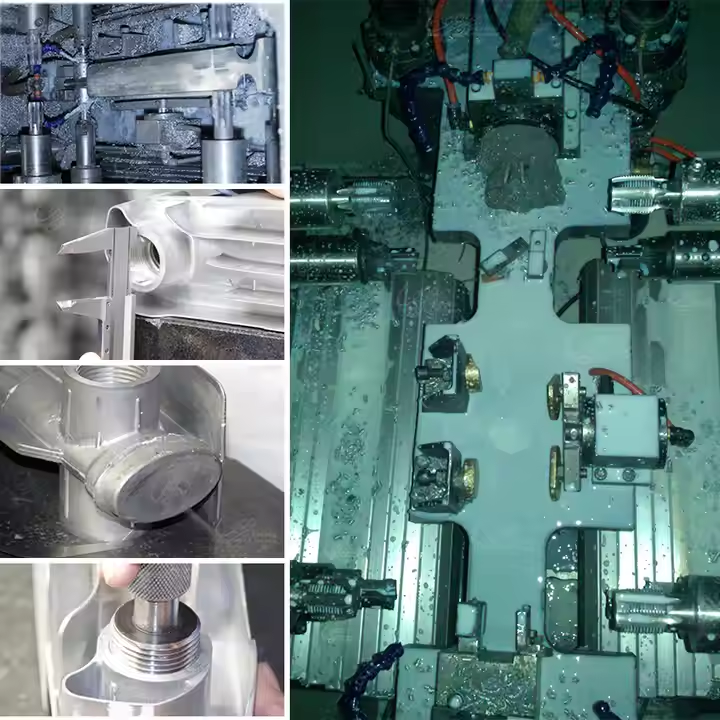
Fully Automated Metal Forming System: An End-to-End Sheet Forming Automation Line refers to a fully automated production system that takes flat sheet materials (typically metal, plastic, or composite) and processes them through various stages to form, cut, assemble, and finish them into a final product — all with minimal human intervention. Here’s a breakdown of what such a system typically includes:
Core Components of an End-to-End Sheet Forming Automation Line
- Material Loading System
- Coil or Sheet Feeder: Loads raw material (sheet or coil) onto the line.
- Uncoilers / Decoilers: For coil-fed systems, unwinds the coil and straightens it.
- Leveling and Feeding System
- Straightener: Removes coil set and flattens the material.
- Servo Feeder: Precisely feeds the sheet into the forming equipment.
- Punching / Notching / Blanking (optional)
- CNC-controlled punch presses or laser cutters to shape or prepare the sheet.
- Forming Equipment
- Press Brake / Hydraulic Press / Roll Forming Machines: These shape the sheet into the required form.
- Can involve deep drawing, stamping, bending, or roll forming depending on application.
- Transfer System / Robot Automation
- Robotic arms or linear transfer systems move sheets between stations.
- Often coordinated with vision systems and sensors for precise handling.
- Welding / Fastening (if needed)
- Integration of spot welding, laser welding, riveting, or other joining methods.
- Quality Inspection & Measurement
- Vision systems or laser measurement for dimensional accuracy and defect detection.
- Inline sensors and cameras ensure part consistency.
- Stacking / Palletizing / Unloading
- Robotic stacking or conveyor systems to collect finished parts.
- Could include sorting, labeling, and packaging.
Smart Automation & Integration
- PLC / SCADA / MES Integration:
- Seamless control and data acquisition throughout the line.
- Real-time monitoring, predictive maintenance, and analytics.
- Industry 4.0 Ready:
- IoT sensors, cloud connectivity, and AI-driven optimizations for smart manufacturing.
Benefits
- Increased throughput and consistency.
- Reduced labor costs and human error.
- Enhanced safety and ergonomics.
- High adaptability for various product types.
Applications
- Automotive body panels
- HVAC ducting
- Electrical enclosures
- Appliance components
- Aerospace structures
An end-to-end sheet forming automation line is a fully integrated manufacturing system designed to transform flat sheet material, such as metal or plastic, into finished components through a continuous and automated process. It begins with the loading of raw material, either in coil or flat sheet form, using uncoilers or sheet feeders. For coil-based lines, straightening equipment flattens the material and ensures it is properly tensioned and aligned. A servo feeder then precisely advances the sheet into the processing stations.
Depending on the product, the sheet may undergo initial operations like punching, notching, or blanking using CNC-controlled presses or lasers. This prepares the material for the main forming operations, which may include bending with press brakes, deep drawing in hydraulic presses, or continuous roll forming. Each forming stage is carefully synchronized to maintain alignment and timing across the line.
Transfer systems, often using robotic arms or linear transfer units, move parts between stages efficiently. These robots may also be equipped with vision systems and sensors for positioning, inspection, and part verification. If the design requires assembly or joining, stations for welding, riveting, or adhesive application are integrated into the line. These are commonly used in automotive and appliance production.
Quality inspection is embedded throughout the process, with cameras, laser scanners, and other non-contact measuring tools ensuring dimensional accuracy and identifying defects in real time. Data collected can be fed into a central control system such as a PLC or SCADA platform, allowing operators to monitor and control the entire process from a central interface. These systems can be tied into higher-level manufacturing execution systems (MES) or enterprise resource planning (ERP) tools, creating a smart factory ecosystem.
The final stages involve stacking, sorting, labeling, and unloading finished components using automated palletizers or conveyor systems. Some lines also include packaging or wrapping units for protection and logistics. Overall, an end-to-end sheet forming automation line dramatically increases production speed and consistency, reduces labor costs, minimizes errors, and enhances safety. It’s a vital setup for high-volume, precision-focused industries like automotive, aerospace, HVAC, and electrical enclosures.
In addition to the mechanical and electrical integration, modern sheet forming automation lines are increasingly incorporating software intelligence and data analytics to boost performance and adaptability. Machine learning algorithms can be used to predict maintenance needs, optimize tool paths, or adapt to material inconsistencies in real time. For example, if a sensor detects minor dimensional drift or material springback, the system can auto-correct forming parameters on the fly, minimizing waste and downtime.
Energy efficiency is another growing focus. Many systems now include regenerative drives, energy monitoring modules, and low-power standby modes. These allow manufacturers to track and reduce their energy consumption, contributing to sustainability goals without compromising throughput.
Flexibility is also key in advanced automation lines. Tooling stations can be designed for rapid changeover, allowing manufacturers to switch between different part designs with minimal interruption. This is especially useful in sectors like automotive or appliances where part variety is high and batch sizes vary. Robotic end-effectors may be modular or adjustable to handle different shapes and weights, and forming tools can be swapped automatically using tool magazines or robotic changers.
Safety is built into every level of the line. Light curtains, safety interlocks, emergency stops, and integrated safety PLCs ensure that the entire system operates within strict safety protocols. In collaborative environments, cobots (collaborative robots) may work alongside humans for tasks that require fine manipulation or flexible decision-making, without compromising safety.
Remote monitoring and diagnostics have also become standard, allowing engineers to track production metrics, receive alerts, or even troubleshoot issues from anywhere. This helps reduce downtime and supports continuous improvement initiatives. With integration into the cloud, companies can compare performance data across facilities, benchmark operations, and implement global process standards.
All of this comes together to create a manufacturing line that is not just automated, but intelligent, responsive, and capable of adapting to changing demands. Whether producing thousands of identical components or handling varied small-batch runs, an end-to-end sheet forming automation line is a cornerstone of modern, scalable manufacturing.
As production demands evolve, one of the strongest advantages of an end-to-end sheet forming automation line is scalability. These systems can be designed to operate in modular fashion, meaning new stations or capabilities—like laser marking, deburring, part washing, or robotic inspection—can be added without needing to overhaul the entire line. This modularity makes it easier to future-proof the operation, accommodate new product lines, or react to shifts in customer requirements.
For example, in automotive panel production, a line might start with basic blanking and roll forming, but over time, expand to include hem flanging, adhesive application, or even in-line surface treatment for paint prep. All of this can be programmed, scheduled, and monitored through centralized control architecture, minimizing training requirements and maintaining process stability.
Automation lines also benefit from closed-loop control systems, which use real-time feedback to fine-tune forming forces, tool positions, and material feeds. Instead of relying solely on fixed settings, the machines “listen” to sensors—measuring tonnage, displacement, heat, and vibration—to dynamically adjust and stay within tight tolerance bands. This level of control ensures consistency in even the most complex formed shapes, like aerospace components or consumer electronics casings, where a tiny deviation can cause misalignment or failure downstream.
Another important aspect is traceability. In regulated industries, every part that passes through the line may need to be tracked by batch, date, material source, or forming parameters. This is often achieved by incorporating part marking (such as QR or dot peen marking) early in the line, then recording all process data against that mark as the part progresses. Should a defect arise, manufacturers can isolate affected units instantly, identify root causes, and prove compliance with quality standards like ISO 9001, IATF 16949, or AS9100.
From a logistics perspective, full automation improves plant layout efficiency. With robotic handling, buffer zones and intermediate storage can be minimized or eliminated entirely. Finished parts can be automatically sorted by type, sent directly to subassembly or packing lines, or even passed to autonomous mobile robots (AMRs) for further distribution in the factory. This creates a tightly integrated, lean production ecosystem.
In the long run, the return on investment (ROI) for an end-to-end sheet forming automation line is driven not just by labor savings, but by cycle time reduction, defect rate elimination, material utilization, and overall equipment effectiveness (OEE). For companies aiming to compete on quality, speed, and flexibility—especially in global markets—this kind of automation line is a strategic enabler.
If you’d like, I can prepare a sample layout or specification sheet for a line suited to a specific product—say, automotive brackets, HVAC ducts, or appliance panels. Just let me know what you’re targeting.
Smart Sheet Metal Production Line
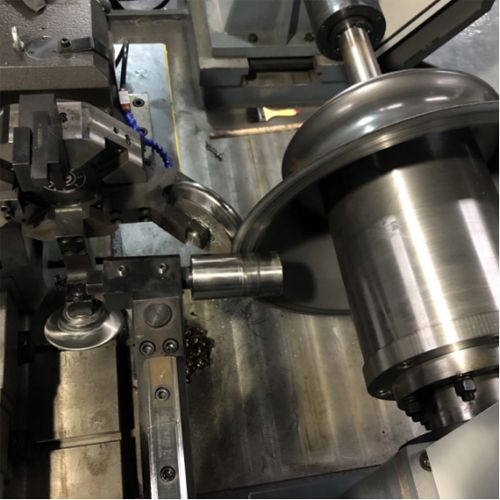
A Smart Sheet Metal Production Line takes traditional sheet metal processing to a whole new level by integrating advanced automation, data analytics, and interconnected systems under the umbrella of Industry 4.0. The result is a self-optimizing, adaptive manufacturing environment that can produce complex parts with minimal human intervention, high efficiency, and full traceability.
In a smart line, the process begins with digitally managed material intake. Whether it’s sheets or coils, the system knows what material is being loaded thanks to barcode or RFID scanning, matching it to a digital job file. A central Manufacturing Execution System (MES) or ERP automatically schedules and routes the job through the line, assigning priority based on deadlines, material availability, and current line load.
Once in motion, each machine along the line is connected through an industrial network (like EtherCAT, Profinet, or OPC UA), sharing real-time data about status, output, and health. Smart feeders use sensors to detect material thickness, flatness, and temperature, adjusting their output accordingly. CNC-controlled punching, laser cutting, or combination machines execute cutting programs that have been optimized using AI-powered nesting software, reducing material waste dramatically.
The forming section—press brakes, roll formers, panel benders—is equally smart. Tools are automatically loaded based on the job ID, with robotic tool changers and digital tool libraries. Cameras or laser alignment systems measure the part during forming, feeding data back to adaptive control systems that tweak bending angles or compensate for springback instantly. If a part is slightly off, it’s corrected in-line—no need to scrap or rerun it.
Smart robotics and AGVs (Automated Guided Vehicles) or AMRs (Autonomous Mobile Robots) move parts between stations. These robots are equipped with machine vision and AI, enabling them to identify, pick, and orient parts correctly without fixtures or manual help. Their paths are calculated dynamically, avoiding bottlenecks and adapting to the current workload on the shop floor.
Along the way, real-time quality control is integrated using cameras, laser scanners, and even AI-based surface defect detection. Every part’s journey and parameters are recorded—force applied, temperature, tool ID, machine status—creating a digital twin of the part for full traceability. This is critical for industries like aerospace, medical devices, or automotive, where compliance is strict.
The smart line also supports predictive maintenance. Sensors continuously monitor machine health—vibration, temperature, tool wear—and AI models predict when maintenance is required before breakdowns happen. This minimizes downtime and maximizes OEE (Overall Equipment Effectiveness).
All data collected flows into dashboards where engineers and managers can monitor KPIs, analyze trends, and make real-time decisions. The system can alert operators to deviations, suggest optimizations, or even auto-correct programs on the fly. In many cases, these systems are cloud-connected, allowing remote diagnostics, over-the-air updates, and benchmarking across multiple facilities globally.
Finally, finished parts are automatically sorted, stacked, labeled, and even packed, ready for shipping or assembly. This seamless integration from raw sheet to packaged part not only accelerates production but also enables mass customization—running multiple part types or customer variants on the same line without manual reconfiguration.
In a smart sheet metal production line, the entire system functions as a connected ecosystem where machines, materials, software, and operators communicate continuously. The intelligence of the line doesn’t just lie in its mechanical precision, but in its ability to adapt in real time, to learn from every cycle, and to optimize both its own performance and the quality of its output without needing manual intervention. As production begins, job data is sent from the central digital control system directly to the machines. This includes not only the geometry of the part to be produced, but also material-specific instructions, toolpath optimizations, bend allowances, laser parameters, and inspection criteria. Each step of the process executes based on this unified data model, ensuring consistency from design to finished product.
Machine learning algorithms running in the background analyze production data continuously. If a press brake, for example, starts to show signs of performance drift due to minor tool wear or material springback, the system automatically compensates for the deviation, often before it even affects the quality of the parts. Over time, the system becomes more accurate, drawing on historical data to improve bending angles, cut paths, or forming sequences, reducing the need for rework and boosting first-pass yield.
Energy management is embedded throughout. Sensors track the energy consumption of each machine and operation, and the system can dynamically adjust production scheduling to balance power loads. For instance, it can delay a high-energy laser cutting task slightly if multiple heavy-forming machines are running simultaneously, thus avoiding spikes in energy usage and lowering operational costs. This level of intelligence allows manufacturers to meet sustainability targets while maintaining throughput.
The logistics side of smart production is equally advanced. With real-time part tracking, managers know exactly where every piece is in the workflow, how long each process takes, and when the final product will be ready. If there’s an urgent order, the system can reshuffle job queues, reroute material, or activate backup machines without manual rescheduling. Parts can be custom-tracked using embedded barcodes or RFID chips that carry not only ID data but also links to the digital production record, including tooling history, process parameters, and inspection outcomes.
Remote visibility into the entire line is another core strength. Engineers can access dashboards from mobile devices or web portals anywhere in the world, seeing live machine status, output counts, scrap rates, or upcoming maintenance needs. In the event of a fault or bottleneck, remote diagnostics tools allow technicians to access machine logs, camera feeds, and sensor data in real time, often resolving issues without ever needing to be on-site.
Smart lines also excel in enabling mass customization. Because job data is managed digitally, switching from one product type to another requires no physical setup beyond automatic tool changes and minor machine adjustments. This allows the production of highly varied part types in sequence, even down to batch sizes of one, without losing time or increasing costs. For industries that rely on rapid response to market demands or customized solutions—such as interior systems, HVAC components, or architectural metalwork—this capability is transformative.
As manufacturing moves into a data-driven era, the smart sheet metal production line becomes not just a factory tool, but a source of strategic advantage. It brings together physical production with virtual modeling, machine automation with human insight, and operational control with cloud-scale intelligence. The result is a system that doesn’t just make things—it continuously learns how to make them better.
Want me to take all this and draft a whitepaper or proposal for a smart sheet metal production line investment or presentation? I can also create diagrams or system architecture layouts to go with it.
As the smart sheet metal production line continues to evolve, it’s also becoming more deeply integrated with enterprise-level systems, closing the loop between design, engineering, production, and even customer feedback. One of the most powerful concepts in this space is the use of a digital twin—a virtual model that mirrors the physical production environment in real time. Every machine, part, tool, and process is represented digitally, enabling simulations, stress testing, and process validation before anything hits the shop floor. Engineers can tweak forming sequences, predict failure points, and optimize workflows in the virtual environment, pushing those updates instantly to the real line when validated.
This tight feedback loop also extends to suppliers and customers. With smart integration, suppliers can get real-time insights into inventory levels and usage rates, enabling just-in-time replenishment without overstock. Likewise, customers can track their orders live, see when their parts are being formed, inspected, and packed, and even get automated reports including measurement data, images, and digital certificates of conformity. This level of transparency is increasingly becoming a differentiator in competitive industries, where speed, traceability, and quality assurance are as valuable as the product itself.
On the workforce side, a smart line doesn’t eliminate the need for skilled labor—it redefines the role. Operators shift from machine controllers to process supervisors, system analysts, and continuous improvement specialists. Human-machine interfaces (HMIs) are now touch-based, intuitive, and multilingual, often supported by voice guidance, augmented reality (AR), and AI assistants. Training time drops dramatically, and operators can quickly be cross-trained across multiple machines and tasks. For complex maintenance or troubleshooting, AR glasses can guide technicians step-by-step through procedures, even overlaying 3D diagrams or allowing remote experts to view what they’re seeing in real time.
Safety is another domain where smart technology excels. Not only do smart lines employ standard safety measures like light curtains, interlocks, and emergency stops, but intelligent systems continuously assess operator location, movement, and machine behavior. Vision systems and LiDAR sensors can identify if a person enters a restricted area and stop or slow machines proactively, creating a safer, more adaptive environment. Collaborative robots (cobots), designed to work safely alongside humans, add flexibility to tasks where a balance of precision and human judgment is needed.
Finally, the smart sheet metal line becomes a source of continuous innovation. Because it captures and stores so much granular data, companies can perform deep process mining, uncovering inefficiencies that would otherwise be invisible. They can benchmark between different lines or facilities, test hypotheses, and trial new forming strategies digitally. This fosters a culture of improvement grounded in hard data rather than guesswork or tradition.
Ultimately, the smart sheet metal production line isn’t just a technological upgrade—it’s a transformation in how products are designed, built, and delivered. It breaks down silos between departments, enables ultra-responsive production, and lays the groundwork for sustainable, scalable, and data-driven manufacturing. Whether for high-volume commodity parts or low-volume complex components, the future of sheet metal lies in these intelligent, fully connected ecosystems.
Let me know if you’d like to take this and build it into a pitch, presentation deck, concept study, or plant layout proposal. I can even help generate visual diagrams or simulate a production flow based on your specific application.
Continuous Sheet Metal Forming System
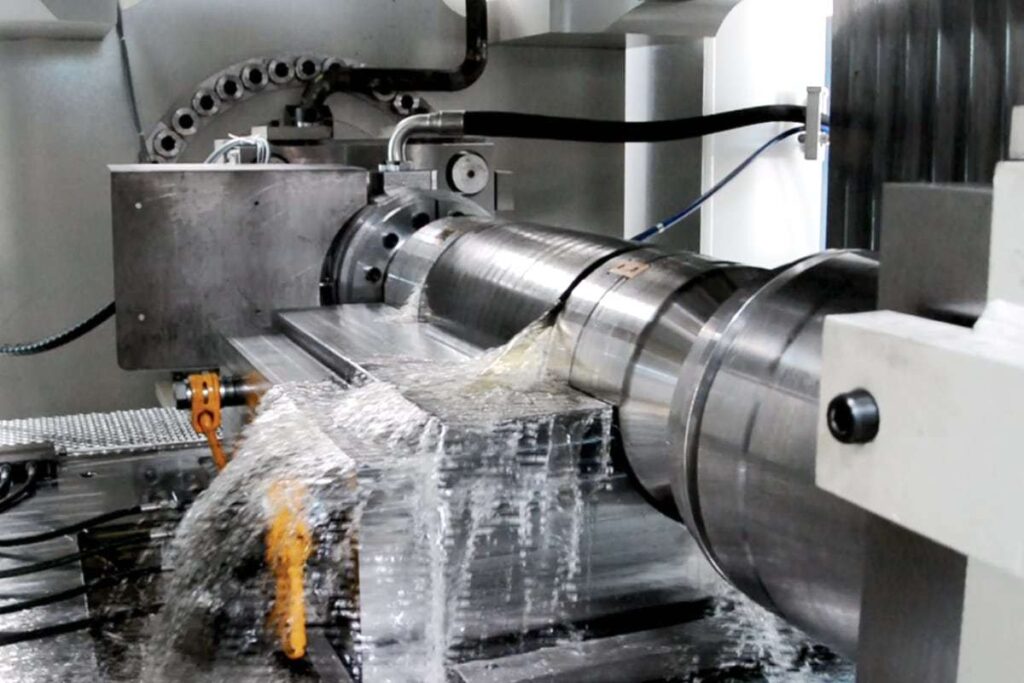
A Continuous Sheet Metal Forming System is a high-efficiency manufacturing solution designed to shape sheet metal into desired profiles or components through an uninterrupted, streamlined process. Unlike batch forming or individual press operations, this system feeds sheet metal—often from coils—through a sequence of forming stations without stopping, making it ideal for high-volume, consistent production of long or repetitive parts.
At the heart of the system is the roll forming process, where the sheet is gradually bent into shape as it passes through a series of precisely aligned roller dies. Each station incrementally adjusts the metal, reducing internal stresses and avoiding cracking, even with complex profiles. Because the material remains in motion throughout the entire line, cycle times are minimized, and material handling is simplified.
A continuous sheet forming line typically begins with a decoiler, which unrolls metal coils and feeds them into a leveling unit to flatten the material and remove coil set. The sheet then enters a servo feeder, ensuring precise advancement into the forming section. As the sheet moves through the roll forming mill, it progressively transforms into the final profile, whether it’s a structural channel, roofing panel, cable tray, or automotive trim component.
Additional inline processes can be integrated, including punching, notching, embossing, or marking, which are synchronized with the material’s movement. For example, CNC-controlled punching heads can operate in tandem with the line speed, enabling features like holes, slots, or part numbers to be added without halting production. Similarly, cut-off units—often flying shear or rotary cutting systems—trim the profile to the required length on the fly, without stopping the line.
In advanced systems, inline quality control technologies are also embedded. Vision systems, laser gauges, or eddy current sensors measure dimensions, check surface finish, and confirm feature placement in real time. If a deviation is detected, the system can adjust forming parameters on the spot or flag the product for rejection downstream.
One of the most powerful aspects of continuous forming is its ability to produce long-length parts without seams or welds, improving structural integrity and reducing post-processing. These systems can run at high speeds—often exceeding 30 meters per minute—while maintaining tight tolerances and consistent repeatability, making them highly efficient for large-scale production.
From an automation standpoint, the entire line is typically governed by a PLC-based control system, integrated with HMI touch panels and often linked to MES or ERP software. This enables centralized job control, production tracking, and data logging. Operators can monitor performance, change job recipes, and adjust line parameters with minimal downtime.
Maintenance and uptime are key factors in these systems. Many modern lines include condition monitoring sensors for predictive maintenance, alerting operators to bearing wear, die misalignment, or lubrication needs before breakdowns occur. Tooling can be changed quickly using cassette systems or servo-actuated die changers, enhancing flexibility.
Applications for continuous sheet metal forming systems span across multiple industries—construction (roofing, studs, gutters), automotive (bumpers, reinforcements), appliances (frames, brackets), logistics (shelving, racking), and energy (solar panel frames, cable trays). The system’s continuous nature and integration-friendly design make it an ideal choice for manufacturers looking to maximize throughput, maintain consistency, and reduce labor and handling costs.
In a continuous sheet metal forming system, the coordination between mechanical components and digital controls is critical. Every motion, from the decoiler’s rotation to the cut-off action at the end of the line, must be precisely timed and synchronized. This is achieved through servo motors and intelligent drive systems that constantly communicate through industrial networks, allowing even small adjustments in speed or pressure to be made on the fly without interrupting the process. The line operates like a living system, adapting in real time to slight changes in material thickness, tension, or environmental conditions such as temperature or humidity, which can subtly affect forming behavior.
As the sheet metal flows through the rollers, the design of the tooling becomes a major determinant of part quality and system efficiency. The roll tooling is carefully engineered using CAD/CAM and FEA (Finite Element Analysis) to predict how the metal will behave under gradual deformation. Advanced simulations help eliminate common issues like warping, bowing, or end flare before any physical tool is cut, shortening development time and minimizing costly trial-and-error runs. Once finalized, these forming rolls are precision-machined and mounted in sequence, each one responsible for just a fraction of the overall shape transformation.
One of the distinctive features of these systems is the ability to add modular capabilities along the line. For instance, embossing stations can create textured surfaces, ribbing can be introduced for added rigidity, or multi-material feeding can allow for hybrid components. In some advanced applications, laser welding or clinching can be done inline, enabling the assembly of complex multi-piece profiles directly as they are formed. The system does not treat the sheet as a static material to be shaped, but as a dynamic flow of raw potential being sculpted at speed.
The control software plays a critical role in managing this complexity. It not only governs machine actions but also collects performance data continuously. Every formed part carries with it a stream of metadata—material batch, tool ID, line speed, ambient temperature, forming pressure, and more. This data is logged and stored, enabling manufacturers to trace every component back to its exact process conditions. This full digital record is invaluable for quality assurance, regulatory compliance, and process optimization. Over time, machine learning algorithms can analyze this data to detect subtle patterns, flag early indicators of tool wear or drift, and recommend corrective actions.
In high-volume manufacturing, line uptime is everything. To support this, predictive maintenance technologies are embedded throughout the system. Sensors monitor vibration levels on rollers, temperature at critical bearings, fluid levels in hydraulic systems, and power draw of motors. When trends begin to move outside normal ranges, alerts are issued automatically, allowing service teams to act before a breakdown occurs. Maintenance windows can be strategically planned, and spare parts pre-positioned, ensuring that production targets are met without unexpected downtime.
Efficiency is not limited to the mechanical line itself. The entire production flow—from raw coil loading to finished part unloading—is often supported by autonomous logistics systems. Coils can be automatically shuttled into place, and formed parts may be robotically sorted, stacked, or transferred to subsequent lines like painting, assembly, or packaging. These post-forming logistics are orchestrated with the same precision as the forming itself, all driven by centralized production scheduling software that balances capacity, demand, and delivery commitments.
The environmental footprint of such systems is also being addressed through energy-efficient drives, regenerative braking, and smart load balancing. Cooling systems, lubrication systems, and waste handling units are optimized to reduce consumption, meet regulatory requirements, and support green manufacturing initiatives. Sustainability is no longer an afterthought—it’s embedded in the system’s design.
A continuous sheet metal forming system, when fully optimized, represents not just a production tool but a strategic manufacturing asset. It enables faster time-to-market, consistent product quality, lower labor costs, and flexible production capabilities that can pivot quickly as market needs evolve. Whether installed in a traditional factory setting or as part of a fully automated, lights-out manufacturing cell, this system is a key enabler of modern industrial competitiveness.
As the continuous sheet metal forming system evolves, its integration with smart factory infrastructure becomes more seamless. The line doesn’t operate in isolation—it connects with upstream and downstream systems, enabling a closed-loop manufacturing environment where information flows as smoothly as material. Orders from customers or ERP systems feed directly into the production planning module, which schedules coil loads, tooling changes, and machine settings automatically based on real-time availability and capacity. Instead of static production plans, the system adapts fluidly to demand fluctuations, rush orders, or unexpected downtime, rebalancing workload across shifts or even across multiple production lines if needed.
Flexibility is becoming a core performance metric. Older forming systems were designed around long production runs of a single profile, but market demands are shifting. Now, the ability to run short batches, switch between part geometries, or introduce product variations without prolonged setup is a competitive advantage. To support this, manufacturers are adopting rapid tool-change systems, modular roll units, and universal forming platforms where different roll sets can be swapped with robotic assistance. With quick recipe changes via touch-panel HMIs and automated calibration routines, the downtime between jobs is reduced to mere minutes, enabling true just-in-time production without compromising throughput.
There’s also a growing move toward multi-profile lines, capable of forming different shapes from the same material input on demand. These systems use servo-driven roll stands that adjust position dynamically, allowing the same rollers to be reconfigured electronically rather than manually replaced. This approach supports high product diversity and is particularly valuable in industries like construction, where product customization by region or client is standard. In addition, hybrid forming lines are emerging—systems that combine roll forming, bending, and even stretch forming capabilities in a single process chain, enabling more complex shapes and design freedom without secondary operations.
Digitalization continues to play a central role. Each part produced can be assigned a unique digital signature or tag—QR codes, RFID, or laser etching—linking it directly to its production data. If a customer reports an issue months later, manufacturers can instantly retrieve that part’s forming pressure, tool wear state, batch ID, and even a video of it moving through the line. This level of traceability transforms both quality control and customer service, giving companies the ability to respond with precision and confidence.
On the innovation frontier, AI-driven process optimization is beginning to take root. Instead of relying on fixed rule-based control logic, the system can learn from historical runs, adjust parameters to match material behavior, and even suggest alternative forming paths to reduce stress concentrations or eliminate cosmetic defects. AI can also identify subtle degradation in tool performance—such as tiny alignment shifts or wear patterns—long before a human could notice, triggering maintenance recommendations or pre-emptive tool swaps. This adds a self-healing quality to the line, where errors are not just corrected, but anticipated and avoided altogether.
All of this contributes to a broader transformation: the sheet metal forming line as not just a machine, but as a dynamic, intelligent manufacturing platform. It’s capable of adapting to new designs with minimal lead time, collaborating with logistics systems, communicating with cloud-based analytics platforms, and providing live feedback to designers and engineers. In effect, it closes the loop between digital product development and physical product realization—turning CAD files into actual components in minutes, at industrial scale.
The competitive edge this delivers is significant. Manufacturers can respond to customer needs faster, enter new markets more confidently, reduce overhead tied to inventory and rework, and maintain higher overall equipment effectiveness over the machine’s lifetime. As technology continues to mature, future systems may incorporate real-time voice control, autonomous self-setup routines, and even swarm robotics for adaptive post-processing—all building toward a factory that thinks, adapts, and evolves alongside its users.
Automated Workflow for Sheet Metal Shaping
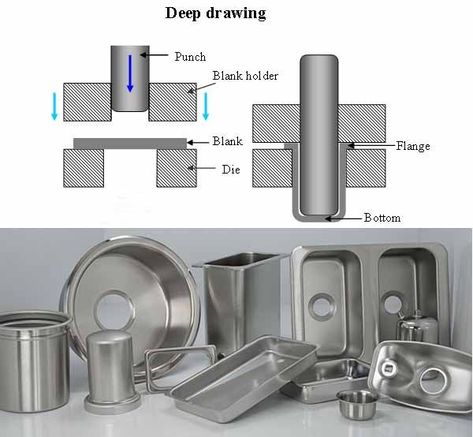
An Automated Workflow for Sheet Metal Shaping integrates various stages of the manufacturing process into a cohesive, automated system. This end-to-end solution aims to streamline production, increase efficiency, reduce human error, and enable high flexibility in manufacturing sheet metal parts. Through interconnected systems, real-time data analysis, and intelligent decision-making, the workflow is optimized to meet modern demands for both high volume and mass customization.
The workflow begins with material handling. Coils of sheet metal are automatically loaded onto the decoiler, which unrolls the material into the system. This is done with precision, as the decoiler is integrated with sensors to monitor material thickness and coil tension. The material is then fed into a leveling machine that flattens the metal sheet, ensuring that it is uniform in thickness and free from defects like coil set or waviness. A sensor-based inspection system can detect any issues at this early stage and flag coils that may need further attention.
Next, the sheet enters the servo-driven feeder, which automatically advances the material through the line based on predetermined program parameters. The feeder adjusts for any variations in material thickness or size, ensuring the sheet moves smoothly through the upcoming forming processes. The servo-driven feeder system ensures that the metal is precisely fed without deformation or skewing.
The forming process is driven by roll forming technology, which gradually shapes the sheet into the required profile. This is done through a series of rollers that apply incremental bending, with each station refining the shape step by step. The rollers can be quickly adjusted using servo motors or hydraulic presses to achieve different bending angles or curvatures. For more complex shapes, additional modules like punching, embossing, or stamping stations can be seamlessly integrated into the line. These processes are synchronized with the material feed, allowing the system to create multi-featured parts without stopping.
Inline cut-to-length systems are also automated to ensure that once the desired profile is formed, the sheet is cut to the correct length without delay. Flying shear systems or rotary cutters operate at the same speed as the line, ensuring no interruption to the flow. These automated cutting systems are synchronized with the overall line speed and programmed to cut parts based on the final specifications.
Simultaneously, quality control and inspection systems are embedded throughout the workflow. Inline vision systems or laser measurement devices constantly monitor the dimensions, surface quality, and any potential defects of the formed metal. As each part moves through the line, these systems can identify any deviations from the specified tolerances. If a defect is detected, the system can automatically reject the part, mark it for rework, or adjust the process parameters to correct the issue in real time, ensuring consistently high-quality output.
Once the part is formed and cut to size, automated material handling systems like robotic arms, conveyors, or automated guided vehicles (AGVs) move the parts to the next station or prepare them for packaging and shipment. These robots are integrated with the factory’s Warehouse Management System (WMS) and Material Requirement Planning (MRP), allowing for optimized inventory management and ensuring that the correct parts are processed and dispatched according to the schedule.
In the final stages, automated packing and labeling systems are employed to ensure that parts are correctly stacked, labeled, and packaged for shipment. Each part is tagged with RFID or QR codes, which store production data such as material type, batch ID, processing conditions, and quality assurance results. This ensures complete traceability and provides the customer with a digital record of the part’s production journey.
Throughout the entire workflow, data analytics platforms monitor and collect performance metrics from every stage of the process. These systems analyze machine performance, material usage, output quality, and downtime, providing real-time feedback to operators and managers. Over time, this data is used to optimize the entire workflow, adjusting variables like feed rates, tool changes, and cutting sequences based on historical performance. This continuous feedback loop helps improve efficiency and reduces the risk of human error or suboptimal production.
Moreover, the system’s centralized control software allows operators to monitor the entire production process through HMI (Human Machine Interface) panels or even mobile devices. The control software is also connected to the Enterprise Resource Planning (ERP) and Manufacturing Execution System (MES), enabling seamless integration of production schedules, inventory management, and supply chain processes. This integration supports real-time updates on production progress, delivery timelines, and inventory levels, providing transparency and agility in meeting customer demands.
The beauty of an automated workflow for sheet metal shaping lies in its ability to scale. Whether the factory is running high-volume orders for standardized parts or low-volume, highly customized pieces, the workflow can adapt without significant changes in labor or manual intervention. The system can also run continuously, providing manufacturers with a 24/7 production capability, ideal for industries where quick turnaround times are crucial.
By incorporating advanced features such as predictive maintenance, adaptive tooling, and real-time data feedback, the entire sheet metal shaping process becomes more efficient, cost-effective, and agile. Predictive maintenance systems analyze machine health data, such as vibration or temperature levels, and schedule maintenance before a failure occurs, reducing downtime and increasing operational efficiency. Adaptive tooling allows for quick adjustments to the tooling based on material types or product specifications, minimizing the need for manual reconfiguration.
In conclusion, an automated workflow for sheet metal shaping is a powerful solution for manufacturers looking to improve efficiency, reduce errors, and scale operations. By combining robotics, AI, real-time data analytics, and smart automation, manufacturers can deliver high-quality parts faster, at lower costs, with more consistent results. If you’d like, I can help you design or visualize a custom automated workflow suited for your specific production needs, helping you assess potential hardware, software, and integration points for your operations.
As automated workflows in sheet metal shaping continue to evolve, there are several additional areas where technological advancements are playing a key role in enhancing the system’s capabilities and efficiency.
One such advancement is the integration of additive manufacturing or 3D printing technologies alongside traditional sheet metal forming processes. In certain cases, 3D printing can be used to create complex geometries or tooling inserts that would be difficult or costly to manufacture using conventional methods. For example, 3D-printed forming tools can be quickly prototyped and tested, allowing manufacturers to experiment with new designs or modify existing tools for specific parts without a lengthy lead time. This hybrid manufacturing approach combines the flexibility of additive manufacturing with the high-throughput efficiency of traditional metal forming, enabling the production of both custom parts and high-volume runs in the same system.
The ability to integrate augmented reality (AR) and virtual reality (VR) for both design and maintenance is another significant innovation. In the design phase, AR can be used to visualize how sheet metal parts will behave during forming processes, allowing engineers to make real-time adjustments to tooling, material choice, or process parameters before physical production begins. Operators can use AR glasses to receive live instructions on the factory floor, guiding them through setup procedures, tool changes, or maintenance tasks. For complex troubleshooting, VR can simulate entire production lines, enabling technicians to test different repair scenarios without needing to interact directly with the physical equipment.
In terms of material flexibility, modern automated workflows are increasingly capable of handling a wide variety of sheet metal types and grades, from lightweight aluminum to high-strength steel alloys, all while maintaining high precision. Advanced material tracking systems—often integrated with RFID or barcode technology—allow the system to automatically adjust forming parameters based on the specific material grade being processed. This ensures that each metal type receives the appropriate treatment, whether in terms of heat, pressure, or speed, optimizing the forming process and improving product quality. These systems can also track material consumption and give real-time updates on material availability, helping to prevent shortages or overstock situations.
Automation also extends to the customization of end products. Today, customers demand more than just a “one-size-fits-all” product. Automated workflows are increasingly designed to accommodate small-batch production with minimal downtime. Customizable tooling libraries, which can be called up and adjusted dynamically, allow for the easy switch between different product configurations without halting production. For example, a roof panel production line could easily switch from producing panels with standard profiles to customized profiles for a specific building or client, with no more than a few minutes of automated reconfiguration. Additionally, digital twin technologies enable customers to specify custom features directly into the production system, which can then be validated and produced in real time, reducing lead times and improving customer satisfaction.
Cloud-based monitoring is also playing an increasingly important role in managing these automated workflows. By connecting production lines to the cloud, manufacturers can access real-time data on machine performance, part quality, and overall system health from anywhere in the world. This remote accessibility allows factory managers to monitor operations during off-hours, troubleshoot issues remotely, and even optimize production schedules to meet shifting demand. In addition, cloud connectivity allows for the aggregation of data across multiple factories or lines, enabling global performance benchmarking and facilitating the identification of trends, inefficiencies, and opportunities for continuous improvement across the entire operation.
The energy efficiency of automated sheet metal shaping workflows is another important consideration. As sustainability becomes a higher priority in manufacturing, automated systems are being designed with energy consumption in mind. From regenerative braking systems in servo motors to optimized heating and cooling processes, each part of the workflow is examined to minimize energy use while maintaining output. Energy recovery systems can capture and store excess energy from one part of the system—such as from hydraulic presses or forming stations—and redirect it to power other parts of the line. This can result in significant cost savings over time, as well as a reduced environmental impact.
Finally, one of the most critical elements of an automated workflow is its ability to scale without sacrificing quality or efficiency. As manufacturers are tasked with producing increasingly complex parts with diverse designs, automated systems can scale up to meet higher volumes or handle larger product variations with minimal adjustments. Flexible manufacturing systems (FMS) allow the workflow to switch seamlessly between high-volume, standardized parts and small-batch, custom orders. This scalability is further enhanced by intelligent scheduling systems that optimize production runs based on real-time order demand, production capacity, and material availability, ensuring that manufacturers can stay agile in the face of market shifts.
By combining all of these technologies, automated workflows for sheet metal shaping can achieve unprecedented levels of efficiency, flexibility, and quality control. The factory becomes more responsive, adaptable, and integrated, with fewer human interventions required at each stage of the production process. These systems not only improve operational metrics but also foster innovation in product development and customer service, ultimately creating a more sustainable and competitive manufacturing environment.
Should you wish to explore specific technologies, product configurations, or integration possibilities for your application, I can assist in further detailing the setup and flow tailored to your needs. Feel free to share more details about the type of products you’re producing or the scale you’re operating at.
Building on the advancements mentioned, as automated workflows continue to evolve, there’s an increasing push towards fully autonomous factories where the system operates with minimal human intervention. These factories, often referred to as lights-out manufacturing, are able to run continuously, 24/7, with the majority of operations being self-monitored and self-adjusting. With AI-driven process control and machine learning algorithms, these systems are able to analyze vast amounts of production data to predict and preemptively address inefficiencies or failures before they occur.
For instance, machine learning can be employed to continuously analyze the conditions of the material being processed. The system can track factors like temperature, humidity, and material variations across multiple batches and adapt the machine’s settings dynamically. This ensures that the optimal process parameters are always applied to every part, increasing efficiency, reducing scrap rates, and improving product consistency. The system can also learn from historical performance to refine its processes and predict future needs, such as when tooling needs maintenance or when material properties are likely to change.
In these smart, autonomous factories, human roles shift to higher-level decision-making and system oversight, rather than direct interaction with the machines. Operators, engineers, and managers can monitor the system remotely, receiving real-time notifications about potential issues, performance statistics, or production KPIs. Augmented reality (AR) or virtual reality (VR) can assist in remote diagnostics, enabling workers to “see” the production line and troubleshoot problems without physically being on-site.
One of the most exciting developments is the integration of cobots (collaborative robots) into these automated workflows. Unlike traditional robots that are often fenced off for safety, cobots are designed to work side-by-side with humans. They can assist in material handling, packaging, inspection, or even in adjusting tooling for specific parts. For instance, cobots can help load sheet metal onto automated feeders or make fine adjustments to parts on the fly. These robots are equipped with sensors that allow them to adapt to human movements and environments, ensuring that they work in harmony with the human workforce, rather than replacing them entirely.
Another emerging trend is the use of digital twins for real-time simulation and performance monitoring. A digital twin is a virtual replica of the physical production line, created using data from sensors and other monitoring systems. This digital representation can be used for a variety of purposes, from optimizing workflows and predicting machine failures to performing virtual tests on new parts or tooling before they are implemented on the factory floor. A digital twin of the sheet metal forming process can simulate material flow, part quality, and even energy consumption, helping manufacturers fine-tune their operations for maximum efficiency and output.
The use of edge computing is another important factor in the ongoing automation of sheet metal shaping. Traditionally, data from factory machines would be sent to a centralized cloud for processing, which could introduce delays due to bandwidth limitations or latency. With edge computing, data is processed locally at the machine level, reducing response times and enabling faster decision-making. This is particularly useful for time-sensitive operations, such as adjusting the speed of the sheet feeder or the pressure of the forming rollers in real-time. Edge computing can also help ensure that machines continue to operate optimally even if the network connection to the cloud is temporarily disrupted.
Additionally, 5G connectivity is beginning to revolutionize the way manufacturing systems operate. With its ability to support ultra-fast data transfer and low latency, 5G allows for real-time communication between machines, robots, sensors, and control systems, enabling faster adjustments and more efficient workflows. This is particularly advantageous for systems that rely on continuous feedback and high-speed operation, such as sheet metal forming lines that require constant monitoring and adjustment.
Sustainability continues to be a key focus in the design of these automated systems. Green technologies are being integrated into every stage of the workflow, from reducing waste and scrap through more precise forming techniques to optimizing energy usage across the entire production process. For example, closed-loop cooling systems that recycle water and reduce energy consumption or energy-efficient motors and drives that reduce the factory’s overall energy footprint are becoming standard. In addition, the use of recyclable materials and eco-friendly lubricants is being emphasized to reduce the environmental impact of the manufacturing process.
