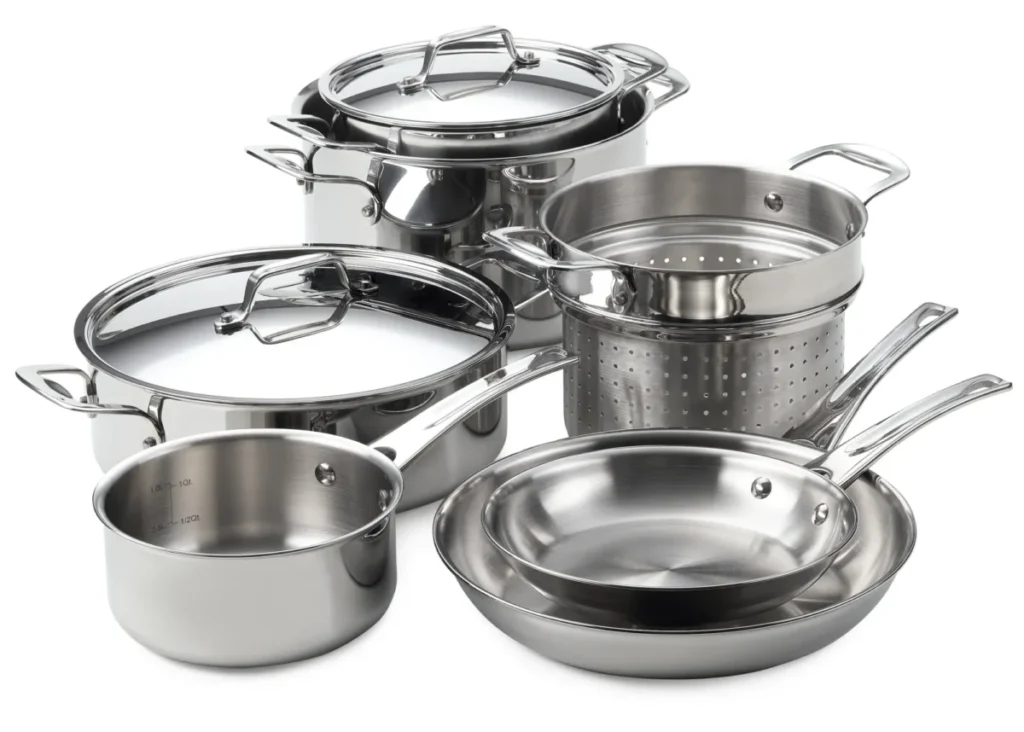
Sheet Metal Serving Platter Manufacturing Machine: When it comes to shaping, cutting, and forming sheet metal, manufacturers rely on a broad ecosystem of specialized machinery. Below is an overview of the most common types of sheet‑metal machinery, what they do, and key considerations when selecting equipment:
Shearing & Cutting Equipment
- Guillotine Shears
- Function: Straight‑line cutting of sheet‑metal stock.
- Key Specs: Maximum thickness, blade length, throat depth, cut angle adjustability.
- Use Cases: Cutting large plates into smaller blanks for further processing.
- Nibblers
- Function: Punch‑and‑die style cutting for free‑form shapes without heat.
- Key Specs: Sheet‑thickness capacity (typically up to ~3 mm mild steel), scrap‑minimizing head design.
- Use Cases: Complex contours, internal cutouts (e.g. louvers, vents).
- Plasma / Laser / Waterjet Cutters
- Function: High‑precision contour cutting via thermal (plasma/laser) or abrasive‑jet (waterjet) processes.
- Key Specs: Cutting speed, kerf width, tolerances (laser: ~±0.1 mm; waterjet: ~±0.2 mm), material thickness limits.
- Use Cases: Intricate patterns, thick/hard alloys, minimal heat‑affected zones (waterjet).
Punching & Perforating Machines
- CNC Turret Punch Presses
- Function: Tool‑changing turret holds multiple punches to blank, pierce, and form holes/shapes.
- Key Specs: Number of tool stations, turret indexing speed, sheet‑handling loader capacity.
- Use Cases: High‑volume hole patterns, louvers, embossing features.
- Rotary & Flatbed Punches
- Function: Similar to turret presses but optimized for specific tasks (e.g., high‑speed punching of simple hole arrays).
- Key Specs: Stroke rate (SPM), sheet thickness, bed size.
Bending & Forming Machinery
- Press Brakes
- Function: Bends sheet metal along straight lines using punch‑and‑die sets.
- Key Specs: Tonnage capacity, bed length, axes (2‑ to 9‑axis CNC), back‑gauge precision.
- Use Cases: Boxes, enclosures, frames; repeatable, programmable bends.
- Folding Machines (Pan Brakes)
- Function: Manual or hydraulic folding of small flanges/profiles.
- Key Specs: Maximum width, folding depth, angle stops.
- Roll Benders / Plate Rolls
- Function: Gradually roll sheets into cylinders or cones.
- Key Specs: Maximum thickness, roll diameter, segment rolls for cone bending.
Stretching & Deep‑Drawing Presses
- Hydraulic Presses
- Function: Apply uniform high pressure for forming deep shapes (e.g., automotive panels).
- Key Specs: Force (tonnage), stroke length, bed size, controllable cushion zones.
- Mechanical Presses
- Function: High‑speed stamping for drawing, blanking, and coining.
- Key Specs: Strokes per minute, slide adjustment, quick die change.
Joining & Assembly Equipment
- Spot Welders
- Function: Resistance welding for joining sheet overlaps.
- Key Specs: Throat depth, electrode force control, weld current programming.
- Riveting Machines & Clinching Presses
- Function: Mechanical joining without heat (blind rivets, clinch joints).
- Key Specs: Stroke force, speed, tooling variety.
- Adhesive Dispensing Robots
- Function: Automated glue or sealant application for structural bonding or sealing.
- Key Specs: Flow‑rate control, robot reach, nozzle types.
Finishing & Secondary Processes
- Deburring & Edge‑Rounding Machines
- Function: Remove burrs and sharp edges via brushes, tumbling, or belt grinders.
- Key Specs: Throughput speed, abrasive media types, adjustable angles.
- Press‑Fit & Insertion Machines
- Function: Insert nuts, studs, or threaded inserts into sheet‑metal parts.
- Key Specs: Insertion force, turret capacity, vision‑inspection integration.
- Coating & Painting Lines
- Function: Powder‑coat or wet‑paint finish with conveyance, curing ovens.
- Key Specs: Line speed, oven length/temperature, filter/reclaim systems.
Selecting the Right Machinery
- Production Volume & Batch Size
- High‑volume—favor automated CNC turret punches, press brakes with automatic tool changers, and robotic welding.
- Low‑volume/prototyping—manual nibblers, smaller press brakes, bench‑top brakes.
- Material & Thickness Range
- Thicker or harder alloys may require more robust presses, waterjet cutting, and higher‑capacity brakes.
- Light‑gauge stainless or aluminum may be handled by lower‑tonnage equipment.
- Precision & Tolerance
- Laser cutters and CNC brakes for tight tolerances; manual methods if tolerances are loose.
- Flexibility vs. Specialization
- General‑purpose machines (e.g. press brakes, turret punches) vs. dedicated lines (e.g. high‑speed stamping press).
- Integration & Automation
- Consider material handling (sheet loaders, conveyors) and CNC/robotic add‑ons for efficiency and safety.
This machinery landscape evolves rapidly with Industry 4.0 trends—CNC controls, IoT monitoring, and robotic integration are becoming standard for competitive throughput and quality control. If you have a specific application or production context in mind (e.g., enclosure fabrication, HVAC panels, automotive stamping), let me know and I can drill into the optimal machine selections, vendors, and process flows!
When you work sheet metal, you need machines that can slice, shape, bend, join and finish flat stock with accuracy and speed. Cutting starts with shears—guillotine shears that chop straight lines in thick plate, nibblers that step‑cut curves without creating heat, or high‑precision contour cutters such as lasers, plasma torches or waterjets (the latter excels at thick or exotic alloys with minimal thermal distortion). Once you’ve blanked out your basic shapes, punch presses—either CNC turret machines with dozens of tool stations or dedicated flat‑bed/rotary punches—drive stamps through the sheet to create holes, louvers, embosses and internal cutouts. Bending comes next, typically on a press brake: hydraulic or electric brakes with two to nine CNC axes and programmable back‑gauges deliver repeatable bends, while folding brakes (pan brakes) and segment roll benders handle lighter or cylindrical forms.
Deep‑drawing and stretching presses—mechanical or hydraulic—then form complex three‑dimensional parts, like automotive panels or enclosures, by forcing the metal into dies under high tonnage. To join parts, resistance spot welders, rivet inserters, clinching presses and robotic adhesive dispensers clamp, squeeze or bond overlapping flanges. Finally, every edge may need deburring—through brushes, tumblers or belt grinders—before nuts, studs or threaded inserts are press‑fitted into bosses, and parts move through powder‑coat or paint‑spray lines with conveyors and curing ovens.
Selecting the right line hinges on your batch size (low‑volume shops lean manual nibblers and bench‑top brakes; high‑volume plants invest in CNC turret punches, auto‑tool‑change brakes and robotic welders), material thickness and alloy (thicker steel or titanium demands more robust equipment), tolerance requirements (lasers and multi‑axis brakes for ±0.1 mm, manual tools for ±0.5 mm or looser), and your desire for automation and Industry 4.0 connectivity—sensors, IoT dashboards and full robotics can boost throughput and trace every bend, cut and weld for quality control.
When scaling up to medium‑volume production, material handling becomes just as critical as the machines themselves. Automated sheet loaders and stackers minimize manual lifting and align blanks precisely for each operation, reducing cycle times and fatigue. Integrating robotic arms for part transfer between cutting, punching, and bending stations not only speeds throughput but also maintains repeatability—robots can reposition parts within ±0.05 mm, ensuring each bend or hole aligns perfectly with the program.
Tooling strategy also evolves: instead of manually swapping punch and die sets, turret punch presses with quick‑change stations can swap dozens of tools in under a minute, and press brakes paired with auto‑tool changers can switch punch/die combinations via magazine systems. Dies may incorporate quick‑clamp features and hydraulic crowning to compensate for deflection when bending wide or thick sections.
On the control side, Manufacturing Execution Systems (MES) tie CNC machines into a central network, scheduling jobs, tracking material usage, and logging machine health data. Predictive maintenance algorithms analyze spindle loads, hydraulic pressures, and vibration signatures to preempt failures—downtime drops by up to 30%.
Quality inspection tightens: in‑line laser scanners and vision systems measure blank dimensions, verify hole placements, and detect burrs or surface defects before parts leave each cell. Data feeds back to the MES, enabling real‑time adjustments—if a laser cutter’s kerf varies by more than 0.05 mm, the CNC program auto‑compensates on the next part.
Investing in modular, reconfigurable cells lets you pivot between product lines with minimal downtime: quick‑disconnect power and data couplings, movable guards, and standardized fixturing mean a cell can transition from HVAC ductwork to precision enclosures in under an hour. This agility, combined with digital twin simulations for process validation, positions manufacturers to respond swiftly to custom orders or design changes, all while maintaining lean inventories and high OEE (Overall Equipment Effectiveness).
For high‑precision or highly automated operations, consider the following advancements: plug‑and‑play End-of-Arm Tooling (EOAT) for robots, which lets a single robotic arm seamlessly switch between grippers, suction cups, and magnetic clamps—ideal for handling various sheet sizes and part geometries without manual intervention. Collaborative robots (cobots) equipped with force‑torque sensors can safely assist operators on tasks like manual loading or deburring, blending human dexterity with machine consistency.
Augmented Reality (AR) is emerging on the shop floor: maintenance technicians wear AR glasses that overlay step‑by‑step repair instructions on machines, reducing service times by up to 40%. Similarly, operators can use AR to visualize bend lines and bend sequences directly on the sheet before the first bend is made, cutting programming time and trial‑and‑error scrap.
Edge computing hubs collect data from sensors on each press, cutter, and robot, processing it locally to trigger immediate responses—like pausing a press brake if a back‑gauge collision is detected—while less time‑sensitive data streams to the cloud for long‑term analytics. This hybrid architecture ensures safety and uptime without clogging network bandwidth.
Finally, sustainability initiatives are reshaping equipment choices: waterjet systems now recycle up to 95% of their abrasive media, while laser cutters with advanced fume extraction and closed‑loop gas systems significantly cut operating costs and environmental impact. Electric press brakes, replacing hydraulic systems, offer 40% energy savings and eliminate oil leaks. By embedding circular economy principles—remanufactured tooling, energy recovery from ovens, and digitally optimized nesting to reduce scrap—manufacturers not only lower costs but also meet growing regulatory and customer demands for greener production.
Sheet Metal Coffee Pot Manufacturing Machine
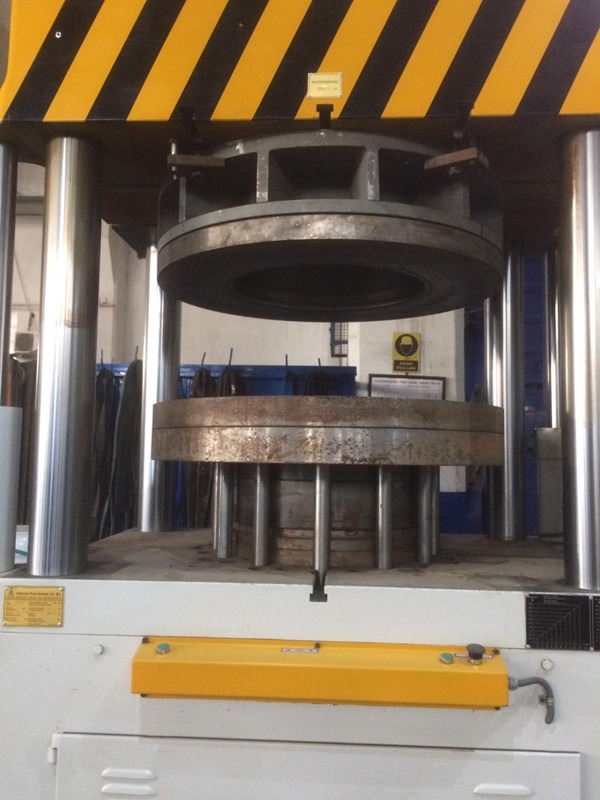
A dedicated sheet‑metal coffee‑pot manufacturing machine is essentially a small, highly integrated production cell that takes flat sheet stock all the way through cutting, forming, joining, and finishing to produce a fully assembled kettle or moka pot. Here’s what a turnkey line might include and how each stage operates:
1. Sheet Loading & Nesting
– Automated Sheet Feeder: Holds a coil or stack of pre‑cut sheet blanks and feeds them one at a time into the cell.
– Nesting Software: Optimizes the blank layout on the sheet to minimize scrap, especially important given the curved profiles and tight tolerances of coffee‑pot parts.
2. Contour Cutting
– Laser or Waterjet Cutter: Cuts out the main body blank, lid blank, handle bracket blanks, and any decorative or ventilation holes. Laser is typical for stainless‑steel pots; waterjet can be used for thicker, exotic materials.
3. Flanging & Forming
– Roll Former / Flanger: Creates the 90° flanges around the body blank, prepping it for welding or seaming.
– Hydraulic Deep‑Draw Press: Draws the flat body blank into the classic pot shape in one or two stages (blanking, then redrawing), controlling wall thickness and radii.
4. Spinning & Necking
– Spinning Lathe: Further refines the neck of the pot, achieving smooth curvature and precise inner diameters for a snug lid fit.
5. Handle and Spout Fabrication
– Wire‐bending Machine: Bends and shapes the handle wire or bracket.
– Tube‐forming Press: For machined spouts, a small hydroforming station can shape the spout blank before trimming.
6. Welding & Seaming
– Seam Welder: Typically a high‑precision laser or TIG welding station that joins the spun body seam and welds on handle brackets.
– Roll‑Seaming Machine: Mechanically rolls and crimps the lid to the body or secures the flame‑break valve assembly.
7. Machining & Trimming
– CNC Trimming Station: Removes excess flange material around the lid and body openings to ensure crisp edges.
– Chamfering & Edge‐Rounding Tool: Deburrs and rounds all cut edges in one pass.
8. Surface Treatment
– Pickling & Passivation Tank: Cleans and passivates stainless‑steel surfaces to prevent corrosion.
– Brushing/Polishing Station: Automated brushes create a uniform finish or decorative pattern.
9. Assembly & Inspection
– Automated Riveting or Spot‐Welding: Fastens the handle to the body.
– Vision Inspection: Cameras check dimensions, weld integrity, and finish quality (no scratches, uniform polish).
10. Packaging
– Robotic Pick‑and‑Place: Places finished pots into cartons or display trays.
– Labeling & Sealing Machine: Applies stickers or shrink‑wraps and seals boxes for shipping.
Key Considerations
- Throughput: A cell of this type might produce 30–60 pots per hour, depending on the number of forming stages and welding cycle times.
- Material: Stainless steel (typically 0.5–0.8 mm gauge) is standard; aluminum or coated steels may require different welding or seaming methods.
- Footprint: A fully automated turnkey cell could occupy 40–60 m²; modular cells allow you to scale up or down.
- Quality & Traceability: Integrate MES and barcode/RFID tracking on each pot for batch traceability, especially important for food‑contact items.
- Flexibility: Quick‑change tooling and programmable CNC stages let you switch between pot sizes or designs in under an hour.
This type of machine lineup embodies a miniaturized version of an automotive or appliance manufacturing plant, optimized for the geometry and sanitary requirements of coffee pots. If you’re exploring a purchase or retrofit, let me know your desired daily output and budget range, and I can recommend specific vendors and configurations.
A sheet‑metal coffee pot line begins by automatically feeding stainless‑steel or aluminum blanks, nesting each layout to squeeze maximum yield from the coil. A laser cutter then pierces and contours the body, lid, spout and handle‑mount brackets in one seamless program. The flat ring that becomes the pot’s flange is formed next—either by roll‑flanging the blank or by a tandem deep‑draw press that first blanks and then redraws the cup‑shaped body, controlling wall thickness to prevent thinning at the curve. Once drawn, the neck is spun on a CNC lathe, smoothing inner radii for a perfect lid seal, and the flange ring is trimmed to exact diameter.
Handles and spouts arise from their own mini‑cells: wire‑benders shape the handle rod to ergonomic curves while tube‑forming presses hydroform or mandrel‑bend the spout. CNC trimming stations shave off burrs, then a precision TIG or laser welder fuses the seam of the spun body and tacks on handle‑brackets. A roll‑seaming head crimps the lid to the body with a food‑safe gasket or flame‑break valve nestled between.
After welding, the pot passes through a robotic deburring cell where brushes and small belt grinders remove any sharp edges before a pickling and passivation bath neutralizes surface oxides. Polishing stations equipped with rotating brushes or belts impart a satin or mirror finish, while in‑line vision cameras inspect for scratches, weld uniformity and dimensional accuracy.
The final cell fastens the handle—either by automated riveting or MIG spot‑welding—then a vision system verifies torque and alignment. Pots are then picked by a delta robot and placed into cartons or trays, labeled with batch IDs and RFID tags for full traceability. A small conveyor then moves them through a shrink‑wrap or carton sealer, completing a turnkey process that, depending on cycle times and the number of parallel cells, can yield anywhere from 40 to 80 finished coffee pots per hour with less than 1% scrap.
The heart of the cell is its synchronized timing: as one pot completes its final weld, the next blank has already been cut and is halfway through forming. By staggering operations across parallel modules—two draw presses alternating strokes, three laser welders cycling seams, and four polishing heads working in shifts—the line achieves continuous flow. Sheet‑feeding robots deliver blanks precisely to the laser cutter, then retrieve finished bodies with vacuum grippers and hand them off to the spin lathe. Meanwhile, custom PLC logic and an MES coordinate changeovers: when you switch from a three‑cup capacity pot to a six‑cup model, the software automatically adjusts draw press depths, lathe tooling offsets, and laser seam patterns based on digital templates, all without halting the cell for more than a few seconds.
Energy recovery systems capture heat from the passivation and curing ovens to pre‑heat incoming water for pickling baths, trimming overall energy consumption by up to 20%. Centralized lubrication and hydraulic power units feed multiple presses, reducing footprint and simplifying maintenance. And with cloud‑connected dashboards, plant managers monitor cycle counts, reject rates, and OEE in real time, drilling down to the individual actuator level to identify bottlenecks.
Safety is baked in: light‑curtain zones around robot cells, collision‑detection sensors on all moving axes, and AR‑guided lock‑out/tag‑out procedures ensure technicians can service the line without risking injury. All modules are mounted on leveling pads and connected via quick‑disconnect couplings for power, air, and data—so the entire cell can be relocated or reconfigured in a matter of hours.
In essence, a sheet‑metal coffee‑pot manufacturing machine is less a single “machine” and more a miniaturized factory: an ensemble of cutting, forming, joining, finishing, inspection, and handling modules orchestrated by advanced controls and data analytics to deliver consistent, high‑quality pots at automotive‑plant scale.
Sheet Metal Serving Platter Manufacturing Machine
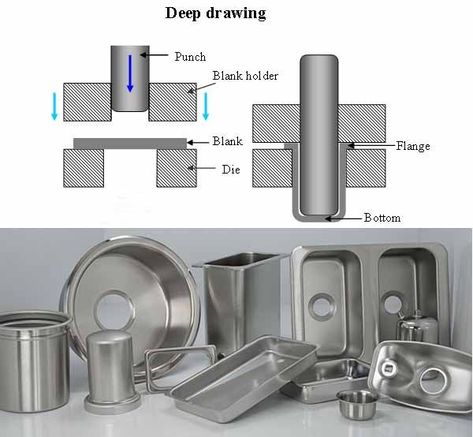
A serving platter line follows much the same principles as a coffee‑pot cell but swaps forming stages to suit the platter’s flat, shallow geometry. Blanks are fed from coil or sheet stacks into a laser cutter or turret punch that nests multiple platter profiles per sheet, cutting outline and any decorative perforations or vent slits in one operation. The cut blanks go next to a shallow die station—either a low‑tonnage hydraulic press or a servo‑electric forming press—that flanges the edge upward by a few millimeters to create the platter’s rim. For platters with decorative raised patterns or embossed logos, a second press station with custom embossing dies imparts the design in one quick stroke.
Edge finishing is automated: a series of rotating brushes and abrasive belts chamfer and deburr the rim, then an ultrasonic washer cleans the metal of lubricants and particulates. If a decorative finish is needed—brushed, bead‑blasted, or patterned—a robotic arm applies abrasive media or polishing pads in a programmed path to achieve uniform texture. A vision system inspects each platter for dimensional accuracy (rim height, flatness, profile radius) and surface quality, flagging any that exceed tolerance for automatic rejection.
For stainless‑steel platters, parts may then pass through a passivation bath and rinse station before drying in a heated tunnel. Aluminum or coated steel platters might receive a powder‑coat or anodized finish—an integrated spray booth and curing oven handle this in‑line, complete with reclaim systems for overspray. Once dry, platters travel to a final inspection cell where cameras verify finish consistency and check for scratches or coating defects.
Finished platters are picked by delta robots or suction‑cup gantries and placed into protective trays or stackers. A labeling station applies batch codes, and a robotic palletizer or case packer bundles them for shipment. Throughput typically runs 100–200 platters per hour per line, depending on the number of forming stations and finish steps. Modularity allows you to add or remove embossing, finishing, or coating cells to dial in just the features you need—whether it’s a simple brushed stainless look or a fully decorative, coated product ready for retail.
Blanks feed from coil or sheet stacks into a high‑speed cutter—laser or turret punch—that nests platter outlines and any decorative slots to maximize material yield. The cut parts move directly into a low‑tonnage press that flanges the rim only a few millimeters, creating the platter’s signature shallow lip. If embossing or logos are required, a secondary stamping station presses custom dies into the flat pan, adding texture or branding in a single stroke. Immediately afterward, rotating brushes and abrasive belts round and deburr the edges, while ultrasonic washers strip away oils and tiny particulates.
When a decorative finish is specified—bead‑blast, brushed or patterned—a robotic arm carries abrasive media or polishing pads across the surface in a precise, repeatable path. Vision cameras stationed before and after finishing verify rim height, flatness and surface uniformity, automatically rejecting any piece that falls outside tight tolerances. Stainless‑steel platters then go through pickling and passivation baths and dry in heated tunnels; aluminum or coated steels enter enclosed spray booths for powder‑coating or anodizing, complete with overspray reclaim systems.
Once plates are dry, robots equipped with suction‑cup gantries lift each platter onto trays or stackers. A labeling head prints and applies batch and traceability codes before a delta‑robot or case packer bundles them into cartons or onto pallets. With modular cells, lines can be reconfigured—adding or removing embossing, polishing or coating stations in minutes—to switch between simple, brushed stainless designs and fully decorated retail‑ready platters. Throughput ranges from 100 to 200 units per hour, scrap rates under 1%, and integrated MES dashboards provide real‑time OEE, cycle counts and reject statistics to optimize performance.
The synchronized choreography of a platter line hinges on parallelism and quick changeover. While one blank is being cut, another is deburred, a third is embossed, and a fourth is finishing its coat. Robots on linear rails shuttle parts between cells with vacuum end‑effectors, timing their moves to the sub‑second. Presses are served by centralized hydraulic power units with load‑sensing valves, so tonnage is precisely metered for both flanging and embossing dies.
Job recipes stored in the MES trigger automatic tool changeovers: hydraulic press platens swap die sets via quick‑release clamps in under 30 s, and spindle‑driven flanging rolls adjust their gap based on electronic thickness gauges that scan each blank’s actual gauge before forming. Vision‑guided robots correct pick‑positions on the fly, compensating for any lead‑edge deviation from nesting.
Energy efficiency comes from heat reclaim: waste heat from the passivation tunnel and curing ovens pre‑heats wash water and ambient air for powder booths. A digital twin of the line runs in parallel, simulating each station’s cycle to predict and smooth bottlenecks before they occur.
Safety and maintenance go hand‑in‑hand: AR‑guided technicians scan QR‑codes on each module to receive interactive maintenance procedures overlaid on the real hardware. Collision‑detection sensors and light curtains ensure safe co‑working zones for humans and robots, while centralized lubrication systems with flow sensors alert the MES when oil or grease levels drop below thresholds.
In effect, a serving‑platter machine is an agnostic platform—sheet feeder, cutter, flanger, stamper, finisher, robot handler—tied together by sophisticated controls, vision, and data analytics to churn out hundreds of decorative or utility platters per hour at consistent quality and minimal downtime.
Sheet Metal Tea Infuser Manufacturing Machine
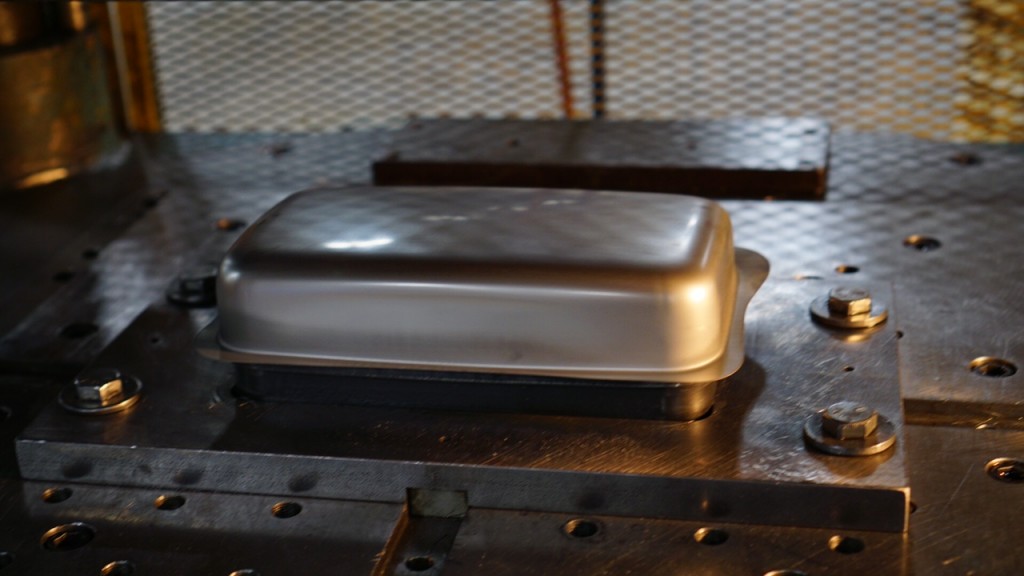
A sheet‑metal tea infuser manufacturing machine is designed to create the intricately perforated, typically cylindrical or spherical tea infuser shapes from thin sheet stock. The process involves several stages—cutting, forming, perforating, assembly, and finishing—each focused on delivering precise perforation patterns and maintaining a smooth, seamless design for the infuser to be both functional and visually appealing.
The process begins with feeding sheets of stainless steel, aluminum, or other suitable alloys into an automatic feeder, which aligns the sheets for cutting. A laser or turret punch cuts out the circular blanks that form the base of each infuser, optimizing material usage with intelligent nesting software. For larger batch runs, a blanking die might be used to shear multiple blanks in one stroke, increasing throughput. Once the blanks are prepared, they move to the next station, where they are shaped into the desired form—typically a cylindrical or rounded shape.
Forming occurs using a hydraulic press or a precision rotary press. In this stage, a shallow drawing or deep‑drawing press molds the blank into the body of the tea infuser. If the infuser requires a spherical design, a second deep‑draw press or a spinning lathe will be used to further refine the shape to a tight radius.
The next stage is perforating the metal. The tea infuser must have a uniform and fine mesh of holes to allow for proper infusion while retaining tea leaves. This can be done using a high‑precision laser, water jet, or a perforating die that stamps tiny holes into the surface of the metal. Laser perforation offers the best precision, allowing for a consistent pattern that is free of burrs. For larger production runs, a rotary press with perforating dies may be used for high‑speed punching of thousands of holes in one pass.
Once the metal is perforated, the parts move to the welding or joining stage, where any required components are attached. For infusers that have handles or chains for hanging, robotic welding or laser welding is used to attach metal handles, hooks, or chains securely. This can also involve ultrasonic or resistance welding for finer components.
After assembly, the tea infuser is placed into an automated polishing or finishing cell. This step ensures that there are no sharp edges left from the perforation or welding processes and that the surface of the infuser is smooth and free of burrs. The parts may go through a passivation process to improve corrosion resistance, especially if stainless steel is used, followed by a final polishing stage that enhances the appearance and smoothness of the metal.
The final inspection involves automated vision systems that check for hole placement, alignment, finish quality, and structural integrity. Any parts that do not meet the specifications are rejected automatically by a robotic sorting system, ensuring that only fully compliant products move forward.
Once inspected, the finished tea infusers are either stacked into protective packaging or loaded onto conveyors for packaging machines. Depending on the desired packaging (individual boxes, bulk packs, etc.), robotic pickers place the items into their respective containers. The entire process can be highly automated, offering an output range that can exceed 100 infusers per minute, depending on part complexity and the desired automation level.
The efficiency of the line is enhanced with a fully integrated MES (Manufacturing Execution System), which ensures precise tracking of each part’s progress, monitors machine performance, and collects data for predictive maintenance. By monitoring every stage, from the cutting of the sheet metal to the final packing, manufacturers can optimize production, reduce waste, and improve overall throughput.
The beauty of a tea infuser manufacturing system is in its combination of high‑precision operations with consistent, high‑quality outputs, producing a product that not only functions effectively but also appeals to consumers in terms of both aesthetics and durability.
Once the tea infusers are fully assembled and finished, they undergo rigorous inspection. Automated vision systems check for consistent perforation patterns, correct alignment of welded components, and overall surface finish. Any parts that show imperfections, such as misaligned holes or sharp edges, are automatically rejected by sorting robots, ensuring that only the highest quality pieces move forward. The remaining units are then ready for packaging. Depending on the packaging requirement—whether it’s individual boxes for retail or bulk packaging for wholesale—robots pick and place the tea infusers into their appropriate containers.
The packaging process itself is just as automated. Packaging lines can shrink-wrap individual units or stack multiple infusers into larger boxes. The boxes are sealed, labeled with product and batch information, and placed onto pallets for shipment. Robotic palletizers ensure that the products are stacked efficiently and securely for transportation.
Throughout the entire production process, the use of an integrated Manufacturing Execution System (MES) ensures that every step is tracked in real time. This system monitors each machine’s performance, detects any issues early on, and provides the production team with data for process optimization. Predictive maintenance algorithms analyze data from sensors on each machine to identify potential failures before they occur, reducing unplanned downtime.
The result is a fully automated production line that efficiently manufactures tea infusers at scale, with minimal waste and maximum precision. The combination of high-speed cutting, forming, perforating, welding, and finishing, along with real-time monitoring, enables the production of a high volume of quality tea infusers while ensuring consistency and reliability across every unit. This level of automation and integration makes the entire manufacturing process streamlined and cost-effective, meeting both high throughput demands and tight quality standards.
As the manufacturing process continues, the line adapts to varying design specifications or material changes with ease, thanks to its modular setup. For example, if the design of the tea infuser changes—such as adjusting the perforation pattern or adding a new handle design—operators can quickly reprogram the machines through the MES interface without needing extensive downtime for retooling. The system stores preset configurations for different part designs, allowing for swift transitions between production batches with minimal manual input.
The flexibility extends to material handling as well. The sheet-metal feeder is equipped with sensors that detect material thickness and adjust the cutting, forming, and perforating processes in real time. If a new material type is introduced, like a higher-grade stainless steel, the machine adjusts cutting speeds, laser settings, and press tonnage to accommodate the different properties of the material, ensuring that the final product maintains the desired quality and consistency.
Additionally, as part of ongoing sustainability efforts, energy recovery systems are embedded into the production line. Heat from the welding and curing stations is recycled and used to preheat water for cleaning or passivation processes, reducing overall energy consumption. Closed-loop water systems in the ultrasonic cleaning stage minimize water waste, while the powder coating booth uses advanced filtration and reclamation techniques to recover overspray, reducing material waste and improving efficiency.
The final stage of production benefits from real-time analytics provided by the MES. Key performance indicators such as production rate, defect rate, machine uptime, and operator efficiency are tracked and displayed on digital dashboards visible to the entire production team. This data allows for continuous process improvements and enables operators to take corrective actions on the fly, ensuring that production goals are met and quality is upheld.
At the same time, automation doesn’t just stop at the production floor. Packaging is equally optimized with smart systems that determine the optimal packing configuration, minimizing empty space and maximizing the use of packaging materials. This helps reduce shipping costs and waste while also ensuring that the final product is securely packed for transit, minimizing the risk of damage during delivery.
As a result, tea infuser manufacturing becomes not just a high-efficiency operation but a highly flexible and sustainable one. The integration of advanced automation, real-time monitoring, and data analytics ensures that the production process remains responsive to demand fluctuations, capable of handling design changes, and continuously improving in terms of speed, precision, and environmental impact.
Sheet Metal Beverage Dispenser Manufacturing Machine
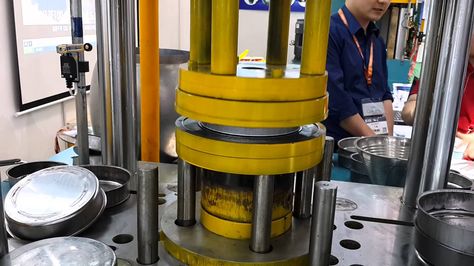
A sheet-metal beverage dispenser manufacturing machine is designed to create high-quality, durable dispensers used in both commercial and residential settings. These dispensers typically involve components like tanks, spouts, handles, and faucets, all of which must be formed, welded, and finished with high precision to ensure the proper flow of beverages and easy maintenance. The manufacturing process includes several key stages—sheet loading, cutting, forming, welding, assembly, and finishing.
The process begins with a sheet-metal coil or stacked sheets, which are automatically fed into a high-speed turret punch or laser cutting system. This machine cuts the flat metal sheets into blanks, forming parts like the body, lid, base, and other necessary components. The cutting pattern is optimized through nesting software to maximize material efficiency, ensuring minimal waste. The laser cutter is used for precise edges and holes, especially for dispensing nozzles or spouts, while a turret punch might be employed for faster, high-volume punching of simple shapes or holes.
Once the blanks are cut, they are transferred to a forming station. For the main body of the beverage dispenser, a deep-drawing press is used to form the cylindrical or tank-like structure from the flat sheet. Depending on the design, additional presses or rotary forming machines can create the curves for the dispenser’s handles, spouts, and other curved parts. For more intricate shapes or those requiring complex angles, spinning or hydroforming might be used to achieve precise geometries.
The next critical stage involves perforating and shaping smaller parts, such as dispensing nozzles, spouts, or decorative elements. A laser or water jet cutting machine is often employed here to create precise holes or designs on the surface of the metal for visual appeal or functionality, such as allowing liquid flow through the spout or aerating the beverage as it dispenses. Depending on the design, some dispensers might require a separate tube-forming press to create the spout or additional parts.
Once all parts are formed, the assembly process begins, which often involves welding, riveting, or ultrasonic welding. For stainless-steel beverage dispensers, precision TIG or laser welding is commonly used for joining the parts, especially where clean, durable seams are needed. The body of the dispenser is welded shut, the handle and spout are securely attached, and any decorative elements, such as logos or trim, are also welded or riveted into place.
Following assembly, the parts are deburred and polished. Automated robotic arms equipped with brushes or abrasive pads remove any sharp edges from the welded seams or cut parts, while also smoothing out rough spots on the exterior. If needed, the dispensers are passivated through a chemical bath to enhance corrosion resistance, particularly if they are made of stainless steel, ensuring the product remains hygienic and resistant to rust.
For aesthetic finishes, the beverage dispenser may undergo powder coating or anodizing, particularly for aluminum parts or to add an extra layer of protection to stainless steel. Powder coating offers the option to add a variety of colors or textures, while anodizing enhances the metal’s durability and appearance, giving it a sleek, shiny finish. If the design requires a particular pattern or surface treatment, robotic arms are used for precise and uniform application of finishes across each unit.
Final inspection involves using vision systems and other automated checks to ensure that each dispenser is correctly formed, welded, and finished. The dispensers are measured for any dimensional discrepancies, and any defective units are rejected from the line. This ensures that the dispensers are produced to the highest standards, meeting both functional and aesthetic requirements.
Once approved, the dispensers are transferred to packaging stations. Depending on the order, packaging can range from individual boxes for retail sale to bulk packaging for commercial shipments. Robotic pickers or conveyors automatically place each dispenser into protective packaging, ensuring that the items are safely cushioned for transit and delivery.
Throughout the entire process, the use of an integrated MES system allows manufacturers to monitor real-time production data, including machine efficiency, output rates, and quality control statistics. This helps to optimize workflows, predict maintenance needs, and ensure that the beverage dispensers are produced as efficiently as possible, all while maintaining top-tier quality.
In total, the beverage dispenser manufacturing line is a complex, highly automated system designed for precision, speed, and flexibility, capable of producing large volumes of high-quality dispensers for various commercial and residential needs.
The process flow is meticulously coordinated to achieve optimal efficiency. After the sheets are fed into the cutting machine, the blanks are carefully aligned and moved between stations using automated conveyors, ensuring that there are no delays or misalignments. The forming stage is equally precise, with presses and forming machines equipped with sensors to monitor pressure, speed, and temperature, guaranteeing consistent part quality. Each station is synchronized to ensure a seamless transition from cutting to forming to welding.
At the welding stage, advanced robotic arms equipped with precision lasers or TIG welders perform the necessary joins, ensuring that the body, spout, and handle are securely attached without compromising the aesthetic or structural integrity of the dispenser. These robotic systems are equipped with advanced feedback loops that monitor weld quality in real time, adjusting parameters automatically if any issues are detected, such as inconsistent power levels or incorrect positioning.
Following welding, the dispensers are moved to the finishing stage, where automated polishing systems, including robotic arms with polishing pads, smooth out any rough edges from welding or cutting. For dispensers made from stainless steel, this process is particularly crucial, as it not only improves the appearance but also ensures there are no sharp edges that could pose a safety risk to consumers.
After finishing, dispensers undergo a thorough inspection using a combination of machine vision and laser scanning technologies. These systems assess every dimension of the dispenser, checking for potential defects such as misalignments, weld imperfections, or finish inconsistencies. If any defects are detected, the part is automatically flagged and removed from the line, ensuring only products meeting stringent quality standards proceed to packaging.
Packaging is a critical step in ensuring that the dispensers reach their destination in pristine condition. Automated pickers and conveyors load finished dispensers into protective boxes or packaging trays. Depending on the customer’s requirements, the dispensers are either packaged individually for retail or grouped together in larger cartons for bulk shipping. Labeling systems apply batch codes, product details, and barcodes for traceability, and robotic arms place the finished packages onto pallets for transport.
Real-time data collected through the Manufacturing Execution System (MES) plays a pivotal role in optimizing the entire process. Operators can access detailed analytics on machine performance, production rates, and quality control metrics. This data allows them to quickly identify and address any potential bottlenecks in the production line or maintenance issues, minimizing downtime and maximizing throughput. Furthermore, predictive maintenance systems based on sensor data alert operators to potential equipment failures before they occur, ensuring the machines are always operating at peak performance.
The entire production system is designed with flexibility in mind. If a design change is requested—such as a new dispenser model with a different shape, size, or feature—operators can quickly adjust the system parameters through the MES interface. This enables manufacturers to respond rapidly to market demand without disrupting production, allowing for efficient short-run manufacturing of custom or specialized beverage dispensers alongside regular, high-volume runs.
In summary, a sheet-metal beverage dispenser manufacturing machine integrates cutting-edge automation, precision forming, high-quality welding, advanced finishing techniques, and real-time monitoring to produce dispensers that meet both functional and aesthetic standards. With minimal waste, high throughput, and reduced labor costs, this type of manufacturing setup ensures that beverage dispensers are made with the utmost efficiency and quality, serving the diverse needs of both commercial and consumer markets.
The manufacturing system continues to evolve as it adapts to more sophisticated technologies aimed at increasing both efficiency and product variety. The use of advanced robotics extends beyond just welding and finishing; robots are also deployed in part handling and assembly, eliminating the need for manual intervention. For instance, robotic arms are responsible for picking up the formed bodies of dispensers and positioning them with precision into subsequent welding stations. These robots use vision-guided systems to identify part orientations and ensure accurate placement without any errors, streamlining operations and reducing the risk of human error.
One key innovation is the integration of collaborative robots (cobots) that work alongside human operators in the final assembly and packaging stages. These cobots are designed to handle the lighter, more repetitive tasks, such as placing spouts or handles onto the bodies of dispensers. This frees up human workers to focus on tasks that require more finesse or oversight, such as quality control or troubleshooting.
The entire system is connected through a robust network of Internet of Things (IoT) devices. Sensors embedded in each machine monitor variables like temperature, pressure, humidity, and vibration to provide real-time feedback on machine performance. If a machine starts to deviate from its optimal parameters—such as a press operating at slightly too high or low pressure—alerts are sent to the operator or maintenance team to address the issue before it affects the quality of the product. This predictive approach to maintenance helps reduce downtime and extends the lifespan of the machinery.
Material tracking is another critical component of the automated beverage dispenser line. Each sheet of metal is tagged with RFID chips that allow the system to track its journey through the entire process. This ensures that materials are correctly matched to the right production run and that there’s full traceability in case of defects or recalls. It also helps with inventory management, as operators are notified when supplies are running low, and new materials are needed, minimizing delays.
The system’s flexibility is key to its success. With the ability to quickly switch between different types of dispensers, from small, single-use models to large, commercial-grade units, the line is equipped to meet a broad range of customer specifications. Whether the order requires dispensers with multiple spouts, adjustable faucets, or decorative finishes, the MES system automatically adjusts parameters for the necessary tooling, material specifications, and machine settings, allowing for rapid changeovers with minimal downtime.
Energy efficiency remains a priority throughout the production line. The integration of heat recovery systems helps capture waste energy from the curing or drying ovens used in the coating process. This recovered heat is used to preheat water for cleaning stages or assist with temperature control in other parts of the system. Additionally, the entire line is equipped with energy-efficient motors, LED lighting, and optimized air systems, ensuring that the production process is as sustainable as possible.
