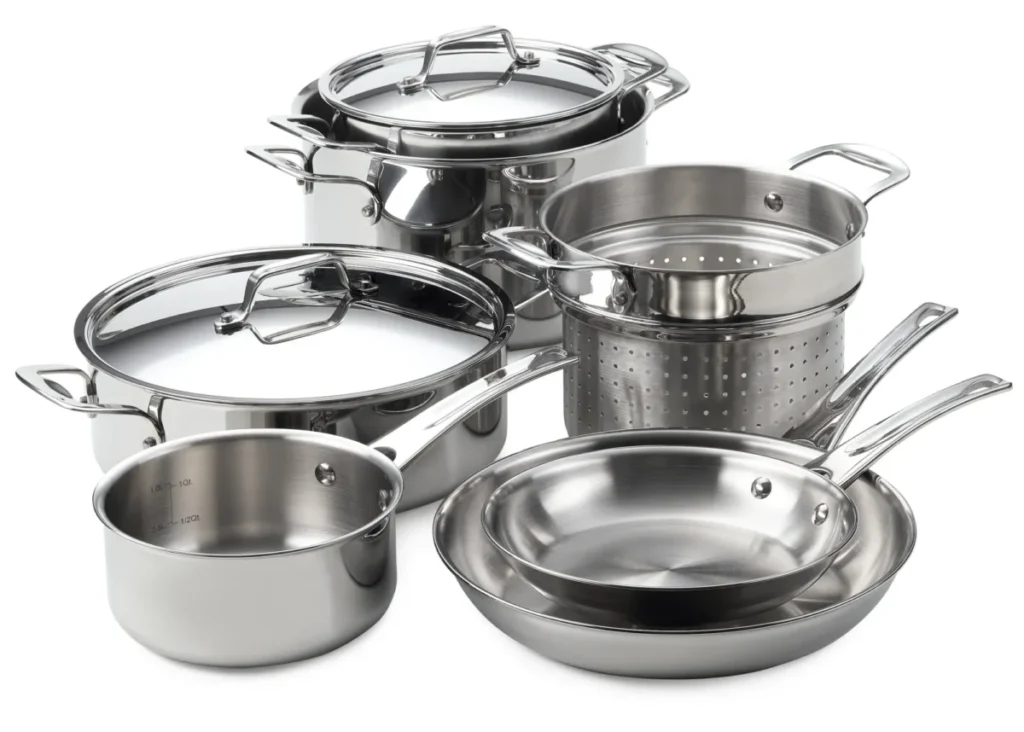
Machinery and Machine for Metal Pot and Pan Manufacturing: A Metal Pot Manufacturing Line is a series of automated and semi-automated machines designed to transform raw metal sheets into finished cooking pots. The production process typically integrates forming, shaping, trimming, surface finishing, and coating steps. Below is a typical flow of such a production line, especially for aluminum or stainless-steel pots:
Raw Material Preparation
- Material: Aluminum, stainless steel, or copper sheets/discs.
- Process: Sheets are cut into circular blanks using sheet cutting machines or hydraulic shears.
Deep Drawing
- Machine: Deep Drawing Press
- Process: A hydraulic press forms the metal blank into a pot shape in one or more steps.
- Tooling: Punch and die set specific to pot dimensions.
- Output: Rough-formed pot.
Trimming
- Machine: Trimming Machine
- Purpose: Remove excess material from the rim to ensure uniform height and clean edges.
Necking / Beading (Optional)
- Machine: Beading Machine or Necking Machine
- Process: Forms a rolled rim or neck to add strength and improve aesthetics.
Ironing (Optional)
- Machine: Ironing Press
- Purpose: Thin the walls uniformly, used in high-speed aluminum pot production.
Handle Hole Punching
- Machine: Hydraulic or Pneumatic Hole Punching Machine
- Purpose: Create mounting holes for handles (side or top).
Bottom Impact Bonding (for multi-layered pots)
- Machine: Impact Bonding Press
- Purpose: Bond layers (e.g., aluminum + stainless steel + copper) for better heat distribution.
Annealing (if needed)
- Machine: Annealing Furnace
- Purpose: Relieve stresses in the metal and soften it for further processing.
Surface Treatment
- Options:
- Polishing (Mechanical or Electrochemical)
- Sandblasting
- Brushing
- Machines: Polishing Machines, Buffing Wheels, or Vibratory Finishing Equipment
Non-stick or Decorative Coating (Optional)
- Machines: Spray Booths, PTFE / Ceramic Coating Ovens
- Process: Non-stick coating application and baking.
Handle Assembly
- Machine: Riveting Machine or Spot Welder
- Process: Mounting plastic, wooden, or metal handles.
Quality Inspection
- Steps: Dimensional check, coating adhesion test, leakage test, visual inspection.
Packaging
- Machine: Shrink Wrapping, Cartoning, or Labeling Machines
- Purpose: Final packaging for retail or wholesale distribution.
Optional Automation Add-ons
- Robotic arms for material handling
- CNC-based forming stations
- Inline sensors for defect detection
- Conveyor systems for process flow
In a metal pot manufacturing line, production begins with the preparation of raw material, typically in the form of circular blanks cut from aluminum, stainless steel, or copper sheets. These blanks are produced using hydraulic shears or sheet cutting machines, ensuring consistent dimensions and thickness. Once cut, the blanks are transferred to a deep drawing press, where the primary shaping occurs. This process transforms the flat disc into a cylindrical or rounded pot shape using a punch-and-die mechanism under high hydraulic pressure. Depending on the design and material, this might require one or multiple drawing stages.
Following deep drawing, the pot undergoes trimming. The trimming machine removes any excess material at the rim, ensuring a uniform height and clean edge finish. For added strength and ergonomic quality, many pots proceed to a beading or necking machine, where the rim is rolled or flared. If the production line is geared towards high-speed or high-volume output, ironing presses may be introduced to achieve consistent wall thickness, particularly for aluminum pots.
Subsequently, holes are punched into the body using pneumatic or hydraulic punching machines, preparing the pot for handle installation. For cookware requiring multilayered bottoms—such as stainless steel pots with aluminum or copper cores—impact bonding is employed. Here, multiple layers of metal are bonded under high pressure and temperature to create a thermally efficient base. Depending on the mechanical stress introduced during shaping, some pots go through annealing furnaces, where controlled heating softens the material and removes internal stresses.
Surface finishing follows, employing a range of polishing, brushing, or blasting machines. This not only enhances appearance but also prepares the surface for any subsequent coating. For non-stick or decorative finishes, spray booths apply PTFE or ceramic layers, which are then cured in high-temperature ovens. After coating, handles made of plastic, metal, or wood are affixed using riveting machines or spot welding units.
The almost-complete pots are then subjected to rigorous quality control. This includes dimensional checks, visual inspections, adhesion tests for coatings, and water tightness evaluations. Once approved, the pots are passed through automated or manual packaging stations, where they are labeled, shrink-wrapped, or boxed, ready for distribution. Throughout the line, conveyor systems and robotic arms may be used to automate transitions and improve production efficiency. The entire process, when well-integrated, ensures high throughput, consistency in quality, and minimal waste, making modern pot manufacturing lines highly productive and adaptable to various cookware types.
Advanced manufacturing lines often incorporate smart control systems and sensor-based monitoring to maintain consistency and minimize defects. Temperature sensors in annealing furnaces, pressure monitors in deep drawing presses, and thickness gauges during ironing help ensure every pot meets strict specifications. In modern setups, programmable logic controllers (PLCs) synchronize different machine stations, optimizing cycle times and coordinating robot arms for loading and unloading tasks. This results in a smoother workflow and reduced human intervention, which is especially important for large-scale production.
Customization options are integrated early in the line. Different pot sizes and shapes can be manufactured by simply changing the tooling sets in the deep drawing and trimming stations. Quick-change dies and servo-controlled machines make it possible to switch from one product line to another with minimal downtime, which is a key advantage in today’s flexible manufacturing environments.
For premium products, additional features like encapsulated bases, heat-diffusing disks, or laser-etched branding may be added near the final stages. Laser engraving systems are often used to apply logos or measurement marks on the inner wall or base. Some pots, particularly in high-end or export markets, are subjected to more refined finishing stages such as mirror polishing or satin brushing to enhance aesthetic appeal.
In non-stick pot manufacturing, the application of multiple coating layers—primer, mid-coat, and top-coat—is done in succession, often with automated spray systems that ensure uniform thickness. Each layer is cured in high-temperature ovens between applications. These ovens are typically tunnel-type with conveyor belts to allow continuous processing. Quality of the coating is verified using scratch resistance and adhesion tests to ensure durability during cooking and cleaning.
The handle assembly step varies depending on material and design. Plastic or bakelite handles are usually riveted using pneumatic presses, while stainless steel handles might be spot welded for a seamless look. Some designs include detachable handles, which require special fastening mechanisms and tighter dimensional control.
Final inspection is supported by vision systems or manual inspectors who verify shape, finish, handle fit, coating integrity, and overall workmanship. Some lines include leak-testing stations, where pots are filled with water or pressurized air to detect micro-perforations or weak welds.
After passing inspection, pots enter the packing zone, where automated systems may insert instruction booklets, lid accessories, or separators before final wrapping. Packaging can range from simple shrink-wrap to fully branded printed cartons, depending on the market segment. Palletizing robots or semi-automated stackers then prepare the goods for shipment.
Overall, the metal pot manufacturing line is a synergy of heavy-duty forming machinery, precision finishing systems, and increasingly intelligent automation. Whether producing basic aluminum pots or high-end multi-layer stainless steel cookware, the process is designed to balance quality, speed, and cost-efficiency while adapting to evolving consumer and industry demands.
In high-capacity factories, material flow is carefully engineered to minimize manual handling and idle time. Blank feeding systems automatically load discs into the deep drawing press, often using magnetic or vacuum-based loaders. After forming, conveyor belts or robotic arms transfer the semi-finished pots through each station, reducing labor costs and improving safety. These systems are programmed to adapt to different production sequences, making the line suitable for batch or continuous production.
For manufacturers targeting export or compliance with food safety regulations, additional treatments may be included. Stainless steel pots, for example, often undergo passivation to remove surface contaminants and improve corrosion resistance. This involves immersing the pots in a controlled acid bath, followed by thorough rinsing and drying, ensuring hygienic and long-lasting cookware.
Energy efficiency is also a growing priority. Modern furnaces, dryers, and presses are equipped with energy recovery systems, such as heat exchangers or insulation layers that reduce thermal loss. In addition, some lines integrate induction-based heating instead of traditional gas or electric systems to shorten cycle times and reduce emissions. Factories with environmental certifications often include filtration systems that manage dust from polishing stations and fumes from coating ovens.
When producing copper or copper-clad cookware, additional challenges arise due to the softness and oxidation tendency of copper. These lines may include special cleaning or coating stages to preserve surface shine. In such cases, clear lacquer may be applied to prevent tarnishing, or a stainless steel lining may be bonded inside the pot for safe food contact.
The design of the tooling—particularly dies and punches—is critical for the line’s flexibility and longevity. Tool steel is commonly used, and precise CNC machining ensures tight tolerances. Tool maintenance is scheduled regularly, with spare parts kept in stock to prevent downtime. Advanced facilities use simulation software to test drawing and forming processes virtually before full-scale production begins, reducing material waste and trial cycles.
Traceability is another important aspect in modern production. Each batch or even each pot may be marked with a serial or lot number—either engraved, stamped, or printed—linking it to production data such as raw material origin, press cycle parameters, coating batch, and operator ID. This allows for effective recall management, process optimization, and warranty service.
Finally, feedback loops between quality control and process control systems enable real-time adjustments. For instance, if a polishing defect is detected by a vision sensor, the line may automatically alert technicians or slow down until the issue is corrected. Similarly, if a drawing die shows signs of wear based on force sensors or cycle time anomalies, predictive maintenance systems can schedule replacement before failures occur.
Altogether, the metal pot manufacturing line is a tightly coordinated system that combines metallurgy, mechanical engineering, surface chemistry, and automation. It is scalable for small artisanal workshops or large industrial plants and can be tailored for various markets—from basic cooking vessels to designer cookware lines with strict performance and aesthetic standards.
Pot Factory Automation Solutions
Pot Factory Automation Solutions are designed to streamline production, enhance consistency, reduce labor dependency, and improve overall efficiency in metal cookware manufacturing. These automation systems integrate robotics, sensors, and intelligent controls across various stages of the pot production line. The degree of automation can be scaled based on production volume, product variety, and budget. Here’s a detailed view of key automation solutions in a modern pot factory:
Automation begins with blank handling systems, where robotic arms or gantry loaders automatically load metal sheets or discs into cutting or deep drawing machines. Vision systems and alignment sensors ensure precise positioning, reducing material waste and misfeeds. For high-speed operations, servo-driven feeders work in sync with press cycles to keep up with rapid production rates.
In deep drawing and forming, automation focuses on press synchronization, die lubrication, and part ejection. Smart hydraulic presses with programmable logic controllers (PLCs) allow for recipe-based operations, enabling quick changeovers between different pot models. Ejector arms and automated die changers reduce downtime and operator fatigue.
After forming, automated trimming and beading stations use robotic transfers or indexed conveyors to handle semi-finished pots. Servo-controlled rotary trimming machines automatically adjust to different diameters and heights, offering greater flexibility for mixed-model production lines.
Robotic handle hole punching systems integrate multi-axis positioning and sensor verification to punch precise holes regardless of pot shape or size. For factories producing pots with various handle types, vision-guided robots can adapt their position dynamically without the need for manual adjustment.
Impact bonding and base-cladding processes can also be automated. Advanced presses feature automated disc feeding, alignment correction, and bonding force control, ensuring consistent thermal diffusion properties in layered cookware bases. Automated annealing systems equipped with conveyors and temperature control ensure uniform heat treatment while minimizing energy usage.
In surface finishing, robotic polishing arms or multi-head polishing stations replicate manual polishing movements with far greater consistency. These systems are often coupled with dust extraction units and feedback loops to maintain finish quality. Robotic buffing arms can follow complex curves using force sensors and adaptive path control.
Coating automation includes spray robots in enclosed booths, ensuring even coverage of non-stick or decorative coatings. Coating thickness is monitored by inline sensors, while automated ovens cure coatings with precise thermal profiles. Conveyor-based curing tunnels optimize throughput and reduce manual handling.
Handle assembly benefits from robotic riveting or welding cells, capable of handling varying handle types and materials. These systems can identify handle orientation, position it with high accuracy, and complete the attachment process within seconds.
For inspection and quality control, machine vision systems detect dimensional errors, surface defects, or coating inconsistencies in real-time. These systems are often mounted above conveyors and work with reject diverters to separate defective products without stopping the line. Leak-testing machines automate water or air pressure checks, recording results for each unit.
End-of-line automation includes robotic packaging systems that insert instruction manuals, place lids, and pack pots into cartons. Shrink-wrapping and palletizing robots streamline final logistics steps. Labeling systems can automatically apply QR codes, barcodes, or branding stickers, tying each pot to digital traceability systems.
A fully automated pot factory is typically managed by a centralized SCADA or MES (Manufacturing Execution System), which collects data from every machine, tracks performance, predicts maintenance needs, and allows real-time control adjustments. Remote access features allow plant managers to monitor operations, perform diagnostics, or implement changes without being on-site.
Overall, automation in pot manufacturing not only boosts productivity but also ensures repeatable quality, reduces safety risks, shortens lead times, and enables agile responses to market changes. Whether it’s a semi-automated line or a fully lights-out factory, automation solutions are increasingly essential for competitiveness in the global cookware market.
In a fully automated pot factory, the production environment is orchestrated like a synchronized system where each element communicates with the next to maintain flow, consistency, and high output. From the moment raw materials enter the facility, automation ensures minimal manual intervention. Coils or stacks of metal sheets are automatically unrolled, leveled, and fed into blanking presses where discs are cut with precision. These discs are picked up by robotic arms or feeding systems and delivered directly into the deep drawing presses without the need for human handling. Servo-controlled presses automatically adjust their stroke and force based on the type and thickness of the metal, enabling the production of different pot shapes and sizes with minimal tooling changeover time.
Once the initial shape is formed, robotic pick-and-place systems or linear transfer units carry the semi-finished pots through trimming, beading, and ironing stations. These stations operate in tight coordination, with real-time data exchange ensuring each step is tailored to the exact dimensions of the product. For instance, if the deep drawing press outputs a slightly taller pot due to a minor tooling shift, the trimming station adjusts automatically to maintain consistent finished dimensions. Robots equipped with force sensors handle tasks like beading with sensitivity that mirrors a human craftsman, ensuring quality without deforming the pot.
In high-end pot lines, particularly those making layered-bottom cookware, bonding stations incorporate advanced automation that includes layer alignment, induction preheating, and synchronized impact pressing. Once bonded, the pots are automatically conveyed into annealing tunnels where temperature profiles are precisely controlled to relieve internal stresses. Automated cooling zones ensure safe handling temperatures for subsequent stages.
As pots proceed to surface preparation, automated systems polish or brush them using pre-programmed paths. Multi-axis robotic arms equipped with polishing wheels or abrasive pads adjust in real-time to pot curvature and diameter, delivering uniform surface finishes. Dust and residue are continuously extracted by integrated filtration systems to keep the environment clean and maintain operator safety, even in partially automated plants. If the cookware requires non-stick or decorative coatings, robotic spray arms coat the surfaces with exceptional consistency. These arms are equipped with flow meters, atomization sensors, and motion tracking to maintain optimal spray patterns and prevent overspray or undercoating.
Post-coating curing ovens, usually designed as conveyor tunnels, apply exact temperature and timing parameters depending on the type of coating used. Smart temperature zoning, airflow regulation, and exhaust management systems ensure energy efficiency while maintaining coating integrity. Once cooled, the pots are routed to handle assembly stations. Here, machine vision systems recognize the orientation and handle type, directing robotic riveters or welders to install side handles and knobs with micron-level alignment. Torque sensors verify rivet or weld strength, ensuring that every handle meets quality standards before proceeding.
The next critical step—quality control—is handled by integrated vision systems that scan the pot for cosmetic defects, surface irregularities, or dimensional deviations. High-resolution cameras and 3D scanning sensors operate at line speed, automatically rejecting flawed units. Additional automated leak-testing systems use air pressure or water immersion techniques, logging results against each pot’s serial number in the MES system.
Finally, finished pots are routed to end-of-line packaging. Automated lines insert manuals, attach lids, and load pots into customized packaging boxes. Robotic arms then stack cartons onto pallets with optimal space utilization. For direct-to-retail shipments, label applicators mark boxes with destination data, QR codes, or barcodes for easy traceability and inventory management. All these actions are monitored in real time via centralized dashboards that allow factory managers to track line performance, energy consumption, output quality, and production rates. If an issue arises, such as a misaligned spray nozzle or a jammed feeder, the system can pause the affected section, notify maintenance, and reroute production to minimize downtime.
In the most advanced setups, AI-powered analytics help forecast tool wear, optimize cycle times, and even recommend design adjustments to improve manufacturability. These smart systems learn from production data, improving accuracy and efficiency over time. In such factories, the workforce shifts from operating machinery to supervising systems, performing maintenance, and managing production flow, making the facility more resilient, scalable, and globally competitive.
In the context of lean manufacturing and Industry 4.0, automation in pot factories extends beyond physical machinery to include digital integration, data management, and predictive control. Each machine, sensor, and robot is part of a connected ecosystem where operational data is collected continuously—temperature, pressure, vibration, torque, cycle times, defect rates, energy consumption—all of which are fed into a central platform. This infrastructure enables real-time diagnostics, historical data analysis, and automated reporting that supports informed decision-making by plant managers and engineers.
Digital twins of the production line can be created, allowing operators to simulate changes in parameters or product types before applying them to the physical system. This reduces the risk of downtime or quality issues during actual production. A change in the design of a pot, such as altering the depth or wall thickness, can be virtually tested across all relevant stations—from deep drawing to polishing to coating—ensuring compatibility and optimal output before a single blank is processed.
Supply chain integration also benefits from factory automation. ERP systems communicate directly with the production floor, automatically adjusting production schedules based on order changes, material availability, or shipment deadlines. If a specific batch of stainless steel blanks arrives with slightly different hardness, the press parameters can be adapted accordingly to prevent tool damage or product rejection. RFID or barcode tagging at the raw material stage allows complete traceability through the production chain, enabling root-cause analysis if any product fails quality assurance at a later point.
Preventive and predictive maintenance are also fully digitized. Vibration sensors on motors, thermal sensors on bearings, and load sensors on hydraulic cylinders detect signs of mechanical stress or wear. When thresholds are breached, alerts are sent to maintenance teams, and replacement parts are automatically requested from inventory. This approach not only reduces unplanned downtime but also extends the life of expensive components like forming dies, polishers, and coating sprayers.
Human-machine interfaces (HMI) at each station are designed for ease of use, often with touchscreens displaying process parameters, alerts, and suggested actions in real time. Operators can adjust settings within authorized ranges, view instructional videos, or check system logs without leaving their station. Multilingual support and visual interfaces also help reduce training time for new staff, making the plant more adaptable to workforce changes.
Safety systems are fully integrated into the automation framework. Light curtains, laser scanners, and emergency stop zones are monitored digitally. When a worker enters a restricted area or a fault is detected, the system safely halts the relevant machines and triggers a cascade of warnings. Restart procedures are controlled and logged, ensuring that machines only resume operation under verified safe conditions.
Waste reduction is another major benefit. Automated systems optimize material use during blanking, monitor overspray in coating booths, and capture excess polishing dust for recycling. Scrap rates are continuously monitored and analyzed to detect trends and correct root causes—whether due to tool wear, incorrect parameters, or inconsistent raw materials. This not only improves sustainability but also increases profitability by reducing rework and material costs.
As customer expectations rise and product lines diversify, flexible automation becomes essential. Pot factories increasingly adopt modular automation cells that can be reconfigured or expanded as needed. For example, a plant might introduce a new line of induction-compatible cookware that requires ferritic stainless-steel bases bonded to aluminum bodies. Instead of building a separate line, a modular bonding station can be added, programmed, and integrated into the existing flow with minimal disruption.
Ultimately, full-factory automation in pot manufacturing offers a platform for scaling up production, ensuring consistent high quality, and remaining agile in a highly competitive market. It transforms the factory from a collection of isolated machines into a coordinated, intelligent system capable of adapting to both internal demands and external shifts in market trends or supply chain conditions.
Metal Pot Surface Polishing Equipment
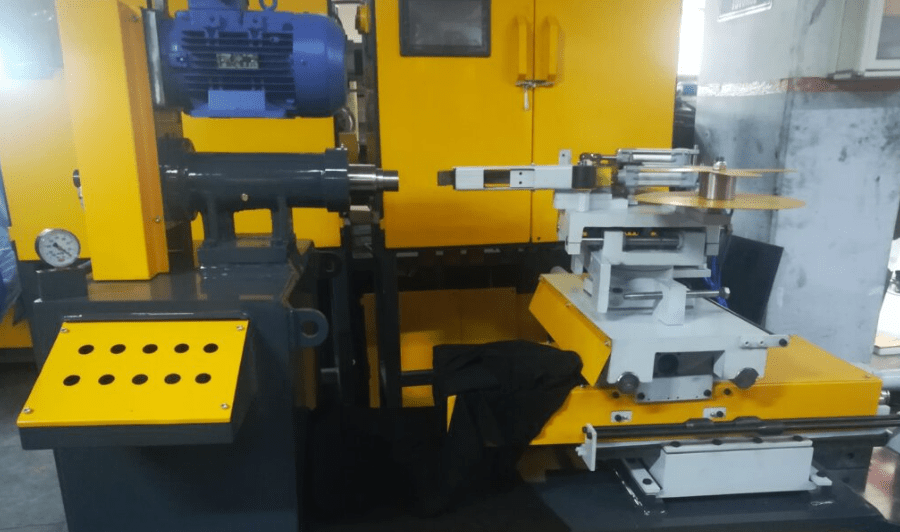
Metal pot surface polishing equipment is crucial in cookware manufacturing to enhance the aesthetic appeal, improve hygiene, and prepare surfaces for coating or branding. These machines are designed to handle different metals—such as stainless steel, aluminum, or copper—and adapt to varied pot shapes and sizes. They range from manual polishing units to fully automated robotic polishing cells, depending on production scale and finish requirements.
Rotary polishing machines are among the most commonly used. These feature multiple polishing heads that rotate at adjustable speeds while the pot is held and spun on a horizontal or vertical axis. They can perform mirror finishing, satin brushing, or matte texturing by using different polishing wheels—abrasive belts, non-woven pads, or buffing mops. High-end models include CNC control to vary the contact pressure and path, ensuring consistent results on curved surfaces and complex geometries.
For high-volume operations, robotic polishing systems are widely adopted. These use multi-axis robotic arms equipped with force-feedback sensors and rotary polishing tools to polish the interior and exterior of pots with precise control. The robot follows pre-programmed polishing paths, adapting to different diameters and profiles automatically. Vision systems can detect part orientation and surface condition, allowing dynamic adjustment of pressure and path to maintain a uniform finish.
Flat surface polishers or belt-grinding machines are used for pots with straight sides or flat bottoms. These machines use oscillating abrasive belts and adjustable pressure systems to maintain even polishing across the surface. Some are designed with auto-feed conveyors, allowing continuous processing of stacked cookware.
Double-sided polishing machines are ideal for simultaneous treatment of the inside and outside of the pot. These machines hold the pot between two rotating polishing heads, often with adjustable spacing and tilt angles. This dual action improves efficiency and ensures uniformity in one pass.
Vibration polishers or centrifugal barrel finishers are sometimes used for small or specialty cookware components, such as handles or knobs. These machines use abrasive media and motion to deburr, smooth, and lightly polish metal surfaces in bulk.
Dust and heat generated during polishing are managed through integrated extraction systems and cooling jets. High-end polishing equipment also includes automatic compound application systems that dispense polishing wax or liquid at set intervals, enhancing efficiency and finish quality.
In summary, metal pot surface polishing equipment is highly versatile and configurable. Whether for high-gloss mirror finishes or subtle brushed textures, the right combination of polishing machinery, abrasive tools, and automation ensures that each pot meets both functional and visual standards.
In an industrial setting where metal pots are manufactured in large volumes, the polishing stage is both critical and highly technical. The selection of polishing equipment depends on factors like pot geometry, base metal, desired surface finish, and downstream processes such as coating or engraving. For stainless steel pots requiring a mirror-like finish, rotary buffing units are fitted with fine cotton wheels or sisal wheels treated with abrasive compound. These machines operate with variable speed drives, allowing operators or controllers to fine-tune RPM and pressure based on material thickness and heat sensitivity. For matte or satin finishes, non-woven abrasive wheels or fine-grit flap wheels are preferred, giving a consistent grain pattern without causing surface overheating or discoloration.
Robotic polishing cells take this process further by integrating CNC controls and force-feedback technology. These systems enable the polishing head to maintain constant pressure on the pot surface, even if the pot has slight dimensional variations. The robot arm moves with precision across the contour of the pot, whether it’s a shallow frying pan or a deep stockpot, adjusting its angle, speed, and pressure automatically. This ensures uniform polishing from the top rim down to the rounded base, including complex areas around riveted handles or embossed logos. In many high-end installations, the polishing robot is coupled with a vision system that scans each pot prior to polishing, optimizing the path based on exact surface measurements. This minimizes rework and produces consistent surface reflectivity across every unit.
Some polishing lines feature rotating turret systems where pots are clamped onto turntables that rotate continuously as the polishing heads apply force. These systems are ideal for polishing the exterior of symmetrical cookware at high speed. Each turret can be customized with different types of abrasive wheels to create multi-step polishing processes within a single machine cycle—starting with coarse abrasives for surface leveling and progressing to fine abrasives for luster finishing. Automated compound feeders dispense polishing wax onto the wheels at pre-set intervals, maintaining their efficiency and preventing overheating.
Interior polishing, which is equally important for hygienic and aesthetic reasons, is handled by inner-surface polishing machines. These units use flexible polishing tools that conform to the curvature of the interior surface. Often installed as part of a conveyorized polishing station, pots are inverted and clamped while spinning brushes or flaps polish the internal surface. High-end machines monitor vibration and torque to adjust pressure and rotational speed dynamically, preventing damage to the thin inner walls of aluminum or stainless steel cookware.
Edge finishing is another specialized process often integrated into polishing lines. Rim polishers, usually composed of spinning brush heads or fine-grit belts, smooth out the sharp edges left by trimming or beading operations. These polishers may also slightly round the rim for safety and comfort in handling. For cookware with rolled edges, polishing heads are mounted on pivoting arms to access the tight radii and ensure a clean, smooth profile.
Dust and debris generated during polishing are managed through centralized extraction systems connected to each polishing station. These systems use high-efficiency filters and negative pressure to draw fine metal particles away from the work area, keeping both the machinery and the shop environment clean. Many robotic cells also include enclosures with fume extraction hoods, reducing airborne contamination and ensuring compliance with occupational health regulations.
For facilities that require high surface uniformity for downstream coating or laser marking, quality control checkpoints are installed after polishing. Automated inspection systems use light sensors, cameras, and reflectometers to measure surface smoothness, gloss level, and defect patterns. Any product falling outside acceptable ranges is diverted for rework or rejected automatically. This inline inspection improves yield and ensures that only fully qualified cookware advances to the next stage of production.
Maintenance of polishing equipment is also partially automated in advanced systems. Machine diagnostics track wheel wear, motor load, and spindle temperature, alerting operators when servicing or part replacement is needed. Polishing wheels can be automatically dressed or replaced using robotic changers in some high-throughput factories. These features reduce downtime and keep surface quality consistent over long production runs.
All polishing data—from cycle time and wheel consumption to surface gloss level and defect counts—can be logged in real-time and integrated with the factory’s digital production system. This allows managers to analyze trends, forecast consumable usage, and make adjustments to tooling or machine parameters to optimize performance over time. The result is a fully traceable and consistent polishing process that supports the high standards required in today’s competitive metal cookware markets.
In facilities aiming for zero-defect output and premium surface quality, metal pot polishing systems are further enhanced with intelligent synchronization between pre-polishing, fine polishing, and final buffing stations. Each station is configured to recognize the specific model of cookware passing through, either through barcode identification or shape recognition via 3D scanners. This enables dynamic adjustment of polishing parameters such as spindle angles, wheel type, abrasive grade, and contact time. Some systems are designed to store hundreds of polishing recipes, allowing instant switching between products without manual recalibration—ideal for flexible manufacturing environments with frequent batch changes.
The robotic polishing arms are often equipped with interchangeable tool heads mounted via automatic quick-change couplings. These heads can carry different abrasives or compounds depending on the stage of polishing. For example, a single robot may first use a coarse flap disc to eliminate micro-scratches from forming, then automatically switch to a soft cotton buffing wheel for the final luster finish. In ultra-high-end cookware production, these arms polish in several coordinated passes, mimicking the varied hand motions of traditional craftsmen but with perfect repeatability. The polishing path can be adjusted in real time by feedback from contact sensors that feel subtle variations in pressure across the pot surface.
Energy management is another key aspect of modern polishing equipment. Smart drives monitor motor loads and optimize spindle RPM and pressure to minimize power usage during idle or light-duty cycles. Advanced polishing systems can adjust torque in response to pot wall thickness to prevent overheating or warping thin aluminum or copper cookware. Additionally, some setups utilize regenerative braking systems in polishing spindles to recover energy during deceleration phases, contributing to overall plant efficiency.
For high-mirror finishes, cleanroom-compatible polishing cells are sometimes installed in isolated chambers with constant air filtration. These cells feature temperature-controlled environments to prevent thermal expansion of parts or tools that could cause micro-scratches or uneven polishing patterns. Buffing compounds in these applications are dispensed with medical-grade precision to avoid contamination. This level of surface finishing is typically reserved for cookware designed for luxury markets or display models where flawless surface reflection is essential.
The layout of a fully automated polishing section is designed for minimal material handling. Pots move through polishing stages on robotic conveyors or gantry systems equipped with part orientation correction mechanisms. These systems rotate, tilt, or re-position pots between stages to ensure correct alignment for each polishing operation. At the end of the polishing line, automatic blow-off or washing systems remove residual compound or dust before the pot proceeds to coating, branding, or packing.
For small to mid-sized operations, semi-automated polishing stations are often used. These include motorized polishing wheels on articulated arms, where operators manually guide the pot but benefit from assistive features like programmable speed control, digital load monitoring, and safety enclosures. Some setups offer hybrid solutions—robotic polishing for the exterior, and operator-assisted tools for interiors or decorative areas. This balances automation benefits with lower investment costs, making it accessible for niche cookware producers.
Over time, the integration of AI in polishing processes is gaining momentum. AI algorithms analyze surface finish data from previous production runs and continuously fine-tune variables such as wheel speed, compound application rate, and robot movement profiles to achieve optimal gloss and uniformity. Predictive analytics identify subtle wear patterns in polishing wheels or mechanical misalignments before they cause visible defects. These systems not only enhance output quality but also reduce waste, downtime, and the need for skilled manual polishers—whose availability is declining in many regions.
Ultimately, metal pot surface polishing equipment today represents a sophisticated combination of mechanical engineering, sensor integration, software intelligence, and ergonomic design. Whether in a high-volume, lights-out facility or a boutique cookware workshop, the goal remains the same: to deliver visually appealing, smooth, and defect-free pots that meet consumer expectations and brand standards. The right polishing technology becomes a critical competitive advantage, particularly in cookware segments where finish quality is directly linked to perceived product value.
Pot Rim Forming Machine
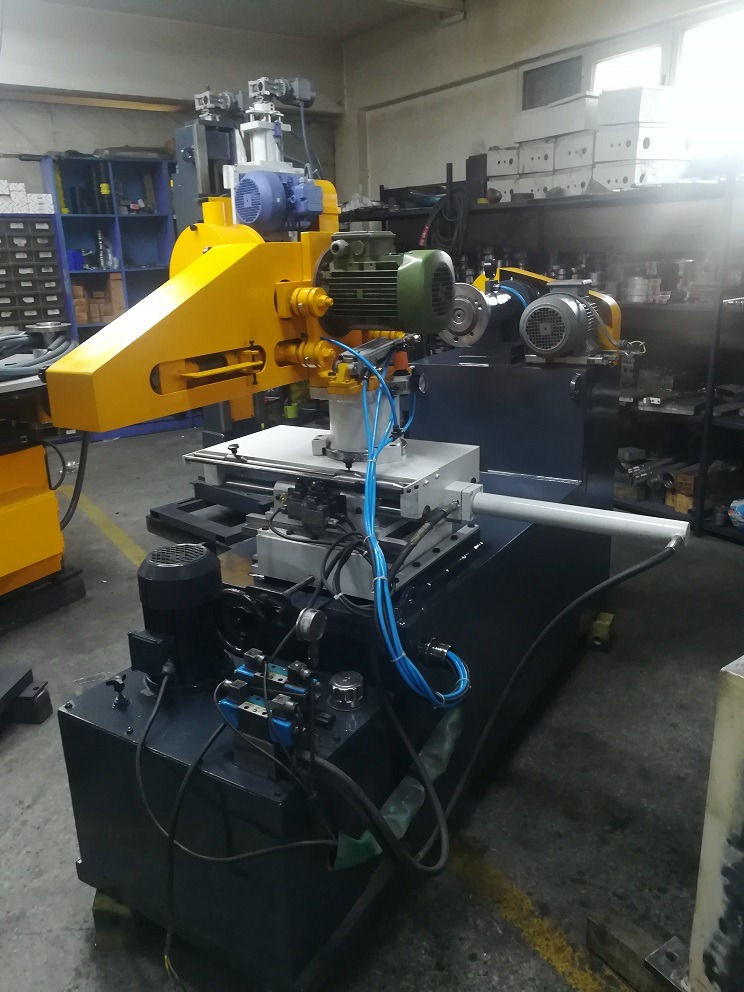
A Pot Rim Forming Machine is a specialized piece of equipment used in cookware manufacturing to shape, smooth, and reinforce the rims or edges of metal pots and pans. The rim or flange of a pot is critical both for structural integrity and safety, as it provides strength, prevents sharp edges, and often serves as the attachment point for lids or handles.
These machines are designed to perform several key functions such as rolling, curling, flanging, or beading the rim to achieve the desired profile. The process typically follows initial deep drawing and trimming, ensuring the raw edge is reshaped into a smooth, consistent, and often rounded or rolled form.
Pot rim forming machines come in various designs:
- Roller-type rim formers use a set of rollers—fixed and adjustable—that progressively curl or flange the edge by passing the pot through a rolling gap. The rollers can be configured to produce different rim profiles, including rolled edges, bead rims for aesthetic appeal, or double-flanged edges for added strength.
- Spinning rim formers use a rotary chuck that holds and spins the pot while a forming tool presses against the rim, gradually shaping it by controlled force. This method is often employed for pots with complex profiles or thicker materials that require gradual, precise deformation.
- Hydraulic or servo-driven rim formers offer programmable control over forming speed, pressure, and tool movement, enabling the production of a wide variety of rim shapes with high repeatability and minimal manual adjustment.
The machine typically includes adjustable guides and clamps to hold the pot securely and align it properly during forming. Sensors monitor rim thickness and profile to ensure quality, and automatic adjustment systems can compensate for slight variations in pot dimensions or material properties.
Some advanced rim forming machines integrate multiple forming steps into one unit, combining rolling, beading, and flanging operations in a continuous sequence to improve efficiency. Others are part of modular production lines where rim forming is synchronized with downstream processes like handle riveting or coating preparation.
In addition to forming rims, these machines often remove any burrs or sharp edges generated during trimming, ensuring the rim is safe to handle and ready for further processing.
Modern pot rim forming machines can be equipped with user-friendly interfaces, allowing operators to select or program rim profiles digitally. This flexibility is essential for manufacturers producing a range of cookware styles or customizing rim designs for branding and functional purposes.
Overall, the pot rim forming machine is essential for ensuring cookware durability, safety, and aesthetic quality, serving as a key step in automated and semi-automated pot manufacturing lines.
Pot rim forming machines play a vital role in enhancing both the functionality and appearance of cookware. The rim not only reinforces the structural integrity of the pot but also contributes significantly to user safety by eliminating sharp edges that could cause injury during handling. Additionally, the rim often serves as a sealing surface for lids, impacting heat retention and cooking performance, so precision in forming is critical.
In production lines, rim forming machines are typically positioned immediately after trimming and before surface finishing stages such as polishing or coating. After the pot blank is deep drawn and trimmed to the approximate shape, the rim forming machine engages to smooth and shape the edge to exact specifications. This sequence ensures that any sharp burrs created during trimming are removed or folded inward, preventing damage to workers and downstream equipment.
The forming process involves gradual plastic deformation, where the metal at the rim is bent, curled, or flanged by the forming tools. For thinner gauge materials like aluminum or stainless steel, care is taken to control the speed and pressure to avoid cracking or thinning that could weaken the rim. This is particularly important for cookware intended for induction cooking, where the rim must maintain dimensional stability under thermal cycling.
Many modern rim forming machines use servo motors and CNC controls to precisely regulate tool movement and forming force. This allows manufacturers to easily switch between different rim profiles—such as single or double rolled edges, bead rims for decorative purposes, or reinforced flanged rims designed for heavy-duty use—without mechanical retooling. Operators can load digital recipes for each product variant, speeding up changeovers and reducing human error.
Quality assurance during rim forming is increasingly automated. Integrated laser micrometers and optical scanners continuously measure rim thickness, diameter, and shape during operation. Any deviation beyond preset tolerances triggers alarms or automatically pauses the machine for adjustment. These inline inspection methods ensure consistent product quality and minimize scrap rates.
Advanced machines also feature real-time force sensors that monitor the forming pressure applied to the rim. If the force exceeds safe thresholds—indicating potential tool wear or material anomalies—the system alerts maintenance personnel or adjusts parameters dynamically to prevent damage. This predictive maintenance capability helps extend the life of expensive forming dies and reduces unexpected downtime.
In high-capacity manufacturing plants, rim forming machines are often linked with automated material handling systems. Robots or conveyors load pots into the forming station, orient them precisely, and transfer them onward to polishing or assembly stations. This integration enables continuous “lights-out” operation with minimal human intervention, increasing throughput and reducing labor costs.
Some manufacturers incorporate multi-stage rim forming units that combine edge rolling, beading, and deburring in a single machine. This compact setup optimizes floor space and reduces handling time. For example, after the rim is rolled, the machine may perform a bead pressing operation that strengthens the edge by creating a narrow raised ridge. This bead not only adds rigidity but also serves as an aesthetic design element, enhancing brand recognition.
The flexibility of modern rim forming machines makes them suitable for a wide range of cookware materials and styles. Whether producing lightweight camping pots from aluminum alloys or heavy-duty stainless steel stockpots, manufacturers can adjust machine settings to accommodate material thicknesses, alloy compositions, and rim shapes with high precision.
Safety features are integral to rim forming machines due to the high forces involved. Machines are equipped with protective guards, emergency stops, and light curtains that immediately halt operation if an operator enters the danger zone. Ergonomic designs minimize operator fatigue during loading and unloading, and user interfaces provide clear status indicators and troubleshooting guidance.
In summary, pot rim forming machines are indispensable in metal cookware manufacturing, ensuring the final product meets mechanical, safety, and aesthetic standards. Their integration into automated production lines contributes significantly to consistent quality, operational efficiency, and the ability to swiftly adapt to new product designs or market demands.
Beyond the core rim forming functions, many pot rim forming machines incorporate additional capabilities to further streamline production and enhance product quality. For example, some models include integrated edge trimming or flash removal tools that clean up excess material left after stamping or deep drawing. This integration reduces the need for separate deburring operations and minimizes handling time, helping to maintain a smooth, clean rim ready for subsequent processing.
In lines producing pots with handles, rim forming machines are often synchronized with handle attachment stations. The precise shape and consistency of the rim are critical to ensure secure and accurate riveting or welding of handles. Automated rim forming guarantees uniform edge geometry, improving joint strength and reducing the risk of assembly defects or post-sale failures.
Customization options for rim forming machines have also expanded to include variable rim height and thickness adjustments within the same production run. This feature allows manufacturers to produce multiple pot models with different rim specifications without changing tooling, increasing versatility. Some machines employ hydraulic or servo-actuated tooling that can raise or lower forming dies on the fly, controlled by programmable logic controllers (PLCs).
Material handling systems feeding pots into rim forming machines often include robotic vision systems that inspect each pot’s orientation, rim condition, and dimensional compliance before forming. If a pot fails inspection, it can be automatically rejected or sent to rework stations, preventing defective products from advancing down the line. This closed-loop quality control is vital for maintaining high standards in modern cookware manufacturing.
The control software of advanced rim forming machines integrates with factory-wide Manufacturing Execution Systems (MES), providing real-time data on machine performance, output rates, and quality metrics. Plant managers can monitor trends, predict maintenance needs, and optimize production schedules based on accurate and up-to-date information. This connectivity supports lean manufacturing principles and continuous improvement efforts.
In terms of physical footprint, rim forming machines vary from compact benchtop units suitable for prototyping and small-batch production, to large, fully automated inline systems designed for mass production. Modular designs allow manufacturers to add or remove forming stations as needed, tailoring the system to evolving product lines and market demands.
Environmental considerations are also addressed in modern rim forming equipment. Efficient power usage, reduced noise levels, and integrated dust or chip extraction systems contribute to safer and more sustainable operations. Some machines incorporate recyclable tooling materials and biodegradable lubricants to minimize ecological impact.
Training and user support are critical aspects of deploying rim forming machines. Manufacturers provide intuitive human-machine interfaces (HMIs) with touchscreens, graphical programming, and step-by-step setup guides. Remote diagnostics and software updates enable quick troubleshooting and minimize downtime. Operators receive comprehensive training to handle routine maintenance, changeovers, and quality checks confidently.
Looking forward, advancements in sensor technology and artificial intelligence are expected to further revolutionize pot rim forming. Adaptive control algorithms could adjust forming parameters in real time based on material behavior, wear patterns, and environmental conditions. Predictive maintenance systems will become more sophisticated, using machine learning to foresee failures before they occur. Such innovations will enhance precision, efficiency, and reliability even further.
Ultimately, the pot rim forming machine is a cornerstone of modern cookware manufacturing, balancing mechanical robustness, precision engineering, and digital intelligence. It ensures that each pot leaving the production line not only meets stringent technical standards but also delivers the safety, usability, and aesthetic qualities demanded by consumers worldwide.
Pot Spout Forming Machine
A Pot Spout Forming Machine is a specialized industrial machine designed to create and shape spouts on metal pots, kettles, or similar cookware. The spout is an important functional feature that allows controlled pouring of liquids, such as water, soups, or sauces, and is often integrated seamlessly into the pot’s body during manufacturing.
This machine automates the complex forming process required to produce consistent, precise spouts that meet quality and ergonomic standards. Typically, the pot or kettle body is positioned securely in the machine, and specialized tooling bends, stretches, and shapes a portion of the metal rim or side wall into the spout profile.
Depending on the design and material, pot spout forming machines can employ various technologies:
- Mechanical Press Forming: Using stamping or progressive dies, the machine presses the pot wall or rim into the desired spout shape in a single or multiple stages. Dies are custom-designed for each spout style and size.
- Hydraulic or Servo-driven Forming: These machines apply controlled force and motion to gradually shape the spout with high precision, reducing the risk of metal cracking or distortion. Servo control allows variable speed and pressure profiles.
- Roll Forming and Curling: For pots with rolled spouts, specialized rollers bend and curl the metal edge outward, producing a smooth, rounded lip that improves pouring flow and prevents drips.
- Spinning and Stretch Forming: In some cases, rotary tools spin the pot body while shaping the spout by pressing or stretching the metal, especially for complex or ergonomic spout designs.
Pot spout forming machines often include clamps or fixtures to hold the pot firmly without damaging the surface or geometry during forming. Alignment systems ensure that spouts are positioned consistently relative to handles and lids for ergonomic use and aesthetic harmony.
Some machines are integrated into automated production lines, where pots are fed sequentially by conveyors or robots. After spout forming, pots proceed directly to trimming, deburring, or surface finishing stations, maintaining efficient workflow and minimizing manual handling.
Quality control is an essential feature. Vision systems and laser scanners inspect spout dimensions, angles, and edge smoothness inline. If any irregularities or defects are detected—such as incomplete forming, cracks, or sharp edges—the system can reject the pot or flag it for rework.
Adjustability is crucial to accommodate different pot models and spout designs. Modern pot spout forming machines offer quick-change tooling, programmable parameters, and CNC controls, allowing rapid product changeovers and high flexibility.
In addition to functionality, the spout’s aesthetic appearance is important. The machine’s forming process ensures smooth, consistent curves and edges, contributing to the overall cookware design quality and brand identity.
Safety features like protective enclosures, emergency stops, and interlocks prevent operator injury during operation. Ergonomic design considerations facilitate easy loading and unloading of pots.
Overall, pot spout forming machines are integral to producing high-quality cookware that balances usability, durability, and visual appeal. Their precision and automation capabilities support efficient, scalable manufacturing while maintaining consistent product standards.
Pot spout forming machines are essential in ensuring the functionality and ergonomic quality of cookware, especially in products like kettles, saucepans, and specialty pots where controlled pouring is a key feature. The spout must be designed to provide a smooth flow of liquid without drips or spills, which requires precise shaping and finishing.
During the forming process, the machine handles the pot carefully to avoid deforming the main body or compromising its structural integrity. The metal used for pots—often stainless steel, aluminum, or copper alloys—has varying ductility and thickness, so the forming parameters such as pressure, speed, and tooling configuration are carefully controlled to match the specific material characteristics.
Many pot spout forming machines operate as part of a larger, integrated production line, enabling continuous and automated manufacturing. After the spout is formed, the pot typically moves immediately to trimming or deburring stages where any excess metal or sharp edges are removed. This sequence is crucial to guarantee user safety and product quality.
Automation systems, including robotic arms or conveyors, often load and unload pots into the spout forming station. These systems can include vision-guided alignment to ensure the spout is formed precisely in the correct position relative to other features like handles or lids. This precision is especially important for pots with ergonomic or aesthetic designs, where misalignment could affect usability or customer perception.
Tooling versatility is a key advantage of modern pot spout forming machines. Quick-change dies and programmable servo controls allow manufacturers to switch between different spout designs efficiently, supporting product diversification and customization without significant downtime or retooling costs.
Inline quality inspection is often integrated, using cameras and laser sensors to detect defects such as incomplete forming, cracks, or rough edges. This real-time monitoring helps maintain high production yields and reduces waste by catching issues early.
The forming process may also include secondary operations such as embossing brand logos or applying decorative patterns on or near the spout area. Some machines are equipped with multi-functional tooling capable of combining forming with light stamping or texturing in one cycle.
Energy efficiency and sustainability are increasingly important considerations. Pot spout forming machines are designed to optimize power usage, often through servo-driven systems that use energy only when actively forming. Lubricants and coolants used during forming are managed carefully to reduce environmental impact, with closed-loop systems recycling fluids and minimizing waste.
Operator safety and ease of use are priorities in machine design. Protective guarding, emergency stop systems, and intuitive control panels help prevent accidents. Ergonomic features such as adjustable loading heights and assistive handling tools reduce operator fatigue and improve productivity.
With advancements in Industry 4.0, pot spout forming machines are becoming smarter and more connected. Data from sensors and controls are collected for analysis, enabling predictive maintenance, production optimization, and seamless integration into smart factory environments. These capabilities help manufacturers increase uptime, improve product consistency, and respond flexibly to changing market demands.
In summary, pot spout forming machines combine mechanical precision, automation, and intelligent control to produce high-quality spouts that meet functional and aesthetic requirements. They are integral to modern cookware production, ensuring each pot delivers reliable pouring performance while maintaining the brand’s design standards and manufacturing efficiency.
Beyond the core forming process, pot spout forming machines also contribute significantly to the overall manufacturing efficiency and product differentiation. In competitive cookware markets, the ability to quickly introduce new spout designs or customize existing ones for different product lines offers manufacturers a distinct advantage. Machines with modular tooling and programmable control enable rapid transitions between styles, such as narrow pour spouts for precision pouring or wide lips for faster filling and cleaning.
Some advanced systems incorporate multi-axis forming heads that can manipulate the spout geometry in three dimensions, allowing more complex shapes that improve ergonomics or aesthetics. For example, angled or flared spouts can be formed to enhance liquid flow and reduce drips, features that are increasingly valued by consumers.
Integration with upstream and downstream processes enhances line efficiency. For example, after spout forming, the pots may proceed directly to automated handle attachment, lid fitting, or coating stations. Synchronizing these processes reduces manual handling and cycle times, increasing throughput while maintaining consistent product quality.
Maintenance and durability of pot spout forming machines are also critical. High-strength tool steels and wear-resistant coatings extend tooling life, reducing downtime and costs. Machines often include automated lubrication and cooling systems to protect both tools and material during forming, ensuring consistent results and preventing premature wear or damage.
Operators benefit from user-friendly software interfaces with graphical programming, diagnostic tools, and recipe management. These features simplify setup and troubleshooting, reduce human error, and allow less experienced personnel to manage complex forming tasks effectively.
Emerging technologies such as machine learning and AI are beginning to influence pot spout forming operations. By analyzing forming parameters and production data, these systems can optimize process settings in real time, compensating for material variations or wear and improving yield. Predictive maintenance alerts based on sensor data help avoid unexpected breakdowns.
The environmental footprint of pot spout forming processes is also a focus for manufacturers. Efforts to reduce energy consumption, recycle materials, and use environmentally friendly lubricants align with sustainability goals and regulatory requirements. This is especially relevant as cookware producers increasingly market eco-conscious products.
In conclusion, pot spout forming machines represent a sophisticated blend of mechanical engineering, automation, and digital innovation. They enable cookware manufacturers to produce durable, functional, and attractive pots with precision and efficiency, meeting evolving consumer expectations and industry standards. Their continued development supports the competitiveness and sustainability of modern cookware production.
Metal Pot Lid Production Line
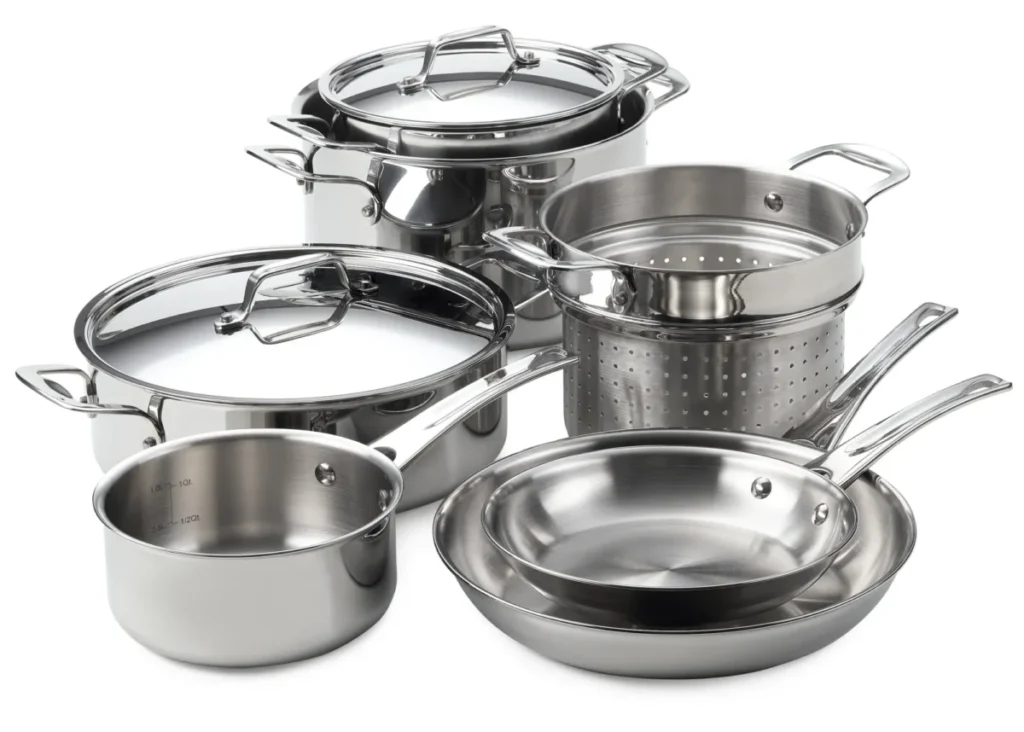
A Metal Pot Lid Production Line is a specialized automated or semi-automated manufacturing system designed to produce metal lids for pots, pans, and cookware efficiently and with consistent quality. These lids, made from materials such as stainless steel, aluminum, or sometimes copper, require precise shaping, trimming, finishing, and sometimes assembly of components like handles or vents.
The production line typically involves several key stages:
- Blanking and Cutting: Metal sheets or coils are fed into blanking presses or stamping machines that cut out circular or shaped lid blanks to the required diameter and shape.
- Deep Drawing/Forming: The lid blank is formed into a shallow dome or flat profile using deep drawing presses or hydraulic forming machines. This shaping gives the lid its characteristic curvature, improving strength and fit on the pot.
- Trimming and Edge Forming: After forming, excess material is trimmed to exact dimensions. The edges are then rolled, flanged, or curled using specialized rim forming machines to create smooth, safe, and strong rims. This process may include beading or embossing for structural reinforcement or aesthetic detail.
- Surface Finishing: The lids undergo surface treatments such as polishing, buffing, or brushing to achieve the desired finish — whether mirror-like shine, matte texture, or brushed patterns. Automated polishing machines, often using abrasive belts, brushes, or wheels, improve efficiency and consistency.
- Handle and Accessory Attachment: Many metal lids have handles, knobs, or steam vents attached. These components are usually riveted, welded, or screwed in place by robotic or manual assembly stations integrated into the line.
- Quality Inspection: Vision systems and sensors inspect dimensions, surface quality, handle attachment integrity, and overall appearance to ensure conformity with specifications. Defective lids are automatically rejected or diverted for rework.
- Packaging: Finished lids are stacked, counted, and packaged using automated systems, ready for shipping or further assembly.
Modern metal pot lid production lines emphasize automation to increase throughput, reduce labor costs, and maintain tight tolerances. Programmable controls and modular machinery allow quick product changeovers and customization for different lid sizes, shapes, and designs.
Integration with factory-wide manufacturing execution systems (MES) enables real-time monitoring of production metrics, predictive maintenance, and inventory management, further optimizing efficiency and product quality.
Safety features like guarding, emergency stops, and ergonomic design protect operators throughout the production process.
Overall, a metal pot lid production line is a critical component of cookware manufacturing, delivering high-quality lids that complement pots in durability, fit, and appearance while supporting scalable and flexible production.
The metal pot lid production line is designed to optimize every step of lid manufacturing for consistency, speed, and quality. Starting from the raw metal coil or sheet, precision feeding and blanking systems ensure minimal material waste by cutting lids with high accuracy and repeatability. Advanced blanking presses use high-strength tooling capable of handling various metals and thicknesses, accommodating a wide range of lid sizes from small saucepans to large stockpots.
Once blanks are cut, the deep drawing or forming stations use hydraulic or mechanical presses to shape the lids. This forming process is carefully controlled to prevent metal thinning, cracking, or wrinkling, which can compromise the lid’s strength and aesthetics. Adjustable stroke lengths, blank holders, and pressure settings allow operators to fine-tune the process for different materials and designs.
Edge trimming and rim forming follow, where specialized machines trim the excess metal and create rolled or flanged edges that provide structural rigidity and a safe, smooth surface for handling. Beading or embossing may be added during this phase to enhance strength or contribute to brand-specific design elements. The rim forming machines typically incorporate servo-driven controls for precise and repeatable edge shaping.
Surface finishing is a critical step, as the appearance of the lid greatly affects the perceived quality of the final cookware product. Automated polishing machines use belts, brushes, or pads with varying abrasives to achieve finishes ranging from high-gloss mirror polish to uniform brushed textures. These finishing machines are often equipped with dust extraction and coolant systems to maintain a clean work environment and prolong tool life.
Attachment of handles or knobs is usually integrated into the production line. Robotic arms or semi-automated stations align and fasten components through riveting, welding, or screwing, depending on the design. Steam vents or other features may also be added at this stage. These processes are synchronized with upstream operations to maintain smooth workflow and minimize bottlenecks.
Inline quality control systems equipped with cameras, laser scanners, and force sensors continuously monitor lid dimensions, surface quality, and handle security. Real-time data acquisition allows immediate rejection of defective lids or adjustments to process parameters to correct deviations, thereby reducing scrap rates and enhancing overall yield.
The entire production line is managed through advanced programmable logic controllers (PLCs) and human-machine interfaces (HMIs), providing operators with intuitive control panels, recipe management for different lid models, and diagnostic tools. Integration with manufacturing execution systems (MES) enables monitoring of production efficiency, downtime, and maintenance schedules, contributing to lean manufacturing goals.
Material handling throughout the line is often automated, with conveyor belts, robotic loaders, and stackers ensuring smooth and efficient transfer of lids between stations. This automation reduces manual labor, minimizes the risk of damage, and increases throughput.
Environmental considerations have become increasingly important in modern production lines. Energy-efficient drives, servo motors, and process optimization reduce power consumption. Recycling systems for metal scrap and polishing compounds help minimize waste. Additionally, noise reduction measures and dust control enhance workplace safety and comfort.
Operator safety remains a priority, with guards, interlocks, emergency stops, and ergonomic designs incorporated into each machine. Training programs and clear operational protocols help ensure safe handling of materials and machinery.
Flexibility and scalability are key features of contemporary metal pot lid production lines. Modular machine designs allow manufacturers to expand capacity or add new processing steps, such as laser engraving or anti-fingerprint coatings, without major overhauls. Quick-change tooling and programmable settings facilitate rapid product changeovers to meet evolving market demands.
Ultimately, the metal pot lid production line delivers high-quality lids that meet stringent standards for fit, durability, and aesthetics, playing a vital role in the overall success of cookware manufacturing operations. By combining advanced mechanical design, automation, quality control, and digital integration, these lines help manufacturers achieve competitive efficiency and product excellence.
In addition to the core manufacturing processes, many metal pot lid production lines now incorporate advanced customization and branding options to meet market differentiation needs. Laser engraving or etching stations can be integrated inline to apply logos, product information, or decorative patterns directly onto the lid surface with high precision and permanence. These markings enhance brand recognition and add value without requiring separate labeling or printing steps.
Another growing trend is the application of functional coatings during or after production. Anti-fingerprint, anti-corrosion, or scratch-resistant coatings may be applied via automated spray booths or dip coating stations. Some lines include curing ovens or UV treatment units to ensure coatings bond properly, enhancing the durability and appearance of the lids.
For lids requiring glass inserts or transparent windows, specialized assembly modules handle the precise placement and sealing of glass components. Robotic arms, vision systems, and adhesive dispensers work together to achieve strong, leak-proof bonds while maintaining tight tolerances. These hybrid lids offer consumers improved visibility during cooking while preserving heat retention and safety.
Steam vent mechanisms or pressure release valves are often incorporated into lid designs for advanced cookware. Automated assembly lines integrate these components with exact positioning and secure fastening, sometimes combining mechanical installation with electronic testing to verify functionality.
Modern production lines also emphasize digital traceability. Each lid can be assigned a unique identifier, such as a barcode or RFID tag, allowing manufacturers to track production history, quality inspections, and batch information throughout the supply chain. This traceability supports warranty claims, quality audits, and regulatory compliance.
Continuous improvement and data analytics play a key role in optimizing line performance. Sensors and data acquisition systems monitor equipment health, material usage, cycle times, and defect rates. Advanced software tools analyze this data to identify bottlenecks, predict maintenance needs, and suggest process adjustments that reduce downtime and improve yield.
Maintenance strategies have evolved with condition-based and predictive approaches replacing traditional scheduled maintenance. Smart sensors detect vibrations, temperature changes, or wear patterns, alerting technicians before failures occur. This reduces unexpected stoppages and extends equipment lifespan.
Energy management is increasingly integrated, with lines equipped to monitor and minimize electricity and compressed air consumption. Waste heat recovery systems may be installed on processes like forming or coating curing to improve overall plant efficiency.
Training and workforce development are essential for operating sophisticated production lines. Virtual reality (VR) and augmented reality (AR) tools offer immersive training experiences, allowing operators to practice machine setups, troubleshooting, and safety procedures without interrupting production.
In terms of layout, flexible manufacturing cells allow quick reconfiguration of machines and workstations to accommodate new product designs or volume changes. Collaborative robots (cobots) work alongside human operators to assist with loading, inspection, or assembly tasks, combining automation with human flexibility.
Environmental sustainability is a priority, with manufacturers seeking to reduce scrap metal through optimized nesting and cutting algorithms, recycle polishing compounds, and use eco-friendly materials wherever possible. Certifications such as ISO 14001 for environmental management are increasingly pursued to demonstrate commitment to responsible manufacturing.
In summary, modern metal pot lid production lines blend precision engineering, automation, digitalization, and sustainability to deliver high-quality, customizable lids efficiently. These capabilities empower cookware manufacturers to meet diverse market demands, improve operational resilience, and maintain competitive advantage in a dynamic industry.
Baking Pot Manufacturing Machines
Baking Pot Manufacturing Machines are specialized equipment designed to produce baking pots, which are cookware items typically used for oven baking, roasting, and slow cooking. These pots can be made from various metals such as cast aluminum, stainless steel, carbon steel, or coated steel, and often feature thick walls for even heat distribution and durability.
The manufacturing process involves several key machines and stages that work together to shape, finish, and assemble baking pots:
- Metal Sheet or Coil Preparation Machines: These include decoilers, straighteners, and feeders that prepare metal sheets or coils by flattening and feeding them precisely into subsequent machines.
- Deep Drawing Presses: Since baking pots usually have deep, round, and sometimes complex shapes, hydraulic or mechanical deep drawing presses are employed. These presses draw flat metal blanks into cup or pot shapes through one or multiple drawing steps, controlling material flow to avoid thinning or cracking.
- Ironing and Wall Thickness Control Machines: Some baking pots require uniform wall thickness for optimal heat transfer. Ironing presses or wall thickness control machines reduce the thickness of the pot walls while increasing height, ensuring consistent thickness and strength.
- Trimming Machines: After forming, excess metal around the pot rim or base is trimmed to precise dimensions. This can involve mechanical trimming presses or laser trimming for high accuracy and minimal waste.
- Flanging and Beading Machines: The rim or edge of the pot is formed to improve strength and safety by rolling, flanging, or beading. This process creates smooth, rounded edges that prevent injury and help in lid fitting.
- Surface Treatment Equipment: To prepare pots for use or coating, machines for cleaning, degreasing, and surface roughening may be used. Some lines incorporate shot blasting or brushing machines to improve surface texture for better coating adhesion.
- Coating and Baking Ovens: For non-stick or protective coatings, automated spraying systems apply coatings evenly, followed by curing ovens that bake the coating onto the pot surface. This is essential for durable, food-safe finishes.
- Handle and Accessory Assembly Machines: Robotic or semi-automated stations attach handles, knobs, or lid assemblies. Depending on design, attachment methods may include riveting, welding, or screwing.
- Quality Inspection Systems: Vision inspection, dimensional measurement, and coating thickness gauges ensure each pot meets design and safety standards. Defective products are automatically rejected or diverted for rework.
- Packaging Machines: Automated stacking, counting, and packaging equipment prepare finished baking pots for shipment, often including protective materials to prevent damage during transport.
Modern baking pot manufacturing machines emphasize automation, precision, and flexibility to produce a variety of pot sizes, shapes, and finishes efficiently. Integration with digital controls and monitoring systems supports high throughput, consistent quality, and quick product changeovers.
These machines are critical for producing durable, high-performance baking pots that deliver even cooking results and meet consumer expectations for quality and safety.
Baking pot manufacturing machines form a tightly integrated production system that combines mechanical precision, automation, and quality control to produce reliable cookware. The process begins with raw metal in sheet or coil form, which passes through feeders and straightening equipment to ensure flatness and correct dimensions before forming. Deep drawing presses then shape the metal into the pot’s characteristic rounded, deep form. This step is critical, as the metal must flow evenly into the die cavity without wrinkles, cracks, or thinning that could compromise durability or performance. Multiple drawing stages are often employed to gradually achieve the desired depth and shape, especially for larger or more complex pots.
After forming, trimming machines precisely cut away excess metal to finalize the pot’s dimensions and prepare it for edge treatment. Flanging and beading machines roll or curl the rim to enhance strength, improve safety by eliminating sharp edges, and facilitate secure lid fitting. These machines use servo-controlled tooling to ensure consistent, repeatable results that meet strict tolerances.
Surface preparation is a vital part of the manufacturing process. Automated cleaning and degreasing equipment remove oils, contaminants, and scale from forming to ensure proper adhesion of coatings and improve corrosion resistance. Depending on the pot’s material and finish requirements, shot blasting or brushing machines refine the surface texture, creating a uniform profile ideal for coating application.
Coating lines are integrated to apply non-stick, ceramic, or enamel layers that enhance cooking performance and ease of cleaning. Automated spray systems deliver coatings evenly across the pot’s interior and exterior, often with multiple layers applied. Curing ovens bake the coatings at controlled temperatures to achieve strong chemical bonds and durable finishes. Environmental controls manage overspray and emissions to comply with regulations and maintain worker safety.
Handle and accessory attachment machines are synchronized with earlier stages to maintain smooth flow through the line. Robotics or specialized assembly stations affix handles via riveting, welding, or mechanical fastening. These machines often include vision systems to verify correct positioning and secure attachment, reducing defects and improving product reliability.
Throughout the line, inline inspection systems use cameras, laser scanners, and sensors to monitor dimensions, surface quality, and coating integrity. Data collected supports real-time adjustments and quality assurance, reducing waste and rework. Defective pots are automatically removed from the line or flagged for manual inspection.
Material handling is highly automated, with conveyors, robotic arms, and stacking equipment minimizing manual intervention. This reduces the risk of damage, increases throughput, and supports continuous operation. Control systems coordinate all machinery, providing operators with intuitive interfaces for monitoring, recipe management, and troubleshooting.
Energy efficiency is a priority, with modern machines employing servo motors and optimized process controls to reduce consumption. Waste management includes recycling metal scrap from trimming and forming stages and reclaiming coating materials. Safety features such as guarding, emergency stops, and ergonomic design protect workers and enhance productivity.
The modular design of baking pot manufacturing machines allows manufacturers to scale capacity and adapt to new product lines quickly. Quick-change tooling and programmable controls facilitate rapid transitions between pot sizes, shapes, and finishes, enabling responsiveness to market trends and customer demands.
In essence, baking pot manufacturing machines form a sophisticated ecosystem that combines forming, finishing, assembly, and inspection into a seamless production flow. This integrated approach delivers high-quality, durable baking pots with consistent performance, supporting efficient and flexible cookware manufacturing operations.
Advancements in baking pot manufacturing machines continue to focus on increasing automation, precision, and flexibility while reducing production costs and environmental impact. One significant development is the integration of smart sensors and Industry 4.0 technologies into the machinery. These sensors continuously monitor parameters such as press force, temperature, vibration, and cycle times, transmitting data to centralized control systems. This real-time feedback allows for predictive maintenance, minimizing unplanned downtime by identifying wear or faults before failures occur.
Artificial intelligence and machine learning algorithms analyze production data to optimize forming parameters automatically, compensating for variations in material properties or environmental conditions. This adaptive control enhances product consistency and reduces scrap rates, improving overall equipment effectiveness (OEE).
Robotic automation is increasingly employed beyond handle assembly, including loading and unloading of presses, transfer of parts between stations, and packaging. Collaborative robots (cobots) work safely alongside human operators to assist with tasks that require dexterity or decision-making, increasing operational flexibility without sacrificing safety.
In coating applications, more environmentally friendly processes are being adopted, such as powder coatings and water-based coatings that emit fewer volatile organic compounds (VOCs). Automated coating lines with closed-loop monitoring ensure precise application thickness and uniformity, reducing material waste and improving finish quality.
Energy-saving technologies such as regenerative drives, energy-efficient motors, and optimized heating systems contribute to lowering the carbon footprint of baking pot production. Heat recovery systems capture waste heat from ovens or presses and reuse it within the facility, improving overall energy utilization.
Digital twin simulations of the manufacturing line allow engineers to model and test process changes virtually before implementing them on the floor. This reduces trial-and-error, speeds up product development, and helps plan expansions or modifications with minimal disruption.
Customization is becoming more accessible with flexible tooling and modular machine components. Manufacturers can quickly switch between different pot designs, sizes, or finishes to meet diverse market demands or seasonal trends. This agility helps maintain competitiveness in a dynamic consumer environment.
Quality assurance systems now often include automated defect detection using advanced vision technology, including 3D scanning and surface texture analysis. These systems identify issues such as dents, coating flaws, or dimensional inaccuracies that may be invisible to the naked eye, ensuring only the highest-quality pots reach customers.
Sustainability extends beyond manufacturing processes, with companies seeking recyclable or reusable packaging solutions and implementing closed-loop systems to reclaim scrap metal and coating overspray. These practices not only reduce environmental impact but can also lower raw material costs.
Worker training has also evolved, utilizing augmented reality (AR) and virtual reality (VR) tools for immersive learning experiences. Operators can practice machine setups, safety procedures, and troubleshooting in a risk-free virtual environment, increasing skill levels and reducing errors on the production line.
In conclusion, baking pot manufacturing machines are at the forefront of combining traditional metal forming expertise with cutting-edge automation, digital technologies, and sustainable practices. These innovations enable cookware manufacturers to deliver superior baking pots efficiently while adapting to market needs and environmental responsibilities, ensuring long-term success in the industry.
Steamer Pot Production Equipment
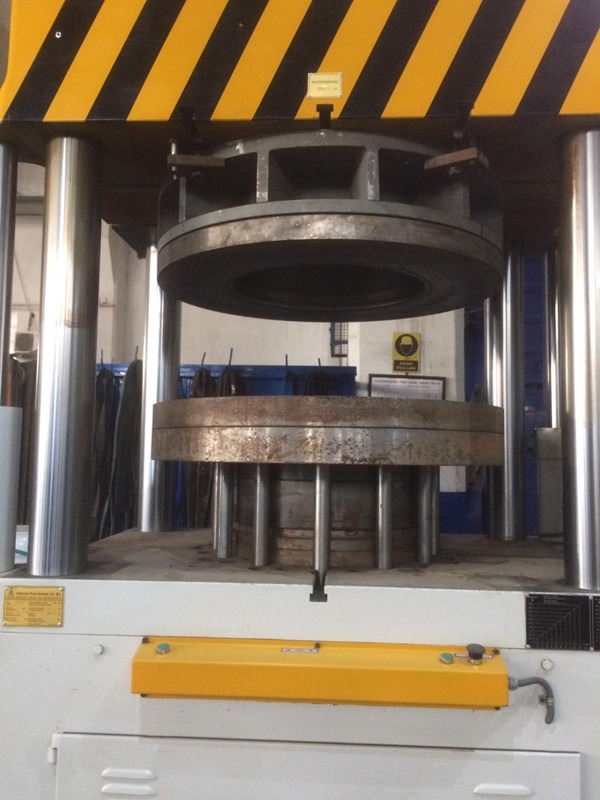
Steamer pot production equipment encompasses the specialized machinery and systems used to manufacture steamer pots—cookware designed to cook food with steam by stacking perforated tiers over a boiling water base. These pots are commonly made from metals like stainless steel, aluminum, or sometimes coated steel, and require precise forming, joining, and finishing processes to ensure functionality, durability, and safety.
The production equipment typically includes:
- Sheet Metal Preparation Machines: These feed and straighten raw metal sheets or coils, preparing them for forming operations with consistent thickness and flatness.
- Deep Drawing Presses: Since steamer pots often have deep, rounded shapes with smooth walls, hydraulic or mechanical deep drawing machines form the base and tiers from metal blanks, drawing the material into the desired cup-like shapes without cracking or wrinkling.
- Perforation or Punching Machines: A key feature of steamer pots is their perforated tiers that allow steam to pass through. Specialized CNC-controlled punching presses or laser cutting machines create precise, uniform perforations in the metal sheets before or after forming, depending on design.
- Trimming and Flanging Machines: After forming and perforation, trimming presses remove excess metal, and flanging machines roll or curl the edges of the pot and tiers to create smooth rims for safe handling and to enable stacking and lid fitting.
- Assembly Equipment: Since steamer pots are often composed of multiple stackable sections and lids, semi-automated or automated assembly stations fit and secure components. Welding or riveting machines may attach handles or other fittings.
- Surface Finishing Machines: Polishing, buffing, or brushing machines provide the pots with smooth, attractive finishes and remove forming marks or burrs. These machines often incorporate dust extraction and coolant systems.
- Quality Inspection Systems: Vision systems and dimensional gauges verify perforation quality, forming accuracy, surface finish, and assembly integrity to ensure products meet specifications.
- Packaging Machines: Automated conveyors and packagers prepare finished steamer pots for shipping, including stacking, wrapping, and boxing.
Modern steamer pot production lines emphasize precision, repeatability, and efficiency, often integrating digital controls, robotic handling, and inline inspection to reduce defects and increase throughput. The specialized perforation and forming equipment differentiate steamer pot production from general cookware manufacturing, ensuring the final product functions properly to steam food evenly and safely.
Steamer pot production equipment operates as a coordinated system designed to efficiently manufacture durable, functional steamers with high precision and consistent quality. The process begins with raw metal sheets or coils that are fed through straightening and leveling machines to ensure uniform thickness and flatness, essential for flawless forming and perforation.
