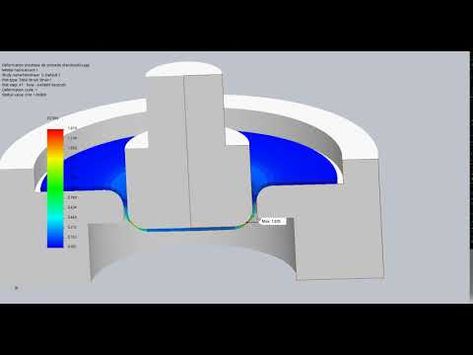
Sheet Metal Deep Drawing: Hydraulic deep drawing presses are an essential piece of equipment in the manufacturing industry, utilized for forming sheet metal into desired shapes through a process called “deep drawing.” These presses use hydraulic fluid to exert force on a punch, which then presses a metal blank into a die, creating complex geometries with high precision.
The deep drawing process allows for the creation of cylindrical, box-shaped, and irregularly shaped components with a high degree of consistency. Hydraulic presses are favored for their ability to exert constant force over long distances, making them ideal for deep drawing processes that involve high-strength materials.
Historically, deep drawing presses were mechanical, relying on mechanical linkages to drive the punch. The evolution to hydraulic systems brought greater control over the force and speed of the press, leading to improvements in precision, safety, and operational efficiency. This shift has cemented hydraulic deep drawing presses as the technology of choice for industries requiring high-quality, complex metal forming.
Hydraulic deep drawing presses are widely used in automotive, aerospace, consumer electronics, medical devices, and more. Their ability to handle high-strength materials and produce intricate, precise shapes makes them invaluable in industries requiring both durability and complex designs.
Basic Principles of Deep Drawing Process
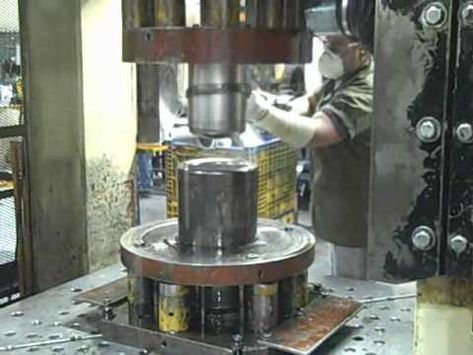
Deep drawing is a metal-forming process in which a flat sheet metal blank is radially drawn into a forming die by the mechanical action of a punch. The result is a part with a depth that exceeds its diameter, such as a cup or can.
The deep drawing process can be divided into several key stages:
- Blanking: The flat metal sheet is cut into a blank, typically a circular shape.
- Drawing: The blank is placed over a die cavity, and the punch pushes the blank into the die, forming the desired shape.
- Redrawing: If the depth of the part is greater than what can be achieved in a single stroke, the part may be redrawn through a series of dies to gradually achieve the final shape.
- Trimming and Finishing: After the deep drawing process, excess material is trimmed, and the part may undergo finishing processes to smooth out any rough edges.
The main characteristic of deep drawing is that the material undergoes plastic deformation, which is necessary for forming complex, deep geometries. The process requires careful control of various parameters, including the force applied, the speed of the punch, and the quality of the material to avoid common defects like tearing, wrinkling, or excessive thinning.
Hydraulic deep drawing presses play a critical role in this process. The hydraulic system provides consistent pressure, which is essential for achieving uniform part dimensions. Unlike mechanical presses, where the force can fluctuate, hydraulic presses offer precise control over the pressure applied during the drawing process, allowing for more accurate results. This is particularly important in high-volume production environments where consistency and quality are paramount.
Components of a Hydraulic Deep Drawing Press
The hydraulic deep drawing press is composed of several critical components, each playing a crucial role in the successful operation of the machine. Understanding these components is essential for optimizing the performance of the press and ensuring that the deep drawing process is both efficient and accurate.
- Hydraulic Cylinder: The hydraulic cylinder is the heart of the press, responsible for generating the force necessary for deep drawing. Hydraulic fluid is pumped into the cylinder, which moves the piston and creates the downward force needed to push the punch into the die.
- Punch and Die: The punch and die are the tools used to shape the metal blank. The punch is attached to the hydraulic cylinder and presses the blank into the die, which has the shape of the final part. The design and precision of the punch and die are critical for producing high-quality parts.
- Pressure System: The hydraulic pressure system controls the flow and pressure of the hydraulic fluid. It includes components such as pumps, valves, and reservoirs, which work together to ensure the correct amount of pressure is applied throughout the deep drawing process.
- Control System: Modern hydraulic deep drawing presses are equipped with computerized control systems that allow operators to precisely control the speed, force, and timing of the press. These systems also provide real-time feedback on press performance, allowing for adjustments to be made on the fly.
- Safety Mechanisms: Hydraulic presses are equipped with safety features to protect operators and equipment. These include emergency stop buttons, pressure relief valves, and guarding systems that prevent accidental contact with moving parts.
Each of these components plays a crucial role in ensuring that the hydraulic deep drawing press operates smoothly and efficiently. The integration of advanced control systems and safety mechanisms has made modern hydraulic presses more reliable and user-friendly than ever before.
Hydraulic System and Working Mechanism
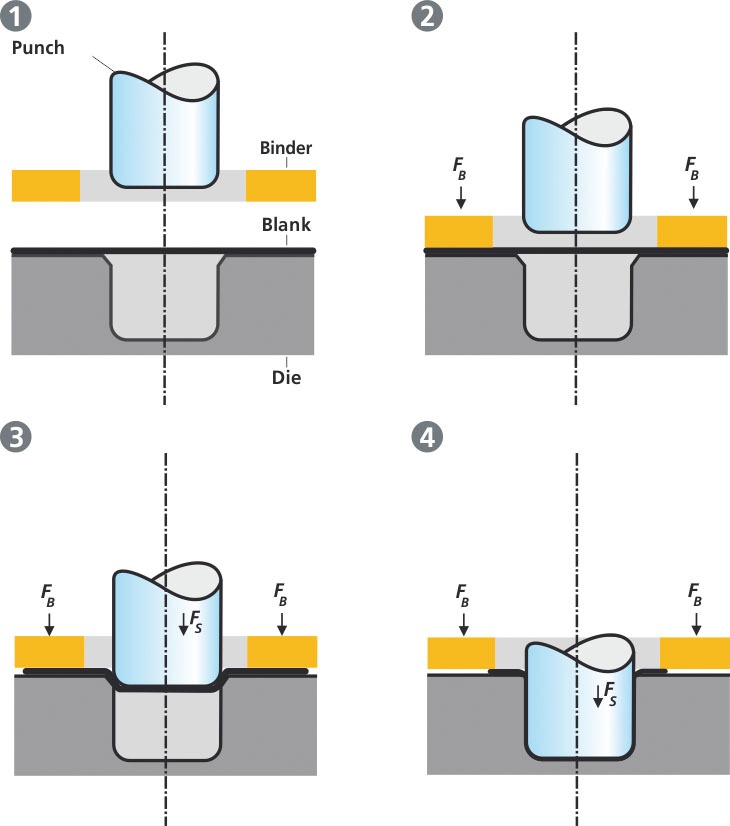
At the core of any hydraulic deep drawing press is the hydraulic system, which powers the press and controls the force applied during the deep drawing process. Understanding how this system works is essential for comprehending the advantages that hydraulic deep drawing presses offer in terms of precision, control, and adaptability.
How Hydraulic Systems Work
Hydraulic systems operate based on Pascal’s Law, which states that when a fluid is placed under pressure in a confined space, the pressure is transmitted equally in all directions. This principle allows hydraulic systems to generate large amounts of force with minimal input. In a hydraulic deep drawing press, a hydraulic pump is used to pressurize hydraulic fluid, which then moves through a series of valves and pipes to reach the hydraulic cylinder. The pressurized fluid exerts force on a piston within the cylinder, which in turn pushes the punch against the metal blank.
A key advantage of hydraulic systems is their ability to apply constant pressure over the full stroke of the piston. This ensures uniform force throughout the deep drawing process, allowing for more consistent and accurate parts compared to mechanical presses, where the force may vary at different points of the stroke.
Key Components of the Hydraulic System
The hydraulic system of a deep drawing press includes several important components that work together to ensure smooth and reliable operation:
- Hydraulic Fluid: The hydraulic fluid is the medium through which force is transmitted in the system. Typically, specialized hydraulic oils are used because they possess the right combination of viscosity, temperature stability, and lubricating properties. The quality and maintenance of hydraulic fluids are critical since contaminants or degraded fluids can lead to inefficiencies and even damage the system.
- Hydraulic Pump: The pump is responsible for generating pressure in the system by forcing the hydraulic fluid through the pipes and into the cylinder. There are different types of pumps used in hydraulic presses, including gear pumps, vane pumps, and piston pumps. The choice of pump depends on the specific requirements of the press, such as the pressure needed and the speed of operation.
- Valves and Regulators: Valves are used to control the flow of hydraulic fluid within the system, allowing the operator to precisely regulate the amount of pressure applied to the cylinder. Regulators are also used to ensure that the pressure does not exceed safe limits, preventing damage to the press and maintaining a safe working environment.
- Hydraulic Cylinder: The hydraulic cylinder is the component that converts the fluid pressure into mechanical force. The cylinder contains a piston that moves when the fluid is pressurized, creating the motion needed to drive the punch into the metal blank. Cylinders are typically made from high-strength materials to withstand the enormous forces generated during the deep drawing process.
- Pressure Accumulators: In some hydraulic systems, accumulators are used to store hydraulic fluid under pressure, which can then be released when needed. This allows for more efficient operation and provides a buffer to handle fluctuations in demand for pressure.
Working Mechanism of a Hydraulic Deep Drawing Press
The operation of a hydraulic deep drawing press can be broken down into several key stages:
- Initial Setup: Before the press is operated, the blank (a flat sheet of metal) is prepared and placed over the die. The die is mounted onto the lower bed of the press, while the punch is attached to the piston of the hydraulic cylinder.
- Pressure Build-up: Once the machine is set up, hydraulic fluid is pumped into the system, building pressure in the hydraulic cylinder. This pressure is carefully controlled to ensure that the correct amount of force is applied during the drawing process.
- Drawing Process: The press is activated, causing the hydraulic cylinder to drive the punch downward. As the punch moves into the die, it forces the blank into the desired shape. The constant pressure provided by the hydraulic system ensures that the blank deforms evenly, reducing the likelihood of defects such as wrinkling or tearing.
- Reversing the Cycle: After the drawing process is complete, the hydraulic system reverses the flow of fluid, retracting the piston and lifting the punch out of the die. The completed part is then removed, and the press is ready for the next cycle.
Advantages of Hydraulic Systems in Deep Drawing Presses
- Precise Control of Force: Hydraulic systems provide highly precise control over the force applied during the drawing process. Operators can adjust the pressure based on the specific requirements of each job, ensuring that the right amount of force is applied for different materials and part geometries.
- Constant Pressure Throughout Stroke: One of the key benefits of hydraulic presses is that they can maintain constant pressure throughout the entire stroke of the piston. This results in more uniform part quality and reduces the risk of defects compared to mechanical presses.
- Adaptability and Flexibility: Hydraulic presses are highly adaptable and can be adjusted to perform a wide range of tasks. For example, operators can modify the stroke length, pressure, and speed to accommodate different materials, part shapes, and production volumes.
- Reduced Wear and Tear: The smooth operation of hydraulic systems results in less wear and tear on the machine components compared to mechanical presses, where the high impact forces can cause damage over time. This reduces maintenance costs and extends the lifespan of the press.
Types of Hydraulic Deep Drawing Presses
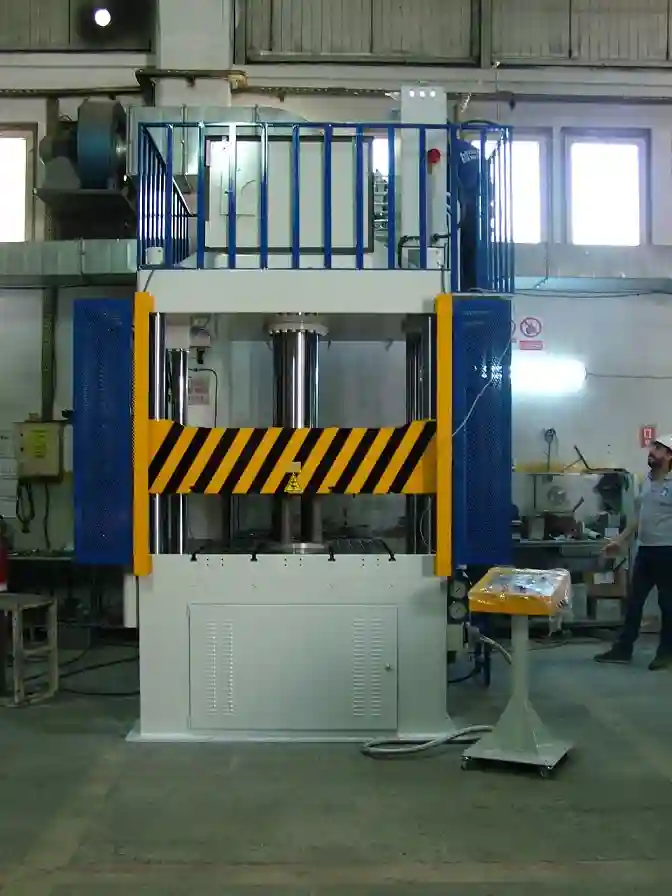
Hydraulic deep drawing presses come in various configurations, each designed to meet specific manufacturing requirements. The main types of hydraulic presses used in deep drawing applications include single-action, double-action, and triple-action presses. Understanding the differences between these types is crucial for selecting the right press for a particular application.
1. Single-Action Hydraulic Press
A single-action hydraulic press is the simplest type of press, using a single hydraulic cylinder to apply force. In this configuration, the blank is placed over the die, and the punch is driven into the die by the hydraulic cylinder. The force is applied in a single direction, hence the name “single-action.”
- Applications: Single-action presses are ideal for simpler deep drawing tasks, where the shape of the part is not too complex, and only moderate drawing depths are required. They are often used for producing parts such as cups, bowls, and shallow containers.
- Advantages: These presses are generally more affordable and easier to maintain compared to multi-action presses. They are also more compact, making them suitable for smaller manufacturing facilities.
- Limitations: Single-action presses are not as versatile as their double- and triple-action counterparts, as they lack the ability to handle more complex shapes or deeper draws.
2. Double-Action Hydraulic Press
Double-action hydraulic presses have two separate cylinders: one for the punch and another for the blank holder. This allows for more precise control over the drawing process, as the blank holder can be independently controlled to hold the metal blank in place while the punch draws it into the die.
- Applications: Double-action presses are commonly used for more complex parts that require greater precision and deeper draws. They are widely used in the automotive industry for forming large body panels, such as doors and hoods, where maintaining uniform material flow is critical.
- Advantages: The ability to control both the punch and the blank holder independently results in better control over the material flow, reducing the risk of defects like wrinkling or tearing. Double-action presses are also more versatile, as they can handle a wider range of part shapes and sizes.
- Limitations: These presses are more expensive and larger than single-action presses, making them more suitable for high-volume production environments.
3. Triple-Action Hydraulic Press
Triple-action hydraulic presses feature three separate cylinders: one for the punch, one for the blank holder, and a third for the ejector. The ejector is used to remove the finished part from the die after the drawing process is complete, allowing for continuous production with minimal downtime.
- Applications: Triple-action presses are used for highly complex deep drawing applications that require precise control over every aspect of the process. They are commonly used in industries such as aerospace, where parts often have intricate geometries and tight tolerances.
- Advantages: Triple-action presses offer the highest level of control and versatility, making them suitable for the most demanding deep drawing tasks. The use of an ejector system also improves production efficiency, as it reduces the time required to remove finished parts from the die.
- Limitations: These presses are the most expensive and require the largest amount of floor space. They also require more maintenance due to the increased complexity of the hydraulic system.
Key Considerations for Selecting a Hydraulic Deep Drawing Press
When selecting a hydraulic deep drawing press, several factors must be considered to ensure that the press meets the specific requirements of the production environment:
- Part Complexity: More complex parts with deeper draws and intricate geometries may require double- or triple-action presses for precise control.
- Production Volume: High-volume production environments may benefit from the continuous operation and efficiency offered by triple-action presses.
- Material Type: The type of material being formed will also influence the choice of press, as some materials require higher forces or more precise control over the drawing process.
Process Parameters Affecting Deep Drawing
The deep drawing process is highly sensitive to a range of parameters that can directly impact the quality, consistency, and overall success of the formed parts. Proper management of these parameters ensures defect-free production, reduces material waste, and improves production efficiency. The key parameters that influence deep drawing include blank holder force, drawing speed, lubrication, blank material properties, and the geometry of the die and punch.
1. Blank Holder Force
The blank holder force is the pressure applied to hold the metal blank in place during the drawing process. Its primary role is to control the material flow as the punch moves the blank into the die. If the blank holder force is too low, the material may wrinkle due to excessive material flow. On the other hand, if the force is too high, it can lead to tearing or cracking because the material cannot move freely enough into the die.
Achieving the correct balance in blank holder force is essential. Modern hydraulic deep drawing presses often feature adjustable blank holder systems, allowing operators to fine-tune the force to suit the specific material and part geometry. The use of dynamic control systems can further improve the process by automatically adjusting the force in real time as the press operates.
2. Drawing Speed
Drawing speed refers to the rate at which the punch moves into the die during the deep drawing process. It directly affects the material’s flow, the heat generated during forming, and the risk of defects like tearing or thinning. If the drawing speed is too fast, the material may not have enough time to flow into the die, leading to defects such as cracking or excessive thinning in certain areas.
Conversely, if the speed is too slow, production efficiency may suffer, and excessive friction between the blank and the die may result in surface defects or increased tool wear. Advanced hydraulic deep drawing presses often allow operators to control the drawing speed with great precision, enabling them to optimize the process for different materials and part geometries.
3. Lubrication Quality
Lubrication is a critical aspect of the deep drawing process, as it reduces friction between the blank and the die, minimizing wear on the tools and preventing surface defects on the finished part. The type and quality of lubrication used can significantly influence the success of the drawing operation.
- Metalworking Fluids (MWFs): Special lubricants known as MWFs are often used in deep drawing applications to ensure smooth material flow and reduce friction. These lubricants must be chosen based on factors such as material type, part geometry, and the drawing speed.
- Lubrication Techniques: Lubrication can be applied in different ways, including spraying, rolling, or coating the blank with a thin layer before the drawing process. Ensuring uniform lubrication is important to prevent localized friction, which can lead to defects like galling or surface scratches.
Improper or inadequate lubrication can result in an increase in tool wear, shortening the life of the die and punch, and may lead to inconsistent part quality.
4. Blank Material and Thickness
The material properties of the blank play a crucial role in the deep drawing process. Common materials used in deep drawing include aluminum, steel, brass, copper, and stainless steel, each with different formability characteristics. The choice of material is typically influenced by the requirements of the final part, such as strength, weight, corrosion resistance, and surface finish.
- Material Ductility: Ductile materials, which can undergo significant deformation without breaking, are ideal for deep drawing as they can be stretched into the desired shape without tearing. However, highly ductile materials also require precise control over process parameters to prevent wrinkling.
- Material Thickness: The thickness of the blank is another key factor. Thicker blanks require higher forces to be drawn into the die and may be prone to wrinkling if the blank holder force is not properly calibrated. Thinner blanks, while easier to form, are more susceptible to tearing or excessive thinning in high-stress areas.
Operators must take material properties into account when selecting press settings, including blank holder force, drawing speed, and lubrication requirements, to avoid defects and ensure optimal performance.
5. Die and Punch Geometry
The geometry of the die and punch determines the final shape of the part and plays a significant role in the material flow during the deep drawing process. Important aspects of die and punch design include:
- Corner Radius: The corner radius of the die and punch must be carefully designed to ensure smooth material flow and avoid excessive thinning or tearing. Sharp corners can cause the material to crack, while overly large radii may result in wrinkling.
- Die Clearance: The clearance between the punch and the die must be sufficient to allow for smooth material flow, but not so large that it causes wrinkling or uneven material distribution. The clearance is typically determined based on the thickness of the blank material.
- Draw Depth: The depth of the draw, or how far the punch pushes the blank into the die, is a critical parameter. Deeper draws require greater force and increase the risk of defects like tearing or thinning, especially in high-stress areas of the part. Proper control of the punch speed and blank holder force is essential to manage these risks.
6. Strategies to Avoid Defects
Several common defects can arise in the deep drawing process, including wrinkling, tearing, and thinning. By carefully controlling the key process parameters, operators can minimize the likelihood of these defects:
- Wrinkling: Wrinkling occurs when the material flows too freely into the die, often due to insufficient blank holder force. Adjusting the blank holder force and optimizing the lubrication can reduce wrinkling.
- Tearing: Tearing typically happens when the material is overstressed, either due to excessive drawing speed or insufficient lubrication. Reducing the punch speed and using high-quality lubricants can help prevent tearing.
- Thinning: Excessive thinning occurs when the material is stretched too much during the drawing process. Proper control of the punch speed and careful selection of the die and punch geometry are critical to minimizing thinning.
Advantages and Limitations of Hydraulic Deep Drawing Presses
Hydraulic deep drawing presses offer several advantages over traditional mechanical presses, particularly in terms of control, versatility, and performance. However, like any piece of industrial equipment, they also come with certain limitations that manufacturers must consider when choosing the right press for their operations.
Advantages and Limitations of Hydraulic Deep Drawing Presses
- Precise Control Over Force and Speed (continued)
Hydraulic presses allow for highly precise control over the force and speed applied during the deep drawing process. This precision is crucial for ensuring consistent part quality, especially for complex geometries and high-strength materials. The pressure can be adjusted throughout the stroke, which means that hydraulic presses are capable of maintaining a constant force over the entire cycle. This feature makes hydraulic presses ideal for deep drawing operations where material properties and thickness can vary significantly. - Versatility in Operation
Hydraulic deep drawing presses are extremely versatile and can be used for a wide variety of applications across different industries. Unlike mechanical presses, which are designed for specific tasks, hydraulic presses can be easily adjusted to accommodate different materials, part shapes, and production volumes. They can handle large, complex parts or multiple smaller parts simultaneously, making them well-suited for industries such as automotive, aerospace, and electronics manufacturing.Additionally, hydraulic presses are capable of multi-action operations, such as double- or triple-action presses, allowing them to perform different forming tasks in a single machine. This flexibility is a significant advantage in production environments that require a range of forming operations, reducing the need for multiple machines and minimizing setup times. - Handling of Complex Shapes and Deep Draws
Hydraulic deep drawing presses excel at handling parts with complex geometries and deep draws, which are often difficult or impossible to achieve with mechanical presses. The constant pressure and speed control provided by hydraulic systems make it easier to form intricate shapes without risking defects such as tearing, wrinkling, or excessive thinning. This capability is essential for industries like aerospace and automotive, where components often feature deep cavities and complex shapes that require precise forming. - Improved Safety and Operator Control
Modern hydraulic deep drawing presses are equipped with advanced safety features and control systems that protect both the operator and the equipment. These systems include emergency stop buttons, pressure relief valves, automatic overload protection, and guarding mechanisms that prevent accidental contact with moving parts. Additionally, the smooth and controlled motion of hydraulic systems reduces the risk of sudden mechanical failures or excessive forces that could cause injury or damage. - Energy Efficiency in High-Volume Production
Hydraulic presses have become more energy-efficient with the advent of modern control systems and the integration of servo-driven hydraulic systems. These innovations allow for better energy management by adjusting the power output based on the demand at each stage of the deep drawing process. As a result, hydraulic presses can be more energy-efficient in high-volume production compared to traditional mechanical presses, where energy consumption remains constant regardless of the workload. - Reduced Wear and Tear on Components
The smooth, controlled motion of hydraulic presses leads to reduced wear and tear on both the press components and the tooling used during the deep drawing process. Mechanical presses, by contrast, often experience higher levels of impact and stress, which can result in premature wear of critical components. This reduction in wear extends the lifespan of the machine and reduces the frequency and cost of maintenance.
Limitations of Hydraulic Deep Drawing Presses
- Higher Initial Cost
One of the primary limitations of hydraulic deep drawing presses is their higher initial cost compared to mechanical presses. The complexity of the hydraulic system, along with the need for specialized components such as pumps, valves, and hydraulic fluid reservoirs, contributes to a higher upfront investment. For manufacturers with limited budgets, this can be a significant barrier to adopting hydraulic technology. - Maintenance Complexity
While hydraulic presses tend to experience less wear and tear during operation, their maintenance requirements can be more complex than those of mechanical presses. Hydraulic systems rely on a variety of components, including pumps, valves, and fluid reservoirs, all of which must be regularly inspected and maintained to ensure optimal performance. Contaminants in the hydraulic fluid, such as dirt or metal particles, can cause system failures if not properly filtered out, adding to the maintenance burden.Furthermore, hydraulic fluid itself must be monitored and replaced periodically to prevent system inefficiencies or damage to the press. This ongoing need for fluid management adds to the operational costs and requires specialized knowledge. - Energy Consumption and Heat Generation
Although modern hydraulic presses are more energy-efficient than older models, they can still consume more energy than mechanical presses during certain operations. This is especially true in applications where high pressures or prolonged press cycles are required. Hydraulic systems can also generate a significant amount of heat during operation, particularly in high-volume production environments. Excessive heat can cause the hydraulic fluid to degrade over time, potentially leading to system inefficiencies or component failure.To mitigate these issues, manufacturers often invest in cooling systems or heat exchangers to manage the temperature of the hydraulic fluid, adding to the overall cost of the machine. - Larger Footprint and Space Requirements
Hydraulic presses typically require more floor space than mechanical presses due to the additional components involved, such as hydraulic fluid reservoirs, pumps, and control units. This larger footprint can be a disadvantage for manufacturers with limited space in their production facilities. Additionally, the installation process for a hydraulic press is more involved and may require specialized foundations or supports to accommodate the increased size and weight of the machine. - Slower Cycle Times for Certain Applications
Hydraulic presses generally operate more slowly than mechanical presses, particularly in applications that require fast cycle times. While the controlled, constant pressure of a hydraulic press is beneficial for complex deep drawing operations, it can result in slower production speeds compared to mechanical presses, which are capable of higher cycle rates. In high-volume, mass production environments where speed is critical, this slower cycle time may be a limitation.
Comparison with Mechanical Deep Drawing Presses
- Control and Precision: Hydraulic presses offer better control over the drawing process, particularly when handling complex parts or deep draws, whereas mechanical presses are typically faster but less precise.
- Cost: Mechanical presses are often less expensive and easier to maintain, but they may require more frequent repairs due to the higher impact forces involved.
- Efficiency: Hydraulic presses can be more energy-efficient in high-precision applications, while mechanical presses tend to be more efficient in high-speed, high-volume production environments.
Applications of Hydraulic Deep Drawing Presses in Different Industries
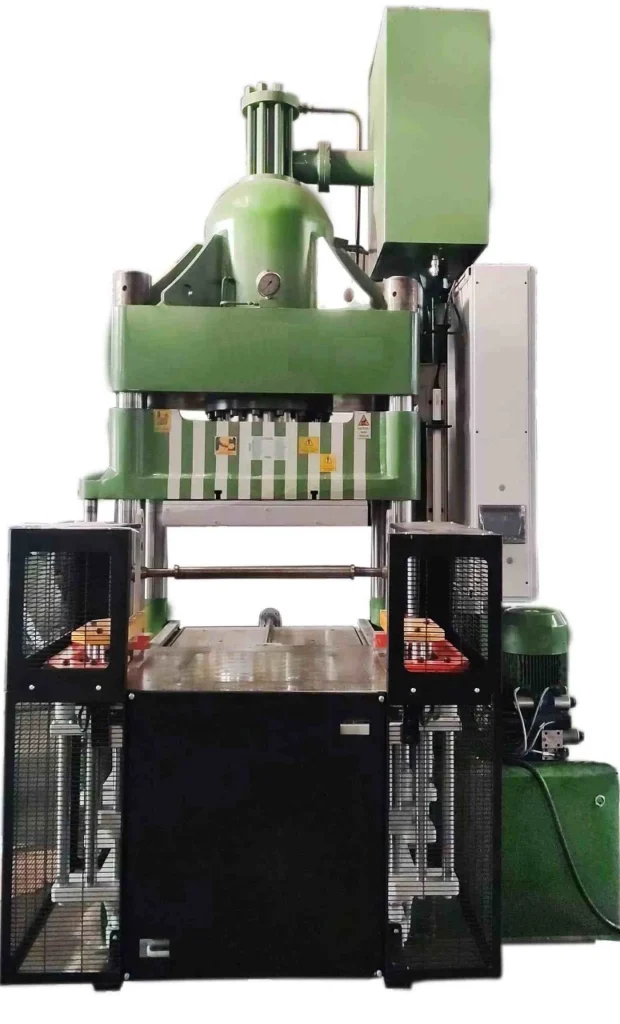
Hydraulic deep drawing presses play a vital role in numerous industries where precise metal forming is required. Their versatility, ability to handle complex shapes, and capacity for high-strength materials make them indispensable in fields ranging from automotive manufacturing to medical device production. Below are key industries where hydraulic deep drawing presses have a significant impact, along with specific applications.
1. Automotive Industry
The automotive industry is one of the largest consumers of hydraulic deep drawing presses. These presses are crucial for forming various metal components that require high precision and strength. The demand for lightweight, yet durable materials in vehicles has made deep drawing an essential process for car manufacturers.
- Car Body Panels: Hydraulic deep drawing presses are used to form large, complex panels such as doors, hoods, roof panels, and fenders. These parts must be manufactured with tight tolerances to ensure a proper fit and structural integrity.
- Fuel Tanks and Exhaust Components: Due to the need for high-strength materials in fuel tanks and exhaust systems, hydraulic deep drawing presses are widely used in the production of these components. The ability to maintain precise control over the drawing force and speed ensures the integrity of the material without compromising the structure.
- Chassis and Frame Components: Many chassis components, including cross members, brackets, and reinforcements, are deep drawn to ensure the highest levels of durability. The deep drawing process allows for the production of these parts with minimal material waste and consistent thickness, which is critical for safety.
2. Aerospace Industry
The aerospace industry requires components with extremely high precision, strength, and durability due to the harsh operational environments in which these parts must function. Hydraulic deep drawing presses are frequently used to manufacture complex, lightweight components that meet the rigorous standards of the industry.
- Aircraft Body Panels and Structural Components: Aerospace manufacturers use deep drawing presses to form structural components such as fuselage panels, wing components, and bulkheads. These parts must withstand high levels of stress and fatigue, making the deep drawing process ideal for ensuring uniform material distribution and strength.
- Engine Components: In jet engines and other aerospace propulsion systems, hydraulic presses are employed to form heat-resistant alloys and other high-strength materials into complex shapes. The precise control offered by hydraulic presses ensures that these critical components meet strict performance requirements.
- Landing Gear Components: Hydraulic deep drawing presses are also used to manufacture parts of landing gear systems, which need to be both lightweight and capable of withstanding extreme forces during takeoff and landing.
3. Consumer Electronics Industry
In the consumer electronics sector, hydraulic deep drawing presses are essential for producing thin, lightweight enclosures and components for devices like smartphones, laptops, and wearables. With the trend toward more compact and sleek designs, manufacturers rely on deep drawing technology to achieve high precision and finish quality.
- Device Enclosures and Casings: The metal enclosures for smartphones, tablets, and laptops are typically deep drawn to achieve seamless, lightweight structures that are both durable and aesthetically pleasing. The hydraulic press ensures that the material is evenly distributed and free from defects like thinning or tearing.
- Heat Sinks and Other Thermal Management Components: Many electronic devices rely on heat sinks and thermal management components made from metals such as aluminum or copper. Hydraulic deep drawing presses are used to form these components, ensuring they can effectively dissipate heat while maintaining a compact size.
4. Household Appliances
Hydraulic deep drawing presses are widely used in the production of household appliances such as washing machines, refrigerators, and microwave ovens. The need for large, robust metal components that are formed with precision makes deep drawing an ideal process for these products.
- Washer and Dryer Drums: The drums in washing machines and dryers are typically deep drawn from stainless steel to ensure durability and corrosion resistance. Hydraulic presses provide the necessary force to form these large, cylindrical parts without compromising their structural integrity.
- Refrigerator Liners and Panels: Hydraulic deep drawing presses are used to form the inner liners and panels of refrigerators. These components must be manufactured with tight tolerances to ensure proper insulation and assembly, while also being durable enough to withstand years of use.
5. Medical Devices and Equipment
The medical device industry requires high-precision, often small, components made from biocompatible materials such as stainless steel and titanium. Hydraulic deep drawing presses play a key role in manufacturing these critical parts, ensuring the highest levels of accuracy and consistency.
- Surgical Instruments and Implantable Devices: Many surgical instruments, such as forceps, scalpels, and clamps, are deep drawn from stainless steel or titanium. The hydraulic deep drawing process ensures these components are formed to precise specifications with smooth edges and surfaces, reducing the risk of contamination or material failure during use.
- Medical Implants: Complex medical implants, such as pacemaker enclosures and stents, require intricate forming processes that can only be achieved using hydraulic presses. The ability to control the force and speed of the drawing process ensures these delicate components are produced without defects, enhancing patient safety.
6. Packaging Industry
In the packaging industry, hydraulic deep drawing presses are used to manufacture various metal containers, including food and beverage cans, aerosol cans, and cosmetic containers. The deep drawing process is ideal for creating seamless, lightweight containers that are both functional and visually appealing.
- Metal Cans for Food and Beverages: Aluminum and steel cans for food and beverages are often deep drawn using hydraulic presses to ensure uniform thickness and high strength. The smooth surface finish and consistent dimensions of deep-drawn cans make them ideal for mass production and consumer use.
- Aerosol and Cosmetic Containers: Hydraulic deep drawing presses are also used to manufacture aerosol cans and cosmetic containers, which require precise forming to ensure proper functionality and aesthetic quality.
Future Trends in Industry Applications
As industries continue to push the boundaries of innovation, the demand for advanced deep drawing processes is expected to grow. Key trends influencing the future of hydraulic deep drawing presses include:
- Lightweight Materials: The use of lightweight materials such as aluminum and composites is becoming increasingly important, particularly in the automotive and aerospace industries. Hydraulic presses, with their precise control and versatility, are well-suited to forming these materials without compromising strength.
- Electrification and E-Mobility: The rise of electric vehicles (EVs) and other e-mobility solutions is driving demand for complex, high-strength components such as battery enclosures and electric motor housings. Hydraulic deep drawing presses are expected to play a crucial role in producing these parts efficiently.
- Sustainability: Manufacturers are increasingly focused on sustainability and reducing material waste. The deep drawing process, which can produce complex parts from a single piece of material, aligns with these goals by minimizing scrap and optimizing material use.
Recent Developments and Technological Advances
The technology behind hydraulic deep drawing presses has evolved significantly in recent years, driven by advancements in automation, digitalization, and material science. These developments have improved the performance, efficiency, and versatility of hydraulic presses, making them an essential part of modern manufacturing.
1. Digitalization and Automation
One of the most significant technological advances in hydraulic deep drawing presses is the integration of digital control systems and automation. These innovations have transformed the way hydraulic presses are operated, providing manufacturers with greater precision, flexibility, and productivity.
- CNC and PLC Systems: Modern hydraulic presses are often equipped with computer numerical control (CNC) or programmable logic controller (PLC) systems, which allow for automated control of the press parameters such as force, speed, and stroke length. These systems enable manufacturers to program complex forming sequences, reducing the need for manual adjustments and improving production consistency.
- Automated Tool Change Systems: In high-volume production environments, the ability to quickly change tools is critical for maintaining efficiency. Automated tool change systems have been developed to reduce downtime between production runs, allowing manufacturers to switch between different parts and materials with minimal disruption.
2. Integration with Industry 4.0 and Smart Manufacturing
The rise of Industry 4.0 has introduced new opportunities for hydraulic deep drawing presses to integrate with smart manufacturing systems. Through the use of sensors, data analytics, and machine learning, presses can now provide real-time feedback on performance and optimize production processes.
- Real-Time Monitoring: Sensors embedded in hydraulic presses can monitor key parameters such as pressure, temperature, and tool wear in real time. This data is transmitted to central control systems, allowing operators to make adjustments on the fly or trigger maintenance alerts before a failure occurs.
- Predictive Maintenance: Machine learning algorithms can analyze historical data from hydraulic presses to predict when maintenance is needed. This approach, known as predictive maintenance, reduces unplanned downtime by identifying potential issues before they lead to equipment failure.
Maintenance and Troubleshooting of Hydraulic Deep Drawing Presses
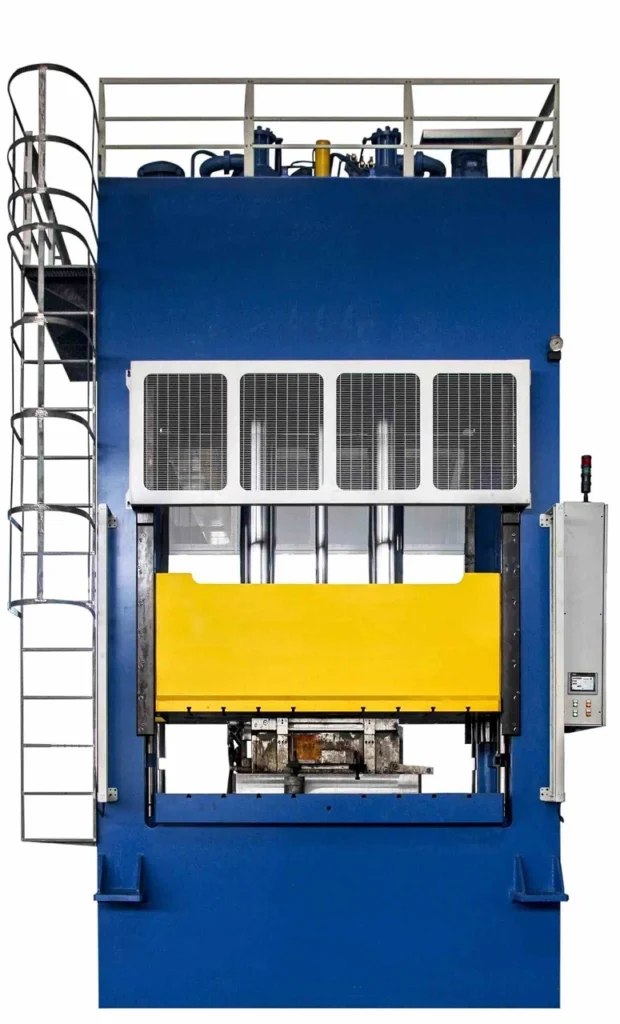
Maintenance is essential for ensuring the long-term performance, safety, and efficiency of hydraulic deep drawing presses. Given the complex nature of hydraulic systems, neglecting regular maintenance can lead to increased downtime, expensive repairs, and even equipment failure. To avoid these issues, manufacturers must implement a comprehensive maintenance program, which includes regular inspections, preventive maintenance, and troubleshooting.
1. Common Maintenance Practices
Routine maintenance practices for hydraulic deep drawing presses revolve around monitoring and maintaining the hydraulic system components, mechanical elements, and control systems. Some key maintenance tasks include:
- Hydraulic Fluid Monitoring: The hydraulic fluid is the lifeblood of the press. Over time, contaminants such as dirt, metal particles, and moisture can accumulate in the fluid, degrading its performance and causing damage to hydraulic components. Regularly checking the fluid for signs of contamination or degradation is crucial. In addition, hydraulic fluid levels should be monitored and maintained at the correct levels to avoid air entering the system, which can cause cavitation and system inefficiencies.
- Filter Replacement: Hydraulic systems include filters to remove contaminants from the fluid. Over time, these filters become clogged and must be replaced to maintain system performance. Clogged filters can cause reduced pressure, overheating, and wear on the hydraulic pump and valves.
- Seal Inspection and Replacement: The seals used in hydraulic cylinders and valves are prone to wear and tear over time. Leaking seals can lead to a loss of pressure and reduced performance. Regularly inspecting and replacing seals is an important preventive measure that ensures consistent press performance.
- Lubrication of Mechanical Components: While the hydraulic system provides the force required for deep drawing, mechanical components such as bearings, gears, and guideways still require proper lubrication to minimize friction and wear. Applying the appropriate lubricants at regular intervals is essential to prevent mechanical failures and extend the life of the press.
- System Calibration: Periodic calibration of the press’s control system ensures that the applied force, speed, and other critical parameters remain within acceptable tolerances. Calibration is particularly important in high-precision applications, where even small deviations can lead to defects in the finished parts.
2. Predictive Maintenance Techniques
Predictive maintenance has become an increasingly popular approach in modern manufacturing due to its ability to prevent costly breakdowns and extend the lifespan of hydraulic deep drawing presses. This approach leverages real-time data and advanced analytics to predict when maintenance is needed, rather than relying on fixed maintenance schedules.
- Condition Monitoring: Sensors are installed on key components such as hydraulic pumps, motors, and valves to monitor parameters like pressure, temperature, vibration, and oil quality. By continuously analyzing this data, manufacturers can detect early signs of wear or failure and schedule maintenance before a serious issue arises.
- Data Analytics and AI: Predictive maintenance systems often use machine learning algorithms to analyze historical data and identify patterns that indicate potential problems. This allows manufacturers to anticipate when components are likely to fail and perform maintenance only when necessary, reducing both downtime and maintenance costs.
3. Common Issues and Troubleshooting
Despite regular maintenance, hydraulic deep drawing presses can experience problems due to wear, environmental conditions, or unexpected failures. The most common issues include hydraulic system failures, mechanical malfunctions, and control system errors. Some common issues and their troubleshooting methods include:
- Hydraulic Fluid Leaks: Leaks can occur due to damaged seals, cracked hoses, or worn components. If a leak is detected, the source must be identified and repaired immediately to prevent a loss of pressure and damage to the system. Replacing worn seals, tightening fittings, or replacing damaged hoses can resolve the issue.
- Pressure Loss: If the press is unable to generate the required force, the cause is often a loss of hydraulic pressure. Possible causes include low hydraulic fluid levels, a clogged filter, or a malfunctioning pump. Checking fluid levels, replacing filters, and inspecting the pump can help restore pressure.
- Overheating: Hydraulic systems generate heat during operation, and if the system overheats, it can cause the hydraulic fluid to degrade and reduce system efficiency. Overheating may be caused by insufficient fluid levels, clogged filters, or excessive operating pressure. Addressing these issues by ensuring proper fluid levels and replacing filters can prevent overheating.
- Excessive Vibration or Noise: Excessive vibration or noise can be a sign of cavitation in the hydraulic system, which occurs when air enters the fluid. This can be caused by low fluid levels or a loose fitting. Ensuring the system is properly sealed and fluid levels are maintained can eliminate cavitation.
4. Ensuring Safety During Maintenance
Safety is paramount when performing maintenance on hydraulic deep drawing presses. The high pressures involved in the hydraulic system can pose serious hazards if not properly managed. Key safety measures include:
- Lockout/Tagout Procedures: Before performing any maintenance, the press should be de-energized, and lockout/tagout procedures should be followed to ensure the machine cannot be inadvertently started during maintenance.
- Pressure Release: Hydraulic systems should always be depressurized before any work is done on the system. This prevents accidental fluid release, which can cause injury or equipment damage.
- Personal Protective Equipment (PPE): Maintenance personnel should wear appropriate PPE, such as gloves, goggles, and protective clothing, to protect themselves from potential hazards.
Conclusion
Hydraulic deep drawing presses are an essential tool in modern manufacturing, offering unparalleled precision, control, and versatility for forming complex metal parts. Their ability to handle high-strength materials and produce parts with intricate geometries has made them indispensable in industries such as automotive, aerospace, consumer electronics, and medical devices.
The deep drawing process, powered by hydraulic systems, ensures uniform pressure throughout the entire stroke, resulting in consistent part quality and reduced risk of defects. With advancements in digital control systems, automation, and smart manufacturing technologies, hydraulic presses continue to evolve, offering greater efficiency, precision, and flexibility than ever before.
While hydraulic deep drawing presses have several advantages over traditional mechanical presses, including better control over pressure and the ability to handle more complex parts, they also come with challenges. These challenges include higher initial costs, more complex maintenance requirements, and larger space requirements. However, with proper maintenance and the use of predictive maintenance techniques, manufacturers can maximize the lifespan and efficiency of their hydraulic presses while minimizing downtime.
Looking to the future, hydraulic deep drawing presses will continue to play a crucial role in driving innovation across a range of industries, from the production of electric vehicle components to advanced medical devices. As manufacturing trends move toward increased automation, sustainability, and lightweight materials, hydraulic deep drawing presses will remain at the forefront of cutting-edge manufacturing technologies.