Finally, the focus on quality assurance continues throughout the packaging process. Before any beverage dispenser is packed, it undergoes a final visual inspection. Robots equipped with high-resolution cameras and laser scanners check for any final cosmetic defects such as scratches, dents, or incorrect finishes. This inspection is complemented by automated functional tests to ensure that all valves, spouts, and handles are securely attached and operate properly. For dispensers that include additional features like built-in filters or temperature controls, automated tests confirm these components are working as intended.
After passing these rigorous quality checks, the dispensers are safely packed, ready for distribution. Automated labeling machines print out shipping labels, QR codes, and batch numbers for traceability. The dispensers are then palletized by robotic systems that arrange the products securely for transit. The fully automated packaging and palletizing system ensures that every unit is packed uniformly, reducing the risk of damage during transportation.
As a result, the beverage dispenser manufacturing line becomes a model of high efficiency, versatility, and reliability. From raw material handling to final packaging, each step of the process is optimized for speed, quality, and sustainability. Through the integration of automation, IoT, predictive maintenance, and real-time data analysis, the entire system is capable of producing high-quality dispensers at scale, ensuring that the final product meets both the functional needs and aesthetic demands of customers in various sectors.
Sheet Metal Food Warmer Manufacturing Machine
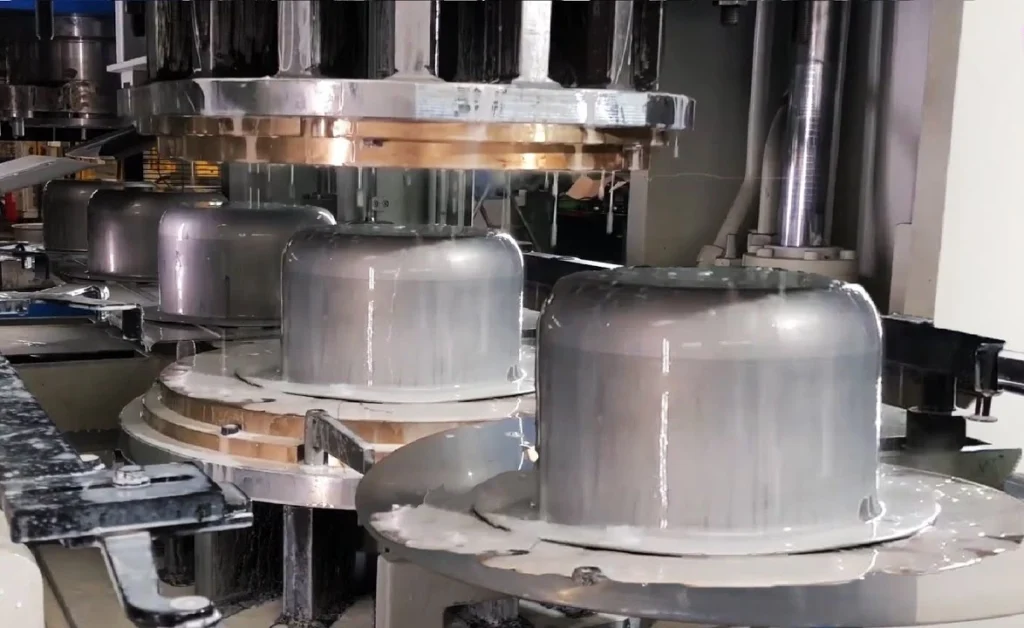
A sheet-metal food warmer manufacturing machine is designed to create durable, high-quality food warming units, which are used in both commercial kitchens and catering services to keep food at optimal serving temperatures. The production process is carefully structured to ensure that each unit is formed, insulated, and finished to meet both functional and aesthetic requirements, with a focus on heat retention, safety, and ease of use.
The process begins with feeding sheet metal, typically stainless steel or aluminum, into the cutting system. This is often done using a high-speed laser cutter or turret punch press. The laser cutter is preferred for its precision, capable of cutting intricate shapes for components such as the outer casing, internal heat trays, vents, and lid supports. The cutting pattern is optimized with advanced nesting software to maximize material utilization and minimize waste. For high-volume production, turret punch presses can quickly punch out simple shapes and holes, offering a cost-effective solution for straightforward designs.
Once the sheets are cut, they are sent to a forming station. The forming process involves using deep-drawing presses or hydraulic presses to shape the metal into the food warmer’s body. These presses are equipped with sensors to ensure that the metal is shaped precisely to the desired geometry, whether it’s for a simple rectangular box for a basic food warmer or a more intricate shape for more specialized models, such as those with curved walls or built-in compartments for trays.
For the insulation stage, the metal is often layered with insulating materials, such as mineral wool or fiberglass, which help maintain the temperature inside the food warmer. These materials are cut and applied to the interior surfaces of the metal casing before the unit is fully assembled. The metal parts are then welded or riveted together, depending on the design requirements. TIG or laser welding is commonly used to ensure a seamless and strong connection between the parts, particularly for stainless steel models. This welding process also ensures that there are no gaps where heat can escape, improving the efficiency of the warmer.
Next, the unit is fitted with heating elements, usually in the form of electric heating coils or infrared lamps. These elements are precisely placed into position using automated systems or robotic arms to ensure proper alignment. Wiring for the heating elements is also handled at this stage, with careful attention given to ensuring that all electrical connections are secure and meet safety standards.
The food warmer’s lid or cover is then created, often using a separate press for forming or cutting. This lid is designed to be easy to open and close while maintaining a secure fit to retain heat. If the warmer is intended for commercial use, the lid might also feature additional mechanisms, such as a self-closing or locking system, to prevent accidental opening.
Once the body of the food warmer is fully assembled, it moves to the finishing stage, which includes deburring, polishing, and cleaning. Robotic arms equipped with abrasive pads or brushes remove any sharp edges from the welded seams and polished surfaces, ensuring there are no hazards for the end-user. Automated ultrasonic cleaning systems may be used to remove any oils or residues left from the manufacturing process. For some models, a powder coating or anodizing process is used to add a protective, aesthetically pleasing finish to the outer surfaces. Powder coating not only provides color options but also enhances the durability of the unit by providing a protective layer against corrosion.
Final inspection ensures that the food warmer meets all quality standards. Automated vision systems and laser scanners check for any surface imperfections, such as scratches or dents, while also measuring key dimensions to verify that the parts are properly aligned and that the assembly is correct. Electrical testing is performed to confirm that the heating elements work efficiently and safely, and temperature sensors are checked to ensure that the unit reaches the desired warming temperature and holds it effectively.
Once approved, the food warmers are carefully packaged for shipment. Depending on the customer’s needs, they may be packed individually in protective boxes or grouped together for bulk shipping. Automated packaging systems use robotic pickers to place the units into packaging, ensuring that they are secured for transport. The packaging process also includes labeling, with batch numbers and product specifications, to ensure traceability and compliance with industry standards.
Throughout the entire process, the use of an integrated Manufacturing Execution System (MES) helps monitor and manage every aspect of the production. This system provides real-time data on machine performance, production rates, and quality control, enabling operators to make adjustments as needed to ensure smooth operations. Predictive maintenance algorithms built into the system monitor the health of key machines, reducing the risk of unplanned downtime by alerting the team when maintenance is required.
Energy efficiency and sustainability are key considerations. The use of heat recovery systems helps capture and reuse energy from the curing or drying process, while energy-efficient motors and equipment reduce the overall energy consumption of the production line. Additionally, material waste is minimized by the intelligent nesting of sheet-metal components, ensuring that the maximum number of parts are produced from each sheet of metal.
In conclusion, the sheet-metal food warmer manufacturing machine integrates high-speed cutting, precision forming, insulation, assembly, welding, and finishing processes to produce durable, high-quality food warmers. The combination of automation, real-time data analysis, and energy-efficient systems ensures that the production line operates efficiently, producing reliable, functional, and aesthetically pleasing food warmers for both commercial and residential use.
The food warmer manufacturing process continues with advanced automation techniques to ensure that each unit is produced at a high standard, with minimal labor and maximum precision. After final inspection, the units are not only checked for structural integrity and functionality but also undergo thorough testing for heat retention capabilities. Automated systems simulate real-world conditions to test how well each unit maintains temperature over time. The food warmers are subjected to a series of rigorous quality control checks, which include evaluating the uniformity of heat distribution and verifying that the temperature remains consistent throughout the warming chamber.
Once a food warmer passes these tests, the packaging process begins. The packaging is handled with the same level of automation and precision as the rest of the manufacturing line. Depending on the model and order specifications, the packaging could range from simple cardboard boxes for individual units to heavy-duty crates for bulk shipments. Robotic arms are employed to carefully pick and place the food warmers into their packaging, while automated labeling systems print out product details, batch numbers, and shipping labels, ensuring proper traceability and compliance with industry regulations. The packaging line is equipped with protective cushioning materials such as foam inserts or air pillows to safeguard the product during transportation.
The finished food warmers are then moved to a dedicated storage area or staging zone, where they are ready for shipment. For high-volume orders, palletizing robots efficiently stack the packaged units onto pallets, optimizing space and ensuring that they are securely packed for safe transportation. The system tracks inventory in real-time, ensuring that the correct quantity of food warmers is always available for shipment according to customer orders.
Throughout the entire production line, the MES system plays a critical role in coordinating every stage. It not only tracks the flow of materials but also monitors the performance of individual machines, detects potential issues early, and alerts operators to address them before they cause disruptions. By collecting data at each stage of production, the MES allows for continuous improvement, helping to fine-tune processes and identify opportunities for cost reduction or quality enhancement. The system also integrates with supply chain management software, providing real-time insights into material inventory, order fulfillment, and delivery schedules, ensuring that production meets customer demand efficiently.
In addition to enhancing operational efficiency, the food warmer manufacturing process places a strong emphasis on sustainability. Efforts to minimize energy consumption are embedded into every part of the production line. From energy-efficient motors to the recovery and reuse of heat energy during various stages, the production system is designed to lower the environmental impact of manufacturing. Waste is minimized by optimizing cutting patterns to reduce scrap material, and any metal by-products or waste materials are carefully sorted and recycled, helping to reduce the carbon footprint of the operation.
Automation and robotics allow for rapid reconfiguration of the production line when needed. If there are changes in product design, such as a shift in the size or shape of the food warmer, operators can adjust the system settings through the MES interface, minimizing downtime and reducing the need for extensive retooling. This flexibility allows manufacturers to quickly respond to market trends, customer preferences, or new design requirements without disrupting overall production.
Moreover, the advanced manufacturing process is not limited to efficiency and sustainability; it also ensures that the food warmers meet the highest standards of safety. The automated testing systems ensure that electrical components are properly insulated, that heating elements function without overheating, and that the product is compliant with industry regulations for electrical safety and thermal efficiency. As safety is a priority, units are tested for potential risks such as overheating or electrical shorts, ensuring that the final product is reliable and safe for use in both commercial and home kitchens.
In summary, the sheet-metal food warmer manufacturing machine integrates cutting-edge technologies in automation, robotics, and data analysis to produce food warmers that are high-quality, energy-efficient, and compliant with safety standards. The entire process—from material handling to final packaging—is designed to ensure consistency and precision, enabling manufacturers to produce food warmers that are not only durable and reliable but also environmentally friendly and cost-effective. The use of real-time monitoring, predictive maintenance, and flexible manufacturing systems ensures that the production process remains efficient and responsive to changing demands, setting the foundation for a successful product line that can meet the evolving needs of customers.
As the production process progresses, the incorporation of additional technologies further enhances the capabilities of the sheet-metal food warmer manufacturing machine. One such innovation is the use of machine learning algorithms to improve the precision of the manufacturing steps. These algorithms are trained on historical production data and are capable of detecting patterns and anomalies that human operators might miss. By analyzing data from the various stages of production—such as material input, machine performance, and environmental factors—these algorithms can optimize the settings for cutting, forming, welding, and finishing, ensuring that the food warmers are consistently produced to the highest standards with minimal waste.
In the forming and welding stages, robotic arms equipped with advanced sensors and feedback mechanisms provide real-time adjustments to ensure the metal is shaped or welded accurately, compensating for any slight variations in material properties or machine calibration. These robotic arms can also work in a more collaborative manner with human operators, particularly in more complex or intricate parts of the process that require human oversight or decision-making. This collaboration ensures that the process is both efficient and adaptable, with the ability to tackle custom orders or specialized designs that may not be feasible on a fully automated line.
In addition to enhancing precision, machine learning is also leveraged for predictive maintenance, a key aspect of the manufacturing system. Sensors embedded in the machines continuously monitor performance indicators such as temperature, vibration, and pressure. Machine learning algorithms analyze this data to detect any signs of wear or malfunction before it leads to equipment failure. By predicting maintenance needs in advance, the system can schedule repairs during off-peak times, reducing unplanned downtime and ensuring the production line remains operational without interruptions.
Furthermore, with the increasing demand for eco-friendly and sustainable products, the food warmer manufacturing process places an emphasis on reducing its environmental impact. The materials used in the construction of the food warmers are selected for their durability, recyclability, and energy efficiency. Stainless steel and aluminum are commonly used for their strength, resistance to corrosion, and ease of recycling. During the production process, scrap metal and excess materials are collected and sent for recycling, helping to close the loop and reduce the overall environmental footprint of the operation. Additionally, energy-efficient heating technologies, such as low-power electric heating elements or infrared heating systems, are being incorporated into the design of the food warmers themselves to further reduce their energy consumption in the field.
The integration of energy-efficient systems extends beyond the production floor and into the design of the food warmers. Manufacturers are increasingly focusing on creating units that offer optimal insulation and heat retention, which helps minimize energy waste during operation. Advanced materials and insulating technologies, such as vacuum-insulated panels or aerogel-based coatings, are being used to improve the thermal efficiency of the warmers. This not only lowers the operational costs for customers but also aligns with growing consumer and regulatory demands for more sustainable, energy-efficient appliances.
In terms of customer satisfaction, the food warmer manufacturing machine is also designed to accommodate varying market needs. Different models of food warmers, such as countertop units, freestanding models, or larger, commercial-grade warmers, can all be produced on the same flexible production line. This flexibility is essential as it allows manufacturers to cater to a wide range of customers, from small cafes and restaurants to large hotels or catering services. Customization options, such as size, finish, and additional features like digital temperature controls, are easily incorporated into the line by simply adjusting the system settings. This makes it possible to produce both standard and specialized food warmers in parallel, maximizing production efficiency without sacrificing product variety.
The importance of user-friendly design is also taken into account in the manufacturing process. The warmers are built with ease of use, maintenance, and cleaning in mind. Features such as removable trays, easy-to-clean surfaces, and intuitive controls are incorporated into the design to enhance the user experience. In addition, safety features such as automatic shut-off mechanisms, temperature controls with safety cutoffs, and non-slip feet are integrated to prevent accidents and ensure that the food warmers operate safely under various conditions.
With the entire production system optimized for speed, quality, and flexibility, manufacturers can respond quickly to changes in consumer preferences and market trends. The MES system plays a central role in this, providing up-to-the-minute data on production progress, order fulfillment, and customer demand. By leveraging this real-time data, manufacturers can make informed decisions about production scheduling, inventory management, and supply chain logistics, ensuring that the right products are delivered to customers at the right time.
In conclusion, the sheet-metal food warmer manufacturing machine is a highly advanced, automated system that integrates cutting-edge technologies to produce durable, energy-efficient, and customizable food warmers. By incorporating machine learning for precision, predictive maintenance, and eco-friendly practices, the system not only ensures high product quality but also minimizes environmental impact and operational costs. This combination of efficiency, flexibility, and sustainability positions food warmer manufacturers to meet the growing demands of a dynamic market while maintaining a competitive edge in the industry. Through continuous innovation, the production process will keep evolving, enabling manufacturers to offer high-quality products that cater to the needs of both commercial and residential customers.
Sheet Metal Chafing Dish Manufacturing Machine
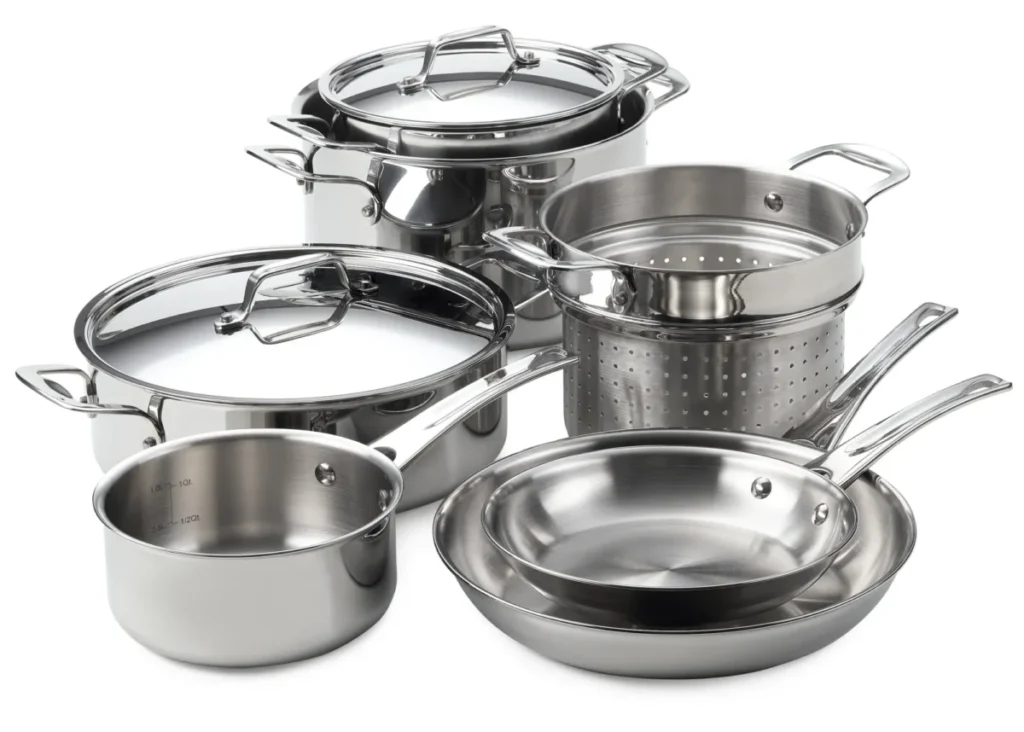
A sheet metal chafing dish manufacturing machine is designed to produce high-quality chafing dishes used in catering, buffet services, and foodservice industries. These dishes are crafted from durable metals such as stainless steel, which ensures they can withstand high temperatures, maintain food temperature, and offer an aesthetic appeal. The production process incorporates precision cutting, forming, welding, finishing, and testing to create functional, attractive, and safe chafing dishes.
The manufacturing process begins with feeding large sheets of metal into the cutting machines. These metals are typically stainless steel or aluminum, chosen for their ability to resist corrosion and heat. Laser cutting or turret punching is used to cut the metal into the required shapes for the base, lid, and side walls of the chafing dish. Advanced nesting software ensures that the sheet metal is efficiently used, minimizing waste and optimizing material utilization. For high-volume production, turret punch presses may be used to quickly punch out simpler shapes, while laser cutting offers the precision needed for intricate designs or components.
Once the metal sheets are cut, the components are sent to the forming stage, where they are shaped into the necessary forms using hydraulic or mechanical presses. The base and side walls of the chafing dish are formed to precise dimensions, ensuring that each unit has the correct shape and size for the food service requirements. Forming presses are designed to handle various materials and thicknesses, ensuring that the metal is shaped accurately without compromising its integrity.
At this stage, insulation materials might be added to the chafing dish to help retain heat. Insulation is often placed between the outer and inner walls of the dish, which helps maintain food temperature while preventing the outer surface from becoming too hot to touch. Materials like mineral wool or fiberglass may be used to provide effective thermal resistance, improving the overall performance of the chafing dish. These materials are cut to size and carefully inserted into the appropriate spaces within the dish.
The next stage involves welding the formed parts together to assemble the chafing dish. TIG (tungsten inert gas) welding or laser welding is commonly used for stainless steel, providing strong, precise, and aesthetically clean joints. Robotic welding systems are used to ensure that each weld is consistent and of high quality, reducing the chances of defects. Robotic arms can be programmed to automatically position the parts for welding, ensuring that the base, side walls, and lid are securely joined with no gaps or weak spots. These robotic systems also feature advanced sensors and feedback mechanisms to monitor the welding process in real-time, making adjustments to parameters like temperature and pressure to ensure uniformity.
After welding, the chafing dish moves to the finishing stage. In this phase, robotic arms equipped with polishing tools smooth out any welds or rough edges left from the manufacturing process. The surface is polished to a high shine to give the chafing dish its aesthetically appealing, corrosion-resistant finish. Additionally, some models may undergo a coating process such as powder coating or anodizing to improve durability, resistance to stains, and overall appearance.
Next, the unit undergoes quality control checks to ensure that it meets the required standards. Automated vision systems and laser scanners are used to inspect the chafing dish for imperfections, such as scratches, dents, or alignment issues. These systems can also measure key dimensions, such as the size of the handles, lid, or pan areas, to ensure the chafing dish is built to precise specifications. If any defects are found, the dish is removed from the production line and either repaired or discarded, ensuring that only high-quality units are sent to customers.
Once the chafing dish passes the quality control checks, it moves to the functional testing stage. Here, heating elements, such as electric coils or gel chafing burners, are installed into the dish to ensure that it can effectively maintain food temperatures. These elements are carefully wired and positioned in a way that allows for efficient heat distribution across the dish. The chafing dish is then tested to ensure the heating elements function properly and that the dish maintains the desired temperature consistently without overheating or underheating.
Following testing, the chafing dish is cleaned thoroughly to remove any oils, residues, or contaminants left from the manufacturing process. Automated ultrasonic cleaning systems are often used in this stage, ensuring the dish is completely free of any manufacturing debris. The unit is then dried, and any final cosmetic touches, such as polishing or buffing, are applied.
Finally, the finished chafing dishes are packaged for shipment. Automated systems handle the packaging, ensuring that each dish is safely enclosed in protective materials like foam inserts or bubble wrap to prevent damage during transport. The packaging also includes labeling with batch numbers, product details, and any necessary safety or usage instructions. For bulk orders, the dishes are palletized and wrapped securely to ensure they arrive in perfect condition. The final product is now ready for distribution to retailers, caterers, restaurants, or other commercial foodservice businesses.
Throughout the production process, an integrated Manufacturing Execution System (MES) tracks every step of the workflow. This system provides real-time monitoring of production rates, machine performance, and inventory levels. It ensures that materials are available when needed, that equipment is running efficiently, and that production meets demand. Additionally, predictive maintenance tools monitor the health of machinery, alerting operators when a part is about to fail or when maintenance is due, preventing costly downtime.
Sustainability and energy efficiency are also key considerations. The production process minimizes waste by optimizing material cutting patterns and recycling any excess metal. Energy-efficient motors and equipment reduce power consumption, and heat recovery systems can be employed to capture and reuse energy from processes like curing or drying. These sustainable practices help reduce the environmental impact of the manufacturing process, aligning with growing consumer and regulatory demands for eco-friendly production methods.
In conclusion, the sheet metal chafing dish manufacturing machine integrates state-of-the-art automation, robotics, and precision technology to produce high-quality, functional, and aesthetically pleasing chafing dishes. The process focuses on efficiency, sustainability, and quality control, ensuring that each dish is durable, easy to use, and capable of maintaining the desired temperature for extended periods. From cutting and forming to welding, finishing, and testing, the production line is designed to deliver consistent results while meeting the demands of commercial kitchens, catering services, and buffet-style foodservice businesses.
The production of sheet metal chafing dishes continues with the integration of advanced robotics and automation to streamline the assembly and packaging process. Once the final inspection is complete, the dishes are carefully packed for distribution. Automated systems use vision cameras and sensors to place each chafing dish into its protective packaging, such as cardboard boxes or custom foam inserts, ensuring that every unit is secure during transit. This system also helps reduce human error, increasing overall efficiency and minimizing the risk of damage during shipment.
The MES plays a vital role in ensuring that the packaging process is synchronized with the production line. It keeps track of packaging materials, monitors inventory, and alerts operators when stock is running low. It also ensures that every unit is correctly labeled and documented, allowing for seamless tracking of products as they move through the final stages of the production process. The system can also provide valuable data on shipping schedules, helping manufacturers coordinate with logistics providers to meet customer deadlines.
Additionally, sustainable practices are embedded in every part of the manufacturing line. Beyond efficient material use, the system has been designed to reduce waste and improve energy consumption. By optimizing production schedules and machine settings, manufacturers can ensure that energy usage is minimized, and any scrap metal or waste from the process is recycled. This not only contributes to reducing the environmental impact but also helps in lowering operational costs, making the entire process more cost-effective.
The machines themselves are designed with longevity and ease of maintenance in mind. Through predictive maintenance technologies, the system ensures that potential issues are identified before they lead to costly downtime. Sensors monitor the condition of key machines, tracking performance metrics like vibration, temperature, and load. When an issue is detected, the system automatically alerts the operators, allowing them to take preventative action, whether it’s lubricating a moving part, replacing a worn-out tool, or adjusting machine settings. This continuous monitoring helps maintain a smooth production flow, ensuring that the manufacturing process remains efficient and consistent.
Furthermore, the introduction of advanced materials, such as more efficient insulation options and energy-saving technologies, has become a priority. Manufacturers are now incorporating materials like vacuum-insulated panels or aerogels into their designs to improve thermal efficiency, ensuring that the chafing dish can maintain food temperatures for longer periods with less energy consumption. This technology aligns with the growing demand for energy-efficient kitchen products and helps provide a competitive edge in a crowded marketplace.
On the consumer end, the manufacturing process focuses not only on functionality but also on design. The chafing dishes are crafted to be both practical and aesthetically appealing. The polished finish, sleek lines, and well-designed handles make them visually attractive while being easy to use and maintain. Customization options, such as different finishes (e.g., brushed stainless steel or chrome plating) or additional features like lids with built-in temperature gauges, allow manufacturers to cater to a variety of customer preferences. These customizable features are seamlessly integrated into the production process, ensuring that each order can be tailored to meet specific needs.
The automated system also tracks customer orders and adjusts production schedules accordingly, ensuring that high-demand items are prioritized and that products are delivered on time. The system can monitor current market trends and predict future demand, allowing manufacturers to plan ahead and adjust production output to match seasonal needs or shifts in customer preferences.
As the chafing dishes are ready for shipment, they are moved into distribution centers where they are organized based on order specifics. For bulk orders, the dishes are carefully palletized to optimize space and ensure safe transport. For smaller orders, they are individually packaged and labeled for easy identification and quick dispatch. The MES continues to monitor the logistics and delivery process, ensuring that orders are shipped on time and that customers receive their products in perfect condition.
Ultimately, the sheet metal chafing dish manufacturing machine is designed to deliver high-quality, durable, and customizable products at scale. It combines advanced technologies in automation, machine learning, robotics, and data analysis to produce chafing dishes that meet the highest standards of safety, functionality, and aesthetic appeal. The integration of sustainability practices, energy efficiency, and predictive maintenance ensures that the production process remains environmentally friendly, cost-effective, and responsive to changing market demands. Through continuous innovation, the production line can adapt to new materials, designs, and consumer trends, ensuring that manufacturers remain competitive and meet the evolving needs of the foodservice industry.
The sheet metal chafing dish manufacturing process continues to evolve with the integration of more advanced technologies and methodologies to enhance product quality, production efficiency, and sustainability. One of the key areas where innovation is being applied is in the design and development of smart chafing dishes. These smart units integrate IoT (Internet of Things) sensors and connectivity, allowing users to monitor and control the temperature remotely via smartphones or digital control panels. By embedding temperature sensors, humidity controls, and Bluetooth or Wi-Fi connectivity into the chafing dish, manufacturers can offer more advanced features that appeal to both commercial and home users.
The smart features include real-time alerts for temperature changes or malfunctions, enabling foodservice providers to ensure that their food is being kept at the ideal temperature at all times. These devices can also track usage data, such as how long the unit has been in operation, when maintenance is needed, or when the heating element may need servicing. This provides valuable insights into the dish’s performance and helps optimize its lifespan. These smart chafing dishes are ideal for catering events, buffet lines, or other foodservice environments where precision and real-time data tracking are essential for food safety and quality control.
The introduction of automated material handling systems further optimizes the production line. Conveyor belts and robotic arms transport the sheet metal from one stage of the manufacturing process to the next, ensuring smooth and consistent movement of parts. Automated guided vehicles (AGVs) or overhead conveyors can be used to move large, heavy components such as the chafing dish bases or lids without the need for manual labor. This helps reduce the risk of human error and speeds up the overall production process while maintaining safety standards.
In addition, manufacturers are increasingly adopting 3D printing technologies, or additive manufacturing, in their prototyping and production processes. 3D printing can be used for creating custom parts, testing design prototypes, and even producing certain components of the chafing dish, such as handles, hinges, or decorative accents. This reduces lead times and allows for more rapid experimentation with new designs or modifications. Additionally, 3D printing offers the ability to create more intricate and complex features that may not be possible with traditional metalworking techniques. It also reduces material waste by using only the necessary amount of material for each part.
Moreover, as the demand for eco-friendly products continues to rise, manufacturers are exploring alternative sustainable materials for the production of chafing dishes. Research into bioplastics and other renewable materials is underway, with some manufacturers beginning to experiment with composite materials that offer similar durability and heat resistance as traditional metals but with a lower environmental impact. This aligns with growing consumer preferences for sustainable and ethically produced products, further enhancing the brand’s appeal to environmentally conscious buyers.
To ensure that the final product is as energy-efficient as possible, manufacturers are investigating and incorporating energy-saving technologies into the chafing dish itself. For example, incorporating LED lighting for any indicator lights or digital controls can reduce the overall energy consumption of the unit. Furthermore, advances in heat-retention technologies, such as improved insulation materials, help to ensure that the chafing dish can maintain food temperature with less energy input. These innovations contribute to reducing the environmental footprint of the product, making it more attractive to consumers and businesses that are looking to reduce their energy usage.
In terms of the post-production phase, a more automated supply chain and logistics management system have been integrated to ensure quick turnaround times and streamlined delivery. The use of RFID (radio-frequency identification) tags and GPS tracking systems enables real-time monitoring of inventory, shipments, and product locations. This allows manufacturers and suppliers to track the progress of each order and ensure that products are delivered on time and to the right location. Furthermore, intelligent warehouse management systems optimize storage and retrieval processes, reducing handling time and improving overall distribution efficiency.
Customer feedback also plays a crucial role in refining the manufacturing process. Manufacturers now have the ability to collect and analyze feedback through online platforms and customer service channels. By leveraging customer insights, manufacturers can continuously improve the design and functionality of their chafing dishes, offering new features or adjusting existing ones based on consumer needs and preferences. This approach ensures that the products remain competitive and aligned with market demands.
The future of sheet metal chafing dish manufacturing holds even more potential for innovation. In addition to refining production processes and incorporating sustainable practices, the integration of artificial intelligence (AI) and machine learning will continue to drive advancements in product development, quality control, and supply chain management. AI can be used to predict consumer behavior, optimize production schedules, and provide insights into operational efficiencies. By combining AI with real-time data from the production line, manufacturers can further enhance the customization and flexibility of the chafing dish production process, allowing for faster response times to market trends and more personalized products.
In summary, the sheet metal chafing dish manufacturing process is becoming increasingly advanced through the integration of automation, robotics, IoT, 3D printing, and sustainable practices. These technologies enable manufacturers to produce high-quality, energy-efficient, customizable products that meet the evolving needs of consumers in the foodservice industry. As the demand for eco-friendly and smart products rises, manufacturers are adapting by exploring innovative materials and features that align with these trends. The continuous improvement of the production line through advanced technologies and customer feedback ensures that the chafing dishes remain relevant, functional, and competitive in the marketplace.
As the sheet metal chafing dish manufacturing process progresses, the ongoing developments in technology and production strategies promise to further elevate the quality, efficiency, and customization of the products. One significant trend is the continued rise of Industry 4.0 technologies, which emphasize the interconnectedness of manufacturing systems, real-time data collection, and advanced analytics. By leveraging the Internet of Things (IoT), artificial intelligence (AI), and cloud-based platforms, manufacturers can create a highly responsive and flexible production environment.
These connected systems enable real-time monitoring of equipment, raw materials, and production progress. Sensors embedded in various stages of the production line capture a wealth of data, which is transmitted to centralized databases for analysis. For instance, data from cutting, forming, and welding machines can be analyzed to detect any subtle variations in performance that may indicate potential issues. This enables predictive analytics that can forecast and mitigate equipment failure before it occurs, further minimizing downtime and maintaining the flow of production.
Through the use of AI, manufacturers can also optimize production schedules in real time. By analyzing historical data and patterns, AI can predict when a machine is likely to need maintenance or when production lines are likely to become congested, allowing operators to make adjustments ahead of time. This predictive capability enhances operational efficiency, reduces bottlenecks, and ensures that resources are utilized optimally.
Additionally, automation continues to be a game-changer in terms of labor efficiency. With advancements in robotic systems, manufacturers can automate many of the more intricate and repetitive tasks. For example, robotic arms equipped with vision systems can autonomously detect imperfections in metal sheets, identifying scratches, dents, or deformities, and sorting out any defective parts. This reduces human intervention and error while maintaining consistency in quality. Robots can also be used in the final assembly stages, installing heating elements, sensors, or other components, ensuring the units are ready for the final testing phase with minimal human touch.
Another exciting advancement is the potential use of augmented reality (AR) and virtual reality (VR) technologies in the manufacturing process. For example, AR could be employed to assist workers during assembly by providing real-time instructions or visual aids superimposed onto the physical environment. This would help reduce errors, improve training, and streamline the assembly process, as workers can receive direct visual guidance on how to perform tasks or troubleshoot problems. Similarly, VR could be used for design reviews or operator training, providing a safe and controlled virtual environment where operators can practice and learn without the need for physical prototypes or machinery.
The implementation of digital twins—virtual representations of physical manufacturing systems—also offers manufacturers greater control over the production process. Digital twins allow manufacturers to simulate and optimize every stage of the chafing dish production cycle before physical production even begins. By mimicking real-world conditions, digital twins can be used to test new manufacturing processes, experiment with different design configurations, and predict how changes in one part of the production process may affect the overall system. This helps reduce costly trial and error and speeds up the development of new designs or improvements.
On the sustainability front, there is a growing emphasis on reducing the environmental impact of manufacturing operations. Beyond using recyclable materials and reducing energy consumption, manufacturers are exploring new methods to minimize waste during the production process. One approach is the increased use of precision laser cutting and advanced nesting algorithms that maximize the material utilization, reducing scrap metal. Additionally, more manufacturers are investing in closed-loop systems for recycling excess metal and by-products from the cutting, forming, and finishing stages. By reusing metal scrap, manufacturers can reduce their reliance on raw material procurement, lowering costs and minimizing the environmental footprint of production.
The use of renewable energy sources in the manufacturing process is also gaining traction. Solar panels, wind energy, and other renewable energy options are being integrated into manufacturing facilities to help power the production process. This not only reduces greenhouse gas emissions but also helps companies meet the growing demand for more sustainable practices. By incorporating energy-efficient machinery and implementing energy recovery systems (such as heat recovery from industrial processes), manufacturers are able to further minimize their environmental impact.
In terms of logistics, manufacturers are adopting more intelligent supply chain management systems that leverage real-time tracking, data analytics, and AI to optimize inventory levels and shipping times. This helps reduce the carbon footprint of the manufacturing and distribution process. Just-in-time (JIT) inventory systems, for example, ensure that materials are delivered to the production line as needed, minimizing excess stock and reducing the need for large storage spaces. By using GPS tracking and RFID technology, manufacturers can also track the movement of raw materials, components, and finished goods throughout the entire supply chain, improving visibility and efficiency.
Customer engagement continues to be a driving force in the development of new chafing dish models. As consumer preferences evolve, manufacturers are adapting to meet these demands by offering more customizable options. Whether it’s the finish (polished, brushed, matte), the design (round, square, or custom), or additional features such as digital temperature displays, built-in timers, or non-stick interiors, the ability to tailor products to meet specific needs is becoming increasingly important. In addition, manufacturers are paying closer attention to the ergonomics and usability of their products, ensuring that the handles are comfortable, lids are easy to open and close, and the units are stable and secure during use.
The rise of e-commerce has also had a profound impact on the sheet metal chafing dish market. Manufacturers are investing in direct-to-consumer sales channels and building online platforms that allow customers to customize, order, and track their chafing dishes. In this digital age, consumers expect seamless online shopping experiences, and manufacturers are adapting to meet these expectations. Providing clear product descriptions, high-quality images, and easy-to-use ordering systems online helps manufacturers stay competitive in a rapidly changing market.
Finally, the shift toward global markets continues to shape the chafing dish manufacturing landscape. As businesses and consumers increasingly demand products for international use, manufacturers are adjusting their production methods to comply with different regulations, certifications, and safety standards in various regions. This requires a deep understanding of global supply chains, market requirements, and consumer behavior, which can vary widely from country to country. Manufacturers who successfully adapt to these global shifts are well-positioned to expand their reach and capture new opportunities in emerging markets.
In conclusion, the future of sheet metal chafing dish manufacturing is defined by advanced technologies, sustainability, and an unwavering focus on customer demands. Automation, AI, robotics, and IoT are streamlining production, reducing waste, and enhancing product quality. Meanwhile, sustainable practices, energy efficiency, and customization are meeting the needs of both environmentally conscious consumers and businesses. With the ongoing integration of smart technologies, digital twins, and renewable energy solutions, manufacturers are poised to create more innovative, high-quality, and eco-friendly chafing dishes that cater to the evolving demands of the foodservice industry.
Sheet Metal Ice Bucket Manufacturing Machine
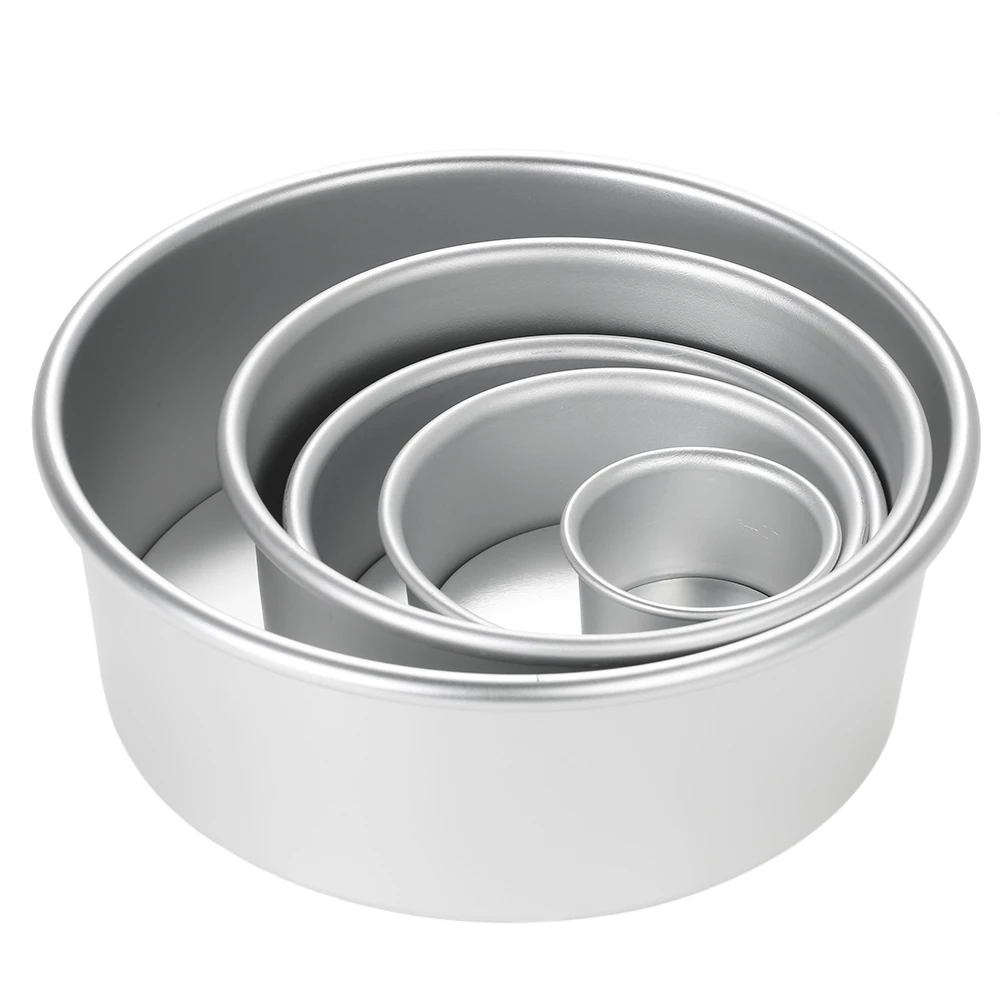
A sheet metal ice bucket manufacturing machine is designed to produce high-quality, durable ice buckets commonly used in the hospitality, catering, and beverage industries. These ice buckets are typically made from stainless steel, aluminum, or other metals that offer strength, heat resistance, and a sleek aesthetic. The manufacturing process involves several stages, from cutting the metal sheets to the final assembly, ensuring the product is functional, attractive, and safe for use in various settings. Here’s an overview of how such a machine might function, focusing on the integration of automated processes, precision, and efficiency.
The process starts with the feeding of metal sheets, typically stainless steel, into a machine that can cut, form, and shape the sheets into the necessary components of the ice bucket. Laser cutting machines or turret punch presses are often employed for this step. Laser cutting is preferred for its precision, allowing for intricate designs and clean edges. The metal sheets are cut into the required shapes for the sides, base, and handle of the ice bucket. These cutting processes are automated, utilizing advanced nesting software that maximizes material efficiency and minimizes scrap.
Once the metal sheets are cut to shape, the next step is the forming process. The components, such as the side walls and bottom of the ice bucket, are then transferred to a hydraulic press or mechanical press. In this stage, the machine uses controlled force to shape the metal into the rounded or cylindrical form needed for the ice bucket. The forming machine ensures precise bending and shaping, ensuring that the dimensions are consistent across all units. For buckets with a more complex or decorative design, such as embossed patterns or a more intricate lip, additional forming techniques like deep drawing or spinning may be used.
Next, the pieces are welded together to form the structure of the ice bucket. This is typically done using TIG (Tungsten Inert Gas) welding or robotic MIG (Metal Inert Gas) welding for high precision. Robotic welding systems are often employed for this purpose, as they can ensure consistency, reduce human error, and speed up the welding process. The welding joints must be smooth and secure to ensure the structural integrity of the ice bucket, as it will be subjected to various conditions, including cold temperatures and water exposure.
After welding, the ice bucket undergoes a finishing process to remove any excess weld material, rough edges, or sharp points that could cause issues during use. Automated grinding or polishing machines are employed to smooth the surfaces and ensure the bucket is free of any imperfections. In some cases, the ice bucket may be polished to a high shine, using abrasive materials and polishing compounds. This not only enhances the appearance of the bucket but also improves its resistance to corrosion and tarnishing.
The next stage involves coating the ice bucket for additional protection and aesthetic appeal. Electroplating or powder coating is commonly used to provide a protective finish. Electroplating applies a thin layer of another metal, like chrome or nickel, to the surface of the ice bucket, which not only enhances its aesthetic appeal but also adds to its corrosion resistance. Powder coating, on the other hand, provides a durable, colored finish and can be applied in a variety of shades, offering a more custom aesthetic to suit different designs.
Once the coating is applied, the ice bucket is subjected to a quality control inspection. Automated vision systems equipped with cameras and sensors inspect each ice bucket for any defects in the metal, coating, or shape. These systems can detect minor imperfections, such as dents, scratches, or uneven coating, and sort out defective units before they proceed to the final assembly phase. The machine can also verify that the dimensions of the ice bucket meet the required specifications, ensuring uniformity across production.
The next step involves the assembly of any additional components, such as handles, lids, or tongs. If the ice bucket is designed to have a handle, it is typically attached using either welding or rivets, depending on the design. In high-end models, handles might be attached with polished screws or other fastening methods for both aesthetic and functional purposes. Robotic arms equipped with tools like riveters or screwdrivers can be used to automatically attach these handles in a precise manner. If the design includes a lid, it would be formed separately and attached similarly, ensuring a secure fit.