In terms of logistics, the integration of autonomous mobile robots (AMRs) is transforming the way materials and finished products are transported throughout the factory. These robots can autonomously navigate the factory floor, picking up and delivering materials to the correct stations based on real-time demand. They also assist in moving finished products to the packaging area or directly to shipping. The flexibility and scalability of AMRs make them ideal for factories that need to adapt to changing production schedules or manage varying order sizes.
Furthermore, as the sheet metal shaping process becomes more automated, integrated supply chain management is gaining importance. Automated workflows can now be directly connected to supplier networks, ensuring that raw materials are ordered and delivered just in time for production. AI-driven supply chain algorithms help anticipate material shortages or delays and proactively adjust production schedules to minimize disruptions. By continuously monitoring global supply chain data, manufacturers can optimize inventory levels and reduce material waste, further improving efficiency and cost-effectiveness.
As for quality control, advanced techniques such as X-ray inspection, ultrasonic testing, and laser-based metrology are increasingly being used in automated sheet metal shaping workflows. These non-destructive testing methods ensure that parts meet stringent quality standards while minimizing the need for manual inspection. These inspection systems are often fully integrated into the production line, enabling real-time quality assurance without interrupting the manufacturing process. If any issues are detected, the system can immediately stop the line, adjust settings, or flag defective parts for removal.
Finally, advanced analytics and big data are becoming indispensable in the continuous improvement of automated workflows. By collecting data from every stage of the process—such as machine performance, material properties, tool wear, and part quality—manufacturers can perform deep data analysis to identify bottlenecks, predict maintenance needs, and optimize the entire production system. Over time, these insights can lead to significant improvements in product quality, process efficiency, and overall factory performance.
In conclusion, the future of automated sheet metal shaping is characterized by a convergence of cutting-edge technologies, all working together to create a more intelligent, efficient, and flexible manufacturing environment. By embracing AI, robotics, IoT, edge computing, and digital twin technologies, manufacturers are well-equipped to meet the demands of an increasingly dynamic market, while improving quality, sustainability, and overall competitiveness. The evolution of automation is not only transforming the production process but is also enabling manufacturers to respond more quickly to customer demands, reduce costs, and drive innovation across industries.
Should you need more specifics, be it a deeper dive into any technology or the design of a specific automated system tailored to your production needs, feel free to let me know. I’d be happy to assist you further.
Flexible Sheet Metal Forming Line
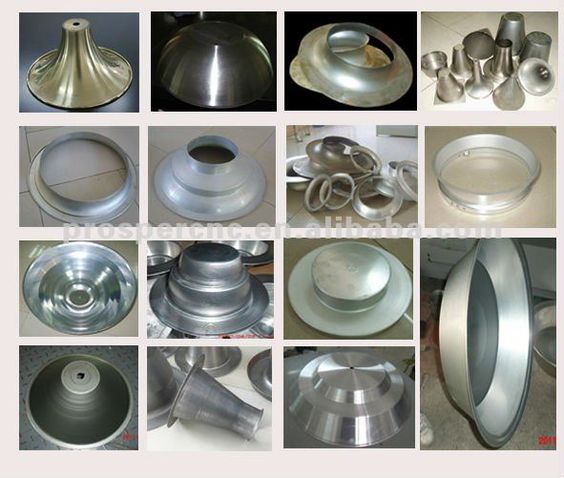
A Flexible Sheet Metal Forming Line is an advanced manufacturing system designed to process a variety of sheet metal materials and product designs with minimal downtime or manual intervention. It integrates various automation technologies and modular equipment that enable it to adapt quickly to different products, materials, and production requirements. The flexibility in such a system is crucial for manufacturers who need to meet diverse market demands, produce a wide range of part sizes, or rapidly switch between different product configurations without significant reconfiguration time.
Key Features of a Flexible Sheet Metal Forming Line
- Modular Tooling System: One of the core features of a flexible sheet metal forming line is a modular tooling system. The tooling, which includes rolls, dies, and punches, can be quickly changed or adjusted according to the specifications of the product being produced. Instead of using fixed tooling for a specific product, modular tooling allows for the easy reconfiguration of the production line for different product profiles and sizes. With a quick-change system, operators can swap out tooling within minutes, minimizing downtime and maintaining high production rates.
- Servo-Driven Roll Stands and Benders: Servo-driven technology plays a crucial role in enabling flexibility. By replacing traditional mechanical drives with servos, the line can adjust forming parameters—such as pressure, speed, and position—dynamically during operation. This means that the system can handle a variety of metal thicknesses, alloys, and profiles while maintaining precision. Servo-driven roll stands, for example, automatically adjust their settings for each batch or part, optimizing the forming process without requiring manual intervention.
- Automatic Material Handling and Feeders: A flexible sheet metal forming line typically incorporates automatic material handling systems that ensure smooth material flow without interruptions. Feeder systems equipped with advanced sensors and vision systems can automatically adjust to different sheet sizes and thicknesses. Automated coil handling ensures that coils are accurately fed into the line, maintaining constant material tension and positioning. These systems also allow for easy integration of different material types, from aluminum to high-strength steels, ensuring that the line can switch between materials without slowing down production.
- Inline Quality Control Systems: To maintain high standards of product quality, flexible forming lines integrate inline quality control systems. These systems use a combination of vision sensors, laser measurements, and ultrasonic testing to continuously monitor the sheet’s quality during the forming process. Any defects, such as dimensional errors, surface imperfections, or structural issues, are detected in real-time, and corrective actions can be taken immediately. If defects are identified, the system can automatically adjust process parameters, reject defective parts, or trigger an alert to the operator.
- Integrated Automation and Control Systems: The entire flexible sheet metal forming line is managed by a central automation and control system, which coordinates the movements of all equipment and integrates with ERP (Enterprise Resource Planning) and MES (Manufacturing Execution System). This central system allows for the real-time management of production schedules, material tracking, tool changeovers, and quality checks. It provides operators with an intuitive HMI (Human Machine Interface) that displays relevant data such as machine status, product specifications, and system health. This level of integration ensures smooth communication between different stages of the production process and enables quick adaptation to changing conditions.
- Customization Capabilities: Flexibility in the forming line is also driven by the ability to accommodate customized product designs. In the past, changing a production line for custom products required significant downtime. However, modern flexible forming lines allow for easy integration of custom part profiles. CAD/CAM (Computer-Aided Design/Computer-Aided Manufacturing) systems directly feed production data to the forming line, automatically adjusting machine parameters, tooling, and even the forming sequence based on the part specifications. This automation allows for quick transitions between standard and custom designs, reducing the need for dedicated production lines for each product.
- Hybrid Forming Techniques: A flexible sheet metal forming line may incorporate multiple forming techniques, including roll forming, punching, press braking, stamping, and even stretch forming. These processes can be combined seamlessly in a single line to create complex parts. For instance, a line might roll-form a base shape, then automatically switch to a stamping station to add holes or embossing, followed by a press brake for additional bending, and then finish with a stretch-forming process to create a more complex geometry. This hybrid approach significantly increases the line’s flexibility, allowing it to produce a diverse range of products without the need for specialized equipment or dedicated production lines.
- Robotic Integration: Robots are increasingly integrated into flexible sheet metal forming lines to handle repetitive tasks and improve flexibility. Robots can handle tasks such as material loading, unloading, part handling, and even complex assembly tasks. For example, robots might load sheets into the press brake station, remove finished parts from the line, or load them into packaging stations. Collaborative robots (cobots) can also work alongside human operators, assisting with tasks that require precision or lifting heavy loads, further enhancing the system’s overall flexibility and productivity.
- Energy Efficiency and Sustainability: A flexible sheet metal forming line can be designed with energy-efficient technologies to reduce its environmental impact. Servo motors, intelligent energy recovery systems, and automated load-balancing reduce energy consumption. Additionally, automated systems for recycling scrap material and using eco-friendly lubricants contribute to a greener manufacturing process. The system can also be designed to be more modular, allowing the manufacturer to scale the production line up or down based on demand, which helps avoid overproduction and waste.
- Data-Driven Optimization: The integration of IoT (Internet of Things) sensors and cloud-based analytics plays a significant role in optimizing flexible sheet metal forming lines. These sensors collect real-time data from each stage of the process, feeding it into advanced analytics platforms. By analyzing this data, manufacturers can identify inefficiencies, reduce scrap, predict when tools will need maintenance, and optimize the overall production flow. With predictive analytics, the system can even forecast potential bottlenecks, ensuring that corrective measures are taken before they impact production.
Benefits of a Flexible Sheet Metal Forming Line
- Quick Adaptability: The ability to switch between different products, material types, and production requirements with minimal downtime is a major advantage. This makes the system ideal for manufacturers that need to handle varying customer demands, complex product designs, or rapid order changes.
- Higher Efficiency: Automation, intelligent feedback systems, and modular tooling contribute to increased throughput and reduced manual intervention. This results in less wasted time, lower operational costs, and improved overall equipment effectiveness (OEE).
- Reduced Lead Times: Flexible forming lines can reduce lead times, as they can handle both high-volume runs and small, customized orders. Automated changeovers and reconfiguration allow the production of smaller batches without the need for a dedicated line for each product.
- Customization and Innovation: The system enables greater design flexibility, allowing manufacturers to explore more complex shapes and parts that were previously difficult to produce. This can lead to innovation in product offerings and provide a competitive edge in markets that demand customization.
- Reduced Inventory Costs: With increased flexibility, manufacturers can produce parts just-in-time (JIT) based on actual demand, reducing the need for large inventory stockpiles and minimizing inventory holding costs.
- Improved Quality Control: Continuous inline inspection and quality monitoring reduce the risk of defects, ensuring that only high-quality products leave the line. Real-time feedback allows for immediate adjustments to maintain quality throughout the production process.
Conclusion
A Flexible Sheet Metal Forming Line is the next generation of automated manufacturing, designed to meet the ever-increasing demands for customization, efficiency, and precision in sheet metal processing. Through a combination of modular tooling, servo-driven automation, integrated robotics, and advanced quality control systems, manufacturers can produce a diverse range of high-quality products with minimal downtime and waste. The ability to seamlessly switch between different products and materials with minimal reconfiguration makes this system ideal for industries that require high flexibility, such as automotive, construction, and consumer electronics.
A flexible sheet metal forming line is designed to seamlessly adapt to various products, materials, and production needs, ensuring manufacturers can stay competitive and agile in a dynamic market. At the heart of its operation lies advanced automation, modular equipment, and intelligent control systems, enabling rapid adjustments and high customization without compromising efficiency or quality. With the demand for increasingly complex, custom-designed metal parts, the need for flexibility in production has never been more critical.
The line’s ability to quickly switch between different products is driven by modular tooling systems. These systems allow for easy swapping of dies, punches, and other tools, reducing setup time and enabling manufacturers to move swiftly from one part design to another. Unlike traditional lines that may require extensive retooling or downtime for changes, a flexible forming line can maintain a continuous flow of production. Additionally, servo-driven technology enhances the system’s flexibility, enabling precise control over critical parameters like pressure, speed, and force, while adapting to varying material thicknesses and types.
Automatic material handling is also an essential feature in ensuring a smooth flow of materials throughout the production process. Advanced feeder systems, equipped with sensors and vision systems, can automatically adjust to different material dimensions, ensuring precise alignment without manual intervention. This capability allows for the use of various sheet metal materials, such as aluminum, steel, or composites, with no need for time-consuming adjustments or reconfigurations between material types. Such systems can also handle automatic coil loading, which helps streamline the process and eliminate the risk of human error.
Quality control becomes more advanced in a flexible forming line as inline inspection systems provide continuous monitoring of the metal parts being produced. Vision sensors, laser measurement tools, and even ultrasonic testing ensure that defects or variations in the part are detected immediately. The system’s ability to adjust in real time based on this feedback means that problems are addressed before they result in a large batch of defective products. For example, if the system detects dimensional deviations or surface imperfections, it can automatically adjust the forming parameters, preventing defective parts from continuing down the production line.
The integration of robotics plays a key role in improving the overall flexibility of the system. Robotic arms or collaborative robots (cobots) can be used for material handling, assembly, and inspection. These robots can work alongside humans, assisting in loading parts onto the line, removing finished products, or adjusting parts during the forming process. By automating repetitive or physically demanding tasks, robots help to enhance the speed and accuracy of the line while reducing human error. Furthermore, their ability to handle custom or delicate parts allows for a higher degree of versatility.
At the core of the line’s operation is a centralized automation and control system, which manages the entire production flow. This system integrates data from sensors, machines, and operators, providing real-time insights into machine status, part quality, and production progress. With an intuitive human-machine interface (HMI), operators can easily oversee the line, make adjustments on the fly, and ensure that everything is running smoothly. This centralization of control allows for optimized scheduling, precise tracking of materials, and automatic adjustments to tooling or process parameters based on product specifications.
Incorporating advanced technologies like IoT (Internet of Things), cloud-based analytics, and edge computing allows the system to monitor performance, predict potential issues, and offer actionable insights for continuous improvement. IoT sensors track data from every stage of the production process, providing feedback on everything from machine performance to material conditions. This data is analyzed to optimize operations, reduce energy consumption, and predict when maintenance will be required, reducing unplanned downtime.
The flexibility of such a system doesn’t just extend to product design; it also allows for rapid customization of parts without significantly affecting production speed. When switching between orders with different specifications, the system can make rapid adjustments to tooling, material handling, and processing speeds. This reduces the time it takes to meet customer demands for customized products while ensuring that throughput remains high.
Energy efficiency is another area where flexible sheet metal forming lines excel. As industries increasingly prioritize sustainability, these systems integrate energy-saving technologies like servo motors, regenerative braking, and closed-loop cooling systems. These technologies help minimize energy waste, lower operating costs, and contribute to a greener manufacturing process. Additionally, the ability to switch between different materials and product designs without overstocking inventory reduces material waste, further contributing to sustainability goals.
In terms of production speed, flexible forming lines are designed to keep up with varying batch sizes and product configurations. Whether producing high-volume standard parts or low-volume custom orders, these systems can switch between production schedules quickly. The ability to seamlessly transition from one configuration to another makes the system ideal for just-in-time (JIT) manufacturing, where demand can shift rapidly, and production needs must remain agile.
Finally, the flexibility of such systems allows manufacturers to stay ahead of market trends. As industries evolve and new product designs emerge, manufacturers need to adapt quickly. A flexible sheet metal forming line allows them to do so, offering the scalability, adaptability, and precision needed to produce a wide range of products with minimal downtime. This system also supports innovation by allowing for the rapid prototyping of new parts, designs, and tooling configurations.
In conclusion, a flexible sheet metal forming line represents the future of manufacturing, where automation, precision, and adaptability combine to create highly efficient, sustainable production environments. These systems allow manufacturers to meet diverse customer demands, reduce lead times, and improve both quality and profitability. As the industry continues to evolve, the integration of robotics, advanced sensors, and AI-driven analytics will continue to enhance the capabilities of flexible forming lines, making them even more agile and efficient. Whether the goal is mass production, custom orders, or rapid prototyping, these systems provide the versatility needed to thrive in a competitive marketplace.
The continued evolution of flexible sheet metal forming lines holds significant potential for the future of manufacturing, especially with the integration of emerging technologies like artificial intelligence (AI), machine learning (ML), and advanced data analytics. These technologies will provide manufacturers with even more precise control over the production process, allowing them to optimize performance and improve output with greater efficiency.
One of the most promising areas is the incorporation of AI and machine learning algorithms that enable the system to “learn” and improve over time. By analyzing vast amounts of data from sensors, quality control systems, and operator inputs, AI systems can predict future production needs, optimize machine settings, and reduce the occurrence of defects. For example, machine learning algorithms can analyze past production runs to detect subtle patterns that lead to failures or inefficiencies, allowing the system to proactively adjust in real-time to avoid these issues in future batches. This predictive maintenance capability is a major asset, as it minimizes the need for manual inspections or repairs, reducing downtime and extending the lifespan of equipment.
Another exciting development is the integration of digital twins, which are virtual representations of the physical production line. A digital twin allows manufacturers to simulate and test production scenarios in a virtual environment before they are implemented on the factory floor. This not only allows for the optimization of machine settings, tooling configurations, and material handling processes but also helps to identify potential bottlenecks or inefficiencies in the workflow. By virtually testing different production scenarios, manufacturers can make more informed decisions and implement changes with a higher degree of confidence. Moreover, digital twins can also provide real-time monitoring, providing insights into the condition of machines and systems, which helps prevent unexpected downtime.
Cloud computing also plays a critical role in the future of flexible sheet metal forming lines. With the increasing amount of data generated by sensors and machines, cloud-based platforms offer the scalability needed to store and process this information. Cloud computing allows manufacturers to access data from any location, enabling remote monitoring, analysis, and troubleshooting of production lines. By combining cloud computing with edge computing, which processes data at the machine level, manufacturers can create a hybrid system that offers both real-time decision-making capabilities and long-term analytics to improve overall production efficiency.
Moreover, the ongoing push toward Industry 4.0 is pushing the boundaries of automation and interconnectedness. As manufacturers adopt IoT (Internet of Things) devices, machines are becoming more intelligent and capable of autonomously communicating with each other to coordinate tasks and share critical data. For example, machines on a flexible forming line can alert each other when they require maintenance or when material is running low, creating a seamless, self-adjusting production environment. IoT-enabled machines and equipment can also track the performance of the production line in real time, providing managers with immediate access to data such as throughput, efficiency, and energy consumption.
As part of the move towards a smarter manufacturing environment, robotic systems will continue to evolve, becoming even more autonomous and adaptive. Future robots will be equipped with more advanced sensors, cameras, and AI-driven capabilities, enabling them to handle an even wider range of tasks, including intricate assembly, packaging, or quality inspections. This evolution will lead to a further reduction in human labor for repetitive or physically demanding tasks, allowing workers to focus on higher-level decision-making or specialized work.
For instance, future robotic arms could not only load and unload materials but also perform complex quality checks in real time. Using machine vision and AI-powered image recognition, robots could scan parts for even the slightest imperfections, automatically making adjustments to the forming process to correct errors. Such robots could also inspect the sheet metal for dimensional accuracy, ensuring that the final product meets the required specifications.
The incorporation of augmented reality (AR) and virtual reality (VR) is also set to revolutionize the way operators interact with the production line. With AR, workers can wear smart glasses or headsets that overlay important production data and instructions directly onto their field of view. For example, during a tool changeover, an operator could see step-by-step guidance on how to swap tools efficiently. In more advanced scenarios, AR and VR could be used for remote troubleshooting or training, where an experienced technician can guide operators through difficult tasks without being physically present, reducing downtime and improving worker productivity.
The focus on sustainability will also drive advancements in flexible sheet metal forming lines. As manufacturers face increasing pressure to reduce their carbon footprint, these systems are incorporating greener technologies to minimize energy consumption and material waste. For example, advanced energy recovery systems can capture excess energy from the machines during operations, which can be used to power other parts of the line or even returned to the grid. Furthermore, companies are increasingly using recyclable materials and eco-friendly lubricants in their production processes, helping to reduce their environmental impact.
Additionally, smart factory analytics and supply chain integration will continue to improve. With real-time data collected from every machine, tool, and process, manufacturers can make more informed decisions about inventory management, ordering materials, and production scheduling. Integration with cloud-based supply chain management systems ensures that materials arrive just in time for production, reducing storage costs and minimizing excess inventory. This also allows for better planning around demand fluctuations, reducing the risk of overproduction and material waste.
In the long term, the combination of these emerging technologies will result in a fully autonomous manufacturing system where human involvement is limited to high-level decision-making and oversight. The automation of routine tasks, the integration of AI for predictive maintenance, and the ability to switch between different products and materials seamlessly will provide manufacturers with unprecedented flexibility, productivity, and agility.
In conclusion, the future of flexible sheet metal forming lines lies in their ability to adapt quickly to a wide range of production demands, material types, and customer requirements. Through the integration of cutting-edge technologies such as AI, robotics, cloud computing, and sustainability-focused innovations, these systems will enable manufacturers to stay competitive in an ever-evolving market. By reducing downtime, improving quality control, and enhancing the speed of production, flexible forming lines will become indispensable to industries that demand high-quality, custom sheet metal parts in shorter lead times. The increased level of automation and intelligence will not only improve efficiency but also drive new levels of innovation in product design and manufacturing processes.
Automated Stamping and Forming Line
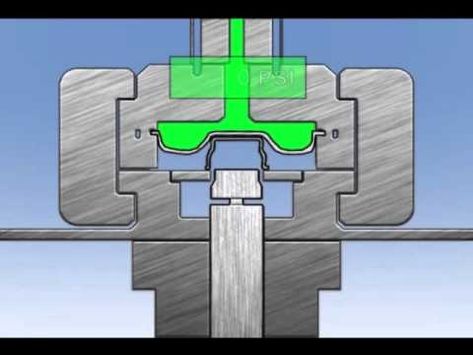
An Automated Stamping and Forming Line is a highly advanced manufacturing system designed to automate the process of shaping sheet metal into parts using stamping, forming, and cutting operations. This system integrates various automation technologies to ensure precision, efficiency, and high throughput. These lines are commonly used in industries such as automotive, aerospace, electronics, and appliance manufacturing, where consistent part quality, speed, and cost-effectiveness are essential.
The automated stamping and forming line combines multiple processes, such as blanking, piercing, bending, drawing, and forming, into a single seamless operation. These processes can be performed using mechanical presses, hydraulic presses, and automated robotic systems. By automating the entire production flow, manufacturers can achieve greater efficiency, improved part quality, and minimized labor costs while also increasing flexibility in handling diverse product designs and materials.
Key Features of an Automated Stamping and Forming Line
- Automated Pressing and Stamping Machines: At the heart of the automated stamping and forming line are presses, which are responsible for applying force to the sheet metal in order to shape it into the desired form. These presses are typically mechanical or hydraulic in nature, with each designed for specific applications. Mechanical presses are generally faster and more suited for high-speed operations, while hydraulic presses offer greater flexibility and are ideal for complex part geometries. The presses are often equipped with automatic feeders and tool changers, enabling them to switch between different stamping and forming operations without manual intervention.
- Servo-Driven Automation: Servo-driven presses are increasingly popular in automated stamping and forming lines due to their precision and energy efficiency. Unlike traditional mechanical presses, servo-driven systems use electric motors to control the motion of the ram. This allows for highly customizable force profiles, which are critical when forming parts with complex shapes or varying material thicknesses. The servo system can also adjust the stroke length and speed of the press, ensuring optimal performance and minimizing material waste.
- Integrated Robotic Handling: To maximize automation, robotic arms or automated guided vehicles (AGVs) are often integrated into the stamping and forming line. These robots handle tasks such as material loading and unloading, part positioning, and even assembly of multiple components. The robots are often equipped with advanced sensors, vision systems, and AI algorithms that enable them to handle and inspect parts with high precision. For example, robots can move stamped parts from the press to downstream operations, such as trimming, deburring, or further forming, without the need for manual labor.
- Automated Material Feeding and Coil Handling: An essential component of an automated stamping and forming line is the automated material handling system. Typically, sheet metal coils are fed into the system by automatic coil handling equipment, which unrolls the material, straightens it, and feeds it into the press. Roll feeders, pneumatic feeders, and servo feeders are used to ensure precise material advancement and alignment. Automated material handling reduces the need for manual intervention, ensuring that the material is consistently fed into the system without interruption, while also preventing damage or misalignment.
- Inline Quality Control and Inspection: To maintain part quality, automated stamping and forming lines are equipped with inline quality control systems that perform real-time inspections throughout the production process. These systems use sensors, cameras, and laser scanners to detect defects such as dimensional inaccuracies, surface defects, or missing features. Automated inspection systems can compare the actual dimensions of parts to the desired specifications and make adjustments in real time to the press settings. This level of quality control reduces the risk of defective products being produced and ensures high-quality, consistent output.
- Tool Changers and Die Maintenance: In an automated system, automatic tool changers allow for quick and efficient swaps between different dies and tooling used for stamping and forming. This is especially useful in high-mix, low-volume production environments where frequent changeovers are required. Tool changers reduce downtime by automatically swapping out tools based on the part design or batch requirements. Additionally, die maintenance systems can be integrated into the line to monitor the condition of dies and alert operators to any wear or damage that may affect part quality.
- Flexible and Modular Design: An automated stamping and forming line can be designed to be highly flexible and modular, allowing manufacturers to switch between different products or part designs without significant downtime. The line can be reconfigured by adjusting press settings, swapping tooling, or repositioning robots and material handling systems. This flexibility makes the system suitable for industries that require the production of a wide variety of parts, such as the automotive industry, where different models or customizations must be produced on the same line.
- Energy Efficiency and Sustainability: Modern automated stamping and forming lines are designed with energy efficiency in mind. Servo-driven presses, for example, consume less energy than traditional mechanical presses, and the ability to optimize energy consumption based on production requirements helps to reduce operational costs. Additionally, the integration of energy recovery systems allows the line to capture and reuse energy that would otherwise be lost during operation, further improving sustainability. These systems also help to minimize material waste by using closed-loop material handling that ensures precise cutting and stamping, reducing scrap.
- Real-Time Data Collection and Analytics: An automated stamping and forming line often incorporates data collection systems that capture real-time data from machines, presses, and quality control systems. This data is sent to a central control system or cloud-based platform, where it is analyzed for performance optimization. By tracking parameters such as machine uptime, part quality, cycle times, and energy consumption, manufacturers can gain insights into potential inefficiencies and optimize the entire production process. The data can also be used for predictive maintenance, ensuring that equipment is serviced before failures occur.
- Downstream Integration: After the stamping and forming processes, parts typically require additional operations such as trimming, deburring, or secondary forming. Downstream integration ensures that these operations are fully automated and coordinated with the main stamping process. For example, once a part is stamped, it can be automatically transferred to a deburring station where robotic arms or specialized equipment remove excess material or smooth rough edges. This seamless integration between stamping and downstream processes reduces the need for manual intervention and accelerates production.
Benefits of Automated Stamping and Forming Lines
- Increased Productivity: Automation reduces the need for manual labor, streamlining operations and significantly increasing production speed. Automated stamping and forming lines can operate 24/7, providing a continuous flow of parts without breaks, improving overall throughput.
- Enhanced Quality Control: Inline quality control systems and real-time feedback loops ensure that parts meet high standards, reducing the likelihood of defects and minimizing scrap. The ability to adjust the production parameters in real time ensures that all parts are produced to exact specifications.
- Reduced Labor Costs: With the integration of robotic systems and automated material handling, manufacturers can reduce their reliance on manual labor, which decreases labor costs and the potential for human error. Additionally, automation frees up workers to focus on more complex tasks, such as maintenance or programming.
- Flexible Production: The ability to quickly change tooling, reconfigure presses, and adapt to different part designs makes automated stamping and forming lines ideal for industries that require flexibility in production. Whether the manufacturer needs to produce high volumes of a single part or small batches of custom parts, the line can easily adjust to meet those needs.
- Lower Operating Costs: Automated systems are designed to be more energy-efficient, use materials more effectively, and require less maintenance, all of which contribute to lower overall operating costs. Additionally, real-time data analysis and predictive maintenance minimize unplanned downtime, keeping the system running efficiently.
- Improved Safety: Automation reduces the need for workers to interact directly with dangerous machinery, such as stamping presses, which improves safety in the production environment. Robots and automated material handling systems can take on dangerous tasks, such as heavy lifting and handling sharp materials, reducing the risk of injury.
- Sustainability: The use of energy-efficient technologies, material optimization, and waste reduction strategies makes automated stamping and forming lines more sustainable. With growing pressure for manufacturers to reduce their environmental impact, these systems are a key part of efforts to lower carbon footprints and improve sustainability in production processes.
Conclusion
An Automated Stamping and Forming Line is a state-of-the-art solution for manufacturers seeking to optimize their sheet metal forming processes. By integrating automation, robotics, servo-driven technology, and advanced quality control systems, these lines offer significant improvements in productivity, part quality, flexibility, and cost-efficiency. Manufacturers can produce a wide range of parts quickly and with minimal downtime, meeting the growing demands for high-quality, low-cost production. With the continuous advancement of automation technologies, automated stamping and forming lines will only become more capable, enabling manufacturers to stay competitive in an increasingly complex and fast-paced market.
An automated stamping and forming line is a highly efficient, integrated production system that uses advanced automation and robotics to streamline the stamping and forming processes for sheet metal. The core of such a line is a series of automated machines and robots that work in coordination to handle material, shape it, and ensure the production of high-quality metal parts with minimal human intervention. These lines are essential for industries such as automotive, electronics, and consumer goods, where precision, speed, and low production costs are crucial.
At the heart of the operation is the press system, which applies significant force to the sheet metal to achieve the desired shape. These presses can be either mechanical or hydraulic, each suited to different types of production. Mechanical presses are often used for high-speed operations, while hydraulic presses are more adaptable and ideal for parts with complex geometries. The integration of servo-driven technology into these presses allows for precise control over the speed, force, and stroke length, optimizing the forming process for different materials and part designs. The servo-driven presses are particularly effective in minimizing energy consumption, as they only use power when required, making them more energy-efficient compared to traditional mechanical presses.
Material handling plays a critical role in ensuring smooth production flow. Automated coil handling systems feed raw sheet metal into the presses with high precision. These systems unroll, straighten, and advance the material into the press, while sensors ensure accurate alignment and positioning. Automated feeders, such as roll feeders and servo feeders, allow for smooth, uninterrupted feeding of materials, reducing human error and improving overall cycle time. This automation also helps in managing different material types, whether it’s steel, aluminum, or other metals, making it easier to switch between different materials without disrupting the production process.
Robotic systems are increasingly integral to automated stamping and forming lines. These robots handle tasks such as loading and unloading the material, moving stamped parts to downstream operations, and performing post-forming processes like trimming, deburring, and assembly. Robots can be equipped with advanced vision systems, sensors, and AI algorithms to inspect parts for defects and even make adjustments during the production process. This ability to detect and address issues in real time ensures that defects are minimized, and production efficiency is maintained.
One of the key features of these lines is their ability to perform inline quality control and inspection throughout the production process. Automated inspection systems use laser scanners, cameras, and other sensors to detect any dimensional inaccuracies, surface imperfections, or other quality issues. These systems can then send feedback to the press, adjusting the parameters or stopping production if a defect is detected, preventing defective parts from continuing down the line. Real-time quality control reduces scrap rates and ensures that the parts produced meet stringent standards.
The flexibility of automated stamping and forming lines is another significant advantage. The systems can be quickly reconfigured to accommodate different part designs, material types, or production volumes. This flexibility is achieved through the use of automatic die changers, which allow for rapid switching between different stamping tools. The ability to change tools and adjust machine settings quickly means that manufacturers can easily transition between different products, making these lines ideal for high-mix, low-volume production environments.
Data collection and analytics are also vital components of automated stamping and forming lines. Sensors embedded in the system collect vast amounts of data during production, including machine performance, material usage, cycle times, and part quality. This data is then analyzed to optimize the production process. Manufacturers can gain real-time insights into system performance, identify potential bottlenecks, and make data-driven decisions to improve efficiency. Predictive maintenance algorithms can be used to monitor the condition of machines, detecting wear or potential failures before they occur, reducing downtime, and extending the life of equipment.
Automation also improves safety on the production floor. By reducing the need for human operators to handle dangerous equipment directly, robotic systems and automated material handling reduce the risk of workplace injuries. Additionally, automated systems can operate in harsh environments, handling hazardous materials or parts with sharp edges, which further enhances worker safety.
Energy efficiency is another key advantage of automated stamping and forming lines. The integration of servo-driven presses, energy recovery systems, and advanced machine controls ensures that the system operates with minimal energy consumption. Regenerative braking systems, which capture and reuse energy during deceleration phases, help further reduce energy waste. These energy-saving measures not only lower operating costs but also contribute to a more sustainable production process, helping manufacturers meet environmental goals.
Another important aspect is the integration of downstream operations, such as trimming, deburring, and secondary forming. These processes are automated as well, ensuring a seamless transition from one operation to the next. Once parts are stamped and formed, they are automatically moved to the next stage of production, whether it’s for finishing operations or assembly. This reduces the need for manual intervention, further speeding up production and improving part consistency.
In terms of scalability, automated stamping and forming lines can be designed to meet a range of production needs, from small batches of custom parts to large volumes of standardized components. The ability to scale production up or down without significant reconfiguration is a major benefit for manufacturers who need to respond quickly to market demand or changes in customer specifications.
The use of cloud-based platforms for data management is another emerging trend in automated stamping and forming lines. These platforms allow manufacturers to access production data remotely, monitor machine performance, and receive alerts for any potential issues. The cloud also enables better collaboration between different production sites, making it easier to share information and coordinate production schedules. As cloud technology continues to evolve, it will play an even more significant role in the optimization and management of automated manufacturing systems.
In conclusion, an automated stamping and forming line is a highly efficient and flexible manufacturing solution that integrates advanced technologies such as servo-driven presses, robotic systems, AI-based inspection, and real-time data analytics. These systems offer significant improvements in productivity, quality control, safety, and sustainability. As the demand for high-quality, low-cost, and customizable metal parts increases, automated stamping and forming lines will continue to play a crucial role in meeting these requirements, providing manufacturers with the flexibility and efficiency needed to stay competitive in today’s fast-paced market.
The future of automated stamping and forming lines continues to evolve with the integration of more advanced technologies and processes that push the boundaries of manufacturing efficiency and customization. As industry demands grow for faster production cycles, higher precision, and more adaptable systems, automation in stamping and forming is increasingly becoming a critical part of the competitive landscape in manufacturing sectors such as automotive, aerospace, and electronics.
One significant area of advancement lies in the integration of Artificial Intelligence (AI) and machine learning (ML). These technologies are enabling stamping and forming lines to become even more intelligent, adaptive, and predictive. AI can analyze production data in real time to identify patterns and anomalies that may not be immediately visible to human operators. For example, machine learning algorithms can predict potential failures or quality issues based on historical data, enabling preemptive maintenance before a failure occurs. This predictive maintenance can help extend the lifespan of expensive equipment and minimize downtime, making operations more efficient and cost-effective. AI systems can also optimize press settings dynamically, adjusting parameters like force, speed, and stroke length based on the specific material and part geometry being processed, improving part quality and reducing waste.
Advanced machine vision systems are another innovation in automated stamping and forming lines. These systems use high-resolution cameras, lasers, and other sensors to inspect parts for even the most minute defects during production. With AI-powered image recognition, these systems can detect dimensional inaccuracies, surface defects, and other imperfections that might be too small for the human eye to catch. The ability to detect these issues in real time allows operators to make immediate corrections, ensuring that only defect-free parts make it to the next stage of production. In some cases, vision systems are also used to guide robotic arms during part handling, ensuring that parts are placed and assembled with the highest degree of accuracy.
Robotics and automation are continuously advancing to become more flexible and capable of handling a wider range of tasks. Robotic arms are now equipped with more sophisticated sensors and AI algorithms that allow them to adapt to changing conditions on the fly. For example, a robot might adjust its grip strength or speed based on the shape or material of a part, reducing the risk of damaging delicate components or creating defects. Additionally, collaborative robots (cobots) are becoming more common in stamping and forming lines. These robots are designed to work alongside human operators safely, without the need for physical barriers, and are increasingly being used to assist in tasks like material handling, quality inspections, and assembly. Cobots allow manufacturers to achieve greater flexibility and throughput while still maintaining a safe working environment.
The concept of digital twins is also gaining traction in automated stamping and forming lines. A digital twin is a virtual representation of the entire manufacturing process, including machines, tooling, and material flows. It allows manufacturers to simulate different production scenarios and predict how changes in one part of the system will impact the overall process. By integrating digital twins with real-time data from the production floor, manufacturers can perform continuous optimization of their systems, making adjustments on the fly to improve efficiency, reduce energy consumption, and minimize material waste. In addition, digital twins can be used for training purposes, allowing operators to interact with a virtual model of the production line and learn how to handle various challenges without interrupting actual production.
Another area of advancement is additive manufacturing and its integration with stamping and forming processes. While stamping and forming traditionally involve subtracting material from a sheet of metal, additive manufacturing (3D printing) allows for the layer-by-layer construction of parts. By combining these technologies, manufacturers can achieve a new level of flexibility in producing highly complex parts. For example, additive manufacturing can be used to produce complex tooling or components that would be difficult or impossible to create with traditional stamping and forming methods. This hybrid approach opens up possibilities for faster prototyping, customized tooling, and more intricate part designs, all of which can be incorporated into the automated production line.
Sustainability is increasingly becoming a driving factor in the design of automated stamping and forming lines. Manufacturers are under growing pressure to reduce their carbon footprint and minimize waste, and automation is a key enabler of this shift. For instance, automated systems can optimize material usage to reduce scrap, and advanced sensors and AI systems can adjust parameters to ensure that parts are formed with minimal material waste. Additionally, energy recovery systems are being integrated into stamping and forming lines to capture excess energy during operations, such as during the press’s deceleration phase, and feed it back into the system. This reduces overall energy consumption and contributes to more sustainable manufacturing practices.
Another promising development is the use of collaborative supply chain networks. As more manufacturers adopt smart technologies, they are also connecting their production systems with external networks through cloud platforms and Internet of Things (IoT) systems. This interconnected approach enables manufacturers to collaborate more effectively with suppliers and customers, exchanging real-time data and ensuring that materials, components, and information flow seamlessly across the entire value chain. For example, if a part is running low on material or requires a specific tool change, the system can automatically communicate with suppliers or other parts of the production process to adjust orders or schedule maintenance. This level of integration improves the overall efficiency of the production process and reduces the risk of delays.
The future of automated stamping and forming lines will also see the rise of flexible automation systems that can quickly switch between different production tasks without requiring extensive reprogramming or tooling changes. This will be especially important for industries with rapidly changing customer demands, such as the automotive industry, where manufacturers must be able to produce a wide variety of parts for different vehicle models in short time frames. By creating more agile and adaptable production systems, manufacturers will be able to respond more effectively to market changes and customer needs, giving them a competitive edge.
Finally, cybersecurity will become an even more critical focus as automated stamping and forming lines become more connected and integrated with digital systems. As production lines become more reliant on cloud platforms, AI, and IoT devices, they also become more vulnerable to cyberattacks and data breaches. Manufacturers will need to invest in robust cybersecurity measures to protect their intellectual property, proprietary processes, and operational data. This will involve implementing advanced encryption, access control, and monitoring systems to safeguard against threats and ensure the integrity of the production process.
In conclusion, the ongoing development of automated stamping and forming lines is set to transform the manufacturing industry. As technology continues to advance, these systems will become even more efficient, flexible, and intelligent, enabling manufacturers to produce high-quality parts faster, with greater precision and less waste. By leveraging AI, robotics, data analytics, and sustainable technologies, manufacturers can not only improve their bottom line but also meet the growing demand for customized, high-performance parts. The integration of these innovations into automated stamping and forming lines will pave the way for the next generation of manufacturing, one that is smarter, more sustainable, and more responsive to the dynamic needs of the market.
Integrated Sheet Metal Shaping Line
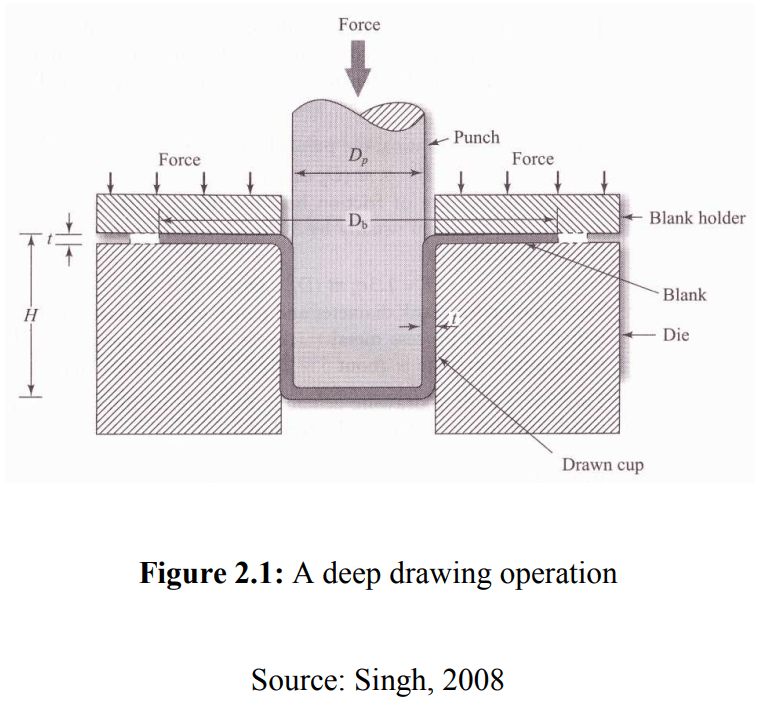
An Integrated Sheet Metal Shaping Line is a sophisticated manufacturing system designed to automate the entire sheet metal forming process from start to finish, integrating various steps such as material feeding, blanking, forming, trimming, and finishing into one continuous, streamlined operation. These systems are commonly used in industries that require precise, high-volume production of metal parts, such as automotive, aerospace, electronics, and appliance manufacturing.
The primary goal of an integrated sheet metal shaping line is to maximize productivity, reduce cycle times, and ensure part consistency by connecting all the key stages of production through automated processes. By linking each stage of the operation, manufacturers can achieve high levels of efficiency, minimize human intervention, and maintain tight control over part quality.
The line typically consists of several key components working together to process the sheet metal into the final product, each with specialized roles. These components often include:
- Automated Material Handling: This includes systems that feed metal sheets or coils into the production line automatically. These systems can include uncoilers, straighteners, and feeders, which ensure the material is correctly aligned and prepared for the stamping or forming processes. By eliminating manual material handling, these systems reduce the chance of misalignment and improve the consistency of the process.
- Blanking and Cutting: Blanking is the process of cutting large sheets of metal into smaller, more manageable pieces (blanks) that are ready for further shaping. This operation is typically performed using automated blanking presses or laser cutting systems. These machines are equipped with automated feeding and tool-changing systems, allowing for quick changes between different part shapes and sizes.
- Forming Presses: After blanking, the metal parts are typically shaped using presses. These presses may be mechanical, hydraulic, or servo-driven, each selected based on the material type, part complexity, and production volume. The press systems apply force to the blanks, shaping them into the desired final form using various techniques, such as deep drawing, stamping, bending, or stretching. Servo-driven presses, in particular, offer high flexibility, allowing for precise control over the force, speed, and stroke length, which is essential for producing complex part geometries.
- Robotic Automation: To ensure smooth transitions between stages and reduce manual labor, robotic systems are often integrated throughout the shaping line. These robots handle tasks such as loading and unloading parts, moving blanks between presses, inspecting parts, and performing secondary operations like deburring or trimming. Robots equipped with vision systems can also perform quality checks during the production process, detecting defects and adjusting production parameters in real-time.
- Trimming and Secondary Forming: After the forming press, many parts require additional operations to remove excess material, such as trimming, edge finishing, and hole punching. These operations are typically automated and integrated directly into the line. For instance, robotic arms or automated trimming presses can perform these tasks without interrupting the flow of the line, ensuring a consistent and high-quality finish on the final part.
- Inline Inspection and Quality Control: Quality control is essential in an integrated sheet metal shaping line to ensure that parts meet strict specifications. Automated inspection systems, including vision systems, laser scanners, and dimensional measurement tools, are used throughout the line to monitor part quality in real-time. These systems can identify defects such as dimensional inaccuracies, surface flaws, or missing features and trigger corrective actions immediately, preventing faulty parts from progressing further down the line.
- Material Waste Management: Minimizing waste is a crucial part of the efficiency of an integrated sheet metal shaping line. Many systems are designed to recycle scrap material generated during blanking or trimming and feed it back into the production cycle. This recycling not only reduces material costs but also supports sustainability goals by minimizing the environmental impact of production.
- Downstream Integration: Depending on the product being produced, the shaping line may integrate additional processes like assembly, welding, or coating. For example, after the metal parts are shaped, they may be automatically transferred to a welding station for assembly or to a painting booth for coating. This integration ensures a seamless production flow, minimizing bottlenecks and downtime.
