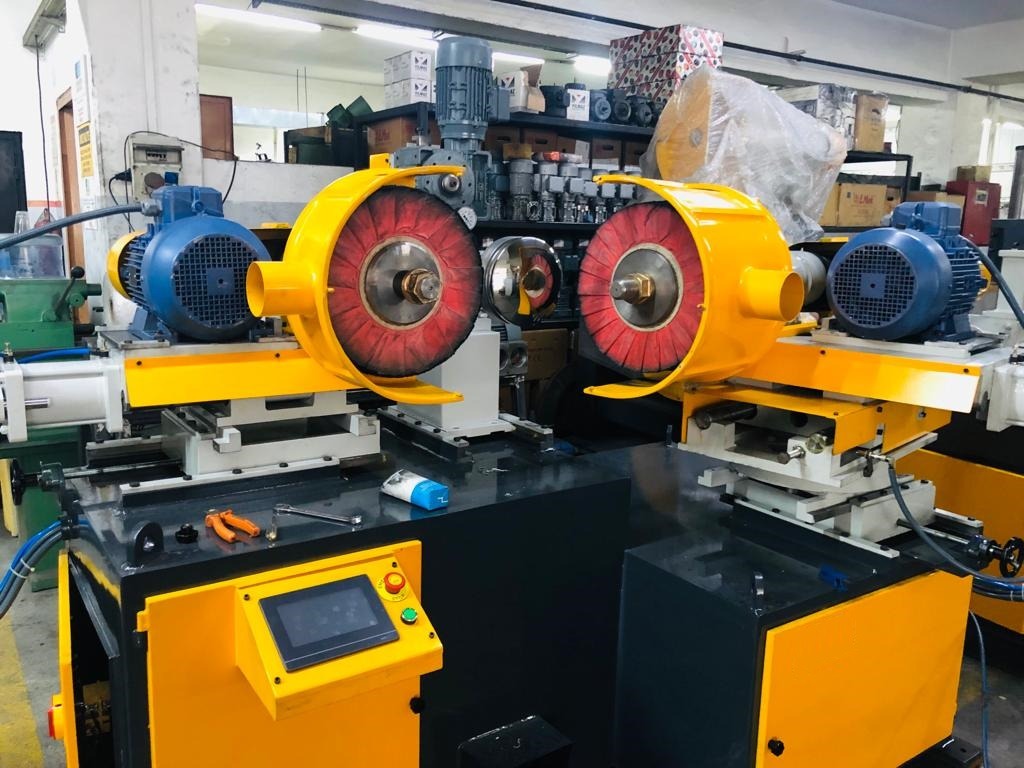
Rotary Buffing Machine: A Polishing and Buffing Combo Machine combines two surface-finishing functions—polishing (removing surface imperfections and achieving a smooth texture) and buffing (enhancing surface gloss and shine)—into a single machine.
Key Components of Polishing and Buffing Machine
- Motor – Powers the rotating wheels, typically ranging from 0.5 to 2 HP depending on application.
- Polishing Wheel – Often made of abrasive materials like emery or silicon carbide, used for initial surface refinement.
- Buffing Wheel – Softer wheels made of cloth, felt, or other flexible materials, used with buffing compounds for shine.
- Work Rest/Support – Provides a platform to steady the workpiece.
- Speed Control (optional) – Allows for variable RPM to suit different materials and finishing stages.
- Dust Collector or Ports (optional) – Helps manage debris and metal dust during operation.
Applications
- Metalworking: Removing rust, smoothing welds, and bright finishing on stainless steel, brass, aluminum, etc.
- Woodworking: Polishing lacquered or painted wood surfaces.
- Jewelry Making: Precision polishing of fine metal items.
- Automotive: Chrome and aluminum trim restoration.
- Plastics and Composites: Edge polishing and surface refinishing.
Advantages
- Space Saving: One unit handles both polishing and buffing.
- Cost-Effective: Eliminates the need to purchase two separate machines.
- Increased Productivity: Enables quick change between operations.
A polishing and buffing combo machine is designed to handle both the initial surface smoothing (polishing) and the final high-gloss finishing (buffing) in a single unit. This type of machine typically features two spindles or shafts, each mounted with a different wheel—one abrasive polishing wheel and one softer buffing wheel made of cloth or felt. The machine is powered by an electric motor, often in the range of 0.5 to 2 horsepower, and may operate at fixed or variable speeds depending on the model. Operators use the polishing wheel to remove oxidation, scratches, or casting marks from metal, plastic, or wood surfaces. Once the desired smoothness is achieved, the workpiece is moved to the buffing wheel, often with an applied buffing compound, to bring out a mirror-like finish. These machines are commonly used in metal fabrication, automotive detailing, woodworking, jewelry making, and plastic finishing. Some models are equipped with safety features like spark guards, adjustable tool rests, and dust collection ports to enhance usability and maintain a clean workspace. Combo units are favored for their efficiency, cost-effectiveness, and the convenience of switching between two essential finishing operations without changing equipment.
Many polishing and buffing combo machines are bench-mounted, making them compact and suitable for workshops with limited space. Industrial-grade models may also be floor-mounted for handling larger or heavier workpieces. The choice of wheel materials and compounds plays a crucial role in achieving specific results—coarse abrasives for heavy material removal during polishing, and finer compounds like rouge or tripoli for delicate buffing tasks. Some machines allow quick wheel changes, which adds flexibility when working on different materials such as aluminum, stainless steel, brass, or even acrylics. Consistent maintenance, such as checking wheel wear and ensuring proper alignment, extends the machine’s life and ensures uniform surface finishes. Proper operator training is essential to avoid issues like over-polishing, which can deform soft metals, or under-buffing, which leaves dull surfaces. Overall, these combo machines provide a streamlined, dual-function approach to surface finishing that saves time and improves productivity across a variety of industries.
In practical use, the polishing and buffing combo machine becomes an integral part of any workshop that deals with surface refinement, whether in fabrication, restoration, or decorative finishing. When a raw or semi-finished part is introduced to the machine, it often carries imperfections such as tool marks, scale, oxidation, or general roughness from casting or machining. The first step is polishing—this is not just about aesthetics but also about preparing the surface for coating, plating, or further mechanical processing. The polishing wheel, usually embedded with abrasive particles or paired with an abrasive compound, cuts into the surface lightly to smooth out these defects. Depending on the material being worked on, wheels may vary from hard rubberized abrasives to cloth-based flaps loaded with cutting compounds.
Once the surface is polished to a uniform level of smoothness, the operator transitions to the buffing side of the machine. Buffing is a more delicate, finishing process aimed at producing a high-gloss, mirror-like shine. It uses soft, pliable wheels—often made from cotton, muslin, or felt—and relies on fine buffing compounds, which can range from brown tripoli for pre-polishing to white rouge or green chrome oxide for final finishing. The operator must be skilled in applying the right amount of pressure and compound to avoid burn marks, streaks, or surface inconsistencies. In many industries, this high-quality finish is not just for appearance—it reduces friction, enhances corrosion resistance, and in some cases, meets critical tolerance requirements for high-performance components.
The machine’s design often includes a solid base to minimize vibration, ensuring steady and safe operation. Some higher-end models come with variable speed controls, allowing the user to adjust the RPM to match the specific task. Lower speeds are ideal for buffing delicate materials, while higher speeds can be used during the polishing stage for quicker material removal. Safety considerations are also crucial—spark guards, eye shields, and even integrated vacuum ports for dust and particulate extraction are common in industrial setups. Metal polishing and buffing generate fine particles and heat, so proper ventilation and personal protective equipment (PPE) are essential for long-term use.
What truly sets the polishing and buffing combo machine apart from separate tools is its ability to streamline workflow. In production settings where throughput and finish quality must be balanced, having both functions integrated into a single station allows operators to move seamlessly from surface preparation to final finishing. This not only reduces equipment cost and space requirements but also cuts down on handling time, which in turn improves consistency and productivity. For small workshops, artisans, or businesses that work with metals, plastics, wood, or composite materials, this machine becomes a core asset—capable of delivering professional-grade finishes on everything from industrial parts to custom-crafted jewelry or automotive components.
Polishing and Buffing Combo Machine
A Polishing and Buffing Combo Machine is a dual-purpose finishing tool designed to perform both polishing and buffing tasks using a single unit. It is widely used in workshops, manufacturing plants, fabrication facilities, automotive garages, and artisan studios where surface treatment is essential. The machine typically features two opposing spindles mounted on a shared motorized base—one side dedicated to polishing, and the other for buffing. This allows the user to transition quickly between the two processes without changing tools or workstations, significantly increasing efficiency and convenience.
In polishing, the goal is to remove surface imperfections such as scratches, oxidation, or tool marks by using an abrasive wheel or polishing compound. This process is aggressive compared to buffing and is usually the first step in surface preparation. Polishing wheels are typically made from harder materials like sisal, impregnated cloth, or synthetic abrasives. They can be combined with various grits of abrasive paste depending on the material being worked—whether it’s steel, aluminum, brass, plastic, or even wood.
Buffing follows polishing and serves as a finishing process. It’s more refined and aims to produce a high-gloss, reflective surface. Buffing wheels are softer, usually constructed from multiple layers of muslin, cotton, or felt. They’re used with buffing compounds—fine, wax-like substances that smooth and brighten the surface without removing significant material. Popular buffing compounds include white rouge (for light metals), green compound (for stainless steel), and red jeweler’s rouge (for soft, precious metals). Proper buffing not only enhances the visual appeal of a component but also improves surface characteristics such as corrosion resistance and cleanliness.
The motor driving the machine typically ranges from 0.5 HP to 2 HP depending on application requirements. Some models are single-speed, while more advanced machines offer variable speed control, which is crucial when switching between materials that require different surface treatments. High RPMs are ideal for aggressive polishing, while lower speeds are safer and more effective for delicate buffing operations.
Modern combo machines often include safety features such as spark guards, eye shields, and non-slip bases. Dust extraction ports or attachments for vacuum systems may also be present, especially in industrial models, as both polishing and buffing generate fine dust and debris that must be controlled to protect both the operator and nearby equipment. Additionally, adjustable tool rests are usually provided to support the workpiece during operation and reduce operator fatigue during extended use.
From a functional perspective, the polishing and buffing combo machine is a highly efficient solution for anyone needing to process metal, plastic, or wood components to a refined finish. It is valued not just for its space-saving design but for its ability to provide consistent and high-quality results. Industries that benefit from this machine include metal fabrication, automotive restoration, aerospace, woodworking, jewelry production, and even consumer electronics repair. Its versatility makes it one of the most practical finishing machines in any multi-material workshop.
The polishing and buffing combo machine continues to stand out in industrial and artisan settings due to its adaptability, ease of use, and the quality of surface finish it can provide. In a typical workflow, operators appreciate the seamless transition from polishing to buffing without the need to interrupt their process or reposition the workpiece between machines. This uninterrupted workflow not only saves time but also helps maintain uniformity in finish, especially on pieces that require consistent surface characteristics across multiple faces or parts. For example, in automotive restoration, chrome parts like bumpers or trim are often polished to remove pitting or discoloration before being buffed to a mirror-like shine. Similarly, in metal fabrication shops, welders and machinists use combo machines to clean up weld seams or machined surfaces before final finishing, enhancing both appearance and performance of the component.
The machine’s effectiveness depends heavily on the choice of wheel and compound combinations. For instance, a coarse polishing wheel combined with a heavy-cut compound is ideal for removing deep scratches or oxidation on hard metals like stainless steel, while a soft buffing wheel with a fine rouge compound is better suited for bringing out a reflective finish on softer materials such as aluminum or gold. Knowing how to match the right wheel, compound, and speed to the material is essential for achieving professional results. This level of control becomes especially valuable in fields like jewelry making or precision engineering, where surface quality has both aesthetic and functional importance.
Beyond its operational features, the polishing and buffing combo machine also contributes to workplace efficiency by consolidating two essential finishing functions into one compact footprint. This is particularly beneficial in smaller workshops where space and budget may not allow for multiple standalone machines. It reduces setup time, minimizes movement between tools, and simplifies maintenance routines, as the user only has to service one motor and one frame. In terms of durability, most commercial-grade combo machines are built with heavy-duty cast iron or steel housings, sealed bearings, and industrial-grade motors to withstand long hours of continuous use. These rugged designs are crucial in production environments where downtime can be costly.
Operator safety and ergonomics are also important considerations in the design and use of these machines. Since both polishing and buffing produce dust, heat, and sometimes sparks, machines are often equipped with shrouds or guards to contain debris, and many allow connection to external dust collection systems. Proper lighting, workpiece support, and non-slip bases also contribute to safer operation. Users are typically trained to wear protective gear, including safety glasses, gloves, and sometimes respirators, particularly when working with fine powders or toxic materials.
Overall, the polishing and buffing combo machine represents a balance of power, precision, and practicality. Whether used for industrial part finishing, fine metalwork, or decorative surface treatment, it provides a reliable and versatile solution that meets the needs of both high-volume operations and custom fabrication shops. Its dual-functionality not only enhances workflow and finish quality but also offers a smart investment for those seeking long-term value and consistent performance in surface finishing tasks.
In continuous operation, the polishing and buffing combo machine plays a critical role in quality assurance, especially where visual appeal and surface integrity are directly tied to product value. This is particularly evident in industries such as aerospace, medical device manufacturing, and high-end consumer goods, where even minor surface flaws can disqualify a part from being accepted. The machine allows for close control over the finishing process, which is vital in environments that demand tight tolerances and repeatable results. By adjusting variables like wheel hardness, compound abrasiveness, motor speed, and pressure applied, skilled operators can fine-tune the outcome to meet highly specific standards. The versatility of the machine extends further when additional accessories are introduced—such as tapered spindles for quick wheel changes, flexible shaft attachments for precision detailing, or specialized jigs for handling complex geometries and delicate parts.
From an economic standpoint, this machine offers both direct and indirect benefits. Directly, it reduces capital expenditure since a single unit performs two processes. Indirectly, it enhances labor productivity by reducing idle time between stages of surface preparation. A worker using a combo machine can complete more parts per hour compared to setups that require moving between separate stations or waiting for other machines to become available. Furthermore, as this tool becomes a central part of production flow, it can be easily incorporated into lean manufacturing systems or continuous improvement programs. The consistency it delivers allows for more accurate scheduling, fewer reworks, and higher customer satisfaction due to the improved finish quality of the end product.
The machine’s relevance also extends into educational and training environments. In technical schools, vocational programs, and maker spaces, combo machines are often used to teach students the fundamentals of surface finishing. Because they combine two essential techniques, they allow learners to understand the complete process flow—from material preparation to final polish—without needing a suite of equipment. This helps build foundational skills while encouraging safe and efficient work habits. Students can experiment with different materials and finishes, gaining insight into how small adjustments in speed, pressure, or compound can lead to dramatically different results. These lessons are invaluable for future careers in machining, fabrication, restoration, and design.
In artisan and craft settings, particularly among metal sculptors, custom knife makers, or furniture builders, the polishing and buffing combo machine becomes a creative tool as much as a technical one. Here, surface finish is not just about function or standardization—it’s part of the product’s identity. Whether aiming for a soft satin sheen on a wooden edge, a deep reflective polish on a custom blade, or a subtly aged patina on a brass fixture, this machine supports a wide range of artistic expressions. The ability to switch quickly between aggressive material removal and delicate final touches allows artisans to bring their visions to life with both efficiency and craftsmanship.
Over time, the durability of the combo machine pays off. With proper maintenance—such as regular cleaning, lubrication of moving parts, replacement of worn wheels, and occasional motor servicing—it can last for decades, becoming a reliable fixture in the workshop. Many users even customize or upgrade their machines with aftermarket parts like extended shafts, upgraded motors, or precision rests to better suit their specific workflow. This adaptability, combined with its dual-purpose design, cements the polishing and buffing combo machine as an enduring staple in both industrial and creative environments.
Angle Buffing Machine
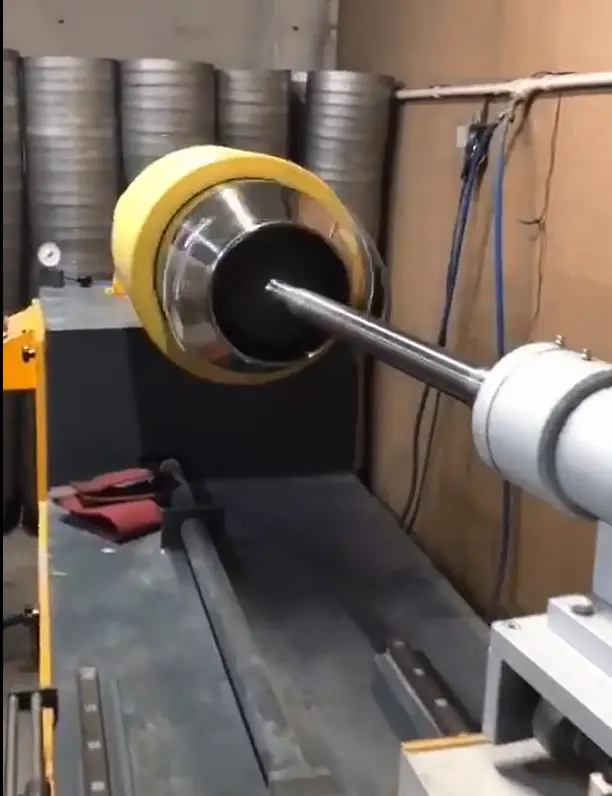
An Angle Buffing Machine is a specialized power tool designed for polishing and buffing surfaces using a rotating abrasive or soft wheel mounted at a right angle to the motor shaft. Unlike standard bench-top or straight-shaft polishing tools, the angle buffing machine features a compact, angled head that allows operators to work on vertical, contoured, or hard-to-reach surfaces with greater control and flexibility. It’s widely used in automotive detailing, metal fabrication, construction, shipbuilding, and maintenance work where surface refinement must be performed in tight or awkward spaces.
The tool resembles an angle grinder in form and function but is optimized for polishing and buffing rather than cutting or grinding. Most models are handheld and powered either electrically or pneumatically. The head, usually set at 90 degrees to the body, holds a spindle or arbor onto which various buffing pads, wool bonnets, foam discs, or abrasive flap wheels can be attached using quick-change systems or threaded mounts. The rotation of the head combined with the angled configuration allows the user to apply consistent pressure across uneven or vertical surfaces such as car panels, stainless steel tanks, pipes, weld seams, and even interior corners of fabricated structures.
The motor in an angle buffing machine typically operates between 1,000 and 3,000 RPM, and many models offer variable speed control to suit different materials and compounds. Lower speeds are essential when working with heat-sensitive surfaces like plastics or paint, while higher speeds may be used for tougher polishing jobs on metal. The tool is often equipped with ergonomic handles, trigger locks, and soft starts for safety and comfort during prolonged use.
Angle buffing machines can be paired with a variety of buffing compounds depending on the material and desired finish—coarse compounds for initial polishing, and finer rouges for high-gloss buffing. In automotive use, for example, detailers use these machines with foam pads and polishing compounds to remove swirl marks, oxidation, and light scratches from painted surfaces. In marine and industrial environments, they are essential for cleaning and restoring stainless steel, aluminum, or coated surfaces subjected to harsh weather and chemicals.
Their portability and versatility make angle buffing machines ideal for on-site work, touch-ups, or maintenance tasks where bench machines are impractical. With proper training and care, they deliver professional-level finishes and are a key tool for anyone working in surface restoration or finishing.
The angle buffing machine continues to be a crucial tool in both professional and hobbyist settings where precision surface finishing is required in challenging or confined spaces. Its right-angle head configuration makes it especially useful for working on irregular geometries, edges, vertical planes, and interiors of structural components where straight or bench-mounted machines cannot reach effectively. For instance, in automotive refinishing, the angle buffing machine is commonly used on contoured body panels, bumpers, and tight areas around mirrors or trim, providing smooth transitions and high-gloss finishes without risking damage to surrounding parts. The angled design also makes it easier to maintain a steady polishing line across vertical surfaces, which is difficult to achieve with flat tools or orbital polishers.
Because it is a handheld tool, operator skill plays a significant role in the final finish quality. Users must learn to apply consistent pressure and maintain the correct angle and movement pattern to avoid issues such as holograms, swirl marks, or overheating of the surface. Variable speed control is an important feature in this context, as it allows the operator to tailor the machine’s performance to the material and stage of the buffing process. Lower speeds may be used to spread compound evenly or to perform finishing passes, while higher speeds are more appropriate for cutting back oxidation or leveling minor scratches. The use of speed-adjustable machines also minimizes the risk of burning through paint or soft coatings, which is a common concern with fixed-speed tools.
The range of attachments available for angle buffing machines adds to their versatility. Depending on the application, users can switch between wool pads for aggressive compounding, foam pads for fine polishing, or microfiber heads for ultra-fine finishing. In metalwork, users might employ abrasive non-woven discs to clean welds or remove oxidation before switching to cloth buffing wheels for a polished shine. The ability to swap out heads quickly means that a single tool can handle multiple stages of finishing without interruption. This modularity makes it highly efficient for professionals who need to maintain productivity while achieving superior surface quality.
In industrial environments such as shipbuilding, railcar fabrication, or pipeline maintenance, angle buffing machines are used to prepare metal surfaces for coating or inspection. Surfaces like aluminum bulkheads, steel hulls, or stainless steel piping require a specific degree of smoothness and cleanliness to meet technical and safety standards. The portability of the angle buffing machine allows technicians to move easily across large structures and perform work directly on-site, reducing the need for disassembly or transport of heavy components. This mobility is also valuable in maintenance settings, where equipment may need to be refurbished or retouched in place, such as in HVAC systems, tanks, or heavy machinery frames.
In more delicate or artistic applications, like musical instrument restoration or architectural metalwork, the angle buffing machine enables highly controlled work on complex or ornamental surfaces. The operator can carefully maneuver the tool around curves, ridges, or recesses to remove tarnish, smooth seams, or enhance luster without flattening detail or causing damage. Artists, conservators, and custom fabricators often rely on the angle buffing machine for this level of tactile precision, as it bridges the gap between coarse grinding tools and fine hand polishing.
Durability and ergonomics are key to long-term use, especially in professional settings where the tool might run for hours at a time. High-quality angle buffing machines are built with reinforced gear housings, sealed bearings to resist dust and moisture, and insulated motors that can handle continuous duty without overheating. Ergonomic design features such as vibration-dampening handles, compact head profiles, and lightweight body construction contribute to reduced user fatigue and more stable handling. Safety features, including soft-start mechanisms, electronic overload protection, and adjustable guard systems, are becoming standard in modern models, enhancing both usability and operator protection.
Ultimately, the angle buffing machine is not just a convenience but a necessity for any work environment that demands consistent, high-quality finishes in complex or confined spaces. Its combination of power, portability, and precision makes it a go-to solution across industries—from car detailing and metalworking to marine maintenance and fine craftsmanship. With proper technique, maintenance, and selection of accessories, it delivers professional-level results that rival more stationary equipment, while offering unmatched flexibility and control. Would you like recommendations on specific models or guidance for selecting pads and compounds for a certain type of material or finish?
As the demand for surface perfection continues to rise across industries, the angle buffing machine is becoming increasingly refined in terms of technology, materials, and performance features. Manufacturers now offer machines with digital speed displays, programmable settings, and intelligent load sensors that adjust torque output based on the resistance encountered during use. These features enhance both the precision and safety of the tool, especially in environments where surface finish standards are tightly regulated, such as aerospace or medical manufacturing. Digital control also allows more consistent performance over extended polishing sessions, reducing the variability that can occur due to operator fatigue or changing surface conditions.
Cordless versions of angle buffing machines have also emerged, thanks to advancements in lithium-ion battery technology. These portable units give users full freedom of movement without sacrificing much in terms of power or run time. In field maintenance, such as on wind turbines, large vehicles, or outdoor pipelines, this mobility can be crucial. While corded machines still dominate in terms of continuous heavy-duty use, cordless versions are gaining ground rapidly, especially in situations where convenience, accessibility, or safety (e.g., avoiding tripping hazards) are primary concerns.
The environmental and workplace health aspects of buffing and polishing are also gaining attention. Angle buffing machines often operate in environments where dust, metal particles, or compound residue are released into the air. These fine particulates pose both respiratory and cleanliness challenges. As a result, many industrial users now integrate dust shrouds, attach vacuum hoses, or work within ventilated booths. Proper personal protective equipment—including respirators, eye protection, gloves, and hearing protection—becomes essential, especially during extended use. Additionally, the compounds used with these machines have evolved to include water-based or low-residue formulas that are safer for the operator and easier to clean from the finished surface.
From a training perspective, the angle buffing machine is relatively easy to learn, but mastering it takes time. Novices often start with practice panels or scrap pieces to develop a feel for the right pressure and motion. Over time, skilled users learn to “read” the sound, vibration, and visual cues from the tool and the workpiece, adjusting their technique instinctively. For companies training multiple employees, this consistency in results becomes critical to maintaining product quality. Some manufacturers now offer training programs, demo units, and even simulator-based systems to accelerate the learning curve and improve safety.
Repair and maintenance of angle buffing machines are generally straightforward. Most models are designed with accessible brush housings, gearboxes, and motor components, making it possible to replace worn parts like carbon brushes, bearings, or power cords without sending the unit out for service. Keeping the machine clean—especially the spindle and venting system—is essential to maintaining its lifespan. If the machine becomes unbalanced due to uneven pad wear or misalignment, it can cause excessive vibration and reduced control, so regular inspection is a good practice. For industrial users, establishing a preventative maintenance routine helps ensure uptime and extends the life of both the machine and consumables.
In terms of innovation, some angle buffing machines are now incorporating orbital motion in addition to rotary action, blending the benefits of rotary and dual-action polishers. This hybrid movement reduces the risk of heat buildup and surface swirl, making the tool more forgiving for users and safer for delicate finishes like clear coats or polished plastics. These tools are especially popular in detailing and finishing work where surface perfection is critical but the risk of overworking an area must be minimized. They represent a natural evolution of the traditional angle buffing machine, pushing the limits of what’s possible with a handheld surface finishing tool.
The longevity and relevance of the angle buffing machine ultimately stem from its ability to adapt to new materials, new processes, and evolving user needs. Whether in the hands of a seasoned professional restoring a classic car, a technician polishing a turbine blade, or an artist finishing a hand-crafted sculpture, this tool continues to offer a blend of control, power, and versatility that few others can match. It remains a bridge between raw fabrication and final presentation, turning unfinished surfaces into polished, functional, and often beautiful results. Would you like to go into detail about compound selection for specific finishes or how to adapt the machine for curved or textured surfaces?
Polishing Cabinet Buffing Machine
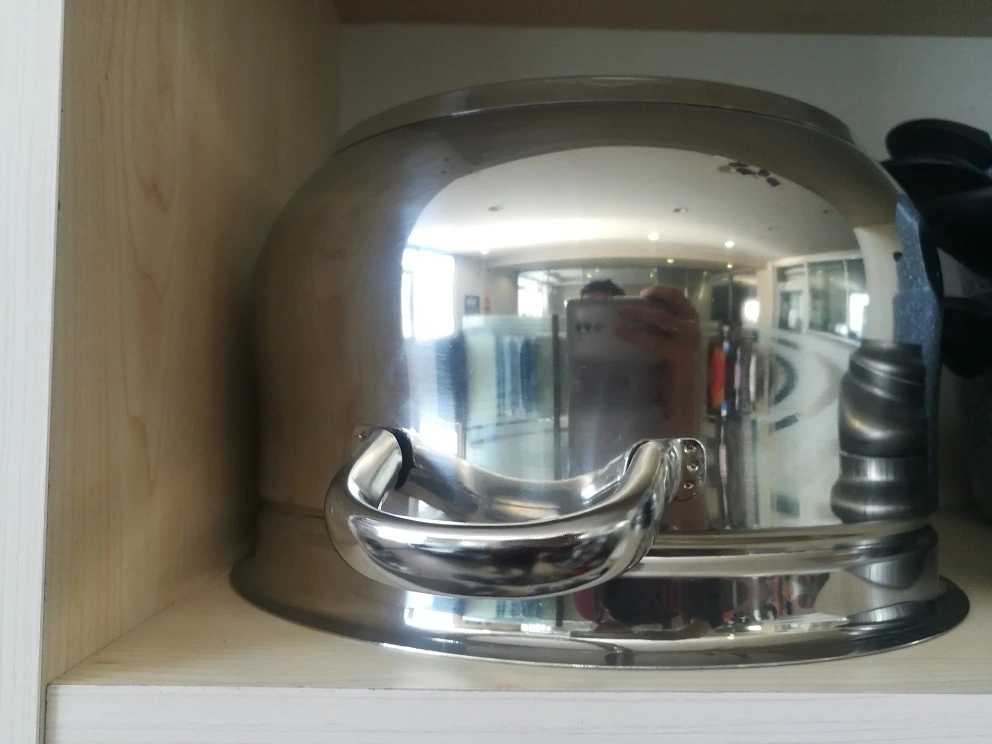
A Polishing Cabinet Buffing Machine is a specialized equipment designed to facilitate safe, controlled, and efficient polishing and buffing operations within an enclosed space. These machines typically consist of a cabinet or booth where the polishing and buffing processes take place, often equipped with one or more buffing wheels, abrasive pads, or brushes, a motor, and integrated systems for dust collection. They are commonly used in industries that require precise surface finishing of small to medium-sized components, such as jewelry manufacturing, electronics, metalworking, and automotive detailing. The primary advantage of a polishing cabinet buffing machine lies in its enclosed design, which helps contain debris, reduces exposure to hazardous materials, and minimizes environmental contamination.