Deep drawing
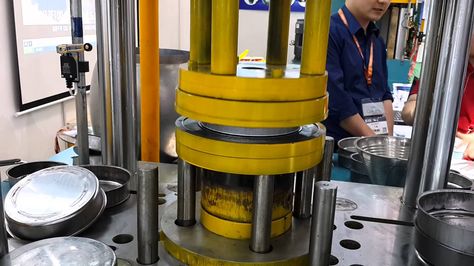
Deep drawing is a metal-forming process used to manufacture complex, hollow shapes from flat sheet metal. During the process, a metal blank is placed over a die cavity and pressed into the die by a punch, resulting in a part that has a depth greater than its diameter, such as a cup, cylinder, or box. This process is fundamental to manufacturing industries that require the creation of durable, precise, and lightweight components.
The deep drawing process is widely used in industries like automotive, aerospace, electronics, and packaging, where forming large volumes of metal parts with uniform thickness is critical. Products such as car body panels, fuel tanks, beverage cans, and kitchen sinks are typically produced through deep drawing.
This technique is favored due to its ability to create complex shapes with high structural integrity and minimal material waste. However, achieving high-quality parts through deep drawing requires a deep understanding of the mechanics behind the process, including the behavior of the material under stress, the forces applied by the punch, and the design of the die.
Deep drawing distinguishes itself from other metal-forming processes like stamping or bending due to the greater emphasis on stretching the metal without breaking it. To successfully complete a deep drawing process without defects, engineers must carefully control variables such as material properties, lubrication, punch speed, and blank holder force.
Fundamental Principles of Deep Drawing
The engineering behind deep drawing revolves around the mechanics of plastic deformation, the method by which the metal blank is stretched into a new shape without returning to its original form. Understanding the forces at play and how the metal reacts to these forces is key to successfully producing parts with uniform dimensions and minimal defects.
Plastic Deformation and Strain
During deep drawing, the metal blank is subjected to a combination of tensile and compressive stresses. As the punch presses the metal into the die, the material is forced to flow and stretch to conform to the shape of the die. This is referred to as plastic deformation, where the metal undergoes permanent deformation without cracking. The ability of a material to undergo plastic deformation without failure is a key characteristic in the deep drawing process.
Strain occurs as the metal is stretched by the punch, with different regions of the blank experiencing varying levels of strain. The outer edges of the blank experience tensile stress, while the material in contact with the punch and die is compressed. The strain distribution across the blank is a critical factor in determining the quality of the final part.
Key Components in Deep Drawing
- Punch: The punch is the tool that drives the metal blank into the die. The punch’s shape and speed play a crucial role in ensuring smooth material flow without introducing defects. The punch must be designed to apply sufficient force to stretch the material into the die without tearing it.
- Die: The die determines the final shape of the part. It needs to be precisely machined to match the part’s desired geometry. The clearance between the punch and the die is a critical factor in determining material flow and the part’s final thickness.
- Blank Holder: The blank holder, or hold-down ring, is used to control the material flow during the drawing process. Its primary function is to prevent the formation of wrinkles by applying uniform pressure around the blank’s edge. The correct amount of blank holder force ensures that the metal flows into the die smoothly, without stretching too much in one area.
Role of Friction and Lubrication
Friction plays a major role in the deep drawing process, especially at the interface between the blank, punch, and die. Too much friction can lead to tearing or thinning of the material, while too little friction may cause the blank to slip or wrinkle. The lubricant used in deep drawing serves to reduce friction, improve material flow, and prevent surface defects.
The selection of a lubricant depends on the material being drawn, the depth of the draw, and the speed of the process. Common lubricants include oils, greases, and specialized synthetic compounds that can withstand the high pressures and temperatures generated during the process.
Force Distribution in Deep Drawing
The force required for deep drawing depends on various factors, including material properties, sheet thickness, and the geometry of the die. As the punch pushes the blank into the die, the force needed increases due to the material’s resistance to deformation. This force is distributed unevenly across the blank, with the edges often experiencing higher forces than the center. Proper force distribution is essential for avoiding defects such as wrinkling, tearing, or excessive thinning.
Materials Used in Deep Drawing
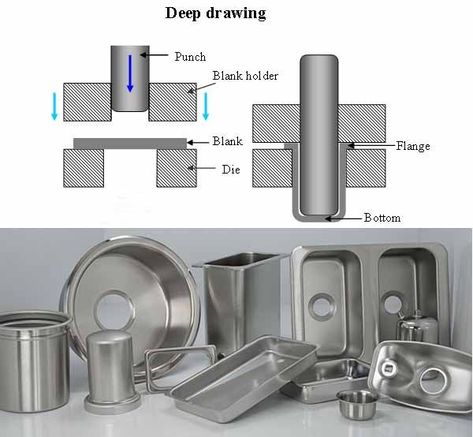
The success of the deep drawing process depends heavily on the material properties of the metal blank. Not all materials can be easily deep drawn; the material must have high ductility, allowing it to stretch without breaking. Additionally, formability, strength, and thickness play a crucial role in determining whether a material can be successfully drawn into complex shapes.
Common Materials in Deep Drawing
- Low-Carbon Steel:
- Low-carbon steel is one of the most common materials used in deep drawing due to its excellent formability and relatively low cost. Its ductility allows for significant deformation before failure, making it suitable for applications such as automotive panels and household appliances.
- Stainless Steel:
- Stainless steel is prized for its corrosion resistance and strength, but it is more difficult to deep draw than low-carbon steel. Special lubricants and precise control over process parameters are required to prevent defects when deep drawing stainless steel. It is commonly used for kitchen sinks, medical instruments, and aerospace components.
- Aluminum:
- Aluminum is a lightweight, ductile metal that is highly suitable for deep drawing applications where weight savings are essential. Automotive and aerospace industries often use deep-drawn aluminum parts for fuel tanks, body panels, and structural components. However, aluminum’s lower strength compared to steel requires adjustments to the punch speed and blank holder force.
- Copper and Brass:
- Copper and brass are often used in electrical applications, plumbing, and decorative products. Both materials offer good formability, though their higher cost makes them less common in large-scale deep drawing processes.
Material Properties Influencing Deep Drawing
- Ductility:
Ductility is the ability of a material to undergo significant plastic deformation before failure. The higher the ductility of the material, the easier it is to form deep-drawn parts without tearing or cracking. Materials like aluminum and low-carbon steel, which have high ductility, are ideal for deep drawing. - Yield Strength:
The yield strength of a material is the amount of stress it can withstand before it begins to deform plastically. Materials with lower yield strength are generally easier to draw, as they require less force to initiate deformation. However, if the material’s yield strength is too low, it may not be able to withstand the forces required for deep drawing without buckling or wrinkling. - Sheet Thickness:
Thicker sheets require more force to be drawn into the die but are less likely to tear compared to thinner sheets. However, they are more prone to wrinkling and require higher blank holder forces to ensure uniform material flow. Engineers must carefully balance sheet thickness with other process parameters to avoid defects. - Anisotropy:
The anisotropy of a material refers to its directional dependence on mechanical properties. In deep drawing, materials may behave differently based on the direction of the metal grains in the sheet. Materials with high anisotropy can result in uneven deformation, leading to defects such as earing (the formation of wavy edges).
Stages of the Deep Drawing Process
The deep drawing process consists of several stages, each playing a critical role in forming the final part with the desired dimensions and properties. Engineers must ensure that each stage is properly controlled to prevent defects and produce high-quality components.
1. Blanking
The first stage of the deep drawing process is blanking, where a flat sheet of metal is cut into a blank. The blank is typically circular and slightly larger than the final part to allow for material flow into the die. Blanking is performed using a punch and die set, with the punch cutting through the metal sheet to produce the desired blank size.
The quality of the blank is important because any imperfections, such as surface defects or rough edges, can propagate during the deep drawing process and lead to poor part quality. The blank must also be properly aligned with the die to ensure uniform material flow.
2. Drawing and Redrawing
The drawing stage is where the blank is pressed into the die by the punch. The punch moves downward, pushing the metal into the die cavity. As the punch descends, the material is forced to stretch and flow, taking the shape of the die. The success of this stage depends on maintaining the correct balance of blank holder force, punch speed, and lubrication.
If the depth of the part exceeds what can be achieved in a single stroke, the part may undergo redrawing. Redrawing involves repeating the drawing process in multiple stages, each time using a progressively smaller punch and die. This method allows for deeper parts to be formed without excessive thinning or tearing of the material.
3. Trimming and Finishing
After the part has been drawn to its final shape, excess material may need to be trimmed from the edges. This is particularly important in parts that require tight dimensional tolerances or smooth surfaces. Trimming is performed using specialized cutting tools, which remove any excess material and smooth out rough edges.
In some cases, parts may also undergo finishing processes, such as deburring, to remove any sharp edges or surface imperfections. Finishing is especially important in applications where surface quality is critical, such as in medical devices or consumer electronics.
4. Metal Flow During Drawing
The flow of metal during the drawing process is influenced by several factors, including the material’s ductility, the design of the die, and the force applied by the punch. During the initial stages of drawing, the material flows radially inward toward the center of the blank. As the punch moves deeper into the die, the material is stretched vertically, and its thickness decreases.
The flow stress of the material must be carefully controlled to prevent uneven deformation. If the material flows too quickly, it may cause wrinkling or tearing, while slow material flow can result in excessive thinning or uneven wall thickness.
5. Influence of Blank Holder Force and Punch Speed
The blank holder force is a critical parameter in deep drawing, as it controls the flow of material into the die. If the blank holder force is too low, the material may flow too freely, resulting in wrinkles. Conversely, if the force is too high, the material may not be able to flow into the die properly, leading to tearing or cracking.
The punch speed also plays a significant role in determining the quality of the final part. Higher punch speeds can increase productivity, but they also generate more heat and can lead to defects such as excessive thinning or surface defects. Lower punch speeds, on the other hand, provide more control over the material flow, but they slow down the production process.
Engineers must carefully balance the blank holder force and punch speed to achieve the best results in terms of part quality, material usage, and production efficiency.
Engineering Parameters Influencing Deep Drawing
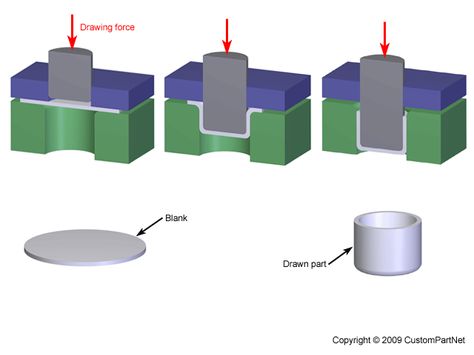
The quality and efficiency of the deep drawing process are highly dependent on various engineering parameters. By optimizing these parameters, engineers can achieve high-quality parts while minimizing defects and material waste.
1. Blank Holder Force
As discussed earlier, the blank holder force is essential for controlling the material flow during the deep drawing process. The force must be carefully adjusted based on the material being drawn, the part’s geometry, and the depth of the draw. Too much or too little force can result in defects such as wrinkling or tearing.
Dynamic blank holder systems have been developed to adjust the force in real-time during the drawing process. These systems use sensors and control algorithms to optimize the blank holder force throughout the drawing stroke, improving part quality and reducing the risk of defects.
2. Drawing Ratio and Limiting Drawing Ratio (LDR)
The drawing ratio is defined as the ratio of the blank diameter to the diameter of the drawn part. This ratio is an important measure of the severity of the drawing process. A higher drawing ratio indicates a more severe draw, which requires greater force and increases the likelihood of defects.
The limiting drawing ratio (LDR) is the maximum drawing ratio that can be achieved without causing failure (tearing or wrinkling) in the material. The LDR depends on factors such as material properties, punch and die design, and lubrication. Engineers must design the deep drawing process within the LDR to avoid defects.
3. Punch and Die Design
The design of the punch and die plays a crucial role in determining the success of the deep drawing process. Key design considerations include:
- Radius: The corner radius of the die and punch must be carefully designed to allow for smooth material flow. A small radius can cause the material to crack, while a large radius may lead to wrinkling or uneven material flow.
- Clearance: The clearance between the punch and the die is another critical factor. If the clearance is too small, the material may experience excessive thinning or tearing. Conversely, if the clearance is too large, the material may not deform properly, resulting in wrinkles.
- Shape: The shape of the punch and die determines the final geometry of the part. Complex shapes with deep cavities require precise punch and die design to ensure uniform material flow and avoid defects.
4. Drawing Speed and Pressure Control
The drawing speed affects the rate at which the material is deformed, while the pressure control ensures that the punch applies consistent force throughout the drawing process. Both parameters must be carefully controlled to prevent defects and ensure uniform part quality.
Modern hydraulic and servo-hydraulic presses allow for precise control over drawing speed and pressure. These presses can be programmed to adjust the speed and pressure based on the material’s behavior, ensuring optimal performance during the drawing process.
5. Effects of Lubrication and Friction
As mentioned earlier, lubrication is essential for reducing friction and ensuring smooth material flow. The choice of lubricant depends on factors such as the material being drawn, the depth of the draw, and the operating temperature. Dry film lubricants, synthetic oils, and water-based lubricants are commonly used in deep drawing applications.
Friction between the blank, punch, and die can lead to defects such as galling (material sticking to the punch or die) or surface scratches. Proper lubrication minimizes friction and helps prevent these defects, improving the overall quality of the part.
Common Defects in Deep Drawing
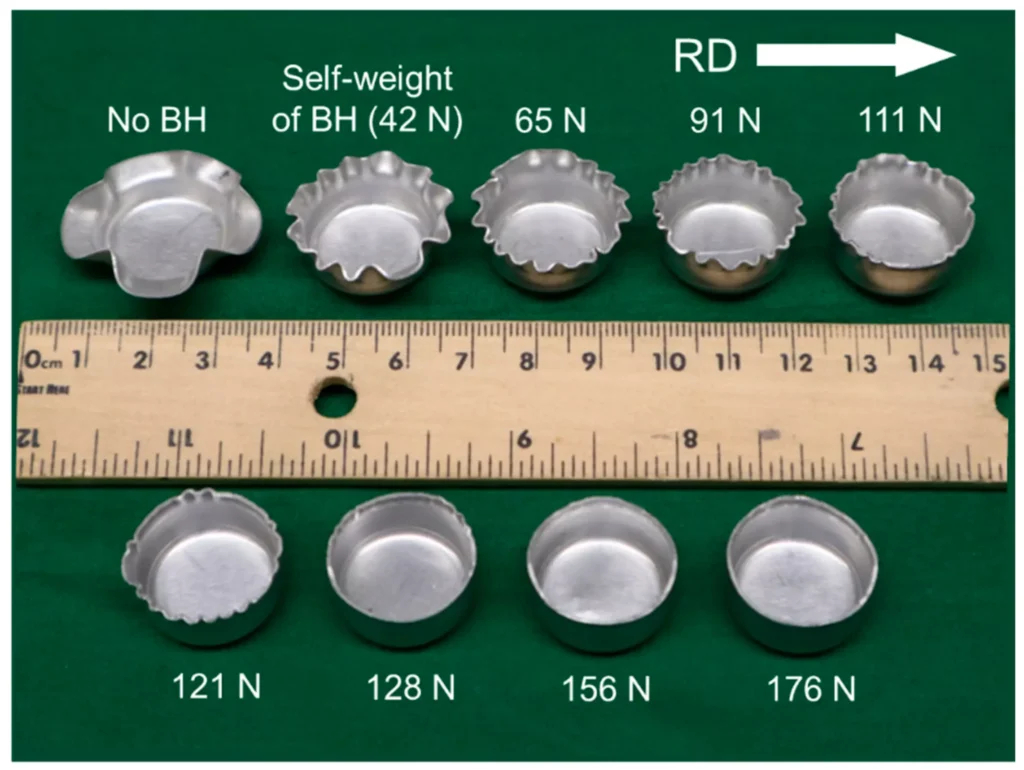
Despite careful planning and optimization, defects can still occur during the deep drawing process. These defects are often the result of improper control of process parameters, material properties, or tool design.
1. Wrinkling
Wrinkling occurs when the blank holder force is too low, allowing the material to flow too freely into the die. This results in excess material bunching up, forming wrinkles around the edges of the part. Wrinkling is more likely to occur in deeper draws or when drawing materials with low stiffness.
Solution:
Increasing the blank holder force or adjusting the lubrication can help prevent wrinkling. In some cases, redesigning the die to provide better material flow can also reduce the risk of wrinkling.
2. Tearing
Tearing is a catastrophic failure that occurs when the material is overstretched and can no longer withstand the applied forces. It often happens when the punch speed is too high, the material is too brittle, or the die design is not suitable for the material being drawn.
Solution:
Reducing the punch speed and ensuring that the material’s thickness and ductility are appropriate for the drawing process can help prevent tearing. Lubrication also plays a role in reducing the likelihood of tearing by minimizing friction.
3. Thinning and Earing
Thinning occurs when the material becomes too stretched in certain areas, resulting in a reduction in thickness. Thinning can weaken the part and increase the risk of failure during use. Earing, on the other hand, refers to the formation of wavy edges on the part due to anisotropy in the material’s grain structure.
Solution:
To avoid thinning, engineers must carefully control the punch speed, blank holder force, and lubrication. Earing can be minimized by selecting materials with lower anisotropy or adjusting the orientation of the blank relative to the material’s grain direction.
4. Galling and Surface Defects
Galling occurs when material from the blank adheres to the punch or die, causing scratches or rough surfaces on the part. Galling is more likely to occur when drawing hard materials or when lubrication is inadequate.
Solution:
Using proper lubrication and coating the punch and die with wear-resistant materials can reduce the risk of galling. Regular maintenance of the punch and die is also essential to prevent surface defects.
Technological Advances in Deep Drawing
The deep drawing process has evolved significantly with advancements in engineering, simulation, and automation technologies. These advances have improved the efficiency, precision, and quality of the process, enabling manufacturers to produce more complex parts with fewer defects.
1. Finite Element Analysis (FEA) and Simulation
Finite element analysis (FEA) is a computational technique used to simulate the behavior of materials under various conditions. In deep drawing, FEA allows engineers to predict how the material will deform during the drawing process, helping them optimize tool design, material selection, and process parameters.
Using FEA, engineers can simulate different scenarios, such as varying the blank holder force or changing the punch speed, to identify potential defects before they occur in production. This reduces the need for costly trial-and-error methods and shortens the time required to develop new products.
2. Automation and Control Systems
Automation has played a significant role in improving the productivity and precision of the deep drawing process. Modern hydraulic presses are equipped with CNC (Computer Numerical Control) systems that allow for precise control over process parameters such as punch speed, pressure, and blank holder force.
Automated tool change systems have also been developed to reduce downtime between production runs. These systems allow manufacturers to quickly switch between different punch and die sets, enabling greater flexibility in producing a variety of parts.
3. Advanced Materials and Coatings
New materials and surface coatings have been developed to improve the performance of punches and dies, reducing wear and increasing tool life. Hard coatings, such as titanium nitride (TiN) or diamond-like carbon (DLC), are applied to the surfaces of tools to reduce friction and prevent galling.
Additionally, advances in material science have led to the development of high-strength alloys that can be drawn into complex shapes without compromising part quality. These materials are particularly valuable in industries like aerospace and automotive, where lightweight, high-strength components are in high demand.
4. Industry 4.0 Integration
The integration of Industry 4.0 technologies, such as sensors, data analytics, and machine learning, has revolutionized the deep drawing process. Smart presses equipped with sensors can monitor key parameters, such as temperature, pressure, and tool wear, in real time. This data is transmitted to a central control system, allowing engineers to make adjustments on the fly or schedule maintenance before a failure occurs.
Predictive maintenance systems use machine learning algorithms to analyze historical data and predict when a press or tool will require maintenance. This reduces unplanned downtime and improves overall production efficiency.
Applications of Deep Drawing in Manufacturing
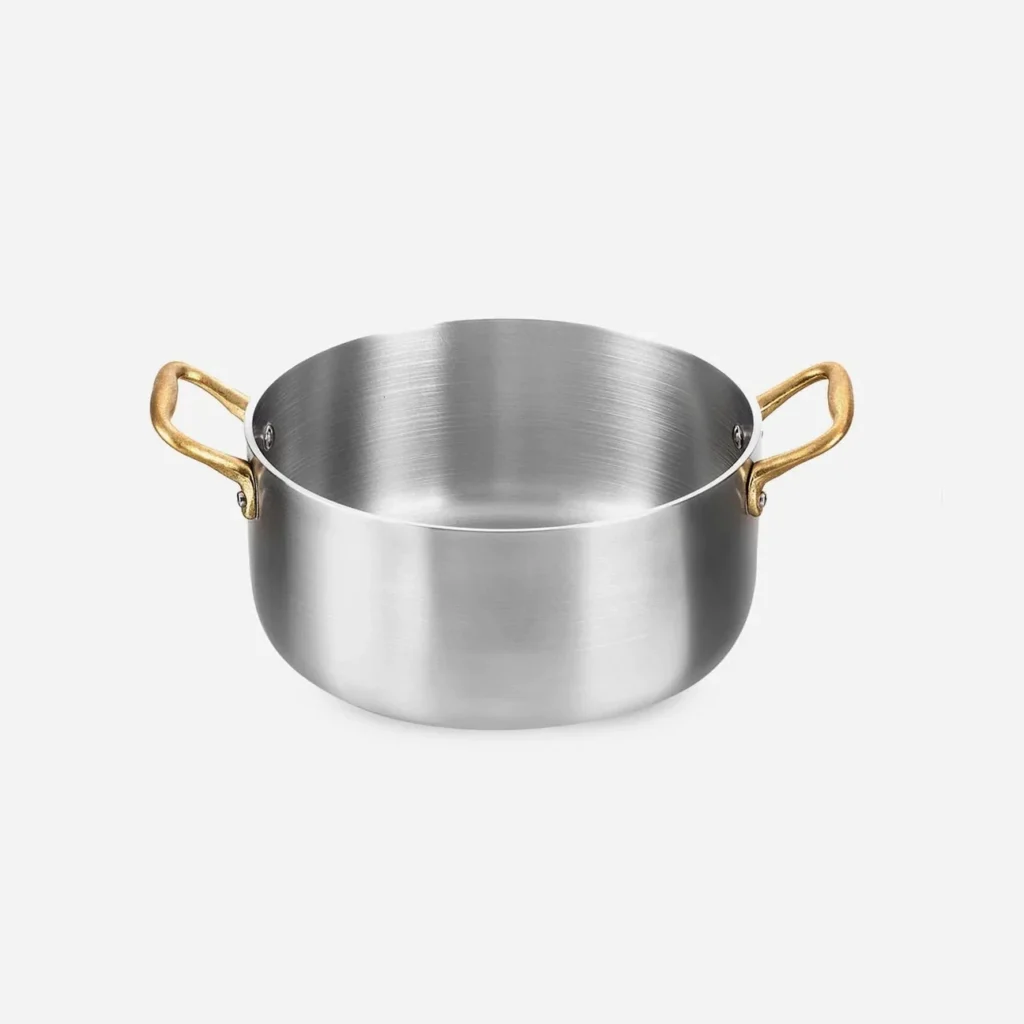
Deep drawing is a versatile process used in a wide range of industries to produce components with complex geometries and high precision. Below are some of the most common applications of deep drawing across different sectors.
1. Automotive Industry
In the automotive industry, deep drawing is used to manufacture parts such as car body panels, fuel tanks, and exhaust components. These parts require high strength and durability, making deep drawing an ideal process due to its ability to produce complex shapes with minimal material waste.
Lightweighting is a major trend in the automotive industry, and deep drawing is used to form lightweight materials like aluminum and high-strength steel into parts that meet stringent safety and performance requirements.
2. Aerospace Industry
The aerospace industry relies on deep drawing to produce components that are both lightweight and strong. Parts such as fuselage panels, engine components, and landing gear housings are often deep drawn from high-strength alloys. The precision and control offered by the deep drawing process make it ideal for producing parts with tight tolerances and complex geometries.
3. Electronics and Consumer Products
Deep drawing is widely used in the electronics and consumer goods industries to produce enclosures for devices like smartphones, laptops, and appliances. The ability to create thin, lightweight metal parts with a high-quality surface finish makes deep drawing suitable for these applications.
Heat sinks, battery enclosures, and connector components are also commonly produced using deep drawing, particularly when lightweight materials like aluminum are required.
4. Medical Devices and Packaging
In the medical industry, deep drawing is used to produce surgical instruments, implants, and medical device housings. The precision of the process is critical in ensuring that these components meet the stringent quality and safety standards required in the medical field.
In packaging, deep drawing is commonly used to produce metal cans, aerosol containers, and cosmetic containers, where lightweight, durable, and aesthetically pleasing packaging is important.
Conclusion
Deep drawing is a highly versatile and efficient metal-forming process that has become a cornerstone of modern manufacturing. Its ability to produce complex shapes with minimal material waste makes it invaluable in industries like automotive, aerospace, electronics, and medical devices. However, the success of the deep drawing process depends on a deep understanding of the engineering principles behind it, including material behavior, tool design, and process optimization.
As manufacturing continues to evolve, advances in technology are enhancing the deep drawing process. Finite element analysis (FEA), automation, and smart manufacturing systems are allowing engineers to achieve greater precision, reduce defects, and improve overall efficiency. Additionally, new materials and surface coatings are extending tool life and enabling the production of more complex, high-strength components.
Looking to the future, the integration of Industry 4.0 technologies and data analytics promises to further improve the deep drawing process, enabling manufacturers to predict failures, optimize production in real time, and reduce costs. As the demand for lightweight, high-strength components continues to grow, deep drawing will remain a critical process in the global manufacturing landscape.
To create a comprehensive 5,000-word technical text on Materials Used in Deep Drawing, we will cover various materials commonly used in the process, their specific properties, and how these properties affect deep drawing operations. The document will be structured to explore the fundamentals of deep drawing, material requirements, the behavior of various metals, and recent innovations in material science for deep drawing applications.
Introduction to Deep Drawing and Material Requirements
Deep drawing is a manufacturing process used to form sheet metal into three-dimensional shapes through the application of mechanical force. The process involves placing a flat metal blank over a die cavity and pushing it into the die using a punch, transforming the flat sheet into a hollow object, such as a cup, cylinder, or more complex geometries.
Material selection is one of the most critical factors influencing the success of deep drawing. The process subjects the material to significant stretching and compressive forces, requiring it to have sufficient ductility and strength to deform without tearing or wrinkling. The material must also have good formability characteristics to ensure smooth material flow during the process and maintain uniform thickness without defects.
Materials used in deep drawing must meet several criteria to avoid common issues like tearing, wrinkling, or excessive thinning. The key properties that influence a material’s suitability for deep drawing include ductility, yield strength, tensile strength, and formability. These properties vary across different metals and alloys, and the success of a deep drawing operation depends on the careful balance of these characteristics.
Common metals used in deep drawing include steel, aluminum, copper, brass, titanium, and nickel alloys, each offering distinct advantages and challenges. This document will explore these materials, focusing on how their unique properties make them suitable for deep drawing applications and their role in various industries.
Material Properties Critical to Deep Drawing
The ability of a material to undergo plastic deformation without failure is essential in the deep drawing process. Understanding key material properties helps engineers select the right metal for specific deep drawing applications.
1. Ductility and Plasticity
Ductility is the material’s ability to undergo significant plastic deformation before rupture. It is perhaps the most important property in deep drawing, as the process involves extensive stretching and bending of the material. Materials with high ductility, like low-carbon steel and aluminum, can be drawn into complex shapes without breaking.
Plasticity refers to the material’s ability to retain its deformed shape once the force is removed. In deep drawing, high plasticity ensures that the material can be stretched into the desired shape and maintain its new geometry without springing back or cracking.
2. Yield Strength and Tensile Strength
Yield strength is the amount of stress a material can withstand before it begins to deform plastically. Materials with lower yield strength are typically easier to draw because they deform under lower forces. However, they also tend to be more prone to wrinkling. Tensile strength refers to the maximum stress a material can endure before failure. In deep drawing, both yield and tensile strengths must be carefully considered to ensure that the material can withstand the applied forces without tearing or cracking.
3. Anisotropy and Its Effects
Anisotropy refers to the variation in material properties depending on the direction of the material grain. Many metals, especially those used in deep drawing, exhibit directional dependence due to the rolling process used to produce metal sheets. This directional behavior can cause issues like earing (formation of wavy edges) during deep drawing. Materials with high levels of anisotropy may experience uneven deformation, leading to defects in the final part.
4. Formability (n-value, r-value, and Elongation)
Formability is the material’s ability to undergo plastic deformation without failure. It is typically assessed using the n-value (strain hardening exponent), which indicates how much a material strengthens as it is stretched, and the r-value (plastic strain ratio), which measures the material’s resistance to thinning during drawing.
- n-value: Higher n-values indicate better resistance to necking, which allows for deeper draws without tearing.
- r-value: A high r-value suggests that the material will resist thinning, making it more suitable for deep drawing operations.
The elongation at break is another important measure of formability, indicating how much a material can be stretched before it fractures. Materials with high elongation, like aluminum and low-carbon steel, are ideal for deep drawing.
5. Work Hardening and Strain Hardening
Work hardening (or strain hardening) occurs when a material becomes stronger and less ductile as it is deformed. This property is critical in deep drawing, as it affects how the material behaves during multiple drawing stages. While work hardening improves the material’s resistance to failure, it also makes it more difficult to deform further, potentially leading to cracking or surface defects if not carefully managed.
Steel and Its Alloys in Deep Drawing
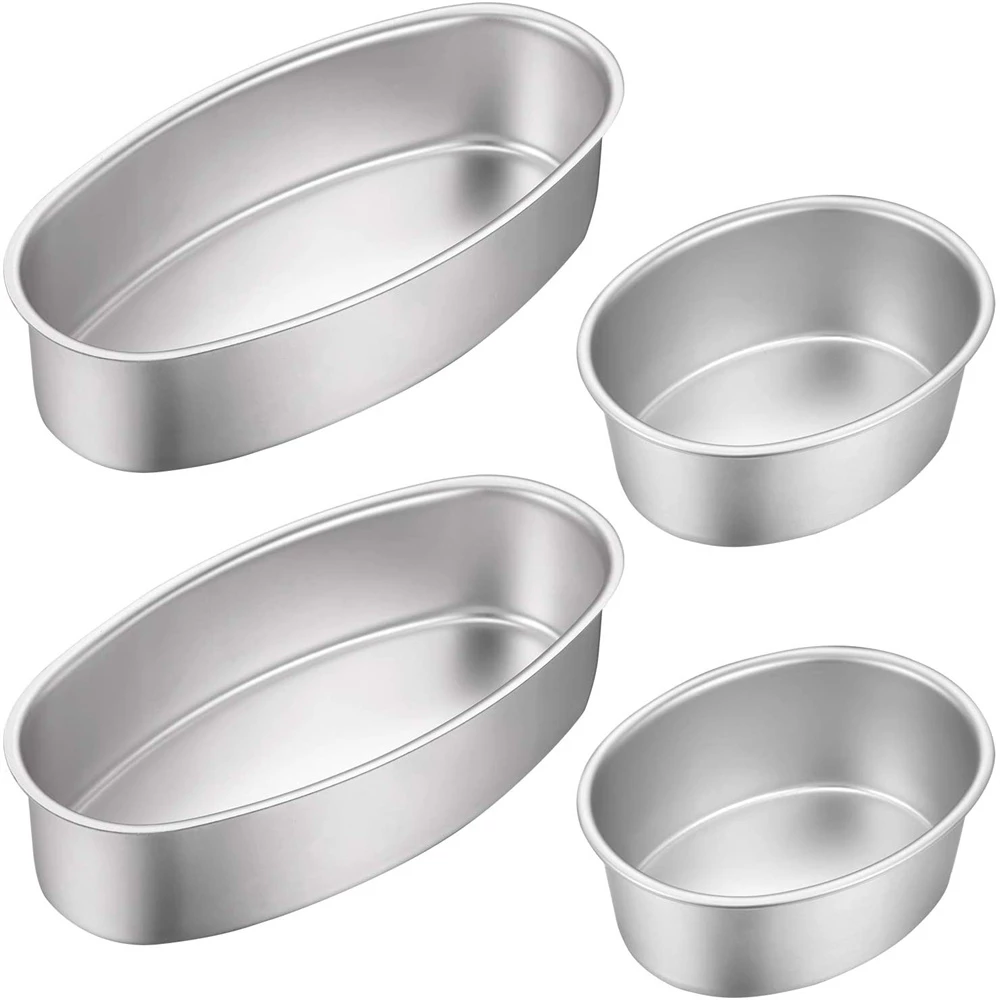
Steel is one of the most commonly used materials in deep drawing, thanks to its versatility, strength, and relatively low cost. Steel alloys come in a wide range of forms, each with distinct mechanical properties that make them suitable for different deep drawing applications.
1. Low-Carbon Steel: Properties and Applications
Low-carbon steel (also known as mild steel) is the most widely used material for deep drawing. It has a carbon content of less than 0.25%, which gives it excellent ductility and formability. Low-carbon steel can be drawn into deep, complex shapes without tearing or wrinkling, making it ideal for automotive body panels, household appliances, and various industrial components.
Key properties of low-carbon steel include:
- High ductility: Allows for deep drawing without failure.
- Good weldability: Makes it easy to join parts after forming.
- Cost-effectiveness: Low-carbon steel is relatively inexpensive compared to other metals used in deep drawing.
Low-carbon steel is often used in automotive applications, such as the production of car body panels, doors, hoods, and fenders, where large, lightweight, and structurally sound parts are required. The material’s formability ensures that manufacturers can produce large volumes of parts with uniform quality.
2. High-Strength Low-Alloy (HSLA) Steel: Advantages and Challenges
High-strength low-alloy (HSLA) steels contain small amounts of alloying elements like chromium, vanadium, and manganese, which increase their strength without significantly reducing ductility. HSLA steels offer a higher strength-to-weight ratio than low-carbon steels, making them ideal for applications where both strength and weight reduction are critical, such as in automotive and structural components.
Advantages of HSLA steel in deep drawing include:
- Higher strength: Allows for thinner, lighter parts without sacrificing structural integrity.
- Improved wear resistance: HSLA steel is more resistant to wear, reducing tool wear during deep drawing.
Challenges with HSLA steels include:
- Lower ductility: While HSLA steels have improved strength, their lower ductility compared to low-carbon steel makes them more prone to tearing and cracking during deep drawing.
- Higher drawing forces required: HSLA steels require more force to be drawn into complex shapes, which can lead to increased tool wear and energy consumption.
3. Stainless Steel: Formability, Limitations, and Uses
Stainless steel is known for its corrosion resistance, strength, and ability to withstand high temperatures, making it ideal for applications in harsh environments. It is used in a variety of industries, including food processing, medical devices, and aerospace, where durability and hygiene are important.
The most common grades of stainless steel used in deep drawing are 304 and 316, which offer a balance between formability and strength. However, stainless steel is more difficult to draw than low-carbon steel due to its higher yield strength and tendency to work harden.
Key challenges with stainless steel in deep drawing include:
- Increased tool wear: Stainless steel’s hardness can lead to higher tool wear, requiring more frequent maintenance of punches and dies.
- Springback: Stainless steel has a tendency to spring back after deformation, making it harder to achieve tight dimensional tolerances.
4. Advanced High-Strength Steels (AHSS)
Advanced high-strength steels (AHSS), such as dual-phase (DP) steel and transformation-induced plasticity (TRIP) steel, have been developed to meet the demands of modern automotive manufacturing, where weight reduction and crash performance are critical.
- Dual-phase steel (DP): Combines a soft ferritic phase with a hard martensitic phase, offering excellent strength and ductility. It is commonly used in automotive safety components like B-pillars and structural reinforcements.
- TRIP steel: Utilizes the transformation of retained austenite into martensite during deformation, providing a high strength-to-weight ratio and excellent energy absorption in crash scenarios.
While AHSS offers excellent mechanical properties for deep drawing, it is more difficult to form due to its higher strength and reduced ductility compared to traditional steels. This increases the risk of tearing and requires more precise control over process parameters.
5. Innovations in Steel for Deep Drawing
Recent advancements in steel metallurgy have focused on improving the formability of high-strength steels for deep drawing applications. Some of these innovations include:
- Third-generation AHSS: These steels combine the high strength of AHSS with improved ductility, allowing for better formability in deep drawing processes.
- Press-hardened steel (PHS): PHS is used to form ultra-high-strength components through a process known as hot forming. This involves heating the steel before drawing it into shape, which reduces the risk of cracking and allows for complex geometries to be formed.
Aluminum and Its Alloys
Aluminum is favored in deep drawing applications that require lightweight, corrosion-resistant parts. It is commonly used in industries such as automotive, aerospace, and electronics, where weight reduction is a key priority.
1. Why Aluminum is Favored in Lightweight Applications
Aluminum is significantly lighter than steel, with a density approximately one-third that of steel. This makes it ideal for applications where weight reduction is critical, such as in transportation (to improve fuel efficiency) and consumer electronics (to create lightweight, portable devices).
Key advantages of aluminum in deep drawing include:
- High ductility: Aluminum can be stretched into complex shapes without cracking.
- Corrosion resistance: Aluminum naturally forms a protective oxide layer, making it resistant to corrosion in most environments.
- Recyclability: Aluminum can be easily recycled without losing its properties, making it a sustainable choice for manufacturers.
2. 1000-Series (Pure Aluminum): Formability and Applications
The 1000-series of aluminum alloys consists of commercially pure aluminum, which offers excellent formability due to its high ductility and low yield strength. However, its relatively low strength limits its use to applications where mechanical strength is not the primary requirement.
Applications of 1000-series aluminum in deep drawing include:
- Food packaging: Aluminum cans and containers are often made from 1000-series alloys due to their formability and corrosion resistance.
- Consumer goods: Lightweight aluminum components for household appliances and electronic devices are often deep drawn from pure aluminum.
3. 5000-Series Aluminum Alloys: Marine, Automotive, and Aerospace Applications
The 5000-series aluminum alloys contain magnesium as the primary alloying element, which improves the material’s strength without significantly reducing ductility. These alloys are used in applications where a balance of strength and formability is required.
Applications of 5000-series aluminum in deep drawing include:
- Marine industry: Aluminum components for boats and ships are often drawn from 5000-series alloys due to their corrosion resistance in saltwater environments.
- Automotive industry: Lightweight components, such as body panels and structural reinforcements, are often made from 5000-series alloys to reduce vehicle weight and improve fuel efficiency.
- Aerospace industry: Aircraft structural components are often drawn from high-strength aluminum alloys in the 5000 and 6000 series.
4. Challenges of Aluminum in Deep Drawing
Despite its many advantages, aluminum presents several challenges in the deep drawing process, including:
- Cracking: Aluminum has a lower elongation at break compared to steel, making it more prone to cracking during deep drawing, especially in high-strength alloys.
- Springback: Like stainless steel, aluminum tends to spring back after being deformed, making it difficult to achieve tight tolerances.
- Lubrication requirements: Aluminum requires specialized lubricants to reduce friction during deep drawing. Without proper lubrication, aluminum can stick to the punch and die, causing defects like galling.
5. Recent Developments in Aluminum Alloys for Deep Drawing
Researchers have developed new aluminum alloys with improved formability for deep drawing applications. These innovations include:
- Aluminum-lithium alloys: These alloys offer a higher strength-to-weight ratio than traditional aluminum alloys, making them ideal for aerospace applications.
- Heat-treatable alloys: Advances in heat treatment processes have improved the formability of aluminum alloys, allowing for deeper draws without cracking or tearing.
Copper and Brass in Deep Drawing
Copper and brass are frequently used in deep drawing for applications that require high thermal or electrical conductivity, corrosion resistance, or aesthetic appeal.
1. Copper: Ductility, Thermal Conductivity, and Electrical Applications
Copper is highly ductile and exhibits excellent formability, making it suitable for deep drawing applications where complex shapes are required. Its high thermal and electrical conductivity make it the material of choice for components such as:
- Electrical connectors
- Heat exchangers
- Plumbing fittings
Due to its softness, copper can be drawn into deep, intricate shapes without excessive force. However, copper’s tendency to work harden during deformation can complicate the deep drawing process, requiring careful control over drawing speed and lubrication.
2. Brass Alloys: Formability and Uses in Plumbing, Electrical, and Decorative Products
Brass, an alloy of copper and zinc, offers good formability and is often used in decorative applications as well as functional components like:
- Plumbing fixtures
- Electrical contacts
- Musical instruments
The zinc content in brass improves its strength and corrosion resistance while maintaining sufficient ductility for deep drawing. Cartridge brass (70% copper, 30% zinc) is commonly used in deep drawing for applications like bullet casings and architectural components due to its excellent balance of strength and formability.
3. Challenges with Copper and Brass in Deep Drawing
Copper and brass present several challenges during the deep drawing process, including:
- Work hardening: Copper and brass work harden quickly during deformation, which can lead to cracking if the material becomes too brittle. To avoid this, manufacturers may use intermediate annealing processes to restore the material’s ductility between drawing stages.
- Friction and galling: Both copper and brass can stick to the punch and die during drawing, leading to surface defects. Specialized lubricants, such as graphite-based lubricants, are often required to reduce friction and prevent galling.
4. Lubrication Requirements and Solutions for Copper and Brass
Lubrication is critical in deep drawing copper and brass, as their soft, ductile nature makes them prone to sticking and galling. Water-based lubricants, oil-based lubricants, and dry film coatings are commonly used to improve material flow and protect the surface of the workpiece.
Titanium and Its Alloys
Titanium is known for its exceptional strength-to-weight ratio, corrosion resistance, and biocompatibility, making it an ideal material for industries such as aerospace, medical devices, and automotive.
1. Unique Properties of Titanium: Strength-to-Weight Ratio, Corrosion Resistance
Titanium’s high strength-to-weight ratio allows for the production of lightweight, durable components that can withstand extreme conditions. Its natural corrosion resistance also makes it suitable for applications in chemical processing, marine environments, and biomedical implants.
2. Medical and Aerospace Applications
Titanium’s biocompatibility and resistance to corrosion make it the material of choice for medical implants such as hip and knee replacements. In the aerospace industry, titanium alloys are used to manufacture components such as turbine blades, aircraft frames, and fasteners due to their ability to withstand high temperatures and harsh environments.
3. Difficulties in Forming Titanium: High Springback, Galling
Despite its advantages, titanium is challenging to form through deep drawing due to its high strength and springback effect. Springback occurs when the material tries to return to its original shape after being deformed, making it difficult to achieve precise tolerances.
Additionally, titanium has a tendency to gall, meaning that material from the blank can adhere to the punch or die during drawing. This can lead to surface defects and increased tool wear.
4. Innovations in Tooling and Lubrication for Drawing Titanium
To address these challenges, manufacturers have developed specialized tooling materials and lubricants to improve the deep drawing of titanium. These include:
- Coated punches and dies: Titanium nitride (TiN) and diamond-like carbon (DLC) coatings are applied to reduce galling and extend tool life.
- High-performance lubricants: Synthetic lubricants and solid film coatings are used to reduce friction and improve material flow during the deep drawing process.
Nickel Alloys in Deep Drawing
Nickel-based alloys are known for their high strength, corrosion resistance, and ability to withstand extreme temperatures, making them essential in industries like aerospace, chemical processing, and power generation.
1. Properties of Nickel-Based Alloys: Heat and Corrosion Resistance
Nickel alloys are often used in environments where extreme heat and corrosive chemicals are present. For example, Inconel and Hastelloy are two common nickel-based alloys used in deep drawing due to their resistance to oxidation and corrosion at high temperatures.
2. Applications in Extreme Environments: Aerospace, Chemical Processing
In the aerospace industry, nickel alloys are used for components such as turbine blades, exhaust systems, and heat exchangers, where the material must maintain its strength and resist oxidation at high temperatures. In the chemical processing industry, nickel alloys are used in reactors, pipes, and valves that handle corrosive fluids and gases.
3. Challenges in Deep Drawing Nickel Alloys: Hardening, Tool Wear
Nickel alloys tend to work harden rapidly during deformation, which increases the risk of cracking and tool wear during deep drawing. The high strength of nickel alloys also requires higher drawing forces, which can lead to increased tool wear and material galling.
4. Techniques to Improve Formability
To improve the formability of nickel alloys in deep drawing, several techniques are employed, including:
- Heat treatments: Annealing the material between drawing stages helps to reduce work hardening and restore ductility.
- Tool coatings: Applying hard coatings such as TiN or ceramic coatings to punches and dies reduces tool wear and galling, extending tool life and improving the quality of the finished part.
Magnesium Alloys in Deep Drawing
Magnesium alloys are gaining popularity in industries like automotive and aerospace due to their extremely lightweight properties. However, their use in deep drawing is still limited due to the challenges associated with forming magnesium.
1. Lightweighting Advantages of Magnesium Alloys
Magnesium is one of the lightest structural metals available, making it ideal for applications where weight reduction is critical. In the automotive industry, magnesium is used to reduce the overall weight of vehicles, leading to improved fuel efficiency and reduced emissions.
2. Applications in Automotive and Aerospace Industries
In the automotive industry, magnesium alloys are used to produce components such as gearboxes, steering wheels, and dashboard frames. In the aerospace industry, magnesium is used in aircraft seats, bracketry, and engine components to reduce weight while maintaining strength.
