A circle cutting machine is a tool used to cut circular shapes out of various materials, such as metal, plastic, paper, or fabric. Here are some parts and features commonly found in circle-cutting machines:
- Cutting blade: The blade is the most important part of the circle cutting machine, and it can be made of different materials such as steel or tungsten carbide. The blade rotates as the machine is in use, cutting out the circular shape from the material.
- Cutting guide: The cutting guide holds the material in place and guides the blade along the cutting path. The guide is adjustable to accommodate different circle sizes.
- Cutting depth adjustment: The cutting depth adjustment allows the user to control the depth of the cut, which can be helpful when working with different materials.
- Base plate: The base plate is the surface on which the material is placed during cutting. It is typically made of a durable material like metal or plastic.
- Pivot arm: The pivot arm connects the cutting blade to the base plate and allows for precise control over the cutting angle and direction.
- Motor: The motor powers the blade and allows it to rotate quickly and efficiently.
- Safety features: Circle cutting machines may have safety features such as blade guards or automatic shut-off mechanisms to prevent injury or damage to the machine.
Circle cutting machines are used in a variety of industries, including metalworking, woodworking, and crafting. They are useful for creating circular shapes for products such as gears, wheels, and decorative items.
A circle cutting machine, also known as a circle cutter or disc cutter, is a specialized tool used to cut circular shapes from various materials, including paper, cardboard, plastic, fabric, and even thin metal sheets. These machines are commonly employed in industrial settings, craft workshops, and DIY projects.
Types of Circle Cutting Machines
Circle cutting machines come in various types, each with its own unique features and applications:
- Handheld Circle Cutters: These compact and portable machines are commonly used for cutting circles from paper, cardboard, and other lightweight materials. They typically feature a rotating blade or a punch-and-die mechanism to cut circles.
- Rotary Circle Cutters: These machines utilize a rotating blade mounted on a track or arm, allowing for precise cutting of circles in a variety of sizes. They are often used for cutting circles from fabric, leather, and other flexible materials.
- Hydraulic Circle Cutters: These powerful machines employ hydraulic pressure to cut circles from thicker materials, such as plastic sheets, thin metal sheets, and rubber. They offer high precision and cutting force for heavy-duty applications.
- CNC Circle Cutting Machines: These computer-numerically controlled (CNC) machines utilize computer programming to cut circles with exceptional precision and accuracy. They are commonly used in industrial settings for cutting circles from a wide range of materials.
Safety Precautions when using Circle Cutting Machines
When operating circle cutting machines, it is crucial to follow safety precautions to prevent injuries and ensure proper operation:
- Wear Personal Protective Equipment (PPE): Always wear safety glasses, gloves, and a cutting mat to protect yourself from sharp blades, flying debris, and potential cuts.
- Securely Clamp the Workpiece: Ensure the workpiece is firmly clamped to the machine’s work surface to prevent it from slipping or moving during cutting.
- Use the Correct Blade or Punch: Choose the appropriate blade or punch size and type for the material and desired circle size. Using the wrong blade or punch can damage the material or cause injury.
- Maintain Proper Blade or Punch Sharpness: Regularly sharpen or replace blades and punches to ensure they are sharp and maintain cutting efficiency. Dull blades can cause ragged edges and increase the risk of injury.
- Handle with Care: Always handle the machine with care, avoiding sudden movements or forceful actions that could lead to accidents.
- Never Touch the Moving Blade or Punch: Never touch the moving blade or punch while the machine is in operation.
- Turn Off the Machine Before Making Adjustments: Always turn off the machine before making any adjustments or changing the blade or punch.
- Store the Machine Properly: Store the machine in a safe, secure location when not in use, keeping it out of reach of children and unauthorized users.
By following these safety guidelines and operating the machine correctly, you can effectively utilize circle cutting machines to create precise circular shapes from various materials with minimal risk of injury.
Circle cutting machines are used in various industries, including:
- Metalworking: Circle cutting machines are commonly used in metalworking industries to cut circular shapes out of metals, such as steel, aluminum, and copper. They are used to make parts for machinery, automotive components, and other metal products.
- Woodworking: Circle cutting machines are also used in woodworking industries to cut circular shapes out of wood. They are used to make decorative wooden objects, such as clocks and signs, as well as to cut circular parts for furniture and other wooden products.
- Textile and apparel: Circle cutting machines are used in the textile and apparel industries to cut circular shapes out of fabric, leather, and other materials. They are used to make clothing, hats, bags, and other textile products.
- Craft and hobby: Circle cutting machines are popular among hobbyists and crafters, as they can be used to cut circular shapes out of a variety of materials. They are commonly used in scrapbooking, card making, and other paper crafts, as well as for creating decorative items like wreaths and ornaments.
- Manufacturing: Circle cutting machines are used in various manufacturing industries to cut circular shapes out of different materials. They are commonly used to make parts for machines and equipment, as well as for creating decorative and functional products.
In factories, where hydraulic presses manufacture deep drawn parts, as blank, sheet metal circles need to be prepared beforehand. These circles can either be manufactured by a mechanical press in serial production or needs to be cut as a square first, then the corners need to be trimmed by a machine to turn these square sheets into circles. This machine is called a circle cutting machine
A circle cutting machine is a machine that is used to cut a circle into a sheet of steel. Circle cutters are mainly used in metalworking to cut round steel sheets into circles. They come in two types: manual and automatic.
The first type of circle cutting machine is the manual type. This type of machine has large handles on both sides which are turned by hand to rotate the blade and produce the circular cut out from the metal sheet. The second type of circle cutting machine is automatic, which is much more efficient than its manual counterpart because it does not require any human input or labor to operate it.
For this purpose, we design and manufacture circle cutting machines, to cut the corners of sheet metals, which are later sent to hydraulic drawing presses for further operation
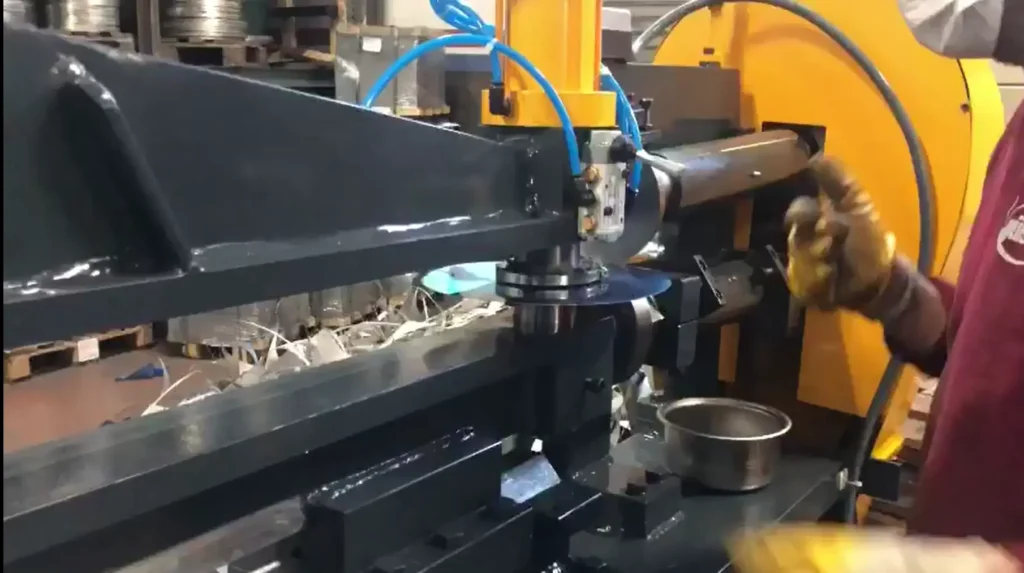
The capacity of our circle cutting machines is exceptionally high where an operator can get as high as 30 pcs per minute
The main body of the circle cutting machine is solid welded steel and knives to cut the sheet are made from high carbon high chromium steel
Circle cutting machine
A circle cutting machine for sheet metal is a specialized tool designed to cut precise circular shapes from metal sheets. These machines are widely used in industries such as metal fabrication, automotive manufacturing, HVAC, and construction. They enable workers to achieve accuracy, consistency, and efficiency in producing round components for various applications. The basic function of a circle cutting machine is to create circular cuts with a defined diameter in metal sheets of varying thicknesses. These machines come in different types, including manual, semi-automatic, and fully automated models, each suited for different levels of production and precision requirements.
Manual circle cutters require an operator to adjust the machine and guide the cutting process, while automated models use CNC technology to program precise cuts without continuous human intervention. The cutting process can be accomplished using different methods such as plasma cutting, laser cutting, oxy-fuel cutting, and mechanical shearing. Plasma cutting is preferred for its speed and ability to cut thick metal sheets with smooth edges. Laser cutting provides high precision and minimal material wastage, making it ideal for intricate designs.
Oxy-fuel cutting is commonly used for thick steel sheets due to its cost-effectiveness, while mechanical shearing relies on rotating blades or punches to create circular cuts. The choice of cutting method depends on factors such as material type, thickness, required precision, and production volume. Some circle cutting machines are portable, allowing workers to cut metal on-site, while others are stationary for industrial-scale operations. The machines typically consist of a base, a cutting head, and an adjustable arm or guide to ensure a consistent circular path. Many modern machines feature digital controls and automated settings to enhance precision and repeatability.
Safety features such as protective shields, emergency stop buttons, and fume extraction systems are integrated into advanced models to protect operators and maintain a clean work environment. Regular maintenance, including blade or nozzle replacement, lubrication of moving parts, and calibration of the cutting mechanism, is essential to ensure optimal performance and longevity of the machine. Choosing the right circle cutting machine involves considering factors such as sheet metal thickness, desired cut quality, production speed, and budget. Proper training for operators is also important to maximize efficiency and reduce errors. By investing in the right circle cutting machine, manufacturers and fabricators can improve productivity and achieve high-quality circular metal components with minimal waste.
Additional features of circle cutting machines can enhance their functionality and efficiency, making them more suitable for specific industrial needs. Some machines are equipped with motorized drive systems that automate the movement of the cutting head, reducing operator fatigue and improving accuracy. Advanced models may also include computer numerical control (CNC) technology, allowing for programmable cutting patterns, automatic diameter adjustments, and precise repeatability. These CNC machines are especially useful in industries requiring mass production of circular components with exact specifications.
The materials that can be processed by a circle cutting machine depend on the cutting method and the machine’s capabilities. Common metals include stainless steel, aluminum, copper, brass, and carbon steel. For high-strength alloys or specialized materials, advanced cutting techniques like fiber laser or waterjet cutting may be preferred to minimize heat-affected zones and material distortion. The ability to adjust cutting speed, pressure, and power settings enables operators to optimize the process for different materials and thicknesses.
In terms of design, some circle cutting machines feature interchangeable cutting heads, allowing users to switch between different cutting methods as needed. This flexibility is particularly beneficial for workshops handling diverse materials and project requirements. Additionally, machines with automated height control can maintain consistent cutting quality by adjusting for variations in sheet metal thickness or surface irregularities.
Efficiency and waste reduction are critical factors in modern manufacturing, and circle cutting machines contribute to these goals by ensuring precise cuts with minimal scrap. Some advanced systems incorporate nesting software, which optimizes the arrangement of circular cuts on a metal sheet to maximize material utilization. This feature is especially valuable in industries where raw material costs are high, such as aerospace and automotive manufacturing.
For heavy-duty applications, industrial-grade circle cutting machines are built with robust frames and high-power motors to handle large-diameter cuts in thick metal sheets. These machines are commonly used in shipbuilding, structural engineering, and heavy machinery production. Portable circle cutters, on the other hand, are designed for on-site applications such as pipeline fabrication, ventilation duct cutting, and maintenance work. Their lightweight and compact design make them easy to transport and operate in confined spaces.
Safety is a key consideration when using circle cutting machines, as high temperatures, sharp edges, and moving parts pose potential hazards. Operators should wear appropriate protective gear, including gloves, eye protection, and fire-resistant clothing, depending on the cutting method used. Machines equipped with fume extraction systems help to remove harmful gases and particulates generated during cutting, ensuring a safer work environment. Emergency stop functions, blade guards, and overload protection are also common safety features in modern machines.
Proper maintenance of a circle cutting machine is essential for ensuring long-term performance and reliability. Regular inspection of cutting components, lubrication of moving parts, and cleaning of dust or slag buildup can prevent downtime and extend the machine’s lifespan. Software updates and recalibration may be required for CNC models to maintain accuracy and efficiency. Operators should also follow manufacturer guidelines for replacing consumables, such as cutting nozzles, blades, or electrodes, based on usage and wear.
Investing in the right circle cutting machine can significantly enhance production efficiency, reduce material waste, and improve the overall quality of metal components. Whether for small-scale workshops or large industrial operations, selecting a machine with the appropriate cutting method, automation level, and material handling capabilities ensures optimal performance and return on investment.
Circle Cutting
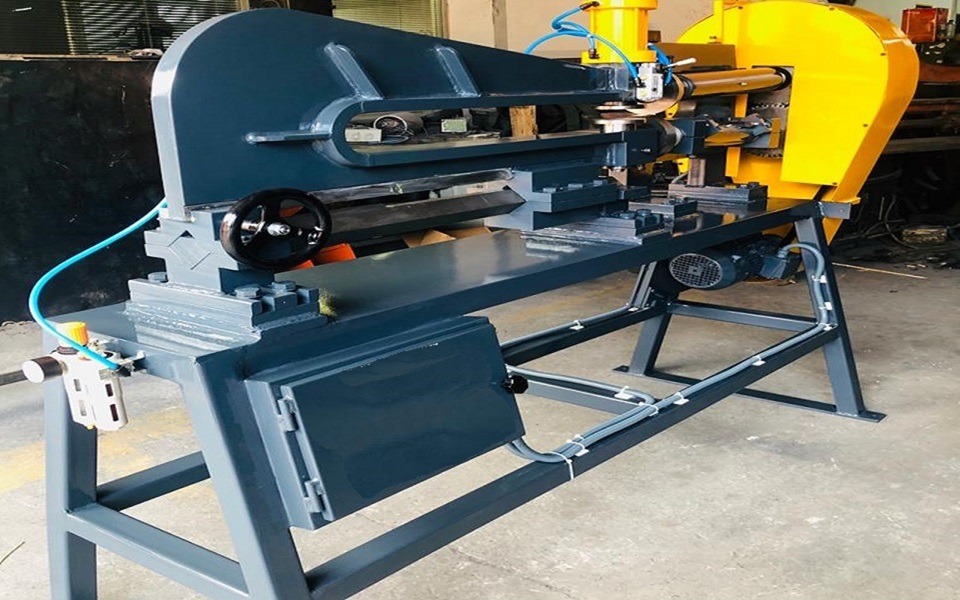
The versatility of circle cutting machines extends beyond standard metal fabrication, as they are used in specialized industries such as HVAC, aerospace, shipbuilding, and custom metalwork. In HVAC applications, for instance, precise circular cuts are necessary for manufacturing ductwork, ventilation openings, and flanges. The ability to quickly and accurately produce circular components ensures proper airflow and system efficiency. In aerospace and automotive industries, where precision is critical, high-tech circle cutting machines equipped with laser or waterjet technology are commonly used to create lightweight yet durable components. These advanced methods minimize heat distortion, preserving the mechanical properties of the materials.
In shipbuilding and heavy machinery manufacturing, thick steel plates often require large-diameter circular cuts for structural components, flanges, and reinforcements. Industrial-grade circle cutting machines with high-powered plasma or oxy-fuel cutting capabilities are typically employed for these tasks. The integration of CNC controls allows for precise customization of cut diameters, reducing manual adjustments and increasing efficiency. In the field of custom metalwork, artisans and fabricators use circle cutting machines to create intricate metal designs, sculptures, and decorative architectural elements. The precision of laser and plasma cutting machines makes them ideal for crafting detailed patterns in metal.
One of the key factors influencing the choice of a circle cutting machine is its power source and cutting capacity. Machines powered by electricity are the most common, offering stable and efficient operation for both manual and automated models. Pneumatic and hydraulic-powered machines provide additional force for cutting thick materials, making them suitable for heavy-duty industrial applications. The thickness and type of metal being processed determine the necessary cutting force, speed, and method. For example, thin aluminum sheets can be efficiently cut using a high-speed laser, while thick steel plates may require oxy-fuel cutting due to its deep penetration capability.
The integration of modern technologies in circle cutting machines has significantly improved accuracy, ease of use, and efficiency. Touchscreen interfaces, digital readouts, and automated positioning systems allow operators to input precise measurements and control the cutting process with minimal manual intervention. Some machines come with remote monitoring and diagnostic features, enabling technicians to track performance, identify issues, and perform maintenance remotely. Smart sensors in advanced models can detect variations in material thickness and adjust cutting parameters accordingly, reducing errors and ensuring uniform results.
Another aspect of circle cutting machines is their compatibility with additional accessories and attachments. For example, rotary indexing tables allow for automatic repositioning of the workpiece, enhancing production speed in mass manufacturing. Magnetic bases provide stability for portable cutting machines, ensuring precise operation even in challenging work environments. For applications requiring beveled edges, some machines include tilting heads or adjustable torch angles to create chamfered cuts, which are essential for weld preparation and assembly processes.
The environmental impact of cutting processes is also a consideration, especially in industries focused on sustainability. Waterjet cutting, for example, is an eco-friendly option that does not produce heat-affected zones or toxic fumes, making it ideal for industries with strict environmental regulations. Laser cutting, while highly precise, requires careful management of energy consumption and fume extraction to minimize environmental impact. Plasma and oxy-fuel cutting generate slag and gases that must be properly filtered and disposed of to comply with workplace safety and environmental standards.
Training and skill development are crucial for maximizing the efficiency of circle cutting machines. Operators must be familiar with machine controls, material properties, and safety procedures to achieve the best results. In industries where CNC cutting is prevalent, knowledge of CAD/CAM software is essential for designing and programming complex cutting patterns. Many manufacturers offer training programs and technical support to help users optimize machine performance and troubleshoot issues.
The future of circle cutting machines continues to evolve with advancements in automation, artificial intelligence, and smart manufacturing. Predictive maintenance using AI-driven analytics can anticipate component wear and suggest timely replacements, reducing unplanned downtime. Robotics integration allows for fully automated cutting cells, where machines can load, position, cut, and unload materials with minimal human intervention. As Industry 4.0 technologies advance, real-time data monitoring and cloud connectivity will enable greater efficiency, quality control, and production flexibility.
Ultimately, circle cutting machines play a vital role in modern metalworking industries by providing precision, efficiency, and versatility. Whether used in small workshops or large-scale manufacturing facilities, these machines enhance productivity and ensure high-quality results. The selection of the right machine depends on specific application requirements, material characteristics, and desired automation levels. With continuous technological improvements, these machines are becoming smarter, more energy-efficient, and more adaptable to the ever-evolving demands of industrial fabrication.
The integration of circle cutting machines into modern manufacturing processes has significantly streamlined production workflows, reducing manual labor while increasing output quality and consistency. These machines are now a fundamental part of industries that require precise circular cuts, from small fabrication shops to large-scale automated production facilities. The ability to automate cutting operations minimizes errors, reduces material waste, and enhances overall efficiency. With advancements in control systems and machine learning, newer models are capable of self-correcting cutting paths, adjusting speed and pressure based on real-time feedback from sensors that monitor material properties.
Customization and adaptability are key advantages of modern circle cutting machines. Many models now support multi-functional cutting heads that allow for different cutting techniques, such as switching between plasma and laser cutting within the same machine. This versatility ensures that manufacturers can handle a wide range of materials and cutting requirements without the need for multiple machines. Some machines are also equipped with interchangeable tooling systems, enabling them to perform additional operations like drilling, marking, or engraving, which can be particularly useful in industries requiring part traceability or branding.
One of the most significant improvements in circle cutting technology is the integration of software-driven precision. Many high-end machines now come equipped with CAD/CAM software that allows users to design cutting patterns digitally before execution. This not only improves accuracy but also reduces setup time and material waste. Operators can program the machine to cut multiple circles from a single sheet with minimal scrap, optimizing material usage. Some machines even feature AI-powered nesting algorithms that automatically arrange cutting patterns in the most efficient layout, further enhancing cost-effectiveness.
The impact of automation on circle cutting machines is particularly evident in large-scale manufacturing operations, where high production volumes require minimal downtime and consistent quality. Robotic arms are increasingly being integrated with CNC cutting systems to automate the loading, cutting, and unloading processes, eliminating manual handling and increasing efficiency. These robotic systems can operate around the clock, significantly boosting productivity while reducing human fatigue and the risk of errors. Additionally, automated material handling solutions, such as conveyor systems and stacking mechanisms, further streamline the workflow by ensuring continuous production without interruption.
For businesses operating in custom metal fabrication, the ability to quickly adjust cutting parameters and produce complex designs is crucial. Modern circle cutting machines offer intuitive user interfaces that allow operators to modify settings on the fly, making them ideal for prototyping and short-run production. The ability to cut intricate designs with minimal post-processing work is especially beneficial in industries such as signage, decorative metalwork, and artistic fabrication, where aesthetics and precision are equally important.
The durability and longevity of a circle cutting machine depend on proper maintenance and adherence to best practices in operation. Regular calibration, lubrication, and cleaning of cutting components are necessary to ensure smooth performance. Many machines now include predictive maintenance features that use sensors to monitor wear and tear, alerting operators when parts need replacement before they fail. This helps prevent unexpected breakdowns and reduces downtime. Additionally, manufacturers are increasingly using modular machine designs, allowing for easy upgrades and component replacements without the need for an entirely new machine.
Safety remains a primary concern in the operation of circle cutting machines, particularly those that use high-temperature cutting methods such as plasma and oxy-fuel. Proper ventilation and fume extraction systems are critical in preventing the accumulation of hazardous gases and particulates. Many machines are designed with automatic safety shutoffs, emergency stop buttons, and protective enclosures to minimize risks to operators. Adequate training is essential to ensure safe handling of both the machine and the materials being cut. In workplaces with high safety standards, compliance with industry regulations and certifications, such as OSHA or ISO safety guidelines, is mandatory for machine operation.
The global demand for more efficient and eco-friendly cutting solutions is driving research into new cutting technologies. Hybrid cutting machines that combine laser and waterjet technologies are being developed to achieve ultra-precise cuts with minimal environmental impact. Additionally, advancements in fiber laser cutting continue to improve energy efficiency and cutting speed while reducing operational costs. As sustainability becomes a growing priority in manufacturing, companies are looking for cutting solutions that minimize energy consumption and reduce waste.
Looking ahead, the evolution of circle cutting machines will likely be shaped by further developments in automation, artificial intelligence, and material science. Smart factories equipped with interconnected CNC cutting machines will be able to operate autonomously, with minimal human supervision, using real-time data analytics to optimize production. Augmented reality (AR) and virtual reality (VR) training modules may also become common, allowing operators to learn machine operation and troubleshooting in a simulated environment before handling the actual equipment.
The continued advancement of these machines ensures that they remain a vital part of modern industry, offering improved efficiency, precision, and versatility. Whether for mass production or custom fabrication, investing in the latest circle cutting technology provides businesses with a competitive edge in an increasingly demanding market.
A circle cutting machine for sheet metal typically consists of five main parts, each playing a crucial role in the cutting process.
- Cutting Head – This is the core component that performs the actual cutting. Depending on the cutting method, the head may contain a plasma torch, laser emitter, oxy-fuel nozzle, or mechanical blade. In advanced models, the cutting head is adjustable to accommodate different angles, depths, and speeds, ensuring precision and smooth edges.
- Base/Frame – The structural foundation of the machine provides stability and support during the cutting process. It ensures minimal vibrations, which is essential for maintaining cutting accuracy. The base may include mounting points, rails, or guides to assist in smooth movement and alignment of the cutting components.
- Rotary Arm/Guide Mechanism – This component controls the circular movement of the cutting tool, ensuring that the cutter follows a perfect circular path. Depending on the design, it may be manually adjustable or automatically controlled in CNC models. Some machines use a pivoting arm, while others rely on a track or programmed coordinates for precision.
- Control System – This includes the interface or software used to operate and program the machine. Manual machines have mechanical dials and levers, while CNC machines feature digital displays, touchscreens, and computer-based programming for precise and automated cutting. The control system adjusts speed, pressure, and cutting depth based on the material and project specifications.
- Power Source and Drive System – The power source varies depending on the machine type. Electric motors drive mechanical cutters, while plasma and laser cutters use high-energy power supplies. Hydraulic or pneumatic systems may also be used in heavy-duty machines to provide additional cutting force. The drive system moves the cutting head along its path, ensuring smooth and controlled operation.
Each of these components contributes to the efficiency, accuracy, and versatility of a circle cutting machine, making it an essential tool in metal fabrication and manufacturing.
Cutting Head
The cutting head is the most crucial component of a circle cutting machine for sheet metal, responsible for executing precise cuts based on the selected cutting method. It serves as the primary interface between the machine and the material, determining the accuracy, efficiency, and quality of the cutting process. Cutting heads can vary widely depending on the cutting technology used, including laser, plasma, oxy-fuel, waterjet, or mechanical blade cutting. The design and functionality of the cutting head must be optimized for the specific material, thickness, and required precision.
In modern machines, cutting heads are often equipped with advanced features such as height adjustment mechanisms, cooling systems, and automated focusing capabilities to enhance performance and durability. A key function of the cutting head is to direct the cutting energy precisely onto the workpiece, ensuring a clean and smooth cut. In laser cutting machines, the cutting head contains a focusing lens that concentrates the laser beam into an intense, fine point capable of melting, vaporizing, or burning through metal with minimal material distortion. The precision of laser cutting heads is enhanced through automated focal length adjustments, which compensate for variations in material thickness and maintain consistent cut quality. Plasma cutting heads, on the other hand, use a high-velocity jet of ionized gas to slice through metal by melting it with intense heat.
These cutting heads require proper gas flow regulation and nozzle maintenance to ensure stable and clean cuts. The nozzle design is critical in plasma cutting heads as it determines the shape and focus of the plasma arc, affecting cut precision and edge quality. In oxy-fuel cutting systems, the cutting head consists of a torch that mixes oxygen and a fuel gas such as acetylene or propane, creating a high-temperature flame that heats the metal to its ignition point before a stream of pure oxygen burns through the material. The cutting head in oxy-fuel machines typically has multiple nozzles to control the flame and oxygen flow, and it requires proper alignment to ensure efficient combustion and cutting performance. Waterjet cutting heads use a high-pressure stream of water, often mixed with an abrasive material, to erode the metal along a programmed cutting path.
These cutting heads require precision nozzles that can withstand extreme pressure levels while maintaining a steady, focused jet stream for accurate cuts. Mechanical cutting heads use rotating blades or punches to physically shear through metal, and they are commonly found in machines designed for thin sheets or softer metals. The durability of the cutting head is a key consideration, as continuous exposure to heat, pressure, and high-speed motion can cause wear over time. Many advanced cutting heads are designed with cooling systems, including air or water cooling, to prevent overheating and prolong their operational lifespan.
Additionally, some cutting heads incorporate automatic height sensing and adjustment systems that detect variations in the workpiece surface and dynamically adjust the head position to maintain optimal cutting distance. This feature is especially important in plasma and laser cutting machines, where inconsistent height can lead to poor cut quality, excessive dross, or material warping. Regular maintenance of the cutting head is essential to ensure consistent performance. Operators must inspect and replace consumable parts such as nozzles, electrodes, lenses, and seals to prevent degradation of cut quality. Calibration of the cutting head is also necessary to maintain alignment with the programmed cutting path, especially in high-precision applications.
In CNC-controlled cutting machines, the cutting head is integrated with motion control systems that allow for intricate cutting patterns and automated adjustments based on programmed designs. Some advanced cutting heads feature multi-axis capabilities, enabling them to tilt or rotate for bevel cutting and more complex geometries. The evolution of cutting head technology continues to drive improvements in cutting speed, accuracy, and energy efficiency. With the integration of smart sensors, AI-driven process control, and adaptive cutting technologies, modern cutting heads are becoming more efficient and user-friendly, minimizing the need for manual adjustments and reducing material waste. As manufacturing demands grow and precision requirements become more stringent, cutting heads will remain a focal point of innovation in metal fabrication and industrial processing.
The efficiency and performance of a cutting head depend on multiple factors, including the quality of its components, the cutting technology used, and its ability to adapt to different materials and conditions. Modern cutting heads are designed to handle a variety of materials, such as stainless steel, aluminum, copper, and carbon steel, with varying thicknesses. The selection of the right cutting head configuration is critical for achieving the desired cut quality, efficiency, and cost-effectiveness. Different cutting methods require specific designs and operating conditions to function optimally. For instance, a laser cutting head requires a precise optical system to focus the laser beam to a fine point, while a plasma cutting head relies on controlled gas flow and electrode stability to maintain a steady arc.
One of the most important aspects of a cutting head is its ability to maintain a consistent distance from the workpiece. In advanced CNC cutting systems, height control mechanisms are integrated into the cutting head to compensate for material warping, uneven surfaces, or variations in sheet thickness. This is particularly essential in plasma and laser cutting processes, where an incorrect distance can result in poor edge quality, excessive slag, or even damage to the cutting head components. Some modern cutting heads utilize capacitive or optical sensors to measure the distance from the material and make real-time adjustments to keep the cut precise and uniform.
