flow during pressing to the behavior of coatings in the curing oven, reducing time-to-market for new products and limiting costly trial runs. These simulations also help with training new operators, who can learn the intricacies of the system in a risk-free virtual environment before working on the live machine.
From a design perspective, the roasting pans themselves are starting to reflect greater consumer expectations around multifunctionality and aesthetic appeal. Machines are now capable of producing pans with integrated pour spouts, textured interiors for better caramelization, or multi-layered metal bottoms for even heat distribution. Some advanced lines also accommodate color-coded or custom-finished handles and accents, meeting retail branding requirements or matching themed kitchen collections.
In terms of logistics, smart factories equipped with these machines often sync directly with warehouse and inventory systems. As soon as a batch of roasting pans is completed, automated guided vehicles (AGVs) or conveyor-based systems transport them to dispatch zones based on real-time demand and shipping schedules. This tight coordination between production and distribution minimizes stockpiling and keeps the supply chain agile.
Ultimately, the sheet metal roasting pan manufacturing machine is no longer just a production tool—it’s part of a broader ecosystem that encompasses intelligent automation, sustainable practices, responsive design, and customer-focused innovation. As culinary trends evolve and kitchen technologies change, these machines ensure that manufacturers can deliver products that are not only functional and durable but also aligned with the lifestyles and expectations of modern cooks. The machine’s adaptability makes it a vital component in the future of cookware manufacturing.
Sheet Metal Stock Pot Manufacturing Machine
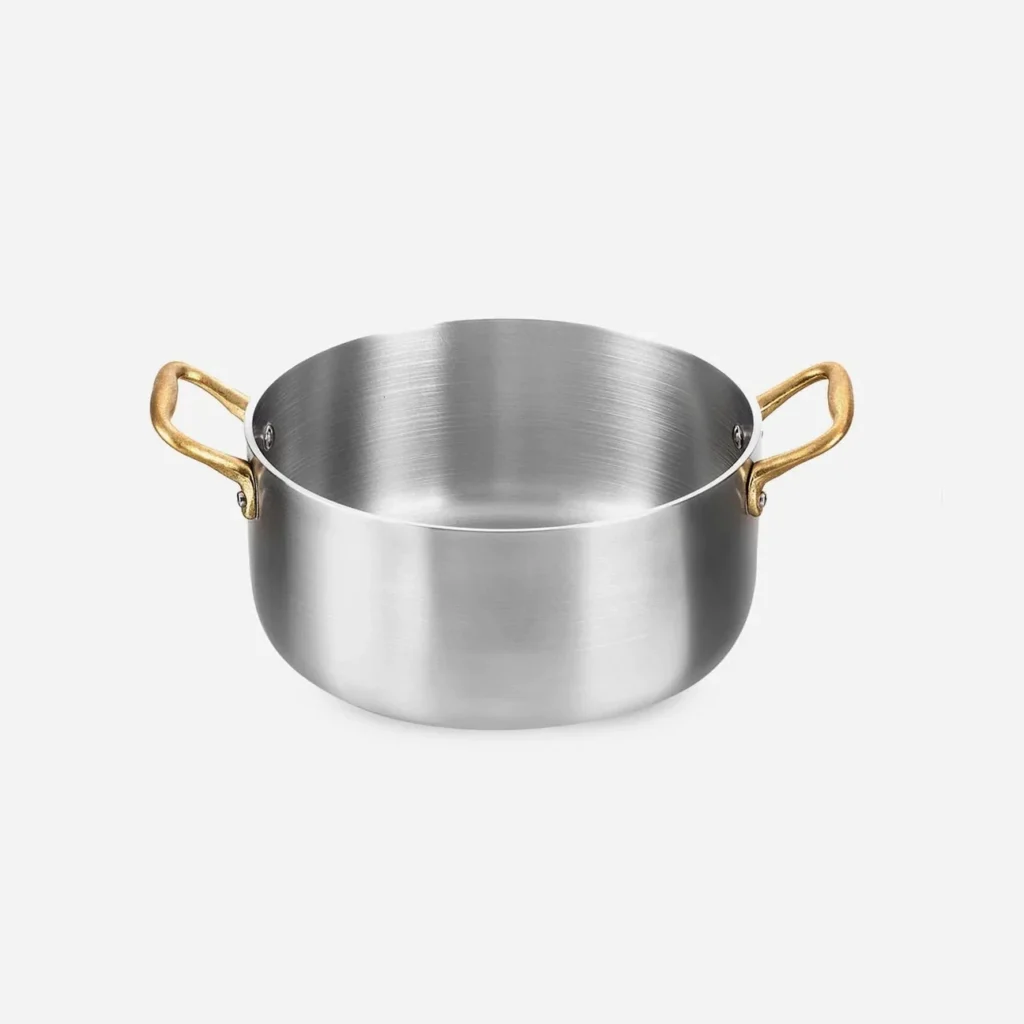
The Sheet Metal Stock Pot Manufacturing Machine is a specialized industrial system designed to efficiently produce stock pots, a vital piece of cookware used in both domestic and commercial kitchens for boiling, simmering, and cooking large quantities of food. Stock pots are characterized by their deep, wide bodies and heavy-duty construction, often made from stainless steel or aluminum to ensure even heat distribution and resistance to rust and corrosion. The manufacturing machine is specifically engineered to handle the various processes involved in producing high-quality stock pots with uniform dimensions, consistent thickness, and durable finishes.
The production begins with raw sheet metal, which is typically stainless steel due to its excellent resistance to heat, corrosion, and staining. Aluminum is another common choice for stock pots, valued for its lightweight nature and superior thermal conductivity. The sheet metal is first unrolled and then cut to size using precision laser cutting or shearing machines, depending on the pot’s design specifications. The blanks are cut to predetermined dimensions, ensuring that each part of the pot will meet the required tolerances.
Once the blanks are prepared, the next step in the process is the forming phase. Using deep drawing or stamping methods, the machine forms the sheet metal into the initial pot shape. Deep drawing is a crucial step for stock pots, as it involves stretching the metal to create the deep, cylindrical shape typical of these cooking vessels. The process must be controlled carefully to avoid thinning or warping of the metal, ensuring that the pot retains its strength and can withstand high heat and frequent use.
Following the forming process, the pots undergo edge trimming to remove any excess material, leaving a clean, smooth rim. The edges are then curled or rolled over to form a flanged lip, which not only reinforces the pot’s structural integrity but also makes it safer and easier to handle. Some advanced systems may include reinforced beads along the rim for added durability, particularly in commercial applications where pots are subject to heavy usage.
At this point, if the stock pot requires handles, the machine proceeds to a robotic or automated welding station. Handles are typically made from heat-resistant materials such as stainless steel or bakelite, and they are securely attached to the sides of the pot using high-precision welding or riveting techniques. The handles are carefully placed and welded to ensure they are firmly bonded, capable of withstanding the high temperatures and frequent use typical in both home kitchens and restaurants. For larger commercial pots, the machine may be configured with a multi-head welding system to handle several pots at once, improving production efficiency.
After handle installation, the stock pots move to surface finishing processes. These can include polishing, brushing, or anodizing to improve the appearance of the pots and enhance their resistance to staining or scratching. For stainless steel pots, electropolishing can be used to give the surface a smooth, shiny finish that is both aesthetically pleasing and easy to clean. If non-stick coatings are required, the machine incorporates a coating station where the pots are sprayed or dipped in a non-stick material, followed by a curing process to harden the coating. Some systems are designed for dual-coating applications, where the interior and exterior of the pot receive separate treatments for maximum durability and functionality.
The stock pots then pass through a quality control system that checks for dimensional accuracy, structural integrity, and any surface defects. Advanced systems use vision-based inspection to detect scratches, dents, or irregularities in the surface, while dimensional scanners ensure that each pot adheres to strict specifications. Any items that fall outside the acceptable quality standards are flagged for rework or rejection.
Once inspected and approved, the pots undergo a final cleaning stage. This typically involves ultrasonic cleaning, high-pressure air jets, or water-based systems to remove any oils, debris, or residue left over from manufacturing. After drying, the pots are ready for packaging.
Packaging is automated, with pots either being individually wrapped or boxed in sets for retail. Packaging is designed to prevent damage during shipping, often using foam inserts or corrugated cardboard to cushion the pots. In some cases, specialized packaging for commercial kitchens ensures that larger pots are handled securely and shipped in bulk.
The manufacturing line is optimized for high efficiency and low manual labor, with most processes being automated to reduce human error and increase throughput. Many systems are programmable and can easily switch between different pot sizes or designs, allowing manufacturers to produce a variety of stock pots—from small home kitchen pots to large, industrial-sized pots used in restaurants, catering, and food processing.
To maintain high production speeds, these machines also incorporate material handling systems such as automated conveyors, robotic arms, or AGVs (automated guided vehicles) to move parts through various stages of the manufacturing process. These systems ensure that the raw materials and finished products are transported seamlessly through the production line, reducing delays and improving overall cycle time.
Energy efficiency is another focus for modern stock pot manufacturing machines. Many of the processes, particularly the heating and curing stages, are optimized to use less energy. Smart manufacturing technologies enable manufacturers to monitor energy usage in real-time, allowing for adjustments to be made for maximum efficiency. This reduces the carbon footprint of the production process and lowers operating costs.
In summary, the sheet metal stock pot manufacturing machine is an advanced, automated system that combines precision, efficiency, and flexibility to produce durable, high-quality stock pots for a wide range of culinary applications. With continuous advancements in automation, materials technology, and sustainable practices, these machines are designed to meet the ever-increasing demands of both consumers and commercial foodservice industries.
The sheet metal stock pot manufacturing machine continues to evolve with advancements in both technology and design, further enhancing production capabilities. As the demand for precision, durability, and sustainability grows, the machine incorporates more intelligent systems to adapt to shifting market needs. The integration of robotics and machine learning into the production line has made it possible for manufacturers to produce a wide variety of stock pots efficiently while maintaining the highest quality standards. This includes adjusting machine parameters on-the-fly, predicting maintenance needs, and optimizing production schedules for different pot sizes or designs, ensuring that production remains flexible and responsive.
One area of significant improvement is the incorporation of predictive maintenance tools. Sensors embedded throughout the manufacturing line can detect wear and tear on critical components such as presses, welders, or coating stations. By analyzing data from these sensors, machine learning algorithms predict when maintenance is required before a failure occurs. This helps prevent costly downtime and ensures the production line runs smoothly. Additionally, these systems provide real-time feedback on the health of the equipment, allowing manufacturers to perform corrective actions more quickly, further minimizing disruption to production.
As environmental concerns continue to shape the global manufacturing landscape, sheet metal stock pot manufacturing machines are increasingly designed with sustainability in mind. These machines now include systems for minimizing waste, such as metal scrap recycling features that redirect offcuts back into the system for reuse. The energy consumption of each stage in the production process is constantly monitored, and energy-efficient motors and heating systems are employed to reduce overall power usage. Many machines are also designed to minimize the environmental impact of coating and cleaning processes by utilizing non-toxic materials and water-based solutions, eliminating the need for harsh chemicals that could harm the environment.