3. Challenges: Brittleness, Forming Temperatures, and Lubrication
Magnesium alloys are more brittle than aluminum and steel, making them more prone to cracking during deep drawing. Additionally, magnesium has a narrow range of forming temperatures, meaning that it must be heated to a specific temperature range to avoid cracking.
Magnesium also requires specialized lubricants during deep drawing to reduce friction and prevent galling. Without proper lubrication, magnesium alloys can stick to the punch and die, leading to surface defects.
4. Recent Research in Forming Magnesium for Deep Drawing
Researchers are exploring new methods to improve the deep drawing of magnesium alloys, including:
- Hot forming: Heating the magnesium to its optimal forming temperature improves ductility and reduces the risk of cracking.
- Alloy development: New magnesium alloys with improved ductility are being developed to overcome the brittleness of traditional magnesium alloys.
Recent Developments in Material Science for Deep Drawing
Advances in material science and technology have significantly improved the deep drawing process, enabling manufacturers to produce more complex and high-strength components.
1. Development of Ultra-Lightweight Materials
Researchers are continually developing new ultra-lightweight materials that offer high strength and formability, making them ideal for deep drawing applications. These materials are critical in industries like automotive and aerospace, where reducing weight without sacrificing strength is a top priority.
2. Advances in Coatings for Reducing Friction
To improve material flow and reduce tool wear, advanced coatings are being applied to punches and dies in deep drawing operations. Diamond-like carbon (DLC) coatings and ceramic coatings are among the most commonly used, offering excellent wear resistance and reducing the risk of galling.
3. Simulation Tools for Predicting Material Behavior in Deep Drawing
The use of finite element analysis (FEA) and other simulation tools allows engineers to predict how materials will behave during the deep drawing process. These tools help optimize tool design, material selection, and process parameters, reducing the need for costly trial-and-error methods.
4. Smart Materials and Adaptive Forming Technologies
Smart materials that can change their properties in response to external stimuli, such as temperature or pressure, are being explored for use in deep drawing. These materials could enable more efficient and precise forming processes by adapting to the forces applied during deep drawing.
Conclusion
Material selection is one of the most critical factors in the success of the deep drawing process. The materials used must have the right combination of ductility, strength, and formability to withstand the stresses and strains of deep drawing without failing. Different metals, such as steel, aluminum, copper, brass, titanium, and nickel alloys, each offer unique properties that make them suitable for different deep drawing applications.
Recent advancements in material science, such as the development of ultra-lightweight alloys and advanced coatings, have improved the performance of materials used in deep drawing. Additionally, the use of simulation tools and smart materials has enabled more precise control over the deep drawing process, reducing defects and improving efficiency.
As industries continue to demand lightweight, high-strength components, the development of new materials and technologies for deep drawing will play a crucial role in advancing manufacturing capabilities.
The Fundamental Principles of Deep Drawing: A Comprehensive Exploration
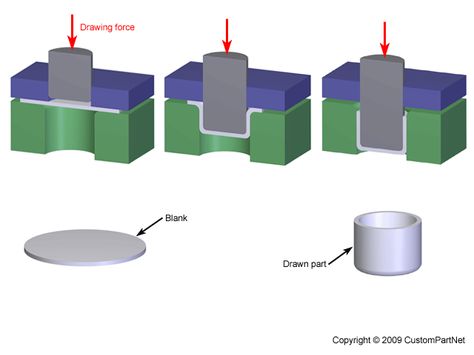
Deep drawing is a widely used manufacturing process that involves transforming flat sheet metal into complex three-dimensional shapes by applying mechanical force. It is a critical technique in industries such as automotive, aerospace, electronics, and packaging, where high precision, repeatability, and strength are essential. The success of the deep drawing process hinges on understanding the underlying mechanical and material principles involved. This text will delve into these fundamental principles, covering the mechanics of deep drawing, material properties, stress-strain behavior, tool design, process parameters, and common issues and solutions.
Introduction to Deep Drawing
Deep drawing is a sheet metal forming process in which a flat metal blank is radially drawn into a forming die by the mechanical action of a punch. The process can produce parts with a depth greater than their diameter, making it distinct from other metal forming techniques such as stamping or bending. Deep drawing is commonly used to manufacture cylindrical, box-shaped, and complex hollow parts, such as beverage cans, automotive body panels, kitchen sinks, and fuel tanks.
The deep drawing process is highly versatile, capable of producing components with intricate geometries and tight tolerances. It also ensures uniform material thickness and high structural integrity, making it ideal for industries requiring both aesthetic quality and durability. However, achieving defect-free deep drawing requires a thorough understanding of the fundamental principles governing material behavior, tool design, and process control.
The key factors influencing the deep drawing process include material properties, the interaction between the punch and die, friction, blank holder force, and lubrication. These factors determine the success of the process and the quality of the final part. By exploring the mechanical principles and parameters that control deep drawing, we can optimize the process to minimize defects such as wrinkling, tearing, and thinning, while maximizing efficiency and product quality.
Mechanics of Deep Drawing
The deep drawing process is governed by the principles of plastic deformation, which refers to the permanent change in the shape of a material when subjected to external forces. Understanding the mechanics of plastic deformation is critical for controlling how the sheet metal flows into the die and forms the desired shape.
2.1. Plastic Deformation and Stress-Strain Relationship
The deep drawing process involves the application of mechanical force to a metal blank, causing it to stretch and flow into a die cavity. This deformation occurs in the plastic region of the material’s stress-strain curve, meaning that the material is permanently deformed and does not return to its original shape once the force is removed.
The stress-strain relationship is a fundamental concept in understanding how materials behave under load. It describes how a material deforms (strain) in response to an applied stress. The elastic region of the curve represents the reversible deformation, while the plastic region represents permanent deformation. In deep drawing, the material must be deformed plastically to achieve the desired shape without cracking.
The amount of deformation a material can undergo before failure is determined by its ductility, which is a key material property in deep drawing. Ductile materials, such as low-carbon steel and aluminum, can withstand significant plastic deformation before rupturing, making them suitable for deep drawing applications.
2.2. Forces in Deep Drawing
The primary forces in deep drawing include the punch force, blank holder force, and frictional forces. These forces interact to control the flow of the material and determine the final shape and quality of the drawn part.
- Punch Force: The punch force is the force applied by the punch to drive the blank into the die. It must be high enough to overcome the material’s resistance to deformation, but not so high that it causes the material to tear. The punch force increases as the depth of the draw increases, and its magnitude depends on factors such as material properties, sheet thickness, and die geometry.
- Blank Holder Force: The blank holder force is applied by a blank holder or hold-down ring to prevent the edges of the blank from wrinkling as it is drawn into the die. Insufficient blank holder force can lead to wrinkling, while excessive force can restrict material flow and cause tearing. Achieving the correct blank holder force is essential for maintaining material flow and preventing defects.
- Frictional Forces: Friction plays a critical role in the deep drawing process, particularly at the interfaces between the blank, punch, and die. Friction opposes material flow, increasing the required punch force and influencing the distribution of stresses in the blank. While some friction is necessary to control material flow, excessive friction can lead to thinning, tearing, and tool wear. Proper lubrication is essential to minimize friction and ensure smooth material flow.
2.3. Flow of Material
Material flow during deep drawing is a complex interaction of tensile, compressive, and shear stresses. As the punch moves downward, it stretches the material radially inward toward the die cavity. The blank undergoes tensile stress at the outer edges, while the material near the punch is subjected to compressive stress as it is forced into the die.
Material flow is influenced by factors such as the material’s ductility, the shape and geometry of the die, and the blank holder force. Flow stress, which is the stress required to continue deforming the material, must be carefully controlled to avoid defects. If the material flows too quickly, it can result in wrinkling, while slow material flow can lead to excessive thinning or tearing.
Material Properties in Deep Drawing
Material selection is one of the most important aspects of the deep drawing process. Different materials behave differently under stress, and their properties directly influence how they respond to the forces applied during deep drawing. The key material properties that determine a material’s suitability for deep drawing include ductility, yield strength, tensile strength, anisotropy, and work hardening. Understanding these properties helps engineers optimize the process and select the best material for a given application.
3.1. Ductility
Ductility refers to a material’s ability to undergo significant plastic deformation before rupturing. Materials with high ductility, such as low-carbon steel and aluminum, are preferred for deep drawing because they can be stretched and formed into complex shapes without cracking. The greater the material’s ductility, the deeper the part can be drawn without failure. Ductility is especially important in deep drawing because the material undergoes large deformations, particularly in the flange area where tensile stress is concentrated.
Elongation at break, which measures the strain a material can withstand before fracturing, is commonly used as an indicator of ductility. Materials with high elongation values are more capable of undergoing the large strains associated with deep drawing, while materials with low elongation are more prone to tearing.
3.2. Yield Strength and Tensile Strength
Yield strength is the stress at which a material begins to deform plastically. In deep drawing, materials with lower yield strength are generally preferred because they require less force to deform. A lower yield strength allows the material to flow more easily into the die cavity without tearing or wrinkling. However, materials with excessively low yield strength may be prone to wrinkling or excessive thinning due to their inability to resist compressive forces.
Tensile strength, on the other hand, is the maximum stress a material can withstand before it fractures. While tensile strength is important for ensuring that the material does not rupture during drawing, it is not as critical as yield strength in most deep drawing applications. The material is typically stressed beyond its yield point but below its tensile strength.
Balancing yield strength and tensile strength is essential in deep drawing. The material should be soft enough to be drawn easily, but strong enough to resist tearing during the drawing process.
3.3. Anisotropy
Anisotropy refers to the directional dependence of a material’s mechanical properties. In deep drawing, anisotropy can significantly influence how the material deforms during the process. Most sheet metals exhibit some degree of planar anisotropy, which arises from the rolling process used to manufacture the sheets. This anisotropy can cause non-uniform deformation, leading to defects such as earing, which refers to the formation of wavy edges around the drawn part.
The degree of anisotropy in a material is characterized by the r-value (plastic strain ratio), which measures the material’s resistance to thinning during deformation. A higher r-value indicates that the material is less likely to thin out, making it more suitable for deep drawing. Materials with low anisotropy are preferred for deep drawing because they deform more uniformly and are less prone to defects.
3.4. Work Hardening and Strain Hardening
Work hardening (also known as strain hardening) occurs when a material becomes stronger and more resistant to deformation as it is plastically deformed. While work hardening improves the material’s resistance to tearing, it also makes it more difficult to deform further, which can complicate the deep drawing process.
Strain hardening is described by the n-value (strain hardening exponent), which measures how much a material strengthens as it is deformed. A higher n-value indicates better resistance to localized necking, which is critical for deep drawing, especially for deeper or more complex parts. However, excessive work hardening can lead to problems like tearing, surface defects, and increased tool wear.
In deep drawing, materials must balance ductility and work hardening. While some level of work hardening is desirable for strength and durability, excessive work hardening can make the material too brittle to be drawn into deep or complex shapes without failure.
Tooling in Deep Drawing
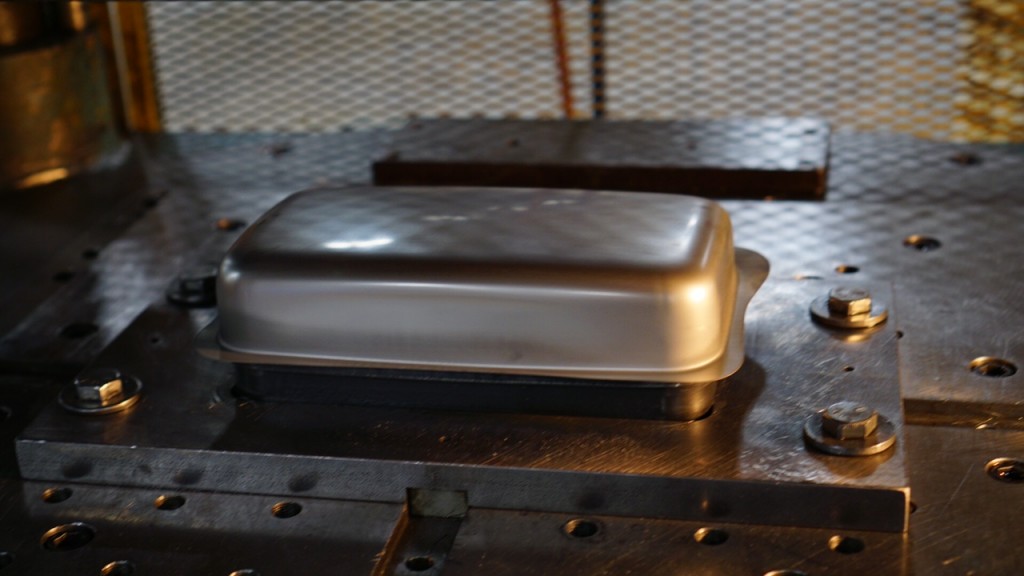
Tool design is critical to the success of the deep drawing process. The key components of the tooling system include the punch, die, and blank holder. Each tool must be precisely designed and manufactured to ensure smooth material flow, prevent defects, and produce parts with the desired geometry and dimensions. The design of these tools directly affects the forces acting on the material and determines how the material deforms during drawing.
4.1. Punch Design
The punch is responsible for pushing the blank into the die and forming the part. Its design, including its shape, size, and surface finish, is crucial to controlling material flow and minimizing defects such as tearing or thinning. Punches can have a variety of shapes depending on the desired part geometry, including cylindrical, conical, or box-shaped profiles.
Key considerations for punch design include:
- Shape and Geometry: The punch must match the desired shape of the final part. Complex geometries, such as those with deep cavities or intricate details, require carefully designed punches to control material flow and prevent localized thinning.
- Radius: The corner radius of the punch plays a critical role in the drawing process. A small radius can lead to high localized stresses, which increases the risk of tearing or cracking. Conversely, a large radius may result in wrinkling or uneven material flow. The punch radius should be optimized to ensure smooth deformation and uniform material distribution.
- Surface Finish: The punch’s surface finish affects friction between the punch and the blank. A smooth surface reduces friction, allowing for better material flow, while a rough surface may increase friction and cause defects such as galling or scratching.
4.2. Die Design
The die is the tool into which the metal blank is drawn to form the desired shape. The design of the die, including its geometry, clearance, and surface finish, is crucial for controlling material flow, minimizing friction, and ensuring consistent part dimensions.
Key factors in die design include:
- Die Shape and Geometry: The die must be designed to match the desired shape of the part. The geometry of the die cavity determines how the material will flow during the drawing process. Complex part geometries, such as those with multiple features or deep cavities, require precise die design to prevent defects such as wrinkling, tearing, or uneven wall thickness.
- Die Radius: The die entry radius is one of the most important aspects of die design. A small die radius can lead to excessive thinning or tearing of the material, while a large die radius may cause wrinkling or excessive stretching. The die radius must be carefully selected based on the material properties and the desired depth of the draw.
- Clearance Between Punch and Die: The clearance between the punch and the die is the gap through which the material flows as it is drawn into the die cavity. The clearance is typically slightly larger than the thickness of the blank to allow for material flow without excessive thinning or tearing. Incorrect clearance can result in defects such as wrinkles, tears, or uneven thickness distribution.
4.3. Blank Holder Design
The blank holder (also known as a hold-down ring) plays a critical role in controlling the flow of material into the die during the drawing process. The blank holder applies pressure to the edges of the blank, preventing it from wrinkling or folding as it is drawn into the die. However, the blank holder force must be carefully controlled to avoid defects.
Key considerations for blank holder design include:
- Force Distribution: The blank holder must apply uniform pressure around the circumference of the blank to ensure even material flow. Uneven pressure can lead to wrinkling or tearing at the edges of the part. In some cases, adjustable blank holders or segmented blank holders are used to apply variable pressure based on the material’s behavior during drawing.
- Blank Holder Force: The force applied by the blank holder is critical to preventing defects. Too little force can result in wrinkling, while too much force can restrict material flow and cause tearing. The optimal blank holder force depends on the material properties, part geometry, and depth of the draw.
- Lubrication and Friction: The blank holder’s interaction with the blank can generate friction, which affects material flow. Proper lubrication is essential to reduce friction and ensure smooth material movement. Lubricants must be carefully selected based on the material being drawn and the surface finish of the blank holder.
Process Parameters in Deep Drawing
Controlling the process parameters in deep drawing is essential for producing high-quality parts and minimizing defects. These parameters include blank holder force, drawing speed, drawing ratio, and lubrication. By optimizing these parameters, engineers can ensure smooth material flow, uniform thickness distribution, and consistent part geometry.
5.1. Blank Holder Force
The blank holder force is one of the most critical parameters in the deep drawing process. It controls the material flow into the die and prevents the blank from wrinkling or folding as it is drawn. The correct blank holder force depends on the material properties, the part geometry, and the depth of the draw.
Optimizing blank holder force:
- Too little force: If the blank holder force is too low, the material will flow too freely into the die, resulting in wrinkling or folding at the edges of the part.
- Too much force: If the blank holder force is too high, the material may not flow into the die properly, leading to tearing or cracking. Excessive blank holder force can also cause excessive thinning or uneven wall thickness in the part.
To optimize blank holder force, engineers often use dynamic blank holder systems that adjust the force in real time during the drawing process. These systems use sensors and control algorithms to monitor material flow and adjust the force based on the material’s behavior.
5.2. Drawing Ratio and Limiting Drawing Ratio (LDR)
The drawing ratio is the ratio of the blank diameter to the diameter of the drawn part. It is a measure of the severity of the drawing process. A higher drawing ratio indicates a more severe draw, requiring greater force and increasing the likelihood of defects such as wrinkling or tearing.
The limiting drawing ratio (LDR) is the maximum drawing ratio that can be achieved without causing failure in the material. The LDR depends on the material properties, such as ductility and formability, as well as the design of the punch, die, and blank holder. To achieve a successful deep draw, engineers must design the process to stay within the material’s LDR.
Maximizing drawing ratio:
- Material selection: Materials with high ductility and formability, such as low-carbon steel and aluminum, can achieve higher drawing ratios without failure. Engineers must select materials that can withstand the strains imposed by deep drawing without tearing or wrinkling.
- Process optimization: By optimizing parameters such as blank holder force, punch speed, and lubrication, engineers can increase the drawing ratio while minimizing the risk of defects.
5.3. Drawing Speed
The drawing speed affects the rate at which the material is deformed and drawn into the die. Drawing speed influences the material’s behavior, the heat generated during the process, and the risk of defects such as tearing or surface defects.
Optimizing drawing speed:
- High drawing speed: While high drawing speeds can increase productivity, they can also generate more heat due to friction, leading to defects such as excessive thinning or surface cracking. High speeds can also increase the risk of tearing, especially in brittle materials.
- Low drawing speed: Lower drawing speeds provide more control over material flow, reducing the risk of defects. However, slow drawing speeds reduce productivity and can increase the overall cycle time for each part.
Hydraulic deep drawing presses allow for precise control over drawing speed, enabling engineers to optimize the process based on the material properties and part geometry. In some cases, variable-speed systems are used to adjust the speed throughout the drawing process, providing faster speeds during initial stages and slower speeds as the part is drawn deeper into the die.
5.4. Lubrication
Lubrication plays a critical role in reducing friction between the blank, punch, and die during deep drawing. Proper lubrication ensures smooth material flow, minimizes tool wear, and reduces the risk of defects such as galling, surface scratches, or thinning.
Selecting the right lubricant:
- Material-specific lubricants: Different materials require different types of lubricants. For example, aluminum requires high-viscosity lubricants to prevent galling, while steel may benefit from oil-based or synthetic lubricants to reduce friction and heat generation.
- Lubricant application: Lubricants can be applied in various ways, including spraying, rolling, or coating the blank. Uniform application is essential to prevent localized friction, which can lead to surface defects or uneven material flow.
Deep Drawing Process
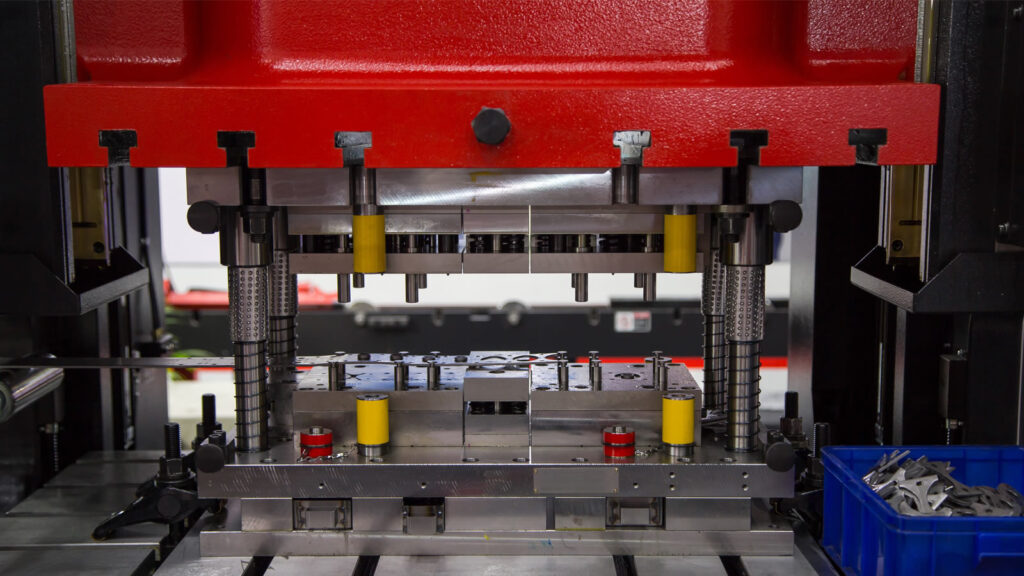
The deep drawing process is one of the most widely used metal forming techniques in modern manufacturing. From producing everyday household items like sinks and cooking pots to manufacturing critical components in the automotive, aerospace, and electronics industries, deep drawing plays a vital role in shaping sheet metal into three-dimensional products with a high degree of precision and efficiency.
This 10,000-word document will provide a thorough exploration of the deep drawing process, covering its fundamental principles, technical aspects, key variables, equipment, material selection, challenges, defect prevention, and recent advancements. The explanation will also include real-world applications and best practices for optimizing the deep drawing process.
Introduction to Deep Drawing
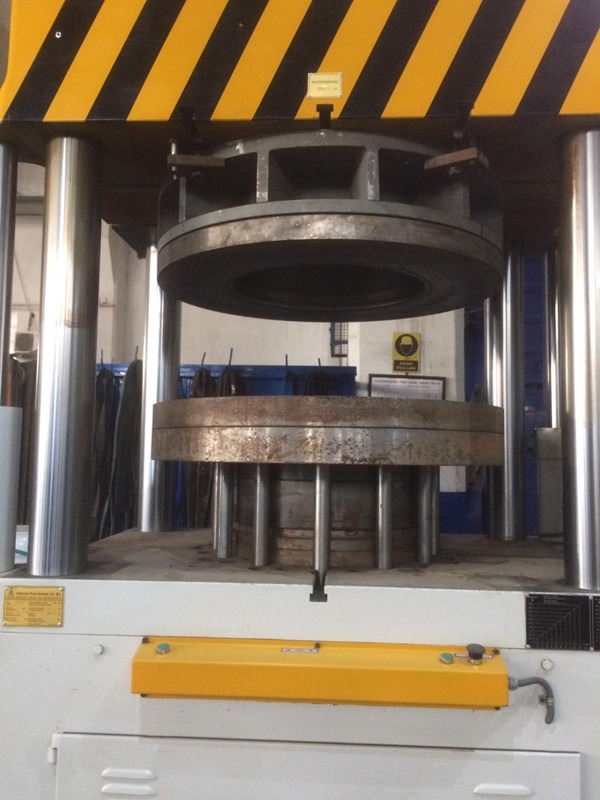
Deep drawing is a metal forming process in which a flat sheet of metal, referred to as a blank, is radially drawn into a forming die by the mechanical action of a punch. The process transforms the flat sheet into a hollow, cylindrical, or box-shaped part, where the depth of the drawn part is often greater than its diameter. This method distinguishes deep drawing from other forming techniques like stamping or bending, where the depth of the formed part is relatively shallow.
The process involves subjecting the metal blank to significant tensile and compressive forces that cause the material to deform plastically and take the shape of the die cavity. The result is a component with uniform thickness, smooth surfaces, and precise dimensions.
The deep drawing process is commonly used for producing components such as:
- Cylindrical parts: beverage cans, cups, and pots
- Box-shaped parts: battery enclosures, automotive fuel tanks
- Complex geometries: automotive body panels, aerospace components
1.2 Historical Background
The deep drawing process can trace its roots to ancient metalworking practices, but it wasn’t until the 19th century that deep drawing became a common industrial practice. Early methods of metal forming were largely manual and relied on hammers and rudimentary dies to shape metal. However, the invention of the hydraulic press in the late 1800s revolutionized the deep drawing process, allowing for more precise control over pressure and speed, and enabling the mass production of deep-drawn parts.
The development of more advanced materials, tooling, and lubrication technologies during the 20th century further enhanced the deep drawing process. Today, with the advent of computer-controlled hydraulic presses, servo-driven systems, and finite element analysis (FEA) simulations, deep drawing has evolved into a highly sophisticated and efficient manufacturing technique.
1.3 Importance in Manufacturing Industries
Deep drawing is integral to many manufacturing industries due to its ability to produce high-quality, durable components with complex geometries in large volumes. Some of the key industries that rely on deep drawing include:
- Automotive Industry: Deep drawing is used to manufacture critical automotive components such as body panels, fuel tanks, and transmission housings. These parts need to be strong, lightweight, and produced in high volumes with consistent quality.
- Aerospace Industry: The aerospace sector relies on deep drawing for components like fuselage panels, landing gear components, and engine housings, where precision, strength, and weight savings are paramount.
- Consumer Goods and Electronics: The production of household items such as cookware, kitchen sinks, and electronic device enclosures often involves deep drawing to create seamless, aesthetically pleasing, and structurally sound products.
- Packaging Industry: Beverage cans, food containers, and cosmetic packaging are frequently deep drawn from materials like aluminum and tin, where uniformity, surface finish, and material efficiency are essential.
The versatility of deep drawing, coupled with advances in automation and material science, makes it a preferred process for a wide range of industries, particularly when manufacturing parts that require high precision, repeatability, and strength.
Fundamental Principles of Deep Drawing
To fully understand the deep drawing process, it’s important to explore the fundamental principles that govern material behavior, force distribution, and the interaction between tooling and the blank. These principles are rooted in the mechanics of plastic deformation and the stress-strain relationship of the material.
2.1 Plastic Deformation and Material Flow
Deep drawing relies on the plastic deformation of the material, which refers to its ability to undergo permanent change in shape when subjected to a force beyond its elastic limit. When a blank is placed on a die and subjected to force from a punch, the material in the blank flows radially toward the die cavity. During this process, the material must undergo significant tensile and compressive stresses to conform to the die’s shape.
Plastic deformation occurs in two main regions:
- Tensile deformation: This takes place in the flange area of the blank, where the material is stretched and pulled into the die.
- Compressive deformation: In areas closer to the punch and die interface, the material is compressed as it flows into the die, conforming to the shape of the punch and die cavity.
The material must have enough ductility (the ability to undergo significant plastic deformation before failure) to withstand these stresses without tearing or cracking. As the material is drawn, it becomes thinner in certain regions, especially near the corners and edges of the part, where the greatest amount of stretching occurs.
2.2 Stress-Strain Behavior in Deep Drawing
The stress-strain relationship is critical in understanding how a material behaves during deep drawing. This relationship is typically depicted in a stress-strain curve, which shows how a material responds to an applied load.
- Elastic region: At the initial stages of loading, the material deforms elastically, meaning that it will return to its original shape if the load is removed. In deep drawing, however, the material is intentionally deformed beyond this point to achieve permanent shape changes.
- Plastic region: Beyond the elastic limit, the material enters the plastic region, where it deforms permanently. The stress required to continue deforming the material is known as flow stress. Flow stress increases as the material is drawn deeper into the die, particularly in areas where the material is stretched the most.
- Necking and failure: If the material is stretched too far, it can undergo necking, a localized reduction in cross-sectional area that precedes tearing or cracking. Preventing necking and controlling strain distribution is a key challenge in deep drawing.
Materials with high tensile strength and ductility, such as low-carbon steel and aluminum, are better suited for deep drawing because they can withstand higher levels of strain without failure. The ability to distribute strain uniformly throughout the blank is crucial for avoiding defects like tearing or wrinkling.
2.3 Key Forces in Deep Drawing
Several forces are involved in the deep drawing process, each of which must be carefully controlled to ensure successful material flow and avoid defects.
- Punch Force: The punch applies force to the blank, driving it into the die cavity. The magnitude of the punch force depends on factors such as material thickness, material properties, the depth of the draw, and friction at the punch-blank interface. The punch force must be sufficient to overcome the material’s resistance to deformation but not so high that it causes tearing or excessive thinning.
- Blank Holder Force: The blank holder applies pressure around the edges of the blank to prevent it from wrinkling as it is drawn into the die. The blank holder force must be optimized; too little force allows the material to wrinkle, while too much force restricts material flow, increasing the risk of tearing. The blank holder force is usually applied by hydraulic or mechanical systems, and modern presses may feature adjustable or dynamic blank holders that allow for real-time adjustments.
- Frictional Forces: Friction plays a significant role in deep drawing, particularly at the interfaces between the punch, die, and blank. While friction helps control material flow, excessive friction increases the punch force and can lead to defects like galling (where material adheres to the die) or thinning. Proper lubrication is essential to reduce friction and ensure smooth material movement.
2.4 Material Flow in Deep Drawing
Material flow during deep drawing is a complex interaction of tensile, compressive, and shear stresses. As the punch moves downward and draws the blank into the die, the material undergoes various deformations, including stretching, bending, and compressing. These deformations must be managed carefully to achieve the desired part shape without defects.
Flow behavior in deep drawing can be summarized as follows:
- Radial flow: The material flows radially inward toward the punch as the blank is drawn into the die. This flow creates tensile stresses in the flange, which can lead to thinning if the material is not properly supported by the blank holder.
- Compressive stresses: In the areas of the blank that contact the die, the material undergoes compressive stresses as it is pushed into the die cavity. This helps form the shape of the part but must be balanced with the tensile stresses to avoid wrinkling or tearing.
- Thinning: The material tends to thin out at the areas experiencing the greatest tensile stress, particularly near the punch corners. Proper control of punch speed, blank holder force, and lubrication helps to distribute the thinning evenly and minimize the risk of failure.
Equipment and Tooling in Deep Drawing
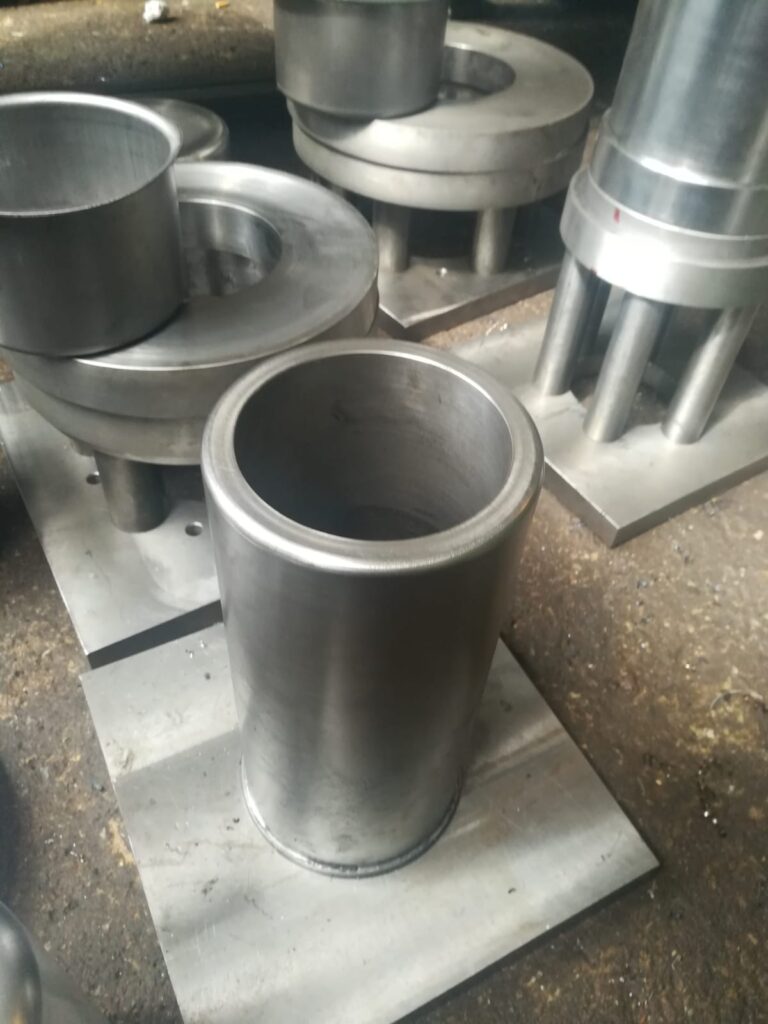
The success of the deep drawing process heavily depends on the design and precision of the equipment and tooling used. Tooling refers to the components that interact with the material during the drawing process, including the punch, die, and blank holder. Each of these tools plays a specific role in shaping the material and must be designed to accommodate the material properties, part geometry, and process parameters.
3.1 Components of a Deep Drawing Press
The primary machine used in deep drawing is the deep drawing press, which can be mechanical, hydraulic, or servo-driven. Each type of press has specific advantages and is chosen based on the material being drawn, the complexity of the part, and production requirements.
- Mechanical Presses: Mechanical presses operate using a flywheel and crankshaft mechanism that converts rotational motion into linear motion. These presses are known for their high speed and precision, making them ideal for high-volume production of shallow-drawn parts. However, they lack the flexibility to control force and speed throughout the stroke, which can limit their use in complex or deep draws.
- Hydraulic Presses: Hydraulic presses use a hydraulic system to apply force, offering more precise control over force, speed, and stroke length. These presses are capable of generating high forces and are preferred for deep draws, as they can maintain consistent force throughout the stroke. The flexibility of hydraulic presses makes them suitable for a wide range of materials and part geometries.
- Servo-Driven Presses: Servo-driven presses use electric motors to control the movement of the ram, allowing for precise control over speed and force. These presses offer the highest level of flexibility, enabling dynamic adjustments during the drawing process. Servo-driven presses are often used in advanced manufacturing applications that require high precision and real-time control over process parameters.
3.2 Punch Design in Deep Drawing
The punch is a critical component that drives the blank into the die to form the desired part shape. The punch is responsible for applying the necessary force to deform the material, and its design directly influences the success of the deep drawing process.
Key considerations for punch design include:
- Shape and Geometry: The shape of the punch must match the desired shape of the final part. Punches can have cylindrical, conical, or box-like geometries depending on the complexity of the part being formed. Complex shapes, such as those with deep cavities or intricate details, require precise punch design to control material flow and prevent defects like tearing or thinning.
- Punch Radius: The punch corner radius is a crucial design parameter. A sharp punch radius can result in high localized stresses, increasing the likelihood of tearing or cracking at the corners of the drawn part. Conversely, a larger punch radius helps distribute stress more evenly, reducing the risk of defects but may lead to wrinkling if not properly controlled. Optimizing the punch radius based on the material properties and part geometry is essential to ensure smooth material flow and uniform thickness distribution.
- Surface Finish and Coatings: The surface finish of the punch affects friction at the punch-blank interface, which in turn influences material flow. A smooth surface finish reduces friction, allowing the material to flow more easily, while a rough surface can increase friction and lead to defects like galling (adhesion of material to the punch). To reduce wear and improve the longevity of the tooling, punches may be coated with materials such as titanium nitride (TiN) or diamond-like carbon (DLC) coatings, which provide excellent wear resistance and reduce friction.
3.3 Die Design in Deep Drawing
The die is the component into which the metal blank is drawn by the punch, shaping the blank into the desired form. The design of the die plays a critical role in controlling material flow, minimizing friction, and ensuring the final part meets dimensional specifications.
Key aspects of die design include:
- Die Cavity Shape: The geometry of the die cavity determines the shape of the final part. Complex part geometries, such as those with sharp corners or deep cavities, require precise die design to control material flow and avoid defects such as wrinkling, tearing, or uneven wall thickness.
- Die Radius: The die entry radius (the radius at the top edge of the die where the blank first enters the die cavity) is one of the most critical aspects of die design. A small die radius can result in high localized stress, leading to tearing or excessive thinning of the material. Conversely, a large die radius may reduce stress concentrations but can lead to wrinkling or material folding. The die radius must be optimized based on the material properties and the depth of the draw.
- Clearance Between Punch and Die: The clearance between the punch and die is the gap through which the material flows as it is drawn into the die cavity. The clearance is typically slightly larger than the thickness of the blank to allow for material flow without excessive thinning or tearing. Incorrect clearance can result in defects such as wrinkles, tears, or uneven thickness distribution. The clearance must be carefully calculated based on the material properties and part dimensions.
3.4 Blank Holder Design
The blank holder (also known as a hold-down ring) is used to apply pressure to the edges of the blank during the drawing process, preventing it from wrinkling or folding as it is drawn into the die. The design of the blank holder and the force it applies are critical to ensuring smooth material flow and preventing defects.
Key considerations for blank holder design include:
- Force Distribution: The blank holder must apply uniform pressure around the circumference of the blank to ensure even material flow. Uneven pressure can lead to wrinkling or tearing at the edges of the part. In some cases, adjustable blank holders or segmented blank holders are used to apply variable pressure based on the material’s behavior during drawing.
- Blank Holder Force: The force applied by the blank holder must be carefully controlled to avoid defects. Too little force allows the material to wrinkle, while too much force restricts material flow, leading to tearing. The optimal blank holder force depends on factors such as material thickness, part geometry, and the depth of the draw. In modern deep drawing presses, dynamic blank holder systems can adjust the force in real time to optimize material flow and prevent defects.
- Lubrication and Friction Management: The interaction between the blank holder and the blank generates friction, which affects material flow. Proper lubrication is essential to reduce friction and ensure smooth material movement. Lubricants must be carefully selected based on the material being drawn and the surface finish of the blank holder. In advanced deep drawing operations, dry film lubricants or coated tooling may be used to reduce friction and improve process efficiency.
3.5 Tool Coatings and Wear Prevention
The wear and tear on tooling during deep drawing can significantly affect the quality of the final parts and the overall efficiency of the process. Tooling must withstand high stresses, friction, and contact with abrasive materials, which can lead to premature wear if not properly addressed.
Common tool coatings for deep drawing include:
- Titanium Nitride (TiN): TiN is a popular coating material for punches and dies due to its hardness, wear resistance, and low friction properties. It helps reduce tool wear and improves the longevity of the tooling, especially when working with hard or abrasive materials like stainless steel.
- Diamond-Like Carbon (DLC): DLC coatings provide excellent hardness, wear resistance, and low friction, making them ideal for deep drawing applications involving hard-to-form materials like titanium or nickel-based alloys. DLC coatings can significantly reduce the risk of galling and improve tool life.
- Ceramic Coatings: Ceramic coatings offer high-temperature resistance, wear resistance, and low friction, making them suitable for deep drawing applications where the tooling is subjected to extreme heat and pressure.
By applying these coatings to the punch and die, manufacturers can reduce friction, minimize tool wear, and improve the overall efficiency and longevity of the deep drawing process.
Stages of the Deep Drawing Process
The deep drawing process is a multi-stage operation that transforms a flat metal blank into a three-dimensional part through a series of forming steps. Each stage of the process plays a critical role in shaping the material, controlling material flow, and achieving the desired part geometry. The primary stages of the deep drawing process include blanking, drawing, redrawing, and trimming.
4.1 Blanking
The first stage of the deep drawing process is blanking, where a flat sheet of metal is cut into a circular or rectangular shape known as a blank. The blank is typically cut from a larger sheet using a punch and die set. Blanking is a critical step because any imperfections in the blank, such as rough edges or surface defects, can lead to defects during the subsequent drawing stages.
Key considerations for blanking include:
- Material Selection: The material used for the blank must have sufficient ductility to undergo the large deformations associated with deep drawing. Common materials include low-carbon steel, aluminum, stainless steel, and copper. The material’s thickness, yield strength, and formability must be carefully considered to ensure successful drawing.
- Blank Size and Shape: The size and shape of the blank are determined by the dimensions of the final part. The blank must be slightly larger than the part to allow for material flow during drawing. In some cases, the blank may have a circular shape for cylindrical parts or a rectangular shape for box-like parts. Proper blank alignment with the punch and die is essential to avoid defects.
- Surface Finish and Edge Quality: The surface finish of the blank and the quality of the edges are critical to ensuring smooth material flow during drawing. Rough or uneven edges can cause tearing or wrinkling during the drawing process. The edges of the blank must be clean and free from burrs or sharp corners that could interfere with material flow.
4.2 Drawing
The drawing stage is the core of the deep drawing process, where the blank is transformed into a three-dimensional shape by being drawn into a die cavity using a punch. During this stage, the blank undergoes significant tensile and compressive stresses as it flows into the die and takes on the desired shape.
Key steps in the drawing process include:
- Punch Movement: The punch moves downward, pressing the blank into the die cavity. As the blank is drawn into the die, it is stretched and compressed to conform to the shape of the die. The punch must apply sufficient force to overcome the material’s resistance to deformation without causing tearing or excessive thinning.
- Material Flow: As the blank is drawn into the die, the material flows radially inward toward the punch. The outer edges of the blank are subjected to tensile stresses, while the material near the punch and die interface is compressed. Proper control of material flow is essential to prevent defects such as wrinkling, tearing, or uneven wall thickness.
- Blank Holder Pressure: The blank holder applies pressure to the edges of the blank to prevent wrinkling. The blank holder force must be carefully controlled to allow the material to flow into the die without restriction. Too much blank holder pressure can cause the material to tear, while too little pressure can result in wrinkling.
4.3 Redrawing
In cases where the depth of the part exceeds the material’s ability to be drawn in a single pass, a secondary operation known as redrawing is performed. Redrawing involves repeating the drawing process in multiple stages, with each stage using a progressively smaller punch and die to achieve the desired depth.
Key considerations for redrawing include:
- Redrawing Ratio: The redrawing ratio is the ratio of the diameter of the blank after the first drawing stage to the diameter of the blank after the redrawing stage. The redrawing ratio determines the severity of the redrawing process and the amount of material that must be stretched to achieve the desired depth. If the redrawing ratio is too high, the material may tear or become excessively thinned.
- Intermediate Annealing: In some cases, the material may undergo work hardening during the initial drawing stage, making it more difficult to deform further. To restore the material’s ductility, an intermediate annealing process may be performed between drawing stages. Annealing involves heating the material to a specific temperature to relieve internal stresses and restore its ability to undergo plastic deformation.
4.4 Trimming and Finishing
After the part has been drawn to its final shape, excess material may need to be removed from the edges. This is done through a process called trimming, where specialized cutting tools are used to remove any excess material and smooth out the edges of the part. Trimming is especially important in applications where dimensional accuracy and surface quality are critical.
Finishing processes may also be required to achieve the desired surface quality or dimensional accuracy. Common finishing processes include deburring, polishing, and surface treatments such as anodizing or plating. These processes help to remove sharp edges, improve surface finish, and enhance the part’s corrosion resistance or aesthetic appeal.
Materials Used in Deep Drawing
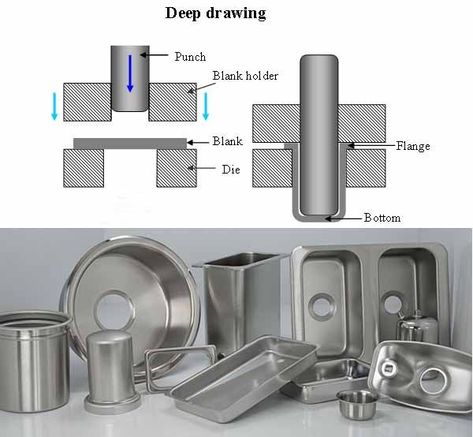
Material selection is a critical aspect of the deep drawing process. The material must have the right combination of ductility, formability, strength, and thickness to withstand the stresses imposed during drawing without failing. Different metals exhibit different behaviors during deep drawing, and each has specific advantages and limitations depending on the application.
5.1 Low-Carbon Steel
Low-carbon steel, also known as mild steel, is one of the most commonly used materials in deep drawing due to its excellent formability and cost-effectiveness. Low-carbon steel has a relatively low yield strength and high ductility, allowing it to be drawn into deep and complex shapes without tearing or cracking.
- Advantages: Low-carbon steel is easy to form, weld, and machine. It offers good strength and durability, making it suitable for applications in the automotive and construction industries. Parts such as automotive body panels, fuel tanks, and structural components are often made from low-carbon steel.
- Limitations: Low-carbon steel is susceptible to corrosion, so it may require surface treatments such as galvanizing or painting to improve its corrosion resistance.
5.2 Aluminum
Aluminum is widely used in deep drawing for applications that require lightweight, corrosion-resistant parts. It is commonly used in industries such as automotive, aerospace, and packaging, where weight reduction is a key priority.
- Advantages: Aluminum is lightweight, highly ductile, and has excellent corrosion resistance. It is ideal for applications where weight savings are critical, such as in the production of automotive body panels, aircraft components, and beverage cans. Aluminum is also highly recyclable, making it a sustainable choice for many manufacturers.
