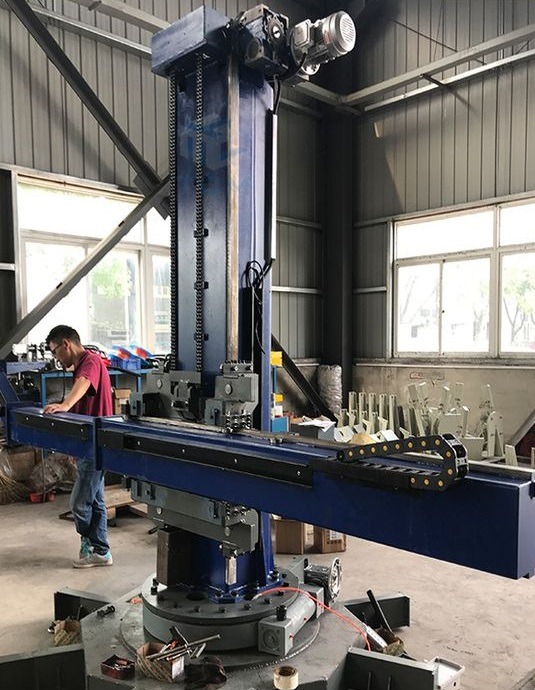
Metal Door Frames Manufacturing Machine: An Automated Machining Line is a highly integrated manufacturing system designed to produce parts with minimal human intervention. It typically consists of a series of machine tools (e.g., CNC lathes, milling machines, drilling machines) that are connected by material handling systems and controlled by a central computer or PLC (Programmable Logic Controller).
Key Components of the Automated Machining Line
- CNC Machines – Perform operations like turning, milling, drilling, etc.
- Robotic Arms / Gantry Systems – Load and unload parts between stations.
- Conveyors / Transfer Lines – Move parts through the line.
- Inspection Stations – Use vision systems or sensors for quality control.
- Tool Management Systems – Monitor and change tools automatically.
- Centralized Control System – Coordinates all operations and collects data for monitoring and optimization.
Advantages:
- High Productivity: Continuous, 24/7 operation.
- Consistency & Precision: Reduced human error.
- Reduced Labor Costs: Fewer operators required.
- Better Data Collection: Enables predictive maintenance and real-time quality tracking.
Applications:
- Automotive components
- Aerospace parts
- Consumer electronics
- Industrial equipment
An automated machining line is a production system where multiple machine tools and handling devices are connected to perform sequential operations on workpieces with minimal human intervention. These lines are typically controlled by centralized computer systems or PLCs that coordinate each stage of the process, from raw material input to finished product output. The core of the system includes CNC machines such as lathes, milling machines, or grinders, which are programmed to carry out precise machining operations. Between these machines, automated material handling systems—such as robotic arms, gantry loaders, or conveyors—transport parts, ensuring smooth workflow and minimal downtime.
The system may also integrate inspection stations equipped with sensors, vision systems, or coordinate measuring machines (CMMs) that verify dimensional accuracy and surface quality during or after machining. This ensures defective parts are identified early and reduces waste. Automated tool changers and tool monitoring systems help keep the line running by switching out worn tools and maintaining machining precision.
Automated machining lines are especially beneficial in high-volume production environments where consistency, speed, and cost-efficiency are critical. Industries such as automotive, aerospace, and electronics rely heavily on such systems to produce complex parts at scale. While the initial investment is high, the long-term benefits include reduced labor costs, improved product quality, faster turnaround times, and better use of manufacturing data for process optimization and predictive maintenance.
In a typical real-world scenario, such as an automotive engine component production line, the automated machining process starts with raw forgings or castings being loaded into the system—often by robotic arms or palletized feeders. The first CNC station might perform rough turning to shape the basic geometry. After this, the part is transferred—usually via a conveyor or robotic gripper—to the next station, where more detailed operations like milling, drilling, or threading take place.
Each machine is pre-programmed with the exact machining instructions and tolerances, ensuring that every part meets the same specifications. Sensors on the machines track cutting forces, spindle speed, vibration, and tool wear. If any parameter deviates from its threshold, the system either compensates automatically or triggers a maintenance alert. Some lines include adaptive machining, where minor real-time adjustments are made based on part variability or tool conditions.
Inspection and quality control are often embedded into the line itself. For example, a vision system might scan the part for surface defects immediately after milling. Later, a contact probe or laser scanner might verify critical dimensions. If a defect is detected, the part can be ejected from the line automatically and logged in a database for traceability and root cause analysis.
Finished parts are either collected in bins, stacked on pallets, or automatically transferred to an assembly line or packing station. Throughout the entire cycle, the central control system logs data from every operation, enabling detailed reporting, traceability, and continuous process improvement through machine learning or statistical process control techniques.
This kind of integration enables not only high-volume output but also flexibility for batch-size variations and product changeovers. With Industry 4.0 and IoT technologies, modern automated machining lines can also be remotely monitored and adjusted, further reducing the need for on-site personnel and enabling centralized control over multiple production facilities.
In traditional automated machining lines without AI or modern digital technologies, the system still relies heavily on mechanical and electrical automation controlled by programmable logic controllers (PLCs), relay-based logic, or basic numerical control (NC) systems. These setups are robust and reliable, often built for longevity and consistent performance in high-volume production environments.
The process begins with manual or semi-automated loading of raw materials into the first machine tool. These machines—typically NC lathes, milling machines, or drills—perform specific operations based on preset programs stored in the machine’s memory. The workpiece is clamped in place, and machining proceeds according to fixed cycle parameters. Once the operation is complete, mechanical transfer systems such as linear tracks, pneumatic pushers, or rotary indexing tables move the part to the next station.
Tool changes are usually scheduled at regular intervals based on time or part count rather than real-time tool condition. Operators may be responsible for monitoring tool life and performing manual replacements when necessary. Likewise, quality checks are typically carried out at regular intervals by human inspectors using gauges, micrometers, or dedicated checking fixtures. In some systems, dial indicators or hard stops are used to maintain dimensional control.
Despite the absence of sensors or real-time feedback, such systems are remarkably effective in stable production conditions where the material and part design do not vary significantly. Maintenance is preventive or breakdown-based, relying on routine inspections, lubrication schedules, and experience-based troubleshooting.
These older automated lines are often found in long-established manufacturing plants, particularly in the automotive, heavy equipment, and appliance industries. They are less flexible than modern systems but are valued for their simplicity, mechanical reliability, and the skill-based approach of their operators and technicians.
In older automated machining lines, the transfer mechanisms are a critical part of the system and are designed for mechanical simplicity and reliability. Common types include chain conveyors, roller conveyors, overhead trolleys, rotary index tables, and linear shuttles. Each is chosen based on the type and size of the part, the required throughput, and the physical layout of the shop floor.
One widely used method is the rotary indexing table, especially in compact setups. It positions the workpiece at different machining stations arranged in a circular configuration. After each operation, the table indexes to the next position, allowing simultaneous machining at multiple stations. This results in high efficiency for parts that require several short, sequential operations.
For heavier parts or larger operations, linear transfer systems are more suitable. These include rigid rails or tracks along which pallets or fixtures holding the parts are mechanically advanced using cams, gears, or pneumatic cylinders. The indexing is precise and repeatable, ensuring each part is aligned correctly at each station. This system may include lifting and rotating units for reorienting parts as needed for subsequent machining.
Another key feature in these systems is dedicated tooling and fixturing. Each station typically has fixed-purpose jigs that precisely position and clamp the workpiece. These fixtures are often hard-mounted to the machine base and require manual adjustment during setup changes. For repeat production of a single part or family of parts, this system works efficiently and minimizes the need for frequent calibration.
Control is handled by relay logic or early PLCs with ladder diagrams programmed to execute sequences such as machine start/stop, indexing, tool changes, and coolant flow. These controls are robust, easy to troubleshoot with basic electrical knowledge, and designed for long-term operation. They don’t adapt in real-time but can reliably run for decades with minimal issues if maintained properly.
Coolant systems in traditional lines are also basic—usually centralized coolant tanks with pumps directing fluid to the tools. Filtration may be rudimentary, involving mesh filters or magnetic separators to remove chips and swarf.
Chip handling is mechanical too—often using screw conveyors or belt-driven systems to move chips away from the machining area to collection bins. Operators are typically responsible for emptying these bins and ensuring the system stays clear to prevent machine stoppage.
Overall, older automated machining lines are engineered for reliability and long production runs of identical parts. Changeovers are time-consuming, and flexibility is limited, but their mechanical simplicity, low software dependence, and proven durability make them well-suited for dedicated manufacturing tasks.
Automated Machining and Grinding Line
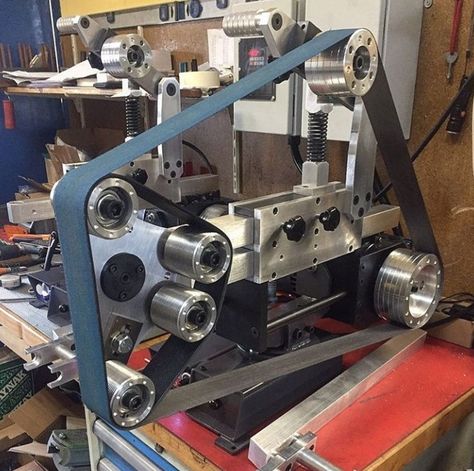
An Automated Machining and Grinding Line is a production system that combines cutting operations (like turning, milling, or drilling) with grinding processes in a continuous, integrated workflow. This setup is commonly used in industries that demand high precision and surface finish, such as automotive, aerospace, and heavy machinery manufacturing. Unlike purely machining lines, these systems can handle parts that require both dimensional accuracy and fine surface quality.
In traditional implementations without modern AI or smart sensors, these lines are built around a sequence of machine tools and grinders, connected via mechanical transfer systems such as conveyors, indexing tables, or robotic arms. Each station is dedicated to a specific operation. For example, a component may first be rough-machined in a CNC lathe, transferred to a milling machine for slots or holes, and finally moved to a grinding station for precision finishing. Grinding is typically done with cylindrical, surface, or centerless grinders, depending on the part geometry.
Parts are usually mounted on dedicated fixtures or pallets designed to maintain consistent orientation and minimize setup time at each station. Fixtures are clamped pneumatically or hydraulically, and the systems are aligned mechanically to ensure accurate positioning. Transfer between stations is timed and controlled by PLCs, which follow a strict logic sequence. These lines often incorporate automated tool changers in the machining stations and fixed grinding wheels in the grinding units.
Grinding stations are equipped with cooling systems and basic wheel dressing mechanisms. In older systems, dressing cycles are timed rather than sensor-driven, and operators rely on scheduled maintenance or visual inspection to identify wear or wheel damage. Coolant filtration may use magnetic separators, paper bed filters, or basic settling tanks to remove fine grinding debris.
Quality control is mostly manual or semi-automated. For high-tolerance parts, operators may use dial indicators, micrometers, or air gauges at designated inspection stations. Some lines include mechanical go/no-go gauges between stages to detect out-of-spec parts before they move to the next operation.
The major advantage of combining machining and grinding in one line is process integration: fewer setups, faster cycle times, and reduced handling between operations. This is particularly beneficial when producing hardened or high-strength materials where post-machining grinding is necessary for tolerance and finish. However, because of the heat, dust, and precision requirements of grinding, these stations are often physically isolated within the line and require more frequent maintenance.
Older automated machining and grinding lines are designed for long runs of standardized parts, with little flexibility for frequent part changes. Changeovers involve manual fixture replacement, program switching, and careful realignment, typically performed by skilled technicians. Despite their limitations, such systems remain in use where durability, consistency, and cost-per-part are more critical than flexibility.
Let’s consider a typical crankshaft production line as an example of an automated machining and grinding line. Crankshafts are complex components that require a combination of heavy material removal and ultra-precise finishing. The line is usually designed for high-volume output, such as in automotive engine manufacturing.
The process begins with forged steel blanks being loaded—either manually or by robot—onto palletized fixtures. These fixtures travel through the line and maintain precise orientation of the crankshaft throughout each station. The first few machines perform rough machining using CNC lathes and milling machines to establish key features like journals, counterweights, and oil passages. Operations at this stage include turning, milling of flat faces, and drilling of oil holes.
Next, the part is transferred—usually by a chain conveyor or robotic arm—to semi-finish machining stations, where closer tolerances are achieved. Here, operations such as journal and pin turning to near-final dimensions are performed. The control is typically PLC-based, with set cycle times and limited part detection logic. Tool changes are pre-programmed based on part count, not real-time monitoring.
After semi-machining, the crankshaft undergoes heat treatment, often offline. It is then reintroduced to the line for hard machining or pre-grinding, depending on the material hardness and required tolerances. The hard surfaces—especially the main and pin journals—now require precise size and surface quality, which is where grinding becomes critical.
The part is now transferred to grinding stations, typically including:
- Cylindrical grinders for the main journals.
- Orbital or crankpin grinders for the offset crank pins.
- Face grinders for end faces and thrust surfaces.
These grinders are built for high rigidity and thermal stability, often with cast-iron beds and hydraulic or electric infeed systems. The grinding wheels are fixed and dressed periodically using diamond dressers. The dressing cycles are scheduled either by time or number of parts, depending on the line’s setup. The grinding process produces significant heat and fine particles, so coolant systems with filtration tanks and magnetic separators are essential.
To maintain accuracy, the line may include mechanical gauging stations after critical grinding operations. These use air gauges or contact probes to measure diameter, roundness, and taper. In some lines, go/no-go fixtures are positioned at intervals to catch out-of-spec parts. If a part fails, it is diverted off the line to a rework or scrap area.
At the end of the line, the crankshaft is washed in a cleaning station to remove residual grinding swarf and oil. It may then be subjected to manual final inspection, including magnetic particle inspection for cracks, followed by balancing and marking before packing.
Older systems like this are not designed for quick changeovers. A model change requires downtime to switch fixtures, adjust machine positions, update programs, and possibly modify transfer settings. But once running, these lines can produce thousands of identical crankshafts with minimal variation, making them ideal for large-scale manufacturing.
Let’s continue with a focus on bearing race production in an automated machining and grinding line. Bearing races require extremely tight tolerances and mirror-like surface finishes, especially on the inner and outer diameters that mate with rolling elements. This makes them ideal candidates for combined machining and grinding lines, particularly where large volumes are involved, such as in automotive wheel hubs or industrial motors.
The process starts with raw steel tubes or forged rings that are cut to approximate length and then loaded onto the line—often using a gravity chute, lift-and-place system, or vibratory bowl feeder for small races. The first station is usually a facing and centering lathe, which squares both ends and generates a center bore or reference surface. The part is then transferred via linear shuttle or rotary table to the next machine, typically a rough-turning lathe, which machines the basic internal and external diameters.
After this, the part might move to a groove turning machine, where the raceways are cut to near-net shape. These operations use fixed tooling and follow numerical control commands via early CNC or PLC systems. At this stage, tolerances are relatively loose, as the final precision will come from grinding.
Following turning, the rings go through a heat treatment process (carburizing or hardening) offline, and are then reintroduced to the line for grinding. This is the critical stage where the inner and outer raceways are ground to final dimension and finish. Here’s how grinding is typically handled in such a line:
- Centerless grinding is used for the external diameters of the outer races. It provides high throughput and good roundness, as the part is supported between a regulating wheel and a grinding wheel without chucks.
- Internal grinding machines are used for the inner diameters of inner races, requiring high spindle speed and careful coolant delivery due to heat buildup in confined spaces.
- Raceway grinding, which may use plunge grinding or oscillating (swiveling) methods depending on the bearing type and production strategy. These machines often have fixed grinding wheels mounted on precision spindles, dressed periodically by a mechanical dresser.
Coolant is heavily used at this stage, delivered through nozzles aimed directly at the contact zone. Coolant systems are relatively basic in older lines, using central tanks with gravity return lines and magnetic or paper bed filters. Since grinding creates very fine swarf and heat, keeping the coolant clean and the grinding wheels dressed is essential to avoid burning or dimensional deviation.
After grinding, the races move to inspection and superfinishing. This may include:
- Lapping or honing to achieve mirror finish and final geometry.
- Air gauging or mechanical comparators to check roundness, diameter, and taper.
- Crack detection using magnetic particle inspection or eddy current testing.
Some lines may also include marking stations where part numbers, batch codes, or hardness zones are engraved using dot-peen or laser systems. In older lines, this is sometimes done manually or semi-automatically.
The final steps involve cleaning, rust prevention coating, and packaging. Rings are passed through a washing tunnel with heated solution and then dried using air blowers. Anti-rust oil is applied via spray or dip tanks before packaging into trays or cartons.
This kind of line, though mechanically complex, operates with high reliability and repeatability over long periods. It’s engineered for mass production with minimal flexibility, but its robustness and mechanical design make it a strong choice where digital technologies are not required or available.
Automated Deep Drawing Production Line
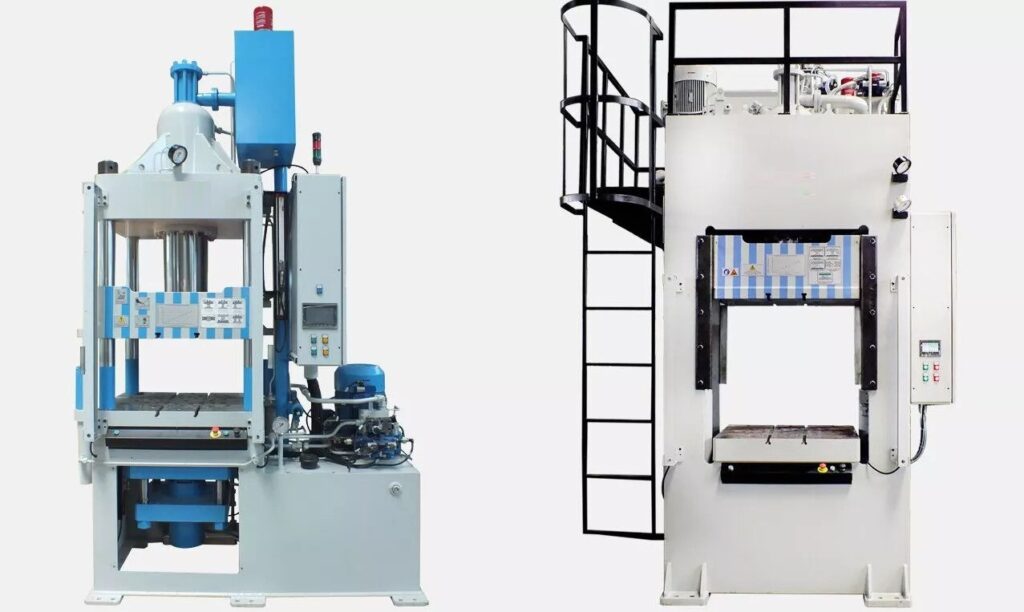
An Automated Deep Drawing Production Line is a high-precision manufacturing system designed for producing complex, hollow metal parts from flat sheets, typically using a process called deep drawing. Deep drawing involves forming a sheet metal blank into a three-dimensional shape, like automotive body panels, kitchen sinks, or pressure vessels, by pulling the sheet over a die with a punch.
In an automated deep drawing production line, the entire process is integrated, often with robotic arms, conveyors, and automated presses working together to form, inspect, and finish the parts with minimal human intervention. The key focus of these lines is to ensure high throughput, precision, and consistent part quality, while reducing labor costs and cycle time.
Key Stages of an Automated Deep Drawing Production Line:
- Blanking and Feeding:
- The process begins with blanking, where flat metal sheets (typically aluminum, steel, or brass) are cut into precise blanks of the required size and shape. In some automated lines, automated blank feeders are used to move the blanks from a material stack to the first forming station.
- A coil-fed system can also be used where a continuous strip of material is unspooled and fed into the line.
- For high-volume production, this stage may involve robotic arms or automatic conveyors to precisely position the blanks into the press.
- Pre-forming/Pre-heating (if necessary):
- Some materials, especially tougher metals, may require pre-heating to make them more malleable before deep drawing.
- A heated die or induction heating system may be employed to soften the metal blank, making it easier to form without cracking or wrinkling.
- Deep Drawing (Forming):
- The core operation of the line is deep drawing, where the metal blank is placed in a die and pressed into the desired shape using a punch.
- In the traditional process, the sheet metal is drawn through a die using a mechanical press, while the punch pulls the metal into the die cavity. The metal may go through several stages of drawing, especially for complex shapes.
- Automated presses are often used in these systems, typically hydraulic or mechanical presses, which provide consistent force and speed. The press may be equipped with automatic stroke adjustments, controlling the drawing depth and force depending on the material and part geometry.
- Multiple drawing stations can be used sequentially, with each one progressively drawing the part deeper and shaping it closer to the final form.
- Lubrication and Cooling:
- A key aspect of deep drawing is the lubrication of the metal blank to reduce friction between the punch and die, and to prevent the metal from sticking or cracking.
- Automated lubrication systems are used, which spray or flood the blank with a lubricant before it enters the die. This ensures consistent application and reduces the need for manual intervention.
- Cooling systems may also be integrated into the die to regulate temperature and prevent overheating of the metal during drawing.
- Ejection and Part Handling:
- Once the part is formed, it is ejected from the die. This is often done using automated ejectors, robotic arms, or mechanical pushers that remove the part from the die without damaging its shape.
- Conveyors are used to transport the ejected parts to the next station for quality inspection, trimming, or other finishing operations.
- If needed, parts may be automatically stacked or placed into containers for downstream processing or shipping.
- Inspection and Quality Control:
- After the drawing process, the parts are automatically inspected for defects such as wrinkles, cracks, or dimensional deviations.
- Vision systems may be employed to inspect the parts for visual defects, while coordinate measuring machines (CMMs) or other contact sensors can check critical dimensions like wall thickness, depth, or diameter.
- Some lines incorporate automatic rejection systems, where defective parts are immediately removed from the line to avoid further processing.
- Trimming and Finishing:
- If the drawn part has excess material (such as a flange or edge), it is sent to a trimming station. This is typically done with automated cutting tools, which trim away the excess metal.
- Parts may then undergo additional processes such as deburred edges, punching, or flange forming as needed for the final design.
- Cleaning and Coating (if required):
- After trimming, the parts may need to be cleaned, either manually or automatically using ultrasonic cleaners or industrial washing systems, to remove oils, lubricants, or other residues from the drawing process.
- Some parts may also require surface coating, such as painting, galvanizing, or coating with protective films. This can be done automatically via spray booths or robotic systems for precise application.
- Packaging and Shipping:
- Finally, the formed and finished parts are ready for packaging and shipment. Automated systems can handle packaging, whether it’s wrapping parts individually, placing them in bulk containers, or preparing them for palletization.
Key Advantages of Automated Deep Drawing Lines:
- High Throughput: With minimal human intervention, the system can operate at high speeds, producing large volumes of parts quickly.
- Consistency and Quality: Automated systems ensure that each part meets the required specifications with minimal variation, reducing scrap and rework.
- Reduced Labor Costs: Many manual steps (such as blank handling, lubrication, and inspection) are automated, reducing the need for operators.
- Flexibility in Material Handling: While deep drawing typically involves metals, automated systems can adapt to different material types, thicknesses, and shapes.
- Process Integration: The entire production process, from blanking to shipping, can be seamlessly integrated into one automated system, reducing downtime and improving efficiency.
Applications:
- Automotive Industry: For parts like car body panels, fuel tanks, or engine components.
- Aerospace: For lightweight, high-strength parts like fuselage panels or wing skins.
- Household Goods: For items such as sinks, tubs, and other kitchen or bathroom products.
- Industrial Equipment: For parts like pressure vessels or enclosures for machinery.
In essence, automated deep drawing lines are highly efficient systems optimized for mass production, especially when complex parts with tight tolerances need to be formed quickly and consistently.
An automated deep drawing production line is designed to streamline the process of forming complex metal parts by transforming flat sheets of material into three-dimensional shapes. The process begins with blanking, where flat metal sheets are precisely cut into blanks, which are then fed into the first stage of the forming process. Depending on the system, blanks may be fed manually or automatically using robotic arms or conveyor belts. After this, the blanks are placed in a die, and a punch is used to draw the material into the die, shaping it into a desired part.
The deep drawing process often occurs in multiple stages, each progressively drawing the part deeper to create the final shape. As the material is drawn, it can be lubricated to reduce friction between the punch and die, helping prevent the material from cracking or sticking. Automated lubrication systems spray or flood the blanks with lubricant, ensuring consistent application and eliminating the need for manual intervention. The metal may also be pre-heated in certain cases to make it more malleable, especially when forming tougher metals that require additional care.
Once the part is formed, it’s ejected from the die using automated ejectors, robotic arms, or mechanical pushers. The parts are then transported via conveyors to the next stages of the process. Automated inspection systems, such as vision systems and coordinate measuring machines, check the parts for defects like cracks, wrinkles, or dimensional inconsistencies. Parts that don’t meet specifications are automatically rejected, ensuring that only quality parts proceed to the next step.
For parts with excess material, an automated trimming station removes the excess through cutting or punching, shaping the part further. Some parts may also go through additional finishing processes like deburring or edge rounding, all carried out by automated systems to maintain precision and reduce manual labor. After trimming, parts are often cleaned in ultrasonic cleaning systems or industrial washing stations to remove lubricants and other residues before any surface coatings are applied. The final step typically involves packaging the parts for shipment, which is often automated, ensuring that the finished products are packaged efficiently for delivery.