The deep drawing presses shape the metal into the pot’s base and the stackable tiers. These presses are engineered to control metal flow carefully, preventing defects such as cracks, wrinkles, or uneven thickness, which could compromise the pot’s strength or steam performance. Depending on the design, multi-stage drawing or redrawing may be used to achieve the required depth and geometry.
A defining feature of steamer pots is their perforated tiers that allow steam to circulate freely. CNC-controlled punching presses or laser cutting machines perform precise and consistent perforations according to programmed patterns and hole sizes. This precision ensures efficient steaming by balancing steam flow and structural integrity. In some cases, perforations are made before forming to optimize metal flow and maintain hole shapes during drawing.
After forming and perforation, trimming machines remove excess material around rims and bases, producing smooth edges that contribute to safety and ease of stacking. Flanging machines then roll or curl the edges, creating sturdy rims that prevent deformation and allow the tiers to nest securely. Some designs may incorporate beading or embossing to enhance rim strength or add decorative elements.
Assembly equipment plays a vital role in integrating handles, lids, and other components. Welding robots, riveting stations, or mechanical fasteners attach handles and locking mechanisms with accuracy and repeatability. Automation in assembly reduces labor costs and ensures consistent fit and finish.
Surface finishing machines polish or brush the pot surfaces, removing marks from forming and cutting while enhancing appearance. These finishing steps improve corrosion resistance and provide an attractive, smooth surface that meets consumer expectations. Dust extraction and coolant systems maintain a clean working environment and extend tool life.
Inline quality inspection systems use high-resolution cameras, laser scanners, and dimensional sensors to monitor every aspect of the production process. These systems detect issues such as incomplete perforations, dimensional deviations, surface defects, or loose assemblies. Real-time feedback allows immediate correction or rejection of faulty items, minimizing waste and maintaining high product standards.
Material handling automation, including conveyors and robotic arms, seamlessly transfers components between stations, increasing throughput and reducing human handling that could cause damage. The entire line is controlled through advanced programmable logic controllers (PLCs) and human-machine interfaces (HMIs), allowing operators to monitor performance, adjust parameters, and manage production schedules efficiently.
Environmental considerations are addressed by recycling metal scrap generated from trimming and perforation, managing lubricant and coolant usage, and incorporating energy-efficient drives and motors. Noise reduction and dust control measures improve worker safety and comfort.
Flexibility in production is achieved through modular machine designs and programmable tooling, allowing manufacturers to switch between different steamer pot sizes, perforation patterns, or finishes with minimal downtime. This adaptability helps meet varied market demands and supports rapid product innovation.
Steamer pot production equipment thus integrates forming, perforating, finishing, assembly, and inspection into a streamlined workflow that delivers high-quality steamers reliably and cost-effectively. By combining mechanical expertise with modern automation and digital controls, manufacturers can produce cookware that offers excellent steaming performance, durability, and consumer appeal.
Further innovations in steamer pot production equipment focus heavily on enhancing automation and data integration to boost efficiency and quality control. Advanced robotics increasingly handle complex tasks such as loading blanks into presses, transferring delicate perforated tiers, and precisely assembling multi-component units. These robots are often equipped with force sensors and vision systems to adapt to slight variations in part geometry and ensure gentle, accurate handling that prevents damage.
Artificial intelligence (AI) and machine learning algorithms are gradually being incorporated into monitoring and control systems. By analyzing production data in real time, AI can predict tool wear, optimize machine settings, and identify subtle defects that might be missed by conventional inspection methods. This predictive capability leads to fewer breakdowns, lower scrap rates, and improved overall equipment effectiveness.
Additive manufacturing (3D printing) is also emerging as a complementary technology in prototyping and tooling for steamer pot production. Custom dies, punches, or specialized assembly jigs can be rapidly produced, enabling faster development cycles and more complex product designs without traditional tooling delays.
Sustainability is a growing priority. New machines are designed to minimize metal waste by optimizing blank nesting and cutting patterns. Lubricant and coolant management systems recycle fluids to reduce environmental impact and operating costs. Energy-efficient motors and regenerative braking on presses cut power consumption, while noise reduction measures contribute to healthier work environments.
Surface treatment technology advances include environmentally friendly coating applications that improve corrosion resistance and ease of cleaning without harmful emissions. Inline curing ovens with precise temperature control ensure consistent coating quality while conserving energy.
In terms of quality assurance, multi-sensor inspection stations combine optical, laser, and tactile measurement technologies to provide comprehensive assessments of pot geometry, perforation accuracy, surface finish, and assembly integrity. Data from these inspections feed into traceability systems that document production history for each pot, supporting warranty claims and compliance with industry standards.
Operator interfaces have become more user-friendly and informative, featuring touchscreen panels with intuitive graphics, real-time performance dashboards, and remote access capabilities. This connectivity allows supervisors and maintenance personnel to monitor multiple production lines from centralized locations and respond quickly to issues.
Ergonomic design improvements in machine layouts and controls reduce operator fatigue and improve safety. Collaborative robots assist with repetitive or strenuous tasks, enabling human workers to focus on supervision and quality management.
Modular and scalable production systems allow manufacturers to expand capacity or adapt quickly to new product variations. Quick-change tooling and flexible automation enable efficient small-batch runs alongside mass production, catering to diverse customer requirements.
Overall, steamer pot production equipment is evolving into a highly integrated, intelligent, and sustainable manufacturing ecosystem. These advancements empower cookware producers to deliver superior-quality steamers with consistent performance while optimizing operational costs, environmental impact, and market responsiveness.
Casserole Pot Manufacturing Line
A casserole pot manufacturing line is a specialized production system designed to fabricate casserole pots, which are durable cookware typically used for slow cooking, stewing, and braising. These pots often feature thick walls and lids to retain heat and moisture, made from metals like cast aluminum, stainless steel, or carbon steel, sometimes with non-stick or enamel coatings.
The manufacturing line integrates various machines and processes to transform raw metal materials into finished casserole pots ready for distribution. It typically begins with metal sheet or coil handling equipment that straightens and feeds the metal into forming machines. Deep drawing presses shape the pot bodies by drawing flat metal blanks into deep, round containers with smooth contours and consistent wall thickness, ensuring structural integrity and even heat distribution.
Following forming, trimming machines remove excess metal from the pot rims and bases to achieve precise dimensions. The rims are then processed in flanging or beading machines that roll or curl edges, enhancing strength, safety, and providing a secure fit for lids. For pots requiring lids, lid forming machines operate similarly, shaping metal blanks into tight-fitting covers with features like handles or vent holes.
Surface preparation is essential for appearance and performance. The manufacturing line includes cleaning, degreasing, and polishing equipment to remove contaminants and smooth surfaces. For non-stick or enamel coatings, coating application systems spray or dip pots and lids with protective layers, followed by curing ovens that bake the coatings to ensure durability and food safety.
Assembly stations attach components such as handles, knobs, or locking mechanisms. These may involve riveting, welding, or screwing machines, often automated or robotic to maintain consistency and efficiency.
Throughout production, quality control systems inspect dimensions, surface finish, coating integrity, and assembly accuracy. These systems use vision cameras, laser measurement, and other sensors to detect defects and ensure compliance with standards.
Finally, packaging machines stack, wrap, and box finished casserole pots for shipment. Automation in material handling and line synchronization ensures smooth workflow and high throughput.
Modern casserole pot manufacturing lines emphasize flexibility, enabling quick changes for different pot sizes, shapes, or finishes. Integration of digital controls and monitoring systems supports efficient operation, reduces waste, and maintains consistent product quality, meeting consumer demands for reliable and attractive cookware.
The casserole pot manufacturing line is designed to maintain a seamless flow from raw material to finished product, maximizing efficiency and ensuring consistent quality. Initially, metal sheets or coils undergo straightening and leveling processes to prepare flat, uniform blanks. These blanks are then precisely cut to size by automated blanking presses that feed directly into the forming machines.
Deep drawing presses shape these blanks into the characteristic bowl-like form of casserole pots. The presses use carefully engineered dies to draw the metal smoothly without defects such as thinning or tearing. For pots with thicker walls or more complex geometries, multi-stage drawing or redrawing steps are employed to gradually achieve the desired shape and thickness. This careful control is critical to produce cookware that distributes heat evenly and withstands daily use.
Once formed, trimming machines cut excess material from the rim and base, ensuring dimensional accuracy and preparing the edges for subsequent treatments. Flanging or beading machines then process the rims, curling or rolling them to add strength and safety by eliminating sharp edges. These rim treatments also facilitate secure fitting of lids, an essential feature for casserole pots designed to trap moisture during cooking.
If the pot design includes a lid, lid forming machines operate in parallel to produce matching covers. These lids are shaped from metal blanks through drawing, pressing, or spinning techniques. Lid rims may be flanged or equipped with reinforcing beads to enhance rigidity. Features like handle mounting points or steam vents are incorporated during this stage through punching or welding operations.
Surface finishing is an integral part of the production line. Automated cleaning stations remove oils, dust, and forming residues that could interfere with coating adhesion or cause corrosion. Polishing and buffing machines smooth the pot’s interior and exterior surfaces, improving both aesthetics and functionality by creating even textures that facilitate cooking and cleaning.
For non-stick or enamel-coated casserole pots, coating application systems precisely spray, dip, or roll coating materials onto the prepared surfaces. These coatings enhance durability, prevent food from sticking, and provide attractive finishes. The coated pots then pass through curing ovens where controlled heating solidifies and bonds the coatings firmly to the metal substrate.
Attachment of handles, knobs, or locking mechanisms is performed at dedicated assembly stations. Automated riveting, welding, or screwing equipment securely fastens these components with repeatable precision. Robotics may assist in handling parts and aligning components to ensure ergonomic and safe designs.
Throughout the manufacturing line, inline inspection systems continuously monitor key quality attributes. High-resolution cameras, laser scanners, and other sensors detect defects such as surface blemishes, dimensional deviations, coating inconsistencies, or loose attachments. Real-time feedback allows operators to make immediate adjustments, reducing scrap and rework.
Material handling is streamlined with conveyors, robotic arms, and stacking equipment that minimize manual intervention and reduce damage risk. Control systems integrate machine operations, providing operators with intuitive interfaces to manage production schedules, monitor performance, and troubleshoot issues efficiently.
Energy efficiency and sustainability are prioritized by using servo-driven machines, regenerative energy systems, and recycling scrap metal generated during trimming and forming. Wastewater and emissions from coating processes are controlled with filtration and treatment systems to meet environmental regulations.
Flexibility in the casserole pot manufacturing line is supported by modular machine designs and programmable tooling. This adaptability allows rapid changes in pot size, shape, or finish to respond to shifting market trends or customer preferences without extensive downtime.
Overall, the casserole pot manufacturing line represents a sophisticated blend of metal forming, finishing, assembly, and inspection technologies. By combining automation with quality control and sustainable practices, manufacturers can produce high-quality casserole pots that deliver durability, performance, and aesthetic appeal to meet consumer expectations worldwide.
Continuous improvements in casserole pot manufacturing lines focus on integrating advanced technologies to further enhance productivity, precision, and sustainability. Automation plays a central role, with more sophisticated robotic systems managing complex tasks such as precise component placement, quality inspections, and packaging. These robots reduce human error and labor costs while increasing throughput and consistency.
Artificial intelligence and machine learning algorithms are increasingly used to analyze process data collected from sensors throughout the production line. These systems predict maintenance needs, optimize machine parameters in real time, and detect subtle defects before they impact product quality. This predictive capability reduces downtime and scrap rates, ensuring more efficient use of resources.
Digital twins of the manufacturing line allow engineers to simulate and optimize workflows virtually, testing new product designs, tooling changes, or process adjustments without disrupting actual production. This reduces development time and accelerates innovation.
In coating and finishing, environmentally friendly materials and processes are emphasized. Water-based coatings and powder coatings replace traditional solvent-based options, lowering emissions and waste. Automated coating lines with closed-loop controls ensure uniform application, reduce overspray, and minimize material usage.
Energy efficiency improvements include using servo motors and variable frequency drives to reduce power consumption and recover energy during braking. Heat recovery systems capture waste heat from curing ovens or presses to preheat incoming air or water, reducing overall energy demand.
Quality assurance benefits from multi-modal inspection systems that combine optical, laser, and tactile measurements for comprehensive evaluation of pot geometry, surface finish, and assembly accuracy. Integration with traceability systems enables tracking each pot’s production history, facilitating warranty management and regulatory compliance.
Flexible manufacturing cells with quick-change tooling enable small-batch and customized production runs, meeting diverse market demands without sacrificing efficiency. Modular line layouts allow capacity expansion or reconfiguration with minimal downtime.
Ergonomic design improvements and collaborative robots enhance operator safety and comfort, allowing humans and machines to work side by side effectively. Training tools using augmented or virtual reality help operators master complex machine setups and troubleshooting in a risk-free environment.
Sustainable practices extend beyond production, including recycling metal scraps, managing waste responsibly, and employing recyclable packaging solutions. These efforts contribute to corporate social responsibility goals and appeal to environmentally conscious consumers.
In summary, casserole pot manufacturing lines are evolving into highly automated, intelligent, and sustainable production systems. These advancements enable manufacturers to produce high-quality, durable cookware efficiently while adapting rapidly to changing market needs and environmental standards.
Frying Pan Production Machinery
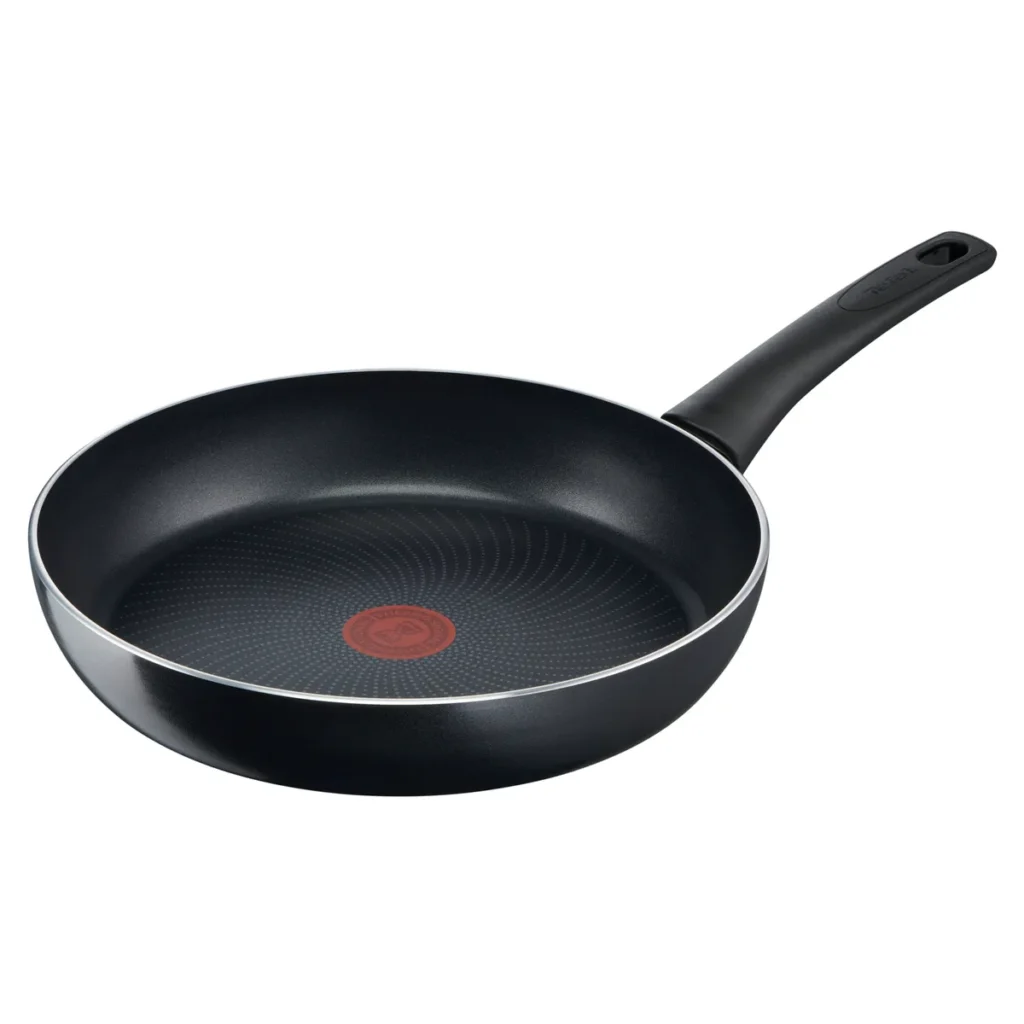
Frying pan production machinery consists of a series of specialized equipment designed to manufacture frying pans efficiently and with consistent quality. Frying pans, typically made from aluminum, stainless steel, or carbon steel, often feature flat or slightly curved bases, flared sides, and handles, sometimes coated with non-stick surfaces.
The production process begins with sheet metal handling equipment that feeds, straightens, and levels metal coils or sheets to prepare uniform blanks. These blanks are cut to size by automated blanking presses.
Deep drawing presses shape the pan bodies by drawing flat blanks into shallow, round containers with smooth walls. Some pans may require multiple drawing stages or ironing presses to achieve thinner walls and uniform thickness, improving heat distribution and durability.
After forming, trimming machines remove excess material from the rims and bases, achieving precise dimensions and preparing the edges for finishing.
Flanging or curling machines process the rims to roll or curl the edges, enhancing strength, safety, and facilitating handle attachment.
Handles are manufactured separately using molding or casting machinery and are attached to the pan bodies using riveting, welding, or screwing machines. Automated assembly lines often perform this step to maintain consistency.
For pans with non-stick or specialty coatings, surface preparation machines clean and polish the metal surfaces before applying coatings via spray, dip, or roll-coating systems. Coated pans then move through curing ovens that bake and set the coating to ensure durability and safety.
Additional finishing steps might include embossing or laser engraving for branding, texture, or anti-slip patterns.
Quality control stations using cameras, sensors, and dimensional gauges inspect frying pans for defects in shape, coating, and assembly throughout the line.
Finally, packaging machines organize, wrap, and box the finished pans for shipping.
Modern frying pan production machinery emphasizes automation, precision, and flexibility, allowing manufacturers to produce various pan sizes, materials, and finishes efficiently while meeting market demands for quality and durability.
Frying pan production machinery operates as an integrated sequence of processes designed to convert raw metal into high-quality cookware with efficiency and precision. The line starts with feeding metal sheets or coils into leveling and straightening machines to ensure consistent thickness and flatness, which is crucial for uniform forming and coating.
Once prepared, the metal blanks are cut to size by automated blanking presses, which provide clean, accurate pieces for forming. The forming stage typically employs deep drawing presses that shape the blanks into shallow pans with smooth, even walls. Some frying pans require additional ironing or wall thinning processes to enhance heat conduction and reduce weight while maintaining strength. These processes carefully control metal flow to avoid thinning or tearing.
After forming, trimming machines remove any excess metal from the pan’s rim and base, ensuring dimensional accuracy and preparing edges for finishing treatments. Flanging or curling machines then roll the rims to create smooth, safe edges and add structural reinforcement, which also facilitates handle attachment.
Handles are manufactured separately using injection molding for plastic or casting and machining for metal variants. Assembly machines attach handles securely to the pan bodies, commonly using riveting or welding methods. Automation in this step improves consistency and reduces labor costs.
Before coating, the pan surfaces go through cleaning and polishing stations to remove oils, dirt, and surface irregularities. This preparation is vital for ensuring that coatings—such as non-stick layers or protective finishes—adhere properly and last through extensive use.
Coating application machinery includes spray booths, dipping tanks, or roller coaters that evenly apply non-stick or specialty coatings. Curing ovens bake the coated pans under precise temperature control to set the coatings, providing durability and food safety. Some lines may include multiple coating and curing stages to achieve desired thickness and finish.
Additional features like embossed patterns, brand logos, or textured surfaces are applied using embossing presses or laser engraving machines, enhancing the pan’s appearance and usability.
Throughout production, inline inspection systems continuously monitor the frying pans’ shape, coating quality, handle attachment integrity, and surface finish using high-resolution cameras, laser scanners, and sensors. These inspections help identify defects early, allowing prompt correction and reducing waste.
Material handling automation, including conveyors and robotic arms, efficiently moves pans between processing stations, minimizing human contact and potential damage. Control systems synchronize operations, provide real-time monitoring, and facilitate adjustments to optimize throughput and quality.
Energy efficiency measures, such as servo drives on presses and ovens with heat recovery systems, help reduce operational costs and environmental impact. Waste management systems recycle scrap metal and capture coating overspray to maintain sustainable production.
The frying pan production machinery is designed to be flexible, supporting a variety of pan sizes, materials, and finishes. Quick-change tooling and programmable automation allow manufacturers to switch product lines rapidly to meet evolving market demands.
Ergonomics and safety are incorporated into machine design, with features like easy-access controls, noise reduction, and protective guards ensuring operator well-being.
Overall, frying pan production machinery integrates forming, trimming, finishing, coating, assembly, inspection, and packaging into a streamlined, automated process. This enables manufacturers to produce cookware that combines durability, performance, and aesthetic appeal while optimizing efficiency and sustainability.
Continuous advancements in frying pan production machinery focus on increasing automation, precision, and adaptability to meet growing consumer demands and sustainability goals. Robotics and automated guided vehicles (AGVs) are increasingly incorporated to handle delicate tasks such as transferring pans between stations, reducing manual labor and minimizing damage risks.
Machine learning and AI-driven analytics monitor equipment performance and product quality in real time, predicting maintenance needs and optimizing process parameters. This predictive maintenance minimizes downtime and extends tool life, while adaptive controls ensure coating thickness, shape tolerances, and assembly accuracy remain within tight specifications.
Innovative coating technologies, such as ceramic-based and diamond-enhanced non-stick surfaces, require precise application and curing methods. Specialized coating lines equipped with advanced spray nozzles and controlled environmental chambers improve coating uniformity and durability, meeting stricter food safety and performance standards.
Energy efficiency is enhanced through the use of servo motors, variable frequency drives, and regenerative braking on presses and conveyors. Heat recovery systems reclaim thermal energy from ovens and curing equipment, reducing overall energy consumption and lowering production costs.
Sustainable manufacturing practices extend to waste management, with metal scraps collected and recycled directly into the production cycle. Coating overspray is captured and reused where possible, and environmentally friendly coating materials replace traditional solvents, minimizing volatile organic compound (VOC) emissions.
Flexible manufacturing systems with modular layouts allow quick product changeovers, enabling manufacturers to respond rapidly to market trends and customer customization requests without significant downtime.
Advanced quality inspection combines multiple sensor technologies—optical, laser, ultrasonic, and tactile—to provide comprehensive, non-destructive testing of frying pans. Real-time data feeds into quality management systems for traceability, ensuring only products meeting stringent criteria proceed to packaging.
Ergonomic designs and collaborative robots improve workplace safety and operator comfort, while augmented reality (AR) tools assist with training, machine setup, and troubleshooting, accelerating staff proficiency.
Packaging machinery has evolved to include automated stacking, wrapping, and boxing systems that protect frying pans during transport and improve warehouse efficiency.
Altogether, these innovations transform frying pan production machinery into highly intelligent, efficient, and sustainable manufacturing ecosystems. This enables producers to deliver premium cookware that meets evolving consumer expectations for quality, performance, and environmental responsibility.
Saucepan Manufacturing Equipment
Saucepan manufacturing equipment consists of specialized machinery designed to efficiently produce saucepans, which are typically smaller, deeper cookware items used for boiling, simmering, and cooking sauces. The production process transforms raw metal sheets or coils into finished saucepans with precise dimensions, durable construction, and often coated surfaces for performance and aesthetics.
The manufacturing line begins with metal sheet feeding and leveling machines that straighten and flatten metal coils or sheets, ensuring uniform thickness and surface quality essential for forming and coating processes. Automated blanking presses cut metal blanks to exact sizes suited for saucepan dimensions.
Forming machinery, such as deep drawing presses, shape the metal blanks into cylindrical or rounded saucepan bodies. In some cases, multi-stage drawing or redrawing is applied to achieve deeper shapes with consistent wall thickness, important for even heat distribution and structural integrity. Ironing presses may thin and smooth the saucepan walls while maintaining strength.
After forming, trimming machines remove excess metal from rims and bases, providing precise and smooth edges. Flanging or curling machines process the rims to roll or fold edges, enhancing strength, safety, and lid compatibility.
If the saucepan design includes lids, separate lid forming machines shape matching covers with features such as handles or vent holes. These lids undergo similar forming, trimming, and finishing processes.
Surface preparation equipment cleans and polishes saucepan interiors and exteriors to remove oils, contaminants, and surface irregularities, improving coating adhesion and final appearance.
Coating application machinery applies non-stick, enamel, or other specialty coatings through spray, dip, or roll-coating systems, followed by curing ovens that bake and bond the coatings to the metal surface for durability and safety.
Handles and knobs are produced separately using molding or casting machines and are attached to saucepan bodies using riveting, welding, or screwing equipment, often automated for consistency and speed.
Throughout the line, quality control systems monitor dimensional accuracy, coating quality, assembly integrity, and surface finish using sensors, cameras, and measuring devices. These systems help reduce defects and ensure compliance with industry standards.
Material handling systems including conveyors, robotic arms, and stacking equipment facilitate smooth, efficient movement of saucepans through the production process, minimizing manual labor and risk of damage.
Packaging machinery organizes, wraps, and boxes finished saucepans for shipment, often tailored to product size and batch quantity.
Modern saucepan manufacturing equipment emphasizes automation, flexibility, and sustainability. Quick-change tooling and programmable controls enable efficient production of various saucepan sizes and designs, while energy-efficient drives, recycling systems, and environmentally friendly coatings reduce environmental impact and operational costs.
This integration of advanced forming, finishing, assembly, inspection, and packaging technologies enables manufacturers to produce high-quality saucepans that combine durability, performance, and aesthetic appeal to meet consumer demands.
Saucepan manufacturing equipment operates as a streamlined sequence of processes designed to transform raw metal into finished cookware with precision and efficiency. The process starts with feeding metal coils or sheets into leveling and straightening machines that prepare flat, uniform blanks. This step is crucial to ensure consistent thickness and surface quality for forming and coating.
Automated blanking presses then cut these metal sheets into exact sizes required for saucepan bodies. The blanks move to deep drawing presses where they are shaped into the characteristic cylindrical or rounded forms of saucepans. In cases where deeper or more uniform walls are needed, multi-stage drawing or ironing presses refine the shape and thickness, ensuring durability and optimal heat conduction.
Following forming, trimming machines remove excess metal from rims and bases, producing smooth, accurate edges. Flanging or curling machines process these edges further, rolling or folding rims to enhance strength, improve safety by eliminating sharp edges, and prepare the saucepan to securely fit lids.
If lids are part of the saucepan design, separate lid forming machines shape the covers through drawing or pressing operations. These lids may include additional features such as vent holes or handle attachments, created using punching, welding, or assembly stations.
Surface finishing equipment cleans and polishes the saucepan interiors and exteriors to remove contaminants and smooth the surfaces. This step ensures proper adhesion for coatings and improves the cookware’s aesthetic appeal and performance.
Coating lines apply protective or functional layers such as non-stick or enamel finishes using spray, dip, or roll-coating methods. The saucepans then pass through curing ovens, which bake the coatings under controlled conditions to provide a durable, food-safe surface resistant to wear and corrosion.
Handles and knobs are manufactured separately using injection molding for plastics or casting and machining for metals. These components are attached to saucepan bodies at dedicated assembly stations employing automated riveting, welding, or screwing machines to ensure strong, consistent connections.
Throughout the manufacturing line, inline inspection systems continuously monitor product dimensions, surface quality, coating integrity, and assembly precision. Advanced sensors, cameras, and measurement devices detect defects early, enabling corrective actions to minimize scrap and maintain high quality standards.
Material handling automation—including conveyors, robotic arms, and stacking equipment—streamlines the movement of saucepans between stations, reducing manual labor and the risk of damage. Control systems synchronize the operation of all machinery, providing operators with real-time monitoring and control interfaces to optimize production flow.
Energy-efficient technologies are integrated, such as servo-driven presses and conveyors, variable frequency drives, and heat recovery systems from curing ovens, which lower operational costs and environmental impact. Waste management practices recycle metal scraps and minimize emissions from coating processes.
Flexibility is built into the equipment through modular designs and quick-change tooling, enabling manufacturers to switch between saucepan sizes, shapes, and finishes with minimal downtime. This adaptability supports small batch production and customization according to market demands.
Ergonomics and operator safety are emphasized with easy-access controls, protective guarding, noise reduction features, and collaborative robots that assist workers with repetitive or physically demanding tasks.
Packaging machinery completes the line by automatically organizing, wrapping, and boxing finished saucepans for transport, ensuring protection and efficient logistics.
Altogether, saucepan manufacturing equipment integrates forming, finishing, coating, assembly, inspection, and packaging into a highly automated and efficient system. This enables manufacturers to produce durable, high-quality saucepans that meet consumer expectations for performance and design while maintaining sustainability and cost-effectiveness.
Advancements in saucepan manufacturing equipment continue to focus on increasing automation, precision, and environmental responsibility. Robotics and automated guided vehicles (AGVs) are increasingly integrated to handle material transport and delicate operations, minimizing human intervention and reducing the potential for damage or contamination.
Smart sensors and AI-powered analytics monitor machinery performance and product quality in real time, enabling predictive maintenance that reduces downtime and extends equipment life. These systems adjust process parameters dynamically to maintain tight tolerances in dimensions, coating thickness, and assembly quality.
Coating technology improvements include more durable and eco-friendly materials such as ceramic-based and PTFE-free non-stick coatings, requiring specialized application and curing processes. Advanced coating lines with controlled atmosphere chambers and precise spray systems ensure uniform coverage and adherence while reducing emissions.
Energy efficiency is enhanced through the use of servo motors, variable frequency drives, and heat recovery systems in ovens and curing stations, lowering energy consumption and operational costs. Waste management systems capture and recycle metal scraps and coating overspray, contributing to sustainable production.
Modular manufacturing setups with quick-change tooling allow rapid product changeovers, enabling flexible production of different saucepan sizes and designs without significant downtime. This agility helps manufacturers respond quickly to market trends and customer preferences.
Quality assurance employs multi-sensor inspection systems combining optical, laser, and tactile measurements to detect any defects in shape, coating, or assembly. Data from inspections feeds into traceability systems, supporting warranty management and compliance with food safety standards.
Ergonomics and safety improvements include collaborative robots working alongside operators, noise reduction technologies, and user-friendly control interfaces. Augmented reality tools assist in operator training, machine setup, and troubleshooting, accelerating skill development and minimizing errors.
Automated packaging lines improve throughput and ensure consistent protection of saucepans during transport, optimizing supply chain efficiency.
In summary, saucepan manufacturing equipment is evolving into a highly intelligent, flexible, and sustainable production ecosystem. These advances allow manufacturers to deliver cookware that meets the highest standards of quality, durability, and environmental responsibility while maintaining competitive efficiency.
Further developments in saucepan manufacturing focus on integrating Industry 4.0 technologies, where interconnected machines communicate seamlessly for optimized production workflows. Real-time data collection and analysis enable dynamic scheduling, resource allocation, and rapid response to any deviations in quality or equipment performance.
Additive manufacturing (3D printing) begins to play a role in producing complex handle designs and custom components, reducing lead times and allowing for greater design innovation. This complements traditional molding and casting processes, offering flexibility for limited runs or prototype development.
Sustainability remains a priority, with manufacturers adopting closed-loop water and air filtration systems in coating and cleaning stages to minimize environmental impact. Use of recycled metals in raw materials and eco-friendly packaging further supports green manufacturing initiatives.
Collaborative robotics and advanced automation reduce physical strain on workers and improve workplace safety. These systems also increase line uptime by automating routine maintenance checks and part replacements, guided by AI-driven predictive maintenance platforms.
Digital twins of the manufacturing line enable virtual testing of process changes, new product designs, or workflow optimizations without halting actual production. This simulation capability shortens development cycles and reduces costly trial-and-error.
Supply chain integration ensures just-in-time delivery of materials and components, reducing inventory costs and improving responsiveness to market demands. Advanced ERP systems connected to manufacturing equipment provide full visibility into production status and quality metrics.
Customization options for saucepans, such as personalized engraving or color variations, are facilitated by flexible machinery setups and automated finishing processes. This supports niche markets and customer engagement.
Overall, saucepan manufacturing equipment is transforming into smart, adaptable, and eco-conscious systems that balance high productivity with quality craftsmanship and sustainability, positioning manufacturers to meet evolving industry and consumer needs effectively.
Pressure Cooker Manufacturing Machines
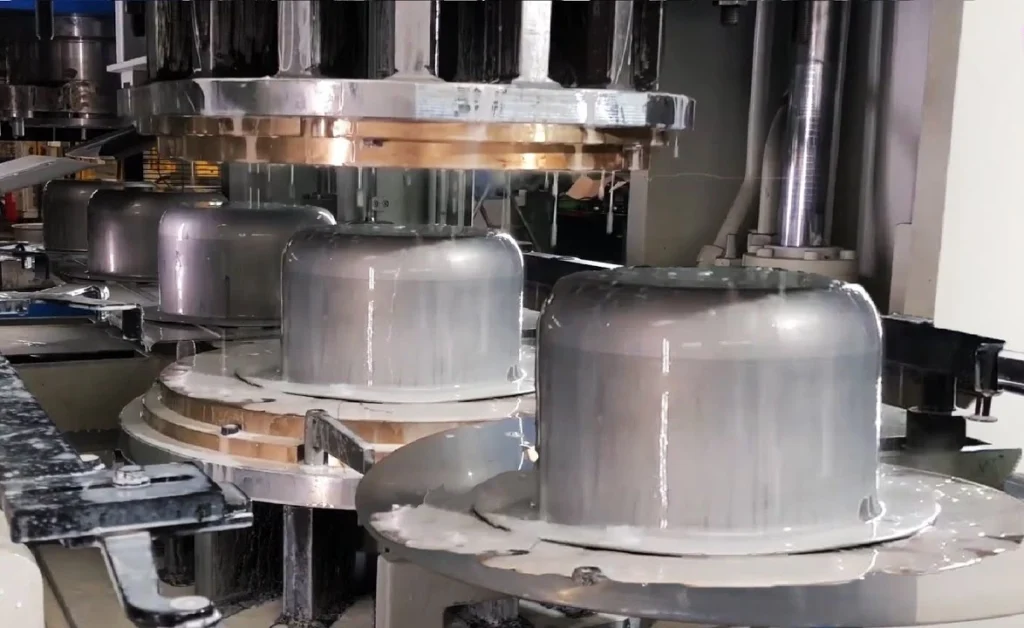
Pressure cooker manufacturing machines are specialized equipment designed to produce pressure cookers with high safety standards, durability, and precise engineering. These machines handle various stages—from shaping thick, high-strength metal bodies to assembling complex sealing and locking mechanisms—ensuring each cooker can withstand high pressure and temperature during use.
The process begins with sheet metal leveling and blanking machines that prepare raw metal coils or sheets, typically stainless steel or aluminum, by straightening and cutting them into blanks of exact sizes for cooker bodies and lids.
Forming machines, such as deep drawing and redrawing presses, shape the metal blanks into thick-walled, cylindrical or rounded pressure cooker pots. Due to the high-pressure requirements, these forming operations often involve multiple stages to achieve the necessary wall thickness and strength without material flaws.
After forming, trimming and edge-flanging machines remove excess metal and roll the rims to create strong, safe edges that support tight sealing and lid attachment.
Pressure cooker lids are formed separately using dedicated presses and stamping machines, which shape and prepare lids with features like safety valves, pressure indicators, locking grooves, and handle mounts.
Specialized machining centers drill and thread holes for pressure release valves, handles, and locking mechanisms. These components require precision to ensure safe and reliable operation.
Surface finishing equipment cleans and polishes cooker bodies and lids to remove oils and contaminants and prepare the surfaces for coatings or polishing, which improves corrosion resistance and aesthetics.
Handles, locking arms, and knobs are manufactured using injection molding (for plastics) or metal casting and machining. Assembly machines then attach these components to bodies and lids using riveting, welding, or screwing equipment, often with automation to ensure consistency.
Safety devices such as pressure release valves, gaskets, and locking systems are installed and tested on dedicated stations to comply with regulatory standards. Automated pressure testing machines simulate working conditions to verify cooker integrity.
Quality control systems, incorporating dimensional checks, surface inspections, and pressure testing, monitor every production stage to detect defects and guarantee product safety and reliability.
Material handling systems, including conveyors and robotic arms, transport parts between machines smoothly and reduce manual handling risks.
Packaging machinery prepares finished pressure cookers for shipment, often including protective inserts to prevent damage during transit.
Modern pressure cooker manufacturing machines prioritize automation, precision, and safety. They integrate advanced control systems, sensor technologies, and energy-efficient drives to maximize throughput while maintaining rigorous quality and safety standards.
Flexibility in tooling and programming allows manufacturers to produce various sizes and designs of pressure cookers, catering to different markets and customer preferences.
Overall, pressure cooker manufacturing equipment combines heavy-duty forming, precise machining, thorough testing, and careful assembly into a comprehensive production line that ensures each cooker performs safely and reliably under high pressure.
Pressure cooker manufacturing machines function as a cohesive production system that transforms raw metal materials into safe, durable, and high-performance cookware capable of withstanding extreme pressure and temperature conditions. The process initiates with metal coil or sheet feeding systems, where leveling and straightening equipment ensures the incoming stainless steel or aluminum stock is flat, uniform, and free of defects essential for subsequent forming steps.
Automated blanking presses precisely cut the metal sheets into blanks sized for pressure cooker bodies and lids. These blanks are fed into multi-stage deep drawing and redrawing presses that form the thick-walled, cylindrical shapes characteristic of pressure cooker pots. The forming sequence is carefully controlled to achieve consistent wall thickness and mechanical strength, crucial for withstanding internal pressure without failure.
Following forming, trimming machines remove excess metal from rims and bases, producing smooth, dimensionally accurate edges. Flanging or curling machines roll these edges to reinforce structural integrity, create safe surfaces for sealing gaskets, and prepare rims for secure lid fitting.
Pressure cooker lids are manufactured separately through specialized stamping and pressing machines that shape the metal into lids equipped with features such as locking grooves, valve mounts, and pressure indicator housings. Precision machining centers drill and thread holes necessary for mounting safety valves, pressure regulators, and handle attachments.
Surface preparation equipment cleans and polishes the interiors and exteriors of cooker bodies and lids, removing oils, contaminants, and surface irregularities. This ensures optimal adhesion for any coatings or finishes applied later and enhances corrosion resistance and appearance.
Handles, locking arms, knobs, and safety components are produced independently via injection molding for plastic parts or casting and machining for metal components. Assembly stations, often automated, attach these parts to the cookware bodies and lids using riveting, welding, or screwing techniques, ensuring strong, reliable connections capable of enduring frequent use and high stress.
Dedicated safety testing stations perform rigorous inspections, including automated pressure testing that simulates actual operating conditions to verify cooker integrity and leak-proof sealing. Pressure release valves and locking mechanisms undergo functional testing to meet regulatory safety standards.
Inline quality control systems incorporate sensors, cameras, and measurement devices to continuously monitor dimensional accuracy, surface quality, assembly precision, and functional performance throughout production. Any detected deviations trigger alerts or automated adjustments, reducing scrap and ensuring consistent product quality.
Material handling is streamlined with conveyors, robotic arms, and automated guided vehicles, facilitating smooth, damage-free transport of parts between processing stations while minimizing manual labor.
Energy-efficient drives, servo motors, and heat recovery systems integrated into presses, ovens, and other equipment reduce operational costs and environmental impact. Waste management systems recycle metal scraps and manage chemical waste from coatings and cleaning processes responsibly.
Modular machine designs and programmable controls offer flexibility for producing different pressure cooker sizes, designs, and safety features, allowing manufacturers to quickly adapt to market demands or customer specifications.
Ergonomic considerations and safety features such as guarded access points, noise reduction, and collaborative robots help protect operators and enhance workplace productivity.
Final packaging lines automate the stacking, wrapping, and boxing of finished pressure cookers, ensuring secure transit and efficient warehousing.
Together, these advanced manufacturing machines and integrated systems create a highly automated, precise, and reliable production line that produces pressure cookers meeting stringent safety regulations and consumer expectations for durability and performance.
Ongoing innovations in pressure cooker manufacturing emphasize integration of Industry 4.0 technologies, where connected machines communicate and coordinate through smart sensors and centralized control systems. Real-time monitoring of equipment conditions, product quality, and process parameters enables predictive maintenance, minimizing unplanned downtime and extending machine lifespan.
Advanced robotics increasingly handle material loading, unloading, and assembly tasks, improving production speed and consistency while reducing manual labor and occupational hazards. Collaborative robots (cobots) work alongside human operators to assist with complex or repetitive steps, enhancing efficiency without compromising safety.
Additive manufacturing technologies are gradually being adopted for producing complex or customized components such as ergonomic handles, locking mechanisms, or valve housings. This reduces tooling costs and accelerates prototyping and product customization cycles.
Sustainability remains a critical focus, with manufacturers implementing closed-loop water and air filtration systems in cleaning and coating areas to minimize environmental emissions. Use of recycled metals and environmentally friendly coatings helps reduce raw material consumption and pollution.
Energy efficiency improvements involve employing servo-driven presses and conveyors, variable frequency drives, and heat recovery systems in curing ovens and machining centers. These innovations lower power consumption and operational costs.
Flexible and modular production lines allow quick changeovers between different cooker models and sizes, enabling manufacturers to respond swiftly to market trends and customer demands without extensive downtime.
Quality assurance benefits from multi-sensor inspection systems that combine optical, laser, and tactile measurements for comprehensive defect detection. Data collected feeds into traceability and analytics platforms, supporting regulatory compliance and continuous process improvement.
Ergonomic design and automation improve workplace safety by reducing operator fatigue and exposure to hazards, while augmented reality (AR) tools facilitate operator training, machine setup, and troubleshooting.
Automated packaging solutions increase throughput and protect products during shipping, incorporating features like customized inserts and smart labeling for inventory management.
Overall, pressure cooker manufacturing machines are evolving into intelligent, adaptable, and eco-conscious systems that maximize productivity, safety, and product quality. These advances enable manufacturers to meet stringent safety standards and growing consumer expectations efficiently while minimizing environmental impact.
Cooking Pots Manufacturing Machinery

Cooking pots manufacturing machinery includes a range of specialized equipment designed to efficiently produce high-quality pots made from metals such as stainless steel, aluminum, or copper. These machines handle all stages from raw material preparation through forming, finishing, assembly, and packaging to create durable cookware suitable for everyday cooking needs.
The process begins with metal coil or sheet feeding and leveling machines that straighten and prepare flat metal blanks. Automated blanking presses cut these sheets into precise sizes for pot bodies and lids.
Deep drawing presses form the pot bodies by shaping the metal blanks into cylindrical or rounded shapes, often through multiple drawing and redrawing stages to ensure uniform wall thickness and structural strength.
Trimming and flanging machines then refine pot rims and edges by cutting away excess material and rolling edges for durability and safety, as well as to facilitate lid fitting.
Separate lid forming machines shape lids with features such as handles, vent holes, or decorative patterns. These lids undergo trimming and finishing similar to pot bodies.
Surface finishing equipment, including polishing and cleaning machines, remove impurities and prepare metal surfaces for coating or final treatments, enhancing corrosion resistance and appearance.
Coating machines apply protective or functional layers like non-stick, enamel, or anti-corrosion coatings using spray, dip, or roll-coating methods, followed by curing ovens to bond the coatings securely.
Handles and knobs are produced separately by injection molding (for plastics) or metal casting and machining. Assembly stations attach these components to pots and lids using automated riveting, welding, or screwing processes.
Inline quality control systems use sensors and cameras to inspect dimensions, surface finish, coating quality, and assembly accuracy throughout production to ensure consistent standards.
Material handling systems, including conveyors and robotic arms, facilitate smooth transfer of parts between stations, improving efficiency and reducing manual labor.
Packaging machines automatically pack finished cooking pots, often incorporating protective inserts and labeling for shipping.
Modern cooking pot manufacturing machinery emphasizes automation, precision, and flexibility. Modular designs and programmable controls allow rapid changes between pot sizes and styles, supporting diverse product lines.
Energy-efficient motors, drives, and recycling systems reduce operational costs and environmental impact, while ergonomic features and safety guards protect operators.
Altogether, these machines form integrated production lines capable of producing durable, attractive, and functional cooking pots that meet market demands for quality and variety.
Cooking pots manufacturing machinery operates as an interconnected production system that transforms raw metal materials into finished cookware through a series of precise, automated steps. The process starts with feeding metal coils or sheets into leveling and straightening equipment to ensure uniform thickness and flatness, critical for consistent forming quality.
Automated blanking presses cut the metal sheets into blanks of exact dimensions suited for pot bodies and lids. These blanks are transferred to deep drawing presses that shape the metal into cylindrical or rounded pot forms. Depending on the required wall thickness and strength, multiple drawing or redrawing stages may be employed to achieve uniformity and durability.
Following forming, trimming machines remove excess metal from rims and bases, producing smooth and accurate edges. Flanging or curling machines roll the rims to strengthen edges, enhance safety by eliminating sharpness, and prepare surfaces for secure lid fitting.
Separate lid forming machines shape lids through stamping and pressing operations, adding features like vent holes or decorative patterns. Lids are trimmed and finished to match the quality of pot bodies.
Surface preparation equipment cleans and polishes pot bodies and lids to remove oils, contaminants, and surface defects. This step is essential for adhesion of coatings and enhances corrosion resistance and visual appeal.
Coating lines apply functional or protective finishes such as non-stick, enamel, or anti-corrosion coatings. Methods include spray, dip, or roll-coating, followed by curing ovens that bake the coatings onto the metal surfaces, ensuring durability and food safety.
Handles, knobs, and accessory parts are manufactured separately using injection molding for plastics or casting and machining for metal components. Assembly stations attach these parts to pots and lids through automated riveting, welding, or screwing, ensuring secure, consistent, and ergonomic fittings.
Inline inspection systems employing sensors and cameras continuously monitor product dimensions, surface finish, coating integrity, and assembly precision. This real-time quality control enables early detection of defects, minimizing waste and maintaining high standards.
Material handling automation, including conveyors and robotic arms, facilitates efficient movement of components between processing stages, reducing manual labor and handling damage risks.
Energy-efficient drives and motors, servo controls, and waste recycling systems contribute to lower operational costs and environmental footprint. Safety features such as guarding, noise reduction, and ergonomic interfaces protect operators and improve workplace conditions.
Modular machine designs and programmable controls enable quick changeovers between different pot sizes, shapes, and finishes, providing flexibility to meet diverse market demands and customization requests.
Final packaging machinery organizes, wraps, and boxes finished pots for secure transport and storage, integrating seamlessly into the production flow.
Together, cooking pots manufacturing machinery forms an advanced, highly automated production ecosystem that balances efficiency, quality, flexibility, and sustainability. This allows manufacturers to deliver durable, attractive, and functional cookware products that satisfy consumer expectations and regulatory standards.
Continuing advancements in cooking pots manufacturing machinery focus heavily on digitalization and smart factory integration, enabling seamless communication between machines, centralized monitoring, and data-driven process optimization. Real-time data collection from sensors embedded throughout the production line allows manufacturers to track equipment performance, product quality, and material usage, facilitating predictive maintenance and reducing downtime.
Robotic automation increasingly handles complex tasks such as precise part placement, welding, and assembly of handles and lids, improving consistency while minimizing human error and labor costs. Collaborative robots assist operators in tasks requiring dexterity or flexibility, enhancing productivity and safety.
Additive manufacturing is being explored for creating prototype parts or complex components like ergonomic handles and decorative elements, allowing rapid design iteration and customized production runs without extensive tooling changes.
Sustainability remains a priority, with machinery designed to reduce energy consumption via servo motors, variable frequency drives, and heat recovery systems in curing ovens and polishing units. Waste management systems recycle metal scraps, coating overspray, and wastewater, contributing to greener manufacturing processes.
Flexible and modular machinery layouts enable quick reconfiguration for different pot sizes, shapes, and surface finishes, supporting shorter product lifecycles and more diverse product lines tailored to consumer preferences.
Advanced inspection technologies using AI-powered image recognition and multi-sensor arrays improve defect detection and quality control accuracy, ensuring every cooking pot meets stringent standards for safety, durability, and appearance.
Augmented reality (AR) and virtual reality (VR) tools assist with operator training, machine setup, and troubleshooting, reducing errors and accelerating skill development.
Smart packaging machines incorporate automation to adapt to different product sizes and shapes, adding protective materials and labeling for efficient logistics.
Overall, cooking pots manufacturing machinery is evolving into an intelligent, flexible, and environmentally conscious production environment. This transformation allows manufacturers to enhance productivity, maintain superior quality, and adapt rapidly to changing market demands while minimizing ecological impact.
Pot Production Process Automation
Pot production process automation involves integrating advanced machinery, control systems, and software to streamline and optimize every stage of manufacturing—from raw material handling to final packaging—reducing human intervention while increasing efficiency, consistency, and quality.
Automation starts with feeding and preparation systems where metal coils or sheets are automatically unrolled, leveled, and cut into precise blanks. These blanks move through robotic or servo-controlled transfer systems to forming presses that shape pot bodies via deep drawing or spinning processes with high repeatability and minimal error.
Subsequent trimming, flanging, and edge-forming stations are equipped with CNC-controlled tools ensuring exact dimensional accuracy. Automated quality inspection units using cameras and sensors monitor shape, thickness, surface defects, and dimensional tolerances at multiple checkpoints, triggering real-time adjustments or alerts.
Surface finishing, such as polishing and cleaning, uses robotic arms and conveyor-mounted polishing machines synchronized to maintain consistent quality and throughput. Coating lines employ automated spraying or dipping systems with controlled parameters for uniform application and curing ovens monitored by precise temperature controls.
Assembly cells utilize robotic arms for attaching handles, lids, knobs, and other accessories, performing welding, riveting, or screwing with programmed precision. These systems often incorporate force sensors and vision guidance for secure, accurate assembly.
Automated pressure and leak testing stations simulate operational conditions to ensure safety and durability of finished pots, rejecting units that don’t meet standards.
Material handling is managed by conveyors, automated guided vehicles (AGVs), and robotic pick-and-place systems that efficiently move parts between processes, reducing manual labor and minimizing damage risks.
Centralized Manufacturing Execution Systems (MES) coordinate all equipment, track production data, schedule maintenance, and provide traceability throughout the pot production cycle. Integration with Enterprise Resource Planning (ERP) systems aligns manufacturing with supply chain and inventory management.
Energy-efficient drives, regenerative braking, and optimized machine cycles reduce power consumption, supporting sustainability goals.
Human-machine interfaces (HMIs) and dashboards offer real-time monitoring and control, enabling operators to oversee multiple production lines, perform troubleshooting, and adjust parameters with minimal downtime.
Automation facilitates quick changeovers through programmable tooling and flexible machine setups, allowing manufacturers to switch between different pot sizes, materials, and finishes rapidly to meet market demands.
Overall, pot production process automation enhances productivity, consistency, safety, and quality while lowering costs and environmental impact, empowering manufacturers to compete effectively in dynamic markets.
Pot production process automation seamlessly integrates advanced machinery, robotics, sensors, and control systems to create a continuous, efficient manufacturing flow with minimal human intervention. Starting from automated feeding systems, metal coils or sheets are precisely unwound, leveled, and cut into blanks using servo-driven equipment that ensures accuracy and repeatability. These blanks are then conveyed automatically to forming stations where deep drawing presses, metal spinning machines, or hydroforming equipment shape the pot bodies with programmed precision, maintaining consistent wall thickness and structural integrity.
Post-forming, automated trimming and flanging machines refine the pot rims and edges, employing CNC controls to achieve exact dimensions essential for proper lid fitting and safe handling. Throughout the process, inline quality inspection units equipped with high-resolution cameras, laser scanners, and thickness gauges continuously monitor product geometry, surface finish, and defect presence, allowing real-time adjustments or rejection of out-of-spec parts.
Surface finishing operations such as polishing and cleaning are conducted using robotic arms and conveyor-mounted polishing machines that adapt their pressure and speed to maintain uniform quality across batches. Automated coating lines apply non-stick, enamel, or protective finishes with precise control over thickness and curing parameters, ensuring durability and compliance with safety standards.
Robotic assembly cells attach handles, lids, knobs, and other accessories using programmed welding, riveting, or screwing tools guided by vision systems and force sensors to guarantee secure, repeatable fittings. Functional testing stations automate pressure, leak, and durability testing to verify product safety and performance, automatically sorting and removing defective units.
Material handling automation employs conveyors, automated guided vehicles (AGVs), and robotic pick-and-place systems to efficiently transport components between process steps, reducing labor costs and minimizing handling damage. Centralized Manufacturing Execution Systems (MES) coordinate machine operations, schedule maintenance, track production data, and facilitate full traceability from raw material to finished product. Integration with Enterprise Resource Planning (ERP) systems aligns production schedules with supply chain and inventory management, optimizing resource use and reducing lead times.
Energy-saving technologies like servo motors, regenerative braking, and optimized machine cycles minimize power consumption, supporting sustainability objectives. Operator interfaces provide intuitive dashboards and controls that enable real-time monitoring, quick troubleshooting, and rapid product changeovers, allowing manufacturers to switch between pot designs, sizes, and finishes with minimal downtime.
Overall, automation in pot production streamlines manufacturing into a highly efficient, flexible, and quality-focused process that enhances throughput, reduces costs, improves workplace safety, and meets evolving market demands while ensuring consistent, high-quality cookware products.
Further advancements in pot production process automation focus on leveraging artificial intelligence and machine learning to optimize operations and quality control. AI-driven analytics analyze data collected from sensors and inspection systems to predict equipment maintenance needs, detect subtle quality deviations, and suggest process adjustments for improved yields.
Vision systems enhanced with deep learning algorithms identify surface defects, dimensional inconsistencies, and assembly errors with greater accuracy than traditional inspection methods, reducing false rejects and rework. These systems can also adapt to new product variants without extensive reprogramming, increasing flexibility.
Collaborative robots (cobots) are increasingly deployed to work alongside human operators for tasks requiring dexterity, adaptability, or visual judgment, such as handling delicate components or performing custom assembly steps. This synergy improves productivity while maintaining safety and operator comfort.
Digital twins—virtual replicas of the production line—allow manufacturers to simulate process changes, forecast outcomes, and optimize machine parameters in a risk-free environment before applying adjustments on the actual line, minimizing downtime and waste.
Cloud connectivity enables remote monitoring and control, facilitating expert support and data-driven decision-making across multiple facilities. This connectivity also supports supply chain integration, allowing dynamic adjustments based on material availability and customer demand.
Sustainable manufacturing is enhanced by automated waste segregation and recycling systems that recover scrap metal and manage chemical byproducts responsibly. Energy consumption is further reduced through smart scheduling algorithms that balance production loads and optimize equipment usage.
Modular and scalable automation solutions allow manufacturers to incrementally upgrade or expand their production capabilities as market needs evolve, protecting investments and ensuring long-term competitiveness.
Training programs using augmented and virtual reality provide immersive learning experiences for operators and maintenance personnel, shortening the learning curve and improving proficiency with complex automated systems.
Together, these cutting-edge automation technologies transform pot production into a smart, resilient, and environmentally responsible process capable of delivering consistent quality at scale, adapting swiftly to market trends, and minimizing operational risks.
Metal Spinning For Round Pots
Metal spinning for round pots is a specialized metal forming process used to create seamless, symmetrical, and durable pot bodies and lids. It involves rotating a metal blank—usually a flat circular disc or pre-formed shallow cup—at high speed on a lathe or spinning machine while a skilled operator or automated tooling applies force with rollers or tools to shape the metal against a mandrel or form.
The spinning process begins with securing the metal blank onto the spinning lathe. As the blank spins rapidly, a forming tool gradually presses and stretches the metal outward and downward over the mandrel, shaping it into a hollow, rounded pot profile. This method enables precise control over wall thickness and contours, producing pots with excellent structural integrity and smooth surfaces.
Metal spinning is well-suited for manufacturing round pots made from ductile metals such as aluminum, stainless steel, copper, or brass. It can accommodate various sizes and shapes, from small saucepans to large stockpots, with relatively low tooling costs compared to stamping or deep drawing.
This technique offers several advantages:
- Seamless construction improves strength and eliminates welds or joints that could weaken the pot or cause leaks.
- Flexibility in design changes, as new mandrels can be made quickly to create different shapes or sizes.
- Efficient material use with minimal waste since the metal is stretched rather than cut away.
- Smooth surface finishes requiring less post-processing.
Automation and CNC-controlled metal spinning machines enable high precision and repeatability, reducing cycle times and labor costs. Multi-axis CNC spinners can produce complex contours and decorative features with consistent quality.
In pot manufacturing, metal spinning is often combined with other processes such as trimming, polishing, and coating to produce finished cookware with aesthetic appeal and functional performance.
Overall, metal spinning is a versatile and cost-effective method for producing high-quality round pots with seamless, durable, and attractive shapes suitable for a wide range of cooking applications.
Metal spinning for round pots operates by firmly holding a flat metal blank or shallow preform on a rotating mandrel, which serves as the shape template. As the mandrel spins at high speeds, skilled operators or CNC-controlled tools gradually press the metal against the mandrel surface, causing the metal to flow and conform to the desired pot shape. The forming tools, often rollers or specialized shaping devices, apply controlled pressure while moving along the blank’s surface, stretching and thinning the material precisely where needed to maintain uniform wall thickness and prevent defects such as wrinkling or tearing.
This incremental forming process allows for complex curves and smooth transitions, creating pots with seamless, continuous surfaces that enhance both structural strength and visual appeal. The ability to adjust tool pressure, feed rate, and rotation speed dynamically enables operators or machines to produce pots with consistent dimensions and quality across large production runs.
Material selection is critical in metal spinning; metals must have sufficient ductility to undergo plastic deformation without cracking. Common choices include aluminum alloys for lightweight cookware, stainless steel for corrosion resistance and durability, and copper or brass for excellent heat conductivity and traditional aesthetics. The spinning process also preserves the metal’s grain structure in a way that can improve mechanical properties, such as tensile strength and hardness, in the finished pot.
After spinning, pots typically proceed to trimming operations where excess material is cut away to finalize rim dimensions and prepare for flanging or curling to strengthen edges. Surface finishing stages include polishing, cleaning, or texturing to achieve the desired appearance and surface quality. Finally, coating or plating processes may be applied to improve corrosion resistance, enhance non-stick performance, or add decorative finishes.
Modern metal spinning machines often incorporate CNC controls and automated tool changers to increase production speed, precision, and repeatability. Multi-axis spinners can create intricate designs, handle varying wall thicknesses, and integrate features like spouts or handles directly during the forming phase. Automated monitoring systems detect force variations and surface anomalies in real-time, allowing for immediate process adjustments and reducing scrap rates.
The metal spinning process for round pots is highly efficient in terms of material utilization, producing minimal waste compared to stamping or casting. Tooling costs are relatively low since mandrels can be machined quickly and affordably, enabling fast product development cycles and flexibility in manufacturing diverse pot shapes and sizes.
Overall, metal spinning remains a vital technique in cookware production, offering a balance of quality, flexibility, and cost-effectiveness that supports both small-scale artisan workshops and large automated manufacturing facilities producing round pots with seamless construction and excellent performance.
Advancements in metal spinning technology have introduced computer numerical control (CNC) systems that automate the spinning process, enabling highly precise and repeatable production of round pots with complex geometries. CNC metal spinning machines control spindle speed, tool pressure, and feed rate with fine accuracy, reducing human error and increasing throughput. This automation allows for consistent wall thickness, tighter dimensional tolerances, and the ability to produce intricate shapes, including tapered sides, flared rims, or integrated spouts.
In addition, modern metal spinning setups often incorporate robotic loading and unloading systems that minimize manual handling, improve workplace safety, and maintain continuous production flow. Sensors integrated into the machinery monitor variables such as torque, vibration, and temperature, providing data for predictive maintenance and process optimization.
Materials science advancements complement metal spinning by developing alloys with enhanced ductility and strength, permitting thinner walls without sacrificing durability or heat distribution. Surface treatments applied post-spinning—such as anodizing aluminum or passivating stainless steel—improve corrosion resistance and aesthetic appeal.
Hybrid manufacturing approaches combine metal spinning with other processes like hydroforming or incremental sheet forming to create pots with complex features that are difficult to achieve through spinning alone. For example, hydroforming can produce more pronounced curves or intricate details, which are then refined by spinning for surface finish and thickness control.
Sustainability is increasingly emphasized, with manufacturers optimizing metal spinning parameters to reduce energy consumption and material waste. Scrap metal generated during trimming and finishing is efficiently recycled back into production. Additionally, improvements in lubricant use and recycling during spinning contribute to environmentally responsible operations.
Training programs using virtual reality and simulation software help operators master the nuances of metal spinning, reducing setup times and improving quality control.
The versatility of metal spinning makes it well-suited not only for traditional cookware but also for specialty pots used in professional kitchens, outdoor cooking, or even decorative purposes. Its ability to produce seamless, high-quality round pots with rapid tooling changes supports small batch runs, custom designs, and mass production alike.
In summary, metal spinning continues to evolve as a cornerstone process in round pot manufacturing, combining tradition with cutting-edge technology to deliver durable, attractive, and functional cookware products efficiently and sustainably.
Pot Forming Press
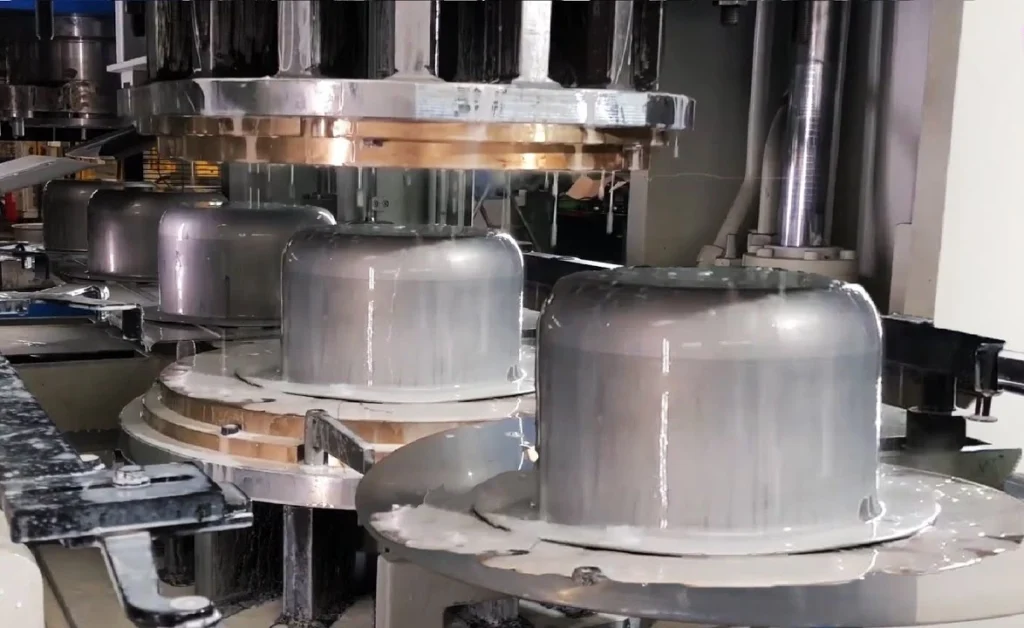
A pot forming press is a specialized machine designed to shape metal blanks into pot bodies through controlled mechanical force. Typically used in cookware manufacturing, the press transforms flat metal sheets or discs into three-dimensional pot shapes by applying high pressure via dies and punches, often in a deep drawing or stamping process.
The forming press consists of a robust frame housing the die set—comprising a punch, die cavity, and blank holder—and a driving mechanism, which may be mechanical, hydraulic, or servo-electric. The metal blank is positioned over the die cavity, and the punch presses down, forcing the metal into the cavity shape. This action stretches and shapes the metal into a hollow pot form with defined walls, rims, and contours.
Modern pot forming presses often use CNC controls to adjust stroke length, pressure, and speed, enabling precise control over metal flow and minimizing defects such as wrinkling, tearing, or uneven thickness. Presses can operate in single or multiple stages, where intermediate steps refine the shape progressively for complex geometries or thicker materials.
Servo-electric presses offer energy-efficient operation and highly repeatable performance, with the ability to program variable speed and force profiles tailored to specific pot designs and materials. Hydraulic presses provide high tonnage and force control, suitable for deep drawing thick metals or larger pots.
Pot forming presses are usually integrated into automated production lines, with robotic or mechanical feeders supplying blanks and transfer systems moving formed pots to trimming, flanging, or finishing stations. Inline sensors monitor force and displacement to detect anomalies early, ensuring consistent quality.
Tooling for pot forming presses is precision-machined, often from hardened steel, and may incorporate interchangeable inserts to allow quick changes between different pot sizes or styles. Proper tooling design is critical to controlling metal flow, wall thickness, and minimizing springback.
In summary, the pot forming press is a central machine in metal pot manufacturing, delivering efficient, high-precision shaping of metal blanks into durable, seamless pot bodies. Its combination of controlled force application, automation compatibility, and tooling flexibility makes it indispensable for modern cookware production.
The pot forming press works by clamping a flat metal blank securely between a blank holder and the die to prevent wrinkling during forming. As the punch descends with controlled force, it pushes the metal into the die cavity, gradually stretching and shaping it into the pot’s desired contour. The process requires precise synchronization of pressure, speed, and stroke depth to ensure uniform wall thickness and avoid common defects such as tearing or uneven material flow. To manage metal thinning and stresses, forming presses may perform the shaping in multiple stages, with intermediate annealing steps if necessary to restore metal ductility.
Modern pot forming presses use sensors to monitor force, position, and speed in real-time, allowing dynamic adjustment of parameters to optimize forming conditions for different metals like aluminum, stainless steel, or copper. This adaptability enhances product consistency and reduces scrap rates. Advanced presses equipped with servo-electric drives offer precise motion control and energy efficiency by consuming power only during active forming strokes, unlike traditional mechanical presses that run continuously.
Tooling for pot forming presses is engineered to tight tolerances and often includes replaceable components for easy maintenance and quick changeovers between different pot designs or sizes. Cooling channels may be integrated into dies to dissipate heat generated during forming, preserving tool life and maintaining dimensional accuracy. Additionally, surface coatings on tooling reduce friction and wear, contributing to smoother metal flow and better surface finishes on formed pots.
Automation integration is common, with robotic arms or conveyor systems loading blanks and unloading finished pots, increasing production speed and reducing manual labor. Inline quality control systems, such as laser scanners or machine vision, inspect pot dimensions and surface quality immediately after forming, enabling prompt rejection of defective parts and minimizing downstream rework.
The pot forming press can be combined with other processes, such as rim flanging, curling, or beading, either in dedicated stations or as multi-step operations within a single press, further streamlining production. Some presses are designed with progressive tooling to perform multiple forming steps in one stroke cycle, improving cycle times and throughput.
In summary, pot forming presses provide the essential shaping force and precision control required to convert flat metal blanks into high-quality pot bodies with consistent dimensions and mechanical properties. Their combination of robust mechanical design, advanced control systems, and integration capabilities makes them the backbone of efficient and scalable cookware manufacturing.
Recent developments in pot forming presses include increased use of servo-electric technology, which provides finer control over the forming process by precisely managing ram speed, position, and force throughout each stroke. This allows manufacturers to tailor the press cycle for different metals, thicknesses, and pot geometries, improving material utilization and reducing defects such as thinning or wrinkling. Servo presses also consume less energy compared to traditional mechanical or hydraulic presses, as they operate only during the forming stroke rather than continuously.
Another innovation is the integration of real-time monitoring and adaptive control systems. Sensors embedded in the press tooling and frame continuously measure parameters like force, vibration, temperature, and displacement. This data feeds into control algorithms that adjust press settings on-the-fly, ensuring optimal forming conditions and compensating for variations in material properties or blank dimensions. These smart presses help maintain consistent product quality and reduce scrap, enhancing overall manufacturing efficiency.
Tooling design has also advanced with modular, quick-change systems that allow rapid switching between different pot sizes or styles, minimizing downtime during product changeovers. Advanced coatings and surface treatments on dies reduce friction and wear, extending tool life and improving surface finishes on formed pots.
Multi-stage forming presses or progressive dies now enable complex pot shapes to be produced in fewer steps, combining deep drawing, trimming, and rim shaping within a single automated cycle. This reduces handling, lowers cycle times, and improves repeatability.
Automation plays a significant role in modern pot forming lines, with robotic loaders, unloaders, and material handling systems integrated tightly with the press. Vision systems and inline gauging verify blank quality before forming and inspect finished pots for dimensional accuracy and surface defects immediately afterward, enabling rapid feedback and quality assurance.
Environmental and sustainability considerations have driven presses to adopt energy-efficient drives, regenerative braking systems, and process optimizations that lower power consumption and reduce material waste. Scrap metal from trimming and forming operations is commonly recycled on-site to improve resource efficiency.
Overall, the pot forming press continues to evolve as a critical machine in cookware manufacturing, combining precision mechanics, intelligent controls, and automation to deliver high-quality, consistent, and cost-effective production of metal pots suited to a wide range of markets and applications.
Metal Pot Manufacturing Machine
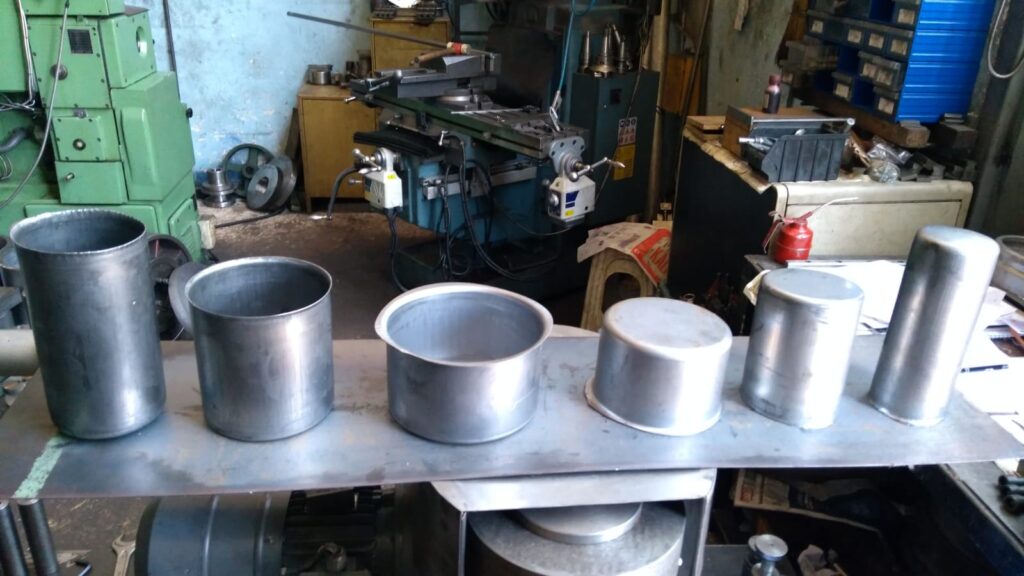
A metal pot manufacturing machine refers to the integrated equipment or a combination of machines used in the industrial production of metal pots. These machines handle various stages of the pot-making process, including blanking, forming, spinning, trimming, polishing, and finishing, often arranged in a production line to ensure efficient, high-volume output with consistent quality.
Typically, a metal pot manufacturing machine setup includes:
- Blanking Machine: Cuts metal sheets or coils into circular blanks of precise size, which serve as the starting material for pot forming.
- Pot Forming Press: Shapes the flat metal blanks into three-dimensional pot bodies using deep drawing or stamping techniques with dies and punches.
- Metal Spinning Machine: For seamless pot shapes, this machine spins and forms the metal blanks over mandrels to produce round, symmetrical pots with controlled wall thickness.
- Trimming and Flanging Machine: Removes excess metal around the pot rim and forms flanges or curls to strengthen edges and prepare the pot for handles or lids.
- Surface Polishing Machine: Buffs and polishes the pot’s surface to improve aesthetics, remove surface imperfections, and prepare for coating or plating.
- Handle and Accessory Fitting Machines: Automate the attachment of handles, lids, or spouts, ensuring consistent placement and secure fastening.
- Coating or Plating Equipment: Applies protective or decorative coatings such as non-stick layers, anodizing, or paint to enhance durability and appearance.
Modern metal pot manufacturing machines are often CNC-controlled and integrated with robotic handling systems, enabling automation from raw material feeding to final product packing. These machines can be customized to accommodate various pot sizes, shapes, and materials like stainless steel, aluminum, copper, or brass.
The entire manufacturing system emphasizes precision, repeatability, and efficiency, minimizing material waste and labor costs while ensuring high product quality suitable for both consumer and commercial cookware markets.
Metal pot manufacturing machines operate in a coordinated workflow where raw metal sheets are first decoiled and fed into a blanking press that punches out circular discs based on the required pot dimensions. These blanks are then automatically transferred to the pot forming press, where deep drawing transforms them into hollow, cylindrical or rounded pot bodies. For designs requiring seamless, high-strength construction, the blanks may instead be processed on a metal spinning machine, where they are formed over a mandrel using rollers under high-speed rotation.
Once formed, the pot body is transferred to a trimming unit that precisely cuts the upper rim to ensure uniform height and removes any uneven or excess material. In the same or subsequent machine, flanging tools curl or fold the rim to add strength and safety. If the pot includes a pouring spout or contour features, additional shaping or pressing machines are used to achieve the specific profile, often with hydraulic or servo-driven presses and matched dies.
Next, the pot surface is subjected to polishing and surface preparation. Automated polishing machines use belts, brushes, or buffing wheels to clean, smooth, and shine the inner and outer surfaces. For higher-end cookware, mirror polishing or satin finishes are achieved using progressively finer abrasives and polishing compounds. At this stage, surface inspection systems can detect dents, scratches, or deformities, automatically rejecting flawed items or flagging them for manual review.
In parallel or subsequent operations, handles and accessories are attached using riveting, welding, or resistance bonding machines. These systems are designed to apply consistent pressure and temperature to ensure strong, long-lasting joints while avoiding damage to the pot body. Robotic arms may perform this step, precisely positioning and fastening components in synchronization with the production flow.
If the pot design requires interior or exterior coatings, such as non-stick layers or decorative finishes, the product passes through spray booths or immersion tanks where coatings are applied evenly. The coated pots then enter curing ovens where heat hardens the coating and bonds it to the metal. Quality control systems check coating thickness, adhesion, and coverage to meet specifications.
Throughout the line, advanced PLCs and HMI panels allow operators to monitor machine status, adjust parameters, and collect production data. Smart sensors detect tool wear, alignment issues, or material inconsistencies, enabling predictive maintenance and minimizing downtime. Automated packing systems at the end of the line collect, stack, and wrap finished pots, ready for storage or shipment.
These machines are highly modular and customizable, allowing manufacturers to produce a wide variety of pot shapes—such as deep stockpots, shallow saucepans, or multipurpose cooking pots—on the same line with minimal tooling changes. They are designed to handle high production volumes while maintaining dimensional precision, strength, and aesthetic quality, ensuring the finished cookware meets global performance and safety standards.