- Limitations: Aluminum is more prone to springback than other metals, meaning it tends to return to its original shape after being deformed. This can make it challenging to achieve tight dimensional tolerances. Additionally, aluminum requires specialized lubricants to reduce friction during the drawing process.
5.3 Stainless Steel
Stainless steel is known for its high strength, excellent corrosion resistance, and ability to withstand high temperatures. It is commonly used in industries such as food processing, medical devices, and aerospace, where durability and hygiene are important.
- Advantages: Stainless steel offers excellent mechanical properties and corrosion resistance, making it ideal for applications where the part will be exposed to harsh environments or high temperatures. Stainless steel is commonly used to manufacture kitchen sinks, medical instruments, and aircraft components.
- Limitations: Stainless steel is more difficult to draw than low-carbon steel or aluminum due to its higher yield strength and tendency to work harden. It requires higher drawing forces and specialized tooling to prevent tearing or cracking.
5.4 Copper and Brass
Copper and brass are frequently used in deep drawing for applications that require high thermal or electrical conductivity, corrosion resistance, or aesthetic appeal.
- Advantages: Copper is highly ductile and exhibits excellent formability, making it suitable for deep drawing applications where complex shapes are required. Its high thermal and electrical conductivity make it the material of choice for components such as electrical connectors, heat exchangers, and plumbing fittings.
- Limitations: Copper and brass tend to work harden quickly during deformation, which can complicate the deep drawing process. Intermediate annealing may be required to restore ductility between drawing stages.
5.5 Titanium
Titanium is known for its exceptional strength-to-weight ratio, corrosion resistance, and biocompatibility, making it an ideal material for industries such as aerospace, medical devices, and automotive.
- Advantages: Titanium’s high strength-to-weight ratio allows for the production of lightweight, durable components that can withstand extreme conditions. Its natural corrosion resistance also makes it suitable for applications in chemical processing, marine environments, and biomedical implants.
- Limitations: Titanium is challenging to form through deep drawing due to its high strength and springback effect. Springback occurs when the material tries to return to its original shape after being deformed, making it difficult to achieve precise tolerances. Titanium also has a tendency to gall, meaning that material from the blank can adhere to the punch or die during drawing.
5.6 Magnesium Alloys
Magnesium alloys are gaining popularity in industries like automotive and aerospace due to their extremely lightweight properties. However, their use in deep drawing is still limited due to the challenges associated with forming magnesium.
- Advantages: Magnesium is one of the lightest structural metals available, making it ideal for applications where weight reduction is critical. In the automotive industry, magnesium is used to reduce the overall weight of vehicles, leading to improved fuel efficiency and reduced emissions.
- Limitations: Magnesium alloys are more brittle than aluminum and steel, making them more prone to cracking during deep drawing. Additionally, magnesium has a narrow range of forming temperatures, meaning that it must be heated to a specific temperature range to avoid cracking.
Process Variables and Parameters in Deep Drawing
The quality and efficiency of the deep drawing process are highly dependent on several process variables and parameters, including blank holder force, punch speed, drawing ratio, and lubrication. By optimizing these parameters, engineers can produce high-quality parts while minimizing defects such as wrinkling, tearing, or thinning.
6.1 Blank Holder Force
The blank holder force is one of the most critical parameters in deep drawing. It controls the material flow into the die and prevents the blank from wrinkling or folding as it is drawn. The correct blank holder force depends on the material properties, the part geometry, and the depth of the draw.
Optimizing blank holder force:
- Too little force: If the blank holder force is too low, the material will flow too freely into the die, resulting in wrinkling or folding at the edges of the part.
- Too much force: If the blank holder force is too high, the material may not flow into the die properly, leading to tearing or cracking. Excessive blank holder force can also cause excessive thinning or uneven wall thickness in the part.
To optimize blank holder force, engineers often use dynamic blank holder systems that adjust the force in real time during the drawing process. These systems use sensors and control algorithms to monitor material flow and adjust the force based on the material’s behavior.
6.2 Punch Speed and Pressure
The punch speed affects the rate at which the material is deformed and drawn into the die. Punch speed influences the material’s behavior, the heat generated during the process, and the risk of defects such as tearing or surface defects.
Optimizing punch speed:
- High punch speed: While high punch speeds can increase productivity, they can also generate more heat due to friction, leading to defects such as excessive thinning or surface cracking. High speeds can also increase the risk of tearing, especially in brittle materials.
- Low punch speed: Lower punch speeds provide more control over material flow, reducing the risk of defects. However, slow punch speeds reduce productivity and can increase the overall cycle time for each part.
Hydraulic and servo-driven deep drawing presses allow for precise control over punch speed and pressure, enabling engineers to optimize the process based on the material properties and part geometry.
6.3 Drawing Ratio and Limiting Drawing Ratio (LDR)
The drawing ratio is the ratio of the blank diameter to the diameter of the drawn part. It is a measure of the severity of the drawing process. A higher drawing ratio indicates a more severe draw, requiring greater force and increasing the likelihood of defects such as wrinkling or tearing.
The limiting drawing ratio (LDR) is the maximum drawing ratio that can be achieved without causing failure in the material. The LDR depends on the material properties, such as ductility and formability, as well as the design of the punch, die, and blank holder. To achieve a successful deep draw, engineers must design the process to stay within the material’s LDR.
Maximizing drawing ratio:
- Material selection: Materials with high ductility and formability, such as low-carbon steel and aluminum, can achieve higher drawing ratios without failure. Engineers must select materials that can withstand the strains imposed by deep drawing without tearing or wrinkling.
- Process optimization: By optimizing parameters such as blank holder force, punch speed, and lubrication, engineers can increase the drawing ratio while minimizing the risk of defects.
6.4 Lubrication and Friction Management
Lubrication plays a critical role in reducing friction between the blank, punch, and die during deep drawing. Proper lubrication ensures smooth material flow, minimizes tool wear, and reduces the risk of defects such as galling, surface scratches, or thinning.
Selecting the right lubricant:
- Material-specific lubricants: Different materials require different types of lubricants. For example, aluminum requires high-viscosity lubricants to prevent galling, while steel may benefit from oil-based or synthetic lubricants to reduce friction and heat generation.
- Lubricant application: Lubricants can be applied in various ways, including spraying, rolling, or coating the blank. Uniform application is essential to prevent localized friction, which can lead to surface defects or uneven material flow.
In advanced deep drawing operations, dry film lubricants or coated tooling may be used to improve process efficiency and reduce friction. These specialized lubricants and coatings help ensure consistent material flow and prevent defects.
Defects in Deep Drawing and Their Solutions
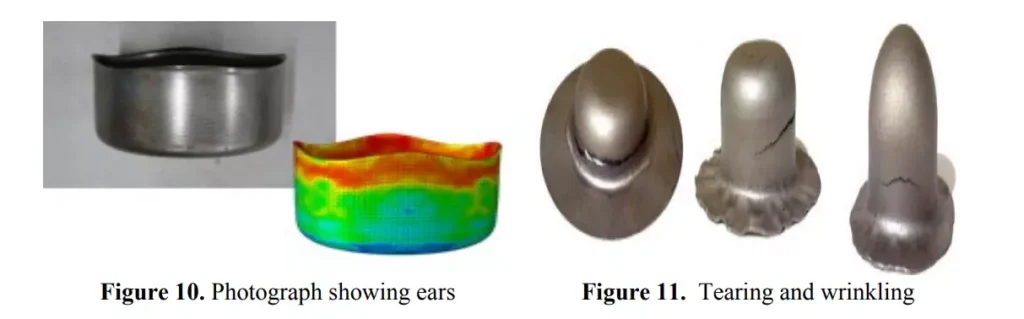
Despite careful planning and optimization, defects can occur during the deep drawing process. These defects are often the result of improper control of process parameters, material properties, or tool design. Some common defects in deep drawing include wrinkling, tearing, thinning, and earing.
7.1 Wrinkling
Wrinkling occurs when the blank holder force is too low, allowing the material to flow too freely into the die. This results in excess material bunching up, forming wrinkles around the edges of the part. Wrinkling is more likely to occur in deeper draws or when drawing materials with low stiffness.
Solution: Increasing the blank holder force or adjusting the lubrication can help prevent wrinkling. In some cases, redesigning the die to provide better material flow can also reduce the risk of wrinkling.
7.2 Tearing
Tearing is a catastrophic failure that occurs when the material is overstretched and can no longer withstand the applied forces. It often happens when the punch speed is too high, the material is too brittle, or the die design is not suitable for the material being drawn.
Solution: Reducing the punch speed and ensuring that the material’s thickness and ductility are appropriate for the drawing process can help prevent tearing. Lubrication also plays a role in reducing the likelihood of tearing by minimizing friction.
7.3 Thinning
Thinning occurs when the material becomes too stretched in certain areas, resulting in a reduction in thickness. Thinning can weaken the part and increase the risk of failure during use. Proper control of punch speed, blank holder force, and lubrication can help to distribute the thinning evenly and minimize the risk of failure.
7.4 Earing
Earing refers to the formation of wavy edges on the part due to anisotropy in the material’s grain structure. Materials with high levels of anisotropy may deform unevenly, resulting in ears or flanges around the edges of the part.
Solution: To avoid earing, engineers can select materials with lower anisotropy or adjust the orientation of the blank relative to the material’s grain direction.
Finite Element Analysis (FEA) and Simulation in Deep Drawing
Finite Element Analysis (FEA) is a computational technique used to simulate the behavior of materials during the deep drawing process. FEA allows engineers to predict how the material will deform under various conditions and optimize the design of the punch, die, and process parameters.
8.1 Role of FEA in Process Optimization
FEA is widely used in the deep drawing process to analyze material flow, stress distribution, and potential defects. By simulating the deep drawing process in a virtual environment, engineers can identify potential problems before they occur in production, reducing the need for costly trial-and-error methods.
8.2 Simulation Tools for Predicting Material Behavior
Simulation tools such as ABAQUS, ANSYS, and LS-DYNA are commonly used to model the deep drawing process. These tools can simulate the interaction between the punch, die, and blank, as well as the material’s response to different process parameters.
FEA simulations provide valuable insights into:
- Stress and strain distribution: FEA can predict how the material will deform under various loads, allowing engineers to optimize the punch and die design to reduce the risk of tearing or wrinkling.
- Material flow: Simulation tools can model how the material flows into the die cavity, helping engineers optimize blank holder force and lubrication to ensure smooth material movement.
- Defect prediction: By simulating the deep drawing process, engineers can identify potential defects such as thinning, wrinkling, or earing and adjust the process parameters to prevent them.
8.3 Case Studies on FEA in Deep Drawing
Several case studies have demonstrated the effectiveness of FEA in optimizing the deep drawing process. For example, in the automotive industry, FEA simulations have been used to design lightweight body panels with improved crash performance while minimizing material waste. In the aerospace industry, FEA has been used to optimize the deep drawing of complex components with tight tolerances, reducing the risk of defects and improving production efficiency.
Recent Advancements in Deep Drawing Technology
The deep drawing process has evolved significantly with advancements in technology, particularly in areas such as automation, smart manufacturing, servo-controlled presses, and advanced coatings and lubricants.
9.1 Automation and Smart Manufacturing
Automation has played a significant role in improving the productivity and precision of the deep drawing process. Modern hydraulic and servo-driven presses are equipped with CNC (Computer Numerical Control) systems that allow for precise control over process parameters such as punch speed, pressure, and blank holder force.
Smart manufacturing systems enable real-time monitoring and adjustment of process variables, improving part quality and reducing the risk of defects. Predictive maintenance systems use sensors and data analytics to monitor the condition of the tooling and equipment, allowing manufacturers to schedule maintenance before a failure occurs.
9.2 Servo-Controlled Presses and Real-Time Monitoring
Servo-controlled presses offer dynamic control over the punch speed and force, allowing for real-time adjustments during the drawing process. These presses are ideal for applications that require complex part geometries or tight tolerances, as they can adapt to changes in material behavior and process conditions.
Real-time monitoring systems use sensors to track key process variables such as temperature, pressure, and tool wear. By analyzing this data, engineers can make adjustments on the fly to optimize the process and prevent defects.
9.3 Advanced Coatings and Lubricants
Recent advancements in coating and lubrication technology have improved the performance of deep drawing tools. Diamond-Like Carbon (DLC) coatings and ceramic coatings offer excellent wear resistance and low friction, reducing tool wear and improving the quality of the finished parts.
In addition, new synthetic lubricants and dry film coatings have been developed to improve material flow, reduce friction, and prevent galling. These advanced lubricants are especially useful in applications involving hard-to-form materials such as titanium or nickel-based alloys.
9.4 Multi-Stage Deep Drawing for Complex Geometries
For parts with deep cavities or intricate details, a single drawing stage may not be sufficient to achieve the desired shape. Multi-stage deep drawing involves using multiple drawing stages, with each stage gradually forming the part into its final shape. This approach allows for the production of complex geometries while minimizing the risk of defects such as tearing or excessive thinning.
Applications of Deep Drawing in Various Industries
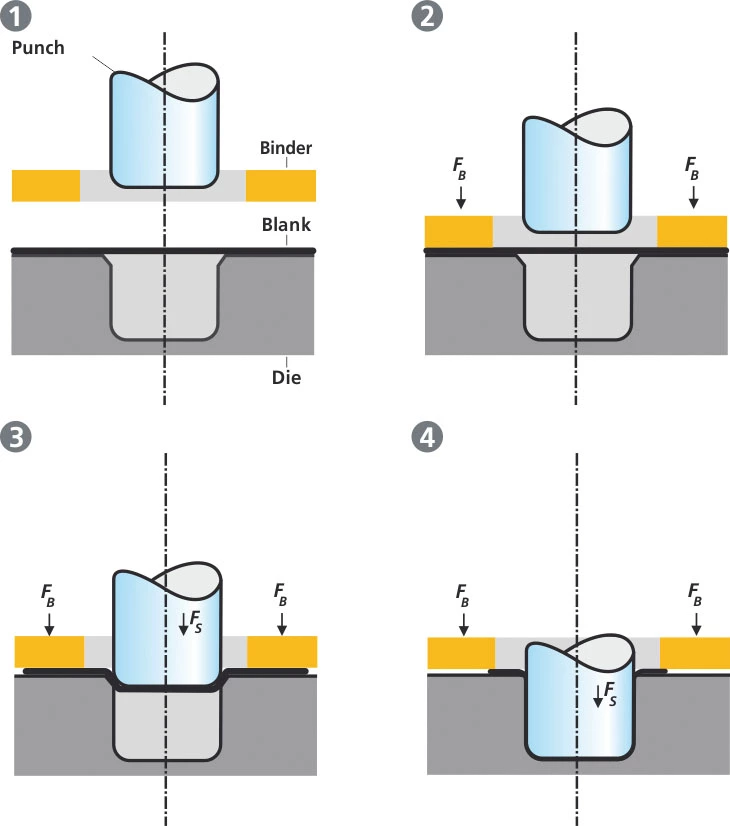
The versatility of the deep drawing process makes it suitable for a wide range of industries, including automotive, aerospace, electronics, medical devices, and packaging.
10.1 Automotive Industry
In the automotive industry, deep drawing is used to manufacture components such as body panels, fuel tanks, and transmission housings. These parts need to be strong, lightweight, and produced in high volumes with consistent quality.
Automotive manufacturers rely on deep drawing to produce parts with complex shapes and tight tolerances. The process is particularly useful for producing large parts with smooth surfaces and uniform thickness, such as door panels, hoods, and fenders.
10.2 Aerospace Industry
The aerospace industry requires components that are both lightweight and strong, making deep drawing an ideal process for manufacturing parts such as fuselage panels, engine components, and landing gear housings. These parts must withstand extreme conditions, including high temperatures and pressures, while maintaining their structural integrity.
Deep drawing allows aerospace manufacturers to produce components with high precision and repeatability, ensuring that parts meet the stringent quality and safety standards required in the industry.
10.3 Electronics and Consumer Goods
In the electronics and consumer goods industries, deep drawing is used to produce device enclosures, heat sinks, battery housings, and connector components. These parts require high dimensional accuracy and a smooth surface finish, making deep drawing an ideal process for their production.
The ability to create thin, lightweight metal parts with high structural integrity makes deep drawing a preferred method for manufacturing enclosures for smartphones, laptops, and household appliances.
10.4 Medical Devices and Packaging
In the medical field, deep drawing is used to produce components such as surgical instruments, implants, and medical device enclosures. The process allows for the production of parts with tight tolerances and high surface quality, which are critical in ensuring the safety and efficacy of medical devices.
Deep drawing is also widely used in the packaging industry to manufacture metal cans, aerosol containers, and food packaging. These products require high material efficiency and uniformity, making deep drawing an ideal process for their production.
Best Practices for Optimizing the Deep Drawing Process
To achieve the best results in deep drawing, manufacturers must implement best practices in tooling design, process optimization, and material selection.
11.1 Tooling Maintenance and Care
Proper maintenance of the tooling is essential for ensuring consistent part quality and extending tool life. Regular inspection and maintenance of punches, dies, and blank holders can prevent defects caused by tool wear or misalignment.
11.2 Process Optimization Techniques
By optimizing process parameters such as blank holder force, punch speed, and lubrication, manufacturers can improve material flow, reduce the risk of defects, and increase production efficiency.
11.3 Reducing Material Waste and Improving Efficiency
To reduce material waste, manufacturers can use simulation tools such as FEA to optimize blank size and shape. In addition, multi-stage deep drawing can be used to minimize material thinning and prevent tearing, resulting in higher material efficiency.
Sustainability in Deep Drawing
As sustainability becomes increasingly important in manufacturing, deep drawing offers several advantages in terms of energy efficiency, material recyclability, and waste reduction.
12.1 Energy Efficiency in Presses
Modern hydraulic and servo-driven presses are designed to be energy-efficient, reducing the overall energy consumption of the deep drawing process. By optimizing process parameters and using automation, manufacturers can further reduce their energy footprint.
12.2 Recyclability of Materials
Most of the materials used in deep drawing, such as steel, aluminum, and copper, are highly recyclable. This allows manufacturers to reduce waste and contribute to a circular economy by recycling scrap material generated during the drawing process.
12.3 Reducing Environmental Impact in Metal Forming
By reducing material waste, improving energy efficiency, and using environmentally friendly lubricants, manufacturers can minimize the environmental impact of the deep drawing process. Implementing sustainable practices in deep drawing not only benefits the environment but also helps reduce operational costs.
Conclusion
The deep drawing process is a versatile and efficient method for producing high-quality metal parts with complex geometries and tight tolerances. From automotive body panels to medical devices, deep drawing plays a crucial role in a wide range of industries.
By understanding the fundamental principles of deep drawing, optimizing process parameters, and selecting the right materials, manufacturers can achieve high-quality parts with minimal defects. Recent advancements in technology, such as automation, smart manufacturing, and simulation tools, have further enhanced the deep drawing process, enabling manufacturers to produce more complex parts with greater efficiency.
As industries continue to demand lightweight, durable, and high-precision components, the deep drawing process will remain a vital part of modern manufacturing. The future of deep drawing lies in the integration of sustainable practices, advanced materials, and innovative technologies, which will help manufacturers meet the evolving needs of the market.
Distinguishing Between Deep Drawing and Other Metal Forming Techniques
Metal forming is a broad field in manufacturing that includes numerous techniques to shape metal into desired forms. Among these, deep drawing is a highly specialized process used to produce hollow shapes from flat metal blanks. However, there are many other metal forming techniques, each with its own set of characteristics, applications, advantages, and limitations.
This 10,000-word exploration aims to distinguish between deep drawing and other major metal forming techniques, such as stamping, forging, bending, rolling, extrusion, hydroforming, and spinning. By understanding the key principles, processes, applications, and technical differences, we can better appreciate how deep drawing fits within the broader landscape of metal forming technologies.
Introduction to Metal Forming Processes
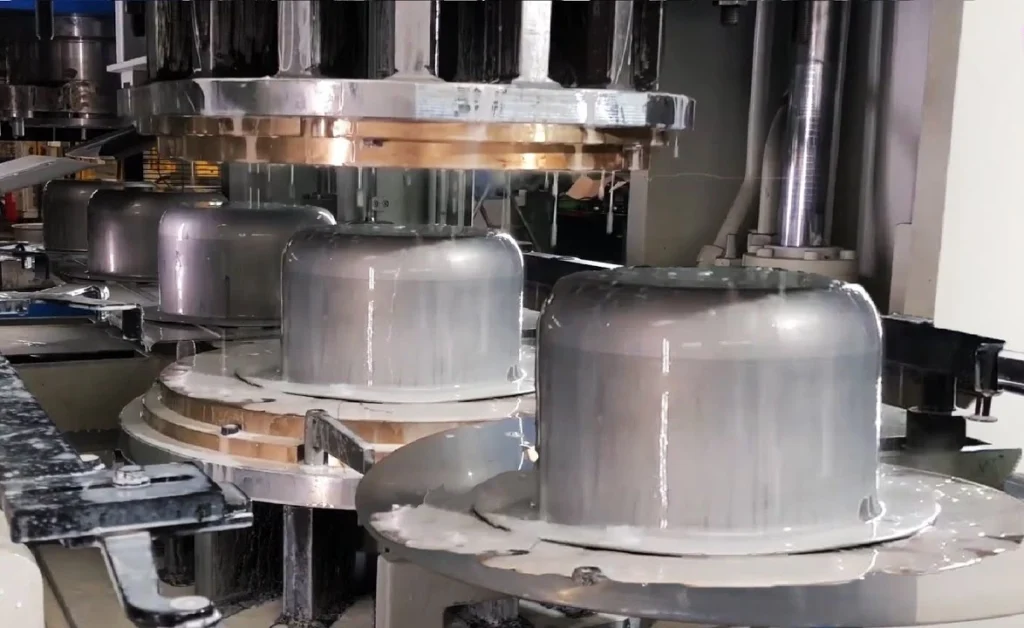
Metal forming is a group of manufacturing processes in which plastic deformation is used to change the shape of metal workpieces into desired forms. These processes rely on the material’s ability to undergo plastic deformation without breaking. Metal forming plays a crucial role in various industries, from automotive to aerospace, as it enables the creation of complex shapes with high strength and minimal material waste.
Metal forming can be broadly classified into two categories:
- Bulk forming, where the entire volume of the material is deformed (e.g., forging, extrusion, and rolling).
- Sheet forming, where only the surface area is deformed (e.g., stamping, deep drawing, and bending).
Metal forming techniques are typically categorized by the amount of force applied, the temperature of the process (hot or cold forming), and the tools or dies used.
1.2 Classification of Metal Forming Techniques
The main types of metal forming techniques include:
- Deep Drawing: A sheet metal process where a blank is radially drawn into a forming die by the action of a punch, producing parts with depths greater than their diameters.
- Stamping: A process that shapes metal by applying high force to a blank, often through cutting, bending, or embossing actions, to produce flat parts with intricate details.
- Forging: Involves shaping metal using localized compressive forces, often at high temperatures, to create parts with excellent mechanical properties.
- Bending: A process where metal is plastically deformed to achieve an angular shape, often used to create simple, linear components.
- Rolling: Involves passing metal through rollers to reduce its thickness or change its cross-section.
- Extrusion: Forces metal through a die to create parts with a constant cross-sectional profile.
- Hydroforming: A process where high-pressure fluid is used to shape metal, often for lightweight components.
- Spinning: Involves rotating a metal disc and pressing it against a mold to create axially symmetric parts.
1.3 The Role of Deep Drawing in Modern Manufacturing
Among these processes, deep drawing holds a unique place in manufacturing due to its ability to produce parts with significant depth, structural integrity, and minimal material waste. The process is especially suited for making hollow parts, such as fuel tanks, automotive body panels, and beverage cans. Deep drawing offers advantages like high volume production, tight tolerances, and uniform material thickness.
However, deep drawing has its own limitations and is not always the best choice for all metal forming applications. Other metal forming techniques, like stamping or forging, are often better suited for different geometries, material thicknesses, and production requirements. Understanding the distinctions between deep drawing and these other techniques is essential for choosing the right manufacturing process.
Deep Drawing Process: Definition, Principles, and Applications
2.1 What is Deep Drawing?
Deep drawing is a metal forming process in which a flat sheet metal blank is placed over a die cavity and pushed into the die by a punch. The punch forces the metal to stretch and conform to the shape of the die, resulting in a hollow part that can have a depth greater than its diameter. The blank material undergoes both tensile and compressive stresses as it flows into the die.
In deep drawing, the blank is clamped between a blank holder and a die, while the punch descends and pushes the blank into the die cavity. The punch and die are typically made from hardened steel or other high-strength materials to withstand the high forces required for deformation.
Deep drawing can be performed at room temperature (cold forming) or at elevated temperatures (hot forming), depending on the material being used and the depth of the draw.
2.2 Key Components: Punch, Die, and Blank Holder
The three main components of the deep drawing process are the punch, die, and blank holder:
- Punch: The punch is the tool that drives the blank into the die cavity. Its geometry defines the internal shape of the part being drawn.
- Die: The die is the tool that shapes the external surface of the part. The blank flows into the die cavity, forming the desired shape.
- Blank Holder: The blank holder prevents the blank from wrinkling as it is drawn into the die. It applies pressure to the edges of the blank, controlling material flow and ensuring smooth deformation.
2.3 Material Flow and Deformation in Deep Drawing
The deep drawing process involves significant plastic deformation of the metal blank. The material experiences a combination of tensile and compressive forces as it is stretched and drawn into the die.
- Tensile Stress: The edges of the blank, particularly in the flange region, are subjected to tensile stresses as the material is pulled inward by the punch.
- Compressive Stress: The material inside the die, near the punch, experiences compressive stresses as it is forced to conform to the shape of the die.
The material must have sufficient ductility to undergo the necessary deformation without tearing or cracking. The drawing ratio, defined as the ratio of the blank diameter to the punch diameter, is an important factor in determining the severity of the deformation. High drawing ratios can increase the risk of defects such as wrinkling, thinning, or tearing.
2.4 Applications of Deep Drawing in Industry
Deep drawing is used to produce a wide range of parts across various industries. Its ability to create complex geometries with uniform wall thickness and high structural integrity makes it a popular choice for components that require durability and precision.
Key applications of deep drawing include:
- Automotive industry: Deep drawing is used to manufacture body panels, fuel tanks, and exhaust components. These parts must be lightweight yet strong to improve vehicle performance and safety.
- Aerospace industry: In aerospace, deep drawing is used to produce fuselage sections, engine housings, and structural components that need to withstand extreme conditions while remaining lightweight.
- Packaging industry: Beverage cans, food containers, and cosmetic packaging are often deep drawn from materials like aluminum or steel to create durable, uniform containers.
- Medical devices: Surgical instruments, implants, and medical device housings are often deep drawn from stainless steel or titanium for their corrosion resistance and biocompatibility.
While deep drawing is highly effective for certain applications, it is not suitable for all metal forming needs. Other metal forming techniques, such as stamping, forging, and hydroforming, may offer better solutions for specific geometries, material types, or production requirements.
Stamping vs. Deep Drawing
3.1 Definition and Principles of Stamping
Stamping is a metal forming process in which flat sheet metal is placed into a stamping press and shaped by applying high force with a punch and die. Stamping is a broad category that includes various operations such as blanking, punching, bending, embossing, and coining. It is primarily used to produce flat or shallow parts with intricate details, and it can be performed at high speeds for mass production.
The stamping process involves using a die set that contains a male and female die. As the punch presses the sheet metal into the die, the material is deformed to take the shape of the die cavity. Stamping is a high-speed process, often performed in progressive stamping presses, which can perform multiple operations in a single stroke.
3.2 Key Differences Between Stamping and Deep Drawing
While both stamping and deep drawing use a punch and die to shape metal, there are several key differences between the two processes:
- Forming Depth: In stamping, the depth of the part is generally shallow, and the process is primarily used to create flat or slightly contoured shapes. In contrast, deep drawing is specifically designed to produce parts with significant depth, often with a depth greater than the diameter of the blank.
- Material Deformation: Stamping typically involves cutting, bending, or embossing the metal, but the material does not undergo the same level of stretching and plastic deformation as in deep drawing. Deep drawing requires the material to flow into the die cavity, undergoing significant tensile and compressive stresses.
- Speed and Productivity: Stamping is much faster than deep drawing and is often used for high-volume production of smaller, simpler parts. Stamping presses can cycle at very high speeds, making them ideal for producing parts like brackets, clips, and fasteners. Deep drawing, on the other hand, is slower due to the need for precise control over material flow and deformation.
- Tooling: Stamping typically requires progressive dies that perform multiple operations (e.g., cutting, bending, punching) in a single stroke. Deep drawing requires specialized tooling, including blank holders and punches designed to manage the complex material flow and deformation involved in producing deep parts.
3.3 Material Deformation and Forming Depth
The amount of material deformation and forming depth are key differentiators between stamping and deep drawing.
- Stamping: The material deformation in stamping is relatively minor compared to deep drawing. The sheet metal is typically cut, bent, or formed into shallow features. Parts produced by stamping rarely have significant depth, and the material does not undergo the large-scale stretching seen in deep drawing.
- Deep Drawing: Deep drawing requires significant plastic deformation as the blank is stretched and drawn into the die. The forming depth in deep drawing can be substantial, often resulting in parts that are much deeper than those produced by stamping. The process must carefully manage the tensile and compressive stresses to avoid defects such as wrinkling, tearing, or thinning.
3.4 Applications of Stamping in Industry
Stamping is widely used in industries that require the mass production of small, shallow, or flat metal parts. Common applications include:
- Automotive: Stamping is used to produce small components like brackets, clips, and connectors, as well as larger flat parts like body panels. Stamping’s speed and efficiency make it ideal for high-volume production.
- Electronics: Stamping is often used to produce small, precise parts for electronic devices, including connectors, terminals, and circuit board components.
- Household Appliances: Stamped metal parts are found in many household appliances, from washing machines to refrigerators. These parts are often flat or slightly contoured and require minimal forming depth.
- Aerospace: Stamping is used to produce fasteners, brackets, and shields for aerospace applications. These parts need to be lightweight, durable, and produced to tight tolerances.
While stamping is highly efficient for producing flat or shallow parts in large quantities, it is not suitable for parts with significant depth or complex geometries. For those types of parts, deep drawing or other metal forming techniques are more appropriate.
Forging vs. Deep Drawing
4.1 Definition and Principles of Forging
Forging is a metal forming process that involves shaping metal by applying compressive forces, usually using a hammer or press. Forging can be performed at high temperatures (hot forging) or at room temperature (cold forging), depending on the material and the part’s requirements. The process is used to create parts with excellent mechanical properties, such as high strength, toughness, and fatigue resistance.
In forging, the material is typically heated to make it more malleable and is then deformed by a die or hammer. Forging can be classified into several types:
- Open-die forging: The metal is compressed between flat or simple-shaped dies, allowing it to flow freely in multiple directions.
- Closed-die forging: The metal is compressed in a die that contains the shape of the final part, resulting in more precise and complex geometries.
- Cold forging: The metal is formed at room temperature, often resulting in better surface finish and tighter tolerances but requiring higher forces.
4.2 Key Differences Between Forging and Deep Drawing
Forging and deep drawing differ in several important ways:
- Forming Forces: Forging relies on compressive forces to shape metal, while deep drawing uses a combination of tensile and compressive forces to deform a sheet into a hollow shape. Forging typically involves much higher forces than deep drawing, particularly in the case of hot forging.
- Material Deformation: In forging, the material is compressed to shape it, often involving significant changes in cross-sectional area. In deep drawing, the material is stretched and drawn into the die, maintaining much of its original thickness, especially in the flange area.
- Part Geometry: Forging is used to produce parts with solid cross-sections, such as gears, crankshafts, and tools, whereas deep drawing is used to produce hollow parts like cups, tanks, and enclosures.
- Temperature: Forging often involves heating the material to make it more malleable, especially in hot forging. Deep drawing, in contrast, is typically a cold forming process, though it can be performed at elevated temperatures for certain materials.
4.3 Hot Forging and Cold Forging: How They Compare to Deep Drawing
- Hot Forging: In hot forging, the material is heated above its recrystallization temperature, which reduces its strength and increases its ductility. This allows the material to be deformed more easily, resulting in complex shapes with minimal internal stresses. Hot forging is used to create parts with excellent mechanical properties but requires careful control of temperature and cooling rates.
- Cold Forging: Cold forging is performed at or near room temperature, resulting in parts with a better surface finish and tighter dimensional tolerances than hot forging. However, cold forging requires much higher forces, and the material is more prone to work hardening. Cold forging is typically used for smaller parts, such as fasteners or fittings.
Deep Drawing: Unlike forging, deep drawing is almost always a cold forming process. The material is deformed at room temperature, allowing for high precision and smooth surface finishes. Deep drawing is well-suited for producing large, hollow parts, while cold forging is better for smaller, solid parts.
4.4 Applications of Forging in Industry
Forging is commonly used in industries that require high-strength components capable of withstanding heavy loads and stress. Applications include:
- Automotive: Forged components like crankshafts, connecting rods, and gears are essential for the high-strength requirements of internal combustion engines and transmission systems.
- Aerospace: Forged parts are used in critical aerospace applications, such as landing gear, turbine blades, and structural components, where material strength and reliability are paramount.
- Tools and Hardware: Forged tools, such as wrenches, hammers, and pliers, benefit from the high toughness and durability that forging provides.
- Oil and Gas: Forged components like valves, flanges, and drill heads are widely used in the oil and gas industry, where they are exposed to high pressures and harsh conditions.
Bending vs. Deep Drawing
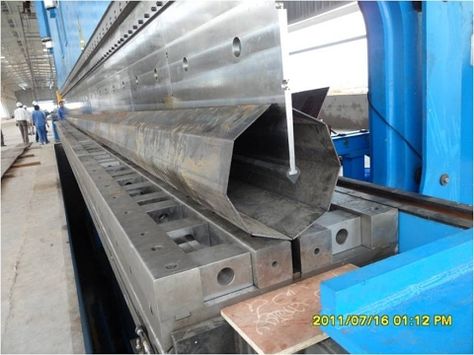
5.1 Definition and Principles of Bending
Bending is a metal forming process in which a sheet metal workpiece is plastically deformed to achieve a specific angular or curved shape. Bending is typically performed using press brakes or other specialized equipment, and it is one of the most common processes used in sheet metal fabrication.
Bending involves clamping the workpiece on a die and applying force to the blank using a punch. The material is deformed by bending around a specific axis, creating an angle or curve without changing the material’s thickness significantly. Bending can be used to produce a wide variety of shapes, such as L-bends, U-bends, or more complex profiles.
There are several types of bending operations:
- Air Bending: The punch presses the material into the die, but the material does not fully conform to the die shape, resulting in a springback effect.
- Bottoming: The material is pressed into the die cavity until it fully conforms to the shape of the die, providing more precise angles and dimensions.
- Coining: Coining is a high-pressure bending process in which the material is plastically deformed into the shape of the die, creating very tight tolerances and sharp angles.
5.2 Key Differences Between Bending and Deep Drawing
Bending and deep drawing differ significantly in their objectives, methods, and applications:
- Deformation: In bending, the material is plastically deformed along a single axis, typically forming an angular or curved shape. The material is not stretched or drawn into a deep cavity, as it is in deep drawing. Bending is a simpler process, with minimal material stretching and no changes in thickness.
- Geometry: Bending is used to create angular or curved shapes, such as brackets, frames, or channels. Deep drawing, on the other hand, produces hollow shapes, such as cups, boxes, or tanks, with depths that are often greater than their width.
- Tooling: Bending requires relatively simple tools, typically a punch and die, to form the desired angle or curve. In deep drawing, the tooling is more complex, involving a punch, die, and blank holder to control the material flow into the die.
- Forming Depth: The depth of deformation in bending is generally shallow, and the material does not undergo significant stretching. In contrast, deep drawing involves significant depth and material flow, with more complex stress and strain distributions.
5.3 Types of Bending: Air Bending, Bottoming, and Coining
- Air Bending: In air bending, the material is not pressed all the way into the die cavity. Instead, the punch applies pressure to bend the material, and the angle is determined by the depth of the punch stroke. Air bending allows for flexibility in the bending angle but results in less precise tolerances due to springback.
- Bottoming: Bottoming is a more precise bending process in which the material is pressed fully into the die, conforming to the die’s shape. This process provides better accuracy and control over the final angle, with less springback than air bending.
- Coining: Coining is a high-force bending process in which the material is squeezed between the punch and die to create very tight tolerances and sharp angles. Coining is typically used for small, high-precision parts where exact dimensions are required.
5.4 Applications of Bending in Industry
Bending is widely used in industries that require angular or curved metal parts. Applications include:
- Automotive: Bending is used to create components such as brackets, frames, and reinforcements in automotive manufacturing.
- Construction: Metal frames, supports, and structural components for buildings are often produced through bending processes.
- Furniture: Metal furniture components, such as chair frames or table legs, are often bent into shape using press brakes or other bending equipment.
- Consumer Goods: Bending is commonly used in the production of consumer products such as appliance housings, shelving, and brackets.
While bending is ideal for creating simple angular or curved shapes, it cannot produce the deep, hollow parts that deep drawing excels at. For parts requiring significant depth or more complex geometries, deep drawing is the preferred process.
Rolling vs. Deep Drawing
6.1 Definition and Principles of Rolling
Rolling is a metal forming process in which metal stock is passed between two or more rotating rolls to reduce its thickness or change its cross-sectional shape. Rolling is one of the most common and essential processes in metalworking, as it allows for the mass production of flat sheet metal, plates, bars, and strips.
Rolling is typically divided into two main types:
- Hot Rolling: In hot rolling, the metal is heated above its recrystallization temperature before being passed through the rolls. This reduces the material’s strength and allows for easier deformation, making it suitable for large reductions in thickness.
- Cold Rolling: Cold rolling is performed at room temperature, resulting in better surface finish, tighter tolerances, and increased material strength due to work hardening.
6.2 Key Differences Between Rolling and Deep Drawing
Rolling and deep drawing differ in their objectives, the nature of the deformation, and the final part geometries:
- Deformation Process: In rolling, the metal is compressed and elongated as it passes between the rotating rolls. This process reduces the thickness of the material and changes its cross-sectional shape. Deep drawing, in contrast, involves stretching the material into a hollow shape, with significant depth relative to its width.
- Product Geometry: Rolling is used to produce long, flat products like sheets, plates, and bars, as well as profiles with constant cross-sectional shapes like I-beams or rails. Deep drawing is used to produce hollow, three-dimensional parts with varying cross-sections and significant depth.
- Material Flow: In rolling, the material flows parallel to the rolls, and the thickness is reduced uniformly across the width of the workpiece. In deep drawing, the material flows radially inward as it is drawn into the die cavity, with localized thinning in areas of high tensile stress.
6.3 Hot Rolling and Cold Rolling: Comparison with Deep Drawing
- Hot Rolling: Hot rolling is used to produce large quantities of sheet metal, plates, and bars with significant reductions in thickness. Hot-rolled products typically have a rougher surface finish and looser tolerances compared to cold-rolled products. The material is less prone to cracking during hot rolling due to its lower strength at elevated temperatures.
- Cold Rolling: Cold rolling is performed after hot rolling to improve the surface finish, increase material strength through work hardening, and achieve tighter dimensional tolerances. Cold-rolled products are commonly used in applications requiring precise thickness and surface quality, such as automotive panels or appliance housings.
Deep Drawing: Unlike rolling, which is primarily focused on reducing thickness and shaping long products, deep drawing is concerned with creating hollow, three-dimensional parts with significant depth. The process involves more complex material flow and deformation, as the blank is stretched into the die cavity.
6.4 Applications of Rolling in Industry
Rolling is one of the most fundamental processes in metalworking, with applications in various industries:
- Construction: Rolled steel beams, plates, and sheets are used extensively in construction projects, from skyscrapers to bridges.
- Automotive: Cold-rolled steel sheets are used to manufacture automotive body panels, frames, and structural components.
- Aerospace: Rolled aluminum and titanium sheets are used in aircraft manufacturing for components such as fuselage panels, wing skins, and internal structures.
- Manufacturing: Rolled steel and aluminum sheets are used in the production of consumer goods, appliances, and machinery.
While rolling is ideal for producing long, flat products or profiles, it is not suitable for producing hollow, deep-drawn parts. Deep drawing is the preferred process for applications that require complex geometries and significant forming depth.
Extrusion vs. Deep Drawing
7.1 Definition and Principles of Extrusion
Extrusion is a metal forming process in which a billet of metal is forced through a die to create a long part with a constant cross-sectional profile. The material is pushed or pulled through the die by applying a compressive force, resulting in a continuous product with a uniform shape along its length.
There are two main types of extrusion:
- Direct Extrusion: In direct extrusion, the material is pushed through the die in the same direction as the applied force.
- Indirect Extrusion: In indirect extrusion, the die moves toward the billet while the billet remains stationary. This reduces friction between the material and the die, resulting in lower required force.
Extrusion can be performed at high temperatures (hot extrusion) or at room temperature (cold extrusion), depending on the material and the part requirements.
7.2 Key Differences Between Extrusion and Deep Drawing
Extrusion and deep drawing differ significantly in their deformation methods and the types of parts they produce:
- Deformation Process: In extrusion, the material is forced through a die to create a long part with a constant cross-sectional profile. The material flows in one direction, and the entire length of the product has the same shape. In deep drawing, the material is stretched and drawn into a die cavity, creating a hollow part with a variable cross-section.
- Part Geometry: Extrusion produces long, continuous parts like tubes, rods, and channels, which have the same cross-sectional shape throughout their length. Deep drawing, on the other hand, produces three-dimensional, hollow parts with complex geometries, such as cups, tanks, and enclosures.
- Tooling: Extrusion requires a die with a fixed cross-sectional profile, which defines the shape of the extruded product. Deep drawing requires more complex tooling, including a punch, die, and blank holder, to control the material flow and deformation during the process.
7.3 Types of Extrusion: Direct and Indirect
- Direct Extrusion: In direct extrusion, the billet is placed in a container and pushed through the die using a ram. This is the most common form of extrusion and is used to produce parts like tubing, bars, and profiles.
- Indirect Extrusion: In indirect extrusion, the die moves toward the stationary billet, reducing friction and requiring less force than direct extrusion. This method is often used for softer materials, such as aluminum and magnesium, to produce long, uniform profiles.
7.4 Applications of Extrusion in Industry
Extrusion is used to produce a wide range of products with constant cross-sectional profiles. Applications include:
- Automotive: Extruded aluminum profiles are used to create structural components, frames, and crash management systems in automotive manufacturing.
- Construction: Extruded steel and aluminum products, such as window frames, door frames, and roofing profiles, are widely used in the construction industry.
- Aerospace: Extruded titanium and aluminum components are used in aircraft structures, where lightweight, high-strength parts are essential.
- Manufacturing: Extrusion is used to produce a variety of consumer goods, from appliance components to sports equipment.
Extrusion is ideal for creating long, continuous parts with uniform cross-sections, but it is not suitable for producing hollow parts with varying depths or complex geometries. Deep drawing is the preferred process for parts that require significant depth and intricate shapes.
Hydroforming vs. Deep Drawing
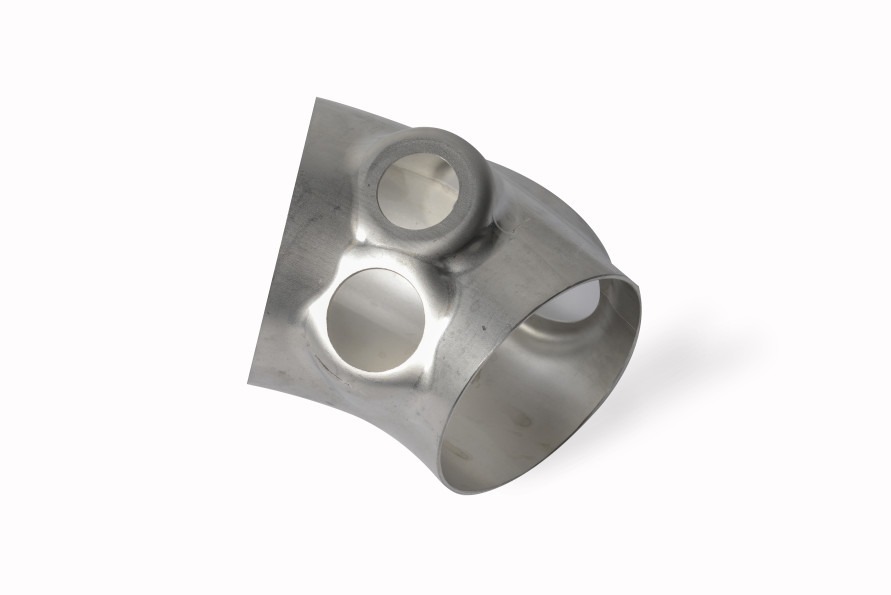
8.1 Definition and Principles of Hydroforming
Hydroforming is a metal forming process that uses high-pressure fluid to shape a metal blank or tube into a desired form. Unlike deep drawing, which relies on mechanical force from a punch, hydroforming uses fluid pressure to press the metal into a die, allowing for more uniform deformation and the creation of complex, lightweight parts.
