A profile bending machine is a specialized tool used to shape and form metal profiles, such as pipes, bars, and tubes, into various curved or bent shapes. It is a versatile and essential piece of equipment in various industries, including metal fabrication, construction, and automotive manufacturing.
Key Components of a Profile Bending Machine:
- Driving System: The driving system provides the power to bend the workpiece. It typically consists of an electric motor, gearbox, and hydraulic or electric actuators.
- Bending Rolls: The bending rolls are the primary components that shape the workpiece. They consist of two or three rotating rolls that apply pressure to the workpiece, causing it to deform into the desired shape.
- Control System: The control system allows the operator to precisely control the bending process, including setting the bending angle, speed, and force. Modern control systems often utilize computer-controlled numerical control (CNC) technology for high precision and automation.
- Workpiece Supports: Workpiece supports provide stability and prevent the workpiece from slipping or twisting during the bending process.
- Safety Features: Safety features, such as safety interlocks, emergency stop buttons, and guards, minimize the risk of accidents and injuries.
Applications of Profile Bending Machines:
- Pipe Bending: Profile bending machines are widely used for bending pipes of various diameters and materials, such as steel, aluminum, and plastic pipes. They are essential for creating curved pipe sections for plumbing, HVAC, and industrial applications.
- Bar Bending: Profile bending machines can also bend bars, such as round, square, and rectangular bars, into various shapes, such as arcs, circles, and custom profiles. They are used in various applications, including structural framing, metal furniture manufacturing, and signage production.
- Tube Bending: Profile bending machines are also suitable for bending tubes, such as rectangular and oval tubes, into various shapes. They are used in applications like automotive exhaust systems, handrails, and furniture frames.
- Structural Bending: Profile bending machines can bend structural shapes, such as I-beams, channels, and angles, into various curved shapes for structural applications. This allows for the creation of custom-shaped beams and supports for buildings, bridges, and other structures.
- Prototyping and Design: Profile bending machines are valuable tools in prototyping and design stages of metalworking projects, allowing for rapid iteration and refinement of prototypes by enabling quick and precise bending of metal profiles.
Choosing the Right Profile Bending Machine:
The selection of the appropriate profile bending machine depends on several factors, including:
- Workpiece Material and Dimensions: Consider the material, diameter, and wall thickness of the workpiece to ensure the machine can handle the bending requirements.
- Bending Capacity: Determine the maximum bending radius and angle required for the desired bending applications.
- Production Volume and Automation Needs: Consider the production volume and whether automation using CNC is necessary for high throughput and consistency.
- Safety Features and Compliance: Ensure the machine complies with safety standards and incorporates necessary safety features to protect the operator.
- Brand Reputation and Service: Choose a reputable brand with a proven track record of quality, reliability, and readily available service support.
Profile bending machines play a crucial role in shaping and forming metal profiles for various applications across industries. Their versatility, precision, and power make them essential tools for metalworkers, engineers, and manufacturers.
A profile bending machine is used to bend profiles in a circular form. The profile bending machines are generally divided into 2 main groups
- Mechanical profile bending machine
- Hydraulic profile bending machine
Mechanical Profile Bending Machine
A mechanical profile bending machine is a type of profile bending machine that utilizes mechanical components, such as gears, levers, and linkages, to apply the force required to bend metal profiles. Unlike hydraulic profile bending machines, which rely on hydraulic pressure, mechanical profile bending machines offer simplicity, robustness, and lower initial cost.
Key Features of Mechanical Profile Bending Machines:
- Mechanical Drive System: The driving system consists of gears, levers, and linkages that transfer the rotational motion of a motor to the bending rolls, providing the necessary force for bending.
- Adjustable Bending Rolls: The bending rolls, typically made of hardened steel, can be adjusted horizontally and vertically to accommodate different workpiece sizes and shapes.
- Manual or Semi-Automatic Controls: Mechanical profile bending machines may feature manual controls for precise bending angle adjustments or semi-automatic controls for repetitive bending operations.
- Compact and Robust Design: Mechanical profile bending machines are often compact and robust in construction, making them suitable for smaller workshops and applications that require durability.