The key benefits of automated deep drawing production lines include high throughput, consistent quality, and reduced labor costs. With the entire process integrated, from blank feeding to packaging, these systems minimize downtime and improve efficiency. By automating the handling, lubrication, inspection, and finishing stages, manufacturers can maintain high-quality standards while reducing manual intervention, making the process ideal for high-volume production.
Continuing from where we left off, an automated deep drawing production line offers significant benefits in terms of efficiency, cost-effectiveness, and scalability. The integration of robotics and automated systems minimizes human error and improves consistency across large production runs. For example, robotic arms in these systems can handle the delicate task of positioning blanks into dies with high precision and speed, eliminating the risk of misalignment and improving cycle time.
In addition to handling blanks, robotic systems can be used for automated lubrication application, ensuring even coverage and reducing wastage of lubricant. The lubrication not only helps to reduce friction but also minimizes wear on the dies and punches, extending their lifespan and reducing downtime for maintenance. Some systems even have automatic lubrication management that adjusts based on the type of material being processed or the drawing process stage, optimizing both lubrication quality and cost.
The automation of part inspection through vision systems and sensor technology is another significant advancement in deep drawing lines. Automated inspection not only checks for visual defects such as cracks or scratches but also measures critical dimensions of the drawn parts. This includes evaluating wall thickness, roundness, and overall dimensional tolerance. If a part fails inspection, it is automatically diverted off the line for rejection, saving time and materials compared to manual inspection methods. In some advanced systems, in-line quality control using X-ray or ultrasonic testing can be implemented to detect internal defects that would be invisible to traditional inspection methods.
Once the part has passed inspection and trimming, finishing operations like deburring (removal of sharp edges or small metal fragments) and polishing are automated. Automated machines can perform these tasks at high speeds while maintaining tight tolerances, ensuring the parts are smooth and ready for final application or coating.
Surface coating, such as painting, galvanizing, or anodizing, is also a key part of the automated deep drawing production line, especially for parts that require additional protection or a finished appearance. These lines often integrate spray booths, robotic arms, or dipping tanks to apply coatings consistently. For example, if the parts are to be coated with a corrosion-resistant layer, an automated system can ensure even coating thickness and proper drying time, reducing the need for human labor and enhancing the quality of the final product.
The final stage of an automated deep drawing line involves packaging and shipping, where finished parts are automatically stacked, boxed, or palletized for shipment. Conveyor systems guide the parts to automated packaging stations, where the parts are grouped, labeled, and wrapped for shipping. These systems often include robotic pick-and-place units for precise placement into shipping containers, ensuring that the parts are well-protected during transportation.
By automating these stages, manufacturers can significantly reduce the labor required for each part of the production process, improve overall cycle time, and increase throughput. The use of integrated systems allows for quicker adjustments to production runs, meaning that the line can handle a range of products with minimal setup time. This is especially beneficial in industries that require both flexibility and high volume, such as the automotive, aerospace, and consumer goods sectors.
The integration of real-time data monitoring and predictive maintenance technologies can further enhance the efficiency of the production line. Sensors embedded in machines can track parameters like temperature, pressure, and vibration, alerting operators to potential issues before they cause significant downtime. This predictive maintenance reduces unexpected failures and extends the life of expensive equipment like presses and dies.
Building on the previous discussion, let’s dive into some of the more advanced technologies and systems that are commonly found in automated deep drawing production lines to ensure maximum efficiency, product quality, and reliability.
One of the key technologies that enhances the functionality of an automated deep drawing line is the use of advanced press technologies. These presses are typically hydraulic or mechanical presses that provide the high force necessary for deep drawing operations. Hydraulic presses are known for their versatility, as they offer variable speed and force control, making them ideal for different types of materials and drawing depths. On the other hand, mechanical presses are faster and more suitable for high-speed production lines, as they can deliver a consistent force with less variation.
In many modern systems, presses are coupled with servo-driven actuators for greater control over the stroke, speed, and force applied during the drawing process. Servo presses allow for real-time adjustments during the drawing operation, optimizing the forming process to reduce defects such as wrinkles, cracks, or tearing, which are common challenges in deep drawing. This precision leads to better material usage, minimizing waste, and ensuring parts meet stringent quality standards.
In-line sensors are another critical element of advanced automated deep drawing systems. These sensors monitor the entire process in real time and provide feedback to the system. For instance, force sensors installed on the punch and die can monitor the amount of force being applied during the deep drawing process. This feedback can be used to adjust the press’s force, preventing damage to the material and die. Additionally, thickness sensors help monitor wall thickness throughout the drawing process, ensuring that the part maintains uniformity and quality across its entire surface.
In material handling, vision systems are commonly used to automatically position blanks and ensure they are accurately aligned in the die before the press cycle begins. These systems can also detect misfeeds or any material defects that could lead to production delays or defective parts. If a problem is detected, the system can either reject the part automatically or alert operators to take corrective action.
Coolant and lubrication management is another area where automation plays a crucial role. In older systems, lubrication may have been a manual process or simply a routine spray, but in modern lines, lubrication is highly controlled through automated systems. This includes centralized lubrication systems, which deliver precise amounts of lubricant to different parts of the machine, especially in the punch-die interface. The correct application of lubricant reduces wear and tear on the tooling, extends the life of the press, and ensures a smoother forming process. Moreover, the lubrication system can be linked to real-time monitoring systems, which adjust lubrication based on the materials being processed and the specific needs of the drawing stage.
In terms of maintenance, predictive technologies are revolutionizing how downtime is managed. Condition-based monitoring systems equipped with sensors provide real-time data on the health of critical equipment like punches, dies, and presses. These systems can track parameters like temperature, vibration, and pressure, which are often the first indicators of potential failure. Using this data, the system can predict when a component is likely to fail, allowing operators to replace or service the equipment before a failure occurs. This approach, often called predictive maintenance, significantly reduces unplanned downtime and maintenance costs, ensuring the line remains in operation for longer periods.
Moreover, data collected from sensors throughout the process can be sent to a central Manufacturing Execution System (MES), which provides an overview of the entire production line. The MES collects data on machine performance, part quality, cycle times, and material usage, and provides operators with actionable insights. These insights can help optimize the workflow, reduce bottlenecks, and improve overall line efficiency.
One significant advantage of automated deep drawing production lines is their ability to easily accommodate small batch production runs or variations in part designs. While traditional deep drawing lines require substantial downtime and manual intervention to adjust for new part designs, automated systems allow for quick changeovers. This flexibility is achieved through the use of robotic part loading systems, quick-change tooling setups, and programmable presses that can automatically adjust stroke and force parameters depending on the new part being produced. In many cases, automated lines can even handle multiple different part sizes and designs within a single production run, making them highly adaptable.
Energy efficiency is also a focus in modern automated deep drawing systems. Hydraulic presses, while energy-intensive, have become more efficient thanks to variable displacement pumps and energy recovery systems that capture and reuse energy during the press cycle. Similarly, automated lubrication systems and cooling systems help ensure that energy consumption is kept in check by only operating when needed, further contributing to sustainability in manufacturing.
Finally, integrated robotics and AI-based control systems allow the deep drawing line to operate with minimal human oversight. These systems can autonomously adjust to changes in material properties, detect part defects, and even optimize the drawing process in real time. Artificial intelligence algorithms can analyze historical production data to predict the best settings for new material batches, optimizing each part of the process for efficiency and quality.
Overall, an automated deep drawing production line is designed to ensure that manufacturers can produce complex, high-quality parts at high volume with minimal human intervention. The integration of robotics, AI, advanced sensors, and predictive maintenance technologies ensures that the production process is more efficient, consistent, and adaptable, while also reducing costs and improving product quality.
Four-Column Deep Drawing Press
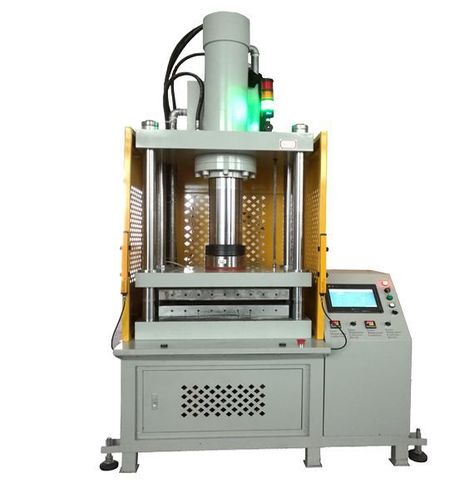
A Four-Column Deep Drawing Press is a type of mechanical or hydraulic press specifically designed for deep drawing operations, where metal sheets are formed into deep, hollow shapes. This type of press gets its name from the four vertical columns that support the press structure, providing stability, strength, and precision during the deep drawing process.
Key Features and Components of a Four-Column Deep Drawing Press:
- Four-Column Frame Structure:
- The press’s four-column design provides a stable and rigid framework that supports the ram (punch), die, and other components. These columns help distribute the load evenly, making the press suitable for high-force applications, such as deep drawing.
- The structure ensures that the vertical movement of the ram is aligned and stable, minimizing any deviations in the part geometry.
- Pressing Mechanism (Hydraulic or Mechanical):
- The pressing action is typically provided by hydraulic cylinders or mechanical systems. In a hydraulic four-column press, hydraulic cylinders are used to apply force to the ram. The advantage of a hydraulic system is its ability to offer precise force control over the entire stroke, making it ideal for deep drawing, which requires varying force levels throughout the forming process.
- Mechanical presses, while faster and more rigid, are less flexible when it comes to force adjustments and are generally used in high-speed stamping rather than deep drawing.
- Die and Punch Setup:
- The die set is positioned on the lower portion of the press and forms the cavity into which the blank is drawn. The punch (ram) is mounted above the die and moves downward to pull the material into the die, forming the part.
- In four-column presses, both the die and punch are aligned vertically with precision, ensuring that the material is drawn consistently without warping or damage.
- Stroke and Force Control:
- The press allows for adjustable stroke length and force settings, which is essential for deep drawing processes that involve materials of varying thicknesses or hardness. By adjusting the stroke, the operator can control how deeply the material is drawn and how much force is applied during each step of the process.
- In hydraulic presses, the stroke can be finely controlled by adjusting hydraulic pressure. In mechanical presses, stroke control is usually limited to pre-set options, but force control can still be achieved by adjusting the ram speed and ram displacement.
- Guiding Mechanism:
- Guides are used to ensure the ram (punch) moves vertically along the four columns without lateral deviations. This precision is crucial, as even minor misalignment can result in defects like wrinkles, uneven thickness, or part failure during drawing.
- Linear guides or roller guides are often employed to reduce friction and ensure smooth, precise motion of the punch.
- Safety and Monitoring Systems:
- Four-column deep drawing presses are typically equipped with safety features such as light curtains, pressure sensors, and emergency stop buttons to protect operators and prevent accidents during operation.
- Force and position sensors can also be incorporated into the system to monitor the press’s operation, ensuring that the correct amount of force is applied at each stage of the forming process.
- Automation Integration:
- Four-column presses can be integrated with automation systems, including robotic arms for part loading and unloading, and conveyor systems for part handling throughout the production line. Automated blank feeders and die changers can also be used to improve efficiency and reduce manual intervention.
- Computer Numerical Control (CNC) or PLC-based control systems enable the press to follow precise part specifications, adjust parameters automatically based on material properties, and even adjust for different part designs without requiring manual retooling.
- Applications of Four-Column Deep Drawing Presses:
- These presses are often used in industries that require high-quality, precision-formed parts, such as automotive, aerospace, appliance manufacturing, and industrial equipment. Common parts include automotive body panels, metal cans, pressure vessels, kitchen sinks, and electrical enclosures.
- Four-column presses are particularly suitable for large, complex parts that require high forming force and precision. They excel in situations where parts have relatively deep profiles, requiring a press capable of applying a large, consistent force over the entire stroke.
Advantages of Four-Column Deep Drawing Presses:
- High Force Capability:
- The four-column structure provides enhanced strength and stability, allowing the press to apply the necessary high force required for deep drawing operations. This makes it suitable for thick materials and larger parts.
- Precision and Alignment:
- The four-column setup ensures precise alignment of the die and punch, leading to consistent quality and uniform part formation.
- Flexibility:
- The adjustable stroke length and force control make the four-column deep drawing press versatile for different materials and part designs. It can handle various thicknesses and hardness levels of materials without the need for retooling or major adjustments.
- Customization and Automation:
- The press can be easily integrated into automated production lines, which increases throughput, reduces human error, and improves overall efficiency. Automation systems can handle part feeding, lubrication, inspection, and part unloading, leading to faster cycle times and lower labor costs.
- Durability and Longevity:
- Due to their robust construction, four-column presses are designed for long-term use, even under the intense pressure of deep drawing. This durability reduces the need for frequent maintenance or replacement, providing a solid investment for high-volume manufacturers.
Potential Drawbacks:
- High Initial Investment:
- Four-column deep drawing presses can be costly to purchase and set up, especially when integrating advanced features like automation or hydraulic systems. However, this is often offset by the high throughput and reduced labor costs over time.
- Space Requirements:
- The four-column frame design requires a significant amount of space to accommodate the press, especially when used in larger configurations for producing big parts. This might require specialized facilities or larger production floors.
- Maintenance Complexity:
- The press’s intricate components, such as the hydraulic systems, guides, and sensors, require regular maintenance to ensure optimal performance. However, predictive maintenance systems can help mitigate unexpected downtime.
Conclusion:
The Four-Column Deep Drawing Press is an advanced, reliable machine that plays a vital role in the production of complex, high-quality formed metal parts. Its ability to provide consistent force, precision, and adaptability makes it a staple in high-performance manufacturing environments, particularly in industries that require intricate metal forming. The press’s ability to integrate with automation systems further enhances its efficiency and flexibility, making it an ideal choice for manufacturers looking to increase production speed and minimize human error.
A Four-Column Deep Drawing Press is built to handle the intense forces required to transform flat metal sheets into deep, intricate shapes, commonly used in industries like automotive, aerospace, and appliance manufacturing. The press operates by using four vertical columns to support and stabilize the press frame, ensuring precise alignment and minimal distortion during operation. This robust design allows for high-tonnage applications, ideal for forming thicker materials or producing larger parts. The frame supports a punch (ram) that applies force to a metal blank, pulling it into a die to form the desired part. The ability to adjust force and stroke length makes this press highly adaptable to different materials, thicknesses, and shapes.
One of the standout features of the Four-Column Deep Drawing Press is its versatility, as it can handle a wide range of part geometries, including deep and complex profiles. The system can be customized to accommodate varying part sizes, and hydraulic or mechanical systems provide the necessary force to ensure high-quality, consistent output. In addition, precise control over the drawing force is possible, which is essential for preventing material defects such as cracks or wrinkles. Furthermore, automation plays a significant role in enhancing efficiency, as robotic arms and conveyor systems can feed, transfer, and unload parts, reducing human labor and improving cycle times.
These presses are typically equipped with sensors and monitoring systems to ensure optimal operation. Force and position sensors monitor the punch’s movement, providing real-time data that helps prevent overloading or misalignment. This data can also be integrated with predictive maintenance systems, which alert operators to potential issues before they lead to unplanned downtime. Automated lubrication systems ensure that the die and punch are consistently lubricated, reducing friction and wear, which prolongs the life of the tooling and helps maintain part quality.
Although the Four-Column Deep Drawing Press offers significant advantages in terms of force, precision, and flexibility, there are some drawbacks to consider. The initial investment can be high, particularly if you incorporate advanced automation or hydraulic systems. The press also requires a considerable amount of space due to its large frame, making it less suitable for smaller production areas. Regular maintenance is crucial for maintaining performance, as components such as hydraulic systems, guides, and sensors need to be serviced to prevent breakdowns. However, these challenges can be mitigated with proper planning and investment in predictive maintenance technologies.
In summary, the Four-Column Deep Drawing Press is an essential piece of equipment for manufacturers who need to produce high-quality, complex metal parts at high volumes. Its combination of force, precision, and adaptability makes it ideal for industries where part integrity and consistency are critical. The integration of automation, monitoring systems, and predictive maintenance further enhances its efficiency, making it a valuable asset in modern manufacturing lines.
As the demand for more complex, high-quality metal parts continues to rise, the Four-Column Deep Drawing Press stands out as an essential tool for manufacturers aiming to keep up with production demands while maintaining high standards of precision and efficiency. The press’s ability to handle deep, intricate forming with uniform quality makes it an ideal choice for industries such as automotive, aerospace, and even the production of consumer goods.
While the Four-Column press excels at deep drawing, it also offers flexibility in terms of part design. It can handle a variety of materials, from soft metals like aluminum to harder materials like stainless steel. The press can be adjusted to accommodate different material properties, thicknesses, and hardness, making it versatile across a range of applications. This adaptability is particularly beneficial in industries where product designs constantly evolve, and flexibility is crucial to staying competitive.
One of the emerging trends in Four-Column Deep Drawing Presses is the integration of smart manufacturing technologies. These presses are increasingly equipped with real-time data analytics, allowing operators to monitor key performance indicators such as force application, stroke length, material flow, and even tool wear. These systems use sensors and cameras to collect data, which is then analyzed using AI and machine learning algorithms. By processing this data, the system can identify patterns, predict potential issues, and suggest adjustments to optimize the production process.
Machine learning algorithms can also help improve part quality by learning from previous drawing cycles. These algorithms can detect subtle changes in material properties and adjust the press parameters in real time to avoid defects, such as wrinkling or tearing. The incorporation of these AI-driven tools enhances the press’s ability to adapt to different conditions and materials, improving both efficiency and product quality. This level of automation and intelligence leads to fewer defects, reduced waste, and increased overall productivity.
Additionally, the trend of energy efficiency has become increasingly important in modern manufacturing. The energy consumption of a Four-Column Deep Drawing Press can be significant, especially when operating at full capacity. However, modern hydraulic systems and advanced control mechanisms have made significant strides in reducing energy usage. Many new systems are equipped with energy recovery features, such as regenerative drives, which capture and reuse energy during the press cycle. This not only helps reduce operational costs but also aligns with sustainability goals by lowering the environmental impact of manufacturing processes.
Another key consideration is the maintenance of the press. Predictive maintenance technologies, already embedded in many modern presses, continuously monitor the condition of the press and its components. By collecting data on things like vibration, temperature, and hydraulic pressure, these systems can predict when maintenance is required, preventing unscheduled downtime. This is a major advantage for manufacturers, as it allows them to plan maintenance around production schedules, reducing costly disruptions and ensuring the press operates at optimal efficiency.
Moreover, the safety features on Four-Column Deep Drawing Presses have evolved significantly over the years. In addition to traditional safety guards and emergency stop buttons, many presses now feature robotic safety systems such as light curtains and laser scanners. These systems can detect the presence of operators or obstacles within the press area, automatically stopping the press before any harm can occur. These innovations not only improve safety but also contribute to a more streamlined, automated production process by reducing human intervention.
In terms of flexibility, some Four-Column presses are now equipped with quick-change tooling systems, allowing manufacturers to switch between different part designs with minimal downtime. The tooling can be swapped automatically, and the press can adjust to the new design parameters, such as stroke length and force, with little to no manual input. This makes it easier to transition between different production runs, which is particularly beneficial in industries that produce a variety of parts in small to medium batches.
Lastly, the integration of robotic automation into the deep drawing process is helping improve both production efficiency and quality. Robotic arms are used to load and unload parts, position blanks accurately in the die, and remove finished parts from the press. These systems can also assist with secondary operations such as part cleaning or sorting. The use of robots minimizes human handling, reducing the risk of part contamination, misalignment, and injury, while also speeding up production cycles.
In conclusion, the Four-Column Deep Drawing Press is a critical piece of equipment in modern manufacturing, offering precision, adaptability, and high force capabilities for forming complex metal parts. As technology advances, these presses continue to evolve, integrating smart technologies, automation, and energy-saving features that optimize production processes. With the added benefits of predictive maintenance and enhanced safety systems, Four-Column presses are now more efficient, reliable, and capable than ever before, making them an indispensable asset for high-volume, high-precision manufacturing operations.
H-Frame Deep Drawing Press
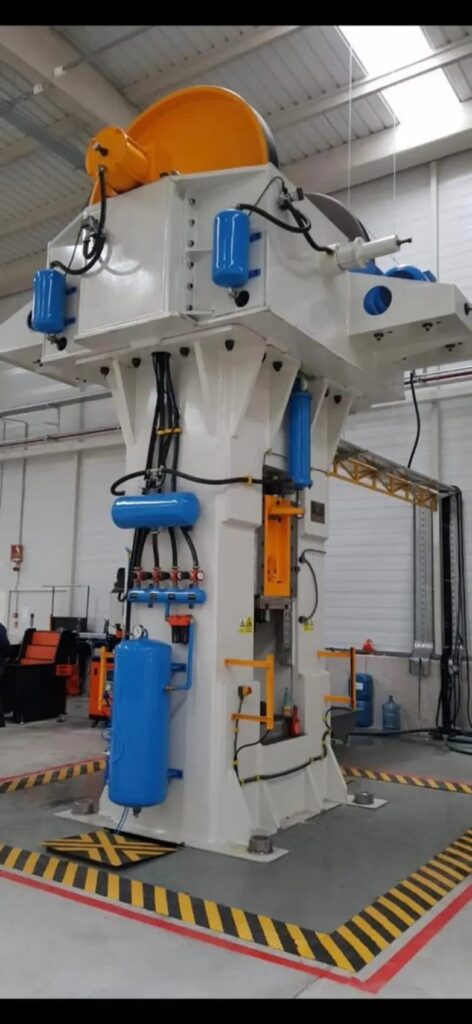
An H-Frame Deep Drawing Press is another type of press used in metal forming, specifically for deep drawing operations, where flat metal sheets are transformed into deep, hollow shapes. The primary difference between the H-Frame press and the more commonly used Four-Column press lies in the frame structure. As the name suggests, the H-Frame press features a frame shaped like the letter “H,” where two vertical columns are connected by horizontal cross members. This design provides the press with a strong and stable frame capable of withstanding high forces during the drawing process.
Key Characteristics of an H-Frame Deep Drawing Press:
- H-Frame Design:
- The H-Frame design consists of two vertical columns connected by a crossbeam or bridge, forming an “H” shape. This configuration provides a robust, rigid structure that distributes the load evenly during the drawing operation.
- The H-Frame press tends to have a more open design compared to the Four-Column press, which can offer better accessibility to the tooling area and facilitate easier maintenance and part handling.
- Hydraulic or Mechanical Drive:
- Similar to the Four-Column press, H-Frame presses are usually powered by either hydraulic systems or mechanical drives.
- Hydraulic systems offer flexibility by providing adjustable force and stroke length, which is essential for handling varying material types, thicknesses, and drawing depths.
- Mechanical systems, typically used for high-speed operations, deliver constant force and are more efficient for quicker, repetitive drawing cycles.
- The hydraulic version, in particular, provides the versatility needed for deep drawing processes where varying force levels are necessary throughout the cycle.
- Similar to the Four-Column press, H-Frame presses are usually powered by either hydraulic systems or mechanical drives.
- Force Application:
- The press uses a ram (punch) that moves vertically, pushing the material into the die to form the desired part. The H-Frame design ensures that the punch remains aligned and that force is applied uniformly to prevent material defects such as cracking or tearing.
- Force control in an H-Frame press can be adjusted to suit the specific material being processed. Some advanced systems include variable displacement pumps or servo-controlled hydraulics to provide precise control of the force, which is vital for the consistency and quality of the formed parts.
- Open Frame Design:
- The H-Frame’s open structure makes it particularly well-suited for large and heavy parts. Its design allows for easier loading and unloading of parts, especially for applications requiring large metal blanks. The open structure also facilitates tool changeover and maintenance access, allowing operators to reach the die and punch areas more easily.
- The lower part of the frame provides additional space for handling equipment or auxiliary machinery such as automatic blank feeders or part stacking systems, enhancing the press’s ability to integrate into a fully automated production line.
- Precision and Alignment:
- H-Frame presses are equipped with guides and alignment mechanisms that ensure the punch and die remain aligned during operation. This helps prevent defects like misformed parts, uneven wall thickness, and material wrinkling.
- In some models, linear guides or roller guides are used to reduce friction and ensure smooth, precise movement of the punch. The rigidity of the frame ensures that the punch applies force in a straight, uniform motion, contributing to the consistent quality of the drawn parts.
- Customization and Flexibility:
- One of the major advantages of the H-Frame design is its customizability. The press can be tailored to accommodate different die sizes, material thicknesses, and part geometries. Adjustments to stroke length, force, and speed can be made quickly to adapt to different production runs, making H-Frame presses suitable for both high-volume and small-batch production.
- The ability to quickly swap tooling and adjust press settings makes H-Frame presses well-suited for industries where part designs frequently change or where there is a need for flexible manufacturing.
- Automation and Integration:
- H-Frame presses can be easily integrated into automated production lines with robotic arms, conveyor systems, and automatic die changers. This integration improves production efficiency, reduces human error, and minimizes downtime between different production runs.