The cabinet typically features transparent viewing panels made from durable acrylic or tempered glass, allowing the operator to monitor the workpiece while maintaining a safe distance from the moving parts. The interior of the cabinet is equipped with buffing wheels or abrasive pads mounted on motor-driven spindles, which rotate at varying speeds depending on the model. These spindles can accommodate different sizes and types of buffing wheels, ranging from coarse to fine materials such as wool, cotton, or felt, which are ideal for different stages of the polishing process. In many cases, the user can switch between polishing and buffing wheels to progressively refine the surface finish, from initial material removal to high-gloss final polish.
A key feature of the polishing cabinet buffing machine is its integrated dust and fume extraction system. Polishing and buffing generate fine dust and debris, particularly when working with metals like aluminum or stainless steel, or with certain composites. These particles can pose health risks when inhaled or cause a mess in the workplace. To mitigate this, polishing cabinet machines are equipped with powerful suction fans or vacuum systems that remove airborne particles from the cabinet, funneling them into filters or external collection bins. This feature is essential for maintaining a clean, safe working environment, especially in compliance with workplace health and safety standards.
These machines are typically designed for ease of use, with access doors or glove ports allowing the operator to insert their hands into the cabinet without opening it, thus maintaining a sealed environment. Glove ports enable precise control over the workpiece, and the compact design of the machine helps in controlling the work area’s lighting and dust levels. The interior often includes adjustable shelves or tool supports, providing convenience for setting the workpiece at the ideal height and angle for the operator.
The buffing cabinet is typically made of sturdy metal, such as steel or aluminum, to provide durability and stability during operation. Some higher-end models also include advanced features like built-in lighting, vibration-dampening components, and optional accessories such as polishing compounds or sprays, which can be applied directly to the workpiece while it is being buffed. These compounds can further enhance the polishing process, especially when working with materials that require a high-gloss finish, such as precious metals, glass, or acrylics.
The polishing cabinet buffing machine is especially valuable in high-precision fields where surface finish quality is critical. In jewelry manufacturing, for example, these machines allow for a meticulous, controlled polishing process that produces a flawless shine on rings, necklaces, bracelets, and other pieces without damaging the delicate details. In automotive applications, such as buffing chrome trim or headlight lenses, the cabinet helps achieve an even, smooth finish that enhances the appearance of the part while also providing a layer of protection against oxidation.
Overall, a polishing cabinet buffing machine provides a controlled, efficient, and safe solution for precision polishing and buffing tasks. The enclosed design ensures both safety and cleanliness, while the versatility in buffing wheel and compound options allows the user to adapt the machine for different materials and finishes. Its application spans a wide range of industries, making it an essential tool for professionals seeking high-quality surface finishes in a secure, effective manner.
The polishing cabinet buffing machine remains an essential tool in environments where precise, high-quality finishes are required. Its enclosed nature offers distinct advantages, not only for the operator’s safety but also for maintaining consistency and cleanliness in the workspace. The ability to control the working environment inside the cabinet makes it easier to handle intricate parts and delicate materials without worrying about contaminants or exposure to harmful polishing compounds and dust. This makes it particularly beneficial in fields like jewelry design and restoration, where intricate detailing and high-shine finishes are a hallmark of quality. The dust and debris removal system ensures that any fine particles produced during the process are efficiently extracted, improving air quality and reducing the risk of cross-contamination or scratches on the workpiece. The machine’s ability to maintain a stable, clean environment also extends the life of polishing wheels and reduces the need for frequent tool changes, as the buildup of abrasive material is minimized.
Another key aspect of these machines is the ability to easily adjust the polishing parameters. Many models come with variable-speed motors, allowing users to tailor the speed of the buffing wheels to suit the material being worked on. Softer materials, like aluminum or plastics, require slower speeds to avoid overheating or gouging, while harder metals like stainless steel might benefit from faster rotation to remove oxidation or achieve a mirror-like finish. These adjustments allow for greater control over the polishing process, ensuring that the finish meets the required standards without risking damage to the workpiece. The variety of polishing pads and wheels that can be used in these machines also makes them versatile, catering to different stages of the polishing process, from coarse grinding to fine polishing and buffing.
The compact and efficient nature of the polishing cabinet buffing machine also makes it ideal for shops or operations with limited space. Instead of needing multiple stations for different polishing tasks, a single polishing cabinet can handle a variety of materials and finishes, making it both a space-saver and a cost-effective solution. Operators can easily switch between tasks without needing to move the workpiece to different machines or setups. This efficiency is particularly valuable in high-volume production environments, where time and workflow are critical.
In addition to its functionality, the ergonomic design of the cabinet makes it easier for operators to perform long hours of buffing and polishing without experiencing undue strain. The ability to perform tasks through glove ports or from an upright position, with the workpiece secured at an optimal height, minimizes operator fatigue and increases overall comfort. This is an important consideration for environments where the operator’s well-being is a priority, such as in workshops with heavy or continuous polishing work.
From a safety perspective, the polishing cabinet buffing machine reduces the risk of accidents that can occur when using traditional open-bench polishing tools. With the operator enclosed within the cabinet, the likelihood of contact with moving parts is minimized. Additionally, the design often includes built-in safety features such as automatic shutoff mechanisms in case of overloads or unexpected malfunctions.
With regular maintenance, a polishing cabinet buffing machine can provide years of reliable service. Routine tasks like cleaning dust filters, inspecting buffing wheels for wear, and ensuring proper lubrication of moving parts keep the machine running smoothly. Many models also allow for easy replacement of worn-out components, such as brushes or wheels, helping to keep downtime to a minimum. This focus on durability and longevity is a significant benefit for businesses that rely on these machines for high-quality finishes on a daily basis.
In terms of application, polishing cabinet buffing machines are not limited to just one sector. Whether it’s polishing automotive parts, fine metal products, glassware, or even medical devices, these machines can adapt to a variety of materials and finishes. The precision offered by the enclosed, controlled environment allows for fine adjustments to the polishing process, ensuring that every part that leaves the machine meets the high standards required by the industry.
As industries continue to prioritize safety, efficiency, and quality, the polishing cabinet buffing machine remains a cornerstone tool for achieving professional finishes. Its ability to handle multiple polishing and buffing tasks while ensuring a safe, clean, and ergonomic workspace makes it a valuable asset in both small workshops and large-scale production facilities. Would you like more insights into choosing the right cabinet buffing machine for specific tasks or comparing models with unique features?
The versatility of polishing cabinet buffing machines extends to various industries, each benefiting from the machine’s ability to handle complex finishing tasks with precision and control. In industries such as aerospace, automotive manufacturing, and metalworking, where component appearance, durability, and surface integrity are paramount, polishing cabinet machines provide consistent, high-quality results. For example, in aerospace, precision-polished metal parts must meet stringent quality standards for both aesthetic and functional reasons, such as ensuring resistance to corrosion or minimizing drag. Polishing cabinet buffing machines allow technicians to fine-tune their processes to meet these exacting specifications, ensuring that even the smallest components, such as turbine blades or fuel fittings, are polished to perfection.
In automotive production, these machines are invaluable for detailing car parts, especially chrome and metal trim, which often require an immaculate finish to meet customer expectations and industry standards. The ability to maintain a controlled environment while polishing intricate surfaces, like grills, rims, or emblems, allows for a high-gloss finish without the risk of contamination from dust or compound residues. Polishing cabinet buffing machines help achieve the signature gleam that’s so important in vehicle aesthetics, from luxury cars to motorcycles.
In the field of medical devices, the quality of the finish on surgical instruments, implants, and prosthetics is crucial not only for the appearance but also for hygiene and functionality. Polishing cabinet buffing machines ensure that these parts are free from imperfections that could harbor bacteria or cause mechanical failure. For example, the smooth, polished finish on stainless steel surgical tools is not just about looks; it’s also essential for reducing the risk of infection and facilitating easier cleaning and sterilization. The precision of these machines makes them ideal for achieving such results.
Another major benefit of polishing cabinet buffing machines is their ability to handle delicate or highly specialized materials, such as gemstones, ceramics, and glass. In industries like jewelry design or glass manufacturing, where the material is often fragile or prone to scratching, the controlled environment inside a polishing cabinet helps prevent unintended damage. The ability to apply a controlled, even buffing action to such materials is essential for creating stunning finishes without compromising their integrity. In jewelry making, for instance, polishing cabinets are used to bring out the brilliance in metals like gold, platinum, and silver, as well as to perfect the clarity and shine of diamonds or other gemstones.
The adoption of polishing cabinet buffing machines in small-scale and artisan settings is also on the rise. Artists and small manufacturers who focus on custom or high-end products often rely on these machines for their precise control and ability to produce professional-grade finishes. Whether creating custom furniture, restoring antiques, or designing bespoke jewelry, the cabinet buffing machine offers a way to ensure consistent, high-quality results. It’s particularly useful in small shops where a single machine can handle multiple materials and finishes, providing versatility without requiring an array of separate machines.
As technology advances, polishing cabinet buffing machines are becoming more integrated with digital systems that allow for greater automation and efficiency. Some high-end models are now equipped with programmable controls, allowing users to input specific parameters such as speed, pressure, and compound type, creating a more automated process that can be repeated consistently. This reduces the potential for human error and ensures that each workpiece receives the exact same level of attention, making the polishing process both more reliable and efficient. This shift towards automation is especially beneficial in high-volume production settings, where consistency is crucial and reducing manual labor can lead to significant time and cost savings.
The environmental impact of polishing operations is another important consideration, and polishing cabinet buffing machines are increasingly designed with eco-friendly features. Many modern models incorporate filtration systems that reduce the amount of waste and pollutants released into the environment. For instance, some units use water-based or biodegradable compounds instead of traditional petrochemical-based polishing pastes, reducing the environmental footprint of the polishing process. Additionally, advancements in energy efficiency are helping to minimize power consumption, making these machines more sustainable for long-term use.
For businesses looking to optimize their operations, integrating polishing cabinet buffing machines with existing workflows is relatively straightforward. These machines can often be incorporated into automated production lines, where multiple parts need to be polished in a consistent and repeatable manner. The compact, enclosed design of the polishing cabinet makes it easy to fit into tight spaces or alongside other finishing equipment. Integration with dust extraction and filtration systems ensures that the entire polishing process remains clean and compliant with workplace health and safety regulations.
In terms of future trends, polishing cabinet buffing machines will continue to evolve, incorporating even more advanced technology such as touch-screen interfaces, real-time monitoring systems, and the ability to work with an even broader range of materials. These machines will continue to support industries that require precision and high-quality finishing, all while enhancing the overall safety, ergonomics, and environmental sustainability of the polishing process.
Whether for industrial, commercial, or artisanal use, polishing cabinet buffing machines represent a perfect balance of safety, efficiency, and high-performance. They provide a secure and controlled environment for achieving flawless finishes, protecting both the operator and the environment. With the right model, maintenance practices, and polishing compounds, businesses can ensure that they achieve the best possible surface finishes on a variety of materials, from metals to plastics and ceramics.
Would you like to explore more about specific polishing compounds or materials suitable for these machines, or perhaps recommendations on optimizing a polishing cabinet for your particular needs?
Industrial Buffing Machine
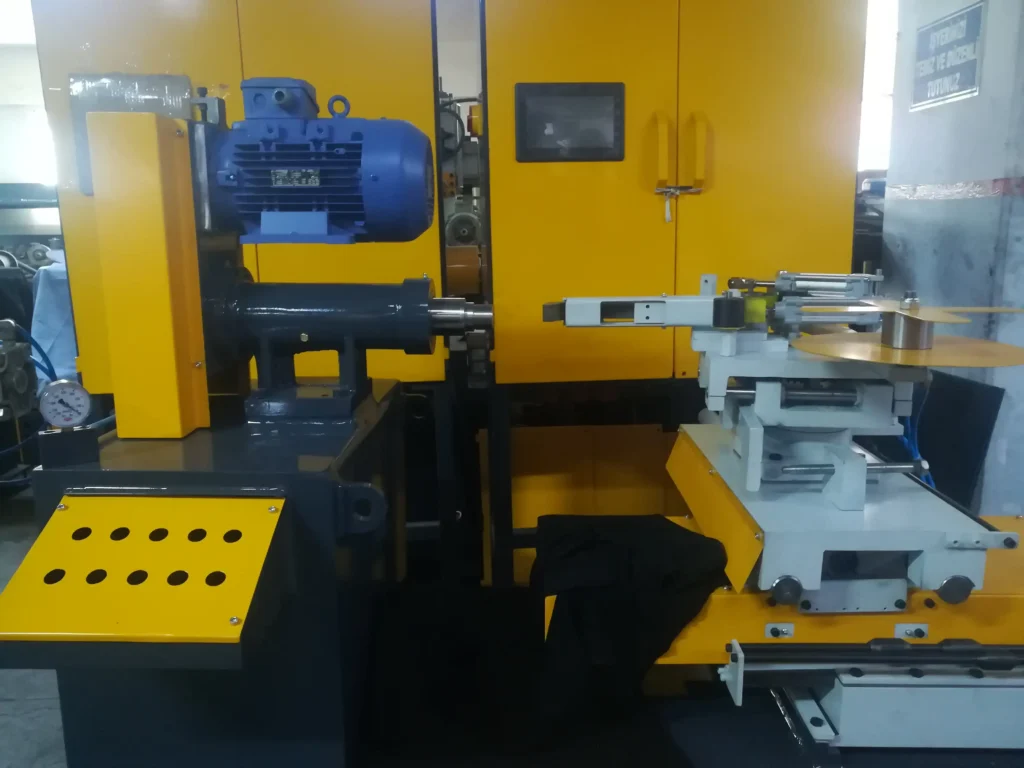
An industrial buffing machine is a high-powered tool used in commercial and industrial settings for polishing and finishing surfaces of various materials, such as metal, wood, plastic, and stone. These machines are designed to perform heavy-duty buffing tasks that require consistent, high-quality results across large quantities of parts or products. Industrial buffing machines are essential in sectors such as metalworking, automotive manufacturing, aerospace, and woodworking, where surface finishing is a critical step in ensuring the quality and appearance of the final product.
Industrial buffing machines come in a wide variety of configurations, from standalone bench-mounted models to larger, more complex systems that integrate multiple stages of polishing or are part of automated production lines. The main components typically include buffing wheels or pads, a powerful motor that drives the rotation of these wheels, and often an adjustable stand or frame to hold the workpiece at the correct angle for polishing. Many models are also equipped with speed controls, allowing operators to adjust the machine’s rotation speed based on the material being worked on and the stage of the buffing process.
The design of industrial buffing machines varies depending on the specific requirements of the task. For example, machines used for polishing large metal parts might feature larger buffing wheels, while those for finer detailing or finishing work might use smaller, more precise wheels. Some models are designed for specific applications, such as polishing automotive parts like chrome trim or buffing metal molds used in manufacturing, while others are more versatile and can handle a range of materials and finishes.
One of the key features of an industrial buffing machine is its motor, which is typically much more powerful than that found in smaller, consumer-grade polishers. These motors can be variable-speed to allow greater control over the polishing process. High RPMs (revolutions per minute) are ideal for quickly removing material or for aggressive polishing, while lower RPMs allow for finer finishing and a smoother, more reflective finish. For example, in metalworking, high speeds are used to cut back oxidation or remove rust, while slower speeds are ideal for fine polishing or creating a mirror-like finish.
Buffing wheels or pads are the heart of the industrial buffing process. These wheels come in a variety of materials such as cotton, felt, wool, and synthetic fibers, and are often treated with polishing compounds or abrasives to enhance their performance. For heavy-duty work, a stiff wheel might be used to remove oxidation or scratches, while softer, more delicate wheels are employed for final finishing. In some cases, the type of buffing compound used will depend on the material being polished. For example, a metal polish or abrasive compound might be used for polishing steel, while a gentler compound might be employed for polishing plastics or softer metals like aluminum or brass.
Industrial buffing machines also tend to feature built-in dust collection systems to manage the debris created during the buffing process. These systems help maintain a cleaner workspace and improve air quality by collecting the dust, metal filings, and polishing compound particles that are generated. This is particularly important in industries where worker health and cleanliness are a priority. In addition, the dust collection systems can improve the longevity of the buffing wheels and other components, as excessive dust buildup can lead to overheating or clogging of parts.
In larger-scale industrial operations, buffing machines may be integrated into automated production lines. These systems allow for consistent and repeatable polishing of high volumes of parts. In these setups, the buffing machine may be programmed to work with robotic arms or conveyors that feed parts into the polishing station, minimizing the need for manual handling and significantly improving efficiency. Such systems can be customized for specific products, enabling companies to meet high throughput requirements without sacrificing quality.
Safety is a major consideration with industrial buffing machines due to their high-speed rotation and potential hazards associated with polishing compounds and airborne debris. Machines are often equipped with safety guards or covers to prevent accidental contact with the buffing wheels. Operators are usually required to wear personal protective equipment (PPE), such as safety goggles, gloves, ear protection, and respiratory masks, especially in environments where fine dust or fumes may be present. Many machines also have emergency stop features and automatic shut-off mechanisms in case of overloads or malfunctions.
In terms of maintenance, industrial buffing machines require regular care to ensure that they continue to operate efficiently and effectively. This includes checking the motor and electrical components for wear, ensuring the buffing wheels are properly balanced, and cleaning or replacing the dust collection filters. Buffing wheels should be inspected for damage or wear, as a worn-out wheel can lead to uneven polishing or potential damage to the workpiece.
Given their durability, power, and ability to handle large-scale tasks, industrial buffing machines are a fundamental tool in many sectors. They ensure that products are finished to a high standard, improving both their appearance and functionality. In industries such as automotive, aerospace, metalworking, and manufacturing, these machines are vital for achieving the precision and surface finishes required for both aesthetic and practical purposes
Industrial buffing machines are designed to tackle demanding polishing tasks that require both power and precision. They are ideal for finishing large quantities of parts or high-volume production environments, where consistency and quality are essential. These machines can be used on a variety of materials, including metals, plastics, ceramics, glass, and composites, making them highly versatile in industries ranging from automotive and aerospace to metalworking, electronics, and manufacturing. The ability to perform both heavy-duty polishing and fine detailing allows these machines to meet the needs of a wide array of applications, such as restoring the shine to automotive parts, polishing turbine blades, buffing metal fixtures, or refining jewelry components.
What sets industrial buffing machines apart from consumer-grade tools is their robustness and ability to handle continuous operation without compromising on performance. High-speed motors, ranging from 1 horsepower (HP) to upwards of 10 HP or more, provide the necessary power for large-scale polishing tasks. This ensures that operators can maintain optimal production speeds while achieving a high-quality surface finish on parts of various sizes and shapes. In some cases, the motor’s power is supplemented by advanced speed control systems, allowing operators to dial in the perfect RPM for each task.
A key component of an industrial buffing machine is its buffing wheel, which can be tailored to specific applications based on the type of material and the level of finish required. Buffing wheels are available in different materials, such as cotton, wool, felt, or synthetic fibers, and they can be impregnated with various polishing compounds to enhance their cutting or finishing ability. For example, a wool wheel might be used for aggressive polishing tasks that involve removing oxidation or rust from metal parts, while a cotton wheel might be used for finer finishing or creating a mirror-like finish on softer metals or plastics.
Many industrial buffing machines come equipped with additional features such as oscillating or dual-action buffing motions. These motions are designed to reduce the risk of swirl marks or uneven finishes, especially when working with delicate or highly reflective surfaces. The oscillating motion helps to distribute the polishing compound more evenly and ensures that the surface being worked on receives consistent attention, which is especially important in industries that require a flawless finish, such as the luxury automotive or jewelry sectors.
Dust extraction and fume control systems are integral to industrial buffing machines, especially in environments where harmful particles or fumes might be released during the buffing process. These systems help capture and remove the fine dust, metal shavings, or polishing compound residues generated, which could otherwise contaminate the work area or pose a health risk to operators. Many machines feature integrated vacuum ports or separate dust collection units that help keep the workspace clean and safe. These systems are particularly important in industrial settings where maintaining air quality is essential for compliance with safety regulations.
Given the heavy-duty nature of these machines, maintenance is crucial to ensure their long-term reliability and performance. Regular inspection and replacement of buffing wheels, motor brushes, and polishing compounds are necessary to keep the machine running smoothly. Additionally, ensuring that the dust collection system is functioning properly, and that no debris or particles are clogging the system, helps prevent overheating and ensures efficient operation.
The integration of industrial buffing machines into production lines can further optimize efficiency in large-scale manufacturing environments. These machines can be automated to feed parts through buffing stations via conveyor belts or robotic arms, reducing manual labor and increasing throughput. In automated setups, buffing machines can be programmed to execute precise polishing sequences, ensuring consistency across large batches of parts. This level of automation not only speeds up production but also enhances product quality by reducing the risk of human error during the polishing process.
As industries continue to prioritize automation, sustainability, and efficiency, industrial buffing machines are also evolving to meet these needs. Many modern machines are designed to be energy-efficient, reducing power consumption and operational costs. Furthermore, advancements in buffing compounds, such as the development of water-based or eco-friendly formulas, help minimize the environmental impact of polishing tasks.
In conclusion, industrial buffing machines are indispensable in industries where high-quality, consistent surface finishes are a must. They are powerful, versatile, and designed for continuous operation, making them an essential part of many manufacturing and finishing processes. With the right maintenance, proper use of buffing compounds, and regular inspection, these machines can deliver exceptional results for a wide range of applications, from metal polishing to automotive detailing and beyond. Whether used in high-volume production environments or for specialized tasks, industrial buffing machines ensure that every part is finished to the highest standards. Would you like to explore specific manufacturers or features of these machines?
The industrial buffing machine’s ability to deliver consistent results in high-demand environments is one of the key reasons it remains indispensable across various sectors. As industries continue to evolve and the need for precision and efficiency grows, the role of buffing machines will likely expand, with advanced technologies integrating seamlessly into automated processes. One area of development is the incorporation of smart technology and sensors into buffing machines. These features can monitor the condition of the buffing wheels, track the pressure applied to the surface, or even detect anomalies in the polishing process. Real-time feedback allows operators to adjust settings or perform maintenance before issues arise, improving uptime and reducing the risk of defects in the final product.
For example, certain modern industrial buffing machines are now equipped with vibration sensors or load monitoring capabilities that can detect when a buffing wheel is out of balance or when the motor is under strain. This early detection can help prevent damage to the machine and the workpieces, ensuring that any issues are addressed before they result in costly downtime or quality control problems. Such advancements in machine diagnostics not only improve the efficiency of polishing operations but also help with predictive maintenance, which can be crucial for operations with high output demands.
Moreover, the flexibility of industrial buffing machines in accommodating a range of materials continues to make them invaluable. From polishing steel and aluminum to working on more delicate materials like plastics, ceramics, or glass, these machines can be tailored with various buffing compounds, pads, and wheels designed to suit the specific requirements of each material. This adaptability allows businesses to handle a wide array of products, from heavy machinery parts to intricate jewelry pieces, all while maintaining the high standards of finish that are expected in industries like automotive, aerospace, medical device manufacturing, and even art restoration.
With advancements in automation, the integration of buffing machines into larger manufacturing lines becomes increasingly seamless. Automated systems allow for continuous, high-speed polishing of parts, reducing manual labor and increasing throughput. This integration often includes conveyor belts or robotic arms that move parts into position for polishing, and some machines can even be programmed to apply specific pressure and speed settings to different parts of the product, ensuring a customized finish for each piece. Such systems are essential for industries like automotive manufacturing, where large quantities of parts need to be polished to the same high standard, or in industries where precision is paramount, such as the aerospace sector.
Environmental concerns and sustainability continue to be important factors in industrial manufacturing, and the development of more eco-friendly buffing systems is becoming increasingly relevant. For instance, using biodegradable or water-based polishing compounds helps reduce the environmental impact of the buffing process. Additionally, dust extraction and air filtration systems are being improved to capture even finer particles, further minimizing environmental exposure to harmful chemicals or metal dust. Some companies are also developing machines that use less energy and produce less noise, addressing both environmental and workplace safety concerns.
Another factor that makes industrial buffing machines essential is their role in quality control. In industries like metalworking, where the aesthetics and functionality of the parts are critical, the buffing process plays a key role in eliminating imperfections such as scratches, rust, or oxidation. Buffing ensures that the finished products have a smooth, even surface, free from defects that could compromise their performance or appearance. High-quality surface finishes can also improve the durability and longevity of products, particularly in industries that require resistance to corrosion or wear, such as the marine or oil and gas sectors.
In woodworking, where polishing and buffing are often done to enhance the natural appearance of the wood and provide a protective finish, industrial buffing machines play an essential role in producing furniture, cabinetry, or decorative items. The buffing process ensures that the wood surfaces are smooth and polished, free from marks or imperfections, and properly sealed. Similarly, in the electronics industry, where components need to have smooth, contaminant-free surfaces for optimal performance, buffing machines are used to polish parts like circuit boards, casings, and connectors, ensuring they meet industry standards for both function and appearance.
As industries move towards more precision-driven and technology-enhanced manufacturing, the role of industrial buffing machines will likely become even more integral. Machines with integrated software and advanced control systems could further reduce human error and improve efficiency, allowing for more complex and intricate finishes. In addition, the incorporation of artificial intelligence and machine learning could help optimize polishing processes by learning from past operations and adjusting settings automatically for the best results.
In summary, industrial buffing machines are continually evolving to meet the increasing demands for precision, efficiency, and sustainability. These machines are critical in industries where surface finish plays an important role in both aesthetics and functionality. From high-volume production settings to specialized craftsmanship, industrial buffing machines ensure that products meet the highest standards of quality and finish. As technology advances, these machines will only become more sophisticated, offering even more benefits in terms of automation, customization, and eco-friendliness. Would you like further details on any specific models or recommendations based on particular industrial needs?
Dust Collection Buffing Machine
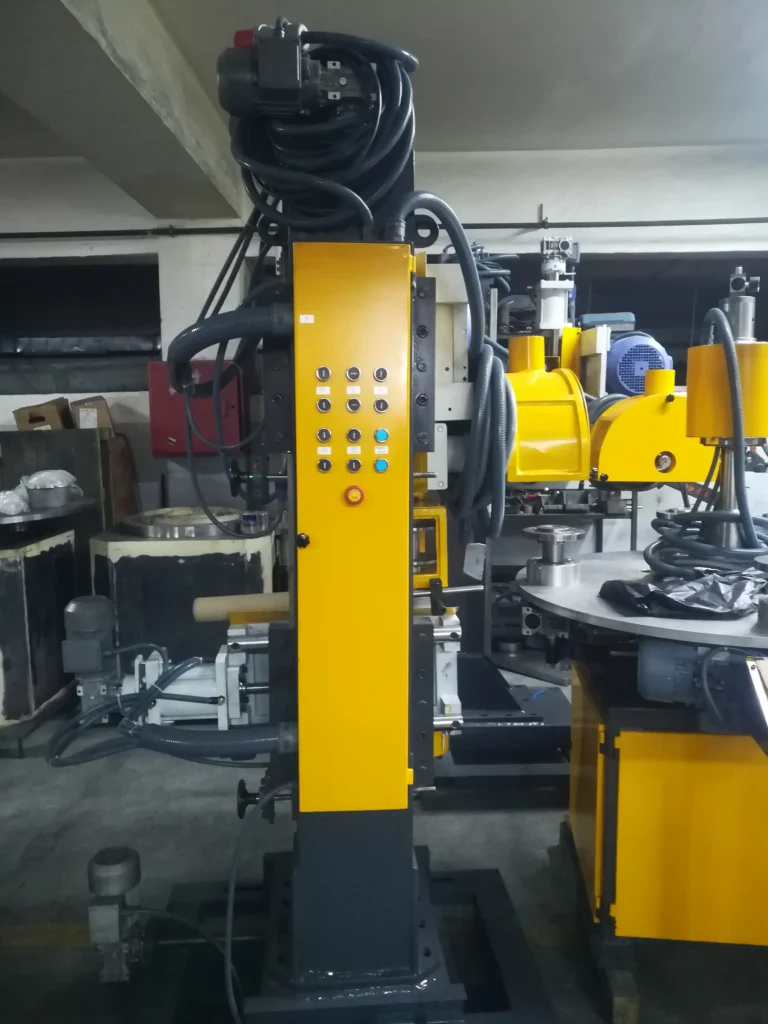
A dust collection buffing machine is a specialized tool designed for polishing and buffing tasks that includes an integrated dust extraction system to capture the debris generated during the buffing process. These machines are widely used in industrial settings, particularly in woodworking, metalworking, automotive manufacturing, and other industries where the polishing process can produce a significant amount of dust, shavings, or particulate matter.
The primary function of a dust collection buffing machine is to ensure a cleaner, safer work environment by capturing and removing harmful dust, polishing compounds, and metal shavings as they are created. This is especially important in environments where dust particles can pose health hazards to workers, create safety risks (e.g., explosions from flammable dust), or interfere with the quality of the finished product.
In a typical dust collection buffing machine setup, the machine is equipped with a high-efficiency dust collection system that either integrates directly with the buffing tool or operates as a standalone component. The dust extraction system usually consists of several key elements:
- Dust Hood or Shroud: A collection hood or shroud is positioned around the buffing wheel to capture the dust and particles generated during the polishing process. These hoods are strategically designed to enclose the work area around the wheel, minimizing the release of dust into the surrounding workspace.
- Vacuum System: The dust captured by the hood is then directed through a vacuum system. This system can be built into the buffing machine itself or connected to an external dust collector via flexible hoses. The vacuum system pulls the dust from the work area and transports it to a filtration unit, where it is safely contained.