The ongoing demand for customization in cookware also impacts the way these machines operate. Today’s stock pot manufacturing lines are often able to produce pots with customized features, such as branding logos, unique handle shapes, or even limited edition designs that cater to specific markets. Using advanced 3D modeling and CAD/CAM systems, manufacturers can quickly adapt their production lines to accommodate new designs, ensuring that the finished products meet the latest market trends or customer specifications. This flexibility is critical in a market that increasingly values personalization and aesthetic appeal alongside function.
Furthermore, the emergence of smart manufacturing has made it easier for manufacturers to track and monitor production data in real time. By utilizing IoT (Internet of Things) technology, machines can communicate with each other and with centralized control systems. This connectivity allows operators to oversee the entire production process from a single dashboard, ensuring that every stage of the manufacturing process runs as efficiently as possible. In addition, these systems can collect data on every pot produced, enabling manufacturers to perform in-depth analysis and identify opportunities for further optimization, both in terms of time and material usage.
In terms of logistics, stock pot manufacturing machines now integrate seamlessly with warehouse management systems (WMS), creating a more streamlined flow of goods from production to distribution. Automated systems handle inventory tracking, and once the stock pots are produced, they are sent directly to packaging and ready for shipping without unnecessary manual handling. In many cases, the products are immediately prepared for just-in-time delivery, meeting the needs of a global customer base with precision and speed. As e-commerce continues to grow, the manufacturing system adapts to smaller batch sizes and quicker turnaround times, allowing manufacturers to cater to both large retailers and individual consumers.
The continuous refinement of the sheet metal stock pot manufacturing machine ensures that manufacturers are better equipped to handle the diverse demands of today’s market. By combining automation with flexibility, sustainability, and technological advancements, these machines are not only improving the production process but also setting new standards for quality, efficiency, and innovation in cookware manufacturing. As the industry moves forward, these machines will play a crucial role in enabling manufacturers to meet the evolving needs of the culinary world, delivering stock pots that are not only functional but also environmentally responsible and tailored to the specific preferences of consumers worldwide.
As the sheet metal stock pot manufacturing machines continue to advance, there’s a growing trend toward integrating artificial intelligence (AI) and advanced analytics into the production process. AI-powered systems are being used to further optimize the efficiency of each stage in the manufacturing cycle. By analyzing vast amounts of data collected throughout the production process, AI algorithms can identify patterns, predict potential bottlenecks, and suggest adjustments to improve throughput. These systems can learn from past production runs and continuously improve their predictions, helping to reduce cycle times and enhance product consistency. This intelligent approach allows manufacturers to react faster to changes in demand, material availability, and production conditions, ensuring smoother and more agile operations.
Additionally, automated quality control systems are evolving with the implementation of machine vision and deep learning technologies. These systems are capable of inspecting each stock pot at various stages of production—such as after forming, welding, and coating—using high-resolution cameras and AI-powered image recognition software. The AI system can detect even the smallest defects, such as scratches, dents, or coating inconsistencies, with far greater accuracy than human inspectors. Once a defect is identified, the system can trigger corrective actions, such as adjusting machine settings or removing the defective product from the production line, reducing the need for manual inspections and ensuring that only products that meet the highest standards reach the market.
Another key development in the manufacturing of sheet metal stock pots is the adoption of modular manufacturing systems. These systems allow for the reconfiguration of production lines to accommodate different sizes, designs, and production volumes. This modular approach not only offers greater flexibility in production but also makes it easier for manufacturers to quickly introduce new products without the need for complete overhauls of their existing equipment. Manufacturers can easily switch between small-batch custom designs and large-volume runs, meeting the diverse demands of both the consumer market and commercial food service providers.
At the same time, manufacturers are increasingly focusing on ergonomics and safety in the design of their machines. New stock pot manufacturing systems are equipped with human-machine interfaces (HMIs) that are intuitive and easy to operate, allowing operators to quickly adjust settings and troubleshoot any issues. These systems also include safety features such as collision detection, automatic shut-off mechanisms, and safety barriers to prevent accidents. These improvements ensure that operators can work efficiently without compromising their safety, creating a more productive and secure work environment.
The global trend toward sustainability also continues to drive innovation in stock pot manufacturing. Manufacturers are exploring new materials that are not only durable and functional but also more environmentally friendly. For instance, many manufacturers are now using recycled metals in their production processes, reducing the need for new raw materials and lowering the environmental impact of their operations. Additionally, water-based coatings and low-VOC (volatile organic compounds) paints are becoming more prevalent, replacing traditional, harmful chemical coatings. This shift is in response to increasing consumer and regulatory demand for products that have a lower environmental footprint.
As 3D printing and additive manufacturing technologies mature, it is also expected that they will be integrated into the production of stock pots in the near future. 3D printing could be used for creating complex pot handles, custom lid designs, or even prototypes for new stock pot models before mass production begins. This would allow for faster iteration of designs and lower development costs. For example, designers could print small batches of customized stock pots for culinary professionals or niche markets, allowing for a more personalized cooking experience.
Furthermore, the increasing shift toward direct-to-consumer sales through online platforms is influencing the way sheet metal stock pots are packaged and distributed. In response to this, stock pot manufacturing machines are being adapted to accommodate specialized packaging requirements, including sustainable packaging materials such as biodegradable plastics or recycled cardboard. These systems ensure that the pots are securely packaged while minimizing waste, which is important for both cost-efficiency and environmental responsibility. Enhanced packaging systems also help in protecting the product during shipping, reducing the likelihood of damage, and increasing customer satisfaction.
As consumer preferences continue to shift toward multifunctional cookware—pots that are suitable for both stovetop cooking and oven use, or pots with specialized features like integrated strainers or vented lids—sheet metal stock pot manufacturing machines are adapting to produce these more complex products. These designs require additional processing steps, such as incorporating ventilation systems, dual-material layers, or smart technology integration that can notify users of cooking progress. The manufacturing machines must be capable of handling these added complexities while maintaining high production speeds and quality.
The future of sheet metal stock pot manufacturing is undeniably focused on automation, sustainability, and consumer-centric innovation. The demand for high-quality, versatile cookware is growing, and manufacturers are investing in cutting-edge technologies to meet these demands while also responding to environmental and safety concerns. As the technology continues to evolve, the industry is poised for even greater advancements that will shape how stock pots are made, distributed, and used in kitchens worldwide. With the introduction of advanced materials, smart features, and eco-friendly practices, the sheet metal stock pot manufacturing machine will continue to be an essential tool in producing cookware that meets the needs of modern consumers and professionals alike.
Sheet Metal Frying Pan Manufacturing Machine
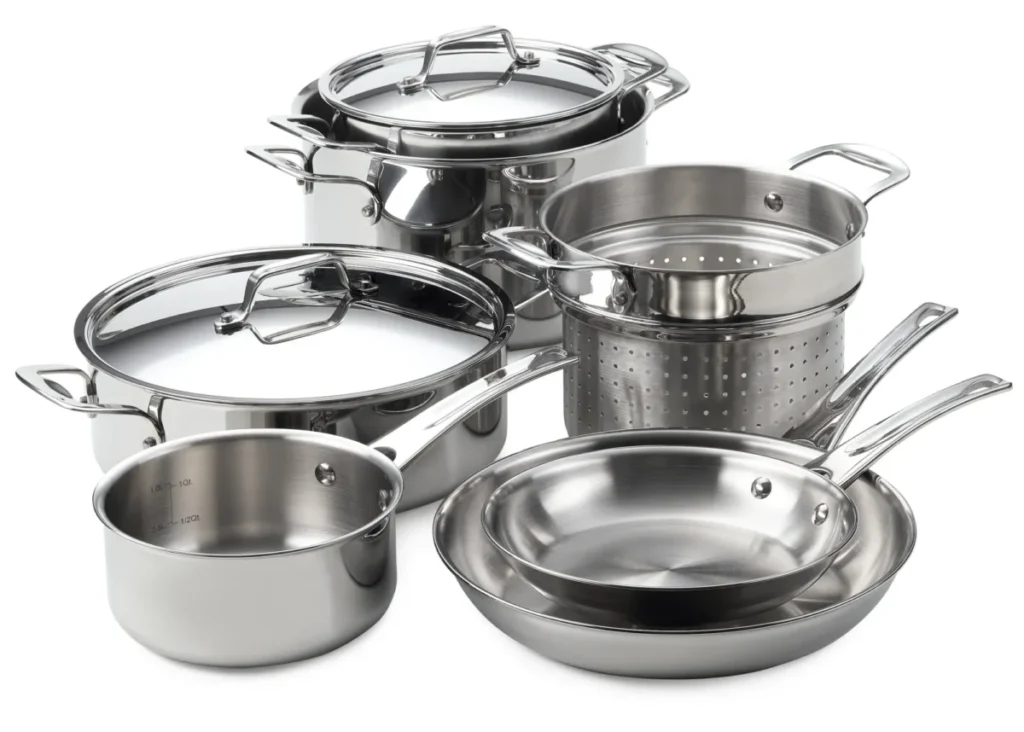
The Sheet Metal Frying Pan Manufacturing Machine is an advanced, high-precision system specifically designed to produce high-quality frying pans for residential, commercial, and industrial use. Frying pans, also known as skillets, are a staple in kitchens around the world, known for their ability to cook a variety of dishes with direct heat. These pans are typically made from metals such as stainless steel, aluminum, or cast iron, but sheet metal variants offer advantages like lighter weight and faster heating times, making them popular in modern cookware lines.
The manufacturing process begins with raw sheet metal, typically stainless steel or aluminum due to their heat conductivity, durability, and resistance to corrosion. The sheet metal is uncoiled from rolls and then processed by precision cutting equipment, such as laser cutters or shearing machines, to produce blanks of the correct dimensions for the frying pans. These blanks are pre-checked for any imperfections, ensuring uniformity in thickness and size before they proceed to the next phase.
Once the blanks are prepared, the next crucial step is forming the pan shape. The sheet metal is placed into a deep drawing press—a machine that uses a die to form the metal into the desired shape. In this case, the machine forms the blank into a shallow, circular bowl shape that will later become the frying pan. During this process, the metal is stretched under high pressure to form the sides of the pan while maintaining consistent thickness. This step must be carefully controlled to avoid thinning the metal, which could compromise the durability and heat retention of the frying pan.
After the forming step, the frying pan undergoes edge trimming to remove any excess material left from the initial pressing process. The machine then rolls the edges of the pan to create a smooth, reinforced lip that makes the pan easier to handle and more structurally sound. In some cases, additional beading or reinforcing of the edges may occur, particularly if the frying pan is intended for commercial or industrial use where more robustness is required.
