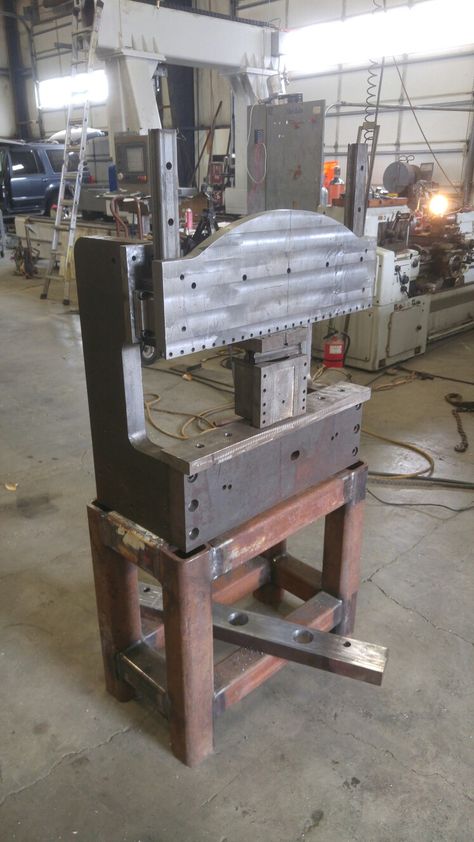
Mini Hydraulic Press Brake: A press brake bending machine is a versatile piece of equipment used in the metalworking industry for bending and shaping sheet metal and plate materials. This machine operates by clamping the metal workpiece between a matching punch and die, applying significant force to create precise bends at specified angles. The press brake machine’s core functionality relies on the application of a predetermined force, which deforms the metal along a straight axis to achieve the desired geometric shape. Its versatility and precision make it indispensable in the production of various components, ranging from simple brackets to complex automotive and aerospace parts.
Press brakes come in various configurations, with hydraulic, mechanical, pneumatic, and servo-electric types being the most common. Hydraulic press brakes dominate the industry due to their reliability, precision, and ability to handle larger workloads. These machines use hydraulic cylinders to deliver consistent force, ensuring uniform bends across the workpiece. Mechanical press brakes, though less common today, employ a flywheel mechanism and are known for their simplicity and speed, albeit with less flexibility in controlling force. Pneumatic and servo-electric machines cater to specific applications, often favoring smaller, lighter tasks or environments where energy efficiency and reduced noise are priorities.
Modern press brakes are equipped with advanced CNC (Computer Numerical Control) systems, which enable precise programming of bending sequences, angles, and dimensions. This technology reduces the need for manual adjustments, minimizes errors, and enhances production efficiency. CNC systems also allow operators to store and retrieve complex bending programs, facilitating the production of intricate designs with repeatable accuracy. In addition, press brakes can be fitted with various tooling options, such as V-dies, U-dies, and gooseneck punches, to accommodate a wide range of bending operations and material types. The selection of the appropriate tooling is crucial, as it directly impacts the quality and consistency of the bend.
The bending process on a press brake typically involves several stages. First, the workpiece is aligned and positioned on the machine bed, often using back gauges or other alignment aids to ensure accuracy. Next, the operator or CNC system initiates the bending cycle, during which the punch descends into the die to apply the necessary force. The force must be carefully calibrated to avoid material deformation beyond the desired bend radius or angle. Factors such as material thickness, type, and grain direction play a significant role in determining the required tonnage and die selection. Overbending is often employed to compensate for material springback, a phenomenon where the metal partially returns to its original shape after the force is removed.
Safety is a critical consideration in press brake operations. Operators must adhere to strict guidelines to prevent accidents and ensure the safe handling of materials. Modern press brakes incorporate safety features such as light curtains, safety sensors, and emergency stop mechanisms to protect operators during operation. Proper training and adherence to safety protocols are essential, as improper use of the machine can result in damage to both the equipment and the workpiece, as well as pose significant risks to personnel.
Energy efficiency and sustainability are growing concerns in the manufacturing industry, and press brakes are no exception. Manufacturers are increasingly focusing on developing energy-efficient machines that reduce power consumption without compromising performance. Servo-electric press brakes, for example, use electric motors rather than hydraulic systems, resulting in quieter operation, lower maintenance requirements, and reduced environmental impact. This shift aligns with industry trends toward greener production practices and the adoption of more sustainable technologies.
In conclusion, the press brake bending machine is a cornerstone of modern manufacturing, enabling the creation of precise, durable components essential to various industries. Its evolution from simple mechanical designs to sophisticated CNC-controlled systems underscores its adaptability and enduring relevance in an ever-changing industrial landscape. As technology continues to advance, press brakes are likely to become even more efficient, versatile, and integral to the fabrication of high-quality metal products.
Press Brake Bending Machine for Sale
The continued evolution of press brake bending machines is driven by the demands of modern manufacturing industries, where precision, speed, and adaptability are critical. Advancements in automation and digital technology have further enhanced the capabilities of press brakes, making them indispensable in the production of high-volume, complex parts. Integration with robotic systems is an increasingly common trend, enabling automated loading, positioning, and unloading of workpieces. This not only increases production efficiency but also reduces the potential for human error and the risks associated with manual handling.
Robotic press brake systems are often equipped with vision systems that allow them to adjust to variances in the material or alignment, ensuring consistent results even in high-speed operations. These systems are particularly valuable in industries such as automotive, aerospace, and electronics, where tight tolerances and repeatability are critical. Additionally, the integration of IoT (Internet of Things) technologies in press brake machines has revolutionized their operational monitoring and maintenance. IoT-enabled machines can provide real-time data on performance metrics, wear and tear of components, and energy consumption, allowing manufacturers to implement predictive maintenance strategies and minimize downtime.
The materials used in press brake operations are as varied as the industries they serve. From aluminum and stainless steel to advanced high-strength steels and titanium, the choice of material often dictates the machine settings and tooling requirements. For example, bending advanced high-strength steels requires significantly higher tonnage and precise control due to their increased resistance to deformation. Similarly, soft metals like aluminum may demand specialized tooling to prevent surface damage and maintain the aesthetic quality of the finished product. Innovations in tooling materials and designs have also enhanced the efficiency and lifespan of press brake tools, enabling manufacturers to handle a broader range of materials with less frequent tool changes.
Environmental considerations are becoming increasingly important in the operation and design of press brake machines. Hydraulic systems, while powerful and reliable, have historically been associated with high energy consumption and the risk of oil leaks. This has led to the development of hybrid press brakes, which combine hydraulic and servo-electric systems to optimize energy usage and reduce environmental impact. These machines use hydraulic power only when high force is needed, relying on electric motors for less demanding operations. This hybrid approach not only improves energy efficiency but also reduces noise levels and maintenance costs, making it a popular choice in modern manufacturing facilities.
Another area of innovation is in the development of adaptive bending technologies. These systems use sensors and advanced algorithms to monitor the bending process in real time, automatically adjusting parameters to compensate for variations in material properties or positioning. This ensures consistent quality across batches, even when working with materials that exhibit slight inconsistencies. Adaptive technologies are particularly valuable in industries where precision is paramount, such as aerospace and medical device manufacturing.
Training and workforce development are critical aspects of effective press brake operation. As machines become more sophisticated, operators must acquire new skills to fully leverage their capabilities. Many manufacturers now offer training programs and certification courses to ensure operators are proficient in using advanced features like CNC programming, adaptive bending systems, and robotic integration. Additionally, the use of simulation software has become an essential tool for training and process optimization. These programs allow operators to simulate bending operations, experiment with different configurations, and identify potential issues before working with actual materials, saving time and reducing waste.
Looking to the future, the role of press brakes in manufacturing is expected to grow even further, driven by advancements in artificial intelligence and machine learning. AI algorithms could enable press brake machines to analyze vast amounts of production data, identify patterns, and optimize settings for maximum efficiency and quality. This level of automation and intelligence would allow manufacturers to respond more quickly to changing market demands, produce highly customized parts, and reduce overall production costs. Moreover, the integration of additive manufacturing technologies with traditional bending processes may open new possibilities for creating hybrid components that combine the strengths of both techniques.
In summary, the press brake bending machine is a cornerstone of modern manufacturing, continuously evolving to meet the challenges of an increasingly dynamic and competitive industry. With ongoing advancements in technology, automation, and sustainability, press brakes are poised to remain a vital tool in the production of high-quality metal components, driving innovation and efficiency across a wide range of applications.
The future of press brake bending machines also includes an increasing focus on customization and adaptability. As industries such as aerospace, automotive, and construction require more tailored solutions, press brake manufacturers are developing machines with modular designs. These modular systems allow for the easy swapping of components, such as tooling, hydraulic cylinders, or CNC units, to meet specific production needs without requiring a complete overhaul of the machine. This flexibility enables manufacturers to respond more quickly to changes in demand, such as shifts in material types, thicknesses, or part designs.
Material science is also playing a significant role in shaping the future of press brake technology. The growing use of advanced composites, lightweight alloys, and ultra-high-strength materials presents both opportunities and challenges for press brake operations. These materials often have unique bending characteristics, such as higher springback, brittleness, or sensitivity to surface damage. To address these challenges, tooling manufacturers are innovating with coatings, heat treatments, and alloy compositions that enhance durability and reduce friction during bending. Additionally, advances in finite element analysis (FEA) software are helping engineers predict how these new materials will behave under stress, allowing for better machine and tooling design.
Sustainability remains a key driver of innovation in press brake systems. As industries strive to reduce their environmental footprint, the energy efficiency of manufacturing equipment becomes a priority. Beyond hybrid and servo-electric press brakes, future designs may incorporate energy recovery systems, where the energy generated during the upward motion of the ram is captured and reused. This concept, similar to regenerative braking in electric vehicles, could significantly reduce energy consumption in high-volume operations. Manufacturers are also exploring the use of biodegradable hydraulic fluids and recyclable materials for machine components to further enhance sustainability.