The durability of a cutting head also depends on the quality of its consumable components, such as nozzles, electrodes, lenses, and focusing elements. In plasma cutting systems, the electrode and nozzle work together to shape the arc and direct it toward the workpiece. These components experience wear over time due to the intense heat and electrical discharge, requiring periodic replacement to maintain cutting accuracy. In laser cutting heads, the lenses or fiber optics that focus the beam must remain clean and free from debris to prevent power loss and beam distortion. Advanced laser cutting heads may include automated lens cleaning systems to extend operational life and reduce maintenance frequency.
Another critical feature in modern cutting heads is cooling technology, which prevents overheating and extends the lifespan of the components. Plasma cutting heads typically use air or water cooling systems to dissipate heat from the electrode and nozzle, while laser cutting heads may incorporate active cooling with circulating coolant to maintain stable temperatures. Effective cooling not only enhances performance but also reduces the risk of thermal damage to the workpiece, ensuring cleaner cuts with minimal distortion.
Automation and integration with digital control systems have significantly improved the functionality of cutting heads in recent years. CNC-controlled cutting heads can execute complex cutting patterns with minimal manual intervention, allowing for greater precision and repeatability. Some cutting heads are equipped with motorized tilting mechanisms, enabling bevel cutting for weld preparation or specialized fabrication needs. Multi-axis cutting heads provide even greater flexibility, allowing for the creation of intricate three-dimensional cuts in a single operation. These advanced capabilities have become essential in industries such as aerospace, automotive manufacturing, and shipbuilding, where precision and efficiency are paramount.
In addition to functionality, safety features in cutting heads are increasingly being prioritized. High-energy cutting methods such as laser and plasma generate intense heat, sparks, and potentially harmful fumes, requiring protective measures to ensure operator safety. Some cutting heads are equipped with enclosed designs to contain sparks and reduce exposure to harmful emissions. In industrial environments, fume extraction systems are often integrated with the cutting head to remove smoke and particulates generated during cutting. In laser cutting systems, automatic beam shutoff mechanisms are implemented to prevent accidental exposure to high-intensity laser radiation.
As technology continues to advance, the future of cutting heads will see even more innovations focused on efficiency, automation, and precision. Developments in artificial intelligence and machine learning are paving the way for smart cutting heads that can analyze material properties in real-time and automatically adjust cutting parameters for optimal performance. Predictive maintenance systems using IoT technology can monitor the condition of cutting head components, alerting operators to potential issues before they lead to downtime. Additionally, advancements in energy-efficient cutting technologies will contribute to more sustainable manufacturing processes, reducing power consumption and material waste.
The role of the cutting head in a circle cutting machine cannot be overstated, as it directly impacts the quality, speed, and reliability of the cutting process. Whether using traditional oxy-fuel, plasma, laser, or waterjet technology, selecting the right cutting head and maintaining it properly ensures consistent results and long-term operational efficiency. With ongoing technological advancements, cutting heads are becoming more intelligent, adaptive, and capable of meeting the ever-evolving demands of modern metal fabrication and manufacturing industries.
The continuous advancement in cutting head technology has led to significant improvements in precision, efficiency, and adaptability across various metal fabrication industries. One of the most critical developments is the integration of adaptive control systems within cutting heads, allowing for real-time monitoring and adjustments during the cutting process. These systems utilize sensors and feedback mechanisms to measure factors such as material thickness, heat distribution, and cutting speed, ensuring optimal performance without manual intervention. This is particularly beneficial for high-precision applications where even minor variations in cutting parameters can impact the final product quality.
For instance, in plasma cutting, modern cutting heads incorporate arc voltage sensing technology to automatically adjust the torch height as the material surface changes. This eliminates inconsistencies caused by sheet metal warping or uneven surfaces, leading to cleaner cuts and reduced material waste. Similarly, laser cutting heads now feature auto-focus and beam diameter adjustment capabilities, enabling them to switch seamlessly between different materials and thicknesses without the need for manual recalibration. This level of automation not only enhances precision but also reduces setup time, making production processes more efficient.
Another major development in cutting head technology is the use of multi-functional heads that can perform additional operations beyond cutting. Some cutting heads are designed to integrate with marking, engraving, or drilling attachments, allowing for more complex manufacturing processes in a single operation. This is particularly useful in industries that require part identification, such as aerospace and automotive manufacturing, where serial numbers or logos must be etched onto components for traceability. Additionally, certain cutting heads are equipped with beveling features that allow them to cut at an angle, making them ideal for weld preparation and specialized fabrication tasks.
Durability and longevity remain critical factors in the design of cutting heads, especially in high-production environments where machines operate continuously. To extend the lifespan of cutting heads, manufacturers have developed advanced cooling techniques and wear-resistant materials for key components such as nozzles, lenses, and electrodes. In laser cutting, for example, cutting heads now include high-efficiency cooling systems that prevent thermal expansion of optical elements, maintaining beam integrity and reducing downtime due to overheating. Plasma cutting heads utilize reinforced electrodes and ceramic nozzle coatings to withstand the extreme temperatures and electrical stress associated with prolonged operation.
One of the most significant challenges in cutting head technology is maintaining consistent performance while minimizing consumable usage and energy consumption. To address this, engineers are developing intelligent power management systems that optimize cutting efficiency based on material properties and job specifications. These systems adjust power output, gas flow, and cutting speed dynamically, ensuring that the cutting head operates at peak efficiency while reducing overall energy costs. This not only makes the process more economical but also contributes to sustainable manufacturing practices by minimizing resource waste.
In addition to technological improvements, the design of cutting heads is evolving to accommodate new manufacturing trends, such as additive manufacturing and hybrid machining. Some modern cutting heads are now being integrated with robotic systems, allowing for more complex cutting geometries and enhanced automation. Robotic arms equipped with precision cutting heads can execute intricate cutting patterns with high repeatability, making them invaluable for industries that require detailed customization, such as medical device manufacturing and custom metal fabrication.
Safety remains a key focus in cutting head development, particularly in high-energy cutting processes like laser and plasma cutting. Advanced safety features are being incorporated into modern cutting heads to protect both operators and the equipment. For example, laser cutting heads now include real-time beam monitoring systems that detect irregularities in laser output and shut down the beam if an anomaly is detected. In plasma cutting, cutting heads are designed with automatic shielding gas control to prevent exposure to hazardous fumes and ensure a stable cutting environment. Many cutting heads also feature integrated collision detection systems that automatically retract the head in case of an unexpected obstruction, preventing damage to both the machine and the workpiece.
As industry demands continue to evolve, the role of cutting heads in precision manufacturing will only become more significant. Future advancements will likely focus on greater automation, enhanced material adaptability, and improved energy efficiency. Artificial intelligence is expected to play a major role in optimizing cutting head performance, with machine learning algorithms analyzing cutting data in real time to make automatic adjustments for optimal results. Additionally, developments in ultrafast laser technology and high-definition plasma cutting will further push the boundaries of what cutting heads can achieve in terms of speed, accuracy, and material versatility.
Ultimately, the cutting head is the heart of any circle cutting machine, and its continued evolution is shaping the future of metal fabrication. By incorporating advanced control systems, improved durability, and smarter automation features, modern cutting heads are becoming more efficient, reliable, and capable of handling increasingly complex manufacturing requirements. Whether used in small workshops or large-scale industrial facilities, the advancements in cutting head technology are revolutionizing the way sheet metal is processed, making production faster, more precise, and more cost-effective than ever before.
Base/Frame
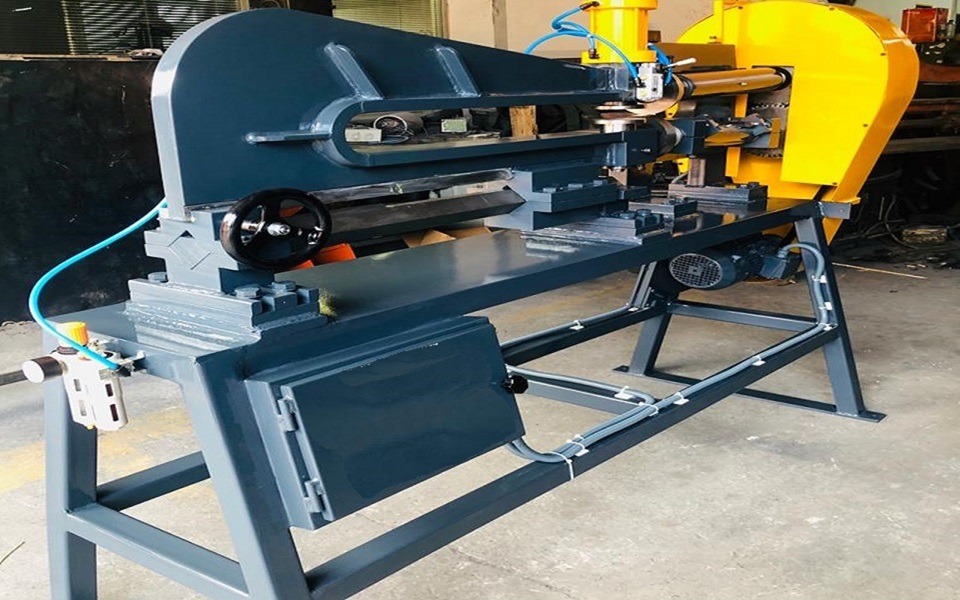
The base or frame of a circle cutting machine for sheet metal serves as the structural foundation, providing stability, support, and alignment for all other components. It plays a crucial role in ensuring precise and vibration-free operation, as any instability in the frame can lead to inaccuracies in cutting, excessive wear on mechanical parts, and reduced overall efficiency. The frame is typically constructed from heavy-duty materials such as steel or cast iron, designed to withstand the stress and forces generated during the cutting process. Its rigidity is essential for maintaining the accuracy of the cutting head’s movement, especially in high-precision applications such as CNC-controlled operations. A well-designed frame minimizes deflection and ensures that all moving parts function smoothly without unnecessary strain or misalignment.
The design of the base varies depending on the size and complexity of the machine. In small, manually operated machines, the base may be relatively simple, consisting of a sturdy metal plate with mounting brackets to hold the cutting head and guiding mechanisms. In contrast, large industrial machines often feature reinforced frames with integrated rails, ball screws, or linear guides that facilitate smooth and precise movement of the cutting components. Some high-end frames include damping systems that absorb vibrations caused by high-speed cutting, preventing distortions and improving the longevity of machine components. The weight and structural integrity of the base also impact the machine’s ability to handle different material thicknesses, as a robust frame can support heavier sheets without flexing or compromising accuracy.
Another key aspect of the base or frame is its role in material handling. Many modern circle cutting machines integrate worktables or slatted surfaces into the frame to support the sheet metal during cutting. These surfaces are often designed with replaceable slats that minimize heat buildup and prevent excessive warping of the material. In plasma and laser cutting machines, specialized bases with water tables or downdraft systems are incorporated to manage fumes, sparks, and slag produced during the cutting process. Water tables help dissipate heat and reduce airborne particulates, while downdraft systems use suction to remove smoke and debris, creating a safer and cleaner working environment.
The frame also provides the necessary support for additional automation features, such as motorized material feeding systems, rotary attachments for tube or pipe cutting, and robotic integration for fully automated production lines. In advanced CNC-controlled machines, the frame houses precision linear motion components that guide the cutting head with extreme accuracy. These motion systems may include servo motors, stepper motors, or rack-and-pinion drives, all of which require a stable and well-aligned base to function correctly. Misalignment or warping of the frame can lead to inconsistencies in cutting path execution, negatively affecting the final product quality.
Durability is a major consideration in frame design, as the machine must withstand years of continuous operation under demanding conditions. Many manufacturers employ stress-relief techniques such as annealing or vibration stress relief to ensure that the frame remains stable and does not deform over time. Protective coatings, such as powder coating or corrosion-resistant treatments, are applied to prevent rust and degradation, particularly in environments with high humidity or exposure to cutting fluids. Regular maintenance of the frame, including checking for loose bolts, structural integrity, and proper leveling, is essential to maintain the machine’s performance and prevent mechanical failures.
Portability and space efficiency are additional factors influencing base design, especially in smaller workshops where space is limited. Some compact circle cutting machines feature modular or foldable frames that allow for easier transport and storage. In contrast, large-scale industrial machines often require fixed, reinforced foundations to handle heavy loads and high-speed cutting forces. For mobile applications, such as on-site fabrication or construction work, lightweight yet sturdy frames are designed to balance portability with stability, ensuring that the machine can be transported and set up without compromising cutting accuracy.
Advancements in machine frame design continue to improve overall machine performance, with manufacturers focusing on enhanced rigidity, better vibration control, and more efficient material handling. The integration of smart sensors and real-time monitoring systems within the frame structure allows operators to detect misalignment, excessive vibration, or wear in critical areas before they lead to performance issues. Some high-end frames now include self-leveling technology, which automatically adjusts to uneven floors or surfaces to maintain perfect alignment for precision cutting.
The base or frame is not just a support structure but an integral component that directly impacts the efficiency, accuracy, and longevity of the entire circle cutting machine. Whether designed for small-scale manual operations or large industrial automation, a well-engineered frame provides the necessary foundation for achieving high-quality cuts with minimal errors. With continuous advancements in material science and machine design, the future of cutting machine frames will likely see further improvements in structural integrity, modularity, and intelligent monitoring capabilities, ensuring that these machines remain at the forefront of precision metal fabrication.
The evolution of base and frame design in circle cutting machines continues to focus on improving stability, precision, and adaptability to different industrial requirements. One of the key advancements in modern base construction is the use of hybrid materials, combining high-strength steel with vibration-dampening composites to enhance rigidity while reducing weight. These materials help minimize the effects of mechanical stress, preventing long-term deformation and ensuring that the machine retains its accuracy even after years of continuous operation. The inclusion of reinforced support structures within the frame, such as crossbeams and gussets, further enhances strength and prevents flexing, particularly in large-format machines designed for heavy-duty sheet metal cutting.
Another significant development in frame design is the integration of modular and customizable structures. Some manufacturers now offer frames that can be expanded or adjusted based on the size of the workpiece or the specific cutting requirements of different industries. Modular frames allow users to add extensions, additional support brackets, or specialized mounting points for attachments such as fume extraction systems, additional cutting heads, or robotic arms. This adaptability makes it easier for businesses to scale their operations without the need to invest in entirely new machines when production demands change.
In CNC-operated circle cutting machines, the accuracy of the frame alignment is crucial for ensuring smooth motion along the cutting path. Modern frames are designed with precision-ground linear rails, hardened guideways, and advanced motion control systems that reduce friction and enable high-speed operation without sacrificing accuracy. High-precision rack-and-pinion or ball screw drive systems are mounted directly onto the frame, ensuring consistent movement with minimal backlash. These systems require perfectly level and stable base structures, making the quality of the frame construction an essential factor in determining the overall performance of the machine.
For plasma and laser cutting machines, heat management is an important consideration in frame design. The intense heat generated during cutting can cause thermal expansion and distortion of the workpiece and even the machine itself. To counter this, manufacturers incorporate temperature-resistant materials and design frames with expansion joints or specialized cooling systems. Water tables, which are integrated into the base of some cutting machines, serve a dual purpose: they help dissipate heat from the cutting process while also reducing smoke, dust, and metal slag. Advanced downdraft tables, designed with powerful ventilation systems, actively extract fumes and airborne particles, maintaining a cleaner and safer working environment.
In the context of industrial automation, the base or frame also serves as a mounting point for auxiliary systems such as conveyor belts, robotic loading arms, and part-sorting mechanisms. Automated material handling solutions rely on a stable and well-aligned frame to ensure smooth transitions between different processing stages. In some high-end machines, the base structure includes embedded sensors that monitor vibrations, surface flatness, and machine alignment in real time. These smart monitoring systems alert operators to potential issues such as misalignment, excessive wear, or instability, allowing for preventive maintenance and reducing the risk of downtime.
Portability remains a key consideration for mobile or field-use cutting machines. Some portable circle cutting machines are designed with lightweight yet durable aluminum frames that allow for easy transport while still maintaining sufficient stability for precision cutting. Foldable legs, adjustable height settings, and compact footprints make these machines suitable for job site applications where space and mobility are critical. Despite their smaller size, these frames are engineered to provide sufficient rigidity to prevent wobbling and ensure consistent cutting performance.
As technology continues to advance, future developments in machine base and frame design are expected to focus on further improving durability, automation, and energy efficiency. The incorporation of smart materials with self-healing or adaptive properties could help enhance longevity by reducing wear and fatigue in high-stress areas. AI-driven frame monitoring systems, capable of predicting structural weaknesses before they lead to performance degradation, could become standard features in next-generation cutting machines. Additionally, advancements in 3D printing and composite manufacturing may enable the production of highly customized and lightweight frame structures that maintain exceptional strength while reducing material costs.
Ultimately, the base or frame of a circle cutting machine is far more than just a supporting structure; it is a fundamental component that affects every aspect of the machine’s performance, from precision and durability to automation and operator safety. Whether used in high-production manufacturing facilities or small workshops, the quality and design of the frame play a crucial role in determining the overall efficiency and reliability of the cutting process. As industries continue to demand higher precision, greater flexibility, and improved sustainability, innovations in frame construction will remain at the forefront of advancements in metal cutting technology.
The future of base and frame design in circle cutting machines is poised to incorporate even more advanced technologies, driven by the growing demands for precision, efficiency, and sustainability. One key trend that will influence frame design is the increased focus on reducing the environmental impact of manufacturing processes. Frames are likely to be designed with lighter, more eco-friendly materials that do not sacrifice strength or durability. For example, the use of recycled metals and sustainable composite materials could become more prevalent, contributing to a greener manufacturing footprint while still maintaining the performance standards required for cutting operations.
Moreover, energy-efficient base designs will become more common. As cutting machines continue to evolve toward greener operations, the base structure will play a significant role in reducing overall energy consumption. Machines may be equipped with integrated power management systems that optimize energy usage, ensuring that all components, including the base and frame, work in harmony to reduce waste. Some advanced frame systems could also include features like regenerative braking or energy recovery mechanisms, allowing excess energy generated during machine motion to be fed back into the system, contributing to overall energy savings.
A growing emphasis on automation and data-driven manufacturing will likely lead to more intelligent base structures. With the increasing integration of IoT (Internet of Things) and AI-powered sensors, the base or frame of a circle cutting machine could be equipped with smart monitoring systems capable of continuously analyzing machine health. These sensors will detect issues such as vibration levels, temperature changes, and wear patterns, providing real-time feedback that can be used to optimize machine performance and prevent breakdowns. These systems will also enable predictive maintenance, where the machine can notify operators of impending issues before they affect performance, thus reducing unplanned downtime. This will increase machine reliability, reduce maintenance costs, and enhance overall productivity.
The integration of autonomous systems into frame design is another area expected to advance. Automated alignment systems embedded into the base can adjust machine components to compensate for any misalignment, ensuring perfect cutting accuracy even under variable operating conditions. This level of automation could be beneficial in industries where cutting machines are used to process a variety of materials or complex geometries, as the system would be able to make real-time adjustments without operator input.
Another innovation on the horizon is the use of 3D printing or additive manufacturing to create custom frame components. As additive manufacturing technology continues to mature, it will allow for the production of complex, lightweight, and strong frame structures that traditional manufacturing methods cannot easily replicate. Custom-designed frames could be tailored to the specific needs of different cutting machines, further enhancing machine performance, reducing material waste, and accelerating production timelines. This process could also help reduce the time and costs associated with producing prototypes or designing bespoke frames for unique applications.
In terms of machine mobility, developments in robotics and advanced mobility systems will lead to more versatile and flexible base designs. For example, mobile circle cutting machines may incorporate robotic bases with autonomous movement capabilities, allowing them to move to different parts of a workshop or factory floor as needed. These autonomous systems could be programmed to transport the cutting machine to different workstations, enhancing workflow efficiency and reducing the need for manual handling of large and heavy equipment. In remote or difficult-to-access environments, such as offshore oil rigs or construction sites, robotic mobility could make it easier to deploy cutting machines where they are needed most.
Additionally, as industries move toward Industry 4.0 and greater connectivity, base structures will increasingly need to be compatible with other automated systems within the factory. This could include robotic arms, automated material handling systems, and centralized data management systems that track and analyze machine performance in real-time. A machine’s base would need to support these systems through integrated mounts, interfaces, and communication channels, allowing the cutting machine to seamlessly interact with other machines and systems in an interconnected production environment.
The importance of ergonomics in frame design will also increase, especially as machine operators’ comfort and safety become more closely tied to productivity and performance. Future base designs may feature adjustable elements, such as height-adjustable frames or tilting components, that can be customized for different operator needs. This adaptability would reduce operator fatigue, improve safety, and enhance overall machine usability, making it easier for workers to handle complex tasks with fewer physical demands.
In terms of structural enhancements, future frames may include integrated vibration-damping technologies that go beyond conventional materials. These damping systems could involve the use of piezoelectric materials or active vibration control systems, which can detect and counteract vibrations in real time, maintaining machine stability even in high-speed or high-torque cutting processes. Such innovations will be especially important in industries where ultra-precise cuts are required, such as in aerospace, automotive, or electronics manufacturing, where even the slightest vibration can lead to defects.
In conclusion, the ongoing development of circle cutting machine frames will continue to enhance the overall performance, flexibility, and sustainability of cutting operations. As industries demand faster, more precise, and environmentally friendly solutions, the base and frame of cutting machines will evolve to meet these needs. With smarter technologies, more sustainable materials, and greater integration with automation systems, the future of base design will ensure that cutting machines can keep pace with the ever-changing demands of modern manufacturing. Whether focusing on energy efficiency, automation, or mobility, these innovations will play a key role in improving the efficiency and precision of metal cutting while reducing costs and environmental impacts.
Rotary Arm/Guide Mechanism
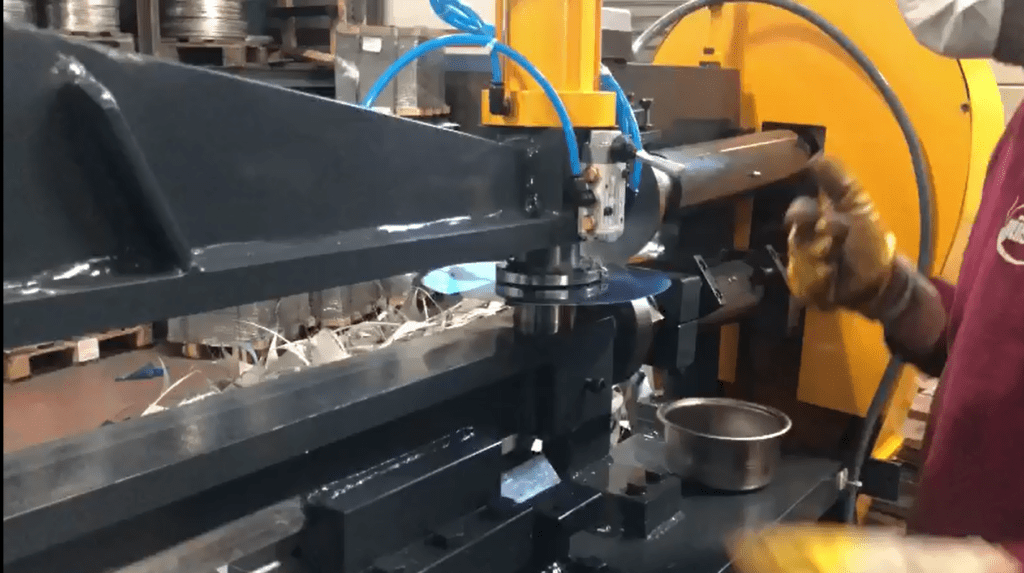
The rotary arm and guide mechanism in circle cutting machines play a crucial role in ensuring the accurate and precise movement of the cutting head. They are responsible for guiding the cutting tool in a circular motion, which is essential for producing consistent cuts on sheet metal. These mechanisms are designed to withstand the forces generated during the cutting process, ensuring that the cutting head remains stable and aligned throughout the operation. The rotary arm typically consists of a rotating shaft or arm attached to a motorized base, which can pivot or rotate around a fixed center point. The guide mechanism, often in the form of tracks, rails, or bearings, ensures smooth and controlled movement, enabling the cutting head to follow the desired path with high precision.
The guide mechanism is a key factor in determining the overall accuracy and quality of the cuts. It ensures that the cutting tool maintains a constant distance from the workpiece, preventing deviations that could result in uneven or imperfect cuts. In some advanced machines, the guide mechanism is integrated with CNC (computer numerical control) technology, allowing for highly precise adjustments based on programmed instructions. This integration enables the machine to automatically compensate for variations in material thickness, surface irregularities, or tool wear, ensuring consistent performance over time.
The materials used in the construction of the rotary arm and guide mechanism are critical to their durability and performance. High-strength alloys, such as steel or aluminum, are commonly used to ensure that these components can withstand the stresses of continuous operation without bending or wearing down. In high-speed machines, bearings and linear guides are often employed to reduce friction and ensure smooth motion. These elements are precision-engineered to minimize backlash and play, which could otherwise lead to inaccuracies in the cutting process.
Over time, advances in technology have led to the development of more efficient and reliable rotary arms and guide mechanisms. For example, the introduction of servo motors and stepper motors has improved the control and responsiveness of these systems, allowing for more precise and faster movements. These motors can be integrated with encoders and feedback systems, which provide real-time data to the machine’s control system. This enables the rotary arm to make minute adjustments during operation, improving cutting accuracy and minimizing the risk of errors.
Another important development in the rotary arm and guide mechanism is the implementation of automation. In modern machines, robotic arms are sometimes used to perform the rotary motion, especially in systems that require high levels of flexibility or complex movement patterns. These robotic arms are often equipped with advanced sensors and cameras, allowing them to detect the position of the cutting tool and automatically adjust the cutting path. This automation improves the overall efficiency of the system and reduces the need for manual intervention, making it possible to produce high-quality cuts with minimal downtime.
In some designs, the rotary arm is coupled with an adjustable counterweight system, which helps to balance the arm during its movement. This system is particularly useful in reducing the strain on the motor and bearings, which can extend the lifespan of these components and improve overall machine performance. Counterweights can be adjusted to accommodate different material sizes and weights, ensuring smooth operation even when cutting thicker or denser materials.
In certain cutting applications, the rotary arm and guide mechanism may also be equipped with a tilting feature. This allows the cutting head to adjust the angle at which it approaches the material, making it possible to cut at varying angles and create beveled edges. This added versatility is beneficial in industries such as automotive manufacturing, where parts often require angled cuts for welding or fitting purposes. The tilting mechanism is typically controlled by the CNC system, ensuring precise and repeatable adjustments.
As cutting technology continues to advance, new materials and coatings are being introduced to improve the performance of rotary arms and guide mechanisms. For instance, anti-wear coatings are applied to reduce friction and increase the lifespan of moving components. Additionally, newer bearing technologies, such as magnetic or air bearings, are being explored for their ability to provide smooth and frictionless motion, further enhancing the precision of the cutting process.
The rotary arm and guide mechanism are not only important for the accuracy of the cuts but also for the overall speed and efficiency of the machine. By ensuring that the cutting tool moves smoothly and steadily, these components help to reduce the time required for each cutting operation. In high-volume manufacturing settings, this can significantly increase productivity and reduce operational costs. Furthermore, because the guide mechanism ensures consistent cutting paths, the need for rework or corrections is minimized, resulting in better material utilization and fewer waste products.
In addition to their mechanical function, the rotary arm and guide mechanism contribute to the overall safety of the machine. In many modern systems, these components are equipped with safety sensors that can detect obstructions or irregularities in the cutting path. If an issue is detected, the system can automatically stop the cutting operation to prevent damage to the workpiece or the machine itself. These safety features help protect both operators and equipment, ensuring a safer working environment.
The development of rotary arm and guide mechanisms will continue to evolve as industries demand even greater precision, speed, and automation. Future innovations may include fully integrated systems that can seamlessly communicate with other machines in a production line, allowing for synchronized operations and higher levels of automation. Additionally, as materials and cutting technologies improve, the rotary arm and guide mechanisms will be designed to handle increasingly diverse materials, thicknesses, and cutting methods, from traditional laser and plasma cutting to newer techniques such as water jet cutting or advanced hybrid systems.
Overall, the rotary arm and guide mechanism are vital components of circle cutting machines, ensuring that the cutting process is precise, efficient, and reliable. Their role in maintaining the alignment and movement of the cutting head directly affects the quality of the final product, making them essential for industries where accuracy and consistency are paramount. With continued advancements in technology, these mechanisms will only become more refined, offering enhanced performance and capabilities for an even broader range of cutting applications.
As industries continue to demand more advanced, precise, and efficient cutting solutions, the role of the rotary arm and guide mechanism in circle cutting machines will evolve to meet these needs. One key area of advancement is the incorporation of artificial intelligence (AI) and machine learning algorithms into the operation of the rotary arm and guide system. These technologies can be used to predict potential issues, optimize cutting paths, and adjust in real-time based on the feedback received from sensors and monitoring systems. For example, AI-driven systems can analyze cutting conditions and make real-time adjustments to optimize speed, accuracy, and efficiency, ensuring that the cutting head maintains its ideal position relative to the material. This level of intelligent control can drastically improve performance and reduce errors, especially in complex cutting operations.
