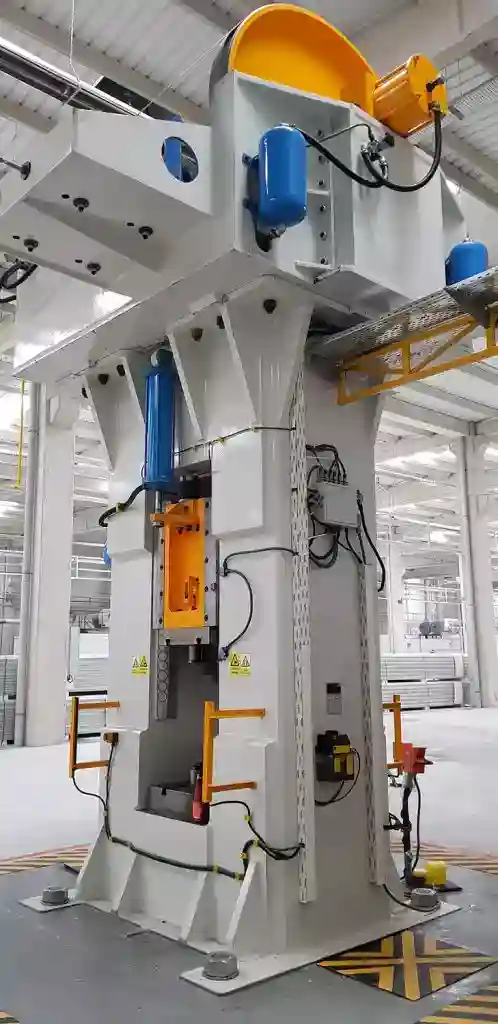
A friction screw press with a capacity of 2000 tonnes is an exceptionally powerful and heavy-duty mechanical press designed to exert a maximum forging force of 2000 metric tonnes (approximately 4,409,246 pounds) during its operation. These presses are among the largest and most robust forging machines available and are used in the most demanding industrial applications where immense forging forces are required to shape and deform very large metal materials effectively. Here are some key details and applications related to a 2000-tonne friction screw press:
- Forging Capacity: A 2000-tonne friction screw press can exert a maximum forging force of 2000 metric tonnes. This force is generated through the frictional resistance between the rotating screw and the fixed nut within the press.
- Working Principle: The operation of a 2000-tonne friction screw press follows the same fundamental principles as other friction screw presses. It involves the use of a rotating screw that threads into a fixed nut. As the screw rotates, it moves vertically, pushing the ram (slide) downward. The ram carries the forging dies, which shape and deform the heated metal workpiece placed between them.
- Applications:
- Heavy-Duty Forging: These presses are primarily used for the most demanding heavy-duty forging processes where metal workpieces are heated to high temperatures (usually above their recrystallization temperature) before being formed and shaped. Common applications include the production of extremely large and massive components used in industries such as heavy machinery manufacturing, shipbuilding, aerospace, and energy generation.
- Die Forging: A 2000-tonne friction screw press is well-suited for die forging operations, where metal blanks are pressed into precision dies to create complex shapes and extremely large-sized components.
- Upsetting: These presses are capable of performing upsetting operations, which are essential for creating very large, high-strength components like massive axles, anchor chains, and heavy bolts.
- Control and Precision: Modern friction screw presses, including 2000-tonne models, are equipped with advanced control systems that allow precise control over the forging process. This ensures that the desired dimensions and quality of the forged components are consistently achieved.
- Energy Efficiency: Despite their immense power, friction screw presses are known for their energy efficiency compared to other types of forging equipment. This is particularly important in large-scale heavy forging applications where energy consumption can be substantial.
- Safety Considerations: Safety precautions are of paramount importance when operating a 2000-tonne friction screw press due to the immense forces involved. Comprehensive safety measures, operator training, and strict adherence to safety protocols are essential to prevent accidents and ensure the safety of personnel working with the press.
In summary, a 2000-tonne friction screw press is an industrial giant used for the most demanding heavy-duty forging applications where extremely high forging forces are required to shape and form very large metal components. These presses are typically found in industries involved in the manufacturing of massive machinery, infrastructure components, and other critical industrial equipment.
Friction Screw Press 2000 Tonnes
A friction screw press with a capacity of 2000 tonnes is a powerful and heavy-duty mechanical press designed to exert a maximum forging force of 2000 metric tonnes (approximately 4,409,246 pounds) during its operation. These massive machines are used for a variety of demanding heavy-duty forging applications where extremely high forging forces are required to shape and form very large metal components.
Key Features of 2000-Ton Friction Screw Presses
- High Forging Force: Capable of generating 2000 tonnes of forging force, enabling the shaping of large and intricate metal components.
- Stable Operation: Employ a friction-clutch mechanism that ensures smooth and stable operation during forging processes.
- Versatility: Can handle a wide range of forging tasks, including upsetting, drawing, and coining.
- Precision Control: Equipped with advanced control systems for precise and consistent forging results.
- Robust Construction: Built with durable materials and robust designs to withstand the demanding forging environment.
Applications of 2000-Ton Friction Screw Presses
- Heavy-Duty Forgings: Production of large and complex metal parts for various industries, including automotive, aerospace, and construction.
- Shaping and Forming: Forming and shaping of metal components into desired shapes and dimensions.
- Upsetting: Shortening and increasing the diameter of metal blanks.
- Drawing: Elongating and reducing the diameter of metal blanks.
- Coining: Impressing patterns or designs onto metal surfaces.
Examples of Components Forged Using 2000-Ton Friction Screw Presses
- Crankshafts
- Connecting Rods
- Gear Blanks
- Flywheels
- Pressure Vessels
- Large Tooling Components
Forging Capacity:
- Maximum forging force: 2000 metric tonnes (4,409,246 pounds)
- Forging speed: Adjustable from 0 to 8 strokes per minute
- Stroke length: Typically 400 to 800 millimeters (15.7 inches to 31.5 inches)
- Bed opening: Typically 600 to 800 millimeters (23.6 inches to 31.5 inches)
- Die area: Typically 900 by 900 millimeters (35.4 inches by 35.4 inches)
Mechanical Structure:
- Rigid and robust frame construction to withstand the high forging forces
- Friction screw mechanism for generating the forging force
- Hydraulic system for controlling the movement of the screw and slide
- Pneumatic system for operating the clutch and brake mechanisms
Control System:
- Advanced PLC (Programmable Logic Controller) for precise and consistent operation
- Touchscreen interface for user-friendly operation
- Real-time monitoring of forging parameters, such as force, stroke, and speed
- Data logging for process analysis and quality control
Additional Specifications:
- Motor power: Typically 75 to 150 kilowatts (101 to 201 horsepower)
- Machine weight: Typically 50 to 100 metric tonnes (110,231 to 220,462 pounds)
- Machine dimensions: Typically 3 meters by 2.5 meters by 2.5 meters (9.8 feet by 8.2 feet by 8.2 feet)
Please note that these are general specifications and may vary depending on the specific manufacturer and model
It’s important to note that the specifications can vary, and specific requirements may depend on the intended application and the manufacturer’s design. When considering the purchase of heavy machinery like a 2000-tonne friction press, it’s advisable to consult with the manufacturer or supplier for detailed specifications, customization options, and any additional features specific to the equipment model.
2000-ton friction screw presses are an essential part of modern industrial manufacturing, enabling the production of large and complex metal components for a wide range of applications. Their high forging force, stability, versatility, and precision control make them indispensable tools for heavy-duty forging operations.
Please let me know if you have any other questions about friction screw presses or if there is anything else I can help you with.
Metal Forming
- Forging: Friction screw presses are commonly used for forging metal components, such as hand tools, automotive parts, and aerospace components. The high force capacity of a 2000-ton press allows for forging thick and dense materials, such as steel or aluminum.
- Stamping: Friction screw presses are also used for stamping metal components, such as washers, brackets, and electrical parts. The press’s precise force control ensures consistent and accurate stamping of complex shapes and features.
- Coining: Friction screw presses can be used to coin metal components, such as coins, medals, and tokens. The press’s ability to apply high force and controlled pressure creates raised or embossed designs on the surface of the coins or medals.
Plastic and Rubber Processing
- Compaction: Friction screw presses are used to compact plastic and rubber powders into dense forms for further processing or molding. The press’s high force capacity ensures that the powders are compacted uniformly and effectively.
- Molding: Friction screw presses can be used to mold plastic and rubber components into various shapes and sizes. The press’s controlled force application ensures that the mold material fills the mold cavity evenly and without defects.
- Trimming: Friction screw presses can be used to trim excess material from molded plastic and rubber components. The press’s precise force control ensures that the trimming process is accurate and consistent, leaving a clean and finished edge.
Packaging and Paperboard Manufacturing
- Die Cutting: Friction screw presses are employed in the packaging and paperboard industry for die cutting a variety of materials, including cardboard, paper, and plastic sheets. The press’s high force capacity and precise force control allow for cutting intricate shapes and patterns for boxes, bags, and other packaging elements with precision and accuracy.
- Embossing: Friction screw presses can be used to emboss packaging materials, creating raised or textured patterns for decorative or branding purposes. The press’s controlled force application ensures that the embossing pattern is evenly applied and consistent across the packaging material.
- Creasing: Friction screw presses are used to crease packaging materials, creating score lines or folds to facilitate bending and shaping without tearing or cracking. The press’s precise force control ensures that the crease lines are sharp and well-defined, allowing for easy and controlled folding of the packaging material.
Cookware Forming and Shaping
- Blanking: Friction screw presses can be used to blank out the basic shapes of cookware components from sheets of metal, such as aluminum, stainless steel, or copper. The press’s high force capacity and precise force control allow for accurate cutting along a predefined die, creating the desired shape for pots, pans, lids, and other cookware components.
- Forming: Once blanked, the metal pieces undergo various forming operations to achieve the desired shape and depth of the cookware components. Friction screw presses provide the controlled force and precision required to form pots, pans, lids, and other cookware pieces with consistent dimensions and smooth surfaces.
- Flanging: Flanging involves creating a rim or edge around the top of a cookware component, such as a pot or pan. Friction screw presses can apply the necessary force and control to form the flange smoothly and evenly, enhancing the strength and aesthetics of the cookware.
- Beading: Beading involves creating a decorative or reinforcing rim around the edge of a cookware component. Friction screw presses can precisely form the beading, enhancing the appearance and durability of the cookware.
- Handle Attachment: Friction screw presses can be used to attach handles to cookware components. They can apply the appropriate force to press-fit or rivet handles securely onto the cookware body, ensuring a strong and durable attachment.
Powder Compaction
Friction screw presses can be used to compact various powders, such as ceramic powders, pharmaceutical compounds, and metal powders, into dense forms for further processing or molding. The press’s high force capacity ensures that the powders are compacted uniformly and effectively, creating a solid and consistent material.
Composite Material Forming
Friction screw presses can be used to shape composite materials, such as fiberglass-reinforced plastic composites or carbon fiber composites, into various shapes and structures. The press’s controlled force application allows for the forming of complex shapes and features without damaging the composite material.
Laboratory Testing
Friction screw presses can be used in laboratory settings for testing the properties of materials, such as compression strength, tensile strength, and fatigue resistance. The press’s precise force control and adjustable stroke allow for controlled testing and accurate
Friction Screw Press
A friction screw press, also known as a screw press or screw press machine, is a mechanical device used for various industrial processes, including forging, forming, and pressing operations. It operates on the principle of converting rotary motion into linear force through the use of a screw mechanism. Friction screw presses are widely used in metalworking, automotive, aerospace, and other manufacturing industries.
Our Friction Screw Press Types
- Friction Screw Press 150 Tonnes
- Friction Screw Press 300 Tonnes
- Friction Screw Press 1000 Tonnes
- Friction Screw Press 1300 Tonnes
- Friction Screw Press 1500 Tonnes
- Friction Screw Press 2000 Tonnes
- Friction Screw Press 2500 Tonnes
Here’s an overview of how a friction screw press works and its key characteristics:
How a Friction Screw Press Works:
- Screw Mechanism: The core component of a friction screw press is a large screw or spindle that runs vertically through the press. This screw is often called the “flywheel screw” because it stores and transfers energy during the operation.
- Motor or Power Source: A motor or power source is used to rotate the screw. The screw is threaded, and as it rotates, it moves either up or down, depending on the direction of rotation.
- Flywheel: The screw is connected to a heavy flywheel or a clutch mechanism. The flywheel stores kinetic energy, and this energy is transferred to the screw when the press is activated.
- Material Placement: The material to be processed, such as a metal workpiece or a forging blank, is placed on the press’s lower die or anvil.
- Pressing Operation: To perform a pressing operation, the operator activates the press by engaging the motor or power source. The screw rotates rapidly, causing it to move downward, applying a compressive force to the material placed on the lower die.
- Compression and Forming: The downward movement of the screw results in the material being compressed, shaped, or formed between the upper die (attached to the screw) and the lower die (the anvil). The force applied can be controlled and adjusted based on the application’s requirements.
- Energy Release: During the pressing operation, energy is transferred from the flywheel to the screw, and this energy is released as mechanical force, creating the pressing action.
- Repetition: The pressing operation can be repeated as needed, with adjustments made to the force, speed, and other parameters to achieve the desired results.
Key Characteristics of Friction Screw Presses:
- Adjustability: Friction screw presses allow for precise control of pressing force and speed, making them suitable for a wide range of applications.
- Energy Efficiency: These presses are known for their energy efficiency because the kinetic energy stored in the flywheel can be reused for subsequent press cycles.
- Versatility: Friction screw presses are versatile machines used for tasks such as forging, extrusion, blanking, bending, and other forming operations.
- High Force Capacity: They are capable of exerting high compressive forces, making them suitable for heavy-duty applications in the metalworking industry.
- Reliability: Friction screw presses are robust and reliable machines, often used in continuous production processes.
- Safety: Modern friction screw presses are equipped with safety features to protect operators and prevent accidents.
- Ease of Maintenance: Routine maintenance is generally straightforward, making them cost-effective to operate.
In summary, friction screw presses are essential machines in metalworking and manufacturing industries, offering the ability to perform various forming and pressing operations with precision, efficiency, and versatility.
Friction Screw Press
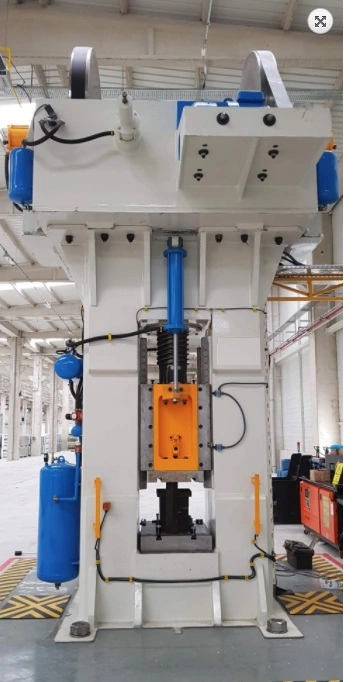
A friction screw press is a type of mechanical press widely used in industrial forging, metal forming, and various manufacturing processes. Unlike other mechanical presses that rely on hydraulic or pneumatic systems, a friction screw press utilizes the principle of friction to drive the motion of the press’s screw and ram. The energy required to deform materials is generated by the friction between rotating discs and the flywheel, which in turn, propels the screw and applies force onto the workpiece.
Importance in Industry
Friction screw presses play a critical role in industries where precise control over force application is essential. These presses are known for their ability to provide high force over short strokes, making them highly effective for various metal forming operations such as stamping, coining, embossing, and hot forging. Additionally, friction screw presses are commonly used in non-metallic applications, such as ceramics, where precise force control is also needed. The versatility of the friction screw press is one of the reasons it remains relevant across a range of industrial sectors.
Historical Development
The origins of the friction screw press date back to the late 19th and early 20th centuries, coinciding with the rise of industrialization and the demand for more efficient manufacturing methods. Early mechanical presses were driven by human or animal power, but the development of friction-based systems revolutionized the way industrial presses operated. With the introduction of the flywheel and friction drive mechanisms, presses could generate greater force while allowing more precise control over the process. The advent of friction screw presses significantly increased production speeds and the ability to form more complex shapes, laying the foundation for modern forging and metalworking industries.
Over time, friction screw presses have undergone continuous development, integrating modern technologies and materials. Today’s presses are designed to be more energy-efficient and feature improved control systems for greater precision. Despite the introduction of hydraulic and pneumatic presses, friction screw presses continue to be favored in many sectors due to their cost-efficiency, durability, and ability to perform well in high-volume production environments.
Principles of Operation
The operation of a friction screw press is based on the fundamental principles of mechanical energy, friction, and screw-driven motion. Understanding these principles helps in appreciating how the machine functions and why it is so effective in its various applications.
Mechanical Energy and Friction
At the heart of the friction screw press is the flywheel, which stores rotational energy. This energy is transferred to the screw mechanism via friction discs. The friction discs are typically connected to a motor, and they rotate when the motor is engaged. As the operator activates the press, the flywheel spins and generates the necessary energy. The friction discs then engage with the flywheel, converting this rotational energy into linear motion by turning the screw.
- Friction as a Driving Force: Friction plays a central role in the operation. By controlling the friction between the flywheel and the discs, operators can control the amount of energy transferred to the screw, thereby controlling the press’s force. The frictional engagement can be modulated depending on the requirements of the pressing operation, whether it’s a light embossing or a heavy forging.
The Screw and Ram Mechanism
The screw is the primary component that converts the rotational motion of the flywheel into linear motion. As the screw rotates, it moves the ram (a heavy component at the bottom of the press) up and down. The downstroke of the ram exerts the necessary pressure to deform or shape the workpiece positioned in the die below.
- The Role of the Ram: The ram is a key component because it applies the actual force required to compress or shape the material. The pressure exerted by the ram is proportional to the rotational speed of the flywheel and the force generated by the friction between the flywheel and friction discs. This provides the press with its characteristic advantage of delivering high force within a short stroke, making it especially useful for metal forming tasks that require significant force over a small area.
Step-by-Step Operation
- Initial Setup: Before operation, the workpiece is placed in the die, which is attached to the lower part of the press.
- Motor Activation: The press operator engages the motor, causing the flywheel to rotate.
- Friction Engagement: Once the flywheel reaches the desired rotational speed, the friction discs engage, transferring the rotational energy to the screw.
- Ram Movement: The screw converts this energy into linear motion, causing the ram to move downward and apply pressure to the workpiece.
- Material Deformation: Under the force of the ram, the material is compressed or shaped according to the design of the die.
- Ram Return: After the pressing operation is complete, the motor is reversed, or the flywheel is decelerated, causing the ram to retract, and the process can be repeated for the next workpiece.
Efficiency and Force Control
The friction screw press excels in applications where force control is essential. Unlike hydraulic presses, where force is generated through fluid pressure, friction screw presses allow for more immediate control of the applied force by adjusting the friction between the flywheel and discs. This level of control is especially useful for operations that require both light touches and high-impact force within the same workflow. Additionally, the short-stroke nature of the press allows it to operate with fewer cycles than other types of presses, resulting in higher production efficiency.
Advantages of the Friction Mechanism
- Precision: The friction mechanism offers exceptional control over the force applied, ensuring precise results in processes like coining or precision forging.
- Energy Conservation: The flywheel stores energy and allows the machine to use it as needed, making the system more energy-efficient than presses that require constant power input, such as hydraulic systems.
- Quick Setup: The operation of a friction screw press is relatively straightforward, and once the correct die and settings are in place, operators can quickly set up the press for mass production.
In summary, the operational principles of a friction screw press revolve around the efficient conversion of mechanical energy into pressing force through the use of friction. This system provides excellent control over force application, making it ideal for industries requiring precision and power in their production processes.
Key Components and Parts
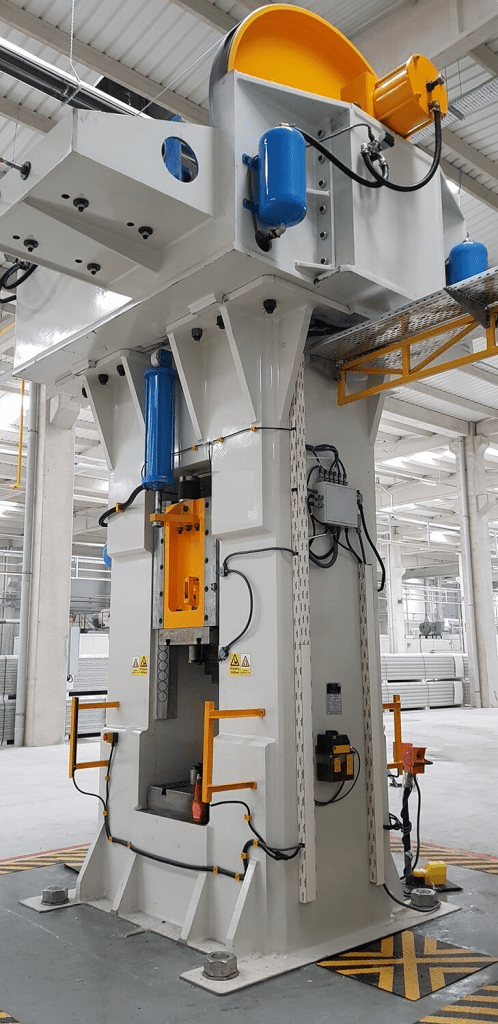
The friction screw press consists of several essential components that work together to deliver the pressing force required in various industrial applications. Each part is carefully designed to withstand high levels of stress, friction, and heat, ensuring the machine’s durability and effectiveness. Below is a detailed look at the key components of a friction screw press:
1. Flywheel
The flywheel is one of the most important components of the friction screw press. It stores rotational energy that is later transferred to the screw mechanism to power the pressing operation. Flywheels in friction screw presses are typically heavy, solid discs designed to minimize energy loss and provide a consistent source of power throughout the press cycle.
- Energy Storage: The primary function of the flywheel is to store kinetic energy. This energy is accumulated when the flywheel spins at high speeds, driven by the motor. Once the friction discs engage, the energy is transferred from the flywheel to the screw and ram system.
- Inertia: Flywheels provide mechanical advantage by maintaining momentum. This is particularly beneficial in operations that require high-impact force over short periods. The larger and heavier the flywheel, the more energy it can store and transfer, contributing to the press’s efficiency.
2. Friction Discs
The friction discs are responsible for engaging and transferring the rotational energy from the flywheel to the screw. These discs are typically made of materials that can withstand high levels of friction and heat, such as composite ceramics or specialized steel alloys.
- Energy Transfer: When the operator initiates the press, the friction discs engage with the flywheel, transferring the stored energy to the screw mechanism. The amount of friction applied determines how much energy is transferred and, consequently, how much force is exerted by the press.
- Durability: Given that the discs are subject to continuous wear due to friction, they are made from materials that resist heat and mechanical stress. Periodic maintenance and replacement of the friction discs are crucial for the longevity of the machine.
3. Screw Mechanism
The screw is the central driving component of the press, responsible for converting the rotational motion from the flywheel into linear force. The screw, typically made of hardened steel, operates in a threaded mechanism that drives the ram downwards.
- Conversion of Motion: The rotational energy from the flywheel is converted into linear motion by the screw. As the screw rotates, it drives the ram downward, applying force to the workpiece. The precise threading of the screw allows for controlled and accurate force application, which is crucial in precision forging and forming tasks.
- Load Capacity: The screw is designed to withstand significant loads and stresses during operation. Proper lubrication of the screw is necessary to reduce wear and tear and ensure smooth operation.
4. Ram
The ram is the component that directly applies force onto the workpiece. Positioned at the bottom of the screw mechanism, the ram transfers the energy from the screw into the material being pressed.
- Force Application: The ram exerts the actual pressing force, deforming the material within the die. The size and design of the ram depend on the specific application of the press, ranging from small, precise rams for light operations to larger rams for heavy-duty forging.
- Precision: The ram’s movement is guided by the threaded screw mechanism, allowing for controlled force application. The accuracy of the ram’s downward stroke is essential in applications such as coin minting or precision metal stamping.
5. Frame
The frame of the friction screw press provides structural support for all the moving parts and components. It needs to be robust enough to withstand the enormous forces generated during the pressing operation. Frames are typically made of cast iron or steel, ensuring both strength and durability.
- Structural Integrity: The frame holds the entire machine together and absorbs the shock generated during pressing. A well-designed frame minimizes vibration and maintains the alignment of the screw, ram, and die during operation.
- Durability: Since the frame bears the brunt of mechanical stress during operation, it is constructed from materials with high tensile strength, such as steel or cast iron, and often reinforced with additional supports.
6. Motor
The motor powers the flywheel, initiating the energy transfer process. Motors in friction screw presses are typically electric and are designed to handle varying loads and speeds, depending on the press’s size and application.
- Power Generation: The motor provides the initial rotational force required to spin the flywheel. The size and power of the motor directly influence the amount of energy the press can store and use during operation.
- Variable Speed Control: In modern friction screw presses, the motor may feature variable speed control, allowing operators to adjust the flywheel’s speed based on the required pressing force. This feature enhances the versatility of the machine for different applications.
7. Die and Workpiece Holder
The die is a critical component that shapes the material during the pressing operation. The workpiece is placed within the die, and the force applied by the ram deforms it into the desired shape. Dies can be customized based on the specific product being manufactured, whether it’s a forged metal part, a stamped component, or a ceramic piece.
- Customization: Dies are typically custom-made for specific applications and can range from simple, flat surfaces to complex, multi-part shapes.
- Precision Manufacturing: The accuracy of the die is crucial for the quality of the finished product. Precision machining and engineering are required to ensure the die can withstand repeated high-pressure operations.
8. Clutch and Brake System
The clutch and brake system provides control over the press’s operation. The clutch engages the flywheel, transferring energy to the screw, while the brake system halts the operation when necessary.
- Clutch Engagement: The clutch allows the operator to control when the flywheel’s energy is transferred to the screw mechanism. This ensures that the press only operates when required, conserving energy and reducing wear on the machine.
- Braking for Safety: The brake system stops the ram and screw from continuing their downward motion, ensuring that the press can be safely halted in the event of an emergency or when the cycle is complete.
Types of Friction Screw Presses
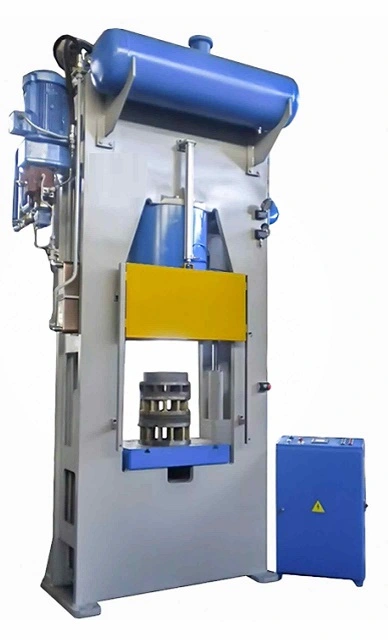
Friction screw presses come in various designs and configurations, each suited to specific industrial applications. The differences between these presses are often based on their mechanical configurations, size, and intended use. The two most common types of friction screw presses are single-disc and double-disc models, though variations exist within these broad categories.
1. Single-Disc Friction Screw Press
A single-disc friction screw press features one friction disc that engages with the flywheel. This design is simpler and more compact, making it suitable for smaller operations or applications where force requirements are moderate.
- Advantages: Single-disc presses are generally easier to maintain and operate due to their simpler design. They are ideal for light forging, stamping, and other medium-duty applications.
- Limitations: While simpler, single-disc presses have limitations in terms of the maximum force they can generate, making them less suitable for heavy forging operations.
2. Double-Disc Friction Screw Press
Double-disc presses feature two friction discs that engage with the flywheel, allowing for greater energy transfer and, consequently, more force generation. These presses are typically larger and used in heavy-duty industrial applications.
- Advantages: The double-disc design allows for a more even distribution of force, which is beneficial in high-pressure operations like forging large metal parts. The additional friction surface enables the press to handle higher loads and provide more consistent force.
- Limitations: Due to their complexity and larger size, double-disc presses require more maintenance and are more expensive to operate and maintain compared to single-disc models.
3. Hydraulic vs. Mechanical Friction Screw Presses
While friction screw presses are mechanical, it is essential to understand how they differ from hydraulic presses.
- Mechanical (Friction Screw): As discussed, friction screw presses rely on mechanical energy stored in the flywheel. These presses provide quick energy release, making them suitable for rapid forging or stamping operations.
- Hydraulic Presses: These presses use fluid power to generate force. While they provide more consistent force over a more extended period, hydraulic presses are slower and often less energy-efficient compared to friction screw presses.
Applications of Friction Screw Presses

Friction screw presses have wide-ranging applications across multiple industries due to their ability to provide precise control over force, energy efficiency, and versatility in material forming processes. Their usage spans from heavy-duty metal forging to delicate precision tasks like coin minting or ceramic molding. Below are some of the most prominent industrial applications where friction screw presses are frequently used:
1. Metal Forging
One of the primary applications of friction screw presses is in metal forging, a manufacturing process that involves shaping metal using localized compressive forces. The energy-efficient operation and ability to deliver high force in a controlled manner make these presses ideal for forging tasks that require precision and strength.
- Hot Forging: Friction screw presses are commonly used in hot forging operations, where metal is heated until it becomes malleable and then pressed into desired shapes. The high energy storage in the flywheel allows the press to apply enough force to deform the heated metal, creating complex shapes with minimal wastage. This process is widely used in industries such as automotive, aerospace, and heavy machinery, where components like gears, crankshafts, and connecting rods are forged.
- Cold Forging: Although less common, friction screw presses can also be used in cold forging, where metals are shaped at room temperature. Cold forging requires more precise force control, as the material’s resistance is higher. Friction screw presses excel in this application due to their ability to generate high, consistent pressure, ensuring uniformity in the finished parts.
2. Ceramics and Powder Metallurgy
Friction screw presses are extensively used in industries that manufacture ceramics and powder metallurgy components. The precision force control provided by these presses makes them ideal for molding fine ceramic powders or metal particles into complex shapes before sintering.