- The press can be equipped with vision systems for automatic part inspection, ensuring that only quality parts move through the production process. Additionally, automated part handling systems can load and unload parts, reducing manual labor and increasing throughput.
- Energy Efficiency and Cost Considerations:
- The energy efficiency of an H-Frame press depends on the hydraulic or mechanical system in use. Hydraulic presses can be optimized for energy use with features like energy recovery systems, which capture and reuse energy during the pressing cycle.
- Servo-driven hydraulic systems are becoming increasingly common in modern H-Frame presses. These systems offer energy savings by using only the energy required for each specific operation, adjusting the force and stroke length dynamically based on the material being processed.
Advantages of an H-Frame Deep Drawing Press:
- Strong Structural Design: The H-Frame press provides excellent support and load distribution during deep drawing, ensuring uniform force application and preventing deflection that could lead to defects.
- Ease of Maintenance and Tooling Changeover: The open frame structure provides easy access to tooling, reducing downtime and maintenance costs. The large space underneath the frame also allows for the addition of auxiliary systems, like automated part handling equipment.
- Customizability and Flexibility: H-Frame presses can handle a wide range of material types and part designs, making them adaptable to different production needs. The quick changeover of tools and settings allows for efficient switching between different jobs or products.
- Higher Production Speed: With the integration of automation systems and fast cycle times in mechanical models, H-Frame presses can produce high volumes of parts at a faster pace, reducing overall production costs and increasing throughput.
Disadvantages:
- Space Requirements: Like other large presses, the H-Frame design requires considerable floor space. The open frame structure, while beneficial for maintenance and part handling, can be cumbersome in smaller production environments.
- Initial Investment: The cost of purchasing and setting up an H-Frame press can be substantial, especially if the press is equipped with advanced features like automated systems, servo-driven hydraulics, and smart monitoring systems. However, this is often offset by the long-term efficiency gains and lower operational costs.
- Energy Consumption in Hydraulic Models: While energy-saving features can be added, traditional hydraulic presses tend to be more energy-intensive compared to mechanical systems, especially when running high-force operations.
Applications of H-Frame Deep Drawing Presses:
H-Frame Deep Drawing Presses are widely used in industries where large, complex metal parts are required. These include:
- Automotive Manufacturing: For producing parts like car body panels, chassis components, and engine parts that require precise forming under high force.
- Aerospace Industry: For parts such as fuel tanks, aircraft panels, and structural components, where precision and material strength are critical.
- Consumer Goods: For the production of kitchenware, metal cans, and appliances, which require deep drawing of thin-gauge metals into precise, uniform shapes.
- Heavy Equipment Manufacturing: For forming large parts like hydraulic cylinders and pressure vessels, where high forces are needed.
Conclusion:
The H-Frame Deep Drawing Press is a versatile and robust piece of equipment well-suited for deep drawing operations that require high force and precision. Its open, customizable design, ease of maintenance, and ability to integrate with automated systems make it a valuable tool in industries producing large, complex metal parts. While there are some drawbacks, such as space requirements and initial investment costs, the benefits of improved flexibility, efficiency, and production speed make the H-Frame press a strong choice for manufacturers looking to optimize their deep drawing processes.
The H-Frame Deep Drawing Press stands out for its versatility in metal forming, particularly in deep drawing applications where large, complex parts need to be created. The “H” frame design, characterized by two vertical columns connected by horizontal cross members, provides a stable and rigid structure capable of handling high forces during the drawing process. This makes it ideal for industries requiring precision in forming thick materials or parts with intricate shapes, such as automotive, aerospace, and appliance manufacturing.
The press operates by using a ram (punch) that moves vertically, pushing the material into a die. The H-Frame’s design ensures that the punch stays aligned, and the force applied to the material is evenly distributed, preventing issues such as wrinkles or material tearing. Its ability to accommodate high-tonnage applications allows it to handle tough, thick materials or parts that demand substantial forming forces. The hydraulic system, in particular, offers great flexibility, as the force and stroke length can be adjusted depending on the material and the specific part requirements. This ensures that the press can adapt to different part geometries and material properties, making it suitable for both high-volume production and smaller batch runs.
One of the major advantages of the H-Frame press is its open structure. Unlike the Four-Column press, which may have a more enclosed design, the H-Frame press offers easier access to tooling, making maintenance and tool changes more efficient. The ability to swap tools quickly is a significant benefit, especially for operations that require frequent adjustments between different part designs. This open frame also facilitates the integration of automated systems, such as robotic arms or conveyor belts, which can improve overall production efficiency by reducing manual labor, enhancing speed, and reducing the chances of human error.
The flexibility in the H-Frame design also extends to energy efficiency. Although hydraulic presses typically consume more energy than mechanical presses, modern H-Frame presses can incorporate energy-saving features like regenerative drives. These systems recover and reuse energy during the pressing cycle, helping to lower operational costs and make the press more environmentally friendly. The integration of servo-driven hydraulic systems further boosts energy efficiency by adjusting the amount of energy used depending on the specific operation, which reduces unnecessary energy consumption.
The automation potential of the H-Frame press can significantly increase throughput. Automated material handling systems, such as robotic feeders and stackers, can load blanks into the die, unload finished parts, and even perform secondary operations such as cleaning or inspection. This reduces the need for human intervention and speeds up the production cycle. Additionally, advanced monitoring and diagnostic tools can be integrated into the system, offering real-time feedback on the press’s performance. This allows operators to make adjustments on the fly, improving both product quality and machine efficiency.
However, the H-Frame press does come with some considerations. Due to its larger frame, it requires significant space, which may not be ideal for smaller production facilities. The cost of acquiring and setting up the press can also be considerable, particularly when equipped with advanced automation or servo-controlled systems. Despite these challenges, the long-term benefits of higher production speeds, reduced downtime, and improved part quality make the H-Frame press a worthwhile investment for manufacturers.
In terms of applications, the H-Frame press excels in sectors like automotive and aerospace, where parts need to be formed with high precision and strength. Components such as automotive body panels, fuel tanks, and structural parts are commonly produced using H-Frame presses. The open design of the press also makes it suitable for larger components, such as pressure vessels and industrial enclosures, where accessibility and tool changeover are critical for maintaining efficiency.
The continued evolution of H-Frame Deep Drawing Press technology, with smart features, energy-saving systems, and integration with automation, further enhances their role in modern manufacturing. Manufacturers are increasingly looking for ways to maximize productivity while maintaining high quality and minimizing environmental impact, and the H-Frame press delivers on all these fronts. The press offers the strength, adaptability, and efficiency required to keep pace with the ever-evolving demands of high-volume, precision manufacturing, making it a crucial asset in industries that rely on deep drawing processes.
The H-Frame Deep Drawing Press continues to be an essential tool in the production of high-quality metal components, particularly in industries that require precision and large-scale production. Its design, offering both robustness and flexibility, ensures it remains a reliable choice for complex, high-tolerance parts. The ability to handle large sheets of metal and apply substantial force while maintaining precise control over the drawing process makes it indispensable for creating parts with deep, intricate shapes.
Moreover, the integration of advanced sensors and monitoring systems is increasingly enhancing the capabilities of the H-Frame press. These systems provide real-time feedback on critical parameters such as force, stroke, material flow, and die condition. This continuous monitoring ensures that the press is running at peak efficiency, helps detect any anomalies in the drawing process, and can prevent part defects before they occur. It also allows for quicker adjustments in force and stroke, which can reduce scrap and improve overall quality. This predictive capability also leads to better quality control, ensuring that each part meets the exact specifications required.
The increased use of robotics in H-Frame presses further increases their efficiency. In addition to loading and unloading parts, robotic systems can now be used for more advanced tasks such as real-time inspection, sorting, and even post-forming operations like trimming or cleaning. The reduced reliance on human operators minimizes the risk of errors or injuries and speeds up the overall production process. The ability to automate these tasks also ensures consistency and repeatability, crucial for high-volume operations.
Furthermore, customization remains a key benefit of the H-Frame press. Different industries often require unique configurations of the press based on the specific materials they are working with or the types of parts they need to produce. The open design of the H-Frame allows for easy modifications and adjustments, such as varying the stroke length, force, or die configuration. These modifications can often be made quickly, improving flexibility and reducing downtime when switching between production runs.
As manufacturers strive for sustainability, the H-Frame press’s energy efficiency becomes increasingly important. The integration of energy-saving technologies, such as servo-driven systems and regenerative drives, ensures that the press operates more efficiently, consuming only the power required for each specific operation. This not only reduces the energy footprint but also lowers operational costs, making the press more cost-effective over time. Additionally, energy recovery systems can be used to harness and reuse energy during the operation, which further reduces waste and maximizes efficiency.
Safety is also a growing concern in modern manufacturing, and the H-Frame press incorporates a variety of safety features to protect operators and prevent accidents. In addition to traditional safety guards and emergency stop buttons, the press may include laser sensors, light curtains, and safety mats that detect the presence of operators or objects in the danger zone. If an obstruction is detected, the press can automatically stop or slow down, preventing injury or damage to the press itself. This high level of safety enhances both productivity and worker confidence in the production environment.
Another important consideration is maintenance. As with any large machine, the H-Frame press requires regular upkeep to ensure it continues to perform optimally. Predictive maintenance systems, which use real-time data to predict when a component might fail, are becoming increasingly common. By analyzing data from sensors monitoring vibration, temperature, pressure, and other metrics, these systems can forecast potential issues and notify operators in advance. This allows for proactive maintenance, reducing downtime and extending the life of the press.
With the ongoing demand for more efficient, sustainable, and customizable manufacturing processes, the H-Frame Deep Drawing Press continues to be an important solution for manufacturers. The combination of strength, precision, and flexibility, coupled with the integration of smart technologies, automation, and energy-saving features, ensures that this press will remain a key asset for years to come. It is particularly effective in industries like automotive, aerospace, and heavy machinery, where high-quality metal parts are critical and where production volumes require both speed and consistency.
In summary, the H-Frame Deep Drawing Press represents a robust, flexible, and efficient solution for the forming of deep-drawn metal parts. Its design ensures it can handle large, complex parts while maintaining precision, and its adaptability to automation, energy efficiency, and predictive maintenance technologies allows manufacturers to stay competitive in an increasingly demanding marketplace.
As industries continue to push for higher production rates, improved quality, and greater sustainability, the H-Frame Deep Drawing Press remains a crucial tool in the evolution of manufacturing. One area where the H-Frame press is particularly making an impact is in smart manufacturing. The shift toward digitalization and Industry 4.0 has led to the integration of advanced data analytics, machine learning, and the Internet of Things (IoT) into production processes. In the context of H-Frame presses, this means real-time monitoring and control over every aspect of the operation.
By utilizing IoT sensors, manufacturers can collect valuable data from the press’s various components. These sensors can monitor the condition of the hydraulic system, detect irregularities in pressure or temperature, and track the wear on dies or punches. This constant flow of data is fed into a central control system where it can be analyzed. If any issues are detected—such as excessive wear on a die or an anomaly in the material flow—the system can automatically adjust parameters to correct the problem or notify the operator of the need for maintenance. This level of real-time feedback enhances not only the efficiency of the press but also the overall quality of the parts being produced, reducing scrap and rework.
Additionally, machine learning algorithms can be applied to the collected data to identify trends and patterns. For example, an algorithm might learn the optimal settings for a given material type, thickness, or geometry based on previous production runs. Over time, the system can refine these settings to achieve even better outcomes, automatically adjusting the press’s parameters without the need for human intervention. This can lead to more consistent part quality and a reduction in defects, as the press continuously adapts to changing production conditions.
The predictive maintenance capabilities of modern H-Frame presses are another critical aspect of their efficiency. As the press operates, it generates wear and tear on components like hydraulic valves, seals, and dies. Traditional maintenance schedules often rely on fixed intervals, which can lead to unnecessary maintenance or unplanned downtime. With predictive maintenance, however, the press can monitor its own condition and alert operators to potential issues before they cause a failure. For example, if the vibration level of a hydraulic pump exceeds a certain threshold, the system can flag this as a potential problem and recommend maintenance before the pump fails completely. This approach minimizes downtime and maximizes the lifespan of critical components, leading to a more reliable and cost-effective operation.
In addition to predictive maintenance, remote monitoring has become an essential feature of modern H-Frame presses. Operators and managers can access data on the press’s performance from virtually anywhere, using cloud-based systems or mobile apps. This enables real-time performance tracking and troubleshooting from remote locations, allowing for quick intervention if necessary. This also facilitates centralized control for manufacturers with multiple facilities, allowing them to monitor the status of presses across different plants from a single location. With this level of connectivity, manufacturers can optimize their operations even more effectively and respond quickly to any issues that arise, improving both uptime and productivity.
The integration of robotic automation continues to complement the performance of the H-Frame press. As robotic systems evolve, they are increasingly capable of performing complex tasks such as precise material placement, post-forming operations, and quality inspection. These robots work alongside the press, enhancing its capabilities and reducing the need for human involvement in repetitive or dangerous tasks. For example, after a part is drawn, a robotic system might inspect the part for defects using high-resolution cameras and AI-driven vision systems. If defects are detected, the part can be automatically sorted out for rework, ensuring only the highest-quality products move through the production line.
Energy efficiency continues to be a major consideration for manufacturers seeking to reduce operational costs and meet environmental standards. The integration of servo-driven hydraulic systems into the H-Frame press is a key innovation in this area. Servo drives allow for precise control over the press’s force and stroke, delivering only the required amount of energy for each specific task. This is in stark contrast to traditional hydraulic systems, which may use constant energy flow regardless of the task. By reducing unnecessary energy consumption, servo-driven systems help manufacturers save on operating costs and reduce their carbon footprint, aligning with broader sustainability goals.
The push for sustainability is not just limited to energy savings but also extends to material usage. H-Frame presses, with their ability to form complex shapes with minimal material waste, are an excellent tool for industries that are working toward zero-waste or reduced-material usage goals. The precision offered by these presses minimizes the amount of scrap generated during the forming process, which not only reduces material costs but also helps in recycling efforts by making it easier to recover and reuse metal scrap.
On a global scale, manufacturers are increasingly seeking ways to optimize supply chains. The H-Frame press, when integrated into a smart manufacturing system, can contribute to this optimization. With the help of digital twins (virtual replicas of the press and production process), manufacturers can simulate various production scenarios, predict supply chain disruptions, and optimize production schedules. This capability allows manufacturers to respond swiftly to changes in demand or material availability, ensuring that production stays on track and resources are used efficiently.
In conclusion, the H-Frame Deep Drawing Press is a highly capable, adaptable, and reliable tool that plays a central role in the future of metal forming. Its ability to handle large, complex parts with precision and speed is crucial in industries like automotive, aerospace, and heavy machinery. With the ongoing integration of smart technologies, robotic automation, predictive maintenance, and energy-saving features, the H-Frame press is becoming even more efficient, flexible, and sustainable. As the manufacturing landscape continues to evolve toward greater automation, digitalization, and sustainability, the H-Frame press will remain a key asset, driving productivity, reducing costs, and ensuring high-quality production for years to come.
The continuous advancements in technology further amplify the potential of the H-Frame Deep Drawing Press, allowing manufacturers to push the boundaries of precision and efficiency in ways that were previously unimaginable. As manufacturing becomes more data-driven and connected, these presses are increasingly capable of performing self-optimization through machine learning algorithms, which assess the process parameters in real-time and adjust them dynamically to ensure optimal performance. This not only increases throughput but also minimizes scrap and downtime by ensuring that the press operates within the best conditions at all times.
A key factor in this evolution is the increasing importance of digital integration across the entire production line. H-Frame presses are no longer standalone machines but are being incorporated into larger, more sophisticated digital ecosystems. These ecosystems connect machines, tools, sensors, and operators through centralized control systems, where everything is monitored and optimized simultaneously. The use of cloud computing allows for the aggregation and analysis of data across multiple machines and even multiple plants, leading to better decision-making, predictive analytics, and supply chain optimization.
Cloud-based platforms also enable manufacturers to perform more accurate production forecasting, helping them better predict when maintenance should be performed or when a machine might experience a failure. In an ideal setup, an operator or manager can receive alerts in advance, allowing them to schedule maintenance before any serious issues arise, thus reducing unscheduled downtime and increasing machine availability. These platforms also facilitate real-time collaboration between engineers, operators, and management, fostering a more agile and responsive production environment.
As Industry 4.0 continues to reshape manufacturing, the role of artificial intelligence (AI) in optimizing the H-Frame Deep Drawing Press’s operations grows increasingly important. AI can be used to analyze historical data to predict the behavior of the press under different operational conditions, such as varying material types, thicknesses, or environmental factors. This allows the press to adjust itself intelligently, reducing human intervention and ensuring that optimal force is applied at every stage of the drawing process. This capability is critical in industries where consistent, high-quality parts are crucial, such as aerospace or medical device manufacturing, where tolerances are strict, and failure can have serious consequences.
One of the most exciting prospects for the future of H-Frame presses is the integration of augmented reality (AR) for both maintenance and operational support. With AR, operators could wear smart glasses or use tablets to get real-time guidance on the press’s performance or to troubleshoot issues. By overlaying relevant data—such as force readings, stroke lengths, or maintenance history—on the operator’s field of view, AR technology can streamline troubleshooting and reduce downtime. It can also be used for training new employees by showing them how to perform maintenance tasks or adjust the settings on the press without needing a physical instructor present.
Another emerging trend is the integration of sustainability initiatives into the H-Frame press’s lifecycle. Manufacturers are increasingly focusing on reducing the environmental impact of their operations, and the H-Frame press is no exception. Beyond energy-efficient features like servo-driven hydraulics, there is a growing emphasis on reducing material waste. The precise force control and accurate part handling of modern presses help minimize material scrap during the forming process. This is particularly important in industries like automotive manufacturing, where lightweight materials such as aluminum and high-strength steel are used. The ability to minimize waste not only reduces costs but also supports the push for more sustainable, circular manufacturing processes.
As materials science continues to evolve, the H-Frame press is poised to handle an even wider array of materials, including advanced composites and high-performance alloys. The press’s adaptability to different material properties and geometries is crucial as industries push the limits of material innovation. For example, with the rise of electric vehicles (EVs), the demand for high-performance, lightweight components—such as battery enclosures and chassis components—has surged. H-Frame presses equipped with the right tooling can form these advanced materials with high precision, enabling manufacturers to meet these new demands.
The future of automation in the H-Frame press looks toward even more seamless integration into smart factories. In these environments, the H-Frame press would be just one component of a fully automated, self-adjusting production line. The press could communicate with other machines, share information with inventory systems, and receive instructions from central management systems that track customer orders and production schedules. This would enable highly flexible manufacturing systems, capable of producing small batches of customized parts at mass-production speeds. As customer demand for personalized products increases, this level of flexibility becomes essential for remaining competitive in the marketplace.
Moreover, the rise of 3D printing technology is influencing the design of press tooling and components. Tooling that is optimized through additive manufacturing could potentially reduce weight, enhance heat dissipation, and improve the efficiency of the drawing process. The combination of 3D-printed tooling and the precision of H-Frame presses may open up new possibilities for innovative part designs, especially in industries that require intricate, complex geometries that are difficult to achieve with traditional methods.
In summary, the H-Frame Deep Drawing Press is evolving alongside the latest advancements in automation, digitalization, and sustainable manufacturing. Its role in the future of industrial manufacturing will likely become even more integral as smart technologies, such as IoT, AI, and robotics, continue to integrate into its operations. These advancements will further enhance its capabilities, enabling manufacturers to produce high-quality, complex parts more efficiently and sustainably. As the press adapts to emerging materials, environmental goals, and production requirements, it will remain an essential tool in industries ranging from automotive and aerospace to electronics and beyond. The combination of force, precision, and adaptability positions the H-Frame press as a cornerstone of modern metal forming, ensuring that it continues to meet the evolving demands of high-tech manufacturing.
C-Frame Deep Drawing Press
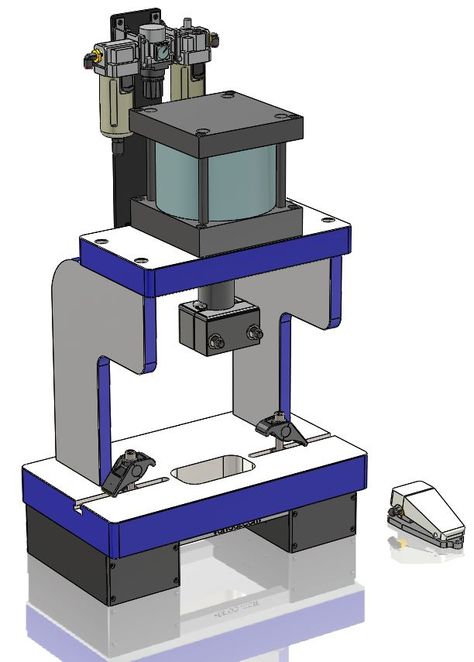
The C-Frame Deep Drawing Press is another important type of mechanical press used in the metal-forming industry, particularly for deep drawing operations. It is named for its distinctive C-shaped frame, which offers several advantages over other press configurations, such as four-column or H-frame presses. This design provides structural support while allowing for easier access to the workpiece, making it especially suitable for a wide range of applications.
Structure and Design
The C-Frame press is characterized by its single vertical frame, which forms a “C” shape. The press has a ram that moves vertically within the frame, pushing the material into a die below. The open nature of the C-frame design provides a significant advantage in terms of accessibility to both the workpiece and the tooling. This allows for easier installation and maintenance of dies, which is an important consideration in high-volume production.
The ram stroke (the distance the ram moves) and the press tonnage (the force exerted by the press) can be adjusted based on the requirements of the part being formed. This adaptability makes C-Frame presses versatile and capable of handling a wide variety of part sizes and material types. C-Frame presses are typically operated using hydraulic or mechanical systems, with hydraulic being more common due to its better control over force application and flexibility.
Advantages of the C-Frame Press
- Accessibility: One of the biggest advantages of the C-Frame design is the easy access to tooling. Since the press’s frame is open, operators can quickly swap dies, load materials, or inspect parts. This is especially beneficial in operations requiring quick tool changeovers or for smaller-scale production runs, where efficiency is key.
- Compactness: The C-Frame press is generally more compact compared to larger frame presses, making it ideal for environments where space is limited. Its design also allows it to fit into smaller factory layouts or even smaller production lines, particularly in operations that do not require the large, heavy presses found in other configurations.
- Cost-effectiveness: Compared to four-column or H-frame presses, C-Frame presses are often more affordable, both in terms of initial investment and maintenance costs. This makes them an attractive option for smaller manufacturers or those looking to expand their production without making a large financial commitment.
- Simplicity and Reliability: The C-Frame press’s simpler design makes it easy to operate and maintain. Fewer components mean less potential for breakdowns, and when issues do occur, repairs are typically straightforward. This simplicity also contributes to its reliability, making it a good option for operations that require consistent performance over time.
Applications of C-Frame Presses
C-Frame presses are typically used in medium to high-tonnage applications, particularly for deep drawing, punching, blanking, and bending operations. They are often seen in industries that require precision forming, such as:
- Automotive: C-Frame presses are used to form body panels, components like brackets, panels, frames, and chassis parts.
- Aerospace: The aerospace industry uses these presses for the production of aluminum or titanium components, such as aircraft panels or structural parts.
- Electronics: Components like casings, brackets, and connectors for electronic devices and appliances can also be produced using C-Frame presses.
- Appliances: Household appliance components, such as washing machine parts, microwave housings, and refrigerator panels, often rely on C-Frame presses for efficient forming.
Hydraulic vs. Mechanical C-Frame Presses
C-Frame presses can be categorized based on their operating mechanisms:
- Hydraulic C-Frame Presses: These presses use hydraulic cylinders to generate the force necessary for the deep drawing process. The hydraulic system allows for a more precise control over force and speed, which is beneficial when forming materials with varying thicknesses or hardness. Additionally, hydraulic systems can be designed to offer adjustable speeds, making them versatile for various forming applications.
- Mechanical C-Frame Presses: These presses use mechanical linkages, cranks, or cams to generate force. While they may not offer the same level of force control as hydraulic presses, they are often faster and more efficient for certain applications. Mechanical presses are generally more durable and better suited for high-speed operations where force consistency is less critical.
Limitations of C-Frame Presses
While C-Frame presses offer many benefits, they also have some limitations:
- Limited Tonnage Capacity: Although C-Frame presses can handle substantial tonnage, they generally cannot achieve the same high tonnage levels as larger H-Frame or four-column presses. As a result, C-Frame presses may not be suitable for extremely heavy or large-forming tasks.
- Deformation Risk: The C-shape design, while offering accessibility, can sometimes lead to structural flexibility issues, especially under high-pressure conditions. This flexibility may cause slight deformations in the press frame, potentially affecting the quality of the formed part. However, this is typically only a concern in extreme cases where the press is operating at or near its maximum tonnage capacity.
- Tooling Restrictions: While C-Frame presses are adaptable, their open structure may not be able to accommodate some larger or more complex tooling configurations compared to larger frame presses. In these cases, manufacturers might need to consider a different press design or adjust the tooling setup.