In addition, the integration of advanced sensors and cameras into the rotary arm and guide mechanism will enable even finer levels of control. These sensors can monitor the position of the cutting head with incredible accuracy, providing instant feedback to the CNC system and allowing for rapid adjustments. This feedback loop helps maintain optimal cutting conditions, even when faced with variations in material characteristics or changes in the environment, such as temperature fluctuations that may affect the material or machine.
The continued miniaturization and refinement of components will also drive improvements in the design of the rotary arm and guide mechanism. Smaller, more efficient motors, coupled with advanced motion control technologies, will allow for smoother and faster movement without sacrificing precision. Additionally, the use of lightweight materials, such as carbon fiber or advanced composites, will reduce the overall weight of the rotary arm, making it easier to handle and reducing the strain on supporting structures. Lighter arms will also allow for more agile motion, which can be especially beneficial for machines that require rapid cutting speeds or need to perform intricate cuts with high precision.
Maintenance and durability will also see significant improvements in future rotary arm and guide mechanisms. As manufacturers seek to reduce downtime and increase operational efficiency, the development of self-lubricating components and longer-lasting bearings will be a focus. These innovations will not only reduce the frequency of required maintenance but also improve the overall lifespan of the machine. Additionally, predictive maintenance systems, which can alert operators to potential wear or mechanical failure before it occurs, will become more prevalent. This technology will allow for proactive repairs and adjustments, preventing costly breakdowns and keeping machines running at peak performance for longer periods.
Moreover, the integration of wireless communication systems and cloud computing will enhance the connectivity and data-sharing capabilities of the rotary arm and guide mechanism. Remote monitoring and control systems will allow operators and managers to track machine performance from any location, enabling faster decision-making and troubleshooting. Real-time data from the cutting process can be analyzed remotely, and any necessary adjustments can be made without the need for physical presence on-site, enhancing flexibility and responsiveness.
As circular cutting machines are used in an increasingly diverse range of industries—from aerospace and automotive to shipbuilding and metal fabrication—the versatility of the rotary arm and guide mechanism will become more critical. Machines will need to be adaptable to different materials, thicknesses, and cutting methods, and the rotary arm and guide system will be integral in achieving this flexibility. The future may see the development of multi-functional systems that can be easily reconfigured for different cutting processes, whether it’s traditional flame cutting, advanced laser cutting, or water jet cutting.
Additionally, safety features will continue to evolve to keep pace with technological advancements. The incorporation of automated safety systems into the rotary arm and guide mechanism will allow for real-time hazard detection, such as obstruction or malfunction of the cutting path. In such cases, the system can stop the cutting operation or trigger an emergency stop to prevent damage to the machine or injury to the operator. These safety features will be further enhanced by real-time data monitoring, ensuring that the machine operates within safe parameters at all times.
The development of hybrid systems, which combine multiple cutting technologies in a single machine, will place additional demands on the rotary arm and guide mechanism. These systems, for example, could use a combination of laser cutting for precision and plasma cutting for speed, requiring the rotary arm to seamlessly transition between different cutting tools. Such flexibility will be achieved through advanced control systems that can dynamically switch between cutting modes, ensuring that the cutting head remains stable and aligned in all settings.
The future of rotary arm and guide mechanisms in circle cutting machines will be marked by continuous innovation, with a focus on automation, precision, and durability. Whether through the adoption of AI, the use of advanced materials, or improvements in machine connectivity, these mechanisms will play a central role in shaping the next generation of cutting technologies. The drive for higher efficiency, greater versatility, and enhanced safety will ensure that these systems remain at the forefront of manufacturing, enabling industries to meet the demands of increasingly complex and diverse production processes.
The advancements in rotary arm and guide mechanisms will also bring about significant changes in machine adaptability and integration with other manufacturing systems. As industries increasingly embrace automation and smart manufacturing principles, the integration of these mechanisms with the broader ecosystem of factory machines will become essential. The rotary arm and guide systems will need to be compatible with automated material handling systems, such as robotic arms, conveyors, and automated inspection units. Seamless communication between these systems will enable more efficient workflows, reducing the need for human intervention and streamlining production lines.
The integration with automated material handling systems will allow the rotary arm to respond to real-time instructions from the factory’s central control system. This means that the machine could not only cut materials with greater precision but could also adapt to changes in the material flow, automatically adjusting its movements based on the arrival of new sheets or changes in the production schedule. For instance, the rotary arm could adjust its path or speed to accommodate different sheet sizes or thicknesses, improving efficiency and reducing the likelihood of errors. These capabilities would enhance production flexibility, especially in environments where quick setup changes and high-volume production are required.
Moreover, the future of rotary arm and guide mechanisms is expected to align with the principles of Industry 4.0, where real-time data exchange and machine-to-machine (M2M) communication are paramount. As more sensors and IoT devices are embedded into the rotary arm, the system will be able to gather and transmit performance data, such as cutting speed, power consumption, and vibration levels. This data can be analyzed by centralized software systems to optimize the cutting process, predict maintenance needs, and provide actionable insights that help operators make informed decisions. This data-driven approach will enhance not only performance but also predictive capabilities, allowing for preemptive actions that can prevent machine downtime and extend the lifespan of critical components.
The increasing sophistication of rotary arm and guide mechanisms will also lead to greater precision in cutting operations. For example, in industries where high-tolerance cuts are required—such as aerospace, medical device manufacturing, and electronics—enhanced rotary mechanisms will be designed to maintain alignment with incredible accuracy. This could involve the use of ultra-precise linear guides, air-bearing systems, or laser-guided alignment systems to ensure that the cutting head stays on track, even during high-speed operations. With these advancements, manufacturers will be able to produce parts with tighter tolerances and higher quality, which is crucial for industries where even small deviations can lead to significant defects.
Additionally, the development of hybrid and multi-tool cutting systems will place new demands on the rotary arm and guide mechanisms. These systems, which combine multiple cutting technologies such as plasma, laser, and oxy-fuel in one machine, will require advanced guidance systems capable of supporting the smooth switching between different cutting heads. The rotary arm and guide mechanism will need to be robust and versatile enough to handle the varying speeds, power levels, and motion requirements of each cutting tool. This adaptability will allow manufacturers to use the same machine for different applications, saving time and cost associated with changing machines or tools for each task.
An emerging trend that will influence rotary arm and guide mechanism design is the use of “smart” materials. These materials possess properties that allow them to respond to external stimuli, such as temperature or pressure changes. For instance, piezoelectric materials could be incorporated into the guide system to enhance precision by actively correcting misalignments in real-time. Smart coatings could also be applied to the rotary arm and guide rails to prevent wear and reduce friction, improving the overall performance and longevity of the system. These innovations would help to create even more reliable and efficient cutting machines capable of maintaining high performance for extended periods.
The influence of sustainability will also extend to the design of rotary arm and guide mechanisms. Manufacturers will increasingly focus on creating energy-efficient systems that not only reduce power consumption but also minimize material waste. By using advanced sensors to monitor the cutting process and adjust parameters in real time, the system can optimize cutting conditions to reduce scrap and maximize material utilization. This level of control, coupled with the ability to adjust speed and power based on the material type and thickness, will help achieve a more sustainable manufacturing process.
Moreover, in industries where cutting machines are used in harsh or remote environments, such as oil rigs or mining sites, the rotary arm and guide mechanism will need to be designed to withstand extreme conditions. This includes exposure to high temperatures, dust, moisture, and vibrations. Manufacturers will use corrosion-resistant materials, protective coatings, and advanced sealing techniques to ensure that the rotary arm and guide mechanism continue to function reliably even in these challenging environments. The addition of robust safety features, such as automatic shutoff systems in case of malfunction, will be critical for preventing accidents and ensuring safe operation in such high-risk settings.
The need for enhanced ergonomics and user-friendly operation will also shape the future of rotary arm and guide mechanisms. As operators play an increasingly important role in monitoring and adjusting machine performance, ease of use will be a key factor in the design of these systems. User interfaces that allow operators to easily adjust settings, monitor machine performance, and receive real-time feedback will be essential. This could include touch-screen controls, intuitive software, and augmented reality (AR) displays that provide a live visual representation of the cutting process. Such interfaces will make it easier for operators to interact with the machine, reduce errors, and improve overall operational efficiency.
Finally, as manufacturing processes become more global and interconnected, rotary arm and guide mechanisms will need to be designed with versatility in mind. Machines will be expected to work across a wide range of materials, cutting methods, and production scales. This means that the rotary arm and guide systems will need to be modular, easily adaptable to different types of materials and production processes. Manufacturers may offer customizable options, allowing operators to tailor the system to specific needs without requiring entirely new machinery for each different application.
In conclusion, the future of rotary arm and guide mechanisms in circle cutting machines is deeply connected to the trends of automation, smart manufacturing, precision cutting, and sustainability. As technology continues to advance, these mechanisms will become more intelligent, adaptable, and reliable, offering enhanced performance, efficiency, and flexibility. By integrating new technologies such as AI, advanced sensors, and smart materials, rotary arms and guide systems will play a pivotal role in transforming the cutting industry and meeting the ever-increasing demands for precision, versatility, and sustainability in manufacturing.
Control System
The control system in a circle cutting machine is the heart of its operation, serving as the brain that directs all of the machine’s movements, processes, and functions. It is responsible for interpreting input data, coordinating various components, and ensuring that the machine operates efficiently, accurately, and safely. Modern control systems in these machines are sophisticated and highly integrated, utilizing advanced technology to deliver precision cutting while enhancing productivity and reducing human error. These systems typically comprise a combination of hardware and software, with the software providing the intelligence and the hardware executing the commands.
At the core of the control system is the computer or programmable logic controller (PLC) that manages all operations, from controlling the motorized movement of the rotary arm and guide mechanism to adjusting the cutting speed and path. The PLC processes the inputs it receives from the operator and sensors, and based on pre-programmed instructions, it generates commands to control the movement of the machine components. The software integrated into the control system is typically customizable, allowing operators to input cutting specifications, adjust settings, and monitor performance in real-time. It also plays a crucial role in optimizing machine performance, reducing waste, and increasing the overall efficiency of the cutting process.
The control system’s interface is a key aspect of machine usability. In many modern systems, a user-friendly graphical interface allows operators to input commands, configure settings, and monitor the machine’s progress through touch-screen panels, buttons, or even voice commands. These interfaces have become more intuitive and feature-rich, enabling operators to easily adjust cutting parameters such as speed, pressure, and depth. In some cases, the system can also suggest optimal settings based on the material type, thickness, and desired cutting quality, streamlining the decision-making process and reducing setup time. This kind of intelligent system allows for greater flexibility and precision in the manufacturing process, accommodating a wide range of materials and cutting requirements.
One of the critical functions of the control system is to ensure the precise synchronization of all the moving parts within the cutting machine. This includes controlling the motors, actuators, and feedback loops to ensure smooth and accurate movement. For example, it must manage the speed and rotation of the rotary arm and guide mechanism, ensuring that the cutting head follows the exact circular path with minimal deviation. The control system also adjusts the pressure and feed rate to maintain consistent cutting performance, even when working with varying material thicknesses or densities. To achieve this, it relies on a network of sensors that constantly monitor the position, speed, and status of various components, feeding this information back into the system to make real-time adjustments.
In addition to basic motion control, the control system is also responsible for integrating with other systems, such as those used for material handling or quality inspection. For instance, the system might communicate with a conveyor belt or robotic arm to automatically feed materials into the machine. The control system can adjust the cutting process based on feedback from sensors that measure material properties or detect defects. If a material is deemed unsuitable for cutting, the system can stop the operation or prompt the operator to replace it. This level of integration helps reduce downtime, optimize workflow, and ensure that the cutting process is always operating under optimal conditions.
Another important function of the control system is safety. Cutting machines often operate under high-speed and high-temperature conditions, and a malfunction or failure could result in significant damage or safety hazards. The control system is designed to monitor critical machine parameters in real-time and to automatically shut down or trigger safety mechanisms when something goes wrong. For instance, if the machine detects an abnormal temperature rise in the cutting head or excessive vibration in the rotary arm, it can stop the process to prevent damage. These safety features are designed to protect both the machine and the operator, ensuring that the cutting process is both effective and safe.
As circle cutting machines evolve, so too does the sophistication of their control systems. The trend toward automation and smarter manufacturing processes has led to the development of control systems that incorporate advanced algorithms and machine learning techniques. These systems can predict and respond to potential issues before they occur, making adjustments to the cutting parameters or machine movements without requiring operator intervention. For example, the system might detect patterns in the way materials are fed into the machine and adjust the cutting speed or pressure accordingly, compensating for slight variations in material properties or environmental conditions. This predictive capability helps ensure that the cutting process remains consistent and high-quality, even as operating conditions change.
Moreover, the integration of Internet of Things (IoT) technology into the control system allows for remote monitoring and control of the cutting machine. Through a network of sensors and cloud-based platforms, operators and maintenance teams can access real-time data about the machine’s performance from anywhere in the world. This remote capability enhances the ability to troubleshoot issues, track machine health, and optimize performance, even if the machine is located in a different facility or on a remote job site. It also facilitates predictive maintenance, as the system can analyze performance data over time and identify trends that suggest potential failure points. By identifying and addressing issues before they cause a breakdown, this capability can significantly reduce downtime and extend the lifespan of the machine.
The increasing complexity and capabilities of control systems also mean that more advanced training and expertise are required to operate and maintain these machines. While earlier systems were often controlled by simple switches or manual settings, modern systems require skilled operators who are familiar with both the machine’s software and hardware. Many cutting machines now feature advanced diagnostic and troubleshooting tools that guide operators through the process of identifying and fixing issues. In addition, operators may need to understand how to interpret the data generated by the system, such as performance metrics, error codes, and sensor outputs, to make informed decisions about machine adjustments.
In the future, control systems will continue to evolve as part of the broader trend toward smart factories and Industry 4.0. The development of artificial intelligence, machine learning, and deep learning technologies will enable control systems to become even more autonomous, making more complex decisions on their own based on real-time data and historical performance data. These systems may even be able to collaborate with other machines in the factory, sharing data and optimizing production processes in real-time to maximize efficiency and minimize waste.
The control system’s role in sustainability will also grow in importance. By optimizing the cutting process, control systems can help minimize energy consumption and reduce material waste. For example, they can adjust the cutting speed and path to reduce the amount of scrap material generated during the process. Additionally, through data analysis and feedback from sensors, the system can detect inefficiencies or suboptimal conditions, enabling operators to make adjustments that reduce the environmental impact of the manufacturing process.
In conclusion, the control system in a circle cutting machine is a vital component that directly influences the machine’s performance, safety, and efficiency. As cutting technology advances, the sophistication of control systems will continue to increase, with a focus on automation, real-time data processing, predictive maintenance, and enhanced safety features. By integrating advanced technologies such as AI, IoT, and machine learning, control systems will be able to handle more complex tasks, make smarter decisions, and optimize machine performance, enabling manufacturers to meet the demands of modern production environments while ensuring sustainability and reducing costs.
As the control system continues to evolve, its role will expand to encompass more sophisticated functions that enhance overall manufacturing processes. One of the key developments will be in the integration of augmented reality (AR) and virtual reality (VR) interfaces. By combining the power of AR/VR with the control system, operators will be able to visualize the cutting process in real-time, as well as simulate various cutting scenarios before the actual operation begins. This would allow them to foresee potential issues, adjust settings, and make more informed decisions, all without physically interacting with the machine.
The integration of these technologies could also make operator training more effective. Instead of relying solely on traditional hands-on training, operators could use VR simulations to familiarize themselves with the system’s operations and troubleshooting methods. They would be able to practice handling emergencies, adjusting parameters, or even maintaining the machine in a safe and controlled environment, minimizing risk and improving skill development. This could be especially beneficial in environments where the machines are complex, and quick, accurate decision-making is crucial.
In addition to AR and VR, the role of big data and analytics in the control system will also continue to grow. As manufacturing becomes increasingly data-driven, the control system will be able to collect vast amounts of data from sensors, production logs, and machine usage patterns. By analyzing this data, manufacturers will gain insights into the overall efficiency of their machines, detecting areas for improvement and further optimization. For example, the system could track the frequency of specific adjustments, performance trends, or even operator behavior. This information could help identify best practices or predict when parts might need replacement, further extending the life of the machinery.
Advanced analytics could also help in achieving greater customization of the cutting process. By tracking the specific requirements of different projects, such as material types, sheet sizes, and cutting complexities, the control system can recommend or automatically apply the optimal settings for each new job. Over time, as the system learns from past performance, it can suggest improvements to cutting strategies, helping manufacturers achieve higher levels of precision while reducing operational costs.
Another area where control systems are likely to advance is in energy management. In industrial settings, energy consumption is a significant cost, and many manufacturers are looking for ways to reduce their energy footprint. The control system can play a crucial role in this effort by optimizing the energy usage of various machine components. By continuously monitoring power consumption, the system can identify patterns that indicate energy waste or inefficiencies and adjust parameters to minimize energy usage without sacrificing performance. For example, the system could lower motor speeds during idle periods, adjust the cooling system to operate only when necessary, or switch off non-critical components during low-demand operations.
The integration of renewable energy sources into the manufacturing process is another possibility. The control system could be designed to prioritize the use of on-site solar or wind power when available, helping companies reduce their reliance on grid energy and lower their environmental impact. Additionally, the system could integrate energy storage solutions, such as batteries, to store excess energy generated during off-peak hours for use during peak demand times, further reducing costs and enhancing sustainability.
Security will continue to be a critical aspect of the control system. As machines become more connected to networks and the Internet of Things (IoT), the risk of cyber-attacks grows. Hackers could potentially gain control of the cutting machine, disrupt production, or cause physical damage. To combat these threats, the control system will need to integrate advanced cybersecurity measures. These could include encrypted communication protocols, multi-factor authentication for remote access, and real-time monitoring of network activity to detect unusual behavior. Additionally, automated backup systems could be implemented to restore machine settings in case of a cyber-attack or system failure.
As the industry continues to adopt artificial intelligence (AI) and machine learning, the control system will increasingly leverage these technologies for decision-making. The ability of AI to analyze large datasets and make decisions in real time will allow the system to make optimizations on the fly, adjusting parameters for maximum efficiency and output. The system could also use machine learning algorithms to continuously improve its performance. By analyzing historical data on cutting jobs, materials, and machine behavior, the system could learn patterns that lead to the best outcomes, and it could apply this knowledge to future jobs, continuously refining its cutting strategy.
For instance, if a certain material consistently produces higher-quality cuts when processed at a slower speed, the AI-powered control system will recognize this trend and recommend—or even automatically implement—slower speeds for similar materials in the future. This level of adaptability ensures that the machine continues to perform at its best, even as variables such as material types, thickness, and external conditions change over time.
In the long term, the control system could even integrate with larger enterprise resource planning (ERP) systems, further enhancing coordination between the cutting machine and other manufacturing processes. By sharing data between departments, such as inventory management, order scheduling, and maintenance, the control system can ensure that the machine operates as part of a larger, more synchronized production workflow. For example, if the system detects a delay in material delivery or a potential scheduling conflict, it could automatically adjust the cutting timeline or pause the operation until the material is ready, optimizing production without human intervention.
The development of more advanced, adaptive, and intelligent control systems will not only improve the performance of circle cutting machines but also redefine how manufacturers approach production. Through automation, real-time data analysis, and increased integration with other systems, these machines will become more flexible, efficient, and capable of handling complex tasks with minimal oversight. As the control systems evolve to support the next generation of manufacturing, they will help companies improve operational efficiency, reduce costs, enhance precision, and contribute to the ongoing trend of smarter, more sustainable production processes.
Looking ahead, the role of control systems in circle cutting machines will continue to expand as new technologies and manufacturing philosophies emerge. One significant advancement on the horizon is the increased use of digital twins. A digital twin is a virtual replica of a physical system, in this case, the cutting machine, which can simulate its behavior and performance in real-time. By integrating a digital twin into the control system, manufacturers will be able to monitor the machine’s performance in a virtual environment, making adjustments and predicting outcomes before implementing changes on the actual machine. This approach not only improves predictive maintenance and troubleshooting but also allows for virtual testing of new cutting strategies or machine configurations, enabling faster innovation cycles and reducing the risks associated with physical changes.
Moreover, digital twins can provide a detailed, real-time view of the entire production process. By linking the virtual model of the cutting machine to the broader factory environment, the control system can synchronize with other machines, sensors, and production lines. This holistic view will allow for real-time optimization across multiple systems, reducing inefficiencies, eliminating bottlenecks, and enhancing throughput. For instance, if the control system detects that a machine downstream of the cutting station is experiencing delays, it could automatically adjust the cutting schedule to minimize idle time and keep the entire production line running smoothly.
In parallel with digital twins, advancements in 5G technology will further transform how control systems operate. The high-speed, low-latency capabilities of 5G will allow machines to communicate with each other and the broader factory network more effectively, enabling even faster data exchanges between systems. This will be particularly beneficial in real-time decision-making, where milliseconds matter. Control systems will be able to send and receive data from sensors, robots, and other machines instantly, allowing for immediate adjustments to the cutting process. This increased connectivity will also facilitate the adoption of cloud-based platforms, where data can be processed, analyzed, and shared across multiple locations. Manufacturers could remotely monitor and control their cutting machines from anywhere, allowing for centralized management of operations, more responsive customer support, and streamlined maintenance processes.
The potential for control systems to integrate with artificial intelligence (AI) and advanced data analytics will also enable more advanced, autonomous decision-making capabilities. AI-powered systems can analyze vast amounts of production data, learning from each cut and optimizing parameters for each new job. For instance, the system could not only adjust for material variations but also adapt cutting strategies based on operator feedback and performance data over time. By continuously refining its approach, the system will be able to reduce cutting time, minimize waste, and ensure the highest quality cuts for every sheet of material.
AI will also support the development of autonomous inspection systems, which can identify defects or quality issues in real-time. These inspection systems can be integrated directly into the control system, allowing the machine to immediately adjust its cutting process in response to detected imperfections. For example, if a defect is identified in the material, the machine could adjust its cutting parameters to ensure that only the usable portion of the material is processed, reducing scrap and improving yield. In more advanced scenarios, AI could predict potential defects in materials even before they are introduced into the cutting machine, allowing for better sorting and preparation of materials ahead of time.
The growing focus on sustainability will drive the development of more energy-efficient control systems. As energy costs continue to rise and environmental regulations become stricter, manufacturers will be under increasing pressure to reduce their energy consumption and minimize their environmental impact. Control systems will play a critical role in this effort by continuously optimizing power usage. For example, advanced algorithms could enable the system to automatically adjust the cutting speed and power consumption based on material properties, thickness, and cutting requirements. This optimization will help minimize energy usage during each phase of the cutting process, while still maintaining the required precision and quality.
Another important area for development is the integration of circular economy principles into the control system’s operation. A circular economy emphasizes the reuse, recycling, and repurposing of materials, which has significant implications for cutting processes. The control system could be designed to track material usage and waste more effectively, allowing manufacturers to identify opportunities to recycle or repurpose scrap materials. For example, the system could automatically sort and process offcuts or remnants, transforming them into usable products for other applications. This not only reduces waste but also contributes to a more sustainable manufacturing process.
As we move toward fully autonomous factories, control systems will need to support increased collaboration between machines. In a smart factory, machines will be interconnected through a centralized digital ecosystem that allows them to work together seamlessly. Control systems will play a key role in coordinating these interactions, ensuring that machines are operating at peak efficiency while sharing information in real time. This interconnectedness will allow for continuous optimization, with each machine adjusting its operations based on data from others, creating a dynamic, self-optimizing production environment.
In such an environment, predictive maintenance will be a key feature of the control system. By continuously collecting data from sensors embedded in the machine, the control system will be able to detect signs of wear and tear, such as excessive vibration or temperature changes. This data will be analyzed in real-time to predict when components are likely to fail, allowing for maintenance to be scheduled before a failure occurs. By preventing unplanned downtime, predictive maintenance will reduce maintenance costs, increase machine availability, and extend the overall lifespan of the equipment.
The ultimate goal for control systems in circle cutting machines is to achieve a high level of automation, precision, and adaptability while also enhancing overall manufacturing efficiency. These systems will not only be able to optimize the cutting process itself but also coordinate seamlessly with other machines, sensors, and enterprise systems to drive continuous improvements across the entire production process. With AI, IoT, and other advanced technologies working in concert, control systems will be able to make smarter, more autonomous decisions, improve machine performance, and contribute to more sustainable and cost-effective manufacturing operations.
As these systems evolve, the role of the operator will change as well. Rather than focusing on day-to-day adjustments and troubleshooting, operators will shift toward overseeing the broader system, making strategic decisions, and ensuring that all components are functioning together smoothly. This shift will require a new set of skills and expertise, as operators will need to understand both the technology behind the control systems and the broader context in which they operate. Training and education will be critical to ensuring that the workforce is prepared for these new roles and can maximize the benefits of increasingly intelligent and interconnected control systems.
In conclusion, the future of control systems in circle cutting machines is closely tied to advancements in automation, AI, machine learning, and digitalization. These systems will become more intelligent, autonomous, and interconnected, offering manufacturers enhanced efficiency, precision, and sustainability. As the technology continues to evolve, control systems will be at the forefront of transforming the cutting industry, enabling manufacturers to meet the demands of a rapidly changing production environment while improving operational performance and reducing environmental impact.
Cutting Blades
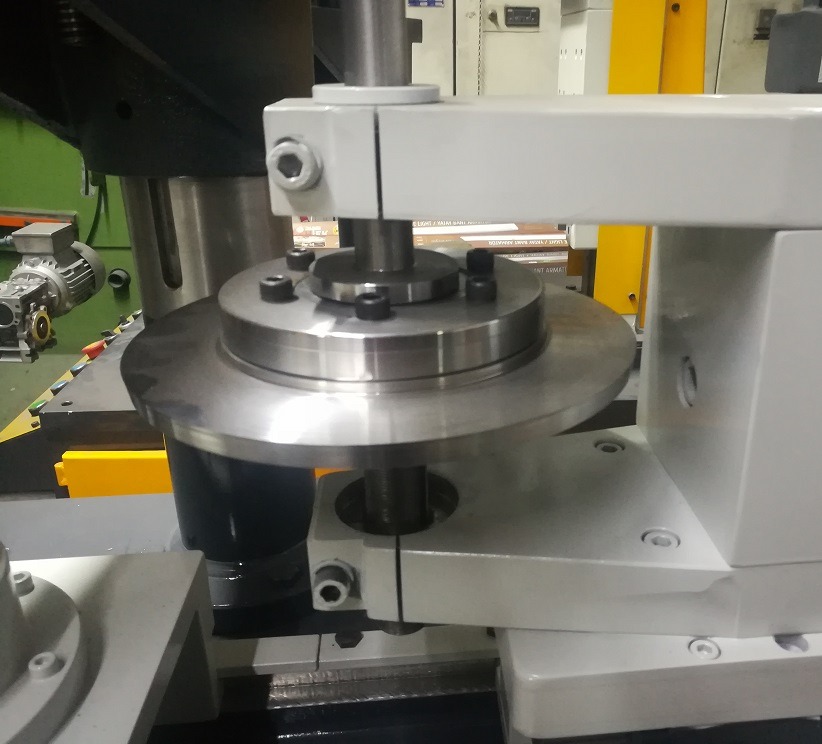
Cutting blades are essential components of any circle cutting machine, serving as the primary tool for achieving the precision cuts that these machines are designed for. They are tasked with cutting through various materials, including metals, plastics, and composites, depending on the specific requirements of the application. The design, material, and sharpness of cutting blades play a crucial role in determining the efficiency, accuracy, and quality of the cutting process. These blades are often subjected to high levels of stress, heat, and wear, making the selection of the right type of blade and proper maintenance essential to achieving optimal cutting performance.
The design of cutting blades varies depending on the specific type of cutting machine and the material being processed. In circle cutting machines, the blades are typically round and feature a sharp edge that can smoothly rotate along a circular path to make precise cuts. They are mounted on a rotating shaft or motorized system that allows them to move around the material, cutting in a smooth, continuous motion. The round shape of the blades makes them ideal for cutting circular shapes, and their sharpness ensures that the material is cut cleanly without excessive burrs or deformation.
The material composition of cutting blades is one of the most important factors influencing their performance and longevity. The blades are often made from high-speed steel (HSS), carbide, or coated with materials like titanium nitride to increase hardness, wear resistance, and cutting performance. High-speed steel blades are commonly used for cutting softer materials such as mild steel, aluminum, or plastic. They offer a good balance of hardness and toughness but are more prone to wear over time, especially when cutting tougher materials. Carbide blades, on the other hand, are used for harder materials like stainless steel, titanium, or high-strength alloys. Carbide is a much harder material, allowing the blades to maintain their sharpness longer and withstand higher cutting temperatures, making them ideal for heavy-duty applications.
The sharpness of the cutting blade is another critical factor that determines its effectiveness. A sharp blade requires less force to make cuts, which reduces the stress on the machine and minimizes the risk of material deformation. It also ensures that the cut is clean and smooth, with fewer imperfections or rough edges. Over time, however, blades will naturally lose their sharpness due to wear and exposure to the cutting material. Dull blades can cause the machine to work harder, leading to increased energy consumption and longer cutting times. They can also result in poor-quality cuts, which may require additional finishing or rework.
To maintain cutting performance, blades must be regularly sharpened or replaced. Some cutting blades are designed with a replaceable tip or edge, allowing for easier maintenance without the need to replace the entire blade. In other cases, the blade may need to be ground or honed to restore its sharpness. Some machines even feature built-in blade sharpening systems, where the blade can be sharpened in place, reducing downtime and improving overall efficiency. Blade sharpening, however, requires precision and care, as improper sharpening techniques can damage the blade, leading to reduced cutting performance or failure.