- Ceramic Forming: In ceramic industries, friction screw presses are utilized to mold materials like clay or porcelain into specific shapes. The short, high-impact strokes of the press enable efficient compaction of the material, ensuring it fills the mold accurately and uniformly. Applications range from decorative ceramic items to industrial components such as insulators and tiles.
- Powder Metallurgy: In powder metallurgy, metal powders are compacted into shapes using friction screw presses. This process is often used to manufacture parts that would be difficult or costly to produce using traditional casting methods. The precise control over the pressing force allows manufacturers to achieve high density and uniformity in the compacted parts, which is essential for high-quality, durable components.
3. Coin Minting and Jewelry Production
The coin minting and jewelry production industries rely heavily on friction screw presses for their precision and ability to imprint fine details. In these applications, the press needs to apply controlled, consistent force to engrave intricate patterns or designs into the metal without damaging the material.
- Coin Minting: The high precision offered by friction screw presses makes them perfect for coin minting. The dies used in coin minting have intricate designs, and even minor inconsistencies in the force applied can result in defective coins. With friction screw presses, operators can control the force down to the smallest detail, ensuring the minting process is flawless. These presses can also be adjusted to mint coins of various sizes and materials, from standard currency coins to collectible medallions.
- Jewelry: Similarly, in the jewelry industry, friction screw presses are used to stamp designs onto metals like gold, silver, and platinum. The ability to finely control the pressure prevents damage to delicate metals while ensuring that the designs are embossed or engraved clearly.
4. Stamping and Embossing
Friction screw presses are frequently used in stamping and embossing processes, where high precision and speed are essential. These operations involve pressing a workpiece into a die to create a specific shape or pattern, often used in the production of metal parts, packaging, or artistic designs.
- Metal Stamping: In the metalworking industry, friction screw presses are used to create a variety of stamped products, including automotive parts, electronic components, and industrial fasteners. The high force generated by these presses allows for deep stamping in hard materials, making them ideal for heavy-duty operations.
- Embossing: Embossing involves creating raised or recessed designs on the surface of materials, often for decorative or functional purposes. Friction screw presses are capable of producing highly detailed embossing on materials like metal sheets, leather, and even certain plastics. This makes them popular in industries like packaging, signage, and decorative arts.
5. Refractory Materials
Another key application of friction screw presses is in the production of refractory materials, which are used in industries like steelmaking, glass production, and cement manufacturing. Refractory bricks and shapes must withstand extreme temperatures, and their production often involves compressing powders and materials into specific forms before they are fired in a kiln.
- Shaping Refractory Bricks: Friction screw presses are widely used to compress raw refractory materials into dense bricks or blocks. The precision control and high-pressure capabilities ensure that the materials are compacted thoroughly, which is essential for creating durable, heat-resistant products.
- Customization: The ability to customize the press settings allows manufacturers to produce a wide range of shapes and sizes, from standard bricks to complex, specialized components used in industrial furnaces and kilns.
6. Other Industrial Applications
Friction screw presses are also utilized in several other industries, showcasing their versatility and effectiveness in a wide range of applications.
- Agriculture: In the agricultural sector, friction screw presses are used to manufacture farming tools and equipment. The press’s ability to handle high-strength materials like steel makes it useful for forming parts for tractors, plows, and harvesting machinery.
- Textile Industry: In some instances, friction screw presses are employed in the production of textiles and related equipment. For example, they are used to shape and press components for textile machinery, ensuring durability and longevity under heavy use.
- Military and Defense: The military and defense sectors utilize friction screw presses for the production of equipment, ammunition casings, and other components that require high precision and durability. The press’s ability to shape metals with intricate detail and strong force is valuable for manufacturing parts for military vehicles, weaponry, and infrastructure.
Advantages of Friction Screw Presses in These Applications
The widespread application of friction screw presses in such a diverse range of industries highlights several inherent advantages of the technology:
- High Precision: Many applications, such as coin minting, jewelry making, and powder metallurgy, require extreme precision. Friction screw presses offer fine control over the force applied, ensuring that intricate details are perfectly replicated in each pressing operation.
- Energy Efficiency: The energy stored in the flywheel allows for high-impact force with minimal energy consumption compared to other press technologies. This makes friction screw presses more cost-effective in the long run, particularly in industries that require continuous, high-volume production.
- Versatility: From shaping ceramics to metal forging, friction screw presses can handle a wide range of materials and applications. Their ability to adjust pressure and force makes them adaptable to both heavy-duty operations and delicate, high-precision tasks.
- Durability and Longevity: Friction screw presses are designed to withstand the rigors of industrial use. Their robust construction and mechanical simplicity (compared to hydraulic systems) make them reliable and durable, which is especially important in industries where equipment downtime can lead to significant financial losses.
Advantages of Friction Screw Presses
Friction screw presses are known for several advantages that make them the preferred choice in various industries, despite the availability of other pressing technologies like hydraulic or pneumatic presses. Below are some key benefits:
1. Energy Efficiency
One of the most significant advantages of friction screw presses is their energy efficiency. The flywheel in these presses stores energy during idle times, which is then released during the pressing cycle. This system reduces the need for continuous energy input, making the press more economical in the long run.
- Lower Operational Costs: The efficient use of stored energy means that friction screw presses consume less power than hydraulic presses, which require constant energy to maintain pressure. This translates to lower electricity bills and operational costs, especially for companies running high-volume production.
2. Precision in Force Application
Friction screw presses offer excellent control over the force applied to the workpiece, making them ideal for industries requiring precision, such as coin minting and jewelry production. Operators can fine-tune the amount of friction applied between the flywheel and discs, ensuring the exact amount of force is transferred to the screw.
- Consistency: This precision also leads to consistent results across multiple operations. For example, in stamping or forging, each workpiece receives the same amount of pressure, reducing defects and waste.
3. Durability and Longevity
The simple, mechanical nature of friction screw presses makes them incredibly durable. Unlike hydraulic presses that rely on complex systems of pumps and fluid control, friction screw presses have fewer moving parts that are prone to wear and tear.
- Low Maintenance Requirements: The robust construction of friction screw presses reduces the need for frequent repairs or maintenance, allowing companies to maintain high production rates without significant downtime. This is especially important in industries that operate around the clock, where downtime can be costly.
4. Flexibility
Friction screw presses can handle a variety of materials and operations, from heavy metal forging to delicate ceramic shaping. The ability to control the force applied also makes them suitable for a range of applications, allowing manufacturers to use the same press for different production tasks.
- Multiple Industries: This flexibility is why friction screw presses are found in so many industries, from automotive manufacturing to pottery. Their versatility helps companies save on equipment costs by using a single machine for different operations.
Limitations and Challenges
While friction screw presses offer many advantages, they also come with certain limitations and challenges. Understanding these drawbacks is essential for industries that rely on these presses to ensure that they are used appropriately and efficiently. Below are some of the common limitations and challenges faced when working with friction screw presses:
1. Mechanical Wear and Tear
One of the primary challenges associated with friction screw presses is mechanical wear. Since the operation of the press relies on friction between the flywheel and friction discs, the repetitive engagement and disengagement create significant wear on these components over time. The constant exposure to high friction forces and heat leads to:
- Wear of Friction Discs: The friction discs in the press are particularly susceptible to wear. As they degrade, their ability to transfer energy efficiently is reduced, potentially leading to inconsistent force application and a drop in the press’s performance.
- Lubrication Needs: The screw mechanism itself requires regular lubrication to reduce wear between the moving parts. Insufficient lubrication can result in increased friction, causing overheating, more rapid deterioration of parts, and even mechanical failure.
Frequent maintenance is required to monitor and replace worn components. While friction screw presses have fewer parts than hydraulic presses, this wear and tear still results in downtime and increased operational costs for maintenance and part replacement.
2. Limited Stroke Length
Friction screw presses are known for their short stroke length compared to other types of presses, such as hydraulic presses. This limited stroke length can restrict the types of operations that friction screw presses can perform. The following challenges arise due to this limitation:
- High-Force, Short-Stroke Operations: While friction screw presses excel at applying high force in short bursts, they are not ideal for operations that require a longer, controlled stroke. For example, deep drawing processes, which involve pulling material into a die to create deep, hollow shapes, are better suited to hydraulic presses that can apply continuous pressure over a longer stroke.
- Difficulty with Large Components: Pressing large components or materials that require gradual deformation can be difficult with friction screw presses. Industries that need to process large workpieces often opt for hydraulic presses due to their ability to apply sustained pressure.
3. Challenges in High-Load Operations
Although friction screw presses can generate significant force, they may struggle in extremely high-load operations or environments where extremely large forces are consistently required. This limitation stems from their reliance on mechanical friction for energy transfer. For very large loads, hydraulic systems may be more suitable due to their superior force generation capabilities over prolonged strokes.
- Force Fluctuations: Because friction screw presses rely on the friction between the flywheel and discs, slight variations in friction can result in fluctuations in the applied force. In operations where extreme consistency is required, such as in precision forging of aerospace parts, these force variations may lead to quality control issues.
4. Energy Consumption at High Speeds
While friction screw presses are generally energy-efficient for many operations, they can consume a considerable amount of energy when operating at high speeds or when used for repetitive tasks over extended periods. This can result in:
- Flywheel Inertia Management: The flywheel must be kept at high rotational speeds to store energy, and maintaining this speed can require significant energy input, particularly for presses handling heavy-duty operations. As the press engages and disengages, energy is lost in the form of heat, leading to inefficiencies.
- Overheating and Heat Dissipation: Continuous use at high speeds can lead to overheating in the friction discs and the screw mechanism. Overheating reduces efficiency and can also lead to safety issues if not properly managed. Operators need to ensure that the press is not pushed beyond its thermal limits, as excessive heat can degrade materials, cause warping, or even result in part failure.
5. Maintenance and Downtime
The need for frequent maintenance is another limitation. While friction screw presses are more durable than their hydraulic counterparts, their reliance on friction and mechanical movement means that key components like the friction discs, screw, and ram are subject to regular wear. Without routine inspection and maintenance, performance can decline, leading to:
- Increased Downtime: As parts wear down, operators must halt production to replace or repair components. For industries that rely on continuous, high-volume production, this can lead to significant downtime, which can affect overall productivity and increase operational costs.
- Part Availability: Depending on the age and model of the press, finding replacement parts for older friction screw presses can be difficult, adding to potential delays in production.
6. Environmental Factors
Friction screw presses may face challenges in environments where extreme temperatures or corrosive conditions are present. The performance of the press can be affected by these external factors in several ways:
- Extreme Heat: In extremely high-temperature environments, the heat generated by the friction discs may combine with the external temperature to push the press components beyond their operational thresholds. This can lead to faster degradation of parts and increased wear.
- Corrosive Environments: In environments where the press is exposed to corrosive materials or humidity, key components such as the screw, ram, and friction discs may be subject to rust or corrosion, reducing their lifespan and efficiency. Special protective coatings or more frequent maintenance may be required to counteract these effects.
Conclusion
In summary, while friction screw presses offer numerous benefits, they do have some inherent limitations and challenges. Mechanical wear and tear, short stroke lengths, energy consumption at high speeds, and maintenance needs are all factors that industries must consider when deciding whether to use friction screw presses for their production processes. However, when used appropriately and maintained properly, these presses can provide long-lasting, reliable service in a variety of applications.
Materials and Construction
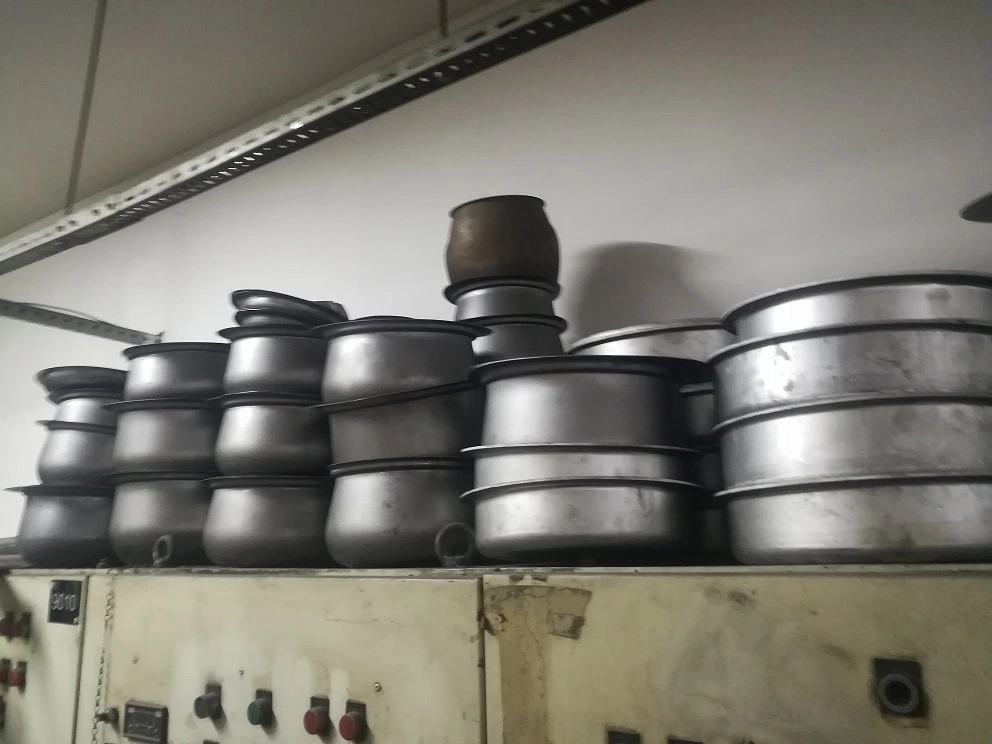
The materials and construction of friction screw presses play a critical role in their overall performance, durability, and efficiency. Given the extreme forces and friction involved in the operation of these presses, the materials used must be able to withstand mechanical stress, high temperatures, and wear over time. Advances in material science have also contributed to the development of more robust and efficient friction screw presses. Below is an overview of the materials commonly used in the construction of friction screw presses and how they contribute to the press’s functionality.
1. Frame and Structural Components
The frame and structural components of a friction screw press are typically made from materials that offer high strength and durability. The frame must be able to absorb and withstand the immense forces generated during the pressing operation without deforming or vibrating.
- Cast Iron: One of the most commonly used materials for the press frame is cast iron. It offers excellent strength, durability, and vibration-damping properties, making it ideal for large, heavy-duty presses. Cast iron is also relatively cost-effective, making it a popular choice for the construction of industrial machinery.
- Steel: In some cases, high-grade steel is used for the press frame and other structural components. Steel offers greater tensile strength compared to cast iron, allowing for thinner yet stronger frames. However, steel is generally more expensive than cast iron, so it is often used selectively in high-stress areas of the press.
2. Friction Discs
The friction discs are a critical component of the friction screw press, responsible for transferring energy from the flywheel to the screw mechanism. As the name suggests, these discs rely on friction to operate, so the materials used in their construction must be able to withstand high levels of heat and wear.
- Composite Ceramics: Modern friction discs are often made from composite ceramics, which offer excellent heat resistance and wear durability. Composite ceramics are designed to maintain their structural integrity even under high temperatures generated by friction, making them ideal for industrial applications where the press is used continuously.
- Hardened Steel Alloys: In some presses, hardened steel alloys are used for the friction discs. These alloys are treated to enhance their wear resistance and thermal conductivity, ensuring they can handle the stress of repeated engagement with the flywheel.
3. Screw Mechanism
The screw is the central component that translates the rotational energy from the flywheel into linear motion, driving the ram down to apply force on the workpiece. The screw must be made from materials that can withstand the high loads and stresses generated during operation.
- Hardened Steel: The screw is typically made from hardened steel, a material chosen for its high strength, toughness, and resistance to wear. Hardened steel undergoes heat treatment processes that enhance its durability, allowing the screw to perform consistently under heavy loads without deforming.
- High-Strength Alloys: In advanced friction screw presses, high-strength alloys may be used for the screw mechanism. These alloys are specifically designed to offer superior mechanical properties, including increased tensile strength, better resistance to fatigue, and improved durability under extreme pressures.
4. Ram
The ram is the component that directly applies pressure to the workpiece, and it must be able to transfer the full force generated by the screw mechanism. The material used for the ram needs to be both strong and wear-resistant, especially in applications where the press is used for heavy-duty forging or stamping.
- Tool Steel: Tool steel is commonly used for the ram because of its hardness and wear resistance. This type of steel is designed to withstand repeated impacts and pressure without losing its shape or structural integrity. Tool steel rams are particularly useful in applications where the press is used for forging hard metals like steel or titanium.
- Forged Steel: In some applications, the ram may be made from forged steel, which offers excellent toughness and fatigue resistance. Forging the steel ensures that the material has a uniform grain structure, increasing its strength and ability to withstand repeated cycles of high-pressure operations.
5. Flywheel
The flywheel is responsible for storing energy and transferring it to the friction discs and screw. The material used for the flywheel must have high inertia, strength, and the ability to withstand repeated rotational forces.
- Cast Iron or Steel: Flywheels are typically made from cast iron or steel due to the high density and strength of these materials. Cast iron is commonly used for its cost-effectiveness and vibration-damping properties, while steel is preferred for its greater tensile strength, which allows for more energy storage in a smaller, lighter flywheel.
6. Bearings and Bushings
The bearings and bushings in a friction screw press support the moving parts, ensuring smooth operation while reducing friction and wear. These components are crucial for the longevity of the press, as they help to minimize wear on the screw and ram mechanisms.
- Bronze: Bronze is a common material for bushings and bearings because of its low friction coefficient and excellent wear resistance. Bronze bearings are self-lubricating, reducing the need for frequent maintenance and ensuring smooth operation.
- Hardened Steel: Hardened steel bearings are also used in heavy-duty applications where the press is subjected to extreme forces. These bearings are heat-treated to enhance their hardness and durability, making them ideal for industrial presses that operate under high loads.
Modern Innovations and Technological Developments
The evolution of friction screw presses has been marked by significant technological advancements and innovations, especially in recent decades. As industries continue to demand higher precision, efficiency, and automation, manufacturers have developed new technologies that enhance the performance, durability, and versatility of these presses. Below, we explore some of the modern innovations and developments that have improved friction screw presses:
1. Computerized Control Systems
One of the most impactful innovations in friction screw presses is the integration of computerized control systems. These systems allow for the automation of many press operations, improving accuracy, consistency, and efficiency.
- Precision Force Control: Modern presses are equipped with computer-based controls that allow operators to precisely control the force applied during pressing operations. This level of control ensures that the press delivers consistent results, which is especially important in applications like coin minting, jewelry production, and precision forging. Computer systems can also monitor the force applied in real-time, ensuring that it matches the required specifications for each workpiece.
- Automated Adjustments: With computerized controls, friction screw presses can automatically adjust their settings for different tasks. For instance, the amount of energy transferred from the flywheel to the screw can be adjusted for different materials or processes, allowing the press to handle a wide range of applications without manual intervention. This level of automation significantly improves the efficiency of production lines and reduces human error.
2. Integration of Sensors and Monitoring Systems
Modern friction screw presses are often equipped with sensors and monitoring systems that track various operational parameters in real-time. These sensors provide critical feedback on the condition of the press, helping to prevent mechanical issues and improve safety.
- Force and Pressure Sensors: These sensors monitor the force applied by the press and provide feedback to ensure that it matches the desired specifications. This is particularly useful in precision applications where slight deviations in force could lead to defective parts or suboptimal performance. The sensors also help prevent overloading, which could damage the machine or compromise the quality of the workpiece.
- Temperature Sensors: Since friction screw presses generate significant heat during operation, temperature sensors are often installed to monitor the condition of the friction discs, screw, and bearings. By detecting excessive heat, the system can alert operators to potential issues before they cause serious damage or downtime. In some cases, the press will automatically reduce its operational speed or pause if temperatures exceed safe limits.
- Vibration Monitoring: Modern presses use vibration sensors to monitor the machine’s structural integrity. Excessive vibrations can indicate problems with the press’s components, such as misalignment or wear. Vibration monitoring helps maintain the longevity of the machine by alerting operators to issues early on, allowing for preventive maintenance before major failures occur.
3. Industry 4.0 and Smart Manufacturing
As part of the broader trend toward Industry 4.0, friction screw presses are becoming more connected and integrated into smart manufacturing systems. Industry 4.0 refers to the digital transformation of manufacturing, where machines, systems, and processes are connected through data exchange and automation.
- Internet of Things (IoT) Integration: IoT technologies allow friction screw presses to be connected to a network where they can communicate with other machines and systems in real time. This connectivity enables remote monitoring, diagnostics, and control, allowing operators to manage press operations from centralized control centers or even offsite locations.
- Predictive Maintenance: With the integration of sensors and IoT technologies, predictive maintenance is becoming a reality for friction screw presses. Data collected from the press during operation, such as temperature, force, and vibration metrics, can be analyzed to predict when maintenance is needed. This approach helps prevent unexpected machine failures and reduces downtime by allowing operators to schedule maintenance during periods of low production activity.
- Data Analytics for Optimization: Data from friction screw presses can be analyzed to optimize production processes. By understanding how the press performs under different conditions and materials, manufacturers can fine-tune their processes for maximum efficiency and output quality. This data-driven approach allows for continuous improvement in manufacturing operations.
4. Advanced Materials and Coatings
The development of advanced materials and coatings has significantly improved the durability and performance of friction screw presses. Innovations in material science have led to the creation of components that can withstand higher forces, temperatures, and wear, extending the lifespan of the machine and reducing maintenance costs.
- Ceramic Coatings: Many modern friction discs are coated with advanced ceramic materials that provide excellent resistance to heat and wear. These coatings improve the longevity of the discs and ensure consistent performance even in high-friction, high-temperature environments. Ceramic-coated components also require less frequent replacement, reducing the overall maintenance requirements of the press.
- Superalloys and Composites: The use of superalloys and composite materials in the construction of key press components, such as the screw and ram, has increased their ability to withstand extreme pressures and temperatures. Superalloys are engineered to maintain their strength and resistance to deformation even under the most demanding conditions, making them ideal for high-force pressing applications.
5. Improved Lubrication and Cooling Systems
Another key area of innovation is the development of enhanced lubrication and cooling systems for friction screw presses. These systems help manage the heat generated during operation and reduce friction between moving parts, leading to smoother operation and longer component life.
- Automatic Lubrication Systems: Many modern presses are equipped with automatic lubrication systems that apply lubricant to key components such as the screw and bearings at regular intervals. This ensures that the press operates smoothly and reduces the risk of component wear due to friction. Automatic lubrication also reduces the need for manual maintenance, increasing overall productivity.
- Enhanced Cooling Mechanisms: In addition to lubrication, modern friction screw presses often incorporate advanced cooling mechanisms to dissipate heat generated during pressing operations. Water-cooled or air-cooled systems are used to maintain optimal operating temperatures, especially in high-volume production environments. These cooling systems help prevent overheating, improving the press’s efficiency and safety.
6. Environmental Considerations and Sustainability
Sustainability has become a significant focus in modern manufacturing, and friction screw presses have benefited from innovations that reduce their environmental impact. The adoption of more efficient designs, materials, and processes helps industries meet their sustainability goals while maintaining high productivity.
- Energy Efficiency Improvements: Recent innovations in friction screw presses have focused on reducing energy consumption by improving the efficiency of the flywheel and friction disc systems. By optimizing the transfer of energy, modern presses can deliver the same level of force with less energy input, leading to lower operational costs and reduced environmental impact.
- Recycling and Waste Reduction: Advanced materials used in the construction of modern presses are often designed to be recyclable, contributing to a circular economy. Additionally, precise control over pressing operations helps reduce material waste by minimizing the number of defective parts produced.
Conclusion
Modern innovations in friction screw presses have dramatically improved their performance, efficiency, and sustainability. The integration of computerized controls, sensors, IoT technologies, advanced materials, and improved lubrication systems has made friction screw presses more reliable and versatile than ever before. These developments ensure that friction screw presses will continue to play a critical role in manufacturing processes across a wide range of industries, from automotive to precision metalworking.
Maintenance and Care of Friction Screw Presses
Proper maintenance is crucial to ensure that friction screw presses operate efficiently and have a long service life. Regular upkeep helps prevent breakdowns, reduces downtime, and ensures consistent performance across various applications. Below, we outline essential maintenance practices and care tips for friction screw presses:
1. Routine Lubrication
One of the most critical aspects of maintaining a friction screw press is routine lubrication of moving parts, such as the screw, bearings, and friction discs.
- Screw Lubrication: The screw mechanism should be regularly lubricated to reduce friction and wear. Without adequate lubrication, the screw can become difficult to operate, leading to mechanical strain and faster wear.
- Friction Discs: Although friction discs are designed to generate friction, they also need proper lubrication to ensure smooth engagement with the flywheel. Care should be taken to use the correct type of lubricant, as some materials are sensitive to certain oils or greases.
- Automated Lubrication Systems: Many modern presses are equipped with automated lubrication systems, which apply lubricant at preset intervals. These systems ensure consistent lubrication and can be monitored for proper operation.
2. Regular Inspection of Key Components
Frequent inspections of the press’s critical components are necessary to identify potential issues before they lead to mechanical failure.
- Friction Discs and Flywheel: Regularly inspect the friction discs for wear and tear. Any visible signs of degradation, such as thinning or heat damage, should prompt immediate replacement. The flywheel should also be checked for balance and alignment to prevent uneven force distribution.
- Screw and Ram: The screw and ram must be inspected for signs of wear, such as scoring or misalignment. Minor issues can often be resolved with proper lubrication or realignment, but major wear may require part replacement to prevent operational failure.
3. Cleaning and Debris Removal
Friction screw presses should be kept clean to avoid the accumulation of debris, dust, or foreign materials, which can interfere with the machine’s operation.
- Clean Press Surfaces: Keeping the press clean, especially around the friction discs and flywheel, ensures that no foreign particles interfere with the engagement of these parts. Cleaning also prevents contaminants from entering critical areas like bearings or the screw.
- Preventive Measures: In high-dust environments, it’s beneficial to use protective covers or enclosures to shield the press from contamination.
Safety Standards and Best Practices
Operating a friction screw press involves significant force and energy, making it essential to adhere to stringent safety standards and implement best practices to protect operators and ensure safe, efficient operations. Proper safety measures not only prevent accidents but also enhance productivity by minimizing machine downtime and reducing the risk of equipment damage. Below, we outline the critical safety standards and best practices for operating friction screw presses.
1. Adhering to Regulatory Safety Standards
Friction screw presses are subject to occupational health and safety regulations, which vary by region but often include similar guidelines for ensuring safe operation in an industrial setting. Compliance with these regulations is mandatory to avoid fines, legal liability, and, more importantly, to safeguard the health and safety of workers.
- OSHA (Occupational Safety and Health Administration) in the United States sets forth guidelines for the operation of mechanical presses, including friction screw presses. These guidelines mandate regular inspections, operator training, and the use of safety features such as emergency stop buttons and guards.
- CE Marking (Conformité Européenne) in Europe certifies that machinery complies with the essential health and safety requirements of the EU. Friction screw presses must meet the standards set out in directives such as the Machinery Directive (2006/42/EC), which governs mechanical safety and operator protection.
2. Operator Training and Certification
Proper training is a critical component of safe press operation. Operators must be trained not only in how to use the friction screw press but also in identifying potential hazards and using the machine’s safety features.
- Comprehensive Training Programs: Operators should undergo comprehensive training programs that cover all aspects of the machine’s operation, including how to start, operate, and shut down the press safely. Training should also address troubleshooting common issues, such as identifying signs of component wear or malfunction.
- Operator Certification: In some jurisdictions and industries, it is mandatory for operators to be certified before they are allowed to operate a friction screw press. Certification ensures that operators have a thorough understanding of safety protocols, which helps to reduce workplace accidents.
3. Use of Safety Guards and Barriers
Friction screw presses must be equipped with safety guards and barriers to protect operators from accidental contact with moving parts, such as the ram, screw, and flywheel. These safety features are essential in preventing injuries during operation.
- Physical Guards: Physical barriers or guards are installed around moving parts to prevent accidental contact. For example, guards around the ram or screw mechanism help to protect the operator from crushing or entanglement injuries.
- Light Curtains and Sensors: In modern presses, light curtains or safety sensors can be used to detect the presence of an operator’s hand or body near dangerous parts of the machine. If the sensor detects an object in its path, the press is automatically stopped to prevent injury.
4. Emergency Stop and Shutoff Systems
Friction screw presses should be equipped with emergency stop systems that allow operators to halt the machine instantly in the event of a malfunction or emergency. These systems are critical for preventing accidents and minimizing the damage to the machine or workpiece.
- Emergency Stop Buttons: The press should have clearly labeled, easily accessible emergency stop buttons that immediately cut power to the machine and disengage the friction discs. Operators must be trained to use these buttons in case of emergencies.
- Brake Systems: Many friction screw presses are equipped with brake systems that engage automatically when the press is stopped. These brakes ensure that the ram does not continue to descend after the machine is powered down, reducing the risk of unintended operations.
5. Regular Maintenance for Safety
Routine maintenance is not only essential for ensuring the longevity and performance of a friction screw press but also for maintaining safety. Worn or damaged components can lead to accidents if not addressed promptly, making regular inspections a crucial part of press operation.
- Scheduled Inspections: Regular inspections of the machine’s key components, such as the friction discs, screw, ram, and bearings, help identify potential issues before they escalate. Operators should look for signs of wear, such as thinning discs or unusual vibrations, and schedule maintenance as necessary.
- Replacing Worn Parts: Worn components must be replaced as soon as they are identified. For example, worn friction discs can reduce the efficiency of energy transfer, leading to erratic press performance. Similarly, worn bearings or bushings can increase friction and heat, potentially causing parts to seize or fail.
6. Personal Protective Equipment (PPE)
Operators of friction screw presses must always wear appropriate personal protective equipment (PPE) to minimize the risk of injury from machine operation or material handling. Depending on the specific application, the following PPE may be required:
- Gloves: Heat-resistant gloves should be worn when handling hot materials during forging operations. Gloves also protect the hands from cuts and abrasions when handling sharp or rough materials.
- Safety Goggles: Eye protection is essential to shield the operator from flying debris, sparks, or fragments of the workpiece that may be ejected during pressing.