If handles are part of the design, they are attached at this stage. Automated welding or riveting machines are used to securely fasten handles to the body of the frying pan. The handles are typically made from stainless steel or heat-resistant materials like bakelite or silicone, and the automated system ensures that they are securely affixed without damaging the metal surface of the pan. For larger frying pans or those with special features, handles may be reinforced with stainless steel inserts to improve strength and heat resistance.
Next, the frying pans go through surface treatment processes. These may include polishing, brushing, or coating. Stainless steel frying pans are often polished to a shiny finish using a buffing machine, giving the pan a smooth, attractive appearance. Aluminum pans may undergo anodizing, a process that thickens the metal’s oxide layer to increase its resistance to scratching and staining while also providing a non-stick surface. If the frying pan is designed to have a non-stick coating, a spray-coating or dip-coating process is used. The pan is coated with a layer of non-stick material (like Teflon or ceramic-based coatings), and then cured in an oven to ensure the coating adheres properly to the surface.
After surface treatments are completed, the frying pans undergo quality control inspections. During this phase, machines equipped with vision systems or laser measurement tools check the frying pans for any deformities, such as surface flaws, incorrect dimensions, or inconsistencies in coating thickness. Automated systems can inspect and reject any substandard products, ensuring that only those meeting the required standards move forward in the process.
Once the frying pans have passed quality control, they move to the cleaning stage, where any residual oils, dirt, or debris from manufacturing are removed. This is typically done using an ultrasonic cleaning system or high-pressure washing system. The pans are thoroughly cleaned to ensure they are free from contaminants before they are packed for shipping.
For packaging, the frying pans are either placed in retail-ready packaging or boxed in bulk for distribution. Packaging is designed to protect the frying pan from damage during transportation and to make the product attractive to consumers. For retail packaging, the frying pans are carefully wrapped in protective materials like foam inserts or cardboard dividers to prevent scratches and dents. In bulk packaging for commercial use, the pans may be grouped together with minimal padding, and the packaging will be designed to facilitate easy handling and storage.
Modern sheet metal frying pan manufacturing machines are often integrated with robotics and automated material handling systems to increase efficiency and reduce labor costs. Robotic arms can be used to move parts between stages, such as transferring formed pans to the welding or coating stations, reducing the need for human intervention and minimizing the risk of errors or injury. Additionally, the production line is typically equipped with inventory management systems to track materials and finished goods in real time, ensuring that the manufacturing process runs smoothly and that inventory is always aligned with demand.
Sustainability is a growing focus in frying pan manufacturing as well. Many manufacturers now prioritize recycled materials, using scrap metal from previous production runs or post-consumer recycled metals to create new frying pans. This reduces the environmental impact of sourcing virgin metals and minimizes waste generated during the manufacturing process. In addition, many manufacturing lines have adopted energy-efficient technologies, such as electric ovens for coating curing and solar power to reduce overall carbon emissions.
As the demand for non-stick, induction-ready frying pans grows, manufacturing machines have adapted to produce pans with specific coatings or designs to meet these needs. Machines now include options to create induction-compatible bases, where the bottom of the pan is specially designed to work with induction cooktops, requiring precision in thickness and metal composition.
In summary, the sheet metal frying pan manufacturing machine combines high-speed automation, advanced materials handling, and precision engineering to produce high-quality frying pans that meet the diverse needs of modern kitchens. The manufacturing process is highly automated, from cutting and forming the metal to welding handles, applying coatings, and packaging the final product. With innovations in automation, material science, and sustainability, these machines continue to evolve, ensuring that frying pans meet the highest standards of performance, durability, and environmental responsibility.
The sheet metal frying pan manufacturing machine also benefits from continuous improvements in machine learning and artificial intelligence (AI), which play an increasing role in optimizing production. For instance, AI-powered systems can track and analyze data from every stage of production, identifying potential inefficiencies or anomalies before they lead to problems. If the system detects a slight deviation in metal thickness, for example, it can automatically adjust machine settings to correct the issue, ensuring that each frying pan is produced to the exact specifications.
The integration of advanced sensors in the machine also allows for real-time monitoring of crucial parameters such as temperature, pressure, and material flow. These sensors help to monitor the forming process and ensure that the metal is not over-stressed, preventing defects such as cracking or warping. Moreover, these sensors can detect variations in coating consistency or surface quality during the non-stick coating application, enabling automatic adjustments to maintain the desired finish.
Collaborative robots (cobots) are becoming more prevalent in frying pan manufacturing lines, especially in tasks that require flexibility, such as manual inspection or finishing. Cobots work alongside human operators to handle delicate tasks or assist in quality control, improving both efficiency and safety. They can quickly swap between tasks, such as welding, attaching handles, or packaging, and provide consistent, high-quality results with minimal human intervention.
The demand for multifunctional cookware is also influencing the design and capabilities of frying pan manufacturing machines. As consumers increasingly look for frying pans that are compatible with induction cooktops, machines are being adapted to manufacture induction-ready frying pans. This requires precise engineering, as the base of the pan needs to have specific ferrous metal properties to work with induction cooking systems. Some machines are now able to apply a magnetic layer to the bottom of the frying pan, ensuring it is compatible with all induction cooktops, while also optimizing energy consumption and cooking efficiency.
Another trend in frying pan manufacturing is the development of eco-friendly and sustainable products. Many manufacturers are now shifting toward producing frying pans with recycled aluminum or steel, reducing their carbon footprint and contributing to a more circular economy. In addition, the coatings used on frying pans are evolving to become more environmentally friendly. Traditional non-stick coatings, which often contain harmful chemicals, are being replaced by PTFE-free alternatives, such as ceramic coatings or other non-toxic options. These new coatings are designed to be just as effective at providing a non-stick surface while reducing the environmental impact of the product.
The packaging process has also been optimized in recent years. Frying pans are often sold in retail-ready packaging, which is designed to minimize waste while ensuring the product is protected during shipping and display. Many manufacturers now use biodegradable or recycled materials for packaging, as well as smart labeling, which allows consumers to scan a QR code for more information about the product’s materials and sustainability practices. This trend is driven by consumer demand for more transparent and responsible manufacturing processes.
The digitalization of the frying pan manufacturing process has also made significant strides in recent years. Through cloud-based software systems, manufacturers can now track production data in real time, optimizing their operations for efficiency, cost reduction, and better resource management. This also allows them to meet the growing consumer demand for customized frying pans. Consumers can now order frying pans with unique designs, colors, or handle shapes, and manufacturers can adjust their production lines accordingly. This level of personalization in cookware is now a reality, thanks to the flexibility of modern sheet metal frying pan manufacturing machines.
In addition, the globalization of the cookware market has pushed manufacturers to create products that can be easily shipped and marketed across different regions, with specific designs and standards that meet local consumer preferences. The manufacturing machines used to produce these frying pans are designed to accommodate various sizes, materials, and specifications, giving companies the ability to target diverse market segments efficiently.
With automation, AI, sustainability, and customization as key drivers, the sheet metal frying pan manufacturing machine is evolving to meet the changing demands of consumers and the environment. By focusing on precision, speed, and flexibility, these machines ensure that manufacturers can produce frying pans of the highest quality while meeting the expectations of modern kitchens and the need for more sustainable production practices. These machines represent the cutting edge of cookware manufacturing, shaping the future of kitchen essentials worldwide.
As the sheet metal frying pan manufacturing machine evolves, it is becoming increasingly integrated with advanced manufacturing technologies that enable greater efficiency, flexibility, and customization. One of the most notable advancements is the use of additive manufacturing or 3D printing in certain aspects of frying pan production. While the main body of the pan is still formed using traditional methods like deep drawing, certain complex parts, such as the handles or auxiliary features, can now be 3D printed. This technology allows for rapid prototyping and the production of intricate designs that were previously difficult or impossible to achieve with conventional manufacturing methods. Custom designs and innovative handle shapes can be tested and produced quickly, offering manufacturers the ability to respond more rapidly to market trends and consumer preferences.
Additionally, robotic automation continues to revolutionize the frying pan manufacturing process. Robotic arms are increasingly used for tasks such as material handling, assembly, quality control, and packaging, ensuring high precision and consistency throughout the production process. These robots are programmed to carry out repetitive tasks quickly and accurately, reducing human error and labor costs while improving production speeds. For example, robotic arms can be used to pick and place the frying pan blanks into the forming dies, weld handles to the pans, or even carefully inspect the pans for any defects. This not only speeds up the process but also ensures that each pan meets strict quality standards.
The rise of IoT (Internet of Things) technologies in manufacturing has also played a key role in advancing the efficiency of sheet metal frying pan production. IoT devices embedded in machines and production lines provide real-time data that can be accessed by operators and managers from anywhere. By monitoring critical metrics such as machine performance, raw material consumption, and energy usage, manufacturers can make data-driven decisions that improve productivity, reduce waste, and lower energy costs. Furthermore, these devices can send alerts for preventive maintenance, ensuring that potential issues are addressed before they result in downtime or costly repairs.
Moreover, cloud-based software solutions now play a significant role in managing the entire manufacturing workflow. These systems allow for real-time tracking of production progress, inventory management, and even customer orders, all from a centralized platform. This digital transformation provides manufacturers with greater visibility and control over their production lines, ensuring that the manufacturing process is as streamlined and efficient as possible. It also enables the production of custom frying pans based on customer preferences, as manufacturers can easily adjust machine settings to accommodate personalized orders.
Another critical advancement in sheet metal frying pan manufacturing is the shift toward environmentally conscious production. Manufacturers are increasingly incorporating energy-efficient technologies into their machines, reducing the overall carbon footprint of the production process. For instance, many machines now use regenerative braking systems to capture and reuse energy during certain phases of production, such as in the forming or pressing stages. Heat recovery systems are also being employed to capture excess heat generated during the manufacturing process and reuse it in other stages, further reducing energy consumption.
In addition to energy efficiency, there is a growing emphasis on material sustainability in the frying pan manufacturing industry. Manufacturers are increasingly sourcing metals that are recycled, further reducing the environmental impact of their products. For example, the use of recycled aluminum or steel not only lowers the demand for virgin materials but also helps reduce the overall carbon emissions associated with mining and refining these metals. Moreover, companies are investing in technologies that reduce waste during production, such as cutting-edge laser systems that provide higher precision in material cutting, thus minimizing scrap metal.
The demand for eco-friendly cookware is also influencing the development of green coatings for frying pans. Non-toxic, PFOA-free (perfluorooctanoic acid) coatings are becoming the standard for non-stick pans, with manufacturers moving away from harmful chemicals traditionally used in non-stick coatings. New materials, such as ceramic-based coatings and water-based enamel, are gaining popularity due to their reduced environmental impact and health benefits. As part of this shift, manufacturers are also exploring more biodegradable packaging materials and innovative ways to reduce the environmental footprint of the packaging process.