The role of software in press brake operation is becoming increasingly sophisticated. Software platforms now offer integrated solutions that connect press brakes with other manufacturing equipment, creating a seamless production environment. This integration allows for the automatic sharing of design files, production schedules, and real-time performance data, enabling more efficient workflow management. Advanced analytics tools can process this data to identify bottlenecks, optimize machine usage, and predict maintenance needs. Some software even includes augmented reality (AR) features, enabling operators to visualize bending sequences and troubleshoot issues with the aid of AR headsets or tablet devices.
Quality control is another area where press brake technology is advancing. High-precision laser and optical measuring systems are being integrated into machines to provide real-time feedback on the bend angle, length, and alignment of workpieces. These systems ensure that each part meets exact specifications, reducing waste and rework. In high-stakes industries like aerospace, these systems are indispensable for maintaining compliance with strict quality standards. Additionally, the data collected from these measuring systems can be stored and analyzed to improve future production runs, contributing to a culture of continuous improvement.
The demand for greater automation in press brake operations has also spurred the development of cobots, or collaborative robots. Unlike traditional industrial robots, cobots are designed to work safely alongside human operators. In press brake environments, cobots can assist with tasks such as positioning heavy workpieces, adjusting tooling, or inspecting finished parts. This collaboration not only boosts productivity but also alleviates physical strain on operators, improving workplace ergonomics and safety.
Education and skill development will remain critical as press brake technology continues to evolve. To keep pace with rapid advancements, manufacturers and training institutions are adopting innovative approaches to education. Virtual reality (VR) training modules, for example, allow operators to practice complex bending tasks in a simulated environment, reducing the learning curve and minimizing the risk of costly errors. These training programs often include interactive tutorials on CNC programming, material handling, and machine maintenance, equipping operators with the skills they need to maximize the capabilities of modern press brakes.
In the broader context of Industry 4.0, press brake machines are becoming smarter and more connected. They are no longer standalone units but integral components of intelligent production lines. Machines equipped with artificial intelligence (AI) can analyze historical production data to optimize future operations, adjust settings autonomously based on material variations, and even predict the lifespan of critical components. This self-learning capability reduces the dependency on operator expertise and ensures consistent performance over time.
As the industrial landscape continues to evolve, press brake machines will play a pivotal role in addressing new challenges and opportunities. Their combination of mechanical precision, digital intelligence, and adaptability ensures they remain at the forefront of metal fabrication. Whether it’s producing lightweight components for electric vehicles, crafting intricate designs for architectural projects, or meeting the rigorous standards of aerospace applications, press brake machines are poised to shape the future of manufacturing with unparalleled precision and efficiency.
Hydraulic Sheet Metal Press Brake
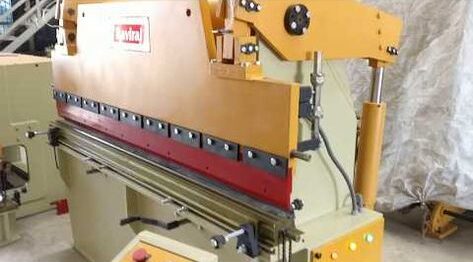
A hydraulic sheet metal press brake is a specialized machine designed to bend and shape sheet metal with high precision and significant force. It operates using hydraulic systems to apply consistent and controllable pressure, making it one of the most reliable and versatile tools in metal fabrication. Hydraulic press brakes are widely used across industries such as automotive, aerospace, construction, and appliance manufacturing, where precision, repeatability, and the ability to handle thick and heavy materials are essential.
The hydraulic system is the defining feature of these press brakes, using pressurized hydraulic fluid to power pistons or cylinders that drive the machine’s ram. The ram moves the punch downward into the die, bending the sheet metal to the desired angle. The pressure applied can be finely adjusted to match the material’s thickness, type, and bending requirements, making hydraulic press brakes suitable for a wide range of tasks, from delicate bends in thin materials to robust folds in thick steel or aluminum sheets.
One of the key advantages of hydraulic press brakes is their ability to deliver consistent force throughout the entire bending process. Unlike mechanical press brakes, which rely on fixed flywheel energy, hydraulic systems can modulate force dynamically, allowing for greater control over the bending operation. This is particularly important for achieving complex bends, tight tolerances, and minimizing springback—the tendency of metal to partially return to its original shape after bending.
Hydraulic press brakes are available in several configurations, including standard, tandem, and synchronized models. Standard hydraulic press brakes are suitable for most applications and come in various sizes and tonnage capacities. Tandem configurations involve two or more press brakes working in unison, enabling the bending of extremely long workpieces such as structural beams or large panels. Synchronized hydraulic press brakes, controlled by advanced CNC systems, offer unparalleled precision by ensuring that the movement of the ram is perfectly aligned across its entire length, even under high loads.
Modern hydraulic press brakes often incorporate CNC (Computer Numerical Control) technology, which automates many aspects of the bending process. CNC systems allow operators to program complex bending sequences, store multiple configurations, and execute operations with minimal manual intervention. These systems are especially useful for high-volume production and jobs that require intricate designs. Operators can input material properties, bend angles, and desired radii into the CNC interface, and the machine calculates the optimal settings, including the necessary tonnage and die positioning.
Tooling is another critical aspect of hydraulic press brake operation. The choice of punch and die directly affects the quality of the bend, with factors such as material type, thickness, and desired angle dictating the appropriate tooling. Hydraulic press brakes support a wide range of tooling options, including multi-V dies, gooseneck punches, and radius dies, making them adaptable to diverse applications. Quick-change tooling systems are also common, allowing operators to switch between setups rapidly and efficiently, reducing downtime and enhancing productivity.
Safety is a top priority in hydraulic press brake operation, as the forces involved can be immense. Modern machines are equipped with advanced safety features such as light curtains, laser sensors, and emergency stop buttons to protect operators from accidents. Light curtains and laser sensors monitor the machine’s operational area and halt the ram’s movement if an obstruction, such as a hand or tool, is detected. Additionally, ergonomic designs and automated systems reduce the need for manual handling, further enhancing operator safety.
The efficiency and environmental impact of hydraulic press brakes have also been areas of focus in recent years. Manufacturers are developing more energy-efficient models that reduce power consumption without compromising performance. Innovations such as variable-speed hydraulic pumps, which adjust motor speed based on the machine’s workload, have significantly improved energy efficiency. Additionally, advancements in hydraulic fluid technology, including biodegradable and longer-lasting fluids, contribute to reducing the environmental footprint of these machines.
Maintenance is an essential consideration for hydraulic press brakes to ensure optimal performance and longevity. Regular inspections of hydraulic fluid levels, seals, and hoses are necessary to prevent leaks and maintain consistent pressure. Filters should be checked and replaced as needed to keep the hydraulic system free of contaminants. With proper maintenance, hydraulic press brakes can deliver decades of reliable service, making them a cost-effective investment for manufacturers.
In conclusion, hydraulic sheet metal press brakes are indispensable tools in modern manufacturing, combining robust force, precise control, and adaptability to handle a wide range of applications. Their ability to produce high-quality bends with repeatable accuracy makes them a cornerstone of metal fabrication, suitable for everything from simple brackets to complex aerospace components. With ongoing advancements in hydraulic technology, CNC integration, and energy efficiency, hydraulic press brakes continue to evolve, solidifying their role as essential assets in the metalworking industry.
The versatility and adaptability of hydraulic sheet metal press brakes make them an indispensable tool for both small-scale fabricators and large industrial manufacturers. As industries push the boundaries of what can be achieved with metal fabrication, hydraulic press brakes continue to evolve to meet increasingly complex demands. The ability to handle a wide range of materials and thicknesses, from delicate thin sheets to heavy-duty structural components, underscores their value in diverse applications.
One of the standout features of modern hydraulic press brakes is their exceptional precision, enabled by advancements in control systems. CNC-controlled hydraulic press brakes allow operators to achieve repeatable accuracy with minimal manual intervention, even on highly intricate bends. These systems use advanced algorithms and real-time feedback from sensors to adjust force, positioning, and speed throughout the bending process. The result is consistent quality, even when working with challenging materials such as high-strength steel or exotic alloys.
Hydraulic press brakes are also renowned for their ability to perform multi-step bending processes in a single setup. With CNC systems, operators can program multiple bends in sequence, allowing the machine to execute complex part geometries without repositioning the workpiece. This capability significantly reduces production time and minimizes the risk of errors associated with manual handling. The ability to store and recall bending programs further streamlines operations, especially for repeat production runs.
As industries demand greater efficiency, hydraulic press brakes are increasingly integrated into automated production lines. Robotic arms and material handling systems can be synchronized with the press brake to automate tasks such as loading, bending, and unloading. This level of automation is especially valuable in high-volume manufacturing environments, where consistency and speed are critical. For example, in the automotive industry, hydraulic press brakes are used to produce components such as chassis parts, brackets, and structural reinforcements with exacting precision.
Another important aspect of hydraulic press brake technology is its capacity for custom tooling and specialized applications. Manufacturers often require bespoke solutions to address unique production challenges, such as creating deep channels, tight radii, or non-standard angles. Hydraulic press brakes can accommodate a wide variety of custom tooling designs, enabling fabricators to meet specific requirements without compromising quality. Tooling innovations, such as segmented punches and dies, also allow for greater flexibility in creating complex shapes or working with challenging materials.
In addition to custom tooling, the development of adaptive bending technologies has revolutionized how hydraulic press brakes handle variations in material properties. Adaptive systems use sensors to measure real-time data, such as material thickness, springback, and alignment. The machine then adjusts parameters dynamically to ensure that each bend meets the specified dimensions and angles. This is particularly beneficial when working with materials that exhibit unpredictable behavior, such as composites or ultra-high-strength steels.