- Hearing Protection: Press operations can generate significant noise, especially in metal forging or stamping applications. Hearing protection, such as earplugs or noise-canceling earmuffs, should be worn to protect against hearing damage.
7. Ergonomics and Operator Fatigue Management
While much of the safety focus is on mechanical hazards, ergonomic considerations are also important to ensure that operators can work comfortably and without strain. Poor ergonomic practices can lead to long-term injuries, such as musculoskeletal disorders.
- Adjustable Workstations: Press workstations should be adjustable to accommodate the height and reach of individual operators. This reduces the risk of back strain, repetitive motion injuries, and fatigue.
- Rest Breaks and Rotation: Operators should be encouraged to take regular breaks and rotate tasks to avoid fatigue, which can lead to mistakes or accidents. Fatigue is a significant factor in workplace accidents, particularly in industries that require repetitive manual tasks.
Conclusion
Ensuring the safe operation of a friction screw press requires a combination of adherence to regulatory standards, proper training, and the use of protective measures. From physical guards and emergency stop systems to the consistent use of PPE and ergonomic practices, every aspect of press operation must prioritize the safety and well-being of operators. By implementing these best practices, companies can not only protect their workforce but also improve efficiency and maintain compliance with safety regulations.
Environmental Impact and Sustainability
With the growing emphasis on sustainability and reducing the environmental footprint of industrial processes, friction screw presses have undergone various changes to align with more environmentally friendly practices. While traditionally associated with high energy consumption due to their mechanical nature, modern friction screw presses have been optimized to minimize energy use and promote sustainability in several ways. Below, we explore the environmental impact of friction screw presses and the steps being taken to enhance their sustainability.
1. Energy Consumption
One of the most significant environmental concerns for any industrial press, including friction screw presses, is energy consumption. Historically, mechanical presses have been energy-intensive, but modern innovations have helped reduce their environmental impact by improving energy efficiency.
- Flywheel Optimization: In friction screw presses, the flywheel stores rotational energy, which is then released as needed during pressing. By optimizing the size and material of the flywheel, modern presses can store energy more efficiently, reducing the amount of energy lost as heat. This leads to lower overall power consumption during operation.
- Variable Speed Drives: Some modern friction screw presses are equipped with variable speed drives that allow operators to adjust the speed of the motor based on the specific needs of the application. By only using the necessary amount of energy for each pressing operation, these systems can reduce energy waste and improve overall efficiency.
2. Sustainable Materials
Another key area of focus for reducing the environmental impact of friction screw presses is the use of sustainable materials in their construction. Advanced materials not only improve the durability and performance of the press but also contribute to a more sustainable manufacturing process.
- Recyclable Components: Many modern friction screw presses are designed with components made from recyclable materials, such as steel and aluminum. When parts wear out or are replaced, these materials can be recycled and reused, reducing waste and the need for new raw materials.
- Advanced Coatings: The use of advanced, eco-friendly coatings on key components, such as the screw and friction discs, helps to extend the life of these parts and reduce the frequency of replacements. Coatings made from non-toxic, environmentally safe materials also contribute to a more sustainable production process.
3. Waste Reduction and Resource Efficiency
Friction screw presses have also been optimized to minimize material waste during production, particularly in industries like metal forging and ceramics, where raw materials can be expensive and resource-intensive to produce.
- Precision Forging: The high level of precision offered by modern friction screw presses ensures that raw materials are used efficiently. By reducing the number of defective parts or excessive material deformation, less waste is produced, leading to more sustainable manufacturing operations.
- Reuse of Scrap Materials: Many industries that use friction screw presses have implemented scrap recycling systems, where leftover or scrap materials from forging or stamping operations are collected and melted down for reuse. This practice reduces the overall demand for new raw materials and minimizes waste sent to landfills.
4. Lower Emissions
While friction screw presses are primarily mechanical and do not directly produce emissions during operation, their overall environmental impact can still be influenced by the energy sources used to power them. Reducing emissions is a critical aspect of making these machines more sustainable.
- Renewable Energy Integration: Some manufacturing facilities that use friction screw presses are incorporating renewable energy sources like solar or wind power to reduce their reliance on fossil fuels. By using cleaner energy to power their presses, companies can significantly lower their carbon footprint.
- Energy Recovery Systems: In certain applications, energy recovery systems can be integrated into the press’s operation, capturing excess heat or mechanical energy and converting it back into usable power. This helps reduce overall energy consumption and lowers the environmental impact of the press.
5. Sustainability Certifications
As part of the broader movement toward sustainability in manufacturing, many companies that use friction screw presses are seeking sustainability certifications such as ISO 14001, which is the international standard for environmental management systems.
- ISO 14001 Compliance: Achieving ISO 14001 certification demonstrates that a company is committed to minimizing its environmental impact. This certification requires companies to implement systems that reduce waste, lower emissions, and conserve resources, which are all relevant for operations that rely on energy-intensive equipment like friction screw presses.
- Lifecycle Assessments (LCAs): Some manufacturers are conducting lifecycle assessments of their friction screw presses to evaluate the environmental impact of the machines from production to disposal. These assessments help identify opportunities to make the press more sustainable throughout its lifecycle, from the materials used in its construction to its energy consumption during operation.
Conclusion
The environmental impact of friction screw presses has been significantly reduced in recent years due to technological innovations and a growing focus on sustainability. By improving energy efficiency, using sustainable materials, and reducing waste, modern friction screw presses align with the broader goals of eco-friendly manufacturing. As industries continue to prioritize sustainability, friction screw presses will play a key role in minimizing the environmental footprint of production processes.
Selecting the Right Friction Screw Press for Your Business
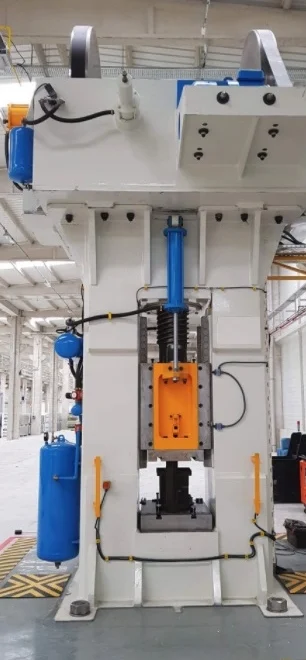
Choosing the right friction screw press for your business involves considering various factors, including the type of materials you will be processing, the production capacity needed, and the specific applications for which the press will be used. Below is a guide to help you select the best friction screw press based on your requirements.
1. Determine Your Production Requirements
The first step in selecting the right friction screw press is to clearly define your production requirements. Understanding the scale of your operations, the materials you work with, and the types of products you produce will guide your decision.
- Material Type: Different materials require different levels of force and precision. For example, heavy metals like steel require higher force presses, whereas softer materials, such as aluminum or ceramics, may need a press with more precise control over force application.
- Production Volume: If your business operates in a high-volume production environment, you will need a press that can handle continuous operation without frequent downtime for maintenance. Presses designed for heavy-duty use tend to have larger flywheels, stronger frames, and more durable components.
- Product Complexity: For complex parts that require intricate designs or multiple stages of pressing, a friction screw press with advanced control systems and precise force application may be necessary.
2. Evaluate Press Capacity
The capacity of the friction screw press refers to the maximum force it can exert during operation. This is a crucial factor to consider, as choosing a press with insufficient capacity can lead to poor product quality or equipment damage.
- Force Rating: Friction screw presses are typically rated by the maximum force they can apply, measured in tons. The size of the flywheel and the strength of the screw mechanism determine this force. Selecting a press with the appropriate tonnage is essential for ensuring that the press can handle the material thickness and workpiece dimensions.
- Stroke Length: The stroke length refers to how far the ram travels during operation. If you are working with deep-drawing processes or large components, a longer stroke length may be required to complete the pressing cycle effectively.
3. Consider Operational Efficiency
Efficiency is an important consideration when selecting a friction screw press, especially in high-volume production environments. Factors such as cycle time, energy consumption, and ease of maintenance can significantly impact overall operational costs.
- Cycle Time: For businesses that rely on quick turnaround times, the speed of the press’s cycle is a critical factor. Presses with optimized friction disc engagement systems and automated controls can achieve faster cycle times, improving throughput and efficiency.
- Energy Consumption: Energy-efficient presses, especially those with advanced flywheel designs and variable speed drives, can lower operational costs by reducing power consumption. Evaluating the energy requirements of a press is especially important if your business is focused on sustainability and reducing its environmental impact.
4. Review Maintenance Requirements
Maintenance plays a key role in the longevity and performance of friction screw presses. Some models are designed with low-maintenance features, such as automatic lubrication systems and durable, wear-resistant components, which can minimize the need for frequent maintenance.
- Component Durability: Choose a press with high-quality materials and components that are designed for durability and longevity. For example, presses with ceramic-coated friction discs or hardened steel screws will require less frequent replacement of critical parts.
- Maintenance Support: Consider the availability of spare parts and the manufacturer’s support services. Choosing a press from a reputable manufacturer with a robust support network ensures that you can easily access parts and technical assistance when needed.
5. Cost-Benefit Analysis
While the upfront cost of a friction screw press is an important consideration, it is also essential to conduct a cost-benefit analysis to understand the long-term value of the machine. Factors such as operational efficiency, durability, and maintenance costs should be weighed against the initial investment.
- Initial Investment: Higher-end presses with advanced features and larger capacities typically have a higher initial cost. However, they may offer greater long-term value due to increased productivity, lower energy consumption, and reduced maintenance requirements.
- Return on Investment (ROI): Consider the potential ROI of the press by estimating how much it will improve your production capabilities. Faster cycle times, fewer defects, and lower energy costs can result in significant savings over the life of the machine.
Conclusion
Selecting the right friction screw press for your business involves evaluating your production needs, capacity requirements, and operational efficiency. By considering factors such as material type, press capacity, energy efficiency, and maintenance requirements, you can choose a press that meets your business’s unique needs and delivers long-term value. Conducting a thorough cost-benefit analysis will help ensure that your investment in a friction screw press pays off in increased productivity and reduced operational costs.
Market Trends and Future Outlook
The market for friction screw presses continues to evolve as industries demand more efficient, reliable, and versatile machinery to meet their manufacturing needs. In recent years, several key trends have emerged, shaping the development of friction screw presses and influencing how they are used in various sectors. Below, we explore the current market trends and the future outlook for friction screw presses.
1. Increased Demand for Automation
One of the most significant trends in the friction screw press market is the growing demand for automation. As manufacturers seek to improve efficiency, reduce labor costs, and increase production speed, friction screw presses are being equipped with more advanced automation features.
- Automated Controls: Presses with computerized control systems and automated adjustments are becoming more common. These systems allow for greater precision and consistency in force application, which is particularly important in industries such as automotive and aerospace manufacturing, where high-quality standards must be maintained.
- Robotic Integration: Many friction screw presses are being integrated into fully automated production lines, where robotic arms handle the loading and unloading of materials. This trend is particularly evident in high-volume production environments, where automation can significantly reduce cycle times and improve throughput.
2. Sustainability and Energy Efficiency
As industries place greater emphasis on sustainability, friction screw presses are being designed with energy efficiency in mind. Reducing energy consumption not only lowers operational costs but also helps companies meet environmental goals.
- Energy-Efficient Designs: Manufacturers are focusing on optimizing the design of friction screw presses to make them more energy-efficient. This includes improvements to the flywheel and friction disc systems to minimize energy loss during operation. Some presses are also equipped with energy recovery systems that capture and reuse excess energy generated during pressing cycles.
- Green Manufacturing Practices: In response to the growing demand for environmentally friendly production methods, friction screw presses are being designed to minimize waste and material usage. This trend is particularly relevant in industries like metal forging and powder metallurgy, where reducing material waste can lead to significant cost savings and environmental benefits.
3. Advanced Materials and Additive Manufacturing
The development of advanced materials and additive manufacturing technologies is also influencing the future of friction screw presses. These technologies enable the production of more durable components and allow for greater customization of press designs.
- 3D-Printed Components: Additive manufacturing is making it possible to produce custom components for friction screw presses with improved precision and durability. For example, 3D-printed dies and molds can be created for specific applications, allowing manufacturers to produce highly specialized parts with minimal lead times.
- High-Strength Alloys: The use of high-strength alloys and composite materials in the construction of friction screw presses is improving their performance and longevity. These materials offer better resistance to wear and heat, reducing the need for frequent maintenance and improving the press’s ability to handle high-stress applications.
4. Global Market Expansion
The demand for friction screw presses is growing in both established and emerging markets. The global expansion of manufacturing industries, particularly in Asia and South America, is driving increased demand for these machines.
- Asia-Pacific Region: Countries in the Asia-Pacific region, such as China, India, and South Korea, are seeing significant growth in industries that rely on friction screw presses, including automotive, aerospace, and metal forging. The availability of lower-cost manufacturing solutions
A friction screw press is a type of mechanical press that utilizes friction to generate force for pressing or shaping materials. It consists of a frame, a flywheel, a screw mechanism, and a table. The flywheel, powered by an electric motor, rotates and transfers kinetic energy to the screw mechanism. The screw mechanism, in turn, converts rotational motion into linear motion, causing the press head to move downward and apply pressure to the material placed on the table.
Key Features of Friction Screw Presses:
- Simple Construction: Friction screw presses have a relatively simple and robust construction, making them easy to maintain and operate.
- High Force Capacity: These presses can generate high forces, making them suitable for pressing or shaping thick or dense materials.
- Smooth Operation: Friction screw presses provide smooth and controlled force application, reducing the risk of defects and improving surface finish.
- Versatility: They can handle a variety of materials and shapes, making them adaptable to different pressing applications.
- Lower Cost: Compared to hydraulic presses, friction screw presses tend to be less expensive to purchase and maintain.
Applications of Friction Screw Presses:
Friction screw presses are widely used in various industries for a range of applications, including:
- Metal Forming: These presses are commonly used for metal forming operations such as forging, stamping, and coining. They can shape and form various metal components, including parts for machinery, tools, and automotive applications.
- Plastic and Rubber Processing: Friction screw presses are also used in plastic and rubber processing for operations such as compaction, molding, and trimming. They can compact powders, mold plastic parts, and trim rubber components with precision and control.
- Packaging and Paperboard Manufacturing: These presses are employed in the packaging and paperboard industry for processes such as die cutting, embossing, and creasing. They can cut, shape, and form various packaging materials, including cardboard, paper, and plastic sheets.
- Textile and Leather Processing: In the textile and leather industries, friction screw presses are used for operations such as embossing, punching, and stitching. They can create patterns, cut shapes, and join textile or leather pieces with accuracy and consistency.
Advantages of Friction Screw Presses:
Friction screw presses offer several advantages over other types of presses, such as hydraulic presses:
- Lower Initial Cost: Friction screw presses are generally less expensive to purchase than hydraulic presses, making them an attractive option for budget-conscious applications.
- Simple Maintenance: These presses have a simpler design and fewer components compared to hydraulic presses, resulting in lower maintenance costs and easier troubleshooting.
- Energy Efficiency: Friction screw presses typically consume less energy than hydraulic presses, contributing to lower operating costs and a smaller environmental footprint.
- Ease of Operation: They are relatively easy to operate and require less specialized training compared to hydraulic presses, making them suitable for a wider range of users.
Conclusion:
Friction screw presses are versatile and reliable machines that play a crucial role in various industries. Their simple construction, high force capacity, smooth operation, and versatility make them well-suited for a wide range of pressing and shaping applications. Their lower initial cost and ease of maintenance further enhance their appeal, making them a cost-effective and user-friendly solution for many manufacturing processes.
Friction Screw Press
A friction screw press is a type of mechanical press that utilizes friction to generate force for pressing or shaping materials. It consists of a frame, a flywheel, a screw mechanism, and a table. The flywheel, powered by an electric motor, rotates and transfers kinetic energy to the screw mechanism. The screw mechanism, in turn, converts rotational motion into linear motion, causing the press head to move downward and apply pressure to the material placed on the table.
Key Features of Friction Screw Presses:
- Simple Construction: Friction screw presses have a relatively simple and robust construction, making them easy to maintain and operate.
- High Force Capacity: These presses can generate high forces, making them suitable for pressing or shaping thick or dense materials.
- Smooth Operation: Friction screw presses provide smooth and controlled force application, reducing the risk of defects and improving surface finish.
- Versatility: They can handle a variety of materials and shapes, making them adaptable to different pressing applications.
- Lower Cost: Compared to hydraulic presses, friction screw presses tend to be less expensive to purchase and maintain.
Applications of Friction Screw Presses:
Friction screw presses are widely used in various industries for a range of applications, including:
- Metal Forming: These presses are commonly used for metal forming operations such as forging, stamping, and coining. They can shape and form various metal components, including parts for machinery, tools, and automotive applications.
- Plastic and Rubber Processing: Friction screw presses are also used in plastic and rubber processing for operations such as compaction, molding, and trimming. They can compact powders, mold plastic parts, and trim rubber components with precision and control.
- Packaging and Paperboard Manufacturing: These presses are employed in the packaging and paperboard industry for processes such as die cutting, embossing, and creasing. They can cut, shape, and form various packaging materials, including cardboard, paper, and plastic sheets.
- Textile and Leather Processing: In the textile and leather industries, friction screw presses are used for operations such as embossing, punching, and stitching. They can create patterns, cut shapes, and join textile or leather pieces with accuracy and consistency.
Advantages of Friction Screw Presses:
Friction screw presses offer several advantages over other types of presses, such as hydraulic presses:
- Lower Initial Cost: Friction screw presses are generally less expensive to purchase than hydraulic presses, making them an attractive option for budget-conscious applications.
- Simple Maintenance: These presses have a simpler design and fewer components compared to hydraulic presses, resulting in lower maintenance costs and easier troubleshooting.
- Energy Efficiency: Friction screw presses typically consume less energy than hydraulic presses, contributing to lower operating costs and a smaller environmental footprint.
- Ease of Operation: They are relatively easy to operate and require less specialized training compared to hydraulic presses, making them suitable for a wider range of users.
Conclusion:
Friction screw presses are versatile and reliable machines that play a crucial role in various industries. Their simple construction, high force capacity, smooth operation, and versatility make them well-suited for a wide range of pressing and shaping applications. Their lower initial cost and ease of maintenance further enhance their appeal, making them a cost-effective and user-friendly solution for many manufacturing processes.
Metal Forming
Friction screw presses are widely used for metal forming operations due to their simple construction, high force capacity, smooth operation, and versatility. They can shape and form various metal components, including parts for machinery, tools, and automotive applications.
Key Principles of Metal Forming with Friction Screw Presses:
- Friction Drive: The rotational motion of the flywheel is transferred to the screw mechanism through friction between the flywheel and a friction disc or clutch. This friction generates the force required to move the press head downward and press the workpiece.
- Controlled Force Application: The screw mechanism converts rotational motion into linear motion, providing precise control over the force applied to the workpiece. This controlled force ensures consistent shaping and forming of the metal component.
- Adjustable Stroke and Speed: The stroke length and pressing speed can be adjusted to suit the specific material and shaping requirements. This adjustability allows for optimal forming of a wide range of metal components.
Common Metal Forming Operations with Friction Screw Presses:
- Forging: Friction screw presses are used to forge metal components by heating the workpiece to a high temperature and then pressing it into a die cavity to form the desired shape.
- Stamping: Friction screw presses are used to stamp metal components by forcing the workpiece through a die to cut or shape it into the desired form.
- Coining: Friction screw presses are used to coin metal components by pressing the workpiece between a punch and a die to create a raised or embossed design on the surface.
- Embossing: Friction screw presses can be used to emboss metal components by pressing the workpiece against a textured die to create a raised pattern or design.
- Swaging: Friction screw presses can be used to swage metal components by forcing the workpiece through a die to reduce its diameter or change its shape.
Advantages of Friction Screw Presses for Metal Forming:
- Simple Construction and Operation: Friction screw presses have a relatively simple design and are easy to operate, making them suitable for a wide range of users.
- High Force Capacity: These presses can generate high forces, making them suitable for forming thick or dense materials.
- Precise Force Control: Friction screw presses provide accurate control over the applied force, ensuring consistent shaping and forming of components with intricate features.
- Smooth Operation: They provide smooth and controlled force application, reducing the risk of defects and improving surface finish of the components.
- Versatility: Friction screw presses can handle a variety of materials and shapes, making them adaptable to different metal forming applications.
Considerations for Metal Forming with Friction Screw Presses:
- Material Properties: The material properties of the workpiece, such as strength, ductility, and strain hardening characteristics, influence the forming process and defect formation.
- Die Design: The geometry and clearance between the punch and die play a significant role in material flow and defect formation.
- Process Parameters: The pressing speed, lubrication, and temperature control affect the forming process and the quality of the formed component.
Conclusion:
Friction screw presses are valuable tools for metal forming operations, providing the force, precision, and versatility required to shape and form various metal components. Their simple construction, high force capacity, smooth operation, and adaptability to different materials make them essential equipment in various manufacturing industries. By carefully selecting appropriate dies, controlling process parameters, and considering material properties, manufacturers can minimize defects and produce high-quality metal components using friction screw presses.
Plastic and Rubber Processing
The production of plastic and rubber products involves various processes, from compounding and mixing to forming and finishing. Hydraulic presses play a crucial role in these processes, providing the force, precision, and control necessary to shape, consolidate, and form these materials into desired products.
Key Stages in Plastic and Rubber Processing:
- Compounding and Mixing: Raw plastic or rubber materials are blended with additives, such as fillers, plasticizers, and pigments, to achieve the desired properties for the final product. Hydraulic presses can be used to mix these materials, ensuring uniform distribution of additives and a homogeneous mixture.
- Forming: The mixed plastic or rubber material is then formed into the desired shape using various techniques, including compression molding, injection molding, and extrusion. Hydraulic presses provide the force required to compress, inject, or extrude the material into the mold or die cavity.
- Vulcanization or Curing: For rubber products, vulcanization or curing is an essential step that involves crosslinking the polymer chains to achieve the desired strength, elasticity, and durability. Hydraulic presses are used to apply heat and pressure during the vulcanization or curing process, ensuring uniform crosslinking throughout the rubber product.
- Finishing: Once formed, plastic and rubber products may undergo various finishing operations, such as trimming, cutting, and surface treatment. Hydraulic presses can be used for some finishing processes, such as trimming excess material or embossing patterns onto the surface.
Role of Hydraulic Presses in Plastic and Rubber Processing:
Hydraulic presses play a critical role in several stages of plastic and rubber processing, including:
- Mixing: Hydraulic presses can be used to mix plastic or rubber compounds, ensuring uniform distribution of additives and a homogeneous mixture.
- Compression Molding: Hydraulic presses apply pressure to molds filled with plastic or rubber material, forcing the material to conform to the shape of the mold cavity.
- Injection Molding: Hydraulic presses are used to inject molten plastic into molds, filling the cavity and forming the desired product shape.
- Extrusion: Hydraulic presses can be used to extrude plastic or rubber compounds through dies, producing continuous shapes such as tubes, sheets, or profiles.
- Vulcanization or Curing: Hydraulic presses provide the heat and pressure required for vulcanization or curing of rubber products, ensuring uniform crosslinking throughout the material.
- Trimming and Cutting: Hydraulic presses can be used to trim excess material from molded plastic or rubber components or cut them into specific shapes.
- Embossing: Hydraulic presses can be used to emboss patterns or designs onto the surface of plastic or rubber products.
Advantages of Hydraulic Presses for Plastic and Rubber Processing:
Hydraulic presses offer several advantages for plastic and rubber processing applications:
- Precise Force Control: Hydraulic presses provide accurate control over the applied force, ensuring consistent forming and shaping of plastic and rubber products.
- High Force Capacity: Hydraulic presses can generate high forces, making them suitable for processing thick or dense plastic and rubber materials.
- Uniform Pressure Distribution: Hydraulic presses ensure uniform pressure distribution across the mold surface, preventing uneven compaction or defects in the products.
- Versatility: Hydraulic presses can handle a variety of plastic and rubber materials and shapes, making them adaptable to different processing applications.
- Automation Capabilities: Hydraulic presses can be integrated with automation systems for high-volume production and consistent quality control.
Conclusion:
Hydraulic presses are essential tools in the plastic and rubber processing industry, providing the controlled force, precision, and versatility required to shape, consolidate, and form these materials into desired products. Their ability to accurately apply force, accommodate different materials, and integrate with automation systems makes them indispensable components in the production of high-quality plastic and rubber products.
Packaging and Paperboard Manufacturing
Friction screw presses play a versatile and crucial role in various stages of packaging and paperboard manufacturing, providing the force, precision, and control necessary to shape, form, and assemble various packaging components. Their simple construction, high force capacity, smooth operation, and adaptability to different materials make them essential equipment in this industry.
Core Applications of Friction Screw Presses in Packaging and Paperboard Manufacturing:
- Die Cutting: Friction screw presses are widely used for die cutting a variety of packaging materials, including cardboard, paper, and plastic sheets. They can cut intricate shapes and patterns for boxes, bags, and other packaging elements with precision and accuracy.
- Embossing: Friction screw presses are employed to emboss packaging materials, creating raised or textured patterns for decorative or branding purposes. They can emboss patterns on cardboard boxes, paper bags, or plastic packaging components, enhancing their aesthetic appeal and brand identity.
- Creasing: Friction screw presses are used to crease packaging materials, creating score lines or folds to facilitate bending and shaping without tearing or cracking. They can crease cardboard boxes, paperboard folders, or plastic packaging components, ensuring clean and precise folds.
- Blanking and Forming: Friction screw presses can be used for blanking and forming various packaging components, such as cardboard inserts, plastic dividers, or paperboard trays. They can cut and shape these components from raw materials, creating the basic shapes required for packaging assembly.
- Assembly and Bonding: Friction screw presses can be used for assembly and bonding operations in packaging manufacturing. They can apply pressure to join components together, such as pressing cardboard inserts into boxes or bonding plastic dividers using adhesives.
- Testing and Quality Control: Friction screw presses can be used for testing and quality control procedures in packaging manufacturing. They can apply controlled forces to evaluate the strength, durability, and performance of packaging components or assemblies.
Advantages of Friction Screw Presses for Packaging and Paperboard Manufacturing:
- Simple Construction and Operation: Friction screw presses have a relatively straightforward design and are easy to operate, making them suitable for a wide range of users in the packaging industry.
- High Force Capacity: These presses can generate high forces, making them suitable for processing thick or dense packaging materials, such as cardboard or heavy-duty plastic sheets.
- Precise Force Control: Friction screw presses provide accurate control over the applied force, ensuring consistent cutting, embossing, creasing, and assembly of packaging components.
- Smooth Operation: They provide smooth and controlled force application, reducing the risk of defects and improving the surface finish of packaging components.
- Versatility: Friction screw presses can handle a variety of packaging materials and shapes, making them adaptable to different manufacturing processes and product designs.
- Cost-Effectiveness: Compared to hydraulic presses, friction screw presses are generally less expensive to purchase and maintain, making them a cost-effective solution for packaging manufacturing.
Considerations for Using Friction Screw Presses in Packaging Manufacturing:
- Material Properties: The properties of the packaging material, such as thickness, strength, and tear resistance, influence the cutting, embossing, and creasing processes.
- Tool Design: The design of the cutting die, embossing tool, or creasing blade plays a significant role in the accuracy and quality of the final product.
- Process Parameters: The pressing speed, pressure, and temperature control affect the cutting, embossing, creasing, and assembly processes.
Conclusion:
Friction screw presses are indispensable tools in packaging and paperboard manufacturing, providing the controlled force, precision, and versatility required to shape, form, and assemble various packaging components. Their simple construction, high force capacity, smooth operation, adaptability to different materials, and cost-effectiveness make them essential equipment in this industry. By carefully selecting appropriate tools, controlling process parameters, and considering material properties, manufacturers can produce high-quality, aesthetically pleasing, and durable packaging using friction screw presses.
Forging
Forging is a manufacturing process that involves shaping metal or other materials through the application of compressive forces. It is a critical process used to create a wide range of components and parts for various industries, including automotive, aerospace, construction, and manufacturing. Forging typically produces strong, durable, and high-quality parts with improved mechanical properties compared to cast or machined components. Here’s an overview of the forging process and its key aspects:
Types of Forging:
- Open-Die Forging: In open-die forging, the metal workpiece is placed between flat or slightly contoured dies, and compressive forces are applied from above and below. This process allows for greater flexibility and can be used to shape large and complex parts.
- Closed-Die Forging: Closed-die forging, also known as impression-die forging, involves placing the workpiece into a die cavity that contains the desired shape. The metal is then compressed within the die cavity, resulting in a precise and highly detailed part.
- Roll Forging: Roll forging uses two or more cylindrical rollers to deform the workpiece. The rollers apply pressure as they rotate, gradually reducing the cross-sectional area of the material and shaping it into the desired form.
- Swaging: Swaging is a cold forging process where a workpiece is reduced in diameter or length by being forced through dies or rollers.
Steps in the Forging Process:
- Material Selection: The forging process begins with the selection of a suitable material, typically a metal alloy with desirable mechanical properties.
- Heating: The chosen material is heated to a specific temperature to make it more malleable and easier to shape. The temperature varies depending on the material but is usually above its recrystallization temperature.
- Forming: The heated material is placed between the forging dies or rollers, and compressive forces are applied. This deforms the material into the desired shape. The choice of open-die or closed-die forging depends on the complexity of the part and the required precision.
- Cooling: After forming, the forged part is often cooled slowly to relieve internal stresses and prevent cracking or distortion. This is known as heat treatment.
- Trimming and Finishing: The forged part may require further machining, trimming, or finishing operations to achieve the final dimensions and surface quality.
Advantages of Forging:
- Strength and Durability: Forged parts are known for their high strength, toughness, and durability, making them suitable for critical applications.
- Improved Grain Structure: Forging refines the grain structure of the material, enhancing its mechanical properties, such as fatigue resistance and impact strength.
- Precision and Tight Tolerances: Closed-die forging allows for the production of parts with tight tolerances and intricate shapes.
- Cost-Efficiency: Forging can be a cost-effective production method, especially for large quantities of parts with complex geometries.