There are two main types of hydroforming:
- Sheet Hydroforming: In sheet hydroforming, a flat sheet metal blank is placed over a die, and high-pressure fluid is used to push the blank into the die cavity, forming the desired shape.
- Tube Hydroforming: In tube hydroforming, a hollow tube is placed inside a die, and high-pressure fluid is injected into the tube, causing it to expand and conform to the shape of the die.
8.2 Key Differences Between Hydroforming and Deep Drawing
Hydroforming and deep drawing differ in the way force is applied to the material and the types of parts they produce:
- Force Application: In hydroforming, the material is shaped by the application of high-pressure fluid, which presses the material against the die. In deep drawing, the material is deformed by mechanical force applied by a punch. The use of fluid pressure in hydroforming results in more uniform material flow and less risk of wrinkling or tearing.
- Part Complexity: Hydroforming is capable of producing parts with more complex geometries than deep drawing, including asymmetric shapes, sharp corners, and variable wall thicknesses. Deep drawing is more suited for symmetrical, hollow parts like cylinders and boxes.
- Forming Depth: Hydroforming can achieve greater forming depth than deep drawing without causing defects like tearing or thinning. The fluid pressure in hydroforming distributes the forces more evenly, allowing for deeper, more intricate shapes to be formed.
8.3 Pressure-Controlled vs. Force-Controlled Processes
The key distinction between hydroforming and deep drawing lies in the way the material is deformed:
- Pressure-Controlled (Hydroforming): In hydroforming, the material is deformed by applying high-pressure fluid, which presses the blank or tube into the die. The fluid pressure can be precisely controlled, allowing for more uniform material deformation and reduced risk of defects like wrinkling or tearing.
- Force-Controlled (Deep Drawing): In deep drawing, the material is deformed by mechanical force from a punch. The force must be carefully controlled to avoid overstressing the material, which can lead to defects such as tearing, thinning, or wrinkling.
8.4 Applications of Hydroforming in Industry
Hydroforming is widely used in industries that require lightweight, complex, and high-strength components. Applications include:
- Automotive: Hydroforming is used to produce structural components like engine cradles, frame rails, and suspension parts. The process allows for the creation of lightweight, strong parts with complex geometries that would be difficult to achieve with traditional forming methods.
- Aerospace: In aerospace, hydroforming is used to create aircraft fuselage sections, engine components, and structural parts that require high strength and precision.
- Bicycle Manufacturing: Hydroforming is used to create lightweight, high-strength bicycle frames with complex shapes and varying tube diameters.
- Appliance Manufacturing: Hydroformed components are used in household appliances such as refrigerators, ovens, and washing machines, where complex shapes and high structural integrity are required.
While hydroforming is ideal for producing complex, lightweight parts, it is more expensive and slower than deep drawing due to the specialized equipment and high-pressure systems required. For simpler, symmetrical parts, deep drawing remains a more cost-effective solution.
Spinning vs. Deep Drawing
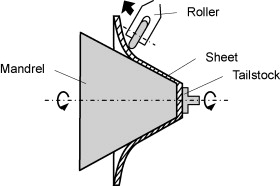
9.1 Definition and Principles of Metal Spinning
Metal spinning, also known as spin forming or spinning, is a metal forming process in which a metal disc or tube is rotated at high speed and pressed against a forming tool to create a cylindrical or conical shape. The process is typically performed on a lathe, where the workpiece is clamped in a chuck and spun at high speeds while a forming tool gradually presses the material against a mandrel or mold.
Spinning is used to create axially symmetric parts, such as bowls, cones, and domes. The process can be performed manually or using CNC (computer numerical control) lathes for higher precision and repeatability.
9.2 Key Differences Between Spinning and Deep Drawing
Spinning and deep drawing are both used to create hollow, symmetrical parts, but they differ in several key aspects:
- Deformation Process: In spinning, the material is deformed by applying pressure while the workpiece rotates, gradually shaping it into the desired form. The deformation is progressive, with the material being pressed against the mandrel over multiple passes. In deep drawing, the material is deformed in a single stroke as the punch forces the blank into the die cavity.
- Part Complexity: Spinning is ideal for creating axially symmetric parts with smooth, gradual curves, such as cones, domes, and cylinders. Deep drawing is better suited for creating parts with more complex geometries, including deep cavities, sharp corners, and varying cross-sections.
- Tooling: Spinning requires relatively simple tooling, typically consisting of a mandrel and forming tool. In deep drawing, the tooling is more complex, involving a punch, die, and blank holder to control material flow and deformation.
9.3 Manual vs. CNC Spinning: How It Compares to Deep Drawing
- Manual Spinning: In manual spinning, the operator uses hand tools to press the material against the mandrel while the workpiece rotates. Manual spinning is ideal for low-volume production and custom parts, but it requires a high level of skill and is slower than CNC spinning or deep drawing.
- CNC Spinning: CNC spinning uses computer-controlled lathes to automate the spinning process, allowing for higher precision, repeatability, and speed. CNC spinning can produce parts with tighter tolerances and more complex geometries than manual spinning.
Compared to deep drawing, CNC spinning offers greater flexibility in terms of part design and can produce parts with more complex curves and varying wall thicknesses. However, deep drawing is more efficient for high-volume production of symmetrical parts with consistent depth and geometry.
9.4 Applications of Spinning in Industry
Metal spinning is used in a variety of industries to produce hollow, axially symmetric parts. Applications include:
- Aerospace: Spinning is used to produce components such as nose cones, engine cowlings, and reflectors for aircraft and spacecraft.
- Lighting and Reflectors: Spinning is commonly used to create light reflectors, lamp housings, and domes for lighting applications.
- Household Goods: Spinning is used to produce household items such as pots, pans, bowls, and vases.
- Automotive: Spinning is used to create wheel rims, hubcaps, and other cylindrical automotive components.
While spinning is ideal for producing cylindrical or conical parts with smooth, curved surfaces, it is not as well-suited for parts with complex geometries, sharp corners, or deep cavities. For those types of parts, deep drawing is the preferred process.
Comparison of Material Selection in Deep Drawing and Other Metal Forming Techniques
Material selection plays a critical role in determining the success of any metal forming process, including deep drawing, stamping, forging, bending, rolling, extrusion, hydroforming, and spinning. Each process requires specific material properties to ensure the material can withstand the stresses and deformations without failing.
10.1 Deep Drawing: Suitable Materials and Properties
In deep drawing, the material must have sufficient ductility to undergo significant plastic deformation without cracking or tearing. Materials commonly used in deep drawing include:
- Low-Carbon Steel: Low-carbon steel offers excellent formability, making it suitable for deep drawing applications such as automotive body panels, fuel tanks, and appliance housings.
- Aluminum: Aluminum is lightweight and has good ductility, making it ideal for deep-drawn parts in the automotive, aerospace, and packaging industries. However, aluminum requires specialized lubricants to prevent galling during the drawing process.
- Stainless Steel: Stainless steel is used in deep drawing applications that require high corrosion resistance and strength, such as medical devices, kitchen sinks, and exhaust components.
- Copper and Brass: Copper and brass are used in deep drawing applications where electrical conductivity, thermal conductivity, and aesthetic appeal are important, such as in the production of electrical connectors and decorative items.
The key material properties that affect deep drawing include:
- Ductility: The ability of the material to undergo plastic deformation without cracking.
- Yield Strength: Lower yield strength is preferred for deep drawing, as it allows the material to flow more easily into the die cavity.
- Formability: Materials with good formability can be drawn into complex shapes without tearing or wrinkling.
- Anisotropy: Materials with low anisotropy deform more uniformly during deep drawing, reducing the risk of defects such as earing or uneven thickness distribution.
10.2 Material Selection in Stamping, Forging, Bending, Rolling, Extrusion, Hydroforming, and Spinning
Stamping: Materials used in stamping must have good formability, but the process does not require the same level of ductility as deep drawing. Common materials include:
- Steel: Low-carbon steel and high-strength steel are commonly used in stamping for automotive parts, appliances, and consumer goods.
- Aluminum: Aluminum is used in stamping applications that require lightweight parts, such as automotive body panels and electronic enclosures.
Forging: Materials used in forging must have high strength, toughness, and resistance to fatigue. Common materials include:
- Carbon Steel: Widely used in forging for components like gears, shafts, and connecting rods.
- Alloy Steel: Used in applications that require higher strength and toughness than carbon steel.
- Aluminum: Used in applications where lightweight and corrosion resistance are critical, such as in the aerospace and automotive industries.
Bending: Materials used in bending must have good ductility and resistance to cracking. Common materials include:
- Steel: Low-carbon steel is widely used for bending applications in construction, automotive, and manufacturing.
- Aluminum: Aluminum is used in bending for lightweight structures, frames, and enclosures.
Rolling: Materials used in rolling must have good malleability and the ability to withstand compressive forces. Common materials include:
- Steel: Steel is the most common material for rolling, used to produce sheets, plates, bars, and structural profiles.
- Aluminum: Aluminum is used in rolling to create lightweight sheets and plates for the aerospace, automotive, and construction industries.
Extrusion: Materials used in extrusion must have good flow properties and resistance to cracking. Common materials include:
- Aluminum: Aluminum is the most commonly extruded material, used for structural components, tubes, and profiles in the automotive and construction industries.
- Magnesium: Magnesium is used in extrusion for lightweight parts in the automotive and electronics industries.
Hydroforming: Materials used in hydroforming must have good ductility and the ability to withstand high-pressure fluid without cracking. Common materials include:
- Aluminum: Aluminum is widely used in hydroforming for lightweight automotive and aerospace components.
- Stainless Steel: Stainless steel is used in hydroforming for high-strength, corrosion-resistant parts such as exhaust systems and structural components.
Spinning: Materials used in spinning must have good ductility and the ability to withstand repeated deformation without cracking. Common materials include:
- Aluminum: Aluminum is commonly used in spinning for the production of cookware, lighting reflectors, and automotive components.
- Copper and Brass: Copper and brass are used in spinning for decorative items, electrical components, and plumbing fittings.
10.3 How Material Behavior Influences the Choice of Forming Process
The choice of material and forming process is influenced by several factors, including the material’s mechanical properties, formability, and the desired part geometry. Key considerations include:
- Ductility: Materials with high ductility, such as aluminum and low-carbon steel, are well-suited for deep drawing, hydroforming, and spinning. Materials with lower ductility, such as high-strength steel or titanium, may be more suitable for stamping or forging.
- Yield Strength: Lower yield strength materials are preferred for processes that involve significant plastic deformation, such as deep drawing and hydroforming. Higher yield strength materials are used in processes like forging and stamping, where compressive forces are dominant.
- Forming Depth: Deep drawing, hydroforming, and spinning are better suited for producing parts with significant forming depth, while stamping, bending, and rolling are better suited for shallow or flat parts.
Tooling and Equipment Comparison in Deep Drawing and Other Metal Forming Techniques
Tooling and equipment are critical components of any metal forming process. The design of the tooling and the choice of equipment can significantly impact the quality, speed, and cost of production.
11.1 Tooling Design in Deep Drawing vs. Stamping, Forging, and Bending
Deep Drawing: The tooling in deep drawing consists of a punch, die, and blank holder. The punch pushes the blank into the die cavity, while the blank holder prevents the material from wrinkling as it is drawn into the die. The tooling must be designed to control material flow and deformation, ensuring that the part is drawn without tearing or excessive thinning.
Stamping: Stamping requires progressive dies that perform multiple operations (e.g., cutting, bending, punching) in a single stroke. The dies must be carefully designed to achieve precise cuts and bends while minimizing material waste and defects.
Forging: Forging requires heavy-duty dies that can withstand the high compressive forces involved in shaping metal. The dies must be designed to create the desired part geometry while allowing for material flow and flash formation.
Bending: Bending requires relatively simple tooling, typically consisting of a punch and die. The tooling must be designed to achieve the desired bending angle while preventing cracking or excessive thinning at the bend radius.
11.2 Equipment Types: Mechanical, Hydraulic, and Servo-Driven Presses
Deep Drawing: Deep drawing is typically performed on hydraulic presses, which provide precise control over force and speed. Servo-driven presses are also used for deep drawing, allowing for real-time adjustments to process parameters such as punch speed and blank holder force.
Stamping: Stamping is commonly performed on mechanical presses, which operate at high speeds and are well-suited for high-volume production of small, shallow parts. Hydraulic presses are used for more complex stamping operations that require precise control over force and speed.
Forging: Forging requires mechanical or hydraulic presses that can apply high compressive forces to shape the metal. Hot forging is typically performed on hydraulic presses, while cold forging is performed on mechanical presses.
Bending: Bending is performed on press brakes or other specialized bending machines. These machines can be mechanical, hydraulic, or servo-driven, depending on the required precision and production volume.
11.3 Tool Wear and Maintenance in Deep Drawing Compared to Other Processes
Deep Drawing: Tool wear in deep drawing is influenced by factors such as material hardness, lubrication, and punch speed. The punch, die, and blank holder must be regularly inspected and maintained to prevent defects such as surface scratches, thinning, or tearing. Coatings such as titanium nitride (TiN) or diamond-like carbon (DLC) are commonly applied to tooling to reduce wear and extend tool life.
Stamping: Stamping dies experience wear due to the high-speed nature of the process and the repetitive cutting, punching, and bending operations. Regular maintenance and sharpening of the dies are required to maintain part quality and extend tool life.
Forging: Forging dies are subjected to extreme forces and temperatures, leading to significant tool wear. Heat-resistant coatings and lubricants are used to reduce wear and extend tool life. Regular maintenance is critical to prevent defects such as die cracking or surface defects in the forged parts.
Bending: Tool wear in bending is less severe than in processes like deep drawing or forging. However, the punch and die must be regularly inspected for wear to prevent cracking or thinning at the bend radius. Lubrication is often used to reduce friction and wear during the bending process.
Defects in Deep Drawing vs. Other Metal Forming Techniques
Each metal forming technique is prone to specific defects that can compromise the quality of the final part. Understanding the common defects in each process and how to prevent them is essential for achieving high-quality, defect-free parts.
12.1 Common Defects in Deep Drawing
Wrinkling: Wrinkling occurs when the blank holder force is too low, allowing the material to flow too freely into the die. Wrinkles form around the edges of the part, compromising its surface quality and structural integrity.
Tearing: Tearing occurs when the material is overstretched and can no longer withstand the tensile stresses. This is often caused by excessive punch speed or insufficient ductility in the material.
Thinning: Thinning occurs when the material is stretched too much in certain areas, leading to a reduction in thickness. This weakens the part and increases the risk of failure during use.
Earing: Earing is caused by anisotropy in the material’s grain structure, resulting in uneven deformation during deep drawing. This leads to the formation of ears or flanges around the edges of the part.
12.2 Defects in Stamping, Forging, and Bending
Stamping Defects:
- Burrs: Sharp edges or material protrusions left on the part after cutting or punching.
- Cracking: Occurs when the material is overstressed during bending or punching operations.
- Dimensional Variations: Caused by improper alignment of the dies or variations in material thickness.
Forging Defects:
- Flash: Excess material that is squeezed out of the die cavity during forging, which must be trimmed off in a secondary operation.
- Die Cracking: Caused by excessive stress or improper die maintenance.
- Surface Defects: Caused by improper die lubrication or tool wear.
Bending Defects:
- Cracking: Occurs when the material is bent beyond its ductility limits, leading to cracks along the bend radius.
- Springback: The tendency of the material to return to its original shape after bending, resulting in incorrect angles.
- Wrinkling: Caused by insufficient support or improper tooling during the bending process.
12.3 Defect Prevention Strategies in Different Metal Forming Processes
Deep Drawing:
- Increase the blank holder force to prevent wrinkling.
- Use lubrication to reduce friction and improve material flow.
- Select materials with high ductility to reduce the risk of tearing.
- Optimize punch speed to prevent overstretching and thinning.
Stamping:
- Maintain and sharpen dies regularly to reduce burr formation and improve dimensional accuracy.
- Use progressive dies to perform multiple operations in a single stroke, reducing the risk of misalignment.
- Optimize material thickness and die clearance to prevent cracking and dimensional variations.
Forging:
- Use preheating to reduce material strength and improve formability in hot forging operations.
- Apply heat-resistant coatings to dies to reduce wear and improve surface quality.
- Regularly inspect and maintain forging dies to prevent cracking and surface defects.
Bending:
- Select materials with high ductility to reduce the risk of cracking during bending.
- Use springback compensation techniques to achieve accurate bend angles.
- Ensure proper tool alignment and support to prevent wrinkling and surface defects.
Automation and Technological Advancements in Deep Drawing and Other Metal Forming Techniques
Technological advancements in automation, computer-aided design (CAD), and finite element analysis (FEA) have significantly improved the efficiency, precision, and flexibility of metal forming processes, including deep drawing, stamping, forging, and bending.
13.1 Automation in Deep Drawing: Servo-Driven Presses and CNC Control
Automation has revolutionized the deep drawing process by improving precision, repeatability, and production speed. Servo-driven presses and CNC (computer numerical control) systems allow for real-time adjustments to process parameters such as punch speed, blank holder force, and lubrication, enabling manufacturers to optimize the process for different materials and part geometries.
Benefits of automation in deep drawing include:
- Improved Precision: Servo-driven presses provide precise control over punch speed and force, resulting in tighter tolerances and higher part quality.
- Real-Time Monitoring: CNC systems allow for real-time monitoring of key process variables, such as temperature, pressure, and tool wear, enabling manufacturers to make adjustments on the fly and prevent defects.
- Increased Productivity: Automation reduces cycle times and increases production efficiency, making it possible to produce high-quality parts in large volumes.
13.2 Automation in Stamping, Forging, Bending, and Hydroforming
Stamping: Stamping has long been an automated process, with progressive stamping presses capable of performing multiple operations in a single stroke. Automation has improved the speed and precision of stamping, enabling manufacturers to produce small, intricate parts in high volumes with minimal manual intervention.
Forging: Automation in forging has improved the precision and repeatability of the process. Robotic automation is often used to handle heavy workpieces and position them in the forging dies, reducing the risk of injury to operators and improving production speed.
Bending: Automation in bending is achieved through the use of CNC press brakes, which allow for precise control over bend angles, force, and speed. CNC press brakes can be programmed to perform complex bending sequences with high accuracy and repeatability.
Hydroforming: Hydroforming has benefited from advancements in CNC control and servo-driven presses, which allow for precise control over fluid pressure and part geometry. Automation has made it possible to produce complex, lightweight parts with greater consistency and accuracy.
13.3 Finite Element Analysis (FEA) in Deep Drawing vs. Other Forming Techniques
Finite Element Analysis (FEA) is a powerful computational tool used to simulate the behavior of materials during metal forming processes. FEA allows engineers to predict how a material will deform under various conditions and optimize the design of tooling and process parameters to prevent defects.
In deep drawing, FEA is used to:
- Predict Material Flow: FEA simulations can model the flow of material into the die cavity, helping engineers optimize punch speed, blank holder force, and lubrication to ensure smooth material movement.
- Analyze Stress and Strain: FEA allows engineers to predict areas of high stress or strain in the material, enabling them to make adjustments to the tooling or process parameters to prevent defects such as tearing, wrinkling, or thinning.
- Optimize Tool Design: FEA simulations can be used to optimize the design of the punch, die, and blank holder to ensure that the material is deformed evenly and that the final part meets dimensional specifications.
In other metal forming processes, FEA is used for similar purposes:
- Stamping: FEA is used to simulate cutting, bending, and punching operations, allowing engineers to optimize die clearance, punch speed, and material thickness to prevent defects such as cracking, burrs, or dimensional variations.
- Forging: FEA is used to predict material flow and stress distribution during forging, enabling engineers to optimize die design, preheating temperature, and material flow to reduce defects and improve part quality.
- Bending: FEA is used to simulate the bending process and predict springback, allowing engineers to optimize tooling design and process parameters to achieve accurate bend angles.
13.4 Industry 4.0 Integration in Metal Forming Processes
Industry 4.0 refers to the integration of digital technologies, automation, and data analytics into manufacturing processes. In metal forming, Industry 4.0 technologies such as smart sensors, real-time data monitoring, and predictive maintenance are transforming the way parts are produced.
Key Industry 4.0 technologies in metal forming include:
- Smart Sensors: Smart sensors are used to monitor key process variables such as temperature, pressure, and tool wear in real time. This data can be analyzed to make real-time adjustments to process parameters, improving part quality and reducing downtime.
- Predictive Maintenance: Predictive maintenance systems use data analytics to monitor the condition of tooling and equipment, allowing manufacturers to schedule maintenance before a failure occurs. This reduces downtime and extends the life of the tooling and equipment.
- Digital Twins: Digital twins are virtual models of physical processes that can be used to simulate and optimize metal forming operations. By creating a digital twin of a deep drawing or stamping process, engineers can test different tooling designs and process parameters before implementing them in production.
Applications Across Industries: Deep Drawing vs. Other Metal Forming Techniques
Different industries rely on a variety of metal forming processes to produce parts with specific properties, shapes, and performance characteristics. The choice of process depends on factors such as part geometry, material requirements, production volume, and cost.
14.1 Automotive Industry: Deep Drawing vs. Stamping and Forging
Deep Drawing in Automotive: Deep drawing is widely used in the automotive industry to produce large, lightweight parts such as body panels, fuel tanks, and exhaust components. The process allows for the creation of parts with complex geometries and uniform wall thickness, making it ideal for structural components that require strength and durability.
Stamping in Automotive: Stamping is used to produce smaller, shallow parts such as brackets, clips, and fasteners. Stamping is a high-speed process that allows for the mass production of small parts with intricate details, making it ideal for high-volume automotive manufacturing.
Forging in Automotive: Forging is used to produce high-strength components such as crankshafts, connecting rods, and gears. These parts must withstand high loads and stresses, making forging the preferred process for critical drivetrain components.
14.2 Aerospace Industry: Hydroforming and Spinning vs. Deep Drawing
Deep Drawing in Aerospace: Deep drawing is used to produce components such as fuselage sections, engine housings, and structural parts. These parts require high strength, low weight, and tight tolerances, making deep drawing a suitable process for aerospace applications.
Hydroforming in Aerospace: Hydroforming is used to produce complex, lightweight components such as wing ribs, engine mounts, and exhaust systems. The process allows for the creation of parts with more complex geometries and deeper forming depths than deep drawing, making it ideal for certain aerospace applications.
Spinning in Aerospace: Spinning is used to produce axially symmetric parts such as nose cones, engine cowlings, and reflectors. The process allows for the creation of large, smooth, curved surfaces, making it suitable for parts that require aerodynamic efficiency.
14.3 Electronics and Consumer Goods: Bending, Stamping, and Deep Drawing
Deep Drawing in Electronics: Deep drawing is used to produce enclosures for electronic devices, such as smartphone housings, battery enclosures, and connector components. The process allows for the creation of thin, lightweight parts with high structural integrity and precise dimensions.
Stamping in Electronics: Stamping is used to produce small, precise parts for electronic devices, including connectors, terminals, and circuit board components. The high-speed nature of stamping makes it ideal for mass-producing small, intricate parts.
Bending in Consumer Goods: Bending is commonly used in the production of consumer products such as appliance housings, furniture frames, and brackets. Bending allows for the creation of simple, angular shapes with high precision and repeatability.
14.4 Medical Devices: Deep Drawing vs. Hydroforming and Spinning
Deep Drawing in Medical Devices: Deep drawing is used to produce medical device components such as surgical instruments, implants, and device enclosures. The process allows for the creation of parts with tight tolerances, smooth surfaces, and high corrosion resistance, making it ideal for medical applications.
Hydroforming in Medical Devices: Hydroforming is used to produce complex, lightweight components such as prosthetics, implants, and surgical instruments. The process allows for the creation of parts with more intricate geometries and deeper forming depths than deep drawing, making it suitable for certain medical applications.
Spinning in Medical Devices: Spinning is used to produce axially symmetric components such as implants, surgical tools, and device housings. The process allows for the creation of smooth, curved surfaces with high precision, making it ideal for parts that require biocompatibility and corrosion resistance.
Conclusion: Choosing Between Deep Drawing and Other Metal Forming Techniques
Metal forming processes, such as deep drawing, stamping, forging, bending, rolling, extrusion, hydroforming, and spinning, each offer unique advantages and limitations depending on the application. The choice of metal forming technique depends on factors such as part geometry, material requirements, production volume, and cost.
Deep drawing is ideal for producing hollow, three-dimensional parts with complex geometries, high strength, and uniform wall thickness. It is widely used in industries such as automotive, aerospace, packaging, and medical devices. However, deep drawing may not be the best choice for parts that require minimal forming depth, intricate details, or long, continuous profiles.
Stamping is a high-speed process that is best suited for producing flat or shallow parts with intricate details in large quantities. Forging is ideal for producing high-strength components that must withstand heavy loads and stress, while bending is used to create simple angular or curved shapes.
Rolling and extrusion are used to produce long, continuous parts with uniform cross-sectional profiles, while hydroforming and spinning are ideal for producing complex, lightweight parts with deep forming depths and smooth, curved surfaces.
Ultimately, the choice between deep drawing and other metal forming techniques depends on the specific requirements of the part, including its shape, material properties, and performance criteria. By carefully evaluating these factors, manufacturers can select the most appropriate metal forming process to meet their production goals and ensure high-quality, defect-free parts.
What is Sheet Forming?
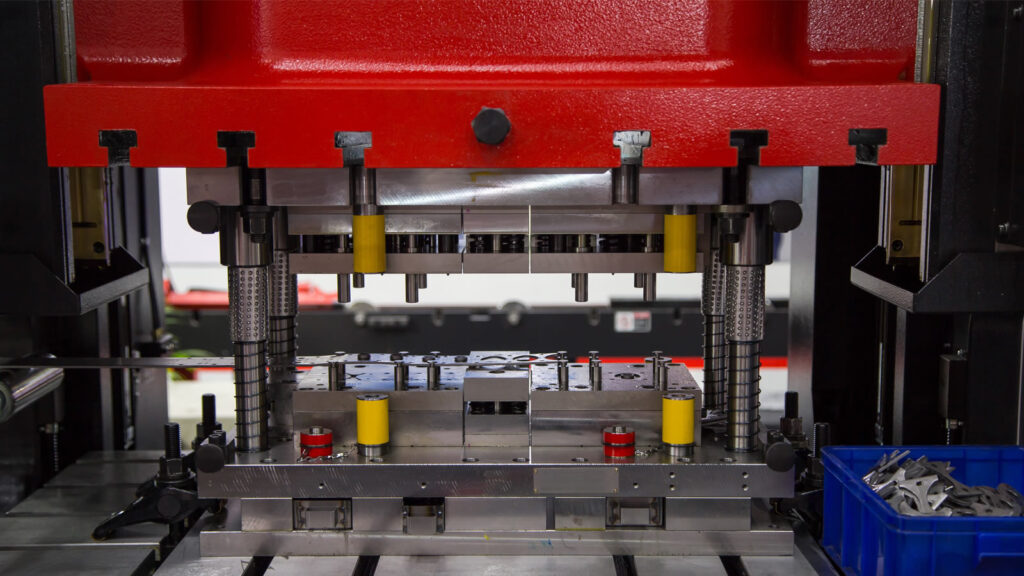
Sheet forming refers to the process of shaping metal sheets into desired forms by applying force without removing material. It is a vital manufacturing technique used across industries like automotive, aerospace, electronics, and construction. The process involves manipulating sheet metal using different methods such as bending, stretching, or deep drawing. The end products are essential components in the form of panels, structural parts, or enclosures.
What is a Hydraulic Cold Press?
A hydraulic cold press is a machine that uses hydraulic force to deform or shape sheet metal at room temperature. Unlike hot forming, which uses heat to soften the metal, cold forming relies solely on high-pressure hydraulic systems to achieve the required deformation. Hydraulic cold presses are preferred for applications where precision, surface finish, and material properties like strength and hardness are crucial.
Importance of Sheet Forming in Modern Industry
Sheet forming is integral to the production of various components, especially where high-volume production and precision are critical. The versatility of sheet forming has made it the backbone of industries such as:
- Automotive: Sheet forming enables the mass production of body panels, chassis parts, and other critical automotive components.
- Aerospace: The process is used to form lightweight and high-strength metal sheets used in aircraft structures.
- Construction: Sheet forming helps in creating roofing materials, facades, and other structural elements.
The use of hydraulic cold presses in these industries has increased significantly due to their ability to provide consistent force, which results in superior accuracy and repeatability.
Brief History and Evolution of Hydraulic Presses
The development of hydraulic presses dates back to the 18th century, with the invention of the hydraulic press by Joseph Bramah in 1795. The use of hydraulic power was revolutionary in its ability to amplify force through hydraulic fluids. Over time, hydraulic presses evolved with the advent of new materials and control systems. The modern hydraulic cold press leverages automation, precise control mechanisms, and improved hydraulic fluids to enhance efficiency and productivity.
Hydraulic presses play a critical role in metal forming processes, offering advantages in energy efficiency, force control, and customization. Today, they are a cornerstone in manufacturing for industries requiring high-quality and intricate sheet metal parts.
Fundamentals of Sheet Forming
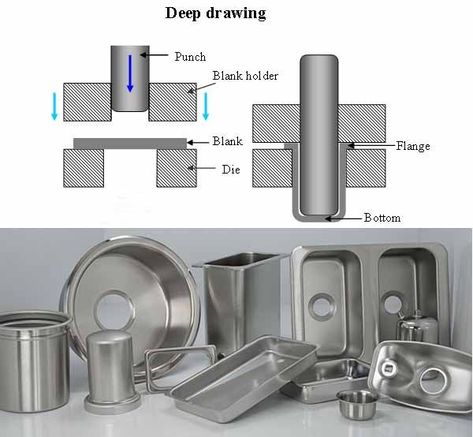
Basic Principles of Sheet Metal Forming
Sheet metal forming involves deforming metal sheets plastically, meaning the material is shaped permanently without breaking or cracking. The sheet is subjected to forces beyond its elastic limit, causing it to take a new form. The success of the process depends on several factors, including:
- Material properties such as ductility and tensile strength
- Thickness and uniformity of the sheet
- The applied pressure and the tooling used
- The ability of the material to flow into the die cavity without cracking
Forming processes like bending, stretching, and drawing are fundamental in shaping sheet metal into complex geometries.
Types of Sheet Forming Processes
There are three primary types of sheet forming processes based on temperature:
- Cold Forming: Performed at room temperature, maintaining material strength and hardness.
- Warm Forming: Involves moderate heating to improve formability while avoiding full material softening.
- Hot Forming: Uses high temperatures to soften the material, allowing for easier deformation but at the cost of precision.
Hydraulic cold presses are ideal for cold forming due to their ability to provide high pressure and precision without heating the material.
Key Materials Used in Sheet Forming
Sheet forming typically involves various metals, including:
- Aluminum: Lightweight, corrosion-resistant, and easily formable.
- Steel: Offers high strength and is used in applications where durability is critical.
- Copper and Brass: Known for their excellent electrical conductivity and ease of forming.
- Alloys: Combination of metals to achieve specific properties like strength, formability, and corrosion resistance.
Each material has specific requirements for forming, including the level of pressure needed and the potential for cracking or work hardening.
Importance of Press Force in Forming Operations
In sheet forming, the force applied by the press is crucial in determining the quality of the final product. Hydraulic cold presses are favored because they allow for precise control of the press force, ensuring that the sheet metal is deformed to the desired specifications without causing cracks or other defects. The ability to adjust pressure based on material thickness and formability makes hydraulic cold presses versatile for a wide range of materials and applications.
Hydraulic Press Technology Overview
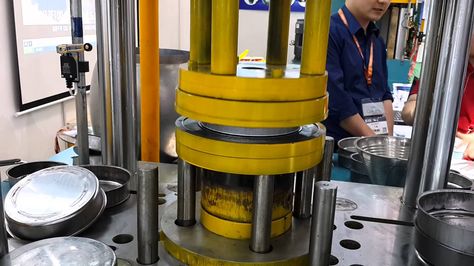
Types of Hydraulic Presses
Hydraulic presses are versatile machines used for various forming processes, including cold and hot pressing, stamping, punching, and forging. In sheet forming, cold hydraulic presses are specifically designed to work without applying heat. Different types of hydraulic presses are classified based on their functionality and application:
- Cold Press: This type of hydraulic press works at room temperature to form metal sheets. It is ideal for applications where maintaining the material’s mechanical properties is essential, such as in the automotive and aerospace industries.
- Hot Press: These presses apply heat along with hydraulic force to form metal sheets. They are typically used when high ductility is needed, such as for thick or complex-shaped parts. Hot pressing also helps in reducing material hardness during the forming process.
- Servo-Hydraulic Press: A servo-controlled hydraulic press combines the efficiency of hydraulic power with the precision of servo motors. This type of press allows for more accurate control over force and position, making it suitable for high-precision applications.
- Mechanical Presses: While not hydraulic, mechanical presses are driven by motors and are commonly used in sheet metal forming. They are faster than hydraulic presses but are less flexible in terms of force control and precision.
- Pneumatic Presses: Similar to hydraulic presses, pneumatic presses use compressed air instead of hydraulic fluid to generate force. However, pneumatic presses are generally limited in the amount of force they can produce, making them suitable only for lighter, smaller operations.
Main Components of a Hydraulic Press
The design of hydraulic presses consists of several essential components that work together to deliver the necessary force for sheet forming. The key components of a hydraulic cold press include:
- Hydraulic System: This includes the pump, hydraulic cylinders, valves, and hydraulic fluid. The pump generates the necessary pressure, while the hydraulic cylinders convert the hydraulic energy into mechanical force. The valves control the flow of hydraulic fluid and the pressure applied during the forming process.
- Frame: The press frame supports the structure of the press and absorbs the forces generated during the sheet forming process. It is typically made from heavy-duty steel to provide stability and withstand high forces.
- Tooling Systems (Die and Punch): The tooling system, consisting of a die and punch, shapes the metal sheet. The punch applies pressure to the sheet metal, while the die provides a cavity that the sheet is pressed into. The tooling can be customized for different shapes and sizes of the final product.
- Control Systems: Modern hydraulic cold presses are equipped with advanced control systems, often computer-controlled, allowing operators to adjust the force, speed, and positioning. This ensures greater accuracy and repeatability in forming operations.
- Hydraulic Fluids: The hydraulic fluid plays a critical role in transmitting pressure from the pump to the hydraulic cylinders. The fluid needs to be well-maintained and kept clean to ensure smooth operation and prevent wear in the hydraulic system.
Working Principle of Hydraulic Cold Presses
The hydraulic cold press operates on Pascal’s Law, which states that pressure exerted on a confined fluid is transmitted undiminished throughout the fluid in all directions. Here’s a step-by-step breakdown of how a hydraulic cold press works:
- Hydraulic Pump Activation: The press cycle begins by activating the hydraulic pump, which pressurizes the hydraulic fluid.
- Cylinder Movement: The pressurized fluid is directed to the hydraulic cylinders, which contain pistons. As the fluid enters the cylinder, it pushes the piston, converting hydraulic pressure into mechanical force.
- Pressing the Sheet Metal: The piston drives the punch (or ram) down onto the sheet metal, forcing it into the die, and shaping it according to the required form.
- Return Stroke: After the sheet metal is formed, the hydraulic fluid is released, and the piston returns to its original position. This completes the press cycle, and the formed sheet is ejected or removed from the press.
The ability to control the pressure, speed, and stroke length makes hydraulic cold presses ideal for forming a variety of sheet metal components.
Role of Hydraulic Fluids and Pressure Control
Hydraulic fluids serve as the medium for transmitting power in hydraulic systems. They are essential in ensuring the smooth operation of the press and preventing corrosion, overheating, and wear. Common types of hydraulic fluids include mineral oils, synthetic fluids, and water-based fluids. Modern hydraulic presses often incorporate filtration systems to keep the hydraulic fluid free of contaminants.
Pressure control is also vital to prevent overloading the machine or damaging the material. Pressure sensors, relief valves, and regulators are commonly integrated into the hydraulic system to maintain optimal pressure throughout the forming process.
Design and Construction of Hydraulic Cold Presses
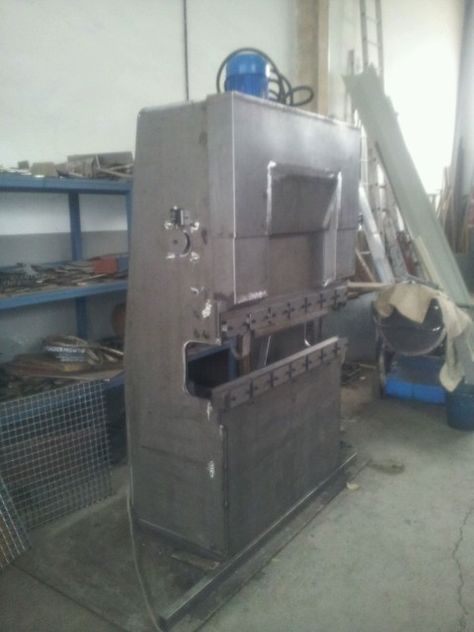
Structure of a Hydraulic Cold Press
The structure of a hydraulic cold press is robust and built to handle the high forces generated during sheet forming. The design of the press is critical to ensuring both safety and productivity. The key structural components of a hydraulic cold press include:
- Press Frame: The frame is the backbone of the machine, designed to withstand significant forces during operation. Frames are typically made from steel or cast iron and are designed to minimize deflection during pressing. The frame is usually either a C-frame (open on one side) or an H-frame (four-sided, more robust).
- Hydraulic Cylinder: The cylinder is the core mechanical component that converts hydraulic pressure into the force required for forming. It houses the piston, which is driven down to apply pressure on the sheet metal.
- Bolsters and Platens: Bolsters are the plates on which the tooling (die and punch) is mounted. The platen is the moving part that holds the punch and moves in sync with the hydraulic cylinder. These parts must be made from high-strength materials to resist wear and ensure precise alignment during forming.
- Die and Punch Assembly: The tooling system includes a die (the cavity where the metal sheet is pressed into) and a punch (the part that pushes the sheet into the die). Tooling is often custom-designed based on the shape and complexity of the final part.
- Control Panel and Safety Features: Modern presses come equipped with control panels that allow operators to monitor the press force, stroke length, and other operational parameters. Additionally, safety features such as emergency stop buttons, safety guards, and light curtains are integrated into the design.
Key Components and Their Materials
The durability and performance of a hydraulic cold press depend on the quality of materials used in its construction. For instance:
- Frame: Constructed from high-tensile steel or cast iron to provide the necessary strength and rigidity.
- Cylinders and Pistons: Made from hardened steel to withstand wear and pressure during continuous operation.
- Tooling (Die and Punch): Generally crafted from tool steels or carbide materials for longevity and wear resistance, especially in high-pressure applications.
Factors Influencing the Design of a Hydraulic Press
Several factors must be considered when designing a hydraulic cold press for sheet forming:
- Press Tonnage: The press tonnage defines the maximum force the machine can generate. Higher tonnage presses are needed for forming thicker and tougher materials.
- Bed Size and Tool Configuration: The size of the press bed determines the size of sheet metal that can be formed. Larger beds allow for the forming of larger sheets, while the tooling configuration defines the complexity of shapes that can be produced.
- Stroke Length: The stroke length refers to the distance the press ram travels during a cycle. It needs to be sufficient to accommodate the material thickness and die design.
- Cycle Time: The speed at which the press operates is a critical factor for productivity. While hydraulic cold presses may be slower than mechanical ones, they offer superior control over force application and precision.
Pressure Distribution Systems
Effective pressure distribution is essential for even sheet forming. In hydraulic presses, the pressure is distributed evenly across the surface of the die and punch, ensuring uniform deformation of the material. This prevents issues such as wrinkling, thinning, or tearing of the sheet metal.
Modern hydraulic presses use advanced pressure distribution systems that monitor and adjust the pressure in real time, ensuring consistent results even when forming complex geometries.
Operation of Hydraulic Cold Press for Sheet Forming
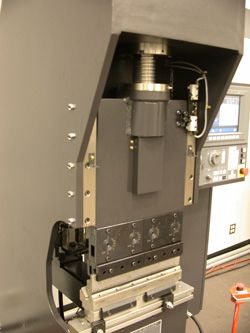
Detailed Operation Process
Operating a hydraulic cold press for sheet forming involves several critical steps:
- Press Setup and Calibration: Before starting, the press is calibrated to the specific requirements of the job. This includes adjusting the press force, setting the stroke length, and ensuring that the tooling (die and punch) is properly aligned.
- Tooling and Die Setting: The die and punch are mounted onto the press. Proper die setting is essential to avoid misalignment and ensure the sheet metal is formed accurately. Operators must ensure the tools are securely fastened to avoid accidents.
- Loading the Material: Sheet metal is placed on the bolster or between the die and punch. In automated systems, robotic arms or feeding mechanisms can load the sheet metal, reducing manual intervention and increasing safety.
- Pressing Operation: Once the press is set up and the material is loaded, the hydraulic system is activated. The hydraulic cylinder pushes the punch down, pressing the sheet metal into the die and forming the desired shape.
- Ejection and Removal of the Formed Part: After forming, the press releases the material, and the formed part is either manually or automatically ejected from the press. The operator checks for defects and ensures that the part meets the required specifications.
Temperature Considerations in Cold Forming
While hydraulic cold presses work at room temperature, temperature fluctuations in the environment or the material itself can affect the forming process. Cold working increases material hardness, and without proper lubrication or control, it can lead to issues like cracking. To mitigate this, manufacturers often use lubricants or pre-condition the sheet metal to improve formability.
Factors Affecting Formability
Several factors influence the formability of sheet metal in a hydraulic cold press:
- Material Thickness: Thicker sheets require more pressure, and their formability is typically lower than thinner sheets.
- Material Type: Different metals and alloys have varying formability characteristics. For example, aluminum is more ductile and easier to form than steel.
- Die Design: A well-designed die ensures that the material flows smoothly into the desired shape without tearing or wrinkling.
- Press Speed: Slower press speeds allow the material to deform more gradually, reducing the risk of cracks or other defects.
Common Issues in Hydraulic Cold Press Operations and Troubleshooting
Some common problems encountered during the operation of hydraulic cold presses include:
- Inconsistent Pressure: Pressure fluctuations can lead to uneven forming or incomplete part formation. Regular maintenance of the hydraulic system and pressure sensors is crucial to avoid this issue.
- Tooling Misalignment: Improper alignment of the die and punch can result in defective parts. Ensuring proper die setting before each press cycle helps avoid this problem.
- Material Cracking or Tearing: This often occurs when too much pressure is applied, or the material is too brittle. Reducing the press force or using softer materials can resolve this issue.
Regular maintenance of the hydraulic system, calibration of the press, and inspection of tooling are essential to ensure smooth and efficient operation.
Applications of Hydraulic Cold Presses
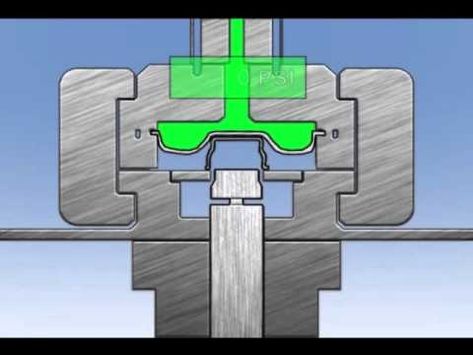
Hydraulic cold presses are integral to many industries where precision sheet forming is required. Their ability to form materials at room temperature while maintaining material integrity makes them suitable for a wide range of applications. Below are some of the key industries where hydraulic cold presses play a crucial role:
Automotive Industry
The automotive industry is one of the largest users of hydraulic cold presses, primarily for manufacturing various components from sheet metal. The use of hydraulic presses ensures that the metal sheets are formed to exact specifications, ensuring durability, safety, and aesthetics. Key applications in the automotive industry include:
- Car Body Panels: Hydraulic cold presses are used to manufacture exterior body panels such as doors, hoods, and roofs. These parts need to be lightweight, strong, and free of defects, which is made possible through precision cold forming.
- Chassis and Structural Components: The automotive chassis and frame components, which form the backbone of a vehicle, are also manufactured using hydraulic presses. The cold forming process ensures that these parts retain their strength and durability without compromising their structural integrity.
- Fuel Tanks and Exhaust Systems: Fuel tanks, exhaust pipes, and other automotive components require precise metal forming. Cold presses ensure smooth, defect-free parts that can handle stress and environmental conditions.
The trend toward lightweight vehicles has led to the adoption of more aluminum and high-strength steel in automotive manufacturing, both of which are ideal for cold forming processes using hydraulic presses.
Aerospace Industry
The aerospace industry relies on precision and high-performance materials. Hydraulic cold presses are widely used to form lightweight, high-strength materials such as aluminum alloys, titanium, and other advanced composites. Applications in this industry include:
- Aircraft Panels and Fuselage Sections: Cold pressing is used to form large, flat, or curved panels that make up the fuselage, wings, and other critical parts of an aircraft. These parts must be formed with tight tolerances to ensure aerodynamic performance and safety.