- Data Analytics and Monitoring: Modern integrated sheet metal shaping lines come equipped with data collection systems that capture key metrics such as machine performance, production speed, material usage, and quality data. This information is sent to a central control system or cloud-based platform, where it can be analyzed in real-time to identify inefficiencies, predict maintenance needs, and optimize the entire production process. This data-driven approach allows manufacturers to make informed decisions and continuously improve operational performance.
- Energy Efficiency and Sustainability: As sustainability becomes an increasingly important focus for manufacturers, energy-efficient technologies are being incorporated into integrated shaping lines. These include energy recovery systems that capture excess energy from presses or other machinery and recycle it for later use, reducing overall energy consumption. Additionally, efficient material handling and forming processes help minimize waste, contributing to a more environmentally friendly production process.
By automating and integrating all of these steps into a single continuous line, manufacturers can achieve several benefits, including:
- Increased Productivity: Automation reduces the need for manual intervention, enabling the line to run continuously, which increases overall throughput.
- Improved Part Consistency: With precise control over each stage of production, the line ensures that each part is manufactured to the exact specifications, minimizing variations and defects.
- Reduced Labor Costs: By reducing manual handling, assembly, and inspection tasks, integrated lines reduce the need for labor while increasing overall operational efficiency.
- Enhanced Flexibility: The ability to easily switch between different part designs or materials without significant downtime is crucial in industries where product variety is essential.
- Lower Operational Costs: Automated systems reduce energy consumption, material waste, and downtime, lowering the overall cost of production.
- Improved Safety: The use of robots and automated material handling systems reduces the need for operators to interact with dangerous machines, improving workplace safety.
In conclusion, an Integrated Sheet Metal Shaping Line provides a comprehensive and efficient solution for manufacturers looking to produce high-quality sheet metal parts with minimal manual intervention. By combining advanced automation, robotics, and data analytics, manufacturers can achieve high throughput, consistent quality, and reduced production costs. These integrated systems are the future of sheet metal forming, offering the flexibility and efficiency needed to meet the demands of modern manufacturing industries.
An integrated sheet metal shaping line is a fully automated production system that combines various stages of sheet metal processing into one seamless, continuous workflow. This system is designed to handle all stages of production, from material feeding to final part inspection, minimizing human intervention and maximizing efficiency. The automation of these processes ensures that manufacturers can produce high-quality metal parts with consistent precision, reduced cycle times, and lower production costs.
At the heart of the system is the automated material handling component, which efficiently feeds sheets or coils of metal into the production line. These systems include uncoilers, straighteners, and feeders that ensure the metal is correctly positioned and aligned for further processing. This step eliminates manual handling, which reduces the chance of misalignment and improves the overall consistency of the material entering the shaping processes. Once the material is in place, blanking machines cut the metal into smaller, manageable pieces, typically referred to as blanks. These blanks are prepared for the forming process, where the bulk of the shaping takes place.
Forming presses, such as mechanical, hydraulic, or servo-driven presses, shape the metal into the desired final form. These presses apply force to the blanks, transforming them through methods like stamping, deep drawing, or bending. Advanced servo-driven presses offer precise control over parameters like force, speed, and stroke length, allowing manufacturers to produce parts with complex geometries while maintaining high consistency and accuracy. These presses can also be adjusted quickly for different part types, making the system more adaptable and capable of handling a variety of materials and part designs.
To ensure smooth transitions between processes, robotic systems are often integrated throughout the line. Robots handle tasks such as material loading and unloading, moving parts between machines, and conducting secondary operations such as trimming, deburring, or assembly. These robotic systems are equipped with sensors and vision systems to inspect parts for quality during the process, ensuring that any defects or dimensional inaccuracies are detected early and corrected before they can propagate through the production cycle. The use of robots also allows for more flexibility and higher throughput, as robots can perform multiple tasks in parallel or adjust their operations as needed to handle varying part sizes and materials.
Once the metal parts are shaped, trimming and secondary forming operations are performed to remove excess material, fine-tune part dimensions, or add additional features like holes or embossments. Automated trimming presses or robotic arms handle these tasks, ensuring that parts meet the desired specifications without requiring manual intervention. These secondary processes are essential for achieving the final quality standards of the part, and their automation helps maintain a high level of consistency throughout the production line.
The inspection of parts is integrated into the process flow to monitor part quality in real-time. Automated inspection systems use advanced vision technologies, such as laser scanning and high-resolution cameras, to detect defects such as surface imperfections, dimensional discrepancies, or missing features. These systems are capable of identifying issues that might be too small for human inspectors to detect, ensuring that only parts that meet strict quality standards progress further down the line. When a defect is identified, the system can automatically trigger corrective actions, such as adjusting machine settings or halting production to prevent defective parts from reaching the next stage.
One of the key advantages of integrated sheet metal shaping lines is their ability to minimize waste. Automation systems are optimized to use materials efficiently, with many lines incorporating recycling systems that recover scrap metal generated during blanking, trimming, and forming. This scrap material can be fed back into the production process, reducing the need for new material and lowering overall costs. Additionally, energy recovery systems are often integrated into the presses and other machinery to capture and reuse excess energy, making the system more energy-efficient and environmentally friendly.
As data collection and analytics play an increasingly critical role in modern manufacturing, integrated shaping lines are equipped with sensors and data systems that continuously monitor production parameters. These systems gather information on machine performance, material usage, cycle times, and part quality. The data is analyzed in real time to identify inefficiencies, predict maintenance needs, and optimize the production process. By using this data, manufacturers can make informed decisions to improve throughput, reduce downtime, and enhance overall system performance. Predictive maintenance tools, powered by AI and machine learning, further increase the efficiency of these systems by forecasting when parts are likely to fail or require servicing, thus preventing costly interruptions and extending the lifespan of the equipment.
Another significant benefit of integrated sheet metal shaping lines is their ability to scale production quickly and efficiently. These lines can be easily reconfigured to handle different part designs, material types, and production volumes without requiring extensive downtime or reprogramming. This flexibility is particularly valuable in industries where customer demands change frequently, such as the automotive and electronics sectors, where manufacturers need to adapt rapidly to market shifts. Automated die changers and quick setup systems allow the line to switch between different parts with minimal disruption, enhancing overall operational agility.
Safety is another important consideration in the design of integrated sheet metal shaping lines. The use of robots and automated material handling systems reduces the need for human operators to interact with dangerous machinery directly. This minimizes the risk of workplace injuries, particularly when dealing with heavy equipment, sharp tools, or high-speed presses. The automated systems are also capable of handling hazardous materials or parts with sharp edges, further enhancing workplace safety. In addition, modern systems often include safety protocols such as emergency stop buttons, sensors, and barriers to ensure that operators remain protected at all times.
In terms of sustainability, integrated sheet metal shaping lines are designed to optimize both material and energy usage. The precise control over machine parameters and material handling processes helps to minimize waste and reduce the environmental impact of production. Energy-efficient components, such as servo-driven presses and energy recovery systems, contribute to lowering the overall energy consumption of the line, while the automated recycling of scrap material reduces the need for raw resources.
The rise of cloud-based platforms for production management and remote monitoring is another emerging trend. These platforms enable manufacturers to access real-time data from anywhere, monitor production performance, and make adjustments remotely. This capability is especially useful for multi-site manufacturers or those with geographically dispersed production facilities. Cloud-based systems also enable better coordination between different stages of production, helping manufacturers optimize their supply chains and reduce lead times.
As the demand for highly customized and precision-engineered parts continues to grow, integrated sheet metal shaping lines will play an increasingly important role in meeting these needs. By incorporating the latest advancements in automation, robotics, AI, and data analytics, these systems enable manufacturers to produce high-quality parts at scale, while maintaining flexibility, reducing costs, and improving sustainability. The continuous development of these lines will ensure that they remain a key driver of innovation and efficiency in the sheet metal forming industry.
As integrated sheet metal shaping lines continue to evolve, manufacturers are increasingly adopting cutting-edge technologies to enhance the capabilities of these systems. One such technology is smart sensors and advanced monitoring systems, which provide deeper insights into the performance of both individual machines and the entire production line. These sensors can track variables such as temperature, pressure, vibration, and force, providing real-time feedback on machine conditions. By monitoring these parameters, the system can identify any deviations from the optimal operating conditions, allowing for immediate corrective actions. This capability not only improves the overall efficiency of the line but also helps prevent potential issues before they cause equipment damage or downtime.
Furthermore, the integration of augmented reality (AR) and virtual reality (VR) technologies into the operation and maintenance of integrated sheet metal shaping lines is gaining traction. These technologies allow operators and maintenance personnel to visualize complex system data in real time, overlaying critical performance metrics on machine components through AR headsets or VR interfaces. For instance, during troubleshooting, AR can provide technicians with step-by-step guidance on repairing or adjusting machinery, increasing the speed and accuracy of maintenance tasks. These innovations reduce the need for specialized training, streamline repair processes, and further enhance operational uptime.
Another important development is the collaboration of human operators with autonomous systems through the use of cobots (collaborative robots). Cobots are designed to work alongside human operators, taking on repetitive or physically demanding tasks while allowing workers to focus on higher-value activities. For example, cobots can assist with material loading and unloading, part inspection, or even packaging. Unlike traditional industrial robots, cobots are built with safety features that allow them to interact directly with humans in shared spaces without the need for safety cages or barriers. This close collaboration between humans and robots increases productivity while maintaining a safe working environment.
The use of artificial intelligence (AI) in the decision-making processes of integrated shaping lines is transforming how these systems operate. AI algorithms can analyze vast amounts of production data to identify inefficiencies or trends that would otherwise go unnoticed. For example, AI can optimize machine settings dynamically by analyzing the material type, thickness, and desired part geometry in real-time. This allows for quicker changeovers, reduces the likelihood of errors, and improves the consistency of finished parts. In addition, AI-powered predictive maintenance systems can use data from sensors and historical machine performance to forecast when a component is likely to fail, helping to schedule repairs before an actual breakdown occurs. This not only prevents costly disruptions but also extends the lifespan of equipment, maximizing the return on investment.
In addition to improving machine performance and quality control, AI and machine learning are enabling new levels of customization in integrated sheet metal shaping lines. With growing customer demand for personalized products, manufacturers are turning to flexible, on-demand production systems that can quickly switch between different part designs or modify existing designs based on customer specifications. AI-driven design software allows for the rapid prototyping of complex parts, while machine learning models predict the best manufacturing parameters for each new design, ensuring that high-quality parts are produced even with changing specifications.
Cloud computing and big data are also revolutionizing the way integrated sheet metal shaping lines are managed. By leveraging cloud platforms, manufacturers can centralize production data from multiple sites, enabling real-time monitoring and control from anywhere in the world. This centralized approach to data management allows for better decision-making, as managers can access detailed insights into production performance, inventory levels, and supply chain conditions. Moreover, cloud-based systems allow manufacturers to collaborate more effectively with suppliers, customers, and other stakeholders, ensuring that material orders, part deliveries, and production schedules are always up-to-date.
Another benefit of cloud computing is its ability to support remote diagnostics and troubleshooting. If an issue arises on the production line, engineers or technicians can remotely access the system to analyze the problem and provide guidance to operators on how to resolve it. This reduces downtime, as engineers do not need to be physically present on-site to address issues, and allows for faster problem-solving.
The concept of digital twins is also becoming a key feature in advanced sheet metal shaping lines. A digital twin is a virtual replica of a physical system, created using data collected from sensors and IoT devices embedded in the production line. By simulating the entire manufacturing process in a virtual environment, digital twins allow manufacturers to test different scenarios and optimize processes without affecting actual production. For example, if a manufacturer wants to experiment with a new material or machine setting, they can use the digital twin to simulate how these changes will impact the production process. This ability to test and optimize processes in a virtual space helps manufacturers avoid costly mistakes, improve system efficiency, and shorten product development cycles.
In line with sustainability goals, energy-efficient technologies and sustainable manufacturing practices are becoming increasingly important in integrated sheet metal shaping lines. Many of these lines are designed to reduce energy consumption through the use of high-efficiency motors, regenerative braking systems, and other energy-saving technologies. Additionally, manufacturers are exploring ways to reduce their environmental footprint by recycling scrap metal, using eco-friendly materials, and minimizing waste generated during the production process. For example, by incorporating closed-loop recycling systems into the production line, manufacturers can reclaim scrap metal and reuse it in future runs, significantly reducing material costs and environmental impact.
The role of supply chain integration is also growing as part of the broader trend towards smart manufacturing. Integrated sheet metal shaping lines are increasingly connected to the larger supply chain ecosystem through advanced Enterprise Resource Planning (ERP) systems and IoT networks. This connectivity enables manufacturers to track material orders, monitor inventory levels, and share production data with suppliers and customers in real time. With better visibility into the supply chain, manufacturers can reduce lead times, improve scheduling accuracy, and make more informed decisions about inventory management. This helps to ensure that the necessary materials are always available when needed and reduces the risk of production delays.
Looking ahead, the future of integrated sheet metal shaping lines will continue to evolve as automation, AI, and digital technologies further advance. Manufacturers will increasingly rely on these systems to meet the growing demand for high-quality, customized parts produced in shorter lead times and with reduced costs. As industry standards shift toward greater flexibility, sustainability, and innovation, integrated shaping lines will be at the forefront of driving these changes, enabling manufacturers to remain competitive in an increasingly complex and dynamic global market.
Ultimately, the ongoing development of integrated sheet metal shaping lines promises a future where manufacturing is more intelligent, efficient, and responsive than ever before. These systems will continue to improve the way sheet metal parts are produced, driving advances in quality, sustainability, and operational performance while offering manufacturers the tools they need to meet the challenges of tomorrow’s industries.
As integrated sheet metal shaping lines continue to advance, the development of smart manufacturing ecosystems will be crucial for improving overall system performance, responsiveness, and adaptability. These ecosystems, powered by IoT (Internet of Things) technology, will connect various machines, sensors, and devices across the production floor. The real-time communication between machines and other systems will allow for a level of synchronization that is unprecedented in modern manufacturing. Machines will be able to share performance data, respond to changing conditions, and even perform self-diagnostics without human intervention. For example, if a machine detects an anomaly in its operation, it could automatically notify the control system to adjust parameters or alert operators before an issue becomes critical. This capability drastically reduces downtime, optimizes performance, and ensures a more streamlined production process.
Additionally, edge computing will become an essential part of integrated sheet metal shaping lines. Edge computing involves processing data locally on machines and sensors rather than sending all the data to the cloud for analysis. This reduces latency and improves decision-making speeds, which is critical in real-time production environments. For instance, if a forming press detects an issue during a cycle, the system can immediately adjust its operation to correct the problem without waiting for cloud-based analysis. This level of immediate responsiveness allows for more precise control over production quality and throughput.
The concept of autonomous manufacturing is another exciting development. In the future, integrated sheet metal shaping lines may become fully autonomous, with machines and systems functioning without the need for direct human oversight. These lines would be capable of performing all tasks, from material handling to production and inspection, based on pre-programmed parameters and continuous data feedback. The line could automatically adjust its operations depending on real-time conditions, optimizing the production process without human input. While humans will still play a key role in system oversight and high-level decision-making, much of the routine operational control could be handled by artificial intelligence and machine learning algorithms. This would result in faster, more efficient production while also reducing human error and the potential for safety hazards.
Supply chain digitization will also play an integral role in shaping the future of integrated sheet metal shaping lines. As production systems become more interconnected, the data flowing between the factory and external stakeholders—such as suppliers, distributors, and customers—will be vital for creating a more responsive and flexible supply chain. Through the use of blockchain technology, for example, manufacturers could track materials in real-time, providing transparency throughout the entire supply chain. This would help prevent delays, identify bottlenecks, and allow for better forecasting, ensuring that materials are available exactly when needed, and production schedules are optimized. Real-time tracking also enables faster and more accurate delivery of parts, improving customer satisfaction.
In addition to these technologies, advanced material science will continue to influence integrated sheet metal shaping lines. New alloys, composites, and advanced metals will require innovative processing techniques that can handle their unique properties. As materials become lighter, stronger, and more versatile, integrated shaping lines will need to be adaptable to handle a diverse range of materials without compromising efficiency or quality. For example, lightweight alloys used in the aerospace industry may require different forming processes than traditional steels used in automotive manufacturing. By incorporating advanced sensors and AI, these lines will be able to automatically adjust their operations to accommodate different material characteristics, ensuring the desired part properties are achieved while maintaining high production standards.
The integration of 3D printing (additive manufacturing) with traditional sheet metal forming techniques is also on the horizon. This hybrid manufacturing approach could revolutionize production by enabling the creation of complex geometries that would be difficult or impossible to achieve using traditional methods. For example, 3D printing could be used for rapid prototyping, tooling, or even for adding intricate internal structures to parts during the production process. These advancements will help manufacturers reduce lead times, lower costs, and improve design flexibility.
Furthermore, the circular economy will be an essential consideration for future integrated sheet metal shaping lines. Manufacturers will increasingly focus on sustainability and the recycling of materials not just within the factory but across the entire product lifecycle. Instead of relying on a linear production model where raw materials are extracted, used, and discarded, the circular economy encourages the continuous reuse and recycling of materials. Sheet metal forming lines of the future will be designed to optimize the reuse of metal scrap, reduce waste, and minimize the environmental impact of production. In the long term, these systems will contribute to a more sustainable approach to manufacturing, ensuring that resources are used efficiently, and less waste is generated.
Artificial Intelligence (AI) and Machine Learning (ML) will continue to drive advancements in predictive maintenance, process optimization, and quality control. These technologies allow manufacturers to proactively manage their equipment and processes by predicting potential failures or deviations from quality standards before they occur. Through the analysis of large datasets gathered from sensors and historical machine performance, AI can identify patterns and correlations that humans may not be able to detect. For instance, machine learning algorithms could predict when a press tool is likely to wear out based on its usage patterns, allowing for preventive maintenance to be scheduled before it leads to a breakdown. This predictive capability improves machine uptime, reduces maintenance costs, and enhances overall production reliability.
Human-centric design will also be an increasingly important aspect of integrated sheet metal shaping lines. As automation levels rise, it’s essential that these systems are designed to be user-friendly and accessible for operators, technicians, and engineers. Interactive interfaces, intuitive control systems, and real-time feedback will allow human workers to collaborate more effectively with automated systems. By reducing the complexity of machine interactions, manufacturers can ensure that their workforce can quickly adapt to new technologies and remain engaged in the production process. Training programs that incorporate virtual reality and augmented reality will also help workers better understand machine functions and improve their ability to troubleshoot issues, resulting in a more efficient and highly skilled workforce.
Lastly, the globalization of manufacturing and the rise of smart factories will continue to drive the evolution of integrated sheet metal shaping lines. As manufacturing becomes more distributed and interconnected, companies will need to find ways to synchronize production across multiple facilities. Integrated sheet metal shaping lines will need to communicate with other factories, warehouses, and suppliers around the world, ensuring that production processes are aligned, resources are used efficiently, and products are delivered on time. These systems will be powered by advanced data analytics, allowing companies to make global production decisions based on real-time market conditions, supply chain disruptions, and customer demand shifts.
In conclusion, the future of integrated sheet metal shaping lines is one of continuous innovation and transformation. The convergence of automation, AI, robotics, IoT, and advanced manufacturing technologies will drive productivity, quality, and sustainability to new heights. These systems will become more intelligent, adaptive, and interconnected, enabling manufacturers to meet the ever-growing demands of global markets. With the ability to handle a diverse range of materials, reduce waste, optimize production processes, and ensure the highest levels of product quality, the integrated sheet metal shaping line of the future will be a critical enabler of tomorrow’s manufacturing landscape.
High-Speed Sheet Forming Line
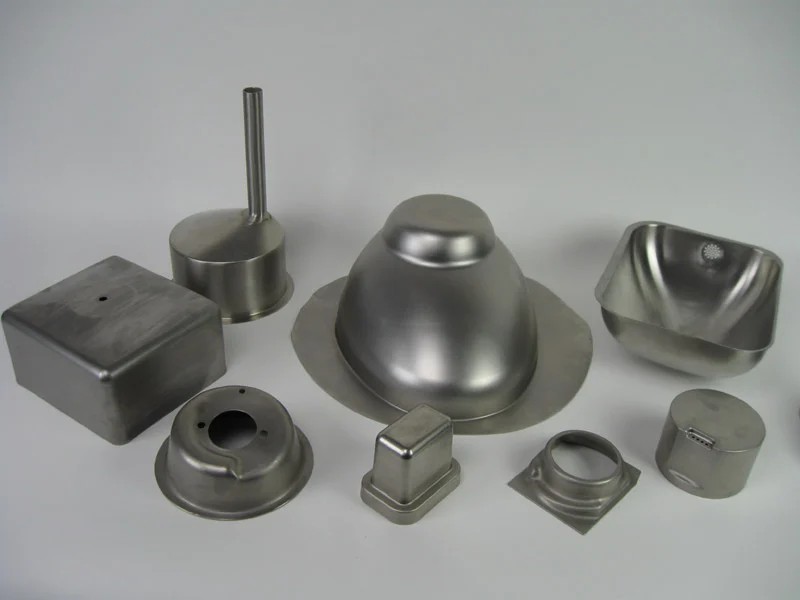
A High-Speed Sheet Forming Line is a specialized automated manufacturing system designed to process sheet metal at high production speeds while maintaining precision and quality. These systems are typically used in industries where large quantities of parts need to be produced efficiently, such as in automotive, aerospace, electronics, and appliance manufacturing. The high-speed sheet forming line integrates advanced automation, robotics, and precision forming technologies to handle the challenges of producing parts quickly without compromising on accuracy or material integrity.
Key Features and Components of a High-Speed Sheet Forming Line:
- Material Handling and Feeding: The first step in a high-speed sheet forming line is material handling, which involves loading coils or sheets of metal into the production system. High-speed feeding systems ensure that the material is fed accurately and consistently to the forming equipment. Coil unwinders or uncoilers are used to feed metal sheets into the line, while straighteners ensure that the metal is flat and free of any coils or curves that could affect the forming process.
- Blanking and Cutting: Once the metal is positioned, it may need to be cut into blanks or pre-formed pieces. Blanking presses or laser cutting systems are employed to quickly and accurately cut the material into the desired size and shape. High-speed cutting technologies are critical for minimizing the time spent on this process while maintaining edge quality and precision. These cutting systems are typically automated, allowing for quick adjustments when changing from one part design to another.
- Forming Processes: The heart of a high-speed sheet forming line is the forming press, where the blanked or pre-cut metal pieces are shaped into the final part. The type of forming press used can vary, but common ones include:
- Mechanical presses for high-speed stamping or punching applications.
- Hydraulic presses for more intricate or deep-drawn parts that require significant force.
- Servo-driven presses for more precision and flexibility, particularly when dealing with a variety of part shapes and sizes. These presses offer quick response times and fine control over parameters such as stroke length, speed, and force, allowing for higher production rates with minimal setup time.
- Progressive dies can be integrated into the press for continuous shaping, enabling the production of multiple parts simultaneously in a single cycle, which enhances speed.
- Automation and Robotics: Automation is essential for maximizing throughput in a high-speed sheet forming line. Robotic arms handle material loading, unloading, and transfer between machines. These robots are equipped with advanced vision systems and sensors that enable them to pick up parts, inspect them for quality, and place them in the next stage of production. Robotic systems can also conduct secondary operations such as deburring, trimming, or inserting additional components into the parts being produced.
- In-Process Quality Control: Maintaining high product quality at high speeds is a major challenge, but advanced in-process quality control systems help ensure consistency. Automated inspection systems using vision systems, laser scanners, and cameras are used to monitor the parts at various stages of the production process. These systems can detect dimensional errors, surface defects, or other issues that might affect part performance. When a defect is detected, the system can automatically reject the part or trigger adjustments in the production process to correct the issue.
- Secondary Operations: After the metal is formed, parts may undergo additional processes to refine their shapes or add features. These processes can include trimming, embossing, hole punching, and bending. Many high-speed sheet forming lines are equipped with automated systems to perform these secondary operations without interrupting the overall production flow. For example, parts may be loaded into a separate trimming press or automated robotic station where excess material is removed, or holes are punched for mounting or assembly.
- Part Handling and Sorting: After forming, parts must be sorted, stacked, or prepared for the next stage of the production process or shipment. High-speed sorting systems, often powered by robots or conveyors, can quickly organize parts based on size, shape, or any other required criteria. The ability to quickly handle and organize parts is essential for maintaining the fast pace of production.
- Energy Efficiency: Since high-speed sheet forming lines often operate at continuous, rapid speeds, energy efficiency becomes a key consideration. Modern lines incorporate energy-saving technologies such as servo-driven motors and regenerative braking systems to capture and reuse energy during operations, reducing overall energy consumption. Additionally, efficient cooling systems may be integrated into the press and forming equipment to prevent overheating and ensure consistent performance.
- Customization and Flexibility: High-speed sheet forming lines are often designed to handle a wide range of part sizes, shapes, and materials. Flexible tooling and quick-change systems allow manufacturers to switch between different part designs with minimal downtime. These systems enable high-speed lines to accommodate both small batches of custom parts and large production runs of standardized parts.
- Data Integration and Analytics: Modern high-speed sheet forming lines are increasingly connected to data networks that allow for continuous monitoring of machine performance and production output. Data analytics is used to track and optimize production metrics such as cycle times, defect rates, and machine efficiency. This data can be used to make real-time adjustments to the line, improving speed and reducing downtime. Predictive maintenance is another benefit, as data analysis can predict when a machine part might fail, allowing for timely repairs and minimizing production stoppages.
Benefits of High-Speed Sheet Forming Lines:
- Increased Productivity: The ability to produce a high volume of parts quickly while maintaining consistency in quality is a key advantage. High-speed sheet forming lines can produce parts much faster than traditional manual methods or slower, less automated systems.
- Cost Efficiency: Automated systems, optimized for speed and efficiency, reduce labor costs and minimize material waste. High-speed lines can process materials with precision, ensuring that each part is produced with minimal scrap.
- High-Quality Parts: The use of automated inspection and precise forming technologies ensures that parts are produced to the highest quality standards. In-process monitoring allows manufacturers to detect and correct any potential issues before they affect the final product.
- Flexibility: While high-speed forming lines are optimized for large-volume production, many can be adjusted to handle a variety of part sizes and shapes, providing manufacturers with flexibility to respond to changing demands or new product designs.
- Reduced Lead Times: With faster processing times, manufacturers can reduce lead times from order to delivery, improving customer satisfaction and allowing companies to be more competitive in the market.
- Improved Safety: The integration of robots and automation in high-speed sheet forming lines reduces the need for human workers to interact with dangerous machinery, improving workplace safety. Automated systems are equipped with safety sensors and features that prevent accidents or injuries.
Applications:
- Automotive Industry: High-speed sheet forming lines are widely used to manufacture body panels, chassis components, and other structural parts for automobiles. The automotive sector benefits from the speed and flexibility of these systems, which can handle high-volume production while meeting tight tolerance requirements.
- Aerospace Industry: The aerospace sector requires high-precision parts made from lightweight metals such as aluminum or titanium. High-speed sheet forming lines are used to produce structural components, aircraft panels, and other parts that need to meet rigorous standards for quality and performance.
- Appliance Manufacturing: Household appliances such as washing machines, refrigerators, and microwaves often require sheet metal parts, which can be produced efficiently using high-speed forming lines. These systems are capable of handling the large volumes and high variety of parts needed in this industry.
- Electronics and Consumer Goods: Sheet metal parts are also used in electronics and consumer goods manufacturing. High-speed sheet forming lines can produce enclosures, chassis, and other components required for products like computers, televisions, and mobile devices.
In conclusion, a high-speed sheet forming line is an essential tool for industries that require the fast, efficient production of high-quality metal parts. These lines are optimized for maximum speed, precision, and automation, helping manufacturers meet the demands of high-volume production while reducing costs and maintaining product integrity. With ongoing advancements in automation, robotics, and data analytics, high-speed sheet forming lines will continue to evolve and play a critical role in modern manufacturing.
A high-speed sheet forming line offers significant advantages to industries that require rapid and efficient production of sheet metal parts. By integrating advanced technologies such as automation, robotics, and precision-forming equipment, these systems are designed to meet the high demands of industries like automotive, aerospace, and electronics, where large volumes of parts need to be produced in a short amount of time without sacrificing quality. The production process begins with the handling of raw materials, where coils of metal are fed into the system, straightened, and pre-cut to the appropriate dimensions for the forming process. This ensures that the metal is in the ideal shape and condition for the next steps.
Once the metal is properly positioned, it is passed through a series of processes, including cutting, blanking, and stamping. High-speed cutting and blanking technologies are employed to quickly prepare the material for forming, often using laser cutting or advanced stamping presses that can rapidly process a variety of metal types and thicknesses. The forming presses, which are the core of the system, then shape the metal into the desired part. These presses can operate at incredibly high speeds while maintaining the accuracy required to meet tight specifications. Whether using mechanical, hydraulic, or servo-driven presses, these systems can handle large production runs efficiently, minimizing downtime and maximizing throughput.
Automation plays a critical role in maintaining the speed and efficiency of these lines. Robotic systems equipped with advanced sensors and vision technology handle the loading and unloading of materials, sorting of finished parts, and even some secondary operations such as trimming or hole-punching. This reduces the need for manual labor, cuts down on errors, and ensures that the production process remains continuous. Robotics also enhances flexibility, allowing for quick changes in part design or production run lengths without causing significant disruptions in the workflow. In parallel with robotics, in-process quality control systems monitor the forming process and check for defects in real-time, ensuring that only parts meeting the desired quality standards move through the production line.
To maintain the high speed of operation, high-speed sheet forming lines are designed for quick changeovers. Tools and dies can be changed rapidly to accommodate different parts, and automated adjustment systems can modify parameters on the fly, reducing the time spent on setup. Additionally, the use of predictive maintenance powered by data analytics helps to ensure that any potential issues with the machinery are detected early, allowing for proactive maintenance and minimizing unplanned downtime.
Energy efficiency is another key consideration in the design of high-speed sheet forming lines. As these systems operate continuously, energy consumption can be significant. To mitigate this, modern lines incorporate features like servo-driven motors, regenerative braking systems, and energy-efficient presses, all of which help reduce overall energy consumption while maintaining optimal performance. Cooling systems are also critical for ensuring that the equipment remains at the right operating temperature, preventing overheating and maintaining production speeds.
The integration of data analytics and cloud-based systems enhances the functionality of high-speed sheet forming lines by providing manufacturers with real-time insights into production performance. This data allows operators to track machine efficiency, monitor the quality of parts being produced, and identify bottlenecks or inefficiencies in the system. By using this data, manufacturers can optimize their production schedules, reduce waste, and ensure that the line operates at maximum efficiency.
A high-speed sheet forming line is also built with future-proofing in mind. As material types evolve and industry demands change, the line can be adapted to accommodate new processes and materials. Whether it’s incorporating hybrid technologies such as 3D printing alongside traditional forming techniques or adjusting to new metal alloys, the flexibility of these systems allows manufacturers to remain competitive in an ever-changing market.
In summary, the high-speed sheet forming line is a sophisticated and highly automated production system that enables manufacturers to produce large volumes of sheet metal parts quickly and accurately. By combining precision-forming technology, robotics, automated quality control, and advanced data analytics, these systems can meet the growing demand for high-quality parts in industries where speed, efficiency, and precision are critical. With advancements in technology and materials, the future of high-speed sheet forming lines will continue to push the boundaries of manufacturing, driving innovation in speed, sustainability, and product quality.
As high-speed sheet forming lines continue to evolve, the incorporation of Industry 4.0 principles will further enhance their capabilities. Industry 4.0, which emphasizes the integration of smart technologies such as the Internet of Things (IoT), artificial intelligence (AI), and machine learning (ML), is set to transform the manufacturing process. In a high-speed sheet forming line, IoT-enabled devices and sensors embedded throughout the system will collect and transmit data in real-time. This data can include information on machine performance, material usage, environmental conditions, and even part quality. By leveraging this data, manufacturers can gain a deeper understanding of their production processes, leading to more informed decision-making, predictive maintenance, and better optimization.
AI and machine learning algorithms will be key to analyzing vast amounts of production data. These technologies can identify patterns and trends that would be impossible for humans to detect, allowing manufacturers to predict and prevent potential failures before they occur. For example, machine learning algorithms could predict when a forming press is likely to experience wear and tear based on its usage patterns, enabling the scheduling of maintenance before a breakdown happens. Additionally, AI can help optimize the entire production process by dynamically adjusting machine parameters to minimize defects and improve throughput based on real-time feedback.
The rise of digital twins will also play a significant role in high-speed sheet forming lines. A digital twin is a virtual replica of a physical asset, such as a forming press or the entire production line. By simulating and monitoring the performance of machines and processes in a virtual environment, manufacturers can test different scenarios, identify inefficiencies, and make adjustments without disrupting actual production. This technology allows manufacturers to optimize processes before implementing changes on the shop floor, reducing the risk of errors and increasing overall efficiency.
The integration of collaborative robots (cobots) alongside traditional robotic systems will increase flexibility and safety in high-speed sheet forming lines. Cobots are designed to work alongside human operators, providing support with tasks such as material handling, quality inspection, and assembly. These robots are equipped with sensors that allow them to interact safely with humans, creating a collaborative environment where humans and robots work together to improve productivity. This human-robot collaboration is particularly valuable in high-speed production lines, where flexibility and adaptability are essential for maintaining high levels of output while ensuring worker safety.
Advanced simulation technologies will also contribute to the development of high-speed sheet forming lines. By using simulation software to model the entire production process, from material handling to final inspection, manufacturers can predict potential issues and fine-tune processes before the production line is even built. These simulations help identify potential bottlenecks, optimize tool and die design, and ensure that the entire system operates smoothly. Simulation can also be used to model different types of materials and part designs, helping manufacturers evaluate the impact of changes to the production process and make data-driven decisions.
Sustainability will be a critical focus for the future of high-speed sheet forming lines. As environmental regulations become more stringent and companies aim to reduce their carbon footprint, these lines will need to adopt greener practices. Energy-efficient motors, regenerative braking, and eco-friendly lubricants are just a few examples of how sustainability can be incorporated into the production process. Moreover, by implementing material recycling systems, manufacturers can reduce scrap material and reuse metal that would otherwise be wasted. Closed-loop systems, where waste material is collected, processed, and returned to the forming process, will become more common as manufacturers strive for greater sustainability in their operations.
As the demand for customization and shorter lead times grows, high-speed sheet forming lines will continue to evolve in their ability to accommodate a wide variety of part designs. Flexible tooling and quick-change systems will be essential in allowing manufacturers to switch between different part configurations without significant downtime. Additionally, the rise of additive manufacturing (3D printing) integrated with traditional forming processes will allow for more complex part geometries that were previously difficult or impossible to achieve. By combining subtractive and additive methods, manufacturers can produce highly specialized components with minimal material waste, further enhancing the versatility of high-speed sheet forming lines.
Lastly, the globalization of supply chains and the need for real-time monitoring across geographically dispersed manufacturing sites will push the adoption of cloud-based solutions and collaborative platforms. These platforms will allow manufacturers to remotely monitor their high-speed sheet forming lines, providing access to real-time production data, performance metrics, and maintenance needs from anywhere in the world. This level of connectivity and visibility will enable manufacturers to quickly respond to supply chain disruptions, manage production schedules across multiple locations, and maintain a high level of operational efficiency.
In conclusion, high-speed sheet forming lines are poised to continue evolving with the integration of advanced technologies such as AI, IoT, robotics, digital twins, and simulation. These innovations will drive higher levels of productivity, quality, and flexibility in manufacturing, helping companies meet the growing demands of industries such as automotive, aerospace, and electronics. With a focus on sustainability, customization, and global collaboration, the future of high-speed sheet forming lines will not only increase the speed of production but also enhance the overall efficiency and adaptability of manufacturing operations.
As the high-speed sheet forming lines continue to evolve, manufacturers will face increasing pressure to adapt to changing consumer demands and market dynamics. One significant trend that will shape the future of these systems is the demand for smaller, more complex parts with shorter lead times. With industries becoming more specialized and product designs becoming more intricate, high-speed sheet forming lines must be capable of handling an ever-expanding range of materials, thicknesses, and geometries. This requires an ongoing investment in both hardware and software that can accommodate such complexity while still maintaining the efficiency and speed that these lines are known for.
One way high-speed forming lines will meet these challenges is through the adoption of multi-material forming technologies. Modern production processes are increasingly using combinations of materials, such as metals and composites, to create parts that are both lightweight and durable. High-speed sheet forming lines will need to be equipped with technology that can handle a variety of material combinations, including hybrid materials, while ensuring that each material is formed with the precision required for its specific properties. This will necessitate more advanced tooling, material handling systems, and process monitoring to ensure that each material is treated optimally.
Moreover, the rise of customized, small-batch production will require high-speed sheet forming lines to become more adaptable. Historically, high-speed lines were used primarily for mass production of standardized parts. However, as demand for more personalized products increases, manufacturers will need to adopt flexible manufacturing systems that can quickly shift between small-batch runs of customized parts. This could involve the use of modular tooling systems that can be easily reconfigured for different product designs or the integration of on-demand manufacturing capabilities that allow for rapid prototyping and adjustment of the production line without significant downtime.
The integration of augmented reality (AR) and virtual reality (VR) into the design and operation of high-speed sheet forming lines will also become more widespread. AR and VR technologies will be used for training operators, monitoring performance, and even conducting virtual maintenance checks. For instance, operators could use AR headsets to access real-time data and guidance directly on the shop floor, allowing them to make quick adjustments or diagnose problems without needing to leave the production line. Additionally, VR simulations could be used during the design phase to visualize the entire production process, test new designs, and optimize workflows before physical implementation.
Furthermore, supply chain integration will play a critical role in the future of high-speed sheet forming lines. As companies become more reliant on global supply chains, the need for real-time communication and coordination across suppliers, manufacturers, and logistics providers will increase. High-speed sheet forming lines will be part of a broader ecosystem that is interconnected through cloud-based platforms. These platforms will enable seamless communication between the production line and the rest of the supply chain, ensuring that materials are available just in time for production and that parts are delivered to customers with minimal delays. This integration will enable manufacturers to respond more quickly to changes in demand and reduce the lead times for their products.
In addition to supply chain integration, traceability will become more important in high-speed sheet forming lines. With increasing concerns over product safety, quality, and compliance with regulatory standards, manufacturers will need to ensure that every part produced on the line is traceable. This can be achieved through the use of RFID tags, QR codes, and blockchain technology, which will track each part’s journey from raw material to final product. This level of traceability will not only improve quality control but also enhance transparency in the supply chain, helping manufacturers meet compliance requirements and provide consumers with greater confidence in the products they purchase.
Another significant development will be the continued push toward zero-defect manufacturing. As the technology for high-speed sheet forming lines advances, manufacturers will aim to eliminate defects entirely through automation and in-process quality control. The implementation of advanced sensor networks and machine vision systems will allow for real-time detection of micro-defects that could otherwise go unnoticed. These systems can identify issues as soon as they arise, allowing the production line to be adjusted immediately to correct any problems, thus minimizing scrap and ensuring that every part produced meets stringent quality standards. The ultimate goal of zero-defect manufacturing is not just to improve product quality but also to minimize waste and maximize resource efficiency.
As high-speed sheet forming lines become more advanced, there will also be a growing focus on human-robot collaboration (cobots). In the past, robots were typically used in isolation, but future systems will involve more dynamic interactions between humans and robots. Cobots will assist operators in a range of tasks, from loading and unloading materials to assembling components, while allowing for safe and efficient collaboration. These robots are designed to work closely with human workers, responding to their actions and adjusting in real-time to help with tasks that may require more dexterity or decision-making. This collaboration will increase the overall efficiency of the production line while reducing the physical strain on human operators.
In terms of sustainability, there will be greater efforts to minimize the environmental impact of high-speed sheet forming lines. Not only will manufacturers focus on reducing energy consumption and material waste, but there will also be an increased emphasis on using sustainable materials in production. As the world moves towards more environmentally friendly solutions, manufacturers will explore alternatives to traditional metals, such as recycled materials or bio-based alloys, that can be processed efficiently on high-speed forming lines. In addition, carbon footprint tracking and energy management systems will become integral parts of the production process, helping manufacturers to monitor and reduce the environmental impact of their operations.
Lastly, the integration of advanced AI-based optimization tools will revolutionize the way production lines are managed. These AI systems will be able to adjust production schedules, allocate resources, and even optimize machine settings in real time based on data inputs from the production process, supply chain, and market demand. This will not only ensure that the high-speed sheet forming line operates at peak efficiency but will also enable manufacturers to achieve greater flexibility and adaptability in an increasingly fast-paced and volatile market environment.
In conclusion, the future of high-speed sheet forming lines will be characterized by greater automation, flexibility, and intelligence. As industries continue to demand faster, more customized, and higher-quality products, high-speed sheet forming lines will evolve to meet these needs through technological advancements such as AI, robotics, digital twins, and data analytics. With a continued focus on sustainability, efficiency, and collaboration, these lines will help shape the future of manufacturing by enabling more responsive, precise, and eco-friendly production processes. Manufacturers will need to stay ahead of these trends to remain competitive and meet the ever-changing demands of the market.
Automatic Press Line for Sheet Metal
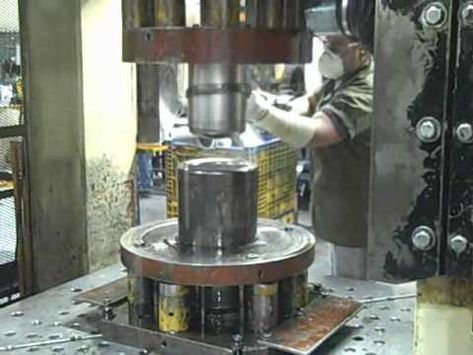
An Automatic Press Line for Sheet Metal is a sophisticated manufacturing system designed for the efficient, high-speed processing of metal sheets to create parts through processes like stamping, blanking, bending, or deep drawing. These press lines integrate various technologies to automate each step of the production process, reducing the need for manual labor, improving part consistency, and increasing throughput. Typically used in industries such as automotive, aerospace, and electronics, an automatic press line can handle high-volume production runs, ensure precise part quality, and reduce operational costs.
Key Features of an Automatic Press Line:
- Raw Material Handling: The process begins with the handling of raw materials, typically coils or sheets of metal. These are fed into the system by an uncoiler, which unwinds the coils, followed by a leveler or straightener to remove any residual curvature or distortions. The metal is then sheared into blanks (pre-cut sheets of metal) that are sized appropriately for the forming process.
- Automatic Stamping or Pressing: The heart of the automatic press line is the press machine, which is responsible for shaping the sheet metal. These presses can be mechanical (using flywheels and cams to deliver power) or hydraulic (using hydraulic force for more controlled and flexible operations). The press may also be servo-driven, providing even more precision and control.
- Stamping presses are commonly used for making parts with shallow depth, such as brackets, panels, or covers.
- Deep drawing presses are used for parts requiring greater depth, such as automotive body panels or cookware.
- The press can operate at high speeds, ensuring that parts are formed quickly and efficiently. Some automatic press lines are capable of producing thousands of parts per hour.
- Tooling: The presses are equipped with dies (tooling used to shape the sheet metal) tailored to specific part designs. In high-volume applications, progressive dies are often used, which allow multiple operations—such as punching, blanking, and bending—to occur in a single pass through the press. Tooling can be easily swapped out or adjusted for different parts, improving flexibility and reducing downtime during production changes.
- Automation and Robotics: Robotic systems are integrated into the press line for material handling, including part loading, unloading, and transfer between operations. Robots may also assist in sorting finished parts or performing secondary operations, such as trimming or hole-punching. This automation not only increases production speed but also reduces human error and ensures higher safety standards for operators.