In addition to the material and sharpness, the blade’s geometry also plays an important role in its cutting efficiency. Blades can have different tooth shapes, angles, and profiles, depending on the cutting requirements. For example, some blades may have a tooth geometry designed for cutting through thicker materials or reducing vibration, while others may be optimized for high-speed cutting or minimizing heat generation. The right blade geometry helps to ensure that the machine operates smoothly and that the material is cut with minimal resistance, reducing the chances of tool breakage or excessive wear.
The coating of cutting blades is another important factor that can significantly impact their performance and durability. Many cutting blades are coated with materials such as titanium nitride (TiN), which provides a hard, wear-resistant layer on the surface of the blade. These coatings increase the blade’s resistance to heat and corrosion, allowing it to last longer and perform better under high-stress conditions. Coatings can also help reduce friction during the cutting process, resulting in less heat buildup and smoother cuts. While coatings can significantly enhance blade performance, they can also add to the cost of the blades, so manufacturers must balance the benefits of coatings with their budgetary considerations.
The cooling of the cutting process is also important for maintaining blade performance and preventing damage. When blades cut through materials, especially metals, they generate a significant amount of heat due to the friction between the blade and the material. Excessive heat can cause the blade to lose its sharpness more quickly, warp, or even crack. To prevent overheating, many cutting systems are equipped with cooling systems that use water, oil, or air to cool the cutting area and reduce the temperature of the blade. Proper cooling not only prolongs the life of the blade but also ensures better cutting performance and quality.
Additionally, the type of material being cut plays a significant role in determining the type of blade needed. For example, when cutting thin sheet metal, a high-speed steel blade may be sufficient to handle the load, but cutting thicker or tougher materials like stainless steel or high-strength alloys may require carbide-tipped or coated blades. The cutting blade must be matched to the material’s hardness, thickness, and density to ensure efficient cutting. Using the wrong type of blade can lead to poor-quality cuts, premature blade wear, or even failure, resulting in downtime and increased operational costs.
One of the emerging trends in the cutting blade industry is the development of more specialized and custom-made blades designed for specific applications. As industries become more diverse and manufacturing requirements grow more complex, the demand for cutting blades that are optimized for specific materials or cutting tasks has increased. Custom-designed blades can incorporate unique features, such as specialized coatings, specific geometries, or materials that are tailored to meet the exact demands of the job. This can result in higher cutting efficiency, longer blade life, and better overall performance.
In industries where high-precision cutting is critical, such as aerospace, automotive, or electronics manufacturing, cutting blades need to meet stringent tolerances and specifications. In these applications, the blades must not only be sharp and durable but also consistently produce high-quality cuts with minimal deviation. These blades are often subjected to rigorous testing to ensure that they can withstand the demands of precision cutting without failure. Specialized blades for these industries may also feature advanced coatings to resist heat, corrosion, and wear, ensuring that they maintain their performance over extended periods of use.
The future of cutting blades in circle cutting machines will likely involve even more advancements in materials science, coatings, and blade geometry. As cutting technologies continue to evolve, the demand for cutting blades that can perform under increasingly challenging conditions will drive innovation in blade design. New materials such as superhard composites, ceramics, and advanced alloys may become more commonly used in blade construction, providing enhanced durability and cutting performance. Additionally, advancements in machine learning and predictive analytics could allow cutting machines to adjust their operations based on the condition of the cutting blade, optimizing performance and minimizing the need for manual intervention.
In conclusion, cutting blades are a fundamental component of circle cutting machines, and their design, material composition, sharpness, and maintenance directly impact the performance and quality of the cutting process. Selecting the appropriate blade for a given application is crucial for achieving efficient and precise cuts while minimizing wear and prolonging the life of the blade. With ongoing advancements in materials, coatings, and blade geometry, the future of cutting blades in circle cutting machines will likely see continued improvements in efficiency, durability, and performance, ultimately contributing to higher-quality manufacturing and reduced operational costs.
As cutting blade technology continues to evolve, there is also an increased focus on sustainability within the industry. One aspect of this is the development of more eco-friendly materials for blades and coatings. Traditional cutting blades often rely on metals and coatings that, while effective, may not be the most sustainable options in the long term. Manufacturers are exploring alternative materials that offer comparable durability and performance but have a lower environmental impact. For example, there is growing interest in the use of recycled metals and composites in blade construction, which can help reduce the demand for new raw materials and lower the overall environmental footprint of the manufacturing process.
In addition to the materials used in the blades themselves, sustainable cutting practices are also becoming more important. As industries seek to reduce waste and improve resource efficiency, manufacturers are looking for ways to optimize the cutting process to minimize scrap and improve material utilization. Cutting blades with higher precision, for example, can help reduce the amount of waste material generated during the cutting process. By achieving cleaner cuts with less burr, deformation, or waste, these blades can contribute to more sustainable production practices.
Another emerging trend is the adoption of digital technologies that can further optimize the cutting process and the performance of cutting blades. Through the use of sensors, data analytics, and machine learning, manufacturers can monitor the condition of cutting blades in real-time and adjust the cutting parameters to extend the life of the blade. These technologies can detect early signs of wear, misalignment, or damage, allowing for proactive maintenance and reducing the need for frequent blade replacements. By keeping blades in optimal condition for longer periods, manufacturers can reduce waste, lower costs, and improve the sustainability of their operations.
Furthermore, advancements in coating technologies may also contribute to more sustainable cutting practices. Coatings like titanium nitride (TiN) or diamond-like carbon (DLC) have been shown to extend the life of cutting blades significantly, reducing the frequency of blade replacements. These coatings help prevent wear, corrosion, and heat buildup, improving both performance and longevity. As coating technologies improve, they may become more cost-effective and environmentally friendly, providing manufacturers with longer-lasting, high-performance cutting blades that reduce waste and lower environmental impact.
The role of automation and robotics in the cutting process also holds potential for further improving the efficiency and sustainability of cutting operations. Automated systems can help optimize the cutting process, reducing waste by ensuring that the material is used as efficiently as possible. Robots can be programmed to adjust cutting parameters based on real-time data, optimizing the angle, speed, and force applied to the cutting blade. These systems can also minimize the risk of human error, which can lead to inefficient cutting practices, increased waste, or damaged blades.
In addition, as manufacturers continue to adopt Industry 4.0 principles and integrate cutting machines into smarter, more connected systems, the entire lifecycle of the cutting blades can be monitored and optimized. Data from multiple sources, such as sensors embedded in the cutting machine, operator input, and material specifications, can be integrated to create a comprehensive view of blade performance. This data-driven approach allows manufacturers to better understand the wear patterns of blades, optimize the timing of maintenance, and forecast when blades are likely to need replacement.
With the increasing push for sustainability, the development of cutting blades will likely focus on both performance and environmental impact. As technologies advance, manufacturers will be able to produce cutting blades that are not only more efficient, durable, and precise but also contribute to a more sustainable, circular economy. This evolution in blade technology will be essential in meeting the growing demands of industries that prioritize environmental responsibility, while still ensuring the highest levels of productivity and quality.
As cutting blades become more specialized and tailored to specific applications, there will also be an emphasis on designing blades that can handle a wider variety of materials and cutting tasks. Advances in blade coatings, materials science, and geometry will enable the production of multi-purpose blades capable of cutting through a range of materials without sacrificing performance or longevity. These all-purpose blades will be increasingly popular in industries where versatility is key, such as the automotive or aerospace sectors, where manufacturers often need to cut a range of materials with varying properties and thicknesses.
The cutting blade market is also likely to see innovations in blade recycling programs. As manufacturers become more environmentally conscious, there is potential for the development of closed-loop systems where used blades can be returned, reprocessed, and reused. By incorporating blade recycling into their operational practices, companies can help reduce the demand for new raw materials and ensure that used blades are disposed of in a sustainable manner. This could also lead to the development of specialized programs where blades are refurbished or reconditioned before being put back into use, extending their life cycle and reducing overall costs.
The demand for longer-lasting and more efficient cutting blades is expected to increase as industries continue to push for higher productivity and better quality. As competition intensifies, manufacturers will focus on maximizing the performance of their cutting machines by investing in cutting-edge blade technology. This will likely involve further research into new materials and advanced coating technologies that enhance the blades’ ability to withstand wear, heat, and corrosion, all while maintaining high cutting precision.
In conclusion, cutting blades will continue to play a central role in the performance of circle cutting machines, and ongoing advancements in materials, coatings, and design will further enhance their effectiveness and longevity. As manufacturers seek to optimize their operations, reduce waste, and improve sustainability, the cutting blade industry will evolve to meet these demands. Through technological innovation and a greater focus on environmental responsibility, cutting blades will not only deliver high-quality performance but also contribute to the broader goals of efficiency and sustainability in modern manufacturing.
Circle cutting machines can easily be used with stainless steel, aluminum, copper, and tin sheets for various industrial applications. The steel circles later are used to deep draw parts with a hydraulic press. For long-duration high-quality parts you can contact us as your supplier from our main page
For a better analysis of our circle blank cutting machine, you can check our video below
Our circle cutting machines are hand-operated. Hand-operated operations are safer as the operator needs to control the machine with his hands and he will need to keep his hands on the control board to operate the machine. Circle cutter machines are essential in production facilities where there is a deep drawing press. Deep drawing presses use round sheets to form vase forms by deep drawings.
With our round corner cutting machines or sheet metal circle cutting machines you can have a capacity as high as 1 piece in 4 seconds. With this capacity, you can feed 2 hydraulic presses with one 1 circle cutting machine easily
Circle cutting machines are versatile tools used in various industries and applications for precisely cutting circular shapes from a wide range of materials. They are commonly employed in industrial settings, craft workshops, and DIY projects.
Industrial Applications
- Manufacturing: Circle cutting machines are used in various manufacturing processes, such as cutting circular gaskets, seals, and components from rubber, plastic, and thin metal sheets. They are also used to cut circular patterns in fabrics and textiles for clothing and industrial applications.
- Packaging: Circle cutting machines are essential in the packaging industry for cutting circular packaging materials, such as cardboard discs, labels, and packaging inserts. They ensure precise dimensions and consistent quality for product packaging.
- Graphic Design and Printing: Circle cutting machines are used in graphic design and printing studios to cut circular shapes from paper, cardboard, and other materials for creating promotional materials, signage, and decorative elements.
Craft and DIY Applications
- Scrapbooking and Paper Crafts: Circle cutting machines are popular among scrapbookers and paper crafters for cutting circular embellishments, decorative shapes, and photo mats. They provide a precise and efficient way to create custom elements for scrapbooking projects.
- Jewelry Making: Circle cutting machines are used in jewelry making to cut circular shapes from leather, felt, and other materials for creating jewelry components, such as pendants, earrings, and bracelets. They ensure consistent shapes and sizes for jewelry designs.
- Home Décor and DIY Projects: Circle cutting machines are versatile tools for DIY projects, such as cutting circular patterns from fabrics for quilting, sewing, and home décor accents. They can also be used to cut circular shapes from materials like felt, foam, and cork for crafting projects.
- Model Making and Architectural Design: Circle cutting machines are used in model making and architectural design to cut circular shapes from various materials, such as cardboard, balsa wood, and foam, for creating models and prototypes. They provide precision and accuracy for detailed work.
General Safety Guidelines
When operating circle cutting machines, safety is paramount. Always follow these general guidelines:
- Wear Personal Protective Equipment (PPE): Always wear safety glasses, gloves, and a cutting mat to protect yourself from sharp blades, flying debris, and potential cuts.
- Securely Clamp the Workpiece: Ensure the workpiece is firmly clamped to the machine’s work surface to prevent it from slipping or moving during cutting.
- Use the Correct Blade or Punch: Choose the appropriate blade or punch size and type for the material and desired circle size. Using the wrong blade or punch can damage the material or cause injury.
- Maintain Proper Blade or Punch Sharpness: Regularly sharpen or replace blades and punches to ensure they are sharp and maintain cutting efficiency. Dull blades can cause ragged edges and increase the risk of injury.
- Handle with Care: Always handle the machine with care, avoiding sudden movements or forceful actions that could lead to accidents.
- Never Touch the Moving Blade or Punch: Never touch the moving blade or punch while the machine is in operation.
- Turn Off the Machine Before Making Adjustments: Always turn off the machine before making any adjustments or changing the blade or punch.
- Store the Machine Properly: Store the machine in a safe, secure location when not in use, keeping it out of reach of children and unauthorized users.
By adhering to these safety guidelines and operating the machine responsibly, you can effectively utilize circle cutting machines for various applications while minimizing the risk of injury.
Sheet Metal Circle Cutter Machine
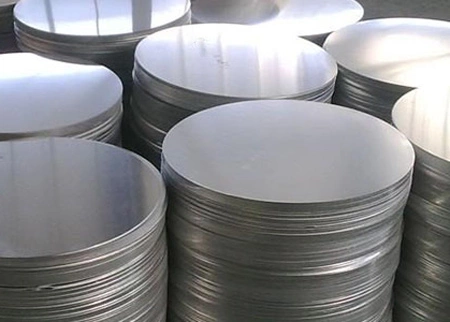
How do you cut a circle in sheet metal?
Our sheet metal circle cutter machine can cut from as small as 2″ of circle blanks on sheet metal surfaces up to 12″ in diameter. The circle diameter to be cut can be arranged on the machine. The cutting tool is made from high-carbon cutting steel specially produced for metal cutting operations. The frame of the machine is complete welded steel and all the machinery goes through stress-relieving after the manufacturing is finished. Circle cutting machines are widely used in the cookware industry.
How do you cut big circles in metal?
with our sheet metal circle cutting machine, you can cut circle blanks from square metal sheets with sheet thickness starting from 0.1 mm up to 5 mm. The diameter also can be arranged from 5 cm up to 30 cm.
The circle cutting machine is a type of machine that can cut circles out of metal sheets. It is also called an automatic circle cutter or a steel circle cutter.
It is used to cut circles out of metal sheets. The machine has a circular blade that rotates around the circumference of the sheet. The operator sets the size and radius of the desired hole and then presses start to begin cutting.
The circle cutting machine is an automatic machine that cuts circles from flat steel sheets.
The circle cutting machine is a type of metalworking equipment that is used to cut circles in sheet metal. This equipment can be used for a variety of purposes, including manufacturing and construction. The round steel sheet, which is the most common material used in the process, can be cut into circles using this machine.
EMS Metalworking Machinery: Your Trusted Partner in Precision Metalworking
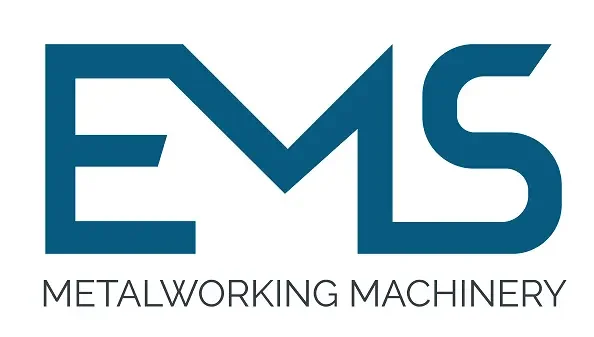
EMS Metalworking Machinery is a leading manufacturer of high-quality metalworking equipment, dedicated to providing innovative solutions that meet the evolving needs of industries worldwide. With a rich history of excellence and a commitment to technological advancement, we have earned a reputation for delivering cutting-edge machinery that ensures precision, efficiency, and durability.
Our Product Range:
- CNC Spinning Lathes: From precision bench lathes to heavy-duty industrial models, our lathes offer unmatched accuracy and performance for a wide range of applications, including machining shafts, gears, and other cylindrical components.
- Trimming Beading Machine: Our trimming beading machines are designed to provide exceptional cutting capabilities and versatility, enabling you to create complex shapes and intricate details with ease. Whether you need a horizontal or vertical trimming machine, we have the perfect solution for your needs.
- Hydraulic Deep Drawing Press Machines: Our hydraulic deep drawing press machines are built to deliver precise and powerful drawing operations, ensuring clean holes and exceptional surface finishes. We offer a comprehensive range to suit various applications.
- Grinding Machines: Our grinding machines are engineered for precision and efficiency, allowing you to achieve the highest levels of surface finish and dimensional accuracy. Whether you need a surface grinder, cylindrical grinder, or tool grinder, we have the equipment to meet your specific requirements.
- Sawing Machines: Our sawing machines are designed for fast and accurate cutting of metals, providing clean cuts and minimal burrs. From band saws to circular saws, we offer a variety of options to suit different materials and cutting needs.
- Custom Machinery: In addition to our standard product line, we also specialize in custom machinery fabrication. Our experienced engineers can work with you to design and build tailored solutions that meet your unique requirements and optimize your production processes.
Why Choose EMS Metalworking Machinery:
- Quality: Our machines are crafted with the highest quality materials and components, ensuring long-lasting performance and reliability.
- Precision: We are committed to delivering machinery that meets the most stringent tolerances and standards, ensuring exceptional accuracy in your metalworking operations.
- Innovation: We continuously invest in research and development to stay at the forefront of technological advancements, offering innovative solutions that enhance your productivity and efficiency.
- Customer Support: Our dedicated team of experts is always available to provide comprehensive support, from machine selection and installation to maintenance and troubleshooting.
- Customization: We understand that every business has unique needs, and we offer flexible customization options to tailor our machines to your specific requirements.
At EMS Metalworking Machinery, we are more than just a supplier of equipment; we are your trusted partner in metalworking success. By choosing EMS, you can be confident in the quality, reliability, and performance of your machinery, enabling you to achieve your business goals and stay ahead of the competition.
A circle cutting machine is a specialized tool designed to cut circles in various materials like metal, wood, plastic, or fabric. These machines are commonly used in industries where precision and efficiency in circular cuts are essential. There are different types of circle cutting machines depending on the application and material:
Types of Circle Cutting Machines:
- Manual Circle Cutters:
- Operated by hand, these are often used for cutting circles in softer materials like paper or thin plastic. They typically feature a circular blade that is manually rotated around a pivot point to create the desired circle.
- CNC Circle Cutting Machines:
- These are automated machines often used in industries like metalworking and manufacturing. A CNC (Computer Numerical Control) machine uses precise computer programming to cut circles with high accuracy. It can handle various materials, including metals, wood, and plastics.
- Laser Cutting Machines:
- Laser cutters use a focused laser beam to cut through materials with high precision. These are used for cutting intricate or complex designs, including circles, in metals, wood, and other materials.
- Plasma Cutting Machines:
- Used primarily for metals, plasma cutters can also be used to cut circles. These machines use a high-temperature plasma jet to melt through the material, allowing for quick and precise circular cuts.
- Rotary Cutters:
- Often used in textile industries, rotary cutters use a round blade that spins to cut through fabric or paper. These are common in crafting and garment manufacturing.
Key Features:
- Adjustable Radius: Many circle cutting machines come with adjustable settings to change the radius or diameter of the circle.
- Precision: High-precision machines are capable of cutting circles with minimal deviation from the desired size.
- Material Compatibility: Depending on the type of machine, circle cutters can handle a range of materials from thin plastics to thicker metals.
- Speed: Automated circle cutting machines like CNC or laser cutters offer high-speed operation, which is essential in industrial settings.
Applications:
- Manufacturing: In industries such as aerospace, automotive, and construction, for cutting components and parts.
- Crafting: Common in the craft and textile industries for making circular cuts in fabric or paper.
- Signage: For cutting circles in materials like acrylic or metal for signs and displays.
- Woodworking: Often used for cutting circular holes or patterns in wood panels.
Do you have a specific application or type of material you’re working with for circle cutting? I can provide more targeted details based on that.
Circle Cutting Machine for metal sheets
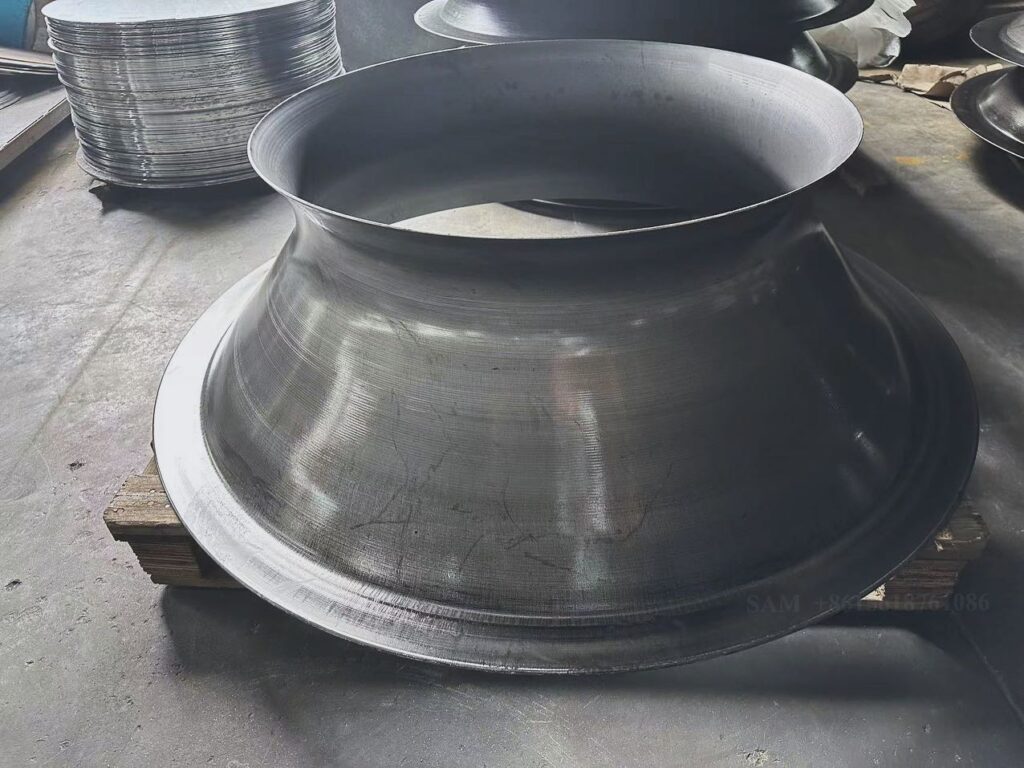
A circle cutting machine for metal sheets is designed to precisely cut circular shapes or holes from metal sheets of varying thicknesses. These machines are highly effective for industries that require precision and high-quality circular cuts, such as aerospace, automotive, construction, and manufacturing.
Types of Circle Cutting Machines for Metal Sheets:
- CNC Plasma Cutting Machines:
- How it works: CNC (Computer Numerical Control) plasma cutters use an electrically charged plasma arc to cut through metal sheets. They are controlled by a computer program, ensuring high precision and repeatability. Plasma cutting machines can cut circles with great accuracy, even in thick metal sheets.
- Applications: Ideal for cutting mild steel, stainless steel, aluminum, and other conductive metals.
- Advantages:
- High speed
- Capable of cutting thick metals
- High precision for intricate designs
- Laser Cutting Machines:
- How it works: Laser cutters use a focused laser beam to melt, burn, or vaporize metal to create a clean, precise cut. CNC laser cutting machines can be programmed to cut circles and other shapes with high accuracy.
- Applications: Laser cutting is widely used for thin to medium-thick metal sheets, including stainless steel, carbon steel, aluminum, and brass.
- Advantages:
- Extremely high precision
- Clean edges with minimal post-processing required
- Ability to cut complex shapes and fine details
- Waterjet Cutting Machines:
- How it works: Waterjet cutters use high-pressure water, often combined with abrasives, to cut through metal sheets. It’s a non-thermal cutting process, meaning it doesn’t affect the material’s properties around the cut area.
- Applications: Suitable for cutting thick metal sheets, including stainless steel, titanium, and other hard metals.
- Advantages:
- No heat-affected zone (HAZ)
- Can cut very thick materials
- Clean and precise cuts
- Punching Machines:
- How it works: A punching machine uses a die and a punch to create circular holes in metal sheets. This method is often used for high-volume, repetitive hole-making.
- Applications: Common in sheet metal fabrication for creating holes, including circular ones, in metal sheets.
- Advantages:
- Efficient for high-volume production
- Cost-effective for simple hole cutting
- Suitable for thinner metal sheets
- Rotary Cutters (for Thin Metals):
- How it works: Rotary cutters or shear cutting machines use a spinning blade to cut metal sheets. Though generally used for straight cuts, certain rotary cutting tools can also make circular cuts.
- Applications: Mostly used for thin metal sheets like aluminum or thin stainless steel.
- Advantages:
- Fast cutting
- Can handle thin materials
- Oxy-Fuel Cutting Machines:
- How it works: Oxy-fuel cutting uses a flame produced by burning oxygen and fuel gases to cut through metal. This method is less common for precision circle cutting but is used for large, simple cuts in thicker metals.
- Applications: Typically used for cutting thick carbon steel sheets.
- Advantages:
- Can cut through very thick metal sheets
- Ideal for rough cuts and large-scale projects
Key Considerations When Choosing a Circle Cutting Machine for Metal:
- Material Type and Thickness:
- Laser and plasma cutters are excellent for thinner to medium-thick sheets.
- Waterjet and oxy-fuel cutters are better for thick materials or when heat distortion must be avoided.
- Cutting Precision:
- If you require high precision, CNC laser or CNC plasma cutting would be the best options, as they can create very accurate circles with minimal tolerance.
- Speed:
- Plasma and laser cutters tend to be faster than waterjet and oxy-fuel cutting machines. However, waterjet cutting is slower but avoids heat distortion.
- Cost Efficiency:
- For high-volume production, punching machines or rotary cutters may be more cost-effective.
- Laser and plasma cutting can be more expensive but offer superior precision and flexibility for complex cuts.
Advantages of Using Circle Cutting Machines for Metal Sheets:
- Precision: High-quality circle cutters can create perfect circular cuts with minimal deviation.
- Versatility: Machines like CNC plasma or laser cutters can handle various shapes and complex geometries, not just circles.
- Speed: Automated machines can cut large quantities of metal sheets quickly and consistently.
- Clean Edges: Laser and waterjet cutting processes offer clean edges that often require little to no post-processing.
A circle cutting machine for metal sheets is designed to create precise circular cuts in various types of metal, including steel, aluminum, and other alloys. These machines are often used in industries where accuracy and efficiency are key, such as in aerospace, automotive, and manufacturing sectors. The primary types of circle cutting machines for metal sheets include CNC plasma cutting machines, laser cutting machines, waterjet cutting machines, punching machines, and oxy-fuel cutting machines.
CNC plasma cutters use an electrically charged plasma arc to cut through metal sheets. These machines are highly efficient and precise, capable of cutting circles quickly and accurately. They are ideal for cutting thicker materials and are often used for applications involving steel, stainless steel, and aluminum. Laser cutting machines use a high-powered laser to cut through metal with incredible precision. They offer clean, sharp edges and are well-suited for cutting thin to medium-thick metal sheets. Laser cutters are often used in industries that require intricate, high-precision cuts.
Waterjet cutting machines are another popular choice for circle cutting in metal sheets. These machines use a high-pressure stream of water, often combined with abrasives, to cut through metal without generating heat. This makes them ideal for cutting thick metal sheets and materials that might be heat-sensitive. Waterjet cutting can also produce very precise, clean cuts without the risk of distortion that can occur with heat-based methods.
Punching machines, which are used for creating holes in metal sheets, can also be used to cut circular shapes. These machines use a die and punch mechanism to shear out the desired circle, and they are often employed in high-volume production environments. Punching machines work well with thinner metal sheets and are commonly used for applications such as perforation in metal sheets.
Oxy-fuel cutting machines are primarily used for cutting through very thick metal sheets. They use a flame produced by burning oxygen and fuel gases to melt and cut through metal. While this method is less precise than laser or plasma cutting, it is effective for larger, rougher cuts, especially in thick steel.
When choosing a circle cutting machine for metal sheets, it’s important to consider the type of metal and its thickness. Plasma and laser cutters are well-suited for thinner to medium-thick sheets, while waterjet and oxy-fuel cutters are better for thicker materials. Additionally, the precision required for the cut is a critical factor—laser cutting is highly precise, while punching machines are faster for high-volume work, but less suitable for detailed cuts.
Circle cutting machines offer several advantages, such as speed, precision, and versatility. They can be used for various materials and applications, from creating simple circular holes to more complex geometric patterns. The choice of machine depends largely on the specific needs of the project, including the material, thickness, and precision required.
For applications requiring high precision and efficiency, CNC plasma cutters are ideal due to their ability to create smooth, consistent cuts on metal sheets at high speeds. These machines excel in cutting through metals like steel and aluminum, even at varying thicknesses. Their programmable nature allows for precise circle cutting without the need for manual intervention, making them highly suitable for complex shapes and designs that would be difficult to achieve with manual methods.
Laser cutting machines are another excellent option for achieving precise circle cuts, particularly for thinner metal sheets. These machines focus a high-powered laser on the metal, effectively melting or vaporizing the material in the cut path. The result is a clean, sharp edge with minimal thermal distortion around the cut area. Because laser cutters can be easily programmed to handle intricate designs, they are often preferred in industries where high precision and detailed cuts are required.