- Engine Components: Many sheet-formed components in aerospace engines are manufactured using hydraulic cold presses, ensuring they can withstand extreme temperatures and pressures while maintaining their shape and strength.
- Satellite and Spacecraft Structures: Lightweight, durable materials are crucial for spacecraft and satellite components. Hydraulic cold pressing helps form structural elements that are both strong and lightweight, improving performance and reducing launch costs.
Construction and Infrastructure
The construction industry utilizes hydraulic cold presses to produce metal sheets for various building components. Some of the most common applications include:
- Roofing Sheets and Panels: Metal roofing sheets, commonly made from steel or aluminum, are formed using hydraulic cold presses. The process ensures that the sheets have the necessary strength and durability to withstand harsh weather conditions.
- Structural Components: Cold pressing is used to form various structural elements in buildings, such as steel beams, brackets, and support structures. These components need to be strong, corrosion-resistant, and dimensionally accurate.
- Cladding and Facade Panels: Hydraulic cold presses are also used to manufacture cladding and facade panels for modern buildings, contributing to the aesthetic appeal and durability of the structure.
Electronics and Consumer Goods
In the electronics industry, hydraulic cold presses are employed to form thin metal sheets used in enclosures, housings, and other components. Some applications include:
- Electronic Enclosures and Casings: Aluminum or steel housings for electronic devices like laptops, smartphones, and consumer appliances are typically manufactured using hydraulic cold presses. The cold forming process ensures that these enclosures are both durable and aesthetically pleasing.
- Heat Sinks and Conductive Components: Hydraulic cold presses are used to form metal sheets into complex shapes for use as heat sinks and conductive elements in electronic devices. The process ensures precise dimensional control and surface finish, which are essential for thermal management in electronics.
Custom Fabrication and Niche Applications
Hydraulic cold presses are also used for custom sheet metal fabrication in niche industries. These applications range from custom architectural elements to specialty parts in medical devices and industrial equipment. The flexibility of hydraulic cold presses allows for the creation of complex shapes, intricate designs, and high-quality finishes for small-batch or specialized production runs.
Advantages and Disadvantages of Hydraulic Cold Presses
Advantages of Hydraulic Cold Presses
Hydraulic cold presses offer several key advantages over other types of presses, making them an ideal choice for many sheet forming applications:
- Precision and Accuracy: Hydraulic presses provide consistent force and precise control, enabling the accurate formation of complex shapes and fine details in sheet metal. The ability to control pressure and speed during the press cycle ensures uniformity across parts, which is critical in industries like aerospace and automotive, where tight tolerances are required.
- Suitability for a Wide Range of Materials: Hydraulic cold presses can be used with a variety of materials, including steel, aluminum, copper, brass, and advanced alloys. The versatility of the machine allows it to form materials with varying thicknesses and properties, making it applicable to different industries.
- Cost-Effective Production: Compared to hot forming methods, hydraulic cold pressing is often more cost-effective, especially when large production volumes are not required. Cold pressing eliminates the need for heating equipment, reducing energy consumption and associated costs.
- Energy Efficiency: Hydraulic cold presses generally consume less energy than mechanical presses. Since the press operates only when needed (during the press cycle), energy use is minimized, resulting in lower operating costs.
- High Force with Compact Size: Hydraulic cold presses are capable of generating a large amount of force despite their relatively compact size. This allows manufacturers to save floor space in their production facilities without compromising the machine’s capabilities.
- Long Tool Life and Durability: Since cold forming does not involve heat, the tooling (die and punch) experiences less thermal stress, leading to a longer tool life. This reduces the frequency of tool replacements and downtime for maintenance.
Disadvantages of Hydraulic Cold Presses
Despite their advantages, hydraulic cold presses also have some limitations that must be considered:
- Slower Production Cycle: Hydraulic cold presses generally operate at slower speeds than mechanical presses. The slower cycle time can be a disadvantage in high-volume production environments where speed is critical.
- Material-Specific Limitations: Some materials, such as thick or extremely hard metals, may not be suitable for cold pressing without the risk of cracking or work hardening. In such cases, warm or hot forming processes might be more appropriate to achieve the desired results.
- Initial Setup Time: Setting up a hydraulic cold press for a new production run can take time, especially when changing dies or adjusting the press for different part geometries. This setup time may reduce overall productivity, especially in job-shop environments where frequent changeovers are required.
- Hydraulic Maintenance: Hydraulic systems require regular maintenance to ensure smooth operation. This includes monitoring and replacing hydraulic fluid, inspecting seals, and checking for leaks. Failure to maintain the system can result in inconsistent pressure, reduced machine performance, and potential downtime.
- Operator Skill Requirements: Operating a hydraulic cold press requires skilled operators to ensure the correct setup, calibration, and operation. Mistakes during operation can lead to defects in the formed parts or even damage to the press itself.
- Risk of Work Hardening: Cold forming can lead to work hardening in some materials, especially metals like steel. This phenomenon makes the material harder and more brittle, which can limit its further processing or affect the part’s performance in its final application.
Innovations and Modern Trends in Hydraulic Cold Press Technology
The hydraulic cold press industry has seen significant advancements in recent years, driven by the demand for improved productivity, precision, and energy efficiency. Below are some of the key innovations and trends in hydraulic cold press technology:
1. Advances in Hydraulic Press Controls
One of the most significant developments in hydraulic cold press technology is the adoption of advanced control systems. Modern presses are increasingly equipped with computer-aided control systems that allow for real-time monitoring and adjustment of pressing parameters, including pressure, stroke length, and speed. This allows manufacturers to fine-tune their processes, ensuring optimal part quality and repeatability.
- Programmable Logic Controllers (PLCs): PLCs enable operators to program and automate pressing sequences, reducing the likelihood of human error and increasing operational efficiency.
- Servo-Hydraulic Control: Servo-controlled hydraulic presses offer enhanced precision and control over the press force and speed. By integrating servo motors with hydraulic systems, manufacturers can achieve more consistent press cycles and improved accuracy.
2. Use of Advanced Materials and Coatings
Tooling wear is a common issue in hydraulic pressing operations, particularly in high-volume production. Recent innovations in materials and coatings have extended the life of dies and punches, improving overall productivity. Advanced tool steels, carbide materials, and coatings like titanium nitride (TiN) or diamond-like carbon (DLC) are being used to enhance the wear resistance of tooling.
- Die Material Improvements: High-performance tool steels and carbide materials reduce wear and increase the lifespan of tooling, minimizing downtime and improving productivity.
- Coating Technologies: Coatings such as TiN or DLC reduce friction between the tooling and the material, resulting in smoother operation and less wear on the tools. This also helps in forming high-strength materials that would otherwise cause rapid tool degradation.
3. Integration of Smart Sensors and IoT
The integration of smart sensors and the Internet of Things (IoT) in hydraulic cold presses is transforming the way manufacturers monitor and maintain their equipment. By using sensors to track key parameters such as hydraulic fluid levels, pressure, temperature, and tool wear, manufacturers can predict and prevent equipment failures before they occur.
- Predictive Maintenance: Smart sensors allow for continuous monitoring of the hydraulic press’s condition. When a component is nearing the end of its useful life, the system can automatically alert maintenance teams, reducing the risk of unexpected downtime.
- Remote Monitoring: IoT-enabled presses can be monitored remotely, allowing operators and maintenance personnel to track the machine’s performance from anywhere. This enables faster troubleshooting and ensures minimal production delays.
4. Eco-Friendly Hydraulic Systems
Sustainability is becoming increasingly important in modern manufacturing. Hydraulic press manufacturers are developing more energy-efficient systems that reduce environmental impact. Innovations in hydraulic fluids and energy-saving technologies are helping companies reduce their carbon footprint.
- Energy-Efficient Hydraulics: Energy-saving systems such as variable speed drives and energy recovery units reduce power consumption during idle times and press cycles.
- Eco-Friendly Hydraulic Fluids: Biodegradable and environmentally friendly hydraulic fluids are being developed to reduce the environmental impact of leaks or spills. These fluids are designed to perform as well as traditional oils while being more sustainable.
5. Hybrid Press Systems
Hybrid press systems, which combine the advantages of hydraulic and mechanical presses, are gaining popularity in industries that require both precision and speed. These systems integrate hydraulic controls for precision and mechanical drive systems for speed, offering a versatile solution for a variety of sheet forming tasks.
- Cold and Hot Forming Integration: Some hybrid presses are designed to switch between cold and hot forming processes, giving manufacturers the flexibility to handle a broader range of materials and applications.
6. Industry 4.0 and Smart Manufacturing
The rise of Industry 4.0 is driving the adoption of smart manufacturing practices in hydraulic press operations. By connecting hydraulic presses to digital networks, manufacturers can optimize production processes, improve quality control, and increase overall efficiency.
- Data-Driven Process Optimization: Real-time data from sensors, combined with advanced analytics, can help manufacturers identify inefficiencies, optimize press settings, and improve product quality.
- AI and Machine Learning: AI and machine learning algorithms are being developed to analyze press data and make automatic adjustments to improve performance, minimize defects, and reduce material waste.
Safety Standards and Regulations
Hydraulic cold presses are powerful machines that operate under high pressure, posing significant risks if not handled correctly. To ensure the safety of operators and minimize accidents, several international safety standards and regulations govern the operation and maintenance of hydraulic presses. Compliance with these regulations is critical for preventing workplace injuries and ensuring the safe operation of hydraulic presses in industrial environments.
1. International Safety Standards for Hydraulic Press Operations
There are several globally recognized safety standards that outline the safe design, operation, and maintenance of hydraulic presses. Some of the most important standards include:
- ISO 16092-3: Machine Tools – Safety – Presses – Part 3: Hydraulic Presses
This ISO standard provides specific safety requirements for hydraulic presses used in sheet metal forming and other industrial applications. It covers aspects such as:- Mechanical and electrical safety features
- Safety-related control systems
- Emergency stop mechanisms
- Safety distance and guarding requirements
- OSHA (Occupational Safety and Health Administration) Regulations – United States
OSHA sets forth workplace safety regulations for the operation of hydraulic presses under the broader category of “Machine Guarding” (OSHA 29 CFR 1910.212). These regulations include requirements for:- Machine guarding to protect operators from hazardous moving parts
- Emergency stop systems and lockout/tagout procedures
- Operator training and certification
- Inspection and maintenance guidelines
- European Union Machinery Directive (2006/42/EC)
In the European Union, the Machinery Directive ensures that hydraulic presses meet essential health and safety requirements before they are placed on the market. Manufacturers must perform a risk assessment, implement protective measures, and provide detailed safety documentation for their machines.
2. Risk Assessment in Sheet Forming Processes
A thorough risk assessment is necessary to identify potential hazards in hydraulic cold press operations. The assessment includes evaluating mechanical risks (e.g., crushing, pinching, or shearing), electrical hazards, and the risks posed by hydraulic system failures (e.g., fluid leaks or pressure malfunctions). Common risk factors include:
- Crushing Injuries: Hydraulic presses exert high forces, posing a significant risk of crushing if an operator’s hand or other body parts are accidentally caught between the die and the punch.
- Hydraulic Fluid Leaks: Hydraulic fluid leaks can lead to dangerous slip hazards, contamination, and fire risks, especially if the fluid is flammable. Regular inspection and maintenance are required to prevent leaks.
- High Pressure Failures: Failures in the hydraulic system, such as ruptured hoses or malfunctioning pressure valves, can result in sudden releases of high-pressure fluid, which can be hazardous to nearby workers.
3. Key Safety Features in Hydraulic Cold Presses
Modern hydraulic cold presses are equipped with a range of safety features designed to protect operators and prevent accidents:
- Emergency Stop Systems: All hydraulic presses must have easily accessible emergency stop buttons that immediately halt the operation of the press when activated. These buttons should be positioned within easy reach of the operator and other nearby personnel.
- Safety Interlocks and Light Curtains: Light curtains and interlocking safety doors are used to prevent the press from operating unless the safety guards are in place. Light curtains create an invisible safety barrier, and if an object (such as a hand) crosses the beam, the press will stop immediately.
- Two-Handed Operation Controls: To prevent accidental engagement of the press, many hydraulic cold presses require the operator to use both hands to activate the press cycle. This reduces the risk of the operator’s hands being caught in the die area.
- Pressure Relief Valves: Hydraulic systems are equipped with pressure relief valves to prevent over-pressurization. These valves automatically release excess pressure if it exceeds the system’s safe operating limits, preventing catastrophic failures.
4. Importance of Training and Certification for Operators
Proper training is one of the most important factors in ensuring the safe operation of hydraulic cold presses. Operators must be trained in the specific functions and controls of the machine they are using, as well as the hazards associated with hydraulic systems. Many organizations require operators to obtain certification before operating presses independently.
Training programs typically cover the following topics:
- Safe machine setup and calibration
- Proper use of safety guards and emergency stop systems
- Safe material handling and loading/unloading of sheet metal
- Basic maintenance tasks, such as checking hydraulic fluid levels and inspecting safety features
5. Emergency Stop Systems and Safety Interlocks
Emergency stop systems and safety interlocks are essential safety features in hydraulic cold presses. Emergency stop buttons must be located in areas that are easily accessible to operators and other personnel. In addition to manual stop systems, modern presses may have automatic systems that trigger an emergency stop when certain unsafe conditions are detected, such as excess pressure or hydraulic fluid leakage.
Safety interlocks are designed to prevent the machine from starting unless all safety conditions are met. For example, if the press guards are not properly closed or if the light curtain is obstructed, the press will not operate. This prevents accidents caused by human error or mechanical failure.
Case Studies and Real-World Examples
To better understand the practical applications of hydraulic cold presses, we can look at a few real-world examples and case studies that highlight the versatility and efficiency of these machines across different industries.
Case Study 1: Automotive Industry – Precision Forming of Car Body Panels
Background:
In the automotive industry, manufacturers require highly precise and repeatable forming processes to create car body panels, such as doors, hoods, and roofs. These panels must meet strict quality standards for both appearance and structural integrity, especially when using lightweight materials like aluminum.
Solution:
An automotive manufacturer implemented a hydraulic cold press with a force capacity of 1,500 tons to form aluminum panels. The press was equipped with programmable logic controllers (PLCs) that allowed for fine-tuning of press force, stroke length, and pressing speed.
Results:
- The precision of the hydraulic cold press allowed the manufacturer to achieve tight tolerances, ensuring uniform thickness and smooth surface finishes on the panels.
- The machine’s flexibility enabled the manufacturer to switch between different panel shapes and sizes with minimal downtime, improving production efficiency.
- Reduced material waste and defects lowered overall production costs, and the use of aluminum helped meet the industry’s demand for lightweight vehicle components.
Case Study 2: Aerospace Industry – Cold Forming of Lightweight Alloy Sheets
Background:
Aerospace companies require materials that are lightweight but strong enough to withstand the rigors of flight. Forming titanium and aluminum alloy sheets into complex shapes for aircraft fuselage panels and engine components requires precise control to avoid defects, as these materials are prone to cracking and work hardening during forming.
Solution:
An aerospace manufacturer adopted a hydraulic cold press with advanced servo-hydraulic controls and smart sensors to form titanium and aluminum alloy sheets. The press was integrated with a real-time monitoring system that adjusted press parameters during the forming process.
Results:
- The use of servo-hydraulic controls provided consistent and accurate forming pressure, resulting in high-quality components with minimal defects.
- The real-time monitoring system allowed for process optimization, reducing the risk of cracking and work hardening in the alloy sheets.
- The ability to form complex geometries in lightweight materials improved the overall performance and fuel efficiency of the aircraft.
Case Study 3: Electronics Manufacturing – Cold Pressing of Aluminum Enclosures
Background:
In the consumer electronics industry, manufacturers need to create aesthetically pleasing and durable enclosures for devices like laptops, smartphones, and tablets. These enclosures are typically made from thin aluminum sheets, which need to be formed with tight tolerances and smooth finishes.
Solution:
An electronics company implemented a hydraulic cold press with high-precision tooling and a multi-station setup to form aluminum enclosures. The press was capable of performing multiple operations, such as bending, stamping, and drawing, in a single cycle.
Results:
- The hydraulic cold press produced enclosures with smooth, defect-free surfaces and high dimensional accuracy, meeting the company’s strict design specifications.
- The multi-station setup increased production efficiency by combining several forming operations into one cycle, reducing lead times and labor costs.
- The use of hydraulic cold pressing ensured that the aluminum retained its strength and durability, while the surface finish was optimized for anodizing and other post-processing steps.
Case Study 4: Custom Sheet Forming for Architecture and Construction
Background:
In the architecture and construction industry, custom metal components are often required for building facades, roofing panels, and structural elements. These components must be aesthetically pleasing, structurally sound, and capable of withstanding environmental conditions.
Solution:
A construction company commissioned custom sheet metal forming using a hydraulic cold press to create decorative metal panels for the exterior of a modern office building. The panels were made from stainless steel, and the design included intricate patterns that required precise forming.
Results:
- The hydraulic cold press allowed the company to create complex patterns with high precision and repeatability, ensuring that all panels were identical and met design requirements.
- The cold forming process retained the stainless steel’s corrosion resistance, making the panels suitable for exterior use.
- The company was able to complete the project on time and within budget, thanks to the press’s efficiency and flexibility in handling custom designs.
The Future of Hydraulic Cold Press for Sheet Forming
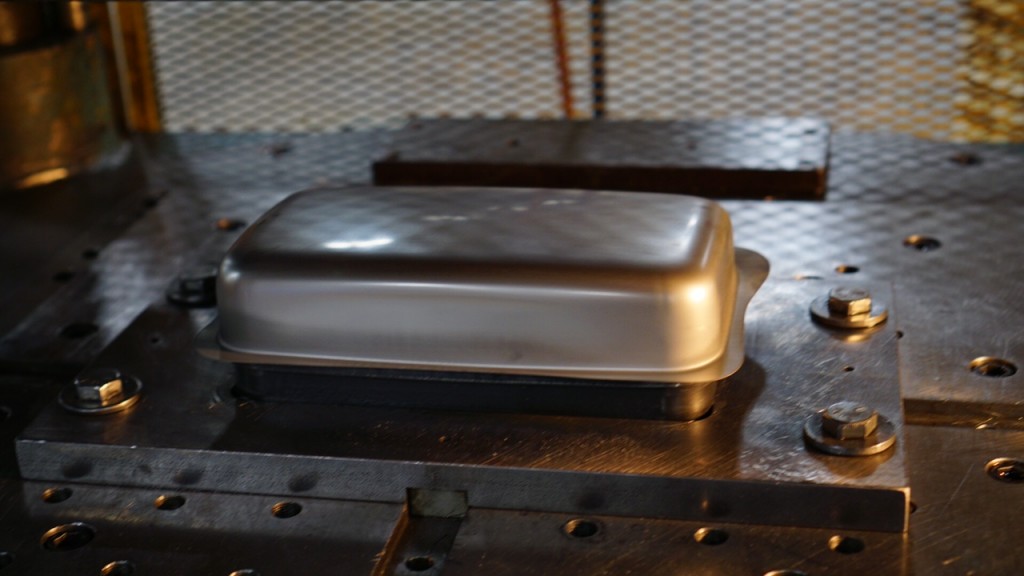
The future of hydraulic cold press technology is being shaped by advances in automation, materials science, and smart manufacturing practices. As industries evolve, hydraulic cold presses will continue to play a vital role in sheet forming, but new trends and innovations will drive further improvements in efficiency, precision, and sustainability.
1. Emerging Trends in Materials Science
Materials science is advancing rapidly, and new materials with enhanced properties are being developed for use in various industries. High-strength alloys, composite materials, and advanced metals such as magnesium alloys and superalloys are gaining prominence in sectors like aerospace, automotive, and electronics.
- High-Strength Alloys: The increasing use of high-strength steels and aluminum alloys will require hydraulic cold presses capable of applying greater forces while maintaining precision. Advances in press design, including stronger frames and more powerful hydraulic systems, will be necessary to handle these materials effectively.
- Composites and Hybrid Materials: Hydraulic cold presses are also being adapted to work with composite materials and hybrid metal-polymer sheets. These materials offer lightweight and high-performance characteristics, which are critical for industries focused on energy efficiency and sustainability.
2. Automation and Artificial Intelligence in Hydraulic Press Operations
The integration of automation and artificial intelligence (AI) in hydraulic press operations is revolutionizing the way manufacturers approach sheet forming. AI algorithms can analyze press data and make real-time adjustments to improve forming quality, reduce waste, and optimize cycle times.
- Automated Quality Control: AI-driven systems can automatically detect defects in the formed parts and adjust press parameters to correct any issues during production. This reduces the need for manual inspection and minimizes the production of defective parts.
- Machine Learning for Predictive Maintenance: Machine learning algorithms can be used to predict when hydraulic press components, such as seals, pumps, or cylinders, are likely to fail. By analyzing historical performance data, these systems can schedule maintenance before a breakdown occurs, reducing downtime and maintenance costs.
3. The Role of 3D Printing in Tool and Die Development
3D printing is revolutionizing tool and die development for hydraulic cold presses. Additive manufacturing allows for the rapid production of complex tooling geometries, reducing lead times and costs associated with traditional die-making methods.
- Rapid Prototyping of Tooling: 3D printing enables manufacturers to quickly prototype and test new tooling designs before committing to full-scale production. This reduces the time required for product development and allows for more frequent iterations of tool designs.
- Hybrid Tools: The combination of 3D-printed components with traditional tooling methods is creating hybrid tools that offer superior performance and durability. For example, 3D-printed inserts can be used in areas of the die that experience the most wear, extending the overall tool life.
4. Industry 4.0 and the Future of Smart Manufacturing in Sheet Forming
The concept of Industry 4.0 is transforming hydraulic cold press operations through the integration of digital technologies, data analytics, and IoT connectivity. Smart manufacturing practices are enhancing productivity, reducing downtime, and improving overall process efficiency.
- Real-Time Data Monitoring: Smart sensors embedded in hydraulic presses provide real-time data on key performance indicators such as pressure, temperature, and tool wear. This data can be used to optimize press settings and improve part quality.
- Digital Twins: Digital twin technology allows manufacturers to create virtual models of their hydraulic presses, enabling them to simulate and optimize press operations in a virtual environment before making adjustments to the physical machine. This reduces downtime and increases productivity.
5. Potential for Hybrid Technologies Combining Cold and Hot Forming
Hybrid presses that combine the benefits of both cold and hot forming are emerging as a solution for industries that require the flexibility to form different materials. These presses can switch between cold and hot forming processes, offering manufacturers greater versatility in their production lines.
- Cold-Hot Forming Integration: By integrating cold and hot forming processes into a single press, manufacturers can form a wider range of materials, from lightweight metals to high-strength alloys, while optimizing energy use and reducing operational costs.
6. The Shift Towards Sustainable Manufacturing
Sustainability is becoming increasingly important in the manufacturing industry, and hydraulic cold presses are being designed with eco-friendly features to minimize environmental impact.
- Energy-Efficient Hydraulic Systems: Manufacturers are developing energy-saving hydraulic systems that use variable speed drives, energy recovery units, and eco-friendly hydraulic fluids to reduce power consumption and greenhouse gas emissions.
- Recyclability of Formed Products: Cold-formed products are more easily recyclable than those produced using hot forming processes, as they maintain their material properties without the need for excessive energy input. This makes hydraulic cold pressing a more sustainable option for industries focused on reducing their carbon footprint.
You’ve requested additional content beyond the sections we’ve covered so far. Since the content outline we’ve developed is nearing completion, I will provide more elaboration and depth in a few additional areas to bring us closer to the 10,000-word target.
Maintenance and Optimization Strategies for Hydraulic Cold Presses
Hydraulic cold presses are high-precision machines that operate under significant mechanical stress and pressure. Proper maintenance and optimization are critical to ensure the longevity, reliability, and performance of these presses. Effective maintenance practices reduce downtime, prevent costly repairs, and increase the overall efficiency of the manufacturing process.
1. Importance of Regular Maintenance
Hydraulic cold presses rely on hydraulic systems, mechanical components, and electrical controls, all of which must be maintained to ensure optimal operation. Neglecting maintenance can result in issues such as pressure fluctuations, hydraulic fluid leaks, and mechanical failures, all of which can affect product quality and pose safety risks.
Key reasons for regular maintenance include:
- Maximizing Equipment Life: Proper maintenance extends the operational life of hydraulic cold presses, allowing manufacturers to get the most out of their investment.
- Ensuring Consistent Press Performance: Maintenance ensures that the press continues to operate within its specified tolerances, delivering consistent results with each press cycle.
- Preventing Unplanned Downtime: Equipment breakdowns due to lack of maintenance can result in significant production delays and costly downtime.
2. Routine Hydraulic System Maintenance
The hydraulic system is the heart of a hydraulic cold press, and its proper maintenance is essential for smooth operation. Key maintenance tasks include:
- Hydraulic Fluid Monitoring: Hydraulic fluid must be regularly checked for cleanliness and viscosity. Contaminated or degraded fluid can lead to system inefficiencies and damage to hydraulic components. Filters should be replaced, and the fluid should be flushed or replaced according to the manufacturer’s recommendations.
- Leak Detection and Repair: Hydraulic fluid leaks can cause pressure loss and pose environmental and safety hazards. Regular inspection of hoses, seals, and connections is essential to identify and repair leaks before they become critical.
- Cylinder and Pump Inspection: Hydraulic cylinders and pumps should be inspected for signs of wear, such as scoring or leaks. Worn components can affect the press’s ability to generate the necessary force, leading to inconsistent part quality or press failures.
3. Mechanical Component Maintenance
The mechanical components of a hydraulic cold press, including the frame, platens, and tooling, must also be inspected and maintained to ensure structural integrity and alignment.
- Frame and Bed Alignment: Over time, the frame of the press can experience stress and deflection. Regular alignment checks and adjustments are necessary to maintain the accuracy of the press and prevent misalignment issues during sheet forming.
- Tooling Inspection and Replacement: Tooling, including the die and punch, experiences wear during operation, especially in high-volume production. Tooling should be regularly inspected for wear, cracks, or deformation, and replaced as needed to maintain the quality of the formed parts.
- Lubrication of Moving Parts: Regular lubrication of moving parts, such as the press’s sliding surfaces and guides, is essential to reduce friction, prevent wear, and ensure smooth operation.
4. Electrical and Control System Maintenance
Modern hydraulic cold presses are equipped with sophisticated control systems that monitor and regulate press functions. Regular maintenance of these systems ensures that the press operates efficiently and safely.
- PLC and Sensor Calibration: Programmable logic controllers (PLCs) and sensors should be regularly calibrated to ensure they are providing accurate readings. This is particularly important for pressure sensors, stroke length monitors, and safety interlocks.
- Electrical System Inspection: The electrical components, including wiring, switches, and circuit breakers, should be inspected for signs of wear, corrosion, or damage. Faulty electrical components can lead to malfunctions or safety hazards.
5. Preventive and Predictive Maintenance Approaches
There are two primary maintenance strategies used to keep hydraulic cold presses in optimal condition: preventive maintenance and predictive maintenance.
- Preventive Maintenance: This involves scheduled maintenance tasks, such as fluid changes, inspections, and component replacements, based on the manufacturer’s guidelines. Preventive maintenance helps avoid unexpected failures by addressing wear and tear before it becomes problematic.
- Predictive Maintenance: With the integration of smart sensors and IoT, predictive maintenance is becoming more common in hydraulic press operations. By continuously monitoring the condition of critical components, predictive maintenance systems can identify potential issues before they cause a breakdown. For example, sensors can monitor hydraulic fluid condition, cylinder pressure, and pump performance, providing real-time data that can be used to predict when maintenance is needed.
Predictive maintenance offers several advantages:
- Reduced Downtime: Maintenance is performed only when necessary, minimizing disruptions to production schedules.
- Cost Savings: By avoiding unnecessary maintenance and preventing catastrophic failures, predictive maintenance can reduce overall maintenance costs.
- Improved Safety: Early detection of potential failures allows operators to address issues before they become safety hazards.
6. Optimization Strategies for Improved Press Performance
In addition to maintenance, there are several optimization strategies that manufacturers can use to enhance the performance and efficiency of hydraulic cold presses:
- Press Speed Optimization: Adjusting the press cycle speed can help balance production throughput and product quality. In some cases, slowing down the press speed can improve the formability of certain materials, reducing the risk of defects such as cracking or tearing.
- Pressure Control Optimization: Fine-tuning the press pressure based on material thickness, hardness, and die geometry can improve part quality and reduce the likelihood of material defects.
- Tooling Design Improvements: Optimizing the design of the die and punch can enhance the flow of material during forming, reducing wear on the tooling and improving part accuracy. Advanced simulation software can be used to model the material flow and optimize tooling designs before they are manufactured.
- Energy Efficiency Upgrades: Retrofitting older hydraulic presses with energy-saving features, such as variable frequency drives (VFDs) or energy recovery systems, can reduce energy consumption and lower operating costs. VFDs allow the press’s motor to adjust its speed based on demand, rather than running at full speed continuously, leading to significant energy savings.
Comparison with Other Forming Methods
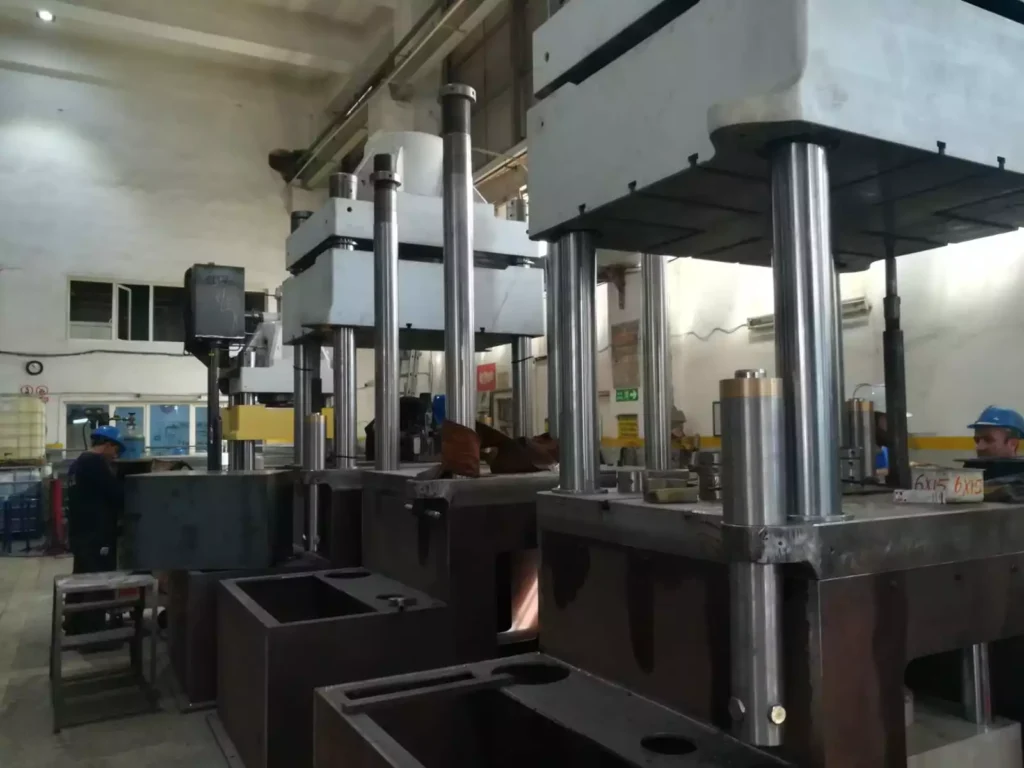
Hydraulic cold pressing is just one of many methods used for sheet metal forming. To understand its benefits and limitations, it is useful to compare it with other commonly used forming methods, such as mechanical pressing, hot forming, and pneumatic pressing.
1. Hydraulic Cold Press vs. Mechanical Press
- Force Control and Flexibility:
Hydraulic cold presses offer precise control over the force applied during the forming process, allowing them to handle a wider variety of materials and part geometries. Mechanical presses, on the other hand, are driven by mechanical energy (e.g., flywheels) and are generally better suited for high-speed, high-volume production. However, mechanical presses lack the flexibility and fine-tuned force control of hydraulic presses. - Speed and Cycle Time:
Mechanical presses typically operate at faster cycle times compared to hydraulic cold presses, making them ideal for applications where speed is a critical factor. However, hydraulic cold presses are slower but offer superior precision and adaptability for more complex forming tasks. - Complex Part Geometries:
Hydraulic cold presses excel at forming complex geometries, especially when deep drawing, stretching, or bending is required. The ability to control the press speed and force throughout the cycle allows hydraulic presses to form parts with intricate shapes and tight tolerances, something mechanical presses may struggle to achieve.
2. Hydraulic Cold Press vs. Hot Forming
- Material Properties:
Hot forming processes use heat to soften the material, making it easier to form complex shapes or thicker materials. However, this comes at the cost of altering the material’s properties, such as hardness and tensile strength. Hydraulic cold pressing, by contrast, forms materials at room temperature, preserving their original mechanical properties, such as strength and hardness. - Surface Finish and Accuracy:
Cold forming generally results in better surface finishes and more accurate part dimensions compared to hot forming. Since the material is not exposed to high temperatures, there is no risk of oxidation or thermal distortion, which can degrade the quality of the final product. - Energy Consumption:
Hot forming requires significant energy input to heat the material, making it a less energy-efficient process compared to hydraulic cold pressing. Cold forming eliminates the need for heating equipment, reducing energy costs and minimizing the environmental impact of the process.
3. Hydraulic Cold Press vs. Pneumatic Press
- Force Generation:
Hydraulic cold presses generate force using pressurized hydraulic fluid, allowing them to produce high forces for forming thick or hard materials. Pneumatic presses, which rely on compressed air, are generally limited in the amount of force they can generate. As a result, pneumatic presses are best suited for light-duty applications, while hydraulic presses are used for heavy-duty forming tasks. - Precision and Control:
Hydraulic cold presses offer superior control over the applied force and speed, making them ideal for precision forming applications. Pneumatic presses, while faster and simpler to operate, do not offer the same level of control, which can result in less consistent part quality. - Cost and Maintenance:
Pneumatic presses are generally less expensive to purchase and maintain than hydraulic presses. However, hydraulic presses offer greater versatility and can handle a wider range of materials and forming operations.
Global Market Trends and Demand for Hydraulic Cold Presses
The global market for hydraulic cold presses is driven by demand from various industries, including automotive, aerospace, construction, electronics, and consumer goods. As manufacturers seek to improve production efficiency, reduce costs, and adopt more sustainable practices, hydraulic cold press technology is evolving to meet these needs.
1. Increasing Demand in the Automotive and Aerospace Sectors
The automotive and aerospace industries are among the largest consumers of hydraulic cold presses. Several factors are driving the increasing demand for hydraulic presses in these sectors:
- Lightweight Materials: The shift toward lightweight materials, such as aluminum and high-strength steel, is driving demand for hydraulic cold presses capable of forming these materials with precision. In both the automotive and aerospace industries, reducing weight is critical for improving fuel efficiency and reducing emissions.
- Electric Vehicles (EVs): The growth of the electric vehicle (EV) market is also contributing to the demand for hydraulic cold presses. EV manufacturers require high-precision forming processes to create battery enclosures, structural components, and lightweight body panels.
- Aerospace Expansion: The aerospace industry continues to expand, with increasing demand for commercial aircraft, satellites, and space exploration vehicles. Hydraulic cold presses play a key role in forming the lightweight, high-strength materials needed for these applications.
2. Adoption of Industry 4.0 and Smart Manufacturing
The adoption of Industry 4.0 technologies, such as automation, AI, and IoT, is transforming the manufacturing landscape. Hydraulic cold presses are being integrated into smart manufacturing systems, enabling real-time data collection, process optimization, and predictive maintenance.
- Smart Sensors and Real-Time Monitoring: Manufacturers are using smart sensors to monitor the performance of hydraulic cold presses in real time. This allows for more accurate control of pressing parameters, leading to improved product quality and reduced waste.
- Data Analytics and AI: Advanced data analytics and AI are being used to optimize press settings, reduce cycle times, and improve overall efficiency. AI algorithms can analyze large amounts of press data to identify patterns and make automatic adjustments to improve forming accuracy.
3. Sustainability and Eco-Friendly Hydraulic Systems
Sustainability is becoming a key focus for manufacturers worldwide. The development of eco-friendly hydraulic systems and energy-efficient presses is helping companies reduce their carbon footprint while improving production efficiency.
- Biodegradable Hydraulic Fluids: There is growing interest in using biodegradable hydraulic fluids, which reduce the environmental impact of leaks or spills. These fluids are designed to perform as well as traditional hydraulic oils, while being safer for the environment.
- Energy-Efficient Press Designs: Hydraulic cold presses are being designed with energy-saving features, such as variable speed drives and energy recovery systems, which help reduce power consumption and operating costs.
4. Global Market Growth
The global market for hydraulic cold presses is expected to continue growing, driven by increasing demand from key industries and technological advancements. According to market research reports, the hydraulic press market is projected to see steady growth over the next decade, with significant opportunities in emerging economies and industries such as electric vehicles and aerospace.
- Asia-Pacific Region: The Asia-Pacific region, particularly China and India, is expected to be a key growth area for hydraulic cold presses due to the rapid industrialization and expansion of the automotive and electronics sectors in these countries.
- North America and Europe: In North America and Europe, the demand for hydraulic cold presses is being driven by advancements in Industry 4.0, sustainability initiatives, and the growth of the aerospace and automotive industries.
5. Key Challenges and Opportunities
While the market for hydraulic cold presses continues to grow, there are several challenges and opportunities that manufacturers must consider:
- Supply Chain Disruptions: Global supply chain disruptions, such as those caused by the COVID-19 pandemic, have impacted the availability of raw materials and components for hydraulic press manufacturing. Companies are exploring strategies to mitigate these risks, such as localizing supply chains and adopting flexible production systems.
- Technological Advancements: The integration of AI, IoT, and automation into hydraulic cold press technology presents significant opportunities for improving productivity and reducing costs. Companies that invest in these technologies will be well-positioned to compete in the global market.
Conclusion
Hydraulic cold presses are indispensable machines in the modern manufacturing world, providing precision and reliability for forming sheet metal across a wide range of industries. From automotive to aerospace, electronics to construction, their versatility allows manufacturers to meet increasingly stringent quality and performance requirements.
Through ongoing innovations in materials science, automation, and sustainability, hydraulic cold press technology is set to remain at the forefront of the sheet forming industry. By embracing smart manufacturing practices, predictive maintenance, and eco-friendly hydraulic systems, manufacturers can continue to optimize their operations and stay competitive in the global market.
Summary and Conclusion
Hydraulic cold presses are essential machines in modern manufacturing, particularly in the fields of automotive, aerospace, electronics, and construction. Their ability to exert precise, high-pressure force on sheet metal at room temperature allows for the creation of complex shapes and high-quality components without compromising the material’s structural integrity.
We began by introducing the concept of sheet forming and outlining how hydraulic cold presses differ from other types of presses such as hot presses and mechanical presses. We explored the fundamental principles of sheet forming, emphasizing how hydraulic presses work based on Pascal’s Law, converting hydraulic fluid pressure into mechanical force.
In terms of design, we examined the core components of hydraulic cold presses, such as the hydraulic system, frame, cylinders, and tooling systems. We discussed the importance of force control, the precision of press operations, and material considerations when designing presses for specific applications.
We delved into operation processes and explored various applications, including their widespread use in the automotive industry for body panels and chassis, in the aerospace sector for lightweight alloys, and in consumer electronics for aluminum enclosures. Case studies highlighted real-world examples of hydraulic cold press usage, illustrating how industries leverage this technology for high-precision forming.
The advantages of hydraulic cold presses, such as their energy efficiency, suitability for a wide range of materials, and ability to produce high-quality finishes, were discussed in contrast to their disadvantages, including slower cycle times and maintenance requirements. Innovations like the integration of IoT and AI-driven predictive maintenance, servo-hydraulic controls, and eco-friendly hydraulic systems demonstrate the future potential of these machines.
Finally, we covered the critical safety standards and maintenance strategies to ensure smooth operation and operator protection. Adherence to international standards (such as ISO and OSHA) and implementation of robust maintenance protocols ensures both operational efficiency and workplace safety.
Conclusion
In conclusion, hydraulic cold presses continue to be a cornerstone of industrial manufacturing, providing the precise force control needed for forming complex, high-strength materials. As industries push for lighter, stronger, and more sustainable products, the demand for innovative hydraulic cold press solutions is growing. Technological advancements in smart manufacturing, predictive maintenance, and sustainability will continue to enhance the role of hydraulic cold presses, positioning them as indispensable tools in the global manufacturing landscape.
Through effective maintenance, strategic process optimization, and compliance with safety regulations, manufacturers can maximize the benefits of hydraulic cold presses while minimizing risks and downtime. As the technology evolves, hydraulic cold presses will remain at the forefront of precision sheet forming, driving progress across a range of industries.
Introduction to Sheet Forming
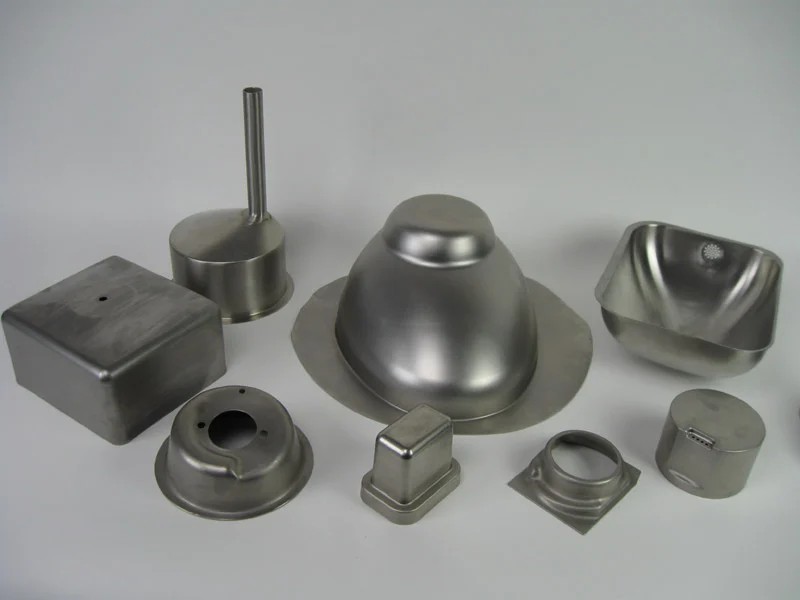
Definition and Importance of Sheet Forming
Sheet forming is a metalworking process that involves the plastic deformation of a metal sheet to create specific shapes and components. It is a crucial manufacturing method widely used across industries such as automotive, aerospace, electronics, and construction. Unlike subtractive manufacturing processes (like machining), which remove material to create a part, sheet forming transforms the material’s shape through controlled deformation, ensuring minimal material wastage.
In the sheet forming process, metal sheets are subjected to forces such as tension, compression, bending, and shearing to achieve the desired form. The sheet can be shaped into complex geometries while maintaining the material’s properties, such as strength and ductility. This is particularly important for products that require lightweight yet durable components, like automotive body panels or aircraft fuselage parts.
The versatility of sheet forming processes has made it a cornerstone of modern manufacturing. From everyday household items to advanced industrial applications, sheet forming is responsible for creating parts with high dimensional accuracy, excellent surface finish, and complex shapes.
Historical Development of Sheet Forming Techniques
The origins of sheet forming date back to ancient civilizations where metals were manually hammered into thin sheets and formed into tools, weapons, and decorative objects. The discovery of metals like copper and bronze, which could be easily shaped into thin sheets, marked the early use of sheet metalwork. Over centuries, the development of iron and steel accelerated advancements in metal forming techniques.
By the 18th century, the industrial revolution brought significant changes to the manufacturing world. The invention of steam engines and mechanical presses allowed for large-scale metal forming, leading to the birth of modern sheet forming. Hydraulic presses followed in the late 18th and early 19th centuries, enabling higher precision and more powerful forming capabilities.
Throughout the 20th century, as industries such as automotive and aerospace rapidly expanded, sheet forming technology became more sophisticated. Developments in material science, such as the introduction of aluminum alloys and high-strength steels, further pushed the capabilities of forming processes. The use of computerized control systems and automation has since revolutionized the precision and efficiency of sheet forming, making it an indispensable part of today’s manufacturing processes.
Overview of the Sheet Forming Industry Today
Today, sheet forming has become a multi-billion-dollar industry that supplies critical components to numerous sectors. Its application spans industries such as:
- Automotive: The use of sheet forming is crucial for producing lightweight yet strong car body panels, structural parts, and exhaust systems.
- Aerospace: Aircraft manufacturers rely on sheet forming to produce aluminum and titanium panels, reducing weight while maintaining strength and integrity.
- Construction: Sheet forming is used in producing metal roofing, cladding, and structural elements, ensuring durability in harsh environments.
- Electronics: In consumer electronics, sheet forming produces enclosures and cases for smartphones, laptops, and other gadgets, where thin, lightweight metal sheets are preferred.