The integration of automation and digital control in metal pot manufacturing machines has significantly increased productivity, product consistency, and operational flexibility. Servo motors and computerized numerical control (CNC) systems enable extremely precise control over all mechanical movements, including drawing depths, trimming accuracy, and polishing pressure. This high level of precision is especially important when working with different metal types, each having unique forming characteristics and stress tolerances. For example, stainless steel may require higher forming pressure than aluminum but allows thinner walls with better strength retention, while copper, being soft and thermally conductive, demands extra care to prevent surface distortion during spinning and finishing.
Production lines can be tailored for either high-volume standard pot designs or flexible, small-batch custom cookware. In flexible setups, quick-change tooling systems allow operators to switch between different dies, mandrels, or polishing heads within minutes, reducing downtime between product runs. Vision-guided robots enhance this flexibility further, enabling real-time adjustments based on product detection and alignment without mechanical reconfiguration.
Material efficiency is a key design factor in these machines. Each process stage—from blanking to finishing—is optimized to reduce scrap, reuse cutoffs, and minimize surface defects that would lead to rework or rejection. Trimming machines use automated measuring systems to determine the minimum amount of material that needs to be removed, while polishing machines equipped with adaptive feedback reduce over-processing and extend polishing media life.
Noise reduction and worker safety are also considered in modern machine designs. Machines are equipped with sound enclosures, dust extraction systems, and safety interlocks to prevent access to moving parts during operation. Operator interfaces are touch-screen based and user-friendly, often supporting multiple languages and visual alerts, which simplifies training and reduces human error.
Maintenance features include automatic lubrication systems, wear sensors, and remote diagnostics modules that alert technicians of potential issues before they lead to failure. This approach not only reduces unscheduled downtime but also extends the lifespan of critical components like press dies, spinning tools, or polishing motors.
The versatility of metal pot manufacturing machines enables the production of various product types beyond standard cookware, including pressure cooker bodies, industrial food preparation vessels, and decorative or specialty kitchenware. With the growing demand for induction-compatible cookware, machines are also adapted to handle layered metal sheets—such as stainless steel-clad aluminum—to ensure even heat distribution while maintaining structural integrity.
In the broader context of smart manufacturing, these machines are increasingly linked to centralized data systems for real-time monitoring, traceability, and production analytics. Managers can track output rates, defect trends, material usage, and energy consumption remotely, making it easier to optimize processes and comply with quality standards like ISO 9001 or food-grade certifications.
Ultimately, the metal pot manufacturing machine is more than a single unit—it is a comprehensive, interconnected system designed to turn raw metal into functional, durable, and appealing cookware products through a series of automated, precision-driven stages, balancing efficiency, customization, and quality in industrial production.
Pot Trimming Machine
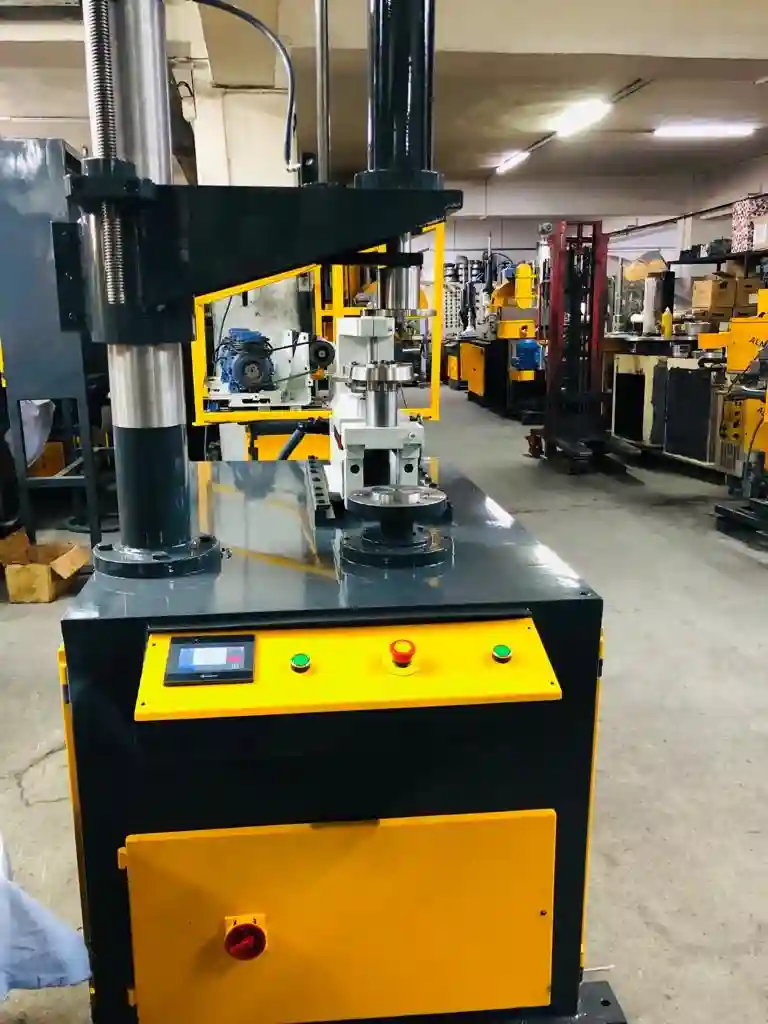
A pot trimming machine is a specialized piece of equipment used in cookware manufacturing to accurately remove excess material from the rim of a formed metal pot. After a pot body is shaped through deep drawing or spinning, its upper edge often has irregularities, uneven height, or excess metal that needs to be removed to ensure a clean, uniform finish. The trimming machine performs this crucial operation, ensuring that every pot meets precise dimensional and quality standards.
The machine typically consists of a rotating chuck or fixture that securely holds the pot body in place while a cutting tool moves along the rim. Depending on the pot’s geometry, the trimming can be done using a lathe-style single-point cutter, a shear blade, or a circular saw blade. The pot rotates at controlled speed, and the cutter follows a programmed path to shave off excess material evenly around the circumference. The trimming can also incorporate contouring, chamfering, or grooving to achieve specific edge profiles.
Most modern pot trimming machines are CNC-controlled, allowing adjustments in trimming height, speed, and tool pressure for different pot sizes and materials. They can handle a wide variety of metals including stainless steel, aluminum, and copper, each of which behaves differently during cutting. The machines are designed to minimize burrs and deformation, producing smooth, straight rims ready for further processing like flanging, curling, or handle attachment.
To boost efficiency, trimming machines are often integrated into automated production lines. Pots are loaded and unloaded by robotic arms or conveyors, synchronized with upstream forming presses and downstream finishing stations. In some setups, the same machine may perform both trimming and beading or flanging operations in a single cycle to save space and reduce handling.
Safety features such as enclosed cutting areas, dust collection systems, and automatic shutdown mechanisms ensure operator protection and maintain a clean work environment. Sensors and quality inspection cameras may be included to monitor cut quality, detect anomalies like incomplete trimming, and reject defective parts automatically.
In summary, the pot trimming machine plays a key role in refining the dimensions and surface quality of cookware products. By delivering accurate, repeatable rim shaping with minimal material waste, it helps ensure that the final pots not only function well but also meet aesthetic and ergonomic standards expected in modern kitchens.
A pot trimming machine is engineered to deliver both precision and efficiency in the post-forming stage of cookware production. Once a pot is drawn or spun into shape, the upper edge often has slight warping, excess metal, or an uneven rim height, which must be corrected before further processing like flanging, curling, or welding handles. The trimming machine addresses this need by mounting the pot onto a rotating chuck or spindle, clamping it firmly in place to ensure concentricity, and then bringing a sharp cutting tool into contact with the rim to remove the excess material in a controlled, even manner.
The machine’s cutting system is typically servo-driven and programmable, allowing the operator to set the exact depth and speed of the cut based on pot diameter, wall thickness, and material type. Stainless steel pots, for example, may require slower cutting speeds and harder tooling, whereas aluminum pots allow faster cycles with lower cutting force. The cutting tool may be a carbide-tipped blade, high-speed steel tool, or even a specialized form tool shaped to simultaneously trim and profile the rim. During trimming, the pot rotates at a consistent speed, and the cutting tool progresses radially inward or outward, guided by a CNC program or mechanical cam system depending on the machine’s design.
Many modern trimming machines are equipped with automated part handling systems that allow pots to be loaded and unloaded without manual intervention. These systems use pneumatic or electric arms that grip the pot and position it precisely, reducing cycle times and operator fatigue. The trimming operation is often combined with in-line inspection, where sensors or vision systems verify the cut quality, rim height, and surface finish. If deviations are detected, the machine can alert operators or automatically divert the part for rework.
The machine’s structure is built for rigidity to prevent vibrations during cutting, which could otherwise cause chatter marks or uneven edges. The chuck mechanism is often adjustable to accommodate a range of pot sizes, and changeover between products is made efficient through quick-clamp tooling and touchscreen interfaces. Some machines even feature dual-station setups, allowing one pot to be trimmed while the next is being loaded or unloaded, effectively doubling output.
Trimming machines are also designed to manage metal chips and dust generated during cutting. Enclosed working areas with chip collection hoods and vacuum extraction systems help maintain cleanliness and prevent debris from contaminating subsequent processes like polishing or coating. Maintenance is straightforward, with easy access to the cutting tools, spindle, and chuck for cleaning or replacement.
Because rim quality directly affects not only the pot’s appearance but also its safety and compatibility with accessories like lids or sealing rings, the precision of trimming is critical. An uneven rim can cause improper lid fit, leakage during cooking, or discomfort during handling. Thus, the pot trimming machine ensures that every product exits the forming stage with a perfectly round, flat, and cleanly finished rim, ready for the next manufacturing steps.
In high-volume cookware production environments, trimming machines are an essential component that bridges the gap between metal forming and final finishing. Their role in ensuring consistency, dimensional accuracy, and aesthetic quality makes them indispensable for both automated and semi-automated pot manufacturing lines.
As cookware design becomes more advanced and consumer expectations for quality increase, pot trimming machines have evolved to meet stricter tolerances and support more complex product geometries. For example, pots with reinforced rims or multi-layered walls require trimming systems that can handle variable hardness across the cross-section without causing delamination or surface tearing. To achieve this, manufacturers integrate adaptive cutting systems with force feedback and real-time monitoring. These systems automatically adjust tool feed rates and angles based on resistance encountered during cutting, which ensures that each trim is smooth and burr-free regardless of material inconsistencies.
Some trimming machines are also equipped with programmable tooling turrets, allowing multiple operations—such as rough trimming, fine finishing, and chamfering—to occur in sequence within a single clamping cycle. This improves precision between cuts and reduces cumulative tolerance errors that could otherwise arise from repositioning the pot. The turret approach also makes it possible to process specialty products, such as pots with decorative flanges, inward-turned rims for pressure cookers, or double-wall insulation lips.
For manufacturers producing a wide variety of pot sizes or designs on the same line, quick-change tooling and automated recipe systems are essential. These features allow an operator to load a new set of parameters through an HMI screen while the machine automatically adjusts chuck diameter, tool position, and cut depth to match the new product. This minimizes downtime and eliminates manual recalibration, making batch changes both fast and accurate.
In facilities with Industry 4.0 integration, pot trimming machines are connected to centralized data networks. They send live performance data—including cycle counts, tool wear trends, error codes, and quality metrics—back to supervisory software. This allows plant managers to monitor line efficiency in real time, plan tool maintenance proactively, and make production adjustments to meet demand without sacrificing consistency. Predictive analytics can also be applied, using historical data from trimming operations to forecast upcoming maintenance needs or detect gradual quality drift before it affects output.
To improve sustainability and reduce operating costs, some trimming machines now incorporate regenerative braking systems and energy-efficient servo motors. These technologies recover energy during deceleration and reduce overall power consumption, particularly important in high-output plants running multiple shifts. Additionally, the machines are often designed with enclosed fluid systems for lubricating the cutting tool and reducing friction heat, helping extend tool life and maintain surface finish without requiring constant coolant replacement.
In cookware plants where cleanliness and hygiene are critical—such as those producing food-safe non-stick or stainless cookware—trimming machines are constructed using corrosion-resistant materials and feature smooth, easy-to-clean enclosures. Chip collection trays, magnetic filters, and oil-mist separators are included to prevent fine metal particles from contaminating downstream processes or compromising worker safety.
Ultimately, the pot trimming machine is not a standalone piece of equipment but a smart, adaptable component within a high-performance manufacturing system. Its ability to deliver precision edge finishing at high speed while supporting flexible production and digital control makes it a key asset in modern cookware production, contributing directly to both the functional integrity and commercial appeal of every finished pot.
Automated Pot Assembly Line
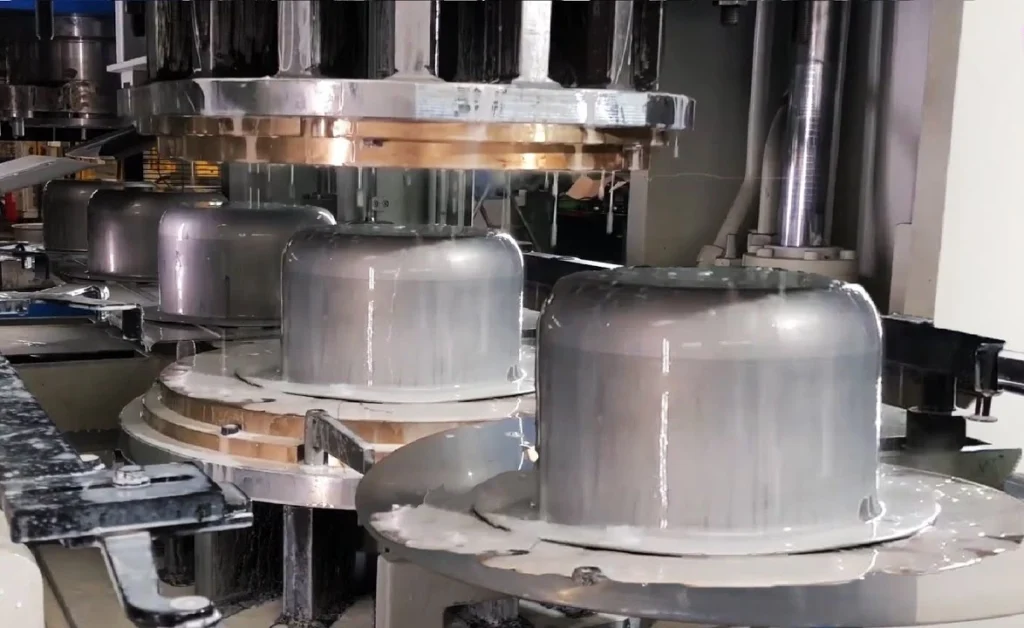
An automated pot assembly line is a fully integrated system designed to streamline and accelerate the process of putting together the various components of a metal cooking pot, transforming formed and finished parts into a complete, ready-for-market product. This assembly line typically follows the forming, trimming, and finishing stages and includes automated operations such as handle attachment, lid fitting, quality inspection, packaging, and labeling.
The core of the automated pot assembly line is a series of interconnected workstations equipped with robotic arms, conveyors, and specialized tooling. Raw components—such as pot bodies, lids, handles, knobs, and accessories—are fed into the system either from upstream production processes or inventory buffers. Advanced feeders and conveyors ensure smooth, continuous flow, minimizing manual handling and the risk of damage or misalignment.
Robotic arms equipped with grippers, welding torches, riveting tools, or adhesive applicators perform precise assembly tasks. For example, handles are positioned and fastened onto the pot body using methods tailored to the product design—mechanical riveting for metal handles, ultrasonic welding for plastic parts, or automated screwing for detachable components. The line can accommodate different handle types and configurations by adjusting robot programming and end-effectors, supporting product variation without significant downtime.
Lid assembly stations automatically fit lids to pots, verifying proper fit and seal quality. Sensors detect misaligned or defective lids and divert those units for rework or rejection. In pressure cooker assembly lines, specialized sealing and locking mechanisms are integrated, with robotic systems ensuring safety-critical components meet strict assembly tolerances.
Inline quality control is a fundamental aspect of the assembly line. Vision systems and laser scanners check for correct handle placement, dimensional accuracy, surface defects, and proper mechanical fastening. Some lines employ force sensors to verify torque on screws or the strength of welded joints. Data from inspections is logged and analyzed to detect trends or recurrent defects, enabling continuous process improvement.
After assembly and quality checks, the pots move to cleaning stations where they may be wiped, air-blown, or washed to remove dust, oils, or residues from manufacturing. Automated packaging systems then take over, arranging pots into cartons, adding protective padding, and sealing boxes with labels and barcodes. Packaging machines can be programmed to handle different product sizes and packing configurations, ensuring safe transport and efficient storage.
The entire automated pot assembly line is governed by a centralized control system, often a programmable logic controller (PLC) network, which coordinates all equipment and synchronizes timing across stations. Operators monitor line status via human-machine interfaces (HMIs) displaying real-time data such as production rates, fault diagnostics, and maintenance alerts. Integration with enterprise resource planning (ERP) software allows for just-in-time inventory management and seamless order fulfillment.
Automation in pot assembly lines offers significant benefits, including reduced labor costs, consistent product quality, minimized human error, and increased throughput. Flexibility built into the system enables rapid changeovers to different pot models or accessory sets, which is crucial for manufacturers serving diverse markets with varying design preferences.
Safety considerations are integral to the assembly line design, with guarded robot cells, emergency stops, light curtains, and interlocks ensuring operators are protected during machine operation. Maintenance access points and modular equipment design facilitate quick servicing and minimize production interruptions.
In summary, an automated pot assembly line combines robotics, precision tooling, quality control, and material handling to transform individual pot components into finished cookware products efficiently and reliably. This approach supports large-scale production while maintaining the high standards expected by consumers and industry regulators.
Automated pot assembly lines are designed to optimize every stage of the assembly process through integration of advanced robotics, intelligent material handling, and real-time quality monitoring. The line begins with loading stations where pot bodies, lids, handles, knobs, and other accessories are automatically sorted and positioned for assembly. These components may come directly from upstream manufacturing or be supplied from storage systems that use automated guided vehicles (AGVs) or conveyor buffers to maintain a steady flow and prevent bottlenecks.
Robotic arms equipped with multi-functional end-effectors perform a variety of joining methods, including mechanical riveting, spot welding, adhesive bonding, and ultrasonic welding, depending on the materials and product specifications. For example, metal handles may be fastened by precision riveting guns that apply consistent force and ensure secure attachment without deforming the pot body. Plastic knobs or silicone seals are often attached using ultrasonic welders that create strong bonds without the need for additional hardware.
The assembly sequence is highly customizable and controlled through programmable logic controllers (PLCs) and industrial PCs, allowing quick adaptation to different pot models or accessory combinations. This flexibility is essential for manufacturers who produce multiple product lines or offer customized options. Tool changers, quick-change fixtures, and adaptive grippers enable the line to handle various shapes and sizes seamlessly.
Throughout the assembly process, inline vision inspection systems continuously scan parts to verify proper positioning, detect surface defects, and ensure fastener integrity. High-resolution cameras combined with AI-powered image recognition can identify scratches, dents, or misaligned components with greater accuracy than manual inspection. Laser measurement systems check dimensional tolerances to ensure that handles are mounted at the correct angles and heights, preventing ergonomic issues or functional defects.
When assembling pressure cookers or pots with complex locking mechanisms, force and torque sensors validate that latches engage properly and seals meet safety standards. Any units failing these criteria are automatically removed from the line for rework or rejection, improving overall product reliability and customer satisfaction.
After assembly, automated cleaning stations remove fingerprints, oils, or debris using ultrasonic baths, high-pressure air jets, or robotic wiping systems. This step is especially critical for pots that will receive coatings, non-stick layers, or surface treatments, as contaminants can negatively impact adhesion and finish quality.
The packaging section of the line is designed for speed and protection. Robotic palletizers and case packers organize products into shipping cartons with foam inserts or protective wraps to prevent damage during transit. Automated labeling machines print and apply product identification codes, QR tags, or compliance markings, which are tracked via barcode scanners to ensure traceability throughout the supply chain.
Data collected from sensors and inspection points feed into a manufacturing execution system (MES), which provides comprehensive analytics on line efficiency, quality rates, and maintenance needs. Predictive maintenance algorithms analyze equipment vibration, temperature, and performance trends to schedule service proactively, reducing downtime and extending machinery life.
Safety is paramount, with robotic work cells enclosed behind safety barriers, light curtains, and emergency stop systems that instantly halt operation if a hazard is detected. Ergonomic design of human-machine interfaces (HMIs) and clear visual indicators reduce operator error and streamline troubleshooting.
The overall result is a highly efficient, flexible, and quality-focused production environment that meets the demands of modern cookware manufacturers. Automated pot assembly lines enable high-volume output while maintaining consistent quality and offering the adaptability needed for evolving market trends and product innovations. This combination of automation, control, and data integration is a cornerstone of Industry 4.0 in cookware manufacturing.
In addition to the core functions, modern automated pot assembly lines often incorporate collaborative robots (cobots) that work safely alongside human operators for tasks requiring dexterity or quality judgment. Cobots can assist with component feeding, quality checks, or manual packaging, blending human flexibility with robotic precision. Their integration enhances overall line efficiency without the need for extensive safety barriers, allowing more compact production layouts.
Advanced assembly lines also leverage machine learning algorithms to optimize processes over time. By analyzing historical production data, these systems can adjust robot paths, tool speeds, and feeding sequences to reduce cycle times and minimize wear on tools. This continuous improvement helps manufacturers achieve higher throughput and lower operating costs.
Traceability and compliance are critical, especially for cookware intended for international markets. Assembly lines integrate serialization and RFID tagging to uniquely identify each pot, linking it to production parameters, inspection results, and batch information. This digital record enables rapid response to quality issues and supports warranty claims or recalls with precise tracking.
Energy efficiency is another growing focus. Automated lines employ variable frequency drives on motors, energy recovery systems, and smart lighting to reduce power consumption. Equipment is designed to enter low-power standby modes during idle periods, contributing to sustainable manufacturing practices.
Integration with upstream and downstream processes enhances supply chain coordination. Real-time communication between forming, trimming, assembly, and packaging stations ensures smooth material flow and enables just-in-time production. This reduces inventory costs and shortens lead times, giving manufacturers a competitive advantage.
Finally, user-friendly interfaces and remote monitoring capabilities allow plant managers and technicians to oversee multiple lines or facilities from centralized control rooms or mobile devices. Alerts for maintenance needs, quality deviations, or equipment faults can be received instantly, enabling rapid interventions that prevent costly downtime.
In sum, automated pot assembly lines represent the convergence of robotics, digital control, and data intelligence tailored specifically for cookware manufacturing. Their ability to deliver consistent quality, flexible production, and operational efficiency makes them indispensable for meeting modern market demands while supporting sustainable and scalable factory operations.
CNC Pot Manufacturing Machine
A CNC pot manufacturing machine is a computer-controlled system designed to automate the precise shaping, forming, and finishing of metal pots through numerical control programming. Unlike traditional manual or semi-automatic forming machines, CNC (Computer Numerical Control) machines utilize advanced software to control motion axes, tool paths, and process parameters with high accuracy and repeatability, enabling complex geometries and tight tolerances in pot manufacturing.
At its core, a CNC pot manufacturing machine combines a rigid machine frame with multiple axes of motion—typically including rotary, linear, and sometimes tilting movements—to manipulate a metal blank or preformed workpiece. The workpiece is mounted on a chuck, rotary table, or fixture, while cutting, spinning, or forming tools are precisely guided along programmed trajectories. This multi-axis control allows for sophisticated shaping operations such as contour spinning, flanging, trimming, and profiling in a single integrated setup.
Programming the CNC machine involves creating detailed toolpaths using CAD/CAM (Computer-Aided Design and Manufacturing) software, where the pot’s 3D model is translated into step-by-step instructions for tool movements, feed rates, spindle speeds, and coolant application. Operators can modify or optimize these programs to accommodate different pot sizes, materials, and design features, making CNC machines highly versatile for batch or custom production runs.
One common application of CNC in pot manufacturing is metal spinning, where a metal disk or tube is rotated at high speed and pressed against a shaped mandrel by CNC-controlled rollers or tools. The CNC system ensures consistent pressure, feed, and tool positioning, producing uniform pot walls and contours with minimal human intervention. This precision reduces material waste and improves surface finish compared to manual spinning.
CNC machines also excel in trimming and profiling operations, where automated tool changes allow for rough and finish cuts to be performed sequentially without repositioning the workpiece. This capability is critical for maintaining concentricity and dimensional accuracy of the pot rim, base, and other features, ensuring proper fit with lids, handles, and accessories.
Advanced CNC pot manufacturing machines integrate real-time monitoring and adaptive control systems that adjust parameters on-the-fly based on sensor feedback such as cutting forces, vibrations, or temperature. This dynamic adjustment enhances tool life, prevents defects, and maintains consistent quality throughout long production runs.
In terms of automation, CNC pot machines are often equipped with robotic loading/unloading systems, pallet changers, and tool magazines, enabling continuous operation with minimal downtime. Integration with plant-wide manufacturing execution systems (MES) allows for centralized job scheduling, quality tracking, and maintenance management.
Safety features include enclosed machining areas with interlocks, emergency stops, and advanced collision detection to protect operators and equipment. User interfaces feature graphical displays, touchscreen controls, and simulation modes that allow operators to verify programs before execution, reducing setup errors.
Overall, CNC pot manufacturing machines provide manufacturers with the capability to produce complex, high-quality metal pots with greater efficiency, flexibility, and precision than traditional methods. Their adaptability to various materials—such as stainless steel, aluminum, and copper—and complex designs makes them essential for modern cookware production facilities aiming for scalability and competitive quality standards.
CNC pot manufacturing machines continue to evolve with improvements in hardware, software, and integration capabilities that enhance productivity and product quality. Modern machines incorporate multi-axis configurations—such as 5-axis or even 6-axis setups—that allow complex three-dimensional shaping without the need for multiple repositioning steps. This reduces cycle times and minimizes errors caused by manual handling.
The precision of CNC control enables the production of pots with intricate features such as embossed patterns, ergonomic handles’ attachment points, and custom flanges for lids or sealing mechanisms. Toolpath optimization software further improves efficiency by calculating the most effective cutting or spinning strategies to reduce tool wear and machining time.
Material handling automation plays a key role in maximizing machine uptime. Automated loading systems use robotic arms or conveyor interfaces to supply raw blanks and remove finished pots seamlessly. This reduces operator fatigue and risk of injury while maintaining consistent feeding rates to match production targets.
Real-time data analytics integrated into CNC machines provide actionable insights to operators and managers. Parameters such as spindle load, vibration levels, and cutting forces are continuously monitored and logged, allowing early detection of tool wear or process deviations. Predictive maintenance algorithms use this data to schedule tool changes or machine servicing before failures occur, thus avoiding costly downtime.
CNC machines also support quick changeover capabilities that are vital for manufacturers producing multiple pot models. Tool libraries and modular fixtures enable rapid reconfiguration for different sizes, shapes, or materials, facilitating flexible batch production without compromising precision.
Integration with other manufacturing systems is a hallmark of CNC pot production lines. Data exchange with upstream processes like blank preparation and downstream finishing or assembly lines ensures synchronization across the entire manufacturing workflow. This holistic approach reduces lead times, inventory costs, and quality issues stemming from misaligned processes.
User experience improvements, such as intuitive graphical user interfaces and simulation environments, empower operators to program and troubleshoot machines with less specialized training. Virtual machining simulations allow validation of toolpaths and collision checks before physical runs, preventing material waste and equipment damage.
Sustainability considerations have driven developments in CNC pot manufacturing as well. Energy-efficient servo motors, regenerative braking systems, and coolant recycling reduce the environmental footprint and operational costs. Some machines incorporate dry machining techniques or minimal lubrication processes to decrease fluid consumption and waste.
In summary, CNC pot manufacturing machines are sophisticated, adaptable platforms that deliver unparalleled precision, efficiency, and flexibility in cookware production. Their advanced control systems, integration capabilities, and data-driven operation support manufacturers in meeting evolving market demands while optimizing costs and maintaining stringent quality standards.
Further advancements in CNC pot manufacturing machines include the incorporation of artificial intelligence (AI) and machine learning (ML) algorithms to enhance process optimization and predictive capabilities. These intelligent systems analyze vast amounts of operational data to automatically adjust machining parameters, such as feed rate, spindle speed, and toolpath trajectories, to maintain optimal cutting conditions and extend tool life without human intervention.
AI-driven quality control systems can detect subtle anomalies in surface finish or dimensional accuracy by processing sensor inputs and high-resolution imagery in real time. When deviations are identified, the CNC machine can pause the operation or trigger corrective measures, such as recalibrating tool alignment or initiating automatic tool changes, ensuring that defective parts are minimized.
The integration of Internet of Things (IoT) technologies enables CNC pot machines to communicate seamlessly with other manufacturing equipment and enterprise systems. This connectivity facilitates real-time monitoring, remote diagnostics, and cloud-based data storage, empowering plant managers to oversee multiple machines or production lines from centralized locations or mobile devices. Such remote capabilities are especially valuable for multi-site operations or during maintenance emergencies.
Additive manufacturing techniques are beginning to complement traditional subtractive CNC processes in pot manufacturing. Hybrid CNC machines equipped with additive heads can build complex features or repair worn tooling directly on the pot surface before final finishing, reducing material waste and expanding design possibilities.
Enhanced automation in CNC pot manufacturing also focuses on environmental and workplace safety improvements. Enclosed machining cells with integrated dust and fume extraction systems improve air quality, while noise reduction technologies create more operator-friendly environments. Furthermore, automated waste handling and recycling systems collect metal scraps and chips for efficient reuse, supporting circular manufacturing practices.
Training and skill development for CNC operators are facilitated by augmented reality (AR) and virtual reality (VR) platforms that simulate machine operation, programming, and troubleshooting. These immersive tools accelerate learning curves and reduce the risk of errors during actual production.
In the future, the convergence of CNC technology with advanced robotics, AI, and smart factory concepts will lead to even more autonomous, self-optimizing pot manufacturing systems. These next-generation machines will adapt dynamically to material variations, design changes, and production schedules with minimal human oversight, driving higher efficiency, lower costs, and superior product quality in cookware manufacturing.
Pot Embossing Machinery
Pot embossing machinery is specialized equipment used to create raised patterns, logos, textures, or decorative designs on the surface of metal pots, enhancing their aesthetic appeal and brand identity. This machinery operates by applying controlled pressure, heat, or mechanical force to imprint detailed designs onto the pot body or lid, often during or after the forming process.
The embossing process typically involves a pair of matched dies—an embossing die with the desired pattern and a corresponding counter-die—that press the pot surface between them. Depending on the material and design complexity, embossing can be performed using mechanical presses, hydraulic presses, or pneumatic systems. High-precision embossing machinery ensures uniform depth and crispness of the design while preserving the structural integrity of the pot.
Modern pot embossing machines often feature CNC controls for precise alignment and pressure adjustment, enabling consistent replication of intricate designs across large production volumes. The dies themselves are manufactured using advanced techniques such as CNC milling, electrical discharge machining (EDM), or laser engraving to achieve fine detail and durability.
Some embossing machines integrate heating elements to soften the metal surface slightly before imprinting, reducing the force required and minimizing the risk of cracking or deformation, especially with harder alloys. Temperature-controlled embossing also improves the sharpness of the embossed patterns and enhances surface finish quality.
Automation plays a key role in modern pot embossing lines. Robotic loading systems position pots accurately into the embossing station, while sensors and vision systems verify correct alignment before pressing. After embossing, automated conveyors transfer pots to subsequent finishing or inspection stations, maintaining smooth workflow and high throughput.
In addition to decorative purposes, embossing can serve functional roles, such as adding textured grips, reinforcing structural stiffness, or marking safety instructions and certification logos. This multifunctionality makes embossing machinery an essential part of comprehensive cookware manufacturing lines.
Some advanced embossing systems support variable designs via quick-change die setups or even use flexible embossing rollers with interchangeable patterns, allowing manufacturers to switch between product lines or customize designs with minimal downtime.
Maintenance of embossing machinery focuses on die care and press calibration. Regular inspection and polishing of dies prevent pattern degradation, while precise control of pressing forces ensures consistent quality and prolongs machine life.
Overall, pot embossing machinery combines mechanical precision, advanced control, and automation to deliver high-quality decorative and functional surface enhancements, enabling cookware manufacturers to differentiate their products in competitive markets through unique and appealing designs.
Pot embossing machinery continues to advance with the integration of digital technologies and enhanced automation to meet growing demands for customization, speed, and precision. One notable development is the use of servo-driven presses that replace traditional hydraulic or mechanical systems, offering greater control over force application, stroke speed, and positioning accuracy. This allows for delicate embossing on thin metal sheets without distortion, as well as the ability to program complex embossing sequences for multi-pattern designs in a single cycle.
The adoption of CNC-controlled embossing machines enables rapid switching between different embossing patterns through automated die changing systems or programmable embossing rollers. This flexibility supports shorter production runs and personalized designs, responding to market trends favoring bespoke cookware and limited editions. Additionally, some systems utilize laser-guided positioning to ensure exact alignment between the pot surface and embossing dies, further enhancing consistency and reducing scrap rates.
Embossing machinery is often integrated into continuous production lines where pots move through forming, embossing, polishing, and inspection stations with minimal human intervention. Advanced sensors monitor parameters such as embossing force, die temperature, and surface deformation in real time, allowing immediate adjustments to maintain quality standards. These feedback loops contribute to reducing defects like incomplete embossing, wrinkles, or cracking.
For materials with special coatings or finishes, embossing machines may incorporate controlled environments, such as inert gas chambers or temperature regulation, to prevent damage during the embossing process. This is critical for pots with non-stick coatings or decorative surfaces that require preservation of functional layers.
Maintenance and tooling innovations also play a significant role in the performance of embossing machinery. The use of wear-resistant coatings on embossing dies, such as titanium nitride (TiN) or diamond-like carbon (DLC), extends tool life and maintains pattern sharpness. Automated lubrication and cooling systems reduce downtime and ensure consistent operation under high production volumes.
Emerging technologies explore the combination of embossing with other surface treatments, such as laser engraving or chemical etching, within the same machinery setup. This multi-process capability enables manufacturers to create complex decorative effects or functional markings without multiple handling steps.
Environmental and ergonomic considerations influence machine design as well. Noise reduction features, vibration dampening, and enclosed safety guards protect operators, while energy-efficient servo motors and intelligent power management reduce operational costs and environmental impact.
In summary, pot embossing machinery represents a sophisticated blend of mechanical engineering, digital control, and materials science that empowers cookware manufacturers to produce visually distinctive and functionally enhanced products efficiently. Its evolving capabilities support the demands of modern production, from mass manufacturing to personalized, high-value cookware lines.
Advancements in pot embossing machinery also include the integration of smart manufacturing technologies that enable predictive maintenance and real-time process optimization. Sensors embedded within the press and dies continuously monitor critical parameters such as pressure consistency, die wear, and temperature fluctuations. This data is analyzed using machine learning algorithms to predict when components need servicing or replacement before failures occur, reducing unplanned downtime and maintaining high production quality.
The connectivity of embossing machines to factory-wide Industrial Internet of Things (IIoT) networks allows for centralized monitoring and control. Operators and managers can track machine performance, production rates, and quality metrics remotely via dashboards and mobile devices. Alerts and diagnostics enable rapid response to issues, improving overall equipment effectiveness (OEE) and minimizing waste.
Customization capabilities have expanded with the adoption of flexible tooling technologies. For example, modular embossing dies with interchangeable inserts can be quickly swapped out to change patterns without requiring a full die replacement. This reduces tooling costs and accelerates changeovers for short production runs or promotional products.
In some cutting-edge systems, digital embossing using laser or electron beam technologies is combined with traditional mechanical embossing. Digital embossing allows for rapid prototyping and the creation of complex, high-resolution textures without physical dies. These hybrid systems can seamlessly switch between digital and mechanical embossing depending on production requirements.
Automation extends beyond the embossing press itself to material handling and post-embossing processes. Robotic arms or conveyor systems ensure precise loading and unloading of pots, maintaining exact positioning needed for accurate embossing. Inline vision inspection systems verify embossing quality immediately after the process, rejecting defective parts and feeding data back to the control system for continuous improvement.
Environmental sustainability is increasingly a priority in embossing machinery design. Efficient energy usage is achieved through the use of servo-electric drives that consume less power compared to traditional hydraulic systems. Additionally, the use of eco-friendly lubricants and cooling fluids minimizes environmental impact and enhances workplace safety.
Training and operator support are enhanced through augmented reality (AR) tools that overlay instructions, troubleshooting guides, and safety information onto the machine interface or through wearable devices. This reduces errors, improves operator confidence, and accelerates onboarding for new personnel.
As consumer preferences continue to evolve, pot embossing machinery will play a pivotal role in delivering differentiated cookware products with unique textures, branding, and ergonomic enhancements. Its continuous technological evolution ensures manufacturers can meet the dual challenges of high-volume production efficiency and flexible customization, positioning them competitively in a dynamic global market.
Pot surface finishing equipment encompasses a range of machines and technologies designed to improve the appearance, texture, durability, and functionality of metal pots by treating their external and internal surfaces. This finishing process is crucial for cookware quality, affecting factors such as corrosion resistance, heat distribution, ease of cleaning, and aesthetic appeal.
The primary types of surface finishing equipment used in pot manufacturing include polishing machines, buffing machines, grinding machines, and surface treatment systems like electro-polishing or chemical etching units. These machines remove surface imperfections, scratches, and oxidation from pots, producing smooth, shiny, or textured finishes as required by the product specifications.
Polishing machines often use abrasive belts, wheels, or pads combined with polishing compounds to achieve the desired surface quality. They can be manual, semi-automatic, or fully automated and vary in size and capacity depending on production volumes. For metal pots, rotary polishing machines are common, where the pot is held securely while a rotating abrasive wheel or brush smooths its surface.
Buffing machines provide a finer finish by using softer wheels and polishing compounds to bring out a high-gloss shine. These machines often follow initial grinding or polishing steps to refine the pot’s appearance and enhance reflectivity.
Grinding machines are used when heavier surface material removal is necessary, such as eliminating weld seams, rough edges, or significant surface defects. They use abrasive discs or belts with higher grit to level and smoothen the pot surface before polishing.
Advanced surface finishing equipment includes electro-polishing systems that use electrochemical processes to dissolve microscopic surface layers, resulting in a highly smooth and corrosion-resistant finish. This method is particularly beneficial for stainless steel cookware, improving both hygiene and appearance without mechanical abrasion.
Chemical etching or passivation units treat the pot surface with acid or other chemicals to remove contaminants and enhance corrosion resistance. These processes can also create matte or textured finishes preferred in certain cookware designs.
Automation plays an important role in surface finishing lines. Robotic polishing and buffing arms can operate with consistent pressure and speed, reducing human fatigue and variability. Conveyor systems move pots through sequential finishing stations, integrating grinding, polishing, and inspection steps to ensure uniform quality.
Surface finishing equipment may also include cleaning and drying stations that prepare pots for coating or packaging by removing polishing residues, oils, or dust. Ultrasonic cleaning machines are sometimes used to ensure thorough contaminant removal.
In addition to improving appearance, surface finishing enhances the pot’s functional performance by smoothing microscopic surface irregularities that could trap food or promote corrosion. Proper finishing also aids in the adhesion of coatings such as non-stick layers or enamel, contributing to product longevity.
Overall, pot surface finishing equipment is essential in transforming raw or formed metal pots into finished cookware that meets aesthetic standards, durability requirements, and consumer expectations. The choice of finishing technologies and equipment depends on the pot material, desired surface characteristics, production volume, and cost considerations.
Continuing with pot surface finishing, modern equipment often integrates real-time monitoring systems that track parameters like abrasive wear, polishing pressure, and surface roughness. These feedback mechanisms help maintain consistent quality across large production runs, minimizing defects and rework. Adaptive control systems can adjust polishing speed and force dynamically to accommodate variations in pot thickness or material hardness, ensuring uniform results without damaging the product.
Robotic automation has become increasingly prevalent in polishing lines. Robots equipped with force sensors can apply precise, repeatable pressure while polishing complex pot shapes, including handles and rims, which are difficult to finish manually. This not only improves quality but also reduces labor costs and ergonomic risks associated with repetitive polishing tasks.
For high-volume manufacturing, multi-station polishing machines allow simultaneous finishing of multiple pots, significantly boosting throughput. These systems may feature rotating fixtures that index pots through sequential grinding, polishing, and buffing stages with minimal operator intervention. Integration with conveyors and automated loading/unloading systems further streamlines the workflow, reducing cycle times and improving overall equipment effectiveness.
Surface finishing processes also address environmental and safety concerns. Dust extraction and filtration units capture metal particulates generated during grinding and polishing, protecting worker health and complying with environmental regulations. Water-based polishing compounds and biodegradable lubricants replace traditional solvents to minimize chemical hazards and waste disposal issues.
Finishing equipment sometimes includes specialty attachments for texturing or patterning pot surfaces, such as brushing tools that create satin finishes or tumbling barrels that impart uniform surface textures. These aesthetic variations cater to consumer preferences and help differentiate product lines in competitive markets.
Advances in material science have led to the development of polishing abrasives and compounds tailored for specific metals, from stainless steel to aluminum and copper alloys. These specialized materials optimize cutting action and surface quality while extending the life of polishing tools.
Digital twin technology is emerging in pot finishing equipment, enabling virtual simulations of polishing processes before physical runs. This helps optimize parameters, predict wear patterns, and prevent costly trial-and-error, especially when launching new product designs or materials.
Overall, the synergy of automation, real-time control, and specialized tooling in pot surface finishing equipment empowers manufacturers to achieve superior surface quality, enhance product appeal, and maintain efficient, safe, and environmentally responsible production operations.
Further innovations in pot surface finishing focus on combining finishing techniques to achieve multifunctional surfaces. For example, hybrid finishing lines may integrate mechanical polishing with laser texturing or micro-engraving, adding both aesthetic patterns and functional features like improved grip or enhanced heat distribution. These combined processes allow manufacturers to create signature designs that stand out in the market while also improving cookware performance.
Another emerging trend is the use of dry polishing technologies that minimize or eliminate the need for liquids and compounds. Dry polishing reduces water consumption, simplifies waste management, and lowers operational costs. These methods often rely on advanced abrasives and high-speed brushes designed to achieve smooth finishes without causing excessive heat or surface damage.
Adaptive finishing machines increasingly use machine vision systems to inspect pot surfaces at multiple stages. High-resolution cameras detect imperfections such as scratches, dents, or uneven finishes, enabling automatic rejection or rework before the product proceeds further down the line. Integrating artificial intelligence algorithms helps these systems learn from defects over time, improving detection accuracy and reducing false positives.
In terms of energy efficiency, servo-driven motors and regenerative braking systems in polishing equipment help reduce electricity consumption, aligning with green manufacturing initiatives. Smart scheduling software optimizes machine usage by balancing workloads and minimizing idle times, further conserving energy.
Maintenance and tooling improvements also contribute to finishing efficiency. Quick-change abrasive modules and self-cleaning polishing pads reduce downtime and keep surface quality consistent. Predictive maintenance tools alert operators to impending wear or mechanical issues, ensuring timely intervention before defects occur.
Worker safety enhancements include improved ergonomic designs for manual finishing stations, noise reduction features in polishing machinery, and better dust extraction systems that comply with the latest occupational health standards.
Finally, sustainability efforts are reflected in the growing use of recycled abrasives, environmentally friendly polishing agents, and closed-loop water recycling systems within finishing lines. These measures reduce environmental footprints while maintaining high-quality output.
Together, these advancements in pot surface finishing technology enable cookware manufacturers to deliver products with superior appearance, functionality, and durability, all while improving operational efficiency and sustainability in their production processes.
Metal Polishing Machine For Pots
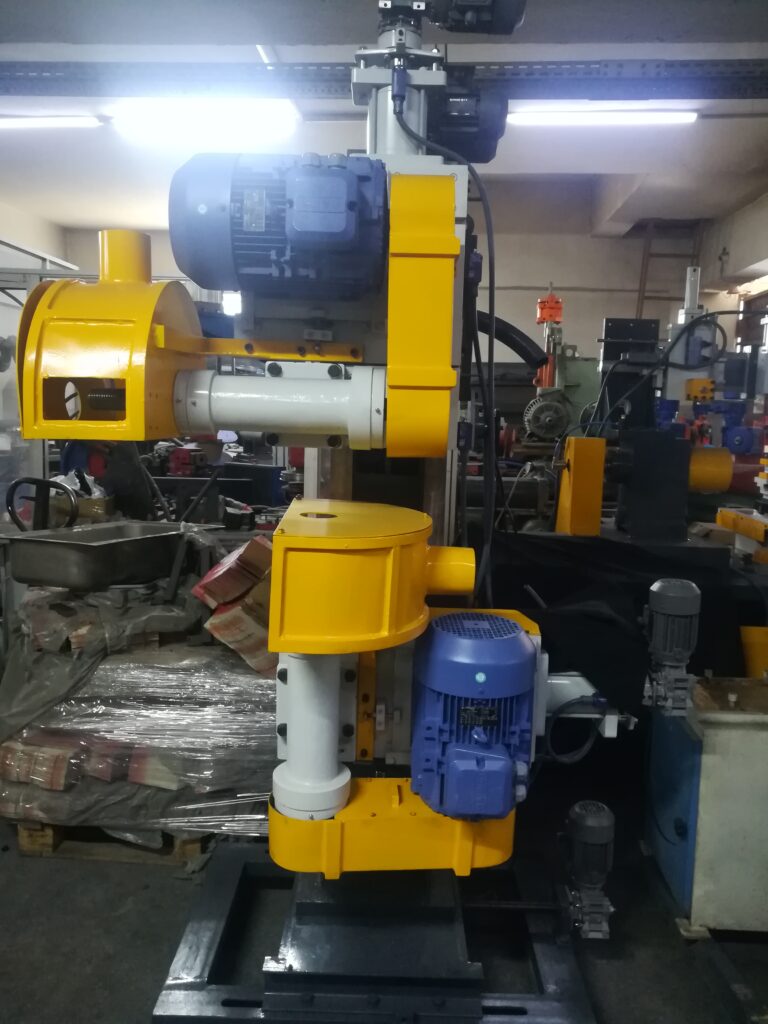
A metal polishing machine for pots is specialized equipment designed to smooth, brighten, and finish the surfaces of metal cookware such as pots, pans, and lids. These machines are essential in the manufacturing process to remove imperfections like scratches, burrs, or oxidation marks from formed metal pieces, resulting in a clean, shiny, and aesthetically pleasing surface that meets quality standards.
Metal polishing machines for pots come in various configurations depending on production scale, pot size, and desired finish. Common types include rotary polishing machines, belt polishing machines, buffing machines, and automated robotic polishing systems.
Rotary polishing machines typically use rotating abrasive wheels or brushes to polish the pot surfaces. The pot is either held stationary while the wheel moves or rotated against the wheel for uniform surface treatment. These machines can achieve different finishes ranging from matte to mirror-like shine by changing abrasive types and polishing compounds.
Belt polishing machines employ abrasive belts moving at high speed. Pots are brought into contact with the belt to remove surface defects efficiently. Belt polishing is suitable for flattening and leveling larger surface areas or removing weld seams and excess material from pot rims.
Buffing machines use softer wheels and finer compounds to produce a high-gloss finish after initial polishing. They are often the final step in the polishing process to enhance the pot’s visual appeal and surface smoothness.
Automated robotic polishing machines are increasingly popular in modern pot manufacturing. Equipped with force sensors and CNC control, these robots can polish complex pot shapes consistently and with minimal human intervention. Robotic arms can adapt pressure and speed in real time, ensuring delicate areas like handles, rims, and spouts receive proper finishing without damage.
Many polishing machines include integrated dust extraction and filtration systems to capture metal particles and maintain a clean working environment, improving operator safety and complying with regulations.
Some advanced machines also feature adjustable fixtures or chucks to securely hold pots of varying sizes and shapes during polishing, enabling quick changeovers and flexible production.
Metal polishing machines for pots are designed for durability and high throughput, often incorporating heavy-duty motors, precision bearings, and vibration-dampening features to maintain stable operation and consistent polishing quality over extended production runs.
In addition to standard polishing, some machines support multi-stage finishing processes, combining grinding, polishing, and buffing within a single integrated line to optimize production efficiency and surface quality.
Overall, metal polishing machines for pots are critical to producing cookware that is both visually attractive and functionally superior, contributing to enhanced corrosion resistance, better heat conduction, and improved consumer satisfaction.
Metal polishing machines for pots often incorporate programmable logic controllers (PLCs) or CNC systems to automate polishing cycles, adjust parameters such as speed, pressure, and polishing time, and enable repeatable high-quality finishes. This automation reduces operator fatigue and errors while increasing throughput and consistency. The machines can be integrated into larger production lines with conveyors, robotic loading/unloading systems, and quality inspection stations to create seamless workflows.
The choice of abrasive materials and polishing compounds is crucial in these machines to match the pot’s metal type—whether stainless steel, aluminum, copper, or alloys—and the desired surface finish. Machines may allow quick swapping of polishing pads, wheels, or belts made from materials like felt, cotton, sisal, or synthetic fibers, paired with different polishing pastes and liquids to optimize results for specific metals or finishes.
Dust and debris generated during polishing are typically managed by built-in extraction systems featuring vacuum hoods, filters, and sometimes water sprays or misting to suppress airborne particles. These systems protect worker health, maintain machine cleanliness, and help comply with environmental and workplace safety regulations.
Some polishing machines offer variable speed drives that enable operators to fine-tune the rotational speed of polishing wheels or belts for delicate finishing or aggressive material removal. Soft start and stop functions prevent sudden jolts that could damage pots or tooling.
Maintenance-friendly designs include easy access to wear parts, modular components for quick replacement, and self-lubricating bearings. Remote monitoring and diagnostics are becoming more common, allowing predictive maintenance that minimizes downtime.
For smaller production runs or artisan manufacturing, compact bench-top polishing machines with versatile fixtures accommodate different pot sizes and shapes. In contrast, large-scale industrial polishing machines prioritize continuous operation, multi-station arrangements, and integration with robotic arms for fully automated handling.
Ergonomic features in manual polishing setups—such as adjustable work tables, vibration dampening, and noise reduction—help reduce operator strain and improve productivity.
Overall, metal polishing machines for pots blend mechanical robustness, process flexibility, automation, and environmental controls to meet diverse manufacturing needs, delivering cookware with durable, attractive, and consistent surface finishes.
Further innovations in metal polishing machines for pots focus on enhancing precision and sustainability. Adaptive polishing technology uses sensors to monitor surface roughness in real time, allowing machines to adjust pressure, speed, or polishing duration automatically to achieve optimal finishes without over-processing. This not only improves quality but also extends tooling life and reduces material waste.
Integration with Industry 4.0 platforms enables data collection and analysis across polishing equipment fleets. Manufacturers gain insights into machine utilization, abrasive wear, and process trends, facilitating continuous improvement and predictive maintenance. This connectivity supports remote troubleshooting and software updates, reducing downtime and operational costs.
Energy-efficient components such as servo motors, regenerative braking systems, and optimized drive trains lower power consumption, aligning with environmental and cost-saving goals. Additionally, many machines now employ water-based or biodegradable polishing compounds instead of traditional solvents, minimizing hazardous waste and improving workplace safety.
Multi-functional polishing lines combine mechanical polishing with complementary surface treatments such as electro-polishing, chemical passivation, or laser texturing to provide enhanced corrosion resistance, improved hygiene, or unique surface aesthetics in one integrated workflow.
Ergonomic designs and user-friendly interfaces reduce operator fatigue and training requirements. Touchscreen controls with guided workflows, customizable programs, and safety interlocks make machines accessible to a broad range of skill levels.
Robotic polishing arms equipped with AI-powered vision systems can handle complex pot geometries, including curved surfaces, handles, and rims, ensuring uniform polishing quality that would be difficult to achieve manually. These robots can work continuously, supporting high-volume production with consistent results.
As consumer demand grows for customized cookware finishes, modular polishing machines with quick-change tooling and programmable patterns enable flexible production runs without extensive downtime or retooling costs.
Together, these advancements empower pot manufacturers to deliver superior products with appealing, durable finishes while optimizing production efficiency, reducing environmental impact, and maintaining competitive advantage in a dynamic market.
Pot Lid Manufacturing Machine
A pot lid manufacturing machine is specialized equipment designed to automate and streamline the production of metal lids used for cookware such as pots, pans, and pressure cookers. These machines perform a series of precise forming, shaping, trimming, and finishing operations to produce lids that fit securely, perform well under heat and pressure, and meet aesthetic quality standards.
The manufacturing process for pot lids typically starts with flat metal sheets or coils, usually stainless steel, aluminum, or other suitable alloys, which are fed into the machine. The machine then uses stamping and pressing techniques to form the basic dome or flat shape of the lid, often incorporating features like rims, handles, vent holes, or steam vents as required by the design.
Pot lid manufacturing machines generally include hydraulic or mechanical presses equipped with custom-designed dies and molds. These dies shape the lid profile in one or multiple stages, including deep drawing for domed lids or progressive stamping for flat lids with integrated features.
Trimming stations remove excess metal and refine the lid’s edge to ensure smoothness and uniformity, critical for a proper seal when fitted onto pots. Some machines include flanging or curling units that bend and finish the lid’s rim to enhance strength and compatibility with pot rims.
Additional stations may perform punching operations to create holes for handles, steam vents, or locking mechanisms. Automated insertion or welding equipment may attach handle components or knobs directly on the line, reducing manual labor and improving assembly speed.
To ensure high precision, these machines often incorporate sensors and quality control systems that monitor dimensional accuracy, detect defects such as cracks or warping, and reject substandard lids automatically.
Advanced pot lid manufacturing lines can be fully automated with robotic arms for material handling, reducing operator involvement and increasing production throughput. Integration with conveyor systems and buffer stations ensures smooth workflow and continuous operation.
Finishing processes such as polishing, brushing, or coating can be integrated inline or performed as separate post-processing steps to improve lid appearance, corrosion resistance, and usability.
Modern pot lid manufacturing machines are designed for flexibility, allowing quick die changes and adjustments to accommodate different lid sizes, shapes, and designs with minimal downtime.
Overall, pot lid manufacturing machines combine high-precision forming, trimming, and assembly capabilities with automation and quality control to produce durable, functional, and attractive cookware lids at scale.
Pot lid manufacturing machines often incorporate programmable logic controllers (PLCs) and CNC technology to enable precise control over each stage of the forming and trimming process. This allows manufacturers to quickly adjust parameters such as press force, stroke length, and timing to accommodate different lid designs and materials without extensive manual recalibration. Automated control systems improve consistency and reduce waste by minimizing off-spec production.
These machines frequently include multiple forming stations arranged in sequence to perform deep drawing, ironing, flanging, and trimming operations in a progressive or transfer press setup. Progressive presses enable continuous production where the metal sheet moves through a series of dies that incrementally shape the lid, improving speed and efficiency for high-volume manufacturing. Transfer presses use robotic or mechanical means to move partially formed lids between stations, allowing more complex forming steps and greater flexibility.
To ensure edge quality, pot lid machines use specialized trimming and flanging dies that produce smooth, uniform rims essential for airtight sealing and safe cooking performance. Some machines offer adjustable curling tools that shape the lid’s edge inward or outward depending on the sealing design, whether for standard pots, pressure cookers, or steamers.
Punching units integrated into the line can create precise holes or slots for steam vents, pressure release valves, or handle attachment points. These holes are often deburred and smoothed automatically to prevent sharp edges that could cause injury or damage seals.
For lid handle assembly, many modern machines include automated welding or riveting stations that attach handles made from metal or heat-resistant plastic. Robotic arms can pick and place handles, align them accurately, and perform spot welding or fastening, eliminating manual steps and ensuring repeatable quality.
Quality control systems with vision cameras and laser measurement sensors monitor critical dimensions such as lid diameter, dome height, and hole placement. Automated rejection mechanisms remove defective lids from the line, maintaining high standards without slowing production.
Material feeding systems, including coil unwinders and straighteners, provide continuous metal input to minimize downtime. These systems synchronize with the press cycles to ensure smooth, consistent feeding without jams or misfeeds.
Some pot lid manufacturing lines also integrate surface treatment processes, such as inline polishing, brushing, or coating applications, to improve corrosion resistance and surface aesthetics immediately after forming.
Ergonomics and safety features are integral to these machines, with guarded enclosures, emergency stop systems, and noise reduction measures protecting operators. User-friendly touchscreens provide real-time monitoring and diagnostics, simplifying operation and maintenance.
Overall, pot lid manufacturing machines combine advanced mechanical design, automation, and quality assurance technologies to deliver high-speed, flexible production of durable and precise cookware lids, meeting the demands of modern manufacturing and consumer expectations.
Emerging trends in pot lid manufacturing machines emphasize increased flexibility and customization capabilities to meet diverse market demands. Machines are now often designed with modular tooling systems that allow quick swapping of dies and fixtures, enabling manufacturers to switch between different lid sizes, shapes, or styles with minimal downtime. This adaptability is crucial for responding to shorter product life cycles and personalized cookware designs.
Incorporation of Industry 4.0 technologies is transforming pot lid production by enabling real-time data collection, process monitoring, and predictive maintenance. Sensors embedded throughout the machine track parameters such as press force, temperature, and cycle times, feeding information into centralized systems for analysis. This connectivity helps optimize machine performance, reduce unplanned downtime, and improve overall equipment effectiveness (OEE).
Robotics and automation continue to play a significant role in enhancing productivity and reducing labor costs. Advanced robotic systems handle material loading and unloading, lid transfer between stations, and complex assembly tasks such as handle attachment. These robots are equipped with vision systems and force sensors that ensure precision and prevent damage to delicate components.
Quality control is becoming more sophisticated, with inline non-contact measurement systems capable of detecting microscopic surface defects, dimensional inaccuracies, or surface finish inconsistencies. Automated feedback loops can adjust machine settings on the fly to correct deviations, maintaining stringent quality standards.
Environmental considerations are also influencing machine design. Manufacturers increasingly adopt energy-efficient drives, servo motors, and regenerative braking systems to reduce power consumption. Use of recyclable and environmentally friendly lubricants and coatings further minimizes the ecological footprint of the manufacturing process.
Ergonomic improvements continue to focus on operator safety and comfort, with intuitive interfaces, adjustable workstations, and advanced safety interlocks. Remote monitoring and control capabilities allow technicians to troubleshoot and optimize machine performance without being physically present, reducing exposure to hazardous environments.
In addition to traditional metals, some pot lid manufacturing machines are being adapted to process emerging materials like coated metals, composites, or hybrid laminates, enabling production of lids with enhanced properties such as improved heat retention, non-stick surfaces, or greater durability.
These advances collectively enable cookware manufacturers to produce pot lids that not only meet high standards of functionality and durability but also offer aesthetic appeal, safety, and environmental responsibility, helping them stay competitive in a dynamic global market.
Pot Bottom Attaching Machine
A pot bottom attaching machine is specialized equipment designed to securely join the base (bottom) of a pot to its cylindrical body during cookware manufacturing. This process is crucial because the strength, durability, and leak-proof quality of the pot largely depend on the precision and reliability of the bottom attachment.
These machines typically use one or a combination of joining methods such as welding (laser, TIG, or spot welding), mechanical fastening, or clinching, depending on the pot material, design, and production volume.
In welding-based pot bottom attaching machines, the pot body and the bottom plate are precisely aligned and held firmly using custom fixtures or clamps. A welding head then applies heat or electrical current to fuse the two parts together, creating a strong, continuous bond. Laser welding is especially favored for its speed, precision, minimal heat distortion, and clean finish, making it suitable for thin metals commonly used in cookware.
Mechanical attaching machines use methods like seaming or clinching, where the pot bottom is mechanically deformed or pressed onto the body edge using rollers or dies. This creates a tight, often leak-resistant joint without adding heat, which can be advantageous for certain metals or coatings sensitive to heat.
Pot bottom attaching machines are often integrated into automated production lines, with robotic arms or conveyors loading, positioning, and removing pots to and from the attachment station. This automation increases throughput and reduces manual labor.
The machines incorporate sensors and control systems to ensure correct alignment and pressure during joining, preventing defects such as gaps, weak welds, or misaligned components. Quality control systems may include visual inspections, ultrasonic testing, or leak detection to verify joint integrity immediately after attachment.
Many machines allow quick changeover of fixtures and tooling to accommodate different pot sizes, shapes, and materials, providing production flexibility.
Overall, pot bottom attaching machines ensure strong, precise, and consistent joining of pot bodies and bottoms, which is critical for manufacturing durable, high-quality cookware that meets safety and performance standards.
Pot bottom attaching machines often feature automated loading and unloading systems, such as conveyor belts or robotic arms, to streamline production and reduce manual handling. These automation elements help maintain high throughput and consistent quality by minimizing human error and physical strain on operators.
Alignment mechanisms are critical in these machines, ensuring the pot body and bottom are perfectly positioned before attachment. Precision sensors, such as laser or optical detectors, verify alignment in real time, allowing for adjustments or halting the process if discrepancies are detected. This prevents defects like leaks or weak joints that could compromise the cookware’s performance.
Welding machines for pot bottoms may employ various techniques depending on the material and design. Laser welding offers high speed and accuracy, producing narrow, clean welds with minimal heat-affected zones. TIG welding provides excellent control for thicker materials or complex geometries, while spot welding is suitable for high-volume production of simpler designs.
Mechanical joining methods like seaming or clinching avoid heat application and are often used for aluminum or coated cookware where heat could damage finishes or cause warping. These methods rely on precision rollers or presses that fold, crimp, or press the pot bottom securely onto the body rim.
Many pot bottom attaching machines include integrated inspection stations that use ultrasonic testing, pressure testing, or leak detection to verify joint integrity immediately after attachment. Automated rejection systems remove defective pots from the production line, ensuring only high-quality products proceed to subsequent stages.
The machines are typically controlled by PLC systems, allowing for programmable adjustments tailored to different pot sizes, materials, or joining methods. Quick-change tooling and modular fixtures facilitate fast setup for different production runs, improving flexibility and reducing downtime.
Energy efficiency and safety features are increasingly emphasized, with servo-driven components reducing power consumption and noise, and safety enclosures and interlocks protecting operators during the joining process.
In some advanced setups, pot bottom attaching is combined with downstream operations such as cleaning, surface finishing, or coating application, creating a seamless production flow that enhances efficiency and product quality.
Overall, pot bottom attaching machines are essential for producing cookware with robust, leak-proof bases that meet durability and safety standards while supporting efficient, scalable manufacturing.
Advanced pot bottom attaching machines increasingly incorporate real-time monitoring and adaptive control systems to optimize joining quality and reduce waste. Sensors track parameters like weld temperature, current, pressure, and alignment, feeding data to control units that can adjust the process dynamically. This ensures consistent weld strength and minimizes defects caused by material variation or machine wear.
Integration with factory automation platforms enables synchronized operation with upstream and downstream equipment, such as metal forming presses, trimming machines, and polishing stations. This holistic approach reduces bottlenecks and maximizes overall production efficiency.
Robotic arms equipped with vision systems are often used for precise handling and positioning of pot bodies and bottoms, especially for complex shapes or larger cookware. These robots can also perform multiple tasks, including flipping, rotating, and transferring parts between stations, reducing cycle times and labor costs.
For cookware made from coated or sensitive materials, machines may employ low-heat joining techniques or specialized mechanical fastening to preserve surface finishes and prevent warping. Some systems even incorporate cooling or post-weld heat treatment processes to maintain material integrity.
Safety remains a top priority, with modern machines featuring comprehensive guarding, emergency stops, and ergonomic designs to minimize operator fatigue and risk. Remote monitoring capabilities allow technicians to troubleshoot issues and perform maintenance without interrupting production.
Finally, many pot bottom attaching machines support quick tooling changes and flexible programming to accommodate varied product lines and custom orders, making them indispensable in agile manufacturing environments where responsiveness to market demands is key.
Together, these innovations in pot bottom attaching technology enable manufacturers to produce high-quality cookware efficiently, reliably, and with greater adaptability, meeting the evolving needs of both producers and consumers.
Pot Edge Rolling Machine
A pot edge rolling machine is specialized equipment used in cookware manufacturing to form, shape, and finish the rim or edge of pots, pans, and similar metal cookware components. The edge rolling process is essential to strengthen the pot’s rim, improve safety by eliminating sharp edges, and enhance the fit between pot and lid, ensuring a secure seal.
The machine operates by feeding the pot body or lid into a series of rolling rollers or forming tools that gradually bend and roll the metal edge inward or outward according to the desired design. This process can create smooth, rounded, or flanged edges that contribute to both the functionality and aesthetic appeal of the cookware.
Pot edge rolling machines often use adjustable tooling to accommodate different pot sizes, shapes, and rim profiles. The rollers are precisely synchronized to apply uniform pressure and maintain consistent edge thickness and shape around the entire circumference of the pot.
Many machines incorporate servo motors and CNC controls to allow programmable rolling speeds, pressure, and roller positions, enabling quick changeovers and high precision. This flexibility is especially valuable for manufacturers producing a range of cookware types or custom designs.
Edge rolling may be combined with other rim-forming operations such as beading, flanging, or curling, either inline or as separate processes, to enhance rim strength, provide grip areas, or improve sealing surfaces.
Safety features like guards and emergency stops protect operators from pinch points during the rolling process. Automated feeding and unloading systems reduce manual handling and improve production speed.
High-quality edge rolling is critical to prevent rim deformation, cracking, or stress concentrations that could lead to failure during cooking. Therefore, many machines integrate sensors and feedback systems to monitor pressure, roller alignment, and edge quality, ensuring consistent results.
In summary, pot edge rolling machines play a vital role in the final shaping and finishing of cookware rims, contributing to product durability, usability, and visual appeal while supporting efficient, repeatable manufacturing processes.
Pot edge rolling machines are typically designed to handle a wide range of materials, including stainless steel, aluminum, copper, and their alloys, which are commonly used in cookware manufacturing. The machine’s rollers and forming tools are often made from hardened steel or other wear-resistant materials to withstand the stresses of shaping metal edges over long production runs without degradation.
These machines can operate in continuous or intermittent modes depending on production requirements. Continuous rolling allows for faster processing of large batches, while intermittent rolling may be used for more precise control on complex rim profiles or smaller production runs.
The feeding system ensures the pot or lid is positioned correctly and fed smoothly into the rolling area. This may involve servo-driven conveyors, grippers, or rotary tables, which work together to maintain consistent speed and orientation. After rolling, parts are typically transferred via automated conveyors or robotic arms to subsequent stations like trimming, inspection, or packaging.
Edge rolling machines often come with adjustable parameters to control roller pressure, rolling speed, and the angle of the rolled edge. Operators can fine-tune these settings via a user-friendly interface, often a touchscreen panel with programmable recipes, allowing for quick changeover between different product types or sizes.
For quality assurance, some machines incorporate inline vision systems or laser measurement tools to check the rolled edge’s dimensions and surface finish. This helps detect defects such as uneven rolling, cracks, or burrs immediately, enabling timely corrections and reducing scrap rates.
Advanced machines may integrate with broader manufacturing execution systems (MES) for real-time monitoring, data logging, and predictive maintenance. This connectivity supports continuous improvement by identifying process trends and preventing unexpected downtime.
In terms of safety, modern pot edge rolling machines include protective guards around moving parts, emergency stop buttons accessible at multiple points, and safety interlocks that halt operation if a guard is opened. Ergonomic design features help reduce operator fatigue during setup and maintenance.
Overall, pot edge rolling machines are essential in delivering cookware products with strong, smooth, and consistent rims that enhance durability, safety, and aesthetics, while enabling manufacturers to meet high-volume production demands efficiently and with minimal waste.
To further enhance productivity, some pot edge rolling machines are equipped with multi-roller setups that can perform complex rolling profiles in a single pass. This reduces cycle times and ensures consistent edge geometry, which is especially important for cookware requiring specialized rim designs, such as those with integrated grip features or decorative flanges.
These machines may also offer capabilities to roll edges on different shapes, including round, oval, or even square pots, by adjusting the positioning and movement of rollers or using flexible tooling. This versatility allows manufacturers to expand their product lines without needing separate equipment for each shape.
In high-end manufacturing environments, pot edge rolling is sometimes combined with inline surface finishing processes like brushing or polishing. This integration streamlines production by smoothing and shining the rolled edges immediately after forming, enhancing the final product’s quality without extra handling.
Maintenance accessibility is another important design consideration. Easily removable rollers and modular components reduce downtime during routine servicing or tooling changes. Some machines also feature automatic lubrication systems that keep moving parts well-maintained, prolonging machine life and ensuring consistent operation.
Environmental factors such as noise reduction and energy efficiency are increasingly addressed in modern machine design. Noise-dampening enclosures and low-energy servo motors create a safer and more comfortable workplace while lowering operating costs.
The precision and repeatability provided by pot edge rolling machines are vital for meeting international cookware standards and customer expectations. Properly rolled edges improve cookware safety by eliminating sharpness, enhance sealing with lids, and contribute to the pot’s structural integrity, preventing warping or deformation during cooking.
In summary, pot edge rolling machines are indispensable in modern cookware manufacturing, offering a blend of precision, flexibility, and automation that supports efficient mass production while maintaining high product quality and safety standards.
Seam Welding Machine For Pots
A seam welding machine for pots is a specialized piece of equipment designed to join the cylindrical body of a pot to its bottom or to weld seams along the pot’s structure with a continuous, airtight weld. This welding process ensures the cookware is durable, leak-proof, and capable of withstanding the stresses of cooking and cleaning.
Seam welding machines use two rotating wheel electrodes—one on each side of the joint—that apply pressure and an electric current to create a continuous weld along the seam. The wheels roll over the joint as the pot moves through the machine, producing a strong, uniform bond without the need for filler materials or additional finishing.
These machines are widely used for stainless steel, aluminum, and other metal pots where a smooth, clean seam is required for both functional and aesthetic reasons. Seam welding is preferred over spot welding for cookware because it offers better sealing and structural strength.
Modern seam welding machines come with adjustable parameters such as wheel pressure, current, welding speed, and cooling to accommodate different pot sizes, materials, and thicknesses. CNC controls or PLC systems often manage these settings for repeatability and precision.
Automation integration allows for synchronized feeding, positioning, and welding of pots, often using conveyors or robotic arms to increase throughput and reduce manual handling. Sensors monitor parameters like wheel alignment, seam temperature, and electrical resistance to ensure weld quality and detect faults early.
Quality control can include inline inspection systems, such as ultrasonic or visual checks, to verify seam integrity. Defective products are automatically rejected to maintain high production standards.
Safety features such as guarding around moving parts, emergency stops, and interlocks are standard to protect operators during operation.
Seam welding machines are essential in producing leak-proof, strong, and visually appealing cookware that meets both performance and safety standards, while supporting efficient, high-volume manufacturing.
Seam welding machines for pots often include adjustable wheel electrode designs that can be tailored to different pot diameters and seam lengths, allowing manufacturers to handle a variety of pot sizes with minimal changeover time. The electrodes are typically made from copper alloys or other conductive, wear-resistant materials to ensure longevity and consistent weld quality.
The welding process involves precise control over the electrical current and wheel pressure to create a continuous molten weld pool that solidifies quickly, minimizing heat distortion and preserving the pot’s shape. Cooling systems, such as water-cooled electrodes, help manage heat buildup and extend electrode life, enabling longer production runs without interruptions.
Automated seam welding lines may incorporate pre-welding positioning stations where pots are accurately aligned and clamped to prevent movement during welding, ensuring seam consistency and reducing defects. Post-welding stations can include seam grinding or polishing to smooth weld beads, improving the cookware’s appearance and making it safer to handle.
Integration with plant-wide automation systems allows real-time data collection on welding parameters and machine performance, enabling predictive maintenance and process optimization. This connectivity supports quality traceability and helps manufacturers meet stringent industry standards.
Many machines are designed for easy maintenance, with quick-release electrodes and accessible components that reduce downtime. Operator interfaces are user-friendly, often featuring touchscreens and programmable welding recipes for different products, streamlining changeovers and reducing training requirements.
Seam welding technology also adapts to different metal types, including thin-gauge stainless steel or aluminum, which are common in cookware production. The machines are calibrated to handle variations in material thickness and surface conditions, maintaining weld integrity without compromising the pot’s structural or aesthetic qualities.
Overall, seam welding machines are critical in delivering cookware with durable, leak-proof joints, supporting efficient, high-quality manufacturing processes that satisfy both regulatory requirements and consumer expectations.
Advanced seam welding machines for pots increasingly incorporate real-time monitoring systems that track critical welding parameters such as current, voltage, wheel speed, and temperature. These data points help maintain consistent weld quality by allowing the machine’s control system to adjust parameters dynamically during production. If any irregularities are detected, the system can trigger alarms or halt the process to prevent defective products.
Many modern machines use servo-driven wheel actuators to achieve precise control over electrode pressure and positioning, which reduces wear on both the electrodes and the workpieces, while ensuring uniform welds along the entire seam length. This level of control is especially important for thin-walled cookware that can deform easily under excessive heat or pressure.
In fully automated production lines, seam welding machines are integrated with robotic handling systems that load and unload pots, position them precisely, and transfer them between different manufacturing stages. This automation minimizes manual intervention, enhances safety, and increases throughput.
Some seam welding systems also offer multifunctional capabilities, combining seam welding with spot welding or projection welding in the same unit. This versatility allows manufacturers to perform multiple joining operations without moving parts between separate machines, saving space and reducing cycle times.
Safety remains a top priority, so machines are equipped with comprehensive protective enclosures, interlocks that prevent operation if safety covers are open, and emergency stop mechanisms accessible from multiple points around the machine.
Energy efficiency improvements, such as optimized power supplies and regenerative braking in servo motors, contribute to reducing operating costs and environmental impact. Additionally, modular designs facilitate easy upgrades or reconfiguration to accommodate new pot designs or materials.
The result is a seam welding solution that balances speed, precision, reliability, and flexibility—key factors for cookware manufacturers aiming to produce high-quality pots that meet durability, safety, and aesthetic standards while maintaining cost-effective mass production.
Metal Pot Welding Equipment
Metal pot welding equipment encompasses various machines and tools designed to join metal components of cookware—such as pot bodies, bottoms, handles, and lids—with precision, strength, and durability. The choice of welding method and equipment depends on factors like material type (stainless steel, aluminum, copper), pot design, production volume, and quality requirements.
Common welding techniques used in pot manufacturing include seam welding, spot welding, TIG (Tungsten Inert Gas) welding, MIG (Metal Inert Gas) welding, and projection welding. Each method offers distinct advantages:
- Seam welding creates continuous, leak-proof joints ideal for attaching pot bottoms or welding cylindrical seams.
- Spot welding efficiently joins overlapping metal parts, often used for handle attachments or lid components.
- TIG welding provides precise, clean welds suited for thicker materials or decorative finishes.
- MIG welding allows faster welding speeds, beneficial for larger or thicker cookware parts.
- Projection welding focuses current on specific projections, enabling strong localized joints with minimal distortion.
Metal pot welding equipment typically features automated or semi-automated operation to improve repeatability and throughput. Machines include adjustable fixtures and clamps to securely hold parts in precise alignment during welding, preventing distortion and ensuring consistent quality.
Advanced systems integrate programmable logic controllers (PLCs) and CNC controls for precise regulation of welding parameters—current, voltage, speed, and timing—tailored to different materials and pot designs. This flexibility enables rapid changeovers between product models.