The market for premium and specialized frying pans is also on the rise, with more consumers seeking cookware that offers unique features or superior performance. These trends are prompting manufacturers to design machines that can produce frying pans with additional characteristics, such as ergonomic handles, reinforced edges, or multi-layered materials that provide improved heat distribution. Multi-material pans, which combine aluminum for quick heat transfer with a stainless steel exterior for durability, are becoming increasingly popular, and manufacturing machines are evolving to accommodate these advanced product designs.
Finally, global market expansion is influencing frying pan manufacturing machines. As consumer preferences and cooking styles vary across regions, manufacturers are tailoring their production processes to meet the specific demands of local markets. For example, frying pans designed for Asian cooking styles may require different shapes or handle types than those intended for Western culinary practices. The ability of modern manufacturing machines to quickly adapt to different specifications ensures that producers can meet the diverse needs of consumers worldwide without sacrificing production speed or cost-effectiveness.
In conclusion, the sheet metal frying pan manufacturing machine is at the forefront of a revolution in cookware production. Through innovations in automation, robotics, AI, sustainability, and customization, these machines are transforming the way frying pans are made, ensuring that they are more efficient, environmentally friendly, and responsive to consumer demand. The future of frying pan manufacturing promises even greater integration of smart technologies, further advancements in eco-friendly practices, and an increased focus on producing high-quality, multifunctional cookware that meets the needs of a global and increasingly eco-conscious market.
Sheet Metal Salt & Pepper Shaker Set Manufacturing Machine
The Sheet Metal Salt & Pepper Shaker Set Manufacturing Machine is a specialized piece of equipment used to produce salt and pepper shakers made from sheet metal materials, typically stainless steel, aluminum, or other corrosion-resistant metals. These sets are a popular choice for households and restaurants due to their durability, sleek appearance, and ease of cleaning. The manufacturing process involves several stages, from the initial cutting of raw material to the final assembly and packaging of the finished shakers. Here’s an overview of the production process for manufacturing metal salt and pepper shaker sets:
1. Raw Material Preparation
The process begins with selecting high-quality sheet metal rolls, typically made of stainless steel for its corrosion resistance or aluminum for its lightweight properties. The metal sheets are uncoiled from rolls and checked for thickness consistency and defects. A variety of thicknesses may be used, depending on the desired weight and durability of the final product.
2. Cutting and Shaping the Shaker Body
The first major step in the process is cutting the metal sheet into blanks that will form the body of the shaker. This is typically done using laser cutting, shearing machines, or punch presses to achieve the correct dimensions for the shaker body. The blanks are carefully inspected to ensure they meet the size specifications and are free of defects.
Next, the metal blanks are moved to a deep drawing press, which uses a die to form the blanks into the cylindrical or domed shape required for the salt and pepper shaker. This deep drawing process stretches and shapes the metal into the hollow bodies of the shakers. The machine applies high pressure, ensuring the walls are even and the desired shape is achieved without causing thinning or tearing of the metal.
3. Edge Trimming and Smoothing
Once the basic shape is formed, the edges of the metal shakers need to be trimmed to ensure smoothness and consistency. A trimming die or edge-finishing tool removes any excess material or burrs left over from the forming process. This step ensures that the shaker edges are smooth and safe to handle.
At this point, the shakers may also undergo deburring or smoothing processes to eliminate any sharp edges or rough surfaces. This step is especially important to ensure that the metal shakers are safe for handling, preventing injury or discomfort during use.
4. Hole Punching for Salt and Pepper Dispensing
The next step is the punching of holes on the shaker tops for salt and pepper dispensing. This is done using precision punch presses equipped with specialized dies that create a series of small holes, arranged in an aesthetically pleasing pattern, on the shaker lid. The number and size of the holes can vary depending on the design and function of the shaker. For example, some shakers may have larger holes for faster dispensing, while others may have smaller holes for more controlled output.
5. Handle and Lid Formation
After the shaker bodies are formed and hole-punched, the next step is the production of the lids and handles (if the design requires handles). The lids are typically made from the same sheet metal material as the shaker body, though they may also be made from different materials like plastic or glass for aesthetic or functional purposes. Lids are typically produced using stamping or deep drawing processes.
In cases where the shaker set has handles, the handles are formed from metal rods or sheet metal that are bent and welded or riveted into place. Automated robots or machines often handle these processes to ensure precision and repeatability.
6. Surface Treatment and Coating
Once the basic structure of the salt and pepper shakers is complete, the next step is applying any desired surface treatment or coating to enhance the durability, appearance, and functionality of the shakers. Common treatments include:
- Polishing: Using abrasive materials or polishing wheels, the shakers are given a smooth, shiny finish. This helps improve their appearance and ensures they are resistant to corrosion.
- Brushing: For a matte or satin finish, the shakers may undergo a brushing process where the surface is mechanically polished with fine abrasive materials to create a textured appearance.
- Coating: Many metal shakers receive an additional protective coating, such as a clear lacquer or powder coating, to prevent corrosion, scratches, or tarnishing. This is especially common for aluminum shakers. Some manufacturers also offer colored coatings for aesthetic purposes.
7. Assembly
Once the individual components are formed and treated, they are moved to the assembly station, where the shakers are put together. The shaker bodies are matched with their respective lids, and handles (if included) are affixed. Automated assembly lines often include robotic arms or conveyor belts to streamline this process, ensuring that all parts are aligned properly and securely fastened.
If any additional components, such as gaskets or seals, are required for air-tightness or preventing leaks, they are inserted into the assembly at this stage. These seals ensure that the shakers retain their contents without spilling, even when the shaker is tilted or shaken.
8. Quality Control
Before the salt and pepper shaker sets are packaged and sent out for distribution, they undergo rigorous quality control checks. This may include visual inspection for surface defects, ensuring that the holes for dispensing are properly aligned, and checking that all components are securely assembled. Automated vision systems can detect minor flaws such as scratches, dents, or coating inconsistencies.
Additionally, some shakers may undergo functional testing to ensure that the dispensing mechanism works smoothly and the shaker is easy to fill and use. If any shakers are found to be defective or below the required standard, they are removed from the production line.
9. Packaging
Once the salt and pepper shakers have passed quality control, they are ready for packaging. Typically, the shakers are carefully placed in protective packaging, such as cardboard boxes, blister packs, or plastic clamshells, to prevent damage during transportation and retail display. For bulk orders, the sets may be packed into larger cartons or shipping containers.
Custom packaging is often used for retail purposes to make the product more appealing to consumers. This packaging may include branded labels, instructions for care, and other product details to enhance the customer experience.
10. Shipping and Distribution
The final step in the process is shipping the finished salt and pepper shakers to distributors, retailers, or direct customers. Logistics management plays a critical role in ensuring that the products arrive on time and in good condition. Depending on the market and distribution strategy, the shakers may be sold in bulk to wholesalers, as individual sets to retail stores, or directly to consumers through online platforms.
Technological Advances in Manufacturing
Modern sheet metal salt & pepper shaker set manufacturing machines often incorporate advanced technologies to improve production efficiency and precision. These technologies include:
- Robotic automation for material handling, assembly, and packaging, reducing labor costs and increasing production speed.
- Laser cutting for precise shaping of the shaker bodies and components.
- Advanced coating technologies to apply more durable, eco-friendly finishes.
- Vision systems for real-time quality control, ensuring defects are identified and eliminated before reaching the consumer.
- AI and machine learning to optimize machine settings and improve production efficiency based on real-time data from the production line.
In conclusion, the sheet metal salt & pepper shaker set manufacturing machine is an advanced, highly automated system designed to produce durable and aesthetically pleasing shaker sets. The use of cutting-edge technology, robotics, and precision manufacturing techniques allows for the production of high-quality products that meet the demands of both residential and commercial customers.
The Sheet Metal Salt & Pepper Shaker Set Manufacturing Machine continues to evolve as technology advances, allowing for further enhancements in efficiency, customization, and sustainability. Let’s explore some additional factors influencing the development and performance of these machines:
1. Advanced Automation and Robotics
One of the key areas of development in the salt and pepper shaker manufacturing process is the use of advanced robotics and automated systems. For example, robotic arms are often used for tasks like assembling shaker bodies, attaching lids, and inserting internal components like gaskets or sprinkler inserts. These robots improve precision, reduce human error, and allow for faster production speeds, making it possible to meet growing consumer demand for these products.
Additionally, collaborative robots (cobots) are becoming more common on the production line. Cobots can work side-by-side with human operators, handling tasks that may be repetitive or require consistent strength, such as lifting heavy components or securing screws. This ensures that human workers are free to focus on more complex tasks, while still increasing overall productivity and safety.
2. Customization and Personalization
With the rise of consumer demand for unique and personalized products, manufacturers are investing in more flexible machinery capable of producing customized salt and pepper shakers. This is particularly relevant in the giftware and premium cookware markets, where consumers want unique designs, colors, or engravings on their shaker sets.
Modern sheet metal manufacturing machines can accommodate these demands by allowing for easy integration of laser engraving or printing technologies. Custom logos, names, or decorative designs can be added to the surface of the shakers during the production process, creating products that are tailored to specific customer preferences.
3. Sustainability Focus
As environmental concerns continue to grow, manufacturers of sheet metal salt and pepper shakers are increasingly focusing on sustainability. Many companies are choosing to use recycled metals, such as recycled aluminum or stainless steel, to reduce the environmental impact of their products. This material choice helps to minimize energy consumption during the manufacturing process, as recycled metals require less energy to produce than new materials.
The trend toward eco-friendly coatings is also gaining traction. Traditional coatings, such as polymer-based finishes and lacquer, are being replaced with more sustainable alternatives that are non-toxic and free from harmful chemicals like PFOA. These coatings not only improve the environmental footprint of the products but also make the shakers safer for consumers.
In addition, manufacturers are optimizing their production lines to reduce material waste, using precision cutting and laser technology to create near-perfect shapes from the metal sheets. This minimizes the amount of scrap produced during the cutting and shaping stages, further reducing waste.
4. Smart Manufacturing Integration
As the manufacturing industry becomes more digitally connected, many sheet metal shaker set production lines are integrating smart manufacturing technologies. These systems allow for real-time monitoring and predictive maintenance, which can significantly reduce downtime and increase the lifespan of machines.
By collecting data from machines throughout the production process, manufacturers can identify potential issues before they lead to failures. For example, if a machine experiences a sudden dip in performance or a tool shows signs of wear, the system can alert operators, allowing them to take action and prevent any disruptions in production. This predictive maintenance can save costs and ensure smooth operations, reducing the risk of costly repairs or production halts.
5. Globalization and Market Trends
The sheet metal salt and pepper shaker market is becoming increasingly globalized, with demand growing in emerging markets as well as established ones. Manufacturers must adapt to meet the demands of various regions, which may require different sizes, shapes, or designs based on local preferences.