Recent Developments and Trends
- Energy Efficiency: Modern C-Frame presses are increasingly incorporating servo-driven hydraulic systems that allow for more efficient energy use. These systems only apply the required amount of force at the right time, improving the press’s energy efficiency and reducing operational costs. Regenerative braking and energy recovery features are also becoming more common, allowing energy to be recovered and reused during certain parts of the cycle.
- Automation Integration: The push for greater efficiency and productivity has led to the integration of robotic automation and material handling systems with C-Frame presses. Automated robots can handle the loading and unloading of parts, tool changes, and even quality control inspections, reducing manual labor and enhancing production speeds.
- Advanced Control Systems: C-Frame presses are increasingly being equipped with advanced control systems that provide real-time feedback on the operation, enabling data collection, remote diagnostics, and predictive maintenance. These features help improve uptime, reduce operational costs, and enhance overall product quality.
Conclusion
The C-Frame Deep Drawing Press is a versatile, cost-effective, and reliable option for manufacturers that need precision in metal forming, especially when ease of access and compactness are important factors. While it may not be suitable for the largest, most demanding forming applications, its advantages—such as accessibility, compact design, and lower operational costs—make it an excellent choice for many industries. The adaptability of C-Frame presses to automation, smart technology, and energy efficiency continues to enhance their performance, ensuring they remain a critical tool in the metal-forming industry for years to come.
C-Frame Deep Drawing Press
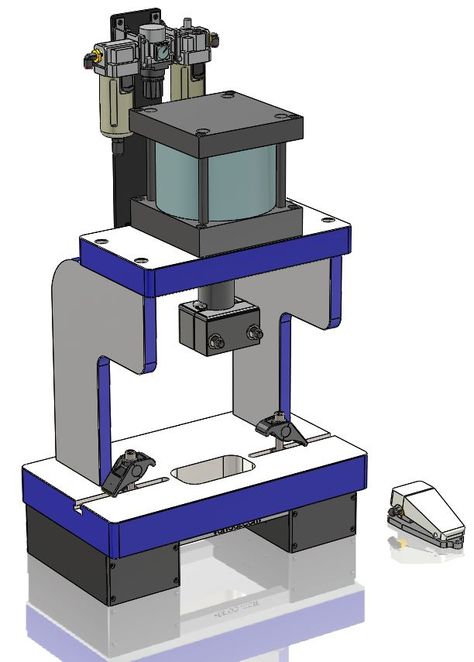
The C-Frame Deep Drawing Press is a specialized mechanical press designed for deep drawing operations, which are commonly used in metal forming, particularly for producing parts with deep, complex shapes from sheet metal. The press is characterized by its distinctive C-shaped frame, which gives it its name. This configuration offers several advantages over other types of presses, especially when access to the workpiece and tooling is crucial. Below is an in-depth look at the key features, benefits, and applications of the C-Frame Deep Drawing Press:
Structure and Design
The C-Frame Deep Drawing Press is designed with a vertical frame shaped like the letter “C.” This frame houses the press mechanism and provides a stable structure for the machine. The ram, which moves vertically, applies pressure to the material placed between a die and a punch. The C-frame’s open design provides several advantages:
- Access to Tooling: The open frame allows easy access to the tooling, which makes setup, maintenance, and adjustments easier compared to more enclosed press designs like the four-column or H-frame presses. Operators can easily load the workpiece, change dies, and perform inspections.
- Space Efficiency: The C-frame design is typically more compact than other press types, which makes it ideal for environments with limited space. Its ability to be used in smaller layouts is a significant advantage for factories with limited room.
- Cost-Effective: Due to the simpler design and lower material requirements, C-Frame presses are generally more cost-effective than their larger counterparts, making them suitable for smaller manufacturers or companies that want to reduce their capital expenditure.
Advantages
- Enhanced Accessibility: The C-shape frame provides superior accessibility to both the die and workpiece. This feature is especially useful for rapid tool changes or for applications where operators need easy access to the parts being formed.
- Compact and Robust: The C-Frame press’s compact nature makes it ideal for areas where space is at a premium. Despite being smaller, it still delivers the necessary force for many deep drawing applications.
- Versatility: The C-Frame press can handle a variety of materials, including steel, aluminum, and copper, and is suitable for medium-tonnage applications. This versatility makes it appropriate for industries such as automotive, aerospace, electronics, and appliances.
- Ease of Maintenance: The open-frame design and simpler mechanics allow for quick and easy maintenance. This reduces downtime and ensures better uptime for high-volume operations.
- Lower Operational Costs: C-Frame presses are known for their lower operating costs, as they require less maintenance and use fewer materials than larger presses. Their energy-efficient designs, particularly in hydraulic versions, also contribute to cost savings.
Types of C-Frame Deep Drawing Presses
- Hydraulic C-Frame Presses: These are the most common type of C-Frame press. They utilize a hydraulic cylinder to exert force, offering better control over the speed and tonnage, which is ideal for deep drawing operations. Hydraulic presses allow for adjustments in force, making them more adaptable to varying material thicknesses and properties.
- Mechanical C-Frame Presses: Mechanical presses use a flywheel and crankshaft to generate force, making them faster and more efficient for high-speed production. While they don’t offer the same level of force control as hydraulic presses, they are well-suited for applications where speed and consistency are key, such as in large-scale stamping or blanking.
Applications
The C-Frame Deep Drawing Press is commonly used in industries that require high precision and quality in the production of metal parts, such as:
- Automotive Industry: For forming components like car body panels, brackets, and structural parts. The high precision needed for these parts makes the C-Frame press ideal.
- Aerospace: The aerospace industry demands parts that meet strict tolerances, such as aircraft skins, aluminum panels, and engine components. The C-Frame press can handle the specialized tooling and high-quality demands of this industry.
- Electronics: C-Frame presses are also used to produce metal casings and connectors for consumer electronics, where precision is critical.
- Appliance Manufacturing: Household appliance parts like refrigerator panels, washing machine components, and microwave casings are commonly produced with the help of C-Frame presses.
Hydraulic vs. Mechanical C-Frame Presses
- Hydraulic C-Frame Presses: These presses are favored for their precise control over force, which is important for deep drawing. They offer flexibility by allowing adjustments to tonnage and stroke speed, making them well-suited for forming materials of varying thicknesses. Hydraulics also offer better force distribution, which is crucial for complex deep drawing operations.
- Mechanical C-Frame Presses: Mechanical presses are typically faster and more efficient, as they generate force through a flywheel system. They are ideal for high-speed operations but may not offer the same degree of force control as hydraulic presses. Mechanical presses are often used when high-speed stamping is required, and the material being processed is consistent in thickness and properties.
Limitations
While the C-Frame press has many advantages, it does have a few limitations:
- Limited Tonnage: The C-Frame design is typically limited in terms of tonnage compared to larger presses, such as four-column or H-frame presses. This makes them less suitable for very heavy-duty applications or for forming extremely large parts.
- Structural Flexibility: The open-frame design, while beneficial for accessibility, can sometimes lead to structural flexibility under high tonnage, potentially causing slight deformations in the frame. This is a consideration when working with very thick or high-strength materials.
- Tooling Compatibility: Although C-Frame presses can be adapted to a wide range of tooling, the open structure might not be suitable for extremely large or complex dies that are needed for certain applications.
Recent Advancements
- Energy-Efficient Designs: Newer models of hydraulic C-Frame presses often incorporate servo-driven hydraulic systems, which use less energy by only applying the necessary force at the right time. This improves efficiency and reduces operational costs.
- Automation Integration: C-Frame presses are increasingly being equipped with automated material handling systems, including robotic arms for loading and unloading parts, which increases throughput and reduces the need for manual labor. Automation also helps maintain consistent part quality and reduce cycle time.
- Intelligent Control Systems: Modern C-Frame presses are incorporating smart control systems that allow real-time monitoring and adjustments. These systems can track the performance of the press, provide data analytics, and predict maintenance needs, improving productivity and reducing downtime.
Conclusion
The C-Frame Deep Drawing Press is a versatile, reliable, and cost-effective solution for deep drawing operations in a variety of industries. Its accessibility, compact design, and lower operating costs make it an attractive choice for manufacturers who need precision and flexibility. While it may have limitations in terms of tonnage capacity and structural rigidity, its overall advantages make it an excellent choice for medium-tonnage, high-precision applications. With continued advancements in automation, energy efficiency, and smart technologies, the C-Frame press is likely to remain a key player in the metal forming industry for years to come.
The C-Frame Deep Drawing Press is a highly versatile and efficient piece of machinery used for metal forming, specifically in applications like deep drawing where precision and access to tooling are crucial. Its design, featuring an open “C” shape, provides easier access to both the workpiece and the tooling, making it highly effective for tasks such as die changes, material handling, and maintenance. This open frame structure ensures that operators can quickly interact with the press, which is a key factor in industries where rapid tool changes or troubleshooting are often required.
Its compact design allows the C-Frame press to be installed in facilities with limited space, making it ideal for manufacturers that need to maximize the use of available floor area. The press is often chosen for its cost-effectiveness, as the simpler design reduces the overall cost of production compared to more robust, multi-column presses. Additionally, the ability to access the components easily contributes to lower maintenance costs, as repairs or adjustments can be made more swiftly.
The C-Frame press can be equipped with either hydraulic or mechanical drives. Hydraulic presses are particularly favored for deep drawing operations because they offer precise control over the tonnage applied, allowing for more flexible handling of different material thicknesses. The force can be adjusted, providing the flexibility needed for a variety of tasks, including high-precision work with complex geometries. Mechanical presses, on the other hand, are often used in high-speed operations, where the rapid application of force is required, such as in stamping or blanking processes. These presses are generally faster than hydraulic presses but might not offer the same level of control over the force applied, which can be a disadvantage in some deep drawing applications.
The C-Frame press is a popular choice in industries such as automotive, aerospace, and electronics due to its ability to produce high-quality parts with a great deal of accuracy. For example, in the automotive industry, C-Frame presses are used to create body panels, brackets, and other components that require deep drawing. These parts must meet strict quality standards, making the C-Frame press an ideal choice due to its ability to consistently produce parts to precise specifications. Similarly, in aerospace, where parts need to meet high standards of precision and strength, the C-Frame press plays a key role in producing structural components, engine parts, and other critical pieces.
In addition to their versatility, C-Frame presses are also being adapted to modern manufacturing needs through automation and digital technologies. The integration of robotic systems for material handling, tool changes, and quality inspection is becoming increasingly common, as manufacturers look to improve productivity while reducing human error and operational costs. This automation not only enhances throughput but also helps maintain consistent quality throughout production runs. Advanced monitoring systems, enabled by sensors and data analytics, allow real-time adjustments to the press settings, improving process efficiency and ensuring that parts are produced to exacting standards.
In terms of energy efficiency, newer models of C-Frame presses incorporate servo-driven hydraulic systems, which only use energy when necessary, making them more sustainable and cost-effective. These systems reduce energy consumption during idle times and contribute to a lower overall environmental footprint for the manufacturing process. Additionally, innovations in material science and tool design are allowing C-Frame presses to work with a wider range of materials, including advanced alloys and composite materials, which are increasingly used in industries like aerospace and electronics.
Despite these advances, the C-Frame press has some limitations. Its capacity is generally lower than other press types, such as four-column or H-frame presses, which means that it might not be suitable for very heavy-duty operations or extremely large parts. The open-frame structure, while advantageous for accessibility, can also result in some structural flexibility, especially when dealing with higher tonnage applications. However, for medium-tonnage tasks that require flexibility and precision, the C-Frame press remains an excellent choice.
Looking to the future, the C-Frame Deep Drawing Press is likely to continue evolving, particularly in its integration with smart manufacturing technologies. The rise of Industry 4.0, with its focus on interconnected systems, real-time data collection, and machine learning, will enable even more sophisticated control of the deep drawing process. Presses will become more autonomous, with systems that predict maintenance needs, optimize production processes, and enhance quality control. As the manufacturing industry continues to shift towards sustainable and highly efficient production methods, the C-Frame press will likely play a key role in meeting the demands of modern industry.
As the manufacturing landscape continues to evolve, the C-Frame Deep Drawing Press is likely to see further enhancements aimed at increasing its versatility, precision, and efficiency. One of the most notable developments in recent years is the integration of smart technologies into the press systems. These advances are not only improving the performance of individual presses but also reshaping entire production lines. The concept of Industry 4.0 is gaining ground in the manufacturing sector, where machines are no longer standalone entities but are interconnected within a broader system that communicates and shares data in real time.
Through IoT (Internet of Things) sensors and data analytics, modern C-Frame presses can now be monitored remotely. These sensors collect valuable data during the forming process, including information on force distribution, material behavior, and machine conditions. This data is then analyzed by machine learning algorithms to identify potential issues before they become serious problems. For instance, predictive maintenance systems can notify operators when parts are wearing out or when a failure is imminent, which helps avoid costly downtime and extends the lifespan of the press. This predictive capability ensures that the press remains in peak condition, thereby improving both productivity and reliability.
The automation of setup and tooling changes is also becoming increasingly sophisticated. Automated tool-changing systems reduce the time required to switch between different die sets, which is particularly useful for manufacturers that need to handle multiple part designs. This reduces the need for manual intervention and minimizes human error, ensuring that parts are produced with high consistency and within tight tolerances. Automation is also improving the material handling processes, with robotic arms now commonly used to load and unload workpieces. This not only speeds up the process but also improves worker safety by reducing the amount of manual labor required in potentially hazardous environments.
Another major area of innovation is in the field of energy efficiency. With rising energy costs and increasing environmental concerns, manufacturers are under pressure to reduce their energy consumption. The introduction of servo-driven hydraulic systems in C-Frame presses has made a significant impact in this regard. These systems are more energy-efficient than traditional hydraulic systems because they only use power when necessary, adjusting the force dynamically to meet the specific needs of each operation. This approach leads to a substantial reduction in energy consumption, lowering operating costs and reducing the environmental footprint of the manufacturing process.
Advanced materials are also playing a role in the ongoing development of C-Frame presses. The increasing demand for lighter and stronger materials, such as high-strength steels, aluminum alloys, and composite materials, is pushing the capabilities of traditional presses. Manufacturers need presses that can handle these advanced materials without compromising on precision or productivity. In response, C-Frame presses are being adapted to accommodate these new materials, often by incorporating specialized tooling and advanced control systems that can adjust to the material’s unique properties.
The versatility of the C-Frame press is also being enhanced with the development of multi-functional tooling systems. These systems allow manufacturers to switch between different types of operations—such as deep drawing, blanking, and punching—without needing to change the entire die set. This further streamlines the production process, saving time and money while increasing the flexibility of the press to handle a wide range of applications.
In addition to these technological advances, there is a growing emphasis on sustainability in the design and operation of C-Frame presses. Many manufacturers are exploring the use of recycled materials and incorporating closed-loop systems that reduce waste and make more efficient use of resources. For instance, some systems can capture and reuse heat generated during the forming process, further reducing energy consumption. The focus on reducing waste and emissions is becoming a significant driver for innovation, as companies strive to meet environmental regulations and respond to the demand for more eco-friendly manufacturing processes.
The increasing trend toward customization and shorter product lifecycles is another factor influencing the future of C-Frame presses. As customers demand more personalized products and rapid prototyping becomes more common, C-Frame presses will need to adapt to quickly changing production runs. This will require machines that can easily be reconfigured for different tasks, allowing manufacturers to stay competitive in a fast-paced market.
As the C-Frame press continues to evolve, it will likely become more integrated into a broader, digitally connected manufacturing ecosystem. This will allow manufacturers to optimize their entire production process, from material procurement to final quality inspection. The continued development of AI-driven optimization algorithms will further enhance the ability to fine-tune the press’s performance, ensuring the highest quality and efficiency.
The future of the C-Frame Deep Drawing Press looks promising, with continued advancements in automation, energy efficiency, and integration with smart manufacturing technologies. These innovations will help manufacturers meet the growing demand for high-quality, customized parts while reducing costs and minimizing environmental impacts. As the industry embraces these changes, the C-Frame press will remain a crucial component in achieving precision, flexibility, and sustainability in modern manufacturing.
Looking ahead, the C-Frame Deep Drawing Press will continue to evolve in several key areas to meet the challenges of the modern manufacturing world. The integration of advanced sensing and monitoring systems will play a critical role in further improving the performance and capabilities of these presses. By equipping presses with advanced sensors that monitor critical parameters such as temperature, pressure, and vibration in real-time, manufacturers will be able to gain deeper insights into the press’s operation. These insights can be used to optimize production, reduce defects, and ensure that the press is operating within ideal parameters at all times.
One of the most promising developments is the use of artificial intelligence (AI) in conjunction with deep learning algorithms. These systems will be able to analyze the data collected from sensors and other connected devices to make real-time adjustments to the press’s operations. For example, the AI could adjust the tonnage or speed of the press based on the material being formed, the thickness of the sheet, or other specific production requirements. This would result in dynamic optimization, where the press is continually improving its performance, adapting to changes in real-time without human intervention.
Another area where we will see significant advancements is in material science. As the demand for lighter, stronger, and more durable materials continues to rise, C-Frame presses will be required to process a broader range of advanced materials. These could include high-strength alloys, new composite materials, or advanced polymers that require highly precise handling. New tool coatings and tooling materials will also be developed to handle the stress and wear associated with forming these tougher materials. Innovations in laser hardening, coating technologies, and tool design will ensure that presses can perform high-quality forming on a wide variety of materials.
The future of C-Frame presses will also be heavily influenced by the trend toward flexible manufacturing systems. As manufacturers are increasingly asked to produce smaller batches of customized parts in shorter timeframes, traditional mass production methods may not be feasible. To meet this demand, C-Frame presses will need to become even more adaptable and modular. This could involve the development of presses with interchangeable components, allowing for rapid reconfiguration to accommodate different part designs. Modular press designs may allow manufacturers to swap out different tool sets, dies, or even entire press components quickly, enabling faster transitions between production runs with minimal downtime.
Additionally, supply chain integration will become a critical component of C-Frame press operations. As manufacturers seek to improve lead times and reduce costs, integrating the press with a digital supply chain network will be essential. This could involve connecting the press to an intelligent inventory management system, enabling it to receive real-time data about available materials, part demand, and other variables. By aligning production schedules with the availability of raw materials and other factors, manufacturers can reduce waste and improve efficiency across the entire production process.
A key area where sustainability will drive change in C-Frame presses is in the optimization of energy use. Green technologies and renewable energy sources will increasingly be integrated into manufacturing facilities, with presses potentially being powered by solar, wind, or other renewable energy sources. The goal will be to reduce the carbon footprint of production while maintaining high productivity and quality. Energy-efficient drives and low-emission systems will be crucial for meeting both economic and environmental goals.
Another aspect of sustainability is circular manufacturing. Manufacturers are beginning to embrace circular economy principles, where products and materials are designed for reuse, repair, and recycling. C-Frame presses will likely play a role in this transition, especially in industries like automotive and electronics, where parts are regularly recycled and repurposed. Presses will be adapted to handle not only virgin materials but also recycled metals and reprocessed composites, requiring presses to be more flexible in terms of material handling and tuning for the specific properties of recycled materials.
As the global market continues to shift, particularly with the growing demand for smaller, custom parts from industries like medical devices, electronics, and aerospace, the need for precision and flexibility in manufacturing will only grow. C-Frame presses, with their ability to form intricate shapes and fine details from a wide range of materials, are poised to meet these demands. As technology progresses, the C-Frame press will remain a versatile, reliable tool that supports high-precision manufacturing for a broad range of industries, from automotive to consumer electronics.
Finally, global competition will drive continuous innovation in C-Frame presses. Manufacturers will look for ways to reduce costs, improve throughput, and enhance product quality to stay competitive in an increasingly globalized marketplace. The adaptation of advanced automation, AI-driven optimization, and data analytics will be key to remaining competitive in the fast-paced world of manufacturing. The C-Frame press, therefore, will remain a cornerstone of modern metal forming, evolving with each new technological breakthrough and expanding its capabilities to meet the ever-growing challenges of the manufacturing sector.
In conclusion, the future of the C-Frame Deep Drawing Press is promising, with ongoing advancements in technology, materials, automation, and sustainability shaping its evolution. By adapting to these changes and embracing the new challenges of modern manufacturing, C-Frame presses will continue to play an essential role in producing high-quality, efficient, and sustainable products for industries across the globe.
Water tank covers Manufacturing Machine

A Water Tank Covers Manufacturing Machine is a specialized piece of equipment designed for the production of covers for water tanks, typically used in various industrial, agricultural, and residential applications. These covers are critical in protecting water from contamination, preventing evaporation, and maintaining temperature regulation. Depending on the type of tank and cover required, the manufacturing process for these covers can vary widely in complexity and the materials used.
The machine designed for manufacturing water tank covers can be fully automated or semi-automated, depending on the production needs and volume. Below is an outline of the different stages and key components of a typical Water Tank Covers Manufacturing Machine:
Key Components of the Manufacturing Machine
- Material Feeding System: The machine is designed to accept raw material, typically metal sheets (e.g., steel, aluminum, or stainless steel), plastic sheets (e.g., polyethylene or PVC), or composite materials, depending on the desired properties of the tank cover. The material is fed into the machine via a feeding system, ensuring consistent material flow.
- Cutting Section: The material is first cut into the required shapes and sizes. For metal covers, laser cutting or plasma cutting might be used to achieve precise dimensions. For plastic or composite covers, the machine might use die cutting or CNC routers. The cutting section ensures that each cover fits the tank it’s intended for, and the cuts are precise to avoid gaps and ensure a proper seal.
- Forming/Stamping Section: The forming section is used to shape the material into the desired cover profile. For metal covers, this may involve deep drawing, press forming, or stamping. In some cases, CNC bending machines or hydraulic presses are used to form the tank cover to the required shape, whether it’s flat or domed. For plastic covers, vacuum forming might be used to create the cover shape, with the material being heated and then drawn into a mold under vacuum pressure.
- Seaming and Welding: For some tank covers, especially those made of metal, the edges may need to be seamed, welded, or riveted to provide a secure, leak-proof cover. This could involve spot welding, TIG welding, or laser welding, depending on the material. In the case of plastic covers, plastic welding methods, such as ultrasonic welding or hot plate welding, may be used to ensure the edges are sealed securely.
- Surface Treatment: After the cover has been formed, the next step is often surface treatment. This ensures the material is durable and resistant to corrosion, particularly important for metal covers used in outdoor environments. Galvanizing, powder coating, or painting might be applied to metal tank covers to protect them from rust and other environmental factors. For plastic covers, a UV-resistant coating might be applied to prevent degradation from exposure to sunlight.
- Inspection and Quality Control: After forming and surface treatment, each cover is carefully inspected to ensure it meets quality standards. The dimensional accuracy, finish quality, and sealing performance (especially for watertight applications) are checked. Automated vision systems or manual checks may be used to inspect the covers for defects, such as cracks, dents, or uneven surfaces.
- Assembly: In some cases, additional components like latches, handles, or gaskets may need to be added to the tank cover. This assembly process can be automated with the help of robotic arms or manual labor, depending on the complexity of the part. Gaskets made of rubber or foam are often placed along the edges of the cover to ensure a tight, waterproof seal when the cover is placed on the tank.
- Packaging: Finally, once the covers are completed and fully inspected, they are packaged for shipment. This step often involves automated packaging systems that wrap, box, or palletize the covers to ensure they are ready for delivery. In high-volume production settings, this can be done quickly and efficiently to prepare for distribution.
Types of Materials Used
- Metal: Metal covers are often used for large industrial water tanks due to their strength and durability. Galvanized steel, stainless steel, and aluminum are commonly used materials because they are resistant to corrosion, have high tensile strength, and provide a long-lasting solution for water storage.
- Plastic: Polyethylene (PE), polypropylene (PP), and PVC are common materials for residential water tank covers, offering a lightweight and cost-effective option. These materials are often preferred in environments where rust or corrosion is a concern.
- Composite Materials: Composite covers, often made from fiberglass or carbon fiber, are used for high-performance applications, where strength-to-weight ratio, resistance to environmental factors, and durability are critical. These materials are more expensive but provide superior protection and longevity.
Types of Water Tank Covers
- Flat Covers: These are the simplest type of covers and are commonly used in both residential and industrial applications. They are typically circular or square, depending on the tank shape, and can be made from metal, plastic, or composite materials.
- Dome-Shaped Covers: These are often used for larger water tanks, especially for those that need to allow for pressure relief or ventilation. Dome-shaped covers are more complex to manufacture due to their curvature and are typically made from metal or fiberglass.
- Vented Covers: These covers are equipped with ventilation holes or valves to allow gases to escape from the water tank. This is common for tanks storing wastewater, chemicals, or other fluids that produce gases. Vented covers can be produced from metal or plastic, depending on the tank’s application.
- Secure or Locking Covers: In some cases, covers are designed with locks or latches to ensure the tank is secure, especially in industrial or commercial settings. These covers are often used for chemical or hazardous material tanks, where tampering or unauthorized access must be prevented.
Automation and Production Efficiency
Modern Water Tank Covers Manufacturing Machines often incorporate automation and advanced manufacturing technologies to increase productivity and reduce costs. Features of automated systems may include:
- Robotic arms for loading, unloading, and assembly of components.
- Automated quality inspection systems that use machine vision and AI to detect defects.