- Filtration System: After the dust and debris are sucked into the vacuum system, they are passed through a filtration unit. Depending on the machine’s design, this filtration unit can include multi-stage filters to remove even fine particles. Common filter types include HEPA filters (high-efficiency particulate air filters), carbon filters for capturing fumes, or cyclone separators that remove larger debris before the air enters finer filters.
- Dust Collector or Hopper: The cleaned air is released back into the room, and the dust and debris are collected in a dust collector or hopper. The hopper or dust bin needs to be emptied regularly to prevent it from becoming clogged, and it may be equipped with a system to alert operators when it’s full.
- Workpiece Area or Booth: In some machines, especially those used in high-precision or sensitive applications, the dust collection system is integrated into an enclosed booth or workpiece area. This setup isolates the polishing process from the surrounding environment, providing an even cleaner working atmosphere and better control over the dust.
The inclusion of a dust collection system in a buffing machine offers several benefits:
- Improved Air Quality: By removing harmful dust particles from the air, these machines help maintain a healthier work environment. In industries like woodworking, metalworking, and automotive, where the polishing process can release fine particulate matter, keeping the air clean is crucial for protecting workers’ respiratory health.
- Enhanced Workplace Safety: Dust accumulation can create fire hazards, particularly when flammable polishing compounds or metals are involved. A dust collection buffing machine minimizes this risk by preventing the buildup of dust, which can otherwise become a source of ignition.
- Better Product Quality: Dust and debris in the environment can contaminate the polishing process and lead to imperfections in the finished surface. A dust collection system helps prevent these contaminants from interfering with the finish, ensuring that parts and products are polished to a high standard without the risk of dust marks or scratches.
- Cleaner Workspace: A cleaner work environment not only improves health and safety but also boosts productivity. Operators can work in a more organized and less cluttered environment, which reduces the time spent cleaning up after each task and keeps the workspace more efficient.
- Compliance with Regulations: In many industries, dust collection is not just a best practice; it’s often a legal requirement. For example, in the woodworking industry, dust is considered a significant health hazard, and businesses must comply with OSHA (Occupational Safety and Health Administration) standards or similar regulations. Using a dust collection buffing machine ensures compliance with these regulations and minimizes the risk of penalties.
In industries like metalworking and automotive production, buffing machines with integrated dust collection systems help to keep surfaces free of contaminants that could affect the quality of polished parts. In metalworking, buffing processes often involve the use of abrasives, which can create fine metal dust. This dust, if not controlled, can result in contamination or affect the surface quality of the finished product. Similarly, in automotive production, using a dust collection system ensures that polishing compounds and fine particles are safely contained, preventing damage to delicate components like mirrors, trim, and bodywork.
In woodworking, dust collection is crucial because the fine dust from sanding, buffing, and polishing wooden surfaces can contain wood fibers that are harmful when inhaled. A dust collection buffing machine helps mitigate the health risks associated with these fine particulates, ensuring that the workspace remains clean and the air quality is improved.
Moreover, the integration of eco-friendly features into modern dust collection systems is becoming more prevalent. Newer systems are designed to be more energy-efficient, reducing the overall environmental impact of polishing operations. This can include optimized vacuum motors that consume less electricity or using sustainable materials for filters that are both effective and biodegradable.
The incorporation of smart technology into dust collection buffing machines is also on the rise. Some machines now feature real-time monitoring and diagnostics, where sensors can detect the level of dust buildup in the filtration system, alerting operators when maintenance is needed or when the filters need to be changed. This ensures that the dust collection system operates at peak efficiency, reducing the chances of downtime and maintaining the cleanliness of the work environment.
In conclusion, a dust collection buffing machine offers a comprehensive solution for industries that require high-quality surface finishes while ensuring that the work environment remains safe, clean, and efficient. The integration of powerful vacuum systems, efficient filtration, and dust collection technologies not only helps protect workers’ health but also ensures the smooth and flawless results that are expected in precision industries. Would you like more details on specific models or features of dust collection systems for buffing machines?
Dust collection buffing machines are a critical advancement in industrial polishing, combining the functions of polishing and dust management into a single, cohesive system. These machines are engineered to perform high-quality buffing while effectively capturing the dust and debris generated during the process, which is essential for maintaining both the quality of the finished product and the safety of the workspace. In industries where dust and particulate matter can negatively impact both product quality and worker health, having an integrated dust collection system helps to address these concerns while boosting operational efficiency.
The dust collection system works by drawing in the airborne particles that are created as the buffing wheel makes contact with the workpiece. This debris can range from polishing compounds to metal shavings, wood dust, or plastic particles, depending on the material being worked on. Without a dust collection system, these particles can scatter into the air and the surrounding environment, potentially contaminating the work area, affecting air quality, and increasing the risk of fire or health issues. In industries like woodworking, metalworking, and automotive, these particles are not only an inconvenience but also a serious safety hazard.
A properly designed dust collection system in a buffing machine includes a powerful suction system that pulls in dust from the immediate work area. This is often achieved by using a combination of collection hoods or shrouds that surround the buffing wheels and vacuum suction hoses that connect to a central dust collector. The dust is pulled through the system, where it passes through various filters designed to trap fine particles, ensuring that only clean air is returned to the workspace. In addition to improving air quality, this system reduces the need for manual cleaning, making the workspace less cluttered and more productive. Moreover, the collection of dust is especially important in environments with high-speed buffing operations, where large amounts of dust are generated quickly.
These machines are also crucial for maintaining the quality of the finish on the workpieces. When dust and other debris are allowed to remain in the environment, they can settle back onto the workpieces and cause imperfections in the final polished surface. Even small particles can lead to scratches, streaks, or uneven finishes. By collecting dust at the source, a dust collection buffing machine helps to preserve the integrity of the surface finish, ensuring that parts remain free from contaminants. This is particularly important in industries such as automotive manufacturing, where high-quality finishes are essential for both aesthetic appeal and functional performance.
Beyond improving air quality and product finishes, dust collection systems in buffing machines also play a significant role in ensuring workplace safety. In industries like woodworking, where wood dust is produced, the dust can be highly combustible, posing a fire risk. Similarly, metal dust, especially from materials like aluminum or steel, can present an explosion hazard if not properly controlled. A dust collection buffing machine helps mitigate these risks by capturing potentially hazardous dust and preventing it from accumulating in the workspace. In doing so, it also helps businesses comply with safety regulations and health standards, which may require the installation of dust extraction systems in certain industries to prevent harmful exposure.
Maintenance of dust collection buffing machines is an essential aspect of keeping them functioning efficiently. Over time, dust can build up in the system, especially in the filters and collection hoppers, so routine cleaning and maintenance are required to keep the system running at peak performance. Regularly checking and replacing filters, ensuring that the vacuum system is not clogged, and keeping the buffing wheels in good condition are all part of maintaining the machine and ensuring optimal dust collection. Many modern dust collection systems are equipped with sensors and monitoring systems that notify operators when the system is nearing full capacity or when the filters need to be replaced, making maintenance easier and reducing downtime.
Another advantage of these machines is their ability to help businesses reduce their environmental footprint. By capturing and containing dust, companies can reduce the amount of airborne particulate matter that is released into the environment. This is particularly relevant in industries where regulations surrounding air quality are stringent, such as woodworking or metalworking. Dust collection buffing machines contribute to a cleaner and more sustainable manufacturing process by preventing the release of harmful pollutants and minimizing waste.
The design and technology of dust collection systems are also evolving to be more energy-efficient and user-friendly. Modern machines often feature adjustable suction power, allowing operators to fine-tune the level of dust extraction based on the material and type of buffing work being done. This helps optimize energy consumption and ensure that the dust collection system is working as efficiently as possible. Additionally, quieter models are available, reducing the noise level in the workspace, which can improve the working conditions for operators and comply with noise reduction regulations.
The incorporation of smart technologies in dust collection buffing machines is also an emerging trend. Some machines now include digital controls, allowing for more precise operation and real-time monitoring of the dust collection process. These systems can track the efficiency of the dust extraction, alerting operators to any potential issues such as blockages or system malfunctions. This real-time data helps ensure that the dust collection system is always functioning optimally, improving both the quality of the work and the safety of the environment.
Overall, a dust collection buffing machine is an essential piece of equipment for many industries that rely on polishing and buffing processes. Whether it is a standalone unit or part of a larger automated production system, the inclusion of a dust collection system enhances safety, improves air quality, and ensures that finished products meet the highest standards of quality. By reducing the environmental impact, increasing workplace safety, and ensuring that the buffing process is efficient and precise, these machines provide a comprehensive solution for a wide range of industrial applications.
The continued development of dust collection buffing machines is driven by the increasing demand for higher productivity, enhanced worker safety, and improved environmental standards. As industries strive to streamline operations, reduce costs, and meet sustainability goals, the role of these machines has evolved beyond simple dust extraction. Modern dust collection buffing machines are now integrating sophisticated features that increase their effectiveness in a variety of applications.
For instance, advancements in filter technology have significantly improved the efficiency of dust extraction. High-efficiency particulate air (HEPA) filters, commonly used in these machines, can capture even the finest dust particles, which are often invisible to the naked eye but can still cause serious health risks if inhaled over time. Additionally, multi-stage filtration systems are now commonly used to enhance dust collection by first removing larger particles and then capturing the finer, more hazardous dust. This progression has made dust collection systems more reliable and effective, ensuring a cleaner and healthier work environment for operators.
The automation of dust collection systems is another notable trend. Many modern machines are designed to integrate seamlessly with automated production lines. For example, buffing machines with dust collection systems are increasingly being equipped with sensors that automatically adjust the suction power depending on the type of material being polished or the volume of dust being generated. This smart functionality helps to ensure optimal dust removal without wasting energy or resources. Automated monitoring systems can also track the condition of the filters, alerting operators when maintenance is needed or when filters should be replaced, thus reducing manual intervention and preventing system failures.
In addition to these technological advancements, compact and modular designs have made dust collection buffing machines more versatile and adaptable. Compact models are especially beneficial for businesses with limited space or smaller production setups, while modular designs allow for greater flexibility. These systems can be customized to meet specific production needs by adding or removing components like extra filtration stages, larger collection hoppers, or additional suction points. This flexibility ensures that businesses can tailor the machines to their operations, whether they are working with large-scale, high-volume manufacturing or smaller, more specialized tasks.
As sustainability becomes a growing concern across all industries, dust collection systems are being designed to reduce their environmental footprint. One such development is the integration of energy-efficient motors and components that reduce electricity consumption while maintaining high performance. Some dust collection buffing machines now use variable speed drives that adjust the motor’s power depending on the workload, further optimizing energy usage. By reducing the machine’s overall energy demand, companies can lower operational costs and contribute to their sustainability goals.
In the automotive industry, the integration of robotic arms with dust collection buffing machines is becoming more common. These robotic systems can be programmed to automatically position parts for buffing and polishing, while the dust collection system ensures that the area around the robot stays clean. This combination of robotics and dust collection enhances the precision and consistency of the buffing process, reduces the need for manual labor, and ensures that parts are finished to a high standard without contamination. This automated setup can be particularly useful for mass production of automotive components, where consistency is key and high-quality surface finishes are essential.
For industries involved in aerospace manufacturing, where polishing and buffing are critical for both the aesthetics and functionality of parts, dust collection systems play an integral role in maintaining a pristine work environment. Aerospace components require precise surface finishes to ensure both performance and safety. A dust collection buffing machine designed for this purpose helps ensure that the surfaces of critical components, such as turbine blades, wing parts, and fuselage sections, remain free from contamination or defects caused by dust particles. By capturing these particles before they settle onto the workpieces, the dust collection system plays a vital role in meeting the stringent standards set for aerospace components.
Woodworking is another industry where dust collection buffing machines are essential. Wood dust, if left uncontrolled, can create a host of problems, including respiratory issues for workers, increased risk of fire, and environmental contamination. By integrating dust collection into the buffing process, these machines not only improve the quality of the wood finish but also ensure compliance with health and safety regulations. In high-end woodworking, such as furniture making or musical instrument crafting, where fine surface finishes are necessary, dust collection buffing machines help create a pristine surface that is free from wood fibers and other contaminants.
In industries that work with metal finishes, such as precision machining or jewelry manufacturing, dust collection buffing machines are indispensable for both quality control and safety. Metals like aluminum, steel, and brass can produce fine dust particles during the buffing process, and the presence of this dust in the air can pose a health risk if not properly managed. By using an effective dust collection system, businesses can ensure that workers are not exposed to harmful metal particles while also maintaining a high standard of finish on the metal surfaces.
Furthermore, in industries like electronics manufacturing, where the cleanliness of the parts is critical for functionality, dust collection buffing machines are often used to polish and buff components such as circuit boards, connectors, and housings. Even a small amount of dust or debris can interfere with the performance of electronic devices, so it is essential to keep the work environment free of dust. These machines help ensure that all parts are polished to the highest standard and free from contaminants that could compromise their performance.
As companies continue to prioritize operational efficiency, worker safety, and environmental responsibility, the demand for dust collection buffing machines that offer both high-performance polishing and effective dust extraction will only continue to grow. Whether for large-scale industrial applications or specialized craftwork, these machines provide a versatile, efficient solution that meets the needs of modern manufacturing and finishing operations. With ongoing advancements in technology, design, and sustainability, dust collection buffing machines will remain an essential tool in a wide range of industries, ensuring cleaner environments, safer workplaces, and higher-quality finished products.
Wet Buffing Machine
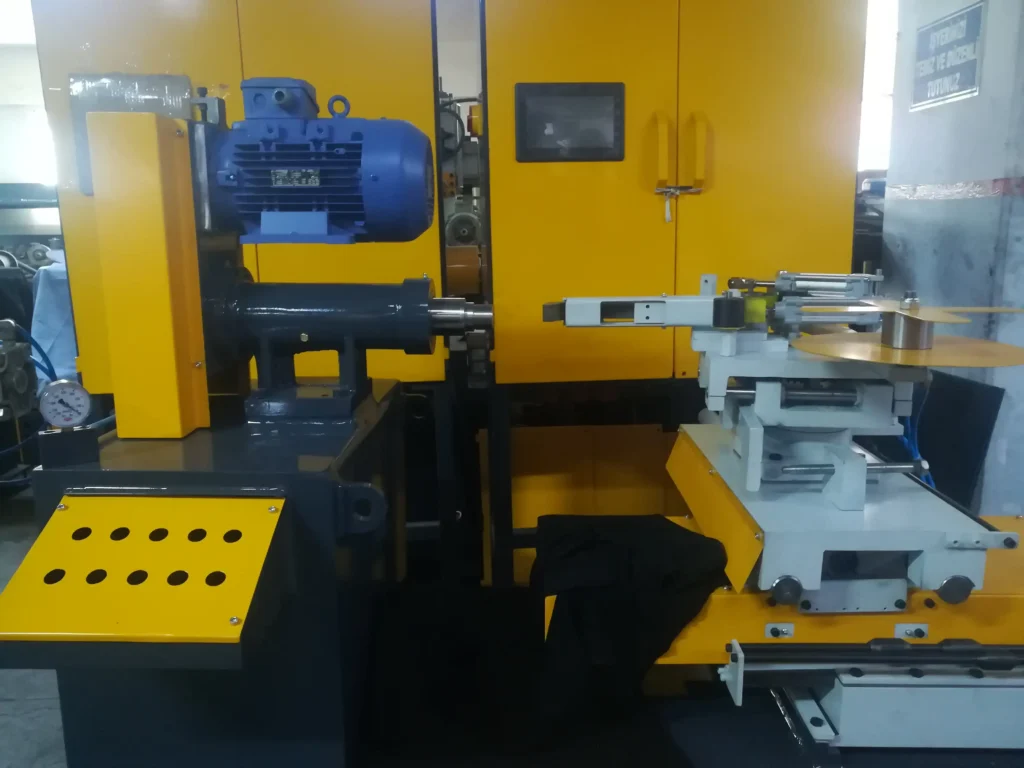
A wet buffing machine is a specialized type of polishing equipment that uses water or a liquid coolant during the buffing or polishing process to reduce friction, manage heat, and enhance the finish of the workpiece. Unlike dry buffing, which generates a lot of heat and can create airborne dust, wet buffing incorporates water or an oil-based compound that cools the surface and collects dust and debris, creating a cleaner and safer environment for both the operator and the workpiece.
Wet buffing machines are used in various industries, including metalworking, automotive, jewelry, and woodworking, and are ideal for applications where heat buildup can damage the material or when a smoother, more refined surface finish is required. These machines are especially useful in processes such as polishing metal, plastics, ceramics, or composites, where the material needs to retain its integrity without being overheated.
The key benefits of wet buffing machines include:
- Reduced Heat Generation: When buffing a surface, the friction between the buffing wheel and the material can generate significant amounts of heat. This heat can cause problems like discoloration, warping, or even material damage. Wet buffing minimizes heat buildup by cooling the surface as it is being polished, preventing heat-related damage and ensuring that the material stays in optimal condition.
- Improved Surface Finish: The presence of a liquid coolant during the buffing process helps to achieve a finer, more polished surface. The liquid helps to lubricate the surface and the buffing wheel, reducing friction and minimizing the chances of scratching or marring the workpiece. As a result, the surface finishes produced by wet buffing are typically smoother and more even, which is particularly important in industries like jewelry and precision machining.
- Dust Control: One of the primary concerns with dry buffing is the creation of fine dust and debris that can contaminate the work environment. Wet buffing helps control this issue by trapping the dust in the liquid, reducing the amount of airborne particulates. This is particularly advantageous in industries where dust can be hazardous to health or affect the quality of the finished product. By capturing the dust, wet buffing machines help maintain a cleaner workspace and improve air quality, contributing to a safer work environment.
- Extended Tool Life: The use of liquid coolant in wet buffing helps extend the life of both the buffing wheel and the workpiece. The liquid prevents excessive wear on the wheel and minimizes the chance of the material becoming overheated or damaged. The lubrication provided by the liquid can also prevent excessive friction, which can cause the wheel to wear down prematurely.
- Enhanced Material Protection: Wet buffing is particularly beneficial for sensitive or delicate materials that could be easily damaged by heat or excessive friction. For example, in industries like jewelry making, where precious metals and stones need to be polished, wet buffing helps preserve the material’s integrity while achieving a brilliant finish. The controlled environment created by the liquid coolant ensures that the materials are polished effectively without risking damage.
- Better Control Over Buffing Process: Wet buffing allows operators to have more control over the polishing process. By adjusting the flow of coolant, operators can manage the speed and temperature of the buffing wheel more precisely, ensuring that the material is polished to the desired specifications. This level of control is crucial in industries that require high precision and quality, such as aerospace or medical device manufacturing.
Wet buffing machines typically consist of several core components:
- Buffing Wheel: This is the main tool for polishing the surface of the material. It is usually made from cloth, felt, or a similar soft material and is designed to spin at high speeds. During the buffing process, the wheel is coated with polishing compounds or treated with the liquid coolant to achieve the desired finish.
- Liquid Coolant Reservoir: Wet buffing machines are equipped with a tank or reservoir that holds the liquid coolant, which can be water or a water-based solution. The liquid is directed to the buffing wheel and the workpiece, where it helps cool the material and carry away any debris or dust generated during the process.
- Pump and Delivery System: A pump circulates the liquid coolant from the reservoir to the buffing wheel. This system is typically designed to ensure that a consistent flow of liquid is delivered to the wheel, maintaining an even cooling effect during the buffing process.
- Suction or Filtration System: In many wet buffing machines, a suction or filtration system is included to capture the liquid and any debris created during the polishing process. This helps to maintain a clean work environment and ensures that the liquid coolant can be reused or filtered for efficiency.
- Workpiece Holding System: Wet buffing machines often include a system for holding or positioning the workpiece securely while it is being polished. Depending on the machine’s design, this can be a manual or automatic setup, ensuring that the workpiece is properly aligned with the buffing wheel for optimal results.
- Control Panel: Modern wet buffing machines typically include a control panel that allows operators to adjust settings such as wheel speed, coolant flow rate, and pressure. Some machines also have built-in monitoring systems that can provide real-time data on the buffing process, ensuring consistency and quality in the finish.
While wet buffing machines provide many advantages, there are some considerations to keep in mind:
- Maintenance: The liquid coolant used in wet buffing systems can become contaminated over time with debris and polishing compounds. This requires regular maintenance, including draining and replacing the coolant, as well as cleaning the filtration and suction systems to ensure that the machine operates efficiently.
- Slipperiness: The use of liquid coolant can create a slippery work environment. Operators should take care to ensure that the floor around the wet buffing machine is properly cleaned and maintained to reduce the risk of accidents.
- Water Quality: In some cases, the quality of the water used in the coolant can impact the effectiveness of the buffing process. Impurities in the water can cause streaks, spots, or residue to be left on the workpiece, requiring additional cleaning after polishing.
- Cost: Wet buffing machines are generally more expensive than their dry counterparts due to the added components like the coolant reservoir, pumps, and filtration systems. However, the additional cost is often justified by the superior finish and increased safety they offer.
Wet buffing machines are an essential tool in industries that require precise, high-quality surface finishes. From polishing metal to fine-tuning the appearance of delicate materials, these machines provide enhanced control, improved safety, and better environmental conditions for operators. Whether in manufacturing, jewelry making, or precision machining, wet buffing machines offer a versatile and effective solution for a wide range of polishing needs.
Wet buffing machines are widely used in industries that require a smooth, polished finish on their workpieces, while also ensuring that the materials remain free from contaminants like dust and debris. These machines are designed to incorporate water or liquid-based coolants into the buffing process, providing several significant advantages over traditional dry buffing methods. The liquid helps manage the heat generated during polishing, which can be crucial when working with sensitive materials that could be damaged by excessive friction. Additionally, it serves as a dust control mechanism, capturing particles and preventing them from becoming airborne, which reduces environmental and health risks. This is particularly important in environments where the dust could be hazardous, such as in woodworking or metalworking operations.
One of the key features of wet buffing machines is their ability to maintain a cool surface temperature during polishing. Buffing generates heat, which, if uncontrolled, can lead to a variety of problems, such as surface deformation, discoloration, or even material distortion. Wet buffing mitigates this risk by using coolants that are applied directly to the workpiece and the buffing wheel. This cooling action ensures that the surface temperature remains stable, allowing for high-quality finishes without the worry of heat-related damage.
Another important benefit of wet buffing is the superior surface finish it provides. The presence of liquid lubricants during the buffing process reduces friction between the buffing wheel and the material, allowing for a smoother, more refined finish. This makes wet buffing especially useful for materials that require a high level of surface precision, such as in the production of jewelry, fine metalworking, and the aerospace industry. The liquid also helps prevent scratches, streaks, or other imperfections that may arise from dry buffing, delivering a flawless, mirror-like finish.
Furthermore, wet buffing machines contribute to a cleaner and healthier work environment. The liquid coolant captures dust and debris that are generated during the polishing process, preventing them from becoming airborne. This eliminates the need for constant cleaning and reduces the risk of respiratory issues for workers who are exposed to dust on a regular basis. It also minimizes the potential for contaminants to settle back onto the workpiece, which could negatively affect the final finish. The built-in dust control system helps ensure that the work area remains clean and safe, and it can improve air quality in the workplace, leading to fewer health concerns for employees.
Wet buffing is particularly advantageous when working with softer or more sensitive materials. For example, materials such as aluminum, brass, or certain plastics are prone to heat buildup and can become damaged or discolored if subjected to excessive friction. By using a wet buffing machine, manufacturers can achieve a high-quality polish while preserving the integrity of these materials. This is especially crucial in industries like automotive or electronics manufacturing, where precision and surface integrity are key.
These machines also offer the benefit of extended tool life. Buffing wheels can wear down more quickly when used for dry buffing due to the increased friction and heat. Wet buffing reduces the wear and tear on the wheel, extending its lifespan and making the process more cost-effective in the long run. Additionally, the coolant helps to prevent the buffing wheel from clogging with polishing compounds, which can compromise its effectiveness and require more frequent maintenance.
A critical component of wet buffing systems is the filtration and recirculation of the coolant. Since the coolant often becomes contaminated with debris and polishing compounds during use, many wet buffing machines are equipped with filtration systems that remove impurities from the liquid. This ensures that the coolant remains effective throughout the process and can be reused, reducing waste and operational costs. Some machines even feature automated systems that monitor the condition of the coolant and alert operators when it’s time for a change. This can help streamline maintenance and prevent disruptions to production.
Another consideration when using wet buffing machines is the potential for water-related issues, such as rust or corrosion on non-stainless steel components. Therefore, manufacturers often design wet buffing machines with materials that resist rust and corrosion to ensure durability and longevity. In some cases, machines may feature additional drainage systems to prevent the accumulation of stagnant water, which can also help minimize the risk of corrosion.
While wet buffing machines are generally more complex than dry buffing machines due to their added components—such as the coolant reservoir, pumps, and filtration systems—the benefits they offer in terms of finish quality, safety, and efficiency often outweigh the added complexity. Moreover, technological advancements in the design of wet buffing machines have made them more user-friendly, with features like digital control panels, automated coolant monitoring, and easy-to-access maintenance points. These features not only improve the machine’s performance but also reduce the operational effort required to keep the system running smoothly.
For businesses that are highly concerned with sustainability, wet buffing machines can be a great asset. By minimizing airborne pollutants and reducing the wear and tear on tools, these machines contribute to both a cleaner work environment and lower operational costs over time. Furthermore, because they often recycle the coolant, these systems reduce water usage and waste, making them an eco-friendly choice for businesses seeking to reduce their environmental footprint.
In summary, wet buffing machines are essential tools for industries that require high-quality, precise, and clean polishing processes. Whether for metalworking, woodworking, or other applications, these machines provide several distinct advantages, such as reducing heat generation, improving surface finish, controlling dust, and extending tool life. The incorporation of advanced filtration and recirculation systems ensures that wet buffing machines operate efficiently, while also maintaining a safe and clean working environment for operators. As technology continues to evolve, wet buffing machines are becoming even more effective, versatile, and user-friendly, making them an invaluable part of many modern manufacturing processes.
Wet buffing machines continue to evolve as advancements in materials, design, and automation reshape the manufacturing and finishing industries. With a growing emphasis on sustainability, efficiency, and the increasing demand for high-quality surface finishes, these machines are integrating even more sophisticated features that make them indispensable in many sectors.
One of the notable developments is the integration of advanced monitoring systems that provide real-time feedback on the performance of the buffing process. These systems can track parameters such as coolant flow, wheel speed, pressure applied, and surface temperature to ensure that the machine operates at optimal conditions. For example, if the coolant flow is too low or the temperature rises above a certain threshold, the system can alert operators and automatically adjust the settings to prevent potential issues. This level of automation not only improves the consistency and quality of the finished product but also reduces the chances of human error.
Another significant trend is the adoption of multi-functional buffing systems that combine various processes, such as wet polishing, dry buffing, and abrasive finishing, into a single machine. These all-in-one systems are designed to streamline production by reducing the number of machines required for different stages of the buffing or polishing process. For instance, a wet buffing machine may have interchangeable wheels or pads that can be used for different materials or finishes, allowing the operator to switch between processes without the need for a full equipment changeover. This versatility can significantly reduce downtime and increase production efficiency.
Moreover, robotic automation is making its way into wet buffing systems, particularly in high-volume industries such as automotive manufacturing or electronics production. Robotic arms equipped with buffing wheels and integrated with wet buffing systems can automatically handle the polishing and buffing tasks. These robotic systems can precisely position the workpieces, ensuring uniform polishing, while the integrated dust and coolant management systems ensure a clean and safe working environment. In addition to improving consistency, automation also frees up human operators to focus on more complex or strategic tasks, increasing overall productivity.
The rise of customizable buffing solutions is another development that has enhanced the utility of wet buffing machines. For instance, some manufacturers now offer machines that can be tailored to specific needs, such as buffing delicate materials or working with specialized polishing compounds. Customization options might include adjustable wheel speeds, specialized buffing pads, or even specialized coolant solutions designed for certain materials or finishes. These machines allow businesses to achieve the highest level of precision and efficiency, while also accommodating the diverse demands of various industries.
In sectors where cleanliness and contamination control are paramount, such as in pharmaceuticals, food production, and biotechnology, wet buffing machines are being designed to meet stricter sanitary standards. These machines are made from materials that are resistant to corrosion and easy to clean, while their coolant systems are equipped with filtration systems that ensure no contaminants affect the workpieces. Additionally, some machines feature closed-loop systems that circulate coolant and prevent exposure to external contaminants, further improving the cleanliness of the process.
The integration of eco-friendly coolant options is also becoming more prevalent. Many manufacturers are moving away from traditional chemical-based coolants, which can be harmful to both the environment and human health, in favor of more sustainable alternatives. Water-based coolants that are biodegradable and less toxic to the environment are being increasingly used in wet buffing systems. Additionally, some machines are designed to handle the disposal or recycling of used coolants in an environmentally responsible manner, reducing waste and the overall environmental impact of the buffing process.
As industries increasingly focus on productivity and cost efficiency, manufacturers are developing wet buffing machines with higher throughput capabilities. These machines are designed to handle larger volumes of workpieces, while still maintaining the high-quality finishes that wet buffing is known for. Features like automated part handling, adjustable buffing speeds, and multi-stage polishing processes enable wet buffing machines to meet the demands of large-scale production runs without compromising on quality.