In the Asian market, for instance, there may be a preference for smaller, compact designs, while in Western markets, larger or more decorative shakers may be favored. To meet these demands, manufacturing machines are becoming more versatile, able to quickly switch between different product styles without significant downtime or reconfiguration. This ability to produce multiple variations of the same product on the same line is essential for competing in a global market.
6. Enhanced Quality Control
Quality control is a crucial part of the salt and pepper shaker manufacturing process, as the products must meet strict standards for durability, functionality, and aesthetics. As production lines become more automated, manufacturers are incorporating more advanced visual inspection systems and 3D scanning technologies to ensure that each shaker is produced to the highest standards.
These inspection systems use cameras and sensors to scan each shaker for defects, such as surface scratches, misaligned lids, or incorrect hole patterns. Any product that fails the inspection is immediately removed from the production line for further evaluation or rework, ensuring that only high-quality shakers reach the consumer.
7. Fast and Efficient Production
The demand for quicker production times, especially in response to seasonal trends or special promotions, is pushing manufacturers to invest in faster, more efficient machinery. The latest sheet metal shaker manufacturing machines are designed to operate at high speeds, with some systems capable of producing thousands of shaker sets per day.
This high-speed production is made possible by advanced automation and precision engineering, which allow machines to perform multiple tasks—such as cutting, forming, punching, and assembly—in a single pass. This not only reduces the overall production time but also improves the overall cost-effectiveness of the manufacturing process.
8. Consumer Demand for Luxury and Premium Products
In addition to the push for more sustainable and customizable products, there is a growing consumer preference for premium, luxury cookware items, which extends to salt and pepper shaker sets. These premium shakers are often made with high-end materials such as brushed stainless steel, gold plating, or even copper finishes.
Manufacturers are increasingly developing machines that can handle these specialized materials and finishes. For example, some production lines now feature equipment capable of applying intricate metal plating or creating embossed designs on the shaker surface. These machines are able to work with these delicate materials without compromising the integrity or quality of the product, catering to the high-end market’s desire for both functionality and beauty.
Conclusion
The sheet metal salt and pepper shaker set manufacturing machine continues to evolve with advances in automation, customization, sustainability, and efficiency. By embracing these innovations, manufacturers can meet growing consumer demand for both standard and custom shaker sets while also keeping costs low and maintaining high-quality standards. As the market for functional yet aesthetically appealing cookware continues to expand, these machines will play a pivotal role in shaping the future of the salt and pepper shaker industry.
As manufacturing technologies evolve, there are even further innovations and enhancements in the sheet metal salt and pepper shaker set manufacturing process that continue to shape the industry. Let’s dive into some emerging trends, challenges, and future outlook for these specialized machines.
1. Integration of Artificial Intelligence (AI) in Manufacturing
Artificial intelligence (AI) is increasingly making its way into manufacturing processes, including the production of sheet metal salt and pepper shakers. AI-driven systems are capable of analyzing data in real-time, optimizing the production process, and ensuring that the products meet the highest quality standards. AI can help identify patterns in manufacturing data that humans might overlook, leading to better decision-making for machine optimization, production scheduling, and inventory management.
For instance, AI-powered systems can predict when a machine is likely to break down or experience a decrease in efficiency, allowing manufacturers to take preemptive measures. This improves overall production efficiency and reduces the costs associated with unplanned downtime. Furthermore, AI can assist in the automated design process, where machine learning algorithms can generate new shaker designs based on consumer preferences and market trends.
2. Advanced Material Science and Alloys
The choice of materials used in manufacturing sheet metal salt and pepper shaker sets is expanding beyond traditional stainless steel and aluminum. Advanced materials such as titanium alloys, copper, and carbon steel are being explored for their unique properties, such as increased durability, resistance to corrosion, and aesthetic appeal.
For example, titanium is known for being lightweight yet incredibly strong, making it ideal for high-end cookware. Copper is not only durable but also adds a rich aesthetic that appeals to consumers looking for premium products. These advanced materials require specialized equipment for shaping and processing, and manufacturers are adapting their production lines to handle these metals without compromising quality.
3. Customization and On-Demand Production
As consumer expectations shift toward personalized and on-demand products, manufacturers of salt and pepper shaker sets are adopting flexible manufacturing systems that allow for greater customization without sacrificing production speed or efficiency. With the rise of 3D printing and additive manufacturing, it’s becoming easier to create bespoke shaker sets in small batches.
These technologies allow for highly detailed and intricate designs to be produced, even for small runs, which was previously difficult and costly with traditional mass-production techniques. Consumers can request engraved names, logos, or even personalized patterns that are unique to their order, making these products more desirable for gifts, special events, and upscale restaurants.
Additionally, the trend toward on-demand production is gaining traction, where customers can place small orders of custom-made products, and machines can adjust to produce these orders with minimal reconfiguration. This reduces overproduction and the need for large inventories, which is especially beneficial for manufacturers aiming to stay ahead in an increasingly environmentally-conscious market.
4. Sustainability in Manufacturing Practices
Sustainability continues to be a key driver in the sheet metal manufacturing process. Manufacturers are increasingly focused on minimizing the environmental impact of their operations. Some of the key strategies in this area include:
- Energy-efficient production: Manufacturers are upgrading to machines that consume less energy while maintaining high production rates. This includes the adoption of more energy-efficient laser cutting, pressing, and forming technologies that reduce energy consumption.
- Closed-loop systems: Waste management is becoming a critical aspect of production. Closed-loop systems that recycle scrap metal, such as small trimmings or leftover material from the cutting process, help ensure that these materials are reused in future production cycles, reducing the environmental footprint of manufacturing operations.
- Packaging innovations: Eco-friendly and sustainable packaging is gaining importance. Many manufacturers are shifting from plastic-based packaging to biodegradable or recycled materials to package salt and pepper shaker sets. Additionally, packaging designs are being optimized to use less material, further reducing waste.
- Low-emission machinery: Many companies are introducing machines that use less toxic or harmful chemicals, which are especially important for coating and finishing processes. This also ensures better working conditions for factory workers and meets stricter environmental regulations in various countries.
5. Smart Sensors and IoT Integration
The Internet of Things (IoT) and smart sensors are becoming increasingly integrated into the manufacturing process. These devices collect data from various machines in real-time, providing insights into machine performance, product quality, and overall production efficiency.
For example, a smart sensor system can detect deviations in temperature, pressure, or vibration during the metal forming process and immediately alert operators if there’s a problem. These systems also allow for predictive maintenance, where machines can be serviced before they break down, avoiding costly disruptions in production.
Moreover, IoT-enabled production lines allow manufacturers to track the entire production process remotely, enabling real-time updates on inventory levels, order status, and quality control measures. This integration enhances transparency, reduces downtime, and facilitates better decision-making across the entire supply chain.
6. Consumer Trends and Market Demand
Changes in consumer preferences are driving new trends in the production of salt and pepper shakers. For example, consumers are increasingly interested in products that align with their values, such as sustainability, ethical production, and local sourcing. This demand is pushing manufacturers to develop eco-friendly products and use locally sourced materials whenever possible.
Another consumer trend is the growing interest in smart kitchen appliances. As kitchens become more connected, the demand for smart salt and pepper shakers that offer features like adjustable dispensing mechanisms or salt-level sensors is rising. Manufacturers are exploring ways to integrate these technologies into their shaker designs, though this requires a more complex assembly process.
In addition, there is a rising demand for luxury kitchenware that combines both functionality and design. Consumers are willing to invest in premium salt and pepper shaker sets that are stylish and durable, often made from high-end metals or featuring artistic, handcrafted designs. Manufacturers catering to this niche market may focus on unique shapes, finishes, and engraving options.
7. Challenges in Sheet Metal Manufacturing
While advancements in technology have revolutionized the production of salt and pepper shakers, there are still several challenges faced by manufacturers:
- Material Costs: The cost of high-quality metals, especially stainless steel and aluminum, can fluctuate based on global supply and demand. Manufacturers must continuously monitor these costs to maintain competitive pricing while ensuring the durability and quality of their products.
- Tool Wear and Maintenance: The cutting, shaping, and forming tools used in manufacturing salt and pepper shakers undergo significant wear and tear, especially when processing hard metals like titanium or stainless steel. Regular maintenance and tool replacement are required to maintain precision and ensure smooth production. This can incur extra costs and downtime.
- Supply Chain Disruptions: Global supply chain disruptions, such as those caused by geopolitical events or natural disasters, can lead to delays in material procurement and machinery parts. Manufacturers must adopt flexible strategies to mitigate the impact of these disruptions, such as developing relationships with multiple suppliers or sourcing materials locally.
- Regulatory Compliance: As regulations around product safety, sustainability, and environmental impact tighten globally, manufacturers must stay up-to-date with evolving standards. This may require frequent updates to production processes or the adoption of new technologies that comply with stricter regulations.
8. Future Outlook
The future of sheet metal salt and pepper shaker manufacturing looks promising, driven by the ongoing evolution of automation, smart technology, and sustainability. As more consumers seek premium, customized, and eco-friendly products, manufacturers will continue to innovate their production processes to meet these demands.
The introduction of next-generation materials, AI-driven design and production, and fully automated manufacturing lines will further revolutionize the industry. Additionally, with the growing interest in smart home devices, there may be a push to create connected salt and pepper shakers that integrate with other kitchen technologies, adding functionality alongside aesthetic appeal.
Manufacturers that can adapt to these trends—while maintaining quality, reducing waste, and staying responsive to market demands—will likely thrive in an increasingly competitive global market.
In summary, sheet metal salt and pepper shaker set manufacturing is undergoing significant changes. Advancements in technology, sustainability, and consumer demands are shaping the future of this industry, offering exciting opportunities for both manufacturers and consumers alike.