Following the assembly of these components, the ice bucket may undergo a functional test to ensure that it meets the desired performance criteria. For example, the machine might check for any leaks if the bucket is intended to hold ice and liquid, ensuring that no moisture escapes and that the bucket maintains its structural integrity. If the ice bucket is designed to be insulated, additional tests might involve checking the thermal properties, confirming that the insulation material performs effectively to keep ice cold for an extended period.
In the final stages of the process, the ice bucket is cleaned to remove any oils, fingerprints, or residues from the manufacturing process. Ultrasonic cleaning systems can be used to gently clean the ice bucket without damaging its surface. Once cleaned, the ice bucket is dried and undergoes a final visual inspection to ensure it meets the manufacturer’s aesthetic and functional standards.
Finally, the finished ice buckets are packaged for shipment. Automated packaging systems handle the packing, ensuring that each unit is securely placed in protective packaging such as foam inserts, bubble wrap, or custom molds. The ice buckets are then placed in sturdy boxes to prevent damage during shipping. The packaging also includes labeling for product identification, which may include the manufacturer’s logo, product specifications, and safety instructions.
Throughout the entire manufacturing process, a Manufacturing Execution System (MES) is often employed to track the progress of each unit, monitor machine performance, and manage inventory. The MES ensures that raw materials are available when needed, production lines are running smoothly, and finished products are shipped on time.
In conclusion, the sheet metal ice bucket manufacturing machine is a highly automated and efficient system that combines advanced technologies such as laser cutting, robotic welding, precision forming, coating, and quality control to produce high-quality ice buckets. By integrating automation at every stage of the process, manufacturers can increase production speed, reduce costs, and ensure a high level of consistency and quality in their products. Additionally, sustainability practices, energy-efficient machines, and eco-friendly materials are increasingly being incorporated into the process to meet consumer demands for environmentally responsible manufacturing practices. The result is a durable, attractive, and functional ice bucket that meets the high standards of both commercial and residential markets.
The automation of the sheet metal ice bucket manufacturing process not only enhances production speed but also ensures that every unit is produced to the highest quality standards. The seamless integration of robotics and AI technology into the process enables precise control at every stage. From cutting the metal sheets to applying the final finish, each task is performed with the utmost accuracy, reducing human error and increasing efficiency. The automated systems can adjust settings in real time, based on feedback from various sensors throughout the production line, which ensures that any deviations from the ideal process are promptly corrected.
The increased use of data analytics throughout the production line has also proven valuable. By continuously monitoring machine performance and material usage, manufacturers can identify areas for improvement. Data collected from the various machines involved in the process—such as laser cutters, presses, and welders—can be analyzed to spot patterns and optimize operational parameters. For example, if certain settings on a press are found to consistently lead to higher-quality buckets, those settings can be automatically adjusted across the entire production line. Similarly, real-time performance data can be used to predict when a machine is nearing a failure point, allowing operators to perform proactive maintenance, which reduces costly downtime and ensures continuous production.
On the sustainability front, manufacturers are increasingly focused on minimizing the environmental impact of the ice bucket production process. This includes not only reducing waste but also incorporating energy-efficient technologies. Energy-saving machines, such as those with variable-speed motors or heat recovery systems, are being integrated into the manufacturing line to minimize power consumption. The automation of material handling, including the use of automated guided vehicles (AGVs) and conveyors, reduces the need for energy-intensive manual labor and ensures that materials are efficiently routed through the production process.
In terms of materials, manufacturers are exploring new ways to improve the environmental footprint of the metal used in ice bucket production. One such approach involves using recycled metals or alloys that are more sustainably sourced. The recycling process itself is becoming more efficient, with closed-loop systems that enable manufacturers to reuse scrap metal generated during production. Additionally, the use of advanced metal forming techniques, like hydroforming or precision stamping, reduces the amount of material waste, ensuring that every sheet of metal is utilized to its fullest potential.
As customer demands evolve, customization options are becoming an increasingly important aspect of the production process. The ability to create ice buckets in a variety of finishes, sizes, and shapes allows manufacturers to appeal to both commercial clients and individual consumers. Whether it’s a highly polished stainless steel finish, a matte powder coating, or a unique, branded design, offering custom solutions is crucial for capturing market share in the competitive beverage accessories market. Automation plays a significant role in this by allowing for flexible production lines that can quickly switch between different designs, finishes, and sizes without significant downtime or retooling.
The rise of e-commerce and online retail platforms has further driven the need for customization and personalization in ice bucket manufacturing. With more consumers seeking unique, bespoke items for their home bars or events, manufacturers are responding by offering easy-to-use online platforms where customers can design their own ice buckets. These platforms allow users to select everything from the material and finish to adding engraved logos or personalized text, creating a product that fits their specific needs. Automated systems help to streamline the process from order entry to production, ensuring that even highly customized orders can be fulfilled quickly and accurately.
As the industry continues to innovate, there is a growing trend toward integrating smart technology into ice bucket designs. Some high-end models now come equipped with built-in cooling elements or features that allow for precise temperature control. IoT sensors embedded in the buckets can track internal temperature and send real-time alerts to a smartphone app if the ice begins to melt or the temperature rises above a preset threshold. These smart ice buckets are increasingly popular in luxury settings, where convenience and high-tech features are highly valued. The production process for these high-tech units requires additional steps, such as integrating cooling elements and ensuring the electronics are properly sealed within the metal structure to avoid damage from moisture.
With a focus on precision, sustainability, and customer customization, sheet metal ice bucket manufacturing is becoming increasingly sophisticated. The use of automation and advanced technologies is enabling manufacturers to produce high-quality products at scale while maintaining cost-effectiveness. At the same time, sustainability initiatives ensure that the environmental impact of the production process is minimized, meeting the demands of both environmentally conscious consumers and businesses. As the market for ice buckets continues to evolve, manufacturers are well-positioned to innovate and meet the growing demand for more personalized, energy-efficient, and technologically advanced products. The result is a more dynamic, responsive manufacturing process that not only delivers superior products but also aligns with global trends in sustainability and technological advancement.
The future of sheet metal ice bucket manufacturing is poised for further innovation, driven by both advancements in technology and shifting consumer demands. One of the key trends is the increasing integration of artificial intelligence (AI) and machine learning (ML) into the production process. These technologies are becoming essential for predictive maintenance, quality control, and production optimization. By analyzing historical production data and real-time inputs, AI can predict when a machine is likely to fail or when adjustments need to be made to optimize the production cycle. This minimizes downtime and ensures that the production line operates as efficiently as possible.
Machine learning algorithms can also be applied to the design phase, where they can analyze consumer preferences and predict design trends. This allows manufacturers to create ice buckets that not only meet functional requirements but also appeal to evolving tastes. For example, AI-driven design tools can suggest materials, finishes, and shapes based on popular market trends or consumer behavior patterns, providing manufacturers with a competitive edge by producing products that are likely to be in high demand.
In addition to AI, the development of advanced sensors and smart materials will play a major role in the evolution of ice bucket designs. Sensors that monitor the internal temperature of the ice bucket, for instance, could help ensure that beverages stay at the desired chill level for longer periods, enhancing the functionality of the product. These smart features could be integrated into the production line, making the process more efficient and allowing manufacturers to produce high-tech products on a large scale without significant additional cost.
3D printing, or additive manufacturing, is another area where the ice bucket manufacturing process could see significant transformation. While metal 3D printing is still in its early stages, it holds great promise for creating custom, intricate designs and components. For example, the handles of ice buckets or decorative accents could be 3D-printed using metal powders, enabling manufacturers to produce highly detailed, one-of-a-kind designs. This could be particularly valuable for luxury or custom orders, where exclusivity and design complexity are key selling points. 3D printing also enables a more sustainable approach by reducing material waste, as parts are built layer by layer rather than cut from larger metal sheets.
The ability to quickly prototype and test new designs using 3D printing can accelerate the development of new products, allowing manufacturers to respond more rapidly to market demands. Furthermore, 3D printing can be used to create lightweight structures, reducing the overall weight of the ice bucket while maintaining strength and durability. This could make the product more attractive to consumers looking for a balance between functionality and ease of use, particularly in commercial settings like hotels, bars, and restaurants.
On the sustainability front, manufacturers are also exploring the potential of alternative, eco-friendly materials. While stainless steel remains a popular choice due to its durability and corrosion resistance, there is increasing interest in materials like recycled aluminum or bioplastics. These materials could reduce the environmental impact of production by lowering the carbon footprint associated with metal extraction and processing. Additionally, using sustainable materials that can be easily recycled or are biodegradable aligns with the growing consumer demand for environmentally responsible products.
Packaging is another area where sustainability efforts are being intensified. Manufacturers are moving toward using more eco-friendly packaging materials, such as recyclable cardboard, biodegradable plastics, or reusable packaging. The goal is not only to reduce waste but also to enhance the overall consumer experience by offering packaging that is both functional and sustainable. For example, using compostable packing peanuts or molded pulp packaging can ensure that the ice bucket is protected during shipping without contributing to plastic pollution.
Moreover, with the rise of e-commerce, manufacturers are increasingly focusing on packaging designs that are optimized for shipping efficiency. This could involve designing packaging that reduces the space required for shipping, ensuring that more units can be transported in fewer shipments, ultimately reducing the carbon footprint of the distribution process. It also opens the door for manufacturers to offer direct-to-consumer sales, cutting out intermediaries and offering a more streamlined shopping experience for customers.
As the global market for premium home and commercial goods continues to grow, manufacturers are also expanding their reach by focusing on international distribution. This requires adapting to different regional preferences, which may include producing ice buckets in sizes or designs that cater to specific markets. For example, while larger, high-capacity ice buckets may be popular in North America, smaller, more compact models may be in demand in regions with more limited space or different consumer habits. In response, manufacturers are utilizing flexible production lines that can quickly shift between different designs and production volumes, ensuring they can meet the needs of a diverse customer base.
The incorporation of digital technologies such as augmented reality (AR) is another possibility that could further enhance customer engagement and the buying experience. Imagine a scenario where a consumer could use an AR app to virtually “place” an ice bucket in their home or bar area to see how it would fit with their existing decor before making a purchase. This ability to visualize the product in its intended environment could reduce hesitation in purchasing and increase overall customer satisfaction.
In terms of innovation, the development of insulated or double-walled ice buckets with better heat retention properties is also gaining momentum. These buckets are designed to keep ice cold for longer periods by adding a layer of insulation between the inner and outer walls. Manufacturers are exploring different insulation technologies, including vacuum-sealed chambers, foam-filled gaps, or other advanced thermal barrier materials that provide enhanced performance. These features not only increase the ice bucket’s functionality but also appeal to consumers looking for more practical, high-performance products.
Finally, as sustainability continues to be a key consideration, manufacturers are exploring the integration of green energy into their production processes. Solar panels, wind energy, or other renewable sources are being incorporated into manufacturing facilities to reduce the reliance on fossil fuels. These sustainable energy practices can contribute significantly to lowering a manufacturer’s overall carbon footprint and demonstrate their commitment to environmentally responsible production.
In conclusion, the future of sheet metal ice bucket manufacturing will likely see further advancements in automation, smart technology integration, sustainable practices, and customization options. As manufacturers respond to consumer demand for eco-friendly, high-performance products, they will increasingly rely on innovative technologies like AI, 3D printing, and sustainable materials to create more advanced and personalized products. At the same time, the evolving market for luxury, high-tech, and customizable ice buckets presents manufacturers with opportunities to explore new designs and features, further pushing the boundaries of what’s possible in the production of these popular beverage accessories.
Looking ahead, the sheet metal ice bucket manufacturing process will continue to evolve, driven by advancements not only in technology and materials but also in consumer behavior and the global business environment. One of the areas that will likely see significant innovation is in the circular economy, where the focus is on reducing waste, reusing resources, and creating products that are easily recyclable at the end of their life cycle.
Circular economy principles are already being incorporated into many industries, and ice bucket manufacturing is no exception. For example, more manufacturers are adopting design-for-recycling practices, ensuring that their ice buckets are made from materials that can be easily disassembled, reused, and recycled. This includes using single-material construction, avoiding the use of mixed materials that are difficult to separate, and making sure that components like handles, lids, or internal mechanisms are recyclable or biodegradable. Moreover, companies are beginning to explore how the metal itself can be sourced more sustainably. This could involve increasing the proportion of recycled metal in the production process, which would reduce the need for raw material extraction and decrease the energy used in production.
Another trend on the horizon is the integration of blockchain technology into the supply chain. Blockchain can provide a secure, transparent, and traceable record of every step in the ice bucket’s journey from raw material procurement to final sale. This allows consumers to verify the ethical sourcing of materials and the sustainability practices of the manufacturers. By providing more transparency, blockchain also enables manufacturers to prove that they are meeting high environmental and ethical standards, which is increasingly important to consumers, particularly those in younger generations who prioritize sustainability.
On the production floor, Industry 4.0 technologies will continue to shape the future of ice bucket manufacturing. This refers to the next phase of industrialization where advanced technologies such as the Internet of Things (IoT), cyber-physical systems, and cloud computing are integrated into manufacturing operations. These technologies create “smart factories” that are highly interconnected and can communicate in real-time, allowing manufacturers to track every aspect of the production process, from raw materials to finished goods. IoT sensors can monitor everything from temperature and humidity to machine health, providing valuable data that can be used for predictive maintenance and ensuring smooth production processes.
In the future, factories may be equipped with more autonomous systems, such as robots capable of not just assembling ice buckets but also independently optimizing production schedules, maintaining inventory, and ensuring quality control. These robots will be increasingly flexible, capable of adapting to different design specifications without the need for manual intervention. For example, a robot could change its tools or settings automatically when switching between different models of ice buckets or adjusting production lines for custom orders. This flexibility will allow manufacturers to create personalized and limited-edition ice buckets at scale, catering to niche markets and evolving consumer tastes without the need for a significant redesign of the production line.
Additionally, advancements in augmented reality (AR) and virtual reality (VR) will further enhance the design and prototyping stages. Designers could use AR to visualize and interact with 3D models of ice buckets in real-world settings, making design decisions faster and more accurately. VR could be used for immersive training experiences, allowing factory workers to simulate operating complex machinery or troubleshoot issues before they occur in real-world settings.
The growth of online sales and direct-to-consumer models will also continue to shape the ice bucket manufacturing process. To meet the increasing demand for direct shipping and faster delivery times, manufacturers will need to continue refining their supply chains. Automation in warehousing and order fulfillment, including robots that can pick, pack, and ship products efficiently, will play a significant role. With more products being sold online, packaging will need to be optimized for both protection and presentation, ensuring that each ice bucket reaches the consumer in perfect condition while also being aesthetically pleasing upon unboxing.
Moreover, the rise of e-commerce platforms has created opportunities for greater customization and personalization, giving manufacturers the ability to offer unique products tailored to individual customer preferences. Consumers will be able to choose not only the color, size, and finish of their ice buckets but also the inclusion of custom engravings, logos, or themed designs. Some companies may even explore augmented reality platforms that allow customers to design their own ice bucket online, preview it in their space, and place an order all within a few clicks. This level of personalization, combined with the convenience of online shopping, will appeal to a growing segment of consumers seeking more individualized products.
The luxury market for ice buckets will also continue to grow, with manufacturers introducing high-end, designer versions that go beyond functionality to become statement pieces. These models may include features such as intricate handcrafting, inlaid precious metals, or innovative technological elements like LED lighting, which adds an extra layer of sophistication and luxury. The fusion of advanced technology with traditional craftsmanship will cater to discerning customers who are looking for products that provide both functional value and aesthetic appeal.
On the other side of the spectrum, manufacturers will need to remain mindful of the increasing demand for affordable, yet well-designed ice buckets. As consumer purchasing power fluctuates across different regions, there will be an increased focus on creating budget-friendly options without sacrificing quality or style. Through smart design choices, automation, and efficient production processes, manufacturers can lower production costs while maintaining high standards of durability and aesthetic appeal, ensuring that ice buckets remain accessible to a wide range of consumers.
In terms of consumer behavior, sustainability is likely to continue driving purchasing decisions. As people become more aware of their environmental impact, many will gravitate towards brands that demonstrate a commitment to responsible sourcing, manufacturing, and disposal of products. The trend of “buying less, but buying better” will encourage consumers to invest in high-quality, durable ice buckets that can withstand years of use, rather than opting for disposable or cheaply made alternatives.
Lastly, the overall consumer experience is becoming an integral part of the product offering. This includes the way products are marketed, the ease of the online shopping experience, and the after-sale services offered. Brands that prioritize customer engagement, offer comprehensive warranties, and create a strong brand identity that resonates with their target market will likely see success in an increasingly competitive market. Personalized customer service, quick resolution of issues, and a clear commitment to sustainability will contribute to customer loyalty and brand reputation.
As ice bucket manufacturing continues to adapt to new trends and technologies, the future promises greater innovation, sustainability, and consumer engagement. By leveraging cutting-edge production techniques, embracing sustainability at every stage, and meeting the evolving needs of the market, manufacturers will remain at the forefront of this industry, producing products that are not only functional but also highly desirable in an ever-changing consumer landscape.
Sheet Metal Condiment Holder Manufacturing Machine
The manufacturing of sheet metal condiment holders involves specialized machinery and automated systems that ensure efficient production and high-quality output. These machines handle various aspects of the production process, from cutting and shaping the metal sheets to assembling and finishing the final product. Here’s an overview of the different stages involved in the manufacturing process of a sheet metal condiment holder.
1. Material Selection and Preparation
The process begins with selecting the appropriate material, typically stainless steel, aluminum, or galvanized steel, which is known for its durability, resistance to corrosion, and ease of cleaning. The metal sheets are sourced in standard sizes and are typically pre-cut into sheets of specific dimensions based on the design requirements of the condiment holder.
Before processing, the metal sheets undergo cleaning to remove any oils, dirt, or other contaminants. This ensures better adhesion of coatings and prevents defects in the finished product. Automated systems often handle this cleaning process, using ultrasonic or mechanical methods to ensure thorough preparation.
2. Cutting
Once the material is ready, the next step is cutting the metal sheets into the desired shapes and sizes. This process is typically carried out using one of the following methods:
- Laser Cutting: Laser cutting is highly precise and is used for intricate designs or complex shapes. It is ideal for creating detailed holes, slots, or patterns in the metal sheet. The laser is controlled by CNC (Computer Numerical Control) systems that follow the exact specifications of the design file.
- Punching: Punching is another common cutting method where a punch press is used to create holes or shapes in the metal. This method is especially useful for creating uniform, repetitive patterns or designs for large production runs.
- Shearing: For straight cuts, shearing machines are used. These machines are designed to cut large sheets of metal into strips or smaller sections that are then used in the construction of the condiment holder.
3. Forming and Shaping
Once the metal pieces are cut to size, they need to be formed into the desired shapes. This process may include bending, rolling, and stamping. The specific method used depends on the design of the condiment holder and the complexity of the shapes required.
- Bending: CNC press brakes are typically used for bending metal sheets into the required angles. The sheet is placed between a punch and die, and the machine applies pressure to bend the metal. The precision of CNC-controlled bending ensures that the angles are accurate.
- Stamping: In stamping, a die is used to cut, shape, or emboss designs into the metal. Stamping machines are used to create patterns, textures, or even brand logos on the surface of the condiment holder.
- Rolling: For cylindrical or curved components, rolling machines are used to bend the metal into the desired shape. The metal is passed through a set of rollers that progressively curve it to the required radius.
4. Assembly
Once the individual parts of the condiment holder are formed, they are assembled into the final structure. The assembly process may involve welding, riveting, or using fasteners like screws or bolts to join the components.
- Welding: For permanent connections, welding is often used. MIG (Metal Inert Gas) welding or TIG (Tungsten Inert Gas) welding is commonly employed for stainless steel and aluminum. Automated robotic welding systems can be used for precise, consistent welds, ensuring strength and stability.
- Riveting and Fastening: In some designs, rivets or screws may be used to join components together. This is particularly common when a design requires the parts to be disassembled or replaced easily.
5. Finishing
Once the condiment holder is assembled, it undergoes a series of finishing processes to improve the appearance and durability of the product.
- Deburring: Any sharp edges or burrs left from the cutting and forming processes are removed using automated deburring machines or hand tools. This ensures that the product is safe to handle and has a smooth finish.
- Polishing: For an aesthetically pleasing, shiny surface, especially in stainless steel or aluminum holders, polishing machines are used. These machines use abrasive materials to achieve a mirror-like finish.
- Powder Coating or Painting: To improve corrosion resistance or to give the condiment holder a colorful or branded appearance, powder coating or painting is applied. Powder coating is commonly used in industrial applications as it is durable and resistant to scratches and fading. The item is typically placed in an oven to cure the powder coating, creating a tough and long-lasting finish.
- Electroplating: For certain premium condiment holders, electroplating (e.g., chrome plating) may be applied to create a shiny, durable surface with high corrosion resistance.
6. Quality Control
Quality control is essential to ensure that the condiment holders meet industry standards and consumer expectations. Each unit is inspected for defects such as dimensional inaccuracies, weld quality, surface finish, and the integrity of coatings. Automated inspection systems, such as cameras and sensors, may be used to check for imperfections.
In addition, the functionality of the condiment holder is tested. This may include ensuring that the sections where condiments are stored are properly sized, stable, and easy to clean.
7. Packaging and Shipping
Once the condiment holders pass quality control checks, they are packaged for shipment. Packaging is designed to protect the product during transit while also promoting the brand. Packaging materials may include cardboard boxes, plastic wraps, or custom-designed cartons with foam inserts to prevent damage. Labels with product information, brand logos, and care instructions are added to the packaging.
The finalized products are then shipped to distributors, retailers, or directly to consumers, depending on the sales model.
8. Automation and Technology Integration
Automation plays a critical role in improving efficiency, reducing labor costs, and maintaining consistent product quality. CNC machines, robots, and AI-based systems can be used at each stage of production, from cutting and forming to assembly and finishing. The integration of sensors and real-time monitoring helps to detect problems early in the process and minimizes downtime.
Additionally, the use of data analytics in the manufacturing process allows manufacturers to monitor trends in production performance and material usage. This data-driven approach helps optimize operations, predict maintenance needs, and reduce waste.
Conclusion
The manufacturing of sheet metal condiment holders is a sophisticated process that relies on precision, automation, and quality control at every stage. By combining advanced cutting, forming, welding, and finishing technologies, manufacturers can produce durable, functional, and aesthetically pleasing condiment holders that meet the diverse needs of consumers and businesses alike. The use of sustainable materials, energy-efficient machines, and environmentally friendly coatings ensures that the production process is increasingly aligned with global sustainability goals.
In the ongoing development of sheet metal condiment holder manufacturing, the emphasis on automation and efficiency will only grow stronger. With advanced technologies such as artificial intelligence (AI), machine learning (ML), and robotics continuing to evolve, the process of designing and producing condiment holders is becoming more streamlined and cost-effective. Automated machines will increasingly take on roles that were once performed by manual labor, especially in tasks like material handling, part assembly, and quality control. Robots and automated systems will be used not only for cutting and shaping metal but also for performing intricate tasks like applying coatings, polishing, and assembling delicate components.
The integration of AI into the manufacturing process allows manufacturers to analyze data in real time and predict potential issues before they arise. For example, machine learning algorithms can be used to monitor machine performance and detect any anomalies or wear-and-tear that could lead to production delays. This predictive capability minimizes downtime, reduces the need for extensive maintenance, and ensures that the manufacturing process remains consistent and efficient.
Additionally, the increased use of robotics will facilitate the handling of repetitive tasks that require high precision, such as the welding of metal parts or the placement of screws and rivets. Collaborative robots (cobots), designed to work alongside human operators, can increase efficiency and reduce the risk of errors in assembly without the need for large-scale automation. These cobots can assist in tasks that involve complex positioning or require a gentle touch, like assembling smaller components that make up the condiment holder.
Beyond automation, the industry will likely see further innovation in materials used for condiment holders. Manufacturers may start to experiment with new alloys or composite materials that are lighter yet equally durable, offering an alternative to traditional metals like stainless steel or aluminum. These new materials might offer additional advantages, such as better resistance to rust and corrosion or the ability to withstand higher temperatures, which could extend the lifespan of the product. Furthermore, incorporating sustainable materials will be key to meeting consumer demand for environmentally responsible products. For instance, manufacturers could explore the use of recycled metals or eco-friendly coatings, which would reduce the environmental impact of production.
The demand for customization is also expected to rise. As consumers become more discerning, the ability to customize condiment holders with personalized engravings, unique designs, or a choice of colors will appeal to both individual customers and businesses looking to create a branded, signature product. Digital printing technologies are likely to play a role in this shift toward personalization, allowing for intricate designs and logos to be directly printed onto the metal surface of the condiment holder, offering endless customization possibilities without compromising on durability.
In terms of consumer preferences, there is a growing trend towards multifunctional designs. Manufacturers will be increasingly focused on developing condiment holders that not only store condiments but also serve additional purposes. For example, condiment holders could be designed with compartments for spices or even integrated with storage for utensils, making them more versatile for home kitchens and commercial settings like restaurants and catering services. Innovations like stackable or modular designs may allow users to customize their condiment holders based on their specific needs, whether for home use, outdoor events, or professional kitchens.
The industry will also see continued improvements in user-centric design, with an emphasis on ease of use and cleanliness. Given the nature of condiment holders, ensuring that they are easy to clean and maintain is essential. Future designs may incorporate features like removable trays, smooth surfaces, and rust-resistant coatings that ensure a long lifespan with minimal maintenance. As consumers look for products that not only serve functional needs but also enhance their dining experience, condiment holders will likely become more refined, offering sleek aesthetics in addition to practicality.
Another factor driving change in the manufacturing of sheet metal condiment holders is the growing influence of e-commerce. As online shopping continues to dominate the retail landscape, manufacturers will need to ensure that their products are optimized for both shipping efficiency and customer satisfaction. This will include designing packaging that is not only protective but also visually appealing, as consumers expect a pleasant unboxing experience. Streamlined production methods will also help reduce lead times and allow manufacturers to fulfill orders more quickly, addressing the growing demand for fast delivery times.
Finally, as sustainability becomes an even more pressing concern, manufacturers will need to adapt their processes to minimize waste and energy consumption. This could involve optimizing the use of raw materials, recycling scrap metal, and investing in energy-efficient machinery. The rise of renewable energy sources, such as solar or wind power, could also see adoption in manufacturing plants, reducing the carbon footprint of production.
In conclusion, the future of sheet metal condiment holder manufacturing is characterized by a shift towards greater automation, sustainability, and customization. With ongoing technological advancements and an increasing emphasis on consumer preferences for quality and design, manufacturers are poised to meet the evolving needs of the market. By embracing innovation in materials, production methods, and consumer engagement, manufacturers will not only enhance the functionality and appeal of their condiment holders but also contribute to a more sustainable and efficient manufacturing process overall.
As the sheet metal condiment holder manufacturing process advances, the next phase will likely involve even more sophisticated digitalization and integration of smart technologies. One major development in manufacturing is the rise of Industry 4.0, a concept that refers to the digital transformation of traditional manufacturing processes through the use of smart machines, interconnected systems, and real-time data analytics. This shift will allow for more agile production lines and greater customization of products, ultimately leading to faster lead times and reduced production costs.
One of the key aspects of Industry 4.0 is the concept of the Smart Factory, where machines are not only interconnected but also capable of communicating with each other. For example, the machines used for cutting, bending, and welding sheet metal could be linked through a centralized network, allowing for real-time monitoring of the production process. This would allow manufacturers to quickly identify and resolve bottlenecks or inefficiencies before they become problems, optimizing the entire production workflow.
In a Smart Factory, machine learning algorithms can analyze data from production lines to continuously optimize the manufacturing process. These systems can predict when maintenance is needed, reducing downtime and ensuring that machines are operating at peak efficiency. Machine learning can also help predict demand trends, allowing manufacturers to adjust production schedules accordingly and ensure that they are meeting consumer demand without overproducing or underproducing.
Robotics will continue to play a critical role in automating repetitive tasks such as assembly and packaging. Collaborative robots (cobots) will work alongside human operators, helping to speed up processes and reduce human error. These robots are increasingly capable of handling more complex tasks, and their flexibility allows them to adapt to various models of condiment holders, which could include changes in shape, size, or design. This adaptability will be a significant benefit for manufacturers who need to accommodate a wide range of customer preferences, especially in industries where customization is becoming increasingly important.
Another critical technology that is likely to shape the future of condiment holder manufacturing is 3D printing. As this technology continues to evolve, it could potentially be used for producing prototype designs, tooling, and even final products. Manufacturers could create highly detailed and intricate parts or features of condiment holders that would be impossible or prohibitively expensive to achieve using traditional methods. 3D printing could also be used for on-demand production, allowing companies to create small batches of customized or limited-edition condiment holders without the need for expensive tooling or molds.
In addition to these advancements in manufacturing technologies, material innovation will also play a major role in the future of condiment holder production. Manufacturers are exploring new, lightweight, and highly durable materials that not only offer strength but also enhance the aesthetic appeal of the product. Nanotechnology and advanced coatings, for example, could provide new ways to enhance the surface properties of metal, offering greater resistance to scratches, corrosion, and wear. Self-cleaning surfaces could be introduced, making condiment holders even more convenient for consumers. These advanced coatings can resist dirt and grime, ensuring that the product remains cleaner for longer and reduces the need for frequent maintenance.
Sustainability will continue to be a driving force behind the industry. Circular economy principles are likely to influence manufacturing methods as companies look for ways to reduce waste, reuse materials, and create products with longer lifespans. This could involve using recycled metal in the production process or adopting processes that minimize the generation of scrap metal. Companies that prioritize sustainability could appeal to environmentally conscious consumers who are increasingly aware of the ecological impact of the products they buy.
Eco-friendly packaging will also become a focal point. As consumers continue to demand more environmentally responsible products, the use of recyclable, biodegradable, or minimal packaging will become standard practice. Manufacturers will likely use more sustainable materials for packaging, such as cardboard made from recycled content or bioplastics that break down more easily than traditional plastic. The packaging will also need to be optimized for shipping, especially for e-commerce, where items are often delivered directly to consumers. Packaging innovations may include designs that reduce the volume of materials used or packaging that can be reused for other purposes.
The growing importance of consumer experience will also shape the future of condiment holder manufacturing. As consumers become more engaged with the products they purchase, they will increasingly seek brands that offer transparency in terms of the materials, production processes, and sustainability efforts behind the products. The digital experience will also play a crucial role, as manufacturers may offer online customization tools that allow consumers to design their own condiment holders. Through virtual platforms, customers could select the size, shape, color, finish, and engraving options for their condiment holders, making them feel more connected to the product. Augmented reality (AR) might also be used, enabling consumers to visualize how their personalized condiment holders would look in their home environments before making a purchase.
Along with greater customization, there will be a focus on personalized service. Customers will expect more from their buying experience, and companies that offer excellent customer service, from responsive communication to fast and reliable delivery, will likely see increased loyalty. Offering warranties, clear return policies, and easy-to-navigate websites will be vital in retaining customers and improving their overall satisfaction.
The increasing use of data analytics and customer insights will also shape the product offerings. By collecting data from sales, customer reviews, and social media interactions, manufacturers will be able to better understand consumer preferences and trends. This insight will allow for the creation of products that are more aligned with market demands, reducing the risk of overproduction and ensuring that companies stay competitive.
Ultimately, the future of sheet metal condiment holder manufacturing is centered around creating smarter, more efficient, and more sustainable products that meet the evolving needs and expectations of consumers. By leveraging cutting-edge technologies, focusing on sustainability, and enhancing the customization and personalization of products, manufacturers can position themselves at the forefront of this ever-changing industry. Through these innovations, they will not only improve the manufacturing process but also deliver products that provide greater value, functionality, and appeal to their customers.
Sheet Metal Sugar Container Manufacturing Machine
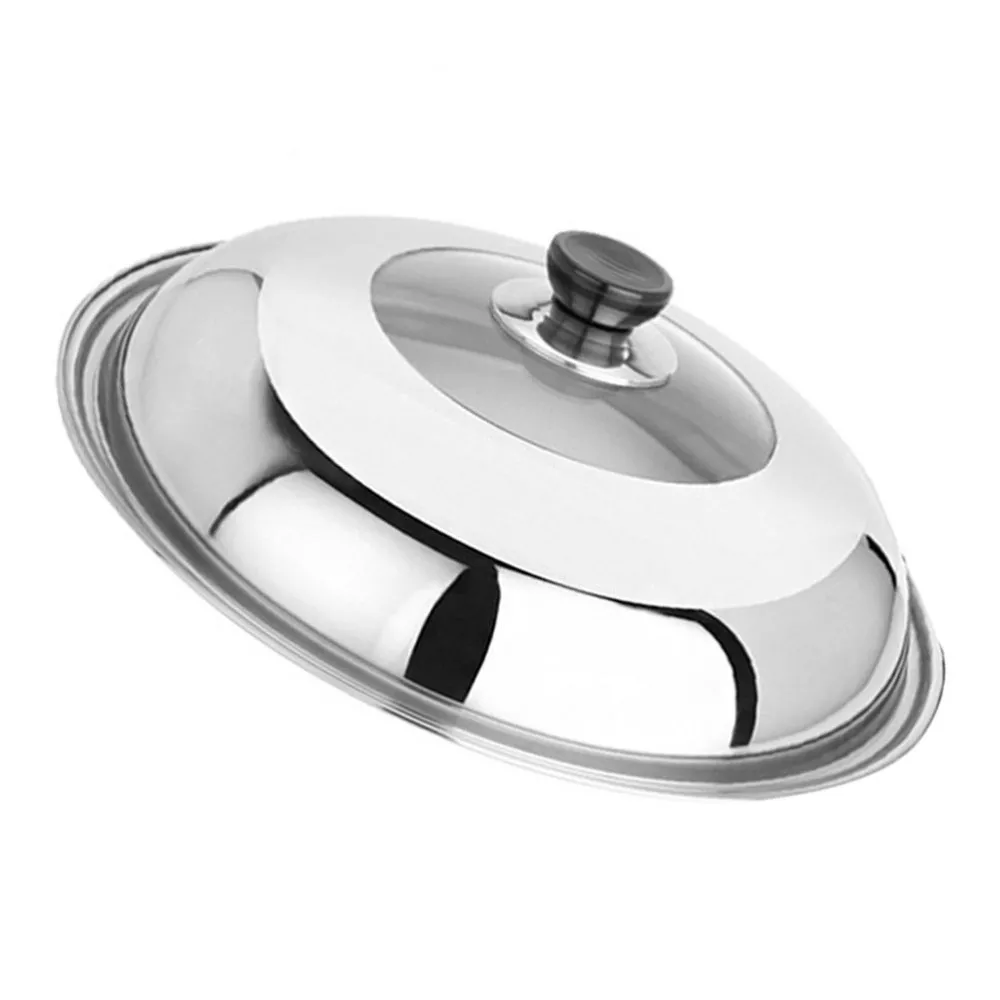
The manufacturing of sheet metal sugar containers involves a highly specialized process where various machines and automated systems are utilized to shape, form, assemble, and finish metal into functional and aesthetically pleasing sugar containers. These containers are commonly made from materials such as stainless steel, aluminum, or other corrosion-resistant metals that can withstand regular handling, contact with sugar, and cleaning. Below is a breakdown of the process for manufacturing sheet metal sugar containers.
The first step involves material selection and preparation, where sheets of metal are chosen based on their durability, resistance to corrosion, and food-safe properties. Stainless steel is particularly popular because it is non-reactive, easy to clean, and resistant to rust. The metal is typically purchased in large sheets, and depending on the container design, the sheets are cut to the required dimensions.
Once the material is ready, the next step is cutting. Cutting is performed using one of several methods depending on the design requirements:
- Laser Cutting: A laser cutting machine is used to cut the metal sheets with high precision. This is particularly useful when intricate shapes or patterns need to be cut into the metal. The cutting process is controlled by a CNC system, ensuring that the design specifications are followed exactly.
- Punching: A punching machine can also be used to create holes or shapes, especially when producing designs that require repetitive patterns.
- Shearing: For straight cuts, shearing machines are employed to cut the metal sheets into strips or smaller sections.
Once the parts are cut, they are subjected to forming and shaping. This process involves transforming the flat metal sheets into the final shape of the sugar container. Common techniques for this step include:
- Bending: A press brake machine is used to bend the sheet metal to create the sides, base, and lid of the sugar container. The metal is placed between a punch and die, which applies pressure to bend the metal at the desired angles. CNC press brakes allow for precision bending and ensure consistent results.
- Stamping: If the design involves embossing or creating specific patterns, a stamping press may be used. This process uses a die to create shapes, logos, or textures on the surface of the metal.
- Rolling: For cylindrical or curved shapes, the metal is passed through a rolling machine, which gradually forms the metal sheet into a round shape, forming the body of the sugar container.
Welding and assembly are critical next steps to join the various parts of the container. After the parts are shaped, they need to be assembled into the final structure. The parts can be welded using techniques like MIG or TIG welding, which ensure strong, secure joints. Rivets or fasteners can also be used for specific designs. For sugar containers that require detachable components or handles, rivets and screws are common choices.
Once the container is assembled, it moves on to the finishing process, which enhances both the appearance and functionality of the product:
- Deburring: Any sharp edges or burrs that remain from the cutting or bending processes are removed using specialized equipment. This is important for safety and helps improve the overall quality of the container.
- Polishing and Buffing: For an attractive, shiny finish, polishing machines are used. These machines buff the surface of the metal to a smooth and reflective surface, especially important for stainless steel sugar containers that will be visible on kitchen counters.
- Powder Coating or Painting: Many sugar containers undergo a powder coating or painting process to enhance durability, provide additional corrosion resistance, or create aesthetic finishes in a range of colors. Powder coating is a popular choice for its durability and smooth, even finish. The powder is applied electrostatically and then baked in an oven to harden the coating.
In some cases, electroplating can also be used to add a layer of shiny chrome or other metals to the container for added visual appeal and increased resistance to wear and corrosion.
Once the container has been fully assembled and finished, it undergoes quality control to ensure that it meets all specifications and is free from defects. The container’s dimensions are checked, and the surface finish is inspected for smoothness and uniformity. In addition, the container is tested to ensure that it is both functional (such as a lid that fits properly) and safe for use with food products.
The final step involves packaging and shipping. Once the sugar containers pass quality control, they are packaged for distribution. The packaging typically involves placing each container in protective materials like bubble wrap or foam inserts to prevent damage during shipping. The containers are then boxed and labeled, with information about the manufacturer and care instructions for the product. After packaging, the containers are shipped to retailers, distributors, or directly to consumers, depending on the sales model.
Throughout the manufacturing process, automation and technology play a critical role. CNC machines, robotic arms, and automated assembly lines increase efficiency and consistency while reducing labor costs. These systems are equipped with sensors and cameras that can detect issues such as misalignment or defects in real-time, enabling manufacturers to address problems early in the process.
Additionally, the use of data analytics and real-time monitoring systems can further optimize production. By tracking the performance of machines and analyzing production data, manufacturers can identify areas for improvement, predict when maintenance will be needed, and ensure that production runs smoothly with minimal downtime.
Sustainability is also an important factor in the manufacturing of sheet metal sugar containers. Manufacturers are increasingly focusing on minimizing waste and using recycled materials where possible. The use of recyclable metals such as aluminum and stainless steel aligns with growing consumer demand for environmentally friendly products. Companies are also adopting more sustainable practices in packaging, with a focus on reducing the use of plastic and opting for recyclable materials.
As consumer preferences evolve, the design of sugar containers will likely become more versatile. Features such as airtight seals, ergonomic handles, and space-saving designs will continue to gain popularity. Some consumers may prefer containers with unique finishes, custom engravings, or even designs that integrate smart technology (such as built-in sensors to measure sugar levels). As a result, manufacturers will continue to innovate in both materials and design to meet the diverse needs of their customers.
In conclusion, the manufacturing of sheet metal sugar containers involves a combination of precision cutting, forming, assembly, and finishing processes. Advances in automation, material science, and sustainability practices will continue to improve efficiency and product quality in the industry. As consumer expectations for durability, functionality, and design continue to rise, manufacturers will adapt their processes to deliver products that meet these demands while staying competitive in the marketplace.
The future of sheet metal sugar container manufacturing will likely see continued advancements in technology, automation, and sustainability. With the integration of advanced robotics, machines will be able to carry out more intricate tasks with higher precision. For example, robots could handle the assembly of smaller components, such as handles or lids, ensuring that the parts are securely fastened and correctly aligned. These robots will also work alongside human operators in a collaborative environment, performing tasks that are repetitive or require fine motor skills, while leaving more complex decisions to the human workers. This blending of human expertise with robotic efficiency will lead to faster production times and reduced risk of error.
Furthermore, the growing emphasis on smart manufacturing will allow for greater real-time monitoring and data collection. Sensors embedded in machines can track various parameters such as temperature, pressure, and speed, providing manufacturers with a wealth of data. This data can be analyzed to predict when a machine is likely to fail or require maintenance, helping to reduce downtime and optimize machine performance. Additionally, machine learning algorithms could be used to further improve the precision of operations, learning from past production cycles and fine-tuning the process to achieve optimal results.
As consumer demand for customization continues to rise, manufacturers will increasingly invest in technology that allows for more personalized designs. Advances in 3D printing technology may enable on-demand creation of parts or components that can be customized to fit specific customer needs. For example, a sugar container could feature personalized engravings, unique patterns, or custom finishes that reflect the style of the buyer or brand. This level of customization may extend to the functional aspects of the container as well, allowing customers to choose specific sizes, lid mechanisms, or handles that best suit their usage preferences.
At the same time, the growing importance of sustainability will continue to drive innovation in materials and processes. Manufacturers will seek to minimize waste, improve the efficiency of raw material usage, and reduce the carbon footprint of their operations. The adoption of recyclable metals and the increased use of recycled materials in production will help companies meet consumer expectations for eco-friendly products. Additionally, manufacturers will explore more sustainable coatings and finishes that avoid the use of harmful chemicals while still providing durability and corrosion resistance.
The increasing focus on energy efficiency will also influence production techniques. Manufacturers will invest in energy-efficient machinery, which reduces overall power consumption and lowers operating costs. The use of renewable energy sources, such as solar or wind power, may become more common in the manufacturing process, further reducing the environmental impact of production. This shift towards greener energy sources could also be a key selling point for brands, appealing to environmentally conscious consumers.
The demand for functional design will also shape the evolution of sugar containers. In response to consumer preferences, manufacturers may create containers with features that improve convenience, such as airtight seals to maintain the freshness of sugar for longer periods or ergonomic handles that make the containers easier to hold and pour. Additionally, designs that allow for easier cleaning and maintenance will likely be prioritized, as consumers seek products that require minimal effort to maintain. Modular designs that allow for stacking or storage efficiency may also be developed to suit different kitchen environments, especially for those with limited space.
Another major trend that will influence the sugar container manufacturing industry is the growing reliance on e-commerce and direct-to-consumer sales models. As online shopping continues to dominate the retail landscape, manufacturers will need to optimize their products for shipping. This means designing packaging that ensures the safe delivery of products while also making the unboxing experience as enjoyable as possible for consumers. Packaging that uses sustainable materials and minimizes waste will align with consumer expectations for environmentally conscious products.
In terms of consumer interaction, digital platforms will increasingly be used to engage with customers and provide a more personalized buying experience. Manufacturers may offer interactive design tools on their websites, allowing customers to customize their sugar containers before purchasing. These platforms could include options for selecting different finishes, colors, or even adding personalized engravings. Furthermore, manufacturers could use augmented reality (AR) technology to let consumers visualize how the containers would look in their kitchen environments before making a purchase.
As sugar containers become more of a lifestyle product, the industry will likely see a blend of traditional craftsmanship and modern technology. While automation will streamline many production aspects, artisanship in design, detailing, and finishing could remain an essential part of creating premium products. Consumers may increasingly gravitate towards brands that offer a combination of innovative design, superior functionality, and high-quality craftsmanship.