- Servo-driven drives that offer precise control over the forming and cutting processes, ensuring consistency and reducing waste.
- Data collection and analytics to monitor performance in real-time and optimize production.
These machines not only improve efficiency but also reduce human error, ensure higher precision in the manufacturing process, and allow for quicker production cycles. The use of CAD/CAM systems allows for the design of highly complex covers that can be fabricated to meet specific customer requirements.
Applications of Water Tank Covers
- Agriculture: Protecting water storage tanks used in irrigation and livestock water management.
- Residential: Covers for water tanks in homes, both for rainwater harvesting and general water storage.
- Industrial: Water tanks in factories, chemical plants, and cooling towers often require specialized covers for safety, environmental, or functional reasons.
- Municipal: Large water treatment facilities and reservoirs require robust and secure covers to prevent contamination and maintain water quality.
Conclusion
The Water Tank Covers Manufacturing Machine plays an essential role in producing durable, reliable, and safe covers for various water storage applications. These machines incorporate cutting-edge technology, from automated forming and cutting to sophisticated quality control systems, ensuring high-quality end products that meet both functional and regulatory requirements. The flexibility to work with various materials like metal, plastic, and composites allows manufacturers to produce a wide range of tank covers tailored to specific industry needs. As the demand for sustainable and secure water storage solutions continues to grow, innovations in manufacturing technology will likely continue to enhance the efficiency and capabilities of these machines.
The production of water tank covers is increasingly becoming more efficient as manufacturers integrate advanced automation, robotics, and smart technologies into the process. These innovations are not just about improving speed but also about enhancing the quality and precision of the covers being produced. For instance, automation in the cutting and forming processes helps reduce human error and ensures that each cover meets the exact specifications required for different types of water tanks.
Another significant trend in water tank cover manufacturing is the customization of covers for different tank sizes, shapes, and materials. The ability to quickly switch between different types of production tasks without long downtimes has become crucial, especially as industries require specialized covers for specific environments, such as industrial, agricultural, or residential tanks. This trend is often supported by modular production lines, where different sets of tools can be swapped in and out, allowing manufacturers to respond quickly to changing demands.
In addition, smart technologies such as IoT sensors and machine learning algorithms are enhancing the capabilities of water tank cover manufacturing. These systems can monitor the condition of the machines in real-time, providing data on factors like wear and tear, temperature fluctuations, and force distribution during the production process. By analyzing this data, manufacturers can optimize machine performance, predict maintenance needs before breakdowns occur, and improve overall production efficiency.
Energy efficiency is another growing consideration. As manufacturing facilities face increasing pressure to reduce their carbon footprint and operational costs, the introduction of energy-efficient systems in the production of water tank covers has become a priority. This includes the use of servo-driven motors for greater precision and less energy consumption, as well as the integration of renewable energy sources like solar or wind power to drive parts of the manufacturing process.
The choice of materials is also a critical factor in the design and manufacturing of water tank covers. Metals like stainless steel and aluminum remain popular for industrial-grade applications, especially due to their durability and corrosion resistance. However, as environmental concerns grow, there is an increasing shift toward using more sustainable materials, such as recycled plastics or biodegradable composites, for residential and agricultural water tank covers. These materials offer a balance between strength, environmental impact, and cost-effectiveness.
The market for water tank covers is expanding in line with the growing need for water conservation and sustainable water management solutions across the world. In particular, rainwater harvesting systems are gaining traction, requiring custom-made covers that ensure the collected water remains clean and safe for use. These covers also need to be designed to withstand harsh weather conditions, such as extreme heat, cold, or heavy rainfall, which may lead to innovations in both material science and design to meet these demands.
As the demand for high-quality, long-lasting water tank covers continues to rise, the manufacturers that adapt to these technological advancements and sustainability goals will have a competitive advantage. The ongoing development of more intelligent systems, coupled with robotic automation and data-driven optimization, will help push the boundaries of what’s possible in water tank cover manufacturing, ensuring that products not only meet today’s standards but also future-proof the industry.
The future of water tank cover manufacturing will likely see increased collaboration between material scientists, engineers, and software developers to create products that are both functionally superior and environmentally friendly. These advancements will allow manufacturers to meet evolving customer needs while addressing global challenges related to water conservation and environmental sustainability.
The future of water tank cover manufacturing is poised to see further innovations driven by the integration of artificial intelligence (AI) and advanced robotics. AI can play a pivotal role in optimizing the production process by analyzing vast amounts of data from various sensors embedded in the machines and the materials. For instance, AI algorithms could predict material behavior during the forming process, fine-tune machine parameters in real-time, and automatically adjust the production line for maximum efficiency. This would not only reduce waste but also ensure that the covers meet strict quality control standards with minimal human intervention.
Robotic systems will continue to enhance automation, particularly in areas such as loading and unloading raw materials, assembling parts, and packaging finished covers. With the development of collaborative robots (cobots), human operators and robots will work side by side on tasks, allowing for flexibility in the production environment. These robots are designed to be easily programmable and adaptable, making them suitable for smaller production runs or even bespoke manufacturing, which could be crucial for customers who require custom tank covers for specialized applications.
The digital twin technology could also be incorporated into the manufacturing process. A digital twin is a virtual replica of a physical system that can be used to simulate the entire production process. This allows manufacturers to optimize the manufacturing line before any actual production begins. By simulating the process in a virtual environment, manufacturers can identify potential bottlenecks, optimize workflows, and test various production scenarios without disrupting actual production. This can be especially useful when introducing new materials or design changes, allowing manufacturers to test and validate changes more quickly.
Moreover, the supply chain aspect of water tank cover production is also evolving. Blockchain technology could play a role in ensuring transparency and traceability throughout the manufacturing process. It could help track the journey of raw materials from their source to the factory and ensure that the materials used in manufacturing meet sustainability standards. Additionally, blockchain could improve inventory management by providing real-time visibility into material availability and demand, allowing for better resource allocation and reducing production delays.
Sustainability will continue to be a major focus for the water tank cover industry. The trend toward circular manufacturing, where materials are reused, recycled, or repurposed, is expected to grow. For instance, some manufacturers might design water tank covers with modular components, making it easier to replace parts of the cover rather than discarding the entire unit. This modularity could help reduce waste and ensure longer product life cycles. As regulations around waste and recycling become stricter, manufacturers will need to ensure that their products can be easily disassembled for recycling at the end of their life.
Additionally, the focus on eco-friendly materials will likely drive further development in the field. Researchers are already working on more sustainable alternatives to traditional plastic and metal, such as bio-based plastics and recycled composites. These materials would not only help reduce the environmental impact of water tank cover production but also appeal to customers looking for greener solutions. The development of eco-friendly coatings that are both durable and biodegradable could also reduce the environmental footprint of manufacturing processes, especially in applications where covers are exposed to harsh weather conditions.
In terms of smart features, water tank covers may increasingly integrate sensors that can monitor the condition of the water tank and cover itself. These sensors could detect changes in pressure, temperature, or moisture levels, providing early warnings about potential issues such as contamination, leaks, or pressure buildup. Some smart covers may even have remote monitoring capabilities, where the tank owner can access data on their mobile device or computer to ensure the water quality is maintained and the cover is secure. This connectivity will align with the broader Internet of Things (IoT) trend in manufacturing and enable more proactive maintenance.
Another interesting avenue for innovation is the design of the water tank covers themselves. Custom-designed covers, tailored to the specific needs of the tank or the environment it’s in, could become more prevalent. With the rise of 3D printing technologies, manufacturers could begin offering covers with highly specialized features or unique shapes, customized for individual customer needs. This could allow for rapid prototyping and smaller production runs without the need for expensive molds or tooling. As 3D printing technologies improve, even more complex and optimized designs could become feasible.
The increasing demand for high-quality, durable, and safe water storage solutions will also fuel further innovation in water tank cover manufacturing. With a growing global emphasis on water conservation and safe water storage, the role of water tank covers will become even more critical. The covers not only need to perform functional roles such as protection from contamination and evaporation, but they must also meet strict safety standards, particularly in industrial and commercial applications. As such, manufacturers will focus on ensuring the reliability and strength of the covers, using advanced materials, designs, and production techniques.
In conclusion, the future of water tank cover manufacturing is moving toward a more automated, connected, and sustainable production process. The integration of advanced technologies such as AI, robotics, and smart sensors will improve efficiency, reduce costs, and ensure higher-quality products. As sustainability continues to be a primary concern, manufacturers will explore eco-friendly materials, energy-efficient systems, and circular production models. This evolution will not only enhance manufacturing processes but also provide end-users with more durable, reliable, and environmentally conscious water tank covers for a variety of applications. With these innovations, the industry will be well-positioned to meet the growing demand for high-performance water storage solutions.
As water tank cover manufacturing continues to evolve, the industry will increasingly embrace data-driven decision-making. This shift toward data-centric production will enable manufacturers to fine-tune processes, optimize performance, and predict potential failures before they occur. The integration of big data analytics will empower manufacturers to track every aspect of the production line—from raw material sourcing to the final packaging—ensuring maximum efficiency and quality control.
With the continued rise of cloud computing, manufacturers can access real-time data from production facilities globally. This cloud-based data sharing will allow for easier collaboration between factories, suppliers, and even customers, enabling a more transparent and coordinated manufacturing process. This can lead to better supply chain management, reduced lead times, and enhanced customer service, as clients will have access to updates on their orders and products at all stages of production.
One key aspect of this data integration will be predictive maintenance. By analyzing historical data from machines and equipment, manufacturers can predict when maintenance or repairs are necessary before a failure occurs. Predictive maintenance systems use machine learning algorithms to detect anomalies in machine behavior and alert operators in advance. This can drastically reduce unplanned downtime, increase the lifespan of manufacturing equipment, and ultimately save costs for the manufacturer. Over time, as more machines are connected and data is collected, the system will become more accurate in predicting when specific parts or machines need attention.
Moreover, with the integration of augmented reality (AR) and virtual reality (VR) in manufacturing, operators and engineers can interact with the production line in more intuitive ways. For example, AR glasses could provide real-time visualizations of machine performance, guiding technicians through troubleshooting or repairs. VR could be used for virtual training of operators, allowing them to simulate manufacturing scenarios without any risk to equipment or materials. This technology could also be leveraged for design verification, where engineers use VR to interact with digital models of the water tank covers, identifying potential design flaws before the physical manufacturing process begins.
The importance of sustainability will continue to be a driving force in the manufacturing of water tank covers. As consumers and industries demand more eco-friendly products, manufacturers will explore alternative materials that reduce the environmental impact of their production. In addition to recycled plastics and bioplastics, innovations in 3D printing could enable more sustainable production methods. 3D printing could reduce material waste by building water tank covers layer by layer, using only the amount of material required. This could be particularly beneficial in producing low-volume, high-customization covers that may otherwise be costly and wasteful to produce using traditional methods.
At the same time, energy consumption will be a key consideration. Manufacturers will increasingly adopt energy-efficient equipment and renewable energy sources to reduce the carbon footprint of production processes. Advanced systems that regulate energy usage based on real-time demand, such as smart grids, will allow factories to optimize power consumption. For example, during non-peak hours, excess energy from solar panels or wind turbines could be stored and used to power operations when electricity demand is higher. This will not only reduce energy costs but also align with global efforts to combat climate change.
The rise of customization in the production of water tank covers will further influence manufacturing practices. With advancements in additive manufacturing and digital fabrication techniques, it will be possible to create covers that are tailored to the specific needs of individual customers. These customized covers could feature specialized ventilation systems, locking mechanisms, or reinforced designs for particular applications. For instance, certain industries, like agriculture, might need covers that allow for water drainage, while industrial applications may require covers that can withstand extreme environmental conditions, such as high pressure or exposure to chemicals. Customization will also be driven by the growing trend of on-demand manufacturing, where covers are produced only when needed, reducing waste and improving resource allocation.
The global market for water tank covers is also set to expand, especially in regions experiencing rapid urbanization and industrialization. As more people move into cities, the demand for reliable water storage solutions in both residential and industrial settings will grow. Developing countries, in particular, may see increased demand for affordable and durable water tank covers as they expand their water infrastructure. These regions will benefit from the ongoing improvements in production efficiency and cost-effectiveness, ensuring that high-quality covers are available at competitive prices.
Moreover, as climate change continues to impact weather patterns globally, the need for resilient and adaptable water tank covers will grow. In areas experiencing increased rainfall or longer periods of drought, water storage systems must be equipped to handle extreme conditions. Manufacturers will need to design covers that are more weather-resistant, capable of withstanding high winds, heavy rainfall, or freezing temperatures. Waterproofing and UV resistance will continue to be critical features, especially for covers exposed to direct sunlight or harsh outdoor conditions.
Another critical factor influencing the future of water tank cover manufacturing will be the increasing emphasis on regulatory compliance. As governments around the world implement stricter environmental regulations and product safety standards, manufacturers will need to ensure their products meet a variety of compliance requirements. These regulations could address issues such as chemical resistance, flammability, or recyclability. Ensuring that tank covers meet these standards will require continuous testing and certification, which can be streamlined with the use of automated quality control systems and certification databases.
In summary, the future of water tank cover manufacturing is deeply intertwined with technological advancements, sustainability initiatives, and a growing demand for customizable, resilient products. Automation, smart technologies, data analytics, and sustainable materials will play central roles in shaping the industry, enabling manufacturers to meet the evolving needs of their customers while reducing environmental impact. The ability to produce high-quality, durable, and cost-effective covers at scale will position the industry to meet the growing global demand for water storage solutions in both urban and rural environments. As the market continues to expand, manufacturers will need to stay agile, embracing new technologies and market trends to stay competitive and fulfill the needs of a water-conscious world.
Metal Door frames Manufacturing Machine
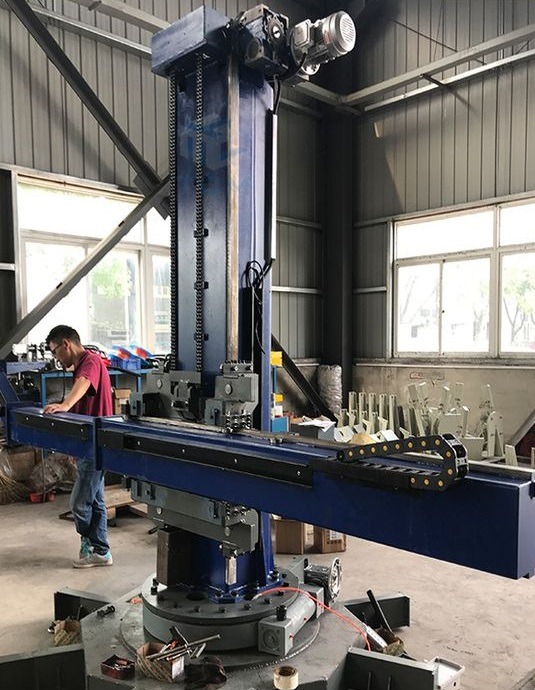
The manufacturing of metal door frames typically involves a combination of precision engineering, automation, and robust materials handling. As with many industries, advancements in technology have led to the development of highly specialized machines and automated systems that streamline the production of metal door frames, reducing labor costs, improving precision, and increasing production efficiency.
Here’s an overview of the process and equipment involved in the manufacturing of metal door frames:
1. Material Selection and Preparation
The process starts with the selection of appropriate metal materials, typically mild steel, stainless steel, aluminum, or galvanized steel. These materials are chosen for their durability, strength, and resistance to corrosion. The raw metal sheets are often delivered in large coils or flat sheets.
The material preparation stage involves uncoiling, shearing, and cutting the metal sheets into the required sizes for the door frame components. This is typically done using automated shearing machines or laser cutting systems. The sheets are then flattened and checked for any defects before proceeding.
2. Cutting and Shaping
The metal door frame components typically include vertical jambs (sides), horizontal rails (top and bottom), and the frame’s support brackets or reinforcements. CNC (Computer Numerical Control) punching or laser cutting machines are often used in this stage to ensure precision cutting. These machines can also cut holes for hinges, locks, and other hardware features, all with tight tolerances.
After cutting, the metal parts may undergo bending or forming to shape the door frame. This process involves using CNC press brakes or rolling machines to bend the metal parts into the correct angles. Automated systems ensure uniformity across large production runs.
3. Welding and Assembly
Once the individual parts are cut and shaped, the next step is welding to join them together. This is where the actual door frame starts to take shape. Depending on the complexity and requirements of the design, various welding methods can be used:
- MIG welding (Metal Inert Gas) or TIG welding (Tungsten Inert Gas) are the most commonly used techniques in the production of door frames, particularly for steel or aluminum frames.
- Spot welding or resistance welding may be used for certain designs, especially when connecting smaller components or reinforcement plates.
Robotic arms equipped with automated welding systems often take over this stage for high-volume production. These robots can work with high precision and at faster speeds, ensuring high-quality welds with minimal human intervention.
4. Surface Finishing
After welding, the frames often undergo various surface treatments to enhance their durability and appearance. Depending on the material and intended use, these treatments may include:
- Powder coating for a smooth, uniform finish that enhances the frame’s aesthetic appeal and provides corrosion resistance. This is often done with automated powder coating machines that apply a layer of powder paint, which is then cured in an oven.
- Galvanizing, where the frames are dipped in molten zinc to create a protective layer against rust.
- Electroplating for metals like steel, where a thin layer of another metal (such as zinc or chrome) is applied to protect against corrosion.
The automated spray booths and drying ovens used in these processes ensure consistent coating and curing.
5. Quality Control and Inspection
At this stage, the metal door frames undergo rigorous quality control checks to ensure that they meet the required specifications and industry standards. Automated vision systems equipped with cameras and sensors can inspect the door frames for defects like cracks, warping, or uneven welds.
Additionally, frames may be tested for dimensional accuracy, strength, and stability. Laser measuring systems or coordinate measuring machines (CMM) are used to verify that the dimensions are within the specified tolerances.
6. Final Assembly and Packaging
After the frames pass inspection, they are ready for final assembly. This may include attaching additional hardware, such as hinges, lock fittings, reinforcements, or weather seals. In many cases, automated assembly lines handle the final steps of attaching these components.
The completed door frames are then packaged using automated packaging systems, such as stretch wrapping machines or cardboard box packers, ready for shipping. Packaging is often designed to ensure that the frames are protected from damage during transportation.
Key Machines Involved in Metal Door Frame Manufacturing:
- Uncoiling and Slitting Machines: These machines uncoil and cut the metal sheets into smaller, manageable strips that are sized for the door frame components.
- Laser Cutting Machines: Used to cut parts to the required shapes, including holes for hinges, locks, and other fittings.
- CNC Punching Machines: These machines punch out holes and slots in the frame components, often for hardware mounting or reinforcement.
- Press Brakes: CNC-controlled machines that bend and shape metal parts with high precision.
- Welding Robots: Automated robots that carry out precise welding operations on the metal frame components, reducing labor and improving consistency.
- Powder Coating Machines: Used for the application of a protective and aesthetic powder coating to the frame surfaces.
- Vision Systems: Automated systems that use cameras and sensors to perform quality inspections on the frames.
- CMM (Coordinate Measuring Machines): High-precision machines used to measure the geometry of the parts and ensure dimensional accuracy.
- Automated Packaging Systems: These machines handle the final stage of packaging the completed door frames for shipment.
Emerging Trends in Metal Door Frame Manufacturing:
- Robotic Automation: The use of robots for welding, assembly, and quality control is significantly increasing in metal door frame manufacturing, as it reduces costs and improves efficiency.
- Customization and Flexibility: With advancements in 3D modeling and CNC technologies, manufacturers are able to offer more customized door frame designs to meet the specific requirements of clients. This allows for shorter lead times for custom orders and small batch production.
- Sustainability: As with many industries, the focus on sustainability is growing. Manufacturers are incorporating recyclable materials, such as recycled steel or aluminum, into their production processes. Additionally, companies are adopting more energy-efficient machinery and eco-friendly coatings.
- Smart Manufacturing: The integration of IoT (Internet of Things) technologies enables real-time monitoring of the production process, allowing for predictive maintenance, real-time adjustments, and optimization of machine performance.
In conclusion, metal door frame manufacturing has become an increasingly sophisticated process, relying on cutting-edge technologies to enhance production efficiency, quality, and customization. The future of this industry lies in the continued adoption of automation, robotics, and data-driven manufacturing processes, all while ensuring sustainability and environmental responsibility.
The evolution of metal door frame manufacturing is heavily influenced by advancements in automation and precision engineering. Modern production systems are designed to streamline the entire process, from raw material handling to final product packaging, allowing manufacturers to increase throughput, reduce costs, and improve consistency across large production volumes.
One of the key innovations is the integration of robotic systems that handle multiple tasks such as welding, cutting, and assembly. These robots work with high precision and speed, ensuring uniformity in the products while reducing the risk of human error. The use of vision systems and machine learning algorithms allows these robots to detect imperfections, identify the right welding points, and even adjust their actions in real time based on the feedback from sensors, which helps ensure the durability and strength of the door frames.
Smart manufacturing technologies have also become a cornerstone of modern production lines. Using IoT (Internet of Things), manufacturers can monitor the health of machines, track the usage of raw materials, and optimize the flow of operations across the factory. Sensors embedded in the production equipment feed data to centralized systems, enabling manufacturers to make data-driven decisions about maintenance schedules and production adjustments. This technology helps in predicting machine breakdowns before they occur, leading to fewer production stoppages and more efficient use of resources.
Sustainability continues to be a growing concern in the industry, leading manufacturers to adopt eco-friendly materials and processes. More manufacturers are turning to recycled metals like steel and aluminum for their production processes, reducing the demand for virgin raw materials. Powder coating is another environmentally friendly option compared to traditional painting methods, as it produces fewer emissions and waste. These practices align with global sustainability goals and appeal to eco-conscious consumers, particularly in sectors like construction and industrial manufacturing, where environmental impact is a key consideration.
With the increasing demand for customization, especially in residential and commercial building projects, manufacturers are investing in technologies that allow for on-demand production and tailored designs. CNC machines and laser cutting systems allow for high levels of precision, enabling manufacturers to produce door frames with specialized features such as custom dimensions, hardware fittings, and even aesthetic elements. This flexibility is becoming a significant competitive advantage, especially as more customers seek personalized solutions for their door frame needs.
As production systems become more automated, labor costs decrease, and manufacturers can focus on quality control and innovation. In the past, much of the manufacturing process required significant human labor, particularly in the welding and finishing stages. Today, however, automated welding systems are capable of completing these tasks with far greater speed and consistency. Additionally, automated packaging systems are now standard, ensuring that the finished door frames are securely packaged and ready for shipment with minimal human intervention.
Another area of focus is the integration of digital technologies in manufacturing. Manufacturers are using 3D modeling and simulation tools to prototype and test door frame designs virtually before committing to physical production. This reduces the risk of design flaws and helps speed up the process of bringing new products to market. It also allows for rapid prototyping, where small batches of new designs can be produced and tested quickly before scaling up to full production.
The use of data analytics is also transforming the industry. Manufacturers can track everything from machine performance to raw material usage, gaining insights into the most efficient ways to operate. Data-driven insights enable manufacturers to optimize production schedules, manage inventory, and ensure that orders are completed on time. This level of visibility across the production process also enhances traceability, making it easier to identify and resolve issues quickly if problems arise.
As the demand for metal door frames continues to rise in sectors like construction, commercial building, and industrial applications, manufacturers are finding ways to meet this demand with higher-quality, more affordable products. Advanced manufacturing techniques are helping to make the production of metal door frames more efficient, flexible, and sustainable, meeting the needs of a modern, fast-paced market. With these advancements, manufacturers are well-positioned to respond to growing consumer expectations for durability, design, and environmental responsibility, ensuring that the industry remains competitive well into the future.
As the metal door frame manufacturing industry continues to evolve, advanced materials are becoming more integrated into production processes. Innovations in alloys and coatings are making it possible to produce frames that are not only stronger but also more resistant to harsh environmental conditions. For instance, the use of corrosion-resistant metals and composite materials ensures that door frames remain durable, even in the most extreme weather conditions, such as coastal regions with high humidity or areas prone to heavy rainfall. The use of galvanized steel and powder-coated finishes provides an additional layer of protection, extending the lifespan of door frames significantly.
Alongside materials innovation, the emphasis on energy-efficient manufacturing has been growing. Companies are increasingly adopting energy-efficient machinery to reduce their carbon footprint. This includes the use of smart sensors and automation to optimize power consumption, ensuring that machinery only uses energy when necessary. Additionally, renewable energy sources, such as solar panels or wind turbines, are being incorporated into manufacturing plants to reduce dependence on fossil fuels and further lower environmental impact.
In terms of global supply chains, the demand for metal door frames in developing markets is increasing. Countries experiencing rapid urbanization are seeing a significant rise in the construction of residential and commercial buildings, thereby driving the demand for metal door frames. These regions often require cost-effective, high-quality door frames for large-scale construction projects. Manufacturers are responding by expanding their production capacities and ensuring that their supply chains are flexible enough to meet global demand, using just-in-time manufacturing to reduce costs and inventory while maintaining production efficiency.