Sheet Metal Butter Dish Manufacturing Machine
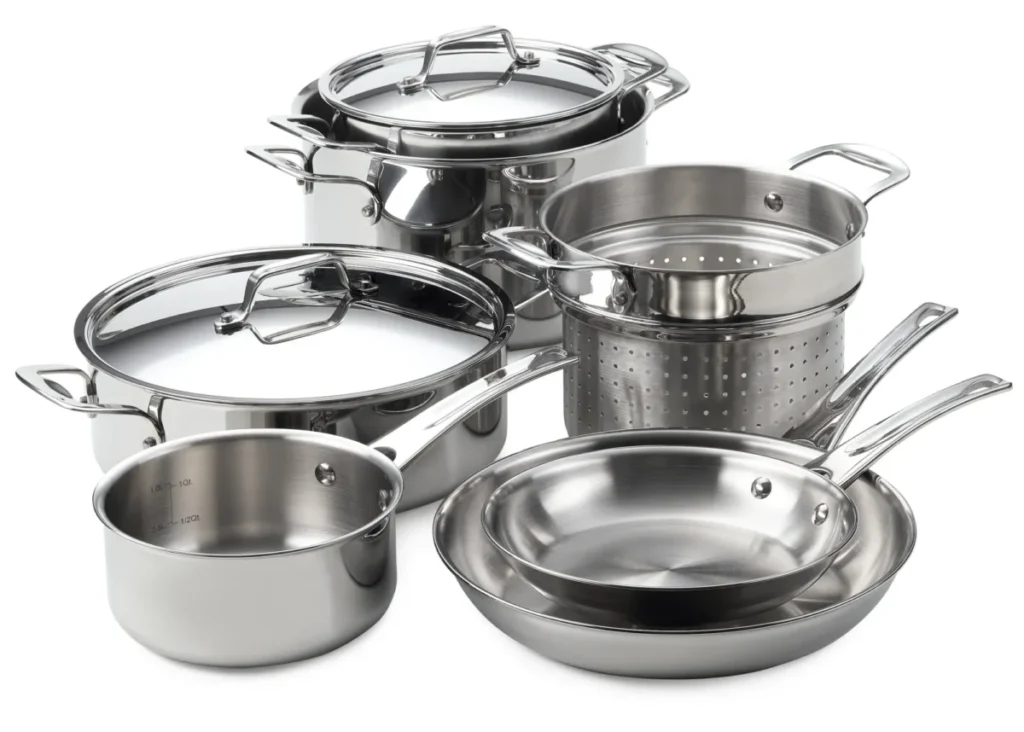
The Sheet Metal Butter Dish Manufacturing Machine is designed to produce butter dishes using sheet metal as the primary material. These machines are equipped with various advanced technologies to ensure precise cutting, forming, and assembling of the components needed to create high-quality butter dishes. Here’s a breakdown of the process and key technologies involved in the manufacturing of sheet metal butter dishes.
1. Design Considerations for Butter Dishes
Before starting the manufacturing process, manufacturers design butter dishes based on consumer preferences for shape, size, and aesthetics. Some common design considerations include:
- Lid Style: Butter dishes can have a hinged or removable lid, depending on the design.
- Shape: Common shapes include rectangular, oval, or square.
- Surface Finish: Manufacturers often opt for finishes like brushed, polished, or matte for visual appeal and ease of cleaning.
- Durability: The material used should ensure long-lasting performance, including resistance to rust and corrosion.
2. Key Components and Materials
- Sheet Metal: The primary material used is typically stainless steel or aluminum, known for their durability, resistance to corrosion, and aesthetic properties. Stainless steel is particularly favored for its non-reactive nature and ease of cleaning.
- Handles/Lids: Some butter dishes may have additional components, such as handles for easy lifting or specially designed lids for better storage and preservation.
3. Manufacturing Process
The process of manufacturing sheet metal butter dishes typically involves the following steps:
A. Material Cutting and Blank Preparation
- The process begins with sheet metal coils or sheets of the chosen material. These sheets are cut into blanks of appropriate sizes, using advanced laser cutting or punching machines.
- For complex designs, laser cutting offers precision and accuracy in producing intricate patterns or designs, such as decorative edges or holes for ventilation.
B. Forming
- After the blanks are cut, they undergo forming or shaping processes to create the dish’s body and lid. This is typically done using press forming or deep drawing techniques, where the sheet metal is pressed into a mold to create the desired shape.
- Hydraulic presses or mechanical presses are commonly used for these forming processes, as they can apply significant force to shape the metal precisely.
C. Edge Finishing
- The edges of the butter dish are smoothed and finished to remove sharpness or burrs that may remain from cutting and forming. This is usually done using a deburring or grinding process.
- For higher-end butter dishes, polishing may be employed to give the dish a smooth, shiny surface.
D. Assembly of Lid and Base
- If the butter dish includes a lid, the base and lid are assembled using spot welding, riveting, or screwing.
- In some designs, a hinged lid is incorporated, which may require additional components like pins or hinges. These components are typically attached using automated assembly machines.
E. Surface Treatment and Finishing
- The final step often involves adding a protective coating to the butter dish. For example, electroplating may be applied to create a glossy finish or provide an additional layer of corrosion resistance.
- Powder coating or anodizing can also be used for a matte finish that resists scratching and tarnishing. This process can also be used to add decorative colors to the butter dish.
4. Quality Control
Throughout the production process, strict quality control measures are implemented to ensure that each butter dish meets the required standards for durability, shape, and surface finish. These measures include:
- Dimensional inspections: Ensuring that the dimensions of the dish, lid, and other components meet design specifications.
- Surface inspections: Checking for any imperfections like scratches, dents, or discolorations.
- Functional testing: For butter dishes with lids or handles, testing ensures proper functionality, such as ease of opening or securely closing the lid.
5. Automation and Robotics
To enhance productivity and reduce labor costs, many modern butter dish manufacturing processes incorporate robotics and automation:
- Robotic arms handle repetitive tasks like assembling the lid, attaching handles, or moving components through different stages of the production process.
- Vision systems ensure accurate placement of components, such as lids and handles, and check for defects during assembly.
6. Packaging and Shipping
Once the butter dishes are manufactured, they undergo packaging. Since these are often high-end items, protective packaging is used to ensure they reach consumers without damage. Packaging might include foam inserts, cardboard boxes, and outer protective wrapping.
7. Sustainability in Manufacturing
Given the growing demand for eco-friendly products, manufacturers are focusing on sustainable practices:
- Using recycled metals for the production of the butter dishes helps reduce the environmental impact.
- Water-based coatings and non-toxic materials are increasingly being used to ensure the product is safe for consumers and the environment.
8. Technological Trends in Butter Dish Manufacturing
Future advancements in sheet metal butter dish manufacturing include:
- 3D Printing: Some manufacturers are exploring 3D printing for creating intricate designs and even testing prototypes before mass production.
- Smart Manufacturing: IoT devices and smart sensors are being integrated into manufacturing equipment to monitor performance, ensure quality control, and predict maintenance needs.
- Customization: The increasing demand for personalized products means that machines will be able to accommodate small-batch or made-to-order designs.
Conclusion
The Sheet Metal Butter Dish Manufacturing Machine is a critical part of the process that ensures high-quality, durable, and aesthetically pleasing butter dishes. Through a combination of advanced manufacturing techniques like laser cutting, press forming, and automation, manufacturers can produce these products efficiently and at scale. With the increasing consumer interest in sustainable, customizable, and premium products, this field is likely to continue evolving, with more emphasis on eco-friendly practices and innovative design features.
The sheet metal butter dish manufacturing machine operates as part of a highly specialized process, where precision, efficiency, and quality are the primary considerations. This process involves the careful transformation of raw materials, typically stainless steel or aluminum, into a durable, aesthetically appealing product that can withstand regular use. The production begins with the careful selection of sheet metal, chosen for its ability to resist corrosion, its ability to be formed into intricate shapes, and its long-lasting durability.
Once the material is selected, it’s processed through advanced cutting techniques, such as laser cutting or punching, to create precise blanks of the required size. These blanks are then subjected to a series of forming processes that turn them into the final shape of the butter dish. These processes typically involve press forming or deep drawing, where the sheet metal is shaped into a mold or die. This is where high precision is critical, as the shape of the butter dish must be uniform across every unit produced, particularly around the edges and corners where the lid and base may meet. The next step in the process is the edge finishing. Sharp edges from the cutting process are smoothed, polished, or deburred to ensure safety, particularly when handling the product. Some manufacturers may also apply additional finishes, such as a polished or matte surface, to enhance the visual appeal and provide a smooth, easy-to-clean surface.
Assembly plays a crucial role in producing high-quality butter dishes, particularly for those models with lids. Depending on the design, the dish may be spot welded, riveted, or assembled with screws. The incorporation of hinged lids may require additional components like pins or special fasteners, which are attached with care to maintain proper functionality. Each component, from the lid to the base, must fit perfectly to ensure ease of use, such as opening and closing without resistance or malfunction. With the final product almost complete, it then undergoes various types of surface treatments like powder coating, electroplating, or anodizing. These treatments not only enhance the durability of the product by preventing rust or corrosion but also provide an aesthetic quality that appeals to consumers. These surface treatments can also add visual appeal by giving the dish a shiny, polished look or a soft, matte finish that enhances its appearance.
To meet increasing consumer demands for quality and precision, manufacturers are increasingly integrating automated systems throughout the production process. Robotic arms and automated assembly lines help streamline the process, ensuring consistent quality across thousands of units. These robots can handle tasks such as placing lids on the base, checking for surface imperfections, or ensuring that the components are correctly aligned before moving to the next production stage. Vision systems are another technological advancement that improves quality control by automatically identifying defects, such as scratches or dents, on the metal surface, helping to catch issues early before they make it to the finished product.
As the demand for sustainable products grows, sheet metal butter dish manufacturers are also focusing on environmentally friendly practices. Recycled materials are increasingly being used to minimize waste, while energy-efficient machines help reduce the carbon footprint of the production process. Additionally, water-based coatings and eco-friendly packaging options are becoming more common, aligning with the broader global push toward more responsible manufacturing.
The manufacturing process also considers customization. As consumer preferences shift toward personalized products, machines are being adapted to accommodate special requests such as custom engravings, unique designs, or limited-edition collections. The rise of on-demand manufacturing and 3D printing technologies is making it easier for manufacturers to offer these personalized products without compromising production efficiency or increasing costs.
In terms of market trends, there’s a clear shift toward higher-end, premium butter dishes that offer both aesthetic appeal and functional durability. Consumers are willing to pay a premium for products that not only serve their intended purpose but also reflect their personal taste or add elegance to their kitchen. This trend has led to a rise in the demand for luxury butter dishes, made from high-end metals such as titanium or copper, which require more specialized equipment to process.
Future advancements in the technology used for manufacturing sheet metal butter dishes will likely continue to be driven by the need for greater efficiency, sustainability, and customization. The growing use of smart technology and IoT sensors in manufacturing machinery will enable manufacturers to monitor machine performance in real-time, predict maintenance needs, and make adjustments to improve production efficiency and reduce costs. Meanwhile, the integration of artificial intelligence into the design process could allow manufacturers to predict consumer preferences more accurately, enabling the creation of butter dishes that are more attuned to the latest market demands.
In summary, the manufacturing of sheet metal butter dishes is a highly advanced process that combines traditional metalworking techniques with modern automation, robotics, and sustainability practices. As consumer demands continue to evolve, the industry will likely see further innovations aimed at improving product quality, production efficiency, and customization options. These developments will continue to make sheet metal butter dishes a durable, stylish, and functional addition to any kitchen.
The manufacturing of sheet metal butter dishes is poised for further advancements as technology continues to reshape the production process. Automation, advanced robotics, and cutting-edge materials are all contributing to the efficiency and precision of butter dish production, while sustainability and consumer demand for customizability continue to drive the evolution of manufacturing practices. As these technologies continue to mature, the process will likely become even more streamlined and tailored to the preferences of individual consumers, allowing for a new level of personalization in mass production.