Many welding machines incorporate cooling systems to manage heat build-up, preserving metal properties and preventing warping. Electrode materials and shapes are selected to optimize contact, wear resistance, and electrical conductivity.
Safety features such as protective guarding, ventilation systems to remove welding fumes, emergency stops, and operator training protocols are essential to maintain safe working conditions.
Integration with production line automation—robotic handling, conveyors, and quality inspection stations—enhances efficiency, reduces manual labor, and maintains consistent weld integrity. Inline inspection may include visual, ultrasonic, or leak testing to detect defects early.
Overall, metal pot welding equipment forms the backbone of cookware assembly, providing strong, reliable joints that ensure product durability, safety, and aesthetic appeal while supporting scalable, cost-effective manufacturing.
Metal pot welding equipment is often customized to suit specific manufacturing requirements, such as the type of pot being produced, the material thickness, and the desired production speed. For example, in high-volume operations, fully automated welding cells are common, where robotic arms load, position, and weld pot components with minimal human intervention. This automation increases consistency and throughput while reducing operator fatigue and errors.
Fixtures and tooling are critical components in welding equipment to ensure parts are held securely and accurately during the welding process. These fixtures are often modular and adjustable to accommodate different pot sizes and designs, allowing manufacturers to switch between product lines quickly without extensive downtime.
Welding parameters are precisely controlled and monitored throughout the process. Parameters such as welding current, voltage, electrode pressure, and welding speed are programmed based on the pot’s material and design to achieve optimal weld strength and appearance. Sensors and feedback systems can detect anomalies like excessive heat or poor contact, prompting automatic adjustments or halting production to prevent defects.
Cooling systems are integrated to dissipate heat generated during welding, protecting both the equipment and the pot materials from damage. Water-cooled electrodes and air-cooling mechanisms help maintain stable operating temperatures, which is particularly important when welding thin metals prone to warping.
In addition to welding the pot body and bottom, metal pot welding equipment can also handle attachments such as handles, spouts, and lids. Spot welding and projection welding are frequently used for these smaller components because they offer strong localized joints without excessive heat input.
Safety is paramount in welding operations. Modern equipment includes protective enclosures, ventilation systems to remove harmful fumes, emergency stop controls, and operator interfaces designed for ease of use and error prevention. Proper training and maintenance protocols further ensure safe and efficient operation.
Quality assurance is integrated into many welding lines through inline inspection techniques such as visual cameras, ultrasonic testing, or leak detection. This helps identify faulty welds early, minimizing waste and rework.
Overall, metal pot welding equipment combines precise mechanical design, advanced control systems, and automation technologies to produce cookware that meets rigorous standards for durability, safety, and appearance, while optimizing production efficiency and reducing costs.
Advancements in metal pot welding equipment also focus on improving energy efficiency and reducing environmental impact. Modern machines utilize power supplies with optimized energy consumption, regenerative braking in servo motors, and efficient cooling systems to lower electricity usage. This not only cuts operational costs but aligns with increasingly strict environmental regulations and sustainability goals.
Modular design is another trend, allowing manufacturers to expand or reconfigure welding lines easily as product demands change. For example, additional welding stations can be added to increase capacity, or the system can be adapted to handle new pot styles or materials without major capital investment.
Data connectivity plays a growing role in welding equipment, with Industry 4.0 integration enabling real-time monitoring and data analytics. Welding parameters, production rates, downtime, and quality metrics can be tracked continuously and accessed remotely. This facilitates predictive maintenance, reduces unplanned outages, and supports continuous process improvement.
User interfaces are becoming more intuitive, featuring touchscreen controls, recipe management, and troubleshooting assistance to reduce setup times and operator errors. Some systems even incorporate augmented reality (AR) support for training and maintenance, helping technicians quickly identify and resolve issues.
In specialty cookware manufacturing, welding equipment can be adapted for exotic materials like titanium or multi-layer clad metals, which require precise heat control and welding techniques to maintain material properties.
Ultimately, metal pot welding equipment represents a critical investment for cookware manufacturers, balancing speed, precision, flexibility, and safety to produce high-quality pots that satisfy both industrial standards and consumer expectations. The ongoing evolution of welding technologies ensures that manufacturers remain competitive while advancing product innovation and sustainability.
Hydraulic Press For Pot Manufacturing
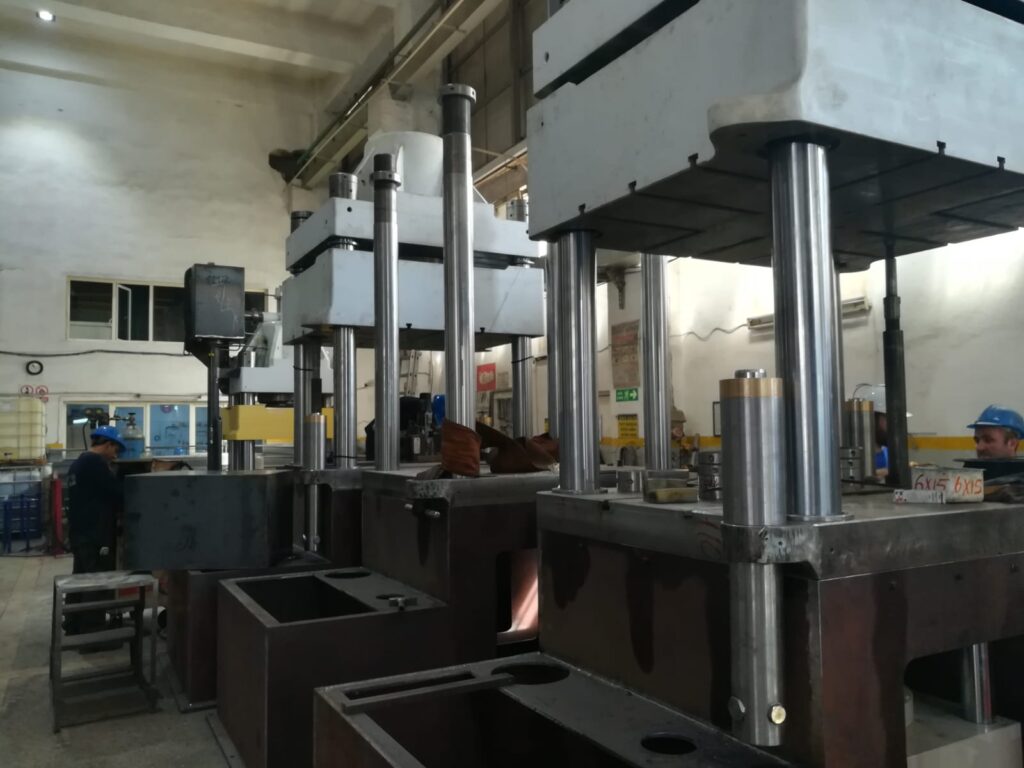
A hydraulic press for pot manufacturing is a powerful machine that uses hydraulic pressure to shape, form, and mold metal sheets into pot bodies, lids, bottoms, or other cookware components. It provides controlled, uniform force, enabling precise deformation of metal without causing cracks or defects, which is essential for producing high-quality, durable cookware.
Hydraulic presses operate by applying pressure through a piston and cylinder system, where hydraulic fluid transmits force to a ram that presses the metal blank against a die or mold. This process can include deep drawing, stamping, embossing, flanging, or trimming operations, depending on the tooling used.
In pot manufacturing, hydraulic presses are ideal for deep drawing—a method where a flat metal blank is stretched into a hollow shape like a pot body. Hydraulic presses offer smoother and more controllable force application than mechanical presses, reducing metal tearing and improving surface finish.
Modern hydraulic presses used in cookware production often have programmable controls for adjusting pressing speed, pressure, stroke length, and hold time. This programmability allows optimization for different metal types (stainless steel, aluminum, copper), thicknesses, and pot designs, improving consistency and minimizing scrap.
Safety features such as two-hand controls, light curtains, emergency stop buttons, and protective guards are standard to protect operators during press operations.
Hydraulic presses vary in tonnage, typically ranging from a few tons for small lids or trims up to several hundred tons for large pot bodies or thicker materials. Presses may be single-acting or double-acting, depending on the complexity of the forming process.
In high-volume production, hydraulic presses can be integrated into automated lines with robotic loading/unloading, part positioning, and transfer systems to maximize throughput and reduce manual handling.
Overall, hydraulic presses are essential equipment in metal pot manufacturing, providing the force, precision, and flexibility needed to form complex shapes with high repeatability and quality, ensuring cookware meets design and performance standards.
Hydraulic presses used in pot manufacturing are valued for their ability to deliver consistent and adjustable force throughout the entire pressing cycle, unlike mechanical presses that have a fixed stroke and force profile. This consistent pressure application is crucial when working with thin metal sheets common in cookware, as it minimizes defects such as wrinkling, tearing, or uneven thickness.
The press tooling, including dies and punches, is custom-designed to match the specific pot shape and size. These tools are made from hardened steel or other durable materials to withstand repeated high-pressure cycles and maintain dimensional accuracy over time. Quick-change tooling systems can reduce downtime during production changes, improving overall efficiency.
Many hydraulic presses feature closed-loop control systems that monitor parameters such as ram position, force, and speed in real time. This feedback allows for precise control and repeatability, which is especially important when manufacturing complex pot designs with tight tolerances.
Hydraulic presses can also perform secondary operations such as trimming excess material from formed pots, embossing decorative patterns, or flanging edges to prepare pots for assembly. This multifunctional capability reduces the need for multiple machines and streamlines production.
Energy efficiency improvements in modern hydraulic presses include variable pump drives and energy recovery systems that reduce power consumption, lowering operational costs and environmental impact. Maintenance-friendly designs with easily accessible components and automated lubrication systems help minimize downtime.
Integration with automated material handling—such as robotic arms or conveyor systems—allows hydraulic presses to be part of a fully automated production line. This integration improves safety by limiting manual handling and enhances productivity by maintaining continuous operation.
Operator interfaces are designed for ease of use, often including touchscreen controls with programmable press cycles, recipe storage, and diagnostic tools to simplify setup and troubleshooting. Training modes and safety interlocks support safe operation and reduce errors.
In summary, hydraulic presses are a cornerstone of metal pot manufacturing, offering the precise force control, versatility, and reliability required to produce high-quality cookware efficiently and consistently. Their adaptability to different materials and pot designs makes them indispensable in modern cookware production facilities.
Hydraulic presses for pot manufacturing also support advanced process monitoring and quality control. Sensors integrated into the press can track force curves, ram displacement, and cycle times, allowing manufacturers to detect deviations from optimal forming conditions. This data enables early identification of tool wear or material inconsistencies, reducing scrap rates and improving overall product quality.
Some hydraulic presses come equipped with servo-hydraulic systems, combining the accuracy and energy efficiency of electric servo drives with the power of hydraulics. These systems offer highly controllable ram motion profiles, including variable speed and dwell times, which are beneficial for delicate forming processes and complex pot geometries.
In specialized applications, multi-stage hydraulic presses are used to perform sequential forming steps without removing the part, such as initial deep drawing followed by flanging or embossing. This approach reduces handling, improves dimensional accuracy, and speeds up production cycles.
The choice of hydraulic press size and capacity depends on the pot size, material thickness, and the complexity of the forming operation. Larger presses are required for bigger pots or thicker materials, while smaller presses are suitable for lids or small accessories.
Maintenance of hydraulic presses is critical for long-term reliability. Routine checks of hydraulic fluid quality, seals, and mechanical components help prevent leaks and breakdowns. Many presses are designed with condition monitoring systems that alert operators to potential issues before failures occur.
Environmental considerations also influence press design. Systems that minimize hydraulic fluid leaks and incorporate eco-friendly fluids contribute to safer, cleaner manufacturing environments.
Ultimately, hydraulic presses provide the strength, precision, and adaptability necessary to meet the evolving demands of metal pot manufacturing, supporting manufacturers in producing cookware that is durable, visually appealing, and consistent in quality. Their combination of force control, programmability, and integration capabilities make them indispensable assets in modern industrial kitchens’ cookware production.
Metal Spinning Lathe For Pots
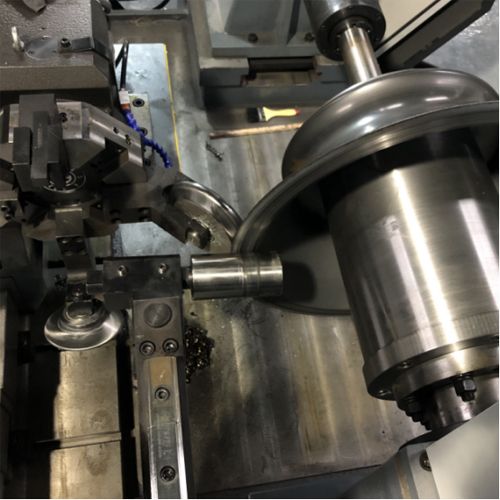
A metal spinning lathe for pots is a specialized machine used to form round, hollow cookware components—such as pot bodies, lids, or pans—by shaping flat metal discs or tubes on a rotating mandrel. This process, known as metal spinning or spin forming, is highly effective for creating symmetrical, seamless, and lightweight cookware with smooth contours.
The spinning lathe operates by clamping a metal blank onto a mandrel, which rotates at high speed. A skilled operator or automated tooling then applies controlled pressure using rollers, spoons, or other forming tools to gradually shape the metal against the mandrel’s profile. This plastic deformation thins and elongates the metal, producing the desired pot shape without cutting or welding.
Metal spinning lathes can be manual, CNC-controlled, or hybrid systems. Manual lathes rely on operator skill for tool manipulation and feed rate control, offering flexibility for custom or low-volume production. CNC spinning lathes automate tool movement and process parameters, ensuring high precision, repeatability, and faster cycle times—ideal for mass production of standardized pot designs.
These lathes accommodate various materials commonly used in cookware manufacturing, including stainless steel, aluminum, copper, and brass. The ability to work with thin sheets while maintaining strength and smooth surface finish is a key advantage.
In addition to forming pot bodies, metal spinning lathes are used for producing other cookware parts such as lids, bottoms, handles, or decorative elements. The process supports a wide range of sizes and shapes, from small saucepans to large stockpots.
Modern metal spinning lathes often include programmable settings for spindle speed, tool feed, and pressure to optimize forming for different metals and thicknesses. Integrated sensors monitor process parameters and detect issues like tool chatter or excessive force, enabling real-time adjustments and protecting both the tooling and workpiece.
Automation options include robotic loading/unloading and tool changers, further increasing throughput and reducing operator fatigue. Some systems also incorporate polishing or finishing stations inline to streamline production.
Safety features like protective guards, emergency stop controls, and ergonomic operator interfaces ensure safe operation. Noise and vibration dampening are also considerations due to the high rotational speeds and force involved.
Overall, metal spinning lathes are essential equipment in pot manufacturing, combining versatility, precision, and efficiency to produce high-quality, seamless cookware components that meet strict standards for durability, appearance, and performance.
Metal spinning lathes are particularly valued for their ability to create seamless cookware parts, which enhances strength and improves aesthetic appeal by eliminating weld lines or joints. The spun metal often exhibits favorable grain flow and work hardening effects, contributing to increased durability and resistance to deformation during use.
The versatility of metal spinning allows manufacturers to produce complex shapes with varying wall thicknesses, enabling lightweight yet sturdy pots. This is especially important for cookware where even heating and handling comfort are priorities. The gradual forming action reduces the risk of cracks or fractures compared to other forming methods.
In CNC metal spinning lathes, operators can store multiple forming programs, allowing quick changeovers between different pot models and sizes. This flexibility supports small batch runs and custom designs alongside high-volume production. Precision servo drives control tool positioning and spindle speed, ensuring consistent quality and reducing material waste.
Tooling for metal spinning includes various rollers, forming spoons, and mandrels, all tailored to the specific pot shape. Mandrels are typically made from hardened steel or aluminum and may be coated or polished to improve surface finish and reduce friction. Quick-change tooling systems help minimize downtime during production shifts.
Many modern spinning lathes incorporate closed-loop feedback systems that monitor force, spindle torque, and tool position. These sensors help maintain optimal forming conditions, prevent tool overload, and detect defects early. Data collected can be analyzed to optimize process parameters and improve yield over time.
Some manufacturers use robotic arms or automated loaders to feed blanks onto the mandrel and remove finished parts, integrating the lathe into fully automated production lines. This automation enhances throughput, reduces labor costs, and improves workplace safety by limiting operator exposure to moving parts.
Post-spinning processes such as trimming excess material, annealing to relieve stresses, or surface finishing are often integrated downstream to prepare pots for assembly or packaging. The quality of the spun surface also minimizes the need for extensive polishing, saving time and cost.
Due to the rotational forces involved, metal spinning lathes require robust construction with vibration damping and precision bearings to ensure smooth operation and long service life. Regular maintenance is important to keep the machine aligned and the hydraulic or servo systems calibrated.
Overall, metal spinning lathes combine traditional craftsmanship principles with modern automation and control technologies to deliver cookware components that excel in strength, appearance, and functional performance. Their adaptability and efficiency make them indispensable in contemporary pot manufacturing facilities.
In addition to their core forming capabilities, metal spinning lathes for pot manufacturing are increasingly incorporating smart technologies to enhance process control and productivity. For instance, integration with Industry 4.0 systems enables real-time data collection and remote monitoring of machine status, spindle speeds, cycle times, and tool wear. This connectivity supports predictive maintenance, reducing unexpected downtime and optimizing production scheduling.
Advanced software algorithms analyze forming parameters to identify the most efficient tool paths and speeds, minimizing material waste and extending tool life. Simulation tools allow manufacturers to virtually test new pot designs and forming sequences before physical production, reducing trial-and-error and accelerating time to market.
Ergonomics is another focus area, with operator cabins designed to reduce fatigue and improve visibility of the spinning process. Noise reduction measures and improved dust and debris extraction systems contribute to safer, cleaner working environments.
For specialty applications, some metal spinning lathes are equipped with multi-axis tool heads or additional forming stations, allowing more complex contours and details to be achieved in a single setup. This reduces handling and potential defects, enhancing overall product quality.
Training programs and virtual reality (VR) tools are sometimes used to help operators gain proficiency with spinning lathe controls and tooling changes, especially important when transitioning from manual to CNC or automated systems.
In summary, metal spinning lathes continue to evolve by combining time-tested metalworking techniques with cutting-edge automation, control, and data analytics technologies. This fusion empowers cookware manufacturers to produce seamless, durable, and attractive pots with greater efficiency, flexibility, and quality assurance, meeting the demands of both traditional and modern markets.
Deep Drawing Machine For Pots
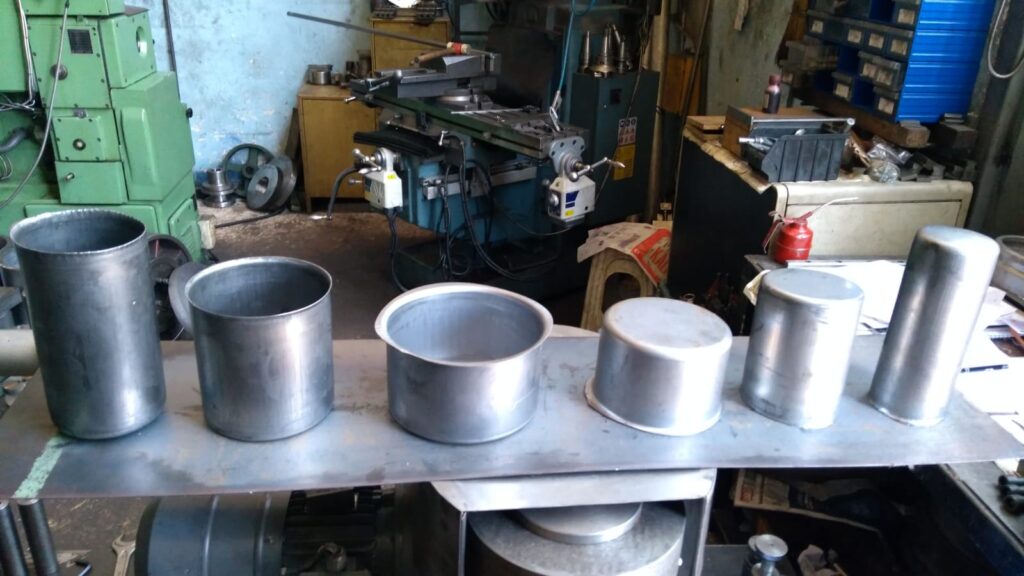
A deep drawing machine for pots is a specialized press system designed to transform flat metal blanks into deep, hollow shapes like cookware bodies through a controlled drawing process. This method involves placing a metal disc over a die cavity and applying downward force using a punch. As the punch descends, the metal is drawn into the die, forming a seamless, cylindrical or rounded pot body with uniform wall thickness.
The machine typically operates hydraulically or mechanically, with hydraulic models offering superior control over speed, pressure, and stroke length—crucial for avoiding defects like wrinkling, tearing, or thinning, especially when forming stainless steel, aluminum, or copper. The depth-to-diameter ratio achieved through deep drawing makes this process ideal for cooking pots, which require both height and structural strength.
Modern deep drawing machines feature programmable control systems that allow operators to adjust parameters for different pot sizes, materials, and shapes. These systems ensure repeatability, reduce operator error, and enable quick changeovers for flexible manufacturing. Some machines also support multi-draw operations, where parts are redrawn through progressive dies to achieve greater depth or more refined shapes.
Blank holders and pressure pads are integral to deep drawing machines, preventing metal from buckling during the punch stroke and ensuring a smooth, controlled flow of material. Lubrication systems are also essential, minimizing friction and tool wear, and contributing to the quality of the final surface finish.
Advanced models are equipped with sensors and force feedback systems that monitor the drawing process in real time, detecting anomalies and allowing on-the-fly adjustments. This leads to higher yield rates and fewer defective products. Some setups include automatic blank feeding, part ejection, and die cleaning to support continuous, high-speed production.
Deep drawing machines can be integrated into complete manufacturing lines, where post-drawing processes like trimming, ironing, flanging, and annealing are carried out sequentially. This integration streamlines workflow and improves efficiency.
Overall, the deep drawing machine is a core component in cookware manufacturing, delivering high-strength, aesthetically clean pot bodies with consistent dimensions. Its ability to produce seamless shapes with excellent material utilization makes it indispensable in both mass production and precision cookware fabrication.
Deep drawing machines used for pot manufacturing are built with heavy-duty frames to withstand the significant forces involved in forming deep, cylindrical parts from metal blanks. The tooling set—comprising the punch, die, and blank holder—is precisely machined to match the specific geometry of the pot being produced. These tools are typically made from hardened tool steel or carbide to endure repeated cycles without degradation. For different pot sizes or materials, interchangeable tooling can be installed, and modern machines often feature quick-change mechanisms to reduce downtime during production shifts.
Hydraulic deep drawing machines provide variable stroke control and adjustable forming speeds, which are essential when dealing with materials that respond differently under stress, such as stainless steel, which tends to harden quickly, or aluminum, which may wrinkle if not managed properly. These machines allow precise regulation of the punch velocity and blank holding force at different stages of the stroke, optimizing material flow and reducing the likelihood of defects like cracking or tearing.
In high-volume cookware production, automation is often integrated into deep drawing operations. Coil feeding lines can automatically cut circular blanks and deliver them to the drawing press. Robotic arms or conveyor systems may handle the transfer of blanks and drawn parts between machines. Sensors monitor critical variables such as punch load, draw depth, and cycle time, and this data is logged for traceability and quality control. Some systems also employ vision cameras to inspect the drawn parts for dimensional accuracy and surface defects before they move to the next station.
To achieve deeper draws or more complex shapes like tapered or contoured pot bodies, a multi-step drawing process may be required. This involves redrawing the part in secondary operations to gradually deepen and shape it further without overstressing the metal. Between stages, annealing ovens may be used to relieve internal stresses and soften the material, ensuring good formability in subsequent steps.
The efficiency of a deep drawing line is also influenced by how well the lubrication is managed. Lubricants reduce friction and help maintain a smooth metal flow, but they must be applied uniformly and cleaned off after forming. Some systems have automatic lubrication units that apply the correct amount at each cycle, while others include in-line cleaning stations to prepare the pot surface for polishing or welding.
Noise reduction, safety interlocks, and user-friendly operator panels are standard features in modern machines to ensure safe and efficient operation. Touchscreen controls allow for recipe storage, error diagnostics, and real-time process visualization, which not only makes the machine easier to use but also supports better production consistency.
In summary, deep drawing machines play a critical role in manufacturing metal pots by delivering fast, accurate, and repeatable shaping of flat metal into strong, seamless cookware. Their adaptability to various materials, pot dimensions, and production scales—combined with automation and digital controls—makes them a cornerstone of advanced cookware production technology.
As production demands grow and product design becomes more refined, deep drawing machines continue to evolve to meet tighter tolerances and faster cycle times without compromising product integrity. Some of the latest machines incorporate servo-hydraulic or fully electric systems instead of traditional hydraulics, which provide more precise movement, improved energy efficiency, and lower noise levels. These systems can execute highly controlled drawing curves, especially important when forming complex or asymmetrical cookware geometries.
To support the manufacture of premium cookware, deep drawing machines are often paired with ironing stations, which help to further refine the wall thickness of the pot body after the initial draw. This ironing process results in uniformly thin and smooth walls, reducing weight while maintaining strength—ideal for high-end aluminum or stainless-steel pots. Such integration is especially common in the production of multi-layer or clad pots, where uniformity is critical for even heat distribution.
In high-output facilities, deep drawing machines are configured as part of a fully automated production cell, where they are synchronized with trimming machines, edge rolling units, and surface polishing lines. This allows the freshly drawn pot to move seamlessly from one station to the next without manual handling. The machine’s control system coordinates with upstream and downstream equipment to avoid bottlenecks and ensure continuous, balanced operation.
Quality control systems are increasingly embedded into these lines. Using non-contact laser or 3D scanners, pot dimensions such as depth, diameter, and wall thickness are measured immediately after forming. Defective parts can be automatically rejected or flagged for secondary inspection. In some cases, forming data is linked directly to MES (Manufacturing Execution Systems) or ERP (Enterprise Resource Planning) software, giving production managers real-time visibility into machine performance, yield rates, and material consumption.
Tool maintenance is another area where technology assists operators. Tool wear is tracked via cycle counters or sensor feedback, and the machine can alert users when a die set needs inspection or replacement. Tool cooling systems, die coatings, and low-friction surfaces help extend tool life and maintain part consistency over thousands of cycles.
Sustainability is also a growing focus. Modern deep drawing machines are designed to minimize hydraulic oil consumption, recycle scrap material efficiently, and reduce power usage through smart energy-saving modes. Waste metal trimmed from the edges of drawn pots is collected and compacted for recycling, often fed back into the raw material loop to improve overall resource efficiency.
In conclusion, deep drawing machines for pot manufacturing have become highly advanced, blending traditional forming power with modern control, automation, and quality systems. Their ability to shape a simple flat disc into a flawless, durable, and precisely dimensioned pot body forms the foundation of modern cookware production. Whether for mass-market aluminum pots or high-end stainless steel cookware, the deep drawing process ensures high repeatability, excellent material utilization, and the structural integrity essential for everyday kitchen use.
Metal Sheet Forming Machine
A metal sheet forming machine is a versatile and essential piece of equipment used to transform flat sheet metal into specific shapes and profiles through mechanical deformation. In the context of cookware and pot manufacturing, these machines play a key role in producing components such as pot bodies, lids, handles, and bases by bending, pressing, cutting, rolling, or stamping metal sheets with high precision.
These machines come in various types depending on the forming method—such as press brakes for bending, stamping presses for blanking and punching, roll forming machines for continuous shaping, and hydraulic or mechanical presses for deep drawing and shaping. Each type is configured with dedicated dies and tools that determine the final geometry of the product. For example, in pot manufacturing, a forming press may stamp out the circular blank that becomes the base of the pot, while another machine may roll the edge or press the sheet into a concave shape.
High-performance metal sheet forming machines are CNC-controlled to ensure repeatable accuracy and efficient production. These systems allow operators to input precise dimensions, angles, and sequences through a digital interface, which improves consistency and reduces the need for manual adjustments. The CNC control also enables rapid switching between different product sizes or models, a major benefit in cookware lines with frequent design changes.
The machines often feature automatic feeding systems that uncoil, flatten, and cut sheet metal to size before feeding it into the forming area. This minimizes human handling, speeds up production, and reduces the risk of material defects. Sensors and feedback systems monitor the entire process, detecting issues such as misfeeds, overloading, or tool misalignment and halting the operation to prevent damage or scrap.
Tooling is central to the performance of a sheet forming machine. Precision-ground dies and punches are tailored to the thickness, type of metal, and shape being formed. Common materials processed include stainless steel, aluminum, and carbon steel, with thicknesses ranging from fractions of a millimeter to several millimeters depending on the application. High wear resistance and easy tool replacement are important to maintain productivity over time.
In advanced setups, multiple forming operations can be combined into a single cycle. For example, a progressive die setup in a stamping press can blank, punch holes, and form contours all in one pass. For cookware, this means not only shaping the pot body but also incorporating ventilation holes, embossed logos, or attachment points for handles—streamlining the workflow significantly.
Sheet forming machines are often integrated with downstream equipment such as welding systems, polishing stations, and assembly lines to create a fully automated production environment. In pot manufacturing, this can include a series of forming presses followed by trimming, edge rolling, and spot welding units, all connected through conveyors and robotic arms.
Ultimately, a metal sheet forming machine provides the structural foundation for nearly every component of a metal pot. Its precision, adaptability, and speed make it a cornerstone of industrial cookware production, enabling manufacturers to meet high volume demands while maintaining the quality, functionality, and design flexibility expected in modern kitchen products.
These machines are typically built with rigid steel frames to handle the high forces required during the forming process. Depending on the forming operation—be it blanking, punching, bending, or deep drawing—the tonnage capacity can vary widely, from small benchtop units to large-scale industrial presses capable of applying hundreds of tons of force. In cookware production, tonnage is carefully matched to the thickness and tensile strength of materials like stainless steel and aluminum to ensure clean forming without tearing or distortion.
The forming speed, stroke length, and die clearance are all adjustable on modern equipment, often controlled digitally. This adjustability allows the machine to accommodate a wide range of products with minimal changeover time. For example, forming machines used in pot manufacturing might switch between making deep stew pots, shallow frying pans, and lids simply by swapping dies and updating control parameters. This makes the production line more agile and reduces the need for multiple dedicated machines.
To further improve cycle efficiency and reduce human error, many sheet forming machines are equipped with automated lubrication systems that apply precise amounts of forming lubricant to the metal surface just before it enters the forming zone. This reduces tool wear, lowers friction, and helps in achieving clean, smooth surfaces without galling or scratches—especially important for kitchenware that demands both functional durability and a clean visual finish.
As safety is paramount in high-force forming operations, machines come equipped with safety light curtains, two-hand control systems, emergency stops, and protective enclosures. Operators are trained to perform tool changes, maintenance, and adjustments safely, and routine diagnostics are often built into the machine’s control system to alert the operator of wear, misalignment, or maintenance needs. In some systems, predictive maintenance algorithms use sensor feedback to schedule downtime before a component fails, avoiding costly production interruptions.
When producing complex cookware shapes or pots with specific ergonomic features, advanced forming techniques like hydroforming or servo-controlled stamping can be employed. These allow more nuanced and flexible shaping of sheet metal, offering better material flow, thinner walls, and smoother transitions without seams or welds. This is particularly beneficial when forming handles, spouts, or contoured bottoms that improve cooking performance or user comfort.
Recycling and material efficiency are also major considerations. The forming process is designed to use as much of the sheet metal as possible. Scrap material from punching or trimming is collected through conveyors or magnetic chutes and sent for re-melting or reuse. This helps reduce raw material costs and environmental impact, especially in operations where sustainability is a competitive priority.
In high-volume production, machine uptime and cycle time are critical. Therefore, manufacturers often run forming machines in multi-shift operations, and modular designs allow for quick maintenance and replacement of wear components. Some factories maintain a dedicated tooling department for sharpening and refurbishing dies, ensuring consistent product quality and extending tool life.
Overall, the metal sheet forming machine is an indispensable workhorse in cookware manufacturing. Its combination of mechanical strength, precision tooling, programmable control, and integration capability with upstream and downstream processes enables a streamlined, cost-effective, and high-quality production system. Whether producing a single model or a diversified range of pots and pans, these machines form the structural backbone of industrial kitchenware manufacturing.
In response to increasing market demand for customized cookware designs, modern metal sheet forming machines are often enhanced with digital tooling libraries and recipe management systems. These features allow operators to select pre-programmed tool settings for various products, minimizing setup time and ensuring repeatability. With digital records, production data for each pot model—such as die pressure, stroke count, feed rate, and part count—can be stored and recalled, enabling manufacturers to quickly resume production runs or analyze performance trends over time.
Forming accuracy is further improved by integrating servo-controlled feeding systems, which ensure the sheet metal is positioned precisely before each forming stroke. In multi-stage operations, this accuracy is vital to maintain alignment across progressive tooling stations. Errors in feed alignment can result in malformed parts or tool damage, so the inclusion of servo feeders, pilot release systems, and real-time monitoring ensures high consistency, especially when producing thousands of units per day.
For cookware with layered bottoms—such as pots with aluminum or copper sandwiched between stainless steel—forming machines are adapted to handle pre-bonded composite sheets. These sheets require controlled deformation to maintain the integrity of the layered structure during shaping. The forming machine’s tooling is calibrated to ensure that the bonding between layers is not compromised, and in some cases, heating elements are included in the press to assist with forming thermally bonded materials.
Post-forming operations are also increasingly integrated into the same machine or production cell. For instance, after forming the pot body, the machine may include an automated trimming station to remove excess metal or a beading system to prepare the edge for rolling or welding. This streamlining reduces handling, improves cycle time, and eliminates alignment errors that could occur when transferring parts between machines manually.
In smart manufacturing environments, metal forming machines are connected to factory-wide networks via industrial communication protocols such as OPC-UA or Ethernet/IP. This connectivity allows real-time data to be collected and shared across the production floor, enabling advanced scheduling, condition monitoring, and remote diagnostics. If an anomaly is detected—such as an unusual force curve during a forming stroke—the system can flag the part, pause production, or notify maintenance personnel before further issues arise.
Training and usability have also advanced. Modern machines feature user-friendly HMI (Human Machine Interface) panels with multilingual support, intuitive graphics, and touch-screen operation. Training operators on machine use, maintenance schedules, and safety procedures has become easier, and manufacturers increasingly provide simulation software that allows operators to rehearse production scenarios digitally before running actual parts.
All these developments reflect the growing complexity and competitiveness of metal cookware manufacturing. From the perspective of efficiency, precision, safety, and product diversity, the metal sheet forming machine has become far more than a mechanical press—it is now a programmable, intelligent hub that drives high-volume production while adapting to changing market and design demands. Its role in turning raw sheet material into perfectly formed pot components, consistently and cost-effectively, continues to make it central to any industrial cookware production line.
Copper Pot Production Machinery
Copper pot production machinery is specially designed to work with copper’s unique properties—its high thermal conductivity, excellent malleability, and aesthetic appeal. However, copper is softer and more reactive than stainless steel or aluminum, so machines used in this process must be finely tuned to handle forming, joining, and finishing without causing surface damage or structural distortion. The production line typically includes several core machines configured to form, shape, and polish copper into high-quality cookware.
The process often begins with a sheet cutting machine or circle cutting machine, which cuts precise circular blanks from copper sheets. These blanks are then transferred to a deep drawing press, where the flat disc is formed into a pot shape using a hydraulic or mechanical press equipped with hardened dies. Because copper flows easily under pressure, deep drawing can be completed in fewer stages than for harder metals, though careful control of pressure and lubrication is needed to prevent wrinkling or tearing.
After the initial draw, spinning lathes—often CNC-controlled—are used to refine the shape, create rounded bottoms, and form flared sides. These lathes rotate the drawn copper blank while a forming tool presses against it, shaping the pot with exceptional smoothness. Spinning is particularly well-suited for copper because of its ductility and ability to retain fine detail without cracking.
To reinforce the pot and improve heat distribution, some copper pots are manufactured with layered or clad bases, combining copper with stainless steel or aluminum. This is achieved using bottom attaching presses or impact bonding machines that fuse a multi-metal disc to the bottom of the pot body. The bonding is done under high pressure—and sometimes with induction heating—to ensure a permanent and thermally conductive joint.
Once the pot shape is finalized, a trimming and edge-beading machine refines the rim, giving it a clean, even finish. In traditional or high-end production, manual edge rolling may still be used, especially if the pot is designed with a hand-rolled rim or decorative detailing. For attaching handles, spot welding machines, rivet presses, or silver brazing stations are used depending on the construction style. Copper’s softness requires precision in these operations to avoid deformation and preserve strength.
Polishing is a critical stage in copper cookware manufacturing. Specialized metal polishing machines equipped with cloth buffs and polishing compounds are used to bring out copper’s rich luster. In high-volume factories, this process is automated with multi-head rotary polishers or robotic arms that follow the pot contour. After polishing, many pots are coated with a protective lacquer or tin lining to prevent oxidation and ensure food safety. Tin lining is typically applied using a hand-tinning station or automated electroplating unit, especially in traditional copper cookware production.
In more modern or large-scale facilities, the copper pot manufacturing process is fully integrated into automated production lines where robotic handling systems move pots from one station to the next, with CNC control ensuring repeatability, and vision systems conducting real-time inspection. These machines reduce human error, improve efficiency, and allow for consistent production quality at scale.
In summary, copper pot production machinery is engineered to respect the material’s softness and value, combining traditional metalworking techniques like spinning and hand-tinning with modern automation and precision forming technologies. The result is a blend of craftsmanship and industrial capability that supports the production of premium cookware used by chefs and home cooks around the world.
These machines must be both delicate and precise, as copper is highly reactive and visually sensitive to scratches, tool marks, or excessive heat during manufacturing. To maintain a high-end finish throughout the process, manufacturers often employ non-marring tooling materials and low-friction coatings on contact surfaces. Additionally, copper’s tendency to oxidize quickly requires the use of inert gas environments or protective coatings during certain forming and welding steps, especially if intermediate storage between process stages is expected.
Many manufacturers integrate inline surface cleaning systems such as acid bath units, ultrasonic washers, or mechanical brushing machines before polishing to ensure the copper surface is free from oil, scale, or particulate matter. Cleanliness at this stage is essential for producing a uniform polish and for the adhesion of any protective coatings or tin linings. These cleaning systems are especially important when bonding stainless steel discs to copper bases, as any contamination can lead to bonding failure or delamination during heating.
Automation is increasingly being adopted in copper pot production, even for artisan-style lines, to reduce human fatigue and guarantee uniformity. For instance, robotic arms can load and unload heavy or awkwardly shaped pots between forming, welding, and polishing stages, minimizing the risk of mishandling and improving workplace ergonomics. Additionally, sensors integrated into spinning and trimming equipment constantly monitor wall thickness and diameter, ensuring the tight tolerances required for nesting pot sets or precise lid fitting.
Quality control throughout the line is typically achieved using digital measurement tools such as laser micrometers and vision inspection systems. These devices check for concentricity, roundness, depth, and uniform surface appearance. Any deviation from the specifications can trigger automatic rejection or re-routing for rework. This systematized inspection is especially vital in premium cookware production, where cosmetic perfection is often just as important as structural integrity.
For manufacturers producing lined copper pots, especially those using traditional tin linings, temperature control and evenness of application are crucial. Manual tinning involves heating the copper pot evenly and applying molten tin with a cloth or brush, which bonds to the inner surface to form a food-safe layer. Machines that automate this process typically employ rotating fixtures and infrared heating systems to maintain constant surface temperatures while robotic applicators spread the tin. Excess tin is spun off or wiped clean to ensure a smooth finish. Electroplated linings—more common in industrial cookware—require a separate line with chemical baths, current controls, and post-plating rinsing and drying stations.
A complete copper pot production facility may include additional systems such as laser engravers for branding and logos, automated packaging lines that prevent scuffing during packing, and barcode tracking systems to manage inventory and traceability from raw material to finished product. The entire process—from copper sheet to boxed cookware—can be fully traceable and quality-assured using factory ERP systems that link each machine’s output data to the final batch records.
Despite the availability of full automation, many copper cookware brands still maintain a hybrid approach, combining industrial-grade machinery with handcrafted finishing to differentiate their products in the premium market. This means machines handle the repetitive or heavy processes—like drawing, spinning, trimming, and polishing—while human artisans apply fine surface detailing, rivet handles, or perform final inspections and packaging.
Ultimately, copper pot production machinery bridges the gap between tradition and innovation. It enables the scalability required for modern cookware demands while preserving the quality and craftsmanship that have long made copper pots a staple in professional kitchens. Whether producing decorative hammered pots, heavy-duty saucepans, or induction-compatible hybrid cookware, these machines form the backbone of a precision-driven manufacturing environment that transforms raw copper into culinary excellence.
As the demand for specialty and induction-compatible copper cookware rises, manufacturers have begun to incorporate advanced bonding and layering technologies into their machinery. This includes systems capable of forming tri-ply or multi-layer cookware where copper is sandwiched between inner and outer layers of stainless steel or aluminum. These layers are bonded using explosive bonding, roll bonding, or impact bonding presses, depending on the production volume and desired material properties. The equipment used in these processes must maintain extremely tight tolerances and uniform pressure across the entire surface to ensure complete fusion of the metals without voids or warping.
Following bonding, hydraulic or servo-hydraulic forming presses reshape these layered sheets into pot bodies. These presses are often CNC-controlled and outfitted with feedback systems that adjust force application in real time to accommodate any material variation, especially crucial in cookware applications where even thermal conductivity across the pot base is essential. Forming composite metals is more challenging than pure copper due to the differing hardness and stretch characteristics of each layer, so forming parameters must be finely calibrated to prevent layer separation or cracking during drawing or spinning.
For applications where aesthetic value is critical—such as hammered copper pots—specialized texturing or embossing rollers are employed to apply decorative finishes either before or after forming. These finishes can be purely decorative or functional, such as enhancing grip or increasing surface area for better heat distribution. In some cases, hammering is done manually or with pneumatic hammers operated by skilled workers, but high-volume operations use automated hammers that replicate traditional patterns with precision and speed.
Once forming and finishing are complete, heat treatment ovens may be used to anneal the copper, restoring ductility lost during forming. These ovens are carefully controlled to prevent discoloration or oxidation, often using a controlled atmosphere with inert gases like nitrogen or argon. Annealing is especially important in traditional copper production, where hand-formed or spun pots must retain flexibility for subsequent handle attachment or rim work.
Another key feature of modern copper pot manufacturing is the integration of induction-compatible ferromagnetic discs onto the pot base. Since copper is not naturally induction-compatible, a stainless steel plate is often added to the base using friction welding or diffusion bonding. Specialized machinery ensures that this plate is perfectly centered, level, and bonded flush to the pot’s bottom to prevent warping during heating. These machines often include in-line testing systems such as eddy current probes to verify the bond quality and ferromagnetic response of the base.
The final polishing and surface treatment stage involves several steps: mechanical polishing for mirror or satin finishes, chemical passivation to neutralize surface impurities, and often the application of a protective lacquer to preserve the shine during shipping and shelf life. For luxury brands or artisanal products, patina finishes or oxidation treatments may be applied intentionally to achieve a vintage or rustic appearance. These surface finishes are achieved using custom equipment like spray booths, rotary tumblers, or dipping stations that provide consistent and repeatable aesthetics.
Packaging lines designed for copper pots are usually equipped with non-abrasive handling equipment, such as fabric belts and foam-padded grippers, to protect the delicate polished surfaces. High-end cookware is often individually wrapped and boxed using robotic arms equipped with vision sensors, ensuring both speed and care. Smart labels and RFID tags may be applied at this stage for traceability and anti-counterfeiting, which is especially important in the luxury kitchenware market.
As copper continues to hold its place in the premium segment of cookware, machinery used in its production evolves to combine industrial efficiency with the preservation of hand-crafted appearance and quality. The ability to precisely control each stage—from bonding and forming to polishing and packaging—defines the competitiveness of modern copper cookware manufacturing. The best production lines not only produce consistently excellent results but also allow for flexibility in design, finishes, and materials, catering to a global market that values both function and form in the kitchen.
Aluminum Pot Manufacturing Equipment
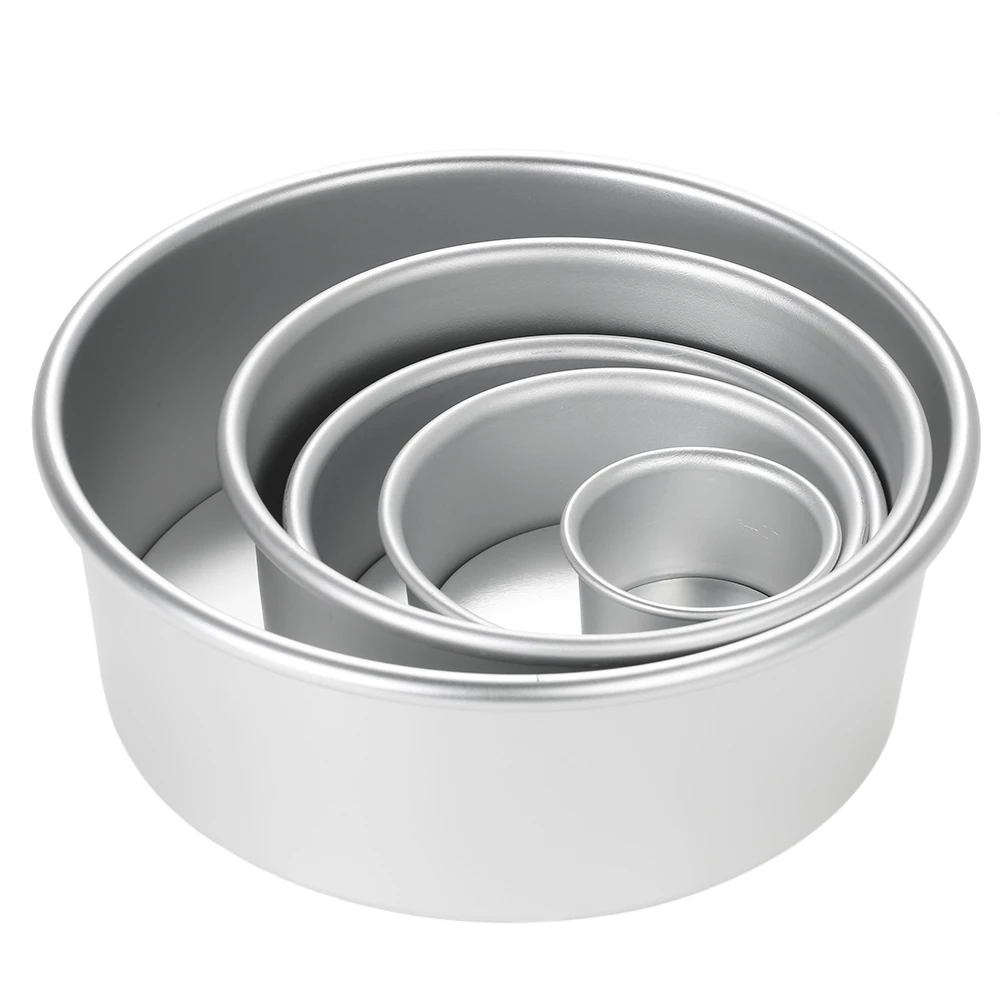
Aluminum pot manufacturing equipment is designed to efficiently handle the forming, shaping, finishing, and assembly of cookware made from aluminum sheets or discs. Aluminum’s lightweight nature, excellent thermal conductivity, and affordability make it one of the most popular materials for mass-market and professional cookware. The equipment used in this industry is engineered for high-speed, high-volume production while ensuring dimensional accuracy, surface smoothness, and proper bonding in multilayer constructions when required.
The process typically begins with circle cutting machines or coil feeders with press lines, which feed aluminum sheets into a blanking die to cut circular discs. These discs are often lubricated and pre-cleaned before entering the next stage. The primary forming process for pots is carried out using a deep drawing press—either hydraulic or mechanical—where the aluminum blank is pulled into a die cavity to form a cylindrical or curved pot body. Because aluminum has excellent formability, it can be drawn deeper than harder metals without tearing, allowing manufacturers to produce taller pots in fewer operations.
After the initial drawing, redrawing presses or ironing machines may be used to refine the shape and wall thickness, especially for tall or thin-walled pots. For better aesthetic and thermal performance, many aluminum pots are manufactured using spinning machines—either manually controlled or CNC—where the pot is rotated and shaped further using forming tools. This step is crucial for making round-bottomed pots or ensuring a consistent wall profile.
To improve heat distribution and induction compatibility, some aluminum pots are manufactured with a bonded base, where a stainless steel or multi-layer disc is attached to the bottom using an impact bonding machine or friction welding system. These machines apply high force and temperature to permanently fuse the metals without adhesives or fasteners. The resulting composite base improves structural rigidity and broadens stove compatibility.
Following forming and base attachment, trimming machines are used to remove any excess material at the rim, and edge rolling machines or beading machines shape the lip of the pot to provide strength and ensure lid compatibility. Some models also use curling machines to fold over the rim if a rolled edge is desired for comfort or safety.
For handles, automatic hole punching units or robotic arm welding stations prepare and attach side handles and top knobs. Riveting machines, robotic MIG welders, or spot welders are commonly used, depending on the design. In high-end models, die-cast handles are also joined using stainless steel rivets or hidden welds.
Surface treatment for aluminum cookware varies by product type. Non-stick aluminum pots undergo sandblasting, etching, or hard anodizing using electrolytic processes to create a durable oxide layer before the application of PTFE or ceramic coatings via automated spray booths or rotational coating lines. Raw or polished aluminum pots are processed through automated polishing machines with multiple buffing heads for satin, mirror, or brushed finishes. For hard-anodized cookware, anodizing tanks, sealing baths, and drying ovens are part of the specialized equipment line.
To ensure product quality, CNC inspection stations, laser measuring systems, and balance testing machines check for dimensional consistency, wall thickness uniformity, and thermal base flatness. Vision systems may also be integrated into production lines for detecting dents, scratches, or coating flaws in real time.
At the end of the line, automatic packaging machines wrap, label, and box the cookware with protective films, cardboard inserts, and branding materials. These packaging systems are often synchronized with barcoding or tracking software to manage inventory and logistics efficiently.
Overall, aluminum pot manufacturing equipment is geared toward speed, reliability, and flexibility. Modern production lines can be fully automated, allowing for minimal manual intervention, fast changeovers between pot sizes and styles, and continuous monitoring. This allows cookware producers to meet high global demand with consistent quality, offering products that range from economy lines to professional-grade, multi-functional pots with induction-ready bases and advanced coatings.
Aluminum pot manufacturing machinery often incorporates integrated lubrication and cooling systems to maintain tool life and ensure smooth metal flow during forming and spinning. Proper lubrication prevents galling and reduces surface defects on the relatively soft aluminum. These systems dispense precise amounts of lubricants or coolants at critical contact points between the tooling and the aluminum blank, enhancing process stability and extending maintenance intervals.
Automation is also widely implemented in aluminum pot production to increase throughput and reduce labor costs. Robotic arms handle material loading, unloading, and transfer between machines such as presses, trimmers, and welders. This reduces human error, minimizes handling damage, and improves safety by limiting operator exposure to hot or sharp parts. Programmable logic controllers (PLCs) and human-machine interfaces (HMIs) allow operators to monitor, control, and optimize the entire production process in real time, often linked to factory-wide ERP and quality control systems.
In multi-layer cookware manufacturing, aluminum cores are clad with stainless steel or other metals to improve durability and stove compatibility. Equipment used for clad material production includes roll bonding mills and heat treatment furnaces that bond and stabilize the layers before forming. Precision cutting and forming machines handle the thicker, composite blanks, ensuring no delamination or distortion occurs during deep drawing or spinning.
For products requiring enhanced corrosion resistance or specialized finishes, aluminum pots may go through chemical conversion coating processes such as chromate or phosphate treatments. These coatings improve adhesion for subsequent painting or powder coating applied by automated spray or dip systems. In cases where decorative patterns or branding are required, laser engraving and pad printing machines add intricate details onto the pot surfaces with high speed and accuracy.
Welding equipment used in aluminum pot assembly must accommodate the metal’s high thermal conductivity and oxidation tendencies. TIG welding machines with inert gas shielding and pulsed current controls are standard for attaching handles and fittings without compromising the pot’s structural integrity or appearance. Some manufacturers employ friction stir welding for seam welding or base attachment, which produces strong, low-distortion joints without melting the metal.
After welding, pots often enter a stress-relief annealing oven to remove residual stresses from forming and welding, preventing warping or cracking during use. Temperature uniformity and atmosphere control in these ovens are critical to maintain surface quality and mechanical properties.
Quality assurance systems in aluminum pot manufacturing lines use laser scanners and 3D optical profilers to verify dimensional tolerances down to microns. Non-destructive testing such as eddy current testing detects subsurface defects or bonding issues in clad materials. Inline cameras and machine vision algorithms inspect surface finishes for scratches, dents, or coating defects before final packaging.
The final packaging stage frequently includes automated wrapping, boxing, and palletizing lines. Protective films and cushioning materials prevent abrasion during transport. Smart packaging solutions with RFID tags or QR codes enable traceability and inventory management throughout the supply chain.
Environmental considerations have also influenced aluminum pot manufacturing equipment design. Modern lines incorporate closed-loop lubrication systems to minimize waste, energy-efficient servo motors for presses and conveyors, and ventilation and filtration units to control emissions from coating or welding processes. Recycling stations for aluminum scrap generated during trimming or defective parts are integrated into factory layouts to reduce material loss.
Together, these advanced manufacturing systems enable aluminum cookware producers to achieve high volumes with consistent quality, offering products that meet diverse consumer demands—from lightweight camping pots to durable, multi-ply kitchen essentials with sophisticated surface treatments and enhanced thermal performance.
Aluminum pot manufacturing lines increasingly incorporate smart manufacturing technologies to optimize efficiency and quality control. Sensors embedded throughout the equipment collect data on parameters such as press force, temperature, spindle speed, and cycle times. This data is fed into centralized manufacturing execution systems (MES) or industrial Internet of Things (IIoT) platforms, where analytics and machine learning algorithms identify patterns and predict maintenance needs. Predictive maintenance helps reduce unplanned downtime by scheduling repairs before critical components fail, thus maintaining smooth production flow.
Flexible manufacturing systems (FMS) allow aluminum pot lines to quickly switch between different pot sizes, shapes, and designs with minimal setup time. CNC-controlled presses, trimming units, and polishing machines can be reprogrammed on the fly, enabling small batch production runs or custom orders without sacrificing productivity. This agility is vital in a competitive market where consumer preferences evolve rapidly and personalized cookware designs are increasingly popular.
Safety features are also integrated into modern manufacturing equipment. Light curtains, emergency stop systems, and interlocked guarding protect operators during high-speed forming, trimming, or welding operations. Automated material handling reduces manual lifting and exposure to hot or sharp parts, enhancing workplace ergonomics and compliance with occupational health regulations.
Energy efficiency improvements include the use of servo-driven presses and conveyors that adjust power consumption based on load, as well as heat recovery systems that capture and reuse energy from ovens or welding stations. Some plants employ renewable energy sources, such as solar panels or wind turbines, to further reduce their carbon footprint.
In terms of finishing, newer coating technologies are being adopted to improve durability and environmental compliance. For example, low-VOC (volatile organic compounds) powder coatings replace traditional solvent-based paints, while PFOA-free non-stick coatings meet stricter safety standards. Automated inspection systems verify coating thickness, adhesion, and appearance, ensuring each pot meets brand quality criteria.
Finally, collaboration with suppliers of raw aluminum and multilayer clad materials ensures consistent input quality, which is crucial for maintaining tolerances and preventing defects. Some manufacturers use blockchain-based supply chain tracking to verify material provenance and compliance with sustainability certifications.
Overall, aluminum pot manufacturing equipment today represents a blend of traditional metal forming expertise and cutting-edge automation, control, and sustainability technologies. This combination enables manufacturers to deliver high-quality, cost-effective cookware that meets diverse market demands while minimizing environmental impact and maximizing operational efficiency.
Stainless Steel Pot Making Machine

Stainless steel pot making machines are specialized equipment designed for the efficient production of cookware using stainless steel sheets or coils. Stainless steel, prized for its corrosion resistance, durability, and aesthetic appeal, requires precise and robust machinery to handle its higher hardness and lower formability compared to aluminum or copper.
The manufacturing process typically starts with sheet feeding and blanking machines, which cut stainless steel coils or sheets into circular blanks sized according to the pot design. Given stainless steel’s tougher nature, these machines feature reinforced blades and powerful hydraulic or mechanical presses to ensure clean, accurate cuts.
Next, deep drawing presses form the blanks into pot bodies by pulling the metal into shaped dies. Stainless steel’s spring-back tendency demands presses with higher tonnage and precise control over stroke and speed to avoid cracking or wrinkling. Both hydraulic and mechanical presses are common, with hydraulic offering greater flexibility for complex shapes.
After initial drawing, pots often go through redrawing and ironing processes to refine shape and achieve uniform wall thickness, especially for taller or thinner-walled models. Ironing machines squeeze the pot walls thinner while increasing height, requiring strong tooling with wear-resistant coatings to withstand the abrasive nature of stainless steel.
Spinning lathes—manual or CNC—are used for fine shaping, especially to produce round bottoms or flared rims. Stainless steel spinning tools are typically made from hardened steel or carbide to maintain sharpness and prevent galling.
To enhance heat conduction, many stainless steel pots include an encapsulated base with an aluminum or copper core. Machines such as impact bonding presses or clad base attachment systems securely join these multi-metal bases to the pot body without adhesives, ensuring excellent thermal performance.
The pot rims are then finished using trimming and beading machines that remove excess metal and shape the edges for strength, safety, and lid compatibility. Curling machines may be used to roll the rim inward for added rigidity and smoothness.
Handle attachment involves hole punching or laser perforation units to prepare mounting points, followed by welding stations (TIG or laser welding) or rivet fastening machines. Stainless steel welding requires inert gas shielding and precise control to avoid discoloration and maintain corrosion resistance.
Surface finishing is critical for stainless steel cookware. Pots undergo grinding and polishing machines to achieve finishes ranging from matte brushed to mirror shine. Automated polishing lines with multiple heads and abrasive belts or pads provide consistent surface quality. Some lines integrate electropolishing stations to enhance corrosion resistance and surface smoothness.
For high-end or decorative products, laser engraving and pad printing machines apply logos, measurement markings, or patterns directly onto the pot surfaces.
Quality control equipment includes dimensional inspection stations with laser scanners and optical systems to ensure tight tolerances, as well as surface defect detection cameras. Testing for weld integrity, base flatness, and handle strength is conducted using specialized fixtures and force measurement devices.
The final stage is packaging, where automated wrapping, boxing, and palletizing machines prepare the pots for shipping. Protective films or foam inserts prevent scratches during transport.
In summary, stainless steel pot making machines form a comprehensive set of high-precision, heavy-duty equipment tailored to the unique mechanical properties of stainless steel. These machines enable manufacturers to produce durable, corrosion-resistant cookware with excellent appearance and functional performance for both consumer and professional kitchens.
Stainless steel pot manufacturing lines emphasize durability and precision due to the metal’s hardness and lower ductility. Advanced blanking presses with servo controls optimize cutting speed and force to minimize burrs and distortion. Deep drawing presses utilize hydraulic systems with adjustable pressure curves to carefully control metal flow, preventing tears or wrinkling. Multiple-stage redrawing and ironing ensure consistent wall thickness, critical for heat distribution and structural strength. CNC spinning lathes enhance the roundness and surface finish, particularly for complex shapes or seamless designs.
Multi-layer base bonding is a key feature, where aluminum or copper cores are attached via mechanical impact or laser welding to improve heat conduction while maintaining stainless steel’s corrosion resistance. Precision rim finishing machines execute trimming, curling, and beading to reinforce edges, ensuring safety and compatibility with lids and handles.
Welding stations incorporate TIG or laser welders with gas shielding to join handles or accessories without compromising aesthetics or corrosion resistance. Automation in handle attachment and riveting improves cycle times and repeatability. Surface finishing lines often integrate multi-stage polishing with abrasive belts and pads, followed by optional electropolishing to enhance surface smoothness and cleanliness. Laser engraving and printing provide customization and branding, meeting diverse market demands.
Inspection systems use 3D scanning and vision cameras to detect dimensional variances, surface defects, and weld integrity. Inline testing rigs verify mechanical strength and flatness, assuring product reliability. The packaging process employs automated wrapping and cushioning to protect the finished pots during transport.
Modern stainless steel pot lines incorporate data acquisition and IoT connectivity for real-time monitoring and predictive maintenance, reducing downtime and improving quality consistency. Energy-efficient servo motors and closed-loop lubrication reduce operational costs and environmental impact. Safety interlocks, light curtains, and ergonomic material handling safeguard operators in fast-paced production environments.
Collaborations with raw material suppliers ensure the stainless steel sheets meet strict chemical and mechanical specifications, critical for consistent forming and finishing. Supply chain traceability and sustainable sourcing practices are increasingly integrated to meet regulatory and consumer expectations.
Overall, stainless steel pot making machines blend robust mechanical design with advanced automation and quality control technologies, enabling efficient production of high-quality cookware that withstands demanding cooking environments and maintains attractive finishes over time.
The trend toward customization and small-batch production in stainless steel cookware manufacturing has driven the adoption of flexible manufacturing systems. CNC-controlled presses, trimming, and polishing machines can be quickly reprogrammed to handle various pot sizes, shapes, and thicknesses, allowing manufacturers to respond swiftly to changing market demands or special orders. This flexibility is supported by modular tooling systems that reduce setup times and tooling costs.
To enhance efficiency, many stainless steel pot production lines now incorporate robotic material handling for loading blanks into presses, transferring parts between stations, and stacking finished products. These robots improve consistency, reduce labor costs, and minimize damage from manual handling. Collaborative robots (cobots) working alongside human operators further optimize processes by assisting in tasks such as quality inspection or packaging.
In terms of environmental impact, stainless steel manufacturing equipment increasingly features waste reduction measures. Scrap metal from trimming and defective parts is collected and recycled on-site, while process water and cooling fluids are treated and reused. Advanced filtration and ventilation systems capture airborne particles and fumes from welding and polishing, ensuring compliance with workplace safety and environmental regulations.
Emerging technologies like laser welding and additive manufacturing (3D printing) are beginning to find roles in prototyping and producing complex handle assemblies or decorative elements. Laser welding offers precision, low heat input, and minimal distortion, which are advantageous for maintaining the integrity of stainless steel pots. Additive manufacturing enables rapid iteration and customization without expensive tooling changes.
Digital twins—virtual replicas of the manufacturing line—are used by some manufacturers to simulate process parameters, predict potential bottlenecks, and optimize production flows before implementing physical changes. This reduces downtime and improves overall equipment effectiveness (OEE).
In quality assurance, machine learning algorithms analyze sensor data and high-resolution images to detect subtle surface defects or inconsistencies that human inspectors might miss. This leads to higher first-pass yield rates and reduced rework.
Safety advancements continue to evolve with real-time monitoring of operator presence and machine status, enabling predictive alerts and automatic shutdowns in hazardous situations. Ergonomic machine designs reduce operator fatigue and injury risk.
By combining traditional metal forming expertise with smart automation, sustainable practices, and flexible production capabilities, stainless steel pot manufacturing machines empower producers to meet the rigorous demands of modern cookware markets efficiently and reliably.
Automatic Metal Pot Production Line
An automatic metal pot production line integrates a series of advanced machines and automated systems to manufacture metal pots—from raw material feeding to final packaging—without requiring constant human intervention. This type of production line is designed to maximize productivity, ensure consistent quality, reduce labor costs, and improve safety.
The process typically begins with an automated coil feeding system that unrolls and straightens metal sheets (stainless steel, aluminum, copper, or clad materials). Precision feeding mechanisms position the metal blank for the next step with exact alignment.
Next, automatic blanking machines punch or shear metal sheets into circular blanks. These machines use hydraulic or servo-driven presses for fast, clean cuts and minimal waste. Blanks are transferred via conveyors or robotic arms to the forming section.
In the forming stage, deep drawing presses or metal spinning machines shape the flat blanks into pot bodies. Modern presses are equipped with CNC controls and servo motors to finely tune stroke speed, force, and dwell times, adapting to different pot sizes and materials. Some lines use multi-stage redrawing and ironing presses to achieve desired wall thickness and height.
After forming, trimming and rim forming machines remove excess material and create smooth, reinforced edges suitable for lids and handles. These machines operate automatically, often linked by conveyors with synchronized speeds to maintain continuous flow.
For pots requiring multi-layer bases, impact bonding machines or laser welding systems attach aluminum or copper cores to improve heat conduction. These machines ensure secure, defect-free bonding while preserving stainless steel surfaces.
Handle attachment stations integrate hole punching, welding (TIG or laser), or riveting. Robotics are increasingly employed here to handle delicate positioning and secure fastening with high repeatability.
Surface finishing is done by automated polishing lines that include grinding belts, abrasive brushes, and buffing wheels. Some lines also incorporate electropolishing or cleaning stations for superior surface quality. Inline vision systems inspect surface finish and detect defects in real time.
Quality control checkpoints with laser scanners and cameras verify dimensions, weld integrity, and surface condition throughout the line. Data collected feeds into manufacturing execution systems (MES) for process optimization and traceability.
The finished pots proceed to automated packaging machines, which wrap, label, and box products before stacking them on pallets. This reduces handling damage and speeds shipment preparation.
Throughout the line, programmable logic controllers (PLC) and industrial IoT sensors enable centralized monitoring and control. Operators can adjust parameters, track production rates, and perform predictive maintenance based on real-time analytics, minimizing downtime.
Safety features such as light curtains, emergency stops, and interlocked guards protect workers around high-speed presses and robotic arms. Ergonomic design reduces manual lifting and repetitive strain injuries.
Overall, automatic metal pot production lines combine high-speed forming, precise machining, surface finishing, and smart automation to produce cookware efficiently with consistent quality and minimal human labor. This approach is ideal for large-scale manufacturers aiming to meet growing demand while controlling costs and maintaining product standards.
Automatic metal pot production lines leverage a seamless flow of interconnected machinery to optimize throughput and consistency. After coil feeding and blanking, blanks are often conveyed via automated transfer systems like servo-driven conveyors or robotic arms that reduce manual handling and improve positioning accuracy. This smooth transfer minimizes cycle times and lowers the risk of damage or misalignment.
In forming stages, multi-station hydraulic or mechanical presses can perform progressive operations—drawing, redrawing, ironing, trimming—in a continuous sequence. These presses often incorporate sensors to monitor force and stroke parameters in real time, allowing adaptive control to accommodate material variations and reduce defects. For more complex shapes, CNC-controlled spinning or hydroforming may be integrated, providing versatility without slowing overall line speed.
Base bonding machines use precise impact or laser techniques to securely join heat-conductive cores without adhesives, maintaining the structural integrity and corrosion resistance of the pot body. Automation in handle attachment ensures consistent welding or riveting, with robots or automated fixtures positioning components rapidly and accurately.
Surface finishing is typically performed on continuous polishing lines featuring multiple abrasive stages, followed by buffing and cleaning. Automated polishing not only ensures uniform appearance but also optimizes abrasive usage, reducing consumables cost. Inline vision inspection systems detect scratches, dents, or uneven polish early, triggering rejection or rework to prevent downstream issues.
Throughout production, integrated quality control systems capture detailed data, including dimensional measurements, weld quality, and surface condition. This information feeds into a centralized MES platform that tracks each pot’s production history, supports traceability, and enables root cause analysis in case of defects.
Packaging automation incorporates robotic arms or conveyors to orient, wrap, label, and box finished pots efficiently. Automated palletizing systems then arrange packages for shipment, maximizing space utilization and reducing manual labor.
The entire line operates under sophisticated control architectures, combining PLCs, human-machine interfaces (HMIs), and IoT connectivity. This setup allows remote monitoring, predictive maintenance, and flexible scheduling, helping manufacturers quickly adjust to order variations or material changes.
Safety and ergonomics are key design considerations. Machines include interlocks, light curtains, and emergency stop systems to protect operators, while automated material handling minimizes physical strain. Ergonomic workstations and user-friendly interfaces improve operator comfort and reduce errors.
Sustainability features are increasingly integrated, such as scrap metal recycling systems, closed-loop coolant filtration, and energy-efficient motors. Waste reduction strategies and environmental controls ensure compliance with regulatory standards and support corporate responsibility goals.
By combining advanced automation, precise forming, real-time quality monitoring, and efficient material handling, automatic metal pot production lines enable manufacturers to deliver high volumes of consistently high-quality cookware while optimizing costs and reducing environmental impact.
To further enhance efficiency, many automatic metal pot production lines incorporate modular design principles. This modularity allows manufacturers to scale production capacity easily by adding or removing machine modules based on demand fluctuations. It also simplifies maintenance and upgrades, minimizing downtime and enabling faster integration of new technologies such as AI-driven quality inspection or advanced robotics.
Integration with enterprise resource planning (ERP) systems enables seamless coordination between production scheduling, inventory management, and supply chain logistics. Real-time data sharing ensures raw materials are replenished just-in-time, reducing storage costs and preventing production delays caused by stockouts.
Advanced robotics continue to expand their roles beyond simple handling to include precision welding, embossing, and even complex assembly tasks such as fitting multi-component handles or attaching lids with locking mechanisms. Collaborative robots (cobots) work alongside human operators to assist with tasks that require adaptability or manual dexterity, creating a hybrid work environment that leverages the strengths of both humans and machines.
In terms of customization, flexible automation systems allow quick changeovers between different pot models or finishes. Programmable tooling and adaptive control systems adjust parameters on the fly, enabling production of a diverse product range without extensive manual intervention. This flexibility supports trends toward personalized cookware and small-batch runs that cater to niche markets.
Energy efficiency is a growing priority, with many lines implementing regenerative drives, LED lighting, and heat recovery systems. Machine cycles are optimized to reduce peak power consumption, and smart sensors help monitor and manage energy usage across the facility.
Environmental sustainability is also addressed through responsible sourcing of metals and the use of environmentally friendly lubricants and cleaning agents. Closed-loop water systems minimize consumption, and waste handling procedures ensure that metal scraps and other byproducts are recycled or disposed of safely.
Operator training and digital assistance tools improve workforce capabilities, with augmented reality (AR) and virtual reality (VR) used for remote diagnostics, maintenance guidance, and skill development. These technologies reduce errors and enhance uptime by enabling faster troubleshooting and knowledge transfer.
Ultimately, the ongoing evolution of automatic metal pot production lines is driven by the need for higher quality, greater efficiency, increased customization, and sustainability. By adopting cutting-edge automation, data analytics, and ergonomic design, manufacturers can meet these demands while maintaining competitive advantages in a global market.
Metal Pots Manufacturing Machinery
Metal pots manufacturing machinery encompasses a wide range of specialized equipment designed to efficiently transform raw metal materials into finished cookware products with precise shapes, sizes, and surface finishes. These machines address each step of the manufacturing process, from material handling to forming, trimming, welding, finishing, and quality inspection.
Raw Material Preparation: The process begins with decoilers or coil feeders that unwind metal sheets or coils (commonly stainless steel, aluminum, copper, or clad metals). Straighteners and levelers ensure flatness and remove stress from the metal before feeding it into subsequent machines.
Blanking Machines: High-speed blanking presses cut metal sheets into round blanks, which serve as the base forms for pots. These presses may use hydraulic, mechanical, or servo-driven systems, depending on production volume and precision requirements.
Deep Drawing Presses: These presses shape the flat metal blanks into three-dimensional pot bodies through controlled deformation. Hydraulic deep drawing machines with CNC controls are preferred for precise and repeatable forming, preventing defects such as wrinkles or tears.
Redrawing and Ironing Presses: For pots requiring taller or thinner walls, redrawing presses re-form the pots to higher dimensions, while ironing presses thin and smooth the walls for uniform thickness and improved mechanical properties.
Metal Spinning Lathes: CNC-controlled spinning machines can also form pots by rotating the metal blank against a shaping tool, allowing for seamless and round shapes with smooth surfaces.
Trimming and Rim Forming Machines: Once shaped, pots undergo trimming to remove excess metal and rim forming to create reinforced edges. These machines ensure clean, uniform rims compatible with lids and handles.
Base Attachment Machines: For pots featuring layered bases, bonding machines attach conductive cores (aluminum or copper) to stainless steel pot bottoms, enhancing heat distribution. Methods include mechanical impact bonding or laser welding.
Handle and Accessory Welding: Specialized welding machines, such as TIG or laser welders, attach handles, spouts, or additional components with precision and minimal heat distortion. Automated robotic welding stations improve consistency and cycle times.
Surface Finishing Equipment: Polishing machines with abrasive belts, brushes, and buffing wheels provide the desired surface texture and shine. Electropolishing stations may be included for corrosion resistance and enhanced appearance.
Quality Inspection Systems: Automated vision and laser scanning equipment measure dimensions, detect surface defects, and verify weld integrity. Data integration allows traceability and process control.
Packaging Machinery: Finished pots are transported to packaging stations featuring automated wrapping, labeling, boxing, and palletizing, reducing manual labor and damage risks.
Overall, metal pots manufacturing machinery combines mechanical forming, precision machining, welding, finishing, and automation to produce cookware that meets stringent standards for performance, aesthetics, and durability. Manufacturers tailor equipment selections based on material type, pot design, production volume, and automation level desired.
Metal pots manufacturing machinery works in a highly coordinated manner to transform raw metal into finished cookware efficiently and consistently. The process begins with feeding metal coils or sheets into decoilers and leveling machines that prepare the material by removing curvature and stresses. This ensures smooth handling in later stages and prevents defects.
Next, blanking presses cut the material into precise circular blanks that serve as the foundation for forming. These presses can operate at high speeds with hydraulic or servo-driven systems, enabling quick and accurate blank production. After blanking, transfer systems such as conveyors or robotic arms move the blanks to forming stations, minimizing manual handling and enhancing line throughput.
Forming is carried out primarily through deep drawing presses that shape the blanks into three-dimensional pot bodies. These presses use controlled force and stroke patterns to avoid common issues like wrinkling or tearing of the metal. For pots requiring taller or thinner walls, multi-stage redrawing and ironing presses refine dimensions and wall thickness, producing consistent, high-quality shapes. Some manufacturers incorporate CNC-controlled metal spinning lathes as an alternative or complement to press forming, allowing for smooth, seamless pot surfaces.
Once formed, pots proceed to trimming machines that remove excess metal and refine edges. Rim forming machines create reinforced, uniform rims that improve durability and compatibility with lids or handles. In cases where enhanced heat conduction is needed, base bonding machines attach aluminum or copper cores to the pot bottoms using techniques like impact bonding or laser welding, maintaining the structural integrity and corrosion resistance of the pot body.
Handle attachment is a critical step where specialized welding machines—often robotic TIG or laser welders—secure handles or spouts with precision. Automation in this stage reduces inconsistencies and increases production speed. Surface finishing machines then polish the pots using multiple abrasive stages, brushes, and buffing wheels, sometimes including electropolishing for improved corrosion resistance and aesthetic appeal. Inline inspection systems monitor surface quality in real time to detect defects early.
Throughout the production line, quality control equipment such as laser scanners and vision systems verify dimensional accuracy, weld integrity, and surface finish. Data from these systems integrate into manufacturing execution systems, enabling traceability and facilitating rapid adjustments to maintain product standards.