Furthermore, the importance of ergonomics in wet buffing machines cannot be overlooked. Many modern machines are being designed with operator comfort and safety in mind. Adjustable workstations, user-friendly interfaces, and noise reduction technologies are all integrated into the design to ensure that the buffing process is as comfortable and safe as possible for operators. Reducing the physical strain on workers and minimizing exposure to hazardous dust and debris not only improves the well-being of employees but also leads to better overall productivity.
In industries where high-precision finishes are required, such as aerospace, medical devices, and precision optics, wet buffing machines are essential for ensuring that each part meets the required specifications. The machines’ ability to control temperature and surface smoothness makes them invaluable in maintaining the structural integrity and aesthetic quality of highly detailed components. Additionally, the low-friction, controlled environment offered by wet buffing reduces the risk of introducing surface defects or imperfections, which is critical in these fields.
Lastly, maintenance and cost-effectiveness are always key considerations for businesses. With modern wet buffing machines, maintenance has become easier and more cost-effective due to the development of automated monitoring systems that can predict when maintenance is needed and alert operators in advance. This predictive maintenance minimizes downtime and reduces repair costs, leading to increased efficiency and longer machine lifespans. Additionally, by using recyclable coolants and integrating features that extend the life of consumables like buffing wheels, these machines can help businesses reduce operational costs over time.
In conclusion, wet buffing machines are crucial tools for industries that demand high-quality finishes, a clean working environment, and efficient production. With ongoing advancements in automation, customization, energy efficiency, and sustainability, these machines continue to evolve and meet the increasingly complex needs of modern manufacturing. Whether it’s for polishing delicate materials, achieving precise surface finishes, or improving worker safety, wet buffing machines offer significant advantages that make them indispensable in many industries.
Double Ended Buffing Machine
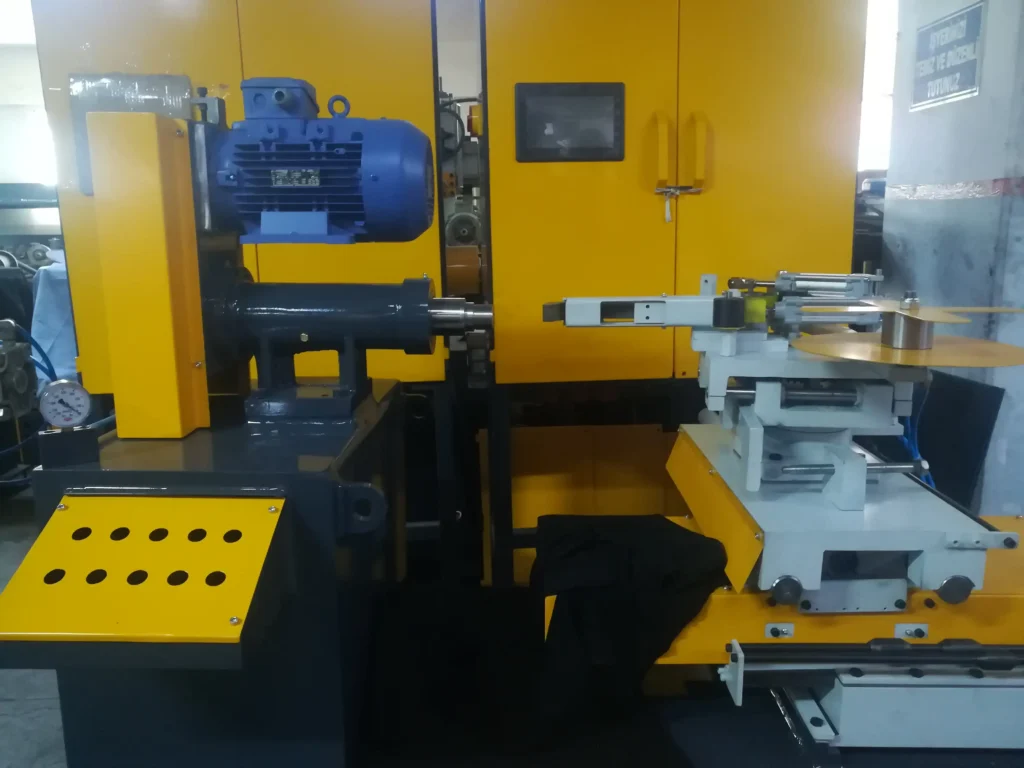
A double-ended buffing machine is a type of polishing or buffing equipment that features two buffing wheels or heads, one at each end of the machine. This design allows operators to buff or polish multiple surfaces of a workpiece simultaneously or switch between different tasks without the need to reposition the workpiece. Double-ended buffing machines are often used in industries where high productivity, efficiency, and precision are required, such as in metalworking, automotive, jewelry, and woodworking.
These machines are versatile and can be used for a wide range of applications, from polishing metal parts to applying fine finishes to delicate materials. The double-ended design allows operators to complete a variety of tasks more efficiently compared to single-ended machines. For example, one end of the machine may be used for rough buffing with a coarser wheel or abrasive, while the other end may be set up with a finer wheel for final polishing. This enables quicker transitions between different polishing stages without having to switch out buffing wheels or adjust the machine.
Key Features and Benefits
- Increased Productivity: With two buffing wheels or heads, a double-ended buffing machine allows operators to work on two parts at once or use different types of wheels for various polishing processes. This helps save time and increases throughput in high-demand production environments, such as in manufacturing or large-scale metalworking operations.
- Dual Tasking: The ability to work with two different types of wheels (e.g., a coarse wheel and a fine wheel) on separate ends of the machine makes it possible to perform multiple polishing steps in a single pass. This versatility reduces the need for additional equipment and streamlines the polishing process, making it more efficient.
- Flexible Operation: Double-ended buffing machines can be equipped with different types of buffing wheels, pads, or brushes depending on the material being polished. This flexibility allows the same machine to be used for a wide range of applications, from heavy-duty metal polishing to fine finishes on delicate materials like wood, plastic, or glass.
- Reduced Downtime: Since operators can change between buffing heads without needing to stop the machine, downtime is minimized. The quick transitions between rough and fine polishing stages enhance the efficiency of the overall operation, particularly in industries where time is critical.
- Space Efficiency: Double-ended buffing machines are designed to accommodate two buffing heads within the same frame, making them space-efficient compared to having separate single-ended machines. This is especially useful in smaller workshops or manufacturing environments with limited space.
- Enhanced Safety: Many double-ended buffing machines come with safety features such as protective shields, dust collection systems, and adjustable speed controls. These features help protect the operator from flying debris, excessive dust, or overheating, making the work environment safer.
- Customization: The machine can be customized to fit the specific requirements of the operation. Buffing wheels of various sizes, materials, and hardness can be used, allowing for tailored results depending on the job. For instance, one wheel could be used for rough grinding, while the other is used for polishing with a finer compound.
Applications
- Metal Polishing: In industries like metalworking, automotive, and aerospace, double-ended buffing machines are commonly used to polish metal parts such as automotive body panels, engine components, and industrial machinery. They are equipped with different buffing wheels or compounds to achieve both coarse and fine finishes on the same machine.
- Jewelry Making: For jewelers, these machines are ideal for achieving fine, mirror-like finishes on metal jewelry pieces. One end may use a coarse wheel to remove imperfections, while the other is used to apply a high-gloss finish, giving the jewelry its final, polished appearance.
- Woodworking: In the woodworking industry, double-ended buffing machines can be used to apply smooth, shiny finishes to wood products. Different buffing wheels can be used for rough sanding, polishing, and buffing, achieving smooth, glossy surfaces on furniture, cabinetry, and decorative wood pieces.
- Plastic Polishing: Plastic manufacturers use double-ended buffing machines to achieve high-gloss finishes on plastic parts or components. The ability to use different types of buffing wheels helps prevent damage to softer materials like plastic while still providing a smooth, polished surface.
- Automotive Detailing: Double-ended buffing machines are frequently used in automotive detailing to polish vehicle surfaces. One end may be used for applying a rough compound to remove scratches and imperfections, while the other end is used for applying a finer compound to achieve a high-gloss, showroom finish.
- Glass and Ceramics: In industries working with glass or ceramics, double-ended buffing machines are used to polish the surface of glassware or ceramic tiles. The fine polishing process enhances the clarity and appearance of glass items, such as mirrors, windows, or glass sculptures.
Types of Buffing Wheels
Double-ended buffing machines can be fitted with a variety of buffing wheels to suit different materials and polishing requirements. Some common types of buffing wheels include:
- Cloth Buffing Wheels: Typically used for general polishing and finishing, cloth wheels are soft and ideal for achieving a smooth, high-gloss finish.
- Felt Buffing Wheels: Felt wheels are more rigid than cloth wheels and are often used for finer polishing or when applying compounds.
- Abrasive Buffing Wheels: These wheels are used for more aggressive polishing and are typically used on harder materials or for removing surface imperfections.
- Wire Brush Buffing Wheels: Wire brush wheels are used for cleaning and deburring surfaces, often in metalworking applications.
Considerations
- Power Requirements: Double-ended buffing machines typically require more power than single-ended models due to the dual motor setup. It’s important to ensure that the machine is compatible with the power supply of the workshop.
- Space and Footprint: While the double-ended design is space-efficient compared to having two separate machines, it still requires adequate workspace for proper operation, particularly if the machine is being used in a high-production setting with multiple operators.
- Dust and Debris: Buffing generates a significant amount of dust and debris, especially when working with abrasive wheels or polishing compounds. Ensuring that the machine has an effective dust collection system is essential for maintaining a clean and safe work environment. Some machines come with built-in dust collectors or can be connected to external dust extraction systems.
- Maintenance: Like any machinery, regular maintenance is essential to keep a double-ended buffing machine running smoothly. This includes checking the buffing wheels for wear, ensuring the motors are functioning correctly, and maintaining the coolant or lubrication systems.
In conclusion, double-ended buffing machines are powerful and efficient tools used across various industries for polishing, finishing, and refining the surfaces of materials. Their dual-wheel design increases productivity by allowing operators to perform multiple polishing steps simultaneously or use different types of wheels for different stages of polishing. Whether for metal, wood, plastic, or other materials, double-ended buffing machines provide a versatile and high-performing solution for a wide range of polishing applications.
Double-ended buffing machines continue to be a cornerstone in many industrial settings due to their efficiency and versatility. The ability to simultaneously operate two buffing heads or wheels allows for faster and more streamlined production, especially when dealing with high volumes of workpieces. These machines are particularly valuable in environments that require rapid transitions between different stages of the polishing process, reducing the time spent switching between machines or tools. As industries become more focused on optimizing productivity and reducing costs, double-ended buffing machines provide a significant advantage by allowing workers to handle multiple tasks in a single setup.
In addition to improving productivity, double-ended buffing machines also help maintain a high level of consistency and quality across a wide range of products. By using different buffing wheels or compounds on each end of the machine, operators can fine-tune the polishing process to achieve the desired finish for each type of material or workpiece. This level of customization is essential in sectors such as metalworking, jewelry making, or automotive detailing, where even the smallest imperfections can affect the final product’s appearance and performance. The flexibility to adjust the polishing stages and compounds on both ends of the machine ensures that each workpiece is polished with the right amount of pressure, speed, and consistency.
Another important benefit is the ergonomic design that many modern double-ended buffing machines offer. These machines often feature adjustable workstations, allowing operators to position the workpiece comfortably without unnecessary strain. The ability to customize the height or angle of the machine ensures that operators can work efficiently while reducing the risk of injury or fatigue. This is especially beneficial in high-volume environments where workers may spend long hours using the machine. The ergonomic setup, combined with the dual heads, ensures that workers can perform tasks without needing to constantly adjust their positions or the workpieces, leading to a more efficient and comfortable workday.
Furthermore, double-ended buffing machines can also incorporate advanced coolant systems or lubrication systems that enhance the polishing process. These systems not only help reduce heat buildup during polishing but also minimize friction, ensuring that the material being polished does not suffer from thermal damage or unwanted scratches. By keeping the surface cool and lubricated, these systems also help to extend the lifespan of both the buffing wheels and the workpieces themselves. The inclusion of coolant systems is particularly important when working with materials that are prone to overheating or warping, such as plastics or softer metals.
In terms of maintenance, double-ended buffing machines often have relatively low upkeep costs, especially when compared to other types of industrial equipment. With proper care, the buffing wheels can last for extended periods, and the machines themselves are built to endure the wear and tear associated with constant use. Regular cleaning and the replacement of worn-out components, such as buffing wheels or belts, are usually sufficient to keep the machine operating at peak performance. Additionally, many modern double-ended buffing machines come with built-in monitoring systems that track performance and alert operators to any issues before they lead to costly breakdowns. This predictive maintenance capability helps reduce downtime and ensures that production schedules are met without interruption.
From an environmental standpoint, double-ended buffing machines can contribute to more sustainable manufacturing processes. Many of these machines now feature energy-efficient motors and closed-loop coolant systems, which reduce the overall environmental footprint of the buffing process. By recycling coolant and using energy-efficient components, these machines help conserve resources and minimize waste, making them a more eco-friendly option for businesses looking to reduce their environmental impact. The dust collection systems, which capture debris and prevent it from becoming airborne, also contribute to cleaner air quality in the workplace, further promoting a safe and healthy environment for workers.
In industries that require precision finishes, such as aerospace or medical device manufacturing, double-ended buffing machines provide the necessary control to achieve exacting standards. The ability to use different wheel types and compounds for various stages of the process ensures that the final surface is smooth, uniform, and free of defects. In these applications, where the tolerance for imperfections is minimal, the versatility of a double-ended machine is essential in maintaining high standards of quality. The precise control over pressure, speed, and polishing compounds ensures that even the most intricate parts or delicate materials can be polished without compromising their structural integrity.
As technology continues to evolve, the integration of smart features into double-ended buffing machines is becoming increasingly common. These smart systems allow for enhanced control and monitoring of the buffing process. For instance, some machines now come equipped with digital displays that show real-time data about the polishing process, such as the speed of the wheels, the temperature of the workpiece, and the pressure applied. This data can be used to adjust settings dynamically, ensuring that each workpiece is polished to the highest standard. Additionally, some machines are now compatible with Internet of Things (IoT) technology, allowing operators to remotely monitor and control the machine via mobile apps or computers, which is especially useful in large production facilities with multiple machines in operation.
The continued development of robotic automation in buffing processes also plays a role in enhancing the capabilities of double-ended buffing machines. Robotic arms or automated systems can be integrated with the machine to handle workpieces, ensuring that each part is positioned and polished with the utmost precision. This automation not only increases the speed of the buffing process but also reduces the risk of human error, ensuring consistent and repeatable results with minimal intervention. For industries with large-scale production needs, robotic automation can drastically increase output while maintaining the quality of the finish.
In conclusion, double-ended buffing machines are an indispensable tool in various industries, offering a combination of productivity, precision, and versatility. Their ability to handle multiple polishing tasks simultaneously, coupled with advancements in automation and sustainability, makes them ideal for modern manufacturing environments. As industries continue to demand higher-quality finishes and more efficient processes, the role of double-ended buffing machines will only continue to grow, providing essential solutions for a wide range of applications. Whether it’s for metal, wood, plastic, or delicate materials, these machines provide the necessary features to achieve flawless surfaces while improving efficiency and reducing operational costs.
As the demand for high-quality finishes increases across a wide range of industries, double-ended buffing machines are likely to evolve further with more advanced features. One key area of development is the integration of artificial intelligence (AI) and machine learning to optimize the buffing process. With AI-powered systems, the machine could learn from the data it gathers during operation and adjust settings automatically to improve efficiency, reduce material waste, and enhance the quality of the final product. These systems could predict when a buffing wheel is becoming less effective and recommend maintenance or adjustments before a decline in performance occurs. This predictive capability could also extend to identifying when the polishing compound needs to be replenished or changed, helping to maintain a consistent finish throughout the production run.
Another trend is the use of advanced materials for buffing wheels and machine components. Manufacturers are experimenting with composite materials, carbon fiber, and diamond-coated wheels to extend the lifespan of the buffing heads and improve their effectiveness on harder or more delicate materials. For example, diamond-coated buffing wheels are particularly effective for polishing very hard surfaces, such as ceramics, stones, or titanium alloys, which are used in aerospace and medical devices. The use of these advanced materials enhances the overall precision and longevity of the machine, which is especially important in industries where quality control and performance are critical.
Additionally, energy efficiency continues to be a driving force in the design of double-ended buffing machines. As sustainability becomes a priority for many manufacturers, the need for energy-efficient equipment that consumes less power while maintaining high performance is more crucial than ever. Modern machines are incorporating features such as variable-speed motors, energy-saving drives, and automatic shutdown systems that reduce power consumption when the machine is not in use. These improvements help companies meet both their production goals and environmental sustainability targets by lowering energy costs and reducing their carbon footprint.
As the industry moves toward greater automation, collaborative robots (cobots) are expected to play an increasingly important role in buffing operations. These cobots can work alongside human operators, taking on repetitive or physically demanding tasks, while still allowing humans to oversee the process and make adjustments as needed. Cobots equipped with buffing tools can work on one side of a workpiece, while the operator can focus on the other side, effectively increasing throughput without sacrificing quality. Moreover, since cobots are often designed to be easily programmable and flexible, they can be adapted for use in various stages of the polishing process, from rough buffing to final finishing.
Furthermore, the globalization of the manufacturing industry and the increased reliance on offshore production have prompted many companies to seek buffing machines that are adaptable to different types of workpieces and materials. Double-ended buffing machines, being versatile, are highly valued in these contexts because they can be used to handle multiple product types in a single production line. Whether it’s polishing automotive parts, consumer electronics, or industrial machinery components, double-ended machines offer manufacturers the ability to process diverse materials while maintaining high-quality finishes. This versatility is a key reason why they are commonly used in contract manufacturing and OEM production.
In line with the growing importance of precision engineering, future developments in double-ended buffing machines will likely focus on further enhancing the machine’s ability to deliver highly consistent results across a variety of material types and geometries. Advances in feedback systems such as force sensors or laser measurement technologies will enable the machine to adjust in real-time to subtle changes in the surface being polished. For example, sensors could detect changes in surface roughness or material hardness and automatically adjust the buffing speed, pressure, and wheel type to compensate for these variations. This would ensure that every workpiece, regardless of its size or complexity, receives the same level of attention and polish.
Moreover, digitalization in the form of cloud-based solutions could become an important feature of double-ended buffing machines in the future. By connecting the machines to cloud-based platforms, manufacturers could monitor the performance of the machines remotely, track maintenance schedules, and analyze production data in real time. This could lead to more efficient scheduling and resource management, as well as better decision-making regarding machine performance and product quality. It also offers the potential for predictive analytics, allowing companies to foresee issues and implement proactive measures to minimize downtime.
The continued evolution of integrated cleaning systems in buffing machines is another area where double-ended machines are expected to see significant improvements. In industries like aerospace and pharmaceuticals, cleanliness is paramount, and buffing machines must be able to handle sensitive materials without introducing contaminants. Future double-ended machines may feature even more advanced in-line cleaning mechanisms that can remove debris and dust from the workpieces automatically during the polishing process. These cleaning systems would integrate seamlessly with the buffing process, ensuring that finished products remain free from dirt, oil, or particles that could compromise their quality or functionality.
Furthermore, the emphasis on worker safety is likely to lead to continued improvements in the design of double-ended buffing machines. Safety standards and regulations are becoming stricter, particularly in industries where hazardous materials are used. Future machines will likely include enhanced safety features such as automated shutdown protocols in case of an emergency, more advanced dust extraction to protect against harmful airborne particles, and safety guards designed to prevent accidental contact with moving parts. These safety features will not only protect workers but will also help companies comply with evolving workplace safety regulations.
Finally, user interfaces will continue to evolve, with many double-ended buffing machines incorporating touchscreen controls and advanced software that allow operators to easily adjust machine settings, monitor progress, and optimize the buffing process. This makes machines more intuitive and user-friendly, reducing the learning curve for new operators and ensuring that the machine operates at its highest efficiency. Operators can also store and recall settings for specific processes or materials, which can further improve productivity and consistency.
In conclusion, double-ended buffing machines are poised to undergo further advancements, particularly in automation, energy efficiency, precision, and safety. As industries increasingly demand high-quality finishes, consistent results, and operational efficiency, the development of these machines will continue to reflect those needs. With advancements in AI, automation, and smart features, these machines will remain essential in industries ranging from automotive and aerospace to consumer goods and electronics. Whether for polishing metal, wood, plastic, or delicate materials, double-ended buffing machines will continue to be indispensable tools in manufacturing environments, providing superior surface finishes with precision, speed, and versatility.
Polishing Lathe Buffing Machine
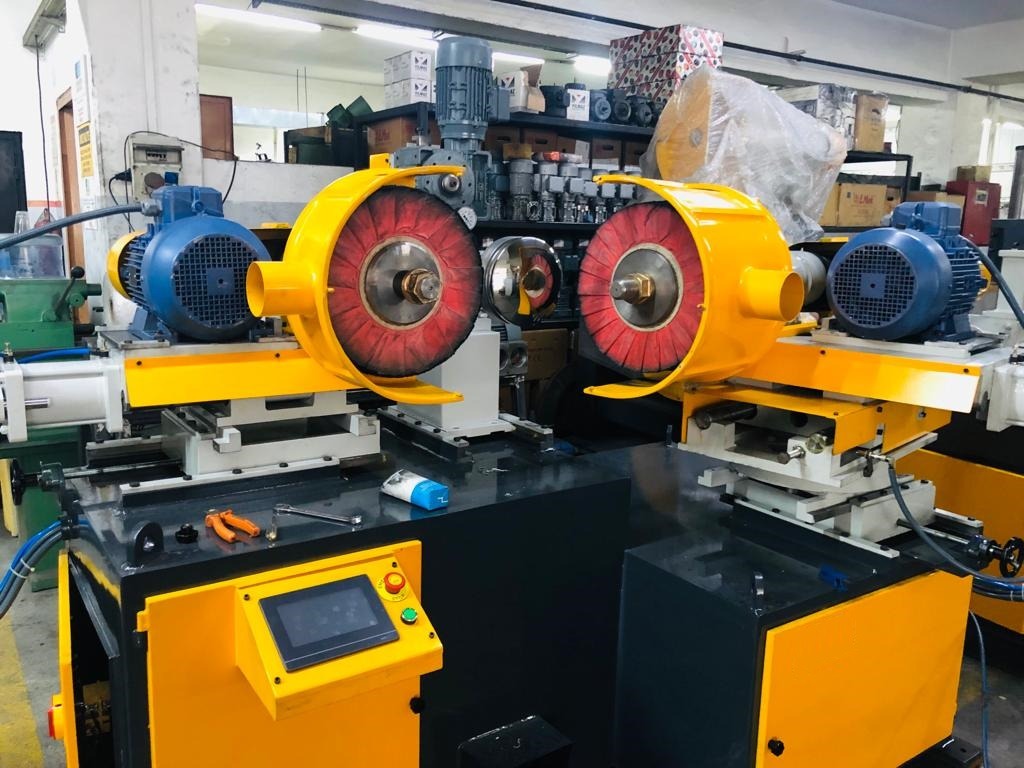
A polishing lathe buffing machine is a specialized piece of equipment designed to polish or buff a variety of materials by rotating the workpiece on a lathe while a buffing wheel or pad is applied to it. This type of machine is often used in industries that require precise, high-quality finishes, such as in metalworking, jewelry making, woodworking, and plastics manufacturing.
The polishing lathe buffing machine typically consists of a rotating spindle where the workpiece is mounted, a motor that drives the spindle, and a buffing wheel or pad attached to another spindle or motor. The workpiece is rotated at high speed, and the buffing wheel or pad is applied to the surface of the piece to remove imperfections, smooth out rough surfaces, and give the workpiece a glossy finish.
Key Features of a Polishing Lathe Buffing Machine
- Precision and Control: One of the primary advantages of a polishing lathe buffing machine is the level of precision it offers. The lathe allows for uniform rotation of the workpiece, ensuring consistent application of the buffing process. This is particularly important in industries where surface quality is critical, such as in jewelry or aerospace applications.
- Versatility: The polishing lathe can be used for a wide range of materials, including metals, plastics, wood, and composites. By changing the type of buffing wheel or pad, operators can adjust the machine for different polishing tasks, from heavy-duty material removal to fine, high-gloss finishes.
- Multiple Buffing Stages: Often, polishing lathe buffing machines allow for different stages of polishing. For example, a rough buffing wheel may be used in the initial stages to remove material and smooth the surface, while a finer buffing wheel is used in later stages to achieve a mirror-like finish. This versatility ensures that the machine can handle multiple polishing processes on the same workpiece.
- Adjustable Speed: Many polishing lathe buffing machines come with adjustable speed controls that allow operators to fine-tune the rotation speed of the spindle and the buffing wheel. This is essential for controlling the level of polishing and ensuring that the workpiece is not overheated or damaged during the process.
- Motorized or Manual Operation: Some polishing lathes are fully motorized, with automated controls that make it easier to operate, while others may offer manual operation for more hands-on control. In industrial settings, motorized versions are typically preferred because they offer consistent speed and less operator fatigue.
- Dust Collection: Since buffing can generate a lot of dust and debris, many polishing lathe buffing machines are equipped with built-in dust collection systems. These systems help to maintain a clean work environment and protect the operator from inhaling harmful particles that can be created during the polishing process.
- Customization Options: Depending on the application, polishing lathes can be fitted with a variety of buffing tools and attachments, such as different sizes of buffing wheels, belts, or pads, as well as accessories like tool rests, adjustable tool holders, and more. This allows the machine to be adapted for specific tasks and materials.
- Safety Features: Modern polishing lathe buffing machines often include safety features like guards around the spinning parts, emergency shut-off switches, and protective covers for the buffing wheel to prevent accidents during operation. These features are particularly important when working with high-speed rotating equipment.
Applications of Polishing Lathe Buffing Machines
- Jewelry Making: Polishing lathes are widely used in the jewelry industry to achieve high-gloss finishes on metal rings, necklaces, bracelets, and other pieces. The controlled rotation of the workpiece on the lathe allows jewelers to achieve a consistent, smooth finish on delicate designs without damaging the material.
- Metalworking: In metalworking, polishing lathe buffing machines are used to give metal parts, such as automotive components, engine parts, or decorative metal items, a smooth, polished surface. These machines are ideal for removing oxidation, scale, and other imperfections from the metal’s surface.
- Woodworking: Woodworkers use polishing lathe buffing machines to polish and buff wooden objects, such as furniture, bowls, and ornamental pieces. These machines help to bring out the natural grain of the wood and give it a high-quality, glossy finish.
- Plastic Polishing: In the plastics industry, polishing lathes are used to give plastic components a smooth and shiny surface. This is often important in the production of high-end consumer products, such as acrylic displays or clear plastic covers, where clarity and smoothness are critical.
- Aerospace and Automotive: Polishing lathes are used in both the aerospace and automotive industries to refine metal and composite parts. Polishing machine components to a high level of precision is essential in these industries, where even small imperfections can affect performance and aesthetics.
Advantages of Polishing Lathe Buffing Machines
- High Precision: The lathe allows for controlled rotation of the workpiece, ensuring that the buffing process is precise and even. This level of precision is especially important in industries like jewelry making, where surface finish quality is paramount.
- Enhanced Surface Finish: By using multiple stages of buffing with different wheels or pads, polishing lathes can achieve a high-quality surface finish. This is especially useful in applications where a mirror-like shine or fine detail is required.
- Increased Efficiency: The ability to adjust the speed and pressure during the buffing process allows operators to optimize their workflow. Since polishing lathes can handle a range of materials and polishing tasks, they offer a highly efficient solution for manufacturers who need to process a variety of parts.
- Reduced Operator Fatigue: The motorized operation of many polishing lathes reduces the physical strain on the operator, making the process less tiring and more productive. The ease of use and ability to adjust settings also make it more accessible for workers.
- Dust and Debris Control: Integrated dust collection systems help to keep the work area clean and reduce the risks associated with airborne particles. This not only improves the work environment but also ensures that the finished products are free of contamination.
Considerations
- Initial Investment: Polishing lathe buffing machines can be a significant investment, especially when they come with advanced features like dust collection systems, adjustable speed controls, or custom attachments. However, their ability to improve efficiency and quality often justifies the cost.
- Maintenance: Regular maintenance is necessary to ensure that the polishing lathe functions smoothly. This includes checking the buffing wheels for wear, cleaning dust collection systems, and ensuring the lathe’s motor is in good working condition.
- Skill Requirement: While polishing lathes can be easier to operate than some other types of polishing machines, they still require a skilled operator to achieve the desired results. Knowledge of different polishing materials, wheel types, and polishing techniques is crucial for achieving a high-quality finish.
- Space Requirements: Polishing lathe buffing machines tend to have a larger footprint than some other polishing machines. Manufacturers need to ensure they have adequate space in their workshop or production area to accommodate these machines.
Conclusion
Polishing lathe buffing machines offer a precise and versatile solution for polishing a wide variety of materials. Their ability to handle different types of polishing tasks, from rough buffing to fine finishes, makes them an essential tool in industries like jewelry making, metalworking, woodworking, and plastic manufacturing. With their high precision, ease of use, and the ability to adjust for different materials and tasks, polishing lathe buffing machines continue to be a popular choice for those seeking high-quality, polished finishes.
Polishing lathe buffing machines are widely recognized for their ability to deliver high-quality finishes with precision and versatility. The ability to control the rotation speed and apply different buffing stages ensures that workpieces are polished uniformly, whether the task is to achieve a high-gloss shine or to smooth rough surfaces. This makes them a valuable tool in many industries that require delicate and detailed work. In addition to the precision they offer, these machines can handle a variety of materials, from metals and plastics to wood and composites, by simply switching out the buffing wheels or pads, allowing operators to easily adjust for different tasks and surface requirements.