- Cost-Effective Solution: Mechanical profile bending machines generally have lower initial costs compared to hydraulic profile bending machines, making them an attractive option for budget-conscious users.
Applications of Mechanical Profile Bending Machines:
- Small-Scale Metal Fabrication: Mechanical profile bending machines are commonly used in small workshops and DIY projects for bending metal profiles, such as pipes, bars, and tubes, into various shapes.
- Prototyping and Design: The simplicity and ease of use of mechanical profile bending machines make them suitable for prototyping and design stages of metalworking projects, allowing for rapid iteration and refinement of prototypes.
- Maintenance and Repair: Mechanical profile bending machines can be used in maintenance and repair tasks to bend metal pipes, conduits, and other components.
- Educational and Training Purposes: Mechanical profile bending machines are often used in classrooms and training workshops to provide students with hands-on experience in metal bending and to introduce them to the principles of metalworking.
Advantages of Mechanical Profile Bending Machines:
- Simple and Reliable Operation: Mechanical profile bending machines are known for their simplicity of operation and reliable performance, making them suitable for both experienced and novice users.
- Low Maintenance Requirements: Mechanical profile bending machines typically require minimal maintenance compared to hydraulic systems, reducing downtime and associated costs.
- Cost-Effective Solution: Mechanical profile bending machines generally have lower initial and maintenance costs compared to hydraulic profile bending machines.
Disadvantages of Mechanical Profile Bending Machines:
- Limited Bending Capacity: Mechanical profile bending machines may have limited bending capacity compared to hydraulic profile bending machines, restricting their suitability for large or thick workpieces.
- Manual Adjustments: Manual adjustments for bending angle and speed may be required, which can be time-consuming for repetitive tasks.
- Lower Automation Potential: Mechanical profile bending machines typically offer lower automation potential compared to hydraulic or CNC-controlled bending machines.
In summary, mechanical profile bending machines are a versatile and cost-effective solution for small-scale metal fabrication, prototyping, and repair tasks. Their simplicity, reliability, and low maintenance requirements make them an attractive option for workshops with limited budgets or those requiring a straightforward bending solution. However, for high-volume production or applications requiring precise automation, hydraulic or CNC-controlled profile bending machines may be more suitable.
This type of profile bending machine is operated by mechanical means. The actuator is an electrical AC motor, that drives the rolls by a worm gear. The mechanical profile bending machine is suitable to bend profiles up to a thickness. The metals that can be bent on this machine is steel, copper, tin and aluminum. Profile bender is widely used in construction, automotive, decoration, defense and agricultural industries.
The profile machine is operated by a foot pedal. When the operator presses on one pedal, the rolls keep turning to one side, and when the operator presses on the other pedal, the rolls keep rotating to the other side.
We produce 2 models for the mechanical profile bending machine
- EMS MPB 30
- EMS MPB 50
Hydraulic Profile Bending Machine
A hydraulic profile bending machine is a type of profile bending machine that utilizes hydraulic pressure to apply the force required to bend metal profiles. Hydraulic profile bending machines offer precise bending control, high bending capacity, and automation capabilities, making them a popular choice for industrial applications.
Key Features of Hydraulic Profile Bending Machines:
- Hydraulic Power Unit: The hydraulic power unit consists of a hydraulic pump, reservoir, and valves that generate and control the hydraulic pressure required for bending.
- Bending Cylinders: The bending cylinders, typically double-acting, convert hydraulic pressure into linear motion, applying force to the bending rolls through pistons or rods.
- Precise Bending Controls: Hydraulic profile bending machines often feature sophisticated control systems, including CNC (computer numerical control), that allow for precise control of bending parameters, such as angle, speed, and force.
- High Bending Capacity: Hydraulic profile bending machines are capable of bending large and thick workpieces, making them suitable for industrial applications involving heavy-duty materials.
- Automation Capabilities: Hydraulic profile bending machines can be integrated with automation systems for high-volume production runs and repetitive bending tasks, increasing efficiency and consistency.