Finally, as the industry evolves, there may be a shift towards smart products that incorporate IoT (Internet of Things) technology. For example, future sugar containers could feature built-in sensors that monitor the sugar level and send alerts to a connected app when it’s time to refill. These smart features would add convenience and cater to the increasing consumer interest in connected home devices. As part of this trend, sugar containers could be designed to integrate with other smart kitchen devices, creating a cohesive, high-tech home environment.
In conclusion, the future of sheet metal sugar container manufacturing is set to be shaped by ongoing technological advancements, sustainability efforts, and growing consumer demand for customization and functionality. Through the adoption of cutting-edge technologies like robotics, 3D printing, and data analytics, manufacturers will continue to improve production efficiency, reduce costs, and create high-quality products that meet the evolving needs of consumers. The integration of smart features, along with a continued focus on sustainability and innovation in design, will ensure that sugar containers remain both practical and appealing to a broad range of consumers.
As the sheet metal sugar container manufacturing industry progresses, manufacturers will also need to stay attuned to broader market trends and societal changes. One key factor is the ongoing shift towards minimalism and multifunctionality in consumer products. Consumers are increasingly seeking items that serve multiple purposes and fit seamlessly into modern lifestyles, where space and utility are prized. In this context, sugar containers may evolve to feature more compact, versatile designs that can not only hold sugar but also accommodate other common kitchen ingredients, such as powdered coffee or sweeteners. These multifunctional containers may feature modular elements, such as removable compartments or interchangeable lids, allowing for greater versatility in how they are used.
Additionally, as the market for home kitchen goods grows, personalization will become a major trend. People are not only looking for functional products but also items that reflect their personal style and taste. To meet this demand, sugar container manufacturers may offer a range of customization options, including engraved names, custom colors, and even patterns that align with current home decor trends. Some companies may also offer limited-edition designs or collaboration collections with renowned artists or designers, turning sugar containers into statement pieces for the kitchen.
Another factor influencing the future of sugar container manufacturing will be the increasing focus on hygiene and safety in the food and beverage sector. As consumers grow more aware of the importance of food safety, especially after global health challenges such as the COVID-19 pandemic, there may be an even stronger emphasis on designs that prevent contamination. Features like antimicrobial coatings or the use of materials that inherently resist bacteria growth could become standard for sugar containers. Additionally, child-proof designs that prevent young children from accessing sugar could also gain popularity, ensuring both the safety and practicality of these products.
In parallel, the rise of sustainable packaging solutions will continue to influence the overall manufacturing process. The global shift toward reducing plastic waste and minimizing the environmental impact of packaging will lead manufacturers to seek alternatives, such as biodegradable or recyclable materials. Sugar container manufacturers may explore the use of eco-friendly packaging that reduces the carbon footprint of the product. Consumers will likely see more emphasis on packaging that can be reused or repurposed, aligning with the growing trend toward circular economy principles.
As consumers continue to prioritize sustainability, cradle-to-cradle design may become an essential concept in the production of sugar containers. Manufacturers will aim to create products that can be fully recycled or reused at the end of their lifecycle, ensuring that the environmental impact is minimized. This could involve designing containers with materials that are easy to disassemble, allowing individual components to be recycled or repurposed. Additionally, using non-toxic, eco-friendly paints and coatings will likely become a standard practice to ensure that the entire product, from the container to its finish, is safe for both consumers and the planet.
Global supply chains will also continue to evolve. With increasing attention on the sustainability and ethical sourcing of materials, sugar container manufacturers may need to adopt more transparent and responsible sourcing practices. This could include sourcing metals from mines that meet environmental standards or using locally sourced materials to reduce the carbon footprint associated with transportation. Manufacturers may also need to ensure that workers involved in the production process are treated ethically and fairly, as consumers become more attuned to social and ethical concerns surrounding the products they purchase.
With the rise of e-commerce and online marketplaces, manufacturers will need to innovate in the way their products are marketed and sold. The growing popularity of platforms like Amazon, Etsy, and other online retailers means that manufacturers must optimize their products for these platforms. This might include ensuring that sugar containers are easy to ship, arrive undamaged, and come with clear, attractive packaging that catches the eye of potential buyers. Social media and influencer marketing will also play a pivotal role in shaping the brand image of sugar container manufacturers, with companies leveraging platforms like Instagram, Pinterest, and TikTok to showcase their products in visually appealing ways.
Alongside e-commerce, the importance of customer reviews and feedback will continue to grow. In a world where consumers have access to a wealth of information online, product reviews and ratings will have a significant impact on purchasing decisions. Manufacturers that prioritize customer satisfaction and use feedback to continuously improve their products will build stronger, more loyal customer bases. Offering excellent after-sales service, such as easy returns and responsive customer support, will be essential for maintaining a positive reputation in the marketplace.
To stay competitive, manufacturers may also invest in research and development (R&D) to continually innovate and improve their products. This could involve experimenting with new manufacturing techniques, such as additive manufacturing (3D printing) for producing intricate parts, or exploring alternative materials that offer enhanced durability or sustainability. R&D teams will be crucial in driving new product features, such as built-in smart technology that syncs with home automation systems. Innovations like these could set manufacturers apart, helping them tap into emerging markets where consumers are looking for the latest in technological advancements.
As the world becomes more interconnected and consumers demand faster, more convenient products, manufacturers will also explore ways to optimize their supply chains through automation and artificial intelligence (AI). AI-powered systems can predict demand trends, monitor inventory levels, and streamline production processes to ensure that products are delivered quickly and efficiently. The ability to rapidly adapt to changes in consumer preferences and market conditions will be crucial for manufacturers looking to maintain relevance in an increasingly competitive marketplace.
Collaboration with other industries and brands will also likely play a role in the evolution of sugar container manufacturing. Strategic partnerships with well-known kitchenware brands, health-conscious companies, or influencers can help bring new products to a wider audience. Cross-industry collaborations can result in unique designs or specialized sugar containers that cater to niche markets, such as those focused on health and wellness or premium kitchen gadgets.
Lastly, with the continuing rise of globalization, sugar container manufacturers will have to consider international markets more closely. Different regions may have varying cultural preferences, aesthetic tastes, and regulatory requirements for food-safe products. Manufacturers that cater to international customers will need to navigate these complexities, ensuring that their products meet the specific demands and standards of each market. Expanding into new geographic regions may require adjustments in manufacturing processes, packaging designs, or even product features to align with local consumer preferences.
In conclusion, the future of sheet metal sugar container manufacturing will be shaped by a combination of technological advancements, changing consumer demands, and a growing emphasis on sustainability and functionality. Manufacturers who embrace automation, innovation, and customization, while staying focused on ethical practices and environmental stewardship, will be well-positioned to thrive in this evolving market. By continuing to adapt to the needs and preferences of modern consumers, sugar container manufacturers can create products that not only meet practical requirements but also resonate with consumers on an emotional and lifestyle level.
Sheet Metal Cocktail Shaker Manufacturing Machine
A sheet‑metal cocktail shaker production cell closely mirrors other small‑appliance lines but is tuned to the unique geometry and quality needs of shakers. Here’s an end‑to‑end flow—no sections:
Blanks feed from coil or sheet stacks into a laser cutter (or turret punch for high volumes) that nests body, cap, and strainer profiles to maximize yield. The flat disks for the body are then deep‑drawn in a hydraulic press to form the classic tapered “Boston” shaker shape—or spun on a CNC lathe for the smooth curves of a three‑piece metal shaker. A secondary redraw or necking die might refine the taper, ensuring a perfect fit between body and cap.
Strainer and cap components are cut separately: the strainer’s perforations are laser‑punched or stamped, then its lip is flanged. Caps (or weighted “top” pieces) are spun or stamped and then trimmed. All parts pass through automated deburring stations—rotating brushes and abrasive belts—to knock down sharp edges.
Welding is minimal: seams on two‑piece bodies are laser‑welded for a clean finish, while three‑piece sets simply press‑fit. Strainers are welded or ultrasonically bonded to their flanges depending on design. Robotic vision systems inspect each weld, perforation pattern, and overall body profile for tolerances down to ±0.1 mm, rejecting any parts outside spec.
Finishing happens in sequence: an ultrasonic wash removes oils, then automated polishing cells with buffing heads impart either a brushed or mirror finish. Some lines include electro‑polishing or passivation baths for stainless steel to enhance corrosion resistance.
A final assembly robot mates bodies, strainers, and caps, torquing any screw‑on parts to spec. Completed shakers move through a last‑pass vision check, then are packed by delta robots into custom trays or boxes, labeled with batch codes, and palletized.
Throughput for a compact cell runs roughly 200–400 shakers/hour with scrap under 1%. Quick‑change tooling and MES‑driven job recipes let you switch between shaker styles—Boston, Cobbler, weighted top—in under 15 minutes. Energy recovery from wash‑tank heat and LED‑lit inspection stations keeps operating costs low. That streamlined, modular approach delivers high‑quality cocktail shakers at bar‑scale volumes.
The cocktail shaker line’s heartbeat is its seamless handoff between stations: as one body blank is drawn, the next is already lined up at the cutter. Robots on linear rails ferry parts—bodies, strainers, and caps—between presses, welders, and finishing cells with sub‑0.1 mm precision. Vision‑guided arms pick drawn bodies straight off the press and place them into deburr stations, then into washing, polishing, or passivation baths without missing a beat.
For two‑piece shakers, laser‑weld heads glide around the seam at thousands of points per second, ensuring zero porosity while keeping heat‑input minimal. Three‑piece models skip welding, relying on precision spun tolerances to press‑fit bodies and caps with perfect alignment. Strainers—whether stamped or laser‑cut—are automatically seam‑bonded via ultrasonic welders that deliver consistent energy across every hole pattern.
Every cell reports status to the MES in real time. If a polishing head’s RPM drifts even 2%, the MES flags the tool, reassigns parts to a spare spindle, and schedules maintenance before any defect occurs. Changeovers are orchestrated by the MES recipe manager: hydraulic press dies retract, robot routines load new tooling, and laser parameters auto‑adjust for new part geometries—all within a 15‑minute window.
Waste streams are tightly controlled: metal scrap from laser cutting is automatically vacuumed into bins for recycling; polishing slurries and wash‑tank effluent pass through closed‑loop filtration so only clean water returns to the system. Energy from heated rinse water is recaptured to pre‑heat incoming wash cycles, shaving up to 15% off utility costs.
With cobots handling lid assembly and inspection, and AMR (autonomous mobile robots) shuttling raw materials and finished pallets, the plant floor runs 24/7 with minimal human intervention—just a small team of technicians overseeing the digital dashboards, optimizing throughput and quality in real time.
The automated system doesn’t just handle routine operations; it adapts dynamically to the fluctuating demands of the market. For example, when a promotional campaign requires a burst of custom-designed cocktail shakers—say, with limited-edition branding or unique engravings—the line can quickly retool. The advanced robot stations can swap between standard assembly tasks and the custom engraving or logo application process, with minimal downtime. The system’s modular design allows for quick switches between different finishes, from polished chrome to matte black, or even more niche finishes like copper plating, allowing manufacturers to meet high-end or boutique market demands without slowing down production.
Furthermore, AI-powered predictive maintenance tools are integrated into the machines. They analyze performance data from the entire line in real time, predicting potential failures before they occur. For example, by monitoring vibration signatures and temperature fluctuations in key components like the hydraulic presses or polishing heads, the AI can notify technicians of parts that are nearing their end of life or need attention—preventing unexpected breakdowns that could disrupt production. These smart maintenance systems help keep downtime to a minimum and ensure that production runs smoothly, even during peak demand periods.
In terms of supply chain efficiency, the system is optimized for just-in-time delivery. Raw materials, such as sheets of stainless steel or aluminum, arrive based on predictive demand algorithms. These materials are stored in high-density shelving units that can be automatically accessed by robotic arms, ensuring that the right materials are always ready for the next stage of production. As the system tracks inventory levels, it can place orders for new materials in advance, keeping the production line constantly fed without overstocking, which minimizes warehousing costs.
Packaging is another area where automation shines. Once the cocktail shakers are fully assembled, they are carefully packaged in custom trays that not only protect the product during transit but also enhance the unboxing experience. These trays are designed with interlocking components to secure each shaker snugly, minimizing any movement during shipping. Automated packing robots use soft robotics to handle delicate packaging tasks, ensuring that each unit is perfectly placed into the shipping box. The packaging is also designed with sustainability in mind, using recyclable materials wherever possible and minimizing waste.
Beyond the manufacturing floor, the system is fully integrated with customer-facing platforms. Real-time tracking is available to consumers, allowing them to follow their orders from production to delivery. E-commerce platforms benefit from seamless integration, where production and stock levels are adjusted based on incoming orders, reducing the risk of stockouts or overproduction. In response to customer demand, the company may also offer customizations directly through its website, allowing consumers to design their own cocktail shakers, choosing everything from finish colors to engraving styles. This process is enabled by a customer-friendly interface that links directly to the manufacturing system, ensuring that personalized orders can be processed without disrupting the overall workflow.
This comprehensive, highly automated manufacturing ecosystem not only supports scalability and efficiency but also drives a cycle of constant improvement. The integration of big data analytics allows the company to continuously monitor every facet of production, from raw material usage to the customer feedback loop. By gathering and analyzing this data, manufacturers can make informed decisions to refine production processes, optimize machine performance, and improve product quality.
In terms of market responsiveness, this level of automation and flexibility allows the manufacturer to react to changing trends swiftly. For instance, if a sudden spike in demand for a particular type of shaker occurs due to a viral social media trend or celebrity endorsement, the system can quickly ramp up production to meet the new demand, while maintaining the high quality and consistency expected from the brand.
As sustainability becomes an even more pressing concern, the system will continue to evolve. For example, the use of eco-friendly coatings—such as PVD (physical vapor deposition) for durable finishes—could become more widespread, providing the same visual appeal and long-lasting results without the environmental impact of traditional coatings. Additionally, by minimizing waste through precision manufacturing and optimizing every step of the process, the facility can reduce its overall carbon footprint and contribute to a more sustainable future.
The automation and high-tech nature of this cocktail shaker manufacturing line also positions the company as a leader in innovation. It paves the way for new opportunities in the smart drinkware market, where connected devices or sensors could be integrated into the shaker itself. Imagine a shaker with a built-in sensor that tracks the amount of liquid being poured or monitors the shaking time for optimal mixing. The potential for such integrations could open up new markets, especially among tech-savvy consumers who enjoy experimenting with both drinks and technology.
Overall, the future of sheet metal cocktail shaker manufacturing is poised to be shaped by innovation, efficiency, and flexibility. By leveraging the power of automation, AI, and smart manufacturing technologies, companies can create high-quality, customizable products that meet the demands of a fast-moving market. Whether catering to mass-market preferences or producing limited-edition, bespoke designs, manufacturers will be able to deliver products that are not only functional but also offer a premium experience for consumers.
As the cocktail shaker manufacturing process becomes more integrated with advanced technologies, manufacturers will also look at supply chain integration and data-driven decision-making as key components to improve both production efficiency and customer satisfaction. By leveraging IoT devices embedded throughout the manufacturing line, every piece of equipment—from presses and welders to polishing stations and inspection systems—will be connected and provide real-time feedback. This interconnectedness allows for a deeper understanding of operational performance, identifying bottlenecks, energy usage patterns, or underperforming machines, all of which can be optimized in real time to increase productivity.
Additionally, the increased automation in manufacturing processes will allow for enhanced precision and reduced human error. As more tasks are taken over by robots and automated systems, not only will efficiency improve, but consistency in product quality will reach a new standard. This becomes particularly valuable in industries where high precision is a must, such as cocktail shaker manufacturing, where even small variations in shape or finish can affect the overall product appeal.
The automation of quality control—through advanced vision systems and machine learning—will also play a key role in ensuring every shaker that leaves the production line meets the strictest standards. Vision systems, in particular, can inspect the most minute details of the product, such as surface imperfections or slight variations in shape, that would typically go unnoticed by human eyes. These systems will automatically reject defective items or flag them for further inspection, ensuring that only products that meet the highest standards make it to packaging and shipment.
AI-driven analytics will help predict production trends, providing manufacturers with insight into demand spikes, seasonal preferences, and emerging consumer trends. For example, if a certain type of shaker finish becomes popular in a specific geographic region, AI can flag this as a trend, enabling the production line to adjust and fulfill these demands promptly. Data gathered from customer purchases, social media feedback, and direct reviews can also be used to adjust product designs, material choices, or even production speed to better cater to customer preferences.
Another emerging trend is the use of sustainable manufacturing practices to appeal to environmentally-conscious consumers. As the importance of eco-friendly production continues to grow, companies in the cocktail shaker industry will need to focus on reducing waste, utilizing recyclable materials, and sourcing metals ethically. Manufacturers may explore using recycled metals, for example, without compromising on product quality, as well as looking into sustainable energy options, such as solar or wind, to power their operations. This shift to more sustainable practices can not only improve the company’s reputation but also reduce operational costs over the long term by cutting down on material waste and energy consumption.
With consumer preferences shifting towards custom and personalized products, manufacturers will need to invest in technology that allows for greater flexibility in design and customization. This might include offering consumers the ability to personalize their cocktail shakers through digital platforms, allowing them to choose colors, engravings, or even incorporate custom materials, such as unique metallic finishes or eco-friendly coatings. By integrating 3D printing technology into the production process, manufacturers can easily create unique prototypes or small-batch runs of shakers with customized features, further enhancing their ability to meet niche demands.
Moreover, as consumer interactions become increasingly digital, manufacturers may look to enhance their direct-to-consumer models by providing virtual shopping experiences. Augmented Reality (AR) apps could allow customers to see how a particular cocktail shaker would look in their kitchen before they buy, helping them make more informed purchasing decisions. These digital tools could also help customers customize their orders, selecting not just the look but the functional features of their shaker, such as the type of cap, built-in strainer design, or grip texture.
Globalization also presents opportunities and challenges. As manufacturers expand into international markets, they must consider the various regulatory standards and cultural preferences that influence the design and manufacturing of products. For example, some markets may prioritize aesthetic design and craftsmanship, while others may be more focused on product functionality and cost. Manufacturers will need to ensure that their products meet local standards for materials, safety, and food contact regulations, which could differ significantly from one country to another. This will require agility in manufacturing systems and logistics, allowing for quick adaptations and compliance across various regions.
In terms of logistics, the need for just-in-time manufacturing and inventory management will continue to grow. With customer demand becoming more unpredictable and often influenced by external factors such as social media trends or seasonal events, manufacturers must be able to respond rapidly to shifting market conditions. Utilizing advanced logistics platforms will allow companies to track inventory, forecast demand, and streamline their distribution networks. Automated warehousing systems will ensure that the right components and materials are always available when needed, reducing delays in production and lowering stockholding costs.
Looking further into the future, smart products may revolutionize the way cocktail shakers are used. Imagine a shaker that is not just designed for mixing drinks but integrates technology to measure liquid contents or track shaking time. This could be especially appealing to professional bartenders or cocktail enthusiasts who want to ensure the perfect mix every time. IoT-enabled shakers could sync with mobile apps, offering drink recipes, storing preferences, or even tracking how often the shaker is used for maintenance scheduling. Such innovations could set a brand apart in a crowded market by adding a layer of high-tech functionality that appeals to both the convenience and performance needs of consumers.
As the industry matures, manufacturers will also need to evolve in terms of their supply chain transparency. Consumers are becoming more interested in where their products come from, and companies that provide clear insights into their sourcing, manufacturing processes, and sustainability practices will likely have a competitive edge. Brands that promote their ethical sourcing of metals, use of recycled materials, or eco-friendly packaging will likely attract environmentally-conscious customers and gain loyalty by demonstrating their commitment to ethical practices.
In conclusion, the future of sheet metal cocktail shaker manufacturing will be shaped by rapid advancements in automation, customization, sustainability, and connectivity. As technologies like AI, IoT, and robotics continue to evolve, manufacturers will have the opportunity to create more innovative, high-quality products faster and more efficiently. At the same time, they will need to remain responsive to shifting market demands, consumer preferences, and global trends, all while embracing sustainability and ethical practices. By adapting to these changes, manufacturers can stay competitive in a rapidly evolving industry, meeting the needs of the modern consumer while maintaining high standards of craftsmanship and quality.
Sheet Metal Coffee Pot Manufacturing Machine
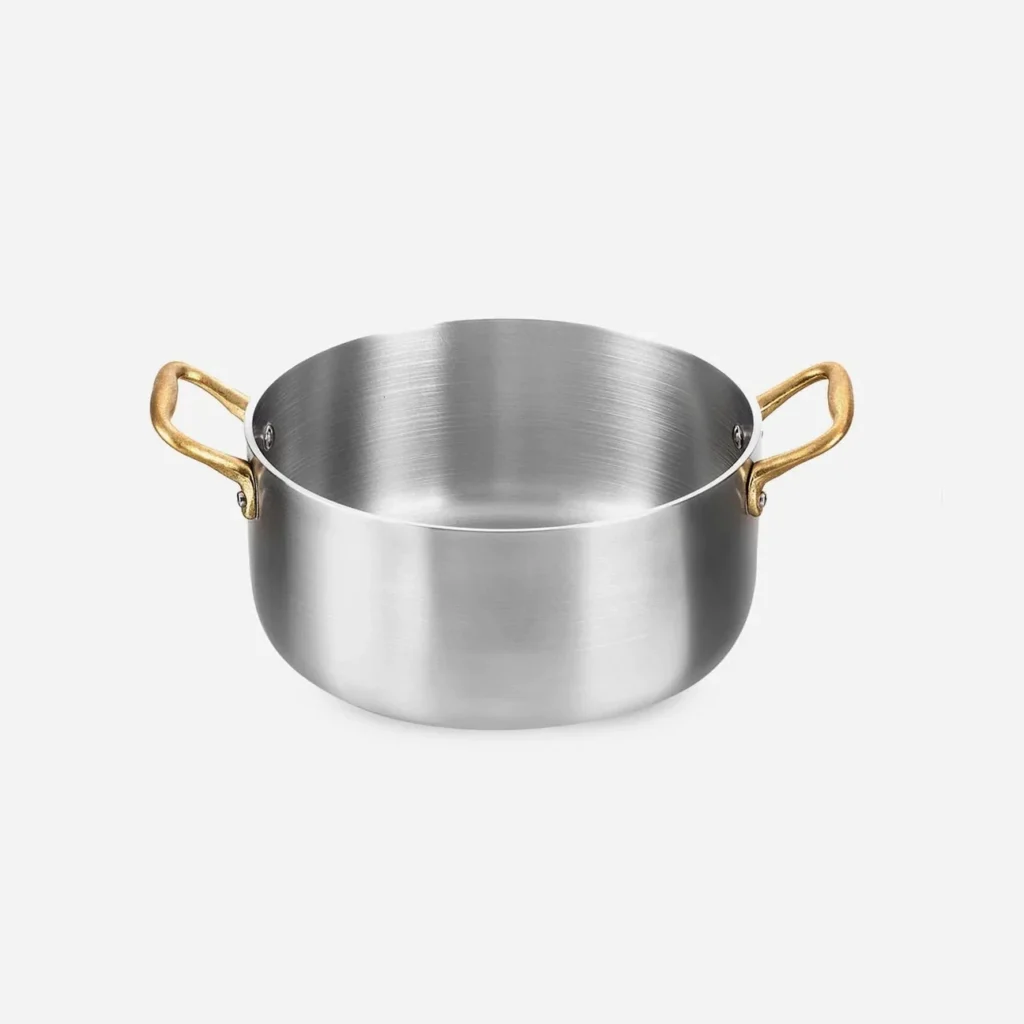
The Sheet Metal Coffee Pot Manufacturing Machine is a high-precision, automated system designed to produce coffee pots from metal sheets, typically stainless steel or aluminum, with a focus on efficiency, high-quality output, and flexibility. The process combines advanced forming, joining, and finishing technologies to create coffee pots that meet both functional and aesthetic standards.
The system starts with raw metal coils or sheets, which are loaded into the machine. These sheets are then cut into blanks using a laser cutter or turret punch press to match the shape of the coffee pot’s main body, handle, lid, and spout. These components are optimized to reduce material waste while ensuring the proper dimensions for each part.
Once the blanks are cut, the next stage is the deep drawing process. In this process, the metal blanks are placed into a hydraulic press equipped with a specialized die. The press forms the body of the coffee pot by pulling the flat metal into a deep, cylindrical shape. This step may require multiple passes to gradually form the desired shape without compromising the integrity of the material. The depth and form of the body are crucial for the functional aspects, such as volume, durability, and ease of pouring.
After the body is formed, the spout and handle are produced. The spout may be stamped or laser-cut from separate metal sheets, while the handle is formed using a similar drawing or bending technique. The handle often requires additional steps such as flanging or curving to ensure ergonomic comfort and secure attachment.
In parallel with the body, the lid is created. Depending on the design, it can be formed from a sheet metal blank and shaped through spinning or die pressing. Some designs include additional features like a knob or a vent hole, which are either molded or stamped into the lid.
Once the parts are formed, the next crucial process is welding or joining. For the two-piece coffee pots, the seam where the body meets the base is welded—typically using laser welding or MIG welding—to ensure a strong, seamless bond. The handle and spout are also attached via welding or riveting, depending on the specific design. Robotic arms equipped with vision systems check each weld and attachment point for accuracy and strength, ensuring that no part is weak or improperly attached.
The finishing phase involves several steps. First, the parts are sent through an ultrasonic cleaning or acid bath to remove any oils, dirt, or residue left from the manufacturing process. The parts are then polished, either manually or automatically, to achieve the desired surface finish—whether it’s a brushed, matte, or high-gloss appearance. In some cases, electro-polishing or passivation is used to improve corrosion resistance, especially for stainless steel coffee pots.
After polishing, some coffee pots are sent through plating or coating processes. This could include a chrome plating or PVD (Physical Vapor Deposition) process, adding both aesthetic appeal and durability to the surface. The coating also provides protection against rust or tarnishing over time.
Once the parts are properly cleaned and finished, they are assembled. Automated assembly lines use robotic arms to attach the handle, spout, and lid to the main body of the coffee pot. For designs that require a lid attachment via screws or rivets, the machine automatically places these fasteners with the correct torque to ensure proper fitment. In high-end models, customized engraving or logo application can be performed during the assembly stage, allowing for branding or product differentiation.
A final quality check is carried out using vision systems that inspect the coffee pot for any defects in the welds, coatings, or overall finish. The machines check for alignment, smoothness, and functionality, making sure the lid fits securely, the handle is properly positioned, and the spout is defect-free.
Once the coffee pots pass inspection, they move into packaging. The pots are individually wrapped or placed into specially designed foam inserts for safe transport. The packaging process is automated, with robots managing the placement of each unit into boxes, which are then labeled and sealed for shipment.
The entire production line is highly automated, with minimal human intervention required outside of supervision and maintenance. The use of robotic arms, machine learning algorithms, and sensors allows for precise control over every aspect of the process, from metal sheet handling to final assembly. Additionally, the system features real-time monitoring for efficiency optimization, with predictive maintenance ensuring that downtime is minimized.
For increased efficiency, the manufacturing cell is designed to handle both high-volume orders and custom or small-batch runs, ensuring flexibility in meeting different market needs. With modular tooling systems, manufacturers can quickly switch between different sizes or designs of coffee pots, enabling short changeover times and reduced production costs.
The key benefits of a fully automated sheet metal coffee pot manufacturing machine are high consistency, reduced material waste, quick changeovers, and low operational costs. As demand for customized or premium coffee pots grows, this technology can quickly adapt to produce specialized versions, meeting the needs of both mass-market and boutique consumers.
The coffee pot manufacturing system is designed to optimize each phase of production with precision and speed. Raw materials are efficiently sourced and fed into automated stock feeders, which ensure that there’s minimal downtime between production runs. The system’s robotic arms quickly and accurately position the metal sheets in cutting and forming stations, reducing handling time and ensuring consistent alignment. Once the metal blanks are formed into the desired body, spout, and handle shapes, the assembly process becomes highly streamlined. Robots not only assemble the parts but also apply precise torques for screws and rivets, ensuring that every coffee pot meets the specified strength and durability standards.
Additionally, real-time data analytics play a pivotal role in the system’s performance. Sensors embedded throughout the machinery track variables like press pressure, temperature, and even air quality in the production area. These insights are transmitted to a central database, where machine learning algorithms continuously optimize operations. If a particular part or machine is showing a slight deviation from its typical performance, the system can automatically adjust parameters to compensate, minimizing waste and maximizing throughput.
The laser welding systems used in this process are capable of producing extremely fine seams, reducing the need for additional finishing steps. This not only improves the product’s appearance but also its functionality, ensuring that each pot has a tight seal that will prevent leaks or defects. Furthermore, welding inspections are made more efficient using visual inspection systems equipped with high-definition cameras that can detect even the smallest imperfections. These inspections happen automatically in the background, ensuring that faulty products are flagged before reaching the final packaging stage.
The entire workflow is designed for minimal human intervention, with most tasks managed by robots and automated systems. This makes it possible to achieve high-volume production without sacrificing consistency or quality. This automation allows human workers to focus on more critical tasks such as monitoring the process, maintaining machines, and handling special orders or customizations. In case of a machine failure or an unexpected event, predictive maintenance systems based on AI help identify potential issues before they cause significant disruptions. This system ensures that replacement parts or repairs are proactively scheduled, avoiding costly downtime.
The sustainability aspect of the production line is another key benefit. The factory’s waste streams—scrap metal from cutting, off-cuts from forming, and other byproducts—are efficiently recycled back into the production cycle. Instead of discarding waste, the system allows for the reuse of materials, minimizing the environmental impact. The energy consumption of the entire line is also optimized using smart controls that adjust for energy use based on production demands, which can help reduce operating costs and make the production process more environmentally friendly.
For manufacturers, flexibility in production is also a crucial aspect of the system. Thanks to modular tooling, the same production line can be easily reconfigured to produce different types or sizes of coffee pots, allowing manufacturers to cater to varying customer preferences or limited-edition runs. Whether it’s a larger pot for family use or a sleek, smaller pot for specialty coffees, the system adapts with minimal downtime, maximizing the return on investment for manufacturers.
Packaging is automated and happens seamlessly at the end of the production line. The system uses robotic pick-and-place mechanisms to carefully place the coffee pots into their protective packaging. The packaging itself is designed to ensure the product arrives in perfect condition, with each pot securely housed in foam inserts that prevent movement during transportation. Labels are applied by machines that scan each unit’s bar code and generate specific shipping labels, ensuring that each product is tracked and properly documented.
The overall production cycle, from raw material intake to packaged product ready for shipment, is tightly controlled, with sophisticated scheduling software ensuring that customer orders are fulfilled in a timely manner. This software integrates with the factory floor, providing live updates on inventory levels, production status, and delivery timelines. The system can prioritize orders based on deadlines, ensuring that customers receive their products quickly, even during peak demand times.
As for market adaptability, the system is flexible enough to support the customization of products, which is increasingly important in today’s market. Consumers often seek unique designs or personalized products, and the coffee pot manufacturing machine can quickly pivot to accommodate these trends. Whether it’s engraving a name, adding a logo, or changing the finish to suit specific consumer preferences, the system can handle small customizations without disrupting mass production flows. This helps manufacturers maintain a competitive edge in the market by offering both high-quality standard products and personalized items.
At the end of the day, the fully automated coffee pot manufacturing line delivers an unparalleled level of efficiency, flexibility, and quality. Manufacturers are able to produce high volumes of coffee pots with minimal human intervention, lower costs, and better control over quality. Whether creating classic designs or accommodating niche customer preferences, the system can adapt to meet evolving market demands while maintaining strict standards for product quality and durability. The integration of predictive analytics, smart automation, and sustainability practices makes this manufacturing approach not only efficient but also forward-thinking, positioning manufacturers to stay competitive in a rapidly changing marketplace.
The continued evolution of coffee pot manufacturing will see even greater advancements in both the technological and market-driven aspects of the production process. With smart manufacturing technologies continuing to gain traction, manufacturers will integrate more advanced IoT (Internet of Things) devices into every stage of production. These devices will allow for the collection of more granular data from the machines, such as real-time machine health reports, operational status, and environmental factors like temperature and humidity. This data will help identify potential areas of improvement in the process, giving manufacturers the ability to make instant decisions to enhance productivity.
Another area of technological innovation is the integration of augmented reality (AR) for the maintenance and operation of the machines. Technicians on the factory floor may wear AR glasses that provide step-by-step guidance for maintenance tasks, highlighting specific components that need attention and showing the proper procedures. This could help reduce training time for new employees and increase the efficiency of on-site repairs, making it easier to maintain continuous production without delays.
The manufacturing of coffee pots will also benefit from further innovations in robotics. For instance, collaborative robots (cobots) are becoming increasingly common in factory settings, as they work alongside human operators rather than replacing them entirely. These cobots can assist with tasks that require precision but may be too delicate for automated systems, such as fine-tuning the attachment of handles or lids, or performing final quality checks. Cobots can adapt to a variety of tasks, making them incredibly flexible and able to handle diverse workflows across different production batches.
In terms of material science, the development of new, advanced alloys could lead to coffee pots that are even more durable, lighter, and resistant to corrosion. Manufacturers might explore the use of titanium or high-grade stainless steel for premium products, which would increase the product’s lifespan and performance. Additionally, sustainable materials such as recycled metal sheets or biodegradable coatings could become more widespread as environmental concerns continue to grow. By sourcing raw materials that have a lower environmental impact, coffee pot manufacturers could reduce their carbon footprint and appeal to the growing market of eco-conscious consumers.
The personalization trend will only continue to grow as consumer preferences shift towards more individualized products. As part of this, manufacturers might introduce on-demand manufacturing for highly customized coffee pots, where customers can design their own products online before ordering. By leveraging 3D printing technology, manufacturers could create limited-edition models, intricate custom designs, or unique finishes that are tailored to each consumer’s specifications. The ability to offer this level of customization could help attract a segment of customers willing to pay a premium for a truly unique coffee pot.
Moreover, the shift towards sustainable business practices will necessitate the adoption of more energy-efficient systems across production facilities. From the machinery that cuts, forms, and assembles to the energy used in finishing processes like electroplating or polishing, manufacturers will need to make efforts to reduce energy consumption. More solar-powered or wind-powered manufacturing facilities could emerge, which would dramatically cut down on energy-related costs and environmental impacts. Moreover, reducing the carbon footprint of each coffee pot produced could provide companies with a marketing advantage, appealing to consumers who prioritize eco-friendly products.
As globalization continues to shape the supply chain dynamics, coffee pot manufacturers will be tasked with optimizing their production lines to meet demand across diverse international markets. This will require maintaining high standards for regulatory compliance in various regions, including food safety regulations for products that come into direct contact with liquid. For instance, different countries may have varying standards for metal safety or environmental compliance. Manufacturers may need to tailor their processes to meet these different regulations without sacrificing efficiency.
In addition, the global marketplace will present new opportunities for manufacturers to introduce their products to emerging markets, where demand for premium or specialty products like high-end coffee pots is growing. For instance, the growing coffee culture in regions such as Southeast Asia, Africa, and South America could lead to increased demand for specialty coffee-making products. Manufacturers that are able to adapt their production lines to meet the preferences of these new markets will find a wealth of opportunities to expand their reach.
At the consumer level, manufacturers can expect increased demand for smart coffee pots, potentially integrating features such as temperature control, built-in timers, or even smartphone connectivity for controlling the brewing process remotely. This could be an extension of the trend toward smart kitchen appliances, where consumers are looking for devices that offer greater convenience, precision, and control over their cooking or brewing experience.
The process of innovation in design will also be integral in maintaining market interest. Companies will focus on producing coffee pots that are aesthetically appealing as well as functional. With consumer attention increasingly turning to interior design, manufacturers might create coffee pots that seamlessly fit into modern, high-tech kitchens with sleek, minimalist designs. These coffee pots may incorporate ergonomic handles, drip-free spouts, or thermal insulation to enhance their usability.
Ultimately, the coffee pot manufacturing industry will continue to evolve towards a model that emphasizes both technological sophistication and consumer-centric design. The blending of automation, sustainable practices, and high-quality materials will define the future of production. The ability to meet the demand for both functional, everyday products and high-end, customizable designs will ensure that manufacturers stay competitive in a fast-paced, evolving marketplace. This progression will not only improve the coffee pot manufacturing process itself but also open up new avenues for creativity and customer engagement, which will drive success in the years to come.
As the coffee pot manufacturing industry continues to advance, integration with other kitchen technologies will become more prevalent. The idea of creating multi-functional or hybrid appliances that combine a coffee pot with other kitchen tools—such as a coffee grinder, coffee maker, or even a milk frother—could revolutionize the way consumers interact with these products. This trend towards convergence of kitchen appliances may also lead manufacturers to innovate in terms of connectivity, allowing coffee pots to interact with other smart home devices. For example, a coffee pot could sync with a smart thermostat to ensure that the water is heated to the perfect temperature, or it could be controlled by voice commands via an AI assistant like Amazon Alexa or Google Assistant.
The increased use of advanced robotics in the production process will likely result in even faster, more cost-effective manufacturing. Robots capable of performing delicate operations such as metal polishing, finishing, or even decorating could add a new layer of customization to the coffee pots while maintaining speed and precision. For example, robotic arm-guided polishing tools could be equipped with artificial intelligence that learns and adapts to different materials, ensuring each coffee pot achieves the desired shine and texture. Likewise, robotic painters could provide a uniform coating of paint or lacquer, offering more control over the finish without the risk of human error.
At the same time, quality control will continue to evolve. As artificial intelligence and machine vision systems become more sophisticated, they will be able to perform real-time inspections with higher precision. These systems can identify even the smallest imperfections, such as slight dents, scratches, or misalignments, and can make corrective decisions on the spot. This level of inspection will significantly reduce defects and returns, helping manufacturers maintain high standards of quality while keeping production costs low.
Customization software for consumers may also be part of the future. Imagine a platform where users can design their own coffee pot—choosing materials, colors, finishes, handle styles, and even engraving options—all through an intuitive online interface. The software could provide a real-time 3D model of the final product, allowing customers to visualize their designs before placing an order. After a design is finalized, the manufacturing system can automatically generate the necessary tooling and adjust the production line to accommodate the custom specifications.
Another direction for the coffee pot manufacturing industry is the emphasis on upcycling and circular economy principles. Instead of relying solely on new raw materials, manufacturers may begin sourcing more of their metal from recycled products, reducing reliance on mining and lowering production costs. By adopting a circular approach, manufacturers could recycle old coffee pots or scrap metal into new products, minimizing waste and increasing sustainability.
The ability to provide bespoke manufacturing solutions will also gain traction. Coffee pot manufacturers might offer services to design and produce one-of-a-kind pieces for luxury markets or specialty collections. This could appeal to boutique coffee shops, high-end hotels, or discerning consumers looking for a unique item. These custom products could be sold at premium prices and potentially feature artisan hand-finishing elements that make each coffee pot a work of art.
The future of coffee pot manufacturing will also see a shift towards smarter supply chains. With blockchain technology, manufacturers will be able to track every component of a coffee pot’s lifecycle—from the sourcing of raw materials to the final product being shipped to customers. This could provide transparency and traceability in the supply chain, which would be especially valuable for environmentally conscious consumers who want to know where the materials come from and how they’re processed. Additionally, it could help manufacturers ensure that they are complying with ethical sourcing standards and maintaining sustainability in every part of their supply chain.
As consumer expectations continue to rise, the demand for premium finishes and unique features will also increase. The ability to customize elements like handles, spouts, or lids through advanced 3D metal printing will allow manufacturers to offer a wide range of designs. These 3D printers can create intricate patterns, textures, and forms that would be impossible to achieve with traditional forming methods. Such features will allow for the creation of coffee pots that are not only functional but also visually striking, appealing to consumers who appreciate design as much as performance.
The environmental impact of manufacturing processes will remain a significant concern. Manufacturers may look to reduce water usage in cleaning processes or implement water-based finishes instead of chemical-based coatings. Additionally, there may be a greater emphasis on modular design, where coffee pots are constructed in a way that parts can be easily replaced or upgraded, further contributing to the product’s longevity. Instead of discarding an entire coffee pot once it has worn out, consumers could replace individual components, extending the product’s lifecycle and reducing waste.
On the production side, lean manufacturing principles will be more widely adopted, further optimizing the production process. This could involve more efficient use of materials, reduced lead times, and continuous improvement cycles. Manufacturers will likely continue to refine their processes using methodologies like Six Sigma or Kaizen to eliminate waste, improve efficiency, and maintain the highest standards of quality.
In terms of global market expansion, the Asia-Pacific region is expected to be a key growth area, with rising incomes and a growing coffee culture. Manufacturers that can tailor their coffee pots to meet regional preferences—whether through size, design, or features—will be well-positioned to tap into these emerging markets. Additionally, localization of production might become a strategy for companies aiming to reduce shipping costs and adapt products to local tastes, which could involve setting up manufacturing facilities in key regions or partnering with local suppliers.
As these developments unfold, the coffee pot manufacturing industry will continue to evolve, balancing innovation, sustainability, and consumer demand. The ability to adapt to technological changes, respond to market needs, and maintain high standards of production will be the key to success in the future. As automation, digitalization, and sustainability continue to drive innovation, manufacturers will remain agile, ready to meet new challenges and create coffee pots that appeal to a more sophisticated, eco-conscious consumer base.
Sheet Metal Tea Pot Manufacturing Machine
The Sheet Metal Tea Pot Manufacturing Machine is a specialized, automated system designed to efficiently produce high-quality tea pots from sheet metal. The process involves several stages, combining advanced technology in cutting, forming, welding, finishing, and assembling to create functional, durable, and aesthetically appealing tea pots. This system integrates precision engineering and automation to achieve high production speeds while ensuring consistent product quality.
The production begins with raw sheet metal coils or sheets, often made from stainless steel or aluminum, which are selected for their durability, resistance to corrosion, and aesthetic qualities. The metal sheets are initially cut into blanks—flat, predetermined shapes—using laser cutting, plasma cutting, or turbine punch presses. This cutting process ensures that the metal sheets are shaped with precision and minimal waste, helping reduce overall production costs.
Next, the deep drawing process takes place, where the metal blanks are placed into hydraulic presses with specialized dies. The press uses high-pressure forces to shape the metal into the body of the tea pot, which is typically a cylindrical or ovoid shape. This is done by drawing the metal into a deep cavity, forming the pot’s main structure while preserving the material’s integrity. Multiple passes may be required, especially for intricate designs, to create smooth curves and even walls without causing tears or deformations.
After forming the body, the spout and handle are manufactured. The spout may be stamped from a separate metal sheet or extruded into shape. The handle is often formed using bending or casting techniques, followed by welding or riveting to secure it firmly to the body of the tea pot. The handle must be carefully designed for comfort, ergonomics, and strength, as it will be subject to frequent handling during use.
Once the main components are shaped, welding is employed to join the pieces together. The body, spout, and handle are typically welded using MIG welding or laser welding, ensuring strong, precise, and seamless joints. For higher-quality products, robotic welding arms are used, enabling high-speed, high-accuracy welding that minimizes human error and ensures uniformity.
After the parts are welded, they undergo a series of cleaning and finishing steps. The welded joints may be smoothed and polished to remove any rough edges, ensuring that the tea pot’s surface is smooth and free of sharp points that could cause injury or affect the product’s aesthetic. Some tea pots undergo electro-polishing or passivation to enhance corrosion resistance, particularly for products made of stainless steel, ensuring they can withstand long-term exposure to hot water and frequent handling.
The next step is typically surface coating. Depending on the design requirements, the tea pot may undergo painting, electroplating, or powder coating to achieve a desired look, be it a matte, glossy, or metallic finish. The coating not only adds aesthetic appeal but also increases the pot’s resistance to rust, stains, and scratching. Automated spray systems or robotic arms can apply the coating evenly and efficiently.
For some tea pots, additional features such as engraving, branding, or decorative elements may be added at this stage. This can include laser engraving or heat stamping to apply logos, designs, or patterns onto the surface of the tea pot, adding a personal touch or branding.
Once the pot is finished, the machine moves on to the final assembly stage. This involves placing the lid (which may have been separately formed and shaped) onto the body, ensuring it fits securely and operates smoothly. In cases where the lid needs a handle or a mechanism for easy removal, these components are attached using automated tools. The spout and handle are double-checked for proper attachment and orientation to ensure they provide optimal usability.