Finished pots are conveyed to packaging stations featuring automated wrapping, labeling, boxing, and palletizing systems. These automated packaging solutions reduce labor costs, minimize product damage, and speed up shipment preparation.
The entire manufacturing setup is managed by programmable logic controllers (PLCs) and integrated control systems that coordinate machine operations, monitor production metrics, and enable remote supervision. IoT sensors provide real-time data on equipment health and process parameters, supporting predictive maintenance and reducing downtime.
Safety is paramount, with machines equipped with interlocks, light curtains, and emergency stops to protect operators. Ergonomic design principles reduce manual handling and operator fatigue, enhancing workplace safety and productivity.
Modern metal pots manufacturing machinery emphasizes flexibility, allowing quick changeovers between pot sizes and designs through programmable tooling and adaptive controls. This versatility supports diverse product lines and smaller batch production without sacrificing efficiency.
Energy efficiency and environmental sustainability are increasingly incorporated, including features like regenerative drives, water recycling systems, and scrap metal collection for recycling. These measures help manufacturers comply with regulations and reduce operating costs.
In sum, metal pots manufacturing machinery integrates advanced forming, welding, finishing, automation, and quality control technologies into streamlined production lines. This integration allows manufacturers to produce high-quality, durable cookware at scale while optimizing cost, safety, and sustainability.
To further optimize production, many metal pots manufacturing lines incorporate modular automation units, enabling manufacturers to scale capacity and customize configurations quickly. Modular design also facilitates maintenance and upgrades, allowing individual machines or sections to be serviced or replaced without halting the entire line.
Robotics play an increasing role beyond material handling and welding. Advanced robotic arms equipped with vision-guided systems perform complex assembly tasks, such as precise fitting of multi-part lids, spout attachment, or embossing decorative patterns. Collaborative robots, or cobots, work alongside human operators to assist with flexible tasks requiring dexterity or judgment, blending automation efficiency with human adaptability.
Data analytics and machine learning are applied to process monitoring systems to predict equipment wear, optimize cycle times, and improve product quality. By analyzing sensor data in real time, manufacturers can detect subtle deviations and adjust machine parameters dynamically, reducing scrap rates and increasing yield.
Flexible manufacturing systems enable rapid changeovers between different pot styles, sizes, or materials without extensive tooling changes. Programmable tooling combined with adaptive forming technologies supports production of diverse product lines, catering to market trends for personalized or premium cookware.
Energy management systems coordinate machine power usage to reduce peak loads and increase efficiency. Technologies such as regenerative braking in presses, LED lighting, and heat recovery systems contribute to lowering overall energy consumption. Water and coolant recycling systems minimize resource waste, aligning with environmental sustainability goals.
Operator training benefits from digital tools including augmented reality (AR) and virtual reality (VR), which provide immersive instruction for machine operation, troubleshooting, and maintenance. Remote support capabilities allow experts to guide onsite technicians through complex repairs, reducing downtime.
Safety systems integrate advanced sensors and interlocks with machine controls, ensuring that hazards are mitigated proactively. Ergonomically designed workstations and automated material handling reduce repetitive strain and enhance workforce well-being.
Environmental compliance is supported through effective waste management, including collection and recycling of metal scraps, responsible disposal of lubricants and chemicals, and emissions monitoring. Some facilities pursue certifications like ISO 14001 to formalize sustainability commitments.
Overall, modern metal pots manufacturing machinery and production lines combine mechanical precision, digital intelligence, and flexible automation. This synergy enables manufacturers to respond to evolving market demands efficiently while maintaining high standards for quality, safety, and environmental responsibility.
Machinery for Production of Cookware with Nonstick Coating
Machinery for the production of cookware with nonstick coating involves specialized equipment that handles both the base metal forming and the application and curing of nonstick surfaces. This equipment ensures that the cookware is shaped precisely, and that the nonstick coating is applied evenly, durable, and safe for cooking use.
The production line typically begins with standard metal forming machinery such as blanking presses, deep drawing machines, and trimming equipment to shape the pots, pans, or other cookware from materials like aluminum or stainless steel. The base cookware must have a smooth, defect-free surface before coating, so finishing machines such as polishing and cleaning stations are integrated early in the process.
Once the cookware bodies are shaped and cleaned, they enter the coating preparation phase. This includes automated cleaning and degreasing units that remove oils, residues, and impurities to ensure strong adhesion of the nonstick layer. Cleaning methods can involve chemical baths, ultrasonic cleaning, or plasma treatments.
After surface preparation, the cookware moves to coating application machines. These may be automated spray booths or dip-coating systems designed to apply one or multiple layers of nonstick coatings, such as PTFE (Teflon) or ceramic-based coatings. Robotic arms often handle the spraying to achieve uniform thickness and coverage, minimizing overspray and material waste.
Next, the coated cookware proceeds to curing ovens where the coating is thermally cured at precise temperatures and times, bonding the nonstick layer firmly to the metal substrate. Conveyors transport the items through curing chambers with controlled atmospheres to optimize coating properties and durability.
Additional machines may perform sanding or polishing between coating layers to improve surface smoothness and adhesion, especially in multi-layer coating systems. Some lines integrate in-line inspection systems using optical sensors or cameras to detect coating defects like bubbles, cracks, or uneven thickness, ensuring quality control before final packaging.
Depending on product design, machines for attaching handles, lids, or other accessories using welding or mechanical fastening may be included downstream, with care taken not to damage the nonstick surface during these operations.
Finally, automated packaging equipment prepares the finished cookware for shipment, including labeling and protective wrapping to prevent damage to the nonstick surface.
This integrated machinery setup allows manufacturers to produce high-quality nonstick cookware efficiently and consistently, combining precision metal forming with advanced surface coating technologies under controlled environmental conditions.
Machinery for producing cookware with nonstick coatings is designed to seamlessly integrate metal forming and advanced coating application processes into a continuous, efficient production line. The process begins with feeding metal sheets or coils into blanking presses that cut precise blanks for pans, pots, or lids. These blanks are then shaped through deep drawing or metal spinning machines, creating the cookware’s body with smooth contours essential for even coating adhesion.
Surface preparation is critical; therefore, the cookware passes through automated cleaning stations where chemical degreasing, ultrasonic baths, or plasma treatments remove oils, dust, and microscopic impurities. This ensures the metal surface is perfectly clean, enabling strong, uniform bonding of the nonstick layers.
Coating application machines employ robotic spray arms or dip-coating systems that apply one or more layers of nonstick materials such as PTFE or ceramic composites. These machines regulate spray pressure, nozzle movement, and coating thickness with high precision, ensuring consistent coverage across complex shapes while minimizing waste. Some advanced lines incorporate electrostatic spraying technology, which charges coating particles to improve adhesion and reduce overspray.
After coating application, the cookware moves through curing ovens where temperature and residence time are carefully controlled to chemically bond and harden the nonstick layers. Conveyor systems with heat-resistant belts or rollers transport the items through multiple curing zones, sometimes under controlled atmospheres to optimize coating properties.
Intermediate sanding or polishing machines may be integrated between coating layers to improve smoothness and adhesion. These use fine abrasives and automated brushes to gently refine the surface without damaging the underlying layers.
Inline quality inspection systems utilize high-resolution cameras, laser scanners, or ultraviolet imaging to detect surface defects such as bubbles, pinholes, or uneven coating thickness. When defects are detected, the system can trigger removal from the line or signal adjustments to coating parameters, minimizing scrap and ensuring product reliability.
Once coating is complete and quality verified, automated assembly stations attach handles, lids, or spouts using precise welding machines or mechanical fastening tools. These operations are designed to avoid contact or abrasion that could damage the nonstick surface.
Finally, the finished cookware is routed to automated packaging machines where protective films, labels, and boxing materials are applied. The packaging lines protect the delicate coating during storage and transport, enhancing product appeal and durability.
Control systems based on PLCs and industrial automation software coordinate all machinery, providing real-time monitoring of process variables, equipment status, and product quality. This integration enables manufacturers to maintain high throughput, reduce downtime, and respond quickly to production changes or quality issues.
Environmental and safety considerations are incorporated with solvent recovery systems for cleaning baths, ventilation for curing ovens, and dust extraction to maintain workplace safety and reduce emissions.
The combination of precise metal forming, advanced surface preparation, controlled coating application, rigorous curing, and thorough inspection enables production of cookware with durable, high-performance nonstick coatings suitable for modern cooking demands.
To enhance efficiency and consistency, many modern nonstick cookware production lines utilize modular automation that can be reconfigured to accommodate different product sizes, shapes, and coating types. This flexibility allows manufacturers to quickly switch between various cookware models without extensive downtime or tooling changes.
Robotic systems play a vital role in material handling and coating application, reducing human exposure to chemicals and ensuring precise, repeatable movements. Collaborative robots may assist operators in tasks requiring human judgment while maintaining high throughput and safety standards.
Advanced process control technologies collect data from sensors throughout the line—monitoring parameters such as spray thickness, curing temperature, and surface cleanliness—and feed it into analytics platforms. Machine learning algorithms analyze this data to optimize coating quality, reduce defects, and predict maintenance needs, enabling proactive interventions that minimize unplanned downtime.
To meet increasingly stringent environmental regulations, machinery often includes solvent recycling systems, closed-loop water treatment, and energy-efficient curing ovens with heat recovery. These features help reduce resource consumption, emissions, and waste generation.
Operator interfaces incorporate intuitive touchscreen controls, enabling easy adjustments, recipe management, and rapid troubleshooting. Remote monitoring and diagnostics allow supervisors and service technicians to access system status in real time, facilitating quick responses to issues regardless of location.
Safety systems integrate interlocks, emergency stops, and ventilation controls to protect personnel from chemical exposure, mechanical hazards, and thermal risks. Ergonomic design of workstations and automated material loading reduce physical strain and improve overall workplace health.
In summary, the machinery for producing nonstick coated cookware merges precise metal forming technologies with sophisticated surface treatment and coating equipment, enhanced by automation, data-driven process optimization, and environmental controls. This integrated approach allows manufacturers to deliver consistent, high-quality cookware products efficiently, safely, and sustainably.
Machinery for Polished Cookware Surfaces
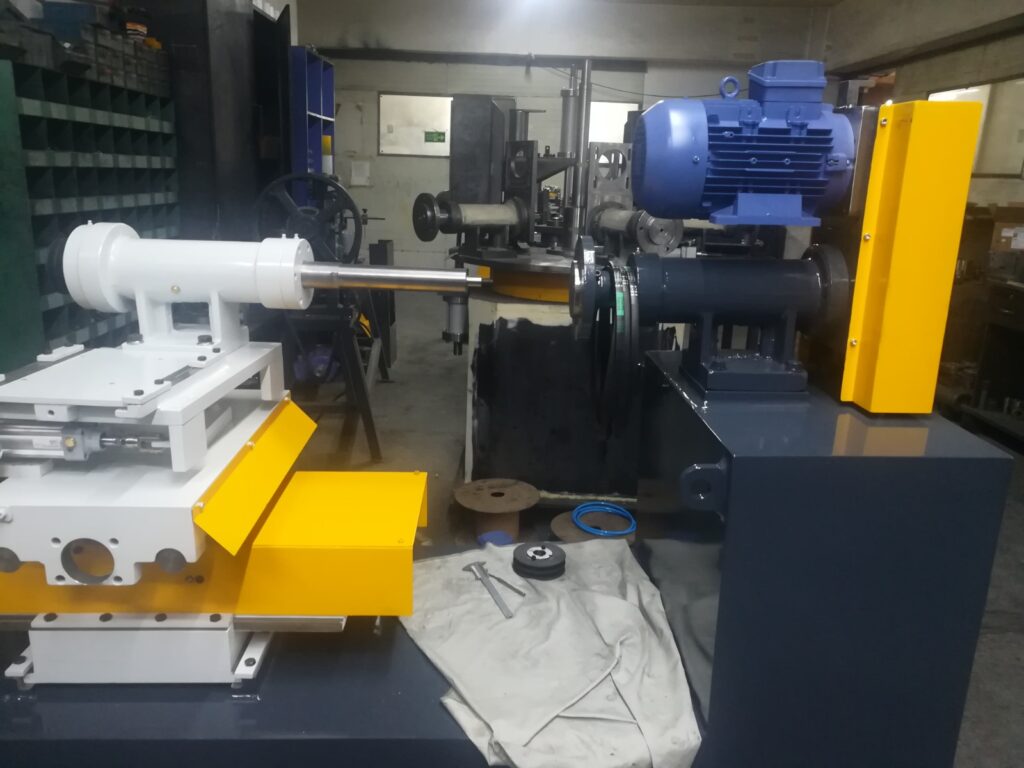
Machinery for producing polished cookware surfaces involves specialized equipment designed to achieve smooth, reflective, and aesthetically pleasing finishes on metal cookware such as pots, pans, and lids. Polishing not only enhances appearance but can also improve corrosion resistance and surface cleanliness, which is important for cookware performance and longevity.
The process usually starts after the cookware has been formed and trimmed. The cookware parts are fed into polishing machines that use abrasive belts, brushes, or wheels to remove surface imperfections, scratches, and roughness. These machines range from manual or semi-automatic bench polishers to fully automated polishing lines with robotic arms for high-volume production.
Automated polishing machines feature multiple polishing stations with varying abrasive grades, arranged in sequence to gradually refine the surface. Coarse polishing belts or pads remove major defects, while finer abrasives provide the final smooth, mirror-like finish. Some systems include buffing wheels with polishing compounds that enhance the shine and surface uniformity.
Polishing lines often incorporate vibration or rotary polishing machines, which rotate or vibrate the cookware parts against abrasive surfaces to ensure consistent contact and uniform finish. These machines can handle different shapes and sizes of cookware, including concave or convex surfaces.
For curved or complex shapes, robotic polishing systems equipped with force sensors and adaptive controls adjust pressure and speed dynamically to avoid over-polishing or deformation. Vision-guided robots use cameras and lasers to detect surface features and guide polishing tools precisely.
Before polishing, cleaning stations remove dust, oils, and residues to prevent contamination or scratching. After polishing, the cookware is cleaned again to remove polishing compounds and prepare it for subsequent coating or packaging.
Some polishing machines are equipped with coolant or lubrication systems to reduce heat buildup and extend abrasive tool life. Dust extraction and filtration systems are integrated to capture fine polishing particles, maintaining a clean and safe working environment.
Advanced polishing machinery includes automated quality inspection using optical sensors that measure surface roughness and detect defects in real time, allowing immediate correction or rejection.
Overall, polished cookware surface machinery combines mechanical abrasion, automation, and quality control to produce cookware with attractive, durable, and hygienic finishes, meeting both functional and aesthetic industry standards.
Polishing machinery for cookware often incorporates flexible fixtures and tooling to securely hold various cookware shapes—such as round pots, frying pans, or lids—ensuring consistent contact with polishing media. These fixtures enable quick changeovers between product types, boosting production efficiency.
High-capacity polishing lines may feature conveyor systems that automatically transfer cookware through multiple polishing stages. Each stage uses different abrasive materials and speeds tailored to progressively refine the surface finish, from initial grinding to fine buffing.
Robotic polishing cells utilize multi-axis arms capable of complex movements to reach hard-to-access areas, such as the inner surfaces of pots or curved edges. Force sensors integrated into the robotic end-effectors adjust polishing pressure in real time, protecting delicate cookware parts from damage while achieving uniform surface quality.
In addition to traditional abrasive belts and wheels, some polishing equipment employs advanced technologies like ultrasonic polishing or electrochemical polishing, which can further enhance surface smoothness and remove microscopic surface defects without mechanical abrasion.
Dust collection and ventilation systems are critical components of polishing machinery, capturing airborne particles generated during abrasion to maintain operator safety and comply with environmental regulations. These systems often include high-efficiency particulate air (HEPA) filters and cyclonic separators to ensure effective dust control.
Post-polishing cleaning stations use ultrasonic baths, high-pressure water jets, or chemical cleaning to eliminate residual polishing compounds and particles, preparing cookware for further processing or packaging.
Polishing machines are controlled via integrated PLC systems with user-friendly interfaces, allowing operators to set process parameters, monitor tool wear, and schedule maintenance. Data logging capabilities enable quality traceability and continuous process improvement.
By combining precision mechanical action, automation, adaptive control, and effective environmental management, polishing machinery ensures that cookware surfaces achieve the desired aesthetic and functional qualities efficiently and sustainably.
Machinery for Production of Cookware with Metal Spinning Process
Machinery for producing cookware using the metal spinning process involves specialized equipment that shapes flat metal discs or blanks into round, hollow cookware forms like pots, pans, lids, and bowls by rotating the metal at high speed and applying force with a roller or other tool.
The core machine is a metal spinning lathe, which holds a metal blank mounted on a rotating mandrel shaped like the desired cookware interior. As the mandrel spins at high RPM, a skilled operator or CNC-controlled roller tool presses against the spinning metal, gradually forming it over the mandrel’s profile. This cold forming process stretches and shapes the metal without cutting, producing seamless, smooth cookware shells with excellent structural integrity.
Modern metal spinning machines are often CNC-controlled to automate the toolpath, speed, and pressure, improving precision, repeatability, and production speed. CNC spinning machines can reproduce complex profiles and contours consistently, reducing scrap and manual labor.
The process begins with loading metal blanks—commonly aluminum, stainless steel, or copper discs—onto the mandrel. The spinning lathe’s rollers then gradually shape the metal by applying controlled pressure, moving along the mandrel’s surface. Depending on design complexity, multiple passes may be required to achieve the final form.
Supporting machinery includes:
- Blanking presses to cut raw metal sheets into discs of precise size and thickness before spinning.
- Mandrel manufacturing equipment to produce hardened, accurate mandrels tailored to specific cookware shapes.
- Tooling sets such as rollers, cones, and pads designed for various forming stages and metal types.
- Material handling systems for loading blanks and unloading finished spun parts, which can be manual or automated.
- Surface finishing stations like polishing or grinding machines to smooth spun cookware surfaces after forming.
- Quality inspection equipment using gauges and optical systems to verify dimensional accuracy and surface quality.
Metal spinning is advantageous for cookware manufacturing because it creates lightweight, seamless, and durable products with excellent strength-to-weight ratios. The process is versatile, capable of producing a wide range of sizes and shapes, and is suitable for both low and high-volume production.
Automation and CNC control have enhanced the metal spinning process by reducing operator dependency, increasing production speed, and enabling complex geometries with tight tolerances, all crucial for modern cookware manufacturing standards.
This machinery setup offers manufacturers a cost-effective, flexible, and efficient way to produce high-quality metal cookware with smooth, consistent shapes ideal for both commercial and consumer markets.
Metal spinning machinery often incorporates advanced servo motors and feedback systems to precisely control spindle speed, roller pressure, and tool path. This level of control minimizes material stress and thinning, ensuring uniform wall thickness and optimal mechanical properties in the finished cookware.
Automated loading and unloading systems improve throughput by reducing manual handling between spinning cycles. Robotic arms or conveyor-fed fixtures position blanks onto mandrels and remove finished parts, enabling continuous operation and integration with downstream finishing processes.
Tooling design is critical in metal spinning, with rollers and form tools custom-engineered from hardened materials to withstand high pressures and repeated use. Quick-change tooling systems allow rapid switches between different cookware designs, enhancing flexibility for varied product lines.
Material selection and preparation directly influence spinning quality. Pre-treated metal blanks, often annealed to increase ductility, reduce the risk of cracking or tearing during forming. Precision blanking machines ensure consistent disc dimensions, critical for maintaining process stability.
Post-spinning operations include trimming excess material from edges using hydraulic or mechanical trimming machines, followed by surface polishing and, if required, coating or anodizing to improve corrosion resistance and appearance.
Quality control is integrated throughout, with in-process sensors monitoring parameters like spindle torque and roller force to detect anomalies early. Finished parts undergo dimensional inspection with laser scanners or coordinate measuring machines to verify adherence to strict tolerances.
By combining precise mechanical forming, automation, and real-time monitoring, metal spinning machinery provides a highly efficient production method for cookware that balances strength, aesthetics, and cost-effectiveness. This technology remains a cornerstone for manufacturing seamless, high-quality metal cookware in modern industrial settings.
Modern metal spinning machines often feature multi-axis CNC capabilities, enabling complex contours and multi-step forming processes in a single setup. This reduces cycle times and eliminates the need for multiple machines, lowering overall production costs and improving consistency.
Integrated cooling and lubrication systems are essential to prevent overheating of both the tooling and the metal during high-speed spinning, which helps maintain material integrity and extends tool life. These systems precisely deliver coolants or lubricants to the contact points, reducing friction and heat buildup.
Advanced metal spinning lines may incorporate real-time vibration monitoring and adaptive control to detect and compensate for any irregularities during the spinning process. This predictive capability helps prevent defects such as wrinkling, cracking, or uneven thickness, ensuring high product quality.
In addition to traditional metals like aluminum, copper, and stainless steel, specialized spinning machinery can process exotic alloys and composite materials, expanding the range of cookware styles and performance characteristics available to manufacturers.
Integration with upstream and downstream processes—such as automatic blank feeding, trimming, polishing, coating, and packaging—allows for fully automated, end-to-end production lines. These integrated systems boost productivity, reduce labor costs, and improve traceability and quality control throughout the manufacturing chain.
User-friendly interfaces and programmable recipe management enable operators to quickly set up and switch between different cookware models, supporting flexible manufacturing and rapid response to market demands.
Environmental considerations are addressed by incorporating energy-efficient drives, waste metal recycling systems, and emissions controls, aligning metal spinning operations with modern sustainability goals.
Overall, metal spinning machinery combines precision engineering, automation, and smart process controls to produce high-quality, seamless cookware with excellent structural integrity and aesthetic appeal, meeting the rigorous demands of both commercial and consumer markets.
Machinery for Production of Forged Metal Cookware
Machinery for the production of forged metal cookware focuses on shaping cookware parts—such as pots, pans, lids, and handles—by applying compressive forces to heated metal billets or blanks. Forging enhances the strength, durability, and grain structure of the metal, resulting in cookware with superior mechanical properties compared to cast or stamped products.
The core forging machines used include:
- Hydraulic Forging Presses: These presses use hydraulic cylinders to deliver controlled, high-force compressive loads that shape heated metal billets between custom-designed forging dies. The presses can be single-action or double-action, depending on the complexity and precision needed.
- Mechanical Forging Hammers: Powered by mechanical linkages or pneumatic systems, these hammers deliver rapid, repeated blows to deform the metal billet. They are suitable for rough forging and initial shaping stages.
- Drop Forging Machines: Drop hammers that repeatedly drop a weighted ram onto the metal workpiece to shape it in dies. Often used for high-volume production where fast cycle times are needed.
- Upsetters: Specialized forging equipment that increases the diameter of metal sections by compressing lengthwise, useful for forming handles or rims.
Supporting equipment includes:
- Heating Furnaces: Induction or gas-fired furnaces heat the metal billets to the forging temperature (typically between 900–1,200°C for steels, lower for aluminum and copper alloys), ensuring the metal is ductile and workable.
- Die Manufacturing Machinery: Precision CNC milling and grinding machines create forging dies with complex cavity shapes tailored to cookware designs. Dies are made from hardened tool steels for durability.
- Trimming Presses: After forging, excess flash material around the forged part is trimmed off using hydraulic or mechanical trimming presses to achieve the final shape and dimensions.
- Heat Treatment Equipment: Post-forging heat treatment (annealing, quenching, tempering) optimizes the metal’s microstructure, enhancing strength and corrosion resistance.
- Surface Finishing Machines: Forged cookware often requires grinding, polishing, or coating to improve aesthetics and functionality.
- Material Handling Systems: Automated conveyors, robotic arms, and loading/unloading stations increase production speed and reduce manual labor.
The forging process produces cookware with improved strength, better heat conduction, and enhanced resistance to warping and impact compared to other forming methods. Forged cookware is often thicker and heavier, prized for its durability and cooking performance.
Modern forging machinery integrates CNC control, programmable forging cycles, and real-time force and position monitoring to ensure precision and repeatability. Automation reduces labor costs and improves safety by minimizing operator exposure to hot metals and heavy machinery.
Environmental controls, such as energy-efficient furnaces and scrap recycling systems, help minimize the ecological footprint of the forging process.
In summary, machinery for forged metal cookware production combines heavy-duty forging presses, precision die making, controlled heating, and finishing equipment to deliver high-performance, long-lasting cookware favored in both professional kitchens and consumer markets.
Forging machinery for cookware production often incorporates advanced hydraulic systems that allow precise control over force application, stroke length, and speed, enabling consistent shaping of metal billets with minimal defects. These systems improve material flow within the die, reducing internal stresses and enhancing the final product’s mechanical properties.
Modern forging presses are frequently equipped with CNC or programmable logic controllers (PLC) that automate the forging cycle, adjust parameters dynamically, and facilitate quick changeovers between different cookware designs. This flexibility supports both small batch runs and large-scale production with high repeatability.
Heating furnaces used in forging lines are designed for rapid, uniform heating to ensure billets reach the optimal temperature for forming while minimizing oxidation or scale formation. Induction heating systems are common due to their energy efficiency and precise temperature control. Some setups integrate inline temperature monitoring and feedback to maintain consistent heating profiles.
Forging dies are engineered with cooling channels and wear-resistant coatings to extend their lifespan and maintain dimensional accuracy over high production volumes. Quick die change systems reduce downtime, allowing manufacturers to switch between cookware models rapidly.
Post-forging, trimming presses remove flash material efficiently, often incorporating automated scrap collection and recycling systems to improve material utilization and reduce waste. Subsequent machining or grinding processes refine edges and surfaces to meet quality standards.
Integrated quality control systems use force sensors, optical inspection, and dimensional scanning to detect defects early and ensure every forged cookware piece meets tight tolerances. Data from these inspections feed into manufacturing execution systems (MES) for traceability and continuous process improvement.
Material handling automation—including robotic arms, conveyors, and palletizing systems—streamlines workflow, reduces manual labor, and enhances safety by limiting operator exposure to hot or heavy components.
Environmental considerations are addressed by optimizing furnace fuel consumption, implementing effective ventilation and dust extraction, and recycling metal scrap generated during trimming and machining.
Overall, forged cookware production machinery blends heavy-duty forging technology with automation, precise process control, and quality assurance to produce durable, high-performance cookware favored for professional culinary applications and premium consumer products.
Advanced forging lines for cookware production also incorporate simulation software during the design phase to optimize die geometry and forging parameters before actual production. This reduces trial-and-error costs, shortens development time, and helps predict material flow, stress distribution, and potential defects.
Some forging systems integrate multi-stage forging processes where a billet undergoes successive forming operations—such as pre-forging, final forging, and trimming—in a fully automated sequence. This approach enhances dimensional accuracy and material properties by controlling deformation more precisely throughout each stage.
Automation extends to billet handling with robotic loading and unloading that synchronize with forging cycles, minimizing idle time and improving throughput. These systems can include sensors and machine vision to verify billet dimensions and orientation before forging.
In addition to traditional metals like aluminum, stainless steel, and copper alloys, modern forging equipment can process specialty materials such as titanium or high-performance alloys used in cookware designed for superior heat retention or lightweight construction.
Integration with Industry 4.0 technologies enables real-time monitoring and data analytics across the forging line. Sensors track machine health, energy consumption, and product quality metrics, feeding data into centralized platforms for predictive maintenance and process optimization.
Safety systems are integral, with guards, emergency stops, and interlocks designed to protect operators from hazards associated with high-temperature materials and powerful mechanical presses.
Forged cookware machinery is often modular, allowing manufacturers to scale production capacity or add new capabilities like surface texturing or embossing without extensive retooling.
Finally, environmental sustainability is addressed through energy recovery systems, optimized furnace combustion, and closed-loop cooling, reducing the ecological footprint of forging operations.
These combined technological advances in forging machinery make it possible to produce cookware that meets demanding standards for strength, durability, and aesthetics while maintaining efficient, safe, and environmentally responsible manufacturing practices.
Machinery for Production of Clad Metal Cookware
Machinery for the production of clad metal cookware is specialized to bond multiple metal layers—typically a core metal like aluminum or copper for excellent heat conductivity, sandwiched between outer layers such as stainless steel for durability and corrosion resistance. This multi-layer construction enhances cookware performance by combining the strengths of different metals.
Key machinery and processes involved include:
Cladding Equipment:
- Roll Cladding Mills: Large rolling mills compress and bond metal sheets or strips together under high pressure, often at elevated temperatures. Precise control of rolling speed, pressure, and temperature ensures a strong metallurgical bond without damaging the individual layers.
- Explosive Cladding Systems: Although less common in cookware manufacturing, explosive bonding uses controlled detonations to join metal layers at high velocity, producing strong bonds with minimal intermetallic formation.
- Diffusion Bonding Furnaces: Used for bonding layers by applying heat and pressure over time, diffusion bonding creates molecular-level bonds without melting metals, preserving layer integrity.
Sheet Preparation and Cutting:
- After cladding, the bonded metal sheets are cut into blanks using high-precision laser cutters, blanking presses, or CNC punching machines tailored for clad materials, ensuring dimensional accuracy for subsequent forming.
Forming Machinery:
- Deep Drawing Presses: Hydraulic or mechanical presses shape the clad metal blanks into cookware forms while maintaining the integrity of the layered structure. Tooling design must accommodate multiple layers and prevent delamination.
- Hydroforming Machines: Utilize fluid pressure to form complex shapes with uniform thickness, ideal for clad cookware with intricate designs.
- Spinning Lathes: Some clad cookware parts can be formed using metal spinning with careful control to avoid layer separation.
Edge Treatment and Joining:
- Specialized edge rolling and trimming machines finish the rims and joints of cookware pieces, ensuring smooth, durable edges without compromising the clad layers.
- Welding and brazing equipment designed for clad metals securely attach handles, lids, and other components without damaging the layered construction.
Surface Finishing:
- Polishing, brushing, and passivation lines prepare the stainless steel exterior for corrosion resistance and aesthetics.
- Coating lines may apply nonstick or other functional surface treatments compatible with the clad structure.
Quality Control Systems:
- Non-destructive testing (NDT) equipment such as ultrasonic testing or eddy current inspection detects delamination or bonding defects within the clad layers.
- Dimensional inspection with laser scanners ensures form accuracy.
Automation and Material Handling:
- Robotic arms and conveyors automate material flow between cladding, cutting, forming, and finishing stages, optimizing throughput and reducing manual handling risks.
These combined technologies ensure clad metal cookware exhibits excellent thermal performance, mechanical strength, and corrosion resistance, meeting the high standards expected by professional chefs and consumers alike. The machinery is designed for precision, efficiency, and careful handling of multilayer materials to maintain the integrity of the clad construction throughout manufacturing.
The production of clad metal cookware requires tightly controlled process parameters throughout to maintain the bond quality and layer uniformity. Rolling mills must precisely regulate pressure and temperature to avoid defects such as wrinkles, voids, or layer separation. Advanced sensor systems monitor these variables in real-time, enabling immediate adjustments and ensuring consistent clad sheet quality.
Following cladding, the cutting and blanking operations use high-precision CNC machines equipped with tooling designed to handle multilayer sheets without causing delamination. These machines often have cooling and lubrication systems to prevent heat buildup and reduce mechanical stresses during cutting.
Forming machines like hydraulic deep drawing presses employ specially engineered dies with surface coatings and polishing to minimize friction and layer damage. The forming speed and stroke profiles are carefully programmed to accommodate the different ductility and deformation behavior of each metal layer, preserving the clad structure throughout shaping.
Hydroforming techniques offer advantages for complex or seamless cookware shapes by applying uniform fluid pressure, which reduces localized stresses and potential separation between layers. This method is increasingly popular for premium clad cookware designs requiring smooth contours and high dimensional accuracy.
Edge finishing processes are crucial because exposed edges are potential weak points for corrosion or layer separation. Edge rolling machines and trimming presses must ensure smooth, uniform edges with no cracks or gaps. In some cases, laser welding or brazing is employed to seal edges or attach handles and lids, using filler materials and parameters optimized for clad metals to maintain bond integrity.
Surface finishing lines are equipped to treat clad cookware exteriors delicately, often involving multi-stage polishing, brushing, and passivation to enhance corrosion resistance and aesthetic appeal without damaging the layered structure. Some manufacturers integrate coating lines applying nonstick or ceramic layers, which require precise surface preparation and environmental controls.
Throughout the production line, quality assurance systems employ ultrasonic or eddy current inspection to detect any internal flaws or delamination within the clad layers before assembly. High-resolution laser scanners measure geometry and thickness, ensuring every piece meets tight tolerances.
Automation plays a significant role, with robotic material handlers, conveyors, and loading systems synchronized to maintain smooth transitions between manufacturing steps, reducing handling damage risk and improving productivity. Centralized control systems collect process data for real-time monitoring and long-term analysis, enabling continuous improvement and traceability.
Environmental controls include energy-efficient rolling mill drives, advanced furnace technologies for any required heat treatments, and recycling systems for metal scrap generated during cutting and trimming, supporting sustainable manufacturing practices.
In summary, machinery for clad metal cookware production integrates precision rolling, cutting, forming, and finishing equipment with sophisticated monitoring, automation, and quality control systems. This ensures the final cookware products combine the best properties of multiple metals—superior heat conduction, durability, and corrosion resistance—delivered consistently at scale to meet consumer and professional demands.
Clad metal cookware production lines often incorporate modular designs, allowing manufacturers to adapt machinery configurations based on specific product types, metal combinations, and production volumes. This flexibility supports rapid switching between different clad constructions, such as stainless steel-aluminum-stainless steel, copper-stainless steel, or other specialized multilayer assemblies.
Roll cladding mills feature adjustable roll gaps, cooling systems, and variable speed drives to accommodate varying metal thicknesses and alloy properties. Some advanced mills use multi-roll configurations for enhanced bonding pressure distribution and improved sheet flatness. These mills are often paired with surface cleaning stations to remove oxides or contaminants before bonding, which is critical for achieving high-quality metallurgical bonds.
Cutting and blanking stations integrate automated loading and stacking systems that reduce manual handling and optimize material flow. Tooling materials and coatings are selected to withstand the increased wear from processing harder clad sheets and to maintain sharp cutting edges for precision blanking.
During forming, the use of computer-controlled servo presses and hydroforming machines enables precise control over force application and deformation rates. This is especially important when working with clad metals, as differing mechanical properties of layers require tailored forming strategies to prevent cracking or delamination.
Robotic welding systems used for attaching handles and assembling multi-component cookware are programmed with specialized parameters to handle clad metals. Techniques such as laser welding or TIG welding with filler materials compatible with both core and cladding metals ensure strong, durable joints without compromising layer integrity.
Surface finishing equipment often includes automated polishing and brushing machines capable of producing various finishes—from mirror-polished to matte textures—while maintaining consistent quality across batches. Passivation lines apply chemical treatments to enhance corrosion resistance, especially for stainless steel surfaces.
Inspection and testing stations employ cutting-edge non-destructive evaluation technologies, including phased-array ultrasonic testing, to detect subsurface defects or bonding irregularities invisible to the naked eye. Inline thickness measurement systems verify that clad layers meet specified dimensions, critical for performance consistency.
Data from sensors and inspection devices feed into manufacturing execution systems (MES) and quality management software, enabling traceability from raw material through final product. This data-driven approach supports compliance with industry standards and customer specifications.
Energy efficiency and environmental sustainability are priorities, with many production lines incorporating regenerative drives, waste heat recovery from rolling mills and furnaces, and water recycling in cooling and cleaning processes. Scrap metal is systematically collected and recycled to minimize waste and reduce raw material costs.
Together, these machinery and process innovations ensure clad metal cookware production is precise, efficient, flexible, and sustainable, meeting the high expectations of both manufacturers and end-users in a competitive market.
Machinery for Production of Anodized Aluminum Pans
Machinery for production of anodized aluminum pans combines precision metal forming equipment with specialized surface treatment systems to produce durable, corrosion-resistant cookware with enhanced aesthetics and performance.
The process typically starts with high-quality aluminum sheet or coil fed into cutting and blanking machines that prepare precise blanks for pan forming. These blanks then move to deep drawing or hydroforming presses that shape the aluminum into pan bodies, rims, and lids while maintaining dimensional accuracy and surface integrity.
After forming, the pans undergo trimming and edge finishing using automated trimming presses and edge rollers to ensure smooth, safe edges and consistent dimensions.
The key step unique to anodized aluminum pans is the anodizing line. This includes a series of stages:
- Cleaning and Degreasing: Automated washing tanks remove oils, dirt, and surface contaminants to prepare the aluminum for anodizing.
- Etching and Brightening: Chemical baths roughen and brighten the surface to ensure uniform anodic layer formation.
- Anodizing Tanks: Large electrolytic tanks apply controlled electric current through the aluminum parts submerged in acidic electrolytes (typically sulfuric acid), forming a hard, porous aluminum oxide layer. The machinery includes power supplies with precise current and voltage controls to regulate layer thickness.
- Sealing: After anodizing, pans are immersed in sealing tanks (hot water or steam) to close the porous oxide layer, enhancing corrosion resistance and surface hardness.
- Drying and Inspection: Automated drying systems prepare pans for quality control, where surface thickness, hardness, and uniformity are inspected using specialized gauges and sensors.
Optional steps may include dyeing or coloring tanks for decorative anodized finishes, followed by protective coating applications like nonstick layers.
Throughout the anodizing process, robotic handling systems transfer pans between tanks and rinse stations, minimizing manual labor and contamination risks.
Supporting equipment includes water treatment and recycling systems for managing chemical effluents, ensuring compliance with environmental regulations.
Integration with automated production lines allows synchronization of forming, anodizing, finishing, and packaging steps, boosting throughput and consistency.
This machinery ensures aluminum pans gain a durable, wear-resistant surface with enhanced corrosion protection and aesthetic appeal, making anodized aluminum cookware popular for both commercial and consumer markets.
Anodized aluminum pan production machinery is designed for high efficiency and precise control over each stage to ensure consistent quality and performance. The forming presses used are often hydraulic or servo-driven to provide smooth, adjustable pressure that shapes aluminum blanks without cracking or deforming the metal. Tooling is carefully engineered and polished to minimize surface defects that could affect anodizing results.
After forming, automated trimming and edge finishing machines quickly and accurately remove excess material and create uniform rims, which are critical for pan durability and user safety. These machines often include sensors to detect dimensional deviations and trigger adjustments or rejects.
The anodizing line itself is a complex system of tanks and conveyors, with programmable logic controllers (PLCs) managing timing, electrical parameters, and chemical flow. Water spray rinse stations between tanks remove residual chemicals, preventing contamination and ensuring uniform oxide layer formation. The electrical power supplies used in anodizing must maintain stable current and voltage levels to control oxide thickness precisely, which directly affects wear resistance and appearance.
Sealing tanks use hot deionized water or steam at controlled temperatures and durations to effectively close the porous anodic layer, locking in the protective properties. Cooling and drying systems after sealing prepare pans for further processing or inspection.
Surface inspection stations use non-contact measurement tools, such as eddy current sensors or optical scanners, to verify layer thickness, surface uniformity, and detect defects like pits or uneven anodizing. Automated rejection systems remove defective parts, maintaining high quality standards.
Optional dyeing processes allow manufacturers to add vibrant colors by immersing anodized pans in dye baths before sealing. These tanks are carefully monitored for temperature, dye concentration, and immersion time to achieve consistent hues.
To enhance corrosion resistance and user experience, some production lines include automated application of nonstick coatings after anodizing. These coating systems use spray or roller technologies, followed by curing ovens that bake the coatings to durability.
Robotic arms and conveyors throughout the production line ensure smooth handling, reducing manual contact that could damage anodized surfaces. This automation also increases throughput and consistency while lowering labor costs.
Wastewater treatment plants integrated with the anodizing facility treat acidic effluents and heavy metals to meet environmental regulations. Closed-loop water recycling minimizes fresh water consumption and chemical waste.
Data acquisition and process monitoring software collect real-time information on all parameters, enabling predictive maintenance and process optimization. This digital integration helps manufacturers maintain consistent quality and reduce downtime.
Overall, machinery for anodized aluminum pan production combines advanced metal forming, chemical processing, and automated handling to produce cookware with superior durability, corrosion resistance, and attractive finishes suitable for commercial kitchens and household use.
To further optimize anodized aluminum pan production, manufacturers often integrate advanced automation technologies such as machine vision systems for detailed surface inspection. These vision systems can detect microscopic defects, discolorations, or surface inconsistencies that are invisible to the naked eye, ensuring only pans that meet strict quality criteria proceed to packaging.
The production line may also feature robotic loading and unloading stations that carefully transfer pans between forming, anodizing, and finishing stages. This minimizes handling damage and contamination, which is particularly important since anodized surfaces are porous and can be prone to staining before sealing.
In some setups, the anodizing line is modular, allowing manufacturers to scale production up or down or switch between different anodizing recipes based on product requirements. For example, thicker anodic layers can be produced for heavy-duty cookware, while thinner layers may be sufficient for lightweight pans. The flexibility of this machinery setup supports a wide range of pan sizes, shapes, and custom surface finishes.
Energy efficiency is another key consideration. Modern anodizing systems utilize power supplies with energy recovery features and process heat exchangers to reduce overall electricity and water usage. These sustainable technologies help manufacturers lower operational costs and meet environmental regulations more easily.
Furthermore, integration with enterprise resource planning (ERP) and manufacturing execution systems (MES) enables seamless tracking of production batches, raw material usage, and quality metrics. This traceability is essential for warranty management, product recalls, and continuous improvement initiatives.
Maintenance of anodizing equipment is facilitated by predictive diagnostics and remote monitoring, which alert operators to potential issues such as electrolyte contamination or power supply degradation before they cause defects or downtime. Scheduled maintenance routines based on actual equipment condition increase uptime and reduce unexpected breakdowns.
Finally, post-anodizing processes may include specialized packaging machinery that applies protective films or cartons designed to prevent scratches during transport and storage. Automated labeling systems print batch codes and product information, ensuring compliance with regulatory standards and facilitating supply chain management.
In summary, the machinery for anodized aluminum pan production encompasses highly automated forming, chemical treatment, inspection, and finishing systems that work in concert to deliver premium cookware products with consistent quality, operational efficiency, and environmental responsibility.
Machinery for Production of Carbon Steel Pans
Machinery for production of carbon steel pans focuses on robust metal forming, surface treatment, and finishing equipment tailored to handle the unique properties of carbon steel, ensuring durable, high-quality cookware suited for heavy-duty cooking applications.
The process begins with feeding carbon steel sheets or coils into cutting and blanking machines that produce precise circular blanks for pan bodies and lids. These machines typically use high-strength steel tooling to cut through the tougher material efficiently while minimizing burrs and edge defects.
Next, deep drawing or hydraulic pressing machines shape the blanks into pan bodies. Carbon steel’s higher tensile strength and lower ductility compared to aluminum require presses capable of delivering greater force with controlled deformation speeds to prevent cracking or wrinkling. Tooling is often specially coated or treated to reduce friction and wear during forming.
Following forming, trimming presses remove excess flange material and ensure uniform rim dimensions. Edge rolling or curling machines then create rolled rims to enhance strength and user safety. Some production lines use flanging machines to prepare the rims for handle attachment.
Surface preparation is a critical step since carbon steel pans are prone to rusting if not properly treated. Machinery for surface cleaning includes abrasive blasting units or shot peening systems that remove mill scale, rust, and surface imperfections while improving adhesion for subsequent coatings or seasoning.
Depending on the production style, pans may pass through pre-seasoning ovens that heat the steel at controlled temperatures to create a stable oxide layer, reducing initial rust formation. Automated seasoning lines spray or apply seasoning oils and bake the pans in curing ovens to develop a natural nonstick surface favored by many chefs.
For handle attachment, robotic or semi-automatic welding stations (such as spot welding, arc welding, or resistance welding machines) join handles securely to pan bodies. Precision fixtures and jigs ensure consistent placement and strong welds while minimizing distortion.
Finishing machines include polishing or buffing systems that smooth edges and surfaces for aesthetics and user comfort. Some manufacturers incorporate powder coating or enamel coating lines, where spray booths and curing ovens apply protective finishes that enhance corrosion resistance and color options.
Inspection stations equipped with dimensional gauges, surface roughness testers, and visual inspection cameras verify product quality throughout the process. Automated rejection systems remove defective units, maintaining stringent quality standards.
Packaging machinery wraps pans with protective materials to prevent scratches during shipping and applies labeling for branding and traceability.
Supporting equipment includes conveyor systems, robotic material handlers, and centralized control units integrating production data for process optimization.
In essence, machinery for carbon steel pan production combines heavy-duty forming presses, surface treatment systems, welding stations, and finishing lines designed to handle carbon steel’s characteristics, delivering cookware that balances durability, performance, and traditional cooking appeal.
Carbon steel pan production lines are typically built for durability and flexibility, accommodating various pan sizes and shapes while maintaining high throughput. The forming presses used are often hydraulic or mechanical, capable of delivering the high tonnage needed to shape thicker steel sheets without causing cracks or defects. Tooling materials are selected for wear resistance and low friction to extend service life and maintain consistent quality.
After forming, trimming machines precisely remove excess flange material to ensure uniform rim dimensions, which is crucial for pan stability and handle attachment. Edge rolling or curling machines then create rounded rims, enhancing strength and preventing sharp edges that could cause injury or damage during use.
Surface preparation equipment is essential due to carbon steel’s susceptibility to oxidation. Shot blasting or abrasive blasting machines clean the pan surfaces thoroughly, removing mill scale and any residual oils or contaminants. This process not only prepares the surface for seasoning or coatings but also improves adhesion.
Pre-seasoning ovens heat the pans to a controlled temperature, allowing a thin, protective oxide layer to form. This step is sometimes combined with automated seasoning systems that apply food-grade oils or waxes uniformly across pan surfaces. Baking ovens cure the seasoning layer, creating a semi-permanent, natural nonstick surface favored in professional kitchens.
For handle attachment, welding stations equipped with robotic arms or precision jigs ensure secure and consistent welding of steel, stainless steel, or cast iron handles. These systems often include spot welding or resistance welding methods, which produce strong joints with minimal heat distortion.
Polishing and buffing machines smooth surfaces and edges to provide a clean, professional finish. In some lines, powder coating or enamel coating stations spray protective layers that enhance corrosion resistance and aesthetic appeal. Curing ovens then bake these coatings for durability.
Inspection stations employ optical sensors, laser measurement tools, and manual checks to verify dimensions, surface quality, and weld integrity. Automated rejection systems divert defective pans to maintain quality standards.
Conveyor systems, robotic handlers, and automated packaging equipment streamline material flow, reduce labor, and protect finished products during shipping. Integrated control systems monitor production parameters, enabling real-time adjustments and data collection for quality control and process optimization.
Environmental controls and dust collection systems are included to maintain workplace safety and compliance with regulations during abrasive blasting and welding operations.
Overall, machinery designed for carbon steel pan manufacturing emphasizes strength, precision, and surface treatment to produce cookware that withstands rigorous use while offering traditional cooking performance and natural nonstick qualities through seasoning.
To enhance production efficiency and product consistency in carbon steel pan manufacturing, many modern facilities incorporate automation and digital controls throughout the line. Programmable logic controllers (PLCs) coordinate presses, welding stations, surface treatment units, and inspection devices to synchronize timing and reduce bottlenecks.
Advanced sensor arrays monitor critical parameters such as forming pressure, temperature in seasoning ovens, and welding current, providing real-time feedback to adjust processes dynamically. This reduces material waste and rework by catching deviations early.
Robotic arms handle repetitive tasks like loading/unloading blanks, positioning pans for welding, and transferring finished products between stations. This not only speeds up the line but also minimizes operator fatigue and safety risks.
Maintenance is streamlined through predictive analytics integrated into machinery, alerting technicians to wear patterns on tooling, hydraulic fluid conditions, or electrical component performance before failures occur. Scheduled maintenance can then be planned to minimize downtime.
Sustainability measures are increasingly common, such as water recycling in surface preparation systems, energy-efficient ovens with heat recovery, and dust extraction systems with particulate filtration to reduce environmental impact.
Customized modular production lines allow manufacturers to adapt quickly to different pan designs, sizes, or surface finishes without extensive retooling, improving market responsiveness.
Quality management software ties together inspection data, process parameters, and production output, enabling traceability of each pan back to raw material batches and machine settings. This facilitates continuous improvement and compliance with customer or regulatory standards.
In summary, carbon steel pan manufacturing machinery today blends heavy-duty forming equipment with precise surface treatment, automated handling, and integrated digital controls, delivering durable, high-quality cookware with efficient, adaptable production capabilities.
Machinery for production of nonstick cookware involves specialized equipment designed to form, treat, coat, and finish cookware surfaces that provide durable, easy-release cooking performance. The manufacturing process integrates traditional metal forming with advanced coating technologies to produce high-quality nonstick pans, pots, and other items.
The process typically begins with metal sheet feeding, cutting, and blanking machines that prepare precise metal blanks for forming. These machines handle aluminum, stainless steel, or other substrates suited for nonstick coating application.
Forming presses—such as hydraulic deep drawing or spinning lathes—shape the metal blanks into cookware bodies with consistent dimensions and smooth surfaces critical for coating adhesion. Tooling used here is precision-engineered to minimize surface defects and ensure uniform wall thickness.
Surface preparation is crucial for nonstick cookware. Specialized cleaning systems—often multi-stage washers, chemical etching tanks, or abrasive blasting units—thoroughly remove oils, oxides, and contaminants to optimize surface roughness for coating adhesion.
Coating application machinery includes automated spray booths or roll-coating lines that evenly apply primers and nonstick coatings, typically fluoropolymer-based (like PTFE) or ceramic formulations. These coating systems often feature robotic arms or conveyorized spray nozzles for consistent coverage and thickness control.
Curing ovens follow, where coated cookware passes through precisely controlled heat zones that polymerize and bond the nonstick layers to the substrate. These ovens use convection or infrared heating to ensure uniform curing without damaging the metal base.
In some lines, multiple coating layers are applied with intermediate curing steps to build up the desired nonstick performance and durability.
After coating, finishing machinery performs edge smoothing, handle attachment via welding or riveting, and quality inspections. Inspection stations employ optical sensors, thickness gauges, and adhesion testers to verify coating integrity and product specifications.
Packaging equipment prepares the cookware for shipment, often including protective films or cartons to prevent surface damage.
Supporting systems include conveyor belts, robotic handling, and integrated production control units that synchronize coating application, curing, and inspection for optimized throughput.
Environmental controls are essential due to volatile organic compounds (VOCs) and particulates generated during coating and curing. Thus, extraction and filtration systems maintain operator safety and regulatory compliance.
Overall, machinery for nonstick cookware production combines metal forming, advanced surface treatment, automated coating application, and precise curing technology, enabling manufacturers to produce cookware that delivers superior cooking performance, durability, and consumer appeal.
Nonstick cookware production lines are carefully designed to maintain a clean, controlled environment, as contamination during coating application can adversely affect product quality. Automated feeding systems ensure a steady supply of blanks to forming presses, reducing manual handling and minimizing surface damage. The forming processes use carefully calibrated force and speed to produce consistent shapes with smooth surfaces, which is critical for subsequent coating adhesion.
Surface preparation is typically multi-step, involving mechanical cleaning like abrasive blasting or brushing, followed by chemical treatments that etch the metal slightly to promote primer and coating adhesion. This preparation must be thorough yet gentle to avoid surface defects that can cause coating failures.
Coating application machinery often incorporates robotic spray arms or precision nozzles arranged on automated conveyors, providing uniform layer thickness and reducing overspray. Process parameters such as spray pressure, nozzle angle, and coating viscosity are tightly controlled. Some facilities employ electrostatic spray coating systems to increase transfer efficiency and reduce waste.
Curing ovens are calibrated to maintain exact temperature profiles, with zones for preheating, curing, and cooling. Uniform heat distribution is vital to ensure complete polymerization of the nonstick coatings without overheating, which can degrade the metal substrate or cause coating blistering.
Multiple coating layers may be applied sequentially, including primers for adhesion, base nonstick layers, and topcoats for scratch resistance and enhanced release properties. Between coating steps, inline quality checks such as thickness measurements and surface inspections identify defects early.
After coating and curing, finishing stations perform critical functions including edge rounding to eliminate sharpness, handle assembly through automated welding or riveting, and visual inspection. Optical and laser-based measurement tools verify coating uniformity, pan dimensions, and handle alignment, ensuring products meet stringent quality standards.
The packaging stage employs automated wrapping and boxing equipment designed to protect delicate coated surfaces from scratches during transport. Some lines integrate inline labeling and serialization for traceability.
Throughout the production line, centralized control systems monitor all machinery and process parameters, enabling rapid adjustments to maintain product quality and throughput. Data collection supports statistical process control and continuous improvement initiatives.
Environmental management includes ventilation, solvent recovery, and particulate filtration systems to minimize emissions and ensure worker safety. Many manufacturers invest in closed-loop water and air recycling systems to reduce environmental impact.
In summary, manufacturing machinery for nonstick cookware integrates precision metal forming, advanced surface preparation, automated coating application, and rigorous quality control within a highly automated and environmentally controlled production line. This ensures the final cookware products combine durability, excellent nonstick performance, and consumer appeal at high manufacturing efficiency.
Modern nonstick cookware production increasingly incorporates Industry 4.0 technologies to further enhance efficiency, quality, and traceability. Sensors embedded throughout the production line collect real-time data on variables such as forming pressures, coating thickness, oven temperatures, and line speeds. This data feeds into centralized manufacturing execution systems (MES), enabling predictive maintenance, process optimization, and rapid troubleshooting.
Robotic automation reduces human error and variability, especially in coating application and handle assembly. Advanced vision systems inspect pans at multiple stages for surface defects, coating inconsistencies, or dimensional deviations, automatically diverting nonconforming products before further processing.
Flexible manufacturing cells allow quick changeovers to different cookware sizes, shapes, or coating types with minimal downtime, supporting customized or limited-run production alongside mass manufacturing.
Energy-efficient curing ovens utilize infrared or microwave heating, reducing energy consumption and cycle times. Some lines integrate real-time coating cure monitoring using infrared spectroscopy or other sensor technologies to ensure optimal bonding without overheating.
Sustainability efforts include replacing solvent-based coatings with waterborne formulations and implementing closed-loop solvent recovery systems to minimize VOC emissions. Recycling scrap metal and overspray coating materials further reduce waste.
Ergonomic design and safety features in machinery protect operators from exposure to fumes, moving parts, and high temperatures, complying with strict workplace safety regulations.
Overall, these innovations make nonstick cookware production machinery more adaptive, precise, and environmentally friendly, enabling manufacturers to meet growing consumer demands for quality, performance, and sustainability in cookware products.
Machinery for Production of Copper Cookware
Machinery for production of copper cookware is specialized to handle the unique properties of copper—its high thermal conductivity, malleability, and softness—which require careful forming, joining, and finishing processes to produce durable, high-quality cookware.
The production line typically begins with copper sheet feeding and blanking machines that cut copper sheets into precise circular or shaped blanks sized for various cookware pieces. These machines are designed to handle copper’s softness without causing surface scratches or deformation.
Forming equipment includes hydraulic presses, deep drawing machines, and metal spinning lathes that shape the copper blanks into pots, pans, or lids. Due to copper’s ductility, forming tools are polished and lubricated to prevent galling and surface damage, ensuring smooth, uniform surfaces that are critical for cookware performance and aesthetics.
Annealing ovens are often integrated into the line to soften copper between forming steps, preventing cracking or work hardening during multiple forming stages. Controlled heating cycles restore copper’s ductility and allow more complex shapes to be achieved without defects.
Trimming machines accurately remove excess flange material after forming, preparing the edges for further processing like rim rolling or handle attachment. Copper-specific edge rolling machines create smooth, rounded rims that enhance strength and safety.
Joining processes for copper cookware frequently involve brazing or soldering rather than welding, due to copper’s thermal conductivity and oxidation tendencies. Automated brazing stations with precise temperature and filler metal control join components like handles or lids. In some advanced lines, laser brazing or TIG welding adapted for copper is used to achieve clean, strong joints.
Surface finishing machinery includes mechanical polishing machines—such as buffing wheels, vibratory finishers, or abrasive belts—that bring out copper’s natural bright, reflective appearance. Electrolytic polishing or chemical patination stations may also be included to create specific aesthetic effects or protective coatings.
Cleaning and degreasing units prepare the cookware for finishing or coating applications, ensuring no residues impair appearance or corrosion resistance.
Optional plating lines may apply tin or stainless steel linings inside copper cookware to provide a safe cooking surface, using electroplating or cladding machinery designed for precise layer thickness and adhesion.
Quality inspection systems, including dimensional measurement and surface defect detection, verify that each cookware piece meets stringent standards before packaging.
Automated material handling, conveyors, and packaging equipment streamline the workflow, reducing manual labor and protecting delicate copper surfaces from scratches during handling.
Environmental controls, such as fume extraction and filtration systems, manage emissions from brazing, polishing, and cleaning operations to ensure workplace safety and compliance.
Overall, copper cookware production machinery balances careful metal forming, controlled heat treatment, precision joining, and fine surface finishing to produce cookware that highlights copper’s excellent thermal properties and timeless aesthetic appeal.
Copper cookware production machinery is carefully engineered to accommodate the softness and high thermal conductivity of copper, ensuring each stage maintains the material’s integrity and aesthetic appeal. Sheet feeding and blanking systems deliver copper sheets with precise dimensional control, often incorporating protective films or coatings to prevent surface damage during handling. Forming equipment such as hydraulic presses and deep drawing machines apply controlled pressure to shape copper blanks into the desired cookware forms without inducing cracks or distortions, with lubricants and polished tooling minimizing friction and galling.
Annealing ovens play a crucial role between forming steps, as copper work hardens rapidly; these ovens heat components to carefully controlled temperatures to restore ductility and reduce internal stresses, allowing for subsequent forming or trimming without failure. Trimming machines remove excess flange material to prepare edges for finishing or assembly, while edge rolling machines create smooth, rounded rims essential for user safety and structural integrity.
Joining copper cookware parts typically involves brazing or soldering processes, favored over welding due to copper’s high thermal conductivity and oxidation susceptibility. Automated brazing stations regulate temperature and filler materials precisely to produce clean, strong joints with minimal oxidation or distortion. In advanced production lines, laser brazing or adapted TIG welding may be utilized for efficiency and joint quality. Handle attachment mechanisms integrate brazing, riveting, or mechanical fastening systems designed to secure handles without damaging the copper body.
Surface finishing equipment includes a variety of polishing machines such as buffing wheels, vibratory finishers, and abrasive belt systems to achieve the characteristic bright, reflective copper surface. Chemical treatments like patination or electrolytic polishing may be applied to create desired finishes or improve corrosion resistance. Cleaning and degreasing units ensure surfaces are free from oils, residues, and contaminants before finishing or plating steps.
Many copper cookware lines incorporate plating or lining processes to apply tin or stainless steel layers on the interior cooking surfaces, enhancing food safety and durability. Electroplating baths or cladding machinery apply these layers uniformly, with precise thickness control critical to performance and longevity.
Throughout the line, automated conveyors and robotic handlers reduce manual contact with delicate copper surfaces, minimizing scratches and defects. Quality control systems featuring optical inspection and dimensional measurement verify surface quality, joint integrity, and compliance with specifications before packaging. Packaging machines often include soft cushioning or protective films to preserve the cookware’s finish during shipping.
Environmental control systems manage fumes and particulates from brazing, polishing, and chemical treatments, ensuring safe working conditions and regulatory compliance. Water recycling and solvent recovery units help minimize environmental impact.
Together, these specialized machines and systems form a coordinated, efficient production line capable of producing high-quality copper cookware that combines excellent heat conduction with durability and aesthetic appeal.
Advanced copper cookware production lines increasingly integrate automation and smart technologies to boost precision, efficiency, and consistency. Robotic arms and CNC-controlled forming presses allow complex shapes to be manufactured with minimal human intervention, reducing variability and scrap rates. Sensors embedded in forming tools monitor pressure, temperature, and metal thickness in real time, enabling immediate adjustments to avoid defects such as thinning or cracking.
Modern annealing ovens use precise atmosphere control to prevent oxidation during heat treatment, maintaining copper’s bright finish and material properties. Automated brazing stations employ computer-controlled temperature profiles and filler feed rates to produce uniform, strong joints with minimal rework. Vision systems inspect brazed seams to detect any flaws or misalignments automatically.
Surface finishing operations benefit from programmable polishing machines that adjust speed, pressure, and abrasive type based on cookware shape and size, ensuring consistent shine and surface texture. Some lines utilize laser cleaning and polishing techniques to enhance surface quality without mechanical contact.
In plating and lining stages, inline thickness gauges and adhesion testers verify that coatings meet strict standards, while robotic sprayers and electroplating systems ensure uniform application with minimal waste. Automated drying and curing ovens maintain optimal environmental conditions for coating durability.
Integrated material handling systems, including conveyors, robotic pick-and-place units, and automated storage, reduce manual labor and the risk of surface damage during transfer between processes. Advanced packaging machines incorporate cushioning materials tailored to protect delicate copper finishes, with options for custom labeling and traceability codes.
Data collected throughout the production line feeds into manufacturing execution systems (MES), supporting predictive maintenance, quality analytics, and continuous improvement initiatives. This data-driven approach helps manufacturers optimize throughput, reduce downtime, and maintain high-quality output in competitive markets.
Environmental sustainability is also emphasized, with water and solvent recycling systems, energy-efficient equipment, and emission control technologies minimizing the ecological footprint of copper cookware manufacturing.
Altogether, the sophisticated machinery and automation systems in modern copper cookware production combine traditional metalworking craftsmanship with cutting-edge technology, enabling efficient, high-quality, and sustainable manufacturing of premium cookware products.
Machinery for Production of Aluminum Cookware
Machinery for production of aluminum cookware is designed to handle aluminum’s lightweight, high thermal conductivity, and formability, enabling efficient shaping, joining, and finishing processes that yield durable, heat-efficient cookware.
The process typically begins with aluminum coil feeding and blanking machines that cut aluminum sheets or coils into precise blanks. These machines feature advanced control to prevent surface scratches and maintain dimensional accuracy, crucial for subsequent forming steps.
Forming machinery includes hydraulic presses, deep drawing machines, and metal spinning lathes that shape aluminum blanks into pots, pans, lids, and other cookware parts. Aluminum’s ductility allows for relatively high-speed forming, but tooling is designed with polished surfaces and optimized lubrication to avoid galling and surface defects.
Annealing ovens are integrated in many production lines to soften aluminum between forming stages, reducing work hardening and preventing cracking. Precise temperature control during annealing ensures consistent material properties across batches.
Trimming machines cleanly remove excess flange material from formed parts, preparing edges for rim rolling or assembly. Edge rolling and curling machines create smooth, rounded rims to improve strength and safety.
Joining methods commonly include TIG welding, laser welding, or resistance welding, suitable for aluminum’s thermal properties. Automated welding stations maintain consistent weld quality while minimizing distortion and heat-affected zones. For parts that require handle attachment, riveting or mechanical fastening machines are also used.
Surface finishing equipment includes mechanical polishing machines—such as abrasive belts, buffing wheels, or vibratory finishers—that provide a smooth, shiny appearance. Some production lines incorporate anodizing tanks where aluminum cookware undergoes electrochemical surface treatment to enhance corrosion resistance and provide decorative finishes.
Cleaning and degreasing stations ensure all surfaces are free of oils and contaminants before finishing or coating. Nonstick coating application systems, including robotic spray booths or roller coaters, apply uniform layers of PTFE or ceramic coatings. Curing ovens then bake coatings to ensure adhesion and durability.
Automated quality inspection systems use vision sensors and laser scanners to detect dimensional deviations, surface defects, coating uniformity, and weld integrity. Defective pieces are automatically removed to maintain product standards.
Material handling systems such as conveyors, robotic arms, and automated storage reduce manual handling, protecting surfaces and increasing efficiency. Packaging machines finalize the process with protective padding and customized labeling for shipping.
Environmental controls manage emissions from welding, coating, and cleaning processes, employing fume extraction and solvent recovery systems. Many modern aluminum cookware lines focus on energy efficiency, water recycling, and waste reduction to meet sustainability goals.
Overall, aluminum cookware manufacturing machinery blends high-speed forming, precision welding, advanced surface treatment, and automated quality control to produce lightweight, durable, and visually appealing cookware suitable for modern kitchens.
Aluminum cookware production lines emphasize speed and precision to capitalize on aluminum’s excellent formability and thermal properties. Coil-fed blanking machines deliver consistent, smooth aluminum blanks, while servo-driven presses and deep drawing equipment shape the cookware efficiently with minimal material waste. These machines feature adjustable parameters to handle various thicknesses and cookware sizes, allowing flexible production runs.
Annealing ovens positioned between forming steps carefully regulate temperature and atmosphere to soften aluminum and relieve stresses, preventing cracking during deep draws or complex shapes. Automated trimming machines swiftly remove excess edges, with integrated scrap collection systems that recycle leftover aluminum.
Rim rolling and edge curling machines finish the cookware rims to enhance strength and safety, producing clean, uniform edges suitable for subsequent handle attachment. Handle assembly lines combine automated riveting, welding, or mechanical fastening stations designed to secure handles reliably without damaging the aluminum body.
Welding stations equipped with TIG or laser welding technology deliver precise, clean welds on aluminum parts, essential for cookware durability and appearance. These systems often include robotic arms programmed for complex weld paths, reducing labor and improving repeatability.
Surface finishing incorporates multi-stage polishing lines with abrasive belts, buffing wheels, and vibratory finishers to achieve smooth, attractive surfaces. Many lines integrate anodizing tanks where cookware pieces undergo electrochemical treatment, boosting corrosion resistance and offering a range of colors and finishes to meet market demands.
Nonstick coating lines apply PTFE, ceramic, or hybrid coatings using robotic sprayers or rollers, ensuring even coverage. Curing ovens bake these coatings at controlled temperatures to optimize adhesion and wear resistance, critical for cookware longevity.
Inline quality control systems utilize high-resolution cameras and laser scanners to inspect dimensions, surface finish, coating uniformity, and weld integrity. Defect detection algorithms enable real-time sorting, minimizing downstream rework or customer returns.
Automated material handling systems—including conveyors, robotic pick-and-place units, and automated guided vehicles (AGVs)—streamline workflow, reduce handling damage, and improve throughput. Packaging machines wrap cookware with protective materials and add customized labels or barcodes, facilitating traceability and retail readiness.
Environmental management is integral, with fume extraction systems capturing welding smoke and coating solvents, water treatment plants recycling rinse water from anodizing and cleaning processes, and energy-efficient equipment reducing operational costs and carbon footprint.
Together, these advanced machinery and process integrations create highly efficient aluminum cookware manufacturing lines that deliver consistent quality, scalability, and sustainability to meet global market needs.
Machinery for Production of Cast Iron Cookware
Machinery for production of cast iron cookware is specialized to handle the heavy, dense material and complex shapes typical of cast iron pots, pans, and skillets, focusing on molding, casting, finishing, and heat treatment processes that ensure durability and excellent cooking performance.
The production begins with molding machines, which prepare sand molds or other refractory molds for casting. These can be automatic or semi-automatic molding lines that compact and shape the molding sand around pattern tools to form precise cavities matching the cookware design. Core-making machines produce internal sand cores when hollow or intricate shapes are required.
Once molds and cores are prepared, the casting process takes place in foundry equipment where molten cast iron is poured into the molds. Furnaces—typically induction or cupola furnaces—melt iron scrap and alloys to produce molten metal at controlled temperatures. Automated pouring systems deliver molten iron efficiently and safely into molds, minimizing defects like cold shuts or misruns.
After cooling, shakeout machines and mold stripping equipment separate the solidified cast iron cookware from the sand molds. This is followed by shot blasting or sandblasting machines that clean residual sand and scale from the surface, preparing the castings for further processing.
Heat treatment ovens perform annealing or stress-relief cycles to improve mechanical properties, reduce internal stresses, and enhance toughness of the cast cookware.
Finishing machinery includes grinding and machining centers that trim excess metal from casting gates and risers, machine flat surfaces, and refine dimensions to ensure consistent fit and finish. CNC machining centers provide precision in critical areas like flat bottoms or handle attachments.
Surface treatment systems include shot blasting, grinding, and polishing machines that produce smooth or textured finishes depending on product specifications. Seasoning ovens bake protective coatings or pre-season layers onto the cookware surface, improving corrosion resistance and preparing it for consumer use.
Automated inspection systems using vision technology and coordinate measuring machines (CMM) check dimensional accuracy, surface defects, and structural integrity, ensuring consistent quality.
Material handling systems such as conveyors, robotic arms, and cranes facilitate the movement of heavy castings safely between stages, reducing manual labor and damage risk.
Packaging machinery is adapted to handle heavy cookware, using protective padding and sturdy materials to prevent damage during transport.
Environmental control equipment manages dust, fumes, and waste generated by molding, casting, and finishing processes, incorporating dust collectors, scrubbers, and recycling units to minimize environmental impact.
Together, this machinery suite enables efficient, precise, and safe manufacturing of durable cast iron cookware products known for their heat retention, longevity, and cooking performance.
Cast iron cookware production lines integrate advanced automation to enhance efficiency while managing the heavy and abrasive nature of the material. Modern molding machines utilize automated sand handling, mixing, and compaction systems to produce consistent molds with minimal human intervention. Core shooters create complex internal geometries with high precision, enabling sophisticated cookware designs such as multi-chambered pots or intricate handle features.
Furnaces equipped with automated controls maintain stable temperatures for melting cast iron, allowing for consistent metal quality and composition. Automated pouring systems use robotics or mechanized arms to deliver molten iron precisely into molds, reducing the risk of spillage and improving worker safety. Continuous monitoring of molten metal temperature and flow ensures optimal casting conditions to minimize defects.
After solidification, shakeout machines separate castings from molds efficiently, while dust suppression systems reduce airborne particulate matter. Shot blasting and vibratory finishing machines clean the rough cast surface, removing sand residues and preparing the cookware for machining.
CNC machining centers perform precise trimming, surface milling, and hole drilling to meet dimensional tolerances and prepare cookware for assembly or packaging. These centers can also machine flat cooking surfaces or intricate details on handles and rims, improving product uniformity and aesthetics.
Heat treatment ovens operate on programmable cycles to relieve stresses and condition the cookware for durability and resistance to cracking. Seasoning ovens apply pre-treatment layers that facilitate initial rust protection and improve seasoning adherence during consumer use.
Quality inspection uses laser scanning and vision systems to detect surface irregularities, measure dimensional accuracy, and verify structural integrity. Any defective units are automatically removed to maintain high product standards.
Material handling throughout the line is optimized with conveyors, robotic pickers, and heavy-duty cranes to transport cookware safely and reduce manual labor risks associated with heavy cast iron parts. These systems are designed to handle the high weight and prevent surface damage.
Packaging stations use custom foam inserts, heavy-duty cartons, and automated strapping to protect cookware during shipping, ensuring products reach customers intact.
Dust collection and fume extraction systems capture particulate and gaseous emissions from molding, casting, and finishing operations, maintaining regulatory compliance and worker safety. Sand reclamation units recycle spent molding material, improving sustainability and cost efficiency.
Overall, cast iron cookware machinery blends robust heavy-duty equipment with automation and precise control to produce high-quality, long-lasting cookware capable of meeting both traditional craftsmanship standards and modern manufacturing efficiency.
The integration of robotic automation in cast iron cookware manufacturing continues to advance, improving both productivity and safety. Robotic arms are increasingly deployed in mold handling, core placement, and pouring operations to reduce human exposure to high temperatures and heavy loads. These robots are equipped with vision systems and force feedback to handle molds delicately, ensuring precise alignment and reducing mold damage.
Advanced simulation software models casting flow and solidification to optimize mold design and pouring parameters, minimizing defects like porosity, shrinkage, and cracking. This predictive approach leads to fewer rejects and higher overall yield.
Additive manufacturing (3D printing) is beginning to complement traditional pattern-making by producing complex and precise patterns or cores rapidly, reducing lead times for new cookware designs. This technology enables rapid prototyping and small batch production runs without expensive tooling changes.
Energy-efficient induction furnaces and waste heat recovery systems reduce the environmental footprint and operational costs of melting processes. Some foundries adopt electric arc or plasma melting to further decrease emissions and improve metal cleanliness.
Post-casting surface treatments are evolving with plasma or chemical polishing techniques that provide smoother surfaces without extensive mechanical finishing. Additionally, innovative coating technologies, such as ceramic or enamel layers, are applied to enhance corrosion resistance, reduce seasoning maintenance, and expand cookware style options.
Smart factory systems monitor equipment health, production rates, and quality metrics in real time, allowing predictive maintenance and minimizing downtime. Data analytics and machine learning help identify process bottlenecks and optimize parameters for consistent output.
Worker safety is enhanced through enclosed casting cells, automated handling, and real-time monitoring of environmental conditions like temperature, dust, and gas levels. Ergonomic design in loading and unloading stations reduces strain during handling of heavy castings.
Sustainability initiatives focus on recycling scrap metal and spent molding materials, reducing water usage in cleaning and cooling, and minimizing airborne emissions through improved ventilation and filtration.
Collectively, these technological advancements in machinery and process control continue to transform cast iron cookware manufacturing into a more efficient, safer, and environmentally responsible industry while preserving the essential characteristics that make cast iron cookware prized for cooking performance and longevity.
Machinery for Production of Stainless Steel Cookware
Machinery for production of stainless steel cookware is designed to handle the unique properties of stainless steel—its strength, corrosion resistance, and work-hardening behavior—while efficiently shaping, joining, and finishing items like pots, pans, saucepans, and lids. The equipment is built to ensure precision, durability, and aesthetic appeal suitable for high-quality kitchenware.
The manufacturing process typically starts with coil or sheet feeding lines, where stainless steel sheets are uncoiled, leveled, and cut into blanks sized for specific cookware pieces. Servo-driven blanking presses stamp out these blanks with high accuracy and repeatability.
Deep drawing presses or hydraulic presses shape the flat stainless steel blanks into bowl or pot forms. These presses are often equipped with multi-stage dies and automatic blank feeders to facilitate high-volume production with minimal operator intervention. Specialized lubricants and precise control of press speed and force help overcome stainless steel’s springback tendency and prevent cracking.
Trimming machines remove excess metal from the edges of drawn cookware to achieve clean, uniform rims. Rim rolling or curling machines shape and strengthen the edges, ensuring safety and functionality.
Handle attachment stations use various joining methods such as spot welding, laser welding, or mechanical fastening depending on design and production scale. Robotic arms often automate these processes to guarantee consistent placement and high throughput.
Seam welding machines—including TIG (Tungsten Inert Gas), laser, or plasma welders—join components such as pot bottoms to sidewalls, lids to rims, or handles to bodies. These machines offer precise heat control to avoid warping and produce smooth, durable welds that maintain corrosion resistance.
Surface finishing lines employ polishing machines with abrasive belts, buffing wheels, and vibratory finishers to achieve desired textures—from mirror finishes to brushed stainless steel appearances. Automated polishing systems improve consistency and reduce manual labor.
Passivation tanks chemically treat cookware surfaces to enhance corrosion resistance by removing free iron and promoting the formation of a stable chromium oxide layer. This step is critical to ensure the cookware’s durability and food safety.
Nonstick or specialty coating lines may be integrated, applying PTFE, ceramic, or hybrid coatings using spray booths and curing ovens to deliver even, durable coatings.