Applications of Hydraulic Profile Bending Machines:
- Industrial Metal Fabrication: Hydraulic profile bending machines are widely used in industrial metal fabrication shops for bending pipes, bars, tubes, and structural shapes into various shapes for construction, machinery, and manufacturing applications.
- Shipbuilding and Offshore Construction: Hydraulic profile bending machines play a crucial role in shipbuilding and offshore construction for bending structural steel members, pipes, and tubes for vessel frames, piping systems, and structural components.
- Automotive Manufacturing: Hydraulic profile bending machines are essential in automotive manufacturing for bending exhaust pipes, chassis components, and other structural parts.
- Heavy Equipment Manufacturing: Hydraulic profile bending machines are used in the manufacturing of heavy equipment, such as cranes, excavators, and agricultural machinery, for bending structural components and piping systems.
- Production of Structural Components: Hydraulic profile bending machines are employed in the production of structural components for buildings, bridges, and other structures, bending beams, channels, and other structural shapes to the required dimensions and angles.
Advantages of Hydraulic Profile Bending Machines:
- Precise Bending Control: Hydraulic profile bending machines offer precise control over bending parameters, ensuring accurate and consistent bends, even for complex shapes and angles.
- High Bending Capacity: Hydraulic profile bending machines can handle large and thick workpieces, making them suitable for industrial applications with demanding bending requirements.
- Automation Capabilities: Hydraulic profile bending machines can be integrated with automation systems for high-volume production runs, increasing efficiency and reducing labor costs.
- Versatility: Hydraulic profile bending machines can bend a wide range of metal profiles, including pipes, bars, tubes, and structural shapes, making them versatile tools for various applications.
- Durability and Reliability: Hydraulic profile bending machines are typically built for heavy-duty industrial use, ensuring durability and reliability over extended periods of operation.
Disadvantages of Hydraulic Profile Bending Machines:
- Higher Initial Cost: Hydraulic profile bending machines generally have higher initial costs compared to mechanical profile bending machines.
- Maintenance Requirements: Hydraulic systems require regular maintenance, including fluid changes, filter replacements, and valve adjustments.
- Complex Troubleshooting: Troubleshooting hydraulic systems can be more complex compared to mechanical systems, requiring specialized knowledge and expertise.
Overall, hydraulic profile bending machines offer a powerful, precise, and versatile solution for industrial metal bending applications. Their ability to handle large and thick workpieces, combined with automation capabilities and precise control, makes them an indispensable tool in various industries, including metal fabrication, construction, and manufacturing.
This type of profile bending machine is operated by hydraulic means. The actuator is an electrical AC motor working with a pressure pump, that drives the rolls. The hydraulic profile bending machine is suitable to bend profiles with bigger dimensions. The metals that can be bent on this machine is steel, copper, tin and aluminum. Profile bender is widely used in construction, automotive, decoration, defense and agricultural industries.
The profile machine is operated by a foot pedal. When the operator presses on one pedal, the rolls keep turning to one side, and when the operator presses on the other pedal, the rolls keep rotating to the other side.
We produce 3 models for the hydraulic profile bending machine
- EMS HPB 50
- EMS HPB 60
- EMS HPB 80
A profile bending machine, also known as a section bending machine or profile rolling machine, is a specialized industrial tool designed to bend and shape various types of profiles, such as beams, channels, angles, tubes, and other structural and architectural components made of metal or other materials. These machines are used across various industries for tasks that involve curving, forming, and shaping profiles to create structural or decorative elements. Here are the key components and features of a profile bending machine:
- Rolls or Rollers:
- Profile bending machines have rolls or rollers specifically designed to accommodate the shape and size of the profiles being bent.
- The rolls come in different shapes, such as cylindrical, conical, and pyramid, depending on the desired bending outcome.
- Frame:
- The frame of the machine provides structural support and stability during the bending process.
- It is usually made of heavy-duty steel to withstand the forces generated during profile bending.
- Bending Rolls:
- Profile bending machines typically have two or three bending rolls, with one or more rolls adjustable to achieve different bending radii.