- Material Savings: Minimal material waste is generated during forging due to precise shaping and controlled deformation.
- Customization: Forging can produce parts of various sizes and shapes, tailored to specific applications.
- Reduced Porosity: Forging reduces the risk of porosity and inclusions in the material, resulting in higher-quality parts.
Forging plays a critical role in the manufacturing industry, producing components for everything from automobiles and aircraft to industrial machinery and hand tools. The process’s ability to create high-strength, reliable parts makes it a fundamental technique for a wide range of applications.
Screw Mechanism
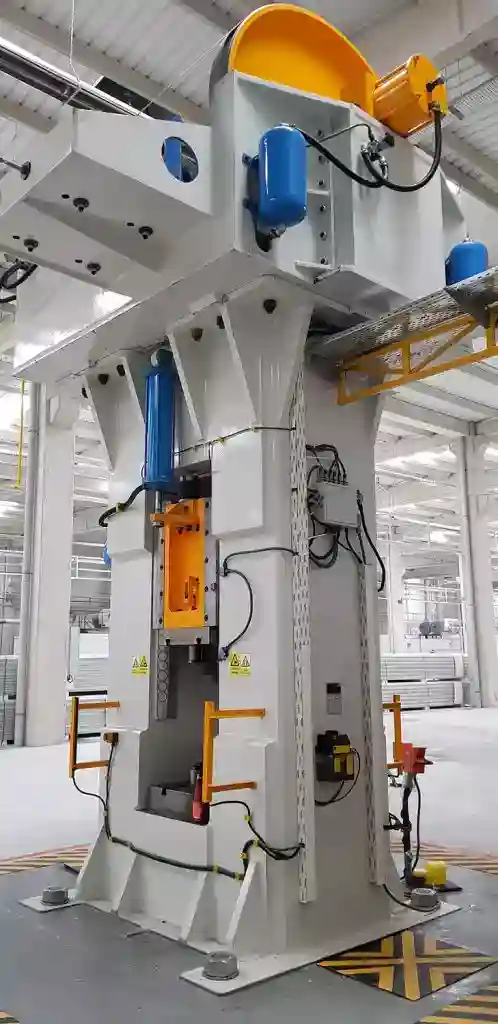
The screw mechanism of a friction screw press is a fundamental component responsible for generating the immense pressure required for various forging and forming operations. It plays a pivotal role in the press’s operation. Here’s an overview of the screw mechanism in a friction screw press:
- Basic Components:
- Screw: The screw is a long, threaded shaft that rotates during the operation of the press. It is usually made of high-strength steel and has a helical thread along its length.
- Nut: The nut is a fixed component positioned below the screw. It has an internal threaded surface that matches the screw’s thread. The screw threads into the nut.
- Ram (Slide): The ram or slide is attached to the screw and moves vertically along with it. The ram carries the forging tooling or dies that apply pressure to the workpiece.
- Drive System: A motor and drive system are responsible for rotating the screw. The drive system may include belts, gears, or other mechanisms to transmit power from the motor to the screw.
- Working Principle:
- When the motor is activated, it rotates the screw in either a clockwise or counterclockwise direction, depending on the press’s design.
- As the screw rotates, it moves vertically, either downward or upward, depending on the direction of rotation. This movement is controlled and precise, allowing for the application of controlled force to the workpiece.
- The screw threads into the nut, and the friction between the screw and nut generates a significant amount of axial force along the length of the screw.
- This axial force is transmitted to the ram, which carries the forging dies. As a result, the ram moves downward (or upward) with substantial force, applying pressure to the workpiece placed between the dies.
- Pressure Generation:
- The key to the friction screw press’s operation is the friction between the screw and the nut. This friction generates an axial force (also called axial thrust) along the length of the screw. The magnitude of this force depends on factors like the screw’s thread pitch, the nut’s design, and the torque applied by the motor.
- The axial force is converted into compressive force when it acts on the ram and the attached forging dies. This force is what enables the press to deform and shape the workpiece.
- Control and Precision:
- The rotation of the screw and, consequently, the movement of the ram can be precisely controlled. This control allows for accurate application of force and precise control over the forging process.
- Control systems may include feedback mechanisms, sensors, and automation to maintain consistent pressure and ensure the quality of the forged components.
- Applications:
- Friction screw presses are used in various metalworking applications, including hot forging, cold forging, coining, extrusion, and more. They are employed in industries such as automotive, aerospace, manufacturing, and metal fabrication for producing a wide range of components and parts.
The friction screw press’s screw mechanism is a critical element that enables the press to exert high pressures and carry out various metalworking processes with precision and control. Its ability to generate substantial axial forces through friction makes it a valuable tool in the manufacturing and forging industries.
Friction Screw Press Application Areas
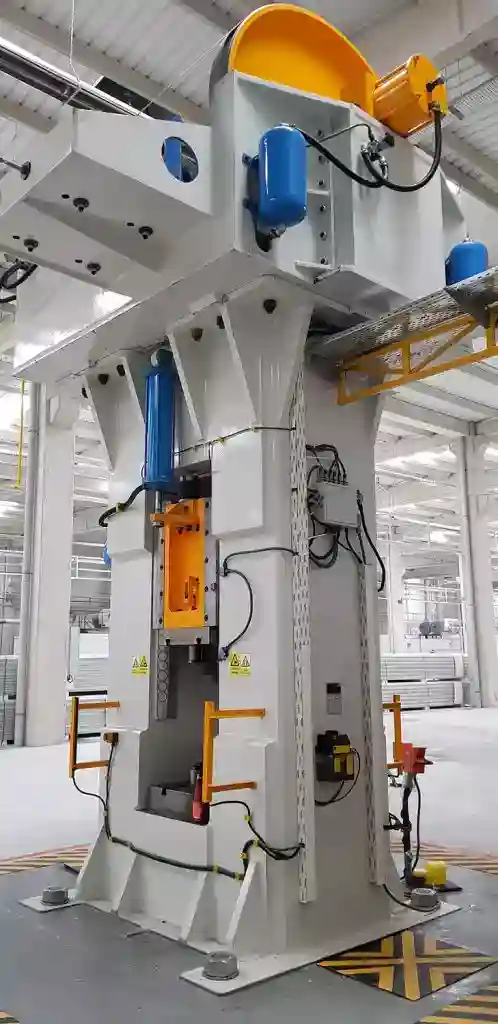
Friction screw presses find applications in various industrial sectors due to their versatility, capability to exert high compressive forces, and precise control over pressing operations. Here are some of the key application areas where friction screw presses are commonly used:
- Forging: Friction screw presses are widely used in forging operations, where metal workpieces are heated and shaped using high pressure. They are employed in the production of automotive parts, aerospace components, hand tools, and various other forged products.
- Extrusion: These presses are used in metal extrusion processes, where metal billets or powders are pushed through a die to create continuous profiles or shapes. Common applications include the manufacture of aluminum profiles for construction and automotive industries.
- Stamping and Coining: Friction screw presses are used for stamping and coining operations, where sheets of metal are cut, stamped, or embossed to create precise shapes or designs. This is common in the production of coins, metal tags, and intricate metal components.
- Cold Heading: In the fastener manufacturing industry, friction screw presses are used for cold heading, where cold-forming processes create fasteners like screws, bolts, and rivets from wire or rod stock.
- Blanking and Shearing: These presses are employed for blanking and shearing processes, where metal sheets or plates are cut or sheared into specific shapes or sizes. Applications include the production of metal blanks for further processing.
- Powder Compaction: In the pharmaceutical, ceramics, and powder metallurgy industries, friction screw presses are used for compacting powders into solid shapes or tablets.
- Bending and Forming: Friction screw presses are utilized for bending and forming operations, which are common in the production of metal components for various industries, including HVAC, construction, and machinery manufacturing.
- Coin Minting: In coin minting facilities, friction screw presses are used to produce coins with precise designs and dimensions.
- Ball and Roller Manufacturing: The production of ball bearings and roller bearings involves precision forming and shaping operations that can be accomplished with friction screw presses.
- Railway Component Manufacturing: Friction screw presses are used to manufacture railway components such as wheels, axles, and rail fasteners.
- Ceramic and Refractory Products: In the ceramics industry, these presses are employed to shape and form ceramic products, including tiles, bricks, and refractory materials.
- Rubber and Plastic Molding: Friction screw presses can be adapted for molding operations in the rubber and plastic industries, allowing for the creation of various molded products.
- Composite Materials: Some industries use friction screw presses for composite material processing, including the shaping and consolidation of composite parts.
- Specialized Applications: Beyond these common applications, friction screw presses are used in numerous specialized manufacturing processes, depending on the specific requirements of the industry and product.
Friction screw presses are valued for their reliability, precision, and ability to handle a wide range of materials and processes. They are an integral part of many manufacturing operations, contributing to the production of diverse products across various industries.
Cookware Production with Friction Screw Press
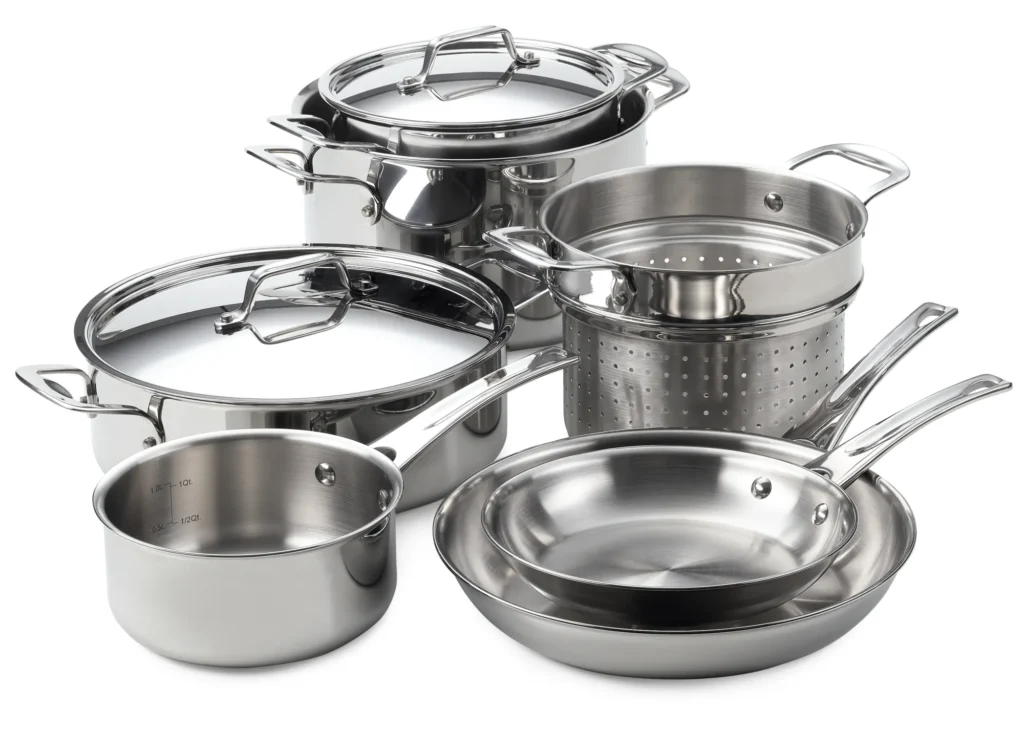
Cookware production with a friction screw press involves the use of this powerful and precise machine to shape and form metal sheets into various types of cookware, such as pots, pans, and utensils. Here’s an overview of the process:
- Materials Preparation:
- The cookware production process begins with the preparation of raw materials, which are typically metal sheets. Common materials used for cookware production include stainless steel, aluminum, cast iron, and copper. The thickness and grade of the metal sheets depend on the type of cookware being manufactured.
- Blanking and Cutting:
- The metal sheets are cut into blanks of the appropriate size and shape using cutting tools or presses. Blanking is the process of cutting out the initial shape of the cookware, often in the form of circular or rectangular pieces.
- Forming and Shaping:
- The friction screw press is used for the forming and shaping of the metal blanks. The press is equipped with specialized dies and molds that define the final shape of the cookware. The blanks are placed between the dies, and the press applies pressure to deform the metal and shape it into the desired cookware shape. For example, in the case of pots and pans, the press forms the metal into the curved, concave, or convex shapes required.
- Handle Attachment:
- If the cookware design includes handles, these are typically attached to the formed pieces. Handles may be welded, riveted, or otherwise securely fastened to the cookware.
- Surface Finishing:
- After forming and handle attachment, the cookware pieces undergo surface finishing processes. These processes may include polishing, grinding, and buffing to achieve a smooth and attractive surface finish. For certain types of cookware, such as non-stick pans, a coating or seasoning process may be applied to the cooking surface.
- Quality Control:
- Throughout the production process, quality control measures are implemented to ensure that the cookware meets the desired specifications. Inspections are performed to check for defects, proper dimensions, and surface finish quality.
- Packaging and Distribution:
- Once the cookware pieces pass quality control, they are packaged and prepared for distribution to retailers or customers. Packaging materials may include boxes, foam inserts, or other protective measures to prevent damage during transportation.
The use of a friction screw press in cookware production offers several advantages, including:
- Precision and Consistency: The press allows for precise control over the forming and shaping of cookware, ensuring consistent dimensions and quality.
- Efficiency: Friction screw presses are efficient in terms of both energy usage and production time, making them suitable for high-volume manufacturing.
- Versatility: These presses can be adapted for various cookware designs and sizes, from small saucepans to large frying pans.
- Strength and Durability: Cookware produced using this method tends to have the strength and durability required for cooking applications.
Cookware production with a friction screw press combines traditional metalworking techniques with modern machinery to create high-quality kitchen utensils that meet industry standards and customer expectations.
Cookware Forming and Shaping with Screw Friction Presses
Friction screw presses play a crucial role in cookware forming and shaping, providing the precise force, controlled pressure, and versatility required to transform raw materials into functional and aesthetically pleasing cookware components. Their simple construction, high force capacity, and smooth operation make them essential tools in the cookware manufacturing industry.
Key Stages of Cookware Forming and Shaping with Friction Screw Presses:
- Blanking: Friction screw presses can be used to blank out the basic shapes of cookware components from sheets of metal, such as aluminum, stainless steel, or copper. The press applies force to cut the material along a predefined die, creating the desired shape.
- Forming: Once blanked, the metal pieces undergo various forming operations to achieve the desired shape and depth of the cookware components. Friction screw presses provide the controlled force and precision required to form pots, pans, lids, and other cookware pieces.
- Flanging: Flanging involves creating a rim or edge around the top of a cookware component, such as a pot or pan. Friction screw presses can apply the necessary force and control to form the flange smoothly and evenly.
- Beading: Beading involves creating a decorative or reinforcing rim around the edge of a cookware component. Friction screw presses can precisely form the beading, enhancing the appearance and durability of the cookware.
- Handle Attachment: Friction screw presses can be used to attach handles to cookware components. They can apply the appropriate force to press-fit or rivet handles securely onto the cookware body.
- Polishing and Finishing: After forming, cookware components may undergo polishing and finishing operations to achieve the desired surface appearance. Friction screw presses can be used to apply polishing compounds or perform light embossing to enhance the finish.
Advantages of Friction Screw Presses for Cookware Forming and Shaping:
- Precise Force Control: Friction screw presses provide accurate control over the applied force, ensuring consistent forming and shaping of cookware components.
- Smooth Operation: They provide smooth and controlled force application, reducing the risk of defects and improving the surface finish of cookware components.
- Versatility: Friction screw presses can handle a variety of metal materials and shapes, making them adaptable to different cookware manufacturing processes.
- Safety Features: Friction screw presses can incorporate safety features to protect operators from potential hazards, such as overheating or sudden pressure release.
- Cost-Effectiveness: Compared to hydraulic presses, friction screw presses tend to be less expensive to purchase and maintain, making them a cost-effective solution for cookware manufacturing.
Considerations for Using Friction Screw Presses in Cookware Manufacturing:
- Material Properties: The properties of the cookware material, such as ductility, strength, and workability, influence the forming process and defect formation.
- Tool Design: The design of the forming dies and tools plays a significant role in material flow and defect formation.
- Process Parameters: The pressing speed, pressure, and temperature control affect the forming process and the quality of the formed cookware component.
Safety Precautions in Cookware Forming with Friction Screw Presses:
- Proper Training: Operators should receive proper training on the safe operation of friction screw presses, including emergency procedures.
- Personal Protective Equipment: Operators should wear appropriate personal protective equipment (PPE), such as safety glasses, gloves, and hearing protection.
- Machine Guarding: Friction screw presses should be equipped with safety guards to prevent accidental contact with moving parts.
- Regular Maintenance: Regular maintenance and inspections of the press are essential to ensure safe operation and prevent malfunctions.
- Clearance Zones: Maintain clear workspaces around the press and avoid obstructions that could hinder safe operation.
Conclusion:
Friction screw presses are indispensable tools in cookware manufacturing, providing the controlled force, precision, and versatility required to shape and form various cookware components. Their simple construction, high force capacity, smooth operation, adaptability to different materials, and cost-effectiveness make them essential equipment in this industry. By carefully selecting appropriate tools, controlling process parameters, considering material properties, and adhering to safety guidelines, manufacturers can produce high-quality, durable, and aesthetically pleasing cookware using friction screw presses.
Friction screw presses
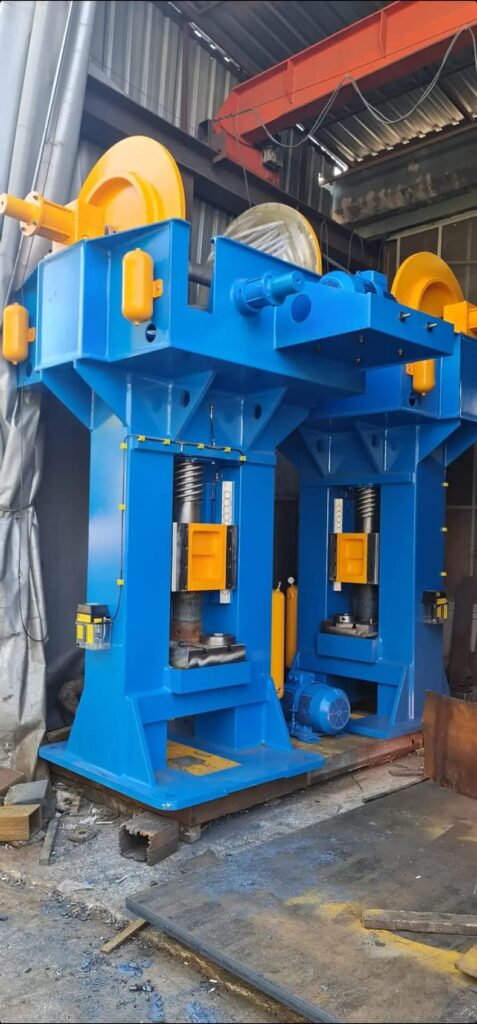
Friction screw presses are essential mechanical tools in forging, metalworking, and manufacturing. They are highly favored for their precision, cost-effectiveness, and relative ease of use. A friction screw press primarily relies on the interaction between a flywheel and a screw, where friction is used to drive the pressing action. As a result, they are commonly found in industries requiring forging, coining, and embossing, offering a balance between manual and automated force application. Unlike hydraulic presses, friction screw presses don’t rely on fluid mechanics; instead, they generate force through the mechanical motion of the flywheel.
The key appeal of friction screw presses is their straightforward, durable design, which makes them suitable for repetitive tasks that don’t demand extreme pressures. However, they come with limitations in terms of maximum force and speed, which can affect high-output industrial processes. In smaller-scale or craft operations, however, friction screw presses offer a reliable and versatile option.
2. Flywheel
The flywheel is perhaps the most crucial component in a friction screw press, as it stores and releases kinetic energy, driving the pressing action. Typically, the flywheel is a large, heavy wheel made from steel or cast iron. The size and weight of the flywheel determine how much energy it can store and, thus, how much force can be applied to the workpiece during pressing.
Key Design Aspects of the Flywheel:
- Size and Weight: A heavier flywheel can store more energy but requires more initial force to spin. Manufacturers must balance these factors to ensure the flywheel provides enough force without being excessively difficult to engage.
- Balancing and Stability: A well-balanced flywheel is critical to prevent excessive vibration, which can damage other components and affect press accuracy.
- Connection to Screw Mechanism: The flywheel is typically attached to the screw via a friction roller mechanism, allowing the operator to start and stop the flywheel’s rotation by applying or releasing friction.
3. Screw Mechanism
The screw mechanism in a friction screw press converts the rotational motion of the flywheel into linear motion, which is essential for generating the downward force required to shape the workpiece. Screws are generally made from hardened steel to withstand the immense pressure and wear involved in each press cycle.
Key Considerations for the Screw Mechanism:
- Thread Design: The design of the threads on the screw affects the force transmission and speed. Coarser threads increase force transmission but reduce speed, whereas finer threads allow for faster movement with reduced force.
- Material and Hardness: Screws must be made from materials that can withstand high stress and wear, typically high-strength steels that are further hardened to extend lifespan.
- Lubrication: Proper lubrication minimizes friction and wear, reducing maintenance requirements and extending the screw’s life.
4. Friction Rollers
Friction rollers play a pivotal role in controlling the engagement of the flywheel, thus managing the press’s force and speed. These rollers are responsible for engaging the flywheel to begin its rotation and disengaging it to stop. Made from heat-resistant and wear-resistant materials, the rollers are designed to handle high-speed friction without excessive wear.
Critical Design Aspects of Friction Rollers:
- Material Selection: Friction rollers are often crafted from durable materials like hardened steel or alloys with high heat tolerance to withstand the constant friction.
- Adjustability: The operator can adjust the friction rollers to regulate the force applied to the flywheel, providing control over the pressing force.
- Wear and Maintenance: Since they are constantly subjected to high friction, rollers require regular inspection and maintenance to prevent excessive wear and ensure consistent operation.
5. Ram or Plunger
The ram, or plunger, is the component that directly applies force to the workpiece. Connected to the screw mechanism, the ram moves downward when the flywheel-driven screw rotates, pressing the material into the die to shape it as desired. This component must withstand repeated impacts and high pressure, so it’s generally made from heavy-duty materials.
Design and Function of the Ram:
- Material and Hardness: Rams are often made from hardened steel or similar materials that can withstand the stresses of continuous, high-pressure usage.
- Connection to Screw Mechanism: The ram is securely connected to the screw, transferring the rotational force of the flywheel into a direct linear motion.
- Wear-Resistance: Since the ram endures high impact forces, it’s essential to consider wear-resistant design choices, such as heat treatment or the use of specialized alloys, to enhance durability.
6. Frame Structure and Base
The frame and base form the structural backbone of a friction screw press, supporting all other components and maintaining the alignment needed for accurate pressing. Frames are typically fabricated from cast iron or steel to provide the necessary rigidity and stability.
Key Aspects of Frame Structure:
- Material Selection: The frame’s material must be robust and resistant to deformation to maintain the press’s alignment over time. Cast iron is commonly used for its vibration-damping qualities.
- Stress Management: The frame must be designed to handle the forces generated during each press cycle without flexing or deforming.
- Mounting Features: Proper alignment between the frame and base helps ensure smooth operation and prevents wear on other components, such as the screw and ram.
7. Safety Mechanisms
Safety is critical in any press operation, and friction screw presses incorporate various safety mechanisms to protect the operator and equipment. Some common safety features include overload protection and emergency stop functions.
Safety Features:
- Overload Protection: This mechanism prevents the press from applying excessive force, which could damage components or cause injury.
- Emergency Stop: An emergency stop button allows the operator to instantly disengage the flywheel and halt the pressing action.
- Operator Guards: Physical guards and shields are often installed to prevent accidental contact with moving parts.
8. Conclusion
Each component of a friction screw press plays an integral role in its operation, from the flywheel’s energy storage to the precise force control of the friction rollers. The screw mechanism, ram, and frame structure work together to create a machine that is both effective and durable, making the friction screw press a versatile tool in manufacturing. Although it has limitations in terms of speed and maximum force, it remains a cost-effective solution for many forging tasks. Innovations in material science and design may continue to improve the performance and longevity of friction screw presses, securing their relevance in the industry for years to come.
1. Overview of Friction Screw Presses
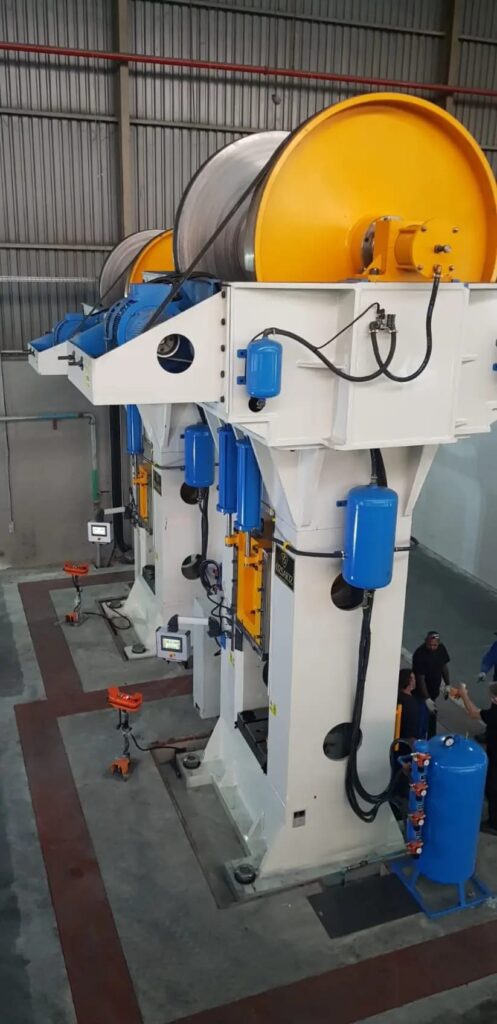
Friction screw presses are a type of mechanical press primarily used in metal forming processes, such as forging, coining, and stamping. These presses generate force through a combination of rotational and linear motion, utilizing a large flywheel and a screw mechanism to exert pressure on a workpiece. Invented during the late 19th century as an economical and practical solution for metalworking, friction screw presses have since evolved to support a wide range of applications.
They are highly valued in industries where precision, cost-efficiency, and durability are essential. By leveraging friction to control the rotation of the flywheel, friction screw presses allow operators to regulate the pressing force, making them ideal for tasks that require moderate but precise pressure. These machines can be found in small-scale blacksmith shops as well as larger manufacturing plants, where they are often used to produce coins, medals, and other detailed metal parts.
2. Working Principles of a Friction Screw Press
A friction screw press operates on a simple yet effective mechanical principle: it converts rotational energy into linear force. This conversion begins when an operator engages friction rollers to spin a large flywheel. The flywheel’s rotation is transferred to a vertical screw, which is threaded in a way that, as it rotates, it moves downward to apply pressure to the workpiece. Once the flywheel stops spinning, the press retracts, resetting for the next cycle.
The key element in this process is the friction rollers. They allow the operator to control the flywheel’s speed and rotation direction with ease, providing flexibility in applying the force required for specific tasks. By adjusting the friction between the rollers and the flywheel, operators can vary the amount of force exerted on the material, which is crucial for tasks like forging and coining, where precision and controlled pressure are essential.
3. Comparison with Other Press Types
When compared to other types of presses, friction screw presses have distinct advantages and limitations:
- Hydraulic Presses: These presses use hydraulic fluid to generate force and are capable of exerting very high pressures, making them suitable for heavy-duty applications. However, hydraulic presses are generally more expensive and require more maintenance than friction screw presses due to the complexity of hydraulic systems.
- Mechanical Presses: Unlike friction screw presses, which use a flywheel-driven screw, mechanical presses often use cams, levers, or other mechanisms to apply force. Mechanical presses can operate faster but often lack the force control and versatility of friction screw presses.
Friction screw presses offer a middle ground between hydraulic and mechanical presses, providing sufficient power for most forging applications without the high maintenance demands of hydraulic systems or the lack of force adjustability found in many mechanical presses. For operations requiring moderate force with high control, the friction screw press is typically preferred.
4. Design and Key Components
The design of a friction screw press centers around a few key components: the flywheel, screw, friction rollers, and ram. Together, these elements create a simple yet powerful machine capable of precise force application.
- Flywheel: This large, heavy wheel stores kinetic energy and releases it to drive the screw mechanism. Its size and balance are critical to the press’s operation.
- Screw: The screw converts the rotational energy of the flywheel into downward pressure. The threading and material of the screw are chosen to handle the high forces generated.
- Friction Rollers: Made from heat-resistant materials, these rollers engage the flywheel, allowing the operator to control the press’s force by adjusting the friction level.
- Ram or Plunger: Connected to the screw, the ram transfers the applied force directly to the workpiece.
These components are usually housed within a strong, stable frame made from cast iron or steel. Proper alignment and material choice are crucial, as they contribute to the machine’s durability and consistent performance over time.
5. Applications of Friction Screw Presses
Friction screw presses are widely used across various industries, including:
- Forging and Metalworking: Common in blacksmithing, jewelry making, and automotive component manufacturing, friction screw presses are ideal for shaping metal due to their controllable force output.
- Coining and Minting: Precision is essential in creating coins and medals, and friction screw presses are well-suited to this task.
- Stamping and Embossing: The ability to apply moderate pressure with control makes friction screw presses useful for producing detailed patterns and designs on metal.
The versatility of friction screw presses allows them to be adapted for a wide variety of metalworking processes, making them a preferred choice in industries requiring consistent, precise forging capabilities.
6. Advantages of Friction Screw Presses
Friction screw presses are popular due to their numerous advantages:
- Cost-Effectiveness: They are generally less expensive to purchase and maintain than hydraulic presses, making them accessible for small- and medium-sized operations.
- Precision Force Control: The friction roller mechanism provides precise control over the force applied, which is crucial in applications requiring detailed work.
- Durability and Low Maintenance: Thanks to their simple design, friction screw presses are durable and require relatively little upkeep.
These qualities make friction screw presses particularly advantageous for operations that don’t require extremely high-pressure applications, allowing operators to achieve quality results with a manageable investment.