Hydraulic press brakes are also being tailored for applications that demand extreme precision and durability. For instance, in the aerospace industry, components must meet stringent standards for accuracy, strength, and surface finish. Hydraulic press brakes equipped with advanced controls, precision tooling, and real-time monitoring systems are uniquely suited to these demanding applications. Similarly, in the medical device sector, where small, intricate parts are often required, the fine control offered by hydraulic systems ensures consistent results without damaging delicate materials.
Energy efficiency and sustainability remain critical considerations for manufacturers investing in hydraulic press brakes. Traditional hydraulic systems, while powerful, can be energy-intensive and require regular maintenance to address issues such as fluid leaks and component wear. To address these concerns, manufacturers are developing hybrid press brakes that combine hydraulic power with servo-electric technology. These hybrid systems reduce energy consumption by activating hydraulic components only when necessary, while servo motors handle less demanding tasks. This approach not only improves efficiency but also reduces operating noise and maintenance costs.
The future of hydraulic press brakes is closely tied to the continued integration of Industry 4.0 principles, such as connectivity, data analytics, and machine learning. Smart hydraulic press brakes are equipped with IoT sensors that collect performance data, enabling predictive maintenance, real-time monitoring, and process optimization. By analyzing this data, manufacturers can identify trends, improve machine utilization, and reduce downtime. For example, sensors can detect early signs of wear in hydraulic components, prompting timely maintenance to prevent costly breakdowns.
Machine learning and artificial intelligence are also poised to play a transformative role in hydraulic press brake operations. AI-driven systems could analyze vast amounts of historical production data to optimize bending sequences, adjust parameters for new materials, or even suggest tooling configurations for specific applications. This level of intelligence would further enhance the efficiency, precision, and adaptability of hydraulic press brakes, making them even more valuable in competitive manufacturing environments.
In conclusion, hydraulic sheet metal press brakes represent the pinnacle of metal bending technology, combining raw power with advanced control and adaptability. Their ability to handle diverse materials, perform complex bending operations, and integrate with modern production systems ensures their continued relevance in an ever-evolving industrial landscape. As technology advances, these machines will become even more efficient, sustainable, and intelligent, cementing their role as essential tools for shaping the future of metal fabrication.
Miniature Press Brake
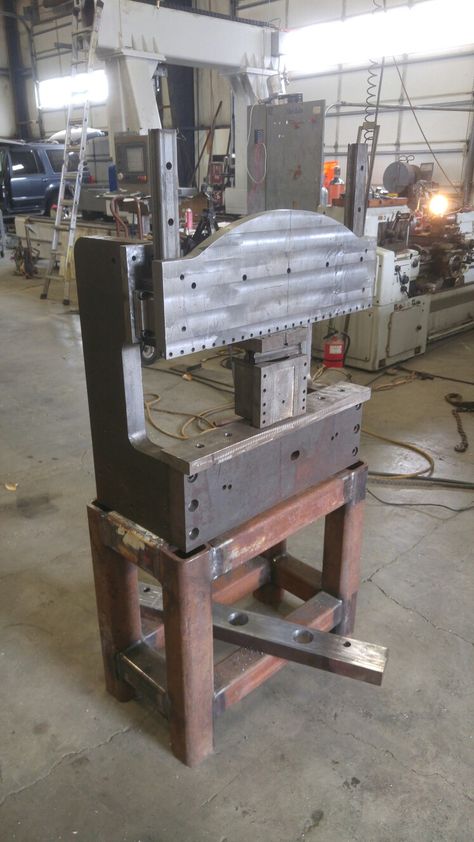
A miniature press brake is a scaled-down version of the standard press brake, designed for bending and shaping smaller metal parts with precision and control. These compact machines are widely used in industries where intricate and delicate components are required, such as electronics, jewelry, medical devices, and small-scale manufacturing. Despite their smaller size, miniature press brakes are capable of delivering remarkable precision and efficiency, making them indispensable tools for specialized applications.
The core functionality of a miniature press brake mirrors that of its larger counterparts, using a punch and die mechanism to bend sheet metal to the desired angle. However, their design is tailored for working with smaller workpieces, thinner materials, and tighter tolerances. Miniature press brakes are particularly suited for precision tasks where even the slightest deviation can compromise the quality or functionality of the finished product.
Miniature press brakes come in various configurations, including manual, hydraulic, and servo-electric models. Manual miniature press brakes are the simplest and most affordable option, relying on the operator’s physical effort to generate bending force. These machines are often used in workshops or low-volume production settings where speed and automation are less critical. Hydraulic miniature press brakes, on the other hand, use a hydraulic system to apply force, providing greater power and consistency. Servo-electric models are among the most advanced, offering precise control, energy efficiency, and the ability to automate complex bending sequences.
One of the key advantages of miniature press brakes is their ability to perform detailed and intricate bending operations. The smaller scale of these machines allows them to achieve tight bend radii, sharp angles, and complex shapes with exceptional accuracy. This makes them ideal for applications such as creating small brackets, enclosures, clips, and other components that require high levels of precision. Many miniature press brakes are equipped with fine-tuned controls that allow operators to adjust parameters such as force, speed, and positioning with extreme precision, ensuring consistent results across production runs.
Tooling plays a crucial role in the performance of miniature press brakes. The punches and dies used in these machines are specifically designed for small-scale operations, often featuring narrow widths and fine geometries to accommodate delicate materials and detailed work. Quick-change tooling systems are also common in miniature press brakes, enabling operators to switch between setups quickly and efficiently. This is particularly useful in applications where multiple bending operations are required on a single workpiece or when frequent changes in production specifications are necessary.
Modern miniature press brakes often incorporate CNC (Computer Numerical Control) technology, which enhances their precision and versatility. CNC-controlled miniature press brakes allow operators to program complex bending sequences, store multiple configurations, and execute operations with minimal manual intervention. This level of automation is particularly valuable in industries such as electronics manufacturing, where high volumes of small, intricate components are produced. CNC systems also reduce the risk of errors and waste, improving overall efficiency and cost-effectiveness.
Safety is another critical consideration in the operation of miniature press brakes. While their smaller size reduces some of the risks associated with larger machines, safety features such as guards, sensors, and emergency stop mechanisms are still essential. Modern miniature press brakes often include advanced safety systems that monitor the machine’s operational area and halt operation if any obstruction is detected. These features ensure that operators can work safely and confidently, even when handling delicate or intricate components.
Energy efficiency is a significant advantage of miniature press brakes, particularly servo-electric models. These machines consume less energy than their hydraulic counterparts, making them an environmentally friendly choice for small-scale manufacturing. Additionally, their compact size and lower power requirements make them ideal for use in smaller workshops or laboratories where space and resources are limited.
The maintenance requirements for miniature press brakes are typically less demanding than those of larger machines. Regular inspections of moving parts, lubrication, and alignment checks are necessary to ensure optimal performance and longevity. The smaller hydraulic systems, if present, require periodic monitoring of fluid levels and seals, but these tasks are generally straightforward and manageable.
Applications for miniature press brakes are as diverse as the industries they serve. In the electronics sector, they are used to fabricate small metal enclosures, connectors, and heat sinks. In jewelry making, they enable the precise bending and shaping of metal for custom designs. Medical device manufacturers rely on miniature press brakes to create components such as surgical instruments, implants, and housings for diagnostic equipment. Additionally, hobbyists and small-scale artisans often use miniature press brakes for crafting decorative items, model components, and prototypes.
The growing demand for customization and precision in modern manufacturing is driving innovation in miniature press brake technology. Features such as adaptive bending, IoT connectivity, and machine learning are beginning to make their way into these compact machines. Adaptive systems use sensors and real-time data to adjust parameters dynamically, compensating for variations in material properties or alignment. IoT-enabled miniature press brakes provide real-time performance monitoring, predictive maintenance alerts, and seamless integration with other manufacturing equipment.
Looking ahead, the role of miniature press brakes in manufacturing is expected to expand further as industries continue to prioritize miniaturization, precision, and efficiency. Advances in materials science, such as the development of thinner, stronger, and more versatile alloys, will open new possibilities for what these machines can achieve. The integration of additive manufacturing with miniature press brake operations may also enable the creation of hybrid components that combine the strengths of both techniques.
In conclusion, miniature press brakes are a vital tool for industries that require precision and adaptability on a smaller scale. Their compact size, advanced capabilities, and ability to handle intricate tasks make them essential for modern manufacturing. As technology evolves, these machines will continue to play a pivotal role in shaping the future of small-scale and high-precision metal fabrication, enabling manufacturers to meet the growing demand for intricate, high-quality components.
As the demand for highly specialized and miniaturized components continues to rise, miniature press brakes are poised to become even more integral in a variety of industries. Technological advancements are pushing these machines to offer greater flexibility, improved performance, and enhanced user experience, while still retaining their compact form factor.
One of the major areas of evolution in miniature press brakes is their increased integration with automation and robotics. As manufacturers strive for higher productivity and reduced labor costs, even small-scale operations are looking to incorporate automated solutions. Miniature press brakes equipped with robotic arms or automated feeding systems can load, bend, and unload materials autonomously. This integration helps improve the overall efficiency of the manufacturing process, reduces human error, and ensures consistent part quality. In some cases, automated systems can even handle parts from the initial setup through to the final inspection stage, providing a fully streamlined production line.
The development of adaptive control systems is another significant trend in miniature press brake technology. Adaptive systems use sensors to monitor the bending process in real time, providing feedback on factors such as material thickness, bend angle, and springback. The system can then adjust the bending force or other parameters dynamically, ensuring that the final result meets the desired specifications. This ability to compensate for variations in material properties or alignment without manual intervention enhances the precision and repeatability of each bend, even when working with less predictable materials or part geometries.