Final quality checks are conducted using automated inspection systems such as machine vision or robotic inspection arms equipped with high-resolution cameras. These systems scan the tea pot for defects like surface scratches, misshaped handles, poorly welded seams, or incorrect sizing. Any units that fail these inspections are removed from the production line for rework or disposal.
After the tea pot passes inspection, it is ready for packaging. The packaging process is often fully automated, with robotic systems handling the placement of each tea pot into protective foam or cardboard packaging to ensure safe transit. The packaging is designed not only to protect the product but also to enhance the consumer’s unboxing experience. Each box is labeled with relevant product information, and shipping labels are applied for tracking purposes.
The entire production process is controlled by a central manufacturing execution system (MES), which monitors each stage of production, tracks inventory, and schedules tasks to optimize efficiency. The MES integrates with other systems, including enterprise resource planning (ERP), for smooth coordination between procurement, production, and sales. The system can also provide valuable data on machine performance, material usage, and labor efficiency, allowing for continuous process improvements.
The machine’s design is modular, allowing for quick changeovers between different tea pot models or sizes. This flexibility is ideal for manufacturers that need to meet the demands of both large-scale production runs and smaller, custom orders. Some systems are equipped with robotic arms that can quickly adapt to handle different types of handles, spouts, or lids, depending on the product design. This means that manufacturers can easily switch between different styles, shapes, or even materials without requiring significant downtime.
The overall benefits of a Sheet Metal Tea Pot Manufacturing Machine include increased production efficiency, consistent product quality, and reduced operational costs. Automated processes lead to lower labor costs and fewer human errors, while real-time monitoring and quality control systems ensure that every product meets the required standards. Additionally, the ability to adapt quickly to customer needs, whether for mass-produced standard tea pots or unique, customized items, positions manufacturers to stay competitive in an evolving market.
In the future, advanced technologies like artificial intelligence (AI) and machine learning (ML) could be integrated into the system to predict maintenance needs, further optimize production schedules, and improve the design of the tea pots based on customer feedback and trends. These innovations would allow manufacturers to remain agile and responsive to changing consumer preferences, improving both production efficiency and product quality.
This manufacturing system not only helps produce high-quality tea pots but also ensures that manufacturers can meet the demand for aesthetic variety, sustainability, and functional innovation in the growing tea pot market. By offering efficient production capabilities, flexibility, and enhanced product quality, manufacturers can maintain a competitive edge in both traditional and emerging markets.
The future of sheet metal tea pot manufacturing will likely involve even more sophisticated technological integration to streamline processes and enhance the product’s overall quality. Smart manufacturing technologies, such as real-time data analytics and machine learning, will play a pivotal role in optimizing production. These technologies will allow manufacturers to monitor every step of the process, from raw material handling to the final assembly. The use of sensors and IoT-connected devices will provide continuous feedback on equipment performance, helping predict and prevent potential malfunctions or maintenance needs. By detecting anomalies early, manufacturers can reduce downtime and improve overall efficiency.
In terms of robotics, we can expect more advanced robotic systems that can autonomously perform tasks like handling delicate components or applying the final coating. Collaborative robots (cobots), which work alongside human operators, will be more common in factories. These robots will be tasked with intricate operations such as assembling small parts, attaching handles, or precise quality inspections. Their versatility and ability to operate safely around humans make them an ideal choice for increasing production capacity without compromising on quality.
On the material side, advances in metal alloys and composite materials could lead to lighter, more durable tea pots with improved performance. For example, the integration of titanium or aluminum alloys could result in a product that is both stronger and more heat-resistant, enhancing the longevity of the tea pot. Additionally, new eco-friendly materials may be adopted as sustainability becomes an even bigger concern in manufacturing. The use of recycled metals or biodegradable coatings could significantly reduce the environmental footprint of the production process, appealing to eco-conscious consumers.
Customization will also become more prominent in the tea pot market. Consumers will increasingly demand personalized, unique products, and advancements in digital manufacturing will allow manufacturers to meet this need. The use of 3D printing technology for creating intricate parts or customized designs will enable manufacturers to produce limited-edition runs or one-of-a-kind pieces tailored to individual customer preferences. Through online platforms, consumers could choose various features such as color, handle style, engraving, or even unique shapes, which would then be manufactured on demand.
At the same time, energy efficiency will remain a critical factor. As energy costs rise, manufacturers will continue to look for ways to reduce energy consumption throughout the production process. Using more energy-efficient machines, solar-powered manufacturing facilities, or sustainable energy sources could lead to cost savings while minimizing the carbon footprint of the tea pot production line. These steps will not only help reduce operational costs but will also align with the growing demand for sustainable products.
Global supply chains will also evolve, especially in light of changing trade dynamics. Manufacturers will look to optimize supply chain management, sourcing materials more locally to reduce lead times and shipping costs. The ability to quickly adapt to local market demands and regional preferences will become increasingly important as manufacturers seek to expand into new international markets. Localized production and assembly might also become more common, enabling manufacturers to produce products closer to the end consumers, which could improve flexibility and reduce time to market.
Artificial intelligence and machine vision systems will continue to revolutionize the quality control process. AI-driven systems will be able to inspect and identify imperfections or deviations from product specifications with high accuracy, far beyond the capabilities of human inspectors. These systems will use advanced algorithms to analyze data from each production stage and flag any defects in real-time, allowing for immediate corrective actions. This will ensure that every tea pot meets the highest quality standards, reducing the rate of defects and returns.
Another significant trend will be the shift towards direct-to-consumer models, facilitated by e-commerce platforms. Manufacturers could set up their own online stores or partner with online marketplaces to sell directly to consumers. This direct relationship allows for better customer engagement, faster feedback loops, and more targeted marketing efforts. Additionally, direct sales could enable manufacturers to reduce the dependency on traditional retail channels, providing them with more control over pricing, distribution, and customer service.
The future of tea pot design will also be influenced by consumer trends in aesthetics and functionality. Tea pots will become more than just tools for brewing; they will be part of a larger kitchen ecosystem. Manufacturers will need to consider how their products fit into modern kitchen environments that prioritize minimalist designs and space-saving features. Tea pots may integrate features like adjustable spouts for precise pouring or temperature control systems that allow users to heat water to the ideal temperature for different types of tea.
Overall, the tea pot manufacturing industry will evolve to meet the increasing demand for efficiency, quality, personalization, and sustainability. Technological advancements, such as AI-driven design, automated production lines, and smart materials, will reshape how tea pots are made, leading to faster production cycles, better products, and a more sustainable manufacturing environment. As consumers continue to seek out products that offer convenience, personalization, and style, manufacturers will need to remain agile, using innovation to stay ahead of the competition.
As tea pot manufacturing evolves, sustainability will remain a major focus, not just in terms of the materials used but also in the overall impact of the production process. The demand for eco-friendly products is expected to increase, and manufacturers will need to align with consumer preferences for environmentally responsible practices. This includes not only the use of recycled or renewable materials, such as recycled steel or plant-based coatings, but also the implementation of closed-loop systems within manufacturing plants. These systems would allow for the reuse of scrap metal and waste by-products, contributing to a circular economy model. By keeping materials in circulation, manufacturers can reduce the amount of waste sent to landfills and minimize the environmental impact of their operations.
The energy-efficient manufacturing process will also become more advanced, with a greater focus on reducing carbon emissions and overall energy consumption. The integration of renewable energy sources, such as solar panels or wind turbines, into production facilities could significantly decrease the industry’s reliance on fossil fuels. Additionally, manufacturers could implement energy-saving technologies like high-efficiency motors or heat recovery systems, which capture and reuse waste heat generated during production. These innovations will not only help reduce operational costs but will also meet the increasing demand for sustainable and carbon-neutral products.
Smart manufacturing systems powered by the Internet of Things (IoT) will provide real-time data on every aspect of production. Sensors embedded in machinery, tools, and production lines will monitor everything from temperature control to material flow to machine performance. This data will be analyzed to identify inefficiencies, prevent machine breakdowns, and optimize the overall production process. Predictive maintenance tools will be increasingly used to anticipate equipment failures before they occur, minimizing downtime and ensuring that production continues smoothly and without interruptions.
The future of tea pot design will also embrace user experience (UX) as a driving force in both aesthetics and functionality. As technology continues to advance, manufacturers will likely integrate features that enhance the consumer experience beyond traditional function. For instance, smart tea pots equipped with sensors could adjust the water temperature automatically based on the type of tea being brewed, or they could connect to a smartphone app to provide brewing instructions, track tea consumption, or even sync with a home assistant like Alexa or Google Assistant. This level of interactivity would elevate the traditional tea pot to a multi-functional, tech-savvy appliance that meets the needs of modern consumers.
Additionally, the ergonomics of tea pot design will become a more significant consideration. As consumers look for more comfortable and functional kitchen tools, the tea pot will likely feature innovative handle designs that enhance the user’s grip and minimize strain, especially for those who might experience discomfort when handling traditional models. The spout could be designed for more precise pouring, ensuring that the tea flows smoothly without dripping or splashing.
The push for greater product personalization will also drive innovation in both design and manufacturing processes. Manufacturers may increasingly offer customizable options, where consumers can choose the material, finish, engraving, and even shape of their tea pot. Technologies like 3D printing or laser engraving will allow for an increased level of detail in these customizations, allowing for personalized patterns, monogrammed designs, or even limited-edition collections. These innovations in personalization will enable consumers to create tea pots that reflect their personal tastes or serve as unique gifts for special occasions.
As the market for tea pots expands globally, manufacturers will need to adapt to regional preferences and cultural trends. For instance, while Asian markets may continue to favor traditional cast iron or porcelain tea pots, Western markets might embrace more modern designs made of stainless steel or aluminum, and incorporate contemporary features like temperature controls or integrated tea infusers. Manufacturers will need to tailor their products to different markets by offering variety in style and functionality, while maintaining consistent quality and craftsmanship across their entire product line.
Automation and artificial intelligence will drive further innovation in manufacturing processes. Advanced AI algorithms will help with designing tea pot prototypes, allowing manufacturers to test and iterate designs more rapidly before moving to production. AI could also be used to predict consumer trends, ensuring that the next wave of tea pot designs is always in line with what consumers want. Robotics will continue to evolve, becoming more dexterous and capable of performing delicate tasks like polishing, engraving, or attaching small parts with increasing speed and precision. These technologies will also reduce the reliance on human labor for repetitive or physically demanding tasks, allowing workers to focus on more complex and creative tasks.
With the rise of smart home integration, manufacturers may also explore opportunities to design tea pots that seamlessly integrate with other kitchen gadgets. For example, a tea pot could be designed to work with an existing smart kitchen system, adjusting water temperature based on pre-programmed settings or sending a notification to a mobile device when the tea is ready. This added layer of connectivity would enhance the product’s appeal to tech-savvy consumers who already use smart appliances like smart refrigerators or smart ovens.
The future of sheet metal tea pot manufacturing will focus on striking a balance between cutting-edge technology and timeless design. While automation, smart technology, and customization will lead the way in production, the product itself will need to preserve the traditional values of craftsmanship, style, and usability. This combination of innovation and heritage will ensure that tea pot manufacturing continues to meet the evolving demands of a global and increasingly sophisticated market, positioning the industry for success in the coming years. As trends shift and consumer preferences evolve, manufacturers who remain adaptable, innovative, and sustainable will have a distinct advantage in the competitive landscape.
As the industry moves forward, collaborations with designers and creative professionals will become increasingly important in distinguishing brands and products. By partnering with renowned industrial designers or artists, manufacturers can create tea pots that are not just functional but also visually appealing and uniquely crafted. These partnerships can result in limited-edition collections or designer lines that attract premium customers who are looking for a piece of art in addition to a functional product. Collaborations like these also offer manufacturers the chance to expand their brand presence in luxury markets and develop a niche for high-end, bespoke items.
Moreover, sustainability practices will extend beyond the materials used in production. Manufacturers will likely place a greater emphasis on reducing the carbon footprint across the entire supply chain. This includes sourcing materials from sustainable suppliers, reducing transportation emissions, and designing products that are easier to recycle at the end of their lifecycle. Manufacturers might adopt cradle-to-cradle principles, where the tea pot can be fully recycled, disassembled, and reused, ensuring that there is no waste in the production and consumption process. The future design of tea pots could incorporate modular elements that allow for parts to be replaced or upgraded, extending the lifespan of the product and reducing the need for consumers to buy entirely new pots.
Modular design in tea pots will allow consumers to mix and match different components, such as the lid, handle, and spout, offering customization without the need for entirely new products. This approach can significantly reduce waste, as consumers would only need to replace parts instead of entire units. Furthermore, modularity can help manufacturers cater to evolving consumer tastes, enabling them to create diverse styles and variations using the same core components, thus improving production efficiency while offering a high degree of personalization.
As more consumers turn to online shopping, the packaging of tea pots will take on greater importance. Not only does the packaging need to protect the product during shipping, but it also becomes a significant part of the consumer’s unboxing experience. Eco-friendly packaging will become the standard, with manufacturers using recyclable or biodegradable materials instead of plastic or other non-sustainable options. The rise of minimalist packaging could also make products more attractive, with sleek, simple designs that highlight the quality of the product itself. Manufacturers may even include interactive elements in the packaging, such as QR codes that link to online resources, videos, or guides about the tea pot’s origins, use, or care instructions.
One of the key drivers for future innovation in tea pot manufacturing will be consumer-driven feedback loops. With the growing influence of social media and online reviews, manufacturers will be able to gather direct feedback from their customer base on design preferences, material choices, and functionality. This real-time data will provide manufacturers with insights into what features or styles are resonating with consumers, allowing them to adjust designs rapidly. Additionally, crowdsourcing could become a more common practice, with manufacturers turning to consumer polls or design competitions to help create new product lines. This ensures that tea pots reflect the current market demand and appeal to a wide range of customers.
As the global tea-drinking culture continues to grow, especially in regions like North America, Europe, and Asia, manufacturers will be able to capitalize on emerging trends in tea consumption. With the increasing popularity of specialty teas such as herbal blends, green teas, and matcha, tea pots will likely evolve to accommodate these different types of brews. For example, matcha tea pots may feature specialized designs that make it easier to whisk the powder into hot water, while herbal tea infusers could be integrated directly into the pot for ease of brewing. As new consumer preferences emerge, manufacturers will need to stay agile in developing products that enhance the tea-drinking experience.
At the same time, globalization will continue to influence tea pot designs. Cross-cultural influences could result in unique hybrid designs that blend traditional elements with modern aesthetics. For example, a tea pot might combine Asian-inspired elements such as ceramic finishes or traditional shapes with Western functionality, such as built-in temperature control systems or integrated smart features. These hybrid designs will appeal to a diverse audience and help manufacturers stand out in a competitive marketplace.
The digitalization of the manufacturing process will likely continue to evolve. 3D printing could play a role in both prototype development and small-batch production of highly specialized or customized tea pots. Manufacturers might use 3D printing to create complex components or prototype designs before moving to mass production, significantly reducing costs and production times for new models. As additive manufacturing technology advances, it could even be used to produce entire tea pots, enabling manufacturers to create intricate and customizable designs without the constraints of traditional manufacturing techniques.
The integration of AI in the design process will also allow for more personalized and adaptive tea pots. AI algorithms could analyze consumer behavior, purchasing trends, and even social media interactions to forecast which features will appeal to the market, helping manufacturers create products that are more aligned with consumer desires. This data-driven approach will ensure that new tea pots are not only stylish but also meet the functional needs of a broad spectrum of customers.
As tea pot manufacturing becomes more advanced, the industry will likely experience increased collaboration between various sectors, including technology companies, design firms, and material science experts. Such cross-disciplinary collaboration will lead to new innovations in both design and production. For example, the development of smart tea pots that can adjust brewing conditions based on the type of tea could involve partnerships with software developers and AI specialists to integrate machine learning and IoT capabilities. Similarly, material scientists might develop new alloys or coatings that enhance the durability and functionality of tea pots, ensuring that they can stand up to the heat and wear of daily use.
Automation in the form of robotic arms, conveyor belts, and AI-powered quality control systems will continue to play an essential role in maintaining high efficiency and reducing production costs. These technologies will allow tea pot manufacturers to scale production quickly, maintain consistency in product quality, and meet the growing demands of the global market. As these automated systems improve, the cost of production will decrease, leading to more affordable prices for consumers without sacrificing the quality of the product.
In conclusion, the future of tea pot manufacturing will be shaped by advancements in technology, sustainability, and consumer-driven trends. Manufacturers will need to adapt to rapidly changing market demands while embracing innovative materials, smart features, and sustainable practices. By staying ahead of technological trends and offering products that are both functional and aesthetically appealing, tea pot manufacturers will ensure their place in the market for years to come. The future holds exciting possibilities for the evolution of tea pot design and manufacturing, blending traditional craftsmanship with modern innovation to create products that satisfy the needs of a new generation of tea enthusiasts.
As tea pot manufacturing continues to evolve, manufacturers will also need to address emerging challenges in the global supply chain. Factors such as fluctuating material costs, political instability, and supply chain disruptions (such as those experienced during the COVID-19 pandemic) could impact the availability of raw materials or increase production costs. To mitigate these risks, manufacturers will need to explore alternative sourcing strategies, such as local sourcing of materials, diversifying suppliers, and developing contingency plans for sudden disruptions. This will help manufacturers ensure consistent access to quality materials and maintain reliable production timelines.
The increasing demand for sustainable products will also lead to eco-friendly innovations in packaging and shipping. Beyond recyclable or biodegradable materials, there is likely to be an increased focus on reusable packaging that encourages consumers to reduce waste. For example, manufacturers may introduce reusable cloth bags or wooden boxes for premium tea pot lines, offering consumers an environmentally conscious way to store or gift their tea pots. These packaging solutions not only reduce waste but can also become part of the overall product experience, contributing to a more sustainable and high-quality image for the brand.
With the rise of online shopping and the increasing importance of direct-to-consumer channels, manufacturers will also need to invest in advanced logistics. This includes real-time inventory management systems that provide insights into stock levels, demand forecasting, and automated reordering. Additionally, last-mile delivery solutions will become more important in ensuring that tea pots arrive safely and on time to consumers. To minimize the environmental impact of shipping, manufacturers might explore more sustainable delivery options, such as carbon-neutral shipping services or local distribution hubs that reduce the distance products travel.
Furthermore, the rise of e-commerce will continue to shape the way tea pot brands engage with consumers. Online platforms allow brands to directly interact with their customers, gather feedback, and cultivate a sense of community. By leveraging social media and digital marketing, tea pot manufacturers can build strong brand identities and engage consumers in creative ways. Manufacturers can also tap into the growing trend of influencer marketing, where tea enthusiasts, lifestyle bloggers, or kitchenware influencers promote tea pots through social media posts, tutorials, or product reviews. These partnerships help spread brand awareness and drive consumer interest in specific models or collections.
In addition, augmented reality (AR) and virtual reality (VR) could become more integrated into the purchasing process. Online shoppers could use AR apps to visualize how a particular tea pot would look in their kitchen environment before making a purchase, enhancing the decision-making process. Similarly, VR technology could allow customers to take a virtual tour of the tea pot’s manufacturing process, learning about the craftsmanship, materials, and design decisions that go into making the product. This level of engagement not only adds value to the consumer experience but also fosters a sense of transparency and trust with the brand.
In terms of consumer education, manufacturers will likely invest more in content creation to inform buyers about the importance of quality materials, the best tea brewing techniques, and the proper care for tea pots. Educational resources such as how-to videos, brewing guides, or even virtual tea parties can help consumers feel more connected to the product and improve their overall experience. Manufacturers may also offer tea pot care kits that include tools and cleaning agents to help preserve the longevity and performance of the product.
As manufacturers continue to innovate, the use of artificial intelligence (AI) will expand beyond just production to encompass other areas of the business. For example, AI-powered chatbots could be used on websites and customer service platforms to help answer consumer questions, provide product recommendations, and even assist with troubleshooting or post-purchase support. AI algorithms could also help optimize pricing strategies, dynamically adjusting prices based on demand, competitor pricing, and market conditions.
Customization technology will also take center stage, offering consumers the chance to personalize their tea pots more than ever before. Tools like laser etching, embossing, and digital printing could enable consumers to add custom designs, monograms, or even artwork directly onto their tea pots. This level of personalization will make each product more meaningful to the consumer, offering a higher degree of emotional value alongside functionality. These personalized tea pots could be used for special occasions, such as weddings, anniversaries, or corporate gifts, further expanding the market for tea pots in both domestic and gift-giving sectors.
As a result, quality assurance in tea pot manufacturing will become even more critical. With the increasing complexity of customization, ensuring that each tea pot meets high standards will require advanced quality control systems. The use of machine vision and AI-driven inspection systems will allow for precise monitoring of product quality at every stage of production. This not only reduces human error but also ensures consistency in the final product, especially when producing customized or limited-edition models.
The future of tea pot manufacturing is poised to see a blend of traditional techniques and modern technologies. The continuous advancements in material science, manufacturing automation, and smart technologies will help tea pot manufacturers stay competitive, while the focus on consumer engagement, personalization, and sustainability will ensure that the products resonate with modern consumers.
As consumer expectations shift toward higher quality, more sustainable products with advanced features, tea pot manufacturers must remain agile, responsive, and forward-thinking. Whether through embracing digital innovation, focusing on eco-friendly materials, or exploring new avenues for global distribution, manufacturers who can balance innovation with craftsmanship will continue to thrive in a rapidly evolving market. In the end, tea pots will remain more than just functional objects; they will become an integral part of the tea-drinking experience, combining tradition, modernity, and sustainability to create a product that is both cherished and practical for a new generation of tea enthusiasts.
Sheet Metal Soup Ladle Manufacturing Machine
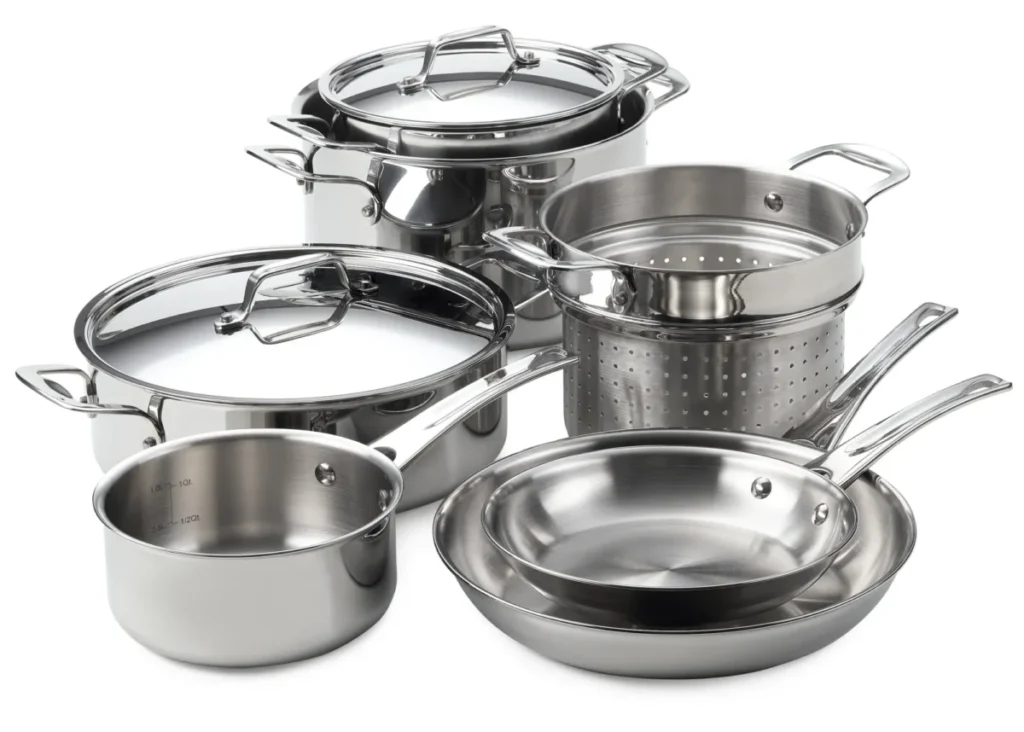
Manufacturing a sheet metal soup ladle involves several key steps, from the selection of materials to the final assembly and quality control. These ladles are essential tools in many kitchens and are primarily made from stainless steel or other durable metals that can withstand high temperatures and regular use. A sheet metal soup ladle manufacturing machine will be specifically designed to automate and streamline the process of shaping, forming, and assembling these kitchen tools efficiently.
Materials and Design
- Material Selection: High-quality stainless steel (SS304, SS316) is commonly used due to its corrosion resistance and durability, which are essential qualities for items like ladles that deal with hot liquids.
- Ladle Design: The ladle typically consists of a bowl (scoop), a handle, and often a hook or ring at the end of the handle for hanging. The bowl is shaped to ensure it can hold a significant amount of liquid, while the handle is long enough to avoid hand burns during use.
Manufacturing Process
- Material Preparation:
- Sheets of stainless steel or aluminum are cut into large flat pieces or coils.
- Coiling or Uncoiling Machine: If coils are used, a coiling/uncoiling machine will unwind and flatten the metal sheet to prepare it for forming.
- Blanking or Punching:
- Blanking Press: A punch press machine is used to cut the raw material into circular blanks, which are the base shape for the bowl of the ladle.
- This process involves using a die and punch system to ensure precise size and uniformity of each metal disc that will form the ladle bowl.
- Forming and Shaping:
- Deep Drawing Press: The blank is then placed into a deep drawing press to form the bowl shape. The machine uses a die to push the metal into a mold, forming the concave shape of the ladle bowl.
- Multiple passes through the drawing process may be required to achieve the final depth and contour.
- Trimming and Edging: After forming, the edges of the ladle bowl are trimmed to ensure smoothness and eliminate any excess metal. This is typically done with a trimming press.
- Handle Fabrication:
- Handle Production: Handles are often produced from separate metal strips or tubes, which are cut, bent, and shaped to the appropriate length. The handle may also be rolled to ensure ergonomic grip and strength.
- Bending Press: A bending press or tube bending machine is used to shape the handle, often forming a slightly curved or straight design depending on the required style of the ladle.
- Welding or Fastening: The handle is then welded or riveted to the bowl using an automatic arc welding machine or spot welding system. Precision welding ensures that the handle is securely attached to the ladle bowl without compromising the structure.
- Surface Treatment:
- Polishing and Finishing: Once the ladle bowl and handle are assembled, the entire piece undergoes a finishing process. This includes polishing, which gives the ladle a smooth, shiny surface that is resistant to staining and easy to clean. Machines like vibratory polishers or rotary polishing machines are used to refine the surface.
- Coating or Electroplating: Some ladles may undergo additional treatments, such as electroplating or powder coating, to improve resistance to rust or provide a decorative finish.
- Assembly and Final Inspection:
- Assembly Line: Once all parts (bowl, handle, hook) are manufactured, they are moved along the assembly line. Here, they are joined using manual or robotic welding. If hooks or additional features are required, they are attached at this stage.
- Final Inspection and Testing: The ladles are then subjected to rigorous quality control checks to ensure they meet specifications. This includes checking for any defects, proper alignment of the handle, smoothness of edges, and functional integrity. The ladles are also tested for resistance to high temperatures and corrosion.
- Packaging and Distribution:
- After passing quality control, the ladles are packaged for shipment. Packaging often includes cardboard boxes, plastic wrapping, or recyclable materials, depending on the manufacturer’s commitment to sustainability.
- Automated Packaging: For high-volume production, automated packaging machines ensure that each ladle is securely packed, and each box is labeled with the appropriate product details.
Automation in Manufacturing
For high-volume production, automation plays a significant role in increasing efficiency and reducing human error. The key automated steps in soup ladle manufacturing include:
- Automated Blanking Presses: These machines can automatically feed, punch, and cut metal sheets into the required ladle bowl blanks.
- Robotic Welding Systems: Robots can be programmed to weld the handle to the bowl, providing precision and speed.
- CNC Machines: Computer Numerical Control (CNC) systems are often used for handle shaping, as they can make precise cuts and bends according to the design specifications.
- Inspection Systems: Automated vision inspection systems equipped with machine vision technology can detect flaws, ensuring that only products meeting strict quality standards are shipped.
Future Trends and Innovations
As manufacturing techniques advance, we are likely to see several trends emerge in the production of sheet metal soup ladles:
- Sustainable Manufacturing: With increasing demand for sustainability, manufacturers will look for ways to minimize waste and use recycled materials. This includes using sustainable energy sources like solar or wind power in the manufacturing plant.
- Smart Manufacturing: Integration of IoT (Internet of Things) technology into the production process will allow manufacturers to collect real-time data on machinery performance, inventory levels, and production efficiency, enabling predictive maintenance and optimized workflows.
- Customization: As demand for personalized products grows, manufacturers may incorporate customized engravings, handle shapes, or even unique colors into the production process, giving consumers the option to design their ladles according to personal taste.
Conclusion:
The sheet metal soup ladle manufacturing machine streamlines the process of creating durable, high-quality ladles for the kitchenware industry. By combining automation, advanced materials, and innovative manufacturing techniques, these machines allow for high-efficiency production while maintaining the standards of durability and precision required for such functional items. The future of soup ladle manufacturing will likely see further integration of sustainability and smart technologies, ensuring that products remain not only functional but also eco-friendly and tailored to modern consumer demands.
The continued evolution of sheet metal soup ladle manufacturing will likely see the integration of advanced materials that offer enhanced performance and durability. Manufacturers may begin to explore composite materials or alloy blends that combine the benefits of stainless steel with other metals to increase resistance to scratching, staining, and thermal conductivity. These materials could offer advantages in terms of both lightweight design and longer lifespan under high-temperature conditions. Additionally, there could be a growing interest in anti-microbial finishes to enhance the hygienic properties of the ladles, especially as more consumers demand tools that are easy to clean and maintain.
Manufacturers may also move towards more customized production processes, as consumer demand for personalization grows. Advanced laser etching or engraving machines could allow buyers to add initials, names, or unique designs to their soup ladles, transforming a simple kitchen tool into a personalized gift or a luxury item. This could cater to both individual consumers looking for custom items for personal use as well as the gift market, which is always looking for unique and high-quality products. Moreover, custom handle designs—whether ergonomic for better grip or aesthetically unique—could become more prevalent as manufacturers seek to differentiate their products in a crowded market.
As global supply chains continue to be challenged by factors like inflation, political instability, and environmental considerations, the focus on local production and shortened supply chains will likely intensify. Manufacturers may seek to source materials locally or set up more decentralized production facilities, reducing shipping costs and time. These strategies not only help improve production efficiency but can also reduce the environmental impact associated with long-distance transportation. Additionally, localized production could foster stronger relationships with customers, particularly in markets where “locally made” goods are highly valued.
Digitalization will continue to influence the manufacturing process. The use of 3D printing could become more integrated into the creation of prototype ladles or small-batch runs, allowing designers and manufacturers to experiment with new designs quickly and cost-effectively. Additive manufacturing offers flexibility in producing complex shapes or incorporating new functionalities, like built-in temperature sensors that alert the user when the soup has reached the optimal temperature. Furthermore, data-driven production systems could optimize the manufacturing process by predicting demand, adjusting production schedules, and reducing downtime, ensuring that ladles are produced as efficiently as possible.
Another emerging trend could be the rise of smart kitchen tools, with soup ladles becoming part of a larger ecosystem of IoT-enabled kitchenware. For example, a soup ladle could feature built-in sensors that interact with a smart pot to adjust the temperature or alert the user when it’s time to stir. Such innovations would align with the growing interest in smart homes and connected devices that provide more convenience and control to consumers.
Sustainability in production and packaging will also remain a significant concern. In addition to using recycled metals and more energy-efficient manufacturing techniques, the packaging used for ladles could become a key differentiator. Eco-friendly packaging, like biodegradable plastic or recyclable paper products, will appeal to consumers who are more environmentally conscious. Manufacturers may even explore minimalistic packaging to reduce waste, with the product itself taking center stage as the primary focus.
In the marketing and sales realm, the rise of e-commerce will continue to shape the way soup ladles are sold. Online platforms allow manufacturers to reach a wider audience, and direct-to-consumer sales models will likely become more prevalent. Enhanced digital tools, such as augmented reality (AR) features that allow customers to virtually “try out” ladles in their kitchen space, could increase engagement and improve the online shopping experience. Furthermore, leveraging social media influencers and user-generated content could help promote ladles, showcasing their functionality in real kitchens and building trust with potential buyers.
Finally, automation will likely remain at the core of the soup ladle manufacturing process. As technology continues to advance, robotic systems and AI-driven quality control will enable faster production cycles with even greater precision. The integration of these systems will not only ensure that the ladles meet the high standards for strength, appearance, and ergonomics but also improve the overall efficiency of the manufacturing line, lowering costs and increasing throughput.
As the industry adapts to these changes, the soup ladle manufacturing process will become more innovative, customized, and sustainable, providing a higher-quality product for consumers while reducing the environmental impact and improving production efficiency. The combination of modern technologies, consumer-driven design preferences, and a focus on quality materials will ensure that soup ladles remain a staple in kitchens worldwide for years to come.
As soup ladle manufacturing continues to evolve, the role of advanced robotics and artificial intelligence (AI) will play an increasingly significant part. Robotics will not only streamline the assembly process, ensuring faster and more precise welding, but also facilitate the handling of delicate components during packaging and inspection. Automated systems could detect any imperfections in the ladle’s surface or construction, ensuring that every unit meets the required safety and functional standards. Additionally, AI-powered machine learning algorithms could be utilized to predict potential production bottlenecks, offering real-time solutions and thus preventing costly delays. The ability of AI systems to analyze large datasets from various manufacturing processes can lead to a more optimized production cycle, lowering waste and increasing overall efficiency.
The growing interest in health and wellness may lead to more focus on safe, non-toxic materials in soup ladle production. Consumers are increasingly concerned about harmful chemicals in their kitchenware, especially in tools that come into contact with hot foods. Manufacturers may respond by using non-reactive, food-safe coatings that are free from harmful substances like BPA or PFOA. These coatings will ensure that soup ladles are both durable and safe for use with a variety of foods, including acidic soups or broths, while also being easy to clean and maintain. Manufacturers could also explore the possibility of creating ladles with handles that feature heat-resistant materials or insulated layers to provide a more comfortable, safer grip during use.
Additionally, there is likely to be a continued emphasis on the ergonomics of the ladle design. Consumers are increasingly looking for kitchen tools that not only perform well but also feel comfortable in their hands. The introduction of soft-touch materials or adjustable handles for varying hand sizes will make soup ladles more user-friendly. Designs could also incorporate angled handles or non-slip grips to ensure a secure hold, especially when lifting heavy pots of hot soup. As the trend toward personalized and custom-designed kitchen tools continues, manufacturers may offer a wider variety of handle styles, colors, and lengths to meet different consumer preferences and needs.
The increase in global consumer awareness of environmental issues will drive manufacturers to focus on carbon footprint reduction within their supply chains. The use of renewable energy sources in manufacturing plants, such as solar or wind power, can help reduce overall emissions, making the production of soup ladles more sustainable. Manufacturers could also explore local sourcing of raw materials to further decrease the environmental impact of transportation. Additionally, waste produced during the manufacturing process could be recycled or repurposed into other products, reducing overall material waste and supporting the circular economy.
Another key consideration in the future of soup ladle manufacturing will be the adoption of smart manufacturing technologies like additive manufacturing (3D printing). This could allow for the creation of highly customized ladles in small batches. For instance, a 3D printer could quickly produce a prototype or one-off design of a ladle, giving manufacturers the ability to test new shapes, sizes, or handle configurations before committing to mass production. This could lead to a more agile approach to design and production, where small runs of unique ladles can be produced on demand, reducing the need for large-scale inventories and lowering the costs associated with unsold stock.
In parallel, cloud-based manufacturing systems will enhance communication across the supply chain, providing real-time updates on inventory levels, production schedules, and order statuses. This cloud integration can also help manufacturers manage orders more efficiently, reducing lead times and helping to meet fluctuating demand. This technology will play an increasingly important role as consumers expect quicker delivery times and more seamless shopping experiences, especially in the growing e-commerce market.
The importance of sustainability in packaging is likely to continue to grow as well. In addition to using biodegradable or recyclable materials for ladle packaging, manufacturers may opt for minimalistic packaging that reduces waste. Some companies may even offer customers the option of receiving their ladles in eco-friendly packaging by default, positioning themselves as more sustainable brands. Furthermore, in line with consumer demand for transparency, manufacturers could include eco-certification labels or offer detailed insights into the sustainability of their products, including the materials used and the manufacturing processes employed.
As the kitchenware market continues to grow and evolve, soup ladle manufacturers will need to embrace a consumer-centric approach. The ability to respond quickly to changing consumer preferences, whether for more ergonomic designs, sustainable materials, or personalized features, will be crucial for maintaining competitiveness. The globalization of markets also means that manufacturers will need to stay attuned to different regional preferences and standards. For example, certain cultures may favor ladles with specific handle shapes or decorative elements, while others may prefer minimalist, functional designs.
The rise of smart kitchens will also influence the design and functionality of soup ladles in the future. As connected devices like smart pots, voice assistants, and temperature sensors become more common in households, ladles might incorporate features like temperature-reading capabilities or sensors that can alert users when their soup has reached the optimal temperature for serving. Imagine a ladle that changes color when the liquid reaches a specific heat threshold, providing users with a visual cue to prevent overcooking or scalding. The integration of IoT (Internet of Things) technology into kitchen tools, including ladles, would provide a highly interactive and user-friendly experience, transforming traditional kitchenware into part of a connected, smart home ecosystem.
Moreover, consumer engagement through platforms like social media will continue to be a powerful marketing tool. Manufacturers could collaborate with influencers or chefs to showcase the versatility and design of their ladles, offering tips, recipes, and demonstrations of the ladles in use. Interactive content, such as polls or custom ladle design contests, could encourage direct consumer participation and further increase brand loyalty.
In conclusion, the future of sheet metal soup ladle manufacturing will likely be defined by the intersection of innovation, sustainability, and consumer engagement. Manufacturers will need to leverage technological advancements, from robotics and AI to smart manufacturing and IoT, to stay competitive and meet evolving consumer expectations. With the demand for personalization, sustainability, and ergonomics growing, the soup ladle of the future will likely be a more customized, intelligent, and environmentally conscious kitchen tool, ensuring its place in kitchens for many years to come.
The future of sheet metal soup ladle manufacturing is closely tied to advancements in robotics and artificial intelligence. These technologies are set to further optimize the production line, ensuring even greater precision, faster production speeds, and reduced waste. As robotics becomes more sophisticated, entire manufacturing processes—from metal sheet handling to final assembly—could be completely automated. This would not only reduce labor costs but also increase production scalability, enabling manufacturers to meet the demands of high-volume and customized orders more effectively. Automated systems may also be designed to handle more complex ladle shapes or even incorporate multi-functional features, such as integrated measuring markings inside the bowl for added convenience.
Furthermore, AI-driven algorithms could play a significant role in predictive maintenance, minimizing downtime by identifying potential issues before they lead to production delays. By continuously monitoring machine performance, these AI systems can alert operators to worn parts or machinery malfunctions, allowing for timely repairs and maintenance. This real-time data analysis will also provide manufacturers with valuable insights to optimize the design and functionality of their ladles, ultimately contributing to better quality control and customer satisfaction.
In addition to technological advancements in production, there is an increasing focus on sustainability and the environmental impact of manufacturing processes. The carbon footprint associated with producing soup ladles will continue to be a major consideration for both manufacturers and consumers. As eco-consciousness grows, the demand for ladles made from sustainable materials and produced through low-energy methods will likely increase. Manufacturers could focus on sourcing recycled metal or exploring alternative eco-friendly metals that have a lower environmental impact during production. These materials would not only cater to environmentally-conscious consumers but also allow companies to align with global sustainability initiatives and eco-labeling standards.
Additionally, the drive toward zero waste in manufacturing could lead to the creation of systems that recycle metal scrap and unused materials back into the production cycle. By implementing closed-loop recycling, manufacturers can reduce the need for virgin materials, minimize waste, and further lower their overall environmental impact. The rise of biodegradable packaging or minimal packaging designs will also become a focal point in ladle manufacturing. Consumers increasingly expect that the products they purchase are environmentally friendly, not just in their usage, but throughout their life cycle, from production to disposal.
In terms of consumer trends, the growing demand for personalization in kitchenware will continue to shape the soup ladle market. Beyond simply choosing between different handle styles and finishes, consumers may want the ability to personalize the engraving, color, or even the shape of their ladles. Manufacturers may introduce online customization platforms, allowing customers to design their ladles in real-time by selecting various features, such as handle length, bowl depth, and material finishes. This trend is likely to be further bolstered by the direct-to-consumer model, where customers can interact directly with the brand, ensuring their specific needs are met.
Smart technology in kitchenware is also on the horizon. Future soup ladles may integrate with smart home systems, enabling them to communicate with other connected kitchen appliances. For instance, a ladle could have a built-in temperature sensor that connects to a smart pot, adjusting cooking times or temperatures based on the ladle’s interaction with the liquid. This type of interconnected functionality will appeal to consumers who are looking to streamline their cooking process and improve the overall efficiency and convenience of their kitchens. Voice-activated features, like those available in other smart kitchen tools, could be added to ladles, allowing users to check the temperature or even send commands to other appliances through voice commands.
As more people embrace healthy eating habits, the importance of non-toxic, food-safe kitchen tools is becoming increasingly important. The emphasis on safe materials will likely lead to greater use of PFOA-free coatings, BPA-free materials, and other substances that ensure the soup ladles are safe for long-term use in food preparation. These ladles will be designed to withstand the high heat of soups and stews without releasing harmful chemicals, ensuring that they not only perform well but are safe for families.
The global market for kitchenware will continue to expand, and with that, the need for localized production and efficient distribution will increase. Manufacturers will need to adapt their production strategies to meet regional preferences and standards. For example, soup ladles designed for the Asian market may have different handle lengths or bowl shapes than those typically used in Western countries. Localization will require manufacturers to tailor their products to fit specific cultural preferences and cooking styles, potentially incorporating new designs and materials that resonate with diverse consumer bases.
As e-commerce continues to dominate the retail landscape, soup ladles will be sold across a range of platforms, from major online retailers to niche, specialized sites. Manufacturers will need to focus on providing an exceptional customer experience in the digital space, from product photography to detailed descriptions and customer reviews. The ability for customers to easily view product details, watch demonstrations, and read testimonials from other users will be critical in driving sales. Additionally, augmented reality (AR) technology could allow customers to visualize the ladle in their own kitchen, helping them make more informed purchasing decisions.
Brand loyalty will become increasingly important as consumers have access to a wider array of choices. Manufacturers can leverage social media and digital platforms to build brand communities, share stories about sustainable production practices, and engage with customers directly. The ability to interact with a brand on a personal level will encourage repeat business and help companies establish themselves as leaders in the sustainable and innovative kitchenware space.
The future of sheet metal soup ladle manufacturing is bright, with technology, sustainability, and personalization paving the way for continued innovation. Manufacturers who can effectively blend cutting-edge production techniques, environmentally conscious practices, and consumer-driven designs will be well-positioned to meet the evolving demands of the global market. By doing so, they will not only create high-quality products that appeal to today’s savvy consumers but will also help shape the future of kitchenware manufacturing for years to come.
The next wave of sheet metal soup ladle manufacturing will likely bring even more refined user experiences and technological integration. As manufacturing technology advances, particularly with innovations in robotics, artificial intelligence, and 3D printing, the potential for creating truly personalized kitchen tools will increase dramatically. Here are some additional areas where these developments will shape the future of ladle production:
Advanced Materials and Performance Enhancements
In the coming years, material science will likely see new breakthroughs that will further optimize the performance of ladles. High-performance coatings could offer increased resistance to corrosion and scratching, especially for ladles used in high-acid or high-salt foods, such as soups containing tomatoes or vinegar-based broths. Manufacturers might also experiment with composite materials—such as carbon fiber or advanced polymers—that provide a lighter weight without sacrificing strength. These composite ladles could become more affordable and accessible to a wider range of consumers, offering both aesthetics and durability in a variety of modern kitchens.