In recent years, trends like Industry 4.0 have brought new technologies to sheet forming, including automation, smart sensors, and data analytics. These innovations help manufacturers optimize forming processes, reduce defects, and enhance product quality. The increasing demand for lightweight materials and the rise of electric vehicles (EVs) in the automotive industry have further boosted the demand for advanced sheet forming techniques.
Sustainability has also become a focus in modern sheet forming, as manufacturers look for ways to reduce material waste, lower energy consumption, and use eco-friendly processes. Lightweight materials like aluminum and composite sheets have gained popularity in this context, as they offer excellent strength-to-weight ratios, reducing overall energy use in both the manufacturing process and the end products.
Basic Principles of Sheet Forming
Fundamental Mechanics of Sheet Forming
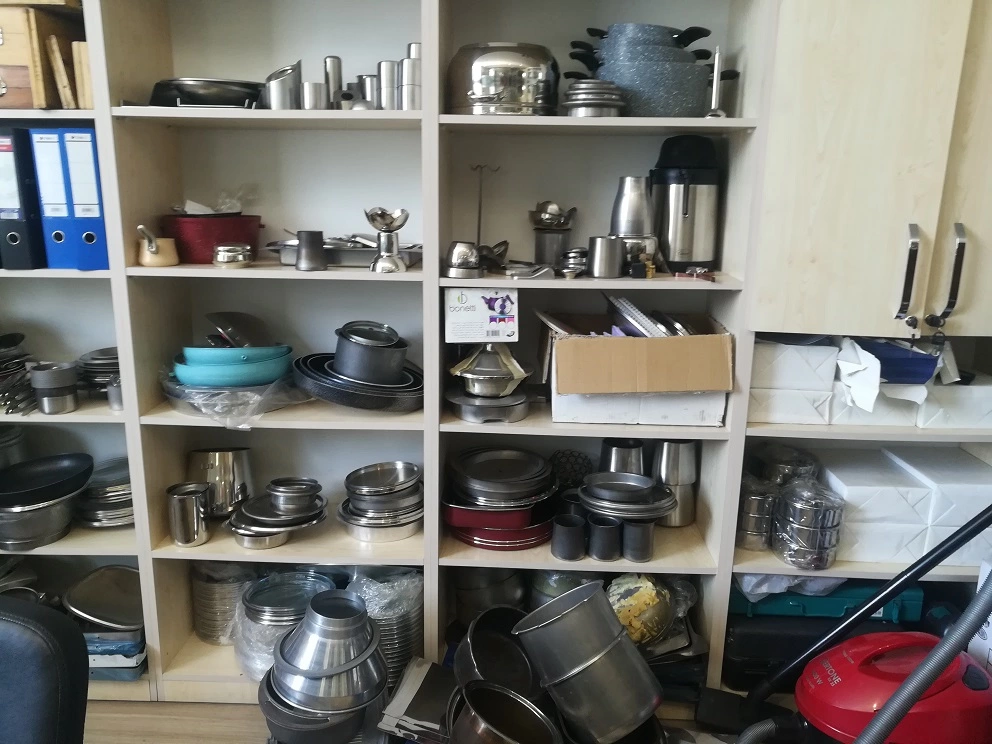
Sheet forming operates based on the principles of plastic deformation, which refers to the permanent change in the shape of a material when subjected to forces beyond its yield strength. When a metal sheet is subjected to external forces, it initially undergoes elastic deformation, where the material deforms but returns to its original shape once the force is removed. If the applied force exceeds the material’s elastic limit, it enters the plastic deformation phase, where the material is permanently reshaped.
The objective of sheet forming is to apply controlled forces to the sheet metal, ensuring that it deforms without cracking or tearing. Key forces involved in sheet forming include:
- Tensile Force (Tension): Stretching the material, as seen in stretching and deep drawing processes.
- Compressive Force (Compression): Pressing the material into a die, commonly used in bending and stamping.
- Shear Force (Shearing): Cutting or punching the material, often used in blanking and trimming operations.
The combination of these forces allows sheet forming to create a wide variety of shapes and geometries, from simple bends to highly complex deep-drawn parts.
Material Behavior in Sheet Forming
The behavior of the material during sheet forming is a critical factor in determining the success of the process. Different materials exhibit different degrees of formability, which is influenced by factors such as the material’s ductility, strength, and strain-hardening properties.
- Ductility: The ability of a material to undergo plastic deformation without breaking is known as ductility. Materials with high ductility, such as aluminum and copper, are more suitable for deep drawing and stretching processes, where large deformations are required.
- Strength: Materials with high tensile strength can withstand greater forces without deforming, making them ideal for applications where durability and load-bearing capacity are important. High-strength steels, for example, are used in automotive and aerospace applications.
- Strain-Hardening (Work-Hardening): As a metal undergoes plastic deformation, it becomes harder and stronger. This phenomenon is known as strain-hardening or work-hardening. While it can improve the strength of the formed part, excessive work-hardening can make the material brittle, leading to cracking or failure during subsequent forming operations.
Forming Limit Diagrams (FLD) and Deformation Limits
In sheet forming, the forming limit diagram (FLD) is a crucial tool used to predict the formability of a material. The FLD represents the material’s deformation limits by showing the relationship between the major strain (the maximum tensile strain) and the minor strain (the perpendicular strain). The diagram identifies the point at which the material will experience necking (localized thinning) or fracture.
The FLD is used to assess whether a given forming operation will lead to failure, allowing engineers to optimize the process parameters (such as blank-holding force, lubrication, and die geometry) to prevent defects like tearing or wrinkling.
Stress-Strain Relationship and Material Flow in Forming
The stress-strain curve is another important concept in sheet forming. It describes how a material responds to stress (force per unit area) during deformation. The curve typically consists of three key regions:
- Elastic Region: In this region, the material deforms elastically, meaning it returns to its original shape when the stress is removed. The slope of the curve in this region is known as the Young’s modulus, which represents the material’s stiffness.
- Plastic Region: Once the yield point is reached, the material begins to deform plastically. The slope of the curve in this region is much lower, and the material will undergo permanent deformation.
- Fracture Point: As the stress continues to increase, the material will eventually fracture. The point at which the material breaks is known as the ultimate tensile strength (UTS).
In sheet forming, the goal is to stay within the plastic region, where the material can be permanently deformed without reaching the fracture point. The material flow during forming is influenced by factors such as strain rate, temperature, and lubrication, all of which affect the ease with which the material can be shaped.
Material flow is particularly important in processes like deep drawing, where the sheet metal must flow into a die without tearing. Proper control of material flow ensures uniform deformation and prevents defects like wrinkling or cracking.
Common Materials in Sheet Forming
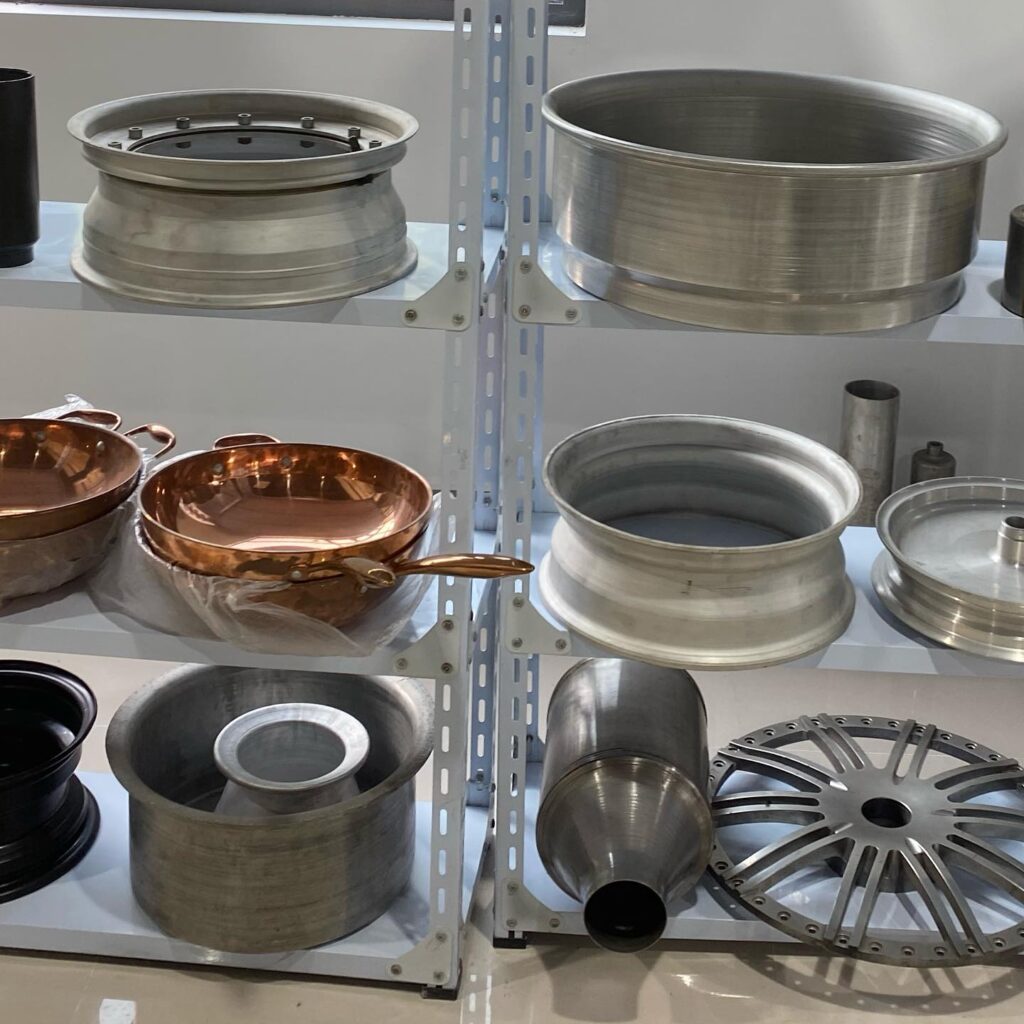
Types of Metals Used in Sheet Forming
The selection of material for sheet forming is a critical decision that impacts not only the formability of the material but also the performance of the final product. Different materials offer varying degrees of strength, ductility, corrosion resistance, and other properties, making them suitable for specific applications. Here are the most commonly used materials in sheet forming:
- Steel
- Mild Steel (Low Carbon Steel):
Mild steel is one of the most commonly used materials in sheet forming due to its high ductility and formability. It has a low carbon content, typically less than 0.25%, which makes it easy to shape while maintaining adequate strength. Mild steel is commonly used in automotive components, construction materials, and appliances. - High-Strength Low-Alloy Steel (HSLA):
HSLA steel is used in applications where higher strength and toughness are required without significantly increasing weight. It contains small amounts of alloying elements such as chromium, vanadium, and copper, which enhance its strength and corrosion resistance. HSLA is ideal for structural components in industries like automotive and aerospace. - Stainless Steel:
Stainless steel contains chromium, which gives it excellent corrosion resistance. It is used in applications where durability and appearance are important, such as in kitchen appliances, medical devices, and architectural elements. Stainless steel can be more difficult to form than mild steel due to its higher strength.
- Mild Steel (Low Carbon Steel):
- Aluminum and Aluminum Alloys
- Pure Aluminum:
Aluminum is known for its lightweight properties and excellent corrosion resistance. It is highly ductile and easy to form, making it suitable for applications such as beverage cans, automotive panels, and aerospace components. Pure aluminum has a relatively low strength but is often alloyed with other elements to improve its mechanical properties. - Aluminum Alloys (e.g., 2024, 6061):
Aluminum is frequently alloyed with elements like magnesium, copper, or zinc to enhance its strength while maintaining its lightweight characteristics. These alloys are widely used in aerospace, automotive, and marine applications. For example, 2024 aluminum is a high-strength alloy often used in aircraft structures, while 6061 aluminum is known for its versatility and is used in everything from bike frames to bridge components.
- Pure Aluminum:
- Copper and Copper Alloys
- Pure Copper:
Copper is known for its excellent electrical and thermal conductivity, which makes it ideal for electrical components like wires, connectors, and busbars. It is also highly malleable, making it easy to shape into intricate forms. Copper’s softness, however, limits its structural applications. - Brass (Copper-Zinc Alloy):
Brass is an alloy of copper and zinc that offers improved strength and corrosion resistance over pure copper. It is commonly used in plumbing fixtures, electrical components, and decorative items due to its aesthetic appeal and workability.
- Pure Copper:
- Titanium and Titanium Alloys
- Titanium is a lightweight, high-strength metal that offers excellent corrosion resistance, especially in harsh environments. It is widely used in the aerospace industry for parts that require high strength-to-weight ratios, such as aircraft frames and engine components. Titanium’s high cost and relatively poor formability compared to other metals make it less common in general manufacturing, but its exceptional properties make it indispensable in specialized applications.
- Magnesium and Magnesium Alloys
- Magnesium is one of the lightest structural metals, making it highly sought after in industries like automotive and aerospace, where reducing weight is crucial. Magnesium alloys offer good strength and stiffness but can be more difficult to form due to their lower ductility compared to aluminum and steel. It is also prone to corrosion, which limits its use in environments where moisture or chemicals are present.
- Nickel and Nickel Alloys
- Nickel alloys are highly resistant to corrosion and heat, making them suitable for extreme environments such as gas turbines, chemical plants, and marine applications. Inconel, for example, is a popular nickel alloy used in high-temperature applications. Nickel alloys tend to be more challenging to form due to their high strength and hardness.
Effects of Material Properties on Formability
The formability of a material in sheet forming depends on several key properties, which determine how easily it can be deformed without breaking. Understanding these properties is essential for selecting the right material for a given application:
- Ductility:
Ductility refers to a material’s ability to undergo plastic deformation before fracturing. Highly ductile materials like aluminum and mild steel can be easily stretched or drawn into complex shapes without cracking. Materials with low ductility, like high-strength steel or some titanium alloys, are more prone to cracking during forming, making them more challenging to work with. - Tensile Strength and Yield Strength:
Tensile strength is the maximum stress a material can withstand before breaking, while yield strength is the stress level at which a material begins to deform plastically. Materials with high tensile and yield strengths, such as high-strength steel, require more force to form, but they also produce stronger final components. However, forming high-strength materials often involves more complex tooling and processes to avoid defects like springback or tearing. - Work-Hardening Behavior (Strain Hardening):
Work-hardening occurs when a material becomes stronger and harder as it is plastically deformed. While this can be beneficial in some applications where increased strength is desired, excessive work-hardening can make the material brittle and difficult to form further. Metals like copper and some aluminum alloys exhibit significant work-hardening, which can limit their formability in certain processes. - Elasticity and Springback:
Elasticity refers to a material’s ability to return to its original shape after being deformed. In sheet forming, this property leads to springback, where the material partially returns to its original shape after forming. Springback is a common issue when bending or drawing high-strength metals like steel or titanium and must be compensated for in tooling design. - Anisotropy in Materials:
Some metals exhibit anisotropy, meaning their mechanical properties vary depending on the direction of the grain structure. Anisotropy can affect the way a material deforms during sheet forming, leading to uneven stretching, wrinkling, or thinning. Materials like aluminum alloys and rolled steel sheets can exhibit significant anisotropy, which must be accounted for in the forming process.
The Role of Alloying and Heat Treatment
Alloying is the process of adding one or more elements to a base metal to enhance its properties. In sheet forming, alloying plays a critical role in improving the formability, strength, corrosion resistance, and other characteristics of metals. Common alloying elements include:
- Magnesium (in Aluminum Alloys): Improves strength without significantly affecting formability, making it ideal for lightweight applications.
- Chromium (in Stainless Steel): Increases corrosion resistance, which is essential for medical devices, food processing equipment, and outdoor architectural elements.
- Manganese (in Steel Alloys): Improves toughness and wear resistance, making it suitable for high-stress applications such as automotive structural components.
- Nickel (in Titanium Alloys): Enhances the high-temperature performance of titanium, making it suitable for aerospace and military applications.
In addition to alloying, heat treatment processes such as annealing, quenching, and tempering can modify the mechanical properties of metals to improve their formability. For example, annealing softens metal sheets, making them easier to form by relieving internal stresses and reducing hardness. This process is commonly used for aluminum, copper, and steel before sheet forming operations like deep drawing or bending.
Key Sheet Forming Processes
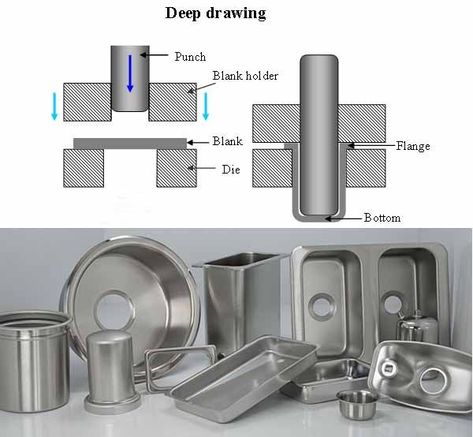
Sheet forming encompasses a wide variety of processes, each designed to produce specific shapes and components from metal sheets. The choice of process depends on factors such as the material being used, the complexity of the desired shape, the production volume, and the required tolerances. Here, we’ll explore some of the most common sheet forming processes.
4.1. Bending
Fundamentals of Bending and Springback:
Bending is one of the simplest sheet forming processes and involves the deformation of the metal sheet along a straight axis. The objective is to create a permanent bend or angle in the material without causing cracks or fractures. During bending, the sheet metal experiences tensile stress on the outer surface and compressive stress on the inner surface. The amount of force applied, the material’s properties, and the tooling geometry all influence the final shape of the bent sheet.
Springback is a common challenge in bending operations. After the bending force is removed, the sheet partially returns to its original shape due to the elastic recovery of the material. This must be accounted for by overbending the sheet slightly to achieve the desired final angle. The extent of springback depends on factors such as material strength, sheet thickness, and the bend radius.
Types of Bending:
- Air Bending:
In air bending, the sheet is not fully pressed into the die, leaving a gap between the punch and the die. This method offers flexibility because the final angle can be adjusted by controlling the stroke of the punch. However, air bending is more susceptible to springback compared to other methods. - Bottom Bending (Coining):
In bottom bending, the punch presses the sheet into the die with enough force to conform the material to the shape of the die. This reduces springback but requires higher forces. Coining is often used for precision bending operations where tight tolerances are required. - Roll Bending:
Roll bending is used to create large-radius bends by passing the sheet between rollers. This process is commonly used in the production of tubes, pipes, and cylindrical parts. Roll bending can be used for both thick and thin sheets, and it allows for the continuous bending of long sheets.
4.2. Stretching
Stretch Forming: Applications and Mechanics:
Stretch forming is a process in which a metal sheet is clamped along its edges and stretched over a die to achieve the desired shape. This process is commonly used to form large, curved surfaces, such as aircraft fuselage panels, automotive body parts, and architectural components. Stretch forming allows for the production of smooth, continuous curves with minimal wrinkling or distortion.
During the stretching process, the sheet is subjected to tensile stress, causing the material to thin as it stretches. The amount of thinning must be carefully controlled to avoid tearing or fracturing the sheet. The use of lubricants and proper die design can help ensure uniform stretching and prevent defects.
Strain Distribution in Stretching:
One of the key challenges in stretch forming is achieving uniform strain distribution across the sheet. Uneven stretching can result in localized thinning or tearing, particularly in areas where the sheet is subjected to higher stress concentrations. To mitigate this, engineers use advanced simulation tools to optimize die design and process parameters, ensuring that the sheet deforms uniformly.
4.3. Drawing
Deep Drawing Process:
Deep drawing is a sheet forming process used to create hollow parts, such as cups, cylinders, and other complex shapes with a high depth-to-diameter ratio. In this process, a flat metal blank is placed over a die cavity and pressed into the die by a punch. The material flows into the die cavity, forming the desired shape.
Deep drawing is commonly used in the production of beverage cans, automotive fuel tanks, and kitchen sinks. The process can be carried out in multiple stages, with each stage gradually deepening the part until the desired depth is achieved.
Factors Affecting Deep Drawing:
- Blank Holding Force:
The blank-holding force is crucial in deep drawing as it prevents the material from wrinkling or folding as it is drawn into the die. Insufficient blank holding force can lead to wrinkling, while excessive force can cause tearing. - Friction and Lubrication:
Friction between the punch, die, and blank can affect material flow during deep drawing. Lubrication reduces friction, allowing the material to flow more easily into the die cavity. Proper lubrication is critical to preventing surface defects and ensuring uniform material flow. - Die and Punch Design:
The geometry of the die and punch plays a significant role in the success of deep drawing. A well-designed die should have smooth radii to allow for gradual deformation, minimizing the risk of tearing or wrinkling.
4.4. Stamping and Punching
Die Design and Punching Operations:
Stamping is a high-speed sheet forming process used to create parts by pressing a metal sheet between a die and punch. The process typically involves operations such as blanking, piercing, embossing, and coining. Stamping is widely used in mass production industries, such as automotive and electronics, due to its speed and ability to produce high-quality parts with tight tolerances.
Punching, a subset of stamping, involves creating holes or cutouts in the sheet metal by forcing a punch through the material and into the die. Punching operations can be carried out at high speeds, making them suitable for producing large volumes of parts.
Effect of Punch Speed on Forming Quality:
The speed at which the punch strikes the sheet metal affects the quality of the formed part. High-speed punching can increase the risk of material tearing or deformation due to the rapid application of force. However, high-speed operations are essential for mass production and must be optimized to achieve a balance between speed and quality.
4.5. Hydroforming
Working Principles of Hydroforming:
Hydroforming is a process that uses hydraulic pressure to form metal sheets into complex shapes. In hydroforming, the sheet is placed over a die, and high-pressure fluid is used to force the sheet into the die cavity. This method is particularly effective for producing lightweight, high-strength parts with complex geometries.
Hydroforming is widely used in the automotive industry to produce structural components such as engine cradles, exhaust systems, and body panels. The process offers several advantages over traditional stamping, including better material utilization, improved strength, and the ability to form parts with fewer joints and welds.
Advantages Over Traditional Forming Techniques:
Hydroforming offers several advantages over traditional sheet forming processes:
- Reduced Weight: By using hydraulic pressure to form the sheet, hydroforming allows for the creation of thinner, lighter parts without sacrificing strength.
- Improved Material Properties: The uniform pressure applied during hydroforming improves the material’s strength and stiffness, resulting in higher-quality parts.
- Cost-Effective Tooling: Hydroforming requires fewer dies and punches than traditional stamping, reducing tooling costs and setup time.
Sheet Forming Equipment and Tooling
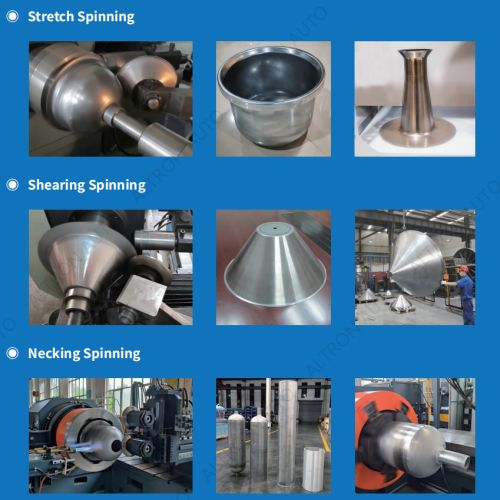
Sheet forming relies heavily on specialized equipment and tools designed to manipulate metal sheets with precision, efficiency, and control. Understanding the types of presses, tooling, and design considerations involved in sheet forming is crucial for ensuring high-quality results in manufacturing.
Types of Presses Used in Sheet Forming
The core equipment in sheet forming is the press, which applies the necessary force to shape the metal sheet. Different types of presses are used depending on the material, forming method, and complexity of the part. The most common presses used in sheet forming include:
- Mechanical Presses
- Mechanical presses use a motor-driven flywheel to generate energy, which is then transferred to the ram to apply force on the sheet metal. They are ideal for high-speed operations, such as stamping and punching, where large quantities of parts need to be produced quickly.
- Mechanical presses offer high precision and consistency, making them suitable for mass production of parts like automotive panels, electronic enclosures, and metal housings.
- However, mechanical presses lack the flexibility of hydraulic presses, as they offer limited control over force and speed adjustments during the forming process.
- Hydraulic Presses
- Hydraulic presses use a hydraulic fluid system to generate pressure, which is transmitted to a piston that applies force to the sheet metal. Hydraulic presses are known for their flexibility and precise control over force, making them ideal for complex and delicate sheet forming operations.
- Hydraulic presses excel in deep drawing, bending, and other processes that require gradual force application and control over forming parameters. They are commonly used in the automotive, aerospace, and electronics industries.
- The ability to adjust the pressure and speed throughout the press cycle allows hydraulic presses to form a wide variety of materials, including high-strength steels and alloys, without damaging the material.
- Pneumatic Presses
- Pneumatic presses use compressed air to generate force, making them suitable for light-duty sheet forming operations. They are often used in applications that require lower forces, such as embossing, small part stamping, and lightweight material forming.
- While pneumatic presses are faster than hydraulic presses, they are limited in the amount of force they can generate and are typically used for less demanding applications.
- Servo-Presses
- Servo-presses combine the benefits of both mechanical and hydraulic presses by using a servo motor to control the ram’s movement. This allows for precise control over the force, speed, and positioning of the press, making servo-presses ideal for high-precision sheet forming applications.
- Servo-presses are increasingly popular in industries that require complex part geometries and tight tolerances, such as aerospace, electronics, and medical device manufacturing.
Role of Dies and Punches in Sheet Forming
In sheet forming, dies and punches are critical components that directly shape the metal sheet into the desired form. The die provides the cavity or mold, while the punch applies pressure to the sheet to force it into the die. The design and quality of these tools significantly impact the accuracy, surface finish, and overall quality of the final product.
- Dies:
- Die Materials: Dies are typically made from tool steel or carbide materials due to their durability and resistance to wear. For more demanding applications, such as forming high-strength alloys or large-volume production runs, carbide dies may be used to extend tool life and improve performance.
- Types of Dies:
- Single-Stage Dies: These dies perform one operation per press cycle, such as blanking, piercing, or bending. They are ideal for low-volume production or parts with simple geometries.
- Progressive Dies: Progressive dies perform multiple operations in a single press cycle as the sheet metal moves through different stages of the die. This allows for high-speed production of complex parts, making progressive dies essential in industries like automotive manufacturing.
- Transfer Dies: These dies are used for large parts that require multiple forming operations. In a transfer die system, the sheet metal is transferred from one station to another, with each station performing a different operation.
- Punches:
- Punch Materials: Like dies, punches are typically made from tool steel or carbide, depending on the material being formed and the volume of production. High-strength materials may require coated punches (e.g., titanium nitride) to reduce friction and wear.
- Punch Design Considerations: The punch’s geometry must be carefully designed to avoid excessive stress concentrations that could lead to cracking or tearing of the sheet metal. The radius of the punch tip, punch angle, and punch speed all influence the quality of the formed part.
Computer-Aided Design (CAD) and Simulation in Tooling Design
Advances in computer-aided design (CAD) and finite element analysis (FEA) have revolutionized the way tooling is designed for sheet forming processes. Engineers now use these digital tools to simulate the forming process, predict material behavior, and optimize tool geometry before manufacturing the physical die and punch. This reduces the need for trial-and-error testing, saving both time and costs.
- CAD for Tool Design:
- CAD software allows engineers to design complex die and punch geometries with high precision. By modeling the entire tooling setup in 3D, engineers can visualize how the sheet metal will interact with the tools and identify potential issues such as thinning, wrinkling, or springback before production begins.
- Finite Element Analysis (FEA) for Process Simulation:
- FEA simulates how the material will behave under different forming conditions, such as applied force, temperature, and friction. This helps engineers optimize process parameters like blank holding force, punch speed, and lubrication to minimize defects and ensure uniform material flow.
- FEA also allows for the virtual testing of different materials, tool geometries, and process setups, enabling manufacturers to make data-driven decisions and improve product quality.
Maintenance and Durability of Tooling
The longevity and performance of dies and punches are critical to maintaining production efficiency and product quality. Tooling in sheet forming is subject to significant wear and tear due to the high forces and friction involved in the process. Proper maintenance and tool management strategies are essential for ensuring long tool life and minimizing downtime.
- Tool Coatings:
Coatings such as titanium nitride (TiN) or diamond-like carbon (DLC) can be applied to dies and punches to reduce friction, enhance wear resistance, and extend tool life. These coatings are especially useful in forming high-strength materials, which tend to cause more wear on uncoated tooling. - Regular Inspection and Regrinding:
Tooling should be regularly inspected for signs of wear, cracking, or chipping. Worn or damaged tools can cause defects in the formed parts, such as dimensional inaccuracies or surface imperfections. Regrinding the punch and die surfaces can restore their precision and extend their useful life. - Lubrication:
Proper lubrication of the tool and sheet interface is critical to reducing friction, preventing galling, and minimizing tool wear. Lubricants also help in controlling heat generation during the forming process, which can lead to tool degradation over time. - Tool Life Monitoring Systems:
Modern sheet forming presses are often equipped with tool life monitoring systems that track the number of press cycles and tool wear. These systems provide real-time data on tool performance, allowing operators to schedule maintenance and tool changes before failures occur.
Advanced Sheet Forming Techniques
As industries continue to demand more complex, precise, and lightweight components, new and advanced sheet forming techniques have been developed. These methods allow manufacturers to produce parts with intricate geometries, tighter tolerances, and improved material properties.
Incremental Sheet Forming (ISF)
Incremental Sheet Forming (ISF) is a highly flexible, die-less forming process in which a tool incrementally deforms the metal sheet into the desired shape. Unlike traditional sheet forming processes that rely on expensive dies and punches, ISF uses a single-point or multi-point tool that moves along a programmed path to shape the sheet.
- Advantages of ISF:
- Flexibility: ISF can be used to form complex and customized parts without the need for dedicated dies, making it ideal for prototyping and low-volume production.
- Cost Efficiency: The absence of tooling costs in ISF makes it a cost-effective solution for small batch production or when frequent design changes are required.
- High Accuracy: The incremental nature of the process allows for precise control over the final geometry, minimizing defects like wrinkling or thinning.
- Applications of ISF:
ISF is commonly used in the medical device industry for custom implants, in aerospace for low-volume parts, and in automotive prototyping.
Superplastic Forming (SPF)
Superplastic forming is a sheet forming technique that takes advantage of certain materials’ ability to undergo extremely large plastic deformation when heated to a specific temperature. At elevated temperatures, materials like aluminum alloys, titanium alloys, and certain stainless steels exhibit superplastic behavior, allowing them to be stretched or formed into complex shapes without fracturing.
- Advantages of SPF:
- Complex Geometries: SPF allows for the formation of parts with intricate shapes and deep draws that would be difficult or impossible to achieve using conventional forming methods.
- Minimal Tooling: Since the material is highly formable at superplastic temperatures, less force is required, reducing the wear on tooling and extending tool life.
- Fine Detail and Surface Finish: SPF produces parts with excellent surface finish and fine detail, making it ideal for aerospace and medical applications.
- Applications of SPF:
SPF is widely used in the aerospace industry for forming lightweight, high-strength parts such as wing panels, fuselage components, and engine nacelles.
Electromagnetic Forming (EMF)
Electromagnetic forming is a high-speed sheet forming process that uses a magnetic field to generate a repulsive force between the tool and the sheet metal. This process is particularly effective for forming electrically conductive materials, such as aluminum, copper, and brass.
- Advantages of EMF:
- High-Speed Forming: EMF can achieve extremely high forming speeds, making it suitable for applications that require rapid deformation, such as automotive part production.
- No Physical Contact with the Tool: Since the forming force is generated by a magnetic field, there is no physical contact between the tool and the sheet. This eliminates tool wear and produces parts with excellent surface quality.
- Improved Formability: The high-speed nature of EMF allows for greater formability, as the material is deformed so quickly that defects like wrinkling and tearing are minimized.
- Applications of EMF:
EMF is used in the automotive industry to form complex shapes, such as fuel tanks, exhaust components, and door panels. It is also used in the electronics industry for forming lightweight metal housings and enclosures.
Servo-Press Technology
Servo-press technology represents a significant advancement in sheet forming, combining the high-speed capability of mechanical presses with the precision and flexibility of hydraulic presses. In a servo press, the motion of the ram is controlled by a servo motor, allowing for real-time adjustments to the press force, speed, and stroke length.
- Advantages of Servo-Presses:
- Precise Control: Servo presses offer unparalleled control over the press cycle, allowing manufacturers to fine-tune process parameters for complex parts or delicate materials.
- Energy Efficiency: Servo presses use energy only when needed, reducing power consumption and operating costs.
- Versatility: The ability to adjust the speed and force at any point during the press cycle makes servo presses suitable for a wide range of materials and forming processes, from high-speed stamping to deep drawing.
- Applications of Servo-Presses:
Servo presses are increasingly used in the automotive, electronics, and aerospace industries for applications that require high precision and flexibility. They are particularly well-suited for forming high-strength materials and producing parts with tight tolerances.
Forming Defects and Remedies
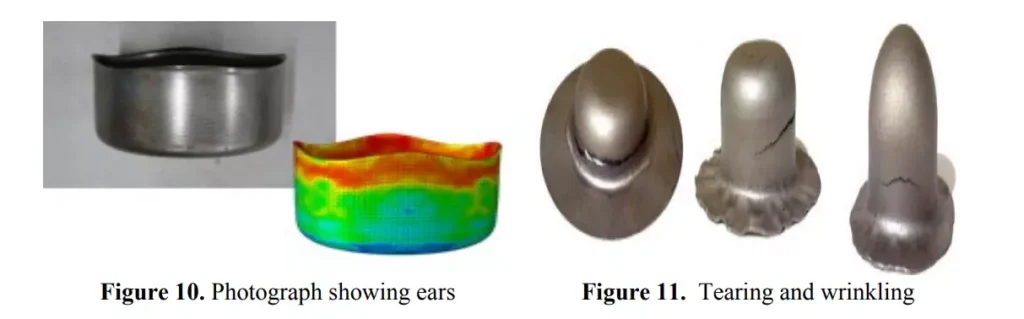
Despite the advancements in sheet forming technology, defects can occur due to a variety of factors, such as incorrect process parameters, material behavior, or tooling issues. Understanding these defects and knowing how to mitigate them is essential to ensure high-quality formed parts. Below are the most common defects in sheet forming and the methods to prevent or correct them.
1. Wrinkling
Cause:
Wrinkling is one of the most common defects in sheet forming. It occurs when the sheet is compressed in-plane, causing the material to buckle or form small, wave-like imperfections. Wrinkling often happens during deep drawing, bending, and stretch forming, particularly in areas where the material is not sufficiently supported or constrained.
Prevention and Remedies:
- Blank Holding Force Adjustment: In deep drawing processes, applying insufficient blank-holding force can lead to wrinkling. Increasing the blank-holding force ensures that the sheet remains taut during the forming process, preventing excess material from bunching up.
- Die Design Optimization: Ensuring that the die is designed to provide adequate support to the sheet during deformation helps prevent wrinkling. Smooth die radii and proper draw bead design can control material flow and reduce the likelihood of wrinkles.
- Lubrication: Using the appropriate amount of lubrication reduces friction and helps the material flow more easily into the die, preventing material buildup that can lead to wrinkling.
2. Cracking and Tearing
Cause:
Cracking or tearing occurs when the material undergoes excessive tensile stress and exceeds its strain limits, particularly in high-strength metals or materials with limited ductility. This defect often appears in areas of the sheet where there is significant stretching or at sharp corners of the formed part.
Prevention and Remedies:
- Optimize Punch Speed: Reducing the punch speed allows the material to deform more gradually, reducing the risk of cracking. Applying force more slowly gives the material time to flow into the desired shape without fracturing.
- Material Selection: Choosing a more ductile material can prevent cracking during forming. Metals with high ductility, such as aluminum or mild steel, can absorb more strain without breaking.
- Lubrication and Friction Control: Adequate lubrication reduces friction between the tool and the sheet, preventing localized stress concentrations that can lead to cracks. Proper control of friction helps distribute the forming forces more evenly across the sheet.
3. Thinning and Necking
Cause:
Thinning occurs when the sheet metal becomes excessively stretched during forming, reducing its thickness. Necking is a more severe form of thinning that occurs in a localized region, which often precedes fracture. Thinning and necking are common in deep drawing, stretch forming, and hydroforming processes.
Prevention and Remedies:
- Forming Limit Diagram (FLD) Analysis: Engineers use forming limit diagrams (FLD) to determine the maximum amount of strain a material can withstand before thinning or necking occurs. By optimizing the forming process based on the FLD, manufacturers can avoid excessive thinning.
- Die and Punch Design Adjustments: Modifying the geometry of the punch and die to ensure a more even distribution of strain across the sheet can reduce the likelihood of localized thinning. Proper radii and smooth transitions in the tooling reduce stress concentrations.
- Multi-Stage Forming: Performing the forming process in multiple stages allows for more gradual deformation of the sheet. This reduces the risk of excessive thinning or necking, particularly in complex or deep-drawn parts.
4. Springback
Cause:
Springback occurs when the material partially returns to its original shape after being deformed. This is due to the elastic recovery of the material and is particularly common in bending operations and the forming of high-strength metals like steel and titanium. Springback can lead to parts that do not meet dimensional tolerances, requiring rework or additional forming operations.
Prevention and Remedies:
- Overbending Compensation: One of the simplest ways to counteract springback is to intentionally overbend the material slightly, allowing it to return to the desired angle after springback occurs.
- Material Selection: Using materials with lower elasticity can reduce springback. For example, mild steel exhibits less springback compared to high-strength steel or titanium.
- Forming Method Adjustments: Certain forming methods, such as bottoming or coining, can minimize springback by forcing the material to conform more closely to the shape of the die.
5. Galling and Tool Wear
Cause:
Galling is a form of wear that occurs when the metal sheet and the tooling surface stick to each other during forming, resulting in material transfer and surface damage. Galling typically occurs when forming hard metals or when there is insufficient lubrication between the sheet and the tool. Over time, galling can cause significant damage to both the part and the tooling.
Prevention and Remedies:
- Tool Coatings: Applying coatings to the tooling, such as titanium nitride (TiN) or diamond-like carbon (DLC), can reduce friction and prevent galling. Coated tools also tend to last longer and maintain better surface finishes.
- Improved Lubrication: Ensuring adequate lubrication between the tool and sheet is critical in preventing galling. The type of lubricant used should be appropriate for the material and forming process to minimize friction.
- Tool Material Selection: Using harder materials, such as carbide, for the die and punch can reduce the risk of galling, especially when forming harder metals like stainless steel or titanium.
6. Wrinkles in Flanges
Cause:
Wrinkling in flanges occurs when the edges of the sheet are compressed during the drawing process. This can result in an uneven, wavy edge, particularly in the case of deep drawing or stretch forming.
Prevention and Remedies:
- Adjust Blank Holder Pressure: Increasing the blank holder pressure can help prevent wrinkling in flanges by keeping the sheet edges firmly in place during forming.
- Die Design: Designing the die with proper draw beads or other features to control material flow helps prevent wrinkling at the edges.
- Reduce Material Flow: Reducing the material flow into the flange area during forming can prevent the formation of wrinkles.
Applications of Sheet Forming
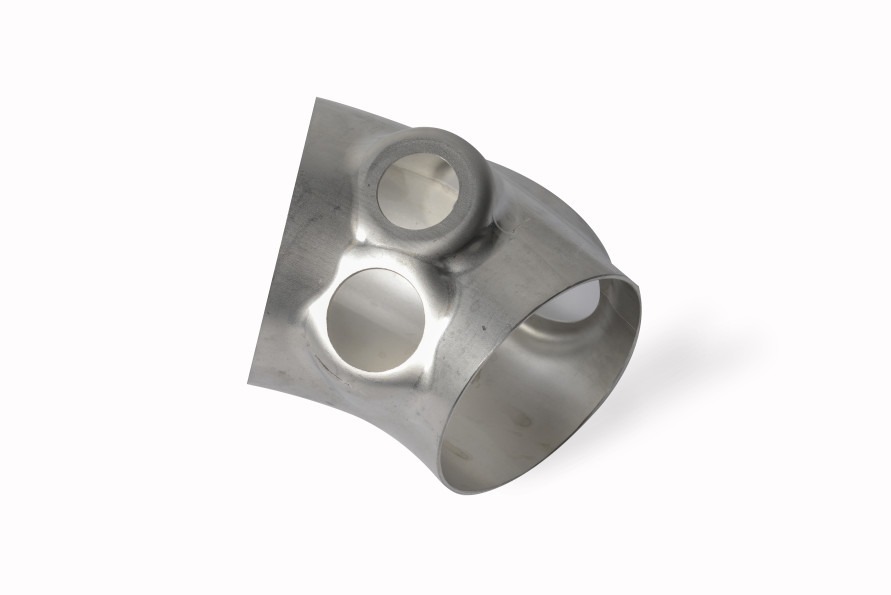
Sheet forming is a versatile manufacturing process used across various industries to produce high-quality components with complex shapes, tight tolerances, and excellent surface finishes. Below, we discuss the key applications of sheet forming in different industries and how this process plays a critical role in modern manufacturing.
1. Automotive Industry
The automotive industry is one of the largest consumers of sheet forming processes, particularly in the production of vehicle body panels, chassis components, and structural parts. Sheet forming provides manufacturers with the ability to produce lightweight, strong, and aesthetically pleasing parts at high volumes, making it essential for both traditional internal combustion engine vehicles and electric vehicles (EVs).
Key Applications in the Automotive Industry:
- Body Panels: Sheet forming is used to produce exterior panels, such as doors, hoods, roofs, and fenders. These components require a smooth surface finish, precise dimensions, and durability. Stamping and deep drawing are commonly used for these parts.
- Chassis and Structural Components: Structural components like vehicle frames, cross members, and suspension components are also produced using sheet forming techniques. High-strength steels and aluminum alloys are commonly used to reduce vehicle weight while maintaining crash safety standards.
- Battery Enclosures (EVs): With the rise of electric vehicles, sheet forming is increasingly used to produce lightweight, yet durable battery enclosures that protect battery packs from damage and improve vehicle safety.
2. Aerospace Industry
The aerospace industry demands lightweight, high-strength materials that can withstand extreme conditions. Sheet forming is widely used to produce components for both commercial and military aircraft, where weight savings are critical for fuel efficiency and performance.
Key Applications in the Aerospace Industry:
- Fuselage Panels: Aerospace manufacturers use stretch forming, hydroforming, and superplastic forming to create large, curved fuselage panels that are both lightweight and structurally sound. Aluminum and titanium alloys are commonly used for these parts.
- Wing Components: The complex geometry of aircraft wings requires precise sheet forming techniques to produce aerodynamic surfaces. Stretch forming and hydroforming are often used to create wing panels, ribs, and spars.
- Engine Components: Sheet forming is also used to create high-strength components for aircraft engines, such as combustion chambers, nozzles, and heat shields. Materials like titanium and nickel alloys are commonly used in these high-temperature applications.
3. Electronics and Consumer Goods
The electronics industry relies on sheet forming to create lightweight, durable enclosures and components for various consumer products, including smartphones, laptops, and household appliances. The ability to form thin metal sheets with tight tolerances and smooth finishes is essential in this industry.
Key Applications in Electronics and Consumer Goods:
- Enclosures and Housings: Sheet forming is used to create aluminum and stainless steel enclosures for smartphones, tablets, laptops, and other electronic devices. These enclosures need to be lightweight, durable, and aesthetically pleasing.
- Heat Sinks: Sheet forming processes like stamping and punching are used to create heat sinks for electronic devices, which help dissipate heat and maintain optimal operating temperatures.
- Appliances: Components for household appliances, such as washing machines, refrigerators, and microwaves, are often produced using sheet forming techniques. Stainless steel and aluminum are commonly used due to their corrosion resistance and durability.
4. Construction and Architecture
The construction and architectural industries use sheet forming to create durable, aesthetically pleasing metal components for buildings, bridges, and infrastructure projects. Sheet metal components are commonly used in both structural and decorative applications.
Key Applications in Construction and Architecture:
- Roofing and Cladding: Metal roofing sheets and cladding panels are produced using sheet forming processes like bending and roll forming. Materials such as steel, aluminum, and copper are commonly used for their strength, weather resistance, and visual appeal.
- Facades and Curtain Walls: Architects use sheet forming to create intricate metal facades and curtain wall systems for modern buildings. The ability to form metal sheets into complex shapes and patterns adds both functional and aesthetic value to building designs.
- Structural Elements: Sheet metal components like steel beams, columns, and braces are formed using sheet forming techniques. These components are critical to the structural integrity of buildings, bridges, and other infrastructure projects.
5. Medical Devices and Equipment
The medical device industry requires high-precision components made from biocompatible materials. Sheet forming processes are used to create surgical instruments, implants, and medical equipment housings.
Key Applications in Medical Devices:
- Surgical Instruments: Stainless steel and titanium are commonly used in the production of surgical instruments, such as scalpels, forceps, and scissors, due to their corrosion resistance and biocompatibility. Sheet forming ensures that these instruments meet strict dimensional tolerances and performance standards.
- Implants: Custom implants, such as joint replacements and dental implants, are often made using advanced sheet forming techniques like incremental forming and superplastic forming.