One of the primary drivers of change in this field is the growing trend toward intelligent manufacturing. With the rise of smart machines that are connected through the Internet of Things (IoT), manufacturers are gaining the ability to monitor their equipment in real-time, gaining insights into machine health, production rates, and potential issues before they occur. These systems use predictive analytics to determine when maintenance is needed, reducing downtime and increasing the overall efficiency of the production process. In addition, data analytics is increasingly being utilized to optimize production schedules and reduce material waste, further improving the sustainability of manufacturing operations.
As artificial intelligence (AI) continues to advance, manufacturers of sheet metal butter dishes are exploring ways to integrate AI into both the design and production phases. AI can be used to assist in product design by predicting consumer preferences based on current trends, allowing for the creation of more appealing and functional butter dish designs. Additionally, AI algorithms can help identify areas of improvement in the production process, optimizing everything from material flow to machine calibration, ultimately resulting in higher-quality products and lower production costs.
The continued development of 3D printing and additive manufacturing also holds significant promise for the future of sheet metal butter dish production. These technologies allow for rapid prototyping, enabling designers to experiment with new designs and shapes for butter dishes without incurring the costs and time delays associated with traditional manufacturing methods. 3D printing can also be used for producing intricate, customized components, such as handles or decorative elements, that would be difficult or impossible to create using conventional sheet metal forming techniques. Additionally, these technologies offer the possibility of creating small-batch, on-demand manufacturing runs, which can be a major advantage in catering to niche markets or fulfilling unique customer requests.
Sustainability is another key consideration driving innovation in butter dish manufacturing. As environmental concerns become more prominent, companies are under increasing pressure to reduce their carbon footprint and minimize waste. Manufacturers are adopting closed-loop systems where metal scraps from the cutting and forming processes are recycled back into the production cycle, reducing the amount of raw material required and limiting waste. Furthermore, advances in green technologies—such as the use of solar power in manufacturing plants or the development of low-energy machinery—are helping to reduce the overall environmental impact of production. Many companies are also opting for more eco-friendly surface finishes, such as water-based coatings or biodegradable packaging, to reduce the environmental impact of their products.
In addition to sustainability, consumers are increasingly interested in the aesthetic appeal of their kitchenware. This has led to the rise in demand for premium, luxury butter dishes that combine both functional design and visual elegance. Manufacturers are responding by introducing a variety of finishes and designs, including polished stainless steel, brushed matte finishes, and even custom engravings or personalized logos. Some high-end models may incorporate wooden accents or other materials like glass or ceramic inserts, creating a more unique and upscale product. The rise of luxury kitchenware has led to the development of artisan butter dishes, where individual pieces are handcrafted or made in limited batches, giving them a sense of exclusivity and craftsmanship.
Additionally, the customization of butter dishes is becoming more prevalent, particularly as consumer preferences become more individualized. Some manufacturers now offer customizable options for the size, shape, and even engraved designs on butter dishes, allowing consumers to create a product that suits their unique tastes. This personalization is facilitated by advanced manufacturing technologies such as laser engraving, which enables highly detailed and accurate designs to be etched into the metal surface of the butter dish. With the ability to customize nearly every aspect of a product, manufacturers can now cater to a broader range of consumers looking for something more distinctive or aligned with their personal tastes.
While automation and robotics have already streamlined many of the production processes, the future will likely see further integration of collaborative robots (cobots) on the shop floor. Cobots are designed to work alongside human operators, assisting with tasks that may be physically demanding or require high levels of precision. For example, a cobot could handle repetitive tasks like placing lids on butter dishes or conducting final quality inspections, reducing the potential for human error and freeing up operators to focus on more complex tasks. The use of cobots is particularly beneficial in small-scale or custom manufacturing environments where flexibility and human oversight are essential.
As global demand for products like sheet metal butter dishes continues to grow, manufacturers will need to balance mass production with the increasing demand for personalized, high-quality products. The convergence of advanced robotics, AI, and smart manufacturing will allow companies to maintain efficient, cost-effective production lines while simultaneously offering tailored products to meet the diverse needs of consumers. This ability to mix customization with high-volume production will be a key factor in the success of manufacturers in the coming years.
In conclusion, the manufacturing of sheet metal butter dishes is evolving in response to technological advancements, changing consumer preferences, and the push for greater sustainability. As companies adopt cutting-edge technologies such as AI, automation, and 3D printing, the production of these items will become more efficient, customizable, and environmentally friendly. With the growing emphasis on personalized products and luxury kitchenware, the future of butter dish manufacturing holds significant promise for innovation, efficiency, and consumer satisfaction. Manufacturers that can leverage these technologies while maintaining quality, durability, and aesthetics will be well-positioned to meet the demands of modern consumers.
Sheet Metal Sugar Bowl Manufacturing Machine
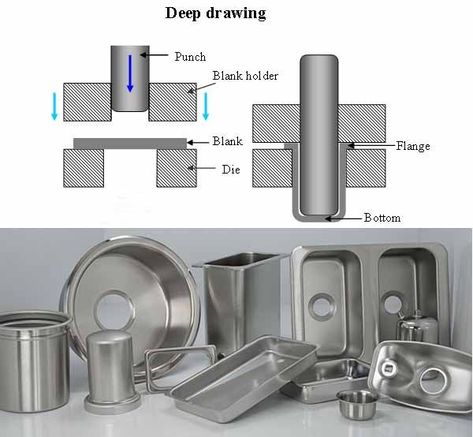
The Sheet Metal Sugar Bowl Manufacturing Machine is designed to produce high-quality sugar bowls using sheet metal materials, primarily stainless steel or aluminum, that are durable, rust-resistant, and easy to clean. These machines are equipped with advanced technologies to ensure precision in cutting, shaping, and assembling the components of a sugar bowl. Here’s an overview of the typical process involved in the manufacturing of sheet metal sugar bowls.
The process begins with the selection of sheet metal in the desired thickness and material. Stainless steel is commonly used for its durability, resistance to corrosion, and aesthetic qualities, while aluminum can be used for lighter weight options. These sheets are fed into automated machines that perform cutting, shaping, and forming to create the desired components of the sugar bowl.
Step 1: Cutting the Metal
The first step in the process is the cutting of the raw sheet metal into specific sizes or blanks. This is typically done using laser cutting or punching machines that precisely cut the sheet metal into the required shapes. For example, circular or oval blanks are often cut to form the base of the sugar bowl.
Step 2: Shaping and Forming
Once the blanks are cut, they undergo the shaping process. The sugar bowl shape is formed through press forming or deep drawing methods, where the cut sheet metal is pressed into a mold. This process creates the body of the sugar bowl, and the metal is shaped into a smooth, uniform form, typically a bowl-like shape with a curved bottom and sides.
For more complex designs, such as decorative edges or handles, additional forming steps may be required. Hydraulic presses or mechanical presses are commonly used in these processes to apply force and create the required shape.
Step 3: Edge Finishing and Smoothing
After the shaping process, the edges of the sugar bowl are smoothed and finished to remove any sharp or rough edges that may have been created during cutting or forming. This is often done using deburring machines or grinding tools. In some cases, the metal may also undergo polishing to ensure a smooth, glossy surface.
Step 4: Assembly of Additional Components
Many sugar bowls have additional features like lids, handles, or decorative elements. The lid is often designed to fit snugly on the top of the bowl to keep the sugar fresh. The lid and other components are added during the assembly process.
Components such as handles or knobs for the lid are typically attached using spot welding, riveting, or screwing methods, depending on the design and material. Spot welding is especially useful for joining two metal components, providing a strong, durable bond. If handles are present, they are usually formed separately and then fixed to the bowl body.
Step 5: Surface Treatment
To enhance the visual appeal and durability of the sugar bowl, it undergoes various surface treatments. Common methods include:
- Electroplating: A coating of nickel or chrome is applied to give the sugar bowl a shiny, metallic finish that is both aesthetically pleasing and resistant to corrosion.
- Powder Coating: For a matte or textured finish, the sugar bowl may be coated with powder, which is then cured in an oven. This provides a durable finish that resists chipping and fading.
- Anodizing: In some cases, especially for aluminum sugar bowls, anodizing is used to create a protective oxide layer on the metal’s surface, providing corrosion resistance and a variety of color options.
Step 6: Quality Control
Quality control is an essential part of the production process. Manufacturers perform strict inspections to ensure that the dimensions of the sugar bowl meet design specifications. Dimensional checks are performed to confirm the accuracy of the shape and size, ensuring that the lid fits properly and that handles or knobs are securely attached.
Surface quality is also closely monitored, as any imperfections in the finish can affect the product’s appeal. The sugar bowls are checked for scratches, dents, or discoloration. Additionally, functional testing ensures that the lids open and close smoothly and that handles are securely attached.
Step 7: Packaging and Shipping
Once the sugar bowls pass quality control, they are carefully packaged for shipment. This may include protective packaging, such as foam inserts or bubble wrap, to ensure the bowls remain undamaged during transit. Packaging is typically designed to reflect the product’s premium quality, and manufacturers may offer eco-friendly packaging options in line with sustainable practices.
Automation and Robotics
To increase production efficiency, many modern manufacturing lines for sugar bowls incorporate automation and robotic systems. Automated material handling systems move sheet metal from one stage of the production process to another, while robots can assist with tasks like placing handles, fitting lids, and inspecting the final product.
Robotic systems also assist in quality control, using vision systems to identify defects such as scratches, dents, or improper finishes. This level of automation improves overall efficiency and reduces human error.
Sustainability in Manufacturing
Sustainability plays an increasingly important role in the manufacturing process. Manufacturers are increasingly using recycled materials, such as recycled stainless steel or aluminum, to reduce waste and conserve resources. Additionally, companies are adopting energy-efficient machinery and utilizing green technologies like solar power to reduce their environmental impact.
Some companies are also exploring eco-friendly finishes, such as water-based coatings or biodegradable packaging, to make their products more sustainable. These steps not only meet consumer demand for greener products but also align with global sustainability goals.
Conclusion
The manufacturing of sheet metal sugar bowls involves a highly intricate and multi-step process that combines cutting-edge technology with traditional metalworking techniques. From cutting and shaping the metal to adding decorative finishes and ensuring quality control, each step is designed to create a durable, aesthetically pleasing, and functional product. As technology continues to advance, the use of automation, robotics, and sustainable practices will further enhance the efficiency and environmental friendliness of the manufacturing process. These innovations will ensure that sheet metal sugar bowls remain a popular choice among consumers who value quality, durability, and sustainability in their kitchenware.
The sheet metal sugar bowl manufacturing machine continues to evolve alongside advances in materials, automation, and sustainability. Beyond the basics of cutting, shaping, and assembling components, manufacturers are adopting more sophisticated technologies to meet growing demands for efficiency, customizability, and eco-conscious production practices.