7. Limitations and Challenges
While friction screw presses are valuable, they also have certain limitations:
- Lower Force Capability: Compared to hydraulic presses, friction screw presses may not generate sufficient force for very heavy-duty applications, limiting their use in some high-force manufacturing processes.
- Slower Cycle Times: Friction screw presses can be slower to operate, which may not be ideal for high-production environments where speed is crucial.
- Wear from Friction: Since the press relies on friction to operate, key components like the rollers and screw can wear over time, necessitating periodic maintenance to ensure smooth operation.
These limitations mean that friction screw presses are best suited for operations that balance precision with moderate force, making them ideal for craft metalworking and forging applications that don’t demand extreme pressures.
8. Future Developments in Friction Screw Press Design
Advances in materials and engineering design have paved the way for potential improvements in friction screw presses:
- Enhanced Materials: Using more wear-resistant alloys and composite materials can reduce friction-related wear, prolonging the lifespan of rollers and screws.
- Automation: Adding automated control systems to regulate friction and force could increase productivity and consistency.
- Hybrid Systems: Combining friction screw mechanisms with hydraulic elements could broaden the range of applications, allowing for higher-force tasks without sacrificing control.
Such innovations could address some of the limitations of traditional friction screw presses, making them more competitive with modern pressing solutions.
9. Conclusion
The friction screw press remains a vital tool in metalworking, offering a blend of precision, durability, and cost-efficiency that appeals to small and large-scale operations alike. While other pressing technologies have emerged, the friction screw press continues to serve industries where moderate force, control, and longevity are valued. With future advancements in materials and automation, friction screw presses may become even more adaptable and reliable, solidifying their place in the manufacturing world.
In friction screw presses, the flywheel is the driving force behind the press’s kinetic energy, creating the motion and pressure needed to shape metal workpieces. This heavy, circular wheel is connected to a screw, and through friction-based engagement, it converts stored rotational energy into linear force, allowing the press to exert considerable pressure. The flywheel’s role is crucial: it both stores energy and modulates the force applied to the workpiece, making it the heart of the friction screw press’s operation.
Historically, flywheels have been used in machinery for centuries, valued for their ability to regulate energy and ensure smoother, controlled power output. In the context of friction screw presses, flywheels enable operators to apply consistent, reliable pressure in forging, coining, and metal shaping tasks. The evolution of flywheel design reflects advancements in material science and engineering, with modern flywheels engineered to deliver high performance in today’s demanding industrial environments.
2. Design and Structure of a Flywheel
The design of a flywheel is paramount to its efficiency and effectiveness in a friction screw press. Typically circular, flywheels are designed with considerable weight and diameter to maximize energy storage. The size, mass, and material distribution of a flywheel directly influence how much kinetic energy it can store, which translates to the press’s force output.
- Shape and Mass Distribution: Most flywheels have a simple disc shape, with weight distributed towards the outer edges. This design leverages the principles of rotational inertia, allowing more energy to be stored when the wheel spins.
- Weight and Size: Heavier flywheels store more energy, but they also require more power to accelerate. The size of the flywheel must be balanced with the press’s energy requirements and operational speed, as overly large or heavy flywheels may slow down operations and increase wear on the system.
- Balance and Precision: A well-balanced flywheel is crucial for smooth operation. Imbalances can lead to vibrations, wear, and inefficiency, potentially damaging the press over time.
The design process involves calculating the optimal size and weight based on the specific pressing force and cycle speed required for the tasks at hand. Engineers must also account for the forces the flywheel will generate, ensuring that both the machine and its surroundings can safely handle the rotational energy involved.
3. Materials and Construction
Flywheels in friction screw presses are constructed from durable materials that can withstand repeated cycles of force application without deformation or excessive wear. The choice of material is based on factors like durability, cost, and energy-storing capability.
- Common Materials: Flywheels are typically made from cast iron, steel, or in advanced cases, composites. Cast iron is preferred for its density and vibration-dampening properties, while steel offers higher strength and durability for higher energy applications.
- Material Properties: The material must have a high tensile strength to resist stress during high-speed rotation, as well as good heat resistance since friction-generated heat can affect performance.
- Manufacturing Techniques: Casting and forging are commonly used to produce flywheels due to the size and density requirements. These processes ensure that the flywheel’s weight distribution is even, enhancing balance and rotational stability.
By selecting the right materials and manufacturing methods, engineers ensure that the flywheel will maintain structural integrity and reliability, even under high-stress conditions.
4. Energy Storage and Release Mechanism
The flywheel’s primary function is to store kinetic energy during its rotation and release it when pressing force is needed. This ability to store energy makes the flywheel a highly efficient power source within friction screw presses.
- Kinetic Energy Storage: When the flywheel spins, its mass generates rotational kinetic energy. The amount of energy stored depends on its rotational speed and mass distribution, which is why flywheels in presses are both large and heavy.
- Energy Release: When engaged, the flywheel’s kinetic energy is transferred to the screw, which moves linearly downward to apply pressure to the workpiece. The energy transfer is almost instantaneous, allowing for precise, forceful pressing action.
- Efficiency Considerations: Higher rotational speeds allow the flywheel to store more energy, but excessive speeds can cause stability issues. Engineers design flywheels to operate within optimal speed ranges for maximum efficiency.
This energy storage and release mechanism enables the press to apply controlled, high-pressure force in short bursts, which is essential for forging and metal shaping processes.
5. Balancing and Stability of the Flywheel
Balancing the flywheel is crucial to achieving a stable, vibration-free operation. An unbalanced flywheel can create significant operational issues, including vibrations that disrupt precision, increase wear, and even damage other press components.
- Importance of Balance: Balance affects both the accuracy and longevity of the press. An imbalanced flywheel leads to uneven forces during operation, which can compromise the quality of the forged product.
- Static and Dynamic Balancing: Engineers use static balancing to ensure that the flywheel’s mass is evenly distributed around its axis. Dynamic balancing is applied to ensure that the flywheel spins evenly under operating conditions, reducing operational vibration.
- Alignment: Proper alignment between the flywheel and other components, like the screw and ram, is essential for smooth energy transfer. Misalignment can lead to uneven force application and increase maintenance needs.
Careful balancing and alignment practices during manufacturing are essential for maximizing the performance and longevity of the friction screw press.
6. Friction Rollers and Flywheel Engagement
The friction rollers allow the operator to control when the flywheel engages, enabling smooth start and stop functions. This friction-driven engagement is key to the press’s force modulation capabilities.
- Engagement Mechanics: The friction rollers make contact with the flywheel to start its rotation, disengaging to halt its motion. This engagement process is critical for controlling the flywheel’s speed and, by extension, the force applied to the workpiece.
- Effects on Wear: The repeated engagement and disengagement of the rollers create wear on both the flywheel and rollers. High-quality, wear-resistant materials are essential to prolong the life of these components.
- Force Modulation: The amount of pressure applied by the friction rollers determines the flywheel’s speed, allowing operators to adjust the press’s force output. This control is particularly valuable for processes requiring variable force application, like precision forging or coining.
By modulating the force through the flywheel’s engagement, operators achieve a fine level of control over the pressing process.
7. Safety and Maintenance of the Flywheel
Given the flywheel’s high-speed rotation and kinetic energy, safety is paramount when operating friction screw presses.
- Safety Risks: A spinning flywheel stores significant energy, which poses a hazard if mishandled. Proper enclosures, shields, and braking mechanisms are essential to prevent accidental contact or energy release.
- Maintenance Practices: Regular inspection of the flywheel and associated components is necessary to detect wear or imbalance. Lubricating the friction rollers and ensuring proper alignment also help maintain safe and efficient operation.
- Emergency Stop Mechanisms: Many friction screw presses include emergency stop features that disengage the flywheel and halt operation, protecting operators and machinery in case of malfunction.
Routine maintenance, combined with stringent safety protocols, ensures the safe operation of the flywheel within a friction screw press.
8. Future Developments and Innovations in Flywheel Technology
Advancements in materials and technology continue to improve flywheel performance in friction screw presses:
- Composite Materials: New composite materials, such as carbon fiber or advanced alloys, offer greater strength-to-weight ratios, allowing for lighter, more durable flywheels with enhanced energy storage.
- Electronic Control Systems: Integrating electronic control systems allows for precise speed regulation, enhancing the press’s control and accuracy.
- Hybrid Systems: Flywheels combined with hydraulic or electric elements can broaden the press’s capabilities, providing both control and high-force output where needed.
These innovations could make friction screw presses more adaptable, efficient, and reliable, keeping them relevant in modern metalworking industries.
9. Conclusion
The flywheel in a friction screw press is an indispensable component, central to the press’s functionality. By storing and releasing kinetic energy, the flywheel enables controlled, powerful force application in metal shaping. The careful design, balancing, and selection of materials allow the flywheel to function efficiently within high-stress environments. Safety measures and regular maintenance ensure that the flywheel remains reliable, contributing to the friction screw press’s reputation as a robust, economical choice in forging.
As advancements in materials and electronic control continue to emerge, the flywheel’s role in friction screw presses may evolve, incorporating features that enhance energy efficiency, precision, and control. These innovations will likely expand the applications and effectiveness of friction screw presses, solidifying their place in modern manufacturing.
Introduction to Flywheel Design in Friction Screw Presses
The flywheel in a friction screw press plays a fundamental role in storing and releasing kinetic energy, allowing the press to apply controlled, high-force impacts to metal workpieces. The flywheel’s design is critical to its performance, influencing everything from energy storage capacity to operational stability and force precision. In friction screw presses, flywheels must be engineered to withstand repetitive, high-stress cycles while ensuring safety and efficiency in industrial applications.
The design aspects of a flywheel are meticulously planned to meet the specific needs of the press. Factors such as mass, moment of inertia, shape, material, and balance all affect how well the flywheel performs under various loads and speeds. These design choices contribute directly to the press’s effectiveness, making the flywheel a central component in achieving consistent, reliable force application for metal shaping processes.
2. Mass and Moment of Inertia
The mass and moment of inertia are among the most important factors in flywheel design. These determine how much energy the flywheel can store and, consequently, how much force the press can apply during operation.
- Mass: The flywheel’s mass contributes directly to its energy storage capacity. Heavier flywheels can store more kinetic energy, which translates to more force during pressing. However, too much mass can lead to operational inefficiencies, so the mass must be optimized based on the press’s energy requirements.
- Moment of Inertia: This is a measure of how the flywheel’s mass is distributed relative to its axis of rotation. The greater the moment of inertia, the more energy the flywheel can store. Distributing mass toward the outer edge increases the moment of inertia, allowing the flywheel to store more energy at a given rotational speed.
- Calculation and Optimization: Engineers calculate the moment of inertia by taking into account the flywheel’s mass distribution and radius. This allows for precise control over the energy output, ensuring that the press can achieve the necessary force without requiring excessive speed.
By carefully balancing mass and moment of inertia, designers can create flywheels that maximize energy storage and improve overall press efficiency.
3. Flywheel Shape and Geometry
The shape of a flywheel is another critical design aspect that affects its performance, energy storage, and stability. While solid discs are common, flywheels can also have a rimmed or spoked design to meet specific operational needs.
- Solid Discs: A solid disc is the simplest and most compact shape, providing balanced weight distribution. However, solid discs can become excessively heavy, limiting efficiency in some applications.
- Rimmed Flywheels: These designs have a central hub with a thick outer rim, allowing mass to be concentrated at the perimeter for higher moment of inertia without adding unnecessary weight to the center. This design maximizes energy storage and is commonly used in applications requiring high force output.
- Spoked Wheels: Spoked designs reduce material weight while maintaining mass at the rim, achieving a balance between energy storage and reduced material usage. This design is advantageous in applications where weight limitations or cooling needs are a priority.
Choosing the appropriate geometry depends on the flywheel’s intended use, the space constraints of the press, and the force requirements of the application.
4. Material Selection and Properties
Selecting the right material for a flywheel impacts its durability, heat resistance, and energy capacity. Common materials used include cast iron, steel, and increasingly, composite materials for advanced applications.
- Cast Iron: Known for its density and vibration-dampening properties, cast iron is a popular choice for flywheels. It can withstand significant stress, but its brittleness can be a drawback in some high-impact applications.
- Steel: Steel offers high tensile strength and is less brittle than cast iron, making it suitable for heavy-duty applications. Alloyed steels can also provide additional resistance to heat and wear, increasing the flywheel’s lifespan.
- Composite Materials: High-performance composite materials, like carbon fiber, offer excellent strength-to-weight ratios, which allow for lighter, stronger flywheels. These materials can be cost-prohibitive, but they are increasingly used in specialized applications where energy efficiency is crucial.
Material selection also involves considering the flywheel’s exposure to high temperatures and friction. Engineers balance these factors to select a material that combines durability with the required energy storage capacity.
5. Flywheel Size and Diameter
The size and diameter of the flywheel have a direct impact on its energy storage capabilities and force application.
- Diameter Influence: Larger diameters enable a higher moment of inertia, allowing the flywheel to store more energy at the same rotational speed. However, increasing diameter also demands more space and can lead to more friction and drag.
- Optimal Sizing: The diameter and overall size are optimized based on the press’s force requirements, ensuring that the flywheel can achieve the necessary energy output without overloading the system.
- Trade-Offs: A larger flywheel can store more energy but may reduce the overall speed and responsiveness of the press. Engineers carefully select a diameter that meets force requirements while balancing speed and efficiency.
Sizing decisions involve trade-offs between energy storage needs and operational speed, with each dimension optimized for the specific press application.
6. Balancing and Alignment Techniques
Proper balancing and alignment are essential for smooth, efficient flywheel operation. Any imbalance can lead to vibration, wear, and even damage over time.
- Static and Dynamic Balancing: Static balancing involves ensuring that the flywheel’s weight is evenly distributed around its axis, while dynamic balancing ensures stability under operational conditions. This minimizes vibration and ensures that the flywheel spins smoothly.
- Alignment with Press Components: The flywheel must be aligned with the screw and ram to ensure efficient energy transfer and prevent misalignment issues that could lead to wear or operational inefficiencies.
- Precision Manufacturing: Techniques like CNC machining are used to achieve the high tolerances necessary for balanced flywheels, improving operational stability and reducing maintenance needs.
Balancing and alignment practices help ensure that the flywheel contributes to the press’s accuracy, stability, and longevity.
7. Friction Control and Engagement Mechanisms
In a friction screw press, the flywheel is engaged through friction rollers, which allow for precise force control. This engagement mechanism affects the flywheel’s performance and longevity.
- Friction Control: Adjusting the pressure on the friction rollers controls the flywheel’s speed, allowing operators to modulate the press force for different applications.
- Wear Considerations: Friction can lead to wear on the rollers and the flywheel’s engagement surfaces, so materials with high wear resistance are chosen for these parts.
- Precision Engagement: By adjusting the friction, operators can control the speed and torque of the flywheel, achieving optimal force for each pressing cycle.
This friction-based engagement system allows for versatile, controlled operation but requires careful design to minimize wear and maximize precision.
8. Safety and Structural Integrity
Safety is paramount in flywheel design, given the high-speed rotation and kinetic energy involved.
- Enclosures and Shields: Safety enclosures prevent accidental contact with the flywheel, and shields help contain any fragments in the rare event of material failure.
- Material Strength and Structural Safety: The flywheel’s material must be able to withstand the high forces generated during operation without fracturing or deforming.
- Load-Bearing and Safety Margins: Engineers incorporate safety margins into the design, ensuring that the flywheel can handle loads beyond typical operating conditions without compromising stability.
Safety measures protect both operators and machinery, ensuring reliable and secure operation of the flywheel over its lifetime.
9. Future Innovations in Flywheel Design
Advancements in materials and electronic controls continue to evolve flywheel design:
- Composite Materials: Advanced composites like carbon fiber offer lightweight, high-strength alternatives to traditional materials, improving energy storage efficiency and wear resistance.
- Electronic Speed Control: Integrating electronic controls for precise speed regulation can enhance the flywheel’s performance, enabling more accurate force modulation.
- Hybrid Press Systems: Flywheels may be used alongside hydraulic or electric components in hybrid systems, expanding their application range.
These innovations will likely make flywheels even more efficient, versatile, and durable, supporting modern manufacturing demands.
10. Conclusion
Flywheel design is a foundational aspect of friction screw press functionality, influencing energy storage, force application, and operational efficiency. Through careful attention to mass, shape, material, balance, and safety, engineers create flywheels that optimize performance while ensuring stability and durability. As new materials and technologies emerge, flywheel designs will continue to evolve, supporting the increasing demands of modern manufacturing and securing the relevance of friction screw presses in the industry.
Introduction to the Screw Mechanism
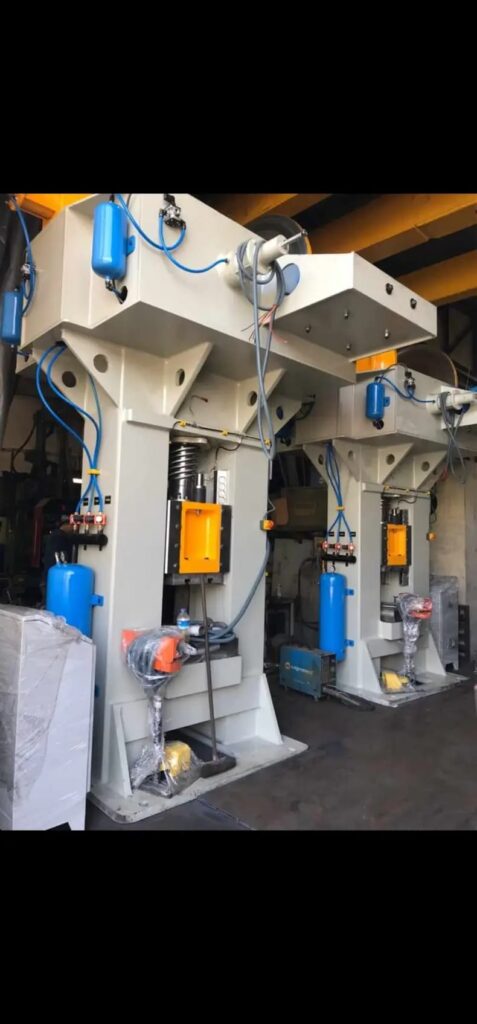
The screw mechanism is a fundamental component in friction screw presses, directly responsible for transforming the rotational energy of the flywheel into the linear pressing force needed for shaping metal workpieces. Acting as the main transmission element, the screw mechanism not only converts energy but also controls the press’s force application, making it integral to achieving consistent and precise results in forging and metal forming.
In a friction screw press, the screw mechanism is designed to withstand high loads and repeated cycles of stress. It must be durable, precisely manufactured, and capable of operating efficiently even under intense pressure. The screw mechanism’s effectiveness depends on a careful balance of materials, threading design, and structural integrity, all of which are crucial to ensuring the longevity and reliability of the press. By examining each of these design elements, we can better understand how the screw mechanism contributes to the overall efficiency and functionality of the friction screw press.
2. Design and Structure of the Screw
The design and structure of the screw in a friction screw press are key to its performance. The screw must be engineered to handle immense loads while maintaining alignment with the press’s other components.
- Length and Diameter: The length and diameter of the screw are carefully calculated to provide the necessary force without buckling under pressure. Longer screws allow for greater force application but must be supported to prevent bending.
- Threading: The type of threading on the screw determines how effectively it can transfer force from the flywheel to the ram. Heavier threading allows for greater force application but may reduce the speed of operation.
- Solid vs. Hollow Screws: While solid screws are more common, some presses use hollow screws to reduce weight without significantly compromising strength. However, hollow screws can be more susceptible to wear under heavy loads.
Overall, the design of the screw must balance force requirements with structural integrity, ensuring that it can endure the repetitive strain of pressing operations while remaining stable and aligned.
3. Material Selection and Heat Treatment
Selecting the right materials and heat treatment processes is crucial for a screw mechanism’s durability. The screw experiences intense stress and wear, requiring materials that can withstand high-pressure cycles and resist deformation.
- High-Strength Steels: Most screws are made from high-strength steels, known for their resilience and ability to retain shape under heavy loads. Alloy steels may also be used, offering additional benefits such as resistance to heat and corrosion.
- Wear Resistance and Toughness: The screw material must be hard enough to resist wear but also tough enough to avoid brittleness. This is especially important in applications where the screw is subjected to repeated impact forces.
- Heat Treatment: Processes like hardening, tempering, and surface nitriding are often applied to enhance the screw’s wear resistance and durability. Heat treatment hardens the surface of the screw while maintaining a tougher core, reducing the risk of cracking or wear under heavy loads.
The combination of strong materials and appropriate heat treatments extends the lifespan of the screw mechanism, reducing the need for frequent replacements and maintenance.
4. Thread Profile and Geometry
The thread profile of a screw greatly impacts its efficiency, strength, and ability to transmit force from the flywheel to the ram. Engineers carefully select thread geometry to meet specific performance requirements.
- Types of Thread Profiles: Common profiles include trapezoidal, square, and ACME threads. Square threads offer high efficiency but are more challenging to manufacture, while trapezoidal and ACME threads balance efficiency with ease of production and wear resistance.
- Thread Pitch and Depth: The pitch and depth of the threads influence how much force the screw can apply with each rotation. A finer pitch allows for greater precision, while a coarser pitch increases force transmission but may reduce control.
- Trade-Offs: Designers must balance the need for high force transmission with the screw’s speed. Coarse threads provide greater force but move more slowly, while fine threads enable quicker motion but reduce the force exerted.
The choice of thread profile and geometry directly affects the screw’s performance, influencing the speed, control, and efficiency of the press.
5. Operation and Mechanics of Force Transmission
The screw mechanism operates by converting the rotational motion of the flywheel into linear force. This conversion process is central to the screw’s function within the press.
- Rotational to Linear Conversion: When the flywheel rotates, the screw mechanism’s threads translate this rotational energy into downward pressure, driving the ram onto the workpiece. This movement is carefully controlled to apply consistent, targeted force.
- Role of Friction: Friction is a necessary part of this energy transfer, as it helps to control the screw’s movement and ensure a steady force application. However, excessive friction can lead to wear, so lubrication is essential.
- Torque and Efficiency: The torque applied by the flywheel influences the screw’s force output. Calculating the appropriate torque and maintaining optimal efficiency are essential for ensuring that the press applies the desired pressure without excessive energy loss.
By understanding the mechanics of force transmission, engineers can optimize the screw mechanism for maximum efficiency and reliability.
6. Lubrication and Maintenance Requirements
Lubrication plays a critical role in the screw’s longevity and efficiency, as it reduces friction and wear on the threads.
- Lubricants: High-performance industrial lubricants are commonly used to minimize wear on the screw threads. These lubricants must be able to withstand high pressures and temperatures without breaking down.
- Application Methods: Lubricants are applied at regular intervals, often through automated systems in larger presses. Consistent lubrication helps maintain smooth operation and prolongs the life of the screw.
- Routine Maintenance: In addition to lubrication, routine inspection of the screw mechanism is essential for detecting early signs of wear. Threads should be inspected for signs of deformation or wear, and alignment should be checked regularly.
Proper lubrication and maintenance are key to ensuring that the screw mechanism operates smoothly and reliably over time.
7. Alignment and Connection to Other Components
The screw mechanism must be precisely aligned with other components, such as the flywheel and ram, to prevent misalignment and ensure smooth energy transfer.
- Connection to Flywheel and Ram: The screw is typically connected to the flywheel via friction rollers, which allow for controlled engagement. The ram is mounted on the screw, allowing it to apply direct force to the workpiece.
- Maintaining Alignment: Misalignment can lead to wear, vibration, and reduced efficiency. Alignment techniques, such as using precision guides or bearings, help maintain the correct positioning.
- Long-Term Stability: Over time, the screw mechanism may shift due to wear or operational stress. Regular alignment checks are essential to keep the mechanism functioning correctly.
Ensuring proper alignment enhances the screw mechanism’s efficiency and prolongs its operational life.
8. Challenges and Common Issues with Screw Mechanisms
Despite careful design, screw mechanisms in friction screw presses are subject to several common challenges and issues.
- Wear and Tear: Threads experience wear over time, leading to degradation of force transmission. Regular maintenance and timely replacement can mitigate this issue.
- Misalignment: Repeated stress and vibration can lead to misalignment, which reduces efficiency and increases wear on the screw.
- Signs of Fatigue: Over time, screws may show signs of fatigue, such as bending or cracking. Operators must monitor for these signs to prevent operational failure.
Understanding these challenges helps operators address issues before they affect the press’s performance.
9. Future Innovations in Screw Mechanism Design
Advancements in materials and design are leading to more durable and efficient screw mechanisms:
- Advanced Materials: New alloys and composite materials are being developed to improve wear resistance and reduce weight.
- Self-Lubricating Screws: Some designs now incorporate self-lubricating materials to reduce the need for maintenance.
- Electronic Monitoring: Sensors can be used to monitor screw wear in real-time, enabling predictive maintenance and reducing downtime.
These innovations promise to make screw mechanisms more reliable and adaptable to future manufacturing needs.
10. Conclusion
The screw mechanism is central to the function of friction screw presses, converting rotational motion into the linear force necessary for metal forming. Through careful design, material selection, and maintenance, engineers ensure that the screw mechanism operates efficiently and withstands the demands of industrial use. As innovations in materials and monitoring systems continue, screw mechanisms are poised to become even more durable and efficient, further solidifying their role in modern manufacturing.
Introduction to the Screw in Friction Screw Presses
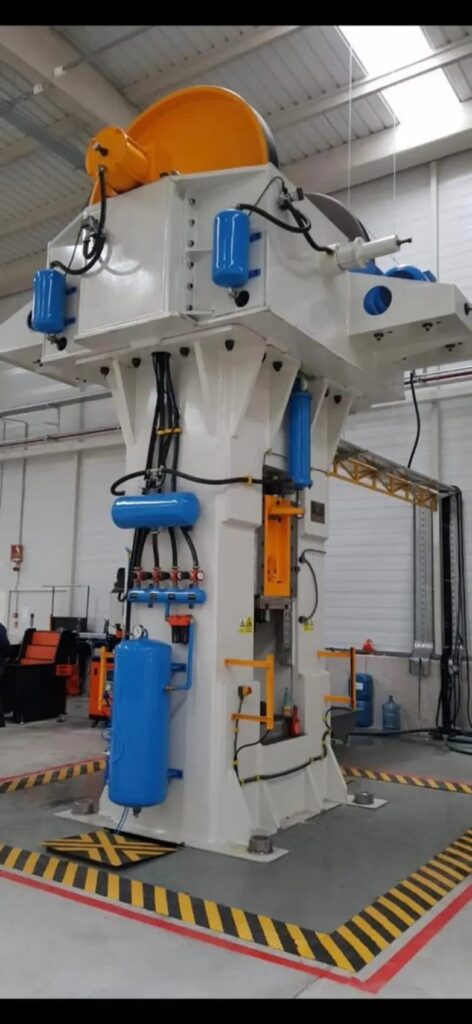
The screw mechanism is one of the core components of a friction screw press, transforming rotational motion into linear force to apply pressing power to metal workpieces. In a friction screw press, the screw bears the load of transferring force from the flywheel to the ram, which directly impacts the workpiece. Consequently, the screw must be durable and precisely engineered to handle repetitive stress without deformation or misalignment.
The design and structure of the screw influence the press’s efficiency, force output, and longevity. Each dimension, from the screw’s length to its thread profile, plays a crucial role in its effectiveness. Careful consideration of these design aspects allows manufacturers to build screws that can endure the rigors of industrial use, ensuring reliable operation and extending the lifespan of the friction screw press.
2. Physical Dimensions: Length, Diameter, and Proportionality
The physical dimensions of the screw in a friction screw press are crucial to its structural integrity and functionality. Length, diameter, and the proportion between the two are all factors that contribute to the screw’s ability to transfer force effectively.
- Length: The length of the screw affects its stability and capacity to withstand load without bending. Longer screws enable greater travel distance for the ram but are more susceptible to bending if not properly supported. Engineers must calculate the ideal length based on the press’s requirements and ensure that it remains stable during operation.
- Diameter: The diameter determines the screw’s strength and load capacity. A larger diameter generally provides greater structural strength and resistance to stress, reducing the likelihood of bending under pressure. However, increasing diameter also adds weight and may affect the flywheel’s ability to drive the screw effectively.
- Proportionality and Balance: Finding the right balance between length and diameter is essential. If the screw is too long relative to its diameter, it may be prone to bending or flexing under heavy loads. Conversely, an overly thick screw may not be as efficient in energy transfer, potentially requiring more rotational force from the flywheel.
By carefully selecting length and diameter proportions, engineers ensure that the screw can handle the press’s operational demands without compromising on stability or efficiency.
3. Thread Types and Profiles
The thread profile of a screw directly influences how it transmits force from the flywheel to the ram. Common thread types in screw press applications include trapezoidal, square, and ACME profiles, each of which has specific characteristics suited to different pressing needs.
- Trapezoidal Threads: Known for their high load-bearing capacity, trapezoidal threads offer a good balance of efficiency and durability. They are commonly used in applications where the screw experiences heavy, repetitive loads.
- Square Threads: Square threads provide high efficiency for linear force transfer but are more challenging to manufacture. They generate less friction than trapezoidal threads, making them suitable for applications requiring precise force with minimal energy loss.
- ACME Threads: ACME threads are a compromise between trapezoidal and square threads, combining load-bearing strength with easier manufacturing. They are robust and offer reliable force transfer, which makes them a popular choice for friction screw presses.
Selecting the right thread profile is critical in achieving optimal performance for the press’s intended application. Each thread type provides distinct advantages in terms of efficiency, ease of production, and durability, allowing engineers to match thread design with operational requirements.
4. Pitch, Lead, and Thread Depth
Pitch, lead, and thread depth are crucial parameters that affect the screw’s performance. These dimensions determine how fast the screw moves in response to rotation and how much force it can apply.
- Pitch: The pitch refers to the distance between threads. A finer pitch allows for more precise control but may require more rotations to achieve the same linear movement. Coarser pitches increase the rate of movement per rotation, allowing for faster operation but potentially reducing control.