- In-Process Quality Control: Automated vision systems and sensors are used to monitor the quality of parts during the forming process. These systems check for defects, such as dimensional inaccuracies or surface imperfections, and can provide real-time feedback to adjust the press parameters or stop production to correct any issues before defective parts are produced. Laser measurement systems can be integrated to measure part thickness, shape, and dimensional accuracy, ensuring that all parts meet the required specifications.
- Cutting and Trimming: After the metal sheet has been shaped, it often requires additional operations, such as cutting, trimming, or punching, to remove excess material or add holes and slots to the part. These secondary operations are automated to ensure consistent quality and speed. Laser cutting or shear cutting can be employed to perform these tasks with high precision.
- Part Handling and Transfer Systems: Once formed, the metal parts are transferred to the next stage of the production process, such as assembly or packaging. Automated conveyors or robotic arms are used to move parts efficiently through the press line. The system is often designed to handle parts with various shapes and sizes, allowing for flexibility in the types of products it can produce.
- Quick Die Change (QDC): High-speed production often requires rapid changeovers to accommodate different part designs or sizes. Automatic press lines may incorporate quick die change systems, enabling operators to swap dies quickly and easily. This minimizes downtime, enhances productivity, and supports the production of small-batch or customized runs.
- Energy Efficiency: With rising energy costs, manufacturers are increasingly focused on reducing energy consumption in their press lines. Technologies such as servo motors in press machines provide energy savings by reducing the power required during idle times. Additionally, energy recovery systems, such as regenerative braking, can store and reuse energy from the press, further optimizing energy consumption.
- Data Analytics and Remote Monitoring: Modern automatic press lines integrate data analytics platforms that collect performance data from all aspects of the press line. Sensors and IoT devices track parameters like press speed, part quality, equipment wear, and energy usage. This data is analyzed in real-time to optimize the press line’s performance, predict maintenance needs, and ensure continuous improvement. Manufacturers can also remotely monitor the press line’s performance from any location, enabling quick responses to potential issues and improving operational management.
- Maintenance and Predictive Maintenance: Maintenance is a critical aspect of keeping an automatic press line running efficiently. Many systems include predictive maintenance capabilities, utilizing sensors and data analytics to monitor the condition of key components (like dies, motors, and hydraulic systems). By analyzing patterns of wear and tear, manufacturers can predict when maintenance is needed and prevent unexpected downtime, ensuring continuous and efficient operation.
- End-of-Line Operations: At the end of the press line, additional automated systems can perform tasks like part stacking, sorting, and packaging. Parts may be packaged automatically into boxes or bins for delivery to downstream operations or to customers, ensuring a smooth and efficient end-to-end production process.
Benefits of an Automatic Press Line for Sheet Metal:
- Increased Efficiency and Throughput: The combination of automation, high-speed presses, and robotics enables higher production rates with consistent part quality.
- Reduced Labor Costs: By automating most of the processes, these systems significantly reduce the need for manual labor, resulting in lower operational costs.
- Improved Quality and Precision: Automated quality control, real-time feedback, and precision tooling ensure that parts are made to exact specifications with minimal defects.
- Flexibility in Production: With quick die change capabilities and automated tooling adjustments, automatic press lines can quickly switch between different part designs, making them suitable for a wide range of products.
- Cost-Effective for High-Volume Production: While the initial investment may be substantial, the ability to run at high speeds and with minimal downtime makes the automatic press line cost-effective for large-scale, high-volume production.
- Enhanced Safety: Automation reduces the risks associated with human operators interacting with heavy machinery, enhancing workplace safety.
Applications of an Automatic Press Line:
- Automotive Industry: High-speed press lines are commonly used to produce body panels, chassis components, brackets, and other parts.
- Aerospace Industry: Press lines form lightweight yet durable components for aircraft, including structural panels and parts for the fuselage and wings.
- Consumer Electronics: High-precision metal parts for mobile devices, appliances, and other consumer goods are produced using automatic press lines.
- Appliance Manufacturing: Parts for appliances such as refrigerators, washing machines, and ovens are made using press lines.
- Medical Equipment: Some press lines are designed for the production of parts used in medical devices, where precision and quality control are crucial.
Conclusion:
An automatic press line for sheet metal is a highly efficient and cost-effective solution for producing metal parts at scale. With automation, high-speed presses, and integrated robotics, these systems allow manufacturers to produce parts quickly and accurately while minimizing labor costs and improving part quality. As technology continues to advance, we can expect further integration of AI, IoT, and data analytics, enabling even greater optimization of these systems and further reducing waste and downtime. Whether for high-volume mass production or small-batch runs, an automatic press line offers a powerful tool for manufacturers across a wide range of industries.
An automatic press line for sheet metal is designed to streamline and optimize the entire metal forming process, from raw material handling to the production of finished parts. By automating each step, it minimizes human intervention, reduces operational costs, and boosts production efficiency, making it ideal for high-volume manufacturing environments. The line begins by feeding raw material, often in coil form, through uncoilers and straighteners that ensure the sheet is properly aligned and free from any warping. This raw material is then pre-cut into blanks of the required size, ready for the press. The press itself, whether mechanical, hydraulic, or servo-driven, applies the necessary force to shape the metal into the desired part using dies.
Automation plays a significant role in the efficiency of the press line, especially with the integration of robotic arms or conveyors that handle materials, unload parts, or transfer items between different stages of production. These robotic systems ensure that production continues uninterrupted, significantly reducing the time spent manually moving components between stations and allowing for faster changeovers. Sensors and vision systems are integrated into the line to continuously monitor part quality in real-time. These technologies allow for immediate detection of defects such as dimensional inconsistencies, scratches, or irregular shapes, enabling prompt corrective actions.
The tooling used in the press is crucial for shaping the sheet metal with precision. Dies, which are customized for specific parts, ensure that the metal is formed accurately in each pass. These dies can be progressive, allowing multiple forming steps in a single operation, which improves throughput and reduces the number of processes required. The incorporation of quick die change systems further enhances the system’s efficiency by reducing the downtime needed when switching between part designs or sizes.
As the parts move through the press line, secondary processes like trimming, punching, and cutting are carried out to remove excess material and add necessary features such as holes or slots. These operations are also automated, with technologies like laser cutting and shear cutting being commonly employed for their speed and precision. Once the parts are fully formed and trimmed, they are transferred to the next phase, whether for assembly, packaging, or further processing. Conveyors or robotic arms facilitate the efficient handling and sorting of parts, ensuring that they move seamlessly to the next stage.
An advanced automatic press line also benefits from in-depth data analytics and real-time monitoring. Sensors connected to IoT devices continuously gather information about every part of the production process, including press speed, material usage, energy consumption, and part quality. This data is analyzed to optimize performance, predict when maintenance is needed, and even suggest improvements to the production process. Cloud-based platforms enable operators to monitor the press line remotely, offering greater flexibility and control. Predictive maintenance systems, which use data gathered from sensors, can anticipate potential issues before they cause downtime, ensuring the press line runs smoothly without unexpected interruptions.
As sustainability becomes increasingly important, many manufacturers are integrating energy-efficient technologies into their press lines, such as servo motors, regenerative braking, and optimized power usage during idle times. These efforts help reduce overall energy consumption and lower the carbon footprint of the production process. Additionally, material waste is minimized through precise cutting and forming techniques, and recycling systems are often in place to handle scrap metal, turning it back into usable material for future production runs.
The automatic press line is not only a tool for efficiency but also for quality control. By incorporating real-time inspection systems and continuous feedback mechanisms, the line ensures that every part produced meets the necessary standards. The ability to trace each part back to its origin using barcodes or RFID tags adds an extra layer of traceability, which is especially important in industries with strict regulatory requirements, like automotive or aerospace.
In the future, the role of artificial intelligence and machine learning will further transform automatic press lines. These technologies will be used to analyze production data in real-time, adjusting machine parameters to optimize output, detect emerging problems, and even predict trends in demand. AI-driven predictive maintenance will become even more accurate, identifying subtle patterns in machine performance that humans may not be able to detect, leading to more proactive and effective maintenance schedules.
In addition, the push for customization and flexibility in production will lead to the development of multi-functional presses that can handle a wider variety of parts and materials, switching between operations with minimal downtime. Automated lines will be able to manage shorter production runs and customized orders without sacrificing the speed and efficiency typically associated with high-volume production. With the integration of advanced tools like 3D printing for prototyping and hybrid manufacturing systems, automatic press lines will become more versatile, accommodating an even broader range of part designs and applications.
Ultimately, an automatic press line for sheet metal is more than just an assembly line. It’s an integrated system that combines cutting-edge automation, robotics, data analytics, and smart technologies to create a highly efficient, cost-effective, and flexible manufacturing solution. As industries continue to demand faster, more accurate, and customizable products, the automatic press line will remain a critical component of modern manufacturing, continually evolving to meet the challenges of the future.
The evolution of automatic press lines for sheet metal will be heavily influenced by several key technological advancements and emerging trends in manufacturing. The increased integration of artificial intelligence (AI) and machine learning (ML) will allow for greater automation and intelligence within the press lines. AI can help optimize the press parameters dynamically in response to changing material properties, part complexity, and environmental conditions. For instance, AI algorithms can analyze production data in real-time, adjusting press forces, speeds, and temperatures to ensure optimal part quality and minimize defects.
With machine learning, the system will become more adaptable over time, learning from past production runs to identify patterns in machine performance and part quality. By doing so, the press line can not only detect issues but also predict potential failures before they occur, allowing for timely interventions and reducing the need for reactive maintenance. This will significantly reduce unplanned downtime and contribute to a more sustainable and cost-effective operation.
Robotic integration will continue to advance, leading to more collaborative robots (cobots) that work alongside human operators on the press line. These cobots will be able to handle a broader range of tasks, from loading and unloading parts to performing secondary operations like trimming or deburring. With sensor fusion and real-time feedback loops, cobots will be able to adapt to changes in the production environment, making them incredibly versatile and efficient. These robots will ensure smoother transitions between production batches, especially in industries where product designs are constantly changing or where customization is in demand.
Another major area of development is in augmented reality (AR) and virtual reality (VR). These technologies will be used not only for operator training but also for real-time troubleshooting and machine setup. For example, an AR headset could provide operators with step-by-step instructions or visual overlays, allowing them to quickly resolve issues or change tooling. This would be particularly useful in high-speed production environments where speed and accuracy are critical. VR could also be used to simulate production runs, allowing manufacturers to optimize the press line configuration before initiating production, reducing the risk of costly errors.
The growing need for sustainability and reduced environmental impact is driving the development of more energy-efficient and eco-friendly press lines. Manufacturers are increasingly adopting green practices and integrating sustainable materials into their production lines. The focus is on reducing energy consumption through the use of servo-electric drives, which are more energy-efficient than traditional hydraulic or mechanical presses, as well as incorporating energy recovery systems that can capture excess energy during the press operation and repurpose it for other tasks. Additionally, recycling systems for scrap metal and the use of biodegradable lubricants are becoming more prevalent, aligning with the industry’s goal of minimizing waste and reducing its carbon footprint.
The trend toward customization is becoming more pronounced, especially with the rise of small-batch production and the need for rapid prototyping. Automatic press lines will evolve to accommodate shorter production runs without compromising speed or efficiency. This will be achieved through the development of flexible press lines that can easily switch between different part designs and materials without significant downtime. The press lines will integrate modular tooling systems that can be quickly reconfigured for different jobs, enabling faster product changes. 3D printing technology may even play a role in the future, enabling the rapid creation of complex parts or tooling inserts, which can be used on press lines to produce unique or highly customized products.
As Industry 4.0 continues to transform the manufacturing landscape, IoT (Internet of Things) devices will become even more ubiquitous within automatic press lines. These devices will provide real-time data on machine performance, part quality, and environmental conditions. This data can be collected and analyzed to improve decision-making, optimize production processes, and enable predictive maintenance. The integration of cloud-based platforms will also allow manufacturers to monitor and control press lines remotely, improving flexibility and response time. Big data analytics will be used to identify trends, improve efficiency, and even assist in supply chain management, ensuring that materials are delivered just in time to keep the press line running smoothly.
Additive manufacturing may also play a role in the future of automatic press lines, particularly in the creation of hybrid products that combine traditional sheet metal forming with 3D-printed parts. This could be particularly useful in industries where lightweight, high-strength materials are needed, such as aerospace or automotive manufacturing. By combining additive and subtractive technologies, manufacturers could create complex, custom parts that would be difficult or impossible to produce with conventional methods.
The future of quality control in automatic press lines will also see significant advancements. The integration of machine vision systems will allow for more accurate and faster inspections of parts during production. These systems will not only check for common defects such as cracks, wrinkles, or dimensional errors but will also perform real-time analysis of surface finish and other subtle features that are difficult to detect manually. With the help of AI-powered image recognition, the press line will be able to conduct high-precision inspections at speeds far beyond what a human operator could achieve.
In addition to improving part quality, traceability will become more critical. With the increase in demand for custom parts and more stringent regulatory requirements, manufacturers will need to be able to trace every part from raw material to finished product. This will be facilitated by the integration of RFID tags, barcodes, or blockchain technology, which can securely record every stage of a part’s journey through the production process. This ensures compliance, enhances product integrity, and improves the ability to recall parts in case of defects.
Finally, the role of cybersecurity in automatic press lines cannot be overstated. As these systems become more interconnected and reliant on digital technologies, they also become more vulnerable to cyber threats. Manufacturers will need to implement robust cybersecurity measures to protect sensitive production data, safeguard intellectual property, and prevent disruptions to the production process. Regular updates, secure communication protocols, and continuous monitoring will be necessary to defend against cyberattacks and ensure the resilience of these automated systems.
In conclusion, the future of automatic press lines for sheet metal will be characterized by greater automation, intelligence, and flexibility. By integrating advanced technologies such as AI, machine learning, robotics, AR/VR, and IoT, these lines will be capable of handling more complex, customized parts with greater efficiency and higher quality. The push for sustainability, energy efficiency, and reduced environmental impact will drive the adoption of eco-friendly practices, while Industry 4.0 technologies will provide manufacturers with greater data insights and remote capabilities. As the demand for high-quality, customizable, and environmentally responsible products grows, the automatic press line will continue to evolve, becoming an even more critical component of modern manufacturing processes.
Sheet Metal Forming Assembly Line
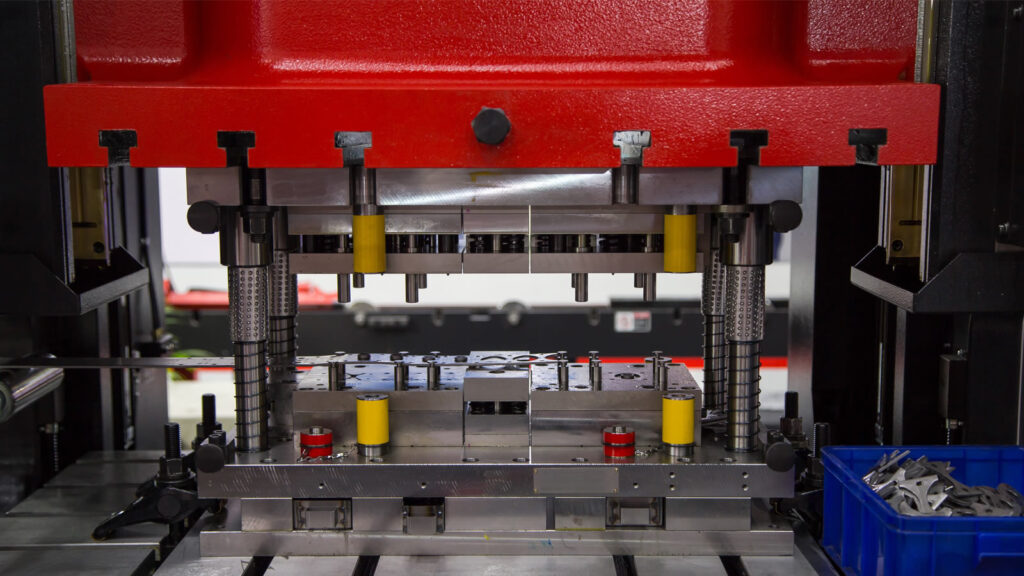
A Sheet Metal Forming Assembly Line refers to a highly automated manufacturing system used to process sheet metal into various shapes and components through a series of forming operations, followed by assembly. This type of line is commonly employed in industries such as automotive, aerospace, electronics, and appliance manufacturing, where precision and efficiency are crucial for producing high-quality metal parts in large volumes.
Key Features of a Sheet Metal Forming Assembly Line:
- Raw Material Handling: The process begins with the delivery of raw materials, typically in the form of metal coils or sheets. These materials are unwound, straightened, and cut to the desired size using uncoilers and levelers. The sheets are then prepped for the forming process.
- Sheet Metal Forming Operations: The core of the line consists of various sheet metal forming operations, which may include:
- Stamping: The sheet metal is pressed into molds (dies) to create parts with a variety of shapes, from simple components like brackets to complex body panels.
- Punching: Holes and slots are punched into the sheet metal for further processing or to add specific features like fastener holes.
- Bending: The sheet is bent into the desired angles and shapes, which is a common operation for forming parts like panels, frames, and brackets.
- Deep Drawing: This is used to form deeper, more complex shapes, such as automotive body panels or cooking pots, by pulling the sheet metal into a die cavity.
- Rolling: For cylindrical or curved components, the sheet metal can be passed through rollers to achieve the desired curvature.
- Tooling and Die Management: The forming processes rely on precise tooling and dies, which can be customized for specific part shapes. Progressive dies are often used in high-volume production to perform multiple operations in a single pass, improving throughput and reducing handling time. Die changeover systems (Quick Die Change, or QDC) allow the line to switch between different part designs with minimal downtime.
- Automation and Robotics: Robotic arms and automated conveyors play a critical role in handling materials, loading, unloading, and transferring parts between stations. This reduces manual labor and speeds up the entire assembly line. Robotic systems can be employed for various tasks such as part assembly, welding, screwing, and even inspection.
- Assembly Operations: After the forming process, the sheet metal parts move to the assembly stage. Here, various parts are brought together to form a final product. For instance, in the automotive industry, different sheet metal components like panels, frames, and brackets are welded, riveted, or fastened together. The assembly process can also include operations such as spot welding, riveting, laser welding, or screwing.
- In-Line Inspection and Quality Control: Quality control is integrated throughout the assembly line, with systems in place to detect defects during each stage of production. This can include visual inspection using machine vision systems, laser sensors, or ultrasonic testing to check for dimensional accuracy, surface defects, and part integrity. Automated inspection ensures that parts meet the required tolerances and quality standards.
- Part Transfer and Handling: Automated conveyors or robotic transfer systems are used to move parts between stations efficiently, minimizing handling time. The parts are transferred from one forming station to another, or from forming to assembly, with minimal human intervention, which improves speed and reduces risk of damage to the parts.
- Secondary Operations: Once the main forming and assembly processes are completed, secondary operations may be needed to finalize the product. These include trimming (removal of excess material), deburring (removal of sharp edges), and surface finishing (painting, coating, or polishing). These operations can be automated using robotic arms or other automated machinery to ensure consistency and precision.
- Packaging and Shipping: After final assembly, parts are packaged for shipment. Automated systems handle packaging, labeling, and sorting for shipping, ensuring that the final product is ready for delivery to the customer or next phase of production. This step is crucial in high-volume production lines, where efficiency and accuracy are paramount.
Benefits of a Sheet Metal Forming Assembly Line:
- Increased Productivity: The integration of automated material handling, forming, assembly, and inspection processes increases throughput, enabling the production of large volumes of parts in a shorter amount of time.
- Consistency and Precision: Automation ensures that each part is produced with high precision and uniformity, which is essential in industries requiring tight tolerances, like aerospace or automotive.
- Reduced Labor Costs: Automation reduces the need for manual labor, lowering operational costs and allowing human workers to focus on more complex tasks or supervisory roles.
- Flexibility: The line can be designed to handle various products and part types, especially if it includes quick changeover capabilities for tooling and dies, allowing manufacturers to produce different parts with minimal downtime.
- Reduced Waste: Advanced sensors and monitoring systems help to detect defects early in the process, reducing scrap and rework. Efficient material handling and use of energy-efficient machines also contribute to less waste.
- Improved Safety: By automating many dangerous tasks, such as heavy lifting or working with high-precision machinery, the risk of accidents is reduced, contributing to a safer work environment.
Applications of Sheet Metal Forming Assembly Lines:
- Automotive Manufacturing: Used for producing body panels, frame components, and other metal parts.
- Aerospace: Parts for aircraft structures, engine components, and interior fittings.
- Consumer Electronics: Housing and structural components for devices like smartphones, laptops, and other electronic equipment.
- Appliance Manufacturing: Parts for household appliances like refrigerators, washing machines, and ovens.
- Heavy Machinery: Structural components and frames for construction or mining equipment.
Future Trends in Sheet Metal Forming Assembly Lines:
- Smart Manufacturing and IoT Integration: The use of Internet of Things (IoT) sensors and smart systems allows for the continuous monitoring and analysis of production data, enabling predictive maintenance and real-time adjustments to optimize the line.
- Additive Manufacturing Integration: 3D printing could play a role in producing complex or customized sheet metal components that are then incorporated into traditional assembly lines.
- Advanced Robotics and AI: The continued advancement of artificial intelligence and robotics will further enhance the flexibility and precision of sheet metal forming and assembly. Robots may be able to handle increasingly complex tasks, including high-precision welding or part handling.
- Sustainability Initiatives: There will be a greater emphasis on energy-efficient machinery, material recycling, and waste reduction to make sheet metal forming and assembly processes more sustainable.
- Modular Design for Flexibility: As product demand continues to fluctuate, manufacturers will seek modular production lines that can be quickly reconfigured to handle different products, reducing downtime and increasing flexibility.
In conclusion, a sheet metal forming assembly line is a highly efficient and automated manufacturing solution that is critical for producing metal parts in high volumes with consistency and precision. By integrating cutting-edge technologies such as robotics, AI, and smart manufacturing systems, these lines are becoming more flexible, adaptable, and capable of meeting the demands of modern manufacturing industries.
A sheet metal forming assembly line is an advanced automated system designed to efficiently process and assemble sheet metal parts. It starts with the delivery of raw materials, typically in the form of metal coils or sheets, which are unwound and straightened to ensure the material is ready for forming. The metal is then cut to the desired size, often using uncoilers, levelers, and shear cutting machines. The forming process itself involves several techniques, including stamping, punching, bending, deep drawing, and rolling, depending on the shape and design of the final parts. These processes can be done using progressive dies, which perform multiple operations in a single pass, thereby improving throughput and reducing the number of manual handling steps.
Automation plays a crucial role in improving efficiency and precision within these lines. Robotic arms, conveyors, and other automated material handling systems move the parts from one stage to the next, minimizing human intervention and ensuring that the materials are handled swiftly and safely. Once the metal parts are formed, they often move to the assembly stage, where they are joined together using various techniques such as welding, riveting, or screwing. Automated robotic systems are often employed in this stage as well, performing complex tasks like spot welding, laser welding, or assembling parts with high precision.
In addition to forming and assembly, secondary operations such as trimming, deburring, and surface finishing are performed to ensure the parts meet quality standards. These steps can be automated using machines equipped with sensors and robotic arms to maintain accuracy and speed. Inspection systems, often integrated with machine vision and laser sensors, monitor parts for defects during every stage of production. These systems detect any dimensional inconsistencies, surface defects, or other issues early, reducing the need for rework and scrap material.
Once the final parts are assembled and inspected, they are moved to the packaging and shipping stage. Automated packaging systems are employed to wrap, label, and prepare the parts for delivery, ensuring that the right products are sorted and sent to the correct destinations. Throughout the entire process, automated systems collect data on machine performance, material usage, energy consumption, and product quality. This data is analyzed to optimize the production process, predict maintenance needs, and improve overall efficiency.
As technology continues to evolve, future sheet metal forming assembly lines will incorporate even more advanced features. The integration of AI and machine learning will enable systems to adapt to changing production conditions, continuously improving performance over time. Robotics will become even more advanced, with collaborative robots (cobots) working alongside human operators in more flexible and adaptable ways. Additionally, the integration of Industry 4.0 technologies, such as the Internet of Things (IoT), will allow manufacturers to monitor and control the production line remotely, enabling real-time data analysis and predictive maintenance.
Sustainability efforts will also drive future developments. Manufacturers will increasingly focus on energy-efficient equipment, material recycling, and reducing waste through more precise cutting and forming techniques. The use of servo-electric presses, for example, will help reduce power consumption compared to traditional hydraulic presses. Meanwhile, additive manufacturing techniques such as 3D printing may begin to play a role in producing complex metal components that can be integrated into the assembly line, providing more flexibility for customized or low-volume parts.
In conclusion, sheet metal forming assembly lines are becoming increasingly automated, flexible, and efficient. The integration of robotics, advanced sensors, AI, and data analytics is revolutionizing the way sheet metal parts are produced and assembled. These innovations not only improve productivity but also help manufacturers maintain high-quality standards while reducing costs and environmental impact. As the demand for more customized and sustainable products grows, the technology behind sheet metal forming assembly lines will continue to evolve to meet the challenges of modern manufacturing.
The continued development of sheet metal forming assembly lines is shaped by emerging trends in automation, data analytics, artificial intelligence, and sustainability. As the industry moves forward, more advanced robotic systems and machine learning algorithms will be introduced to enhance the flexibility, precision, and adaptability of production lines.
In particular, AI-driven optimization will allow the forming processes to dynamically adjust based on material variations, environmental changes, or the specific requirements of the part being produced. Machine learning will also enable predictive analytics, anticipating potential failures and maintenance needs before they become critical. This shift towards predictive maintenance helps reduce downtime, lower maintenance costs, and increase the overall reliability of the production system.
In terms of robotics, collaborative robots, or cobots, are expected to play an even greater role in assembly lines, not just as automated assistants, but as active participants in tasks traditionally performed by human workers. Cobots can adapt to different tasks, assist with assembly, or inspect parts with extreme precision, all while ensuring that operators remain safe within the workspace. These robots are becoming smarter, more flexible, and able to work seamlessly alongside humans, which significantly boosts productivity while maintaining a safe working environment.
Another key advancement in sheet metal forming will come from the integration of augmented reality (AR) and virtual reality (VR) in the assembly process. These technologies can be used to guide operators through complex assembly tasks by overlaying digital instructions on physical components, helping them to identify part orientations, assembly steps, or even potential issues during the assembly process. Additionally, VR will allow for virtual simulations of assembly lines before they are set up in the real world, helping manufacturers optimize layouts and workflows for maximum efficiency.
The Internet of Things (IoT) will continue to enhance connectivity between machines, tools, and operators. With IoT-enabled sensors, the production line can collect and analyze vast amounts of data, allowing manufacturers to gain insights into everything from machine performance to energy consumption and product quality. This connectivity will also enable remote monitoring and real-time adjustments, giving managers and engineers the ability to troubleshoot, fine-tune settings, and make decisions from virtually anywhere.
Sustainability will continue to be a driving force behind the development of green technologies in sheet metal forming. The implementation of energy-efficient equipment such as servo-electric presses or energy recovery systems will help reduce the carbon footprint of the production process. Manufacturers will also look to adopt more sustainable materials, utilize recycled metal, and improve material utilization to reduce waste. Recycling systems, particularly for scrap metal, will become more sophisticated, enabling manufacturers to repurpose material more efficiently and reduce overall material costs.
3D printing could also have a greater influence on sheet metal forming processes. While additive manufacturing is not yet fully integrated into traditional assembly lines, it offers unique opportunities for producing complex or low-volume parts. 3D printed metal parts can be integrated with traditionally formed parts in certain industries, such as aerospace and automotive, where lightweight, high-strength materials are required. This combination of additive and subtractive manufacturing techniques could lead to the production of highly customized components, allowing manufacturers to meet increasing demand for personalized products.
The future of quality control will also be heavily influenced by technological advancements. With the introduction of advanced machine vision systems and AI-powered inspection, assembly lines will become more capable of identifying micro-defects, even those that are invisible to the human eye. These systems will use high-definition cameras, 3D scanning, and AI algorithms to inspect parts at every stage of the manufacturing process, ensuring that defects are detected and corrected before they become costly issues.
As assembly lines become more connected and integrated, the concept of smart manufacturing will take center stage. Smart manufacturing incorporates real-time monitoring, machine learning, and big data analytics to create highly adaptive and efficient production systems. Through this integration, manufacturers will be able to respond more rapidly to changing market demands, optimize production schedules, and minimize waste. With the help of advanced software systems, manufacturers will be able to dynamically adjust production workflows, prioritize jobs based on demand, and coordinate the entire production process across multiple facilities and supply chains.
One more important consideration for the future of sheet metal forming assembly lines is cybersecurity. As these systems become more connected through IoT and cloud-based technologies, the risk of cyber threats increases. Manufacturers will need to implement robust cybersecurity measures to protect their intellectual property, production data, and the integrity of the entire system. This could involve securing communication networks, implementing data encryption, and using blockchain technologies to ensure the traceability and authenticity of parts throughout the supply chain.
Looking ahead, automation will continue to drive innovation in sheet metal forming assembly lines. Manufacturers will invest in highly flexible, adaptive systems that are capable of producing a diverse range of parts with minimal downtime. These advancements will not only improve productivity but also enhance customization options, allowing for more unique, personalized, and complex designs.
In conclusion, the future of sheet metal forming assembly lines will be marked by an increasing reliance on automation, intelligence, and sustainability. By integrating advanced technologies such as AI, machine learning, robotics, IoT, and 3D printing, these lines will become more efficient, adaptable, and capable of producing high-quality parts at scale. As industries continue to evolve and demand for customized, sustainable, and high-performance products grows, the sheet metal forming assembly line will remain a cornerstone of modern manufacturing, constantly evolving to meet new challenges and opportunities.
Servo-Controlled Sheet Metal Processing Line
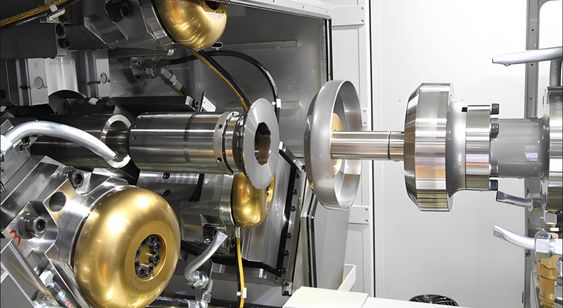
A Servo-Controlled Sheet Metal Processing Line is an advanced manufacturing system that utilizes servo motors to control the various processing stages of sheet metal fabrication with precision and high flexibility. This type of processing line is designed to offer superior control over every aspect of the forming, punching, bending, and other metalworking processes. Servo-controlled systems provide more accurate, faster, and more energy-efficient performance compared to traditional hydraulic or mechanical systems, making them increasingly popular in industries like automotive, aerospace, electronics, and heavy machinery.
The core feature of a servo-controlled sheet metal processing line is the use of servo motors to precisely control the movements of machines at various stages of sheet metal processing. These systems are highly adaptable, with the ability to adjust speed, position, and force in real time based on the specific requirements of the part being produced.
Here’s an overview of how a servo-controlled sheet metal processing line typically operates:
- Raw Material Handling: The process begins with the delivery of sheet metal in coil or sheet form. This raw material is typically fed into the line by an uncoiler or sheet feeder. Servo-controlled systems can regulate the speed and tension of the material, ensuring that it is fed into the forming machines smoothly and without distortion.
- Cutting and Blanking: The material is often cut into blanks or shapes that are required for the next steps in the forming process. Servo-controlled cutting tools, such as laser cutters or punch presses, ensure high precision when cutting the metal. The servo motors adjust the speed and pressure according to the type and thickness of the material, resulting in clean cuts with minimal material waste.
- Forming and Stamping: Servo-controlled presses are widely used in stamping operations to shape the sheet metal into desired forms. The servo motor adjusts the press’s stroke speed, force, and timing to ensure that the metal is shaped accurately. This allows for more flexible production processes, as the machine can easily adapt to different part designs and thicknesses. The servo motor’s precision improves the quality of the formed parts and reduces the likelihood of errors, such as overstretching or warping of the material.
- Bending and Folding: In bending operations, servo-controlled presses or press brakes are used to shape the sheet metal into angles or curves. The servo motor controls the speed, position, and force applied by the press brake, enabling it to make precise and repeatable bends. This is especially important in applications that require parts with tight tolerances or complex geometries.
- Punching: Servo-driven punching machines are used to create holes or other specific shapes in the sheet metal. These machines use servo motors to control the punching speed and depth, allowing for high-speed operation and consistent results. The servo system can be programmed to execute a variety of hole patterns or shapes, ensuring flexibility in the production of different components.
- Automatic Material Handling: In a servo-controlled processing line, automated material handling systems, including robotic arms and conveyors, are employed to move parts between different stages of the process. Servo motors drive these systems with high precision, enabling quick and efficient transfers. Robots may be used to load and unload parts, pick up components from conveyors, or perform secondary operations like assembly, all while minimizing errors and downtime.
- Inspection and Quality Control: In servo-controlled systems, machine vision and sensor technologies are often integrated for real-time quality control. These systems inspect parts for defects such as dimensional inaccuracies, surface imperfections, or material inconsistencies. Servo-controlled machines can adjust parameters in real-time based on feedback from these inspection systems to correct any issues immediately, ensuring high-quality output.
- Energy Efficiency: One of the main advantages of a servo-controlled processing line is its energy efficiency. Unlike traditional hydraulic systems, which continuously consume power to maintain pressure, servo motors only draw power when needed, adjusting their output in real-time to match the load. This results in significant energy savings compared to conventional systems, making servo-controlled lines more environmentally friendly and cost-effective.
- Precision and Flexibility: The use of servo technology in sheet metal processing provides exceptional control over speed, force, and position. This means that manufacturers can easily adapt the system to process different materials, thicknesses, and part designs without the need for extensive retooling or machine adjustments. Servo systems also offer faster cycle times, enabling high-throughput production while maintaining precision.
- Integration with Digital Manufacturing Systems: A servo-controlled sheet metal processing line is often integrated with digital manufacturing technologies, including CAD/CAM systems, PLM software, and IoT-enabled monitoring systems. These systems allow for seamless communication between the design, production, and quality control processes. The integration of digital technologies enables the real-time collection and analysis of data, which can be used to further optimize the processing line, improve productivity, and ensure consistent product quality.
Advantages of a Servo-Controlled Sheet Metal Processing Line:
- High Precision and Consistency: Servo motors provide precise control over the processing stages, ensuring that each part is produced within tight tolerances and with minimal variation.
- Increased Speed and Throughput: The ability to control speed, position, and force allows for faster cycle times, resulting in higher throughput and more efficient production.
- Energy Efficiency: Servo motors are more energy-efficient than traditional hydraulic systems because they only consume power when necessary, reducing energy costs and environmental impact.
- Flexibility: The system can easily be reprogrammed or adjusted to accommodate different sheet metal thicknesses, part designs, or production volumes, making it highly flexible and adaptable to changing manufacturing needs.
- Reduced Maintenance: Servo systems have fewer moving parts compared to traditional hydraulic systems, resulting in less wear and tear and reduced maintenance requirements.
- Lower Operating Costs: Due to their energy efficiency and reduced maintenance needs, servo-controlled lines often result in lower overall operating costs.
- Real-Time Monitoring and Control: The ability to monitor the entire process through digital systems ensures that any issues can be detected and addressed in real-time, minimizing downtime and defects.
Applications of Servo-Controlled Sheet Metal Processing Lines:
- Automotive Industry: For producing high-precision parts such as body panels, brackets, and structural components that require consistent quality and flexibility.
- Aerospace Industry: For the manufacturing of complex and lightweight parts with tight tolerances, where precision and material handling are critical.
- Electronics: For producing metal enclosures and components for consumer electronics, where high precision and high-speed processing are essential.
- Heavy Machinery: For creating large structural components used in construction, mining, and agricultural machinery, where high-force stamping and bending are required.
- Appliance Manufacturing: For producing metal parts used in household appliances like refrigerators, washing machines, and ovens.
Future Trends and Developments:
The evolution of servo-controlled sheet metal processing lines will continue to be influenced by technological advances, including machine learning, AI, and IoT. These technologies will enable even more sophisticated automation, improving not only precision and throughput but also the ability to predict and prevent machine failures before they occur. Furthermore, as sustainability becomes a more important focus, the development of energy-efficient, environmentally friendly solutions will continue to drive the adoption of servo-controlled systems in the manufacturing sector.
In conclusion, a servo-controlled sheet metal processing line represents a significant advancement in the field of metalworking. By utilizing the precision, flexibility, and efficiency offered by servo motors, manufacturers can improve product quality, increase throughput, reduce energy consumption, and minimize operational costs. As the demand for high-quality, low-cost, and sustainable manufacturing solutions continues to grow, servo-controlled systems will play a central role in shaping the future of sheet metal processing.
A servo-controlled sheet metal processing line offers a level of precision and adaptability that greatly enhances the efficiency of modern manufacturing. The core benefit lies in its ability to precisely control the various movements of machines using servo motors, which respond dynamically to the demands of the production process. This allows manufacturers to optimize every phase of sheet metal processing—from material handling and cutting to forming, stamping, and bending—ensuring high-quality output while reducing waste and energy consumption.
The adaptability of servo-controlled systems enables manufacturers to process a wide range of materials and thicknesses with minimal downtime, as the machines can be easily reprogrammed or adjusted for different jobs. This flexibility is critical in industries where product designs are frequently updated, and small batch production is common. The real-time adjustment of speed, position, and force during operations ensures that each part is created to precise specifications, and the use of servo motors reduces the reliance on traditional hydraulic systems that can be less responsive and less energy-efficient.
In terms of energy savings, the servo-controlled line stands out by only consuming power when necessary. Unlike hydraulic systems, which maintain constant pressure regardless of the load, servo motors adjust their power output to match the task at hand. This not only cuts down on overall energy costs but also reduces the environmental impact of the production process, aligning with the growing push for sustainable manufacturing practices.
Additionally, the integration of advanced digital technologies like machine vision, AI, and IoT into these lines helps improve overall productivity and quality. Machine vision systems can inspect parts in real-time, detecting defects that might otherwise go unnoticed, and the data collected can be used to optimize the production process continually. AI algorithms can anticipate maintenance needs, improving uptime by identifying potential issues before they cause significant downtime, which further reduces costs and improves the longevity of the equipment.
Servo-controlled systems also allow for better integration with other automation technologies, such as robotic arms and automated material handling systems. These robots, often programmed to work collaboratively with human operators, can take on repetitive tasks such as loading and unloading material, performing secondary operations, and assembling parts, reducing the risk of human error and increasing the speed of production. The ability to connect these systems seamlessly with the servo-controlled machines enhances the overall efficiency of the line, creating a highly automated and flexible production environment.
The future of servo-controlled sheet metal processing lines is increasingly intertwined with Industry 4.0 concepts. The evolution toward smarter factories will see more advanced data analytics and cloud-based solutions that enable manufacturers to monitor and control every aspect of production remotely. With real-time data analytics, manufacturers will be able to track performance metrics, identify areas for improvement, and make data-driven decisions that enhance productivity and product quality.
At the same time, as product designs become more complex and demand for customization increases, the ability of servo-controlled systems to adapt to a wide variety of designs will make them essential in sectors like automotive, aerospace, and electronics. The combination of high precision, flexibility, and speed makes these lines ideal for industries where innovation and cost-efficiency must go hand in hand. The ability to quickly change tooling, adjust settings, and fine-tune the production process in real-time also enables manufacturers to meet the demands of low-volume, high-mix production runs that are becoming increasingly common.
Looking forward, robotics and additive manufacturing will likely play a greater role in servo-controlled sheet metal processing. As 3D printing technologies continue to improve, the ability to integrate them with traditional sheet metal forming could allow manufacturers to produce highly customized parts with complex geometries. Furthermore, as robotic automation continues to advance, it could further improve flexibility, enabling production lines to quickly reconfigure to handle different parts, materials, and processes without significant downtime.
Finally, the adoption of cybersecurity measures will be critical in the future as these systems become more connected and digitized. Manufacturers will need to safeguard sensitive production data, intellectual property, and machine settings from potential cyber threats, ensuring that their operations remain secure and their data remains protected from malicious attacks.
In summary, the servo-controlled sheet metal processing line is revolutionizing the manufacturing process by offering unmatched precision, flexibility, and energy efficiency. These systems reduce operational costs, improve product quality, and increase production speed, while also contributing to a more sustainable manufacturing process. The integration of smart technologies, coupled with automation and advanced data analytics, will continue to shape the future of sheet metal fabrication, making it possible to produce complex, high-quality parts with greater ease and efficiency than ever before. As industries continue to push for greater customization, sustainability, and cost-effectiveness, servo-controlled processing lines will play an increasingly central role in meeting these demands.
As the demand for customized products and shorter production cycles increases across various industries, the capabilities of servo-controlled sheet metal processing lines will continue to evolve to meet these needs. One of the key benefits of servo-controlled systems is their ability to handle low-volume, high-mix production. This is particularly important in industries like automotive, aerospace, and electronics, where customized and intricate parts are often required in smaller quantities. In such cases, the ability to quickly adjust settings and switch between different part designs without significant retooling or downtime becomes a critical advantage.
With real-time adaptability, servo-controlled systems can handle rapid changes in design or material specifications. This makes them ideal for prototype development and just-in-time manufacturing, where speed and precision are key. Designers and engineers can modify the production process on the fly, allowing for faster iteration cycles and reducing the lead time for new product designs.
The integration of advanced robotics will likely push the boundaries of what’s possible in servo-controlled sheet metal processing lines. The use of collaborative robots (cobots) will allow operators and machines to work together more efficiently and safely. Cobots, which are designed to work in close proximity to human operators, can assist in tasks that require fine motor skills, such as assembly, quality inspection, or part handling. The ability of cobots to perform these tasks alongside humans means less downtime between shifts and fewer manual errors, improving overall productivity while maintaining a high level of safety on the shop floor.
Another advancement that will enhance these systems is the ongoing development of machine learning and artificial intelligence (AI) algorithms that can continuously optimize the production process. By analyzing large volumes of data generated by the sensors, cameras, and monitoring systems integrated into the line, AI-driven systems can detect inefficiencies, predict maintenance needs, and make real-time adjustments to the operation. This creates a self-optimizing production environment where the system learns and adapts to improve quality and throughput over time without the need for human intervention.
The IoT-enabled sensors in these systems will play a key role in predictive maintenance and real-time process monitoring. The data collected by these sensors can not only provide insight into machine health and performance but also allow for the analysis of broader production trends. By using this data to predict failures before they occur, manufacturers can reduce unplanned downtime, minimize repair costs, and extend the lifespan of equipment.
Energy efficiency remains a crucial focus for manufacturers looking to reduce operational costs and environmental impact. The inherent energy savings of servo-controlled systems—due to their ability to adjust power usage according to load—are expected to drive further adoption. In addition to improving the energy efficiency of individual machines, servo-controlled lines can be integrated into energy management systems that optimize energy use across the entire production facility. This can result in significant cost savings, particularly for industries with high energy consumption.
Another future direction for servo-controlled sheet metal processing lines is the deeper integration of additive manufacturing and conventional subtractive processes. As 3D printing technologies continue to mature, manufacturers are beginning to experiment with combining traditional sheet metal forming techniques with additive processes to create more complex and customized parts. In this hybrid approach, servo-controlled machines could be used to form the basic shape of a part, while 3D printing could be employed to add intricate details, internal structures, or specialized features. This combination would significantly expand the range of parts that could be produced, particularly for industries that require high levels of customization or low-volume production.