As mentioned, automation plays a crucial role in modern production lines. With automated machines performing repetitive tasks, manufacturers can maintain high-speed production while minimizing human error. One major innovation in the field is the use of smart machinery, which incorporates IoT (Internet of Things) technology to enable real-time monitoring and predictive maintenance. These systems collect data from various parts of the machine, such as motor performance, temperature, and pressure, allowing operators to anticipate potential failures and reduce downtime. This predictive approach ensures that the machines stay in optimal working condition, thus enhancing productivity and reducing operational costs.
Manufacturers are also increasingly relying on robotic arms and collaborative robots (cobots). These machines are designed to work alongside human operators, performing tasks that require precision or heavy lifting, such as assembling handles or lids. Cobots are particularly useful for quality control inspections, where robots can quickly spot defects or inconsistencies in the metal surface that human eyes might miss. This integration of robotics not only streamlines production but also helps ensure consistent quality across large batches.
As demand grows for more personalized and customized products, manufacturers are integrating technologies that enable greater flexibility. For example, laser engraving allows for custom designs, names, or logos to be added to the sugar bowl. This personalization is increasingly popular in the consumer market, with customers looking for items that reflect their style or make unique gifts. These features are made possible by the precision of modern manufacturing systems that can accommodate small-scale or batch productions, allowing for high-quality custom designs without compromising efficiency.
On the materials front, advanced coatings and finishes are becoming an essential part of the sugar bowl’s appeal. In addition to traditional finishes like electroplating, anodizing, and powder coating, newer methods such as nano-coatings are being explored. These coatings are not only more environmentally friendly but also provide enhanced properties, such as improved scratch resistance and antimicrobial features. This can add significant value to the final product, especially for consumers who are concerned with hygiene and durability.
A major push within the industry is also the shift towards sustainability. Many manufacturers are now focusing on reducing their carbon footprint and energy usage, with initiatives like using recycled metals and green energy sources for production. In line with these goals, companies are also adopting closed-loop systems where the scraps from the sheet metal are collected and recycled back into production, reducing waste and conserving materials. Furthermore, eco-friendly packaging solutions are gaining traction, where sugar bowls are packaged in recycled or biodegradable materials, appealing to environmentally conscious consumers.
Another significant trend in the industry is the movement toward multi-material manufacturing. Sugar bowls may no longer be confined to just one type of metal. Manufacturers are experimenting with hybrid designs that incorporate different materials, such as wood accents, ceramic inserts, or silicone handles, which add unique textures and designs to the product. These hybrid designs are not only aesthetically appealing but also create functional advantages, such as improved heat resistance or better grip.
Looking toward the future, the integration of artificial intelligence (AI) in manufacturing will likely continue to advance. AI can assist in everything from optimizing production schedules to improving design processes. Generative design algorithms powered by AI can propose new shapes or structures that are not only aesthetically pleasing but also more efficient in terms of material usage and durability. By analyzing vast amounts of data, AI can predict what designs will perform best in the marketplace, allowing manufacturers to stay ahead of consumer trends and preferences.
In summary, the manufacturing of sheet metal sugar bowls is undergoing a transformation driven by the need for greater efficiency, customization, and sustainability. Through the integration of smart manufacturing technologies, robotics, and eco-friendly practices, companies can produce high-quality, durable products while reducing waste and energy consumption. As the demand for personalized and high-end kitchenware continues to rise, the sheet metal sugar bowl manufacturing machine is evolving to meet these changing consumer needs. With technological innovations on the horizon, the future of sugar bowl production promises even more advancements in design, efficiency, and environmental responsibility.
As the sheet metal sugar bowl manufacturing process continues to advance, there are several emerging trends and innovations on the horizon that will likely reshape the industry. These developments are driven by technological advancements, changing consumer preferences, and a growing focus on sustainability. Let’s explore the future of manufacturing in more detail:
1. Integration of Additive Manufacturing (3D Printing)
The use of 3D printing (additive manufacturing) is already transforming many industries, and the sheet metal sugar bowl production line is no exception. While traditionally associated with prototyping and small-scale production, 3D printing has increasingly found a place in mass production as well. In the future, manufacturers may use metal 3D printers to create parts of the sugar bowl that are too intricate or complex to be easily made with traditional methods.
For example, customized components such as decorative patterns, lids, or even handles could be produced using 3D printing. It allows for high precision and design flexibility, especially in cases where intricate patterns or unique shapes are desired. 3D printing also reduces material waste by using only the required amount of metal, which is a significant advantage in terms of both cost and environmental impact.
Additionally, this technology allows manufacturers to quickly iterate on design ideas without needing expensive molds or tooling. This speed in prototyping accelerates the innovation cycle, enabling more rapid testing and consumer feedback loops.
2. Smart Manufacturing and Industry 4.0
As part of the Industry 4.0 movement, the integration of cyber-physical systems (CPS) into the manufacturing environment will play a major role in shaping the future of sheet metal sugar bowl production. Smart manufacturing systems, which include connected machines, sensors, and data analytics, will create highly responsive, automated production lines capable of adjusting in real time to changes in demand, material availability, and equipment performance.
For instance, machines equipped with sensors can monitor the temperature, speed, and pressure during each manufacturing step, instantly feeding data to a centralized cloud-based system. This data can then be analyzed by AI systems to predict maintenance needs, identify areas for efficiency improvements, or optimize production schedules.
Through these systems, manufacturers will be able to create real-time supply chain visibility, adjust production processes to customer demands, and enhance product quality through continuous feedback loops. This smart approach will help eliminate bottlenecks and improve overall productivity, ensuring that the production of sheet metal sugar bowls is more agile and efficient.
3. Sustainability and Circular Economy
The shift toward more sustainable production practices is becoming a defining characteristic of the manufacturing industry, including in the production of sheet metal sugar bowls. The increasing focus on circular economy principles is changing how manufacturers approach the lifecycle of their products. Instead of relying on a linear model of “take-make-dispose,” the circular economy seeks to maximize the use of resources, reduce waste, and create products that can be reused, refurbished, or recycled.
For sugar bowl manufacturers, this means adopting closed-loop systems where metal waste generated during the production process, such as cuttings, trimmings, and scrap, can be recycled and reintegrated into production. Recycled metals, particularly stainless steel and aluminum, are being increasingly used as a way to reduce the reliance on virgin resources and minimize environmental impact.
Another significant development in sustainability is the move toward eco-friendly coatings and finishes. Non-toxic, biodegradable coatings, such as those made from plant-based materials, could replace traditional chemical-based finishes. These alternatives not only reduce the environmental impact but also appeal to consumers who are looking for environmentally responsible products.
Manufacturers are also exploring more sustainable packaging options. Recyclable and biodegradable packaging materials will replace plastics and excessive packaging, aligning with broader sustainability trends in consumer products.
4. Customization and Personalized Products
Consumers are increasingly seeking personalized and unique products. The rise of online shopping platforms and direct-to-consumer models has made it easier for buyers to request customizations on a wide variety of products, including kitchenware like sugar bowls. This trend is pushing manufacturers to explore new ways of offering customization without sacrificing efficiency or cost-effectiveness.
One way to achieve this is by leveraging on-demand manufacturing. Instead of producing large batches of identical products, manufacturers can use advanced CNC machines or robots to quickly create small batches with customized features, such as engravings, sizes, or finishes. This approach allows manufacturers to offer personalized sugar bowls at scale while maintaining cost efficiency.
5. Collaboration with Designers and Artists
As kitchenware products become more integrated into home decor, manufacturers may find it increasingly beneficial to collaborate with designers and artists to produce limited-edition or high-end collections. The luxury kitchenware market is growing, and custom-designed sugar bowls with artistic patterns, unique shapes, and premium finishes are increasingly sought after.
Collaborating with artists can bring new levels of creativity and exclusivity to the product. For instance, using advanced laser engraving or 3D printing techniques, artists can design intricate patterns, logos, or even personalized touches to be applied to each sugar bowl. Such collaborations would cater to consumers who seek distinct, high-quality kitchenware that doubles as decorative items.
6. Advances in Metal Alloys
Another avenue for innovation is the exploration of new metal alloys that enhance the properties of the sugar bowl while also improving its durability, weight, and aesthetic appeal. Advances in stainless steel or the development of new, lightweight alloys can lead to products that are more resistant to corrosion, stains, and discoloration, improving the lifespan and overall value of the product.
Additionally, alloys that allow for better heat resistance or non-stick properties could be explored for more versatile uses of the sugar bowl, allowing it to be used in a variety of applications beyond its primary function, such as in serving hot or cold dishes.
7. Global Trends in Kitchenware and Design
The design preferences for kitchenware are also evolving in response to global trends. For example, the minimalist aesthetic, popularized by Scandinavian design, is influencing how products like sugar bowls are designed. Sleek, functional, and simple shapes with clean lines are becoming the norm, and manufacturers are responding by producing designs that emphasize both form and function.
Furthermore, the demand for multifunctional kitchenware is rising. Consumers want products that serve multiple purposes or can be easily stored, making stackable designs or compact storage solutions more popular. Manufacturers are exploring ways to make sugar bowls not just a container for sugar but also a part of the broader kitchen experience, which could include features such as integrated scoops, dual-function lids, or modular stacking options.
Conclusion
The future of sheet metal sugar bowl manufacturing is characterized by the integration of cutting-edge technologies, such as 3D printing, smart manufacturing, and AI, which are all leading to more efficient, sustainable, and customizable production methods. As the demand for eco-friendly products, personalization, and luxury kitchenware increases, manufacturers must adopt new materials, advanced machinery, and innovative techniques to stay competitive. The trends shaping the industry point to a future where sheet metal sugar bowls are not only functional but also a stylish, sustainable, and personalized addition to the home kitchen.
EMS Metalworking Machines
We design, manufacture and assembly metalworking machinery such as:
- Hydraulic transfer press
- Glass mosaic press
- Hydraulic deep drawing press
- Casting press
- Hydraulic cold forming press
- Hydroforming press
- Composite press
- Silicone rubber moulding press
- Brake pad press
- Melamine press
- SMC & BMC Press
- Labrotaroy press
- Edge cutting trimming machine
- Edge curling machine
- Trimming beading machine
- Trimming joggling machine
- Cookware production line
- Pipe bending machine
- Profile bending machine
- Bandsaw for metal
- Cylindrical welding machine
- Horizontal pres and cookware
- Kitchenware, hotelware
- Bakeware and cuttlery production machinery
as a complete line as well as an individual machine such as:
- Edge cutting trimming beading machines
- Polishing and grinding machines for pot and pans
- Hydraulic drawing presses
- Circle blanking machines
- Riveting machine
- Hole punching machines
- Press feeding machine
You can check our machinery at work at: EMS Metalworking Machinery – YouTube
Applications:
Flange-punching
Beading and ribbing
Flanging
Trimming
Curling
Lock-seaming
Ribbing