Moreover, the trend toward sustainable materials will likely grow, with the increasing focus on sourcing metals and other materials that are both renewable and recyclable. This could help reduce the environmental footprint of ladle manufacturing while also aligning with the growing global push for sustainable production practices. Manufacturers may explore biodegradable coatings or metal alloys that require less energy to produce, contributing to an eco-friendly approach.
Integration of Artificial Intelligence (AI) for Smarter Designs
The rise of AI-based design systems will make it possible to create ladles that are tailored to specific cooking tasks. For instance, through the use of machine learning algorithms, a manufacturer could develop ladles that are optimized for different types of soups or stews. A ladle designed for use in broth-based soups might have a longer, more flexible handle, while one intended for stew might have a more rigid handle with a deeper bowl. The AI systems could analyze customer preferences, cook times, and soup characteristics to suggest the ideal ladle design. 3D modeling tools driven by AI could allow customers to visualize, adjust, and even prototype their own designs from home.
In addition to design, AI could play a central role in quality assurance and production optimization. For instance, computer vision systems powered by AI could be employed to inspect the ladles for imperfections during production. This technology can detect even the slightest defects, such as scratches, dents, or dimensional inaccuracies, ensuring only the highest quality ladles are sent to customers. AI can also help in managing production workflows to reduce waste, predict demand, and optimize manufacturing processes, leading to lower costs and better product availability.
Smart Features for Enhanced Cooking Experience
The integration of smart features in soup ladles will likely become a major differentiator in the future of kitchenware. Just as smartphones and smart home devices have transformed our daily lives, smart kitchen tools will make cooking more interactive and efficient. Future soup ladles could include embedded sensors that monitor the temperature of the soup or even detect if the ladle is submerged in liquid, triggering an alert if the soup is too hot, too cold, or if it’s time to stir.
In addition, a smart ladle could be designed to sync with other smart kitchen devices. For example, it could connect with a smart stove to regulate the temperature of the soup in real-time, adjusting heat levels for optimal cooking. Similarly, it could communicate with a digital recipe assistant on a smart display, providing step-by-step cooking guidance based on the ingredients detected in the ladle. For example, the ladle could automatically sync with an app, helping track nutritional data like calories or sodium content, which is especially useful for health-conscious consumers or those with dietary restrictions.
Furthermore, some ladles might incorporate features like LED indicators along the handle to alert users when it is safe to remove the ladle from a hot pot, or even sound alerts when the soup has reached the ideal serving temperature. Bluetooth or Wi-Fi connectivity could also enable consumers to track their cooking progress remotely through smartphone apps, giving them greater control over their kitchen environment.
Consumer-Centric Customization
The growing demand for personalization will continue to influence ladle designs. Customization options will be driven by a combination of consumer preferences and advancements in on-demand production technologies like 3D printing and digital fabrication. In the future, customers will likely be able to design their own ladles from scratch, choosing from various bowl sizes, handle types, colors, and even engravings. These options could be offered through an easy-to-use online platform that allows consumers to visualize their custom designs before making a purchase.
Additionally, for customers with unique needs—such as those with arthritis or other mobility limitations—ladles could be designed with ergonomics in mind, offering adjustable handles, anti-slip grips, or weighted designs for ease of use. Modular ladles could also be developed, where users can swap out handles or bowl sections depending on their preference, thus offering multiple functions with a single tool.
Social and Digital Influence on Ladle Design
The role of social media and influencers will continue to shape consumer expectations. As more individuals share their experiences with kitchen products online, manufacturers will need to cater to the demand for visually appealing, socially shareable products. Ladles could be designed with unique shapes, colors, or even artistic finishes that encourage users to post photos of their kitchens and cooking setups. This focus on aesthetics could extend to limited edition designs, collaborating with well-known chefs, artists, or designers to create exclusive ladle collections.
Manufacturers may even utilize crowdsourcing platforms to gather feedback on potential ladle designs or allow customers to vote on the next big innovation. Interactive digital campaigns could engage the community, encouraging customers to share recipes or cooking tips using their ladles, thus fostering a sense of connection with the brand.
Increased Focus on Sustainability
As environmental concerns intensify, sustainability will continue to be a driving force in the manufacturing process. Beyond using eco-friendly materials, manufacturers will increasingly focus on reducing their carbon footprint through more energy-efficient production processes. The use of solar energy or wind power in manufacturing plants could become standard practice, while the adoption of carbon-neutral practices could be an attractive selling point for consumers who prioritize environmental responsibility.
In addition, ladles could be designed with recyclability in mind, ensuring that once their useful life is over, they can be easily broken down and reused. Some companies might even introduce repair and replacement programs, where handles or bowls can be swapped out for upgrades, ensuring a longer lifecycle for the product and minimizing waste.
Manufacturers will likely continue to push the envelope when it comes to reducing packaging waste, as well. The move towards zero-waste packaging solutions may lead to the use of compostable packaging materials, biodegradable wraps, or minimalist packaging that can be recycled or reused in creative ways.
Conclusion: The Future of Soup Ladle Manufacturing
The future of sheet metal soup ladle manufacturing will be driven by technological innovation, personalization, and a growing demand for sustainable production practices. Manufacturers who embrace smart technologies, consumer-driven design, and eco-conscious manufacturing will be well-positioned to cater to the evolving needs of a more connected, health-conscious, and environmentally aware consumer base.
The integration of advanced materials, customization options, and AI-driven design tools will make soup ladles not only more functional but also more personalized and interactive than ever before. As smart kitchens and IoT-enabled devices continue to evolve, soup ladles could soon be part of a much broader network of connected kitchen tools, enhancing the cooking experience and making meal preparation more efficient, enjoyable, and sustainable.
Ultimately, the soup ladle of the future will be a product that combines precision engineering, cutting-edge design, and consumer customization, offering an experience that blends functionality with creativity, health, and sustainability. The market for these innovative tools will continue to grow, and manufacturers who can adapt to these changes will have the opportunity to define the future of kitchenware for years to come.
The future of sheet metal soup ladle manufacturing is likely to witness even greater transformations, as advancements in technology, consumer demands, and manufacturing processes continue to reshape the industry. As more manufacturers pivot towards digitally-driven, smart, and sustainable production, we can expect additional enhancements in design, functionality, and consumer interaction. Here are some further developments that are likely to emerge:
1. Further Integration with Smart Kitchens
As the demand for smart kitchens grows, the soup ladle may evolve beyond just a utensil for stirring. It could integrate into the IoT (Internet of Things) ecosystem, communicating seamlessly with other connected kitchen devices. For instance, the ladle could use a smart handle embedded with sensors to measure the temperature or viscosity of soup in real-time. These sensors could provide real-time feedback to a mobile app, offering updates like “soup is too hot” or “the broth is ready to be stirred.”
In a more futuristic scenario, the ladle could even adjust its shape or temperature based on real-time data provided by a smart pot or smart stove. For instance, a self-heating ladle could keep the soup at an optimal temperature during serving, or a sensor-activated ladle might adjust its design to better handle the soup’s density. These technologies could greatly enhance the cooking process by creating seamless connectivity between kitchenware and appliances, enabling cooks to be more efficient and precise in their meal preparation.
2. 3D Printed Ladles and On-Demand Production
The future of manufacturing soup ladles could also see 3D printing becoming a central element. This additive manufacturing method would allow for the on-demand creation of ladles with bespoke features, including intricate designs, ergonomic handles, and custom shapes that cannot be achieved with traditional metalworking. The ability to print ladles as needed eliminates excess production, reducing material waste and inventory costs. This could be especially beneficial in industries requiring limited editions, such as high-end restaurants or artisanal kitchenware brands.
3D printing technology also allows for greater experimentation in terms of material composition. For example, bio-based plastics, metal composites, or recycled materials could be combined to create ladles that are both durable and sustainable. Furthermore, 3D printing could open up new opportunities for customers to design their own ladles or select from a variety of pre-set designs to customize the perfect tool for their kitchen.
3. Collaborative Design and Crowdsourcing
As part of the growing consumer-centric approach in manufacturing, manufacturers could shift towards collaborative design models. Consumers may be invited to participate in the design process through crowdsourcing platforms. These platforms could allow users to submit ideas or vote on the next ladle design, offering personalized features or limited-edition collections. This approach would create a stronger connection between manufacturers and customers, leading to more innovative products tailored to consumer preferences.
Moreover, co-branding with influencers or celebrities could play a significant role. Imagine a celebrity chef or food blogger designing their own line of ladles, with custom engravings or aesthetic features that reflect their brand identity. These collaborations could generate increased interest and buzz, enhancing customer engagement and loyalty.
4. **Focus on Sustainability and Eco-Friendly Manufacturing
As the environmental impact of manufacturing continues to be a pressing concern, the industry will likely see a surge in sustainable production practices. Manufacturers will be encouraged to find alternative materials such as recycled metal or biodegradable alloys that reduce their environmental footprint. Additionally, energy-efficient manufacturing methods, such as solar-powered factories or the use of green energy sources, will become more common.
Sustainable packaging will also take center stage, with manufacturers adopting zero-waste principles. The shift towards minimalistic packaging or even no packaging for certain products will resonate with eco-conscious consumers. Efforts to ensure that packaging is 100% recyclable, compostable, or made from recycled materials will be critical for brands aiming to appeal to environmentally-aware customers.
A more ambitious approach might be the establishment of closed-loop manufacturing systems that continuously reuse metal and other materials in the production process. This circular economy model would drastically reduce the need for raw material extraction and significantly cut waste.
5. Sustainable Consumer Education and Transparency
The growing interest in ethical consumerism and transparency will likely push manufacturers to be more open about the origins of their materials and the environmental impact of their production processes. Consumers are increasingly asking questions about the products they buy, such as: “Where is this ladle made?” or “What is the environmental cost of its production?”
In response, manufacturers will offer greater transparency by providing detailed information about sourcing, production practices, and supply chains. Tools like QR codes on product packaging could allow customers to access full data on material sourcing, energy consumption, and waste management practices used during the production of the ladle. This information could help consumers make more informed decisions when choosing kitchen tools that align with their values.
Furthermore, brands might engage in eco-certification programs, earning certifications that prove their commitment to sustainability. As consumers become more environmentally conscious, these labels could become a major differentiator, pushing companies to adopt more sustainable practices across the board.
6. Health and Safety Features in Ladle Design
As people become more aware of the health risks associated with certain materials used in cooking, such as BPA, PFOA, and other potentially harmful chemicals, the demand for non-toxic, food-safe kitchen tools will likely grow. Future ladles will be designed with health-conscious materials like food-grade stainless steel, ceramic coatings, or PFOA-free non-stick surfaces.
Additionally, ladles might be designed with hygiene and safety in mind. For example, handles could be made from antimicrobial materials to prevent the growth of harmful bacteria. Ladles could also incorporate heat-resistant features, ensuring that the handle remains cool to the touch even when the ladle is used in hot liquids. For families with small children, a child-safe version of the ladle could be produced, featuring non-toxic materials and rounded edges for safety.
7. Enhanced User Experience with Augmented Reality (AR) and Virtual Reality (VR)
As part of the evolving retail landscape, Augmented Reality (AR) could be used to allow customers to visualize how a ladle will fit in their kitchens. For example, a consumer could use their smartphone to project a 3D model of a ladle into their own kitchen space. This technology could help customers select the right ladle for their kitchen design, offering a more personalized shopping experience.
In a similar vein, Virtual Reality (VR) could be used to provide an immersive, interactive shopping experience where customers can “virtually” test different ladles before purchase. This technology would allow customers to feel as though they are physically interacting with the product, enhancing their confidence in making a purchase.
8. Evolution of the Soup Ladle’s Form and Function
As global cuisine continues to evolve, soup ladles will likely undergo design changes to better suit international cooking styles. Ladles for Asian soups, for instance, might feature wider, shallow bowls with a longer handle for easier stirring of large pots, while those made for European-style soups could be designed with deeper, narrower bowls for serving.
In addition, the multifunctional design of ladles will continue to evolve. Some ladles may incorporate additional features, such as straining capabilities, allowing users to pour liquid without taking the ladle out of the pot. Multi-purpose ladles could also serve as measuring spoons, strainers, or even tongs for lifting ingredients directly from the pot. The flexibility of design could make ladles more versatile, reducing the number of tools needed in the kitchen and streamlining the cooking process.
Conclusion: The Future is Bright for Ladle Manufacturing
As technology continues to evolve and consumer demands shift, the sheet metal soup ladle manufacturing process will become increasingly dynamic. Smart kitchen tools, personalized designs, and sustainable production practices will drive innovation and reshape how ladles are made, sold, and used. The emphasis on health, functionality, aesthetics, and environmental impact will ensure that soup ladles remain an essential and evolving part of our kitchens.
Manufacturers who can adapt to these changes and remain forward-thinking will be well-positioned to thrive in this competitive, consumer-driven market. By embracing smart technologies, offering customization options, and prioritizing sustainability, they will continue to meet the needs of tomorrow’s consumers while defining the future of kitchenware manufacturing.
Sheet Metal Salad Bowl Manufacturing Machine
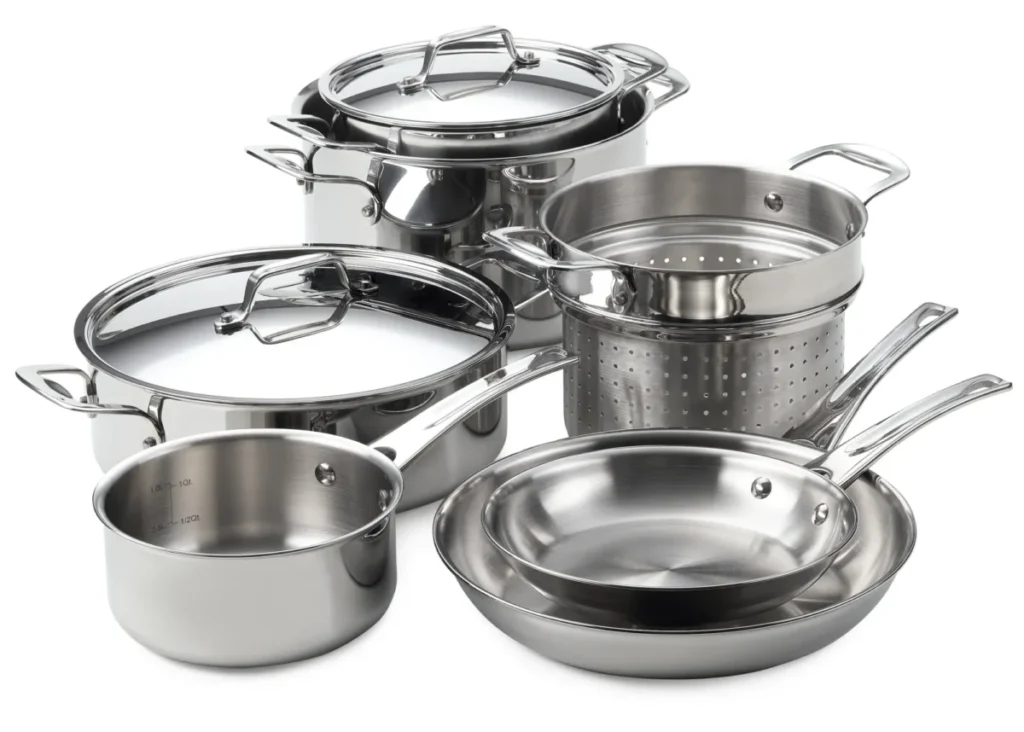
The sheet metal salad bowl manufacturing machine is designed to produce high-quality, precision-made metal bowls used for serving salads and other food items. These machines utilize a combination of advanced technology, automation, and specialized processes to create bowls that are both durable and aesthetically pleasing, with the right shape and surface finish. The following outlines the typical machine setup and key processes involved in manufacturing sheet metal salad bowls.
Key Stages of Production
1. Material Selection and Sheet Metal Preparation
The process begins with selecting the appropriate sheet metal material for manufacturing the salad bowls. Common materials used include:
- Stainless steel: Popular for its durability, rust resistance, and aesthetic appeal. It’s often chosen for higher-end bowls.
- Aluminum: Lightweight and resistant to corrosion, though often less durable than stainless steel.
- Copper or brass: These materials are less common but are used for their unique aesthetic qualities.
The material is supplied in large coils or flat sheets, which are then prepared for further processing. The sheets are often cleaned and coated if necessary, to prevent oxidation or to add an aesthetic layer, such as a matte or polished finish.
2. Cutting and Shaping
The next step involves cutting the sheet metal into the necessary shapes for the bowls:
- Cutting: The sheets are typically cut using laser cutting, water jet cutting, or punching machines to ensure precision. A cutting machine will precisely carve out a circular blank of the metal, which will form the base of the bowl.
3. Forming (Deep Drawing or Spinning)
Once the base metal shape is cut, the next process is to form the actual bowl shape. This can be done using two primary methods:
- Deep drawing: A pressing machine is used to pull the metal into a die that forms the bowl shape. The metal is stretched, so it becomes deeper and wider.
- Spinning: For some salad bowls, metal spinning is used, where the blank metal sheet is mounted on a rotating spindle. A tool is then pressed against the spinning metal to gradually form it into a bowl shape.
Both of these processes require specialized tools and precision control to ensure the correct depth, width, and curvature of the bowl, while maintaining material integrity without deforming or cracking.
4. Trimming and Edge Finishing
After the forming process, the bowl will have edges that need to be trimmed to the desired size and shape. This can be done using laser cutting or mechanical shearing. The edges are then smoothed to ensure they are safe to touch and have a high-quality finish.
- Edge deburring: A process of smoothing out any rough or sharp edges using a grinding machine, deburring tool, or polishing machine. This step is critical for safety and aesthetics, especially if the bowls are intended for high-end consumer markets.
5. Surface Finishing
The metal surface can be finished in several ways to enhance the aesthetic appeal and durability of the bowl:
- Polishing: This can be done using a polishing machine to give the bowl a high-gloss, shiny finish. Electropolishing is another method used, particularly for stainless steel, to provide a smooth, corrosion-resistant surface.
- Brushed finish: For a more matte or industrial look, a brushed finish can be applied using abrasive pads or machines. This gives the bowl a textured surface that resists fingerprints.
- Coating: For certain applications, a protective coating such as PVD (Physical Vapor Deposition) or powder coating might be applied to give the bowl color or added resistance to stains and scratches.
6. Forming the Final Shape
Depending on the design and size of the salad bowl, some designs may require additional forming steps to ensure the metal is perfectly shaped. This might involve pressing or calibrating the bowl into specific proportions, especially when making larger bowls or specialized designs that require fine adjustments.
7. Inspection and Quality Control
Each salad bowl produced goes through a rigorous quality control process to ensure it meets the required standards for dimensions, weight, and surface finish. This typically includes:
- Visual inspection: Checking for defects, imperfections, or color inconsistencies.
- Dimensional measurement: Ensuring that the bowl meets specified measurements for diameter, depth, and other design aspects.
- Strength testing: Conducting basic tests to ensure the metal’s integrity, especially when the bowls are intended to be used for food service in high-volume environments.
8. Packaging and Shipping
Once the salad bowls have passed inspection, they are carefully packaged for shipment. Depending on the intended market, the bowls might be sold in bulk or individually packaged. The packaging typically includes protective materials such as foam or bubble wrap to prevent damage during transportation. For consumer goods, the bowls might be branded with labels or placed in decorative boxes for retail sales.
Machinery and Equipment Involved
To create high-quality sheet metal salad bowls, manufacturers use a range of specialized machinery:
- Laser cutting machines: For precise cutting of the metal sheets into the correct shape.
- Pressing machines: For deep drawing and shaping the metal into a bowl.
- Spinning lathes: For creating smooth, round shapes in the metal.
- Polishing and buffing machines: For finishing the bowl’s surface to a high gloss or matte look.
- Deburring machines: To ensure smooth edges and remove any imperfections.
- Inspection equipment: Includes digital calipers, microscopes, and measurement tools for quality control.
Innovations in Sheet Metal Salad Bowl Manufacturing
As technology continues to advance, there are several trends in the manufacturing of sheet metal salad bowls that can be anticipated:
- Automated production lines: With automation increasingly becoming the norm in manufacturing, more processes such as cutting, shaping, and finishing can be automated for increased precision, speed, and reduced labor costs.
- 3D printing for design customization: In the future, 3D metal printing might be used to create customized designs for salad bowls, allowing consumers or businesses to request unique shapes or features.
- Sustainability practices: More companies are focusing on using recycled metals and adopting eco-friendly manufacturing processes, such as water-based coatings or energy-efficient machinery, to reduce the environmental impact of production.
Conclusion
The sheet metal salad bowl manufacturing machine combines advanced technology, automation, and precision to create high-quality, durable, and aesthetically pleasing bowls. As consumer demand for unique designs, sustainable practices, and smart kitchenware grows, the production processes and machinery used in manufacturing these salad bowls will continue to evolve, ensuring high-quality, customizable, and sustainable products for years to come.
The sheet metal salad bowl manufacturing machine begins with the selection of materials, typically stainless steel, aluminum, or occasionally copper, depending on the desired aesthetic and durability of the final product. These metals are chosen for their rust resistance, corrosion resistance, and strength, all essential for a bowl that will frequently be used for food service. The sheets of metal are first prepared, often cleaned or coated to ensure that they are free from contaminants or oxidation before they move on to the shaping process.
Once the metal sheets are ready, they undergo cutting. The sheets are cut into circular blanks, which will form the base of the salad bowl. Advanced cutting methods such as laser cutting, water jet cutting, or punching machines are used for precise, clean edges. These methods help ensure that each piece is uniform and ready for the next stage of production.
After cutting, the metal blanks are ready to be formed into a bowl. This can be done through either deep drawing or spinning. In deep drawing, a press applies force to stretch the metal over a mold, transforming the flat metal blank into a 3D bowl shape. For spinning, the metal is fixed to a rotating spindle and shaped by pressing a tool against it as it spins. Both techniques require careful attention to ensure the metal doesn’t tear or crack during the forming process, especially since the material is being stretched and shaped.
Once the bowl shape has been formed, the edges are trimmed to the desired dimensions using mechanical shearing or laser cutting. This step is crucial for ensuring that the bowl’s edges are smooth and safe to touch. Edge deburring is also performed to remove any sharp edges or burrs that may result from the cutting process. This ensures a high level of safety and quality in the final product, preventing any injury when handling the bowl.
The surface of the bowl is then finished to improve both its appearance and its resistance to wear and corrosion. Polishing, for example, can give the metal a high-gloss, shiny finish that is both aesthetically pleasing and functional, as it helps the bowl resist stains and marks. A brushed finish, which offers a more matte and industrial look, may also be applied, depending on the design specifications. Some bowls may even undergo additional processes such as anodizing, which further enhances the bowl’s durability and resistance to corrosion, particularly for aluminum products.
The final shape and finish of the salad bowl are checked through quality control procedures, where the bowl is inspected for dimensional accuracy, surface quality, and overall structural integrity. This ensures that each bowl produced meets the required standards for both functionality and aesthetics. Any imperfections found during this phase are addressed, either through manual rework or by rejecting the defective products.
Once approved, the bowls are packed for shipment. Depending on their intended market, the packing process may involve wrapping the bowls in protective materials like foam or bubble wrap to prevent damage during transport. Retail packaging may also be used, especially for consumer goods, where the bowls are placed in boxes or other packaging materials that highlight their design and make them attractive for store display.
As technology continues to evolve, there are several exciting innovations on the horizon for salad bowl manufacturing. Automation and robotics are increasingly being integrated into the production lines, improving efficiency, consistency, and reducing labor costs. The use of 3D printing, particularly metal 3D printing, may become more prevalent, allowing for even more intricate and customizable designs that are difficult or impossible to achieve through traditional methods. Additionally, the growing demand for sustainability in manufacturing is leading to the adoption of recycled metals and energy-efficient manufacturing processes. These innovations will likely continue to drive the evolution of sheet metal salad bowl manufacturing, making the process more efficient, customizable, and eco-friendly.
The continued advancement of technology and materials in the sheet metal salad bowl manufacturing process is expected to introduce even more groundbreaking innovations in both design and production. One such advancement could be the integration of smart manufacturing technologies. These include the use of artificial intelligence (AI) and machine learning to optimize production processes, predict potential defects before they occur, and streamline quality control. AI-driven systems could monitor every step of the production process in real-time, adjusting machine settings to ensure the highest possible quality output, reducing waste, and increasing throughput.
Furthermore, as the Internet of Things (IoT) continues to expand, we could see smart bowls being developed, particularly in the high-end market. These could feature integrated sensors to monitor the freshness or temperature of food stored inside the bowl. While this might not be common for all salad bowls, it could find a niche market in smart kitchens, where consumers demand more from their cookware. These sensor-enabled bowls could provide valuable feedback to consumers through connected apps, making the experience more interactive and data-driven.
Another exciting area of development in the future of salad bowl manufacturing is the customization and personalization of products. As consumer demand for unique, personalized items increases, manufacturers may offer more tailored design options. With the help of advanced digital design software, consumers could input specific preferences, such as the size, shape, or engraving details on the bowl. 3D printing technology could play a major role here, allowing manufacturers to produce one-off or limited-edition bowls based on customer input. This could lead to a more customized consumer experience, with businesses leveraging direct feedback to design products that better meet their customers’ needs.
Sustainability will remain a key focus in the future of manufacturing. More companies are likely to adopt a circular economy approach, where materials are reused and recycled to minimize waste. This could lead to innovations in the way metal sheets are sourced and repurposed, with a focus on sustainable sourcing and reducing the environmental impact of the production process. In addition, energy-efficient machines that use renewable energy sources, like solar or wind, could become the standard in manufacturing plants, further reducing the carbon footprint of the production process.
In terms of material science, we may see new metal alloys developed that are both lightweight and highly durable, with improved corrosion resistance. These advanced materials would allow for thinner metal sheets to be used in bowl manufacturing, reducing material costs while maintaining the strength and aesthetic quality of the final product. Nano-coatings might also become more common, providing bowls with ultra-resistant surfaces that are both easy to clean and maintain, while also offering enhanced protection against rust and stains.
As the demand for aesthetically pleasing and functional kitchenware continues to rise, manufacturers will increasingly focus on creating bowls with multi-functional features. For example, a salad bowl may evolve to include features such as built-in drainage systems or stackability for easy storage. Innovative designs might allow bowls to transform from a simple salad serving dish into a storage container or a mixing bowl for various cooking tasks. This could be achieved through the use of modular components or interlocking parts that make the bowls more versatile and adaptable to different kitchen environments.
Moreover, there will likely be a growing emphasis on the health and safety of materials used in manufacturing. Consumers are becoming more conscious of the substances they come into contact with, especially when it comes to food preparation. In response, manufacturers may increasingly adopt food-grade, non-toxic materials for salad bowls, ensuring that the bowls are safe to use with a variety of food types. This could include the use of BPA-free and PFOA-free metals, as well as coatings that ensure the bowls are safe for direct food contact and do not leach harmful chemicals.
Finally, globalization and global supply chains will play an important role in the sheet metal salad bowl industry. As demand for these products grows in emerging markets, manufacturers will have to adapt to a wider range of consumer preferences. This could lead to the development of specialized designs for different cultural markets, as well as changes in production strategies to cater to global logistics and delivery needs.
In conclusion, the future of sheet metal salad bowl manufacturing is poised for exciting developments. From smart technology integration to sustainable practices and customization options, the industry will continue to evolve to meet the changing needs and expectations of consumers. As manufacturers embrace advanced technologies, environmentally friendly processes, and personalized design options, the sheet metal salad bowl will not only remain a kitchen essential but could also become a symbol of innovation and sustainability in the food industry.
The future of sheet metal salad bowl manufacturing will continue to adapt as the global demand for eco-conscious products and technological innovation rises. As these changes unfold, several key trends are likely to shape the future of the industry.
Advancements in Automation and Robotics: In the coming years, sheet metal salad bowl manufacturers are likely to adopt more advanced robotic automation systems to improve efficiency and reduce labor costs. These robots would not only assist with repetitive tasks like cutting, shaping, and polishing, but could also help with more intricate processes such as finishing and inspection. With artificial intelligence and machine learning integration, robots could continually improve their processes, learning from previous productions to optimize every cycle. Automation would also help increase the consistency and quality of the products produced, minimizing the chances of defects and human error.
3D Metal Printing and Customization: As additive manufacturing (3D printing) technology improves, it is expected that more manufacturers will explore its application in metal production. 3D printing of sheet metal bowls would allow for custom designs that were once impossible to achieve through traditional methods. This opens up the possibility for consumers to create bespoke salad bowls with unique designs, textures, or functional features, such as integrated utensils or compartments for toppings. This could also reduce material waste since 3D printing allows manufacturers to only use the exact amount of metal required for each product.
Sustainable Manufacturing Practices: With growing consumer awareness of environmental impact, manufacturers are increasingly adopting sustainable production methods. This might include using recycled metal materials, such as recycled stainless steel or aluminum, reducing the amount of new raw material required for production. Additionally, companies might focus on making their manufacturing processes more energy-efficient, cutting down on emissions and waste. More use of biodegradable or recyclable packaging and more efficient transportation networks to reduce carbon footprints are likely to become industry standards as well.
Advanced Coating Technologies: To improve the durability and performance of the bowls, we may see advanced coating technologies such as nano-coatings or self-healing coatings applied to the finished products. These coatings not only help protect the metal from rust and stains but could also have antimicrobial properties, ensuring that the bowls remain hygienic even with regular use. This is especially important in the food industry, where cleanliness and safety are a top priority.
Consumer-Centric Designs and Innovation: With more customization options and consumer-driven design requests becoming common, manufacturers will likely offer consumers more choices in terms of size, shape, finish, and functionality. The industry could see a wider range of designs tailored to various culinary traditions or preferences. In addition to aesthetic choices, manufacturers may also focus on making bowls more ergonomically friendly or easier to store. Stackable designs, collapsible features, or even bowls with modular attachments could cater to consumers who prioritize functionality in addition to style.
Smart Technologies and IoT: One of the most exciting possibilities for sheet metal salad bowls is the integration of smart technology. For example, a salad bowl might incorporate a temperature-sensing system to alert users if their salad has reached an optimal serving temperature. The bowls could also have integrated scales to measure the weight of ingredients, or even embedded smart sensors to detect the freshness of salad greens or other ingredients. These bowls could sync with mobile apps or smart kitchen systems, providing valuable data to enhance the user’s cooking and dining experience. In a more advanced version, manufacturers might even produce bowls that can track nutritional information or pair with diet-planning apps, offering personalized recommendations based on a user’s dietary preferences.
Global Market Expansion: As the popularity of salad bowls continues to rise globally, manufacturers will need to consider regional preferences and market demands. For instance, some regions may prefer larger or smaller bowls, or specific finishes that align with local culinary traditions. Understanding and responding to cultural tastes will be crucial for companies looking to expand into new international markets. This will involve research and development into local material preferences, design aesthetics, and price points. As emerging markets become more economically prosperous, demand for high-quality kitchenware will likely increase, creating new growth opportunities.
Customization via Online Platforms: The rise of e-commerce platforms will likely drive the customization trend further. Consumers will increasingly want the ability to design their own salad bowls through online configurators where they can choose the material, finish, size, and engraving options. This will allow manufacturers to serve customers directly, cutting out the middleman and offering highly personalized products. E-commerce platforms may also allow for limited edition runs of specific designs, leveraging social media trends or influencer collaborations to drive sales.
Collaboration Between Manufacturers and Designers: In the future, we may also see more collaborations between manufacturers and industrial designers, resulting in more aesthetically sophisticated salad bowl designs. These collaborations could combine artisanal craftsmanship with cutting-edge technology, resulting in unique, limited-edition pieces that are highly desirable to consumers. Designers might also create bowls with multifunctional capabilities, where the bowls serve not only as serving dishes but as pieces of interactive kitchenware.
As consumer expectations evolve toward higher quality, more sustainability, and personalized products, the sheet metal salad bowl manufacturing process will likely continue to evolve to meet these needs. From incorporating high-tech smart features to creating eco-friendly, aesthetically pleasing designs, the future of this industry looks both exciting and innovative. Manufacturers that can successfully combine technology, sustainability, and customization will be well-positioned to thrive in a competitive global market, ultimately providing consumers with products that are not only functional but tailored to their needs and desires.
Sheet Metal Buffet Tray Manufacturing Machine
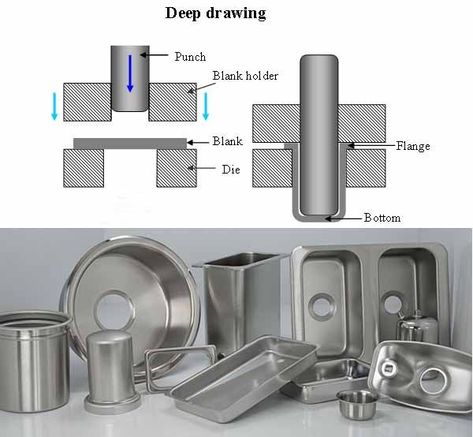
The sheet metal buffet tray manufacturing machine is a highly specialized production system designed to create durable and aesthetically pleasing buffet trays typically used in catering, restaurants, and other food service applications. These trays need to meet specific requirements: they must be strong, resistant to corrosion, easy to clean, and capable of withstanding constant use. The manufacturing process involves several stages, from material selection to finishing, ensuring that each tray produced meets industry standards for quality and functionality.
1. Material Selection and Preparation
The first step in the production process involves selecting the appropriate metal for the trays. Most buffet trays are made from stainless steel due to its excellent durability, resistance to corrosion, and ability to maintain a polished, shiny appearance. Aluminum can also be used for lighter, more cost-effective options, but it is generally less durable than stainless steel.
- Metal Sheets: Stainless steel or aluminum sheets are typically rolled into large coils. The material is carefully inspected to ensure there are no defects, such as rust or dents, which could compromise the final product’s appearance and strength.
- Coating: Some trays may undergo a coating process (like electroplating or anodizing) to enhance their surface properties, providing additional protection against corrosion and giving them a uniform, shiny finish.
2. Cutting
Once the metal sheets are prepared, they are cut into the desired shapes for the trays. This is typically done using high-precision cutting methods, such as laser cutting, water jet cutting, or mechanical shearing.
- Laser Cutting: A laser cutter precisely cuts the metal sheet into the required tray shapes. It is especially useful for creating intricate designs, clean edges, and tight tolerances. The laser cutting process ensures that the trays have consistent dimensions and smooth edges, which is essential for both aesthetic appeal and functionality.
- Water Jet Cutting: In cases where a softer cut is needed (to prevent any potential distortion or heat damage to the material), water jet cutting is often used. It uses a high-pressure stream of water to cut the metal, which helps maintain the integrity of the material.
3. Forming
The cut metal blanks are then formed into their 3D tray shapes. This process typically involves deep drawing or stretch forming.
- Deep Drawing: A press machine is used to push the flat metal blank into a mold, creating the tray’s depth. The metal is carefully stretched and formed into the desired shape without compromising its integrity. This method is common for trays with a deep or curved design.
- Stretch Forming: For trays with simpler designs, stretch forming may be used. In this process, the metal is mechanically stretched over a mold to achieve the required shape. This method is ideal for creating flat or shallow trays.
4. Edge Treatment
After the trays are formed, the edges are often rough or sharp from the cutting and forming processes. To ensure the trays are safe to handle and aesthetically appealing, the edges are smoothed through a deburring or edge rounding process. This involves either mechanical grinding or hand-finishing to remove any sharp edges that could cause injury during use.
- Deburring: This is the process of removing burrs (rough edges or raised areas of metal) created during the cutting or forming processes. It is typically done using grinding machines or abrasive wheels.
- Edge Rounding: In some cases, a machine tool will round the sharp edges of the tray to give it a more finished look and feel.
5. Surface Finishing
Surface finishing is critical in both aesthetics and functionality. Buffet trays are typically polished to a high sheen, which not only makes them more visually appealing but also makes them easier to clean and more resistant to staining and rust.
- Polishing: Mechanical polishing or electropolishing techniques can be used to create a smooth, shiny surface on the trays. Polishing machines use abrasives or polishing compounds to buff the surface, removing minor imperfections and achieving a glossy, reflective finish.
- Brushed Finish: Some trays may require a matte finish, achieved by using a brushed technique. This gives the tray a more industrial or contemporary look and hides fingerprints and water spots better than a shiny finish.
6. Additional Functional Features
At this stage, additional features that enhance the tray’s functionality are added. These can include:
- Handles: Depending on the design, trays may require handles to facilitate easy transport. Handles are typically made by welding or riveting additional metal parts onto the tray. Handles can also be coated with heat-resistant materials or have ergonomic grips to improve usability.
- Compartmentalization: In some cases, the trays may include built-in compartments or dividers. This can be achieved by adding inserts or creating specific mold designs that allow the tray to hold multiple types of food separately.
7. Quality Control
Once the trays are fully formed, finished, and equipped with any additional features, they undergo a strict quality control inspection. This step ensures that the trays meet the required standards for:
- Dimensional Accuracy: Trays are checked for correct size, shape, and consistency across batches.
- Surface Quality: The finish is examined for any imperfections, such as scratches, dents, or discoloration.
- Strength and Durability: The trays are tested for their structural integrity to ensure they can withstand regular use in a buffet or catering setting.
- Safety: The trays are also inspected for sharp edges, and any required modifications are made to ensure they are safe to handle.
8. Packaging and Shipping
Finally, once the trays have passed inspection, they are packed and prepared for shipment. Depending on the customer or retailer’s requirements, trays are usually individually wrapped in protective materials (such as foam or bubble wrap) to prevent scratches and dents during transport. Larger orders may be packed into boxes or pallets for bulk shipping. Packaging design often highlights the tray’s aesthetic appeal, with branding or instructions for care and maintenance included.
Technological and Industry Trends
Looking ahead, the sheet metal buffet tray manufacturing process may incorporate new technological advancements, including:
- Automation and Robotics: More automated machines will be integrated into the production line to increase efficiency, reduce labor costs, and improve consistency.
- Advanced Coating Technologies: More trays may be treated with advanced coating technologies that increase their resistance to heat, stains, and scratches. For example, ceramic coatings or nano-coatings could be used to improve durability and reduce cleaning time.
- Customization and Personalization: With advances in laser engraving and digital printing technologies, manufacturers may offer greater opportunities for custom designs, where logos, patterns, or text can be added to the trays, catering to unique business needs or personal preferences.
In conclusion, the sheet metal buffet tray manufacturing machine is integral to producing high-quality, durable trays that meet the needs of food service industries. Advances in materials, production techniques, and technology will continue to improve the manufacturing process, making it more efficient, customizable, and sustainable in the future.
The future of sheet metal buffet tray manufacturing will likely involve significant advancements driven by technology, sustainability, and consumer demand for customized products. As automation continues to evolve, manufacturers are increasingly incorporating more advanced robotics and artificial intelligence into the production process. Automated machines will not only increase the efficiency of manufacturing but also enhance precision and reduce human error, ensuring consistent, high-quality trays. These innovations will streamline operations, cut down on costs, and increase the overall speed of production.
In addition to automation, the use of 3D printing in the production of sheet metal components could become a game changer. While 3D printing is more common in plastic and composite materials, the technology is advancing to include metals, and this could allow manufacturers to create custom molds or even produce trays directly from metal powder. This could provide greater flexibility in design, reduce waste, and make it easier to produce intricate, custom-shaped trays that may have been difficult or costly to produce with traditional methods.
As sustainability remains a critical focus, manufacturers will likely continue to refine their processes to reduce waste and carbon emissions. The circular economy approach could lead to the reuse of scrap metal or excess material from the production line, helping to minimize environmental impact. More and more, manufacturers are looking to recycle and repurpose old trays or other metal products to create new ones, which is not only eco-friendly but also cost-effective.
Another significant trend is the increasing demand for customization. Consumers and businesses alike are becoming more interested in personalized products. Manufacturers are responding to this by offering greater flexibility in design, allowing for a wide range of options from size, shape, and finish to personalized engravings or logos. Customization could also extend to the material choices, as consumers may prefer specific alloys, finishes, or coatings based on their preferences for durability or aesthetic appeal. With the rise of online configurators, customers could easily design their own trays and order them directly from manufacturers, opening up a new direct-to-consumer channel for sales.
The focus on health and safety will also continue to influence the industry. Buffet trays need to meet strict hygiene standards, and with rising concerns about food safety, manufacturers may develop new technologies and finishes that ensure trays are easier to clean and more resistant to bacteria and mold. Advances in antimicrobial coatings or even the incorporation of UV sanitizing features could become a staple in buffet tray production, making them more hygienic and safe for food service environments.
In terms of material innovation, there could be a shift toward more sustainable or advanced materials that combine the strength and appearance of metals with the benefits of other materials. For example, using alloy blends that are more lightweight or resistant to corrosion could extend the lifespan of buffet trays while maintaining their visual appeal. Additionally, the development of smart materials that adapt to different conditions (e.g., expanding or contracting based on temperature) could lead to trays that are more versatile in holding food at optimal temperatures for longer periods.
Manufacturers are also likely to improve the ergonomics of their products. While buffet trays are already designed to be functional and easy to handle, future designs may incorporate handles that are easier to grip or stacked designs for easy storage. Trays with modular components that can be adjusted or reconfigured to suit different buffet setups might become more common, especially in large catering environments where flexibility is key.
In parallel, the global market for sheet metal buffet trays will likely expand as dining trends evolve worldwide. As more international markets grow and develop, catering and buffet services will become more prevalent, increasing the demand for these products. Regional preferences will likely influence the style and material of trays, with manufacturers tailoring designs to suit local tastes or specific food service requirements.
Ultimately, the combination of advanced manufacturing techniques, sustainability, customization, and health-conscious innovations will shape the future of the sheet metal buffet tray industry. These trends will allow manufacturers to produce more efficient, eco-friendly, and consumer-focused products while staying competitive in a rapidly evolving market. As the demand for high-quality, durable, and aesthetically pleasing buffet trays continues to rise, the industry will continue to innovate, leading to exciting new developments in both design and production processes.
As the sheet metal buffet tray manufacturing industry evolves, there are several additional factors that will further influence its future, ranging from technological advancements to shifts in consumer behavior and environmental concerns.
One of the key areas likely to see growth is the integration of smart technologies into buffet trays. The concept of smart kitchenware is gaining traction, and buffet trays could become more than just serving pieces. Imagine trays that are equipped with temperature control features, allowing them to keep food at the ideal temperature throughout a buffet or catering event. Integrated sensors could monitor the temperature of the food and alert service staff when it’s time to replace or reheat certain items. This could improve the overall dining experience and ensure that food quality is maintained consistently, particularly in large events where food may sit for extended periods.
Along with smart technologies, energy-efficient manufacturing processes will continue to be a focus. Many of the traditional manufacturing processes, such as metal forming and heat treatment, can be energy-intensive. Manufacturers are likely to adopt sustainable energy sources, such as solar or wind power, to reduce their carbon footprint. Some might implement more energy-efficient machinery that minimizes the use of electricity during production. The push for reducing energy consumption aligns with both regulatory requirements in various countries and the growing demand for green manufacturing practices.
Lean manufacturing practices will also play a key role in improving production efficiency and minimizing waste. By streamlining the production process and utilizing methods like just-in-time inventory, manufacturers will be able to reduce excess stock and material waste, contributing to cost savings and environmental sustainability. Automation in inventory management will allow for more precise control over the use of raw materials, leading to better overall resource management.
Furthermore, as consumers become more socially conscious about the environmental impact of the products they purchase, there will be a growing preference for products that are made with recycled or upcycled materials. Manufacturers may source post-consumer recycled metals or repurpose metal waste from other industries to produce their trays. This approach not only reduces the need for virgin materials but also supports a more circular economy by reintroducing scrap metal back into the production cycle.
The aesthetic trends in buffet tray design will also evolve. While functionality is crucial, design innovation will be a key differentiator in the market. Manufacturers may explore minimalistic, modern designs that appeal to a younger demographic seeking stylish and sleek kitchenware. As consumer preferences shift toward more sustainable and functional designs, we may see trays with modular capabilities, allowing them to be resized or adapted based on the buffet’s needs. Some trays may even incorporate multi-functional features such as serving stations that double as food warming units or have built-in coolers for chilled items, making them more versatile for a variety of events.