- Lead: The lead is the distance the screw advances with each full rotation. In single-thread screws, pitch and lead are equal, while in multi-thread screws, lead is the pitch multiplied by the number of thread starts. A higher lead increases the speed of linear movement, which can be advantageous in presses requiring rapid cycling.
- Thread Depth: Thread depth influences load capacity and wear resistance. Deeper threads provide greater surface area for force transfer, increasing durability. However, they also add friction, which can impact efficiency.
Engineers must carefully balance these parameters to achieve the right mix of speed, control, and force for the screw’s specific application.
5. Solid vs. Hollow Screw Design
The choice between a solid or hollow screw design impacts the weight, strength, and resilience of the screw mechanism.
- Solid Screws: Solid screws are the traditional choice for high-strength applications. They are straightforward to manufacture and can withstand heavy loads without risk of collapse. However, solid screws can be heavy, which may place additional demands on the flywheel and increase wear on other components.
- Hollow Screws: Hollow screws are lighter and offer certain operational advantages, such as faster response time and reduced inertia. However, they are more complex to manufacture and may not be suitable for very high-load applications unless made from advanced, high-strength materials.
For applications requiring a balance of weight and strength, hollow screws can offer advantages. However, in high-stress environments where maximum durability is necessary, solid screws are often preferred.
6. Material Choices and Heat Treatment
Material selection is fundamental to the screw’s durability and resistance to wear. Common materials for screw construction include alloy steels, carbon steels, and, in some cases, composite materials for specialized applications.
- Alloy Steels: Alloy steels provide a balance of strength, toughness, and cost-effectiveness, making them suitable for screws that bear heavy loads. Alloying elements like chromium and molybdenum improve resistance to wear and heat.
- Carbon Steels: Carbon steels offer high strength but are more susceptible to corrosion and wear. They are often used in less demanding applications or when cost is a primary concern.
- Heat Treatment: Processes like hardening, tempering, and nitriding are commonly applied to screws to improve wear resistance and durability. Heat-treated screws have a hardened surface layer, which provides resilience to surface wear while maintaining a tough core to resist cracking.
Selecting the right material and heat treatment enhances the screw’s ability to handle the stress of repeated operation, reducing the risk of wear or breakage.
7. Structural Reinforcement Techniques
To increase durability, various reinforcement techniques are used in screw manufacturing.
- Surface Hardening: Surface hardening strengthens the screw’s exterior while maintaining a tough, ductile core. This is useful in high-wear applications where the threads experience continuous friction.
- Nitriding: Nitriding introduces nitrogen into the surface of the screw, creating a hard, wear-resistant layer. This process is especially beneficial for screws exposed to high temperatures and friction.
- Coatings: Certain coatings can provide additional wear and corrosion resistance, enhancing the screw’s longevity and performance in demanding environments.
These reinforcement techniques increase the screw’s resilience, enabling it to withstand extended periods of operation without excessive wear.
8. Connection Points and Alignment with Other Components
The screw must be securely and accurately connected to the flywheel and ram for effective energy transfer.
- Connection to Flywheel: The screw connects to the flywheel through friction rollers, which engage to initiate rotation. This connection must be stable to ensure consistent force transfer.
- Ram Alignment: The ram is attached to the screw, translating its downward force onto the workpiece. Proper alignment is essential to prevent off-center force, which can cause wear or damage to both the screw and ram.
- Wear Prevention: Connections and alignments are regularly inspected to prevent uneven wear and ensure smooth operation. Any misalignment can reduce efficiency and increase wear on components, making routine checks essential.
By ensuring correct alignment, engineers maximize the screw’s operational life and maintain consistent press performance.
9. Maintenance and Wear Management in Screw Design
Screws in friction screw presses are designed for high endurance, but they still require regular maintenance to manage wear.
- Lubrication Channels: Many screws are designed with channels for lubricant application, which reduces friction and wear on threads.
- Coatings for Wear Resistance: Some screws feature specialized coatings that minimize surface wear and extend lifespan.
- Monitoring Wear: Engineers monitor the screw’s condition as part of routine maintenance, looking for signs of thread degradation, surface damage, or misalignment.
These maintenance features support the screw’s long-term performance and reduce downtime due to unexpected breakdowns.
10. Conclusion
The design and structure of the screw in a friction screw press are key to its functionality and durability. Through careful selection of dimensions, materials, and threading profiles, engineers create a screw that can withstand high-stress cycles while providing precise force application. Advanced reinforcement techniques and regular maintenance help to further extend the screw’s life. As new materials and technologies emerge, the design of screws will continue to evolve, enhancing their resilience and efficiency in modern industrial applications.
Introduction to Material Selection and Heat Treatment
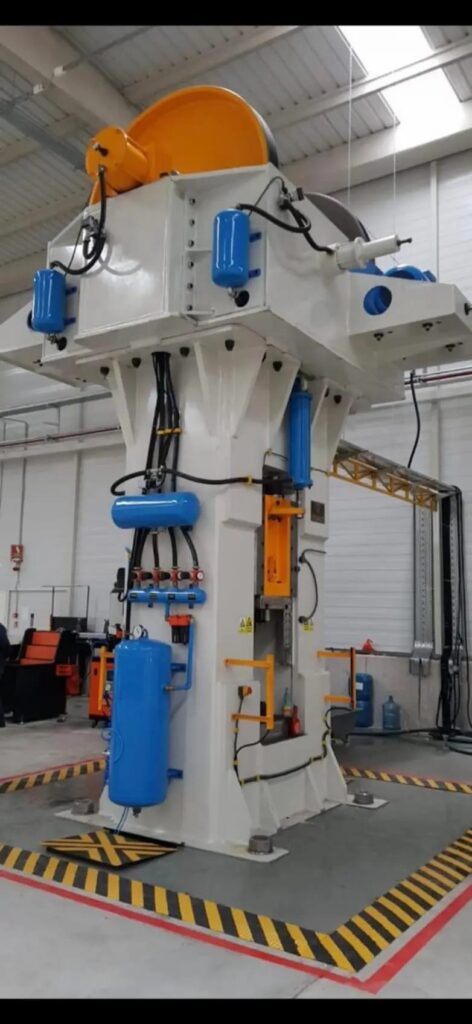
The screw in a friction screw press is subjected to intense, repetitive stress, necessitating careful selection of materials and heat treatment processes to ensure durability and optimal performance. As the core component that translates rotational energy into linear force, the screw must maintain its structural integrity under high loads and withstand friction-related wear. The choice of material and the application of specific heat treatment techniques directly influence the screw’s ability to handle these conditions without compromising performance.
In high-stress industrial applications, the material must offer a combination of strength, hardness, and toughness, while heat treatment further enhances these properties, especially in terms of surface hardness and wear resistance. By carefully selecting materials and applying tailored heat treatments, engineers can optimize the screw’s lifespan and effectiveness, making it resilient against wear, high temperatures, and repetitive impact.
2. Key Material Properties for Screw Performance
Material properties significantly impact the screw’s durability and operational effectiveness. For screws in friction screw presses, several key properties are prioritized:
- Hardness: The ability of a material to resist deformation is critical for withstanding the intense friction and pressure exerted on the screw. Harder materials typically offer better wear resistance, especially at the surface.
- Toughness: Toughness, or the material’s ability to absorb energy without fracturing, is equally important. Tough materials can endure sudden impacts and cyclical loads without failing, which is essential in high-pressure pressing applications.
- Tensile Strength: This property is crucial for preventing deformation under load. High-tensile-strength materials maintain shape and alignment even under repeated heavy loads, preserving the press’s precision and efficiency.
- Ductility: While screws benefit from hardness, they must also retain some ductility to avoid becoming overly brittle. A small degree of ductility allows the screw to flex slightly under stress, reducing the risk of sudden fractures.
- Thermal Stability: Since friction screw presses generate heat during operation, materials must be thermally stable to avoid expansion, warping, or degradation at elevated temperatures.
These material properties collectively determine how well a screw will perform in demanding conditions. By selecting materials that balance hardness, toughness, and thermal stability, engineers create screws capable of long-term, reliable operation.
3. Common Materials Used in Screw Manufacturing
In friction screw presses, a variety of materials are used for screws, with choices typically revolving around alloy and carbon steels due to their favorable properties.
- Alloy Steels: Common alloys include chromium-molybdenum and chromium-nickel-molybdenum steels. These materials offer excellent strength, hardness, and heat resistance, making them suitable for screws exposed to repetitive high-pressure loads. The addition of chromium enhances corrosion resistance, while molybdenum increases hardness and toughness.
- Carbon Steels: Carbon steels are often used in applications where cost is a concern. Medium- to high-carbon steels can be heat-treated to achieve substantial hardness and wear resistance. However, they are more susceptible to corrosion and lack some of the high-temperature resistance seen in alloy steels.
- Emerging Materials: For specialized applications, composite materials or advanced steels, such as martensitic stainless steels, are increasingly used. These materials are designed for environments where extreme durability and resistance to high temperatures or corrosion are required.
Each material has specific advantages, and the choice depends on the operational requirements of the friction screw press. Alloy steels are generally preferred for their durability, but carbon steels remain a cost-effective alternative for less demanding applications.
4. Material Selection Based on Application Requirements
The operational requirements of a friction screw press heavily influence material selection for the screw.
- Load-Bearing Applications: Screws that must endure heavy, repetitive loads benefit from alloy steels with high tensile strength and toughness, ensuring they can withstand pressure without deformation or fracture.
- High-Temperature Environments: Some applications generate significant heat, requiring thermally stable materials that won’t degrade under these conditions. Molybdenum and chromium-enhanced steels are often chosen for their ability to maintain structural integrity at elevated temperatures.
- Type of Press: Different types of friction screw presses may have unique requirements based on their load and cycle characteristics. Presses used for high-frequency or precision operations may benefit from high-strength, wear-resistant materials, whereas simpler presses can rely on medium-strength materials that are more cost-effective.
Material selection is, therefore, a balance between performance needs and economic considerations, with specialized applications often necessitating more advanced and durable materials.
5. Overview of Heat Treatment Processes
Heat treatment is essential for enhancing the screw’s durability and performance, particularly for increasing hardness and wear resistance. Several common heat treatment processes are used to achieve these improvements:
- Hardening: This process increases the screw’s surface hardness, typically through heating followed by rapid cooling (quenching). Hardening is essential for screws that need high resistance to wear and deformation.
- Tempering: Following hardening, tempering reduces brittleness by reheating the screw to a lower temperature, then cooling it slowly. This process maintains hardness while adding toughness, making the screw less prone to cracking under heavy loads.
- Case Hardening: In case hardening, only the outer surface of the screw is hardened, leaving a tough core. This is achieved through techniques like carburizing, where carbon is introduced to the surface. Case-hardened screws combine a hard exterior with a flexible core, enhancing wear resistance without sacrificing toughness.
Heat treatment is a precise process that requires careful control of heating and cooling rates. When done correctly, it increases the screw’s ability to handle high-pressure and high-friction applications, extending its lifespan.
6. Hardening and Tempering Processes
Hardening and tempering are complementary processes that work together to improve the screw’s durability.
- Quenching for Hardening: During hardening, the screw is heated to a specific temperature to alter its crystalline structure, then rapidly cooled. This hardens the surface, making it more resistant to wear. However, quenching can make the metal brittle, so it’s often followed by tempering.
- Tempering to Balance Toughness: Tempering involves reheating the screw to a temperature below its hardening point, which reduces brittleness without significantly lowering hardness. This process adds toughness, making the screw more resilient to the cyclical loads seen in press applications.
Together, hardening and tempering enhance the screw’s strength and flexibility, allowing it to endure intense friction and pressure without fracturing.
7. Surface Treatments for Enhanced Durability
In addition to bulk heat treatment, surface treatments are applied to increase wear resistance, especially in high-friction environments.
- Nitriding: Nitriding diffuses nitrogen into the surface, creating a hard, wear-resistant outer layer without the need for quenching. This process is beneficial for screws exposed to high temperatures, as it doesn’t distort the material.
- Carburizing: Carburizing introduces carbon to the surface layer, hardening it through subsequent heat treatment. The resulting case-hardened surface is highly resistant to wear while maintaining a tough core.
- Other Surface Hardening Techniques: Techniques like flame hardening and induction hardening offer localized hardening for specific parts of the screw, increasing durability in targeted areas.
These surface treatments create a hardened exterior that withstands the repetitive contact and frictional forces, reducing the rate of wear on the screw.
8. Coatings and Composite Treatments
In high-friction applications, coatings can be applied to improve wear and corrosion resistance further.
- Diamond-Like Carbon (DLC) Coatings: DLC coatings are highly wear-resistant and reduce friction. They are particularly useful in applications where lubrication is challenging, as they help the screw move smoothly.
- Physical Vapor Deposition (PVD) Coatings: PVD coatings are thin, hard layers applied to the screw surface. They provide excellent hardness and are useful for corrosion resistance in harsh environments.
- Combining Coatings with Heat Treatment: Some applications combine coatings with traditional heat treatment to improve both surface and core properties. This layered approach increases the screw’s longevity and resilience to wear.
Coatings add a layer of protection that complements heat treatment, enhancing the screw’s durability and allowing it to perform well under intense stress.
9. Future Trends in Material Selection and Heat Treatment
Advances in materials science and heat treatment techniques continue to improve the durability and performance of screws in friction screw presses.
- Self-Lubricating Materials: New materials with self-lubricating properties reduce the need for external lubricants, improving wear resistance in high-friction applications.
- Eco-Friendly Heat Treatments: Environmentally friendly heat treatments, such as salt bath nitriding, are being developed to reduce the environmental impact of traditional methods.
- Digital Monitoring: Real-time monitoring of heat treatment processes using AI and IoT technologies enables better control over treatment quality, resulting in more consistent and durable parts.
These innovations enhance screw design, ensuring that friction screw presses remain reliable and efficient.
10. Conclusion
Selecting the right materials and applying effective heat treatment processes are crucial for the durability and performance of screws in friction screw presses. Through careful consideration of material properties and heat treatment techniques like hardening, tempering, and surface hardening, engineers optimize screws to withstand high-stress, high-friction environments. Future advancements in materials and heat treatments promise even greater durability and performance, ensuring that friction screw presses continue to meet the demands of modern manufacturing.
Introduction to Thread Profile and Geometry
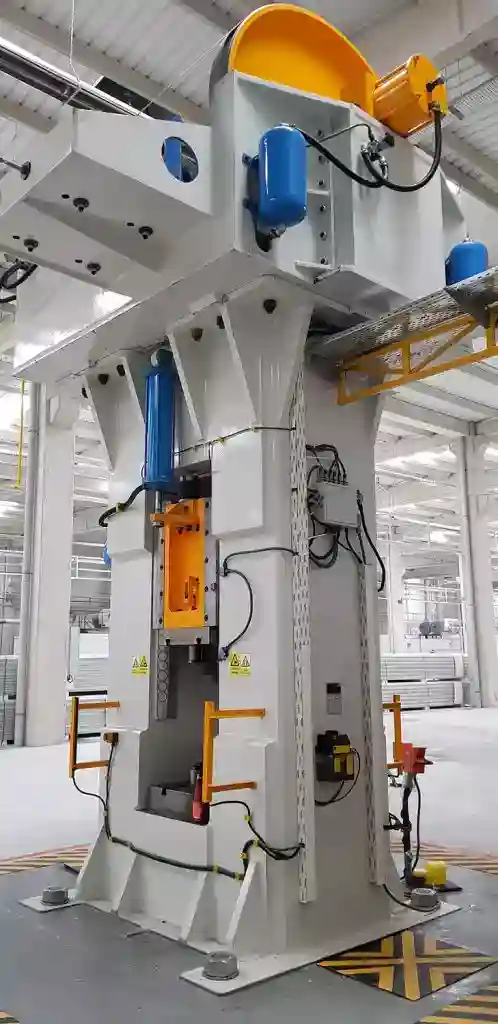
The design of the thread profile and geometry in the screw of a friction screw press plays a critical role in converting rotational force into linear motion, a key operation in pressing and forging applications. In these presses, the screw threads bear high loads repeatedly, and the design of each thread—its profile, pitch, lead, and depth—directly impacts the efficiency of force transmission, wear resistance, and operational longevity.
Choosing the right thread profile and geometry allows manufacturers to optimize the press for specific applications, whether it’s coining, forging, or shaping metals. Thread profile and geometry influence not only the efficiency of force transfer but also the screw’s durability and performance under various loads. Understanding these design aspects is essential for achieving precise, controlled pressing action while minimizing energy loss and wear.
2. Types of Thread Profiles
In friction screw presses, the choice of thread profile significantly affects the screw’s load-bearing capacity, efficiency, and durability. Some common profiles include:
- Trapezoidal Threads: Trapezoidal threads are known for their robustness and load-bearing ability. Their sloped sides reduce friction while offering a larger contact area, distributing force evenly. These threads are common in heavy-load applications due to their balance of efficiency and strength.
- Square Threads: Square threads are designed for efficient power transmission, as their perpendicular thread flanks create minimal friction. This profile is excellent for force-heavy applications where high efficiency is required, though they are more difficult to manufacture due to their geometry.
- ACME Threads: The ACME profile is a modified version of square threads, designed for easier manufacturing while retaining a significant portion of the square thread’s efficiency. The trapezoidal shape of the ACME thread offers greater durability and load capacity, making it a preferred choice for friction screw presses.
- Buttress Threads: Buttress threads are designed to handle heavy axial loads in one direction, with one flat and one angled flank. They are less common in friction screw presses but are useful for applications that require unidirectional force application, offering high efficiency with minimal friction.
The selection of thread profile depends on the specific load and speed requirements, with trapezoidal and ACME threads often being favored for their load-bearing capabilities and ease of manufacturing.
3. Thread Pitch and Lead
Pitch and lead are crucial factors in the operation of a friction screw press, determining the speed and control of the screw’s linear motion.
- Pitch: Pitch is the distance between successive thread peaks. A smaller pitch results in finer control, as it requires more rotations to achieve a given linear displacement. Finer pitches allow for better precision but may reduce the speed of operation.
- Lead: The lead is the distance the screw advances per full rotation. In single-start threads, lead and pitch are the same, but in multi-start threads, lead is the pitch multiplied by the number of starts. A higher lead increases the screw’s linear movement per rotation, which is beneficial for applications requiring faster press cycles.
Selecting the right pitch and lead balance is essential. For precision applications, finer pitches with lower leads offer more control, while coarse pitches and higher leads are preferable for faster, high-force applications.
4. Thread Depth and Engagement
The depth of the screw threads determines how much surface area is in contact during operation, affecting load capacity and wear resistance.
- Deeper Threads for High Load: In applications where the screw must bear heavy loads, deeper threads provide more contact surface, enhancing load distribution and reducing wear. However, deeper threads also increase friction, which can reduce efficiency.
- Shallow Threads for Speed: Shallower threads allow for faster movement with reduced friction but may lack the load capacity of deeper threads. They are ideal for applications where speed is prioritized over heavy load capacity.
Balancing thread depth with the press’s operational requirements ensures that the screw can handle the load without excessive wear.
5. Single-Start vs. Multi-Start Threads
Single-start and multi-start threads offer different advantages based on the desired speed and force application.
- Single-Start Threads: These threads have one continuous helix along the screw’s length, providing high force at lower speeds. Single-start threads are often preferred for applications where precision and control are critical, as they offer steady, incremental motion.
- Multi-Start Threads: Multi-start threads (e.g., double or triple-start) have multiple helical threads, which allow the screw to move linearly more quickly with each rotation. Multi-start threads are used in applications where speed is essential, as they reduce the number of rotations needed for a given movement.
Choosing between single-start and multi-start threads depends on the press’s speed and precision requirements, with multi-start threads favored in high-speed applications.
6. Thread Angle and Friction
The angle of the thread’s flank influences the amount of friction and efficiency of the screw.
- Thread Angle and Efficiency: A smaller thread angle reduces friction, allowing for more efficient force transmission. However, shallow angles can reduce the screw’s load-bearing capacity, so a balance must be found based on the application.
- Optimizing for Reduced Wear: The ideal thread angle for a friction screw press balances efficient force transmission with minimized wear. In applications requiring high force, angles are carefully chosen to reduce friction while maintaining load-bearing strength.
Properly selecting the thread angle helps maintain efficiency while minimizing wear over time.
7. Load Distribution and Stress Concentration
Load distribution across the thread’s surface area affects durability and wear resistance.
- Uniform Load Distribution: Designing threads to distribute load uniformly along the screw prevents localized stress points, which can lead to premature wear or even thread failure.
- Reducing Stress Concentration: Stress concentration points are areas where loads are disproportionately high. Engineers minimize these points through optimized thread geometry, such as rounded or tapered thread edges.
By carefully managing load distribution, designers extend the lifespan of the screw and improve press reliability.
8. Manufacturing Considerations for Thread Profiles
The precision of the thread profile affects performance, necessitating careful manufacturing and quality control.
- Thread Milling and Rolling: Thread milling and rolling are common methods for producing screw threads, with rolling often used for stronger threads due to its work-hardening effect.
- Thread Grinding: In high-precision applications, thread grinding is used to achieve tighter tolerances and smoother finishes, which can reduce friction and improve efficiency.
Ensuring thread accuracy during manufacturing is critical for the long-term performance of the screw in a friction screw press.
9. Innovations and Future Trends in Thread Design
Technological advances are paving the way for improved thread design.
- CAD and FEA: CAD modeling and FEA (Finite Element Analysis) allow engineers to simulate thread performance under various loads, enabling optimized designs for durability and efficiency.
- New Materials and Coatings: Advanced materials and wear-resistant coatings can extend thread life, reducing the frequency of replacements in high-wear environments.
These innovations help create threads that are more resilient and efficient, enhancing the overall performance of friction screw presses.
10. Conclusion
The thread profile and geometry in friction screw presses are essential for efficient force transmission, durability, and operational efficiency. Through careful selection of thread profile, pitch, depth, and angle, engineers optimize the screw’s performance to meet specific pressing requirements. As advancements in design and materials continue, the screws in friction screw presses will become even more resilient and adaptable, further extending the utility and reliability of these machines in modern manufacturing.
Introduction to Force Transmission in Friction Screw Presses
Force transmission in friction screw presses is the core process that enables metal forming and forging. These presses utilize a straightforward yet powerful mechanism where rotational force generated by a flywheel is converted into linear force applied to a workpiece. This conversion process, driven by the interaction between the flywheel, friction rollers, and screw, allows friction screw presses to exert controlled, repeatable force that is crucial for forging and shaping materials.
Understanding the mechanics of force transmission is essential for optimizing press performance, efficiency, and durability. The way force is generated, transmitted, and applied impacts the precision, speed, and lifespan of the press. By examining each stage of the process—from friction initiation to the final application of force—engineers can design presses that meet specific operational demands with high efficiency and minimal energy loss.
2. The Role of Friction in Power Transmission
Friction is a fundamental principle that drives force transmission in friction screw presses. The press utilizes friction rollers to engage with the flywheel, initiating the process of force generation. By adjusting the frictional contact between these rollers and the flywheel, operators control the force exerted by the press.
- Friction Rollers and Flywheel Engagement: The friction rollers apply pressure to the flywheel, creating friction that causes the flywheel to rotate. This rotation stores kinetic energy in the flywheel, which can be released to drive the screw. The amount of frictional force is determined by the roller material, pressure, and surface characteristics.
- Engagement and Disengagement: The rollers are designed to engage and disengage quickly, enabling rapid starts and stops. Effective force transmission relies on precise engagement timing, which ensures smooth operation without energy waste or excessive wear.
- Factors Affecting Frictional Efficiency: The efficiency of friction-based transmission is influenced by roller materials, lubrication, and pressure control. High-friction materials improve force transmission but can increase wear, so a balance is necessary.
Friction plays a critical role in power transmission, with the efficiency and precision of force application directly tied to how well friction is managed.
3. Kinetic Energy Storage and Release Mechanism
The flywheel in a friction screw press stores kinetic energy, which can be released to drive the screw and apply force to the workpiece. This energy storage and release mechanism is central to the press’s operation.
- Energy Storage in the Flywheel: When the flywheel rotates, it accumulates kinetic energy proportional to its mass and rotational speed. The formula E=12Iω2E = \frac{1}{2} I \omega^2E=21Iω2 (where EEE is energy, III is the moment of inertia, and ω\omegaω is angular velocity) quantifies the energy stored, which is later converted into linear force.
- Energy Release and Conversion: Once engaged, the kinetic energy from the flywheel is transferred to the screw, which, through its thread design, converts the rotational motion into linear force. The timing of this energy release is crucial for consistent force application.
- Calculating Flywheel Energy: Engineers calculate the optimal flywheel size, speed, and mass to ensure adequate energy is stored for each press cycle, balancing force output with operational stability.
The flywheel’s ability to store and release energy efficiently is vital to the press’s effectiveness, allowing it to apply controlled, high-force impacts with each cycle.
4. Conversion of Rotational Motion to Linear Force
The screw mechanism converts the rotational energy of the flywheel into linear force, a key operation that makes the friction screw press functional.
- Role of the Screw: As the flywheel rotates, it drives the screw, whose threads translate rotational motion into downward linear force. The screw’s geometry, pitch, and lead directly impact how efficiently this conversion occurs.
- Mechanics of Force Transfer: The screw’s thread profile and angle determine the speed and force of the linear movement. A coarser pitch increases the force per rotation but may reduce precision, while a finer pitch enhances control but reduces the force exerted per cycle.
- Thread Geometry Influence: The screw’s thread geometry affects how much rotational energy is converted into linear force. For example, trapezoidal threads distribute load evenly, reducing friction and wear, while square threads offer high efficiency but are more challenging to manufacture.
This conversion process is optimized by selecting the appropriate screw geometry and ensuring the flywheel delivers consistent rotational energy, maximizing the press’s operational efficiency.
5. Calculations in Force Transmission
Calculating force transmission in a friction screw press involves understanding torque, friction, and linear force.
- Torque Calculation: Torque (τ\tauτ) is a measure of rotational force, calculated by τ=r⋅F\tau = r \cdot Fτ=r⋅F, where rrr is the radius of the flywheel and FFF is the force applied by the rollers. Torque determines how much rotational energy is available for conversion to linear force.
- Relationship between Torque and Linear Force: The linear force applied by the ram is a product of torque, thread pitch, and friction within the screw mechanism. The formula F=τrF = \frac{\tau}{r}F=rτ, where rrr is the screw radius, helps engineers determine the linear force.
- Efficiency and Energy Loss: Not all energy is transmitted perfectly due to frictional losses, which are calculated using friction coefficients and material properties. Engineers optimize materials and lubrication to minimize these losses.
These calculations allow for precise force control, enabling friction screw presses to operate efficiently without overloading components.
6. The Role of Thread Pitch, Lead, and Angle in Force Efficiency
The screw’s pitch, lead, and angle influence force transmission efficiency in friction screw presses.
- Pitch and Lead: The pitch and lead of a screw determine how much force is generated with each rotation. A higher pitch provides greater force but reduces control, while a lower pitch increases control but requires more rotations for the same movement.
- Thread Angle: The thread angle affects how easily force is transmitted. A steeper angle reduces friction but may decrease load capacity, while a shallower angle increases friction but provides better force distribution.
- Optimization for Efficiency: Engineers select pitch, lead, and angle based on the press’s required force, speed, and precision. Fine adjustments to these parameters enhance energy transfer and reduce wear.
Optimizing these variables ensures the press operates with minimal energy loss, enhancing both performance and durability.
7. Interaction of Components in Force Transmission
Each component in a friction screw press contributes to force transmission, working in unison for effective operation.
- Flywheel and Screw Connection: The flywheel’s rotational energy initiates force transfer, driving the screw through frictional contact with rollers. This connection is designed for minimal slippage to ensure consistent force application.
- Ram Movement: The ram, connected to the screw, applies force to the workpiece. The efficiency of force transmission from screw to ram is essential for precise, controlled pressing.
- Alignment and Synchronization: Proper alignment of the flywheel, screw, and ram is crucial to prevent wear and ensure smooth energy transfer.
By synchronizing these components, the press achieves efficient force transmission, reducing wear and maximizing operational life.
8. Factors Affecting Efficiency and Energy Loss
Energy losses in force transmission are primarily due to frictional forces and component wear.
- Frictional Losses: Friction within the screw threads and between the rollers and flywheel reduces force efficiency. Lubrication and optimal thread angles are used to mitigate these losses.
- Heat Generation: Friction generates heat, which can cause material expansion and reduce efficiency. Heat-resistant materials and cooling mechanisms help maintain operational stability.
- Material and Lubrication Choices: Selecting durable, low-friction materials and applying high-performance lubricants minimize energy loss, preserving force transmission efficiency.
Reducing these factors allows the press to maintain high performance with less energy input, optimizing operational costs.
9. Future Trends and Innovations in Force Transmission
Advancements in materials and technology promise to improve force transmission efficiency in friction screw presses.
- New Friction Materials: Development of wear-resistant materials for friction rollers can improve durability and reduce energy loss, increasing the lifespan of the press.
- Electronic Control Systems: Integrating electronic controls allows for real-time force adjustments, improving efficiency and control, especially in high-precision applications.
- Innovative Energy Storage: Improved flywheel materials and design reduce weight while maintaining energy storage capacity, enhancing press speed and reducing maintenance needs.
These innovations are likely to make friction screw presses more efficient and adaptable for modern manufacturing.
10. Conclusion
The operation and mechanics of force transmission in friction screw presses involve a coordinated process where friction initiates power, and carefully designed components transmit force with efficiency and precision. By optimizing thread geometry, friction management, and material selection, engineers ensure that the press operates with minimal energy loss and maximum durability. As innovations continue to improve friction materials and electronic controls, friction screw presses will become even more effective, meeting the growing demands of the manufacturing industry with precision and efficiency.