- The rolls are positioned at different angles to bend profiles in various configurations.
- Drive Mechanism:
- These machines can be powered by hydraulic, mechanical, or electric drive systems.
- Hydraulic systems offer precise control and are often preferred for heavy-duty applications.
- Control Panel:
- Modern profile bending machines are equipped with control panels that allow operators to set and control parameters like bending radius, speed, and angle.
- CNC (Computer Numerical Control) systems may be used for automated and precise bending operations.
- Support Rollers:
- Support rollers are often placed on both sides of the bending rolls to guide and support the profile as it passes through the machine.
- These rollers help ensure uniform bending and prevent material distortion.
- Tooling and Dies:
- Tooling and dies are used to shape and bend the profile accurately according to the desired specifications.
- Different tooling and dies are used for various profile shapes and sizes.
- Safety Features:
- Safety features like emergency stop buttons, guards, and interlocks are important to protect operators during bending operations.
- Material Compatibility:
- Profile bending machines can handle a variety of materials, including steel, aluminum, stainless steel, and even plastic, depending on the machine’s design and capabilities.
- Applications:
- Profile bending machines are used in various applications, including metal fabrication, construction, shipbuilding, aerospace, and architectural metalwork.
- They are essential for producing curved and bent profiles used in building structures, bridges, handrails, and other architectural and industrial elements.
- Flexibility:
- Profile bending machines offer a high degree of flexibility and can be used to bend profiles into a wide range of shapes, including circles, spirals, and complex curves.
- They can accommodate different sizes and types of profiles with appropriate adjustments.
Profile bending machines are versatile tools that enable the creation of complex and curved shapes with precision. They are essential for industries that require the fabrication of curved and arched components used in various structural and decorative applications.
Components and Features
Profile bending machines are versatile tools used in various industries for bending and shaping profiles, such as beams, channels, angles, and tubes, to create curved and custom shapes. Here are the key components and features of a profile bending machine:
Components:
- Rolls or Rollers:
- Profile bending machines have sets of rolls or rollers that are responsible for bending the profile. These rolls come in various shapes and sizes to accommodate different profiles and bending requirements.
- Common roll configurations include three-roll and four-roll designs. Three-roll machines have one fixed bottom roll and two adjustable top rolls, while four-roll machines typically have two bottom rolls and two adjustable top rolls.
- Frame:
- The frame provides structural support for the machine and ensures stability during the bending process.
- It is typically made of heavy-duty steel to handle the high forces generated during bending.
- Drive Mechanism:
- Profile bending machines can be powered by various drive mechanisms, including hydraulic, mechanical, or electric systems.
- Hydraulic systems offer precise control and are often preferred for heavy-duty and high-precision bending tasks.
- Control Panel:
- Modern profile bending machines feature control panels that allow operators to set and adjust bending parameters. These panels provide control over bending radius, speed, and angle.
- Some machines may have CNC (Computer Numerical Control) systems for automated and precise bending operations.
- Support Rollers:
- Support rollers are positioned on both sides of the bending rolls to guide and support the profile as it passes through the machine.
- They help ensure uniform bending and prevent material distortion or misalignment during the process.
- Tooling and Dies:
- Tooling and dies are used to shape and bend the profile accurately according to the desired specifications.
- Different sets of tooling and dies are available to accommodate various profile shapes and sizes.
- Safety Features:
- Safety is paramount when operating profile bending machines. These machines are equipped with safety features such as emergency stop buttons, guards, and interlocks to protect operators from accidents and injuries.
Features:
- Material Compatibility:
- Profile bending machines can handle a wide range of materials, including steel, aluminum, stainless steel, and various alloys. The machine’s design and capabilities determine the materials it can work with.
- Applications:
- Profile bending machines find applications in metal fabrication, construction, shipbuilding, aerospace, and architectural metalwork, among others.
- They are used to create curved and bent profiles for building structures, bridges, handrails, and other architectural and industrial elements.
- Flexibility:
- Profile bending machines offer a high degree of flexibility and versatility. They can produce a wide range of shapes, including circles, spirals, and complex curves.