Machine learning and artificial intelligence (AI) are also being explored to enhance the performance of miniature press brakes. AI algorithms can analyze production data and suggest optimal bending parameters or tooling configurations based on past experiences. Over time, these systems can learn from previous setups and continuously improve the bending process, offering more accurate results and faster setup times. AI-driven systems may even be able to predict maintenance needs by analyzing machine performance data, allowing operators to schedule maintenance proactively, reducing downtime, and extending the lifespan of the press brake.
In addition to performance improvements, manufacturers are focusing on making miniature press brakes more user-friendly and intuitive. Advances in user interface (UI) design, touchscreen controls, and intuitive software platforms are simplifying machine operation. Operators can now program complex bending sequences and access machine diagnostics with ease. This makes it easier for even those with minimal experience to operate the press brake efficiently and safely. In some models, augmented reality (AR) interfaces are used to guide operators through setup procedures and visualize the bending process, enhancing both the ease of use and the accuracy of the operation.
Another important consideration for the future of miniature press brakes is their environmental impact. As part of the broader trend toward sustainability, manufacturers are designing machines with energy-efficient components, recyclable materials, and reduced fluid consumption. Hybrid systems that combine hydraulic and servo-electric technologies are becoming more common, offering energy savings and a lower environmental footprint while still providing the high force needed for bending. These eco-friendly systems reduce both energy consumption and the need for regular maintenance, making them attractive choices for companies looking to minimize their carbon footprint.
The growing interest in precision engineering and customization in fields like aerospace, medical device manufacturing, and electronics is also driving the development of miniature press brakes. These industries often require small, highly detailed components made from specialized materials. The ability of miniature press brakes to handle high-precision bending and complex geometries, combined with their ability to process a range of thin and exotic materials, positions them as essential tools for these demanding applications. Additionally, the trend toward miniaturization in consumer electronics and the increasing use of advanced materials, such as composites and specialized alloys, further highlights the value of miniature press brakes in meeting the evolving needs of these industries.
The use of specialized tooling for miniature press brakes also continues to improve, allowing manufacturers to produce increasingly complex parts with minimal setup time. Tooling innovations such as modular dies, quick-change systems, and customized punches allow for rapid adjustments, enabling operators to quickly transition between different production runs. In the context of prototyping, the ability to quickly adjust tooling and bending parameters makes miniature press brakes invaluable for testing new designs and materials. Manufacturers can iterate on designs faster and more efficiently, reducing lead times and speeding up time-to-market.
As global manufacturing trends continue to shift towards more localized production, miniature press brakes are well-suited for smaller production facilities or workshops that require flexible, high-quality manufacturing capabilities without the large footprint of traditional equipment. Their compact size allows them to be easily integrated into smaller spaces, such as labs, R&D facilities, or pilot production lines. Additionally, these machines are more cost-effective than larger industrial press brakes, making them an attractive option for small businesses, startups, or companies looking to explore new production techniques or niche markets.
In conclusion, miniature press brakes represent the future of precision metal forming for small-scale, intricate parts. With advancements in automation, control systems, tooling, and energy efficiency, these machines continue to evolve to meet the increasing demands of industries requiring high-quality, small-scale components. Their ability to perform precise, complex bending operations on thin, delicate materials while maintaining compactness and affordability makes them indispensable tools in sectors such as electronics, medical devices, jewelry, and more. As technology continues to progress, miniature press brakes will remain at the forefront of innovation, helping manufacturers stay competitive and meet the growing need for miniaturized and customized components in an increasingly complex world.
Compact Press Brake
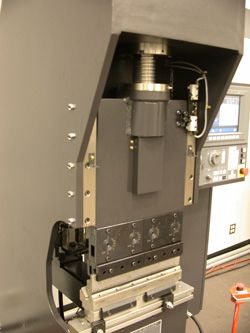
A compact press brake is a smaller and more space-efficient version of the standard industrial press brake, designed to deliver high-precision metal bending and shaping capabilities while occupying less floor space. These machines are ideal for applications in industries where space is at a premium but the need for accuracy and reliability remains high. Compact press brakes are typically used in small to medium-sized workshops, educational institutions, prototyping labs, and in industries such as automotive, electronics, appliance manufacturing, and sheet metal fabrication, where versatility, speed, and compactness are key.
The functionality of a compact press brake is similar to that of larger machines, but its design is optimized for smaller-scale operations. It uses a punch and die setup, with the machine applying force through either a hydraulic, mechanical, or servo-electric drive system to bend sheet metal into the desired shapes. The compact size of the press brake makes it particularly advantageous in environments where space is limited, such as crowded workshops or factory floors that house multiple machines.
One of the primary benefits of a compact press brake is its ability to handle precise, repeatable bends on small to medium-sized workpieces, often with intricate details. These machines are often used for bending thin sheet metal or components that require tight tolerances. Whether the material is aluminum, steel, or stainless steel, compact press brakes can be configured to process a variety of metals with consistent results. The smaller footprint does not compromise the bending force, making compact press brakes effective at delivering the required tonnage for typical applications in smaller setups.
Compact press brakes come in a variety of configurations. The most common are hydraulic, mechanical, and servo-electric models. Hydraulic compact press brakes utilize pressurized fluid to generate force, offering excellent precision and the ability to handle a variety of materials and thicknesses. These machines are popular for their versatility and ease of control, making them suitable for different types of metalworking tasks. Mechanical compact press brakes use a flywheel system, offering a more traditional and cost-effective solution. However, they may not offer the same level of force modulation or energy efficiency as hydraulic systems. Servo-electric press brakes combine the precision of electric drives with the energy efficiency of electric motors, providing superior control, lower energy consumption, and minimal maintenance requirements, making them an ideal choice for precision-driven industries where energy efficiency is critical.
Another significant feature of compact press brakes is their ability to integrate with modern control systems. Many compact machines are equipped with CNC (Computer Numerical Control) systems, which enable operators to program complex bending sequences, store bending profiles, and automate processes. CNC-controlled compact press brakes provide the flexibility to handle intricate designs, manage multiple bend angles, and execute high-precision tasks with minimal operator intervention. This is particularly valuable for industries where part designs are constantly changing or where production runs need to be executed quickly and efficiently.
Tooling is a key factor in the performance of compact press brakes. These machines are designed to accommodate a wide range of tooling options, including segmented dies, quick-change tooling systems, and custom punches. The ability to quickly change dies is an important feature, particularly for workshops that need to switch between different types of workpieces or production runs frequently. The smaller size of compact press brakes typically means that the tooling is more compact as well, allowing for greater flexibility in terms of the types of parts that can be produced. Additionally, compact press brakes can support multi-function tooling, allowing multiple operations to be carried out on the same workpiece, which reduces setup time and increases productivity.
Safety is always a top priority in metalworking, and compact press brakes are no exception. Although their size reduces some of the risks associated with larger machines, modern compact press brakes are still equipped with safety features such as light curtains, safety guards, emergency stops, and advanced sensors. These features protect operators from potential hazards by monitoring the area around the machine and ensuring that the machine stops immediately if any obstruction or safety breach is detected. Some compact models also include features like anti-twist safety mechanisms to prevent the sheet metal from shifting during the bending process, further reducing the risk of accidents.
In terms of energy efficiency, compact press brakes have several advantages. Many of these machines use servo-electric technology, which reduces energy consumption compared to traditional hydraulic systems by using only the energy required for the specific operation. This makes compact press brakes a more sustainable option for manufacturers who are conscious of their energy usage and environmental impact. The reduced energy demand, coupled with the smaller overall size of the machine, contributes to lower operating costs, which can make a big difference for small businesses and workshops operating on a tight budget.
Maintenance of compact press brakes is relatively simple and less demanding than larger machines. Given their smaller size and less complex hydraulic systems, these machines require fewer maintenance interventions, which reduces downtime and operational costs. Operators still need to regularly check for issues such as wear on the tooling, alignment of the punch and die, and hydraulic fluid levels (in hydraulic models). However, the overall maintenance procedures are generally easier to manage and less time-consuming compared to their larger counterparts.
One of the most significant advantages of compact press brakes is their ability to cater to small-scale production runs and prototyping. In industries like automotive, aerospace, and electronics, the ability to produce small batches of high-precision components is a key requirement. Compact press brakes provide manufacturers with the flexibility to produce smaller quantities of parts while maintaining the accuracy and consistency needed for these industries. The machines are also ideal for prototyping, where a company might need to test new designs or components before scaling up production.
As manufacturers increasingly focus on customized products and rapid prototyping, compact press brakes are becoming more common in research and development (R&D) departments. Their ability to handle a wide range of materials and bend angles with high precision makes them an essential tool for companies that are exploring new technologies or testing innovative ideas. Compact press brakes are also useful for small manufacturers or businesses looking to develop specialized parts in-house without the need to invest in larger, more expensive equipment.
Looking ahead, the continued demand for efficient, space-saving, and cost-effective metalworking solutions will likely drive further developments in compact press brake technology. Innovations in automation, artificial intelligence, and smart manufacturing will likely integrate with compact press brakes, providing even greater precision, faster setup times, and improved overall performance. Additionally, the ongoing push toward sustainability will encourage the development of more energy-efficient machines, with lower environmental impact, and more recyclable materials used in the construction of compact press brakes.
In conclusion, compact press brakes are versatile, efficient, and space-saving solutions for a wide range of metal forming and bending applications. Whether used in prototyping, small-scale manufacturing, or for producing custom metal parts, these machines offer the precision and flexibility required in today’s fast-paced and demanding industries. Their smaller size and advanced control systems make them a perfect fit for businesses and workshops that need to balance quality, speed, and limited space, while their energy efficiency and low maintenance requirements help keep operational costs down. As technology evolves, compact press brakes will continue to play an essential role in driving the future of metalworking and fabrication.