The demand for versatility will also continue to grow. Buffet trays are no longer just used in traditional catering events but have expanded into various industries like hotels, restaurants, and even food trucks. As the nature of food service changes, manufacturers will adapt to produce trays that cater to new serving needs. For example, the growing popularity of food delivery services might lead to the creation of trays that can be easily packaged for transport, keeping food fresh and presentable during delivery.
Another noteworthy trend is the rise of personalization in product offerings. Consumers increasingly seek items that reflect their individual tastes and preferences. In the buffet tray industry, this could translate into personalized engravings, custom finishes, or unique shape configurations tailored to specific occasions like weddings, corporate events, or holidays. The growing trend of personalization, fueled by e-commerce platforms, will allow consumers to easily customize their buffet trays through online tools, further enhancing their product appeal.
The influence of globalization cannot be overlooked, either. As international travel and trade continue to grow, manufacturers will look to expand into new markets, tailoring their products to meet specific regional tastes and demands. Buffet trays manufactured in one country may be distributed and used globally, with designs and materials adjusted to fit local cultures and foodservice practices. For instance, Asian markets may prefer buffet trays that cater to their unique culinary styles, such as small, compartmentalized trays for sushi or dim sum, while Western markets may favor larger, more open designs.
Finally, digital tools for design and production will continue to improve the product development process. Advanced CAD (Computer-Aided Design) systems will enable designers to create more intricate and functional tray designs that are tested and optimized virtually before production begins. Virtual prototyping can minimize the risks associated with traditional trial-and-error methods, reducing the time and costs involved in bringing a new product to market. Similarly, 3D printing technology will allow for the rapid prototyping of tray components, enabling manufacturers to test new features and materials on a smaller scale before committing to mass production.
As manufacturers look to differentiate themselves in a competitive market, brand partnerships and collaborations with renowned designers may become more common. By partnering with famous chefs, celebrities, or popular lifestyle influencers, manufacturers can create exclusive lines of buffet trays that appeal to a broader audience. These special editions may be positioned as premium offerings, targeting niche markets that desire higher-end, designer kitchenware.
In summary, the future of sheet metal buffet tray manufacturing will be shaped by a combination of technological advancements, sustainability, consumer demand for personalization, and a greater focus on functional design. As the industry adapts to changing market conditions, manufacturers will continue to innovate, improving production processes, reducing environmental impact, and offering a wider range of customizable and high-quality buffet trays that meet the evolving needs of the global food service market.
As the sheet metal buffet tray manufacturing industry continues to progress, several more aspects will come to the forefront, shaping how these products are designed, produced, and consumed in the future.
Customization and Consumer Experience will be an increasingly important factor. With the rise of e-commerce and the proliferation of online marketplaces, consumers will expect an even greater degree of personalization and flexibility in their products. Manufacturers are likely to embrace mass customization techniques, allowing customers to select from a range of sizes, colors, finishes, or additional features that meet their specific needs. The ability to personalize trays with engravings, logos, or custom designs will become a major selling point for catering businesses, hotels, or event planners looking to create unique, branded dining experiences. Customers could even design their own trays using digital tools on websites or apps, offering a more interactive and engaging shopping experience.
The role of smart manufacturing systems will also grow significantly in the future. The integration of IoT (Internet of Things) technology into the manufacturing process will allow real-time data collection, improving efficiency and enabling predictive maintenance. For instance, machines on the production line could automatically detect when maintenance is required or when a component is nearing the end of its lifespan, preventing costly downtime and ensuring that production runs smoothly. Furthermore, machine learning algorithms will optimize manufacturing workflows by identifying areas where bottlenecks occur and suggesting improvements, leading to more streamlined operations.
Manufacturers may also look to advanced automation to reduce costs, improve speed, and maintain consistency in production quality. In particular, robots and automated guided vehicles (AGVs) can be used to move materials between different stages of production, reducing labor costs and improving safety by minimizing the need for human intervention in potentially hazardous tasks. In some facilities, automated laser welders or robotic arms could take over complex forming or assembly tasks, ensuring that each tray is produced to exact specifications.
Another significant trend is the growing focus on eco-friendly materials and production techniques. The demand for sustainable products is not just a passing trend but a long-term shift in consumer preferences. In response, manufacturers will explore more sustainable materials, including biodegradable coatings, eco-friendly paints, or recycled metal alloys. The use of green energy in the manufacturing process—such as solar, wind, or hydroelectric power—will become more common, reducing the carbon footprint of production. Additionally, there will be increased emphasis on reducing waste in the manufacturing process by employing methods such as zero-waste production, where scrap materials are recycled back into the production process, minimizing material losses.
Supply chain optimization will continue to be a major consideration for sheet metal buffet tray manufacturers. With global supply chains becoming increasingly complex, manufacturers will seek to streamline their operations and reduce their dependency on single suppliers or geographic regions. By diversifying sources for raw materials and components, manufacturers can mitigate risks associated with supply disruptions. Additionally, the use of blockchain technology could enhance transparency in the supply chain, enabling customers and manufacturers to track the origin of materials and ensure ethical sourcing practices.
The shift towards online retail and direct-to-consumer (DTC) sales will change the way buffet trays are marketed and sold. Traditional distribution methods, such as wholesale or retail partnerships, will be complemented by more direct online platforms where manufacturers engage directly with consumers. This trend will lead to greater price transparency, allowing customers to compare prices and find the best value for their needs. With the increase in consumer reviews and user-generated content, customers will play a larger role in influencing the reputation and marketing of these products, especially in online communities or on social media.
Looking ahead, collaboration between manufacturers and end-users will become a key factor in product development. As food service providers and catering businesses become more involved in the design process, there will be an emphasis on developing trays that are highly functional in real-world settings. Feedback from these users will lead to improvements in ergonomics, such as lighter trays that are easier to carry, or trays with additional features like self-warming capabilities, built-in cooling compartments, or modular sections for more versatile food serving.
The potential for global expansion in emerging markets presents a massive growth opportunity for sheet metal buffet tray manufacturers. As economies in countries like India, China, and parts of Africa continue to develop and grow their middle-class populations, the demand for higher-end catering products will rise. Manufacturers who can tap into these markets early, tailoring their products to local preferences and offering competitive pricing, will be well-positioned for long-term success. Export strategies that leverage the growing popularity of international food service practices will become more crucial, and companies will look to form local partnerships to facilitate distribution.
Furthermore, the increasing popularity of sustainable packaging for buffet trays will lead to changes in how these products are presented to customers. Biodegradable, recyclable, or compostable packaging will become the norm, as consumers and businesses become more conscious of their environmental impact. Manufacturers will also explore minimalist packaging solutions that reduce excess waste, ensuring that products are well-protected during transit but without unnecessary plastic or paper.
The demand for integrated food service solutions is also on the rise. Manufacturers may begin offering complete catering systems that combine buffet trays with food warming stations, cutlery racks, and even buffet counters. These systems will help caterers and event organizers streamline their operations by providing a one-stop solution that ensures the efficiency and aesthetics of their service setup. Companies that can offer these integrated solutions will be in high demand, as they reduce the complexity of catering setups and allow clients to focus on the food and guest experience.
The role of technology in design will also become more prominent. Advanced 3D modeling and virtual prototyping software will allow manufacturers to create detailed digital representations of buffet trays before they are physically produced. This will speed up the development cycle, allow for more complex designs, and enable customers to see and even interact with digital models of the trays. With augmented reality (AR) and virtual reality (VR) technologies, customers may be able to visualize how different designs look in a real-world setting, helping them make more informed decisions before purchasing.
Lastly, the customer experience and branding will play a pivotal role in the success of sheet metal buffet tray manufacturers. As consumers become more discerning and selective about the products they purchase, manufacturers will need to focus on building strong brand identities that resonate with consumers. This can be achieved through storytelling, high-quality imagery, and demonstrating a commitment to sustainability, innovation, and customer satisfaction. A strong, recognizable brand can create loyalty and drive repeat purchases, especially in an increasingly competitive market.
In conclusion, the sheet metal buffet tray manufacturing industry is set to undergo a transformation driven by technological advances, sustainability efforts, and changing consumer demands. By embracing these trends—ranging from automation and material innovation to customization and enhanced customer engagement—manufacturers will not only stay competitive but also lead the way in creating functional, eco-friendly, and aesthetically appealing products that meet the evolving needs of the global food service industry. As the market expands and diversifies, the future looks bright for those who can adapt and innovate in response to these emerging trends.
Sheet Metal Serving Tray Manufacturing Machine
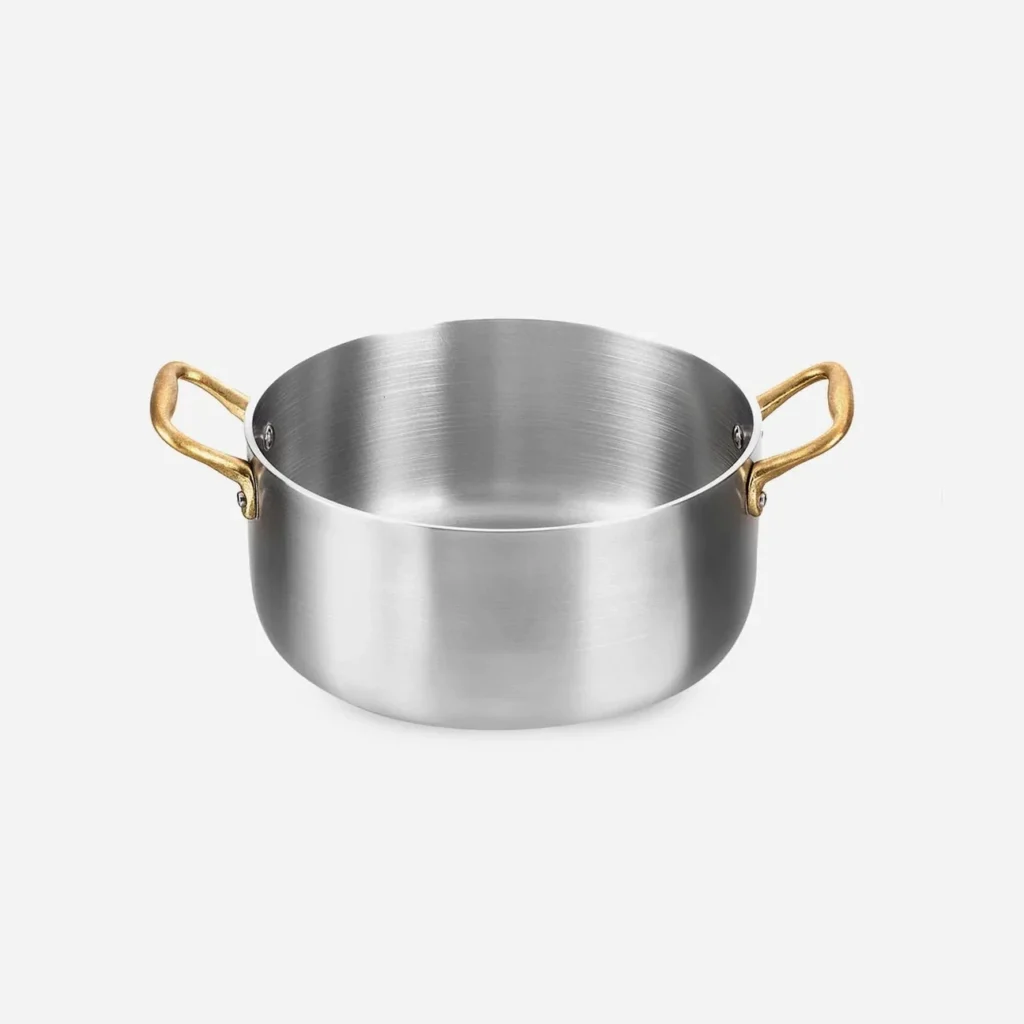
A Sheet Metal Serving Tray Manufacturing Machine is designed to produce high-quality serving trays made from various metals, typically stainless steel, aluminum, or other alloys. These machines integrate several stages of manufacturing to efficiently create trays that are functional, durable, and aesthetically pleasing. Below is a breakdown of how such a machine typically operates, and the key processes involved in its design and functionality.
Key Processes Involved in Sheet Metal Serving Tray Manufacturing:
1. Material Loading and Preparation
- Metal Coil Loading: The process begins with loading large metal coils into the machine. These coils are typically made from stainless steel, aluminum, or other sheet metals, which are unrolled and fed into the production line.
- Cleaning: The metal sheets are cleaned to remove any oil, grease, or debris. This ensures that the trays have a clean surface, which is critical for both the aesthetic quality of the final product and for any coating or finishing that may be applied later.
2. Cutting
- Shearing: After the metal sheets are prepared, they are cut into the required shapes and sizes. Shearing machines are used to cut the metal into basic tray outlines. This process is highly precise and can be done in one pass, depending on the complexity of the design.
- Laser Cutting: For more intricate designs or precise cuts, laser cutting technology may be employed. Laser cutting is especially useful when making decorative patterns or ensuring that the tray edges are perfectly straight.
3. Stamping/Forming
- Hydraulic Pressing: Once the metal sheet is cut, it is fed into a stamping press. A large hydraulic press is used to stamp the shape of the tray. The process involves placing a metal die inside the press, which molds the metal sheet into the desired shape. This is where the curvature of the tray is formed.
- Deep Drawing: For trays that require a deeper shape or sides, deep drawing machines are used. This process pulls the metal sheet into the desired depth using a punch and die, making it ideal for creating dishes with taller edges, such as round or square serving trays.
4. Edge Trimming and Finishing
- Edge Trimming: The edges of the tray are often trimmed to remove any excess metal or sharp edges, giving the tray a smooth and uniform appearance. This can be done with automated trimming tools or robotic systems.
- Bending: If the tray requires bent or angled edges, a bending machine is used. The metal sheet is bent around a die to form the desired angles for handles or sides.
- Smoothing and Polishing: In some cases, additional machines are used to smooth out any rough spots left after the stamping or cutting process. Polishing machines ensure the trays have a shiny, smooth finish, especially important for trays designed for high-end or decorative uses.
5. Hole Punching and Custom Features
- Punching: Holes or slots may be punched into the tray for drainage, handles, or decorative elements. This is done using punching presses, which quickly create holes of different sizes in specific areas.
- Handles and Cutouts: If the tray requires handles or cutouts, specialized equipment can create these features. This could involve additional cutting or punching steps, depending on the design specifications.
6. Coating and Finishing
- Surface Treatment: After the tray is formed, it may undergo surface treatments such as galvanizing, anodizing, or powder coating to enhance its appearance and durability. These treatments prevent rusting, corrosion, and wear over time.
- Heat Treatment: For trays made from materials like stainless steel, heat treatment may be used to strengthen the metal or alter its properties, ensuring it can withstand the rigors of daily use in both domestic and commercial settings.
- Decorative Finishes: Some manufacturers may add decorative finishes, including embossing, engraving, or printing designs directly onto the tray. This adds a level of customization, particularly for high-end or personalized trays.
7. Assembly (if needed)
- Handle Attachment: For trays with handles, the handles are attached using mechanical fasteners, welding, or rivets. This is typically done in an automated assembly line or with robotic arms to increase precision and speed.
- Additional Features: Depending on the tray design, additional components, such as dividers or legs, may be added in this stage.
8. Quality Control and Inspection
- Inspection: Before the trays are packaged, they undergo rigorous quality control checks. This ensures that they meet the required specifications for size, shape, finish, and structural integrity.
- Testing: Depending on the type of tray being produced, testing for strength, resistance to corrosion, and overall durability may be conducted. This could involve mechanical tests or exposing the trays to certain environmental conditions to simulate real-world usage.
9. Packaging and Distribution
- After passing the quality checks, the trays are carefully packaged to protect them from damage during shipping. Packaging can vary depending on the tray’s use case—commercial catering trays might be packed in bulk, while individual serving trays for retail may be packaged in boxes with protective inserts.
- The trays are then ready to be distributed to wholesalers, retailers, or directly to consumers.
Technological Innovations in Sheet Metal Tray Manufacturing:
- Automation and Robotics: Many aspects of the manufacturing process, such as cutting, forming, and assembly, have been automated, using robotic arms, conveyor belts, and automated presses to speed up production and ensure consistency. Automation not only reduces labor costs but also increases the precision and repeatability of the process.
- 3D Printing in Metal: While not yet mainstream in mass production, the use of 3D printing technology for metal manufacturing is a growing trend. This could allow for the production of highly complex and customized trays with reduced material waste, offering opportunities for bespoke designs that traditional manufacturing methods may not be able to accommodate.
- Laser Cutting and Engraving: Advanced laser cutting technology enables precise cuts and can create intricate patterns or logos directly onto the surface of the tray, adding a layer of customization that appeals to both consumers and businesses.
- Sustainability: The trend toward eco-friendly production methods is gaining momentum. Manufacturers are exploring the use of recycled metals and adopting green energy solutions in production to reduce the environmental impact of the manufacturing process. In addition, water-based coatings and other low-VOC (volatile organic compounds) materials are being used in the finishing processes to reduce harmful emissions.
Future Trends in Sheet Metal Tray Manufacturing:
- Smart Trays: The future of serving trays may involve the integration of smart technology. This could include temperature-regulating features or embedded sensors that alert users when the contents of the tray need attention (for example, if the food has cooled down).
- Advanced Customization: As consumer demand for personalized products grows, manufacturers might offer an increased range of customization options, including custom engravings, shapes, and finishes.
- Sustainable Manufacturing: Increased focus on circular economy principles will drive the use of recycled metals and sustainable production methods. There may be a move toward producing serving trays that are biodegradable or made with completely recyclable materials.
- Hybrid Production: Combining traditional and additive manufacturing (like 3D printing) could allow for faster prototyping, more intricate designs, and reduced material waste in the creation of serving trays.
In conclusion, sheet metal serving tray manufacturing is a complex and multi-step process involving high levels of precision, technology, and efficiency. With advancements in automation, material science, and customization options, manufacturers will be able to create increasingly high-quality, sustainable, and customizable products that meet both commercial and consumer demands.
The sheet metal serving tray manufacturing process is continuously evolving with the integration of new technologies and production methods aimed at increasing efficiency, reducing costs, and enhancing product quality. As consumer preferences shift toward more customizable and eco-friendly products, manufacturers are adjusting their processes to meet these demands. The entire manufacturing journey begins with selecting high-quality metal sheets, usually stainless steel, aluminum, or galvanized steel, which are then processed through various stages, including cutting, shaping, and finishing.
The first step in the production line is preparing the raw material, where metal coils or sheets are unrolled, cleaned, and prepped for further processing. A key part of the preparation includes ensuring that the metal surface is free from oil, rust, or debris, ensuring a smooth and clean surface for the subsequent stages. After preparation, the metal is either sheared or laser-cut to the desired shape, forming the outline of the serving tray. Laser cutting is especially advantageous when intricate patterns or designs are required, as it provides a higher level of precision than traditional methods. Once the basic shape is cut, the metal undergoes a forming process. The forming process involves stamping or deep drawing, where the metal is pressed into molds that shape it into the tray’s final form. Depending on the design, additional forming steps may be necessary to create the edges or add features like handles or decorative cutouts.
To ensure the trays are both durable and visually appealing, the edges are often smoothed and polished to remove any sharpness from the manufacturing process. This step also enhances the appearance, giving the trays a clean and uniform finish. If necessary, additional features like handles are attached, often using mechanical fasteners or welding to ensure that they are securely affixed to the tray. Depending on the design, trays may also receive coating treatments, such as powder coating or anodizing, to improve durability and prevent corrosion, especially when they are designed for food service environments where durability and hygiene are paramount.
The finishing touches on the trays may include decorating the surface with logos, engravings, or embossing, which is often done for branding purposes or to provide a premium aesthetic. These steps are particularly common for trays that are marketed for high-end catering or giftware. The use of laser engraving or other high-tech methods allows manufacturers to add these decorative elements without compromising the integrity or strength of the metal.
Once the trays are fully formed and finished, they undergo rigorous quality control checks to ensure they meet the required specifications. These checks include visual inspections to catch any cosmetic flaws, dimensional checks to ensure that all measurements are accurate, and stress tests to ensure that the trays can withstand the intended load. Only after passing these quality control steps are the trays packaged and shipped to retailers or directly to customers.
With the rise of automation in manufacturing, many of these processes are now handled by robotic arms and automated systems. This helps increase production speeds, reduce human error, and maintain consistent product quality. Automation also improves safety by minimizing the need for workers to be involved in potentially hazardous tasks such as welding or handling heavy materials.
Sustainability is also becoming a key focus in the sheet metal serving tray manufacturing process. Manufacturers are increasingly adopting eco-friendly practices by using recycled materials, minimizing waste through precision cutting, and employing sustainable energy sources for production. The trend towards eco-friendly manufacturing is driven by both consumer demand for greener products and regulatory pressures to reduce environmental impact.
The future of sheet metal serving tray manufacturing is likely to see even more advancements in materials, design capabilities, and automation. Manufacturers are exploring the potential of 3D printing with metals to create more intricate designs and customized trays. This technology could offer greater flexibility in production and the ability to create highly specialized products with fewer constraints compared to traditional methods.
As the industry continues to evolve, manufacturers will need to remain agile, adopting new technologies and practices to stay competitive in the market. The ability to offer customizable and sustainable products, paired with increased production efficiency, will be key to success in the future of sheet metal serving tray manufacturing.
As the sheet metal serving tray manufacturing industry progresses, several additional factors are influencing its growth, sustainability, and innovation. One of the most notable changes is the integration of digital technologies into manufacturing processes. This includes Industry 4.0 innovations such as smart manufacturing systems, machine learning, and artificial intelligence. These technologies enhance efficiency and ensure higher precision throughout the production line. For example, predictive analytics can forecast when a machine or component might fail, allowing for scheduled maintenance before it causes unexpected downtimes, thus minimizing disruptions to production schedules.
With the increasing demand for customization in consumer products, the ability to offer personalized designs will be a crucial aspect of the manufacturing process. Manufacturers may implement digital design tools that allow customers to modify aspects of the tray’s size, shape, or decorative features, which will be realized through advanced 3D modeling software. This will enable direct-to-consumer sales models where customers can design their trays and receive unique products tailored to their specifications, all while streamlining the production process.
Additionally, robotic automation is becoming even more prominent. In advanced production lines, robots can handle repetitive and labor-intensive tasks like material handling, welding, polishing, and even packaging. These robots can work round the clock, improving production capacity and reducing the overall cost of labor. Collaborative robots (cobots) can work alongside human operators, performing tasks that complement human efforts and further enhancing safety and productivity. For instance, cobots could be used to feed metal sheets into laser cutters or help with the installation of handles on the trays.
With the rise of eco-consciousness among consumers, there is an increasing emphasis on the sustainability of materials used in manufacturing. Many companies are looking at recycled metals as a viable material source, which reduces the environmental impact of the production process. These metals are often just as durable and effective as new materials but come with a lower environmental footprint. Companies are also investigating the use of biodegradable coatings or eco-friendly finishes for trays to enhance their sustainability.
At the same time, green manufacturing practices are becoming essential to meet environmental regulations and consumer demand for sustainable products. This could include reducing waste during production, employing energy-efficient machinery, and even utilizing renewable energy sources like solar or wind power for operations. Some manufacturers are also seeking certifications such as ISO 14001, which indicates that a company adheres to international environmental management standards, further strengthening their eco-friendly image.
Another significant aspect driving innovation in sheet metal serving tray manufacturing is global supply chain optimization. With globalization, many manufacturers are exploring ways to improve their supply chains to ensure that materials are sourced efficiently and cost-effectively. By implementing more advanced tracking and logistics technologies such as blockchain or RFID (Radio Frequency Identification), manufacturers can gain better control over inventory management and ensure the ethical sourcing of materials.
As demand for high-end commercial-grade trays grows, manufacturers will also focus on increasing their product quality. High-quality finishes and design features, such as anti-slip surfaces, stackability, and ergonomically designed handles, will continue to play an important role in the product offerings. For commercial kitchens, event planners, or hotels, trays must not only be durable and functional but also aesthetically pleasing to maintain a certain level of brand image or presentation.
Customization in serving trays is expected to reach new heights as advancements in technology make it easier for businesses to offer bespoke designs to customers. Manufacturers will begin offering more varied options for pattern engraving, logo printing, and color coatings that allow businesses to imprint their branding onto trays. This customization could also extend to the functional aspects of the trays, such as having compartments for organizing items or features that allow for temperature regulation, keeping food either warm or cool during service.
Moreover, there will likely be greater emphasis on the ergonomics of serving trays. As the service industry continues to focus on enhancing the comfort of its staff, manufacturers will design trays that are lighter, easier to carry, and more comfortable to handle. This could mean trays with handles that are ergonomically shaped or materials that make the trays easier to carry, such as using alloys that combine strength with lightness.
Looking ahead, the global market expansion in emerging economies presents a growth opportunity for sheet metal serving tray manufacturers. Countries with rapidly expanding middle classes, such as in Asia and Africa, will see increased demand for dining products, including serving trays. Manufacturers may need to adapt to these new markets by considering local preferences, cultural dining habits, and price sensitivity when designing and marketing their products. This could involve offering more affordable, yet durable, products for these regions while continuing to focus on higher-end trays for more developed markets.
Smart integration into the design of serving trays might also play a significant role in the future. For example, temperature-sensitive trays or those with integrated cooling or heating elements could revolutionize the way food is served, ensuring that it remains at an optimal temperature for longer periods. These trays might also be equipped with sensors that detect temperature or moisture levels, providing feedback on when food might need to be reheated or when the tray should be cleaned. This integration of smart features could be a major selling point in high-end restaurants or catering services where presentation and food quality are paramount.
Finally, digital supply chain management and automated production will streamline operations and improve the agility of the manufacturing process. By utilizing digital tools for inventory management, demand forecasting, and supply chain logistics, manufacturers can reduce lead times, manage resources more effectively, and optimize production schedules. This will ensure that serving trays can be produced quickly to meet consumer demands without overextending inventory.
In conclusion, the future of sheet metal serving tray manufacturing lies in technology integration, sustainability, and customization. Manufacturers who embrace automation, eco-friendly practices, and consumer-driven design will be well-positioned for success. With innovations in material science, smart manufacturing, and global market expansion, the sheet metal serving tray industry is set for a future that meets the evolving needs of both consumers and the food service industry at large.
Sheet Metal Pastry Roller Production Machine
A Sheet Metal Pastry Roller Production Machine is specifically designed to manufacture pastry rollers from sheet metal, typically stainless steel or aluminum. These rollers are commonly used in bakeries, restaurants, and home kitchens to roll out dough for pastries, cakes, and other baked goods. The production of a pastry roller involves several key processes to ensure that the rollers are durable, smooth, and of high quality. Below is an overview of the manufacturing process and the role of the production machine in creating a sheet metal pastry roller.
Material Preparation
The production begins with the loading of metal coils (often stainless steel or aluminum) onto the machine. The metal coil is unrolled and fed into the production system. These coils are typically cleaned and coated to ensure that they are free from any contaminants like oil, dust, or debris, which could interfere with the manufacturing process or the quality of the final product. Some machines may incorporate a cleaning station to remove any residues left on the metal before processing.
Cutting and Shaping
Once the material is prepared, it is then cut to the required size and shape. Shearing is commonly used to cut the metal into long strips, which are then further processed to form the base of the pastry roller. The size of the metal strip depends on the dimensions of the roller being produced. In some cases, laser cutting may be used to achieve more intricate designs, especially if the rollers feature decorative patterns or embossing.
Rolling and Forming
The next step involves rolling and forming the metal strip into the cylindrical shape of the pastry roller. This can be done through a series of machines that gradually bend the sheet metal into a round shape. In many production lines, forming machines with rotating dies or rollers are used to gradually bend the metal strip into the desired cylindrical form. The ends of the metal strip are then welded or joined to form a seamless connection. If the roller has handles or other components, these are usually added during the forming stage.
For rollers that require more intricate shapes (for example, rollers with textured or patterned surfaces), embossing or stamping machines may be used. This process imprints a design or texture onto the surface of the roller, ensuring that it has the necessary grip or aesthetic quality.
Handle Attachment (If Applicable)
Some pastry rollers come with handles for easier use. The handles can either be made of the same sheet metal or another material such as wood, plastic, or rubber. The handles are attached to the metal body of the roller using mechanical fasteners such as screws, rivets, or by welding. In high-precision systems, robotic arms or automated assembly lines may handle this task for increased accuracy and speed.
Surface Treatment and Finishing
Once the pastry roller is formed, it undergoes a series of finishing steps to improve both its durability and appearance. Polishing is one of the primary finishing processes, as it ensures the roller is smooth and shiny, which is important for both aesthetics and functionality. The polished surface also helps in reducing dough sticking to the roller during use.
Depending on the material used, the rollers may undergo additional treatments like electropolishing or anodizing to improve corrosion resistance, especially for rollers made from aluminum. Powder coating or painting may also be applied for decorative purposes or to add extra protection against wear.
Quality Control
Quality control is critical throughout the production process. Each pastry roller is inspected for defects such as surface imperfections, incorrect dimensions, or weak welds. Additionally, specific checks are made to ensure the handles are securely attached, and the surface is free from any irregularities. Some manufacturers also test the rollers for durability, ensuring that they can withstand the stress of rolling dough without deforming.
Packaging
After passing quality control checks, the finished pastry rollers are carefully packaged for shipping. Packaging often involves placing the rollers in protective materials to prevent scratches or damage during transit. For high-end products, the packaging may also include branded boxes or packaging to enhance the product’s appeal for retail sales.
Automation and Efficiency
Modern pastry roller production lines often include automated systems to increase efficiency, speed, and accuracy. Robotic arms may handle tasks such as loading and unloading materials, assembling parts, and even applying finishes. Automation significantly reduces labor costs while increasing the precision of the manufacturing process.
In addition, digitalization in manufacturing systems allows for real-time monitoring and adjustment of processes to maintain high quality and minimize defects. IoT (Internet of Things) technologies may be incorporated into machines to track machine performance, detect potential failures before they occur, and improve maintenance schedules.
Sustainability in Production
As in many modern manufacturing processes, sustainability is becoming an important consideration in the production of sheet metal pastry rollers. Manufacturers are increasingly focusing on energy efficiency, using renewable energy sources when possible, and recycling scrap metal to minimize waste. Environmentally friendly coatings and finishes are also becoming more common, allowing for low-VOC (volatile organic compounds) materials that are less harmful to the environment.
Conclusion
The production of sheet metal pastry rollers involves a combination of cutting-edge technology, precision manufacturing, and quality control. The use of automation, advanced forming processes, and finishing techniques ensures that each roller is durable, functional, and aesthetically pleasing. As consumer demand for high-quality kitchen tools continues to grow, the manufacturing process for pastry rollers is evolving, incorporating more sustainable practices, customizable options, and innovative designs. With these advances, manufacturers can continue to meet the needs of both professional bakers and home cooking enthusiasts while maintaining efficient and cost-effective production methods.
The production of sheet metal pastry rollers is a highly automated and streamlined process designed to create high-quality, durable products. Initially, the process begins with the preparation of raw materials, typically stainless steel or aluminum. These metal sheets or coils are unrolled, cleaned, and inspected to ensure they are free of contaminants that could affect the quality of the finished product. Once prepared, the metal sheets are cut into the desired length using cutting machines, such as shears or lasers. For intricate designs or more precise cuts, laser cutting is preferred due to its ability to deliver high accuracy and clean edges.
After cutting, the metal sheets are shaped into cylindrical forms, the hallmark of a pastry roller. This process is done through rolling or bending the metal in specialized forming machines. These machines gradually shape the metal until it reaches the desired diameter. Once the cylindrical form is achieved, the edges of the metal are either welded or mechanically joined to create a seamless piece. In the case of rollers with handles, these are often added at this stage, either by welding or by using mechanical fasteners like screws or rivets to securely attach them to the body of the roller. The choice of materials for handles can vary from metal to wood, rubber, or plastic, depending on the desired aesthetic or functionality.
With the roller formed and handles attached, the next step is surface treatment and finishing. The rollers are often polished to achieve a smooth, shiny surface that prevents dough from sticking during use and provides an attractive finish. The surface can also undergo additional treatments such as electropolishing, anodizing, or coating with powder to improve durability and corrosion resistance. This ensures the rollers maintain their appearance and function over time, especially when exposed to moisture or frequent handling in a bakery setting.
Once the rollers are finished, they undergo thorough quality control checks. Each roller is inspected for any defects, such as surface blemishes, cracks, or imperfections in the welding or forming process. The rollers are also tested for consistency in size and functionality, ensuring they meet the required specifications for performance and durability. After passing these inspections, the rollers are carefully packaged to prevent damage during transportation. Packaging may include protective materials like bubble wrap or foam, and for premium models, custom-branded boxes may be used for retail sale.
To increase production speed and reduce costs, many modern factories employ automated systems throughout the process. Robots and automated conveyors handle tasks such as moving metal sheets, loading materials, and assembling parts. Automation helps reduce human error, improve precision, and speed up production cycles, allowing manufacturers to meet high demand while maintaining quality. This also leads to reduced labor costs and more consistent product output. Additionally, digital monitoring systems may be employed to track production progress and identify any bottlenecks or potential issues, further optimizing the manufacturing flow.
In addition to production efficiency, sustainability is becoming an increasingly important factor in pastry roller manufacturing. Companies are exploring ways to reduce their environmental footprint by utilizing recycled materials, implementing energy-efficient machines, and adopting eco-friendly finishing techniques. The goal is to reduce waste during production, use fewer harmful chemicals in coatings, and minimize overall energy consumption. As the demand for eco-conscious products grows, manufacturers are likely to continue investing in greener practices, such as recycling metal scrap and using environmentally safe coatings that avoid harmful emissions.
Technological advancements also allow for the potential integration of smart features into pastry rollers. For example, rollers could be designed with embedded sensors that provide real-time feedback on dough thickness or detect temperature fluctuations to help bakers achieve the perfect results. Such innovations are still emerging but could enhance the functionality of pastry rollers and cater to professional bakers who require precise and consistent results.
As the global market for baking products continues to expand, particularly in regions with growing culinary industries, there is an increasing demand for high-quality, durable, and well-designed pastry rollers. Manufacturers are adapting to these needs by improving their production techniques and offering customizable products, allowing customers to select rollers tailored to their specific preferences, such as handle materials, roller size, and surface textures. This customizability also extends to branding opportunities for businesses looking to create signature products.
Looking ahead, the pastry roller manufacturing process is likely to become more sophisticated, with continuous advancements in automation, material science, and sustainable practices. As consumer expectations for quality and functionality continue to evolve, manufacturers will need to stay agile, adopting new technologies to improve the performance, design, and environmental impact of their products. Through these innovations, sheet metal pastry rollers will continue to play a vital role in both professional and home kitchens, helping bakers achieve perfect results while keeping up with the latest trends in kitchenware manufacturing.
As the manufacturing of sheet metal pastry rollers evolves, new trends and technologies are likely to shape the industry further. For instance, advanced materials are becoming a key focus, with manufacturers exploring alloys and composite materials that combine strength and lightness while also improving the roller’s resistance to corrosion and wear. Stainless steel remains a popular choice for its durability and resistance to rust, but there is growing interest in alternatives that can offer similar or superior performance at a lower cost or with additional environmental benefits.
The design flexibility of sheet metal pastry rollers is another area of potential growth. With advancements in digital fabrication techniques, such as 3D printing and laser engraving, manufacturers can explore more intricate and personalized designs for pastry rollers. These could include rollers with textured or embossed surfaces, ergonomic handles, or even customizable features such as adjustable roller diameters or interchangeable parts. 3D printing could be especially useful for creating prototype models of innovative designs before committing to full-scale production, allowing manufacturers to rapidly test and iterate on new concepts.
Ergonomics is another factor that is increasingly being integrated into the design of pastry rollers. The comfort and ease of use are critical for bakers, especially in commercial settings where rollers may be used for extended periods. Manufacturers are focusing on creating ergonomically designed handles that reduce strain on the wrists and arms, making the rollers more comfortable to use. Some of these designs incorporate soft-touch grips or anti-slip handles to ensure better control and prevent hand fatigue.
Another area of focus is smart technologies. While still in the early stages, the integration of sensors or Bluetooth-enabled features in kitchen tools could be the next frontier for pastry rollers. Imagine a pastry roller with a built-in sensor that communicates with a smartphone app to track and control dough thickness or temperature. These smart rollers could be used in professional kitchens to ensure precise results, allowing chefs to fine-tune their recipes and procedures with greater accuracy. Such innovations could enhance the functionality of a seemingly simple tool by making it more interactive and adaptive to the baker’s needs.
Additionally, the shift toward more sustainable manufacturing practices is continuing to gain momentum across many industries, including kitchenware production. Manufacturers are increasingly focusing on circular economy principles, such as designing products that can be easily recycled or reused at the end of their lifecycle. For instance, scrap metal from the manufacturing process can be melted down and reused to produce new rollers or other kitchen products, reducing waste and minimizing the environmental impact of production.
Moreover, consumers’ growing demand for eco-friendly products has led manufacturers to look for alternatives to traditional coatings and finishes that may contain harmful chemicals. For example, plant-based coatings and eco-friendly finishes are being explored to reduce the reliance on synthetic materials. Similarly, some companies are experimenting with biodegradable lubricants or water-based cleaning solutions for use in the manufacturing process, contributing to a greener production cycle.
On the global stage, manufacturers are keeping an eye on emerging markets where the demand for high-quality kitchen tools is increasing. As culinary trends shift globally, especially in regions like Asia, Africa, and South America, manufacturers will need to adapt their production methods and designs to cater to different market needs. Local tastes, preferences, and culinary practices will influence the materials, designs, and features offered in various regions. For example, markets with a higher emphasis on traditional cooking methods may prefer more classic, manual pastry rollers, while developed markets might be more inclined toward innovative, smart-enabled kitchen tools.
Additionally, automation will continue to play a pivotal role in reducing production time and costs. As robotics and artificial intelligence improve, they will allow for faster, more precise manufacturing. Collaborative robots (cobots) are particularly important in the food manufacturing industry, where they can assist workers with tasks like lifting heavy metal sheets, assembling parts, and handling delicate items without compromising quality or safety. These robots are designed to work alongside human operators, enhancing productivity without replacing the human workforce entirely.
Manufacturers are also exploring lean production methods to minimize waste and improve efficiency. Lean techniques, which involve continuous improvements and the elimination of inefficiencies, are being integrated into production lines to create more streamlined, cost-effective manufacturing processes. By minimizing the use of resources and reducing time spent on non-value-adding activities, lean manufacturing ensures that pastry rollers can be produced at a lower cost while maintaining high quality.
In terms of marketing and sales, the growing trend of direct-to-consumer models is expected to reshape the way pastry rollers are sold. Online platforms, particularly those that focus on kitchen tools and culinary products, provide a unique opportunity for manufacturers to showcase their products directly to end users. Customization options, such as engraving a name or logo onto a pastry roller, could become popular in this model, offering a personalized touch that appeals to both consumers and businesses like bakeries and restaurants.
As manufacturers look toward the future, they will continue to face the challenge of balancing quality, cost, and sustainability. The ongoing development of new materials, manufacturing techniques, and technologies will likely open up new possibilities for innovation in the pastry roller market. However, the importance of maintaining high-quality standards and ensuring that the products meet the specific needs of both professional and home bakers will remain at the core of the production process.
Ultimately, the evolution of sheet metal pastry roller production is guided by the pursuit of creating better, more efficient, and more sustainable products that meet the diverse needs of consumers. With advancements in materials, technology, and automation, the future of pastry roller manufacturing promises to bring new levels of precision, personalization, and sustainability to an essential kitchen tool.
Sheet Metal Wok Production Machine
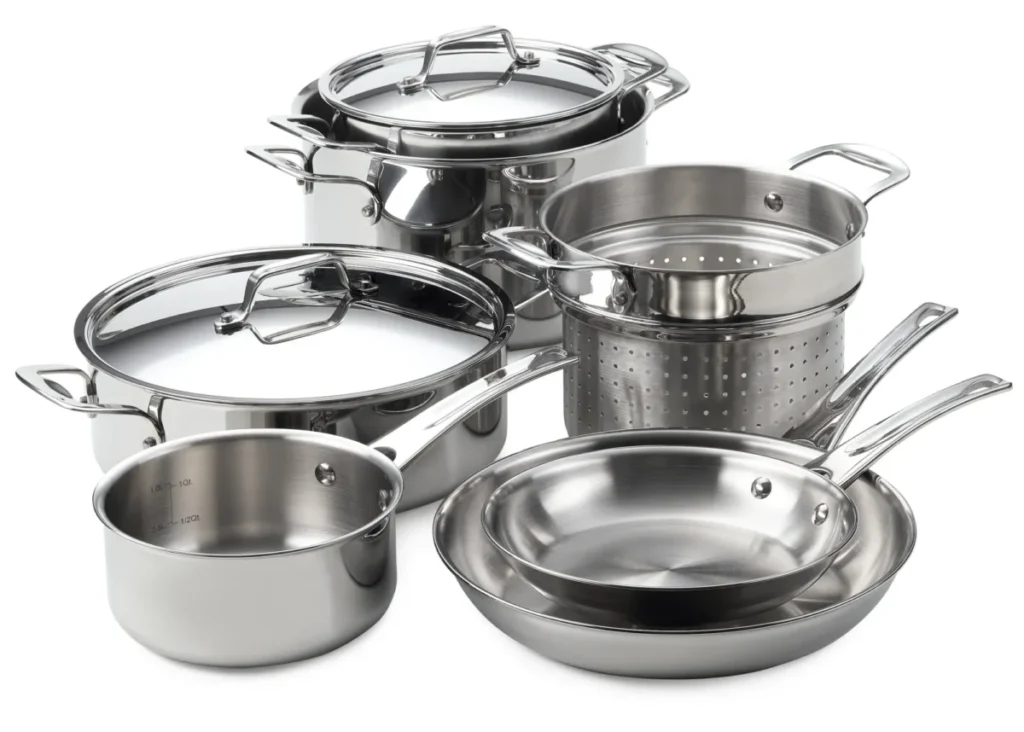
A Sheet Metal Wok Production Machine is designed to manufacture woks, a traditional cooking vessel used widely in Asian cuisine. The process of producing a wok from sheet metal involves various stages, including cutting, forming, welding, surface treatment, and finishing. The production of woks requires precision, as the shape, durability, and surface characteristics are critical for both cooking performance and aesthetic appeal. Below is an outline of how the production machine works and the key steps involved in manufacturing a sheet metal wok.
The process typically starts with the selection of materials. High-quality metals, such as carbon steel or stainless steel, are commonly used for woks because of their ability to distribute heat evenly and resist rust. These metals are usually supplied in coils or sheets, which are then prepared for the manufacturing process. The coils or sheets are first unrolled, cleaned, and inspected for any imperfections.
Next, the material is cut to the required size. This can be done using a shearing machine, which cuts the sheet into discs or circular blanks, depending on the design and size of the wok being produced. Laser cutting is often employed for more intricate designs, especially if the wok has additional features such as drainage holes or decorative patterns. The sheets must be cut precisely to ensure the wok’s shape and size are consistent throughout the production batch.
Once the material is cut to the correct shape, it is ready for forming. This stage is crucial in giving the wok its characteristic bowl-like shape. In a production machine, press forming or deep drawing is used to shape the metal into the curved bowl of the wok. The metal disc is placed into a forming die, and pressure is applied, typically by a hydraulic press, to stretch and form the metal into the desired shape. This process requires significant force to ensure the metal forms smoothly without any tearing or warping.
After the wok’s bowl is formed, reinforcing the edge is typically the next step. The edges of the wok are sometimes rolled or flanged to add strength and to make it easier to attach the handle. The rim rolling process can be done using a set of rollers or dies, which smooth out and reinforce the edge of the wok, making it more durable and preventing it from deforming under stress during cooking.