As manufacturing processes become more automated and demand for consistent, high-quality products increases, polishing lathe buffing machines continue to evolve. In some cases, they are integrated with more advanced technologies, such as sensors that monitor the temperature of the workpiece or the pressure applied by the buffing wheels. These sensors can automatically adjust settings to optimize the process, preventing overheating or damaging the surface. The use of automated systems also helps reduce the need for manual intervention, ensuring more consistent results, even in high-volume production settings.
Another area of improvement is the integration of advanced dust collection and filtration systems, which are becoming increasingly important in ensuring cleaner, healthier working environments. As buffing can generate a significant amount of fine dust, these systems help reduce the amount of airborne particles that may be harmful to workers. The ability to manage this dust more efficiently also contributes to cleaner final products, as contaminants from dust or debris can compromise the finish.
Polishing lathe buffing machines are also benefiting from innovations in smart technology. The implementation of IoT (Internet of Things) capabilities in some machines allows operators to monitor real-time data on performance, including variables such as speed, temperature, and pressure. This data can be accessed remotely, enabling operators or maintenance teams to spot potential issues before they lead to machine failure or production delays. These advancements further enhance the machine’s efficiency, reducing downtime and allowing for more predictive maintenance schedules.
Additionally, improvements in the materials used for the buffing wheels themselves are contributing to the performance of these machines. The development of longer-lasting, more durable materials helps extend the lifespan of the buffing heads, reducing the frequency of wheel replacements and improving the consistency of the polishing results. Innovations such as diamond-coated or ceramic wheels are particularly useful for polishing harder materials, providing even finer finishes while maintaining their durability.
With the continuous improvements in energy efficiency, many polishing lathe buffing machines are now designed to use less power, reducing operational costs while still delivering optimal performance. The integration of variable-speed motors and energy-efficient components ensures that these machines can operate with minimal energy consumption, even during long hours of operation. This focus on sustainability is an essential consideration for manufacturers looking to reduce their environmental impact.
As industries increasingly seek automation and precision in polishing, the future of polishing lathe buffing machines lies in further integration of robotic systems. Robotic arms or collaborative robots (cobots) could work alongside human operators to load and unload workpieces, ensuring that the polishing process remains consistent and efficient. These robots could also handle repetitive tasks, freeing up human operators to focus on more complex aspects of the production process.
In conclusion, polishing lathe buffing machines are a critical tool for industries that require high-quality, precise finishes on a wide range of materials. With continuous advancements in technology, automation, and energy efficiency, these machines will continue to play an essential role in manufacturing, delivering both speed and precision while maintaining high standards of quality. Their versatility, adaptability, and the potential for further innovation make them indispensable in modern production lines, from jewelry manufacturing to automotive and aerospace applications.
The future of polishing lathe buffing machines looks promising with continuous advancements in several key areas. One of the major trends is the increased automation of polishing processes. As industries continue to push for higher levels of efficiency, more polishing lathe buffing machines are being integrated into automated production lines, reducing the need for manual intervention. Automation allows these machines to run continuously, improving output and minimizing human error. Automated loading and unloading systems, for example, ensure that workpieces are handled efficiently and consistently, leading to faster processing times and reduced labor costs.
Additionally, robotic integration is becoming more prevalent. Collaborative robots (cobots) are being used to assist with the polishing process by working alongside human operators. Cobots can take over repetitive and physically demanding tasks, such as loading parts into the lathe or applying a consistent level of pressure to the polishing wheel. These robots are designed to be easily programmable and flexible, allowing them to adapt to different polishing tasks and work seamlessly with other machines on the production line. The use of cobots not only increases efficiency but also enhances the quality of the finished products by maintaining consistent polishing results.
As the demand for smart manufacturing continues to grow, polishing lathe buffing machines are being equipped with advanced sensors and data analytics capabilities. These systems can monitor key variables such as speed, pressure, temperature, and vibration in real time, allowing operators to track the machine’s performance and make adjustments when necessary. The integration of artificial intelligence (AI) is also enhancing the machine’s ability to learn from past operations and optimize its settings for different types of materials and workpieces. For example, AI algorithms can analyze the data from previous polishing sessions to automatically adjust the machine’s speed, pressure, and polishing wheel type, ensuring optimal results every time.
In addition to performance monitoring, the development of predictive maintenance systems is improving the reliability and uptime of polishing lathe buffing machines. By analyzing the machine’s operating data, predictive maintenance software can identify potential issues before they become major problems, allowing for timely repairs or adjustments. This reduces the risk of unexpected downtime and ensures that the machine remains in peak operating condition, leading to greater productivity and reduced maintenance costs.
The evolution of material science is also playing a significant role in the future of polishing lathe buffing machines. Buffing wheels are being made from more advanced, durable materials that can handle higher speeds and provide finer finishes. For example, diamond-coated wheels are becoming increasingly popular for polishing hard metals and ceramics, providing longer life and a superior finish. The development of new abrasive materials also enables polishing machines to work more efficiently with a wider range of materials, including difficult-to-polish alloys and composites used in high-tech industries such as aerospace and electronics.
As environmental concerns grow, there is an increasing push towards sustainable manufacturing practices. Polishing lathe buffing machines are being designed with more eco-friendly features, such as energy-efficient motors, low-emission dust collection systems, and the use of biodegradable polishing compounds. Additionally, the increased use of closed-loop systems that recycle and reuse polishing fluids is helping to reduce waste and improve the environmental footprint of polishing operations. Manufacturers are also focusing on reducing the use of hazardous chemicals in the buffing process, opting for safer alternatives that meet environmental and safety regulations.
The future of polishing lathe buffing machines will also see a continued focus on ergonomics and operator safety. As the machines become more advanced, manufacturers are incorporating features that enhance user comfort and reduce the risk of accidents. For example, machines are now equipped with more user-friendly interfaces, including touchscreen controls and intuitive software, making it easier for operators to set up and monitor the machine. Safety features such as automatic emergency shutdown, dust and noise reduction, and protective barriers around the buffing wheels are becoming standard in many models to ensure a safer working environment.
Moreover, the rise of digitalization in manufacturing is transforming the way polishing lathe buffing machines are operated. Cloud-based platforms are being used to connect polishing machines to centralized control systems, allowing for remote monitoring and control of multiple machines from a single location. This connectivity also enables real-time collaboration between operators, engineers, and maintenance teams, improving communication and efficiency across the production floor. By having access to real-time data on machine performance and output, manufacturers can make more informed decisions, streamline operations, and improve product quality.
In specialized industries such as aerospace, medical device manufacturing, and luxury goods production, polishing lathe buffing machines will continue to play a crucial role in achieving the exacting standards required for highly finished, high-performance parts. For instance, in the aerospace industry, where components must meet stringent requirements for both aesthetics and functionality, polishing lathe buffing machines are essential for ensuring that parts are free of defects and have a flawless surface finish. Similarly, in medical device manufacturing, where precision is critical for the safety and performance of devices, polishing machines will remain indispensable for creating smooth, contamination-free surfaces on implants, surgical instruments, and other critical components.
As these industries evolve, polishing lathe buffing machines will continue to advance to meet new challenges, providing the flexibility, precision, and speed required to keep up with the increasing demands for high-quality finishes. In this context, manufacturers are likely to see more customizable machines that can handle a wider range of materials, sizes, and shapes, as well as advanced technologies that help optimize the polishing process for maximum productivity and minimum waste.
In conclusion, the future of polishing lathe buffing machines is marked by ongoing advancements in automation, smart technology, material science, and sustainability. As industries demand higher levels of precision, efficiency, and sustainability, polishing lathe buffing machines are poised to evolve into even more powerful, versatile, and eco-friendly tools. With the integration of AI, robotics, predictive maintenance, and eco-conscious design, these machines will continue to be a critical part of modern manufacturing, providing the quality and consistency needed for a wide variety of applications.
Vertical Buffing Machine
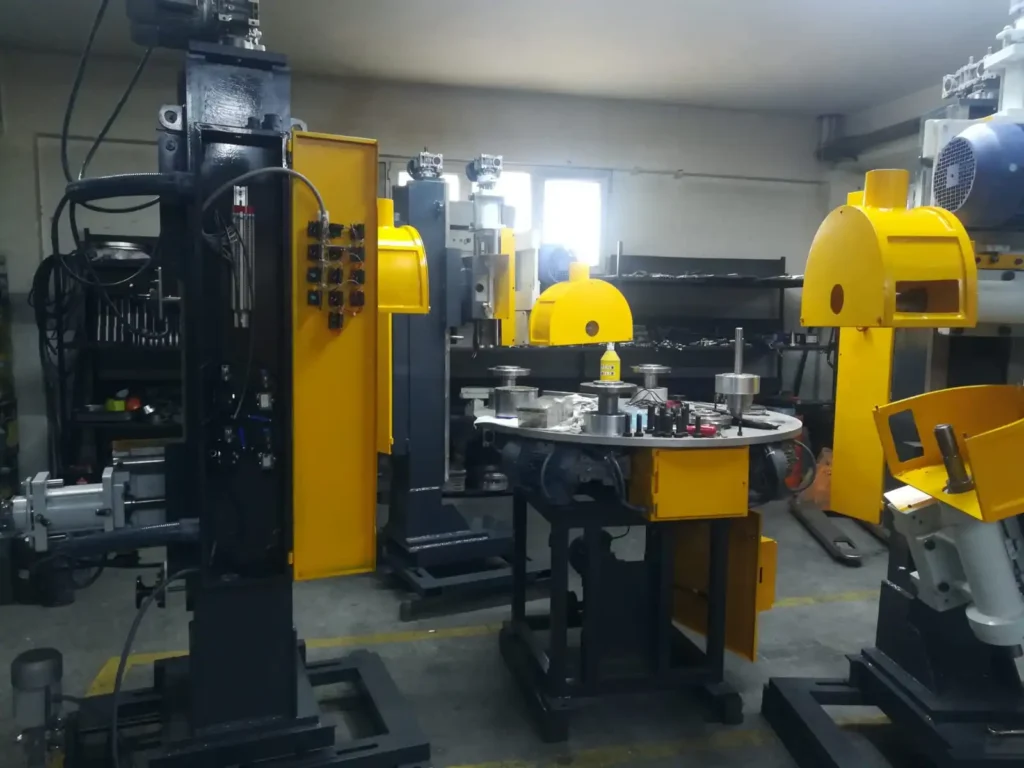
A vertical buffing machine is a type of buffing equipment commonly used in manufacturing and finishing processes to polish and buff surfaces of various materials. The key distinguishing feature of this machine is its vertical spindle orientation, meaning that the buffing wheel or pad is mounted vertically rather than horizontally. This design allows for more precise control over the polishing process, making it ideal for polishing tall or intricate parts that may be difficult to process with a horizontal machine.
The vertical buffing machine typically consists of a vertically mounted spindle driven by a motor, with the buffing wheel or pad attached to the spindle. The workpiece is usually held stationary or rotated by a fixture or support platform. As the buffing wheel makes contact with the workpiece, it spins at high speeds, removing imperfections, smoothing rough surfaces, and giving the material a high-gloss finish.
Key Features of a Vertical Buffing Machine
- Vertical Spindle Configuration: The vertical orientation of the spindle allows for better access to parts that might be difficult to polish using a horizontal machine. This is particularly beneficial for polishing long, thin, or complex shapes, such as rods, bars, tubes, or other vertical components.
- Precision Buffing: The vertical setup provides a stable environment for controlled buffing, ensuring that the polishing process is even across the surface of the workpiece. This precision is essential in industries where high-quality finishes are required, such as in automotive parts, jewelry, and metalworking.
- Variable Speed Control: Many vertical buffing machines come equipped with adjustable speed controls, allowing operators to tailor the polishing process to different materials and workpieces. For instance, lower speeds may be used for more delicate materials, while higher speeds are suited for tougher surfaces that require more aggressive polishing.
- Dust Collection Systems: Buffing generates a significant amount of dust and debris, which can be harmful to both the operator and the environment. Many vertical buffing machines are equipped with dust collection systems to capture these particles and maintain a clean and safe workspace.
- Ergonomic Design: The vertical configuration of the machine can also contribute to a more ergonomic work setup. Operators can work at a comfortable height without having to bend over or exert unnecessary physical strain, especially when polishing large or heavy workpieces.
- Rotary and Stationary Buffing: Depending on the specific model, vertical buffing machines may either rotate the workpiece while the buffing wheel remains stationary, or both the workpiece and the buffing wheel may rotate. This flexibility allows the machine to be adapted to various types of polishing operations.
- Adjustable Workholding: Vertical buffing machines often feature adjustable clamps, chucks, or fixtures that can securely hold the workpiece in place. This ensures that the workpiece remains steady during the polishing process, improving the consistency and quality of the finish.
- High Precision Buffing Heads: Many vertical buffing machines are equipped with high-precision buffing heads that can be easily swapped out to suit different materials, finishes, or polishing stages. This versatility allows operators to use the machine for various polishing applications without needing multiple machines.
Applications of Vertical Buffing Machines
- Metal Finishing: Vertical buffing machines are commonly used in metalworking applications to achieve a polished, smooth surface on metal parts. Industries like automotive, aerospace, and construction use vertical buffing machines to polish components such as engine parts, decorative trim, or structural metal pieces.
- Jewelry Polishing: In the jewelry industry, vertical buffing machines are used to create a mirror-like finish on rings, necklaces, bracelets, and other metal jewelry. The ability to control the speed and pressure of the buffing process is critical in achieving high-quality finishes without damaging the delicate components.
- Plastic Polishing: Vertical buffing machines are also used to polish plastic parts, especially in applications where clarity and smoothness are important, such as in the production of clear acrylic displays, lenses, or automotive parts.
- Woodworking: Vertical buffing machines can be used in woodworking to polish and finish wooden items, such as furniture, cabinetry, or carved objects. These machines are ideal for achieving a glossy surface finish on wooden pieces without causing damage.
- Aerospace and Medical: In specialized industries such as aerospace and medical device manufacturing, vertical buffing machines are essential for polishing critical components. For instance, aerospace components such as turbine blades or medical implants require a flawless finish to meet regulatory standards.
Advantages of Vertical Buffing Machines
- Improved Access to Workpieces: The vertical orientation allows for easier access to certain types of workpieces, especially those that are tall, cylindrical, or awkwardly shaped. This makes the machine highly versatile in polishing parts that would otherwise be challenging to process with other types of buffing machines.
- Consistent Finishes: The vertical design of the machine helps ensure a uniform polishing process. With a stable and controlled approach, operators can achieve more consistent results, which is important in industries that demand high-quality surface finishes.
- Space Efficiency: Vertical buffing machines often have a smaller footprint than horizontal models, which can be beneficial in shops or production lines where space is limited. The vertical design can be integrated into tighter workspaces while still providing efficient polishing capabilities.
- Increased Flexibility: The ability to adjust speed, pressure, and the type of buffing wheel allows for greater flexibility in the polishing process. Operators can fine-tune the settings to suit different materials and desired finishes, making the machine adaptable to various tasks.
- Ergonomics and Operator Comfort: The vertical configuration can improve operator comfort by reducing the need to bend or strain during operation. This can help reduce fatigue, improve safety, and make it easier for workers to operate the machine for extended periods.
- Enhanced Productivity: Vertical buffing machines are designed for high-speed operation, which can improve throughput and productivity. By offering fast polishing speeds while maintaining high precision, these machines help streamline the finishing process and reduce turnaround times.
Considerations for Vertical Buffing Machines
- Initial Cost: Vertical buffing machines can be a significant investment, especially those with advanced features such as variable speed control, high-precision buffing heads, and integrated dust collection systems. However, the long-term benefits in terms of precision, productivity, and finish quality often justify the initial expense.
- Maintenance: Like all machinery, vertical buffing machines require regular maintenance to keep them in optimal working condition. This includes routine checks on the buffing wheels, cleaning of dust collection systems, and ensuring the motor and spindles are functioning properly.
- Operator Skill: Although vertical buffing machines are designed for efficiency and ease of use, operators still need a certain level of skill and experience to achieve the best results. Proper training is essential to ensure that the machine is used correctly and safely.
- Workpiece Compatibility: While vertical buffing machines are versatile, some workpieces may require specific adjustments or fixtures to be properly polished. Operators need to ensure that the workpiece is securely held in place and that the right buffing wheel or pad is used for the material.
- Space Considerations: While the vertical design can save space compared to horizontal buffing machines, it’s still important to ensure that there is sufficient clearance around the machine for both operation and maintenance.
Conclusion
Vertical buffing machines are a powerful and versatile tool used in a variety of industries to achieve high-quality, precise surface finishes. Their ability to handle tall, cylindrical, and irregularly shaped parts makes them ideal for polishing a wide range of materials, including metals, plastics, wood, and more. With features such as variable speed control, dust collection, and ergonomic design, vertical buffing machines offer both efficiency and ease of use. While they require a significant initial investment and regular maintenance, their precision, consistency, and flexibility make them an invaluable asset in any manufacturing or finishing operation.
Vertical buffing machines are highly valued in various industries due to their unique ability to handle workpieces that require precise polishing and finishing. Their vertical spindle configuration allows for more controlled and efficient polishing, especially when working with tall, cylindrical, or intricately shaped components. The versatility of these machines makes them suitable for a wide range of materials, including metals, plastics, wood, and composites. This adaptability enables manufacturers to achieve the desired surface finish without the need for multiple types of machines.
One of the standout features of vertical buffing machines is their ability to adjust to different polishing requirements. The machines often come equipped with variable speed controls, allowing operators to tailor the process to the specific material being polished. This capability is essential, especially in industries like automotive, aerospace, and medical device manufacturing, where the finish quality must meet stringent standards. By adjusting the speed, pressure, and buffing wheel type, operators can achieve a wide range of finishes, from satin to high-gloss, depending on the specific needs of the workpiece.
Another advantage of vertical buffing machines is the dust collection system that is often integrated into the design. Buffing and polishing processes can generate fine dust and debris, which can be harmful to both the environment and the health of workers. The dust collection system ensures that these particles are captured efficiently, maintaining a cleaner and safer workspace. This feature is especially important in industries that handle materials like metal, plastic, or composite, where fine particles can create health hazards if not properly managed.
Moreover, vertical buffing machines can improve operator ergonomics. The vertical design of the machine allows for a more natural and comfortable working posture, reducing the strain on workers during long hours of operation. This ergonomic design can help to improve productivity and reduce the likelihood of work-related injuries. The ability to access the workpiece from different angles, combined with an adjustable workholding system, further enhances the flexibility of these machines.
The productivity benefits of vertical buffing machines are also significant. By offering high-speed operation and the ability to fine-tune polishing parameters, these machines help reduce production times while maintaining excellent finish quality. This makes them an essential part of high-volume production environments, where time and efficiency are critical. In addition, the consistent quality of the finishes achieved by vertical buffing machines leads to fewer rework cycles, which can further improve overall manufacturing efficiency.
Vertical buffing machines are often equipped with specialized features designed to accommodate different types of workpieces. For instance, they may have adjustable workholding devices, such as clamps or chucks, that securely hold the workpiece in place during the polishing process. This ensures that the workpiece remains stable, allowing for even and uniform polishing across its surface. The flexibility to adjust the workholding system also enables these machines to accommodate various sizes and shapes, making them highly versatile tools in a wide range of industries.
Another benefit is the energy efficiency that modern vertical buffing machines offer. Many newer models are designed with energy-saving features, such as variable-speed motors that adjust power consumption based on the task at hand. This reduces the overall energy usage, making these machines more cost-effective to operate over the long term. With an increased emphasis on sustainability in manufacturing, energy-efficient machines that minimize waste and reduce operational costs are becoming more desirable.
In terms of maintenance, vertical buffing machines are generally designed to be low-maintenance, but regular care is still essential for ensuring long-term performance. Regular checks on the buffing wheels, spindles, and motor components are necessary to prevent breakdowns. In addition, operators should clean the dust collection system and inspect it for any blockages to ensure optimal air quality and machine performance. By adhering to a maintenance schedule, manufacturers can ensure that the machine operates at peak efficiency and that production is not interrupted due to unexpected downtime.
The market for vertical buffing machines continues to grow as industries demand higher-quality finishes and more efficient manufacturing processes. With the advancement of technology, these machines are becoming even more sophisticated, integrating features such as sensor technology, real-time data monitoring, and AI-driven adjustments. These innovations allow for greater precision, improved control over the polishing process, and better overall results, especially when working with complex or delicate parts.
Vertical buffing machines are also becoming more adaptable to a wide range of industries. For example, in the aerospace sector, where components must meet exacting tolerances and surface finishes for both performance and aesthetics, vertical buffing machines play a crucial role. Similarly, in the automotive industry, these machines are used to polish engine components, trim parts, and other elements where surface quality is a critical factor in both function and appearance. Medical device manufacturers rely on vertical buffing machines for polishing implants and surgical instruments, ensuring that the surfaces are smooth and free from imperfections that could compromise functionality or safety.
The future of vertical buffing machines lies in further innovation aimed at improving efficiency, sustainability, and quality. With ongoing advancements in automation and robotics, future vertical buffing machines may be able to operate with minimal human intervention. Collaborative robots (cobots) may assist in tasks like loading and unloading parts, while sensors could monitor and adjust the polishing process in real-time to ensure the optimal finish is achieved. The integration of smart technology will enable manufacturers to remotely monitor and control machine performance, allowing for more efficient management of production schedules and quality control.
As industries continue to demand faster, more precise, and more cost-effective manufacturing processes, vertical buffing machines will remain a key component in achieving high-quality finishes on a wide range of materials. The combination of precision engineering, ergonomic design, and the flexibility to handle different materials and workpieces makes them a valuable asset for manufacturers aiming to meet the demands of modern production. The continued evolution of these machines, driven by technological advancements and a focus on sustainability, will further cement their role as essential tools in the manufacturing landscape.
As vertical buffing machines evolve, several trends are likely to shape their future. One such trend is the integration of smart manufacturing and Industry 4.0 technologies. With the growing adoption of the Internet of Things (IoT), vertical buffing machines are becoming increasingly interconnected with other machines and systems on the shop floor. This interconnectivity allows for real-time data sharing, enabling operators and managers to monitor machine performance, track production progress, and detect potential issues before they lead to downtime. For instance, sensors can continuously monitor key parameters like wheel speed, pressure, and temperature, and send alerts when maintenance is needed or when the polishing process is deviating from the optimal conditions.
Moreover, the use of artificial intelligence (AI) is becoming more prevalent in the operation of vertical buffing machines. AI algorithms can analyze historical data to identify patterns in the polishing process, optimize settings for specific materials or components, and even predict when maintenance or repairs will be needed. This predictive capability reduces the likelihood of unexpected machine failures and helps to streamline operations by ensuring that machines are always running at their best. AI-driven systems can also help operators adjust polishing techniques on the fly, adapting to variations in material properties or changes in environmental conditions, thereby ensuring consistent results across large production runs.
The growing demand for sustainability in manufacturing is another factor that will influence the future of vertical buffing machines. With increasing environmental regulations and a push for more eco-friendly practices, manufacturers are seeking ways to reduce the environmental impact of their polishing operations. In response, vertical buffing machines are being designed with greater energy efficiency, reduced waste generation, and improved material recycling systems. For example, closed-loop water and fluid recycling systems are being incorporated into buffing machines to minimize the amount of polishing fluid consumed and reduce wastewater production. Similarly, dust collection systems are becoming more efficient, capturing a greater percentage of particles and improving the air quality in production facilities.
The materials used in buffing wheels and pads are also advancing. Manufacturers are increasingly using high-performance materials that last longer, provide better polishing results, and are less prone to wear. These advanced materials improve the overall efficiency of vertical buffing machines by reducing the need for frequent wheel replacements, lowering maintenance costs, and enhancing the consistency of the polished finish. For example, the use of diamond-impregnated buffing wheels allows for finer and more precise finishes, especially when working with hard metals or ceramics. These wheels not only offer superior polishing performance but also have a longer lifespan, reducing downtime and material waste.
The rise of customization in manufacturing is also influencing the design and capabilities of vertical buffing machines. As industries move toward more specialized and bespoke products, buffing machines are being designed with greater flexibility. Manufacturers are increasingly looking for machines that can be easily adapted to different workpieces, finishes, and materials. This has led to the development of vertical buffing machines with customizable features, such as adjustable spindle speeds, interchangeable buffing heads, and programmable polishing cycles. This level of flexibility enables manufacturers to handle a wide variety of polishing tasks, from mass production runs to low-volume, high-precision work.
Additionally, the integration of robotics in polishing and buffing operations is expected to continue to grow. Robotic arms can be used to automate the process of loading and unloading parts, ensuring that the workpieces are handled precisely and without manual intervention. This automation reduces the risk of human error, speeds up the production process, and enhances the overall consistency of the finished product. In some cases, robots may also be used to perform the polishing itself, particularly in applications that require high precision and a high degree of repeatability. This shift towards automation allows manufacturers to increase their productivity while reducing labor costs and minimizing the risk of injuries associated with manual polishing tasks.
Safety will continue to be a key consideration in the design of vertical buffing machines. As manufacturing environments become more automated, ensuring that machines operate safely and do not pose a risk to workers will be a priority. Modern vertical buffing machines are likely to come equipped with a variety of safety features, such as automatic shut-off mechanisms, emergency stop buttons, and protective enclosures that prevent operators from coming into direct contact with the spinning buffing wheels. Additionally, there will be a continued emphasis on minimizing noise and vibration during operation, both of which can contribute to worker fatigue and potential hearing loss over time.
The trend towards integration with enterprise resource planning (ERP) systems is another factor that will shape the future of vertical buffing machines. By connecting polishing equipment to the broader production management system, manufacturers will be able to track production metrics, manage inventory, and plan maintenance schedules more effectively. This integration improves the overall efficiency of the manufacturing process, as it allows for better coordination between polishing operations and other stages of production. For instance, real-time data from the buffing machine can be used to adjust scheduling, ensuring that parts are polished at the optimal time in the production process.
In the aerospace, medical, and automotive industries, where precision is paramount, vertical buffing machines will continue to evolve to meet the increasingly demanding requirements of these sectors. 3D polishing technologies and advanced simulation tools are expected to be integrated into vertical buffing machines, enabling manufacturers to virtually simulate the polishing process before it is executed. This will help identify potential issues early on, reduce trial and error, and ensure that the final product meets the desired specifications. In addition, precision polishing capabilities are likely to advance further, allowing manufacturers to achieve even finer and more uniform finishes on critical components.
Training and skill development for operators will also play a crucial role in the future of vertical buffing machines. As these machines become more advanced, operators will need to be skilled in working with high-tech features such as automation, robotics, and AI-driven systems. Manufacturers are likely to invest in specialized training programs to ensure that their workforce can effectively manage and maintain these sophisticated machines. Moreover, as the technology continues to evolve, operators will need to stay updated on the latest features and techniques to maximize the performance of their buffing machines.
In conclusion, the future of vertical buffing machines is shaped by advancements in automation, robotics, AI, and sustainability. These machines are becoming more efficient, precise, and flexible, allowing manufacturers to meet the growing demands for high-quality finishes across a wide range of materials and industries. With the integration of smart technologies, predictive maintenance, and eco-friendly features, vertical buffing machines will continue to play a crucial role in modern manufacturing. By adapting to these trends, manufacturers can improve productivity, reduce costs, and maintain the high standards required for a variety of demanding applications. As the technology continues to evolve, vertical buffing machines will remain at the forefront of the finishing process, enabling industries to produce high-quality, polished products with greater efficiency and consistency.
Swing Arm Buffing Machine
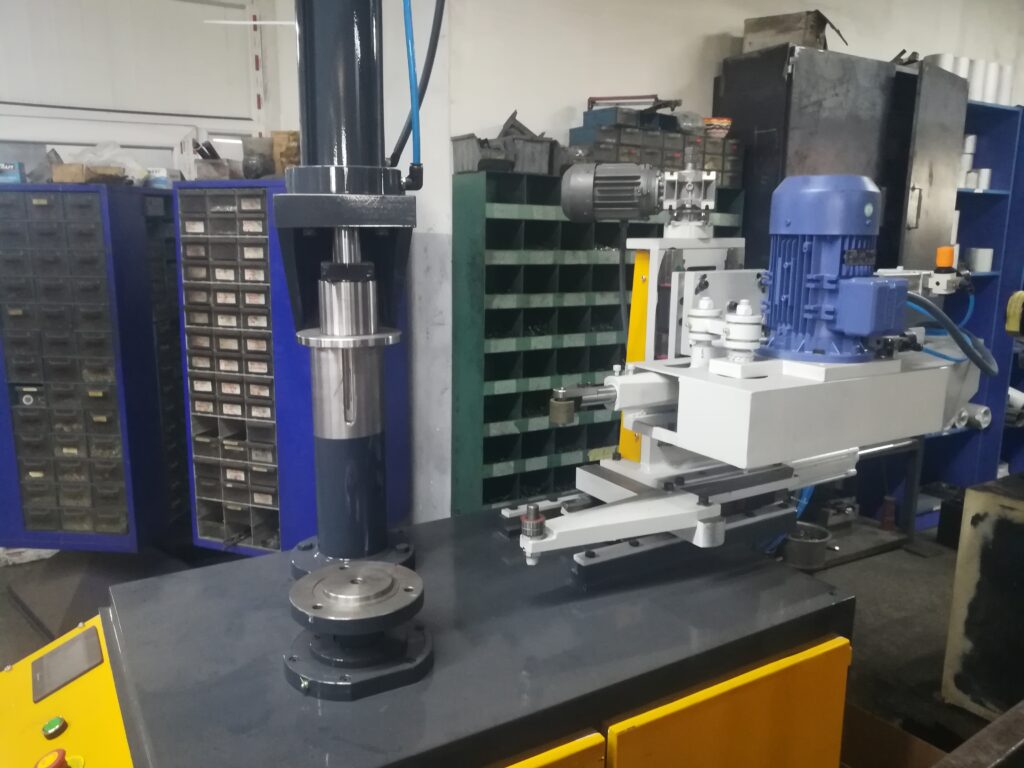
A swing arm buffing machine is a specialized polishing tool used in various manufacturing industries to achieve high-quality surface finishes on workpieces. The machine features a distinctive design that includes a swing arm mechanism, which allows the buffing wheel or polishing pad to move in a circular or sweeping motion. This setup makes it easier for operators to handle workpieces of varying shapes and sizes while maintaining a consistent and smooth finish. Swing arm buffing machines are widely used for polishing metal, wood, plastic, and other materials.