As customer preferences evolve, the demand for smarter and more integrated products in door frame manufacturing is also increasing. Smart door frames, for example, are beginning to emerge in the market, equipped with features like integrated sensors, RFID systems, or electronic locks. These frames are designed to offer enhanced security and convenience for both residential and commercial buildings. As technology continues to advance, door frame manufacturers are exploring how to integrate features like IoT connectivity, enabling real-time monitoring of security systems, access controls, or even the structural integrity of the door frame itself.
The use of AI (Artificial Intelligence) and machine learning algorithms in production is also making strides. These technologies allow for continuous improvement in production lines, helping manufacturers predict failures and optimize processes in ways that were previously not possible. AI-driven systems can analyze production data and suggest modifications to improve output quality, machine performance, and overall efficiency. Machine learning models can also help in demand forecasting, allowing companies to better align production schedules with market requirements.
Additionally, the logistics and distribution aspects of the industry are undergoing changes as well. With increasing demand for fast delivery, manufacturers are leveraging automated warehousing and drone technology to expedite shipping processes. Autonomous vehicles are being used for large-scale transportation, further reducing delivery times and ensuring timely product availability across wide geographical areas. In regions with logistical challenges, these technologies can offer more reliable and efficient transportation solutions.
Customer engagement is another area seeing significant change. The rise of e-commerce platforms has allowed manufacturers to directly reach customers, offering door frames and related products online. Some manufacturers are now offering virtual consultations and online configurators, allowing customers to select, customize, and order metal door frames to their specific requirements without leaving their homes or offices. This seamless, customer-driven approach is reshaping how the manufacturing process is perceived, making it more accessible and convenient for end-users.
Moreover, the shift towards sustainability is creating a demand for door frames that not only meet high-performance standards but are also environmentally friendly. Consumers are increasingly looking for products that are energy-efficient, recyclable, or have a lower overall environmental impact. Metal door frames, when produced with sustainable practices in mind, can offer a significant advantage in environmentally conscious markets. Manufacturers that prioritize eco-design and the use of sustainable materials will be better positioned to cater to this growing segment of the market.
Lastly, there is an increased focus on safety and security in the design of metal door frames. Given the increasing concerns around security in both residential and commercial properties, there is a rising demand for door frames that provide superior intrusion resistance, especially in high-risk areas. Advanced locking mechanisms, reinforced frames, and bulletproof or fire-resistant materials are becoming standard offerings for security-conscious consumers. Manufacturers are responding to these needs by incorporating high-strength alloys and innovative locking systems that enhance the safety and durability of the frames.
In conclusion, the metal door frame manufacturing industry is undergoing a technological transformation, driven by advancements in automation, smart technologies, sustainable practices, and customer-centric innovations. As manufacturers continue to adopt more advanced production techniques and respond to growing demand for customizable, secure, and eco-friendly products, the industry is poised for even greater efficiency, innovation, and global reach.
As the metal door frame manufacturing industry continues to evolve, the integration of advanced materials and innovative manufacturing processes will only deepen. One notable trend is the use of smart materials such as self-healing coatings, which can automatically repair minor scratches or damage over time, improving the durability and lifespan of the door frames. These materials could significantly reduce maintenance costs and increase the overall service life of the frames, particularly in environments prone to wear and tear.
The push towards modular construction is also gaining momentum. Metal door frames are increasingly being designed to be part of a larger modular building system. This allows for faster construction times, as the frames are pre-assembled or pre-fabricated off-site and then quickly integrated into the overall structure. The use of standardized components across projects leads to greater cost-efficiency and speed while maintaining high levels of quality control. This approach not only makes it easier to scale production but also allows manufacturers to better respond to the needs of the construction industry, which is often subject to fluctuating demands.
In terms of manufacturing processes, additive manufacturing (commonly known as 3D printing) is beginning to make its mark in metal door frame production. While the technology is still in its early stages for large-scale manufacturing, it has shown great potential for prototyping and customization. With 3D printing, manufacturers can create highly complex frame components or fittings that would be difficult, if not impossible, to produce with traditional methods. This opens up opportunities for bespoke designs or low-volume production runs that were previously cost-prohibitive.
The role of artificial intelligence (AI) in optimizing production scheduling and quality control cannot be understated. AI-powered systems can predict and manage fluctuations in demand, ensuring that manufacturers can maintain optimal stock levels while avoiding overproduction. AI can also analyze data from the production process to detect anomalies in real-time, triggering corrective actions that improve product quality and reduce waste. Furthermore, AI-assisted robots are capable of adaptive learning, meaning they improve their performance over time as they interact with the production environment.
In response to the growing focus on building codes and regulations, manufacturers are adapting their production lines to comply with new safety and environmental standards. This includes meeting higher standards for fire resistance, security features, and energy efficiency in metal door frames. Manufacturers are investing in testing and certification processes to ensure that their frames meet the increasingly stringent requirements of various markets. Some regions have adopted regulations that mandate the use of fire-rated or blast-resistant door frames, pushing the industry to innovate in material science and engineering to meet these challenges.
The demand for integrated building solutions is another driver of change. Builders and contractors are looking for turnkey solutions that include everything from the frame and door to the locking mechanism, hardware, and finish. Manufacturers who can provide a comprehensive solution that meets these requirements are becoming more competitive in the market. Additionally, the integration of advanced locking systems and electronic access controls is increasingly seen as a value-added feature, especially for commercial and high-security applications.
The role of big data and analytics is continuing to grow, particularly in managing the supply chain and production processes. Through real-time data monitoring and predictive analytics, manufacturers can anticipate potential disruptions, such as supply shortages or machine downtime, and take proactive measures to mitigate them. By analyzing data from the entire production cycle—starting from the procurement of raw materials to the final delivery—manufacturers can make more informed decisions and continuously improve their operations.
In addition, the industry is embracing collaborative platforms where manufacturers, contractors, and even end customers can work together more effectively. Through cloud-based platforms or BIM (Building Information Modeling) systems, all stakeholders in the construction process can have access to real-time data about the door frames, including design specifications, production progress, and delivery timelines. This improves communication, reduces errors, and speeds up the overall construction process.
Globalization continues to shape the industry, as manufacturers are expanding their reach into emerging markets. The construction boom in countries like China, India, and Brazil is driving demand for high-quality and cost-effective metal door frames. Manufacturers are adapting to local market conditions by either establishing manufacturing facilities in these regions or partnering with local distributors to meet the needs of the growing construction sectors. These global partnerships help manufacturers mitigate the risks of fluctuating exchange rates, transportation costs, and regional trade policies.
At the same time, localization is becoming increasingly important. Many markets now demand products that are tailored to local tastes, building codes, and environmental conditions. Manufacturers are adjusting their designs to meet these needs, offering greater flexibility in size, shape, and finish. This trend toward localization also aligns with the desire for more sustainable practices, as local production reduces the carbon footprint associated with shipping and transportation.
In the long term, robotic process automation (RPA) is likely to play an even more significant role in the metal door frame industry. RPA technologies are already being used to automate repetitive tasks such as parts handling, packaging, and inventory management. As technology advances, manufacturers will increasingly turn to RPA for more complex processes like material sorting, quality inspection, and even adaptive production scheduling. This will allow for even more efficient and flexible manufacturing systems, capable of responding to rapidly changing market demands.
As the industry continues to evolve, the customer experience is becoming a more important focus. Manufacturers are enhancing their digital presence by offering virtual consultations, online design tools, and interactive product configurators. These tools allow customers to visualize how different door frame styles and finishes will look in their specific spaces, providing a more engaging and personalized experience. Manufacturers are also leveraging augmented reality (AR) to allow customers to virtually “install” door frames in their homes or offices, helping them make more informed purchasing decisions.
In conclusion, the future of metal door frame manufacturing is marked by rapid advancements in technology, sustainability, and customer-centric innovations. As manufacturers embrace automation, robotics, AI, and smart technologies, they will be able to offer more efficient, customized, and sustainable products. At the same time, they will need to stay agile in a rapidly changing global market, responding to evolving customer demands, regulatory requirements, and technological developments. The ongoing integration of digital tools, eco-friendly materials, and advanced manufacturing processes will shape the next generation of metal door frames, driving further growth and innovation in the industry.
White Goods Outer Casing Panels Manufacturing Machine
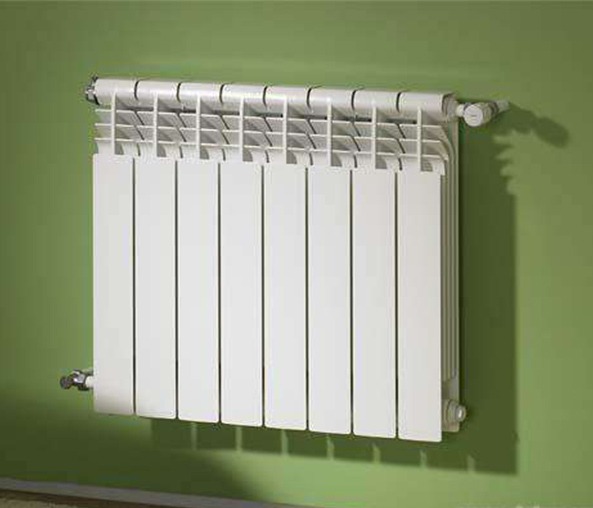
The manufacturing of white goods outer casing panels—which are the external enclosures of appliances like refrigerators, washing machines, and dishwashers—requires specialized equipment designed to meet both aesthetic and functional demands. These outer casings serve not only as protective covers but also contribute to the durability and visual appeal of the appliance. Modern manufacturing machines for white goods casing panels integrate advanced technologies to ensure precision, speed, and flexibility in the production process.
Key Aspects of White Goods Outer Casing Panels Manufacturing Machines:
1. Material Handling and Pre-Treatment
White goods outer casing panels are typically made from sheet metal (commonly steel or aluminum) or plastic materials. The material handling system is designed to efficiently load, unroll, and feed the raw material into the manufacturing line. Some key features of these systems include:
- Coil unwinders to feed sheet metal or plastic film into the production line.
- Surface pre-treatment stations, such as cleaning, degreasing, or priming, which are crucial for ensuring good paint adhesion and long-term corrosion resistance. These pre-treatment systems often include chemical baths or plasma treatment.
2. Stamping and Forming Machines
Once the material is properly prepped, the next step is shaping the outer casings. Stamping and forming machines are used to cut, bend, and shape the panels into their desired form. Common processes involved here include:
- Deep drawing: For forming complex curves, like the body of a refrigerator or washing machine.
- Hydraulic or mechanical presses: For stamping and cutting the sheet metal to create precise shapes.
- Roll forming: Used for producing continuous parts, such as the sides or frames of the panels.
The stamping process is usually highly automated and may include robotic arms to load and unload materials, improving efficiency and reducing human error.
3. Welding and Joining
For many white goods applications, the outer casings are assembled from multiple parts, such as the top, bottom, and sides. Welding or riveting systems are often used to join these parts. Key welding techniques include:
- Spot welding: Often used for joining steel panels together at specific points.
- Laser welding: For high-precision, low-distortion welding of thin sheets.
- TIG (Tungsten Inert Gas) welding: For delicate or highly visible seams, particularly when the casings need to maintain an aesthetic standard.
- Riveting and clinching: In some cases, mechanical fastening techniques like rivets or clinching are used for joining non-weldable materials or creating removable panels.
4. Surface Treatment and Coating
The finished panels undergo surface treatments to enhance their appearance and protect them from rust, corrosion, and wear:
- Powder coating: A popular choice for applying a durable, smooth finish to metal casings. It is applied electrostatically and cured under heat.
- Spray painting: In some cases, traditional liquid paints are used for a specific aesthetic finish.
- Electroplating or galvanizing: For providing a corrosion-resistant coating, especially in environments with higher humidity or exposure to chemicals.
- UV coating: For plastic panels, UV-resistant coatings may be applied to maintain appearance and prevent fading under prolonged exposure to sunlight.
5. Automated Assembly Lines
After surface treatment, the panels are often integrated into automated assembly lines. These lines can handle multiple stages of the assembly process, which includes:
- Panel insertion into frame structures.
- Fastening of internal components such as insulation, electric wiring, or metal supports.
- Attachment of functional components, such as hinges, latches, or ventilation grills.
At this stage, robots or automated arms may assist with part handling and installation, minimizing manual labor and improving consistency. These assembly lines often integrate vision systems to ensure precise alignment and correct assembly.
6. Quality Control and Inspection
Throughout the manufacturing process, quality control systems are critical to ensuring that the panels meet industry standards. These may include:
- Dimensional checks: Automated inspection systems using lasers or cameras to measure the size and shape of the panels.
- Visual inspection: For detecting cosmetic defects such as scratches, dents, or uneven finishes.
- Strength testing: Some machines are equipped with load-testing stations to ensure the structural integrity of the panels.
- Corrosion resistance tests: Ensuring that the coatings and materials used meet durability standards.
7. Packaging and Distribution
Once the panels are fully assembled and inspected, they are typically ready for packaging. Automated packaging systems ensure that each panel is carefully wrapped and prepared for shipment. This includes:
- Stacking and wrapping: Panels may be stacked in pallets and wrapped to prevent damage during transport.
- Labeling: Automated labeling machines print and apply shipping information and barcodes for easy tracking.
- Storage and dispatching: The finished goods are sent to warehousing systems or directly to distributors.
Trends in White Goods Outer Casing Panel Manufacturing
1. Customization and Flexibility
As consumer preferences for color, texture, and style evolve, manufacturers are increasingly focused on customization. The machinery used for panel manufacturing now often includes capabilities for batch production and on-demand customization. This allows for the production of panels with varying finishes, textures, and even integrated design features that can align with a wide range of product aesthetics.
2. Sustainability
Sustainability is becoming a key focus in the manufacturing of white goods. The adoption of recyclable materials and the reduction of waste during production is increasingly important. Newer technologies are designed to minimize energy consumption, reduce water usage, and enhance material recycling capabilities. For example, water-based paints and low-emission welding techniques are being integrated into production lines to reduce environmental impact.
3. Smart Manufacturing
The shift towards smart manufacturing means that more white goods casing panel factories are utilizing IoT (Internet of Things) devices to monitor and optimize production in real-time. Sensors embedded within machines can provide data on performance, downtime, and maintenance needs. Predictive maintenance algorithms help prevent unplanned downtime, which can improve operational efficiency and lower maintenance costs.
4. Automation and Robotics
Increasing automation with robotic arms is streamlining production processes, particularly in material handling, welding, and assembly. These robots are programmed to perform complex tasks with high precision, reducing the reliance on human labor and minimizing potential errors. Automation is also driving the production of high-mix, low-volume products without compromising on speed.
Conclusion
The manufacturing of white goods outer casing panels has evolved into a highly automated, flexible, and sustainable process. By integrating advanced materials, automation, smart technologies, and eco-friendly practices, manufacturers can meet the growing demands for high-quality, customized, and environmentally responsible products. These innovations not only improve the manufacturing process but also ensure that the end products align with modern consumer preferences for design, durability, and sustainability.
As the manufacturing of white goods outer casing panels continues to evolve, several emerging technologies and trends are further reshaping the production process. The integration of Industry 4.0 principles—such as cyber-physical systems, data analytics, and artificial intelligence—is enhancing the flexibility, efficiency, and intelligence of manufacturing lines. Here’s a deeper look into the ongoing advancements and their potential impact on the industry.
1. Industry 4.0 Integration
The shift toward Industry 4.0 is accelerating across manufacturing sectors, and the white goods industry is no exception. By incorporating cyber-physical systems, which combine physical manufacturing processes with digital technologies, white goods manufacturers can achieve higher levels of automation and data integration. Key components of Industry 4.0 in panel manufacturing include:
- Smart Sensors and IoT: Sensors embedded in production machines can continuously monitor machine performance, material quality, and even environmental conditions. This data can be sent to cloud-based platforms for real-time analysis, allowing for predictive maintenance, process optimization, and quality control.
- Big Data Analytics: With the continuous collection of data from manufacturing lines, manufacturers can use advanced analytics to identify patterns, predict demand fluctuations, and optimize production schedules. This data-driven approach enhances decision-making across all stages of production.
- Digital Twin Technology: Digital twins are virtual representations of physical machines and processes. In the context of casing panel manufacturing, digital twins can simulate the entire production process, helping to identify potential bottlenecks or inefficiencies before they occur in the physical world.
2. Robotics and Automated Systems
The application of robotics in white goods panel manufacturing is expanding beyond material handling to include more complex processes such as welding, assembly, and even quality inspection. Here are some specific applications:
- Robotic Welding: Robotic systems are being increasingly employed in welding processes, such as spot welding and laser welding, to ensure consistency and precision. These robots can perform repetitive welding tasks with high accuracy, reducing the likelihood of defects.
- Collaborative Robots (Cobots): Unlike traditional industrial robots that operate in isolation, cobots are designed to work alongside human workers in a shared space. They are ideal for tasks that require flexibility, such as loading and unloading materials, assembling parts, or applying coatings. Cobots enhance productivity without compromising safety.
- Automated Quality Inspection: Robots equipped with advanced vision systems can inspect finished panels for defects such as scratches, dents, or misalignments. These robotic systems can perform inspections faster and more consistently than human workers, ensuring that only flawless panels proceed to the next stages of production or packaging.
3. Advanced Materials and Coatings
The use of advanced materials and innovative coatings is a growing trend in the manufacturing of white goods outer casing panels. These materials provide better performance in terms of durability, appearance, and environmental impact.
- High-Strength Steels: Manufacturers are increasingly turning to high-strength steels for casings, which offer greater durability without adding weight. These materials can withstand harsh environments, making them particularly useful for outdoor appliances or regions with extreme weather conditions.
- Polymer Coatings and Laminates: For plastic panels, the use of polymer coatings and laminates is becoming more popular. These coatings provide a high-quality finish while improving scratch resistance, UV protection, and overall appearance. Advances in nanocoatings and self-healing materials also contribute to a more durable and aesthetically pleasing product.
- Recycled and Sustainable Materials: With an increasing focus on sustainability, manufacturers are exploring the use of recycled materials or biodegradable plastics for white goods panels. Using recycled steel, aluminum, or plastics not only reduces costs but also minimizes the environmental impact of production.
4. Sustainability and Circular Economy
The concept of sustainability is at the forefront of white goods manufacturing, and manufacturers are looking for ways to reduce energy consumption, minimize waste, and improve the recyclability of their products. Key initiatives include:
- Energy-Efficient Manufacturing: Advanced energy recovery systems and energy-efficient machinery are being adopted to reduce power consumption during the production of metal and plastic panels. Manufacturers are also integrating solar panels or other renewable energy sources into their production facilities to reduce their reliance on traditional energy grids.
- Zero-Waste Production: By optimizing material usage and implementing more efficient cutting and forming processes, manufacturers are striving to eliminate material waste. Techniques like nesting (optimizing part layouts) and advanced cutting methods (such as laser cutting) allow for minimal material loss.
- End-of-Life Recycling: As part of a circular economy, manufacturers are focusing on designing panels that can be easily disassembled and recycled at the end of their lifecycle. Using recyclable materials and creating products with less mixed-material construction allows for easier separation and recycling when the appliance reaches the end of its life.
5. Customization and Modular Design
As consumer preferences shift towards personalization and greater variety, manufacturers are offering more customization options for the outer casing panels of white goods. These include:
- Color and Texture Customization: Consumers now expect to be able to choose their appliance’s exterior finish. The introduction of advanced color-matching systems and automated coating lines has made it easier for manufacturers to offer a wide range of colors and textures, catering to different tastes and interior designs.
- Modular Design: Modular manufacturing systems allow for quicker adaptation to changing market trends or customer demands. Instead of producing large volumes of a single design, manufacturers can adapt their production lines to produce various panel designs using interchangeable components. This reduces production time and costs while providing greater flexibility.
- Integrated Features: Some manufacturers are adding functional features directly into the panels, such as integrated ventilation systems, lighting, or smart technology interfaces. These innovations can help differentiate brands and provide added value to consumers.
6. Digitalization and Consumer-Centric Solutions
With the rise of digital platforms, manufacturers are increasingly turning to online tools and technologies to connect directly with consumers, improve engagement, and streamline the purchasing process. This includes:
- Online Customization Tools: Consumers can design their own white goods panel finishes, upload custom logos, or even choose specific materials and coatings through easy-to-use online configurators.
- Virtual Reality (VR) and Augmented Reality (AR): These technologies are being used in showrooms or e-commerce platforms to allow customers to visualize how appliances with custom-designed outer casing panels will look in their homes. VR and AR can also assist with remote maintenance and repair by guiding technicians through troubleshooting processes.
- Smart Appliances: Manufacturers are integrating IoT technology into the casing itself, allowing consumers to monitor and control their appliances remotely via smartphone apps. This trend is especially important for white goods like refrigerators, washing machines, and dishwashers, where smart features can help optimize performance, maintenance, and energy use.
Conclusion
The future of white goods outer casing panel manufacturing lies in the convergence of advanced materials, smart technologies, and sustainable practices. Manufacturers are increasingly adopting robotic automation, data-driven manufacturing, and customization tools to improve efficiency, product quality, and customer satisfaction. At the same time, growing demand for environmentally friendly products is driving innovation in materials and processes, pushing manufacturers to reduce waste and enhance recyclability. As technology continues to evolve, the white goods manufacturing industry will remain at the forefront of efficiency, innovation, and sustainability, creating products that meet the needs of both consumers and the environment.
As we look ahead, the white goods outer casing panels manufacturing sector will continue to embrace new technological innovations that not only enhance production efficiency but also improve the quality of the final product. Some of the key developments in the near future include:
1. Artificial Intelligence and Machine Learning in Production Optimization
The integration of artificial intelligence (AI) and machine learning (ML) is poised to revolutionize the manufacturing of white goods outer casing panels. These technologies enable the automation of decision-making processes that were once dependent on human intervention. AI and ML can significantly improve several areas of production, including:
- Predictive Maintenance: AI algorithms can predict when a machine or equipment will likely fail by analyzing historical data and real-time sensor readings. This allows for preventative maintenance, reducing downtime and increasing overall efficiency.
- Process Optimization: Machine learning models can analyze vast amounts of production data to identify inefficiencies in the manufacturing process. By optimizing material flow, cutting patterns, and energy use, manufacturers can significantly reduce waste and improve throughput.
- Defect Detection: AI-powered vision systems, combined with deep learning techniques, can improve the accuracy of defect detection in real-time during the production process. This means that surface imperfections, misalignments, or dimensional inconsistencies can be flagged immediately, improving product quality.
2. 3D Printing and Additive Manufacturing
The role of 3D printing (or additive manufacturing) is gradually expanding within the white goods manufacturing industry, particularly in the development of prototype parts and small-volume production. While the technology is still emerging for large-scale production, it holds immense potential for:
- Rapid Prototyping: 3D printing enables designers to quickly produce prototypes of new outer casing designs or specific components, reducing the time it takes to go from concept to production.
- Customized Components: For highly specialized or niche product requirements, 3D printing could allow manufacturers to produce custom-shaped panels, integrated features, or brackets that would be difficult or expensive to make with traditional manufacturing methods.
- Low-Volume Production: In cases where only a limited number of white goods are required (for example, customized appliances for specific markets or customers), additive manufacturing can offer a cost-effective and flexible alternative to traditional injection molding or stamping.
3. Sustainability and Closed-Loop Manufacturing
The push for sustainable production will only grow stronger as regulations become stricter and consumers demand more eco-friendly products. The concept of closed-loop manufacturing is one that is gaining traction across industries, including white goods manufacturing. This approach seeks to minimize waste, energy consumption, and raw material usage by recycling products back into the production process.
- Recycling and Reuse: Manufacturers are increasingly implementing systems to recycle the metal and plastic materials used in the outer casing panels, either by reusing the raw material in the production of new panels or by refining the scrap metal/plastic to be used in other parts of the production process.
- Eco-Friendly Materials: The industry is moving toward using biodegradable materials or recycled plastics for panel production. Additionally, companies are exploring bio-based coatings that are both durable and non-toxic, contributing to the overall sustainability of the product.
- Energy-Efficient Production: Implementing energy-efficient technologies such as heat recovery systems and using solar or wind energy in manufacturing plants will reduce the carbon footprint of production processes. This includes not only powering the machinery but also implementing green building designs in manufacturing facilities.
4. Smart Manufacturing and the Role of IoT
The concept of smart manufacturing, powered by the Internet of Things (IoT), is fundamentally changing how white goods manufacturers operate. By embedding IoT sensors in both machines and products, manufacturers can collect a wealth of data to monitor, optimize, and control every aspect of production. IoT will enable manufacturers to:
- Real-Time Monitoring: IoT sensors can track the performance of machines, energy usage, and material consumption in real time. This data allows manufacturers to monitor production closely, detect anomalies, and make real-time adjustments to optimize performance.
- Smart Factory Integration: In a fully connected smart factory, all machines, robots, and systems can communicate with each other, enabling seamless integration across the production line. This level of interconnectivity improves workflow, reduces errors, and ensures consistent product quality.
- Supply Chain Efficiency: IoT can also extend to the supply chain, where sensors can monitor inventory levels, track material deliveries, and even forecast demand. This helps prevent delays, reduce excess inventory, and streamline logistics, ensuring that production is not hampered by supply chain disruptions.