Waterjet cutting machines provide a versatile solution, especially for metals that are sensitive to heat. Using high-pressure water mixed with abrasive particles, waterjet cutters can slice through thick metal sheets without creating any heat-affected zones, ensuring that the material’s properties remain unchanged. While these machines tend to be slower than laser and plasma cutters, they excel in cutting thick materials, and the resulting edges often require little to no post-processing.
Punching machines, which use a punch-and-die mechanism to create holes, are particularly effective for high-volume production of circular holes in metal sheets. These machines work by applying pressure to the metal sheet using a punch that is shaped to the desired hole size. Punching is a fast process, but it’s best suited for thinner metals and applications where large quantities of identical holes are required. The machines are generally cost-effective for simple cuts but may not provide the same level of precision as laser or plasma cutters for intricate shapes.
Oxy-fuel cutting, which involves the use of an oxy-acetylene flame to cut through thick metal, is often chosen for large, simple cuts where speed is more critical than precision. This method is commonly used in heavy industries, such as shipbuilding or structural steel fabrication, where thick metal sheets are regularly processed. Though it’s slower and less precise than other cutting methods, oxy-fuel cutting remains an essential technique for certain applications due to its ability to handle very thick materials.
Ultimately, selecting the right circle cutting machine for metal sheets depends on the specific requirements of the project. If high precision is needed, laser or CNC plasma cutters are preferred, while for thicker materials, waterjet or oxy-fuel cutting machines are better suited. Punching machines offer a cost-effective option for mass production of simple cuts. Understanding the material thickness, cutting speed, and quality requirements will help in choosing the most suitable machine for the job.
Aluminium Circle Cutting Machine
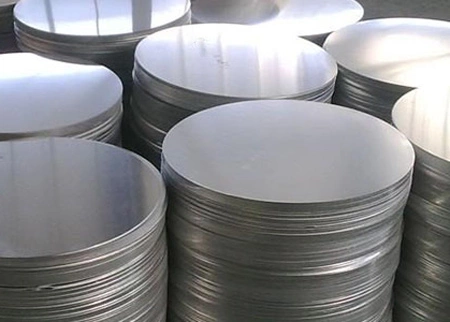
An aluminum circle cutting machine is specifically designed to cut precise circular shapes from aluminum sheets. Aluminum is a relatively soft metal compared to steel, making it easier to cut, but still requiring the right equipment for efficient, high-quality cuts. Depending on the required precision and the thickness of the aluminum sheet, different types of machines can be used for cutting aluminum circles.
CNC Plasma Cutting Machines can be used for aluminum circle cutting, especially for thicker sheets. These machines use a plasma torch that emits an electrically charged plasma stream to melt and cut the aluminum. CNC control ensures high precision, and it’s ideal for cutting circles with minimal distortion and high-speed performance. This method works well for medium to thick aluminum sheets and can easily produce clean, round cuts.
Laser Cutting Machines are another excellent choice for cutting aluminum circles, particularly for thin to medium-thick sheets. Laser cutting is known for its high precision and clean edges, making it ideal when fine details and tight tolerances are required. The laser beam melts the aluminum along the path of the cut, producing smooth, burr-free edges. Laser cutting is typically preferred when the final cut quality is important and minimal post-processing is desired.
Waterjet Cutting Machines are especially useful when cutting thicker aluminum sheets or when heat distortion needs to be avoided. The waterjet uses a high-pressure stream of water, often mixed with abrasive particles, to cut through the aluminum. Since this method is non-thermal, it ensures that the aluminum’s properties are preserved around the cut area, making it ideal for thicker aluminum sheets and applications where the material’s integrity must be maintained.
Punching Machines are used for creating holes in metal sheets, and they can also cut circles in aluminum sheets. The punching process involves a punch and die, where the aluminum sheet is placed between them, and the punch creates a circular hole by applying pressure. Punching machines are typically used for thinner aluminum sheets and high-volume production runs, where many identical circular cuts are needed quickly.
Shearing Machines can also be used for aluminum, though they are more commonly used for straight cuts. Some shearing machines are equipped with a circular blade or can be adapted to create circular cuts in aluminum, but they are less common for precise circular cuts compared to lasers, plasma, or waterjet machines.
Key Considerations for Aluminum Circle Cutting:
- Material Thickness: The thickness of the aluminum sheet determines the best cutting method. Laser cutting is generally more suitable for thinner aluminum, while plasma and waterjet cutting are better for thicker sheets.
- Precision: For high-precision cuts with minimal burrs or distortion, laser cutting is typically preferred. Plasma and waterjet cutting can also achieve good precision, but may leave more rough edges depending on the thickness and machine settings.
- Cut Quality: If a clean, polished edge is critical, laser cutting or waterjet cutting would be the best options. Plasma cutting, while faster, may result in slightly rougher edges that may need post-processing.
- Production Speed: Punching machines are very efficient for mass production of circular holes in thin aluminum sheets, while laser and plasma cutters offer greater flexibility for intricate designs.
Advantages of Aluminum Circle Cutting Machines:
- Speed and Efficiency: Automated machines, such as CNC plasma or laser cutters, provide fast, accurate cutting, which is ideal for large batches.
- Versatility: These machines can handle different sizes and thicknesses of aluminum sheets, offering flexibility in manufacturing processes.
- Minimal Material Waste: Cutting circles precisely minimizes the amount of scrap material left behind, optimizing material usage and reducing waste.
If you’re planning to cut aluminum circles, your choice of machine will depend on factors like the thickness of the material, the level of precision required, and the volume of production. Laser and plasma cutting are often favored for high-precision work, while punching machines are more suitable for mass production of simple circular holes. Waterjet cutting can offer high-quality results, especially for thicker aluminum sheets where heat distortion is a concern.
For cutting aluminum circles, the type of machine you choose will largely depend on the specifics of your project, such as the thickness of the aluminum sheet, the required precision, and the volume of production.
CNC Plasma Cutting Machines are an excellent choice for cutting aluminum circles, especially for thicker sheets. These machines use an electrically charged plasma arc to cut through the metal, and their CNC control allows for precise, repeatable cuts. Plasma cutters are typically faster than other methods, making them ideal for larger production runs. The machine can cut circles of various diameters, and adjustments can be easily made to handle different sheet thicknesses. While plasma cutters work well on aluminum, the edges may need some post-processing to smooth out roughness, especially for intricate designs.
Laser Cutting Machines are another popular method for aluminum circle cutting, particularly when high precision is required. The laser cutting process uses a highly focused beam of light to melt and vaporize the material along the cut path. This method is ideal for cutting thin to medium-thick aluminum sheets with excellent edge quality and minimal distortion. The precision of laser cutting allows for tight tolerances, making it perfect for applications where exact measurements and clean edges are essential. Additionally, laser cutting machines can handle more intricate designs, cutting circles and patterns with high accuracy. Because laser cutting does not produce significant heat-affected zones, the material around the cut remains largely unaffected, ensuring that the properties of the aluminum are preserved.
Waterjet Cutting Machines are highly effective for cutting thicker aluminum sheets or when you need to avoid heat distortion entirely. Waterjet cutting uses a high-pressure stream of water mixed with abrasive particles to cut through the aluminum. This non-thermal cutting method means there is no heat-affected zone, making it suitable for applications where precision and material integrity are essential. Waterjet cutters are slower than plasma and laser cutters, but they are perfect for thick materials and projects that require a high level of detail without the risk of warping. Waterjet cutting also leaves smooth edges and often requires little or no post-processing.
Punching Machines are another common option for cutting circles in aluminum sheets, particularly when producing large volumes of identical parts. Punching works by placing a metal sheet between a punch and a die, and the punch forces a circular hole through the sheet. This method is best suited for thin aluminum sheets and for producing simple, repeatable circular cuts. Punching is fast and efficient, especially in mass production environments, but it does not offer the same level of precision or flexibility as laser or plasma cutting, especially for more intricate or detailed shapes.
For applications requiring high-speed and high-volume production of simple circular holes, shearing machines or rotary cutters can also be used, though they are typically more common for straight cuts and are less effective for high-precision or intricate circle cutting.
Ultimately, your choice of a circle cutting machine will depend on the material thickness, cut quality required, production volume, and the need for precision. Laser and plasma cutters are ideal for high-precision and fast cutting, while waterjet cutting is perfect for thicker materials where heat distortion is a concern. Punching machines are excellent for high-volume, simple cuts in thinner materials.
When considering aluminum circle cutting, it’s important to understand the advantages and limitations of each cutting method, as well as their impact on the final product and production process.
CNC Plasma Cutting Machines are known for their speed and versatility, especially when cutting thick sheets of aluminum. These machines work by creating an ionized gas (plasma) that melts the aluminum as it moves along the pre-programmed path. CNC control ensures that the machine can accurately follow the design to produce circles or other complex shapes. Plasma cutting is ideal for industrial-scale operations where large volumes of aluminum need to be processed quickly. However, plasma cutting can leave rougher edges compared to laser cutting, which may require additional finishing steps, such as grinding or polishing, to achieve the desired surface finish.
On the other hand, Laser Cutting Machines offer superior precision and a high-quality finish. The laser’s fine beam melts or vaporizes the aluminum along the cutting path, resulting in clean edges with minimal thermal distortion. Laser cutting is ideal for thin to medium-thick aluminum sheets and is commonly used for high-precision applications such as electronic housings, decorative panels, and automotive components. The clean cut edges eliminate the need for post-processing in most cases, which can reduce time and costs in the production process. However, laser cutting machines tend to be slower than plasma cutting and are generally more expensive, especially for thicker sheets of aluminum.
Waterjet Cutting Machines provide a unique advantage in applications where heat distortion must be avoided. Since waterjet cutting uses high-pressure water mixed with abrasive particles to cut through aluminum, there’s no heat generation, meaning that the aluminum’s material properties remain intact. This makes waterjet cutting ideal for more sensitive applications where maintaining the material’s integrity is crucial, such as aerospace and medical components. Waterjet cutting can also handle thicker materials than plasma or laser cutting, which is a key advantage when working with aluminum sheets greater than 1 inch thick. However, the process is slower than both laser and plasma cutting, and waterjet cutting machines can be more expensive to operate due to the cost of abrasives and water pressure equipment.
Punching Machines offer an efficient and cost-effective solution for cutting circles in thin aluminum sheets. Punching is a mechanical process where a punch is used to shear out a circular shape from a metal sheet. The high-speed operation makes punching machines ideal for high-volume production runs where thousands of identical holes or circles are required. However, punching machines are less flexible than plasma or laser cutters, as they are limited to making simple shapes and are not suitable for intricate designs. Punching can also cause the aluminum edges to be slightly rougher, although this can be minimized by adjusting the machine settings.
For high-speed mass production of simple aluminum circles, shearing machines or rotary cutters are also viable options, though they are not as precise as other cutting methods. Shearing machines are typically used for straight cuts, but some can be modified or equipped with a circular blade to handle round cuts. They work best with thin aluminum sheets and are often used in manufacturing settings where speed is prioritized over precision.
In summary, the ideal choice of aluminum circle cutting machine will depend on the specific requirements of your project. If you need high precision, clean edges, and minimal post-processing, laser cutting is the way to go, especially for thinner sheets. Plasma cutting is faster and suitable for thicker aluminum but may require additional finishing. Waterjet cutting provides superior results when heat distortion must be avoided and for thicker materials. Punching is great for high-volume production of simple circles in thin aluminum, while shearing or rotary cutting is an option when cutting speed is the primary concern, though it comes with limitations in terms of precision and complexity. Understanding your material’s thickness, the precision required, and the production scale will help in selecting the best cutting method for your needs.
When it comes to aluminum circle cutting, the operational efficiency, precision, and application-specific requirements will dictate the choice of machine. Each machine type offers distinct advantages and is better suited for different production scenarios. It’s essential to explore how each cutting method affects the production process and the resulting product quality in more detail.
CNC Plasma Cutting Machines are a popular choice when cutting aluminum, particularly for thicker sheets. They offer a combination of speed and precision that is unmatched when dealing with industrial-scale projects. Plasma cutters are capable of cutting through materials up to several inches thick, making them ideal for large-scale, heavy-duty cutting jobs. Plasma cutting is also well-suited for cutting complex shapes, including circles, in aluminum. However, the key downside is that plasma cutting can create rougher edges compared to laser cutting, which may require post-cut finishing, such as grinding or deburring, to achieve a smooth finish. For larger, industrial projects that need high throughput and can tolerate slightly rougher edges, plasma cutting provides an efficient and cost-effective solution.
Laser Cutting Machines take the lead when it comes to precision and finish quality. Laser cutting works by using a high-powered laser beam to melt, burn, or vaporize the material along the cutting path. For aluminum, this ensures highly accurate cuts with smooth, clean edges, which are especially valuable when the final product requires a polished look. Laser cutting is often chosen for applications where detail and accuracy matter, such as in electronics enclosures, decorative aluminum panels, or components requiring high tolerances. However, laser cutting machines are generally slower than plasma cutters, which may not be ideal for projects with extremely tight deadlines or for handling thick aluminum sheets that can slow the process further. Despite this, the lack of rough edges or thermal distortion typically means that laser cutting reduces the need for post-processing, which can save both time and money in the long term.
Waterjet Cutting Machines offer another advantage when it comes to maintaining material integrity. Since waterjet cutting is a cold-cutting process, it doesn’t introduce heat into the aluminum, preventing thermal distortion and maintaining the material’s original properties around the cut. This makes waterjet cutting ideal for cutting thick aluminum sheets or when the aluminum must retain its mechanical properties, such as in aerospace applications where part strength and precision are critical. Waterjet cutting is also highly versatile and can handle a variety of aluminum thicknesses, from thin sheets to thick plates, without compromising on cut quality. However, waterjet cutting is slower than both plasma and laser cutting, and the operational costs can be higher due to the use of abrasives and high-pressure water systems. As a result, waterjet cutting is best suited for applications where precision is paramount, or when working with thick materials that would otherwise be difficult to cut.
For high-volume, simpler cuts, punching machines can be an effective solution, especially for mass production of aluminum circles or holes. Punching machines are designed to quickly punch out circular holes in thin aluminum sheets, making them ideal for applications where large quantities of identical parts are required. The punch-and-die mechanism allows for fast, efficient cutting with minimal material waste. While punching is fast, the precision may not be as high as other methods like laser cutting. Additionally, the edges of punched aluminum can be rougher, requiring additional finishing work if high-quality cuts are necessary. Nonetheless, punching machines are a cost-effective choice for basic, high-volume production and are commonly used in industries such as automotive or HVAC where uniform, simple shapes are in demand.
Shearing Machines and rotary cutters are also options for cutting aluminum, but these are less common for creating precise circles compared to other methods. Shearing machines are typically used for straight cuts, although some models can be adapted with circular blades to make basic round cuts in thin aluminum sheets. While these machines offer speed, they are typically limited in terms of precision and the complexity of cuts. Shearing is ideal for simple, rapid cutting tasks, especially when working with thin aluminum sheets. However, these machines are not well-suited for intricate or high-precision designs, so their use is mostly limited to projects where cutting speed is more important than cut quality.
Ultimately, choosing the right machine for cutting aluminum circles depends on a few critical factors: the material thickness, the required precision, the production volume, and the desired finish quality. For precision and clean edges, laser cutting is often the best option, especially for thinner aluminum sheets. For larger, thicker sheets or when speed is crucial, plasma cutting can handle the job more efficiently, though the edges may require additional processing. Waterjet cutting is the best choice when material integrity and the avoidance of heat distortion are key, especially for thicker aluminum. Punching is ideal for high-volume production of simple circular cuts in thin sheets. Lastly, shearing machines or rotary cutters are suitable for basic, high-speed tasks when precision isn’t a primary concern.
By evaluating the specific needs of your project—whether that’s cutting thick sheets or achieving intricate designs—you can select the most suitable cutting method, ensuring both efficiency and quality in the final product.
Circle cutting machine manufacturing
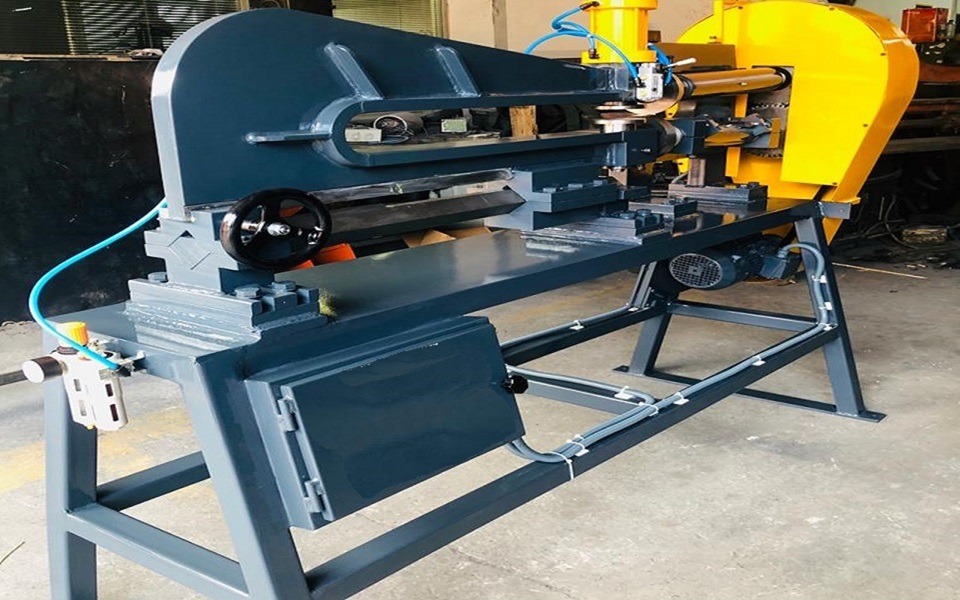
Manufacturing a circle cutting machine involves several steps, from the design and development phase to the final assembly and testing. These machines are used for cutting precise circular shapes from metal sheets, typically used in industries such as manufacturing, construction, automotive, aerospace, and more. The machines themselves can be powered by various technologies, such as CNC (Computer Numerical Control) for higher precision, or mechanical systems for more basic applications.
Here’s an overview of the process involved in manufacturing a circle cutting machine:
1. Concept and Design Phase
The first step in manufacturing a circle cutting machine is to define the specifications and requirements based on the application. This will guide the design of the machine, including the size, cutting method (plasma, laser, waterjet, punching, etc.), and material type (metal, plastic, composite materials).
Key design considerations:
- Type of Cutting Mechanism: The choice of plasma, laser, waterjet, or mechanical punch determines the design of the machine. For precision cutting, a laser cutter or plasma cutter will require a stable framework to support the laser or plasma head.
- Control System: For automated machines, a CNC (Computer Numerical Control) system or PLC (Programmable Logic Controller) system is essential to control the cutting process. The software should be capable of importing design files, managing machine movements, and monitoring the cutting process.
- Power Supply and Cooling Systems: A reliable power supply and cooling system are crucial, especially for plasma and laser cutters, as these require high energy and efficient cooling to prevent overheating.
Prototyping: Once the design specifications are finalized, a prototype or a scaled-down model is usually created for testing and adjustments. CAD (Computer-Aided Design) software is used for creating detailed machine schematics, followed by 3D modeling to simulate the cutting process.
2. Material Selection
The materials used for the construction of the circle cutting machine must be strong, durable, and able to withstand the stresses of the cutting process. Common materials used in the frame of the machine include:
- Steel: For heavy-duty machines, the frame is often made of high-strength steel to ensure rigidity and durability.
- Aluminum: For lighter machines, aluminum may be used as it is easier to machine and lightweight.
- Specialized Alloys: In some cases, heat-resistant alloys or composites are used in parts exposed to high temperatures, such as the laser or plasma cutting heads.
3. Fabrication of Components
The various components of the circle cutting machine are fabricated through different methods, including machining, welding, and casting:
- CNC Machining: Parts of the frame, cutting heads, and support systems are manufactured using CNC machines. Precision machining ensures that the components fit together perfectly and are strong enough to withstand the operational stresses.
- Welding: Structural components such as the frame and support brackets are often welded together for additional strength.
- Casting: Some parts may be cast, especially for components that need to have a specific shape or thickness.
Key components include:
- Cutting Head: This is the mechanism that holds and directs the cutting tool (plasma, laser, waterjet, or punch) onto the material.
- Drive System: Motors and gear systems control the movement of the cutting head, ensuring precise positioning and movement across the material.
- Cutting Tool: The tool itself varies depending on the cutting method chosen—plasma torch, laser, water jet nozzle, or punching die.
- Control System: This is the brain of the machine, directing the movements and operations of the cutting head based on the input from the operator or design software.
- Cooling and Exhaust Systems: Depending on the type of cutting tool, a cooling system (for lasers or plasma cutters) and exhaust system (for fume extraction) will be designed and integrated.
4. Assembly
Once the components are fabricated, they are assembled into the machine:
- Frame Assembly: The steel or aluminum frame is welded and bolted together to form the base of the machine. The machine’s precision and stability depend heavily on the rigidity of the frame.
- Electrical Wiring: The electrical components, including the control system, motors, power supplies, and sensors, are wired into the machine.
- Integration of the Cutting Head: The cutting tool (plasma torch, laser, etc.) is mounted onto the cutting head, which is connected to the driving mechanism for precise movement.
- Final Calibration: After assembly, the machine must be calibrated to ensure the cutting head moves along the correct paths and that the cutting tool operates at the right parameters.
5. Testing and Quality Control
After assembly, the circle cutting machine undergoes a series of tests to ensure it meets the design specifications and quality standards:
- Functional Testing: The machine is run through a series of test cuts to check the accuracy and smoothness of the cuts. This may include cutting a range of materials and thicknesses to ensure the machine performs well across the intended spectrum.
- Precision Testing: The cutting precision is checked using specialized measuring tools to ensure the circle cutting is accurate and that edges are clean and precise.
- Stress and Durability Testing: The machine is subjected to high-stress tests to ensure it can handle long-term use without failure, particularly under continuous operation or with thick materials.
- Safety Checks: Ensuring that safety features such as emergency stop buttons, fume extraction systems, and machine guards are working properly.
6. Final Adjustments and Finishing
After testing, any adjustments or fine-tuning are made to optimize the machine’s performance. This might involve tweaking the cutting speed, adjusting the control system, or improving the finishing processes. Any cosmetic finishes, like painting or coating the machine for protection against rust and wear, are applied at this stage.
7. Delivery and Installation
Once the machine is fully assembled and tested, it is ready for delivery. The installation process involves setting up the machine on-site, ensuring proper electrical and air supply (if necessary), and conducting a final operational test to ensure the machine works as expected in the working environment.
8. User Training and Support
Manufacturers typically provide training to operators on how to use and maintain the circle cutting machine effectively. Training includes understanding the software interface, setting up materials, and troubleshooting common issues. Additionally, manufacturers often offer ongoing technical support and maintenance services.
Conclusion
Manufacturing a circle cutting machine requires a combination of precise engineering, advanced technology, and expert craftsmanship. From the initial design and component fabrication to assembly, testing, and final delivery, each step is critical in ensuring the machine meets the highest standards of performance and reliability. The end result is a machine capable of producing high-quality, accurate circular cuts in various materials, including metals, plastics, and composites.
9. Software and Automation Integration
For modern circle cutting machines, automation plays a significant role in precision and ease of operation. The software integration is an essential part of the machine’s operation. This software controls the cutting process, from loading design files to guiding the machine through the cutting path. Here’s a breakdown of what this includes:
a. CNC Control System:
- The heart of the automation is the CNC (Computer Numerical Control) system, which uses digital inputs to control machine movements.
- The CNC system processes the design file, usually in formats like DXF (Drawing Exchange Format) or G-code (the language used to control CNC machines) and translates these into commands for the machine’s motors.
- In a circle cutting machine, the CNC system moves the cutting head in a specific path to ensure that the circle is cut with the exact diameter and position, as specified by the design file.
b. Software Packages:
- CAD/CAM software (Computer-Aided Design and Computer-Aided Manufacturing) is used to design the shape and cutting path. The CAD software creates the design (for example, a circular pattern), and the CAM software translates it into machine-readable instructions.
- Some machines come with proprietary software that is specifically tailored to the cutting machine, offering features like path optimization (to minimize material waste) and automated nesting (for efficient material usage).
c. Automation Features:
- Auto-loading: Automated systems can be implemented to load the material (like aluminum sheets) onto the cutting bed without manual intervention.
- Auto-calibration: This feature helps adjust the machine automatically for precise cutting based on real-time feedback from sensors. It ensures the machine remains in alignment, even if the material or machine shifts slightly.
- Cutting Speed Optimization: The software can adjust the cutting speed in real-time to match the material type and thickness, ensuring optimal cut quality and efficiency.
d. Monitoring and Diagnostics:
- Many modern machines are equipped with IoT (Internet of Things) integration or sensor-based systems that allow for real-time monitoring of machine performance. This can track aspects such as motor status, cutting head condition, power consumption, and more.
- Diagnostics features can alert operators to potential issues, such as tool wear, overuse, or cooling failures, enabling preventive maintenance to avoid downtime.
10. Material Handling and Management
Efficient material handling is crucial when operating a circle cutting machine, particularly for high-volume production environments. Here are some important considerations for material handling:
a. Loading and Unloading Systems:
- In high-volume operations, a material loading system is used to feed metal sheets onto the machine’s cutting bed automatically. This can be achieved using robotic arms, conveyors, or even automated vacuum lifters.
- Unloading systems may include automated systems that remove cut pieces and move them to the next stage in the production process, minimizing manual labor and reducing handling time.
b. Material Nesting and Optimization:
- Nesting software allows for the most efficient arrangement of circular cuts (and other shapes) within a single sheet of metal. This is especially critical for reducing material waste, which can improve the cost-efficiency of the entire cutting process.
- Automated nesting software takes into account factors such as material thickness, cutting speed, and kerf width (the amount of material removed by the cutting tool) to ensure optimal use of material.
c. Sheet Positioning and Clamping:
- Proper sheet clamping mechanisms ensure that the aluminum sheets do not move during the cutting process, which is critical to maintaining cutting accuracy.
- Advanced machines use vacuum systems, pin systems, or hydraulic clamps to hold the sheet securely in place. These systems can be adjusted based on the size and thickness of the material to avoid shifting.
11. Post-Cutting Processing
Although many circle cutting machines provide clean cuts with minimal burrs or rough edges, post-cutting processes may still be necessary, especially in high-precision industries. Some common post-cutting processes include:
a. Deburring:
- Deburring is the process of removing sharp edges or rough spots from the cut aluminum circles. This can be done manually with abrasive tools or using automated deburring machines.
- Mechanical deburring uses brushes, wheels, or abrasives to smooth out rough edges left from the cutting process.
b. Polishing:
- For applications requiring a high-quality finish, polishing may be used to give the aluminum circles a smooth and shiny surface.
- This can be done with vibratory polishers, rotary polishing machines, or hand-held polishing tools.
c. Heat Treatment (Optional):
- For certain applications, heat treatment processes like annealing may be necessary to adjust the hardness of the cut aluminum or to relieve internal stresses that may have developed during cutting.
d. Inspection:
- Quality inspection is crucial for ensuring that the cut circles meet dimensional specifications and that the edges are smooth and free from defects.
- Automated vision inspection systems or manual gauges can be used to check the accuracy of the cuts, ensuring the final product matches the design specifications.
12. Maintenance and Support
Long-term maintenance of the circle cutting machine is key to ensuring its longevity and optimal performance:
a. Preventive Maintenance:
- Routine tasks, such as lubricating moving parts, replacing worn components, and checking the cutting head for wear, should be performed regularly to prevent costly downtime.
- Cleaning the machine to remove dust, metal shavings, or debris helps maintain the machine’s efficiency and cutting quality.
b. Machine Calibration:
- Machines should be recalibrated periodically to ensure that the cutting head and control system remain aligned for precise operation.
- Laser alignment tools or CNC system software calibration might be used to verify the positioning accuracy and precision of the machine.
c. Technical Support and Troubleshooting:
- Manufacturers of circle cutting machines often provide ongoing technical support, including troubleshooting, software updates, and training for operators.
- Having a support network in place ensures quick repairs and minimizes operational downtime.
13. Cost Considerations and ROI
Finally, it’s essential to consider the cost-effectiveness of the circle cutting machine. The initial investment in a high-quality machine can be substantial, but the ROI (return on investment) is typically realized through increased efficiency, reduced waste, and higher quality in the final product. Factors that influence ROI include:
- Machine purchase price vs. production volume and cycle time.
- The cost of material waste—efficient nesting and material handling can significantly reduce this.
- The cost of maintenance and downtime, which can be minimized through regular maintenance and proper calibration.
- Energy consumption, particularly in processes like laser or plasma cutting, which can be high.
By considering these factors, manufacturers can ensure they select a circle cutting machine that not only meets their operational needs but also offers the best value in terms of productivity, material savings, and product quality.
Conclusion
The manufacturing process of a circle cutting machine involves multiple stages, from design and fabrication to integration of automation systems and software. The machine’s components are crafted with precision, ensuring that the final product offers reliability, efficiency, and accuracy in cutting aluminum circles or other materials. With the right software integration, material handling systems, and post-cutting processes, these machines can significantly streamline production and improve the overall manufacturing workflow.
14. Emerging Trends in Circle Cutting Machines
The cutting technology landscape is evolving rapidly, driven by advancements in automation, precision, and efficiency. The following trends are shaping the development of circle cutting machines:
a. Industry 4.0 Integration and IoT
- The future of manufacturing is highly connected, with Industry 4.0 bringing automation, data exchange, and manufacturing technologies to the forefront. Circle cutting machines are becoming part of a larger ecosystem, where sensors, robotics, and smart factory systems interact seamlessly.