Looking forward, the evolution of servo-controlled systems will also be influenced by cloud computing and big data analytics. The ability to analyze data from production lines in real time, combined with cloud-based solutions, will allow manufacturers to make data-driven decisions about everything from machine operation to supply chain management. This could result in more efficient resource allocation, better demand forecasting, and enhanced production planning, helping companies stay competitive in a rapidly changing market.
As manufacturers strive to meet increasing demands for sustainability, we can expect to see more widespread adoption of servo-controlled systems due to their ability to minimize waste and energy consumption. Manufacturers will continue to seek ways to recycle materials, such as reusing scrap metal, and reduce their carbon footprint by implementing energy-efficient technologies. These sustainable practices will be critical for companies looking to align with both regulatory requirements and consumer demand for environmentally responsible products.
Additionally, smart factories and digital twins will become more commonplace in the future of sheet metal processing. A digital twin is a virtual representation of the physical production line that can simulate the entire production process in real time. By combining the capabilities of IoT, AI, and machine learning, digital twins allow manufacturers to run simulations, identify bottlenecks, test process optimizations, and improve predictive maintenance. The integration of digital twins with servo-controlled lines will give manufacturers greater control over their operations, enabling faster and more informed decision-making.
Automation in the workforce will also evolve as part of this transformation. While servo-controlled systems will continue to replace many manual processes, human operators will still play an essential role, particularly in tasks that require creative problem-solving or direct interaction with complex designs. As technology advances, the role of the operator will shift from managing individual tasks to overseeing entire automated production lines. Human-robot collaboration will be key to achieving optimal performance while keeping operators safe and productive.
In conclusion, servo-controlled sheet metal processing lines represent the next generation of flexible, high-precision manufacturing systems. As they evolve, they will integrate with cutting-edge technologies such as robotics, AI, IoT, 3D printing, and cloud computing, enabling manufacturers to improve speed, quality, and energy efficiency while reducing costs and waste. These systems will be at the forefront of smart manufacturing, responding dynamically to changing production needs and creating new opportunities for customization, sustainability, and innovation in industries around the world.
Programmable Sheet Metal Shaping Line
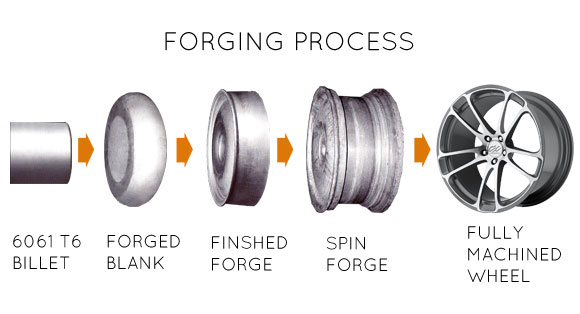
A Programmable Sheet Metal Shaping Line is an advanced manufacturing system that allows for the shaping, forming, and processing of sheet metal through programmable, automated equipment. This line combines high precision, flexibility, and efficiency by leveraging the power of programmable controllers, often integrated with advanced sensors and servo motors to manage various processes such as bending, stamping, punching, and cutting. It enables manufacturers to create complex metal parts with tight tolerances and in a variety of shapes, without the need for frequent retooling or manual intervention.
The programmable nature of the system means that operators can input specific design parameters into the control system, which then directs the machines accordingly. This allows for quicker transitions between different products or designs, offering flexibility in production while maintaining high accuracy. This type of line is particularly valuable in industries where customization and rapid prototyping are necessary, such as automotive, aerospace, electronics, and heavy machinery.
Key Features of a Programmable Sheet Metal Shaping Line:
- Flexibility and Customization: The programmable system offers immense flexibility in how sheet metal is shaped. Different parts with varied shapes, sizes, and materials can be processed on the same line without the need to overhaul machinery. For example, the system can handle tasks like punching, bending, cutting, and forming all in a single line, adjusting quickly to accommodate a range of part designs.
- Advanced Control Systems: The core of a programmable sheet metal shaping line is the programmable logic controller (PLC) or a computer numerical control (CNC) system. These controllers allow operators to input detailed specifications for each part, including parameters such as dimensions, material thickness, and the type of forming operation required. The programmable system ensures precise execution of these instructions, making it ideal for mass production as well as custom, low-volume runs.
- Precision and Repeatability: One of the main advantages of using a programmable line is the high level of precision and repeatability it offers. Programmable machines, equipped with servo motors and linear actuators, can repeat the exact same process for thousands of parts, ensuring consistent quality across all pieces. This reduces errors and material wastage, especially important when working with expensive or hard-to-process materials.
- Increased Speed and Efficiency: The automation of various tasks, such as material feeding, cutting, and shaping, significantly reduces cycle times compared to manual or less automated processes. By programming the entire workflow, manufacturers can optimize each step of the process, minimizing downtime and improving throughput.
- Real-Time Monitoring and Adjustment: Programmable lines often integrate real-time monitoring systems that use sensors and feedback loops to constantly check for discrepancies in the production process. If the system detects any deviation from the programmed specifications, it can adjust the parameters on the fly to ensure the final product remains within the desired quality standards. This capability is crucial for reducing scrap and rework, which can be costly in high-precision manufacturing.
- Energy Efficiency: The ability to program specific parameters based on the job requirements allows for energy optimization. Machines can be set to adjust their power consumption according to the load and operational needs. This is particularly important for energy-intensive processes like stamping or bending, where energy usage can be controlled more effectively through smart programming.
- Integration with Digital Manufacturing Systems: Programmable sheet metal shaping lines are often integrated into broader digital manufacturing ecosystems. This allows for seamless communication with CAD/CAM software, product lifecycle management (PLM) systems, and enterprise resource planning (ERP) systems, ensuring that designs are easily translated into the production process. This integration further enhances the flexibility of the line and improves communication between the design and production teams.
- Reduced Human Intervention: Programmable lines automate many of the tasks that were traditionally manual, reducing the need for operators to constantly intervene. This not only lowers the risk of human error but also improves worker safety by reducing their exposure to heavy machinery and hazardous environments.
Stages in a Programmable Sheet Metal Shaping Line:
- Material Feeding: The process begins with the automated feeding of sheet metal into the line, where the system adjusts the feed rate according to the size and thickness of the material. Servo motors control the speed and tension to ensure smooth feeding, which is critical for consistent processing.
- Cutting: A programmable cutting machine, such as a laser cutter, water jet, or punch press, then cuts the sheet metal into the desired shape or blanks. These machines are programmed to handle different cutting paths, material types, and thicknesses. By using servo-controlled systems, the cutting process can be carried out with high precision, reducing waste and improving part quality.
- Forming and Bending: The metal is then transferred to a press brake or forming press, which is programmed to create specific shapes. This can include tasks like bending, punching, or deep drawing. The programmable system ensures that the right pressure, speed, and angle are applied, producing parts that meet strict dimensional tolerances.
- Secondary Operations: In addition to primary forming and shaping, secondary operations like tapping, deburing, or spot welding may be performed on the same line. These operations can be programmed into the system to ensure the smooth handling of all tasks within a single workflow. Robotic arms can be used for tasks like loading and unloading parts, further enhancing automation.
- Inspection and Quality Control: After forming and shaping, parts are typically inspected for defects. This can be done through machine vision systems, which scan the parts for any imperfections such as dimensional inaccuracies or surface defects. The inspection data is fed back into the system, allowing for immediate adjustments to the process if necessary. This feedback loop ensures high-quality standards are maintained throughout the production process.
- Packaging and Output: Once the parts pass inspection, they are either further processed or packaged for shipment. Automated robotic arms or conveyors handle the transportation of parts to the next stage or final product packaging. The line can be programmed to handle different batch sizes and to ensure that each part is carefully packaged and labeled.
Benefits of a Programmable Sheet Metal Shaping Line:
- High Precision and Flexibility: Programmable systems can quickly adapt to different part designs, ensuring high-quality production without the need for significant retooling or adjustments.
- Faster Production Cycles: Automation and programmability reduce the time between tasks, enabling faster production and quicker turnarounds.
- Reduced Waste: Accurate control over material feeding, cutting, and shaping leads to less scrap and material waste, which is crucial for reducing production costs.
- Enhanced Customization: Manufacturers can program the system to handle a wide variety of designs, materials, and thicknesses, enabling customization of parts according to customer specifications.
- Improved Safety: By automating dangerous tasks and reducing human intervention, these lines improve the safety of the workplace.
- Cost-Effective: The combination of automation, precision, and efficiency lowers operating costs in the long term by reducing labor costs, material waste, and energy consumption.
Applications of Programmable Sheet Metal Shaping Lines:
- Automotive Industry: For producing car body parts, brackets, and other components that require high precision and flexibility.
- Aerospace: For making lightweight, high-performance parts that must meet strict quality standards and exacting tolerances.
- Electronics: For the production of metal enclosures, connectors, and other parts used in consumer electronics.
- Heavy Equipment: For creating structural components used in construction, mining, and agricultural machinery.
- Consumer Goods: For manufacturing sheet metal parts used in household appliances, furniture, and other consumer products.
Future Trends:
- AI and Machine Learning Integration: Future programmable systems will incorporate more AI-driven capabilities, allowing machines to optimize the production process based on real-time data, improving efficiency and quality.
- Collaborative Robots: Increased integration of collaborative robots (cobots) will enhance flexibility and enable even higher levels of automation while still allowing human operators to provide oversight.
- Sustainability Focus: With sustainability becoming a key priority, programmable sheet metal lines will continue to evolve to minimize energy usage, reduce material waste, and use environmentally friendly materials.
- Cloud-Based Manufacturing: The integration of cloud computing will enable manufacturers to access and control production lines remotely, monitor performance, and make adjustments from anywhere in the world, enhancing the overall flexibility of the manufacturing process.
In conclusion, programmable sheet metal shaping lines represent a leap forward in the manufacturing of high-precision, flexible, and efficient parts. These systems offer manufacturers a powerful tool to meet the demands of today’s fast-paced, customized production environment, while also improving safety, reducing waste, and lowering overall operational costs. As technology continues to evolve, these lines will become even more advanced, enabling even greater levels of automation, optimization, and customization.
A programmable sheet metal shaping line is designed to automate and optimize the process of shaping sheet metal in a highly flexible and precise manner. By utilizing advanced programmable control systems, such as PLC (Programmable Logic Controller) or CNC (Computer Numerical Control), the production line can execute a range of operations, including cutting, bending, punching, and forming, with minimal manual intervention. This integration of automation allows manufacturers to process different materials, sizes, and thicknesses on the same line without major retooling or downtime, making the system ideal for high-mix, low-volume production.
Programmable systems enable fast switching between different product designs, offering customization and precision that traditional machines cannot match. Operators can input detailed instructions into the system, specifying the shape, size, and features of the parts. The system then ensures that each step in the process—whether it’s cutting, bending, or punching—is executed with high accuracy. This precision is particularly valuable in industries that require complex, detailed parts, such as automotive, aerospace, and electronics, where tolerances are tight, and quality must be guaranteed.
The flexibility of a programmable sheet metal shaping line allows for rapid prototyping and short lead times. With the ability to quickly adapt to new part designs, manufacturers can produce custom parts or make adjustments to existing designs without the need for lengthy retooling. This makes the system an excellent fit for industries with frequent design changes, such as automotive or electronics, where innovation is constant, and customization is in demand.
By automating various processes, the system also enhances efficiency. Operations like material feeding, cutting, forming, and secondary operations can be carried out simultaneously or sequentially, reducing the overall time required to complete a part. The servo motors used in these systems ensure that each step is completed with precision, reducing material waste and improving throughput. Additionally, real-time monitoring systems can track the progress of each operation and detect any issues before they lead to defects or downtime. These features contribute to higher productivity and quality control, as adjustments can be made on the fly based on real-time feedback.
A significant advantage of programmable systems is their energy efficiency. Unlike traditional mechanical or hydraulic systems that require constant power, servo-driven systems adjust their energy usage to meet the needs of the task at hand, significantly reducing energy consumption. The precision of programmable systems also ensures that the optimal amount of force is applied during each stage of the shaping process, further reducing energy waste.
As the system is programmable, it also supports advanced features like automated inspection and quality assurance. Parts are inspected during or after each operation, often using machine vision or sensors to check for dimensional accuracy, surface defects, and other quality metrics. This automation not only improves consistency but also minimizes the potential for human error, resulting in higher-quality products and less waste. Additionally, by collecting and analyzing production data, manufacturers can make real-time adjustments to optimize operations, further improving efficiency and product quality.
The future of programmable sheet metal shaping lines looks promising with the increasing integration of AI, machine learning, and data analytics. These technologies will enable predictive maintenance, allowing the system to anticipate when parts will need to be serviced or replaced, preventing unplanned downtime. They will also help optimize production schedules, identifying the most efficient use of resources and improving overall production planning.
Moreover, robotics and additive manufacturing will likely play an increasingly significant role. As robotic systems become more advanced, they can take on tasks such as material handling, assembly, or complex forming operations, further improving automation and flexibility. Combining 3D printing with programmable sheet metal shaping systems may also lead to hybrid processes, where parts are first formed on the line and then customized with additive manufacturing techniques. This could open new opportunities for creating highly complex and customized parts with minimal waste.
As these systems evolve, cloud-based technologies will also play a larger role in enabling manufacturers to monitor and control production remotely, access data, and perform real-time analysis from anywhere. This not only improves operational visibility but also enhances the ability to make data-driven decisions that increase productivity and quality. With the growing demand for smart factories, this level of connectivity and integration will continue to push the boundaries of what’s possible in automated sheet metal processing.
In summary, a programmable sheet metal shaping line is a highly flexible and efficient manufacturing solution that allows for precise, customizable, and automated processing of sheet metal. The system’s ability to rapidly adapt to different designs, coupled with real-time monitoring and advanced control systems, makes it a valuable asset for industries requiring high-quality, low-volume, and customized parts. As technology continues to evolve, the integration of AI, robotics, and cloud computing will further enhance the capabilities of these lines, making them even more adaptable, efficient, and capable of meeting the demands of modern manufacturing.
As programmable sheet metal shaping lines continue to evolve, new trends and advancements are emerging that will further enhance their efficiency, flexibility, and sustainability. With the integration of Industry 4.0 technologies, these systems are becoming more interconnected, intelligent, and automated, enabling manufacturers to streamline operations and improve decision-making processes.
One of the most significant trends is the increased use of advanced robotics. The collaboration between programmable sheet metal shaping lines and robotic arms is expanding beyond basic material handling to include more intricate tasks such as assembly, secondary processing, and even inspection. Collaborative robots (cobots), in particular, are becoming more prevalent, working alongside human operators to perform tasks that are either repetitive, dangerous, or require precision. These robots not only help with physically demanding tasks but also improve workflow efficiency by working in sync with the rest of the automated system, reducing bottlenecks and human error.
Additionally, the rise of smart sensors and machine vision systems integrated within the shaping lines is taking quality control to new levels. These systems are capable of monitoring part quality in real time, making adjustments to the process if defects are detected. For example, machine vision can be used to inspect the surface of the sheet metal for imperfections such as scratches, dents, or misalignments, while laser sensors measure thickness and ensure dimensional accuracy. These real-time feedback loops help to minimize scrap and rework, increasing yield and improving overall product quality.
Another key development is the increased focus on sustainability in manufacturing processes. Programmable sheet metal shaping lines are becoming more energy-efficient, with the ability to adjust energy consumption based on the size and complexity of the parts being processed. By optimizing the machine’s power usage throughout the production cycle, manufacturers can significantly reduce their carbon footprint and operating costs. Additionally, manufacturers are increasingly implementing material recycling technologies, such as collecting scrap metal for reuse, and utilizing eco-friendly materials in their production processes. These efforts align with growing regulatory requirements and consumer demand for more sustainable practices in manufacturing.
The incorporation of additive manufacturing (AM) into programmable sheet metal shaping lines is also a notable trend. By combining traditional subtractive processes with 3D printing techniques, manufacturers can create parts with complex geometries that were once impossible or cost-prohibitive to produce. For instance, additive manufacturing can be used to create intricate features or internal structures in a part that would be challenging to form using traditional sheet metal processes alone. This hybrid approach offers a powerful way to produce highly customized and lightweight parts with minimal material waste.
With the expansion of data-driven manufacturing, cloud computing is becoming an essential tool for monitoring and controlling programmable sheet metal shaping lines remotely. By connecting machines to cloud-based platforms, manufacturers can access real-time data on machine performance, production status, and maintenance needs from anywhere in the world. This integration allows for enhanced predictive analytics, as historical data and machine learning algorithms can be used to predict potential failures, optimize scheduling, and improve operational efficiency. Additionally, this connectivity enables a more collaborative approach to production, as teams from different locations can work together on optimizing production lines, troubleshooting issues, or conducting remote audits.
The shift towards digitization is also impacting how programmable sheet metal shaping lines are integrated with digital twins. A digital twin is a virtual replica of the physical manufacturing system, which can be used to simulate production processes, test new configurations, and troubleshoot potential issues before they arise. By integrating digital twins into programmable systems, manufacturers can gain valuable insights into the performance of their machines and production lines, allowing them to make data-driven decisions and test improvements in a virtual environment before implementing them on the shop floor. This capability is particularly useful in reducing downtime and optimizing production processes, as it enables proactive adjustments and simulations based on real-time data.
Artificial intelligence (AI) and machine learning (ML) are also transforming the way programmable sheet metal shaping lines operate. These technologies allow the system to continually improve its performance by analyzing large sets of data and identifying patterns that might not be visible to human operators. For example, AI algorithms can optimize production schedules based on historical data, demand forecasting, and machine availability, leading to better resource allocation and reduced downtime. In addition, AI can be used to fine-tune the process parameters (such as speed, pressure, and material feed rate) in real-time, leading to more consistent product quality and higher efficiency.
As customer demands continue to grow for highly customized, low-volume production runs, programmable sheet metal shaping lines will increasingly be able to meet these needs with rapid changeover capabilities. Instead of the lengthy and costly retooling processes traditionally required for each new product design, these lines will be able to switch between different part designs and configurations quickly and with minimal setup. This flexibility will be particularly valuable for industries such as aerospace, automotive, and consumer electronics, where the need for short production runs and customized components is growing.
Lastly, the ability to integrate with the supply chain will continue to evolve, with programmable sheet metal shaping lines becoming part of a broader smart manufacturing ecosystem. Through supply chain integration, manufacturers will have real-time visibility into inventory levels, material availability, and customer demand, allowing them to optimize production schedules and reduce lead times. This end-to-end integration, from design through to delivery, will enhance collaboration across the entire manufacturing process, ensuring that parts are produced on time, to specification, and with minimal waste.
In conclusion, the future of programmable sheet metal shaping lines will be shaped by the ongoing advancements in automation, data analytics, robotics, and sustainability. These lines will continue to evolve to meet the demands of modern manufacturing, offering greater flexibility, precision, and efficiency than ever before. By leveraging new technologies such as AI, robotics, additive manufacturing, and cloud computing, manufacturers will be able to stay competitive in an increasingly fast-paced and customized production environment. The ultimate goal will be to create more sustainable, energy-efficient, and intelligent production systems that can adapt to changing market needs and contribute to the growth of the manufacturing industry.
Automated Line for Sheet Forming
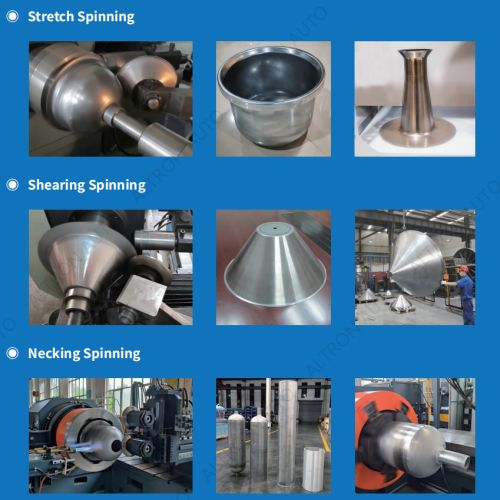
An automated line for sheet forming refers to a fully integrated, high-efficiency manufacturing system designed to automate the various processes involved in shaping and forming sheet metal. This type of system is typically used in industries such as automotive, aerospace, electronics, and construction, where precision, speed, and scalability are crucial. The automation within the system reduces the need for manual intervention, speeds up production cycles, and ensures higher consistency and quality in the finished products.
The system usually includes multiple stations, each responsible for a specific process, such as cutting, bending, stamping, punching, forming, and inspection. These stations are interconnected by conveyors and robotic arms to seamlessly move parts through each stage of production without manual handling, leading to optimized throughput and reduced human error. The automated line often operates with programmable logic controllers (PLC) or computer numerical control (CNC) systems to ensure precision and flexibility in part design and processing.
At the heart of an automated sheet forming line is its control system, which allows operators to input specific design parameters and control the machines accordingly. This enables quick setup times and easy transitions between different product designs or part sizes, a feature that is particularly useful for high-mix, low-volume production. The line can handle various materials like steel, aluminum, and copper, as well as different material thicknesses, making it highly adaptable to various industry requirements.
Key Features of an Automated Sheet Forming Line:
- Automation and Robotics: The use of robotic arms and automated material handling systems reduces manual intervention. Robots may be tasked with material feeding, loading/unloading parts, and even executing complex operations like assembly, welding, or quality inspection. These systems increase throughput and improve overall production speed.
- Advanced Control Systems: Modern sheet forming lines are equipped with sophisticated control systems that allow precise programming of every aspect of the manufacturing process. CNC or PLC controllers enable accurate control over part dimensions, material properties, machine speed, and operational settings. These systems also offer advanced real-time monitoring and diagnostics, ensuring that production proceeds smoothly with minimal disruption.
- Flexibility and Quick Changeover: Automated lines are designed to be flexible, capable of processing different part designs without significant retooling. With automated changeover mechanisms, parts can be adjusted quickly to accommodate new designs or specifications. This reduces setup times and allows manufacturers to meet the demands of smaller production runs or customized orders.
- High Precision and Repeatability: Precision is a critical factor in sheet metal forming, as even slight deviations can affect the quality of the final product. Servo motors and linear actuators control key movements with high precision, ensuring that each part is shaped according to exact specifications. The automation ensures repeatable results, reducing variability between parts and minimizing scrap.
- Integrated Quality Control: Automated systems can incorporate real-time quality monitoring through sensors and machine vision systems. These technologies continuously inspect parts for defects like dimensional inaccuracies, surface imperfections, or alignment issues. If a defect is detected, the system can adjust its parameters or flag the issue for manual inspection, ensuring that only parts that meet quality standards are passed along the production line.
- Material Handling and Feeding: The line is typically designed with automated material handling systems that feed sheets of metal into the line, ensuring they are aligned correctly for processing. Servo-controlled feed systems ensure smooth and precise material advancement to prevent material distortion or damage. These automated systems also manage the cutting, shearing, or blanking processes at the beginning of the forming line.
- Energy Efficiency: Automated sheet forming lines are often equipped with energy-efficient components that reduce energy consumption. Servo motors, for example, adjust power usage based on the task being performed, ensuring that the system uses only as much energy as needed for each operation. This not only lowers operational costs but also contributes to more sustainable manufacturing practices.
- Safety and Ergonomics: Automation increases safety by reducing the need for human operators to be directly involved in hazardous or physically demanding tasks. Machines are often designed with safety sensors and guards that ensure operators are not exposed to risks, such as moving parts or heavy machinery. Ergonomically designed workstations and robotic assistance reduce physical strain on workers.
Process Flow in an Automated Sheet Forming Line:
- Material Loading: The process begins with the automated loading of sheet metal onto the production line. Automated systems move the material from storage or from a supply conveyor to the cutting station, ensuring it is properly aligned and tensioned.
- Cutting and Blanking: The sheet metal is then cut to size using automated laser cutters, punch presses, or shearing machines. These tools are programmed to handle specific cutting operations based on the design specifications. Accurate cutting ensures that the material is prepared properly for the subsequent forming processes.
- Forming and Bending: After cutting, the metal sheets are moved to the forming station, where they undergo bending, stamping, or deep drawing operations. Press brakes or hydraulic presses are often used to shape the material according to the desired design. These processes can be programmed with high precision to ensure the final part meets design specifications. Depending on the part, forming can include processes like roll forming, stretch forming, or shear forming.
- Secondary Operations: Depending on the part requirements, secondary operations like tapping, deburring, welding, or spot welding may be automated. These operations are often handled by robots equipped with specialized tools, and can be integrated directly into the automated line to minimize handling time.
- Inspection and Quality Control: As parts progress through the line, they are often inspected using automated vision systems, 3D scanners, or laser sensors. These systems check for defects in geometry, surface quality, and alignment. Real-time feedback allows the system to make immediate corrections or notify operators of any issues. This ensures that only defect-free parts continue through the line.
- Packaging and Output: Once the parts are formed and inspected, they are moved to the packaging area, where they are either bundled together, boxed, or prepared for shipment. Automated systems handle the sorting and packaging of the parts, ensuring that the correct quantities and types are prepared for delivery. In some cases, robotic arms can also assist in this phase by stacking and organizing parts.
Benefits of an Automated Sheet Forming Line:
- Increased Productivity: Automation ensures that parts move through the system faster, with less downtime between processes, resulting in higher production rates.
- Improved Quality: Automated systems maintain consistent quality by reducing human error, ensuring parts are formed within specified tolerances.
- Reduced Labor Costs: With automation taking over repetitive tasks, manufacturers can reduce their labor costs while improving overall efficiency.
- Flexibility and Customization: The line can be reprogrammed for different parts, making it ideal for manufacturers that need to respond to customer orders with short lead times or frequent design changes.
- Energy Efficiency and Sustainability: Automated systems can optimize power consumption, reduce waste, and incorporate environmentally friendly practices into the production process.
- Enhanced Safety: By minimizing manual intervention and automating hazardous tasks, the risk of injury is significantly reduced.
Applications of Automated Sheet Forming Lines:
- Automotive Manufacturing: For producing body panels, brackets, and other structural components.
- Aerospace Industry: For creating lightweight, high-precision parts that must meet strict safety and performance standards.
- Electronics: For producing enclosures, connectors, and other sheet metal components.
- Heavy Equipment Manufacturing: For the creation of durable, large-scale components used in machinery and construction.
- Consumer Products: For manufacturing parts used in appliances, furniture, and other consumer goods.
Future Trends:
- Increased Use of Artificial Intelligence: AI will further enhance the flexibility and performance of automated sheet forming lines by enabling predictive maintenance, process optimization, and real-time adjustments based on data collected from the line.
- Collaborative Robots: The integration of cobots will allow for even greater flexibility, where robots can safely work alongside human operators, assisting with tasks such as part handling or assembly.
- Sustainability Initiatives: As sustainability becomes more critical, automated lines will increasingly adopt green technologies, focusing on reducing material waste, energy consumption, and the environmental impact of manufacturing processes.
In conclusion, an automated line for sheet forming offers a highly efficient, flexible, and precise way to manufacture sheet metal components, making it an invaluable asset for industries requiring high-volume production with consistent quality. With advancements in automation, robotics, and AI, these lines will continue to evolve, offering manufacturers the ability to meet the growing demands for customized, high-quality, and environmentally friendly products.
An automated sheet forming line offers a comprehensive solution for high-precision, high-efficiency manufacturing of sheet metal components. It integrates various processes, from material loading and cutting to forming, bending, and quality control, creating a seamless workflow that minimizes manual intervention and maximizes throughput. Automation plays a pivotal role in improving production efficiency, reducing costs, and maintaining consistent quality throughout the manufacturing cycle.
At its core, the system utilizes advanced control technologies, such as programmable logic controllers (PLC) and computer numerical control (CNC) systems, allowing operators to program specific tasks and adjust parameters to accommodate different designs or specifications. These systems ensure that each stage of production runs smoothly, with machines operating in harmony to deliver precise and accurate results, reducing errors and the need for frequent retooling.
Robotics further enhances the efficiency of automated sheet forming lines. Robots can be deployed to perform tasks such as material handling, loading and unloading parts, and conducting secondary operations like welding or assembly. Their ability to work continuously and with high precision increases productivity while reducing human error and fatigue. The flexibility of these robotic systems allows them to handle a variety of materials, sizes, and shapes, adapting quickly to changes in production requirements.
The integration of machine vision systems plays a critical role in ensuring that parts meet high-quality standards. These systems can detect defects, dimensional inaccuracies, and surface imperfections in real time, allowing for immediate adjustments or rejection of faulty parts. By automating the inspection process, the system ensures consistent quality and minimizes the chances of defects reaching the customer, reducing scrap and rework.
The use of servo motors and linear actuators provides fine control over the movement and forces applied during each operation. Whether cutting, bending, or stamping, these actuators ensure that the correct amount of force is applied with precision, resulting in high-quality, defect-free parts. This level of control allows for quick adjustments between different part designs, further enhancing the system’s flexibility and reducing setup times.
Automated sheet forming lines are designed with energy efficiency in mind. By utilizing servo-driven systems, energy consumption is optimized based on the specific demands of the task at hand. Unlike traditional mechanical or hydraulic systems that operate at full power throughout the entire process, servo motors adjust power usage to match the exact requirements of each operation, reducing overall energy costs and contributing to more sustainable manufacturing practices.
The material handling process in an automated sheet forming line is critical for ensuring that raw materials are efficiently fed into the system and that finished parts are correctly sorted and packaged. Automated material handling systems can move sheets of metal into cutting or forming stations, where they are precisely aligned and fed through each step in the production process. Conveyors, robotic arms, and other automated systems work together to move materials with minimal human intervention, reducing labor costs and the risk of errors.
As the sheet metal progresses through the various stages, secondary operations like tapping, deburring, and welding can also be automated. These operations can be carried out by robotic arms equipped with specialized tools, ensuring that each part meets the required specifications. The integration of secondary operations into the automated line reduces the need for additional machines and setups, making the entire production process more efficient.
Predictive maintenance is becoming increasingly important in automated sheet forming lines. By integrating sensor technologies and real-time data monitoring, manufacturers can predict when a machine is likely to fail or require maintenance. This proactive approach reduces downtime, minimizes production interruptions, and extends the lifespan of machines, ultimately improving overall productivity and reducing maintenance costs.
Cloud-based platforms are also playing a more prominent role in automated manufacturing systems. By connecting machines to cloud services, manufacturers can remotely monitor the performance of their sheet forming lines, track production data, and receive alerts on potential issues. This level of connectivity improves operational visibility, allowing manufacturers to make data-driven decisions that optimize production efficiency and improve supply chain management.
Sustainability is becoming a key focus in the development of automated sheet forming lines. Manufacturers are increasingly adopting green technologies that reduce waste, lower energy consumption, and use eco-friendly materials. Automated lines can incorporate material recycling systems to reclaim scrap metal and reuse it in the production process, reducing material costs and environmental impact. Furthermore, energy-efficient machines and systems help to lower the carbon footprint of the manufacturing process.
As customization becomes more important to consumers, automated sheet forming lines are evolving to accommodate high-mix, low-volume production runs. The ability to quickly change between different product designs and part configurations without significant downtime makes these systems ideal for manufacturers that need to respond to frequent design changes or customer-specific requests. This flexibility allows manufacturers to stay competitive in industries where product innovation and customer customization are critical.
In the future, artificial intelligence (AI) and machine learning (ML) will play an even greater role in optimizing the performance of automated sheet forming lines. By analyzing large volumes of production data, AI algorithms can identify inefficiencies, predict potential failures, and even optimize machine settings for better performance. These technologies will further enhance the automation of manufacturing processes, making them more intelligent, adaptive, and capable of handling complex tasks without human intervention.
Ultimately, an automated sheet forming line represents a major advancement in manufacturing, offering a range of benefits, including higher productivity, better quality control, reduced labor costs, and increased sustainability. By integrating robotics, machine vision, AI, and cloud-based technologies, these lines are poised to become even more efficient, flexible, and capable of meeting the ever-evolving demands of modern industries.
As the evolution of automated sheet forming lines continues, several exciting advancements and trends are poised to shape the future of manufacturing, driving further efficiency, flexibility, and sustainability. These innovations aim to address the challenges faced by manufacturers, such as increasing demand for customization, maintaining high production rates, and meeting stricter environmental standards.
One of the most notable trends is the continued integration of advanced robotics. As robotic capabilities improve, we are seeing more complex tasks being handled by robots, such as fine-tuning sheet metal shapes, advanced welding techniques, and even automated quality inspection. Collaborative robots (cobots), designed to safely work alongside human operators, will become more common, helping to bridge the gap between manual and automated labor. These cobots can be used for tasks that require human dexterity, such as assembly or fine-tuning, while robots handle the heavy lifting and repetitive processes.
Moreover, the integration of artificial intelligence (AI) and machine learning (ML) technologies will enhance the adaptability of automated sheet forming lines. These technologies will allow systems to learn from historical production data, identify patterns, and continuously improve their performance. AI and ML will enable predictive maintenance capabilities, where the system can forecast potential machine failures or inefficiencies, preventing unexpected downtimes and reducing maintenance costs. Additionally, AI will help optimize the production process by adjusting parameters such as speed, pressure, and temperature in real-time based on incoming data from sensors and quality control systems.
The application of Internet of Things (IoT) technology in automated sheet forming lines is also expanding. IoT-connected sensors embedded in machinery can communicate with each other and with central control systems, providing valuable data about machine performance, material flow, and process conditions. This real-time feedback allows manufacturers to make immediate adjustments, track performance metrics, and proactively address any issues that arise during production. Additionally, IoT integration helps manufacturers achieve end-to-end traceability of the production process, ensuring that every part can be tracked from its initial material state to the final product.
As sustainability becomes a driving force in global manufacturing, automated sheet forming lines are being designed with energy efficiency and environmental considerations in mind. For instance, manufacturers are increasingly using energy-efficient motors and regenerative braking systems in automated equipment. These innovations reduce overall power consumption and make it easier for manufacturers to meet increasingly stringent energy efficiency standards. Additionally, the reuse and recycling of materials are being prioritized, with systems designed to reclaim scrap metal and repurpose it into the production process, reducing material waste and lowering raw material costs.
The development of hybrid manufacturing systems, which combine traditional subtractive processes like stamping and cutting with additive manufacturing techniques like 3D printing, is another exciting trend. By blending these two methods, manufacturers can produce highly complex parts with intricate internal geometries or customized features that would be difficult or impossible to achieve using conventional sheet metal forming techniques alone. This hybrid approach also offers the advantage of reducing material waste by enabling more precise part design and material usage.
Furthermore, cloud-based platforms are becoming increasingly vital in the management of automated sheet forming lines. Cloud computing allows manufacturers to access real-time data from their production lines, monitor machine performance remotely, and integrate the system with other manufacturing processes across the supply chain. This level of connectivity not only improves operational visibility but also enables manufacturers to collaborate more effectively across different locations, enhance decision-making, and quickly adjust production schedules based on demand fluctuations.
The digital twin technology is also gaining traction in automated sheet forming systems. A digital twin is a virtual replica of a physical asset, such as a machine or entire production line, that allows manufacturers to simulate and monitor performance in real time. By using digital twins, manufacturers can run simulations to predict outcomes, test new configurations, or troubleshoot problems without the need to physically stop production. This leads to faster response times, reduced downtime, and better overall efficiency.
Another key development in automated sheet forming is the improvement of smart material handling systems. These systems use AI-powered robots and vision-guided automation to detect, track, and manipulate parts as they move through the line. Advanced material handling technologies, such as automated guided vehicles (AGVs) and automated palletizing systems, ensure that parts are moved efficiently and correctly, minimizing human intervention and reducing the likelihood of errors in part orientation or misplacement.
Flexibility in automated systems is also becoming more important as manufacturers are increasingly required to produce smaller batches with varying designs. This flexibility is facilitated by the development of multi-functional machines that can handle multiple forming processes, from cutting and stamping to bending and welding, all within the same line. This eliminates the need for multiple dedicated machines, streamlining the production process and enabling manufacturers to quickly switch between different product designs without extensive retooling.
The growing demand for customized products is another area where automated sheet forming lines excel. With programmable setups, manufacturers can respond to market changes and customer-specific requests without long lead times. The automation of this process reduces the complexity of switching between different part designs and configurations, allowing companies to produce a wide variety of products with high precision and minimal setup time.
The future of automated sheet forming lines also lies in the integration of big data analytics. With advanced data collection and analytics platforms, manufacturers can gather vast amounts of information from sensors, machines, and production processes. This data can be analyzed to uncover insights that drive improvements in efficiency, quality, and throughput. Predictive analytics will play a central role in forecasting production trends, adjusting manufacturing processes, and optimizing inventory management, leading to more efficient operations and reduced costs.
In addition to these technological advancements, the human element in automated sheet forming lines will also evolve. While automation reduces the need for manual labor in many areas, skilled operators will continue to play a vital role in overseeing system operations, making high-level decisions, and managing the integration of new technologies. Manufacturers are focusing on upskilling workers to operate advanced systems and interpret the data generated by these machines, ensuring that the workforce remains adaptable and capable of handling the complexities of modern manufacturing.
In conclusion, the future of automated sheet forming lines will be marked by even greater integration of advanced technologies like AI, IoT, cloud computing, digital twins, and robotics. These innovations will enhance the flexibility, efficiency, and sustainability of automated systems, allowing manufacturers to respond quickly to changing customer demands, reduce waste, and improve product quality. As these systems evolve, manufacturers will be better equipped to meet the challenges of modern production, maintaining competitiveness in an increasingly globalized and fast-paced market.
Metal Sheet Forming Automation Setup
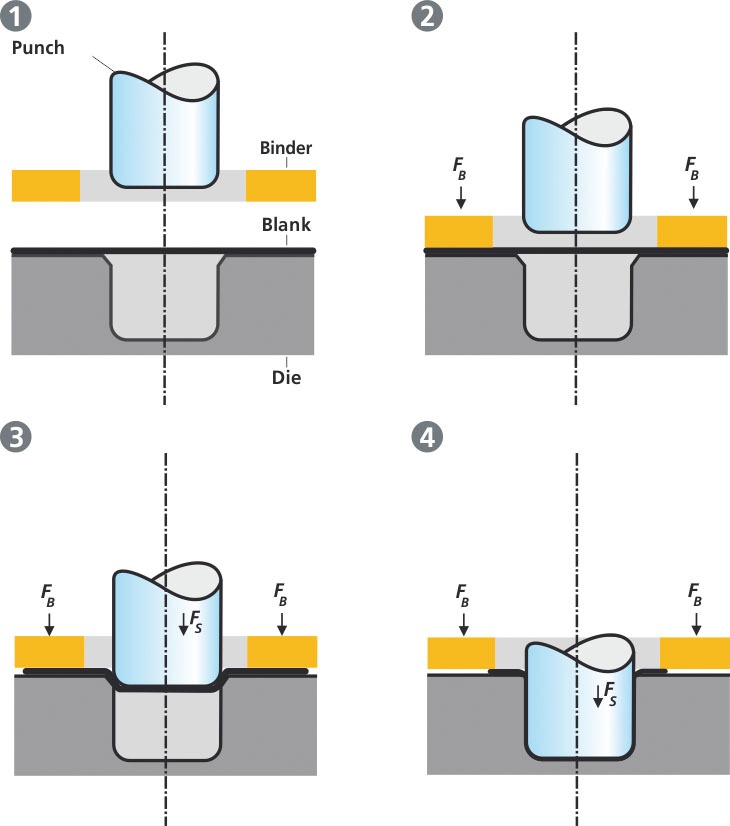
A metal sheet forming automation setup refers to a fully automated system designed to handle the various stages of sheet metal processing, including cutting, forming, bending, stamping, punching, and assembly. This system is engineered to streamline production workflows, enhance precision, increase speed, and minimize the need for manual labor, all while maintaining high-quality standards. Such setups are widely used in industries like automotive, aerospace, construction, electronics, and appliances, where sheet metal components need to be produced with consistency and efficiency.
An automated metal sheet forming system is typically composed of several key components and stages, each optimized for specific tasks. The system utilizes robotics, advanced control systems, sensors, and feedback loops to ensure that parts are processed accurately and efficiently.
Key Components of a Metal Sheet Forming Automation Setup:
- Material Handling and Feeding Systems: The setup begins with an automated material handling system that retrieves metal sheets from storage or input areas and feeds them into the forming line. These systems can be conveyors, robotic arms, or automated guided vehicles (AGVs), which ensure that sheets are aligned correctly and fed into the first machine with high precision.
- Cutting and Blanking Stations: After feeding, the first operation typically involves cutting the metal sheet to the desired size or blanking it into specific shapes. Automated systems such as laser cutting machines, water jet cutters, or punch presses are used for this task. These machines are controlled by CNC (computer numerical control) systems, which enable precise cutting according to design specifications. Automated blanking ensures that the sheet is ready for further processing without the need for manual measurements or adjustments.
- Forming and Bending Stations: After the sheets are cut or blanked, they are moved to forming stations where various shaping operations are performed. This can include bending, deep drawing, or stretch forming depending on the design. Machines like press brakes, hydraulic presses, and roll formers are often used to bend or shape the material to the required dimensions. These stations are equipped with servo motors and actuators that provide precise control over the amount of force applied, ensuring high precision and repeatability.
- Stamping and Punching Stations: For parts that require holes or intricate shapes, stamping or punching operations are performed. Automated punch presses and progressive die stamping systems can handle high-speed operations for mass production of parts with consistent quality. These stations can also incorporate automated die changeovers to quickly adjust to different part designs.
- Secondary Operations (Welding, Tapping, Deburring): Once the primary forming and shaping tasks are completed, secondary operations such as welding, deburring, tapping, or coating can be integrated into the automated line. For example, robotic welding cells or spot welding machines can automatically join metal parts together, while robotic arms can handle deburring to remove sharp edges. Other operations like surface coating or painting can also be automated to apply protective layers or finishes on the formed parts.
- Inspection and Quality Control: Automated quality control systems play a crucial role in ensuring that the finished parts meet the required specifications. Vision systems, laser scanners, and 3D measurement tools are often used for real-time inspection during the production process. These systems detect defects such as dimensional inaccuracies, surface imperfections, or alignment issues. If a defect is detected, the system can make immediate adjustments or alert operators for intervention.
- Packaging and Sorting Systems: After all the forming, shaping, and quality control processes are complete, the parts are moved to packaging and sorting stations. Robotic arms or automated sorting conveyors can handle the grouping, stacking, or packaging of finished parts. This ensures that parts are delivered to the correct location or packaged for shipping without manual handling, reducing labor costs and improving productivity.
- Control Systems and Automation Software: The entire automated sheet forming setup is controlled through a centralized control system, which manages the flow of materials, coordinates machine operations, and ensures synchronization between all components. PLC (programmable logic controllers) or CNC systems manage machine functions and collect data from sensors to monitor performance. Manufacturing Execution Systems (MES) and Enterprise Resource Planning (ERP) software can also be integrated into the setup to monitor production status, track material usage, and ensure efficient resource management across the entire operation.
Benefits of an Automated Metal Sheet Forming Setup:
- Increased Efficiency: Automation speeds up the production process by eliminating manual handling and reducing cycle times. This leads to higher throughput, faster time-to-market, and improved overall productivity.
- Precision and Consistency: Automated machines, controlled by CNC or PLC systems, deliver highly accurate results with minimal deviation from design specifications. This consistency ensures that parts meet strict quality standards, reducing the likelihood of defects and waste.
- Reduced Labor Costs: By automating repetitive tasks such as material handling, cutting, and forming, manufacturers can reduce the number of operators required on the production floor, thus cutting labor costs.
- Flexibility and Scalability: Automated setups are flexible and can be reprogrammed or adjusted to handle different types of sheet metal products. This flexibility makes them suitable for both high-volume production runs and low-volume, high-mix orders. Manufacturers can easily switch between different product designs with minimal downtime.
- Enhanced Quality Control: Automated inspection systems ensure that parts are constantly monitored for defects, reducing the risk of defective parts reaching customers. Real-time feedback allows for quick adjustments to the production process, preventing quality issues before they escalate.