As the demand for versatility, precision, and compactness continues to grow in various manufacturing sectors, compact press brakes are expected to undergo further advancements. Manufacturers are actively exploring ways to enhance their capabilities, expand their range of applications, and improve ease of use. As industries become increasingly focused on customization, efficiency, and sustainability, compact press brakes are positioned to play a pivotal role in meeting these needs.
Advancements in Automation and Integration
In the next generation of compact press brakes, automation will continue to be a significant factor. The integration of automated loading and unloading systems with these machines is becoming increasingly popular, especially for industries dealing with high-mix, low-volume production. By automating these processes, manufacturers can significantly reduce manual handling, increase throughput, and improve worker safety.
Robotic arms, conveyor systems, and automated material handling equipment can work in conjunction with compact press brakes to create a fully integrated production line. For example, a robotic arm could load the material onto the press brake, while a secondary robotic arm might unload the finished parts. This level of automation minimizes human intervention and allows for continuous, uninterrupted production, which is ideal for industries requiring high precision and consistent results.
Additionally, Industry 4.0 principles are beginning to make their mark on compact press brake technology. Through the use of IoT (Internet of Things) sensors, these machines can provide real-time data about their performance, which can then be monitored remotely. This data can be used to assess machine health, optimize production schedules, predict potential failures, and allow for proactive maintenance. Smart machines will provide more transparent insights into production, enabling operators to make informed decisions that improve efficiency and reduce downtime.
Improved User Interfaces and Smart Controls
The user interface (UI) and software systems used in compact press brakes are also evolving. Modern compact press brakes are now equipped with intuitive touchscreens and advanced software platforms that allow operators to input parameters with ease, access detailed diagnostic reports, and quickly adjust machine settings. User-friendly control systems are essential in lowering the learning curve for new operators and ensuring that production runs smoothly.
With the integration of advanced AI and machine learning, compact press brakes will have the ability to automatically adjust settings based on material data, bending requirements, and production history. This means the machine can “learn” the optimal bending process for specific materials, automatically selecting the best tooling and bending parameters for each job. Over time, the system will improve its own efficiency and accuracy, further minimizing the risk of errors and maximizing productivity.
Material Diversity and Customization
Compact press brakes are becoming increasingly capable of working with a broader range of materials. While traditionally used for sheet metal, newer versions of these machines can handle materials like composites, plastics, and advanced alloys. The ability to bend a diverse set of materials is especially valuable in industries like aerospace, automotive, and electronics, where high-performance materials are often required.
The ongoing development of flexible tooling solutions will allow manufacturers to bend even more complex materials with ease. Quick-change tooling systems, for instance, enable fast and precise switching between tooling sets, optimizing the machine for different materials or bending operations. Furthermore, the ability to create customized tools on-demand, either through 3D printing or other fabrication methods, will enable compact press brakes to handle increasingly specialized parts and applications without needing to invest in entirely new machines.
Energy Efficiency and Eco-Friendly Technologies
As sustainability becomes an ever-larger focus, compact press brakes are likely to feature even more energy-efficient technologies. Servo-electric models, which use electric motors to provide precise control over motion, already offer significant energy savings compared to traditional hydraulic systems. This trend toward energy-efficient technologies will continue, with future machines consuming less power while still delivering high performance.
Hybrid systems, which combine the benefits of hydraulic power with electric drive systems, are also expected to see more widespread adoption. These hybrid models are not only more energy-efficient but also help reduce maintenance costs by minimizing the wear and tear on hydraulic components. As environmental regulations become more stringent, these energy-saving solutions will become essential for manufacturers seeking to reduce their carbon footprint while maintaining high productivity.
Precision and Fine-Tuning Capabilities
The future of compact press brakes will be closely tied to further improvements in precision and fine-tuning capabilities. As industries continue to demand increasingly intricate and complex parts, the need for high-precision bending solutions will grow. New developments in machine controls and sensor technology will allow compact press brakes to provide even greater accuracy, even with smaller or thinner materials. Advanced sensors that measure material properties, such as thickness, hardness, and tensile strength, can enable real-time feedback to adjust bending parameters for optimal results.
For example, compact press brakes equipped with adaptive bending systems can compensate for material springback during the bending process, ensuring that parts meet the exact required angles and dimensions. The integration of laser scanning or vision systems can further enhance precision by verifying the final shape of the bent component before it is released from the machine.
Future Applications and Market Trends
In the coming years, compact press brakes will continue to see widespread use in industries that prioritize customization, small-scale production, and rapid prototyping. The ability to quickly and efficiently produce customized parts in low volumes is becoming increasingly important in sectors such as automotive (for custom parts and prototypes), electronics (for intricate casings and components), and medical device manufacturing (for specialized tools or enclosures).
Additionally, as smaller businesses and startups seek more cost-effective and flexible production solutions, the demand for compact press brakes will likely increase. Small manufacturers who previously might have been priced out of the market for traditional, larger press brakes can now access high-precision bending capabilities without the need for large capital investment. The rise of online and on-demand manufacturing platforms will further fuel this trend, as these businesses turn to compact press brakes for short runs and customized orders.
Conclusion
Compact press brakes represent an ideal solution for a wide range of applications that require precision, flexibility, and efficiency in a space-efficient package. With ongoing advancements in automation, control systems, material handling, and energy efficiency, these machines are evolving to meet the ever-changing demands of modern manufacturing. Their versatility in handling a diverse range of materials, their ability to accommodate precise bending operations, and their integration with cutting-edge technologies like AI and IoT will ensure that compact press brakes remain at the forefront of small-scale manufacturing for years to come.
As manufacturers continue to seek ways to improve production efficiency, reduce costs, and embrace sustainable practices, the role of compact press brakes in shaping the future of metalworking and fabrication will only grow. With their combination of compact size, advanced capabilities, and increasing adaptability, compact press brakes are poised to be an essential tool for industries ranging from automotive to aerospace, electronics to medical devices, and beyond.
Mini Hydraulic Press Brake
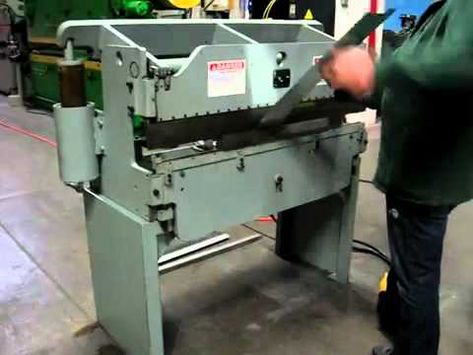
A mini hydraulic press brake is a smaller, more compact version of the traditional hydraulic press brake, designed to perform precise bending and forming operations on sheet metal, but with a focus on small-scale production and limited space. These machines are widely used in workshops, laboratories, and small-scale manufacturing operations where high-precision bending is required but the footprint and tonnage of larger machines are not needed. Despite their smaller size, mini hydraulic press brakes still deliver the power and flexibility needed to bend various materials with precision, making them a popular choice in industries like prototyping, electronics, medical device manufacturing, automotive, and even the jewelry industry.
Key Features and Design
The main feature that differentiates a mini hydraulic press brake from larger models is its size and tonnage. Typically, these machines are designed for bending smaller sheets of metal, often in the range of 0.5mm to 6mm thickness, and can handle materials such as aluminum, steel, and stainless steel. However, the compact design does not mean a sacrifice in performance—mini hydraulic press brakes are capable of delivering the bending force required for small to medium-scale metalworking tasks.
One of the most significant design features of a mini hydraulic press brake is the hydraulic system itself. In these machines, a hydraulic pump and cylinder work together to provide consistent bending force, allowing the machine to handle bending tasks with high precision. The hydraulic system’s ability to provide smooth, controlled force enables it to handle a variety of bending operations, from simple angles to more complex geometries, depending on the tooling used.
The mini hydraulic press brake’s compact design makes it an excellent choice for workshops with limited space. These machines are ideal for applications where there is a need for high precision but not a lot of floor space. The hydraulic components are typically housed in a compact frame, often with a modular design, so that the machine can be configured for specific tasks, making it a flexible and versatile option.
Hydraulic System and Bending Force
Despite its small size, the hydraulic system in a mini hydraulic press brake is often optimized to deliver sufficient force for bending thin to medium-gauge materials. The hydraulic system works by using a pump to pressurize the fluid, which is then directed into a cylinder to move the ram or press brake tool. This system is highly efficient for bending applications because it can apply consistent and adjustable force, which is essential for achieving the correct angles and bend profiles.
In general, mini hydraulic press brakes are available in tonnages ranging from around 10 to 60 tons, which is more than enough for most small to medium-sized sheet metal bending tasks. The hydraulic control system ensures that the bending force is distributed evenly across the sheet, resulting in smooth and accurate bends. Advanced models come with features that allow users to adjust the bending speed, stroke length, and pressure, ensuring that the bending operation matches the material and desired result.
Precision and Control
One of the most important benefits of mini hydraulic press brakes is the precision they offer, especially for delicate or small parts. These machines can achieve precise bend angles, repeatability, and minimal springback due to the controlled hydraulic force. This precision is especially valuable in industries such as electronics and medical device manufacturing, where small parts require tight tolerances.
Many mini hydraulic press brakes are equipped with digital or CNC controls, allowing operators to program and monitor the bending process with high accuracy. These systems allow users to store bending sequences, input precise measurements, and even control the machine remotely in some cases. The use of digital control systems significantly reduces human error, improving consistency and ensuring that each part is bent to specification.