- IoT integration enables real-time data collection, allowing for predictive maintenance, remote monitoring, and enhanced machine performance analytics. Operators can access key metrics like machine health, cutting precision, and energy consumption directly from their devices, ensuring that maintenance issues are detected early, preventing costly breakdowns.
b. Artificial Intelligence and Machine Learning
- AI-powered software is beginning to play a more significant role in optimizing cutting paths, improving material usage, and reducing waste.
- Machine learning algorithms analyze historical performance data to predict potential issues before they occur. These systems can adapt cutting parameters based on real-time conditions, improving precision and speeding up the cutting process.
- AI-assisted error detection helps identify flaws in the cut quality by analyzing images or laser scans of the finished cut.
c. Laser Technology Advancements
- Fiber laser cutting is gaining popularity over traditional CO2 lasers due to its higher efficiency and lower operational costs. Fiber lasers use a solid-state laser source, which allows for better beam quality, reduced energy consumption, and faster cutting speeds.
- The intensity of fiber lasers enables faster cutting of thicker materials, while providing more precise cuts compared to traditional methods, making them highly effective for aluminum and other metals.
- Laser beam shaping and multi-beam technology are innovations that will allow even more precise and faster cutting, enhancing the capabilities of future circle cutting machines.
d. Hybrid Cutting Systems
- A growing trend in the industry is the development of hybrid cutting machines that combine multiple cutting technologies. For example, machines may combine laser and waterjet or plasma and laser cutting, providing versatility in cutting different materials and thicknesses.
- These hybrid systems can reduce operational costs and provide greater flexibility, allowing manufacturers to choose the best cutting method for the specific material or task at hand.
15. Customization and Flexible Production
- Customization has become an essential factor in the modern manufacturing process. Manufacturers are increasingly demanding machines that can handle a wide range of materials, shapes, and sizes with a high level of flexibility.
- Many modern circle cutting machines are designed with modular components that allow for quick reconfiguration depending on the material or cutting method required. For example, changing the cutting head or switching from a punching system to a laser cutter can be done more quickly, enhancing the machine’s ability to adapt to varied production runs.
- This flexibility also includes the ability to process non-circular shapes or modify existing designs without significant downtime, making these machines more versatile for small-batch production or custom orders.
16. Sustainability and Environmental Impact
The environmental impact of manufacturing and material processing is becoming increasingly important. Manufacturers of circle cutting machines are focusing on sustainable practices and energy efficiency, driven by both regulatory requirements and consumer demand for eco-friendly solutions.
a. Energy Efficiency
- Energy-efficient designs are at the forefront of new circle cutting machines. For example, fiber lasers are more energy-efficient than traditional CO2 lasers, resulting in reduced power consumption during operation.
- Low-power consumption features such as sleep mode or automated shutdown after periods of inactivity are integrated into many modern cutting systems.
b. Material Waste Reduction
- Advanced nesting software plays a crucial role in minimizing material waste during the cutting process. By optimizing the layout of cuts on the material, manufacturers can reduce scrap rates and use fewer raw materials.
- Additionally, some machines can incorporate recycling systems for metal shavings or waste material, further contributing to a circular manufacturing process.
c. Green Manufacturing Standards
- Manufacturers of circle cutting machines are adhering to environmental standards such as ISO 14001 (Environmental Management Systems) and other green manufacturing practices.
- Use of eco-friendly lubricants and coolants, along with efficient waste management systems, helps ensure that the environmental footprint of the machine and its operation is minimized.
17. Safety and Compliance with Industry Standards
The design and operation of circle cutting machines must comply with stringent safety standards to protect operators and ensure the safe handling of materials. Compliance with industry-specific safety regulations and standards is critical to ensure the machine’s operational safety.
a. Safety Features
- Automatic shutdown and emergency stop buttons are standard on modern circle cutting machines, ensuring that the machine can be quickly powered down in case of an issue.
- Safety enclosures and laser shielding (for laser cutting machines) are designed to protect workers from potential hazards such as flying debris, intense heat, and radiation exposure.
- Fume extraction systems are integrated into the machines, especially in plasma and laser cutting systems, to remove harmful fumes and particles from the air and protect operators’ health.
b. Regulatory Compliance
- Machines must comply with local regulations, such as the CE certification in Europe or OSHA standards in the United States, ensuring that safety features are built into the machine from the ground up.
- Machines may also need to meet environmental regulations regarding emissions and material handling, particularly for processes like plasma cutting, which produce hazardous fumes.
18. Market Demand and Industry Applications
The demand for circle cutting machines varies across industries, and several factors are influencing market trends:
a. Growth in the Automotive Industry
- The automotive industry is one of the largest consumers of aluminum, and the demand for high-quality, precise cuts for parts such as body panels, wheels, and engine components is driving the market for advanced circle cutting machines.
- Automotive manufacturers require machines capable of cutting both large volumes of metal and highly precise, intricate parts, pushing the need for machines that can handle both high-speed production and fine-tolerance cuts.
b. Aerospace and Electronics Industries
- The aerospace and electronics industries require machines that can cut through thin sheets of high-strength aluminum and other materials with extreme precision. Applications include parts for aircraft, satellites, and circuit boards.
- With these applications, the trend is toward laser cutting machines and waterjet systems that maintain the material’s integrity and avoid heat-induced distortion.
c. Construction and Architecture
- Architectural and construction industries use circle cutting machines to produce decorative metal elements, fittings, and other components for building facades, bridges, and infrastructure. The demand for these types of machines is growing, especially for precision cutting of larger, thicker materials.
19. Cost Considerations for Manufacturers
Manufacturers should take into account several factors when purchasing circle cutting machines to ensure profitability:
a. Initial Investment
- Circle cutting machines, especially those with advanced features like lasers and CNC control, require a substantial initial investment. However, this cost is often justified by the precision and efficiency they offer, which can lead to significant savings over time.
b. Operational Costs
- Energy consumption, maintenance, and consumables (such as cutting gas, laser optics, and waterjet abrasives) are ongoing costs to consider. Machines with higher energy efficiency or lower maintenance requirements can reduce the long-term operational costs.
c. Training and Support Costs
- Comprehensive operator training and ongoing technical support are essential for ensuring that the circle cutting machine operates at peak efficiency, which may also contribute to ongoing costs.
20. Conclusion
The manufacturing landscape for circle cutting machines is continuously evolving, driven by advancements in technology, automation, and sustainability. As industries demand greater flexibility, efficiency, and precision, circle cutting machines will continue to integrate more intelligent systems, reduce environmental impact, and improve operational safety. By focusing on the latest trends and innovations, manufacturers can ensure that their circle cutting operations are future-proof and aligned with the needs of modern industry.
21. Selecting the Right Circle Cutting Machine
Choosing the right circle cutting machine for your operation depends on several factors. While every business might have unique requirements, there are common factors that should be evaluated to ensure the chosen machine meets production needs effectively.
a. Material Type and Thickness
- Material compatibility is one of the first considerations. Different circle cutting machines (laser, plasma, waterjet, mechanical) are suited for specific materials. For example:
- Laser cutting machines are ideal for precise cutting of metals like aluminum, steel, and stainless steel up to moderate thicknesses.
- Plasma cutters are effective for thicker metals but may not offer the same level of precision as laser cutters.
- Waterjet cutters excel in cutting metals, composites, and other materials without thermal distortion.
- The thickness of the material being processed also impacts the choice of machine. For thicker materials, plasma and waterjet machines are preferred, while laser cutters are better suited for thin to medium-thick sheets.
b. Precision and Tolerances
- Cutting precision is a critical factor for industries like aerospace, automotive, and electronics, where tight tolerances are essential. Machines with high precision ensure that parts meet stringent specifications and fit perfectly into complex assemblies.
- For fine cuts and intricate designs, laser cutters and waterjets tend to provide the highest precision. On the other hand, for larger, less detailed cuts, mechanical cutting might suffice.
- Tolerances in the range of ±0.1 mm to ±0.2 mm are often acceptable in many industries, but for specialized industries, you might require even finer tolerances.
c. Production Volume and Speed
- High-volume production environments need machines that can operate at faster speeds without sacrificing accuracy. Laser and mechanical cutting machines are often used for faster, high-volume cutting, while waterjets may be better for lower-volume, high-precision applications.
- Cutting speed is important for meeting deadlines and maximizing throughput, but operators should balance speed with cut quality and material utilization. High-speed machines often have automated features like auto-focus, servo motors, and quick-change tooling to optimize throughput.
d. Operational Cost vs. ROI
- The initial investment and ongoing operational costs must be weighed against the potential ROI (Return on Investment). High-performance machines like fiber lasers or robotic arms tend to have higher upfront costs, but they offer substantial long-term benefits, such as reduced labor costs and improved efficiency.
- Consumables such as laser gas, waterjet abrasives, and cutting heads can contribute significantly to operating costs, so these factors need to be carefully evaluated to calculate total cost of ownership over time.
- For businesses with high-volume production, the ROI will typically be realized faster due to reduced production time, lower material wastage, and enhanced part accuracy.
e. Machine Flexibility and Customization
- Flexibility in production processes is essential, especially in industries that require customization and adapt quickly to new product designs. Circle cutting machines with customizable tooling and adaptable cutting heads can switch between different materials and cutting methods quickly.
- Machines with modular designs allow manufacturers to reconfigure their equipment for different tasks, such as switching from cutting circles to cutting irregular shapes, reducing downtime and boosting flexibility.
22. Integration with Existing Production Systems
The ability of the circle cutting machine to integrate with existing production systems and workflows is critical to maximizing productivity.
a. Integration with MES (Manufacturing Execution Systems)
- MES integration enables seamless communication between the cutting machine and the broader factory management system. This integration facilitates real-time tracking of machine performance, production output, and inventory, improving scheduling and supply chain management.
- ERP systems can also be integrated with circle cutting machines to automatically track the cost of raw materials, labor, and machine downtime, ensuring accurate financial reporting.
b. Automation in Material Handling
- Automated material handling systems, such as robotic arms, conveyors, and stackers, help ensure smooth operations. These systems automatically load and unload sheets, reducing manual labor and material handling errors.
- Automatic nesting and cutting path optimization software can be integrated into the system to maximize material utilization and reduce waste.
c. Networked Machines and Remote Monitoring
- With the rise of smart factories, circle cutting machines are increasingly networked to allow for remote monitoring and management. Operators and managers can monitor machine health, productivity, and material usage remotely, even through mobile devices.
- Cloud-based platforms enable centralized data storage, ensuring that performance data from different machines can be analyzed to predict maintenance needs, optimize production processes, and make real-time adjustments.
23. Adapting to Market Demand and Customization
As consumer preferences shift toward more customized products, circle cutting machines are evolving to accommodate low-volume, high-mix production.
a. Low-Volume, High-Mix Production
- The trend toward customization in industries such as fashion, automotive, and architecture is pushing manufacturers to use machines that can quickly adapt to new designs and materials. This involves implementing quick-change tooling, modular cutting heads, and programmable CNC controls that can easily switch between different materials and cutting patterns.
- Batch production for customized products is on the rise, and multi-functional machines that can switch between different cutting technologies (like from laser to mechanical cutting) offer versatility that traditional systems may lack.
b. Rapid Prototyping and Agile Manufacturing
- Rapid prototyping is increasingly important, especially in industries like automotive and aerospace, where manufacturers must quickly produce and test new parts. Circle cutting machines that can cut intricate, high-precision prototypes with minimal setup time are essential in supporting these agile manufacturing processes.
- Manufacturers that can deliver prototypes faster than competitors often gain a competitive edge. The machines designed for this purpose need to have high-speed cutting capabilities, flexible settings, and integrated design software.
24. Key Supplier Partnerships and Market Growth
The circle cutting machine market is growing globally, driven by innovation and demand for more specialized and customizable cutting solutions. Companies looking to invest in cutting-edge machinery should consider forming strategic partnerships with key suppliers and vendors.
a. Supplier Collaboration
- Long-term relationships with machine manufacturers and suppliers can offer access to the latest technologies, service packages, and customization options. For example, suppliers might offer ongoing support for software updates, cutting head modifications, and precision upgrades, ensuring the machine remains efficient over time.
- It’s also essential to select suppliers who provide high-quality replacement parts and offer efficient technical support. For cutting machines, uptime is crucial, so having quick access to parts and technical service can minimize downtime.
b. Global Market Trends
- The demand for circle cutting machines is expected to rise in regions such as Asia-Pacific, driven by the growing industrial base in countries like China and India. The adoption of advanced cutting technologies is also gaining momentum in Latin America, where industries like construction and automotive manufacturing are booming.
- As sustainability becomes a growing priority, the market for energy-efficient cutting solutions will likely see increased demand, particularly in industries like aerospace, automotive, and heavy machinery, which prioritize precision and eco-friendly operations.
c. Future Supplier Collaboration and Co-Innovation
- In the future, co-innovation between manufacturers of circle cutting machines and their suppliers will be critical to producing next-generation systems. Suppliers can collaborate with manufacturers to improve laser beam technology, cutting head design, and machine intelligence, enhancing performance and expanding the range of materials and applications the machines can handle.
25. Future Innovations and Next-Generation Circle Cutting Machines
The next generation of circle cutting machines will be shaped by several key innovations, leading to machines that are faster, more accurate, more energy-efficient, and easier to use.
a. Autonomous Systems
- Future machines may incorporate autonomous capabilities, where AI systems not only detect potential issues but also optimize cutting paths, adjust cutting parameters in real-time, and manage material handling without human intervention.
- Self-learning algorithms will enable machines to adapt to new materials and changing production demands, streamlining setup times and ensuring consistently high-quality cuts.
b. Integration of 3D Cutting Technologies
- 3D cutting technologies, such as multi-axis lasers and waterjets, are set to revolutionize how manufacturers cut and process complex parts. These technologies allow the cutting head to move in multiple dimensions, making it possible to cut more intricate shapes and curved surfaces with precision.
- The integration of robotic arms or multi-axis CNC controls with circle cutting machines will make it easier to produce complex, geometrically challenging components for industries like aerospace, automotive, and robotics.
c. Smart Machines with Predictive Maintenance
- Predictive maintenance will be a hallmark of future circle cutting machines. By integrating sensors and machine learning, these machines will anticipate when parts need replacing or when preventive maintenance is required, minimizing unplanned downtime.
- Real-time diagnostics will notify operators of potential issues before they affect the machine’s performance, ensuring continuous production and reducing maintenance costs.
26. Conclusion
As circle cutting machines evolve, they will play an increasingly crucial role in industries that demand precision, speed, and flexibility. The integration of advanced technologies, such as AI, IoT, and laser advancements, will push the boundaries of what’s possible, offering businesses the ability to create high-quality, customized parts faster and more efficiently. By choosing the right machine, integrating it with existing systems, and embracing the latest innovations, businesses can stay competitive in a rapidly evolving manufacturing landscape.
SS Circle Cutting Machine
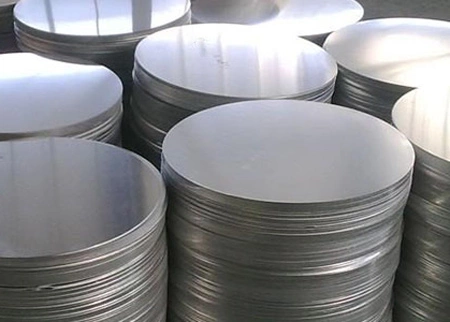
An SS (Stainless Steel) Circle Cutting Machine is a specialized piece of equipment designed for cutting stainless steel sheets into circular shapes with precision. Stainless steel is a widely used material in various industries like automotive, construction, kitchenware, and aerospace due to its strength, corrosion resistance, and durability. These machines are engineered to handle the specific characteristics of stainless steel, which is harder and more resistant to cutting than some other metals.
Key Features of SS Circle Cutting Machines
- Precision Cutting
- These machines provide high precision in creating smooth, uniform circles with tight tolerances. This is crucial for industries that require exact measurements, such as in the manufacturing of stainless steel parts for machinery, appliances, and decorative components.
- Laser Cutting Technology
- Laser cutting is one of the most common technologies used for SS circle cutting due to its ability to handle the hardness of stainless steel. Fiber lasers are particularly popular as they offer high cutting speed, precision, and energy efficiency.
- Laser cutting offers minimal thermal distortion, which is important for maintaining the integrity of stainless steel, ensuring the cut is both accurate and clean.
- Plasma Cutting Technology
- Plasma cutting can also be used to cut stainless steel, though it might not be as precise as laser cutting. Plasma cutters use a high-temperature plasma jet to melt and blow away metal, offering a fast and cost-effective solution for cutting thick stainless steel plates.
- Waterjet Cutting Technology
- Waterjet cutting is another method commonly used for cutting stainless steel circles. It uses a high-pressure stream of water, sometimes mixed with abrasives, to cut through metal without generating heat. This method preserves the material’s properties and is perfect for intricate cuts or thick sheets of stainless steel.
- CNC Controls
- Many SS circle cutting machines feature CNC (Computer Numerical Control) to ensure precise cuts and automated operations. This allows operators to input design specifications into the machine’s software, minimizing human error and increasing production efficiency.
- CNC machines also enable batch processing, which is essential for high-volume production of stainless steel circles.
- Hydraulic and Pneumatic Presses
- For high-volume sheet metal processing, hydraulic or pneumatic presses can be used to punch out circles from stainless steel sheets. These machines offer fast cutting speeds and can handle relatively high thicknesses.
- Adjustable Cutting Parameters
- Many advanced SS circle cutting machines allow for the adjustment of key parameters like cutting speed, power, and tooling configurations. This flexibility allows the machine to be used for a variety of stainless steel grades (304, 316, etc.) and thicknesses.
- Material Handling System
- Automated material handling systems are often incorporated into SS circle cutting machines. These systems load and unload stainless steel sheets automatically, reducing the need for manual labor and improving safety.
- Edge Quality and Finish
- SS circle cutting machines are designed to deliver clean, smooth edges without significant burrs or roughness. This is particularly important when the circles need to be used in visible or high-quality applications like kitchen appliances, architectural elements, or medical equipment.
Applications of SS Circle Cutting Machines
- Manufacturing of Stainless Steel Parts
- In industries like automotive, aerospace, and machinery, precision-cut stainless steel circles are used for making various components such as gears, seals, and casings.
- Kitchenware and Cookware
- Stainless steel circles are commonly used in the production of cookware items such as pots, pans, and lids. The precision cutting ensures uniformity and fits for components that must be welded or joined.
- Architecture and Construction
- Stainless steel circles are used for decorative purposes in buildings and structures. They can be used for cladding, facades, railings, and interior design elements, requiring machines that can handle aesthetic and functional cuts.
- Medical Devices and Equipment
- Stainless steel discs are used in the production of various medical instruments, implants, and surgical tools. The precision and cleanliness of the cut are crucial for these applications.
- Filtration and Engineering
- Stainless steel circles are used in filtration systems and engineering components where high strength and resistance to corrosion are required.
Advantages of SS Circle Cutting Machines
- High Precision
- These machines deliver highly accurate and repeatable cuts, which are essential when working with stainless steel, a material that can be difficult to cut due to its hardness.
- Versatility
- They can handle different sizes, thicknesses, and grades of stainless steel, making them suitable for a wide range of industries and applications.
- Efficiency and Speed
- The use of automation and advanced cutting technologies, such as CNC control and laser cutting, significantly enhances cutting speed and reduces operational costs.
- Clean Cuts and Reduced Material Waste
- Advanced technologies like laser cutting provide clean, smooth edges with minimal waste, ensuring higher material utilization and reduced post-processing work.
- Reduced Heat Affected Zone (HAZ)
- Cutting methods like laser and waterjet cutting generate minimal heat, reducing the heat-affected zone (HAZ) and preventing warping, which is essential for maintaining the quality of stainless steel.
- Automated Operations
- With automation and CNC control, SS circle cutting machines offer increased productivity and reduced labor costs. Automated material handling systems improve the flow of materials and reduce downtime.
Conclusion
An SS Circle Cutting Machine is a vital tool in industries that require high precision, high-quality cuts, and efficiency when working with stainless steel. The integration of advanced technologies like CNC control, laser cutting, plasma cutting, and waterjet cutting allows manufacturers to produce stainless steel circles quickly and with minimal waste. Whether in automotive, aerospace, medical, or construction, these machines offer versatility, precision, and reliability, making them indispensable in many high-performance manufacturing environments.
1. Advanced Cutting Methods for Stainless Steel Circles
The choice of cutting method for stainless steel depends on several factors, such as the material thickness, the required cut quality, and the intended application. Here are a few advanced cutting methods commonly used in SS circle cutting:
a. Fiber Laser Cutting
- Fiber lasers have become increasingly popular for cutting stainless steel circles. The laser beam is generated by a fiber-optic cable, providing higher efficiency and precision.
- Advantages:
- High precision: The laser beam focuses tightly on the material, resulting in incredibly accurate cuts.
- High-speed cutting: Fiber lasers provide faster cutting speeds compared to traditional methods like plasma or mechanical cutting.
- Energy efficiency: Fiber lasers are more energy-efficient than traditional CO2 lasers, reducing overall operational costs.
- Minimal heat distortion: Because of the focused nature of the laser beam, there is minimal heat build-up, which reduces the risk of warping and distortion in stainless steel, particularly important in thin sheets.
b. Plasma Cutting
- Plasma cutting uses a high-temperature plasma jet to melt and blow away material from the workpiece. While plasma cutting is generally considered less precise than laser cutting, it has advantages when cutting thicker stainless steel sheets.
- Advantages:
- Cost-effective for thicker materials: Plasma cutting is often the most affordable method when dealing with thicker stainless steel plates (typically above 6 mm thickness).
- High cutting speed: It allows for fast cutting, which is beneficial in high-volume production settings.
- Minimal burr formation: Plasma cutting typically generates cleaner cuts with fewer burrs compared to mechanical cutting methods.
c. Waterjet Cutting
- Waterjet cutting uses a high-pressure stream of water mixed with abrasive particles (such as garnet) to cut stainless steel.
- Advantages:
- No heat distortion: Since waterjet cutting does not generate heat, there’s no risk of thermal distortion, which is essential for maintaining the structural integrity of stainless steel, especially in sensitive applications.
- Versatility: Waterjets can cut through almost any material, not just stainless steel, which makes them useful for cutting multiple materials in a production environment.
- Intricate shapes and high precision: Waterjet cutting allows for very precise cuts, making it suitable for intricate designs and high-quality finishes.
d. Mechanical Cutting (Shearing and Punching)
- Mechanical cutting involves shearing, punching, or stamping stainless steel into desired shapes using presses and dies.
- Advantages:
- High speed for mass production: Mechanical cutting methods are fast, which makes them ideal for high-volume manufacturing.
- Cost-effective for simple cuts: If only basic shapes or circles are needed and the material is not too thick, mechanical cutting can be a very affordable solution.
2. Optimization Strategies for SS Circle Cutting Machines
To enhance efficiency and reduce costs, manufacturers can implement several optimization strategies when using SS circle cutting machines:
a. Nesting Software
- Nesting software optimizes the arrangement of circles on a sheet of stainless steel, ensuring minimal material waste. The software calculates the best possible layout for the cutting patterns, taking into account the material dimensions, part geometry, and the specific machine capabilities.
- Benefits:
- Material saving: Reduces the amount of scrap material by optimizing how parts are cut from a sheet of stainless steel.
- Enhanced efficiency: Increases the number of parts cut per sheet, reducing the frequency of material changes and improving overall production time.
b. Cutting Path Optimization
- Optimizing the cutting path refers to the algorithm that determines the most efficient route for the cutting head to follow during the process. This minimizes unnecessary movement, cutting time, and energy consumption.
- Benefits:
- Reduced cutting time: More efficient cutting paths minimize delays between cuts, leading to faster production.
- Increased machine life: Reducing unnecessary movements can extend the lifespan of the machine’s components, as they experience less wear.
c. Automation and Robotic Integration
- Integrating robotic arms or automated material handling systems with SS circle cutting machines can streamline the workflow. These systems automatically load and unload material, remove cut parts, and position sheets for the next round of cutting.
- Benefits:
- Increased throughput: Automation ensures that the machine runs continuously, reducing downtime caused by manual labor or material handling.
- Enhanced accuracy: Automation reduces human error in material handling, ensuring that sheets are positioned and cut exactly as needed.
- Improved safety: Automated systems reduce human exposure to potentially hazardous equipment, increasing workplace safety.
d. Predictive Maintenance
- Predictive maintenance involves using sensors and data analytics to predict when maintenance is needed for a machine before it breaks down. For SS circle cutting machines, this is particularly important for maintaining cutting quality and reducing unexpected downtime.
- Benefits:
- Reduced downtime: Predictive maintenance helps ensure that machines are maintained proactively, preventing costly breakdowns and disruptions in production.
- Improved machine longevity: By addressing wear and tear early on, machines can operate at peak performance for a longer period.
3. Trends in SS Circle Cutting Machine Technology
The SS circle cutting machine industry is evolving with advancements in technology and the rising demands for better productivity, quality, and cost-efficiency. Below are some of the key trends shaping the future of SS circle cutting:
a. Integration of Artificial Intelligence (AI)
- AI-driven optimization is transforming the manufacturing process by enhancing cutting path algorithms, material nesting, and machine diagnostics. AI allows machines to learn from past cuts, continuously improving cutting accuracy, speed, and material utilization.
- Smart scheduling: AI algorithms can predict the optimal production schedule based on order volumes, machine availability, and material availability.
b. Industry 4.0 and IoT Integration
- Industry 4.0 technologies, including the Internet of Things (IoT), are allowing SS circle cutting machines to become smarter and more connected. IoT sensors can provide real-time performance data to operators, while cloud-based platforms enable remote monitoring and diagnostics.
- Real-time data: IoT integration allows manufacturers to track production in real-time, helping to make faster decisions and improve overall operational efficiency.
c. Laser Technology Advancements
- Fiber lasers and CO2 lasers are continually improving, with newer models providing higher power, faster cutting speeds, and better beam quality. These innovations result in better precision and fewer defects in stainless steel circle cutting, which is especially important for industries requiring high-quality parts, like aerospace and medical devices.
d. Energy Efficiency and Sustainability
- As energy costs rise and environmental concerns become more prominent, manufacturers are seeking energy-efficient cutting machines. Newer technologies, such as fiber lasers, consume less power compared to older CO2 lasers. Furthermore, the reduction of material waste through nesting software and cutting path optimization directly contributes to more sustainable manufacturing practices.
- Sustainable practices: The adoption of eco-friendly materials (such as recyclable stainless steel) and energy-efficient cutting technologies can significantly reduce the environmental footprint of SS circle cutting operations.
e. Customization and Flexibility
- As customer demands for customized products grow, SS circle cutting machines are evolving to offer greater flexibility in terms of material compatibility, cut complexity, and speed. Many modern machines are multi-functional, capable of switching between cutting stainless steel, aluminum, and other materials seamlessly.
- Tailored solutions: The ability to produce bespoke parts with varying thicknesses, sizes, and designs makes SS circle cutting machines more adaptable to various industries like automotive, medical, and construction.
Conclusion
The SS circle cutting machine plays an essential role in industries that require high-quality, high-precision stainless steel parts. As technology advances, these machines are becoming more versatile, efficient, and capable of meeting the increasingly complex demands of modern manufacturing. With innovations such as AI, IoT integration, and advanced laser cutting technologies, SS circle cutting machines are poised to deliver even greater accuracy, speed, and sustainability, positioning manufacturers to meet the challenges of tomorrow’s production environment.
4. Specific Use Cases for SS Circle Cutting Machines
SS circle cutting machines serve a broad range of industries, each with unique requirements. The versatility of these machines allows them to be adapted for various applications. Here are some of the most prominent use cases:
a. Aerospace Industry
- Stainless steel parts are essential in the aerospace industry for components like engine parts, turbine blades, and seals due to their excellent strength-to-weight ratio and corrosion resistance.
- Precision is key, as many of these parts need to adhere to strict tolerances to ensure safety and performance. SS circle cutting machines with laser or waterjet cutting are ideal for producing these critical components with tight tolerances and smooth, burr-free edges.
b. Automotive Industry
- Stainless steel circles are used in the automotive sector for a variety of parts, such as brake discs, exhaust systems, and clutch components. The use of stainless steel in vehicles improves durability and corrosion resistance, especially for parts exposed to high temperatures or harsh conditions.
- High-volume production is a key aspect of the automotive industry. With CNC-controlled cutting machines, manufacturers can produce large quantities of high-precision stainless steel components quickly and efficiently.
c. Medical Devices and Equipment
- Stainless steel is widely used in the medical field for products such as surgical tools, implants, needles, and diagnostic equipment. These applications require high-precision cutting and a smooth finish to meet strict standards for safety and biocompatibility.
- SS circle cutting machines help ensure that these medical parts are consistently manufactured to the exact specifications, crucial for both functionality and patient safety.
d. Consumer Appliances and Kitchenware
- The home appliance industry heavily relies on stainless steel due to its aesthetic appeal, durability, and corrosion resistance. Stainless steel is used for parts like refrigerator doors, microwave casings, and cookware.