Key Features of a Swing Arm Buffing Machine
- Swing Arm Mechanism: The most distinctive feature of this machine is the swing arm, which holds the buffing wheel or pad and allows it to move in a sweeping motion. This feature offers flexibility, as the operator can maneuver the buffing wheel around the workpiece to achieve a uniform polish. The swing arm is typically mounted on a rotating base, enabling the buffing wheel to reach multiple angles of the workpiece without requiring it to be moved manually.
- Adjustable Arm Length and Angle: Most swing arm buffing machines allow for adjustable arm lengths and angles, providing greater control over the buffing process. This adjustability enables operators to work with various workpiece sizes and shapes, whether they are polishing small intricate parts or larger components. The ability to adjust the arm length also helps when dealing with awkwardly shaped items that may require more precise polishing.
- Variable Speed Control: Many swing arm buffing machines come equipped with variable speed controls, allowing operators to adjust the speed of the buffing wheel. This feature is essential for achieving different types of finishes, from light polishing to aggressive buffing. By controlling the speed, operators can optimize the process for different materials, ensuring a smooth and even finish without damaging the workpiece.
- Heavy-Duty Construction: These machines are built to handle tough polishing tasks and typically feature robust, heavy-duty construction to ensure long-term durability. The frame is usually made from high-quality steel or other strong materials, providing stability and reducing vibrations during operation. The solid build allows the machine to handle both light and heavy-duty polishing tasks with ease.
- Dust Collection Systems: Buffing and polishing processes generate significant amounts of dust and debris, which can pose health risks to operators and contribute to a dirty work environment. Many swing arm buffing machines are equipped with dust collection systems that capture the fine particles produced during polishing. These systems help maintain a clean and safe workspace, prevent clogging of the buffing wheels, and improve air quality.
- Ergonomic Design: Swing arm buffing machines are often designed with ergonomics in mind. The swing arm design allows operators to adjust the height and angle of the buffing wheel, reducing strain on the operator’s body. The ability to work at different angles also reduces fatigue, as the operator doesn’t need to constantly reposition the workpiece or buffing wheel.
- Easy Workpiece Handling: The swing arm mechanism simplifies the process of handling workpieces. Rather than manually repositioning the part, the operator can move the buffing wheel around the part, which is particularly helpful for large, bulky, or oddly shaped items. The setup also helps in achieving a uniform and consistent finish across all surfaces of the workpiece.
- Interchangeable Buffing Wheels: Swing arm buffing machines typically offer interchangeable buffing wheels or pads, which allow operators to choose the best type of wheel for the job. This makes it easy to adapt the machine to different materials and polishing stages, such as rough buffing, fine polishing, or achieving a mirror-like finish.
Applications of Swing Arm Buffing Machines
- Metal Polishing: Swing arm buffing machines are commonly used in the metalworking industry for polishing metal parts like automotive components, engine parts, jewelry, and decorative pieces. The ability to adjust the buffing wheel’s angle and speed makes these machines ideal for achieving high-quality metal finishes without damaging delicate surfaces.
- Plastic Polishing: These machines are also used for polishing plastics, especially in the automotive and consumer electronics industries. Whether it’s achieving a glossy finish on car trim or polishing acrylic or polycarbonate parts for electronics, the swing arm buffing machine provides the precision needed for these delicate materials.
- Woodworking: In the woodworking industry, swing arm buffing machines can be used to polish and finish wood surfaces, ensuring a smooth and glossy finish on furniture, cabinets, and decorative items. The adjustable arm length and angle help to efficiently buff large wooden pieces or intricate carvings, reducing manual labor and improving finish consistency.
- Glass Polishing: Swing arm buffing machines are also used in glass polishing applications, such as polishing glass edges, mirrors, and other glass components. The precise control over the buffing wheel helps prevent damage to glass surfaces while achieving a smooth, shiny finish.
- Jewelry Polishing: In the jewelry industry, swing arm buffing machines are used to achieve highly polished, mirror-like finishes on rings, necklaces, bracelets, and other fine jewelry items. The precision and flexibility of the swing arm mechanism are ideal for working with delicate and intricate pieces that require a high-quality finish.
- Aerospace and Automotive: Swing arm buffing machines are used in the aerospace and automotive industries to polish various parts, including turbine blades, car body parts, and other components that need a precise finish to meet aesthetic and functional requirements. The machine’s versatility makes it ideal for polishing both small and large parts with high precision.
Advantages of Swing Arm Buffing Machines
- Flexibility and Versatility: The ability to adjust the swing arm’s angle and length allows for greater versatility in polishing a wide range of workpieces. Whether the task requires polishing flat, cylindrical, or intricate surfaces, the swing arm mechanism makes it easier to achieve the desired finish without having to reposition the part.
- Consistency of Finish: The swing arm buffing machine provides consistent results by enabling the operator to maintain uniform pressure and speed across the workpiece. This results in a high-quality, consistent finish, which is critical in industries where precision and appearance are important.
- Increased Productivity: The ease of handling workpieces and the ability to achieve a smooth, even finish quickly can help improve productivity. Operators can polish more items in less time, which is particularly important in high-volume manufacturing environments.
- Reduced Operator Fatigue: The ergonomic design and adjustable features of swing arm buffing machines help reduce strain and fatigue on operators. By allowing for better access to workpieces and minimizing the need for constant repositioning, operators can work more efficiently and comfortably for extended periods.
- Cost-Effective: Swing arm buffing machines are relatively cost-effective when compared to other types of polishing equipment. They are designed for durability, and their ability to handle a wide variety of tasks makes them a good investment for businesses that require versatile polishing machines without a significant upfront cost.
- Improved Safety: With built-in dust collection systems and the ability to control the speed and pressure of the buffing process, swing arm buffing machines help improve safety in the workplace. Dust and debris are minimized, reducing the risk of inhalation or contamination. Furthermore, the ergonomic design helps prevent repetitive strain injuries, which are common in industries that require extended polishing sessions.
- Easy to Operate and Maintain: Swing arm buffing machines are typically easy to operate, with simple controls for adjusting speed and arm positioning. Additionally, maintaining these machines is straightforward, as many models have replaceable components such as buffing wheels and dust filters, which can be easily swapped out as needed.
Considerations for Swing Arm Buffing Machines
- Initial Investment: While swing arm buffing machines are generally affordable, higher-end models with advanced features (such as variable speed control and precision dust collection systems) can have a higher initial cost. However, the long-term benefits in terms of efficiency and finish quality often justify this investment.
- Space Requirements: Swing arm buffing machines typically require more space than other types of buffing equipment due to the swing arm’s extended reach. It’s important to ensure that the workspace is large enough to accommodate the machine and allow for easy movement of both the workpiece and the buffing wheel.
- Skill and Training: Although swing arm buffing machines are relatively easy to operate, they still require a certain level of skill to achieve the best results. Operators need to be trained in the proper handling techniques to ensure that the workpiece is polished uniformly without damage.
- Maintenance: Regular maintenance, such as checking the buffing wheel for wear and tear and ensuring the dust collection system is functioning properly, is necessary to keep the machine running efficiently. Neglecting maintenance can lead to reduced performance and potentially costly repairs down the line.
Conclusion
Swing arm buffing machines are versatile and efficient tools that play a vital role in achieving high-quality surface finishes across a wide range of industries. With their adjustable swing arm, variable speed control, and ergonomic design, these machines provide operators with flexibility and precision in polishing various materials. Whether used for metal, plastic, wood, or other materials, swing arm buffing machines help improve productivity, consistency, and safety in manufacturing environments. By providing a cost-effective and adaptable solution for polishing tasks, they remain an essential part of the finishing process in many industries.
The ongoing development of swing arm buffing machines reflects a broader movement in industrial finishing technology toward automation, precision, and efficiency. As manufacturers seek to increase throughput while maintaining high standards of quality, swing arm machines are becoming increasingly integrated with smart features that enhance both control and consistency. Modern models now incorporate digital controls that allow for precise setting of parameters such as speed, pressure, and cycle time. This level of precision not only improves finish quality but also reduces material waste and operator error. Operators can now program polishing routines that the machine follows consistently, making it possible to achieve uniform results across large production batches without constant supervision or adjustment.
Another major trend in swing arm buffing machine development is the adoption of servo motors and programmable logic controllers (PLCs). These technologies enable more nuanced and automated movement of the buffing arm, ensuring that complex geometries and surfaces are polished with uniform contact and pressure. With servo-driven motion, the arm can be made to follow intricate paths, adapting to workpiece contours with a level of precision that manual systems cannot match. In applications such as aerospace or medical device manufacturing, where surface perfection is critical, this capability is essential. It ensures that each component is finished to exact specifications, thereby reducing post-processing and quality control rework.
Manufacturers are also increasingly focused on reducing the physical strain on operators. Traditional buffing tasks can be physically demanding, often involving repetitive motion and extended periods of manual handling. Swing arm machines, particularly those with motorized arm movement and height-adjustable features, alleviate this strain by allowing the operator to bring the tool to the workpiece, rather than the reverse. This ergonomic benefit not only improves worker comfort but also reduces the risk of repetitive strain injuries, a concern in many industrial settings. Furthermore, with the integration of foot pedals and hands-free operation modes, productivity increases as workers can maintain steady control while keeping their hands free to position the workpiece or make adjustments.
In terms of sustainability, the push for greener manufacturing has also influenced the design of swing arm buffing machines. Energy-efficient motors are now standard in many models, reducing power consumption without sacrificing performance. Additionally, advanced dust and particle collection systems are being refined to better capture airborne debris generated during the polishing process. These systems not only improve air quality in the workspace, creating a safer environment for workers, but also allow for the reclamation and recycling of valuable materials such as metal dust. Some machines are even equipped with filters that separate and store different particle types for reuse or proper disposal, aligning with modern environmental and health standards.
The rise of hybrid materials and composites in manufacturing has further driven innovation in buffing equipment. Swing arm buffing machines must now accommodate a wide array of surface types, each with distinct hardness, thermal properties, and abrasion responses. To meet this challenge, manufacturers are developing machines with interchangeable buffing heads and materials that can be quickly swapped out to match the specific requirements of each job. Whether working with delicate plastics that can be easily marred, or hard metals that require aggressive polishing, the swing arm machine offers the versatility needed to adapt to each situation without requiring a complete equipment changeover.
Another noteworthy evolution is the use of real-time monitoring and feedback systems. Sensors embedded within the machine can now monitor pressure applied to the workpiece, temperature at the point of contact, and the condition of the buffing wheel. When certain thresholds are exceeded or components show signs of wear, the system can alert the operator or automatically adjust parameters to compensate. This minimizes the risk of surface damage due to overheating or over-polishing and extends the life of consumables like wheels and pads. In high-volume or precision-critical applications, this smart feedback loop adds a layer of quality assurance that manual inspection cannot match.
Looking to the future, swing arm buffing machines are likely to become even more connected through integration with broader factory systems. As part of a smart manufacturing environment, these machines can communicate with other equipment, feed data into enterprise systems, and even be monitored remotely. This connectivity allows managers to track machine performance, diagnose issues in real time, and schedule maintenance based on actual usage rather than fixed intervals. In large production environments, this contributes to more predictable operations, fewer breakdowns, and lower overall cost of ownership.
Customizability is another area where swing arm buffing machines excel and will continue to evolve. Depending on the production context, machines can be tailored with features like dual-head setups for simultaneous buffing, retractable arms for space-saving configurations, or modular designs that allow for easy upgrading as production needs change. These options enable businesses to start with a base model and scale capabilities over time, making swing arm machines a flexible investment that grows with the operation. Combined with improvements in software and user interfaces, even operators with limited experience can quickly become proficient, reducing training time and allowing for more fluid workforce deployment.
All of these developments underscore the continued importance of swing arm buffing machines in modern manufacturing. Whether used for mass production, precision finishing, or highly customized projects, they provide a unique blend of flexibility, control, and reliability that few other systems can match. As industries from automotive to aerospace continue to demand higher performance from their surface finishing processes, the swing arm buffing machine is poised to remain a vital part of the production landscape, evolving alongside advancements in materials, automation, and sustainability.
In addition to technical advancements, the role of swing arm buffing machines in optimizing workflow efficiency cannot be overstated. In many production facilities, particularly those engaged in small-batch or custom manufacturing, minimizing downtime between setup changes is crucial. Swing arm buffing machines support this requirement by allowing for rapid tool changes, intuitive repositioning of the buffing head, and fast adjustment of operational parameters. This adaptability means that operators can transition between tasks with minimal interruption, maintaining a smooth and continuous production cycle even when dealing with diverse components or short production runs. The reduction in changeover time directly impacts overall throughput, enabling businesses to meet tighter deadlines without compromising on finish quality.
Moreover, these machines provide a distinct advantage when it comes to handling components that have irregular geometries or complex contours. Traditional fixed-head polishing machines often struggle to maintain consistent contact pressure across varying surfaces, resulting in uneven finishes or the need for additional post-processing steps. The articulated nature of the swing arm allows for more natural movement around curved, concave, or angular parts, ensuring that the buffing wheel conforms better to the surface. This capability is especially beneficial in industries such as automotive restoration, musical instrument production, and high-end furniture finishing, where aesthetic details are as critical as structural integrity.
Another benefit is the ability to integrate these machines into semi-automated production cells. In such configurations, a swing arm buffing station might work in concert with robotic part loaders, conveyors, or inspection systems. The machine’s buffing cycle can be triggered automatically, and polishing routines can be synchronized with other stages of the manufacturing process. While fully robotic polishing systems are available, swing arm machines offer a more economical and modular step toward automation. They strike a balance between hands-on craftsmanship and programmable control, preserving the tactile quality of manual work while streamlining repetitive tasks.
In workshops focused on craftsmanship, such as those in the musical instrument, jewelry, or luxury goods sectors, swing arm buffing machines continue to serve as invaluable tools for artisans. Unlike rigid, fully automated systems, these machines allow operators to exercise nuanced control over the polishing process, making minute adjustments in real-time based on the material’s response and the visual feedback they receive. This human-guided flexibility ensures that each piece meets a high aesthetic standard—something that’s difficult to replicate with automation alone. The swing arm mechanism provides just enough mechanical support to reduce fatigue and increase consistency, while still giving the user the freedom to apply their expertise and finesse.
Even in high-volume settings, such as appliance manufacturing or architectural metalwork production, the durability and repeatability of swing arm buffing machines contribute to leaner and more cost-effective operations. These machines are designed for extended use under rigorous conditions, and many come with built-in safeguards to prevent overheating, excessive wheel wear, or operator misuse. Some models also include digital counters and timers that assist in production logging, helping supervisors keep track of cycle times and maintenance intervals. This data can be used to analyze performance trends, reduce waste, and implement continuous improvement initiatives within the production line.
Furthermore, as global supply chains become more decentralized and demand shifts toward more regional, responsive manufacturing, the versatility of swing arm buffing machines becomes even more relevant. These machines can be deployed effectively in both large-scale industrial plants and smaller, agile workshops. Their relatively compact footprint and low infrastructure requirements make them suitable for operations with limited space or resources, while still delivering professional-grade polishing results. This scalability allows manufacturers of all sizes to maintain competitive quality standards without making prohibitive capital investments.
In terms of consumables, the range of compatible buffing wheels and polishing compounds available for swing arm machines continues to expand. From sisal and cotton wheels to non-woven abrasives and diamond-impregnated pads, users can select the ideal medium for each material type and finish requirement. This compatibility with modern abrasive technology ensures that the machines remain relevant across a broad spectrum of applications. It also allows for experimentation and process refinement, as operators can fine-tune the combination of speed, pressure, and media to achieve custom finishes—whether matte, brushed, satin, or mirror-polished.
Lastly, the training and skill development associated with swing arm buffing machines should not be overlooked. These machines are ideal platforms for teaching new operators the principles of surface finishing, such as correct buffing angles, pressure control, and compound selection. Their manual interaction allows learners to develop a deeper understanding of how materials respond to polishing, which is knowledge that can be applied even when working with automated systems later on. For companies investing in workforce development, swing arm machines represent a practical tool for cultivating craftsmanship while supporting production needs.
In sum, the swing arm buffing machine embodies a unique intersection of tradition and innovation. It honors the hands-on precision of skilled labor while embracing technological enhancements that make polishing processes faster, safer, and more consistent. As industries continue to prioritize quality, adaptability, and efficiency, the swing arm buffing machine will remain a cornerstone of surface finishing operations—reliable, flexible, and ready to evolve with the demands of modern manufacturing. Would you like to continue with another machine type or expand on any specific use case?
Dual Spindle Buffing Machine
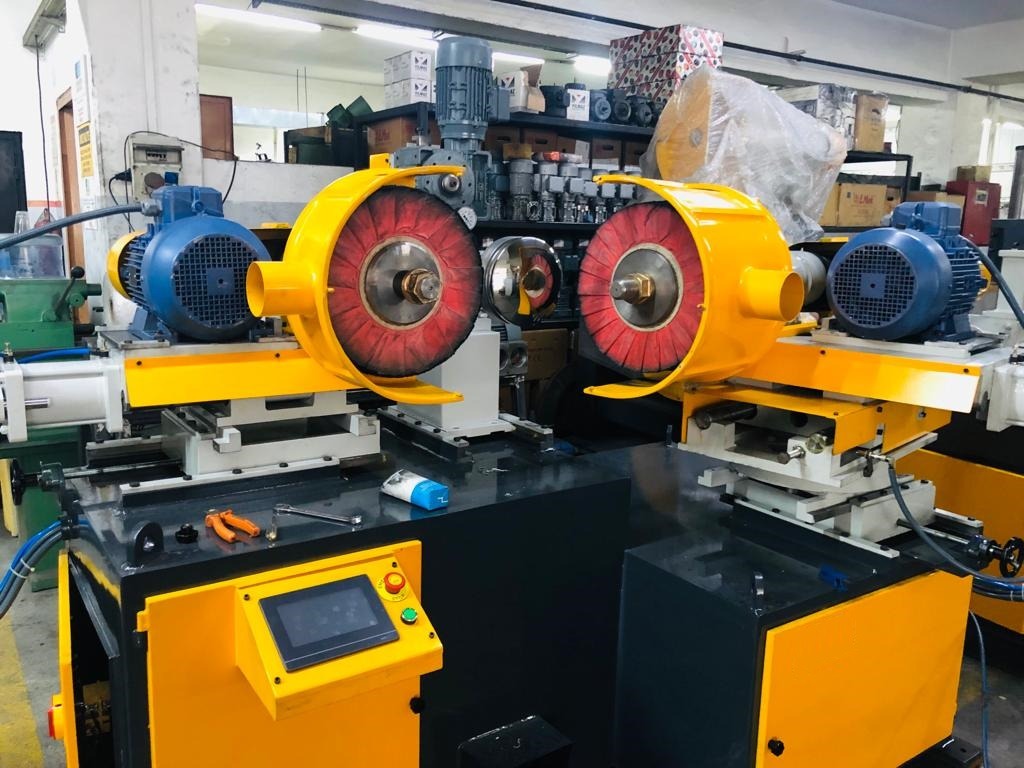
The dual spindle buffing machine represents a significant evolution in surface finishing equipment, offering enhanced productivity, versatility, and operational efficiency. Designed with two independent or synchronized buffing spindles, this machine is particularly well-suited for medium to high-volume manufacturing environments where speed and consistency are critical. Each spindle can be outfitted with a different buffing wheel—varying in size, material, or abrasive level—allowing operators to perform sequential polishing operations without switching tools or setups. This setup streamlines the workflow, making it possible to move from a coarse to a fine finish in a single pass, significantly reducing process time and manual handling.
One of the key advantages of the dual spindle configuration is its ability to support either simultaneous or independent operation. In simultaneous mode, both spindles can be used by a single operator working on larger or more complex workpieces, or by two operators working on separate tasks at the same time, effectively doubling output capacity. This flexibility is invaluable in environments where a variety of product sizes and finishing requirements are present. For instance, in automotive component polishing or metal hardware manufacturing, operators can adapt the machine on the fly to different part geometries or finishing specifications without needing to reconfigure the system extensively.
Precision control is another hallmark of modern dual spindle buffing machines. Many models now come equipped with variable speed drives for each spindle, allowing the operator to fine-tune rotation speed to match the workpiece material and desired surface finish. Some machines even incorporate digital controllers and user interfaces that store preset configurations for different jobs, further improving repeatability and reducing operator error. The ability to independently set each spindle’s speed and direction also opens up opportunities for more specialized applications, such as cross-polishing or compound layering, where different abrasives are used in sequence to achieve a superior finish.
From an ergonomic and safety standpoint, dual spindle machines are designed to minimize operator fatigue and ensure a safer working environment. Features such as adjustable working heights, built-in lighting, and accessible emergency stop controls contribute to a more user-friendly experience. Additionally, integrated dust extraction systems can be installed between the spindles or externally to remove fine particulates generated during polishing. This not only helps maintain air quality in the workshop but also extends the life of buffing wheels and compounds by keeping them free from contamination.
Durability is a major design focus in dual spindle buffing machines, as they are often used in continuous-duty applications. Heavy-duty motors, reinforced spindle shafts, and vibration-resistant frames ensure stable, long-lasting performance even under rigorous operating conditions. These machines are typically constructed from high-grade steel or cast iron to minimize deflection and provide a solid platform for precision polishing. Many models are also designed for easy maintenance, with quick-access panels and modular components that simplify part replacement or service tasks.
In specialized industries, dual spindle buffing machines can be customized to meet highly specific needs. For example, in the aerospace or medical device sectors, where ultra-smooth finishes and contamination control are paramount, machines can be equipped with cleanroom-compatible enclosures and precision-tuned spindles. Alternatively, in woodworking or decorative metalwork, dual spindle units may be configured with larger diameter wheels and slower speeds to accommodate softer materials that are prone to burning or deformation. This adaptability makes the machine a valuable asset across a wide range of production environments.
As automation continues to advance, dual spindle machines are increasingly integrated into semi-automated and fully automated finishing lines. Robots or mechanical arms can be tasked with feeding parts into the machine, rotating workpieces for uniform coverage, or applying consistent pressure during buffing. Sensors and feedback systems monitor variables such as torque, vibration, and temperature, automatically adjusting machine settings or alerting operators to potential issues. These capabilities ensure not only consistent results but also prolonged equipment life and reduced downtime due to premature wear or operator oversight.
In conclusion, the dual spindle buffing machine offers a powerful combination of speed, versatility, and control, making it an ideal solution for high-precision, high-volume polishing applications. Its ability to perform multi-stage finishing processes in a compact footprint significantly enhances productivity while maintaining superior finish quality. Whether in metal fabrication, plastic polishing, or composite finishing, this machine provides a scalable, customizable, and efficient polishing solution that meets the evolving demands of modern manufacturing. Would you like to explore the next machine type or focus more deeply on a particular industry application?
As manufacturing demands continue to evolve toward higher throughput and increasingly diverse product ranges, the dual spindle buffing machine becomes even more indispensable. Its ability to handle two different buffing configurations at once not only saves time but also enhances finish quality by eliminating the need to move the workpiece between separate stations. This reduces the risk of handling damage, maintains alignment accuracy, and allows for smoother transitions between abrasive stages. In facilities where precision and cycle time are critical—such as in stainless steel appliance production or aerospace part finishing—the dual spindle setup streamlines operations while minimizing variability between parts. Operators can easily tailor each spindle for specific roles: one for heavy material removal and one for polishing, or one set up for hard metals and the other for softer or coated materials.
Beyond the sheer efficiency, this machine type offers an ideal balance between automation potential and human oversight. Unlike fully automated systems that often require extensive programming and rigid tooling, the dual spindle buffing machine gives operators control over the tactile elements of polishing while still benefiting from mechanical precision. This is particularly useful for jobs that involve slight variations in part geometry or surface condition—where operator judgment adds value but repetitive tasks need to be completed consistently. Additionally, the machine’s design supports both right-handed and left-handed operators with symmetric layout options and adjustable working positions, which is valuable in multi-operator settings where shift handovers are frequent.
The expanding role of Industry 4.0 technologies has also impacted the development of dual spindle machines. Newer models are now equipped with sensor arrays and digital integration features that allow them to collect and transmit performance data in real time. Operators and supervisors can monitor usage trends, identify inefficiencies, and plan preventive maintenance based on actual operating hours and stress loads rather than estimates. These smart capabilities make the dual spindle buffing machine not only a production tool but also a data-generating asset within the larger ecosystem of modern digital manufacturing. With integration into ERP and MES systems, machine usage can be tracked against production targets, material costs, and quality control metrics, offering insights that lead to better planning and resource management.
Another emerging feature in some advanced models is spindle synchronization, which allows both spindles to mirror each other’s movement or work in precisely timed opposition. This function is especially useful when symmetrical parts need to be polished simultaneously, such as in the production of pairs or mirrored assemblies. The coordination reduces human error and ensures uniform surface treatment, contributing to better part matching and improved visual aesthetics. In industries where symmetry and consistency matter—such as in consumer electronics casings, decorative fixtures, or automotive trim—this capability adds measurable value.
Consumable management is also more efficient with a dual spindle system. Since operators can dedicate one spindle to high-abrasion wheels and the other to finishing pads, each type of media experiences wear at a consistent and predictable rate. This separation reduces cross-contamination between abrasives and finishing compounds, ensuring cleaner finishes and extending the life of each wheel. Moreover, tool life can be monitored independently on each spindle, and digital prompts or visual alerts can notify users when a change is due, ensuring that the quality of work doesn’t degrade unnoticed.
Noise and vibration control are further considerations in machine design, particularly in installations where environmental comfort or safety regulations are paramount. Dual spindle buffing machines are often built with isolation mounts, sound-dampening enclosures, and precision-balanced spindles that minimize vibrations even at high RPMs. This not only protects the integrity of the surface finish but also reduces fatigue and long-term strain on operators working nearby. Some installations take this a step further with integrated soundproof booths or fully enclosed cells that contain dust and sound while allowing for visual monitoring through transparent panels.
Portability and modularity are also increasingly sought-after features, especially for workshops or production environments that deal with frequent layout changes. Some dual spindle machines are available in semi-mobile versions with lockable casters or modular bases that allow them to be repositioned easily. Others can be configured with interchangeable spindles, mounts, or attachments to serve as combination buffing, deburring, and sanding stations. This adaptability makes them especially valuable in prototyping labs, contract manufacturing shops, or mixed-use fabrication areas where versatility is key.
Ultimately, the dual spindle buffing machine represents not just a step up in capacity but a strategic advantage in achieving better throughput, improved quality control, and operational flexibility. Its dual-head configuration introduces a level of process efficiency that helps meet increasing market demands without sacrificing the craftsmanship and attention to detail required for high-quality finishes. As materials and manufacturing techniques continue to advance, the dual spindle buffing machine is well-positioned to remain a critical piece of finishing equipment, bridging the gap between manual dexterity and industrial-scale performance.
In expanding the capabilities of the dual spindle buffing machine even further, manufacturers have begun integrating programmable logic controllers (PLCs) and human-machine interfaces (HMIs) to streamline operation and enhance repeatability. These digital enhancements allow for the programming of precise operating sequences, including speed ramp-up, dwell times, and shutdown cycles, which can be repeated with high fidelity across multiple production runs. This is especially advantageous in sectors where finish consistency is not only aesthetic but also functional—such as in sealing surfaces for valves or aerospace components that require extremely tight tolerances. With PLC-based control, even relatively unskilled operators can manage sophisticated processes reliably, reducing training overhead and minimizing operator-dependent variation in output.
The use of robotic assistance in conjunction with dual spindle buffing machines is also increasing, especially in high-throughput operations. Collaborative robots, or cobots, can be deployed to hold, rotate, and manipulate parts against the buffing wheels, allowing for highly repeatable polishing of parts that would otherwise require considerable manual dexterity. These robotic integrations are often designed to work safely alongside human operators, using force sensors and adaptive feedback loops to maintain safe working conditions. The result is a hybrid workflow where robots handle repetitive or ergonomically challenging tasks, while humans focus on quality assurance and oversight, optimizing labor efficiency and reducing injury risk from prolonged exposure to vibration or dust.
Another area of advancement is the customization of spindle heads and arbor configurations. Depending on the specific application, dual spindle machines can be fitted with extended shafts for deep or recessed polishing, tapered spindles for quick wheel changes, or multi-mount hubs for compound wheel assemblies. This allows for further specialization, making it possible to polish both internal and external surfaces of complex assemblies within a single workstation. In industries such as tool and die making or medical device manufacturing, where intricate geometries and critical surface properties are standard, these custom spindle configurations provide both the flexibility and precision necessary to maintain competitive quality standards.