- Safety: Automation reduces the risk of human error and minimizes worker exposure to hazardous environments. Robots can handle dangerous tasks, such as welding or high-speed cutting, keeping workers safe and reducing workplace injuries.
- Sustainability: Automated metal forming lines can incorporate features like material reclamation systems, which reduce waste by recycling scrap metal. Energy-efficient equipment helps lower power consumption, contributing to more sustainable manufacturing practices.
Future Trends in Metal Sheet Forming Automation:
The future of metal sheet forming automation lies in the continued integration of cutting-edge technologies. Artificial intelligence (AI) and machine learning (ML) will play an increasingly significant role in optimizing production processes. These technologies will help predict machine maintenance needs, identify inefficiencies, and optimize machine settings in real time. Additionally, advancements in robotics will allow for even more intricate and adaptable manufacturing processes, enabling the production of complex parts with ease.
Cloud-based systems will continue to be integrated into automation setups, allowing for real-time monitoring, remote access, and improved data analysis. Smart sensors and Internet of Things (IoT) technology will enable better monitoring and control of production lines, providing insights into machine performance, material usage, and energy consumption.
With the rise of customization and on-demand production, automated sheet forming lines will become even more flexible, enabling manufacturers to respond quickly to customer requirements with smaller batch sizes and faster changeover times. Additionally, additive manufacturing (3D printing) may be integrated into sheet forming lines, enabling hybrid processes that combine traditional and additive techniques for creating complex geometries.
In conclusion, a metal sheet forming automation setup offers a highly efficient, flexible, and scalable solution for producing high-quality sheet metal components. By integrating advanced technologies such as robotics, AI, machine vision, and IoT, these systems will continue to evolve, providing manufacturers with new opportunities to improve production processes, reduce costs, and meet the ever-growing demand for precision and customization in metal fabrication.
An automated metal sheet forming setup is designed to streamline the entire process of sheet metal production, eliminating the need for extensive manual labor while ensuring high precision, consistency, and efficiency. By integrating a series of interconnected systems, from material handling to forming, bending, punching, and even quality control, the automation setup works cohesively to achieve the optimal production process. The system is equipped with advanced control technologies such as CNC (Computer Numerical Control) systems and PLC (Programmable Logic Controllers) that guide the machines through precise operations, ensuring that each step aligns with the required specifications.
At the beginning of the process, the automated setup begins with material handling systems, which are responsible for transporting sheets of metal from storage to the production area. These systems often include conveyors, robotic arms, or automated guided vehicles (AGVs) that transport the metal sheets to various processing stations. The automation of material handling reduces manual labor and ensures that sheets are fed into the system in the correct orientation and at the appropriate speed.
Once the material is positioned, the first major step typically involves cutting or blanking the metal sheets. This can be achieved using automated laser cutters, water jet cutters, or punch presses, each of which is guided by CNC or other advanced control systems. These cutting processes are highly accurate, producing clean edges and shapes that are ready for further processing.
The next stage usually involves forming or bending the metal to the desired shape. Press brakes, hydraulic presses, and roll formers are used to apply controlled force to the sheet metal, bending it according to the design specifications. The automation in these stations helps ensure that each bend or form is executed precisely, minimizing waste and reducing the likelihood of errors in the final product. Advanced systems equipped with servo motors and linear actuators provide the ability to apply fine-tuned control over force, angle, and speed, improving both the flexibility and accuracy of the process.
For parts that require holes or other complex features, punching or stamping stations are integrated into the line. These machines can operate at high speeds, cutting or shaping the metal to produce holes, slots, or intricate patterns. Progressive die stamping is often employed to produce multiple parts simultaneously in a single pass, increasing production rates and improving efficiency.
Secondary operations such as welding, deburring, tapping, and coating are also incorporated into the automation setup. Robotic welding cells or spot welding machines can automatically join metal parts, ensuring consistent and high-quality welds. Similarly, robotic arms handle deburring tasks, removing sharp edges and improving the safety and appearance of the parts. Tapping and threading operations, as well as surface treatments like coating or painting, can also be automated, reducing the need for separate machines and minimizing the overall production footprint.
Quality control is a crucial aspect of the setup, and automated systems such as vision-based inspection and laser scanning are used to monitor the parts throughout the process. These systems can identify defects, dimensional inaccuracies, and surface imperfections, allowing for real-time corrections to be made. This ensures that only parts meeting the required quality standards are produced, reducing waste and ensuring customer satisfaction.
Once the parts are completed, they move to packaging and sorting stations, where they are organized and prepared for shipment. Automated sorting conveyors or robotic arms can be used to arrange finished parts in a specific order, package them, or prepare them for delivery, further reducing the need for manual labor in the final stages of production.
In terms of control, the entire system operates under a unified network that allows operators to monitor and adjust the flow of materials, coordinate machines, and ensure that everything is functioning smoothly. PLC systems or supervisory control and data acquisition (SCADA) systems provide a real-time view of the production status, allowing for adjustments to be made as necessary to maintain optimal throughput and minimize downtime.
The automation of sheet metal forming provides numerous advantages, such as increased efficiency, reduced labor costs, and improved product quality. With precise control over the entire production line, the system ensures that parts are consistently manufactured to exact specifications, reducing the risk of defects. The integration of machine learning and AI technologies into the setup allows for predictive maintenance, where potential issues with equipment can be identified and addressed before they cause significant downtime, thus enhancing system reliability.
As industries demand higher levels of customization and flexibility, automated metal sheet forming systems are evolving to handle smaller production runs and frequent changes in part designs. The ability to quickly adjust machine settings or switch between different types of products without significant downtime is a critical feature in modern manufacturing. This adaptability ensures that manufacturers can meet customer needs without sacrificing efficiency.
Sustainability is another growing focus within automated metal forming systems. The use of energy-efficient motors, systems for material recycling, and advanced energy recovery technologies are helping manufacturers reduce their environmental impact. Additionally, the automation setup often incorporates more precise material handling, reducing the amount of scrap generated during production and increasing overall material utilization.
Looking toward the future, digital twin technology is expected to play a bigger role in these setups. By creating virtual replicas of the physical production line, manufacturers can simulate different production scenarios, optimize workflows, and predict potential issues before they arise. This helps improve both the planning and performance of automated systems, leading to increased efficiency, reduced waste, and better resource management.
As the use of robotics and AI continues to advance, it is likely that even more complex tasks—such as intricate forming or multi-step assembly processes—will become automated, making metal sheet forming lines even more efficient, flexible, and capable of handling a broader range of products.
Ultimately, the automated metal sheet forming setup is poised to revolutionize the way metal components are produced, driving further advancements in precision, speed, and sustainability. With the integration of smart technologies, advanced robotics, and data analytics, these systems are not only improving manufacturing capabilities but also creating new opportunities for manufacturers to respond to rapidly changing demands in the market.
As automation in metal sheet forming continues to advance, the future of these systems will likely see even more sophisticated integrations of emerging technologies and innovative approaches that redefine manufacturing standards. The push for higher efficiency, lower costs, and greater flexibility will drive the development of highly adaptable systems capable of managing complex, multi-step processes with minimal human intervention.
One of the most exciting developments is the increased adoption of artificial intelligence (AI) and machine learning (ML), which will enable automated metal sheet forming lines to not only monitor real-time data but also predict and optimize production outcomes. These technologies will enable the systems to make intelligent decisions on the fly, adjusting machine settings to account for variations in materials, product specifications, and production conditions. AI will also facilitate advanced predictive maintenance, where machine learning algorithms analyze historical data and sensor inputs to forecast potential issues before they lead to equipment failure or downtime, thus ensuring continuous and efficient operation.
Additionally, AI-powered systems will improve quality control by detecting even the smallest defects in parts during the production process. Through image recognition and vision systems, AI can be trained to identify issues that are too subtle for traditional inspection methods. This not only ensures higher-quality products but also increases throughput by reducing the need for manual quality checks.
Robotic automation will continue to evolve, becoming more flexible and capable of handling a wider range of tasks in sheet metal forming lines. Robots will become increasingly adept at performing tasks that require higher levels of dexterity and precision. Collaborative robots (cobots), designed to work alongside human operators, will be widely implemented to assist in assembly tasks, fine-tuning operations, and performing detailed work such as intricate bends or spot welding in small batches. This will further increase productivity and enable manufacturers to scale their operations while minimizing the workforce required for complex or repetitive tasks.
The growing interest in smart manufacturing will also transform how metal sheet forming lines are controlled and monitored. Internet of Things (IoT) technology will play a critical role in connecting various elements of the production line. By embedding smart sensors into machines, material handling equipment, and even the metal sheets themselves, manufacturers can collect real-time data on every aspect of the process. These systems can then share this data with centralized platforms or cloud-based solutions to enable real-time decision-making. For example, if a sensor detects a slight deviation in material temperature or thickness, the system can automatically adjust the machine parameters to correct it before the issue affects the final product.
The integration of cloud computing will further extend these capabilities, allowing manufacturers to remotely monitor and manage production lines from any location. Cloud platforms will provide manufacturers with access to detailed data analytics, allowing them to track efficiency, identify areas for improvement, and optimize resource utilization. The ability to manage production processes remotely will become increasingly essential as manufacturers look to streamline operations across multiple facilities or respond to customer demands in real time.
Sustainability remains a key driver in the development of automated metal forming lines. To meet the growing demands for eco-friendly production practices, manufacturers are focusing on energy-efficient equipment and sustainable materials. As the industry faces stricter environmental regulations, automated systems will be designed to optimize power consumption, reduce waste, and ensure compliance with environmental standards. For instance, energy recovery systems will allow machines to reuse power from actions like braking or during idle time, improving overall energy efficiency. Additionally, automated systems will help minimize material waste by using more accurate cutting, stamping, and forming techniques, as well as facilitating the recycling of scrap metal during production.
Another aspect of sustainability is the potential for additive manufacturing (AM), or 3D printing, to integrate with traditional sheet metal forming processes. Hybrid systems that combine traditional forming methods with additive manufacturing could become more common, enabling manufacturers to create more complex geometries or produce components with features that would be difficult to achieve through conventional means. This could result in lighter, stronger, and more efficient parts that are tailored to specific needs, all while reducing material waste.
The demand for customization in metal products is rapidly growing, particularly in industries like automotive and aerospace, where unique or bespoke components are frequently required. Automated sheet forming lines will increasingly be able to cater to these demands by providing high levels of flexibility. Advanced servo-controlled machines and multi-functional tooling systems will allow for quick and easy changes between different product designs without requiring extensive retooling or downtime. The ability to program machines for short runs or rapid product changes will enable manufacturers to serve both mass production needs and niche markets, while minimizing lead times.
Furthermore, digital twins—virtual models of the production line—are likely to become integral in modern automated setups. By simulating the entire process, manufacturers can experiment with different configurations, predict machine behavior, and optimize performance before making physical adjustments. Digital twins will allow for real-time monitoring of the actual production line, ensuring that the system operates at peak efficiency. These models will also enable manufacturers to simulate potential failure scenarios and proactively address issues, improving operational reliability.
Another trend that will shape the future of automated sheet metal forming is the increased use of modular manufacturing systems. These systems consist of flexible, interchangeable modules that can be combined in various configurations to form different production lines. This modular approach offers manufacturers the ability to quickly reconfigure their production lines for new products or processes, providing greater flexibility in adapting to changing customer demands or market conditions. Modular systems can also reduce downtime during system upgrades or retooling, which is crucial for maintaining production continuity.
As automation continues to evolve, the human element in metal sheet forming will also change. While machines and robots will handle the bulk of the work, human operators will play an increasingly important role in overseeing operations, interpreting data, and making strategic decisions. The need for skilled workers who can manage, troubleshoot, and optimize automated systems will increase. Manufacturers will need to invest in training programs and upskilling initiatives to ensure that their workforce is equipped to handle the complexities of advanced manufacturing systems.
In the future, the entire lifecycle of a product—from design and production to end-of-life recycling—will become more integrated within the automated sheet forming line. Manufacturers will use data collected from every stage of production to optimize designs for manufacturability, ensure efficient material usage, and minimize waste. Additionally, automated systems will likely be linked with post-production systems that handle packaging, distribution, and even recycling, creating a closed-loop production system that reduces the environmental impact of manufacturing.
In conclusion, the future of automated metal sheet forming lines will be defined by the integration of smart technologies like AI, IoT, robotics, and cloud computing. These advancements will enable manufacturers to achieve higher efficiency, greater flexibility, and improved sustainability in their operations. As customization becomes more important and demand for precision increases, automated systems will provide manufacturers with the tools they need to meet evolving market needs while maintaining competitiveness and reducing costs. With continued innovations, the automation of sheet metal forming will play a pivotal role in transforming modern manufacturing processes across various industries.
Automated Sheet Forming Production Line
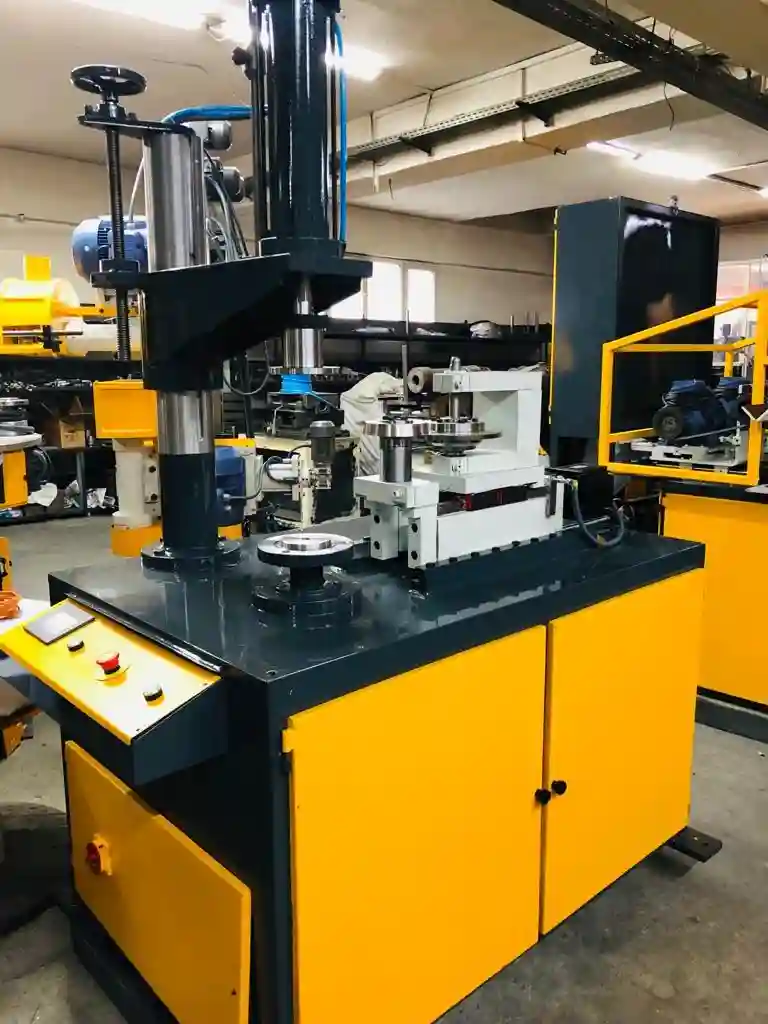
An Automated Sheet Forming Production Line is an advanced manufacturing setup designed to automatically process and shape sheet metal into a wide range of products. These systems are typically employed in industries such as automotive, aerospace, electronics, and construction, where precision, efficiency, and scalability are paramount. The automated system reduces human labor, improves production speed, enhances consistency, and ensures high-quality output, all while minimizing material waste and production downtime.
The core of an automated sheet forming production line includes several interconnected systems and processes, each focused on specific tasks like material handling, cutting, forming, bending, stamping, and quality control. These systems are powered by technologies such as CNC (Computer Numerical Control), robotics, machine vision, AI, and IoT (Internet of Things), enabling seamless automation and real-time adjustments for optimal performance.
Key Features of an Automated Sheet Forming Production Line:
- Material Feeding and Handling:
- The production line begins with an automated material handling system designed to move sheets of metal from storage to the processing area. This could involve robotic arms, conveyors, or automated guided vehicles (AGVs), all designed to transport the metal efficiently. The system ensures that the material is fed in the correct orientation and position, reducing errors that could arise from manual handling.
- Cutting and Blanking:
- The first step in processing is often cutting or blanking the metal to a predefined size or shape. This can be achieved using high-precision laser cutters, water jet cutters, or punch presses controlled by CNC systems. These automated cutters ensure that the metal is cut precisely and consistently, minimizing scrap and reducing labor costs associated with manual cutting.
- Forming and Shaping:
- After cutting, the metal sheets are transferred to forming stations, where they undergo processes like bending, stretch forming, or deep drawing. Machines such as press brakes, hydraulic presses, and roll formers are used to bend or shape the metal to match specific design requirements. These processes are highly controlled using servo motors, which allow for precise adjustment of force, angle, and speed, ensuring high-quality parts with minimal deviation from design specifications.
- Stamping and Punching:
- If the parts require holes, slots, or intricate shapes, the system integrates stamping and punching operations. Stamping presses and progressive die stamping systems are typically used to handle high-speed, high-volume tasks, creating detailed features in the metal sheets. These operations are highly automated and can produce multiple parts in a single stroke, increasing throughput and reducing cycle time.
- Secondary Operations (Welding, Deburring, Coating):
- Once the primary forming and shaping steps are complete, the parts may undergo secondary operations. Automated robotic welding systems or spot welders can join metal parts together, while deburring machines can remove sharp edges or excess material from the finished parts. Coating and painting can also be automated using robotic arms or spray systems, ensuring consistent and high-quality finishes.
- Inspection and Quality Control:
- Quality control is a critical component of automated sheet forming production lines. Automated vision systems, laser scanners, and 3D measurement tools monitor parts as they move through the line. These systems check for defects, dimensional inaccuracies, and surface imperfections. If a defect is detected, the system can automatically adjust machine settings or alert operators, ensuring that only high-quality parts reach the end of the line.
- Sorting and Packaging:
- After the parts have been formed, shaped, and inspected, they are automatically sorted and packaged. Robotic arms or automated conveyors are used to arrange the parts according to size, type, or customer specifications. The parts are then packaged, ensuring minimal manual intervention and a fast, efficient packaging process that prepares them for shipment.
- Control Systems and Data Integration:
- The entire production line is managed and controlled through an integrated system that uses PLC (Programmable Logic Controllers) or CNC systems. These systems ensure smooth coordination between each station, manage machine parameters, and collect data on production performance. MES (Manufacturing Execution Systems) or ERP (Enterprise Resource Planning) systems can be integrated to allow for real-time tracking, performance analysis, and efficient scheduling of tasks.
- Advanced Automation Technologies:
- The automation setup is enhanced with advanced technologies like AI, machine learning, and robotics to optimize production efficiency and reduce errors. AI algorithms can predict machine performance, enabling predictive maintenance and ensuring that machines are operating at optimal capacity. Robots and cobots (collaborative robots) work alongside human operators to handle intricate tasks and adapt to a wide variety of parts without extensive retooling.
- Sustainability and Energy Efficiency:
- In modern automated sheet forming lines, sustainability plays a significant role. Energy-efficient equipment and systems for material reclamation and scrap recycling are incorporated to minimize waste and reduce energy consumption. The integration of smart energy management systems ensures that machines consume power only when necessary, improving overall energy efficiency and reducing the environmental impact of production.
Benefits of an Automated Sheet Forming Production Line:
- Improved Efficiency: Automation dramatically reduces cycle times and increases throughput, allowing for faster production without compromising quality. This leads to better resource utilization, lower costs per unit, and quicker time-to-market.
- Enhanced Precision and Consistency: Automated systems provide high levels of precision, ensuring that each part meets strict design specifications. This eliminates variability caused by human error and enhances product consistency across large production runs.
- Reduced Labor Costs: Automation reduces the need for manual labor, especially for repetitive or dangerous tasks. This lowers labor costs, reduces the risk of workplace accidents, and improves worker safety.
- Flexibility and Scalability: Automated systems can be reprogrammed and reconfigured to accommodate different product designs or changes in production demand. This flexibility is especially valuable in industries that require frequent design changes or small batch production.
- Better Quality Control: Integrated quality control systems ensure that every part is inspected for defects as it moves through the production line. This reduces waste, ensures that only high-quality parts are shipped, and provides valuable data for process improvement.
- Increased Sustainability: Automation helps to reduce waste, recycle scrap material, and optimize energy consumption. These environmentally friendly practices contribute to a more sustainable manufacturing process.
- Advanced Data Analytics: By integrating IoT, AI, and machine learning, the production line can be continuously monitored, and performance data can be analyzed in real time. This data-driven approach helps optimize machine settings, predict maintenance needs, and improve overall production performance.
The Future of Automated Sheet Forming Production Lines:
The future of automated sheet forming production lines will likely see the continued integration of advanced robotics, artificial intelligence, and digital twin technology to further enhance production capabilities. Additive manufacturing may also play a larger role in hybrid systems, enabling the production of more complex parts and designs that are difficult to achieve through traditional forming methods. Furthermore, the increased focus on sustainability will drive the development of even more energy-efficient and environmentally friendly automation technologies.
As industries increasingly demand customized and on-demand production, automated systems will be capable of adapting quickly to new product requirements, providing manufacturers with the flexibility to meet changing customer needs. The continued development of machine learning and smart manufacturing systems will also lead to greater optimization and real-time decision-making, reducing downtime and increasing overall production efficiency.
In conclusion, an automated sheet forming production line offers manufacturers significant advantages in terms of efficiency, precision, and flexibility. By leveraging cutting-edge automation technologies, manufacturers can improve their production processes, reduce costs, and meet the demands of an increasingly complex and fast-moving market.
An automated sheet forming production line operates as an integrated system that efficiently converts raw metal sheets into finished components with minimal human intervention. It brings together various automated processes, from material handling to shaping, cutting, welding, inspection, and packaging, working seamlessly together to produce high-quality parts quickly and consistently. By automating these processes, manufacturers can achieve faster production cycles, reduce labor costs, minimize material waste, and ensure uniformity across large production runs.
The process begins with an automated material handling system that transports metal sheets from storage to the processing area. Using robotic arms, conveyors, or automated guided vehicles (AGVs), the system positions the metal precisely, ensuring it enters the production line in the correct orientation and at the proper speed. This automation reduces the risk of errors caused by manual handling and accelerates the flow of materials.
Once the material is in place, the next step involves cutting the metal sheets into blanks or specific shapes. Using advanced cutting technologies such as laser cutting, water jet cutting, or high-speed punching presses, the system performs the task with high precision and minimal waste. These processes are all controlled by CNC systems that ensure each cut is made according to the exact specifications required.
After cutting, the metal moves to the forming stations where various shaping processes are performed. Using machines like press brakes, hydraulic presses, and roll formers, the metal is bent, stretched, or molded into the desired shape. These systems are powered by servo motors, which allow for fine control of bending angles, speed, and force, ensuring accuracy and minimizing variations in product quality.
In cases where the parts require holes or intricate features, the production line incorporates stamping and punching machines. These machines are capable of processing high volumes of metal quickly, producing parts with complex shapes or patterns with minimal cycle time. Progressive die stamping systems are often used to perform multiple operations in a single pass, increasing throughput while maintaining consistency.
Once the primary shaping is complete, the line may incorporate secondary operations, such as welding, deburring, and coating. Robotic welding systems handle the assembly of parts, ensuring strong and precise welds without the need for manual labor. After welding, automated deburring systems remove sharp edges and excess material, improving both the safety and finish of the parts. Automated coating and painting systems provide a consistent finish across all parts, further enhancing their durability and appearance.
Throughout the production process, the quality of each part is closely monitored using advanced inspection technologies, such as vision systems, laser scanners, and 3D measurement tools. These systems detect defects, dimensional discrepancies, and surface imperfections. If any issues are identified, the system can automatically adjust machine settings or alert operators to prevent defective products from moving further down the line.
Once the parts are formed and inspected, they are sorted, packaged, and prepared for shipment. Robotic arms or automated conveyors can sort the parts according to size, type, or customer specifications, reducing manual labor in the packaging process. Automated packaging systems then secure the parts, ensuring that they are ready for delivery without any additional human intervention.
Control of the entire production line is managed through integrated systems, such as PLCs (Programmable Logic Controllers) or CNC controllers. These systems synchronize the machines, monitor performance, and make real-time adjustments to optimize production efficiency. By collecting data from all stages of the process, manufacturers can gain valuable insights into production performance and identify areas for improvement.
The incorporation of advanced technologies like AI, machine learning, and IoT enhances the system’s capability to learn, adapt, and predict future outcomes. AI systems can analyze performance data and adjust machine settings in real time to optimize production based on factors such as material quality, machine wear, and operational conditions. IoT sensors embedded throughout the production line provide real-time data on machine health, material conditions, and production progress, allowing operators to make informed decisions and preemptively address potential issues before they cause significant downtime.
The sustainability aspect of automated sheet forming lines is increasingly important. These systems are designed to minimize material waste by using precise cutting, bending, and stamping techniques. Scrap metal generated during production can be recycled back into the system, reducing waste and lowering material costs. Additionally, energy-efficient motors and systems for energy recovery, such as regenerative braking, reduce the overall power consumption of the production line, helping manufacturers meet environmental standards and reduce their carbon footprint.
As demand for customization and flexibility in manufacturing grows, automated sheet forming systems are evolving to accommodate smaller production runs, quick changes in design, and the ability to handle complex geometries. Modular and flexible production setups allow manufacturers to easily switch between different products or designs without significant downtime, improving the overall agility of the production process. This flexibility is particularly valuable in industries like automotive or aerospace, where rapid design changes and bespoke components are common.
The future of automated sheet forming production lines will likely include even more advanced integrations of robotics, AI, and machine learning. For instance, collaborative robots (cobots) could be deployed to work alongside human operators for tasks that require fine dexterity or troubleshooting, improving efficiency and safety. Digital twin technology, which involves creating a virtual replica of the entire production line, could be used to simulate different production scenarios, optimize workflows, and predict potential failures, thus improving the reliability and performance of the system.
As these technologies continue to evolve, automated sheet forming lines will become more intelligent, adaptable, and capable of meeting the growing demands for faster production, higher precision, and greater sustainability. The increased use of data analytics and predictive maintenance will allow manufacturers to optimize their operations further, ensuring that the production lines run at peak efficiency and that any potential issues are addressed proactively.
Overall, an automated sheet forming production line offers numerous advantages, from improved quality and efficiency to lower operational costs and reduced environmental impact. By embracing the latest advancements in automation, manufacturers can stay competitive in an increasingly fast-paced and complex market, meeting customer demands while maintaining high standards of quality and sustainability.
As the landscape of automated sheet forming production lines evolves, further advancements in technology will continue to push the boundaries of what is possible in manufacturing. One key area that will shape the future is the development and integration of smart manufacturing systems. These systems are equipped with sophisticated sensor networks, AI-driven decision-making algorithms, and cloud-based platforms that provide real-time data and allow for remote monitoring and control of the production line.
With IoT sensors embedded throughout the production equipment, each machine and system within the line can generate detailed data, which can then be analyzed using advanced data analytics platforms. This real-time data feeds into predictive maintenance algorithms, allowing the system to foresee wear and tear on equipment before it results in failures or costly downtime. By identifying and addressing maintenance needs proactively, manufacturers can reduce machine downtime, lower maintenance costs, and improve overall line efficiency.
Another significant advancement is the ability to leverage digital twins in the manufacturing process. A digital twin is a virtual replica of the production line, created using real-time data from sensors, machines, and the entire system. By simulating real-world conditions and running virtual tests, manufacturers can optimize the design and layout of the line, experiment with different process configurations, and predict outcomes without any physical changes. This not only helps identify potential issues but also provides valuable insights into energy consumption, material flow, and overall system performance.
As customization becomes more prevalent in consumer demands, automated systems are expected to become even more adaptable. Flexible manufacturing systems that integrate modular components and reconfigurable machines will allow for rapid changes in product designs without extensive downtime or retooling. Advanced robotics and cobots will further support this by being programmed to handle new tasks with ease, ensuring that production lines can handle both high volumes of standard parts and low-volume, highly customized parts, without compromising on efficiency or quality.
In line with growing demands for sustainability, automated sheet forming lines will integrate even more energy-efficient and resource-saving measures. For example, new innovations in energy recovery will allow systems to recapture and reuse energy that would otherwise be lost, such as the energy generated during braking or idle times. Additionally, the use of sustainable materials and recycling loops within the production process will continue to reduce waste and lower the environmental impact of manufacturing.
The future of automated sheet forming also includes a greater focus on supply chain integration. As more manufacturers turn to just-in-time (JIT) production systems, automated lines will need to be able to quickly adapt to fluctuations in material availability, production schedules, and customer demand. Blockchain technology could be used to improve supply chain transparency and traceability, allowing manufacturers to track the entire lifecycle of materials and parts, from sourcing to production, and even to recycling. This will ensure that companies maintain efficient production processes while staying compliant with regulatory requirements and sustainability goals.
Furthermore, the integration of advanced materials into automated sheet forming lines is expected to revolutionize product design and manufacturing capabilities. As industries demand lighter, stronger, and more complex materials, sheet forming lines will be equipped to process a wider variety of materials, including composite metals, alloys, and even advanced polymers. This will require enhanced precision and control systems to account for the varying properties of these materials, but it will enable manufacturers to create products that meet the specific performance requirements of next-generation applications, such as electric vehicles, aerospace components, and renewable energy technologies.
Finally, the human role in the future of automated sheet forming will evolve to focus more on overseeing, optimizing, and troubleshooting systems rather than performing manual tasks. As machines take over routine operations, human operators will act more as supervisors, interpreting data from machine learning algorithms, adjusting settings based on real-time conditions, and ensuring that the production line runs smoothly. The need for skilled workers in areas such as robotics programming, AI model training, and data analysis will grow significantly, requiring manufacturers to invest in continuous training and workforce development programs.
The collaboration between human and machine will be further enhanced by the use of cobots that work alongside human operators to handle tasks that are either too dangerous, too repetitive, or too delicate for humans alone. These robots will be designed with advanced sensing technologies, allowing them to work safely in close proximity to human workers and assist with tasks such as material handling, part assembly, and quality inspection. This collaborative approach will increase productivity while maintaining safety and flexibility in the manufacturing process.
In conclusion, the future of automated sheet forming production lines will be marked by a convergence of technologies that enable smart, flexible, sustainable, and efficient manufacturing. Automation will continue to reduce the reliance on manual labor, improve product quality, and accelerate production speeds, while AI, robotics, and IoT will create more intelligent systems that optimize performance and adapt to changing demands. With these advancements, manufacturers will be better equipped to meet the increasing demands for custom products, sustainable production practices, and high-performance components across a wide range of industries.
Robotic Sheet Shaping Line
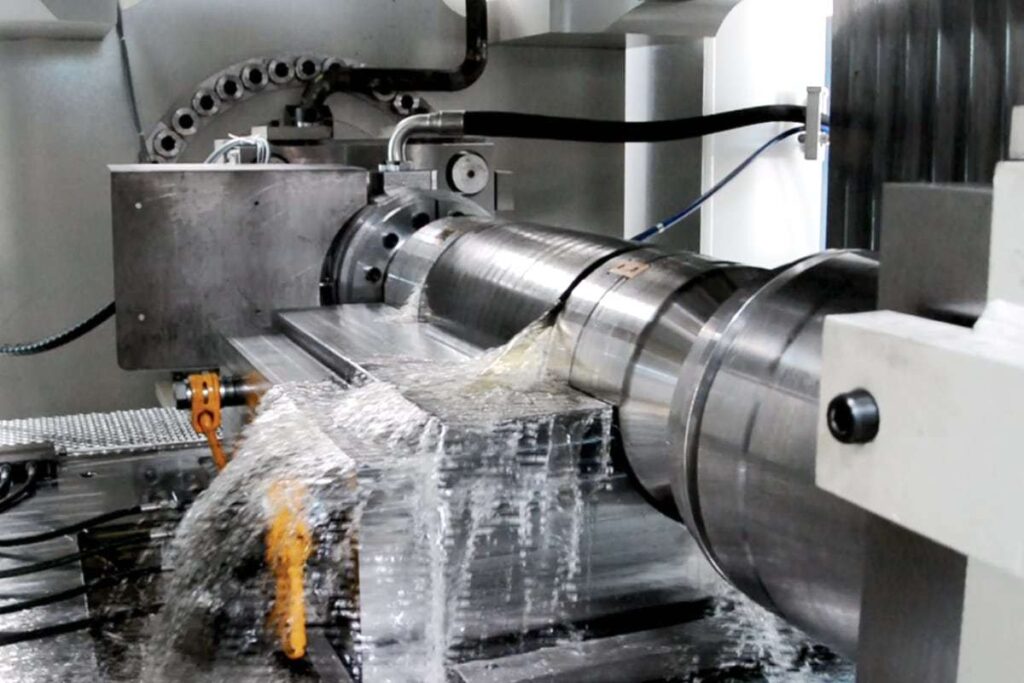
A Robotic Sheet Shaping Line is an advanced manufacturing system that integrates robotics with traditional sheet metal forming processes to achieve high levels of precision, flexibility, and efficiency in shaping sheet metal. This system is designed to automatically handle, manipulate, and shape sheet metal into various complex forms without the need for extensive human intervention. The line leverages robotic arms, automated systems, and advanced sensors to improve production speed, consistency, and quality, making it suitable for industries like automotive, aerospace, electronics, and construction.
The core of a robotic sheet shaping line involves a series of robotic arms or cobots (collaborative robots) equipped with various end-effectors, such as grippers, welding tools, or bending tools, to perform specific tasks. These robots are often integrated with CNC (Computer Numerical Control) systems, machine vision, and AI-driven algorithms, allowing them to execute precise operations while adapting to different product designs or production requirements.
A typical robotic sheet shaping line consists of several stages:
- Material Handling and Loading:
- The process begins with an automated material handling system that moves the sheet metal from storage to the processing area. Robotic arms equipped with vacuum grippers or magnetic tools are used to pick up, position, and load the sheet metal into the shaping stations. This reduces manual labor, minimizes the risk of damage to the material, and ensures precise positioning for the next steps.
- Cutting and Blanking:
- In the first step of shaping, robotic systems may work alongside automated cutting equipment such as laser cutters, plasma cutters, or water jet cutters to achieve highly accurate cuts in the sheet metal. The robots can position the metal at the right angles, ensuring precision in cutting and minimizing waste. Depending on the complexity of the design, CNC punching presses may also be integrated to handle blanking and punching operations.
- Forming and Bending:
- After cutting, the robotic arms can perform bending, stretch forming, or deep drawing on the sheet metal. For bending, the robot is often equipped with a press brake tool or bending die that applies precise force to bend the sheet into the required shape. The flexibility of the robotic arms allows them to perform multiple forming tasks without the need to reconfigure the system for each change in product design.
- Assembly and Welding:
- The robotic sheet shaping line may include robotic welding stations for joining parts together. These robotic systems can perform tasks like spot welding, TIG welding, or laser welding with exceptional speed and precision. The robots are programmed to handle complex welding paths, ensuring strong, clean welds while maintaining a high level of consistency. Robotic arms can also handle assembly tasks, such as aligning and securing parts before welding or fastening.
- Surface Treatment and Coating:
- After the sheet metal has been shaped and assembled, the parts may need surface treatment or coating. Robotic arms can be equipped with spray guns for applying paints, coatings, or anti-corrosion treatments. This automation ensures uniform coverage and a high-quality finish on every part. Additionally, robotic deburring systems can remove excess material and sharp edges, ensuring safety and smoothness.
- Inspection and Quality Control:
- Integrated vision systems allow the robotic arms to inspect parts as they move through the line. Using machine vision and 3D scanners, the robots can detect defects such as dimensional discrepancies, surface imperfections, or misalignment. The system can make real-time adjustments, reject defective parts, or notify operators if manual intervention is needed. This continuous quality control ensures that each part meets strict specifications, reducing the likelihood of defects reaching the final product stage.
- Packaging and Sorting:
- Once the parts are shaped, welded, and coated, they are ready for packaging. Robotic sorting systems can organize parts based on size, type, or customer specifications. Automated conveyors move the parts to packaging stations, where robotic arms can carefully pack the products into boxes or crates for shipment. This final stage eliminates manual handling and accelerates the time to market.
Key Benefits of a Robotic Sheet Shaping Line:
- Increased Precision and Consistency: The integration of robotics allows for high-precision tasks, ensuring consistent quality across every product. Robots can work with incredible accuracy, reducing human error and improving the overall reliability of the products.
- Flexibility and Adaptability: Robotic arms can be reprogrammed to handle various shapes, sizes, and designs, making the system adaptable to changing production requirements. This flexibility allows manufacturers to produce a wide range of products without significant downtime or reconfiguration.
- Reduced Labor Costs: Robotic systems replace manual labor for repetitive and physically demanding tasks, which not only reduces labor costs but also improves worker safety by reducing the risk of injury.
- Faster Production: Robotic automation accelerates many tasks that would otherwise require human intervention. The ability to perform cutting, shaping, bending, welding, and coating without pauses significantly increases production speed, leading to faster time-to-market for products.
- Improved Safety: Robotic systems can perform dangerous or strenuous tasks, such as welding and handling heavy metal sheets, minimizing the risk of injury for human workers. Additionally, robots can work in hazardous environments where human presence would be unsafe, such as areas with high temperatures or dangerous fumes.
- Real-time Monitoring and Quality Control: With advanced vision systems and integrated sensors, the robotic line can continuously monitor the quality of parts and make adjustments in real-time. This results in higher product quality, fewer defects, and less waste.
- Energy Efficiency: Robotic systems are often designed to be energy-efficient, using only the power necessary for each task. This reduces the overall energy consumption of the production line, leading to cost savings and more environmentally friendly operations.
Future Developments:
As technology advances, robotic sheet shaping lines will continue to evolve. The integration of AI and machine learning will enable even more sophisticated control systems, where robots can learn from past operations and optimize future production runs automatically. Robots will become more collaborative, working seamlessly with human operators and other automated systems to ensure that production processes run smoothly.
The incorporation of advanced sensors and 3D printing into robotic systems will also open new possibilities. For example, robots could use 3D printing technology to create custom tooling or parts on demand, further increasing the flexibility of the system. Additionally, robots could use advanced vision systems with AI to detect and correct defects in real-time with greater accuracy than ever before.
As manufacturers strive for sustainability, robotic systems will play an important role in reducing waste, recycling scrap material, and improving the energy efficiency of production. Automation will allow for better management of resources, ensuring that materials are used more effectively and reducing the environmental impact of the manufacturing process.
In conclusion, a robotic sheet shaping line offers significant advantages in terms of efficiency, precision, flexibility, and cost savings. As the technology continues to evolve, these systems will become even more intelligent, adaptable, and capable of meeting the demands of an increasingly complex and fast-paced manufacturing environment. By embracing robotics, manufacturers can stay competitive, improve product quality, and meet the growing demands for faster, more customized production.
A robotic sheet shaping line integrates robotic systems with traditional metal forming processes, revolutionizing the way sheet metal is processed in industries like automotive, aerospace, and electronics. By automating tasks such as material handling, cutting, bending, welding, and coating, this type of production line enhances speed, precision, and consistency while minimizing human error and reducing labor costs.
The process starts with automated material handling, where robotic arms equipped with specialized grippers or magnets transport sheets of metal to the shaping stations. These robots precisely position the material for cutting or blanking. Laser cutters, plasma cutters, or water jet systems can be used to cut the metal, with robotic arms providing accurate placement for the material to ensure clean, precise cuts with minimal waste. The cutting process is controlled via advanced CNC systems, ensuring the cuts meet strict dimensional tolerances and are consistently applied.
Following the cutting stage, the robotically controlled systems perform various shaping operations. These include bending, stretching, and deep drawing, with robotic arms outfitted with press brake tools or bending dies. The ability to reprogram these robotic systems for different product designs gives manufacturers unparalleled flexibility. The process can be adjusted in real-time to accommodate different material types, thicknesses, and forming requirements.
In many cases, robotic arms are also used for welding operations. Robotic welding systems, whether using MIG, TIG, or spot welding techniques, provide highly precise and repeatable joins between metal parts. These robots are programmed to follow specific paths to ensure strong, clean welds, which are crucial in applications where the integrity of the joint is vital, such as in automotive or aerospace components. Additionally, robots can perform assembly tasks by securing parts into place before welding or attaching components with bolts or fasteners.
After shaping and welding, parts are often sent to surface treatment stations where robotic arms apply coatings or paints. The robots, equipped with spray guns, ensure that the coatings are applied evenly and consistently, contributing to the part’s durability and appearance. Robotic deburring systems are also used to remove sharp edges and excess material, improving the overall safety and quality of the final product.
As the parts move through the line, integrated vision systems play a crucial role in quality control. High-resolution cameras and 3D scanners inspect parts for defects or dimensional inconsistencies. If any issues are detected, the system can automatically adjust machine parameters or reject faulty parts, ensuring that only high-quality products reach the final stages of production.
The final stage in the process involves packaging and sorting, where robotic systems handle the finished parts. Automated sorting systems ensure that parts are organized according to size, type, or customer specifications. The robots can then place the parts into boxes or crates for shipment, reducing the need for manual labor and speeding up the packaging process.
The integration of AI and machine learning into robotic sheet shaping lines further enhances their capabilities. These systems can learn from past performance data, predicting potential issues and optimizing processes in real-time. This predictive capability allows manufacturers to adjust production schedules, improve machine settings, and reduce waste before problems arise. IoT sensors integrated into the robots provide real-time data on machine health, part quality, and operational status, allowing for continuous monitoring and fine-tuning of the system.
As sustainability becomes a key focus in manufacturing, robotic sheet shaping lines also contribute to greener production practices. Precision cutting, bending, and welding reduce material waste, while the recycling of scrap metal further decreases environmental impact. Additionally, energy-efficient robotics and regenerative braking systems help reduce power consumption, contributing to more sustainable operations.
Looking to the future, robotic sheet shaping lines will become even more advanced. Collaborative robots (cobots) that work alongside human operators will increase productivity while ensuring safety and flexibility. These robots will be capable of performing more intricate tasks, and their ability to interact with humans will enable them to assist in more complex operations without interrupting the workflow. As 3D printing and additive manufacturing technologies improve, they may be integrated into the robotic shaping line, further enhancing the customization of parts and allowing for on-demand production of specialized tooling or components.
Additionally, the use of digital twins—virtual replicas of the entire production line—will enable manufacturers to simulate operations, optimize workflows, and predict potential failures before they occur. This technology will provide valuable insights into energy consumption, material flows, and system performance, helping manufacturers improve efficiency and reduce costs.
In summary, a robotic sheet shaping line transforms sheet metal production by automating and optimizing every step of the process, from material handling and cutting to welding, coating, and packaging. This integration of robotics, AI, and machine learning enhances flexibility, efficiency, and quality control, while reducing labor costs and environmental impact. As these technologies continue to evolve, manufacturers will benefit from even greater precision, speed, and adaptability in meeting the growing demands for custom and high-performance products.
As robotic sheet shaping lines continue to evolve, the future promises even more transformative changes that will redefine manufacturing practices. The integration of artificial intelligence (AI) and machine learning will allow for systems to not only optimize in real-time based on performance data but also adapt to dynamic changes in production needs without requiring manual intervention. AI-driven algorithms will analyze historical and real-time data from various sensors embedded throughout the production line to predict when maintenance is required, forecast production bottlenecks, and enhance overall system efficiency. These advancements will ensure minimal downtime and significantly reduce the chances of failure.