- Precision cutting is important for ensuring uniformity and smooth edges, particularly when stainless steel parts are visible to consumers. SS circle cutting machines enable manufacturers to produce these components in high volumes with high precision.
e. Construction and Architecture
- Architectural components, such as cladding, facades, and decorative panels, often require the use of stainless steel due to its aesthetic appeal and resistance to the elements.
- Stainless steel circles may be used for decorative elements, window frames, or structural supports, which require high precision and quality cuts. These circles may also be used for ceiling tiles, wall panels, or brackets in commercial buildings.
f. Food Processing Equipment
- Stainless steel is commonly used in food processing due to its resistance to corrosion, ease of cleaning, and durability. Stainless steel circles are used in filtering systems, tanks, and machines for food production.
- SS circle cutting machines provide the precision and speed required to maintain sanitary standards and production efficiency in food processing operations.
5. Market Dynamics of SS Circle Cutting Machines
The market for SS circle cutting machines is influenced by several factors, including technological advancements, regional demand, and economic trends. Key dynamics shaping the market include:
a. Demand for Precision Engineering
- As industries such as aerospace, automotive, and medical devices continue to grow, there is a rising demand for precision-engineered stainless steel components. SS circle cutting machines equipped with CNC controls, laser technology, and automation are crucial to meeting this demand.
- Manufacturers are increasingly focusing on producing parts with tighter tolerances, cleaner edges, and better surface finishes to cater to high-end markets that require high-quality stainless steel parts.
b. Cost-Effectiveness and Automation
- The need for cost-effective solutions is driving the adoption of automated SS circle cutting machines. These machines can handle large volumes of production with minimal human intervention, reducing labor costs and improving overall productivity.
- Automation also enables manufacturers to operate at higher speeds while maintaining consistent cut quality. With the increasing availability of affordable automation and robotic integration, smaller manufacturers are also able to incorporate advanced cutting technologies.
c. Rise of Energy-Efficient Technologies
- As energy costs rise, there is an increased focus on energy-efficient cutting technologies. Fiber lasers, in particular, are becoming popular for their lower energy consumption compared to older CO2 lasers.
- Sustainability is also a growing concern. Energy-efficient technologies, along with waste reduction through improved nesting and cutting path optimization, are helping manufacturers reduce their environmental footprint.
d. Customization and Flexibility in Manufacturing
- The trend toward customization is influencing the demand for flexible SS circle cutting machines that can easily adapt to varying sizes, materials, and design specifications. In industries like automotive, aerospace, and medical devices, manufacturers need machines capable of producing both large batches of standard parts and small runs of customized components.
- Manufacturers are also investing in multi-functional machines capable of switching between various cutting methods, such as laser, plasma, and waterjet cutting, to maximize production capabilities and cater to diverse customer needs.
e. Growth in Emerging Markets
- Emerging economies, particularly in Asia-Pacific, Africa, and Latin America, are experiencing rapid industrialization, driving demand for advanced manufacturing equipment. This trend is expected to lead to an increase in the adoption of SS circle cutting machines in these regions.
- Rising construction activities, automotive production, and demand for medical equipment in these regions are contributing to the growing demand for stainless steel parts, further boosting the market for SS circle cutting machines.
6. Emerging Technologies and Innovations
The SS circle cutting machine industry is continuously evolving, with innovations that improve the efficiency, quality, and capabilities of these machines. Here are some of the emerging technologies that are likely to shape the future of SS circle cutting:
a. Hybrid Cutting Machines
- Hybrid cutting machines combine multiple cutting technologies, such as laser and plasma or waterjet and laser, to offer increased versatility and the ability to cut a wider range of materials.
- Advantages:
- Adaptability: Hybrid machines allow manufacturers to switch between different cutting methods depending on the material and thickness, providing greater flexibility.
- Improved quality: Combining different technologies can help improve the overall cut quality, especially when working with materials that require specific cutting methods.
b. Artificial Intelligence (AI) and Machine Learning
- The integration of AI and machine learning is taking automation to the next level by allowing SS circle cutting machines to adapt to real-time variables and improve cutting performance autonomously.
- Benefits:
- Self-optimization: AI-driven systems can analyze cutting data to automatically adjust parameters for optimal performance.
- Predictive maintenance: AI can predict machine failures and automatically schedule maintenance, reducing downtime and improving overall operational efficiency.
c. 3D Laser Cutting
- 3D laser cutting technology, which allows for cutting complex shapes and curves in stainless steel, is gaining traction. This technology expands the possibilities for producing intricate designs and shapes beyond traditional flat cutting.
- Benefits:
- Increased design flexibility: 3D laser cutting allows for more complex geometries and designs to be cut from stainless steel sheets, opening up new possibilities for parts used in architecture, aerospace, and automotive applications.
- Enhanced precision: 3D laser cutting offers high accuracy, which is essential for industries requiring tight tolerances and complex shapes.
d. Additive Manufacturing (3D Printing) for Tooling
- Additive manufacturing is being explored as a way to create custom tooling for SS circle cutting machines, such as custom cutting heads or fixtures that are tailored to specific jobs.
- Benefits:
- Customization: Additive manufacturing allows for rapid prototyping and the production of specialized tools without the need for expensive molds or tooling changes.
- Reduced downtime: Custom tooling can be produced quickly, minimizing the downtime associated with retooling for specific jobs.
e. Cloud-Based Monitoring and Control
- Cloud-based systems allow manufacturers to monitor and control SS circle cutting machines remotely. This enables real-time tracking of performance, diagnostics, and production data, making it easier to optimize workflows and improve decision-making.
- Benefits:
- Remote monitoring: Operators can monitor machine performance, receive alerts, and perform diagnostics remotely, improving overall efficiency.
- Data-driven insights: Cloud platforms can provide insights into production patterns, machine usage, and efficiency, allowing manufacturers to make data-driven decisions to improve operations.
Conclusion
As industries demand greater precision, speed, and customization, the future of SS circle cutting machines will be shaped by ongoing technological advancements, including AI integration, hybrid cutting technologies, and cloud-based solutions. With emerging trends such as the growth of emerging markets, the increased adoption of energy-efficient technologies, and innovative hybrid machines, manufacturers will continue to push the boundaries of what SS circle cutting machines can achieve. By embracing these innovations, manufacturers can stay ahead in a competitive market, improving productivity and meeting the evolving needs of industries such as aerospace, automotive, and medical devices.
Circle Cutting Machine Manufacturing
Circle Cutting Machine Manufacturing involves the design, development, and production of specialized machinery used for cutting circular shapes out of various materials, such as metals, plastics, rubber, and composites. These machines are essential for industries where precise and repeatable circular cuts are required, including metalworking, automotive, aerospace, construction, and more.
Here’s a detailed overview of the process involved in manufacturing a circle cutting machine:
1. Designing the Circle Cutting Machine
The design phase is the first critical step in the manufacturing process of a circle cutting machine. The design must consider various factors, including:
- Material Handling: The design must accommodate the material size and type to be processed, such as metal sheets, stainless steel, or plastic. The material’s thickness will determine the type of cutting method (e.g., laser, plasma, waterjet, mechanical).
- Cutting Mechanism: Circle cutting machines can use several mechanisms, including:
- Laser Cutting: For precise, high-speed cutting, especially in thin materials like stainless steel or aluminum.
- Plasma Cutting: Ideal for thicker materials.
- Waterjet Cutting: Suitable for materials sensitive to heat.
- Mechanical Cutting (Shearing or Punching): Often used for cost-effective, high-volume cutting of metals.
- Customization Options: The machine should be designed with flexibility in mind, allowing for different sizes of circular cuts and adaptability to various materials.
- User Interface (Control Systems): Modern circle cutting machines are often equipped with CNC (Computer Numerical Control) or PLC (Programmable Logic Controller) to ensure precision and ease of operation. These systems allow operators to input cut parameters (e.g., diameter, cutting speed) and monitor the process remotely.
- Safety Features: The design should integrate multiple safety measures, such as safety sensors, emergency stop buttons, and protective shields, to ensure worker safety during operation.
- Size and Weight: The machine’s dimensions should be suitable for the workspace and material sizes it will handle. It should also be optimized for transportation and installation.
2. Material Selection for Circle Cutting Machines
Selecting the right materials for constructing the machine is essential for durability and performance. Key components and their material selections include:
- Frame: The frame is typically made from steel or cast iron due to its high strength and ability to withstand the forces involved in cutting operations. A rigid frame ensures minimal vibrations during operation, which is crucial for maintaining cutting precision.
- Cutting Tools: The cutting tools, such as laser heads, plasma torches, or waterjet nozzles, are made from high-performance materials like tungsten carbide or ceramic for their resistance to wear and heat.
- Electrical Components: Copper, aluminum, and other conductive materials are used for wiring and electrical systems. High-quality PCB (printed circuit boards) and semiconductors are selected for control systems to ensure optimal machine functionality.
- Bearings and Drives: Linear guides and ball bearings are chosen for smooth movement of the cutting head or gantry. Servo motors and stepper motors are used for precise control of the cutting head movement.
- Protective Coatings: Some parts of the machine, especially those exposed to heat or chemicals, are coated with corrosion-resistant materials, such as chromium or nickel, to prolong the lifespan of the machine.
3. Manufacturing Process for Circle Cutting Machines
Once the design and material selections are finalized, the manufacturing process begins. This process typically involves the following steps:
a. Fabrication of Frame and Structure
- The frame and structure of the circle cutting machine are fabricated using welding, machining, and casting methods. The base frame is typically welded from heavy-duty steel to ensure strength and stability. Cast iron may be used for critical structural parts requiring superior vibration damping.
b. Assembly of Mechanical Components
- Cutting Mechanism Installation: Depending on the chosen cutting method, the machine will be equipped with laser heads, plasma cutters, or mechanical shearing tools.
- Axis and Movement Systems: The linear motion systems (e.g., gantry systems, X-Y tables, or rotary axes) are assembled with servo motors, ball screws, and linear rails for accurate positioning.
- Drive Motors: The system is powered by stepper motors or servo motors that drive the cutting head along specific paths, controlled via the CNC or PLC systems.
c. Installation of Electrical and Control Systems
- The electrical components are installed, including the power supply for the cutting tool, CNC controllers, PLC systems, sensors, and monitoring systems. The electrical wiring is carefully arranged to prevent overheating or short circuits, and to ensure safe operation.
- The user interface is also integrated, allowing the operator to easily input parameters such as cutting speed, depth, and diameter.
d. Integration of Cutting Technology
- Laser Cutting: For laser-based machines, the laser generator, focusing lenses, and cutting heads are installed. The machine is calibrated to ensure the laser beam is precisely focused on the material for optimal cutting performance.
- Plasma Cutting: For plasma cutters, the torch assembly is mounted, along with the cooling system to ensure the torch remains within optimal operating temperatures.
- Waterjet Cutting: If the machine uses waterjets, the high-pressure pump, abrasive delivery system, and nozzle are integrated.
- Mechanical Cutting: Mechanical shearing machines will have high-quality cutting dies installed.
e. Calibration and Testing
- Calibration: Once the machine is assembled, it undergoes a series of calibrations to ensure all axes are aligned, cutting tools are functioning properly, and the CNC or PLC system is correctly programmed to handle different cutting profiles.
- Testing: The machine undergoes rigorous testing under different conditions to ensure the accuracy and precision of the cuts. Sample cuts are made on various materials (such as stainless steel, aluminum, or plastic) to check for alignment, quality of the cut edge, and repeatability.
- Quality Control: The machine is inspected for compliance with international quality standards (ISO, CE) and local regulations to ensure safety and performance.
4. Final Assembly and Shipping
After the machine has passed testing, it undergoes a final assembly phase, where all parts are tightened, aligned, and inspected one last time. Final adjustments to the cutting systems, electrical systems, and safety features are made. Afterward, the machine is cleaned, packed, and prepared for shipment.
- Documentation: A complete set of user manuals, maintenance instructions, and warranty information is provided to the customer along with the machine.
- Shipping: The circle cutting machines are carefully packed to avoid damage during transit. Depending on the size and complexity, machines may be shipped fully assembled or in modular parts that can be easily assembled on-site.
5. Installation and Training
Once the circle cutting machine arrives at the customer’s facility, the installation team ensures that it is correctly set up, tested, and calibrated for the customer’s specific needs. Operators are trained to operate the machine, input cutting parameters, and perform routine maintenance tasks.
6. Maintenance and Support
After installation, manufacturers typically offer ongoing support and maintenance services, which may include:
- Regular maintenance checks.
- Software updates for control systems.
- Spare parts replacement (e.g., cutting heads, motors, and bearings).
- Remote troubleshooting services via connected systems.
7. Cost Considerations and Pricing
The cost of manufacturing a circle cutting machine depends on various factors, including:
- Material costs: High-quality materials like steel, copper, and high-performance cutting tools add to the overall cost.
- Technology: Advanced technologies like laser and waterjet cutting increase the price compared to mechanical cutting machines.
- Customization: Custom-built machines tailored to specific customer requirements tend to be more expensive.
- Labor: Skilled labor for design, fabrication, and assembly adds to the cost.
Typically, circle cutting machines range in price from several thousand to hundreds of thousands of dollars, depending on their complexity and cutting technology.
Conclusion
The manufacturing of circle cutting machines is a complex process that requires precision engineering and attention to detail at every stage. From initial design and material selection to the final assembly and testing, manufacturers must ensure that these machines are capable of delivering high-quality, precise cuts across a variety of materials. As industries demand greater efficiency, precision, and flexibility, the evolution of cutting technologies will continue to shape the future of circle cutting machine manufacturing, offering even more advanced capabilities to meet the needs of modern production environments.
Let’s continue by delving deeper into the various aspects of circle cutting machine manufacturing. We’ll explore the market trends, challenges faced in manufacturing, and innovations that influence the design and production of these machines. These additional points will provide a more comprehensive understanding of the dynamics within the circle cutting machine industry.
8. Market Trends in Circle Cutting Machine Manufacturing
The global market for circle cutting machines has evolved significantly over the years, driven by advancements in technology, increased demand for precision, and the rise of automation. Here are the major market trends currently shaping the industry:
a. Increased Automation and CNC Integration
- Automation is a key factor in driving the growth of circle cutting machines, particularly in high-volume production environments. Machines equipped with CNC (Computer Numerical Control) systems offer improved precision, repeatability, and efficiency.
- Automated features, such as automatic loading and unloading, material handling systems, and real-time diagnostics, allow manufacturers to optimize their processes and reduce labor costs.
- CNC systems enable users to program precise cutting patterns, adjust for material thickness variations, and monitor machine performance remotely, improving overall productivity.
b. Customization for Specific Applications
- Industries such as aerospace, automotive, and medical device manufacturing often require highly customized circle cutting solutions. The demand for machines that can handle diverse cutting requirements (e.g., cutting different shapes, sizes, and materials) is on the rise.
- Manufacturers are increasingly offering customizable options for their machines, allowing for features like adjustable cutting diameters, multi-functional heads, and integration with other tools such as punching or stamping.
c. Advances in Cutting Technologies
- The cutting technology used in circle cutting machines is rapidly advancing. Technologies such as fiber laser cutting are replacing older CO2 laser systems due to their improved cutting speed, energy efficiency, and cost-effectiveness.
- Waterjet cutting technology is also gaining popularity because of its ability to cut a wide range of materials without introducing thermal stresses, which can distort the material.
- Plasma cutting remains a popular option for thicker materials, though newer machines are offering improved precision and better edge finishes.
d. Global Expansion and Emerging Markets
- The growth of industrial sectors in emerging economies, particularly in Asia-Pacific, Africa, and Latin America, is driving demand for circle cutting machines.
- Countries with expanding manufacturing sectors—such as China, India, and Brazil—are investing in advanced production equipment to improve efficiency and stay competitive.
- As emerging markets develop, there is an increasing need for affordable yet reliable cutting solutions. Manufacturers are focusing on providing cost-effective options without compromising quality or performance.
e. Sustainability and Energy Efficiency
- Energy-efficient technologies are becoming more crucial as industries seek to reduce operational costs and meet environmental standards.
- Circle cutting machines using fiber laser technology are more energy-efficient compared to traditional cutting methods (such as CO2 lasers or plasma), helping manufacturers reduce their carbon footprint and lower energy consumption.
- Waterjet machines also contribute to sustainability since they don’t generate heat, which reduces material waste and improves cutting quality.
f. Industry 4.0 and Smart Manufacturing
- Industry 4.0 concepts are increasingly influencing the design of circle cutting machines. These smart machines are equipped with IoT (Internet of Things) sensors and AI-powered software that allow real-time monitoring of production processes.
- Manufacturers are increasingly integrating predictive maintenance features into their circle cutting machines. This allows the system to predict wear and tear on parts, reducing unexpected downtime and increasing machine reliability.
- Data analytics plays a crucial role in optimizing machine performance, where manufacturers can gather insights into cutting efficiency, material usage, and overall workflow to make data-driven decisions.
9. Challenges in Circle Cutting Machine Manufacturing
While the circle cutting machine industry continues to grow, it also faces various challenges that manufacturers need to address:
a. High Initial Investment
- The initial cost of setting up a circle cutting machine—especially advanced systems with CNC, laser, or waterjet cutting technologies—can be substantial. The high upfront cost can be a barrier for smaller manufacturers or those operating in regions with limited access to financing.
- Manufacturers must carefully consider the return on investment (ROI) for customers and offer financing options or leasing models to make these machines more accessible.
b. Skilled Labor Shortage
- The increasing complexity of circle cutting machines—particularly with the integration of CNC and automation—requires highly skilled workers to operate, maintain, and troubleshoot the machines.
- There is a shortage of skilled labor in many regions, and this creates a challenge for manufacturers who need a well-trained workforce to maintain the machines.
- Training programs, certifications, and industry partnerships are crucial to ensuring a skilled labor force.
c. Material Handling and Waste Management
- Handling large sheets of metal or other materials can be a challenge in circle cutting, particularly when dealing with heavier or larger materials.
- Waste management, such as cutting scrap and material efficiency, is also a concern. Manufacturers are working on improving nesting algorithms and cutting patterns to minimize waste and improve material utilization.
- Ensuring that the cutting head remains accurate and aligned during the process is critical to avoid material waste due to miscuts.
d. Competitive Pressures
- As more players enter the circle cutting machine market, competition has intensified. Manufacturers need to constantly innovate to stay ahead, focusing on product quality, performance enhancements, and cost-effectiveness.
- Moreover, global supply chain issues and tariffs can impact material costs and availability, making it harder to maintain profit margins.
10. Innovations in Circle Cutting Machines
Continuous innovation is key to keeping pace with evolving industry demands. Here are some of the cutting-edge innovations in circle cutting machine technology:
a. Advanced Cutting Software and CAD Integration
- Modern circle cutting machines are often integrated with advanced CAD (Computer-Aided Design) and CAM (Computer-Aided Manufacturing) software systems, which streamline the design-to-production process.
- These software systems offer intuitive interfaces, automated nesting capabilities, and the ability to simulate cutting paths, allowing for optimized machine operation and minimized material waste.
b. Hybrid Cutting Machines
- Hybrid machines combine multiple cutting methods, such as laser cutting and plasma cutting, into a single unit. This flexibility allows manufacturers to handle a broader range of materials and thicknesses without needing separate machines for each cutting method.
- This multi-functionality saves space, reduces costs, and enhances operational flexibility.
c. Robotic Integration
- Some modern circle cutting machines incorporate robotic arms to automate material loading, unloading, and sometimes even the cutting process itself.
- This integration further increases automation and efficiency, especially in high-volume production environments, while also improving safety by minimizing human interaction with the cutting process.
d. Improved Cooling and Dust Management Systems
- For processes like laser cutting and plasma cutting, maintaining cooling systems is critical to prevent overheating, especially during prolonged cutting sessions.
- Newer models of circle cutting machines come with advanced cooling technologies that ensure optimal cutting performance without material distortion.
- Dust extraction systems are also more effective, removing hazardous fumes and particulate matter produced during the cutting process.
e. Integration of Augmented Reality (AR) for Maintenance and Training
- Some manufacturers are incorporating augmented reality (AR) technologies into their machines, allowing operators to receive step-by-step guidance on maintenance and machine troubleshooting in real time.
- AR can also be used for operator training, providing visual overlays of machine operation and enhancing the learning experience for new operators.
Conclusion
The manufacturing of circle cutting machines is a complex process that involves advanced engineering, careful material selection, and sophisticated manufacturing techniques. As industries evolve and demand for precision and speed increases, circle cutting machines are incorporating more advanced technologies like CNC control, AI integration, and hybrid cutting systems. Despite challenges such as high initial costs and skilled labor shortages, the market continues to grow, driven by technological advancements and the expanding needs of industries like aerospace, automotive, and medical devices.
By focusing on innovation, customization, and automation, manufacturers of circle cutting machines are positioning themselves to meet the demands of a rapidly changing industrial landscape. As these machines become more efficient, flexible, and user-friendly, they will continue to play a pivotal role in a wide range of applications where precision circular cuts are essential.
11. Future Trends in Circle Cutting Machine Manufacturing
The future of circle cutting machines will be shaped by several exciting trends as industries evolve and demand for more advanced, efficient, and sustainable solutions increases.
a. Greater Focus on Precision and Tolerances
- Ultra-precision cutting will continue to be a major trend. As industries like aerospace, medical devices, and electronics demand ever-higher tolerances and quality, circle cutting machines will need to meet these stringent requirements.
- Technologies like nanosecond lasers (which have extremely short pulse durations) could be integrated into circle cutting machines to achieve microscopic precision and finer cuts, making them suitable for high-precision applications like microelectronics and medical implants.
b. Intelligent and Autonomous Systems
- Artificial intelligence (AI) and machine learning will play an increasingly important role in the optimization of circle cutting machines. These systems will continuously learn and adapt, adjusting cutting parameters for the best performance based on real-time data.
- Autonomous systems may be introduced to fully automate the entire production process, from material loading to cutting and finished part removal. This will reduce human intervention and the potential for errors, making machines even more efficient.
c. Additive Manufacturing and Hybrid Machines
- The integration of additive manufacturing (3D printing) with traditional cutting processes is an emerging trend. Hybrid machines that combine subtractive (cutting) and additive manufacturing processes are expected to provide more flexibility and capability for creating complex parts in industries like aerospace and automotive.
- Hybrid machines could allow for the creation of parts with complex geometries, including circular components that are simultaneously cut and built up in layers of material, all within a single system.
d. Energy Efficiency and Sustainability
- There will be a continued push for energy-efficient machines, especially as industries strive to reduce their carbon footprints. Manufacturers are likely to invest in cutting technologies that minimize energy consumption and maximize performance, such as fiber lasers, which consume significantly less energy than traditional CO2 lasers.
- Additionally, sustainability will continue to be a focal point, with a greater emphasis on recycling scrap materials and using eco-friendly consumables (e.g., cutting gases, water filtration systems for waterjet cutters).
e. Smart Maintenance and Remote Monitoring
- As machines become more connected, remote monitoring and predictive maintenance will become more prevalent. This will allow manufacturers to detect and resolve potential issues before they lead to downtime, improving productivity and reliability.
- Machines may be equipped with sensors that collect data in real-time, feeding this information back to the manufacturer for data analysis, optimizing everything from cutting speed to material consumption.
- Condition-based monitoring systems can predict when parts such as cutting heads, motors, or guides need maintenance or replacement, thereby extending the lifespan of the machine.
12. Emerging Technologies in Circle Cutting Machines
Several emerging technologies are expected to revolutionize the performance and capabilities of circle cutting machines in the coming years.
a. Laser Cutting Advancements
- Ultrafast Lasers: Lasers with femtosecond (quadrillionth of a second) or picosecond (trillionth of a second) pulse durations are being developed for precise cutting of even the most delicate materials. These lasers generate less heat, meaning the material around the cut remains largely unaffected.
- High-power fiber lasers: These lasers are replacing traditional CO2 lasers in many applications due to their higher efficiency, faster cutting speeds, and reduced maintenance.
b. Waterjet Cutting Enhancements
- Multi-axis waterjets: These advanced waterjet systems provide even more cutting flexibility, enabling 3D cutting and intricate shapes. Multi-axis systems can tilt, rotate, and move in multiple directions to achieve complex, high-precision cuts without the need for a secondary operation.
- Abrasive waterjet cutting: Waterjets combined with abrasive materials allow for cutting much harder materials like stone, ceramic, or titanium. Innovations in abrasive delivery systems are helping increase the speed and reduce the wear on the cutting head.
c. Plasma Cutting Innovations
- High-definition plasma cutting: This technology improves the precision of plasma cuts, producing better-quality edges and finer tolerances. It also reduces the need for post-cut finishing, saving time and cost.
- Dual gas plasma cutting: This is becoming popular for cutting thicker materials, as it utilizes two gases for different cutting operations, optimizing the plasma’s performance and enhancing cut quality.
d. Hybrid Laser-Plasma Machines
- Some manufacturers are developing hybrid laser-plasma cutting machines. These machines combine the advantages of both technologies, using laser cutting for thin material cuts and plasma cutting for thicker materials. The integration of both systems into one machine increases versatility and overall cutting capacity.
e. Digital Twin Technology
- Digital Twin technology—creating a virtual replica of the physical machine—will become more common in the industry. This allows manufacturers to simulate cutting operations before actually starting the physical process, enabling better decision-making, efficiency, and error prediction.
13. Key Players in the Circle Cutting Machine Industry
Several companies dominate the circle cutting machine market, driving innovation and providing cutting-edge solutions to various industries. These players specialize in different cutting technologies (e.g., laser, plasma, waterjet) and provide customized solutions for specific industries. Some of the key players in the market include:
a. TRUMPF
- TRUMPF is one of the largest and most well-known manufacturers of industrial laser cutting systems. They provide a wide range of high-precision machines, including fiber laser systems and CO2 lasers, for cutting metal sheets into various shapes, including circles.
- TRUMPF’s innovations in laser cutting technology, combined with its CNC control systems, have made it a leader in precision cutting.
b. Bystronic
- Bystronic is another major player in the field of laser cutting machines, with a strong presence in the market for sheet metal cutting. Their systems are known for being energy-efficient, precise, and highly automated.
- Bystronic’s focus on automation and user-friendly interfaces has positioned them as one of the preferred manufacturers in industries requiring high-precision cuts.
c. Hypertherm
- Hypertherm is a global leader in plasma cutting technology, particularly for cutting thick materials with high precision. Their HyPerformance Plasma systems are used widely for applications requiring high-quality cuts on metals like stainless steel and carbon steel.
- They continue to innovate with HD plasma cutting technology that delivers faster cuts and improved edge quality.
d. Omax
- Omax is one of the top suppliers of abrasive waterjet cutting machines. Their machines are highly regarded for their ability to cut a wide variety of materials without introducing heat distortion.
- They offer multi-axis waterjet systems that can make complex cuts with extreme precision, making them a leader in industries requiring intricate designs.
e. Mazak
- Mazak manufactures laser cutting systems as part of their broader portfolio of manufacturing equipment. Known for their high-speed cutting, their fiber laser machines are particularly well-suited for high-precision cutting, including circular parts in metal sheets.
f. KUKA Robotics
- KUKA Robotics focuses on automation and robotics, including robotic arms for automated material handling and cutting. Their integration of robotics into cutting processes is transforming industries by enabling high levels of automation in circle cutting.
g. Amada
- Amada is renowned for its sheet metal processing equipment, including punching, laser cutting, and shearing machines. They offer solutions for a range of materials and cutting needs, including specialized systems for precise circular cutting.
Conclusion
The circle cutting machine manufacturing industry is continuously evolving, with advancements in laser cutting, waterjet cutting, and plasma technologies leading the charge. As automation, AI, and energy efficiency become more integrated into machines, manufacturers will be able to meet the demands of precision, speed, and cost-efficiency in modern production environments.
Future trends suggest even more sophisticated systems with hybrid cutting technologies, smart maintenance, and increased customization to meet specific industrial needs. As global competition intensifies and new players enter the market, manufacturers will need to focus on innovation and adaptability to stay competitive, providing solutions that address the increasingly complex needs of industries like aerospace, automotive, and electronics.
The continual push for sustainability and cost-efficiency will shape the future of circle cutting machines, as industries strive for greener, more efficient production methods. With innovations on the horizon, the next generation of circle cutting machines promises to be faster, smarter, and more reliable than ever before.