Advanced models can even incorporate features such as automatic back gauges, which automatically adjust to the thickness and length of the material being processed. These back gauges allow operators to maintain consistent bend positioning without manually measuring and adjusting the workpiece, streamlining the process and improving efficiency.
Tooling and Versatility
Another standout feature of mini hydraulic press brakes is their versatility when it comes to tooling. These machines can be equipped with a wide variety of dies and punches to accommodate different bending applications. The tooling can be customized or replaced depending on the material and the desired bend. Additionally, quick-change tooling systems are available on many models, which allows operators to switch tooling sets rapidly, minimizing downtime between production runs.
Mini hydraulic press brakes are particularly useful for prototyping and small batch production. Their ability to handle a wide range of materials and tooling configurations makes them suitable for a variety of industries that require custom or low-volume parts. Whether the task involves creating small brackets, housings, or precision parts, the mini hydraulic press brake can be adapted to the requirements.
Tooling options for these machines include V-dies, radius dies, and custom tooling for specialized applications. The ability to quickly and easily swap out tooling for different parts is crucial in fast-paced environments where turnaround times are short, such as for manufacturers who need to produce prototype parts for new designs or small production runs for specialized products.
Applications
Mini hydraulic press brakes find a wide range of applications in industries that demand precision and flexibility, often in environments where space is a limiting factor. Some of the key applications include:
- Prototyping and R&D: The mini hydraulic press brake is ideal for rapid prototyping in industries like automotive and electronics. Manufacturers can quickly create small quantities of parts, refine designs, and test new materials without needing to invest in large-scale equipment.
- Sheet Metal Fabrication: In small sheet metal shops, mini hydraulic press brakes are used to bend and shape parts for various products, including enclosures, brackets, frames, and more. Their precision and adaptability make them essential for producing custom or low-volume parts.
- Medical Device Manufacturing: Medical device manufacturers often use mini hydraulic press brakes to produce precision parts, such as custom housings for medical equipment, surgical instruments, or protective casings. The high precision and repeatability offered by these machines ensure that parts meet stringent regulatory standards.
- Jewelry and Small-Scale Manufacturing: In jewelry production or small-scale manufacturing of metal products, mini hydraulic press brakes are invaluable for making intricate bends and precise shapes in metals like gold, silver, and platinum. Their ability to work with small pieces while maintaining high accuracy is crucial in these industries.
- Aerospace and Electronics: Industries like aerospace and electronics, which require small, high-precision components, benefit from the mini hydraulic press brake’s ability to handle complex geometries on thin and exotic materials, ensuring that the parts produced meet exact specifications.
Energy Efficiency and Sustainability
The growing emphasis on sustainability in manufacturing has made energy efficiency an increasingly important factor in the design of mini hydraulic press brakes. Many of these machines are now designed with energy-saving technologies, such as more efficient hydraulic systems and optimized motors, which reduce overall power consumption without sacrificing performance. The use of servo-electric hybrid systems, which combine the precision of electric motors with the energy efficiency of hydraulic components, is also becoming more common in mini hydraulic press brakes.
The reduction in energy consumption is particularly important for small businesses, as it can significantly lower operating costs over time. Additionally, mini hydraulic press brakes generally have smaller reservoirs of hydraulic fluid, which reduces waste and improves environmental sustainability.
Maintenance and Cost-Effectiveness
Maintenance is relatively straightforward for mini hydraulic press brakes, particularly because they have fewer hydraulic components than larger machines, which makes them easier to maintain. Regular maintenance includes checking the hydraulic fluid levels, inspecting the dies and punches for wear, and ensuring proper alignment. However, the compact design of these machines means they generally require less maintenance than larger counterparts, making them an economical choice for small workshops or businesses with limited resources.
Overall, mini hydraulic press brakes offer a cost-effective solution for manufacturers who need the power of a hydraulic press brake but lack the space or budget for larger machines. Their precision, versatility, and ability to handle a variety of materials make them ideal for custom work, prototyping, and small-batch production.
Conclusion
Mini hydraulic press brakes are versatile, space-saving machines that offer high-precision bending for small to medium-scale sheet metal processing. Their compact size, adaptability to various materials and tooling configurations, and precise control systems make them a valuable tool for a wide range of industries, including prototyping, small-scale manufacturing, medical devices, and electronics. With continued advancements in energy efficiency, automation, and user interfaces, mini hydraulic press brakes will continue to be essential in modern metalworking environments, offering reliable performance in an increasingly competitive marketplace.
Mini hydraulic press brakes are an increasingly popular choice for small-scale metalworking operations due to their compact size, high precision, and versatility. These machines are specifically designed to perform bending operations on sheet metal with efficiency and accuracy, but they differ from traditional hydraulic press brakes in that they are smaller in both physical size and tonnage. Despite their compact design, mini hydraulic press brakes are equipped with powerful hydraulic systems that deliver the required force to bend materials with the same level of accuracy as larger machines. They can handle various metals such as steel, stainless steel, and aluminum, and they are especially useful in situations where space is limited or when only smaller, thinner materials need to be processed.
One of the primary advantages of mini hydraulic press brakes is their ability to produce precise, repeatable bends in sheet metal. This is particularly important in industries where tight tolerances are required, such as medical device manufacturing, electronics, and aerospace. The hydraulic systems in these machines are designed to provide consistent, adjustable force, ensuring that the bend angles are accurate and that material springback is minimized. Additionally, mini hydraulic press brakes offer flexibility in terms of tooling, as they can accommodate a wide range of die and punch configurations, allowing users to create custom parts for a variety of applications.
These machines are particularly valuable in environments where low-volume production or prototyping is needed. Small workshops or manufacturers can use mini hydraulic press brakes to create a wide variety of components, such as brackets, enclosures, and frames, without needing to invest in large, expensive equipment. The flexibility of the machine allows it to be quickly reconfigured to handle different types of parts or materials, making it ideal for small manufacturers who work with many different designs or customer orders.
While the physical footprint of mini hydraulic press brakes is significantly smaller than their larger counterparts, they still retain many of the features that make traditional hydraulic press brakes reliable and efficient. These include the ability to adjust bending speed, stroke length, and pressure, which can be crucial for achieving high-quality bends. The compact design of mini hydraulic press brakes also means they are more energy-efficient than larger machines, as they consume less power and are often equipped with energy-saving technologies like servo-electric motors or optimized hydraulic systems.
Maintenance for mini hydraulic press brakes is generally less demanding than for larger machines due to their simplified hydraulic systems. Regular maintenance tasks often involve checking hydraulic fluid levels, inspecting tooling for wear, and ensuring proper alignment of the ram and dies. These machines are also more cost-effective to operate and maintain, making them an appealing choice for smaller operations that need precise metalworking capabilities without the overhead associated with larger machines.
With advances in automation and control technology, many modern mini hydraulic press brakes come equipped with CNC (Computer Numerical Control) or digital controls, allowing operators to input precise measurements, store bending sequences, and monitor the machine’s performance in real-time. This technology enhances the precision and repeatability of bending operations, making it easier for operators to achieve consistent results across multiple parts. Automated back gauges, which can adjust to the material’s thickness or length, further improve productivity by eliminating the need for manual adjustments during the bending process.
The future of mini hydraulic press brakes looks promising, as manufacturers continue to refine their designs to meet the evolving needs of modern industries. The integration of smarter controls, better energy efficiency, and automation will likely continue to increase the value of these machines for small-scale manufacturers. As industries increasingly rely on rapid prototyping and customized production, the ability to efficiently produce small batches of high-quality, precise parts will make mini hydraulic press brakes an essential tool for businesses that need to remain competitive in an ever-changing market. These machines will continue to play a crucial role in supporting the growing demand for small-scale, high-precision manufacturing across various industries.
Small Electric Press Brake
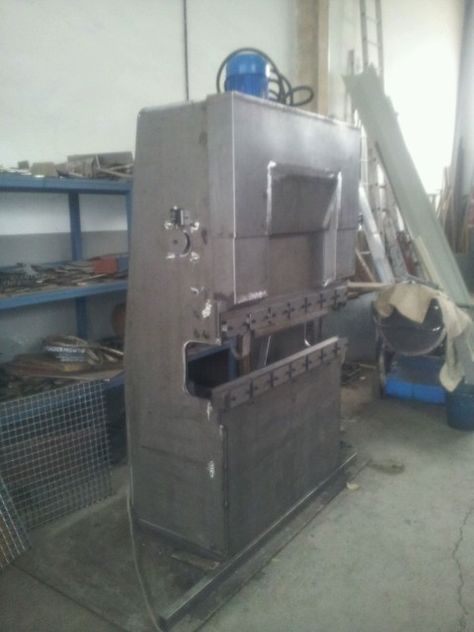
Small electric press brakes are becoming an increasingly popular choice for sheet metal bending operations, particularly in environments where space, energy efficiency, and precision are critical. These machines are compact, easy to operate, and ideal for businesses that require high-precision metalworking without the large footprint and power consumption of traditional hydraulic press brakes. Small electric press brakes utilize electric motors instead of hydraulic systems to provide the force needed for bending, making them quieter, more energy-efficient, and easier to maintain than their hydraulic counterparts.
The core advantage of small electric press brakes lies in their ability to deliver precise and consistent bending force with high energy efficiency. Electric press brakes typically use servo-electric motors that generate the necessary force to bend sheet metal. These motors can be finely controlled, allowing for precise adjustments in the bending process, including the bending speed, pressure, and stroke length. This level of control makes electric press brakes particularly valuable in industries that require tight tolerances, such as electronics, aerospace, and medical device manufacturing.