Introduction to Lubrication and Maintenance in Friction Screw Presses
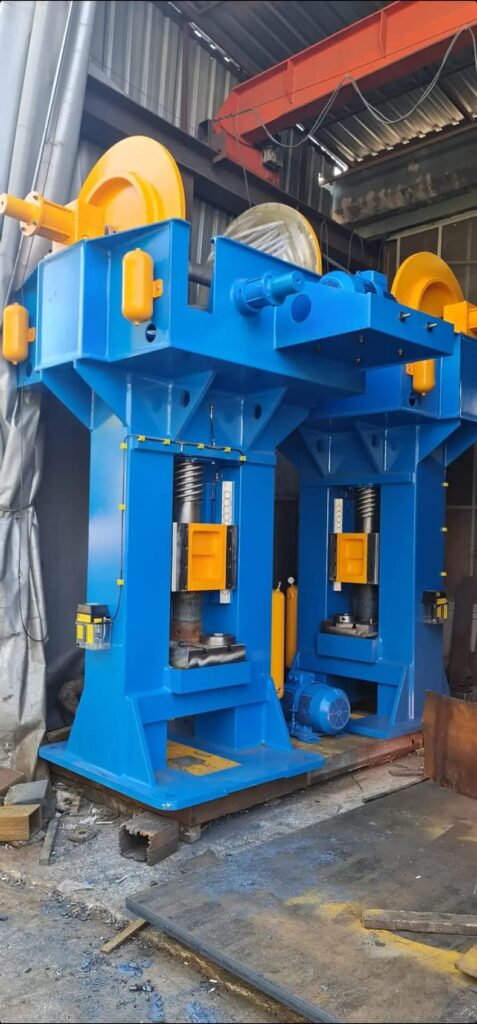
In friction screw presses, lubrication and maintenance play crucial roles in ensuring efficient operation, longevity, and reduced downtime. These presses are used in forging and metal shaping, where components like the screw, rollers, and bearings undergo significant wear due to high-pressure and high-friction conditions. Proper lubrication minimizes friction between moving parts, reducing energy loss and preventing premature wear, while routine maintenance helps catch potential issues before they result in costly breakdowns.
Effective lubrication and regular maintenance schedules are essential to maintain consistent performance and protect the press from excessive wear. By establishing a structured maintenance routine, manufacturers ensure that friction screw presses operate efficiently and safely, ultimately extending the machine’s lifespan and improving productivity.
2. Types of Lubricants Used in Friction Screw Presses
Friction screw presses require various lubricants, each suited to specific components and operating conditions.
- Oils: Lubricating oils are commonly used in components where low viscosity and high penetration are beneficial, such as in bearings and the screw threads. Oils reduce friction without creating excess buildup and are ideal for areas needing frequent lubrication.
- Greases: Greases offer thicker, longer-lasting lubrication than oils and are used in high-pressure components like bearings and rollers. They provide a protective film that helps reduce wear and can withstand higher loads and pressures.
- Dry Lubricants: In applications where oils and greases are impractical, such as in high-temperature zones, dry lubricants like graphite or molybdenum disulfide are used. They provide a low-friction coating without the risk of breakdown from heat.
- High-Temperature and Anti-Wear Lubricants: Specially formulated lubricants with additives are used to improve wear resistance and thermal stability, especially in components like the screw and rollers that are exposed to extreme heat and pressure.
Selecting the appropriate lubricant for each component depends on factors like operating temperature, pressure, and frequency of use. Choosing the right lubricant enhances the efficiency and longevity of the press.
3. Lubrication Points and Methods
Effective lubrication involves applying the correct type and amount of lubricant to specific components, including:
- Key Components Requiring Lubrication:
- Screw: Lubricating the screw threads reduces friction and wear, preserving force transmission efficiency.
- Friction Rollers: The rollers that engage with the flywheel benefit from frequent lubrication to prevent overheating and wear.
- Flywheel Bearings: Bearings in the flywheel require lubrication to maintain smooth rotation and reduce friction.
- Ram: Lubrication reduces wear on the ram, which is under significant pressure during each press cycle.
- Methods of Application:
- Manual Lubrication: In smaller operations, manual lubrication is applied periodically based on usage and operating conditions.
- Automatic Lubrication Systems: Automated systems dispense lubricants at set intervals, ensuring consistent coverage without interrupting operations.
- Centralized Lubrication Systems: A centralized system distributes lubricants to multiple points, simplifying maintenance for larger presses.
- Frequency and Quantity of Lubrication: Lubrication frequency and quantity depend on usage and operational demands. High-load components like the screw and rollers may require more frequent lubrication than other parts to maintain efficiency and prevent overheating.
Consistent and accurate lubrication of these key points ensures that each component functions optimally, reducing frictional wear and improving press performance.
4. Preventive Maintenance for Friction Screw Presses
Preventive maintenance involves scheduled inspections, cleaning, and re-lubrication of components to prevent breakdowns.
- Routine Inspections: Regular inspections allow operators to detect early signs of wear, such as pitting, abrasions, and misalignment. Inspecting components like the screw, bearings, and rollers helps identify potential issues before they lead to major failures.
- Cleaning and Re-Lubrication: Removing dust, debris, and old lubricant is essential to prevent abrasive wear. After cleaning, components are re-lubricated to ensure optimal performance.
- Setting Preventive Maintenance Schedules: Maintenance schedules are based on usage patterns, operational conditions, and manufacturer recommendations. High-frequency presses require more regular maintenance than those used sporadically.
Implementing preventive maintenance helps maintain operational consistency, reduces downtime, and extends the lifespan of the friction screw press.
5. Common Wear and Tear Issues and Their Solutions
Despite regular lubrication, certain components in friction screw presses experience natural wear and tear due to their high-stress roles.
- Screw Wear: Thread wear and pitting are common on screws, affecting force transmission efficiency. Regular inspection of screw threads is important, and re-machining or replacement may be necessary in severe cases.
- Roller and Bearing Wear: Friction rollers experience wear due to their engagement with the flywheel. Bearings can also wear down, leading to misalignment. Replacing worn rollers and bearings prevents vibrations and operational instability.
- Flywheel Surface Wear: Continuous friction contact with rollers can cause the flywheel surface to wear down. Periodic resurfacing or coating helps maintain friction efficiency.
Addressing wear early helps avoid further damage and reduces the likelihood of costly repairs or replacements.
6. Troubleshooting Lubrication and Maintenance Problems
When lubrication and maintenance issues arise, troubleshooting helps restore smooth operation.
- Overheating: Excessive heat may indicate inadequate lubrication or excessive friction. Increasing lubrication frequency or switching to high-temperature lubricants often resolves this issue.
- Excess Friction and Wear: If components show signs of accelerated wear, it may be due to insufficient lubrication or misalignment. Ensuring proper alignment and re-evaluating lubricant type and application frequency can reduce wear.
- Leakage: Leaks are common in high-pressure lubrication systems. Regularly inspecting seals and gaskets, and replacing them when needed, prevents leakage and ensures efficient lubrication.
Effective troubleshooting identifies the root causes of lubrication problems, allowing for timely intervention and minimizing operational disruptions.
7. Impact of Lubrication and Maintenance on Efficiency
Proper lubrication and maintenance significantly impact the efficiency of friction screw presses.
- Energy Efficiency: Reduced friction through proper lubrication decreases energy loss, allowing the press to operate with less force while achieving the same results. This efficiency translates to lower operating costs.
- Wear Reduction: Lubrication minimizes wear, which preserves the precision of components like the screw and rollers. Reduced wear means fewer replacements and lower maintenance costs over time.
- Improved Press Longevity: Consistent maintenance and lubrication extend the life of the press, ensuring that it operates effectively for longer periods without requiring major repairs.
Optimizing lubrication and maintenance leads to a more efficient, durable press, contributing to lower operational expenses and improved productivity.
8. Best Practices for Long-Term Maintenance
Establishing best practices in lubrication and maintenance helps ensure long-term press performance.
- Maintenance Log: Keeping a detailed log of maintenance activities, including lubrication schedules and inspections, helps track the health of the press and anticipate component replacements.
- Operator Training: Training operators on proper lubrication techniques and maintenance routines improves consistency and minimizes errors.
- Component Monitoring: Monitoring high-wear components like the screw and rollers allows for proactive maintenance, preventing breakdowns and extending lifespan.
By following these practices, operators maintain a friction screw press in optimal condition, enhancing reliability and reducing downtime.
9. Innovations in Lubrication and Maintenance Technology
Advances in lubrication and maintenance technology offer new ways to improve press efficiency and durability.
- Self-Lubricating Materials: New materials with self-lubricating properties reduce the need for external lubrication, especially in high-wear components.
- Automated Monitoring Systems: Sensors can provide real-time data on component wear and lubrication levels, enabling predictive maintenance. These systems alert operators to lubrication needs before problems arise.
- Advanced Lubricants: Specialized synthetic lubricants provide better high-temperature and anti-wear properties, improving durability and reducing maintenance intervals.
These innovations help streamline maintenance and extend component life, making presses more reliable and efficient.
10. Conclusion
Lubrication and maintenance are critical for the optimal performance and longevity of friction screw presses. Proper lubrication minimizes frictional wear, while preventive maintenance ensures the reliability of each component. By adhering to a structured maintenance schedule, using suitable lubricants, and embracing new technologies, operators can enhance press efficiency, reduce downtime, and extend operational life. Implementing these practices ultimately results in a more efficient, cost-effective, and durable friction screw press, enabling it to meet the demands of modern manufacturing with improved consistency and performance.
Introduction to Friction Rollers in Friction Screw Presses
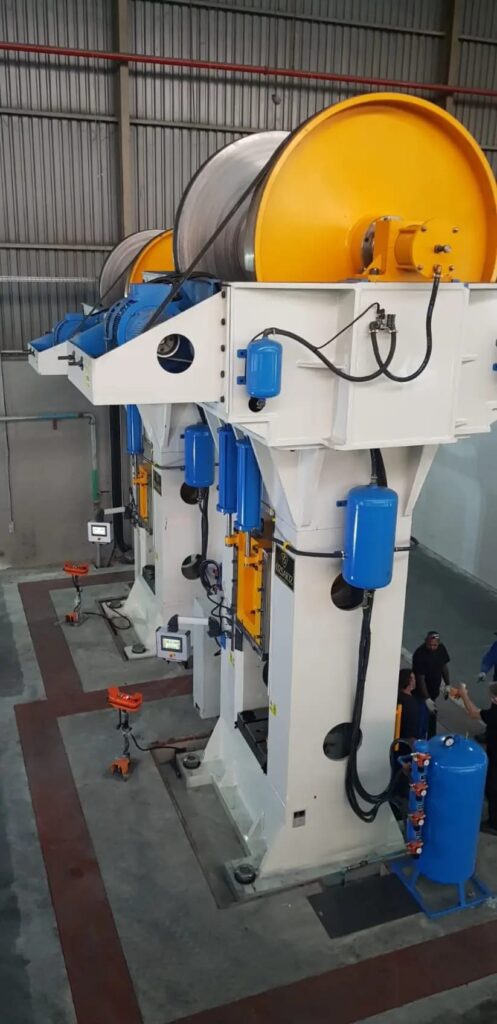
Friction rollers are critical components in friction screw presses, responsible for transferring energy from the flywheel to initiate the pressing motion. These rollers engage with the flywheel, creating friction that spins the wheel and subsequently drives the screw, which then applies the necessary force to the workpiece. By controlling the engagement and disengagement of the friction rollers, operators can modulate the press’s speed and force, allowing for precise control over the pressing cycle.
The friction rollers’ role is foundational to the press’s functionality, as they determine how much rotational force is converted into linear pressure. This makes the rollers crucial for achieving the desired results in applications like forging, metal forming, and precision coining. Due to their continuous exposure to high friction and pressure, friction rollers must be durable, heat-resistant, and carefully maintained to prevent wear and ensure consistent performance.
2. Design and Structure of Friction Rollers (500 words)
The design and structure of friction rollers impact their efficiency, durability, and ability to transmit force effectively. Key design considerations include:
- Shape and Size: Friction rollers are typically cylindrical to maximize surface contact with the flywheel, but the diameter and width can vary based on the press’s force requirements. Larger rollers provide more contact area, which can improve force transmission but may also increase the demand on the motor driving the press.
- Surface Texture: A textured surface improves friction by increasing the contact area, which helps reduce the likelihood of slipping during operation. Some friction rollers have grooves or tread patterns to enhance grip and ensure consistent contact with the flywheel.
- Balancing Durability and Efficiency: The rollers must be strong enough to withstand repeated engagement with the flywheel without losing their shape or surface texture. Engineers balance the roller’s durability with the need for efficient force transmission, ensuring that the rollers contribute to the overall efficiency of the press without becoming a maintenance burden.
The design of friction rollers aims to optimize force transmission while resisting wear and maintaining alignment, which is essential for achieving long-lasting performance in industrial applications.
3. Material Selection for Friction Rollers
Choosing the right materials for friction rollers is essential, as they must resist wear, handle high temperatures, and maintain their structural integrity over time.
- Steel and Alloyed Steels: Steel is a common choice for friction rollers due to its strength, toughness, and ability to withstand repeated friction without significant deformation. Alloyed steels with elements like chromium or molybdenum offer enhanced hardness, wear resistance, and heat tolerance, making them suitable for heavy-duty applications.
- Composite Materials: In advanced presses, composite materials are increasingly used to reduce weight while maintaining strength and durability. Composites can be engineered to resist heat and wear, and they are sometimes chosen for applications where minimizing roller weight can improve press responsiveness.
- Ceramic-Coated Rollers: Some friction rollers have ceramic coatings, which provide exceptional hardness and wear resistance. These coatings reduce friction, which helps improve efficiency and prolong the lifespan of the roller, although they can be more expensive.
Selecting a material for friction rollers involves evaluating the application’s requirements, including force, temperature, and cycle frequency. High-quality materials reduce maintenance needs and extend the rollers’ lifespan, leading to more reliable press performance.
4. Mechanics of Friction Engagement
Friction rollers operate by creating contact with the flywheel, producing the friction necessary to initiate rotation and drive the screw.
- Engagement with the Flywheel: Friction rollers press against the flywheel’s surface, generating rotational motion that is transferred to the screw. The friction generated by this contact is carefully calibrated to ensure smooth, controlled movement without excessive slippage.
- Speed and Pressure Impact: The speed at which the rollers engage and the pressure applied influence how much force is transmitted. Higher pressure increases friction, allowing for greater force transmission, but also increases wear. Finding the optimal pressure ensures efficient operation without unnecessary frictional loss.
- Rolling vs. Sliding Friction: Rolling friction is generally preferred over sliding friction because it generates less wear and heat, extending the lifespan of the rollers. Most friction rollers are designed to rotate along with the flywheel, minimizing wear by reducing the amount of direct sliding contact.
Understanding these mechanics enables engineers to fine-tune the roller’s engagement, achieving efficient force transmission and smooth press operation.
5. Maintenance and Wear Prevention
Due to their critical role and exposure to friction, friction rollers require regular maintenance to function optimally.
- Lubrication Requirements: Although friction rollers rely on friction for their operation, controlled lubrication is often applied to reduce wear on the bearings supporting the rollers. Proper lubrication helps maintain smooth motion and reduces heat buildup in high-friction areas.
- Common Wear Issues: Friction rollers are susceptible to surface abrasion, material degradation, and flattening of contact surfaces over time. Regular inspection for signs of wear, such as changes in surface texture or shape, helps prevent unexpected failures.
- Preventive Maintenance: Preventive maintenance includes periodic cleaning, resurfacing, and re-lubricating rollers to preserve their performance. Some maintenance routines may involve grinding down worn surfaces or replacing rollers entirely if wear is excessive.
Following a structured maintenance schedule extends the rollers’ lifespan, reducing downtime and improving the press’s efficiency.
6. Troubleshooting Common Friction Roller Issues
When friction rollers experience performance issues, troubleshooting helps identify the cause and prevent operational delays.
- Signs of Wear: Signs of wear include flattening, cracking, or visible abrasion on the roller surface. Operators should monitor for uneven wear, as it can affect force transmission and lead to misalignment.
- Diagnosing Friction Loss: If the press experiences reduced force or slipping, friction loss may be the cause. This can result from improper lubrication, insufficient roller pressure, or worn roller surfaces. Adjusting roller pressure or replacing worn parts can restore performance.
- Heat Generation Issues: Excessive heat can be a sign of friction inefficiency or inadequate lubrication. Checking lubrication levels and ensuring that the roller bearings are properly maintained can prevent overheating and extend roller life.
Addressing these issues promptly prevents further damage and ensures that the rollers continue to function effectively.
7. Impact of Friction Rollers on Force Control and Efficiency
Friction rollers play a vital role in controlling the force transmitted through the press, impacting both precision and efficiency.
- Force Modulation: By adjusting the roller’s pressure on the flywheel, operators control the force transmitted to the screw. This modulation enables precise force application, which is essential for tasks requiring controlled pressure.
- Precision in Pressing Cycles: Friction rollers enable fine control over the pressing action, allowing for incremental adjustments to achieve the desired results. This is especially valuable in processes that demand accuracy, such as coining or fine metal forming.
- Balancing Efficiency with Friction: Excessive friction can lead to energy loss, but inadequate friction reduces force transmission. Optimizing roller pressure and material choices improves the press’s energy efficiency while maintaining effective force control.
Efficient force control by the rollers enhances press accuracy and reduces energy consumption, making them integral to efficient press operation.
8. Innovations and Future Trends in Friction Roller Design
Advances in material science and engineering have led to innovations in friction roller design.
- Advanced Materials: New materials like nano-composites and ceramic-coated rollers offer improved durability, wear resistance, and heat tolerance, making them suitable for demanding applications.
- Self-Lubricating Rollers: Some friction rollers are being developed with self-lubricating properties, which reduce maintenance needs and improve lifespan by minimizing friction-related wear.
- Automated Monitoring Systems: Sensors can monitor roller wear, friction levels, and temperature in real-time, enabling predictive maintenance and reducing downtime by alerting operators before issues arise.
These innovations make friction rollers more durable and efficient, supporting the evolving demands of modern industrial processes.
9. Best Practices for Optimizing Friction Roller Performance
To maximize the effectiveness and lifespan of friction rollers, certain best practices are recommended.
- Proper Setup and Alignment: Ensuring accurate alignment between the rollers and the flywheel prevents uneven wear and maximizes force transmission.
- Routine Inspections: Regular inspection of roller surfaces, alignment, and lubrication levels helps detect wear early, reducing the risk of unexpected failures.
- Training Operators: Training operators on proper handling and maintenance routines for friction rollers ensures consistent performance and reduces wear over time.
By following these practices, operators help maintain the press’s efficiency, prolonging the rollers’ lifespan and ensuring smooth operation.
10. Conclusion
Friction rollers are essential components in friction screw presses, enabling efficient force transmission, control, and precision. Through careful material selection, regular maintenance, and adherence to best practices, friction rollers perform effectively even in high-stress applications. Innovations in material technology and automated monitoring continue to improve roller durability and efficiency, making friction screw presses more adaptable and reliable. Proper care and optimization of friction rollers ensure that presses operate with high efficiency, precision, and reduced energy loss, supporting the long-term productivity and cost-effectiveness of industrial processes.
Introduction to the Ram or Plunger
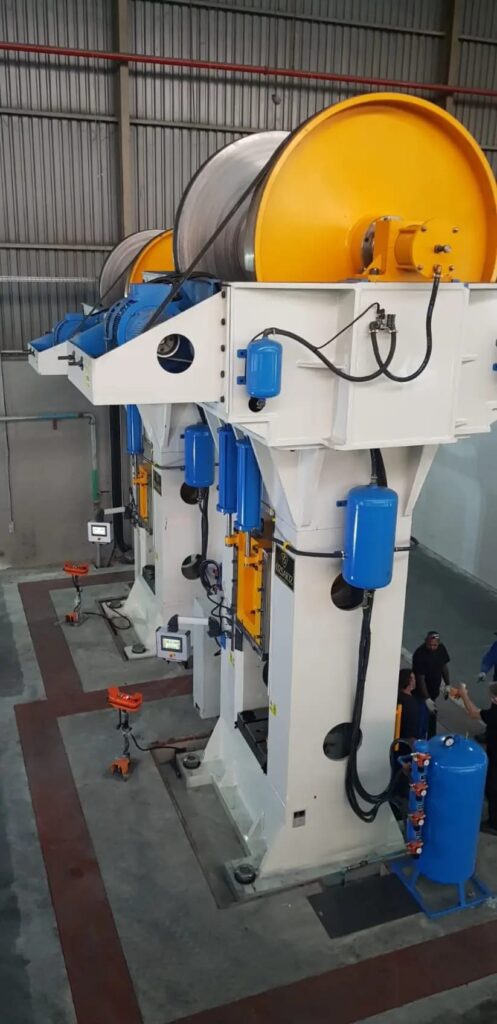
In friction screw presses, the ram or plunger is a critical component responsible for applying force directly to the workpiece, effectively transferring energy from the flywheel and screw. The ram’s precise design and robust structure are essential, as it endures high-stress cycles, frequently subjected to intense pressure during each pressing operation. Positioned at the end of the screw mechanism, the ram’s alignment, shape, and material directly impact the quality, efficiency, and consistency of the press’s output.
The ram’s role is fundamental to the success of various metal-forming processes, including forging, coining, and precision stamping. Its performance determines the force’s accuracy and distribution, which affects the shape and quality of the final product. Understanding the design, materials, and maintenance needs of the ram helps in optimizing its efficiency and longevity, ensuring consistent press performance and reduced downtime.
2. Design and Structure of the Ram
The design and structure of the ram are carefully considered to handle high loads and ensure efficient force application. Key design aspects include:
- Shape and Size: The shape of the ram often corresponds to the workpiece’s shape and the pressing requirements. Rams may be cylindrical, square, or customized for specific applications. The size and mass of the ram influence the force applied, with larger rams providing greater surface contact and stability, though they may also require more force to operate effectively.
- Alignment: Alignment of the ram with the screw and the pressing axis is crucial for consistent force application. Misalignment can lead to uneven force distribution, which reduces precision and may cause premature wear on the ram and other components.
- Structural Reinforcements: To handle the high-pressure cycles without deformation, the ram is often reinforced. Some designs feature hardened surfaces or additional supports at stress points to prevent bending or warping under heavy loads.
Each of these design elements ensures the ram can endure continuous operation, accurately transferring force to the workpiece while minimizing wear. By optimizing the ram’s structure, engineers maximize both efficiency and durability, making it suitable for heavy-duty applications.
3. Material Selection for the Ram
Selecting the right material for the ram is essential, as it must withstand high forces and resist wear from repeated contact with the workpiece.
- Hardened Steel: Hardened steel is a common choice for rams due to its high strength, wear resistance, and ability to handle extreme pressures without deforming. Hardened steel is often used in applications where high loads are involved.
- Alloyed Metals: Alloyed metals, such as chromium-molybdenum or nickel-based alloys, provide enhanced properties like improved toughness and heat resistance. These materials are used in high-temperature applications and where increased durability is required.
- Composite Materials and Coatings: Advanced applications may use composite materials or surface coatings, like carbide or ceramic, which offer excellent hardness and wear resistance. Coatings can extend the ram’s life by creating a hard, abrasion-resistant surface that can handle high-stress contact without degrading.
Material selection depends on the press’s operating conditions, with choices balancing cost, durability, and specific performance needs. Advanced materials and coatings are increasingly used to maximize ram lifespan, reduce maintenance needs, and ensure consistent press performance.
4. Mechanics of Force Application
The mechanics of force application through the ram are fundamental to a friction screw press’s operation, translating rotational energy into linear pressing power.
- Force Transmission from the Screw: The ram receives force from the screw, which rotates under the influence of the flywheel. The threads on the screw convert this rotational force into linear motion, pushing the ram downward onto the workpiece. The efficiency of this process depends on the screw’s design, the material properties, and the alignment of the ram.
- Role in Precision Pressing: The ram must apply force evenly to prevent damage to the workpiece and ensure uniform shaping. Its surface is often designed to distribute force consistently, which is particularly important in processes that require fine detail or uniform thickness across the workpiece.
- Force Distribution: The ram’s design determines how the force is distributed on the workpiece. A well-designed ram reduces stress concentration points, which helps in achieving a more uniform force application, essential for producing high-quality forged or pressed parts.
Understanding these mechanics helps in designing a ram that effectively applies force without compromising precision or causing excessive wear on the press components.
5. Impact of Ram Design on Efficiency and Precision
The design of the ram has a significant impact on the efficiency, precision, and quality of the output in a friction screw press.
- Influence on Accuracy: A well-aligned and properly shaped ram ensures that force is applied uniformly, improving accuracy and preventing defects in the workpiece. Accurate alignment and a carefully designed pressing face contribute to the press’s overall precision.
- Energy Efficiency: The ram’s weight and shape also impact energy efficiency. If the ram is too heavy or misaligned, the press will require more energy to operate. Optimizing the ram’s mass and balance minimizes energy loss, making the press more efficient.
- Balancing Precision and Durability: The ram must be durable enough to handle repeated cycles without losing its shape or alignment. At the same time, it should be precise enough to produce high-quality output. Engineers balance these factors to design a ram that performs effectively under various operational demands.
By refining the design, engineers can maximize the ram’s efficiency, enabling the press to operate at lower energy costs while maintaining high precision.
6. Maintenance and Wear Management
Due to continuous contact with the workpiece and high forces, the ram is subject to wear, necessitating regular maintenance.
- Common Wear Issues: Surface wear, pitting, and material fatigue are common issues affecting rams. Repeated high-pressure contact can gradually degrade the surface, reducing its ability to apply consistent force and compromising the quality of the press output.
- Lubrication Requirements: Some rams require lubrication to minimize wear, particularly where the ram and screw connect. Proper lubrication reduces friction and prevents overheating, both of which can accelerate wear.
- Surface Treatments for Longevity: Surface treatments like nitriding or carburizing can increase the ram’s hardness, improving wear resistance. These treatments create a tough surface layer, enhancing the ram’s durability and reducing the need for frequent maintenance.
Regular maintenance practices, including inspection, lubrication, and surface treatment, help extend the ram’s life, ensuring consistent performance and minimizing downtime.
7. Troubleshooting Common Ram Issues
When problems arise with the ram, troubleshooting helps identify the issue and restore optimal function.
- Signs of Wear and Misalignment: Common signs include uneven force application, visible surface damage, or alignment issues. Operators should watch for defects in pressed parts, which may indicate misalignment or surface wear on the ram.
- Diagnosing Surface Damage: If the ram’s surface shows signs of wear, such as pitting or cracks, it may need resurfacing or replacement. Surface damage often affects force application and may cause inconsistencies in the press output.
- Solutions for Reconditioning: In some cases, worn rams can be reconditioned by grinding down the surface or applying a coating. Replacement is necessary if the wear is extensive or affects the ram’s structural integrity.
Addressing issues early helps prevent further damage and ensures that the ram continues to function effectively within the press.
8. Innovations and Future Trends in Ram Design
Advances in materials and technology are driving innovations in ram design, making them more durable and efficient.
- High-Performance Materials: New alloys and composite materials are being developed to enhance the ram’s strength, wear resistance, and thermal stability. These materials reduce maintenance needs and extend the lifespan of the ram.
- Sensors and Real-Time Monitoring: Some rams now incorporate sensors that monitor wear, alignment, and pressure in real time. These sensors provide feedback to operators, enabling predictive maintenance and reducing the likelihood of unexpected failures.
- Self-Lubricating Materials: Self-lubricating materials are also being explored to reduce the need for manual lubrication, especially in high-wear applications, enhancing efficiency and minimizing maintenance.
These innovations make rams more resilient and efficient, supporting the increasing demands of modern manufacturing.
9. Best Practices for Optimizing Ram Performance
Following best practices ensures that the ram performs optimally and maintains its lifespan.
- Proper Setup and Alignment: Ensuring the ram is correctly aligned with the screw and pressing axis helps prevent uneven force application, which reduces wear and improves precision.
- Routine Inspections: Regular inspection for signs of wear, pitting, or misalignment allows for early intervention before significant issues arise, maintaining consistent performance.
- Operator Training: Training operators in the correct handling, maintenance, and troubleshooting techniques ensures that the ram is properly cared for and operates efficiently.
These practices help extend the ram’s life and enhance press performance, reducing downtime and maintenance costs.
10. Conclusion
The ram or plunger is a crucial component in friction screw presses, responsible for applying force directly to the workpiece. By carefully selecting materials, optimizing design, and maintaining proper alignment, the ram can function effectively and withstand the demands of high-pressure applications. Regular maintenance and adherence to best practices further extend its lifespan, ensuring consistent press performance. Innovations in materials and monitoring technologies continue to improve ram durability and efficiency, helping friction screw presses meet the evolving requirements of modern manufacturing with reliability and precision.
Introduction to Frame Structure and Base in Friction Screw Presses
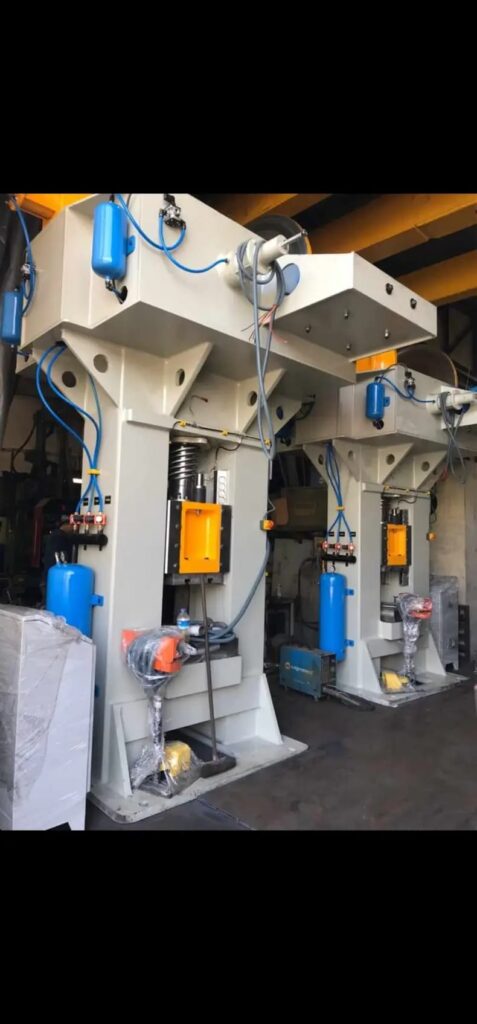
In friction screw presses, the frame structure and base are foundational components that ensure stability, alignment, and durability during high-pressure operations. These elements provide the necessary support for all other components, allowing the press to operate effectively and maintain alignment under heavy loads. The frame bears the brunt of the force exerted during pressing, and any misalignment or instability can negatively impact the accuracy and efficiency of the press.