Thermal control also plays a crucial role in advanced applications. Excessive heat generated during buffing can degrade surface finishes, warp delicate materials, or cause compounds to break down prematurely. High-end dual spindle buffing machines often incorporate active cooling systems, such as forced air, misting nozzles, or temperature monitoring at the spindle hub, to manage thermal buildup during prolonged polishing cycles. These systems not only preserve material integrity but also extend the life of both the machine and its consumables, contributing to lower total cost of ownership over the long term.
Training and process documentation have likewise evolved alongside machine capabilities. Operators using dual spindle buffing machines are now frequently equipped with digital tablets or touchscreens that display real-time operating instructions, standard operating procedures (SOPs), and visual quality benchmarks. This ensures a consistent process across shifts and locations, particularly important for multi-site operations or when onboarding new staff. Many manufacturers even include video-based training modules or augmented reality (AR) overlays as part of their training systems, offering intuitive, on-the-job guidance that shortens the learning curve without compromising safety or productivity.
Environmental compliance and sustainability are also shaping how these machines are designed and used. With stricter regulations on particulate emissions, volatile compounds, and energy usage, modern dual spindle machines often feature closed-loop dust collection systems, low-emission motor technology, and energy-efficient inverters. Some models are equipped with monitoring systems that track consumable use and energy consumption, generating sustainability reports or alerts when thresholds are exceeded. This not only ensures compliance with regulations such as OSHA, EPA, or REACH, but also helps companies meet internal ESG (Environmental, Social, and Governance) targets without sacrificing operational capability.
As surface finishing continues to evolve beyond purely functional polishing into realms of decorative and branding differentiation, the dual spindle buffing machine’s ability to deliver customizable, high-quality finishes becomes increasingly important. From mirror-polished stainless steel architectural panels to intricately detailed brass fittings, the level of finish achievable with this machine can significantly influence a product’s perceived value and brand appeal. Its dual setup enables multi-step finishing sequences that would otherwise require separate machines, helping companies shorten lead times while delivering premium results that stand out in competitive markets.
In essence, the dual spindle buffing machine is more than just a polishing tool—it is a production enabler. Its dual-head configuration, digital integration, robotic compatibility, and adaptability to industry-specific requirements make it a cornerstone of modern finishing operations. Whether used in manual workflows or integrated into smart manufacturing systems, it delivers unmatched efficiency, consistency, and precision. As production demands continue to push the boundaries of quality and scalability, the dual spindle buffing machine is poised to remain an essential asset for any organization focused on high-quality surface finishing. Would you like to continue to the next machine type or further expand this one with diagrams, technical specs, or use-case examples?
Rotary Buffing Machine
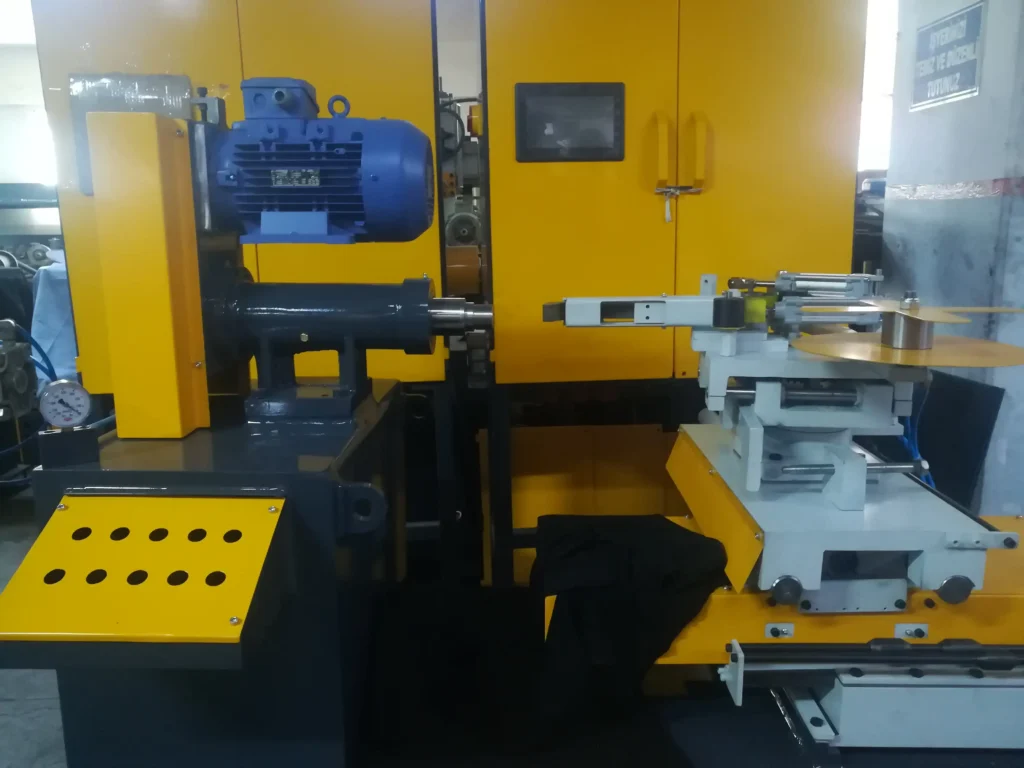
The rotary buffing machine stands as a cornerstone in the surface finishing industry, known for its circular motion that delivers uniform, high-quality finishes across a variety of materials and part geometries. Unlike linear or belt-based polishing systems, the rotary action facilitates even distribution of pressure and compound, resulting in consistent polishing without streaks, burn marks, or uneven gloss. This makes rotary buffing machines particularly suited for applications where aesthetic appearance is critical, such as in the production of kitchen appliances, automobile parts, musical instruments, and architectural hardware.
At the heart of the rotary buffing machine is a rotating table or disc—often motorized and controlled for speed and torque—that holds the workpiece while one or more buffing heads move into position. These heads may be fixed, articulating, or robotically actuated, depending on the machine’s level of sophistication. The rotational movement of the workpiece, in conjunction with the spinning buffing wheels, ensures that every surface contour receives uniform exposure to the abrasive media. This dual motion is especially valuable for components with rounded, convex, or cylindrical profiles, such as cookware bottoms, faucet handles, or metal bowls, which are notoriously difficult to polish using linear methods.
One of the primary advantages of rotary buffing machines is their ability to be configured for both manual and automated operations. In manual setups, an operator positions and holds the workpiece while the rotary table and buffing head perform the polishing. In automated or semi-automated systems, parts are loaded onto fixtures or jigs mounted on the rotating disc, allowing for unattended or lightly supervised operation. The flexibility to move between manual craftsmanship and high-volume production makes the rotary buffing machine highly attractive to small workshops and large factories alike. Moreover, modern systems often incorporate quick-change fixtures and programmable buffing sequences, reducing setup times and increasing productivity across varied product lines.
The ability to control rotational speed independently for both the table and the buffing wheel is a defining characteristic of advanced rotary buffing systems. This feature enables operators to fine-tune the contact dynamics between wheel and surface, optimizing results for different material types and finish requirements. Softer materials like aluminum, brass, or plastics require gentler pressure and slower speeds to prevent distortion or melting, while harder materials like stainless steel or titanium benefit from higher surface speeds and more aggressive compound applications. Variable-speed drives and digital feedback systems ensure these parameters remain stable throughout the polishing cycle, regardless of load variations or environmental conditions.
Another key strength of the rotary buffing machine is its modularity. Machines can be outfitted with a variety of buffing heads—ranging from standard cotton or sisal wheels to more specialized nylon or flap wheels—depending on the level of aggressiveness or finish desired. Multiple heads can be arranged at various angles around the rotating work surface to simultaneously address different areas of the part, significantly reducing cycle times. This 360-degree coverage is ideal for symmetrical parts or assemblies where a uniform finish is critical. Some systems even include compound dispensing nozzles that apply polishing agents in a controlled manner, ensuring consistent application and minimizing waste or overspray.
Dust collection and workplace cleanliness are also thoughtfully addressed in many rotary buffing machine designs. Enclosed or semi-enclosed units often include integrated suction ports, downdraft tables, or peripheral dust skirts that capture airborne particulates at the source. This not only keeps the work area clean and safe but also preserves the clarity and effectiveness of the buffing compound on the wheel. Proper dust management is essential in industries such as food equipment manufacturing or medical device polishing, where surface contamination can lead to product rejection or failure.
The rotary buffing machine is especially effective when integrated into robotic polishing cells or CNC-controlled systems. In such setups, robotic arms handle the loading, unloading, and positioning of parts with exact precision, while the rotary table presents the part to multiple buffing wheels arranged in a predefined pattern. This orchestration allows for highly repeatable and consistent results, even on complex shapes or in tight tolerance applications. In addition, sensors can be used to monitor wheel wear, detect excessive vibration, or verify surface finish via optical scanning, enabling real-time quality control and proactive maintenance.
In summary, the rotary buffing machine is a versatile and highly efficient polishing solution that adapts to a wide range of materials, finishes, and production volumes. Its circular motion ensures even treatment of curved surfaces, while its compatibility with both manual and automated workflows makes it ideal for shops seeking a balance between precision and scalability. As finishing requirements become more demanding across industries, the rotary buffing machine continues to be an essential tool for achieving consistent, high-quality surface finishes. Would you like to expand further into applications or move on to another type of machine?
The rotary buffing machine’s capability to deliver continuous and smooth surface finishing without interruptions also lends itself well to high-volume production environments where part consistency is non-negotiable. Manufacturers dealing with components that must meet strict cosmetic standards, such as luxury goods or consumer electronics housings, often rely on the rotary motion to eliminate visible polish lines and achieve a mirror-like gloss across every unit. This consistency, combined with the machine’s ability to operate in a cyclical manner, makes it highly suitable for batch processing where identical results are required across thousands of parts. Operators or robotic arms can place multiple pieces on a rotating fixture, allowing the system to work on several units simultaneously in timed cycles, thereby multiplying output without increasing floor space.
Because the rotating motion naturally reduces the chance of overheating a specific section of the workpiece, the rotary buffing process is particularly gentle on delicate surfaces or coatings. This is critical when polishing plated parts, composite materials, or parts with thin-wall geometries, which could otherwise be compromised by localized friction or excessive contact pressure. The movement helps dissipate heat more evenly, extending the lifespan of both the polishing wheel and the part being finished. For this reason, rotary buffing machines are frequently used in industries where fine detail and surface preservation are paramount, such as jewelry, optical components, or musical instruments.
Another advantage lies in the ergonomic and operational benefits offered by the rotary configuration. Since the part is rotated under a stationary or adjustable buffing head, the operator does not need to reposition the component repeatedly to access various surfaces. This reduction in manual handling minimizes fatigue, improves safety, and ensures that even hard-to-reach areas receive equal polishing attention. Machines equipped with tilting tables or adjustable axes further expand this accessibility, allowing for compound angles or stepped contours to be polished in one uninterrupted cycle. This is especially useful in tool and die shops, where molds and complex dies must be finished to extremely tight tolerances with uniform texture and reflectivity.
The rotary buffing machine is also a favorite in rework and repair environments, particularly where parts need to be resurfaced or restored to their original shine after use. Automotive body shops, for instance, use rotary polishers to bring back the luster of aluminum wheels, stainless trim, or vintage chrome parts without damaging the underlying structure. The circular motion, when paired with the right compound and wheel combination, can gently remove oxidation, scratches, and blemishes while preserving sharp lines and details. This makes it an invaluable tool for restoration professionals working with both metals and plastics, where too much pressure or inconsistent buffing can lead to surface distortion or color change.
In advanced production settings, rotary buffing machines can be fitted with closed-loop control systems that monitor parameters such as torque resistance, surface pressure, and wheel RPM in real time. These systems adjust performance automatically to ensure that the polish quality remains constant, even as buffing wheels wear down or slight variances in part geometry occur. Integration with plant-wide data systems allows supervisors to track machine efficiency, identify bottlenecks, and schedule maintenance based on usage data rather than fixed intervals, increasing uptime and reducing the likelihood of unexpected breakdowns.
Moreover, many rotary buffing machines are now being designed with modular footprints and scalable configurations. A basic single-head, single-table system can later be upgraded with additional polishing heads, automated part changers, or compound feeding systems as production needs grow. This allows businesses to invest incrementally without having to replace their core machinery entirely. For contract manufacturers or small-to-midsize shops, this flexibility helps balance capital expenditure with operational growth, making the rotary buffing machine a future-ready platform that evolves alongside the business.
From a material standpoint, rotary buffing machines can handle a wide spectrum of substrates, including ferrous and non-ferrous metals, hard plastics, glass, and composites. This makes them ideal for operations that serve diverse industries or produce varied product lines. A single machine, with the right combination of wheels and compounds, can be used to polish stainless steel medical equipment in the morning, aluminum lighting fixtures in the afternoon, and acrylic display panels by evening, all with minimal changeover time. This adaptability maximizes machine utilization and reduces downtime associated with frequent setup adjustments.
In practice, the machine’s reliability and versatility often become central to a plant’s finishing operations. The repeatability of results and ease of operator training make it possible to maintain high quality without an overreliance on skilled labor. Because the motion and pressure dynamics are built into the machine’s design, the risk of human error is greatly minimized. Operators can be quickly trained to manage settings, load parts, monitor wheel wear, and apply compounds without needing years of experience, accelerating onboarding and cross-training processes in dynamic production environments.
As a cornerstone of both traditional and advanced manufacturing processes, the rotary buffing machine continues to play an essential role in achieving precise, consistent, and high-quality surface finishes. Its circular action, compatibility with automation, and scalability make it a powerful tool for industries that demand both beauty and function from their finished parts. Whether used in artisanal workshops or high-speed production lines, the machine delivers a level of polish and professionalism that meets the standards of even the most demanding applications.
The ongoing innovation in rotary buffing machines highlights their expanding role in modern manufacturing environments, particularly in industries where precision and aesthetic quality are equally important. One notable advancement is the incorporation of adaptive control systems that allow the machine to respond in real-time to changes in the workpiece or polishing conditions. These systems continuously monitor variables like wheel speed, pressure, and temperature, adjusting the machine’s behavior automatically to maintain optimal polishing conditions. For example, if the workpiece material is found to be slightly harder or softer than expected, the system will reduce or increase the speed of the buffing wheel accordingly, ensuring that the quality of the finish remains consistent regardless of material variation.
Furthermore, as manufacturing processes become more automated, rotary buffing machines are being integrated into fully automated production lines that handle the entire finishing process from start to finish without the need for human intervention. These systems often use robotic arms to load and unload parts onto rotating tables, while the rotary buffing machine performs the necessary surface treatments. Sensors and cameras positioned around the work area can monitor part positioning and wheel wear, while real-time feedback ensures the system is always operating at peak performance. Such fully automated cells are beneficial in environments where high production volumes, tight tolerances, and uniform finishes are crucial, such as in automotive parts manufacturing or electronics assembly.
In addition, rotary buffing machines are seeing increased use in specialized applications, such as the polishing of delicate or intricate parts that require a fine touch. For instance, in the production of high-end watch components, jewelry, and luxury products, the rotary action allows for an even and gentle polishing process that enhances the natural luster of the materials without damaging the intricate designs. In these sectors, where a flawless surface finish is a key selling point, rotary buffing machines are often chosen for their ability to produce results that meet both aesthetic and functional standards.
Another area of development is the application of rotary buffing machines in eco-friendly or sustainable manufacturing practices. Many modern systems incorporate energy-efficient motors, low-emission dust collection systems, and environmentally friendly polishing compounds to reduce the environmental impact of the polishing process. The integration of renewable energy sources, such as solar or wind power, into the operation of rotary buffing machines is also being explored, as companies seek to meet increasingly strict environmental regulations while maintaining high production standards. Additionally, innovations in compound recycling and waste reduction are helping to minimize the consumption of raw materials and reduce the overall ecological footprint of the buffing process.
The rotary buffing machine’s potential is also expanding in the realm of additive manufacturing, or 3D printing. As more industries adopt 3D printing technologies to create complex, customized components, the need for post-processing solutions, including polishing, becomes more significant. Rotary buffing machines are being used to smooth and finish 3D-printed parts, particularly those made from metals or plastic materials. In these applications, rotary buffing machines help to eliminate layer lines, enhance surface smoothness, and prepare the parts for coating or further assembly. The adaptability of rotary buffing machines to handle a wide variety of materials makes them ideal for these emerging applications, where the precision of the surface finish is critical to the part’s performance.
The versatility and reliability of rotary buffing machines also position them as crucial tools in industries where parts undergo multiple stages of surface treatment. For example, in the aerospace industry, components often undergo a series of processes, including deburring, grinding, polishing, and final buffing, to ensure that they meet the stringent standards required for safety and performance. The rotary buffing machine plays a key role in the final stages of this process, helping to achieve a smooth, reflective surface that reduces friction and enhances the part’s resistance to wear and corrosion. Similarly, in the medical device industry, rotary buffing machines are used to polish and finish surgical instruments, ensuring that they not only meet functional requirements but also have an aesthetically pleasing finish that meets regulatory standards.
As technology continues to evolve, the rotary buffing machine will likely continue to incorporate features that improve precision, efficiency, and adaptability. Future innovations may include even more advanced robotic integrations, AI-driven diagnostics, and smart machine learning systems that can predict when maintenance is required or suggest process adjustments based on historical data. Additionally, advancements in materials science may lead to new types of buffing compounds and wheels that offer superior performance while reducing wear and tear on both the machine and the parts being polished.
Ultimately, the rotary buffing machine’s enduring presence in the manufacturing world is a testament to its ability to adapt to changing production needs and technological advancements. Its simple yet effective rotational motion, combined with continuous improvements in automation, precision, and sustainability, ensures that the rotary buffing machine will remain an essential piece of equipment for achieving high-quality surface finishes across a wide range of industries. Whether used in high-volume production or specialized, small-batch applications, the rotary buffing machine provides the flexibility, consistency, and quality needed to meet the demands of modern manufacturing.
Cylindrical Buffing Machine
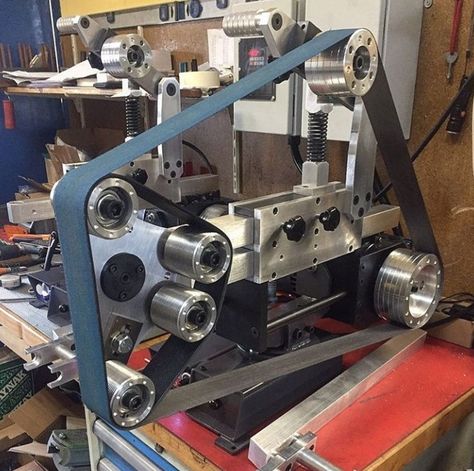
The cylindrical buffing machine is specifically designed for polishing cylindrical, tubular, or round parts, making it a critical tool in industries that require the finishing of pipes, rods, shafts, or other similar components. These machines provide an efficient method of achieving a uniform surface finish, removing imperfections, scratches, and oxidation, while improving both the aesthetic appeal and functional characteristics of the workpieces.
At its core, the cylindrical buffing machine operates by rotating the workpiece along its axis, while one or more buffing wheels or brushes, often mounted on adjustable spindles, move in a parallel or perpendicular motion to the cylinder’s surface. This allows for consistent pressure distribution over the full length of the cylinder, ensuring an even polish across the entire surface. Depending on the setup, multiple buffing heads may be used simultaneously to cover large surface areas quickly, making these machines well-suited for mass production environments or high-volume polishing of cylindrical parts.
One of the key advantages of the cylindrical buffing machine is its ability to handle both small and large diameter components with precision. Whether polishing a thin tube or a large pipe, the machine can be adjusted to accommodate varying sizes. The workpieces are typically secured in a fixture or held by specialized clamping systems, which can either rotate the part or move it along a linear path while the buffing wheels maintain contact with the surface. The precision of this system ensures a consistent finish on the cylindrical surface, which is particularly important in industries such as automotive, aerospace, and plumbing, where surface integrity and appearance are critical.
Cylindrical buffing machines are often equipped with features that optimize both the quality of the finish and the speed of the operation. These include adjustable speed controls for the rotation of the workpiece and the buffing wheels, as well as the ability to regulate pressure and the application of polishing compounds. In high-precision environments, where even minor surface imperfections can impact product quality, these adjustments allow operators to fine-tune the process to meet exact specifications.
Additionally, many modern cylindrical buffing machines integrate automatic compound feeding systems that apply polishing agents directly to the buffing wheel or workpiece. This ensures consistent and efficient compound application, helping to reduce waste while achieving optimal polishing results. For companies focused on sustainability, some systems are designed with closed-loop or filtration systems that capture and recycle excess compounds, further reducing environmental impact and operational costs.
The construction of the cylindrical buffing machine is typically robust, with heavy-duty frames and components designed to withstand continuous operation. These machines are built to provide long-lasting performance, even under the demands of high-production environments. In some cases, the machine may also include a cooling system to prevent excessive heat buildup during prolonged buffing, especially when working with harder materials like stainless steel, titanium, or hardened alloys.
The adaptability of the cylindrical buffing machine also allows it to be integrated into automated production lines. For example, robotic arms can be used to load and unload parts, while the cylindrical buffing machine performs its polishing function automatically. Such integration streamlines the production process, reduces labor costs, and minimizes human error, while increasing throughput and consistency. These automated systems are particularly valuable in industries where large quantities of similar cylindrical parts are produced, such as in the manufacturing of automotive components like drive shafts, exhaust pipes, or shock absorbers.
In industries such as food processing or pharmaceuticals, where hygiene is paramount, cylindrical buffing machines are sometimes used to polish pipes or tubes to a smooth finish, minimizing areas where bacteria or contaminants could accumulate. By achieving a mirror-like finish, these machines help to reduce the risk of contamination and ensure compliance with health and safety regulations.
Another emerging trend is the use of cylindrical buffing machines in the finishing of 3D-printed or additive-manufactured parts, especially those created from metal or composite materials. These parts often exhibit rough surfaces due to the layering process of 3D printing, and cylindrical buffing machines offer a reliable way to smooth out these surfaces. With the ability to polish both the interior and exterior surfaces of cylindrical 3D-printed components, the cylindrical buffing machine plays a crucial role in bridging the gap between additive manufacturing and traditional finishing processes.
Cylindrical buffing machines are also designed with flexibility in mind, able to handle a range of different materials, including ferrous and non-ferrous metals, plastics, and composites. The choice of buffing wheel material—cotton, wool, sisal, or specialized compounds—can be tailored to suit the specific hardness and texture of the workpiece, ensuring optimal results without causing damage to the surface.
In terms of maintenance, cylindrical buffing machines typically feature systems that allow for easy access to key components such as the buffing wheels, spindles, and motors. Regular maintenance of these parts ensures optimal performance and helps prevent unexpected downtime. Many machines are also designed to allow for quick wheel changes, which is especially beneficial when switching between different materials or finish types. Preventative maintenance programs, combined with easy access to machine components, help maintain operational efficiency and extend the lifespan of the machine.
In conclusion, cylindrical buffing machines are indispensable in the finishing process of cylindrical parts across various industries. Their ability to produce high-quality, consistent surface finishes with minimal operator intervention makes them a versatile and efficient solution for high-volume production environments. Whether used in automated systems, small-scale operations, or specialized sectors such as aerospace, automotive, or food processing, cylindrical buffing machines ensure that components meet both functional and aesthetic standards. Their ongoing evolution, particularly in terms of automation, sustainability, and material adaptability, guarantees that they will remain a crucial tool in the surface finishing industry for years to come.
The cylindrical buffing machine continues to evolve in terms of technology and design, adapting to the ever-growing demands of industries seeking higher precision and greater efficiency. As manufacturing processes become more automated, the integration of advanced technologies such as artificial intelligence, machine learning, and robotics into cylindrical buffing machines has become more common. These technological innovations allow for predictive maintenance, automatic adjustments to polishing parameters based on real-time data, and even the detection of defects during the buffing process. For instance, with AI-powered vision systems, cylindrical buffing machines can now scan parts in real time to identify surface defects or imperfections, automatically adjusting the buffing process to correct them before they become an issue, ensuring a higher level of consistency and quality control.
Furthermore, advancements in user interface design and digital control systems have made cylindrical buffing machines more intuitive and easier to operate. Operators can now use touchscreen panels or computer interfaces to set specific parameters, monitor machine performance, and receive real-time feedback on key metrics like wheel speed, pressure, and compound application. This level of automation not only improves efficiency but also reduces the likelihood of operator error, leading to more reliable and repeatable results. In high-volume environments, this digital integration streamlines operations by making it easier to set up, operate, and adjust the machine according to the specific needs of the job.
Another notable trend is the increasing use of cylindrical buffing machines in industries where material integrity and surface finish are crucial. For example, the oil and gas sector often requires the polishing of large cylindrical pipes and valves to ensure they meet industry standards for pressure resistance and corrosion resistance. In these cases, a cylindrical buffing machine not only improves the surface appearance but also ensures that critical surface imperfections that could lead to failure in high-stress environments are removed. Similarly, in industries like aerospace and automotive manufacturing, the machine plays a key role in polishing parts that need to meet strict dimensional tolerances and surface finish specifications to ensure performance, durability, and safety.
In sectors such as medical device manufacturing, cylindrical buffing machines are used to polish and finish components like surgical tools, dental implants, and other medical instruments. The ability to achieve smooth, precise finishes on these small but critical components is vital for both functional performance and patient safety. A well-polished surface can reduce the risk of bacterial growth, prevent damage to delicate tissues during use, and ensure that the device performs as intended over its entire lifecycle. The precision and adaptability of cylindrical buffing machines make them essential tools in these high-stakes industries, where any defect in surface quality could have significant consequences.
Cylindrical buffing machines also contribute to advancements in sustainable manufacturing practices. Many of these machines are being designed with more energy-efficient motors and processes that reduce waste and energy consumption during operation. Additionally, some models incorporate closed-loop filtration and recycling systems for polishing compounds, reducing the environmental impact of the buffing process. These systems help manufacturers comply with environmental regulations and reduce costs by minimizing the consumption of compounds, while also improving safety by ensuring that hazardous materials are properly contained and disposed of.
The versatility of cylindrical buffing machines extends beyond traditional materials like metals and plastics. As additive manufacturing (3D printing) continues to gain traction, cylindrical buffing machines are becoming an essential tool in post-processing 3D-printed parts. Additive manufacturing often results in rough surfaces, particularly in metal parts produced through techniques like powder bed fusion. Cylindrical buffing machines can help smooth these surfaces, giving 3D-printed components the desired finish and dimensional accuracy necessary for use in high-performance applications. This ability to process both traditional and 3D-printed materials makes cylindrical buffing machines an increasingly valuable asset in industries that utilize additive manufacturing for producing complex, customized components.
With all these advancements, cylindrical buffing machines are poised to continue their evolution in both functionality and application. The combination of automation, precision, and sustainability is shaping the future of surface finishing across a wide range of industries. The ability to seamlessly integrate these machines into broader production systems, reduce operator involvement, and improve the quality and consistency of finishes is driving their increasing adoption. Whether in high-volume manufacturing, precision industries, or specialized sectors like aerospace or medical devices, cylindrical buffing machines are essential tools for achieving the high-quality surface finishes that modern manufacturing demands.
As the demands of modern manufacturing continue to evolve, cylindrical buffing machines are increasingly being equipped with features that enhance not only their precision but also their versatility and adaptability. One area of focus is the integration of smart technologies, including the Internet of Things (IoT), into cylindrical buffing machines. This connectivity allows for real-time monitoring and diagnostics, which can help prevent unplanned downtime, improve maintenance schedules, and optimize machine performance. With IoT-enabled systems, manufacturers can track the health of the machine, monitor usage patterns, and even receive alerts when specific components need attention, ensuring a more proactive approach to machine care.
Additionally, the role of machine learning in the operation of cylindrical buffing machines is becoming more prominent. By utilizing historical data and predictive algorithms, these machines can anticipate the ideal settings for polishing, adjusting parameters like wheel speed, pressure, and compound application automatically based on the material type, part geometry, and desired finish. This level of sophistication reduces the need for manual adjustments and ensures that the polishing process remains consistent, even when parts vary slightly from one another. This is particularly valuable in industries where parts need to meet tight tolerances and any deviation in surface finish can affect overall performance or quality.
The growing demand for customizable and flexible manufacturing processes has led to further advancements in the design of cylindrical buffing machines. Modular designs now allow for the easy addition or removal of buffing heads, compound dispensers, or automated loading/unloading systems, allowing businesses to tailor the machine to specific production needs. For example, a company that specializes in polishing parts for multiple industries, from automotive to medical devices, can adjust the machine to handle a wide variety of part sizes, shapes, and materials without significant downtime or reconfiguration. This modularity is especially beneficial for smaller manufacturers or job shops that require the flexibility to handle both large-volume production runs and smaller, more specialized orders.
Another significant development is the enhancement of the buffing wheels and polishing compounds used in cylindrical buffing machines. Advances in materials science have led to the creation of more durable, efficient, and specialized buffing wheels that can work on a broader range of materials with greater precision. For instance, composite buffing wheels with enhanced resilience are being used to polish harder materials, like titanium or ceramics, while also extending the lifespan of the wheels themselves. New polishing compounds that are more effective at removing surface imperfections while being gentler on the material are also becoming more widely available. These improvements not only enhance the quality of the finish but also reduce the environmental impact by decreasing the amount of compound needed and minimizing waste.