Adjustable Circle Cutter for Metal
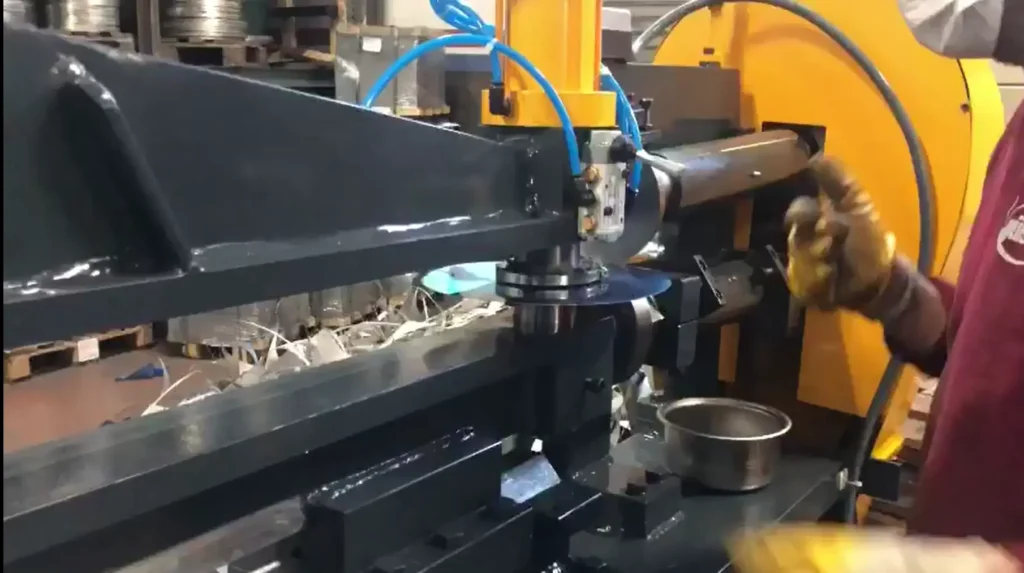
An adjustable circle cutter for metal is a specialized tool or machine used to cut precise circular shapes from metal sheets. This tool is particularly useful for industries that require accurate and efficient circular cuts in a range of sizes and material thicknesses. Adjustable circle cutters are often designed for use in sheet metal fabrication, HVAC manufacturing, automotive, and other sectors where round cuts are frequently needed.
Here’s an overview of the different types of adjustable circle cutters for metal, their features, and their applications:
1. Types of Adjustable Circle Cutters for Metal
a. Manual Adjustable Circle Cutters
- Design: These are often hand-held tools with a blade or rotary cutter that can be adjusted to cut different diameters. They typically consist of a pivoting arm, a cutting wheel, and a scalable ruler that allows the operator to set the diameter of the circle to be cut.
- Usage: Manual adjustable circle cutters are commonly used for small-scale, low-volume production and prototyping. They are useful for cutting metal sheets, plastics, and other materials with ease and accuracy.
- Adjustability: The diameter of the circle can be adjusted by changing the position of the pivot point or adjusting the cutting wheel’s position along the arm. The size of the circle is marked on a scale for quick reference.
b. CNC Adjustable Circle Cutting Machines
- Design: These are fully automated systems integrated with CNC (Computer Numerical Control) technology. They offer precise and adjustable circle cutting through laser, plasma, or waterjet cutting methods.
- Usage: Ideal for high-precision, high-volume production where different circle sizes need to be cut rapidly and accurately. CNC systems allow for programmable adjustments to cut circles of varying diameters with high consistency.
- Adjustability: Users can adjust the diameter of the circle via the machine’s control interface, enabling the cutting of various sizes without the need to manually reposition parts. The cutting tool can also be adjusted for different thicknesses and materials.
c. Rotary Adjustable Circle Cutters
- Design: These machines use a rotary blade that spins at high speed to cut circular shapes from metal. The adjustable part of the tool typically refers to a pivoting center or adjustable cutting radius.
- Usage: Rotary circle cutters are used for both manual and automated operations. In a manual setup, the operator adjusts the pivot point and uses the cutter to rotate around the fixed center. In automated setups, the machine controls the rotary cutter’s speed and radius.
- Adjustability: The cutter’s radius can be easily adjusted to change the diameter of the circle. The process involves rotating the cutter around a fixed point at the desired radius.
d. Hydraulic and Pneumatic Adjustable Circle Cutters
- Design: These types of cutters use hydraulic or pneumatic pressure to drive the cutting mechanism. The adjustable feature is typically related to the pressure control or the cutting head’s positioning, allowing different diameters to be cut by changing the settings.
- Usage: Hydraulic or pneumatic circle cutters are ideal for high-capacity operations in heavy industries such as construction, steel manufacturing, and metalworking. They provide fast cutting speeds and can handle large and thick metal sheets.
- Adjustability: The adjustability is managed through controls that regulate the cutter’s speed, pressure, and cutting size. The machine can be set to cut various circle sizes based on the material’s thickness and type.
2. Key Features of Adjustable Circle Cutters for Metal
a. Adjustable Cutting Radius
- The primary feature of an adjustable circle cutter is its ability to change the diameter of the circles being cut. This flexibility allows the user to create circles of various sizes without the need for additional tools or setups.
- Manual tools typically have a scale or gauge that lets the operator easily adjust the size, while CNC machines allow precise input through digital controls.
b. Durable Cutting Blades
- Circle cutters for metal typically feature durable, high-quality cutting blades, such as tungsten carbide or HSS (High-Speed Steel), capable of cutting through tough materials like steel, aluminum, copper, and stainless steel.
- These blades are designed to withstand heat and friction and maintain sharpness over time for consistent results.
c. Precision and Accuracy
- Precision is a key benefit of adjustable circle cutters, especially those integrated with CNC or laser cutting technologies. These systems can create circles with very tight tolerances, which is essential for industries where high-quality and repeatable cuts are required.
- Manual circle cutters also offer decent precision but are more suited for smaller, low-volume tasks or prototypes.
d. Ease of Use
- Adjustable circle cutters, especially manual models, are generally easy to use, requiring minimal setup and adjustment. The ability to quickly change the size of the circles and move between materials makes these tools convenient for various cutting tasks.
- CNC and robotic models, while more complex, offer greater automation, reducing the need for human intervention and enabling faster production times.
e. Versatility
- Many adjustable circle cutters can be used for a variety of metal types, including steel, aluminum, brass, and stainless steel, as well as for plastic, wood, and ceramics, depending on the type of cutting tool used (laser, plasma, or waterjet).
- These tools are highly versatile and can handle various thicknesses and material grades by simply adjusting the cutting parameters or settings.
3. Applications of Adjustable Circle Cutters for Metal
Adjustable circle cutters are used in several industries for various purposes, including:
a. Sheet Metal Fabrication
- In sheet metal fabrication, adjustable circle cutters are used to create round components for products such as air vents, flanges, circular covers, and gaskets. The adjustable cutting radius allows fabricators to work with materials of different thicknesses and sizes.
b. Automotive Manufacturing
- In the automotive industry, adjustable circle cutters are used to cut wheel rims, brake components, engine parts, and other circular metal components with high precision. These tools allow manufacturers to produce parts in large quantities with consistency.
c. HVAC Systems
- HVAC manufacturers use adjustable circle cutters to create ductwork and ventilation components. The ability to cut circular holes in various sizes is crucial for ensuring proper airflow and ventilation in buildings.
d. Aerospace Industry
- The aerospace industry demands precise circular cuts for parts such as engine components, circular fuselage sections, and rotor blades. Adjustable circle cutters can provide the level of accuracy needed for high-performance, high-stress components.
e. Signage and Custom Metal Products
- Companies that produce custom metal signs or decorative pieces also rely on adjustable circle cutters to create consistent, round shapes for their designs. The ability to adjust the cutting radius ensures that they can cater to various customer specifications.
f. Prototyping
- Adjustable circle cutters are invaluable in prototype development, where designers and engineers need to quickly create models with varying sizes, shapes, and materials. The flexibility of these cutters allows for rapid iteration and adjustments during the prototyping phase.
4. Considerations When Choosing an Adjustable Circle Cutter for Metal
a. Material Compatibility
- It’s essential to select a circle cutter that can handle the specific type of metal you plan to cut. Make sure the tool is compatible with the material in terms of cutting ability, blade hardness, and required precision.
b. Cutting Diameter Range
- Choose a cutter with a sufficient diameter range to meet your needs. The cutter should be able to produce the smallest and largest required circle sizes without compromising precision or cutting quality.
c. Machine or Manual Operation
- If you are looking for high-volume production, CNC-based or automated circle cutters may be the best choice, offering speed, precision, and minimal operator intervention. For low-volume, more cost-effective operations, manual or semi-automatic cutters may suffice.
d. Cutting Speed and Efficiency
- Depending on your production volume and time constraints, consider the cutting speed of the machine. Laser and plasma cutters are typically faster than manual models and can be more suitable for larger operations.
e. Maintenance Requirements
- Consider the ease of maintaining the cutter, especially if it is part of an automated system. CNC machines may require more regular calibration, while manual cutters are easier to maintain but may require blade replacements more frequently.
Conclusion
An adjustable circle cutter for metal is an essential tool for many industries that require precise and efficient circular cuts. Whether used in manual, CNC, or automated settings, these cutters offer flexibility in cutting various metal types and sizes, making them suitable for a wide range of applications. When choosing the right cutter, factors like cutting precision, material compatibility, and production volume should be considered to ensure that the cutter meets your specific needs.
5. Advanced Features in Adjustable Circle Cutters for Metal
Modern adjustable circle cutters, especially automated and CNC-driven models, are equipped with a variety of advanced features designed to improve performance, precision, and efficiency in metal cutting.
a. Automated Calibration and Setup
- Automated calibration systems are increasingly incorporated into CNC circle cutting machines. These systems allow the cutter to self-adjust and recalibrate according to the material thickness, type, and cutting radius, reducing human error and ensuring consistent cuts.
- Some machines come with automatic tool changers to switch between different cutting tools (e.g., from laser cutting to plasma), enhancing their versatility.
b. Cutting Head Tilting and Rotation
- Adjustable cutting heads allow for tilting and rotation of the tool to cut angled or beveled edges, which is useful when cutting cones, sloped designs, or curved components that go beyond simple circular cuts.
- Multi-axis CNC machines are particularly well-equipped with this feature, offering a high degree of flexibility and precision in complex cutting operations.
c. Water-Cooled Cutting Tools
- Some advanced laser and plasma circle cutters include water-cooled cutting heads to prevent overheating and maintain cutting efficiency over extended periods. This feature is especially useful in high-speed cutting operations, where the heat generated can cause tool wear and material distortion.
- The water-cooling system helps to keep the cutting tool and workpiece cool, improving both the quality of the cut and the longevity of the machine.
d. Integrated Material Handling Systems
- Many high-end CNC circle cutting machines come with integrated material handling systems. These systems automatically feed sheets of metal into the machine, hold them in place during the cutting process, and remove the finished parts after cutting.
- Automated material handling increases productivity and ensures that parts are accurately placed in the cutting zone, reducing errors related to manual loading and unloading.
e. Advanced Software and Control Interfaces
- Advanced software allows users to precisely control every aspect of the cutting process, including speed, feed rates, and cutting paths. Software packages are becoming increasingly user-friendly and intuitive, making the machines accessible to both seasoned professionals and new operators.
- Many systems also include simulation features that allow operators to visualize the cutting process before actual cutting begins, minimizing waste and material defects.
- Cloud connectivity is an emerging feature that allows users to monitor the machine remotely, access real-time data, and optimize the cutting process based on feedback from the machine.
6. Cutting Techniques for Adjustable Circle Cutters
The technique used to cut the metal often depends on the type of adjustable circle cutter in use. Below are the common cutting methods used with these machines:
a. Laser Cutting
- Laser cutting uses a focused laser beam to melt or vaporize metal. The high precision of fiber lasers and CO2 lasers makes them ideal for cutting detailed, intricate circles in metal sheets.
- Advantages: Laser cutting provides smooth edges, minimal distortion, and the ability to cut intricate patterns or small holes within a circular shape.
- Best suited for: Stainless steel, aluminum, and copper; ideal for thin materials and precision cuts.
b. Plasma Cutting
- Plasma cutting uses an electrically ionized gas (plasma) to melt the metal along a specific cut line. This method is widely used in cutting thicker materials, and is known for being fast and efficient.
- Advantages: Plasma cutters are faster and cost-effective for cutting thicker materials compared to lasers.
- Best suited for: Carbon steel, stainless steel, aluminum (up to 2 inches thick), and other non-ferrous metals.
c. Waterjet Cutting
- Waterjet cutting uses a high-pressure stream of water mixed with abrasive particles to cut through metal. This method is ideal for cutting thick materials and is often used when heat distortion needs to be avoided.
- Advantages: Waterjet cutters can handle a wide range of materials without causing thermal deformation or introducing mechanical stresses.
- Best suited for: Thicker materials, such as brass, titanium, copper, and alloys, and for applications where heat-affected zones (HAZ) must be avoided.
d. Oxy-Fuel Cutting
- Oxy-fuel cutting uses a combination of oxygen and fuel gases (typically acetylene or propane) to cut through metal by heating it to a temperature at which the metal burns in the presence of oxygen.
- Advantages: Oxy-fuel cutting is cost-effective and efficient for thicker metal cutting, especially in heavy industries such as shipbuilding and construction.
- Best suited for: Carbon steel and thick plate materials.
e. Mechanical Cutting (Rotary Cutters)
- Rotary cutting uses a rotating cutting wheel or blade to shear the metal along the desired circle. The adjustable center of the rotary cutter allows for different circle sizes to be created manually or automatically.
- Advantages: Mechanical cutters are suitable for simpler, lower-precision cuts and provide a cost-effective solution for smaller applications.
- Best suited for: Thin sheet metals and non-ferrous materials.
7. Maintenance Tips for Adjustable Circle Cutters
Maintaining an adjustable circle cutter is essential to ensure its longevity, precision, and reliability over time. Below are some key maintenance tips for different types of circle cutters:
a. General Maintenance
- Regularly clean the machine to remove metal debris, dust, and buildup that can affect cutting performance. Pay special attention to the cutting head, guides, and moving parts.
- Check alignment and calibration to ensure the cutting tool is properly aligned and provides accurate, consistent cuts. Misalignment can lead to errors in cutting circles, requiring additional setup time or material waste.
- Lubricate moving parts regularly, especially in mechanical systems, to reduce friction and prevent premature wear.
- Replace worn-out blades or cutting tips, as dull tools can lead to uneven cuts and longer cutting times.
b. Laser Cutting Maintenance
- Clean the lenses and mirrors frequently to ensure a clear beam path. Contamination or dirt buildup can degrade the quality of the laser cut.
- Check the gas supply (for CO2 lasers) to ensure it’s at the correct pressure and concentration for optimal cutting.
- Inspect the cooling system, as laser cutters often generate significant heat. Keeping the cooling system in good working condition helps avoid overheating and maintains cutting quality.
c. Plasma Cutting Maintenance
- Inspect the consumables (electrodes, nozzles, and swirl rings) regularly, as they wear out with use. Replacing these parts will ensure the plasma cutter operates at peak performance.
- Check the air supply to ensure it’s dry and clean. Moisture and contamination can affect the quality of the plasma cut and shorten the lifespan of the consumables.
- Ensure the torch height is properly calibrated to maintain a consistent cutting distance from the workpiece.
d. Waterjet Cutting Maintenance
- Monitor the pump pressure and cleanliness to avoid debris and buildup, which can affect the jet stream and cutting performance.
- Change abrasive materials periodically to ensure consistent cutting speeds and high-quality results.
- Flush the system to remove any residual material after each cutting session, ensuring there are no blockages in the nozzle or plumbing.
8. Considerations When Selecting an Adjustable Circle Cutter
When choosing an adjustable circle cutter for metal, here are several factors to consider:
a. Production Volume
- For high-volume production, you may want to invest in a CNC-based or automated circle cutting system to minimize manual labor and maximize speed. These machines are best suited for mass production of parts that require consistent precision.
- For low to medium volumes, a manual or semi-automatic circle cutter may suffice, offering flexibility and lower upfront costs.
b. Material Type and Thickness
- Consider the materials you plan to cut and their thicknesses. For instance, plasma cutters are effective for thick materials, while laser cutters excel at thin sheets with intricate designs. Waterjets work well for thick and hard-to-machine materials, like metals with heat sensitivity.
c. Cutting Precision
- The level of precision required will influence the type of cutter you choose. If you need to achieve tight tolerances for parts like aerospace components, a laser or CNC-based system may be the best choice. For general fabrication or prototyping, manual or rotary cutters may suffice.
d. Cutting Speed
- Speed may be a priority for some industries that need fast turnarounds. Laser and plasma cutters offer high-speed cutting, while waterjets tend to be slower but provide better quality for thicker materials.
Conclusion
An adjustable circle cutter for metal is a highly versatile tool, with applications spanning from small-scale manual cutting to advanced automated solutions for high-precision production. Understanding the different cutting techniques, advanced features, and maintenance needs of these machines will help you make informed decisions about which cutter is best suited for your specific needs. With continuous advancements in cutting technology, adjustable circle cutters are becoming more efficient, accurate, and user-friendly, enabling manufacturers to achieve better results faster and with lower costs.
9. Cutting-Edge Advancements in Adjustable Circle Cutters
Recent advancements in technology have made adjustable circle cutters more efficient, precise, and adaptable to a wider range of applications. Here are some of the cutting-edge features in today’s systems:
a. AI-Powered Optimization
- Artificial intelligence (AI) and machine learning (ML) are increasingly being integrated into circle cutting systems, especially those with CNC capabilities. These systems can learn from previous cutting patterns and automatically optimize parameters like cutting speed, pressure, and tool paths based on material types and thicknesses.
- Benefits: AI integration helps improve cut quality, reduce errors, and adapt to new materials quickly. It also enhances process efficiency by predicting wear and tear on parts and providing recommendations for maintenance before issues arise.
- Example: An AI-powered system could predict the exact time to switch out consumables like cutting tips, nozzles, or laser lenses, reducing downtime and preventing costly delays.
b. Hybrid Cutting Systems
- Hybrid cutting machines that combine different cutting technologies (like laser and plasma) are gaining popularity. These systems offer the flexibility to choose the most suitable cutting method based on material type, thickness, and desired cut quality.
- Example: A hybrid cutter might switch between plasma cutting for thicker materials and laser cutting for thinner, more detailed sections, improving overall productivity and material flexibility.
- Benefits: These systems enable faster production times, reduce waste, and optimize energy use by applying the right cutting method to the right part of the process.
c. Integrated 3D Modeling and Simulation
- Advanced CAD/CAM (Computer-Aided Design/Computer-Aided Manufacturing) software now allows operators to create 3D models of the parts to be cut. These models can be fed directly into CNC machines, which use them to guide the cutting process.
- Benefits: 3D modeling and simulation allow for preemptive troubleshooting, minimizing material wastage and ensuring that cuts are made exactly as planned. These systems also enable virtual prototyping, reducing the need for physical mock-ups and speeding up the design process.
d. High-Speed Laser Cutting (Femtosecond Lasers)
- The use of femtosecond lasers, which can fire pulses in the range of femtoseconds (quadrillionths of a second), allows for ultra-precise cutting without the heat-affected zones that traditional lasers might create.
- Benefits: This technology is particularly useful for cutting thin metals and delicate materials without causing thermal distortion or changes in material properties. It’s ideal for industries that require micro-level precision, such as electronics, aerospace, and medical device manufacturing.
10. Cost Considerations for Adjustable Circle Cutters
The cost of an adjustable circle cutter depends on several factors, including its cutting technology, size, complexity, and features. Understanding these costs will help in making an informed decision.
a. Initial Investment
- Manual and Semi-Automatic Cutters: These are generally less expensive, making them a good choice for smaller businesses or low-volume operations. They may cost anywhere from a few hundred to several thousand dollars, depending on the size and quality of the cutter.
- CNC and Automated Systems: High-end automated systems with laser, plasma, or waterjet cutting capabilities can cost significantly more, ranging from tens of thousands to several hundred thousand dollars. These systems are designed for high-volume production and can be a significant investment for large-scale manufacturers.
b. Operational Costs
- Energy Consumption: Different cutting technologies consume varying amounts of energy. Laser cutters, especially high-powered systems, tend to be energy-intensive, while plasma cutters and waterjets may have slightly lower energy requirements depending on the material and thickness being cut.
- Consumables: Consumables such as cutting tips, nozzles, laser lenses, and abrasives contribute to ongoing operating costs. The cost of replacing consumables can add up over time, particularly in high-volume operations.
- Maintenance: Regular maintenance is essential to keep adjustable circle cutters running smoothly. For CNC systems, there might be additional costs related to software updates, machine calibration, and technical support.
c. Return on Investment (ROI)
- While CNC and automated circle cutters have higher upfront costs, they can provide significant ROI in the long run due to faster cutting speeds, reduced labor costs, and the ability to produce high-precision parts consistently. Automated systems also minimize the chances of human error, which can lead to wasted material and costly mistakes.
- For smaller operations, manual circle cutters can provide a solid ROI by fulfilling basic cutting needs without the overhead of a large-scale automated system. However, the potential for higher labor costs and slower production may impact ROI over time.
11. Future Trends in Adjustable Circle Cutters for Metal
The future of adjustable circle cutters for metal is shaped by innovations in technology, materials, and process efficiency. Here are a few trends to watch for:
a. Increased Automation and Robotics
- The rise of robotic automation in manufacturing is transforming how circle cutting is done. Robots equipped with advanced vision systems and collaborative AI can work alongside human operators to handle material loading, unloading, and even adjusting cutting parameters based on real-time feedback from sensors.
- Benefits: Increased automation can reduce labor costs, improve safety by limiting human exposure to hazardous cutting operations, and boost overall productivity.
b. Cloud-Based Monitoring and Control
- Cloud technology is poised to play a major role in the future of circle cutting. Manufacturers can use cloud-based platforms to monitor machines in real-time, access data analytics, and even remotely control machines or diagnose problems.
- Benefits: Cloud integration allows for better data collection, predictive maintenance, and more responsive customer support. It enables manufacturers to optimize their operations across multiple sites.
c. Smart Machines and IoT Integration
- The integration of IoT (Internet of Things) into circle cutting machines is already underway. These machines are being equipped with sensors that can send real-time data to operators, alerting them to potential issues such as tool wear, material discrepancies, or machine faults before they lead to operational stoppages.
- Benefits: IoT integration leads to smart factories where machine downtime is minimized, parts are produced more efficiently, and quality is constantly monitored.
d. Sustainability and Eco-Friendly Manufacturing
- There’s a growing emphasis on eco-friendly practices in manufacturing, including minimizing material waste and energy consumption. For example, laser cutting can produce minimal waste compared to traditional cutting methods. Waterjet cutting produces zero hazardous fumes, and the waste material (abrasives) can often be recycled.
- Benefits: Companies that adopt sustainable cutting practices can reduce costs associated with waste disposal, improve their environmental footprint, and align with industry regulations and standards.
e. 3D Printing and Additive Manufacturing Integration
- As 3D printing continues to evolve, some industries are combining traditional circle cutting with additive manufacturing (AM). This allows for more intricate, multi-functional parts to be created through a combination of cutting and 3D printing processes.
- Benefits: Combining these technologies can reduce production time, improve design flexibility, and lead to innovative part geometries that would be impossible or extremely costly to achieve through conventional manufacturing methods.
12. Training and Skills for Operating Adjustable Circle Cutters
Operating an adjustable circle cutter, especially automated systems like CNC or laser cutters, requires specialized skills. Here’s an overview of the necessary training:
a. Machine Operation Training
- Operators need to understand how to set up, calibrate, and operate the machine effectively. This includes selecting the right cutting parameters, adjusting for different materials and thicknesses, and troubleshooting common issues.
- CNC and automated cutters require knowledge of G-code programming, which controls the machine’s movement and cutting actions. Training in programming is critical to ensure the system performs optimally.
b. Safety Protocols
- Operators should be well-versed in safety protocols related to cutting operations. This includes wearing protective gear, handling hazardous materials safely, and adhering to machine-specific safety procedures.
- Laser and plasma cutters pose particular risks, such as exposure to high-powered lasers, electrical hazards, and flying metal debris. Ensuring proper safety training can prevent workplace injuries.
c. Maintenance and Troubleshooting
- A good understanding of how to maintain the cutting tools, replace consumables, and troubleshoot common machine faults is essential. Regular hands-on training helps operators identify early signs of wear or malfunction and resolve issues before they lead to downtime.
d. Software and CAD/CAM Systems
- Knowledge of CAD/CAM software is increasingly important, especially for CNC and automated cutting systems. Operators need to be trained in using design software to import and optimize cutting plans.
- Simulation software is also vital for predicting cutting paths, ensuring efficiency, and avoiding material waste.
13. Energy Efficiency and Environmental Impact
a. Energy Consumption
- As energy prices continue to rise, manufacturers are looking for ways to reduce energy consumption. Laser cutting, plasma cutting, and waterjet cutting technologies are becoming more energy-efficient, with newer machines requiring less power to produce the same or better results.
- Benefits: Using energy-efficient machines reduces operational costs and helps meet sustainability goals.
b. Waste Reduction
- Efficient cutting systems like laser and waterjet cutters produce minimal waste, which is especially beneficial for expensive metals like titanium or copper. Additionally, advancements in automated material handling reduce the chances of error during material loading, cutting, and unloading.
- Recycling: Many modern systems support material recycling by using advanced collection systems to capture waste for reuse, contributing to reducing environmental impact.
Conclusion
The world of adjustable circle cutters for metal is rapidly advancing, driven by innovations in automation, AI, sustainability, and cutting technologies. Whether you’re focused on precision cutting, cost efficiency, or environmental responsibility, today’s systems offer impressive capabilities that help meet the needs of various industries. By staying informed about the latest trends and technologies, manufacturers can make smarter investments in their cutting equipment, optimize operations, and reduce costs while enhancing product quality and sustainability.
As adjustable circle cutters continue to evolve, there’s a growing focus on improving automation and increasing machine intelligence. One of the key developments in this space is the rise of AI-driven systems. These systems use machine learning algorithms to analyze past cutting data, optimizing parameters like cutting speed, pressure, and even tool paths. Over time, the system “learns” the optimal settings for different materials, cutting geometries, and thicknesses, providing not only better precision but also reducing material waste and energy consumption. Additionally, these systems can predict maintenance needs, identifying parts that are likely to wear out before they cause downtime.
Another significant trend is the integration of hybrid cutting technologies. These systems combine multiple cutting methods, such as laser and plasma or plasma and waterjet, to achieve better results. For example, a system might start cutting a thick metal sheet with plasma to quickly remove the bulk of the material, and then switch to a laser for finer, more detailed cutting. This adaptability makes hybrid systems highly efficient, especially in industries where a mix of materials and cutting precision is needed.
The advent of 3D modeling and simulation software has also changed how manufacturers approach circle cutting. With these tools, it’s possible to visualize the entire cutting process in a virtual environment before the machine ever touches the material. This preemptive step not only helps in detecting potential errors but also allows operators to optimize the cutting pattern, minimizing waste. These innovations in software, paired with advanced CNC systems, enable manufacturers to push the boundaries of what’s possible in terms of cutting complexity and accuracy.
From an operational standpoint, the importance of operator training cannot be overstated. As circle cutters become more advanced, there’s a greater need for skilled professionals who understand both the machine’s hardware and the associated software. Operators must be familiar with not just the basic machine setup but also how to interpret the data provided by smart systems. This includes understanding how AI optimization works and how to tweak settings for non-standard or complex materials. Additionally, the ability to troubleshoot and repair cutting tools, such as laser heads, nozzles, or abrasives, is a critical skill that ensures minimal downtime.
The financial side of investment is another important consideration. While the initial cost of high-tech systems may be prohibitive for smaller operations, the long-term benefits—such as increased cutting speed, precision, and lower material wastage—can make the investment worthwhile. Businesses should carefully assess their needs, production volumes, and the materials they work with before committing to a particular cutting method. For some, a semi-automatic cutter might be sufficient, while others may benefit more from fully automated systems.
Sustainability is becoming an increasingly important factor in the choice of equipment. Many of the latest circle cutting machines are designed to minimize energy use and reduce environmental impact. For example, waterjet cutters are known for their zero-emission operation, producing no harmful fumes or gases, making them ideal for industries with strict environmental regulations. Laser cutting, on the other hand, is highly efficient in terms of energy use, particularly with fiber lasers, which consume less power while maintaining high cutting speeds and quality.
Finally, as robotic automation becomes more common in manufacturing, circle cutters are increasingly integrated into automated systems for larger-scale production. Robots equipped with vision systems can handle materials, monitor the cutting process in real-time, and even make adjustments on the fly, ensuring the highest quality cuts while reducing labor costs and improving safety. These robotic systems are particularly useful for high-volume production environments, where consistency and speed are paramount.
In conclusion, the landscape of adjustable circle cutters is rapidly changing, driven by advancements in automation, AI, hybrid technologies, and sustainability. These innovations allow manufacturers to not only improve their cutting capabilities but also reduce costs, increase production speed, and meet environmental standards. As the technology continues to evolve, it will be important for businesses to stay updated on new developments, training programs, and cost-benefit analyses to make informed decisions about which systems best suit their specific needs.
EMS Metalworking Machinery
We design, manufacture and assembly metalworking machinery such as:
- Hydraulic transfer press
- Glass mosaic press
- Hydraulic deep drawing press
- Casting press
- Hydraulic cold forming press
- Hydroforming press
- Composite press
- Silicone rubber moulding press
- Brake pad press
- Melamine press
- SMC & BMC Press
- Labrotaroy press
- Edge cutting trimming machine
- Edge curling machine
- Trimming beading machine
- Trimming joggling machine
- Cookware production line
- Pipe bending machine
- Profile bending machine
- Bandsaw for metal
- Cylindrical welding machine
- Horizontal pres and cookware
- Kitchenware, hotelware
- Bakeware and cuttlery production machinery
as a complete line as well as an individual machine such as:
- Edge cutting trimming beading machines
- Polishing and grinding machines for pot and pans
- Hydraulic drawing presses
- Circle blanking machines
- Riveting machine
- Hole punching machines
- Press feeding machine
You can check our machinery at work at: EMS Metalworking Machinery – YouTube
Applications:
- Beading and ribbing
- Flanging
- Trimming
- Curling
- Lock-seaming
- Ribbing
- Flange-punching