A well-designed frame and base are essential for force distribution, vibration control, and structural integrity, supporting the operational demands of forging and metal forming. By choosing the right materials, optimizing design, and implementing preventive maintenance, manufacturers can enhance the performance and lifespan of friction screw presses. Proper attention to the frame and base helps reduce the likelihood of breakdowns and ensures consistent quality in the press’s output.
2. Design and Structural Requirements of the Frame
The design and structural integrity of the frame are critical to the performance of a friction screw press. Key considerations include:
- Shape and Size: The shape and size of the frame vary based on the force requirements and intended application of the press. For example, high-load presses may have reinforced or thicker frames to handle greater force without deformation.
- Load-Bearing Capacity: The frame must be able to withstand significant forces during operation without bending or cracking. Engineers calculate load-bearing capacity based on expected pressures, ensuring that the frame can handle maximum loads while maintaining stability.
- Frame Variations for Different Applications: Frames may vary in design depending on whether the press is used for high-frequency, high-force operations or precision applications. For example, some frames may feature reinforced sections to handle greater localized stresses.
By designing frames that meet structural and operational requirements, engineers ensure that friction screw presses can operate effectively and withstand heavy use without risk of structural damage. Optimized frame design improves the longevity and reliability of the press, supporting high-performance applications.
3. Material Selection for Frame and Base
Material selection for the frame and base of a friction screw press is a crucial decision that affects the press’s durability, vibration resistance, and heat management.
- Cast Iron: Cast iron is a popular choice for frames because of its excellent vibration-damping qualities and robustness. It’s also highly durable, making it suitable for applications where stability is crucial. However, it can be brittle under extreme stress, which may limit its use in very high-force applications.
- Steel and Alloyed Steels: Steel and alloyed steels provide high tensile strength and resistance to bending, making them suitable for high-load presses. These materials are often alloyed with elements like chromium or molybdenum to improve durability and wear resistance.
- Reinforced Alloys and Composites: For advanced applications, reinforced alloys or composites may be used to reduce weight while maintaining high strength. Composites offer excellent heat resistance and strength-to-weight ratios, but they can be more expensive than traditional materials.
The choice of material depends on factors like expected load, environmental conditions, and cost considerations. Advanced materials provide enhanced performance, especially in demanding environments, reducing the likelihood of wear and structural failure over time.
4. Mechanics of Force Distribution and Load Management
The frame and base are essential for managing and distributing the forces generated by the pressing action in a friction screw press.
- Load Management: The frame is designed to distribute force evenly across its structure, minimizing localized stress that can lead to wear or deformation. Proper load management is crucial for maintaining structural integrity over time, especially in applications requiring repetitive high-force operations.
- Preventing Deformation: Frame geometry is designed to prevent deformation under load. Reinforcements are often added to sections of the frame that experience the highest stresses, such as the areas directly supporting the screw and ram.
- Stress Concentration Management: By avoiding sharp angles and ensuring smooth transitions in the frame structure, engineers minimize stress concentration points. This reduces the likelihood of cracks or fractures developing over time.
Effective load distribution and stress management ensure that the frame can handle intense pressure without sustaining damage, improving the durability and performance of the press.
5. Vibration Control and Damping Mechanisms
Vibration control is essential in friction screw presses, as excessive vibrations can reduce precision, cause component wear, and impact the quality of the workpiece.
- Material Selection for Damping: Cast iron is often chosen for its excellent vibration-damping properties. Materials with inherent damping qualities reduce vibrations naturally, which helps maintain accuracy during pressing cycles.
- Design for Vibration Control: Frames are often designed with added mass in specific areas to reduce vibrations. Heavier frames tend to vibrate less, though this may increase the overall weight of the press, which can be a trade-off in some applications.
- Shock Mounts and Damping Pads: Some presses incorporate shock mounts or damping pads between the frame and base to isolate vibrations. These mounts absorb and dissipate vibrations, reducing their impact on the overall system.
Efficient vibration control improves precision, reduces wear on moving parts, and enhances the press’s ability to produce consistent results.
6. Alignment and Stability Considerations
Alignment and stability are critical in friction screw presses to ensure that force is applied evenly and accurately.
- Importance of Alignment: Proper alignment of the frame with other press components ensures that force is transmitted efficiently without causing misalignment or wear. Misalignment can lead to uneven force application, which may damage components or result in imprecise press output.
- Maintaining Stability: Stability is particularly important in presses that handle high loads. Structural features such as reinforcements or stabilizing elements are often included to prevent the frame from shifting or twisting under load.
- Alignment Techniques: Techniques like precision machining, guide rails, and reinforced base structures help maintain alignment throughout the press’s lifespan. Routine checks and adjustments ensure the frame remains aligned with other press components.
Proper alignment and stability contribute to the efficiency and accuracy of force transmission, reducing wear and extending the lifespan of the frame and other components.
7. Maintenance and Inspection of Frame and Base
Regular maintenance and inspection are essential to preserve the structural integrity of the frame and base.
- Routine Inspections: Operators should inspect the frame for signs of wear, cracks, or other damage regularly. Checking for alignment issues and verifying that components remain properly secured helps prevent structural problems from worsening.
- Cleaning and Surface Maintenance: Dust and debris can accumulate on the frame, potentially affecting lubrication and causing wear. Regular cleaning and re-lubrication help maintain a clean, effective surface, preventing corrosion or abrasion.
- Preventive Maintenance: Preventive maintenance schedules ensure that the frame and base are inspected regularly, reducing the likelihood of failures. Reinforcing or welding minor cracks can prevent larger structural issues, extending the frame’s operational life.
Effective maintenance practices protect the frame from damage, helping ensure long-term durability and reliability.
8. Common Frame Issues and Solutions
Even with proper maintenance, frames in friction screw presses can develop issues over time.
- Cracking and Fractures: Repeated high loads can cause cracks to form in areas with high stress concentration. Weld repairs, reinforcement plates, or part replacements can address these issues before they compromise the entire structure.
- Deformation and Warping: Deformation can result from excessive loads or prolonged exposure to stress. Engineers may reinforce weakened areas or adjust load distribution to prevent further warping.
- Misalignment: Misalignment often results from gradual wear or improper installation. Routine inspections and adjustments help keep the frame aligned, while guide rails or alignment markers ensure consistent positioning.
Addressing these issues promptly helps prevent further damage and maintains the press’s precision and efficiency.
9. Future Trends and Innovations in Frame Design
Advancements in materials and structural design are leading to new innovations in frame and base construction for friction screw presses.
- Advanced Materials: High-strength alloys and composites provide improved strength-to-weight ratios, allowing for lighter yet more durable frames. These materials improve performance in applications requiring frequent high-force cycles.
- Real-Time Monitoring: Integrated sensors can monitor stress levels, alignment, and vibration in real time, providing feedback for preventive maintenance. This technology helps operators detect and address issues before they result in significant downtime.
- Optimized Engineering Techniques: New engineering methods, such as finite element analysis (FEA), enable designers to optimize frame geometry for minimal weight and maximum strength. This approach creates frames that are more efficient and adaptable to a variety of press applications.
These innovations enhance frame durability and precision, supporting the evolving needs of modern manufacturing.
10. Conclusion
The frame structure and base of a friction screw press are vital to its stability, efficiency, and durability. Proper design, material selection, alignment, and vibration control ensure that the frame can withstand high loads while maintaining precision. Through regular maintenance and prompt repairs, operators can extend the lifespan of the frame, ensuring consistent performance and reducing downtime. As new materials and real-time monitoring technologies continue to advance, frame designs will become even more durable and efficient, supporting the rigorous demands of industrial metal forming applications with greater reliability.
Introduction to Safety in Friction Screw Presses
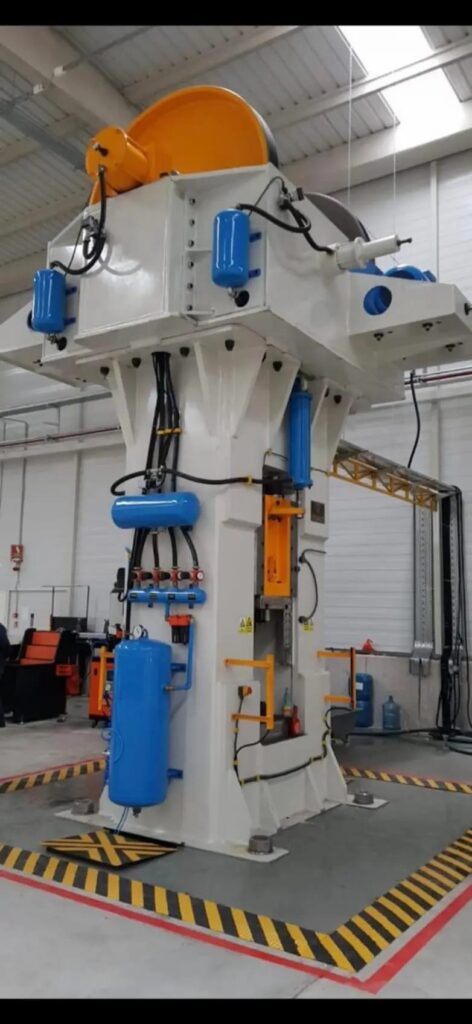
Operating a friction screw press involves handling substantial forces, moving parts, and heavy materials, all of which create potential hazards. High pressures, rapid movement, and intense heat produced during pressing operations pose significant risks to operators if not managed carefully. Safety mechanisms, therefore, play a central role in protecting operators from injuries, ensuring safe operation of the press, and preventing damage to the equipment itself.
Effective safety mechanisms minimize the risk of accidents and create a controlled environment that limits exposure to hazardous conditions. These mechanisms include a combination of physical barriers, automated safety interlocks, emergency stop systems, and thorough operator training protocols. The integration of these systems enables presses to operate safely and efficiently, supporting a productive work environment while adhering to regulatory safety standards.
2. Mechanical Safety Mechanisms
Mechanical safety mechanisms in friction screw presses are the first line of defense against accidents, providing physical protection and control over machine operation.
- Physical Barriers and Guards: Physical barriers, such as guards around the press’s moving parts, prevent accidental contact by operators. These barriers can include transparent shields that allow visibility while protecting from debris or accidental touch.
- Locking Systems: Mechanical locking systems prevent the press from engaging unless it’s safe to operate. These locks secure the flywheel, screw, or ram when the press is idle, ensuring that no accidental movements occur when the machine is not in use.
- Interlock Devices: Interlock mechanisms prevent the press from operating if certain conditions are not met. For example, if a guard is open or if an inspection panel is removed, the interlock prevents the press from starting. This ensures that the machine only operates when all safety conditions are met.
Mechanical safety mechanisms are essential for providing physical barriers that prevent accidents and control the press’s movement, especially in high-risk areas. Proper placement and maintenance of these systems ensure that the press remains secure, even during power fluctuations or emergency stops.
3. Electrical Safety Systems
Electrical safety systems are integral to friction screw presses, offering emergency stop capabilities and protection from electrical hazards.
- Emergency Stop Buttons: Emergency stop buttons, often located at multiple points around the press, provide a quick way for operators to halt the machine instantly. These buttons are typically designed to be easily accessible, and some systems may include foot-operated stops for convenience.
- Power Disconnects and Circuit Breakers: Power disconnects allow operators to cut off electrical power before performing maintenance, ensuring safety during inspection or repair. Circuit breakers protect against electrical overload, automatically stopping the press if it experiences excessive current.
- Safety Interlocks and Control Systems: Advanced interlock systems monitor the operational status of the press, preventing it from engaging if it detects abnormal conditions. For example, an interlock may stop the press if it detects a malfunction in the hydraulic or pneumatic systems, protecting operators and equipment from potential failures.
Electrical safety mechanisms provide immediate shutdown capabilities, protecting operators from electrical hazards while also ensuring that the press can be safely deactivated in emergencies.
4. Hydraulic and Pneumatic Safety Features
Hydraulic and pneumatic systems are often used to control force and movement in friction screw presses, especially in larger, high-force models.
- Pressure Relief Valves: Hydraulic and pneumatic systems can produce high pressures that, if uncontrolled, pose risks to operators and equipment. Pressure relief valves prevent over-pressurization, releasing excess pressure when it exceeds safe limits.
- Overload Protection: Overload protection systems monitor hydraulic and pneumatic pressure levels, stopping the press if levels rise beyond safe thresholds. This protects the equipment from damage and prevents accidents caused by excessive force.
- Fail-Safe Mechanisms: In the event of a hydraulic or pneumatic failure, fail-safe mechanisms prevent sudden drops or uncontrolled movements. These systems ensure that, even during system malfunctions, the press halts safely and gradually without posing risks to operators.
Hydraulic and pneumatic safety features are essential in managing high-force applications, protecting operators and equipment from pressure-related hazards.
5. Emergency Protocols and Shutdown Systems
Emergency shutdown protocols are critical for minimizing risk in the event of equipment malfunctions or accidents.
- Rapid Shutdown Procedures: Emergency shutdown procedures are designed to halt the press quickly and safely, allowing operators to prevent potential injuries or equipment damage. These protocols often involve a combination of emergency stops and power disconnects.
- Emergency Stop Control Placement: Emergency stops are strategically placed around the press for easy access. In some cases, multiple stop buttons or foot pedals are used to ensure that operators can reach a stop control from any position.
- Post-Emergency Protocols: After an emergency shutdown, specific procedures must be followed to reset the press safely. Operators must inspect the press for damage, check all safety mechanisms, and ensure proper alignment before restarting operations.
Effective emergency protocols provide a structured response to unforeseen events, minimizing risk and allowing for quick recovery after shutdowns.
6. Operator Training and Safety Protocols
Thorough operator training is essential to press safety, as it ensures that personnel understand safety mechanisms and proper operational procedures.
- Operator Training Programs: Training programs educate operators on safety mechanisms, emergency protocols, and best practices for safe operation. These programs include both theoretical knowledge and practical demonstrations to ensure a deep understanding of press safety.
- Safety Protocols for Operation: Key protocols include proper use of emergency stops, adherence to maintenance schedules, and understanding load limits to avoid overloading the press. Operators are also trained to recognize signs of wear and potential safety issues.
- Emergency Drill Practices: Regular emergency drills help operators respond effectively to emergency situations. By practicing shutdowns and evacuations, operators become familiar with the protocols, reducing response time in real emergencies.
Operator training ensures that personnel can safely operate the press and respond appropriately to potential safety hazards.
7. Monitoring and Diagnostic Systems for Safety
Real-time monitoring and diagnostic systems improve safety by detecting unsafe conditions and notifying operators before issues escalate.
- Real-Time Condition Monitoring: Sensors monitor parameters like pressure, temperature, and vibration, alerting operators if values exceed safe thresholds. For example, sensors can detect excess pressure in hydraulic systems or overheating in electrical components.
- Diagnostic Tools for Preventive Maintenance: Diagnostic systems track component wear and operational data, identifying potential issues before they lead to safety hazards. This allows for proactive maintenance, reducing the likelihood of mechanical failures.
- Alarms and Alerts: Visual and audible alarms notify operators when unsafe conditions are detected. These alarms are essential for immediate responses to potential safety risks, enabling operators to shut down the press if needed.
Monitoring systems enhance safety by providing operators with real-time data, reducing the risk of accidents from undetected faults.
8. Common Safety Issues and Troubleshooting Solutions
Certain safety issues are common in friction screw presses, and troubleshooting these problems helps maintain a secure operational environment.
- Operational Hazards: Common hazards include jamming of moving parts, misalignment, and overloading. These issues can often be resolved by following safety protocols, using proper lubrication, and performing regular maintenance.
- Troubleshooting Mechanical Failures: Mechanical issues such as loose bolts, cracked guards, or misaligned frames can compromise safety. Regular inspections help identify these issues early, allowing for timely repairs.
- Solutions for Recurring Issues: If certain safety issues are recurring, operators should review maintenance logs and investigate potential causes, such as incorrect alignment or insufficient lubrication, to prevent future occurrences.
Addressing these issues promptly helps maintain a safe and efficient work environment, reducing the risk of accidents.
9. Innovations and Future Trends in Safety Technology
New technologies are advancing safety in friction screw presses, making operations safer and more efficient.
- Machine Vision and Automated Monitoring: Machine vision systems and automated monitoring technologies detect operator presence and unsafe conditions, preventing operation if hazards are detected.
- IoT and AI Integration: IoT sensors and AI algorithms analyze operational data to predict safety risks and maintenance needs, allowing for preventive interventions. These systems can detect unusual patterns or deviations, alerting operators before issues arise.
- Emerging Protective Materials: New materials, such as impact-resistant composites and transparent safety shields, enhance safety without compromising visibility or efficiency.
Innovations in safety technology make friction screw presses more adaptable to modern safety standards, creating safer environments for operators and enhancing operational reliability.
10. Conclusion
Safety mechanisms are essential in friction screw presses to protect operators and maintain equipment integrity. Through a combination of mechanical barriers, electrical systems, hydraulic controls, and real-time monitoring, presses can operate safely while minimizing risk. Training operators, adhering to maintenance protocols, and leveraging advanced technologies further enhance safety. As new safety innovations continue to emerge, friction screw presses are becoming more secure, reliable, and adaptable to evolving industry demands, supporting a safer and more productive work environment.
1. Introduction to the Working Principle of Friction Screw Presses
Friction screw presses are powerful machines used in metal forming and forging industries for applications like coining, embossing, forging, and precision shaping. By converting rotational energy into linear pressing force, these presses enable accurate shaping of workpieces, even under high pressures. Understanding the working principle of a friction screw press is essential for optimizing its operation, improving efficiency, and maintaining precision in the production process.
The friction screw press relies on a sequence of coordinated steps, beginning with energy storage in a rotating flywheel and culminating in the controlled application of force by a ram onto the workpiece. Key components—including the flywheel, friction rollers, screw, and ram—work together to convert stored kinetic energy into linear motion, which presses or shapes the material. This process involves a unique combination of mechanical energy storage, friction-based motion transfer, and precise force application, making friction screw presses a versatile choice for high-force applications in metalworking.
2. Energy Storage and the Role of the Flywheel
The flywheel is a critical component in friction screw presses, responsible for storing the rotational energy needed for pressing operations.
- Function in Storing Energy: When the flywheel rotates, it accumulates kinetic energy that can be harnessed to power the press. This energy storage allows the press to apply significant force in short bursts, which is crucial for metal forming. The flywheel’s mass and speed determine how much energy it can store; a larger and faster-spinning flywheel will store more energy, providing greater pressing force.
- Mechanics of Energy Buildup: Energy is imparted to the flywheel by an electric motor or another power source. As the flywheel spins, it builds up rotational energy, which remains stored until the friction rollers engage it to drive the screw. The ability to store energy efficiently is key to the flywheel’s role in making the press operationally effective.
- Controlling Force Output: The rotational speed of the flywheel can be adjusted to control the force output. By varying the flywheel’s speed, operators can achieve different force levels, enabling the press to perform diverse tasks from light coining to heavy forging.
Through effective energy storage, the flywheel ensures that the press can generate sufficient force for each pressing cycle, supporting high productivity and operational efficiency.
3. Friction Rollers and Force Transmission
Friction rollers play a central role in transferring energy from the flywheel to the screw, initiating the pressing motion in a controlled manner.
- Engaging the Flywheel: When friction rollers engage the rotating flywheel, they create the friction necessary to drive the screw. The engagement process is controlled by adjusting the pressure between the rollers and the flywheel. This frictional contact initiates motion without direct physical locking, enabling smooth and adjustable force transfer.
- Mechanics of Friction-Based Energy Transfer: The friction rollers’ contact with the flywheel generates torque, which is then applied to the screw. This torque translates the flywheel’s rotational energy into linear force, driving the ram downward. The rollers’ surface material, texture, and pressure influence the amount of friction generated and thus control the press’s force output.
- Modulating Force: Operators can adjust the pressure exerted by the friction rollers, modulating the amount of force transmitted. This modulation is useful for varying the pressing power needed for different metal-forming applications, from delicate shaping to heavy forging.
By controlling friction through the rollers, the press achieves adjustable, efficient force transfer from the flywheel to the screw, which is essential for precision operations.
4. Conversion of Rotational to Linear Motion via the Screw
The screw mechanism is responsible for converting the rotational force from the flywheel into linear motion, enabling the application of pressing force by the ram.
- Mechanics of Conversion: As the flywheel rotates and transfers energy to the screw, the threads on the screw convert this rotational motion into downward linear force. The screw’s design—including thread pitch, profile, and lead—affects how efficiently this conversion occurs, as well as the speed and force of the ram’s movement.
- Impact of Thread Profile and Pitch: Thread pitch and profile determine how much force is applied with each rotation. A coarser thread pitch allows for greater linear force per rotation but may reduce precision. Conversely, a finer pitch provides more control and smooth motion, which is beneficial for high-precision tasks.
- Optimizing Motion Conversion: Engineers design the screw to maximize force conversion while minimizing energy loss due to friction. High-quality materials and surface treatments are used to reduce wear, ensuring that the screw can perform repeated cycles without degradation.
Through the screw mechanism, the press achieves efficient, controlled transformation of rotational energy into linear pressing force, allowing precise metal shaping.
5. Force Application by the Ram or Plunger
Once the screw converts rotational energy into linear force, this force is applied by the ram or plunger to the workpiece.
- Role of the Ram: The ram is attached to the end of the screw and applies direct force to the workpiece, pressing it into the desired shape. The force level and precision depend on the ram’s alignment, material, and design, as well as the accuracy of the screw mechanism.
- Ensuring Precision: Proper alignment of the ram with the screw and the pressing axis is crucial for achieving even, accurate force distribution. Misalignment can lead to uneven pressing, potentially damaging the workpiece or reducing the quality of the final product.
- Controlled Force Application: The ram’s surface may be customized to match the workpiece’s shape, allowing for precise and consistent shaping. This control over force application makes friction screw presses versatile in handling various metal-forming tasks.
The ram’s precise force application capability is critical to the success of metal-forming operations, ensuring high-quality output in terms of shape, detail, and finish.
6. Return Mechanism and Cycle Completion
After the pressing cycle, the ram and screw must return to their starting position, preparing the press for the next cycle.
- Returning to Start Position: The ram and screw are returned to their starting positions through various mechanisms. Some presses use springs to provide reverse force, while others rely on reverse torque from the motor to reset the components.
- Role of Springs or Reverse Torque: Springs are common in smaller presses, where they provide a reliable way to return the ram to its starting point. For larger presses, reverse torque may be applied to the flywheel to drive the screw and ram back to the ready position.
- Cycle Preparation: Once reset, the press is ready for the next cycle. The flywheel begins spinning again, building up energy for the subsequent pressing operation.
The return mechanism enables the press to operate continuously, with each cycle reset allowing for efficient, repetitive production processes.
7. Control of Force and Speed in Press Operations
Controlling force and speed is essential for achieving desired results in different pressing applications.
- Variable Flywheel Speed: Adjusting the flywheel’s speed controls the amount of energy stored, which affects the force generated. Faster speeds provide more force, while slower speeds allow for gentler pressing, suitable for precision tasks.
- Friction Roller Adjustments: The friction rollers’ pressure on the flywheel is another way to control the press’s force. By modifying roller pressure, operators can fine-tune the force applied to the workpiece.
- Achieving Precision in Diverse Applications: Operators can adjust both the speed and force to accommodate different materials and pressing requirements, ensuring that each application receives the optimal level of force and precision.
These adjustments make the friction screw press versatile, allowing it to handle a range of applications from heavy forging to delicate shaping.
8. Efficiency and Energy Loss in the Pressing Process
Energy efficiency is a key consideration in friction screw presses, as energy loss can reduce productivity and increase operational costs.
- Sources of Energy Loss: Friction between components, heat generation, and material deformation can lead to energy loss in the pressing process. Maintaining proper lubrication and using wear-resistant materials help mitigate these losses.
- Improving Efficiency: Design adjustments, such as optimizing the screw’s thread profile and using low-friction materials for friction rollers, help reduce energy waste. Routine maintenance, including lubrication and alignment checks, also enhances efficiency.
- Benefits of Optimized Efficiency: By minimizing energy loss, friction screw presses operate more economically, with reduced power consumption and lower wear on components, leading to longer equipment life.
Optimizing efficiency is essential for achieving cost-effective, high-performance operation in friction screw presses.
9. Innovations and Future Enhancements in Friction Screw Press Technology
Recent technological advancements have led to significant improvements in friction screw press design and function.
- Advanced Materials and Lubricants: New materials, such as high-strength alloys and self-lubricating composites, reduce wear and improve efficiency, extending press lifespan and reducing maintenance needs.
- Electronic Control Systems: Integration of electronic controls and sensors allows for real-time monitoring of parameters like force, speed, and alignment, improving precision and enabling preventive maintenance.
- Potential Future Developments: Emerging technologies, such as AI-driven optimization and IoT connectivity, offer potential enhancements in automation, predictive maintenance, and real-time performance adjustments, making presses even more adaptable to modern manufacturing demands.
These innovations support safer, more efficient, and versatile press operation, keeping friction screw presses competitive in the metal-forming industry.
10. Conclusion
The working principle of friction screw presses involves a coordinated sequence of energy storage, friction-based force transfer, and precise application of pressing force. By understanding the mechanics behind each component—from the flywheel to the ram—operators can optimize press performance, achieve high-quality results, and improve operational efficiency. As innovations continue to enhance materials, control systems, and monitoring technology, friction screw presses will become even more effective, supporting modern metal-forming needs with greater precision and versatility.
EMS Metalworking Machinery: Your Trusted Partner in Precision Metalworking
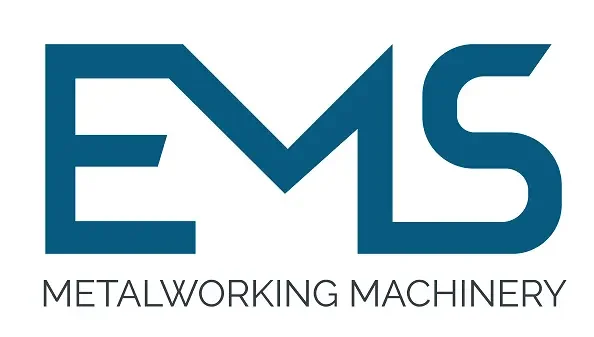
EMS Metalworking Machinery is a leading manufacturer of high-quality metalworking equipment, dedicated to providing innovative solutions that meet the evolving needs of industries worldwide. With a rich history of excellence and a commitment to technological advancement, we have earned a reputation for delivering cutting-edge machinery that ensures precision, efficiency, and durability.
Our Product Range:
- CNC Spinning Lathes: From precision bench lathes to heavy-duty industrial models, our lathes offer unmatched accuracy and performance for a wide range of applications, including machining shafts, gears, and other cylindrical components.
- Trimming Beading Machine: Our trimming beading machines are designed to provide exceptional cutting capabilities and versatility, enabling you to create complex shapes and intricate details with ease. Whether you need a horizontal or vertical trimming machine, we have the perfect solution for your needs.
- Hydraulic Deep Drawing Press Machines: Our hydraulic deep drawing press machines are built to deliver precise and powerful drawing operations, ensuring clean holes and exceptional surface finishes. We offer a comprehensive range to suit various applications.
- Grinding Machines: Our grinding machines are engineered for precision and efficiency, allowing you to achieve the highest levels of surface finish and dimensional accuracy. Whether you need a surface grinder, cylindrical grinder, or tool grinder, we have the equipment to meet your specific requirements.
- Sawing Machines: Our sawing machines are designed for fast and accurate cutting of metals, providing clean cuts and minimal burrs. From band saws to circular saws, we offer a variety of options to suit different materials and cutting needs.
- Custom Machinery: In addition to our standard product line, we also specialize in custom machinery fabrication. Our experienced engineers can work with you to design and build tailored solutions that meet your unique requirements and optimize your production processes.
Why Choose EMS Metalworking Machinery:
- Quality: Our machines are crafted with the highest quality materials and components, ensuring long-lasting performance and reliability.
- Precision: We are committed to delivering machinery that meets the most stringent tolerances and standards, ensuring exceptional accuracy in your metalworking operations.
- Innovation: We continuously invest in research and development to stay at the forefront of technological advancements, offering innovative solutions that enhance your productivity and efficiency.
- Customer Support: Our dedicated team of experts is always available to provide comprehensive support, from machine selection and installation to maintenance and troubleshooting.
- Customization: We understand that every business has unique needs, and we offer flexible customization options to tailor our machines to your specific requirements.
At EMS Metalworking Machinery, we are more than just a supplier of equipment; we are your trusted partner in metalworking success. By choosing EMS, you can be confident in the quality, reliability, and performance of your machinery, enabling you to achieve your business goals and stay ahead of the competition.
EMS Metalworking Machinery
We design, manufacture and assembly metalworking machinery such as:
- Hydraulic transfer press
- Glass mosaic press
- Hydraulic deep drawing press
- Casting press
- Hydraulic cold forming press
- Hydroforming press
- Composite press
- Silicone rubber moulding press
- Brake pad press
- Melamine press
- SMC & BMC Press
- Labrotaroy press
- Edge cutting trimming machine
- Edge curling machine
- Trimming beading machine
- Trimming joggling machine
- Cookware production line
- Pipe bending machine
- Profile bending machine
- Bandsaw for metal
- Cylindrical welding machine
- Horizontal pres and cookware
- Kitchenware, hotelware
- Bakeware and cuttlery production machinery
as a complete line as well as an individual machine such as:
- Edge cutting trimming beading machines
- Polishing and grinding machines for pot and pans
- Hydraulic drawing presses
- Circle blanking machines
- Riveting machine
- Hole punching machines
- Press feeding machine
You can check our machinery at work at: EMS Metalworking Machinery – YouTube
Applications:
- Beading and ribbing
- Flanging
- Trimming
- Curling
- Lock-seaming
- Ribbing
- Flange-punching