In response to environmental concerns, manufacturers are also exploring ways to reduce the overall energy consumption of cylindrical buffing machines. Energy-efficient drive systems, as well as optimized motor control systems, are helping reduce the electrical consumption of the machines. Some newer models are designed to use less power while still maintaining high output and finishing quality, which is especially important as companies strive to meet sustainability goals and reduce operational costs. The incorporation of regenerative braking systems, where energy is captured and reused during certain parts of the buffing cycle, is also being explored as a way to further enhance energy efficiency.
The use of cylindrical buffing machines is also being expanded in sectors that were previously not associated with traditional polishing operations. For example, in the rapidly growing electric vehicle (EV) market, cylindrical buffing machines are used to finish components like electric motor housings, battery enclosures, and aluminum frames. These parts often require precise surface finishes to ensure they meet both functional and aesthetic standards. The ability to handle a variety of materials, including aluminum alloys and composite materials, positions cylindrical buffing machines as essential tools in the EV manufacturing process.
In the field of renewable energy, cylindrical buffing machines are being used to finish components for wind turbines and solar panels. These large-scale components require smooth, durable finishes to optimize performance and ensure long-term reliability, making the cylindrical buffing machine ideal for polishing critical parts like turbine blades, rotors, and frames. As the demand for renewable energy sources continues to rise, the ability to maintain high-quality surface finishes on these large parts becomes increasingly important, further driving the need for advanced cylindrical buffing technologies.
The customization options available in cylindrical buffing machines also open the door for their use in highly specialized fields, such as jewelry and luxury goods manufacturing. Polishing jewelry, watches, and other luxury items requires not only a flawless finish but also delicate handling to ensure that intricate designs and fine details are not damaged during the buffing process. Cylindrical buffing machines with fine-tuned controls allow for the precision required to polish these small, complex components without compromising their integrity.
Moreover, as global supply chains become increasingly interconnected, cylindrical buffing machines are being designed for easy integration into international manufacturing processes. With the ability to communicate with other machines, track parts throughout the manufacturing process, and share data with global production systems, these machines can seamlessly become part of larger, networked production lines. This connectivity enables manufacturers to achieve higher levels of productivity, better coordination across different stages of production, and more transparent tracking of part quality across global facilities.
As cylindrical buffing machines continue to evolve, the focus on adaptability, automation, and precision will likely drive their future development. The need for machines that can handle a broader range of materials, parts, and production volumes, while also improving energy efficiency and sustainability, will continue to shape the industry. Whether in traditional manufacturing, advanced industries like 3D printing, or emerging fields like renewable energy and electric vehicles, cylindrical buffing machines will remain integral to producing high-quality, consistent surface finishes that meet the demands of modern manufacturing.
Floor Buffing Machine
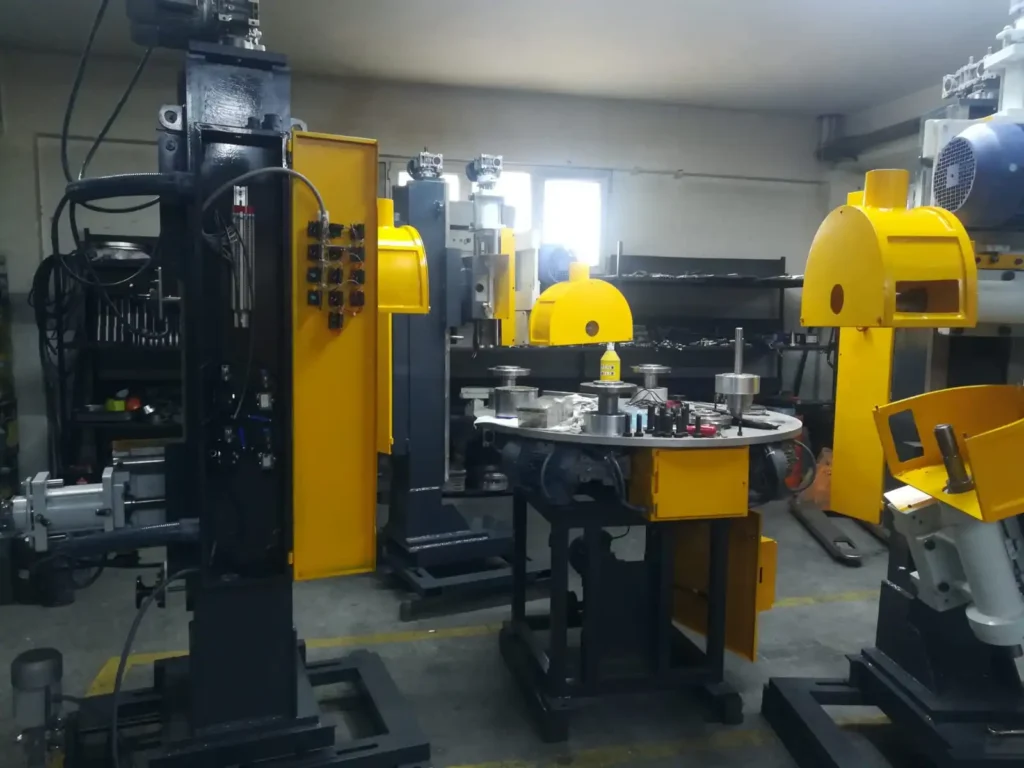
A floor buffing machine is an essential tool used in commercial and industrial settings to maintain clean, polished, and well-maintained floors. These machines are specifically designed for buffing, polishing, and maintaining the shine of various flooring types, including hardwood, vinyl, tile, concrete, marble, and more. Floor buffing machines are commonly used in environments such as schools, hospitals, shopping malls, office buildings, hotels, and factories to keep high-traffic areas looking clean and professional.
Floor buffing machines typically consist of a motorized base unit with a rotating pad or brush that moves across the floor’s surface. The machine uses rotational motion to apply pressure on the floor surface while also distributing polishing compounds, waxes, or cleaning solutions to enhance the floor’s appearance. The rotational speed of the buffer can be adjusted, depending on the type of floor and the desired finish.
These machines are designed to offer several key functions, including cleaning, polishing, and restoring the floor’s luster. Buffing works by smoothing out imperfections, scratches, and dull spots, and it is ideal for floors that have been stripped or waxed. Depending on the floor’s condition, buffing can remove surface-level dirt, stains, and scuffs, leaving behind a polished, glossy finish.
There are different types of floor buffing machines available, each tailored for specific purposes and types of flooring. The two most common types are:
- Single Disc Buffing Machines: These machines feature a single rotating disc that moves in a circular pattern across the floor. Single disc buffers are versatile, lightweight, and typically easier to maneuver, making them ideal for smaller areas or areas with limited access, such as corners. They can be used for both wet and dry polishing and can handle a variety of floor types.
- Dual-Disc Buffing Machines: Dual-disc machines feature two rotating pads, providing more power and coverage than single-disc models. These machines are more efficient in larger spaces and are better suited for commercial or industrial use. They are particularly useful when there is a need for a high level of polishing or restoration on floors that have been heavily used or are more worn down.
The most important feature of a floor buffing machine is its ability to apply even pressure to the floor surface, preventing damage while still achieving an effective clean. Buffing machines can be equipped with a variety of pads or brushes, depending on the task at hand. For instance, soft pads are ideal for polishing, while more aggressive brushes or pads are used for scrubbing or cleaning floors.
In addition to their basic functionality, modern floor buffing machines often come with various enhancements to improve performance and ease of use. Some advanced models come with features such as:
- Variable Speed Control: This allows the operator to adjust the machine’s speed depending on the floor type, the condition of the surface, or the desired level of polishing.
- Dust Collection Systems: These systems capture dust and debris generated during the buffing process, improving the air quality and reducing the need for post-cleaning of the floor.
- Ergonomic Handles: Adjustable and comfortable handles help operators work for extended periods without fatigue, improving both the efficiency and safety of the job.
- Heavy-Duty Construction: Many floor buffing machines are built with durable, industrial-grade materials that can withstand continuous use in commercial or industrial settings. This includes strong motors, heavy-duty frames, and long-lasting pads.
- Automatic Solution Dispensing: Some models come with automatic solution dispensers that release floor cleaner or polish as the machine operates, improving efficiency and ensuring consistent coverage.
For floor buffing to be most effective, it should be performed regularly as part of an ongoing floor maintenance program. Buffing helps to preserve the integrity of the floor, extending its lifespan while maintaining its aesthetic appeal. Additionally, it enhances the safety of the floor by reducing the accumulation of dirt, grime, and debris that could lead to slips or falls.
Floor buffing machines are also used as part of the broader process of floor care, which often includes stripping, waxing, and sealing. Stripping involves the removal of old wax or polish buildup, followed by the application of fresh wax or polish. After waxing, a floor buffing machine is used to bring out the shine and provide a smooth, glossy finish. In some cases, floor buffers are used to maintain floors between more intensive waxing cycles.
In conclusion, a floor buffing machine is an essential tool for maintaining high-quality floors in environments where appearance and cleanliness are priorities. Whether you are looking to maintain a pristine shine in a luxury hotel lobby, keep a retail space looking polished, or ensure a safe, clean environment in a hospital, floor buffing machines offer a reliable and efficient solution for floor care. With technological advancements making them more user-friendly, effective, and adaptable to different surfaces, floor buffing machines remain a key piece of equipment in the world of commercial and industrial cleaning.
Floor buffing machines continue to evolve with new technologies and innovations designed to enhance performance, ease of use, and sustainability. As the demand for higher-quality finishes and more efficient cleaning processes grows, manufacturers are developing more advanced features that cater to specific needs, particularly in industries where cleanliness and floor aesthetics are paramount.
One of the latest trends in floor buffing machines is the increasing emphasis on environmentally friendly cleaning solutions. Manufacturers are focusing on creating buffers that minimize water and chemical usage, making them more eco-conscious. Some models feature a “dry” buffing process, which uses minimal or no liquid, reducing water waste and the need for cleaning chemicals. Additionally, floor buffing machines are now being designed with biodegradable polishing pads and eco-friendly compounds that are safer for both the environment and the user.
The incorporation of advanced motor technologies is another significant advancement. Many modern machines are equipped with brushless motors, which are not only more energy-efficient but also require less maintenance. Brushless motors reduce wear and tear on the machine, extending its lifespan and ensuring quieter, smoother operation. These motors also reduce the amount of carbon emissions generated by the machine, aligning with the growing trend of green technologies in cleaning equipment.
Another key innovation is the integration of robotic automation in floor buffing machines. Robotic floor buffers are beginning to gain popularity, especially in large facilities such as airports, shopping centers, and warehouses. These autonomous machines are equipped with sensors and cameras that allow them to navigate the environment, avoiding obstacles and adjusting their cleaning paths accordingly. Robotic floor buffing machines can operate autonomously for long hours, reducing the need for manual labor while maintaining consistent cleaning standards. This automation also allows operators to focus on other tasks, improving overall efficiency in large-scale cleaning operations.
The digitalization of floor buffing machines has also brought about significant improvements. Modern machines are now equipped with smart technology, allowing users to monitor performance, track maintenance schedules, and even troubleshoot potential issues remotely through mobile apps or cloud-based systems. Some machines are equipped with data analytics tools that provide detailed reports on machine performance, floor conditions, and usage patterns, helping facilities better manage their maintenance and cleaning schedules. This level of connectivity enhances operational efficiency, reduces downtime, and ensures that machines are functioning at their optimal capacity.
Ergonomics and operator comfort are becoming a higher priority in the design of floor buffing machines. Many newer models feature adjustable, padded handles that allow operators to adjust the height and angle of the machine for greater comfort during use. Some machines also incorporate vibration-reducing technology, which helps minimize hand and arm fatigue, especially when operators are using the machine for extended periods. These ergonomic improvements are especially important in environments where staff must operate the machines for long shifts, ensuring that their health and well-being are prioritized.
The mobility and maneuverability of floor buffing machines have also improved significantly. For example, lighter models with more compact designs are available, making it easier to transport and store the equipment. Additionally, some machines are designed with swivel casters and low-profile bodies, allowing them to navigate tight spaces, corners, and under furniture more easily. This flexibility is valuable in environments where space is limited, and it allows operators to reach areas that would be difficult for larger, bulkier machines to access.
As businesses continue to embrace smart cleaning solutions, floor buffing machines are becoming an integral part of a larger ecosystem of connected equipment. Many businesses are opting for integrated cleaning systems that connect floor buffing machines with other cleaning tools like vacuums, mops, and scrubbers. This integration ensures a holistic cleaning approach that enhances both efficiency and the overall cleanliness of facilities. For instance, floor buffing machines in these integrated systems can automatically adjust their cleaning parameters based on the specific floor type or area being cleaned, ensuring optimal results every time.
In addition to these technological advancements, training and safety features are also gaining attention. Manufacturers are developing machines that include safety sensors to prevent accidents, particularly when operators are working in busy, crowded environments. Some machines include automatic shutoff mechanisms or warning systems that alert operators to potential hazards, such as a blocked pad or an improperly secured floor. Training programs and online resources are also becoming more widespread, helping operators get the most out of their machines and stay up-to-date with the latest cleaning techniques and best practices.
The need for customization in floor buffing machines is also becoming more apparent. Different types of flooring require different care, and facilities are looking for machines that can be adjusted to meet specific cleaning needs. For example, certain buffing machines are designed specifically for hardwood floors, with gentler pads and specific pressure settings that preserve the floor’s integrity while still providing a polished finish. On the other hand, concrete or terrazzo floors may require more aggressive cleaning and polishing techniques, which can be accommodated with different pad options and higher-speed settings.
In industries like healthcare and foodservice, where cleanliness is critical, floor buffing machines can also be designed to meet specific health and safety standards. Hygienic design principles are being incorporated into the machines to minimize bacterial buildup and ensure that cleaning procedures adhere to industry regulations. For example, machines may feature sealed, non-porous components that are easy to disinfect, preventing contaminants from hiding in crevices.
The future of floor buffing machines lies in continued innovation that meets the growing demands for sustainability, efficiency, and safety. Whether it’s through the integration of AI, automation, or enhanced ergonomic designs, the evolution of floor buffing machines will continue to play a key role in the cleaning industry. As businesses strive for cleaner, greener, and more cost-effective solutions, these machines will adapt to meet these challenges, ensuring that floors remain spotless, safe, and polished for years to come.
Bench Buffing Machine
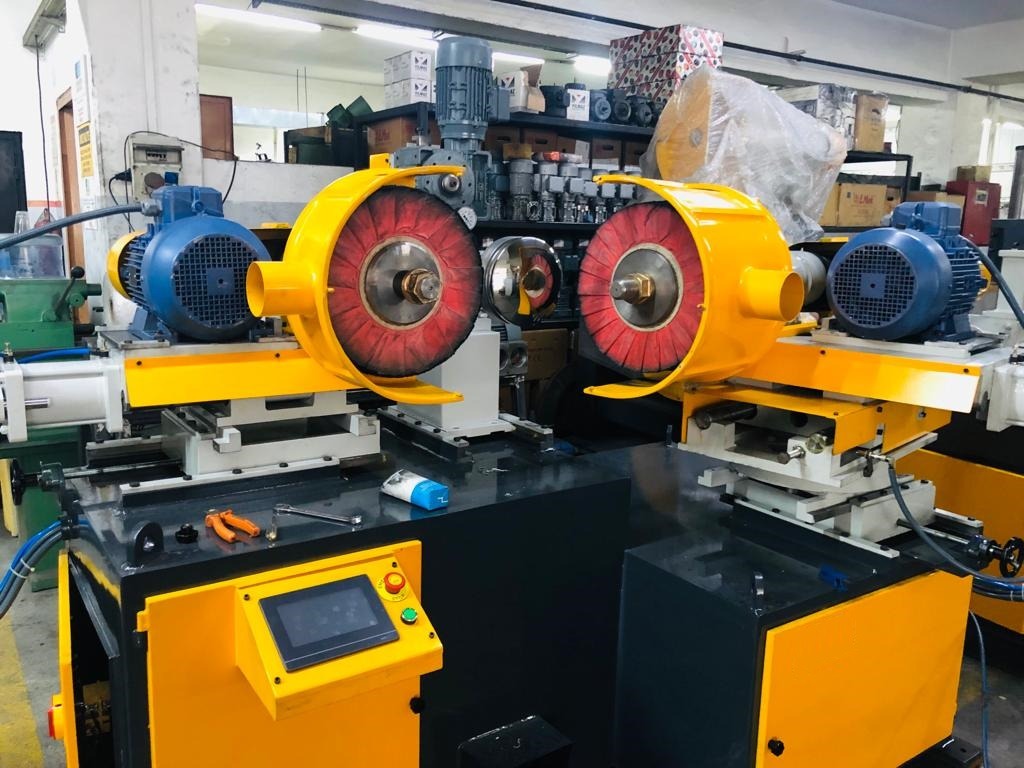
A bench buffing machine is a type of polishing and finishing tool that is commonly used in small to medium-sized workshops for polishing, buffing, and cleaning metal, plastic, and other materials. These machines are typically mounted on a workbench or table, providing stability and precision for various tasks such as polishing jewelry, automotive parts, tools, and small machinery components. Bench buffing machines are known for their compact size, ease of use, and versatility, making them a popular choice for businesses and hobbyists alike who need a high-quality finish on smaller parts.
Key Features of Bench Buffing Machines:
- Compact Design: As the name suggests, bench buffing machines are designed to be mounted on a workbench or placed on a solid surface. Their compact size allows them to fit into smaller workshops or spaces where larger floor-standing machines may not be practical.
- Rotating Buffing Wheels: The primary feature of a bench buffing machine is its rotating buffing wheels or polishing pads. These wheels spin at high speeds, applying pressure to the surface of a material to smooth it out, remove imperfections, and create a glossy finish. The wheels can vary in size and texture depending on the job at hand. Common materials for buffing wheels include cotton, wool, and synthetic fibers, which can be fitted with different compounds or abrasives to achieve the desired finish.
- Motorized Operation: Bench buffing machines are powered by electric motors that drive the rotation of the buffing wheels. These motors vary in power depending on the size of the machine and the type of work it’s designed for. More powerful motors are typically used for buffing harder materials or larger components, while smaller machines may have lower-powered motors for lighter polishing tasks.
- Adjustable Speed: Many bench buffing machines offer adjustable speed controls, allowing users to customize the rotation speed of the wheels based on the type of work they are doing. For example, lower speeds are typically used for finer polishing, while higher speeds are often required for heavy-duty buffing or removing scratches and imperfections from hard materials.
- Versatility: Bench buffing machines can be used for a wide range of polishing tasks, including:
- Metal polishing: Commonly used in the automotive, jewelry, and manufacturing industries to give metals like aluminum, brass, and steel a mirror-like finish.
- Wood polishing: Although primarily used for metal, some bench buffing machines can also be used with softer materials like wood, often for finishing or detailing.
- Plastic and acrylic buffing: Bench buffing machines are often used to buff plastic or acrylic surfaces to achieve a smooth, high-gloss finish.
- Small tools and equipment polishing: Polishing small tools, knives, and other handheld devices to remove scratches and restore their shine.
- Safety Features: Since buffing machines involve high-speed rotating parts, safety is an important consideration. Many bench buffing machines come equipped with safety guards that shield the user from flying debris or sparks. Additionally, some models feature dust collection systems to capture debris, preventing buildup on the workbench and reducing the amount of airborne dust and contaminants.
- Dust Collection: Some advanced bench buffing machines are equipped with integrated dust collection systems that help to keep the workspace clean and minimize exposure to harmful particles. These systems are particularly useful when buffing metals and plastics that can produce a fine dust that may be hazardous if inhaled over time.
- Compatibility with Buffing Compounds: Bench buffing machines are often used in conjunction with a variety of polishing compounds. These compounds help to improve the polishing process and achieve the desired finish. For instance, abrasive compounds can be used to remove scratches, while polishing compounds can provide a shiny, reflective finish. The type of compound used depends on the material being buffed and the desired result.
Types of Bench Buffing Machines:
- Single-Wheel Bench Buffing Machines: These are the simplest type of bench buffing machines, featuring a single rotating wheel for polishing. They are ideal for smaller jobs or when only one polishing surface is needed at a time.
- Dual-Wheel Bench Buffing Machines: Dual-wheel machines have two buffing wheels that allow for more efficient polishing by enabling the user to use two different compounds or materials at once. One wheel might be used for coarse polishing, while the other can be reserved for fine polishing or finishing work. This configuration is ideal for more versatile and complex tasks.
- High-Speed Bench Buffing Machines: These machines are designed for high-speed applications, often used for polishing harder materials or for tasks that require more power and precision. They are typically equipped with stronger motors and faster rotation speeds.
- Variable-Speed Bench Buffing Machines: Some bench buffing machines offer variable speed control, which allows the user to adjust the speed of the buffing wheels for different tasks. This feature is especially useful when working with delicate materials that require slower speeds for a finer finish or when faster speeds are needed to remove heavier imperfections.
Applications of Bench Buffing Machines:
- Jewelry Polishing: Bench buffing machines are commonly used in the jewelry industry to give jewelry pieces a high-quality finish. Polishing gold, silver, and precious stones can be done with a bench buffing machine to achieve a mirror-like shine.
- Automotive Detailing: Automotive detailers use bench buffing machines to restore the finish on car parts like wheels, bumpers, and chrome fixtures. The precision of a bench buffing machine allows for detailed work, such as buffing small areas of the car’s exterior or polishing metal components.
- Tool Restoration: Bench buffing machines are frequently used to polish and restore the edges of tools, such as chisels, knives, and saw blades. The high-speed rotation of the buffing wheel can help to remove rust and imperfections, restoring the tools to their original condition.
- Restoring Antique Objects: Antique collectors and restorers often use bench buffing machines to restore and polish antique metal objects, like old coins, brass fixtures, and other collectibles, without causing damage to delicate surfaces.
Conclusion:
In summary, a bench buffing machine is an indispensable tool for small to medium-sized polishing and finishing jobs, offering both precision and versatility in various industries. From jewelry polishing to tool restoration, these machines provide a high-quality finish with minimal effort. Whether you’re working in a workshop or a larger production facility, a bench buffing machine can help maintain the appearance and performance of metal, wood, plastic, and other materials, providing the ideal solution for achieving smooth, glossy, and professional-quality surfaces.
Bench buffing machines are versatile and efficient tools that play a crucial role in many industries by offering precise polishing and buffing capabilities. Their compact and user-friendly design makes them perfect for smaller spaces, such as workshops, jewelry studios, and automotive detail shops, where a high-quality finish is necessary. These machines can handle a wide variety of materials, including metals, plastics, wood, and acrylics, making them an essential piece of equipment for polishing, restoring, and enhancing the appearance of various components.
The core functionality of a bench buffing machine lies in its ability to rotate buffing wheels at high speeds, applying pressure to the surface of materials. The machine’s motor drives the rotation, allowing for a smooth and glossy finish on the workpiece. Users can customize the process by choosing different types of buffing wheels, each designed for specific tasks, such as coarse buffing for removing surface imperfections or finer wheels for achieving a polished, reflective surface. The ability to switch between various buffing compounds, such as abrasives for cleaning or polishing compounds for shine, further enhances the flexibility of these machines.
Safety features are also critical, given the fast-moving components of the machine. Bench buffing machines are designed with guards that protect the operator from debris or sparks. In many cases, dust collection systems are integrated to reduce airborne dust, which is especially important when buffing metals or plastics that can produce fine particles. These features not only ensure the safety of the user but also contribute to maintaining a clean and safe work environment.
The design and construction of a bench buffing machine make it adaptable to various polishing needs. Many machines are built with heavy-duty components that allow them to withstand continuous operation, especially in commercial settings where high levels of efficiency are necessary. At the same time, their relatively small size means they can be easily stored and transported, making them suitable for workshops that may be limited on space.
As technology advances, modern bench buffing machines incorporate more sophisticated features. Variable speed control is one such feature that gives users greater control over the buffing process. This control allows for a more tailored approach, adjusting the machine’s speed depending on the material being worked on or the desired level of finish. Additionally, ergonomic improvements in machine handles and controls make these tools more comfortable to operate for extended periods.
For industries that require highly specialized polishing, such as jewelry making or tool restoration, bench buffing machines offer an unparalleled combination of precision and power. Whether used for fine detailing on small, intricate pieces or for more robust buffing tasks, these machines remain indispensable tools in any workshop. As a result, they are integral in maintaining and enhancing the appearance, functionality, and lifespan of a wide range of materials and components.
Overall, the bench buffing machine is a versatile and indispensable tool for professionals in various fields. It continues to be an essential piece of equipment for anyone looking to achieve a high-quality, polished finish with precision and efficiency.
In addition to the core features of a bench buffing machine, one of its greatest advantages is its adaptability. The ability to interchange buffing wheels and compounds allows users to fine-tune their approach depending on the material they are working with. For example, a softer buffing wheel might be used for delicate items like jewelry, while a stiffer, more abrasive wheel could be employed for heavy-duty tasks like polishing metal components or removing rust from tools. The versatility in wheel choice ensures that users can achieve the right balance between aggressiveness and finesse in the polishing process.
Furthermore, bench buffing machines are increasingly becoming part of integrated workshop systems. These systems allow for greater efficiency by connecting the buffing machine with other machinery, such as grinders, drills, or sanders. This integration enables a smoother workflow, allowing operators to move from one task to the next without needing to switch equipment. This is particularly useful in environments where time is critical, such as in industrial settings or production lines.
When it comes to materials, bench buffing machines are used to enhance the appearance of a wide range of substrates. Metals, especially, benefit from the buffing process, as it removes oxidation, scratches, and imperfections, creating a smooth and shiny surface. In industries like automotive manufacturing and repair, this is essential for ensuring the parts are not only functional but aesthetically pleasing. Polishing automotive parts like bumpers, rims, and chrome trim is commonly done with bench buffing machines, allowing them to achieve a near-mirror finish that adds to the vehicle’s overall appeal.
For jewelry making, bench buffing machines are indispensable in creating high-quality, fine finishes on rings, necklaces, bracelets, and other pieces. The ability to polish precious metals such as gold, silver, platinum, and even softer metals like brass and copper is a key application of these machines. By using specialized polishing compounds, jewelers can restore the original luster of pieces or add a reflective shine to newly created items, giving them a professional, pristine look.
Another area where bench buffing machines shine is in tool restoration and maintenance. Over time, tools like knives, chisels, and other cutting instruments accumulate wear, scratches, and rust. The buffing process can help restore the tool to its original state, not only improving its appearance but also ensuring its functionality. Polishing edges helps to refine their sharpness, which can enhance the tool’s performance and prolong its lifespan. In addition, buffing is useful for the final step of tool manufacturing, providing a clean and polished finish that improves both appearance and durability.
The compact nature of the bench buffing machine also means that it can be used for small-scale production or for occasional polishing tasks without taking up too much space. For hobbyists or small businesses, this is a major advantage, as it allows for high-quality finishes without needing a large and expensive setup. The ability to fine-tune the polishing process based on individual projects is particularly beneficial for those working on unique, custom pieces that require extra attention to detail.
As workplace safety remains a key consideration, the design of modern bench buffing machines increasingly incorporates advanced safety features. Some machines come equipped with automatic shutoff mechanisms that engage if the machine overheats or if an obstruction is detected. Additionally, enhanced vibration control systems are being built into newer models to reduce operator fatigue, making the machines easier to handle during extended use. Protective eye shields, noise reduction features, and better dust collection systems also contribute to a safer and more comfortable working environment.
In terms of maintenance, bench buffing machines are relatively easy to maintain compared to more complex machinery. Regular cleaning of the buffing wheels, checking for wear, and ensuring the motor remains in good working condition can extend the life of the machine and maintain optimal performance. Many models also allow for quick wheel replacement, enabling the user to switch between different types of buffing materials as needed without significant downtime.
The ongoing evolution of bench buffing machines also reflects broader trends in the manufacturing and crafting industries, where precision, efficiency, and quality are paramount. With continued advancements in automation, energy efficiency, and smart technologies, the future of bench buffing machines holds exciting possibilities. Some models may soon integrate with cloud-based systems, offering users the ability to track machine performance, manage maintenance schedules, and even optimize polishing routines based on real-time feedback.
Ultimately, the bench buffing machine is not just a tool for polishing—it is an investment in achieving superior finishes, extending the life of materials, and enhancing the overall quality of products. Whether for small-scale craftsmanship or larger production runs, its ability to deliver consistent, high-quality results makes it an indispensable part of many industries. As technology continues to improve, these machines will only become more powerful, efficient, and user-friendly, providing even greater capabilities to those who rely on them for their work.
EMS Metalworking Machines
We design, manufacture and assembly metalworking machinery such as:
- Hydraulic transfer press
- Glass mosaic press
- Hydraulic deep drawing press
- Casting press
- Hydraulic cold forming press
- Hydroforming press
- Composite press
- Silicone rubber moulding press
- Brake pad press
- Melamine press
- SMC & BMC Press
- Labrotaroy press
- Edge cutting trimming machine
- Edge curling machine
- Trimming beading machine
- Trimming joggling machine
- Cookware production line
- Pipe bending machine
- Profile bending machine
- Bandsaw for metal
- Cylindrical welding machine
- Horizontal pres and cookware
- Kitchenware, hotelware
- Bakeware and cuttlery production machinery
as a complete line as well as an individual machine such as:
- Edge cutting trimming beading machines
- Polishing and grinding machines for pot and pans
- Hydraulic drawing presses
- Circle blanking machines
- Riveting machine
- Hole punching machines
- Press feeding machine
You can check our machinery at work at: EMS Metalworking Machinery – YouTube
Applications:
Flange-punching
Beading and ribbing
Flanging
Trimming
Curling
Lock-seaming
Ribbing