Inline inspection systems with vision cameras and laser scanners verify dimensions, weld quality, surface finish, and coating uniformity, enabling immediate defect detection and removal.
Material handling solutions such as conveyors, robotic arms, and automated guided vehicles (AGVs) streamline workflow, minimizing handling damage and optimizing production flow.
Packaging machinery designed for stainless steel cookware applies protective films or pads, labels, and sturdy cartons for safe transport.
Environmental controls, including fume extraction during welding and coating, water treatment for rinse cycles, and dust collection systems, ensure regulatory compliance and workplace safety.
Together, this machinery suite provides flexible, scalable, and efficient production capabilities, enabling manufacturers to produce high-quality stainless steel cookware that meets strict performance, durability, and aesthetic standards demanded by consumers worldwide.
Stainless steel cookware production lines increasingly emphasize automation and precision to meet growing market demands for quality and consistency. Advanced coil feeding and leveling machines prepare raw material with minimal surface defects, reducing scrap and improving downstream processing. Servo-electric and hydraulic presses equipped with multi-stage deep drawing tools enable the forming of complex shapes such as tapered pots, saucepans, and flared rims while controlling springback inherent in stainless steel.
Trimming and rim rolling machines operate with high accuracy to ensure smooth, burr-free edges that enhance user safety and product aesthetics. Integration of robotic welding cells using TIG or laser welding technologies improves joint strength and appearance, while also reducing heat distortion and maintaining corrosion resistance critical to stainless steel cookware.
Polishing lines incorporate automated belt and buffing systems with adjustable pressure and speed, allowing customization of surface finishes—from high-gloss mirror polish to matte or satin textures—tailored to brand specifications. Vibratory finishing units and electro-polishing stations further refine surface quality and enhance corrosion resistance.
Passivation stations use controlled acid baths and rinsing systems to form and stabilize the protective chromium oxide layer on stainless steel surfaces, crucial for long-term durability and hygiene. These chemical treatment steps are monitored for temperature, concentration, and timing to ensure consistency.
Some production lines integrate coating application units for specialty finishes such as nonstick layers or decorative coatings. Automated spray booths and curing ovens maintain uniform coating thickness and adhesion, with inline sensors verifying coating quality in real time.
Vision inspection systems throughout the line detect surface defects, dimensional deviations, weld integrity, and coating uniformity. Defective units are automatically segregated to maintain high quality standards and reduce customer returns.
Material handling solutions utilize conveyors, robotic pick-and-place arms, and automated guided vehicles to reduce manual labor, minimize contamination or damage, and improve workflow efficiency. These systems also facilitate quick product changeovers and flexible batch sizes.
Packaging stations deploy protective films, foam inserts, and custom cartons designed specifically for stainless steel cookware, ensuring product safety during shipping and retail display. Automated labeling and barcode printing systems enhance traceability and inventory management.
Environmental and safety equipment address fume extraction during welding and coating processes, water treatment for rinse cycles, and air filtration systems to reduce particulate emissions. Recycling and waste management units recover and reuse metal scraps, spent chemicals, and process water to support sustainability goals.
Overall, the machinery for stainless steel cookware production combines robust mechanical systems with advanced automation, process control, and quality assurance technologies. This integration enables manufacturers to produce durable, attractive, and high-performance cookware that meets strict consumer and regulatory requirements globally.
To further optimize stainless steel cookware manufacturing, many factories implement Industry 4.0 principles, integrating IoT sensors and real-time data analytics across the production line. These systems continuously monitor machine conditions, production rates, and quality parameters, enabling predictive maintenance and reducing unplanned downtime. Data-driven process adjustments improve yield and consistency, while dashboards provide operators and managers with actionable insights.
Advanced robotics continue to replace manual tasks, especially in material handling, welding, and finishing stages. Collaborative robots (cobots) work alongside human operators to enhance flexibility and safety without requiring extensive physical barriers. This hybrid approach allows for small batch customization alongside mass production, meeting diverse market needs efficiently.
In the forming stage, incremental forming machines and servo presses provide highly controllable deformation, accommodating new cookware designs with thinner walls or ergonomic shapes that were previously difficult to achieve with traditional presses. These technologies reduce tool changeover times and scrap rates.
Welding technologies are advancing with hybrid laser-arc systems that combine deep penetration and high-speed welding to improve seam quality while reducing thermal distortion. Seam sealing and surface conditioning post-weld ensure both structural integrity and aesthetic appeal.
Surface finishing innovations include plasma treatments and nanocoatings that improve scratch resistance, reduce fingerprint visibility, and enhance corrosion protection beyond traditional polishing and passivation. These treatments contribute to premium product positioning in competitive markets.
Sustainability practices are increasingly embedded throughout stainless steel cookware manufacturing. Closed-loop water systems recycle rinse water, and energy-efficient machinery reduces overall consumption. Use of recycled stainless steel feedstock and minimizing chemical waste align with environmental regulations and corporate responsibility goals.
Flexible automation platforms allow manufacturers to rapidly switch production lines between different cookware types or customized orders, supporting just-in-time manufacturing and reducing inventory costs. Modular machinery design facilitates quick upgrades and integration of emerging technologies.
Quality control systems are evolving with AI-powered vision inspection that can detect subtle surface defects, weld anomalies, or coating inconsistencies beyond human capability. Automated sorting and feedback loops enable continuous improvement cycles and lower defect rates.
Overall, the machinery and processes for stainless steel cookware production are becoming smarter, greener, and more adaptable—delivering superior products at scale while meeting stringent safety, quality, and environmental standards demanded by modern consumers and regulators worldwide.
Machinery For Metal Cookware Finishing Polishing
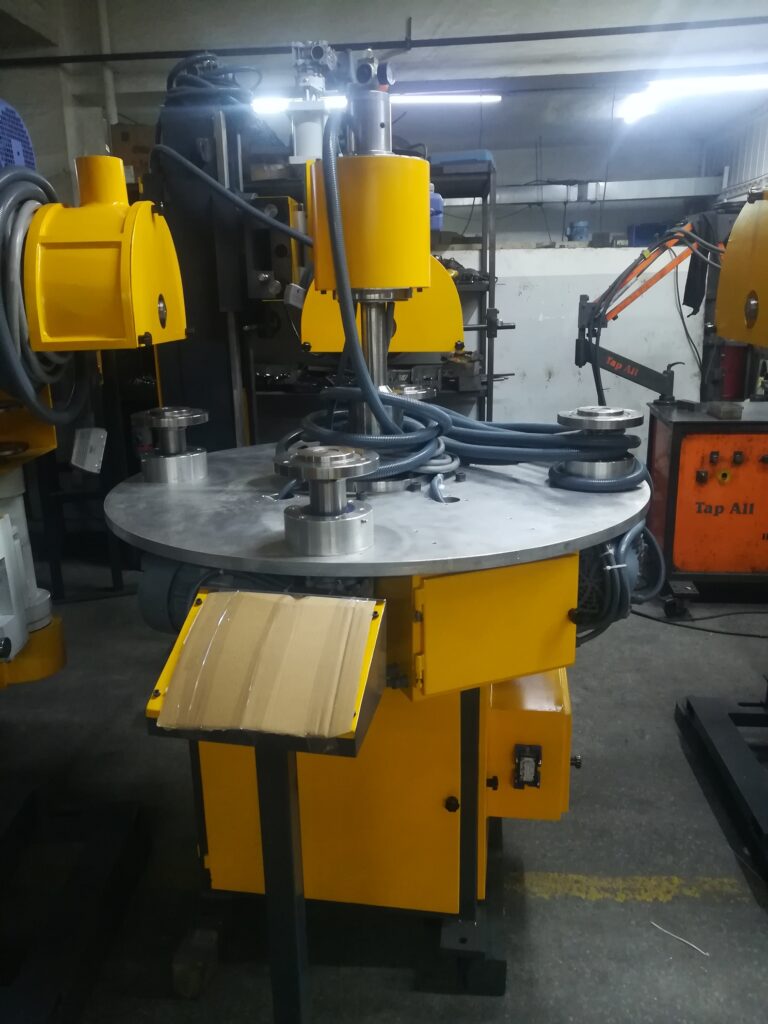
Machinery for metal cookware finishing and polishing plays a crucial role in enhancing both the functional and aesthetic qualities of cookware products made from materials such as stainless steel, aluminum, copper, and cast iron. This equipment is designed to deliver smooth, uniform surfaces that improve corrosion resistance, ease of cleaning, and visual appeal, while also preparing cookware for additional surface treatments or coatings.
The finishing and polishing machinery typically includes:
- Abrasive Belt Polishers: These machines use abrasive belts of varying grit sizes to remove surface imperfections like scratches, scale, or oxidation. Adjustable speed and pressure controls allow operators to tailor the finish from coarse grinding to fine smoothing.
- Buffing Machines: Equipped with rotating buffing wheels and polishing compounds, these machines produce high-gloss, mirror-like finishes. Buffing wheels come in various materials (cotton, sisal, felt) to suit different polishing needs.
- Vibratory Finishers: These machines utilize a vibrating or tumbling action with abrasive media (ceramic, plastic, or organic) to deburr, smooth, and polish cookware surfaces in batches. Vibratory finishing is efficient for handling multiple small parts or complex shapes.
- Centrifugal Disc Finishers: Similar to vibratory finishers but with a rotating disc that spins abrasive media at high speed, offering faster finishing times and more aggressive material removal for stubborn imperfections.
- Electropolishing Equipment: This electrochemical process removes a thin layer of metal from the cookware surface, enhancing smoothness, brightness, and corrosion resistance. Electropolishing is especially common for stainless steel cookware.
- Automated Polishing Robots: Robotic polishing arms equipped with force and speed control provide consistent, repeatable finishes on cookware with complex geometries, reducing manual labor and improving throughput.
- Surface Grinding Machines: Used for flattening and refining cookware bases to ensure even contact with cooking surfaces, enhancing heat distribution and stability.
- Spray Cleaning and Rinsing Systems: Often integrated with polishing lines to remove residues and prepare cookware for final inspections or coating applications.
- Inspection and Quality Control Stations: Vision systems and surface roughness testers check polishing quality and surface uniformity, ensuring that products meet specified standards.
- Dust and Fume Extraction Systems: These maintain a clean working environment by capturing polishing dust and airborne particles generated during finishing operations.
By employing this range of machinery, manufacturers achieve high-quality surface finishes that not only enhance the cookware’s performance and durability but also contribute significantly to its market appeal and customer satisfaction.
Continuing with metal cookware finishing and polishing machinery, many manufacturers focus on integrating flexible automation to boost efficiency and consistency. Automated conveyors feed cookware through sequential polishing stages where abrasive belts or buffing wheels progressively refine the surface finish. Programmable logic controllers (PLCs) manage parameters such as belt speed, pressure, and polishing duration, enabling precise control and reproducibility for different cookware types or grades.
Advanced polishing compounds formulated for specific metals optimize surface quality while minimizing material loss. For instance, aluminum cookware benefits from compounds that reduce oxidation and improve brightness without excessive abrasion, while stainless steel polishing focuses on achieving corrosion-resistant mirror finishes.
Robotic polishing cells increasingly use adaptive force sensors and computer vision to dynamically adjust polishing pressure and contact angles based on real-time surface feedback. This capability is crucial for maintaining uniform finish on cookware with varying geometries, such as curved handles, flared rims, or embossed logos.
Vibratory and centrifugal finishing machines are favored for batch processing of smaller cookware components like lids, knobs, or handles, achieving consistent edge rounding and surface smoothing with minimal operator intervention. These systems often include automatic media replenishment and cleaning cycles to maintain finishing quality.
Electropolishing lines, integrated with rinsing and drying stations, provide chemically enhanced surface finishes that improve cookware hygiene and resistance to staining or discoloration. Inline monitoring of electrical parameters and solution chemistry ensures optimal material removal rates and surface characteristics.
Dust and fume extraction systems designed for polishing environments are critical to comply with occupational health regulations and protect worker safety. These systems use multi-stage filtration to capture fine metallic particles and volatile polishing agents, maintaining air quality and minimizing equipment contamination.
Final inspection stations equipped with high-resolution cameras and 3D surface scanners enable detection of minute surface defects, scratches, or uneven finishes before cookware moves to packaging or coating lines. Integration with factory data systems supports traceability and continuous process improvement.
Many finishing lines are also designed with sustainability in mind, recycling polishing compounds and abrasive media, and reducing water and energy consumption through closed-loop systems and energy-efficient motors.
Overall, modern machinery for metal cookware finishing and polishing combines precision mechanical design, advanced automation, and environmental controls to produce cookware that meets high standards for durability, safety, and visual appeal in competitive global markets.
Additionally, manufacturers are increasingly adopting modular polishing systems that can be quickly reconfigured or scaled to meet changing production demands. This flexibility allows for rapid adaptation to new cookware designs or material specifications without extensive downtime or capital investment.
Integrated maintenance and diagnostic features in polishing machinery help predict wear on belts, wheels, and other consumables, enabling just-in-time replacements that minimize production interruptions. These smart systems often alert operators when tool changes or recalibrations are needed, improving overall equipment effectiveness (OEE).
Surface treatment options beyond traditional polishing are also being incorporated into finishing lines. For example, plasma cleaning or coating deposition units can be added to enhance surface energy and adhesion properties, preparing cookware for advanced coatings such as ceramic or diamond-infused layers.
Environmental compliance is a major driver behind innovations in finishing machinery. Water recycling systems capture and treat rinse water used during polishing and cleaning processes, reducing freshwater consumption. Waste abrasive media and polishing compounds are collected and processed for reuse or safe disposal, aligning with circular economy principles.
Operator ergonomics and safety have improved with machinery designed to reduce repetitive strain and exposure to noise or airborne particulates. Enclosed polishing stations with automated feed and discharge reduce direct human contact with moving parts, while sound-dampening enclosures and ventilation systems improve workplace conditions.
The adoption of digital twins and simulation software allows manufacturers to model polishing processes virtually, optimizing parameters before physical trials. This reduces trial-and-error efforts, saves material, and accelerates the development of new cookware finishes.
Lastly, collaborative robotics (cobots) are increasingly utilized to assist skilled workers with intricate polishing tasks, combining human dexterity and judgment with robotic precision and consistency. This partnership enhances quality while maintaining production flexibility.
Together, these advancements in machinery for metal cookware finishing and polishing empower manufacturers to deliver products with superior surface quality, consistent aesthetics, and enhanced performance, all while improving operational efficiency, worker safety, and environmental sustainability.
Machinery For Metal Bowl Deep Drawing
Machinery for metal bowl deep drawing is specialized equipment designed to transform flat metal sheets into bowl-shaped parts through a controlled plastic deformation process. This manufacturing method is widely used for producing kitchenware such as mixing bowls, serving bowls, and other hollow metal components with smooth, uniform walls and precise dimensions.
The primary machinery involved in metal bowl deep drawing includes:
- Deep Drawing Press: This is the central machine that applies controlled force to draw a metal blank over a die using a punch. Presses vary in type—mechanical, hydraulic, or servo-driven—with capacities tailored to bowl size and material thickness. Hydraulic and servo presses offer precise control of speed, force, and stroke, improving product quality.
- Blanking Press or Shearing Machine: Prior to drawing, metal sheets are cut into round blanks of specific diameter and thickness. Accurate blank preparation is crucial for consistent deep drawing results.
- Drawing Dies and Punches: Custom-designed tooling forms the metal into the bowl shape. Dies and punches are made from hardened tool steel or carbide for durability, featuring smooth surfaces and precise geometries to minimize friction and prevent defects like wrinkling or tearing.
- Blank Holder or Hold-Down Ring: This component controls material flow during drawing by applying pressure on the metal blank’s outer edges, preventing excessive wrinkling and ensuring uniform wall thickness.
- Lubrication Systems: Proper lubrication between the metal blank and tooling reduces friction, improves metal flow, and extends tool life. Lubricants may be oil-based or synthetic and are applied manually or via automated spray systems.
- Multiple Drawing Stations: For deeper or more complex bowls, progressive deep drawing presses with multiple stations incrementally shape the metal in successive steps, reducing strain and improving dimensional accuracy.
- Redrawing Presses: These machines perform additional drawing stages on previously formed bowls to achieve greater depth or specific shapes, often necessary for thick or hard-to-form metals.
- Trimming Machines: After deep drawing, excess material or flash around the bowl edges is trimmed to final dimensions using hydraulic or mechanical trimming presses.
- Flanging Machines: These machines create rolled edges or flanges on bowl rims to enhance rigidity, safety, or for joining purposes in assembly.
- Annealing Furnaces: Intermittent annealing may be required between drawing stages to soften the metal and relieve stresses, preventing cracking during further deformation.
- Inspection Equipment: Dimensional gauges, surface defect detectors, and thickness measurement tools ensure bowls meet quality specifications.
- Automation Systems: Conveyor belts, robotic arms, and CNC controls streamline material handling, tool changes, and process monitoring, boosting throughput and repeatability.
By using this suite of machinery, manufacturers produce metal bowls with high structural integrity, smooth finishes, and consistent shapes suitable for a wide range of consumer and industrial applications.
Continuing with metal bowl deep drawing machinery, advances in servo-electric press technology have enhanced the precision and flexibility of the deep drawing process. Servo presses provide accurate control over punch speed, position, and force throughout the stroke, enabling optimization of forming parameters for different metals such as stainless steel, aluminum, and copper alloys. This results in reduced material waste, lower tool wear, and higher quality bowl shapes.
Modern deep drawing lines often incorporate automated blank handling systems to feed metal blanks consistently and accurately into the press, minimizing manual intervention and improving cycle times. Robotic arms or conveyor systems remove finished bowls from the press area and transfer them to subsequent processing stations like trimming or flanging.
Tooling innovations have focused on reducing friction and enhancing metal flow during drawing. Coatings such as titanium nitride (TiN) or diamond-like carbon (DLC) on punches and dies extend tool life and allow for higher-speed operations without compromising surface finish. Additionally, modular die sets facilitate quick tool changes, supporting diverse product ranges or shorter production runs.
Integrated process monitoring systems with sensors measure parameters like punch force, stroke depth, and material thickness in real time. These data enable immediate adjustments or alarms to prevent defects such as wrinkling, tearing, or excessive thinning. Closed-loop feedback systems improve process stability and reduce scrap rates.
Inter-stage annealing ovens are designed to work seamlessly with automated lines, ensuring that metal blanks or partially formed bowls receive precise heat treatment at the right intervals. Controlled atmosphere furnaces prevent oxidation and maintain surface quality during the annealing cycles.
In more complex applications, deep drawing machinery is combined with incremental forming techniques or hydroforming. Hydroforming uses fluid pressure to shape metal sheets, allowing more intricate shapes and better control of wall thickness, especially useful for ergonomic or decorative bowls.
To support quality assurance, optical inspection stations with laser scanning and vision systems check dimensional accuracy and surface defects at high speed. Non-contact thickness gauges ensure uniformity and detect thinning that could compromise bowl integrity.
Environmental considerations have led to the adoption of closed-loop lubrication systems that recycle drawing oils and reduce waste. Energy-efficient hydraulic systems and servo motors lower power consumption while maintaining performance.
Overall, the integration of advanced controls, automation, tooling technology, and quality monitoring in metal bowl deep drawing machinery allows manufacturers to achieve high productivity, consistent product quality, and flexibility to meet diverse market demands for metal bowls across kitchenware, industrial, and decorative sectors.
Further enhancements in metal bowl deep drawing machinery include the adoption of Industry 4.0 technologies, enabling smart manufacturing and data-driven process optimization. Machine learning algorithms analyze historical production data to predict tool wear and adjust press parameters proactively, minimizing downtime and maintaining consistent quality.
Collaborative robots (cobots) are increasingly integrated into deep drawing lines for tasks such as loading blanks, unloading finished bowls, and performing quality checks. These cobots work safely alongside human operators, improving efficiency without requiring extensive safety barriers.
Advanced simulation software allows engineers to virtually test and optimize deep drawing processes before physical production. Finite element analysis (FEA) models predict material flow, stress distribution, and potential failure points, guiding tool design and process parameters to reduce trial runs and material waste.
The machinery is also evolving to accommodate a broader range of materials, including advanced high-strength steels (AHSS) and lightweight aluminum alloys used in premium cookware. These materials require precise force control and lubrication management to prevent cracking and maintain surface finish during deep drawing.
Modular press designs support rapid retooling and format changes, enabling manufacturers to switch between bowl sizes and styles with minimal downtime. This flexibility is critical for meeting diverse customer demands and shorter product life cycles.
In addition to traditional single-action deep drawing presses, tandem or transfer presses streamline multi-stage forming within a single automated line. This arrangement reduces handling time and improves throughput while maintaining tight process control.
To enhance sustainability, many systems incorporate energy recovery solutions that capture and reuse hydraulic or kinetic energy during press cycles. This reduces overall energy consumption and operating costs.
Safety features have been upgraded with light curtains, pressure-sensitive mats, and emergency stop systems that comply with international standards, ensuring operator protection in increasingly automated environments.
Overall, modern machinery for metal bowl deep drawing combines mechanical precision, advanced automation, data intelligence, and flexible manufacturing capabilities to meet the demands of high-volume, high-quality bowl production while reducing costs and environmental impact.
Machinery For Industrial Metal Polishing
Machinery for industrial metal polishing is designed to efficiently smooth, brighten, and finish metal surfaces on a large scale, suitable for applications in automotive, aerospace, cookware, machinery parts, and construction industries. These machines enhance surface quality by removing burrs, oxidation, scratches, and imperfections, delivering consistent finishes from matte to mirror-like polish.
Key types of industrial metal polishing machinery include:
- Belt Grinders and Sanders: Utilize abrasive belts moving at high speeds to grind and polish metal surfaces. These machines are versatile for both rough and fine polishing, capable of handling large workpieces or continuous production lines.
- Vibratory Tumblers: Batch-processing machines where parts are placed in a vibrating bowl with abrasive media and compounds. The vibration causes the media to polish all surfaces of the parts simultaneously, ideal for mass finishing of small to medium-sized components.
- Centrifugal Disc Finishers: Combine centrifugal force with abrasive media in a rotating disc setup to polish parts quickly and uniformly, often used for deburring and surface smoothing.
- Rotary Drum Polishers: Similar to vibratory tumblers but with rotating drums that gently polish metal parts, especially suited for delicate or intricately shaped items.
- Buffing Machines: Employ rotating cloth or felt wheels with polishing compounds to achieve high-gloss finishes. Available in bench, floor-standing, or automated configurations.
- Automated Robotic Polishing Systems: Integrate robotic arms equipped with polishing heads, vision systems, and force sensors for precise, repeatable polishing on complex or large metal components. They improve consistency and reduce manual labor.
- Electropolishing Equipment: An electrochemical process that removes a thin layer of metal to improve surface smoothness and corrosion resistance, often used for stainless steel and specialty alloys.
- Shot Blasting Machines: Propel abrasive particles at high velocity to clean and polish metal surfaces, effective for removing rust, scale, and old coatings before final polishing.
- Chemical Mechanical Polishing (CMP) Systems: Combine chemical etching and mechanical polishing, widely used in precision industries such as semiconductor manufacturing but adaptable for certain metal finishing applications.
- Surface Grinding Machines: For flat metal parts, these machines use abrasive wheels to achieve precise surface finishes and tight tolerances.
- Multi-Head Spindle Polishers: Feature multiple polishing spindles working simultaneously to increase throughput on production lines.
- Dust Extraction and Filtration Units: Integrated with polishing machinery to capture airborne particles and maintain clean working environments, essential for worker safety and quality control.
Industrial metal polishing machinery often incorporates programmable logic controllers (PLCs) and human-machine interfaces (HMIs) for process control, allowing adjustment of speed, pressure, and polishing time based on metal type and desired finish.
Materials commonly polished include stainless steel, aluminum, brass, copper, titanium, and various alloys, each requiring specific abrasives and parameters for optimal results.
Through the combination of mechanical action, abrasive media, chemical agents, and automation, industrial metal polishing machinery delivers high-quality, uniform finishes that enhance both the aesthetic appeal and functional performance of metal products.
Industrial metal polishing machinery continues to evolve with a strong focus on automation, precision, and environmental sustainability. Advanced systems now incorporate sensors that monitor polishing force, temperature, and vibration to ensure consistent quality and prevent damage to delicate parts. Real-time feedback allows for adaptive control, adjusting parameters on the fly to maintain optimal polishing conditions.
Robotic polishing cells have become increasingly prevalent in high-volume manufacturing environments. These robots can handle complex geometries and execute multi-axis movements, reaching difficult areas while maintaining uniform pressure. Equipped with machine vision, they identify surface defects and adjust polishing paths, greatly reducing scrap rates and manual rework.
Hybrid polishing techniques are also emerging, combining mechanical polishing with chemical or electrochemical processes to achieve superior surface finishes. For example, combining traditional buffing with electropolishing can enhance corrosion resistance and surface cleanliness, particularly for stainless steel components used in medical or food industries.
Energy efficiency is a key design consideration in modern polishing machines. Variable frequency drives (VFDs) optimize motor speeds to reduce power consumption, while regenerative braking systems recover energy during deceleration. Additionally, closed-loop water and chemical recycling systems minimize waste and reduce environmental impact.
Dust and particle management are critical due to health and quality concerns. Integrated dust extraction with HEPA filtration and mist collection ensures operator safety and maintains a clean work area. Some systems also incorporate automated cleaning cycles for polishing media and abrasive compounds, extending their usability and reducing operational costs.
Customization options allow manufacturers to tailor polishing lines to specific product requirements, from coarse deburring to ultra-fine mirror finishes. Interchangeable polishing heads, adjustable spindle speeds, and modular conveyor systems provide flexibility for varying batch sizes and product types.
Maintenance and downtime reduction are addressed through predictive maintenance technologies. Sensors track wear on belts, wheels, and abrasive media, alerting operators before failures occur. Remote diagnostics and software updates facilitate quick troubleshooting and process optimization.
Industrial metal polishing machinery is integral to producing high-quality metal components that meet stringent standards for aesthetics, durability, and performance. Its continued advancement supports diverse industries, enabling efficient, precise, and environmentally responsible surface finishing solutions.
Further advancements in industrial metal polishing machinery focus on integrating artificial intelligence (AI) and machine learning to enhance process optimization and quality control. AI-driven systems analyze vast amounts of operational data, learning patterns that correlate machine settings with final surface quality. This allows predictive adjustments that preemptively correct deviations, improving yield and reducing scrap.
Smart polishing machines are increasingly connected within Industry 4.0 frameworks, enabling seamless communication between production line components. Data from polishing equipment feeds into centralized manufacturing execution systems (MES), facilitating real-time monitoring, reporting, and coordination with upstream and downstream processes such as machining or coating.
Customization through modular tooling and quick-change polishing heads enables rapid adaptation to different product sizes, shapes, and materials without significant downtime. This flexibility supports shorter production runs and diversified product portfolios, crucial in markets demanding customization and fast turnaround.
Emerging abrasive materials, such as nano-structured polishing compounds and diamond-enhanced pads, deliver higher efficiency and longer tool life. These innovations reduce polishing time and energy consumption while achieving finer surface finishes, especially on hard metals and complex alloys.
The adoption of ultrasonic-assisted polishing technology introduces high-frequency vibrations to polishing tools, improving material removal rates and surface smoothness with less mechanical force. This technique reduces wear on both the workpiece and tooling, making it suitable for delicate or precision components.
Safety and ergonomics are enhanced through fully enclosed polishing cells, automated loading and unloading systems, and operator-friendly interfaces. Noise reduction technologies and vibration dampening also contribute to healthier work environments.
Waste management advancements focus on recycling spent abrasives and polishing fluids. Closed-loop filtration and separation systems recover reusable materials, lowering environmental footprint and operational costs.
In summary, the evolution of industrial metal polishing machinery is driven by smart automation, advanced materials, and sustainable practices. These innovations collectively enable manufacturers to deliver superior quality metal finishes at higher speeds, lower costs, and with greater environmental responsibility.
Machinery For Metal Cookware Forming
Machinery for metal cookware forming encompasses a range of specialized equipment designed to shape raw metal sheets or blanks into finished cookware components such as pots, pans, lids, and bowls. These machines handle forming processes including deep drawing, stamping, spinning, pressing, and bending to achieve the precise shapes, dimensions, and structural integrity required for high-quality cookware production.
Key types of metal cookware forming machinery include:
- Deep Drawing Presses: Hydraulic or mechanical presses that pull a metal blank into a die cavity to create seamless, rounded cookware shapes like pots and pans. These machines provide controlled force to stretch the metal without tearing, ideal for forming bowl-shaped items with uniform thickness.
- Metal Spinning Lathes: Rotational forming machines where a metal disc is spun at high speed while a tool presses against it to shape cookware parts such as lids or round bases. Spinning allows for seamless, symmetrical shapes with smooth surface finishes.
- Stamping Presses: High-speed mechanical or hydraulic presses that use dies to cut, shape, or emboss flat metal sheets into cookware parts. Stamping is common for producing lids, handles, and decorative features efficiently in large volumes.
- Hydraulic and Mechanical Presses: Versatile machines used for bending, flanging, and shaping metal cookware components with precise force control. They handle forming of rims, edges, and flanges essential for cookware assembly and sealing.
- Rim Forming Machines: Specialized presses or rollers designed to form and finish the edges or rims of pots and pans, ensuring uniformity and smoothness for safety and functionality.
- Flanging and Curling Machines: Equipment that bends or curls the edges of cookware parts, often used to create secure joints or prepare surfaces for handle attachment or lids.
- Embossing and Patterning Machines: Presses equipped with dies that imprint decorative or functional patterns on cookware surfaces, such as non-slip textures or brand logos.
- Multi-Station Transfer Presses: Automated lines combining several forming operations in sequence, enabling high-volume, precise, and repeatable cookware part production.
- Roll Forming Machines: Used for creating continuous profiles or components such as handles or rims by gradually bending metal strips through rollers.
- Servo-Driven Forming Machines: Advanced forming equipment with electronically controlled drives allowing precise speed, position, and force adjustments, enhancing process flexibility and energy efficiency.
Cookware forming machinery supports a wide range of materials, including stainless steel, aluminum, copper, and clad metals. They are designed to maintain material properties and surface quality during forming, preventing defects like cracks, wrinkles, or excessive thinning.
Integration with automation systems, robotics, and quality inspection tools ensures consistent part quality and efficient production workflows. Modern forming machines often feature quick die change capabilities to accommodate different cookware designs and sizes with minimal downtime.
Together, these machines form the backbone of metal cookware manufacturing, transforming flat metal inputs into durable, aesthetically pleasing, and functional cookware components ready for further processing such as welding, polishing, coating, or assembly.
Metal cookware forming machinery plays a critical role in shaping raw materials into precise cookware components with consistent quality and efficiency. These machines utilize controlled force and tooling to deform metal sheets without compromising structural integrity or surface finish. The forming processes are optimized for different metals, including aluminum, stainless steel, copper, and composite clads, each requiring specific parameters to prevent cracking, wrinkling, or uneven thickness distribution.
Advanced deep drawing presses apply hydraulic pressure to stretch the metal uniformly into die cavities, producing seamless pots, pans, and bowls with smooth contours. These presses often incorporate servo-driven controls for fine-tuning stroke speed and force, which improves precision and reduces material waste. Progressive dies in stamping presses enable multi-step forming operations, combining cutting, bending, and embossing in a single stroke to enhance productivity for components like lids and handles.
Metal spinning machines transform flat discs into symmetrical shapes by rotating the workpiece at high speed while a skilled operator or automated tool applies pressure. This method achieves excellent surface quality and allows quick adaptation for different product sizes. In addition, rim forming and flanging machines finish edges by rolling or bending, preparing cookware pieces for secure joining and aesthetic appeal.
Automation integration with robotics and conveyors streamlines metal cookware forming lines, allowing for continuous production with minimal manual intervention. Sensors and vision systems monitor the forming process in real time, detecting defects such as wrinkles, tears, or dimensional inaccuracies early to prevent downstream rework. Tooling changeover systems reduce downtime between different product batches, enabling flexible manufacturing for diverse cookware designs.
Modern forming equipment emphasizes energy efficiency and operator safety through features like variable frequency drives, ergonomic controls, and enclosed working zones with dust extraction. Maintenance is facilitated by modular machine designs and predictive diagnostics, ensuring high uptime and consistent output quality.
The precise control over forming parameters, combined with robust machinery and smart automation, ensures that metal cookware formed through these processes meets stringent standards for durability, usability, and appearance. This machinery is indispensable for producing cookware that withstands high thermal and mechanical stresses while offering consumer-friendly designs and finishes.
Further innovations in metal cookware forming machinery include the integration of smart manufacturing technologies and adaptive control systems. These advancements allow machines to dynamically adjust forming parameters based on real-time feedback from sensors that monitor material behavior, thickness variation, and tool wear. This ensures optimal forming conditions are maintained throughout production, reducing scrap rates and improving part consistency.
Robotic assistance in metal forming lines is becoming increasingly common. Robots handle material loading, unloading, and transfer between forming stations, minimizing human intervention and enhancing safety. Collaborative robots (cobots) work alongside operators to perform precise tasks such as tool changes and quality inspections, increasing overall line flexibility.
Additive manufacturing techniques are starting to complement traditional forming methods, especially for producing complex tooling and custom dies. This reduces lead times and allows rapid prototyping of new cookware shapes, accelerating product development cycles.
Energy-efficient servo drives and regenerative braking systems reduce power consumption during forming strokes, lowering operational costs and carbon footprint. Many forming machines now include comprehensive diagnostics and predictive maintenance modules that analyze vibration, temperature, and force data to forecast potential failures before they cause downtime.
Material handling within forming lines benefits from modular conveyors and automated storage systems, which optimize workflow and support just-in-time manufacturing approaches. Integration with factory-wide manufacturing execution systems (MES) provides real-time data tracking, production scheduling, and traceability for each cookware piece formed.
These technological advances collectively enable manufacturers to produce high-quality metal cookware faster, more economically, and with greater customization capabilities than ever before. As market demands evolve, forming machinery continues to adapt by incorporating smarter controls, automation, and sustainable design principles to maintain competitive advantages in cookware production.
Machinery For Food-Safe Metal Bowl Manufacturing
Machinery for food-safe metal bowl manufacturing is specialized to produce bowls that meet stringent hygiene, durability, and safety standards required for food contact applications. These machines handle forming, finishing, and inspection processes while ensuring compliance with food safety regulations such as FDA (USA), EU food contact standards, or similar regional certifications.
Key equipment and features include:
- Deep Drawing Presses: Hydraulic or mechanical presses shape metal blanks into smooth, seamless bowl forms without cracks or wrinkles. Food-safe bowls typically require uniform thickness and no sharp edges, so deep drawing machines with precise force control and high-quality tooling are essential.
- Metal Spinning Lathes: Used to produce round, symmetrical bowls by rotating and forming metal discs. Spinning ensures a smooth, continuous surface ideal for food safety and easy cleaning.
- Edge Forming and Curling Machines: These machines roll or curl the bowl rims to eliminate sharp edges, enhancing user safety and structural strength while maintaining a hygienic finish.
- Surface Polishing Equipment: Automated polishing lines using fine abrasives and buffing compounds deliver smooth, shiny surfaces free of burrs or contaminants. Polished surfaces resist bacterial growth and facilitate cleaning.
- Washing and Cleaning Systems: Specialized washing units remove oils, dust, and residues after forming and polishing, preparing bowls for coating or direct use. Cleanliness at this stage is critical for food-grade certification.
- Passivation Systems: For stainless steel bowls, passivation treatments remove free iron particles and enhance corrosion resistance, critical for food safety and longevity.
- Automated Inspection Systems: Vision systems check surface quality, dimensional accuracy, and absence of defects such as dents or cracks. Inspection ensures only compliant bowls proceed to packaging.
- Material Handling Automation: Robots and conveyors minimize manual contact with the bowls, reducing contamination risks and improving production efficiency.
Materials commonly used include stainless steel (304, 316 grades), aluminum alloys, and food-grade coated metals. All machinery components contacting the bowl surfaces are made of or coated with corrosion-resistant, non-toxic materials to avoid contamination.
In sum, food-safe metal bowl manufacturing machinery integrates precise forming, finishing, and cleaning processes, combined with strict quality controls and hygienic design, to produce bowls that are safe, durable, and suitable for direct food contact.
Food-safe metal bowl manufacturing relies heavily on maintaining absolute cleanliness, structural integrity, and smooth surface finishes throughout the entire production process. The machinery involved must not only shape the metal precisely but also eliminate any potential for contamination, making stainless steel the most preferred material due to its corrosion resistance, non-reactivity with food, and ease of sanitation. During the initial stage, hydraulic deep drawing machines form the metal into bowl shapes in a single or multi-stage operation, ensuring even distribution of material with no thinning or tearing that could compromise food safety. Precision tooling is crucial here to avoid surface imperfections that could harbor bacteria. After forming, trimming machines remove excess material around the edges, preparing the bowl for safe handling and further processing. To eliminate sharp edges, rim forming and curling units smooth and roll the bowl lip, preventing injury and reducing crevice formation.
Surface treatment is perhaps the most critical step for food-safe applications. Automated polishing lines apply multiple stages of fine abrasives and polishing compounds to achieve a mirror or satin finish, depending on the design. This not only improves aesthetics but also eliminates micro-scratches where food particles and bacteria might accumulate. Advanced polishing systems include enclosed dust extraction and slurry recycling to maintain a clean processing environment. Some operations incorporate electrolytic or electrochemical polishing for a flawless, passivated finish that enhances corrosion resistance, particularly important for acidic or salty food use. Inline cleaning units then remove all residues from forming and polishing, using high-pressure deionized water jets, ultrasonic cleaning, or detergent cycles. These systems are often followed by hot air or filtered air dryers to prevent watermarks or microbial growth.
Automated conveyors and robotic arms are integrated into most stages to minimize human contact with the bowls, supporting hygienic production and consistent handling. Quality assurance is conducted by automated vision systems that detect surface flaws, dimensional variances, or deformities. Bowls that do not meet tolerances are automatically rejected to maintain batch consistency. The entire system is often enclosed in cleanroom-style environments with temperature and humidity controls to meet regulatory compliance for food-grade production. Software-driven process monitoring collects data on each bowl’s manufacturing history, useful for traceability and audits.
As consumer and regulatory demands increase for food-safe, high-performance kitchenware, these machines continue to evolve toward even tighter tolerances, greater automation, and cleaner operations. Modern designs focus on tool-free changeovers, fast cleaning protocols, and energy-efficient drives, ensuring not only product safety and quality but also sustainable and flexible manufacturing.
In the final stages of manufacturing, specialized machinery may be employed for additional functional or aesthetic treatments, depending on the intended application of the metal bowls. For example, bowls designed for mixing or industrial food processing may undergo bead blasting or matte finishing to provide grip or reduce glare, all while maintaining food contact compliance. In contrast, consumer-grade kitchen bowls might receive decorative surface textures or laser-etched branding, applied using CNC-controlled engraving systems with food-safe parameters. Coating systems are also sometimes integrated, especially when manufacturing aluminum bowls that require non-stick or protective interior finishes. These coatings are applied in clean, dust-controlled booths using automated spray arms and then cured in precision temperature-controlled ovens to ensure chemical bonding without contamination.
Packaging is another critical step in the food-safe manufacturing workflow. Automatic packing lines wrap or seal finished bowls in protective film or place them directly into sanitized cartons using robotic pick-and-place systems. This process is usually conducted in a clean area with filtered air and minimal operator involvement. Labels indicating food safety compliance, batch numbers, and material specifications are printed and applied automatically to support traceability and meet international export requirements.
From a production management standpoint, advanced machinery is increasingly integrated with manufacturing execution systems (MES) and enterprise resource planning (ERP) platforms. These digital tools allow operators and managers to monitor performance metrics such as production speed, defect rates, maintenance schedules, and compliance reporting in real time. Predictive maintenance algorithms analyze vibration, temperature, and wear data from key machinery components, allowing interventions before failures occur. This not only protects the expensive tooling and machines but also ensures uninterrupted compliance with stringent hygienic manufacturing standards.
The entire production setup is designed to meet or exceed regulatory benchmarks like ISO 22000 (food safety management), NSF/ANSI standards, and Good Manufacturing Practices (GMP). As demand grows for sustainable and transparent cookware production, manufacturers also prioritize eco-friendly lubricants, water recycling systems in polishing lines, and energy recovery systems in hydraulic presses. The use of modular machine architecture allows lines to be reconfigured for different bowl shapes or sizes, enabling small-batch customization without sacrificing cleanliness or efficiency.
In essence, machinery for food-safe metal bowl manufacturing merges mechanical precision, hygiene-first design, digital control, and robust automation. The outcome is a consistently high-quality, contamination-free product line that meets the evolving expectations of both regulatory bodies and health-conscious consumers worldwide.
Machinery For Metal Cookware Surface Grinding
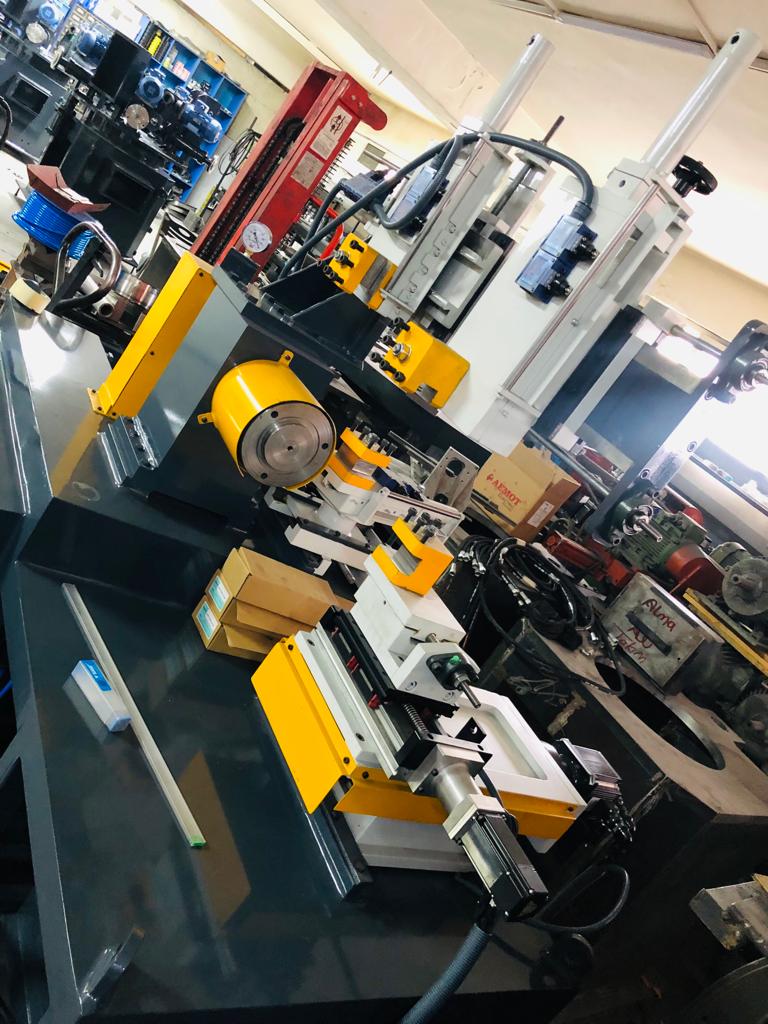
Machinery for metal cookware surface grinding is engineered to ensure smooth, flat, and visually appealing finishes on items like pots, pans, and lids. These machines are critical in removing weld seams, oxidation marks, tool impressions, and other surface imperfections that occur during earlier manufacturing processes like spinning, deep drawing, or welding. The goal is not only to enhance appearance but also to prepare the surface for polishing, coating, or direct food contact by achieving precise texture and flatness.
Typically, flat surface grinders or belt grinding machines are used for cookware bases, especially for pans and pots that require even heat distribution. These machines use abrasive belts or grinding wheels to level the bottom surface, ensuring perfect contact with cooking elements like induction plates or gas burners. The cookware item is fixed on a rotating or clamping table while the grinding head moves across the surface with controlled pressure and speed, achieving uniform material removal.
For curved surfaces or round bowls, CNC-controlled contour grinding machines are used. These machines follow the shape of the cookware using programmable motion systems and flexible abrasive tools. The grinding pressure, feed rate, and abrasive grit can be adjusted automatically based on the metal type (stainless steel, aluminum, copper) and the desired finish. This is essential to avoid excessive stock removal or surface overheating, which could compromise the cookware’s quality or safety.
Edge grinding machines are often employed to remove burrs and sharpness from the rims after forming or trimming processes. These machines use radial abrasives or flap wheels and are commonly integrated into automated finishing lines.
Modern cookware surface grinding machines are equipped with dust extraction systems to manage metallic particles and ensure a clean working environment. Many systems include cooling and lubrication units that reduce heat buildup during grinding, which not only protects the surface but also extends tool life.
In advanced setups, robotic arms load and unload cookware pieces, aligning them precisely to maintain consistency. These robots can also manipulate the workpiece during grinding to maintain optimal contact angles, particularly on complex surfaces.
The surface grinding stage is often followed by polishing or brushing, but in some cases, it serves as the final finish for brushed-look cookware. Machine configurations may support single or multiple stations, enabling continuous, high-speed processing in industrial-scale production.
Overall, this machinery ensures that metal cookware not only meets high-performance criteria like heat transfer efficiency and safety but also delivers the visual quality and tactile refinement expected in modern kitchens.
Surface grinding machinery for metal cookware is typically integrated into automated production lines to maximize consistency, throughput, and finish quality. These machines can handle various cookware geometries and materials, including stainless steel, aluminum, and copper, each requiring distinct grinding techniques and abrasive media. The process begins with securely fixing the cookware item, often using pneumatic or magnetic fixtures, to prevent any vibration or movement that could result in uneven grinding.
The grinding unit, equipped with abrasive belts, discs, or wheels of calibrated grit, traverses the surface using servo-driven actuators that allow high precision in movement, pressure, and timing. This motion can be linear, rotary, or multi-axis depending on whether the machine is working on flat bases, contoured interiors, or vertical sidewalls. For applications demanding extremely flat bottoms—particularly for induction-compatible cookware—dual-head bottom grinders are employed. These machines grind both sides of the base simultaneously, minimizing thermal warping and ensuring perfect stovetop contact.
Cookware that requires a textured appearance, like a brushed steel finish, goes through specific machines using non-woven abrasive belts that impart directional grain while preserving the metal’s integrity. In the case of aluminum, which is softer, machines use lower pressure and finer abrasives to avoid gouging or deep scratches that could affect anodizing or coating stages later. Grinding machines designed for high volumes often incorporate multiple stations where each unit progressively refines the surface, transitioning from coarse to fine grit abrasives. These are enclosed in dust-tight cabins fitted with extraction hoods and filters to meet air quality standards and reduce fire risks from airborne metal particles.
To improve efficiency and reduce operator fatigue, many surface grinding systems are now coupled with vision systems and sensors that scan the cookware surface in real time, adjusting parameters dynamically to correct for surface waviness or inconsistencies in material hardness. Some systems even incorporate AI-driven control software that learns optimal grinding cycles based on previous jobs, adjusting feed rates and belt replacements automatically. For specialty cookware with embossed logos, ridged surfaces, or composite metal layers, grinding must be done with utmost care to preserve the design and avoid delamination or distortion. In such cases, customized fixtures, slower grinding speeds, and intermittent cooling sprays are used. The end result of a properly executed surface grinding operation is cookware that not only performs better in heat distribution and mechanical strength but also exudes a high-quality finish that appeals to both consumers and professional chefs. This machinery plays a vital role in bridging the gap between functional industrial metalworking and refined consumer product aesthetics.
To further enhance production versatility and meet the demands of diverse cookware lines, surface grinding machinery is often modular and configurable. Manufacturers may choose between vertical or horizontal grinding axes depending on space constraints and the shape of the cookware. Vertical grinders are ideal for deep pots and vessels with significant sidewall height, as they allow for better access along the vertical contour. Horizontal grinders, on the other hand, are commonly used for flat-bottomed frying pans or sauté pans, ensuring high-speed planar grinding.
The abrasives used in cookware surface grinding range from zirconia and ceramic belts for aggressive stock removal to fine silicon carbide or aluminum oxide belts for finishing operations. In multi-pass grinding systems, automatic grit changing mechanisms reduce downtime by switching belts or wheels between roughing and finishing sequences without operator intervention. This is particularly useful for operations requiring consistent finishes across multiple SKUs or materials.
Automation also extends to in-process measurement systems, which use laser or contact sensors to evaluate flatness, roundness, or surface roughness (Ra value) during or after grinding. Data from these sensors feed into closed-loop control systems, which can automatically adjust feed speed or grinding force to ensure every piece meets specification without manual rework.
For cookware manufacturers focused on sustainability and energy efficiency, modern grinding machines are often equipped with regenerative braking systems, variable frequency drives (VFDs), and water recycling systems for cooling circuits. This minimizes energy consumption and supports compliance with ISO 14001 or other environmental certifications.
In high-end cookware lines, such as those involving clad metals (e.g., stainless-steel-aluminum-stainless sandwiches), surface grinding must be executed with extreme care to prevent smearing between layers or exposing core material. Specialized multi-material grinding heads with adjustable dwell times and pressure settings are used to treat these items without compromising the laminated structure.
Some production lines also integrate grinding stations with robotic deburring tools or flap disc polishing units to perform additional refinement immediately after surface grinding. This continuous flow reduces handling time, labor costs, and potential damage from excessive movement between processes.
Training and safety protocols are equally critical in operations involving surface grinding. Modern machines include full enclosures with interlocks, automatic shutdowns in case of vibration anomalies, belt breakage detection, and emergency stop systems. Touchscreen HMI panels allow operators to monitor and adjust machine parameters quickly, with built-in recipe management for quick changeovers.
Ultimately, surface grinding in metal cookware manufacturing is not just a finishing step—it’s a precision process that significantly impacts cookware quality, durability, thermal efficiency, and aesthetic value. With advanced machinery and automation, manufacturers can achieve consistent results at industrial scale while maintaining the flexibility to serve both commercial and consumer markets.
Machinery For Non-Toxic Metal Cookware Manufacturing
Machinery for non-toxic metal cookware manufacturing focuses on producing safe, durable, and environmentally friendly cookware that meets strict health and safety standards. These machines are designed to use materials and processes that avoid harmful substances like lead, cadmium, or toxic coatings, ensuring the cookware is safe for food contact and long-term use.
The manufacturing process begins with metal sheet preparation machines that handle food-grade metals such as stainless steel (especially 304 and 316 grades), high-purity aluminum, copper with food-safe linings, or clad materials combining multiple metals without harmful adhesives or fillers. These sheets are cut, cleaned, and prepared for forming using automated shearing and cleaning lines that ensure surface purity and avoid contamination.
Forming machines include deep drawing presses, metal spinning lathes, and hydraulic or mechanical stamping presses specifically adjusted to work with non-toxic alloys. The machinery maintains strict control over temperature and pressure to prevent micro-cracking or stress points that could harbor bacteria or degrade over time.
Surface treatment machinery emphasizes mechanical finishing methods—such as polishing, grinding, and brushing—over chemical treatments to avoid introducing toxic substances. When coatings are applied, specialized equipment uses PFOA-free, PTFE-free, ceramic, or enamel coatings that are certified food-safe. These coating lines incorporate robotic spray or dipping systems with precise environmental controls to ensure even application and curing without off-gassing.
Welding and joining machines utilize laser or TIG welding techniques that create strong, clean seams without filler materials that may contain heavy metals or toxins. Seam welding machines designed for cookware prioritize airtight, smooth joints that resist corrosion and prevent contamination.
Throughout the line, automated inspection systems using vision and spectrometry sensors verify surface quality, coating thickness, and material composition to certify compliance with food safety standards such as FDA, LFGB (Germany), or EU regulations.
Additional machinery includes non-toxic handle attachment stations that use mechanical fastening or food-safe adhesives rather than toxic glues or soldering. Packaging and sterilization machines then prepare the finished cookware for distribution while maintaining hygienic conditions.
Overall, machinery for non-toxic metal cookware manufacturing integrates precision forming, mechanical finishing, safe coating application, and rigorous quality control to deliver products that are safe, eco-friendly, and meet modern consumer and regulatory demands.
These manufacturing lines often incorporate closed-loop process control to ensure that every step—from raw material input to finished product—is monitored and adjusted in real time. For example, metal sheet suppliers provide certification of material composition, which is verified on-site with handheld or inline analyzers using X-ray fluorescence (XRF) or optical emission spectroscopy (OES). This guarantees that only food-safe metals enter the production stream.
Cutting and forming machines are engineered to minimize scrap and contamination, employing precision servo-driven tooling and CNC controls that reduce burrs and metal deformation. This precision also helps preserve the integrity of the metal surface, reducing the need for aggressive finishing or chemical treatments afterward.
Surface finishing equipment is tailored to avoid toxic chemical baths; instead, mechanical polishing, grinding, and brushing dominate. These methods not only preserve the natural qualities of the metal but also enhance its corrosion resistance and food safety by eliminating residues that could harbor bacteria. For manufacturers adding coatings, robotic application systems utilize certified non-toxic coatings applied under controlled temperature and humidity conditions to ensure proper curing without harmful emissions.
Joining and welding technologies focus on high-precision laser welding or TIG welding, which produce clean, durable seams without the use of toxic filler materials or solder. These methods also reduce heat-affected zones, preventing metal degradation or unwanted material migration that might compromise food safety.
Advanced inspection stations equipped with high-resolution cameras, 3D scanners, and spectroscopy devices perform continuous checks for surface defects, weld integrity, coating consistency, and material composition. This real-time quality control ensures compliance with strict food contact regulations and reduces the risk of product recalls.
Automation and robotics play a key role in maintaining sanitary conditions, reducing human contact with the product, and minimizing contamination risk. For instance, robotic arms can handle delicate assembly steps like attaching handles with food-safe mechanical fasteners or adhesives, and packing finished cookware into sterilized containers.
Environmental control systems integrated into the production facility manage air quality, humidity, and particulate filtration to maintain an ultra-clean manufacturing environment. Wastewater treatment and scrap recycling systems are often included to align with environmental regulations and corporate sustainability goals.
Overall, the machinery and equipment for non-toxic metal cookware manufacturing create a seamless, precise, and hygienic production ecosystem that prioritizes consumer health and environmental responsibility while delivering high-quality, durable cookware products.
In addition to the core manufacturing machinery, non-toxic cookware production often integrates traceability systems that log every batch and component through RFID tags or QR codes. This allows manufacturers and end consumers to verify the origin of materials and the processing history, ensuring transparency and building trust in product safety.
Maintenance-friendly machine designs are also essential, with easy-to-clean surfaces and modular components that prevent buildup of contaminants and allow for quick sanitation. Many machines include CIP (Clean-In-Place) capabilities or are designed to be disassembled rapidly for deep cleaning without using harsh chemicals.
Energy-efficient drives, LED lighting, and heat recovery systems are commonly employed to reduce the environmental footprint of the production line. This commitment to sustainability often aligns with the non-toxic philosophy, as manufacturers seek to minimize the overall impact of cookware production on people and planet.
Training and certification for machine operators focus heavily on hygiene, safe handling of materials, and proper monitoring of critical control points within the process to prevent cross-contamination or material mix-ups.
Finally, modular line configurations enable manufacturers to adapt quickly to new regulations or emerging consumer preferences, such as switching to new food-safe coating technologies or integrating more advanced inspection methods like AI-powered visual defect recognition.
Together, these elements create a comprehensive, future-proof machinery ecosystem that supports the efficient, safe, and sustainable manufacture of non-toxic metal cookware for global markets.
Machinery for metal bowls used in food preparation manufacturing is specialized to produce durable, hygienic, and food-safe bowls that meet industry standards. The production process typically involves forming, finishing, and quality control equipment designed specifically for the shapes and sizes common in kitchen and commercial food prep bowls.
The manufacturing line usually begins with metal sheet preparation machines that handle food-grade stainless steel, aluminum, or sometimes copper. Automated coil feeders straighten and cut sheets or blanks to precise dimensions, optimizing material usage and reducing scrap.
Bowl forming machines include deep drawing presses and hydraulic stamping presses that shape the metal sheets into smooth, uniform bowl shapes. These presses are equipped with precise tooling to ensure consistent wall thickness, roundness, and smooth edges, critical for food safety and durability. Some lines use metal spinning lathes for custom or smaller batch production, allowing flexible bowl shapes with excellent surface finish.
Following forming, trimming machines remove excess metal from the bowl edges to ensure smooth rims without sharp edges that could cause injury or compromise food safety. Edge rolling or flanging machines may be used to strengthen rims and improve ergonomics.
Surface finishing equipment is vital for food prep bowls, focusing on polishing, grinding, and brushing to achieve a sanitary, corrosion-resistant finish. Automated polishing machines use belts or brushes with food-safe abrasives to create mirror-like or matte surfaces, depending on product specifications. These machines often include dust extraction systems and are enclosed for operator safety.
In more advanced lines, automated inspection stations with vision systems check bowl geometry, surface finish, and detect defects such as scratches or dents. Inline measurement tools verify dimensions to maintain strict tolerances required in food prep environments.
Assembly machines may be included if the bowls incorporate handles or lids, using food-safe welding, riveting, or mechanical fastening systems. Robots or automated fixtures ensure repeatable, hygienic assembly processes.
Quality control and packaging machinery complete the line, providing sanitary handling, sterilization (if required), and protective packaging for transport.
Overall, machinery for metal food prep bowl manufacturing integrates precision forming, finishing, and inspection technologies to deliver safe, durable, and aesthetically pleasing products suitable for commercial kitchens and household use.
The production workflow starts with high-quality metal sheets—usually stainless steel grades like 304 or 316 due to their corrosion resistance and food safety certifications. These sheets are fed into coil straighteners and precision cutting machines that produce clean, burr-free blanks tailored to bowl dimensions.
Forming machines then shape these blanks via deep drawing or stamping, carefully controlling pressure and speed to avoid metal cracking or thinning. The design of dies and punches is optimized to maintain uniform wall thickness and preserve the integrity of the metal surface, which is crucial to prevent bacterial buildup and ensure durability.
After forming, trimming stations remove any excess metal and sharp edges, often followed by rim flanging to reinforce the bowl’s lip, enhancing strength and user comfort. These processes employ CNC-controlled tools to maintain consistency across production batches.
Surface finishing equipment polishes the bowls to a smooth, hygienic finish. Automated polishing machines use abrasives and brushes compatible with food-grade standards, removing microscopic imperfections and enhancing corrosion resistance. Dust extraction and closed enclosures protect operators and maintain a clean environment.
Inspection systems are integrated inline, employing high-resolution cameras and laser scanners to detect surface defects, dimensional inaccuracies, or contaminants. Such quality assurance measures reduce waste and ensure compliance with strict food safety regulations.
If bowls require handles or lids, automated assembly stations use food-safe welding or mechanical fastening methods, ensuring robust, hygienic joins without introducing harmful substances. Robotics often handle these tasks to minimize human contamination.
Finally, packaging systems wrap and box the finished bowls in sanitary conditions, sometimes including sterilization steps for commercial or medical-grade products. The entire line is supported by process monitoring software and traceability systems that track material batches and production parameters, ensuring full compliance with food safety standards and facilitating recalls if necessary.
This combination of specialized machinery and strict process controls ensures that metal food prep bowls are manufactured efficiently, safely, and to the highest quality standards demanded by both consumers and regulators.
To enhance efficiency and maintain hygiene, many modern metal bowl manufacturing lines incorporate automation and robotics at multiple stages. Automated guided vehicles (AGVs) or conveyor systems transport raw materials and finished products between stations, minimizing manual handling and reducing contamination risks. Robotics perform repetitive tasks such as loading and unloading forming presses, polishing, and assembly, improving precision and consistency.
Energy efficiency is also a critical consideration. Machines are often equipped with servo motors and variable frequency drives to optimize power consumption, while waste heat recovery systems capture and reuse energy from presses and polishing equipment. This approach not only reduces operational costs but also aligns with environmental sustainability goals.
Material traceability systems are integrated throughout the line, using RFID tags or barcode scanning to track each batch of metal sheets, ensuring that only certified food-grade materials are processed. Data from inspections, machine settings, and operator inputs are recorded in centralized quality management systems, facilitating real-time monitoring and regulatory reporting.
Maintenance and cleaning protocols are built into the machinery design, with easy-access panels, smooth surfaces, and sanitary fittings to allow thorough cleaning and reduce downtime. Some machines feature Clean-in-Place (CIP) systems or are compatible with food-safe cleaning agents, further supporting hygienic production environments.
Customization capabilities allow manufacturers to produce bowls with varied sizes, shapes, and finishes on the same line. Quick-change tooling and flexible software controls enable rapid adjustments, accommodating small batch runs or new product designs without lengthy reconfiguration.
Overall, the synergy of advanced forming, finishing, inspection, and automation technologies creates a highly productive, safe, and adaptable manufacturing ecosystem for metal food preparation bowls, meeting the evolving demands of the foodservice industry and end consumers.
Machinery For Metal Wok Manufacturing
Machinery for metal wok manufacturing is designed to handle the unique shape, thickness, and strength requirements of woks, which typically feature a rounded, deep bowl with a flat or slightly curved bottom. The equipment combines precision forming, finishing, and assembly technologies to produce durable, heat-conductive, and ergonomically shaped woks suited for both commercial and household cooking.
The production begins with feeding metal sheets—commonly carbon steel, stainless steel, or aluminum—into coil straighteners and automatic blanking machines that cut precise circular blanks sized for the wok diameter. These blanks must be burr-free to ensure smooth forming and safe handling.
Forming machines include deep drawing presses and metal spinning lathes. Deep drawing presses use custom-designed dies to shape the metal into the classic wok bowl form in one or multiple stages, carefully controlling pressure to avoid cracks or thinning. Metal spinning lathes can also be employed to spin and shape the wok from a rotating blank, providing excellent surface finish and allowing for adjustable thickness and contour.
For flat-bottom woks, additional pressing or ironing machines create a stable base, ensuring even contact with heat sources. Edge forming machines then roll or flange the wok rims to add strength and improve usability.
Surface finishing machines polish or brush the wok interior and exterior, achieving a smooth, food-safe finish that enhances cooking performance and corrosion resistance. Some lines incorporate seasoning stations, especially for carbon steel woks, where controlled heating and oil application create a protective patina.
If the wok includes handles, automated welding, riveting, or mechanical fastening machines attach wooden, metal, or composite handles securely, ensuring durability and heat insulation. Robots often perform these tasks to maintain precision and hygiene.
Quality inspection stations with vision systems check dimensions, surface quality, and handle attachment integrity. Defect detection ensures consistent product quality before packaging.
Finally, packaging machinery wraps and boxes the woks, sometimes including protective inserts to prevent damage during shipment.
Overall, metal wok manufacturing machinery integrates specialized forming, finishing, and assembly equipment tailored to wok geometry and material properties, producing high-quality cookware ready for various cooking styles.
The wok manufacturing process begins with high-quality metal sheets selected for their heat conductivity, durability, and food safety. Carbon steel is most commonly used due to its excellent heat retention and seasoning properties, though stainless steel and aluminum options are also popular.
The sheet metal is first leveled and fed into blanking machines that cut out precise circular blanks for wok bodies. These blanks must be perfectly flat and free from defects to ensure smooth forming and uniform thickness. Automated feeding systems optimize material use and reduce waste.
Forming is typically done via deep drawing presses or metal spinning lathes. Deep drawing uses a series of dies to progressively shape the flat blank into a deep, round bowl while controlling metal flow to prevent thinning or cracking. This method is efficient for mass production. Metal spinning, in contrast, involves rotating the blank on a lathe while a forming tool shapes the wok, allowing for custom thickness adjustments and smooth finishes. Some factories combine both methods depending on product range and volume.
For woks with flat or slightly curved bottoms, secondary pressing or ironing machines flatten and shape the base for stable placement on stovetops. This step ensures proper heat distribution and user safety.
Rim rolling or flange forming machines create smooth, reinforced edges that add strength and facilitate handling. The rim design can also be functional, allowing for lid fitting or stacking.
Surface finishing involves polishing, brushing, or coating, depending on the wok material. Polishing machines remove surface irregularities and produce a smooth interior for better cooking performance. For carbon steel woks, seasoning lines apply controlled heat and oil layers to develop a natural non-stick patina. Stainless steel or aluminum woks may receive electro-polishing or anti-corrosion coatings.
Handle attachment is automated where possible. Welding machines, riveting tools, or mechanical fastening stations secure handles made from heat-resistant materials like wood, bakelite, or metal. Robotic arms ensure precise placement and consistent weld quality, reducing manual labor and contamination.
Quality inspection is critical. Vision systems and dimensional gauges check for shape accuracy, surface finish, and attachment security. Defects such as dents, cracks, or improper welds are detected early to prevent faulty products reaching the market.
Packaging equipment wraps woks in protective materials and boxes them for shipping. Automated lines may include labeling, palletizing, and inventory tracking, supporting efficient warehouse management.
Advanced wok manufacturing lines incorporate automation, real-time monitoring, and data collection systems to enhance productivity, maintain strict quality standards, and reduce downtime. Flexible tooling allows for quick changes in wok size, shape, and finish to respond to market trends.
Overall, metal wok manufacturing machinery blends specialized forming, finishing, and assembly technologies with automation to produce durable, high-performance cookware that meets culinary and safety demands worldwide.
Material handling systems in wok manufacturing lines play a vital role in streamlining production flow and minimizing manual labor. Automated conveyors, robotic arms, and magnetic lifters transport blanks, formed wok bodies, and finished products between stations efficiently and safely. This reduces cycle times and protects sensitive surfaces from scratches or contamination.
To ensure consistent wok thickness and structural integrity, thickness measurement systems using laser or ultrasonic sensors are integrated after forming stages. These sensors detect uneven metal distribution or thinning, enabling immediate adjustments or rejection of defective parts. Maintaining uniform thickness is crucial for cooking performance and product longevity.
For specialized wok designs such as multi-layered clad woks or those with non-stick coatings, additional processing stations are incorporated. Cladding machines bond layers of different metals for improved heat conduction and durability, while coating lines apply PTFE or ceramic layers with precision spraying and curing ovens. These stations require careful environmental controls and quality monitoring.
Environmental and safety considerations are integral to modern wok manufacturing. Equipment is designed with dust and fume extraction systems to capture metal particles and volatile compounds, protecting workers and equipment. Noise reduction features, ergonomic controls, and safety interlocks ensure compliance with industrial regulations and create safer workplaces.
Maintenance and downtime reduction are addressed through predictive maintenance technologies embedded in machinery. Sensors monitor vibration, temperature, and wear, alerting operators to potential failures before breakdowns occur. Modular machine designs enable quick replacement of worn parts, minimizing production interruptions.
Customization options in manufacturing machinery allow producers to offer various wok sizes—from small household models to large commercial woks—with different bottom shapes and handle configurations. Tooling changeover systems use quick-release dies and programmable CNC controls to switch between product types with minimal downtime.
Training simulators and digital twins of the manufacturing line help operators understand machine functions and optimize settings without risking actual production. These technologies enhance workforce skills and improve overall efficiency.
In summary, the combination of precise forming equipment, advanced finishing processes, automated assembly, and intelligent control systems makes modern metal wok manufacturing highly efficient, flexible, and capable of meeting diverse market demands while maintaining high quality and safety standards.
Machinery For Stainless Steel Pans Manufacturing
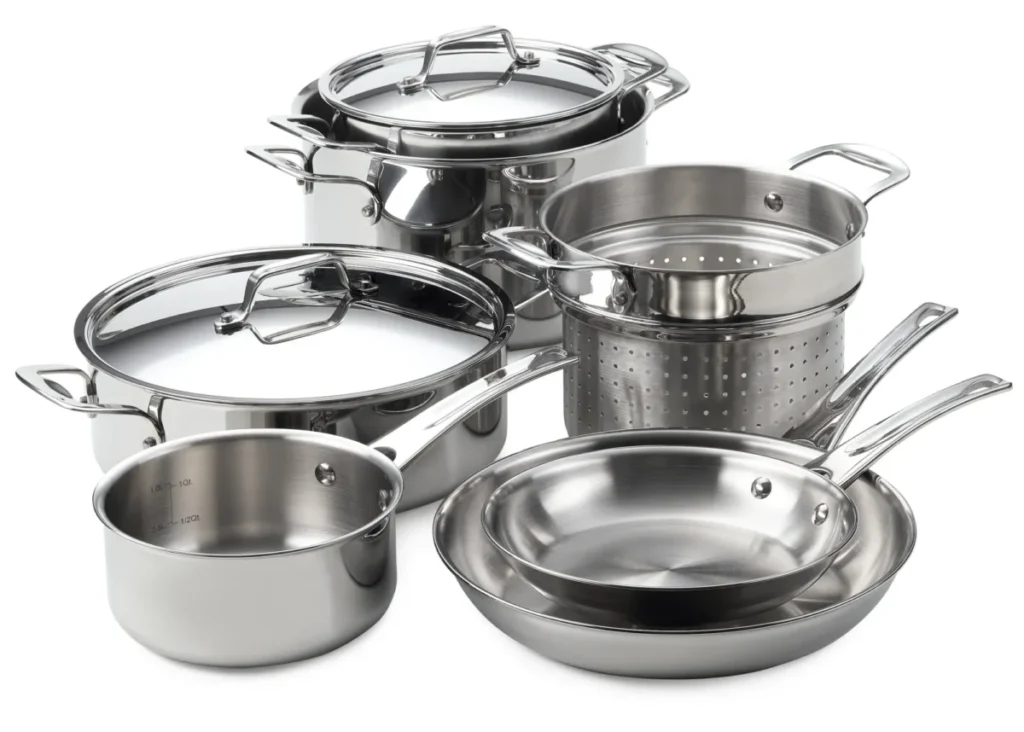
Machinery for stainless steel pans manufacturing is designed to handle the unique properties of stainless steel — such as its hardness, corrosion resistance, and thermal conductivity — while shaping durable, high-quality cookware. The process integrates metal forming, surface finishing, and assembly equipment tailored to stainless steel’s characteristics to produce pans with excellent performance, appearance, and longevity.
The manufacturing line typically begins with stainless steel coil or sheet feeding systems. These include automatic uncoilers, straighteners, and feeders that deliver perfectly flat blanks cut by high-precision blanking presses or laser cutters. Accurate blank dimensions ensure efficient forming and minimize material waste.
Forming machines include deep drawing presses and hydroforming systems. Deep drawing presses progressively shape the flat stainless steel blanks into pan bodies using custom dies designed to maintain material thickness and prevent cracks or wrinkles. Hydroforming uses high-pressure fluid to press the metal into a die cavity, producing smooth, uniform pan shapes and allowing for complex designs or integrated features like pour spouts.
For pans requiring flat or slightly domed bottoms, ironing or stamping presses refine the base thickness and shape, improving heat distribution and stability on cooking surfaces. Edge rolling machines then form strong, smooth rims, sometimes incorporating rolled beads or flanges for enhanced durability and aesthetics.
Surface finishing equipment is crucial for stainless steel pans to achieve both functional and visual quality. Polishing machines with abrasive belts or brushes smooth out forming marks and create the desired finish—ranging from mirror polish to brushed textures. Electro-polishing stations may also be employed to enhance corrosion resistance and surface cleanliness.
Some lines include machines for adding additional layers, such as clad or multi-ply bases combining stainless steel with aluminum or copper for better heat conduction. These clad layers are bonded by rolling mills or explosive welding machines before pan forming.
Handle attachment involves automated welding robots, riveting machines, or mechanical fastening systems that secure handles made from stainless steel, heat-resistant plastics, or composites. Precise welding ensures strong joints without compromising pan aesthetics.
Inspection stations equipped with laser measurement tools and vision systems verify dimensions, thickness, surface quality, and weld integrity. Automated defect detection helps maintain consistent product quality.
Finally, packaging machines prepare the pans for shipment with protective wrapping, boxing, and labeling. Integrated logistics systems can manage inventory and batch tracking.
Modern stainless steel pan manufacturing lines emphasize automation, precision tooling, and flexible configurations to handle various pan sizes and designs while ensuring efficiency, durability, and top-tier quality in finished cookware.
Stainless steel pan manufacturing machinery often incorporates advanced CNC-controlled forming presses that allow for precise control over pressing speed, force, and stroke, minimizing material stress and enhancing consistency across batches. These machines can be quickly retooled for different pan dimensions or designs, enabling manufacturers to respond flexibly to market demands.
Hydroforming technology is increasingly used due to its ability to create complex shapes with minimal tooling changes, reducing setup time and increasing product variety. The uniform pressure applied by hydroforming helps maintain metal thickness evenly, which is particularly important for stainless steel to avoid weak spots that could cause deformation during use.
Surface finishing lines are integrated with automated buffing and polishing machines that use variable-speed abrasive belts and polishing wheels to achieve finishes from satin to high gloss. The finishing process not only improves aesthetics but also impacts cleanability and corrosion resistance. Some advanced lines include ultrasonic cleaning and passivation steps that remove surface contaminants and form a protective oxide layer, enhancing the stainless steel’s natural corrosion resistance.
Cladding processes add thermal performance to stainless steel pans by bonding conductive metals like aluminum or copper beneath the stainless steel surface. Rolling mills compress and bond these layers before pan forming, ensuring strong adhesion and durability. Multi-ply clad pans undergo additional forming and trimming steps to shape the combined layers precisely.
Automated welding robots use TIG (tungsten inert gas) or laser welding to attach handles and other components securely, minimizing heat distortion and providing consistent weld quality. Quality control systems monitor weld seam integrity through sensors and cameras.
Throughout the production line, integrated vision systems scan pans for defects such as scratches, dents, or surface inconsistencies, while laser micrometers measure thickness and dimensions to tight tolerances. Data from these systems feed into centralized quality management software, enabling real-time adjustments and traceability.
Packaging lines often include automated wrapping with anti-scratch films, box erection, and labeling machines that incorporate barcodes or RFID tags for inventory tracking and supply chain management.
Incorporating IoT-enabled sensors and predictive maintenance systems reduces downtime by monitoring machine health, scheduling maintenance proactively, and optimizing production schedules. This ensures continuous, efficient operation with minimal waste.
Overall, machinery for stainless steel pan manufacturing blends precision engineering, automation, and quality control to produce cookware that meets high standards for durability, appearance, and cooking performance while maintaining production flexibility and cost-effectiveness.
Additional machinery in stainless steel pan manufacturing includes automated edge finishing systems that refine the pan rims after forming, ensuring smoothness and safety for users. These machines can deburr, roll, or curl the edges to the desired profile, reducing sharpness and improving durability. Some systems feature multi-stage abrasive belts combined with polishing heads to create a seamless transition between the pan body and the rim.
For pans with integrated features like pour spouts, measuring marks, or decorative patterns, CNC stamping and embossing machines are employed. These machines use programmable dies and punches to imprint precise designs onto the stainless steel surface without compromising structural integrity.
To improve heat distribution and reduce warping during cooking, stress-relief annealing furnaces may be incorporated in the production line. Controlled heating and cooling cycles relieve internal stresses caused by forming and welding, enhancing pan performance and lifespan.
For pans requiring non-stick or ceramic coatings, additional coating lines apply these finishes via spraying, dipping, or roll coating methods, followed by curing ovens with precise temperature controls. Surface preparation equipment like plasma cleaners or sanding machines ensure optimal adhesion of coatings.