5. Flexible and Modular Manufacturing Systems
As market demands become more dynamic, the need for flexible and modular production systems is becoming increasingly evident. Traditional manufacturing lines were often designed for high-volume, single-product runs. However, with the rising demand for customization and shorter production cycles, manufacturers are adopting more flexible production methods that allow them to switch between different panel designs and configurations quickly.
- Modular Equipment: Modular production systems are designed to be easily reconfigured, allowing for adjustments in production volume or product type without extensive downtime or retooling.
- Flexible Workforce: Alongside flexible production lines, there is a growing need for a more adaptable workforce. With more robots, cobots, and automated systems, human workers are shifting roles toward overseeing, programming, and maintaining the machines, while ensuring the overall production system remains agile and responsive to market shifts.
- Batch Production: The ability to produce smaller batch quantities of customized panels, or even limited edition designs, will allow manufacturers to meet specific customer demands and target niche markets.
6. Enhanced Customer Experience Through Digital Tools
The focus on customer-centric manufacturing continues to shape the white goods sector. As customer preferences become more diverse, offering personalized experiences in product selection and design is increasingly important. Manufacturers are leveraging digital tools to provide a more interactive, transparent, and engaging process for consumers, which could include:
- Virtual Product Customization: Online platforms enable consumers to visualize and select custom designs, materials, colors, and finishes for white goods panels. These tools often incorporate 3D rendering to allow customers to see how different panel styles will look in their home environment.
- Augmented Reality (AR) for Product Testing: Consumers can use AR to virtually place a model of an appliance with custom casing in their home, helping them make purchasing decisions with more confidence.
- E-Commerce and Direct-to-Consumer Models: Some manufacturers are embracing direct-to-consumer (DTC) models, cutting out traditional distribution channels and allowing customers to design and order their appliances directly from the manufacturer. This model enables brands to offer unique product lines, provide greater transparency, and ensure faster delivery times.
7. Global Expansion and Localization
The globalization of the white goods industry has opened up new markets, especially in developing regions where rising disposable incomes and urbanization are driving demand for household appliances. However, as manufacturers expand into these new markets, they are increasingly adopting localization strategies to cater to the specific needs, preferences, and regulations of each region.
- Localized Manufacturing: Establishing manufacturing plants closer to key markets reduces shipping costs, allows for faster delivery, and helps manufacturers better understand and serve local customer demands.
- Tailored Product Features: Local market preferences can affect design, materials, and functionality. For instance, certain regions may prioritize energy efficiency, specific aesthetic styles, or adapt to regional climates, prompting manufacturers to customize their panel designs accordingly.
Conclusion
The future of white goods outer casing panel manufacturing is characterized by innovation, efficiency, and sustainability. Through the adoption of Industry 4.0 technologies, AI, robotics, and smart manufacturing systems, manufacturers will continue to enhance the production process, allowing for greater customization, higher quality, and lower environmental impact. At the same time, the shift towards eco-friendly materials and circular economy practices will ensure that the industry can meet both consumer demand for sustainability and the need for cost-effective, high-quality products. Ultimately, by staying at the forefront of technological advancements and embracing evolving market demands, manufacturers can secure their position in a highly competitive and ever-changing global market.
As we continue exploring the future of white goods outer casing panels manufacturing, several key factors and trends are driving transformation in the industry, further impacting product quality, production efficiency, and customer engagement.
1. Digital Supply Chains and Blockchain Technology
With the growing complexity of global supply chains, digital supply chains powered by blockchain technology are becoming more critical for enhancing transparency, traceability, and efficiency in white goods manufacturing.
- Blockchain for Traceability: Blockchain allows for the secure, transparent tracking of materials as they move through the supply chain, from raw material suppliers to manufacturers. This can help verify the authenticity of sustainable sourcing practices (such as the use of recycled materials) and ensure compliance with environmental and labor standards.
- Smart Contracts and Automated Payments: Blockchain-based smart contracts can automate transactions between suppliers, manufacturers, and customers, reducing administrative overhead and speeding up the supply chain process. This can lead to faster procurement, better inventory management, and smoother delivery schedules.
- Enhanced Inventory Management: Digital supply chains, combined with IoT and real-time data analytics, allow manufacturers to track and manage inventory in real-time. This minimizes overproduction, prevents stockouts, and improves the efficiency of the manufacturing process.
2. Automation and Industry 5.0
While Industry 4.0 focuses on integrating advanced technologies to enhance automation and data-driven decision-making, Industry 5.0 is emerging as a concept that brings humans and machines into even closer collaboration.
- Human-Machine Collaboration: Industry 5.0 emphasizes the importance of human creativity, intuition, and flexibility alongside increasingly capable robots and AI systems. In the white goods manufacturing context, this means workers might focus more on overseeing complex tasks, programming robots, and solving problems that machines cannot handle, while robots handle repetitive, high-precision tasks.
- Personalized Production: Industry 5.0 enables more mass customization through the use of advanced robotics, flexible automation, and human expertise. Consumers will increasingly be able to design and specify their own white goods products with more options, all while ensuring the production line can quickly switch between personalized products without losing efficiency.
3. Augmented Reality (AR) in Training and Maintenance
The adoption of augmented reality (AR) technologies is improving both training and maintenance processes in white goods manufacturing. AR is enabling manufacturers to train workers more effectively and provide real-time assistance for complex repairs and maintenance tasks.
- Training and Skill Development: AR headsets and applications can superimpose instructions and visual aids onto real-world objects, enabling employees to learn and practice tasks in a hands-on, interactive environment. This is particularly useful for training operators on complex equipment or systems, like robotic arms, welding machines, or automated quality inspection systems.
- Remote Maintenance Support: AR is also useful for remote assistance. Maintenance technicians can wear AR glasses while working on machines, and experts from across the world can guide them through repairs or troubleshooting steps without being physically present. This reduces downtime and improves the efficiency of machine servicing.
4. Sustainability: Carbon Footprint Reduction and Eco-friendly Materials
As climate change concerns continue to rise, the white goods manufacturing industry is increasingly pressured to reduce its carbon footprint and adopt more sustainable practices. In addition to energy-efficient production processes, manufacturers are considering the full lifecycle impact of their products, from material sourcing to disposal.
- Low Carbon Manufacturing: Manufacturers are looking for ways to reduce emissions across the entire production process. This includes the use of green energy sources such as wind, solar, and hydroelectric power to run production facilities. Energy-efficient machinery, along with advanced energy management systems, helps optimize power consumption throughout the manufacturing process.
- Sustainable Materials: Companies are exploring the use of eco-friendly materials such as bio-based plastics, recycled steel, and composite materials that are not only durable but also biodegradable or recyclable at the end of the product’s life. These materials can replace traditional metals and plastics, contributing to a more circular economy.
- Product Take-Back Programs: Many manufacturers are implementing take-back programs that encourage customers to return their old appliances. These products are then disassembled, and the materials are reused, which further reduces the need for virgin raw materials and promotes recycling.
5. Advanced Packaging Solutions
Packaging is another area in which manufacturers of white goods outer casing panels are innovating. With sustainability becoming more of a consumer priority, packaging solutions must be environmentally friendly while maintaining product protection and transportation efficiency.
- Eco-Friendly Packaging: Companies are shifting away from single-use plastics and opting for biodegradable or recyclable packaging materials. This includes cardboard, corrugated paper, and plant-based plastics, which can all be recycled or composted.
- Protective and Lightweight Packaging: Advanced foam technologies and customized packaging reduce material usage and weight while still ensuring products are protected during shipping. Additionally, innovations like air-filled cushioning can replace traditional, heavier packaging materials.
- Smart Packaging: Some manufacturers are also integrating smart packaging that includes sensors to track product conditions during transportation. These sensors can measure temperature, humidity, or shock levels, ensuring that the outer casing panels arrive at their destination in perfect condition.
6. Robotics and Automation in Post-Production
In post-production, robotic systems are playing an increasingly important role in automating the final stages of manufacturing, such as sorting, packaging, and quality control. The use of robotics can help reduce human labor in these areas and improve speed and consistency.
- Automated Sorting and Handling: Robotic systems equipped with vision sensors can inspect and sort finished panels based on quality, size, or finish. These systems can also handle panels carefully to avoid any damage, ensuring that only products meeting the required standards proceed to the next stage.
- Automated Packaging Lines: Once the panels pass quality inspection, automated systems can quickly package them for shipment. These systems can wrap, box, and label products with minimal human intervention, speeding up the process and reducing errors.
- Integrated Testing: Before products are shipped, they are subjected to various tests to ensure their durability, finish, and dimensional accuracy. Robotics can be integrated with testing stations to automatically conduct tests such as impact resistance, UV exposure, and dimensional checks, streamlining the quality assurance process.
7. Global Competitiveness and Emerging Markets
As the global white goods market continues to grow, particularly in emerging markets, manufacturers are facing increased competition. To maintain a competitive edge, companies must look beyond cost-cutting measures and focus on innovation, product differentiation, and customer satisfaction.
- Regional Adaptation: As manufacturers expand into new markets, especially in Asia, Africa, and South America, they must adapt their product offerings to meet local preferences, cultural factors, and environmental conditions. For instance, some regions may favor appliances that are more energy-efficient due to higher electricity costs, while others may prioritize durability in harsh climates.
- Technology Leapfrogging: Many emerging markets are adopting new manufacturing technologies faster than developed nations due to their ability to bypass legacy systems. This is allowing companies to build more efficient and advanced manufacturing operations in these regions, helping to close the technological gap with traditional manufacturing powerhouses.
8. Consumer Preferences and Product Differentiation
To maintain market leadership, white goods manufacturers are becoming more customer-centric, focusing on understanding evolving consumer needs and offering tailored products that meet those expectations.
- Smart Appliances: Consumers are increasingly looking for appliances with integrated smart technology, such as connectivity with home automation systems, voice control, or energy-monitoring features. Manufacturers are adding IoT features into the panels, allowing customers to monitor and control their appliances remotely through smartphone apps.
- Aesthetics and Design Customization: As consumers place more importance on the look and feel of their appliances, there is greater demand for personalized design options. Offering a wide range of customizable finishes, colors, and textures for outer casing panels allows manufacturers to cater to various interior styles and preferences.
- Energy Efficiency and Eco-Consciousness: With growing environmental awareness, consumers are increasingly prioritizing energy-efficient appliances. Manufacturers must meet higher standards for energy ratings and eco-friendly certifications to appeal to eco-conscious buyers.
Conclusion
The future of white goods outer casing panel manufacturing is driven by a combination of advanced manufacturing technologies, sustainability, customer-centric innovation, and globalization. Manufacturers who embrace digitalization, automation, and eco-friendly practices will be better positioned to thrive in the competitive global market. By integrating AI, robotics, sustainable materials, and smart manufacturing systems, the industry is on track to not only improve the efficiency and quality of its products but also to create more personalized, sustainable, and consumer-focused solutions.
As we continue to look at the evolving landscape of white goods outer casing panel manufacturing, it’s clear that new innovations and shifts in industry dynamics will shape the future of production, quality, and customer experience. Let’s explore further some critical areas where this transformation is taking place.
1. Circular Economy and the Rise of Recycling Innovation
The circular economy model is quickly becoming a cornerstone of the manufacturing industry, particularly in sectors like white goods manufacturing, where product lifecycle management and recycling are critical for reducing waste and environmental impact.
- Closed-Loop Recycling Systems: Manufacturers are increasingly adopting closed-loop recycling to repurpose materials from end-of-life products back into the production cycle. This reduces the need for virgin raw materials and supports the movement toward more sustainable manufacturing practices. The focus is on designing products that are easier to disassemble, reuse, and recycle, ensuring that materials can be recovered and reused efficiently.
- Innovative Recycling Technologies: Companies are investing in cutting-edge material recycling technologies, such as advanced sorting systems and chemical recycling methods, that can handle a wider variety of materials used in white goods panels (e.g., plastics, metals). These technologies allow for higher purity and quality in the recycled materials, which can then be used in the manufacturing of new products, creating a more sustainable closed-loop system.
- Design for Disassembly: To facilitate better recycling and reuse, manufacturers are focusing on designing products with disassembly in mind. This ensures that components, like metal frames or plastics, can be easily separated and processed at the end of the product’s life, making it easier to recycle materials without contamination.
2. Energy-Efficient Manufacturing Processes
As part of the broader push for sustainability, energy efficiency has become a critical focus in the production of white goods panels. Manufacturers are incorporating technologies that help reduce the energy consumed during production, which in turn reduces costs and the environmental impact.
- Energy Recovery Systems: Some manufacturers are integrating energy recovery systems into their production lines, such as heat recovery systems, which capture excess heat generated during manufacturing processes and reuse it for heating or powering other parts of the facility. This reduces overall energy consumption and lowers operational costs.
- Low-Energy Manufacturing Equipment: Advanced machinery and equipment that consume less energy are being adopted across manufacturing plants. Variable frequency drives (VFDs) for motors, energy-efficient compressors, and LED lighting systems are just a few examples of how manufacturing operations can reduce energy usage while maintaining high levels of productivity.
- Smart Grids and Sustainable Energy: Many manufacturers are transitioning to smart grids that integrate renewable energy sources, such as solar or wind power. These grids allow manufacturing plants to source energy more sustainably, manage energy usage more efficiently, and even sell excess energy back to the grid, improving the overall sustainability of the manufacturing process.
3. Advanced Data Analytics for Production Efficiency
The role of data analytics in modern manufacturing cannot be overstated. With the availability of big data and powerful analytics tools, manufacturers are optimizing nearly every aspect of production to increase efficiency and reduce waste.
- Predictive Analytics for Maintenance: By using predictive analytics, manufacturers can foresee potential equipment failures before they happen. This helps in scheduling maintenance at optimal times, thus preventing unexpected breakdowns, reducing downtime, and maximizing machine uptime.
- Data-Driven Process Improvements: The use of data from machines and sensors enables manufacturers to gain real-time insights into production lines. By analyzing this data, manufacturers can optimize processes such as machine calibration, temperature control, and material flow, leading to reduced waste and improved quality.
- Supply Chain Visibility: Data analytics can also be applied to manage the supply chain more effectively. By tracking materials in real time, forecasting demand, and optimizing inventory levels, manufacturers can avoid stockouts or overproduction, ensuring smooth production schedules and reducing costs associated with inventory management.
4. Customization and Personalization at Scale
The growing demand for customized products is reshaping how white goods manufacturers approach production. As customers increasingly seek personalized solutions that meet their specific needs, manufacturers are exploring ways to efficiently produce customized outer casing panels without sacrificing speed or quality.
- Flexible Manufacturing Systems: Flexible manufacturing systems (FMS) allow manufacturers to produce different versions of the same product without extensive downtime for retooling. By incorporating automation, robotics, and digital technologies, manufacturers can rapidly adjust production to meet changing customer preferences and market demands.
- Mass Customization: Using modular production techniques and 3D printing, manufacturers can offer consumers a variety of customizable options, such as color, finish, and panel design, all while maintaining mass production efficiency. This approach enables manufacturers to meet the growing desire for personalized products without the cost and time penalties typically associated with bespoke manufacturing.
- Smart Configurators: Online tools, such as product configurators, allow consumers to design their own appliances by selecting from various customization options for the outer casing panels. These digital interfaces simplify the design process and give manufacturers a clear view of demand trends, which can be used to adjust production accordingly.
5. Global Supply Chain Resilience and Risk Management
In an increasingly interconnected world, supply chain resilience has become a top priority for manufacturers. Disruptions like the COVID-19 pandemic, geopolitical tensions, and environmental disasters have highlighted the vulnerability of global supply chains.
- Diversified Sourcing: Manufacturers are diversifying their supply chains to mitigate risks associated with over-reliance on a single source or region. By sourcing raw materials and components from different suppliers and geographic regions, companies can maintain production continuity in the face of disruptions.
- Localizing Production: To reduce dependency on global supply chains, some manufacturers are opting to localize production closer to key markets. This helps lower transportation costs, reduce lead times, and minimize the risk of delays caused by supply chain bottlenecks.
- Advanced Risk Modeling: Predictive analytics and AI-based modeling are increasingly used to assess and manage supply chain risks. By analyzing historical data and simulating different disruption scenarios, manufacturers can proactively prepare for potential supply chain challenges and respond quickly to minimize impact.
6. Collaborative Industry Ecosystems
In the future, the white goods manufacturing industry is likely to see increased collaboration among manufacturers, suppliers, technology providers, and even competitors. The idea of collaborative ecosystems is gaining momentum, with companies joining forces to drive innovation and create more efficient solutions across the supply chain.
- Partnerships with Tech Companies: White goods manufacturers are increasingly partnering with technology companies to integrate cutting-edge technologies into their production processes. These partnerships enable manufacturers to access expertise in AI, IoT, machine learning, and robotics, speeding up the adoption of advanced manufacturing technologies.
- Joint Ventures for Sustainable Practices: To meet sustainability targets, manufacturers are forming joint ventures with materials suppliers, recyclers, and waste management companies to create more efficient and sustainable processes. These partnerships focus on reducing waste, enhancing recycling capabilities, and advancing the circular economy.
- Industry Consortia and Shared R&D: Manufacturers are also collaborating within industry consortia to share research and development costs, innovate jointly, and influence industry-wide standards. This collaboration accelerates the adoption of new technologies and drives collective progress in improving manufacturing processes, materials, and product sustainability.
7. Consumer-Centric Innovations
As the market for white goods continues to evolve, consumer preferences are playing a central role in shaping product designs and manufacturing approaches. Manufacturers are focusing more on delivering value-added features that meet the expectations of modern consumers.
- Enhanced User Experience: Manufacturers are increasingly integrating user-centric features into appliances. For instance, the design of outer casing panels is no longer just about aesthetics; it also includes functionality, such as ease of cleaning, reduced noise, and improved ergonomics.
- Integration with Smart Home Systems: Many consumers now expect their appliances to be connected to their smart home systems, enabling remote monitoring and control. Manufacturers are designing panels that accommodate the installation of IoT sensors and connectivity features, facilitating integration with other household devices.
- Increased Durability and Sustainability: Consumers are becoming more focused on the durability and sustainability of their products. Manufacturers are responding by developing long-lasting, energy-efficient, and eco-friendly white goods that are built to last and minimize their environmental footprint over time.
Conclusion
The future of white goods outer casing panels manufacturing will be defined by a complex interplay of technological advancements, environmental concerns, evolving consumer demands, and global competition. Manufacturers that embrace digital transformation, sustainability, and innovation in their production processes will be better positioned to meet the challenges of a rapidly changing industry landscape.
By leveraging cutting-edge technologies such as AI, IoT, robotics, 3D printing, and sustainability-driven innovations, manufacturers can create products that not only meet the needs of consumers but also contribute to a more efficient, circular, and eco-friendly industry. As the pace of change accelerates, staying ahead of these trends will be crucial for ensuring long-term success and competitiveness in the global market.
Sheet Metal Coffee Pot Manufacturing Machine
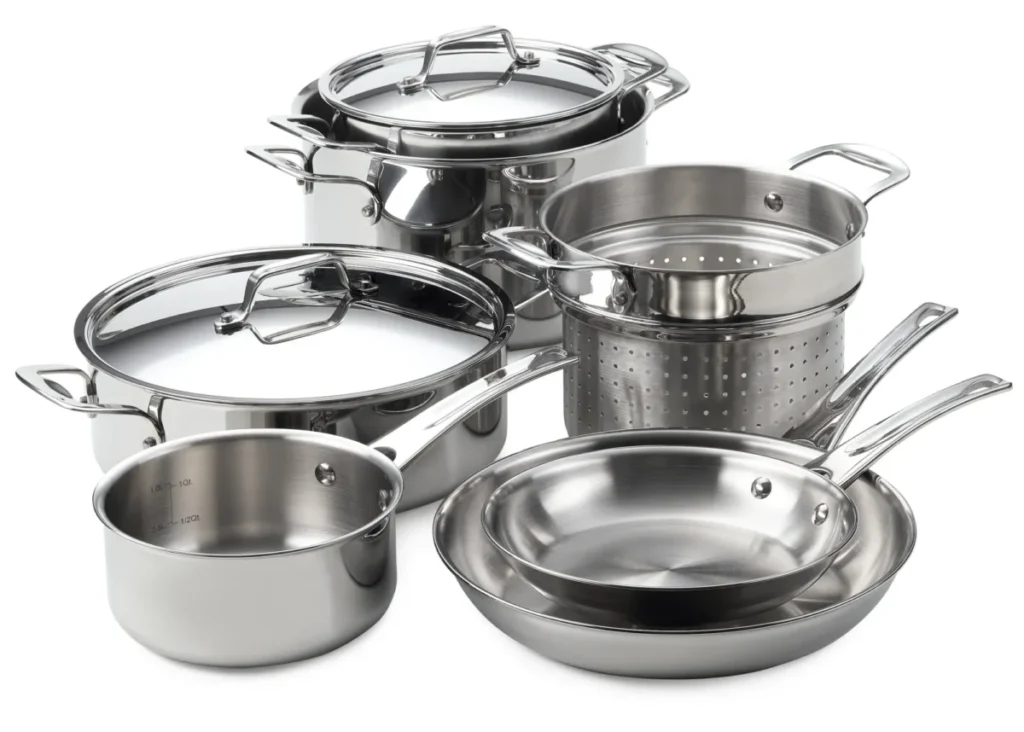
A Sheet Metal Coffee Pot Manufacturing Machine is designed to automate the process of creating coffee pots or other similar kitchenware from sheet metal. The manufacturing process for these coffee pots typically involves several key steps, such as cutting, forming, welding, assembling, and finishing. Let’s explore the different processes and technology involved in the production of sheet metal coffee pots using specialized machinery.
1. Material Preparation
- Sheet Metal Selection: The process begins with selecting the appropriate metal sheet, typically stainless steel, aluminum, or copper, depending on the desired characteristics of the final product, such as durability, appearance, and heat resistance. Stainless steel is a common choice due to its resistance to corrosion and its aesthetic appeal.
- Sheet Metal Cutting: The metal sheet is cut into the required shapes (such as circular blanks for the pot’s body and lid) using a laser cutting machine or punching press. The cuts need to be precise to ensure smooth edges and to minimize waste.
2. Forming and Shaping
- Deep Drawing or Stamping: The cut metal sheets are placed into a deep drawing press or hydraulic stamping machine, which is used to form the main body of the coffee pot. This process involves pushing the sheet metal into a die to create the curved, cylindrical shape of the pot. The depth and form of the drawing are carefully controlled to prevent cracking or deformation.
- Spinning or Stretch Forming: For more intricate shapes, some manufacturers may use spinning or stretch forming techniques, where the metal is rotated at high speed and shaped over a mandrel or die to form the required contours of the pot.
3. Assembly
- Joining Components: The coffee pot typically consists of multiple parts: the body, lid, handle, spout, and sometimes a base. The assembly process involves joining these components together. Common joining methods include:
- Welding: Parts like the handle or spout are welded onto the main body using TIG welding (Tungsten Inert Gas) or MIG welding (Metal Inert Gas) to ensure a strong bond without compromising the metal’s integrity.
- Riveting: Riveting can be used for joining parts where welding may not be suitable or desired.
- Soldering: For smaller or delicate components, soldering may be used for joining parts like the spout to the pot.
4. Finishing
- Surface Polishing and Buffing: Once the parts are assembled, the surface of the coffee pot is usually polished to a smooth, glossy finish. This is typically done using polishing machines or buffing wheels to give the product a high-quality appearance.
- Cleaning and Degreasing: The coffee pot goes through a cleaning and degreasing process to remove any oils, dirt, or residues from the manufacturing process. This ensures that the metal surface is free of contaminants before coating or packaging.
- Electroplating or Coating: If the design calls for it, the coffee pot may undergo electroplating (e.g., for a shiny chrome finish) or powder coating for added durability and an aesthetic finish.
5. Handle and Lid Attachment
- Handle Fabrication and Attachment: The handle is typically made of metal but may also incorporate other materials, such as plastic or wood, for a more ergonomic grip. It is attached securely to the pot using rivets, welding, or screws, depending on the design.
- Lid Attachment: The lid of the coffee pot is often attached using hinges or a snap-fit design. If necessary, a seal may be incorporated to prevent spillage.
6. Quality Control and Inspection
Before the coffee pots are packaged, each unit undergoes a rigorous quality control process. This may include:
- Dimensional Inspection: Ensuring that all components are correctly sized and aligned.
- Leak Testing: For coffee pots that require holding liquids, leak testing may be performed by filling the pot with water and checking for any leaks.
- Visual Inspection: Checking the exterior for any scratches, dents, or other surface imperfections.
7. Packaging and Shipping
Once the coffee pots have passed the final inspection, they are cleaned, packaged, and prepared for shipping. Packaging ensures that the pots are protected during transportation and arrive at the retailer or customer in perfect condition.
Automation in Sheet Metal Coffee Pot Manufacturing
Many modern Sheet Metal Coffee Pot Manufacturing Machines incorporate automation to improve production speed and consistency. Key automation features include:
- Robotic Welding: Robots equipped with welding arms can precisely weld components, reducing human error and increasing production speed.
- Automated Assembly Lines: Conveyors and automated assembly systems are used to move parts through various stages of the production process without manual handling, ensuring a continuous workflow.
- CNC Machines: Computer Numerical Control (CNC) machines can be used to perform precision cutting, forming, and drilling operations with high accuracy.