One of the main benefits of small electric press brakes is their energy efficiency. Unlike hydraulic press brakes, which require a constant supply of hydraulic fluid and use large motors to generate the necessary bending force, small electric press brakes only consume energy when they are in use, leading to reduced power consumption and lower operating costs. This makes them an excellent choice for companies looking to reduce their carbon footprint and operating expenses. Furthermore, electric press brakes do not require hydraulic fluid, which eliminates the need for regular maintenance and the associated costs of fluid replacement, leaks, and disposal.
Another key advantage of small electric press brakes is their compact size. These machines are often designed with a smaller footprint, which makes them ideal for workshops or production environments with limited space. Their smaller size does not compromise their bending capacity, as they can handle a variety of materials and thicknesses with the same level of precision as larger, hydraulic press brakes. This makes them suitable for small batch production, prototyping, or custom manufacturing tasks, where space is at a premium, and large, industrial machines are impractical.
Small electric press brakes are also easier to maintain than traditional hydraulic press brakes. Because they do not use hydraulic fluid, there are fewer components that require regular maintenance, such as hydraulic pumps and hoses. Electric press brakes also tend to have fewer moving parts overall, which reduces the likelihood of breakdowns and extends the machine’s overall lifespan. Regular maintenance typically involves checking the electric motor, ensuring the tool alignment is correct, and maintaining the control system, but the overall maintenance demands are significantly lower than those of hydraulic machines.
The precision offered by small electric press brakes is one of their standout features. These machines provide exceptional accuracy in bending, ensuring that the finished parts meet tight tolerances required in industries like electronics, automotive, and medical device manufacturing. The ability to program and store bending sequences in the machine’s control system further enhances the precision and consistency of the bending process. Operators can input the exact measurements for each bend, allowing for repeatable and high-quality results across multiple production runs.
Advanced control systems are commonly integrated into small electric press brakes, allowing operators to program the machine to perform a wide range of bending tasks. These machines can be equipped with digital or CNC controls, which provide greater flexibility and ease of use compared to manual or mechanical press brakes. With digital controls, operators can set specific parameters for each bend, such as angle, depth, and position, and the machine will automatically adjust the force and stroke to ensure the part is bent accurately. This level of automation not only improves precision but also enhances productivity by reducing setup times and eliminating human error.
Another feature of small electric press brakes is their quick tooling change capabilities. Many models are designed with quick-change tooling systems, which enable operators to swap out dies and punches in a matter of minutes. This reduces downtime between production runs and makes the machine more versatile in handling a variety of bending tasks. The quick-change tooling systems are especially valuable for manufacturers who work with different materials, sizes, and bending configurations, allowing them to efficiently produce custom parts with minimal delays.
Small electric press brakes are also well-suited for applications that require high-speed production. Their precision and efficiency enable fast, consistent bending, making them ideal for industries where short lead times and high throughput are critical. These machines can quickly produce large quantities of parts with minimal setup, making them particularly useful for custom or low-volume production. With the ability to handle a variety of materials and thicknesses, small electric press brakes are flexible enough to meet the needs of diverse industries, from automotive to electronics, to small-scale manufacturing.
Sustainability is another key consideration in the development of small electric press brakes. As businesses and industries seek ways to reduce their environmental impact, the energy efficiency and lower maintenance requirements of electric press brakes make them an attractive option. These machines use less energy than hydraulic press brakes, contributing to a reduction in overall energy consumption. Furthermore, the absence of hydraulic fluid not only eliminates waste but also reduces the potential for fluid spills, further promoting sustainability in the manufacturing process.
Small electric press brakes are ideal for small businesses, workshops, or manufacturers with limited space, resources, or energy consumption needs. Their versatility, precision, and lower operational costs make them a practical solution for a wide range of applications. Whether it’s bending metal for prototypes, custom parts, or small batch production, these machines offer the flexibility and performance required to meet the demands of modern metalworking operations.
In conclusion, small electric press brakes offer an innovative solution for companies looking for high-precision, energy-efficient bending in a compact and easy-to-maintain machine. Their ability to handle a variety of materials with consistent quality, combined with the flexibility of digital or CNC controls, makes them ideal for industries that require accurate, small-volume production. As the demand for sustainable manufacturing practices continues to grow, small electric press brakes are poised to become an essential tool in modern fabrication and sheet metal working, offering both cost-saving benefits and high-quality results.
Small electric press brakes are continuing to evolve as manufacturers look for ways to enhance their capabilities, improve energy efficiency, and reduce costs. As technological advancements continue to be incorporated, these machines are expected to become even more versatile, with additional features such as integrated robotics and advanced material handling systems. With these enhancements, small electric press brakes could become even more automated, enabling businesses to further streamline production processes and reduce manual intervention.
For instance, the integration of robotics for automated loading and unloading of sheet metal can help eliminate bottlenecks during production, improving overall throughput. By automating material handling, the process becomes more efficient, reducing the time needed for setup and manual labor. This is particularly beneficial for industries that demand high volumes of parts with a short turnaround time, such as automotive, electronics, and appliances.
Furthermore, the ability to interface small electric press brakes with a networked production environment offers significant advantages in terms of data collection and analysis. By connecting these machines to a central control system, manufacturers can monitor performance, track the wear and tear of tooling, and predict maintenance needs before they result in downtime. This predictive maintenance is made possible through sensors embedded in the machines, which can detect early signs of mechanical issues, such as deviations in motor performance, wear on dies, or pressure inconsistencies. By addressing these issues proactively, manufacturers can reduce unscheduled downtimes, leading to greater productivity and lower maintenance costs.
In terms of operator ergonomics, modern small electric press brakes are designed with user-friendly controls and enhanced safety features. The control systems often feature intuitive touchscreens that make programming and adjusting parameters easier, reducing the likelihood of operator error. These controls also allow for remote diagnostics, so issues can be identified and addressed quickly without needing to send technicians on-site. Safety features, such as light curtains, emergency stops, and advanced sensors, ensure that operators can work in a safe environment without compromising productivity. These features help minimize the risk of injury and ensure compliance with safety regulations, further enhancing the machine’s appeal to businesses.
Another trend in the development of small electric press brakes is the increasing use of hybrid technology. Some modern machines are adopting a hybrid design that combines both electric and hydraulic elements. These hybrid press brakes maintain the energy efficiency and precision of electric machines while retaining the bending power of hydraulic systems. By integrating the best aspects of both technologies, hybrid machines can handle a wider range of materials and thicknesses, making them more adaptable to diverse production needs.
As manufacturers continue to prioritize sustainability and cost efficiency, the compact, low-maintenance design of small electric press brakes will continue to provide an important solution for businesses. The reduced environmental impact, due to the absence of hydraulic fluids and lower energy consumption, positions small electric press brakes as a key player in the green manufacturing movement. Furthermore, their ability to produce high-quality bends in small to medium-volume runs makes them an essential tool in industries that require precision but also need to remain agile and adaptable in a competitive marketplace.
In industries where customization and quick turnaround are crucial, such as custom metal fabrication, signage, or small-batch production, small electric press brakes offer a reliable solution. Their ability to process smaller sheets of metal with high accuracy ensures that manufacturers can meet the varied needs of their customers, whether they are producing one-of-a-kind pieces or short production runs.
The growing demand for small electric press brakes also highlights a shift toward more flexible manufacturing systems. These machines are well-suited for modern, lean production environments where manufacturers need to remain responsive to changing customer demands and quickly adjust production schedules. The precise control of bending angles, stroke lengths, and pressure settings makes it easier to switch between different types of products, increasing overall manufacturing flexibility.
In conclusion, small electric press brakes are increasingly becoming an integral part of the metalworking and manufacturing landscape, offering businesses the benefits of precision, energy efficiency, reduced maintenance, and space-saving design. As advancements in automation, robotics, and data analytics continue to integrate into these machines, their capabilities will only improve, offering even greater efficiency and flexibility to manufacturers. Their combination of small size, energy-saving features, and high precision positions small electric press brakes as a leading option for modern fabrication shops that require cost-effective solutions for a range of bending tasks. Whether used for prototyping, small batch production, or high-precision custom parts, small electric press brakes provide the flexibility and performance that modern manufacturers need to stay competitive and meet the demands of a rapidly changing market.
Press Brake Small
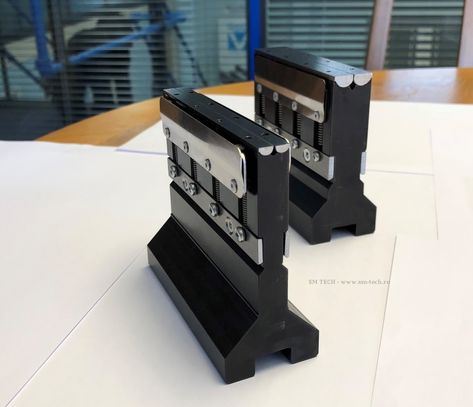
A small press brake is a highly versatile and efficient machine designed for sheet metal bending in applications where space is limited, and high precision is required. These compact machines offer many of the same features as their larger counterparts, but in a smaller form factor, making them an excellent choice for smaller workshops, prototyping, and small-scale production runs. Despite their size, small press brakes can handle a wide range of bending tasks with remarkable accuracy, ensuring that they can meet the needs of industries like metalworking, electronics, automotive, aerospace, and more.
The primary benefit of small press brakes is their ability to offer high-precision bending for sheet metal. Typically, small press brakes come in tonnages ranging from 10 to 60 tons, which makes them ideal for bending thinner materials or smaller batches. They are capable of producing a variety of parts, including brackets, enclosures, panels, and other sheet metal components, with consistent quality and accuracy. The compact nature of the machine does not compromise its ability to achieve the necessary bending forces for these tasks, and advanced control systems ensure that bends are made to exact specifications.