Quality assurance is further enhanced by computerized data collection systems that track every stage of production, from raw material input to final inspection. This allows manufacturers to maintain batch traceability, analyze defect trends, and comply with food safety regulations.
Modern stainless steel pan manufacturing machinery is often modular, enabling rapid reconfiguration to produce various pan models—from shallow skillets to deep sauté pans—while minimizing changeover time. Integration with robotic systems for material handling and assembly increases throughput and reduces manual labor, improving workplace safety and consistency.
Energy-efficient drives and servo motors optimize machine performance, reduce power consumption, and provide fine control over forming and finishing processes. Noise and vibration dampening technologies enhance operator comfort.
In essence, stainless steel pan manufacturing machinery is a synergy of robust mechanical forming, high-precision finishing, advanced automation, and comprehensive quality management, all tailored to produce durable, attractive, and high-performing cookware at scale.
Machinery For Metal Cookware Safety Manufacturing
Machinery for metal cookware safety manufacturing focuses on ensuring that cookware meets strict safety, durability, and usability standards to protect consumers during cooking and handling. This includes specialized equipment designed to address structural integrity, heat resistance, non-toxicity, and safe user interfaces.
Key machinery and systems include:
1. Material Testing and Inspection Machines:
- Tensile and impact testers verify metal strength and flexibility to ensure cookware can withstand thermal cycling and mechanical stress without cracking or deforming.
- Ultrasonic and X-ray inspection systems detect internal defects, cracks, or inclusions in metal parts before assembly.
- Surface contamination analyzers check for harmful residues or coatings that may leach toxins during cooking.
2. Heat-Resistant Handle Manufacturing:
- Injection molding machines produce handles from heat-resistant plastics or composites, designed to stay cool during cooking.
- Robotic assembly stations attach handles securely using welding, riveting, or adhesive bonding, ensuring mechanical safety and durability.
3. Seam and Joint Welding Equipment:
- Precision TIG and laser welding machines create strong, clean welds on pan rims, handles, and lids, preventing weak points that could cause breakage or injury.
- Seam welding machines seal joins to eliminate leaks, critical for pressure cookers and sealed cookware.
4. Edge Finishing and Deburring Machines:
- Automated edge rollers and grinders smooth sharp metal edges on rims, lids, and bottoms to prevent cuts and injuries during handling.
- Multi-stage polishing systems eliminate burrs and sharp points while enhancing surface quality.
5. Coating and Surface Treatment Lines:
- Non-toxic coating application machines apply FDA-approved non-stick or ceramic layers evenly, followed by curing ovens that ensure strong, durable finishes resistant to chipping or peeling.
- Passivation and electro-polishing units enhance corrosion resistance and reduce the risk of metal ion leaching into food.
6. Pressure Testing Systems (for pressure cookers and sealed cookware):
- Automated pressure chambers simulate cooking conditions to test seals, valves, and structural integrity, ensuring safe operation under pressure.
7. Temperature and Thermal Shock Testing Equipment:
- Thermal cycling chambers expose cookware to rapid heating and cooling cycles to confirm resistance to warping, cracking, or handle failure.
8. Automated Quality Control and Safety Inspection:
- Vision systems identify surface defects, coating inconsistencies, or assembly faults.
- Laser micrometers and thickness gauges verify material uniformity and ensure compliance with safety tolerances.
9. Traceability and Compliance Software:
- Integrated systems log production parameters, inspection results, and material batch data to guarantee compliance with food safety regulations and enable recall tracking if necessary.
10. Ergonomic and Anti-Slip Handle Manufacturing Machines:
- Equipment that shapes and textures handles with grip-enhancing materials reduces risk of slips or burns during use.
Together, these machines create a manufacturing environment that prioritizes safety at every stage — from raw material validation and forming through assembly, finishing, and final testing — producing cookware that protects users and complies with international safety standards.
Further advancing metal cookware safety manufacturing, automation plays a critical role in reducing human error and ensuring consistent product quality. Robotics integrated into welding, assembly, and inspection stages provide precision and repeatability, minimizing defects that could compromise safety.
Heat sensors and thermal imaging cameras monitor equipment temperatures during production to prevent overheating that could degrade materials or coatings. Automated alerts and shutdowns safeguard the process, maintaining product integrity and worker safety.
Advanced coating technologies, such as plasma-enhanced chemical vapor deposition (PECVD), offer ultra-thin, uniform layers that are free of harmful chemicals and enhance cookware durability and food safety. These coatings are applied in controlled environments to ensure purity and adhesion.
Material handling systems, including conveyor belts with controlled speeds and robotic arms, reduce manual contact, preventing contamination and mechanical damage. Cleanroom or controlled-atmosphere zones are sometimes incorporated where sensitive coatings or assemblies take place.
Safety-focused testing continues through product lifecycle simulations using mechanical fatigue testers that mimic repeated use stresses to predict long-term durability. This data guides process adjustments and material selection to further enhance user safety.
Environmental control machinery manages dust, fumes, and waste, maintaining a clean and safe manufacturing environment that protects both workers and the final cookware products.
Emerging technologies like AI-powered vision inspection systems provide real-time defect detection beyond human capability, spotting micro-cracks, coating anomalies, or assembly misalignments instantly and accurately.
Integration of Industry 4.0 standards connects machinery and sensors in a smart factory setup, enabling centralized monitoring and predictive maintenance that reduces unexpected downtime and maintains consistent safety compliance.
By combining mechanical precision, advanced materials science, automated quality assurance, and smart manufacturing technologies, metal cookware safety manufacturing machinery ensures that every piece meets rigorous safety criteria, providing consumers with reliable, durable, and safe cookware products.
In addition, ergonomic considerations in machinery design help produce cookware that is comfortable and safe to handle. Machines that shape handles and grips with textured or heat-insulating materials reduce the risk of burns and slipping during cooking. Automated systems can precisely control these features to maintain consistent quality across batches.
Environmental sustainability is also a growing focus in safety manufacturing machinery. Equipment designed to minimize waste, recycle metal scraps, and reduce energy consumption contributes to safer workplaces and eco-friendly production. Efficient filtration systems capture airborne particles and fumes generated during welding or coating, protecting worker health and preventing contamination of cookware surfaces.
Maintenance and calibration machinery ensure that safety-critical equipment remains in optimal condition. Regular automatic calibration routines on welding robots, inspection sensors, and coating applicators maintain precision and reliability, preventing deviations that could affect product safety.
Training simulators and virtual reality tools are sometimes integrated with manufacturing setups to educate operators on safe machine handling, emergency procedures, and quality standards, further enhancing overall safety culture.
Finally, collaboration between machinery manufacturers, material scientists, and regulatory bodies continually drives innovation, refining manufacturing processes and equipment to meet evolving safety standards worldwide. This synergy results in metal cookware that not only performs well but also adheres to strict health, safety, and environmental regulations, assuring consumer confidence and satisfaction.
Machinery For Metal Pan Manufacturing
Machinery for metal pan manufacturing encompasses a wide range of specialized equipment designed to efficiently shape, form, finish, and assemble pans made from various metals like stainless steel, aluminum, carbon steel, copper, and clad metals. These machines enable high precision, consistent quality, and scalable production to meet market demand.
Key machinery types include:
1. Sheet Metal Cutting Machines:
- Hydraulic or mechanical shears cut metal sheets into blanks for pan bodies and lids.
- CNC laser cutters offer precise, customizable cutting for complex shapes or patterns.
2. Deep Drawing Presses:
- Hydraulic or mechanical deep drawing machines form flat metal blanks into pan shapes by pressing them into dies, creating smooth, seamless bodies.
- Multi-stage drawing presses enable deeper and more complex pan profiles.
3. Metal Spinning Lathes:
- Used for shaping round pans by rotating metal blanks on a mandrel while applying pressure with tools to form curved sides and contours.
- Ideal for smooth, symmetrical pans with uniform thickness.
4. Stamping and Punching Machines:
- Punch holes or slots for handles, vents, or rivet placements.
- Stamping presses emboss brand logos, measurement marks, or decorative patterns.
5. Edge Rolling and Flanging Machines:
- Roll or bend pan edges for strength, safety, and handle attachment points.
- Flanging machines create rims that reinforce pan shape and facilitate lid fitting.
6. Handle Manufacturing and Assembly Systems:
- Injection molding machines produce plastic or composite handles.
- Robotic or manual assembly stations attach handles using welding, riveting, or adhesive bonding.
7. Welding Equipment:
- Seam welding machines join pan components or attach handles with strong, clean welds.
- Laser welding offers precision with minimal heat distortion.
8. Surface Finishing Machinery:
- Polishing and buffing machines create smooth, shiny surfaces.
- Grinding machines remove burrs and sharp edges.
- Brushing or sandblasting equipment offers matte or textured finishes.
9. Coating and Treatment Lines:
- Non-stick coating applicators spray or roll Teflon or ceramic layers, followed by curing ovens.
- Anodizing and electro-polishing equipment improve corrosion resistance and aesthetics.
10. Quality Inspection Systems:
- Vision inspection cameras check surface defects and dimensional accuracy.
- Thickness gauges verify material uniformity.
11. Automated Material Handling and Conveyors:
- Transport components and finished pans between production stages, reducing manual labor and contamination risk.
Together, this machinery suite allows manufacturers to produce metal pans that meet exacting standards of durability, safety, appearance, and performance. Modern production lines integrate automation, robotics, and smart controls for efficient, cost-effective pan manufacturing.
In metal pan manufacturing, automation plays a vital role in increasing production speed and ensuring consistent quality. CNC-controlled machines enable precise shaping and cutting with minimal human intervention, reducing errors and material waste. Robotics assist in tasks like handle attachment, welding, and packaging, improving safety and efficiency.
Material selection impacts the choice of machinery and process parameters. For example, stainless steel pans often require specialized welding and polishing equipment to achieve corrosion resistance and aesthetic appeal, while aluminum pans focus on lightweight forming and anodizing lines. Copper pans may need tailored spinning and brazing machines due to their distinct thermal properties.
Environmental considerations are increasingly integrated into manufacturing machinery, with energy-efficient presses and waste recycling systems becoming standard. Equipment with closed-loop coolant systems minimizes contamination and resource usage. Air filtration units capture fumes from welding and coating processes, protecting both workers and the environment.
Quality control is embedded throughout the production line, with inline sensors and cameras monitoring dimensions, surface finish, and weld integrity in real-time. Data from these systems feed into production management software, enabling immediate adjustments and traceability. Predictive maintenance algorithms help prevent machine downtime by analyzing wear patterns and scheduling timely repairs.
Ergonomic design of machinery interfaces and workstations supports operator comfort and reduces fatigue, contributing to overall production reliability. Safety features such as light curtains, emergency stops, and interlocks protect personnel from moving parts and hazardous operations.
The combination of advanced forming presses, precise cutting tools, robotic assembly, surface treatment systems, and integrated quality inspection creates a comprehensive solution for modern metal pan manufacturing. This integrated approach ensures high output volumes with consistent product quality, meeting stringent industry standards and customer expectations across various market segments.
Further advancements in metal pan manufacturing machinery include the adoption of Industry 4.0 technologies, where interconnected machines communicate data to optimize production flow and quality. Smart sensors embedded in presses, cutters, and finishing equipment collect real-time metrics like pressure, temperature, and vibration, enabling adaptive process control and early detection of anomalies.
Additive manufacturing techniques, such as 3D printing of tooling and prototype components, accelerate development cycles and allow rapid customization of pan designs. These innovations reduce tooling costs and enable manufacturers to respond quickly to market trends.
Hybrid machines that combine multiple forming operations—like deep drawing followed by spinning or stamping—within a single setup reduce handling time and improve precision by maintaining consistent alignment throughout the process.
Energy recovery systems integrated into hydraulic presses and ovens improve overall plant efficiency by capturing and reusing waste heat or kinetic energy. This not only lowers operational costs but also aligns with sustainability goals.
Advanced coating lines now incorporate environmentally friendly, solvent-free materials applied via electrostatic spray or dip coating methods, reducing volatile organic compounds (VOCs) and ensuring safer working conditions.
Collaborative robots (cobots) increasingly support human workers by handling repetitive, ergonomically challenging tasks such as loading/unloading heavy blanks or finishing delicate pan surfaces, enhancing productivity while minimizing injury risks.
Finally, modular machinery designs allow manufacturers to scale production capacity and switch between pan types or materials quickly, improving flexibility and reducing downtime during product changes. This adaptability is crucial for meeting diverse consumer demands and maintaining competitive advantage in a dynamic market.
Overall, metal pan manufacturing machinery continues evolving through integration of automation, smart technologies, sustainable practices, and ergonomic design to deliver superior products efficiently and responsibly.
Machinery For Heat-Resistant Metal Bowls Manufacturing
Machinery for heat-resistant metal bowl manufacturing is specially designed to produce bowls that can withstand high temperatures without deforming or degrading. These bowls are often made from metals like stainless steel alloys, aluminum with heat-resistant coatings, or clad metals combining different layers for durability and thermal stability.
Key machinery and equipment involved include:
1. Sheet Metal Cutting Machines:
Precision hydraulic shears, CNC laser cutters, or plasma cutters slice metal sheets into blanks sized for bowl forming, ensuring clean edges for heat-resistant materials that can be sensitive to stress concentrations.
2. Deep Drawing Presses:
Hydraulic or servo-driven deep drawing machines form the metal blanks into bowl shapes with smooth contours. Multiple-stage presses allow gradual shaping to prevent cracking or thinning in heat-resistant alloys.
3. Spinning Lathes:
Metal spinning machines shape round bowls by rotating and pressing blanks against a mandrel, ideal for producing symmetrical, uniform walls that maintain strength under thermal stress.
4. Annealing Furnaces:
Heat treatment ovens soften metal blanks or partially formed bowls, relieving stresses introduced during forming. Controlled annealing prevents brittleness and enhances heat resistance.
5. Surface Treatment Lines:
- Electro-polishing or passivation systems enhance corrosion resistance critical for heat-exposed surfaces.
- Coating machines apply heat-resistant non-stick or ceramic coatings evenly, followed by curing ovens designed for high-temperature coatings.
6. Edge Rolling and Flanging Machines:
Roll or flange bowl rims for structural integrity and safe handling, with precise control to avoid cracks in heat-resistant materials.
7. Welding and Joining Equipment:
Laser or TIG welding machines assemble multi-layered bowls or attach handles, ensuring strong, heat-tolerant joints.
8. Inspection Systems:
Vision inspection cameras and ultrasonic thickness gauges detect surface defects and verify uniform wall thickness critical for heat resistance.
9. Automated Material Handling:
Robotic arms and conveyor systems manage the bowls during forming, coating, and inspection stages to minimize contamination and damage.
Together, this specialized machinery enables production of metal bowls designed to perform reliably under high-heat cooking conditions, maintaining safety, durability, and aesthetic quality.
Heat-resistant metal bowl manufacturing lines often integrate advanced automation to optimize throughput while maintaining strict quality standards. The forming processes are carefully controlled to accommodate the mechanical properties of heat-resistant alloys, which can be less ductile and more prone to work hardening than standard metals. This requires precise control over pressing speeds, force application, and tool geometry to avoid cracks or deformation.
The annealing stage is crucial to restore ductility after cold working and to enhance the bowl’s resistance to thermal cycling. Furnaces used here employ programmable temperature profiles tailored to specific alloy compositions, ensuring consistent metallurgical properties throughout production batches.
Surface treatments not only improve corrosion resistance but also enhance thermal emissivity or reflectivity, depending on the bowl’s intended use. For example, some bowls receive a brushed finish to disperse heat evenly, while others might be polished to a mirror finish to reflect radiant heat.
Welding and assembly techniques are designed to create joints capable of withstanding repeated thermal expansion and contraction without failure. Automated welding robots with high-precision sensors ensure uniform weld beads, reducing weak points that could lead to cracks under heat stress.
Quality assurance systems employ non-destructive testing methods, including ultrasonic thickness measurement and eddy current scanning, to detect sub-surface flaws invisible to the naked eye. High-resolution imaging combined with AI algorithms can spot surface irregularities or coating defects, enabling real-time rejection of non-conforming parts.
Ergonomic considerations in the machinery layout minimize manual handling of heavy or hot components, improving worker safety and reducing the risk of contamination. Collaborative robots assist with tasks such as stacking, packaging, and transporting bowls within the production line.
Energy-efficient designs in presses, furnaces, and finishing equipment reduce operational costs and environmental impact. Many modern lines incorporate heat recovery systems that capture and reuse waste heat from annealing furnaces and curing ovens, contributing to sustainable manufacturing practices.
This combination of specialized machinery, automation, and quality control ensures the reliable production of heat-resistant metal bowls suited for demanding culinary applications, industrial uses, and commercial kitchens, meeting both safety standards and customer expectations.
To further enhance heat-resistant metal bowl production, manufacturers increasingly implement modular machinery setups that allow quick switching between different bowl sizes, shapes, and alloy types. This flexibility supports shorter production runs and custom orders without extensive downtime or retooling costs.
Advanced process monitoring systems use IoT-enabled sensors embedded in presses, furnaces, and coating lines to continuously track parameters such as temperature, pressure, and humidity. Data analytics platforms process this information to predict maintenance needs, optimize production cycles, and reduce scrap rates by catching deviations early.
In addition to traditional deep drawing and spinning, some manufacturers employ hydroforming technology, where high-pressure fluid shapes the metal into complex, uniform bowl geometries. Hydroforming is especially beneficial for heat-resistant alloys that require gentle forming forces to maintain material integrity.
Integration of additive manufacturing is emerging as well, particularly for creating custom tooling and mandrels tailored to specific bowl designs. This accelerates tooling development and allows rapid prototyping of innovative bowl geometries or features, such as integrated handles or heat-dissipating patterns.
Environmental sustainability is a growing priority. Many production lines now use water-based coatings and low-VOC materials for surface treatments, alongside closed-loop water recycling systems and energy-efficient equipment. Compliance with environmental regulations and certifications like ISO 14001 enhances market acceptance and brand reputation.
Worker safety is addressed through automation of hazardous tasks, such as handling hot metal parts or operating high-pressure forming machines. Safety interlocks, real-time monitoring, and ergonomic design reduce injury risks and improve overall workplace conditions.
The cumulative effect of these technological and operational improvements is a manufacturing process capable of producing high-quality, durable heat-resistant metal bowls at competitive costs and with minimal environmental impact. This supports a broad range of applications—from consumer cookware to industrial kitchen equipment—while meeting evolving market demands for performance, safety, and sustainability.
Machinery For Metal Embossing Pans Manufacturing
Machinery for metal embossing pans manufacturing is specialized equipment designed to create decorative, textured, or patterned surfaces on metal cookware such as pans. Embossing enhances aesthetic appeal, improves grip, and can also influence heat distribution. The embossing process involves mechanically pressing or rolling patterns onto the metal surface without compromising the structural integrity of the pan.
Key machinery used in metal embossing pans manufacturing includes:
- Embossing Press Machines:
Hydraulic or mechanical presses equipped with custom embossing dies imprint raised or recessed patterns onto flat metal sheets or formed pan surfaces. These presses provide precise control over pressure and speed to ensure consistent embossing without damaging the metal. - Roller Embossing Machines:
These machines use engraved rollers that continuously press patterns onto metal strips or sheets as they pass through. Ideal for high-volume production, roller embossing ensures uniform patterns over large surface areas with minimal cycle times. - CNC Engraved Dies and Rollers:
Custom dies and rollers are crafted using CNC machining to produce intricate and repeatable designs. This allows for rapid prototyping and easy changes in embossing patterns according to market trends or customer requirements. - Metal Sheet Feeding and Positioning Systems:
Automated feeders precisely position metal sheets or partially formed pans for embossing, increasing throughput and reducing manual labor. Servo-controlled systems maintain alignment to ensure pattern accuracy. - Forming and Deep Drawing Machines:
In many manufacturing lines, embossing occurs either before or after forming the pan shape. These machines form the metal into the desired pan shape while maintaining or accommodating embossed patterns. - Surface Finishing Equipment:
Post-embossing finishing machines such as polishing buffers or brushing units enhance the appearance of embossed patterns, removing burrs and refining surface texture without diminishing embossing depth. - Quality Inspection Systems:
Vision inspection cameras and surface scanners detect embossing defects, inconsistencies, or misalignments, enabling real-time quality control. - Automation and Robotics:
Robotic arms and conveyors integrate embossing machines within fully automated pan production lines, reducing cycle times and maintaining consistent quality.
This specialized machinery setup enables efficient and precise production of embossed metal pans, combining durability with decorative and functional surface enhancements to meet market demands.
Embossing machinery for metal pans often incorporates advanced control systems to fine-tune pressure, speed, and temperature, adapting to different metal types such as stainless steel, aluminum, or carbon steel. The embossing process must balance the force applied to ensure clear pattern formation without thinning or weakening the metal, especially in cookware where structural integrity and even heat distribution are critical.
To achieve this, many embossing presses are equipped with sensors that monitor force feedback and sheet deformation in real time, allowing automatic adjustments during production. This reduces waste caused by over- or under-embossing and helps maintain consistent quality across batches.
Roller embossing machines often use a tandem setup, where multiple rollers apply sequential patterns or layered textures to create complex surface effects. This approach enables manufacturers to produce distinctive designs that differentiate their cookware in competitive markets.
Custom tooling fabrication is a key aspect of embossing machinery, with CNC machining enabling rapid creation of detailed dies and rollers. This flexibility allows manufacturers to quickly respond to new design trends or customer requests, offering unique embossed patterns or branding directly on the pan surface.
Integration with forming processes is crucial, as embossing can be performed either on flat blanks before shaping or on partially formed pans. Embossing after forming requires machinery capable of handling curved or irregular shapes without compromising pattern clarity.
Surface finishing after embossing involves careful polishing or brushing to enhance visual appeal while preserving the texture. Automated finishing lines use a combination of abrasive pads, brushes, and buffing wheels that can be programmed for different finishes, from matte to mirror-like.
Quality control systems employ high-resolution cameras and laser scanners to detect defects such as incomplete embossing, misalignment, or surface imperfections. These systems often use AI algorithms to classify defects and trigger alerts or automatic rejection, improving overall yield and customer satisfaction.
Automation plays a significant role, with robotic arms handling the transfer of parts between embossing, forming, and finishing stations. This reduces manual labor, minimizes handling damage, and maintains a steady production flow.
Environmental considerations include minimizing lubricant use during embossing and employing eco-friendly cleaning and finishing processes to meet modern sustainability standards.
Together, these technologies enable manufacturers to produce high-quality embossed metal pans that combine aesthetic appeal, functional performance, and durability, meeting both industrial standards and consumer expectations.
Modern metal embossing machinery for pans often incorporates modular designs that allow quick changeover between different embossing patterns and pan sizes. This flexibility is critical for manufacturers who produce multiple product lines or customize designs for different markets. Quick tooling change systems, such as hydraulic die clamps and automated roller exchanges, significantly reduce downtime and increase overall equipment effectiveness (OEE).
The machinery also frequently integrates with Industry 4.0 technologies. IoT sensors gather detailed operational data — pressure, temperature, speed, vibration — that feed into centralized monitoring platforms. Predictive maintenance algorithms analyze this data to foresee wear or failure in embossing dies and rollers, preventing costly breakdowns and ensuring continuous production.
In some advanced setups, embossing presses are combined with laser engraving or etching stations, allowing hybrid surface decoration. This expands creative possibilities, blending tactile embossing with intricate laser patterns or branding marks in one seamless production flow.
For handling materials with special coatings or treatments, embossing equipment is adjusted to maintain surface integrity without damaging coatings that enhance pan performance, such as nonstick layers or anodized finishes. This requires precise control of pressure and tooling surface finishes.
Safety is also prioritized with protective guards, emergency stops, and operator training modules integrated into embossing machine systems, ensuring compliance with workplace safety standards and reducing accidents.
To meet global standards, embossing machinery suppliers often provide certification support (CE, ISO) and after-sales services including training, spare parts, and remote troubleshooting, helping manufacturers maintain high uptime and consistent product quality.
Altogether, these capabilities make metal embossing machinery a vital part of modern cookware manufacturing, enabling production of pans with appealing designs, enhanced grip, and unique market differentiation while maintaining efficiency, quality, and safety.
Machinery For Metal Cookware Production
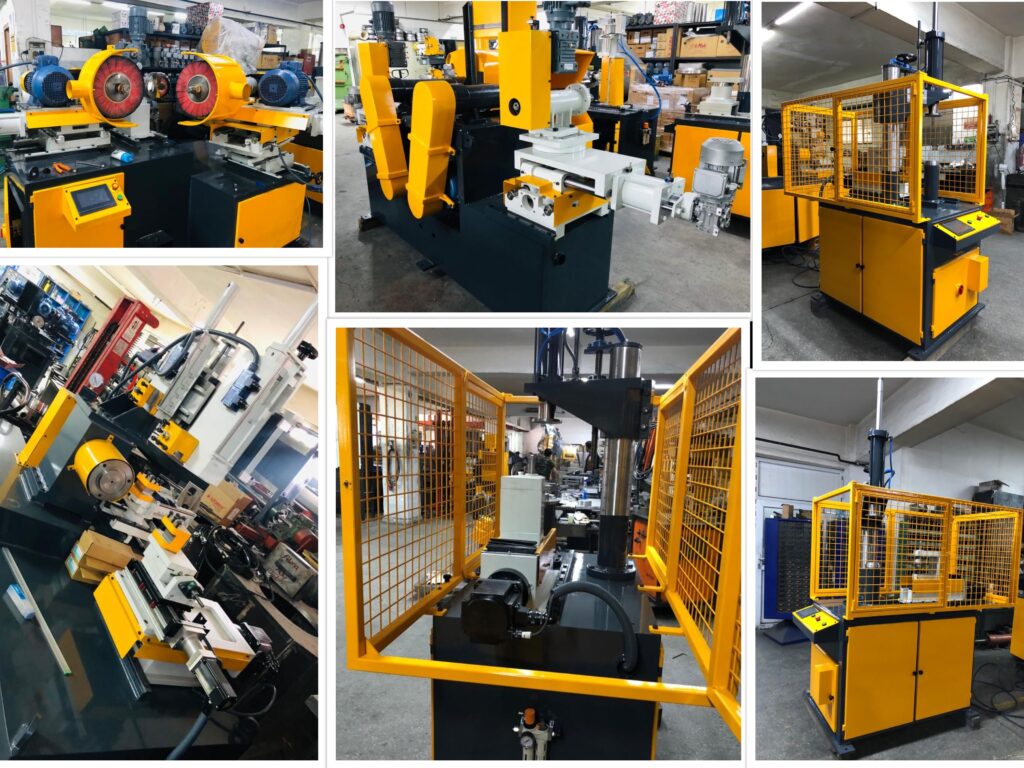
Machinery for metal cookware production encompasses a comprehensive set of specialized equipment designed to transform raw metal materials into finished cookware items such as pots, pans, lids, and related accessories. These machines streamline the manufacturing process, ensuring precision, efficiency, and consistency while accommodating various metal types including stainless steel, aluminum, copper, cast iron, and clad metals.
Key machinery used in metal cookware production includes:
- Metal Sheet Preparation Machines:
These machines cut, flatten, and clean metal sheets to prepare them for forming. Shearing machines, leveling rollers, and surface cleaning systems remove imperfections and ensure uniform thickness. - Deep Drawing Machines:
Essential for shaping flat metal blanks into three-dimensional cookware bodies, deep drawing presses apply high pressure to form pots, pans, and bowls while maintaining metal integrity and thickness. - Metal Spinning Lathes:
Used for creating round, symmetrical cookware components by rotating metal discs against shaping tools, ideal for smooth, seamless pots and pans. - Stamping and Pressing Machines:
These apply force to shape or cut metal parts, including rims, handles, lids, and decorative features. Hydraulic or mechanical presses enable high-volume, precise forming. - Embossing and Engraving Equipment:
Machinery for adding textures, patterns, logos, or branding to cookware surfaces enhances aesthetics and user experience. - Edge Rolling and Flanging Machines:
These machines finish edges, roll rims, and prepare cookware parts for assembly, ensuring smoothness and safety. - Seam Welding and Spot Welding Machines:
Welding equipment joins cookware parts, such as attaching handles, spouts, or bases, providing strong, durable bonds without compromising material quality. - Surface Finishing Machines:
Buffing, polishing, grinding, and brushing machines enhance the visual appeal and surface smoothness of cookware, often including automated systems for consistent results. - Coating Application Machinery:
Specialized lines apply nonstick coatings, anodized layers, or other surface treatments, including spraying booths, curing ovens, and inspection systems. - Assembly and Automation Systems:
Conveyor belts, robotic arms, and automated feeders coordinate production steps, reduce manual labor, and improve throughput. - Quality Inspection Systems:
Optical scanners, dimensional gauges, and defect detection sensors ensure each cookware piece meets specifications and safety standards. - Packaging Machines:
Final packaging lines wrap, label, and box cookware products ready for shipment.
By integrating these machines into a streamlined production line, manufacturers can produce high-quality metal cookware efficiently while minimizing waste and labor costs. Advances in automation, precision controls, and material handling continue to enhance productivity and product innovation in the metal cookware industry.
In modern metal cookware production, the seamless integration of machinery is crucial to achieving high output and consistent quality. Automation plays a central role, with programmable logic controllers (PLCs) coordinating various machines along the production line to ensure smooth workflow and real-time adjustments. This reduces human error and increases production speed.
Material handling systems, such as automated feeders and robotic arms, transport metal sheets and components between different machines with precision, reducing damage and improving safety. These systems are often equipped with sensors to detect positioning and alignment, which is essential for processes like deep drawing and welding that require exact tolerances.
Advanced forming machines use servo-driven technology for precise control over stroke length, pressure, and speed, allowing manufacturers to produce cookware parts with complex geometries and consistent thickness. This is particularly important when working with materials like clad metals that combine layers for enhanced thermal properties.
Surface finishing technologies have evolved to include multi-stage polishing, brushing, and grinding systems capable of producing a wide range of finishes, from satin matte to mirror polish. These finishes not only improve aesthetics but also affect cookware performance, such as heat distribution and ease of cleaning.
Coating application lines utilize electrostatic spraying and advanced curing ovens that ensure uniform coating thickness and strong adhesion, essential for nonstick cookware longevity. Inline inspection systems detect coating defects early, allowing for immediate correction and reducing waste.
Welding and joining machinery employ laser welding and precision spot welding techniques to minimize heat-affected zones, preserving the cookware’s material properties and enhancing durability. These processes are often monitored with real-time quality control to maintain strong, defect-free joints.
Cutting-edge quality inspection combines vision systems and 3D scanning to check dimensions, surface quality, and structural integrity at multiple stages, enabling manufacturers to maintain strict tolerances and compliance with international standards.
Overall, the synergy of these advanced machines within an automated, flexible production environment enables manufacturers to respond rapidly to market demands, customize products, and optimize resource use, driving efficiency and innovation in metal cookware manufacturing.
Continuous advancements in machinery for metal cookware production have also emphasized sustainability and energy efficiency. Modern equipment is designed to minimize material waste through precise cutting, forming, and recycling systems that collect scrap metal for reuse. Energy-efficient motors, regenerative drives, and optimized process cycles reduce power consumption across the production line.
The adoption of digital twins and simulation software allows manufacturers to virtually model and optimize manufacturing processes before physical implementation. This reduces setup times, tooling wear, and trial-and-error adjustments, saving costs and improving product quality from the outset.
Modular machinery designs facilitate rapid reconfiguration of production lines, supporting the manufacture of diverse cookware styles and sizes without extensive downtime. This flexibility is critical as consumer preferences shift towards customized or premium products with unique shapes, finishes, or materials.
Safety enhancements have become integral, with machines equipped with advanced guarding systems, light curtains, and emergency stop mechanisms to protect operators while maintaining high productivity. Training simulators and augmented reality (AR) tools help workers quickly learn machine operation and maintenance, reducing errors and accidents.
Furthermore, many production lines are integrating smart sensors and IoT connectivity to enable real-time monitoring, predictive maintenance, and data analytics. This connectivity helps identify bottlenecks, optimize machine performance, and schedule maintenance proactively, minimizing unplanned downtime.
Collaborations between machinery manufacturers and cookware producers foster innovation in tooling, materials, and process parameters, continually pushing the boundaries of what metal cookware production lines can achieve in terms of quality, speed, and environmental responsibility.
Altogether, the machinery used in metal cookware production is evolving into highly automated, flexible, and intelligent systems that not only meet increasing market demands but also contribute to sustainable manufacturing practices and product excellence.
Machinery For Anodized Aluminum Cookware Manufacturing
Machinery for anodized aluminum cookware manufacturing involves a series of specialized equipment designed to shape, treat, and finish aluminum cookware with an anodized surface that enhances durability, corrosion resistance, and aesthetic appeal. The process combines metal forming with electrochemical surface treatment, requiring precise and integrated machinery.
Key equipment includes:
- Aluminum Sheet Cutting and Preparation Machines:
These machines cut aluminum sheets or coils into blanks suitable for cookware forming. They ensure uniform size and thickness, and may include surface cleaning systems to remove oils and contaminants before anodizing. - Deep Drawing Presses:
Used to shape the aluminum blanks into pots, pans, and bowls, deep drawing machines apply controlled pressure to form complex shapes without cracking or thinning the material. - Trimming and Flanging Machines:
These machines trim excess metal and create rolled edges or flanges for cookware rims, lids, and other components, preparing them for assembly and surface treatment. - Surface Cleaning and Pre-Treatment Systems:
Before anodizing, cookware parts undergo thorough cleaning in automated washing lines to remove grease, dirt, and oxides. This step often includes alkaline cleaning, rinsing, and etching tanks. - Anodizing Tanks and Electrochemical Equipment:
Large anodizing baths filled with electrolytes (usually sulfuric acid) are equipped with power supplies that create an electrochemical reaction, forming a hard, porous aluminum oxide layer on the cookware surface. Tanks have temperature controls, agitation systems, and filtration units for uniform coating. - Sealing and Coloring Lines:
Post-anodizing, cookware is immersed in hot water or steam sealing tanks to close the oxide pores, enhancing corrosion resistance. Optional coloring tanks with organic or inorganic dyes can impart decorative finishes. - Drying and Curing Machines:
Drying ovens or tunnels remove moisture from sealed cookware parts, ensuring coating stability and preventing defects. - Inspection and Quality Control Systems:
Automated inspection stations check anodized layer thickness, surface uniformity, and adhesion, using non-destructive testing methods like eddy current or optical sensors. - Assembly and Welding Machines:
Once anodized, parts are assembled using welding, riveting, or mechanical fastening equipment designed to handle anodized surfaces without damaging the coating. - Polishing and Finishing Equipment:
Some anodized cookware requires additional finishing, such as buffing or brushing, using automated polishing machines that enhance the final appearance without compromising the anodized layer. - Packaging Machines:
Final anodized cookware is packaged with protective materials in automated lines to avoid scratches or damage during shipment.
This integrated machinery setup ensures anodized aluminum cookware meets high standards of performance, durability, and visual appeal, supporting large-scale production with consistent quality.
In anodized aluminum cookware manufacturing, precise control of the anodizing process parameters is critical for achieving consistent coating thickness and quality. Advanced power supply systems with programmable current density and voltage settings allow manufacturers to tailor the anodic layer properties according to the cookware’s intended use, whether for enhanced wear resistance or decorative appeal. Temperature control within anodizing tanks is maintained through cooling and heating units, ensuring optimal electrolyte conditions to prevent defects like uneven coating or burning.
Automation is increasingly integrated into the entire anodizing line, with robotic arms handling delicate cookware parts to minimize human contact and contamination. These robotic systems load and unload racks, transfer items between cleaning, anodizing, sealing, and drying stages, improving throughput and consistency. Real-time monitoring with sensors measuring pH levels, electrolyte concentration, and bath temperature helps maintain process stability, with feedback loops adjusting parameters dynamically.
Environmental considerations have driven the adoption of closed-loop electrolyte filtration and recycling systems that reduce chemical waste and water consumption. These systems prolong electrolyte life and reduce the environmental footprint of anodizing operations, aligning with stricter regulations and sustainability goals.
Post-anodizing finishing machinery complements the coating by preparing the cookware surface for branding or packaging. Laser etching machines can imprint logos or patterns without damaging the anodic layer, while automated buffing machines apply uniform surface textures that enhance aesthetic qualities and user experience.
Integration with upstream and downstream production stages, such as forming presses and assembly lines, is facilitated by centralized control systems, often utilizing Industry 4.0 technologies. This enables seamless data exchange, predictive maintenance scheduling, and rapid response to production issues, minimizing downtime and improving overall equipment effectiveness (OEE).
Machinery manufacturers continue to innovate by developing modular anodizing lines that can be quickly reconfigured or expanded to accommodate new product designs or increased capacity. This flexibility supports manufacturers in responding to market trends, such as the demand for multi-layered anodized coatings or combination treatments with nonstick surfaces.
Overall, the sophisticated machinery employed in anodized aluminum cookware production not only ensures high-quality, durable products but also enhances efficiency, environmental compliance, and adaptability, securing a competitive advantage in a dynamic marketplace.
Advancements in machinery for anodized aluminum cookware manufacturing also focus on reducing energy consumption and improving worker safety. Newer anodizing lines incorporate energy-efficient rectifiers and power management systems that optimize electricity use during the electrochemical coating process. Additionally, improved ventilation and fume extraction equipment protect operators from harmful acid vapors, while enclosed or semi-automated workstations reduce direct exposure to hazardous chemicals.
To further enhance production quality, inline surface inspection machines equipped with high-resolution cameras and AI-driven defect detection systems identify surface anomalies such as pits, scratches, or uneven anodizing immediately after processing. This rapid feedback allows for real-time corrections and reduces the amount of scrap or rework.
The machinery used for sealing anodized layers has also evolved, with modern sealing systems using steam or hot water under controlled pressure and temperature to ensure pore closure without compromising coating hardness. Some lines incorporate chemical sealing baths with additives that enhance corrosion resistance or prepare the surface for subsequent coatings.
Integration of conveyor systems with precise timing and positioning capabilities ensures smooth transitions between each manufacturing step, reducing mechanical stress on cookware and maintaining coating integrity. This conveyor automation can be combined with RFID tagging for full traceability of batches, aiding in quality assurance and regulatory compliance.
Moreover, hybrid machinery that combines anodizing with other surface treatments, such as powder coating or ceramic impregnation, is becoming more prevalent. These multifunctional lines enable manufacturers to produce cookware with unique properties, such as enhanced scratch resistance or color variety, without multiple handling stages.
In summary, the machinery landscape for anodized aluminum cookware manufacturing is continuously improving through automation, energy efficiency, environmental management, and advanced quality control. These enhancements enable producers to meet the growing demands for high-performance, visually appealing, and sustainable cookware products.
Machinery For Metal Surface Finishing
Machinery for metal surface finishing plays a crucial role in improving the appearance, durability, and performance of metal products across industries like cookware, automotive, aerospace, and construction. These machines perform processes such as polishing, grinding, buffing, deburring, and coating preparation to achieve desired surface qualities.
Common types of metal surface finishing machinery include:
- Grinding Machines – Equipped with abrasive wheels or belts, grinding machines remove surface irregularities and prepare metals for finer finishing. They offer precise control over material removal, essential for achieving flatness and smoothness.
- Polishing Machines – Using soft polishing wheels and compounds, these machines enhance surface shine and luster. They range from bench-top models for small parts to large automated polishing lines for bulk production.
- Buffing Machines – Similar to polishing but often using softer wheels and finer abrasives, buffing machines refine metal surfaces to a mirror-like finish. They help remove minor scratches and oxidation.
- Vibratory Finishing Machines – Employing vibrating tubs filled with abrasive media, these machines deburr, clean, and polish multiple small parts simultaneously, improving efficiency for mass production.
- Shot Blasting and Peening Machines – These machines project abrasive particles or shot at high velocity onto metal surfaces, cleaning and strengthening them by inducing compressive stresses, enhancing fatigue resistance.
- Electropolishing Equipment – An electrochemical process where metal surfaces are smoothed and brightened by selectively removing microscopic peaks, often used for stainless steel and medical-grade metals.
- Automated Robotic Finishing Systems – Integrated with sensors and CNC controls, robotic systems perform consistent and repeatable finishing tasks, improving quality and reducing labor costs.
- Surface Preparation Machines – Including sanding and abrasive blasting units that prepare metal surfaces for coatings, plating, or painting by ensuring proper texture and cleanliness.
- Chemical Finishing Stations – Machines designed for processes like passivation, anodizing, or conversion coating, improving corrosion resistance and surface hardness.
Modern metal surface finishing machinery often features adjustable speed controls, programmable operation sequences, and real-time monitoring for process consistency. They can handle various metal types and shapes, from flat sheets and tubes to complex castings and forged parts.
The choice of finishing machinery depends on the product requirements, production volume, and desired surface characteristics, balancing factors like cost, throughput, and finish quality. With ongoing technological advances, surface finishing machinery continues to evolve toward greater automation, precision, environmental friendliness, and adaptability.
Advances in metal surface finishing machinery increasingly incorporate automation and smart technology to enhance productivity and precision. Sensors and vision systems enable real-time quality inspection during finishing operations, detecting surface defects such as scratches, pits, or uneven texture immediately and allowing for corrective actions. This reduces waste and ensures higher product consistency.
Robotic finishing systems can be programmed to handle complex geometries and delicate surfaces, adjusting pressure and tool paths dynamically to avoid damage. Such flexibility is especially valuable in industries producing high-value or safety-critical components.
Environmental considerations drive the development of finishing equipment with improved dust and waste collection systems, minimizing airborne particles and abrasive media loss. Water-based and eco-friendly finishing compounds are being adopted to reduce hazardous chemical usage, while machinery designs increasingly emphasize energy efficiency.
Integration with digital factory systems allows finishing machines to communicate with upstream and downstream processes, optimizing workflow and enabling predictive maintenance through data analytics. This interconnected approach reduces downtime and improves overall equipment effectiveness.
The capability to handle a wide range of materials, from soft aluminum to hardened steel and specialty alloys, makes modern finishing machinery versatile. Customizable abrasive types, speeds, and finishing cycles cater to diverse surface requirements, whether matte, glossy, textured, or mirror-like finishes.
Overall, metal surface finishing machinery is becoming more intelligent, adaptable, and environmentally conscious, meeting the demands of modern manufacturing for higher quality, efficiency, and sustainability.
Emerging trends in metal surface finishing machinery also focus on combining multiple finishing processes within a single integrated system. Hybrid machines that can perform grinding, polishing, and buffing sequentially without manual intervention save time, reduce handling errors, and ensure uniform quality.
Additive manufacturing and 3D-printed tooling are beginning to influence finishing equipment design, allowing for customized polishing heads or abrasive media tailored to specific part geometries. This customization enhances finishing accuracy and can reduce cycle times.
In industries like cookware manufacturing, finishing machinery is tailored to maintain food safety standards, using FDA-approved polishing compounds and hygienic machine designs that prevent contamination. Machines with easy-to-clean surfaces and sealed components help maintain sanitation during production.
The adoption of AI and machine learning in finishing equipment helps optimize parameters such as speed, pressure, and abrasive selection based on real-time feedback, adapting dynamically to variations in material or surface condition. This results in reduced wear on tools, lower energy consumption, and consistently high finish quality.
Furthermore, the trend toward miniaturization and precision finishing drives the development of compact, high-speed finishing machines capable of working on micro-components or intricate details without compromising surface integrity.
Overall, metal surface finishing machinery continues to evolve by integrating automation, customization, sustainability, and intelligent control systems to meet increasingly stringent manufacturing demands and support the production of high-performance, aesthetically superior metal products.
Machinery For Automated Metal Press Manufacturing
Machinery for automated metal press manufacturing is designed to perform high-precision, high-speed forming operations with minimal human intervention. These systems are central to the production of metal components across industries such as cookware, automotive, aerospace, and appliance manufacturing. The core of such setups is the metal press itself, but full automation requires integration with multiple auxiliary systems.
Automated metal press lines typically consist of a decoiler or uncoiler to feed raw metal coils, a straightener to flatten the material, and a servo feeder that precisely positions the sheet for pressing. Once the material is in place, the hydraulic or mechanical press carries out forming operations like blanking, punching, deep drawing, embossing, or coining.
Modern presses are equipped with CNC and PLC controls to manage stroke depth, pressure, timing, and die position with extreme precision. Tooling changeover is often automated using quick-die-change systems, reducing downtime and enabling flexible production of multiple part types on the same line.
Robotic arms or linear transfer units are often employed to move parts between stations, stack finished components, or remove scrap. These robots are integrated into the press line’s control system for synchronized motion, ensuring safety and continuous workflow.
In quality-critical applications, in-line sensors, vision inspection systems, and load monitoring devices are used to detect defects or misfeeds in real time. Data from these systems can be used for process optimization, predictive maintenance, and traceability.
Safety features like light curtains, interlocks, and emergency stop systems are standard to protect operators during manual interactions such as die changes or maintenance.
Automated metal press machinery improves output rates, consistency, and material utilization. It also reduces labor costs and workplace injuries. These systems can be scaled from compact servo presses for precision parts to large progressive-die press lines for mass production, making them essential in modern metalforming operations.
Automated metal press manufacturing systems are increasingly integrated with Industry 4.0 technologies, enabling real-time data collection and process monitoring across the entire production line. Press machines are now capable of self-adjustment based on feedback from sensors that monitor variables like force distribution, alignment, and temperature. This helps maintain consistent quality even during long production runs. Modern systems also employ servo-driven presses that offer greater control over the ram motion and allow for variable speed and pressure profiles within a single stroke, which is especially useful for forming complex geometries or sensitive materials.
Die life and maintenance schedules are monitored through embedded sensors and software that track tool wear and usage cycles. When anomalies are detected, the system can automatically alert maintenance teams or even halt production to prevent costly damage. Press automation also extends to post-press operations such as part ejection, stacking, labeling, and packaging, which are handled by synchronized robotic systems or automated conveyors.
Flexibility is another major benefit of these systems, as they can quickly switch between product types with minimal manual reconfiguration. This is achieved through servo feeders with programmable feed lengths, modular die sets, and touch-screen interfaces that allow operators to load new job recipes instantly. Automation allows presses to run unmanned for extended periods, including overnight or weekend shifts, boosting productivity and lowering operating costs.
Energy efficiency has also improved with regenerative drives, smart motor controls, and optimized press stroke designs that reduce power consumption during idle or low-load periods. All these features contribute to higher throughput, lower defect rates, and better overall equipment effectiveness. As labor shortages and the demand for high-mix, low-volume production grow, automated metal press systems continue to evolve as a critical solution in competitive manufacturing environments.
In fully automated metal press manufacturing environments, integration with enterprise-level software systems such as MES (Manufacturing Execution Systems) and ERP (Enterprise Resource Planning) allows production data to flow seamlessly between the shop floor and management. This enables real-time tracking of inventory levels, production rates, machine performance, and maintenance needs. The ability to analyze this data supports better decision-making, rapid response to production issues, and enhanced forecasting accuracy.
Another advancement is digital twin technology, which enables manufacturers to create a virtual replica of the entire press line. Engineers can simulate and test process changes, material behavior, or tooling designs without interrupting actual production. This reduces setup time, speeds up new product introductions, and minimizes risk.
Human-machine interfaces (HMIs) have also become more intuitive, often using touchscreen panels with visual guides, diagnostics, and multilingual support. This simplifies operation and reduces the learning curve for machine operators. In addition, remote access capabilities allow engineers and technicians to troubleshoot or optimize press settings from off-site locations, improving uptime and support responsiveness.
In terms of tooling, press systems are now often equipped with smart dies that include embedded sensors and microchips. These dies provide real-time feedback on pressure distribution, alignment, temperature, and cycle counts. Such intelligent tooling enables predictive maintenance and reduces the risk of die failure, which can cause significant downtime and product defects.
Press lines are also being designed with modularity in mind. This allows manufacturers to add or remove stations such as cleaning units, embossing heads, or additional forming tools based on product requirements. Such modularity enhances versatility and capitalizes on shared infrastructure to reduce costs.
Overall, the machinery used in automated metal press manufacturing represents a convergence of mechanical engineering, automation, software, and data intelligence. It delivers unparalleled precision, repeatability, and scalability, making it a cornerstone of modern metalworking industries that demand high productivity, minimal waste, and agile production capabilities.
Machinery For Metal Bending Manufacturing
Machinery for metal bending manufacturing encompasses a wide range of equipment designed to shape metal sheets, bars, tubes, and profiles into precise angles or curves without breaking or weakening the material. These machines are essential in producing components for cookware, construction, automotive, HVAC, furniture, and countless other industries. The core of metal bending machinery includes press brakes, tube and pipe benders, profile benders, and roll bending machines, all of which offer varying capabilities based on material thickness, type, and required bend geometry.
Press brakes are the most common machines used for bending flat metal sheets. These machines use hydraulic, electric, or servo-driven systems to press a punch into the metal against a die, creating accurate bends with tight tolerances. Modern CNC press brakes come with programmable controls, automatic back gauges, and angle measurement systems, allowing complex multi-bend parts to be produced with minimal operator input and high repeatability.
For cylindrical or curved products like metal pots, tubes, and piping systems, tube and pipe bending machines are widely used. These machines come in several configurations including rotary draw benders, compression benders, and roll benders. CNC tube benders can handle multiple radii, variable angles, and even 3D bending tasks in a single automated cycle. Some machines are capable of mandrel bending, which supports the interior of the tube to prevent wrinkling or collapse during tight-radius bends.
Roll bending machines are ideal for forming gentle curves or full circles, using three or four rolls to progressively shape metal sheets or bars. These are commonly used for creating circular components like pot bodies, tanks, and flanges. They are available in manual, hydraulic, and CNC-controlled versions depending on the required precision and throughput.
Profile bending machines are specialized for bending structural metal profiles such as channels, angles, T-bars, and square tubes. These machines use adjustable roller systems to accommodate different profiles and bend radii, ensuring that cross-sectional deformation is minimized even with complex shapes.
In modern manufacturing environments, bending machinery is often equipped with automation features like robotic loading/unloading systems, automatic tool changers, and real-time angle correction using optical or laser systems. These enhancements improve productivity, reduce setup time, and eliminate human error.
The material type—such as stainless steel, aluminum, copper, or carbon steel—also influences the choice of bending machinery, as each has different elasticity and strength properties. Safety is a major consideration in bending operations, and machines are typically equipped with light curtains, interlocks, and emergency stop systems to protect operators.
Overall, metal bending machinery plays a crucial role in enabling precise, efficient, and repeatable shaping of metal components, supporting both high-volume industrial production and custom fabrication tasks.
Advanced bending machinery integrates servo-electric drives for more energy-efficient and precise operations, reducing hydraulic oil dependency and allowing cleaner, quieter manufacturing environments. These machines also feature intelligent control systems that adjust for spring-back in real-time, ensuring that each bend angle remains accurate across different batches and materials. Some systems use AI-assisted software to simulate bends beforehand, avoiding collisions or material waste.
In high-throughput applications, machines are configured with automatic part feeders and conveyors, enabling uninterrupted bending cycles and integration into full production lines. This is especially useful in cookware production, where pot handles, rims, or reinforcement rings may require consistent and complex bends. Sensors embedded in the tooling and machine body monitor strain, position, and pressure, sending data to central control systems for diagnostics and quality assurance.
Modern bending systems support Industry 4.0 protocols, meaning they can communicate with factory-wide networks to optimize job sequencing, material tracking, and maintenance scheduling. This reduces downtime and extends equipment life. Additionally, remote monitoring capabilities allow manufacturers to oversee machine performance, troubleshoot issues, and make process adjustments from offsite locations.
Material-specific bending strategies are applied as well—copper requires lower force but precise control to avoid cracking, stainless steel demands higher tonnage and sharp tooling to handle its strength, and aluminum benefits from careful support to prevent surface marks or distortion. This diversity in capability is supported by modular toolsets and flexible machine programming.
Ergonomics and operator usability have also improved significantly. Touchscreen HMIs, multilingual interfaces, and guided setup procedures make operation accessible even to less-experienced users. Quick-change tooling systems and automatic alignment reduce downtime during product switches. Safety remains a priority, with laser safety guards, two-hand controls, and automated shutoff protocols enhancing worker protection.
Bending machinery remains a cornerstone of metal forming processes, providing the accuracy and flexibility required for an ever-evolving range of applications—from cookware to construction elements, automotive panels to decorative trims. The integration of high-precision mechanics with smart controls ensures consistent performance, faster turnaround times, and lower rejection rates, even under demanding production schedules.
As manufacturing demands grow more sophisticated, bending machinery continues to evolve with multi-axis capabilities that allow not only vertical bending but also lateral and rotational positioning. This makes it possible to form highly complex geometries—especially valuable in custom cookware, furniture frames, or architectural metalwork. Machines capable of processing multiple bends in one continuous cycle reduce the need for repositioning, cutting labor costs and boosting efficiency.
In cookware production specifically, bending machines are crucial for shaping handles, forming rims, attaching spouts, or reinforcing pot bases. For instance, thick aluminum or stainless steel strips used for handles may be bent into ergonomic shapes with consistent radii, while edge flanges or rolled rims on pot bodies are formed with precision bending or curling machines integrated into the line. These steps ensure durability, safe handling, and an appealing finish.
Tooling flexibility is another critical advantage. Interchangeable die sets can be swapped quickly to accommodate different product models or material types. In mass production, this versatility is paired with pre-programmed recipes stored in the machine’s control system—so switching from one batch to another requires minimal setup time. This feature supports just-in-time (JIT) production models, where efficiency and responsiveness are essential.
To further improve production outcomes, many machines now include built-in quality control features such as vision systems or laser scanners. These monitor the dimensions of each bent part immediately after processing, automatically flagging or rejecting pieces that deviate from specifications. Over time, these systems collect data that can be used for statistical process control (SPC), helping manufacturers fine-tune their operations and reduce material waste.
The global focus on sustainability has also led manufacturers to favor bending machinery with low energy consumption and minimal maintenance requirements. Servo-electric models not only consume less power but also eliminate hydraulic fluid leaks, reducing environmental risk. Their precision allows thinner materials to be used without compromising strength—further lowering raw material usage.
Bending machinery today is more than just a mechanical solution; it is a programmable, data-driven part of an intelligent production system. Whether used for small-scale specialty cookware or high-volume industrial items, it ensures uniformity, speed, and scalability. As automation and smart controls become standard, metal bending technology continues to shape modern manufacturing with unparalleled adaptability and performance.
Machinery For Metal Welding for Cookware
Machinery for metal welding in cookware manufacturing plays a vital role in assembling components like handles, bases, spouts, or layered bottoms, especially in stainless steel, aluminum, and copper cookware. These machines ensure strong, clean, and food-safe welds that meet both structural and aesthetic standards. Various welding techniques are applied depending on the design, material, and production volume.
One of the most common systems used is resistance spot welding, especially for attaching stainless steel handles or brackets to pot bodies. This method uses electrodes to apply pressure and electrical current at precise spots, creating a clean and reliable weld without the need for filler material. Spot welders are typically automated and can be integrated into robotic arms or indexed production lines for high-volume output.
TIG (Tungsten Inert Gas) welding is preferred when a more refined, clean, and corrosion-resistant weld is required—often used in premium or seamless cookware. TIG welders provide better control and lower heat distortion, making them suitable for thin-walled metals and for producing high-end finishes. Automation in TIG welding now includes programmable weld paths, torch angle control, and adaptive current settings.
Laser welding is gaining popularity in cookware manufacturing due to its ability to create narrow, deep, and clean welds with minimal thermal distortion. It is especially useful for attaching layered or clad bottoms where multiple metal types—such as aluminum and stainless steel—need to be fused together without compromising the base flatness. Laser welders are also capable of welding intricate geometries and small parts, and they operate at high speeds suitable for mass production.
Seam welding machines are used when long, continuous welds are needed, such as when joining rolled rims or reinforcing bands. These machines apply continuous current through rotating wheel electrodes, producing uniform and leak-proof seams. This is especially important for products that hold liquids or for base-to-wall transitions in multi-material cookware.
Some cookware, such as pressure cookers or thermal-based multi-layer pots, require friction welding or inert gas shielded MIG/MAG welding, particularly when thicker parts or dissimilar metals are involved. These machines are often custom-designed to hold the cookware in specific jigs and apply the welds under computer-controlled parameters.
Modern welding machines feature integrated cooling systems, automatic torch cleaning, seam tracking sensors, and advanced HMI interfaces. They also support data logging and quality traceability, which is essential for ensuring consistent weld strength, alignment, and surface appearance.
In cookware production, welding must balance aesthetics with strength. Therefore, post-welding processes like grinding, buffing, or electropolishing are often integrated nearby to ensure smooth and polished finishes. With automation, real-time process monitoring, and high-speed operation, welding machinery ensures cookware products are safe, durable, and visually appealing.
Advanced welding machinery for cookware production continues to evolve toward higher precision, speed, and integration with fully automated manufacturing lines. Robots equipped with welding torches now handle complex operations that once required manual skill, including variable-angle handle welding, deep-draw vessel joint sealing, or layered base fusions. These robotic systems not only increase throughput but also drastically reduce human error and inconsistency. They can be taught complex welding paths via offline programming or teach pendant, allowing fast adaptation for new cookware designs.
In high-end cookware, especially those using tri-ply or multi-layer materials, accurate thermal bonding is essential for optimal heat distribution. This is where hybrid welding techniques—combining laser and arc processes—are applied to fuse dissimilar metals like aluminum and stainless steel while preserving thermal conductivity. Such fusion is critical for ensuring energy efficiency and even heating, which are key selling points for professional-grade cookware.
Cookware production also demands that welds be hygienic and resistant to corrosion. Therefore, modern machines often include inert gas shielding systems—especially in TIG and MIG setups—to prevent oxidation during welding. This is essential for ensuring that weld seams are smooth and won’t harbor bacteria or rust over time. Some systems go further by incorporating internal purging systems for enclosed joints, especially in pressure cooker rings or multi-layered bottoms.
Process monitoring has become standard. Sensors continuously measure arc stability, temperature, weld bead shape, and penetration depth. Deviations trigger automatic shutdown or correction, protecting both equipment and product integrity. Such intelligent systems support Industry 4.0 principles by connecting welders to factory networks for centralized data logging, remote diagnostics, and predictive maintenance.
To further improve product quality, some systems are designed to combine welding and polishing functions in a single cell. This streamlines production, reducing the need for manual handling and ensuring consistent surface finish. Seamless integration with conveyors, pick-and-place robots, or rotating fixtures ensures that cookware items move efficiently from welding to inspection to packaging with minimal human intervention.
For cookware with visual branding or embossed reinforcement, laser welding also allows near-invisible welds that don’t interfere with the product’s design. These fine welds are also ideal for maintaining a uniform thickness in food-contact areas, meeting both safety regulations and consumer expectations for clean lines and smooth surfaces.
Whether it’s lightweight aluminum saucepans, heavy-duty steel stockpots, or intricate steamers with multiple parts, modern metal welding machinery ensures they are joined with strength, speed, and elegance. As demand grows for energy-efficient, durable, and aesthetically appealing cookware, welding technology will remain at the heart of quality-driven production lines.
As cookware design trends shift toward more ergonomic, multi-functional, and induction-compatible products, welding machinery is adapting accordingly. One major area of innovation is in welding for induction base attachment—especially in stainless steel cookware. This process requires precision in attaching ferromagnetic discs (often made of carbon steel) to non-magnetic cookware bases. Specialized circular seam welding machines, often assisted by induction heating, are used to create uniform bonds that maintain perfect flatness and ensure proper energy transfer on induction cooktops.
Another growing application involves welding composite handles or hybrid assemblies that combine metal and non-metal components. In these cases, the metal parts—like mounting plates—are welded to the pot body before overmolding or fastening with polymer or wooden grips. The welding must be highly precise to avoid deformation or heat damage to parts that will later be paired with temperature-sensitive materials.
High-frequency welding is also emerging in certain niche segments where thin sheet metal or fine mesh parts (like steam trays or insertable baskets) need to be assembled quickly without adding bulk. This non-contact technique offers extremely clean results and minimal thermal distortion.
To meet international quality and safety standards, modern metal cookware welding systems are increasingly equipped with automatic inspection stations. Vision systems and laser scanners check the weld integrity in real time, measuring factors like seam continuity, alignment, and surface smoothness. These systems flag defective units automatically, reducing reliance on manual quality control and improving overall line efficiency.
Energy efficiency is another key focus. In response to sustainability goals, manufacturers are choosing inverter-based welding power sources that adjust energy output dynamically based on the material thickness and weld progress. This not only reduces power consumption but also extends electrode life and minimizes heat-affected zones, which is critical in preserving the appearance and performance of the final product.
Lastly, safety in operation is being elevated with features like automatic shielding, emergency stops, enclosed welding cells with fume extraction, and operator access restrictions. As many factories move toward lights-out manufacturing, these safety mechanisms support round-the-clock operation without risk.
In summary, metal welding machines for cookware production are no longer simple joiners—they are precision, intelligent systems that serve a vital role in combining form, function, and food safety in every pot and pan. Their continued evolution will enable cookware manufacturers to produce increasingly sophisticated products at higher speeds, with greater consistency, and in more sustainable ways.
Machinery For Metal Casting Cookware Manufacturing
Machinery for metal casting cookware manufacturing is specialized equipment designed to produce cookware items by pouring molten metal into molds where it solidifies into the desired shapes. This process is ideal for creating thick, durable cookware such as cast iron skillets, Dutch ovens, and certain aluminum or bronze pots.
Key machinery and equipment involved include:
- Melting Furnace:
- Crucial for melting raw metal such as cast iron, aluminum, or bronze.
- Furnaces can be induction, gas-fired, or electric resistance types.
- Modern furnaces offer precise temperature control and energy efficiency.
- Mold Making Equipment:
- Molds are often made from sand, ceramic, or metal depending on the casting method.
- Sand molding machines automate the process of packing sand around patterns to create molds.
- Ceramic shell mold making machines are used for investment casting of finer details.
- Pouring and Casting Machines:
- Automated pouring systems ensure accurate and consistent filling of molds with molten metal, improving safety and reducing waste.
- Some lines include tilt-pour machines or robotic arms for precise control.
- Cooling and Shakeout Systems:
- After solidification, cooling conveyors or cooling pits ensure controlled cooling to reduce internal stresses.
- Shakeout machines remove sand or ceramic material from the solid castings efficiently.
- Casting Cleaning and Fettling Machines:
- Shot blasting or grit blasting machines clean the surface of cast cookware to remove residues.
- Grinding and trimming machines remove excess metal and smooth out edges.
- Heat Treatment Furnaces:
- Controlled heat treatment may be applied to improve mechanical properties like hardness and toughness.
- Surface Finishing Machines:
- Polishing, grinding, or coating lines finalize the cookware’s appearance and protect against corrosion.
- Inspection Systems:
- Non-destructive testing equipment such as X-ray or ultrasonic machines check for internal defects.
- Visual inspection stations ensure dimensional accuracy and surface quality.
In cast cookware manufacturing, automation is increasingly integrated to improve consistency, reduce manual labor, and enhance safety due to the high temperatures and heavy components involved. Casting also allows for complex shapes and thick-walled products not easily achieved by sheet metal forming, making it essential for premium cookware segments.
Casting cookware manufacturing starts with melting metal in furnaces that precisely control temperature to ensure the metal is at the ideal pouring consistency. Once molten, the metal is poured into molds shaped exactly like the final cookware product, such as skillets, pots, or Dutch ovens. These molds are typically made from sand or ceramic materials, designed to withstand the extreme heat and allow cooling in controlled conditions to prevent cracking or warping.
Automated pouring machines help reduce the risk of spillage and improve the consistency of fill, which is critical for maintaining uniform wall thickness in cast cookware. After the metal solidifies and cools, the castings are extracted from the molds by shakeout machines that break away the sand or ceramic shell. This process is carefully timed to optimize the balance between mold integrity and production speed.
Post-casting, the cookware pieces undergo extensive cleaning to remove any remaining mold material, often through shot blasting or grit blasting, which also improves surface finish and prepares the cookware for further processing. Excess metal, such as sprues and runners left from the casting process, are trimmed off by grinding or machining operations, ensuring the cookware’s edges and surfaces are smooth and safe for handling.
Heat treatment furnaces are used to alter the metal’s microstructure, increasing strength and durability to withstand everyday use and thermal cycling. This stage is especially important for cast iron cookware to achieve the desired hardness and wear resistance.
After heat treatment, surface finishing steps like polishing or applying protective coatings enhance corrosion resistance and aesthetic appeal. Inspection is rigorous, often involving non-destructive testing methods such as X-ray or ultrasonic scanning to detect internal flaws that could cause product failure during use.
The entire casting cookware production line increasingly incorporates automation, robotic handling, and real-time quality control systems to boost efficiency and consistency while reducing labor costs and safety hazards. With these technologies, manufacturers can produce complex, thick-walled cookware items with superior durability and design precision that are highly valued in the premium cookware market.
Would you like more information on automation trends, specific casting methods like sand casting versus investment casting, or how foundry safety is managed in cookware production?
In cookware casting, sand casting remains one of the most popular methods due to its flexibility and cost-effectiveness, especially for larger items like cast iron skillets and Dutch ovens. Sand molds are relatively easy to produce and can be reused with minor adjustments, allowing manufacturers to create various sizes and shapes without extensive tooling costs. However, sand casting usually results in a rougher surface finish, necessitating additional grinding and polishing.
Investment casting, also known as lost-wax casting, is employed when finer detail and smoother surfaces are required. This method involves creating a wax model of the cookware, coating it with a ceramic shell, and then melting the wax out to leave a detailed mold cavity. Molten metal is then poured into this cavity, producing highly accurate and smooth castings. Investment casting is more expensive and time-consuming but is valuable for specialty cookware pieces with intricate designs or thin walls.
Automated molding and shell building machines improve the consistency and throughput of both sand and investment casting processes. Robotics are increasingly used for pouring molten metal to minimize human exposure to hazards and improve precision. Cooling control is critical—slow, uniform cooling reduces internal stresses and helps prevent warping or cracking. Advanced cooling conveyors and temperature sensors are integrated into modern lines to optimize this phase.
After casting and initial cleaning, CNC machining centers are often employed for finishing operations such as flattening pot bottoms, trimming rims, and drilling holes for handles or lids. This ensures precise dimensional accuracy and compatibility with assembly components.
Heat treatment furnaces are customized with programmable cycles tailored to the specific metal alloys, adjusting factors like heating rate, soak time, and cooling speed to achieve desired hardness, tensile strength, and ductility.
Surface treatments may include polishing for a shiny finish, sandblasting for a matte look, or application of protective coatings such as enamel or nonstick layers. Some manufacturers also use chemical treatments like passivation for stainless steel to enhance corrosion resistance.
Quality control integrates visual inspections, dimensional measurements with laser scanners, and non-destructive testing such as ultrasonic or dye penetrant inspection to detect cracks or porosity. Data from these systems feed into digital quality management platforms, allowing real-time monitoring and traceability.
Safety is a paramount concern in metal casting facilities due to high temperatures, molten metal handling, and heavy equipment. Modern foundries implement strict safety protocols including heat-resistant protective gear, ventilation systems to control fumes, automated handling to reduce manual labor, and emergency shutdown procedures.
The combination of traditional casting methods with modern automation and quality control enables cookware manufacturers to produce high-quality, durable metal cookware at scale while minimizing waste and ensuring worker safety.
Would you like me to elaborate on specific machinery used in casting, alloy choices, or environmental considerations in casting cookware production?
Machinery For Forged Metal Pans Manufacturing
Machinery for forged metal pans manufacturing is designed to transform metal blanks into durable, high-quality cookware through processes that involve shaping metal under high pressure and heat. Forging improves the metal’s grain structure, resulting in enhanced strength, heat conductivity, and durability—key qualities for premium pans.
The typical machinery involved in forged pan manufacturing includes:
- Forging Presses
These hydraulic or mechanical presses apply tremendous force to shape heated metal billets or blanks into the desired pan shape. The forging press may have custom dies to form the pan body, sides, and base in one or multiple steps. Precision and repeatability are crucial for uniform thickness and shape. - Heating Furnaces
Prior to forging, metal blanks are heated to high temperatures in specialized furnaces (such as induction or gas-fired) to increase ductility. Controlled heating ensures the metal softens uniformly without overheating, which could weaken it. - Trimming and Flash Removal Machines
After forging, excess metal known as flash is trimmed off. Automated trimming presses or CNC cutting machines remove the flash cleanly to refine the pan’s edges and overall shape. - Cold Forging and Forming Equipment
Some parts of the pan, like rims or handles, are formed using cold forging presses or bending machines to add precision features without reheating. - Machining Centers
CNC machining centers finish surfaces, machine flat bottoms, drill holes for handles, and perform any additional contouring. This step ensures dimensional accuracy and consistency. - Heat Treatment Equipment
Post-forging heat treatment (annealing, quenching, tempering) optimizes the metal’s mechanical properties, balancing hardness with toughness. - Surface Finishing Machines
These include grinders, polishers, and shot blasting machines that prepare the pan surface for coating or polishing. The finish affects both aesthetics and cookware performance. - Coating Application Systems
For nonstick or protective coatings, automated spray booths or dipping systems apply coatings evenly. Curing ovens then bake these coatings to durability. - Quality Control Stations
Inspection equipment such as laser scanners, hardness testers, and visual inspection stations ensure each pan meets strict specifications before packaging. - Automated Handling and Conveyor Systems
To improve efficiency and worker safety, robotic arms, conveyors, and automated guided vehicles move parts between manufacturing stages.
Forged pan manufacturing machinery balances heavy-duty forging operations with precision machining and finishing, combining robust construction and fine detail to deliver cookware that lasts.
If you want, I can provide details on specific forging press types, recommended alloys for forging, or the typical production workflow for forged pans.
Forged pan manufacturing machinery often incorporates advanced automation to enhance production speed and consistency. Robotic systems can load and unload metal billets into heating furnaces and forging presses, minimizing manual handling and reducing cycle times. Automated tool changers and servo-driven presses enable quick adaptation to different pan sizes and shapes without extensive downtime.
The forging presses themselves vary widely depending on the scale and complexity of production. Mechanical forging presses use flywheel energy to deliver rapid, repeated impacts and are suitable for high-volume production of simpler shapes. Hydraulic forging presses, on the other hand, provide slower but more controlled and powerful strokes, allowing for precise forging of thicker or more complex parts. Some plants employ a combination of both to optimize efficiency and quality.
Induction heating furnaces have become popular for their rapid, energy-efficient, and uniform heating of metal billets before forging. These furnaces reduce thermal stress on metals, prolonging die life and improving product consistency. Precise temperature control is crucial because overheating can lead to grain growth and reduced mechanical properties, while underheating causes incomplete forming and increased tool wear.
After forging, flash removal is critical not only for aesthetics but also to ensure safety and proper fit in downstream assembly processes. CNC trimming machines equipped with sensors adjust cutting paths dynamically to handle variations in flash thickness, improving scrap reduction and dimensional accuracy.
Cold forging operations complement hot forging by adding features like flanged rims or pre-formed handle attachment points without additional heating, which saves energy and speeds up production. These processes also help refine grain structure and improve surface finish in certain areas.
CNC machining centers are essential for delivering precise flat bottoms and tight tolerances on handle holes, allowing seamless integration with handles and lids. High-speed milling and drilling ensure that pans meet stringent quality standards for professional and consumer markets.
Heat treatment cycles are carefully designed based on the specific alloy and product requirements. Some forged pans require solution annealing to relieve internal stresses, followed by quenching and tempering to achieve an optimal balance between hardness and toughness. These processes enhance durability, impact resistance, and lifespan.
Surface finishing is another critical step, where shot peening or blasting removes scale and surface imperfections, preparing the pan for coating or polishing. Multi-stage polishing lines using abrasive belts, wheels, and brushes create a smooth, uniform finish that affects both cooking performance and visual appeal.
Coating application technologies vary depending on the coating type—fluoropolymer-based nonstick coatings require clean, smooth surfaces and precise curing ovens to ensure adhesion and durability. Automated spray systems maintain consistent coating thickness and minimize waste, while quality checks detect defects like bubbles or uneven coverage.
Quality control integrates both manual and automated inspection. Vision systems detect surface defects and dimensional deviations, while hardness and thickness testers verify mechanical properties and coating uniformity. Traceability systems log production data for each pan, enabling quality tracking and continuous improvement.
In addition to manufacturing equipment, modern forged pan production lines often include advanced data collection and analytics platforms. These systems monitor equipment status, process parameters, and product quality in real-time, enabling predictive maintenance and reducing downtime.
Environmental considerations also play a role in modern forging operations. Energy-efficient induction heating, waste heat recovery systems, and scrap metal recycling help reduce environmental footprint and operational costs.
Integration of Industry 4.0 principles allows forging plants to optimize production flow, adjust parameters dynamically based on real-time feedback, and achieve higher yields with less resource consumption.
Overall, machinery for forged metal pans manufacturing is a sophisticated blend of traditional heavy forging processes and cutting-edge automation, aiming to deliver durable, high-quality cookware at competitive production rates.
Continuing with machinery for forged metal pans manufacturing, ergonomic design and operator safety are key considerations in modern equipment. Machines incorporate advanced guarding systems, emergency stop controls, and user-friendly human-machine interfaces (HMIs) that simplify setup, monitoring, and troubleshooting. Touchscreen panels with intuitive software allow operators to quickly adjust forging parameters, monitor production data, and respond to alerts, minimizing downtime and errors.
Robotic arms equipped with vision systems handle material loading, transfer, and unloading tasks, reducing operator fatigue and exposure to hot or heavy components. Collaborative robots (cobots) can work alongside human workers to perform repetitive or hazardous tasks such as deburring, polishing, or quality inspection, increasing throughput and consistency without compromising safety.
Material handling conveyors are often integrated throughout the forging line to transport billets, semi-finished pans, and finished products seamlessly between heating, forging, trimming, machining, and finishing stations. Automated guided vehicles (AGVs) or overhead cranes manage bulk material movement, optimizing workflow and reducing manual labor.
In terms of tooling, forging dies are made from high-grade tool steels with coatings like titanium nitride (TiN) to resist wear and thermal fatigue. Die maintenance is streamlined with quick-change die holders and modular designs, allowing rapid replacement and minimizing downtime. Some facilities employ die monitoring systems that track die temperature, force, and wear, triggering preventive maintenance before failures occur.
Process simulation software assists engineers in designing forging sequences and tooling, predicting metal flow, stresses, and potential defects. This virtual modeling reduces trial-and-error on the shop floor, saving costs and accelerating new product development.
To support sustainability, modern forging plants use closed-loop cooling systems to manage die and machine temperatures efficiently, minimizing water consumption. Air filtration and dust extraction systems control particulate emissions from forging and finishing operations, ensuring compliance with environmental regulations and improving workplace air quality.
Some manufacturers adopt modular line setups, enabling rapid reconfiguration to produce different pan models or sizes. This flexibility supports shorter production runs and quicker market response without extensive retooling.
Finally, integration with enterprise resource planning (ERP) and manufacturing execution systems (MES) provides end-to-end visibility over production schedules, inventory, quality, and maintenance. This connectivity enhances coordination across departments and suppliers, ensuring timely delivery of forged pans that meet customer specifications.
In summary, forged metal pan manufacturing machinery today is a comprehensive ecosystem combining mechanical robustness, digital intelligence, ergonomic safety, and environmental responsibility—enabling manufacturers to stay competitive and deliver premium cookware products efficiently.