The expansion of cobots—collaborative robots that work alongside human operators—will enhance the flexibility of robotic sheet shaping lines. Cobots are designed to be intuitive, user-friendly, and capable of working safely with human workers. These robots can assist with tasks such as material handling, part alignment, or quality inspection, while allowing humans to focus on tasks requiring advanced decision-making or creativity. This collaboration between human workers and robots will allow for more streamlined production processes, while maintaining high levels of safety, especially in environments where heavy lifting or complex assembly processes are involved.
Another exciting development is the integration of 3D printing with robotic sheet shaping lines. 3D printing, or additive manufacturing, enables the creation of complex parts and tooling on-demand, without the need for traditional molds or dies. In the future, robotic systems could be used to print custom components or add features to existing parts during the forming process. For instance, robots may print localized reinforcements on a sheet metal part to improve its structural integrity or add intricate details that are difficult to achieve with conventional forming methods. This level of customization and flexibility will be particularly valuable in industries like aerospace, automotive, and medical device manufacturing, where precision and design complexity are paramount.
Digital twins—virtual replicas of physical systems—will also revolutionize how robotic sheet shaping lines are managed and optimized. These digital models, which simulate the entire production process, will allow manufacturers to monitor and adjust workflows in real time. With a digital twin, engineers can test different production scenarios, optimize machine settings, and simulate how the system would respond to changes in material properties, temperature, or machine configuration. This virtual testing environment will reduce the need for costly physical prototypes, speeding up product development while ensuring that only the most efficient and cost-effective processes are used in actual production.
Advanced sensors and machine vision systems will further increase the capability of robotic systems by allowing them to “see” and respond to changes in their environment with greater precision. These sensors, combined with AI, will help robots detect subtle defects in parts, even at microscopic levels. If a defect is detected, the system can immediately make adjustments to the process, such as halting the production line, altering machine parameters, or sorting defective parts for further inspection. Machine vision systems will also enable robots to handle increasingly complex geometries, ensuring that parts meet the strictest tolerances without the need for extensive manual checks.
The focus on sustainability will continue to grow, with robotic sheet shaping lines playing a central role in reducing the environmental footprint of manufacturing. Through resource optimization, manufacturers will be able to use materials more efficiently, cutting down on waste. The systems will be designed to recover energy where possible—such as through regenerative braking during robot movements—and recycle scrap metal during the shaping process. Additionally, the use of more eco-friendly coatings, processes, and materials will help reduce the carbon footprint of the entire production cycle.
As the market for customized products continues to grow, robotic sheet shaping lines will become even more adaptable. Flexible manufacturing systems (FMS) will enable the production of a wide variety of parts with minimal downtime. These systems will allow for quick adjustments to the production process, enabling manufacturers to switch between products of varying sizes and complexities without significant reconfiguration. This is crucial in industries like automotive, where customer demand for personalized vehicles is increasing.
Additionally, the growing demand for smaller batch sizes and just-in-time (JIT) production will make automation even more essential. Robotic systems can be reprogrammed on the fly to handle different production runs, reducing setup times and improving inventory management. As production lines become more agile, manufacturers will be able to respond to fluctuations in customer demand without maintaining large inventories, thus reducing storage costs and improving overall efficiency.
Finally, as more manufacturers adopt cloud-based systems, robotic sheet shaping lines will be more interconnected than ever. These cloud platforms will allow for real-time monitoring of production lines, predictive analytics, and seamless communication between various production sites. The cloud will also enable manufacturers to aggregate data from multiple machines across different locations, providing a comprehensive view of operational performance and enabling better decision-making. Remote diagnostics and troubleshooting will become more commonplace, allowing experts to resolve issues without the need for on-site visits, which will reduce response times and improve service efficiency.
In conclusion, the future of robotic sheet shaping lines is one of unprecedented flexibility, precision, and intelligence. Through the integration of AI, 3D printing, digital twins, cobots, and advanced sensors, these systems will become more adaptable, efficient, and sustainable. As manufacturers seek to meet the growing demands for customized, high-quality products while maintaining low costs and minimal waste, robotic sheet shaping lines will play a crucial role in driving the next wave of innovation in manufacturing. With these advancements, the capabilities of sheet metal forming will reach new heights, enabling the creation of parts and components that were once unimaginable, all while enhancing the overall sustainability and profitability of the manufacturing process.
CNC Sheet Metal Forming Line
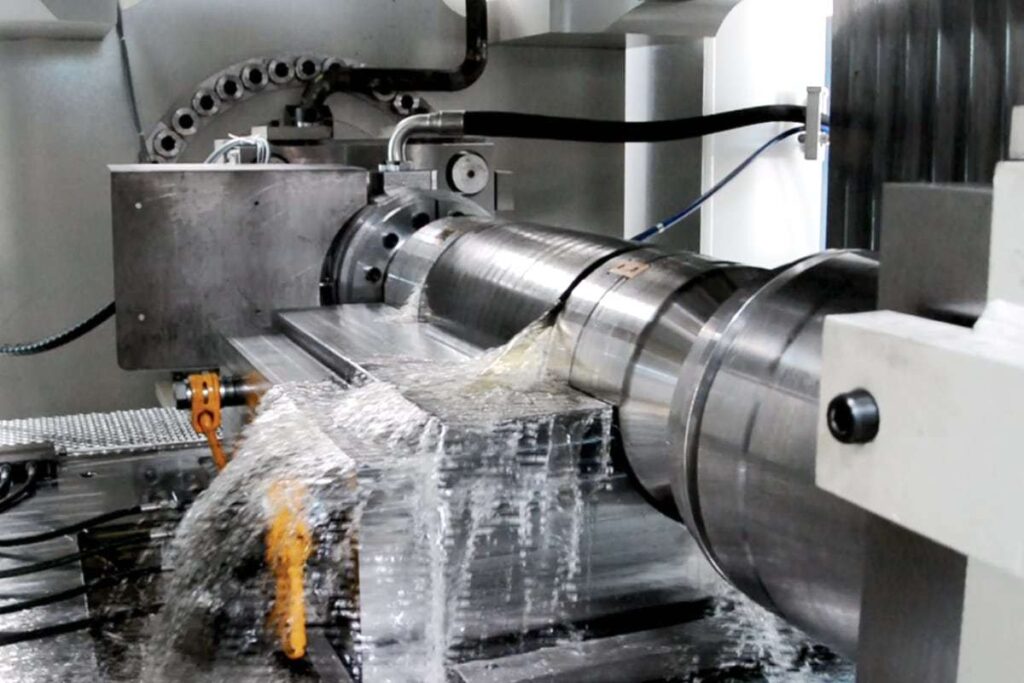
A CNC (Computer Numerical Control) Sheet Metal Forming Line is a highly automated production system designed to efficiently shape, cut, and form sheet metal into precise, complex components using CNC technology. CNC machines use computer-controlled systems to perform various operations such as cutting, punching, bending, and welding, providing high accuracy, repeatability, and flexibility in manufacturing. This technology is essential for industries where precision and customization are critical, such as automotive, aerospace, electronics, and construction.
The main advantage of a CNC sheet metal forming line lies in its ability to automate the process of sheet metal shaping, which reduces human error, improves product consistency, and speeds up production. The integration of CNC systems ensures that every operation, from material handling to the final product, is done with high precision, significantly improving the efficiency of manufacturing processes.
Key Components of a CNC Sheet Metal Forming Line:
- Material Handling System: The first stage of the CNC sheet metal forming line is the automated material handling system, which moves raw sheet metal from storage to the workstations. This system may include conveyor belts, robotic arms, or automated guided vehicles (AGVs) that transport the sheets to the CNC machines. The material handling system ensures that the metal sheets are placed accurately and consistently at each workstation for the next forming process.
- CNC Laser Cutting/Plasma Cutting: In the cutting phase, CNC machines with laser cutting or plasma cutting technologies are employed. These machines use focused lasers or high-velocity plasma to cut through sheet metal with high precision and speed. The CNC control system allows for precise adjustments in cutting speed, power, and movement, enabling the cutting of complex shapes, curves, and intricate designs without the need for manual intervention. These systems are typically paired with CNC punching machines for perforating or punching holes into the sheet metal.
- CNC Bending/Punching: After cutting, the sheet metal is often subjected to bending or punching to achieve specific shapes or features. CNC press brakes are used for bending operations, where they apply controlled force to bend the sheet metal into desired angles. These systems are extremely precise and can create complex bends in different directions, making them ideal for producing components with multi-axis geometries.
CNC punching machines can be used to create holes or cutouts in the sheet metal. The CNC system controls the punch’s speed and position, ensuring that holes are precisely aligned and spaced according to design specifications.
- CNC Forming: For more complex sheet metal components, CNC forming equipment is used. This includes deep drawing presses, stretch forming machines, or roll forming systems, all of which are automated and controlled by CNC systems. CNC forming allows for the production of components with intricate curves and detailed shapes that are difficult to achieve using conventional methods. The CNC control provides consistent pressure and speed, ensuring uniform quality throughout the production run.
- Welding and Assembly: Many CNC sheet metal forming lines incorporate automated CNC welding stations. Robots or CNC-controlled welding equipment can perform various types of welding, such as TIG (Tungsten Inert Gas), MIG (Metal Inert Gas), and spot welding. These systems ensure that joints are welded with high precision and strength, maintaining the quality and structural integrity of the assembled parts.
For assembly purposes, CNC robotic arms are used to pick and place parts, assemble components, or attach fasteners such as screws, rivets, or bolts. These robotic arms are guided by CNC instructions and can handle tasks that require high levels of precision and repeatability.
- Surface Treatment: After the sheet metal has been formed and welded, it may undergo surface treatment or finishing processes, such as coating, painting, or anodizing. CNC-controlled robots equipped with spray guns can apply coatings uniformly across the surface, ensuring an even and high-quality finish. Automated polishing or deburring systems may also be used to remove sharp edges or imperfections, providing a smooth and safe surface.
- Inspection and Quality Control: A critical aspect of the CNC sheet metal forming line is integrated quality control. CNC inspection systems, such as 3D scanning, laser triangulation, or vision systems, are used to detect dimensional deviations and surface defects. These systems continuously monitor the workpieces as they move through the production line and can immediately identify parts that do not meet quality standards. If a part is found to be defective, the system can reject it or alert operators for further inspection.
- Packaging and Sorting: Once the sheet metal components have been shaped, welded, and finished, they are sorted and packaged. Automated systems sort the parts based on size, type, or customer specifications. Robotic arms or conveyors move the finished parts to packaging stations, where the components are packed and prepared for shipment. This step is fully automated, minimizing labor costs and improving the overall efficiency of the production process.
Benefits of CNC Sheet Metal Forming Lines:
- High Precision and Accuracy: CNC technology provides superior precision, allowing manufacturers to create parts that meet tight tolerances. The automation ensures that every part is produced with the same level of accuracy, reducing the risk of errors and rework.
- Increased Efficiency and Speed: The automation of processes such as cutting, bending, and welding accelerates production. CNC systems can operate continuously, reducing downtime and increasing throughput, which is essential for high-volume manufacturing.
- Customization and Flexibility: CNC systems allow for easy changes in design and production parameters. With the ability to quickly reprogram machines, manufacturers can switch between different product designs without lengthy setup times. This flexibility is essential for industries that require small batch runs or customized products.
- Consistency and Repeatability: CNC-controlled operations are highly repeatable. Once a program is written for a specific part or component, it can be used to produce thousands of identical parts with consistent quality, ensuring that the final product matches design specifications.
- Reduced Labor Costs: CNC sheet metal forming lines reduce the need for manual labor, particularly in high-skill tasks like cutting, bending, and welding. Robots and automated machines can perform these tasks efficiently, allowing human workers to focus on higher-level operations, such as programming and maintenance.
- Improved Safety: The automation of dangerous tasks like cutting, welding, and heavy lifting reduces the risk of injury for human workers. CNC sheet metal forming lines often include safety features such as barriers, sensors, and emergency stop systems to protect workers.
- Better Resource Management: The precision of CNC systems helps reduce material waste, as cutting and shaping are done with minimal scrap. Additionally, the ability to recycle scrap metal back into the production process further reduces material costs and supports sustainability.
Future Trends:
The future of CNC sheet metal forming lines will continue to be shaped by advancements in technology. As AI and machine learning become more integrated into CNC systems, these lines will become even smarter, learning from past performance to predict maintenance needs and optimize production schedules. Additionally, advancements in robotics and cobots (collaborative robots) will improve the flexibility of these systems, allowing them to perform a wider range of tasks and interact safely with human operators.
The rise of Industry 4.0 will further transform CNC sheet metal forming lines, with the integration of IoT sensors and cloud computing allowing for real-time monitoring and remote control. Manufacturers will be able to track production data, monitor machine health, and make adjustments to processes on the fly from anywhere in the world.
Furthermore, additive manufacturing (3D printing) may increasingly play a role in CNC sheet metal forming lines. Some systems may incorporate 3D printing to create complex parts or tooling that traditional methods cannot achieve, offering even greater flexibility in production.
In conclusion, a CNC sheet metal forming line is a powerful, versatile tool for modern manufacturing, providing the precision, speed, and flexibility necessary for producing high-quality sheet metal components. By automating the processes of cutting, bending, punching, welding, and finishing, manufacturers can achieve greater efficiency, consistency, and cost savings while meeting the demands for customization and high-performance parts. With ongoing advancements in robotics, AI, and IoT, CNC sheet metal forming lines are poised to continue revolutionizing industries that rely on sheet metal components.
As CNC sheet metal forming lines continue to evolve, the potential for further innovation and improvement is vast. Below are some of the trends and technologies that are expected to shape the future of CNC sheet metal forming:
1. Advanced CNC Programming and AI Integration
The integration of artificial intelligence (AI) and machine learning in CNC systems will enable them to become increasingly autonomous. AI algorithms will analyze real-time data from sensors, cameras, and machine feedback to optimize production in real time. This could include adjusting speed, pressure, and other operational parameters without human intervention based on the specific requirements of the material or part being produced. Additionally, machine learning will allow the system to continuously improve its performance by learning from previous production runs, making adjustments to minimize material waste, energy usage, and processing time.
These advances will also enhance predictive maintenance, allowing machines to foresee potential failures or required repairs based on wear patterns and usage data. This not only reduces downtime but also extends the lifecycle of the machines, contributing to long-term cost savings.
2. Increased Use of Robotic Systems
Robotics will play an even greater role in CNC sheet metal forming lines, enhancing flexibility and precision. In particular, collaborative robots (cobots) will become more common. These robots are designed to work safely alongside human operators, enabling greater collaboration between humans and machines. Cobots could assist in tasks like loading and unloading parts, aligning materials, or even performing post-processing tasks like quality inspections or painting.
The use of multi-axis robotic arms with greater dexterity will allow for more intricate and complex parts to be handled without the need for rigid tooling setups. The flexibility of these robotic systems can also reduce the need for specialized tooling for different products, making production lines adaptable to multiple part designs without long changeover times.
3. Smart Manufacturing with IoT and Cloud Connectivity
As part of the Industry 4.0 movement, CNC sheet metal forming lines will increasingly incorporate Internet of Things (IoT) devices and cloud computing. Sensors embedded throughout the production line will collect data on everything from machine health to production speed, energy consumption, and material usage. This data will be transmitted to a central cloud platform where it can be analyzed in real time, giving operators and managers complete visibility over the production process.
IoT-enabled CNC systems will allow for remote monitoring and control, meaning engineers can manage and troubleshoot production lines from anywhere in the world. This connectivity will also enable real-time data sharing with suppliers and customers, improving coordination and responsiveness in supply chain management.
Furthermore, the integration of digital twins—virtual replicas of the CNC production line—will allow manufacturers to simulate and optimize the production process before physical production even begins. This can help identify potential bottlenecks, inefficiencies, or quality control issues before they occur, leading to smoother and faster manufacturing processes.
4. Sustainability and Eco-Friendly Technologies
Sustainability will continue to be a key driver in the development of CNC sheet metal forming lines. As environmental concerns rise, manufacturers are under increasing pressure to reduce their environmental footprint. CNC systems are already efficient at minimizing material waste, but new technologies will push this even further. For example, energy-efficient machines and regenerative braking systems in robots will help reduce energy consumption.
Additionally, advancements in water-based coatings or eco-friendly surface treatments will further contribute to more sustainable manufacturing practices. Closed-loop recycling systems will allow manufacturers to recover scrap metal and remelt it for reuse, reducing the need for raw material procurement and cutting down on waste.
Additive manufacturing technologies, such as 3D metal printing, may become integrated into CNC sheet metal forming lines to produce complex geometries or add custom features to parts. This could reduce the need for traditional tooling and minimize material waste, as 3D printing only uses material where it is needed.
5. Customization and Shorter Production Runs
Demand for customized products and shorter production runs is increasing, especially in industries like automotive, electronics, and consumer goods. CNC sheet metal forming lines will continue to adapt to this shift by offering greater flexibility in switching between different product designs. Automated systems can be reprogrammed quickly to accommodate new designs, reducing the downtime required for tool changes or setup adjustments.
The ability to produce low-volume, high-mix parts with the same efficiency as mass-produced components will give manufacturers a competitive edge in the market. With increased automation and flexibility, manufacturers can provide customers with more customized solutions without sacrificing cost-efficiency.
6. Integrated Quality Control and Inspection
The next generation of CNC sheet metal forming lines will feature even more advanced quality control (QC) and inspection systems. These systems will leverage machine vision, 3D scanning, and AI-based defect detection to automatically inspect parts throughout the production process. The use of automated optical inspection (AOI) will ensure that parts meet strict dimensional and surface quality standards, without the need for human intervention.
AI systems will enable continuous monitoring of part quality and machine performance, triggering immediate adjustments if deviations from specifications are detected. In the event of a defect, the system can either rework the part or reject it, preventing faulty products from continuing down the line.
Additionally, real-time data logging will make it easier for manufacturers to comply with regulatory requirements and track product quality over time. This integrated quality control system will help manufacturers achieve the highest levels of product consistency and traceability.
7. Hyper-Personalization Through Advanced CNC Systems
As consumer expectations for hyper-personalized products rise, CNC sheet metal forming lines will become increasingly capable of producing unique parts in small batches. This could include custom enclosures for electronics, personalized automotive components, or tailored metal structures for specific building projects. The ability to quickly change setups and produce high-quality, bespoke items will be a significant advantage in industries such as consumer electronics, medical devices, and luxury goods.
To support this level of customization, the design-to-manufacture process will become more interconnected. Design software will be tightly integrated with CNC systems, enabling quicker transitions from digital models to physical products, all while maintaining precision and high quality.
Conclusion
The future of CNC sheet metal forming lines is poised to be transformative, driven by advancements in AI, robotics, IoT, sustainability, and custom manufacturing. These systems will become more intelligent, adaptive, and efficient, offering manufacturers greater flexibility, faster production cycles, and the ability to meet growing consumer demands for customization and personalized products.
The integration of robotic systems, advanced CNC technologies, and data-driven automation will streamline processes, improve quality, and reduce costs across the manufacturing sector. Additionally, the focus on sustainability and eco-friendly practices will play a crucial role in making sheet metal forming processes more resource-efficient and environmentally friendly.
As these technologies evolve, the future of CNC sheet metal forming will offer unprecedented opportunities for manufacturers to innovate, enhance productivity, and maintain high standards of quality, all while staying competitive in a rapidly changing market.
Fully Automated Metal Forming System
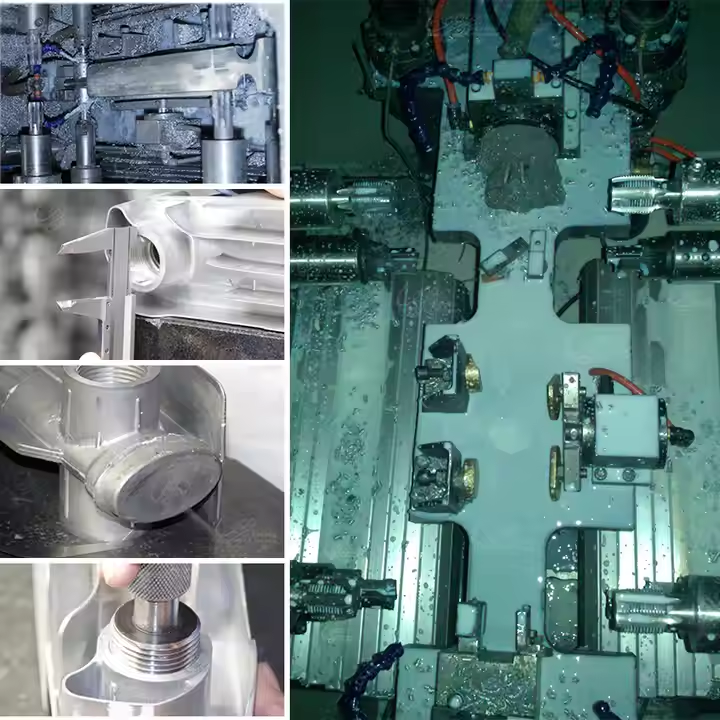
A Fully Automated Metal Forming System refers to a production line where all aspects of the metal forming process—from material handling to final product inspection and packaging—are completely automated, requiring minimal human intervention. These systems integrate advanced technologies like robotics, CNC machining, AI-driven optimization, and real-time monitoring to create a seamless and highly efficient manufacturing process. Fully automated systems are particularly valuable in industries where precision, speed, and consistency are crucial, such as automotive, aerospace, electronics, and heavy machinery manufacturing.
Key Features of a Fully Automated Metal Forming System
- Automated Material Handling
- The system typically begins with automated material handling. Raw materials, usually in the form of metal sheets or coils, are transported by robotic arms, conveyor belts, or Automated Guided Vehicles (AGVs) to the various processing stations in the line.
- Robotic arms equipped with grippers or vacuum systems are used to pick, place, and position the metal sheets accurately on the forming equipment.
- The material handling system ensures that the metal sheets are consistently positioned for the forming process, improving efficiency and reducing the risk of errors.
- Automated Cutting and Punching
- CNC cutting machines (such as laser cutters, plasma cutters, and waterjet machines) are used to cut metal sheets into the desired shapes or sizes. These machines are controlled by a CNC system that interprets design files (e.g., CAD drawings) and adjusts cutting parameters for optimal performance.
- CNC punching machines are often integrated for perforating or punching holes in the metal. These machines can handle complex punching patterns with high precision, ensuring that parts meet strict specifications without requiring manual adjustments.
- Laser or plasma cutting systems can be programmed to handle intricate and customized designs, making it possible to produce parts with complex geometries and tight tolerances.
- Bending and Forming
- CNC press brakes are employed to bend the metal sheets to the required angles and shapes. These machines use hydraulic or electric actuators controlled by CNC systems to apply precise force on the metal, allowing for high-accuracy bends in a wide range of sizes and shapes.
- For more complex forms, roll forming or stretch forming machines can be used. These machines can be fully automated and programmed to create detailed curves and complex parts by stretching or rolling the metal into the desired shapes.
- In systems where large volumes of parts are required, automated die change systems are incorporated, allowing the press brakes to be quickly reconfigured to handle different part designs with minimal downtime.
- Welding and Joining
- Automated welding systems are employed to join metal parts or components. These systems can include robotic welding arms that perform MIG, TIG, or spot welding processes with high precision and consistency.
- Welding robots are typically programmed to handle repetitive tasks, ensuring that the welds are made to exact specifications every time. These systems can also inspect the quality of the welds during the process using real-time sensors.
- Automated riveting, bolting, or fastening systems may also be included in the process for joining parts that are not suitable for welding, or for adding additional components to the metal structure.
- Surface Treatment and Finishing
- Once the metal parts are formed and welded, automated finishing processes such as coating, painting, or polishing can be employed to enhance the appearance or corrosion resistance of the parts.
- Robotic spray systems can be used to apply coatings such as powder coating, electroplating, or painting to metal parts in a uniform and consistent manner.
- Automated deburring systems remove sharp edges or unwanted burrs from the formed metal parts, ensuring that the parts are safe for handling and meet quality standards.
- Real-Time Quality Control and Inspection
- Automated inspection systems integrated with machine vision, 3D scanning, or laser measurement technologies ensure that every part meets quality standards.
- Machine vision systems use cameras and sensors to detect defects, such as surface flaws, dimensional inaccuracies, or misalignments. These systems can automatically reject defective parts or trigger alerts for corrective actions.
- In-line measurement using 3D laser scanners or tactile probes allows for continuous monitoring of part dimensions during the forming process, ensuring that deviations from specifications are caught immediately, and adjustments can be made in real time.
- Packaging and Sorting
- Once the metal parts are fully formed and inspected, they are sorted based on predefined criteria such as size, type, or customer requirements. This sorting process is automated through robotic arms or automated conveyors.
- Parts are then sent to automated packaging stations, where they are appropriately packaged for shipment. Packaging robots can arrange parts, secure them, and label them according to shipping specifications without manual input.
- Automated labeling systems can print and apply barcode labels or RFID tags, ensuring that each part is traceable throughout the production and shipping process.
Advantages of Fully Automated Metal Forming Systems
- High Precision and Consistency
- Automation ensures that each part is manufactured with the same high level of precision, reducing the potential for human error and ensuring that each product meets stringent specifications.
- Increased Efficiency and Reduced Downtime
- Automated systems operate continuously, reducing downtime between processes. Systems are often designed for quick changeovers, allowing manufacturers to switch between different products or designs without significant delays.
- With automated material handling, cutting, bending, welding, and inspection, the production process is streamlined, leading to faster cycle times and higher throughput.
- Lower Labor Costs
- By reducing the need for manual intervention in tasks like material handling, cutting, welding, and inspection, a fully automated system minimizes labor costs. Operators can focus on programming, maintenance, and oversight instead of performing repetitive tasks.
- Enhanced Safety
- The use of automated systems reduces the need for human operators to be directly involved in potentially hazardous tasks such as welding, cutting, or handling hot metal. This improves worker safety and reduces the likelihood of injuries on the production floor.
- Scalability and Flexibility
- Fully automated metal forming systems can be scaled up or adapted to handle different product types. Automated systems can be reprogrammed to accommodate various designs and production volumes, making them flexible for different market demands.
- These systems also offer customization capabilities, allowing manufacturers to easily adjust production parameters to meet specific customer requirements.
- Higher Quality Control
- Integrated quality control systems provide continuous monitoring of production, allowing manufacturers to catch defects early in the process. This ensures that only high-quality parts are produced, leading to fewer rejections, less waste, and higher customer satisfaction.
- Sustainability
- Automation can help reduce material waste, energy consumption, and the environmental impact of manufacturing. For example, precise cutting and forming processes minimize scrap metal, while advanced energy-saving technologies help optimize power usage throughout the production line.
- The use of closed-loop recycling systems in some fully automated setups can allow manufacturers to recover scrap metal and reuse it in future production cycles, making the process more sustainable.
Future Trends in Fully Automated Metal Forming Systems
- Integration with Industry 4.0
The rise of Industry 4.0 technologies—such as the Internet of Things (IoT), cloud computing, and AI-driven analytics—will further enhance the capabilities of fully automated metal forming systems. These technologies will enable real-time monitoring and optimization of production lines, predictive maintenance, and even autonomous decision-making. - Smart Robotics and AI-Driven Operations
As AI and machine learning technologies evolve, robots and automation systems will become even smarter. These systems will not only perform tasks based on pre-programmed instructions but will be capable of learning from past experiences and adapting to new conditions. For example, robots may autonomously detect defects in parts and make real-time adjustments to the manufacturing process to prevent the production of faulty parts. - Additive Manufacturing (3D Printing) Integration
3D printing or additive manufacturing may be integrated into fully automated metal forming systems to produce more complex parts or tooling on-demand. This could complement traditional subtractive forming techniques, enabling the production of highly intricate parts without the need for traditional molds or dies. - Increased Customization and Short Run Production
As demand for customized products grows, fully automated metal forming systems will become even more flexible. These systems will be able to handle short run production and custom orders without the need for expensive retooling, making them highly attractive for industries where personalization and unique designs are key.
Conclusion
A Fully Automated Metal Forming System represents the future of precision manufacturing, offering benefits such as improved efficiency, quality, safety, and flexibility. By integrating cutting-edge technologies like robotics, CNC systems, AI, and advanced quality control, these systems streamline the entire production process, enabling manufacturers to produce high-quality metal components at scale while minimizing costs and downtime. As the demand for customization and sustainability increases, the role of automation in metal forming will continue to expand, allowing manufacturers to meet new challenges and stay competitive in an ever-evolving marketplace.
The evolution of Fully Automated Metal Forming Systems is poised to bring even more transformative changes to the manufacturing sector, particularly as industries push towards higher levels of automation, customization, and efficiency. Here are some additional factors and trends shaping the future of fully automated metal forming systems:
1. Advanced Simulation and Virtual Prototyping
- With the increasing sophistication of simulation software and virtual prototyping tools, manufacturers can design and test their metal forming processes in a digital environment before implementing them on the shop floor. This virtual testing eliminates the need for costly physical prototypes, allowing for more efficient design iterations.
- Finite element analysis (FEA) and other simulation techniques will enable engineers to predict how materials behave under stress, heat, or pressure during the forming process, optimizing tooling, machine parameters, and material usage.
- Virtual prototyping also extends to the complete production line, where digital twins of the manufacturing system can be used to simulate and test production scenarios, improving efficiency and identifying potential bottlenecks before physical production starts.
2. Real-Time Data Analytics and Decision-Making
- As more sensors and IoT devices are integrated into manufacturing lines, the ability to collect and analyze data in real-time will be a game-changer for metal forming. Big data analytics will help manufacturers identify trends, optimize production parameters, and predict potential failures before they occur, leading to predictive maintenance and reduced downtime.
- Machine learning algorithms will become increasingly adept at analyzing this data and offering insights into optimizing speed, energy use, and raw material consumption. Over time, this real-time data could also be used to automatically adjust machine settings, such as pressure, speed, or tooling, ensuring optimal performance at all times.
3. Autonomous Maintenance Systems
- As automation in metal forming systems progresses, the role of autonomous maintenance systems will become more prominent. These systems use sensors and AI to monitor equipment health and detect early signs of wear, preventing unplanned downtime.
- For example, vibration sensors, thermal imaging systems, and oil quality sensors could be integrated into automated systems to monitor the condition of key components, such as motors, hydraulic systems, or CNC machines.
- These maintenance systems will be able to predict when parts will need servicing or replacement, minimizing costly repairs and extending the lifespan of the machinery.
4. Collaboration Between Humans and Robots
- Although fully automated systems can handle most tasks independently, there will still be a need for human involvement in certain high-level tasks, such as system programming, troubleshooting, or final quality assurance.
- Collaborative robots (cobots) will be used to enhance human-robot collaboration, enabling operators to work alongside robots to improve the flexibility of the production line. These robots will assist with tasks like loading parts, organizing materials, performing inspections, or even handling delicate components that require human precision.
- This collaboration will not only optimize the workflow but also enhance safety by allowing robots to perform the physically demanding tasks, reducing the risk of injury to human workers.
5. Sustainability and Energy Efficiency
- As environmental sustainability becomes more important, manufacturers will continue to push for energy-efficient, low-waste production processes in fully automated metal forming systems.
- Green manufacturing initiatives will drive the adoption of low-energy equipment, such as electric press brakes and high-efficiency motors, as well as environmentally friendly technologies like solar-powered manufacturing facilities.
- Closed-loop systems will reduce waste generation by reusing scrap metal directly in production, while smart energy management systems will monitor and optimize energy consumption across the entire production process. Additionally, water and air usage can be minimized, and systems will monitor these parameters to reduce the plant’s environmental footprint.
6. Integration with Global Supply Chains
- The advent of digital supply chains will allow automated metal forming systems to communicate directly with suppliers, customers, and other production lines. This interconnected ecosystem will provide real-time visibility into material availability, production progress, and inventory levels, improving decision-making and collaboration across the supply chain.
- Advanced technologies such as blockchain may also be used to track and authenticate the origin of materials and components, ensuring transparency and quality throughout the production process. Automated metal forming lines can integrate with enterprise resource planning (ERP) systems to streamline operations and improve logistics management.
7. Modular and Scalable Systems
- Modular automation will allow manufacturers to easily scale and reconfigure their metal forming systems to meet changing production needs. Manufacturers can add or remove modules, such as additional press brakes, robotic arms, or material handling units, to adjust the capacity of the production line without significant investment in new equipment.
- This flexibility is crucial for industries that demand frequent product changes, such as automotive or electronics manufacturing, where production runs are often shorter, and product designs are continually evolving.
- The ability to reconfigure production lines with minimal downtime will significantly enhance a manufacturer’s ability to quickly adapt to market demands and custom orders.
8. Artificial Intelligence in Design and Customization
- AI is not only transforming the manufacturing process itself but also the design stage. AI-driven generative design tools can automatically create optimal designs for metal parts based on performance and manufacturing constraints.
- In fully automated metal forming systems, these designs can then be directly fed into the CNC machines or robots, eliminating the need for human intervention and allowing manufacturers to produce complex and highly customized parts efficiently.
- In sectors like aerospace, automotive, and medical devices, where customization is critical, AI algorithms will allow for the mass production of highly personalized components, enabling customers to get the exact specifications they need without sacrificing production efficiency.
9. Faster Time-to-Market
- Automation allows manufacturers to reduce production times, enabling faster time-to-market for new products. With a fully automated system, the production line can be quickly reprogrammed to handle different designs and sizes without the need for time-consuming tooling changes or setup processes.
- Additionally, real-time tracking and monitoring of production schedules will allow manufacturers to quickly adapt to delays, supply chain disruptions, or changes in customer demand, ensuring that deadlines are met without sacrificing quality or efficiency.
10. Human-Centric Automation
- While automation reduces human involvement in repetitive and dangerous tasks, it also opens the door for more human-centric roles in the production process. Operators and engineers will shift from manual labor to overseeing complex automation systems, managing production lines, and working on optimization and improvement strategies.
- Training for these roles will focus on developing skills in robotics programming, data analysis, and system monitoring. As such, workers will become highly skilled technicians, equipped to manage and optimize advanced automation systems.
11. Advanced Additive and Subtractive Manufacturing Integration
- As additive manufacturing (3D printing) and subtractive manufacturing (traditional CNC) continue to evolve, manufacturers will integrate both technologies into a hybrid system for more flexibility.
- Additive manufacturing can be used to produce intricate or low-volume components alongside traditional sheet metal forming techniques. For instance, in aerospace or automotive sectors, additive processes could create complex geometries for specific parts that are later incorporated into larger, traditionally formed assemblies.
- A hybrid manufacturing system will also enable on-demand tooling—using 3D printing to produce tooling or dies quickly without waiting for long lead times, thus enhancing production flexibility.
Conclusion
The future of Fully Automated Metal Forming Systems is characterized by the fusion of cutting-edge technologies, including robotics, artificial intelligence, IoT, and sustainable manufacturing practices. These systems will offer greater flexibility, efficiency, and precision while driving down production costs and improving quality. As industries demand more customized, sustainable, and high-quality products, the ability of manufacturers to implement fully automated systems that are intelligent, adaptive, and connected will be crucial.
The combination of these technologies will not only enhance the manufacturing process but also pave the way for innovations in product design and production strategies. Fully automated systems will be the cornerstone of a new era in metal forming, allowing manufacturers to meet the evolving demands of customers while maintaining a competitive edge in an increasingly globalized and digitalized marketplace.
12. AI-Enhanced Process Optimization
In the future, artificial intelligence (AI) will play an even greater role in optimizing metal forming processes. AI algorithms will continuously analyze data collected from sensors, cameras, and other monitoring systems throughout the production line. By learning from historical data and real-time performance metrics, AI can make immediate adjustments to the production process, optimizing parameters such as:
- Temperature control for heat-treated metals
- Pressure settings in press machines or stamping processes
- Speed and feed rates in CNC machines
- Tool wear predictions, ensuring tools are replaced or serviced at the optimal time
This real-time, self-adjusting capability will help eliminate inefficiencies and reduce the likelihood of defects in metal parts, leading to higher throughput, better part quality, and reduced waste.
13. Digital Twin Technology
The integration of Digital Twin technology will revolutionize how fully automated metal forming systems are monitored and optimized. A Digital Twin is a virtual replica of a physical system (like a metal forming production line) that can be used to simulate, predict, and optimize real-world operations.
- Digital twins will enable manufacturers to model the entire metal forming process, from material handling to final inspection. They can simulate different production scenarios, such as changes in material properties, tool wear, or equipment failure, to predict how the system will respond.
- These models will allow manufacturers to test new settings or designs virtually, reducing the need for physical trials and minimizing risks associated with changing operational parameters.
- By continuously updating the digital twin with real-time data, manufacturers can detect inefficiencies, optimize production schedules, and implement predictive maintenance strategies before problems arise, ultimately reducing downtime and maximizing equipment lifespan.
14. Multi-Tasking Robotics and Collaborative Systems
The evolution of multi-tasking robots will further enhance the automation of metal forming lines. Instead of using specialized robots for each task (cutting, bending, welding, etc.), modular robotic systems that can be easily reprogrammed to perform different tasks will become more prevalent. These robots will:
- Switch between tasks such as picking, placing, welding, and inspecting without needing manual reconfiguration.
- Be programmed to handle diverse types of material, from stainless steel to aluminum and even composites, depending on the application.
- Work alongside humans in collaborative environments, where the robot may assist operators with handling large parts, moving heavy components, or providing real-time feedback on quality checks.
These robots will reduce the need for specialized equipment and streamline workflows, enabling faster production changes and more flexible operations.
15. Sustainability Integration with Circular Economy Principles
Sustainability is becoming a primary focus in manufacturing processes, including metal forming. Circular economy principles will drive innovation, ensuring that materials and energy are used efficiently, and waste is minimized or repurposed. The adoption of closed-loop manufacturing systems is a critical step in achieving sustainability:
- Material recycling: Scrap metal from the forming process can be automatically sorted and sent back into the production line for reuse, creating a more sustainable system by minimizing material waste. Additionally, waste material from forming, cutting, and finishing processes can be processed and used for other parts of the production line or repurposed in other applications.
- Energy recovery: Excess energy from processes such as heating or cooling can be recaptured and reused within the production system. For instance, heat generated during metal forming could be stored and used in other parts of the process, reducing overall energy consumption.
- Environmentally friendly materials: The future of fully automated systems may see the integration of materials with lower environmental impact, such as sustainable alloys or bio-based composites, which will be incorporated into the automated production systems to meet environmental standards.
By aligning with circular economy principles, metal forming systems can reduce their environmental footprint and contribute to more sustainable industrial practices.
16. Autonomous Quality Assurance
While automated systems already include some quality control features, the future will see fully autonomous quality assurance systems that use a combination of machine vision, AI, and sensor technologies to inspect products throughout the production process.
- Machine vision systems equipped with high-definition cameras and advanced imaging algorithms will be used to detect minute surface defects, dimensional deviations, or even minor scratches that could compromise the integrity of the product.
- AI-powered systems will learn to identify specific defect patterns and adjust production parameters to eliminate defects in real time. These systems will also be capable of evaluating the texture and finish of parts, ensuring high-quality surface treatments.
- The automation of these quality control processes will reduce the need for human inspection, improve defect detection rates, and ultimately deliver more consistent, higher-quality products.
17. Real-Time Supply Chain Integration
The evolution of real-time supply chain integration within fully automated systems will allow for a seamless flow of materials and components, enabling just-in-time manufacturing and reducing inventory costs. Automated systems will:
- Communicate with suppliers to ensure that raw materials are available on-demand, avoiding delays or production halts due to material shortages.
- Track inventory in real-time, ensuring that only the necessary amounts of materials are ordered, minimizing excess stock, and reducing material waste.
- Adjust production schedules based on customer demand, production capacity, and material availability, ensuring that products are manufactured and delivered on time.
This integration will result in more agile and cost-efficient production lines, allowing manufacturers to respond to shifts in market demand more quickly and with less risk of overproduction or stockouts.
18. Integration of Additive Manufacturing and Metal Forming
As additive manufacturing (3D printing) technologies mature, there will be increasing opportunities to integrate them into traditional sheet metal forming systems. This combination of additive and subtractive manufacturing will lead to new production capabilities, including:
- Tooling on-demand: Instead of relying on traditional die-casting or forging methods, manufacturers can use 3D printing to create custom tooling for sheet metal forming. This ability to produce tools quickly and cost-effectively will allow for more flexible and rapid product prototyping, as well as short-run production.
- Complex geometries: Additive manufacturing will enable the production of complex internal features or custom geometries that are difficult or impossible to achieve through traditional forming methods. These parts can be incorporated into the larger metal forming process, creating more intricate designs with minimal material waste.
- Hybrid production: Manufacturers will be able to print complex shapes or geometries and then use traditional forming techniques (such as stamping or bending) to refine or finalize the part. This hybrid process could reduce time and cost for the production of customized parts or low-volume production runs.
19. Augmented Reality (AR) for Production and Maintenance
The use of augmented reality (AR) in production and maintenance workflows will enhance operator decision-making and improve system efficiency in fully automated metal forming systems.
- AR-based training: Operators and technicians will use AR glasses or smart devices to receive real-time guidance, such as system diagnostics, machine settings, and assembly instructions. This will reduce the learning curve and allow for faster onboarding of new workers.
- Maintenance support: AR technology can be used to assist with maintenance tasks by overlaying real-time information, such as maintenance manuals or repair instructions, onto the physical machinery. This could help technicians identify issues and perform repairs faster and with greater accuracy.
- Remote troubleshooting: Experts can use AR to guide operators through troubleshooting and repairs in real-time, even if they are located at different facilities, reducing downtime and the need for on-site technical support.
Conclusion: A New Era for Metal Forming
The future of fully automated metal forming systems represents a new era of manufacturing, one characterized by greater flexibility, precision, sustainability, and intelligence. As digital technologies like AI, IoT, 3D printing, and augmented reality continue to evolve, they will further integrate into automated metal forming lines, creating smarter, more responsive production environments. These advances will enable manufacturers to produce highly customized, complex parts with unprecedented speed and efficiency, while minimizing waste and energy consumption.
In this new age of manufacturing, companies that embrace fully automated metal forming systems will not only improve their competitive edge but will also play a crucial role in shaping a more sustainable and connected industrial future. As these systems become more advanced and integrated with broader supply chain and production networks, they will unlock new possibilities for product innovation, quality control, and operational optimization across industries.
Sheet Metal Shaping Automation Line
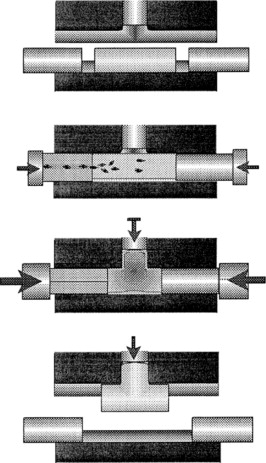
A Sheet Metal Shaping Automation Line is a highly efficient and advanced production setup designed for the automated processing and shaping of metal sheets into complex parts or products. This system integrates various technologies such as robotics, CNC (Computer Numerical Control) machines, sensors, and intelligent control systems to handle everything from material handling and forming to quality inspection and packaging. The goal of such a line is to maximize production speed, consistency, and quality while reducing labor costs, human error, and waste.
Here’s an overview of how a Sheet Metal Shaping Automation Line operates and the key technologies involved:
1. Material Handling and Feeding System
- Automated Feeding Mechanism: Raw metal sheets are loaded onto the system via conveyor belts, robotic arms, or automated forklifts. The material is moved to the appropriate station for processing, ensuring precise alignment and smooth transitions between machines.
- Sheet Leveling: If necessary, an automated leveling station may be included to remove any distortions or bends in the raw metal sheets, ensuring they are perfectly flat before they enter the forming or shaping stages.
2. Cutting and Shearing
- Laser Cutting: In some setups, a laser cutting system may be used to precisely cut the sheets into specific shapes or sizes. Lasers provide high precision and can handle intricate designs with minimal material waste.