- Quality Control Automation: Automated systems using vision sensors and AI-based defect detection can ensure high standards in terms of quality and consistency across all products.
By integrating these automation technologies, manufacturers can reduce labor costs, minimize production errors, and increase throughput while maintaining high-quality standards.
This process can be customized depending on the design and features of the coffee pot. For example, some manufacturers may focus on premium handcrafted designs with more manual involvement, while others may prioritize speed and volume through full automation. The right approach depends on the target market and the specific needs of the consumer.
In addition to the primary manufacturing steps already covered, there are several auxiliary processes and considerations that further refine the production of sheet metal coffee pots, enhance efficiency, and ensure regulatory compliance and market readiness.
8. Tooling and Die Maintenance
A critical part of maintaining consistent quality in deep drawing and stamping operations is ensuring that dies and molds are well-maintained:
- Precision Tooling: Dies used in forming the body and lids of the pots must be manufactured with high precision and made from hardened steel to resist wear.
- Regular Maintenance: Scheduled regrinding, polishing, and alignment of tooling components help prevent defects like wrinkling, tearing, or thinning of the sheet metal.
- Quick Die Change (QDC) Systems: For high-mix, low-volume production, many facilities implement QDC systems that reduce downtime during tooling changes, improving flexibility and productivity.
9. Production Line Layout and Workflow Optimization
An efficient layout ensures smooth movement of materials and components, reducing cycle times and minimizing manual handling:
- U-shaped Cells: These are often used for compact coffee pot lines where an operator can monitor and intervene in several stations.
- Inline Buffering and Staging: Between forming, assembly, and finishing stations, buffer zones prevent bottlenecks and allow one section to continue operating even if another is momentarily paused.
- Ergonomics: For semi-automated lines, workstations are designed to reduce operator fatigue and injury, especially in processes like handle assembly or final packaging.
10. Compliance with Food Contact Regulations
Since coffee pots are used for preparing consumable liquids, they must meet stringent health and safety standards:
- Material Compliance: Metals used, particularly stainless steel, must meet FDA or EU (e.g., EC No. 1935/2004) regulations regarding food contact safety.
- Surface Treatments: Any coatings or platings must be non-toxic, non-reactive, and resistant to leaching or degradation under heat and cleaning conditions.
- Traceability: Manufacturers often maintain lot tracking systems to ensure traceability of materials and parts for quality assurance and recalls, if necessary.
11. Product Testing and Endurance Validation
In addition to basic inspections, coffee pots may undergo advanced testing:
- Thermal Shock Testing: Simulating rapid temperature changes to ensure that the pot can handle real-world conditions without deformation or cracking.
- Handle Load Testing: The strength of the handle is tested under static and dynamic loads to prevent failure during use.
- Drop Tests: Simulating common accidents in domestic use to verify product durability.
12. Variants and Product Line Diversification
Modern coffee pot lines may be designed to support multiple product types:
- Espresso Makers and Percolators: Variants with additional features like valves, chambers, or built-in heating elements require extra machining or assembly stations.
- Size Variants: The same base machine line can often accommodate different volumes (e.g., single-cup, 4-cup, 8-cup) by using interchangeable dies and fixtures.
- Design Features: Embossed logos, decorative patterns, or multi-color finishes can be added via stamping, engraving, or laser marking stations downstream.
13. Sustainability and Waste Management
Efficiency in manufacturing today also includes minimizing environmental impact:
- Scrap Recovery Systems: Sheet metal offcuts from blanking operations are collected and either reused or sent for recycling.
- Water and Coolant Recycling: In operations like polishing or cutting, closed-loop water systems filter and reuse water and coolant, reducing both cost and discharge.
- Energy Monitoring: Sensors and smart systems track energy consumption by machine, allowing operators to identify inefficiencies or overuse.
14. Packaging and Branding
Before final shipment, the coffee pots go through:
- Automated Packaging Machines: Machines fold cartons, insert user manuals, and package the coffee pot automatically.
- Laser Engraving or Screen Printing: For brand identity, machines may apply logos, barcodes, or compliance labels directly to the product or packaging.
- Barcode/QR Coding: Used for product tracking, warranty management, and in some cases, digital manuals or promotional materials.
With the integration of these additional systems and best practices, a Sheet Metal Coffee Pot Manufacturing Machine or production line becomes a highly coordinated and efficient operation. It combines precision forming, automated assembly, and rigorous quality control to meet the demands of global markets—balancing speed, safety, aesthetics, and compliance.
Another important dimension of the Sheet Metal Coffee Pot Manufacturing Line involves process integration, digital monitoring (non-AI), operator safety, and global adaptability, which are often implemented even in traditionally automated, non-AI production environments.
15. Integrated Line Control Systems (PLC-Based)
Though AI is excluded, programmable logic controllers (PLCs) remain central in classic automated lines:
- Sequential Control: PLCs manage step-by-step sequences — from sheet feeding to forming, trimming, and welding — ensuring coordination without manual intervention.
- Sensor Feedback Loops: Sensors (e.g., proximity, pressure, and temperature) provide real-time feedback to the PLC, helping control actuator motion and machine timing.
- Human-Machine Interfaces (HMIs): Operators use basic touch panels to adjust press stroke, speed, or perform diagnostics, offering user control without AI-based decision-making.
16. Tool and Die Changeover Efficiency
For high-variety manufacturing, minimizing downtime during changeover is essential:
- Manual Quick-Lock Fixtures: These systems allow tooling to be swapped in minutes using standardized mounting points.
- Color-Coded Tool Sets: Simplifies identification and setup for operators managing multiple part variants.
- Dedicated Storage Racks: Tooling is organized in racks adjacent to the line to reduce tool retrieval time and potential damage.
17. Operator Safety and Ergonomics
In legacy-style manufacturing lines, robust mechanical safety systems remain vital:
- Two-Hand Press Controls: Prevent accidental activation of drawing presses or forming equipment, ensuring hands are clear of the working area.
- Mechanical Interlocks and Light Curtains: Stop the press when operators inadvertently enter guarded zones.
- Fume and Dust Extraction: Grinding and welding processes often generate fine particulates and fumes, requiring localized extraction systems for a clean and compliant work environment.
18. Mechanical Transport Systems
Without robotic arms or AGVs, movement between stations is handled by:
- Roller Conveyors and Chain Drives: Simple and reliable transport systems to move semi-finished pots from one station to another.
- Pneumatic Lifts and Pushers: These raise, align, or transfer components between vertical and horizontal process positions.
- Rotary Indexing Tables: Often used in multi-stage assembly for spout attachment, handle welding, and lid placement.
19. Global Supply Chain Compatibility
Manufacturers catering to multiple markets must adapt to:
- Regional Material Standards: Adjusting to varying grades of stainless steel (e.g., 304 vs. 430) depending on price and customer requirements.
- Electrical Compatibility: Machines are designed to work on both 50Hz and 60Hz grids and with variable voltage inputs to match international standards.
- Modular Production Layouts: Enables lines to be replicated or modified easily for factories across different countries without needing total redesign.
20. Service and Maintenance Simplicity
Traditional systems prioritize ease of maintenance over smart diagnostics:
- Manual Lubrication Points: Clearly labeled lube points simplify preventive maintenance.
- Interchangeable Spare Parts: Fast access to replacement parts like belts, pulleys, valves, and sensors minimizes downtime.
- Printed Maintenance Schedules: Checklists and charts posted near the machines keep the service routine simple and consistent.
By combining precision engineering, durable mechanical systems, and classic automation logic, these legacy-style production lines maintain high throughput and repeatability without relying on AI or digital optimization. They are particularly valuable in settings where:
- Labor is semi-skilled but well-trained
- Production volumes are stable
- Investment budgets prioritize robustness over digital sophistication
A Sheet Metal Water Heater Tank Manufacturing Machine is a specialized production system designed to fabricate the cylindrical tanks used in residential, commercial, or industrial water heaters. These machines and integrated lines handle processes from raw sheet metal to fully formed and sealed pressure vessels, typically made from steel (often stainless or galvanized) and sometimes coated internally with enamel or polymer layers for corrosion resistance.
Here’s how such a manufacturing system operates, focusing purely on traditional automation and mechanical processes, without the use of AI.
1. Sheet Metal Blanking and Preparation
The process begins with coil-fed or sheet-fed decoilers, where flat steel sheets are prepared:
- Decoiling and Straightening Units: Unwind steel coils and straighten the material.
- Blanking Press: Cuts the sheets into rectangular or circular blanks based on tank dimensions.
- Edge Trimming: Ensures smooth, straight edges to aid in consistent rolling and welding.
2. Rolling and Seam Welding
The cut sheets are passed through a plate rolling machine:
- Cylindrical Forming: Three or four-roll bending machines shape the sheet into a cylindrical tube.
- Longitudinal Seam Welding: Typically using MIG/MAG or submerged arc welding, the open edge is welded longitudinally to form a pressure-resistant shell.
- Weld Bead Grinding: Internal and external welds are smoothed for aesthetic and functional quality.
3. End Cap Forming and Assembly
- Dished Head Pressing: Hydraulic presses form the tank’s end caps (heads) using deep drawing or stamping dies.
- Edge Flanging: The edges of the dished heads are flanged to match the cylindrical shell diameter.
- Circumferential Welding (Seam Welding): The ends are joined to the shell using rotary positioners and circumferential welders, ensuring a leak-proof seal.
4. Nozzle and Fitting Installation
- Hole Punching or Drilling: Dedicated fixtures locate and cut holes for nozzles (inlet, outlet, T&P relief valve, drain, etc.).
- Stub Welding: Threaded or flanged pipe stubs are manually or automatically inserted and welded.
- Reinforcement Collars: Reinforcing rings are added at openings if pressure regulations require.
5. Internal Coating or Lining (If Applicable)
- Enamel Coating (common for domestic tanks): Tanks are cleaned, pre-heated, and sprayed internally with a vitreous enamel layer.
- Curing Ovens: The enamel is fused to the steel at high temperatures in gas or electric ovens.
- Polymer Lining: Some tanks use drop-in polymer bags or sprayed-on epoxy for corrosion resistance.
6. Insulation and Outer Shell Application
- Foam Injection or Wrapping: Polyurethane foam is injected between the tank and an outer jacket, or fiberglass is wrapped around the tank.
- Outer Casing Installation: Sheet metal jackets (usually color-coated steel or aluminum) are wrapped and crimped around the insulation, completing the exterior.
7. Leak Testing and Inspection
- Hydrostatic Testing: Tanks are filled with water and pressurized to check for leaks or weld failures.
- Air Pressure Testing: In some cases, air under pressure is used along with submersion for visual leak detection.
- Visual and Dimensional Inspection: Operators inspect welds, seams, and overall dimensions for compliance.
8. Final Assembly and Packaging
- Labeling and Fitting Installation: Thermowells, anode rods, or control fittings are inserted.
- Packaging Line: Tanks are shrink-wrapped, palletized, and labeled for shipment.
Line Characteristics (Non-AI, Legacy Style)
- PLC-Driven Automation: Process logic is handled by programmable logic controllers, ensuring repeatability and sequence integrity.
- Manual Loading and Unloading Stations: Though semi-automated, operators handle some transitions and monitor stations.
- Mechanical Interlocks and Safety Barriers: Protect personnel without requiring smart sensors.
- Tooling and Die Changeover Systems: Modular dies and welding fixtures allow changeovers for different tank sizes.
This type of machine line can be customized based on whether the tanks are pressurized or non-pressurized, vertical or horizontal, and for gas, electric, or solar water heaters. It’s a robust and efficient approach for mass production with proven reliability in global markets.
Once the water heater tanks have passed hydrostatic or air pressure testing, they proceed to the finishing and assembly stages. In traditional non-AI manufacturing lines, this includes processes like anode rod insertion, port thread cleaning, and in some designs, thermostat pocket welding. These steps are executed using manually adjustable jigs or pneumatic tools to maintain consistency without digital automation. Following this, tanks are dried internally if any moisture remains from leak testing. Drying is often achieved by hot air blowers or heat tunnels that maintain internal tank temperature for a set period.
If the tank is enamel-coated internally, a high-voltage spark test may be performed to detect pinholes or coating discontinuities that could lead to corrosion. Operators use handheld testing wands that arc across the internal surface, and any insulation breach is visibly or audibly detected. These are low-tech but highly effective in ensuring long-term tank durability.
On the exterior, insulation foam is injected through ports at set fill volumes, often timed pneumatically. The polyurethane expands and hardens in a matter of minutes inside the outer casing, which was previously clamped into place with a mechanical roller system. Older-style wrap insulation may still be used, in which glass wool or synthetic batts are manually fitted between the tank and outer jacket. Once the insulation is in place, the outer shell—typically pre-painted steel—is closed and crimped or spot welded shut using standard mechanical presses or roller seamers.
At the end of the production line, the water heaters are moved by conveyor or roller tracks to the labeling and accessory station. Here, control panels, user manuals, warning stickers, and electrical covers are applied. Depending on market destination, units may be fitted with specific voltage elements, gas burner assemblies, or solar coil connections. These variants are addressed through manual sub-assembly stations positioned adjacent to the main line. Cartoning and palletizing are done with semi-automatic equipment, where tanks are lowered into custom cardboard sleeves and either strapped or shrink-wrapped for distribution.
Maintenance of the machines used in the line is carried out through scheduled routines: grease points are serviced weekly, weld tips are replaced based on duty cycles, and die alignment is manually verified using gauges. The overall reliability of this setup lies in its mechanical simplicity, rugged construction, and reliance on skilled human oversight rather than predictive digital controls. Quality assurance relies heavily on checklists, gauge blocks, and operator experience, making the system ideal for regions with stable production demand and consistent tank specifications.
Additional auxiliary equipment plays a crucial role in completing the sheet metal water heater tank production process and enhancing line efficiency without relying on AI systems. For example, pipe nipple threaders are typically stand-alone machines that use hardened dies and motor-driven spindles to thread short pipe sections that will be welded onto the tank body as inlets, outlets, or relief valve ports. These machines operate with mechanical stops, foot pedals, and manual oilers to maintain thread quality and longevity of tooling. The threaded nipples are later inserted into pre-punched holes in the tank body and joined using MIG or TIG welding equipment, usually mounted on a rotary positioning table or a fixed jig setup to ensure alignment and seal integrity.
For the outer jacket, jacket seamers are essential. These are often roller-based mechanical presses that use overlapping or locking seam profiles to wrap and fasten the outer metal skin around the insulated tank. Operators feed the pre-cut and rolled jacket sheet into the seamer, and the machine mechanically locks the longitudinal seam by folding or crimping it shut. The base and top edge of the jacket are then either rolled over or riveted using rotary crimping tools to form a neat finish that secures the insulation and provides a weather-resistant barrier.
In enamel-lined tank production, the enamel furnace is a key piece of infrastructure. These high-temperature kilns, often gas-fired, operate in the range of 850–900°C. Tanks that have been sprayed internally with enamel slurry are placed onto steel racks or mandrels and conveyed into the furnace chamber. The heating cycle is precisely timed using traditional thermocouple feedback and relay-based temperature controllers. The enamel vitrifies and bonds to the steel surface, forming a hard, glass-like interior coating. After the enamel is cured, tanks exit the furnace and are air-cooled before further processing. These furnaces are built with ceramic insulation and zone-based burners to manage heat uniformity.
Also integral are hydraulic test benches, which use manually operated pressure pumps or PLC-timed cycles to fill the tanks with water and apply pressure through high-pressure hoses. The tank is held for a set duration at test pressure (typically 1.5 to 2 times the rated pressure), and the operator visually checks for leaks or deformation. These test benches are simple, robust units with analog pressure gauges and safety relief valves, suited for batch testing and field-serviceable environments.
Lastly, manual jig welding stations or turntables are used to mount tanks for tasks like element flange welding, base ring attachment, or decorative trim application. These stations rotate the tank slowly while the operator applies welds or fasteners. Because these are manual or semi-automatic, they are highly adaptable to different tank sizes and product variants without needing robotic programming or reconfiguration.
This configuration allows a single line to produce thousands of tanks per month with a relatively low level of automation, favoring durability, mechanical simplicity, and operator oversight. Would you like to include packaging line integration or storage and logistics layout for this type of production environment?
Following the final welding and assembly stages, the completed water heater tanks are transferred to the packaging and dispatch line, which in traditional manufacturing setups is designed for high throughput with minimal digital automation. Tanks typically exit the main line via gravity-fed rollers or low-speed conveyors, then proceed to a manual or semi-automatic packaging station.
At this station, each unit is manually inspected one last time for cosmetic defects, label accuracy, and correct accessory installation. Labels are applied using thermal transfer or inkjet printers mounted on simple adjustable brackets. Barcodes, serial numbers, model information, and safety warnings are affixed based on a reference list or product run sheet, which operators follow using printed checklists.
The next step is protective wrapping. Tanks are enclosed in plastic film using manual or semi-automatic shrink tunnels, where low-level infrared heaters contract the film tightly around the tank for protection during shipping. In some factories, foam or cardboard corner protectors are inserted before wrapping to prevent denting during transport. Alternatively, in bulk shipment formats, units may be bagged and stacked on pallets without shrink wrap but secured with plastic strapping using tensioners and buckles.
Palletizing is done either manually with pallet jacks or by using lift tables to adjust the working height as units are placed in layers. Edge protectors and top boards are sometimes added to stabilize the stack before it is strapped. Tags indicating batch numbers, destination, and production date are stapled or tied to each pallet. In high-volume setups, a rotary stretch wrapper might be used to secure the entire pallet automatically, but the wrapping process itself is still mechanically controlled without sensor feedback or AI integration.
Once secured, pallets are moved to a staging area or temporary warehouse using forklifts. The warehouse layout is typically organized with painted floor zones or simple paper logs indicating batch number, order status, or shipment route. Inventory tracking may be done with printed ledgers or basic terminal entries into a legacy MRP (Material Requirements Planning) system, sometimes using barcode scanners but without smart stock prediction or autonomous coordination.
Maintenance crews handle daily inspections of packaging equipment—checking tension rollers, blade sharpness on film cutters, and heating elements in shrink tunnels. Preventive maintenance is managed through wall charts or logbooks that list inspection tasks by shift, not by predictive algorithms. Spare parts for these systems (such as strapping heads, film rolls, motors, and casters) are stored in a centralized toolroom and are ordered by technicians through paper-based requisition slips.
This final stage completes a fully traditional manufacturing flow: sheet metal enters as coil or blanks at one end, and a sealed, insulated, and palletized water heater tank exits the other, all accomplished through mechanically automated but operator-supervised processes. Despite lacking AI, such a line is highly efficient when maintained and staffed by experienced workers. Would you like to continue into the tooling standards or process time estimates for each production step?
Continuing further, once the water heater tanks have been packaged and prepared for shipment, we can focus on tooling standards and process time estimates that ensure smooth operation of the line. These factors are crucial in maintaining consistent quality, minimizing downtime, and optimizing production efficiency in a non-AI-driven setup.
Tooling Standards
Tooling plays a central role in shaping, joining, and finishing the components. Since this manufacturing process is mechanical and non-AI-driven, it’s essential that all tooling is built to precise specifications and regularly maintained for optimal performance. Here are the main tool types and their standards:
- Blanking Dies: These are used in the initial cutting of sheet metal. The dies are typically made of high-carbon steel or tool steel and are designed to produce consistent, burr-free cuts. They are sharpened and tested regularly for wear to maintain dimensional accuracy.
- Forming Dies: For rolling the sheet metal into cylindrical shapes, forming dies must have a durable surface and be calibrated to the required radius for each tank size. These dies are typically made from hardened steel, and regular inspection is required to ensure that the formed metal fits the welding seam precisely.
- Welding Fixtures: Fixtures that hold parts in place during welding, whether MIG or TIG welding, are built for specific tank sizes and configurations. They are designed to maintain the correct alignment between the cylindrical shell and dished heads to ensure high-quality, leak-proof welds. These fixtures must be checked for deformation after frequent use.
- Nozzle Dies: These dies are used to punch or drill holes for inlet and outlet nozzles. They are custom-designed for each model based on required dimensions, and maintaining sharp edges is crucial to avoid distortion in the tank body.
- Seam Rollers and Crimping Tools: Used in the jacket assembly process, these tools ensure a tight and secure seal of the outer casing. They must be calibrated for different thicknesses of metal and ensure the seam is sealed without causing damage to the tank’s insulation layer.
- Spray Nozzles (for Enamel Coating): The nozzles used to apply the enamel coating must be maintained regularly to avoid clogging. These are typically made of stainless steel and should be cleaned after each batch to maintain coating consistency and prevent defects.
- Threading Tools (for Pipe Stubs): These tools are used to thread the pipe nipples for the inlet, outlet, and valve stubs. They must be carefully aligned to ensure threads are consistent and precise, as improper threading could cause leaks or difficulty in installation.
- Grinders and Polishing Tools: For finishing and smoothing welds, grinders with adjustable speeds are essential. These are used to eliminate sharp edges and imperfections and ensure that the welds are smooth and consistent.
Process Time Estimates
Efficient management of cycle times for each operation helps ensure optimal throughput in traditional, mechanically driven manufacturing lines. Here’s a rough estimate of process times for each key stage:
- Blanking and Preparation:
- Cycle Time: ~10-15 minutes per sheet.
- Description: The coil is unspooled, and sheets are blanked, then trimmed. The cutting and preparation process involves both the decoiling and blanking machines, with material handling time factored in.
- Rolling and Seam Welding:
- Cycle Time: ~20-30 minutes per tank (depending on tank size).
- Description: The sheet is rolled into a cylinder, and the longitudinal seam is welded. This process involves the coordination between the rolling machine and welding robot or operator.
- End Cap Forming and Assembly:
- Cycle Time: ~15-25 minutes per set of caps.
- Description: Dished caps are stamped or pressed, then aligned with the tank body for welding. Time varies depending on the complexity of the end caps and the ease of aligning the parts.
- Internal Coating (if applicable):
- Cycle Time: ~30 minutes to 1 hour per tank (depending on the furnace size and coating type).
- Description: Enamel or polymer coating is applied and cured in a furnace. The drying and curing cycles vary based on the materials used, but each tank typically spends several minutes in the furnace.
- Insulation and Outer Shell Application:
- Cycle Time: ~20-30 minutes per unit.
- Description: Foam insulation is injected, and the outer shell is wrapped and sealed. The time needed for this process depends on whether foam or fiberglass is used and the speed of the wrapping equipment.
- Welding and Fitting Installation:
- Cycle Time: ~10-15 minutes per fitting.
- Description: Inlets, outlets, and other pipe fittings are welded into place. The cycle time is dependent on the type of weld being applied and whether fittings are pre-threaded.
- Leak Testing:
- Cycle Time: ~10-20 minutes per tank.
- Description: Tanks are hydrostatically or air-pressure tested for leaks. This process includes filling the tank with water or air, pressurizing it, and visually inspecting for leaks.
- Packaging and Palletizing:
- Cycle Time: ~5-10 minutes per unit.
- Description: After final inspection, tanks are wrapped, labeled, and placed on pallets. Packaging can be done manually or with semi-automated systems, depending on the factory layout.
Maintenance and Downtime Considerations
Even in non-AI lines, maintenance is a key factor in minimizing downtime and ensuring consistent production rates. The primary equipment that requires regular attention includes:
- Welding Machines: These require regular inspections of electrodes, nozzle tips, and cooling systems. Maintenance can be scheduled monthly or after a set number of hours of use.
- Rolling and Forming Dies: Regular lubrication and alignment checks ensure smooth metal flow and reduce wear. Dies are typically serviced or replaced every 2-3 months, depending on usage.
- Conveyors and Material Handling Equipment: Regular checks for jams, broken chains, or misalignment help keep the line moving smoothly.
- Furnaces and Curing Ovens: These should be cleaned and calibrated regularly to ensure consistent heating and optimal curing of enamel or coatings.
By maintaining tooling to precise standards and managing process times efficiently, this non-AI, mechanical production line can produce water heater tanks in high volumes while minimizing defects and maintaining cost-effectiveness.
EMS Metalworking Machines
We design, manufacture and assembly metalworking machinery such as:
- Hydraulic transfer press
- Glass mosaic press
- Hydraulic deep drawing press
- Casting press
- Hydraulic cold forming press
- Hydroforming press
- Composite press
- Silicone rubber moulding press
- Brake pad press
- Melamine press
- SMC & BMC Press
- Labrotaroy press
- Edge cutting trimming machine
- Edge curling machine
- Trimming beading machine
- Trimming joggling machine
- Cookware production line
- Pipe bending machine
- Profile bending machine
- Bandsaw for metal
- Cylindrical welding machine
- Horizontal pres and cookware
- Kitchenware, hotelware
- Bakeware and cuttlery production machinery
as a complete line as well as an individual machine such as:
- Edge cutting trimming beading machines
- Polishing and grinding machines for pot and pans
- Hydraulic drawing presses
- Circle blanking machines
- Riveting machine
- Hole punching machines
- Press feeding machine
You can check our machinery at work at: EMS Metalworking Machinery – YouTube
Applications:
Flange-punching
Beading and ribbing
Flanging
Trimming
Curling
Lock-seaming
Ribbing