- Operators can adjust the machine to accommodate different sizes and types of profiles, making them suitable for a variety of projects.
- Precision:
- These machines are known for their precision and ability to consistently produce accurate and uniform bends, critical in industries where tight tolerances are required.
- Ease of Use:
- Modern profile bending machines often feature user-friendly interfaces and controls, making them accessible to operators with varying levels of experience.
- Automation:
- Some advanced profile bending machines are equipped with CNC systems, allowing for automated and programmable bending operations. This enhances efficiency and repeatability.
Profile bending machines are invaluable tools in industries that demand the creation of curved and customized components. They provide the capability to bend profiles with precision and consistency, meeting diverse project requirements.
EMS Metalworking Machinery: Your Trusted Partner in Precision Metalworking
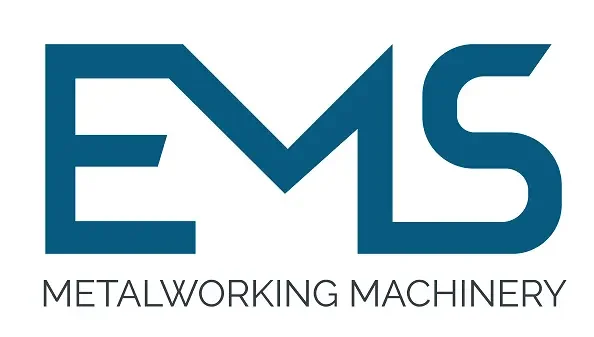
EMS Metalworking Machinery is a leading manufacturer of high-quality metalworking equipment, dedicated to providing innovative solutions that meet the evolving needs of industries worldwide. With a rich history of excellence and a commitment to technological advancement, we have earned a reputation for delivering cutting-edge machinery that ensures precision, efficiency, and durability.
Our Product Range:
- CNC Spinning Lathes: From precision bench lathes to heavy-duty industrial models, our lathes offer unmatched accuracy and performance for a wide range of applications, including machining shafts, gears, and other cylindrical components.
- Trimming Beading Machine: Our trimming beading machines are designed to provide exceptional cutting capabilities and versatility, enabling you to create complex shapes and intricate details with ease. Whether you need a horizontal or vertical trimming machine, we have the perfect solution for your needs.
- Hydraulic Deep Drawing Press Machines: Our hydraulic deep drawing press machines are built to deliver precise and powerful drawing operations, ensuring clean holes and exceptional surface finishes. We offer a comprehensive range to suit various applications.
- Grinding Machines: Our grinding machines are engineered for precision and efficiency, allowing you to achieve the highest levels of surface finish and dimensional accuracy. Whether you need a surface grinder, cylindrical grinder, or tool grinder, we have the equipment to meet your specific requirements.
- Sawing Machines: Our sawing machines are designed for fast and accurate cutting of metals, providing clean cuts and minimal burrs. From band saws to circular saws, we offer a variety of options to suit different materials and cutting needs.
- Custom Machinery: In addition to our standard product line, we also specialize in custom machinery fabrication. Our experienced engineers can work with you to design and build tailored solutions that meet your unique requirements and optimize your production processes.
Why Choose EMS Metalworking Machinery:
- Quality: Our machines are crafted with the highest quality materials and components, ensuring long-lasting performance and reliability.
- Precision: We are committed to delivering machinery that meets the most stringent tolerances and standards, ensuring exceptional accuracy in your metalworking operations.
- Innovation: We continuously invest in research and development to stay at the forefront of technological advancements, offering innovative solutions that enhance your productivity and efficiency.
- Customer Support: Our dedicated team of experts is always available to provide comprehensive support, from machine selection and installation to maintenance and troubleshooting.
- Customization: We understand that every business has unique needs, and we offer flexible customization options to tailor our machines to your specific requirements.
At EMS Metalworking Machinery, we are more than just a supplier of equipment; we are your trusted partner in metalworking success. By choosing EMS, you can be confident in the quality, reliability, and performance of your machinery, enabling you to achieve your business goals and stay ahead of the competition.