Machinery For Stainless Steel Cookware Manufacturing
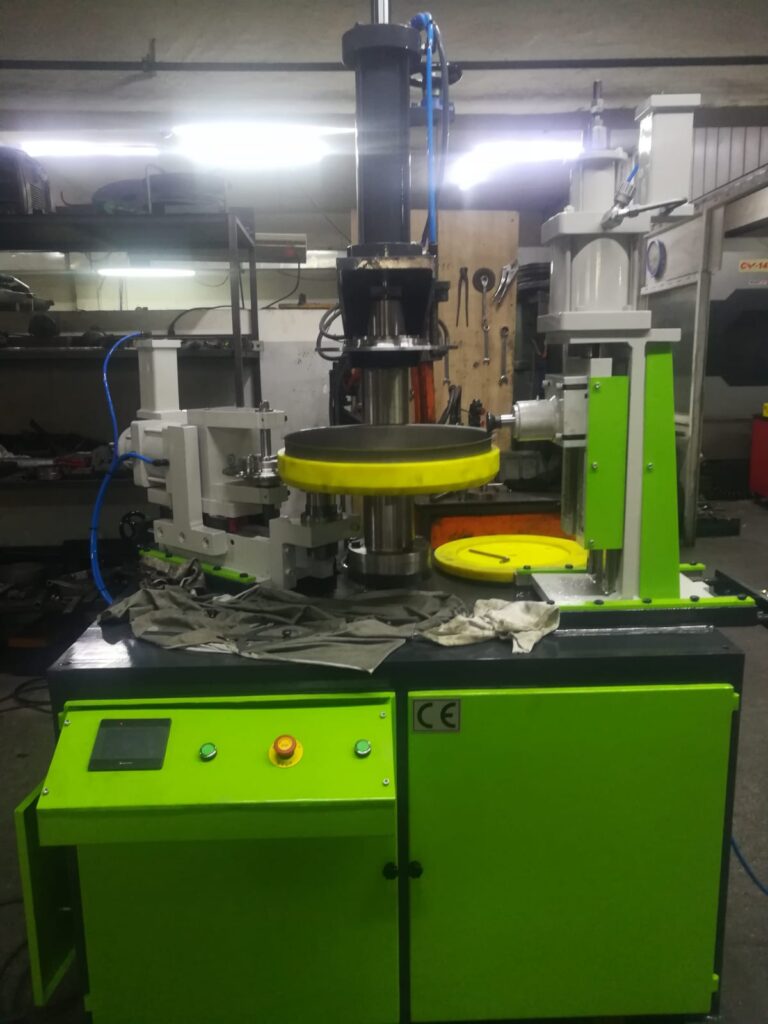
Machinery for stainless steel cookware manufacturing involves a series of specialized equipment designed to efficiently transform raw stainless steel sheets or blanks into finished cookware items such as pots, pans, saucepans, and lids. Here’s an overview of key machines commonly used in stainless steel cookware production:
- Sheet Metal Decoiling and Flattening Machines
These machines uncoil stainless steel sheets from large rolls and flatten them to prepare for further processing. Precision flattening ensures uniform thickness and surface quality. - Blanking Presses
Blanking presses cut out circular or shaped blanks from flat stainless steel sheets. These blanks form the initial shape for cookware bodies and lids. - Deep Drawing Machines
Deep drawing presses shape the flat blanks into cup or pot forms by drawing the metal into a die cavity with a punch. They ensure smooth, uniform walls without cracks or wrinkles. - Hydraulic or Mechanical Presses
Presses perform forming, flanging, or bending operations such as creating rims, spouts, or handles. They provide the force needed for precise shaping and assembly features. - Spinning Lathes (Metal Spinning Machines)
Used for forming round cookware items, spinning machines rotate stainless steel blanks at high speed while a tool shapes the metal over a mandrel, enabling smooth contours and curves. - Edge Rolling and Curling Machines
These machines form rolled or curled edges on pots and pans for strength and safety, preventing sharp edges. - Seam Welding Machines
Seam welding equipment joins cookware components like bodies and lids, or attaches handles and spouts with strong, clean welds. Techniques include TIG, laser, or ultrasonic welding. - Surface Polishing and Buffing Machines
Polishing lines utilize abrasive belts, brushes, and buffing wheels to achieve smooth, mirror-like finishes on stainless steel surfaces, enhancing aesthetics and corrosion resistance. - Grinding and Deburring Machines
These machines remove excess material, weld spatter, or sharp burrs left from forming and welding processes, ensuring safety and a refined appearance. - Handle and Accessory Attachment Machines
Automated or semi-automated systems attach handles, knobs, or lids using riveting, welding, or screwing processes, improving production speed and consistency. - Coating and Surface Treatment Equipment
Some stainless steel cookware may receive additional treatments like passivation, electro-polishing, or nonstick coating applications using spray booths and curing ovens. - Quality Inspection Systems
Vision inspection machines, dimensional gauges, and leak testers ensure that finished cookware meets stringent quality and safety standards before packaging. - Packaging Machines
Automated packaging lines wrap, box, or label cookware ready for shipment, often integrated with production tracking systems.
These machines, often integrated into semi-automated or fully automated production lines, optimize productivity while maintaining high quality and consistency in stainless steel cookware manufacturing. Advances in CNC controls, robotics, and sensor technology continue to enhance precision and efficiency in this sector.
Additional machinery and technologies that complement stainless steel cookware manufacturing include:
- CNC Machining Centers: Used for precision cutting, drilling, and milling operations on cookware parts, such as handle fittings or decorative embossing, enhancing customization and consistency.
- Laser Cutting Machines: Provide high-precision cutting of stainless steel sheets and components with minimal heat-affected zones, improving edge quality and reducing material waste.
- Robotic Welding Cells: Increase the speed and uniformity of welding operations, especially for handle attachment and seam welding, while improving worker safety by automating repetitive tasks.
- Automated Material Handling Systems: Conveyor belts, robotic arms, and palletizers streamline the movement of components and finished products across various stages of manufacturing, reducing manual labor and production time.
- Heat Treatment Furnaces: Some cookware components require heat treatment to improve hardness, durability, or stress relief; specialized furnaces with controlled atmospheres are used for these processes.
- Inspection and Testing Equipment: Beyond visual inspections, nondestructive testing methods like ultrasonic testing or dye penetrant inspection ensure structural integrity and detect hidden defects.
- Environmental Control Systems: Waste management units, dust collectors, and cooling systems maintain a clean, safe, and environmentally compliant manufacturing environment.
By integrating these machines and systems, stainless steel cookware manufacturers can achieve scalable, flexible, and high-quality production suited for a wide range of cookware products—from basic everyday pots to premium, designer-grade kitchenware. Continuous innovation in automation, material science, and process optimization drives cost-effectiveness and product performance in the competitive cookware market.
Further enhancing stainless steel cookware manufacturing, advanced technologies and specialized equipment include:
- Automated Welding Inspection Systems: These use cameras and sensors to monitor weld quality in real-time, ensuring consistent seam strength and appearance, reducing rework and defects.
- Press Brake Machines: High-precision press brakes form complex bends and flanges in cookware components, especially for lids, handles, and accessory parts, allowing customized shapes with minimal manual intervention.
- Electropolishing Equipment: This electrochemical process smooths and brightens stainless steel surfaces beyond mechanical polishing, enhancing corrosion resistance and hygiene — critical for cookware safety and longevity.
- Robotic Assembly Stations: Robots equipped with vision systems and precision grippers handle tasks like fitting lids, attaching handles, or inserting gaskets, increasing throughput and reducing labor costs.
- Nonstick Coating Lines: For cookware requiring nonstick surfaces, fully automated spray booths, drying ovens, and curing chambers apply PTFE or ceramic coatings uniformly, ensuring durability and performance.
- Cleaning and Degreasing Systems: Automated cleaning lines remove oils, dust, and contaminants before surface finishing or coating, improving adhesion and final product quality.
- Smart Manufacturing Systems (Industry 4.0): Integration of IoT sensors, real-time data analytics, and predictive maintenance allows monitoring of machine health, process parameters, and production output, optimizing efficiency and reducing downtime.
- Energy-Efficient Presses and Motors: Modern hydraulic and mechanical presses equipped with variable frequency drives (VFDs) reduce power consumption and improve operational control, aligning with sustainability goals.
Together, these sophisticated technologies help stainless steel cookware manufacturers meet high standards of quality, design complexity, and production speed, while also addressing environmental and economic considerations. The focus is increasingly on automation, precision, and smart factory concepts to remain competitive globally.
Machinery For Non-Stick Cookware Manufacturing
Machinery for non-stick cookware manufacturing involves specialized equipment designed to produce durable, high-quality cookware with effective non-stick surfaces. The typical machinery includes:
- Metal Forming Machines: These shape raw metal sheets (usually aluminum or stainless steel) into pots, pans, and lids through processes such as deep drawing, stamping, or metal spinning.
- Surface Preparation Equipment: Before applying the non-stick coating, surfaces must be cleaned, degreased, and roughened. This includes:
- Shot Blasting Machines to create surface texture for better coating adhesion.
- Ultrasonic Cleaning Units to remove oils and residues.
- Chemical Etching or Abrasive Treatment lines for surface activation.
- Non-Stick Coating Application Machines: These automated systems apply non-stick coatings uniformly. Types include:
- Spray Coating Booths that spray PTFE or ceramic-based coatings onto cookware surfaces.
- Roll Coaters for flat components or lids.
- Dip Coating Systems for even coverage on complex shapes.
- Drying and Curing Ovens: After coating application, cookware passes through controlled ovens where coatings are cured and hardened, typically at high temperatures to achieve durable bonding.
- Quality Inspection Systems: Automated visual and thickness measurement systems check coating uniformity, adhesion, and surface defects.
- Polishing and Buffing Machines: Some non-stick cookware requires polishing to smooth edges or exterior surfaces after coating.
- Handle Attachment and Assembly Lines: Automated or semi-automated stations attach handles and accessories, often using rivets, welding, or screws.
- Packaging Equipment: Automated packing machines prepare finished cookware for shipment, including protective wrapping and boxing.
This machinery set ensures efficient, repeatable production of non-stick cookware with consistent quality, excellent coating performance, and durability. Modern lines often incorporate automation, robotics, and quality control systems to minimize defects and optimize throughput.
Continuing with machinery for non-stick cookware manufacturing, advanced production lines may integrate robotics for precision and speed, especially in coating application and assembly stages. Robotics ensure even coating thickness and reduce human exposure to coating chemicals. Environmental controls such as ventilation and filtration systems are crucial to safely handle volatile organic compounds (VOCs) and particulates during spraying and curing processes. Automated conveyors transport cookware through sequential stages—from forming and surface prep to coating, curing, inspection, and packaging—ensuring smooth workflow and minimizing manual handling. High-precision temperature and humidity controls in curing ovens optimize coating durability and performance.
Additionally, modern non-stick production often uses multi-layer coating machines capable of applying primer, mid-coats, and top coats in a single automated pass to improve adhesion and longevity. Inspection systems employ cameras and sensors to detect pinholes, uneven coatings, or surface defects in real time, allowing immediate correction or rejection. Integration with factory management software enables tracking of production data, quality metrics, and maintenance schedules, enhancing overall efficiency and traceability. Energy-efficient equipment, such as induction ovens and low-emission spray booths, reduce environmental impact and operational costs. Specialized machinery also exists for applying ceramic or diamond-infused coatings, which require different curing profiles and surface preparations compared to traditional PTFE coatings. Overall, these technologies combine to produce high-performance non-stick cookware at scale while maintaining strict quality standards and environmental compliance.
Further expanding on machinery for non-stick cookware manufacturing, some production lines incorporate automated robotic arms equipped with precision nozzles to apply coatings in multiple passes, ensuring optimal layer thickness and minimizing waste. These robots can adapt to various cookware shapes and sizes, providing versatility for different product lines. In addition, some facilities utilize laser or infrared sensors to continuously monitor coating thickness and surface temperature during curing, allowing real-time process adjustments to maintain uniformity.
Innovations also include eco-friendly coating systems that reduce solvent use and emission levels, employing water-based or solvent-free non-stick formulations. Machinery designed for these coatings often feature closed-loop spray booths with advanced recovery and recycling systems, minimizing environmental impact.
On the forming side, machinery advancements such as servo-driven deep drawing presses allow for more precise control over pot and pan shapes, reducing material waste and improving dimensional accuracy. Integration of CNC-controlled trimming and edge rolling machines ensures consistent, smooth edges essential for both safety and coating adherence.
Some high-end manufacturing setups employ automated cleaning and inspection cells where parts are conveyed through ultrasonic cleaning, drying, and then passed under machine vision systems for defect detection before proceeding to coating. This closed-loop quality control helps reduce scrap and rework.
Furthermore, handle and accessory assembly lines are increasingly automated with robotic screwdrivers, riveters, and ultrasonic welders, ensuring strong, reliable joints while speeding up production. Final packaging machinery often includes automated labeling, boxing, and palletizing robots to streamline logistics.
In summary, the machinery for producing non-stick cookware is a complex integration of forming, surface preparation, advanced coating application, curing, inspection, assembly, and packaging equipment. The emphasis is on automation, precision, environmental safety, and quality control to meet growing market demands efficiently.
Machinery For Heat Distribution Pans Manufacturing
Machinery for manufacturing heat distribution pans focuses on producing cookware that ensures even heat transfer and retention during cooking. The production involves specialized equipment and processes designed to optimize the pan’s base and body structure for superior thermal performance.
Key machinery includes:
- Multi-Layer Cladding Machines: These machines bond different metal layers—such as aluminum or copper sandwiched between stainless steel—to create clad pans with excellent heat conduction and durability. Roll bonding or diffusion bonding presses are commonly used to produce these multi-layer sheets.
- Deep Drawing and Forming Presses: Hydraulic or mechanical deep drawing machines shape the clad metal sheets into the desired pan form, preserving the integrity of the layered structure while achieving smooth contours and consistent thickness.
- Edge Rolling and Flanging Machines: After forming, edge rolling machines create reinforced rims that improve pan strength and support lids. Flanging machines prepare edges for handle attachment or lid fitting.
- Surface Finishing and Polishing Equipment: To enhance heat transfer and aesthetics, surface polishing machines provide smooth, uniform finishes on the cooking surfaces and exteriors, which can also assist in coating adhesion.
- Base Attachment and Bonding Systems: Some heat distribution pans require an added heat-conductive base, often bonded using ultrasonic welding, brazing, or high-frequency induction bonding machines to ensure a strong, seamless connection.
- Thickness and Flatness Inspection Systems: Precision measurement equipment, including laser scanners and micrometers, verify base thickness uniformity and flatness—critical factors in heat distribution performance.
- Handle Assembly and Welding Machines: Automated riveting, welding, or screwing machines securely attach heat-resistant handles, ensuring durability and safety.
- Coating Application Machinery: For pans requiring additional non-stick or protective coatings, automated spray booths and curing ovens integrate with the manufacturing line.
Overall, machinery for heat distribution pans manufacturing combines advanced metal forming, bonding, finishing, and assembly technologies to produce cookware that delivers superior thermal performance, durability, and user safety. Automation and precision control throughout the process ensure consistent quality and efficiency.
Expanding on heat distribution pan manufacturing, modern production lines increasingly incorporate automation for enhanced precision and throughput. Multi-layer clad metal sheets are first produced by rolling mills that bond layers of aluminum or copper with stainless steel under high pressure and temperature, ensuring metallurgical bonding for optimal heat conductivity. These sheets then move to servo-controlled deep drawing presses that shape them into pans with minimal variation, preserving layer alignment and preventing defects such as delamination or wrinkling.
Following forming, advanced edge finishing machines roll and flange pan rims to reinforce structural integrity and provide clean, safe edges. These machines are often CNC controlled, allowing customizable shapes and consistent quality across batches. Surface finishing equipment like robotic polishing cells smooth the inner cooking surfaces to reduce hotspots and improve heat transfer while also enhancing the visual appeal.
Base attachment processes use ultrasonic welding or high-frequency induction bonding to securely affix heat-conductive discs or layers without compromising the clad structure. Real-time inspection systems equipped with laser profilometers and infrared thermography verify thickness uniformity and flatness to tight tolerances, as any warping can lead to uneven heating.
Automated handle assembly lines use precision robotics to attach heat-resistant handles with rivets or screws, often integrating torque control for consistent fastening. Some lines include ultrasonic or laser welding for metal handles, combining strength with aesthetic appeal.
Coating application machinery features enclosed spray booths equipped with multi-axis robots applying non-stick or protective layers with precision control of thickness and coverage. Curing ovens with zoned temperature control ensure uniform polymerization of coatings, critical for durability and food safety.
Final quality assurance stations utilize machine vision and tactile sensors to detect surface defects, coating inconsistencies, or assembly issues. Packaging automation then prepares the pans for shipping, including protective wrapping, labeling, and palletizing.
Throughout the process, integration with Industry 4.0 technologies enables real-time monitoring and data collection, allowing manufacturers to optimize machine parameters, reduce waste, and ensure consistent product quality. This holistic approach in machinery and process design results in heat distribution pans that combine efficient thermal performance with durability and consumer safety.
Continuing further, manufacturers often integrate modular machinery systems that allow flexible adaptation for different pan sizes, shapes, and materials within the same production line. This flexibility reduces downtime during product changeovers and increases responsiveness to market demands. Advanced servo drives and programmable logic controllers (PLCs) coordinate the timing and operation of forming, finishing, and assembly equipment to ensure smooth workflow and synchronization across stages.
In the metal forming stage, incremental forming technologies and hydroforming presses are sometimes employed to achieve complex shapes with minimal material stress, preserving the integrity of multilayer cladding. These methods enable the production of pans with ergonomic designs and optimized heat distribution geometries.
Surface treatments before coating, such as plasma cleaning or chemical etching, enhance coating adhesion, preventing peeling or blistering during use. Post-coating inspection may utilize spectroscopic analysis to verify the chemical composition and thickness of non-stick layers, ensuring compliance with food safety standards.
Waste reduction and sustainability are also key focuses. Scrap metal from trimming and forming is collected and recycled internally, while energy-efficient presses and ovens lower overall production costs and environmental impact. Water-based or low-VOC coatings are increasingly preferred to meet regulatory and consumer demands for greener products.
Maintenance of machinery is optimized through predictive analytics based on sensor data, reducing unplanned downtime and extending equipment life. Operator interfaces are designed for intuitive control and quick troubleshooting, with remote monitoring capabilities allowing supervisors to oversee multiple lines or factories simultaneously.
In summary, machinery for heat distribution pan manufacturing now encompasses a blend of precision forming, advanced bonding, high-quality finishing, and intelligent automation, all supported by data-driven process control and sustainability initiatives. This comprehensive approach ensures the production of cookware that delivers superior cooking performance, durability, and consumer appeal.
Machinery For Metal Deep Drawing Manufacturing
Machinery for metal deep drawing manufacturing is specialized equipment designed to transform flat metal sheets or blanks into complex, hollow shapes by stretching the metal into a die cavity using a punch. This process is widely used in producing components like pots, pans, automotive parts, kitchen sinks, and various industrial containers.
Key machinery components and types include:
- Deep Drawing Presses: These hydraulic, mechanical, or servo-driven presses provide the necessary force to draw the metal blank into the die. Hydraulic presses offer smooth, controlled force suitable for thicker materials, while mechanical presses excel in high-speed production of thinner sheets. Servo presses combine precision and flexibility, allowing programmable stroke profiles to optimize forming.
- Drawing Dies and Punches: Precision-engineered tooling that shapes the metal. Dies consist of a die cavity and a blank holder that prevents wrinkling by controlling metal flow. Punches push the metal into the die cavity, shaping the final part. Dies are typically made from hardened steel or carbide for durability.
- Blanking and Feeding Systems: Automated feeders and blanking machines cut sheet metal into blanks with exact dimensions, ensuring consistent quality and efficient material usage. Integration with robotic arms or conveyors can streamline feeding into the press.
- Lubrication Systems: Deep drawing requires lubrication to reduce friction between the blank and the die, preventing tearing and extending die life. Automated spray or drip lubrication systems apply lubricants precisely.
- Trimming and Piercing Machines: Post-drawing, parts often require trimming to remove excess material and piercing for holes or features. These can be integrated inline or operate as standalone stations.
- Ejector Systems: Mechanisms to safely remove drawn parts from the die without damage, essential for high-speed operations.
- Process Monitoring and Quality Control: Sensors and vision systems monitor parameters such as force, stroke length, and part dimensions in real time to detect defects like thinning, wrinkling, or cracking. Data is fed into control systems to adjust process parameters or trigger alarms.
- Automation and Robotics: For large-scale manufacturing, robotic systems handle material loading/unloading, part transfer, and stacking, enhancing safety and throughput.
Deep drawing machinery is often modular, allowing adaptation to various part sizes and thicknesses. Advances include servo-electric presses for energy efficiency and more precise control, along with simulation software to optimize die design and forming parameters before production.
Overall, metal deep drawing machinery enables high-volume, precise production of complex metal parts with excellent surface finish and structural integrity, essential for cookware, automotive, aerospace, and appliance industries.
Continuing on metal deep drawing manufacturing machinery, it is important to highlight the role of advanced materials and tooling technologies that enhance the process. Tool steels with superior wear resistance and coatings such as titanium nitride extend the life of punches and dies, reducing downtime and maintenance costs. The use of quick-change tooling systems enables rapid die swaps, increasing production flexibility and minimizing machine idle time.
Modern deep drawing presses are often equipped with adaptive control systems that monitor forming forces and adjust press speed or blank holder pressure dynamically to prevent defects. This real-time feedback loop helps maintain consistent part quality across long production runs and varying material batches. Additionally, digital twin technology and simulation tools are increasingly used in planning and optimizing deep drawing processes, allowing engineers to predict issues like springback, thinning, or wrinkling before physical tooling is made.
Incorporation of servo drives in presses provides highly programmable motion profiles, enabling multi-step forming in a single stroke. This capability reduces the number of required operations and tooling sets, thus lowering overall production costs and improving efficiency.
Automation is another critical aspect, with robotic arms handling blank feeding, part removal, stacking, and transfer between process stations. This reduces manual labor, increases safety, and ensures higher throughput. Integration with Industry 4.0 platforms allows remote monitoring, predictive maintenance, and data analytics, which help in optimizing production schedules and reducing unplanned downtime.
Lubrication systems have also evolved to more environmentally friendly formulations, with precise application methods to minimize waste and maintain operator safety. These systems work seamlessly with the machinery to ensure consistent lubrication throughout the forming cycle.
Furthermore, finishing operations such as annealing, surface cleaning, and coating application are often integrated into the production line to prepare drawn parts for subsequent use or assembly. Quality control technologies, including 3D scanning and non-destructive testing, verify dimensional accuracy and detect internal stresses or surface defects early.
Overall, the synergy of high-precision tooling, intelligent presses, automation, and digital process control makes modern metal deep drawing manufacturing machinery highly efficient and capable of producing complex shapes with excellent repeatability and material utilization. This is vital for sectors requiring high-quality metal components, such as cookware production, automotive body panels, and household appliances.
Building further on metal deep drawing manufacturing machinery, customization and scalability are key trends shaping current equipment designs. Manufacturers often offer modular press lines that can be expanded or reconfigured to accommodate new part geometries or increased production volumes without major capital expenditures. This modularity supports just-in-time manufacturing and rapid response to market demand changes.
Another important feature is energy efficiency. Modern presses are designed to consume less power by employing servo motors and energy recovery systems. These systems capture braking energy during press cycles and reuse it, reducing overall electricity costs and environmental impact. Additionally, variable speed drives help optimize energy usage by matching motor speed to process requirements rather than running at constant full power.
Safety enhancements are integrated throughout these machines, including light curtains, emergency stop systems, and interlocks. Operator ergonomics are improved by designing easy access to controls and reducing manual handling, which minimizes fatigue and risk of injury.
Material handling innovations, such as automated coil feeders, servo-driven straighteners, and robotic pick-and-place units, streamline the workflow from raw material to finished part. These systems reduce scrap by precisely controlling material feed and alignment, contributing to sustainability goals.
Advanced monitoring tools employ sensors and machine vision to detect defects like cracks, wrinkles, or inconsistent thickness during or immediately after forming. This inline inspection enables corrective actions to be taken promptly, reducing waste and rework.
In the context of cookware manufacturing, deep drawing machinery is often paired with subsequent processes such as flange forming, trimming, and surface treatment stations to create ready-to-use pots, pans, or lids. This integrated approach reduces handling time and improves throughput.
Finally, the adoption of digital platforms allows manufacturers to gather extensive operational data, enabling predictive maintenance that anticipates component wear or failure before it occurs. This minimizes downtime and extends machine life.
Together, these advancements make metal deep drawing machinery highly adaptable, reliable, and efficient — essential qualities for producing high-quality metal cookware components in competitive markets.
Machinery For Metal Spinning Manufacturing
Machinery for metal spinning manufacturing is specialized equipment designed to form hollow, symmetrical metal parts such as pots, pans, bowls, and other roundware by rotating a metal blank on a lathe and shaping it using a tool or roller. Metal spinning is a highly efficient process for producing thin-walled, seamless components with excellent surface finish and strength.
Key machinery involved includes:
- Metal Spinning Lathe: The core of the metal spinning process. It features a rotating chuck or mandrel on which the metal blank is mounted. The lathe spins the workpiece at high speeds while a skilled operator or CNC-controlled tool applies pressure to shape the metal over a forming tool or mandrel.
- CNC Metal Spinning Machines: Advanced versions of traditional lathes, these machines use computer numerical control (CNC) to automate the spinning process, improving precision, repeatability, and speed. CNC systems allow complex shapes and consistent wall thicknesses to be achieved with minimal manual intervention.
- Mandrels and Formers: Custom-designed tools that provide the shape over which the metal is spun. Mandrels must be highly durable and precisely machined to match the desired finished product geometry.
- Spinning Tools and Rollers: These apply controlled pressure to the spinning metal blank, gradually stretching and thinning it over the mandrel to form the final shape. Tools vary depending on the material, thickness, and complexity of the part.
- Material Feed and Handling Systems: Some metal spinning lines integrate automated loading and unloading to improve cycle times and reduce manual labor, especially in CNC setups.
- Annealing Furnaces: In some cases, metal spinning requires intermediate annealing to soften the metal for further forming, especially with harder alloys or thicker blanks.
- Surface Finishing Equipment: After spinning, parts often go through polishing, deburring, or coating machines to achieve the desired finish and protect against corrosion.
- Quality Control Systems: Inline inspection tools, including laser scanners and thickness gauges, help ensure spun parts meet strict dimensional and structural specifications.
Metal spinning machinery is widely used in cookware manufacturing due to its ability to produce durable, lightweight, and aesthetically pleasing metalware efficiently. It is also common in lighting fixtures, musical instruments, aerospace components, and decorative metal arts.
Advances in CNC technology, automation, and tool materials continue to expand the capabilities and applications of metal spinning manufacturing machinery.
Metal spinning manufacturing machinery enables high flexibility in producing a wide variety of metal shapes without the need for expensive dies or molds, making it ideal for small to medium batch production as well as prototyping. It supports multiple metals, including aluminum, stainless steel, copper, brass, and carbon steel, accommodating various thicknesses and alloys.
The integration of robotic arms and automated tool changers in CNC metal spinning machines enhances throughput and reduces operator fatigue, while sophisticated control software optimizes spindle speed, feed rate, and tool pressure to minimize defects like wrinkling or tearing.
Additionally, some advanced systems combine metal spinning with incremental forming or flow forming techniques, further improving precision and material properties. These hybrid approaches allow manufacturers to achieve complex geometries, uniform wall thickness, and superior surface finishes, meeting stringent industry standards for cookware and other metal products.
Maintenance of metal spinning machinery focuses on precise alignment of mandrels, lubrication of spindles, regular inspection of tools for wear, and calibration of CNC systems to ensure consistent output quality. Safety features such as emergency stop buttons, protective enclosures, and real-time monitoring systems are standard to protect operators and equipment.
Overall, metal spinning machinery forms a crucial part of modern metal cookware manufacturing lines, delivering efficiency, adaptability, and quality in the production of various round and cylindrical metal products.
Metal spinning machinery also supports customization and design flexibility, allowing manufacturers to quickly adapt to changing market demands or create bespoke cookware designs. By adjusting mandrel shapes and spinning parameters, unique patterns, textures, or embossed details can be incorporated without extensive tooling costs.
Energy efficiency is another benefit of modern metal spinning machines. Many CNC units employ energy-saving motors and regenerative braking systems, reducing power consumption during operation. This contributes to lower operating costs and a smaller environmental footprint, aligning with sustainability goals in manufacturing.
Integration with upstream and downstream processes—such as automated blank preparation, annealing, trimming, polishing, and final assembly—can create seamless production lines. These integrated systems improve workflow, reduce cycle times, and enhance overall productivity.
Training and skill development remain important for metal spinning operations. While CNC automation simplifies many tasks, understanding material behavior, machine setup, and troubleshooting is essential to maximize machine capabilities and maintain high-quality output.
As technology evolves, emerging trends include the use of AI-driven process optimization, real-time defect detection via machine vision, and remote monitoring for predictive maintenance. These advancements are shaping the future of metal spinning manufacturing, pushing the boundaries of precision, efficiency, and innovation in cookware and related industries.
Machinery For Sheet Metal Stamping Manufacturing
Machinery for sheet metal stamping manufacturing is essential in producing precise, high-volume metal parts for cookware and many other industries. This machinery uses dies and presses to shape, cut, or emboss flat metal sheets into desired forms with high repeatability and speed.
Key equipment in sheet metal stamping includes:
- Stamping Presses: These can be mechanical, hydraulic, or servo-electric, providing different force ranges and speeds suited to various metals and thicknesses. Mechanical presses are fast and efficient for high-volume jobs, while hydraulic presses offer flexibility and precise control.
- Progressive Dies: Designed for multi-stage stamping operations, progressive dies enable sequential cutting, bending, and forming in one continuous process, increasing production efficiency and consistency.
- Transfer Presses: These machines move sheet metal blanks automatically through multiple stamping stations, ideal for complex parts requiring several operations.
- Blanking Machines: These cut raw metal sheets into blanks of specific sizes, preparing materials for stamping.
- Coil Feeders: Automated systems that feed metal coils into presses, allowing continuous operation and reducing manual loading.
- Die Maintenance Tools: Including die setting, alignment, and sharpening equipment, ensuring dies stay precise for long production runs.
Advantages of sheet metal stamping machinery include rapid production rates, excellent dimensional accuracy, and the ability to produce complex shapes with tight tolerances. The process is highly repeatable, making it ideal for mass production of cookware components such as lids, pot bottoms, handles, and decorative elements.
Modern stamping machines often incorporate CNC controls for programmable precision and can be integrated with robotic systems for loading/unloading, quality inspection, and part handling, enhancing automation and reducing labor costs.
Material considerations such as metal type, thickness, and hardness influence the choice of stamping machinery and die design. Proper lubrication and cooling systems are also crucial to reduce tool wear and maintain surface quality.
Overall, sheet metal stamping machinery plays a vital role in efficient, high-quality production of metal cookware components, combining speed, precision, and versatility.
Sheet metal stamping machinery is widely used for producing cookware parts with intricate shapes and consistent quality. The stamping process involves placing a flat sheet metal blank into a stamping press where a die forms the metal into the desired shape through a combination of cutting, bending, and embossing. This process can be highly automated to achieve rapid production cycles and minimize waste.
The versatility of stamping machines allows manufacturers to produce a variety of cookware parts such as pot lids, handles, rims, bases, and decorative surfaces. High-precision dies ensure tight tolerances, which are critical for components that must fit together perfectly during assembly. Additionally, stamping can create textured or patterned surfaces that enhance cookware aesthetics and functionality.
Advanced stamping presses use servo-electric drives, providing improved energy efficiency, adjustable stroke speeds, and precise control of the forming process. This flexibility allows operators to optimize parameters for different materials, such as stainless steel, aluminum, or copper, each requiring specific handling due to their mechanical properties.
Automation integration includes robotic arms for material handling, automated die changing systems to reduce downtime, and inline quality control stations with cameras and sensors to detect defects early. These technologies collectively improve throughput, reduce scrap rates, and ensure consistent part quality.
Maintenance of stamping dies and presses is crucial; regular inspection and repair prevent downtime and maintain production accuracy. Many modern setups use predictive maintenance systems that monitor machine conditions and alert operators before failures occur, optimizing equipment lifespan.
Material handling systems paired with stamping lines facilitate smooth logistics, from coil feeding and blanking to finished part stacking and packaging. Such comprehensive automation allows cookware manufacturers to scale production efficiently while maintaining strict quality standards.
Environmental considerations include managing lubricant use, controlling noise and vibration, and recycling scrap metal generated during stamping. Implementing eco-friendly practices aligns with sustainable manufacturing goals increasingly demanded in the cookware industry.
In summary, sheet metal stamping machinery is integral for efficient and high-volume production of cookware components, enabling manufacturers to deliver durable, precisely formed, and aesthetically appealing products that meet market demands.
The continuous advancement of sheet metal stamping machinery has significantly enhanced the flexibility and capabilities of cookware production facilities. Modern machines are designed not only for speed and precision but also for versatility, allowing quick transitions between different product types and sizes without extensive retooling. This adaptability is especially valuable in cookware manufacturing, where producers often need to switch between different models of pots, pans, and lids to meet diverse market preferences.
Tooling innovations, such as modular dies and quick-change die systems, have reduced setup times and improved uptime. These features are particularly beneficial in short to medium production runs or when producing customized batches, offering a competitive edge in markets demanding fast delivery and product variation.
Stamping operations are also tightly integrated with computer-aided design and manufacturing (CAD/CAM) software. Engineers can simulate forming operations virtually before physical production begins, optimizing the die design, minimizing material usage, and identifying potential forming issues in advance. This digital workflow shortens development cycles, reduces tooling errors, and accelerates time-to-market.
Noise and vibration, traditional concerns in stamping operations, have been addressed with newer machine frames engineered for stability and dampening, as well as acoustic enclosures. These improvements contribute to a safer and more comfortable working environment, while also aligning with increasingly stringent occupational safety regulations.
In multi-step cookware production, stamping is frequently the first operation that prepares parts for subsequent processes like deep drawing, trimming, hole punching, or edge rolling. Therefore, the dimensional accuracy and surface quality achieved during stamping directly influence downstream performance and overall product quality.
Automation does not end at forming—finished stamped parts are often transferred via conveyors or robotic arms to washing stations, surface finishing units, or storage racks, reducing human intervention and potential for handling damage. Machine vision systems further enhance quality assurance by identifying even minute defects in shape, finish, or edge uniformity.
Sustainability in stamping operations is supported by closed-loop lubrication systems that reduce oil consumption, as well as by energy-efficient motors and press drives. Additionally, the scrap metal from stamped sheets can be collected, sorted, and recycled, contributing to circular production practices and reducing raw material costs.
Altogether, machinery for sheet metal stamping in cookware manufacturing serves as a foundational element of a fully integrated, high-efficiency production line. It ensures that each component starts with the right shape, structural integrity, and finish, setting the stage for a final product that meets both performance standards and consumer expectations.
Machinery For Industrial Metal Forming
Machinery for industrial metal forming plays a central role in the manufacturing of a wide range of products, including cookware, automotive parts, structural components, and precision tools. These machines are engineered to manipulate metal sheets, rods, bars, or billets into complex shapes through mechanical force, thermal processes, or a combination of both. They operate with high precision and speed, enabling mass production while maintaining strict tolerances and material integrity.
At the core of industrial metal forming are processes such as deep drawing, forging, stamping, bending, rolling, spinning, and extrusion. Each of these operations relies on dedicated machines—such as hydraulic presses, mechanical presses, rolling mills, spinning lathes, and forging hammers—that are designed to apply the necessary pressure or deformation forces without compromising the properties of the metal.
Modern metal forming machines are highly automated and digitally controlled. CNC systems and PLCs allow operators to set complex forming sequences, monitor real-time parameters, and adjust for variables like material thickness, deformation speed, and die wear. This level of control enhances consistency, reduces waste, and improves safety by minimizing manual interventions.
Hydraulic forming presses are frequently used for deep drawing and complex shape formation, especially when precision and controlled speed are required. These presses can deliver consistent pressure across the entire stroke and are capable of handling high-strength materials without cracking or wrinkling. Mechanical presses, on the other hand, offer higher speed and are commonly used for blanking, coining, and shallow drawing operations.
Roll forming machines continuously bend long strips of metal into desired profiles by passing them through successive sets of rollers. This method is widely used in the production of structural components and cookware rims, offering excellent uniformity and surface finish. For cylindrical or rounded shapes, metal spinning lathes are employed to form cookware, bowls, and other hollow parts using rotational force and forming tools.
In the forging segment, machines such as screw presses and drop hammers shape heated metal billets into highly durable forms. These are ideal for creating components that require exceptional strength, such as cookware handles or base rings. Extrusion machines are used for producing seamless tubes, rods, or custom profiles, pushing metal through a die under high pressure.
The integration of robotics and material handling systems has further increased the efficiency of metal forming operations. Automated feeders, transfer systems, and pick-and-place units reduce downtime and ensure accurate positioning of materials. These machines are often linked through Industry 4.0 protocols, enabling predictive maintenance, production monitoring, and energy optimization.
Industrial metal forming machinery also incorporates advanced safety features, including interlocks, safety curtains, overload protection, and emergency stop systems, ensuring safe operation in high-volume settings. Additionally, energy-efficient drive systems and regenerative braking contribute to sustainability goals by reducing power consumption.
Overall, machinery for industrial metal forming forms the backbone of manufacturing infrastructure, delivering high-volume, high-quality metal components with repeatable accuracy. These machines are indispensable in sectors where durability, precision, and scalability are non-negotiable.
These machines are built to accommodate a broad spectrum of metals, including stainless steel, aluminum, copper, carbon steel, and specialty alloys. Their versatility allows manufacturers to switch between product types with minimal downtime, thanks to modular tooling systems and programmable controls. In cookware manufacturing, for example, the same forming lines can be adapted to produce frying pans, saucepans, or pressure cooker bodies by changing dies and updating machine parameters.
In high-speed production environments, servo-driven presses and hybrid systems are becoming more common. These machines combine the force of traditional hydraulic or mechanical systems with the precision and speed of servo motors. The result is improved forming control, lower noise, faster cycle times, and reduced maintenance. These attributes make them well-suited for both thin-gauge and high-strength material processing, which is often needed in cookware with multi-layer bases or reinforced structures.
Tooling design is another critical component. Dies, punches, mandrels, and rollers must be made from high-strength tool steels or carbide materials to withstand the repeated stress and wear of continuous forming. Modern simulation software helps in optimizing tool geometry before manufacturing, reducing development time and improving first-pass yield.
In terms of process integration, many metal forming machines are now part of fully automated production cells. These cells can include coil feeders, lubrication systems, infrared heaters for thermal forming, automated quality inspection cameras, and even robotic arm stackers. The goal is to create a continuous, self-adjusting workflow that requires minimal human oversight but delivers consistent, defect-free parts.
Cooling systems, vibration dampers, and dust extraction units are also integrated into forming lines to preserve machine life and improve working conditions. For cookware, where hygiene and surface finish are vital, post-forming processes like annealing, cleaning, and polishing are often directly attached to the forming line, ensuring a seamless transition between stages.
With increasing demand for sustainable production, newer machines feature regenerative energy systems that recover and reuse kinetic energy generated during press cycles. Additionally, real-time monitoring of energy usage, lubricant consumption, and tool wear allows for smarter production management and lower operational costs.
These advancements have transformed industrial metal forming from a labor-intensive and noisy operation into a precise, efficient, and largely automated process. Whether forming flat sheets into deep pots, spinning cylindrical stock into bowls, or forging robust handles, modern machinery ensures each component is made with the highest standards of accuracy, repeatability, and material efficiency.
To support high-throughput and flexible production, many industrial metal forming systems now integrate advanced digital control interfaces. Human-Machine Interfaces (HMI) with touchscreen displays allow operators to select product types, adjust forming parameters, and monitor performance metrics in real time. These interfaces can store presets for different cookware models, drastically reducing setup time during changeovers and minimizing errors.
Closed-loop feedback systems are also increasingly used in high-precision forming operations. These systems use force sensors, encoders, and vision-based inspection to detect anomalies such as misfeeds, wrinkles, or material springback during each cycle. When a deviation is identified, the system can automatically adjust stroke pressure, die alignment, or feed rate, effectively self-correcting without stopping the line. This ensures consistently high product quality even over extended production runs.
Another major development is the rise of collaborative robots (cobots) in supporting tasks such as part loading/unloading, visual inspection, packaging, or post-forming assembly. Cobots can work safely alongside human operators and are easily reprogrammed to handle new tasks, giving manufacturers more flexibility without major infrastructure changes.
When it comes to forming cookware with special features—such as encapsulated bases for induction cooking or embossed logos—multi-stage forming setups are used. These include a sequence of stations, each dedicated to a specific forming, trimming, or embossing operation. For example, a pot body may be deep drawn in the first stage, its edge rolled in the second, the base fused or pressed on in the third, and finally the whole piece polished or cleaned in subsequent stages.
Material flow and handling between stages are streamlined with conveyors, pneumatic lifters, or linear transfer arms. This not only boosts productivity but also reduces the risk of part damage. For delicate materials like aluminum or copper, contact surfaces in handling equipment are coated with non-marring materials or Teflon to preserve cosmetic finish.
In response to environmental regulations and worker safety, forming equipment now includes enclosed housings, noise-dampening panels, and mist extraction units. Additionally, many systems are designed with quick-access panels and predictive maintenance alerts to minimize downtime and enhance serviceability.
Ultimately, the latest industrial metal forming machinery empowers cookware manufacturers to maintain consistency, reduce production waste, ensure ergonomic operation, and rapidly adapt to changing market demands. Whether producing budget aluminum saucepans or premium stainless steel pots with multi-layer construction, these machines form the technological backbone of modern metal cookware production.
Machinery For Metal Mixing Bowls Manufacturing
Machinery for metal mixing bowls manufacturing encompasses a sequence of forming, finishing, and assembly operations tailored to create lightweight, food-safe, and aesthetically refined bowls used in both household and industrial kitchens. The production process begins with the selection of high-grade stainless steel, aluminum, or occasionally copper sheets—materials favored for their corrosion resistance, hygiene, and formability.
The core forming operation typically involves deep drawing presses. These hydraulic or servo-hydraulic machines shape flat metal blanks into bowl-shaped forms in a single or multiple drawing stages, depending on the required depth and diameter. To ensure uniform wall thickness and prevent wrinkling or tearing, blank holders and precision dies are employed, often lubricated with food-safe compounds.
For hemispherical or gently tapered mixing bowls, metal spinning lathes offer an alternative or complementary forming method. In this process, the metal blank is rotated at high speed while a roller tool gradually presses it over a mandrel, shaping the bowl with high accuracy and smoothness. CNC spinning machines allow for programmable control of shape profiles, enabling consistent replication of bowl geometries with minimal operator intervention.
Once formed, the edges of the bowl are processed using rim forming and trimming machines. These machines ensure the top edge is smooth, rounded, and safe to handle. Depending on the product specification, this step may include curling or reinforcing the rim to enhance durability.
Surface finishing is carried out using automated polishing and buffing systems, which remove oxidation, tool marks, and fine imperfections. For high-end products, a mirror finish is applied via multi-stage polishing using progressively finer abrasives. If a matte or brushed texture is preferred, belt grinding machines or orbital finishers are used.
To ensure food safety, surface passivation and cleaning stations are integrated to remove any residual contaminants or metal particles. For bowls with volume markings, brand logos, or decorative elements, laser marking or embossing units may be included.
If the bowl includes features such as silicone bases, handles, or measurement guides, assembly cells equipped with robots or pick-and-place units perform precise placement and joining—via adhesives, press-fit techniques, or fasteners. Quality control is finalized with vision inspection systems, checking dimensional accuracy, surface quality, and structural integrity before packaging.
These integrated manufacturing lines enable consistent high-volume production of metal mixing bowls in a wide range of sizes and designs, while maintaining compliance with food-grade standards and ergonomic consumer preferences.
Additional process enhancements in the manufacturing of metal mixing bowls include automated material feeding systems, such as coil feeders and blanking presses, which streamline the supply of raw metal sheets to forming machines. These systems ensure precise blank size and shape, optimizing material usage and reducing waste. Integration with programmable logic controllers (PLCs) and human-machine interfaces (HMIs) allows real-time monitoring of operations, recipe selection for different bowl types, and rapid changeovers between production batches.
Tooling precision is essential in deep drawing and spinning operations. Progressive die sets and interchangeable spinning mandrels are frequently employed to accommodate various bowl diameters and depths with minimal downtime. In high-speed lines, robotic arms may be used to transfer semi-finished bowls from one station to another, enhancing efficiency and minimizing manual handling, which also reduces contamination risks in food-grade production environments.
Thermal treatments, such as annealing, may be applied to bowls made from work-hardened materials, restoring ductility and reducing internal stresses developed during forming. This is particularly relevant for stainless steel variants that require multiple drawing stages or spinning passes. Controlled atmosphere furnaces or induction heating units are commonly used in these steps.
Final surface treatments may include electrochemical polishing or electroless coating, depending on the desired finish and corrosion resistance. For aluminum bowls, anodizing is an option to enhance durability and surface hardness while adding decorative appeal. Integrated leak testing and weight control mechanisms ensure that all bowls meet functional and quality criteria before being transferred to automated packing lines.
Packaging machinery adapted to the cookware industry handles stacking, wrapping, and labeling of bowls in nested sets or individually, using shrink film, cartons, or customized inserts. Data tracking via QR codes or RFID tags
For expanded capabilities in metal mixing bowl manufacturing, some advanced facilities incorporate hybrid forming techniques—combining deep drawing with ironing or hydroforming. These processes allow for ultra-smooth wall surfaces and tighter dimensional tolerances, essential for premium-grade bowls used in commercial kitchens or high-end culinary applications. Hydroforming, in particular, can produce complex contours without wrinkling, making it ideal for ergonomic bowl shapes or integrated handles.
In terms of materials, production lines are often configured to handle multiple metal types—such as stainless steel, aluminum, copper, or clad metals—with quick-change tooling systems and adaptable feed controls. This flexibility allows manufacturers to cater to a wider market, including both budget-friendly and luxury product lines, without needing to overhaul entire setups.
Post-forming operations play a crucial role in final bowl quality. Edge trimming and beading machines are used to create uniform and safe rim profiles, while automated deburring stations ensure no sharp edges remain—important for both user safety and dishwasher compatibility. If the bowl design includes measurement markings or branding, laser engraving or stamping units are positioned after forming but before finishing, ensuring permanent and precise placement.
In polishing and finishing lines, robotic polishing arms equipped with variable-speed abrasive belts or polishing wheels deliver consistent mirror or matte finishes. These systems are programmed for different bowl sizes and shapes, maintaining a uniform finish across all units. For a high-luster appearance, a multi-stage polishing process with compound application may be used. Dust and particulate extraction systems are integrated to ensure environmental safety and compliance with workplace standards.
Another critical component is the quality assurance framework. Vision systems with AI-based inspection algorithms can identify surface defects, dents, or shape deviations in real-time. Coupled with automated rejection systems, they significantly reduce the risk of defective products reaching final packaging. Production data is stored in centralized servers or cloud platforms, accessible for auditing, traceability, and continuous improvement analysis.
For bowl sets or items meant for retail, automated sorting and nesting machines align and stack bowls based on diameter and height before passing them to the packaging station. Packaging machines apply branding, barcode labels, and user instructions with high precision, supporting brand consistency and logistical accuracy.
Overall, modern machinery and integrated automation enable scalable, flexible, and cost-effective production of metal mixing bowls. Manufacturers benefit from reduced labor dependence, faster time-to-market, and consistent product quality—key competitive advantages in the cookware industry.
Machinery For Metal Mixing Bowls Manufacturing
Machinery for metal mixing bowl manufacturing includes a range of forming, shaping, finishing, and quality control equipment, designed to automate the production of durable, food-safe kitchen bowls used in domestic and professional settings. The process begins with flat metal sheets—typically stainless steel or aluminum—cut to size by a sheet metal cutting machine such as a CNC laser or hydraulic shear.
The cut blanks are then transferred to deep drawing presses, where the flat sheet is drawn into a bowl shape in one or multiple stages. This process ensures uniform wall thickness and structural integrity. For bowls with larger depths or higher walls, multi-stage deep drawing lines are used, sometimes incorporating ironing stations to reduce wall thickness and improve surface smoothness.
After forming, edge trimming machines clean and shape the bowl rims, and beading machines may be used to curl or reinforce the edges for safety and rigidity. If the bowls require embossed designs, logos, or capacity markings, embossing or engraving presses are integrated into the line.
Polishing machines, either robotic or manual, follow to achieve desired surface finishes—from brushed satin to mirror-polished effects. These machines often feature rotary or belt-driven heads with varying abrasive compounds tailored to the type of metal and finish requirements.
Cleaning and degreasing machines remove residues before or after polishing to ensure hygienic surfaces suitable for food contact. For higher productivity and consistency, automated robotic arms are used for part handling between operations, while vision inspection systems perform surface defect checks.
At the end of the line, stacking and nesting machines organize finished bowls for packing. Fully integrated lines may include automated packaging machines that apply protective films, labels, and box the products for shipping.
This level of automation allows manufacturers to produce large volumes of mixing bowls efficiently while maintaining consistent quality, surface finish, and dimensional accuracy—ideal for both private-label cookware brands and OEM production.
These production lines can be customized depending on the specific design of the mixing bowl, such as flat base or rounded base, varying diameters, or inclusion of features like pouring lips or handles. When handles are required, separate handle-forming presses or stamping tools create the components, which are then attached to the bowl using robotic or semi-automatic spot welding or riveting units. These systems ensure precise and consistent handle alignment, strength, and durability, all while maintaining production speed.
For premium product lines, especially those targeting professional kitchens or upscale markets, additional finishing steps may be integrated. This includes electropolishing units for ultra-smooth, corrosion-resistant surfaces, and laser marking machines to apply branding or identification codes without compromising the surface finish.
In facilities producing both aluminum and stainless-steel bowls, dedicated lines may be used to avoid cross-contamination, or quick-change tooling systems enable flexibility between materials with minimal downtime. Advanced PLC and HMI controls allow for real-time monitoring and adjustment of all machinery parameters, helping operators ensure optimal production flow, reduce scrap, and maintain quality.
Noise and dust control are also considered in modern setups, with enclosed polishing cells fitted with high-efficiency filtration systems and acoustic insulation. Maintenance is streamlined through centralized lubrication systems, modular machine design, and predictive maintenance software that alerts operators before failures occur.
Safety is integral, with interlocked safety doors, light curtains, and emergency stop systems embedded throughout the production line to protect personnel without compromising efficiency. The entire line can be connected to a central data system, enabling Industry 4.0 integration for performance analytics, traceability, and remote diagnostics.
As demand increases for hygienic, durable kitchenware, these advanced manufacturing systems provide the scalability, consistency, and quality control essential to meet global market expectations while minimizing labor costs and maximizing output.
In addition to the core manufacturing steps, many modern metal mixing bowl production lines incorporate automated quality inspection systems. These use machine vision cameras to detect surface defects such as dents, scratches, or uneven polishing in real-time, allowing immediate rejection or rework of defective parts before they move further down the line. This ensures that only flawless products reach packaging.
Furthermore, automated stacking and packaging machines are often integrated at the end of the line. These systems carefully stack the finished bowls, insert protective interlayers if needed, and pack them into boxes or crates ready for shipment. This reduces manual handling and speeds up the shipping preparation process.
For manufacturers targeting eco-conscious markets, some lines include material recycling systems that collect and recycle metal scraps, polishing residues, and defective parts, reducing waste and environmental impact. Additionally, energy-efficient motors and drives are used throughout machinery to reduce power consumption.
Training modules with augmented reality (AR) interfaces are increasingly being adopted, allowing operators to receive hands-on guidance through smart glasses or tablets. This helps reduce operator error, speeds up onboarding, and improves overall line productivity.
Overall, the combination of precision machinery, automation, quality control, and smart integration makes modern metal mixing bowl manufacturing highly efficient, adaptable, and capable of producing large volumes while maintaining premium quality standards.
Machinery For Copper Cooking Pots Manufacturing
Machinery for copper cooking pots manufacturing involves specialized equipment designed to handle copper’s unique properties — its softness, excellent thermal conductivity, and susceptibility to oxidation. A typical copper pot production line includes these key machines and processes:
- Copper Sheet Decoiling and Flattening Machine:
- Unrolls copper coils and flattens sheets to prepare for forming.
- Ensures uniform thickness and smooth surface for consistent pot quality.
- Deep Drawing Press:
- Forms the copper sheets into pot bodies by pressing them into dies.
- Uses hydraulic or mechanical presses tailored for copper’s ductility to prevent cracking.
- Spinning Lathe / Metal Spinning Machine:
- Shapes and refines pot contours by rotating and pressing the copper sheet against a form.
- Enables creation of complex shapes like rounded bottoms or tapered sides.
- Annealing Furnace:
- Copper is periodically annealed (heated and cooled) to restore ductility after forming steps.
- Prevents brittleness and cracking in subsequent processing.
- Trimming Machine:
- Removes excess material from edges for uniform rims and smooth finishes.
- Handle Forming and Attachment Machines:
- Forging or casting machines produce handles.
- Attachment can be done manually, semi-automatically, or fully automated via riveting, soldering, or brazing equipment.
- Polishing and Buffing Machines:
- Copper requires thorough polishing to achieve a bright, mirror-like finish.
- Machines include rotary buffers, tumblers, and abrasive belt polishers.
- Cleaning and Surface Treatment Systems:
- Removes oxidation and oils using chemical baths or ultrasonic cleaners.
- Sometimes involves protective lacquer coating to maintain shine and prevent tarnish.
- Seam Welding or Soldering Equipment:
- For pots made from multiple pieces, seam welding or soldering machines join parts securely.
- Quality Control and Inspection Systems:
- Machine vision or manual inspection to check for defects, dimensional accuracy, and surface quality.
- Packaging Automation:
- Automated stacking, wrapping, and boxing equipment to prepare pots for shipment.
These machines are often integrated with computer control systems for precise operation and repeatability. Copper cookware manufacturing demands skilled craftsmanship along with automation to balance efficiency and the high-quality aesthetic finish copper is known for.
Copper cooking pot manufacturing requires careful handling of copper’s softness and malleability to produce durable, visually appealing cookware. The production line typically starts with copper coil uncoiling and sheet flattening, ensuring consistent thickness and smoothness for forming. The sheet metal is then shaped by deep drawing presses, where copper is pressed into molds to create the basic pot body. Due to copper’s work-hardening tendency, annealing processes are integrated at intervals to restore softness and prevent cracking during successive forming stages.
Metal spinning machines refine the shape, allowing for rounded or tapered designs by spinning the copper sheet against a mandrel. Excess material is trimmed precisely to form smooth edges, and handles are formed separately through forging or casting, then attached using riveting, brazing, or soldering machines. Seam welding or soldering equipment is used if the pot consists of multiple components, ensuring strong and leak-proof joints.
Polishing machines, including rotary buffers, tumblers, and abrasive belts, are essential for achieving the classic shiny copper finish. Surface treatments such as chemical cleaning or ultrasonic baths remove oxidation, and some lines include protective lacquer coating to maintain appearance and reduce maintenance for end-users. Automated quality control systems help detect dimensional inaccuracies, surface imperfections, or structural defects.
The manufacturing workflow is optimized for efficiency while preserving the aesthetic and functional qualities unique to copper cookware. Integration of CNC controls, robotics, and computer vision enhances precision, repeatability, and throughput. Final packaging lines automate stacking and protective wrapping to prepare pots for distribution. Throughout the process, careful coordination between automated machinery and skilled craftsmanship is vital to produce high-quality copper pots with excellent durability and thermal performance.
Continuing with copper cooking pot manufacturing, advanced automation systems further streamline production by synchronizing each stage for minimal downtime. Robotic arms handle material transfer between forming, trimming, welding, and polishing stations, reducing manual labor and contamination risks. Real-time data monitoring collects parameters like pressure, temperature, and cycle times to optimize machine performance and predict maintenance needs, improving overall equipment effectiveness (OEE).
For customization, CNC-controlled metal spinning lathes allow quick adjustments for different pot sizes and shapes, enabling small batch production alongside large runs. Decorative embossing or engraving machines add branding or patterns directly onto the copper surface without compromising structural integrity. Additionally, integrated laser cleaning or precision sanding systems prepare surfaces for better coating adhesion or finishing.
Environmental considerations are also addressed: closed-loop coolant systems, solvent recovery units, and energy-efficient motors minimize waste and emissions. Some facilities use renewable energy sources or recycle copper scrap generated during trimming and machining, reducing material costs and ecological footprint.
Final assembly may include fitting lids, handles, and additional components like steamer inserts or non-stick liners, depending on product design. Automated leak testing equipment verifies pot integrity before packaging. The entire process, from raw copper coil to finished cookware, reflects a balance of traditional metalworking techniques enhanced by modern industrial automation to produce high-quality, durable copper pots suited for professional kitchens and home use alike.
Machinery For Steel Woks Manufacturing
Manufacturing steel woks requires specialized machinery designed to shape, form, and finish the thin, large-diameter metal sheets that give woks their characteristic shape and cooking properties. Here’s an overview of key machinery used in steel wok production:
- Steel Sheet Decoiler and Flattening Machine
Raw steel sheets or coils are first uncoiled and flattened to ensure a smooth, even surface before forming. - Deep Drawing Press or Hydraulic Press
Large deep drawing presses form the concave wok shape by pressing steel sheets into wok molds. This process may be done in multiple stages to avoid cracking and ensure uniform thickness. - Spinning Lathe (Metal Spinning Machine)
After initial forming, metal spinning machines refine the wok’s shape by rotating and shaping the steel sheet against a mandrel, allowing precise control over curvature and thickness. - Edge Trimming and Beading Machine
Excess metal from the wok rim is trimmed for a clean edge, and beading machines add rolled edges to strengthen and smooth the rim, preventing sharpness. - Handle Forming and Attaching Equipment
Handles—often made of steel or wood—are forged or molded separately, then attached via spot welding, riveting, or screwing. Automatic handle feeders and positioning devices speed up this step. - Surface Treatment and Polishing Machines
Buffers, rotary polishers, or vibratory finishing machines smooth and polish wok surfaces to enhance appearance and prevent rust. Some lines also apply seasoning or protective coatings. - Quality Inspection Systems
Automated dimension measuring and visual inspection ensure each wok meets specifications and has no surface defects. - Packaging Machines
Finished woks are automatically stacked, wrapped, and boxed for shipment.
Advanced manufacturing lines often integrate robotics and CNC controls to improve precision, reduce manual labor, and enable rapid product changeovers between different wok sizes and styles. Environmental controls, such as coolant recycling and dust extraction, help maintain clean working conditions and reduce waste. This machinery combination ensures efficient production of durable, high-quality steel woks favored by both professional chefs and home cooks.
Metal Forming Presses: These are essential for shaping the wok’s body, using multiple stamping stages to gradually form the curved sides without causing cracks or wrinkles in the steel sheet.
Hydraulic Deep Drawing Machines: Deep drawing presses are favored for their ability to form complex shapes with uniform thickness, critical for woks that require a deep, rounded bottom.
Automatic Edge Rolling Machines: To create a smooth, reinforced rim that’s safe to handle, edge rolling machines curve and finish the wok edges, improving strength and user comfort.
Welding and Riveting Machines: These machines attach handles securely. Welding machines provide strong, seamless joins, while riveting machines offer alternative fastening, especially for wooden or heat-resistant handles.
Surface Finishing Units: Polishing and buffing machines use abrasive belts, brushes, or tumbling to give the wok a smooth surface, which helps prevent sticking and rust. Some systems include chemical cleaning or passivation for corrosion resistance.
Heat Treatment Furnaces: In some manufacturing lines, heat treatment may be applied to relieve stresses from forming and improve metal durability.
Automated Quality Control: Vision systems and laser measurement devices inspect wok dimensions, surface finish, and weld quality, ensuring each product meets strict standards.
Packaging Lines: After production, automated conveyors and robotic arms package the woks efficiently, readying them for distribution.
The combination of these machines allows manufacturers to produce steel woks with consistent quality, optimized strength, and attractive finishes, suitable for both commercial kitchens and consumers worldwide.
Coating Application Machines: For some steel woks, a layer of seasoning or non-stick coating is applied to improve cooking performance. Spray or dip coating machines evenly distribute oils or polymer coatings before curing.
Curing Ovens: After coating, woks pass through curing ovens where controlled heat sets the coating, bonding it permanently to the metal surface for durability and non-stick properties.
Handle Assembly Robots: In advanced lines, robotic arms assemble and attach handles, which may be wooden, plastic, or metal. Automation ensures precision and speeds up production while maintaining ergonomic standards.
Heat Source Testing Units: Some factories include testing stations where woks undergo heat resistance and distribution tests, verifying that the final product meets thermal performance criteria.
Surface Treatment Baths: Electrochemical polishing or passivation baths enhance corrosion resistance and improve aesthetic appeal, particularly for stainless steel woks.
Deburring Machines: After forming and welding, burrs and sharp edges are removed by automated deburring machines using brushes, grinding wheels, or abrasive belts to ensure safety and quality.
Laser Marking Machines: For branding and traceability, laser engraving machines mark the wok’s surface with logos, serial numbers, or product information without affecting the metal integrity.
Final Inspection Stations: Human inspectors or AI-powered vision systems conduct final quality checks for surface defects, weld integrity, and dimensional accuracy before packaging.
This integrated machinery suite maximizes efficiency, reduces waste, and guarantees that steel woks leaving the production line meet high standards of quality and performance. Would you like details on any specific machinery or step?
Machinery For Aluminum Cookware Manufacturing
1. Aluminum Sheet Decoiling and Straightening Machines:
These machines feed aluminum sheets or coils into the production line, straightening the metal for smooth processing.
2. Deep Drawing Presses:
Used to form the basic shape of pots, pans, and lids by pressing aluminum sheets into molds with high force, producing seamless cookware bodies.
3. Metal Spinning Machines:
For shaping round cookware like bowls and pans, these lathes spin aluminum blanks against a forming tool to create uniform curved surfaces.
4. Hydraulic Presses:
Apply controlled pressure to form complex shapes or emboss patterns on cookware surfaces.
5. Trimming Machines:
Remove excess material or flashing from edges after forming, ensuring precise dimensions and smooth edges.
6. Edge Rolling and Flanging Machines:
Form and strengthen rims of pots and pans for durability and to prepare for handle attachment or lid fitting.
7. Handle Welding and Riveting Machines:
Attach handles using automated welding (often spot welding) or riveting, securing handles firmly to cookware bodies.
8. Surface Treatment Equipment:
Anodizing lines or chemical baths enhance corrosion resistance and surface hardness of aluminum cookware. Some lines include cleaning, anodizing, coloring, and sealing stages.
9. Polishing and Buffing Machines:
Automated systems polish cookware surfaces to achieve smooth, shiny finishes, improving aesthetics and ease of cleaning.
10. Coating Machines:
Spray or roll non-stick coatings onto cookware surfaces, followed by curing ovens that bake the coatings to durable finishes.
11. Quality Inspection Systems:
Vision systems and manual checks for surface defects, dimensional accuracy, and coating consistency.
12. Packaging Automation:
Automated packaging lines wrap, box, and label finished cookware for shipping.
These machines together create efficient, high-quality aluminum cookware production with consistent output and minimized waste. Want me to dive deeper into any of these machines or processes?
Aluminum cookware production starts with selecting high-quality aluminum sheets or coils that meet specific alloy standards for strength and thermal conductivity. The sheets are first uncoiled and straightened to remove any bends or curls, ensuring smooth feeding into forming machines.
Deep drawing presses play a critical role in shaping cookware bodies. The aluminum sheets are blanked into circular discs, then progressively formed into pots, pans, or lids by high-pressure punches pushing the metal into matching dies. This process can produce seamless bodies that are strong and lightweight.
For round cookware like mixing bowls or frying pans, metal spinning machines are widely used. A disc of aluminum is rotated at high speed while a tool presses it against a mandrel, shaping the metal precisely with minimal waste. These lathes allow for smooth curves and consistent thickness.
Hydraulic presses with specialized dies can add decorative embossing or reinforce rims by controlled bending and flanging. This enhances the cookware’s durability and visual appeal.
After forming, trimming machines remove any excess material around edges, achieving tight tolerances for lids and handles. The edges are then rolled or flanged to strengthen and prepare for assembly.
Handle attachment is often automated, using robotic welders or riveting machines that position and secure handles consistently. This automation improves assembly speed and reduces human error.
Surface treatment for aluminum cookware usually involves anodizing, where the metal is immersed in an electrolytic bath creating a hard oxide layer. This layer improves corrosion resistance and wear. Some plants integrate multi-stage anodizing lines, including pre-cleaning, anodizing, coloring, sealing, and drying.
Polishing and buffing machines use rotating brushes or pads with abrasives or polishing compounds to achieve a bright, smooth finish. This step is important both for aesthetics and for creating surfaces that are easy to clean.
Non-stick coating application systems typically use automated spray booths or roll coaters to apply layers of PTFE or ceramic-based coatings evenly. After coating, curing ovens bake the cookware at high temperatures to fix the coating firmly to the aluminum surface.
Throughout production, advanced quality inspection systems use cameras and sensors to detect surface defects, measure dimensions, and verify coating thickness. This ensures only top-quality products proceed to packaging.
Finally, packaging machines automate the stacking, wrapping, and boxing of cookware sets. Some lines include labeling and palletizing robots for efficient shipping preparation.
Together, these machines form a highly integrated, efficient aluminum cookware production line capable of meeting large-scale manufacturing demands while maintaining quality and safety standards.
One key aspect of modern aluminum cookware production is the integration of CNC (Computer Numerical Control) technology in forming and finishing machines. CNC deep drawing presses and CNC spinning lathes provide precision control over shaping parameters, enabling consistent product dimensions and reducing material waste. Programmable tooling changes allow quick switching between different cookware models, enhancing flexibility for manufacturers.
Advanced robotics are increasingly used for handling and assembly tasks. Robotic arms can pick and place formed pots and pans between stations—such as from the deep drawing press to trimming, or from anodizing baths to drying ovens—minimizing human contact and contamination risk. Automated welding cells equipped with laser or ultrasonic welding technologies attach handles or reinforcing components with high repeatability and strength.
In coating processes, robotic spraying systems combined with precise flow and temperature controls ensure uniform application of non-stick or ceramic coatings, improving coating durability and performance. Inline curing ovens with adjustable temperature zones optimize the baking process, reducing defects like bubbling or peeling.
Surface finishing also benefits from automated brushing and polishing stations equipped with sensors that adjust pressure and speed based on real-time surface condition feedback. This adaptive finishing ensures a consistent, high-quality sheen across batches.
Quality control is enhanced with AI-driven vision inspection systems that detect microscopic surface flaws or coating irregularities beyond human capability. Integrated data collection allows traceability from raw material to finished product, enabling root-cause analysis and continuous improvement.
Energy-efficient machinery design reduces operational costs and environmental impact. For example, servo-driven presses consume less power than traditional hydraulic systems and provide finer control. Closed-loop water treatment and recycling systems in anodizing and washing stages minimize water consumption.
Some modern plants implement Industry 4.0 principles, where interconnected machines communicate via IoT networks. This enables predictive maintenance alerts, minimizing downtime, and real-time production monitoring dashboards improve throughput and quality tracking.
In summary, aluminum cookware manufacturing combines traditional metal forming techniques with cutting-edge automation, robotics, and quality control to produce durable, attractive, and high-performing cookware at scale. Manufacturers that invest in these technologies gain competitive advantages through higher efficiency, product consistency, and faster response to market demand.
Would you like to explore automation in another type of cookware production or focus on specific machinery?
Machinery for Production of Cookware with Metal Spinning Process
Machinery for production of cookware using the metal spinning process involves specialized equipment designed to shape flat metal discs into round, seamless cookware items such as pots, pans, lids, and bowls. Metal spinning is a highly efficient forming method that offers precise control over wall thickness, contours, and surface finish, making it ideal for cookware manufacturing.
Key machinery and equipment used in the metal spinning process for cookware production include:
- Metal Spinning Lathe (Spinning Machine):
- The core equipment that rotates a metal blank (usually aluminum, stainless steel, or copper) at high speed.
- A skilled operator or CNC control presses a forming tool (roller or mandrel) against the rotating blank to shape it over a preformed form or mandrel.
- CNC-controlled spinning lathes enable complex shapes with high repeatability and reduced labor.
- Mandrels and Forming Tools:
- Mandrels serve as the shaping core over which the metal blank is spun. They are made precisely according to the cookware design (e.g., pot body, bowl shape).
- Forming rollers or tools apply pressure to the metal, gradually stretching and shaping it around the mandrel.
- Multiple mandrels and tooling sets allow for different cookware sizes and styles.
- Coiling and Feeding Systems:
- For continuous or semi-automated production, coil-fed spinning lathes can feed sheet metal directly from rolls, minimizing waste and speeding up the process.
- Some setups include automatic blanking machines to cut metal discs from sheet coils before spinning.
- Annealing Furnaces:
- During spinning, metal work hardens and can crack if not softened periodically. Annealing furnaces are used to heat-treat spun parts between stages to restore ductility.
- Controlled annealing improves metal formability and surface finish.
- Trimming and Flanging Machines:
- After spinning, excess metal around rims is trimmed to precise dimensions.
- Flanging machines roll or curl the edges to create smooth, safe rims or to prepare the part for handle attachment.
- Polishing and Surface Finishing Machines:
- Metal spinning creates a smooth but sometimes rough surface that requires finishing.
- Automated polishing and buffing machines enhance aesthetics and prepare cookware for coatings or anodizing.
- Quality Inspection Systems:
- Vision systems and gauges check for dimensional accuracy, wall thickness uniformity, and surface defects.
- Automation and CNC Integration:
- CNC metal spinning lathes and robotic arms enable higher throughput with reduced manual labor.
- Integrated process controls monitor force, speed, and temperature for consistent quality.
Metal spinning is favored for producing high-quality, seamless cookware with good structural integrity and attractive finishes. It is common in manufacturing copper pots, stainless steel bowls, and aluminum pans.
The metal spinning process starts with a flat metal blank, typically cut into discs from sheet metal. This blank is mounted onto a rotating spindle of the spinning lathe, which can be either manually operated or CNC-controlled. The mandrel, shaped to the desired interior profile of the cookware, is positioned behind the blank. As the spindle spins at high speed, forming tools press the metal blank against the mandrel, gradually stretching and shaping the metal into the cookware’s shape through incremental passes.
The forming tools may include rollers, styluses, or other specialized tooling, depending on the shape complexity. The operator or CNC program carefully controls the pressure and position of these tools to avoid tearing or thinning the metal excessively. Throughout the process, the metal work hardens, so intermediate annealing steps may be applied to soften it, allowing further deformation without cracking.
Once the desired shape is achieved, the spun cookware part often requires trimming to remove excess metal around the edges. Trimming machines use blades or rotary cutters to cleanly cut the rims to precise dimensions. Following trimming, flanging or curling machines may be employed to roll the edges, enhancing safety and preparing the parts for handles or lids.
Surface finishing is crucial in cookware production to ensure a smooth, attractive appearance and prepare the metal for additional coatings or treatments like anodizing or non-stick layers. Polishing machines use abrasive wheels, brushes, or buffing compounds to remove surface imperfections and impart a mirror-like or matte finish as specified.
Automation plays a key role in modern metal spinning production lines. CNC metal spinning lathes allow for repeatable, precise shaping with minimal operator intervention. Integration with robotic handling systems speeds up loading and unloading of blanks and finished parts, improving productivity and reducing labor costs.
Quality inspection is typically integrated into the process, using laser measurement tools or vision systems to verify wall thickness uniformity, overall dimensions, and surface defects. This ensures that every piece meets stringent quality standards required in cookware manufacturing.
Materials commonly used in metal spinning for cookware include aluminum, stainless steel, and copper. Each material requires specific tooling and process parameters to optimize forming and finish quality. For example, copper’s high ductility makes it excellent for complex shapes but requires careful annealing to prevent cracking, while stainless steel demands higher forces and more robust tooling due to its hardness.
In summary, machinery for cookware production using the metal spinning process is designed to efficiently transform flat metal blanks into high-quality, seamless cookware parts with precise shapes, smooth finishes, and consistent quality, combining traditional craftsmanship with modern automation technology.
Following the metal spinning and initial forming stages, additional machinery is often employed to assemble and enhance the cookware. Handle attachment machines weld or rivet handles made from metal or heat-resistant materials securely to the pot or pan bodies. This can be done through automated robotic welding cells or manual welding stations depending on production scale.
Lid manufacturing lines may run in parallel, using similar metal forming processes followed by edge rolling and handle fixing. The lids often require precise fitting to ensure proper sealing and heat retention during cooking.
For cookware requiring special surface treatments, lines for anodizing, powder coating, or applying non-stick layers are integrated downstream. Anodizing equipment uses controlled electrolytic baths to create a durable oxide layer on aluminum cookware, improving corrosion resistance and surface hardness. Powder coating systems spray polymer powders onto the cookware, which are then cured in ovens to form tough, decorative finishes. Non-stick coating lines apply PTFE or ceramic-based coatings with precise layering and curing processes to ensure adhesion and longevity.
Post-coating, automated ovens cure or bake the coatings at controlled temperatures. Quality control stations use visual inspection, adhesion testing, and thickness gauges to verify coating uniformity and durability.
Packaging machinery completes the production flow, wrapping, boxing, or bundling cookware sets for shipment. Modern packaging lines incorporate conveyors, robotic arms, and automated labeling systems to speed up output while maintaining accuracy.
Overall, a complete metal cookware manufacturing line integrates metal forming, finishing, assembly, coating, inspection, and packaging into a streamlined automated process. This reduces production time, minimizes manual labor, and ensures consistent high quality across large batches of products.
Such integrated machinery solutions are customizable to different cookware types—pots, pans, pressure cookers, casserole dishes, woks, and more—accommodating variations in material, thickness, size, and finishing requirements. The result is a flexible, efficient manufacturing setup that can meet market demands while maintaining stringent quality and safety standards.
EMS Metalworking Machines
We design, manufacture and assembly metalworking machinery such as:
- Hydraulic transfer press
- Glass mosaic press
- Hydraulic deep drawing press
- Casting press
- Hydraulic cold forming press
- Hydroforming press
- Composite press
- Silicone rubber moulding press
- Brake pad press
- Melamine press
- SMC & BMC Press
- Labrotaroy press
- Edge cutting trimming machine
- Edge curling machine
- Trimming beading machine
- Trimming joggling machine
- Cookware production line
- Pipe bending machine
- Profile bending machine
- Bandsaw for metal
- Cylindrical welding machine
- Horizontal pres and cookware
- Kitchenware, hotelware
- Bakeware and cuttlery production machinery
as a complete line as well as an individual machine such as:
- Edge cutting trimming beading machines
- Polishing and grinding machines for pot and pans
- Hydraulic drawing presses
- Circle blanking machines
- Riveting machine
- Hole punching machines
- Press feeding machine
You can check our machinery at work at: EMS Metalworking Machinery – YouTube
Applications:
Flange-punching
Beading and ribbing
Flanging
Trimming
Curling
Lock-seaming
Ribbing