- Punching and Shearing: Automated punching presses or shear blades can be used to cut parts from the sheets, creating holes, slots, or other features required for the final product.
- CNC Plasma or Waterjet Cutting: These cutting technologies can also be integrated into the automation line for cutting thicker or more complex parts from metal sheets.
3. Bending and Forming
- Press Brakes: CNC-controlled press brakes automatically bend sheets into specific angles and shapes. These machines can be programmed to handle multiple bending operations, including complex geometries.
- Stamping and Deep Drawing: For high-volume production of parts with more intricate or deep shapes, a hydraulic or mechanical press can be used for stamping and deep drawing. These presses apply controlled force to shape metal sheets into desired forms.
- Roll Forming: This process involves feeding metal sheets through a series of rollers that progressively shape the sheet into the desired profile. Roll forming is typically used for long, continuous profiles like metal roofing or framing.
- Stretch Forming: In this process, metal sheets are stretched over a mold using hydraulic or mechanical force to create curved or complex 3D shapes, which is especially useful in the aerospace or automotive industries.
4. Welding and Joining
- Robotic Welding: Automated robotic arms equipped with welding tools can perform high-precision welding tasks, such as spot welding, MIG welding, or TIG welding. This ensures that parts are joined accurately and consistently, reducing the chance of defects.
- Automated Riveting and Fastening: For applications that require non-welded connections, robotic riveting or fastening systems can be integrated into the line to automatically insert rivets, bolts, or other fasteners.
5. Surface Treatment and Coating
- Automated Painting and Coating: After shaping, the metal parts may require a surface coating to prevent corrosion or enhance their appearance. Automated spray booths or electrostatic powder coating systems can apply uniform layers of paint or coating.
- Passivation and Galvanizing: For added protection, certain parts may undergo galvanizing (coating with zinc) or passivation (treating with acid) to improve their resistance to rust or environmental damage.
6. Quality Control and Inspection
- Machine Vision Systems: High-resolution cameras and image processing systems are often used to inspect the parts at various stages of the forming process. These systems can detect defects such as surface blemishes, dimensional errors, or misalignment in real-time.
- Dimensional Measurement: Automated measurement systems using laser scanning or probe-based techniques ensure that the parts meet precise size and shape requirements. If a part is out of specification, the system can trigger an automatic correction or rejection.
- Non-Destructive Testing (NDT): Techniques like ultrasonic or X-ray inspection may be used to detect internal flaws in welded parts, ensuring product quality without damaging the components.
7. Robotic Packaging and Sorting
- Automated Sorting: After the metal parts have been shaped and inspected, robotic arms or conveyors can sort the finished products according to their type, size, or quality for further processing or shipment.
- Packaging Systems: Automated packaging machines can wrap, box, or palletize the parts, streamlining the final step in the production process.
8. Control Systems and Integration
- Centralized Control System: All stages of the sheet metal shaping automation line are typically controlled through a centralized computer system. Operators can monitor the production line, input machine settings, and track the status of each component in real time.
- Data Analytics and Feedback Loops: Advanced systems collect data from various sensors throughout the process. This data can be analyzed to identify inefficiencies, optimize performance, and predict when maintenance is required.
- IoT Integration: The production line is often connected through the Internet of Things (IoT), enabling seamless communication between machines and monitoring systems, which ensures a smooth workflow and real-time troubleshooting.
Benefits of a Sheet Metal Shaping Automation Line
- Increased Efficiency: Automation significantly reduces manual labor, accelerates production cycles, and minimizes the time spent on changeovers or setup adjustments.
- Consistent Quality: Automated systems offer precise control over every step of the process, ensuring parts are shaped and finished with high consistency and minimal defects.
- Cost Reduction: Automation lowers labor costs and reduces the likelihood of costly mistakes, while also minimizing material waste.
- Flexibility: Many automated systems can be easily reprogrammed to handle different sheet metal types, sizes, and part configurations, providing flexibility in meeting changing customer demands.
- Safety Improvements: By reducing human involvement in hazardous tasks (such as welding, cutting, and material handling), automation enhances worker safety and reduces the risk of accidents.
Future Trends in Sheet Metal Shaping Automation
- AI-Driven Process Optimization: The use of artificial intelligence (AI) for real-time decision-making and process optimization will continue to evolve. AI can analyze data from sensors and cameras to make adjustments on the fly, improving part quality and production efficiency.
- Additive Manufacturing Integration: As 3D printing and additive manufacturing technologies advance, they will be integrated with traditional sheet metal forming lines, enabling the production of more complex geometries and parts with less waste.
- Collaborative Robots (Cobots): The integration of cobots into the sheet metal shaping process will allow for more seamless collaboration between human workers and robots, further improving productivity and flexibility.
- Sustainability Focus: As manufacturers face increasing pressure to reduce their environmental impact, automation lines will be designed to minimize waste, improve energy efficiency, and facilitate the recycling of scrap metal.
Conclusion
A Sheet Metal Shaping Automation Line represents a significant leap forward in manufacturing technology, offering enhanced speed, precision, and flexibility in metalworking. By integrating advanced robotics, AI, and IoT systems, these lines can automate a wide range of processes, from cutting and bending to welding and packaging, ensuring optimal production rates and consistent product quality. As the technology continues to evolve, we can expect even greater advancements in automation that will lead to more sustainable, cost-effective, and adaptable manufacturing solutions for the metalworking industry.
9. Advanced Robotics and Automation Integration
The integration of advanced robotics into the sheet metal shaping automation line will enhance capabilities such as:
- High-Speed Robotics: The use of ultra-fast robots can speed up processes like material handling, bending, and welding, drastically reducing cycle times. These robots can quickly and accurately handle sheet metals, perform repetitive tasks without fatigue, and execute high-precision movements for intricate designs.
- Flexible Robotic Cells: Flexible robotic cells can be programmed to perform multiple tasks in the production line. For example, a single robot could handle tasks like loading, unloading, and sorting parts, adapting to different job requirements with minimal downtime for reprogramming or setup changes.
- Collaborative Robots (Cobots): Cobots can work alongside human operators, sharing the workspace while performing tasks like light assembly, part inspection, or material handling. Their ability to adapt and safely interact with humans will help increase productivity without compromising safety. They could assist in tasks such as moving large or heavy parts, while operators can focus on quality control or troubleshooting.
10. Real-Time Process Monitoring and Predictive Maintenance
The future of sheet metal shaping lines will involve enhanced real-time process monitoring and predictive maintenance:
- Predictive Maintenance: Through the use of IoT sensors and machine learning algorithms, the automation system can track the health and performance of key equipment like press brakes, stamping machines, and welding robots. These sensors monitor variables such as temperature, vibration, and load, which can indicate early signs of wear or failure. This predictive maintenance can significantly reduce unplanned downtime by alerting operators to potential issues before they cause machine breakdowns.
- Real-Time Data Analysis: Real-time data from sensors, cameras, and machines will be analyzed using AI and machine learning algorithms to detect anomalies or inefficiencies in the process. For example, if a certain bending press starts to produce parts that are slightly out of tolerance, the system can automatically adjust the press settings to compensate, ensuring that every part meets the required quality standards.
- Edge Computing: Edge computing technology will play a role in processing data locally on the production floor, reducing latency and ensuring quick responses to any issues. This enables faster decision-making and allows the system to make adjustments on the fly without needing to rely on cloud-based processing.
11. Integration with Advanced Manufacturing Software
In addition to the physical hardware, the sheet metal shaping automation line will rely heavily on advanced manufacturing execution systems (MES) and enterprise resource planning (ERP) software. These systems help manage and optimize the entire production process, from raw material procurement to finished product delivery:
- Manufacturing Execution Systems (MES): MES software can integrate with the automation line to track every step of the production process, monitor machine performance, and collect detailed data on work in progress. This allows for better scheduling, real-time visibility, and tracking of order fulfillment.
- ERP Integration: ERP systems link the production process to broader business functions such as inventory management, procurement, and customer relationship management. Integration with an automated sheet metal shaping line can help synchronize production with demand, ensuring that resources are efficiently allocated and minimizing the chances of stockouts or overproduction.
- Computer-Aided Design (CAD) and Computer-Aided Manufacturing (CAM): As the designs for sheet metal parts become increasingly complex, the integration of CAD and CAM software with the automation line will allow for faster design-to-production cycles. CAD software enables the creation of detailed 3D models of parts, while CAM software translates those models into machine instructions that can be directly fed into the automation system.
12. Flexible Production for Customized Parts
The ability to produce customized parts in high volumes is a growing trend in manufacturing, and automated sheet metal shaping lines are evolving to meet this demand:
- Customization on Demand: Automated systems will increasingly be capable of handling low-to-medium volume production runs of custom parts. The flexibility of these lines, combined with the precision of CNC machines and advanced robotics, will allow manufacturers to easily adjust the line to accommodate varying part designs, thicknesses, and material types.
- Dynamic Tooling Changes: Some automated systems can dynamically change the tools used for cutting, bending, or welding in response to different part requirements. This eliminates the need for extensive manual interventions or long setup times, enabling the line to switch between different part types quickly.
- Mass Customization: With advancements in AI and machine learning, manufacturers can provide mass-customized products that meet the individual specifications of each customer. These products can range from highly personalized consumer goods to complex parts for industries like automotive, aerospace, or medical devices.
13. Human-Machine Collaboration
While automation reduces human labor in the production process, the need for human oversight and expertise remains critical. The future of automated sheet metal shaping lines will see an increased focus on human-machine collaboration:
- Augmented Reality (AR) and Virtual Reality (VR): Operators will use AR glasses or VR systems to visualize machine data, part specifications, and maintenance instructions directly within their field of view. This reduces errors, improves training, and makes troubleshooting easier and more efficient. For example, AR can overlay machine diagnostics, part assembly instructions, or step-by-step troubleshooting procedures directly onto the machine or part being worked on.
- Remote Monitoring: Operators and supervisors will have the ability to remotely monitor production lines through connected devices and applications. This allows them to make adjustments, receive alerts, or monitor the production status without being physically present on the floor. Remote support can also be provided by experts who can assist with troubleshooting or guide on-site operators through complex tasks.
14. Energy Efficiency and Sustainability
As global environmental concerns increase, the future of sheet metal shaping automation will focus heavily on energy efficiency and sustainability:
- Energy-Efficient Machinery: The development of energy-efficient machines that consume less power during operation will become a key feature of automated sheet metal shaping lines. This includes the use of more efficient hydraulic systems, regenerative braking in robots, and energy recovery systems.
- Recycling and Waste Reduction: Automated systems will include integrated solutions for scrap metal recycling. Parts of the production process will be designed to collect scrap and waste materials, which will be processed and reused within the system, reducing overall material waste and improving the sustainability of the process.
- Carbon Footprint Reduction: Automation lines will be optimized to reduce the carbon footprint of manufacturing operations. This includes using renewable energy sources, reducing material waste, and improving production scheduling to minimize idle times, all of which contribute to a more sustainable production environment.
15. Enhanced Safety Features
Automated sheet metal shaping lines will incorporate more safety measures to protect both operators and the machinery:
- Safety Sensors and Cameras: The integration of advanced sensors, machine vision, and safety cameras will ensure that human operators are not exposed to dangerous areas of the production line. These systems can automatically stop the machines if a worker enters a restricted area or if there’s an imminent risk of injury.
- Collaborative Workspaces: As cobots (collaborative robots) work alongside human operators, safety features will be built into the robots to prevent injury. For example, if a cobot detects a human nearby, it may slow down or stop its motion to ensure safe interaction.
- Remote Monitoring and Control: Operators can monitor and control automated systems remotely, reducing the need for direct interaction with potentially hazardous equipment. This reduces human exposure to high-risk tasks, such as welding or heavy lifting.
16. End-to-End Automation
In the future, end-to-end automation will connect every stage of the sheet metal shaping process. From initial material handling and shaping to final inspection, packaging, and shipping, the entire workflow will be managed by a combination of intelligent systems, robotics, and AI-powered decision-making tools. The seamless connection between these systems will:
- Improve efficiency by minimizing downtime and human intervention.
- Enable real-time adjustments based on production needs, material availability, or customer orders.
- Increase flexibility by allowing for custom designs, quick prototyping, and low-volume production runs without interrupting the overall production flow.
Conclusion
The future of Sheet Metal Shaping Automation Lines will focus on creating highly efficient, flexible, and intelligent manufacturing systems that integrate advanced robotics, AI, real-time data analysis, and sustainable practices. The ability to produce high-quality, customized parts at faster speeds while minimizing waste and improving safety will give manufacturers a competitive edge in the evolving market.
By leveraging these technologies, manufacturers can achieve faster turnaround times, reduce costs, and offer more innovative and personalized products to meet the diverse needs of industries like automotive, aerospace, electronics, and construction. The ongoing evolution of these automated systems promises to push the boundaries of manufacturing capabilities, bringing about a new era of smart, sustainable, and efficient production.
17. Artificial Intelligence and Machine Learning Integration
As the demand for smarter and more efficient production lines grows, the integration of artificial intelligence (AI) and machine learning (ML) into sheet metal shaping automation lines will continue to expand. These technologies will play a pivotal role in optimizing processes and making real-time decisions that improve overall efficiency and product quality.
- AI-Based Process Optimization: AI algorithms will continuously analyze production data to identify inefficiencies, predict bottlenecks, and recommend process adjustments. This could involve optimizing speed settings, altering tooling configurations, or adjusting robotic paths for the most efficient part production.
- Quality Prediction and Control: Machine learning algorithms will analyze historical data to predict quality outcomes for parts, identifying patterns that lead to defects before they occur. These systems can monitor production conditions in real-time (e.g., temperature, pressure, material properties) to predict and prevent potential issues.
- Self-Learning Systems: Over time, machine learning models integrated into the automation line can “learn” from production data, improving their accuracy and predictive capabilities. This self-learning ability means that the system becomes increasingly more efficient, with reduced intervention needed from human operators.
18. Smart Supply Chain Integration
An increasingly important aspect of automated sheet metal shaping lines will be their integration with the smart supply chain. Automation lines will not only be optimized for internal processes but will also be part of a larger, interconnected network of suppliers, distributors, and customers.
- Just-in-Time (JIT) Manufacturing: Automated lines can be integrated with supply chain management systems to ensure that the right materials are available at the right time, minimizing inventory costs and production delays. This involves integrating real-time demand data with automated material handling systems, ensuring a smooth and responsive production process.
- Supply Chain Visibility: IoT devices and sensors integrated into the line can provide detailed data on material usage, part progress, and shipping status. This data can be shared with suppliers or distributors, enabling greater transparency and quicker responses to supply chain disruptions.
- Demand Forecasting: AI-driven demand forecasting tools can predict changes in customer demand, allowing the automated line to adjust production schedules dynamically. By linking production directly to market trends, businesses can reduce the risk of overproduction or stockouts, ensuring that products are always available when needed.
19. Human-Centered Automation
While automation will continue to reduce labor requirements for repetitive or dangerous tasks, human-centered automation will emphasize the collaboration between humans and machines to leverage the strengths of both.
- Human Supervision and Decision-Making: Despite the advanced capabilities of automated systems, human expertise will still be essential for high-level decision-making, troubleshooting, and complex problem-solving. Operators will be able to oversee multiple machines and systems simultaneously, using intuitive user interfaces and remote monitoring tools to maintain control of the production line.
- Employee Training and Upskilling: As automation continues to evolve, there will be an increased focus on training and upskilling workers to operate, maintain, and troubleshoot advanced automated systems. This shift will move factory workers from traditional manufacturing roles to roles focused on overseeing automated processes, ensuring system performance, and maintaining equipment.
- Collaborative Interfaces: User interfaces that are intuitive, user-friendly, and data-driven will help human workers make informed decisions about production processes. Augmented Reality (AR) or heads-up displays could provide real-time data visualizations of machine performance, error detection, and step-by-step troubleshooting instructions.
20. Modular Automation Systems
Modular automation systems are gaining traction as a way to enhance the flexibility of sheet metal shaping lines. These systems consist of interchangeable, standardized modules that can be easily reconfigured or expanded to accommodate changing production needs.
- Scalability: Manufacturers can scale their production capacity up or down depending on demand. If production needs increase, additional modules can be added to expand capacity without the need for a complete overhaul of the existing automation system.
- Customizable Production Lines: Modular systems allow for rapid changes to production workflows. If a new product design requires different forming or cutting methods, modular machines can be easily reprogrammed or swapped to meet new requirements. This flexibility is especially useful for businesses that need to quickly respond to changing customer demands or market conditions.
- Cost-Effective Upgrades: Rather than investing in an entirely new system, businesses can update their production lines in a cost-effective manner by adding or upgrading individual modules. This reduces the need for large capital expenditures and allows manufacturers to stay competitive with the latest technology.
21. Blockchain for Traceability and Security
The integration of blockchain technology into automated sheet metal shaping lines will enhance traceability and security across the entire production and supply chain.
- Product Traceability: Blockchain can be used to track the journey of materials and components from suppliers to finished products. Every step in the process (from material sourcing to production and final delivery) will be recorded on a secure, immutable ledger. This ensures that each product is traceable and verifiable, providing transparency and reducing the risk of counterfeit parts or faulty materials entering the production process.
- Supply Chain Security: Blockchain ensures the security of data exchanges between manufacturers, suppliers, and customers. By using smart contracts, manufacturers can automate payments and other supply chain transactions securely, reducing the potential for fraud or errors.
- Quality Assurance: With blockchain, quality control and inspection results can be recorded and stored securely, ensuring that every part produced meets the required standards. This data can be used to resolve disputes, track the origin of defects, and demonstrate compliance with industry regulations.
22. Advanced Simulation and Digital Twin Technology
The use of simulation and digital twin technology in sheet metal shaping automation lines will allow manufacturers to simulate entire production processes before they are executed in the real world.
- Digital Twin: A digital twin is a virtual representation of a physical system that mirrors its real-time performance. In the case of automated sheet metal shaping lines, a digital twin could simulate the behavior of machines, robots, material flow, and even entire factory layouts. Manufacturers can use digital twins to predict performance, optimize machine settings, and troubleshoot problems before they occur in the physical world.
- Process Simulation: Before initiating production, manufacturers can run simulations of sheet metal forming, bending, and cutting processes to analyze the effects of different variables such as material thickness, temperature, and machine speed. This allows for optimization of processes and reduces the likelihood of defects or failures.
- Predictive Maintenance and Failure Prevention: By combining real-time data with digital twin simulations, predictive maintenance models can be created. These models can predict when a machine is likely to fail or when its performance might degrade, allowing maintenance to be performed proactively to avoid unplanned downtime.
23. Enhanced Customization for Niche Markets
As the market for specialized and niche products continues to grow, automated sheet metal shaping lines will be able to cater to small-batch production with high levels of customization:
- Low-Volume Production: Automation systems that can quickly switch between different part configurations and production runs will be crucial for industries that require low-volume, high-variability production. For example, aerospace and automotive companies often require custom parts with strict tolerances but in smaller quantities. Automation lines will make it easier to produce these specialized parts without excessive costs.
- Rapid Prototyping: Automated sheet metal lines will integrate more advanced rapid prototyping capabilities, enabling manufacturers to produce prototypes and test designs faster. Automated systems can produce prototype parts in small quantities, allowing engineers to evaluate and refine designs more quickly before full-scale production begins.
- Tailored Part Production: Customization features could include the ability to engrave, mark, or personalize individual parts, allowing manufacturers to offer unique solutions to customers, such as branded or tailored metal components for consumer goods or specialty industries.
24. Smart Factory and Industry 4.0 Integration
Finally, sheet metal shaping automation lines will be integral to the broader concept of Industry 4.0 and the Smart Factory. These factories are characterized by interconnected, data-driven machines and systems that operate with minimal human intervention, offering several key benefits:
- Self-Optimizing Systems: Smart factories will use AI, machine learning, and real-time data to self-optimize production processes. Machines can communicate with one another, adjust their settings based on incoming orders, and adapt to changes in demand or material availability.
- Cross-Industry Integration: Automation lines will integrate seamlessly with other aspects of manufacturing, such as 3D printing, additive manufacturing, and assembly. This will create a more cohesive, flexible manufacturing ecosystem where various technologies work together to produce complex, customized products.
- Smart Supply Networks: Industry 4.0 will bring about the development of fully interconnected supply networks, allowing for real-time tracking of materials, predictive stock management, and efficient resource allocation, leading to reduced lead times and more responsive production schedules.
Conclusion
The evolution of sheet metal shaping automation is poised to revolutionize manufacturing by integrating advanced robotics, AI, real-time data analysis, sustainability practices, and Industry 4.0 technologies. The increased flexibility, precision, and efficiency of these systems will enable manufacturers to meet the growing demand for customized, high-quality products while reducing costs, downtime, and waste.
As automation continues to advance, manufacturers will be able to produce more complex, tailored parts at higher speeds and with greater consistency than ever before. The integration of smart, interconnected systems across the entire production line will lead to a more adaptable, resilient, and efficient manufacturing ecosystem capable of responding to the evolving demands of the market. With these innovations, the future of sheet metal shaping automation holds immense potential for driving forward industrial productivity, innovation, and sustainability.
Automated Sheet Metal Forming Line
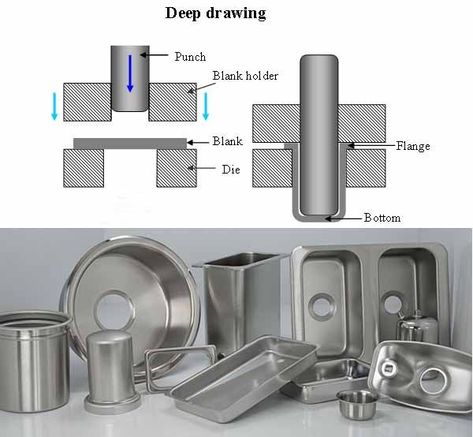
An Automated Sheet Metal Forming Line is a highly efficient manufacturing system designed to shape sheet metal into specific forms or components using automated processes. These systems incorporate robotics, sensors, AI-driven controls, and other advanced technologies to streamline production, reduce human intervention, and improve precision. Here’s a breakdown of the key components and features that make up such a system:
Key Components of an Automated Sheet Metal Forming Line:
- Material Handling System:
- Automated conveyors or robotic arms move sheets of metal from one stage of the process to another.
- Systems for automatic material loading and unloading, minimizing manual intervention.
- Pressing and Forming Stations:
- CNC Press Brakes: These are automated to bend the sheet metal to precise angles, powered by CNC (Computer Numerical Control) for enhanced precision and flexibility.
- Stamping Presses: Used to punch, cut, or form the metal sheets into desired shapes. These presses can operate with minimal human intervention through automation.
- Roll Forming Machines: Roll forming is often used for creating continuous profiles or shapes by feeding metal sheets through a series of rollers.
- Hydraulic Presses: Hydraulic systems are used for high-force shaping and forming, ideal for thick or rigid metal sheets.
- Robotic Arms:
- Used for tasks like loading/unloading materials, handling parts, or even performing secondary operations like welding or assembling components.
- Robots can be programmed for precise movements, reducing the risk of errors and increasing throughput.
- Laser Cutting and Welding Stations:
- Laser Cutting: High-precision laser systems cut sheet metal to the required shape. The automation ensures quick setup and adjustment to different part designs.
- Laser Welding: Laser welding systems used for joining metal parts, providing strong welds with minimal distortion, often automated for repetitive tasks.
- Spot and MIG Welding: Automated robotic welding arms can handle spot or MIG (Metal Inert Gas) welding with precision and speed.
- Inspection and Quality Control Systems:
- Vision Systems: Automated optical systems inspect parts for defects, ensuring only high-quality parts are passed through.
- AI and Machine Learning: These systems analyze production data to predict potential issues, helping operators optimize processes in real time and maintain part quality.
- Thickness Sensors: To ensure uniformity in the metal sheet thickness and ensure consistency across all produced parts.
- Flexible Automation Controls:
- Programmable Logic Controllers (PLCs): Manage machine operations and ensure synchronization across the entire production line.
- Advanced Human-Machine Interface (HMI): Operators can monitor and control the line using touchscreen interfaces, adjusting settings or accessing diagnostic information.
- Industry 4.0 Integration: Integration of the line with cloud systems and IoT (Internet of Things) devices for real-time monitoring and remote troubleshooting.
- Post-Processing Stations:
- After the primary forming process, parts may undergo secondary operations such as trimming, deburring, or coating.
- Automated systems ensure uniformity in these post-processing stages, enhancing the final product quality.
- Packaging and Shipping Automation:
- After the sheet metal parts are formed and inspected, the automated system can handle sorting, packaging, and labeling for shipping.
- Automated packaging systems ensure that products are securely packed and ready for delivery, with minimal handling.
Benefits of an Automated Sheet Metal Forming Line:
- Increased Productivity: Automation allows the system to operate 24/7, reducing downtime and maximizing throughput.
- Improved Precision and Consistency: With automated CNC machines, robotics, and AI-based control systems, the line ensures high-quality, repeatable results with minimal deviation.
- Reduced Labor Costs: Automation reduces the need for manual labor, which not only lowers costs but also reduces human error.
- Scalability: The system can be adjusted to handle different product volumes, from small-batch production to large-scale manufacturing, by simply reprogramming the automation system.
- Enhanced Flexibility: Automated systems can quickly adapt to changes in design or material specifications, making it easy to switch between different products or part designs.
- Reduced Material Waste: Precise control over the cutting and forming processes minimizes scrap and maximizes the efficient use of raw materials.
Future Trends in Automated Sheet Metal Forming Lines:
- AI-Driven Optimization: Future systems will be capable of learning from past data and optimizing production parameters for faster cycle times and higher product quality.
- Advanced Robotics: Robotic arms and cobots (collaborative robots) will play a bigger role in performing complex tasks such as assembly, part inspection, and adaptive adjustments.
- Sustainability: Energy-efficient machines and better material recovery systems will reduce environmental impact, while also lowering operating costs.
- Integration with Additive Manufacturing: In the future, automated forming lines could integrate with 3D printing systems to create hybrid manufacturing processes, where sheet metal components are combined with additive parts for more complex assemblies.
- Real-Time Data Analytics: Using real-time data from connected devices and sensors, manufacturers will gain insights into machine performance, part quality, and even supply chain status, enabling proactive decision-making.
Conclusion
The Automated Sheet Metal Forming Line is an integral part of modern manufacturing, providing a combination of speed, precision, and flexibility. By reducing the need for human intervention, minimizing errors, and optimizing production, these systems help manufacturers meet the growing demands for high-quality, cost-effective sheet metal products across various industries, such as automotive, aerospace, construction, and electronics.
As technology advances, the automation in sheet metal forming will continue to evolve, making manufacturing processes even more intelligent, interconnected, and efficient, paving the way for next-generation manufacturing practices.
25. Advanced Data Analytics for Process Optimization
The integration of advanced data analytics into automated sheet metal forming lines is set to revolutionize manufacturing efficiency and product quality. These systems use big data and machine learning algorithms to analyze vast amounts of data generated by machines and sensors throughout the production line.
- Predictive Analytics: By analyzing historical data and real-time sensor inputs, predictive models can forecast potential failures, such as equipment malfunctions or quality issues, before they occur. This allows manufacturers to perform maintenance at optimal times, preventing unexpected downtime and reducing the risk of defects.
- Process Optimization: Data analytics can continuously monitor process parameters (e.g., pressure, speed, temperature) and adjust them in real-time to maximize throughput and minimize material waste. Optimization algorithms can make adjustments faster and more accurately than human operators, leading to more efficient and cost-effective production.
- Production Insights: Manufacturers can use the data generated by automated systems to uncover patterns in production performance. These insights enable them to fine-tune processes, optimize machine usage, and improve energy consumption, leading to a more sustainable operation.
26. Augmented Reality (AR) and Virtual Reality (VR) for Operator Assistance
Augmented Reality (AR) and Virtual Reality (VR) technologies are increasingly being used to improve operator interaction with automated sheet metal forming lines.
- AR for Maintenance and Troubleshooting: Operators can use AR glasses or devices to receive real-time guidance during equipment maintenance or troubleshooting. The system can overlay step-by-step instructions or highlight potential issues directly in the operator’s field of vision, making the repair process quicker and reducing downtime.
- Training with VR: VR can be used for immersive training simulations, allowing workers to practice operating the automated system in a safe, virtual environment before handling real equipment. This helps operators become familiar with the system’s controls and workflow, improving their efficiency when working with the real machinery.
- Remote Assistance: AR can also allow for remote troubleshooting. Experts can guide operators through complex procedures or address issues from a distance, improving response time and reducing the need for on-site personnel.
27. Advanced Robotics and Collaborative Systems
The role of robots in automated sheet metal forming lines will continue to expand, particularly through the use of collaborative robots (cobots) that work alongside human operators to enhance efficiency and flexibility.
- Collaborative Robotics: Cobots are designed to work safely alongside human workers without the need for safety cages. They can assist with tasks such as loading and unloading materials, welding, or assembling components. These robots adapt to changes in production schedules and work alongside humans, enabling manufacturers to achieve higher efficiency without sacrificing flexibility.
- Precision and Flexibility: Robots in the forming line can be reprogrammed or reconfigured to handle different parts or complex shapes, increasing the line’s adaptability to various product designs. The use of robotic arms for tasks like bending, welding, or picking parts reduces manual labor and ensures higher consistency in the final product.
- Automated Assembly: In addition to forming, robotic arms can be used to assemble parts, add fasteners, or perform other post-processing operations. These collaborative systems can seamlessly handle parts from one stage of the process to the next, enhancing overall throughput and quality control.
28. Energy-Efficiency and Sustainability
As industries shift towards more sustainable practices, energy efficiency and sustainable manufacturing will be critical components of future automated sheet metal forming lines.
- Energy-Efficient Machinery: Automation systems will increasingly integrate energy-efficient motors, sensors, and process controls to minimize energy consumption while maintaining performance. For instance, energy recovery systems can be implemented in machines like presses or roll formers, capturing and reusing energy during operation.
- Green Manufacturing: Automated systems can also optimize resource usage, reducing waste generation and enabling manufacturers to minimize their environmental impact. For example, automated cutting and stamping processes can be adjusted to maximize material usage and reduce scrap. Additionally, sustainable materials such as recycled metals could be integrated into the supply chain, with the automation line being optimized for these materials.
- Emission Reduction: As the production of sheet metal parts is often energy-intensive, automating the processes can also help reduce emissions by improving energy efficiency and reducing waste. Cleaner technologies, such as electric-powered machines, can be utilized to further reduce the carbon footprint of the factory.
29. Digital Twin Technology for Real-Time Monitoring and Simulation
Digital Twin technology is becoming a game-changer in automated sheet metal forming lines. A digital twin is a virtual representation of the physical production line that updates in real-time, allowing manufacturers to monitor performance, predict failures, and optimize operations.
- Real-Time Monitoring: The digital twin can be connected to all machines, sensors, and control systems on the production line. This allows operators to observe the line’s performance in real-time, identify inefficiencies, and troubleshoot potential issues before they affect production.
- Simulating Process Changes: Manufacturers can simulate changes in the production process, such as adjustments to speed or temperature, before making those changes in the physical environment. This helps predict the outcome of different adjustments and optimize the production flow without causing disruption.
- Predictive Maintenance: By analyzing data from the digital twin, predictive maintenance algorithms can forecast when equipment will need repairs, reducing unplanned downtime and extending the lifespan of machines.
30. Advanced Automation Software and Integration
The success of an automated sheet metal forming line depends heavily on the software systems that control and integrate the various machines and processes. Advanced automation software plays a critical role in managing the entire production process, from material handling to final packaging.
- Centralized Control Systems: Modern automation lines are managed by centralized control systems that allow operators to monitor and control each stage of the process from a single platform. These systems provide real-time updates, track production progress, and help operators make adjustments as needed to optimize the workflow.
- Cloud-Based Systems: The adoption of cloud-based software solutions allows manufacturers to access real-time data and production metrics from anywhere, improving decision-making and allowing for remote monitoring. Cloud-based platforms can also enable easier software updates, ensuring that the automation system stays current with the latest features and improvements.
- ERP and MES Integration: Automated lines are increasingly integrated with Enterprise Resource Planning (ERP) and Manufacturing Execution Systems (MES) to provide seamless communication across departments. For example, an ERP system could send real-time inventory data to the automation line to ensure that the right materials are always available, while an MES system ensures that production is aligned with customer orders and schedules.
31. Customization and Quick Changeover Capabilities
An essential feature of automated sheet metal forming lines is their ability to quickly changeover between different products or designs. This flexibility is crucial in industries where product demand changes frequently, and manufacturers need to respond quickly.
- Quick Tool Change Systems: Advanced automated lines can include quick-change tooling that allows for fast switching between different molds or dies, reducing setup time. This is especially useful for businesses that handle multiple products or custom orders with varying specifications.
- Flexible Automation: Robotic systems and programmable machinery allow the automation line to be easily reconfigured to accommodate different product designs or batch sizes. This is particularly valuable for industries such as automotive or aerospace, where parts may vary in size, shape, and complexity from one production run to another.
- Modular Systems: Modular automation systems make it easy to scale production up or down, allowing businesses to adjust production capacity based on current demand. By adding or removing machines and modules, manufacturers can tailor the system to meet changing production needs without significant downtime or retooling costs.
32. Smart Factory Integration
Finally, automated sheet metal forming lines will play a significant role in the development of the smart factory. These factories integrate automation, IoT, and real-time data analytics to create highly efficient, interconnected production environments.
- Machine-to-Machine Communication: Automated lines will increasingly rely on machine-to-machine (M2M) communication to enable seamless interaction between equipment, sensors, and control systems. This connectivity ensures that all parts of the line are synchronized, and any issues can be addressed in real-time.
- Real-Time Performance Metrics: Smart factories use sensors and data collection points across the production line to monitor machine performance, product quality, and overall production efficiency. Real-time performance data will be used to optimize operations, identify bottlenecks, and make data-driven decisions about machine usage and scheduling.
- Autonomous Production Lines: In the most advanced smart factories, automated sheet metal forming lines could operate autonomously, with minimal human intervention. These lines would self-adjust based on production requirements, perform predictive maintenance, and even optimize production schedules based on demand forecasts.
Conclusion
The future of automated sheet metal forming lines is bright, driven by advancements in robotics, AI, data analytics, and smart manufacturing. These systems will not only increase productivity, reduce waste, and improve precision, but they will also enable manufacturers to meet the growing demands for customized products, quick changeovers, and flexible production runs. As technology continues to evolve, the possibilities for innovation in automated sheet metal forming lines are virtually limitless, opening up new opportunities for industries around the world.
33. Artificial Intelligence (AI) and Machine Learning Integration
The role of Artificial Intelligence (AI) and Machine Learning (ML) in automated sheet metal forming lines is rapidly expanding, enhancing both the decision-making process and the adaptability of manufacturing systems. These technologies are utilized for tasks ranging from quality control to predictive maintenance and process optimization.
- Real-Time Process Monitoring: AI-powered systems can monitor production processes in real-time, analyzing vast amounts of data collected from sensors and cameras. By identifying patterns or anomalies, AI can immediately alert operators about potential issues or deviations from the expected production standards.
- Predictive Quality Control: AI can be trained to recognize minute defects or inconsistencies in sheet metal parts that might be too small or subtle for the human eye. This leads to higher quality control by detecting flaws early in the production process and enabling corrective actions before defective parts are produced in large quantities.
- Process Adjustment: AI systems can analyze production data to predict the ideal settings for different types of materials or designs. By continuously learning from previous batches, AI algorithms can make real-time adjustments to speed, pressure, and other variables, ensuring optimal production parameters for each job.
34. Cloud-Based Manufacturing and Remote Management
As manufacturing lines become more interconnected, cloud-based systems are offering new levels of accessibility and management. These platforms allow manufacturers to monitor, manage, and control automated sheet metal forming lines from anywhere in the world, providing numerous benefits for global manufacturing operations.
- Global Operations Monitoring: Cloud-based systems enable manufacturers to monitor multiple facilities or production lines in real-time. This is especially beneficial for companies with operations across multiple locations, providing a unified dashboard to oversee performance, quality, and efficiency across the entire network.
- Remote Troubleshooting and Support: With cloud-based monitoring, experts can access production data remotely, providing real-time support for troubleshooting issues or optimizing processes. This reduces the need for on-site intervention and ensures that problems can be addressed quickly, even if the team is located elsewhere.
- Data Storage and Analytics: Cloud systems offer extensive data storage capabilities, allowing manufacturers to keep a history of production data, including machine performance, material usage, and quality control. By analyzing this historical data, companies can gain valuable insights that help improve future production runs and predict market trends.
35. Customizable Automation and Modular System Design
As the demand for product diversity and customization continues to rise, the ability to easily reconfigure automated sheet metal forming lines will be crucial for manufacturers to maintain flexibility and respond to customer needs.
- Modular Automation Systems: Modular systems are designed to be reconfigured easily by adding or removing components based on specific production needs. This modularity allows for greater customization and ensures that the line can be adapted to various part designs, volumes, or manufacturing requirements without major retooling.
- Quick Reconfiguration for New Product Lines: With modular automation systems, companies can quickly shift production between different types of products. For instance, a single automated line could switch from producing automotive components to creating electronics casings, with minimal downtime and without the need for significant new investments in machinery.
- Flexible Tooling and Changeovers: As part of the modular system design, tools and dies can be quickly changed or adjusted for different sheet metal thicknesses, designs, or finishes. This reduces the setup time required between production runs and allows for faster transitions from one product type to another.
36. Cybersecurity for Automated Manufacturing
As automated sheet metal forming lines become more connected to the internet and various industrial networks, ensuring cybersecurity becomes a critical concern. Protecting the data, equipment, and networks from cyber threats is essential to maintain the integrity and continuity of production.
- Secure Data Transmission: All communication between machines, control systems, and the cloud must be encrypted to prevent unauthorized access or tampering. Secure data transmission protocols and multi-factor authentication systems are necessary to protect sensitive production data and prevent hacking or sabotage.
- Risk Management and Threat Detection: Advanced cybersecurity systems can be integrated into automated production lines to continuously monitor for potential threats. Machine learning algorithms can help identify abnormal activity or vulnerabilities in real-time, enabling immediate responses to cyber threats.
- Regulatory Compliance: As industrial networks become more interconnected, compliance with cybersecurity regulations and industry standards (e.g., ISO/IEC 27001 for information security management) is essential. Automated sheet metal forming systems must adhere to these standards to ensure data security and prevent disruptions in the manufacturing process.
37. Enhanced Ergonomics and Worker Safety
Although automated systems reduce the need for manual labor, ergonomics and worker safety continue to be crucial considerations in the design and operation of sheet metal forming lines. Automation is not just about replacing workers but ensuring that human operators are safe, comfortable, and able to interact efficiently with the machines.
- Collaborative Robot Safety: Cobots that work alongside human workers are designed to prioritize safety. These robots have built-in sensors that allow them to detect nearby humans and stop or slow down their movements to prevent accidents. In addition, their tasks are often limited to repetitive or physically demanding work, reducing the risk of injury for human workers.
- Operator Safety Stations: Safety features such as emergency stop buttons, safety fences, and light curtains are implemented in automated systems to protect operators. These features ensure that operators can work in proximity to the machines without risk of harm, while still being able to intervene if necessary.
- Ergonomic Workspaces: Automation systems can also be designed with ergonomics in mind. For instance, adjustable workstations and robotic arms with precise control can help operators perform tasks such as part inspection or machine maintenance without putting undue strain on their bodies.
38. Real-Time Feedback and Continuous Improvement
To foster a culture of continuous improvement, automated sheet metal forming lines can be equipped with real-time feedback loops that help operators and managers quickly identify areas for enhancement.
- Continuous Monitoring of Performance: Sensors embedded in the production line can collect data on machine efficiency, part quality, and environmental conditions. This data is processed in real-time and displayed on dashboards, allowing operators to take immediate corrective action if any part of the process falls below standard.
- Production Line Feedback Systems: Real-time feedback from workers and operators can be incorporated into the control system to continuously optimize the line. This may include feedback on material defects, mechanical issues, or even suggestions for adjusting process parameters to improve efficiency.
- Employee Involvement in Process Improvement: Automation can also support a more inclusive approach to continuous improvement by empowering workers to provide feedback on the systems they interact with. Employees can be equipped with tools that allow them to submit ideas for process changes, fostering a sense of ownership and collaboration in improving the line’s performance.
39. Advanced Material Handling and Automation Integration
Material handling is a critical part of sheet metal forming, and advancements in automated material handling are helping streamline workflows by reducing bottlenecks and ensuring seamless movement of materials throughout the entire production line.
- Automated Guided Vehicles (AGVs): AGVs are used to transport raw materials, finished components, and waste products throughout the production line without requiring human intervention. These vehicles are equipped with sensors to navigate obstacles and optimize transportation routes, reducing downtime and improving overall efficiency.
- Smart Conveyors: Conveyors integrated with IoT sensors and real-time tracking systems allow for precise monitoring of the movement of materials. This ensures that parts are always in the right place at the right time and prevents materials from being delayed or misplaced during the forming process.
- Dynamic Routing and Scheduling: Automated systems can use data analytics to dynamically adjust material flow and scheduling. For example, if there’s a bottleneck in one part of the production line, the system can reroute materials to another station to keep production running smoothly.
40. Sustainability and Circular Manufacturing in Sheet Metal Forming
The future of sheet metal forming will not only be about speed and efficiency but also about integrating sustainability into the entire manufacturing process. As the demand for eco-friendly practices increases, automation will play a key role in reducing the environmental footprint of manufacturing operations.
- Circular Economy Practices: Automated systems can be designed to support circular manufacturing practices by reducing waste and enabling the reuse or recycling of materials. For example, excess scrap metal from the forming process can be automatically sorted, cleaned, and fed back into the production line.
- Reduced Energy Consumption: Automation systems that optimize process parameters can also help minimize energy consumption by ensuring that machines run at their most efficient settings. Additionally, energy-efficient motors, regenerative braking, and energy recovery systems can further reduce the energy needed for forming operations.
- Environmentally Friendly Materials: Automated lines will increasingly use materials that have minimal environmental impact, such as recycled metals or bio-based coatings. Automation allows for better handling of these materials, ensuring that the production process is optimized for sustainability.
Conclusion
The future of automated sheet metal forming lines is poised for remarkable advancements, driven by the integration of AI, machine learning, robotics, cloud computing, and sustainable practices. These innovations will not only enhance the speed and quality of production but also increase flexibility, reduce costs, and contribute to greener manufacturing practices. As the industry continues to evolve, companies that invest in cutting-edge automated technologies will be well-positioned to meet the demands of an ever-changing global market while achieving higher levels of efficiency, quality, and sustainability.
EMS Metalworking Machinery
We design, manufacture and assembly metalworking machinery such as:
- Hydraulic transfer press
- Glass mosaic press
- Hydraulic deep drawing press
- Casting press
- Hydraulic cold forming press
- Hydroforming press
- Composite press
- Silicone rubber moulding press
- Brake pad press
- Melamine press
- SMC & BMC Press
- Labrotaroy press
- Edge cutting trimming machine
- Edge curling machine
- Trimming beading machine
- Trimming joggling machine
- Cookware production line
- Pipe bending machine
- Profile bending machine
- Bandsaw for metal
- Cylindrical welding machine
- Horizontal pres and cookware
- Kitchenware, hotelware
- Bakeware and cuttlery production machinery
as a complete line as well as an individual machine such as:
- Edge cutting trimming beading machines
- Polishing and grinding machines for pot and pans
- Hydraulic drawing presses
- Circle blanking machines
- Riveting machine
- Hole punching machines
- Press feeding machine
You can check our machinery at work at: EMS Metalworking Machinery – YouTube
Applications:
Flange-punching
Beading and ribbing
Flanging
Trimming
Curling
Lock-seaming
Ribbing