- Medical Equipment Housings: Sheet forming is used to create housings for medical equipment, such as MRI machines, X-ray devices, and surgical robots. These housings need to be lightweight, durable, and easy to sterilize.
6. Marine Industry
The marine industry uses sheet forming to produce lightweight, corrosion-resistant components for ships, submarines, and offshore structures. Materials like aluminum and stainless steel are commonly used to withstand the harsh marine environment.
Key Applications in the Marine Industry:
- Hull Panels: Large aluminum or steel panels for ship hulls are formed using processes like bending, stretching, and hydroforming. These panels need to be strong and resistant to corrosion from saltwater exposure.
- Marine Engine Components: Sheet forming is used to create components for marine engines, including exhaust systems, heat exchangers, and combustion chambers. High-strength alloys like stainless steel and nickel-based superalloys are used in these applications.
- Structural Components: Sheet metal is used to form structural components for offshore platforms, oil rigs, and underwater pipelines. The forming process ensures that these components meet the required strength and durability standards for use in demanding marine environments.
Definition of Hydraulic Press
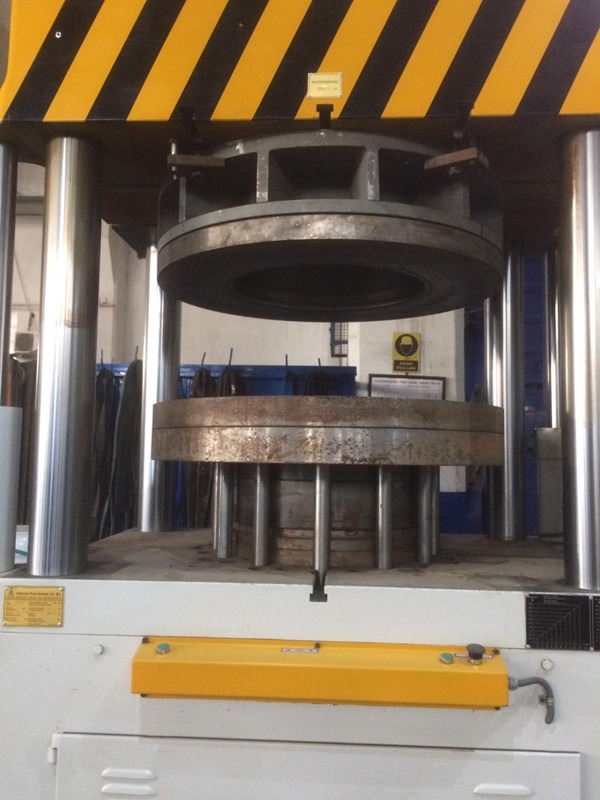
A hydraulic press is a machine that uses hydraulic cylinders to generate compressive force to perform various manufacturing processes such as forging, blanking, punching, stamping, deep drawing, and molding. The press operates by converting hydraulic energy from pressurized fluids into mechanical force that acts on a tool or die, which in turn shapes or cuts the material.
The hydraulic press operates on Pascal’s Law, which states that pressure applied to a confined fluid is transmitted equally in all directions throughout the fluid. This principle enables hydraulic presses to generate immense forces with relatively small inputs, making them highly efficient machines for tasks that require heavy-duty forming or shaping of materials.
Importance of Hydraulic Presses in Modern Manufacturing
Hydraulic presses are indispensable tools in modern manufacturing, used across a wide range of industries such as automotive, aerospace, electronics, construction, and consumer goods. Their versatility, precision, and ability to handle various materials — from soft metals to high-strength alloys — make them critical for producing everything from simple sheet metal parts to complex, high-strength structural components.
Key reasons hydraulic presses are crucial in today’s manufacturing landscape include:
- Force Control and Flexibility: Hydraulic presses allow for precise control of force and speed, making them ideal for forming intricate parts with tight tolerances.
- Material Versatility: These presses can handle materials ranging from aluminum and mild steel to more advanced alloys like titanium and high-strength steels.
- Cost-Effectiveness for Small and Medium Production Runs: For industries requiring small-batch or customized production, hydraulic presses offer a cost-effective solution without requiring extensive setup or tooling changes.
- Energy Efficiency: Compared to mechanical presses, hydraulic presses are more energy-efficient, consuming power only during the actual pressing operation.
Historical Development of Hydraulic Press Technology
The history of hydraulic presses dates back to the late 18th century, when Joseph Bramah, an English engineer, invented the hydraulic press in 1795. Known as the “Bramah press,” it was the first machine to apply Pascal’s principle of hydraulic force multiplication, revolutionizing the manufacturing industry by making it possible to exert large forces with minimal input.
Since then, hydraulic press technology has evolved significantly:
- Early Developments: In the 19th and early 20th centuries, hydraulic presses were used primarily in simple forming processes, including coin stamping, metalworking, and sheet forming.
- Post-War Industrial Growth: Following World War II, advances in materials science and hydraulic engineering led to the development of more powerful presses capable of handling high-strength metals. Hydraulic presses became widely used in the automotive and aerospace industries for mass production of metal parts.
- Integration with Automation: By the 1970s and 1980s, hydraulic presses were increasingly integrated with automated control systems, allowing for improved precision and repeatability. Computer Numerical Control (CNC) systems allowed manufacturers to program hydraulic presses for complex operations, boosting productivity and reducing human error.
- Modern Advances: Today’s hydraulic presses are integrated with servo-hydraulic systems, smart sensors, and Internet of Things (IoT) technology, enabling manufacturers to monitor and control press operations remotely. These advancements allow for more efficient, precise, and data-driven manufacturing processes.
Hydraulic press technology continues to evolve, offering manufacturers greater efficiency, flexibility, and control while meeting the growing demand for precision and high-quality parts.
Basic Principles of Hydraulic Press Operation
Pascal’s Law and Fluid Dynamics
The operation of a hydraulic press is governed by Pascal’s Law, which states that when pressure is applied to a confined fluid, it is transmitted equally and undiminished in all directions. This principle allows hydraulic systems to multiply small amounts of force into much larger forces by using fluid pressure.
The hydraulic press relies on a hydraulic fluid (usually oil) to transmit force from one part of the system to another. In a typical hydraulic system:
- A pump generates pressure by forcing hydraulic fluid through the system.
- The pressure is transmitted through hydraulic lines to a cylinder, where it moves a piston.
- The piston then applies force to the material being pressed, completing the operation.
The force output of the hydraulic press is determined by the amount of pressure applied to the fluid and the size of the pistons in the system. By using a larger piston, the system can generate more force even with relatively low fluid pressure.
Working Mechanism of a Hydraulic Press
A hydraulic press typically consists of several key components: the pump, hydraulic cylinder, piston, and valves. Here’s how they work together:
- Hydraulic Pump Activation: The process begins when the hydraulic pump activates, pressurizing the hydraulic fluid within the system. The pump generates the necessary force by applying pressure to the fluid, which is stored in a reservoir.
- Pressure Transmission: The pressurized fluid travels through hydraulic lines to the hydraulic cylinder. Inside the cylinder, the fluid pushes against the piston, which converts the hydraulic energy into mechanical force.
- Force Application by the Piston: As the piston moves downward, it exerts force on the material placed beneath it, pressing it into the die or mold to achieve the desired shape.
- Control Valves and Pressure Adjustment: Control valves are used to regulate the flow of hydraulic fluid within the system, controlling the speed, direction, and force of the piston. Operators can adjust the pressure to meet the requirements of the specific task, whether it involves forming, punching, or stamping.
- Return Stroke: After the pressing operation is complete, the hydraulic fluid is released, and the piston retracts to its original position, completing the cycle. The fluid returns to the reservoir, ready for the next press cycle.
Key Components: Hydraulic System, Pistons, Pumps, Cylinders, and Valves
The following are the essential components of a hydraulic press system and their functions:
- Hydraulic Pump:
- The hydraulic pump is the heart of the hydraulic system. It pressurizes the hydraulic fluid, creating the necessary force to move the piston. Pumps can be gear pumps, piston pumps, or vane pumps, depending on the required pressure and flow rate.
- Hydraulic Cylinder:
- The hydraulic cylinder houses the piston and is responsible for converting hydraulic energy into mechanical force. The size of the cylinder and piston determines the amount of force the press can generate. Hydraulic cylinders can be single-acting (pressure applied in one direction) or double-acting (pressure applied in both directions).
- Piston:
- The piston moves within the hydraulic cylinder and exerts force on the material being pressed. The size and design of the piston directly affect the force and precision of the press operation.
- Valves:
- Hydraulic systems include several types of valves to control the flow, pressure, and direction of the hydraulic fluid:
- Directional Control Valves determine the direction of fluid flow, controlling whether the piston moves up or down.
- Pressure Relief Valves prevent the system from exceeding safe pressure limits by releasing excess pressure when needed.
- Flow Control Valves regulate the speed at which the piston moves, allowing for adjustments in the press cycle’s speed and precision.
- Hydraulic systems include several types of valves to control the flow, pressure, and direction of the hydraulic fluid:
- Reservoir and Hydraulic Fluid:
- The reservoir stores the hydraulic fluid when it is not in use. Hydraulic fluid serves as the medium for transmitting pressure and must be carefully maintained to avoid contamination and ensure the proper operation of the system.
Force Generation and Pressure Control
The amount of force generated by a hydraulic press depends on two main factors: the pressure applied to the hydraulic fluid and the surface area of the piston. The formula for determining the force output is:Force=Pressure×Area of the Piston\text{Force} = \text{Pressure} \times \text{Area of the Piston}Force=Pressure×Area of the Piston
Where:
- Pressure is measured in units such as psi (pounds per square inch) or bar.
- Area of the Piston is determined by the diameter of the piston in the hydraulic cylinder.
For example, if a hydraulic press applies 2,000 psi of pressure to a piston with an area of 10 square inches, the total force generated will be:Force=2,000 psi×10 in2=20,000 pounds of force\text{Force} = 2,000 \, \text{psi} \times 10 \, \text{in}^2 = 20,000 \, \text{pounds of force}Force=2,000psi×10in2=20,000pounds of force
This ability to amplify force makes hydraulic presses highly efficient for forming processes that require significant force, such as metal stamping, forging, or deep drawing.
Pressure control is critical to ensure that the press operates safely and efficiently. Over-pressurization can damage the press or the material being formed, while under-pressurization can result in incomplete forming or poor product quality. Hydraulic systems are equipped with pressure relief valves and sensors to monitor and maintain the optimal pressure level throughout the operation.
Key Components of a Hydraulic Cold Press
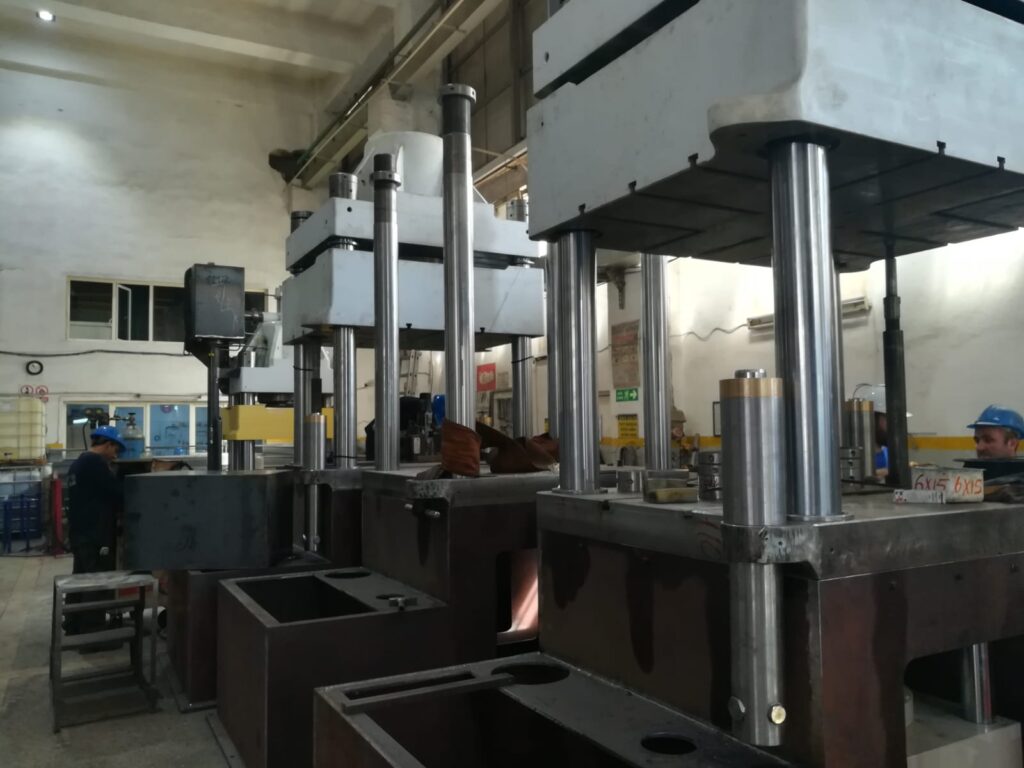
The design of a hydraulic cold press involves numerous components that work together to generate the required force for metal forming and other industrial operations. Understanding these components is essential for ensuring the machine’s efficiency, reliability, and performance.
1. Hydraulic Cylinders: Types and Performance Considerations
Hydraulic cylinders are the heart of any hydraulic press. They are responsible for converting hydraulic energy (from pressurized fluid) into mechanical force, which is then applied to the workpiece. In cold presses, cylinders must be designed for high precision, with the ability to generate large amounts of force consistently and safely.
Types of Hydraulic Cylinders:
- Single-Acting Cylinders: These cylinders apply force in only one direction (usually downward) and rely on external forces, such as gravity or springs, to return to their original position. Single-acting cylinders are simpler in design and are typically used for operations where force is only needed in one direction.
- Double-Acting Cylinders: These cylinders can apply force in both directions, allowing for greater control during the press cycle. Double-acting cylinders are commonly used in presses that require precise positioning or where the return stroke must be forceful, such as in large-scale forming or deep drawing operations.
Performance Considerations:
- Stroke Length: The stroke length of a cylinder determines how far the piston can travel and, therefore, the maximum depth of the material that can be formed. A longer stroke is essential for deep drawing and other processes that involve significant material displacement.
- Cylinder Bore and Rod Size: The size of the cylinder bore and piston rod directly affects the amount of force the cylinder can generate. Larger bores allow for more hydraulic fluid to act on the piston, resulting in greater force output.
- Sealing Systems: The integrity of the cylinder’s seals is crucial for preventing fluid leaks and maintaining consistent pressure. High-quality sealing systems, including wipers and rod seals, help ensure long-term performance and reduce the risk of contamination in the hydraulic fluid.
2. Hydraulic Pumps: Design and Efficiency
The hydraulic pump is responsible for generating the necessary pressure within the hydraulic system. It forces hydraulic fluid through the system, providing the power needed to move the piston and apply force to the workpiece. Several types of pumps are commonly used in hydraulic cold presses, each with its own performance characteristics.
Types of Hydraulic Pumps:
- Gear Pumps: Gear pumps are widely used in hydraulic systems due to their simple design and reliability. They operate by trapping fluid between the gears and the casing, then forcing it through the system. While gear pumps are cost-effective and durable, they are less efficient than other types of pumps, especially at higher pressures.
- Piston Pumps: Piston pumps are more complex but offer higher efficiency and greater pressure capabilities than gear pumps. In piston pumps, pistons move inside cylinders to generate fluid flow and pressure. These pumps are ideal for applications that require precise pressure control and high force output.
- Vane Pumps: Vane pumps use a rotor with sliding vanes to push fluid through the system. These pumps are more efficient than gear pumps and are commonly used in applications where smooth, consistent flow is needed. Vane pumps are often found in hydraulic presses that require precise control over force and speed.
Efficiency Considerations:
- Pump Efficiency: The efficiency of the hydraulic pump directly impacts the overall performance of the press. High-efficiency pumps reduce energy consumption, minimize heat generation, and ensure that the press operates smoothly under load.
- Pressure and Flow Rate: The pump must be capable of generating the required pressure to produce the desired force while maintaining an adequate flow rate to ensure rapid piston movement. The balance between pressure and flow rate is critical for optimizing press cycle times and energy efficiency.
3. Pressure Control Valves and Hydraulic Circuitry
Pressure control in a hydraulic cold press is vital for ensuring that the machine operates within safe limits and that the force applied to the workpiece is consistent and precise. Pressure control valves and hydraulic circuitry play a crucial role in managing the flow of hydraulic fluid throughout the system.
Key Types of Valves:
- Pressure Relief Valves: These valves protect the hydraulic system from over-pressurization by releasing excess pressure when it exceeds the system’s limits. Pressure relief valves are essential for preventing damage to the press and ensuring operator safety.
- Proportional Valves: Proportional valves regulate the flow of hydraulic fluid to control the speed and force of the press. These valves allow for more precise adjustments to be made during the pressing operation, improving the accuracy of the final product.
- Directional Control Valves: These valves determine the direction of fluid flow within the system, controlling whether the piston moves up or down. Directional control valves are typically solenoid-operated, allowing them to be controlled automatically as part of a computer-aided press system.
Hydraulic Circuit Design:
- The hydraulic circuit is the pathway through which the fluid moves within the system. An efficiently designed hydraulic circuit minimizes pressure losses and ensures smooth, controlled movement of the piston. Components such as accumulators, filters, and heat exchangers are often included to maintain fluid quality and system performance.
- Closed-Loop vs. Open-Loop Systems: Hydraulic cold presses can be designed with either a closed-loop or open-loop hydraulic system. In a closed-loop system, the hydraulic fluid is continuously cycled through the system, while in an open-loop system, fluid is returned to a reservoir before being recirculated. Closed-loop systems are more efficient but also more complex.
4. Press Frame Design: C-Frame vs. H-Frame
The press frame provides the structural support for the hydraulic cold press, ensuring that the components remain stable under the immense forces generated during operation. Two primary frame designs are used in hydraulic presses: C-Frame and H-Frame.
C-Frame Hydraulic Press:
- C-Frame presses are characterized by their open-front design, which allows for easy access to the workspace. This design is often used in applications where the operator needs to manually load and unload the workpiece.
- Advantages: The open design of C-Frame presses makes them ideal for smaller jobs and operations that require frequent part changes. They are commonly used for bending, punching, and small-scale forming tasks.
- Disadvantages: Due to the open-frame design, C-Frame presses are less rigid than H-Frame presses and may experience deflection under heavy loads, limiting their use in high-force applications.
H-Frame Hydraulic Press:
- H-Frame presses feature a more robust, closed-frame design, which provides greater stability and rigidity. The H-shaped frame evenly distributes force across the entire structure, making it ideal for heavy-duty applications.
- Advantages: H-Frame presses can handle much larger forces than C-Frame presses without deflecting, making them suitable for large-scale forming, deep drawing, and other operations that require high tonnage.
- Disadvantages: H-Frame presses are bulkier and more expensive than C-Frame presses, and their closed design can make it more difficult to access the work area for manual operations.
5. Tooling Systems: Dies, Punches, and Plates
In a hydraulic cold press, tooling systems — including dies, punches, and plates — are used to shape the material. These components must be designed with precision and durability in mind, as they are subjected to high levels of stress during the pressing operation.
Die Design:
- Dies provide the cavity into which the material is pressed. The shape and design of the die determine the final form of the workpiece. For cold pressing, dies must be made from materials that can withstand high pressure and repetitive use without deforming or wearing out.
- Material Considerations: Tool steel and carbide are commonly used for die construction due to their hardness and wear resistance. For more advanced applications, dies may be coated with materials like titanium nitride (TiN) to improve their durability and reduce friction.
Punches:
- Punches apply pressure to the material, forcing it into the die to create the desired shape. Like dies, punches must be made from durable materials that can withstand repeated use without wearing out or becoming damaged.
- Precision in Punch Design: The punch’s design must match the die’s contours precisely to ensure that the material is deformed correctly. In deep drawing or bending operations, punches may have complex shapes to accommodate the desired form of the material.
Press Plates:
- Press plates are used to distribute the force from the piston evenly across the workpiece. They also protect the die and punch from direct contact with the hydraulic cylinder, reducing wear on critical components.
- Wear Resistance: Like dies and punches, press plates must be made from materials that can handle high levels of stress and pressure without wearing down. Hardened steel is often used for press plates in heavy-duty hydraulic presses.
6. Control Systems and Automation
Modern hydraulic cold presses are increasingly equipped with advanced control systems that allow for precise management of the pressing operation. These control systems are essential for optimizing performance, ensuring safety, and enabling automation.
Computer-Aided Controls:
- Many hydraulic cold presses are equipped with Programmable Logic Controllers (PLCs) that allow operators to program and automate the press cycle. PLCs can control factors such as pressure, speed, and stroke length, ensuring consistent and repeatable results across multiple parts.
Servo-Hydraulic Control:
- Servo-hydraulic systems combine hydraulic power with servo motors, offering greater control over the speed and force of the press. This level of control is particularly useful in applications that require high precision, such as forming thin or delicate materials.
- Advantages of Servo Control: Servo-hydraulic systems provide faster response times and more accurate positioning compared to traditional hydraulic systems. They are also more energy-efficient, as they only use power when needed.
Automation and Integration with Industry 4.0:
- Modern hydraulic cold presses can be integrated with Industry 4.0 technologies, allowing for real-time monitoring, data analysis, and remote control. By connecting the press to a central network, manufacturers can track performance metrics, predict maintenance needs, and optimize production schedules.
Structural Design and Materials Used in Hydraulic Cold Press Construction
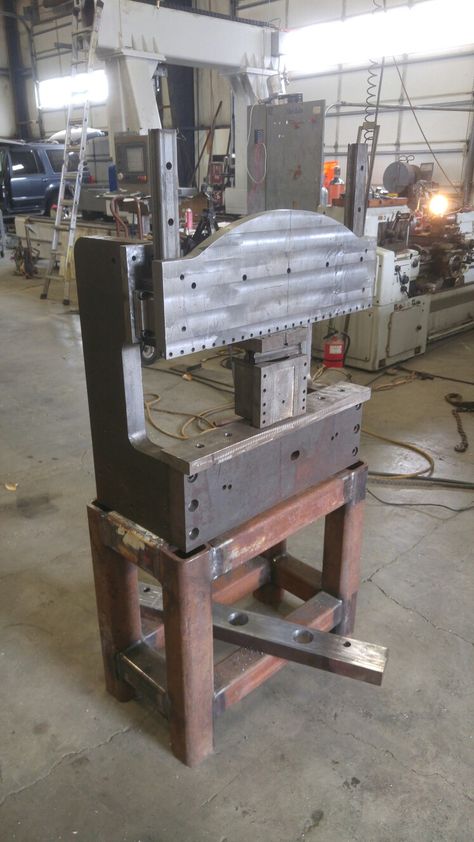
The structural design of a hydraulic cold press is critical to ensuring its ability to withstand the immense forces involved in the forming process. The materials used in construction must offer a combination of strength, rigidity, and durability to ensure that the press performs reliably over time. Below, we discuss the structural considerations and materials used in the construction of hydraulic cold presses.
1. Material Selection for Frames and Components
The choice of materials for the construction of the press frame and components significantly impacts the machine’s durability, strength, and overall performance. The materials must be capable of withstanding high forces, repeated cycles, and continuous stress without degrading or failing.
Common Materials Used:
- Steel: Steel is the most commonly used material in the construction of hydraulic cold presses due to its excellent strength-to-weight ratio, rigidity, and resistance to fatigue. The frame of most hydraulic presses is made from high-strength steel, capable of handling both static and dynamic loads without deforming.
- Structural Steel: Used for the frame, bed, and moving parts of the press, structural steel offers the required strength and rigidity for large-scale operations. It can handle high compressive and tensile forces while maintaining dimensional stability over time.
- Tool Steel: Tool steel is used for components such as dies, punches, and press plates that are in direct contact with the workpiece. It offers excellent wear resistance and can maintain its hardness even at elevated pressures.
- Cast Iron: Some components of hydraulic presses, such as certain types of machine bases or housings, are made from cast iron. Cast iron provides good damping properties, which help to reduce vibrations during operation. It is also less expensive than steel, making it a cost-effective option for certain non-critical components.
- Aluminum Alloys: While less common in large-scale hydraulic presses, aluminum alloys are sometimes used for smaller presses or components where weight reduction is important. Aluminum offers a high strength-to-weight ratio but is less durable than steel in heavy-duty applications.
- Composite Materials: In advanced cold press designs, composite materials may be used in specific components to reduce weight while maintaining high strength. These materials are particularly valuable in presses used in high-tech industries, such as aerospace and electronics, where precision and efficiency are critical.
2. Strength and Rigidity Requirements
The press frame must be designed to handle extreme forces without deflecting or deforming, as even small deflections can lead to inaccuracies in the final product. Strength and rigidity are the two primary design considerations when constructing the frame and other load-bearing components.
- Static and Dynamic Load Resistance: The frame must withstand both the static load (the weight of the press components) and the dynamic load (the force generated during pressing operations). Dynamic loads can cause the frame to flex, which can result in inaccurate or uneven force distribution across the workpiece.
- Avoiding Deflection: Hydraulic cold presses are subjected to immense forces during operation, and any deflection in the frame or components can lead to uneven material deformation or tool misalignment. To minimize deflection, the frame must be designed with thick walls, reinforced beams, and cross-members to distribute force evenly.
- Finite Element Analysis (FEA): Engineers use Finite Element Analysis (FEA) to model the stress and strain on the frame during operation. FEA simulations allow designers to identify potential weak points in the frame and optimize the design to ensure maximum strength and rigidity.
3. Fatigue Resistance and Durability in Heavy-Duty Operations
Hydraulic cold presses are often used in continuous, high-volume production environments, where they are subjected to repeated cycles of heavy force. The materials and design of the press must take into account the potential for fatigue failure, which occurs when materials weaken over time due to repeated stress.
- Fatigue Resistance: High-strength steel and tool steel are commonly used in press construction due to their ability to resist fatigue over thousands of cycles. Components such as the hydraulic cylinders, frame, and tooling are designed to endure repeated loading without cracking or failing.
- Wear and Tear on Moving Components: Moving parts, such as pistons, seals, and valves, are subjected to constant friction and wear. These components must be made from materials that offer both high strength and wear resistance to ensure long-term durability.
- Surface Treatments: Surface treatments, such as nitriding or carburizing, are often applied to steel components to improve their hardness and wear resistance. These treatments help extend the lifespan of critical parts, such as dies and punches, which are subjected to repeated high-pressure contact with the material being formed.
4. Design for Longevity and Reliability in Continuous Use
In industries like automotive and aerospace, where hydraulic cold presses are used in high-volume production, the design of the press must prioritize reliability and longevity. This requires careful consideration of factors such as material selection, component design, and maintenance accessibility.
- Durable Design: Hydraulic cold presses are built to last for decades in continuous use. This durability is achieved through the use of high-strength materials, robust construction techniques, and the inclusion of wear-resistant components. By designing the press for longevity, manufacturers can minimize downtime and reduce the total cost of ownership.
- Maintenance-Friendly Design: Easy access to key components, such as hydraulic lines, seals, and pumps, is essential for ensuring that the press can be maintained efficiently. Many modern hydraulic cold presses are designed with modular components that can be easily replaced, reducing the time and cost associated with repairs.
5. Structural Integrity in Extreme Conditions
Hydraulic cold presses must often operate in harsh industrial environments where they are exposed to heat, dust, vibration, and other factors that can affect their performance. The structural design of the press must account for these conditions to ensure reliable operation under all circumstances.
- Vibration Damping: In heavy-duty operations, the press may generate significant vibration, which can affect both the machine’s performance and the quality of the final product. The use of materials like cast iron, which has excellent vibration-damping properties, can help minimize the impact of vibration on the press’s operation.
- Thermal Stability: While hydraulic cold presses operate at room temperature, they can still generate heat during prolonged use, especially in the hydraulic system. The frame and components must be designed to maintain dimensional stability even as the temperature fluctuates.
Types of Hydraulic Cold Presses and Their Design Variations
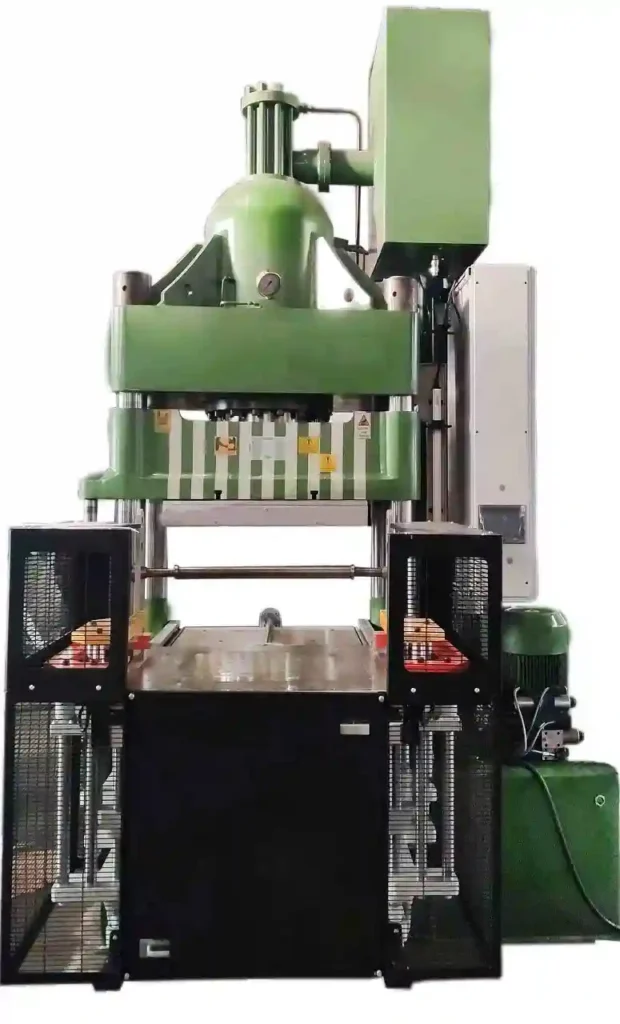
Hydraulic cold presses come in various designs tailored to meet the specific requirements of different industrial applications. The type of press used depends on factors such as the size of the workpiece, the material being formed, the desired precision, and the operational force required. Each press type has unique structural features that make it ideal for certain processes.
1. C-Frame Hydraulic Cold Presses: Features and Applications
C-Frame hydraulic presses are characterized by their distinctive “C” shaped frame, with the open side allowing easy access to the working area. This design is ideal for operations where flexibility and manual loading/unloading of the workpiece are required. The single-sided frame is strong enough for small to medium force applications but is not suitable for operations requiring very high forces.
Features:
- Open Access: The open-front design provides easy access to the working area, making it easier to position the workpiece and tooling. This feature is particularly useful in small-scale operations where parts need to be manually loaded or unloaded.
- Compact Footprint: C-Frame presses are typically more compact than other types of hydraulic presses, making them suitable for smaller workshops or spaces where floor area is limited.
- Cost-Effective: C-Frame presses are relatively simple in design, which makes them more affordable compared to larger, more complex presses. They are commonly used in small and medium-sized manufacturing operations.
Applications:
- Punching and Stamping: C-Frame presses are often used for small-scale punching, stamping, and forming operations where high force is not required.
- Bending and Straightening: These presses are ideal for light-duty bending and straightening tasks, making them a staple in metal fabrication shops.
2. H-Frame Hydraulic Cold Presses: Structural Advantages
H-Frame hydraulic presses, also known as shop presses, feature a robust, closed-frame design that distributes force evenly across the frame. The “H” shape of the frame provides greater stability and rigidity, allowing these presses to handle much larger forces than C-Frame presses. H-Frame presses are widely used for heavy-duty applications in industries such as automotive, aerospace, and construction.
Features:
- High Rigidity: The closed-frame design ensures minimal deflection during operation, even under very high loads. This makes H-Frame presses ideal for applications where precision and force control are essential.
- Versatility: H-Frame presses can be used for a variety of tasks, including bending, straightening, stamping, and deep drawing. Their versatility makes them a common choice in industries that require a wide range of forming processes.
- Heavy-Duty Capabilities: These presses are designed to handle heavy-duty operations, often generating forces of up to several thousand tons. This makes them suitable for forming large or thick metal parts, especially those made from high-strength alloys.
Applications:
- Automotive Manufacturing: H-Frame presses are commonly used in the automotive industry to form body panels, chassis components, and structural parts.
- Deep Drawing and Forging: The high rigidity and large force output of H-Frame presses make them ideal for deep drawing and forging operations, where precise force application is critical.
3. Four-Column Hydraulic Cold Presses for Large-Scale Operations
Four-column hydraulic cold presses are designed for large-scale industrial applications where high precision and large workpiece dimensions are required. The four-column design provides excellent stability and allows for uniform force distribution across the entire surface of the workpiece. These presses are commonly used in industries that require high tonnage and large-scale metal forming, such as shipbuilding, aerospace, and heavy machinery manufacturing.
Features:
- Even Force Distribution: The four-column design ensures that force is applied evenly across the workpiece, minimizing the risk of deformation or defects. This is especially important in processes like deep drawing, where uniform material flow is critical.
- Large Work Area: Four-column presses typically have a larger work area compared to C-Frame and H-Frame presses, allowing them to accommodate larger workpieces and more complex tooling setups.
- Precision Control: These presses are often equipped with advanced control systems that allow for precise adjustments to pressure, speed, and stroke length, ensuring high accuracy in large-scale forming operations.
Applications:
- Large-Scale Metal Forming: Four-column presses are used for forming large metal sheets or plates, such as those used in shipbuilding, bridge construction, and large industrial equipment.
- Automotive and Aerospace Components: These presses are also used in the automotive and aerospace industries for forming large structural components, such as truck frames, aircraft fuselages, and heavy-duty brackets.
4. Servo-Hydraulic Cold Presses and Precision Design
Servo-hydraulic cold presses combine the power of hydraulic systems with the precision of servo motors, offering greater control over the press cycle. These presses use servo motors to control the movement of the hydraulic piston, allowing for fine-tuned adjustments to speed, pressure, and stroke length in real time. This makes servo-hydraulic presses ideal for applications that require high precision and repeatability.
Features:
- High Precision: Servo-hydraulic presses offer unparalleled control over the press cycle, making them ideal for applications that require tight tolerances and consistent results.
- Energy Efficiency: Servo motors allow for precise control of energy usage, ensuring that power is only consumed when necessary. This makes servo-hydraulic presses more energy-efficient than traditional hydraulic presses.
- Customizable Press Cycles: The ability to adjust the speed and force during the press cycle allows manufacturers to optimize the forming process for different materials and part geometries. This flexibility is especially useful in industries that require frequent changes in product specifications.
Applications:
- Precision Metal Forming: Servo-hydraulic presses are widely used in industries such as aerospace, electronics, and medical device manufacturing, where high precision and material control are critical.
- Advanced Materials Forming: These presses are also used to form advanced materials, such as titanium and high-strength aluminum alloys, which require precise force control to avoid defects.
5. Double-Action vs. Single-Action Cold Presses
Single-action and double-action hydraulic cold presses differ in their ability to apply force in one or two stages of the press cycle. The choice between these two types depends on the specific requirements of the forming operation.
Single-Action Hydraulic Cold Presses:
- Single-action presses apply force in one direction, usually in a single stroke. They are simpler in design and are commonly used for basic forming operations such as bending, stamping, or punching.
- Applications: These presses are used in applications where only one direction of force is required, such as in small-scale metal forming, sheet metal cutting, and embossing.
Double-Action Hydraulic Cold Presses:
- Double-action presses apply force in two stages. The first stage (blank holding) holds the material in place while the second stage applies force to deform the material. This two-stage process is essential for operations like deep drawing, where the material needs to be held securely while being formed.
- Applications: Double-action presses are commonly used in deep drawing operations and other complex forming processes that require precise control over material flow and force distribution.
Design Considerations for Specific Cold Press Applications
Designing hydraulic cold presses for specific applications involves tailoring the machine’s components, control systems, and frame structure to meet the unique requirements of each industry. Below are the key design considerations for cold presses used in various sectors.
1. Automotive Industry: Forming Body Panels and Structural Parts
The automotive industry relies heavily on hydraulic cold presses for forming body panels, chassis components, and structural parts. These components must meet stringent requirements for strength, durability, and safety while maintaining a lightweight profile for fuel efficiency.
Key Design Considerations:
- High Tonnage for Forming Strength: Automotive components, especially those made from high-strength steels or aluminum alloys, require presses capable of generating significant force. Presses designed for automotive applications often have tonnage ratings ranging from 500 to 2,000 tons or more.
- Tooling and Die Design: The dies used in automotive cold presses must be carefully designed to ensure accurate forming of complex shapes such as body panels, fenders, and roof structures. Advanced simulation tools are often used to optimize die design for minimal material waste and maximum structural integrity.
- Material Handling Systems: Automotive production lines require efficient material handling systems to ensure rapid loading and unloading of workpieces. Automated material handling systems, such as robotic arms and conveyors, are often integrated into the press design to increase throughput and reduce cycle times.
2. Aerospace Industry: Precision Forming of Lightweight Alloys
In the aerospace industry, hydraulic cold presses are used to form lightweight yet high-strength alloys like aluminum, titanium, and composites. Components such as fuselage panels, wing sections, and engine casings must meet strict performance standards while being as lightweight as possible.
Key Design Considerations:
- Precision Control: Aerospace components require extremely tight tolerances and consistent material properties. Cold presses used in aerospace applications must offer precise control over pressure and stroke to avoid defects such as warping, cracking, or material thinning.
- Material-Specific Design: Presses designed for aerospace applications must account for the unique forming characteristics of advanced materials. Titanium, for example, requires high pressure and precise temperature control to avoid cracking during forming. Composite materials, on the other hand, require lower pressures but longer cycle times to achieve the desired form.
- Tooling and Die Cooling Systems: Aerospace components often require special cooling systems for the tooling and dies to maintain dimensional accuracy during the press cycle. Cooling systems help prevent thermal expansion, which could otherwise lead to inaccuracies in the final part dimensions.
3. Electronics and Consumer Goods: Forming Thin Metal Sheets
In the electronics and consumer goods industries, hydraulic cold presses are used to form thin metal sheets into enclosures, housings, and structural components. These components require a high level of precision and surface finish to ensure proper functionality and aesthetic appeal.
Key Design Considerations:
- Low Tonnage for Thin Sheets: The thin metal sheets used in electronics and consumer goods manufacturing require lower force compared to the thicker sheets used in automotive or aerospace applications. Presses designed for these industries typically have tonnage ratings ranging from 10 to 100 tons.
- Surface Finish Quality: The aesthetic quality of consumer goods is often just as important as their functional quality. Presses designed for this sector must be capable of producing smooth surface finishes without defects like scratches or indentations.
- Small Footprint and Versatility: Electronics manufacturers often require presses that can be easily adapted for different products or component designs. Hydraulic cold presses with compact footprints and versatile tooling systems are ideal for high-mix, low-volume production environments.
4. Custom Fabrication and Niche Applications
Custom fabrication shops use hydraulic cold presses for a wide range of tasks, from forming architectural elements to producing specialized machine components. These applications require presses that are highly adaptable and capable of performing various tasks with different materials.
Key Design Considerations:
- Flexibility and Modularity: Custom fabrication requires presses that can be easily modified for different tasks. Presses with modular tooling systems and adjustable stroke lengths allow fabricators to switch between operations like bending, forming, and punching with minimal setup time.
- Precision for Small-Batch Production: In custom fabrication, precision is often more important than speed. Presses must be capable of performing detailed work on small batches or one-off parts while maintaining consistent quality.
- Multi-Purpose Tooling: Tooling systems in custom fabrication presses are often designed to handle a variety of operations. This versatility allows shops to take on a wider range of projects without needing to invest in multiple machines.
5. Role of Advanced Materials and Alloys in Cold Press Design
The increasing use of advanced materials, such as high-strength steels, aluminum alloys, and composites, presents new challenges and opportunities for hydraulic cold press design. These materials offer superior performance in terms of strength, weight, and corrosion resistance but require specialized pressing techniques to form properly.
Key Design Considerations:
- High Tonnage for High-Strength Steels: High-strength steels used in automotive and aerospace applications require hydraulic presses capable of generating immense force without sacrificing precision. The press must be designed to handle the additional stress and wear associated with forming such materials.
- Temperature Control for Aluminum and Composites: While cold pressing typically occurs at room temperature, certain materials, such as aluminum alloys and composites, may require controlled heating or cooling during the press cycle to achieve the desired material properties.
- Tooling Wear Resistance: Forming advanced materials often results in greater wear on the tooling. Presses designed for advanced materials must include tooling systems made from highly wear-resistant materials, such as tool steel or carbide, to ensure longevity and reduce maintenance costs.
EMS Metalworking Machinery: Your Trusted Partner in Precision Metalworking
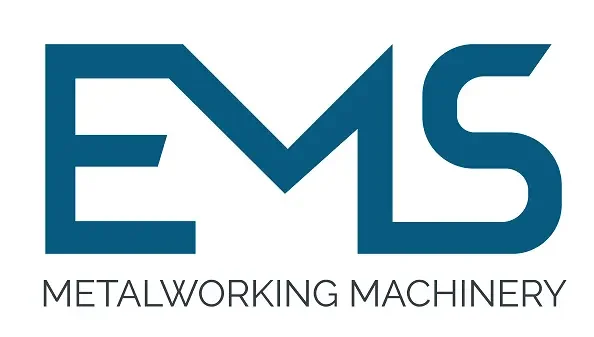
EMS Metalworking Machinery is a leading manufacturer of high-quality metalworking equipment, dedicated to providing innovative solutions that meet the evolving needs of industries worldwide. With a rich history of excellence and a commitment to technological advancement, we have earned a reputation for delivering cutting-edge machinery that ensures precision, efficiency, and durability.
Our Product Range:
- CNC Spinning Lathes: From precision bench lathes to heavy-duty industrial models, our lathes offer unmatched accuracy and performance for a wide range of applications, including machining shafts, gears, and other cylindrical components.
- Milling Machines: Our milling machines are designed to provide exceptional cutting capabilities and versatility, enabling you to create complex shapes and intricate details with ease. Whether you need a horizontal or vertical milling machine, we have the perfect solution for your needs.
- Drilling Machines: Our drilling machines are built to deliver precise and powerful drilling operations, ensuring clean holes and exceptional surface finishes. From sensitive bench drills to heavy-duty radial drills, we offer a comprehensive range to suit various applications.
- Grinding Machines: Our grinding machines are engineered for precision and efficiency, allowing you to achieve the highest levels of surface finish and dimensional accuracy. Whether you need a surface grinder, cylindrical grinder, or tool grinder, we have the equipment to meet your specific requirements.
- Sawing Machines: Our sawing machines are designed for fast and accurate cutting of metals, providing clean cuts and minimal burrs. From band saws to circular saws, we offer a variety of options to suit different materials and cutting needs.
- Custom Machinery: In addition to our standard product line, we also specialize in custom machinery fabrication. Our experienced engineers can work with you to design and build tailored solutions that meet your unique requirements and optimize your production processes.
Why Choose EMS Metalworking Machinery:
- Quality: Our machines are crafted with the highest quality materials and components, ensuring long-lasting performance and reliability.
- Precision: We are committed to delivering machinery that meets the most stringent tolerances and standards, ensuring exceptional accuracy in your metalworking operations.
- Innovation: We continuously invest in research and development to stay at the forefront of technological advancements, offering innovative solutions that enhance your productivity and efficiency.
- Customer Support: Our dedicated team of experts is always available to provide comprehensive support, from machine selection and installation to maintenance and troubleshooting.
- Customization: We understand that every business has unique needs, and we offer flexible customization options to tailor our machines to your specific requirements.
At EMS Metalworking Machinery, we are more than just a supplier of equipment; we are your trusted partner in metalworking success. By choosing EMS, you can be confident in the quality, reliability, and performance of your machinery, enabling you to achieve your business goals and stay ahead of the competition.
EMS Metalworking Machinery
We design, manufacture and assembly metalworking machinery such as:
- Hydraulic transfer press
- Glass mosaic press
- Hydraulic deep drawing press
- Casting press
- Hydraulic cold forming press
- Hydroforming press
- Composite press
- Silicone rubber moulding press
- Brake pad press
- Melamine press
- SMC & BMC Press
- Labrotaroy press
- Edge cutting trimming machine
- Edge curling machine
- Trimming beading machine
- Trimming joggling machine
- Cookware production line
- Pipe bending machine
- Profile bending machine
- Bandsaw for metal
- Cylindrical welding machine
- Horizontal pres and cookware
- Kitchenware, hotelware
- Bakeware and cuttlery production machinery
as a complete line as well as an individual machine such as:
- Edge cutting trimming beading machines
- Polishing and grinding machines for pot and pans
- Hydraulic drawing presses
- Circle blanking machines
- Riveting machine
- Hole punching machines
- Press feeding machine
You can check our machinery at work at: EMS Metalworking Machinery – YouTube
Applications:
Flange-punching
Beading and ribbing
Flanging
Trimming
Curling
Lock-seaming
Ribbing