One of the key features of small press brakes is their flexibility. These machines are able to handle a range of materials, such as steel, aluminum, stainless steel, and even certain alloys, with ease. The ability to adjust parameters such as stroke length, bending force, and speed ensures that small press brakes can work with different material thicknesses and types without sacrificing performance or quality. The modular nature of small press brakes also allows for easy tool changes, enabling operators to switch between different bending configurations quickly and efficiently. This adaptability is particularly valuable in industries where custom parts or short production runs are common.
Another advantage of small press brakes is their reduced energy consumption compared to larger machines. Many small press brakes, especially those with electric or hybrid systems, consume less power than hydraulic press brakes while still offering the necessary force for precise bending. The energy efficiency of small press brakes not only reduces operating costs but also aligns with growing demands for sustainable manufacturing practices. By using less power and often eliminating the need for hydraulic fluid, these machines help minimize the environmental impact of the bending process.
Maintenance for small press brakes is also simplified compared to larger, more complex machines. With fewer hydraulic components and a simpler design, these machines generally require less maintenance and are easier to service. Regular maintenance tasks typically involve checking the alignment, inspecting tooling for wear, and ensuring the electrical or mechanical components are functioning properly. Since they do not rely on hydraulic fluid, small press brakes avoid the complications associated with fluid leaks and hydraulic system failures, making them more reliable and cost-effective in the long term.
Small press brakes are often equipped with advanced control systems that allow for precise programming of bending sequences. These control systems, which can include CNC (Computer Numerical Control) or digital interfaces, give operators the ability to input exact bending parameters, such as bend angles, stroke lengths, and pressure. This makes the process more automated, reducing the likelihood of operator error and ensuring that each part is bent consistently. Many small press brakes also feature automatic back gauges, which adjust to the length of the workpiece, further streamlining the bending process and improving accuracy.
The compact design of small press brakes makes them ideal for workshops or production environments with limited space. These machines can be easily integrated into smaller facilities, offering high performance without taking up the valuable floor space required for larger machinery. This makes them a popular choice for small-scale manufacturers, prototyping shops, and businesses that need to maximize their use of available space.
Additionally, small press brakes are highly suitable for industries that require high-precision metalworking, such as electronics, medical devices, and aerospace manufacturing. The precise bending capability of these machines ensures that parts meet strict tolerances, which is crucial for these industries where accuracy is paramount. The ability to quickly and efficiently produce high-quality parts in small quantities is another reason small press brakes are favored in these fields.
Another important factor in the growing popularity of small press brakes is the reduced cost compared to larger machines. These machines generally have a lower initial purchase price, and their energy efficiency and simplified maintenance contribute to reduced operating costs over time. This makes small press brakes an attractive investment for smaller businesses or startups looking to produce high-quality sheet metal components without the significant capital investment required for larger machines.
As with other types of press brakes, small press brakes are designed to work with various dies and punches, making them suitable for a wide range of bending applications. The tooling for these machines can be customized or replaced as needed to handle specific tasks. Quick-change tooling systems allow operators to swap out tooling sets efficiently, reducing downtime between production runs and improving overall productivity. The versatility of these machines is further enhanced by their ability to bend various shapes and angles, making them an ideal choice for applications where multiple bends or complex geometries are required.
Small press brakes are also becoming more advanced with the incorporation of automation and smart technologies. Features like automatic sheet loaders, material handling systems, and advanced safety features are being added to enhance the performance of small press brakes, making them more efficient and safer to operate. These features help reduce human intervention, improve part quality, and increase throughput, particularly in high-demand manufacturing environments.
In conclusion, small press brakes offer a combination of precision, energy efficiency, and versatility, making them ideal for smaller workshops, prototyping, and small-scale production environments. Their compact size does not hinder their performance, allowing them to produce high-quality parts with exacting precision. Whether used in industries like aerospace, automotive, electronics, or custom fabrication, small press brakes deliver the flexibility and power needed for a wide range of bending applications. With the continued evolution of automation, digital controls, and energy-efficient systems, small press brakes are likely to play an increasingly important role in modern manufacturing, offering cost-effective solutions for businesses looking to maximize their production capabilities while minimizing their environmental impact.
Small press brakes are also benefiting from ongoing innovations in safety and automation, making them even more effective in fast-paced production environments. In terms of safety, modern small press brakes often come equipped with advanced safety features such as light curtains, protective barriers, and emergency stop systems. These safety systems help prevent accidents by ensuring that operators are kept at a safe distance from the bending area, while still allowing them to monitor and control the machine. Some machines even feature automated safety checks that verify correct machine operation before starting a bending cycle, further reducing the risk of injury or malfunction.
Additionally, the integration of automated material handling systems is becoming more common in small press brakes. These systems can include automated loading and unloading systems, which streamline the process and reduce the need for manual intervention. For instance, an automated sheet feeder can bring in the material to be bent, while an automated unloading system can remove the finished parts from the machine. These enhancements significantly improve efficiency, as they reduce downtime between cycles and enable operators to focus on other tasks, such as quality control or setup for new jobs.
The use of computer numerical control (CNC) and programmable logic controllers (PLC) in small press brakes is also improving their flexibility and precision. CNC systems allow operators to program complex bending sequences, enabling the production of intricate shapes and parts with minimal human input. This capability is especially beneficial in industries such as aerospace, automotive, and electronics, where the parts being produced may require multiple bends, intricate geometries, or tight tolerances. With the ability to store and recall bending programs, small press brakes can quickly transition between different tasks, making them ideal for small batch production and quick turnaround times.
In terms of material types, small press brakes are capable of processing a wide range of materials, from thin sheet metal to more challenging materials such as high-strength steels, aluminum alloys, and stainless steel. This versatility is especially important in industries where multiple materials are used for different applications. The machine’s ability to adjust bending parameters based on the material type ensures consistent and accurate bends, even when working with more difficult-to-bend materials.
The ability to handle various material thicknesses is another benefit of small press brakes. While their size limits their bending capacity compared to larger machines, modern small press brakes can still handle a wide range of sheet thicknesses, from thin metal sheets to thicker, heavier plates. This makes them suitable for applications where precision bending of thinner materials is needed, such as for electronic components, consumer products, or small structural components.
As the demand for sustainability continues to grow in the manufacturing sector, small press brakes are meeting this challenge through improved energy efficiency and environmentally friendly features. The transition to electric-powered systems, for example, has significantly reduced the energy consumption of small press brakes compared to traditional hydraulic models. Electric machines are more energy-efficient because they only consume power when the machine is in use, unlike hydraulic models that maintain a constant flow of hydraulic fluid, leading to higher energy costs. This makes small press brakes an attractive option for manufacturers aiming to reduce their environmental impact while maintaining high-quality production standards.
Moreover, because small press brakes are generally easier to maintain than larger hydraulic models, businesses can save on both operational and maintenance costs. With fewer moving parts and a simpler design, electric or hybrid small press brakes require less frequent servicing, and the absence of hydraulic fluid eliminates the costs associated with fluid replacement, leaks, and disposal. This low-maintenance design contributes to lower overall ownership costs, allowing small businesses to keep their operating expenses under control while still benefiting from the performance of a high-quality press brake.
Furthermore, the small size of these machines makes them ideal for businesses operating in facilities with limited space. Traditional press brakes require a large amount of floor space and substantial clearance for material handling. Small press brakes, on the other hand, can be placed in compact workspaces, allowing businesses to make the most of their available area. This space efficiency is particularly beneficial for small-scale manufacturers, prototyping shops, or businesses that need to maximize production in a limited footprint.
The increasing adoption of small press brakes also reflects broader trends in modern manufacturing, where there is a focus on flexibility, customization, and fast production cycles. Small press brakes are especially well-suited for low-volume production runs, prototype development, or custom parts manufacturing, where traditional, high-volume machinery might not be as effective or efficient. Their ability to quickly adjust to new designs, materials, and production specifications allows businesses to stay competitive in industries that demand flexibility and responsiveness to changing customer needs.
In industries where rapid prototyping is essential, such as in the development of new products or design iterations, small press brakes can quickly produce small batches of parts, allowing manufacturers to test and refine their designs before moving to larger-scale production. The precision and repeatability of small press brakes ensure that the prototypes meet the same high standards as mass-produced parts, making them invaluable tools for engineers and designers.
Overall, the small press brake market is expected to continue growing as manufacturers seek more efficient, cost-effective, and versatile solutions for sheet metal bending. With continued innovations in automation, energy efficiency, and precision control, small press brakes will remain a vital tool for businesses that require high-quality metalworking without the need for large, expensive machinery. As industries evolve and demand for smaller, more customized parts increases, small press brakes will continue to offer the adaptability and performance needed to meet these challenges.
EMS Metalworking Machinery
We design, manufacture and assembly metalworking machinery such as:
- Hydraulic transfer press
- Glass mosaic press
- Hydraulic deep drawing press
- Casting press
- Hydraulic cold forming press
- Hydroforming press
- Composite press
- Silicone rubber moulding press
- Brake pad press
- Melamine press
- SMC & BMC Press
- Labrotaroy press
- Edge cutting trimming machine
- Edge curling machine
- Trimming beading machine
- Trimming joggling machine
- Cookware production line
- Pipe bending machine
- Profile bending machine
- Bandsaw for metal
- Cylindrical welding machine
- Horizontal pres and cookware
- Kitchenware, hotelware
- Bakeware and cuttlery production machinery
as a complete line as well as an individual machine such as:
- Edge cutting trimming beading machines
- Polishing and grinding machines for pot and pans
- Hydraulic drawing presses
- Circle blanking machines
- Riveting machine
- Hole punching machines
- Press feeding machine
You can check our machinery at work at: EMS Metalworking Machinery – YouTube
Applications:
Flange-punching
Beading and ribbing
Flanging
Trimming
Curling
Lock-seaming
Ribbing