For woks that require handles, the next step involves attaching metal handles or wooden handles to the wok’s body. Depending on the design, handles can be attached using welding, riveting, or screwing. If the handles are made of metal, welding is typically used to ensure a strong bond. Wooden handles are often riveted or bolted to the wok for added strength. The handles are designed to be ergonomic and heat-resistant, ensuring they are easy to grip during cooking. In some cases, heat-resistant silicone or rubber is applied to the handles for better user comfort.
Once the handles are attached, the wok proceeds to the surface treatment phase. This is where the wok’s cooking surface is prepared for use. Woks, especially those made from carbon steel, often require seasoning. Seasoning is a process in which the wok is heated to a high temperature and coated with oil to create a non-stick surface. This also helps to prevent rust and enhances the wok’s performance. Some woks may also undergo pre-coating with black enamel or non-stick coatings to provide additional protection and to make cleaning easier.
After the seasoning or coating is applied, the wok undergoes a finishing process. This may include polishing or grinding to remove any excess material, burrs, or rough spots left from the forming and welding processes. If needed, the wok’s surface is further smoothed to create a uniform texture and ensure there are no sharp edges that could cause discomfort during use.
The final step is quality control. Each wok is carefully inspected to ensure it meets the required standards for shape, size, durability, and finish. Any woks that do not meet the quality standards are set aside for rework or scrap. After passing inspection, the woks are packaged and prepared for shipment.
Key Features of the Sheet Metal Wok Production Machine:
- Cutting Mechanism: Uses shearing or laser cutting for precise shaping of metal discs.
- Forming Die: Deep drawing or press forming to create the characteristic wok shape.
- Edge Rolling or Flanging: Strengthens the edge of the wok for durability.
- Handle Attachment: Welding, riveting, or bolting for handle installation.
- Surface Treatment: Seasoning, coating, or polishing to enhance the wok’s performance and appearance.
- Automated Quality Control: Ensures the woks meet all specifications before they leave the factory.
Modern sheet metal wok production machines typically include automation and robotic systems to speed up the production process, reduce labor costs, and maintain consistent quality. For instance, robotic arms may handle tasks such as inserting the woks into seasoning stations, applying coatings, and packaging. Automation also helps to optimize the workflow and improve production efficiency, enabling manufacturers to meet high demand.
With sustainability being a growing concern in manufacturing, recycled materials and eco-friendly coatings are increasingly used in wok production. Manufacturers are exploring methods to reduce energy consumption and minimize waste during the manufacturing process. Some companies are also working on creating biodegradable coatings or offering recyclable woks to appeal to environmentally conscious consumers.
In conclusion, the production of sheet metal woks requires a combination of advanced manufacturing techniques, high-quality materials, and strict quality control processes. The use of automation, surface treatments, and innovative handle designs makes the process efficient while maintaining the wok’s performance and aesthetic quality. As consumer demand for durable, high-quality kitchen tools continues to rise, the manufacturing of woks will likely continue to evolve with technological advancements and a greater emphasis on sustainability and customization.
The production of sheet metal woks is a complex, highly detailed process that involves a range of techniques and advanced machinery. Starting with the selection of raw materials, such as carbon steel or stainless steel, these metals are chosen for their excellent heat conductivity, durability, and resistance to rust. The process begins with unrolling the metal sheets or coils, followed by thorough cleaning and inspection to ensure the material is free from any imperfections. The metal is then cut into circular blanks using precision cutting machines, such as shears or laser cutters. The cutting process needs to be accurate, as any discrepancies could affect the final shape and functionality of the wok.
After the blanks are cut, the next step is to form the wok’s characteristic bowl shape. This is typically done through press forming or deep drawing, a process where a circular sheet of metal is placed in a forming die and then drawn into shape under high pressure. This step is crucial in creating the wok’s smooth, curved interior. Precision is key during this stage, as an uneven curve can affect how the wok performs during cooking. Once the bowl shape is formed, the edges are often rolled or flanged to enhance the wok’s structural integrity. This process helps to strengthen the wok and create a finished edge that can accommodate handles securely.
The handles themselves are a critical component, as they must be strong, ergonomic, and heat-resistant. Metal handles are often welded onto the wok, while wooden handles are typically attached with rivets or bolts to provide extra support and comfort for the user. If the wok is designed with a loop handle, it may be welded or fastened onto the wok’s side to make it easier to lift and maneuver during cooking. The attachment of handles is a crucial step, ensuring that the finished wok is durable and can withstand frequent use without the handles loosening or becoming damaged.
Surface treatments play a significant role in the overall quality and performance of the wok. Seasoning is a common process for carbon steel woks, where the surface is heated and coated with oil to create a natural non-stick layer. This layer not only improves the cooking experience by preventing food from sticking but also helps protect the metal from rust. Some woks may undergo additional treatments like enamel coatings or non-stick finishes to enhance their usability and longevity. These coatings improve the wok’s resistance to food build-up and make it easier to clean.
Once the wok is coated and seasoned, it undergoes a polishing or grinding process to remove any rough edges or imperfections. This ensures the wok has a smooth, uniform surface free of burrs or sharp points that could be uncomfortable to handle or cook with. Quality control checks follow, where each wok is inspected for shape, size, handle attachment, and surface finish. Any woks that don’t meet the quality standards are set aside for rework or recycling.
Automation has become an essential part of wok production, especially in high-demand settings. Robotic arms or automated systems can take over tasks such as moving sheets of metal, forming the wok shapes, applying surface coatings, or assembling parts. This speeds up production, improves consistency, and reduces the risk of human error. Additionally, automated systems are often used for packaging, where the woks are carefully packed in protective materials to prevent damage during shipping.
Sustainability is also gaining traction in wok production. Recycling is a key aspect, with manufacturers seeking ways to minimize waste during production. The metal scraps produced during cutting and forming are often recycled to create new woks or other products. The use of eco-friendly coatings and water-based lubricants further reduces the environmental footprint of wok manufacturing. Moreover, as consumers become more eco-conscious, there is a growing demand for products made from sustainable materials or that feature biodegradable coatings.
Manufacturers are also focusing on creating woks with customizable features to meet the specific preferences of different markets. Some woks are designed with detachable handles, adjustable handles, or multi-functional features, such as a wok that can be used on both gas and induction stovetops. In addition, there is a growing trend for woks with innovative surface treatments that offer even better non-stick properties or resistance to corrosion. Some woks may even include digital temperature sensors to help chefs or home cooks achieve precise cooking results, allowing for more control over the cooking process.
As the global market for kitchenware continues to expand, especially in regions where Asian cuisine is becoming more popular, the demand for high-quality woks will continue to rise. Manufacturers are not only focused on improving the performance and design of their products but are also exploring ways to make woks more accessible, functional, and appealing to a broader range of consumers. From ergonomic designs to smart technologies, the future of sheet metal wok production looks to be one of continual innovation, sustainability, and adaptability to the ever-changing needs of the kitchenware industry.
As the production of sheet metal woks continues to evolve, the focus on precision engineering and advanced manufacturing technologies will become even more significant. The incorporation of AI-driven design tools allows manufacturers to fine-tune wok shapes and sizes based on customer preferences, local cooking traditions, and ergonomic requirements. 3D modeling and simulations help in optimizing the forming process, ensuring that every wok produced has consistent quality and performance.
Customization is another area of growth. Consumers and professional chefs alike are increasingly seeking products tailored to their needs. This trend is leading to the development of woks with specialized features, such as adjustable handles, variable depths, or even interchangeable components that allow for more versatility in cooking. For example, a wok with a detachable base could provide more flexible cooking options, such as transforming it into a deep fryer or a flat-bottomed pan. These customizable features can cater to both home cooks and restaurants, allowing for a more personalized cooking experience.
In terms of supply chain and logistics, manufacturers are increasingly adopting just-in-time (JIT) manufacturing methods. This approach helps to minimize inventory costs and reduce the risk of overproduction, ensuring that woks are only produced when they are needed, based on real-time demand. This allows companies to respond more quickly to shifts in market trends, customer preferences, or seasonal demand surges. The use of digital supply chain management systems also enables better tracking of raw materials, components, and finished products, improving the overall efficiency and reducing delays in production and delivery.
The introduction of robotic automation in wok production isn’t limited to just material handling and assembly; it’s also playing a crucial role in quality assurance. Vision systems equipped with high-resolution cameras and sensors are used to inspect woks at multiple stages of production. These systems can detect minute defects such as cracks, imperfections, or inconsistent surface finishes, ensuring that only high-quality products make it to market. This technology significantly reduces the chances of human error and ensures that each wok meets the high standards expected by consumers and professional kitchens.
Another critical area of development is the integration of smart technologies into the production and usage of woks. For instance, smart woks equipped with temperature sensors could be a game-changer for precision cooking. These woks might feature a Bluetooth connection that communicates with an app, allowing cooks to monitor and adjust the temperature of the wok remotely, ensuring optimal cooking conditions at all times. Such woks could automatically adjust their heat distribution based on the type of dish being prepared, which would be particularly useful in commercial kitchens, where consistency is key to delivering high-quality dishes every time.
Sustainability continues to be a driving force in the design and manufacturing processes. Companies are investing in energy-efficient production methods, using renewable energy sources, and reducing carbon emissions associated with the manufacturing of woks. As part of this shift toward more sustainable practices, many manufacturers are working toward eco-friendly packaging solutions, eliminating excessive plastic and opting for recyclable or biodegradable materials.
Additionally, the trend of material innovation will continue to shape wok production. Manufacturers are experimenting with lighter, more durable metals or coatings that improve the wok’s performance while reducing its overall environmental impact. For example, the use of titanium-coated woks could offer superior non-stick properties and corrosion resistance without compromising the traditional characteristics of a wok. Similarly, recycled metals could become a more prominent feature in wok manufacturing, providing an environmentally conscious alternative to virgin metals while maintaining the high quality and performance expected from a well-made wok.
As global demand for woks grows, manufacturers will need to consider the diverse cooking needs and preferences of consumers from different regions. This might involve offering a wider variety of wok designs and sizes to accommodate different cuisines and cooking methods. For example, flat-bottomed woks are increasingly popular in regions with induction stoves, as they offer better contact with the cooking surface, whereas round-bottomed woks continue to be favored in traditional Asian cooking, particularly for stir-frying over high heat. Additionally, the inclusion of induction-compatible materials in wok production will cater to the growing number of households and restaurants adopting induction cooking technologies.
The future of wok production will also be shaped by changing consumer expectations. As more people become interested in cooking at home, there will be an increasing demand for high-quality, professional-grade cookware that delivers excellent cooking results without the need for a commercial kitchen. To meet this demand, manufacturers are likely to focus on creating woks that not only perform well but also offer exceptional aesthetic appeal. Woks with polished finishes, decorative details, or customizable features will continue to attract consumers looking for both functionality and beauty in their kitchen tools.
Furthermore, manufacturers are expected to provide greater support for the maintenance and care of their products. Providing detailed instructions on how to properly season and maintain woks, along with offering refillable seasoning kits or specialized cleaning tools, can help customers extend the lifespan of their woks and improve their cooking experience. Woks with self-cleaning capabilities or anti-rust coatings may become more popular, offering consumers the convenience of low-maintenance cookware without sacrificing performance.
In conclusion, the production of sheet metal woks will continue to evolve in response to technological advancements, market demands, and the global trend toward sustainability. The incorporation of smart technologies, innovative materials, and eco-friendly practices will drive the future of wok manufacturing, while the focus on quality, customization, and functionality will ensure that these kitchen tools remain an essential part of cooking culture worldwide. Whether through robotic automation, precise temperature control, or sustainable practices, the wok manufacturing industry will adapt to meet the changing needs of the modern kitchen, while maintaining the traditional characteristics that make the wok such a beloved cooking tool.
Sheet Metal Griddle Production Machine
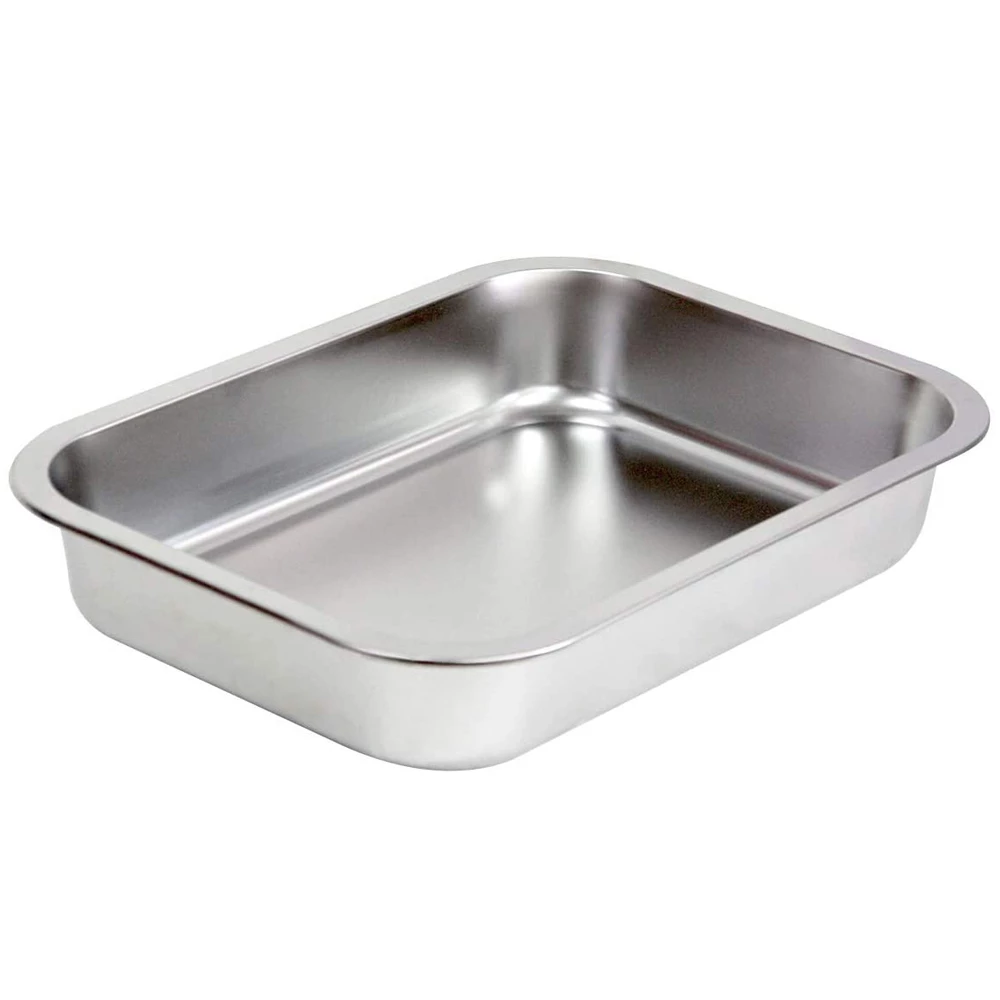
A Sheet Metal Griddle Production Machine is designed to manufacture griddles, a flat cooking surface typically used for frying, searing, and grilling various foods. Griddles are widely used in both commercial kitchens and home cooking setups, often made from carbon steel, cast iron, or stainless steel for their excellent heat conduction properties and durability. The production of sheet metal griddles involves various stages, from material preparation to final finishing and quality control. Below is an overview of the manufacturing process.
The process begins with selecting the appropriate raw material, typically stainless steel or carbon steel for its high heat retention and resistance to rust. The sheet metal used for the griddle is often supplied in coils or large sheets, which are unrolled and inspected for any surface defects or contamination. This ensures that the material is clean and free from imperfections that could affect the quality of the final product.
Once the material is selected, it is cut into the required size for the griddle surface. This is typically done using a shearing machine for straight cuts or a laser cutter for more intricate designs. The sheet metal is then transferred to the forming station, where the flat metal sheet is shaped into the desired form. The most common method for this step is press forming or deep drawing, where a large metal press applies pressure to the sheet metal to mold it into a flat, cooking surface. This step is crucial for ensuring the griddle has a uniform thickness and smooth surface.
After the griddle surface is formed, the next step is to reinforce the edges. This is typically done through edge rolling or flanging, which strengthens the edges of the griddle and prepares it for any additional parts, such as handles or drip trays. The edges are rolled to make them smooth, preventing any sharp spots that could cause injury or discomfort during use.
If the griddle is to have handles for easier maneuvering, these are attached during the next phase. Metal handles are often welded onto the sides of the griddle, while wooden handles are riveted or bolted into place. This step requires precision to ensure the handles are securely attached and can withstand the high temperatures the griddle will be exposed to during cooking.
The next crucial step in the manufacturing process is surface treatment. Since griddles are subjected to high heat and frequent use, the surface must be treated to prevent rust, improve durability, and provide a non-stick surface. Some griddles are seasoned, where the metal is coated with oil and heated to create a protective layer. Other griddles may receive enamel coatings or non-stick finishes, which are applied to ensure ease of cleaning and long-lasting performance. The surface treatment process also helps in achieving the desired anti-rust properties.
Once the surface treatment is applied, the griddle goes through a polishing or grinding process to remove any excess material, rough spots, or imperfections left from the forming and welding stages. This step ensures that the griddle has a smooth, even surface with no sharp edges or burrs.
Quality control is an essential part of the production process. Every griddle is carefully inspected for consistency in size, shape, surface finish, and overall quality. Any griddles that do not meet the required standards are set aside for rework or recycling. The final product is then tested for heat retention, evenness, and durability to ensure it meets the necessary performance criteria.
Once the griddle has passed quality control, it is packaged for shipment. The packaging is designed to protect the griddle during transportation and storage. Many manufacturers use eco-friendly packaging materials, such as recycled cardboard, to reduce the environmental impact of the packaging process.
Key features of the Sheet Metal Griddle Production Machine include:
- Cutting Mechanism: Shearing or laser cutting machines for precise shaping of the metal.
- Forming Die: Press forming or deep drawing equipment to shape the metal into a flat griddle surface.
- Edge Rolling or Flanging: Strengthens the edges of the griddle to enhance durability and ease of handling.
- Handle Attachment: Welding or riveting handles onto the griddle for secure and ergonomic use.
- Surface Treatment: Seasoning or non-stick coating to improve performance and longevity.
- Polishing and Grinding: Ensures a smooth and uniform surface, free from imperfections.
- Quality Control: Automated inspection systems to verify the final product meets the required standards.
- Automated Packaging: Packaging systems designed to protect the griddle during transportation and storage.
Modern production machines often incorporate robotic arms, automated presses, and vision systems for quality assurance to enhance the speed and precision of the manufacturing process. These technologies allow manufacturers to produce griddles at a faster rate while maintaining consistency and reducing human error.
The future of sheet metal griddle production is likely to be influenced by trends in sustainability, material innovation, and customization. Manufacturers are increasingly using recycled materials in their production processes, as well as exploring new surface treatments that are both eco-friendly and effective. The demand for customizable griddles, including those designed for specific cooking styles or stove types (such as induction-compatible griddles), is also expected to grow.
In conclusion, sheet metal griddle production combines several advanced manufacturing processes to create durable, high-performance kitchen tools. The focus on precision, surface treatments, and quality control ensures that the final product can withstand the demands of everyday cooking. As consumer preferences evolve, the production of griddles will continue to innovate, incorporating new materials, technologies, and designs to meet the changing needs of the market.
The process of manufacturing sheet metal griddles continues to evolve with advancements in materials and manufacturing techniques. After the cutting, forming, and edge rolling processes, the griddle is often tested for uniform heat distribution to ensure optimal cooking performance. The goal is to create a cooking surface that allows for consistent heat retention across the entire surface, whether it’s used on a stovetop, grill, or in a commercial kitchen.
Heat treatment is another critical part of the process for certain types of griddles, particularly those made from carbon steel or cast iron. The griddle may undergo a tempering process, where it’s heated to high temperatures and then slowly cooled to improve its strength and resistance to wear. This step helps improve the longevity of the griddle, allowing it to withstand the rigors of frequent use and extreme cooking conditions.
Once the griddle has been treated and polished, non-stick coatings may be applied to improve ease of use and cleaning. These coatings, typically made from PTFE (polytetrafluoroethylene) or ceramic-based materials, prevent food from sticking to the cooking surface, making the griddle easier to clean and reducing the need for excessive oil or butter during cooking. In some cases, seasoning is applied to create a natural non-stick layer that enhances the griddle’s performance over time. For carbon steel or cast iron griddles, seasoning involves coating the surface with oil and heating it until it forms a patina that prevents rust and creates a non-stick layer. This process is crucial for improving the functionality of the griddle and increasing its resistance to corrosion.
At this stage, the griddles are often subjected to additional testing, including thermal cycling, where the griddle is heated and cooled several times to ensure it can handle temperature fluctuations without warping or cracking. This is particularly important for griddles that will be used in commercial settings, where they will be exposed to high heat and extreme temperature changes frequently.
Packaging is the final step in the process. Griddles are carefully packed to ensure they arrive at their destination undamaged. The packaging is designed to protect the griddle from scratches, dents, and other forms of damage that may occur during shipping. Many manufacturers are now using sustainable packaging materials, such as recyclable cardboard and biodegradable plastics, in response to growing concerns about environmental impact. The griddles are often packed with clear instructions for care and maintenance, helping consumers get the best use out of their products.
The use of robotic systems and automated machinery throughout the production process ensures that each griddle is made to exact specifications, maintaining consistency and quality. This automation has greatly improved the efficiency of production lines, allowing manufacturers to produce large quantities of griddles without sacrificing quality. In addition, automated inspection systems with vision cameras and sensors can detect defects that might otherwise be overlooked, such as surface imperfections or incorrect dimensions, ensuring that each griddle meets the required standards before it’s shipped.
With the increasing popularity of induction cooking, manufacturers are incorporating induction-compatible bases into their griddles. These griddles are designed with special magnetic properties that allow them to work on induction cooktops, providing even heat distribution and energy efficiency. As more homes and restaurants switch to induction cooking, the demand for induction-compatible cookware is expected to grow, leading manufacturers to adapt their griddle production processes to accommodate this shift.
The growing interest in sustainable materials is also influencing the design and production of griddles. Some manufacturers are exploring recycled metals to reduce the environmental footprint of their products. Using sustainable coatings that are free of harmful chemicals is also becoming a priority for many brands, particularly as consumers become more eco-conscious. These environmentally friendly alternatives are not only better for the planet but also align with the increasing demand for healthier, safer cookware options.
Customization is another key trend in the griddle manufacturing process. Consumers are looking for products that can suit their specific needs, whether that means different sizes, shapes, or surface textures. Manufacturers are responding by offering a wider range of options, such as griddles with detachable handles, adjustable heating zones, or those with specific coatings for grilling, frying, or even baking. Some manufacturers are even offering personalized engraving or custom designs on the griddle surface, allowing consumers to add a unique touch to their kitchenware.
As the market for griddles grows, particularly in commercial kitchens and among home cooks who want restaurant-quality results, the production of sheet metal griddles will continue to innovate. Manufacturers will focus on improving the performance and sustainability of their products, responding to consumer demands for high-quality, durable, and versatile cookware. Technological advancements will continue to play a major role in driving efficiency and precision in the production process, while the increasing emphasis on eco-friendly manufacturing practices will help reduce the environmental impact of the industry. Ultimately, the future of griddle production will combine innovation, sustainability, and customization to meet the diverse needs of modern kitchens around the world.
As the demand for high-quality cookware continues to rise, particularly in both home and commercial kitchens, the sheet metal griddle production process is poised to adapt even further. Precision manufacturing will play an increasingly important role in ensuring griddles are crafted to exacting standards. As consumers seek more specialized cooking tools, manufacturers will likely invest more in advanced machining and robotic automation to ensure that every griddle meets high-quality standards while keeping production costs competitive.
The future of sheet metal griddle production will likely see further material innovations that enhance the griddle’s cooking performance, heat retention, and energy efficiency. New alloys and composite metals, for example, could provide an even better balance of durability and conductivity, making griddles not only more effective at cooking but also longer-lasting. Research into metals that resist warping under high heat or those that improve the non-stick properties of griddles will be a focal point of future advancements.
At the same time, the global supply chain for griddle production will continue to evolve, with a greater emphasis on localization to reduce lead times and transportation costs. By localizing production, manufacturers can respond more quickly to shifts in demand, such as spikes in popularity during certain seasons or cultural events. This flexibility also reduces the environmental impact of long-distance shipping, aligning with growing consumer preferences for sustainable products.
Smart technologies will also play a role in the future of griddle manufacturing. The integration of Internet of Things (IoT) technology into griddles could lead to a new generation of “smart griddles” that are capable of regulating their own temperature. These IoT-enabled griddles could allow users to monitor and adjust cooking conditions through mobile apps or directly through smart kitchen systems. In professional kitchens, such technology would enable chefs to precisely control cooking temperatures in real-time, enhancing cooking efficiency and consistency.
Moreover, energy-efficient production technologies will likely gain traction, reducing both operational costs and the environmental impact of manufacturing griddles. Companies may embrace green energy sources such as solar or wind power, particularly for high-energy processes like casting or forging. Additionally, water usage in production will be optimized to ensure sustainable practices are followed at every step of the process.
Another trend on the horizon is the growing importance of ergonomics in cookware design. As more consumers invest in high-end, professional-grade griddles, attention will shift towards making griddles that are not only functional but also comfortable to use. Innovations in handle design, such as heat-resistant or ergonomically shaped handles, could enhance the cooking experience. Non-slip grips or adjustable handles for easier storage and maneuverability will become increasingly popular as cooks prioritize ease of use, even in high-volume commercial settings.
As more consumers embrace healthy cooking habits, the demand for griddles that promote health-conscious cooking will rise. Non-stick surfaces that are free from harmful chemicals like PTFE and PFOA will become a standard, pushing manufacturers to develop safer, more effective coatings. Additionally, as cleaning convenience becomes more important, griddles that feature scratch-resistant surfaces and easy-to-maintain designs will be highly sought after.
Customization is likely to take an even bigger role in future griddle production. As more people look to add personal touches to their kitchenware, offering bespoke designs or unique materials for griddles, such as special wood accents or color finishes, could be a new revenue stream for manufacturers. Providing custom branding for businesses in the hospitality industry, like hotels, restaurants, and catering services, will also become a viable option for manufacturers looking to attract commercial clients.
Sustainability in griddle production is not just limited to eco-friendly materials and manufacturing processes. The entire lifecycle of the product is becoming an area of focus. Manufacturers will likely continue to embrace the concept of circular economy, which encourages reusing, refurbishing, and recycling materials. Griddles made from recycled metals will be increasingly common, and companies might offer refurbishment services for older models, allowing them to be restored to like-new condition instead of being discarded.
With these trends in mind, the future of sheet metal griddle production will be shaped by a combination of technological innovation, sustainability, and customization. Manufacturers will focus on creating high-performance, durable, and aesthetically pleasing griddles that meet the needs of diverse consumers—from professional chefs seeking precision and durability to home cooks looking for high-quality tools for everyday use. As competition intensifies, those who prioritize innovation, eco-conscious practices, and consumer-centric designs will be best positioned to succeed in the evolving cookware market.
Sheet Metal Baking Pan Production Machine
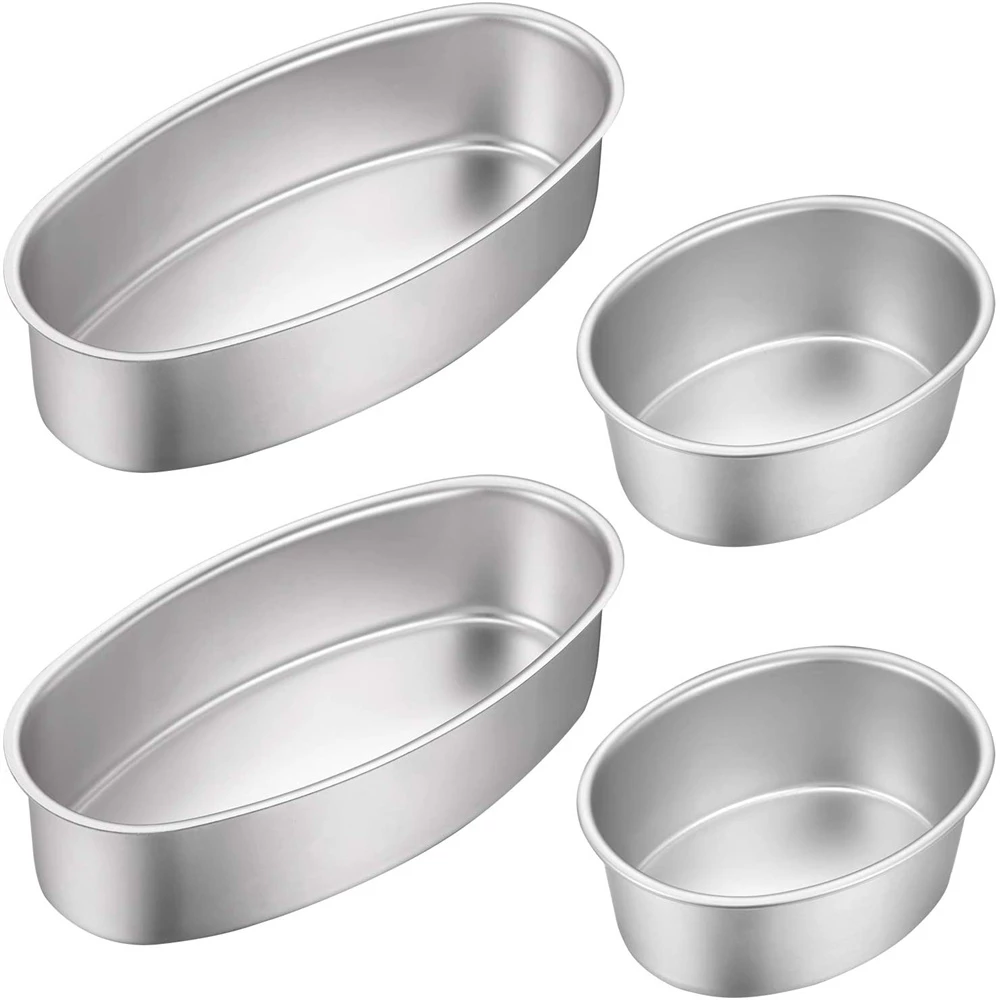
A Sheet Metal Baking Pan Production Machine is designed to efficiently manufacture high-quality baking pans, which are essential kitchen items used for baking cakes, cookies, breads, and other pastries. These pans are typically made from aluminum, stainless steel, or carbon steel, as these materials provide excellent heat distribution and are durable enough to withstand frequent use in home and commercial kitchens.
The production of baking pans from sheet metal involves several key steps, from material selection to final packaging. Here’s an overview of the manufacturing process:
The process begins with the selection of the raw material. Aluminum is one of the most common materials used in the production of baking pans because it is lightweight, conducts heat well, and is resistant to rust. Other materials such as carbon steel and stainless steel are also used, particularly for high-end or commercial-grade baking pans. The sheet metal used for baking pans is typically provided in coils or large flat sheets, which are then unrolled and inspected for any defects, ensuring that they are free of contaminants and imperfections.
Once the raw material is prepared, the first step in the manufacturing process is the cutting of the sheet metal. This is usually done with a shearing machine, which precisely cuts the metal into the appropriate sizes for the baking pan. The dimensions are critical to ensure that the final product fits the standard baking sizes, such as square, rectangular, or round pans. Alternatively, laser cutting technology may be used for more intricate designs, particularly for custom shapes or pans with complex features like handles or decorative edges.
The next step is the forming of the metal into the shape of a baking pan. This is typically done using a pressing machine or die press. The sheet metal is placed into a die, and a large press applies force to the metal to shape it into the pan’s desired form. This could include a flat baking surface with raised edges, as well as any added features like handles, lips, or indentations for stacking. The forming process ensures that the pan has a smooth, uniform thickness and consistent dimensions.
If the baking pan design includes handles, they are attached during this phase. The handles can be welded, riveted, or screwed onto the pan, depending on the design and material used. For instance, metal handles may be welded onto the sides, while plastic or silicone handles could be riveted or fastened with screws. This step is particularly important for ensuring that the handles are securely attached and can withstand the weight and heat of the pan during use.
After forming, the next phase involves surface treatment. This step is crucial for improving the baking pan’s performance and durability. Many baking pans undergo anodizing or coating with a non-stick layer. Anodizing is a process where the aluminum is treated to create a hard, protective layer on the surface that is resistant to scratches, rust, and corrosion. Non-stick coatings, typically made from PTFE (Polytetrafluoroethylene), are also applied to reduce the need for excessive oils or greasing, making cleanup easier for consumers.
Alternatively, some pans may receive a seasoning process, where a thin layer of oil is applied to the metal and heated to create a protective coating. This is often seen in carbon steel or cast iron pans, where the seasoning improves the non-stick properties and helps prevent rusting over time. Regardless of the surface treatment chosen, it ensures that the pans are easy to clean, resistant to wear, and provide consistent baking results.
Following the surface treatment, the pans undergo a quality control process. This includes a visual inspection for any defects, such as surface imperfections, cracks, or uneven coating. Machines equipped with vision systems or sensors may be used to inspect the pans for defects that could affect performance or safety. In addition, some pans are tested for heat distribution properties to ensure they bake evenly.
Once the baking pans pass the quality control stage, they are then subjected to polishing or grinding to smooth out any rough edges or areas that may have been created during the forming and cutting processes. This is done to ensure that the pans are comfortable to handle and free from sharp edges that could cause injury.
Packaging is the final step in the manufacturing process. The finished baking pans are carefully packed to prevent damage during transportation. This often involves placing each pan into protective packaging such as bubble wrap, cardboard boxes, or plastic wrap. Packaging may also include instructions for care and use, particularly for pans that require specific cleaning or maintenance, such as those with non-stick coatings or seasoning.
The packaging is also designed to be as eco-friendly as possible, with many manufacturers now opting for recyclable materials to reduce environmental impact. Once packaged, the baking pans are ready for shipment to retailers, wholesalers, or directly to consumers.
Key features of a Sheet Metal Baking Pan Production Machine include:
- Cutting Mechanism: Machines that provide precise cuts to sheet metal, such as shearing or laser cutting.
- Pressing/Stamping Equipment: Used for shaping the metal sheet into the desired pan form using dies.
- Handle Attachment: Systems for securely attaching handles, whether through welding, riveting, or screwing.
- Surface Treatment: Processes such as anodizing, coating, or seasoning to enhance the pan’s non-stick properties and durability.
- Polishing and Grinding: Smoothing out rough edges and imperfections to improve the pan’s safety and usability.
- Quality Control Systems: Automated systems using vision cameras and sensors to inspect pans for defects.
- Packaging Systems: Automated packaging lines that protect the pans during shipment and provide clear labeling.
With the increasing demand for high-quality kitchenware, automation has become an integral part of baking pan production. Robotic arms, automated presses, and conveyor systems are used to streamline the process, improving efficiency and reducing human error. These machines also allow manufacturers to produce a higher volume of pans while maintaining consistent quality across batches.
The future of sheet metal baking pan production will likely see further advancements in material innovation, customization, and sustainability. Manufacturers may continue to explore new eco-friendly coatings and heat-resistant materials to improve the durability and cooking performance of the pans. Additionally, there may be growing interest in custom-designed pans for specific baking needs, such as pans for particular cake designs, cookies, or specialty breads.
In conclusion, the production of sheet metal baking pans combines traditional craftsmanship with modern technology to create durable, high-performance cookware. From raw material selection to surface treatments and packaging, each step in the process is designed to ensure that the final product meets the highest standards of quality, functionality, and consumer satisfaction. As trends in sustainability and innovation continue to shape the cookware industry, sheet metal baking pans will evolve to meet the changing needs of home bakers and professional chefs alike.
The production of sheet metal baking pans begins with the selection of high-quality materials such as aluminum, stainless steel, or carbon steel. These materials are chosen for their ability to conduct heat evenly, resist corrosion, and withstand the high temperatures often encountered in baking. The raw material typically arrives in coils or large flat sheets, which are then unrolled and inspected to ensure they meet the necessary standards for thickness, surface quality, and durability.
Once the material is prepared, the first step in the manufacturing process is cutting the metal into the appropriate size. This is often done using a shearing machine, which ensures precise cuts. In some cases, laser cutting may be employed for more intricate or custom designs. The cuts must be accurate because even small deviations can result in an imprecise baking pan that could affect cooking performance.
After the metal is cut, the next step is to shape it into the form of a baking pan. This is typically done using a pressing machine, where the metal sheet is placed in a mold and subjected to force. The press shapes the metal into the correct dimensions, creating the base and the raised edges that are characteristic of baking pans. If handles are a part of the design, they are either welded, riveted, or screwed onto the sides of the pan. This ensures the handles are secure and can withstand heat and weight during use.
Following the shaping process, the pan undergoes surface treatment. This is where the pan receives its final coatings or finishes. Many baking pans are anodized, which hardens the metal surface, making it more resistant to scratches, rust, and heat damage. Some pans also receive non-stick coatings made from materials like PTFE (polytetrafluoroethylene), which make them easier to clean and improve their cooking performance by reducing the need for greasing. Carbon steel and cast iron pans might undergo seasoning, a process in which a layer of oil is heated onto the surface to create a natural non-stick coating.
After surface treatments are applied, the pans are inspected for any defects. This may involve both visual inspections and automated systems with sensors and cameras that detect imperfections such as cracks, uneven coatings, or incorrect dimensions. The goal is to ensure that every pan meets high standards of quality and functionality before it moves to the next stage of production.
Once the pans pass the quality control checks, they are polished or ground to smooth out any rough edges or surfaces left over from the forming process. This step is crucial to ensure that the pans are safe to handle and that there are no sharp edges that could cause injury. After polishing, some pans may be given additional heat treatments or stress tests to ensure they can withstand the rigors of constant use in a kitchen environment.
Finally, the baking pans are packaged for shipment. Packaging is done in a way that protects the pans from damage during transit. The pans may be wrapped in protective materials like bubble wrap, placed in sturdy cardboard boxes, or individually wrapped in plastic to prevent scratches. Along with the pans, consumers may receive care instructions, particularly for those with non-stick coatings or those requiring seasoning. Sustainable packaging materials are increasingly being used as manufacturers and consumers become more conscious of environmental impacts.
The production process of sheet metal baking pans is heavily automated, incorporating robotic arms, automated presses, and conveyor systems. These innovations help streamline the production, allowing manufacturers to produce large volumes of pans while maintaining consistent quality and reducing the potential for human error. Automation also contributes to reducing the production time, which makes it possible to meet growing consumer demand.
In addition to the standard manufacturing processes, manufacturers are continuously exploring new materials and technologies to improve the performance of baking pans. Future developments may include the use of more sustainable materials, advanced non-stick coatings that are safer and more durable, or even smart technologies that enable users to monitor or control the baking temperature through mobile apps or IoT devices. Furthermore, as custom cookware becomes more popular, manufacturers might offer more personalized options, allowing consumers to select specific sizes, shapes, or finishes for their baking pans.
Overall, the production of sheet metal baking pans is a highly refined process that combines material science, advanced manufacturing techniques, and quality control to create products that meet the needs of both home bakers and professional chefs. The evolution of this process will continue to focus on enhancing the cooking performance, durability, and environmental impact of baking pans, ensuring that they remain a staple in kitchens around the world.
As the market for high-quality cookware continues to grow, manufacturers of sheet metal baking pans are likely to embrace additional innovations that enhance both the functionality and user experience of their products. One potential avenue for improvement is the development of advanced coatings that offer superior non-stick properties while being safer for the environment. Manufacturers may explore ceramic-based non-stick coatings, which are free from harmful chemicals like PTFE and PFOA, and offer a safer alternative that can withstand high temperatures without degrading.
There may also be a growing trend toward eco-friendly materials in baking pan production. As consumers become increasingly conscious of environmental issues, manufacturers will likely respond by using materials that are more sustainable and easier to recycle. For instance, the use of recycled aluminum in the production of baking pans could become more common, allowing manufacturers to reduce their carbon footprint and appeal to eco-conscious consumers.
Customizability will also continue to be a major trend in the baking pan market. While traditional pans come in standard sizes and shapes, there is an increasing demand for bespoke baking pans tailored to specific needs. This might include personalized engraving, special designs for unique recipes, or even pans with adjustable dimensions for home bakers who want greater flexibility in their kitchenware. Manufacturers might invest in technologies that allow them to quickly produce customized pans without significantly increasing production costs.
Additionally, smart technology could make its way into the baking pan industry. Similar to other kitchen gadgets, smart baking pans could be equipped with sensors that monitor the pan’s temperature and send real-time data to a smartphone or tablet. This would allow bakers to precisely control the cooking process and receive alerts when the ideal temperature is reached, improving the consistency of their baking results. Such advancements could be particularly useful for professional chefs or avid home bakers who require exacting precision.
Another area of innovation will be in the ergonomics of baking pans. As home bakers look for more comfortable and user-friendly kitchen tools, manufacturers may develop lightweight pans with heat-resistant handles designed for ease of use. Additionally, stackable designs could be developed, allowing consumers to store multiple pans in a more compact and organized manner. Innovations like these would help increase the convenience of owning multiple pans while keeping kitchen space organized.
Multi-functional baking pans could also see growth in popularity. These pans might feature interchangeable inserts or modular components that allow them to serve different purposes. For example, a baking pan could be designed to accommodate various types of baked goods, such as cakes, cookies, or breads, with adjustable sections or inserts that make the pan versatile enough for multiple uses. This would appeal to consumers who want to minimize the number of kitchen tools they need without sacrificing the quality of their cooking.
As demand for high-performance kitchen products grows, the importance of energy-efficient production processes will continue to rise. Manufacturers will look for ways to reduce energy consumption during the baking pan production process. This could include the use of solar-powered machinery, more efficient casting and forging technologies, or reducing waste through better material management. Energy-efficient production not only lowers costs but also aligns with global sustainability goals and can improve a manufacturer’s reputation as an environmentally responsible company.
With the rise of online shopping and direct-to-consumer sales models, manufacturers will also need to focus on effective digital marketing and customer engagement. Offering an online platform that allows customers to customize, review, and purchase their baking pans directly from the manufacturer could become a common practice. Additionally, manufacturers may invest in subscription models where consumers receive a new, specialized pan or accessory every few months, keeping their kitchen tools fresh and up to date.
Moreover, the ongoing global interest in home cooking—fueled by trends like baking as a hobby, especially during events like the pandemic—has led to an increase in demand for quality kitchen products. As a result, brand differentiation will become more important in the sheet metal baking pan industry. Companies that can emphasize their craftsmanship, heritage, or unique features (like handmade, eco-friendly materials, or limited edition collections) may attract more loyal customers.
In conclusion, the future of sheet metal baking pan production will likely be shaped by a combination of technological advancements, sustainability efforts, customization opportunities, and a focus on consumer experience. Manufacturers will continue to innovate and respond to shifting consumer preferences, creating products that are not only functional but also environmentally conscious and tailored to individual needs. The industry is poised for continued growth, with a focus on quality, performance, and sustainability, ensuring that baking pans remain an essential tool for both professional chefs and home bakers worldwide.
EMS Metalworking Machines
We design, manufacture and assembly metalworking machinery such as:
- Hydraulic transfer press
- Glass mosaic press
- Hydraulic deep drawing press
- Casting press
- Hydraulic cold forming press
- Hydroforming press
- Composite press
- Silicone rubber moulding press
- Brake pad press
- Melamine press
- SMC & BMC Press
- Labrotaroy press
- Edge cutting trimming machine
- Edge curling machine
- Trimming beading machine
- Trimming joggling machine
- Cookware production line
- Pipe bending machine
- Profile bending machine
- Bandsaw for metal
- Cylindrical welding machine
- Horizontal pres and cookware
- Kitchenware, hotelware
- Bakeware and cuttlery production machinery
as a complete line as well as an individual machine such as:
- Edge cutting trimming beading machines
- Polishing and grinding machines for pot and pans
- Hydraulic drawing presses
- Circle blanking machines
- Riveting machine
- Hole punching machines
- Press feeding machine
You can check our machinery at work at: EMS Metalworking Machinery – YouTube
Applications:
Flange-punching
Beading and ribbing
Flanging
Trimming
Curling
Lock-seaming
Ribbing